{"pages":{"page":[{"#text":"PACKAGING / PALLETISING PETplanet Insider Vol. 22 No. 04/21 petpla.net 36 Next-generation case packer featuring collaborative robot automation system Layer by layer Proco Machinery Inc., the Ontario, Canada-based manufacturer of automation systems for the blow moulding industry, has unveiled the next generation of its Pakman case packer, which is integrated with Yaskawa Motomon HC10 and HC20 collaborative robots. Proco says that this integrated, automated arrangement offers more efficient handling and will deliver improved efficiency and cost reductions, compared with conventional automation. Proco has focused for years on achieving greater efficiencies through the implementation of innovative technologies and automation in bottle packaging. The company says that the collaborative robotic (cobotic) automation system in the latest iteration of Pakman works interactively with human staff and needs minimal training for new tasks. The systems reduce container handling container and provide a good return on investment (ROI), according to Siva Krish, vice president of sales for Proco Machinery. “These systems are being designed in such a way that they complement the production line and provide simplified operation, a smaller footprint, and enhanced efficiencies,” he said. Proco’s Pakman case packer features a collating indexing accumulation system to accumulate complete layers of bottles inside the packaging cell. It stages bottle layers so they can be picked up by Proco’s end-of-arm (EOA) tooling and placed inside the box. The accumulation indexing conveyor helps to increase the line speed of the Pakman packaging cell by requiring only one movement of the robot per layer. The high static in heated PET bottles leads them to repel each other when they are close together. Proco says that Pakman’s layer pack EOAT technology ensures that containers are placed inside the box as complete layers, preventing any change of bottle position. Proco’s recently-launched Integrated Rotary Inverting Technology helps to rotate a layer of bottles to The Proco Pakman case packer is a totally integrated packaging module, including a safety door and interlocking as standard. It is supplied with a six-axis collaborative robotic arm, infeed conveyor and a box conveyor, all mounted onto a common subframe that is fitted with levelling pads and castor wheels. This means it can be easily moved into position, set up, and be in production quickly. The system’s compact footprint of just 2,540mm x 1,780mm (100 in x 70) means that it can fit between blow moulding lines. As well as Yaskawa HC10 or HC20 cobots, the Pakman includes an integrated collating table and container inverting system; inbuilt secondary PLC with HMI; vacuum feature for polybags; a box alignment mechanism; and both bottle and box infeed and exit conveyors. www.procomachinery.com PACKAGING neck-down orientation. The Pakman packaging cell equipped with this optional feature will help the processor pack bottles in all neck-down orientation in a layer formation and without any impact on cell size. The feature can be specified at outset or added at a later date. The system’s flexibility enables it to handle different pack configurations and the company’s engineering team can develop a custom designed system to provide an efficient, cost-effective solution. Proco was able to provide a recent customer with a multiple packing solution within a single cell, to handle both re-shipper containers and regular full boxes. Its quick-release tooling enabled the customer to complete changeovers to new pack patterns within 30 minutes; programs to change tooling and run different bottles can be recalled from the human machine interface (HMI).","@ID":38} "MATERIALS / RECYCLING PETplanet Insider Vol. 22 No. 04/21 petpla.net 15 However, low weight is not a be-all and end-all. Consideration also needs to be given to the notion that a welldesigned but heavier PET bottle, with a PET label, may actually in the end prove more sustainable than a lighter one that has a multilayer structure or a PVC label, both of which hinder recycling efforts. Sipa uses something called the Green Plastic Factor to show how light a bottle is in comparison with what it holds. The Green Plastic Factor (or GPF) is the ratio of the volume of the container contents in ml to the weight of the unfilled container in g. For a collapsible 10 l bottle, the GPF is around 125, while for a singleserve 500ml bottle it is around 55. This clearly shows the high level of sustainability of large-format bottles, production of which Sipa has developed specific equipment. For a returnable 2 l bottle, the GPF is also low, at around 20. But if such a bottle fulfils its purpose and makes multiple trips, it can be assigned a “virtual” GPF, which can be close to 200. Green Plastic Factor is just one tool that Sipa uses in its design projects: it is a means rather than an end. So, for example, an ultra-light 5 l water bottle may have a high GPF – possibly around 85 – and also have very good performance as indicated by high top-load strength, but these have to be weighed against factors that are not so positive, such as the fact that it is single-use, and it requires the implementation of good logistics. From flake to preform in a single step One issue still in the balance is just how all those used PET bottles are converted back into new ones. Reducing them to flake, converting the flake into granules and then reprocessing the granules into preforms and then bottles is the obvious solution is the most obvious one – but it is not necessarily the most economic one. Xtreme Renew process incorporates technologies that enable rPET to be converted in a fully integrated system directly into injection-compression moulded preforms. Xtreme Renew eliminates an entire section of the heat history of rPET, making it considerably more cost-effective, while offering extra benefits in terms of carbon footprint. Sipa believes that for converters considering the use of high volumes of rPET, it is a highly attractive proposition. At the same time, Sipa acknowledges that Xtreme Renew does require investment in equipment that many converters are unfamiliar with. This is why it also supplies more conventional Xform injection moulding systems, and SFL or Xtra linear and rotary stretch-blow moulding systems, incorporating special features that make processing with rPET a relatively simple affair. In many cases, customers will not even have to invest in new systems, but rather make highly affordable adjustments to equipment they already have. But they will still be able to produce bottles with up to 100% rPET if they so choose (and if the application allows). Fromflakes to preforms in a single step Modified hot runners For converters producing preforms, for example, it will make a lot of sense to use hot runner systems that have been upgraded to prevent accumulation of PET powder. Sipa has developed Xactive Cleaning, a patented system, which adapts the compressed air flows, normally used to move the hot runner valves stems, to also blow out the very few plastic particles that deposit inside the actuators each cycle. Cleanliness is an issue not only in hot runner systems, but also in the injection moulds that they feed. So Sipa has also been developing ways to keep mould cavities as clean as possible. A system incorporating new vacuum technology reduces the need for maintenance and increases line efficiency. Pulling a vacuum during injection All moulds incorporate tiny vent holes at key points on the surfaces of the cavities, to allow the escape of air in the cavities when the PET is injected. But the vents can become dirty if the air flowing through them is not completely clean – impeding the passage of the air. Sipa has patented a solution that pulls the air out of the mould during injection. Net result is that the need for operations to clean the vents is also drastically reduced. Accounting for colour variations in rPET Not all rPET preforms are the same. Because the raw material usually comes from a variety of sources, it is quite possible that there will be, for example, slight variations in colour. This may affect behaviour when the preforms are heated in infrared ovens, since different colours absorb different amounts of infrared energy. Sipa has developed ways to take account of such variations – making automatic adjustments to the oven settings for example – making it possible to have a high level of consistency in the way the preforms behave when they are formed into their final blown shape. Preform heating can be adjusted from one batch of preforms to another, based on the variation in colour. Related to this, special vents, known and patented as X-Vents, can be inserted into the bottle moulds, making it possible to manage pressure changes in the cavities caused by the process adjustments relating to the different levels of energy absorption of the preforms. Sipa’s Product Manager for Blow moulding Systems, says: “The specification of any container can always be ensured. The use of X-Vents, is particularly useful for managing these situations when bottles with complex geometries are being produced, or for controlling the bases of bottles for carbonated soft drinks.” He also points out that the extra wide processing angle on the new generation of Xtra rotary stretch-blow moulding machines provides further help in processing ‘difficult’ materials like rPET. www.sipasolutions.com","@ID":17} "PREFORM PRODUCTION PETplanet Insider Vol. 22 No. 04/21 petpla.net 18 Hot runners for the plastic industry “We are providing solutions based on application” Mold-Masters is a well known global player in the plastics industry. The company designs, manufactures, distributes, sells and services highly engineered and customised plastic processing equipment and systems. Hot runners, temperature controllers, auxiliary injection and co-injection systems are utilised by customers of all sizes in plastics industry, from small local manufacturers to large worldwide OEM manufacturers. PETplanet talked with Mr Igor Kim, Global Sales Director for PET & Co-injection about the PET industry and future plans of Mold-Masters how they will serve the market. PETplanet: Igor, what is the vision of Mold-Masters to serve the PET industry? Igor: Mold-Masters’ core business is to manufacture different types of hot runners: monolayer, co-injection and multi-component injection. With this kind of technology we are focussing on providing the right solutions to the plastic industry including the packaging segment. Packaging customers are looking for solutions based on application – and we at MoldMasters have the best expertise: We can design the whole system. And of course, to serve the PET industry, we are focusing on how to make monolayer PET hot runners for preforms or co-injection hot runners - for PET performs or preforms made of any other material. PETplanet: At this point Kortec comes in, another company under the umbrella of Milacron and MoldMasters. Igor: Yes, it was a logical step that Kortec, that became part of Milacron in 2014, is now fully integrated within Mold-Masters. Combining co-injection know-how and R&D expertise from both companies under one leadership makes the engineering team the strongest team in terms of co-injection solutions. PETplanet: What are special services solutions Mold-Masters offers its customers? Igor: We know what the PET industry requires. As a company our strength is flexibility, I would like to mention just two products here: The new PET hot runner and the Coinjection Connect. Within the last 18 months we made a lot of investment and dedicated resources to advance our PET hot runner. Our foundation here is “iflow” technology, where melt channels are optimised to provide natural balance and the shortest path. This allows a faster injection time and reduces injection pressure. Also, the machine needs less energy. The next step was to increase robustness, reliability and maintenance interval, especially when running in an aggressive moulding environment. As a result, our PET hot runner delivers superior processing performance and lowest running costs, independent from the machine generation. Moreover, we can make PET hot runners with any pitch and for any cavitation. Co-injection Connect is another unique offering, allowing to convert a standard single-shot machine into co-injection system. We can size the system based on the customer’s needs, making it as low as with 2 cavities or up to 144 cavities. And of course, we can offer complete turnkey systems, both in monolayer and coinjection. PETplanet: As we know co-injection is not only for PET applications. In which packaging market is demand as high? Igor: For example, in the medical industry we have a significant increase, in particular blood culture bottles and vaccine vials. The coffee capsules segment, where usage of biodegradable and compostable resins is in high demand. Thin-wall packaging is a growing segment, where co-injection technology offers better return than thermoforming or extrusion, plus it’s more sustainable. In fact, specifically related to co-injection (multilayer) product, both extrusion and thermoforming require 5-7 layers, including tie-layers (adhesive) and some regrind. The smaller the part, the higher the skeletal waste, which can be as high as 50%. In case of 5/7 layer it’s difficult to return everything to the process, plus it requires additional energy. Co-injection, whether it’s injection moulding or injection blow moulding, doesn’t generate such scrap, no additional energy waste, produce better dimensionally stable parts and normally it’s 3 layers (no adhesive) – thus easy to recycle.","@ID":20} "TOP TALK PETplanet Insider Vol. 22 No. 04/21 petpla.net 13 equipment, which will lead to reduced dependence on human personnel while increasing production efficiency, expanding productivity, developing e-commerce and ensuring product safety and quality. The traditional technology and production line will be replaced much faster, because of the pandemic. At the same time, consumers are more aware of food health, safety and traceability. PETplanet: How fast can the entire beverage and food industry adapt to these change, do you expect? Tony Ho: We have already found that more and more customers are partnering with us to find safer and more efficient solutions, and to provide consumers natural, fresh, healthy and nutritious products. PETplanet: Many exhibitions have been cancelled and it is still unclear when this situation can return to normal. Some of them have been or will be hosted digitally instead. What do you think about such formats and do you see effects for Newamstar? Tony Ho: With the help of 5G, IIoT, AI and other technologies we will attend a variety of exhibitions. We believe that, in the future, we will communicate and interact more and more closely with customers online. PETplanet: We regularly hear from a lot of our readers and partners that physical events like exhibitions, in-house meetings and so on cannot be replaced by online sessions, as people want to see and feel technology in action and to network live at such occasions. Do you agree with that and do you see digital contents as a good addition or as a replacement? Tony Ho: Liquid product packaging machinery is a large-scale equipment with high precision and a strong presence. Only by personal experience can we discover beauty and value, and better understand the industry’s technological development. Digital demonstrations can be used as a supplement, in conjunction with the offline display, to present the product in an all-round way. PETplanet: Agreed. One final question: What can we expect next from Newamstar? Tony Ho: We will fully embrace Industry 4.0, actively participate in the global market, constantly develop and innovate technologically and stay close to customers, to provide quality service. We will focus on new aseptic technology, multifunctional integrated equipment and the digital factory, and pay even more attention to continuously improve our ability to help customers build the ideal factory. PETplanet: Thank you, Mr Ho. www.newamstar.com Respeto Respect PET is a respectful material with nature due to the minimum amount of fossil resources necessary to be produced. This amount can even be reduced by including the r-PET in the production cycle. www.novapet.com","@ID":15} "26 TRADE SHOW REVIEW PETplanet Insider Vol. 22 No. 04/21 petpla.net Instead of TRADE SHOWpreview What you would have seen at NPE… Even though the NPE cannot take place in Orlando this year, developments in the PET industry are not standing still. And because they are too good not to be shown, we have collected some of them for you here. Have fun reading our collection “what you would have seen at NPE”. Dry ice blaster for the PET industry Offering the PET industry one smart machine with the ability to adapt the cleaning process to so many different applications was the intention why Cold Jet planned to present the PCS 60 dry ice blasting machine during the 2021 NPE show. Cold Jet’s new PCS 60 machine is claimed to present many technological advancements which help PET processors to achieve an even more efficient and faster cleaning process with the additional benefit of lower costs for consumables such as compressed air and dry ice. The PCS 60 features Cold Jet’s patented Particle Control System (PCS). This allows moulders to have a greater degree of versatility in all of their cleaning applications. With the PCS, a PET processor can use one machine to clean many types of surfaces. The cleaning of lock rings, neck rings, cavities, take out tubes, cores, and gate inserts can all be cleaned on-site, without disassembly of the stripper plate. Cold Jet states that the PCS 60 is a very easy-to-use dry ice blaster. With a 7” LCD colour screen and digital controls, it provides an intuitive display that allows the user to easily view and adjust blasting parameters and machine settings. The machine also features programmable and passwordprotected application recipes. A PET processor can save one application recipe for one of their injection moulds and another application recipe for their blow moulds or even the air conveyors. In addition, the PCS 60 is IoT enabled via Cold Jet’s Industry 4.0 solution, Cold Jet Connect. The system provides remote monitoring and diagnostics while allowing users to collect and manage data and employ tools for optimum performance and productivity. Also, Cold Jet recommends a new accessory package for PET moulders with a specially designed J-Hook nozzle for backside taper cleaning. It is the only solution on the dry ice cleaning market that fits all cavities. www.coldjet.com New size 110 for rotary filtration systems Gneuss Filtration Technology is introducing an additional size across its line of rotary filtration systems. The models RSFgenius, SFXmagnus, SFneos and CSFprimus are now available in a size 110, which offers almost 20% more active screen area than the size 90 for each model, 46 to 62 square inches, depending on the specific model. In the past the next size up was the size 150, with a jump of more than 50% in active filtration aera. The new intermediate size is intended to ensure an optimised and cost efficient filtration solution for every application. Rotary filtration systems operate continuous, automatic, process and pressure constant. They are characterised by a filter disk on which the screen cavities are located in a ring pattern. Screens can be changed on the part of the filter disk that is not active in the melt channel, while the production process continues to run without any interruptions or disturbances. The various models differ in terms of e.g. drive design, encapsulation and whether they offer integrated back-flushing. www.gneuss.com","@ID":28} "TRADE SHOW REVIEW PETplanet Insider Vol. 22 No. 04/21 petpla.net 48 Kick-off ceremony of Chinaplas in Shenzhen Chinaplas was held for the first time at the 350,000m2 Shenzhen World Exhibition & Convention Centre. Under the theme of “New Era - New Potential - Innovation for Sustainability”, the event took place from April 13-16, 2021. Over 3,600 exhibitors showcased the latest innovations and technologies. rubber technological innovation and development. 2021 sees the start of China’s 14th Five-Year Plan, the latest version of the country’s overall strategy for social and economic development. During the opening ceremony experts from the plastics and rubber industries illustrated current situation and presented forecasts of various aspects of the industry. Wang Zhanjie, Vice President & Secretary General, China Plastics Processing Industry Association Mr Wang Zhanjie, Vice President & Secretary General, China Plastics Processing Industry Association, delivered a speech on “China’s Plastics Processing Industry: Essential Information and 14th Five-Year Plan Development Proposals”. He described how the speed of technological innovation in China’s plastics industry accelerated during the 13th Five-Year Plan, making huge progress in functionality, lightweighting, environmental sensitivity and smart manufacturing. Mr Zhanjie outlined the main challenges and changes that will be faced and delivered during the 14th Five-Year Plan, including acceleration of technological innovation and the transformation and development of the industry, which should take advantage of China’s huge domestic market to On March 24, 2021, show organisers Adsale Exhibition Services, Ltd., hosted the “Chinaplas Shenzhen Kick-off Ceremony”. After Mr Stanley Chu, Chairman of Adsale Exhibition Services, Ltd., and Mr Marius Berlemann, General Manager of Messe Duesseldorf (Shanghai) Co., Ltd., co-organisers of the exhibition, delivered welcome speeches, representatives from the plastics and rubber industries made presentations to about 150 representatives from associations, exhibitors, buyers and media attending the event in person. By relocating the exhibition to Shenzen in the GuangdongHong KongMacao Greater Bay Area, Chinaplas sought to stimulate awareness of and demand for manufacturing upgrades in the Greater Bay Area, and encourage enterprises to grasp the opportunities of economic recovery, transform to smart environmental protection and promote China’s plastics and SidelSuperCombiCompact integrates five process steps into a single system: preform feeder, blower, labeller, filler/capper and cap feeder. This solution drastically reduces the space required, while enhancing performance thanks to new dynamic filling technology that produces up to 54,000 bph. This makes it the ideal solution for maximising water production and increasing line efficiency while reducing your TCO. That’s one compact, super-efficient solution. sidel.com/supercombicompact MORE PERFORMANCE, LESS SPACE. SUPER COMBI COMPACT","@ID":50} "TRADE SHOW REVIEW PETplanet Insider Vol. 22 No. 04/21 petpla.net 46 Pandemic-compliant hybrid event concept for market launch Introducing the new Netstal PET line with sideways removal system Netstal has introduced the new PET line with a new hybrid in-house trade fair concept. Ongoing demand from customers means that the planned three-month event has grown to nine months. We spoke to Michael Birchler, Chief of Marketing for the Netstal brand. PETplanet: Mr Birchler, you made a virtue of necessity and developed the introduction of the new Netstal PET line in September 2020 as a hybrid event concept. You have established a showroom in Näfels that could also have been set up at an industry trade fair. Its centrepiece is your new PET line. Birchler: The pandemic has of course affected the trade fair scene and this includes our in-house trade fair. We had planned a large customer event for September to introduce the new Netstal PET line but when we could see that the virus was going to scupper our plans, we decided to run a limited hybrid event, initially until the end of 2020. Because of its great popularity, we have extended the event to May 2021. PETplanet: Hybrid means that both visiting the site in person and viewing it live online are possible? Birchler: Precisely. In late summer, PETplanet also had the opportunity to travel and get an impression in person of the system and the concept. On average, we have 1 to 2 customer visits live onsite or live online each day. How did you like the concept? PETplanet: I have to say, I found the new approach very promising (see article edition 10/2020 page 22). Compared to a normal trade fair where the next appointment is already waiting, you have the opportunity to inspect the machine quite intensively, almost “to get right inside it”. What feedback did you get from customers? Birchler: As indicated above, we have extended the initiative again and again because of the high level of interest. We had positive feedback from our visitors for having this presentation concept during the coronavirus pandemic. But of course, the technology is always the main focus. High on the list of topics for discussion were the unit costs that are at their lowest because of the shortest cycle time and the reduced energy consumption. We can calculate these individually for each customer for the preform to be produced. Another topic mentioned frequently was the advantage given by the PETX screw, with its wide processing window for recyclate. This can be ordered for retrofitting in existing systems. The new PET-Line Michael Birchler, Chief of Marketing for the Netstal brand","@ID":48} "PREFORM PRODUCTION PETplanet Insider Vol. 22 No. 04/21 petpla.net 20 Voices from industry experts of Alpla and Gneuss A closed loop of PET preforms by Markus Halabi, Guest Author The PET preforms market is booming. So does the circular economy. How does the closed circle of such a product look like and which points does a manufacturer need to factor in if he wants to recirculate its production waste? Our interview partners of Alpla and Gneuss delivering important notes. We talked with Jens Seifried , Global Sales Director at Alpla Groupabout his view on preform trends, circular economy and ‘greendesign’. Halabi: Concerning the PET preform market which current trends do you observe? Seifried: At the moment, the overall objective of the market is to reduce CO2emissions. To this end, the localised production of preforms and rPET helps to reduce CO2 emissions by eliminating the need to transport the products. This multi-site approach is one of our major strengths at Alpla. And as a system supplier, we use our rPET in our preforms. Another trend is the increased proportion of rPET content up to 100%. Here we are ensuring the long-term availability. Therefore, we design our products to be optimised for recycling by, for example, producing them preferably without any colours or additives that are harmful to the recycling stream. We offer closed-loop solutions from a single source – from the input bale materials of the customer to a climate-neutral recycling process, through to the production of preforms. We are also seeing an increase in specialisation through the implementation of separate rPET streams for non-food (e.g. ‘yellow bag’ in Germany) and food products, as well as customised rPET solutions for specific applications with properties tailored to the needs of the customer. Finally, measures such as lowering the weight in the neck and base of the preforms, reducing energy and water consumption in processes and an active dedication to recycling around the globe with increased capacities for rPET and rHDPE are trends which we also see in the industry at the moment. Halabi: Regarding the sustainability goals of the European commission in terms of recycling quotes, how do you handle the recirculation process of PET? Seifried: In our view, the joint target of the European Union, local governments and all market participants involved has to be the establishment of closed-loop systems on a local level. This is the only way to guarantee the highest possible collection rates, recyclability and quality of the input bale materials. This will also ensure that as much rPET as possible is being used and offsetting virgin materials. Additionally, logistical efforts must be reduced as much as possible on a local level. Alpla is working hard with all stakeholders involved to support and create solutions in this regard. Halabi: What is your core approach of ensuring a ´green-design´ of your PET products – maybe you have a specific example out of your portfolio? Seifried: Werner & Mertz provides a good example of the use of optimised PET solutions. The familyowned company specialises in cleaning and care products. They have relied on our expertise for more than 25 years for production of recycled plastics and processing them into bottles for the company’s own recycling initiative. Our joint efforts have resulted in sustainable packaging solutions that have received recognition in the form of multiple international awards. The ‘Frosch’ brand of Werner & Mertz is considered to be an ecological pioneer and develops its products according to the cradle-tocradle principle. It was the first brand to introduce PET bottles made from 100% recycled plastic, with a certain proportion of rPET from the ‘yellow bag’ recycling system. Halabi: Thanks you for your words. www.alpla.com Andrew Prangnell, Manager of Technical Sales at Gneuss summarises the processing of food-contact material, working with post-industrial waste and introduces the Gneuss MRS Extrusion system. Halabi: Gneuss pelletising systems produce high quality pellets which are due to the MRS extrusion process suitable for processing to food-contact products. What are your first thoughts when it comes to PET preforms, clean post-industrial waste, and its pelletising process? Prangnell: When people refer to PET recycling, they usually mean ‘reprocessing post-consumer bottle flake’. This is an area in which we have a great deal of experience, whether PET bottle flake to sheet for thermoforming, to strapping tape, to fibres or bottle-to-bottle recycling. The reprocessing of PET post-industrial is often overlooked and can pre-","@ID":22} "PETplanet Insider Vol. 22 No. 04/21 petpla.net 54 PETbottles Beverage + Liquid Food A one-litre liqueur in a moulded bottle The first “drinkable mouthwash” is how Nordbrand Nordhausen GmbH is describing a limited version of their peppermint liqueur “Pfeffi” which has an 18% alcohol content. The shape of the bottle that could almost be mistaken for the familiar mouthwash container is made from PET and holds one litre of the liqueur. The easy-to-grip, tapered bottle has two labels that provide information about the product. The black screw cap is similar to the “original” version and is covered by a tamper-proof shrink film. www.pfeffi.com Syrup in a slim bottle The Austrian company, S.Spitz GmbH, is selling the Wiesgart brand’s ice sweet flavoured syrup which comes in a tall, slim 700ml bottle. The 1-part syrup and 6-parts water mixture have created a refreshing ice sweet flavoured drink. The colour of the product is easily visible through the transparent bottle which has a film label that provides information about the ingredients and how the product should be applied. The syrup is poured via a two-tone, hinged press-down lid with dispensing spout. A sealed cap needs to be removed prior to the initial opening of the bottle. www.spitz.at","@ID":56} "7 NEWS PETplanet Insider Vol. 22 No. 04/21 petpla.net Henkel and Plastic Bank open first collection centres in Egypt Henkel and Plastic Bank have opened their first three plastic waste collection centres in Cairo. The project is part of Henkel’s long-term partnership with the social enterprise. The opening of three collection centres in Egypt marks the first step in the commitment to deliver environmental, social and economic impact in the country. Working together, Henkel and Plastic Bank aim to steadily expand their engagement in the coming years and to reach a yearly collection capacity of 5,000t of plastic waste in 2023. At the collection centres, people can return collected plastic waste and exchange it for money. This prevents the plastic from entering the rivers and oceans, and at the same time Henkel and Plastic Bank support the local population by improving the lives of collector communities. Plastic Bank reprocesses the material and returns the so-called Social Plastic back to the value chain – for example in Henkel’s product packaging. Henkel was the first global consumer goods company to partner with Plastic Bank in 2017 and has already launched first product packaging made from Social Plastic in the market. David Katz, Founder and CEO of Plastic Bank says “Since the beginning of our partnership, Henkel has helped to collect over 1.7 million kilograms of plastic waste, preventing over 86 million plastic bottles from entering the ocean. With our collection centres in Egypt, we are taking a significant step towards stopping ocean plastic and improving lives on the African continent.” Plastic Bank establishes recycling ecosystems in countries that still lack adequate waste management infrastructure. Collectors receive a premium for the materials they collect which helps to provide basic family necessities such as groceries, cooking fuel, school tuition or health insurance. The collected plastic is processed as Social Plastic which can be reintegrated into products and packaging as part of a closed-loop supply chain. In Egypt alone, Henkel and Plastic Bank aim to create 1,000 jobs over a two-year period which will directly impact over 4,000 Egyptian citizens through the establishment of a long-term recycling infrastructure. The companies will build on a successful partnership in Haiti, which began in 2017. Henkel has already integrated Social Plastic into several of its products. The Beauty Care brand Nature Box was the first cosmetic brand to introduce Social Plastic as a packaging material for its complete bottle portfolio, with all bottle bodies being made of 98 per cent Social Plastic. And Henkel’s Laundry & Home Care Pro Nature cleaners have transitioned to PET bottle bodies that are made of 100 per cent recycled plastic, of which up to 50 per cent is Social Plastic. www.henkel.com www.plasticbank.com +44 (0) 1254 584210 [email protected] petmachinery.com Active for over 25 years, our global network and specialist knowledge makes us the go-to company for the sale or purchase of a PET machine. Commercially savvy, we work closely with our customers and our global network, to make sure everyone gets the best deal. Providing comprehensive advice throughout your sale or purchase; we can arrange dismantling, loading, packing, shipping, specialist insurance and commissioning. If you have amachine to sell or you’re looking to purchase, please get in touch. THE INDUSTRY EXPERTS Repi announces acquisition of Novosystems GmbH Repi, a leading supplier of high-performance liquid colour and additive solutions for polyurethanes and thermoplastics, has acquired Novosystems GmbH, one of the few independent European players in the field of liquid colours and additives for thermoplastic materials. With the acquisition of the Germanbased company, Repi intends to strengthen its position in one of the key polyurethanes and plastics markets in the world, as well as improving the Group’s geographical footprint in Central and Northern Europe, with the aim of providing better and faster response to the market. Novosystems will also contribute with interesting complementary technology platforms, which can be leveraged by Repi’s global presence, and will accelerate value creation through superior level of expertise in liquid formulation and dispersion technologies. “Welcoming a private, family-owned company in our Group is another exciting milestone for Repi, as both companies shared a common history in liquid colourants for plastics, and we are looking forward to shaping our future together based on common values and a long-term vision and strategy. Germany has long been one of the most important markets for Repi, and this investment strengthens our commitment to a country served by Repi for over 40 years”, comments Filippo Angiolini, Repi Group CEO. www.repi.com","@ID":9} "MATERIALS / RECYCLING PETplanet Insider Vol. 22 No. 04/21 petpla.net 16 Technology for recycling PCR PET trays Recovering the iV loss The global trend towards increased post-consumer recycled (PCR) content, in water and carbonated soft drink segments especially, has driven up demand for clear PCR PET bottle flakes. A shortage of supply has led to increased prices for PCR and the search for additional sources. Starlinger viscotec’s solution is to source, process and prepare PET tray flakes for recycling. PET tray flakes are currently underutilised; only around one-fifth of PET thermoformed materials, such as clamshells, cups, trays, or boxes, are recovered from the recycling stream in Europe, according to Plastic Recyclers Europe, eunomia report, 2018. The situation in the US is very similar, according to Napcor. “Post-consumer thermoforms are generally not captured in the PET recycling stream,” Jeff Cornell, Vice President of Sales at Starlinger-Sahm, Inc., observed. “This is changing with new legislation and improved technologies to sort out this valuable material.” The Plastic Recyclers Europe association estimates that more developed reprocessing routes can enable PET trays to be collected and recycled at a similar rate to overall plastic packaging. Starlinger viscotec say that recyclers are now preparing recycling lines for processing it. However, it has lower intrinsic viscosity (iV) and needs pre-treatment. Tray to tray recycling requires the intrinsic viscosity of the sheet and the final thermoformed packaging to be maintained at an optimal level. When Starlinger viscotec presented deCon iV+ in 2019, it described it as a turnkey solution to close the tray recycling loop. “With viscotec’s experience, we are poised to meet the demand for true tray to tray circular economy requirements with the deCon iV+: offering crystallisation, super cleaning decontamination and IV increase, all in one unit,” Cornell said. Starlinger reports that it has sold its new decontamination dryer to customers in the US, Great Britain, Poland, Japan, Germany and Italy. The deCon iV+ is designed for the production of dry, iV increased, crystallised, de-dusted post-consumer flakes. The unit processes thermoform flakes, bottle flakes, or in-house skeleton waste and is installed directly in front of a production extruder. Intrinsic viscosity is increased in the deCon iV+ in every recycling cycle; IV losses are recovered while quality is kept at an optimal level. Starlinger viscotec says that the technology delivers decontamination of PCR materials that exceed EFSA and FDA standards, while increasing IV for dedicated tray recycling. The equipment processes on a FIFO (first in-first out) basis. deCon iV+ is also claimed to offer excellent de-dusting as well as drying below 50ppm and good colour values. www.viscotec.at Jeff Cornell, Vice President of Sales at Starlinger-Sahm, Inc. deCon iV+ decontamination unit","@ID":18} "BOTTLING / FILLING PETplanet Insider Vol. 22 No. 04/21 petpla.net 23 zone, in a previously sterilised package. It differs from traditional aseptic technology because the package sterilisation takes place at the preform rather than at the bottle phase. It offers a sterilised blowing process as well as fast and safe product and format changeovers with limited manual intervention for continuous aseptic production time up to 200 hours. Plus, the producer can lower its Total Cost of Ownership (TCO) as the Versatile Aseptic Combi Predis does not use any water and very few chemicals (less than 0.7 l of H2O2 per hour) for preform sterilisation. GAWiSD featuringAutoJob ™ – job set up in seconds +1.724.482.2163 AGRINTL.COM ACCURATE • FAST • REPEATABLE SEE GAWIS4D IN ACTION Dimensional and thickness measurements for plastic containers and preforms. ® The sparkling drinks are produced with a Sidel carbonator that adds carbon dioxide (CO2 ) after the beverage processing phase. With this integrated carbonation just before filling, the dosing performance is optimised, allowing accuracy, reduced product waste and improved beverage stability. Moreover, it ensures one aseptic treatment for both still and carbonated products. PET bottle designs Sidel not only provided the Versatile Aseptic Combi Predis, but they also partnered with Sangaria for the PET bottle designs of their products. Sangaria wanted to keep the same brand identity critical for recognition purposes, and Sidel therefore supported them in adapting the bottles they were handling in hot-fill to aseptic production. Thanks to the dry preform sterilisation solution they could also lightweight some of their bottles up to 30%, as this system does not require any thermal treatment of the blown bottle. www.sidel.com Versatile Sidel Aseptic Combi Predis can both handle aseptic carbonated and still drinks in PET bottles on the same line. Sidel’s integrated aseptic blow-fillseal solution, Aseptic Combi Predis, includes the dry preform sterilisation.","@ID":25} "PETcontents 4 PETplanet Insider Vol. 22 No. 04/21 petpla.net 04/2021 Page 36 Page 10 Page 62 TOP TALK 10 Complete production lines from China - From single machines to turn-key solutions MATERIAL / RECYCLING 14 Taking a holistic approach to PET packaging with AWArPET 16 Recovering the iV loss - Technology for recycling PRC PET trays PREFORM PRODUCTION 18 “We are providing solutions based on application” Hot runners for the plastic industry 20 A closed loop for PET preforms - Voices from industry experts of Alpla und Gneuss BOTTLING / FILLING 22 When aseptic matters - Sangaria tackles green tea and sparkling water boom 24 Enough plastic to re-use it - A sustainable solution at Ice River Spring MARKET SURVEY 31 Suppliers of preforms and preform inspection systems PACKAGING SPECIAL 35 Shrink film made of 100% recyclate 36 Layer by layer - Next generation case packer featuring collaborative robort automation system 38 New filler for Central and Eastern Europe - Thermo-Pack rises to Covid challenges 40 US PET packaging market - Set to recover from Covid-19 to face sustainablility challenge 42 Packaging PET products TRADE SHOW PREVIEW 28 ‘Instead of NPE 2021’ products 29 Increased service portfolio 30 Overmoulding Cube applications TRADE SHOW REVIEW 46 Introducing the new Netstal PETline with sideways removal system - Pandemic-compliant hybrid event concept for market launch 48 Kick-off ceremony of Chinaplas in Shenzhen DIGITALISATION 52 Spare parts 24/7 - Swiss company Bevazar offers food and beverage companies their own dedicated, digital sales channels CERTIFICATION 53 “More work is required to drive harmonisation” - Interview with Fabricio Di Georgio, Technical Director at PRE BUYER’S GUIDE 56 Get listed! INSIDE TRACK 3 Editorial 4 Contents 6 News 54 PET bottles Beverage + Liquid Food 62 Outer Planet PACKAGING","@ID":6} "CERTIFICATION PETplanet Insider Vol. 22 No. 04/21 petpla.net 53 More work is required to drive harmonisation PETplanet Insider talked to Mr Fabrizio di Gregorio, PRE Technical Director about the Recycled Plastics Traceability Certification PETplanet: Generally speaking, how does this certification work? Di Gregorio: Recycled Plastics Traceability Certification recognises the actual use of recycled plastics in finished or semi-finished products in a transparent manner. It allows for an adequate determination of any share of the recycled material, via a percentage-based calculation. It is destined to any company which plays a part in the value chain and holds custody of the recycled plastics including but not limited to compounders, converters, blow moulders and brand owners. The Certification guarantees the verifiability and traceability of the material along the different actors, up to the consumers. In practice, it attests to the origins, sourcing, recycling processes and incorporation of the material in the final product. This practice is ensured via and based on the Chain of Custody approach as well as the Recycled Plastics standards. Within such a system the ownership and the certification are verified and passed from one actor of the value chain to another. Chain of Custody, among others, guarantees the traceability and origins of waste. This in turn means that the certification must be paired with a scheme that transparently verifies that information. Additionally, to guarantee its full impartiality the Certification has an inbuilt independent audit system. It brings confidence in the use of recycled material not only to the value chain but also to consumers. Via its labelling system, the certification allows for providing clear messages destined to end-users who can make conscious choices about the environmental impact of the products they buy. PETplanet: What are the points where your clients most often struggle/ what are the biggest challenges? Di Gregorio: The companies strive to make their products more sustainable and are looking for trustworthy and wellreputed schemes to prove their claims to the consumer, as any environmental claim must be easily verifiable and reliable. To be considered green or environmentally friendly, such claims must be based on easily verifiable, transparent certification schemes and not based on self-claims. This is necessary to ensure a level playing field and to deliver on the goals of the circular economy. The key here is that such a claim reflects reality (i.e., the actual level of recycled content, waste source, level of recyclability, without making any estimations or assumptions). Secondly, it must be endorsed by a third-party body that will attest its authenticity. Lastly, it must be easily verifiable by consumers – ensuring its full transparency. RecyClass is equipped with certifications that allow for making such verified and trustworthy claims for both recycled content and recyclability. PETplanet: What are the advantages for the certified companies? Di Gregorio: With the upcoming regulatory requirements at the EU level which call for a structured, consistent, and transparent approach to recycled content verification, it is now of utmost importance to ensure that they are guided by verifiable and tangible principles. This will bring clarity and eliminate void environmental claims used purely as a marketing tool without genuinely reducing the impact on the environment. This is where the Recycled Plastics Traceability Certification comes into play. It recognises the actual use of recycled plastics in finished or semi-finished products in a transparent manner. RecyClass Recycled Plastics Traceability Certification allows for an adequate determination of any share of the recycled material, via a percentage-based calculation. Another benefit is that it is destined to any company which plays a part in the value chain and holds custody of the recycled plastics including but not limited to compounders, converters, blow moulders and brand owners. PETplanet: How do you see the future of the European plastics recycling market? Di Gregorio: RecyClass’ mission, beyond supporting the industry in redesigning plastic packaging and boosting recycled material in new products, is to harmonise the approach of recyclability assessment and recycled content calculation – the genuine drive for circularity of plastic packaging in Europe. The shelves of European retailers are very similar in different EU countries; we often find the same products. Why should not we find a common approach to recyclability, collection and sorting systems? One of the aims of the RecyClass is therefore to harmonise recyclability definition, approach to design-for-recycling guidelines, recycled content source and share and methodologies behind these documents. To give an example, without finding a common ground for what is currently recyclable, it is impossible to reach a consensus on which kind of products are genuinely compatible with state-of-the-art mechanical recycling technologies. As a result, Plastics Recyclers Europe (PRE) and the Association of Plastic Recyclers (APR) developed a global recyclability definition. It stipulates that to be considered recyclable, a product must be able to be collected and sorted in sufficient quantities. At the same time, it must be compatible with existing industrial recycling processes, or be available in sufficient quantities to justify the development of new recycling processes to become a raw material for new products. The definition allows for the establishment of a global and harmonised approach by providing a common direction for the industry. However, more work is required to drive harmonisation. This additional work must focus also on harmonising the different documents including design for recycling guidelines or protocols. RecyClass works on guidelines for the so-called “recyclability and recycled content claims”, i.e., a set of instructions on how to report correctly on the recyclability and shares/type of recycled plastic in packaging. If we consider that the platform includes the main world FMCG brands, it is easy to imagine how this document could become a sort of shared specification. Going a step ahead, RecyClass collaborates with many like-minded organisations in Europe and strives for harmonising the existing guidelines and reporting on recycled content to allow for one set of rules that should be applied to lead on a common approach within the EU market. www.recyclass.eu","@ID":55} "PETplanet Insider Vol. 22 No. 04/21 petpla.net 55 BOTTLES Vöslauer Junior in 100% rPET Vöslauer Mineral Water has redesigned its natural mineral water bottles for kids. The easy-to-grip, tapered 0.33 l bottles now consist of 100% rPET and are lightly coloured to make the product more attractive to children. The bottles are secured via tamper-proof hinged press-down lids with drinking spout. www.voeslauer.com Immune-supporting drinks from Aldi South For a limited time only, Aldi South is selling three immune system-supporting drinks under their own “Westminster Tea” label and are available in caloriefree and low-calorie varieties. Each drink contains zinc and vitamins B6 and C and comes in a clear 500 ml bottle with a conveniently-sized spout, a film label and coloured screw cap with tamper-proof strip. The drinks are produced by the Austrian company, S.Spitz. ww.aldi-sued.de A protein drink from dm The German pharmacy discount firm, dm, is selling a protein drink under its “Sportness” brand which comes in a tapered, clear 500ml deposit bottle made from 100% recycled material. The sugar-and lactose-free drink with the taste of blueberry cassis contains 20g of protein per bottle. A shrink sleeve label provides consumer information, with a red screw cap and tamper-proof strip completing the sports drink’s appearance. www.dm.at “ ”","@ID":57} "TOP TALK PETplanet Insider Vol. 22 No. 04/21 petpla.net 12 refreshment. Representative products such as Dali Group’s peanut milk and Panpan Group’s raw coconut juice are typical products bottled using aseptic technologies. In 1999, we became the first supplier in China to engage in aseptic technology. Building on our experiences and continuous improvement through six generations of aseptic technology, we initiated, developed and launched our 7th generation aseptic equipment, which features integrated combiblocs and high speed lines. Newamstar offers a complete range of sterilisation, including wet, dry and e-beam technologies. PETplanet: What do you see as the general PET trends, today and in future? Tony Ho: PET is still the most widely used beverage package format. Its recyclability is way better than paper, glass and metal. Demand for PET is growing in non-food sector, such as cleaning chemicals and homecare, an area where we developed good relationships with manufacturers. PETplanet: The Covid-19 pandemic caused the whole world to stop. Whilst China was able to control the virus in a short time, other countries and regions globally haven’t. What does that mean for you as a Chinese supplier with a global customer base? Tony Ho: We expect that the world economy will emerge from the impact of the Covid-19 pandemic gradually. After the pandemic was controlled in China, Newamstar recovered production and operation quickly and was soon able to resume good standards of service for our customers in China and around the world. PETplanet: Did you encounter issues affecting supply for your products or difficulties in logistics, for example? Tony Ho: Logistics and transportation were somewhat affected but control of the situation has seen the impact essentially eliminated. PETplanet: How did the pandemic affect your daily work in your HQ? What arrangements did you implement to ensure safety? Tony Ho: Our company recovered production and operation quickly and was able to maintain on-time delivery. Our intelligent remote service and online service systems, introduced in 2016, provide customers with remote technical support and assistance. The system helps reduce support waiting time and has improved customer service responsiveness and efficiency. Our technical support centre is accessible online, 24/7, for customers in China and abroad. PETplanet: How do you deliver after-sales and service on-site, at customers facilities? Tony Ho: New technologies, such as 5G, big data, industrial internet of things (IIoT), Cloud computing, AI and so on, are deeply integrated with the real economy and facilitate digitalisation, networking and intelligent factories. We have already developed an intelligent service system for customers, which provides remote technical support and assistance. During the pandemic, installation, commissioning and maintenance of several projects outside of China were carried out smoothly through that system. PETplanet: In many cases customers also need service support in person, on site, in their factories. Do you still face that sort of demand from your customers as well, is it just a small portion or is it not even really necessary anymore, because of your remote and online services? Tony Ho: Currently, the proportions of on-site and remote service support vary in different regions. In the future, with the upgrading of the service system and improvement of the technical level of the operators, more and more on-site service support will be replaced with remote services. We are already finding that our intelligent remote service system is being relied upon by a growing number of customers. PETplanet: What do you, as an industry leader, think the situation could develop, now that there are vaccines available? Tony Ho: It is believed that the pandemic will be further controlled as the availability of vaccines increases. The international business communication environment will be safer and more stable, which will lay the foundation for global economic recovery. PETplanet: When do you think the world will be ‘back to normal’? Tony Ho: According to the World Health Organisation (WHO), the global roll-out of vaccines are leading to the pandemic being controlled more and more effectively. However, we cannot predict when it will come to an end. We still need to do a good job in pandemic prevention and control, maintaining production, operation and customer service. PETplanet: What major changes, on both the industry and customer sides, do you expect to see when the pandemic is over? Tony Ho: Digital transformation and AI are already happening. We expect the food and beverage industry to speed up its deployment of intelligent manufacturing technology and Juice ultra-clean blowing-filling-capping production line","@ID":14} "BOTTLING / FILLING PETplanet Insider Vol. 22 No. 04/21 petpla.net 22 Sangaria tackles green tea and sparkling water boom with Sidel’s aseptic PET packaging solution When aseptic matters To handle aseptic carbonated and still drinks in PET bottles on the same line was the intention of Japanese beverage company Sangaria when acquiring Sidel’s Aseptic Combi Predis. This investment is also intended to support Sangaria to widen its production portfolio in the future. In Japan, the local, fast-ageing consumer base is becoming increasingly health-conscious. For food and beverage producers, this puts an increasing focus on the introduction of new, added-value products and demands a careful tailoring of the existing ones to tackle specific needs and expectations around health and packaging functionalities. Alongside, premiumisation is also projected to show strong development in this market. According to Global Data 2020, enhanced and flavoured water, as well as tea and energy drinks, are the best performing beverages in Japan with substantial forecast growth in the upcoming years. Seasonality, as a key purchasing factor, plays an important role for these beverages, as sparkling water is particularly preferred in summer, but green tea and coffee are more popular in the winter season. Therefore, Sangaria is continuously innovating to diversify its portfolio of drinks, which includes many soft drink brands infused with vitamins and marketed for their health benefits. The company’s motto ‘Sangaria, always searching for natural beverages’ summarises this business strategy. From hot-filling to aseptic Initially, Sangaria was using hot-fill technologies to manufacture its sensitive beverages like green teas and juices. When the company decided to increase sales with milk-based products in 2011, moving to aseptic PET production was chosen as a better choice. For this strategic step, Sangaria turned to Sidel. Sangaria’s CEO, Ishiyama san, was personally involved in the decision and visited different Sidel customers active in aseptic beverage manufacturing. Sangaria became the first bottling company in Japan to acquire the Aseptic Combi Predis, the Sidel integrated aseptic blow-fill-seal solution including the dry preform sterilisation. Increased production capacity The main objective for Sangaria was to invest in a new aseptic PET packaging line, able to produce sparkling water, carbonated soft drinks (CSD) and still beverages while offering production flexibility for new product launches in the future. As carbonated beverages, including sparkling water and green tea, are booming in Japan, Sangaria was looking for an increase in its production capacity. With the Sidel Versatile Aseptic Combi Predis, they enlarged their capability to produce still beverages and CSD aseptically in PET bottles on the same line. This allows increased production flexibility with the same filling magnetic valve to aseptically handle all sensitive low and high acid products with no need for valve changeovers while ensuring reliability and product integrity. Sangaria now can manage various milk-based products and barley green tea – previously bottled on hot-filling lines – as well as healthy sparkling water in 500 ml and 1 l containers. With the new filling line, Sangaria is running the production of 500 ml bottles at 24,000 bph. The production flexibility is also enhanced with the toolless mould changeover, the Bottle Switch, which enables fast interventions. Sterilised blowing process The technology at the core of the Sidel Versatile Aseptic Combi Predis merges dry preform sterilisation with aseptic blowing, filling and sealing functions within a single production enclosure. As such, it respects the fundamental concept that underpins state-of-the-art aseptic packaging rules: producing a commercially sterile product, filled in a sterile Enhanced and flavoured water, as well as tea and energy drinks, are the best performing beverages in Japan.","@ID":24} "PREFORM PRODUCTION PETplanet Insider Vol. 22 No. 04/21 petpla.net 19 Overall, co-injection is the better solution to achieve sustainability goals, plus it brings savings in costs and flexibility to run small scale production. PETplanet: While observing the market where do you see market trends? Igor: The main market trend in the packaging and of course in the PET industry can be summarised in one word: sustainability. Everybody wants to have a sustainable solution, but without any cost increase, nor capital investment. Another trend is e-commerce, demanding that the packaging has to be lighter but also stronger because of handling. The shelf life is also a very important topic, even now during the pandemic where products needs to be shipped worldwide. This means that the packaging has to increase barrier properties. A third trend I would like to mention is the time of product changes. Brand owner and packaging companies are bringing many different shapes in the market, this means a new kind of equipment is required. Small scales are produced to test, this means addition capital investment. The return of this has to come as fast as possible. This is where Mold-Masters has the right solution to the industry: Co-injection Connect delivers a wide process window to mould bio-resins, challenging engineering resins and high content of PCR. On the cost side, we are offering dedicated solutions based on two criteria: How to reduce investment and to ensure that the running costs are as low as possible. www.moldmasters.com www.milacron.com PETplanet Insider talked withRussell Gray, Chief Operations Officer at NGOC Nghia Industry , Vietnam, about his Mold-Masters equipment: PETplanet: How long has MoldMasters been a customer of NNI? And why do NNI decide to work with them? Ngoc Nghia Industry - Service - Trading Joint Stock Company (NN) is a leading PET converter in Vietnam, specialising in bottle blow-moulding, injection moulding, and cap compression moulding. Founded in 1993, NN is a leading company in PET manufacturing with modern PET packaging production lines in Vietnam. NN have achieved a commanding position within the Vietnam market, one out of every three PET bottles in the market is produced by NN. The success harvested from their core business which has allowed NN to diversify to the manufacturing of plastic closures, with a specific focus on compression cap moulding. NN’s standards are backed by the certification of FSSC 22000 Certification, HACCP Certified, BRC Food Certified inclusive of Cosmetics and Packaging, Halal Certified; therefore, more than 1,000 companies from various industries have trusted and chosen NN as their strategic packaging partner. Russell: After I joined NNI in May of 2018, we started discussions on this project with Mold-Masters in Q4 of 2018. NNI had made a strategic decision to invest in new technologies to meet the demanding and evolving requirements of the rigid packaging industry and provide advantaged technical and cost effective solutions to our customers. I was aware of the Mold-Masters Connect solution, knew that this could be applied and developed for preforms and would be a perfect entry level solution to adapt to our existing preform systems for multilayer preforms. PETplanet: What technologies do you use at NNi and for what kind of application are they used? What are the advantages of using Mold-Masters technologies? Russell: NNI has a significant number of Husky and Niigon preform systems, Sacmi systems for closures, Sidel, Blomax, Sipa and Techlong blowers as well as ASB single stage machines for bottles. We have moulds and hot runners from Husky, Stackteck/ Yudo and GDXL for our preform business; Mold-Masters offered a solution that was not available from our existing partners including a well established hot runner solution for co-injection preforms. The E-Multi unit had a similarly proven track record in the market so we felt comfortable choosing Mold-Masters as a partner. PETplanet: Are you satisfied with the machines and the service from Mold-Masters (MM)? Russell: The overall project from concept to the system integration and acceptance in Canada and final start-up and acceptance in Vietnam has been a great experience. MM drew on people from across their company to ensure the project was a success. The real challenge came with the installation and start-up in Vietnam in a year with Covid. MM worked with our technical team to provide remote start-up support including detailed instructions on installation and start-up as well as on-line support. Our team was able to successfully install and operate the Mold-Masters Connect having never seen the equipment and without training. Installation to preform acceptance was completed in less than 2 weeks and our team was very impressed with how user friendly the interface and controls were to use and the robust construction of the hardware. Their team also worked closely with our QA team on the detailed inspection process for co-injection preforms including validation of our results with samples sent to their own QA Lab in NA. PETplanet: Are there plans for future cooperation? Russell: We continue to work with MM on a number of applications for our co-injection preforms and they are always more than willing to engage and provide support on this. As the demand for co-injection preforms increases we are confident that MM can provide scalable higher cavitation systems for our existing machines. www.nnc.vn Niigon 150NPET with a 32 cavity coinjection hot runner and E-Multi from Mold-Masters.","@ID":21} "TOP TALK PETplanet Insider Vol. 22 No. 04/21 petpla.net 10 From single machines to turn-key solutions Complete production lines from China Equipment manufacturer Jiangsu Newamstar Packaging Machinery is headquartered in Jiangsu Province, around 130 km north-west of Shanghai. Since the early 2000s the company has evolved from a local filling machine producer to become a world-renowned turnkey supplier that covers the whole packing process chain, from water treatment, blowing and filling up to downstream and logistics. We met Mr Tony Ho, Vice president, and spoke with him about Newamstar’s crucial milestones. PETplanet: Newamstar has become an internationally recognised all-in-one solutions supplier for liquid processing, packaging and storage systems. The company began in the mid-90s with filling equipment and expanded associated manufacturing and packaging processes over the following years. What were the main strategic steps that led your company to where it stands today? What is the story behind its success? Tony Ho: Technology innovation has always been regarded as core to competitiveness right from the beginning, from when the company was established. Newamstar started with a single filling machine in the product range. Since 2003, our product portfolio has been extended from that single machine to a complete production range, aligned with market trends. Newamstar aims to be recognised as China’s leading, expert company for beverage packaging machines, providing high quality equipment as well as complete turn-key projects. Since 2006, Newamstar has been active in five key markets: beverage, dairy, alcohol, edible oils and chemical cleaning products. Over time, we have been recognised as a leader in high-end liquid packaging machinery in China. In 2016 we got involved in smart logistics, a new area for us and for much of the market. We developed a full-service solution that integrates production and inventory in our industry. Throughout our existence, we have retained true to the vision that development is driven by innovation and market share is gained by quality. Our focus remains on food and beverage machinery; we are aiming to become the world’s leading integration solution supplier for liquid processing, packaging and storage. PETplanet: When did Newamstar turn from a domestic to an international equipment supplier? Was there any key event that prompted this development? Tony Ho: China joining the World Trade Organisation (WTO) in 2001 provided a good opportunity for more and more Chinese companies to enter the global market. We closely watched market trends and projected developments from the early stages of WTO membership; our R&D, standards management, market and technology strategies are conducted in line with world developments. Consequently, co-operation developed between Newamstar and global enterprises like Nestlé, Pepsi-Cola, Coca-Cola, Danone, Otsuka, Wilmar, Mayora, Kraft Heinz, ITO EN, Oishi, Tsingtao and so on. We have grown into a global equipment supplier. PETplanet: How many Newamstar machines are currently installed and running across the world? Tony Ho: We have provided more than 2,200 production lines, in more than 80 countries and regions. PETplanet: Apart from your domestic market, where has Newamstar sold most of its machines? Blowing-labellingfilling-capping Starbloc Vice President Mr Tony Ho by Kay Barton","@ID":12} "TRADE SHOW PREVIEW PETplanet Insider Vol. 22 No. 04/21 petpla.net 29 Instead of Increased service portfolio At NPE, Spanish blow moulding specialist Urola would have presented its increased range of services; Urola Performance, Urola Design and Urola Teleservice. Urola Solutions offers a variety of 100% electric and compact linear PET stretch blow moulding machines for medium production needs. The machine range, all under the name of URBI, goes from 2 to 8 cavities and it has a capacity to produce from 2,000 up to 13,000bph for bottles and jerrycans of a capacity of up to 10l for any type of application reaching outputs of 5,000 containers/hour. But, beyond improvements and additional developments on the equipment, for several years now, Urola has increased its service portfolio with the aim of offering a more complete and higher quality service to its customers. These services Urola Performance, Urola Design and Urola Teleservice are the result of combining advanced technologies with a 40-year knowledge and experience in the blowmoulding industry. Urola Design Urola Design is an integral service covering the bottle, moulds, process, and industrialisation through a collaborative dynamic that takes into account our know-how on blowmoulding technology, a focus on technical feasibility and cycle optimisation, guaranteeing the manufacturability of the container. Helping customers to position themselves in the market, defining the packaging together and accompanying them in the manufacturing process once the bottle has been prototyped and accepted. Urola Performance Urola Performance is a productivity improvement service through a digital platform with which the process and operating data of the plant / line are captured and analysed. This is a proactive service that improves the performance of the customer´s business. A comprehensive service that monitors, analyses and proposes improvement interventions assuring an encrypted communication. Urola Teleservice This is a remote assistance service, which gives the possibility of one of Urola´s engineers to assist remotely the machine or the operator. The communication with the operator is based on an AR (Augmented Reality) technology which includes a video camera, drawing tools, a simultaneous translation chat and driving, sharing and tracing tools. It is easily used on a smartphone, tablet or smart glasses. In case of the direct machine assisting option, there is the possibility of accessing any equipment connected to the machine’s network using encrypted communication channels from point to point or VPN. To illustrate the achievements obtained using Urola Performance, a highlight is the case of one of the biggest processors of dairy products in Spain using one of the company’s blowers, URBI-4 series, producing two bottle sizes. By monitoring through the cloud the operation of the line, analysing the main reasons for inefficiencies due to various external factors and applying the necessary recommendations and correctives actions, the OEE (Overall Equipment Effectiveness) of the line was increased to 96% on average, having increased also the machine capacity by 19%. www.urola.com • Food grade • Superclean • High iV Closing the PET loop Upcycle post-consumer bottle and tray flakes with Starlinger viscotec rPET solutions viscotec.at foodgrade without compromise","@ID":31} "PACKAGING / PALLETISING PETplanet Insider Vol. 22 No. 04/21 petpla.net 35 Sustainable alternative for secondary packaging Shrink film made of 100% recyclate Day after day, valuable plastics are lost from the recycling loop. At the same time, the demand for resource-conserving packaging systems is constantly on the rise. By enabling film made entirely of recycled material to be processed on all KHS shrink packers, the KHS Group now provides a further sustainable alternative for secondary packaging. Martin Thyssen, packaging expert for cardboard, paper and shrink film at KHS. “Consumers, retailers and the food and beverage industries are increasingly calling for environmentallyfriendly packaging systems that aren’t merely recyclable but also made of recycled materials,” says Martin Thyssen, packaging expert for cardboard, paper and shrink film at KHS. With the option of now processing shrink film made of 100% recyclate, the KHS Group meets this demand and adds a further sustainable alternative to its packaging portfolio. With immediate effect, the use of film made entirely of recyclate is possible on all KHS shrink packers in the TSP, WSP, SP and PSP series. Thanks to their modular design, existing machines can be easily adapted. Fully recycled film is suitable for use with both PET and glass bottles as well as beverage cans. KHS offers manufacturers who work with their own film suppliers a wide range of services. “At our inhouse laboratory we can test whether the film destined for use is compatible with our machines,” explains Thyssen. Experienced KHS service engineers are also on hand to assist their customers with commissioning directly on site or through remote services. Using recycled film is to the operator’s advantage in several respects. “On the one hand, compared to new material it reduces the carbon footprint by up to 65%, according to market information supplied by various film manufacturers, and this thus helps to significantly save on resources,” Thyssen states. On the other, bottlers would then be prepared for the planned changes to legislation in some countries regarding fixed quotas. In Great Britain, for example, by April 2022 plastic packaging must be made up of at least 30% recyclate. France is already one step further: since January 1, 2021, throughout the entire country plastic packaging must contain at least 50% post-consumer recycled materials. In both states, companies face increased taxes should they undershoot these quotas. It cannot be denied that the use of film made of recycled material is more expensive than conventional new film. Experience shows that up to 10% in additional costs are incurred for 50% rPE, with this surcharge rising to a maximum of 15% for 100% rPE. However, Thyssen is convinced that the benefit of acting sustainably by using recycled film overrides the increase in expenditure – especially when failing to meet statutory thresholds means paying environmental taxes in the future. www.khs.com PACKAGING Innopack Kisters SP: Film made of recycled material can now be used on all KHS shrink packers, including the flexible Innopack Kisters SP. Fully recycled film is suitable for use with PET and glass bottles as well as beverage cans.","@ID":37} "PETplanet Insider Vol. 22 No. 04/21 petpla.net 49 TRADE SHOW REVIEW expand and enhance its applications, the quality of plastic products and services, following to the expansion of the consumer market. The industry will continue to strengthen environmental development. Su Dongping, Executive Deputy President of China Plastics Machinery Industry Association Ms Su Dongping, Executive Deputy President of China Plastics Machinery Industry Association, presented on the Development Status and Prospects of China’s Plastics Machinery Industry. During the 13th Five-Year Plan, revenues reached RMB81billion (US$12.4 billion), at an average annual growth rate of 5.7%. Average annual growth in export value, major business income, total profit, and research and development expenses of the leading plastics machinery companies reached 6.34%, 10.03%, 11.33%, and12.11% respectively. During the 14th Five-Year Plan, annual revenues may well exceed RMB100 billion (US$15.3 billion); they and total profits are expected to grow by over 6% annually. R&D investment will account for more than 6% of business income and professional technical personnel will account for more than 25% of industry employees. In his presentation on Europe’s Plastics Machinery Industry - Economic Situation and Sustainability Goals 2020/2021, Mr Thorsten Kuehmann, Secretary General of Europe’s Association for Plastics and Rubber Machinery Manufacturers (Euromap) said that the industry is in good shape, overall. Plastics and rubber machine sales grew by 7% in 2020, despite plastics’ image being under pressure. The industry has to drive towards the circular economy and to get across the message that plastic is good for climate. Fu An, President of the Guangdong Plastics Industry Association Mr Fu An, President of the Guangdong Plastics Industry Association, presented on the Development of & Forecast for the Plastics Industry in the Greater Bay Area. China strongly supports the development of the Area, as evidenced by the Outline Development Plan for the Greater Guangdong-Hong Kong-Macao Bay, implemented in February 2019. The Guangdong Provincial Key Construction Project Plan in 2020, issued by the Guangdong Provincial DevelopWhether it is inhouse, postconsumer or bottle recycling: you can only close loops in a precise and profitable way if machines are perfectly tuned for the respective application. Count on the number 1 technology from EREMA when doing so: over 6000 of our machines and systems produce around 14.5 million tonnes of high-quality pellets like this every year – in a highly efficient and energy-saving way. WE DRIVE THE CIRCULAR ECONOMY. CHOOSE THE NUMBER ONE. VISIT OUR virtual showroom ShowHello! 2103029ERE_PETplanet.indd 1 24.03.21 09:54","@ID":51} "TRADE SHOW REVIEW PETplanet Insider Vol. 22 No. 04/21 petpla.net 50 ment and Reform Commission, said that there are more than 400 projects in the nine cities of the Greater Bay Area, with a total investment of more than RMB2.8 trillion (US$ 428.1 billion). These projects involve automotive, smart manufacturing, new materials, home appliances and commodities. These industries offer a huge market for the plastics industry and demonstrate good prospects for sustainable development. In addition to the representatives of industry associations, representatives of exhibitors and buyers participating in Chinaplas also discussed the business opportunities arisen from the development in the Greater Bay Area, as well as demands for new technologies. Mr Li Jianjun, Director & CSO of Kingfa Sci. & Tech. Co., Ltd. delivered a speech on the Sustainable and Innovative Development of China’s Plastics Industry, in which he shared his views on sustainable development and the prevention and control of plastic waste pollution, as well as his experience in green and low-carbon circular development and addressing aspects of degradation, reuse and recycling. Kingfa produced more than 1.2 million tonnes of quality recycled plastics from 2004 to 2019. James Zhang, General Manager of Yizumi IMM Division, Director & DGM of Yizumi Group The Application-driven, Smarter Future presentation, delivered by Mr James Zhang, General Manager of Yizumi IMM Division / Director & DGM of Yizumi Group, Guangdong Yizumi Precision Machinery Co., Ltd., highlighted a range of environmental protection trends, including lightweighting, personalisation, multifunctionality, recyclability, degradability, energy savings and emission reduction. Automation, smart machines, industrial interconnection and digital transformation should help to reduce cost and enhance efficiency, providing new functions and stimulating new demand for industrial development. The company exhibited applications and technologies including injection moulding and intelligent factory solutions. Ms Christine Li, Marketing Manager of Arburg (Shanghai) Co., Ltd., introduced Arburg’s exhibits such as a pipette tip, LSR lens for car lights and lightweight-FDC, digital and intelligent PM. Mr Gence Shi, the R&D Director of Lenovo Research Institute, said that the demand for special dielectric materials, high-strength and weightreducing materials, environmentally friendly, healthy, and degradable, recyclable/antiviral materials, etc. has soared significantly. From 4G to 5G, consumer electronics materials have","@ID":52} "BOTTLING / FILLING PETplanet Insider Vol. 22 No. 04/21 petpla.net 24 A sustainable solution at Ice River Spring Enough plastic to re-use it “Our philosophy is based on the three Ps: people, planet, and profit.” Howe firmly believes that coordinating the three Ps is crucial. “PET and plastics in general have been getting a lot of negative attention lately worldwide. But Ice River Springs is already ahead of the game. By completely reusing PET plastic in a closed loop, we’re being part of the solution.” The year 2009 was an important one for Ice River Springs as the company received a permission to use 100% recycled PET plastic in its water bottles. “We were the first bottler in North America to produce food-grade recycled PET and use it to manufacture 100% recycled content bottles. We’re still the only one to maintain a closed loop today,” Howe says with visible pride and she adds, “We’ve done it to protect the environment. What’s special about our company is that we don’t base our decisions primarily on cost but rather on sustainability.” Closed plastics loop Sandy and Jamie Gott tried a few different options before deciding to produce their own recycled PET. “PLA (polylactic acid) couldn’t offer the shelf life we needed, and it gave the water an off taste. Carton-based packaging isn’t easily recyclable and has a much larger carbon footprint,” says Howe. “We then started to use recycled PET, but the quality of the pellets we were buying on the open market wasn’t very consistent from batch to batch. So, my parents decided to build their own recycling plant and produce their own rPET.” The company’s Blue Mountain Plastics plant now converts 25,000 metric tons of post-consumer PET material a year into food-grade resin pellets. Ice River Springs buys around 80% of the total volume of PET plastic collected by municipal recycling programs in Ontario for this purpose. Three of the company’s seven bottling plants are equipped with injection moulders that turn the recycled pellets into preforms. All seven plants have Contiform blow moulders that inflate the preforms into bottles. Ice River Springs also manufactures its own caps and printed shrink films, which already contain 20% recycled material. The company’s subsidiary C.R. Plastic Products transforms HDPE cap material, that is collected through the recycling line, into durable outdoor furniture. Every addition to the Ice River Family of Companies drives forth the belief that “there’s enough plastic in the world – we need to re-use it.” 108,000 containers per hour Until recently, Ice River Springs had used one Krones/Kosme filling line for 4 l containers and another for 500ml bottles (which included a Contiform blow moulder) at their Lachute plant, west of Montreal. Since the 500ml line was no longer able to keep up with increased demand, Ice River Springs has now replaced it with a twin line featuring two ErgoBloc L systems that can process a total of 108,000 containers per hour. “We don’t have a lot of space here in Lachute. So this line’s compact layout was a perfect fit,” says Howe. The line isn’t Ice River Springs’ first high-speed line from Krones. Back in 2002, the company installed one at its home base in Feversham. In 2016, they replaced that line with a new one featuring an ErgoBlocL for blow moulding, labelling, and filling 81,000 containers per hour. The Miami plant has also had a 108,000bph twin line from Krones in operation since 2018. That line is identical to the one just commissioned in Lachute. High-speed twin line In designing this turnkey line, Krones combined two 55,000bph block systems for the wet end to bring the total capacity up to 108,000bph. Each ErgoBloc L system consists of a Contiform 3 Pro stretch blow moulder, a Solomodul labeller with four Contiroll HS stations, a Modulfill VFJ filler, and a Checkmat FEM-X inspector. The two streams converge in the dry end, where the finished PET containers are processed. The Variopac Pro FS packer produces shrink packs in four different sizes. Palletising is being handled by a Modulpal Pro 1AD with a Robobox grouping system. The ErgoBloc L meets all of Ice River Springs’ expectations in terms of sustainability: “The machines process recycled PET plastic preforms with no problems,” explains Howe. “The bottles run as if they were made of virgin PET. We have actually had Krones technicians comment on how well the preform processes.” Crystal Howe, Sustainability Manager Ice River Springs As Sustainability Manager at Ice River Springs Co. and Blue Mountain Plastics, Crystal Howe has, of course, made sustainability a top priority. But she’s not alone. The entire company shares her passion.","@ID":26} "MARKET SURVEY 33 PETplanet Insider Vol. 22 No. 04/21 petpla.net Sacmi Imola S.C. Via Selice Provinciale 17/A, 40026 Imola (BO), Italy +39 0542 607111 www.sacmi.com Mr Stefano Severi Sales Specialist Manager +39 335 6594236 [email protected] PVS002C PVS-3 PVS10L 1,200 preforms/h 72,000 preforms/h 72,000 preforms/h Shape, diameters, ovalisation, contamination, inclusions, crystallisation, unmelts, bubbles, black specks, gate length, colour shade variations, wrong colours, scratches, thermal degradation, mould marks, haze, opacity, moisture Shape, diameters, contamination, inclusions, crystallisation, unmelts, bubbles, black specks, gate length, colour shade variations, wrong colours, scratches, thermal degradation, mould marks, haze, opacity, moisture Shape, diameters, contamination, inclusions, crystallisation, unmelts, bubbles, black specks, gate length, colour shade variations, wrong colours, scratches, thermal degradation, mould marks, haze, opacity, moisture Contaminations, cavity number recognition, diameters, flashes, black specks Contaminations, cavity number recognition, flashes, black specks Contaminations, cavity number recognition, flashes, black specks Diameters, ovality, thickness, scratches, short shots, flashes, notches, contaminations, black specks Diameters, ovality, thickness, scratches, short shots, flashes, notches, contaminations, black specks Diameters, ovality, thickness, scratches, short shots, flashes, notches, contaminations, black specks Craters, holes, crystallisation, inclusions, injection point out of center, bubbles, unmelts, contaminations, grooves, cracks, black specks Craters, holes, crystallisation, inclusions, injection point out of center, bubbles, unmelts, contaminations, grooves, cracks, black specks Craters, holes, crystallisation, inclusions, injection point out of center, bubbles, unmelts, contaminations, grooves, cracks, black specks Colour deviations, intensity deviations, LAB measurement Colour deviations, intensity deviations, LAB measurement Colour deviations, intensity deviations, LAB measurement Cavity number recognition with AI algorithms, cavity related statistics, sorting by cavity number Cavity number recognition with AI algorithms, cavity related statistics, sorting by cavity number Cavity number recognition with AI algorithms, cavity related statistics, sorting by cavity number Weighing module: Polarised light inspection with AI algorithms for detection of unvisible defects, such as: - local deformations of the sidewall - signs of chipping - irregularities, material contraction - orange peel surface (part of performs having smaller thickness) - water marks - haze - thermal degradation - absence of stress - irregular material flow Polarised light inspection with AI algorithms for detection of unvisible defects, such as: - local deformations of the sidewall - signs of chipping - irregularities, material contraction - orange peel surface (part of performs having smaller thickness) - water marks - haze - thermal degradation - absence of stress - irregular material flow Polarised light inspection with AI algorithms for detection of unvisible defects, such as: - local deformations of the sidewall - signs of chipping - irregularities, material contraction - orange peel surface (part of performs having smaller thickness) - water marks - haze - thermal degradation - absence of stress - Irregular material flow Fully automated and patented format changeover: thanks to DRIVA (Drive and Recognize through Intelligent Vision Algorithms) the machine changes format (different finish, diameters, length and colour) in about 1min. If the supply includes also Sacmi PLO030 feeder, the automatic changeover also involves the feeder and the total changeover time is still about 1min. No No No No No No No No No Yes Yes Yes Yes Yes Yes Yes, n.1 camera with 360° rotation of the preform No, patented cavity recognition with top camera Yes, 4 side cameras. CVs software includes CVS360-3D for a perfect reconstruction of the sidewall .;;;...... ; AI algorithms for the highest reading performance Non destructive Non destructive Non destructive SQL database, possibility to extract data in XLS format, possibility of connection to ERP system, HTTP and OPC/UA communication protocol available SQL database, possibility to extract data in XLS format, possibility of connection to ERP system, HTTP and OPC/UA communication protocol available SQL database, possibility to extract data in XLS format, possibility of connection to ERP system, HTTP and OPC/UA communication protocol available","@ID":35} "MARKET SURVEY 32 PETplanet Insider Vol. 22 No. 04/21 petpla.net Preform inspection The right tools and expertise to help with your rPETgoals! Agr is uniquely positioned to support your venture into rPET bottle manufacturing with a powerful combination of Process Control tools, Process Consultants, and decades of industry experience. AGRINTL.COM • +1.724.482.2163 Company name Pressco Technology Inc IMD Ltd. Sprana Ltd. Postal address Telephone number Web site address Contact name Function Direct telephone number E-Mail 29200 Aurora Road, Cleveland, OH, USA +1 440 498 2600 www.pressco.com Mr Tom Murphy VP, Sales & Customer Service +1 440 498 2600 [email protected] Industriestrasse 37A, 2555 Bruegg, Switzerland +41 32 366 80 66 www.imdvista.ch Mr Martin Gerber Sales Director (CSO) +41 32 366 80 66 [email protected] Mokslininkųg. 6A, Vilnius, Lithuania +370 699 92823 www.sprana.eu Mr Ričardas Razgaitis Business Development Manager +370 640 04521 [email protected] Preform Inspection Systems Intellispec IMDvista Peco V3 for 100% inline or re-sorting IMDvista Peco Lux for inline monitoring PSIS - Express on-line PET preforms colour inspection system Inspection speed Up to 2,500/min According to IMM speed (depending on preform type and geometry) On-line, 30 frame per 1s Inspected parameters: Geometry / Body Unmelts, heat splay, burn marks, water spots, bent/warped preforms, contamination, carbon streaks, bubbles/blisters, colour, crystallinity & clarity/hazing, gate length Colour defects, contamination, bubbles, unmelts; preform dimensions, shape, burnt marks, water marks, scratches, crystallinity and all visual defects - transparent, translucent and opaque preforms Contaminations and black specks Thread area Contamination, flash, dimensions, pulled threads Contamination, dimensions, flash, short shots, diameter, ovality and all visual defects - transparent, translucent and opaque preforms Mouth / Sealing surface Contamination, ovality and diameter, dirt & debris in the preform, nicks, gouges, short shots & dips Short shots, notches, flash, diameter, ovality and all visual defects - transparent, translucent and opque preforms Gate / Dome Bent/warped preforms, dirt/debris, cracked gates Holes, cracks, position of injection point, too long injection point, crystallisation and all visual defects - transparent, translucent and opque preforms Colour Colour variations, incorrect colour Precise detection of colour deviation (LAB values) - transparent, translucent and opaque preforms Colour and intensity deviation Cavity number No Cavity reading available on all available preform types, cavity related statistics and preform sorting by cavity number - transparent, translucent and opque preforms No limit Further criteria Additional inspection modules include: neck support ring, inner barrel Stress test by polarisation filter Measurement of absence or presence of barrier material Yes Layer thickness & position measurement at distinctive points No Layer thickness & position measurement at the complete body by scanning No Features: · Installation: · Stand-alone On customer-supplied starwheel Stand alone for 100% re-sorting · Inline Mounting and installation inside major OEM blowmoulding machines; options available for stand-alone and inline systems 100% inline or inline monitoring Inline · Side camera for cavity recognition No 360° side view for cavity recognition with IMDvista Neuron (AI) 2 recognition cameras · Methode: destructive/non destructive Non-destructive Non destructive · Data base connection Yes Via IMDvista Portal Cloud based connection MODBUS RTU/ASCII via RS485/RS232 MODBUS TCP/IP (via ethernet) MODBUS RTU via TCP (ethernet)","@ID":34} "BOTTLING / FILLING PETplanet Insider Vol. 22 No. 04/21 petpla.net 25 High-speed line reduces costs The aim is to run the line 24/7 and to consistently achieve 90-95% efficiency with the same number of operators a slower line would require. “Margins on bottled water are very narrow. That makes it all the more important to control cost with a highspeed line like this. Of course, when we’re looking at investing in a new line, we look at all the options. But it makes sense to use the same technologies in all of our plants,” says Howe. “Once you know and understand Krones’ machines, you won’t want anything else.” The Krones Academy supports the line ramp-up phase with specialised training to continuously improve line efficiency. Ice River Springs also has a service contract with Krones. The twin line handles 500ml containers exclusively. Ice River Springs developed the bottle in house following a “function over aesthetic” principle. “It just has to do its job as a container for water – although we still think it looks beautiful,” says Howe. From farmers to water bottlers You might say Crystal Howe’s loyalty to Ice River Springs has been instilled in her from birth. After all, she’s not only the company’s Sustainability Manager but also the daughter of Ice River Springs’ founders and owners, Jamie and Sandy Gott. Her parents started out as farmers, raising chickens and trout in Feversham, two hours’ drive north of Toronto. The natural spring they used as a water source for the trout farm provided a supply of high-quality water, which Jamie and Sandy initially sold in bulk to water bottlers. At some point, they began bottling the water themselves on a small scale, in large HDPE containers. Soon after that, Y2K loomed and an apocalyptic mood set in, driven largely by the media especially in North America. People feared that all computer systems would stop working on January 1, 2000. So they started stockpiling emergency supplies, including bottled water. Demand for Ice River Springs water exploded. “My dad had the vision, and mom helped make them happen,” says Howe. They built one bottling plant after another, at first only in Canada and later in the US as well. Howe explains that Ice River Springs sold off four of its US plants in 2018, “because the market there works differently than in Canada.” The company still maintains a facility in Miami, Florida, in addition to its six plants across Canada – all of which are in close proximity to consumers to minimise transport distances. www.krones.com www.icerivergreenbottleco.com The short-neck bottles weigh only 8.5 g each, another important environmental criterion. “But we don’t want to reduce the weight any more than that since it would make it harder to separate the caps from the bottles in the recycling process.” Clear and transparent blue, purple, and yellow postconsumer PET plastic can be used to produce Ice River Spring’s blue bottles. Green plastic can’t be used in this bottle. Since green PET plastic makes up about 5% of the incoming recycling stream, Jamie Gott devised an alternative use for it instead of downcycling: Following their own ideal of sustainability, the company now produces a green 100% rPET bottle that it uses for its own Ice River Springs brand. The company will now begin marketing the green bottle more heavily in Canada under the name Ice River Green Bottle Co. German Technology Innovative hotrunner optiRun","@ID":27} "PACKAGING / PALLETISING PETplanet Insider Vol. 22 No. 04/21 petpla.net 38 Challenges faced by the epidemic Thermo-Pack has responded to the challenges presented by the Covid-19 pandemic and consequent changes in client companies’ development strategies by enhancing the versatility of its equipment and by developing a new product line. The Thermo-Pack MP6-3.12, which is aimed particularly at meeting the needs of customers in Central and Eastern Europe, is designed for rinsing and filling PET bottles with soft drinks and mineral water, and sealing them with a plastic screw cap. The machine can operate at speeds of up to 15,000 bph, and handle bottles ranging from 250ml to 3,000ml. Changeover tooling kits are designed to be easy to install, in order to minimise changeover time and cut downtime. The versatility of the MP2-3.12 is in keeping with Thermo-Pack’s approach to meeting the needs of customers for non-standard and specialised solutions. The company has developed lines for bottling Kyrgyzstan national drinks, such as bozo, chalap, maksim and aralash. An equipment order is in the process of preparation for shipping to and Indian company, which will be bottling a national drink that features products of different densities. Thermo-Pack rises to Covid-19 challenges New filler for Central and Eastern Europe Ukrainian engineering company Thermo-Pack Ltd, headquartered in Bila Tserkva, about 90km south-west of Kiev, manufactures filling, labelling, packaging and conveyor systems machinery and complete solutions for beverage companies. The company’s approach to projects is to work with clients at all stages, from initial technical approval and design, through to manufacture, installation and staff training. PACKAGING “There are several factors that may prevent companies from using standardised production lines. The composition of the product, the feature and/or the shape of the PET container, the environmental conditions – all these require a creative approach to the technical task,” explains Valery Yumagulov, Chief Engineer of Thermo-Pack. Pallet-packing The company offers a range of solutions for automation of group packaging processes, including an automatic pallet-packing complex that is used in light, food and chemical industries. It can load up to 15 pallets per hour. Thermo-Pack says that automation enables a single operator to supervise all aspects of the entire complex. Thermo-Pack was founded in 1996, initially to supply the domestic market in Ukraine. Its first machine was a manually-operated unit, which was followed just a year later with an in-house designed automatic packing machine. It began exporting in 2000 and made its international exhibition debut in 2002, when it attended Rosupak, in Moscow, and Riga Food, in Latvia. The company now occupies a 9,000m2 factory and employs over 200 people. Thermo-Pack says that its range today meets all international standards and regulations. The company has customers in more than 30 countries across the world, including Cote d’Ivoire in Africa; Canada; India; and New Zealand. www.tp-eu.com Thermo-Pack’s site near Kiev, Ukraine","@ID":40} "imprint EDITORIAL PUBLISHER Alexander Büchler, Managing Director HEAD OFFICE heidelberg business media GmbH Vangerowstraße 33 69115 Heidelberg, Germany phone: +49 6221-65108-0 fax: +49 6221-65108-28 [email protected] EDITORIAL Kay Barton Heike Fischer Gabriele Kosmehl Michael Maruschke Ruari McCallion Waldemar Schmitke Anthony Withers WikiPETia.info [email protected] MEDIA CONSULTANTS Martina Hirschmann [email protected] Johann Lange-Brock [email protected] phone: +49 6221-65108-0 fax: +49 6221-65108-28 LAYOUT AND PREPRESS EXPRIM Werbeagentur | exprim.de Matthias Gaumann READER SERVICES Till Kretner [email protected] PRINT Chroma Druck Eine Unternehmung der Limberg-Druck GmbH Danziger Platz 6 67059 Ludwigshafen, Germany WWW www.hbmedia.net | petpla.net PETplanet Insider ISSN 1438-9459 is published 10 times a year. This publication is sent to qualified subscribers (1-year subscription 149 EUR, 2-year subscription 289 EUR, Young professionals’ subscription 99 EUR. Magazines will be dispatched to you by airmail). Not to be reproduced in any form without permission from the publisher. Note: The fact that product names may not be identified as trademarks is not an indication that such names are not registered trademarks. 3 PETplanet Insider Vol. 22 No. 04/21 petpla.net The Chinaplas trade fair has closed its doors. After the cancellation of the event last year, the industry was looking forward to this year’s fair. It is the first trade fair in the plastics industry to take place as a face-to-face event post-pandemic. New to the event was the new location in Shenzhen, near Hong Kong. The fair now takes place alternately with Hong Kong and Shanghai. Guangzhou is history. As is well known, China is already well on the way to containing the pandemic. So the fair was able to take place in pretty much the usual conditions. In order to keep the pandemic under control, the country has largely isolated itself from the outside world, as is shown by the number of foreign visitors which fell dramatically from 42,005 in 2019 to 2,363 visitors in 2021. To compensate for the predictable decline in foreign visitors, the fair organisers set up a streaming platform. 363,000 users took part over the 4 days. However, the fair was able to increase the very high proportion of local visitors from 121,309 visitors in 2019 to 149,771 visitors in 2021, thus maintaining the total number of visitors at a high level despite the adverse circumstances. The next event will take place in Shanghai in April 2022, and I am already looking forward to visiting it. Yours sincerely, Alexander Büchler Dear readers,","@ID":5} "PETplanet Insider Vol. 22 No. 04/21 petpla.net 51 TRADE SHOW REVIEW changed: filter materials have shifted from metal to microwave ceramic; key PCB materials have migrated from copper foil to high-frequency substrates, and antenna materials have changed from PI to LCP/MPI, and so on. These changes offer huge scope for the application of plastics. Mr Chen Shou, Chairman of Shenzhen Beauty Star Co., Ltd., covered recyclable design, multi-channel recycling, and classified and graded utilisation of plastics packaging under the circular economy in a discussion on Sustainable Development of Plastics Packaging. He said that Chinaplas, as an “accelerator” to promote innovation in the plastics packaging industry, is looking forward to seeing recycling equipment, post-consumer recycled materials, single structure recyclable materials, CMF surface treatment process, biodegradable materials and smart and efficient equipment. Mr Stanley Chu, Chairman of Adsale Exhibition Services Ltd., declared that China has ranked first in the world for 15 consecutive years in plastics machinery production and opined that this is strong evidence that China is transforming from a large manufacturer to an influential one. Chinaplas has made a significant contribution to this process, by facilitating technical exchanges, trades, collaboration and joint ventures between China and overseas countries. From 2021, Chinaplas will be held in Shenzhen every odd year, in response to the demand of high-end industry development as well as the thriving development of the Greater Bay Area. Stanley Chu, Chairman of Adsale Exhibition Services Ltd. In her speech entitled “Chinaplas 2021 Show Highlights & Concurrent Events” Ms Ada Leung, General Manager of Adsale Exhibition Services Ltd., identified the five key technology areas for the industry: 5G, plastics and rubber technology, circular economy, green technology and industry 4.0 plus artificial intelligence. These and high performance materials, engineering plastics, reinforced carbon fibre composite materials and flexible product design solutions will make the future. www.chinaplasonline.com l l","@ID":53} "PACKAGING / PALLETISING 40 PETplanet Insider Vol. 22 No. 04/21 petpla.net Set to recover from Covid-19 to face sustainability challenge US PET packaging market by John Nelson, Smithers Exclusive new data from Smithers show that the North American rigid plastics packaging market will grow by 6.6% to reach a projected $ 42.79 billion in 2021. This marks a return to positive growth following a drop of 1.1% from 2019 to 2020, in a year scarred by the human and economic consequences of the Covid-19 pandemic. New challenges and market opportunities will foster growth across the decade pushing total value forward at a compound annual growth rate of 2.1% to reach $ 47.55 billion in 2026. Smithers’ new report – The Future of Rigid Plastic Packaging to 2026 – shows that at 3.37 million tonnes, PET is the most widely used plastic in this segment in the US. As firms reorientate themselves to a post-Covid market, there will be many new challenges, especially in sustainability. This trend largely defined design and R&D priorities for much of the second half of the previous decade, and disappeared only temporarily under Covid-19. The poor perception that plastics have in consumers’ minds is leading brands to and trial alternative formats, such as aluminium cans for mineral waters. Within plastics, the leading contemporary solution is to use greater stocks of rPET in a new generation of packaging, especially beverage bottles. Coca-Cola for example announced in February that it was moving to transition several of its North American product lines to 100% rPET containers across 2021. This accords with regulatory developments; though for now these are confined to a state-level. As is often the case, California has pioneered green legislation in this area. It has set a requirement for an average of 15% recycled material to be used in beverage bottles by 2023. This will come into effect before targets set by the EU‘s Singleuse Plastics Directive 2019/904 – 25% recycled content from 2025. Several other state legislatures, including New Jersey and New York, are now actively considering similar commitments. Realising the vision of a sustainable, circular economy is a laudable aim, and one that will lean heavily on the PET industry to deliver. This is because mechanical recycling processes and collection infrastructures are more advanced – with California among 10 States of the Union that have bottle deposit schemes in place for PET formats. The wide use of PET in food and beverage packaging also supports this from a technical and legal perspective. In the US, to be authorised for reuse in such packaging, PET from any facility must have its processes approved via the issuance of a Letter of No Objection from the Food and Drug Administration (FDA). As Alistair Irvine, senior manager for food contact testing at Smithers, explains: “PET is a great candidate for recycling because it is resistant to the absorption of contaminants from its environment and can also be processed at a high temperature, which enables the effective removal of any contaminants. Whereas polyolefins tend to absorb more contaminants during use and have to be processed at a lower temperature.” This is already being reflected in resin prices, with rPET consistently selling higher than virgin grades. As demand from food brands and other segments, such as personal care, expands over the 2020s there will be further pressure. This will involve brands switching over to PET and increasing their use above levels mandated in state or corporate targets, to compensate for the lack of viable recycled content for other polymers. In the longer term, heavy investment in chemical recycling – which breaks polymer waste down to its base monomers – has the potential to increase supply for all rigid polymer types. This will take time to come on stream at a commercial level however, and will be available at volume to help deliver on goals with 2025 deadline. www.smithers.com PACKAGING Rigid plastic packaging, percentage share of global consumption by weight, by polymer type, 2020 (source: Smithers)","@ID":42} "44 PRODUCTS PETplanet Insider Vol. 22 No. 04/21 petpla.net Case packer for lids and containers Muller Technology, a leading global supplier of moulds and automation solutions for thin-wall packaging, has announced the launch of the industry’s first self-contained collaborative robot (Cobot) case packer for the packing of lid and container packaging. The new automation product, which incorporates an Omron 6-axis cobot, helps processors bridge a major labor shortage gap in the U.S. plastics processing industry while also delivering versatility, flexibility, and productivity. “In these tough economic times, the cobot case packer helps processors who struggle filling unskilled labor positions while also meeting Covid-19 social distancing requirements,” said Taras Konowal, Director of Sales and Marketing for North America. The jobs of packers are highly repetitive and unfulfilling, but highly needed, according to Konowal. The new case packer enables moulders to re-allocate their workforce to more productive, fulfilling jobs. Industry data show that while baby boomers age 55 and older represent 27% of the U.S. manufacturing workforce, a total of 10,000 boomers are reaching retirement age every day. The problem for plastic manufacturers is that millennials and Generation Xers are not interested in filling manufacturing gaps left by boomers, surveys show. The cobot works side-by-side with an employee doing many basic tasks. When an employee comes close to the cobot, it slows down but continues to work. Unlike traditional industrial robots, the cobot system doesn’t require external guarding and all safety features are built into the cobot. The cobot case packer incorporates a standard Muller Human Machine Interface (HMI) which eliminates any programming requirements and stores multiple recipes for a wide range of stack and box sizes. The case packer can be purchased separately or integrated into an automation line such as Muller’s new M-Line system, a new integrated robotic and automation system which delivers significantly greater flexibility and versatility for production of injection moulded packaging. The cobot case packer offers portability, quick part changeover for different size configurations, and a return on investment of less than one year. The product platform will be manufactured in Switzerland and Colorado. Muller has already sold several units for lids and containers in the U.S. and Europe. www.muller-technology.com","@ID":46} "27 TRADE SHOW REVIEW PETplanet Insider Vol. 22 No. 04/21 petpla.net","@ID":29} "OUTER PLANET 62 PETplanet Insider Vol. 22 No. 04/21 petpla.net OUTER PLANET Water bottle lid prevents consumption of microplastics Keeping microplastics at bay The consumption of microplastics is suspected of having a negative impact on human health. Hence, Korean start-up Real Water has come up with a solution to filter out microplastics from bottled water to reduce synthetic polymer contamination. A study done by the State University of New York in 2018 found that tiny pieces of plastics exist in more than 90% of the samples collected from the world’s most popular bottled water brands. Real Water’s simple yet unique design of a water bottle cap that fits on almost all plastic bottles is claimed to have the potential to save millions of people from health issues that may arise from this contamination. To conduct the study, 259 bottles of packaged drinking water of 11 different brands were collected as samples from nine countries; China, Brazil, India, Indonesia, Mexico, Lebanon, Kenya, Thailand, and the U.S. After the results of the study were made public, the World Health Organisation (WHO) sought a review of the potential risks arising from plastic particles in drinking water. The study revealed that, on average, a person can consume 2,000 microplastics amounting to around 5 g of plastic in a week. Real Water’s uniquely designed lid is capable of filtering up to 0.005mm of fine plastic particles and can save people from consuming microplastics, which some voices consider a next big health hazard. The start-up’s story Real Water was started by Kwon Hyeok Jae, who developed the product with the goal of helping to make drinking water safe for human consumption. Kwon and his team came out with the final product after 10 months of intense research. The team studied microscopic plastics’ size, investigated available filters in the market, studied the characteristics, pore sizes, and principles of each filter before finally introducing the Real Water filter cap. “It took us more than 10 months to develop the product. I kept repeating the experiments by changing the shape and size of the filter frame. I designed the prototype after numerous trial and error, using a 3D printer. Eventually, I had to find a factory to mass produce the product,” said Kwon Hyeok Jae. Real Water’s filter cap can filter around 120 l of water. If, on average, a person drinks two litres of water a day, the cap will last for two months. However, it should be cleaned by rinsing it under running water to achieve better life of the product and stored in a dry place when not in use. The company will also provide a case for storing the filter. The company released its first product in June 2020 and received good reviews. Real Water also launched its crowdfunding in the same month for mass production and received funding. Safety certificates & overseas expansion Real Water’s product has received the ‘Hazardous Substances NonDetection Certification’ after undergoing the Korea Testing and Research Institute’s test. Also, it has been confirmed as ‘Bisphenol A non-detection’ as a result of the Korea Institute of Construction Living Environment Test and received ‘BPA Free’ certification. After its successful launch facilitated by a crowdfunding drive, Real Water got several customer inquiries from the overseas market as well. The start-up is currently preparing to export its unique bottle cap filters to Japan and Taiwan. “Our company’s motto is ‘Make water that can be drunk with real peace of mind.’ In addition, the issue of microplastics in bottled water is more serious overseas than in Korea. Some brands abroad have up to 10,000 microplastics per litre of water. As the demand is high, we are preparing to enter the overseas market in earnest,” said Kwon Hyeok Jae. www.realwater.modoo.at Real Water bottle cap What are microplastics? As a category, microplastics encompass a wide range of materials composed of different substances, with different densities, chemical compositions, shapes and sizes. There is no scientificallyagreed definition of microplastics, although they are frequently defined as plastic particles 5mm in length. A subset of microplastics 1μm in length are often referred to as nanoplastics. www.who.int","@ID":64} "TOP TALK PETplanet Insider Vol. 22 No. 04/21 petpla.net 11 Tony Ho: The majority of our sales are in Asia and Africa. We have installed production lines in over 80 countries and regions across the world and have set up several technical service centres in other countries, to provide customers with convenient and efficient service and technical support, locally. PETplanet: Which countries and sectors do you see as offering the greatest potential for growth, and why? Tony Ho: Growth in the global food and beverage industry will continue, especially in nutritious foods, plant-based beverages and products aimed to improve health, well-being and immune systems. We have gained an abundance of experience in technological development and application, as well as the project planning and management, at home and abroad. We believe that we can provide professional project solutions and technical services for customers in a growing number of countries and regions but we expect that countries in Asia and Africa offer the greatest potential for growth. PETplanet: Have changing demands over the past 10 years been driven primarily by the manufacturers and bottlers or by changing consumer needs? Tony Ho: Consumer demand for natural, fresh, healthy and nutritious food and beverage rises with improved living standards and changing lifestyles, which drives requests for new production lines in manufacturing companies, who also focus on safety, automation, integration and flexibility. We are implementing digitalisation, networking and artificial intelligence and can provide complete “smart factory” solutions. These will help to reduce operating costs and improve production efficiency and energy usage. Labour intensity and management costs will also be reduced, helping return on investment (RoI) times to be cut. Food and beverage quality, safety and traceability can be improved and made more reliable through the integration of production, packaging, inventory and logistics, linked with artificial intelligence. PETplanet: Your portfolio includes combination solutions, which can also be found with many other equipment suppliers today. Are these bloc solutions the way to go, for now and in future, and why? Tony Ho: Pressure on global resources is intensifying and, at the same time, we are seeing a growing trend towards ‘intelligent manufacturing’. The combination, monobloc offers the advantages of smaller footprint along with lower operating costs, higher stability and efficiency, convenient maintenance, and intelligent management and control. They mean that flexible manufacturing can be made a reality for users. PETplanet: Which machine models or types are your best-sellers? Tony Ho: We are responding to market demand with a range of advanced technology and products, including the Combiblock blowing-filling-capping machine for bottled water, edible oils, CSD, hot filling and aseptic product, and our Starbloc blowinglabelling-filling-capping unit. Aseptic PET bottle packaging solutions, intelligent warehouses and smart factory management systems are also in demand from our customers. PETplanet: Which are your overall top three application areas by machine sales? Tony Ho: In the field of beverages, bottled water, CSD and non-carbonated drinks are the top three application areas. PETplanet: Newamstar has been listed on the stock exchange since 2016. What impact has this had on the company? Tony Ho: Newamstar had an IPO in April 2016. Public listing encouraged us to optimise our management system and build a better brand culture. It means that, worldwide, customers are able to get a understanding of the company, through more channels, which enables us to build the better working relationships. PETplanet: What is the company’s strategy for future development and what investments are planned? Tony Ho: We will increase investment in key markets, establish subsidiaries, strengthen exchanges and interactions with local partners, and jointly promote economic development. PETplanet: Around a year ago you have introduced Starbloc, a very compact all-in-one system. How did it perform since then? Tony Ho: Starbloc got good feedback from customers and industrial experts. We are confident that it represents the future development path. PETplanet: Sounds good; how many Starblocs are already in operation, worldwide? Tony Ho: At present, several sets are on being trialled in customers’ factories. We are very optimistic about its market prospects. PETplanet: Aseptic filling technology is a significant part of your business. How did that evolve, and in response to what demands? Tony Ho: Newamstar is a pioneer of PET aseptic cold filling in China. No preservatives are added to drinks that are bottled using PET aseptic filling technology, so taste, colour and nutrition values can be maintained. These drinks, including fruit and vegetable juice, protein, special-purpose, tea, coffee and plant beverages, satisfy consumer demands for tasty and healthy CSD blowing-filling-capping Combiblock","@ID":13} "TRADE SHOW PREVIEW PETplanet Insider Vol. 22 No. 04/21 petpla.net 30 Instead of Simultaneous moulding of preforms with multiple layers Overmoulding Cube applications StackTeck Systems Ltd. announces a successful introduction of technology for overmoulding PET preforms with multiple layers. The first overmoulding system has been designed to achieve a light barrier for light sensitive applications. The system incorporates two preform moulds used in concert with a Niigon rotary cube injection moulding machine, using its horizontal rotating table and dual injection units. The rotary cube rotates 180 degrees during every cycle, bringing the first shot parts to a second cavity for overmoulding the second shot. “We are very pleased with the new system, which provides competitive cycle times while dramatically reducing the overall part weight and light blocking additives of a monolayer bottle by means of a multi-shot process. This results in a dramatic reduction in part cost, while delivering improved light barrier properties. We chose to work with StackTeck and Niigon, as innovative suppliers who bring state-of-the-art capabilities to high volume moulding systems,” said Russell Gray, COO of Ngoc Nghia Industry. “The StackTeck mould includes an advanced Yudo hot runner, which helps improve our part quality with superior hot runner balance. At the same time, the hot runner pressure drop is much lower than conventional hot runners, which enables the moulding of the thin layers needed for this multi-layer part design.” Mr Gray continued, “It’s an exciting technology to work with, we’ve expanded our testing to include parts with pearlescent colours in the inner layer and clear PET in the outer layer; the final parts have a glossy, “candy-apple” look that gives great shelf appeal and significant savings over a monolayer bottle with 100% blended pearlescent colours. We see opportunities for cosmetics and personal care packaging beyond the original focus on beverage packaging.” Rick Unterlander, General Manager of PET at StackTeck, explains the set up: “This technology is distinct from traditional co-injection, because an inner layer is initially moulded on one side of the cube, then rotated 180 degrees where the outer layer is over-moulded. Both moulding stages operate as conventional injection moulding processes, which is simpler to set up, maintain, and run continuously in comparison to a more complex co-injection system. It’s comprised of two standard moulds, with stacks designed to accurately and repeatably produce the individual layers of the preform.” Overmoulding with rPET possible Instead of the light barrier approach, this technology can be used with significant rPET content in the overmoulded shot. For some applications, up to 75% of the total part weight can be moulded with rPET on the outside surface, which is much higher than some competing preform moulding processes. Stackteck states that PET preform overmoulding allows: Cost reduction through isolation of non-virgin materials from product contents (regrind/flake); use of lower cost materials; reduced additive/colourant content. Increased use of recycled material/ rPET which addresses environmental concerns and/or government regulations. The development of new approaches to applications requiring light barrier/shielding such as dairy. New product differentiation. www.stackteck.com Cube mould as it rotates in the machine. Single serve dairy bottles and PET preforms – 250ml PET preforms showing internal light barrier layer","@ID":32} "PETproducts 42 PETplanet Insider Vol. 22 No. 04/21 petpla.net Cups with an rPET inlet Paccor presents new additions to its DuoSmart range. Coming to the market is RecycleDuo which stands for our DuoSmart (DS) products without glue and new DuoSmart solutions with rPET or foamed PP inlets. DuoSmart is a packaging solution that combines paper and plastic. It contains up to 50 % less plastic compared to standard injection moulded packaging, and with a “zip”, the inner cup and paper banderole can be easily separated into different waste streams. DuoSmart with rPET inlet responds to the market request of recycled content increase which today is mainly possible with rPET reincorporation up to 100%. The new generation of DuoSmart solutions allow having the Digimarc barcode printed on the paper outer layer and engraved on the plastic cup. The packaging is stated to be suitable to protect the nutritional value, colour, aroma, and taste of food products, including those stored in ambient, chilled, or frozen conditions. Hot filling and microwaving are also options. Available in a wide range of sizes, DuoSmart runs on standard food industry filling lines, with fast and smooth performance. www.paccor.com EcoFloat sleeve solution CCL’s 360° sleeves are claimed to offer design freedom whilst also ensuring a strong visual impact at the point of sale. With their expertise in the field of film manufacturing, CCL have created a sustainable TD sleeve material enabling customers to meet their recycling targets. The EcoFloat material complies with all CCL conformity standards and has been engineered to improve the sink/ float separation process relating to PET bottles. Maximum PET recycling performance The clear polyolefin film material has been specifically developed for PET bottle-to-bottle recycling: It is based on polyolefin; the TD shrink is less than 60% and it has a thickness of 50μ . These are the same process conditions as other TD films. Its specific gravity is 0.93g/cm³. The material floats with ink during the separation process and supports the PET bottle-to-bottle recycling process. Meeting the Association of Plastic Recyclers (APR) standards in the US and the European PET Bottle Platform (EPBP) standards in Europe is becoming increasingly important. The EcoFloat material has now been approved by the European PET Bottle Platform (EPBP). EPBP is a voluntary industry initiative that provides PET bottle design guidelines for recycling and evaluates PET bottle packaging solutions and technologies. www.ccllabel.com Condensed milk in PET instead of HDPE The Spanish dairy producer Delifactory Originia Foods recently launched two new 900g and 450g easy-pour anti-drip containers on the market of its Benestare condensed milk (whole and skimmed) manufactured in PET. These new packages are claimed to constitute a complete novelty in the market, as they are the first ones made in PET in their category; they replace a previous version produced in multi-layer HDPE. The new easy-pour anti-drip bottle is stated to guarantee perfect long-term preservation (12 months) which this product requires. The change in material offers good dosing and improves recovery of its original shape after use. Additionally, the single-layer structure used in this new container, the functional additives used in it for perfect preservation of the milk, and the fact that it is produced in PET ensure its complete recyclability within the existing recycling streams of this material. The production and supply of these new bottles have been entrusted by Delifactory Originia Foods to Novapet which has integrated the action of all its divisions to achieve the goals set with this new development. Thus, the project of technical definition and of functional verification of the container have been managed by the Novapet PET Packaging Technical Centre, using resins, concentrates and additives produced by the company itself. The preforms are injected by Novapet Envase (Noven) at its Spanish Barbastro factory, and the final containers blown by Noven Farmaplás at its Fuenlabrada plant. Finally, REnovaPET has studied the behaviour of these containers in the PET recycling streams in order to ensure the incorporation of post-consumption material into them, as provided in European regulations. www.novapet.com PACKAGING","@ID":44} "MATERIALS / RECYCLING PETplanet Insider Vol. 22 No. 04/21 petpla.net 14 Taking a holistic approach to PET packaging with AWArPET Sipa’s philosophy for PET containers is a holistic one – it looks at the big picture of how low-weight, high-performance, aesthetically pleasing, consumer-friendly PET packaging fits best into the new circular economy. Sipa is well known among the globe as a supplier of equipment systems for producing (and filling) PET preforms and large and small containers. This offering is backed up by a comprehensive design service that helps customers take early ideas about containers all the way through drawings, virtual and real prototypes – functional as well as decorative – testing and validation, through to the definite article. “We are strongly focused on optimising the use of PET in liquid packaging,” says Sipa’s Packaging Development Manager. “We identify and implement the proper lightweight solution, based on customer and market demands, transport and handling logistics, local scenarios, and other influencing factors. Secondary packaging may also play a part. It almost goes without saying that Sipa is a strong advocate of the use of post-consumer recycled materials.” Design, engineering, and production with 100% rPET PET bottles containing postconsumer recycled material – rPET – have in a relatively short time become a common sight, rather than the exception that they were just a few years ago; use of rPET is destined to increase further, with a growing number of bottles made in 100% rPET. Sipa has built up experience through its expertise in bottle design and in process technologies to enable the use of rPET. This means not only creating designs that take into account differences and variations in processing characteristics of rPET, but also other less obvious factors such as the increased level of powder that rPET processing creates. Containers incorporating rPET will only be accepted by brand owners and consumers if they perform as well as containers made from virgin material. That means rPET arriving at the converter has to be clean and consistent, and with processability during preform production and bottle blowing that is almost, if not exactly, the same as virgin PET. A new brand - AWArPET Sipa states that sustainability has for many years been at the heart of its thinking, about everything it does, whether it is the way its equipment is built and works, or how its customers containers are produced, filled, used, disposed of, and, increasingly, recovered and converted back into containers again. These days, Sipa’s product design experts are involved in the development of 3,000 or more new packaging designs every year. The three R: Reduce, Reuse, Recycle – are constant principles in all of these projects, says the company. That’s why Sipa has now established a new brand -AWArPET- which stands for an environmentally conscious approach to the design and production of PET packaging. Recyclass rules Sipa strictly follows the Recyclass Design for Recycling guidelines established by EPBP, the European PET Bottle Platform. This voluntary industry initiative provides PET bottle design guidelines for recycling, evaluates PET bottle packaging solutions and technologies, and facilitates understanding of the effects of new PET bottle innovations on recycling processes. EPBP is supported by the European Federation of Bottled Waters (EFBW), the European Association of Plastic Recycling and Recovery Organisations (EPRO), Petcore Europe, Plastics Recyclers Europe (PRE) and European Soft Drinks Industry (Unesda). It has established several test procedures in order to assess the impact on recycling of new packaging technologies. Products that pass the tests should not cause any problems during recycling. The Green Plastic Factor AWArPET bottles are very light. Sipa has for example been involved in one design project, code-named Mario, for a 1 l water bottle weighing just 16 g, far lighter than most 1 l bottles currently on the market. The company believes that over the next three-to- five years, the weight could come down even more.","@ID":16} "MARKET SURVEY 34 PETplanet Insider Vol. 22 No. 04/21 petpla.net Preform inspection Company name Intravis GmbH Postal address Telephone number Website Contact name Function Direct telephone number E-Mail Rotter Bruch 26a, 52068 Aachen, Germany +49 241 9126 0 www.intravis.de Markus Juppe CMO +49 241 9126 0 [email protected] Preform Inspection Systems PreWatcher offline PreWatcher inline Sample-PreWatcher PreMon LayerWatcher Inspection speed Up to 100,000 objects/h with 18 cameras Up to 72,000 objects/h with 8 cameras Up to 1,200 objects/h with weight check Up to 72,000 objects/h with 5 cameras Up to 144 objects/h Inspected parameters: Geometry / Body Contamination; short shots; length; diameter; shape; unmelted material; oil & water marks; burn spots; scratches; opacity; crystallisation; streaks; bubbles; colour and colour deviations; barrier; stress test with polarised light Contamination; short shots; length; diameter; shape; unmelted material; oil & water marks; burn spots; scratches; opacity; crystallisation; streaks; bubbles; colour and colour deviations Contamination; short shots; length; diameter; shape; unmelted material; oil & water marks; burn spots; wall thickness; inner wall damage; core shift; scratches; opacity; cystallisation; streaks; stress test with polarised light; bubbles; colour and colour deviations; barrier Colour and colour deviations; contamination; short shots; unmelted material; oil; burn spots; opacity; crystallisation; streaks; bubbles; yellowness; Presence of barrier layers; thickness of barrier layers; position of barrier layers; structure of barrier layers; position of barrier leading edge; position of barrier trailing edge Thread area Contamination; thread dimensions; defects at the neck support ring; flash; pulled thread Contamination; short shots Mouth / Sealing surface Diameter; ovality; short shots; flash; scratches and notches on the sealing surface; defects at the neck support ring; contamination Diameter; ovality; short shots; flash; scratches and notches on the sealing surface; contamination Diameter; ovality; short shots; flash; scratches and notches on the sealing surface; inner mouth wall inspection; contamination Short shots; flashes; scratches; ovality; contamination Gate / Dome Contamination; grooves; holes; cracks; crystallisation; postitioning of injection point; unmelted material; gate length; gate deformation; stringing Length of injection point; contamination Colour Colour and intensity deviations ( ΔL*, Δa*, Δb*); presence of UV blocker; presence of barrier; presence of IR absorber (reheater) Colour and intensity deviations ( ΔL*, Δa*, Δb*); yellowness; grayness Cavity number Cavity number reading; cavity related statistics; preform sorting according to cavity number; powerful cavity reading without need for learning for most fonts; possibility to share information based on cavity number with IMM Cavity number reading; cavity related statistics; preform sorting according to cavity number; enables collection of reference samples; powerful cavity reading without need for learning for most fonts; possibility to share information based on cavity number with IMM Cavity related statistics; powerful cavity reading without need for learning for most fonts; possibillity to share information based on cavity number with IMM Further criteria Reference sample collection based on defect and/or cavity, footprint of less than 4m², connectable with IntraVisualizer: wireless reports, alarms operator in extraordinary events, share product quality with factory QMS or ERP Combination of sorting, feeding and inspection unit with only 8m² foot print, connectable with IntraVisualizer: wireless reports, alarms operator in extraordinary events, share product quality with factory QMS or ERP High precision weight measurement; high precision dimension measurement, reference sample collection based on defect and/or cavity, connectable with IntraVisualizer: wireless reports, alarms operator in extraordinary events, share product quality with factory QMS or ERP Bad part ejection, high precision through preform orientation, connectable with IntraVisualizer: wireless reports; alarms operator in extraordinary events, share product quality with factory QMS or ERP Visualization of barrier layers in 3D images in less than 30s, connectable with IntraVisualizer: wireless reports, alarms operator in extraordinary events, share product quality with factory QMS or ERP Measurement of absence or presence of barrier material Yes Yes Yes No Yes Layer thickness & position measurement at distinctive points No No No No Yes Layer thickness & position measurement at the complete body by scanning No No No No Yes Features: · Installation: · Stand-alone Yes Yes Yes No Yes · Inline Yes, but optimised for offline Yes, optimised for inline after IMM and before blower and filler Yes, sampling Yes, optimised for inline after IMM Yes, sampling · Side camera for cavity recognition Yes, 4 cameras Yes, 3 cameras Yes, rollout of the complete thread area No Yes, rollout of the complete thread area · Method: destructive/non destructive Non destructive Non destructive Non destructive Non destructive Non destructive · Data base connection Yes, all industry standards supported; ready for Industry 4.0 applications: XLS formats; SQL and several others; connectable to IntraVisualizer, ERP & QMS","@ID":36} "PETnews 6 NEWS PETplanet Insider Vol. 22 No. 04/21 petpla.net Over half of the total EU plastics recycling capacity certified with EuCertPlast With the release of the record number of 4.6 million tons, the EuCertPlast certification was granted to more than half of the total EU recycling capacity covering both pre- and post-consumer streams. The scheme grew by 27% in comparison to 2019, and with 45 new recycling facilities, there are now 214 companies certified by EuCertPlast, demonstrating its wide recognition in the plastics industry. The leader, with a share of 30% of the EuCertPlast certified facilities, is Germany. Italy with the 12% share is in the second place, followed closely by the Netherlands and France, having respectively 11% and 10% share of the certified capacity. Additionally, LDPE and PET are the most widely certified polymers representing almost half of the total capacity. Despite the pandemic, which affected the ability of the auditors to travel to recyclers’ facilities, EuCertPlast certified companies grew substantially in the course of 2020. The positive trend of a steady increase of certifications shows the increasing demand for third-party verification of the origin of waste and recycled content calculation, and consequently the growth and the maturing of the plastic recycling market in Europe. By promoting transparency and the highest standards, the EuCertPlast certification contributes, as well, to the Circular Plastics Alliance’s objective to increase the uptake of recycled materials to 10 million tonnes by 2025. www.eucertplast.eu Ground-breaking inauguration of recycling plant in Indonesia Coca-Cola Amatil Indonesia (Amatil Indonesia) and Dynapack Asia announced the construction of a 20,000m2 PET recycling facility located in Bekasi, West Java. The newest investment valued at AUD50.51 million (IDR556.2 billion) will enable the collaboration of Amatil Indonesia and Dynapack Asia to create a closed loop plastic packaging supply chain by producing food and beverage safe plastic pellets made from post-consumer plastic bottles. During the groundbreaking ceremony, Amatil Indonesia and Dynapack Asia introduced PT Amandina Bumi Nusantara and Mahija Parahita Nusantara with the following roles: PT Amandina Bumi Nusantara – the entity which will run that state-of-the-art rPET facility, leading the transformation process of low-quality PET waste back to virgin-quality, food-grade PET using the latest renewable technology; Mahija Parahita Nusantara – the non-profit foundation which will support collection centres’ management, ensuring the observance of human rights and regulation in the waste collection supply chain, execute activities to improve the welfare of waste pickers and communities, as well as conducting research and development on recyclability improvement and other opportunities related to PET utilisation and plastic collection. The facility will start its operation in 2022 and has the capacity to reduce the amount of new plastic resin companies use by an estimated 25,000t/a. Amatil Indonesia continues to strengthen its commitment to reduce plastic usage, among others with light-weighting PET bottles that has successfully reduced 28.5% plastic content since 2014, as well as transitioning from coloured to clear bottles which are easier to recycle. Together with Dynapack Asia, Amatil Indonesia continues its support on many grassroots initiatives to help collect and recycle beverage containers including daily beach clean-up program, Bali Beach Clean-Up, which has successfully collected more than 40,000 t of waste for more than 13 years and other similar programs. www.ccamatil.com www.dynapackasia.com Alpek & ContourGlobal create JV to develop a CO2 recovery facility Alpek, S.A.B. de C.V. announced that it has formed a new joint venture company with ContourGlobal plc to develop a CO2 capture and liquefaction facility. The site would be integrated into ContourGlobal’s cogeneration facility in Altamira, Mexico. Each party holds a 50% stake in the JV. The JV was created to meet the rising need of food-grade CO2 for Mexico´s food and beverage industry, which is currently undersupplied by around 80,000 t/a, and used in the carbonation of soft drinks, beer, and mineral water, among others. This venture is well aligned with the three pillars of Alpek’s LongTerm Strategic Growth Plan: Foster a Circular Economy / Sustainable Product Portfolio: Alpek intends to continue growing its share of products that promote a lower carbon footprint and are well aligned with a fully circular economy. The proposed CO2 recovery facility would be a carbon negative asset, helping Alpek reduce its carbon footprint, as the company works towards full carbon neutrality. Strategic & Focused Growth / Product Innovation: When Alpek began negotiating the sale of CGA to ContourGlobal in 2019, both companies were already contemplating the construction of a CO2 recovery facility. In this sense, this venture represents the fruit of a proactive mindset of both teams. The Innovation team will continue to actively look for new products that can help Alpek grow by drawing on its core strengths. Strengthen the Core Business / Value Added Products: This venture diversifies Alpek’s portfolio with a new product that can be commercialised through its existing PET customer base, moving us further into new, attractive and growing markets. www.alpek.com","@ID":8} "8 NEWS PETplanet Insider Vol. 22 No. 04/21 petpla.net product development caps & closures design high cavitation moulds multi-component moulds closure production systems after sales service competent – professional – inspiring +43 5572 7272-0 | [email protected] | www.z-moulds.com Nissei ASB concludes US patent litigation against R&D Tooling Nissei ASB Machine Co., Ltd. filed a lawsuit against R&D Tool & Engineering Co., Ltd. alleging the infringement of ASB’s patents in the United States District Court for the Northern District of Georgia on February 1, 2018. The lawsuit was transferred to the United States District Court for the Eastern District of Missouri on January 18, 2019. Nissei ASB Machine Co., Ltd. has now reached a settlement with R&D. ASB alleged that R&D’s mold of the ASB-150DPW, ASB’s one-step injection stretch blow moulding machine, infringed upon ASB’s US Patent Nos. 8,608,466, 8,998,602, and 8,613,614. Under this settlement, ASB will receive an undisclosed amount from R&D for the past sales of R&D’s mould of the 150 DPW. ASB will grant R&D a limited, nonexclusive, royalty-bearing license to sell its molds for the 150DPW. The patents-in-suit remain fully valid and enforceable. The details of the settlement terms are subject to confidentiality. ASB states that it will continue to take appropriate measures against any entities anywhere in the world to provide suitable protection of ASB’s patents and other intellectual property rights. www.nisseiasb.co.jp Consolidation at PackSys Global AG The companies Combitool AG, Texa AG and Madag Printing Systems AG have merged or will merge together into PackSys Global AG. The goal is to create a stronger force and focus on the continuity of their strengths. The complete merger process of all companies will be completed by August 1, 2021. The organisational prerequisites have already been created to operate in the markets with the new structure. The individual companies have been on the market since 1969 and the drive for their entrepreneurial development was and is the passion for mechanical engineering. In order to best take advantage of the benefits of the merged companies, the management structure was reorganised fromApril 1, 2021 with flat and agile hierarchies under the leadership of Beat Rupp as CEO and Angela Strigl as CFO for quick and goal-oriented decisions. The company is newly organised in four divisions: Premium Cosmetics, Health and Pharma, Beverage and Specialties and Customer Service. www.packsysglobal.com","@ID":10} "MARKET SURVEY 31 PETplanet Insider Vol. 22 No. 04/21 petpla.net 04/2021 MARKETsurvey Suppliers of preforms and inspection systems for preforms In this survey we would like to present you preform manufacturers and the inspection system suppliers who are taking care of the preforms before, during or after processing. We thank all the participating companies: PDG Plastiques, Novapet S.A., Europlast, Plastipak, Société Générale des Techniques (SGT), Retal, Sacmi Imola, Pressco Technology, IMD Ltd, Sprana Ltd, Intravis GmbH. Although the publishers have made every effort to ensure that the information in this survey is up to date, no claims are made regarding completeness or accuracy. Resins & additives Preform machinery Preform production & inspection systems Preform & SBM mould manufacturer SBM 2-stage Compressors Caps & closures & inspection systems Filling equipment & inspection systems Recycling machinery Palletising & shrink film machinery Preforms Company name PDG Plastiques Novapet, S.A. Europlast Plastipak Société Générale des Techniques (SGT) Retal Industries LTD Postal address Telephone number Web site address Contact name Function Direct telephone number E-mail ZI secteur 2 45330 Malesherbes, France +33 238 3461 95 www.pdg-plastiques.com Mr Francois Desfretier General Manager +33 238 3461 95 [email protected] Paseo Independencia 21, 3rd floor, Zaragoza 50001 - Spain +34 976216129 www.novapet.com Mr Antonio Lázaro Preform business manager +34 976 216129 [email protected] Novopresnensky lane, 7 123557 Moscow, +7 4957778887 www.europlast.ru Ellice Way Wrexham LL13 7YL, UK www.plastipak.com Mr David Albeniz Sales & Marketing Director [email protected] 3 Rue de l’Île Macé 44412 Rezé, France +33 (0)240 050937 www.sgt-pet.com Mr Pierre-Henri Jany Sales Manager +33 (0)240 050937 [email protected] Epimitheos St. 6, Industrial Area A, Limassol, 3056, Cyprus ++357 25 270 500 www.retalgroup.com Mr Milos Kuzman Vice President Sales and Service +357 25 270 500 [email protected] Preforms Multilayer preforms (Yes/No) No No No Yes Yes Yes PEN prefoms (Yes/No) No No No Yes No No Preforms in alternative materials (PP/PLA/PEF) Which? BioPET - PP No Only PET prefoms Yes - PLA, PEF / Subject to customer specification Yes, BioPET and PEF apllicable Preforms incorporating rPET (rPET content in %) Yes up to 100% Yes, from 10-100% Yes, from 10-100 % Yes, from 10-100% Yes, from 1-100% ( according to customer requests); SGT also proposes to incorporate its own made and food grade rPET CirPET Yes, rPET content 10 - 100% List of additives available Prelactia 100% light barrier for UHT sterilized long shelf-life, milk, oxygen, UV, CO2barriers Concentrates (for milk and light sensitive products), colours, lubricants, nucleants, under customer requirements All standard additives including UV, barrier technologies, colourants All colours and barrier technologies; UV blocker, AA reducer, O2 scavenger, CO2 scavenger, reheat additive, white colour for UHT milk, slip agent CO2and O2 scavangers; AA reducers; Slip agent; UV blockers; Brighteners; Preform range Coloured preforms, Preblow technology, Mint-Tec technology 29/25 shorty: 8 - 10.5 - 11.7 - 18.7 -2122- 23 - 23.5 - 24 - 24.5 - 28g 30/25 high: 17.5 - 24.5 - 26 - 28 - 31 - 33 - 36 - 39 - 50g 26/22: 10.5 - 17- 23 - 28.5 - 30 - 34g 38mm 3 start: 18 - 22 - 28 - 33.5 - 35 - 44 - 50g Prelactia 38mm 3 start: 17 - 24 - 28 - 38g 48/40: 47- 55 - 62g 21/29: 22.5g 27/32: 6.5g dairy and smoothies 25/20: 6.5 - 8g dairy PCO 1810: 20 - 33.6g PCO 1881: 18.5 - 30 - 32 - 36.5g 29/23: 24 -27- 33g chemical BVS 30H60: 50g wine (high oxygen barrier) 22H30: 19g wine (high oxygen barrier) ultra-lightweighting 2.4g preform standard and specific preforms for mineral water, dairy, juice, CSD..etc Overmolding technology for 2-layer preforms, Preblow and Mint-Tec technology for lightweigthing bottles Ø 29/25 W (short neck) 3302,000ml: 10-32g Ø 30/25 W (std neck) 3302,500ml: 11.6-47g Ø 48mm W 5,000-10.000ml: 77g, 82g & 98g Ø PCO 1810 (std neck) 5003,000ml: 18-50g Ø PCO 1881 (std neck) 3002,000ml: 18-38.7g Ø 38mm: 300-8,000ml: 21-93g Ø 29/21 edible oil 1l: 22g & 25g Ø 42/34 edible oil 3-5l: 75g & 85g Ø Pilfer 28mm: 17.5g & 25g Ø 28/410: 30g, 36.5g & 42.5g Any other shape and weight under customer requirements Wide range of preform sizes and weights - too numerous to list. Plastipak supplies preforms for use in bottled water, CSD, food, dairy, home and personal care, alcohol, industrial and other applications. Please contact us with your requirements. SGT supplies preforms for use in bottled water, CSD, food, dairy, juices, oil & vinegar, sauces & condiments, home and personal care, wine & spirits, industrial and other applications. Neck finish: 27/31: 36 g, 45g, 66g; 55mm for 5 gallon (refillable application): 450-650g 30/25 high neck and low neck: 13-44g 30/25 BB Light: 22.50-28g 29/25 (without step): 9.3-35.8g 29/25: 9.5-36g 28 PCO 1810: 16-52.5g PCO 1881: 14.5-50g 26/22: 17-30g 28 BPF: 20.5-53g 38mm 42/36, 38mm 43/36, 38mm 43/36.5 (without step), 38mm 43/36.5: 14-44g 45/52 (yogurt cup): 11g 48/40: 77-160g 21/29: 20-52g 28/22: 23g 28/410: 19.5-40g 28/410 with anti back off system: 34-40g 22H30: 18g BVS 30 H: 40-53.50g CRC63: 385g - 400g - 450g 38/400: 18-28g Around 800 diffrent preforms designs with different weight (9,7 - 485g) and neck (PCO 1881, PCO1810, PET cycle Pco 1810, High PCO 1810, PCO HYBRID, BPF, 30/25, 29/25, Hexalite 26/22, Obrist, 34/29, 38 mm, 29/21, 28/410,etc.","@ID":33} "PREFORM PRODUCTION PETplanet Insider Vol. 22 No. 04/21 petpla.net 21 sent specific challenges. Whereas reground PET preforms are clean and relatively easy to handle, the reprocessing of PET post-industrial fibre waste for example is quite another matter. The Gneuss MRS devolatilising extruder is well suited to processing fibre waste which usually has a high residual moisture level and is often coated with spin finish oils. The dynamic viscosity control of this extrusion system ensures a uniform IV of the material which is important if the material is to be put back into fibres. Halabi: What does it take to process a polymer into a pellet which is fully capable of being recirculated? Prangnell: Post-industrial preform regrind is a sought after material and usually used for high quality applications. With the MRS extruder, it is possible to process this material without the need for pre-drying or any kind of heat treatment prior to extrusion. For this reason, the MRS extruder offers the processor the ability to reprocess raw material with the minimum of quality loss through re-processing. Halabi: For preforms manufacturers the PET pellets need to be of highest quality with regard to transparency and yellowness. Can you describe the way how your machines handle these factors? Prangnell: With the MRS extruder, it is possible to process PET without any thermal pre-treatment whatsoever and in the case of post-consumer PET bottle flakes, thermal pre-treatment for the purpose of decontamination for food contact applications is likewise unnecessary. This means that one major cause of yellowing of the material is taken out of the equation completely. The multiple satellite screws of the MRS extruder provide excellent distributive mixing which ensures good clarity and transparency. Halabi: Together, Europe and North America are expected to capture more than half of the global PET preforms market by end of 2030. However, East Asia is anticipated to have highest growth trajectory, at a CAGR of 4.6%. How do you prepare your company in order to participate and profit best possible? Prangnell: Gneuss has always worked hard to embrace worldwide markets and to adopt different approaches to different markets in different regions. In some regions we operate via daughter companies and in other regions we operate via highly trained representatives with the aim of providing the same level of advice and support as direct from Germany, but with a local touch. The Covid-19 pandemic has shown us that this approach is more important today, than it ever has been. Halabi: Thank you for your time. www.gneuss.com","@ID":23} "28 TRADE SHOW REVIEW PETplanet Insider Vol. 22 No. 04/21 petpla.net Instead of Bottle inspection system including calibrated measurements During recent years, IMD engineers were designing new lighting techniques, algorithms and hardware to improve their bottle inspection system IMDvista Boco Scan. Market research was performed to understand the requirements of potential customers; hundreds of types of bottles were collected and thousands of hours of R&D were logged studying these bottles. The first major challenge was the ability to inspect multiple different types of bottles using the same system; transparent, natural, opaque, shiny, flat smooth and structured. Each of these types of bottles require different lighting and camera techniques to achieve optimal inspection results. For example, a customer may run a clear PET bottle and a white shiny PET bottle on the same line. Traditionally this would require two completely different designs of hardware configurations; backlighting for clear and front lighting for opaque as well as different camera angles due to the clear bottles. The shiny white bottles would cause multiple lighting reflections causing a limited side inspection for contamination, scratches or burn marks. The Boco Scan has the capability of inspecting all of these bottles within a compact single module. Using four special high-resolution cameras (12.5 megapixels) and proprietary lighting configuration even the most complex bottle designs are now capable of inspection. Additionally, usingArtificial Intelligence (AI) the system can learn and easily distinguish a good bottle from a defective bottle. Most bottles have some natural defects to them especially extruded bottles. These defects do not affect the integrity or performance of the bottle. Recognising the difference between natural process driven bottle marks and actual defects is alleviated with the use of A.I., as the Boco Scan gets smarter over time. This is especially useful with bottle with strong structural features. The second major challenge was the ability to perform accurate measurements on the finish. IMD took on the challenge to introduce lab quality measurements in an automated online inspection system. By implementing telecentric camera, telecentric lighting and new algorithms, the result are a fully calibrated measurement system capable of measuring to an accuracy of +/- 5μm (T/E) on 100% of the bottles. Through the IMDvista Portal Software, these measurements can be saved and exported directly to quality management systems. To guarantee sucurity, the system includes a state-of-the-art vein scanner. This hardware features uses an infrared sensor to “scan” the blood veins in the operators hand as this method is more secure than traditional methods of fingerprints or RFID tags. Complete inspection solution To round out the system additional inspections are available: Thin wall inspection and material flow 360° IR control for monitoring of heat profile - prevention of deformation after cooling of the bottle Base control - panel inspection Parting line (also in the handle area) Neck inside inspection (choked necks) Thread inspection www.imdvista.ch Retal introduces US sales team Retal would have introduced its new sales team of the US plant in Donora, PA at NPE. Retal’s US plant reports increased productivity across their operation. CEO and president Darius Janulionus, who took over the running of the fast-growing plant from his role as production director for Retal Lithuania, says, “Of course we all know that 2020 was full of challenges, and 2021 is still not plain sailing, but thanks to the strength and hard work of our team, we can happily say that we have achieved better than hoped for results. We have seen increased productivity across our operation, which is largely due to the team working together, utilising opportunities to share our expertise and listening closely to our customers’ changing needs. Staying agile has been crucial.” The sales team is led by chemical engineer Bob Phillips, a well-known face in the US plastic packaging industry, alongside sales coordinator Brittany Brooks and latest recruit Vlad Nyemstov. Biochemist Brittany worked in the RPA quality laboratory prior to joining the sales team and brings knowledge about preform production. The latest addition to the RPA sales team is Vlad Nyemstov, an Ukraine native who has lived in the US for five years. The Programming Engineer joined Retal in the middle of February. www.retalgroup.com Bob Phillips, Brittany Brooks and Vlad Nyemstov are the new sales team at Retal PA","@ID":30} "47 TRADE SHOW REVIEW PETplanet Insider Vol. 22 PETplanet: Surely the topic of compatibility with other sideways removal moulds was also discussed? Birchler: Processers would naturally like to use their existing moulds for sideways removal on the new PET line, but the focus was actually more on the unit costs. In tough competition, the costs are crucial and producers must be convinced that they are making a good choice with Netstal in this regard. We also discussed many related topics like general handling, safe operation, ease and expense of maintenance and servicing options. PETplanet: How did cooperation with your system partners work? Birchler: There, too, we received a positive response. We set up the entire system with the mould from MHT and the periphery from Piovan and integrated the activation of these components into our aXos controls. We also integrated an inline inspection system from IMD Vista into the removal unit. PETplanet: So, you have created a nine-month event out of an event scheduled to last three months. Will the exhibition become a permanent fixture? Birchler: No. However brilliant the whole initiative has been, it cannot replace a face-to-face meeting. In many individual appointments, we have been able to offer comprehensive advice to interested parties. Because of the longer timespan, this has even been somewhat better than at a trade fair. However, we have missed the spontaneous networking with those visitors and interested parties that drop in unplanned for a coffee and a chat. This group is also very important to us and is hard to reach without trade fairs. PETplanet: Does this mean you won’t repeat the concept after the pandemic? INDUSTRY- LEADING SOLUTIONS FOR SUSTAINABLE APPLICATIONS Mold-Masters’ industry-leading Co-injection Multi-Layer BarrierTechnology offers proven processing capabilities for your sustainable applications. This includes the use of high content post-consumer recycled materials (up to 50% of total part weight) and a wide range of Bio-Resins. For more information, contact [email protected] Preserving Freshness • Maintaining Flavour • Extending Shelf Life Birchler: We use many different touchpoints and all are justified. The current situation has shown us how important trade fairs and personal contact are. However, in a comparable situation, we would do just the same, so the concept is not dying out entirely. Even when we can travel again normally, we will use the resources we have created for “digital visits” in certain situations in the future. Furthermore, we are planning a reconstruction of our technology and customer centre - and many suggestions and experiences from recent months are contributing to that. PETplanet: Many thanks, Mr Birchler! www.kraussmaffei.com","@ID":49} "DIGITALISATION PETplanet Insider Vol. 22 No. 04/21 petpla.net 52 Swiss Company Bevazar offers food & beverage companies their own, dedicated, digital sales channels Spare parts 24/7 Founded by its managing Katja Ceynowa, who worked for Krones for 11 years and rose to divisional managing director level, Bevazar describes itself as “the first independent online procurement platform for operational goods and services for companies in the beverage industry”. It went live in May 2020 and has been engaged since then in expanding the product portfolio and customer base, and integrating new functionalities. On April 1, 2021, Bevazar started offering a new feature that enables sellers to set up their own digital sales channel, very quickly and without making huge investments. Manufacturers can control access to their products and product data, which means they can decide which platform users can see their products and buy them. The conception and integration of this new functionality were based on market demands mentioned by several machine building companies in the industry. Spare parts digitally available The new feature was piloted by project partner (and first project customer) M. Tanner AG, which is based in Illnau in Switzerland and supplies complete solutions for preform handling to bottlers and beverage manufacturers. The company had already been thinking about how to make its standard spare parts digitally available to its customers. The Bevazar digital procurement platform enables operators to simplify the purchase of standard spare parts, saving time and money. The channel with access control developed for M. Tanner AG’s exclusive use enables order clarification for standard spare parts and savings in the preparation of offers. B2B trade is changing fundamentally, and not just in spare parts. The upcoming generation of business people now arriving in decision-making positions want speed, transparency and independence. Long searches or waiting times in the procurement process will be punished, quickly, with a change of supplier. “Manufacturers need to offer their products not only directly or in their own shop, but also in accordance with a multichannel sales strategy on different channels and platforms - wherever their individual customers are to be found,” Ms Ceynowa says. “Nobody wants to invest in large quantity of spare parts in stock anymore,” says Marco Tanner, Managing Director of M. Tanner AG. “For us, this [digital sales channel] means fast and reliable delivery within the shortest possible time.” The ordering process has to be quick, easy and digital, in order to achieve it. Tanner says that the Bevazar platform enables the company to order spare parts online, 24/7, from anywhere in the world. “There are many end customers who operate several of our preform feeders but are integrated in PET lines from different machine suppliers. The spare parts are identical,” he explains Marco Tanner. “Today, many customers ask for quotes by email. They send screenshots from the operating instructions or photos of the required items. That costs time both on the customer side and in our offer preparation. Our goal is to make all standard spare parts available online, in order to save both sides time.” The project team is currently now working on the possibility of displaying products individually, for each machine or customer, according to the respective spare parts list, to ensure that correct spare parts are actually being ordered. M. Tanner AG customers can now request access to products directly via the M. Tanner AG website, or on the M. Tanner AG profile page on Bevazar. Interested parties register on Bevazar first and can then send an access request via the M. Tanner company profile page. After conducting necessary checks, M. Tanner AG approves the new user, which is then automatically informed and enabled to order necessary parts online thereafter. www.bevazar.com","@ID":54} "45 PRODUCTS PETplanet Insider Vol. 22 No. 04/21 petpla.net 45 PRODUCTS ENDLESS INNOVATION SINCE 1919 Pulsed Light sterilisation for sport closures Aptar Food + Beverage, a global leader in dispensing solutions, has announced a technical collaboration with Claranor, a world leader in Pulsed Light packaging sterilisation. This synergy highlights the benefits of the Fullcap sterilisation solution with the Uno sport cap family in PP material, specifically adapted for use with functional beverages. Functional beverages containing vitamins and minerals, boosting energy and helping recovery, capped with advanced sport closures, require a specific sterilisation process that Claranor provides. The company’s Fullcap Pulsed Light sterilisation solution goes through the closure, allowing sterilisation under the cap, where chemicals cannot penetrate or could be trapped. Claranor equipment is compact (600mm high), and provides an instant treatment. It can be used on speed lines up to 60,000 bph with no chemical nor residue. This solution is claimed to provide ultimate inner and outer decontamination when applied to Aptar’s Uno PP sport closure family in the translucent material version. It is adapted for high acid aseptic lines. With its non-chemical and non-thermal treatment, it respects the integrity of the packaging and the product inside. Aptar Uno sport cap is a one-piece design, made with mono-material for improved recyclability. Its active hinge provides a comfortable, one-hand opening and closing, and the 28mm version is tethered to the bottle helping to improve the closures’ recyclability rates, and contribute to a more circular economy. Uno is suitable for dry aseptic filling and approved by Claranor Fullcap sterilisation with pulsed light. This closure is available in 1881, 38mm 2S and 3S neck finishes. The development of Uno, and its ability to be sterilised with pulsed light was driven by the continuous growth of aseptically processed, shelf stable beverages, such as preservative-free functional drinks. Thanks to this development, Aptar and Oshee have recently strengthened their partnership as Uno 38mm 3S was the perfect fit for Oshee’s new functional drink, RL-9 Junior, launched on the Polish market. Oshee, market leader in functional beverages in Poland, inspires and motivates physical activity and a healthy lifestyle. www.aptar.com","@ID":47} "43 PRODUCTS PETplanet Insider Vol. 22 No. 04/21 petpla.net rPET water bottle concept inspired by Greenland Sidel’s art designers have created the Nuuk bottle concept. Taking its name from Greenland’s capital and the fjords, the clear, 100% PET Nuuk container was designed for high-quality, fjordsourced premium water brands. The 500ml bottle showcases the water it contains and reflects the brand’s essence. Thanks to its asymmetric shape, Nuuk stands out on the shelves, putting traditional water bottle designs in the shade. “The specific ice shape on the lower part of the bottle constitutes a great asset and reinforces its structure. It gives the impression that the bottle is surging up from the ice,” explains Laurent Lepoitevin, Packaging Design Engineer at Sidel. In line with its origins, the deep bottle base resembles a rock glacier and is produced by Sidel’s patented Base Over Stroke System (BOSS). The mechanical forming which takes place during the blowing process optimises the material distribution in the final bottle base profile. The consistent blowing process uses a minimum amount of material. The wide cap, with its ice shape and blue colour, enhances the brand’s premium look and perception. The bottle is also compatible with tethered cap solutions to meet environmental requirements and forthcoming regulations. Geometric Viking art influences label design The transparent PressureSensitive Label (PSL) decoration is inspired by authentic Viking art, more specifically the Borre style. In the 10th century, the Nuuk area was inhabited by Vikings who left their cultural imprint, including their art. Laurent explains: “The Borre style embraces a range of geometric interlacing, knot patterns and zoomorphic (single animal) motifs.” Five versions of the label show different graphic designs based on this geometric interlacing. The brand logo is a snowflake combined with an ancient Norse symbol, Vegvisir, a symbol of protection and guidance believed to be used as a compass by Vikings. The other labels represent important symbols of Viking culture, including the drakkar ship, two head-to-tail fishes, the artic fox, and the polar bear. Consumers can collect each bottle from this unique family. www.sidel.com IS STILL 50% TOO MUCH. 50% L SS P CK G NG The KHS solution for more sustainability: New avenues in packaging technology. We are continuously improving our packaging. By applying innovative technologies and switEJKPI QXGT VQ OQPQ OCVGTKCN RCEMCIKPI YG JCXG JCNXGF QWT RCEMKPI OCVGTKCNU QXGT VJG NCUV ƂXG [GCTU #PF YG CTG UQQP VQ VCMG CPQVJGT DKI UVGR HQTYCTF KP WUKPI PGY VJKPPGT V[RGU QH ƂNO khs.com/packaging-systems","@ID":45}]}}
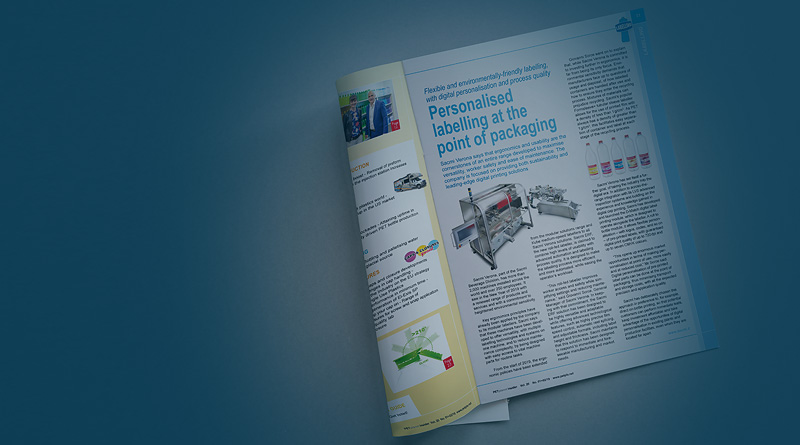