{"pages":{"page":[{"#text":"MOULD MAKING PETplanet Insider Vol. 22 No. 09/21 petpla.net 25 shown to be reliable when changing moulds within the 200 t KraussMaffei CX series machine. The optimised fastening system makes it possible to change a mould in just 30 minutes,” Mr Wanasoontornkul is happy to report. Operating the system is simple and user-oriented. “We benefit from the frugal principle when teaching the machine: You only need to enter a few tool data to start production,” the Powerpack managing director continues. Operating conditions are kept simply MHT says that the demands that the frugal mould places on the customer’s injection moulding system are reduced. All that’s needed is a standard injection moulding machine. The set-up of the peripherals includes machines and components that are common for PET-processing operations. From the chiller to the dryer to the dehumidifier, users can draw on existing components from their own inventory. For the best preform quality, the injection moulders at Powerpack make use of an HPS auger. This ensures gentle processing of the PET, contributes to uniform melting and protects the machine from excessive wear. The reduced demands regarding the customer’s peripherals enable the frugal mould to be used anywhere in the world. In configuring the overall system, the customer was able to rely on the expert support of Mr Prawit Yodprechavigit / KraussMaffei Group SEA. The improved offer made possible by a frugal design also offers cost-conscious customers a possibility to take advantage of the benefits of MHT’s moulds, states the company. This new mould has been designed to offer reliability and an optimal preform quality. www.mht-ag.com Frugal mould","@ID":27} "MARKET SURVEY 32 PETplanet Insider Vol. 22 No. 09/21 petpla.net Inspection Company name Sacmi Imola S.A. IMD Ltd. Postal address Telephone number Web site address Contact name Function Direct telephone number Fax E-Mail Via Selice Prov. Le 17/A 40026 Imola (Bo), Italy +39 0542 607111 www.sacmi.com Mr Stefano Severi Sales Specialist Manager +39 335 659 4236 [email protected] Industriestrasse 37A 2555 Bruegg, Switzerland +41 32 366 80 66 www.imdvista.com Mr Martin Gerber Sales Director (CSO) +41 32 366 80 66 [email protected] Inspection system CHS102/202 PFMC Vision inspection systems for closures, preforms, bottles + barrier testing Inspection speed Up to 4,500 caps/min Up to 200 caps/h Up to 4,500p/min. - depending on closure type and geometry. Inspection method Artificial computer vision algorithms, spark tester Mechanical and destructive breaking force test Non contact inspection Inspected objects Flat top caps, tethered caps, sport caps, hinge caps, multicomponents caps Flat top caps and tethered caps All types and shapes Inspected parameters: -Inner inspection Inspection of the whole product side, including mouth, plug seal (one piece caps), gasket (two pieces caps). Dedicated algorithms for a precise thread inspection. Detection of small flashes and voids in Tamper Evident Band wings. Detection of colour variations, discolourations, contaminations, black specks, pulled threads, voids, flashes of material. Inspection of standard or tethered cut produced in the mould: flashes in the windows, windows partially closed, bridges, number of bridges, thickness of the bridges. 100% inspection - guaranteed Available -Outer inspection Complete inspection of the public side, including sidewall. Special CVS3603D module to unroll the sidewall in a 2D image making a compensation of any deformation coming from lens deformation, perspective and spatial position of the object. Inspection of the decoration with automatic recognition of colours and areas with a specific colour. Colour variation ( ΔE), wrong colour, colour planes registration, off-centre, stains, black specks and many others. Available -Geometry From a top view: Ovalisation, indicative measurement on inner and outer diameter; from side views: outer diameters measured long the cap body, bulged caps, cap height. Available -Cavity number reading Yes, through artificial intelligence algorithms for the highest reliability and performance. Statistics of defects by cavity number, sorting by cavity number. Yes, through CVScut vision system Available -Microhole inspection Yes, with dedicated and integrated spark tester device Available -Additional inspection criteria for inserts Yes, (presence/absence, integrity, black specks, voids, flashes, contaminations…) Available - depending on your requirements Further inspection options Side inspection Breaking force test Specific tethered closures inspection & slit inspection (after slitting machine), print inspection Colour Camera: CHS features up to 7/12 high resolution and high speed colour cameras to control the whole cap Yes Installation: · Stand-alone (offline) Yes CHS 102, no CHS 202 Yes Available · Inline CHS family includes two machines: CHS102 (single vacuum conveyor belt) and CHS202 (double vacuum conveyor belt). Both machines are very compact and have been designed to match the highest production speeds required by the market (up to 4500ppm). PFMC takes samples of plastic caps and performs destructive tests: breaking forces of the bridges and of the lugs that keep the cap tethered to the bottle. The machine records the detected values and provides a set of statistics. It also produces chart showing force as a function of time, and can export that data via Ethernet or USB. Available Softwarefeatures: Graphical HMI translated in more than 20 languages, artificial intelligence algorithms, colour analysis, special tools dedicated to a precise thread inspection, runs under Windows 10 IoT. IMDvista Neuron (AI software for tethered closures) IMDvista Portal (one overview of all running IMDvista systems - connects your vision systems Industrie 4.0)","@ID":34} "Editour PETplanet Insider Vol. 22 No. 09/21 petpla.net 15 HIGH PERFORMANCE L IQUID COLOURS & ADDI T IVES FOR POLYOLEFINS STAND B3-3209 Alessandra Funcia, Head of Sales & Marketing at Sukano AG 1) The pandemic has definitely impacted our business. Most importantly, it affected our daily way of working, requiring immediate and quick rearrangement and highest flexibility for our entire organisation globally. Our supply chain team strategically negotiated supply conditions, we operated even closer to our partners and our employees, supported by the management, demonstrated extreme resilience, making our family business style even more intimate. Because our business was from the very beginning designated as “essential”, we never stopped. On the contrary, we faced increased demand from customers, some to ensure business continuity, some due to higher demand in areas such as medical applications and food packaging materials. The market and safety situation seem poised to remain volatile and uncertain for the coming months, and we therefore expect business to continue at the same pace, with our regional and local suppliers slowly accommodating raw material availability and stock levels. The question that remains to be answered is what demand may be for end of the year festivities, and how our supply chain will be able to react to that. We expect to be ready for different scenarios, as we plan and further strengthen our supply chain and customer relationship to grant their needs on time in full. 2) The SUPD impacts about 40% of the total plastic packaging business in Europe. The Green Deal is expected to impact our entire business as it takes shape. And we find it much more of an opportunity than a threat. At Sukano we closely follow the regulatory and legislative evolution to ensure we are ahead of changes or, if we are able through our innovations, to proactively make our products and customer applications compliant with them before they are enforced. Whether it’s mandatory recycling rates, design for recycling conditions or alternative end of lives, the Sukano portfolio is a direct result of the company’s strategy which is derived from our foundations: pioneering ideas, an entrepreneurial spirit that guides our way of working and servicing the market. The goal is to continuously cause positive social impact, ensuring we are part of the solution (#wearepartofthesolution) through our product offerings and performance. Sukano focuses on masterbatches and compounds in PET, the number one and most recycled plastic in the world, by targeting mainly closed loop or circular applications. We are also a leading company in biodegradable masterbatches that help to catalyse conversion of conventional plastics to biobased and degradable options, where the end application makes sense and infrastructure is in place to accommodate compostability as end of life. 3) The entire plastics value chain - and I dare expand this to any material value chain players that are active in the packaging market segment - must assess their current business models and identify where rapid change is needed to accommodate the societal and environmental demand at its forefront and heart of its operations. We need to do this now: It is urgent and so we need to act urgently to address it. The same goes for the PET industry. Of course, here there is a clear advantage in that we have a head start, with existing collection and recycling rates of over 50% of the PET placed in the ma r ke t ( sou r ce PRE report 2020). The PET industry is actively working to promote collection of its plastic packaging that are not yet collected such as trays, while the industry players are investing and adapting methods and equipment technology to recycle PET trays. The PET industry is also looking deeply into relatively smaller PET applications, such as opaque white and coloured PET bottles, as well as functional PET bottles, to make sure they are not only collected but sorted into dedicated streams to be effectively recycled. This is all in place right now, and is a high priority for our industry, which is already familiar and transparent with regard to recycling operations and reporting. Similar to the PET industry, our vision and strategic pillars at Sukano aim to ensure that all PET packaging placed in the market is designed for recycling, collected, sorted, and effectively recycled. This will help ensure its value is maintained and sustained in the next life and application the material will have. www.sukano.com","@ID":17} "53 PRODUCTS PETplanet Insider Vol. 22 No. 09/21 petpla.net 53 PRODUCTS Horizontal feeding and conveying of preforms With its product-range, the company M. Tanner AG from Illnau in Switzerland, is known for manufacturing preform handling in front of blow moulding machines and inspection systems. As early as 1983, the mechanical development company ventured on its first test trials in the field of PET feeding systems. Two years later, the first system was delivered. From preform tippers to complete preform lines, the company offers complete solutions for every need regarding preform handling. Systems for all output ranges are designed, manufactured and delivered. “Our strengths are to be found in the general handling of preforms. With our experience of more than 30 years in this field, we want to offer our customers the possibility to purchase a complete solution for their preform handling,” says CEO Marco Tanner. The Tanner service engineers are located worldwide and guarantee high flexibility and fast customer service. Now the company has launched its latest innovation named “ErgoFlow”. ErgoFlow is a state-of-the-art system that enables horizontal feeding and conveying of preforms in the highest output range. Using a newly developed system from M. Tanner AG, up to 100,000 preforms per hour are transported through a belt guide. One of the main advantages, according to the company, is that the belt guide does not require air, as is the case with comparable systems that transport preforms horizontally. ErgoFlow is installed directly in front of the blow moulder, inspection system or other downstream machines. Regardless of which machine the ErgoFlow is installed in front of, it impresses with its highly efficient function. Other advantages include a very manageable maximum height and operation and maintenance close to the floor in all performance classes. Despite its high efficiency, ErgoFlow is an compact system that can be used in limited spaces as well. M. Tanner AG offers a solution to companies that already have a preform feeding system. ErgoFlow is also available as a retrofit for already installed systems. www.mtannerag.ch 27th Fakuma International trade fair for plastics processing - Injection moulding technology - Thermoforming and forming technology - Extrusion technology - Additive manufacturing / 3D printing technology - Tooling, materials, process engineering and services @ www.fakuma-messe.com Ä #fakuma2021 ü ? ägB Organizer: SP. E.SCHALL GmbH & Co. KG f +49 (0)7025 9206-0 [email protected] D12.– 16. Oct. 2021 a Friedrichshafen MesseFriedrichshafen SAFE EXPO","@ID":55} "No.09 2021 petpla.net D 51178; ISSN: 1438-9452 27 . 09 . 21 PETplanet is read in more than 140countries MAGAZ I NE FOR BOT T L E R S AND BOT T L E - MAK E R S IN THE AMERICAS, ASIA, EUROPE AND ALL AROUND THE PLANET MARKETsurvey All about caps and closures! Page 31 Page 10 Page 35","@ID":1} "EVENT REVIEW PETplanet Insider Vol. 22 No. 09/21 petpla.net 48 Lahnstein pilot plant At a press briefing on July 8, Borealis and Tomra showcased their pilot plant for advanced mechanical recycling in Lahnstein, Germany. It is capable of sorting post-consumer plastic waste – valuable material that would otherwise be lost to incineration and landfill. This not only keeps feedstock in circulation that are urgently needed by industry to meet its recycling quotas, but also saves CO2 that would otherwise be produced twice - in the manufacture of virgin material and in the incineration, too. The plant recycles household waste made from both films and rigid plastic, which is delivered as presorted baled product from all over Europe. “In Germany, around two million tonnes of plastic waste that could be mechanically recycled is currently incinerated,” explains Jürgen Priesters, SVP Circular Economy, Head of Business Development Tomra. In Lahnstein, these thermoplastics and polyolefins are reprocessed mechanically. Furthermore, in contrast to many other recycling facilities, the plant delivers advanced material solutions that are needed for high-quality and sophisticated plastic applications in a wide variety of areas, such as consumer goods or automotive applications. Currently, these are provided in the form of odourless flakes but a further stage of expansion is already in progress, in which completely compounded material can be produced. The purpose of this demo plant is to manufacture products for brand owners and processors and to test and demonstrate their suitability for sophisticated applications. Successful technical implementation will form the basis for an advanced recycling facility at commercial scale. Volker Rehrmann, who is also Head of Circular Economy at Tomra, says: “After bringing to life this new department for a circular economy, it is clear that the waste economy and key projects like this one play a huge role in our path to a sustainable future. We are proud to have taken the initiative. The plant is among the most advanced mechanical recycling facilities for post-consumer polymer waste. It is and will be an important prerequisite for further accelerating the switch to a circular economy over the coming years and we are delighted to be part of this pioneering project.” The plant is operated jointly by Borealis, Tomra and Zimmermann. Borealis is responsible for the economic success of the facility and contributes its specialist skills and extensive knowledge in the fields of innovation, recycling and compounding. Tomra supplies its thorough specialist expertise and comprehensive process and market knowledge, which in turn contribute to the circular economy though the advanced collection and sorting systems. Zimmermann is a waste disposal company with experience in the field of separating various waste types, including plastics, and is responsible for successful plant operation and product quality. www.tomra.com www.borealisgroup.com www.eunomia.co.uk www.zimmermann-recycling.com The pre-sorted household waste comes in bales from all over Europe. WATER DESIGN - YOUR WAY UNLOCK THE VALUE OF YOUR BRAND Wouldyou likeyourconsumers toengage inacompletely immersiveexperiencewithyourbrand?WithSidel’s packagingexpertise,youcanrelyoncustomisedbottles thatperfectlymatchyourneeds in termsofperformance andrecognition.Fromvalue-based lightweightbottlesand designdifferentiation topremiumdecoration, wehave thebestsolution foryourwater inPET. Findoutmoreaboutourwaterpackagingat: sidel.com/packaging ADV_Water PET Campaign_ 1 08.09.21 13:17","@ID":50} "42 TRADE SHOW PREVIEW PETplanet Insider Vol. 22 No. 09/21 petpla.net Sumitomo-Demag - hall B1 booth 1105 One stop shopping-machine and process technology from a single source All-electric injection moulding machines for LSR, IMD, medical and packaging applications. The trade fair presentation will be supported by three all-electric injection moulding machines from the IntElect series, plus one from the company’s El-Exis SP packaging range. An IntElect 130/520-450, including an LSR package, showcases state-of-the-art elastomer injection moulding integrated with the Servomix Z200 metering system from partner Nexus Elastomer Systems GmbH, Eberstalzell, Austria. An El-Exis SP 250 proves its high-speed capabilities in cup manufacturing applications. The hybrid packaging machine demonstrates high speed, user-friendliness and durability. “Opening and closing sides are the fastest on the market,” reports Arnaud Nomblot, Director Packaging. “The origins of the short cycle times and 1,000mm/s injection speeds can be attributed to the hydraulic accumulator. As a result, processors can produce even thinner and lighter packaging items, resulting in a significant reduction in raw material requirements, packaging waste and shipping costs.” Permanent condition monitoring of machine status Another booth highlight is the inaugural launch of a series of permanent machine status condition monitoring systems. Reducing maintenance costs while maintaining reliability, they can be used to determine the actual degree of wear and tear, enabling early detection and optimal maintenance planning towards the end of the service life of the injection moulding machine. Utilising condition monitoring, complex processes can be reliably analysed directly on the machine, making it possible to monitor critical parameters, which typically requires considerable effort and resources. Commitment to sustainability At the trade fair, Sumitomo (SHI) Demag draws special attention to the ecological progress being made within the production landscape. The company states to be committed to the new slogan “Act! Sustainably”. Firmly integrated into the company’s corporate and CSR mission statement, only machines and equipment that contribute to this sustainability statement will be showcased. Future proof Industry 4.0 networking tools and web-based software Meeting all future networking and communication requirements in the context of Industry 4.0, all of the company’s robots and machines are now completely aligned to the OPC/UA control, monitoring and integration interface. Additionally, Sumitomo (SHI) Demag presents its advanced web-based software solution MyConnect. This central platform gives customers direct access to a wide range of fully networked support services. The MyConnect system helps to enhance the management of inefficiencies, reduce costs, improve total cost of ownership, troubleshoot errors and minimise downtime. www.sumitomo-shi-demag.eu rPET100 HOT CUPS · DAIRY PRODUCTS · INSTANT SOUPS · TO-GO MEALS · COFFEE LIDS Designed for recycling. Made from recycling. • Heat resistant • Fully recyclable • Thermoformable like PET BENEFITS foodgrade without compromise","@ID":44} "PETcontents 4 PETplanet Insider Vol. 22 No. 09/21 petpla.net 09/2021 Page 54 EDITOUR 10 Kick-off European Road Show 2021 16 “The need for exchange of information is immense” - Interview with Petra Westphal and Markus Kosak, Drinktec, Messe München MOULD MAKING 20 Almost 50 years of PET stretch blow mould production 23 Control over the smallest details - PET hot runner spare parts and refurbishment services 24 Focus on core functions, reduce components - A frugally designed mould generation CAPS & CLOSURES 26 Tethered caps: Production requirements and strategies PACKAGING 29 Recycle - Regenerate - Reuse Environment protection combined with product protection MARKET SURVEY 31 Suppliers of caps & closures, mould manufacturers and suppliers of inspection systems TRADE SHOW PREVIEW 35 Fakuma 2021 preview 44 High-performance injection moulds - Indian mouldmaking group Vasantha establishes VTW in Austria EVENT REVIEW 45 European techologies and projects for a global circular economy - Decarbonisation through comprehensive recycling and use of resources 49 5. PETinar: Disruptive technologies and innovative additives for PET recycling BUYER’S GUIDE 56 Get listed! INSIDE TRACK 3 Editorial 4 Contents 6 News 52 Products 54 PET bottles for Home + Personal Care 55 Patents 62 Outer Planet Page 62 Page 20","@ID":6} "MARKET SURVEY 34 PETplanet Insider Vol. 22 No. 09/21 petpla.net Producer Company name Corvaglia group Has Plastik San Tic. A.S. Alpla Werke Alwin Lehner GmbH & Co KG Retal Industries Ltd Postal address Telephone number Web site address Contact name Function Direct telephone number E-Mail Hörnlistrasse 14, 8360 Eschlikon Switzerland +41 71 973 77 77 www.corvaglia.com Mr Vaidotas Bucevicius Director Sales & Service +41 71 973 77 10 [email protected] Firuzkoy Bulvari No, 34325 Avcilar, Istanbul, Turkey +90 212 695 50 00 www.hasplastik.com Mr Unal Haspaylan Commercial Director +90 212 695 50 00 [email protected] Mockenstraße 34, 6971 Hard, Austria +43 5574 602 0 www.alpla.com Ms Gabriele König Key Account Manager - Corporate Sales IM +43 5574 602 555 [email protected] Epimitheos St. 6, Industrial Area A, Limassol, 3056, Cyprus 357 25 270 500 www.retalgroup.com Mr Milos Kuzman Vice President Sales & Service +357 25 270 500 [email protected] Product Range One-piece closures for beverages (Yes / No - If Yes, please specify material) Yes - HDPE Yes , HDPE Yes, HDPE Yes, HDPE Two-piece closures for beverages (with liner) (Yes / No - If Yes, please specify material No No No No Applications relevant to PET containers (e.g. CSD, water, juice, beer, etc.) CSD & carbonated bottled water, still bottled water (pressurised & non-pressurised), sensitive drinks (juices, teas, flavored waters, ...), sports & energy drinks, others (dairy, edible oil, …) CSD, water, juice, energy drinks, beer etc. CSD, water, juice, dairy CSD, water, dairy, juice, Neck finishes available as standard Several standard finishes from 25 to 48mm, e.g. Cetie standard necks GME 30.21 to GME 30.26, GME 30.28 to GME 30.33, GME 30.36 to GME 30.43 26 mm, 29-25 mm, 30-25 mm, 38 mm, 48 mm, 1810, 1881, HOD 55 mm (non standard solutions upon request) PCO1881; PCO1810; 38mm 2-start(GME30.29); 38mm 3-start(GME30.25); 30/25H; 48mm; glass (MCA 7,5R); SPI-necks; 26mm 3 start (GME30.28); 26mm 1 start (GME30.37) 1881, 1810, BPF, 48/41,29/25, 38mm 3 starts, 29/21 Printed caps available (Yes / No) Yes Yes Yes Yes Colour matching service (Yes / No) Yes Yes Yes Yes, tampoprint and laserprint Child-proof closures (Yes / No) No No Yes No Push-Pull / sports caps (Yes / No) Yes Yes Yes No Special comments/special closures (e.g. tethered cap solution, flipt-tops, drinking spouts, lightest cap for 28mm PCO, 26mm for water etc including non-beverage closures...) Closure manufacturing sites in Switzerland, Mexico, USA, corvaglia designed caps are available all around the world via our partner network. Tethered caps for carbonated and noncarbonated drinks according to requirements of EU Directive 2019/904. Tethered caps, flip top caps, lightest 1881 caps for high CSD, global technical service is available. Non aerosol pumps in various neck finishes, buckets & canisters for various applications, tethered cap solutions for 1810, 1881, 38mm neck finishes; CRC caps; standard packaging for pharma applications; 2-chamber caps; bi-and multicomponent injection moulding; custommade closures; Colour printing up to 3 colours, UV & IR laser engraving are available, caps embossment upon request. Tethered solution for closures with slit-folded band – at pre-industrial stage and tethered solution for injected TEB – prototyping ongoing in its final stage. Special patented closures or marketing features Digital printing capabilities installed at production sites HOD caps for 5 gallon, laser marking inside the caps (alfanumeric codes , artwork etc), engraved logo designs Mould Company name z-moulds Corvaglia Mould AG Sacmi Imola S.A. Postal address Telephone number Web site address Contact name Function Direct telephone number E-mail z-werkzeugbau GmbH, Dr.-Walter-ZumtobelStrasse 9, 6850 Dornbirn, Austria +43 5572 7272 0 www.z-moulds.com Mr Michael Fink VP Sales & Marketing +43 5572 7272-610 [email protected] Hörnlistr. 14 8360 Eschlikon, Switzerland +41 71 973 77 77 www.corvaglia.com Mr Albert Brunner Director Sales & Service +41 71 973 77 52 [email protected] Via Selice Prov. Le 17/A 40026 Imola (Bo), Italy +39 0542 607111 www.sacmi.com Mr Stefano Severi Sales Specialist Manager +39 335 659 4236 [email protected] Filling good: - beverages Carbonated and non-carbonated drinks, water, juices, beer, coffee & tea, dairy, etc. CSD & carbonated bottled water, still bottled water (pressurised & non-pressurised), sensitive drinks (juices, teas, flavored waters, ...), sports & energy drinks, others (dairy, edible oil, …) Still water CSD and sparkling water Juice, RTD tea, isotonic, cold /hot filled - other Edible oil, soy sauces and other filling goods possible on request Coffee, beer, detergents, other contents/applications upon request Diary, pharma & food - individial cap solutions Possible on request Individual cap solutions are possible upon request Closure: -type All single-piece standard closure dimensions for all neck finishes, sports closures, flip-tops, push-pulls, multi-component closures… Flat top & sports closures for neck finishes from 25 to 48mm, e.g. all Cetie standard necks GME 30.21 to GME 30.43 Flat top, 25-48mm Flat top, 26-38mm Flat top, 28-38mm / 48mm Flat top, child proof & stoppers -material HDPE, LDPE, PP, TPE, … HDPE (PP for transparent parts) HDPE HDPE and PP HDPE and PP PP, HDPE and TPE -weight Lowest from 0.7g Starting from 0.8g From 0.8g up From 1.45g up From 1.65g up /1.95g up from 1.5-2.5g up Moulds: Clamping dimensions/cavities 16 - 128 cavities 24 - 96 cavities From 12-64 cavities Preferred hot runner suppliers Mold Masters and others Various Special features Several patented technologies for most efficient closure production, with lowest downtimes and spare parts usage. Closure design approvals from all major beverage brand owners. Most economical closure designs for private labels. Tethered cap solutions for carbonated and non-carbonated drinks according to requirements of EU Directive 2019/904","@ID":36} "EDITOUR PETplanet Insider Vol. 22 No. 09/21 petpla.net 16 Tour Sponsors: Interview with Petra Westphal and Markus Kosak, Drinktec, Messe München “The need for exchange of information is immense” by Kay Barton PETplanet: The new road show is at the starting gate and we are delighted to be able to talk to you as the gun is fired. The most important question first: How are you and the Drinktec team health-wise, and how is the vaccination programme at Messe München progressing? Petra Westphal: We are doing great and really looking forward to Drinktec 2022. Two halls of the venue are being used as a vaccination centre. A voluntary vaccination offer has been made to Messe München’s employees. PETplanet: Can you briefly tell us how you, as managers, have felt about not being able to organise and conduct trade fairs combined with all the global uncertainties? Petra Westphal: Of course, the last 18 months have been quite different as well as challenging. Nonetheless, it has also been an exciting period of time with plenty of scope for creativity, both in terms of developing our trade fairs and re-thinking and organising the internal operational workflow. As always we are totally on brand with our slogan: everything is in a state of flow. Markus Kosak: The current climate has further strengthened the relationship with our customers because the need for exchange of information is immense as new questions and challenges naturally arise during such unique times. PETplanet: You were, and still are, all working from home just like us. Was that a big challenge for the team, for your work and for communication? Petra Westphal: On March 16th , 2020 it was clear that starting the very next day we would all have to start working from home. Luckily all employees had the right equipment at hand. This meant that remote working from the beginning was seamless. In addition to that, we are lucky enough to have a strong, cohesive team, which enabled us to maintain our excellent team spirit whilst all working remotely. Overall, the team quickly found creative and effective ways of continuing to work well together within a new operational environment. PETplanet: And are you looking forward to going back to a vibrant office life again? Petra Westphal: Yes indeed. In fact, for us, office life began again on July 1st this year. Even before Covid, we regularly made use of mobile work. Of course, with all the experiences we have made in the last year and a half, it is now much easier to successfully combine office and remote work. For me it is a great mix that further strengthens our team cohesion and productivity as now we have clearly defined the parameters of hybrid working. PETplanet: We have known you, Ms Westphal and Mr Kosak, for many years and are aware that you have always met challenges openly and positively during your involvement with Messe München. As we speak now, how excited are you about the future? Petra Westphal: Super optimistic. Of course, many question marks and uncertainties still remain. However, we have learnt from our customers across all industries that we serve with our trade fair programme that there is still a definite need for physical trade fairs. Of course, you can easily share knowledge digitally but to really create something new, to exchange ideas, to build up sustainable business relationships, and perhaps, most importantly in these current times, for the feel good factor, physical events are needed more than ever. A trade fair cannot be replaced by digital formats – that’s the clear and mutual statement from the industry. In addition, shows that have already taken place in Germany like “Trendset” in July in Munich, or “Caravan Salon” in Düsseldorf, have clearly shown that trade fairs are feasible in all regards. Currently IAA Mobility is taking place in Munich with a new concept that enables visitors to not only find out about latest and future concepts of the industry in the exhibition halls, but also in open space areas in downtown Munich. Our thorough and approved hygienic and safety measures make all of that possible. Trade fairs are back on track - without a doubt. Let us be optimistic that by September next year, or earlier hopefully, all countries will have access to vaccines, we will have learned to live with the virus and measures will be in place that enable us to travel globally. PETplanet: That is our impression too. For our industry, personal contacts and seeing innovations first-hand is immensely important and makes international trade fairs vital as a platform for the sector, particularly for Drinktec of course. For obvious reasons, this has not always been possible. What do you think are the consequences for machine and plant suppliers and for their customers? Markus Kosak: Of course, our customers are best placed to answer this question. Our view is that the industry’s access to new customers is currently being made more difficult and is even lacking in some cases. What is desperately missing is stimulating interaction with the industry in its entirety, i.e. those interactions that go further than your own backyard.","@ID":18} "35 TRADE SHOW PREVIEW PETplanet Insider Vol. 22 No. 09/21 petpla.net TRADE SHOW preview Welcome back to Fakuma 2021 More than 1,900 exhibitors will present their international offerings on the technical event for industrial plastics processing. The 27. Fakuma will take place in Friedrichshafen Exhibition Centre from October 12-16, 2021. Attention will be focused on the latest technologies which promise highly advantageous benefits, as well as processes and tools for efficient plastics processing by means of injection moulding, extrusion, thermoforming and 3D printing. PETplanet put together some PET-relevant presentations at the show. www.fakuma-messe.de Technotrans solutions GmbH - hall B1 booth 1205 Competence bundling: gwk and Reisner as Technotrans solutions GmbH at the Fakuma trade fair New name, proven technology, familiar contacts: true to this motto, gwk Gesellschaft Wärme Kältetechnik mbH and Reisner Cooling Solutions GmbH will be presenting themselves for the first time at this year’s Fakuma under the new name Technotrans solutions GmbH, giving visitors an insight into the ongoing integration. On display will be proven and new solutions from a portfolio of highly efficient cooling and temperature control systems for a temperature range of -80 to +400 °C. The focus will be on sustainable technologies as well as remote service solutions as the basis for CO2 -neutral production in the plastics and rubber industry. In addition, the two companies will ensure a safe stand concept at Fakuma 2021 with room ventilators. www.gwk.com","@ID":37} "PETplanet Insider Vol. 22 No. 09/21 petpla.net 54 PETbottles Home + Personal Care Hyaluron micellar water by Nivea Beiersdorf has combined the active ingredient hyaluron with micellar water to create an enhanced skin care product. The micellar water gently cleanses the skin of makeup residue and dirt while the hyaluron adds moisture and a light replenishing effect which makes the skin look fresher and younger. The 400 ml Nivea bottle is made from 95% recycled material, the colour of which may vary slightly. The liquid is applied via a two-tone hinged press-down cap with the embossed brand name and dispensing spout. www.nivea.de Body milk in a tapered bottle The German company Fit has brought out a vegan-based body milk product under its “Fenjal intensiv” brand. Avocado oil and shea butter provide nourishing moisture to the skin that is claimed to last for 24 hours. The colours of the 400 ml tapered bottle reflect the brand and has twin-colour matching selfadhesive labels. The body milk is applied via a screw-on hinged lid and dispensing spout. www.fit.de Green action from Aldi South The range of products under Aldi South’s “green action” label is being constantly extended or supplemented by new varieties. For example, there are several dishwashing liquids, including one with the scent of apple and another as a balm. The products come in 500ml bottles with recessed grips on both sides. The dishwashing detergents are produced by using plant-based surfactants that are grown in Europe and have several seals of environmental approval. Push-pull caps are used for easy and controlled application. www.aldi-sued.de Hand wash lotion from Neutrogena Neutrogena, a Johnson and Johnson brand, has recently launched a moisturising and antibacterial hand wash lotion. According to the manufacturer, the product gently cleanses and nourishes the skin while removing any bacteria. The clear bottle has three grooved embossments on both sides, making it easy to grip and use with one hand when applying the product. There is also a bead below the bottle thread. The screw-on pump dispenser has a locking function and the two self-adhesive labels provide essential information about the product. www.neutrogena.de","@ID":56} "43 TRADE SHOW PREVIEW PETplanet Insider Vol. 22 No. 09/21 petpla.net Lindner - hall A6 booth 6108 PET hot-wash system and Micromat premium shredder Besides digitalisation and automation, the circular economy is a key topic in the plastics processing industry. Changing from a linear to a circular economy, the quality of the recycled material plays an increasingly important role. Lindner, manufacturer of shredders, system solutions and industrial washing systems for plastics recycling, is taking on this challenge and will be presenting a new hot-wash system for recovering PET. Equipped with the new hot-wash tower and the also new Lindner step dryer, the company is setting new standards in PET recycling. When shredding the plastic to be recovered, the focus of Lindner’s Micromat series is firmly on quality, reliability, robustness and experience. The Micromat, Lindner Recyclingtech’s original powerhouse, shreds waste materials reliably and efficiently. The signature feature of the Micromat series is its Mono Fix rotor, which guarantees universal applicability by enabling different or mixed rotor configurations. Various pointed or flat knives and special counter knives can be fitted to one and the same rotor as required depending on the input material. As a result, this Mono Fix technology ensures a high and consistent throughput with a wide range of materials that are often classified as difficult. The latest product from Lindner’s subsidiary Washtech is the hot-wash system with the PET hot-wash tower and Lindner’s step dryer, which were developed specifically for the PET sector. The innovative stainless steel step dryer dries the material particularly gently by slowly adjusting the rotation speed infive steps. This results in less friction and a lower fines content. The compact step dryer delivers throughputs of 1,000-3,000 kg/h at a drive power of 30 kW. Thanks to the new hot-wash, the last remaining contaminants such as adhesives, labels and prints are completely removed from PET bottles. The PET hot-wash tower can be operated with or without caustic solution and works with a separate water circuit. Gentle cleaning and defined dwell times guarantee high-quality output materials, which are the perfect basis for producing food grade rPET. Lindner Washtech supplies the turnkey line including NIR sorting, label remover and water treatment. “With our new washing components, we also want to set new standards in the PET sector and make an important contribution to a functioning circular economy,” emphasises Harald Hoffmann, Managing Director at Lindner Washtech. www.lindner.com","@ID":45} "39 TRADE SHOW PREVIEW PETplanet Insider Vol. 22 No. 09/21 petpla.net Gneuss - hall A6 booth 6501 Extrusion technology Innovative MRSjump extruder with high decontamination performance and a viscosity boost in one single extrusion step. Gneuss is presenting its new MRSjump extruder. As with the proven MRS extruder, the extrusion process does not require any pre-treatment of the input material, such as crystallisation or pre-drying of the material. Short residence times, low thermal and mechanical stress on the melt and efficient degassing have characterised MRS technology, says Gneuss. With the new MRSjump extruder, the MRS screw section has been modified and extended so that, in combination with a 1mbar vacuum unit developed for this purpose, the viscosity of the polyester can be raised or stabilised to the desired level directly in the extrusion step. A downstream IV build-up in a solid state polycondensation (SSP) is not necessary. For the first time, the processing of materials with low or highly fluctuating input viscosities is possible in a single extrusion step. The compact design of the MRSjump extrusion line requires little space, energy and maintenance compared to other solutions on the market. Filtration technology Gneussfiltration technology is introducing an additional size across its line of rotary filtration systems. The models RSFgenius, SFXmagnus, SFneos and CSFprimus are now available in a size 110, which offers almost 20% more active screen area than the size 90 for each model, depending on the specific model. In the past the next size up was the size 150, with a jump of more than 50% in activefiltration aera. The new intermediate size will ensure an optimised and cost-efficientfiltration solution for every application. Pressure and process constant Gneuss rotaryfiltration systems Rotary filtration systems operate continuous, automatic, process and pressure constant. They are characterised by a filter disk on which the screen cavities are located in a ring pattern. Screens can be changed on the part of the filter disk that is not active in the melt channel, while the production process continues to run without any interruptions or disturbances. Gneuss meltfiltration systems can be integrated into an existing process and are perfectly suited as a retrofit solution e.g. for demanding recycling applications. The various models differ for example in terms of drive design, encapsulation and whether they offer integrated back- flushing. Gneussflange pressure sensor Measurement technology As a machinery manufacturer, Gneuss has the manufacturing capabilities to manufacture even unusual sensor requirements. The lean manufacturing structure at Gneuss allows the company to offer very short delivery times. Gneuss sensors are available to match regional or application-specific requirements such as Atex, Hart Communication or EAC and are also available with digital IO-Link communication. For special process conditions or difficult places of installation, Gneuss offers individual sensor solutions; new are the rotatable sensor shaft and a flange mounting solution. www.gneuss.com Swiss Made | www.imdvista.ch Inspection Systems for the Plastic Packaging Industry CLOSURE Tethered ready – Ready since more than 2 years – Flexible with IMDvista NEURON (AI) – Already more than 30 running lines successful in the market PREFORM Factory Concept 4.0 – In-line monitoring, process control – 100% In-line inspection – 100% Off-line inspection (re-sorting) CLOSURE Factory Concept 4.0 – In-line after IMM – In combination with slitter/folder – Flexible OEM integration","@ID":41} "EVENT REVIEW 50 Vol. 22 No. 09/21 petpla.net TheOnline Viscometer (VIS) is used in a by-path, as a closed loop. By using a small amount of the material from the main flow conveyed by a gee-pump into a slip capillary, which is a defined measure capillary, the differential pressure and the temperature are measured. With the capillary, one can calculate the viscosity during the process. It is possible to monitor and to control the viscosity anytime in the process. Gneuss tray-to-tray recycling solution Dr Carl-Jürgen Wefelmeier stated that for the tray-to-tray recycling a different concept is needed. The question is how to keep or to increase the input IV? Gneuss offers the new MRSjump system, that combins decontamination performance of the established MRS devolatilising extruder with viscosity boost in one processing step. The MRSjump extrusion system can be used in pellet processing, direct recycling (e.g. fibre or strapping tape production) or in a tray-to-tray closed loop recycling system. The extruder is an advance on a simple single screw extruder, equipped with a multi screw section for optimum devolatilisation. The MRS technology enables efficient and gentle decontamination of PET, without the need for predrying whilst achieving the required decontamination for food contact standards. What is new about the MRSjump is the longer, modified version of the multi-rotation section which ensures both a longer residence time of the material and surface area exchange under vacuum. At the same time, material shearing has been reduced. As the thermal and mechanical stress on the polymer melt is minimised, PET processed on the MRSjump extruder has very good optical and mechanical properties. Dr Axel Hannemann further explain, that the longer Multi Rotation Section, coupled with a powerful vacuum system with 1 mbar can be used to boost the viscosity of rPET and to hold it at a stable level in spite of variations in the input material. In this way, there is no need for any liquid phase (LSP) or solid-state polymerisation (SSP) for many applications. With the stabilisation and/or increase of the intrinsic viscosity in the extrusion process, the MRSjump is well suited to recycling for example reground PET film waste or fibre recycling – cases in which direct recycling with an extruder was previously impossible due to the too low intrinsic viscosity or variable input viscosities. Sukano masterbatches for processing rPET application Ms Alessandra Funcia, Head of Sales and Marketing at Sukano spoke about the use of Sukano masterbatches to ensure a high quality and productivity in the final rPET application. She started by taking a look at the European rPET market. Alessandra explained that in 2019 there was un uplift in the collection rate in Europe. This was an organic growth because the consumption growth level was little bit lower than the collection rate. The growth of the collection rate was about 5%. She pointed out that there is a great room for improvement in the collection of PET and that there is a big lack of harmonisation in collection systema and this leads to a varied rate across Europe. This throws up the problem of waste quality and variety. An un-harmonised collection system leads to a significant variety of waste quality of anything between 20 to 99%. The food contact bottles are one of the most important applications when it comes to rPET output (32%), and they are also the most significant growth area. Sheets, or more specifically PET trays are the major outlet for rPET (38%). Recycling PET thermoforms has become a business opportunity. Out of one million tons of PET sheet consumed in Europe, just 15% is collected. The major country for the collection of PET waste is the UK. At the moment there are very little data from other countries. By 2025 and 2030 when the industry has organised itself correctly we will be up at 550 kgt PET from trays in less than 10 years. As an example for upcycling PET trays, a project by Gneuss, Illig, Veolia and Sukano was started. The aim was to convert out of mixed APET flakes thermally stable rCPETfood trays that can go back to a closed loop. As material source, the wide variety of PET collected in the yellow bin by German households was used. To crystallise the PET polymer a masterbatch is needed. Sukano PET Nucleating Combimasterbatch for rPET increases the crystallisation capacity of the rPET film and ensures faster and uniform crystallisation. This results in a higher processing window and leads to a temperature resistance of up to 200 °C for the end application. Additionally, a temperature-resistant colour pigment improves aesthetics. In the example the following result was recorded: “Veolia supplied the rPET collected from the yellow bin from Germany. We mixed it with a combimasterbatch of Sukano which contains a colour and additive package that leads to nucleation and some other functionality. We put it together in the MRS extruder from Ms Alessandra Funcia, Global Head of Marketing & Head of Sales EMEA at Sukano","@ID":52} "PETplanet Insider Vol. 22 No. 09/21 petpla.net 51 EVENT REVIEW Gneuss to produce the desired homogenisation and which purified the PCR with the high vacuum technology. And finally, the MRS extruder will help to stabilise and control the viscosity. By combining these technologies we were able to produce an extrudable PET sheet that can be formed in a CPET process. Oven testing at 200°C for 20 minutes did proof that the CPET tray would resists temperature conditions of conventional ovens up to 200°C. That is the proof we have been looking for, to make tray to tray recycling possible even for CPET menu tray applications.” Sukano offers a full portfolio of additive and colour masterbatches to enable the use of rPET in various applications. The Sukano Melt Enhancer Masterbatches recover the rPET original properties, allowing a higher rPET content. One of the latest innovation is the transparent impact modifier for cold, flash frozen and room temperature applications, which can replace specialised co-polyester resins with recycled or virgin PET resin that is modified with a new masterbatch, allowing the end application to be monomaterial, and recyclable. Apart from the high performance cristalliser mentioned in this project, the company offers not only NIR detectable black but also a full colour portfolio formulated to be detected by sorting machines. And to technically prove that also white opaque PET bottles from recycled materials is possible with the same throughput and without contaminating the recycling stream, the company teamed up with another industry leader and provdided a formulated monolayer PET white bottles masterbatch. For more information about this PETinar, please visit our homepage. There you have the possibility to view and save the presentations of the speakers. You can also watch a full-length version of the PETinar including a lively discussion and Q &A session. www.gneuss.com/en www.sukano.com/en petpla.net/category/petinars","@ID":53} "imprint EDITORIAL PUBLISHER Alexander Büchler, Managing Director HEAD OFFICE heidelberg business media GmbH Vangerowstraße 33 69115 Heidelberg, Germany phone: +49 6221-65108-0 fax: +49 6221-65108-28 [email protected] EDITORIAL Kay Barton Heike Fischer Gabriele Kosmehl Michael Maruschke Ruari McCallion Waldemar Schmitke Anthony Withers WikiPETia.info [email protected] MEDIA CONSULTANTS Martina Hirschmann [email protected] Johann Lange-Brock [email protected] phone: +49 6221-65108-0 fax: +49 6221-65108-28 LAYOUT AND PREPRESS EXPRIM Werbeagentur | exprim.de Matthias Gaumann READER SERVICES Till Kretner [email protected] PRINT Chroma Druck Eine Unternehmung der Limberg-Druck GmbH Danziger Platz 6 67059 Ludwigshafen, Germany WWW www.hbmedia.net | petpla.net PETplanet Insider ISSN 1438-9459 is published 10 times a year. This publication is sent to qualified subscribers (1-year subscription 149 EUR, 2-year subscription 289 EUR, Young professionals’ subscription 99 EUR. Magazines will be dispatched to you by airmail). Not to be reproduced in any form without permission from the publisher. Note: The fact that product names may not be identified as trademarks is not an indication that such names are not registered trademarks. 3 PETplanet Insider Vol. 22 No. 09/21 petpla.net Dear readers, Here in Europe, the first significant trade fair is just around the corner in mid-October: Fakuma 2021 at Lake Constance. It is a plastics trade fair of transregional significance with a catchment area of around 1,000 km. We are anxious to see what the 1,900 exhibitors will be showcasing, what visitor numbers will look like and whether meetings will be intensive. We have found around 50 exhibitors from the PET sector at the trade fair. In light of the constantly increasing proportions of rPET, the topic of recycling is sure to be a key focus. Our Editour will also be setting off: from October, our reporters will be on the road again with the Editourmobil. The European Road Show has now attracted a great deal of attention – read the first part of our sponsors’ interviews on page 10ff. Another slice of normality is being offered by the leisure and sporting events now cautiously taking place once more with spectators. In recent months, the drinks industry has sorely missed these and missed out on a large proportion of single-serve bottle sales. The usual summer highs were never reached. Even if the coming autumn cannot make up for the drop in sales, the events that are taking place can at least sustain the low production levels of the summer. In regions where the virus continues to spread almost unchecked, such as South America, Africa and India, we will have to wait somewhat longer for markets to recover. Stay well. Yours sincerely, Alexander Büchler","@ID":5} "OUTER PLANET 62 PETplanet Insider Vol. 22 No. 09/21 petpla.net OUTER PLANET Sustainable urban project – Muzzi Cycles Bicycles made from old plastic bottles Bicycles themselves offer great potential for recycling old plastics. The Brazilian manufacturer Muzzi Cycles manufactures the frames of its bicycles from plastic obtained from post-consumer PET bottles. Juan Muzzi, founder of the the company, had the idea of recycling bicycles early on, as he explained in an interview with Plastics Magazine: “I worked on a polyamide bicycle frame in the early 2000s. Over time I became aware of the environmental problems caused by plastic. I therefore decided to make the frame out of recycled plastic”. The Brazilian company produces 132,000 bicycle framesper year. The post-consumer The right tools and expertise to help with your rPETgoals! Agr is uniquely positioned to support your venture into rPET bottle manufacturing with a powerful combination of Process Control tools, Process Consultants, and decades of industry experience. AGRINTL.COM • +1.724.482.2163 PET, which now serves as the starting product, is crushed into small pieces for this purpose. These are further crushed and chemical additives are added to give the frame more strength and protect it from weathering. In the injection moulding process, the frame is produced within four minutes and can be further processed into a bicycle after cooling for five hours. The start–up idea 1998 was to develop an urban mobility from photosynthesis for circular economy without the need to extract minerals, nor produce alumina and aiming to reduce the cost of CO2 . In 2010 was the beginning of the injection process with PET and Nylon, perfected by 2016. Currently Muzzi recycle 15,000t of polymers, out of this they manufacture 132,000 bicycle frames. It is stated to save 980t of oil and to reduce the greenhouse gas emissions by approximately 6,000t of CO2 . The ultimate goal at first is to reuse the fossil fuel spread by society and then use renewable sources with no need to extract minerals, thus making the injected parts organic to be absorbed by nature. 90% of bicycle components are manufactured in Brazil. The aluminum parts contain a recycles percentage. In addition the packing boxes are made from recycled materials. The features of the Muzzi Cycles are that disposable plastic is reused, that a colour injection eliminates the painting and finally the bicycles are certificated with a lifetime warranty. They are produced with renewable energy sources from photosynthesis and manufactured out of recycled thermoplastic resin blends. The rust free cycles with an organic and comfortable design eliminates soldering and shock absorber. Let’s padel on! www.muzzicycles.com.br www.plasticsindustry.org www.mobility-logistics.messefrankfurt.com","@ID":64} "8 NEWS PETplanet Insider Vol. 22 No. 09/21 petpla.net The TEM machine offers possibilities for slitting or slitting and folding of tamper evident bands for specialty caps. The TEM, a highly versatile machine for beverage, food, beauty & home, chemical and other products. Modular design machine for slitting / folding or folding /slitting of tamper evident band Large variety of cap dimensions, including sport caps All size parts located in the outside for easy adjustment and changeover Heating system for the blade. Blade position sensor Servo-driven infeed star wheel, integrated cap stop and sensor controlled upside down closure detection Operator friendly interface Match the output of associated moulding and downstream machines Easily integrated into any production line due to independent control and optional vision inspection system Our packaging machines are perfectly suited for a wide variety of industrial sectors: for the production of premium cosmetics, health and pharmaceutical products as well as for beverages and specialties. Complete lines for laminate and extruded tubes Plastic closures slitting and folding machines Packing solutions for unfilled tubes, cans, cartridges and containers High precision automatic hot stamping solutions We stand for Swiss engineered innovation and performance. Creating Packaging Technology. PackSys Global AG T +41 55 253 38 31 [email protected] www.packsysglobal.com SPECIALTY CLOSURES TAMPER EVIDENCE","@ID":10} "MOULD MAKING PETplanet Insider Vol. 22 No. 09/21 petpla.net 20 Almost 50 years of PET stretch blow mould production If there were a synonym for PET stretch blow moulds it could be Röders. Röders, together with Corpoplast, from its very beginning made PET stretch blow moulding suitable for largescale production almost 50 years ago. Later Röders supported well-established machine producers like Krones and Sipa with their development of modern mould concepts for their blowing machines. The PET stretch blow moulding technology is still one of the most important packaging technologies for liquids today. Jürgen Röders, managing director of Röders, has a long-held passion for PET stretch blow moulding - so we visited him at Soltau. Röders is a sixth-generation family-run business with a history of more than 200 years. Apart from technology, there is only one matter of concern for Jürgen Röders and that is reliability. This means meeting short delivery times as well as ensuring that he provides solutions that are tailor-made to his customers’ requirements. Röders, together with Corpoplast, was the first to venture into the PET stretch blow moulding technology for packaging soft drinks in 1975 in a move away from PVC to PET. For years, Röders had designed and produced PET blow moulds exclusively for machines from Corpoplast. Later, in the 1990s, Röders started offering PET blow moulds also for machines made by Sidel and others. Röders has not only left its mark on the history of PET stretch blow moulding. Today, too, significant industry innovations are coming out of Soltau, including its rapid mould change system and the development of coatings for stainless steel moulds to reduce cleaning efforts at the customers as well as protection against scratches and damages. For all innovations, it often comes down to fine details which will be decisive for whether or not a mould will fit and function. “Even within machine generations, the mounting arrangement for the PET stretch blow moulds can be different. Here, we have to take particular account of the machine’s varying and therewith special features”, says Jani Rickert, Head of PET Blow Mould Sales. Innovations in production are very important for reducing delivery times and improving cost efficiency. More than 30 years ago, Jürgen Röders already felt challenged by the fact that aluminium is relatively easy and fast to machine, but only slow machines were available to produce moulds made of aluminium. Finally, he started the development of High Speed Cutting machines (HSC machines) and Röders became a pioneer in this evolving technology. Today, the production of its high precision, high speed milling and grinding machines account for more than 80% of Röders’ turnover. Jürgen Röders is the sixth generation in his family running Röders as managing director. When he started at Röders, the major business had been pewter and at a lower scale PET stretch blow moulds. Under his responsibility, the new business field of High Speed Cutting machines was developed, which today accounts for over 80% of the turnover and increased the competitiveness of the PET blow mould production. +44 (0) 1254 584210 [email protected] petmachinery.com Active for over 25 years, our global network and specialist knowledge makes us the go-to company for the sale or purchase of a PET machine. Commercially savvy, we work closely with our customers and our global network, to make sure everyone gets the best deal. Providing comprehensive advice throughout your sale or purchase; we can arrange dismantling, loading, packing, shipping, specialist insurance and commissioning. If you have amachine to sell or you’re looking to purchase, please get in touch. THE INDUSTRY EXPERTS","@ID":22} "9 NEWS PETplanet Insider Vol. 22 No. 09/21 petpla.net New PET recycling facility to be built by industry partnership Pact Group, Cleanaway, Asahi Beverages and Coca-Cola Europacific Partners (CCEP) have announced they have signed a Memorandum of Understanding (MoU) to form a joint venture that will build and operate a new PET recycling facility. Under the MoU, the parties intend to come together to provide an industry model for recycling solutions in Australia. This will include the new facility as well as the PET recycling facility currently being built by Pact Group, Cleanaway and Asahi Beverages through Circular Plastics Australia (PET) in Albury-Wodonga, which is intended to be completed later this year. The proposed facility is expected to provide a massive boost to Australian recycling by processing raw plastic material collected via Container Deposit Schemes and kerbside recycling. It will process the equivalent of around 1 billion bottles each year to produce over 20,000 t of new recycled PET bottles and food packaging. The facility will use state-of-the-art sorting, washing, decontamination and extrusion technology. The cross-industry solution combines the complementary expertise of each participant to enhance their individual sustainability goals. Cleanaway will provide available PET through its collection and sorting network, Pact will provide technical and packaging expertise and CCEP, Asahi Beverages and Pact will buy the recycled PET from the facility to use in their respective products. The plant, when fully operational, will be run by Pact. A decision on the plant’s location is anticipated in the coming months and construction is expected to be complete by 2023. CCEP and Asahi Beverages, while competitors in the beverage market, have, for the purpose of this joint venture, joined with Pact and Cleanaway to increase the production and availability of recycled PET resin in Australia. The parties are proud to work with one another to advance the cause of sustainability and recycling. This proposed plant is an important step forward in creating a local plastics circular economy in Australia. This new self-sustaining industry is expected to create dozens of new jobs during the construction phase and operation of the plant. The arrangements set out in this announcement remain subject to the finalisation of legally binding documents between the parties. www.pactgroup.com product development caps & closures design high cavitation moulds multi-component moulds closure production systems after sales service competent – professional – inspiring +43 5572 7272-0 | [email protected] | www.z-moulds.com Mould at FAKUMA 29/25mm 3-start water 24-cavity @Ferromatik Milacron, booth B3-3202 Amcor expands global network of innovation centres Amcor, a global leader in developing and producing responsible packaging, announced plans to build two new stateof-the-art innovation centres. The new facilities in Ghent, Belgium, and Jiangyin, China, will welcome customers as of mid2022, with full build-out over the next two years. The total investment is expected to be approximately $35 million. The new centres expand the global reach of Amcor’s innovation network, which currently includes flagship sites such as Neenah, Wisconsin, and Manchester, Michigan, in the US, as well as smaller sites around the world. The broader network will allow customers globally to tap into the company’s deep material science expertise and packaging development capabilities. The centres will include differentiating features that are in high demand from customers: Immersive customer experience facilities to generate consumer insights, run co-creation sessions and conduct rapid prototyping. Advanced analytical and material science labs. Dedicated pilot manufacturing equipment. Packaging machinery that replicates customer operations to run trials without disruption to customer production. The latest packaging recycling and composting know-how across multiple materials. Amcor dedicates more than $100 million annually to its industry-leading research and development activities. The company claims that it was the first packaging solutions provider pledging to develop all its products to be recyclable or reusable by 2025 and is on track to meet that commitment. www.amcor.com","@ID":11} "EDITOUR PETplanet Insider Vol. 22 No. 09/21 petpla.net 18 of vaccinated and recovered people will increase significantly in the upcoming months globally. This should have a positive affect on the probability of being able to travel. Ultimately, we are all responsible with our behaviour and attitude in helping the new normal become reality. PETplanet: That’s true: Can you draw any positive conclusions on how things stand at present? Markus Kosak: We have once again shown how flexible and resilient we are as a trade fair company. We have honed our creative skills and advanced digitisation at lightning speed. Hybrid work offers great opportunities and video calls enable us to become even closer with our customers, as well as colleagues at our subsidiaries as we can “see” each other more often. Nonetheless, if you really want to be inspired, build strong relationships and make business, a physical meeting is a must. PETplanet: How is Messe München, and the Drinktec team more specifically, positioned and equipped for dealing with upcoming events taking into account all the changes that have taken place as a result of the pandemic? Petra Westphal: We have adapted to the new situation extremely well. With some new operational frameworks in place, we are ideally equipped for the hybrid world. PETplanet: Can you give us an indication of what might be in store for us in terms of innovations at Drinktec? Markus Kosak: In addition to the webinars I mentioned earlier, there will be an inspiration hub@ Drinktec and at China Brew China Beverage. We will give more details during the fourth quarter. PETplanet: As a long-standing partner of Messe München, we will again be heavily involved in supporting Drinktec events, including your foreign trade shows as soon as travel without restrictions is possible again. Despite all the difficulties of the first pandemic year in 2020, we managed to organise a very interesting, partially digital Editour with you in the Australasian markets. Now we are bridging the gap from the other end of the world to the technology hub of Europe. From now until Drinktec 2022, we will travel to various countries under the banner “Let your inspiration flow – the European tour”, interviewing market leaders in the drinks and mechanical engineering industries to discussing technologies, market developments and innovations. Important topics such as sustainability, digitisation and global changes brought about by the pandemic will also be raised. The interviews and articles will appear in PETplanet Insider in the next few months. What do you both want to come out of this initiative, and why is it crucial for you to be on board as the Drinktec team? Petra Westphal: The tour will enable us to get much closer to our customers, thereby learning more about their specific needs, as well as hearing about current and real time market information and industry trends. PETplanet: How will you use Editour as a source of information, or as a tool, and how will you present it at the trade show? Markus Kosak: The collected information of the tour is extremely valuable for us, as it helps us to understand the individual needs of our clients even better. Together with hbmedia we will summarise the output into a joint market report. This will be shared with the Drinktec community through our Drinktec blog and social media channels. PETplanet: Finally, what message do you have for our readers, many of whom will also be your Drinktec exhibitors and visitors? Petra Westphal: Let us go forward confidently together and ensure that an entire industry can continue to benefit from a unique interaction and source of inspiration that only a physical trade fair can offer in all its varied forms. Markus Kosak: And let us also highlight the added value that digital platforms offer in terms of knowledge transfer alongside these physical events. With this symbiosis, we are sure to be a perfect partner for our industry in this new world. PETplanet: Thank you! www.drinktec.com","@ID":20} "41 TRADE SHOW PREVIEW PETplanet Insider Vol. 22 No. 09/21 petpla.net Koch-Technik - hall A3 booth 3213 Mixing, dosing, conveying and drying Koch-Technik will be showcasing the broad portfolio of its product range in the areas of mixing, dosing, conveying and drying, as well as a variety of sustainable solutions for applications in the automotive, consumer goods, health care and several others industries. The new Eko-N dry air dryer, already presented in its original version at K 2019 exhibition, will celebrate its debut at this year’s Fakuma. The dryer has been developed further with respect to energy efficiency. Together with the patented Koch-Öko energy system control, the new dryers can save up to 50% energy. Another highlight is the KKT mobile granulate dryers, which will be presented with a new touch control. The new colour displays are larger than before and offer further advantages such as the simple, intuitive operation of the control unit, the integrated central conveying system - which is Industry 4.0-compatible as a result of the OPC UA communication standard - and the option of full integration into the Koch visualisation. Another innovation will be the MCGT control unit for the gravimetric mixers, Graviko. Together with the control units of the volumetric pre-mixers and the mobile KKT dryers, the new control units of Koch-Technik present themselves in a uniform and modern appearance. Thanks to the OPC-UA communication interface, the complete and easy integration of the Gravikos into the client´s production processes is possible. The clear illustration and easy entry of process parameters on the touch-panel is one of many advantages. The control unit calculates the necessary process parameters automatically and guarantees a continuous and consistent dosing. www.koch-technik.com Maag Pump Systems AG - hall A6 booth 6202 Filters for use in PET recycling Maag Group is a broadly diversified global solutions provider of pump & filtration systems, pelletising & pulverising systems, recycling systems and digital solutions. Maag experts will be on hand to discuss the company’s product portfolio for the polymer industry: Maag Ettlinger has unveiled a new generation of tried-and-tested Eco high performance melt filters for use in PET recycling. Their new features take into account the need for systems with a higher product throughput and are initially available in sizes suitable for mediumsized recycling lines. The new performance enhanced Eco 350 replaces the former Eco 250, while the new Eco 500, capable of achieving capacities of up to 4,000 kg/h, replaces the former Eco 250 Twin. The Eco 200 completes this range. New high-performance pelletising machines for the polymer industry including direct crystallisation. Efficient systems for the production of biopolymers. Technology-based, optimised pellet shape up to micro pellets. Recycling systems with added value. Tools with significantly longer service life until knife change and/or die plate grinding. Innovation in strand pelletising: From lab size to compounding/ masterbatch and large scale polymerisation. All Maag Group extrex gear pumps in x6 class design are completely re-engineered and have redesigned components, from the shafts through to the bearings and seals, and optimised the interaction of the components. Specially developed gear teeth with low compression allow high pressures to be achieved with low shear rates. The result is a further increase in achievable product quality, volumetric efficiency, as well as production consistency and safety. www.maag.com Ettlinger’s new Eco 500 high performance melt filter November 7-9, 2021, Dubai At the KRONES booth A1-34 German Technology Innovative hotrunner optiRun","@ID":43} "MARKET SURVEY 31 PETplanet Insider Vol. 22 No. 09/21 petpla.net 09/2021 MARKETsurvey Resins & additives Preform machinery Preform production & inspection systems Preform & SBM mould manufacturer SBM 2-stage Compressors Caps & closures & inspection systems Filling equipment & inspection systems Recycling machinery Palletising & shrink film machinery All about caps! For the scond time PETplanet decided to put all our surveys about caps & closures manufacturing together in one comprehensive overview - from mould maker, systems manufacturer, inspection systems provider to cap producer. Please find out about state of the art closure equipment. We thank all participants: z-mould, Corvaglia, Engel, Netstal (KM), Sumitomo Demag, Retal, Has Plastik, Alpla, IMDvista, Pressco Technology, Intravis and Sacmi. Although the publisher has made every effort to make sure that the information in this survey is up to date, no claims are made regarding accuracy and completeness. Systems Company name Netstal Maschinen AG Engel Austria GmbH Sumitomo (SHI) Demag Plastics Machinery GmbH Sacmi Imola S.C Postal address Telephone number Web site address Contact name Function Direct telephone number E-mail Tschachenstrasse 1 8752 Näfels, Switzerland +41 55 618 61 11 www.netstal.com Mr Stefan Kleinfeld Product Manager +41 55 618 62 41 [email protected] Ludwig-Engel-Straße 1, 4311 Schwertberg, Austria +43 50 620 0 www.engelglobal.com Mr Christoph Lhota Vice President, Packaging +43 50 620 3400 [email protected] Altdorferstrasse 15 90571 Schwaig, Germany +49 91150610 www.sumitomo-shi-demag.eu Mr Arnaud Nomblot Director - Bus. Develpmt. Pack. +49 911 5061 625 [email protected] Via Selice Prov. Le 17/A, 40026 Imola (BO) - Italy +39 0542 60 7111 www.sacmi.com Mr Stefano Severi Sales Area Manaer +39 335 659 4236 [email protected] Systems for cap/closure production Turnkey systems Injection moulding machine Model Elion Engel e-cap El-Exis SP CCM24SC /CCM32CM /CCM48SD/ CCM64MC Procession technology Injection moulding Injection moulding Compression Clamp force 1,200 - 4,200kN 2,200 - 4,200kN 1,500 - 10,000kN Not applicable Cycle time (guaranteed 98% closure system efficiency for): 2 - 20s 2s (dry cycle times of 1.3s with the e-cap 380) 26/22mm - up to 2,800 caps/min 29/25mm - up to 2,300 caps/min PCO1881 - up to 1,800 caps/min GME30.40 - up to 1,800 caps/min - High speed production: closure type/ weight/cavities: caps/min 26/22 / 0.8g / 96 / 2298 29/25 caps/1.3g/96 cavities/2,880 caps/min (e-cap 380, Plastisud mould, HDPE) 29 mm water/ 1.2 g / 24 cavities: 1,000caps/min, 28 mm CSD/ 2g / 32 cavities: 980caps/min, 29 mm water/ 1.2 g / 48 cavities: 2,000 caps/min, 28 mm CSD/ 2.4 g / 64 cavities: 1,600caps/min - Individual cap solution: closure type/ weight/cavities: caps/min 38 / 2.8g / 72 / 1026 Drive concept Electric + hybrid All-electric Hybrid Electric / hydraulic Energy consumption (kwh/kg) 0.40 0.37kWh/kg (e-cap 380) 0.40kWh/kg, varying upon application Equal or more than 0.4 kwh/h Preferred mould makers Corvaglia, z-moulds, Plastisud z-moulds / Plastisud Sacmi Special features SmartOperation, twin-valve technology, high-speed toggle lever clamp myConnect Possibility to assemble only 12-32 moulds, inline quality control on all caps, cap weight adjustable from HMI, without mould change","@ID":33} "PETplanet Insider Vol. 22 No. 09/21 petpla.net 45 EVENT REVIEW Decarbonisation through comprehensive recycling and use of resources European technologies and projects for a global circular economy In July, PETplanet accepted two invitations from circular waste management expert and equipment manufacturer Tomra: On July 7, the company hosted a webcast on the topic of CO2 reduction and how climate change can be encouraged by comprehensively optimising waste management and recycling. The company worked with UK sustainability consultancy Eunomia and their experiences and findings are now available online. Speakers for the event were Tomra’s Executive Vice President Dr Volker Rehrmann and Eunomia’s Director of Circular Economy Policy Strategy & Operations, Joe Papineschi. On July 8, Tomra and Borealis invited us into their pilot plant in Lahnstein, Germany, where extensive renovation and expansion measures have now enabled the sorting and recycling of an incredible range of plastics. sumed and that generates CO2 in its manufacturing, and finally 26% to the food system. “We are focusing on the materials sector,” explained Joe Papineschi, “as this is where we see great potential for improvement regarding a lower use of new material, improved and more frequent recycling loops with existing resources and overall, a fundamental lowering of consumption.” The ever-increasing consumption in this sector, resulting from better living conditions and growing purchasing power, also leads to increased energy use and CO2 emissions. According to Eunomia, this would be much lower using recycled material rather than processing virgin material. Mr Papineschi demonstrated this by comparing the aluminium, steel, glass and plastic sectors, where savings of CO2 emissions are significantly better with recycled materials: this, he explained, should dictate how choices are made when the aim is decarbonisation. A further slide showed a scenario for 2030, where the adoption of global installations for the optimised collection and processing of urban waste would lead to a reduction of 2.8 billion tonnes of CO2 annually. “The technologies to take this step are currently available,” said Joe Papineschi. He went on to outline the essence of the Holistic Resource System, which is a mixture of a deposit system, separate material collection of certain material streams and the collection and sorting of mixed waste as it occurs in household waste. A key consideration would be to strengthen the responsibility of producers in this process. Following this, Dr Volker Rehrmann gave more detail about the advantages of deposit systems in recycling, especially for PET bottles but also for metal and glass packaging, and discussed a diagram that compared separate collection and a deposit system. “Alongside the aforementioned CO2 impact resulting from avoiding new bottle production, we can simply continue to process the available secondary resources,” stated Dr Rehrmann. “Flagship systems are normally used for beverage containers and these have been operating for many years in all the Scandinavian countries, in Germany and for Tomra’s “Holistic Resource Systems” webcast essentially examined the levers that must be pulled to decrease CO2 emissions and went on to examine to what extent improvements in recycling systems can contribute to this. Tomra had commissioned Eunomia to carry out a study to examine the effects that a combined waste management system would have on CO2 output and resource optimisation if it were made up of the most ingenious and comprehensive systems currently available in Europe. The focus here was particularly on collecting and processing waste. Initially, by way of illustration, Eunomia presented some figures on the three main causes of CO2 emissions. Of a global output of 50 billion tonnes of CO2 , 51% is due to the energy industry, 23% to the materials sector, i.e. everything that is conDr Volker Rehrmann from Tomra Joe Papineschi from Eunomia by Kay Barton & Gabriele Kosmehl","@ID":47} "37 TRADE SHOW PREVIEW PETplanet Insider Vol. 22 No. 09/21 Herbold Meckesheim - hall A6 booth 6312 Plastics recycling solutions The key for the efficiency of the Herbold Meckesheim granulators is the rotor design and the special construction design of the granulators in addition to the cutting geometry and the real double cross cutting action. Herbold can offer a multitude of rotor geometries, customised according to the individual application. The entire anti-wear coating of the housings and the exchangeable wear parts of special rotors have scrupulously been thought out and guarantee a long service life of the machines, easy to maintain. Washing technology The demand for high-performance and efficient recycling plants is currently extremely high. Projects covering investments of up to €12 million keep surging and high-end product qualities are in focus. The use of hydrocyclones in separation technology and the hot wash have been important components of the Herbold plant solutions and vital criteria of Herbold technology for years. Herbold has almost doubled its turnover business in the last 2 years. For the following applications in particular Herbold is able to offer tried-and-tested solutions: Post-industrial postconsumer film Post-consumer rigid plastics PET bottles PET trays Big-bags and other monofilaments Bottle crates and pulper residues The hot wash offilm has now become an essential component in a multitude of orders to yield the high qualities of postconsumer materials currently required. In the PET realm, plant technology continues to be set on efficiency and product output. We can also showcase efficient solutions for PET trays and due to a gentle treatment, only few fines loss in this brittle material flow. Herbold technology can also be used as a preliminary processing step for chemical recycling. Dry cleansing solutions, wash lines as well as Herbold agglomerators tailor the input material for the chemical procedure solution. “We are committed to an expert and comprehensive consultation with our customers,“ highlights Achim Ebel, Division Manager for Washing Lines – „A ready-made washing line does not exist at Herbold – in cooperation with our customers, it is an individual process to devise a solution that corresponds exactly to the application.” www.herbold.com INDUSTRY- LEADING SOLUTIONS FOR SUSTAINABLE APPLICATIONS Mold-Masters’ industry-leading Co-injection Multi-Layer BarrierTechnology offers proven processing capabilities for your sustainable applications. This includes the use of high content post-consumer recycled materials (up to 50% of total part weight) and a wide range of Bio-Resins. For more information, contact [email protected] Preserving Freshness • Maintaining Flavour • Extending Shelf Life","@ID":39} "PETnews 6 NEWS PETplanet Insider Vol. 22 No. 09/21 petpla.net New CEO at Tomra Tove Andersen has joined global resources sustainability company Tomra as president and CEO effective August 16th , 2021. She took over from Stefan Ranstrand, who held the position for the past 12 years.She became the first female president and CEO of the company since it was founded in 1972. Tove Andersen comes to Tomra from the leading global fertiliser company Yara International, which is also headquartered in Norway, where she was Executive Vice President Europe. Commenting on starting her new role, Tove Andersen said: “With the increased focus worldwide on sustainability and, in particular, the circular economy, Tomra is more relevant than ever before and is perfectly placed to continue being a very successful company. “What especially excites me about Tomra is that it is a technology-based business which is purpose-led and delivering on a truly global scale. It is a business that is making a positive difference to the world we live in. www.tomra.com Spin-off of Netstal into an independent group KraussMaffei Group announced that its Swiss business unit KraussMaffei HighPerformance AG (formerly NetstalMaschinen AG) and the associated Netstal brand will be expanded into an independent group under the name Netstal. In addition to the headquarters in Näfels, Switzerland, sales and service subsidiary based in Stuttgart, Germany, as well as the two sales and service units in Barcelona, Spain and Singapore will be transferred to the new Netstal Group. Employees from the Netstal sales and service organisation in existing KraussMaffei subsidiaries will also be transferred to the new group and integrated into existing or newly founded subsidiaries. As part of this restructuring, around 500 employees will transfer from the KraussMaffei Group to the Netstal Group, which will in future be managed from Näfels. The restructuring is scheduled to be completed by October 1st , 2021. The existing organisational units will be renamed to the familiar Netstal name at the earliest possible date. With the spin-off of Netstal into an independent group, the leading supplier of high-speed, high-performance injection moulding machines and systems is to be further developed and expanded. With the creation of an independent group, Netstal will gain promising strategic options for the further development of a growth-oriented Netstal Group, with its own sales and service companies in the most important markets. www.kraussmaffei.com Joint research project on returnable PET for sensitive beverages In the beverage packaging market, returnable PET containers currently play a rather small role. Unjustifiably so, say the results of a joint research project of Krones and Alpla. In the project’s first phase, the material and process parameters underwent a comprehensive scientific evaluation. Based on these findings, Krones and Alpla developed a returnable PET container that provides an optimal environment for sensitive ESL (Extended Shelf Life) products such as juice and milk in the cold chain. Bottle samples and cleaning processes tested Krones and Alpla teamed up to make these benefits available for use for a wide range of beverages. “Until now, the main applications for returnable PET containers have been carbonated soft drinks and water,” explains Jörg Schwärzler, returnables expert and project lead at Alpla. “But we were certain that, if we combined our expertise in materials science, preform design, container design, and systems engineering, we could find a solution for sensitive beverages like juices and dairy products. The option of using a 38mm bottle neck offers particular advantages for sensitive returnable applications.” The partners dedicated particular attention to the container cleaning process because “PET is less heat-resistant than glass,” explains developer Ines Bradshaw. “So we had to find a way to ensure both a high level of microbiological safety and a high number of use cycles while cleaning at lower temperatures.” To obtain an objective and meaningful base of data, Krones’ development plant for washing technology in Flensburg, Germany, carried out an elaborate series of tests, analysing the interaction of different bottle designs and cleaning processes. “The tests provided us with a very clear picture of the respective thermal, chemical, and mechanical factors,” says Bradshaw. “Among the findings: With the right combination of parameters – especially lye concentration, temperature, additive, and mechanical impact – temperatures around 60 °C are sufficient to reliably remove even dried protein, fat, and starch contamination from the containers.” Direct comparison with returnable glass A direct comparison of returnable PET and returnable glass brought to light another interesting discovery: Over the course of several cleaning cycles, the alkaline cleaning medium visibly roughened the surface of the glass bottle, whereas nothing comparable could be observed with the PET containers. “For the filling of sensitive beverages in particular, consistent container quality can be an advantage that should not be underestimated,” notes Ines Bradshaw. Microbiological tests are currently being conducted to definitively establish whether the technology is safe. Initial results confirm the observations made thus far: “Microbiologically, PET bottles that had gone through 25 cycles could not be distinguished from new ones,” says Ines Bradshaw. With this proof of concept, the project has reached an important milestone and is now ready for the next major step: preparations are already well underway for the technical field test. www.krones.com www.alpla.com","@ID":8} "MOULD MAKING PETplanet Insider Vol. 22 No. 09/21 petpla.net 23 PET hot runner spare parts and refurbishment services Control over the smallest details HRC, which operates out of Győr, Hungary, was founded by brothers Árpád and Tamás Horvath in 2006. The company’s core business consists of servicing of PET hot runners and providing high-quality spare parts to the industry. HRC has established itself as a trustworthy supplier for both small and large customers, with fast return times and the smooth start-ups of serviced hot runners once they are going back into operation. Its revenues have now reached 1.5 million Euros/year (US$1.8 million; £1.3 million) Árpád Horvath, HRC’s CEO, says that its business model is based on working closely with customers to understand how they operate, including their cost structure. “Producing quality preforms on a battery of multi-cavity systems ‘flatout’ requires control over the smallest details of the hot runner system,” he says, and highlights the importance of well-executed preventative maintenance programs. However, these require robust technologies and the use of high-quality components. HRC has learned from experience that the quality of hot runner parts available in the market vary significantly, with consequences for users. HRC’s solution is to deploy 100% part inspection and to accept zero faults. It says that this results in service and maintenance completed without unscheduled delays, enabling reliable planned downtime and fast turnaround. The company does not base its offer on lowest cost but, rather, on value in terms of total cost of ownership (TCO). HRC’s main customer base is in Europe, where it supports some of the industry’s biggest names. It has also, more recently, established itself in Russia, India, and Japan, where its attention to detail and high quality standards have been rewarded with a growing turnover. HRC’s reservoir of expertise, which covers different types of hot runners ranging from two to 144 cavities, grew through the need to respond to urgent requests of customers who were depending on their systems. While converters and food packaging companies plan major maintenance and refurbishment activities for quiet periods during the year, unforeseen problems and machine failures cause unscheduled production interruptions and downtime. “Production managers can shut down the problematic cavities and keep running with reduced output but this is a temporary solution and such actions can cause more serious issues down the line,” Árpád Horvath explains. “Some of our customers now contact us directly when an issue occurs, so we can assist in a brief root-cause analysis and help them make the best decision.” He says that HRC’s fast turnaround time is an advantage, as it can be more effective to send the faulty system to its workshop, for repair and fast return, in full-cavity configuration. HRC takes pride in its very clean workshop which includes a hot-cleaning section, a large ultrasonic bath array, a QC lab featuring a Mitutoyo CMM, a hardness gauge and a contour measurement unit. “A few microns’ variation can cause headaches for precisely dimensioned parts, such as valve bushings and valve stems, and we simply do not want to bring that risk to our customers,” he says. In response to requests from customers for solutions for co-injection hot runners, HRC has provided yearround support and refurbishment services for multilayer preform systems since 2012. “Reliability is key, and we believe that our customer stays with us for exactly that reason. Zero risks and proven performance, with the fastest lead times,” Tamás Horvath concludes, on behalf of the two brothers. www.hotrunnercomponents.eu General Manager Árpád Horváth founded HRC hot runner components together with his brother Tamás Horvath in 2006.","@ID":25} "PETproducts 52 PETplanet Insider Vol. 22 No. 09/21 petpla.net PETproducts 52 Configuration system SynchronizAir ABC Compressors, headquartered in the province of Guipuzkoa in NE, Spain, has announced the commercial launch of SynchronizAir, a configuration system that can coordinate different compressor brands from a single location, helping to eliminate cascade regulation. It offers a series of GUI onscreen displays with an integral display of the whole plant; advanced monitoring arranged according to customers’ own priorities; customised records of each machine; and automation sequence preselection. ABC says that SynchronizAir offers a range of benefits including energy saving, through simultaneous pressure regulation of several compressors with variable speed drives, even when operating in different ranges, which eliminates idling and reduces overall compression pressure. Lower pressure bands can be set for all compressors in the plant, individually and simultaneously. SynchronizAir incorporates machine learning technology, which enables it to record trends and identify and predict pressure and flow variations. Personalised ‘intelligent parametrisation’ helps to optimise compressor fleet management. “SynchronizAir offers to our clients versatile and efficient configuration by reducing the compression pressure and avoiding idling scenarios,” said Eriz Cristóbal, ABC Compressors’ International Sales Area Manager for Eastern Europe. “Sustainability and 4.0 technologies enabled us to keep our strength in the international markets especially these days, when all customers value any energy savings.” www.abc-compressors.com","@ID":54} "EVENT REVIEW PETplanet Insider Vol. 22 No. 09/21 petpla.net 46 the last two years in parts of Australia. Implementation is planned in the UK and in many other countries, especially in Europe. High collection rates are achieved because of the value of the packaging, on average around 90% and in Germany up to 95-98%. In terms of emission reduction, the high collection rate is a crucial factor.” According to estimates, 100 new PET bottles could be made into over 200 rPET bottles, thanks to repeated recycling. “For 90 out of 100 collected bottles, we deduct a few losses in the recycling process and achieve a recycling rate of around 75%, which is a conservative estimate; some systems achieve up to 85% or more. However, based on this assumption, 208 recycled bottles could be created from the 100 original new bottles in the specific example.” In countries without a deposit system, the return rate lags behind at around 50% and despite the discipline of many people who separate their waste themselves, half the bottles are lost because they have not been collected separately. Using the aforementioned model, this would mean only 60 recycled bottles would be made from 100 new bottles. “In the example of Lithuania, where there is now a deposit system, collection rates for containers were initially only 34%. Just one year after the introduction of the deposit system, it was already 74% and at the end of the second year 92%.” According to Tomra, a significant loss of potentially recyclable material occurs in mixed waste, e.g. household rubbish. This area has long been considered too complex for sorting and the waste usually ends up in incinerators or landfill. “In Europe, a lot of incineration takes place and a great deal ends up in landfill sites,” says Dr Rehrmann. “However, these landfills should broadly disappear over the coming decades and then everything will be incinerated. But this doesn’t have to happen; we are currently in a position technologically to sort waste and offer alternatives.” A Norwegian study shows that a few European countries can filter out more than twice as much plastic before incineration or landfill dumping by using current technology to sort mixed waste. A pilot project by Tomra with Borealis and Zimmermann Germany offers further evidence, and this recycling demonstration plant achieves a throughput of 10,000 t/a. “Of course, the recycling process requires more effort in terms of sorting and washing because of contamination,” explains Dr Rehrmann. “But very good recycling quality can be achieved for plastics using this method; plastic can be reused so should not be incinerated.” Dr Rehrmann continued: “From a greenhouse gas perspective, incineration also generates CO2 . With separation and the avoidance of new manufacturing going hand in hand, emissions can be reduced significantly.” Dr Rehrmann also discussed the costs for installing these systems and suggested that in comparison to decarbonising the energy or transport systems, the costs of installing these recycling systems would not be very high. *Non-deposit containers. Collection rate based on 2017 European average. New bottles made with recycled content are based on a 75% recycling rate for PET in a closed-loop system. Source: Tomra Source: Eunomia","@ID":48} "PATENTS www.verpackungspatente.de PETplanet Insider Vol. 22 No. 09/21 petpla.net 55 Bottle with folding neck Intern. Patent No. WO 2019 / 106347 A1 Applicant: Creanovate Ltd., Isleworth (GB) Application date: 26.11.2018 The shoulder area of a PET bottle is designed so that the bottle neck / spout can be folded to the side by pressing on the specified place. This makes pouring or drinking directly from the bottle easier. Thin-walled container Intern. Patent No. WO 2020 / 208243 A1 Applicant: Société Anonyme des Eaux Minerales D’Evian et an Abrège, Evians-les-Bains (FR) Application date: 10.4.2020 Thin-walled container (50-150μm) with special base form. The container is made from at least 50% rPET. Base of a plastic bottle Intern. Patent No. WO 2020 / 202727 A1 Applicant: Suntory Holdings Ltd., Osaka (JP) Application date: 23.1.2020 Thin-walled, reduced-weight bottle to hold a “sugar-free” drink. The bottle is specially shaped in the base area to prevent unwanted misshaping during chilling. PETpatents Space-saving PET bottle Intern. Patent No. WO 2019 / 054866 A1 Applicant: Creative Cloud Comp. B.V., Hilversum (NL) Application date: 13.9.2018 The application proposes a screwcapped PET bottle specially shaped for reasons of spatial economy, weight and handling and for use on board aeroplanes. Size and diameter can be adjusted to the serving quantity. Plastic bottle Europ. Patent No. EP 3677522 A1 Applicant: Suntory Holdings Ltd., Osaka (JP) Application date: 6.6.2018 The application describes the shaping of a plastic bottle for use in varying temperature ranges with embossing on the outer wall. The compensation areas required by temperature variations are created by the shaping and reshaping of the bottle shoulder. Changed surface optics Intern. Patent No. WO 2020 / 210590 A1 Applicant: Procter & Gamble Comp., Cincinnati (US) Application date: 10.4.2020 Multi-layer preform and the bottle it creates, which accommodates more interesting and improved optics to meet consumer wishes through special colour effects. The pigments worked into the material create these special optics.","@ID":57} "TRADE SHOW PREVIEW PETplanet Insider Vol. 22 No. 09/21 petpla.net 44 Indian mouldmaking group Vasantha establishes VTW in Austria High-performance injection moulds After a construction period of only nine months, the European headquarters of the Indian tool making group VTC (Vasantha Tool Crafts) in Waidhofen, Austria went into operation in May of this year. It operates under the name VTW (Vasantha Tool Waidhofen) GmbH, reminiscent of the former toolmaking company KTW in Waidhofen. The latter has developed over 40 years from 1979 into one of the leading suppliers of closure systems and highperformance injection moulds for closures. At Fakuma, VTW will celebrate its trade fair debut in hall 1, booth 1117. VTW functions as a majorityowned subsidiary and the European headquarters for VTC. The facility went into operation, in May this year as VTW (Vasantha Tool Waidhofen) GmbH. The name reflects former toolmaking company KTW, which was also based in Waidhofen for over 40 years. VTW was founded in 2019 VTC, as majority shareholder, with four former Husky-KTW executives, including Managing Director Manfred Schinko. KTW had established a reputation as one of the leading suppliers of systems and high-performance injection moulds for closures – a legacy that VTC seeks to build upon by establishing its European centre of excellence and a competence and production centre for tool and mould making. It will complement the Vasantha North American Technical Center in Westchester, Ohio, which manufactures micro injection moulds for medical LSR moulded and medical precision parts. The new production premises are equipped with the latest technologies for achieving high levels of efficiency and environmental standards. The factory is built to a compact design and uses thermal building core activation for temperature control via the building fabric, heat pumps and heat recovery systems. The planned addition of a photovoltaic system and the sourcing of other electricity from wind and water energy means that VTW is poised to become a CO2 -neutral company in the short term. The factory is equipped with machinery that offers advanced levels of precision, efficiency and automation. The IoT-capable equipment, in combination with the integrated ERP and MES systems already installed, are the basis for digital manufacturing, which has already been implemented in some areas. Focus on multi-cavity high performance moulds The focus of the Vasantha Group at the Austrian VTW facility will be high-performance injection moulds, for applications in a range of sectors. Its machines will produce pharmaceutical closures and components; medical technology and laboratory components; beverage closures, sports caps and closures for carton packages for liquids; tamper-evident caps and packages, as well as child-resistant closures; dosing and pouring systems; and flip-top closures and spray caps. Performance test and qualification included All moulds are tested, optimised and qualified in-house. Applications are tested to the respective customer requirements under practical conditions. The company has three high-performance injection moulding machines with clamping forces from 1,500-6,500 kN available on site. In addition, VTW offers bays, equipped with all the necessary infrastructure facilities, for qualification of customerspecified production cells. www.vtw.co VTW’s machine equipment is tailored to multi-cavity injection moulds for the packaging industry and medical technology.","@ID":46} "Editour PETplanet Insider Vol. 22 No. 09/21 petpla.net 12 Tour Sponsors: Stefan Zatti, CEO at Otto Systems AG 1) We have sensed a real reluctance to take on new projects. In my view, this is due to planning uncertainty that the pandemic has created in many companies. On the other hand, we were able to record a significant increase in the volume of orders for spare parts and mould reconditioning. All in all, 2020 was a moderate year for us in terms of sales. We have been able to register orders that exceed our budget since the beginning of the year. We do not expect this encouraging trend to change in the coming months either given the fact that projects that could not go ahead from 2019/2020 will now be implemented this year. 2) The introduction of EU approved tethered caps seems to us to be the most important change in the PET bottle market. Although our company does not directly produce any capping moulds, we are still affected by this regulation. Some of the new caps need modification or a completely new design in the thread area of the bottle. This means that our customers will have to redesign or in some cases remake the respective preform moulds. This year, we received orders from two well-known major customers in Europe to convert their preform moulds and believe that more will follow during 2021. We increased our manufacturing capacity accordingly at the beginning of the year. 3) The use of recycled PET will be an extremely important issue. Many well-known brands have already made commitments in this area and developed the necessary targets to meet them. Preforms and bottles made from 100%rPET are no longer an impossible pipedream. However, the biggest challenge for some countries is to establish a functioning take-back system for used bottles. In addition, we must continue to try and optimise the weight of preforms in order to reduce the consumption of PET granules per bottle. www.otto-systems.com Michael Perl, Group Director Sales Division Sorting Recycling at Sesotec GmbH 1) Our work and also our business performance were inevitably affected by Corona in Q2 and Q3 2020. There were many uncertainties, but these brightened towards the end of the year. Nevertheless, I would classify the business performance in 2020 as good overall. With the exception of the severe disruptions in overseas travel, our work and the course of business have developed very well this year. The PET industry in Europe will certainly face some challenges in connection with collection and recycling quotas, among other things. I am confident about the development of the industry in the coming months. 2) As a manufacturer of sorting and analysis equipment for the recycling industry, we are right in the middle of the discussions about collection and recycling quotas, the design and labeling of plastic packaging and, of course, the ways in which this packaging can be sorted and recycled in the best possible way. We want to support our customers with our solutions and experience in order to ensure material quality and yield, as this is the basis for a profitable and therefore longterm successful circular economy of plastics. 3) On the one hand, I think it is enormously important to promote the collection and thus the availability of PET bottles and trays in order to have sufficient recycla - ble material available at all. This would also mean that fewer plastics would end up in the environment or be incinerated. Furthermore, it is important to use plastics for packaging that on the one hand protect the goods and on the other hand are really recyclable. In addition to the plastic itself, the design, colours and composition (keywords: mono/multilayer and additives) of the packaging play a decisive role here. This is where we have to work together. www.sesotec.com Matthias Müller, CEO Sales at Contexo GmbH 1) The pandemic has challenged everyone´s lifestyle, habits and daily life. Looking at Contexo, it has been a successful year, even though we were facing a number of challenges: Not meeting customers face-to-face, the cancelling of trade fairs, the difficulty of machine installation at factories across the world. New ways of working had to be developed and installed. This has become a routine now. We are looking optimistically in the future, as we see an increasing demand for machines on different sectors. That´s why we are actively investing in the future and continue strong execution. 2) Contexo has been working on a high number of projects, clearly with a focus on tethered caps, which will become the new standard for beverage bottles. The demand has risen - driven by the EU SUP directive - but we see an increasing demand coming fromOverseas. Contexo launched successfully the “All-in-one”- machine for tethered caps, which includes slitting, folding and assembling. This machine solution turned out to be a bestseller on the European market. As the system also works for multi-part tethered caps, we notice an increasing European demand. Users benefit from a particularly powerful, flexible machine concept that is characterised by its high speed, outstanding precision and the lowest energy consumption on the market. 3) In the context of climate change and protection, packaging, particularly plastic packaging has received significant atten - tion. Sustainability and environmental protection is the key topic. The use of recycled materials is a growing trend among brands. But the discussion goes far beyond PET packaging. There also is a focus on secondary packaging such as shrink wrap. As a machine builder we are constantly striving to optimise the carbon footprint. www.contexo-automation.com","@ID":14} "Sponsors to date The worldwide round trip with Editours Back to Europe The second part of PETplanet’s bipartite Drinktec Editour is right ahead! After the successful first part “From Down Under to Japan” in 2020, our second stage of the project takes us back to the flourishing European hub where we will be exploring the latest technologies, news, innovations and developments that move our PET industry. It is time for a new start, for renewal and for developing new ways of thinking. During and especially after the pandemic, it will be vital to make every effort to get the global economy back on track in the medium term. Sustainability will be the key. Once again, PETplanet will be at the forefront. It will again be a partner in Drinktec, the world’s leading beverage trade fair, which is to be held in Munich from 12-16 September 2022. After the success of our previous Drinktec Road Shows, in 2017 in South East Asia and 2020 in Australasia, we will be back on the road in Europe for a whole year. Starting in Autumn 2021 with our Editourmobil, we will be ready for a new get-together with the industry. We will be revealing the results of our meetings and discussions at Drinktec with the leading thinkers in PET processing, packaging and recycling. Apart from new technologies we will be also taking stock of how things stand. We will be asking how global thinking might change as a result of Covid-19. How will bilateral business relationships cope with the aftermath of the pandemic? What opportunities will there be for the drinks industry and its suppliers? Our planning, in terms of precise timeframes and details of the countries to be visited will be flexible, in order to take account of the rapidly changing pandemic situation. However, this much we can confidently say: in these challenging times we, as the voice of the PET industry, will be at the very heart of the roadshow as usual and are already looking forward to welcoming you back on board the Editourmobil! Share this exciting experience with us! Interested in being interviewed? [email protected] Let Your Inspiration Flow. The European Road Show Part2 Empowered by drinktec Interested in becoming a Sponsor? [email protected] Autumn 2021 - 2022","@ID":16} "CAPS & CLOSURES 26 PETplanet Insider Vol. 22 No. 09/21 petpla.net Tethered caps: Production requirements and strategies What are the specific requirements of the new EU directive for caps & closures for producers? Jörg Leonhartsberger, Sales Director Packaging Engel Austria, sheds light on the effects on equipment and the manufacturing process. Tethered caps are caps which remain firmly attached to the bottle after opening and during the product’s service life or life cycle. The relevant part of this EU regulation for caps & closures production reads: “Plastic closures and lids used for beverage containers are among the single-use plastic items most frequently found as litter on the beaches of the European Union. Therefore, the placing on the market of single-use plastic beverage containers should only be allowed if they comply with certain product design requirements in order to significantly reduce inputs of plastic container closures and lids into the environment. For beverage containers that are both single-use plastic articles and packaging, this is an additional requirement to the basic composition, reusability and recoverability, including recyclability, requirements for packaging set out in Annex II to Directive 94/62/EC.” This Regulation shall apply to the caps of all beverage containers up to a capacity of 3 l, i.e. containers used to hold liquids, such as beverage bottles, including their closures and lids and composite beverage containers, including their closures and lids, but not: Glass or metal beverage containers with plastic closures or lids; Beverage containers intended for liquid foodstuffs for special medical purposes. The legal foundations based on this regulation must be created in the EU member states by July 31, 2021, and the entry into force of the legal and administrative regulations is scheduled for July 3, 2024 at the latest. Basic requirements for tethered caps The requirements for the design and function of tethered caps resulting from this regulation are currently still being defined and can be summarised as follows at the moment: GAWiSD featuringAutoJob ™ – job set up in seconds +1.724.482.2163 AGRINTL.COM ACCURATE • FAST • REPEATABLE SEE GAWIS4D IN ACTION Dimensional and thickness measurements for plastic containers and preforms. ®","@ID":28} "Editour PETplanet Insider Vol. 22 No. 09/21 petpla.net 10 Tour Sponsors: Kick off European Road Show 2021 In the run-up to our European Road Show, we asked a first group of our sponsors and experts from the whole PET value chain about topics that are currently relevant: 1) PETplanet’s latest Roadshow takes a critical look at the European market, which is picking up steam this year after pandemic-related slumps. How has the pandemic affected your business and what are your expectations for the coming months? 2) The European PET bottle market is on the move - not least due to the potential impact of various EU directives. Which of these are particularly relevant for your company and how are you placed to meet them? 3) What future challenges do you see for the PET industry? Karel Keersmaekers, Managing Director at Nissei ASB GmbH 1) During the initial period of the pandemic, there was a high demand for packaging for hand gels and cleaning products. The one step ISBM technology is extremely suitable for the production of this type of packaging, which led to a huge sudden increase in the demand for new machines and moulds for this application. As the pandemic worsened and with longer delivery times due to increased demand for machines and a temporarily production stop at one of our factories, customers began to pre-order machines to ensure future delivery. So overall, I can conclude that the pandemic had a positive effect on our business although it took a tremendous effort for the entire organisation to meet the increased demand and to continue to offer service to our customers amidst the devastating pandemic. 2) The EU packaging directive is the most relevant for our European business and we already witnessed a strong increase in the number of projects for bottles and jars with recycled material content from 25% up to 100%. In addition we have developed new technologies that focus on reducing bottle weight without compromising it’s quality and performance, we have developed returnable PET bottles with reduced weight with our double blow technology and recently have started to market our newest double layer moulding machine that can produce containers with an inner layer of virgin PET and an outer layer of PCR material, enabling the use of recycled materials that are not food approved even for food products. 3) Plastic packaging has received a lot of bad press because of the pollution of land and sea due to careless handling of plastic waste. It is the shared responsibility of the producer, consumer and government to make every effort to improve collection to increase circularity and reduce plastic that ends up in the environment. PET is already the world’s most recycled plastic material and with new recycling capacities and recycling methods put in place, I believe it has a bright future ahead as one of the most sustainable materials for all kinds of packaging. At ASB, we continue to develop environment-conscious machines and moulding technologies for every segment of the 3R principle to meet those challenges. www.nisseiasb.co.jp Josep Jimenez, Commercial Director at Side S.A. 1) Our business has grown significantly in the last two years. There have been effects directly related to the pandemic, such as the growth of domestic consumption or of cleaning and hygiene products, but they have also been the result of effort and work in recent years, offering the best services and products. 2) We are seeing how the new European directives may affect but we believe that in some cases PET can benefit and we must take advantage of these circumstances. One of the points in which our company believes the most and to which we are committed is recycling and the use of rPET in an ever more extensive way. In this sense, we are conducting a support campaign for our clients to make the transition to rPET as soon as possible, and we are also socially aware of recycling. 3) Newmaterials, new resins, new applications for PET, specialisation of sectors, increased energy costs and therefore reduced consumption in production and reduction of resin available on the market. These are the new challenges and also new opportunities that we have for the future. www.sidemachines.com","@ID":12} "47 EVENT REVIEW PETplanet Insider Vol. 22 The future starts in our heads Discover our digital innovations at krones.com In the subsequent Q & A session with the audience, the options for recycling food trays were discussed. These are not yet very widespread but according to Dr Rehrmann, Tomra is also working on solutions for tray-2tray recycling. Tray-2-bottle is also an option; a prototype PET bottle development has just been manufactured from recycled food trays and was shown during the event. The question was also raised of how influential a circular economy system could be at a European level when this is actually a global problem. Joe Papineschi responded: “The developments and systems can be applied around the world. If a 2.8 billion tonne CO2 reduction is to be achieved, there must be some fundamental rethinking about environmental matters. We are doing a great deal in Europe in terms of technology and policy, and these applications can be adopted with appropriate adjustments. Europe is certainly far from being the template for the world as there is still a great deal of inconsistency here. But with appropriate adaptation for other parts of the world, these things can definitely function and there is an incredible amount of potential. Also, it could be started there immediately, as the whole learning and development process has broadly been completed and already exists here in Europe. The political will to take action is of course also important in other countries. A fundamental re-think as regards sustainability and recycling is necessary but this must also be identified and appropriately regulated.” Emission, kg CO2 equivalent per tonne of waste managed. Source: Eunomia","@ID":49} "PACKAGING / PALLETISING PETplanet Insider Vol. 22 No. 09/21 petpla.net 29 Environment protection combined with product protection Recycle – Regenerate – Reuse The growing consumers’ awareness towards the problems of the ecosystem in which we live influence the activity of the companies that prefer the use of sustainable packaging, such as rPET and cutting-edge technical solutions, in order to save energy and reduce the production environmental impact. Design of sustainable containers Today all the main food and beverage manufacturers aim at promoting sustainable lifestyles in compliance with circular economy and support the importance of the responsible use of resources and recycle. Their commitment starts from the use of PET plastics: a 100% recyclable and regenerable material. Thanks to its advanced CAD center for 3D design, SMI supports companies in the design and graphic realisation of a wide range of 100% recyclable PET containers, featuring high quality and lightweight in order to save energy and material. Green solutions for the primary packaging The wide range of SMI rotary stretch-blow moulders from EBS Ergon range is able manufacturing PET or rPET containers of different shapes and capacities from 0.10l up to 10l. SMI says that the advantages of these machines are further enhanced in terms of space, energy and cost saving, when the blower is combined with afiller and a capper, which allows companies, actively involved in the environmental protection, to bottle their products in 100% recyclable, sustainable, light, unbreakable and safe containers with a high level of hygiene and suitable for the food and beverage storage. A need to preserve product quality and protect the environment led for example Société des Eaux de Volvic to invest in SMI’s Ecobloc Ergon integrated system for stretch-blow moulding, filling and capping 8l rPET containers. The new bottles are made from 100% recycled plastic and thus are 100% recyclable: a result that has been possible thanks to a joint work between the specialists at Danone and at SMI. Ecobloc Ergon HC, resulting from an intense activity of R&D, is claimed to stand Circular economy-material savings Clear PET packaging with a handle Fast production changes (QHUJ\\ HIÀFLHQW H[WUXVLRQ BENCHMARK FOR BLOW MOULDING MACHINES Bekum Maschinenfabriken GmbH Phone: +49 (0)30 7490-0 • [email protected] • www.bekum.com CONSUMER PACKAGING FOOD & BEVERAGE INDUSTRIAL PACKAGING PHARMA PET Handleware out for its compactness andflexibility, making this solution suitable even for those who do not have large spaces in their production plants. The system does not need a rinser, nor conveyor between thefiller or accumulation; this means benefits in terms of space and costs. Primary packaging plays a vital role for Volvic, as it has to maintain the purity of the spring water and preserve the product quality until it is consumed. That’s the reason why environment protection is combined with product protection: bottles in fact go through a long series of controls during the whole bottling process, thanks to the integration of sophisticated inspection systems, that, starting from the preforms, carry out a long series of checks to maintain the quality and purity of the spring water and prevent any non-compliance issues or contamination. Solutions for tethered caps The tethered caps, that stay attached to the bottle after having been opened, will become an object of everyday use for European consumers from 2024, when 2019/904 directive will enter into force. The EU directive establishes the minimum recyclate percentage in plastic beverage bottles (25% starting from 2025 and 30% starting from 2030) and states that the caps of PET bottles have to be attached to the container, so that they can be recycled together with the bottle, thus avoiding they end up as waste in the environment. SMI, aware of the challenges posed by this directive to beverage manufacturers, offers solutions for producing containers with a percentage of recycled PET in compliance with 2019/904 and supports customers in order to evaluate the right tethered cap solution. www.smigroup.it","@ID":31} "Editour 13 PETplanet Insider Vol. 22 Michael Fink, Vice President Sales & Marketing at z-moulds 1) The pandemic itself did not affect our business directly - as a mould supplier we still had good projects to deliver. The only affecting part was that some of the new projects got stopped or delayed due to less man power in times of lock-downs and homeworkers. 2) Definitely the Directive (EU) 2019/904 – Article 6. For us, the last two years were very interesting. We developed so many new designs with our customers to fulfil the tethered cap requirements. Now as the companies start introducing their solutions to the market, it’s even more exciting. I hope that the new solutions will be accepted by the customers and will help achieving the environmental targets in the upcoming years. 3) The years of plastic bashing harmed our business and the reputation of plastics. Now it’s important to act with responsibility. The way how the industry is driving innovations on circular economy solutions is terrific and will help recovering. www.z-werkzeugbau.com Christoph Wöss, Business Development Manager Application Bottle at Erema Group GmbH 1) During the pandemic we still had a very high demand from the PET market, especially from the bottle-to-bottle segment. Problems arose from limited cash-flow in some countries (banks were partially closed) and extended startup times due to quarantine, delayed deliveries etc. Also in Europe we could not be on site, especially at the beginning of the pandemic. 2) SUPD and PPWD but more than that the voluntary pledges from the brands. By doubling the manufacturing space, expanding the customer test centre at Eremas´s headquarters in Austria and increasing the number of employees involved in the specific bottleto-bottle application, we are prepared for meeting the upcoming challenges. 3) On one hand the lagging collection rate, availability of input material; on the other hand the huge delay from Efsa side to grant positive Efsa opinions. I’m afraid with this delaying process it would become difficult to achieve the EU´s recycling regulations for 2025/2030. www.erema.com","@ID":15} "Editour PETplanet Insider Vol. 22 No. 09/21 petpla.net 11 DISCOVER MORE www.novapet.com Respeto Respect E A R T H PET is a respectful material with nature due to the minimum amount of fossil resources necessary to be produced. This amount can be even reduced by including the r-PET in the production cycle. Brad Molnar, European Sales Manager at Pressco Technology Inc. 1) Like many suppliers, we saw some delays in our customers’ projects as the pandemic began, yet over the past 12-18 months it appears that the food & beverage packaging business has grown tremendously. We are now experiencing record-level demand for our Intellispec inspection systems, and we see this trend continuing for some time. A fascinating side-effect of the travel restrictions and lockdowns was that it provided opportunities for Pressco to work extra-hard in support of our customers during their most challenging times, which resulted in much more purposeful interactions and a deepening of trust. This further opening of the communication channel is proving to be critical as production and demand increases. 2) Directives from the EU are largely driven by consumers who want change to help improve the world. The conversion to 100% rPET in combination with the tethered closures is resulting in the increased need for quality control/monitoring as the next wave of light-weighting initiatives hit the market. The increased use of recycled material continues to be a significant challenge for many high-speed production lines, as bottles tend to be more prone to manufacturing process-related defects. This puts additional burden on the inspection system to identify these process issues quickly, so Pressco’s real value to our customers is shifting from an emphasis on defect detection to placing a higher priority on process visibility and control. Our commitment to Industry 4.0 allows our entire family of high-speed inspection systems to be integrated into the plant network so that valuable data is available immediately. Additionally, there is less reliance on the operator to react to problems when the inspection system can detect issues and take action reliably before time and/or product is wasted. 3) It will be interesting to watch how the use of rPET continues its dynamic impact on the market – there are many who are asking if 100% rPET is sustainable over the long haul. The broader challenges of supply chain shortages and longer lead times continue to make project timing difficult to manage. Although increased automation is widely regarded as critical to operational efficiency, the upfront capital burden can pose finan - cial obstacles for many smaller operators. www.pressco.com","@ID":13} "EDITOUR PETplanet Insider Vol. 22 No. 09/21 petpla.net 17 PETplanet: And what does that mean for you as a trade fair company and promotor of Drinktec? Markus Kosak: As mentioned earlier by Petra the need for physical trade fairs is immense due to the reasons she has already explained. I am confident that the new given framework brings both the need and ability to perfectly combine the opportunities of both worlds: the physical and digital. Therefore, we have put in place our digital Drinktec Talks starting in December this year where our global road show will be fully digital. Both formats will enable us to reach a broader audience and hopefully will result in more traffic onsite. PETplanet: Have there been, or will there be any fundamental changes or innovations to the trade fair business as a result of the pandemic? How does the industry need to adjust? Petra Westphal: The big change is that all customers will have to think more and more about the purpose of their physical or digital events. How do they decide on which format? What are the different targets for each format? And how can the digital presence enhance the results of the physical event? Of course, this is applicable for us as well. We need to have a good understanding how our future digital events need to be designed to provide the perfect level of suspense for the physical event as well as bridging the gap between events. And last but not least, communication, particularly between exhibitors and trade fair organisers, is as important as ever. It is only by knowing the needs, problems and concerns of our customers that we can provide or develop solutions that will address them. Working together is our path to success. EDITOUR 17 www.sacmi.com Product design Product development Product validation Industrial production plant Process & quality control On-site and start-up assistance After-sales and Customer service SACMI 4.0 THE COMPLETE CLOSURE, PREFORM AND CONTAINER SOLUTION FOR YOUR SMART FACTORY ENDLESS INNOVATION SINCE 1919 PETplanet: What alternative channels emerged during the pandemic and which of them can be considered sustainable? Markus Kosak: With Drinktec Talk, Drinktec is offering a series of webinars for the first time. On a total of four dates, innovations and solutions for the beverage and liquid food industry will be presented in compact online live events that match the main themes of the trade fair. This provides the community with the opportunity to to get into exchange with each other nine months before Drinktec. PETplanet: Will such ideas become a fundamental part of the new Drinktec? Markus Kosak: If they prove to be successful, then yes, definitely. PETplanet: You are both in regular contact with your global customers. What key needs have been expressed to you most in recent months? Petra Westphal: On the one hand, planning reliability. On the other hand, the capability to travel. Here, we were able to offer some respite with the postponement of Drinktec to September next year. In addition, we are also organising 2 events for next year, ChinaBrew China Beverage and Drinktechnology India. One way or another Drinktec’s global customers will get the opportunity to come together. PETplanet: Drinktec was affected by Covid in a way which resulted in the event being postponed to the second half of the trade fair year 2022. What opportunities does this offer for the event itself and for exhibitors and visitors? Petra Westphal: First and foremost, the previously mentioned improved planning certainty. I am confident that the number","@ID":19} "MOULD MAKING PETplanet Insider Vol. 22 No. 09/21 petpla.net 21 The use of High Speed Cutting machines can dramatically reduce the processing times for mould parts and almost completely cut down the manual polishing work of the inner surfaces of those mould parts. Smallest details and complex geometries may directly be produced with this specialised machinery and timeconsuming die-sinking (EDM) work is avoided. EISBÄR TROCKENTECHNIK GMBH / Wuhrmühle 22 / 6840 Götzis / T +43 5523 55558-0 / F –50 / [email protected] / www.eisbaer.at GDS GRANULE DRYING SYSTEM 94 % WATER SAVING We took a closer look at our GDS granule drying systems. The result is astounding. We were able to reduce the cooling water consumption drastically. You are having a GDS granule drying system from Eisbär and would like to take advantage of the savings? Please contact us: [email protected] As example for GDS1100: New water consumption litre per minute 12 Water saving litre per hour 9,180 Water saving litre per year 78,030,000 Calculation based on an assumption of 8,500 operational hours per year and a cooling water temperature of 12 °C. VISIT US AT FAKUMA IN FRIEDRICHSHAFEN BOOTH A7-7312 HALL A7 The flat company hierarchy helps shortening delivery times also. If necessary, it takes only a few days from the design stage to an initial sample mould to be completed. Processes within the plant are carefully time and quality monitored and supervised. In case a customer requires a sudden change, for example in priority, production may immediately react. In most projects, customers usually come up with a suggestion for a bottle design and already send a detailed construction (CAD file). Then Röders with its comprehensive experience consults with respect to feasibility in PET stretch blow moulding. Sometimes, the customer only has a vague idea about a bottle design, may be a sketch. Then Röders will develop also the construction of the new PET bottle suitable for stretch blow moulding. Technical requirements like top load, minimum weight, choice of preform etc. are considered. For testing Röders has a fully certified blowing laboratory, in which also larger numbers of sample bottles may be produced and tested. Renowned companies like PepsiCo and CocaCola have certified Röders’ capabilities and laboratory. A very important trend in the industry with respect to saving resources has been the development of bottle designs for low-pressure stretch blow moulding. This mainly concerns the base design. Again, Röders has made own developments and brought down the blowing pressure to approx. 20 bar helping the customers to achieve significant energy savings. Today, Röders produces an average of 6,000 moulds/year. Business has been stagnant during the year of Covid. When answering the classic parting question “Where will Röders be in five years’ time?” Mr Röders did not mention any specific targets but said “We are flexible, follow the market and remain open for new opportunities. This has been our solid business foundation for more than 200 years company history”. www.roeders.de It is not only the very rapid production that ensures short delivery times, but also the company’s flat hierarchical structure. Here, Jani Rickert (right), and Steffen Lühning (left), are responsible for the blow mould sales and its worldwide business.","@ID":23} "36 TRADE SHOW PREVIEW PETplanet Insider Vol. 22 No. 09/21 petpla.net Avient - hall B5 booth 5316 Solutions for improving recyclability in the PET market As part of a sustainable circularity focus, Avient launched the following new solutions in 2021 aimed at improving recyclability in the PET market: ColorMatrix Optica toners & colours for enhanced recyclability. When added to PET resin, preforms and recycled PET (rPET), it corrects and reduces the yellowing that occurs during the recycling process. Aside from aesthetics, there are also processing benefits for PET resin during the manufacture and recycling processes, and further downstream for convertors, bottle blowers and brand owners during packaging production. ColorMatrix Amosorb 4020R oxygen scavenging additive specifically formulated for use with rPET. The solution delivers full oxygen scavenging performance with up to 100% rPET content with a focus on improving the aesthetics of the recycled bottle in terms of haze and colour. ColorMatrix Lactra low TiO2 . The new Four, One and Zero formulations offer dairy contents protection with superior whiteness & low inorganic content. With TiO2 content between 4% and 0%, ColorMatrix Lactra Four, One and Zero offers light blocking up to 99.9%, improved performance in thin wall sections, superior whiteness, and can be processed with standard PET grades and rPET. Rejoin PCR masterbatch for polyolefins enables post-consumer recycled (PCR) to be used as a carrier resin, effectively allowing a bottle or part to be manufactured with 100% PCR. It combines pigments and functional additives into one solution without creating a negative impact on colour or mechanical properties. Avient will also be showcasing its full portfolio of speciality engineered materials, and colour & additive solutions for PET and rPET, including formulations developed to support the circular economy. www.avient.com www.prseventeurope.com Organised by Silver Event Sponsors Registration now OPEN atprseventeurope.com Registration is free of charge The PRSE exhibition, conference and awards are the annual focal point of the Plastics Recycling industry in Europe, bringing together respected global brands and professionals. The 2021 event will be a ‘Hybrid’ event. Whilst the live event will take place at the RAI, there will be virtual elements of the show – livestreaming, exhibitor profiles, networking – also available for those unable to attend the event in person.","@ID":38} "PETplanet Insider Vol. 22 No. 09/21 petpla.net 49 EVENT REVIEW 5. PETinar: Disruptive technologies and innovative additives for PET recycling The fifth PETinar organised by PETplanet insider took place on June 16, 2021. PETplanet invited Dr Axel Hannemann and Dr Carl-Jürgen Wefelmeier from Gneuss and Alessandra Funcia from Sukano to talk about Disruptive Technologies and Innovative Additives for PET Recycling. Gneuss and Sukano presented new recycling technologies focussed on shifting towards recycling PET waste from sources such as post-industrial fibre waste or other post-consumer sources, such as thermoformed PET trays. Dr Axel Hannemann, Head of Fibers & Pellets at Gneuss, started the PETinar introducing the company Gneuss by explaining its four business units: the first unit is about filtration technology, where rotary screen changers were developed. The second business unit covers the measurement technology designing melted pressure- and temperature sensors. Some 15 years ago, Gneuss started with the third business unit - extrusion technology. And finally in the fourth unit, Gneuss brought all production areas together to offer turnkey solutions to its customers. Gneuss bottle-to-tray recycling solution Dr Carl-Jürgen Wefelmeier took over and continued with some detailed information on the various Gneuss PET recycling lines with a special focus on Gneuss post-consumer tray recycling concept. As a bottle-to-tray recycling solution, Gneuss offers its Gneuss Processing Unit (GPU) consisting of a rotary filtration system, an MRS extruder, a vacuum system for the extruder and an online Viscometer system (VIS). The whole Processing Unit can be integrated, for example in a sheet line. The MRS extruder works without any pre-treatment, no pre-drying and no crystallisation of hygroscopic polymers. Its flexibility means the system saves a lot of space and energy. For processing postconsumer rPET Gneuss adds after melting a special multi-rotation step, where degassing and decontamination in vacuum takes place. This leads to an EFSA or FDA foodapproved application. The MRS extruder is based on the conventional single screw extruder. It is equipped with a multiple screw section, for optimum devolatilisation. The polymer melt is delivered into a large single screw drum. The drum contains eight small extruder barrels, parallel to the main screw axis. Installed in these small extruder barrels are the satellitescrews, which are driven by a ring gear in the main barrel. The satellite screws rotate in the opposite direction to the main screw while they rotate around the screw axis. This disproportionately increases the surface exchange of the polymer melt, so that the volatiles can be freely evacuated. The extruder is equipped with a large opening for venting (exposing the full length of the satellite screws) which is completely under vacuum. This provides unrestricted access to the polymer melt, the surface of which is constantly replaced at an extremely high rate by the action of the satellite screws in the multiple screw section. Precise control of the melt temperature is possible as the temperatures of all the surfaces in contact with the melt can be controlled accurately. The special rotary filtration system called RSFgenius , is fullyautomatic and extremely pressure- and process constant. With an integrated back flushing system, it is possible to reuse the screens very often. Self-cleaning and backflushing waste of the RSFgenius filter system is five times less then with conventional purging filter. Dr Axel Hannemann, Head of Fibers & Pellets at Gneuss Dr Carl-Jürgen Wefelmeier, Head of Film & Sheet at Gneuss by Heike Fischer PETINAR","@ID":51} "40 TRADE SHOW PREVIEW PETplanet Insider Vol. 22 No. 09/21 petpla.net www.sise-plastics.com - e-mail: [email protected] - Tel : +33 4 74 77 34 53 PRODUCTION & PROCESS MONITORING HOT RUNNER CONTROL VALVE GATE CONTROL MOLD TEMPERATURE CONTROL Hall A4 – Booth A4-4006 INDUSTRIAL PROCESS CONTROL INTERNATIONAL SPECIALIST IN INTEGRATED TEMPERATURE AND PROCESS CONTROL SYSTEMS FOR THE PLASTICS, COMPOSITES, CALENDARING AND CHEMICALS INDUSTRIES. Engel - hall A5 booth 5204 Thin-wall injection compression moulding for stack mould technology Engel’s stand will put the spotlight on sustainability. The production of decorated mono-material food packaging and the processing of regrind from labelling waste is supporting the circular economy by creating a process chain. At the same time, the company is celebrating the world première of the 4,200 kN version of the Engel e-speed injection moulding machine. The sophisticated packaging application combines extreme thin-wall injection compression moulding with stack mould technology. Over the five days of the trade event, an e-speed 420/90 injection moulding machine with integrated in-mould labelling (IML) will be used to produce ready-to-use margarine tubs from polypropylene in a fully automated injection compression process. The containers, which have a wall thickness of 0.4mm (including the label), will be removed from the 4+4-cavity stack mould via high-speed, side-entry automation and stacked on a discharge conveyor following camera-based quality control. Corporate partners at the trade show will be MCC Verstraete, Plastisud, Campetella, Mevisco and Borealis. Intelligent labelling technology The labels of MCC Verstraete, which will be used for the production of the margarine tubs at Fakuma, are interactive. These labels are based on technology by Digimarc and, much like a QR code, Digimarc codes can be scanned with any smartphone camera. The main advantage of these is that they extend invisibly over the entire label surface. The camera can scan any point. Moreover, the codes do not interfere with the packaging design. From production through retail and recycling, the interactive labels offer added value. Consumers can discover the details of the ingredients and manufacture for both the product and the packaging while shopping. And when the packaging has reached the end of its useful life, the label provides information on the recycling process. Where the containers and labels are made of the same material, interactive IML packaging becomes fully recyclable. www.engelglobal.com Erema - hall A6 booth 6314 Shredder-extruder combination Pure Loop, an Erema Group company, will present its Isec evo series. This shredder-extruder combination is rapidly becoming established as an efficient recycling solution in injection moulding production thanks to its high flexibility in processing different materials, simple operation and low maintenance requirements. Re-injection instead of rejection Isec evo is a high-performance material all-rounder that has been specially designed for recycling different types and shapes of material, regardless of whether solid parts or hollow bodies, roll stock or punched waste or waste from injection moulding production such as sprues, sprue patties and regrind. This is made possible by the unique input technology that features a combination of a double feed ram system and single shaft shredder. The wide range of applications for this technology is confirmed by consulting the list of Pure Loop customers. In a series of tests carried out together with Engel, an injection moulding machine manufacturer, and Profol, a cast film manufacturer, Pure Loop recently proved that recycled pellets produced from glass fibre reinforced organo sheets can be processed in the injection moulding process just as well as virgin material. www.erema-group.com The Isec evo shredder-extruder combination is an efficient material all-rounder","@ID":42} "MOULD MAKING PETplanet Insider Vol. 22 No. 09/21 petpla.net 24 A frugally designed mould generation Focus on core functions – reduce components MHT AG introduces a new frugal mould generation. The simplifications are in the first injection moulding cycle: instead of the usual transfer to a removal unit that guides the preforms out of the mould after injection, a free fall is used. The frugal mould does without a complex post-cooling unit. Although this increases the cycle time, this fact is less important to users in niche areas, newcomers or producers in emerging regions. Some changes have been made inside the mould. The designers reduced the mould cavity to a small number of components by replacing the support ring with a much smaller retaining ring and dispensing with the conical ring. The simplification approach also offers room for change in the neck ring. This has now been designed without cooling. Test series confirm good cooling of the preform thread during production. If necessary, though, the cooling can still be upgraded at any time. That is the basic idea of the frugal principle: the tool grows with the increasing requirements of the user. The frugal principle is applicable to a fixed mould cavity distance in small moulds with 24 or 32 mould cavities. The hot runner components come from the Legacy series, which is known for its space-saving use and robust design. Reduction without compromise To ensure the highest preform quality, frugally designed mould components are subject to the same requirements as components of a high-performance mould. MHT AG manufactures all components on the same equipment and subjects externally sourced components to equally extensive quality monitoring. There are no differences, even in the choice of materials. This ensures the dimensional accuracy of the end product. By maintaining fine tolerances in the production of the shaping components, the strip line appears just as precise and fine in frugal tools from MHT as in high-performance tools. This strip line is often unclean and coarse in preform production using cheap tools from alternative suppliers. When demoulding preforms, users of a frugal mould also expect the slides to run smoothly. The solution is to guide the slide frame over roller bearings. This reduces maintenance intervals and the wear on the mould components. Powerpack quality Two frugal moulds are already in the possession of one of MHT’s long-standing partners and customers. Powerpack Quality approached MHT looking for a cost-effective offer comprising an injection mould that still manages to produce high-quality preforms. Powerpack Quality has been active in the PET bottle business since 2009. Two years later, the company started its preform production, primarily to supply customers in Thailand. Within just eleven years, the company succeeded in expanding its machine pool to 16 systems. Various 16- and 24-cavity moulds from MHT are used in these systems. In total, Powerpack processes 200-240 t of plastic per month, from a granulate to the bottle preform. When inquiring about new moulds, General Manager Amnart Wanasoontornkul focuses on three factors in particular: High mould accuracy, durability and preform quality. These are the absolute requirements that a cost-effective small mould is expected to meet. It was immediately clear that a “frugal engineering” project was needed. The shared motto was: “High quality at affordable prices.” After the first frugal mould was a complete success, Powerpack 2020 put another 24-cavity mould into operation. “The production of the preforms is distinguished by excellent quality. The concept was also F.l.t.r.: Mr Prawit Yodprechavigit (KraussMaffei Group SEA), Mr Amnart Wanasoontornkul (General Manager, Powerpack Quality), Mrs Mayuree Wanasoontornkul (Managing Director, Powerpack Quality)","@ID":26} "38 TRADE SHOW PREVIEW PETplanet Insider Vol. 22 No. 09/21 petpla.net Weima - hall A6 booth 6201 Focus on circular economy After more than one and a half years without events and personal interactions, the anticipation of face-to-face trade shows is palpable. Weima will present fundamental process steps on the way to efficient recycling of plastics at a joint booth with its long-standing partner Neue Herbold. The topic of the circular economy will also be in the foreground at the booth of the German Ilsfeld-based shredder specialist. After all, a functioning recycling economy can only be realised with high-quality recyclate. To meet the strict quality criteria, the best possible processing of the plastic is necessary. Weima WLK 1000: Single-shaft shredder for large-volume plastic parts, films, and fibres At the booth, Weima will present the versatile WLK 1000 single-shaft shredder. It stands out for its high throughput andflexibility in daily use. The WLK 1000 shreds not only massive start-up lumps, production waste or large-volume plastic parts made of PE, PP, PVC, PU or PET, but also tear-resistant fibres and films to a homogeneous size; thefirst step on the way to producing high-quality recyclate. Shredding results The shredder can be optimally adapted to any application with various equipment options. The V-rotor, with a working width of 1,000mm and a diameter of 370mm, delivers first-class shredding results. For flexible materials such as films, filaments, and fibres, Weima also offers the F-rotor for a particularly precise cut. The counter knives of the WLK 1000 are manually adjustable and reversible. This allows the appropriate cutting geometry to be optimally configured for each material stream. As a result, shredding remains energy-efficient, wear costs can be minimised, and knife service life can be significantly extended. Flexible for varying material flows The speed of the rotor can be continuously adjusted via the optional frequency converter. This makes the machine particularlyflexible, especially with changing material flows. The large-volume hopper with the innovative log spacer shape prevents the formation of material bridges even when shredding particularly large parts. Direct filling takes place via the low loading edge by conveyor belt, gripper, wheel loader or manually and is therefore convenient to operate. Two-stage processing of plastic waste A two-stage processing system is often required to achieve particularlyfine particle sizes. In cooperation with the granulator specialist and long-standing partner, Neue Herbold, Weima has already implemented many joint customer solutions. Shredders fromWeima can be precisely operated and controlled via Siemens PLC control. They have common interfaces (such as Profibus or Profinet) and can thus be integrated into existing production systems. This also includes peripherals such as extraction, metal detection and secondary crushers. This optimises the use of downstream production machines (such as washers and extruders) and increases the efficiency of the recycling line. www.weima.com Two-stage shredding solution with Weima shredder and Neue Herbold granulator Enhanced cavitation Superior tool steel Balanced HR system Acme Drinktec Solutions LLP Email: [email protected] Website: www.acmedrinktec.com Phone +91-9810418975 +91-9819020785 +91-9810631426 SINGLE STAGE ISBMMOLDS CREATING MOLDS WITH A DIFFERENCE","@ID":40} "CAPS & CLOSURES 27 PETplanet Insider Vol. 22 No. 09/21 petpla.net CAPS & CLOSURES 27 The closure must be compatible with existing preform designs, openings and thread types. Impact on the end customer should be kept as low as possible, i.e. comfort of use should not be reduced. Closures are compatible with existing filling equipment. Closures are connected to the container throughout the entire product life cycle until recycling. Materials for the closures are not changed. Impact on existing production lines should be minimised and output not reduced. 15 times opening and closing of the cap without loss of function must be guaranteed. The connection between cap and container must withstand at least 25 N tensile force. Strategies for the production and design of tethered caps Currently, two main production concepts exist to achieve the new requirements for the production of tethered caps: With the “slit concept”, the cap is cut after injection - this has the advantage that the current tools can continue to be used, but requires an additional work step in production and significantly restricts the design scope of the cap. With the “bridge concept”, a band is injected along with the cap, which requires new tools. The advantage of this concept, however, is that no additional work step is required afterwards, greater freedom of design is possible for the caps and the injection-moulded connection between the cap and the band can withstand higher loads. Engel sees two variants currently dominating in the design of tethered caps: The “lasso design” refers to caps that are connected to the bottle with a two-part band. The cap is connected to the upper band and the bottle to the lower band. This design is relatively easy to implement with existing tools, usually only the sliders need to be reworked. Do you want high-quality and modern technology for the production of high-class Post Consumer Resin (PCR) and would like to source everything - from sorting to extrusion - from a single supplier? With STADLER you can. +49 7584 9226-0 [email protected] www.w-stadler.de STADLER Anlagenbau GmbH PLASTIC RECYCLING SYSTEMS: WITH STADLER! OF COURSE Contact us to know more! STADLER: for a clean world! The “hinge design”, on the other hand, allows the permanent connection of cap and container by means of a hinge, which optionally also allows the cap to be fixed in a defined position. The use of existing moulds is practically impossible. Impact of tethered caps on production “The new requirements for beverage closures necessitate fundamental changes in production,“ explains Jörg Leonhartsberger, Sales Director Packaging Engel Austria. “Due to the high demand in the market, many manufacturers are expected to start with the Lasso solution first as the Hinge design requires high investments in both time as well as financial terms due to the need for a new mould. In addition, the hinge design may require adjustments to the filling line and the feeding of the caps, resulting in further costs.” As a trend for the future, it is expected that in the course of the changeover to tethered caps, many producers will consider switching from 1810/1811 cap types to 26mm caps. The advantage here is a possible reduction in cycle time and material usage. For the injection moulding machine, tethered caps require higher injection speeds and increased injection pressure, as the required cavity internal pressure will tend to be higher. The reason for this is the changed filling behaviour with an increased number of filling points on the TE belt. The necessary clamping force, on the other hand, will not increase with a change to a 26 mm closure. www.engelglobal.com Engel e-cap","@ID":29} "MARKET SURVEY 33 PETplanet Insider Vol. 22 No. 09/21 petpla.net Pressco Technology Inc Intravis GmbH 29200 Aurora Road, Cleveland, OH USA +1 440 498 2600 www.pressco.com Mr Tom Murphy VP, Sales & Customer Service +1 440 498 2600 [email protected] Rotter Bruch 26a, 52068 Aachen, Germany +49 241 9126 0 www.intravis.de Mr Markus Juppe CMO +49 241 9126 0 [email protected] Intellispec CapWatcher Q-Line CapWatcherSC (specialty closures) IntraOne! Up to 3,600ppm 60cps / 3,600cpm / 216,000 cph 80 cps / 4,800 cpm / 288,000 cph 50cps / 3,000cpm / 180,000cph Vision 3 cameras for inner inspection (sealing elements, thread, tamper evident), 4 cameras for shell inspection, 1 camera for topwall inspection, contactless microhole inspection, temperature measurement, cavity reading Fully customised inspection systems that are tailored to the needs and wishes of our customers The perfect system for OEMintegration into capper-, filler-, assembly-, laser- or printingsystems Food, beverage, pharma, specialty, dispensing, sport, plug seal or liner, injection or compression moulded Tethered caps, standard one-piece beverage closures, standard two-piece beverage closures Tethered caps, carton fitment, flip-top, sports cap, push-pull, 3-piece closures, screw top cap, spout & dosing, beauty & home-care, food & beverage, pharma, automotive, inserts, cutters, lids, dustcover Tethered caps, standard one-piece beverage closures, standard twopiece beverage closures, carton fitment, flip-top, sports cap, push-pull, 3-piece closures, screw top cap Yes Measurement of inner seal cone diameter ( σ =0.02mm), pulled thread inspection, tamper evident band inspection, black specks, contamination, colour deviation, inner seal cone, outer seal cone, plug seal, constant distance between inner seal and outer seal, homogeneity between inner seal and outer seal Measurement of inner seal cone diameter, pulled thread inspection, tamper evident band inspection, black specks, contamination, colour deviation, inner seal cone, outer seal cone, plug seal, constant distance between inner seal and outer seal, homogeneity between inner seal and outer seal, liner, laser engraving, QR-codes, promotion codes, cavity number reading. Yes Measurement of outer closure diameter ( σ =0.02 mm) and height ( σ =0.02 mm), long gate inspection, slit quality for slitted closures, broken bridges, hinges, flashes between bridges, colour deviation, black specks Measurement of outer closure diameter & height, long gate inspection, slit quality for slitted closures, broken bridges, flashes between bridges, colour deviation, black specks, contamination, ovality, short shots, flashes, angel hairs. Yes High precision measurement of the outer closure dia-meter: accuracyσ =0.02mm, high precision measurement of the inner seal cone diameter: accuracyσ =0.02mm, high precision measurement of the outer closure height: accuracyσ =0.02mm Diameter and ovality, height, assembly faults, missing & damaged components, damaged seal cone, vertical long shots, open & closed short shots, horizontal/radial long shots, tamper evident band, damaged flaps, turned up flaps, damaged pull tabs, missing or damaged quality seal. No Robust cavity reading with special illumination technology, cap-oriented imaging & machine-learning algorithms for cavity recognition. No time-consuming teaching or learning procedure necessary. This enables the creation of real-time heat maps of moulds. Problems in temperature control of individual cavities or entire heating & cooling circuits can be detected & eliminated. Robust cavity reading with specially developed illumination technology, cap-oriented imaging and machine-learning algorithms for outstanding cavity recognition. No time-consuming teaching or learning procedure necessary. No New contactless microhole inspection, no need to dip into the closure - must-have for tethered caps with inserts New contactless microhole inspection - no need to dip into the closure Wide range of insert types and materials Missing components, closure height, diameter and ovality, flow lines, weight, Label, l*a*b values, barrier inspection, layer inspection, tactile measurement Colour, UV, print/deco, liner/wad, caps on filled containers Pull-off test, TE-features Available Yes Yes Yes Yes Yes Yes Yes Yes Yes Yes Yes Real-time trend data, last 100 images, defective image database/ archive, remote access, biometric user login, customisable reports, OPC connectivity Data base connection, reject rate monitoring, production monitoring, integrated control of up- and downstream equipment, integrated trend statistics with pre-warning. IntraVisualizer - data analytics to improve production quality visualises the data of all Intravis systems on site simultaneously. Most importantly, it helps to investigate defective product (Root-cause analysis) predicting and avoiding quality failures and material waste. In addition, it detects negative trends before faulty products are produced. It is possible to integrate data from different production machines with a robust OPC-UA interface according to Euromap standard.","@ID":35}]}}
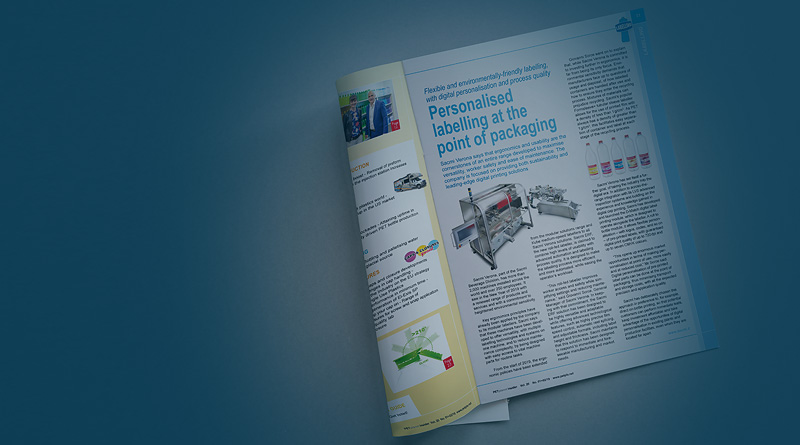