{"pages":{"page":[{"#text":"8 NEWS PETplanet Insider Vol. 22 No. 10/21 petpla.net First products granted RecyClass recycled plastics certifi cation RecyClass recycled plastics traceability certifi cation was granted to the first products covering both flexible and rigid, as well as food and non-food applications. The certification attests the inclusion of recycled plastics in products containing between 10-100% of recycled content. With the growing pressure to demonstrate to consumers that products are genuinely circular manufacturers, brand owners and retailers are increasingly looking for a reliable and transparent certification. The RecyClass certifi cation is destined to all actors in the plastics value chain, beyond packaging, for virtual ly any plastic product. It attests to the physical traceability of recycled plastics as described in EN 15343:2007, following a controlled blending chain of custody approach ISO/IEC 22095 where origins of plastic waste are verifi ed starting with the recycler and moving up the value chain. The certifi cation allows as well for an adequate determination of the share of the post and pre-consumer plastic. Nine companies were granted the RecyClass recycled plastics traceability certifi cation include: Alpla with 89% post-consumer recycled content in PET bottle in Germany; Selenis Portugal S.A., certifying the use of 30 and 50%of post-consumer recycled content in PET compounds in Portugal. Silvalac, S.A., certifying the use of 20, 30, 50, 60, 75, and 95% recycled content (both pre-consumer and post-consumer) in fi lms in Spain; Macresac, S.A. with 30, 50 and 70% of post-consumer recycled content in fi lms in Spain; Mornos S.A. with 30% pre-consumer recycled content in LDPE bags in Greece; Neemann LIteFlexPackaging, certifying the use of recycled plastics in fi lm bags 23, 40, 60, 80% post-consumer and 20, 40 and 50% pre-consumer in Germany; Versalis S.p.A. with 10 and 35% postconsumer recycled in expandible polystyrene in Italy; Sleever Technologies with at least 30% post-consumer recycled plastics in PET shrink fi lms for shrink sleeve labels in France; Colpack S.r.l. certifying the use of both at least 60, 95, 98, and 99% recycled plastics in garbage bags from the postconsumer origin and the use of at least 87, 92, and 97% mixed pre-consumer and post-consumer recycled plastics in garbage bags as well. The certified products come from all over Europe including Germany, Greece, Italy, Portugal, France, and Spain, further certifi cations are presently ongoing also in, among others, Belgium and the UK. Meeting consumer demand for transparency and verifi ed claims remains high on the agenda of the plastic value chain as the target of placing 10 million tonnes of recycled materials on the European market by 2030 is approaching. With the aim of increasing the robustness of theAudit Scheme, the organisation is currently in the process of being accredited under the ISO 17065 standard. www.recyclass.eu Plastics Recycling Show Europe announces conference programme The Plastics Recycling Show Europe (PRSE) conference programme has been published ahead of the event’s return to the RAI Amsterdam, The Netherlands on November 4-5, 2021. The latest trends in the plastics recycling sector will be explored in depth throughout the free-to-attend two-day event, providing a holistic view of the whole plastic recycling value chain and drawing together political leaders, major brands, recyclers and the plastics recycling and manufacturing industry. Virginijus Sinkevičius, Commissioner for Environment, Oceans and Fisheries at the European Commission will deliver the opening keynote updating delegates on the latest political and legislative developments in plastics recycling in Europe. Additional speakers in the opening session entitled Making plastics fully circular – what’s next? are Ton Emans, President of Plastics Recyclers Europe (PRE) and Peter Goult, Associate at Sytemiq. Prominent speakers from major brands at the plastics recycling conference include: Thor Tummers, External Affairs manager at Unilever Eelco Smit, Sustainability Leader at Philips Domestic Appliances Gian De Belder, Technical Director – R&D Packaging Sustainability at Procter & Gamble Anne Guillou, Sustainable Packaging & Product Development Manager, L’Oréal Ermis Panagiotopoulos, Sustainability Director at Natural Mineral Waters Europe Materials focus sessions on the fi rst day will explore the challenges, issues and opportunities within the sector for mechanical recycling, covering PET, PVC, technical plastics and PS recycling. In the PET session, Ermis Panagiotopoulos covers PET: EU legal obligations on rPET & beverage industry’s actions. In the PVC session Charlotte Röbber, Managing Director, EPPA presents Circular Economy in action – Implementing Collection and Recycling schemes for Windows in Germany, France and Poland. Topics covered in the Technical Plastics and PS session include: Plastics recycling in domestic appliances Sustainable plastics solutions; and The future of food contact and low carbon footprint: Circular Polystyrene. The second day’s opening session recyclability and recycled content: how to make it happen? is chaired by Paolo Glerean, PRE Board Member and Chairman of RecyClass. The following polyolefi n material focus sessions will examine the current status of polyolefi n waste streams including LDPE and HDPE. In the LDPE sessions Mik Van Gaever, COO, FostPlus looks at recycling of flexible household packaging in Belgium. A highlight of the HDPE session is expected to be Thor Tummers, External Affairs Manager at Unilever with accelerating the transition for a circular economy for packaging with all stakeholders. The conference concludes with a fi nal session looking at PP recycling. The hybrid event will allow people unable to visit the event in person to view elements of the two-day conference programme via livestream including the welcome address, keynote speeches and sponsored as well as the announcement of winners of the Plastics Recycling Awards Europe. Online-only visitors will also be able to interact directly with exhibitors. www.prseventeurope.com","@ID":10} "PETplanet Insider Vol. 22 No. 10/21 petpla.net 49 TRADE SHOW REVIEW A new plastics recycling technology Solvent-based recycling by Heike Fischer Interview with Florian Riedl, Director Business Development at APK AG, Merseburg, Germany. APK was founded in 2008 with the vision of producing pure polymers with properties close to virgin plastics from plastic waste. After many years of research, development and testing of various waste fl ows, the vision has become a reality with an industrial scale plant. The plant in Merseburg has around 57,000m² for R&D, production and administration. For conventional recycling process the input capacity is 12,000 t/a, for the Newcycling process the plant has a capacity of 8,000 t/a. 100 employees work for the success of APK AG. Mr Florian Riedl, Director Business Development at APK AG PETplanet: Dear Mr Riedl, may I ask you to briefl y introduce you and your company? What were your reasons for looking at an alternative to mechanical and so-called “chemical” recycling? Florian Riedl: APK is a plastic recycler based in Germany. The focus of APK is its Newcycling technology, a solvent-based recycling process that enables to generate from multilayer plastic packaging and mix plastic waste fractions again pure sorted polymers. Myself, I’m responsible for the Business Development within APK and focus on strategic cooperation partners. The demand from brand owners and packaging converters in highquality recyclates that can replace virgin plastics is already today higher than the market availability of such recyclates. And this trend will accelerate the coming years. From our perspective, solvent-based recycling can close this gap and provide recyclates that can substitute virgin plastics and at the same time reduce the carbon foot print of plastics packaging. PETplanet: Would you please be so kind and explain the technology of solvent-based recycling? What are the differences and advantages to other plastics recycling processes? Florian Riedl: Mechanical recycling comes in most cases quickly to a limit in terms of mixed plastic waste streams. For example if the waste contains multimaterial packaging with a mix of different polymers, e.g. PE and PET, then the generated recyclates consist also of a mix of these polymers what limits the range of suitable end applications. Chemical recycling processes enable pure polymers also from mixed and complex waste streams. But most of the chemical recycling technologies include two highly energy intensive steps: First they break down the polymers chains to monomers or other chemical base units, and afterwards synthesise again the monomers to polymers. Theses two energy consuming steps are not needed by solvent-based recycling, as solvent-based recycling does not break down the polymer chain. It is selectively dissolving polymers and generates this way pure sorted plastics. PETplanet: What is the state of development of this technology at APK? Is it already ready for the market? For which types of plastics is it suitable? Florian Riedl: APK has its fi rst Newcycling plant with a capacity of 8,000t/a in operation since June 2019. The technology is fully commercialised and recyclates from the Newcycling process are sold to customers for already over two years. The technology is suitable for a huge range of polymers and polymer combinations, such as LDPE, HDPE, PP or PA. PETplanet: What are the future plans for Newcycling? Florian Riedl: In the next step we make the technology ready for the usage in postconsumer household waste. We are already far ahead in these developments but cannot share details at this stage. PETplanet: Thank you so much for this brief overview. www.apk-ag.de/en www.kreyenborg.com [email protected] FDA & EFSA approved lj Easy retrofitting for existing lines lj Decontamination & drying in one step lj FOR DIRECT FOOD CONTACT PACKAGING rPET FLAKE DECONTAMINATION Continuous processing lj MADE IN GERMANY","@ID":51} "7 NEWS PETplanet Insider Vol. 22 No. 10/21 petpla.net Carbios launches industrial demonstration plant for its enzymatic recycling technology Carbios, a company pioneering new enzymatic solutions to reinvent the lifecycle of plastic and textile polymers, announced the offi cial opening and launch of an industrial demonstration plant operating with its enzymatic recycling technology, C-Zyme, which was installed on the Cataroux site in Clermont-Ferrand, France. The demonstration plant marks the culmination of the development of the C-Zyme technology. It will allow the validation of the enzymatic PET recycling process’ technical, environmental, and economic performance, as well as the design of future industrial units. By the end of 2022, its operation will enable the complete engineering documents for the process (Process Design Package) to be drawn up for the building and operation of a 40,000 t/a capacity reference unit as well as future factories to be run under licensing agreements. The optimisation of the operating parameters as well as the production of the monomer batches are now carried out by a team of ten people. An initial hydrolysis has been successfully realised, confi rming the upscaling of the process. The C-Zyme recycling process uses an enzyme capable of depolymerising PET which is found in a variety of plastic and textile items. The depolymerised monomers are purifi ed before being repolymerised into PET of comparable quality to virgin PET derived from petrochemicals. Unlike traditional methods, Carbios’ breakthrough enables unlimited recycling of all sorts of PET waste (clear, coloured, opaque, complex plastics, polyester textiles) as well as the production of 100% recycled and 100% recyclable PET goods that maintain their virgin quality throughout the process. www.carbios.com New launch of the PET returnable bottle in Austria Austria’s market leader in the mineral water market, Vöslauer Mineralwasser GmbH, is concretising its plans to relaunch the fi rst and so far only PET returnable container in Austria. “In Austria, PET reusable containers were common until the 1990s, but they disappeared from the shelves completely due to a lack of demand. The change in consumer behaviour, but also the improved technological conditions in the meantime, make a new generation of PET returnable products possible that fi t into today’s world and are an ecologically sensible addition to our product range,” explains Herbert Schlossnikl, Managing Director of Vöslauer. “To this end, we are investing around seven million euros in new plants, despite economically challenging times,” adds Birgit Aichinger, Managing Director of Vöslauer. In the fi rst quarter of 2022, Vöslauer will launch Austria’s fi rst returnable PET bottle in the fl avours sparkling, mild & plain, with more to follow in the future. The current 9×1 l rePET twoway deposit bottle will be completely replaced with the new solution. “Amajor advantage of the new returnable PET bottle is the reduction of the CO2 footprint by up to 30% compared to our existing deposit containers,” says Schlossnikl. The lightweight PET returnable bottle also comes with 90% less weight compared to the glass returnable bottle. “This is an unbeatable advantage in handling, logistics and for the end consumer,” emphasises Aichinger. When it is launched on the market, the PET returnable bottle will have a recycled content of 30 %, which is to be continuously increased. The PET monomer material used is also 100% recyclable and the labels are also made of 100% recycled material. “We aim for 12 cycles for our returnable PET bottles and thus also the Austrian Eco-label,” explains Schlossnikl. A bottle is thus expected to be in use for around three to four years and saves around 80% of material over this period. Calculated in tonnes, that is about 400 t/a of material, which corresponds to a CO2 equivalent of 420 t. The reusable crates manage at least 50 cycles. www.voeslauer.com GAWiSD featuring AutoJob™–job set up in seconds +1.724.482.2163 AGRINTL.COM ACCURATE • FAST • REPEATABLE SEE GAWIS4D IN ACTION Dimensional and thickness measurements for plastic containers and preforms. ®","@ID":9} "9 NEWS PETplanet Insider Vol. 22 No. 10/21 petpla.net \r \t \t \t \r ","@ID":11} "PATENTS PETpatents PETplanet Insider Vol. 22 No. 10/21 petpla.net 55 Bottle base Intern. Patent No. WO 2018 / 110301 A1 Applicant: Sidel Participations, Octeville-sur-Mer (FR) Application date: 21.9.2018 The international application describes the shaping for the base of a thin-walled PET bottle. Plastic container Europ. Pat.issue No. EP 3290345 B1 Applicant: Yoshino Kogyosho Co. Ltd., Tokyo (JP) Application date: 8.4.2016 Plastic container for hot fi lling. The compensation areas for the low pressure arising during cooling are slanted. This should make the deformation more defi nable. Bottle with handle Intern. Patent No. WO 2020 / 234125 A1 Applicant: Sidel Participations, Octeville-Sur-Mer (FR) Application date: 14.5.2020 A PET bottle is given a hollow / indentation on one side. The bottle can be gripped securely with a separately manufactured handle piece. PET bottle base shape Disclosure No. DE 102019119984 A1 Applicant: Krones AG, Neutraubling (DE) Application date: 24.7.2019 One-piece container or bottle with special shaping of the base with carriage strap grooves. Bottle base shape Europ. Patent No. EP 3763628 A1 Applicant: Nissei ASB Machine Co. Ltd., Nagano (JP) Application date: 5.3.2019 Application is made for the base shape of a bottle for a product that is heat-treated only after bottling. Stable plastic bottle Europ. Patent No. EP 3763629 A1 Applicant: Suntory Holdings Ltd., Osaka (JP) Application date: 22.1.2019 This describes the shaping of a plastic bottle that remains suffi - ciently stable in shape even under “high” pressure fl uctuations / pressure changes. The base and side wall areas are specially shaped for this.","@ID":57} "MATERIALS / RECYCLING PETplanet Insider Vol. 22 No. 10/21 petpla.net 25 possibility of installing robots. Stadler addressed this demand by including two independent sorting lines – one for the treatment of multi-material and one for hollow material – a set-up that gives more fl exibility. Meeting the growing demand for recycling The push to address the global waste issue by working towards a circular economy is driving a growth in the recycling sector. As a result, Stadler has seen an increase in the demand for new sorting plants as well as upgrades and expansions of existing facilities. This was the case of Viridor, one of the UK’s leading recycling, resource and waste management companies, which undertook a £ 15.4m (US$ 21,2m) upgrade of its Masons Materials Recycling Facility (MRF) in 2020. As one of two developers of this plant, Stadler transformed its operation, increasing its capacity from 65,000 tpa to 75,000 tpa and signifi cantly improving output quality, achieving 98.5% purity on newspapers and pamphlets and 95% for polymers such as PET, HDPE and mixed plastics. Viridor is focused on developing opportunities to put quality recycling materials back into the economy where they belong. The Masons investment plan has been specifi cally designed not only to achieve greater capacity but to match the quality of its output with market requirements. The plant now has the same infeed material as before, but the upgrade has resulted in the facility being able to cope with an additional 10,000 t/a of material. www.w-stadler.de Inside of the UK-based Viridor plant Flexible sorting plant for the Schroll Group, France","@ID":27} "43 TRADE SHOW REVIEW PETplanet Insider Vol. 22 No. 10/21 petpla.net Recycling line - RecoStar dynamic Starlinger showed its latest recycling technology for the processing of fi lms, fi bres, and washed post-consumer waste from materials such as PE, PP, PET / PES, PA, PLA, PS and PPS. Ecological, economical, energy-saving These are the three keywords, Starlinger uses to describe the new RecoStar dynamic recycling line. The machine concept is characterised by a energyeffi cient production process as well as a high grade of automation, which accounts for reliable and constant production, higher output, and wider range of applications says Starlinger. The RecoStar dynamic will be the fi rst of the Starlinger recycling lines to carry the “rEco” stamp. By using exclusively motors with the best effi ciency ratings, energy consumption and CO2 emissions are reduced signifi cantly. Features such as energy recovery systems in various process steps as well as infrared heating further slim down the energy costs for machine operation. Designed for recycling plastic scrap from industrial and post-consumer applications, the new recycl ing l ines are especially suited for processing hygroscopic, wet and/or preground and foamed materials. The Smart feeder prepares the material prior to extrusion through performing simultaneously the following: Shrink & cut Mix & homogenise Active feed & control Rotate & friction Temperature & dry The dynamic automation package regulates that the system is running at the best operating point. Consequently, higher output is achieved with lower energy consumption, and higher levels of humidity can be processed. The produced highquality regranulate is suitable for a wide range of end use applications. The RecoStar dynamic series is available in six sizes and covers an output range of 150-2,600 kg/h. Technical Data Output: 150-2,600 kg/h (depends on extruder dimensions and the material to be processed) Energy consumption: 0.2-0.35kWh/kg Diameter Smart feeder: 900-2,050mm Smart feeder drive power: 37-400kW Extruder screw diameter (L/D): 65(24;40)-215(24;40)mm Extruder AC drive: 45-560 kW www.starlinger.com","@ID":45} "CAPS & CLOSURES 38 PETplanet Insider Vol. 22 No. 10/21 petpla.net Swing-top PET bottle by Kay Barton In the small town of Personico in the Ticino region just under an hour’s drive north of Lugano, the Gazzose Ticinesi company produces the Gazzosa, a typical soft drink from the Italian region of Switzerland. The bottler, whose history goes back as far as 1890, is now fi lling PET as well as glass bottles as a result of increased demand from promotors and retailers. The PET bottles have a special feature which is a fi tted resealable swing-top, previously only found on glass bottles. With this innovative and contemporary plastic design, the fi rm is bringing the original glass bottle into the 21st century. We spoke to the company’s Director, Luca Bianda, about his “Fizzy” product. From 1890 until the late 1960s, the factory operated under the name “Gazzosa Cantoni” and was based in the nearby town of Bodio. It then moved to Personico following a takeover that resulted in a change of company name to “Gazzosa Sassi Grossi”, a reference to the Battle of Giornico in which a heroic force of 600 Swiss routed an invading 10,000 strong Milanese army in 1478. In 1972, the fi rm was taken over again and was renamed “Gazzosa Ambra”. Signifi cant expansion and renovation work was carried out which enabled the current company to vastly increase its production capacity for the fi rst time. Finally in 2008, the Ticino entrepreneur and pharmacist Luca Bianda took over the company and formed what is now Gazzose Ticinesi SA, with plans to establish the Ticino-based business on a supra-regional and national scale. In addition to extensive refurbishment and upgrading of the production facilities, ISO 9001 certifi - cation, HACCP and IFS Food Standard systems were also incorporated. The company has grown from 3 to 22 employees. “We promote and develop our Gazzosa mainly through food stores, distributors and caterers. By relaunching our carbonated soft drinks under the “Fizzy” brand, the aim is to connect with our cultural food heritage. The idea is for Fizzy to become a kind of synonym for Gazzosas so that in future, people will order Fizzy when they really mean Gazzosa. We have already achieved this in Ticino and are now intent on doing the same in the rest of Switzerland and beyond”, Mr Bianda explained in an interview. All the latest sizes are produced on a 4,000 bph production line with machinery from various manufacturers. The line is equipped with a bottle washer for glass bottles from Akomag, a bottle rinser for PET bottles from Enopoggio, an inspection unit for empty and full bottles from Digital Controls, a C.E.M. fi lling machine customised by Gazzose Ticinesi. Capping machines for the various formats are from AMS Getränketechnik and Kompass, labelling machines from Kosme and Simac, a Fipal case packer customised by the company, a Giemme Thermo shrinkwrapper and a Twinpack handle applicator. “We have made modifi cations to each machine in-house where necessary”, outlined Mr Bianda. The Fizzy Fizzy PET bottles with screw cap Director Luca Bianda Fizzy PET bottle with swing-top closure","@ID":40} "47 TRADE SHOW REVIEW PETplanet Insider Vol. 22 No. 10/21 petpla.net in reverse direction back through the screen, carrying away contaminant for removal from the system. The sequence is performed for each cavity one after the other. In normal operation, polymer is fl owing through all four cavities. While one of the cavities is cleaned, production continues through the other three. There are two challenges to improving this type of screen changer: fi rst, to reduce downtime by extending the working life of the screens and thus reducing the frequency of required screen changes; and second, to cut back on material loss by reducing both the amount of polymer expended per backflush cycle and the number of cycles needed in a given period of time. With a ton of PET bottle fl ake selling at € 920 (US$1,000), material losses with a standard backfl ush screen changer, operating on a 24/7 basis, can amount to more than €100,000 (US$108,467) per year. To address these issues, Nordson has developed a fi lter stack composed of multiple so-called FlexDiscs which replaces the standard screen in each cavity, substantially enlarging fi ltration area while decreasing the melt loss caused by backfl ushing. Each fi lter stack consists of two to four cassettes, with two screen packs in each cassette. In PET recycling, backfl ush screen changers combined with FlexDisc fi lter stacks have provided fi ltration as fi ne as 25-30 μm, increased screen lifetime, and exhibited more than 50% less material loss versus comparable screen changers. Comparative data from trials at one recycling company appear in Table 1. Pelletising systems Two types of pelletising system are used in PET recycling - strand pelletisers and underwater pelletisers (UWPs). A third type, water ring pelletisers, is not appropriate for lower-viscosity materials like PET. Widely used for recycling, UWPs provide several advantages over strand pelletisers. The UWP can achieve by far the greatest throughput rates and is more capable of automation, making possible linkage with the upstream process. (Unfortunately a larger capital investment is required for realising these benefi ts.) Unlike strand pelletising, underwater production of pellets is a closed process, minimising emissions as well as the generation of dust during production and in the fi nal product. With constant melt fl ow (ideally ensured by a gear pump) and the fl ow uniformity provided by a round die plate, underwater pelletising yields the most consistent pellet size distribution. The spherical shape of pellets produced under water results in 5-10% greater bulk density compared to cylindrical pellets, and it reduces their tendency to clog in subsequent post-pelletising equipment as well as in hoppers and feed throats. Downstream of the pelletiser are the pellet dryer and the tempered water system. After process water has been used in the pelletiser cutting chamber and for transporting pellets to the dryer, it needs to be cleaned of fi nes and cooled to within a strictly maintained temperature range for reuse in the pelletising cycle. Fines-removal components in tempered water systems range from a woven wire mesh screen that periodically must be removed and cleaned manually, to systems that reduce downtime and operator intervention by providing continuous, automated fi ltration. Still more advanced is an automated, self-cleaning system that reduces overall pelletiser energy consumption by 10-17% by eliminating the need for a separate fi nes-removal system, which in standard systems requires a secondary, dedicated water pump. Energy-saving inline crystallisation For the bottle-to-bottle recycling process, systems have been developed that reduce energy costs by combining the pelletising and crystallisation step in a single integrated process. This technology uses the thermal energy of the molten polymer in PET pelletising for subsequent crystallisation, avoiding the need to cool PET after pelletising and then reheat it for crystallisation. The inline crystallisation system developed by Nordson, called CrystallCut, is designed to work with the spherical pellets generated by UWPs and is an integrated network incorporating pelletiser, dryer, and crystallising unit. rPET pellets achieve a crystallisation level of up to 32% (in production of virgin polymer, by comparison, the fi gure is approximately 40%, depending on the initial quality of the material). Subsequently, a solid state polycondensation (SSP) reactor raises the intrinsic viscosity of the polymer and carries out a fi nal decontamination step by removing trace substances like acetaldehyde, which have a deleterious effect on taste in food applications. Pellet temperature in the CrystallCut system is maintained at 140-180 °C. The system eliminates the intervening step of holding pellets in a silo at a maximum 60 °C (to avoid pellets sticking together) and a separate pre-crystallisation step before the pellets are transferred to the SSP reactor. Alternatively, by adjusting process parameters, it is possible to bypass the CrystallCut step or to produce amorphous polymer. Compared with a traditional operation with UWP and SSP operating at 2.5 t/h, the CrystallCut system provides thermal energy savings of 30-50 kWh/t, electrical","@ID":49} "PETplanet Insider Vol. 22 No. 10/21 petpla.net 53 BOTTLES The right tools and expertise to help with your rPET goals! Agr is uniquely positioned to support your venture into rPET bottle manufacturing with a powerful combination of Process Control tools, Process Consultants, and decades of industry experience. AGRINTL.COM • +1.724.482.2163 Sustainable brand of Colgate Palmolive Many large manufacturers are developing and establishing new brands as part of their portfolio that are intended to appear sustainable, trendy and independent. One example is Colgate Palmolive’s “For the future Now!” brand. Four hand dishwashing liquids with and without fragrances are available on the market. The vegan dishwashing liquids contain no microplastics, no dyes and the ingredients are 99.4% biodegradable. The bottles are made of 100% recycled material and can be easily recycled after removing the foil label via a perforation. The closure is a one-handed hinged cap with a dispensing opening. www.fürdiezukunftnow.de Foaming wash for kids Unde r t he own b r and “alverde Naturkosmetik Kids”, German discount pharmacy Dm is selling a foaming wash especially for kids’ hands and faces. The vegan foam contains organic strawberries and organic apple extract from organic farms and is free from microplastics. The bottle consists of 99% recyclate, is decorated with two self-adhesive labels and the screwed-on, lockable pump dispenser produces foam when pumped and product is dispensed. www.dm.de Pro Climate Range from Dm Consumer demand for special products as regards sustainability and ingredients presents an ongoing challenge for manufacturers. The result of this trend at Dm is the “Pro Climate” Range for environmentally neutral products. One of these is the alcohol-free, vegan mouthwash with organic balm. The 500ml bottle consists of 100% recyclate and the product is developed overall with the best possible life cycle assessment and a minimal environmental footprint. According to the printed information, compensation is made for the remaining environmental effects, making the product “environmentally neutral”. The screw cap is protected before opening by a tamper-evident seal. www.dm.de","@ID":55} "PREFORM PRODUCTION PETplanet Insider Vol. 22 No. 10/21 petpla.net 35 Preform range for hand sanitiser applications and cosmetic products Tried and tested for new uses The post-Covid world brings with it a greater demand for products that were previously used relatively infrequently. Whereas hand sanitiser, for example, was perhaps bought by consumers once a year, now many people keep a bottle of this liquid with them most of the time. And it’s not just consumers that want a handy bottle of sanitiser: supermarkets, shops, offi ces and public spaces are now routinely stocked with bottles of alcohol gel, which are either regularly changed or refi lled, with the heavy usage requiring sturdy products. For plastic packaging manufacturers, diverting existing or customisable bottles and closures suitable for this newly-crucial application is a good way to respond to this trend. For Retal Iberia, the Girona factory for the global Retal group of PET preforms, fi lms and closures producers, its fast-acting team has created a range of preforms that are suitable for hand sanitiser applications, as well as other cosmetic products. Raquel Oller Bosch, commercial manager at Retal Iberia, explains how the lexpertise of the team has allowed it to quickly create a viable solution. She says, “We have extensive knowledge of creating and manufacturing PET preforms that can include rPET, and we are always looking for ways to utilise our portfolio. With the increased appreciation for hygienic packaging solutions, and the greater demand for hand sanitiser and alcohol gels, we wanted to offer a cost-effective preform that was available at a range of sizes.” The new Retal DIN preform is available in a range of neck fi nishes and weights, with sizes ranging from 0.5 l up to 1.5 l, making it suitable for both individual use and more commercial volumes of hydroalcoholic gels. The neck weights available with the Retal DIN preform are 23/410 (2.23 g) and 28/400 (2.85 g). Oller Bosch continues, “This preform is based on our very successful design for mineral water and carbonated soft drinks, but the variation comes from the different demands of hand sanitiser when compared to CSD as the product is dispensed; the cap needs to be pushed or squeezed, rather than poured or drunk directly. So we’ve not reinvented anything . We’ve taken what we know inside and out and made it suitable for a new demand.” Transposition to other segments Production capabilities for these preforms are al ready establ ished at a possible 13.6 mi l l ion units per month, depending on size and order requirements. Retal Iberia has invested in state-ofthe-art equipment in order to manufacture at volume and speed, offering costconsc i ous so l u t i ons to brand owners and blowers across Europe. Wi th up to 100% rPET ‘not a problem’, the Retal Iberia preform range can be offered as standard or customised, wi th al l the product ion faci l i t ies and equipment already up and running with experienced teams. Oller Bosch explains how the long-term experience of Retal Iberia’s team in p r oduc i ng p r e f o rms a t high volumes for food and beve r age app l i ca t i ons means that this value can be transposed to the hand sanitiser segment, as well as other cosmetic products. She notes, “We’re used to producing huge volumes for the very cost-conscious bottled water market, so we are able to pass on that advantage to customers in the hydroalcoholic gel segment.” With the wider neck available on the preform, this PET bottle is also suitable for a range of other cosmetic and personal care applications, particularly with the push button closure option. Body lotions, face creams, shampoo and conditioner are all suited, as well as sprays when coupled with the right closure. www.retalgroup.com Retal Iberia premises","@ID":37} "EVENT REVIEW PETplanet Insider Vol. 22 No. 10/21 petpla.net 40 19. GSI PET Day 2021, Webinar edition Flexibility - the PET industry’s way forward This year’s PET day, organised by GSI (Global Service International), took place on September 30, 2021. Held as a webinar edition for the second time, it re-united top decision-makers under one (virtual) roof for a passionate discussion of actual and realistic issues related to the current status of the industry. The most pressing question was what can be done to change for the better the industry position in this planet without affecting its environment, but more importantly acting and moving effectively and quickly to a more sustainable future. PET Day is not just a place where lectures are read in front of an audience. Here they are forensically analysed and openly discussed in a creative atmosphere. Francesco Zanchi, founder and CEO of GSI, opened this 19th edition of PET Day, welcoming the selected audience, those fortunate enough to receive the precious invitation from GSI. The morning session started with Mr Paul Hodges, Chairman of New Normal, a regular presence at the event, who addressed the climate change issue and the great opportunities ahead for the polyester industry. Considering the shifts in sourcing strategies, in consumers’ preferences, reduction in oil transformation and increase in recycling attitudes, he pointed out that we are going to witness the biggest transformation in the chemical industry since the industrial revolution. The transition may happen now very quickly. For its part, the oil companies are moving too slowly, whilst the polyester industry is moving swiftly into larger use of recycled materials, even before the deadline of 2030. In fact, it is starting to realise and raise awareness that PET waste is actually a resource, stimulating bigger efforts in plastic collection, with better connections among industry, local communities, managers, converters. Eventually money is made available by institutions to support this change: what is needed is the will to act, and the need is now urgent, Mr Hodges stated. The right behaviour is the only way in which the PET industry can succeed in getting the necessary solutions for enhanced sustainability and thus lead to a brighter future. Mr. Zanchi, agreed on the strategic approach underlined by Mr. Hodges, but reflected on the point that the industry must also consider the reality, with current materials prices and freight rates moving on a crazy rollercoaster. Mr. Hodges however insisted that, as far as energy policies are concerned, we should not take our governments as examples, because their actions today are too short-term. The industry needs to take a long-term perspective, since they cannot bring about change overnight. And a big change is vital. At this point Mr. Francesco Zanchi took the virtual podium to give a long-term global overview of the PET market. Capacity is still increasing in 2021, for PET and PTA. The overcapacity in PET is around 8 million tons, and 50% of that is in China. In Europe, demand for virgin is slowing due to more rPET in the pipeline: the EU is the driving force behind the move to recycled material. A doubling of rPET production in EU is forecast by 2025, but it will still not be sufficient for the projected demand. Also, is the 2029 collection target of 90% achievable? That is a big question. In Europe, there are currently 150","@ID":42} "MATERIALS / RECYCLING PETplanet Insider Vol. 22 No. 10/21 petpla.net 23 Producing food contact compliant rPET “The demand for rPET is increasing“ One of the fi rst Vacunite bottle-to-bottle systems by Erema started operation in Werne, Germany, in spring 2020. Using this system, the RCS Group, who already produced PET fl akes for the non-food sector, is expanding their plastics recycling division to include the production of food-grade PET recyclate for food and beverage packaging, fi lms and blisters. RECYCLING For the further processing of PET fl akes, the waste disposal and recycling group has built a new location on a 10,000m2 site, creating 20 additional jobs. Here, the Vacunite recycling system launched by Erema a few months previously will process up to 15,000t/a of PET fl akes from the German deposit bottle collection system and other European sources to make high-quality recyclate - vacuumassisted and in a nitrogen atmosphere. Due to the strict travel restrictions during the Corona-lockdown in spring, commissioning the plant became an unexpected challenge for everybody involved. The plant components had already been delivered, but since the installation team was not permitted to travel to Germany, RCS started to assemble the recycling plant themselves. An Erema team was then able to be on site for commissioning. New standard for recycled material quality RCS now operates seven days around-the-clock to produce rPET that meets all existing FDA and Efsa specifi cations for direct food contact and the often even stricter regulations of wellknown beverage brands. It also clearly exceeds the customer’s expectations. “Our analyses indicate that for all potential contaminants we achieve values that are signifi cantly below our target values or are not detectable at all,” explains Alexander Rimmer, Managing Director of the RCS Group. Vacunite is based on the combination of Vacurema technology - which has been proven over the past 20 years and Erema has further developed for this application - together with newly patented vacuum-assisted Solid State Polycondensation (SSP) technology, which was also specially developed by Polymetrix for this demanding application. All thermal process steps now take place in nitrogen and/or vacuum atmosphere. Discolouration of fl akes and pellets is largely eliminated and additives that could lead to undesired reactions in the melt are reliably removed. In addition to these quality factors, this new technology minimises energy consumption. The process requires 40 per cent fewer components and consumes up to 36 per cent less energy than comparable systems on the market. The energy consumption for the entire production process from fl akes to the fi nal pellets is only 0.35kWh/kg, which also complies with the internal sustainability standards at RCS. Following the commissioning of the Vacunite system with a throughput capacity of up to 1.8t/h, RCS can now offer its customers not only high-quality rPET fl akes but also rPET pellets that are food contact compliant. The cooperation between RCS and a leading PET bottle and preform manufacturer illustrates how a closed plastic cycle can be implemented, taking the PET material obtained from the German deposit system as an example. Alexander Rimmer says: “The recycling process of PET bottles returned by consumers to deposit machines begins in our group of companies as early as the collection stage. We turn the bottles into washed fl akes, which are then processed using the new Vacunite system to produce food contact compliant recycled pellets. Our customer uses this in proportions of up to 100 per cent to produce new preforms and bottles, which in turn end up in the retail trade and in households. This means that the cycle is completely closed and completely transparent to consumers, who can trace the route from the deposit machine back to the retailer.” Christoph Wöss, Business Development Manager at Erema Group GmbH, is also convinced that this route will be a successful one in the future: “Like our customers, we are convinced that plastic recycling will not lose its importance as a signifi cant contributor to the circular economy and that the demand for high-quality recycled pellets will continue to increase over the medium term.” The reasons for this are both the voluntary commitments of all well-known brand manufacturers in the beverage industry, as well as legal conditions such as the European Union’s requirements for the recycling of PET bottles and for the minimum recyclate content in new PET bottles. Due to the positive experience with the fi rst Vacunite plant, RCS has already set the course for starting up a second recycling line. It should enter production as early as spring 2022. “The decision to go for another Vacunite machine was easy for us,” says Rimmer: “The demand for rPET is increasing, the quality has exceeded our expectations, and the entire process from planning to installation and commissioning has been trouble-free.” With the second Vacunite bottle-to-bottle line, RCS will then be able to increase its recycled pellet capacity to over 50,000t/a. www.erema.com www.rcs-entsorgung.de/en","@ID":25} "10 NEWS PETplanet Insider Vol. 22 No. 10/21 petpla.net Tethered caps industrial trial In recent months Arol has been cooperating with CocaCola, together with several closures manufactures, in the validation process of the new GME 30.40 CSD (carbonated soft drinks) PET fi nish, both at laboratory level (c/o Arol premises) and at industrial level (c/o CCEP production line in Barcelona plant Spain). GME 30.40 (CETIE code) PET fi nish is the fi rst international standard specifi cally developed for tethered closures to be compliant with SUP EU Directive. The industrial trial at the CCEP Barcelona plant involved the production of more than 6 million sellable bottles 500ml size closed with new 26/22 CSD tethered closures. The directive requires the lids and caps of single use plastic (SUP) bottles and composite packaging with a capacity of up to 3l to remain tethered to the containers for as long as they are used. For the changeover to tethered caps, Arol is working with packaging manufactures and bottling line manufactures to minimise the impact of the changes. The company states that in most cases, a simple chuck cones replacement in the equipment will be enough to run these new caps. www.arol.com Fakuma 2021 review The 27th Fakuma international trade fair for plastics processing celebrated a restart in Friedrichshafen from October 12-16, 2021. 1,470 exhibitors from 39 countries came to Lake Constance for the fi rst major international on-site event for the plastics industry this fall, and presented injection moulding, extrusion technology, thermoforming and 3D printing on a world-class level. Overall emphasis was placed on the issues of sustainability, circular economy and recycling. After the compulsory one-year hiatus, the event on 85,000m2 of overall exhibition fl oor space. The fact that 40% of the exhibitors came from outside of Germany substantiates Fakuma’s signifi cance all over the world, especially in these exceptional times. “I’m delighted that something like this is possible again,” said Prof. Dr.-Ing. Martin Bastian, Institute director of the SKZ in Würzburg, at the trade fair’s opening ceremony. In his technical presentation to an auditorium full of trade press and guest listeners, he pointed out impressively what needs to be done in the industry: “We have to take more responsibility for what happens with plastic.” Martin Bastian made a passionate plea for the cause of plastics. The exhibition halls in Friedrichshafen were very well frequented right from the fi rst day of the event. Interested expert visitors were able to gain an impression of the latest developments and perspectives for concrete solutions in the fi eld of plastics processing. www.fakuma-messe.de/en Alpla acquires BTB PET-Recycling The Alpla Group, a global packaging solutions and recycling specialist, is acquiring BTB PET-Recycling based in Bad Salzufl en, Germany. The company turns used PET bottles from Germany’s reverse vending system into recycled material which is then predominantly used for the production of new beverage bottles. Its bottle-to-bottle packaging cycle is a closed loop. In acquiring BTB PET-Recycling GmbH & Co. KG, Alpla is investing in further developing the region’s recycling loop. Bottle-to-bottle BTB pre-sorts, shreds and washes the input material, then sorts it again. It is then melted down in an extrusion process and turned into pellet form, resulting in valuable food-grade rPET. The processing volume is around 20,000 t/a of PET bottles. The company has approximately 35 employees, all of whom will be kept on by Alpla. Georg Pescher, Managing Director of Alpla in Germany, says: “By acquiring BTB, we are investing in a very structured company which has been operating successfully within the local circular economy for years and which is already supplying our preform business in Germany with rPET. What’s pivotal here is a functioning system comprising a bottle return infrastructure, bottle production and bottling companies in the direct vicinity of the recycling plant.” The parties signed the contract on September 28, 2021. They have agreed not to disclose the purchase price or any further details. Expansion of recycling activities Just recently, Alpla and its partners announced the founding of the joint venture PET Recycling Team Targu Mures for the recycling of post-consumer PET bottles in Romania. The target is annual production of 15,000t of food-grade rPET to strengthen the local materials cycle in Central and South-Eastern Europe. In the UK, Alpla has been cooperating with the British waste management company Biffa since this year and sources food-grade rPET pellets from the Biffa recycling plant in Seaham. With this collaboration, Alpla is increasing the proportion of British recyclate used to manufacture packaging in the UK. In early 2021, theAlpla Group announced that it would invest an average of 50 million EUR/a until 2025 in the ongoing expansion of its recycling activities. In particular, it plans to globalise its activities in the area of high-quality recyclates in order to close the materials cycle in as many regions as possible. In all, the annual capacity of the Alpla recycling companies, joint ventures and partnerships amounts to approximately 130,000 t of PET and 60,000t of PE. www.alpla.com","@ID":12} "11 NEWS PETplanet Insider Vol. 22 No. 10/21 petpla.net","@ID":13} "MATERIALS / RECYCLING PETplanet Insider Vol. 22 No. 10/21 petpla.net 28 Tomra Recycling opens new test centre in Italy by Ruari McCallion September 21 saw the offi cial opening ceremony of Tomra Recycling’s latest test centre, located in Parma, Italy. The company says it will use the facility to develop new applications and solutions for polyolefi n and PET fl ake sorting and offer testing and demonstration services to its customers. Parma is a two-hour drive down the Autostrada from Milan. One reason for choosing the city as the location for the new centre is because of its good communications. “Parma is in the middle of a cluster of airports that put everywhere in Europe and the Mediterranean area in reach within two hours, including Turkey,” said Alberto Piovesan, Plastic Segment Manager EMEA & Americas in Tomra Recycling. It is also conveniently placed for Italy’s cluster of food packaging machinery companies, as well as big European recycling plant builders. Testing, development and demonstration The session was hosted by Fabrizio Radice, Head of Global Sales and Marketing at Tomra Recycling, and Tom Eng, Senior Vice President, Head of Tomra Recycling. Fabrizio gave an infectiously enthusiastic and charismatic introduction to the new centre and explained its role as part of Tomra’s research and development activity, as well as a demonstrator. “We use this facility and equipment to develop the software, hardware, monitoring systems and tools,” he said. The opening event was presented under the banner of ‘Testing is Believing’. The allusion to the more familiar phrase that ‘seeing is believing’ seems to be deliberate. Tomra’s sorting equipment rely on optical sensor technology for sorting and purifi cation of fl akes of different polymer types, colours, and with different material and colour impurities. The company’s operations include reverse vending solutions (RVMs) for ‘clean loop’ recycling, collecting aluminium, plastic and glass beverage containers for recycling into new bottles and cans; sorting technologies for mineral processing and mining; and grading, sorting, peeling and analytical technology for the food industry, as well as metal and waste sorting solutions in Tomra Recycling. Common technology “The common technology is sensors,” Tom Eng explained. “Optical equipment and optical technology are what Tomra brings to the process of fl ake sorting.” There is a high and rising demand for high quality recycled material and the challenge is to take input material with increasing levels of impurity and turn it into high purity output product, according to Alberto Piovesan. As a result of this, the effi ciency demands of the fl ake sorting machines has increased signifi cantly in a short period of time, from a typical 85-87% performance in PET to 95-97% for PP and PE. Tomra’s fl ake sorting portfolio includes two machines: Autosort Flake and Innosort Flake. Autosort Flake, which is designed for highend applications like PET bottle-tobottle recycling, incorporates Tomra’s Flying Beam NIR (near infra-red) sensor with 2mm resolution, as well as full-colour RGB camera, and a highly sensitive metal sensor, which can detect ferrous and non-ferrous metals down to 1mm in size. When asked whether this was sensitive enough, Product Manager Recycling Ida Semb explained that smaller particles – including paper – would have already been removed from the fl ake mix earlier in the sorting process by screening and windsifters. Ribbon cut by Tom Eng (Senior VP, Head of Tomra Recycling - in the middle), framed by Robert Glaser (left) and Fabrizio Radice (right) Fabrizio Radice, Head of Global Sales and Marketing, Tomra RECYCLING","@ID":30} "PETplanet Insider Vol. 22 No. 10/21 petpla.net 51 BOTTLES Luxury water in PET Fillico is a brand of luxury water that comes from the Kobe region in Japan. The natural mineral water is bottled in specially shaped glass bottles fi nished as limited editions by famous designers. The range also includes a more affordable variety. This polygonal PET bottle holds 500ml. Parts of the bottle surface have a pebblelike impression. The shiny gold label is transparent in the writing area, which is eye-catching in the light. A white screw cap with guarantee band closes almost flush with the shape of the neck ring, giving the bottle its unique appearance. www.fi llico.com Sinalco Extra Tradi t ional German brand “Sinalco” is expanding its range of drinks in di fferent direct ions. On the one hand, there is the new drink “Extra Fruity” containing a proportion of high-carb juice; on the other hand, the range includes “light” or sugar-free drinks. The image shows the Extra Fruity variety with the exotic blend of lime and melon and the Extra Sugar-Free variety with guava and passionfruit. The product is available in slightly contoured 750ml single-use bottles with a structured surface with bubbles. The circulating paper label and a red screw seal with a win code for an online game complete the packaging. www.sinalco.de Protein drink from LiveFresh LiveFresh GmbH & Co. KG fi lls 250ml of a vegetable protein drink into a transparent bottle made from 100% recycled material. The vegan organic product contains 16 g of protein - without soy - and is available in several juice combinations and is supposed to support the maintenance of muscles and bones. Two selfadhesive labels draw attention to the product and the colourful design attracts attention in the chiller cabinet. The sufficiently large drinking opening is closed with a screw cap with fi rst-opening protection. www.livefresh.de Frumate in 100 % recycled material The German Drink Star GmbH from Rosenheim now sells its well-known drink “Frumate Citro” in a bottle made of 100% recycled material. The bottle is decorated with two embossings in the style of a stylised head, decorated with a plastic label and closed with a brown screw cap. The drink contains 20mg of caffeine per 100ml, an extract of mate leaves and 2% lemon juice. www.frumate.de","@ID":53} "OUTER PLANET 62 PETplanet Insider Vol. 22 No. 10/21 petpla.net OUTER PLANET Inspection for highly demanding applications Advanced sorting Sortco GmbH & Co. KG is a specialist for optical and mechanical sorting of shape and colour deviations in plastic pellets. In addition, the company offers dust removal and metal separation of plastic raw materials. Since March 2021, Sortco has been using two Purity Scanner Advanced systems from Sikora in its new, state-of-the-art sorting service center in Niederzissen, Germany. With these, the pellets to be sorted are inspected 100% optically, and impurities from a size of 50 μm are automatically sorted out. Technically demanding plastics, such as those used in the medical sector or in the aircraft and automotive industries, require the highest quality standards as well as reliable control and processing of raw materials. Accordingly, the requirements for the purity of the materials are very high. Sortco has been specialised in contract sorting since 2015 and professionally prepares plastic pellets according to customer requirements. In the sorting service center, which was opened in spring 2021, the company sorts standard plastics as well as optically demanding technical plastics. For this purpose, Sortco uses two online inspection and sorting systems from Sikora. “The decision for Sikora was made due to the best detection for us, an excellent analytics and the proximity to the company, which is not unimportant for us,” says Hilger Groß, Head of Sales & QM at Sortco, and continues: “The Purity Scanner Advanced is typically used where other sorting systems have diffi culties. Namely, in the detection of very small optical defects from a size of 50 μm.” Sortco uses the Purity Scanner Advanced to sort primarily transparent, natural-coloured and, to a lesser extent, coloured pellets. The focus is on unreinforced materials which, after sorting, fi nd their use in high-quality optical applications. Each system is equipped with three optical cameras, which detect even the smallest optical impurities from 50 μm in size and automatically sort them out by compressed air pulse. If required, the Purity Scanner Advanced can also be extended by an X-ray camera for the detection of metal particles in the raw material. “Black specks are the focus of our sorting work. In addition, we remove all discolourations that have a different colour than the polymer to be sorted,” explains Groß and continues: “As a service provider, Sortco is confronted with new materials and new and old contamination every day. This means that we also have to adjust the Purity Scanner Advanced to constantly changing products and customer requirements. We therefore create a special recipe for each product that can also be used and adapted for future jobs.” During sorting, the Purity Scanner Advanced automatically records the number of all defects, the smallest edge length of the optical defect, the contamination area and, for example, the size class of the defect, which can be freely adjusted and specifi ed according to customer requirements. In addition, the system detects the intensity with which the colour deviation was detected. “All key data is checked again at the end of the job, stored and a test report is generated for the customer. Logging of the results is also possible but must be decided due to the large volume of data,” sums up Lars Ruttmann, Managing Director at Sortco. “Our customers appreciate that we understand their problem about the cause and effect of the defect, i.e. we dispose of plastics know-how, offer the appropriate solution and take over all the work necessary to produce the optimal quality,” summarises Groß, adding, “By commissioning optical sorting, our customers contribute to a very signifi cant extent to protecting our environment and avoiding waste.” He advises interested customers for whom sorting is an option to take a closer look at products that have recently shown higher reclamation costs. “It is comparatively easy to calculate a comparison between sorting costs and potential savings. However, if the customer also takes into account his lost sales, his loss of image and all the costs for unnecessarily consumed resources such as energy, machines, personnel, materials, freight, etc., many people get very wide-eyed. The advantages of sorting always outweigh the disadvantages,” concludes Groß. Ruttmann also sees an increasing demand for optically sorted raw materials in the future. “Sorting is in demand because manufacturers have recognised that special requirements also necessitate special measures. We are pleased to have found such a reliable partner in Sikora and its sorting system, with whom we successfully cooperate in our core business.” www.sortco.de/en www.sikora.net Plastic pellets are optically inspected and sorted by the Purity Scanner Advanced. Mr Lars Ruttmann, Managing Director at Sortco, presents Sikora‘s Purity Scanner Advanced for inspection and sorting of plastic pellets.","@ID":64} "CAPS & CLOSURES 39 PETplanet Insider Vol. 22 No. 10/21 petpla.net brand with its added lemon, tangerine, raspberry, muscatel and blueberry fl avours, and the Sprell label with tonic water, bitter lemon and ginger beer, roll off the production line. In 2020, around 1.6 million litres of water were processed. The PET bottle ratio was 37% to 63% glass for a total production volume of 1.5 million bottles. Fizzy comes in 0.46 l, 0.5 l and 1.5 l PET bottles, and Sprell in exclusively 1 l bottles. Fizzy glass bottles come in 0.35 l and 1.0 l sizes and Sprell in 0.20 l. Swing-top bottle with 65mm neck fi nish All other PET bottles have a conventional PCO1810 neck with the usual screw cap, apart from the new 0.46 l swing-top bottle which has 65mm in diameter neck fi nish. The bottles are not currently being produced in-house but are sourced instead via third-party suppliers. There are no immediate plans for in-house production. “As part of our general business operations, the bottler underwent extensive modifi cations to enable it to process the PET swingtop bottle, which was followed by minor adjustments across the whole production line”, said Mr Bianda. The new bottle is recycled by separating the swing-top from the PET body and then disposing of all the components separately. www.fi zzy.ch rPET100 Designed for recycling. Made from recycling. • Heat resistant • Fully recyclable • Thermoformable like PET BENEFITS HOT CUPS · DAIRY PRODUCTS · INSTANT SOUPS · TO-GO MEALS · COFFEE LIDS foodgrade without compromise Gazzose Ticinesi’s manufacturing plant","@ID":41} "42 TRADE SHOW REVIEW PETplanet Insider Vol. 22 No. 10/21 petpla.net The Compounding World Expo and Plastics Recycling World Expo returned to Messe Essen in Germany on September 29-30, 2021. This year they were joined by the new Plastics Extrusion World Expo and Polymer Testing World Expo. Organised by Ami, the free-toattend exhibitions featured more than 200 exhibitors - a 20% increase compared to when the shows previously ran in 2018. They also boast fi ve free conference theatres with more than 100 speakers covering the latest market trends and technical developments in plastics compounding, recycling, extrusion and testing. Companies showcasing their latest products and solutions include APK, Aquafi l, B+B, Bühler, Erema, ExxonMobil, Kreyenborg, NGR, Pellenc, Rodepa, Sorema, Steinert, Starlinger, Van Werven, Vecoplan, Veolia, Weima and lots more. This year visitors came from over 100 countries in the world. PETplanet Insider selected some highlight from the show! www.plasticsrecyclingworldexpo.com Sorting systems for separating PET fl akes with a multi-sensor into pure colour and material fractions For some time now, environmental awareness has been rising at every level of society. Consumers are increasingly interested in recycled materials, and in order to meet this growing demand, more and more companies are committing to the use of a fi xed proportion of recyclate in their products. In the case of PET, there is a growing focus on the production of food grade PET recyclate for use in remanufactured beverage bottles (bottle-to-bottle) and packaging trays. Impurities in raw materials Purity is essential to the quality of recycled PET. This is especially true for food-grade applications, such as bottle-tobottle recycling processes, in which purity standards are particularly high. Metal particles and other foreign contaminants found in the starting materials may cause disruptions in the production process, especially during extrusion. Such issues can degrade product quality. In order to enable large-scale use of recyclate, contaminants must be avoided and eliminated. The key concerns of the recycling process are producing pure recyclates, protecting processing machinery, and increasing overall equipment effectiveness. The right process technology is critical in all of these regards. Flake sorting systems are one solution for improving the quality of PET fl akes. The multi-sensor sorting system Flake Purifi er+ CMN from Sesotec can be equipped with three sensors: for colour detection (C), for metal detection (M), and for material detection (N). Data from each individual sensor is evaluated in the processing unit using Octa-Core technology. Poor-quality material is separated by a high-precision air ejection system with a 3.2mm valve and nozzle grid. Use of the multi-sensor sorting system makes it possible to ensure downstream partners receive food grade rPET in varying colors, sorted by material type, and free of metallic particles. With the Flake Purifier+ CMN, offcolours, foreign plastics, and metal contaminants are reliably sorted out before processing. This increases the throughput and thus the production volume of the entire recycling process. Multi-sensor sorting systems are an optimal solution with key advantages: high material purity to fulfi ll even the strictest quality requirements; high material throughput for greater profi tability; minimal loss of good material for higher effi ciency. In addition, the use of multi-sensor sorting systems in rPET processing prevents contaminants from accumulating in extrusion fi lters. By reducing the frequency of fi lter changes, processors are claimed to benefit from reduced maintenance costs and downtime. Also, the use of recycled PET helps to save both raw materials and CO2, thereby contributing to climate protection and resource conservation. www.sesotec.com PLASTICS RECYCLING WORLD EXPO review Bartosch Jauernik, Director Product Management PI Plast, Sesotec GmbH","@ID":44} "44 TRADE SHOW REVIEW PETplanet Insider Vol. 22 No. 10/21 petpla.net Bühler unveiled its 4-in-1 optical sorter for PET recyclers With increasing demand for bottle-tobottle and food-packaging applications, the global plastics market can now get the superior quality and purity levels it needs thanks to the pioneering Sortex A Glow Vision, launched recently in London and presented at the World Recycling Expo in Essen, Germany. This one-machine solution and its host of intricate features includes a custom-built inspection system, highly accurate double-sided cameras, and fl exible chute confi guration. In response to growing demand, the Sortex AGlowVision offers a simultaneous re-sort function, which delivers the high reject concentration (up to 40% when the re-sort channel is deployed). The Sortex A GlowVision is available in three to fi ve chute models on a fi ve-module frame and features a custom-built inspection system designed specifi cally for PET sorting. As a 4-in-1 sorting solution for bottleto-bottle and food applications, the Sortex A GlowVision has been designed with the increasing industry requirements in mind. In this respect the Sortex A GlowVision will be of great interest to PET processors looking to reduce contamination levels on key colour and polymer defects, providing one of the most comprehensive solutions. Thanks to its double-sided camera viewing technology, the Sortex A GlowVision provides convincing results, performing on a broad range of defects typically found in PET streams. The Sortex A GlowVision deals effectively with opaque, white, and transparent coloured fl akes, as well as on polymer defects including polyvinyl chloride (PVC), polycarbonate (PC), polystyrene (PS) and polyamide (PA), and a high performance on metals and signifi cant reduction of loose labels. Sortex monitoring system The Sortex A GlowVision comes with Bühler’s built-in Sortex monitoring system subscription. The cloud-based system continuously analyses data straight from the Sortex A GlowVision and provides operators with real-time monitoring of key performance indicators such as yield and throughput. This helps to improve productivity and keep yield consistently high. The at-a-glance dashboard of the Sortex monitoring system, which can be viewed on a mobile phone, laptop, or tablet, provides a simple yet comprehensive overview of each sorter, with alarms able to notify the customer when their key parameters are out of specs. Performance reports The Sortex monitoring system, which tracks the sorter’s performance in realtime, sends operators’ instant mobile alerts should any unusual sorter performance occur. Operators can then make adjustments to avoid any wastage, while minimizing downtime. Processors can use the generated sorter data to track key performance indicators (KPIs) in weekly or monthly performance reports. Control and support The Sortex A GlowVision has a SortControl – as optional – which helps to integrate the sorter with a local automation system via a compatible programmable logic controller (PLC), enabling central data collection. An interface between the optical sorter and the automation system will be achieved using a proprietary gateway. Through the integration of automation protocols, SortControl enables the implementation of requirements for Industry 4.0 compatibility. www.buhlergroup.com Thomas Neureiter, Market Development Manager (CEE) at Sortex, Bühler Group TOTAL SOLUTION PET BOTTLE RECYCLING SYSTEM SUPER CLEAN PROCESS ĞƐŝŐŶĞĚ ĨŽƌ ŵŝĐƌŽͲĚĞŶŝĞƌ ĮůĂŵĞŶƚ ŐƌĂĚĞ ĂŶĚ ĨŽŽĚͲŐƌĂĚĞ ďŽƩůĞͲƚŽͲďŽƩůĞ ƌĞĐLJĐůŝŶŐ͕ ƚŚĞ ƉƌŽĐĞƐƐ ŝƐ ĚŝǀŝĚĞĚ ŝŶƚŽ ĚƌLJ ĂŶĚ ǁĞƚ ĂƌĞĂƐ͘ Capacity3000 kg/h 6000 kg/h, 9000 kg/h. 燨' Clean Production High Automation Modular Design TOTAL SOLUTION OTAL SOLUTION PET BOTTLE RECYCLING SYSTEM SUPER CLEAN PROCESS ĞƐŝŐŶĞĚ ĨŽƌ ŵŝĐƌŽͲĚĞŶŝĞƌ ĮůĂŵĞŶƚ ŐƌĂĚĞ ĂŶĚ ĨŽŽĚͲŐƌĂĚĞ ďŽƩůĞͲƚŽͲďŽƩůĞ ƌĞĐLJĐůŝŶŐ͕ ƚŚĞ ƉƌŽĐĞƐƐ ŝƐ ĚŝǀŝĚĞĚ ŝŶƚŽ ĚƌLJ ĂŶĚ ǁĞƚ ĂƌĞĂƐ͘ Capacity3000 kg/h 6000 kg/h, 9000 kg/h. 燨' Clean Production High Automation Modular Design More than 170 W d ďŽƩůĞ ƌĞĐLJĐůŝŶŐ ůŝŶĞƐ ĨƌŽŵ ŽZĞdĞĐŚ ĂƌĞ ƌƵŶŶŝŶŐ Ăůů ŽǀĞƌ ƚŚĞ ǁŽƌůĚ","@ID":46} "MOULD MAKING PETplanet Insider Vol. 22 No. 10/21 petpla.net 37 Moldintec claims its NoLabel PET bottle helps brand owners develop new visions for “iconic assets”. More of less Label-less PET bottles are becoming increasingly popular across the world. A new generation of packaging is emerging from branding agencies, striving for distinctive and iconic assets. Moldintec says that NoLabel bottles, using its Advanced Laser Mould Decoration technology, provoke and engage with consumer opinions and emotions that go beyond traditional “features and benefi ts” marketing. The Covid-19 pandemic has strengthened the trend for health and wellness issues to be a major part of consumer interest. The idea that plastics are polluting materials is becoming more entrenched in consumers’ minds. Single-use plastics, PET bottles, especially, have attracted a lot of attention, manifested in taxes, deposit fees, and an increasing array of regulations. The PET industry’s deployment of new water and CSD bottles without an added label reduces materials and improves recyclability. Double award-winning The Brazilian Bonafont Naked 100% PCR bottle (Danone), which embodies the brand’s manifesto for environmental protection, has been recognised as an example of the new packaging generation, with a prize from packaging professionals in its home country, by Brazil Abre (Associação Brasileira de Embalagem), and globally with the Silver Award by the Pentawards 2021 in the water category. Pentawards recognises global excellence in packaging design in its annual competition. The development of PET bottles featuring new technologies including 100% PCR and label - free packaging continues, under ongoing pressure to minimise resource util isat ion and to present packages with the lowest number of features necessary to communicate the idea. In packaging design, the essential is minimise resources to few features to communicate the essential details and concept of the packaged contents. Moldintec claims that NoLabel is iconic of itself, enabling verbal and non-verbal communication of environmentally responsible, ease of recycling and use of PCR in the bottles designed and made from it. “Clean labelling” is an established trend; NoLabel is a response to it. The company says that elimination of the traditional, ink-printed, colourful cylindrical label panel presents brand owners and their design teams with both challenges and opportunities. It is working on a number of labelless projects for plain water and CSD bottles worldwide and is expanding its role and involvement beyond that of a a supplier of moulds only, to involvement in design and branding, where Moldintec is changing its role from just a tooling supplier; the company is now more involved in the branding design process, helping its customers open their minds towards this new generation of bottles. “NoLabel changed the PET packaging rules, but now we are going forward, creating more iconic shapes that connect to consumer emotions in deeper.”, says Jorge Pucci, CSO and head of design at Moldintec. He says that NoLabel satisfi es the requirement for recycling and has opened the door to a new generation of “Iconic Bottles” for the creative industry, helping producers to keep the brand identity and purpose clear while encouraging consumers to recognise a business model that is environmentally responsible. www.moldintec.com www.tridimage.com","@ID":39} "46 TRADE SHOW REVIEW PETplanet Insider Vol. 22 No. 10/21 petpla.net Herbold Meckesheim GmbH Your Partner for Plastics Wash Lines www.herbold.com As a one-stop supplier, we provide all relevant process components: Pre-washing units Hydro-cyclone separation systems Friction washers Mechanical and thermal driers Water treatment As a specialist for plastics recycling we are your contact for complex applications. We have the long lasting expertise in washing, separation and drying - to recycle new, used and contaminated plastics waste. Thanks to our modular technology, we are able to develop customized overall concepts or to optimize your already-existing plant. Key points for your profitability: Best flake quality High energy efficiency Minimized fresh water quantities Low downtimes and labour utilization Durable equipment made for tough applications fi bre applications in order to extend the working life of the screen packs on the spinning line. In bottle-to-bottle recycling, fi nenesses are now increased from a typical former level of 60 μm or more up to 40 μm or less. By comparison, a young, healthy human eye cannot distinguish particles fi ner than 50 μm. Minimal losses of polymer: The widely used “backfl ush” screen changer ejects some of the polymer melt as part of the process of removing contaminants. Over time, the amount of material loss can be substantial. One goal of innovation in screen changers is to reduce such losses. Energy efficiency: In conventional underwater pel let ising systems, three phases where an energy input is required are 1) maintenance of the tempered water system circulating through the pelletiser; 2) drying of pellets; and 3) crystallisation. One goal of innovation is to reduce energy consumption in these stages. High product ivi ty: The maximum throughput now considered the state of the art in producing rPET pellets for bottle applications is approaching 5 t/h. For post-extrusion components, achieving these rates depends on three factors: 1) component designs that yield streamlined fl ow properties; 2) enhanced control over melt pressure and temperature; and 3) reduction in downtime for troubleshooting and maintenance. Gear pump The gear pump shifts part of the job of building melt pressure from the extruder, thereby reducing stress on the extruder and on the processed material while delivering melt at the pressure level required by the screen changer and the following downstream equipment. In addition, the gear pump provides uniform fl ow, reducing surges and other process variations that can negatively affect the pelletising process and pellet uniformity. With use of a gear pump, the degassing system of an extruder can be made more reliable, and the extruder length can be reduced. Screen changer While typically deployed immediately downstream of the extruder and upstream of the screen changer, the gear pump may be preceded by an additional screen changer that provides “pre-fi ltration” at a fi neness level down to 1,000 μm, removing large particles that can cause excessive wear to the gear pump. At this particle size, the contamination level is less than 0.1%, provided that there has been effi cient washing and sorting prior to extrusion. Otherwise, the contamination level is larger. For the main fi ltration step in PET processing, a piston-actuated system with a self-cleaning feature based on a hydraulically powered process called backfl ushing is state-of-the-art. In a screen changer with four screen cavities, for example, melt fl ow is split into four streams. Backfl ushing starts automatically when the pressure differential caused by contaminant build-up increases to a pre-set level. Melt is then compressed and discharged","@ID":48} "","@ID":21} "MATERIALS / RECYCLING PETplanet Insider Vol. 22 No. 10/21 petpla.net 14 RECYCLING Christian Strasser, CEO of PET to PET Recycling Österreich GmbH, on toxic trends in the raw materials market and how to ensure consistent material quality over the long term in the circular economy. Seamless and resourcesaving recycling of PET bottles by Gabriele Kosmehl Pandemic-related lockdowns have changed beverage consumption, working conditions and the market for secondary raw materials. The recycling industry has also been greatly affected by economic developments. Nevertheless, thanks to coordinated efforts and strict adherence to its pandemic plan, the Austrian PET to PET Recycling company has not only managed to maintain a high volume of PET bottle recycling but even invested in plant expansion. Christian Strasser, CEO of PET to PET Recycling Österreich GmbH, tells us the secret of his success. PETplanet: At the beginning of August, you drew a positive interim balance for the fi rst half of 2021: 14,048 t PET beverage bottles were kept in the resource cycle. How did you manage this despite the special challenges posed by the Corona pandemic? Strasser: The fact that we were able to maintain production and even achieve record levels of performance is mainly due to three factors. Firstly, having a detailed pandemic plan tailored specifi cally to production operations, including extremely strict hygiene measures and rapid Covid testing, enabled us to ensure the safety of our workforce. Secondly, the Austrian beverage industry continues to play a pioneering role in the use of recyclates in new PET bottles which has helped our sales. And thirdly, we are continually growing our business through on-going system optimisation, as well as expanding our facilities in the interests of the circular economy. PETplanet: Have you noticed any pandemic-related changes in the last year, such as a different consumption of beverages or a change in the way consumers return empty bottles? And if so, have all the changes now settled down again? Strasser: Major changes did indeed occur during the pandemic. If we look at consumer behaviour, it is clear that the partial disappearance of hospitality, tourism and limited leisure opportunities also resulted in a sharp decline in the use of small bottles. On the other hand, the number of large-volume packaged varieties, which are mainly sold via retail outlets, has grown strongly. The change in demand has also caused huge upheaval in the raw materials market. Primary raw material prices have fallen sharply, while at the same time, there has been high demand in the secondary raw material market, with a corresponding lower volume of bottles. This year in particular, prices for bales and the recyclates to be produced from them have risen to unprecedented levels. In some cases, we have a situation where secondary material is being traded at almost twice the price of primary raw material. The term unhealthy is not suffi cient to characterise this state of affairs - for a shift towards a circular economy a more appropriate word would be toxic. I would characterise the behaviour of customers in relation to the separate collection of bottles as consistent even though there is great potential for a further increase in the amount collected. PETplanet: What development do you expect for the second half of 2021? Strasser: The situation has improved as a result of the lifting of many restrictions. However, we will probably not be able to speak of normality for some time yet. The best outcome would be expecting sales fi gures to be similar to those of 2020. Christian Strasser is CEO of the PET to PET recycling plant, which went into operation in 2007. (Photo: Andi Bruckner) Dipl.-Ing. Christian Strasser (photo: Eva Kelety)","@ID":16} "MARKET SURVEY 33 PETplanet Insider Vol. 22 No. 10/21 petpla.net Newamstar Packaging Machinery Co., Ltd. Sacmi Imola S.C. Krones AG East Xinjing Road, Zhangjiagang Economic & Technological Development Zone, Jiangsu 215618, P.R. China +86 512 5869 1111 www.newamstar.com Marketing Manager +86 512 5699 3303 [email protected] Via Selice Prov.le 17/A Imola (BO) Italy +39 0542 607111 www.sacmi.com Mr Stefano Severi Sales Area Manager +39 0542 607553 [email protected] Böhmerwaldstr. 5 93073 Neutraubling, Germany +49 9401 70 0 www.krones.com Yes No Yes Yes No Yes Yes No Yes Yes Yes Yes and high frequency Equipped with recovery system No Yes Yes Yes Yes Yes Yes Yes Yes Yes Yes Yes Yes Yes Yes Yes Yes Camera with special peripheral lens to control 360° of the sidewall, real 3D technology for 360° precise inspection Yes Yes Yes, +/- 1° Yes Yes Yes, +/- 1mm Yes Yes Yes, both inkjet or laser printed, through proprietary AI algorithms Yes Yes Camera 360° with real 3D technology Yes Yes No Yes Up to 50-250mm Up to 150mm 50-105mm Up to 100-470mm Up to 340mm 60-340mm & closure diameter 27-46mm Single or multi push devices Yes, without air consumption 1,000-72,000bph Up to 72,000bph Up to 84,000bph Panorama supervisor Yes SMI S.p.A. KHS GmbH Newamstar Packaging Machinery Co., Ltd. Via Carlo Ceresa, 10 24015 San Giovanni Bianco, Italy +39 0345 40111 www.smigroup.it Mr Pietro Volpi Marketing Dept. Manager +39 0345 40316 [email protected] Juchostraße 20 44143 Dortmund, Germany +49 231 569-0 www.khs.com Mr Manfred Härtel Product Manager Filling +49 231 569-0 [email protected] East Xinjing Road, Zhangjiagang Economic & Technological Development Zone, Jiangsu 215618, P.R. China +86 512 5869 1111 www.newamstar.com +86 512 5699 3303 [email protected] Sensofi ll FMa / FMac Blowing, fi ller and capping machine in Ecobloc confi guration; rinser, fi ller and capper machine in Monobloc confi guration Innofi ll PET DRV Innofi ll PET NV XGF 27-150 9-126 48/216 32/144 20-120 0.2-3.0 0.25-10 0.1/3.0 0.1/3.0 0.25-15 6,000-60,000 1,000-68,100 Up to 82.000 Up to 82.000 1,200-81,000 Up to 68,100 Up to 82.000 Up to 82.000 Up to 48,000 36,000 Up to 36,800 Up to 72.000 Up to 36,000 48,000 Up to 36,000 Up to 50.000 Up to 36,000 48,000 Up to 36,000 Up to 60.000 Up to 60.000 Up to 36,000 Yes Yes Yes Yes Yes Yes Yes Yes No Yes No Yes Yes Yes Yes No No No Yes Yes No No Yes Yes Electronic volumetric fi ller, magnetic fi lling valve Electronic volumetric fi lling valves Flowmeters (metering system) Volumetric fi lling system; pneumatic cylinder; MID (inductive fl owmeter); Mass-fl ow (Coriolis) Volumetric fi lling system; pneumatic cylinder; MID (inductive fl owmeter); Mass-fl ow (Coriolis) Water valve, hot fi lling valve, isobaric valve, electronic valve; Flometer, weight, liquid level inspection Up to 60,000bph (500ml bottle format); 200 production hours without cleaning/sterilisation; fl exible aseptic fi lling for a wide range of beverages, including still water, still and carbonated drinks, particles up to 6x6x6mm, viscous products, etc. Compact modular frame, with a wide choice of customisation options; operating and maintenance costs dramatically cut; easy and quick format changeover, with no need to replace mechanical components CSDwarm-fi lling up to 24°C; simple fi lling valve; compact unit; slow & fast-fi lling; gentle fi lling with low foaming; no beverage loss during production; PTFE-sealing technology prevents aroma transfer Contact-free fi lling Intelligent Factory Management Platform","@ID":35} "MATERIALS / RECYCLING PETplanet Insider Vol. 22 No. 10/21 petpla.net 17 MATERIALS / RECYCLING 17 PET to PET Recycling Österreich GmbH was founded in April 2006 and is operated by leading companies in the Austrian beverage industry. Today, the 53,000m² site is claimed to be one of the most modern PET recycling plants in the world. In 2010, a granulation plant was added to the recycling plant in Müllendorf. This was followed in the following year by the start of the new automatic bottle sorting stage and the installation of a silo plant, both of which were expanded again in 2017. In 2018, the PET to PET in-house laboratory was expanded, and in 2020 the handling areas and the granulation plant were extended. www.pet2pet.at additives and, especially, to foreign polymers that change the material’s properties. In particular, if the added substances are thermally overloaded at PET processing temperatures, the optical and mechanical components are severely compromised. Last but not least, all elements used to manufacture and confi gure a beverage bottle must meet the criteria for full recyclability. PETplanet: In 2009, Austria took PET returnable bottles off the market. Now the mineral water bottler Vöslauer has announced that it will revert to returnable PET bottles from 2022. How do you assess this changeover and does it affect you as a recycling company? Strasser: Based on studies which show that the disposable PET beverage bottle when combined with a closed bottle-to-bottle cycle has the same ecological impact compared to the returnable glass bottle and that only a returnable PET bottle is better for the environment, I see the impact being relatively minor and would expect a slight decrease in returnable glass bottles. PETplanet: Thank you very much Mr Strasser. Sorting station (photo: Andi Bruckner) E N D L E S S I N N O V A T I O N S I N C E 1 9 1 9","@ID":19} "MATERIALS / RECYCLING PETplanet Insider Vol. 22 No. 10/21 petpla.net 30 In the second test, Alberto Piovesan and Ida Semb then described the purifi cation process of a natural HDPE fraction . As HDPE normally is more contaminated than PET, the throughput was lower; initially, 800kg/h/m and 900kg/h/m on the second run. In two stages, contamination was brought down from 7.7% to below 1%. The team demonstrated the same equipment in sorting red PE with different colour and material contaminants, using either only the colour cameras or only the NIR sensoron the Innosort Flake; sorting shredded white PVC window frames in two steps over both machines; and fi nally HIPS (high impact polystyrene), the material used in yoghurt pots, for example, especially showcasing the capabilities of the metal sensor as such material often is contaminated with metal from the lids. Same machines, different settings All the sorting and purifi cation processes were carried out on the same two machines. Their sorting classifi ers and fl ow rates were adjusted on the control panel; there was no exchange of tooling at all. Ida Semb explained that the Flying Beam optical technology can identify and separate between different polymer and material types in the NIR spectrum. The colour cameras use the RGB colour space and back- and foreground illumination from long-life time LED-bars for transmission and refl ection sorting; enabling sorting of transparent and coloured, opaque fl akes independent of material type. The machine were set up so that the demonstration sample buckets were handled manually by the test engineer but in a big sorting plant the material fl ow is normally automated so that material is transported in pipes to the next stage, whether within the same unit or transferred from one to the other. Autosort Flake is particularly suited for high-end applications with lower levels of initial contamination and high end-purity requirments; Innosort Flake is appropriate for more contaminated streams and the dual-sided colour camera is specifi cally benefi cial in sorting polyolefi ns, material that is typically more contaminated. Innosort Flake’s sorting capacity is up to 6 t/h, depending on input material. “The Parma Test Centre can also show potential customers what Tomra’s machines can do. The customers can bring their own recyclate to run through it and see their performance in practice,” Fabrizio Radice concluded. www.tomra.com BEYOND THE HORIZON PROCESS SOLUTIONS FOR POLYMER RECYCLING AND SOLID STATE POLYMER UPGRADING Polymetrix, a Sanlian Buhler Company, provides process technology including EPCM services for the polymer recycling and manufacturing industry. Leading supplier of rPET systems and intergated rPET plants for single line capacities up to 70’000 tons per year. www.polymetrix.com www.slhpcn.com","@ID":32} "45 TRADE SHOW REVIEW PETplanet Insider Vol. 22 No. 10/21 petpla.net The newest generation AUTOSORT® enhances capacity, quality and purity levels across every application. Thanks to its integrated patented features, the multifunctional sorting solution offers the perfect combination of state-of-theart technologies in a single, compact unit. See how it works PRECISION THAT PAYS OFF NEW AUTOSORT® – the most advanced sorting functionality in one machine. WITH TOMRA INSIGHT Pelletising and melt-delivery systems for producing virgin-like rPET by Frank Asmuss, Business Development Manager, and Stefan Wöstmann, Application Engineer, Nordson Corporation The worldwide boom in demand for recycled PET (rPET) has generated new challenges for polymer processing systems used to transform molten polymer from PET fl ake into high-quality material for reuse. By far the biggest challenge involves bottle-to-bottle recycling, where regulatory and marketing mandates now call for a dramatic increase in bottle collection and use of rPET in new packaging. Downstream of the extruder, the key equipment in rPET production lines includes so-called “melt delivery” components - gear pumps and screen changers; pelletising systems; and, as required, systems for crystallising pelletised material. Among the major post-extrusion challenges faced by processors of PET fl ake are intensifying requirements for: High levels of purity. Bottle fl ake feedstock includes considerable amounts of contaminants such as labels, metals, paper, wood, and plastics other than PET. These substances must be fi ltered out by the screen changer. Melt pressure stability. A gear pump provides the uniform melt flow and pressure required for the process to operate effi ciently and with uniformly high-quality product. The pressure requirements for each component downstream of the extruder must be calculated to determine the appropriate extruder drive rate and type of gear pump. Fineness of melt fi ltration. A fi neness of 25-30 μm is essential for bottle-to-","@ID":47} "Sponsors to date The worldwide round trip with EDITOURS Back to Europe The second part of PETplanet’s bipartite Drinktec Editour is right ahead! After the successful first part “From Down Under to Japan” in 2020, our second stage of the project takes us back to the flourishing European hub where we will be exploring the latest technologies, news, innovations and developments that move our PET industry. It is time for a new start, for renewal and for developing new ways of thinking. During and especially after the pandemic, it will be vital to make every effort to get the global economy back on track in the medium term. Sustainability will be the key. Once again, PETplanet will be at the forefront. It will again be a partner in Drinktec, the world’s leading beverage trade fair, which is to be held in Munich from 12-16 September 2022. After the success of our previous Drinktec Road Shows, in 2017 in South East Asia and 2020 in Australasia, we will be back on the road in Europe for a whole year. Starting in Autumn 2021 with our Editourmobil, we will be ready for a new get-together with the industry. We will be revealing the results of our meetings and discussions at Drinktec with the leading thinkers in PET processing, packaging and recycling. Apart from new technologies we will be also taking stock of how things stand. We will be asking how global thinking might change as a result of Covid-19. How will bilateral business relationships cope with the aftermath of the pandemic? What opportunities will there be for the drinks industry and its suppliers? Our planning, in terms of precise timeframes and details of the countries to be visited will be flexible, in order to take account of the rapidly changing pandemic situation. However, this much we can confidently say: in these challenging times we, as the voice of the PET industry, will be at the very heart of the roadshow as usual and are already looking forward to welcoming you back on board the Editourmobil! Share this exciting experience with us! Interested in being interviewed? [email protected] Let Your Inspiration Flow. 7KH (XURSHDQ 5RDG 6KRZ PART2 Empowered by drinktec Interested in becoming a Sponsor? [email protected] Autumn 2021 - 2022","@ID":65} "imprint EDITORIAL PUBLISHER Alexander Büchler, Managing Director HEAD OFFICE heidelberg business media GmbH Vangerowstraße 33 69115 Heidelberg, Germany phone: +49 6221-65108-0 fax: +49 6221-65108-28 [email protected] EDITORIAL Kay Barton Heike Fischer Gabriele Kosmehl Michael Maruschke Ruari McCallion Anthony Withers WikiPETia. info [email protected] MEDIA CONSULTANTS Martina Hirschmann [email protected] Johann Lange-Brock [email protected] phone: +49 6221-65108-0 fax: +49 6221-65108-28 LAYOUT AND PREPRESS EXPRIM Werbeagentur | exprim.de Matthias Gaumann READER SERVICES Till Kretner [email protected] PRINT Chroma Druck Eine Unternehmung der Limberg-Druck GmbH Danziger Platz 6 67059 Ludwigshafen, Germany WWW www.hbmedia.net | petpla.net PETplanet Insider ISSN 1438-9459 is published 10 times a year. This publication is sent to qualifi ed subscribers (1-year subscription 149 EUR, 2-year subscription 289 EUR, Young professionals’ subscription 99 EUR. Magazines will be dispatched to you by airmail). Not to be reproduced in any form without permission from the publisher. Note: The fact that product names may not be identifi ed as trademarks is not an indication that such names are not registered trademarks. 3 PETplanet Insider Vol. 22 No. 10/21 petpla.net Dear readers, A lot in this issue revolves around PET recycling. When we included the topic in the planning last year, it was not clear to us how vigorously the topic is now being discussed not only in the professional world, but also by politicians and citizens. In Germany, for example, the big discounters Lidl and Aldi have created their own closed loop for recycling PET bottles. In addition to recyclable material recycling, chemical recycling is constantly being touted. “The chemical processing of plastic waste is actually old hat in the industry and yet it keeps on cropping up. At the moment it is hyped under the label of chemical recycling,” reports Dr Dirk Textor, chairman of the bvse-Fachverband Kunststoffrecycling. He believes that “chemical recycling is a new greenwashing campaign by the European plastics industry that should not be allowed to go through.” It is undisputed, he continued, that recycling is the better method. Chemical recycling is CO2 intensive. If we look at PET waste streams: the majority of the bottles arrive at the plant sorted by type, or can be sorted by type, so that they are suitable for recycling. Depending on the quality of the collection and the country, more or fewer PET bottles are left that have been thermally recycled up to now. Be it coloured bottles, be it multilayer bottles, etc. Here chemical recycling can defi nitely be a better alternative to incineration. For Dr Dirk Textor designing the packaging directly for recycling is certainly a viable option for general plastic packaging, but the advantages of the PET bottle, light, CO2-saving, and safe for some products can only be achieved through barrier layers. Stay well. Yours sincerely, Alexander Büchler","@ID":5} "MATERIALS / RECYCLING PETplanet Insider Vol. 22 No. 10/21 petpla.net 24 Dry recyclables and light packaging The sorting challenge The varying and constantly changing composition of waste materials poses a challenge for designers of sorting plants, which need to deliver consistently high purity rates while managing an increasing degree of complexity. Stadler, a leading supplier of sorting plants for the recycling industry, has the broad wealth of experience and know-how to develop high-performance facilities with the best plant concept for each type of material that will meet the specifi c requirements of every individual customer. The recycling and waste disposal sector is in constant evolution, with an increasing degree of complexity and growing volumes. New regulations, policies and targets have been introduced across the world to address the global waste issue. Different countries have adopted varying approaches to collecting and separating dry mixed recyclables and light packaging as they strive to reduce the quantity of materials going to landfi ll. The composition and density of this waste is also constantly changing, with an increasing proportion of fi lms and plastic trays. At the same time, the recycling industry is demanding high purity levels of the sorted fractions so that their recycled end-products can compete with virgin materials on the market. These factors are driving a demand for sorting plants capable of processing multiple materials fl exibly while delivering consistently high purity rates. Design considerations: waste material composition The composition of waste materials arriving at sorting plants can vary depending on different factors, starting from the way waste is collected and separated, which can vary from country to country or even at a regional level. Drop-off systems tend to lead to cleaner waste than collection. The way local authorities charge for Municipal Solid Waste collection can infl uence how much people sort their waste for recycling. Different demographics in rural and urban areas will result in strong variations in the composition, and there will even be seasonal fl uctuations. Managing increasing complexity The introduction of new European recycling targets is driving changes in the way waste is collected. In Belgium, the decision was taken to extend the types of plastics collected in the blue bag for packaging waste to include all plastic packaging. As a result, the sorting plant in Willebroek, operated by sustainable waste management solutions provider Indaver, would have to process much bigger volumes and manage the greater complexity involved in sorting more materials. The company decided to invest in a new facility, three times bigger than the previous one. They chose Stadler for the design of a plant with the necessary capacity and capability to manage the complexity. Stadler’s experience came into play, as it developed and built a new plant capable of sorting the high volume of packaging waste into 14 fractions at a throughput of over 20 tph using a bag ripper, drum screens, magnets, wind sifters, eddy current separators, ballistic separators and optical sorters. Flexibility built into the design and delivery process “The key challenges to address when designing and building a plant for dry mixed recyclables and light packaging are the changes in material composition, in the packaging and in purity requirements, because they can affect the quality and recovery of the products” explains Jürgen Berger. “These changes can happen between the design phase and fi nal plant commissioning, and this possibility needs to be factored in. At Stadler, we have the experience to address these issues by integrating fl exibility and spare capacity in our design.” This approach was particularly important when Stadler designed a future-proofed, fl exible sorting plant for the Schroll Group in France, for whom the company had previously designed and built fi ve plants. On the customer’s request, the facility was designed to allow for future expansion and the sorting of further fractions, as well as the RECYCLING Mr Jürgen Berger, Sales Director at Stadler The Indaver plant in Belgium Flacipel recycling plant","@ID":26} "EDITOUR PETplanet Insider Vol. 22 No. 10/21 petpla.net 12 Tour Sponsors: Kick off European Road Show 2021 Part 2 In the run-up to our European Road Show, we asked the 2nd group of our sponsors and experts from the whole PET value chain about topics that are currently relevant: 1) PETplanet’s latest Roadshow takes a critical look at the European market, which is picking up steam this year after pandemic-related slumps. How has the pandemic affected your business and what are your expectations for the coming months? 2) The European PET bottle market is on the move - not least due to the potential impact of various EU directives. Which of these are particularly relevant for your company and how are you placed to meet them? 3) What future challenges do you see for the PET industry? Mr Carsten Lurz, Vice President Sales, Service & Marketing at MHT 1) The pandemic defi nitively affected our business due to the fact that our customers faced a high degree of planning uncertainty. In this t ime, we received a g r owi ng numbe r o f requests regarding spare parts and overhauling of moulds. Moreover, travel limitations, home office r egu l a t i ons and l ock downs all over the world had a crucial infl uence on the way of interaction with our business partners as well. Nevertheless, the year 2020 was an acceptable year in terms of sales fi gures under the given circumstances. 2) The implementat ion of the EU approved tethered caps directive will change our business as a mould manufacturer. We expect an up-coming high demand of new preform designs including the thread area. With a recent ly instal led ful ly automated manufacturing line for neck-rings in our factory, we are well prepared for this new directive by a drastically increased output capacity. The close and strong cooperation with our parent company Krones in PET preform-/bottle-design enables us to provide our customers with an excellent support on this fi eld. 3) The on-going plastic bashing will redefi ne the questions and discussions around the topic PET bottle and the use of recycled PET in the next few years. As part of Krones PET recycling circle, we act with social responsibility. Accordingly, to optimise the preform and bottle weight in order to reduce the PET consumption will be in our focus. Moreover, we will strive to offer our customers digitalisation service solutions as this is an essential tool for the future. In conclusion, I´m convinced that the PET bottle will not lose its importance for the beverage industry, but light-weighting and recycling will become more mandatory. www.mht-ag.com Mr Dario Previero, General Manager at Previero N. Srl - Sorema 1) During the pandemic, we had to follow all the safety procedures in order to safeguard the health of our workers. Nevertheless, our industry got the permission to continue its activity and that enabled us to never stop providing services for our customers and, in the meantime, to pursue the negotiations for new projects. Since the demand for recycled polymers is always very strong, the medium-long term prospects for this industry are positive, especially for companies like us that produce and sell recycling plants. 2) For the PET bottles sector, the most important EU directive is the one concerning the single-use plastics which has placed very specifi c objectives for the amount of both the bottles to be collected and the rPET content to use in the production of new bottles. 3) To achieve the goals imposed by the new directives on the circular economy, the future challenges affect all the industrial chain. The fi rst challenge is to improve the communication between the parties involved so that a better design for recycling can be obtained and the volumes of collected material, which are not always suffi cient to meet the EU criteria, can be increased (on average, of course, some European countries have already reached these targets). The second challenge will be a technological one. As a matter of fact, it should be important to reach a high level of technology in all the recycling chain, in order to be able to produce recycled polymers with the requested quality and quantity. www.previero.it","@ID":14} "48 TRADE SHOW REVIEW PETplanet Insider Vol. 22 No. 10/21 petpla.net Whether it is inhouse, postconsumer or bottle recycling: you can only close loops in a precise and profitable way if machines are perfectly tuned for the respective application. Count on the number 1 technology from EREMA when doing so: over 6000 of our machines and systems produce around 14.5 million tonnes of high-quality pellets like this every year – in a highly efficient and energy-saving way. WE DRIVE THE CIRCULAR ECONOMY. CHOOSE THE NUMBER ONE. VISIT OUR virtual showroom ShowHello! 2103029ERE_PETplanet.indd 1 24.03.21 09:54 energy savings of 10 kWh/t, a reduction in cooling water of up to 40%, and a reduction in fresh water for refi ll of up to 90%. As energy costs vary from region to region globally, plant operators need to calculate their cost savings individually. The system can be used to yield rPET with near-virgin properties. Because process heat is retained in the core of the pellets, crystallisation takes place uniformly from the core to the outside surface. By means of process optimisation, it is possible to achieve this crystallinity at small pellet sizes, making the rPET more compatible with virgin PET when blended. At the same time the higher bulk density of the rPET increases SSP capacity and reduces costs for transportation and packaging. Complete polymer processing systems Polymer processing systems for PET recycling - from gear pumps through in-line crystallising systems - are available individually, but there are benefi ts in sourcing them from a single company. Apart from the obvious one of reducing the number of interfaces during the engineering and purchasing phase, single-sourcing enables the supplier to design a system to maximise the effi ciency with which the various equipment components interact. For example, the pressure demands of the screen changer and pelletiser affect the selection of the gear pump. Another important advantage of working with a single supplier is that of using a single control or software solution to integrate the entire post-extrusion system. With UWPs, the operator can use a single interface on the pelletising system to access the extruder, feeding equipment, screen changer, and melt pump. To meet the surge in demand anticipated for rPET, the recycling industry will have to achieve massive increases in new capacity. Along with the extensive equipment needed for producing high-quality fl ake from post-consumer PET bottles, recycling companies will have to invest in extrusion and post-extrusion systems capable of yielding rPET with properties as close as possible to those of virgin material. In helping these companies to supply a fast-growing market for rPET, new-generation post-extrusion systems will be key to increasing productivity and profi tability. www.nordson.com","@ID":50} "PETplanet Insider Vol. 22 No. 10/21 petpla.net 52 November 7-9, 2021, Dubai At the KRONES booth A1-34 German Technology Innovative hotrunner optiRun PETbottles Home + Personal Care 600ml as standard size for Listerine The consumer goods manufacturer Johnson & Johnson always had bottles with a capacity of 500 ml in its range for standard Listerine products and only changed to bottles with a capacity of 600 ml for promotional or sales campaigns. For some time now, one can only fi nd the 600ml as standard bottles in the shops. The picture shows a 600 ml bottle for Listerine mouthwash for daily use. It is Advanced White with a mild taste for removing stubborn discolouration. The slightly milky coloured bottle is shaped for easy grip and combined with a screw cap with dosing function and fi rst-opening safety device. www.listerine.de Today Men as Limited Edition “Free Your Spirit” is the name given by the German retail group Rewe to the shower gel of its own brand “today men” in a special bottle. While the other bottles in the range allow a direct view of the product, this bottle is decorated with a full sleeve label. The 300 ml bottle is made of 100% recycled material, with 20% coming from the “yellow bag”. The product does not contain microplastic. For disposal, the label can be easily removed via a perforation. www.rewe.de Washing-up liquid in an easy-grip bottle Via a subsidiary in Switzerland, Unilever is selling “Sun” brand washing-up liquid in a bottle shaped for easy gripping. The slightly green coloured bottle is easy to handle and can even be held securely with wet hands. The bottle is made of 100% recyclate and can be recycled after removing the partially transparent sleeve label using the perforated strip. The concentrated washing-up liquid is dispensed via the screwed-on hinged cap with dosage opening. www.sun-online.ch","@ID":54} "MATERIALS / RECYCLING PETplanet Insider Vol. 22 No. 10/21 petpla.net 20 PET diamonds for the Indian fl ake market India is one of the rare countries where the estimated bottle collection is in the range of 80-90%. This is probably one of the highest in the world. There is an informal organised system in place since the last 20 years. Due to the weight of each bottle, there is a reasonable value for collection. The major challenge in plastic waste is segregation at source. If waste is properly segregated into different categories, almost everything can be recycled or put to a better use. However, a large percentage of the plastic waste generated still ends up in landfi lls or in water resources. It will be a much cleaner and greener world, if 100% of our plastic waste is given a new life and a new value. If we, as responsible global citizens, want to leave this world a better place for future generations, then we have to take a proactive stance to buy sustainable products, ethical brands, clean up the beaches and be mindful of where and how to dispose of products. This gives hope for a better future, where there is no “waste” but just another life for the material. The Mumbai-based company AeroFibre is in its third generation of plastic waste business. In the late 80s, the family-owned business started in the recycling and processing of PET industrial waste. In 2008, AeroFibre commissioned the fi bre recycling plant to further process the industrial waste. “After completing my graduation in UIUC, I decided to join the family business in 2009. I was excited about the recycling of polyester waste and was elected to head this business. In 2017, we commissioned a stateof-the-art recycling plant that has the capacity to process 18,000mta of hollow and hollow conjugate fi bre. We are the fi rst company in India to have two German bottle sorters in our wash-line. Our main focus was to enhance the quality of fl akes which will result in higher fi bre quality,” stated Director Mr Ankit Jain. In 2021, the company realised that there was an increasing demand for high quality fl akes for bottle-to-bottle and bottle-to-fi lament segments; and there was a paucity of good quality PET fl akes in the market. To fi ll this gap, Aero Fibres installed an advanced laser sorting machine from Germany to process fl akes which are as clean and consistent as diamonds – hence the brand is called DiamondPET Flakes. The DiamondPET fl akes provide a consistent high purity value of fewer than 100 ppm. “We create this with the help of dual automatic bottle sorters, manual sorting as well as a fi nal check with an automatic laser sorter. Just like high pressure makes diamonds, we employ heat washing and pressure sorting to make diamonds out of trash,” Mr Ankit Jain explained. He continued, “We have a team that is 150 strong today who work on three shifts to produce PET fl akes that are of precise and consistent quality. We have installed an effl uent treatment plant to reuse and recycle all our water used in the PET fl ake production. Our plant qualifi es as a zero liquid discharge site. We also generate a portion of power needs via solar power. Our goal is to produce high value products from plastic waste. To that end we want to process as much of the by-products generated while processing the PET bottles – from segregating caps and wrapper, we now wash and produce granules that can be made into injection moulded products like crates and other items.” The goal for AeroFibre is that they want to produce the best value for their customers, treat team as family and give back to the communities that the company is a part of. AeroFibre believes in doing well by doing good. “Hopefully, one day in the near future, we will be part of the reason India will be able to recycle 100% of plastic waste, creating value from waste.” www.aerofi bre.com RECYCLING","@ID":22} "No.10 2021 petpla.net D 51178; ISSN: 1438-9452 30 . 10 . 21 PETplanet is read in more than 140 countries MAGAZ I NE FOR BOT T L E R S AND BOT T L E - MAK E R S IN THE AMER ICAS, AS IA, EUROPE AND AL L AROUND THE PLANET MARKETsurvey Suppliers of fi lling equipment and fi lling inspection systems Page 31 Page 12 Recycling Page 14","@ID":3} "PETnews 6 NEWS PETplanet Insider Vol. 22 No. 10/21 petpla.net U.S. plastics industry trade improves in 2021 after 2020 pandemic slump The Plastics Industry Association released its annual Global Trends report at the 27th Fakuma International trade fair for plastics processing. The report, which analyses trade data from all of 2020 and the fi rst six months of 2021, paints a complex but promising portrait of the U.S. plastics industry in the international market. For those around the world interested in the American plastics market, the global trends report and its accompanying dataset provides a comprehensive account of U.S. plastics exports to and imports from around the world in each of the four categories of the plastics industry – resin, products, machinery and moulds. According to the report, Mexico and Canada remained the U.S. plastics industry’s largest export markets. In 2020, the industry exported $13.7 billion to Mexico and $11.7 billion to Canada, maintaining its largest trade surplus - $8.2 billion - with Mexico. The coronavirus pandemic caused the merchandise trade to decline. In 2020, total U.S. plastics industry exports fell 8.2%, and imports were 1.8% above 2019. The report found that the U.S. plastics industry had a trade defi cit of $5.5 billion last year. For many years, the plastics industry enjoyed a trade surplus, which in 2019 was $727 million. Last year, the U.S. had an $18.6 billion surplus in resin. The U.S. plastics industry had a $15.3 billion defi cit with China - the third-largest export market of the U.S. plastics industry. However, the U.S. had a $3.0 billion trade surplus with China with resin. China is still the world’s largest resin buyer and a large importer of U.S.-produced resins. The 2021 Global Trends report also explores a broader international view of plastics, covering production, consumption and more details of important trading partners for the U.S. It also discusses apparent consumption, a broad measure of the domestic market size. U.S. apparent consumption of plastic products fell marginally by 0.1% to $288.4 billion in 2020. “Although the merchandise trade outlook is much brighter this year, uncertainties remain and depend largely on global economic recovery. While the U.S. plastics industry trade volume rose 27.9% in the fi rst six months of 2021 compared to the same period in 2020, it still has a plastics trade defi cit,” said the association’s Chief Economist Perc Pineda, PhD “The large and growing plastics industry outside the U.S. will continue to compete with the U.S. for overseas markets as well as for their own domestic markets.” Canada and Mexico will continue to be the two largest export markets and are also the top sources of U.S. plastics imports. Proximity matters. The manufacturing sector’s supply chain in these countries was strengthened with the passage of the North American Free Trade Agreement (Nafta). The updated free trade pact, United States Mexico Canada Agreement (USMCA), should further enhance trade among the three countries, which is important particularly as global manufacturing is experiencing supply chain diffi culties. The 2021 complete Global Trends report is available to download for free for members and is available for purchase to non-members. www.plasticsindustry.org Matthias Hermle hands over the CEO position of IMD Ltd. to Marc Wymann Marc Wymann will take over as the new CEO of IMD AG on November 1, 2021. After a transition period of three months, he will take over the executive lead from company founder, Matthias Hermle. Matthias Hermle will then focus on the strategic area of IMD Ltd. and CAPrint Ltd. as active Chairman of the Board of Directors and support innovations. IMD Ltd. is in a good position, stable and ready to grow further. After more than 25 years in the lead of IMD Ltd., the perfect time has come for Matthias Hermle to hand over into new hands and take care of the strategic area. He will actively support the management in order to align IMD Ltd. well for the future in the medium and long term. He sees a lot of potential in approaching innovations differently. With Marc Wymann, he has found a successor who fi ts perfectly into the IMD family. With his passion for technology and sales, a fl air for employee management, business know-how and a backpack full of management experience, he is ideally equipped to lead the IMD family into the future together with the well established management team and the employees. “I’m not coming to turn everything upside down, I’m coming to support and develop what already exists», tells Marc Wymann about his goals. During his introduction period, he fi rst wants to get to know the company with all its employees, customers, processes and all the other exciting facets and understand how the market works. His main goal is to continue the company, which has been successfully built up over the past 25 years, in the spirit of the company’s founder, to optimise where reasonable and to break new ground where appropriate. www.imdvista.ch Matthias Hermle (left) hands over the CEO position of IMD Ltd. to Marc Wymann (right). The company owner and founder, Matthias Hermle, will focus on his role as active Chairman of the Board of Directors of IMD Ltd. and CAPrint Ltd.","@ID":8} "MATERIALS / RECYCLING PETplanet Insider Vol. 22 No. 10/21 petpla.net 21 Test installation validates new techniques for plastic recycling B+B Anlagenbau has recently put into operation a testing facility where potential clients can test their plastic recycling requirements, in order to substantiate the business case before building. B+B Anlagenbau is part of Heilig Group and is a specialist in designing, building, installing and maintaining complete plastic recycling installations and individual machines. There has been a substantial investment in a test facility where solutions for the future are devised. RECYCLING “We have built the test facility for the somewhat more diffi cult issues facing the plastic recycling industry. Together with the customers who are considering giving plastic a new life in some way, we are showing the possibilities with our machines through testing and validation. Customers will receive a validation report and get to see the result. In the end, a tailor-made solution will probably be developed for them, but in the test installation they can already see whether the method they came up with really does produce the intended result,” explained Innovation Manager Arjan Wever at Heilig Group. Transparency This test installation makes the entire process of recycling and washing of plastic much more transparent for customers. “It is more than just putting a piece of plastic through a centrifuge or a washer. All facets of the technology are involved; heat, water, air, chemistry, etc.” continued Arjan Wever. B+B Anlagenbau build standard machines for washing plastic waste. However, what the optimal solution is for a customer who wants a certain washed end-product, differs. The type of product also makes a difference to the set-up: PET requires different techniques than laminated plastic or foils. Arjan Wever adds, “Each issue stands on its own and we look for the best answer to it together with our customer. This way, we offer the customer some extra goodwill. We show that we want to work together and make a case to show investors what something can be worth. By working together in the early stages of a major investment, we hope to win trust and loyalty of our customers.” Subjects The test report answers the main questions of the customer, but of course it also will raise new ones. “That is precisely why we can put innovative steps into practice.” says Wever. “It’s a lot more nuanced than ‘you throw something in and something comes out’. Many different disciplines come together in washing plastic: sorting techniques, washing techniques, thermodynamics, but also fl uid dynamics, for example. Within Heilig Group we have all this knowledge and specialities. This test installation is specifi - cally intended for plastic recycling, but there is a lot of cross-fertilisation with other business units.” The test installation can also be at the basis of innovations. Wever outlines: “Customers come to us with products that are not yet washed. Our approach is that we fi rst clearly set out the basic question with the aim of achieving a functionally optimal process and the highest possible customer return. In doing so, we are not limited by our existing machine portfolio. We can convert or expand machines very fl exibly - we have more than enough capable mechanics and engineers in house for that.” Thinking about what goes into an installation and how it comes out again is really in Heilig Group’s DNA. “With this test installation, we hope to share that knowledge more widely with the market.” www.bub-anlagenbau.de www.heilig-group.com","@ID":23} "MATERIALS / RECYCLING PETplanet Insider Vol. 22 No. 10/21 petpla.net 16 RECYCLING PETplanet: During the pandemic, work was cut back and tightly managed in many companies. You, on the other hand, expanded. Can you please briefl y explain what investments you have made and what might be next on the agenda? Strasser: Increased demand for resource-saving recycling prompted us to invest in expanding our facilities despite the Covid crisis. This involved extending the outdoor and storage areas and increasing production capacity with a second granulation plant, which can produce 2 t/h of food-grade PET recyclate. An additional label removal system prior to wet washing helps in improving the cleansing process. In addition, the silo facility for washed flakes was expanded as a storage unit before food-grade processing. With these investments, we have not only ensured the seamless and resourcesaving recycling of PET bottles but also created eight additional jobs. PETplanet: From which area do you obtain the bale goods that are processed by you? Strasser: The demand for recyclable PET bottles is very high throughout Europe. These recyclates can be used in all applications, even if high-quality recycling is no longer possible afterwards. Therefore, PET to PET must also source bottle bales from all over Europe, as far as transport costs will allow. PETplanet: How long does a process take from the fi rst processing step of the baled goods to the compounded rPET ready for delivery? Strasser: The recycling operation takes 10-12 hours, depending on the process used. Two different techniques are used to convert PET bottles into PET flakes or PET granules. One plant thoroughly washes PET flakes using patented URRC (United Resource Recovery Cooperation) technology while in the second, PET is melted down and processed into granules. This produces quality that meets the highest food standards. PETplanet: In the EU, an average of 25% rPET content in bottles will become mandatory from 2025, with some brands pledging themselves to 100% rPET. In your eyes, what is the most appropriate recycled content ratio to ensure good material quality in the long term? Strasser: Many manufacturers have increased recyclate usage rates in recent years, with new bottles now being produced from 100% recyclate. It ultimately all comes down to the average value that is fi xed on the market as a whole. As is readily apparent, a 100% closed loop for all bottles is neither realistically achievable nor sustainable. Based on previous experience, we believe a sensible recyclate usage rate of 50% on average is reasonable in order to ensure consistent material quality over a long period of time. This includes very ambitious quotas of 100%, as well as very low ones of less than 30%. The average value that emerges on the market is relevant in all this. PETplanet: When Europe switches to 25% rPET initially and 30% rPET from 2030 onwards, the demand for food-grade material will also continue to increase. Can you imagine opening more locations? Strasser: Such options cannot be ruled out but there are currently no specifi c plans to do so. In any case, further expansion of the bottle-to-bottle cycle of the PET beverage bottle will require additional capacity for high-quality recycling plants. PETplanet: Which “design for recycling” aspects, implemented in PET bottles, would make your work easier - or which additives, colourants, material combinations… are the most challenging to recycle? Strasser: Any change or modifi cation to the molecular structure of PET is problematic. This applies both to PET bottles, sorted by colour and pressed into large bales. One bale weighs about 250 kg and contains around 10,000 PET bottles. (Photo: Andi Bruckner) PET to PET recycles bottles from all over Europe. (Photo: Andi Bruckner)","@ID":18} "PETcontents 4 PETplanet Insider Vol. 22 No. 10/21 petpla.net 10/2021 Page 23 EDITOUR 12 Kick-off European Road Show 2021, Part 2 MATERIALS/RECYCLING 14 Seamless and resource-saving recycling of PET bottles - Interview with Christian Strasser, CEO of PET to PET Recycling Österreich GmbH 18 Bottle-to-bottle recycling line at Srichakra Polyplast in India 20 PET diamonds for the Indian market 21 Test installation validates new techniques for plastic recycling 23 “The demand for rPET is increasing” - Producing food contact compliant rPET 24 The sorting challenge - Dry recyclables and light packaging 26 Direct PET processing - Economical and FDA-compliant recycling of PET fl akes 28 Tomra Recycling opens new test centre in Italy PREFORM PRODUCTION 35 Tried and tested for new uses - Preform range for hand sanitiser applications and cosmetic products MOULD MAKING 37 More of less - Moldintec claims its NoLabel PET bottle helps brand owners develop new visions for “iconic assets”. CAPS & CLOSURES 38 Swing-top PET bottle MARKET SURVEY 31 Suppliers of fi lling equipment & inspection systems EVENT REVIEW 40 Flexibility, the PET industry’s way forward - 19. GSI PET Day 2021 42 Plastic Recycling World Expo review BUYER’S GUIDE 56 Get listed! INSIDE TRACK 3 Editorial 4 Contents 6 News 50 PET bottles for Beverage + Liquid Food 52 PET bottles for Home + Personal Care 54 Products 55 Patents 62 Outer Planet RECYCLING Page 14 Page 38","@ID":6} "PETplanet Insider Vol. 22 No. 10/21 petpla.net 50 PETbottles Beverage + Liquid Food Multi-facetted bottle Hamburg company Lifestyle Drinks GmbH is selling 500ml of “healsi”- branded natural mineral water in colourful bottles. The facets of the bottles are reminiscent of crystal glass or diamonds. The water comes from a source in Portugal. Several small transparent foil labels contain the necessary product and retail information. The seal is a 2K screw cap with guarantee band. The outer cap of the seal is coloured to match the bottle colour and closes fl ush with the neck ring, which improves the visual appearance of the bottle. www.healsi.eu Bottle with bonus With its bottle offering an added bonus, US-based company Surprise Drinks is perfectly combining the drink experience with a surprise / toy for children. The offer is continually expanded with new bonus ranges, which are based on current characters loved by children. The bottle has an indentation that holds the capsule. The capsule contains a toy fi gurine and is then attached with the sleeve label and protected before removal. The idea for the bottle arose when the subsequent founder of the company looked at his pregnant wife and asked himself whether it would be a boy or a girl. The low-calorie drink is free from colours, preservatives and added sugars. A screwed-on push-pull cap makes the product easy for children to drink. www.eu.surprisedrinks.com Salad dressing from the convent kitchen Based on recipes from his grandmother, the chef of the Johanneum Centre in Neu St. Johann, Switzerland, has developed these salad dressings and is marketing them across the country via sales partners. The fi ve varieties have female names and are very different from one another. The dressings are prepared using natural ingredients, are lactose and gluten free and do not contain fl avour enhancers, preservatives or colourings. The products are available in 500ml transparent bottles with a screw seal. The bottles are decorated with transparent fi lm labels with pictures of women and names like “Amélie” for a French-style salad dressing or “Marianelli” for a Swiss-style dressing. www.klosterkueche.ch","@ID":52} "MARKET SURVEY 31 PETplanet Insider Vol. 22 No. 10/21 petpla.net 10/2021 MARKETsurvey Resins & additives Preform machinery Preform production & inspection systems Preform & SBM mould manufacturer SBM 2-stage Compressors Caps & closures & inspection systems Filling equipment & inspection systems Recycling machinery Palletising & shrink fi lm machinery Supplier of fi lling equipment and fi lling inspection systems It’s time to present some state-of-the-art fi lling equipment and fi lling inspection systems in our annual market survey. Please have a look at the up to date technical details provided by: Sacmi Imola S.C., SMI S.p.A., Sipa S.p.A, Pressco Technology Inc., Sidel, KHS GmbH, Newamstar Packaging Machinery Co., Ltd.,Krones and Fogg Filler. Although the publisher has made every effort to make sure that the information in this survey is up to date, no claims are made regarding accuracy and completeness. Filling Equipment Company name Sipa Postal address Telephone number Web site address Contact name Function Direct telephone number E-Mail Via Caduti del Lavoro n. 3 31029 Vittorio Veneto (TV), Italy +39 0438 911 511 www.sipasolutions.com Mr Matteo Tagliaferri Marketing and Communication +39 0438 911 511 [email protected] 1. Machine designation / model number Isofi ll P Stillfi ll Evo Flextronic C Flextronic SE Flextronic S Flextronic W Bigfi ll 2. Number of fi lling heads (range: from/to) 20-160 20-120 50-180 20-180 20-180 20-96 12-24 3. Min to max bottle contents (in liters) 0.125-3 0.125-3 0.125-3 0.125-3 0.125-3 0.125-3 3-20 4. Filling speed: output (bph) (min to max): specifi y: 1l bottle / still water (bph) 60,000 62,000 60,000 62,000 63,000 36,000 16,000 (3 l ) 1l bottle / CSD (bph) 51,000 (CMW) 55,000 (CMW) 1l bottle / Milk (bph) 62,000 62,000 36,000 1l bottle / Juice (bph) 53,000 60,000 59,000 62,000 62,000 36,000 5. Filling process Pressureless (still drinks) Yes Yes Yes Yes Yes Yes Yes Pressure fi lling (carbonated drinks) Yes Yes Hot fi lling Yes Yes Cold aseptic fi lling Juices with high pulp content Yes Yes 6. Type of fi lling valve and metering system Isobaric mechanical level fi lling Mechanical gravity fi lling Isobaric volumetric fi lling valve Gravity volumetric fi lling valve Gravity volumetric fi lling valve Electronic weight fi ller Gravity volumetric fi lling valve 7. Special features (short description/keywords) AISI 316L SS valve, product defl ection without defl ector on the fi lling tube, quick changeover for different neck diameters, automatic dummy bottle insertion, mobile vent tube, centralised remote fi ll level adjustment AISI 316L SS valve, product defl ection without defl ector on the fi lling tube, quick changeover for different neck diameters, seperated bottle air return, hot fi ll kit for product recirculation, constant and controlled recirculation rate in bottle, centralised remote fi ll level adjustment no bottle no fi ll system AISI 316L SS valve, product defl ection without defl ector on the fi lling tube, quick changeover for different neck diameters, automatic dummy bottle insertion, magnetic fl ow meter product control, fi lling speed control, XFill confi guration without tank on board, dry pressurisation separated bottle air return AISI 316L SS valve, no contact between valve and bottle neck, quick changeover for different neck diameters, ultra clean version available, magnetic fl ow meter product control, fi lling speed control, automatic dummy bottle insertion, XFill confi guration without tank on board AISI 316L SS valve, no contact between valve and bottle neck, quick changeover for different neck diameters, ultra clean version available, 3 positions membrane valve fi lling speed control, automatic dummy bottle insertion, XFill confi guration without tank on board AISI 316L SS valve, no contact between valve and bottle neck, quick changeover for different neck diameters, load cell integrated in the bottle neck support, 3 positions membrane valve fi lling speed control, automatic dummy bottle insertion AISI 316L SS valve, no contact between the valve and the bottle neck, quick changeover for different neck diameters, ultra clean version available, 3 positions membrane valve fi lling speed control, automatic dummy bottle insertion, high fl ow performance","@ID":33} "MATERIALS / RECYCLING PETplanet Insider Vol. 22 No. 10/21 petpla.net 29 Innosort Flake, which is equipped with a front and a rear full-colour RGB camera and the Flying Beam NIR optical sensor, allows for a dual-sided colour detection and can therefore detect and sort out transparent, opaque and two-sided colour contaminants, as well as polymer and metal contaminants. Tomra’s Technical Flake Expert, Robert Glaser, explained, the company is benefi ting from what they call the ‘Common Sorting Platform’, where they are in-house developing the same core technologies for e.g., sensors, software and ejector for their recycling, mining and food machines, all apart from mechanical differences due to different applications and sorting tasks. This also applies for the two fl ake sorting machines. They have their own PCB (printed circuit board) ‘brains’ but the common platform means that upgrades developed within Tomra’s R&D department and tested at the test centres, can be brought to market faster. There is reduced risk to the customer; a common platform ensures wider experience in operation and faster detection and remedy of any problematic issues, as well as development and implementation of improvements. Practical demonstrations After the theory was explained, Fabrizio Radice introduced the practical demonstration, which was orchestrated and explained in real time by Alberto Piovesan and Ida Semb, using the machinery that had, until that point, sat silently in the corner of the test centre. The fi rst batch to be processed was a typical mixture of clear-light blue PET fl akes, with an initial contamination level of 5.4%. The fi rst sorting step on the Innosort decreased the contamination level down to 1.8% and did so with a throughput of 1,500 kg/h/m. Running the accept fraction from the Innosort Flake through the Autosort Flake brought the contamination further down to 0.2% Alberto Piovesan explained that for Tomra as well as the whole recycling industry, in PET there is a strong focus on getting PVC content reduced as much as possible. The boxes of initially rejected material from both machines were then put through the same process again to further concentrate the contaminations and recover any ejected good PET fl akes. As the purifi ed, good material from this ‘recovery step’ is mixed in with the initial input material, it is required that it has the same or a lower input contamination, so that over time the input material will have the same or a lower contamination level. This can then improve the whole process and was proved by the recovery steps demonstrated. SUSTAINABLE SOLUT IONS TO BOOST A CIRCULAR ECONOMY L IQUID COLOURS & ADDI T IVES FOR RECYCLED PET Stand E22 Team Tomra at the Test Center Opening","@ID":31} "MATERIALS / RECYCLING PETplanet Insider Vol. 22 No. 10/21 petpla.net 18 Bottle-to-bottle recycling line at Srichakra Polyplast in India The well-established Indian recycler commissioned a PET bottle-to-bottle recycling line from Starlinger by mid of September. With the new line Srichakra Polyplast upgraded its facilities and now offers the highest grade of recycled PET to customers in India and international markets such as Europe and the United States. RECYCLING Srichakra Polyplast, a leading plastic recycling and waste management company based in in Hyderabad, invested US$10 million (€8.6 million) for upgrading and expanding its plastics recycling capabilities. The new RecoStar PET 165 iV+ features technology for processing post-consumer PET bottle fl akes approved by the US Food and Drug Administration authority (FDA) and is the fi rst of its kind Starlinger has installed in India. The produced rPET pellets are suitable for food-contact and can be used for food and beverage packaging like bottles for water and carbonated soft drinks, food trays, etc. at levels of up to 100% recycled content. With this technology upgrade, Srichakra is now able to provide premium foodgrade quality rPET for food packaging. In addition to the new PET bottleto-bottle recycling line the company also installed a Starlinger recycling line for post-consumer polyolefi n packaging with odour reduction technology. New life for local plastic scrap “Our approach at Srichakra is focused on using leading-edge technology to create reliable, high-quality materials that help brand-owners reduce their use of virgin plastic”, said Ravindra Venkata, CEO and Cofounder of Srichakra Polyplast. “The new world-class technology not only enables us to produce food-grade quality recycled plastic for customers, but also gives locally-sourced plastics a new life, preventing it from entering the environment. We’re proud to be the fi rst in India to achieve this standard and continue our work towards making the world a better place by cleaning up the environment.” Elevating plastics recycling standards in India According to the UN Plastic Waste Management Programme India, only one fourth of the country’s plastic waste is currently recycled. The recycled materials themselves are generally not high quality, which results in low levels of re-usage. With the newly installed equipment, Srichakra produces high-quality recycled plastics that can be used to substitute virgin resin. This way, the company contributes to the development of a sustainable plastic waste management model in India. „Srichakra Polyplast is a pioneer of the circular economy in India, and we are proud to be their technology suppliers”, said Paul Niedl, Commercial Head of Starlinger recycling technology. “With the new Starlinger PET bottle-to-bottle recycling line with SSP treatment they have expanded their scope of products now into the important fi eld of food-grade rPET. With their high-quality products Srichakra Polyplast is going to set new standards for the Indian plastics recycling industry.” www.recycling.starlinger.com Founded in 2010, Srichakra Polyplast (India) Pvt Ltd is a leading plastics recycling and waste management company based in Hyderabad, India. The company produces premium PET and polyolefi n fl akes and regranulate from plastic waste and specialises in offering high-quality recycled products in large volumes for the packaging industry. To help brand owners reduce virgin plastic use, Srichakra is constantly striving to improve, resulting in the development of its technically advanced bottle-tobottle solutions and food-grade recycled pellets. For ten years, Srichakra has championed the transformation of locally sourced plastic waste and strives to divert plastic from the ocean and encourage the advancement of the circular economy. www.srichakra.in The Starlinger PET bottle-to-bottle recycling line at Srichakra’s production facilities in Hyderabad produces rPET for food-grade applications. A new life – used PET bottles become new bottles again.","@ID":20} "EDITOUR PETplanet Insider Vol. 22 No. 10/21 petpla.net 13 Mr Thomas Schmidt, Group Marketing Director at Bericap Holding GmbH 1) As with most other businesses, the pandemic has of course impacted our daily way of working internally as well as with our business partners. From a business point of view, we were facing opposite developments in demands resulting from different consumer and customer behaviours: whereas the out-of-home related smaller volume beverages segment collapsed, the demands from hygiene and food sectors by far exceeded the production capacities. We have already experienced a return towards pre-pandemic levels over the last months but only the future can tell us to what extend the pandemic has changed consumer behaviour and market segments in the long term. 2) For Bericap, as one of the leading manufacturers of caps and closures for the beverage, food and industrial sectors, the EU single use plastic directive 2019/904 (SUP) defi nitely has the highest impact. The conversion of the European beverage industry to tethered caps by 2024 is truly a challenge; starting from technical product requirements and consumer preferences via closure production, testing, approvals and equipment, scaling up to customer fi lling line trials, approvals and market introductions. Besides several approved solutions on hand, we see that our ClipAside tethered cap offers the most robust and consistent per formance across all relevant neck fi nishes with minimum changeover cost for our customers. A key argument for many of our customers is the fl exibility that the slitted TE band offers to their tethered cap project. Our customers can start preparing and testing their lines today based on a tethered cap shell with standard TE band, and once they are ready with their market preparations it is only a change of the slitting geometry with no impact to the prepared lines. 3) Several studies prove the signifi cant environmental advantages that the PET bottle offers compared to potential alternative materials especially when kept in the recycling loop. Some of the major future challenges go beyond the PET industry’s immediate scope, such as a necessary shift in the political, public and consumer opinions and establishing the appropriate infrastructures, certifi cations and re-collection behaviours across the world. The immediate challenges of the PET and related industries are to optimise PET and rPET materials (usage of rPET and PCR material), designs (e.g. light weighting), processes and technologies (e.g. chemical recycling) which further improve the usage and recycling of the PET / PE materials. www.bericap.com","@ID":15} "MATERIALS / RECYCLING PETplanet Insider Vol. 22 No. 10/21 petpla.net 26 PET recyclate manufactured using this process has received approval from the United States Food and Drug Administration (FDA) for food-contact uses. Coperion says that the effi cient plastifi cation within the ZSK extruder enables bottle-tobottle recycling at throughput rates between 2 t/h and 8 t/h. The company asserts that recycling companies will gain from high product quality, reduced operating and logistic expenses, and from energy cost savings up to 30% lower than conventional PET recycling methods. Increased effi ciency Before PET can be reprocessed, it must fi rst be shredded to fl akes and then cleaned. Ordinary technologies require pre-drying, crystallisation or agglomeration of the PET fl akes following washing. However, Coperion says that its specialised technology enables shredded PET to be fed directly into the ZSK twin screw extruder and compounded. The shredded fl akes are fed reliably into the ZSK extruder using high-accuracy SWB (Smart Weigh Belt) feeders or gravimetric feeders from Coperion K-Tron. Other regrind materials, new materials, or mixtures can be added at this stage. Melting, intensive devolatilisation and complete homogenisation take place in the ZSK process section before the melt is transferred, via a gear pump and fi lter with an automatic screen pack changer, to a strand or underwater pelletiser for pellet production. Pellets are then condensed in an SSP reactor. The pellets’ quality meets the requirements of virgin material. They have received FDA Letter of Non Objection which certifi es that they meet the standards for food-safe plastics and thus, can be processed into bottles once again. With this direct processing of PET into bottles, recyclers profi t particularly from the high product quality. Product handling in the bottle-to-bottle process is very gentle. Residence time in the ZSK extruder is short and dispersion is good. The ZSK extruders’ high torque enables processing at low temperatures and with almost no viscosity loss and their self-cleaning capacity enables rapid recipe and colour changes, states the company. The machines’ devolatilisation options mean that volatile components such as monomers, oligomers, and water are reliably removed and channelled away from the exhaust fl ow in suitable separators before discharge from the process section. High-accuracy Coperion K-Tron SWB feeder that feeds PET fl akes into the extruder. (Photo: Coperion K-Tron, Niederlenz, Switzerland) Economical and FDA-compliant recycling of PET fl akes Direct PET processing Coperion Gmbh, headquartered in Stuttgart, Germany, says that the drive towards a circular economy for PET has taken another step with its Coperion ZSK twin screw extruders, which can process PET fl akes without predrying into pellets. The fl akes are then condensed in the SSP (solid state polycondensation) reactor and reprocessed back into bottles, with virgin material quality. Coperion ZSK twin screw extruders are claimed to provide good devolatilisation with short residence times in the process section as well as high dispersion. (Photo: Coperion, Stuttgart) RECYCLING","@ID":28} "The TEM machine offers possibilities for slitting or slitting and folding of tamper evident bands for specialty caps. The TEM, a highly versatile machine for beverage, food, beauty & home, chemical and other products. Modular design machine for slitting / folding or folding /slitting of tamper evident band Large variety of cap dimensions, including sport caps All size parts located in the outside for easy adjustment and changeover Heating system for the blade. Blade position sensor Servo-driven infeed star wheel, integrated cap stop and sensor controlled upside down closure detection Operator friendly interface Match the output of associated moulding and downstream machines Easily integrated into any production line due to independent control and optional vision inspection system Our packaging machines are perfectly suited for a wide variety of industrial sectors: for the production of premium cosmetics, health and pharmaceutical products as well as for beverages and specialties. Complete lines for laminate and extruded tubes Plastic closures slitting and folding machines Packing solutions for unfilled tubes, cans, cartridges and containers High precision automatic hot stamping solutions We stand for Swiss engineered innovation and performance. Creating Packaging Technology. PackSys Global AG T +41 55 253 38 31 [email protected] www.packsysglobal.com SPECIALTY CLOSURES TAMPER EVIDENCE","@ID":24} "PETplanet Insider Vol. 22 No. 10/21 petpla.net 41 EVENT REVIEW local producers (for 1.5 million tonnes), and the situation is chaotic. Mr Zanchi’s belief is that imports will always be necessary, and it is estimated that about 400,000 t will have to be imported in 2025. Will all the imported material have to meet all Reach regulations? But, even more important, how much imported material really conforms to Reach today? There are question marks over how to evaluate fairly the feasibility of sustainability targets, whether they are claimed by large groups or imposed by institutions. Without a great push to increase collection rates, problems are expected to increase. The logistics situation also is a big issue currently. The extraordinary speculation by a few companies may kill an industry. If this situation persists, dramatic changes in world trade could be seen. Bulk carriers may be a temporary solution for large importers, and GSI is offering urgent support to secure them in the shortest time frame until the rates are economically advantageous. Finally, Mr. Zanchi updated the audience of GSI and the St. Lawrence Foundation social arm in Sierra Leone (Social Business Development). Its agri-food activity is moving forward rapidly and is now providing feed and poultry to other farmers in the area, and eggs to local communities. Its success is spreading fast, bringing work and food to one of the poorest areas in Africa. The afternoon session of the webinar, whose theme was based on evaluating the impact of the pandemic on business, began with Christian Wöss (Erema), Uwe Neumann (NGR) and Matteo Calloni (Bandera), who discussed their companies’ latest technologies for recycling polyester wastes by eventually improving the quality of the final product. Market trends and the latest developments in developing a real circular economy were discussed by, amongst others, David Feber (McKinsey) who underlined how hygiene requirements are going to be stricter in the packaging field, Hans Van Bochove (Coca-Cola) and Fabiana Marchini (Nestlé San Pellegrino). Mr. Van Bochove warned about the race to please customers by promising 100% rPET bottles in a short time period, while recycled raw materials are still scarce. Mrs Marchini insisted on the need to support the right behaviour and awareness amongst consumers on correct waste disposal. Werner Bosmans, from the EU Commission (Team leader “Plastics” DG Environment) and a member of the panel, confirmed that, from the EU standpoint, it is necessary to improve the quality of the recycling process and curb plastic waste and littering, since all packaging in the EU market must be reusable and recyclable by 2030. Aldo Scalini (counsellor at Van Bael & Bellis) gave an insight on latest EU trade laws and regulations, particularly detailing on the possibility of additional anti-dumping investigations, even though none is actually on the table at present. The final group of panellists explained the challenges faced by the PET industry in overcoming various issues caused by the pandemic, around the world, and the related consequences. Herman Sharma (Reliance Ind.) said the supply chain was the most affected area of the business chain, while PET applications showed good resilience; Christian Mayr (Alpla) underlined first the change in trade flows, as countries in the Far-East may not be competitive for some time, and then the great crisis in the Horeca business which impacted the beverage sector negatively. Stefano Marini, CEO of San Pellegrino, revealed the prompt actions taken by his company to support struggling restaurants, major customers of the Nestlé Company, just three weeks into the worst pandemic period. In times of crisis, companies often respond positively. Coert Michielsen (Refresco) moved the discussion towards collection; his proposal was to include the retail sector in such operations. He also suggested that retailers could be invited to the next PET Day as part of a round table discussion on this issue. Finally, the hot topic of the logistics crisis was left to Salvatore Feraco (DHL) who explained the causes and the reasons for what happened and is still ongoing in world trade. There were few signs of optimism, with the current excessive rates forecast to remain well into 2022. The use of bulk vessels is growing but this will not change the scenario: big corporations like Walmart and Ikea are being compelled to buy their own ships to ensure reliable supply. With DHL’s gloomy picture, the 19th PET Day came to an end, leaving participants facing a number of scenarios which are likely to cause huge changes in the entire structure of the polyester industry, and which will be witnessed in the years to come. www.gsiplastic.com","@ID":43} "PETproducts 54 PETplanet Insider Vol. 22 No. 10/21 petpla.net EC washing process opens a new way for PET bottle recycling The global PET bottle recycling rate is approximately 50%, but it still needs to be improved. With restrictions on the import and export of plastic waste in various countries around the world, the local plastic recycling model is imperative. The demand usage for recycled PET by global brands has increased, so the recycling rate of waste PET must be increased year by year. It took two years to investigate and analyse the variation tendency in global PET bottle packaging and composition of waste PET bottle bales for BoReTech. As a professional supplier of recycling equipment that has been deeply involved in the plastic recycling industry, BoReTech has proposed how to reduce the concentration of such a huge PET bottle recycling process due to the global land area is gradually decreasing, prompting to consider environmental friendliness to reduce equipment footprint and equipment production energy consumption, which responding to global energy conservation and emission reduction, and reducing carbon footprint. Compared with the traditional recycling process, the EC washing process PET bottle recycling system by BoReTech has greatly reduced land and plant investment, and at the same time, the investment in production costs and the manpower requirements are relatively reduced. For the developed countries and regions, tight land, and high labor costs, the EC washing process has signifi cant advantages. The EC washing process has 3,000kg/h and 6,000kg/h input capacity as the standard design. Compared with the same input capacity of the traditional process, the equipment land occupied will be reduced by half, and the fi nal product rPET fl akes quality is the same, which can be directly applied in bottle-to-bottle production and micro-denier fi lament production. The EC washing process adopts a modular design concept to reduce the equipment maintenance points, reduce the failure rate of equipment operation, and be conducive to the unifi cation and standardisation of spare parts. To emphasise the concept of environmental protection, the water circulation system of the EC washing process will pass through the online fi ne fi ltration system to achieve more than 50% of the water that can be reused in the washing process. At present, the EC washing process technology has been successfully developed and internal trial running. BoReTech is expecting to launch the technology on the market next year. www.bo-re-tech.com Evian unveils 100% rPET bottles created by Loop Industries’ recycling technology Evian has launched an rPET prototype bottle using technology from technology company Loop Industries. As the demand for more sustainable packaging solutions continues to grow, Loop Industries states to offer a technology that allows no and low value PET plastics that would otherwise go to waste to be recycled endlessly into new, virgin-like PET plastic. The process breaks down plastic into its base building blocks, or monomers. The monomers are then purifi ed and repolymerised into Loop PET plastic. This technology is intended to allow more plastic to be kept in use, reduces reliance on fossil fuels and avoids the creation of new plastic. The technology is claimed to enable a continuous loop for recycling at large scale, meaning that all types of PET plastic waste can be transformed into high quality plastic bottles. To bring to life this latest concept, Evian has renamed its prototype bottles to ‘Evian Loop’ to highlight each bottle’s recycling potential. Evian’s partnership with Loop Industries spans four years, during which time Loop Industries worked on perfecting its technology for commercial production on a global scale. The partnership will see this pioneering technology rolled out across markets beginning in 2022 and is part of Evian’s effort to accelerate the development of innovative sustainable packaging solutions. www.evian.com www.loopindustries.com RECYCLING","@ID":56} "MATERIALS / RECYCLING 27 PETplanet Insider Vol. 22 As well as high product quality, direct processing of PET fl akes offers further advantages including reduced operating costs and energy consumption as well as lower logistic expense, according to Mr Jochen Schofer, Business Segment Manager, Recycling & Direct Extrusion at Coperion. “With FDA certifi cation, we have offi cially confi rmed the high product quality of the PET recyclates. With the Coperion solution, we make a technology available to recyclers that is economical and at the same time allows them to make a decisive contribution to the plastic industry’s path towards a circular economy.” Coperion is an international market and technology leader in compounding and extrusion systems, feeding and weighing technology, bulk materials handling systems and services. It has 2,500 employees and nearly 30 sales and service companies worldwide. www.coperion.com Typical set-up of a recycling system for processing PET fl akes into PET pellets that can be used in turn to manufacture bottles: 1 SWB (Smart Weigh Belt) feeder 2 ZSK twin screw extruder 3 Addition of PET fl akes 4 Devolatilisation of volatile components 5 Discharge via gear pump and fi lter 6 Water bath 7 Strand drying 8 Strand pelletising","@ID":29} "No.10 2021 petpla.net D 51178; ISSN: 1438-9452 30 . 10 . 21 PETplanet is read in more than 140 countries MAGAZ I NE FOR BOT T L E R S AND BOT T L E - MAK E R S IN THE AMER ICAS, AS IA, EUROPE AND AL L AROUND THE PLANET MARKETsurvey Suppliers of fi lling equipment and fi lling inspection systems Page 31 Page 12 Recycling Page 14","@ID":1} "MARKET SURVEY 32 PETplanet Insider Vol. 22 No. 10/21 petpla.net Filling inspection systems Company name KHS GmbH Pressco Technology Inc Postal address Telephone number Web site address Contact name Function Direct telephone number E-Mail Juchostraße 20 44143 Dortmund, Germany +49 231 569-0 www.khs.com Mr Helmut Schmitt Project & Production Manageement Inspection Technology +49 231 569 10124 [email protected] 29200 Aurora Road, Cleveland, OH USA +1 440 498 2600 www.pressco.com Mr Tom Murphy VP, Sales & Customer Service +1 440 498 2600 [email protected] Fill level control Infrared No X-ray Yes Yes Gamma Yes Camera Yes, high frequency controll Yes, high frequency Contamination control Foreign Substance Inspection (sniffi ng) for empty ref PET bottles No Closure inspection Presents of cap Yes Yes Crooked cap Yes Yes Lifed cap Yes Yes Wrong cap Yes Yes Tamper evident band control Yes Yes Camera: 360° / sensor Yes, both Yes Label inspection Torn label Yes Vertical / horizontal misalignment Yes Yes Best-before date control Code presence inspection No Camera: 360°/ sensor Camera and sensor Yes Pressure leak detector Squeezer No Applicable bottle type Diameter 40-110mm Up to 150mm Height 150-360mm Up to 400mm Rejecting bottle Into bin and onto collecting table Push reject and diverter reject options available Inspection speed PET: up to 86,000 bph Over 3,000ppm Monitoring Filler-/sealer management Filler valve, capper head correlation Filling Equipment Company name Krones AG Fogg Filler Sidel Postal address Telephone number Web site address Contact name Function Direct telephone number E-Mail Böhmerwaldstr. 5 93073 Neutraubling, Germany +49 9401 70 0 www.krones.com Mr Philipp Schön Product Manager Filling Division +49 9401 4567 [email protected] 3455 John F Donnelly Dr Holland, MI 49424, USA +1 616 786 3644 www.foggfi ller.com Mr Cody Peterson Sales +1 616 786 3644 [email protected] Via La Spezia 241/A, 43126 Parma, Italy +39 0521 9991 www.sidel.com Mr Stefano Baini Filling Product Manager [email protected] 1. Machine designation / model number Modulfi ll F2 - F12 (2' fi lling bowl to 12' fi lling bowl) Sidel Matrix SF 300 FM Sidel Matrix SF 100 FM Sidel Matrix SF 700 FM 2. Number of fi lling heads (range: from/to) 16-216 6-120 32-216 24-144 32-108 3. Min to max bottle contents (in liters) 0.1-5 0.05-5 0.2-3.0 0.2-3.0 0.2-2.0 4. Filling speed: output (bph) (min to max): 20bpm - 1,200bpm 4,000-81,000 (18°C) 5,000-90,000 6,000-60,000 specifi y: 1l bottle / still water (bph) Up to 72,000 38-746 80,000 75,000 1l bottle / CSD (bph) Up to 65,000 No carbonated beverages 68,000 (18°C) 1l bottle / Milk (bph) Up to 60,000 38-786 1l bottle / Juice (bph) Up to 60,000 38-786 48,000 5. Filling process Pressureless (still drinks) Yes Yes - gravity fi ll Yes Yes Yes Pressure fi lling (carbonated drinks) Yes No Yes Hot fi lling Yes Yes- gravity fi ll Yes Cold aseptic fi lling Yes Yes - cold fi ll - esl and near aseptic Juices with high pulp content Yes Yes - gravity fi ll with special agitation system Yes Yes Yes 6. Type of fi lling valve and metering system Volumetric fi lling system: inductive and mass-fl owmeter, net weight fi lling system with weighing cell and height fi lling system with electronic fi ll height measuring Gravity fi lling valves Electropneumatic volumetric fi ller with fl owmeter volume control Electropneumatic volumetric fi ller with fl owmeter volume control, with no bottle/valve contact Electropneumatic volumetric fi ller with fl owmeter volume control 7. Special features (short description/keywords) Monotec (starwheel columns with servo drives), cap disinfection (UV light / PAA / H2O2, optional), clean room cover, foam cleaning system, nitrogen injection system, automatic CIP-cups, capcade, Bloc solutions Hot Fill, Cold Fill, ESLFill, Spirits Fill All pourable liquids that are noncarbonated Fully automatic operating computer control; external beverage tank (no ring bowl); electropneumatic components integrated on fi lling valve For mineral and demineralised water ie R.O. (reverse osmosis) water; fully automatic operating computer control; external beverage tank (no ring bowl) Quick changeover procedure fully automatic operating computer control; food safety due to recirculation and CIP (Clean In Place) minimum fl owrate control during operatio","@ID":34}]}}
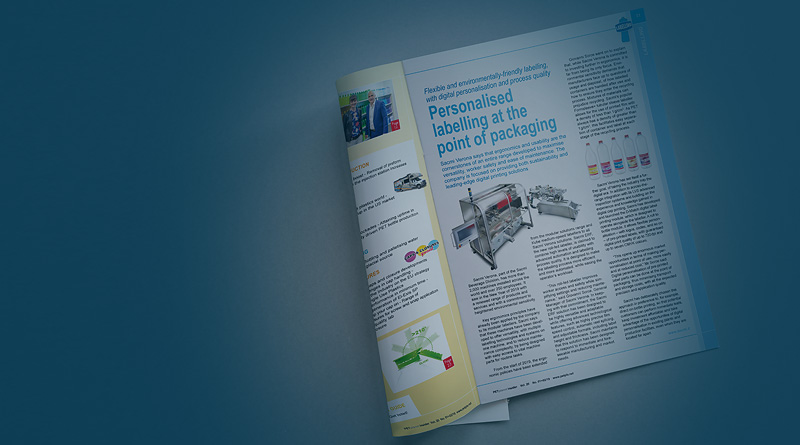