{"pages":{"page":[{"#text":"ClipAside with parallel tethers prevents overbending or breakage, even when misused. Fill, Seal, ClipAside! Added functionality meets easy integration Contact us and arrange your line trials now! www.bericap.com PET 38 PET 29/25 PCO 1881 PET 33 PET 26 PET 26 GME 30.40 In the years to come, tethered closures are going to become the new standard for beverage bottles. Our innovative ClipAside solution is ideal for all major neck finish standards from 26mm to 38mm and for liquid products ranging from carbonated soft drinks to water, juices, teas, syrups, dairy and others. ClipAside does not require major adaptations of the capper or the filling equipment. If necessary at all, small capper feeding or capping head adjustments can be performed by our in-house technical service. ClipAside opens as wide as 180° and is easy to use with no spills or splashes. More convenient for consumers, ClipAside generates less waste too*. *Conforms to the EU Single Use Plastics Directive","@ID":58} "AFTER SALES SURVEY 4 PETplanet Insider Vol. 23 No. 03/22 www.petpla.net OUTER PLANET Global market research study on cap and preform production and bottle-fi lling by PETplanet Insider How satisfied are you with your After Sales service? Dear Friends of PETplanet, In the next few weeks you will be receiving an e-mail from us asking you to take part in a survey on the After Sales service provided by your machine suppliers. As a thank you, you will be given a confidential assessment of similar companies in your area. For you as a processor and manufacturer of caps, preforms, bottles and fillers in PET bottles, the results of this detailed customer satisfaction survey of After Sales service can be an additional factor to consider when purchasing new machinery or in improving the servicing of your existing machines. I am really looking forward to receiving your input which will of course be anonymised. Mrs Trotter will be happy to send you the link and access code if you have not received your questionnaire by the end of April (e-mail: [email protected]). As it has been eight years since our last market research study on this subject, we felt it was high time to take a closer look at the quality of After Sales service. The online questionnaire asks for information on which manufacturers provide the machines used in your plant and how satisfied you are with their After Sales service. This includes the following elements: Speed, reliability, skill; Reasonable price-performance ratio; Availability of mechanical replacement parts; Availability of electrical replacement parts; Emergency hotline; Retrofit / upgrade services; Monitoring and digitalisation of the machines / systems; Employee training / continued training. It would also be fascinating to know what level of After Sales service you receive from the machine manufacturer OEM or from third-parties. We realise this will be a subjective view but having made many on-site visits, we are sure that every company will be able to make a realistic assessment. This can be between 0% (no After Sales service from the machine manufacturer) up to 100% (all-round carefree package provided by the manufacturer). In evaluating the many questionnaires, we will be able to identify clear trends in particular areas and highlight regional, machine manufacturer or size of company differences. The success of this study depends on your cooperation. I look forward to receiving your contributions. Yours, Alexander Büchler Publisher of PETplanet Insider AFTE SALES SURVEY","@ID":6} "EDITOUR PETplanet Insider Vol. 23 No. 03/22 www.petpla.net 14 Tour Sponsors: Interview with Universal Closures Ltd. Making the best of the worst of times by Ruari McCallion February 3, 2022 We met: Mr Mark Smith, Senior Vice-President Universal Closures Ltd seized the opportunity presented by the reduced level of primary activity during the Covid-19 pandemic to bring forward a number of design innovations – but the impossibility of face-to-face interaction was an inconvenience. Universal Closures, which is based in Tewkesbury, near Gloucester in England’s West Country, is quite a small company but it casts a giant shadow. It specialises in the design and development of closure systems, mostly in HDPE, for plastic bottles ranging in size from 100ml to 5 l. Its client list includes Coca-Cola, PepsiCo, P&G and Nestle. It has over 30 licensees across the world using its designs and works closely with Z-Moulds in Austria, in developing the tooling for the caps involved in complete closure systems. Its main focus has been beverages; over 80% of its revenues have, traditionally, come from that market. But that is likely to change, mainly thanks to its most recent partner, Westfall Technik in the USA. Its primary market is homecare and personal care, which is becoming a commercially attractive area for the company – of which more later. Mark Smith, Senior Vice-President of Universal Closures, made the trip from Tewkesbury to meet PETplanet Insider’s Editor-at-Large, Ruari McCallion, in Salisbury, in the south of England – the first time we have sat down face-to-face since June 2020. It has been an eventful 20 months since then and we started by discussing the impact of Covid-19 on the business. It was good to hear that the pandemic and associated shutdowns, border closures and restrictions have not had an immediate effect on Universal Closures. EU Directives, tethered caps and new GME 30/40 finish and closure standards “We have a business model that has a strong and regular income from royalties,” he said. There have been fluctuations but there has not been any discernible trend, either commercially, by sector or geographically. Sales have remained pretty constant. The impact is more likely to be felt further down the road, because the normal five-year cycle of machinery renewal has been interrupted. A number of changes are arriving in the market, including EU Directives on tethered caps, single-use plastics and incorporation of recycled material, as well as recyclability. The standard for caps and closures is also changing. The 1881 closure systems, which have become common for over 15 years, are being superseded by the new GME 30/40 or 30/41 standard. “Coca-Cola specifically has been working with several of their key partners – UCL being one of them – to develop a replacement finish for 1881, which is known as GME 30/40. They wanted a lighter weight neck finish but also needed to ensure that they didn’t score an own-goal and not have enough space to accommodate the tethered cap that is coming,” Mark explained. The GME 30/40 PET finish is the first international standard that Mark Smith, Senior Vice-President of Universal Closures Ltd, came to visit PETplanet Insider’s Editor-at-Large, Ruari McCallion (photo on the left), at the Salisbury, England offices. Mark noticed an interesting article in PETplanet Insider about Z-Moulds, a long-time partner of Universal Closures.","@ID":16} "CAPS & CLOSURES 30 PETplanet Insider Vol. 23 No. 03/22 www.petpla.net Interview with Mr Pankaj Bafna, General Manager at Nishant Mouldings Ltd. about Sacmi’s compression moulding technology “CCM is our calling card on the market” Based in Bangalore, the Indian company Nishant Mouldings has played a key role in the fast-paced growth of closure production in recent years. In 2019, the company decided to establish itself with a complete preform-cap solution on the market. PETplanet talked with Mr Pankaj Bafna about his experience with Sacmi’s CCM. Nishant Mouldings Ltd., founded in 2001, is a protagonist in manufacturing caps, preforms and container for the beverages & FMCG markets. The brand name is well renowned in the industry as Fortunapet. PETplanet: What is the reason for the company’s success in recent years? Pankaj Bafna: Three main factors, firstly – keen attention to customers requirements, constantly evolving to provide better products and services. Secondly – sixth sense in pre-empting the market requirement well ahead resulting in development of successful designs of products. Thirdly - the ideology of choosing the best technology available. Hence, the partnership with Sacmi for a compression made cap mould came into existence. PETplanet: Which points were particularly decisive? Pankaj Bafna: A key year for Nishant was 2012. We expanded our business and produced our own preforms offering a broad range of preforms from 25mm to 120mm to the market. The second big step came in 2019. Our decision to present ourselves in the market with a complete cap-preform product, keeping the highest industry standards. In the closures business, we’d had our sights set on Sacmi’s compression technology for some time. Indeed, we believe it’s the best competitive one-piece cap manufacturing system. That’s why, following meticulous cost-benefit analysis, we opted for this solution and installed the first 48-cavity CCM. And the results were exceptional. PETplanet: What products are made with CCM and in what volumes? Pankaj Bafna: We started off by producing the standard 27 mm Alaska, a water cap weighing 1.28 g. With CCM we managed to raise productivity to 70 million caps per month, improving both products and efficiency to an extent that allowed us to grow rapidly in this segment. We can now attend trade fairs and explain to our customers that we use Sacmi compression technology to make their products. It’s a valuable calling card, a guarantee of quality for our partners. PETplanet: In recent years, the industry has changed a lot. How has the management dealt with this? Pankaj Bafna: Accelerating change is a key feature of our time. More specifically, the issue of sustainability is increasingly important in cap and preform manufacturing, as are quality and an optimised consumer experience. It’s vital to know how to adapt quickly to customer demand, how to develop customised products and work on new standards and designs with the fastest possible time-to-market. For example, we were able to install and start up the Sacmi machine in very short time and work as a team with our own technicians, allowing us to get the maximum potential from the new line immediately. PETplanet: What about other projects? Pankaj Bafna: The first is to double line output capacity by purchasing an additional CCM press. In fact, we have the full scope of CSDs to consider and, here too, company’s aim to work with the major India-based international brand owners. Last but not least, our satisfaction with the partnership with Sacmi means we’re also assessing IPS preform production technology. PETplanet: Thank you so much for your statements, Mr Pankaj Bafna. www.sacmi.com www.nishantmouldings.com F.l.t.r.: Mr Ashish Narang, Sales Area Manager Sacmi Rigid Packaging Technolgies, Mr Pankaj Bafna, General Manager at Nishant and Nishant stuff member.","@ID":32} "MARKET SURVEY 29 PETplanet Insider Vol. 23 No. 03/22 www.petpla.net Sipa Otto Systems AG Via Caduti del Lavoro 3 31029 Vittorio Veneto, Italy +39 04389 11 511 www.sipa.it Mr Gianfranco Perricci Global Sales Director, Preform Systems & Tooling +39 0438911 511 [email protected] Zürcherstrasse 73 8730 Uznach, Switzerland +41 55 285 22 11 www.otto-systems.com Mr Stefan Zatti CEO +41 55 285 22 09 [email protected] IPS300 IPS400 XForm 250 XForm 350 XForm 500 Xtreme 72 Xtreme 96 PET-Series 160, PET-Series 240, PET-Series 320 24 - 128 48 - 144 96 128 200 72 96 2-128 cavities 140g 140g 69,000 preforms per hour (pph) 87,000pph 135,000pph 52,000pph 69,000pph Max. shot weight 7,980g 900 1,250 Up to 1,220 Injection cylinder (shooting pot), electrical drive for plasticising screw, T-belt for preforms extraction, Cool+ system (inside cooling), belt free robot linear motor with KERS, take out plate with 4 postcooling stations, HMI with control of all auxiliaries, boosters on moving platen for fi rst phase ejection, double cylinders for preform ejection, digital valves for each actuator, water unloading system prior to mould changing. XForm: available in GEN4 XP version (low energy consumption, fast cycle time, complete new HMI); XTreme: injectioncompression technology, ultra-thin wall capability, 2 preforms can be produced simultaneously Consulting & engineering of preform systems, complete preform production system including auxiliaries, full electric clamping unit, hybrid injection solution with shooting pot or electric injection with Time Safe Unit (TSU) Injection shot completition device (power failure), water pumps for mould cooling assembled on main machine platform, quality control vision system with multiple camera, soft handling package, walkway, high temperature environment package, cooling water sensoring kit XForm GEN4 XP: XP technology, LongLife tooling coating, XMold for ultra-thin preform injection capability, wide-mouth preforms capability XTreme: built-in inspection system for 100% quality check, 100% recyled fl akes processing capability, direct connection with Xtra SBM Extra large preform capability (up to 380mm), compatible to a selection of top entry moulds, co-injection technology up to 72 cavities, integrated dust-evacuation (OH-XTract), enhanced neck-cooling (OH-XCool), wearprotection coating (OH-XTreme) Resins & additives Preform machinery Preform production & inspection systems Preform & SBM mould manufacturer SBM 2-stage Compressors Caps & closures & inspection systems Filling equipment & inspection systems Recycling machinery Palletising & shrink film machinery","@ID":31} "AFTER SALES SURVEY 5 PETplanet Insider Vol. 23 No. 03/22 www.petpla.net OUTER PLANET AFTER SALES SURVEY 5 Sumitomo Demag Engel Netstal Sacmi Corvaglia Z moulds Husky StackTeck GDXL Intravis Pressco Sacmi IMDVista Otto Systems Sipa Mold Master Otto Hofstetter Electra Form MHT R&D Leverage Petka Mold Agr Ingersoll Rand ABC AF Compressors Kaeser Dalgakiran Shangair Boge Siad LMF Atlas Copco 1Blow KHS Side SMI Kosme Technopet Machineries Luxber Newamstar Krones Flexblow Amsler Sidel STM Pack Fogg Filler Serac PE Labellers Filtec Finpac Heuft European Polymers Conference PET, Polyolefins and Recycled Plastics VIENNA 2022 9-10 MAY 2022 Use code MEDPETPLANET10 to save 10% Evaluate the After Sales service of your machine manufacturer OEMs","@ID":7} "CHINA SPECIAL & CHINEPLAS 2022 PETplanet Insider Vol. 23 No. 03/22 www.petpla.net 33 is a hot topic within China. Although China is the world’s largest producer of rPET, accounting for around 45% of current global rPET capacity, rPET flake is almost exclusively used in the production of textiles and fibre. Within China, until now rPET in food-grade applications been heavily restricted by food standards, Czarnikow explains. Quality safety certificates are required for local manufacturers to produce food packaging materials made of plastics and paper, and very few have ever been granted for the use of food-grade rPET. However, this could change in the future. The Chinese government is pushing efforts for the circular economy, and new standards are being established. Only recently, on 1st of March, a new national standard became effective, the “Ecological technical requirements for recycled Poly(ethylene terephthalate) fibre” (GB/T 40351-2021), focusing technical requirements such as chemical residues, colourants or dyestuff. Although the food contact regulations in China are not expected to be changed in the short term, they will have a major impact on the rPET market, which is already experiencing higher demand than supply. Market situation for foreign companies Mid-January, the German Chamber of Commerce (AHK) in China, in cooperation with KPMG AG Wirtschaftsprüfungsgesellschaft, published the results of the annual “Business Confidence Survey”. Results show that confidence in the growth of the China market remains strong. German companies in China are confident about the current year: in 2021, almost 60% of companies in China reported improved business, and more than half expect an improvement of the development in their industry in China in 2022. Also, the VDMA members reported that in 2021, revenue developments in China were better than originally expected for many machinery and plant manufacturers. In spring, respondents estimated their revenue growth for 2021 at an average of 17 per cent; the autumn survey forecasted an encouraging 22 per cent. Expectations for 2022 are significantly lower at plus 10 per cent, but still at a good level. However, even a few months ago there were already some developments that cast a shadow over the China business. According to the survey conducted by the VDMA China, the shortage of raw materials and supplies, are regarded as an essential factor hampering business operations; 62 per cent of the companies see themselves affected by this. Bottlenecks in the supply of electricity posed a challenge for 32 per cent of the companies. This problem has been largely solved in the meantime. The preferential treatment of domestic competitors against the background of a political focus of the Chinese economy on itself, has become a major challenge, as it is stated by AHK. This moves the challenge from 6th to 1st place in the study’s ranking compared to the previous year. Also among the top operational challenges are ongoing travel restrictions. The strict Covid-related entry regulations increasingly induce foreign companies to localise in China. “Of course, the Russian aggression in Ukraine could not yet play a role in January [when the survey was conducted], and the effects of the war will not be seen in the order figures until March at the earliest,” VDMA economic expert Mr Olaf Wortmann comments the current development which might become the next top challenge, not only for China. EC PROCESS on energy consumption, PET RECYCLING PLANT Compact process, modular design equipment space. Sources: PETplanet Pulse, www.china.ahk.de, www.vdma.org, www.marketsandmarkets.com, www.czarnikow.com, www.chinesestandard.net, www.imarcgroup.com, www.prnewswire.com","@ID":35} "MARKET SURVEY 28 PETplanet Insider Vol. 23 No. 03/22 www.petpla.net 03/2022 MARKETsurvey Suppliers of preform machinery In this issue we focus on new developments in perform machinery. We are very proud to present the most exciting brand-new data from the following perform machine manufacturers: Nissei ASB Machine Co. Ltd., Netstal Maschinen AG, Sacmi Imola, Sipa and Otto Systems. Although the publishers have made every eff ort to ensure that the information in this survey is up to date, no claims are made regarding completeness or accuracy. Company name Nissei ASB Machine Co., Ltd. Netstal Maschinen AG Sacmi Imola Postal address Telephone number Web site address Contact name Function Direct telephone number E-Mail 4586-3 koo, Komoro-shi, Nagano-ken, 384-8585 Japan +81 267 23 1565 www.nisseiasb.co.jp Mr Paul Atkin Manager, Sales Coordination Team +81 267 23 1565 [email protected] Tschachenstrasse CH-8752 Näfels, Switzerland +41 55 618 6111 www.kraussmaffei.com Mr Stefan Kleinfeld Application & Product Manager +41 55 618 6241 [email protected] Via Provinciale Selice 17/A 40026 Imola BO, Italy +39 0542 607111 www.sacmi.it Mr Moraldo Masi Director of Business Unit PET +39 0542 607888 [email protected] Preform injection moulding systems Machine model number / name PM-70/65NII, PM-70/111N, PM-170/111M Side entry systems: Netstal PET-Line 3000, 4000 / top entry systems: Netstal PET-Line 2400, 4000, 5000, 2C; IPS220 Number of cavities (min/max units) 6 - 48 24 - 144 16 - 72 Maximum individual preform weight 240g Max shot weight 6,600g 140g Max resin through-put (kg/h of PET) 250 (approx.) Up to 1,350 625 Standard features (short description / keywords) Vertical clamping, built-in preform aftercooling stations, extremely compact All systems: intrusion; side entry systems: smart operation (= safe and guided operation); PETX-screw (= optimised 100% rPET processing); energy recuperation (lowest energy consumption) Injection cylinder (shooting pot); electrical drive for plasticising screw, T-belt for preforms extraction, Cool+ system (inside cooling), belt free robot linear motor with KERS, take out plate with 3 postcooling stations, HMI with control of all auxiliaries, double cylinder for preform ejection, digital valves for each actuator, water unloading system prior to mould changing, injection shot completition device (power failure) Options / special features (short description / keywords) Outputs are tailored to ASB's own range of 2-step blowing machines for hot fi ll application. PM-170/111M is designed for bottle and jar preforms with capability of neck size up to 120mm Cycle guard (= controlled production shutdown during a power outage); NRS (= Netstal remote support); energy measurement; Cool plus (= preform inside cooling); staggered EOAT (= additional cooling station); Q-Vision control Fast change over system with plug-and-play mould fi xing system, plug-and-play take out plate fi xing system, water pumps for mould cooling assembled on main machine platform, secondary belts system for an easier collection of preforms sampling, quality control vision system with multiple camera, soft handling package, walkway; high temperature environment package, cooling water sensoring kit","@ID":30} "43 CHINA SPECIAL & CHINAPLAS 2022 PETplanet Insider Vol. 23 No. 03/22 www.petpla.net Maag: Pelletising systems, melt filter & gear pumps Maag Group is a broadly diversified global solutions provider of pump & filtration systems, pelletising & pulverising systems, recycling systems and digital solutions. More and more new developments in plastics are being made in China, one of the strongest growth markets in the world. Maag Group takes this into account and will be present at Chinaplas in Shanghai, with a booth of over 120m2 in hall 2.1, booth F82. Pearlo 350 EAC with liquid-heated die plate for high capacities: The underwater pelletising system Pearlo 350 EAC is especially designed for high throughputs of like 18,000 kg/h of virgin polymer production. The cutting blade design and optimum water and material flow conditions within the cutting chamber provide a homogeneous cooling effect which results in a high pellet quality. Another design feature of the Pearlo is the cutting blade advance system, which permits axial movement of the cutter shaft resulting in a precise blade advance as well as a regrinding of the blades during production. This allows higher equipment availability, elongated production runs and thus saves costs. Maag Ettlinger is presenting the ERF 350, a high performance melt filter for the filtration of heavily contaminated polymer feedstock. The filter is self-cleaning with a rotating, perforated drum, through which there is a continuous flow of melt from the outside to the inside. A scraper removes the contaminants that are held back on the surface and feeds them to the discharge system. This enables the filter to be used fully automatically and without any disruptions over long periods without having to replace the screen. Strand pelletising: the Primo Plus Flex which will also be on display is claimed to provide Short unguided length in combination with an enlarged rotor diameter; Throughputs up to 5,000 kg/h; Prof i table product ion due to high machine availability with wear resistant cutting tools. For applications such as pelletising of base polymers, recycling products, processing of highly filled compounds or ETPs at different pellet lengths from micro to LGF, the Primo Plus enables a reliable dry cut strand pelletising process. All Maag Group extrex gear pumps in x 6 class design are completely re-engineered and have redesigned components, from the shafts through to the bearings and seals, and optimised the interaction of the components. Specially developed gear teeth with l ow comp r es - sion allow high pressures to be achieved wi th low shear rates. www.maag.com MAAG Hall 2.1 Booth F82","@ID":45} "42 CHINA SPECIAL & CHINAPLAS 2022 PETplanet Insider Vol. 23 No. 03/22 www.petpla.net NEWAMSTAR Hall 8.1 Booth D50 Newamstar and Ganten launch new barrelled water packaging The traditional barrelled water industry faces a number of constraints and challenges. The service life of a reusable barrel is limited but it is also difficult to monitor. Cleaning and sterilising returned barrels are not straightforward and there are other risks that may arise during processing; quality and safety of products are hard to guarantee. The cost of production is quite low, which attracts criminal elements, including counterfeiters, as well as makers of shoddy, low quality products. Furthermore, deposit, recycling and empty barrel storage issues lead the industry to focus on very short logistics radiuses. In order to save production cost, barrelled water is usually fulfilled from local sources; high-quality mineral water is almost completely unavailable in barrelled packaging. The list of challenges is extended by the physical characteristics of the expansion cap; altogether, the shelf life of barrelled water is relatively short, in stark contrast to the 12 months or more of bottled water. Altogether, options for consumers are extremely limited. The opportunity to upgrade to a new generation of barrelled water is impossible to ignore and hard to resist. Ganten, the largest exporter of bottled water in China, has proposed a solution utilising food-grade PET for disposable packaging. It claims that this approach will greatly extend shelf life and make the product safer and more environmental-friendly. In this way, people can buy barrelled water in much the same way as ordinary bottled mineral water. After considering the ideas and requirements put forward by the Ganten team, Jiangsu Newamstar Packaging Machinery Co., Ltd. commissioned its technical departments to conduct further research. A program of testing and analysis lasting 100 days led to a technical solution of for 15 l PET bottles, produced on a single-stage Newamstar combibloc. Ganten officially signed a strategic cooperation agreement with Newamstar for the 15 l PET bottled water packaging solution project and set up production in Beijing, Shanghai and Guangzhou, equipped with Newamstar 2,500 bph (15 l) combibloc production lines. The company says that they offer potential savings in energy and manpower and that the 15 l PET water barrel can help to minimise the risk of microbial contamination and improve the assurances of food safety and quality. Newamstar and Ganten say that using the blowing-fillingcapping combibloc eliminates the area for empty barrel storage, barrel cleaning equipment and disinfecting chemicals, as well as occupying a smaller area, requiring less staff and saving water. A customised robot palletising solution overcomes of longdistance transportation problems. Newamstar and Ganten say that their joint venture brings to the barrelled water market a technological innovation that enables more consumers to have access to wholesome water. www.en.newamstar.com +44 78175 32087 +34 676 986 962 [email protected] petmachinery.com Looking to sell your used PET machinery? We can help you. We offer a free valuation service, 50 years of industry experience, and a global network that guarantees you the best market value. Contact us today to find out more. THE INDUSTRY EXPERTS","@ID":44} "37 CHINA SPECIAL & CHINAPLAS 2022 PETplanet Insider Vol. 23 No. 03/22 www.petpla.net SMI S.p.A., Italy 1) We will not exhibit in 2022, but we will probably attend the event and take into consideration a presence for future editions. 2) The Chinese market is definitely one of the main objectives for SMI, which is very aware of its prominent role in the international scene. The Chinese clients are very demanding and well aware of the newest technologies. Their expectations are reasons for SMI to constantly improve and raise the performance bar of its products. We are already present in the territory with WFOE in Beijing and representative office in Guangzhou. 3) As the pandemic contingency is returning to a milder degree, we are now taking into account new business sectors with new awareness by the final consumer for products and environmental protection. New materials, such as rPET, represent the effort of our industry to demonstrate that plastic is still a protagonist in the market of packaging and blow filling. This policy is giving an enthusiastic return by the final users in China and worldwide. We are very confident about the future of the industry! www.smigroup.net","@ID":39} "MOULD MAKING PETplanet Insider Vol. 23 No. 03/22 www.petpla.net 19 MOULD MAKING 19 must be included in the technical data package, in order to obtain the effects created through hundreds of hours of design and financial investment. NoLabel is novel in multiple ways; a constantlychanging range of challenges has to be faced while moving forward in expanding the scope of its application, Juan Manuel Colmenares concludes. “The new bottle definitions goes far beyond dimensions and tolerances. Indicating which parts of the design require lasers is something that we include in bottle drawings that we generate for our clients. We also help them create the quality control procedures to follow with these new kinds of tools, since they will include legal information that is to be present in the bottle’s skin, a fusion between ancient label printing with bottle approval protocols”, he continues. Engineer Juan Manuel Colmenares has been part of the Moldintec NoLabel project research team since its launch in 2017. He has been involved in multiple no-label projects, including the 2022 WorldStar award winner. www.moldintec.com E N D L E S S I N N O V A T I O N S I N C E 1 9 1 9 Laser machining: Sharp edges for an exact logo definition Sharp edges and detailed small fonts, realised via laser machining High Speed Milling: Logo distortion due to tool radius 0.5mm","@ID":21} "PACKAGING/PALLETISING PETplanet Insider Vol. 23 No. 03/22 www.petpla.net 27 standards, currently leads to barriers to their industrial use. Regulatory restrictions can also often not be met. Finally, there is a lack of information along the value chain of plastic products to guarantee optimisations in an ecologically sustainable way. The IKV is pursuing a cross-value-added approach to establish digital solutions for the sustainable use of recycled materials. In the BMBF joint research project “PlasticBond”, prototype concepts are being developed together with a broad-based research and industry consortium, which take product and process properties into account at every stage of the life cycle and provide them as information along the lines of the material passport introduced by the “Platform Industry 4.0”. Use cases where the digital passport can be a benefit are many and varied. At the meta-level, for example, the focus is on efficient recyclate processing, holistic optimisation of ecological sustainability (e.g. CO2 footprint of packaging) and fulfilment of extended producer responsibility (EPR). The research project also ties in with the crosscompany initiative “R-Cycle” founded by the Reifenhäuser company for the traceability of plastic packaging, in which the IKV is one of the consortium members. The effects of the use of different recyclate qualities and varying recyclate proportions on plastics processing are also taken into account. However, the focus here is less on increasing individual recyclate qualities or optimising processing, but rather on standardising secondary raw material flows. Recyclates are to be used in a targeted manner depending on their classification and thus increasingly integrate the political goals into practice in the sense of a “circular economy”. www.ikv-aachen.de Figure 2: Recyclable barrier packaging for the chemical industry (image: IonKraft)","@ID":29} "imprint EDITORIAL PUBLISHER Alexander Büchler, Managing Director HEAD OFFICE heidelberg business media GmbH Vangerowstraße 33 69115 Heidelberg, Germany phone: +49 6221-65108-0 fax: +49 6221-65108-28 [email protected] EDITORIAL Kay Barton Heike Fischer Gabriele Kosmehl Michael Maruschke Ruari McCallion Anthony Withers WikiPETia. info [email protected] MEDIA CONSULTANTS Martina Hirschmann [email protected] Johann Lange-Brock [email protected] phone: +49 6221-65108-0 fax: +49 6221-65108-28 LAYOUT AND PREPRESS EXPRIM Werbeagentur | exprim.de Matthias Gaumann READER SERVICES Till Kretner [email protected] PRINT Chroma Druck Eine Unternehmung der Limberg-Druck GmbH Danziger Platz 6 67059 Ludwigshafen, Germany WWW www.hbmedia.net | www.petpla.net PETplanet Insider ISSN 1438-9459 is published 10 times a year. This publication is sent to qualified subscribers (1-year subscription 149 EUR, 2-year subscription 289 EUR, Young professionals’ subscription 99 EUR. Magazines will be dispatched to you by airmail). Not to be reproduced in any form without permission from the publisher. Note: The fact that product names may not be identified as trademarks is not an indication that such names are not registered trademarks. 3 PETplanet Insider Vol. 23 No. 03/22 www.petpla.net Dear readers, On Thursday, March 24th we are starting our PETinar on the subject of closures, which is currently the most hotly discussed topic in our PET industry. Presenting the event will be Intravis, Universal Closures and Z Moulds. They will oversee all aspects of closures, from mould making to production to inspection. The tethered cap will be the common thread running through the talks. Based on the experiences of the previous PETinar we will be giving give the auditorium enough space to broaden the topic with questions. We look forward to a lively discussion. Chinaplas 2022 opens its doors from April 25 to 28. It is still difficult for visitors from outside China to visit Asia’s leading trade fair for the plastics industry. Nevertheless, Chinaplas lives up to its claim as a national trade fair. It takes place at a difficult time. Prime Minister Li Keqiang said at the opening of the National People’s Congress, “The Chinese economy is currently facing many more risks and challenges.” The Corona pandemic and the Evergrande Real Estate conglomerate, which is threatened with bankruptcy, are leaving their mark. Nevertheless, the PET industry in China is positive about the future. According to GDXL (see interview on page 34), Chinese consumers are turning to safer packaged foods and therefore also packaged beverages, and as a result of steadily increasing prosperity, more and more people are now able to afford packaged beverages. Despite difficult economic circumstances, the Chinese PET market remains the driving force behind the PET industry. In its last annual report, Krones forecast annual growth rates for bottled beverages of 2.5% by 2023 in China (245.5 billion litres in 2020 plus 18.7 billion litres by 2023). By contrast, Africa and Asia-Pacific are around 2% and the rest of the world lags behind at around 0%. Yours sincerely, Alexander Büchler","@ID":5} "40 CHINA SPECIAL & CHINAPLAS 2022 PETplanet Insider Vol. 23 No. 03/22 www.petpla.net SUKANO Hall 8.2 Booth C26 Sukano Masterbatches activities on Chinese market by Colin Newton, Director of Sales & Marketing Asia Pacific at Sukano 1) Are you exhibiting at the Chinaplas fair? - Yes, Sukano is exhibiting at the Chinaplas this year. With travel restrictions in place, we are working closely with our local distribution partners who will be welcoming customers and prospects at our booth. Our Malaysia team will be available virtually for meetings with customers and visitors at the fair. The Greater China market is indeed a market of high relevance for Sukano and we are delighted to have the possibility to be part of this trade show once again. 2) What innovations will your company be presenting? - One of the main highlights is our latest project CPET light, jointly developed with our long-term partner Illig. It is aimed for transparent applications where temperature resistance up to 100 °C is required. Up until today, commonly used PE and PP was either not recyclable or not food contact compliant. CPET offers both, but is also temperature resistant up to 220 °C, which is not necessarily needed and lowers the output. CPET light offers it all: transparency, temperature resistance up to 100°C, and recyclable to ensure no contamination of recycling streams. We see a high market demand in this new material as it provides a great alternative to PP and PE and improves the production efficiency compared to CPET. It provides food contact compliance and ensure recyclability of the end application. Another recent development is our transparent impact modifier for flash frozen applications, which again goes under the umbrella of circularity. Our impact modifier enables the replacement of non-recyclable frozen food trays with PET monomaterial structure, while increasing the use of rPET. With this newly formulated Sukano Impact Modifier, customers have an alternative at hand to replace products made of, for instance, amorphous copolyesters or GAG film structures, while enjoying the benefits that go beyond mechanical property modification: improved durability and toughness, enhanced impact resistance, higher rPET content, shatter resistance – and all without a loss in transparency. With local biopolymer producers being established, we now see an increasing demand in biopolymer masterbatches. At Chinaplas, Sukano will showcase its complete PLA portfolio, which enables and expands the use of biopolymers in various end applications, since biopolymers play an important role in the goal of a circular economy. 3) How important is the Chinese market for you? - For Sukano as a global additive and colour masterbatch specialist for PET, biobased, biodegradable polymers and specialty resins, the greater China market is of high relevance. Sukano has a very large presence in BOPET thin films and shrink film markets and has been active in these market segments since the development of BOPET manufacturing in China. We continue to grow and develop our market presence and sales for thin films, rigid film for thermoformed packaging and injection moulded containers. We are experiencing increasing interest and demand for masterbatches that enhance the properties and characteristics of the various polyester products as the focus on recycling and biopolymer usage increase, and Sukano has extensive experience in both markets and a complete portfolio that supports customers inquiries. Investment in biopolymer manufacturing in China is expanding rapidly and is expected to account for the vast majority of world capacity by 2030. Sukano is proud to have embarked this journey towards biobased, biodegradable polymers from the very beginning over a decade ago. By leveraging our expertise, focus and dedication in conventional polyester plastics to bioplastics, our bio-based masterbatches portfolio has grown significantly with a product range for PLA, PBS(A) and now also expanding into PHA Masterbatches. 4) Are you planning to invest or establish yourself there? - We have established great long-term partnership with local distributors that are familiar with the market and demand. We work very closely to ensure we meet and fulfill the needs of our customers in China. Our global presence allows us to develop in one place and deploy everywhere. Our strategically located manufacturing site in Malaysia allows a local and agile service with unique technical support while ensuring prompt availability of our products. We firmly believe – and practice - customer centricity via dedicated collaboration, cooperation and partnership. 5) How do you see the PET industry developing this year? - We see an increasing demand in recycling and biopolymers, especially with the Chinese legislation for polymer waste imports and the huge emphasis that has been placed on internal recycling management initiatives. Both recycling and biopolymers are core founding principles of Sukano. Sukano offers an extensive rPET portfolio to enable the use in various end applications, supporting our customers in switching to circular solutions via a dedicated rPET masterbatch formulations. For a long time, the reuse of PET was limited to applications like fibres or trays; rPET was perceived as low value, hence a source of cost reductions. One of our core products in our rPET portfolio is our Sukano Melt Enhancer Masterbatches, which enables upcycle instead of just recycle. This masterbatch ensures uniform cell structure, improving mechanical performance and processing stability, allowing the use of recycled PET in high quality end applications and closed loop systems. Since different end applications require different product performances – and processing technology is not uniform at every industrial centre – our specialists can assist you in the selection of the most accurate and appropriate reactive chemistry to allow you enjoy the greatest value over benefit ratio. At Sukano, it is clear that only by joint forces and efforts along the entire value chain we can be impactful in achieving a circular and sustainable future. All our products are designed for circularity, enabling or improving production, sorting and recycling and, in the end, ensuring the most suitable end-of-life option with the best value that together leads us towards the common goal. www.sukano.com","@ID":42} "EDITOUR PETplanet Insider Vol. 23 No. 03/22 www.petpla.net 11 Tour Sponsors: MHT prepares for tethered caps and new threads We met: Dipl. Ing Christian Wagner, CEO at MHT Hochheim, Germany In the EU, tethered caps will be mandatory from 2024 and worldwide entirely thread geometries like 26/22 are expanding their market share. While the remainder of the preform can retain its original size, in many moulds the neck rings will need to be replaced with new geometries. As an independent mould producer, MHT has responded to the increased demand by building a fully automated production line for neck rings. PETplanet met with Christian Wagner, CEO at MHT. PETplanet: Everybody is talking about the introduction of tethered caps and we also see new threads for CSD and water coming up. How does that affect a highly specialised mould makers like MHT? Christian Wagner: At the moment there are different kinds of tethered caps entering the market but there is no standardised solution yet. As soon as the big players have figured out which caps they are heading for, there will be a huge demand for the reworking of existing moulds. The same is true for new threads which offer very interesting possibilities for saving material. If you look at a 26/22 for example with 2.4 grams compared to a PCO 1881 with 3.81 grams. PETplanet: Why is tethered caps such an issue? It’s only the caps, isn’t it? Christian Wagner: Many of our customers are still not aware that in most cases tethered caps will involve new neck geometries for the preform. There simply has to be some space for the tethering. As a reliable partner, we are trying to get ahead of the wave, talk about challenges and opportunities now – and prepare our production facilities for the rising demand. PETplanet: What does that mean in detail? Christian Wagner: We invested a lot in a fully automated manufacturing Dipl. Ing. Christian Wagner, CEO, talks to PETplanet Insider. The fully automated neck ring process inter-connects several machines by multi-axis robots. On tour with Editourmobil outside the gates of MHT in Hochheim, Germany. line for neck rings. This is the part that forms the contour of the thread and must be exchanged when preforms get a new geometry. The crucial thing is that we combined several operational phases and only need to clamp the neck rings once for everything that follows. The component can be machined from both sides and the machines used for high-speed milling, grinding, polishing and eroding are inter-connected by means of multi-axis robots. The neck rings pass through a cleansing unit that removes dust created before being measured at another station. The machine can run on its own for the weekend by means of an efficient magazine support system. The system has been designed in such a way that throughput can be increased by using additional machines. PETplanet: You mentioned opportunities that might open up regarding the thread exchange. Christian Wagner: Well, if you need to rework the mould anyway you can just as well look into lightweighting and material saving. That is why we are talking to our customers two years in advance about tethered caps. It often takes some time to check on patent situations and find the perfect solution for an application. PETplanet: MHT builds moulds for almost all PET systems on the market. Do you also exchange neck rings on moulds of different makes? Christian Wagner: Yes, that it is no problem at all. We measure the existing neck rings very precisely and manufacture the new ones accordingly – with the tethered cap geometry and maybe a lightweight thread, of course. PETplanet: Thank you so much Mr Wagner. www.mht-ag.de","@ID":13} "No.3 2022 www.petpla.net D 51178; ISSN: 1438-9452 21 . 03 . 22 PETplanet is read in more than 140 countries MAGAZ I NE FOR BOT T L E R S AND BOT T L E - MAK E R S IN THE AMER ICAS, AS IA, EUROPE AND AL L AROUND THE PLANET MARKETsurvey Suppliers of preform machinery Page 28 Page 36 Page 11 Page 44 AFTER SALES SURVEY","@ID":1} "ENERGY COSTS reduced by 15 %? UNLIMITED life time ! MAINTENANCE COSTS reduced by 50 %? Drinktec Munich Hall 5 / Stand 520 Messe München, 12-16 Sep. 2022 www.afcompressors.com [email protected] YES! AF Compressors can provide sustainable and long life 8 bar & 10 baroil free air compressors! Can AF Compressors also supply 8 bar & 10 bar, oil free air compressors? AF COMPRESSORS","@ID":12} "EDITOUR PETplanet Insider Vol. 23 No. 03/22 www.petpla.net 15","@ID":17} "38 CHINA SPECIAL & CHINAPLAS 2022 PETplanet Insider Vol. 23 No. 03/22 www.petpla.net SIPA Hall 4.1 Booth C07 Starlinger & Co Gesellschaft m.b.H., Austria by Paul Niedl, Commercial Head of Starlinger recycling technology 1) One of the main topics Starlinger will focus on at this year‘s Chinaplas fair is polyester fibre recycling. We will present various options for IV increase and melt filtration to achieve high-quality recyclate that will enable fibre producers to make their products more sustainable. Other topics will be PET bottle-to-bottle recycling for direct food contact applications, and PE and PP post-consumer recycling solutions featuring Starlinger’s highly efficient odour reduction technology. 2) China is one of the most important markets for Starlinger. Recognising the high potential of this country and in order to best serve this market, Starlinger founded a subsidiary with production facilities already in 2006. By now the Starlinger team in China has grown to more than 70 people, and our sales and service department provides quick support to our customers. 3) In China, the use of recycled PET for direct food contact is still not legally permitted. Only two companies with a special permission are allowed to recycle PET bottles for food contact applications – one of them uses Starlinger PET iV+ technology. We hope there will be changes in the legal framework soon because China has huge potential in the area of B2B recycling. www.starlinger.com STARLINGER Hall 2.1 Booth C52 Sipa Spa., Italy Sipa will be in Hall 4.1 on booth C07 at Chinaplas 2022, providing information on its latest developments in PET packaging design, processing equipment and moulds. Innovations will be highlighting in multimedia presentations including production and upgrades for preform injection moulds, their refurbishment (where Chinese plant in Hangzhou is very strong), to stretch-blow moulding moulds and machines, as well as systems processing post-consumer recyclate. For example, XForm Gen4 preform moulding systems can now be equipped with moulds made by Sipa that have 200 cavities – up from the previous maximum (already a market-leading figure) of 180. In China Sipa’s SFL linear stretch-blowing system is very well known especially for large size containers, both one-way such as collapsible or refillable with handle as the machine is quite a reference for inmould handle containers. As matter of fact, though, SFL are machines featured for producing a range of containers that is covering virtually all the specialties for the most diverse applications. The Xtreme Renew, a solution for the circular economy, with its ability to produce preforms for food-contact applications directly from 100% post-consumer flakes – providing important savings in energy over alternative recycling technologies as well as systems processing virgin PET. China has for a long time been an important market for Sipa. The company has operated a subsidiary– Sipa Machinery Hangzhou (SMH) – for many years. It employs close to 200 employees, involved in commercial activities, mould manufacturing and servicing, as well as a team of skilled packaging designers and engineers that is working very close to customers to provide new design & engineering both for preforms and bottles. The plant, extended over a total area of around 6,000m2, has the capacity to produce up to 800 injection stacks and 300 blowing moulds every month. PET, with its applications in food and beverage, chemical, medical and pharmaceutical fields, is one of the high-tech industries supported by the Chinese state. With market demand still increasing, Sipa expects local growth in the PET packaging sector to continue at high speed. What is changing is the increasing emphasis on recycling and the use of rPET in a growing number of food and non-food applications. At the same time, Sipa remains at the forefront of developments in container lightweighting, whether the PET material used is virgin or recyclate. www.sipasolutions.com","@ID":40} "CHINA SPECIAL & CHINAPLAS 2022 PETplanet Insider Vol. 23 No. 03/22 www.petpla.net 35 improvements in product shelf life and market appeal. Application of barrier materials into PET packages in the form of a laminated structure can improve the package’s resistance to permeability of gases and light depending on the type of barrier applied. Durability and shelf life of the product contained are extended as a result. It is particularly suitable for products which are sensitive to oxygen such as juice, and light such as dairy products. The technology also helps retain CO2 content in carbonated drinks, thus preserving their taste and flavour for a longer period. Moreover, multilayer co-injection can also realise colour gradation, delivering a new option for market appealing impression. PETplanet: Can you say something about the recyclability of the finished product? GDXL: While multilayer packages have potential in enhancing food safety and food conservation, their recyclability is worth improving from technological and commercial aspects. Research in bio-based and bio-degradable barrier materials, and a realisable way to process them in existing sorting and recycling systems are needed to attain sustainability goals. PETplanet: GDXL is strongly committed to research and development. What improvements/modifications in the field of preform, cap or blow moulds have been realised recently? GDXL: Continuous dedication in R&D of mould products have improved our overall competitiveness in the sector. For moulds, recent developments involve further improvement in performance. For instance, we developed a new structural design for enhancing uniform cooling capability of mould cavities, and a new base mould design achieving low pressure blowing, etc. There are also developments in preform designs. For instance, we are developing a preform design with an optimised base to achieve uniform distribution of base material during the blowing process, enhancing the performance of the resulting bottle while creating a bonus in the possibility for weight. Developments in other areas include inspection methods and improvements in our digital production system, etc. PETplanet: Thank you very much! www.gdxl.com Three questions for Boretech Group New projects in Taiwan What are new projects of Boretech? In 2022, the subsidiary of Boretech Group in Taiwan introduced the latest EC process technology of the PET bottle recycling system developed by Boretech. The EC process has been completed development in 2021, it is the first time to be applied in the PET recycling project. What is special about the EC process? The project adopts the hot washing and rinsing modular of the EC process PET bottle washing system. Compared with the traditional recycling process, it includes pre-mixing, hot washing, and drying, it occupies an area of only 110m2. The entire hot- washing module can replace the hot-washing machine, screw conveyor, and friction washer with the minimum equipment, which reduces equipment and civil engineering investment, and the process design is rationalised, compact and simplified. The special structure design of MegaWasher and the frequency control greatly improve hot washing efficiency and the rPET flakes’ cleanliness. The impurity content of the flakes after high-speed hot washing with MegaWasher can be stably produced. The Hydro rinsing module includes high-speed rinsing, floating, ultrasonic washing and dehydration. It is applied to PET recycling, either for HDPE, PP, PE recycling. The Hydro Washer replaces the continuous rinsing, which not only occupies a small area but also has higher rinsing efficiency. After rinsing, the pH value of flakes is stable in the range of 7.5±0.5, and the inline water reuse system reduces industrial water by 50%. The structure design of the floating washing machine ensures the material is under the water and achieves the complete separation of the sinking and floating materials. Where do you see future markets for PET recycling? Recently, the Food Safety and Standards Authority of India (FSSAI) issued direction under Section 16(5) of the food safety and standards act, which involved guidelines for recycling of post-consumer PET for food contact applications. It means that India has opened access to the food-grade application of recycled PET. As the second-largest populated country in the world, India has pushed the global recycled PET food application to a new chapter. The food-grade recycling equipment of Boretech provides a new option for India to open up food-grade applications for waste PET bottle recycling. www.bo-re-tech.com/en","@ID":37} "BOTTLING / FILLING PETplanet Insider Vol. 23 No. 03/22 www.petpla.net 20 How African edible oil producers have taken advantage of growing demand Efficient in a competitive market Based on statistics from Global Data, the edible oil market shows significant growth potential in Africa over the coming years. While product differentiation plays a big role in attracting consumers, packaging cost savings and production efficiency are important to maintain competitiveness. Moreover, it is crucial to bring sustainability to the fore in both package design and production. How can edible oil players take advantage of growing demand and the trends? According to Global Data, bottled oil accounts for the majority of the market with six billion units; edible oil is expected to reach a compound annual growth rate (CAGR) of 4.4% by 2024 within the food category in the Middle East, Africa and India region. Across the African continent, price is a key driver that influences consumers’ purchase decisions in edible oil. Domestic players dominate the market. Hence, their ability to rapidly fulfil consumer demand for competitive prices and availability plays a crucial role. Despite the outbreak of the pandemic, the edible oil market continues to grow, since it is essential for cooking. For producers, cost and productivity are therefore key to being competitive. To make a product that will stand out on the shelves, but simultaneously be lightweight, Sidel’s packaging experts are able to provide customised bottle design. With modern bottle design techniques from bottle digital mock-ups, technical designs to prototypes with 3D printed models, the bottle design can match customers’ preferences and be presented in real size before mass production. When it comes to production, either with a complete line or standalone equipment, Sidel provides a full range of solutions, from blowing and labelling to end of line equipment with shrink-wrappers, case packers and palletisers. The right tools and expertise to help with your rPET goals! Agr is uniquely positioned to support your venture into rPET bottle manufacturing with a powerful combination of Process Control tools, Process Consultants, and decades of industry experience. AGRINTL.COM • +1.724.482.2163","@ID":22} "PATENTS PETpatents PETplanet Insider Vol. 23 No. 03/22 www.petpla.net 47 Vacuum control International Patent No. WO 2021 / 154209 A1 Applicant: Amcor Rigid Packaging USA LLC., Ann Arbor (US) Date of application: 28.1.2020 A bottle made from PET intended for hot filling has a moveable segment in the base area with which vacuum pressure created during the cooling process can be effectively controlled. An easily detachable label International Patent No. WO 2021 / 182004 A1 Applicant: Tokyo Seikan Co. Ltd., Tokyo (JP) Date of application: 12.2.2021 A specially shaped plastic container which has a label that for disposable purposes can be easily removed from the container by pressing it at a certain point and then peeling it off with a spiral action. Uneven grooves International Patent No. WO 2021 / 183810 A1 Applicant: Niagara Bottling LLC., Diamond Barr (US) Date of application: 11.3.2021 A plastic bottle with all-round grooves with a specially designed base. The wave-shaped grooves ensure that the peaks and troughs of the waves do not overlap one another. An oval-shaped plastic bottle International Patent No. WO 2021 / 194506 A1 Applicant: Amcor Rigid Packaging USA LLC., Ann Arbor (US) Date of application: 27.3.2020 A standard oval-shaped highvolume bottle made from PET. The container, which is made stabile due to its grooves and balancing surfaces, is light in weight and prevents problems caused by deformation in the evolving structure of PET. A plastic bottle International Patent No. WO 2020 / 081248 A1 Applicant: Pepsico. Inc., Purchase (US) Date of application: 3.10.2019 A plastic bottle with a specially designed base and stability “feet” at the base. A sturdy plastic bottle International Patent No. WO 2020 / 079122 A1 Applicant: Société des Produits Nestlé S.A., Vevey (CH) Date of application: 17.10.2019 A lightweight plastic bottle that has been specially adapted to withstand force applied from the side.","@ID":49} "BOTTLING / FILLING PETplanet Insider Vol. 23 No. 03/22 www.petpla.net 22 After a terrible fi re: Serbian milk producer Imlek relies on an up-to-the-minute block system from KHS Phoenix from the ashes In 2018, a huge fire caused severerebuilt damage to Serbian milk producer Imlek’s production site. One of the many items destroyed was a KHS aseptic filler, just six years old. When it came to procuring a replacement, the company again opted for the German systems supplier – and for a block system featuring the latest in stretch blow moulding technology. neighbouring countries of Montenegro, Bosnia-Herzegovina and Macedonia. Further sales markets include Croatia, Albania, Slovenia and Russia. The diary giant was the very first in the Balkans to invest in an aseptic filler in 2012 in order to enable germfree filling of a section of its portfolio into PET bottles. Its prime aim was to facilitate the export of sensitive products by lengthening shelf lives and lowering transportation weights. Back then Imlek decided to invest in a linear KHS Asbofill ABF 711 filler, as with its very small aseptic zone this machinery permits sterile filling without the need for intermediate sterilisation. Focus on flexibility With its vast product range, fast format changeovers are important for Imlek so that it can react with the utmost flexibility during production, where extended shelf life (ESL) and ultra-heat-treated (UHT) milk products are bottled alternately. ESL milk keeps up to four weeks longer than standard bottled milk, for example, with unopened UHT products staying fresh for as long as three to six months. Short, trouble-free product changeovers for the many different smaller product batches in particular give the company greater flexibility, safety and speed over the use of cartons, for instance. Regarding flexibility, the Asbofill ABF 711 provides a vast range of bottle and closure design options, the use of which requires no mechanical intervention. One of the aseptic filler’s special features is its small sanitary room that measures just 1.5m3: in combination with the machine’s room-within-a-room concept, it cuts the risk of recontamination down to practically zero, says KHS. Limiting sterilisation to the necessary areas only – namely just the neck on the outside of the bottle – means that sterilisation media can be used more sparingly. Thanks to its compact design the filler also takes up less space and is easier to clean. And as it needs no extra water during the production cycle, for example, it also scores on sustainability. Devastating fire and successful rebuild In September 2018, a devastating fire tore through Padinska Skela, destroying much of the production shop and causing serious damage to property. Like so many other lines and machines, the exemplary technology of the aseptic filler was consumed by the flames. “The end of 2018 and the whole of 2019 were an extremely challenging time for us,” remembers Darko Samardžija, chief supply officer of the Imlek Group. “To guarantee market supply with our products, we had to redirect our contracted milk quantities to our other plants in the region for further processing and to production sites outside the Imlek system. Here, we needed to make sure that all the dairies This low-fat, sugar- and lactose-free chocolate shake is one of the products in Imlek’s new protein range. Darko Samardžija, chief supply officer for the Imlek Group What is now the Imlek Group has its origins in a farmstead in Glogonjski Rit, a suburb of Belgrade, where in 1953 an artisan dairy farm was established. This transported between 3,000 and 5,000 l of milk a day from the farm’s 800 or so cows to the city’s markets, initially in metal churns loaded onto horse-drawn carts and tractors. Just four years later the company installed its first pasteurising and filling line. Its development then gathered pace: by 1963 the dairy was already producing over 20 million litres of milk a year. The 1970s were also marked by growth, with more and more dairies becoming part of the consortium. Since 1991, the company has been run as a stock corporation under the name of Imlek. It now fills over one million litres of milk a day, with its annual turnover amounting to around €300 million. This makes Imlek a market leader – also beyond the Serbian border in the","@ID":24} "PACKAGING/PALLETISING PETplanet Insider Vol. 23 No. 03/22 www.petpla.net 26 Recycling in packaging by Dr.-Ing. Martin Facklam, Managing Director Training and Further Education at Institute for Plastics Processing in Industry and Craft (IKV) at RWTH Aachen University With the European Green Deal, the course has been set at EU level for an international shift towards a circular economy. A key objective is to promote sustainable products, business models and services, to adapt consumption patterns with the aim of avoiding or reducing waste, and also to establish a well-functioning internal market for high-quality secondary raw materials in the EU. For this reason, the basic requirements for packaging for approval on the EU market are to be tightened by 2030. The main topics in this context are: A reduction in packaging volumes and waste by reducing packaging complexity, including product-specific material variety; Promoting the reusability and recyclability of packaging through appropriate designs; Regulations for the safe recycling of plastics as food approved material. These focal points give rise to technical issues that can be addressed with the help of plasma technologies and digital solutions. The Institute for Plastics Processing in Industry and Craft (IKV) has been researching in the field of plastics recycling for many years and is currently developing highly functional layer systems in the field of packaging for various specific fields of application, which are outlined below. Reduction of complex (multi-material) packaging through plasma technology Complex multilayer composites made of different plastics, each of which fulfils a necessary packaging function, are currently still strongly represented in packaging technology. After use, these composites can only be thermally recycled because they can no longer be separated by type. With the help of Plasma Enhanced Chemical Vapour Deposition (PECVD) technology, plastics can be equipped with a high-quality gas barrier, whereby the recyclability of the plastic is not impaired. In the discussions on the circular economy, plasma technology has developed into a highly dynamic field of research with broad relevance and decisive innovative power. The packaging market is facing major changes due to the challenges of transitioning to a circular plastics economy. Films are already being successfully coated with a barrier layer in discontinuous “roll-to-roll” coating processes. To improve the process economy, however, there is currently still a lack of a continuous process variant to avoid the unavoidable dead times in previous batch processes. This disadvantage is to be circumvented with an innovative system development for continuous PECVD film coating. The film is unwound under ambient pressure and fed through a double door system into a vacuum chamber, where a SiOx coating is efficiently applied using a so-called “in-plasma concept”. The film is then guided back through the double door system to ambient pressure and wound up. The process can be carried out without interruption by means of commercially available tying procedures. To work out the complex airlock and vacuum system, the required pumping capacity is currently being evaluated and a sealing concept is being developed (see Figure 1). Figure 1: Experimental set-up for pump design (image: IKV) Reusable and recyclable design in the Deep Tech start-up IonKraft The potential and innovative power of plasma technology for the circular economy is demonstrated by the founding of the Deep Tech startup IonKraft, which has its roots at the IKV. IonKraft transfers scientific findings from plasma research into industrial production technology. Building on research and development work in the 1980s at the IKV, which today has led to marketable products in the form of the internal coating of PET bottles, IonKraft focuses on developing a system technology for coating large-volume hollow bodies. For these packagings, which are frequently used in agricultural technology, for example, also require barrier properties for various reasons, which up to now can only be solved by multi-material systems that are difficult to recycle. Scaling up the process to larger volumes certainly places new demands on coating plant technology, which must be achieved through design innovations in vacuum technology and microwave technology. Furthermore, the sometimes aggressive agricultural products also place new demands on the PECVD barrier layer, which must have a media-specific resistance for this purpose (see Figure 2). The business project is funded by the Exist research transfer programme of the Federal Ministry for Economic Affairs and Energy. Digitalisation as a solution approach for sustainable recyclate use The complex and highly variable composition of recyclates, in combination with the lack of evaluation","@ID":28} "PETcontents 6 PETplanet Insider Vol. 23 No. 03/22 www.petpla.net 03/2022 Page 36 AFTER SALES SURVEY 4 How satiesfied are you with your After Sales service? - Global market research study by PETplanet Insider EDITOUR 11 MHT prepares for tethered caps and new threads - Interview with MHT Mold & Hotrunner Technology AG 12 ‘Ich bin ein Berliner’ - Interview with Bekum Maschinenfabriken GmbH 14 Making the best of the worst of times - Interview with Universal Closures Ltd. MOULD MAKING 18 Challenge accepted - From R&D+I to producing moulds of label-less bottles BOTTLING / FILLING 20 Efficient in a competitive market - How African edible oil producers have taken advantage of growing demand 22 Phoenix from the ashes - After a terrible fire: Serbian Milk producer Imlek relies on an up-to-the-minute block system from KHS PACKAGING 26 Recycling in packaging MARKET SURVEY 28 Suppliers of preform machinery CAPS / CLOSURES 30 “CCM is our calling card on the market” - Interview with Nishant Mouldings about Sacmi’s CCM technology CHINA SPECIAL & TRADE SHOW PREVIEW 32 Outlook clear but overcast 34 PET - the ideal candidate - China’s consumers are increasingly demanding healthy drinks in sustainable packaging 35 New projects in Taiwan - Three questions for Boretech Group 36 Chinaplas 2022 preview 44 Anuga FoodTec 2022 preview 44 Aseptic line and packaging systems BUYER’S GUIDE 48 Get listed! INSIDE TRACK 3 Editorial 6 Contents 8 News 31 Onsite 46 PET bottles for Home + Personal Care 47 Patents 54 Outer Planet Page 22 Page 11 AFTER SALES SURVEY","@ID":8} "TRADE SHOW PREVIEW PETplanet Insider Vol. 23 No. 03/22 www.petpla.net 45 Aseptic line and packaging systems KHS Group will be presenting its entire portfolio of filling technology and environmentally-friendly packaging systems at Anuga FoodTec. With its InnoPET BloFill ACF-L block system the company provides a system solution for sensitive beverages in PET bottles that is low in space. A further focus will be on the new standard interfaces for communication between KHS machines and customer IT systems. For the filling of sensitive beverages in a hygienic environment, the turnkey supplier provides a portfolio of environmentally-friendly systems for various container designs and materials. With the InnoPET BloFill ACF-L stretch blow moulder/filler block, the Dortmund engineering company presents a further development for sensitive beverages in PET bottles that is especially low on space. The new system is claimed to come with a multitude of innovations, one being its new switching valve. This controls the volume of the inflow to the actual filling valve and thus permits a total of four different filling speeds. Bottle volumes both large and small with varying viscosities can be perfectly processed on this machinery – with low foaming an added bonus. The filling process is stored in the product recipes; there is no need for manual conversion. This makes for a reproducible filling quality and improves filling accuracy. The result is a stable output of beverages with different properties, in turn boosting efficiency and the flexibility required to fill a wide assortment of products. New standard interfaces As part of its Basic Line Monitoring process, KHS has developed new standard interfaces for line monitoring and order control. The respective modules facilitate communication between KHS machines and beverage producers’ IT systems. Furthermore, regular updates and new versions ensure a high, reliable quality of data. With this new standardised approach the systems supplier’s and customer’s own IT environments can be connected up to the machines even better and even more economically than before. This renders previously required time- and cost-intensive customised harmonisation and programming superfluous. Secondary packaging systems KHS will also be putting its range of packaging systems on display. Film made of up to 100% recyclate can now be used to wrap containers, as can paper or cardboard. The newly developed Innopack CNP or Carton Nature Packer turns beverage cans into stable packs using toppers or clips made of corrugated cardboard or solid board. Another packaging alternative is Nature MultiPack. This system joins beverage containers together with dots of adhesive to form a stable pack and is intended to save up to 90% in materials by doing away with the secondary packaging. Nature MultiPack is now also available for the highperformance range, with throughputs of up to 108,000 containers per hour possible when running at overcapacity. Depending on the format, the machine manufactures up to 450 packs of four a minute. Retrofits on existing packaging machines KHS offers extensions for existing Innopack machines. The new alternative that wraps beverage cans in paper instead of film is one such retrofit, for instance. Customers can opt for more flexibility by switching between film and paper packaging as required or permanently switch to paper. www.khs.com Hall 5.1 Booth B051 C058 InnoPET BloFill ACF-L stretch blow moulder/filler block In addition to its filling technology and various digital solutions the KHS Group will be exhibiting its range of packaging systems in Cologne.","@ID":47} "EDITOUR PETplanet Insider Vol. 23 No. 03/22 www.petpla.net 12 Tour Sponsors: Extrusion blow moulding machines from the German capital - Interview with Bekum Maschinenfabriken GmbH ‘Ich bin ein Berliner’by Kay Barton January 27, 2022 We met: Mr Christian Richard, Sales Administration & Corporate Communications Manager the Berlin Wall looming nearby, we had to come up with some way to expand. The solution was in Traismauer, Austria, where industrial areas and qualified employees for the further development and production of machine parts were available. With the growing product range, capacities in Traismauer increased, where in the course of time complete large blow moulding machines of our Large Blow Moulder series “BA” started. Traismauer’s full responsibility for the development and production of the BA series was finally taken over in 1994. In addition, at Traismauer, there is a state-of-the-art mechanical inhouse and job-order manufacturing facility, which supplies a comprehensive range of flexible and precision manufacturing activities. After With its machinery and systems, Bekum serves both the food and beverage industry and various nonfood sectors, such as the automotive and pharmaceutical industries. The manufacturer has recorded growth of over 10% annually in the years 2019 to 2022 and has managed to take advantage of supply shortages in other engineering firms caused by the pandemic and achieve record sales. Currently, its principal markets are in the packaging sector with handleware bottles for food and beverage. Interview partner Christian Richard, Sales Administration & Corporate Communications Manager at Bekum, has been with the company for more than 27 years and is almost part of the furniture. As an introduction, he told us the history of the company sites: “Back in 1968, with business booming and Bekum Maschinenfabriken GmbH has its headquarters on an industrial estate in the south of Berlin’s Tempelhof-Schöneberg district. It is an original Berlin company and after more than 60 years of its existence, the world of extrusion blow moulding has long been unimaginable without it. Founded in 1959 by Gottfried Mehnert, the company remains family-run and has trodden a continually successful path, delivering various important inventions and patents. When it all started, the still new company became a talking point with its development of the first ring neck calibration. This was followed in 1963 by the first double-station blow moulding machine in the world and then, 13 years later, the first blow moulding machine for six-layer coextrusion. Full order books in the Berlin Wall era and the resulting expansion restrictions in the city led to the establishment of the Traismauer site in Austria in 1968. In 1979, another site was added in Williamston, Michigan, USA, to serve the North American market. But Berlin always remained the nerve centre and beating heart of Bekum, uniting the departments for Sales, Customer Service, Design and Development. The upcoming generation of the entrepreneurial family is ready in the starting blocks to secure the company in the long term. A reason for us to drop into the company’s headquarters. Christian Richard, Sales Administration & Corporate Communications Manager, Bekum","@ID":14} "9 NEWS PETplanet Insider Vol. 23 No. 03/22 www.petpla.net Klӧckner Pentaplast: rPET/PET capacity expansion Klöckner Pentaplast, a global leader in recycled content products and high-barrier protective packaging, has announced its intention to expand its post-consumer recycled content (PCR) PET capacity in North America with an investment to further grow its sustainable innovation offering in consumer health, pharmaceutical, and food packaging markets. The expansion will add an extrusion line and two thermoformers delivering a total of 15,000 metric tonnes of new rPET/PET capacity. The extrusion line will support the production of sustainable product lines such as kpNext recyclable pharmaceutical blister films, and Smartcycle recyclable label and consumer packaging films. The thermoformers will produce kp Elite mono-material protein trays which are made using up to 100% rPET and are claimed to be easily recycled. The location for multimillion-dollar expansion is currently under review and will sit next to one of its six North American plants that is best situated to serve its customer base. It is targeted to be fully operational in Q1 2024. www.kpfi lms.com Alpla Group continues international growth trajectory The Alpla Group, the global packaging solutions and recycling specialist, increased its turnover in the 2021 financial year by 8.4 per cent to four billion euros. The number of employees worldwide increased to 22,100. In addition to investments in recycling and in the development of bio-based and biodegradable plastics, the company expanded through acquisitions and participations. Since 2021, the Alpla Group has invested an average of 50 million euros annually in the expansion of recycling activities. By 2025, the recycling loops are to be closed in as many regions as possible. “Our customers’ demand for high-quality recycled materials is also growing outside Europe. In the long term, we want to cover between 70 and 80 per cent of demand with our own production,” says CEO Philipp Lehner. Outlook 2022 Growth of three to five per cent is the target for the 2022 financial year. “Numerous projects and acquisitions in the USA, Mexico, Asia-Pacific region and Western Europe enable us to strengthen existing and enter new product and market segments,” Lehner emphasises. With the new Asia-Pacific (APAC) region coming on stream in early 2022, Alpla is also expanding the reach of its industry-leading mould technology in the growing Asian market and driving the expansion of the circular economy in the region. www.alpla.com Coca-Cola pledges to increase share of sales in refillable bottles With an eye to curbing plastic waste, The Coca-Cola Co. announced the goal to increase the share of its beverages delivered in returnable/refillable containers. The company committed to selling 25% of beverages in refillables by 2030, up from a current 16%. The pledge was in response to a pending shareholder proposal filed by As You Sow and Green Century Capital Management, asking the company to set stronger refillables goals. A recent analysis by Oceana indicated considerable potential to reduce ocean plastic by increasing refill market share. It concluded that boosting the share of refillable bottles by 10% in all coastal countries in place of single-use PET bottles could reduce plastic bottle marine plastic pollution by 22%. Nearly half of the company’s packaging consists of singleuse PET plastic bottles, generating 3 million tons of plastic packaging annually, the equivalent of producing 200,000 bottles/minute. The company states that single-use bottles are far more likely to be improperly disposed of and become ocean pollution, harming marine life. Refillables are claimed to provide opportunities for faster, larger cuts in single-use plastic, since they do not need to be remanufactured each time they are used. Refillables have demonstrated their ability to substantially cut plastic waste while providing substantial profits with a 90% collection rate, says Coca-Cola. The bottles can be reused from 20 to 40 times. By comparison, less than 30% of single-use PET beverage containers are recycled in the U.S. Refillables account for 50% or more of company sales in more than 20 global markets, and 25% or more in another 40 markets, yet Coke had not committed until now to strategically increase refillables targets and timelines except in one country - Brazil. As You Sow filed the shareholder proposal in conjunction with Green Century Capital Management as co-lead filers. After additional analysis of the details of the company’s goal, the filers will determine whether to withdraw the proposal. www.coca-colacompany.com www.asyousow.org","@ID":11} "TRADE SHOW PREVIEW PETplanet Insider Vol. 23 No. 03/22 www.petpla.net 44 Global trends of the international food and beverage industry Anuga FoodTec 2022 Following the Corona-related postponement of Anuga FoodTec from March 2021 to April 26-29 this year, organiser Koelnmesse is expecting a high number of registrations. The trade show offers the food and beverage industry an information and ordering platform for all sections of the production, processing and packaging. Liquid processing and sustainable packaging are among this year’s focus themes. The latest technical updates make it possible for machinery in the beverage industry to adapt to as many different containers as possible and fill the most varied products – from carbonated refreshment drinks to water. Step-by-step, the system manufacturers are networking production processes with the help of digital and smart technologies, so that machines can communicate and coordinate with one another more efficiently. Filling under hygienic conditions Mixed milk beverages, juices, smoothies and near-water products present especially stringent requirements for hygienic filling, as Manfred Härtel from KHS knows. As Product Manager Filling, Härtel is responsible for all filling technology at the Dortmund filling and packaging systems manufacturer. “Filling under aseptic conditions in particular is a protecting process for recontamination-free filling and sealing“, he explains – a technology for which there are hardly any alternatives. In order to ensure the safe filling of sensitive beverages, the linear fillers of KHS can be blocked with a rotative stretch blowing machine. Thanks to the blocking, a possible introduction of contaminants is minimised, which has a positive effect on hygiene and system availability. A transfer module developed to this purpose harmonises the continuous flow of PET bottles with the stepby-step filling process. The containers are divided up into units of ten pieces each in the process with the help of a handover carousel. In keeping with the industry wish for greater flexibility, the module is available in three variants: for blocking with the stretch blowing machine, with an additional outflow for the Plasmax coating machine or an optional bottle inflow that makes it possible to process both PET and HDPE bottles. The requirements for volumetric dispensing modules in the filling systems are also high. Thus, for example, the required output quantity must be precisely maintained at high frequencies, which is a challenge, especially for highly viscous liquids and chunky ingredients. In-line dispensers that function completely automatically and aseptically and are installed between processing and filling machines assume this task. Dual filling systems of this kind are equipped with two separate filling modules, which are located in the same microbiological isolator. More room to manoeuvre for ESL beverages The Whitebloc Aero from Gea is also based on proven aseptic technology, but was optimised for the specific requirements of ESL (Extended Shelf Life) products. The kicker: the bottle sterilisation with the help of dry H2O2 and the subsequent activation with hot air are possible in one and the same carousel. Sterilisation, filling and sealing take place in a clean room, in which sterile air that is evenly guided upwards under slight overpressure ensures the maintenance of the hygienic and protected environment. Depending upon the product sensitivity and the required minimum shelflife, various sterilisation goals can be defined to determine which are best suited depending upon the acidity of the products. Reusable PET containers, which are primarily used for carbonated soft drinks and water, have acquired a large market share in the past decade. However, PET packaging has played a more subordinate role for ESL products to date. A research project from Krones should now change this. Together with the cooperation partner, the plant manufacturer from Neutraubling was able to develop a reusable PET container that provides sensitive products optimal protection in the cooling chain. A special focus of Ines Bradshaw, responsible development engineer at Krones, was on the cleaning process of the containers, because: “PET is less heat-resistant than glass. We therefore had to find a way to ensure a high degree of microbiological safety and a large number of cycles at lower cleaning temperatures.“ This was successful thanks to the right choice of the cleaning parameters, especially with regard to the alkaline solution concentration, additive and mechanical impact. In microbiological terms, the PET bottles that had already gone through 25 cycles could not be distinguished from new ones. “Temperatures of around 60 °C are now adequate to reliably remove dried protein, fat and starch contamination from the containers“, according to Bradshaw. www.anugafoodtec.com","@ID":46} "MOULD MAKING PETplanet Insider Vol. 23 No. 03/22 www.petpla.net 18 From R&D+I to producing moulds of label-less bottles Challenge accepted While PET label-less bottles are gaining shelf space and other commercialisation channels, the legal information printed on the container could be less than before. However, the multitude of technical and design resources involved in a label-free bottle make it complex for the mould maker to define in a technical document. It is no longer enough to use a drawing with the code of an etching pattern is shown, solely. Precisely defining textures, glosses, reliefs and other forms of communication involved in a label-less container becomes a necessity for global R&D+I teams. Branding agencies are having more influence than ever on PET bottle design teams. Inevitably, this will require changes in the way designers communicate with engineers at blow mould suppliers. The multiplicity of technical and design resources used in a label-less bottle adds layers of complexity to the way that information is transmitted. The 3D model of a PET bottle contains detailed shape information but a challenge raised by label-less bottles is merging or integrating graphic design resources with industrial design. Engraving texts within a blow mould is not new. Small diameter cutting tools, which rotate at high RPM, have been used until now but the advent of laser technology in mould manufacturing has changed results and greatly expanded possibilities. Is it possible to create exactly the same text if the mould is made using CNC milling machining equipment instead of laser equipment? The answer is: No. A similar result in the blown bottle compared with the laser mould version can, in some cases, change what the branding agency sought to communicate to the target consumer. The beam of light from the laser creates pure shapes on the metal, just like ink on a label, so the logos and fonts are transmitted to the mould as designed – but what happens when a toolmaker changes manufacturing technology from laser to milling machine? Could the shine on the production bottle’s skin not be exactly what was initially achieved in the R&D+I laboratory? And could this ultimately lead to on-shelf performance being affected? Something similar happens with the textures and many other technical resources applied to develop this new high-tech packaging generation. The new design paradigm is associated with the need to communicate more than a shape by the blow mould. Deformations of even a minimal tool radius distort bottle details and, ultimately, the transmission of information. The brand logo, texts, textures, polishing – and more – must be accurate, in order to reproduce every effect that initially was approved in the pilot mould and avoid unexpected commercial results. The success of a NoLabel bottle is not only the industrial design itself, says Juan Manuel Colmenares, Senior Engineer at Moldintec’s TechCenter Buenos Aires. The mould plays a decisive role in creating the effects that make designs legible and attractive, in practice. It brings the virtual into the real world. The use of laser has changed the definition of what we manufacture, as well as the limits of what is possible. The historic corner radius distortion is no longer an issue but getting PET to copy the mould faithfully requires several other factors to be resolved, first. Engineering of the venting channels is an example. Its calculation, location and how they are manufactured will radically influence bottle results. Drilling a hole in a NoLabel bottle is not the same as making a continuous venting frame with the laser, or even combining the two techniques. Something similar happens with textures and fonts. Etching patterns are no longer two-dimensional image applications on a mould surface with a fixed depth. It is now possible to apply specific depths to each part of a pattern and create amazing 3D effects. To make the stunning effects of a NoLabel container, a texture needs a pattern (an image created by designers) but also definitions of density, height or depth, levels of application, roughness, and numerous other fundamental parameters. Companies’ R&D+I teams face the challenge of converting graphic design information into an engineering document. With labels, it is about transmitting the font, the printing colour coding through standards such as Pantone, the technology of printers to be used, the substrate, along with other parameters, to create a label is the same, globally. During the R&D+I process of a novel label-less bottle, several design parameters exceed the 2D drawing and 3D model limits. The techniques and technologies used in the pilot mould must be replicated, in order to manufacture those that will operate at commercial scale in industrial production. This means that they Blow mould shells for label-less mineral water bottles from Danone Villavicencio","@ID":20} "PETnews 8 NEWS PETplanet Insider Vol. 23 No. 03/22 www.petpla.net PETINAR Evergreen to install AI-enabled sorting robotics in third recycling, rPET manufacturing plant Evergreen, one of North America’s three largest producers of food grade rPET, has announced that it will be installing artificial intelligence (AI)-enabled bottle sorting robotics at its Albany, New York plastics recycling and rPET manufacturing facility. When the installation is completed in mid 2022, Evergreen will have deployed 15 high-speed, highly accurate robotic lines at its three of its United States locations. Supplying the robotics sorting lines to Albany is AMP Robotics Corp., a pioneer in AI robotics and infrastructure for the waste industry. AMP installed the AI-enabled robotic sorting lines in Evergreen Clyde in April 2021 and Evergreen Riverside in August 2021. Evergreen President and CEO Omar Abuaita says replacing previously manual sorting processes with high-tech robotics is part of a strategic vision to transform not just his company, but the overall plastics recycling industry. “With demand for recycled PET at the highest levels in history, we simply can’t rely on outdated ways of doing business. Evergreen is playing for keeps. Automating our sorting lines allows us to support ever larger PET recycling streams, provide the millions of pounds of food grade rPET our customers have committed to purchasing, and achieve a safer, more efficient work environments for our team.” Last month Abuaita revealed that Evergreen, a portfolio company of private equity firm the Sterling Group, has invested more than $ 200 million in modernisation, capacity expansion, and acquisitions over the last 12 month. The AMP robotics are part of that investment. Evergreen currently recycles more than 11.6 billion postconsumer PET bottles a year, up from 2 billion in 2021. General Manager Greg Johnson says the AI-enabled sorting lines are an absolute necessity to increase both the speed and accuracy of sorting the monumental volume of bottles Evergreen processes. www.evergreentogether.com Carbios to build in France a manufacturing plant for fully bio-recycled PET in partnership with Indorama Ventures After having successfully started-up its demonstration plant in Clermont-Ferrand, Carbios is now moving one step further towards the industrialisation and commercialisation by partnering with Indorama Ventures. The goal is to build and operate in France the world’s first industrial-scale enzymatic PET bio-recycling plant, with a processing capacity estimated at ca. 50,000 t of post-consumer PET waste per year, equivalent to 2 billion PET bottles or 2.5 billion PET trays. After the positive results of Indorama Ventures’ initial analysis on the technical soundness of Carbios’ technology over the past several months, both parties agreed to complete a due diligence process. A feasibility study will be conducted for the industrialisation of Carbios’ technology on Indorama Ventures’ French production site. Subject to the successful completion of these technical and economical evaluations, Indorama Ventures would co-invest in the project. With its world-first enzyme-based biological process, Carbios’ technology, named C-Zyme, converts PET into its core monomers, which can then be used to manufacture 100% recycled and infinitely recyclable PET. This manufacturing plant is claimed to combine Carbios’ science and technology with Indorama Ventures’ world-class manufacturing capabilities. This collaboration will meet the growing needs of both demanding consumers and large consumer goods companies including Carbios’ partners and shareholders (L’Oréal, Michelin, L’Occitane, Nestlé Waters, PepsiCo, Suntory Beverage & Food Europe) for more sustainable packaging. www.carbios.com www.indoramaventures.com On 24 March 2022 at 2 p.m. PETplanet Insider will host another PETinar on the topic of Tethered Caps! Learn from Sascha Baumanns, Director of Sales at Intravis about the possibilities of inspecting tethered caps. Mark Smith, Senior Vice President at Universal Closure and Michael Fink, CEO of z-Moulds will report on their joint projects and present their moulding concepts and systems. All three companies are well established in the market and will be available to answer your questions! PETplanet’s Editor-at-large Ruari McCallion will guide through the PETinar. Register now: https://petpla.net/category/petinars","@ID":10} "CHINA SPECIAL & CHINAPLAS 2022 PETplanet Insider Vol. 23 No. 03/22 www.petpla.net 32 Outlook clear but overcast China is a main player in the PET market. This applies not only to production but also to demand. A circumstance that, in the current situation with rising energy and raw material prices, is raising worry lines on the foreheads of many processors from abroad: supplies from the Far East are not forthcoming or are only available at a significant price premium. At least for 2021, machinery and plant manufacturers in China however, including foreign companies, have had positive economic developments to report. However, just before this issue went to press, the head of government Li Keqiang issued a target of 5.5% economic growth for this year, which is the lowest figure since 1991. And at this point, it is not yet possible to estimate what effects the conflict in Ukraine will have additionally. Globally, the PET bottle market reached a value of US$ 39.7 billion in 2021, according to a projection of Imarc Group. Looking forward, the analysts expect the market to reach US$ 52 billion by 2027, exhibiting at a CAGR of 4.46% during 2022-2027. The Chinese market is seen as one of the global PET bottle market drivers. The rising trend of westernisation, inflating disposable incomes and altering food patterns of consumers have increased the demand for bottled beverages. Additionally, hectic lifestyles have enabled consumers to opt for on-the-go beverages. These developments result in the fact that China – which is considered the cheapest supplier of PET in the Asian region – meets high demand at home and is sold out. This also applies to the situation on the feedstock market. Changing recycled PET market The global recycled PET market size is expected to grow from USD 8.9 billion in 2021 to USD 11.7 billion by 2026, at a CAGR of 5.7% during the forecast period, according to figures provided by Markets andMarkets. Flakes are the fastest-growing type segment in the recycled PET market. Growth is attributed to the rising demand in various end-use applications such as food-grade bottles & containers, sheets, and fibre. Bottles are the largest and fastest-growing application segment in the recycled PET market. Increasing demand for rPET bottles in food & beverage packaging is driving the market. Growth of this segment is attributed to the rising demand for bottle-to-bottle recycling across the world. It accounted for a share of about 36.5% of the recycled PET market, in terms of value, in 2020, says a report by Research and Markets. Asia Pacific (APAC) is the largest and market of recycled PET, with China being the major emerging market. Czarnikow market analysts see an rPET boom coming in Asia: attempts to use food-grade rPET in Asia has been contested by many of Asia’s largest food packaging producers like China and India. Now, more Asian countries are revising their stance on the use of rPET in food contact materials: India, Thailand, and South Korea have amended food packaging standards and food-grade rPET","@ID":34} "36 CHINA SPECIAL & CHINAPLAS 2022 PETplanet Insider Vol. 23 No. 03/22 www.petpla.net Chinaplas 2022 preview Chinaplas 2022, to be held from April 25 to 28, will bring together more than 4,000 exhibitors from all over the world to launch innovative green solutions. A lot of events will be organised during Chinaplas 2022, focusing on green topics such as carbon neutrality and sustainable development. For this year’s edition, PETplanet has launched a three-question survey. 1) Are you exhibiting at the Chinaplas fair? What innovations will your company be presenting? 2) How important is the Chinese market for you? Are you planning to invest or establish yourself there? 3) How do you see the PET industry developing this year? Exhibit presentations are also included. We are pleased to be able to inform our readers in such detail about the Chinese market and invite you to our booth in Hall 8.1, booth no. A08. Enjoy reading and have a great show! www.chinaplasonline.com Previero N. srl - Sorema div. of Previero, Italy 1) Yes, Previero - Sorema is going to be present also this year at Chinaplas, booth Nr. F71, Hall 2.1. Sorema will present its new developments in the mechanical recycling of plastics (PET, PP, PE and fibres) including proven technology for deinking industrial and post-consumer waste. 2) China is undoubtedly an extremely important market for us. At present, there is a plan to establish a Previero office in China within the next 24 months. 3) We believe that the PET industry will develop like last year when large producers of mineral water and soft drink bottlers and the producers of fibres led the market towards a high quality target of recycled materials. Sorema is a leading company in the recycling technology and its well proved plants are the solution to reach the upgrading of recycled materials requested by these industries. www.sorema.it And&Or, Spain 1) Yes, And&Or will be present at booth C07, Hall 4.1. The company exhibits its lateral handle applicator for PET bottles. It is an equipment that automatically inserts handles in PET bottles. 2) The Chinese market is currently representing 10-15% of our total sales. We already established a sales office in Suzhou. 3) The Chinese market is recovering this year again, and we expect to achieve the numbers from pre-Covid situation in 2022. More efficiency of blow moulding line with automatic handle applicators Moving from HDPE to eye-catching PET bottles with inserting handles automatically with And&Or handle applicator machines: by inserting the handle outside the mould, the speed of the packaging line can be much higher. The system is appropriate to be installed in the existing blowing/filling/packaging line. Finally, the high-quality PET bottle is more attractive because the handle can be coloured. And&Or applicators were developed with specialised technology allowing the automatic insertion of different types of handles. They are adaptive for low, medium or high-speed lines, with different sort of operation: rotary, interval linear or continuous linear. And&Or offers a wide range of handle insertion machine systems, approaching state of the art premium application technology to bottlers and bottle manufacturers willing to transition to PET handle-ware containers. And&Or will offer brands expertise and professional advice in all the transition, accompanying the customer throughout the complete process with support in the design and conception of the handle, bottle, preform specs, etc. with a team of design members and partners to ensure a successful and cost effective final handle-ware bottle. www.andyor.com SOREMA Hall 2.1 Booth F71 AND&OR Hall 4.1 Booth C07","@ID":38} "PETplanet Insider Vol. 23 No. 03/22 www.petpla.net 46 PETbottles Home + Personal Care An artistically-designed sleeve label In some countries, Ecover sells a variety of cleaning agents under its “Method” brand which have their own distinctive styles. The sleeve labels have been designed by artists and are intended to be pleasing to the eye of the buyer and to offer something different when the products are put in the sink at home. Pictured are two dispensers from the “art collection” plant-based liquid soap range. The product comes in 100% recycled 354 ml bottles which have a lockable pump dispenser. www.methodproducts.co.uk A limited edition detergent The German discount pharmacy company Dm has brought out a limited edition of an allpurpose liquid detergent under its “Denk mit” label. According to the manufacturer, it washes at lower temperatures, guaranteeing a brilliant white finish while reliably removing stains. The orangescented, green-coloured product comes in a clear 1 l bottle with a sleeve label which is transparent on both sides, making it easy to see the liquid level. The bottle is secured with a screw cap and has a dispensing aid. www.dm.de Pril in a special sized bottle A promotional campaign has been advertising the availability of the well-known Pril detergent in a special sized 600ml bottle. The light pink-coloured product containing pomegranate, orange blossom and natural mineral pearls comes in a clear bottle made from 100% recycled material. The colour of the bottle and product, along with the transparent label, ensure the pearls are easily visible as well as generating a lot of interest when displayed on shop shelves. A screw-on, one-handed hinged press-down lid with dispensing spout enables the product to be easily applied. www.pril.de A messy bun-cream in PET The market for hair-styling products has always followed the latest fashion trends. The latest example of this is a “messy bun cream” from Balea. Dm’s own label promises to create a natural look of the bun and a matt finish of the hair when using the cream. The styling product, which is made from ingredients including jojoba oil and rose water, comes in a pink-coloured 150ml bottle and is applied using a lockable pump dispenser in a contrasting colour. A wrap-around self-adhesive label provides information on the product and on how it should be applied. www.dm.de","@ID":48} "BOTTLING / FILLING PETplanet Insider Vol. 23 No. 03/22 www.petpla.net 21 Redesigned bottle with increased practicality Sidel recently supported one of Africa’s leading edible oil producers, Willowton, with redesigning the bottle and installing two standalone blowers – EvoBlow SBO 10 and SBO 16. The new cylindrical Sunfoil silhouette bottle not only had an elevated aesthetic level, but also increased practicality due to its easy-to-handle beltinspired design and reduced diameter. The company also benefited from its two blowers, ensuring higher performance and production integrity. “With the Sidel blowers, we have already increased our yearly production volume by 50% and we are ready to handle any future additional demand as well,” says Faisal Modi, Operations Manager at Willowton. Enhanced productivity and cost-saving Sidel has a strong heritage in edible oil, acting as a one-stop-shop partner in proposing complete and integrated PET lines including a combi configuration, which can help minimise equipment and conveying footprint by up to 30%. Agrimed chose Sidel’s complete edible oil line solution to sustain its leading market position in Tunisia and other export regions such as Libya and the Middle East. The company already owned a Sidel blower and labeller for various bottle sizes. As a result of good performance from their existing Sidel equipment, Agrimed invested in a new complete line including the new blowing/filling/capping combi with Serac. Net weight filling technology dedicated for its 1 l bottle line, running at 18,000 bph. The highspeed complete line has enhanced its productivity by reducing the previous long changeover time. Mohamed Laamouri, Plant Manager at Agrimed stressed that many costs had been saved with bottle lightweighting options while bottle robustness has also been optimised. This aspect is especially important to him as these bottles will be in wrap around cases. Today, edible oil is a very competitive market category, essentially driven by product and brand differentiation as well as competitiveness through packaging cost savings, production efficiency and permanent asset optimisation. Sidel states that it has generated many success cases with edible oil players in the Middle East and Africa, both in the low and high speed market. Sidel addresses the low speed market through Synergy, its linear blow moulding provider. www.sidel.com September 12-16, 2022 Munich, Germany Hall C5, Booth 440 Innovative solutions for special preforms PMC units for all major PET systems German Technology","@ID":23} "39 CHINA SPECIAL & CHINAPLAS 2022 PETplanet Insider Vol. 23 No. 03/22 www.petpla.net 39 TRADE SHOW PREVIEW Otto Hofstetter AG - High quality injection moulds and systems from Switzerland Following the successful trade fairs of previous years, the Swiss firm Otto Hofstetter is present with its own stand, the products and services this year. Otto Hofstetter will inform customers regarding the complete portfolio of high quality injection moulds. Besides the well know high quality injection moulds, Otto Hofstetter will inform about the services which start at begin of a project with an idea for a product, follow with the competence to consult and design the product. Once the injection mould is build, the after sales service will round up the complete package. Otto Hofstetter is well known for PET preform moulds from 2 up to 192 cavities, as well as for injection moulds for thin-walled packaging, medical articles and in mould labelling solutions. Otto Hofstetter will present products for thin-walled packaging and medical industry as well as the competence for complete systems to produce PET preforms. Under the roof of the Otto Hofstetter Holding Otto Systems AG is presenting system solutions for PET preforms at the same booth. www.otto-hofstetter.swiss OTTO HOFSTETTER Hall 2.2 Booth K21","@ID":41} "31 ON SITE PETplanet Insider Vol. 23 No. 03/22 www.petpla.net ONsite Upcoming facility expansion to recycle 3.5 million PET bottles per year BariQ based in Giza, Egypt, a PET bottle-to-bottle recycler in MENA region is expanding and upgrading its existing plant with another Starlinger PET recycling system and an additional solid-state-polycondensation (SSP) reactor. The new recycling system, a reco-Star PET 215 HC iV+ including a visco-Star 350 SSP reactor, reaches an output of 2,700 kg/h and will enable BariQ to increase its total production capacity to 35,000 metric tonnes of food-grade rPET pellets per year. The viscoStar 350 SSP reactor – the biggest size of the latest reactor generation – provides extended processing capacity and residence time while it keeps the footprint of the new recycling line compact like the first Starlinger PET recycling line BariQ installed in 2012. BariQ will also upgrade its existing Starlinger recoStar PET 165 iV+ recycling line with a new melt filter for fine filtration and an additional SSP reactor. This setup not only increases the line’s output, it also allows the production of rPET types beyond the regular bottle-to-bottle grades, guaranteeing good decontamination results and 24/7 production of rPET with highest quality specifications. BariQ’s investment also includes the latest sorting equipment from Tomra Recycling to ensure optimum quality of the input material. According to BariQ, the high variability of the input material and the rising quality requirements of the customers are the biggest challenges the company has been facing since it started operations in 2012. BariQ sources its post-consumer bottles mainly from local collection and GCC countries. As bottle quality and decontamination vary greatly, the recycling equipment must be able to handle such demanding conditions in order to achieve top rPET quality and meet customer requirements. Founded in 2011, BariQ is the first food-grade rPET producer in Egypt and the biggest in the MENA region. The company started production of food-grade rPET with a Starlinger PET recycling line in 2012 and holds a positive EFSA opinion and an FDA Letter of Non-Objection (LNO). It is also the first non-European recycling company to be registered with ECOEMBES Spain. In November 2021 BariQ was acquired by Intro Resource Recovery, a member of Intro Group, to strengthen its waste management portfolio. With the upcoming facility expansion, BariQ aims to recycle 3.5 million PET bottles per year, producing 35,000t of food-grade rPET for new bottles and saving 80,000t of CO2. BariQ supplies the foodgrade rPET to major converters and brand-owners in Europe and worldwide. www.bariq-eg.com www.starlinger.com In front f.l.t.r.: Andreas Pechhacker, General Manager Starlinger recycling technology, Mostafa Khairat, CEO BariQ, and Tasos Bereketidis, Sales Director Emerging Markets at Tomra Sorting Recycling, signed the contracts for the plant expansion. Symbolic picture","@ID":33} "EDITOUR PETplanet Insider Vol. 23 No. 03/22 www.petpla.net 16 Tour Sponsors: has been specifically developed for attached closures. The thread diameter of the neck is just 26mm, down from 28mm of the PC 1881. This enables the tethered cap strength requirements and performance standards to be met while, at the same time, reducing the weight of the finish – often the single heaviest element in a PET bottle. It’s a step forward but its emergence, at the same time as the two years of the Covid pandemic, has led to a downturn in investment in new equipment. “We hit the beginning of the pandemic with the 1.9 g CSD closure. Under normal circumstances, that would have been quite an easy sell,” he continued. “If you’ve had the 2.1 g for the previous five years then, in the normal course of refurbishment, you would go for the lighter version – it would save a lot of money in raw materials. But the pandemic has led people to delay investing in new equipment and, probably, now to look to the GME 30/40.” Driving development However, the hiatus in investment has not impacted on UCL’s development activity; rather, the opposite. Enquiries have been coming in about tethering systems and the company itself has been looking to develop markets complementary to its historic heartland of CSD and waters. “Westfall Technik, our newest partner, is based in the USA. Our MD, Rod Druitt, is spending a lot of time over there right now,” Mark said. “They have an interest in broader areas of the market, including healthcare, personal care and homecare, as well as beverages. Our relationship with them means that we have had a lot more enquiries from sectors outside beverages than has been the case, historically. As a result, in terms of design activity, developing new closures and prototyping them we have been as busy as ever.” Opening new markets The fact that international travel has largely been out of the question means that UCL has hunkered down, take those enquiries and developed a whole new market. A lot of enquiries have enabled it to bring its beverage expertise to bear on liquids with different viscosities, developing resolutions through innovative technology, eliminating components and materials from caps and closures. “We were the first to design an effective cap that didn’t need a liner to create a seal on extrusion blow moulded bottles,” he continued. “Eliminating materials means reducing cost, cutting energy consumption, reducing waste and improving recyclability.” A lot of the package materials being used in homecare, healthcare and personal care are different – and processed differently – from CSD’s PET. Drink bottles are likely to be used fairly quickly; a large bottle of cleaning material is likely to be around for longer and to be treated more roughly, so the typical material is more likely to be HDPE. A single-stage extrusion blow-mould process, for example, will typically use a guillotine to cut the bottles away from the mould. This leads to a finish that is not even and smooth, like PET, but may feature a lot of flashing – dairy is another area where this is the case. UCL has designed a single-piece cap that incorporates a flexible blade within it, that can cope with the variations in neck finish and still maintain a full seal. Universal Closures’ Blade cap is designed to eliminate liners in closures for extrusion blow-moulded neck finishes. Sealing the deal: a new solution to eliminate liners “We created a seal, called a wedge seal, that looks a little bit like a liner. Its blades lie diagonally and, when they compress, they don’t form a complete, uniform line; they follow what a liner would do in the critical areas,” he explained. “If you think of a conventional liner, it’s a disc and, in fact, the bit in the middle is wasted. What our design does is to mimic the behaviour of a liner, in a blade. We designed that and worked closely with Z-Moulds to develop the tooling to allow the shape to be created and we had to do a lot of trials on the angle and with the ultimate client – a major producer of household goods – to prove the concept and demonstrate that it works, at scale.” Mark and UCL as a company believe that the new blade-seal cap has a great deal of potential, across the world and across several markets. UC’s ‘Eagle’ closure for the new GME 30.40 closure system standard for CSD","@ID":18} "OUTER PLANET 54 PETplanet Insider Vol. 23 No. 03/22 www.petpla.net OUTER PLANET New SodaStream bottle resin requires Sipa technology Standing up to pressure and heat SodaStream, the manufacturer of in-home carbonation systems, is known for products that transform tap water into flavoured or unflavoured sparkling soda water, at the touch of a button. The company now collaborates with PTI and Sipa to produce new generation Tritan copolyester bottles. SodaStream decided to develop a new sturdy, refillable container that would handle high dishwasher temperatures and accommodate high-pressure filling, as well as offer clarity in the material and dent/scratch resistance. SodaStream approached American company PTI (Plastics Technologies, Inc) to assist it in engineering a solution that would be appropriate for its markets and customers. PTI is headquartered in Holland, Ohio and has a European facility in Yverdon-les-Bains, Switzerland. It became part of Sipa in March 2021. Selection of material SodaStream worked directly with Eastman Chemical to identify a Tritan resin grade that would deliver the necessary properties. It was important that the resin have amorphous glass-like clarity without crystallinity and haze. The next part of the of the process was to research and develop a preform that could be commercially blow moulded. Tritan grade has to be approximately 30°C hotter than PET to make the plastic preform malleable enough for blow moulding. It was at this point that the company approached PTI to assist them in developing the right preform. After a series of blow moulding and performance simulations, PTI determined that an 83g Tritan preform would deliver optimum performance. This represented a 15% weight reduction from SodaStream’s existing 1l PET container. Prototyping trials and performance evaluations were conducted to ensure application pressure safety. The Tritan material required higher stretch ratios and reheat temperatures, compared to PET, which proved challenging for injection and reheat cycle times. Custom bottle manufacturing solution The thick-walled plastic container presented challenges in both injection and blow moulding. Special care must be taken during the manufacturing process, so that scuffing is minimised when the preforms are transported from injection to blow moulding. Sipa was able to engineer a blow moulding machine with enough lamp power to heat a very thick preform close to 140°C, without having to carry over the heat of injection for blow moulding. The process Sipa developed also eliminates scrap that had been generated when the blow moulding line went down inadvertently. Sipa’s preform manufacturing system starts with an XForm 350/48 Gen4 injection moulding unit. This can produce several different types of preform both in PET and in Tritan. Once moulded, preforms are automatically taken out by a robot fitted with a “cool pick plate” and transferred to a stabilisation station, where they remain for several cycles. Transfer and bottle blowing Preforms are then picked up by a second robot; a six-axis anthropomorphic type, fitted with special end-of-arm tooling equipped with vacuum suction, and immediately transferred to a Sipa SFL 6/6 Evo linear stretch-blow moulding machine.The bottles are formed and then transferred using star wheels and subject to 100% in-line optical scanning, to ensure their quality. www.sipasolutions.com Sipa integrated injection and blowing solution for zero defect bottle Robotised preform transfer","@ID":56} "41 CHINA SPECIAL & CHINAPLAS 2022 PETplanet Insider Vol. 20 EREMA Hall 2.1 Booth F53 Erema, Austria - Solutions to meet the needs of the Chinese recycling market This year, Shanghai is the venue of Chinaplas, making this high-profile trade fair a home game for the Erema subsidiary in China. The team from the company’s Shanghai subsidiary will be at the Erema trade fair hall 2.1, booth F53. Customers and interested parties can also talk to their contacts at the company’s headquarters in Austria in a video call if personal consultation is required. The ent ire range of services in the areas of PET recycling, post-consumer and in-house recycling solutions will be presented. Erema has enjoyed a very successful year in China with significant growth in turnover and orders for all of these applications. Strong demand for recycling solutions The increase in demand is strongest in the PET recycling sector. Ten Vacurema systems and, for the first time, a Vacunite system for bottle-to-bottle applications were commissioned during the past calendar year by Erema. There were also three Intarema TVEplus systems with ReFresher modules for recycling postconsumer material. A team of technicians from Austria was on the road in China for ten months to commission these systems on-site at customers’ plants, right across the country. Quality, process stability and flexibility The great demand for Vacurema technology is due to its high flexibility for bottle-to-bottle recycling, because it offers a wide spectrum of applications - including food contact packaging materials. Processes include inline preform technology, which enables post-consumer PET flakes to be processed directly into preforms, proven Vacurema prime systems, and the Vacunite systems, which brings together the power of Vacurema technology with vacuum-assisted Solid State Polycondensation (SSP). Delivering efficient decontamination, good colour values, IV stability, low energy consumption end-toend, and a compact design, this process is claimed to meet the highest specifications for producers of food contact compliant rPET pellets. Growing interest is also noticeable in the post-consumer segment. In Europe, the use of post-consumer recyclate has become a major topic in the plastics industry due to legal recycling regulations imposed by the European Union. With its Intarema TVEplus RegrindPro technology featuring ReFresher module, Erema plays a major role in making recyclates suitable for high-quality applications in the cosmetics and food industries, opening up new sales markets for their customers. Erema expects further growth in the production waste recycling segment as a result of China supporting companies in implementing suitable recycling solutions. Erema doubled production area At the company’s headquarters in Austria, Erema has been gearing up in recent months to meet the increasing demand worldwide for its recycling technologies. The construction of a new manufacturing plant doubled the production area in Ansfelden by the end of 2020. The expansion phase also saw an extension to the Customer Centre, where tests are carried out on a range of recycling machines using input materials supplied by customers. This was followed in January 2021 by the acquisition of a 40,000m² site very close to the company’s headquarters, increasing production capacity by a further 60 per cent. www.erema-group.com","@ID":43} "CHINA SPECIAL & CHINAPLAS 2022 PETplanet Insider Vol. 23 No. 03/22 www.petpla.net 34 China’s consumers are increasingly demanding healthy drinks in sustainable packaging PET – the ideal candidate As a company that is active in moulds and services for bottles, with a considerable R&D department, Foshan-based GDXL has a good overview of the latest market requirements. In our interview, they explain current trends and developments in the Chinese market and beyond. PETplanet: How do you see the PET industry in China developing? GDXL: Consumers are now more interested in safe, healthy, individualised and sustainable products, which in turn creates corresponding requirements for the packages. PET is by its nature one of the ideal candidates. Its demand should go in pace with the growth and consumption ability of the economy, whose prospect is good and steady. On the contrary, sustainability of the material can be further improved by means of R&D of biobased raw materials, development of the collection and recycling industry, and product design, etc. Meanwhile, safety and performance of the package should not be compromised amid the post-pandemic era. These lead to opportunities and challenges to brand owners and suppliers in the industry. PETplanet: Do you observe any trends that are particularly in demand from customers in the PET bottle sector? GDXL: In response to the pandemic, customers have developed a consumption preference for choosing food and beverage products which are safe, healthy and credible, especially for essential commodities such as PET bottled water. Traditional renowned brands have intrinsic advantages in terms of consumer confidence. Meanwhile, compared with general consumers, younger generations tend to be more satisfied with creative, individualised and sustainable products which reflect their values. Adoption of sustainable materials, green and fashionable design, as well as cross-boundary elements into PET bottles may give some insights. PETplanet: Last year you announced turnover growth for the first pandemic year 2020, which was mainly due to growth in the domestic market. How have things progressed since then? Has the foreign business already recovered somewhat, and how did the 2021 financial year develop for GDXL? GDXL: In 2021, we achieved turnover growth year-on-year both in our domestic and overseas markets. The growth rate in overseas business is higher than that in our domestic market, with overseas turnover exceeding the pre-pandemic figure in 2019. It somehow reflects a sign that some of the foreign suppliers and converters are becoming more optimistic towards their local or regional beverage markets. PETplanet: In the last few years, you have focused on the multilayer coinjection area solutions strongly. Can you briefly explain the advantages and the applications for which the system is particularly suitable? GDXL: The main advantages of multilayer co-injection are the 144 cavities preform mould (photo: GDXL) by Gabriele Kosmehl","@ID":36} "BOTTLING / FILLING PETplanet Insider Vol. 23 No. 03/22 www.petpla.net 24 we sent raw milk to were able to meet our high production standards. After all, we wanted consumers to continue to have Imlek products in their usual top quality.” At the start of reconstruction a clear decision was made to make the new factory the most modern in the region – a complex task that was completed quickly and so successfully that the impact of the fire, in which luckily no-one was hurt, was soon forgotten. The new InnoPET BloFill ACF-L block system is largely instrumental in this, where a latest-generation KHS stretch blow moulder, an Inno-PET Blomax V, has been combined with a KHS aseptic filler, the Innofill PET ACF-L, for the first time ever. The block boasts a number of developments that make it more powerful than the previous filler and also more sustainable and economical – by saving up to 40% in energy, for example. A special transfer module has been designed to join both machines that feeds the continuous PET bottle flow from the rotary stretch blow moulder to batch processing on the linear filler. To this end, ten consecutive containers at a time are picked from the bottle flow, accelerated and separated from the following units as a group so that they can then be easily removed by grippers at their downstream stop position and placed in the filler’s carrier plates. Combining the stretch blow moulder and filler does away with the need for an air conveyor, resulting in a system that saves space, cuts energy consumption and eliminates a potential source of error. Despite the misfortune of losing their proven system and the considerable amount of extra organisation this subsequently incurred, Imlek can now enjoy a new machine that thanks to its numerous further developments is much more than simply a replacement investment. However, the Serbian dairy group does not need to risk any experiments here. “Our specifications were basically the same as when we commissioned the first machine,” Samardžija explains. “The main emphasis was to ensure product quality and production stability. And with our new acquisition we again attached great importance to a high degree of flexibility so that we can produce our various volume formats on the same machine.” The block setup means that a full format changeover can now be performed in the space of just ten minutes, taking up to 40% less time compared to single machines with an air conveyor. The filling volume accuracy has also been improved by around 30% over the old filler. Electromagnetic induction flow meters with new evaluation software and tried-and-tested algorithms are also used in the aseptic zone to achieve this. They ensure consistent head space volumes and thus identical fill levels in the bottles and minimise the risk of excessive foaming. Modular aseptics The modular design of the Innofill PET ACF-L aseptic filler is also new. It allows optional empty modules to be planned for on procurement. These leave space for filler retrofits, such as foil sealers or dosing units for fruit chunks, should these need to be later included in the portfolio. Finally, the KHS Innopack Kisters SP Basic from 2012, a shrink packer that can wrap up to 10,800 packs/hour in film, also forms part of the restored line at Imlek. The packaging unit is one of the few pieces of equipment in the machine park to have survived the fire unscathed. Following a general overhaul, it’s again now fully functional. In the near future Imlek wishes to further exploit the various new options already provided by its state-of-the-art technology and associated increase in flexibility. “We can imagine expanding the portfolio of our aseptic filler in the future to also include milk shakes and flavoured milk,” the dairy’s chief supply officer tells us. Product range The Serbs currently process around 200 products. The majority of its sales are generated with fermented milk products and fresh and ultra-heat-treated milk. Financially no less significant but much smaller in volume are product categories such as dairy spreads, butter and standard value-added products. The company is not just looking ahead when it comes to its production technology but also with respect to its portfolio: besides standard and organic milk products this includes lactose-free products and the probiotic Imlek Balans+ line for all those who pay particular attention to digestion and immunity. “This year we launched Imlek Protein to market, a protein-rich, lactose- and sugar-free milk beverage specially geared towards people who watch their diet and do sport,” states Samardžija. “Products like these have been a focus of the international milk industry for some time now.” The milk magnate’s modernity also encompasses a strategic commitment to more sustainability. “With a mind to our responsibility to the environment, we’re the first local milk producer to fill our Moja Kravica brand into packaging made of recyclable, bio-based plastic,” Samardžija tells us. “Even the caps are made of plastic that comes from plants, namely from sugar cane.” www.khs.com The roof of the block also serves as the filler’s service module with easy access to the maintenance area. Filled and capped PET bottles leaving the stretch blow moulder/filler block on their way to the sleever.","@ID":26} "EDITOUR PETplanet Insider Vol. 23 No. 03/22 www.petpla.net 13 will make PET bottles with handleware,” continues Mr Richard. “New applications in the field of PET carry handle packaging are currently being developed. We are seeing even greater growth here.” Besides food and beverage, nonfood sectors are also being kept in view, where customers do not want to do without the brilliant appearance of PET. The current best-selling machines are the models Eblow/ Hyblow 607D 2x3-fold and 407D 2x2-fold. “PET handleware bottles need excellent clamp performance, which we deliver with the C-frame. The design of the C-frame, which utilises mould platens that move along precise, low-friction linear guides, enables completely symmetrical clamp force distribution along the entire mould area, while maintaining high parallelism of the mould platens. The full clamp force is available independent of the mould thickness without adjustment. A precise clamp force distribution during the clamping process results in ideal article weld formation.” Besides the initial successful business years mentioned above, the pandemic years have also given the company a boost in terms of service development. “We have expanded everything relating to digitalisation in day-to-day business as regards customer interaction and the remote maintenance of machines.” In other ways too, they are doing a great deal and equipping themselves further for the future, for example in the processing of rPET, where successes have been reported in various test runs. “This is one of the many topics we’re tackling. Just last year, we expanded our site in Williamston with a 3,700 m2 production hall so we can keep up with the increased demand for machines. At this year’s K trade fair, we will be presenting our new equipment and new technologies to the public.” www.bekum.com significant investments, since 2015, the complete Bekum production capability for the European market has been located there.” With the expansion into the American market in Williamston in 1979, there was finally synergy between German technology and American entrepreneurial spirit, which led to an independent product range. “It was more than just a simple adaption of a German machine for the market there,” explained Mr Richard. “The Americans successfully established their own machine line. The sense of responsibility of a family business is always present in the US: for example, Bekum America depends strongly on their own apprenticeship program. Today around half of the manufacturing employees come from this program.” The group has around 350 employees in total; 50 in Berlin, 150 in Traismauer and 150 in Williamston. “Our 60-year company philosophy sets us apart, as well as the specialist staff that implement it. It enables us to get close to our customers both in person and digitally. Alongside our own sites, we also have more than 30 local sales offices and onsite service centres with appropriate spare parts stores to accelerate processing and service. Careful expansion of the PET business Besides Bekum’s machines and equipment for processing various thermoplastics, the PET sector is also being carefully expanded – its current contribution to overall turnover is still under 10%. In the past few years, there have been various projects in this field, such as the successful production of handleware bottles for juice bottler POM Wonderful in 2005 using Eastman’s copolyester EB062, and a bottle for Coca-Cola in 2007, which helped the EB062 achieve its breakthrough. Christian Richard explained: “Packaging trends, which we support with our equipment, often place global food and drinks manufacturers in the premium sector, and the same is true for PET. One example is fresh juices from the chiller, where marketing at POS is also guided by the premium packaging.” New applications of PET carry handle packaging The beating heart of a finished PET bottle like this, the “C-frame closing” unit, was reported as a patent by Bekum in 2010 for electric and hydraulic blow moulding machines. It was to simplify the processing of copolyester and PET and can be found in the models of the Eblow and Hyblow ranges. In 2019, the new System Concept 808 was presented, which was to combine improved plastification while simultaneously saving energy, an interactive user interface and the option to manufacture multi-layer packaging, alongside the use of the C-frame and a revised design feature including a quick-change system for moulds. “This year, in 2022, over 40 extrusion blow moulding machines","@ID":15} "EDITOUR PETplanet Insider Vol. 23 No. 03/22 www.petpla.net 17 BEYOND THE HORIZON PROCESS SOLUTIONS FOR POLYMER RECYCLING AND SOLID STATE POLYMER UPGRADING Polymetrix, a Sanlian Buhler Company, provides process technology including EPCM services for the polymer recycling and manufacturing industry. Leading supplier of rPET systems and integrated rPET plants for single line capacities up to 70’000 tons per year. www.polymetrix.com www.slhpcn.com “There are lots of these HDPE bottles with PE or PP closures. Our’s is a solution that will cost less, it uses the same HDPE resin and their environmental message gets stronger,” said Mark. Dairy is an obvious example. It has very tight margins, is dominated by HDPE as a material and uses tonnes of liner material. Being able to get rid of the liners – and the challenges associated with collection and recycling – could be a major step forward. Personal relationships: key to satisfaction One thing that UCL has always regarded as very important is personal relationships, for sales, trials, service and support, and the pandemic has got in the way. Quarantine periods before and after site visits – if they are even allowed – mean that a trial that should take just a few days can extend to five weeks or so. Rod Druitt gave up his Christmas to help smooth the installation process at a customer in Thailand. He took responsibility, rather than expect an employee to shut themselves away for such a long time. And it goes further. “You need to have a line trial to prove a product is fit for purpose. We have our own product laboratory at UCL and we can undertake all the validation – we are fully Pepsi accredited and there’s nothing we can’t do to prove that the closure is functional,” Mark explained. “But key projects tend to get over the line when you are face to face and that is a key element that has been missing. It’s being able to look someone in the eyes and being able to read subtleties, better than you can in a Zoom or Teams call. We can be working on something for several months, we can develop and demonstrate all the concepts, then you do the pilot and being there is crucial. It’s being able to spot that there’s a query that hasn’t been raised, so you haven’t answered it. You can see someone look at someone else, press to understand the issue and answer their concerns immediately. We simply cannot do that as well virtually.” Like many of us, UCL is willing and eager to get back to normal, to working closely with clients all over the world. As restrictions are lifted in territory after territory, its clients will find Universal Closures coming to see them with a wider range of ideas and solutions, with better performance and more cost saving than ever before. It’s a company full of ideas and it hasn’t wasted time during lockdowns. www.universalclosures.com UC 2925 HMC (hinge-moulded closures) for still beverages","@ID":19} "Sponsors to date The worldwide round trip with EDITOURS Back to Europe The second part of PETplanet’s bipartite Drinktec Editour is right ahead! After the successful rst part “From Down Under to Japan” in 2020, our second stage of the project takes us back to the ourishing European hub where we will be exploring the latest technologies, news, innovations and developments that move our PET industry. It is time for a new start, for renewal and for developing new ways of thinking. During and especially after the pandemic, it will be vital to make every effort to get the global economy back on track in the medium term. Sustainability will be the key. Once again, PETplanet will be at the forefront. It will again be a partner in Drinktec, the world’s leading beverage trade fair, which is to be held in Munich from 12-16 September 2022. After the success of our previous Drinktec Road Shows, in 2017 in South East Asia and 2020 in Australasia, we will be back on the road in Europe for a whole year. Starting in Autumn 2021 with our Editourmobil, we will be ready for a new get-together with the industry. We will be revealing the results of our meetings and discussions at Drinktec with the leading thinkers in PET processing, packaging and recycling. Apart from new technologies we will be also taking stock of how things stand. We will be asking how global thinking might change as a result of Covid-19. How will bilateral business relationships cope with the aftermath of the pandemic? What opportunities will there be for the drinks industry and its suppliers? Our planning, in terms of precise timeframes and details of the countries to be visited will be exible, in order to take account of the rapidly changing pandemic situation. However, this much we can con dently say: in these challenging times we, as the voice of the PET industry, will be at the very heart of the roadshow as usual and are already looking forward to welcoming you back on board the Editourmobil! Share this exciting experience with us! Interested in being interviewed? [email protected] Let Your Inspiration Flow. The European Road Show PART2 Empowered by drinktec Interested in becoming a Sponsor? [email protected] Autumn 2021 - 2022","@ID":57}]}}
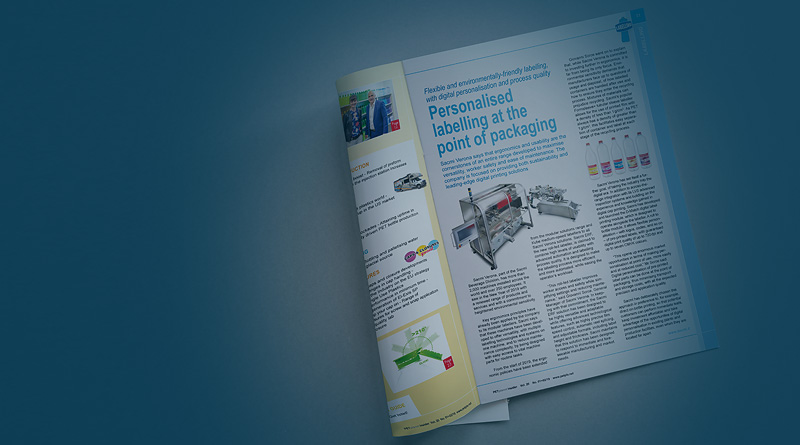