{"pages":{"page":[{"@ID":45, "CAPS & CLOSURES 43 PETplanet Insider Vol. 23 No. 05/22 www.petpla.net In practical use situations the quality of the Bericap ClipAside closure is evident: after it had been opened and closed 30 times the closure did not detach from the bottle. The parallel tethers, a design element of ClipAside, prevent overbending or breakage, even when misused. Image gains and sustainability improvements As the study revealed, many consumers are not aware of the ecological benefits of tethered caps. This indicates how important it is for beverage manufacturers to communicate them. High-visibility information about the benefits and correct handling on the label will help to educate consumers and contribute to a more positive brand image for the beverage manufacturers. Although it is unlikely that consumers will change their brand because of a closure, they will welcome the fact that their chosen beverage brand has closures that meet their requirements. rPET100 Designed for recycling. Made from recycling. • Heat resistant • Fully recyclable • Thermoformable like PET BENEFITS HOT CUPS · DAIRY PRODUCTS · INSTANT SOUPS · TO-GO MEALS · COFFEE LIDS foodgrade without compromise Flexible switchover to tethered caps for the beverage industry Bericap has created the technical framework for the beverage industry to switch over to the new Bericap ClipAside tethered closure system thanks to its consistent performance across all relevant neck finishes from 26 to 38mm. The flexible slit band technology allows customers to make the adaptations to their production lines for the new closure dimensions today and then decide spontaneously whether to initially continue with the current TE band slit or change over to the new tethered caps. Customers can remain flexible in this respect because a changeover from the current TE band geometry to tethered caps doesn’t necessitate any further adaptations to the production lines. When the customer is ready to launch bottles with the new caps they can then execute the switch without any further modifications to the filling equipment. This is very useful for beverage manufacturers outside Europe, where tethered requirements are not mandatory yet, but might be in future. www.bericap.com Bericap ClipAside parallel tethers"},{"@ID":36, "BOTTLE MAKING 34 Vol. 23 No. 05/22 www.petpla.net Looking for a suitable SBM machine PET bottle production in Uruguay The Sirte plant, dedicated to the production and bottling of water and soft drinks, is located in the Pajas Blancas resort, in the southwest of the department of Montevideo. There, 150m deep, the natural mineral water is born. It is a stainless steel pipe which then brings the water to the plant, where it is filled into glass and PET containers. Key facts: Blow mould quick change enables the production of several types of bottles using the same equipment without down time; The oriented bottle outfeed allows the equipment to be integrated into the filling line of any brand; Simple logic, PLC and manuals in Spanish make operation and maintenance easy; Intense preform heating and its simultaneous cooling enable the production of bottles with sophisticated designs. ODOUR REDUCTION TECHNOLOGY IR-FRESH® Made in Germany FOOD GRADE DECONTAMINATION & DRYING rPET FLAKE IR-CLEAN® www.kreyenborg.com [email protected] The roots of the company go back to the beginning of the 20th century, when the water spring was discovered in Pajas Blancas. It was baptised with the name “Sirte” which means “water under the sand”. In 1915, Sirte Mineral Water was founded. The company’s importance outside the resort was growing. The consumption of bottled water was increasing. Home water distribution is one of the pillars that led to the expansion of the Sirte company. Bottled water is often perceived as safer and can offer a higher quality product. This is where machinery comes into play, be it conveying, blowing, filling or palletising systems. Thus, the fruitful cooperation between PET Technologies and Sirte was born. The well-known bottling company from Uruguay contacted the European manufacturer of PET stretch blow moulding machines to implement the project to manufacture its own PET bottles. It was the APF-3002 model that perfectly met the needs of the Sirte company. It has an output of 3,000 bph and is able to produce up to 2.32 l. The equipment is integrated into the water and carbonated soft drink filling line. Sirte sells water in glass and PET bottles from 600ml to 7 l and in jars. The APF-3002 blowing machine helps to make the formats of 0.6 l, 1.65 l, 2.32 l. They are sold in bags of six units each. All the bottles have the same design that makes the product recognisable in the market. The containers are ergonomic and reflect the product inside. Water droplets decorate the narrowing line of the bottle. The cavities for the finger make it comfortable to handle, especially the family formats. www.pet-eu.com"},{"@ID":4, "MATERIALS / RECYCLING PETplanet Insider Vol. 23 No. 05/22 www.petpla.net 16 Plastics separation of household plastics waste on particle level via magnetism Do you know the CO2 impact of your recycled bottle? Author: Lucy van Keulen, Commercial director, Umincorp Recycling has everyone’s attention. But what is the source of this recycled plastic: Does it come for example from the Netherlands or from Turkey? Does it come from households or from companies? How sustainable is it recycled? One recycled plastic is not like another, and there are large differences in emissions between plastic recycling methods, Lucy van Keulen from Netherlands-based Umincorp points out, and shares her opinion in this article on how post-consumer plastic waste can be recycled efficiently and what role the CO2 level is playing. The different plastic recycling methods vary in many aspects. The most common recycling approach in Europe uses infrared sensors to recognise the type of plastic to be recycled. This method has three challenges. First, it is limited in recognising packaging that consists of different types of plastic (broadly speaking PP, HDPE and PET), and the different types of plastics have to be pre-separated in a first step. The second challenge is that with this approach, a lot of input material is lost in getting from the mixed packaging to a pure end product. As a result, a significant portion cannot be sorted and ultimately recycled. The final challenge is that sorting often takes place somewhere other than the actual recycling. This leads to additional transportation, less optimisation and higher CO2 emissions. Magnetic density separation MDS (magnetic density separation), a mechanical recycling technique codeveloped by the founders of the Dutch company Umincorp, is an alternative to conventional mechanical recycling in which different types of plastic are separated using magnetism. In this process, the plastic is first split into small particles after which the particles, consisting of the three most common types of plastic, can be accurately separated from each other. Because the plastic can be separated at particle level, the recovery rate of this technique is claimed to be higher compared to conventional methods. It also allows both sorting and recycling to take place at the same location, thus reducing CO2 emissions. CO2 reduction remains underexamined in the current way we look at recycling. If we hold producers responsible for the total CO2 emissions in the chain, the actual impact of a product, including production, packaging and recycling becomes clear. The current discussion in the market about mechanical versus chemical recycling, becomes also direct clear when CO2 emissions are taking into account. An example can be seen with supermarkets that put minced meat in multilayer bags, thus saving on the amount of packaging compared to the original container. Often, however, the sachet is less recyclable, or not recyclable at all, whereas the PET container was. By approaching packaging on the basis of CO2 emissions, companies can make the right choices while explaining them to consumers. A kind of CO2 label for packaging, similar to the nutrition label, could also give consumers more insight and thus help them make the most sustainable choice. Insight into the chain Another risk of the increasing popularity of recycling is the lack of understanding of the origin of the recycled plastic. There is already not enough PET or HDPE available in Europe to meet the demand of packaging producers. If new plastic is produced outside of Europe, chopped up and then sent to Europe as recyclate, this completely misses the point. However, due to a lack of full insight of the supply chain, such procedures cannot be ruled out. Legislators also play a stimulating role in this. In the UK, companies have to pay extra tax on packaging that does not consist of at least 30% recycled material. The expectation is that this will increase the proportion of recycled material in packaging by 40%, saving about 200,000t of CO2 emissions in the short term. There are several levers that the entire plastic chain can pull simultaneously to reduce the climate impact of plastics. Every step in the chain, whether it is the producer, designer, legislator, recycler or consumer, should look at actually reducing the CO2 impact. More traceability, knowledge and understanding is needed to properly compare the different options. www.umincorp.com CO2 reduction remains underexamined in the current way we look at recycling, Lucy van Keulen states. RECYCLING"},{"@ID":32, "PREFORM PRODUCTION PETplanet Insider Vol. 23 No. 05/22 www.petpla.net 30 Recent developments in PET preforms and bottles Preforms for the Indian market Packaging technologies have evolved to make industrial processes more efficient and production faster, more environmentally sustainable and of consistently higher quality. In the Asia Pacific region, PET containers are not only widely used for drinking water, carbonated soft drinks (CSD) or fruit juices but also for edible oils, ghee, vanaspati (hydrogenated vegetable fat), alcohol, pharmaceuticals, detergent powders, personal care products, and more. Chemco Plastics Industries Pvt Ltd, one of India’s leading manufacturers of PET preforms, supplies a wide range of products to established FMCG brands. The Asia Pacific region, already the largest market by revenue, is seeing the world’s fastest growth in demand for PET preforms, forecast at over 6% CAGR between 2016 and 2026. China is the primary market and expected to be the largest market for PET preforms in the Asia Pacific, followed by India - a fast-growing market - and Japan where PET is also wellestablished. Consumption of CSD, liquor, personal care, food products, and other items has increased as the youthful population grows across the region and disposable income increases. Health and lifestyle trends have boosted the popularity of juices and non-carbonated drinks. Preform design Several factors are involved in delivering required bottle characteristics such as overall shape, neck finish and mechanical and barrier properties. A lesser bottle thickness will deliver material savings and make the finished container lighter but mechanical strength will be reduced and the choice of shapes may be limited. The bottle neck can also be made lighter and customised and preforms can be designed to incorporate special characteristics, such as large size, stackability, asymmetric shapes, or suitability for hot-fill. Chemco manufactures PET preforms with neck diameters of 28mm, 29/25mm, 30mm and 48mm and weights ranging from 10 g to 270 g for packaged drinking water, 12.3 g to 48 g for carbonated soft drinks with a neck diameter of 22mm and 28mm, and other products. Preform manufacturing Machine and mould technical characteristics determine production speed, product quality, power consumption, process costs and maintenance intervals. PET preforms are generally manufactured by a threestep process. Drying: Hopper drying is the most common method of extracting humidity from PET. Even drying is achieved by continuous conveyance by autoloaders. Dehumidifiers use a closed-loop system that provides consistently good surface finish and physical properties. Melting: Temperatures within the injection cavity vary by as much as 8-10 °C, from 270-275 °C at the front and 280-285 °C at the back, depending on mould design. Cooling and moulding: Cooling is usually by water, circulated at about 5 bar. This pressure has to be consistently maintained, to avoid breakage or deformities. Automated grippers deposit cooled preforms onto conveyor belts that take them for packaging for external delivery, or for reheating if they are to be blow-moulded immediately. Preform inspection Chemco’s laboratory tests each production batch. Every preform undergoes inline visual/optical checking for holes, scratches, chips and cracks, as well as internal and external dimensions. They are packed in corrugated fibreboard boxes. Sustainability Chemco has responded positively to the drive for improved sustainability, including reduced material consumption, increased use of post-consumer recycled (PCR) PET and a stronger network for collection of plastic waste. The company’s in-house recycling facilities allow it to monitor and control the quality of input materials. Advanced machinery and an on-site laboratory ensure that recycled materials are safe and can be used for food packaging applications. While bottle designs are largely determined by customers, Chemco is able to introduce recycled content without affecting quality, to minimise damage in transit, and enable retailers and end-users to reduce environmental impacts by using less protective packaging. www.chemcogroup.com"},{"@ID":3, "No.5 2022 www.petpla.net D 51178; ISSN: 1438-9452 30 . 05 . 22 PETplanet is read in more than 140 countries MAGAZ I NE FOR BOT T L E R S AND BOT T L E - MAK E R S IN THE AMER ICAS, AS IA, EUROPE AND AL L AROUND THE PLANET MARKETsurvey Suppliers of preform and SBM moulds Page 27 Page 10 Recycling Page 12"},{"@ID":57, "Sponsors to date The worldwide round trip with EDITOURS Back to Europe The second part of PETplanet’s bipartite Drinktec Editour is right ahead! After the successful first part “From Down Under to Japan” in 2020, our second stage of the project takes us back to the flourishing European hub where we will be exploring the latest technologies, news, innovations and developments that move our PET industry. It is time for a new start, for renewal and for developing new ways of thinking. During and especially after the pandemic, it will be vital to make every effort to get the global economy back on track in the medium term. Sustainability will be the key. Once again, PETplanet will be at the forefront. It will again be a partner in Drinktec, the world’s leading beverage trade fair, which is to be held in Munich from 12-16 September 2022. After the success of our previous Drinktec Road Shows, in 2017 in South East Asia and 2020 in Australasia, we will be back on the road in Europe for a whole year. Starting in Autumn 2021 with our Editourmobil, we will be ready for a new get-together with the industry. We will be revealing the results of our meetings and discussions at Drinktec with the leading thinkers in PET processing, packaging and recycling. Apart from new technologies we will be also taking stock of how things stand. We will be asking how global thinking might change as a result of Covid-19. How will bilateral business relationships cope with the aftermath of the pandemic? What opportunities will there be for the drinks industry and its suppliers? Our planning, in terms of precise timeframes and details of the countries to be visited will be flexible, in order to take account of the rapidly changing pandemic situation. However, this much we can confidently say: in these challenging times we, as the voice of the PET industry, will be at the very heart of the roadshow as usual and are already looking forward to welcoming you back on board the Editourmobil! Share this exciting experience with us! Interested in being interviewed? [email protected] Let Your Inspiration Flow. 7KH (XURSHDQ 5RDG 6KRZ PART2 Empowered by drinktec Interested in becoming a Sponsor? [email protected] Autumn 2021 - 2022"},{"@ID":21, "MATERIALS / RECYCLING PETplanet Insider Vol. 23 No. 05/22 www.petpla.net 19 MATERIALS / RECYCLING 19 PETplanet: Extrupet recently announced an expansion of the food-grade PET recycling operations in South Africa. Can you please explain the background and the capacities you are aiming to achieve? Wadhwani: We will double our food-grade operations by adding a second food-grade rPET facility, which will increase our recycling capacity by an additional 33,000 t/a. Currently Extrupet has one Vacurema and two Starlinger lines based out of Johannesburg. PETplanet: Can you envisage transferring your expertise to other African countries and expanding further outside South Africa? Wadhwani: We are currently in dialogue to make investments in West and East Africa, namely Nigeria, Ghana and Kenya, Tanzania and Uganda. PETplanet: What directives or legally prescribed recycling quotas must be complied with in S. Africa? Wadhwani: November of 2021 saw the beginning of this kind of legislation. Extended producer responsibility (EPR) was gazetted across three main sectors, namely, 1) electrical and electronic equipment, 2) the lighting sector, and 3) paper, packaging and single use products. For PET beverage packaging specifically, there would need to be a 10% inclusion rate of rPET in year 1, 12.5% in year 2, 13% in year 3, 15% in year 4 and 20% in year 5 in order for the bottle to comply. PETplanet: To meet these quotas, how could a reliable and predictable availability of in coming material be further improved? Wadhwani: In South Africa, most of the bottle raw material originates from landfill. Separation at source projects spearheaded by government would be a great starting point and certainly help the quality of incoming raw material. There would however be a cost associated with this, and to get the process subsidised as in Europe would be the ultimate goal. PETplanet: What is the quality of the material you receive? Wadhwani: Most of the raw material collected originates through an informal collection system, and once delivered to our factory the yield loss is as much as 35% from beginning to end. PETplanet: Which markets are you supplying with your food-grade rPET? Wadhwani: Africa, EU, UK, Australia, and the USA. There are different approval / certification levels needed for each; however our main food approval agencies, BRC, FDA, EFSA, SMETA and ISO cover most of our customer needs. PETplanet: Recently, the price for vPET was fetching around 1,700€/t, a very high value, but the price for rPET flakes was as high as 1,950€/t and for granules even 2,200€/t or more. Are you concerned about this development? Wadhwani: Yes, we are very concerned as pricing will have a huge impact on the availability of feedstock. Without which one cannot produce food grade rPET. PETplanet: Thank you very much, Mr Wadhwani! Expanding recycling capabilities South Africa’s PET recycling industry is performing well. In 2019, a total of 2.2 billion bottles were collected which amounted to a 62% recycling rate. Recycling company Extrupet announced in April a further expansion of their food-grade plastics recycling operations. We spoke to Chandru Wadhwani, Extrupet’s Joint Managing Director. STADLER’s Label Remover is just what your plastic bottles need! No bottleneck losses Better subsequent NIR detection, due to rougher surfaces of the bottles after leaving our Label Remover Economic advantage for washing systems Outstanding results with PET, PE and PP STADLER: for a clean world! STADLER Anlagenbau GmbH +49 7584 9226-0 [email protected] www.w-stadler.de LABELS: SUPERBLY REMOVED by Gabriele Kosmehl"},{"@ID":17, "44 PETplanet Insider Vol. 23 No. 05/22 www.petpla.net ONsite Starlinger recycling technology for Australia’s largest PET recycling plant Circular Plastics Australia (PET) is a joint venture partnership between Pact Group, Cleanaway Waste Management Ltd, Asahi Beverages, and Coca-Cola Europacific Partners (CCEP) aiming to create a circular economy for PET beverage and food packaging. The newly installed Starlinger RecoStar PET 215 HC iV+ at the Albury-Wodonga facility turns post-consumer PET flakes into food-contact rPET pellets, starting with a two-stage heating and drying process of the hot-washed flakes for preparation for the extrusion process. After extrusion, thorough filtering and underwater pelletising, the resulting rPET pellets undergo vacuum treatment in the downstream SSP reactors for IV increase and decontamination that readies the pellets for food-contact applications. Circular Plastics Australia (CPA) plans to recycle 30,000 t of post-consumer PET collected via container deposit schemes and kerbside recycling each year and use the food-grade rPET pellets as raw material to produce new beverage bottles and other food and beverage packaging. Each member of the joint venture provides its knowledge and expertise in the project: Cleanaway supplies the plastic to be recycled through its collection and sorting network, Pact operates the facility and provides technical and packaging expertise, while Asahi Beverages, CCEP and Pact buy the recycled plastic from the facility to use in their packaging. The output of the Albury-Wodonga plant will help to increase the amount of locally sourced and recycled PET by two thirds from around 30,000 t/a to over 50,000 t/a and reduce Australia’s reliance on virgin plastic and recycled plastic imports. The CPA Albury-Wodonga faci l - ity was supported by an AUD 5 million grant through a New South Wales Government’s initiative, with the support of the Australian Government’s Recycling Modernisation Fund. CPA is building a second PET recycling facility in Altona North in Melbourne, Victoria, which will be equipped with a Starlinger RecoStar PET 330 HC iV+ recycling line featuring the largest SSP reactor currently installed worldwide. It will have the capacity to recycle the equivalent of around one billion PET beverage bottles each year. Construction has been scheduled to begin in April 2022 and be completed in 2023. www.starlinger.com www.pactgroup.com www.cleanaway.com.au www.asahi.com.au www.cocacolaep.com/au COMPLETE RECYCLING SOLUTION FROM PCR PET BOTTLES TO FOOD GRADE RPET PELLETS - FDA Approval - Low TCO (Total Cost of Ownership) - Energy Saving - Low Loss CONTACT US TO LEARN MORE ! WWW.BO-RE-TECH.COM | +86-573-85120186 | [email protected] K FAIR 2022 H9 E21 3HOOHWL]LQJ /LQH 663 :DVKLQJ /LQH Vacuum treatment in the ViscoStar SSP reactors for IV increase and decontamination makes the recycled PET safe for food-contact packaging. (Photo: CPA) RECYCLING"},{"@ID":27, "CAPS & CLOSURES 42 PETplanet Insider Vol. 23 No. 05/22 www.petpla.net Bericap’s ClipAside solution Consumer survey on tethered cap The Bericap ClipAside Tethered Caps comply with EU Directive 2019/904 to improve recycling performance. The majority of consumers surveyed rated the Bericap tethered caps more positively than conventional closures. at Bericap. “The ClipAside design impressed respondents in every respect: from handling, convenience, hygiene and sustainability to robustness in daily use. When the user experiences this level of convenience in use it has positive impacts for beverage brands. It has been stated that beverage manufacturers offering the new tethered caps now were considered as customercentric, innovative and sustainable brands.” Specific results of the consumer survey: Intuitive and easy handling Consumers felt that the biggest advantage of ClipAside was its simplicity of use. It looks and is used very much like a conventional screw closure, so most people can open it intuitively – without prior knowledge and without looking on the bottle for instructions. In fact, the closures can easily be opened with one hand while performing other tasks, by elderly people with mobility limitations or by children. Only very few people in the survey had to get used to the new closure, for example, because they did not realise that there is no need to remove it from the bottle. However, by the time they had opened their third bottle, virtually all of them were able to perform the ‘twist and clip aside’ mechanism just as well as the other respondents. Visible and clear instructions should be provided on the bottle label to explain handling and answer any questions the user may have. Robust solution with health and hygiene benefits Since the closure is tethered to the bottle, the survey respondents rated it positively for hygiene and health reasons, and because the closure cannot be lost. Consumers also liked the fact that the closure is 100% leakproof during transportation and storage after being opened and closed multiple times. The tethered cap can be opened 180 degrees and fixed in place for easy pouring or drinking straight out of the bottle. This is one of the findings of a consumer survey commissioned by Bericap involving citizens aged between 18 and 80 as well as their families. Survey respondents tested the new closures on 1.5 l mineral water bottles in real-life scenarios for a period of a week. The users emphasised the easy and intuitive handling when opening, closing and drinking, as well as the fact that the closures are very hygienic. This is because it is impossible for the closure to fall onto the floor and get dirty, which is what often happens with conventional closures when bottles are carried by small children, taken along in the car or in other everyday situations. Tethering the cap to the bottle also ensures that the closure and bottle remain together in the recycling process. Many consumers are not aware of this ecological advantage of tethered caps, which will be mandatory for disposable beverage containers up to 3 l from July 2024 onwards. However, as soon as they realise it – e.g. after reading information on the bottle label – they rate the sustainability aspect positively. The very good user experience associated with the ClipAside closure will also have a positive impact on consumer perceptions of beverage brands and customer loyalty. The first well-known customers in the carbonated soft drinks, mineral water and fruit juices segments already have products with the new Bericap ClipAside closure on the market. Proven practicality ClipAside has gone through the design, development to market readiness and market launch phases, and is now in the fourth phase: postlaunch monitoring. The adjustments that had been made to optimise the user-friendliness of the new closure system – based on the consumer and handling tests conducted in the design phase – met with a positive response from the testers, as did the high quality of the closures and their ability to withstand being opened and closed multiple times. Most users rated the Bericap ClipAside better than conventional bottle closures in many respects and would recommend it for that reason, and because it combines the advantages of screw and hinge cap closures. “The consumer survey has confirmed that the ClipAside offers many benefits to users aside from its recycling advantages,” said Thomas Schmidt, Group Marketing Director Bericap’s ClipAside closure solution on an OGEU bottle. This bottle was used for the consumer survey."},{"@ID":15, "BOTTLING / FILLING PETplanet Insider Vol. 23 No. 05/22 www.petpla.net 40 From hotels and restaurants to retail penetration A water brand makes it big by Kay Barton Interview with Mr Nayan Shah, Chief Managing Director at Energy Beverages Pvt. Ltd. India’s water market is huge. Okay, admittedly you can take this for granted in the world’s largest democracy with a population of 1.3 billion people. It is only when you hear that there are well over 5,700 licensed bottlers, as reported in an article in “The Hindu Business Line” from mid-2018, that the sheer size of the market really becomes apparent. And this does not include the countless unauthorised bottlers which the report also mentions. Such an enormous diversification finds thirsty consumers both regionally and locally. In the 2021 fiscal year, the value of the bottled water market is said to have been over US$ 2.4 billion, with future growth estimated at over 13%. PETplanet has been familiar with the Indian water and beverage market almost from the company’s inception and encountering genuine players in the water market has always been an easy task. The ubiquitous presence of Aquafina (Pepsico), Bailley (Parle-Agro), Bisleri or Kinley (Coca-Cola) – we have interviewed all the country’s major brands over the years – is testament to wellestablished brand imaging. Ordering “Bisleri” in a restaurant, for example, is usually generally synonymous with a bottle of water. However, we are not talking here about the previously mentioned brands but of one whose market strategy up until 2020 was based exclusively on the hotel and catering business. With more than a decade experience in the beverage industry Clear fills an estimated half a billion bottles each year, namely Energy Beverages Pvt. Ltd., with its “Clear Premium Water” brand from the state of Gujarat with a presence in over 18 states with more to follow. We have come across this water time and again on the Indian market, mostly as PET ultra-lightweight bottles on domestic flights or in hotels. It was time to take a closer look at this up-and-coming business. From energy drinks to water The under-supplied sub-continent of the 2000s in terms of energy drinks could do with a new product, thought Nayan Shah, the current Chief Managing Director of Energy Beverages who has a degree in Strategy and Business Management from the University of Technology in Sydney. In 2005, he decided to establish the company with the aim of creating “refreshing, revitalising and rejuvenating” drinks, as he himself puts it. The result was the “Current” energy drink which saw the business rise and fall in equal measure in the years that followed until 2009. While business with the rather high-priced lifestyle product was healthy in the beginning, demand stagnated after 2007 which ultimately forced a rethink of the company’s strategy. Drawing on his previous years’ experience, an idea took shape with Mr Shah deciding on a way into the growing bottled water market. So, in 2010, the Clear Premium Water brand was born. Many things different while some are new As was mentioned at the beginning, we had already come across these bottles on a number of occasions on planes and in hotels, most notably the company’s best-selling standard, single-serve 200ml version, weighing 6.5g and 500ml version weighing 9.5g which is lowest in the country, according to the company. What is immediately noticeable here is the bottle design which has a square shape instead of the usual round format. Just for its appearance and haptic value alone, the product stands out and stays in the memory, “Our first major customer following the launch of Clear was the Grand Bhagwati nationwide hotel chain with its main office in Ahmedabad”, said Mr Shah. Other chains, including internationally-known ones such as Marriott, Holiday Inn, Ritz-Carlton, Crowne Plaza and Hilton were added over time, together with airlines including Air India, Jet Airways and Spice Jet. The brand recognition and its association have become part of Energy Beverages’ marketing and strategy, at least since the water became available in ordinary shops and supermarkets in 2020. “We were the first bottlers to have both a square bottle design and a vertical logo on the container. We also have a customised labelling machine for vertical printing which can also be used to add co-branding on the label. This can be the Chief Managing Director Nayan Shah in his office"},{"@ID":56, "PETplanet Insider Vol. 23 No. 05/22 www.petpla.net 54 PETbottles PETbottles Beverage + Liquid Food Olive oil in PET The supermarket chain Albert Heijn, part of the Ahold Group, sells one litre of olive oil in a PET bottle strongly reminiscent of a glass bottle under its own brand “ah”. The slim bottle has grooves that improve grip and stability. It is closed with a multipiece screw cap with a tamper-evident cap that can be removed before the first opening. www.ah.nl San Pellegrino flavoured water Co n s ume r s ’ g r ow i n g awareness of the amount of sugar contained in beverages requires all manufacturers to offer beverages that contain either less sugar or no sugar at all. San Pellegrino responded to this consumer demand by launching the flavoured and carbonated sof t dr ink S. Pellegrino Essenza. There are two flavours, Lemon & Lemon Zest and Dark Cherry & Pomegranate. 500 ml are bottled in a disposable bottle, closed with a grey screw cap and decorated with a sleeve label wi th colour gradient. www.sanpellegrino.com Home + Personal Care A gentle hygiene soap for kids A sl ight ly bluish-coloured gentle hygiene soap for kids has been brought out by dm under its “Balea” label. The “Swimming Buddies” product comes in a clear, secure 300 ml bottle. The vegan formula does not contain microplastics and consists of 93% natural ingredients. A screw-on, lockable pump dispenser allows for controlled application of the liquid soap. A transparent label with marine animals creates a kind of underwater effect. www.dm.de All-in-One from Colgate Colgate Palmolive’s latest All- in-One Breathtaking Mouthwash features an eye-catching package design that stands out from the more discreet packaging of its competitors. The brand-typical, easy-to-grip and transparent bottle contains 500ml mouth rinses that promise not only fresh breath but also optimal protection for teeth and gums. The colourful sleeve label visually colours the contents. It can be easily separated from the bottle via a tear strip. The screw cap with dosing function is secured via a shrink sleeve before initial removal. www.colgate.de"},{"@ID":28, "MATERIALS / RECYCLING PETplanet Insider Vol. 23 No. 05/22 www.petpla.net 26 The all-new PET-LINE comes with a variety of advantages to maximize output and minimize costs: • Maximum compatibility with legacy molds and PMC • Shortest cycle times for increased output • Lowest level of energy consumption to minimize the ecological footprint • Improved 100 % rPET processing to enable the circular economy • New control unit including Smart Operation to ensure easy, fast and safe start-up and production • Now available with 3000 and 4000 kN clamping force More details on www.netstal.com FLIPPING THE WORLD OF PET UPSIDE DOWN AND EVEN SIDEWAYS THE ALLNEW PETLINE WITH SIDE ENTRY. drinktec 2022 I 12-16 September I C5.363"},{"@ID":8, "PETnews 6 NEWS PETplanet Insider Vol. 23 No. 05/22 www.petpla.net Europe’s non-alcoholic beverage industry calls for mechanisms to accelerate circular economy Europe’s non-alcoholic beverage industry, represented by the European Fruit Juice Association (AIJN), Natural Mineral Waters Europe (NMWE) and Unesda Soft Drinks Europe, together with leading NGOs, including Changing Markets Foundation and Zero Waste Europe, are calling on EU decisionmakers to create the right enabl ing policy framework to help accelerate the transition to a circular economy in Europe. These organisations underline the need to ensure resource-efficient waste management systems to enable closed-loop recycling. They also call for a “priority access”, or a similar mechanism that guarantees a “right of first refusal” to beverage producers to facilitate their fair access to the food-grade recycled materials coming from the products they placed on the market and which were successfully collected. The EU Circular Economy Action Plan has the ambition of accelerating the transition to a circular economy. This will require significant changes in the way recycled materials are collected, reused, recycled and incorporated, the statement says. Achieving fully closed and resource-efficient waste management systems for all materials should be the primary objective. The more closed-loop a system is, the more resource efficient it will be by delivering quality recycled materials which can be re-used multiple times for the same application. Therefore, for each sector, the ultimate goal should be to achieve closed-loop recycling, the organisations state and are confident that this can be achieved with the right enabling policy framework. The organisations suggest that the main policy conditions that should be created are: mandatory minimum requirements for Deposit Refund Schemes (DRS) to facilitate the roll-out of efficient waste collection schemes and the achievement of the EU 90% separate collection target; a mechanism that grants beverage producers fair and necessary access to the recycled materials deriving from the beverage containers they put on the market and which were successfully collected. This way, these materials can be used again as recycled content for new beverage packaging. This legal mechanism to guarantee a ‘’right of first refusal’’ to beverage producers will enable them to comply with the mandatory EU targets for the incorporation of rPET and ideally meet their more ambitious voluntary pledges (e.g. Unesda’s Circular Packaging Vision of achieving 50% rPET in 2025 and 100% in 2030 and NMWE’s commitments to achieving 50% rPET by 2030) towards circular packaging. a harmonised definition of high-quality recycling and, based on this definition, a ranking of recyclability classes. In such ranking, the highest position (priority) should be attributed to packaging that does not pose any recyclability issues and the recycled material can feed a closed-loop scheme and allow further recyclability of the same quality (for example, food-contact) when reaching their end-of-life. Nicholas Hodac, Director General of Unesda Soft Drinks Europe, adds: “Recent reports have illustrated that postconsumer recycled PET from beverage bottles is increasingly used by non-food sectors (textiles, automotive, etc.) to boost their environmental sustainability credentials. […] ‘Breaking the loop’ (a loss from the circular bottle stream) goes against the very principle of circularity. In addition, it also creates an unfair situation because food and drink producers are obliged to comply with strict EU health and safety requirements for food contact materials.’’ A priority of upcoming EU legislation should be, according to the organisations, to look beyond beverage containers and enable the creation of closed loops for all products and packaging applications. Joan Marc Simon, Executive Director of Zero Waste Europe, says: “It is time to raise EU ambitions and define highquality recycling. Introducing such a definition in the EU legislation will incentivise investments in recycling infrastructure and foster resource efficiency across the whole production of products and packaging materials.’’ www.unesda.eu New figures for installed plastics recycling capacities reveal a 13% growth The total installed plastics recycling capacity in 2020 in EU27+3 grew by 1.1 mt compared to the previous year. The new figures show that the plastics recycling industry remains resilient while continuing its path towards making plastics genuinely circular. The growth in the sector, despite the difficulties brought on by the pandemic, was possible thanks to the booming demand driven, among others, by the new legislative targets. The dataset shows that PET, flexible PO and rigid HDPE & PP retain the biggest share of the overall plastics recycling capacity, representing nearly 80%. Moreover, Germany, Italy, Spain, UK and France have the highest capacities for plastic waste recycling. Rigid HDPE & PP registered the highest increase in recycling capacities (a rate of over 20%), while for flexible PO it grew by roughly 10%. Fast-paced technological developments in collection, sorting and recycling were among the factors that facilitated these developments. With €7.7 billion in turnover and a total of 9.6 million tonnes of installed recycling capacity, European recyclers are an essential part of the puzzle in addressing plastic waste and play a significant role in contributing towards a carbon-neutral Europe. Comprehensive legislative support would unlock additional collection and high-quality sorting tonnages while incentivising investments in recycling technologies & infrastructures leading to a tripling of plastics recycling capacities by 2030. www.plasticsrecyclers.eu"},{"@ID":40, "BOTTLING / FILLING PETplanet Insider Vol. 23 No. 05/22 www.petpla.net 38 Low oxygen pickup The solid jet principle of the NV filling system with its practically drip-free gas lock also helps to ensure a high product quality. “From a microbiological standpoint, it’s beneficial if the beverage doesn’t come into contact with the bottle neck,” Härtel continues. The product manager also always keeps an eye on the amount of oxygen pickup. It’s important to avoid this wherever possible, for instance when hot filling juice: too much oxygen pickup could cause pulp to float to the surface and thus form clumps. It would also lower the vitamin C content in the products. Oxygen pickup is a relevant topic for breweries in particular. “Bottom-up filling on our DVF and DRF long-tube valves significantly reduces oxygen pickup and allows beer and mixed beer beverages of excellent quality to be filled into PET bottles.” The exact filling volume is determined with the help of an inductive flow meter or – optionally – a mass flow meter. Two different filling speeds are configured as standard that ensure good flow behaviour and low-foam filling. A number of optional additional components are available for the best possible processing of different volumes and viscosities, such as a large spectrum of bottle sizes or juices with a low or high viscosity. A control valve upstream of the filling valve can freely regulate the filling speed for production within a capacity range ideally suited to the type of beverage, amount of foaming, bottle volume and viscosity. Together with a gentle container control, this results in less product loss, says KHS. Because of the design and deployment of the components on the filling valves, the new filler platform is intended to achieve a high-power density regardless of the type of beverage. Härtel underlines: “We’ve implemented this modularity and standardisation in both the machine controller and the mechanical equipment. As our fillers will always have the same construction in the future, installation and commissioning will be much faster.” This shortens the time to the start of production and the first commercial product. Here, semi- and fully automated format changeovers especially are claimed to ensure a permanently high level of availability during ongoing operation. Some parts of the cleaning system are already automated, such as the CIP sleeves. In addition to providing hygienic safety, the use of quick functions also means that they save considerably on time. As several operator tasks are now redundant, the number of potential sources of error is reduced to boot. Moreover, the durability of all components makes for greater efficiency, so that maintenance intervals can now be much longer. Diagnostic assistance system The technical functions of the new filler platform are supplemented by the optional KHS Dias diagnostic assistance system. This enables all aspects of the entire filling process to be monitored. For this purpose, pressure sensors are installed in every filling valve that constantly The clear design with its mostly enclosed surfaces increases hygiene and makes cleaning and disinfection easier."},{"@ID":10, "8 NEWS PETplanet Insider Vol. 23 No. 05/22 www.petpla.net Plastics Industry Association announces top leadership appointments The Plastics Industry Association Board of Directors appointed Matt Seaholm to the position of Chief Executive Officer and Glenn Anderson to the position of Chief Operating Officer. Matt Seaholm has served as Plastics’ Vice President of Government Affairs for the past two years and prior to that was the Executive Director of the American Recyclable Plastic Bag Alliance at Plastics. Before joining the association, Matt was Vice-President of Public Affairs at Edelman. He is a veteran of political and policy campaigns, having worked on everything from local ordinance fights to state-wide political campaigns to national issue advocacy initiatives. He has been a public voice on behalf of the plastics industry for more than five years, testifying before more than thirty legislative bodies and being interviewed by more than one hundred media outlets. Glenn Anderson is currently the Vice President, Member Engagement for Plastics and has been in that role since April of 2020. Glenn has been an industry leader for nearly 40 years. Prior to joining Plastics, Glenn worked for member company and NPE exhibitor, Milacron LLC (now a division of Hillenbrand) for over 30 years. During his time at Milacron, Glenn held numerous roles and responsibilities including Vice-President & General Manager for both their injection & extrusion businesses for the America’s and most recently, as Senior Vice-President – Global/Strategic Accounts working with key global customers for all Milacron branded companies including Mold Masters and DME. www.plasticsindustry.org Erema Group: Growing revenues, plant sizes and production capacities The Erema Group, which comprises Erema Group GmbH and its subsidiaries Erema, Pure Loop, Umac, 3S, Keycycle and Plasmac, closed the 2021/22 financial year with a 17 per cent increase in revenue. Consolidated Group revenue amounted to EUR 295 million, and the number of employees increased to over 840. The Erema Group remains on course for continued growth. A total of 220 extruders manufactured in Ansfelden were supplied to customers all over the world. If one includes individual components and modules such as filter systems and ReFresher anti-odour technology in that figure, the total was around 320. Then there are another 53 extruders from Plasmac, the Italian subsidiary. The recycled pellet production capacity of all extrusion systems de l i vered i n f i nanc i a l year 2021/22 adds up to around 1.34 million tonnes per year. A closer look at the post-consumer segment clear ly shows a t rend towards larger plants, both for PET recycling and for processing polyolefins. For example, the first Vacurema Basic 2628 T machine with an annual capacity of up to 40,000 t was recently commissioned at a customer’s site in Brazil. This plant features a ten-metre-long special geometry screw with a diameter of 280mm and a weight of 3.5 t. The screw was developed and manufactured by 3S, a subsidiary of Erema GmbH. Demand for prev i ous l y-owned machines at Umac also remained high during the past financial year. In addition to the general trend towards plastics recycling, the decisive factor here is that customers are more frequently opting for previously-owned systems available at short notice due to the tense situation on the procurement markets. At the same time, businesses that have so far had little contact with recycling are also becoming increasingly interested in this topic. Their need for feasibility studies, consulting and engineering services, project management and turnkey projects are now also very successfully catered for by Keycycle, an Erema Group company. www.erema-group.com F.l.t.r.: Matt Seaholm, CEO & Glenn Anderson, COO Herbold Meckesheim GmbH Your partner for plastics recycling www.herbold.com As a specialist for plastics recycling we are your contact for complex applications. We have the long lasting expertise in washing, separation and drying – to recycle new, used and contaminated plastic waste. Thanks to our modular technology, we are able to develop customized overall concepts or to optimize your already-existing plant. Herbold Hydrocyclone Ten times higher separation effect compared to a swim-sink tank for higher purity Higher washing effect due to additional intensive friction Continuous water cleaning circuit Compact design"},{"@ID":23, "MATERIALS / RECYCLING 21 PETplanet Insider Vol. 23 The future starts in our heads Discover our sustainable innovations at krones.com drinktec 2022 Munich 12-16 September Hall B6 pensates this number by adding an additional shot to the octabin. In this way, the PreMon ensures that not only the preform quality increases but also that the quantity delivered per octabin is always approximately the same. Product reference The setup of a new product is one of the essential tasks of the operator of a vision inspection system like the PreMon. Thanks to the product reference, the system can detect which products meet the specified quality standards and which do not. If this product reference is set incorrectly or not optimally, it has a lasting effect on the inspection quality and the corresponding customer satisfaction. With the new PreMon software add-on Wizard the reference creation becomes easier for the operator. The Wizard actively supports the operator in finding the optimal settings. The operator is guided through the setup process by simple steps, some of which are even carried out automatically by the system. In this way, the operator can create a new reference with only a few steps – even while the production process is running, and the products are being inspected. With the PreMon, Intravis has already had a system in its portfolio for several years which, due to its inspection criteria, is suitable for the application in preform production lines that increasingly rely on recycled material. With new developments at software level – the informative dashboards, ejection compensation as well as the PreMon Wizard – the system contributes the desired information for decision making and immediate production optimisation. www.intravis.com"},{"@ID":31, "MARKET SURVEY 29 PETplanet Insider Vol. 23 No. 05/22 www.petpla.net PET Technologies Sacmi Imola S.C. Sipa Spa GDXL Precise Machinery Co., Ltd. KHS GmbH Grünlandgasse 5/1/12 2620 Neunkirchen, Austria +43 720 775 196 www.pet-eu.com Mr Maxim Poliansky CEO +43 720 902 169 offi [email protected] Via Provinciale Selice 17/a, 40026 Imola, Italy +39 54260 7111 www.sacmi.it Via Caduti del Lavoro 3 31029 Vittorio Veneto, Italy +39 0438911511 www.sipa.it Mr Paolo De Nardi Product Manager SBM +39 0438 9 11511 [email protected] No.18 Changjiang Rd., Guicheng, Nanhai, Foshan City, Guangdong Province, Postcode: 528251, China +86 757 8677 7168 www.gdxl.com Mr Billy Ay Marketing Specialist +86 757 8677 7168 ext. 8681 [email protected] Juchostr. 20, 44143 Dortmund, Germany +49 231 569 0 www.khs.com Mr Dennis Jacobi Manager Service Sales +49 40 67907 225 [email protected] 40 l 3.3 l (std machines) - 12 l (big format machines) 30 l Up to 5 l Depending on bottle geometry: - typically 100ml-2,500ml with regular moulds, inner shell & outer shell system (requires additional maxi pencake at approx. 1,500ml to hold the mould closed) - up to 3,900ml with compact moulds (outer=inner shell, still usable at standard blow moulder) - up to 5,500ml with compact large moulds (only applicable at special compact large blow moulder) Yes No No Yes Yes Yes Yes Yes Yes, moulds applicable to various brands of SBM machines such as Sidel, Krones, KHS, Sipa, TechLong, Newamstar, etc. Yes Rotary and linear blow moulders: Sidel, KHS, Krupp, Sipa, SMI, Krones, Kosme, Siapi, Mag Plastic, ADS, Lonza, Side, Chumpower etc. Sidel, Krones, KHS/SIG/Krupp, SMI, Siapi, Kosme, Side Bottlers/converters which supply bottle to beverage brands such as Coca-Cola, Pepsi-Cola, Danone, Nongfu Spring, etc.; as well as applications in food, cosmetic, pharmaceutical, home and personal care industries. Customers from different branches (soft drinks, water, beer, non-food, food, …), including global key accounts such as Coca-Cola Creation of unique bottle design, branding, product naming, logos and labels, 3D models, prototyping, bottle sampling, PET containers laboratory tests Yes Brandbuilding, product repositioning, market analysis, packaging engineering, lightweightening of existing bottles, technical feasibility; newAWArPET analysis (Design for Recycling), label and secondary packaging Yes, GDXL designs bottles according to customers' requirements on technical performance and appearance. Yes, preform and bottle design (technical/marketing), fi nite elements analysis, 3D modelling, use of rPET Moulds for 100ml - 40l containers, fi lling line conversions, bottles for chemicals and detergents, sanitisers, hot fi ll, wide neck jars, lightweight designs, laboratory tests Double cavity concept, low pressure base moulds, stainless steel moulds Wide mouth, large sizes (up to 30 liters), asymmetrical, Nitrogen hot fi ll, containers with handles, HDPE to PET conversions, pharma & cosmetics. Bottle designs for light-weighting, optimised CSD base, re-inforced structure, market-appealing styles and imitated texture, etc. Light weighting, low pressure, complete PET line optimisation, carbon dioxide calculator, global key account certifi ed laboratory Short lead time VACUNITE® definiert den Maßstab für Leistungsfähigkeit im Bottle-to-Bottle Recycling neu: Höchste Dekontamina- tionseffizienz für kompromisslose Lebensmitteltauglichkeit, rPET-Granulate mit besten Farbwerten, Top IV-Stabilität, Kompaktheit der Anlage sowie ein geringer Energieverbrauch über den gesamten Prozess sorgen für überzeugende Sicherheit, Produktivität und Qualität. Vereint Vakuum- & Stickstoff-Technologie"},{"@ID":34, "BOTTLE MAKING 32 PETplanet Insider Vol. 23 No. 05/22 www.petpla.net Sipa ECS SP one-stage system boosts Şimşek Plastik’s production Flexible & fancy Several months ago, major Turkish converter Şimşek Plastik made an investment in singlestage injection-stretch blow moulding technology (ISBM) from Sipa. After acquiring an ISBM ECS SP 25 unit in early 2020, it subsequently purchased three larger model ECS SP 80 units. All are now in full operation. Moulds made in high-performance stainless steel are equipped in a standard configuration with valvegated hot runners for the production of premium quality containers. An important advantage for a company like Şimşek Plastik, which produces containers in diverse shapes and sizes, is that the same hot runner system can be used with moulds producing different types of preforms, with only the cold half needing to be changed. This saves money, as well as time at format changeovers. Şimşek Plastik is among the leading companies in its sector in Turkey. “We are happy to add value to the products of dozens of international brands in many different sectors,” the company states. “With our internationally accepted production power in the sector, we have delivered Şimşek Plastik quality to many locations outside our country.” Up to 30% lower changeover times Sipa’s ISBM offering is claimed to provide answers to companies producing at all levels, from as few as 100 bph, up to 36,000 bph for Sipa’s ECS SP ISBM machine has been designed for high quality containers on challenging shapes. to our needs. The ECS machine is robust and highly efficient, and can operate with as many as 16 cavities, offering the maximum versatility”. High performance, low energy consumption ECS SP machines use a hybrid drive technology, obtaining precision and speed for injection from servoelectrics, while hydraulics perform more “workhorse” tasks (e.g. to apply clamping tonnage). The result is a combination of high performance and low energy consumption, helping the machines achieve a small carbon footprint. Şimşek Plastik is a leading manufacturer of plastic bottles for a variety of sectors such as food, healthcare, cosmetics or detergents. From Turkey, the company supplies many international brands. The most recent additions to Şimşek Plastik’s machinery are currently operating with different cavitations: the first has five cavities, the second has six, and the third has nine. They produce high-quality bottles between 200 and 1,000ml, for various applications, including detergent, personal care, and beverages. Outputs are up to 70,000 bottles per day. “We wanted to diversify our existing ISBM machines and renew the installation with a system that can cope with new demands from different markets,” says Zeynel Abidin Şimşek, CEO of Şimşek Plastik. “We found in Sipa ISBM technology the solution"},{"@ID":35, "BOTTLE MAKING 33 PETplanet Insider Vol. 23 No. 05/22 www.petpla.net both cold and hot product filling. The ECS SP units are fast, flexible, and resource-efficient, all the while producing high-quality bottles under safe conditions, says Sipa. Speed comes from such factors as short lock-to-lock time, while flexibility manifests itself in many ways, including the ability to use legacy moulds, fast mould changeovers, and the capability of hot runners to be used on different cold halves. Changeover times can be up to 30% lower than on other machines, while operator safety is always a factor of utmost importance in the design of each Sipa system. Blow mould clamping force can be simply adjusted via the HMI; optional servo drive stretching rods makes it possible to use the same preform for different shapes. Sipa ECS SP machines have large mould pitches, so even bottles with large diameters can be produced with high levels of cavitation. Meanwhile, the optimal use of resources comes from the use of a single pump in a hybrid configuration while using a minimal amount of oil. Additional blowing pressure for challenging shapes High bottle quality derives from different factors, including mould material, process technology and control, and from the robustness of the Sipa machines. A massive clamping force together with 15% of additional blowing pressure available allows to blow complicated shapes and challenging sharp edges as well as simple designs. Cleanliness is ensured as clamping force for stretch-blowing is generated by short-stroke hydraulic cylinders positioned below the working area and requiring limited amount of oil. The safety features include special protection for all high-pressure hydraulic hoses, the cabin can be opened only after high-pressure air has been released and interlocking guards activated on all operator access. Sipa ECS SP machines are fully CE compliant. www.sipasolutions.com Şimşek Plastik’s team Şimşek Plastik is a leading manufacturer of plastic bottles for a variety of sectors such as food, healthcare, cosmetics or detergents. Production of several bottle shapes and neck finishes up to 215mm diameter on ECS SP"},{"@ID":41, "BOTTLING / FILLING PETplanet Insider Vol. 23 No. 05/22 www.petpla.net 39 record and document the internal bottle pressure and step sequence. The data collected is displayed as a pressure graph on the KHS ClearLine HMI operator panel. Any deviations from target values immediately trigger an alarm, meaning that faults can be quickly detected, localised and independently remedied by the customer. At the same time, the data enables results to be statistically evaluated. InnoPET Blomax Series V PET fillers are seldom a solitary phenomenon but instead a fixed feature of the KHS portfolio of block systems. The latest generation of KHS stretch blow moulders, the InnoPET Blomax Series V, is no exception. Its output was recently increased to a maximum of 2,800 bottles per blowing station. Thanks to intelligent process control, NIR heating and a simple modular design, the stretch blow moulder is specified with an efficiency of 98%. The InnoPET Blomax Series V is claimed to be thoughtoutwhen it comes to sustainability, not only with its ability to save on bottle weight but also regarding flexibility in the processing of recycled or virgin PET. Moreover, numerous technical optimisations considerably reduce the amount of energy and blow air used by up to 40% compared with the previous series. www.khs.com Manfred Härtel, filling product manager at KHS"},{"@ID":1, "MATERIALS / RECYCLING PETplanet Insider Vol. 23 No. 05/22 www.petpla.net 20 Inline inspection also for colour deviation Monitoring rPET preforms In recent years, the proportion of recycled material in preforms has gradually increased - initially for reasons of cost and image, and recently because it was required by law. Although this regulation makes sense from the point of view of resources conservation, the use of rPET has some negative effects on the quality of the preforms. To address these directly, it makes sense to have a monitoring system in the production line that is fully dedicated to inspecting recycled preforms. RECYCLING Yellowing is certainly the most obvious quality-reducing effect that occurs when rPET is used to produce preforms. By yellowing, a slight discouloration of the preform caused by the recycled material is meant. Just imagine how water can look in a yellowed PET bottle for the end consumer. That is why the yellowing effect is considered particularly critical by any preform producer. Targeted inspection for yellowing Intravis launched the preform monitoring system PreMon which is used inline directly behind the injection moulding machine. It provides comprehensive information about the products’ quality to the system operator. It has been optimised especially for the inspection of rPET preforms: In addition to the inspection of typical criteria such as contaminations in the body area as well as short shots and defects at the sealing surface, the PreMon also features a sophisticated colour inspection that outputs an explicit yellowing value. Thus, the operator can immediately determine the influence more or less rPET has on the quality of the produced preforms and can react accordingly, for example by adding certain additives. Clear dashboards to keep track of production As a monitoring system, the PreMon provides its operator with a comprehensive quality picture without the need to thoroughly inspect each preform. The data and information obtained is presented in a newly designed dashboard. The PreMon’s Octabin Statistics will provide the information which is needed. If one would rather find out about the quality of the whole production based on a time interval or specific inspection criteria, then the PreMon supports data with the IntraVision statistics dashboard. A special feature of the PreMon is the so-called ejection compensation. In addition to shot counting, the PreMon offers an ejector as an optional extension. Both combined, the operator is able to control the amount of preforms in his octabins in a targeted manner, and to actively influence the quality in his octabins. If a specified amount of defective preforms are ejected, the PreMon com-"},{"@ID":12, "EDITOUR PETplanet Insider Vol. 23 No. 05/22 www.petpla.net 10 Machine builder Nissei ASB during and post pandemic Strong growth in cosmetics, health care and pharmaceutical products by Kay Barton March 25, 2022 We met: Mr Karel Keersmaekers-Michiels, Managing Director While many companies have experienced serious disruption during the past two years, Nissei ASB made further gains in sales, posting record revenues of JPY35,9 billion in the 2021 fiscal year which ended in September, with a 31.7% growth in sales from 2020 to 2022 despite restrictions imposed on pandemic-related commercial activities. Just over 600 machines and 1,400 moulds were sold during this period by the company which employs 2,093 staff worldwide. Tour Sponsors: Karel Keersmaekers-Michiels explains: “At the start of the pandemic, there was an urgent demand for disinfectants and cleaning products which, of course, required the necessary packaging machinery and moulds. We had made major investments in new factories in India and Japan during 2018-2019 which enabled us to manage the sudden demand for this as well. The trend continued for more than a year. At the same time, demand for cosmetic products dropped significantly due to various lockdowns and travel restrictions. But then, the situation changed once again. Following the saturation of the market by disinfectant and cleaning products, demand again fell markedly while global easing of restrictions greatly boosted areas such as standard and high-priced cosmetics. By the way, we only had a temporary shutdown of our plant in India in the spring of 2020 but were fully operational again by the autumn”. During the pandemic, Nissei ASB also continued to fine-tune its Zero Cooling technology, as well as processing quite a few orders for its high-performance PF36 machine used in the production of drinks bottles and launched in 2018. There were also developments in the area of environmentally-friendly packaging such as double-layer containers; lightweight, large-sized bag-in-box containers and lightweight reusable bottles. “On the manufacturing side we have optimised our global production system by enhancing our mould manufacturing capacity at our India plant and restructuring a flexible production system at the factories in Japan to respond to the increase in production and the spreading of risk. We will continue to invest for the future expansion aiming at increasing in-house production, shortening lead times and enhancing profitability”, explained Mr Keermaekers-Michiels. This year, he is expecting a yield of JPY30 billion due to disruption in supply chains and a weakening global economy caused by rising material and energy prices. The war in Ukraine is also likely to have an adverse impact on Nissei ASB’s operations, particularly in Europe. “We will probably sell around 500 machines and systems this year”, said Keersmaekers-Michiels. The best-selling line is the 4-station ASB series which comes in three different sizes and on which a range of containers made from various plastics can be produced. The basic customer structure is around 35% from hygiene products and cosmetics, 25% food, 20% pharmaceuticals and 10% each from drinks to household cleaners. But back to Europe. The market, Mr Keersmaekers-Michiels explains, is not only the most advanced in terms of plastic packaging but also a trendsetter in sustainability and contributes 20% to the company’s total sales. “In our strongest segment, cosmetics and personal care products, the design and functionality of the packaging plays an important role in both positioning and protecting the product as well as providing convenience to the consumer. Several global brands have their headquarters and R&D centres in Europe and their packaging developments have an impact on the rest of the world.” The importance of sustainable production is also a constant issue with customers. Recyclate is already being processed on a broad scale, with future European legislation expected to further increase the demand for rPET Managing Director Karel KeersmaekersMichiels"},{"@ID":29, "MARKET SURVEY 27 PETplanet Insider Vol. 23 No. 05/22 www.petpla.net 05/2022 MARKETsurvey Suppliers of preform and SBM moulds In this issue of PETplanet we are very glad to present you an update of mould manufacturing for perform and SBM moulds. Please have a close look at the companies showing their newest developments: Wentworth Mold, Kosme, SMI, Röders Tec, KHS, Sipa, Kiefer Werkzeugbau, PET Technologies, GDXL, Sacmi Imola, MHT Mold & Hotrunner Technology AG and Otto Hofstetter. Although the publishers have made every eff ort to ensure that the information in this survey are up to date, no claims are made regarding completeness or accuracy. Resins & additives Preform machinery Preform production & inspection systems Preform & SBM mould manufacturer SBM 2-stage Compressors Caps & closures & inspection systems Filling equipment & inspection systems Recycling machinery Palletising & shrink film machinery Preform moulds Company name Otto Hofstetter AG GDXL Precise Machinery Co., Ltd. Sacmi Imola S.C. Kiefer Werkzeugbau GmbH Sipa Spa MHT Mold & Hotrunner Technology AG Postal address Telephone number Web site address Contact name Function Direct telephone number E-Mail Zürcherstrasse 73, 8730 Uznach, Switzerland +41 55 285 22 11 www.otto-hofstetter.swiss Mr Markus Feldmann Division Manager PET +41 55 285 22 97 [email protected] No.18 Changjiang Rd., Guicheng, Nanhai, Foshan City, Guangdong Province, Postcode: 528251, China +86 757 8677 7168 www.gdxl.com Mr Billy Ay Marketing Specialist +86 757 8677 7168 ext. 8681 [email protected] Via Provinciale Selice 17/a, 40026 Imola, Italy +39 54260 7111 www.sacmi.it Mr Moraldo Masi Preform Division Director [email protected] Steinhäldenstraße 11, 74193 Schwaigern, Germany +49 7138 97320 www.kiefer-mold.de Mr Maik Weber Sales & Project Manager +49 7138 973 270 [email protected] Via Caduti del Lavoro 3 - 31029 Vittorio Veneto , Italy +39 0438911511 www.sipa.it Mr Gianfranco Perricci Global Sales Director +39 04389 11511 [email protected] Dr. Ruben-Rausing-Str. 7 65239 Hochheim am Main, Germany +49 614 69060 www.mht-ag.de Mr Ralph Gauß Area Sales Manager [email protected] Preform moulds Horizontal opening Yes Number of cavities 2 up to 192 From 32 to 144 cavities 16-32-48-72-96-128-144 Up to 200 2 to 192 cavities Preform sizes up to 500g Various neck fi nish standards:1810, 1881, 30/25, 29/25, 26/22, 38mm, etc. Preform weight from approx. 3.5g to 750g (for applications from pharmaceutical/cosmetic bottle to 5-gallon keg) L 190mm UP to 750g Up to 750g, for bottles up to 30 l Moulds already built for (makes) Netstal, BMB, Husky, Arburg, Husky Husky, Netstal, Niigon, KraussMaffei, Sipa, etc. Sacmi , Husky Sipa, Husky, Netstal, KraussMaffei, Sacmi Sacmi, Husky, Netstal, KraussMaffei, Sumitomo, Niigon, Arburg, BMB, Demark, Cincinnati, Unique, NegriBossi, Sipa Vertical opening Yes Number of cavities 2 up to 112 From 16 to 96 cavities Up to 96 2 to 112 cavities Preform sizes up to 500g Various neck fi nish standards: 1810, 1881, 30/25, 29/25, 26/22, 38mm, etc. Preform weight up to 69g Up to 150g Up to 600g, for bottles up to 30 l Moulds already built for (makes) Arburg, Krauss-Maffei Sipa, Krauss-Maffei, etc. Standard and custom Sipa, Krauss-Maffei KraussMaffei, Arburg Do you produce single stage tooling sets? (Preform moulds AND blow moulds) No No Yes Yes, for Sipa machines No Other - Multilayer moulds up to 72 cavities - Moulds for PP - Moulds for thinwall packaging - Moulds for cartridges and tubes - Moulds for medical products We also provide: preform R&D service for specialised container purposes; engineering solutions together with our partners for: multilayer co-injection containers with barrier properties and marketappealing elements; and complete preform production systems - Preformmoulds for PE, PP, PLA - Bag in bottle moulds - Wide mouth - Moulds for vacuum blood test tubes - Up to 5 gallon - Moulds for toner cartridges - 2K hotrunner (e.g. milk application) - AFM technology (Active Flow Moulding) - Test plaque mould for rPET"},{"@ID":25, "MATERIALS / RECYCLING 23 PETplanet Insider Vol. 23 ensuring a clear, high-resolution image of the base at the start of production. The high-resolution imaging is suited for managing bottles with rPET where the presence of small particle contaminants can increase the incidences of holes in the highly stretched regions of the foot and base. The Pilot Vision+ system offers a number of tools to assist operators with setup and job management. These include adjustable ROI tools, digital image filtering, zone scaling and the ability to display live and historical inspections images that can be used for evaluation or setup purposes. Defects are correlated to the mould/spindle to easily identify the source of a defect. Defects are also categorised using colour codes for quick and easy identification of offending characteristics. Process control for managing rPET variability One of the challenges to efficient bottle production is variability in the resin and as a result, lack of consistency in preforms. Recycled resin significantly compromises preform consistency, and as a result, the bottle becomes increasingly more difficult to make. Preforms made of recycled PET, because they are inconsistent in makeup and colour, behave differently in the blowmoulder and require continuous adjustments to the blowmoulder controls in order to maintain proper material distribution. The Process Pilot system takes and analyses real-time measurements of sidewall thickness of every bottle leaving the mould, then adjusts the blowmoulder control parameters if material distribution starts trending out of spec. The result is an optimised blowing process that ensures consistent container quality and performance over the entire production run. Process variability related to rPET material, such as variations in colour that affect heat absorption, can be effectively managed by the Process Pilot system, eliminating the need to constantly adjust the blowmoulder. This avoids the production of defective and non-conforming containers, minimising product waste and related downstream issues. The Pilot Vision+ and Process Pilot automated blowmoulder control system are part of a complete line of products offered by Agr International Inc. to help bottle manufacturers and brand owners manage container quality and production efficiency, particularly with the ever-increasing use of rPET. www.agrintl.com"},{"@ID":16, "MATERIALS / RECYCLING PETplanet Insider Vol. 23 No. 05/22 www.petpla.net 14 mass of PET used in fibres will end up as leakage from the circular system. Upper limits to PET circularity in the future Upcoming policy is driving increased bottle collections, likely only achievable through the introduction of deposit return systems (DRS) for PET beverage bottles. The widescale introduction of DRS, coupled with improvements in bottle product design, is also likely to offer advantages in the quality of rPET derived from bottles. Petcycle, a German DRS closed loop circular system, demonstrates that continued circularity can be achieved with 55% rPET content of bottles (recycled content target for members for the past eight years). Recent laboratory test results indicate that bottles can be made from 75% recycled content in a closed loop circular model by adding 25% of vPET at each manufacturing stage, without any significant loss of bottle quality characteristics, other than a grey discolouration in the bottle appearance. Within the total European PET bottle market this means that bottles POM contain on average 17% rPET, which means only 17% will be carried over from the previous loop and the PCR content within the system is swiftly reduced. Taking anticipated policy changes, the Petcycle case study as well as the experiment results by other studies into account, we can see that the impact on the longevity of PCR content in each case is significant. A future scenario will likely see bottles being managed in a much more circular way than currently is the case. With a high PCR content (a maximum of 75% was used in an example in the study), a high amount of rPET flake is returned into bottles of the same colour, with reduced levels of cascading from bottles to lower value streams. Noticeable also is a significant reduction in loss from the bottle system, both in terms of waste and rPET cascading into other, lower grade PET applications. Due to lack of availability of rPET from clear and light blue bottles, in this best-case scenario only 61% instead of 75% recycled content in bottles is possible. Considering only the traditional mechanical recycling market there are two potential scenarios considered in more detail in this report which could increase the recycled content in bottles: A further improvement in collection rates (e.g., meeting higher collection rates in DRS schemes); and/or A move from coloured and opaque bottles to clear bottles (this would require a ca. 91% reduction in coloured and opaque bottles). To generate 75% recycled content purely with a further increase in the DRS collection rate alone is not possible, even when assuming that all current and future DRS systems would achieve the current collection rate of the highest performing DRS system (i.e., 97% reported in Germany). Therefore, manufacturers would need to consider changes to the design of their bottles, more specifically the colours they use for their products. Reducing the current opaque and coloured beverage bottles POM by 91% and thereby increasing the clear and light blue bottles POM by the same absolute numbers means that 75% recycled content in bottles overall can be achieved. In addition to the two scenarios considered for mechanical recycling there is potential for chemical recycling technologies, such as chemical depolymerisation, to contribute to PET circularity and achieve a 75% recycling content in all bottles. This industry has not reached maturity, however, and its true potential is not fully known at present, but it does appear that there is planned input capacity (sorted and clean post-consumer PET flake) of approximately 350 ktpa by 2025, that could be sufficient to achieve 75% content in bottles if food contact regulations allow. It is estimated in the report that in the future, we could see an increase in the upper limit of bottle-to-bottle recycling with a recycled content of somewhere between 61% and 75%, up from currently 17%. This is, however, on the assumption of prioritising closed loop recycling (ie., using rPET from bottles in bottles as opposed to other PET applications) to ensure maximum circularity. More realistically, based on market conditions, the study estimates the future use of recycled content in bottles to lie somewhere between a minimum policy driven target of 30% and the upper possible limit of 75%. When considering the impact the changes might have on all PET packaging, an increase of recycled content from 28% to somewhere in the region of 47% to 56% could be envisaged. For all PET applications, recycled content shifts from currently 24% to an upper limit of 41% to 42% in the future. This will happen only by: Prioritising bottle-to-bottle closed loop recycling instead of using rPET from bottles in other PET applications; Increasing the use of Deposit Return Schemes, which will improve collected material quantity and quality; and/or Switching from coloured and opaque PET to clear PET. www.zerowasteeurope.eu 17% 80 70 60 50 40 30 20 10 0 bottles current Recycling content future future with shift from coloured all PET packaging all PET 28% 24% 61% 47% 41% 75% 56% 42% Recycled content by manufacturing scope (source: Zero Waste Europe)"},{"@ID":39, "BOTTLING / FILLING PETplanet Insider Vol. 23 No. 05/22 www.petpla.net 37 Design improvements help to save energy – from the compact tubular ring bowl to the effective servo-drives. As the new filler permits filling temperatures of up to 24 °C, no additional investment and operating costs are incurred for energy-intensive cooling devices. A further plus is that at these temperatures no condensation is formed that needs to be dried using a high amount of energy before the bottles are packaged in film or cardboard. The hygienic design also contributes to the overall sustainability of the new technology: the clear, straightforward design of the machine surfaces enables a free runoff of liquids. This is claimed to make cleaning and disinfection easier and shorter. Finally, as bottles are conveyed through the machine by their neck rings, the handling of lightweight containers is supported, thus helping to ensure that products are packaged safely and reliably while saving on resources. Avoiding flavour carryover In view of the increasing variety of products and ever more frequent type changeovers, avoiding flavour carryover is of central importance. One key prerequisite needed to achieve the level of flexibility beverage fillers require is thus to choose the right sealing material for the expansion joint seals on valve pistons and switching cylinders. “KHS uses polytetrafluorethylene (PTFE) here,” emphasises Härtel. “This material can be excellently cleaned and absorbs practically no flavouring substances – unlike standard seals made of elastomers such as ethylene-propylene-diene rubber (EPDM), that soak up liquid like a sponge during production. When there’s a drop in concentration with the next product in the filling sequence, the EPDM again releases these flavourings – water, for example, then tastes of the beverage previously filled.” In order to prevent this unwanted effect, the production plan has to be scheduled by flavour, states Härtel. “The week thus starts off with a mineral water, for instance, and continues with the filling of products with an increasingly intensive taste, such as energy drinks. After these have been processed, the filler then has to be thoroughly cleaned before water can be bottled. By considerably reducing the flavour transfer, our filling valves give our customers more freedom in their production planning.” 26\"-*5: \"4463\"/$& GPS ZPVS QSFGPSNT BOE 1&5 QSPEVDUT 888 */53\"7*4 $0. The new KHS filler is featuring a servo screw capper."},{"@ID":49, "47 PRODUCTS PETplanet Insider Vol. 23 No. 05/22 www.petpla.net Fixed blades on a rotating drum to cut the label Despite being widely used in industries such as soft drink and water, traditional roll-fed labellers have several areas that can notoriously cause downtime and frustration for users. One of the biggest complaints about traditional roll-fed labellers is downtime associated with the frequent cleaning of the vacuum drum that transfers labels after they are cut. In traditional rollfed labellers, glue can accumulate on the drum and in the vacuum holes. Eventually, the machine must be taken out of operation and cleaned. Additionally, the label cutting area of traditional roll-fed labellers presents inherent challenges for maintenance personnel. Typically, the setup time for the cutting blades is long and expertise is required to optimally set them up. With Simpl-Cut, PE Labellers offers a solution to solve these problems. One special feature of the Simpl-Cut system is the simplicity of the cutting system itself. Unlike traditional roll-fed labellers that use contrasting blades to cut the label, SimplCut uses fixed blades on a rotating drum to cut the label. The fixed blades are contained in a cartridge which can be changed out and ready to run in less than ten seconds. In the Simpl-Cut process, hot-melt glue is applied prior to the cutting of the label, virtually eliminating glue buildup on the drum. In traditional roll-fed labellers, glue is applied after the label is cut, leading to glue buildup on the drum which has to be cleaned often by maintenance staff. For the labelling process, only one drum is needed to transfer and cut the label, whereas traditional rollfed labellers require two separate drums for each function. This feature is intended to reduce maintenance, to improve uptime, and to allow for faster format changes. www.pelabellers.com The PRSE exhibition, conference and awards are the annual focal point of the plastics recycling industry in Europe PRSE 2022 will return to the Rai, Amsterdam on 22-23 June 2022 Register today for your FREE entry badge www.prseventeurope.com Follow PRSE on social media: l linkedin.com/company/plastics-recycling-show-europe/ T twitter.com/PRS_Europe f facebook.com/PlasticsRecyclingShowEurope 22-23 June 2022 RAI, Amsterdam Platinum Sponsor Awards Platinum Sponsors: Silver Sponsors Organised by"},{"@ID":55, "MATERIALS / RECYCLING PETplanet Insider Vol. 23 No. 05/22 www.petpla.net 17 MATERIALS / RECYCLING 17 www.sacmi.com Product design Product development Product validation Industrial production plant Process & quality control On-site and start-up assistance After-sales and Customer service SACMI 4.0 THE COMPLETE CLOSURE, PREFORM AND CONTAINER SOLUTION FOR YOUR SMART FACTORY E N D L E S S I N N O V A T I O N S I N C E 1 9 1 9 Magnetic density separation (MDS) principle Umincorp’s patented mechanical recycling process is based on flake sorting. In an early stage of the process, all incoming plastics are cut into flakes and separated via MDS. The MDS application, with a capacity of 10,000 t/a, makes use of specially designed magnets in combination with a unique water-based process fluid to separate heterogeneous input flows on density levels of each individual particle in one step. The magneto-responsive fluid, produced in-house at Umincorp, together with the permanent magnet, creates the required density gradient so that there are different densities at different heights in the machine. Particles flow through the density field, with light particles floating on the surface while heavier particles are suspended in the liquid below at different depths according to their density. The separation for the production of pure material fractions of equal densities are combined into one process by setting splitters in the right positions. The use of MDS in the plastics industry is claimed to result in high purity PP, HDPE, PS, PET, ABS, PVC, or other plastics fractions that can be used directly in new end products. Umincorp was established in 2012 to develop and market its MDS technology. The idea was born in 2005 under the lead of Professor Peter Rem at the Delft University of Technology, the Netherlands."},{"@ID":20, "MATERIALS / RECYCLING PETplanet Insider Vol. 23 No. 05/22 www.petpla.net 18 New extended producer responsibility (EPR) legislation is a benefi t, one of Africa’s largest PET recyclers explains Team work in the plastics value chain Plastic strapping is used to secure unstable goods during transit. From a circular economy perspective, both PET bottles and PET strapping can be diverted from landfill, and economically recovered and recycled into new products, without compromising the quality of the end product. As a manufacturer of strapping, Extrupet, like other packaging producers, is now obligated to either join an existing producer responsibility organisation (PRO), start a new PRO or run an individual compliance scheme, as part of the National Environmental Management Waste Act (NEMWA) Section 18 mandatory EPR regulations, which came into effect in South Africa in November 2021. In terms of the regulations, producers must take practical and financial responsibility for the full lifecycle of their products. This means designing packaging with recyclability and circularity in mind and also including more recycled content in their products. “Many companies are still importing rPET strapping, so closing the loop locally provides another high-value end-use for rPET, aside from bottle-tobottle recycling, or turning it into polyester staple fibre,” said Extrupet joint managing director Chandru Wadhwani. While clear PET plastic bottles had the highest commercial value for bottle-tobottle recycling, Wadhwani explained that green and brown PET bottles had limited end-use products associated with them, because they discoloured the recyclate and could not be used for bottle-to-bottle recycling. “In the past, plastic strapping has provided a viable end-use market for coloured rPET. As producers begin to move away from coloured to clear bottles for maximum recyclability, the clear bottles can now also serve as feedstock for strapping,” he said. “I would like to encourage companies to support homegrown circular initiatives. The more enduse markets we develop for rPET, the more the benefits will be felt along the entire value chain – right down to the waste pickers.” Petco CEO Cheri Scholtz said the Section 18 regulations essentially compelled all organisations and companies involved along the plastics value chain to work as a team to ensure that less waste ended up in landfill. In terms of the regulations, every brand owner, converter, or retailer that places more than 10t/a of identified plastic packaging onto the consumer market is deemed a producer and is required to pay an EPR fee per tonne. The knock-on effect of mandatory EPR is set to be heightened investment in infrastructure to support the sustainability of the recycling sector – from the waste pickers who collect recyclables, to the buy-back centres who purchase and re-sell the materials, and the largescale recyclers who turn these into recyclate that can be made into new products. “Without EPR, we wouldn’t be able to scale collection and recycling rates sufficiently to make a meaningful difference to the amount of packaging waste that ends up in the environment each year,” she said. Wadhwani said there was a delicate balance between collection, recycling capacity and demand for rPET in the recycling value chain: “As the only Section 18-registered strapping producer in South Africa, our strapping helps to maintain that balance by providing another end-use market for rPET. Growth in rPET production and consumption is ultimately key to ensuring the sustainability of both the PET and recycling industry,” he said. Strapping falls into the PET flexibles category where legislated targets state that 50% of the product must comprise rPET, 10% must be collected, and 9% recycled. Petco and Extrupet will be working together to achieve these mandated targets. www.petco.co.za www.extrupet.com RECYCLING To reduce the amount of packaging waste sent to landfill and to accelerate the circular economy, South Africa has implemented EPR regulations. One of the biggest recyclers of PET bottles on the African continent, Extrupet, has been guided in its journey by long-standing producer responsibility organisation Petco. At the same time – and in a first for South Africa – Extrupet is helping its partner to develop an additional end-use market for recycled PET (rPET) in the manufacture of rPET industrial strapping. rPET strapping Chandru Wadhwani, Joint Managing Director Extrupet"},{"@ID":51, "45 ON SITE PETplanet Insider Vol. 23 No. 05/22 www.petpla.net DGrade opens its first sorting facility in Abu Dhabi Under the name “DGrade Recycling Factory Launch: Supporting a Closed-loop for Plastic Bottles”, DGrade, UAB, has held an opening ceremony on March 23 to celebrate the establishment of its PET bottle and flake sorting plant that features Tomra’s plastic sorting systems. The new plant started operating on March 20 and targets to process 3 t/h of PET with the latest equipment including one Autosort unit for pre-sorting and one Autosort Flake for subsequent flake purification. The high-purity flakes are then processed by DGrade and turned into the company’s Greenspun yarn for sustainable clothing or sold to local converters who use the recycled content to produce new packaging. The plant utilises the new generation Autosort to pre-sort PET bottles originating from surrounding communities. Thanks to the combination of the most advanced technologies, including its Flying Beam illumination unit, the machine removes contamination and separates PET bottles by colour. The sorted fractions are shredded into flakes and undergo additional purification and colour sorting with Autosort Flake. The high-precision flake sorter is claimed to detect even small contaminants and separates other polymers such as polyolefins coming from the bottle lids. In combination, the sorting systems can process a billion PET bottles into high-purity flakes, closing the loop on PET. The establishment of the new plant benefits the environment, but also society and businesses as well. Local packaging converters now have direct access to feedstocks and are no longer dependent on high-priced virgin materials or market availability. Furthermore, the amount of recycled content in packaging can be increased, making it easier to meet recycled content targets. DGrade for its part uses rPET to produce its Greenspun yarn for the production of sustainable clothing that also reduces dependency on primary resources. Being the only plant in the region to produce high-purity rPET flakes, DGrade is expected to play a crucial role in the promotion of a circular economy in plastic packaging and more sustainable production of textiles, supported by Tomra’s sorting machines and consultancy. www.tomra.com www.dgrade.com EISBÄR TROCKENTECHNIK GMBH / Wuhrmühle 22 / A–6840 Götzis / T +43 5523 55558-0 / F –50 / [email protected] / www.eisbaer.at RECYCLING Conveying Drying Crystallizing Mixing&Dosing Decontamination Testing"},{"@ID":48, "PETproducts 46 PETplanet Insider Vol. 23 No. 05/22 www.petpla.net +44 78175 32087 +34 676 986 962 [email protected] petmachinery.com Looking to sell your used PET machinery? We can help you. We offer a free valuation service, 50 years of industry experience, and a global network that guarantees you the best market value. Contact us today to find out more. THE INDUSTRY EXPERTS Cooperation and integration make the difference Claranor introduced pulsed light technology to beverage and dairy markets 12 years ago, as a packaging sterilisation process. One important feature was the cup decontamination, as the efficiency enabled to replace chemical processes. Together with Primoreels, Claranor is now able to retrofit the lid station with a sustainable and economical solution due to Primoreels lidding system. The Primoreels precut lids are delivered on reels, which removes the continuous check and refilling of lids magazine; it thus increases productivity. Less handling and the smart integration of the Claranor module offers a high level of hygiene, 3 to 4 log reduction on moulds and bacteria, depending on the product and aligned with Class IV VDMA code of practices. The lids are found in various structures. Even PP lids are used, so together with PP cups, the recyclability is ensured. The reels system allows the use of thin films and the Primoreels patented layout reduces film and overpack consumption. Claranor pulsed light lid decontamination, as a nonthermal treatment, is well adapted to respect even very thin films. This enables material savings. Claranor technology is claimed to save around 80% energy compared to UVC or chemical treatments. The integration of the Claranor in the Primoreels is simpler than on a conventional lidding station (less lamps, simple optical shielding), says Claranor. www.claranor.com Plug & Dry - material drying all-in-one-solution Eisbär Plug & Dry is an all-in-one-solution for material drying. A power connection and material supply line is all that is required to start the process as this system runs without cooling water. The energy-efficient compact module Plug & Dry for drying PET granules and flakes consisting of material dryer, drying hopper and material conveyance is characterised by its compact design. Among the benefits claimed for the device are high efficiency for low throughputs (25 to 200 kg/h) combined with a lower space requirement compared to conventional drying systems. The system is capable of operating under all ambient conditions using a closed circuit for continuous and rapid material drying. The adsorption drying technology offers user-optimised design and easy maintenance. The continuous drying process, low energy consumption and long life are advantages of the system, the company claims. The heart of the continuous material drying process is the slowly rotating adsorption wheel with its multitude of honeycombed, axially aligned tunnels. The inner walls of the tunnels are lined with a desiccant. As it flows through the lower half of the adsorption wheel, the process air is dehumidified by the dessiccant. During the next quarterturn, hot regeneration air flows through the tunnel and in turn dehumidifies the desiccant. In the next quarter-turn, the adsorption wheel is cooled to operating temperature and is then able to dehumidify process air again. Eisbär’s test centre, located at its Austrian headquarters, enables customers to undertake a range of different tests, with granules or flakes. Eisbär systems are intended to support a higher quality of regranulated plastics by focusing on the purification of monymers and other pollutions. www.eisbaer.at"},{"@ID":43, "BOTTLING / FILLING PETplanet Insider Vol. 23 No. 05/22 www.petpla.net 41 logo of a hotel chain, for example”, Mr Shah explained. “With the Covid pandemic and the consequent downturn in the hotel, restaurant and airline sectors, we decided to take the risk of moving into the retail sector. The demand for packaged water rose dramatically almost overnight and we are continuing to take advantage of this. Our second offering is our eco-friendlier bottles Clearth which was born with the need of sustainable packaging which has 40% less plastic leaving less carbon footprint, also called our earth edition clear water made of PET. Processing and bottling The company has two plants in Gujarat – the original facility in Ahmedabad and a second one in Surat, north-west of Nashik since 2009. Capacity is said to be over 270 million bottles per year. Still water that comes in 0.2 l, 0.5 l, 1-litre, and 2-litre bottles is produced over a work area of 14,000m2. Around three billion litres of water are processed annually, drawn from the River Tapi in Surat and from a well borehole in Ahmedabad. In addition, 20 other locations throughout India bottle Clear Premium Water under licence, with Energy Beverages producing almost half a billion bottles each year. AFM Active Flow Molding Core movement for less preform weight German Technology September 12-16, 2022 Munich, Germany Hall C5, Booth 440 “We make some of the preforms and caps ourselves”, said Mr Shah. “We are currently using two preform machines supplied by Chinese manufacturer Unique (U-PET23OE-2000. OP90/90 EE80) with 48 cavities. We make two types of preforms ourselves, both with a 26/22 neck that weighs 6.5 g and 9.5 g. We also use 28 mm preforms weighing 8.4 g,13 g and 21 g. Furthermore we have a Jeepine compression moulding cap machine with 24,000 caps per hour each along with Tech-Long DSL-60X20 Combi blocks with 32,400 bottles per hour. Additionally we buy caps that are produced on Sacmi equipment. The Combi blocks take care of bottle blowing, filling, capping, labelling and all the peripherals. We also use ABB transport robots. We have around 50% share in PET bottles and depending on what further changes are made to legislation governing the use of rPET in beverage and food packaging in India – such work has already been approved here for the first time after years of effort on the part of manufacturers – Energy Beverages is also planning to use recycled material in its bottles.” Sustainable expansion The business plan is geared to growth. Over the next five years, the company plans to acquire two more co-packers each month and purchase another bottling plant every year. Dedicated preforming and capping facilities are also to be added in Gujarat. “On the one hand, our approach is always to be goal-oriented and to produce unique products using state-of-the-art equipment that meets all international standards”, said Mr Shah. “On the other, we also want to focus our efforts increasingly on sustainability with our Clearth packaging strategy. I believe the combination of our product made and distributed with heart and soul by a committed team and our willingness to explore sustainable ideas already sets us apart from many other manufacturers. We want to continue to be close to the heart of the market and respond to consumer needs and trends as necessary”. www.clearpani.com Automatic palletising of the finished water bottles Clear Premium Water"},{"@ID":11, "9 NEWS PETplanet Insider Vol. 23 No. 05/22 www.petpla.net Talk to our specialist team [email protected] Making a positive impact on plastic Partnering for a sustainable future bmt-ni.com Netstal establishes subsidiary in the USA Netstal is strengthening its presence in the North American market with its new US subsidiary. Doug Haberman will lead Netstal Inc. as president. He will report to Renzo Davatz, CEO of Netstal, Member of the Executive Committee of the KraussMaffei Group and Board Director of the new company. Netstal Inc. is headquartered in Hebron, Kentucky. Netstal Inc. moved into its new headquarters at the beginning of March. The team will provide support to customers from the U.S. and Canada, and continue to expand North American business. The Netstal Inc. team currently consists of 24 employees. Doug Haberman brings 30 years of experience in the plastics industry. His previous positions include both machine and material suppliers. Between 1996 and 2007, he held various positions in injection moulding machine sales at KraussMaffei Corporation. Since 2007, Doug Haberman has held several leadership positions at Audia Group of Companies, a compounding and colour masterbatch company. Most recently, he managed Audia’s European business from Slovakia. For his new role as president of Netstal Inc, Doug Haberman is returning home to the United States. New facilities for sales, service and applications engineering The new North American headquarters in Hebron will serve as administrative hub for the United States and Canada. “Beyond warehousing our growing spare parts inventory, this location will also have a machine demonstration area and a separate space to refurbish machines in the future. Netstal’s field-based service, applications development, and sales team remains solely focused on helping our customers to fully realise the advantages of the Netstal technology”, emphasises Doug Haberman. www.netstal.com"},{"@ID":5, "imprint EDITORIAL PUBLISHER Alexander Büchler, Managing Director HEAD OFFICE heidelberg business media GmbH Hubweg 15 74939 Zuzenhausen, Germany phone: +49 6221-65108-0 fax: +49 6221-65108-28 [email protected] EDITORIAL Kay Barton Heike Fischer Gabriele Kosmehl Michael Maruschke Ruari McCallion Anthony Withers WikiPETia. info [email protected] MEDIA CONSULTANTS Martina Hirschmann [email protected] Johann Lange-Brock [email protected] phone: +49 6221-65108-0 fax: +49 6221-65108-28 LAYOUT AND PREPRESS EXPRIM Werbeagentur | exprim.de Matthias Gaumann READER SERVICES Till Kretner [email protected] PRINT Chroma Druck Eine Unternehmung der Limberg-Druck GmbH Danziger Platz 6 67059 Ludwigshafen, Germany WWW www.hbmedia.net | www.petpla.net PETplanet Insider ISSN 1438-9459 is published 10 times a year. This publication is sent to qualified subscribers (1-year subscription 149 EUR, 2-year subscription 289 EUR, Young professionals’ subscription 99 EUR. Magazines will be dispatched to you by airmail). Not to be reproduced in any form without permission from the publisher. Note: The fact that product names may not be identified as trademarks is not an indication that such names are not registered trademarks. 3 PETplanet Insider Vol. 23 No. 05/22 www.petpla.net Dear readers, The PET bottle recycling rate in the USA has been languishing below 30% for years. The reasons are complex and have already been questioned several times at this point. Now, from Texas, comes a proposal from a completely different direction. The idea, from the University of Texas in Austin, is to depolymerise PET in just 24 hours using enzymes and then repolymerise it again later. “The possibilities are endless across industries to leverage this leading-edge recycling process,” said Hal Alper, Professor in the McKetta Department of Chemical Engineering at UT Austin. “Beyond the obvious waste management industry, this also provides corporations from every sector the opportunity to take a lead in recycling their products. Through these more sustainable enzyme approaches, we can begin to envision a true circular plastics economy.” Research into enzymes for plastic recycling has been going on for over 15 years, but never at this speed of just 24 hours. For mixed PET fractions, this is perhaps a viable option so that one do not have to sort them according to type. So in the study, 51 different post-consumer plastic containers, five different polyester fibres and fabrics and water bottles all made from PET were examined. Researchers at the Cockrell School of Engineering and College of Natural Sciences used a machine learning model to generate novel mutations to a natural enzyme called PETase that allows bacteria to degrade PET plastics. The model predicts which mutations in these enzymes would accomplish the goal of quickly depolymerising postconsumer waste plastic at low temperatures. Despite all the enthusiasm for these fast enzymes, we must not lose sight of the fact that post-consumer PET waste still has to be collected, even in the USA... For the more down-to-earth amongst our readers, you will find many substantive articles about bottle recycling in this issue. Yours sincerely, Alexander Büchler"},{"@ID":9, "7 NEWS PETplanet Insider Vol. 23 No. 05/22 www.petpla.net PELabellers.com | Simpl-Cut.com Simpl-Cut™ introduces the cutting-edge next generation of automatic labelers. Completely innovative cutting system and gluing concept that revolutionize the traditional operating principle of the Roll-fed world. Ingenious Cutting System change blade in 10’’ without adjustment Revolutionary Gluing glue roller before label cutting Single Drum for three operations: gluing, cutting, label application Total Flexibility 3, 4, 5 and even 6 different division drums on the same station All-In-One Roll-fed cold glue and linerless pre-glued technology What’s on the line? The Simple Revolution Roll-fed Labelling will never be the same."},{"@ID":13, "EDITOUR 11 PETplanet Insider Vol. 23 for example. “Of course, rPET is not the same as virgin PET and there are technical challenges such as colour consistency, batch to batch consistency, IV stability, crystallinity level, etc.“, said Mr Keersmaekers-Michiels, “but the processibility on our machines has been sufficiently proven, given the large number of projects with rPET that we have already realised. Besides rPET we also offer processing of PET flakes and we continue to test newly developed materials such as biodegradables. Our machines have been proven to be very flexible when it comes to processing different plastic materials.“ In order to prepare itself for the future, Nissei ASB GmbH will continue to invest in staff development, communication and adaptability to enable the company to respond effectively to situations such as the pandemic with a high level of resilience. We also wanted to know how the market for single-stage technologies is likely to develop in the future, to which Mr Keersmaekers-Michiels replied as follows: “Single stage machines are extremely versatile and suitable for the production of high-quality containers and hygienic container production as the machines produce containers starting from the raw material. This also makes the production process energy efficient because cooling, reheating, handling and transport of preforms as in the 2-step system are eliminated. The trend towards short chains makes these small and medium output machines very suitable for local production to avoid expensive and polluting transport costs. I believe that we will see a further transition from mass production to small-scale local production in the coming years and the single step machine is a perfect match for this.” www.nisseiasb.co.jp Nissei ASB’s Technical Centre in Düsseldorf"},{"@ID":6, "PETcontents 4 PETplanet Insider Vol. 23 No. 05/22 www.petpla.net 05/2022 Page 47 EDITOUR 10 Strong growth in cosmetics, health care and pharmaceutical products - Machine builder Nissei ASB during and post pandemic MATERIALS / RECYCLING 12 How circular is PET? - A report shows how far PET, the most circular of all plastics, is from real circularity 16 Do you know the CO2 impact of your PET bottle? - Plastics seperation of householde plastics waste on particular level via magnetism 18 Team work in the plastics value chain - New extended producer responsibility (EPR) 19 Expanding recycling capabilities 20 Monitoring rPET preforms - Inline inspection also for colour deviation 22 Inspecting bottles with increased levels of rPET 24 It’s all in the mix - rPET preform production, flakes and granules in one hopper MARKET SURVEY 27 Suppliers of preform & SBM moulds PREFORM PRODUCTION 30 Preforms for the Indian market - Recent developments in PET preforms and bottles BOTTLE MAKING 32 Flexible and fancy - Sipa ECS SP one-stage system boosts Şimşek Plastik’s production 34 PET bottles production in Uruguay - Looking for a suitable SBM machine BOTTLING / FILLING 36 More flexibility and future viability - KHS develops modular PET filler platform 40 From hotels and restaurants to retail penetration - A water brand makes it big CAPS AND CLOSURES 42 Consumer survey on tethered cap - Bericap’s ClipAside solution BUYER’S GUIDE 48 Get listed! INSIDE TRACK 3 Editorial 4 Contents 6 News 44 On site 46 Products 54 PET bottles for home + personal care & PET bottles for beverage + liquid food Page 32 Page 10 RECYCLING"},{"@ID":24, "MATERIALS / RECYCLING PETplanet Insider Vol. 23 No. 05/22 www.petpla.net 22 Inspecting bottles with increased levels of rPET When producing PET bottles with significant recycled PET (rPET) content, there are several factors to consider - including the visible quality issues related to rPET as well as the challenges related to processing bottles with this material. RECYCLING Agr international offers a combined solution for these challenges with two products in its Process Pilot portfolio; the Pilot Vision+ inspection system and the Process Pilot blowmoulder management system. While either product can work on a stand-alone basis, the combination of Pilot Vision+ and Process Pilot provide bottle producers with a powerful duo that can manage rPET in a manner that ensures quality, maximises production efficiency and minimises waste. Vision inspection for contaminants and defects The Pilot Vision+ system, Agr’s latest generation of vision-based inspection systems, is designed to work in conjunction with today’s highspeed reheat stretch blow moulding equipment and identify contaminants and defects present in preforms and bottles. The Pilot Vision+ can be configured with up to six cameras, positioned at optimal locations within the blowmoulder in order to facilitate effective inspections. Typically, units are configured in four separate inspection stations; preform inspection in the oven area, and then immediately after mould takeout for bottle seal surface, base and sidewall inspection. The preform inspection module of the Pilot Vision+ system acts as a preform filter. Multiple colour cameras provide the imaging for 360º preform sidewall inspection as well as end cap and gate. Optics, LED illumination and image analysis routines are optimised to identify preform defects that impact bottle integrity, particularly the black specs and particle contamination associated with rPET. Preforms with visible defects can be accurately identified and removed before the bottle is blown, saving energy and resources. With the increased use of rPET, challenges related to colour consistency are also an issue. In the Pilot Vision+ system, the colour preform cameras can monitor the colour of preforms entering the blowmoulder and ensure that colours are consistent and within acceptable ranges. A valuable tool incorporated into this system provides the capability to learn multiple reference image sets for colour inspection. With this, it is possible to process a preform supply with slight colour variations and manage the range of colour by accepting those that match the reference images, while rejecting those that do not match. The base inspection on the Pilot Vision+ system incorporates a set of inspection algorithms that identify the smallest defects and anomalies regardless of bottle base size, shape or design. In addition, the base inspection features a unique liquid lens that adjusts focus for bottle heights from five to sixteen inches, without mechanical components. This feature eliminates the need for mechanical lens adjustment when changing between bottles of different heights. Focus settings are saved with each job and focus is automatically adjusted to accommodate new bottle heights, saving changeover time and Agr’s Pilot Vision+ and Process Pilot provide comprehensive inspection and control for rPET bottle processing. Agr’s Pilot Vision+ system provides vision-based inspection for identifying rPET-related contaminants and defects during the PET bottle production."},{"@ID":2, "MATERIALS / RECYCLING PETplanet Insider Vol. 23 No. 05/22 www.petpla.net 24 rPET preform production - fl akes and granules in one hopper It’s all in the mix Sacmi and its partner Piovan present a new solution that enables an increase in the percentage of flakes in the mixture by up to 70%-75%, with consequent advantages in terms of cost reductions, ease of use and management. A solution that Sacmi proposes for new generation preform presses, starting from the IPS 300 model. RECYCLING The sustainability ‘r-evolution’ in the PET world has led the major technology manufacturers to evolve their solutions to make a complete supply chain of PET viable and recyclable for food grade options. The possibility of using recycled PET on standard preform production lines has been a key element of Sacmi R&D projects for many years. Already, with the current range of IPS preform presses, it is possible to process up to 100% of rPET in granules and up to 50% of rPET in the form of flakes. This question is the starting block when presenting the new developments that Sacmi is launching together with its partner Piovan, wellknown for its development and production of production process automation systems for the storage, transport and processing of plastic and foodgrade powders and polymers. The solutions typical of this market, except for small percentages, process flakes differently from granules, due to the differences in shape and specific weight. The new solution developed is a technical solution that offers the possibility to skilfully manage the mixtures of flakes and granules without having to resort to using two distinct processing hoppers. Flakes production A new step in the IPS plasticisation unit supported by a new single hopper dryer solution which conveys the granule-flake mixture internally. This solution offers: Firstly, the possibility of increasing the percentage of flakes in the mixture to up to 70-75% (no solution on the market with this configuration can currently operate using these percentages, according to Sacmi). Secondly, simplifying the process: two hoppers are no longer required to manage the granule and flake lines with all the complexities that this involves in terms of the management of different dryers, temperatures, recipes – but a single solution that is more economical and easy to use. The new Sacmi IPS 300 Sacmi has been operating on the preform press market for over ten years, expanding its range of solutions, from the IPS220 to the IPS400, and the IPS300, launched in 2021. The characteristics of this press – which offers a range of possibilities including that of integrating the vision system which continuously controls the production – are accompanied by the development of the auxiliary unit, which will be assembled on it and, therefore, on all the new generation Sacmi IPS units. Another offer is the maximum versatility depending on the manufactured product and the quality and type of raw material (recycled or virgin) available to the customer. With the new automation developed with Piovan it is possible to work with up to 70-75% of recycled PET in flakes, but also 100% of virgin material or 100% of rPET in granules. All of this on a standard platform, that is, one that does not impose any particular adaptation at a productive or management level. www.sacmi.com www.piovan.com"},{"@ID":58, "Buyer’sguide 48 PETplanet Insider Vol. 23 No. 05/22 www.petpla.net www.repi.com 1.0 MATERIALS [email protected] www.loginplast.com NOVAPET, S.A. Paseo Independencia, 21, 3° 50001 Zaragoza fon +34 976 232 069 www.novapet.com 1.1 Materials for bottle and cap production 1.1.9 Additives and colorants HIGH PERFORMANCE LIQUID COLOURS & ADDITIVES REPI.COM Masterbatches & Compounds www.sukano.com 1.2 Packaging components and accessories 1.2.1 Preforms HIGH QUALITY PREFORMS +91-9699610000 [email protected] www.chemcogroup.com ESKAPET PET PREFORM [email protected] www.eskapet.com Special Preforms [email protected] www.flexblow.com Ph: +91 44 4340 4340 [email protected] www.nationalgroup.in PDG PLASTIQUES F-45330 Malesherbes - France Tel. 00 33 2 38 34 61 95 [email protected] www.pdg-plastiques.com Preform manufacturer 3 Rue de l’île Macé 44 412 REZE France Tel: + 33 (0)2 40 05 09 37 Fax: + 33 (0)2 51 70 01 55 [email protected] www.sgt-pet.com 1.2.2 Bottles 1.2.4 Caps and Closures Closure Solutions BERICAP GmbH & Co. KG Kirchstr. 5 55257 Budenheim Tel: +49 (6139) 2902-0 [email protected] www.bericap.com IT’S ALL ABOUT CAPS www.corvaglia.com Caps-Closures-Bouchons [email protected] www.uner.com.tr 2.0 MACHINES AND EQUIPMENT Perfect Inspection System for Cap, Preform, PET/Glass bottle & Can Email: [email protected] 2.1 Preform production (machines and equipment) ARBURG GmbH + Co KG Arthur-Hehl-Strasse 72290 Lossburg Tel.: +49 7446 33-0 [email protected] www.arburg.com BMB SpA Via Enrico Roselli 12 25125 Brescia (BS) - Italy Tel.: +39 030 2689 811 Fax: +39 030 2689 880 [email protected] www.bmb-spa.com [email protected] www.netstal.com SACMI IMOLA www.sacmi.com SIPA S.p.A via Caduti del Lavoro,3 31029 Vittorio Veneto, Italy Tel. +390438911511 Fax +390438912273 [email protected] www.sipa.it"},{"@ID":30, "MARKET SURVEY 28 PETplanet Insider Vol. 23 No. 05/22 www.petpla.net Stretch blow moulds Company name Kiefer Werkzeugbau GmbH SMI S.p.A. Kosme Gesellschaft mbH Röders Tec Wentworth Mold Ltd. Postal address Telephone number Web site address Contact name Function Direct telephone number E-Mail Steinhäldenstraße 11, 74193 Schwaigern, Germany +49 7138 97320 www.kiefer-mold.de Mr Maik Weber Sales & Project Manager +49 7138 973 270 [email protected] Via C.Ceresa, 10 24015 San Giovanni Bianco (BG), Italy +39 0345 40 111 www.smigroup.it Marketing department +39 0345 40111 [email protected] Gewerbestr. 3, 2601 Sollenau, Austria +43 2628 411 0 www.kosme.at Mr Johann Gugler Managing Director +43 2628 411 125 [email protected] Scheibenstraße 6, 29614 Soltau, Germany +49 5191 603 53 www.roeders.de Mr Steffen Lühning & Mr Jani Rickert Sales Manager +49 5191 603 822 / +49 5191 603 340 [email protected] 156 Adams Blvd., Brantford, ON, N3S 7V5, Canada +1 519 754 5400 www.wentworthmold.com Mr Tar Tsau General Manager +1 519 754 5400 ext 611 [email protected] Stretch blow moulds Bottle size (max.) (in litres) Up to 30 l 10 l 30 l Up to 30 l 10 l Moulds supplied directly to blowing machine manufacturers Yes Yes No Yes Yes Do you supply retrofi t moulds for existing SBM machines? Yes Yes Yes Yes Yes, also manufacture multiplatform compatible mould systems For which bottle maker have you already produced moulds Kosme, Krones, Sipa, Sidel, ADS, Sacmi, KHS, Bekum, Tetra Pak, Side, SMI, MAG Up to now, SMI engineers have produced numbers of moulds, featuring from the most simple to the most sophisticated shape Kosme, Krones, Sidel, KHS Sidel, KHS Corpoplast, Krones, Sipa, Kosme, ADS, Nissei, Chumpower, Terekas, 1 blow and other major machine types For all blow moulding machine platforms. e.g. Sidel, Krones, KHS, Sipa, etc. Bottle design service Yes SMI design, develop and virtually prototype a wide range of packaging solutions in rPET and PET, according to the customers' specifi c requirements. Yes Bottle design development Yes, container design, prototype sampling and bottle performance tests Specialities Lightweight design, special design for functional drinks, juices, oil and vinegar, household chemistry, dairy products, cosmetic industry, petrochemical industry Moulds are manufactured using a special aluminium alloy. SMI relies on a special laboratory for the production of moulds and mechanical components, equipped with an FMS line consisting of 12 CNC machining centres: highly automated machines, running 7 days a week round the clock, even operator-less, according to pre-set production programmes (CAM). Bottle development service free of charge, if blow moulds are ordered Quick and fl exible bottle sampling & qualifi cation in Röders laboratory with certifi ed equipment. New: Diamond milling technology and Röders Racecut system will lead to shorter lead times for customers. Hot-fi ll/heat-set moulds with energy effi cient system and multi-platform interchangeable quick mould systems Other one-stage The “ReduxAir” system allows to carry out stretch-blow moulding operations at lower pressures than usual. It allows for the air in between the bottle's outer walls and the mould's surface to be more quickly released; thus, the PET bottle manufacturing process can be carried out with compressed air pressure at 15-20 bars (such a value depends on the preform and bottle features and on the stretch-blowmoulding process conditions). Solutions for compatibility of moulds between different machine types, new Röders RMC-system for quick mould change to reduce changeover times and cut mould costs Joint development projects for special applications and new blow mold development. GAWiSD featuring AutoJob™–job set up in seconds +1.724.482.2163 AGRINTL.COM ACCURATE • FAST • REPEATABLE SEE GAWIS4D IN ACTION Dimensional and thickness measurements for plastic containers and preforms. ®"},{"@ID":52, "MATERIALS / RECYCLING PETplanet Insider Vol. 23 No. 05/22 www.petpla.net 12 A report shows how far PET, the most circular of all plastics, is from real circularity How circular is PET? Research produced for Zero Waste Europe by sustainability consultancy Eunomia shows that most PET plastic recovered from bottles in Europe does not make its way back into new PET bottles. Significant improvements in PET design, collection and recycling will be needed to improve circularity, the study says. The “How circular is PET?” report presents a picture of the state of circularity of this material in bottles in Europe – including how much material from bottles is collected for recycling; how much of it is actually recycled; and how much of recycled PET is put into new bottles. Current circularity The majority of PET is not currently managed in a circular model since leakage from the circular system is high, with material lost at all stages of the PET lifecycle. As it is technically and economically more challenging to deliver manufacturing quality requirements from rPET than virgin PET, and as this is especially the case for closed loop applications, rPET can ‘cascade’ from one product stream to another, usually from higher quality to lower. Once cascaded, it is unlikely to return up the cascade and, in some cases, rPET may exit the circular recycling system through the cascade. What are the root causes of this problem? Ineffective collection systems leading to high losses of post-consumer PET. Lack of availability of recyclers means some collected material cannot be reprocessed. Contaminants from collection and sorting. Product design and material quality, including coloured PET and multimaterial applications as well as foodgrade standards for rPET. rPET economics, i.e., the market rate of rPET compared to vPET, which is dependent on many drivers including the demand by end markets. PET bottle stream Of the entire PET family, bottle recycling has the most developed technology and infrastructure. Across Europe, collection schemes for PET bottles vary. Some countries are achieving high recycling rates with beverage deposit refund schemes (DRS), while other countries and regions are achieving lower recycling rates with separate collection schemes. The report shows that PET bottles have a recycling rate of around 50% (calculated using the weight of PET material at the stage after wash and flake vs the weight of PET bottles (including lids and labels) placed on the market). rPET used in bottle manufacturing has high overall quality criteria and must be derived from bottles. It is estimated that bottles placed on the market (POM) only comprise an average of 17% rPET, with the remaining rPET downcycled into other, lower grade manufacturing applications and therefore considered a loss from the circular bottle stream. While bottles make up the largest share of PET packaging, PET is used in other PET applications, such as in fibres, single-use tray manufacturing, films, and strapping. There is no standardised collection and sorting of non-bottle PET applications in Europe. The lack of appropriate sorting and recycling technologies as well as the design of these applications makes them currently difficult to recycle. Although some tray and film recycling does happen on a small scale, the amount is negligible in the greater scheme of the PET packaging manufacturing scope currently. Therefore, only bottle recycling has been considered in the current scenario. Trays use approximately one third (31%) of the total rPET generated from bottle recycling. In total, PET packaging uses 74% of rPET derived from bottles. While this means that the rPET generated by bottles finds use in new packaging products, the lack of large-scale recycling for anything other than bottles means that it is eventually lost as leakage from the circularity of PET packaging. Approximately 14% of the global polyester market is recycled polyester, the majority of which is produced from PET bottles. Clear/light blue bottle material is typically most desirable for textile production, as this produces fibre with reduced discolouration. Although fibres may have a recycled content (rPET from bottles), there are no known current market scale recycling processes for post-consumer fibres. Therefore, as is similarly seen in other non-bottle PET applications, the RECYCLING"},{"@ID":38, "BOTTLING / FILLING PETplanet Insider Vol. 23 No. 05/22 www.petpla.net 36 KHS develops modular PET fi ller platform More flexibility and future viability The demands made of beverage producers regarding product variety and quality have grown immensely over the past few years. With its new PET filler platform, the KHS Group now offers its customers a modular setup to their requirements which can be reconfigured or expanded as needed. Other benefits include low energy consumption, low carbon emissions and a hygienic machine design for optimum product quality. Bottlers today face a number of economic and ecological challenges regarding the packaging of their products. One factor is that they are under a great deal of pressure in relation to time and cost: new and ever more powerful packaging systems and technologies need to be developed and commissioned as quickly as possible; materials, media and energy consumption needs to be further reduced yet efficiency and productivity increased. A second consideration is that the beverage industry is currently very much the focus of specific legislation and has to answer to increased regulation. Doing their bit for the protection of the climate is the kind of commitment which is also increasingly being expected of them by consumers who, however, neither wish to do without a high variety of products nor packaging that is both practical and affordable. PET block systems In light of these developments KHS offers its customers a range of block systems, particularly for the filling of products into PET bottles. These include its latest stretch blow moulding technology – with or without fully recyclable barrier protection – and a powerful labeller. The filler is naturally a core component of these systems. What’s new about the Dortmund systems supplier’s PET filling equipment is the modular, configurable and expandable platform. Consistently implemented on its glass fillers in 2020, its machines for plastic bottles now satisfy equally demanding customer requirements for adaptability and future viability. “The beverage market is undergoing an extremely dynamic process of change as regards its products,” says Manfred Härtel, filling product manager for KHS. “Where possible, bottlers want to and must therefore keep all options open when investing in their production technology so that their portfolio can be tailored to consumer demands at any time.” The aspects of flexibility, sustainability, product quality and efficiency are thus very much in focus – in combination with smart technology that ensures trouble-free production monitoring and control. Greater flexibility “Nobody can predict which trends will still prevail in the industry in five years’ time,” Härtel maintains. “This is why we’ve made our platform so modular that it can be converted to other beverages or PET containers at any time according to market requirements.” Individual components can thus be bought in at a later stage and integrated into the existing machinery with relatively little effort, according to KHS. “Depending on which filling system a customer goes for, they can react to changing market requirements. Thanks to the modularity of the filling systems, functions and features can be easily added.” KHS’ DRV system, for instance, can process both carbonated and still beverages. For the non-contact filling of water and the hot filling of juice at temperatures of up to 95 °C, there is the NV filling system. And for beer and mixed beer beverages, the Dortmund systems provider has its DVF and DRF longtube filling systems. Flexibility is also enhanced by the high degree of automation during format and product changeovers. “Even now, for example, operators don’t need more than a quarter of an hour to change a 0.5-litre bottle over to a 1.0-litre PET bottle,” Härtel says. More climate protection Customers can achieve energy savings and low CO2 emissions with the new PET filler platform, the company says. “On the DRV filling system, for instance, CO2 consumption has been cut from 150 g per hectolitre to practically zero,” explains Härtel. “We also no longer use CO2 as a pressurisation gas, instead favouring sterile air.” The KHS Innofill PET DRV filler for the filling of carbonated soft drinks"},{"@ID":37,
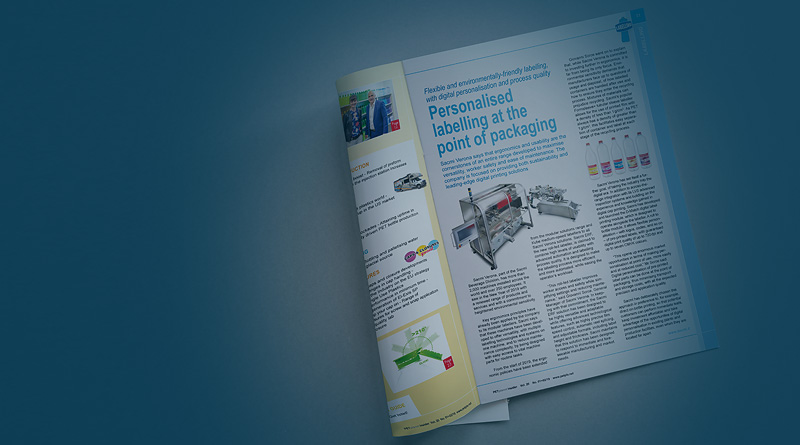