{"pages":{"page":[{"@ID":5, "imprint EDITORIAL PUBLISHER Alexander Büchler, Managing Director HEAD OFFICE heidelberg business media GmbH Hubweg 15 74939 Zuzenhausen, Germany phone: +49 6221-65108-0 fax: +49 6221-65108-28 [email protected] EDITORIAL Kay Barton Heike Fischer Gabriele Kosmehl Michael Maruschke Ruari McCallion Anthony Withers WikiPETia. info [email protected] MEDIA CONSULTANTS Martina Hirschmann [email protected] Johann Lange-Brock [email protected] phone: +49 6221-65108-0 fax: +49 6221-65108-28 LAYOUT AND PREPRESS EXPRIM Werbeagentur | exprim.de Matthias Gaumann READER SERVICES [email protected] PRINT Chroma Druck Eine Unternehmung der Limberg-Druck GmbH Danziger Platz 6 67059 Ludwigshafen, Germany WWW www.hbmedia.net | www.petpla.net PETplanet Insider ISSN 1438-9459 is published 10 times a year. This publication is sent to qualified subscribers (1-year subscription 149 EUR, 2-year subscription 289 EUR, Young professionals’ subscription 99 EUR. Magazines will be dispatched to you by airmail). Not to be reproduced in any form without permission from the publisher. Note: The fact that product names may not be identified as trademarks is not an indication that such names are not registered trademarks. 3 PETplanet Insider Vol. 24 No. 05/23 www.petpla.net Dear readers, In Germany, there is a deposit of €0.25 on disposable PET bottles, so it is little wonder that over 98% of them are returned. Bottle return machines are located in supermarkets. Now, the Schwarz Group with its 4,000 supermarket branches has put its money where its mouth is and published its own life cycle assessment study on their rPET bottles. The Group recycles the returns into 100% rPET bottles that come in clear, green and blue colours. For years, their portfolio has included five bottling plants, two preform facilities, one of which produces caps, and two recycling sites in Germany. Following the latest expansion of their recycling plant near Aachen, the Schwarz Group can now recycle 100% of its 2.3 billion bottles using its own bottle-to-bottle material. As a leading advertising partner, the company was able to persuade the well-known presenter of the “Who Wants To Be A Millionaire?” television programme Günther Jauch to explain the environmental benefits of disposable PET bottles compared to reusable glass PET containers to the end-consumer. Videos on the https://diekreislaufflasche.de website are well worth watching also for the non-German speaking PET enthusiast. On average, PET bottles in Germany have a rPET content of over 44.8%. According to Coca-Cola, their own proportion is slightly higher at 52.5% (both are 2021 figures). However, of the high return rate of 98% only around 44% of rPET for bottles is produced during recycling outside the Schwarz Group, with the rest going into fibre, foil or thermal recycling. This means there is a lack of bottleto-bottle material for higher rPET content on the market. And so Tilmann Rothhammer, a management board member of the Coca-Cola Europacific Partners Company in Germany, argued in WiWo [‘Business Week’] on May 1, only two weeks after the launch of Günther Jauch’s promotional campaign, that “if a bottle is to become a bottle again then beverage producers must be allowed to purchase recycled bottle material at a preferential rate” and that “we want a pre-emptive strike on recycled disposable deposit PET bottles”. The short amount of time between the response and the use of the term “pre-emptive strike”, borrowed from language used by the military and police, suggests that the Schwarz Group took Coca-Cola by surprise with its Günther Jauch promotional campaign. Sometimes, the mid-tier sector operates faster than international multinationals. Yours Alexander Büchler (Sources: Life Cycle Assessment Study MEG – The Schwarz Group 2023; Coca-Cola Sustainability Report 2021; PET Forum 2022 and WiWo, [‘Business Week’] 1 May 2023)."},{"@ID":53, "MATERIALS / RECYCLING PETplanet Insider Vol. 24 No. 05/23 www.petpla.net 13 Working with us bears a risk RI VWDUWLQJ D ORQJ WHUP SURƓWDEOH UHODWLRQVKLS IRU \\HDUV yellow.agency 3(7 SUHIRUP SURGXFWLRQ OLQHV HQJLQHHUHG E\\ 2WWR 6\\VWHPV URXWLQHO\\ VHW LQGXVWU\\ EHQFKPDUNV IRU SHUIRUPDQFH DYDLODELOLW\\ HQHUJ\\ HIƓFLHQF\\ and lowmaintenance costs. This is because the consultants and engineers at Otto Systems meet your production challenge with open minds, decades of experience and deep knowledge about PET production processes and techniques to ensure high quality at the best possible price. That’s why they are able to plan and implement production systems that are uncompromisingly tailored to your needs, independently selecting the best components from experienced manufacturers to achieve your goals. &DOO RWWR V\\VWHPV FRP"},{"@ID":38, "PREFORM PRODUCTION PETplanet Insider Vol. 24 No. 05/23 www.petpla.net 36 The PET material dryer - an often unrecognised key point for economical preform production by Stefan Bock, Managing Director at ReduPET GmbH In most cases, a dryer is an energy guzzler and/or a process killer because it rarely runs at the optimum operating point. The energy content in the PET granulate cannot be directly determined economically during preparation for processing in the production plant, so an average of 40Wh is lost unnoticed per kilogram of PET raw material processed - largely through the heat exchanger, connected to a cooling machine, which requires a further 12Wh/kg. For a preform system with, for example, 96 cavities and an average throughput of 900 kg/h, this amounts to almost 400,000 kWh/a - or, depending on the price of electricity or gas US$ 44,000-88,000 per production system. A lost profit that can be easily and precisely realised with a clear effort. How it works The problem in almost all preform production plants is that hardly any operator really knows how his dryer uses energy. If the material is sufficiently dried, there is general satisfaction - the real energy consumption is usually not asked about, as the understanding of these figures is complex and therefore difficult to classify anyway. But how is a dryer set correctly so that it runs optimally in terms of energy? In almost all cases, this is left to the dryer manufacturer - the easiest way at first. However, if the operator stands at the dryer and really tries to understand the energy management, he quickly reaches the limits. The setting values are based on rough experiences in the past that have led to good preforms - or have been recommended by the dryer manufacturer. The end result need not be doubted: if enough dried process air is blown through the material, the preparation of the material is usually sufficient and the process satisfactory. But then usually far too much air is blown through the material: 30-50% too much is not uncommon - and the excess energy disappears via the heat exchanger into the cooling machine. When processing rPET, it is very likely that the material will turn yellow due to the higher dwell time at the heat maximum. Another strategy employed by operators is to keep the energy input at the dryer as low as possible - as long as the desired degree of dryness is achieved below 50 ppm. In this case, it is easy for the material to still be 25-40% short of thermal energy when it is heated in the drying hopper, despite the degree of dryness achieved. This missing energy then has to be added to the plasticising process - usually relentlessly in conjunction with increased friction and a significantly higher energy input. The preform quality then also suffers, which shows itself with an increased appearance of bubble formation and “black specks”. In addition, this is generally accompanied by increased acetaldehyde (AA) cleavage and IV degradation. Continuous dryer monitoring can do even more The above explanations clearly show that a dryer has an ideal operating point which, however, the operator finds difficult to determine due to a lack of sufficient information - certainly not continuously and adapted to the current processing procedure. It is also not possible to determine instabilities during the drying process in retrospect - and then to assign them to quality problems on the preform. These can occur, for example, if the material feed does not continuously and reliably supply the hopper with PET material. It is also not possible to determine when a drying hopper needs maintenance and cleaning, especially in the area of the air filters. For this reason, the filter is also cleaned here - often as a precaution - usually far too early - or far too late. Both mean losses in preform production. How can a dryer be continuously and reliably monitored? As explained at the beginning, the energy content in PET material cannot be measured economically. The erroneously circulated “bucket method” of pouring the PET material from the drying hopper into a bucket to measure the temperature of the PET granules is misleading, as it only measures the temperature of the hot air between the highly insulating PET"},{"@ID":44, "TRADE SHOW REVIEW PETplanet Insider Vol. 24 No. 05/23 www.petpla.net 42 ers in China. “We were able to forecast an 11.8% increase in PTA capacity in Asia from 2022 to 2023, and this to remain steady until 2024. For PX, we saw a 14.8% increase from 2022 to 2023 and we see only a 3.7% increase by 2024,” said Mr Zhang. Contrary to high capacities, the production rates of the textile industries in China and Southeast Asia are at a low level due to lower clothing consumption as a result of the weakening economic situation worldwide. On average, the textile industry was running about 20% lower than normal at the beginning of the year. However, a potential improvement is expected in the coming year. For the current year, Icis showed an outlook into apparel (polyester, 75% PTA demand), beverages (virgin PET, 20% PTA demand) and tourism. The demand for clothing within China, for example, is expected to rebound due to the lifting of the lockdowns, but not so global consumption due to high inflation. Demand for beverages is expected to increase due to outdoor activities, while the area of disinfectants is expected to decline. Last but not least, the tourism sector in Asia is expected to recover and open up new business opportunities due to the end of pandemic restrictions. Continued demand for PET material from Western markets is leading to tight supply in Asian PET resin market, while Asian PET resin demand growth should be around 6%. For 2023, in addition to new capacity, Icis forecast an average lower price level of US$30/t less for PX and US$20/t less for PTA with an oversupply for PTA during the year. Icis sees a recovery in Asia only in the long term. The leading Chinese PET producers keep the PTA wheel turning by constantly investing in capacity expansions, while PX production is increasingly integrated with refining and the production of various petrochemical products, leading to other product manufacturing or new factories together with PTA, which limits the necessary expansions, so that in the case of China, PX imports are still necessary. However, a trend towards a long-term reduction in import dependency is measurable. While this was still 29% in 2022-2023, it would probably fall to 26% in 2027. In Northeast Asia, production rates for PX are expected to decline over the coming years. For PTA, China’s exports were expected to increase from about 2.4 million t in 2022 t to over 3 million t in 2027. The main customers in 2022 were India with 28%, followed by Turkey with 20%. Interesting also was a comparison chart in which Mr Zhang showed the increased utility costs in relation to the total costs in Europe and Northeast Asia: while these were quite different in Northeast Asia from the beginning of 2022 to 2023, they climbed to 28% of total costs in Europe compared to 11% at pre-energy crisis levels, fuelling imports from Asia. www.icis.com"},{"@ID":48, "PETplanet Insider Vol. 24 No. 05/23 www.petpla.net 46 PETbottles Beverage + Liquid Food Tea in a striped dress Peak Punk, a young brand distributed by the Swiss company Fruver AG, sells sustainable and natural products related to nutrition for athletes. Among them is an Organic Energy Tea in two variants, one with Black Tea, the other with Green Tea and Ginger - both with Mate. The brandtypical striped bottles each contain 500ml of the vegan, low-calorie drink with 75 mg of caffeine. A black screw cap with a tamper-evident band and adhesive label on the top completes the eye-catching packaging. www.peakpunk.com Ginger Shot in XXL The Swiss beverage producer Fresh Drink sells sustainable, cold-pressed and non-heated products such as shots, juices and smoothies under the “Sluups” brand. These include a Ginger Shot Reload - a fruit juice blend with ginger content - in XXL for special ginger fans or as a family pack. The transparent bottle contains 500ml of drink with a 25% ginger juice content. The lid remains uncoloured for sustainability reasons. A nonlook sleeve label makes the product as visible as possible. www.sluups.ch Repeat by Marco Reus Under licence from MR Repeat, the Hamburg-based Columbus Drinks GmbH has launched several functional vitamin drinks. In keeping with the names and objectives, the individual drinks contain corresponding vitamins or additives. The low-sugar, vegan vitamin waters are intended to support the body before, during and after sport or other exertion. Each of the bottles contains 500ml, is decorated with a foil label and sealed with a screw cap with a tamper-evident band. www.repeatbyreus.com"},{"@ID":8, "PETnews 6 NEWS PETplanet Insider Vol. 24 No. 05/23 www.petpla.net Sidel guides Niche Cocoa Industry Ltd’s move into aseptic beverage production in Ghana Niche Cocoa Industry Ltd, Ghana’s largest fully integrated cocoa processor, has successfully installed its first-ever aseptic line through Sidel. The line marks the company’s first venture into milk-based products in PET, with the assistance of Sidel’s expertise in aseptic production. Having chosen PET for its 100% recyclability, affordability, food integrity, and lightweight properties, Niche Cocoa Industry Ltd opted for Sidel’s Predis aseptic dry preform sterilisation technology. Besides its ease of operation, Predis also reduces water usage and chemicals consumption, says Sidel. Since its launch, it has successfully decontaminated more than 120 billion bottles globally. Aseptic PET solution The 16,000 bph aseptic PET complete solution integrates Tetra Pak Processing Systems technologies and the Sidel Aseptic Combi Predis with dry preform and cap sterilisation systems, two units of Gebo OptiDry, a sleeve labeller, a VersaFilm Access shrink-wrapping system, and finally a stretch wrapper. Sidel also supplied its EIT (Efficiency Improvement Tool) data acquisition and plant intelligence system. It is widely used to support its beverage company customers in decreasing unplanned downtime, reducing waste and costs, and increasing factory output. www.sidel.com Alpek maintains dividend in difficult conditions Alpek S.A.B. de C.V., headquartered in San Pedro Garza García, Greater Monterrey, Mexico, is one of the largest PET and PTA producers in the Americas and is the sole producer of polypropylene and caprolactam in Mexico. The company’s two business segments are: Polyester (including PTA, PET, rPET and polyester fibres) and Plastics & Chemicals (PP, expandable styrenics, and other speciality and industrial chemicals). Alpek’s Q1 2023 report demonstrated that challenging conditions continue in the industry, including the consequences of stockbuilding during the Covid period. Total sales volumes were down five per cent in Q1 2023 compared with Q1 2022, from 1.216 million tonnes to 1.161 this year. Plastics and chemicals were down quite heavily, by 13% year-on-year (0.254 million tonnes to 0.222), although this segment has shown a recovery between Q4 2022 and Q1 2023 of two per cent, from 0.217mt. Production volumes were are higher than sales. Q1 2023 production was 1.381mt (down 9% from Q1 2022 and 11% from Q4). Polyester was down 8% year-on-year (1.172mt Q1 2023 from 1.277mt 2022) and 12% since Q4. Polyester revenues were the stronger of the two segments. Total year on year receipts declined 12%, from US$ 2,332 million to US$ 2,062m, but Polyester was down only 2%, from US$ 1,521m to US$ 1,490m. Q4 2022 showed an increase over the first 3 months of last year to Q1 2023 (US$ 1,630) but that was not maintained into Q1 2023. Plastics and chemicals fell more heavily, by 30% year on year and 2% quarter to quarter. Margins and EBITDA have also been affected but the Board declared a dividend of US$159 million. The company has reviewed its capital expenditure strategy and will be delaying some projects, while the current situation stabilises and consolidates. PET resin operations at Alpek’s Cooper River site near Charleston, South Carolina, have been shut down indefinitely. CEO Jorge Young reported that oil prices have stabilised at an average US$ 81/ bbl Brent Crude, down on Q4 2023. PP prices have increased in the USA, despite a disconnect in prices between the Americas and the Far East, with some recovery towards historical levels. www.alpek.com Retal Iberia gains ISO50001 energy certificate The ISO50001:2018 energy certificate has recently been awarded to Retal Iberia following an external audit. Quality Manager Xavi Mora says, “This international standard is a tool to support us improve on energy consumption by developing and implementing an energy management system. The aim of this certification is to for continual improvement when it comes to energy consumption and efficiency.” The process of gaining the certificate involved the whole of the Girona-based facility, with the production zone, offices, storehouses and all processes assessed. During the audit, different simulations were done to see what consumptions are the most important in the plant’s processes, giving an opportunity to identify improvement measures to increase efficiency. Successful audit This analysis was followed by an evaluat ion, wi th a str ict process of documentation, checks and improvements implemented on the actual plant system. Only once this was complete, the audit from the certification body could be granted. Mora adds, “Everybody is involved in this process; we all use energy, so everybody must know that they can contribute to reducing the energy consumption, from switching off the lights, changing the climatisation of the different areas, reaching more efficient production procedures or implementing new controls or even changing some equipment for new ones. To reach new goals, we all have to participate!” www.retalgroup.com"},{"@ID":3, "PETcontents 4 PETplanet Insider Vol. 24 No. 05/23 www.petpla.net 05/2023 Page 20 MATERIALS / RECYCLING 10 PPWD: Reality-check 12 Study on environmental benefits of a PET material cycle for single-use bottles - Consistent circulation management of PET bottles can save 60,000 t of CO2 in Germany alone MOULD MAKING 14 XpBottle, dynamic bottle’s capacity - Designing PET bottles and blow moulds to improve the shelf-life through the filling process 18 200-fold hot collaboration - MHT technology used in ASB Nissei single-stage process 19 Even tighter tolerances than for bottle preforms 20 The easy solution - Swiss made tethered closure 22 “The hot runner is the heart and artery system of the mould” - Saving money and reducing CO2 emissions through hot runner refurbishment BOTTLE MAKING 25 Injection Stretch Blow Molding Machines - Stretch Blow Molding, part 15 30 Complex process made simple - Flexible production with faster neck changes on the stretch blow moulder 32 Highspeed bottle design - Digital bottle designer as automated web application MARKET SURVEY 27 Suppliers of preform & SBM moulds BOTTLING / FILLING 34 Keeping natural effervescence PREFORM PRODUCTION 36 The PET material dryer - an often unrecognised key point for economical preform production TRADE SHOW REVIEW 39 “The demand to recover recyclables from waste is at a record high” - Tomra Recycling Sorting hosts event to celebrate the extension of its test facilities in Germany 40 Icis PET Value Chain Conference 2023 BUYER’S GUIDE 48 Get listed! INSIDE TRACK 3 Editorial 4 Contents 6 News 43 Products 45 PET bottles for home + personal care 47 PET bottles for beverage + liquid food 54 Outer Planet MOULD MAKING Page 32 Page 34"},{"@ID":40, "PREFORM PRODUCTION PETplanet Insider Vol. 24 No. 05/23 www.petpla.net 38 lap, indicating that the PET material is energetically saturated (see Figure 1). If the process air flow is now too low, it is obvious that the green curve will drop below the blue curve. The material does not have enough energy, the plasticising and the PET material are thus more stressed, the quality of the preforms decreases (acetaldehyde value, bubbles, unmelts, black specks etc.). The balance of power consumption also increases, as plasticising has a lower energy input efficiency than an extruder. If the process air flow is too high, there is energy left over after the PET material has passed through the drying hopper, which the material is not able to absorb because of the degree of saturation. However, because this air is too hot for renewed drying in the drying cartridges, it has to be cooled down by means of a heat exchanger. This means that the already unnecessarily heated air feeds further energy to the cooling machine via the heat exchanger - the energy loss is therefore reflected twice - in the heat generation - and in the heat dissipation. The software records this energy loss in a specific graph (red curve). In this graph, the energy loss of the process air via the heat exchanger is determined, which is then apportioned to the throughput. Sources: ReduPET The user enters only a few parameters in the setting, number of active cavities, preform weight and the desired pellet temperature - when using two dryers on one system, the material proportion of the respective dryer must also be entered. Figure 1 Before the airflow optimisation, it can be seen that the green graph (energy input) lies on the blue graph and the material is thus energetically saturated. The red graph shows the energy losses via the heat exchanger, which is generated by a much too high airflow. This means that twice as much energy is used here as is necessary. Figure 2 After the airflow optimisation, the PET material is still energetically saturated (optimal for the processing) but the loss has been significantly reduced - by approx. 40Wh/ kg PET. At a throughput of 800 kg/h, for example, this would be a loss of 262,000KWh/a. With optimal filling of the dry hopper, a further reduction in losses would be conceivable. If the machine is switched off while the dryer is still running, the material in the upper area of the drying hopper heats up, while the losses increase. Figure 3 The visualisation with its graphs on the timeline not only shows how optimally the drying process is running, but also the changes. This means that a malfunction in the material feed can be detected immediately - and thus in good time. The effectiveness of the filters for the process air in the drying hopper can also be constantly monitored. This allows the filters to be cleaned when necessary - and not when the maintenance schedule calls for it, which can often be too early - or too late. The graph and display also warn when the heat exchanger is not running as it should. In very many cases, the process air is cooled down too much because the valve is no longer working cleanly - these losses hit twice: on the process air heater and on the cooling machine. These losses are not only unnoticeable, but usually significant. Also, when using two different materials (e.g. mixture with rPET) when using two different dryers, the energy input of both hoppers can be used to determine whether the proportions are plausible - or not. Summary WAVE succeeds for the first time in the preform industry in visualising the energy efficiency of a dryer on a timeline by means of three simple graphs with current data. Especially in times of rising energy costs, the advantages are obvious: the return on investment can be steadily reduced to a few months and employees are constantly made aware of the energy consumption in the drying process through the visualisation. ReduPET GmbH also offers recognised training courses that not only focus on drying, but also consider the PET system as a production unit whose entire energy and process optimisation is in focus. www.redupet.swiss"},{"@ID":28, "PREFORM PRODUCTION PETplanet Insider Vol. 24 No. 05/23 www.petpla.net 26 particular position with respect to an oblong bottle shape. This requires an expensive device in two-stage moulding but is “free” in ISBM as the neck start can be chosen deliberately and the preforms are held in place between injection and blow without spinning. Vertical injection tooling leads to longer tool life because gravity does not try to pull tools off-centre as is the case with horizontal injection machines. Many custom bottles have special neck finishes for which it is hard to find preforms on the open market. In this case, a single-stage solution may be the most cost-effective solution as it is often cost-prohibitive to build and run injection tooling for preforms of low volumes. The inside of the preform is always hotter than the outside. This is of great advantage as the inside always has to stretch more than the outside (Chapter 6, Section 6.2). The reason why this is happing in single stage is that the cooling area on the core side is always smaller than on the cavity side and often with less flow (see Chapter 9, Section 9.6 for a more detailed explanation). This explains the ease of forming difficult container shapes. There are also a number of disadvantages mentioned as follows: Cycle times are relatively slow even when comparing the same thickness and weight preform moulded on a modern injection machine. Part of this has to do with the way the machine rotates requiring several tool movements that accumulate dead time. Long changeovers: Injection tooling is very cumbersome to remove as each injection core must be replaced individually. Machines are also difficult to access making it more timeconsuming to work on them. Each blow cavity requires one injection cavity. Because injection usually takes 2 to 3 times longer than blowing the blow section is idle for half to two thirds of the cycle time. In two-stage moulding it is much easier to match the output of an injection machine with that of a blow machine. For example, a 72-cavity injection machine running a 8s cycle time produces around 32,000pph. A blow machine with 16 cavities running at 2,000 bph per cavity will be the ideal candidate to match. Both machines can run at full capacity, a great advantage given capital and footprint limitations. As explained in greater detail in Chapter 9, Section 9.7 processors are not in complete control of the preform temperature profile limiting the uniformity of bottle wall thickness and reducing bottle quality (Fig. 8.4). Fig. 8.4 8.2 Machine controls Melting in Extruder The resin that enters the extruder throat is a mix of crystals and amorphous parts. In order to melt the resin the extruder must heat and soften the amorphous fraction and melt the crystalline fraction. By rubbing the pellets against each other and against barrel and screw the extruder generates the necessary shear heat for melting. All crystals must be melted or they will become nuclei (starting points) for crystallisation in the preform. Heat transfer from barrel through heater bands is only about 30%, may even be negative in some zones. Negative heat transfer would be the case when the temperature readout of an extruder zone is higher than the set point. In this case the friction inside the barrel is so high that it actually overheats the barrel and must be cooled down to maintain the temperature that is selected. This usually happens at the end of the barrel in the so-called metering zone of the screw. Most heat (about 70%) comes from pellet inlet temperature (dryer) and from friction (screw and barrel). The operator has control over the heats, the screw rotational speed, and the back pressure during screw rotation, which is called recovery. While temperature screens differ from machine to machine, they all convey the same information. They may show: the location of the heater band (usually going right to left) °C or °F the set point the actual temperature a display of a temperature without set point is the temperature of the incoming resin as measured just above the extruder throat. A temperature of about 165°C is optimal for PET processing the percentage of power the controller puts out to the heater band. For example, if this value is 40%, the heater band is on for 4s, then off for 6s. The controller will use a value that is best suited to keep the heater band at the set point. This is regulated by a so-called PID loop and all controllers use some form of this control program. A typical temperature profile starts at 270°C (518°F) at the feed zone and increases to 285°C (545°F) toward the extruder nozzle. This can be used for most PET applications. The extruder cannot be started until all heaters are at the set point and a soak timer has timed out. The machine heats have to be enabled either by a physical switch or by a switch on a screen before the machine starts heating. If a “soft start” feature is available and is selected heater bands heat up slowly. Soak time may be available on some machines and is the time between the moment when the last heater band has reached its set point and the moment the machine allows the extruder to start. Soak time is different for extruder and hot runner. A longer soak time does not harm the process but too short of a soak time may. Use 30min for the extruder and 15min for the hot runner. If a “standby” function is available it allows the dialing in of a second, lower set point. When the machine is expected to be down for longer than 30min, this feature is used to prevent material from burning without turning heats all together off. Older machines may not have a protection against a “cold start,” which is the (often accidental) turning on of the extruder before the heats are up and have had time to soak. This will usually break the screw at the thinnest point in the feed section. On these machines a note should be kept on the machine during the heating up process to indicate when it will be safe to start the extruder."},{"@ID":41, "TRADE SHOW REVIEW PETplanet Insider Vol. 24 No. 05/23 www.petpla.net 39 Tomra Recycling Sorting hosts event to celebrate the extension of its test facilities in Germany “The demand to recover recyclables from waste is at a record high” Tomra Recycling Sorting welcomed industry partners, customers and media representatives from February 28 to March 2, 2023 for the opening of a second test facility at its headquarters in Mülheim-Kärlich in Germany. Intended to meet growing demand for material trials, the company now operates one test centre each for waste and metal sorting applications at the same location. The event took place within the framework of the company’s Integrator’s Conference. More than 200 participants from 26 countries joined the two-day event and enjoyed a diverse conference and event program. On the first conference day, participants listened to presentations detailing the company’s strategic direction, including one held by Tomra CEO, Tove Andersen. The second day focused on the extension of the test facilities that marked another milestone in Tomra Recycling Sorting’s long-term goals. “With more stringent legislation and higher recycling targets, the demand to recover recyclables from waste is at a record high and so is the demand for our sorting solutions and material tests. We’ve observed this situation over the last few years and came close to our test capacity limits in Germany. We had to act to ensure the best service for customers and partners”, states Fabrizio Radice, VP and Head of Global Sales and Marketing at Tomra Recycling Sorting. Previously, Tomra’s test centre incorporated both its waste and metal sorting solutions and is one of eight facilities operated at seven locations worldwide that give recyclers and plant operators the opportunity to test their materials on Tomra’s advanced sorting machines before making an investment. “Apart from the increasing demand for tests, we are continuously developing new sorting systems that are all installed in our test centre. In the last few years, we have introduced multiple new products into the market and will roll out more in the future. Thus, we needed to make sure that we have sufficient space for our growing portfolio and decided to invest in an additional building”, adds Radice. Tomra itself will use the extra space for the development of innovations that can be tested and optimised by specialised teams on-site. The company conducts approximately 650 customer and internal trials each year and anticipates the demand to grow in the future. The decision to extend capacities entailed another important change. Ralph Uepping, VP, Head of Technology at Tomra Recycling Sorting explains: “Until recently, we’ve combined both metal and waste sorting machines in one area. Now, each test hall will be dedicated to one segment only. While waste sorting trials are done in the first established facility, the focus of the new facility is on metal sorting.” Tomra’s new X-Tract, Finder, and Combisense, as well as a soon-to-be release machine for advanced aluminium sorting, have been installed in the new facility measuring 1,000m2. The original test center started as a mobile test station in Andernach, Germany, moved to Mülheim-Kärlich in 2009, and steadily grew in sophistication. Today, it offers 1,500m2 for waste sorting trials. The test possibilities range from the recovery of recyclable polymers from mixed and source-separated waste streams, to flake sorting, the separation of wood by material type, and many more. Also, deep learning technologies, as a subset of AI, are part of Tomra’s product portfolio and can be tested in different sorting tasks. Available as a complementary solution to its core technologies, deep learning is a future-forward tool that helps improve sorting performance by detecting previously hard or impossible-to-detect materials. Summarising the advantages of the new test centre setup, Ralph Uepping stresses: “All our products are installed and can be tested in a complete circuit. Together with our expert teams, we can simulate the entire sorting process with eddy currents, magnets, screens and a ballistic separator. This allows us to demonstrate the importance of material pretreatment and define processes that are stable and economically viable even with changing input streams.” www.tomra.com Ribbon cut: (f.l.t.r.) Volker Rehrmann (EVP and Head of Tomra Recycling), Fabrizio Radice (VP and Head of Global Sales and Marketing), Tove Andersen (CEO), Tom Eng (SVP and Head of Tomra Recycling Sorting), André Lehmann (Test Center Manager)"},{"@ID":42, "TRADE SHOW REVIEW PETplanet Insider Vol. 24 No. 05/23 www.petpla.net 40 Icis PET Value Chain Conference 2023 by Kay Barton From March 7-8, the UK-based Independent Commodity Intelligence Services (Icis) from London again organised the annual PET Value Chain Conference, this time in the centre of Vienna in Austria. The focus was on PET recycling and rPET, circular economy, energy and resource stability in times of crisis, as well as macroeconomic outlooks on changing global markets. The conference was attended by 96 top executives and industry experts from across the supply chain from 26 countries. In addition to exciting presentations from the industry, the analysts from Icis provided interesting data and facts on current developments in the recycling world, which we have summarised for you. Icis’ Senior Analyst for Polyester Chain Mrs Jincy Varghese addressed virgin material developments in her presentation “Virgin PET Supply and Demand Dynamics: Mapping Market Instability”. Icis is forecasting the global polyester incremental capacity to increase by 8.4 million tonnes for food-grade PET, fibre and film in 2023. Foodgrade PET would account for 2.5 million tonnes. The largest share, 66%, would go to beverage applications, followed by 20% packaging in general and 14% miscellaneous (e.g., pharma, hygiene and other industrial applications such as strapping). The largest growth between 2022 to 2025 will be driven primarily by Southeast Asia, followed by Northeast Asia, Africa and Middle East. Overall, the company forecasts an average PET demand increase of 3.0% growth for this period, with the largest demand coming from the AsiaPacific region. While the earthquakes in Turkey did not have a significant impact on European supply chains, according to Mrs Varghese, economic changes such as inflation and higher energy and production costs due to the Ukraine war caused lower yields. Concerns about developments in the energy crisis would persist through 2023 and 2024, according to Icis. “We don’t expect gas prices in Europe to remain at a high level in the long term, but they will command premium,” Mrs Varghese said. International dependencies on polyester imports would continue. From 2021 to 2022, PET imports in Europe increased by about 80% from around 550 kt to 900 kt. Northeast Asia and Asia-Pacific are the most important trading partners for the EU polyester imports. Globally, China was the largest PET exporter with over 4 million tonnes of material exported in 2022. In response to an audience question on how Asian exports might change in the future, Jincy Varghese pointed out that Europe is a structurally short market, so Europe’s dependence on imports is expected to continue. Similar to Europe, United States is a net importer as well. However, with the new PET-PTA Corpus Christi plant, which is under construction, this situation is going to change. The initiation of an antidumping investigation into imports of PET originating in China could potentially open up opportunities for other Asian exporters. In response to a question about the development of bio-PET, Jincy Varghese explained that this area is expected to grow on the premise that appropriate factories are built. Sources: Icis"},{"@ID":12, "MATERIALS / RECYCLING PETplanet Insider Vol. 24 No. 05/23 www.petpla.net 10 PPWD: Reality-check by Heike Fischer The re-usable targets of the Packaging and Packaging Waste Directive (PPWD) for the European countries are controversial. The EU countries are at a completely different infrastructural, technological and economic level. Consumer behaviour is also different. Many other factors have to be taken into account in order to be able to use reuse in a really meaningful way. Reusable doesn’t really make sense in every application, says Tobias Bielenstein, Public Affairs Sustainability Manager at Genossenschaft Deutscher Brunnen. PET planet: On the German mineral water market there has been glass reuse as well as PET reuse for a long time. The word `single-use` is not popular in Germany as the recycling and return rate is around 99%, which is why the term `PET circular` is used. How did Germany manage to successfully set up this overall system? What special challenges did it face and how much time did it take? Bielenstein: Germany has a re-use tradition since many decades. The first deposits for re-use bottles were introduced at the beginning of last century. So, when the mandatory deposit for single-use beverage containers – which includes PET and glass-bottles as well as cans – was introduced in 2003, it was not necessary to explain to German consumers how to return containers with a deposit. In fact, our numbers show that around 50% of German consumers still believe today that all bottles with a deposit are re-use bottles – while the market share of reuse is only around 43% in the beverage market. This is also because returning a bottle with a deposit is very easy to consumers. No matter whether it is re-use or single-use, most RVMs (reverse-vending machines) are set-up at the POS and they will accept both types of bottles as well as crates. It is only the two big discounter-chains that don’t sell nor accept returning re-use bottles. Of course, there were challenges in operational terms when the DRS was introduced. This included set-up of RVMs and a clearing-mechanism and -institution for deposits. But this was solved after a short transition period. Today it is easy for consumers. And this is key in my view: no matter whether it is re-use or singleuse with a deposit – it must be easy and convenient to consumers to become a success. PET planet: What exactly does the PPWD provide for and what problems arise specifically for the German system as a result of the targets set? Especially since Germany already has a higher value of recycled content than the EU demands. Bielenstein: The PPWR draft as well as the amendments discussed in the European Parliament are putting our successful re-use systems at risk and will lead to higher operational costs, which will weaken them in competition. The reason is that the commission has defined too specific requirements regarding the management of re-use systems. This poses a huge issue for existing and future re-use systems in Europe. There are many varieties among re-use systems. A re-use system for to-go-beverages is very different to a system of re-use bottles filled in an industrial production. The current draft does not reflect these differences. It would be more effective in regulatory terms if we would have a good framework and less detailed regulation in the PPWR to allow for effective governance and options for innovation for re-use systems. If this is not reflected, we will pledge for an exception of markets that exceed the goals of the regulation – like we do in Germany. But this is definitely only the second-best choice. PET planet: Re-usable is a system - not just a package in itself. It is made up of the producers, the retailers and of course the consumer. What challenges do you see in introducing and implementing this in any EU country? Bielenstein: Re-use systems need to be simple and easy for consumers and effective for all other stakeholders involved. Therefore they have to build on consumer behaviour and the structure of retail in each country. And we all know these structures are very different from country to country within Europe. This is again a call for a strong regulatory framework and space for individual implementation in each country. Europe and EU are not about harmonisation in every details. In our view it is most important to be “united in diversity” – which should be also the guideline when it comes to re-use systems. PET planet: Which SUP beverage applications make sense in which EU countries and why? Do you have any suggestions or assessments? Bielenstein: In Germany, most mineral water companies have a mix of re-use and single use packaging offers. This give brands space to be relevant to all consumers in all consumption situations. As an example: you might prefer a glass re-use bottle if you have guests at home for dinner, but you will go for a PET bottle whenever you are on the road or doing sports. Tobias Bielenstein, Public Affairs Sustainability Manager at Genossenschaft Deutscher Brunnen (Photo: Francois de Ribaucourt)"},{"@ID":17, "MOULD MAKING 15 PETplanet Insider Vol. 24 filling-capping block capable of improving the performance of the PET container in retaining CO2 in the product by the expansion coming from the counterpressure. “We have worked on many other developments as strategic partners with Moldintec’s TechCentre in Sao Paulo on blow moulding technology. This project goes beyond the blowing process itself, and we are excited to collaborate with our suppliers to go that one step further. We want to know more about the possibilities of this new concept and verify that shelf-life improvement is possible. At Coca-Cola Andina Brazil, we’re working with Moldintec to validate this new technological concept in our bottling lines at the Duque de Caxias plant, RJ. It is our most modern facility with the fastest equipment. We trust that if we achieve the expected results, we can quickly implement them in other productive units. We know that it is a long journey conducting this R&D+I development, especially for a new technology company such as Moldintec. That’s why we are always here to help and it is a pleasure to test their inno-"},{"@ID":19, ""},{"@ID":20, "MOULD MAKING PETplanet Insider Vol. 24 No. 05/23 www.petpla.net 18 MHT technology used in ASB Nissei single-stage process 200 times hot collaboration 128, 144 or even 192 preforms in a single shot. Everything in the drinks industry is geared towards high flow rates, and the two-stage procedure, where preforms are only later blown into bottles, has become established. But for special applications and moderate item quantities, the single-stage process also has its strengths. ASB Nissei and MHT have been working on this together for several years. in terms of size and weight so they can transport the preforms to their subsequent production stage. For this reason, they have a lower number of cavities than usual. Horizontal injection moulding machines dominate elsewhere in the PET sector but here, a vertical construction is used. This means that the cold half is already in the correct position for the subsequent process and the preforms can be demoulded using gravity. In the hot half, the filling of the cavities is effected not in the usual way but by using a lateral sprue bushing. The balancing of the hot runner therefore becomes more sophisticated so as to avoid crystallinity and other preform flaws. MHT builds its hot runners in-house and in 1998 was a sector pioneer for vertical moulds. Itself a pioneer since 1979 in the single-stage process, ASB Japan uses this experience for ambitious projects or its own capacity bottlenecks. Since 2012, the Indian subVisiting ASB India: Prince Rudra (Sales Manager MHT), Christian Wagner (CEO MHT) and Jérémie Cuny (Business Development Director MHT, from left) MOULD MAKING sidiary has also been placing orders with the mould specialist from Hesse in Germany. CEO Christian Wagner, Jérémie Cuny (Business Development Director) and Sales Manager Prince Rudra have already visited the site in Maharashtra. The single-stage procedure is especially suitable for applications with somewhat lower quantity requirements, for example in the food or cosmetics sector, and also for reusable PET bottles. www.mht-ag.de MHT Mold & Hotrunner Technology is well-known for its multi-cavity moulds and for pushing the cavity count just a little higher on each machine type. But since 2006, also almost 200 hot halves with up to 24 cavities have been created for one special customer: ASB Nissei. In the Japanese company’s singlestage procedure, the entire process from granulate to finished container takes place in one complete system which is also interesting regarding the energy consumption. The preforms are injection moulded, then immediately conditioned and stretch-blown into the final shape. The cold mould halves need to be easily movable MHT 24-drop hotrunner for production of single stage process bottles"},{"@ID":29, "MARKET SURVEY 27 PETplanet Insider Vol. 24 No. 05/23 www.petpla.net 05/2023 MARKETsurvey Suppliers of preform and SBM moulds In this issue of PETplanet we are very glad to present you an update of mould manufacturing for perform and SBM moulds. Please have a close look at the companies showing their newest developments: Wentworth Mold, Kosme, SMI, Röders Tec, KHS, Sipa, Kiefer Werkzeugbau, PET Technologies, GDXL Precise Machinery, Sacmi Imola, MHT Mold & Hotrunner Technology AG, Flexblow and Otto Hofstetter. Although the publishers have made every eff ort to ensure that the information in this survey are up to date, no claims are made regarding completeness or accuracy. Resins & additives Preform machinery Preform production & inspection systems Preform & SBM mould manufacturer SBM 2-stage Compressors All about caps Filling equipment & inspection systems Palletising & shrink film machinery Recycling machinery Preform moulds Company name Otto Hofstetter AG MHT Mold & Hotrunner Technology AG Sipa SpA GDXL Precise Machinery Co., Ltd. Kiefer Werkzeugbau GmbH Postal address Telephone number Web site address Contact name Function Direct telephone number E-Mail Zürcherstrasse 73, 8730 Uznach, Switzerland +41 55 285 22 11 www.otto-hofstetter. swiss Mr Markus Feldmann Division Manager PET +41 55 285 22 97 [email protected] Dr. Ruben-Rausing-Str. 7, 65239 Hochheim am Main, Germany +49 614 690 60 www.mht-ag.de Mr Jérémie Cuny Business Development Director [email protected] Via Caduti del Lavoro 3 31029 Vittorio Veneto, Italy +39 0438911 511 www.sipa.it Mr Gianfranco Perricci Gl. Sales Dir., Preform Systems & Tooling +39 0438911 511 [email protected] No. 18 Changjiang Road, Guicheng, Nanhai, Foshan city, Guangdong Province, China. Postcode: 528251 +86 757 8677 7168 www.gdxl.com Mr Billy Ay Marketing Specialist +86 757 8677 7168 ext 8681 [email protected] Steinhäldenstraße 11, 74193 Schwaigern, Germany +49 7138 97320 www.kiefer-mold.de Mr Rüdiger Lang Sales & Project Manager +49 7138 973270 [email protected] Preform moulds Horizontal opening Number of cavities 2 up to 144 2 to 192 cavities Up to 200 From 32 to 144 cavities Preform sizes Up to 500 g Up to 750 g, for bottles up to 30 l Up to 750 g Various neck fi nish standards including 1810, 1881, 30/25, 29/25, 26/22, 38mm, etc. Preform weight from approx. 3.5g to 750g (for applications from pharmaceutical/cosmetic bottle to 5-gallon keg) Moulds already built for (makes) Netstal, BMB, Husky, Arburg, Sipa Sacmi, Husky, Netstal, Krauss-Maffei, Sumitomo, Niigon, Arburg, BMB, Demark, Cincinnati, Unique, Negri-Bossi, Sipa Sipa, Husky, Netstal, Krauss-Maffei, Sacmi Husky, Netstal, Krauss-Maffei, Sipa, etc. Vertical opening Number of cavities 2 up to 112 2 to 112 cavities Up to 96 From 16 to 96 cavities Preform sizes Up to 500g Up to 600g, for bottles up to 30 l Up to 150 g Various neck fi nish standards including 1810, 1881, 30/25, 29/25, 26/22, 38mm, etc. Preform weight up to 69g Moulds already built for (makes) Arburg, Krauss-Maffei Krauss-Maffei, Arburg Standard and custom Sipa, Krauss-Maffei Sipa, Krauss-Maffei, etc. Do you produce single stage tooling sets? (Preform moulds AND blow moulds) No No Yes, for Sipa machines No Yes Other - Multilayer moulds up to 72 cavities - Moulds for PP - Moulds for thinwall packaging - Moulds for cartridges and tubes - Moulds for medical products - Preform moulds for PE, PP, PLA - Bag in bottle moulds - Wide mouth - Moulds for vacuum blood test tubes - Up to 5 gallon - Moulds for toner cartridges - 2K hotrunner (e.g. milk application) - AFM technology (Active Flow Moulding) - Test plaque mould for rPET We also provide: - Preform R&D service for specialised container purposes; - Engineering solutions together with our partners for: multilayer co-injection containers with barrier properties and market-appealing elements, preforms with integrated moulded handle in cooperation with patent holder); and turn-key production systems"},{"@ID":30, "MARKET SURVEY 28 PETplanet Insider Vol. 24 No. 05/23 www.petpla.net Stretch blow moulds Company name Röders Tec KHS GmbH SMI SpA Sacmi Imola SC Sipa SpA Postal address Telephone number Web site address Contact name Function Direct telephone number E-Mail Scheibenstraße 6, 29614 Soltau, Germany +49 5191 603 53 www.roeders.de Mr Steffen Lühning & Mr Jani Rickert Sales Manager +49 5191 603 822 & +49 5191 603 340 [email protected] Juchostr. 20, 44143 Dortmund, Germany +49 231 569 0 www.khs.com Mr Dennis Jacobi Manager Service Sales +49 40 67907 225 [email protected] Via C.Ceresa, 10 24015 San Giovanni Bianco (BG), Italy +39 0345 40.111 www.smigroup.it Marketing department +39 0345 40111 [email protected] Via Selice Prov.le, 17/a, 40026 Imola (BO) Italy +39 0542 607 111 www.sacmi.com [email protected] Via Caduti del Lavoro 3 - 31029 Vittorio Veneto, Italy +39 0438 911511 www.sipa.it Mr Paolo De Nardi Product Manager SBM +39 0438 911511 [email protected] Stretch blow moulds Bottle size (max.) (in litres) Up to 30 liters Depending on individual bottle geometry: - typically 100-2,500ml with regular moulds, inner shell & outer shell system (requires additional maxi pencake at approx. 1,500ml to hold the mould closed) - up to 3,900ml with compact moulds (outer=inner shell, still usable at standard blow moulder) - up to 5,500ml with compact large moulds (only applicable at special compact large blow moulder) 12 litres 3.3 l (standard machines) - 12 l (big format machines) 30 liters Moulds supplied directly to blowing machine manufacturers Yes Yes Yes No No Do you supply retrofi t moulds for existing SBM machines? Yes Yes Yes Yes Yes For which bottle maker have you already produced moulds Sidel, KHS Corpoplast, Krones, Sipa, Kosme, ADS, Nissei, Chumpower, Terekas, 1 blow and other major machine types Big number of moulds for a a wide range of company for the industry of food & beverage, household cleaning and personal hygiene products and chemical and pharmaceutical products. No Sidel, Krones, KHS, SIG, Krupp, SMI, Siapi, Kosme, Side Bottle design service Bottle design development Yes: preform and bottle design (technical/marketing), fi nite elements analysis, 3D modelling, use of rPET SMI design, develop and virtually prototype a wide range of packaging solutions in rPET and PET, according to the customers' specifi c requirements. Thanks to an advanced CAD centre for 3D design, SMI has invested in solutions for producing rPET bottles and for supporting companies in the study and graphic realisation of a wide range of containers that are 100% recyclable, of high quality and lightweight for saving energy and material. Furthermore, SMI provides solutions for manufacturing of bottles with the utmost quality, also thanks to accurate checks made on preforms and bottles. Yes Brandbuilding, product repositioning, marketing design, packaging engineering, lightweightening of existing bottles, technical feasibility; new AWArPET analysis (Design for Recycling), etc. Specialities Quick and fl exible bottle sampling and qualifi cation in Röders laboratory with certifi ed equipment. New: Diamond milling technology and Röders Racecut system will lead to shorter lead times for our customers. Light weighting, low pressure, complete PET line optimisation, carbon dioxide calculator, global key account certifi ed laboratory, … The moulds are manufactured using a special aluminium alloy. SMI relies on a special laboratory for the production of moulds and mechanical components, equipped with an FMS line consisting of 12 CNC machining centres: highly automated machines, running 7 days/week round the clock, even operator-less, according to pre-set production programmes (CAM). The 12 machining centres can achieve an output of more than 15,000 moulds/year; they are equipped with linear motors with a speed rate up to 80m/min and mandrels achieving a speed rate of 30,000 rounds/min. As a result, top-level quality standards are constantly provided. Double cavity concept, low pressure base moulds, stainless steel moulds Wide mouth, large sizes (up to 30 liters), asymmetrical, Nitrogen hot fi ll, containers with handles, HDPE to PET conversions, pharma & cosmetics Other Solutions for compatibility of moulds between different machine types, new Röders RMC-system for quick mould change to reduce changeover times and cut mould costs. The “ReduxAir” system allows to carry out stretch-blow moulding operations at lower pressures than usual. By an innovative design and specifi c technical solutions this system allows for the air in between the bottle's outer walls and the mould's surface to be more quickly released; thus, the PET bottle manufacturing process can be carried out with compressed air pressure at 15-20 bars (such a value depends on the preform and bottle features and on the stretch-blowmoulding process conditions). The great advantage the ReduxAir's user can benefi t from in terms of lower power consumption of the compressor requires a few design limitations in the bottle's shape and features."},{"@ID":1, "PREFORM PRODUCTION PETplanet Insider Vol. 24 No. 05/23 www.petpla.net 25 Stretch Blow Molding, part 15 Injection stretch blow moulding machines by Ottmar Brandau Ottmar Brandau has newly revised his book “Stretch Blow Molding”, first published by hbmedia / PETplanet Publisher, and now re-issued in a third edition under the Elsevier Imprint. PETplanet Insider is publishing extracts from successive chapters in a serie of articles. As the name implies this process involves injection of preforms as well as blowing of bottles in the same machine. Preforms are not cooled down completely after injection; instead residual heat inside the preform allows blowing without reheating. Obviously, this makes it inherently more complex than the two-stage process. Processors must know both parts of the process and, as we will see, there is also some interaction present between injection and blow adding to the overall complexity. Machines of this type are commonly (but by no means exclusively) used in the cosmetics, personal care, and household markets. They are hardly used in the water and carbonated soft drinks (CSD) market as their outputs are limited. There are actually two different types of machines that can be summarised under injection stretch blow moulding (ISBM): Indexing with three or four stations where the preform stays in the neck insert, going through injection (conditioning with four-station machines), blow, and ejection. Various designs where the preform is completely removed from the injection tool, put on mandrels, heatconditioned, and then blown. This process may be called integrated two-stretch blow moulding (ITSBM) (Fig. 8.1) Fig. 8.1 8.1 Four-Station machines Preforms and bottles are oriented vertically and in rows, typically one row only but there are also machines with two rows of up to 16 cavities making 32 cavities the current maximum number. They are spaced not with respect to the preform dimension but to the maximum bottle dimension as the pitch between the cavities does not change within the machine. A 90mm wide or round bottle requires spacing of about 100mm in both preform and blow tooling to allow some metal between the blow cavities. A particular machine can produce a 300ml bottle in 16 cavities or a 15 l bottle in single cavity with various bottle sizes and respective cavitation in between (Fig. 8.2). Fig. 8.2 In order to engage the injection tooling vertically, the following two movements are required: Either the cavities move down and the cores move up with the neck inserts staying in place before rotating. This requires the cavity block with the hot runner underneath it to disengage from the extruder that is moved back. One issue with this arrangement is that air or pollutants can enter the melt stream when extruder and hot runner are not connected. Or both cavities and neck inserts move up leaving the cavities in place. This is a superior solution as the aforementioned problem is not an issue (Fig. 8.3). Fig. 8.3 Amachine with four stations rotates 90 degrees moving preforms and bottles around every cycle, whereas a threestation machine rotates 120 degrees. Orientation of each station is vertical allowing a very compact footprint. Other advantages of this system besides the ability to make both preforms and bottles in one machine are as follows: Flexibility to make bottles of different shapes with good wall distribution. Production of blemish-free bottles. Since preforms are not touched, bottles have no marks when they leave the machine. Important feature for cosmetic bottles. Zero contamination between preform and bottle stage. This may decrease sterilisation measures in the filling plant. A neck support ring is not necessary, also interesting for cosmetic bottles. Thermal efficiency; preforms are cooled down only to blowing temperature of about 100°C (212°F), saving energy needed to cool them to about 60°C (140°F) necessary for twostage moulding. Automatic neck orientation; some caps require the neck to start in a Please order your copy at: [email protected] Stretch Blow Molding Third Edition by Ottmar Brandau € 130,00 374 pages © Copyright Elsevier 2017, 2012"},{"@ID":10, "8 NEWS PETplanet Insider Vol. 24 No. 05/23 www.petpla.net Erema Group ends financial year with significant increase in turnover The Erema Group GmbH closed the 2022/2023 financial year in March with around EUR 355 million in overall turnover. “With demand for recycled plastics remaining high, the past financial year brought many challenges that we needed to handle,” says Manfred Hackl, CEO of Erema. The challenges included persistent delays in the supply chain and unexpected supplier outages. Logistics and production processes had to be adapted several times as a result. The situation has improved significantly meantime as a result of these measures and more stable supply chains, says Erema. The production locations in Austria manufactured 270 extruders and delivered them to customers around the globe. Taking the whole group into consideration, this figure rises to 350 including the extruders from Plasmac, the Italian subsidiary. The recycled pellet production capacity of all extrusion systems delivered in financial year 2022/23 adds up to around 1.6 million t/a. On top of that there are around 130 additional components and modules such as filter systems and ReFresher anti-odour units. K’ 2022 saw the Erema Group launch seven new recycling systems and components. “For the first time, we brought all the companies in the group together on one stand, so we were able to provide an excellent overview of our wide range of products and services with the latest innovations as a one-stop-shop concept,” says Hackl. These included the new Intarema TVEplus DuaFil Compact recycling system and the EcoGentle plasticising unit, which was also newly developed. Thanks to their gentle polymer treatment and lower melt temperature, both extrusion innovations are claimed to deliver effective advantages in terms of the quality of the melt, recycled pellets, and final product, as well as energy efficiency in post-consumer and PET recycling applications. www.erema-group.com Berry: cost actions include the rationalising of facilities and labour While announcing the second quarter 2023 results, Tom Salmon, Chairman and CEO of Berry, indicated cost reductions: “Our business delivered solid second quarter and first half results with adjusted earnings per share growth of 4% and 7%, respectively. During the past several quarters, we have seen supply chain constraints continue to ease, prioritised structural cost improvements and continued our efforts to pivot our portfolio to high-value growth products across all of our businesses. Our cost actions include the rationalising of 15 facilities across the world, moving business to more efficient cost facilities, and other labour cost reductions from improved productivity. These cost savings initiatives are expected to provide annualised cost savings of $115 million and we expect to realise $70 million in fiscal 2023. These internal actions helped to offset a 6% volume decline driven by destocking and general market softness. We continued our focus on driving long-term value for our shareholders and repurchased $155 million of shares, or another 2.1% of shares outstanding, in the second quarter, while also paying our quarterly dividend. We believe our shares remain undervalued and our repurchases reflect our confidence in the outlook of our business, our long-term strategy, and the strength of our operating model and cash flows.” Salmon defined health, beauty and foodservice as key end markets that offer greater potential for differentiation and long-term growth. In addition, Berry indicated investments and engagement in emerging markets. In this way, the company aims to achieve long-term structural cost improvements while driving strategic initiatives. Berry says that the net sales decline is primarily attributed to a 6% volume decline, decreased selling prices due to the passthrough of lower resin costs, an unfavorable impact from foreign currency changes, and prior quarter divestiture sales. The volume decl ine is pr imar i ly at tr ibuted to general market softness and ongoing inventory destocking. The operating income decrease is primarily attributed to an unfavorable impact from the volume decline, an increase in business integration costs, an unfavorable impact from foreign currency changes, and an unfavorable impact from increased selling, general, and administrative expenses. These declines are partially offset by a $40 million favorable impact from price cost spread as a result of cost reduction and improved product mix. www.berryglobal.com Interpack 2023 final report Under the heading “Welcome Home”, Interpack trade trade fair welcomed visitors from all over the world in Düsseldorf, Germany from May 4-10. 2,807 exhibitors showcased their technologies and solutions to visitors from 155 countries. Altogether approx. 143,000 visitors travelled to Interpack, two thirds of them coming from abroad. Alongside many European countries, the largest visitor nations were India, Japan and the USA. Around 75% of visitors came from middle or top management. Current market developments were focused at the show. The need to automate, the will to act sustainably and changed consumption habits are all expressions of transformation. Interpack’s strategic orientation towards the four Hot Topics: Circular Economy, Resource Management, Digital Technologies and Product Safety found concrete expression in numerous developments. The trade fair, which has traditionally been a key cornerstone in the innovation cycle of the packaging industry and related process industries, also lived up to this claim this year. Top themes were also all facets of sustainability. Exhibitors presented highend technologies and holistic concepts that consider efficiency and sustainability along their entire production line. The next Interpack will be held in Düsseldorf from May 7 to 13, 2026. www.interpack.com"},{"@ID":25, "MOULD MAKING PETplanet Insider Vol. 24 No. 05/23 www.petpla.net 23 other efforts tend to fall short. The hot runner is the heart and artery system of the mould; at least that’s how we like to think of it.” Árpád explains that on one end, there is one main channel that receives the liquid from a pump, and the hot runner has to deliver this material to all the different areas and consumers, while carefully maintaining the conditions and properties of the material. When one small corner of the melt distribution falters, the impact can eventually be dramatic. It can lead to quality issues, and cycle time losses and can even force complete system shutdowns. All of these effects are detrimental in terms of CO2 emissions. “A slower cycle time mostly means more energy consumed per tons processed. A blocked cavity means more hot runner power is consumed per cavity since the manifold system is still fully heated. And a defective preform eventually is basically more waste-material, which increases CO2 loss per definition since energy that was consumed to Cup preforms for fresh desserts 100% RECYCLABLE 3- and 5-gallon UHȴOO SUHIRUPV 100% RECYCLABLE Dairy preforms, in mono & multilayer 100% RECYCLABLE Wine and spirits Preforms 100% RECYCLABLE PET & RPET preforms manufacturer for food liquids Hot runner before and after refurbishment"},{"@ID":43, "PETplanet Insider Vol. 24 No. 05/23 www.petpla.net 41 TRADE SHOW REVIEW Helen McGeough, Senior Analyst, Plastic Recycling at Icis addressed current and future economics of recyclate, mechanical and chemical recycling in her presentation “RPET Europe: Outlook for supply and demand”. She explained: “Energy and employment costs, as well as the cost of living, are causing a perfect storm on the overall cost situation. At the same time, the demand for rPET is high with comparatively below-average availability. As long as a balanced supply is not guaranteed, the situation will continue.” And the situation in the recycling industry remains difficult. Although market prices in Europe for PET and rPET have fallen slightly in 2023 compared to the beginning of 2022, they are still at a high level overall. While the price difference between food-grade virgin PET pellets and rPET pellets was still marginal in Europe at the beginning of 2018 and rPET was even cheaper for a short time, the current vPET price is now back at a similar level as at the beginning of 2018 (around US$1,200/t) after a price peak in 2022. At the same time, after an increase peak of around 100% in 2022 (approx. US$2,700/t), the rPET price would currently be around 60% above the level experienced at the beginning of 2018 (US$1,360/t versus just under US$2,200/t) and is thus almost twice as expensive as virgin material. According to Icis, the key factors for the high demand for recycled material are, primarily, mandatory minimum quantities in new packaging, as well as sustainability efforts by brand owners, industry and consumers. Other demand drivers are the generally growing demand for polymers in principle. Icis estimates that global consumption of polyester polymers will increase from around 100 million tonnes in 2021 to 140 million tonnes by 2040. With the revision of the EU legislation of November 30, 2022, on the Packaging and Packaging Waste Framework regulation (PPWR), adjusted targets were set until 2040. According to this, single-use plastic bottles and packaging should contain 65% recycled material and packaging for sensitive foods other than single-use bottles 50%. Ms McGeough gave an overview of how recyclers are dealing with the situation globally and which factors are decisive. Despite the current dominance of mechanical recycling systems, particularly in Europe, North America and China/Southeast Asia, continued technological developments in both areas will have a major impact on supply in the future. She explained “Crucial to all recyclers is the input material, its availability and its cost.” Due to the different processing and subsequent applications of the recycled plastics, chemical recyclers would seek to avoid competition with waste sources from mechanical recyclers, allowing the systems to co-exist well. The current capacity of chemical recycling in Europe processes 61% of the annual waste input of 120,000 t by pyrolytic decomposition, according to Icis. The total feedstock for all chemical recycling processes consists of 56% mixed plastics, 10% PET, 8% mixed waste including nonplastics and 26% materials such as PA, PMMA or PU. A comparison of the collection of mixed waste and sorted waste from 2020 showed a recycling rate of 5% for mixed waste, 57% for energy recovery and a landfill disposal rate of 38%. For separated waste, the recycling rate was 65%, 27% went to energy recovery and only 8% ended up in landfill. Ms McGeough summed up: “Chemical recycling will continue because open loop recycling is still better than not recycling plastics at all.” Industry Analyst Jimmy Zhang, responsible for PET & Styrenics industry chain, in his presentation “New market dynamics in Asia - polyester feedstock market” addressed Asia’s price developments of and global influences on paraxylene (PX) and purified terephthalic acid (PTA) and gave a general outlook on polyester trends and imports and exports. While margins for PX increased between January 2022 and 2023 as prices rose in the second quarter of 2022, helped by increased demand for gasoline in the US resulting from shortages caused by the Ukraine war, PTA producers cut production volumes due to shrinking margins, Mr Zhang said. And according to the analyst, the situation could be similar compared to 2022. The expansion of PX production capacity this year, which was in the final stages, would mitigate a shortage in the second quarter, he predicted. On the PTA side, too, capacity would nevertheless be expanded by PET producYOU CAN HAVE FROM THE SAME RESOURCE ACME DRINKTEC SOLUTIONS LLP Enhanced Cavitation Superior Tool Steel IN-House Testing Balanced HR System Faster Mold Delivery Prompt Tech Support Proven 500+ ISBM Molds Globally CREATING MOLDS WITH A DIFFERENCE +91-9810418975 +91-9819020785 +91-9810631426 [email protected] www.acmedrinktec.com #Molds@70DPH"},{"@ID":24, "MOULD MAKING PETplanet Insider Vol. 24 No. 05/23 www.petpla.net 22 Saving money and reducing CO2 emissions through hot runner refurbishment “The hot runner is the heart and artery system of the mould” The company HRC is located near the historic town of Győr in Hungary on the banks of the Danube. HRC’s core business consists of the servicing of PET hot runners and providing highquality spare parts to the PET packaging industry. Keeping their company’s environmental impact as low as possible is something that brothers Árpád and Tamás Horváth, who founded the company in 2006, have seen as an important part of their mission from the very beginning, and they work continuously to reduce the CO2 impact of their processes. “Being owners of an industrial type of business in such a beautiful country as ours, it’s only natural to be aware of the impact on the environment”, Árpád states. “We service the plastic packaging industry, which has had its fair share of challenges in recent years, mostly coming from a growing consumer concern over pollution and emissions, and more recently the pressure to increase the re-use and the recyclability of raw materials. Since we work very closely with the industry leaders in the PET-packaging business, we are subsequently challenged too. Many multinationals that we serve have a specific corporate goal to reduce their environmental impact, looking at every link in their value chain. That also means that we as a supplier and service company have to comply, and we do that by staying ahead of the game. As a company, we have never taken the reactive approach to market trends, technological developments and challenges, so for us, it’s a no-brainer to try and reduce our carbon footprint proactively.” Taking pride in their attention to detail, and keeping their “zero-concessions” policy at the heart of their everyday decision-making, HRC strives to lead the way in low-environmental impact performance as well. The facility has been running on 100% renewable energy since 2019, but that’s not where it ends. Refurbishment minimises carbon footprint “It’s often overlooked, but when comparing newly built machinery versus overhauling such machinery, in many cases there’s a huge offset in CO2 emissions. Especially when there is steel involved, a closer look is often worthwhile. Since the manufacturing and forging of steel is a pretty carbonheavy process”, Árpád continues. “We take a standard 96 cavity PET hot runner as an example. When we make a full refurbishment on such a system, which brings the complete hot runner back to 100% new condition, the carbon footprint is up to 5.6 t less than that of a new manufacturing of such a hot runner. So, not only does a refurbishment save a significant amount of capital expenditure to the customer (without any concession versus a new hot runner), but it also helps achieve the customer’s environmental goals.” “Without a proper working hot runner system, all other efforts tend to fall short” But the biggest impact of the hot runner on emissions is surely its reliability and performance. “When a complete PET system is continuously running at its fastest cycle time, within quality specifications, without stops or breakdowns, that’s when emissions are lowest. When the dryer delivers the material as hot and as consistent as possible, the extruder has to “work” less hard to get to a homogenous melt within the cycle time available. If then the hot runner delivers that melt to all cavities with every shot, that’s the sweet spot of a system. Rigorous preventative maintenance on the complete line is of course a huge must to achieve this, but we take pride in being able to provide the best service to a key part of the process. Without a proper working hot runner system, all MOULD MAKING Tamás Horváth (left) and Árpád Horváth founded HRC in 2006"},{"@ID":32, "BOTTLE MAKING 30 PETplanet Insider Vol. 24 No. 05/23 www.petpla.net Flexible production with faster neck changes on the stretch blow moulder Complex process made simple Beverage producers who process both aseptically filled beverages and juice and carbonated soft drinks need to use 38 mm bottle necks for the former and containers with 28mm openings for the latter. If the bottle neck is to be changed on a PET line, however, to date a comparatively large amount of effort was required to convert the stretch blow moulder in particular. Machine stops of up to four hours are not uncommon. With its new, simplified neck changeovers KHS has now shortened the time needed to convert the InnoPET Blomax stretch blow moulder – including the preform infeed. It is usual to try to only manufacture and fill bottles with an identical neck on one line. If a water bottler wants to produce a still and a carbonated product alternately, until now they had to decide whether to use the higher and heavier neck really only necessary for carbonated water for both products or not. The bottler would then save time but waste material and money in the filling of the still water. The alternative would be to live with the long intermittent downtimes caused by a neck changeover. Besides these considerations, marketing often plays a role in a decision like this, calling for a bottle adapted to suit the various products. Combined lines such as these that require neck changes are very often found in Japan. Complex and timeconsuming process In order to gain an idea of just how complex the exchange of parts for the above process is on the stretch blow moulder alone, it is worth taking a closer look at the individual steps involved. First, the preform infeed needs to be adjusted and what are known as the mandrel heads replaced. These are wedged into the preform necks to guide these safely through the heating module. The grippers that transport the preforms by their necks to the blow wheel are then exchanged on the star wheel. Finally, the moulds in the blow stations, the blow nozzles and often the stretch rods and further grippers downstream that feed the finished containers to the subsequent filler need to be changed over. Here, the number of parts that need replacing depends on the size of the machine. The mandrels and shields especially are of particular importance: the higher the machine output, the longer the heater, as the containers may move faster but always need the same amount of time to heat up. On an InnoPET Blomax 16 stretch blow moulder with a capacity of up to 48,000 bph, around 170 mandrel heads and shields have to be changed by hand, for instance. This means that this part of the neck change is particularly relevant when it comes to the amount of time needed – unlike the exchange of the just 20 grippers that is quick in comparison. needed for two operators to convert the KHS InnoPET Blomax16 stretch blow moulder, for instance, has now been cut by a good two thirds to approximately 86 minutes – including the preform infeed. As the PET bottles in a block like the KHS InnoPET BloFill are held and conveyed by their necks throughout the entire machine, not only the stretch blow moulder but also the filler has been developed further in order to shorten conversion Arne Andersen, stretch blow moulding Product Manager, KHS If both aseptically filled beverages and juice and carbonated soft drinks are to be produced, for example, different sizes of bottle neck are needed. (S urce: Frank Rein old) In order to considerably speed up the conversion process as a whole, KHS has not just simplified the individual work steps involved but also the concept governing the entire procedure. “We started out by analysing how the operators work,” says Arne Andersen, stretch blow moulding product manager. “On this basis we then considered how all tasks could be made easier and organised as perfectly as possible – paying particular attention to the ergonomics. Magazines were thus installed that stop the operator having to repeatedly abandon the machine to fetch and carry change parts, for example. We also replaced the grippers to reduce the number of screws that need to be loosened. At the same time, newly developed mandrel heads are now used that can be simply removed by pressing a release spring. This process used to be much more complex.” In this case, KHS consciously went for an approach that thought all of the specific processes through to the end based on actual customer requirements, Andersen emphasises. Thanks to the simple neck change, the time"},{"@ID":49, "PATENTS www.verpackungspatente.de PETplanet Insider Vol. 24 No. 05/23 www.petpla.net 47 PETpatents Lightweight bottle Intern. Patent No. WO 2022 / 177809 A1 Applicant: The Coca-Cola Comp., Atlanta (US) Application date: 11.2.2022 Lightweight bottle made from PET with a specially shaped base, which saves on materials while still fulfilling stability requirements. Bottle with holder Intern. Patent No. WO 2021 / 064246 A1 Applicant: Sociéte Anonyme des Eaux Minérales d’Evian et en Abrégé, Evian les Bains (FR) Application date: 5.10.2020 This is a proposal for a reducedweight bottle with a special base. The bottle can only stand when set into a special supporting device. Bottle with special base form Europ. Pat.issue No. EP 3390237 B1 Applicant: Sidel Participations, Octeville-Sur-Mer (FR) Application date: 14.12.2016 The patent issued on 10.8.2022 describes a lightweight plastic bottle with a special base shape. Base shaping Europ. Pat.issue No. EP 3523208 B1 Applicant: Sidel Participations, Octeville-Sur-Mer (FR) Application date: 21.9.2017 A European patent is issued for the special base shape of a bottle made from PET. Bottle with champagne base Europ. Pat.issue No. EP 3535192 B1 Applicant: PepsiCo Inc., Purchase (US) Application date: 25.10.2017 A European patent is issued for a plastic bottle with a base shape similar to the base of a champagne bottle. Improved base shape Intern. Patent No. WO 2022 / 185003 A1 Applicant: Société Anonyme des Eaux Minérales D’Evian et en Abrégé, Evian-les-Bains (FR) Application date: 1.3.2022 Improved base shape for a PET bottle. The base should enable a good compromise between stability and material saving."},{"@ID":50, "PETplanet Insider Vol. 24 No. 05/23 www.petpla.net 45 BOTTLES PETbottles Home + Personal Care Liquid soap with organic olive Alverde, a private label of the German drugstore discounter dm, sel ls a l iquid soap wi th a new combination of fragrance and act ive ingredients. This variant has organic olive and organic orange, is CO2-compensated and consists of 99% biodegradable ingredients. It is filled in a 300ml transparent bottle made of 98 % recycled material with a lockable pump dispenser. Two non-label look labels reveal the slightly greenish shimmering product. www.dm.de Micellar water with peeling function The market for micellar water is always coming up with new ideas. The latest development is a “Gentle Micellar Exfoliating Water All-in-1” by Garnier Skinactive. According to the manufacturer, the water cleanses the skin and gently removes make-up and skin flakes. The vegan product is filled in the brand’s typical bottle, which is made of 100% recycled material, with a capacity of 400ml. This is lightly coloured, has two labels and is closed with a screw-on hinged lid with a dosage opening. www.garnier.de Dishwashing Balm with “Iced Coconut” The imagination of product developers always comes up with new creations to tempt consumers to buy. The German drugstore discounter dm, for example, has launched a special scented edition of its dishwashing balm under its own brand “Denk mit”. The coconut-scented product contains a bittering agent to increase child safety. The transparent bottle contains 500ml of the “ice blue” balm. A screw-on push-pull cap allows for easy handling and dosed dispensing. www.dm.de Guhl shampoo with Camomile Guhl Ikebana recently brought a special shampoo designed for natural or blond coloured hair onto the shelves of retailers. According to the manufacturer, the “Blond Fascination” shampoo, which contains active ingredients from chamomile, is intended to strengthen the hair and increase its luminosity. The vegan product was developed without animal testing, consists of 92% natural ingredients and is 98% biodegradable. The body of the bottle is made of 99% recycled material. The screw-on hinged lid with dispensing opening is decorated with embossed brand lettering on the top. www.guhl.com"},{"@ID":35, "BOTTLE MAKING 33 PETplanet Insider Vol. 24 No. 05/23 www.petpla.net Fully automated FE process chain The project with Cadfem - the FEM Bottle Wizard - included a system change to Ansys Workbench in order to design a fully automated FE process chain with pre-processing, calculation and post-processing using ACT (Application Customisation Toolkit). The standardisation and automation of the simulation created an orderly flow of information, including a link to the SAP system. “We use the CAD model to specify which bottle is to be simulated,” explains Maximilian Braun. “Likewise, material data and the wall thickness distribution are defined. Then the load cases to be analysed have to be specified as well as a commission or order number in the request form in order to start the automatism.” Standardisation and automation Six load cases have been implemented so far: top load empty and top load filled as stack load cases, Sideload-filled, hydrostatic pressure simulation, overpressure simulation and the vacuum simulation. These simulate the behaviour on conveyor belts, in processing machines and the haptics for the end user. With the new Wizard, the requirements are defined in 5 minutes instead of the 40 minutes it used to take. It also takes just 10 minutes to set up a simulation project. The ease of use is based on the fact that the user is guided through the process using the structure tree. The speed results from the high degree of automation as well as from the calculations in the cluster. In addition, the results are quickly available in the form of a standardised, automatically generated report. If all calculations are needed, they can now be performed within 24 hours, which used to take several days. With the provision of the Wizard, the number of bottle simulations performed has increased significantly because well-founded results are available quickly. In many cases, this happens within a few hours and not the next day or the day after. Thomas Albrecht explains, “in 2019, we were able to carry out around 150 projects, each with several load cases and simulation runs. That was more than 700 calculations, a number that was previously unimaginable for us. However, it’s not the number that counts, but rather the benefits that come from it. These include an improvement in our consulting expertise, the ease with which we can implement our customers’ design requirements, an acceleration of decision-making processes, and greater customer loyalty.” The entire FEM Bottle Wizard process from data entry to automated report generation. Multiple benefits with Group-wide use The Bottle Wizard can be used throughout the Group by initiating the calculations by employees in the individual branches or subsidiaries. So far, it has been used in Germany, the USA, China, Thailand and Dubai. “With the new Wizard solution, we have been able to expand the user base for simulations to include container designers worldwide,” reports Ulrich Lappe. “There are now a lot of them. Particularly when you are faced with a problem, you can try out similar variants directly in order to solve it. Likewise, errors that occur or are detected late can be resolved more quickly. We have also found that simulation results make it easier for customers to understand why changes are necessary. Time-consuming sampling as verification is usually no longer necessary.” “My future dream for simulation would be a virtual lab report. This would become possible if all test procedures carried out in the laboratory could also be carried out as simulations. For this, we need even more precise models and must integrate further calculations into the digital bottle designer.” - Maximilian Braun, project supervisor of the digital bottle designer - www.krones.com www.cadfem.net Given the production volume of PET bottles, even small material savings have a big impact."},{"@ID":37, "BOTTLING / FILLING PETplanet Insider Vol. 24 No. 05/23 www.petpla.net 35 ronmental sustainability imposed on the Romanian company investment choices that favoured plants and machinery compatible with the best standards for environmental respect and energy saving, as demonstrated by the recent installation of an SMI SFP 30 Ergon stretch film packaging machine. “[…] To achieve and maintain high levels of production quality, within the Carei and Bucharest plants, we use systems supplied by leading companies in the sector, such as rotary stretch-blow moulders for PET bottles and the fully automatic bottling and packaging lines supplied by SMI, who fully satisfy our requests”, says Norbert Varga, CEO of Alconor Company. Currently the company has several production lines in which PET containers of different sizes are bottled: from small formats of 0.33 l and 0.5 l, to standard formats of 1.5 l, 2 l and 3 l, up to large capacity containers of 5 l and 6 l. “We are constantly attentive to the latest technological trends in the market and, within our factories, we adopt the most efficient solutions that meet the most rigorous international quality standards and requirements to offer our customers high-end products at competitive prices”, continues Norbert Varga, CEO of Alconor Company. Focus on quality Alconor Company has paid close attention to all stages of bottling and packaging of its products, which are constantly subjected to scrupulous laboratory checks, to guarantee the high-quality standards that the company offers its customers. For this reason, Alconor adopts a food safety, management system, based on the HACCP (Hazard Analysis Control Critical Points) and ISO 22000 regulations issued by Tüv Rheinland. SMI East Europe: local service The constant support provided by the SMI East Europe branch, allowed Alconor to face the strong changes imposed by the market in the 2000s, a period of time in which both consumption habits and the way of communicating changed. The flexibility offered by the bottling and packaging lines supplied by SMI, has allowed Alconor to embrace new market challenges, seize opportuniPlant in Carei - SMI equipment: 3,600bph PET bottling line with a rotary strech-blower EBS 3 HC Ergon Products worked: 5 and 6 l large capacity bottles End-of-line 24,000bph, PET bottles, consisting of: SK 800F Ergon shrinkwrapper HA 80 handle applicator Packsorter divider and conveyor belts APS 3090P Ergon automatic palletising system Containers worked:0.5 l and 2 l bottles in PET Packs created: 0.5 l bottles in 4x3 film only + handle and 2 l bottles in 3x2 film only + handle Pallets worked: 800x1,200mm 10,800bph PET bottling line, consisting of: SR6 rotary stretch-blow-moulder SK 300F packer SFP 30 Ergon stretch film wrapper DV 200 divider and conveyor belts Containers worked: 0.33 l, 0.5 l, 0.75 l, 1 l, 2 l and 3 l bottles in PET Packs created on the SK 300F packer: 0.33 l and 0.5 l bottles in 4x3 film only, and 2 l and 3 l bottles in 3x2 film only Packs created in stretch film on the SFP 30: 0.5 l bottles in 2x4 film only, and 0.75 l,1 l, 2 l and 3 l bottles in 2x3 film only Pallets worked: 800x1,200mm SK 450T Packer and conveyor belts Containers worked: 0.25 l Slim; 0.5 l cans and 2 l PET Packs created:0.25 l Slim; 0.5l cans in 6x4 in tray + film and 2 l bottles in 3x2 film only ties and adapt quickly to changes. The SMI East Europe S.r.l. branch, located in Timosoara, provides its services throughout the territory of Romania and the surrounding areas; the headquarters of the SMI Group company occupies an area of approximately 100m2 and has spaces equipped for sales, after-sales and administrative assistance. Alconor Company, thanks to the positive experience found in the supply of the first bottling line in 2007 - explains Claudio Begnis - has relied on SMI to face the growth of the market and to invest in new production lines, both for the headquarters of Carei and for the new Bucharest plant. Full of energy and the importance of diversification At the beginning of its business, Alconor Company only bottled carbonated soft drinks in PET containers, while today, thanks to the use of modern technologies, it continues to surprise its customers by launching new products or packaging existing ones in increasingly innovative and original packaging solutions. For example, the fruit-based flavoured water “Aromatic Western Water” is a joy for the palate thanks to the aroma of lemon or strawberries and to the eyes, thanks to sublime “packaging”, made according to the latest market trends. The “Squizzy” lemonade remains among the favourite summer drinks for entire generations, as well as the “Max Speed” brand, energy products, a delicious energy drink to recharge your batteries and vitaminB, which, since 2020, has been the subject of an image “restyling”. www.smigroup.it www.alconor.ro"},{"@ID":23, "MOULD MAKING PETplanet Insider Vol. 24 No. 05/23 www.petpla.net 21 Another advantage is the minimal space requirement of the slitting technology, which, in contrast to slid warranty tapes, creates an almost imperceptible cut line. This feature greatly improves the dimensional stability and resistance of the closure during transport and during application on the filling line. Thus the closure can also be processed mostly without any adjustments on existing or new filling lines. PETplanet: What were the difficulties and technological challenges with the slitting? Büsser: Although slitting is, from our point of view, the best technology for tethering, we had to acknowledge, along with our partners, that every technology has its limitations. Fortunately, we found innovative solutions to work around these limitations. Probably the biggest task was to eliminate the strength degradation at the beginning and end of the cut. This could only be solved by a special cut design, which massively increased the notch strength at these points. The special cut design also makes it possible to optimise the strength of slitted hinged ether rings at the respective cut ends and thus save weight. This is because slit hinged ether ring closures are much more affected by this reduction in strength due to the torsional forces when the closure cap is folded down. PETplanet: In what sizes can EasyCap be produced? What is the material consumption? What features does the closure for your tethering have to have? Büsser: In principle, EasyCap tethering can be implemented on almost all closures with a folded retaining bead, provided certain design features are taken into account. The slit design has been optimised to cut as close as possible to the unfolded retaining bead without negatively affecting the subsequent folding of the retaining bead. PETplanet: In what market segment do you see particularly demand? Büsser: As already mentioned, it was particularly important to us that the consumer can drink directly from the bottle as usual, without having an annoying cap in the immediate vicinity of the face. Therefore, we see a very great potential for our EasyCap tethering in the “on the go consumption” of beverages. This is probably one of the most significant advantages of our tethering! PETplanet: Where are your forms already being used? Büsser: We already have some interested parties with whom we are in talks. Some customers have already tested the first prototypes and are convinced by our solution. In a nationwide survey, the majority of consumers were positive about our solution. PETplanet: What do you want for the future? Büsser: We would like EasyCap to be made available to consumers, through one or more global partners in Europe and around the world. PETplanet: Thank you very much. www.easycap.ch www.ebformen.ch PROCESS PILOT+TM Optimize Blowmolder Performance and Profitability with Automated, Closed-Loop Control +1.724.482.2163 agrintl.com Maximize rPET usability and processing Improve bottle performance and downstream operations Maintain lightweight, targeted material distribution Increase consistent production yield Overcome environmental and process variation Reduce scrap with accelerated start-up"},{"@ID":56, "OUTER PLANET 54 PETplanet Insider Vol. 24 No. 05/23 www.petpla.net OUTER PLANET Israeli headquartered company Watergen has developed patented technology to extract pure water from fresh air. New machines have recently been deployed in water-stressed areas of India. Water from the air The Earth is 74% covered in water but great areas of land suffer from water stress. Some of these are deserts, like the Sahara Desert in North Africa but some are less obvious and over a billion people worldwide do not have access to secure sources of drinking water. Sometimes rainfalls do not happen as expected, leading to drought conditions. Sometimes the rain falls excessively, leading to floods and attendant damage and loss of life. India has seen a shrinkage in the Himalayan glaciers that feed its great northern rivers, the Ganges and Brahmaputra. The Godavari, Krishna and other rivers that flow across the Deccan plateau into the Bay of Bengal or into the Arabian Sea are fed by monsoon rains – which do not always arrive. Drought has led to devastating famines although those days are, thankfully, largely in the past. Other years, they are so fierce that estuaries and flood plans are devastated. Most of India’s water abstraction is used for agriculture, with demand expected to rise a further 89 billion cubic metres by 2030, compared with 2005. About 97 per cent of the population experiences severe water shortage for at least one month annually, according to Statista. India is a huge country and it isn’t all covered by piped water. Its economic expansion has led to dramatic and often unplanned urban development, putting further strain on what infrastructure there is. With the increasing incidence of heatwaves and depleted groundwater, an inconvenience is becoming a crisis. In order to address the problem, a company called Watergen, which is headquartered in Petach Tikva, near Tel Aviv, Israel, has partnered with Indian company SMV Jaipuria Group, of New Delhi, to bring Atmospheric Water Generator (AWG) technology to India. These are devices that suck in air through a specially-designed condenser, which Watergen has named the GENius. Its patented technology enables air to move quickly into and through the system, for greater efficiency and less energy consumption. Watergen is claimed to be the global leader in the AWG market. Scalable, efficient and low cost The technology is highly scalable. The GEN-M1 machines can serve a single family or village school with 225 litres of pure drinking water a day. The medium-sized GEN-M Pro has production capacity of 900 litres a day. The top of the range GEN-L can supply an industrial facility, schools, entire rural villages, hospitals, mines or construction sites with 6,000 litres a day. They can even be linked together to form a ‘water farm’. The GENius heat exchanger uses condensation to produce fresh water. It is powered by electricity – from any reliable source, including wind or solar. Energy consumption for its smallest models is as little as 0.3 kWh; producing a litre of water costs 7-15 US cents, depending on local electricity costs. It doesn’t need supersaturated air to work; it can produce drinking water from air with humidity as low as 20% and at temperatures from 15 °C up. External storage tanks with attached smart quality systems, including controllers and malfunction alert, keeps condensed water fresh by circulating it round the reservoir and thus provides optimum capacity and a ready supply of safe, clean water. Disasters, emergencies and waste As well as established areas of water distress, where management is an increasingly pressing priority, the fact that Watergen systems do not need a piped supply infrastructure means that it can be deployed in disaster areas, such as in the aftermath of earthquakes or any other even that has disrupted or even destroyed water supplies. As the machines can be located on-site, transportation costs are pretty much eliminated, as is the need for extensive and costly piping networks. It also means that the use of disposable bottles can be minimised. www.watergen.com"},{"@ID":55, "MOULD MAKING PETplanet Insider Vol. 24 No. 05/23 www.petpla.net 24 MOULD MAKING 24 make the raw material and the preform is lost.” Understanding these mechanics and the impact on the customer’s P&L and emission targets, HRC maintains that only their true “zero concessions policy” will pay dividends in the end. “We have actively collected a tremendous amount of useful feedback from the market and our customers, about the various levels of hot runner component quality which is available in the market. If we understand the problems of our customers, we can provide the right solutions more efficiently. As with many parts and components, the key is in the details. Take valve stems for example the chamfer on the edge must be precisely made. If not, the valve pin can start wearing out the nozzle tips and the injection mould gates prematurely, leading to preform faults. This is only one of the aspects of a part that we inspect 100%, to ensure there are no such effects impacting our customer’s product down the road.” Over 700,000 units shipped On what the future may bring, HRC is very clear: “The combination of such scrutiny on our side, and the fact that we are ready to directly contribute to our customer’s strategic goals has been our modus operandi since the beginning. We believe it’s this mentality, and the fact that we can guarantee such performance that’s helped us stay in the lead, and continuously helps to increase our market share and customer base across the globe. Our parts and services have received very positive reviews, and very importantly also from our distinguished Japanese customers, and we take big pride in that. But to be frank, we don’t expect anything different, as we for 100% know the precise condition of every part and hot runner that we ship to our customers. That means we can be sure of its performance in its designated PET production line. The future is bright, and we want to contribute to that!” To date, HRC has overhauled more than 140 hot runner systems of various sizes, makes and types, including multilayer systems. They specialise in large 96-144 cavity systems and can handle even larger formats in their state-of-the-art cleaning lines. Over 700,000 units of HRC components have been shipped to their customers, with only positive feedback and returning orders as a result. www.hotrunnercomponents.eu Besides the servicing of PET hot runners, providing high-quality spare parts to the PET packaging industry is part of HRC’s core business. STEPS TO THE PERFECT BOTTLE. www.roeders.de www.roeders.de Idea & Design Technology Manufacturing Blow Mould 100% Service Y O U R PA R T N E R F O R B L OW MO U L D S ."},{"@ID":46, "44 PRODUCTS PETplanet Insider Vol. 24 No. 05/23 www.petpla.net PET masterbatch in sea glass look Ampacet, a global manufacturer in masterbatches, captures the look and feel of the naturally weathered shards of discarded glass polished by the ocean and prised by beachcombers around the world with its new SeaGlass Collection. Ampacet says that the SeaGlass Collection’s carefully curated palette includes the softened blush of Quiet Coral, the highly prised colour found in Rarified Red, the beauty of Pitted Lime, and one of the rarest colours of beach glass, Tumbled Teal. These unique effects for PET are intended to enhance the shelf appeal of packaging and products without a mould change. As with other coloured PET packaging, products made with SeaGlass can find a second life recycled into textile fibres. www.ampacet.com Fiji Water transitions bottles to 100% rPET in the EU and UK Fiji Water, an artesian water from the Fiji Islands, is transitioning its 500ml and 330ml bottles to 100% recycled plastic (rPET), excluding caps and labels, in the UK and EU markets starting in Spring 2023. This move is claimed to be a significant step towards reducing plastic waste and replaces nearly 70% of Fiji Water’s projected bottle volume worldwide (per 2023 sales forecast) with recycled material. The company is committed to transitioning its entire bottle portfolio to rPET by 2025. In addition to introducing 100% rPET bottles (excluding caps and labels), Fiji Water has also invested about FJ$5 million (US$2.27 million) in energy efficiency initiatives on the Fijian islands, which includes the use of microturbine energy generation and adopting low-sulphur fuel standards for shipping, reducing sulphur oxide emissions. Locally in Fiji, the Fiji Water Foundation focuses on sustainability and the preservation of the islands, along with supporting and improving the lives of native Fijians through initiatives such as providing access to clean water, healthcare services, and grants for local schools and organisations, and more. Since 2007, the Fiji Water Foundation has provided funding to large-scale reforestation and conservation efforts to preserve and protect the Sovi Basin, Fiji’s most important forest ecosystem and the largest remaining lowland rainforest, in partnership with Conservation International. Fiji Water is a division of The Wonderful Company. To date, The Wonderful Company and co-owners Stewart and Lynda Resnick have invested more than $1.3 billion USD in environmental sustainability initiatives to help fight climate change. This commitment includes the largest ever gift for sustainability research of $750 million to Caltech, and $50 million USD to TechnionIsrael Institute of Technology for research and sustainability. A portion of the research will focus on decomposable plastics, along with tackling issues of water, energy, food, and waste in a world confronting rapid climate change. Additionally, The Wonderful Company joined RE100, a global initiative made up of some of the world’s biggest companies, which have committed to using 100% renewable energy. www.fi jiwater.co.uk New UV additive for rPET with improved recyclability Avient Corporation announced the launch of ColorMatrix Ultimate UV390R, a new ultraviolet (UV) light-absorbing additive technology for both virgin and recycled PET resins. Part of the Ultimate portfolio, the new additive is claimed to be especially useful with high levels of rPET, offering UV protection that allows less than 10% UV light transmission up to 395 nm, or the edge of the visible spectrum, to protect contents from degradation. When using this additive technology with rPET, other benefits include improved bottle mechanical strength for better bottle-blowing performance, reduced bottle blowouts and stoppages, and lightweighting opportunities. This additive technology also can improve reheat performance and thereby reduce carbon emissions during bottle-blowing. Additionally, by helping to reduce yellowing of rPET upon subsequent heat histories, this additive technology supports improved recyclability. Beverages and personal care products can be affected by UV light, causing degradation of sensitive ingredients such as vitamins, micronutrients, and product emulsifiers, leading to reduced product quality and shelf life. Plastic packaging for these applications often requires an effective UV barrier, ideally allowing less than 10% UV light transmission up to 395 nm, or the edge of the visible spectrum, to protect its contents and increase shelf life. When choosing performance additives for packaging, brand owners and manufacturers typically seek solutions that can help them progress toward their goals for a circular economy and enable them to meet legislation and directives on rPET content without compromising efficacy. www.avient.com"},{"@ID":18, "MOULD MAKING PETplanet Insider Vol. 24 No. 05/23 www.petpla.net 16 vations,” said Guilherme Magalhães, head of Coca-Cola Andina’s Packaging engineering team. Expansion - the essential factor The most common formula for defining a bottle’s capacity is “Brim-full capacity = Net content + Headspace.” This new approach challenges it by considering expansion an essential factor, especially for carbonated beverage packaging. Moldintec’s patent-pending new XpBottle integrates the expansion caused by the filling process itself into the calculation formula. This capacity increase integrates the new equation as a negative term with which Moldintec designs XpBottle. Something that has not been considered before in the basic equation for bottle capacity calculations, especially as a way to improve a particular attribute. Additionally, the term corresponding to headspace (HS) is no longer a value set by a position (distance from the TSS to the liquid) equivalent to a specific millilitre amount. The shape of that area and the transitions of PET thickness (inner side of the preform) play a predominant role in foam generation and minimising HS. The treatment that Moldintec gives HS is based on the minimum required by the filling equipment for a specific product and filling conditions. Factors inherent to the blowing mould and the packaging design are involved here. “When all these factors operate together, we face a bottle that dynamically changes, taking advantage of the filling process conditions in the bottling line. The deformation is projected and controlled by the blow mould itself. We have heard of overfilling or underfilling in the industry, changing a product’s net content for marketing or price reasons. But never from an engineering point of view as a resource capable of improving a physical attribute,” says D.I. Jorge Pucci, CSO and head of Moldintec’s R&D+I. He continues: “We want to integrate filling process information into the blowing stage to optimise the final packaging. The blow mould is a fixed tool during its life cycle now; our challenge is making it dynamic towards a preform weight change, materials, and filling conditions! Today, we work with discrete data taken from the filler. We trust that soon, we will be able to take advantage of the AI agents that equipment manufacturers are integrating into their machines to understand better how counterpressure, speed, and headspace parameters vary with each product. Why not consider adaptive moulds that adjust bottle capacity based on the packaged product and instantaneous filling parameters?” The collaboration of large bottlers allows running tests to be performed under industrial operating conditions, not just in the laboratory. The project is still in the development and operational testing phase at multiple locations. www.moldintec.com You can make 100 % clear preforms without additives Inquiries: [email protected] pramiaplastic.fi The world’s best rPET granulate from Finland"},{"@ID":34, "BOTTLE MAKING 32 PETplanet Insider Vol. 24 No. 05/23 www.petpla.net Digital bottle designer as automated web application Highspeed bottle design based on an article by Gerhard Friederici, Editor, Cadfem Germany GmbH The development didn’t stop here. Together with Cadfem, the Krones engineers developed an automation solution that makes it possible to make complex FEM calculations accessible to a large group of users worldwide. “Our goal was to significantly reduce blow moulding tests by using a digital bottle designer,” explains Ulrich Lappe, Head of PET Pack Design and Application at Krones. “When part of the iteration loops in the laboratory are no longer necessary, we not only save money but also time, which we can use for additional orders. This is because the simulation results can be used to make fundamental optimisations to the container design even before a first blow mould is produced.” An integral part of the development Simulation has been an integral part of product development at Krones for decades, both in new product development and in the further development and optimisation of existing products. “However, the requirements have steadily increased, so that today we are on the way from physical to digital sampling.” explains Thomas Albrecht, who heads the CRD Analytics and Simulations department at Krones. “If we can predict the behaviour of the bottle with simulations, we will be able to produce, fill and transport it faster, more sustainably and more efficiently.” For this purpose, the entire life cycle of a bottle must be considered. Starting with the stretch blow moulding process, the container must then pass through several machine components. During filling and labelling, the bottles are subjected to high pressures. They are also subjected to stresses during storage and transport of empty and filled bottles, which must be taken into account in the design. Ultimately, the feel and look of the bottle for the end customer is an equally important criterion for bottle design. “Each prototype that we have to build and test less because of simulation significantly reduces direct costs. One loop in the real prototype costs several thousand euros, and that doesn’t include the revenue we miss out on by not being able to accept other orders due to time constraints.” - Ulrich Lappe, Head of PET Pack Design and Application - “A PET bottle behaves differently from a glass bottle; in other words, not like a rigid body,” emphasises Maximilian Braun, who oversees the automation project for the simulation process shown here. “A 0.5 l disposable PET bottle weighs much less than a glass bottle of the same volume. Nevertheless, all requirements for stability or for the complete processing line must be met. That’s why we also use simulation to compare bottle variants with each other. This way, we can be sure that we are giving our design teams and our customers the best possible advice. They not only get a good-looking container, but also a functionally flawless product.” In order to further reduce the effort required for the simulations and make them easier to handle overall, Krones invited tenders for a project to standardise and automate the processes for which Cadfem was awarded the contract. Through simulation, Krones AG has successfully optimised the shape and wall thickness of PET bottles so that they are more stable without having to sacrifice individual designs. At the same time, simulation indicates where valuable plastic resources may still be saved. Simulation creates stable bottles with minimal plastic material. (Sources: Krones) The times for the entire simulation process could be reduced. Furthermore, additional load cases (“Topload filled”, “Sideload filled”) that before had not be analysed, could be simulated now."},{"@ID":52, "7 NEWS PETplanet Insider Vol. 24 No. 05/23 www.petpla.net Resilux expands PET preforms factory in Romania The Belgian plastic and preform bottle manufacturer Resilux plans to expand its factory in northern Bucharest, Romania. This was announced by the Belgian Luxembourg Romanian Moldovan Chamber of Commerce on the social media platform LinkedIn. The expansion plans by about 30% include the installation of a recycled PET (rPET) pellets production line and require an investment of under € 3mn. Resilux owns a plot of land of about 3.7 hectares in the northern parts of Bucharest, where it already operates a PET preforms production facility with a surface of about 10,000m2. The new hall will increase the total area of the factory to more than 13,000m2. The raw material for the rPET pellets will be brought from the same group’s units in Hungary. The Romanian factory Resilux Packaging South East Europe, with 55 employees, reported a turnover of €22.5mn in 2021, a historic peak, and a net loss of about € 630,000. Belgian producer Resilux was bought last year by Pascal Vanhalst ‘s family investment fund Quva in a deal that valued the company at € 471m. www.resilux.com Aptar Closures acquires majority stake of Gulf Closures, adding manufacturing capabilities in the Middle East Aptar Closures, a global player in dispensing closures and active material science solutions announced the acquisition of majority stake in Gulf Closures, a closure manufacturer for beverage products in Bahrain. With the acquisition, Aptar Closures will leverage its global business capabilities and Gulf Closures’ manufacturing expertise, regional network, and experienced team to better serve the company’s existing customers in the Middle East, while opening new market opportunities and strengthening its presence in the region. Gulf Closures employs approximately 60 people at its facility in Bahrain and holds ISO and FSSC certifications. Gulf Closures is a partner to several global and other major local beverage brands in Gulf Cooperation Council (GCC) countries, Levant, and Africa. “Aptar has been present in the Middle East since 2019 when the company opened a sales office in Dubai. This acquisition will further accelerate our strategy in the region, now with a local manufacturing footprint. We look forward to building on Gulf Closures’ capacity and expertise to better serve our current customers in the region and to open new market opportunities,” added Hedi Tlili, president of Aptar Closures. As recently announced, Aptar has realigned its segments to provide a specific focus on closures through the segment Aptar Closures, effective January 1, 2023. Aptar Closures leverages its closures expertise to continue to provide best-in-class service to its customers with innovative and sustainable solutions, while strengthening its market position and broadening the served markets with its technologies. www.aptar.com"},{"@ID":33, "BOTTLE MAKING 31 PETplanet Insider Vol. 24 No. 05/23 www.petpla.net times. The capper was one particular area of focus, where the cone responsible for lifting and closing the bottles needs to be replaced manually. No conversion is required regarding the screw cap, however, as there are two cap feeds – one for each neck diameter in the respective format. Retrofittable option Andersen is convinced that the new neck change option will give beverage producers greater flexibility, as they can now also run shorter production cycles for bottles with different necks and therefore reduce their warehousing effort accordingly. “Some of our customers produce just in time; this means that the finished containers are loaded straight onto the truck without any interim storage. The drastically reduced conversion time will now enable filling operations like these to change necks more frequently; they thus profit from totally new options in their production planning.” The same goes for converters who can now produce the generally smaller batches for their customers – often in very different bottles – on a single line much more efficiently. The first customers in Asia who are already using the newly developed quick neck change are pleased with the amount of time and effort they save, says KHS. www.khs.com When converting the stretch blow moulder to a different neck, the shields are first exchanged. (Source: Jörg Schwalfenberg) The mandrel head is released by simply pressing on a spring, enabling it to be changed over quickly and easily. (Source: Jörg Schwalfenberg) 5IF SJHIU TPMVUJPO GPS FWFSZ JOTQFDUJPO UBTL JO ZPVS 13&'03. 130%6$5*0/"},{"@ID":16, "MOULD MAKING PETplanet Insider Vol. 24 No. 05/23 www.petpla.net 14 Designing PET bottles and blow moulds to improve the shelf-life through the fi lling process XpBottle, dynamic bottle’s capacity CO2 retention becomes the top of the list when lightweighting a bottle. It has widely challenged the use of existing blow moulds with lighter preforms, PCR PET, and resins. From this new point of view, the filling process, in combination with the blow mould design, could help to achieve a lightweight bottle and a long shelf-life. In summary, both counterpressure and foaming are important factors to consider in the volumetric filling of carbonated beverages to ensure consistent quality and a pleasant consumer experience. As mentioned earlier, foaming can occur if the counterpressure is too low, adversely affecting the process. However, if it is too high, it can cause deformation problems or even the explosion of the PET container while the drink is being filled. Bottle lightweighting brings significant economic benefits but also a reduction in the physical performance of the containers, including the capacity to preserve the product until consumption. For example, the structural resistance is decreased by reducing the thickness of the walls, producing containers that are difficult for the consumer to handle once opened. The same occurs with the container’s ability to retain CO2 in the product. A correctly carbonated drink that has lost carbon dioxide gas when it reaches the consumer results in a poor consumption experience. Taking the filling process into account The research by Moldintec’s R&D+I team found that the bottle`s CO2 retention could be improved by taking the filling process into account in the container design, calculation formula and mould engineering. They created a dynamically variable bottle between the blowing machine and MOULD MAKING Counterpressure and foaming are two critical factors that must be considered in the volumetric filling of carbonated beverages, as they can affect the quality and stability of the final product. Without going into specific technical details, there are different types of filling machines. They generally work by measuring the drink volume that should be filled in each container. This is achieved using sensors that measure the amount of liquid that enters the container and stop filling once the desired amount is reached. Counterpressure is the pressure exerted on the container while filling the carbonated drink. It is important to maintain an adequate counterpressure to avoid loss of carbonation and thus minimise foam formation. Counterpressure is adjusted by regulating the filling speed and pressure in the beverage storage tank. If the counterpressure is too low, a more significant amount of foam may be generated in the container, which can affect the quality of the final product. Foaming is another essential factor in the filling of carbonated beverages. It refers to the formation of gas bubbles in the container during filling, which can cause stability problems in the final product. Excessive foam formation can result in a lower quality. Maintaining adequate counterpressure and regulating filling speed is vital to avoid foaming. In addition, specific filling techniques can be used to minimise foam formation, such as filling in multiple stages or using special nozzles."},{"@ID":31, "MARKET SURVEY 29 PETplanet Insider Vol. 24 No. 05/23 www.petpla.net GDXL Precise Machinery Co., Ltd. FlexBlow Kosme Gesellschaft mbH Wentworth Mold Ltd. Kiefer Werkzeugbau GmbH PET Technologies No. 18 Changjiang Road, Guicheng, Nanhai, Foshan city, Guangdong Province, China. (Postcode: 528251) +86 757 8677 7168 www.gdxl.com Mr Billy Ay Marketing Specialist +86 757 8677 7168 ext 8681 [email protected] Vytauto str. 114A, 97134 Kretinga, Lithuania +370 445 51431 www.fl exblow.com 0 U $ X ULPDV äLDX ã \\ V Regional Manager, Europe +370 612 42946 blow@fl exblow.com Gewerbestr. 3, 2601 Sollenau, Austria +43 2628 411 0 www.kosme.at Mr Johann Gugler Managing Director +43 2628 411 125 [email protected] 156 Adams Blvd., Brantford, ON, Canada N3S 7V5 +519 754 5400 wentworthmold.com Mr Tar Tsau General Manager +519 754 5400 ext 611 [email protected] Steinhäldenstraße 11, 74193 Schwaigern, Germany +49 7138 97320 www.kiefer-mold.de Mr Rüdiger Lang Sales & Project Manager +49 7138 973270 [email protected] Grünlandgasse 5/1/12 2620 Neunkirchen, Austria +43 720 775 196 www.pet-eu.com Mr Maxim Poliansky CEO +43 720 902 169 offi [email protected] Up to 5 litres From 20ml up to 10 l itres 30 litres 10 litres Up to 30 litres 40 litres Yes No No Yes Yes Yes Yes, moulds applicable to various brands of SBM machines such as Sidel, Krones, KHS, Sipa, Tech-Long, Newamstar, etc. Yes, for FlexBlow machines Yes Yes, also manufacture multiplatform compatible mould systems Yes Yes Bottlers/converters which supply bottle to beverage brands such as Coca-cola, Pepsi-Cola, Danone, Nongfu Spring, etc.; as well as applications in food, cosmetic, pharmaceutical, home and personal care industries. Bottlers and packaging manufacturers from various industries, brick and rotary moulds for FlexBlow, Sidel, Sipa, KHS, Kosme, Krones machines Kosme, Krones, Sidel, KHS For all blow moulding machine platforms, e.g. Sidel, Krones, KHS, Sipa, etc. Kosme, Krones, Sipa, Sidel, ADS, Sacmi, KHS, Bekum, Tetra Pak, Side, SMI, Mag Rotary and linear blow moulders: Sidel, KHS, Krupp, Sipa, SMI, Krones, Kosme, Siapi, Sipa, Mag Plastic, ADS, Lonza, Side, Chumpower etc. Yes, bottle design according to customers' requirements on technical performance and appearance. Feasibility study, container and preform design and engineering, dedicated prototyping, laboratory analysis, real-life testing, mould prototyping with competitor moulds Yes Yes, container design, prototype sampling and bottle performance tests Yes Creation of unique bottle design, branding, product naming, logos and labels, 3D models, prototyping, bottle sampling, PET containers laboratory tests Bottle designs for light-weighting, optimised CSD base, reinforced structure, market-appealing styles, imitated texture, etc. Conversion from glass or HDPE to PET, light-weighting, hot-fi ll/heat-set, extreme vent, deep grip, pinch-grip, moulds with moving parts, lateral handle inserts, interchangeable design inserts Bottle development service free of charge, if blow moulds are ordered Hot-Fill/Heat-Set moulds with energy effi cient system and multi-platform interchangeable quick mould systems Lightweight design, special design for functional drinks, juices, oil and vinegar, household chemistry, dairy products, cosmetic industry, petrochemical industry Moulds for 100ml - 40 l containers, fi lling line conversions, bottles for chemicals and detergents, sanitisers, hot fi ll, wide neck jars, lightweight designs, laboratory tests Complete solution - from preform to working containers. Extreme vent air pressure reduction to 18 bars. PP blow moulding at 8 bars. Joint development projects for special applications and new blow mould development. One-stage Short lead time"},{"@ID":7, "43 PRODUCTS PETplanet Insider Vol. 24 No. 05/23 www.petpla.net PETproducts Consistently high speed achieved with recyclable sleeves Standard PETG sleeve labels remain a major challenge for recycling systems because it is impossible to separate them dependably from the crystallised PET that bottles are made of. This may reduce a recycling system’s efficiency. The label manufacturer CCL has developed the EcoFloat sleeves which consist of polyolefin. They possess a lower density than the PET that bottles are made of. This allows the sleeve labels to be separated from the bottles in recycling systems, using the sink-float method. In a field test conducted on a high-speed Pepsi-Co line in Rodgau, Germany, a sleeving machine from Krones has now successfully dressed 0.5 l and 1.5 l Lipton Iced Tea bottles in these recyclable EcoFloat polyolefin sleeve labels, which are applied using the following kit: a Sleevematic TS sleeve labeller with a Multireel S magazine for the sleeve reels, a Shrinkmat steam tunnel, and two Linadry container dryers, one installed upstream of the labeller and the other one downstream of the steam tunnel. In order to maximise both machine availability and efficiency with the EcoFloat sleeves, the Sleevematic TS has been equipped with special add-on components suitable for processing polyolefin, like specifically adapted rollers and cutting tools. It took one day to install them, with the machine then immediately reaching top speed and maximum efficiency. The shrink-fit quality obtained with the EcoFloat sleeves is at a high level, similar to that achieved with standard PETG sleeve labels. So the Sleevematic TS is able to process polyolefin sleeves with minimal adjustments to its design. www.ccllabel.com www.krones.com Multi-functional label technology Recycling technology providor, Polytag, is set to apply QR codes and UV tags to Co-op own-label PET 2 l spring water bottles in an industry-first, offering the convenience retailer visibility of its packaging during the recycling process. The unique-every-time QR codes will be applied to the pack labels by Co-op’s bottled water supplier at the standard label application speeds. The QR codes are GS1 compliant. A UV tag layer, invisible to the human eye, printed by Tipografic using UV flexographic inks, is applied across the label. This UV tag layer enables barcode level information to be captured in the recycling centre and is uploaded to Polytag’s cloud-based analytics dashboard, providing the retailer with real-time insights on whether packaging is actually recycled, and in what volumes. The UV tag reading technology was developed by Polytag in partnership with researchers at the Advanced Manufacturing Research Centre. It is fitted to the plastics conveyer at Abergele’s Gofer Bulking Centre in Wales. Both the visible QR codes and ‘hidden’ UV tags pave the way for a cost-effective, Digital Deposit Return Scheme (DDRS). In future, scanning the unique QR code on used product packaging, has the potential to allow consumers to reclaim their deposit via their smartphones, from home. The printing of UV tags provides key supply chain stakeholders – manufacturers, retailers and recycling authorities – access to unique packaging lifecycle data, including where and when it was produced and the percentage of recycled material it contains, protecting against fraud. For this trial, the QR codes will be used as a communication tool, transporting customers to the landing page when scanned. Furthermore, with Extended Producer Responsibility (EPR) on the horizon, brands classed as obligated packaging producers maybe required to benchmark their progress. Both on-pack QR codes and UV tags will provide brands with the data to easily ‘describe, tag and trace’ their plastic packaging through the circular economy, while also streamlining packaging and recycling operations. At the same time, the technology will allow legislators to measure business liabilities and enforce legislation by identifying ownership of plastic packaging: Local authorities and recycling centres can capture real-time data on packaging composition and breakdown of bales, to help inform recycling strategy, investment in sorting and recovery equipment, and onward tracking of materials. www.polytag.co.uk"},{"@ID":13, "MATERIALS / RECYCLING PETplanet Insider Vol. 24 No. 05/23 www.petpla.net 11 MATERIALS / RECYCLING 11 PET planet: You are in regular contact with Brussels regarding the PPWD. What are the main criticisms you have of the directive? And what are your recommendations? Bielenstein: First: we are convinced that the regulation is the right approach. We welcome the current directive to become a regulation. We also support the goals of the regulation: all packaging should become recyclable and should be re-use whenever this makes sense. This means to be sustainable in environmental, social and economic terms. Our main criticism is the too detailed approach. This is not only the case regarding the governance of re-use systems. It is also e.g. that there are paragraphs regarding hygiene and food safety. No question: this hygiene and food safety is of highest importance. But the packaging regulation is the wrong place to regulate that. There are two more important things: re-use needs a transition period regarding recyclate rates. And PPWR needs to cover the return of re-use container in an appropriate way. PET planet: What innovative & new types of packaging or materials do you see in the beverage packaging sector? Do you see reusable as an opportunity here? Bielenstein: Our next task is to rise the rPET share of our reusable bottles and to further reduce our carbon footprint on production and logistics of the re-use containers. Anything that’s helps to reach these goals is welcome. And: we should not limit ourself to beverages. PET is a wonderful material: we should further explore how to apply it for re-use packaging solution in other food- and non-foodpackaging whenever this makes sense in environmental terms. It is our job to share our learnings in the beverage sector to make this a success. www.gdb.de www.sacmi.com Product design Product development Product validation Industrial production plant Process & quality control On-site and start-up assistance After-sales and Customer service SACMI 4.0 THE COMPLETE CLOSURE, PREFORM AND CONTAINER SOLUTION FOR YOUR SMART FACTORY E N D L E S S I N N O V A T I O N S I N C E 1 9 1 9"},{"@ID":51, "MOULD MAKING PETplanet Insider Vol. 24 No. 05/23 www.petpla.net 20 Swiss made tethered closure The easy solution From 2024 onwards, all plastic caps have to remain connected to the single-use container, in accordance with the EU Single-Use Plastics Directive, 2019/904, Article 6. As a result, there are now numerous designs of tethered caps with different manufacturing processes on the market. PETplanet spoke to Manuel Büsser, CEO of EasyCap, about his multiple award-winning tethered cap solutions. PETplanet: EasyCap has won both the World Packaging Award and the German Packaging Award. What are the advantages for the consumer when using packaging with EasyCap? Büsser: From the very beginning, our primary goal was to develop a tethering system that not only complies with EU directives, but also puts the needs of consumers first. Our EasyCap solution gives the consumer the greatest possible freedom to open and close the cap with the usual sequence of movements. Another advantage is the freedom to drink that they have been accustomed to up to now. With our tethering solution, the cap is not in the face region during consumption. When the consumer opens a bottle with our EasyCap tethering, he naturally unscrews the cap from the mouth and lifts it off. No unaccustomed flipping over a hinge is necessary. Replacing the cap is also very easy, allowing the consumer to screw the cap back onto the muzzle as usual. With our EasyCap tethering, we assist consumers in easily setting the tethering band length that is most comfortable for them. Through haptic feedback, so-called “stop bridges” show the consumer the predefined band lengths. With all these intuitive functions and the continued natural drinking behaviour, we have been able to convince two independent expert jury groups and many consumers of our tethering solution. PETplanet: Why did you decide on this closure lasso design? What were the challenges in the development? Büsser: Before we started the development of our EasyCap tethering, we first researched the needs of consumers. The most important development goal for us was to develop a tethering that does not interfere with the consumer and does not require the consumer to relearn the already familiar movement sequences. To this end, we analysed the movement sequences learned from childhood for opening and closing a drinking bottle. The analysis showed that the most natural form of the opening process consists of unscrewing and lifting, and that the closing process consists of putting on and screwing down. To realise the two such simple movements in a tethering without adding another movement was a big challenge. The first prototypes were not very well accepted by consumers. The reason for this criticism was that the tethering band was much too short, which consumers found annoying because the cap scratched their face while drinking. After several iterations, we came up with our award-winning tethering solution, where the consumer decides what distance the cap should be from the mouth and thus from the face. Furthermore, our solution also prevents the consumer from tearing off the cap unintentionally. This is because we have observed that consumers who want to drink from bottles with a flip-top tethering cap tear off the cap immediately after opening it so that they can then drink effortlessly from the bottle. PETplanet: What advantages do closure producers have when they opt for EasyCap? Büsser: Our aim was to develop a tethering system that requires no or only minor adjustments to the existing cap design for most cap types. Therefore, it is possible to implement our EasyCap tethering with only minor investments in existing or new injection moulds. We have succeeded in doing this because we do not generate our tethering design with a slide mould, but introduce it subsequently by means of slitting. This also has the advantage that our customers can respond to consumer needs within a very short time and without costly modifications to the injection moulds. Manuel Büsser, CEO EasyCap With EasyCap tethering, consumers can set the tethering band length that is most comfortable for them. MOULD MAKING"},{"@ID":14, "MATERIALS / RECYCLING PETplanet Insider Vol. 24 No. 05/23 www.petpla.net 12 Consistent circulation management of PET bottles can save 60,000 t of CO2 in Germany alone Study on environmental benefits of a PET material cycle for single-use bottles “In order to drive climate protection and the circular economy, the circulation management of single-use PET bottles should be improved,” says Ifeu study leader Benedikt Kauertz. According to the 2021 study, around 425,000 t of plastic are used in Germany for the production of single-use PET bottles. Through the deposit system, 97 per cent of this material can be collected and reprocessed. This recyclable material is already sorted and can even be reused as food packaging. For this reason, it is a sought-after product on the secondary plastics market – and not only for manufacturers of drinks bottles. This is also why it has not yet been possible to reuse all the PET for drinks bottles: around 55 per cent of recycled PET is bought by manufacturers of films, textiles and packaging for cleaning products or cosmetics, and it is used for these products. “When the premium PET comes out of single-use deposit bottle recycling loop and goes into these applications, it is usually lost to the circulation system for new PET bottles – with negative environmental effects,” explains Kauertz. The most important regulatory mechanism for positively assessing bottle circulation is therefore the retention of material. PET from single-use bottles: Nine reuses possible The study shows that the original primary PET is currently reused three times at most. In Germany, it usually ends up in waste incineration after that (“thermal recycling”). If all the PET from the recycling of single-use bottles was reused for drinks bottles, it could theoretically be reused nine times. This makes the amount of material needed in the bottle circulation loop significantly lower than in the other systems. “Closing the bottle circulation loop reduces the use of primary PET considerably. In 2021, manufacturers had to feed in 235,000 t of primary PET. In the closed bottle circulation loop, the use of primary PET would fall by more than 90% to 21,000 t,” says GVM Project Manager Nicolas Cayé. Consistent closure of the circulation loop by prioritising material use in the material stream could reduce the proportion of thermal recycling by 86% and the driftage of materials by 66%. In the scenario where the recyclable PET from deposit-scheme single-use drinks bottles is used as much as possible for new drinks bottles, CO2 emissions fall by 20 per cent or around 60,000 t/a. Here, the study considers the entire value creation chain including all secondary uses, and thus includes a broader system scope than the productrelated packaging life cycle assessments. The benefit of consistent circulation management therefore stands up robustly against methodological stipulations. About the study The study into the environmental potential of a prioritised material cycle for single-use PET bottles in Germany was carried out by the Institute for Energy and Environmental Research (Ifeu) in cooperation with GVM Gesellschaft für Verpackungsmarktforschung, and is a contribution to both scientific and political discussions. The client is Coca-Cola Europacific Partners Deutschland GmbH (CCEP DE). The final report has been available since March 2023. The study investigates what environmental effects an amended, priority materials circulation system has on the environmental record of the PET material cycle for drinks bottles, taking into account the material flow balance, material retention and bonding, and the greenhouse gas balance. Alongside observation of the current situation in 2021, the study also investigates scenarios for 2025. www.ifeu.de If the plastic brought onto the market in Germany as single-use PET bottles was completely reused for the manufacturing of these bottles, around 60,000 t of CO2 could be saved. Instead, too great a proportion of the foodgrade recyclable plastic leaves the single-use container deposit circulation loop for alternative uses and then quickly ends up in waste incineration. These are the findings of a study by Ifeu and the GVM Gesellschaft für Verpackungsmarktforschung [Association for packaging market research]."},{"@ID":57, "1 The worldwide round trip with The Middle East Roadshow EDITOURS PET world in the Middle East New year, new tour! After our successful Drinktec tour, the PETplanet team is going to the Middle East in the last quarter of 2023! In a spectacular project taking us well into 2024, we will be travelling in a wide variety of ways to various countries and regions of the Middle East with different mobile editors. There we will interview machine manufacturers, the supply industry, bottle and beverage producers, as well as PET recyclers and everyone involved in the process chain. What market-specific trends are there now or will arise in the future? What developments and technologies are in vogue on the consumer and plant construction site in some of the hottest regions of the world? What special requirements are there? What role do topics such as food safety, shelf life and sustainability play in PET packaging and how are companies preparing themselves for the coming years? This, and much more we will be discussing face-to-face with all the key players and then our results will be presented to you in a series of must-read reports in PETplanet Insider. Please join on this enchanting voyage to the world of PET in the Middle East. We look forward to welcoming you on board! Our previous Road Shows at a glance 2010-2011-2012-2013-2014-2015- 2016-2017-2018-2019-2020-2022 Interested in being visited? [email protected] Autumn 2023 - 2024 EDITOUR - THE MIDDLE EAST ROADSHOW 6 countries numerous interviews with PET companies Sponsors to date"},{"@ID":36, "BOTTLING / FILLING PETplanet Insider Vol. 24 No. 05/23 www.petpla.net 34 Romania’s secret to bottling and packaging beverages Keeping natural effervescence In Romania, history, culture and traditions are perfectly intertwined with the natural beauties of the environment, which represent a precious resource for human health and well-being. With a third of the mineral and thermal waters of Europe, Romania boasts the presence of 70 resorts, where it is possible to treat various illnesses. The merit of this wealth derives from the geological structure of its mountains. In the north-western part of the country, the pure water springs of the City of Carei, in the county of Satu Mare, have ensured the development and success of Alconor Company, a leading company in the production of beverages and mineral water. The company has distinguished itself in Romania and abroad thanks to the ability to embrace new challenges, to seize the new opportunities offered by the continuous changes in the market. To achieve and maintain high quality levels, within the production lines of the Carei and Voluntari (Bucharest) plants, Alconor uses different types of machines supplied by SMI, such as rotary stretch-blow moulders for the production of PET bottles, within fully automatic bottling and packaging lines which also include secondary and tertiary packaging systems and conveyor lines. The company’s headquarters have been located, since its foundation in 1999, in the city of Carei, in the county of Satu Mare (north-western part of Romania), in the region of Transylvania. Initially Alconor only produced soft drinks, but, in 2014, 15 years after the first plant, it decided to expand the business by inaugurating a new production plant in Voluntari-Bucharest, where three modern fully automated bottling lines are currently installed. Today, Alconor Company is one of the most active and competitive companies in Romania in the production of soft drinks and water and has transformed itself from a family business to an industrial company appreciated at national level, the production of which is carried out entirely in the two factories in Carei and Bucharest, on an area of 7,000m2 and then stored on a total storage area of 15,000m2. From the initial activity of bottling carbonated soft drinks in PET containers, the product range has expanded to spring water, energy drinks and soft drinks. The Romanian company markets both products with its own registered brands, created and developed in over two decades of activity, and private label products of national and international partners. Together with Beverage Drink Srl, the group company specialised in distribution, and the support of reliable partners, Alconor Company perfectly covers 99% of the territory of Romania, easily reaching almost all counties. The company is able to satisfy even very high production requirements, through a daily load capacity of 1,000 t and thanks to five distribution centers in Carei, Chișineu Criș, Târnăveni, Timișoara and Bucharest. In 2019, the Romanian company exceeded 200 million litres of water and soft drinks produced, the equivalent of 10,000 trucks. From that date, the annual production of Alconor is around 250 million litres, an objective achieved thanks to the continual investments in new technologies that allow Alconor to constantly improve its performance at an industrial and financial level. The number of employees, which today sees the presence of around 300 people, is also constantly growing. Transformation and investments The diversification of the products offered by Alconor made it necessary to install various bottling and packaging lines; furthermore, the objective of enviNorbert Varga, CEO of Alconor Company SFP 30 Ergon stretch film wrapper"},{"@ID":21, "MOULD MAKING PETplanet Insider Vol. 24 No. 05/23 www.petpla.net 19 Even tighter tolerances than for bottle preforms Sipa has spent several years developing new injection mould tooling solutions for medical applications sector. A special cold-half core-centring technology that it developed for blood collection tubes (BCTs) is already used successfully at a leading global supplier of these critical and widely-used items. The solution Sipa developed is claimed to be unique in the industry and the subject of a patent application. The development makes it possible to adjust the core alignment from the front face of the cold half, in contrast to competing solutions that require access the back of the core plate. This makes any adjustments easier and faster to carry out during production. Time- and cost-saving core-centring feature is ideal for blood collection tube production Production of high-quality blood collection tubes demands that wall thickness around the circumference is within very tight tolerances. This can only be guaranteed by precise design and especially accurate production of the various elements in the injection mould. While such criteria also apply to more common PET products like bottle preforms, consistently high performance over long-term production is more difficult to ensure with BCTs. Why is this? There are two specific reasons. First, because BCTs have a diameter much smaller than regular preforms, the various components of the mould also have reduced dimensions. In the specific case of the cores, these obviously also have a small diameter, which means that their stiffness is lower than preform cores. As a result, they are more likely to flex under the pressure of the PET melt if the wave front during injection is not perfectly symmetrical. The situation is made more critical by the fact that injection pressures used in BCT moulding need to be higher than in preform production, due to the higher length: thickness ratios of the tubes. This obviously puts the mould components under greater stress, increasing the potential for deflection of the cores. The solution developed by Sipa is claimed to make it easier to fine-tune the positions of the cores, correcting any slightest deviation from the set value, and so enabling production of a product with optimal wall thickness. “Our solution is unique because it allows the processor to make adjustments to the mould while it is still in the machine, simply via access to the front face of the cold, moving half,” says a Sipa spokesperson “No disassembly is necessary, providing the user with a considerable advantage in time taken for the execution of the operations. “Obviously the task is also much simpler than in an MOULD MAKING adjustment operation requiring access to the back of the mould, where the mould, or at least part of it, has to be taken out of the injection moulding machine, dis-assembled, adjusted, reassembled, and then refitted to the machine.” www.sipasolutions.com"},{"@ID":54, "PREFORM PRODUCTION 37 PETplanet Insider Vol. 24 granules. The air may well be at the required temperature, but this is no guarantee that the granules in the core have the same temperature - 25-40% of the energy in the granules may thus be unaccounted for. The company ReduPET GmbH has now developed the monitoring system Waste Analysis and Visualisation of Energy (“WAVE”), which works according to the somewhat modified physical law “energy is not consumed - but only transferred in a different form”. The principle shown in three simple graphs In the first step, only three values are entered on an input page, which determines the PET material throughput at the dryer: The number of active preform cavities and the weight of the preform, optionally the material proportion if a different material is fed through a second dryer (e.g. rPET). With the signal of the machine cycle, the throughput can now be determined precisely on a continuous basis. In continuous measurement, the specific energy requirement of the material currently being processed is determined - only by measuring its input temperature. The output temperature is set by the operator - it is, after all, as mentioned, non-measurable. Due to the known enthalpy values of PET, the specific energy value of PET is known and can be determined by the continuous material throughput of the machine. The process air has the advantage that its temperature can be easily measured. The air also has enthalpy values that change in relation to density, pressure and humidity. However, since the air is extremely dry, the moisture content does not need to be taken into account. The common drying systems on the market work with cubic metres of process air volume, which is not sufficient for determining the energy transport into the PET material. The decisive factor is the air mass, which makes it possible to determine the energy transferred to the PET material by means of the measured temperature loss Delta T (process air inlet temperature - process air outlet temperature). In this way, the specific energy requirement of the PET material and the specific energy delivered by the air to the PET material are compared. Losses and the extraction of moisture are taken into account. WAVE now plots the graph of the specific energy demand of the material (blue curve) and the specific energy given off by the air on a graph (green curve). With a dryer running in thermal equilibrium, both curves over-"}]}}
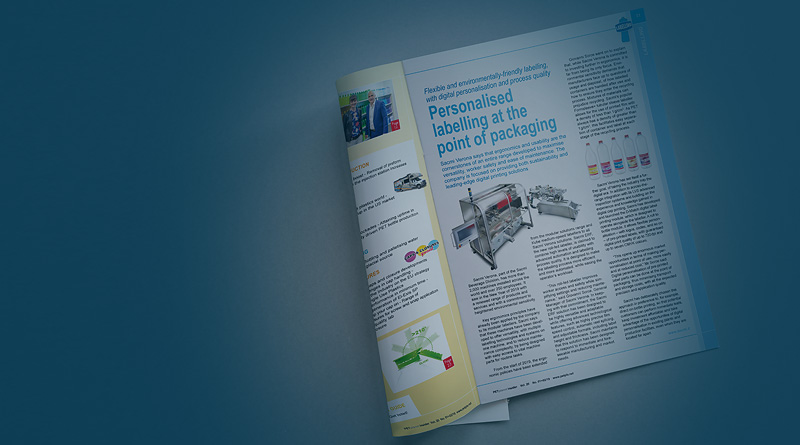