{"pages":{"page":[{"@ID":44 "42 PETplanet Insider Vol. 25 No. 05/24 www.petpla.net PETproducts UPM Raflatac receives APR Design for Recyclability recognitions for three types of label solutions UPM Raflatac, a global supplier of self-adhesive paper and film products, has been formally recognised by the Association of Plastic Recyclers (APR) for three types of biaxially-oriented polypropylene (BOPP) label products for HDPE and PP package recycling. These include Undecorated BOPP with hotmelt adhesive, Undecorated BOPP with RW85C, and metalised undecorated BOPP with general purpose acrylic adhesive. APR Design for Recyclability Recognition provides third-party validation that a package or packaging component’s design is compatible with the North American recycling system. This process has now confirmed that UPM Raflatac’s BOPP products, as stated above, have met the highest criteria for recyclability according to the APR Design Guide. UPM Raflatac’s latest recognitions are all for HDPE and PP recycling. www.upmrafl atac.com Water-washable plates for label printing promises 30% CO2 emission reduction Flexographic printing is a widely used printing method around the world. Currently, the printing plates used are primarily solventwashable plates that require an organic solvent-based washing solution in the wash out step of the plate-making process. Asahi Kasei develops and manufactures water-washable plates that use a water-based washing solution, which is claimed to be more environmentally friendly. Asahi Kasei Corp., headquartered in Tokyo which is the parent company of Asahi Photoproducts, announced that Suntory Beverage & Food Ltd., also headquartered in Tokyo, has switched to AWP water-washable flexographic plates for the printing of beverage labels in Japan on their 550ml PET bottles. This is the first time for AWP plates to be used for printing labels in the beverage industry in Japan. In implementing this next-generation flexo printing technology, Asahi Kasei collaborated with Fuji Seal, Inc. According to research by Fuji Seal, this is expected to reduce CO2 emissions by approximately 30% compared to the plate technology that had previously been used. The AWP water-washable plates adopted for label printing at Suntory Beverage & Food are now used at its Suntory Kyushu Kumamoto Plant, where solvent-washable plates had previously been used. The Asahi Kasei Group will continue to promote its AWP family of water-washable plates to replace solvent-washable plates in beverage label applications. It is expected that this can reduce the environmental impact of printing. www.asahi-photoproducts.com LABELLING"},{"@ID":47 "TRADE SHOW REVIEW PETplanet Insider Vol. 25 No. 0/24 www.petpla.net 45 “The demonstration plant includes a depolymerisation reactor capable of processing 60 kg/h of PET, which is the equivalent of almost 2,000 bottles, the yearly consumption of two people. This is a turning point for Gr3n, as with this plant we will be able to finetune the process the already existing Process Design Package of the 40K tons industrial plant,” added Dr Crippa. Thanks to the MADE technology developed by Gr3n, this approach is now feasible and is claimed to make Gr3n one of the few companies with the potential to provide a reliable enhanced recycling solution that closes the life cycle of PET, offers food grade polymer material, processes a large variety of waste (post-consumer and/or post-industrial polyesters will be both from bottles, i.e., coloured, colourless, transparent, opaque, and textiles, 100% polyester but also with up to 30% of other materials like PU, cotton, polyether, polyurea, etc.) and reduces carbon dioxide emissions. In principle, the obtained monomers can potentially be re-polymerised endlessly to provide brand new virgin PET or any other polymer using one of the monomers. Polymers obtained can be used to produce new bottles,trays and/or new garments, essentially completely displacing feedstock material from fossil fuels, as the recycled product has the same functionality as that derived traditionally. This means that Gr3n can potentially achieve bottleto-textile, textile-to-textile, or even textile-to-bottle recycling, moving from a linear to a circular system. Franco Antonio Cavadini, CTO at Gr3n, explained the MADE technology process. Gr3n developed a new process, based on the application of microwave technology to alkaline hydrolysis, which provides an economically viable approach to the recycling of PET, allowing the industrial implementation. The Gr3n process is claimed to be economically sustainable and industrially viable as it breaks down any type of PET and polyester plastic into its two core components (TPA and MEG monomers), which can then be re-assembled to obtain virgin-like plastics allowing endless recycling loops. The company’s goal is to become a leading supplier of recycled PET and polyester, addressing the global need for virgin plastics and triggering a truly circular approach to plastic recycling. Gr3n is part of Petcore Europe, Chemical Recycling Europe, and Accelerating Circularity. www.gr3n-recycling.com"},{"@ID":62 "25 YEARS ANNIVERSARY 13 PETplanet Insider Vol. 25 No. 05/24 www.petpla.net aldehyde migration. Also acetaldehyde reducing additives are applied in the preform manufacturing process. Acetaldehyde reducing additives Traces of acetaldehyde can migrate from the PET bottle wall into natural mineral water. The main goal in preform and bottle manufacturing is to reduce the acetaldehyde concentration in PET. From migration theory, the bottle wall concentration of acetaldehyde is directly proportional to the migration under the same storage conditions. This means that the reduction by a factor of two results in half of the migrated amount of acetaldehyde into bottled water. 2-Aminobenzamide, also known as anthranilamide, is the most popular acetaldehyde reduction additive and called an acetaldehyde scavenger used in PET preform manufacturing. This additive reacts chemically with acetaldehyde to form a non-odorous and higher molecular weight substance. As any other additive, 2-aminobenzamide must be approved for the application in PET bottles and the specific migration limit of 2-aminobenzamide of 0.05mg/kg food (Table 1) has to be controlled in routine tests by the mineral water filling company. Monomers (ethylene glycol and terephthalic acid) In general terms, the migration of monomers from plastics can never be totally prevented. PET, however, is highly inert compared to other plastics. Thus, only extremely small quantities of monomers may migrate into bottled water. For example, a study has shown that the level of migration of the monomers ethylene glycol and terephthalic acid from PET bottles is far below statutory limits. Nonetheless, water bottling companies constantly monitor levels of monomer migration from PET bottles. Antimony Antimony trioxide is the major catalyst used to polymerise PET. In principle, the catalyst will remain in the PET after polymerisation. Typically, concentrations of antimony in PET bottles are below of 300mg/kg PET. Alternative catalysts for the polymerisation of PET have also been developed, mostly based on titanium, aluminium or germanium. However, to date the alternatives developed have not succeeded in making a major commercial breakthrough and antimony trioxide remains by far the dominant catalyst employed by resin suppliers. As with all the substances employed in the manufacture of PET, antimony is subject to strict statutory regulations in Europe. The maximum permitted level of antimony migration from a PET bottle into the finished product is 0.04mg/l (Table 1). Under normal storage conditions, the level of antimony migration from PET bottles is extremely low. The limit value for antimony migration from PET packaging may not be exceeded during the shelf life of the beverage, even when bottles are stored in warm climates for many months. The limit value for antimony in water is considerably lower than the limit value for migration from PET packaging. In Europe, for example, a maximum of 0.005mg of antimony may be present in one litre of natural mineral, spring or drinking water at the time of packaging. Even if, from a legal point of view, the migration limit of 0.04mg/l is valid for bottled . Bio-PET Traditionally, the monomers of PET are manufactured from fossil-based resources. However, a synthetic route for ethylene glycol, one of the two monomers, was developed from biomass as early as in the late 1980’s. Sugar-cane is transformed to bio-ethanol. In the second step, bio-ethanol is oxidised to the monomer ethylene glycol, which is subsequently used for the polymerisation of PET. A mass fraction of about 30% by weight is realised when using bio-ethylene glycol as monomer for PET. The second monomer of PET, terephthalic acid, is not commercially available using biobased resources. However, synthetic routes from biomass to terephthalic acid are available in laboratory/pilot scale. From a chemical point of view, bio-PET is indistinguishable from fossil-based PET. Therefore, the same manufacturing facilities for PET pellets, preforms and bottles can be used. Also, bio-PET is fully recyclable along with fossil-based PET. Such bio-based equivalents to fossilbased polymer are called “drop-in” biopolymers. * Neumann, E H. Thermoplastic polyesters in Encyclopaedia of Packaging Technology, ed Bakker M. John Wiley, New York 1986. https://www.petcore-europe.org/images/news/pdf/ factsheet_the_facts_about_pet_dr_frank_welle_2018.pdf Substance Specific migration limit in mg per kg food Acetaldehyde 6 Terephthalic acid 7.5 Isophthalic acid 5 Mono- and diethylene glycol 30 Antimony 0.04 2-Aminobenzamide 0.05 Table 1: Requirements according to European Packaging Legislation (EU 2011)"},{"@ID":31 "MARKET SURVEY 29 PETplanet Insider Vol. 25 No. 05/24 www.petpla.net 05/2024 MARKETsurvey Suppliers of preforms & preform inspection systems In this issue, PETplanet’s focus is on new developments in preforms and preform inspection systems. We are very proud to present the brand-new data from the following preform manufacturers and preform inspection system manufacturers: Pressco Technology, Intravis, Sacmi Imola, Hodmeter, Varioform, Retal, PDG Plastiques and Gulf Packaging System. Although the publishers have made every eff ort to ensure that the information in this survey is up to date, no claims are made regarding completeness or accuracy. Resins & additives Cap producers, systems & inspection systems Preform machinery Preform production & inspection systems Preform, cap & SBM mould manufacturer SBM 2-stage Compressors Filling equipment & inspection systems Palletising & shrink film machinery Recycling machinery Preforms Company name PDG Plastiques Hodmeter Retal Industries LTD Gulf Packaging System Co Varioform PET Verpackungen Ges.m.b.H. Postal address Telephone number Web site address Contact name Function Direct telephone number E-mail ZI secteur 2, 45330 Malesherbes, France +33 238 3461 95 www.pdg-plastiques.com Mr Francois Desfretier General Manager +33 238 3461 95 [email protected] 140 rue Louis Pasteur, 76160 Darnéta, France +33 950 373 373 www.hodmeter.com Mr Antoine Brémilts Sales & Marketing +33 684 633 154 [email protected] Epimitheos St. 6, Industrial Area A, Limassol, 3056, Cyprus +357 25 270 500 www.retalgroup.com Mr Fuat Karaev Global Sales Director +357 25 270 500 [email protected] P.O. BOX 20266, Jeddah 21455, Saudi-Arabia +966 126 3600 99 www.3p-gulf.com Mr IbrahimAbushanab Operations Manager +966 505 668 651 [email protected] Industriestaße 5, 3134 Reichersdorf, Austria +43 2783 7114 0 www.varioform.at Ing. Werner Maurer Managing Director +43 2783 7117 -0 offi [email protected] Preforms Multilayer preforms (Yes/No) No No Yes No No PEN prefoms (Yes/No) No No No No No Preforms in alternative materials (PP/PLA/PEF) Which? BioPET - PP No applicable PET No Preforms incorporating rPET (rPET content in %) Yes up to 100% No up 100% rPET Yes - 25% - 100% Yes; up to 100% List of additives available Prelactia 100% light barrier for UHT sterilised long shelf-life milk, Oxygen, UV, CO2 barriers No O2 scavanger (example- Amosorb) AA reducers; slip agent; UV blockers; brighteners; nylon; Polyshield Various colourants, AA reducer, TiO2 Please contact for further information Preform range Coloured preforms, 29/25 shorty: 8-29.5g; 30/25 high: 17.5-50g; 26/22: 9.5-34g; 38mm 3 start: 14-65g; Prelactia 38mm 3 start: 17-38 g; 48/40: 47-62g; 21/29: 20-22.5g; 27/32: 6.5g dairy and smoothies; 25/20: 6.5-8g dairy; PCO 1810: 20-33.6g; PCO 1881: 18.5- 27 - 30-32-36.5g; 29/23: 24-33g chemical; BVS 30H60: 50g wine (high oxygen barrier); 22H30: 19g wine (high oxygen barrier); 87g Ø29 Crown - sparkling wine Ø63: 372-485g; ultra-lightweighting 2.4g preform; standard and specifi c preforms for mineral water, dairy, juice, CSD. etc., overmoulding technology for 2-layer preforms; Preblow and Mint-Tec technology for lightweigthing bottles. 700g 55mm neck Around 800 different preform designs with different weight (9.7 - 485g) and neck (PCO 1881, PCO1810, 26/21, 26/22GME30.37, 26/22GME30.40, BPF, 28/410, 29/21, 29/25, 30/25, 38mm etc.) For still water: 7g - 200g for water 29/25NF, 30/25NF, 38mm, 48mm; for carbonated drinks: 16g-53.5g for CSD 1881 NF; for juice and fl avoured drinks: 11g, 13.5g, 18g, 22g for juice 29/25 and 38mm Varioforms preform portfolio includes different preforms for the beverage and non food usage. We produce preforms from 13.5g up to 54g with PCO 1810, PCO 1881 as well as PETCycle neck fi nishing."},{"@ID":48 "EVENT REVIEW PETplanet Insider Vol. 25 No. 0/24 www.petpla.net 46 All-electric capping systems now on the market Up until now, the hydraulic capping system has been standard practice in the sector. Last year, Sumitomo Demag introduced the first all-electric system. We have been able to see the Pac-E series which is currently under construction at the plant in Schwaig near Nuremberg, Germany. Seven years ago, CEO Gerd Liebig decided that in future his company would only produce fully electric machines at the Wiehe facility. At the time, sustainability was seen as a key issue. The all-electric machine series, together with appropriate automation, digital tools and professional training more than doubled output. Over 90% of all machines currently supplied by Sumitomo Demag to Europe are fully electric. The medical and electronics sectors have been growing as has the number of all-electric machines in the packaging, consumer goods and automotive industries. And so it was only a matter of time before the company launched the fully electric Pac-E series for capping systems last year. At the start of the roadshow, we were able to see the assembly of the classic El-Exis SP 250/630-1600 and The El-Exis SP 250/630-1600 under construction… … and right next to it the Pac-E 350/820 2000 RECYCLING SOLUTIONS HIGH PERFORMANCE CLEANING ADDITIVES & SUPPORT How can your recycled product meet permanently increasing demands? With the CHT range of high performance process solutions with environmental relief for the wet cleaning and recycling process. We support you directly on site and ensure your quality controls in our laboratories with state-of-the-art equipment. Thus, your strong position in the growing market is confirmed day by day. More about us at www.cht.com"},{"@ID":21 "25 YEARS ANNIVERSARY 19 PETplanet Insider Vol. 25 No. 05/24 www.petpla.net to offset the losses.” How would the material loss in recycling be balanced? Kauertz: In fact, the Schwarz Group does not rely on virgin PET for the production of the analysed containers. We verified this during the study’s development by examining documents. Certainly, there are material losses in the collection and processing of used PET single-use bottles, and we have accounted for these losses in the LCA. The study explicitly states at the outset that it examined the Schwarz Group’s circular system. If the Federal Environment Agency takes this into account, it might clarify its statement and focus on the overall market. Then, the statement would be accurate in acknowledging that not all bottles can always consist of 100% rPET if the market is not to shrink. The average rPET content in Germany is still below 50%. There is still plenty of room for improvement, and much material flows into non-recyclable applications, lost to the circular economy. Therefore, there is ample “space” for other highly optimised PET bottles. In the long term, an average rPET content of up to 90% should be achievable if the material can be kept within the bottle cycle. This is also demonstrated by another study published last year by GVM on behalf of Coca-Cola. PETplanet: You yourself point out in your study that the system optimised by the Schwarz Group with 100% rPET cannot represent the entire industry. How does a bottle with a 25% rPET content, as will be mandatory on average in the EU next year, compare? Kauertz: Primary material production is one of the key drivers of the life-cycle assessment of PET bottles. Therefore, all relevant factors such as weight reduction, the use of secondary materials, or the reuse of containers impact this stage of the lifecycle. Reducing the secondary material content from 100% to 25% introduces significant environmental burdens. PETplanet: How do you assess the market development regarding the availability of rPET for the bottling sector? Kauertz: We hear different statements on this matter. Actors who have focused on long-term partnerships and high integration levels across the entire value chain in their procurement strategy seem to have fewer issues with material sourcing than others. Fundamentally, we observe significant competition for secondary materials among various sectors. The textile industry, for instance, has substantial demand for rPET and can offer higher prices. From a LCA perspective, we always advocate that the material should go where it has the highest probability of being recycled again."},{"@ID":42 "LABELLING PETplanet Insider Vol. 25 No. 05/24 www.petpla.net 40 Global push against single-use plastics sparks legislative actions and developments in technologies Adhesive technology spearheads sustainable labelling based on an article by Elizabeth Staab, Global Packaging Sustainability Manager, H.B. Fuller There is growing demand by consumers around the world to limit the proliferation of single-use plastics. Governments are responding with legislation, regulations, and taxes designed to drive change. Globally, the UN is negotiating an end to plastic pollution. In the United States, extended producer responsibility (EPR) legislation is being introduced in various states and the U.S. Plastics Pact brings together organisations and businesses with a vision for plastics circularity. They aim to ensure all plastic packaging will be 100% reusable, recyclable or compostable by 2025. In this context, new adhesive developments offering promise for a more circular economy and reduced environmental impact. Although the goals outlined in the New Plastic Economy are challenging to achieve in a short time frame, producers and brands are seeking packaging designs that are recyclable and avoid single-use plastics. Companies are keenly aware of the impact of perceived environmentally friendly packaging on consumer’s buying decisions, and they are evaluating the impact of their packaging and making design changes. To make a shift towards a circular economic model, recyclability, recycling and use of recycled material are paramount. However, the Recycling Partnership finds that only 21% of U.S. residential recyclables are recycled. The PET recycling rate in the U.S. is higher, at 29% in 2022. These are still comparatively low recycling rates. Globally, PET is the most recycled rigid plastic. Bottle-to-bottle recycling effectively recycled PET bottles into new PET bottles, which can help reduce the use of fossil-based materials and CO2 emissions. The importance of label removal in recycling The cleaning of PET bottles is an essential step of the PET recycling process to remove any remaining liquids, labels, adhesives, or other impurities. An easy and effective label removal, thanks to wash-off adhesive, is essential to a state-of-theart recycling process. Adhesives for wrap-around and full surface labels, that wash-off easily in the initial step of the recycling process, contribute to the overall process and improve the quality of rPET. The Association of Plastic Recyclers (APR) and the Sustainable Packaging Coalition (SPC) collaborate with their members, which include H.B. Fuller, to understand shifting legislation and needs that affect the U.S. packaging industry. Efforts include continued educational outreach and creating clear guidelines, such as APR’s Design Guide, which ensures products are truly recycling compatible. How2Recycle labels on packagLABELLING"},{"@ID":19 "25 YEARS ANNIVERSARY 17 PETplanet Insider Vol. 25 No. 05/24 www.petpla.net 25 YEARS ANNIVERSARY PET recycling infrastructure in Europe - current capacity The PET recycling process starts with the arrival of the material (i.e. PET bales) to the recycling facility, where it is shredded and washed, producing flakes. Flakes can be either directly commercialised by recyclers (for applications such as packaging) or be sent to extrusion into pellets. The first point of the PET recycling value chain where it is possible to measure how much PET can be recycled is the material washing step. The installed washing capacity in the EU27+3 region was around 3 million tonnes in 2022, which accounted for almost 25% of the installed plastics recycling capacity for all polymers. This was an addition of 200,000 t to PET washing capacity in relation to 2020. The first figure below shows the installed washing capacity per country group, with Germany accounting with the largest share of about 630,000 t, followed by Spain & Portugal with almost 500,000 t capacity. Italy (307,000 t), UK & Ireland (292,000 t) and France (286,000 t) are the next countries with the largest capacities. Together, these seven countries account for approximately 67% of rPET flake production capacity. Spain, Germany and Romania witnessed the highest capacity growth between 2020 and 2022. PET polymer recycling capacity for flakes production (washing capacity) has the highest average recycling capacity per plant across all polymers, averaging over 20,000 t per facility, with Benelux, Germany and France having a higher average plant size in terms of geographies. The second figure shows that the extrusion capacity for rPET pellet production from flakes was estimated at around 1.4 million tonnes in 2022, representing a two-fold increase since 2020. This capacity, which absorbs the majority of flakes from the market to extrude into material suitable for food contact applications (mainly food grade pellets), has developed with the demand for rPET materials to comply with mandated targets and voluntary commitments from brand owners and has driven significant investment in this sector of the value chain. Germany accounts for the largest share at over 270,000 t, followed by France (220,000 t) and Benelux (200,000 t). Of the 140 companies reprocessing PET waste into flakes in EU27+3 in 2022, about 40 are integrated with downstream extrusion capacity to produce rPET pellets, i.e. the plant has both washing and extrusion processes. Additionally, over 20 companies only produce pellets from flakes procured from external sources. Thus, about 60% of the rPET extrusion capacity in the region is integrated upstream with flake production, having both washing and extrusion lines within the same facilities. As seen in figures below, the geographical areas of Benelux and France have the highest installed extrusion capacity in relation to the washing capacity, indicating sufficient domestic capacity to convert flakes into pellets locally. Domestic recycling capacity has developed strongly since 2020, with overall available volumes matching demand as set by mandatory recycled content targets for 2025. However, due to the disparity in collection systems across the member states, some capacity was not able to reach its potential due to a lack of available quality feedstocks. Any subsequent gap in supply was met by imports during 2022, with significant increases in rPET flake and pellet imports throughout the year. This displaced domestic supply as the market balance shifted out of typical seasonal patterns, whereby demand spiked early in the year when due to the low season for beverage consumption bale availability was equally low. www.unesda.eu www.icis.com"},{"@ID":56 "25 YEARS ANNIVERSARY 23 PETplanet Insider Vol. 25 No. 05/24 www.petpla.net 25 YEARS ANNIVERSARY The quest to quench by Chris DeArmitt Changing to so-called alternative materials means more materials use, more waste, more GHG, fossil fuel use and more litter. Does that sound like a great plan? At the end of life, PET is one of the most collected and recycled material, which further bolters its environmental credentials. Recycling reduces the impact a further 70-80% compared to new PET. Designers like PET because it is possible to make containers with captivating shapes and colours. Crucially, the transparency of PET allows the customer to see the product they are about to buy and instantly know the amount left as well. - something not possible with opaque materials. The use of a cap means that it can be resealed to prevent waste. One average, packaging has 3% of the impact compared to the food it protects which accounts for the other 97% of impact, so PETs ability to ensure that the drink is preserved and then fully consumed is a big deal. What about safety. As you can imagine, food contact materials are highly regulated and PET has been found to be safe through decades of testing. Having reviewed that data, it is probably fair to say that PET is the saftest of all the options. Claims to the contrary are desperate attempts to get us to spend our money on more expensive products with higher environmental impact like metal or glass. Conclusions As a scientist whose job it is to recommend the perfect material for each application, I would have had to invent PET if it didn’t already exist - it’s that good of a fit! It is the safest, most environmentally responsible and affordable choice. I’ll drink to that. www.phantomplastics.com/why-is-plastic-bad-for-theenvironment-get-the-facts-in-5-minutes Thirst – it can drive you to drink!. In fact, when it comes to survival, we need hydration more than we need food. When at home, we can take satisfy our thirst with tap water, but when we’re on the go, we need other options, but which one is right for you? As an independent materials scientist, I have spent thousands of hours unpaid to read the science around plastic materials and the environment to share the facts for free via my book, podcasts, radio, TV and articles like this one. So, what are the facts around PET? How does it compare to other materials? Is it the perfect choice for drink containers or are there better alternatives? My job as a scientist is to find the ideal material for each application, so let’s take a look. PET is a thermoplastic, meaning that it is easily formed into complex shapes by melting it. It is classified as an “engineering plastic”, meaning that the mechanical properties are extremely good, being stiff, strong, impermeable and so on. Although most people associate PET with the iconic drink container application, many people do not realise that there are other applications including automotive parts, aerospace, toys, medical devices and so on. How is it that such a high performance material came to be used for drink containers? Normally, such materials would be too expensive, but manufacturing efficiencies lowered the price of PET dramatically. Another factor is that the mechanical and barrier properties are so good that the amount of PET needed to make a bottle is extremely low compared to aluminium, steel, glass or other plastics like PE or PP. Over time, the amount of PET used to make a bottle has decreased by over 50% and further reductions are on the way. That lowers price and environmental impact. While we’re on the topic of environmental impact, how does PET stack up? There are multiple life cycle studies comparing different materials used to make drink containers and PET consistently has the lowest impact, especially for carbonated drinks. Any marketing campaign telling you otherwise is soundly refuted by peer-reviewed science."},{"@ID":9 "7 NEWS PETplanet Insider Vol. 25 No. 05/24 Bericap invests in a new production facility in Kunshan Bericap is investing in a new plant in Kunshan that reflects the latest standards and increases production capacity by 50% to help it more effectively cater to customer demand. This marks the next milestone for the leading global manufacturer of plastic and aluminium closures in its international growth strategy – enabling a local presence and ensuring short distances for both customer support and product logistics. Bericap’s customers in China include major edible oil, soy sauce, and vinegar manufacturers, as well as customers in the beverage and automotive sectors. The contract with representatives of the Kunshan Development Zone was recently signed, paving the way for the construction work on the new building in Kunshan to start this year. Bericap is planning to start production at the new facility in 2027. The location of Kunshan, close to Shanghai, remains a strategic fit for Bericap, particularly since the Kunshan Development Zone aims to attract Top 500 companies worldwide as it evolves into an important business cluster focusing on the development, manufacturing, sales and display of high-end food products. www.bericap.com South Korean regulation requires label-free bottled water as of Jan 1, 2026 The South Korean Ministry of Environment (MOE) has announced an amendment to the Regulation on Standards, Specifications, and Labelling Standards for Drinking Water and Similar Products. Under this amendment, individual domestic products of drinking water and similar items will be required to adopt a label-free QR code system. This approach aims to streamline product information while contributing to the reduction of label waste and to promote container recycling. Scheduled to take effect on January 1, 2026, manufacturers are encouraged to transition to the new labelling system well in advance to ensure a seamless implementation process. By embracing label-free QR codes, companies are not only expected to contribute to environmental conservation efforts but also to enhance consumer access to essential product details. www.eng.me.go.kr/eng/web/main.do We will contribute to the realization of a sustainable low-carbon society by leveraging aseptic technologies. www A BETTER FUTURE Through Advanced Filling Systems Aseptic Systems Your Solutions Provider"},{"@ID":24 "25 YEARS ANNIVERSARY 22 PETplanet Insider Vol. 25 No. 05/24 www.petpla.net 25 YEARS ANNIVERSARY Chris DeArmitt: At the moment we are making choices and policies proven to massively increase materials use, waste, GHG, fossil fuel use and total impact and all because we have been intentionally misled. We need to stop trusting NGOs who make bold, false claims without real evidence. They tell us that plastics don’t degrade, which is false. They say there will be more plastic than fish in the ocean but that has been debunked at least three times. They say that we eat a credit card of plastic a week when the best scientific study found that is wrong and it would take over 20,000 years to do that. The main problem is not the attack on plastics because it is not affecting plastic sales which grow around 3-4% a year, just like metal, glass, paper, concrete and other common materials. The problem is that the attacks on plastic distract us from actually helping the environment. Plastics make up under 1% of materials we use and are the least harmful choice in over 90% of applications according to life cycle studies. As long as we obsess over the 1% and ignore the 99% of materials that increase harm 90% of the time, we will not only fail to make progress, but we actively increase harm by taxing and banning our greenest choice. PETplanet: What does it do to you when, for example, multinational brands suddenly engage in supposed greenwashing, jump on the bandwagon of plastic bashing, use it to boost their marketing, even change their packaging and thus manipulate people’s opinions? Chris DeArmitt: Companies and politicians follow the money. We have allowed lies to spread and now customers demand paper over plastic even though 40 life cycle studies say that increases harm. So, we find companies hiding their plastic bottle inside a paper outer layer. We find politicians moving to paper to gain votes. This is the reason that we must not stand by and watch the lies spread. Some of our larger trade associations are funded to take on the fight but been incredibly ineffective to the point that their members express their frustration to me. PETplanet: Last but not least: How do you personally live the circular plastic economy in your everyday life? Chris DeArmitt: I am in a fortunate position to be able to make the right choices because I have the facts at hand. The most impact comes from flying less, driving less, eating less meat and reducing food waste. The problem is that people don’t want to make any such sacrifices, so rather than doing what would help, they waive a cotton bag over their head to look virtuous. Real virtue comes from checking the facts and doing what is right, not pretending just to look good. What I do goes against current public opinion and is not popular, but I do it anyway. I hope that others join me. PETplanet: Thank you, Chris!"},{"@ID":13 "25 YEARS ANNIVERSARY 11 PETplanet Insider Vol. 25 No. 05/24 www.petpla.net 1971: The petaloid base The Continental Can Company was granted a patent for the petaloid base in 1971, which made the base cup of the first PET bottles superfluous in the early 1990s. 1991: Introduction of recycled content Coca-Cola became the first to introduce bottles with recycled content, incorporating 25% rPET into new bottles, marking a significant milestone in sustainability. Hoechst Celanese Fibers and Film Group, a division of Hoechst Celanese Corp., developed the process. 2022: Bottled in PET – but let it sparkle Sipa presented the first PET bottle for sparkling wine. The product is capable of running on existing filling lines. As the bottle neck looks just like the glass version, it accepts the classical mushroomshaped cork with its metal cage. The base also looks the same as the original. The design provides a top-load resistance of 3500N. 1973: Invention of biaxially oriented PET bottle Nathaniel Wyeth obtained a patent for the biaxially oriented PET bottle (US Patent 3733309), designed for “bottling liquids under pressure, such as beer, carbonated beverages, or aerosols”. Wyeth’s invention encompassed a method and apparatus for producing a hollow, biaxially oriented, thermoplastic article, involving a two-stage process comprising the compression moulding of a preform followed by the blowing of the reheated and stretched material into a bottle. 1999: PETplanet Insider With the launch of PETplanet Insider, the PET industry finally got its own trade magazine. From the very beginning, the magazine from a family-run publishing house has provided the industry worldwide with news, on-site reports and exclusive insights. 2024: Status quo Promising growth prospects continue to be attributed to developments aimed at reducing the carbon footprint. These include further lightweighting efforts, increasing the proportion of recycled material in bottles and switching from energyintensive hot filling processes to aseptic filling. Whatever the PET market delivers - read all about it in PETplanet Insider! 1975: Coca-Cola’s plastic bottle debut Coca-Cola`s “Easy-Goer” plastic bottle was unveiled at the St Regis Hotel in New York and praised for its lightweight, durability and environmental advantages over glass bottles. Made from acrylonitrile plastic, the FDA banned the bottle in 1977 due to health concerns. 1986: Compression-moulded caps CSI acquired H-C Industries, Inc., a company that had pioneered a patented compression molding process for manufacturing plastic closures. The H-C Wing-Lok closure emerged as the beverage industry’s premier mechanical tamper-evident closure. MAGAZ I NE FOR BOT T L E R S AND BOT T L E - MAK E R S PAGE 38 PAGE 8 PREVIEW BRAU 99, Trade Fair for the Brewery and Beverage Industry BOTTLE TO BOTTLE everybody wants to do it, PKR in Germany are there! PAGE 16 ROLF KULLEBORN produces 70 million preforms per annum ISSUE NUMBER ONE It´s high time that the industry had its own magazine - covering everything from PET pellets to the filled PET bottle 1/99 ISSN: 1438-9452 PET Source: Imarc Group (www.imarcgroup.com) Outlook of global PET bottles from 2024-2032 Breakup of global PET bottles market volume (for 2023)"},{"@ID":22 "25 YEARS ANNIVERSARY 20 PETplanet Insider Vol. 25 No. 05/24 www.petpla.net 25 YEARS ANNIVERSARY PROCESS PILOT+ Achieve Your Sustainability Goals and Produce Your Best Product TM Agr’s Process Pilot system provides personalized process control response to each unique bottle GHVLJQ EORZPROGHU ȴQJHUSULQW Ȃ VDIHO\\ DQG TXLFNO\\ 1R ELJ GDWD MXVW UHOLDEOH GDWD ZZZ DJULQWO FRP PETplanet: In many countries, there is an ongoing debate about the viability of a mandatory reusable quota, such as the one preferred by the EU Commission. Under what circumstances is PET reusable packaging environmentally sensible? Kauertz: Reusable packaging is always sensible where we have established supplier and customer relationships that reliably function, and where the structures for these systems are therefore sensibly established. The greatest challenges in the way reusable systems operate in the beverage sector today are the individualisation of bottles and the separation of containers during sale and return. All of this leads to high sorting efforts and additional exchange trips, which can quickly counteract the benefits of resource-efficient material handling. A creative approach to the advantages and possibilities of PET bottles can offer advantages over glass reusable systems. I am confident that we will see meaningful PET reusable concepts in the future. However, this is also the weak point of a mandatory reusable quota. Who guarantees that sensibly optimised systems will enter the market? The focus should therefore be more on evaluating what makes reusable and single-use options life cycle-optimised and then addressing these factors through regulation. PETplanet: Finally, a word on other packaging materials. Glass, cardboard, cans, PET – ultimately, does every advantage and disadvantage hinge on the transportation route? Kauertz: Ideally, transportation routes are always short, and transportation vehicles are consistently fully utilised. In general, the heavier the packaging material, the more significant the impact of transportation. However, life cycle assessments are highly complex models. Relying solely on one factor in the system, such as transportation or recyclability, typically oversimplifies the issue and can, in the worst case scenario, lead to incorrect conclusions. PETplanet: Thank you very much, Mr Kauertz! www.ifeu.de"},{"@ID":36 "EDITOUR PETplanet Insider Vol. 25 No. 05/24 www.petpla.net 34 From the preform to the fi nished Safa brand Drinking water from the holy city of Mecca by Kay Barton 25 kilometres west of the central Islamic pilgrimage site of Mecca is the Makkah Water Co. bottling plant, which processes one of the best-known Saudi water brands “Safa” on state-of-the-art Krones equipment and fills it in PET. The production of preforms and closures is also vertically integrated here. The company is headed by General Manager Sheikh Ali Saad Bin Zomah and is part of the Bin Zomah Group, which amongst other activities also operates a second bottling plant with the “Mozn” water brand near the city of Gizan, not far from the border with Yemen. We visited Makkah Water and met Mr Bapu Kumaresh, the master of the injection moulding division, who showed us around his plant. EDITOUR Makkah Water was founded in 1975 with the aim of supplying the population and pilgrims in the region around Mecca with clean drinking water. Where previously PVC bottles were used, PET bottles were used from 1998 onwards. Four Sidel lines for PET filling were commissioned this year, while Husky machines to produce preforms were put into operation in the same year. First, we visited the separate injection moulding area on the large company premises. Bapu Kumaresh’s office and meeting room is virtually right next to the plastics machines for producing preforms and closures. Mr Kumaresh has been on board the company for almost ten years as the Operations Manager responsible for the injection moulding section and can now look back on a career of almost thirty years in the field of plastics processing. He holds a Bachelor of Science in Chemistry and Plastics Processing Technology and worked for many years at plastics processor Savola, among others. “For the production of 9.1 g preforms for 330 ml bottles, we use two 144-cavity Husky HyPET HPP4 systems, as well as two Xform 350s from Sipa with 128 and 96 cavities respectively,” explained Mr Kumaresh. “We also have three Huayan models in operation, two with 96 cavities each for 14.4 g preforms for our 600 ml bottles and one for 81 g preforms for our 5 l bottles. For our 29/25 caps we use Netstal systems, two Elion with 96 cavities each, two Synergy with 72 each and two more Synergy machines with 96 cavities each.” Translated into output, this means 6 million 9.1 g, 1.6 million 14.4 g and 140,000 81 g preforms and closures daily. “We also produce 7.9 g preforms, for 200 ml, in our sister company in Gizan. There are two Netstal PETline and two Elion lines at the Al Janoub plant.” The bottler processes municipal, desalinated seawater for Safa. In the water treatment section on the company premises, one of the largest water treatment systems from Krones to date was designed and built, with a water throughput of 3 x 110 m3/h, which was put into operation as part of a major modernisation phase 2022. The treatment process involves ultrafiltration, reverse osmosis and electro-de-ionisation. Minerals are then added and the water is ozonised. The water treated in this way is finally packaged on a total of six Krones Ergobloc L bottling Bapu Kumaresh (right) with Kay Barton in front of the Sipa Xform F.l.t.r.: Mohammed Elnassag, Production Section Head, Bapu Kumaresh and Bernardino Jr. Enriquez Enrix, Filling Dept. Maintenance Head The injection moulding team with Bapu Kumaresh showing the location of the plant on the Road Show map."},{"@ID":51 "49 ON SITE PETplanet Insider Vol. 25 No. 0/24 www.petpla.net PT Amandina Bumi Nusantara: Recycled PET for Coca-Cola’s first 100% rPET bottles in Indonesia In June 2023, Coca-Cola Indonesia, in partnership with Coca-Cola Europacific Partners Indonesia (CCEP Indonesia), launched the first bottles made from 100% rPET (excluding bottle caps and labels) for its most popular soft drink brands. The recycled PET is supplied by one of Indonesia’s recycling pioneers, Amandina Bumi Nusantara. The company operates a plastics recycling plant on the outskirts of Jakarta with two Starlinger Recostar PET HC iV+ bottle-to-bottle recycling systems and processes 3,000 t of collected PET bottles every month. Two types of clear bottle-grade rPET pellets are produced, one for carbonated beverages and one for spring water. In addition, the company supplies hot-washed flakes in clear and light-blue colours. The installation of the two PET recycling systems was carried out by local technicians from Starlinger’s Indonesian branch office PT Starlinger SEA in autumn 2022. The Starlinger team in the branch office in Surabaya handles machine installations, service and maintenance works as well as spare part orders for Starlinger customers in the South East Asian region and provides immediate support if needed. Responsible sourcing Amandina assists companies in achieving their sustainability targets by providing competitive recycled PET products produced from responsibly sourced input material. For the collection of post-consumer PET bottles, Amandina Bumi Nusantara collaborates with Mahija Parahita Nusantara Foundation, a non-profit organisation founded by CCEP Indonesia and Dynapack Asia. As in many other Asian countries, over 90% of plastic waste collection activities in Indonesia are carried out by waste pickers in the informal sector – called “recycling heroes” by Amandina and Mahija. The remaining percentage is managed through formalised systems such as waste banks and other organised collection efforts. CCEP Indonesia aims to make 100% of its packaging recyclable and to ensure that at least 50% of the plastic bottles are made of rPET by 2025. The company’s targets for 2030 are to collect 100% of their plastic bottles to enter the recycling stream, and to eliminate virgin plastic in their plastic bottles. Certified food-grade quality PT Amandina Bumi Nusantara is the first PET recycling company that has obtained the SNI Marking Product Certificate (SPPT) from the National Standardization Agency (BSN) for implementing the Indonesian National Standard (SNI) 8424:2017. This standard, which was established by the Indonesian Ministry of Industry, protects consumer interests and ensures that the quality of products made of recycled PET resin is maintained. It includes strict qualification stages, high-standard sampling, as well as testing and product assessment procedures to ensure that the PET recycling process meets the desired safety, sustainability and performance criteria. Since its launch in 2017, it has become an important reference in the PET recycling sector. Furthermore, Amandina Bumi Nusantara has obtained standards from the National Agency of Drug and Food Control (BPOM), Halal, and FSSC 22000, which have approved the use of rPET in food and beverage packaging. www.amandinabuminusantara.com www.starlinger.com ONsite"},{"@ID":34 "EDITOUR PETplanet Insider Vol. 25 No. 05/24 www.petpla.net 32 Preforms and now also closures from Riyadh Ready for the future by Kay Barton Future Plus in Riyadh, Saudi Arabia, is the sister company of the Abu Dhabi, UAE-based processor Future Plast Industries LLC. Both are part of the Saudi Printing & Packaging Company (SPPC) which is a prominent provider of packaging and printing solutions in the Middle East. The company is listed on the Saudi Arabian Stock Exchange, employs 1,450 people, and operates 14 manufacturing facilities in Saudi Arabia and the United Arab Emirates. SPPC’s portfolio comprises five main categories: preforms and closures for the beverage industry, flexible packaging and labels, films and pouches, cups, containers, cling film and food packaging solutions, and commercial printing. Its customers include well-known brands such as Almarai, Abar Water, Pure Beverages, Pepsi, Lays, Burger King and McDonald’s amongst many more. EDITOUR Meeting with Future Plus Industries LLC (part of SPPC Group) February 19, 2024 We met: Mr Murali Krishna, General Manager Future Plus & Future Plast Mr Shihab Izzat, Sales Head KSA The company’s sustainability strategy involves creating packaging solutions that utilise renewable, recyclable, recycled, and biodegradable materials. PETplanet was able to meet Mr Murali Krishna, General Manager of Future Plus and Future Plast, in Riyadh. First a look back. Future Plast started its business in 2009 with a plant in Sharjah, UAE, later relocated to its current headquarters in Abu Dhabi and, with the Future Plus plant, expanded its radius of action beyond the country’s borders into neighbouring Saudi Arabia from 2012 in order to better exploit the potential there and respond to the growing needs of this increasingly open and developing country. GM Murali Krishna, is a chemistry graduate with a postgraduate diploma in Plastics Processing Technology from India’s Central Institute of Petrochemicals Engineering. After eight years of professional experience in India in various roles, his career took him to Saudi Arabia, Germany and China with Zamil Plastics and Essel Propack from 1994 to 2003, before moving to the UAE in 2003. He worked at Intergulf, Iffco Group as Business Development Manager until 2010 and then moved to the Enpi Group, where he was General Manager of the preforms and closures business. He has worked in the plastics and packaging industry for 36 years and has led many projects, including weight reduction of preforms and more exotic projects such as processing PLA material for water bottles, a true pioneering project launched in 2020. He currently heads both Future Plus and Future Plast as General Manager. From Riyadh city centre, it takes around 45 minutes, traffic permitting, to reach the “Second Industrial Area”, where the Future Plus plant is located. The plant, which employs 25 people and covers an area of 5,000m2, produces 30/25 high neck and 29/25 short neck preforms on three Husky HyPET 400 systems, each with 96 cavities. Around 900 million units per year, so far exclusively for bottlers of still water, are packaged in recyclable mesh boxes for the local market and an export section in one way jumbo gaylord boxes. “Another five HyPET systems with 96 cavities each are currently running in Abu Dhabi,” explained Mr Krishna. The Abu Dhabi facility is fully approved by Pepsi, Coca-Cola and Nestlé. A new addition to the Saudi machine park is an Engel E-Motion 380 injection moulding machine for closures, which was ordered in 2023 F.r.t.l.: Murali Krishna, Gregor Degasperi (Business Development at Z-Moulds), Kay Barton, PETplanet and Shihab Izzat, Sales Head KSA Freshly produced 29/25 closures in a trendy purple colour Closure inspection with equipment from IMD Vista"},{"@ID":6 "PETcontents 4 PETplanet Insider Vol. 25 No. 05/24 www.petpla.net 05/2024 25 YEARS ANNIVERSARY 8 How it all began 25 years ago 10 The PET bottle’s journey 12 The material of choice for sustainable packaging 14 Advanced recycling on the rise - Advanced recycling technologies to complement mechanical recycling 17 PET recycling infrastructure in Europe - current capacity 18 “Key factors: preform weights and the use of recycled materials” - Criteria on life cycle assessments of PET bottles 21 The crusade of truth - Targeting plastic bashing 23 The quest to quench 24 Raising awareness and engaging with consumers - Interview with Philipp Lehner, CEO Alpla Group, on his social media activities 26 PET production and demand 27 EU Council and EU Parliament agree provisional deal for more sustainable packaging & less waste MARKET SURVEY 29 Suppliers of preforms & preform inspection systems EDITOUR 32 Ready for the future - Preforms and now also closures from Riyadh 34 Drinking water from the holy city of Mecca - From the preform to the finished Safa brand BOTTLING / FILLING 36 Contribution to prosperity in Mexico - Sipa and Gepp mark 25 years of successful collaboration 38 From regional to national - Kazakh mineral water bottler on expansion course with Ukrainian technology LABELLING 39 Shrink sleeves for light sensitive products 40 Adhesive technology spearheads sustainable labelling - Global push against single-use plastics sparks legislative actions and developments in technologies AUXILIARY EQUIPMENT 43 Air-powered plastic drying - RDX PET Rocket uses on-site compressed air to replace desiccants EVENT REVIEW 44 Microwave assisted depolymerisation recycling technology 46 All-electric capping systems now on the market EVENT PREVIEW 48 Plastics Recycling Show Europe - PET Recycling Conference Sessions & Awards finalists confirmed BUYER’S GUIDE 52 Get listed! INSIDE TRACK 3 Editorial 4 Contents 6 News 42 Products 49 On site 50 PET bottles for home + personal care 51 Patents 58 Outer Planet Page 34 Page 38 Page 42 EDITOUR LABELLING 25 YEARS ANNIVERSARY"},{"@ID":33 "MARKET SURVEY 31 PETplanet Insider Vol. 25 No. 05/24 www.petpla.net Pressco Technology Inc Sacmi Imola 29200 Aurora Road, Cleveland, OH, USA +1 440 498 2600 www.pressco.com Mr Tom Murphy VP, Sales & Customer Service +1 440 498 2600 [email protected] Via Selice Provinciale 17/A, 40026 Imola, Italy +39 0542607 111 www.sacmi.com Mr Stefano Severi Sales Specialst Manager +39 3356594236 [email protected] LayerWatcher ColorWatcher Lab Intellispec PVS10L PVS002C PVS156A PVS003 Up to 144 objects/hour Manual feeding, handling time: up to 5s / object measurement time: up to 10ms/object Up to 2,500/min up to 72,000 pph up to 1,100 pph up to 1,200 pph up to 72,000 pph Presence of barrier layers, thickness of barrier layers, position of barrier layers, structure of barrier layers, position of barrier leading edge, position of barrier trailing edge Colour and colour deviations Unmelts, heat splay, burn marks, water spots, bent/warped preforms, contamination, carbon streaks, bubbles/blisters, colour, crystallinity & clarity/hazing, gate length Yes Yes: Includes measurement of the wall thickness in 3 or more points. DUS (diameter under support ledge); TL (total length); BD (body diameter 1, 2, 3); OV (body ovality); WT (wall thickness), PERP (perpendicularity); GL (gate length); CONC (concentricity) Yes Contamination, fl ash, dimensions, pulled threads Yes Yes: Additionally to all the most common detected defects, the machine can: measure the thread in several points as defi ned by the operator with a precision down to 0.03mm and inspect fl ashes in the seaming line. Ø T (thread diameter); Ø E2 (lock ring diameter), Ø I (inner bore diameter); Ø E1 (diameter over pilfer proof); ØA (pilfer proof diameter); Ø Z (support ledge diameter); D (pilfer proof height); X (height under support ledge); B (diameter under pilfer proof) Yes Contamination, ovality and diameter, dirt & debris in the preform, nicks, gouges, short shots & dips Yes, included diameter measurements Yes, included diameter measurements Yes, included diameter measurements Bent/warped preforms, dirt/debris, cracked gates Yes Yes Yes Yes Colour and intensity deviations (ΔL*, Δa*, Δb*), presence of UV blocker, presence of barrier, presence of IR absorber (reheater) Colour variations, incorrect colour Yes, colour inspection applies a colour camera and covers the whole preform body Yes, colour inspection applies a colour camera and covers the whole preform body Yes, colour inspection applies a colour camera and covers the whole preform body Yes, colour inspection applies a colour camera and covers the whole preform body Cavity related statistics, powerful cavity reading without need for learning for most fonts, possibillity to share information based on cavity number with IMM No Yes, using AI algorithms Yes, using AI algorithms Yes, using AI algorithms Yes, using AI algorithms Visualisation of individual barrier layers in 3D images in less than 30s., inspection of up to 100,000 measuring points, layer measurement with OptoSonix scan technology, cavity-related information High precision colour inspection with spectrometer, for translucent, transparent and opaque preforms, analysis of even small colour nuances, no change parts required Additional inspection modules include: neck support ring, inner barrel Patented grid inspection, patented polarised light inspection with AI algorithms. In addition: weighing device to weigh all preforms In addition: measurement of the temperature of the preform body Patented grid inspection, patented polarised light inspection with AI algorithms Yes Yes Yes No No No No Yes No No No No No Yes No No No No No Yes Yes on customer-supplied starwheel Yes Yes No Yes Yes, sampling Mounting and installation inside major OEM blowmoulding machines; options available for stand-alone and inline systems Yes Yes Yes Yes Yes, rollout of the complete thread area No, but manual input No Yes Yes Yes Patented TOP camera for cavity recognition Non-destructive Non-destructive Non-destructive Non destructive Yes, all industry standards supported, ready for Industry 4.0 applications: XLS formats, SQL and several others, connectable to IntraVisualizer, ERP & QMS Yes, all industry standards supported, ready for Industry 4.0 applications: XLS formats, SQL and several others, connectable to IntraVisualizer, ERP & QMS Yes Yes, supported protocols: HTTP, OPC/ UA, Modbus"},{"@ID":53 "PATENTS PETpatents www.verpackungspatente.de PETplanet Insider Vol. 25 No. 05/24 www.petpla.net 51 A built-in bottle handle International Patent No. WO 2022 / 229119 A1 Applicant: Dong-A Precision Co. Ltd., Gyeonggi-do (KR) Registration date: 23.11.2022 This application describes the design and process involved in producing a PET bottle, with a separately manufactured handle built into the container. A flexible bottle International Patent No. WO 2023 / 220675 A1 Applicant: Noah Hammersten, Studio City (US) Registration date: 11.5.2023 A bottle with concertina or helixshaped side walls filled with concentrate or powder. Volume is only increased during use and when liquid is added. Several compressed bottles can be either stored or transported to save space. A sturdy plastic bottle International Patent No. WO 2022 / 132141 A1 Applicant: Amcor Rigid Packaging USA LLC., Ann Arbor (US) Registration date: 16.12.2020 Described here is a thin-walled plastic bottle for hot-filling with associated compensation surfaces and base mouldings. The bottle is resilient enough to withstand increases in stacking pressure. Bottom shape moulding International Patent No. WO 2022 / 125098 A1 Applicant: Amcor Rigid Packaging USA LLC., Ann Arbor (US) Registration date: 10.12.2020 This application describes the special base moulding of a lightweight PET bottle. A plastic bottle European Patent No. EP 4253265 A1 Applicant: Suntory Holdings Ltd., Osaka (JP) Registration date: 25.2.2022 A specially moulded plastic bottle designed to absorb increased pressure both longitudinally and transversally without being damaged in any way. PET bottle European Patent No. EP 3514075 B1 Applicant: Suntory Holdings Ltd., Osaka (JP) Registration date: 16.6.2016 The shape and design of the surface of a PET carbonated drinks bottle will be granted a European patent by the end of 2023. The integrity of its surface structure is maintained even when subject to increased internal pressure."},{"@ID":12 "25 YEARS ANNIVERSARY 10 PETplanet Insider Vol. 25 No. 05/24 www.petpla.net 25 YEARS ANNIVERSARY 1968: PVC bottles as trailblazers In response to a request from Air France, Vittel developed a plastic bottle for still water made from PVC. These early plastic bottles paved the way for the acceptance of other plastics and aligned with the societal trend toward increased mobility. 2011: CSD in 100% rPET PepsiCo Beverages Canada announced the introduction of the 7UP EcoGreen bottle, North America’s first soft drink bottle made from 100% rPET. “Creating a bottle made from 100% recycled plastic for soft drinks is more challenging than creating a bottle for non-carbonated beverages because of the stress on materials from carbonation pressure,” said the press release. 1971: The stretch blow moulding process Otto Rosenkranz of Heidenreich & Harbeck in Hamburg pioneered the development of a stretch blow moulding machine using heat to expand thermoelastic PVC, leading to the inception of the “Corpoplast” process. By 1971, this method had transitioned to PET, and Heidenreich & Harbeck had been acquired by Gildemeister AG in 1972. This, in turn, led to the sale of the BA 3 rotary machine to Dupont and PepsiCo in 1973. 1970: HDPE cap for CSD The Swiss designer Albert Obrist developed the first plastic top for CSD drinks bottles with the injection-moulded one-piece HDPE cap. It was originally intended for use with returnable glass bottles. 2021: 100% plant-based PET bottle Coca-Cola launched a 100% plant-based PET bottle, eliminating virgin oil-based PET from production, in collaboration with biotechnology companies. 2009: Bottles with plant-based material Coca-Cola unveiled the PlantBottle, containing 30% plantbased material, intending to set a new standard for environmentally friendly packaging. The PET bottle’s journey On the journey of development leading to today’s PET bottle, numerous brilliant minds and breakthroughs played pivotal roles, without which the PET bottle might not have achieved its global reach. There are too many to comprehensively list, but we’ve picked out a few highlights for you. 1977/1978: Rise of PET bottles in the USA Pepsi introduced the first 64 oz PET bottle for CSD, followed by Coca-Cola’s 2l PET bottle in 1978. These first PET bottles had a base cup glued under the round bottle base so they could stand up on their own. 1977 The search for the perfect preform mould Representatives of the Continental Can Company, a subcontractor to both Coke and Pepsi, set out to find a mould maker who was able to design and produce a mould for preforms of the desired quality. And although the owner of the Swiss company in Uznach they visited, Otto Hofstetter, didn’t speak a word of English, the Continental Can Company decided in his favour. The order was for twelve moulds with 16 cavities each, which ran on injection-moulding machines of the German manufacturer “Windsor”. Two cycles per minute were being processed. Photo courtesy: Otto Hofstetter, Coca-Cola, PepsiCo, Nestlé, Sipa, CSI"},{"@ID":17 "25 YEARS ANNIVERSARY 15 PETplanet Insider Vol. 25 No. 05/24 www.petpla.net Solvolysis The solvent-based solvolysis describes a chemical process based on depolymerisation which can be achieved with different solvents. This process breaks down polymers (mainly PET) into their building units (e.g. monomers, dimers, oligomers). After breakdown, the building units need to be cleaned from the other plastic components (e.g. additives, pigments, fillers, non-targeted polymers). After cleaning, the component parts are polymerised to synthesise new polymers. With only 24 companies involved, fewer solvolysis technology providers are on the market compared to pyrolysis which likewise offers smaller capacities, typically between 550-8,750 t/a. Of the identified solvolysis technology providers a majority are located in Europe (14 providers) followed by North America (seven), Japan (two), and China (one provider). In the case of nine companies, the majority of providers are mainly small enterprises. Large providers consist of seven companies, whilst five are medium scale and two are micro/start-up enterprises. Among the large enterprises are Aquafil (Arco, Trentino, Italy, Eastman Chemical Company (Kingsport, TN, USA), IFP Energies Nouvelles (IFPEN) (Rueil-Malmaison, France), International Business Machines Corporation (IBM) (Armonk, NY, USA), DuPont Teijin Films (Tokyo, Japan), and Dow (Midland, MI, USA). Dissolution Dissolution describes a solvent-based technology that is based on physical processes. Targeted polymers from mixed plastic wastes can be dissolved in a suitable solvent, leaving the chemical structure of the polymer intact. Dissolution is suitable for PET, but most suppliers primarily focus on PP/PE. However, where high PET content is desired, solutions for PET are available. Other plastic components (e.g. additives, pigments, fillers, non-targeted polymers) remain undissolved and can be cleaned from the dissolved target polymer. Afterwards an anti-solvent is added to initiate the precipitation of the target polymer. The polymer can be obtained directly, and in contrast to solvolysis, no polymerisation step is needed. Currently, the process is achieving a maximum capacity of 8,000 t/a; the majority of the nine identified technology providers is located in Europe (four providers), followed by North America (three), China (one), and the rest of the world (one provider). In the case of three of the companies, most are small enterprises followed by micro/start-up- (two companies), medium- (two companies), and a large (two companies) enterprise which is represented by Shuye Environmental Technology (Shantou, China). Enzymolysis An alternative path is represented by enzymolysis, a technology based on biochemical processes utilising different kinds of biocatalysts to depolymerise a polymer into its building units. Being in an early development phase, this technology is available only at lab-scale. Currently, only one enzymolysis technology provider was identified which is a small enterprise located in Europe. The process is suitable for PET. www.pti-usa.com • [email protected] Engineering Packaging from Concept to Commercialization®"},{"@ID":20 "25 YEARS ANNIVERSARY 18 PETplanet Insider Vol. 25 No. 05/24 www.petpla.net 25 YEARS ANNIVERSARY Criteria on life cycle assessments of PET bottles “Key factors: preform weights and the use of recycled materials” by Gabriele Kosmehl Benedikt Kauertz, Scientific Director of Industry & Products at the Ifeu - Institute for Energy and Environmental Research in Heidelberg, Germany, is an expert on environmental assessments of packaging and life cycle assessments of beverage packaging. In an interview with PETplanet, he delves into the crucial elements for a favourable evaluation of PET bottles, key factors for further optimisation, and the current challenges hindering the establishment of PET reusable systems. PETplanet: Mr Kauertz, you are engaged in the life cycle assessment (LCA) of packaging. What is your perspective on PET bottles? Kauertz: For over 15 years, I have been professionally involved in the environmental assessment of packaging and have conducted numerous studies on beverage containers during this time. Therefore, I primarily approach this subject from a technical standpoint. I am well acquainted with the advantages of packaging, as well as its drawbacks and the challenges involved in optimisation. Based on the findings of these studies, we observe that the selection of beverage packaging should primarily be influenced by the consumption scenario. When the requirements lean towards lightweight and high stability, and there exists a seamless possibility to support recycling loops or return the bottle for refill after use, PET bottles emerge as sensible beverage packaging solutions. PETplanet: How have the life cycle assessments of PET bottles evolved over recent years, and what are the key factors involved in a positive evaluation? Kauertz: Here, we must differentiate between single-use and refillable bottles. For both systems, the key factors are the preform weights and the percentage of recycled material used. While these aspects are more critical for single-use bottles, refillable bottles also benefit from them. In the case of single-use bottles, we also observe that separate collection and material recycling with the aim of reintroducing the material into new bottles have a significantly positive impact on the life cycle assessment. For refillable bottles, increasing the reuse rate is similarly crucial. Systems that have invested in the development of these key factors in recent years have significantly improved their LCA performance. Given that major market players in Europe have also embraced this path, the average life cycle assessment of PET single-use and refillable systems is certainly more positive today than it was ten years ago. However, we must not forget that there are still outliers in both systems that have implemented few optimisations so far. It is essential to create conditions that encourage all stakeholders to implement at least some form of optimisation for their bottle systems in the future. PETplanet: Despite many efforts by the industry to improve bottles, whether through weight reduction, the use of recycled materials, or “design for recycling” aspects, PET bottles overall do not fare well in public perception. What do you think is the reason for this? Kauertz: One reason is the aforementioned outliers. Every bottle that is visibly not optimised or, worse yet, ends up in the environment, serves as evidence that the industry’s efforts are not yielding sufficient results. In general, plastic packaging currently has a negative image, primarily due to issues with littering, especially marine littering. Although these problems are much more apparent in other parts of the world than they are here, in Europe, there is a perceived need to limit the amount of plastic packaging. This mindset involves not only ensuring order within our own homes but also concerns about exacerbating issues through waste exports to Asia. PETplanet: Last year, the Schwarz Group [Lidl, Kaufland] in the German-speaking region made a bold move by informing the public about their in-house circular system for PET bottles through television commercials, which caused quite a stir. Prior to this, the Schwarz Group had commissioned a study from you, using the data to substantiate their campaign. How did you experience the ensuing discussion? Kauertz: From our perspective, the discussion surrounding the study itself was surprisingly rational. Many of the criticisms raised, such as those regarding the data points concerning refillable bottles, had already been thoroughly addressed in the study text. Therefore, for stakeholders genuinely interested in a reasoned discussion, these concerns were easily resolved. PETplanet: One criticism, voiced by the German Federal Environment Agency, was that the Schwarz Group claimed to operate without using virgin PET, stating: “However, on a larger scale, someone must use fresh material"},{"@ID":4 "LABELLING 41 PETplanet Insider Vol. 25 ing guide consumers to place recyclable items into kerbside collection bins, when they need to check locally, bring items back to store or dispose of the packaging. APR recognition is a requirement for recyclability referenced by most EPR legislation. Nine states are debating EPR legislation for packaging in 2024. As more states continue to introduce and pass EPR legislation, prioritising APR recognition and ensuring the recyclability of packaging will be increasingly important for brands. Caustic wash-off adhesive H.B. Fuller says that its Earthic 4010N solution is the first hot melt labelling adhesive for wrap around labelling with recognition from APR for caustic wash off. It is claimed to offer easy wash-off, maintains the label securely in place across a wide temperature range, and is transparent on the label. It also has the Korean wash-off certification and European PET Cycle, allowing brands to use it for export. The company’s global product line includes H.B. Fuller Earthic 4001; a wraparound labelling grade for plastic labels on PET bottles with good wash-off performance according to PET Cycle and Returpack/ Veolia. Labels are removed and separated from the PET bottles to allow for efficient regranulation and the production of new preforms. It is suitable for labelling speeds of up to 37,000 bph. Its flexibility keeps the label in place on carbonated soft drinks across a wide temperature range, says the company. The light colour makes the adhesive barely visible on the label and bottle, meeting high standards for brand integrity and label appearance. The H.B. Fuller adhesive portfolio includes solution needs across many different areas, including labelling and multipack solutions for PET bottles and cans. www.hbfuller.com P E R F O R M A N C E D E TA I L S CIRCULAR SOLUTIONS OF COLOURS AND ADDITIVES FOR RECYCLED POLYMERS PRSE AMSTERDAM – STAND F24"},{"@ID":18 "25 YEARS ANNIVERSARY 16 PETplanet Insider Vol. 25 No. 05/24 www.petpla.net 25 YEARS ANNIVERSARY Gasification Another thermochemical process that is suitable for PET and capable of converting mixed plastics waste and biomass in presence of heat and oxygen into syngas and CO2 is gasification. Overall, 12 gasification technology providers were identified and currently the largest achieved capacity measure is of up to 200,000 t/a; most providers are located in North America (seven providers) followed by Europe (five). The majority of the identified companies (four) are medium-sized enterprises, followed by small- (three companies), micro/start-up (two companies), with just one large enterprise (Eastman). Pyrolysis In the pyrolysis process, a thermochemical recycling process is available that converts or depolymerises mixed plastic wastes (mainly polyolefins) and biomass into liquids, solids, and gases in the presence of heat and the absence of oxygen. Obtained products range, for example, from various different fractions of liquids including oils, diesel, naphtha, and monomers as well as syngas, char, to waxes. Depending on the obtained products these can be utilised as renewable feedstocks for the production of new polymers. With 40,000 t/a, the second-largest capacity found in the report is achieved with pyrolysis. The majority of the 80 identified technology providers are located in Europe (42 providers) followed by North America (21), rest of the world (11), China (four), Cis (one), and Japan (one provider). With 27 companies most providers are small enterprises followed by micro/start-up- and medium- enterprises (both each comprising 18 companies), and large enterprises (16 providers) such as Blue Alp (Eindhoven, the Netherlands), Demont (Millesimo, Italy), Ineos Styrolution (Frankfurt, Germany), Neste (Espoo, Finland), Österreichische Mineralölverwaltung (OMV) (Vienna, Austria), Repsol (Madrid, Spain), Unipetrol (Prague, Czechia), VTT (Espoo, Finland), and Chevron Phillips (The Woodlands, TX, USA). In Europe, pyrolysis is the predominant form of chemical recycling for PE/PP. However, for PET, the process is only suitable to a limited extent of 5%. Evaluation of capacities More than 340 planned as well as installed and operating plants were mapped worldwide providing a total input capacity of 1,477 kt/a. In Europe, there is already a considerable potential of know-how and providers for chemical and physical recycling technologies which is reflected in the comparison with the globally installed plants and capacities. From all installed chemical and physical recycling plants worldwide more than 60 and thus the majority are operating in Europe covering nearly one quarter of the worldwide input capacity. Europe therefore ranks top in the global comparison chart. Globally, the production capacity of advanced recycling is 1,082 kt/a with products ranging from polymers, monomers, naphtha, Secondary Valuable Chemicals (SVC), and fuels & energy. Europe’s circular strategy becomes evident by putting the product shares of polymers, monomers, naphtha, and SVC from chemical and physical recycling into a global context. Here, Europe covers 36 % of the installed global capacity. In the coming five years a strong growth of the market is expected in which the amount of installed chemical and physical recycling plants will steadily grow. A first indicator are the announcements of the technology providers for the construction of new plants. An analysis of these announcements shows that the input capacity in Europe will more than triple by 2027 while globally the capacity will double. However, the projection for Europe might change depending on any additional political measures, such as the revision of relevant directives or the establishment of incentives and investment programmes. www.nova-institut.eu A NEW LEVEL IN RECYCLING Happy 25th Anniversary PETplanet OMNI Recycling Technologies Super Clean Recycling in One Extrusion Step"},{"@ID":26 "25 YEARS ANNIVERSARY 24 PETplanet Insider Vol. 25 No. 05/24 www.petpla.net 25 YEARS ANNIVERSARY Interview with Philipp Lehner, CEO Alpla Group, on his social media activities Raising awareness and engaging with consumers Plastics face a tough battle in public perception, with PET bottles often symbolising increased concern over waste. Shedding light on this issue is crucial. Philipp Lehner, CEO of the Alpla Group, is taking to multiple social media platforms like Youtube, Instagram, and Tiktok to debunk myths surrounding plastics. Through fact-based short videos, he directly addresses consumers, aiming to foster awareness and understanding. PETplanet: You’ve been very active on social media for more than a year now, debunking common myths about plastics and recycling in short videos. How did the idea come about? Lehner: Alpla is a family company. And for us, this means a clear commitment to sustainable social responsibility and transparent communication. We also stand for plastic as a versatile, high-performance and resourcesaving material. We want to expose myths and provide fact-based information about plastic. This is the driving force behind our commitment to social media. In addition to Alpla, I would like to set an example there with my own channels. For this purpose we have also launched the initiative “plastic is fantastic”. With this initiative, we want to raise awareness and seek dialog with consumers. PETplanet: How has this initiative been received by consumers? Lehner: Plastic is fundamental to our lives, but it is not an explicit lifestyle topic. For manufacturers in the industry, communication via social media is still unusual. So, it is clear to us that it takes time to reach people on social media. But we want to continue this open communication. Our video “plastic is fantastic” on Youtube has been viewed over 1.9 million times in three months. That is a good result. Especially when you see that plastic is being criticised. But plastic is an integral part of our daily lives. And there is also a change in thinking: due to its good recyclability, plastic is transformed from a disposable product into a source of valuable material. There is a lot of movement on this topic. This is why people are also becoming aware of the topic on social media. And we will be an active part of it. PETplanet: Users, especially on Tiktok, are typically in their teens or in the 25 to 34 age group. Do you find young people more receptive or concerned about the topic of plastics? Lehner: Young people are influenced by many information channels. They follow stars and influencers on social media and see their opinions. It is important that they form their own opinion based on facts. Plastic is a very emotionally charged topic. Because of the waste. But the material is not the problem. The problem is how we handle it. Plastic saves resources in production and transportation, it can be easily recycled, is therefore sustainable. But we must give waste a value, then there is a market and plastic waste will be collected – and does not end up in the environment. In Mexico, for example, there are collection systems that help us get used plastic and then recycle it and make new bottles from it. With good results. People can earn their livelihood by collecting plastic there. This creates new opportunities on the job market and protects the climate and the environment. If we combine the benefits of new plastic with the value of used plastic, we achieve a good perspective. We can establish a sustainable circular economy. Innovation, not renunciation, secures the future. PETplanet: Do you also engage in discussions in the comment sections? Lehner: Of course we are watching it, we are interested in the reactions and opinions. Our company and I can learn from this. We work as a team and react, but we don’t push ourselves into the foreground. We will see how it develops. PETplanet: What challenges have you faced in trying to educate consumers about plastics and recycling through social media, and how have you met them? Lehner: As mentioned, plastic is an emotionally charged topic and there are many myths about the material. That’s why we want to clear things up - with facts. Personal, informative and with exciting topics about plastic. You need a good team behind you to implement this. You by Gabriele Kosmehl"},{"@ID":41 "LABELLING PETplanet Insider Vol. 25 No. 05/24 www.petpla.net 39 Shrink sleeves for light sensitive products Although plastic labels and films only make up a small but significant part of the overall packaging, they play a major role in the waste stream. Labels can be made from various materials, for example paper or plastic. The labels often have self-adhesive backs. As the material composition of the packaging material varies when packaging or sealing products, the recycling process becomes more complex. CCL Label has introduced a new version of its proven EcoFloat lowdensity polyolefin sleeve material: EcoFloat White. “EcoFloat White will enable greater recyclability for dairy packaging and other products that are light sensitive, we expect it to be a game changer. The dairy industry often uses HDPE bottles for bottles containing yoghurt and probiotic drinks or similar products. However, these white HDPE bottles are rarely recycled back into food grade applications for several reasons, including strict food contact regulations – so the bottles leave the packaging loop,” says Guenther Birkner, member of the management team at CCL. “We have seen a big trend in the food and beverage but also home and personal care industries to move from HDPE to PET, which works well in terms of recycled content for food packaging, and it is our goal to support this with a functional product decoration.” Bottles can now be recycled in a closed loop “Legislation such as the European Green Deal and the Packaging and Packaging Waste Regulation will drive ‘design for recycling’ or eco-design in the coming years, every brand has to come up with packaging that is actually recyclable,” explains Marika Knorr, Head of Sustainability and Communication at CCL Label. “Until now, many white HDPE bottles have left the closed loop for food packaging and are lost for reuse in a circular sense”. By using PET bottles with a white sleeve, companies achieve two benefits at the same time. The entire bottle is fully recyclable, while still achieving the same look and feel that marketing is looking for to maximize the messages and mandatory information given to consumers on the bottle. Millions of additional PET bottles are recycled and turned into a new one giving the packaging many “extra lives”. Additional light blocking barrier can be achieved with carbonfree inks A key requirement for dairy products is light blocking properties to keep the product fresh and maximise shelf life. In the past, this light-blocking barrier was often achieved with a layer of black or silver ink, which is essential for protecting the products but could also be detrimental to sorting and recycling, as the standard near-infrared detection system commonly used could have difficulty detecting the underlying material. “Since 80 percent of recycling is actually sorting, we had to make sure that our solution was detectable by the standard technology used in the recycling industry today,” says Norbert Fenkart, who heads the research and development (R&D) department at CCL’s sustainable sleeve label center in Dornbirn, Austria. “We use carbon-free inks to create additional lightblocking properties on the sleeve. These work well in NIR detection as we have seen in tests and the underlying rigid PET bottle is detected and the bottle is sorted into the correct waste stream.” The sleeve also helps with the crucial sink/float process step in PET recycling because it is made from a low-density polyolefin material that floats. It automatically separates from the PET bottle flakes and the density separation is simple and clean: the heavier PET flakes sink to the bottom of the container, while the floatable material collects at the top of the container and can be easily captured and removed. The recycler is left with high quality, clean PET flakes that can be recycled back into food grade packaging for the dairy and other industries. The transparent EcoFloat sleeve material has been commercialised for over two years and has been adopted by many international brands to increase the recycling of their packaging containers. www.ccllabel.com LABELLING"},{"@ID":57 "BOTTLING / FILLING PETplanet Insider Vol. 25 No. 05/24 www.petpla.net 36 Sipa and Gepp mark 25 years of successful collaboration Contribution to prosperity in Mexico PET machinery and moulds manufacturer Sipa and Grupo Gepp, the largest bottling group in Mexico, have been working together for 25 years. Gepp holds exclusive rights for bottling PepsiCo throughout its home country and has strategic partnerships with other brands such as Jumex and Alpura. Gepp has experienced high levels of growth, since 2018 especially, and recently invested in the latest editions of Sipa’s Xtra rotary blowmoulders and turnkey filling lines. Alfonso Montoya, Director of Purchasing at Grupo Gepp, explained how Gepp came into being and grew to be a leading bottling company in Mexico’s important market. “Gepp began its consolidated business in 2011, after the integration of the existing operations of the companies Geusa, PBG and Gatorade of Mexico, as well as the entry into business of Empresas Polar of Venezuela,” he explained. “Gepp is the only PepsiCo bottler in Mexico. It has more than 45 plants producing various beverages and located in all operating regions of Mexico and has its own preform production plant, Proplasa. Gepp generates direct employment for more than 42,000 workers, consolidating itself as one of the main employers in the private sector in Mexico.” “We are a business group dedicated to the operation, manufacturing, distribution and marketing of water, carbonated, non-carbonated, isotonic beverages, among others. We are leaders in the production and distribution of water in 20 l bottles. Our portfolio is made up of important brands such as ePura, Pepsi-Cola, Gatorade, Manzanita Sol, Mirinda, 7up, Lipton Tea, Canada Dry, B-Light, Jumex Fresh, among others. Additionally, Gepp is a distributor of Alpura products in the Traditional channel in various territories of the Mexican Republic.” The relationship between Gepp and Sipa goes back to 2003, when Sipa supplied blowing equipment and filling lines for the Geusa plants. Later, Sipa installed an SFR 16 model blower and 144-valve filling line at the Celaya Plant in Guanajuato to produce 3 l Pepsi bottles. The filling plant has become recognised as one of the most efficient in the sector. In 2022, Gepp decided to increase collaboration ties with Sipa and selected it as a strategic technological partner for Gepp’s plant technological renewal program, a process that started with the order for four Xtra blowers and a Gatorade filler. After the successful implementation of this line, which was achieved quickly and with an effective start-up and good levels of service both at the time and after sales, based on the good service, speed of installation, start-up and scope of operational efficiencies, Gepp decided to acquire another 2 Xtra blowmoulders, a complete line for water at 57,000 bph, two lines for soft drinks at 48,000 bph and 14 palletisers. Gepp got Proplasa, its subsidiary, involved in a preform lightening program, with which Sipa is involved as the partner for a lightened neck for PCO 1881 LW bottles. “The choice of Sipa as Gepp’s strategic supplier was confirmed due to its ability to provide adequate technical support in Mexico, structuring a greater number of qualified technicians and a well-organised spare parts warehouse, which guarantees fast and accurate response times,” Montoya said. “In addition, the recognition of Gepp by Xtra for connection to Echo and 4.0 digital services stands out.” [see box] Alfonso Montoya, Director of Purchasing at Grupo Gepp Rotary blowing system Xtra"},{"@ID":35 "EDITOUR PETplanet Insider Vol. 25 No. 05/24 www.petpla.net 33 and has just started production. It is equipped with a 72-cavity mould with a cycle time of 2.8 seconds from the Austrian manufacturer Z-Moulds. With this combination, an annual output of almost 730 million 29/25size closures can be achieved. Mr Krishna said: “Moulds like this are almost a rarity in this country, but we are convinced by the Austrian technology, especially in terms of quality and the mould’s cooling system.” For the inspection part, Future Plus relies on equipment from IMD Vista, both for the Engel system and the Husky systems for preform inspection. While the Engel system is the first machine for cap injection moulding in operation here, Future Plast in UAE produces single piece and 2-piece closures with an 1881 neck finish for CSD apart from normal 30/25 high neck and 29/25 short neck for still water applications using six Sacmi compression moulding machines - so the step to add closures to the portfolio in KSA with the new system may just be the beginning. In terms of space, further expansion is still easily possible, as the available open areas clearly showed during the factory tour. PET and PE raw materials are sourced from local producer Sabic, and are also imported from Thailand, India, Oman or China, depending on availability and prices. According to Mr Krishna, the company processes 10,000 t of PET and around 800 t/a of PE p.a. or 30,000 t of PET and around 4,000 t of PE and PP for closures p.a. including Abu Dhabi. “In addition to the Saudi market, around 25% of the preforms produced in Riyadh are intended for export exclusively to Gulf Cooperation Council (GCC) and Yemen markets mainly due to Saudi efforts to strengthen primarily nationally produced products,” Mr Krishna continued. We want to know how the company is positioned in terms of recycling. “The law does not yet insist on the use of recyclate in food packaging,” explained Mr Krishna, “but this is certainly only a matter of time. The topic has already gained momentum in the region and we are certainly technically equipped for it. At Future Plast, we have already produced our first 100% rPET preforms and are currently waiting for a material dosing system with oil condensing unit from Piovan to be ready to dose partial rPET as per the brand owner’s requirements. www.futurepet.ae Three Husky HyPET systems and on the right the new Engel E-Motion The new 72-cavity mould from Z-Moulds F.l.t.r.: Murali Krishna, Mr Palanisamy, Gregor Degasperi, Kay Barton and Shihab Izzat Murali Krishna (right) with Gregor Degasperi from Z-Moulds"},{"@ID":45 "The RDX PET Rocket is directly mounted onto the extruder feed. AUXILIARY EQUIPMENT PETplanet Insider Vol. 25 No. 05/24 www.petpla.net 43 RDX PET Rocket uses on-site compressed air to replace desiccants Air-powered plastic drying Plastics, being highly susceptible to moisture absorption, present a range of challenges during processing due to the presence of moisture within the granules (hygroscopic materials) or condensate on the surface (non-hygroscopic materials). These often present processing and quality issues such as surface defects and compromised mechanical properties. Austrian company Blue Air Systems, which is based in Kundl, in the Tyrol region, has launched a solution that is, it says, a cost-effective alternative to desiccant dryers. Blue Air Systems’ RDX PET Rocket system dries plastic granules using existing, on-site compressed air systems. Blue Air says that RDX PET Rocket delivers good drying results with minimal operational costs and virtually maintenance-free production. The RDX PET Rocket is designed and built to withstand temperatures of up to 180 °C and seamlessly integrates with both central and auxiliary drying systems. It is directly mounted onto the extruder feed and features a 62-litre container that is 110 cm tall and offers both convenience and optimised space usage. The 27- and 42-litre versions are 90 cm in height. Pre-dried PET material can also be easily rehumidified and restored to the required processing temperature, Blue Air Systems says. The RDX PET Rocket is designed to ensure a constant dew point and to deliver reliable performance, regardless of ambient conditions. The company maintains that its product will eliminate the complexities of desiccant and cooling water, without fuss or bother. The RDX series extends beyond PET resin drying. Blue Air Systems has announced the introduction of its Modular Dryer RDL, which can use dehumidified compressed air from customers’ existing compressed air network, an integrated compressor system, or the exhaust air from the blowing process of an injection stretch blowmoulding machine for the drying process. Its throughput capacities range from 24 to 200kg/h, which means that the systems can cater to all plastics, including PET, without requiring a minimum drying temperature or water connection. Using existing compressed air infrastructure means that systems’ special applications, such as resin drying, operate at low cost or even free of charge. Heat and energy recovery further boost the efficiency and sustainability of the drying process, according to the company. Blue Air Systems says that the key features of the RDX series and Modular Dryer RDL systems are: Post-heating granulate dryer designed for PET (180 °C) Compatible with central or auxiliary dryers Directly mounts onto extruder feed – 62 l container, 110 cm in height, 27 and 42 l container with a height of 90 cm Restores pre-dried PET to the required processing temperature Maintains a constant dew point regardless of environmental conditions Operates without the need for molecular sieves and cooling water. www.blue-air.at"},{"@ID":1 "No.5 2024 www.petpla.net D 51178; ISSN: 1438-9452 13 . 05 . 24 M A G A Z I N E F O R B O T T L E R S A N D B O T T L E - M A K E R S I N T H E A M E R I C A S , A S I A , E U R O P E A N D A L L A R O U N D T H E P L A N E T PETplanet is read in 159 countries MARKETsurvey Suppliers of preforms & inspection systems Page 29 EDITOUR LABELLINGPage 39 Page 32"},{"@ID":28 "25 YEARS ANNIVERSARY 26 PETplanet Insider Vol. 25 No. 05/24 www.petpla.net 25 YEARS ANNIVERSARY PET production and demand In 2022, PET converter demand for applications such as bottles, films and sheet in the EU27+3 region stood at 5.0 million tonnes. PET production (including virgin and recycled) reached 3.9 million tonnes in 2022, as illustrated in the figure, showing a downward trend in relation to previous years. The difference between PET demand and production had to be met with imports, as covered in the subsequent sections. Following the years marked by Covid related issues, 2022 saw a converter demand growth of approximately 7% in relation to 2020. In relation to 2019, that change represents 2%, showing recovery and marginal growth compared to pre-pandemic demand levels. Whilst 2022 started with strong demand, unfavourable economic conditions built up, hindering further demand growth. There was an expectation that the lifting of Covid-related restrictions would boost demand on the back of higher consumer spending on travelling, and a return to typical purchasing patterns, but the summer peak season was lower than expected and converter demand was subject to continued uncertainty. 2022 was impacted by the subsequent rise in inflation and costof-living, which put pressure on end-consumer disposable income, as well as the challenging macroeconomic scenario, including recessionary fears towards the end of the year. Compounded by the rise in energy costs, caused by the Russia-Ukraine war, resulting in rapid changes in supply and pricing – affordability was affected for consumers and producers alike. Production In 2022, European virgin PET production for applications such as bottles, films and sheet (trays), strapping and other reached 2.3 million tonnes while production from recycled material reached 1.6 million tonnes. High energy prices and production costs, set against reduced margins and demand for PET, impacted virgin production output significantly in the EU27+3 region, which decreased in 2022 when compared to previous years. rPET production also faced challenges during the year, mainly related to record high energy costs and variable availability of high-quality feedstocks, discussed in more detail further in the rPET section of the report. However, overall production of rPET showed an increase of 0.3 million tonnes in relation to 2020, offsetting the decrease in virgin PET production during the year. In 2022, rPET production represented around 40% of total PET production in the EU27+3 region, an increase in relation to 2020, when rPET represented approx. 30% of total PET production in the region. www.icis.com www.unesda.eu CONTEXO GMBH Tel. +49 (0) 7181 / 606-100 [email protected] www.contexo-automation.de HIGHSPEED ASSEMBLY MACHINES CARTON CLOSURES POUCHES, CANS AND MORE PET CLOSURES + TETHERED CAPS PET total production (virgin and recycled) and converter demand in the EU27+3 region between 2018 and 2022. It only includes PET used in applications such as bottles, films and sheet (trays). Source: Icis"},{"@ID":58 "EVENT REVIEW PETplanet Insider Vol. 25 No. 0/24 www.petpla.net 47 the new Pac-E 350/820 2000 at the factory. Incidentally, both machines are being built for the same customer. This means that the all-electric capping machine is likely to make the transition from a trade fair model to an industry-approved solution. Gerd Liebig estimates the demand for fully electric capping systems to be around 50 machines per year in Europe and globally. Roadshow Demag Sumitomo’s roadshow began at the same time as the machine demonstration. The company has come to realise that new approaches need to be taken when it comes to direct marketing. Prior to the Covid pandemic when customers came to the machine manufacturer, be it at trade fairs or in-house events, Sumitomo Demag recognised that not all clients were treading the same path anymore. And so the idea of taking the machine to the customer was born, from which came a semi-trailer with extendable sides. An IntElect 220-700 is currently in production. Information areas on active melt control (to compensate for material fluctuations), my assist (to document the system process) and the my connect service module complete the mobile display. Gerd Liebig wants to support processors in their quest for greater efficiency, higher production volumes and ultimately improved operating results. The tour will run for four months and visit 14 countries throughout Europe. www.sumitomo-shi-demag.eu “The articulated lorry on the roadshow from Sumitomo Demag is somewhat bigger than our Editourmobil, but the feeling behind the steering wheel when on the way to the consumer is the same as ours,” stated Alexander Büchler, Publisher PETplanet. Gerd Liebig, CEO Sumitomo (SHI) Demag"},{"@ID":14 "25 YEARS ANNIVERSARY 12 PETplanet Insider Vol. 25 No. 05/24 www.petpla.net 25 YEARS ANNIVERSARY The material of choice for sustainable packaging based on an article by Dr Frank Welle, The Facts about PET PET (Polyethylene Terephthalate) was first developed for use in synthetic fibres by British Calico Printers in 1941.* The patent rights were then sold to Dupont and ICI who in turn sold regional rights to many other companies. Although originally produced for fibres, PET began to be used for packaging films in the mid 1960s and then, in the early 1970s, the technique for blowing bi-axially oriented bottles was commercially developed. Bottle now represent the most significant use of PET moulding resins. Making a PET bottle starts from the raw material: ethylene and paraxylene. These two substances’ derivatives (ethylene glycol and terephthalic acid) are made to react in order to obtain the PET resin. The resin, in the shape of small cylinders called pellets, is melted and injected into a mould to make a preform. The preform - a sort of test tube, shorter than the final bottle but with thicker walls - is then blow-moulded. During the blow-moulding phase, high-pressure air is blown into the preform allowing it to take the exact shape of the mould it is set into. The final product is, thanks to the molecular structure of the material, a transparent, unbreakable, resealable and lightweight bottle. The strength of the material It is the strength of the material that contributes to the success of PET. Indeed, carbonated soft drinks can generate pressure inside the bottle reaching up to 6 bar. Such high pressure however, thanks to the alignment of macromolecules (crystallisation) occurring both during the resin spinning process and the blow-moulding process, is not capable of deforming the bottle nor can it make the bottle explode. Another advantage of the material lies in its physical properties that allow for great freedom in design. Throughout the years, the PET industry has increasingly taken on environmental concerns, significantly decreasing the quantity of raw material needed for the manufacture of bottles. Nowadays, a 1.5 l PET container is manufactured with 30 g of raw material. Another striking feature of PET on the environmental side is that it is fully recyclable. In 1977, the first PET bottle was recycled and turned into a bottle base cup. Soon however, the fibre industry discovered the “new” material source and started using it for making textiles, carpets and non-wovens. Today, even though the “bottle to bottle” recycling process is growing, the fibre market is still the major outlet for recovered PET. Lightweighting PET PET bottles are very strong, colourless and lightweight. PET is transparent and it allows the content of the container to remain visible. The strength and lightweight of PET is very important for beverage packaging since it makes the bottles safe for on-the-go or sports use. Over the years, the weight of PET bottles has been reduced and today a 1.5 l bottle can weigh as little as 20 to 30g. This process of light weighting represents a true benefit with regard to the environmental performance a bottle will have during its lifetime: production, transport to the consumer and end of life cycle. With its excellent material properties, PET is widely used today as a packaging material for liquids such as carbonated beverages and is one of the most suitable materials for the packaging of natural mineral and spring water. PET is used in the packaging sector in the form of films, trays or bottles, its principle use being in bottles. The interaction of PET with food and water No packaging material is fully inert and so there will always be some kind of interaction with the beverage or foodstuff it contains. In the case of food, mild oxidation may occur due to oxygen permeation. Likewise, carbon dioxide from carbonated beverages can permeate through the packaging material. In certain instances, there may also be a small degree of migration of components from the plastic packaging into the content. For consumer health protection, all such interaction must be reduced to a minimum. As with all other material in contact with food, PET packaging does comply with all European and national legal requirements. Such requirements include an assessment of the initial raw materials employed (i.e., monomers and additives) and the compliance with any restrictions that are established, such as migration limits. The requirements for the migration of monomers and additives according to the European Packaging Legislation is given in Table 1. Acetaldehyde Acetaldehyde is a by-product of the PET manufacturing process. It is produced when PET is heated to a high temperature to produce bottles. Many beverages and foodstuffs contain natural acetaldehyde. The trace quantities of acetaldehyde that may migrate from PET into bottled water are totally harmless, although they may cause the water to have a slightly fruity offtaste. When the concentration exceeds 0.02mg of acetaldehyde per litre, the consumer may be able to taste it. Based on consumers’ acceptance and local regulation, this is something that should be avoided in some countries whereas it is well accepted in others. PET bottle manufacturers have worked closely with the bottled water companies to optimise the PET bottle production process with a view to minimising levels of acet-"},{"@ID":55 "25 YEARS ANNIVERSARY 25 PETplanet Insider Vol. 25 No. 05/24 www.petpla.net have to stay attentive, develop a feel for topics and you must find an own, distinctive sound. PETplanet: Beyond your own efforts on social media, what other measures would you like to see implemented to improve awareness and practices regarding plastics and recycling? Lehner: In addition to social media, there is also the “aVoice” project with which we are now active in 22 countries worldwide to give plastic a voice that is heard. With this, Alpla aims to raise awareness among the population about the responsible use of plastic as a recyclable material and to start a conversation with people. The raising of awareness succeeds through education. We are not interested in greenwashing and polemics; we want to convince honestly and live our new understanding. This is exactly PET recycling plant in Tabasco, Mexico Packaging specialist Alpla is currently building a recycling plant in partnership with beverage filler Coca-Cola Femsa in the Mexican state of Tabasco. Through the joint venture, approximately 60 million US dollars are being invested in the new high-tech facility, named Planeta, which will be able to recycle more than 50,000 t/a of used PET bottles. The material is sourced from 18 dedicated collection points, where intermediaries deliver it after purchasing it from regional collectors. Overall, the plant will create about 20,000 direct and indirect jobs. The plants compensate collectors for the delivery of recyclable plastic waste - a foundation for active waste management in areas where disposal options are otherwise lacking. Through the 18 collection points already in operation for the Planeta plant, approximately 15,000 t of used PET have already been collected, with 4,000 t set for processing at the planned start of the facility in July 2024. The remainder has been processed by Imer and other recycling facilities in Mexico. The annual production capacity of the new factory will be 35,000 t of recycled material, obtained from over 50,000 t of disposed PET, which is equivalent to roughly 1.6 billion recycled 1.5 l plastic bottles per year (assuming a weight of 30 g for a 1.5 l bottle), thus reducing the amount of waste ending up in landfills or nature. Coverage of structurally weak regions Unlike the Imer recycling plant, where collection points are located in urban centres with good connectivity, the collection points delivering to the Planeta plant, located in southeastern Mexico, also cover structurally weak regions. This primarily supports rural material suppliers, who can already deliver small quantities of 20 to 50 kg through this process. In addition, each of the 18 collection sites has two pickup trucks with trailers, used to collect recyclables from collectors in remote areas. At full capacity, the recycling plant will create about 20,000 direct and indirect jobs, serving as a significant driver for sustainability and economic development. Collectors can earn income equivalent to the minimum wage, depending on the current purchase price, by delivering approximately 30 to 35 kg, or about 1,000 PET bottles. www.alpla.com what “aVoice” stands for. In combination with the initiative “plastic is fantastic”, we can change opinions and things. Now we have over 8 billion people on the planet. Plastic is becoming even more important – in medical care or as a safe packaging for protection and transportation of food. The PET bottle is an important component of a mobile drinking water supply. New products are created from collected plastic waste or energy is generated from it. That’s why we believe in the future of plastic. And that’s what we are working towards. PETplanet: Thank you very much Mr Lehner. https://linktr.ee/alpla_group https://linktr.ee/philipp_lehner https://linktr.ee/aVoice_campaigns"},{"@ID":16 "25 YEARS ANNIVERSARY 14 PETplanet Insider Vol. 25 No. 05/24 www.petpla.net 25 YEARS ANNIVERSARY Advanced recycling technologies to complement mechanical recycling Advanced recycling on the rise Advanced recycling technologies are developing at a fast pace, with new players constantly appearing on the market, from start-ups to chemistry giants and everything in-between. New plants are being built, new capacities are being achieved, and new partnerships are being established. With all these dynamic developments, it is difficult to keep track of what is happening. Nova Institute’s report “Mapping of advanced plastic waste recycling technologies and their global capacities” aims to clear up this jungle of information providing a structured overview and in-depth insight. Besides conventional mechanical recycling and taking account of recent discussions on the improvement of recycling rates, a wide spectrum of advanced recycling technologies is moving into focus. Whilst PET bottle mechanical recycling is well established and performing well, in cases of mixed plastic waste or mixed waste containing various plastics and organic waste, mechanical recycling is not an option, or allows only partial solutions with considerable effort of pretreatment. In consequence, these waste streams mostly end up in landfill or incineration instead of being further processed into a new feedstock. This is why advanced recycling technologies are crucial for the circular economy. With advanced recycling a toolbox of versatile technologies is available to address plastic waste streams in different compositions and qualities in order to transform them into a range of different raw materials that can be reintroduced at different positions along the value chain of polymers and plastics. The technologies include material recycling based on dissolution (physical process) from which polymers can be obtained. Furthermore, numerous chemical recycling technologies are available that are capable of depolymerising a targeted polymer into its component parts (monomers) via enzymolysis (biochemical process), solvolysis (chemical process), and thermal depolymerisation (thermochemical process). Another group of chemical recycling technologies are thermochemical processes which are currently achieving the largest capacities. These technologies are based on pyrolysis, gasification and incineration coupled with Carbon Capture and Utilisation (CCU) which are capable of converting plastic waste into secondary valuable chemicals as well as naphtha, syngas, and CO2 which can be used as feedstock for the production of new polymers. Which technologies are suitable for PET? The Nova Institute report “Mapping of advanced plastic waste recycling technologies and their global capacities” provides an in-depth insight into advanced recycling technologies and their providers. More than 100 technologies and their status are presented in detail listing the companies, their strategies and investment as well as cooperation partners. But which technologies are actually suitable for PET?"},{"@ID":32 "MARKET SURVEY 30 PETplanet Insider Vol. 25 No. 05/24 www.petpla.net Preform inspection Company name Intravis GmbH Postal address Telephone number Website address Contact name Function Direct telephone number E-Mail Rotter Bruch 26a, 52068 Aachen, Germany +49 241 9126 0 www.intravis.com Mr Markus Juppe CMO +49 241 9126 0 [email protected] Preform Inspection Systems PreWatcher Offline PreWatcher Inline Sample-PreWatcher PreMon Inspection speed Up to 100,000 objects/hour with 18 cameras Up to 72,000 objects / hour with 8 cameras Up to 1,200 objects/hour with weight check Up to 72,000 objects/hour with 5 cameras Inspected parameters: Geometry / Body Contamination, short shots, length, diameter, shape, unmelted material, oil & water marks, burn spots, scratches, opacity, crystallisation, streaks, bubbles, colour and colour deviations, barrier, stress test with polarised light Contamination, short shots, length, diameter, shape, unmelted material, oil & water marks, burn spots, scratches, opacity, crystallisation, streaks, bubbles, colour and colour deviations Contamination, short shots, length, diameter, shape, unmelted material, oil & water marks, burn spots, wall thickness, inner wall damage, core shift, scratches, opacity, crystallisation, streaks, stress test with polarised light, bubbles, colour and colour deviations, barrier Colour and colour deviations, contamination, unmelted material, oil, burn spots, opacity, yellowness Thread area Contamination, thread dimensions, defects at the neck support ring, fl ash, pulled thread Contamination, thread dimensions, defects at the neck support ring, fl ash, pulled thread Contamination, thread dimensions, defects at the neck support ring, fl ash, pulled thread, tactile inspection of inner wall diameter Mouth / Sealing surface Diameter, ovality, short shots, fl ash, scratches and notches on the sealing surface, defects at the neck support ring, contamination Diameter, ovality, short shots, fl ash, scratches and notches on the sealing surface, contamination Diameter, ovality, short shots, fl ash, scratches and notches on the sealing surface, inner mouth wall inspection, contamination Short shots, scratches/notches, contamination Gate / Dome Contamination, grooves, holes, cracks, crystallisation, postitioning of injection point, unmelted material, gate length, gate deformation, stringing Contamination, grooves, holes, cracks, crystallisation, postitioning of injection point, unmelted material, gate length, gate deformation, stringing Contamination, grooves, holes, cracks, crystallisation, postitioning of injection point, unmelted material, gate length, gate deformation, stringing, wall thickness Length of injection point, contamination Colour Colour and intensity deviations (ΔL*, Δa*, Δb*), presence of UV blocker, presence of barrier, presence of IR absorber (reheater) Colour and intensity deviations (ΔL*, Δa*, Δb*), presence of UV blocker, presence of barrier, presence of IR absorber (reheater) Colour and intensity deviations (ΔL*, Δa*, Δb*), presence of UV blocker, presence of barrier, presence of IR absorber (reheater) Colour and intensity deviations (ΔL*, Δa*, Δb*), yellowness Cavity number Cavity number reading, cavity related statistics, preform sorting according to cavity number, powerful cavity reading without need for learning for most fonts, possibility to share information based on cavity number with IMM Cavity number reading, cavity related statistics, preform sorting according to cavity number, powerful cavity reading without need for learning for most fonts, possibility to share information based on cavity number with IMM Cavity number reading, cavity related statistics, preform sorting according to cavity number, enables collection of reference samples, powerful cavity reading without need for learning for most fonts, possibility to share information based on cavity number with IMM Further criteria Precise separation and positioning of preforms due to star wheel separation, second ejector for easy collection of sample preforms, spacesaving design on less than 4m², 100%quality control without blind areas, for transparent, translucent and opaque preforms 3-in-1 solution: Combination of sorting, feeding and inspection unit, space-saving design on less than 8m², 100%quality control without blind areas, for transparent, translucent and opaque preforms Precise and extensive measurement of weight and dimension, cavity-correlated information about every detail of the preform, reference sample collection based on defect and/or cavity Comprehensive octabin or time related statistic dashboard, bad part ejection with ejection compensation, high precision through preform orientation, easy reference creation due to PreMon Wizard Measurement of absence or presence of barrier material Yes Yes Yes Layer thickness & position measurement at distinctive points Layer thickness & position measurement at the complete body by scanning Features: Installation: Stand-alone Yes Yes Yes Installation: Inline Yes, but optimised for offl ine Yes, optimised for inline after IMM and before blower and fi ller Yes, sampling Yes, optimised for inline after IMM · Side camera for cavity recognition Yes, 4 cameras Yes, 3 cameras Yes, rollout of the complete thread area · Method: destructive/non destructive Non-destructive Non-destructive Non-destructive Non-destructive · Data base connection Yes, all industry standards supported, ready for Industry 4.0 applications: XLS formats, SQL and several others, connectable to IntraVisualizer, ERP & QMS Yes, all industry standards supported, ready for Industry 4.0 applications: XLS formats, SQL and several others, connectable to IntraVisualizer, ERP & QMS Yes, all industry standards supported, ready for Industry 4.0 applications: XLS formats, SQL and several others, connectable to IntraVisualizer, ERP & QMS Yes, all industry standards supported, ready for Industry 4.0 applications: XLS formats, SQL and several others, connectable to IntraVisualizer, ERP & QMS"},{"@ID":39 "BOTTLING / FILLING PETplanet Insider Vol. 25 No. 05/24 www.petpla.net 37 What does Gepp see as the challenges in the beverage market in Mexico? “Gepp has various commitments, among which are: contributing to the vitality of Mexicans and their families, and acting in accordance with the code of conduct. In addition, we care about applicable laws and regulations and being a competitive option for our consumers by providing them with friendly and dedicated service,” he continued. “We are committed to manufacturing products of excellence and high quality, while generating portfolio growth, building win-win relationships with our clients and suppliers in the short and long term, and providing our workers with decent and dignified work. Gepp seeks to generate maximum potential and return for its partners, actively participating in the communities where we operate, as well as contributing to the prosperity of Mexico,” explained Alfonso Montoya. www.sipasolutions.com Echo digital ecosystem Improving customers’ connectivity and enhance Industry 4.0 integration Sipa says that its new Echo digital ecosystem has been created to connect people, businesses and resources in an interactive environment based on total skill sharing. Transparency, accessibility and usability of information are highlighted by the company as key points on the journey to more intelligent productivity. Echo is claimed to offer customers full control and monitoring of the performance of plants and B2B postsales processes, through a series of new digital technologies, services and information on its installed fleet. Sipa says that it helps to shorten management times of services and helps optimisation of plant efficiency and management costs. The cloud platform allows access to information on the entire fleet of Sipa machines, anywhere and at any time. A data collection hub can be used easily and immediately by a single source, in an interactive environment created to optimise efficiency in the entire manufacturing process. Sipa says that this enables total control of performance and offers the real possibility of improving and streamlining processes and communication. Xcon, the heart of the Echo infrastructure, allows safe and certified connections between people and technology, by accessing IoT and other cloud services using the Echo platform. It is the essential network component to guarantee the connectivity of each system, monitor machine performance and receive real time technical support. www.sipasolutions.com"},{"@ID":52 "PETplanet Insider Vol. 25 No. 05/24 www.petpla.net 50 PETbottles Home + Personal Care Blue Wonder against limescale The Dutch company Blue Wonder al so sel l s a 100% hygieni c and very powerful limescale cleaner in Germany under its own name in a slightly blue-coloured bottle with a lockable pump dispenser. The labels use pictograms to clearly indicate the areas of application of the cleaner. The neck of the bottle has grooves on the sides that come into contact with the heel of the hand to increase the gr ip of the bot t le dur ing use. www.bluewonder.com Respect in PET Under the Respekt brand, the German company Ecol og i ca l C l ean i ng & Ca r e GmbH markets a wide range of detergents and cleaning agents that are environmentally friendly and still achieve good cleaning results. The picture shows two examples: 750 ml each of glass cleaner and bathroom cleaner in handyshaped, t ransparent PET bottles made from 100% recycled material. Opaque, sealable pump dispensers with a plastic spring element round off the sustainable packaging. Two labels explain the product and the packaging. www.ecc-kompetenz.com Two phases for the hair 180ml Guhl Ikebana GmbH fills a transparent bottle in the brand’s typical shape with deep conditioning for damaged and damaged hair. The bottle, made from 98% recycled material, makes the two phases of the product, which must be shaken well before use, particularly visible. The product, which does not need to be rinsed out, is applied to the hair using the silvercoloured pump dispenser. Two labels provide information and a printed QR code leads to even more information. www.guhl.com New design for gum care GSK Consumer Healthcare has revised the design of the 300ml bottle for Parodontax brand Active Gum Care. The slightly pink-coloured product is filled in a waisted bottle with a screw cap, which also serves as a dosing cup. The cap is protected by a green sleeve cap before first use. The cap can be removed via a perforation and the lid can then be unscrewed. www.parodontax.com"},{"@ID":7 "25 YEARS ANNIVERSARY 21 PETplanet Insider Vol. 25 No. 05/24 www.petpla.net 25 YEARS ANNIVERSARY Targeting plastic bashing A crusade for truth by Kay Barton Interview with Chris DeArmitt, President at Phantom Plastics PETplanet: How long have you been interested in plastics and what is your personal story here? And was there a trigger to take action against false reports about plastics with facts? Chris DeArmitt: I have a PhD in chemistry and polymer science, so my experience as a plastic materials scientist goes back nearly 40 years. My personal interest in plastics and the environment was catalysed by my two daughters being taught misinformation at school. As a professional scientist and problem solver, I know that we cannot make progress without sound information. So, as a hobby I began fact-checking what we are told about plastics online because no-one else is checking it. PETplanet: Today, you are known in the industry as a corrective and enlightener when it comes to misinformation and misperceptions about plastics and plastic bashing, and you counter them omnipresently and scientifically. Where does your passion for tirelessly educating people based on facts and setting the record straight come from? Chris DeArmitt: As you say, I appear to have accidentally become the leading expert simply because no-one else have been foolish enough to devote thousands of hours unpaid to reading and sharing the science. To date I have read over 4,000 peer-reviewed studies and found that there is a huge gap between what we are told and what science says. My passion comes not from concern for the environment or plastics but rather it is a crusade for truth. PETplanet: On e.g. social media like LinkedIn, you get the feeling that you comment on anything and everything that could be accused of being a follower of plastic bashing, polemic and negative publicity about plastics and environmental issues. Do you sometimes feel like Don Quixote when you respond to the same unfounded topics for the umpteenth time? Chris DeArmitt: Dispelling myths with facts is a neverending task. Brandolinis Law states that it is vastly more work to dispel nonsense with evidence than it is to make up the nonsense in the first place. The former President of Greenpeace left in disgust and has made it his job to expose so-called environmental groups as charlatans whose business model is to tell lies for money i.e. donations. This has been extremely effective for them, so my one-man unfunded hobby is up against huge NGOs with hundreds of millions of dollars to fund proper marketing campaigns. The upshot is that I am destined to fail but as Elon Musk said, if something is very important, then one must try no matter the probability of failure. PETplanet: In your opinion, what needs to be improved in order to provide more education and a fact-based discourse globally in terms of understanding, perception and handling of plastics, to address their indispensable value in modern civilisation and who do you think is most likely to be responsible for this? Herbold Meckesheim GmbH Industriestrasse 33 I D-74909 Meckesheim I Tel: +49 6226 932-0 I [email protected] I www.herbold.com (QHUJ\\ (ႈFLHQW ƒ (DV\\ 0DLQWHQDQFH ƒ ([FHOOHQW )ODNHV Modular system solutions for automated PET washing lines"},{"@ID":29 "25 YEARS ANNIVERSARY 27 PETplanet Insider Vol. 25 No. 05/24 www.petpla.net 25 YEARS ANNIVERSARY EU Council and EU Parliament agree provisional deal for more sustainable packaging & less waste The EU Council presidency and European Parliament representatives have announced a provisional political agreement on a proposal for regulation on packaging and packaging waste. The stated aim is to tackle the increase in packaging waste generated in the EU while, at the same time, harmonising the internal market for packaging and boosting the circular economy. SOLUTIONS CONSUMER PACKAGING SBM VISIT US AT: Bottle zone | South Hall S17097 Packaging production and waste management generates a total turnover of € 370 bn in the EU. The current Packaging and Packaging Waste Directive was first adopted in 1994 and has been revised several times but, over the past decade, the total amount of waste has increased by nearly 25% and is expected to rise another 19% by 2030 if no action is taken. The expected increase in plastic packaging waste is 46% by 2030. The proposal extends across the full lifecycle of packaging. It establishes requirements to ensure safety and sustainability, requires that all packaging is recyclable and that the presence of substances of concern is minimised. It lays down labelling harmonisation requirements to improve consumer information. Sustainability and recycled content The provisional agreement introduces a restriction of food contact packaging containing per- and polyfluorinated alkyl substances (PFASs) above certain thresholds. It maintains the 2030 and 2040 headline targets for minimum recycled content in plastic packaging. Compostable plastic packaging and packaging whose plastic component"},{"@ID":60 "OUTER PLANET 58 PETplanet Insider Vol. 25 No. 05/24 www.petpla.net OUTER PLANET Coffee consumption meets PET recycling Drinking coffee while making an impact on PET recycling? At first glance, these might seem unrelated, but Cologne-based start-up Plastic2beans is bridging the gap. Every cup of their direct-trade coffee contributes to both ecological and social causes, with proceeds invested in building a circular economy in Ethiopia. Founded in 2018 by Dr KalieMartin Cheng, a polymer chemistry PhD, and Abiye Dagnew, a plastics engineer from Ethiopia, the start-up Plastic2beans emerged from a vision to promote responsible plastic usage globally. The founders identified a significant leverage point in countries where plastic consumption is rising rapidly but recycling technology and know-how remain limited. “When we started in 2018, the PET bottle collection rate in Ethiopia was 40%. However, by 2021, despite a doubling in PET bottle trade volume, collection capacities remained stagnant, leading to a collection rate of 20%,” shares Kalie Cheng. Nevertheless, infrastructure adjustments seem to be adapting to increased consumption levels, explaining the rise to 30% in 2022. Currently, recycled PET in Ethiopia is primarily exported to Eastern Europe for trays and fibres, while domestically manufactured PET bottles rely solely on imported virgin materials. Plastic2beans advocates keeping PET within the local food cycle, but faces hurdles as the use of rPET in bottles is not yet permitted in Ethiopia. “The government is working on legislation for rPET use in Ethiopia. We’ve been in contact with relevant stakeholders, providing information to support a favourable decision. There are some misconceptions to address,” explains Cheng. In collaboration with the German Development Cooperation (GIZ), the Federal Ministry for Economic Cooperation and Development (BMZ), and local industry partners in Ethiopia, the first PET SSP bottle-to-bottle recycling plant in East Africa is planned. Because of current political challenges in Ethiopia, the project is on hold, but partners continue to press for necessary legal reforms. “Our studies for GIZ and BMZ contributed to legislative changes, primarily driven by the NGO PETCO Ethiopia. The new law, effective since September 2022, prohibits coloured PET bottles, improving recycling capability by approximately 140 million kilograms annually. This also boosts material value, benefiting the poorest 1% who collect bottles on the streets,” Cheng reveals, noting visible reductions in street litter. The connection between coffee and PET recycling But how does coffee fit into all of this? Despite partnerships, financing the recycling plant in Ethiopia remains a challenge due to financial constraints. “We exchange knowledge and technology not for dollars, but for fair-trade organic coffee,” explains Cheng. Sourced from cooperatives where farmers cultivate coffee in mixed crops, Plastic2beans’ specialty coffee, 100% organic and sustainable, has a dual impact: better compensation for farmers compared to market prices in addition to the recycling efforts. The coffee can be enjoyed either at the Impact Café in Cologne, Germany, or ordered online through the company’s website. While the system is replicable in other countries, the focus now is on finalising the Ethiopian bottle-to-bottle plant. Interested companies, especially those willing to operate food-grade PET recycling plants in Ethiopia or other African countries, are encouraged to reach out to Plastic2beans. www.plastic2beans.com Founders Abiye Dagnew (third from left) and Dr Kalie Cheng (third from right) with their team in the Impact café in Cologne, Germany PET bottles in Ethiopia are sorted manually."},{"@ID":11 "25 YEARS ANNIVERSARY 9 PETplanet Insider Vol. 25 No. 05/24 www.petpla.net still fresh after 25 years corvaglia is delighted about the close partnership with PETplanet since 2001 and warmly congratulates on the 25th anniversary. www.corvaglia.com Drinktec concept, with an emphasis on beer as part of the whole drinks industry. So we quickly agreed that PETpoint would move to Munich and be one of the initiators of Drinktec’s broader focus. Petra and I moved into the Indian market from 2004. Petra: “I had never been part of such a strategic partnership before. We visited trade fairs in India, met processors, travelled the continent and developed ideas which is how DTI drink technology India was born”. Strategic thinking is still a feature of our work today. One major step forward has definitely been the Editours with which we have been visiting our readers on all the world’s continents for the past fifteen years. This brings us back full circle. Dear Gerd, I am delighted you are now travelling around the country with a roadshow and lorry for the first time this year (see article on p. 46), although I could have lent you our truck right at the outset. And on that note, Yours Alex Büchler Most of the PETpoint exhibitors in 2005 are still our valued customers today. A. Schulman | ADS | AGR Top Wave | Alcoa | Americhem | Arburg | Atelier Francois | Bekum | Bericap | Böhm | Clariant | ColorMatrix Europe | Color Plastic Chemie | Corvaglia | Crown Bender | Dr. Boy | Eastman Chemical | Eisbär | Elixir PET | Engel Austria | Erema | Fostag AG | G. H. Krämer | Gabriel-Chemie | Gala | GEM | gwk | Heinlein Plastik | Henckert Engineering | Holland Colours | HSM Pressen | Husky | Ingersoll-Rand | Intergulf Limited | Josef Mehrer | Kaeser Kompressoren | Kirin Techno-System | KKT | KLZ Servis | Kortec | Krauss-Maffei | Leobersdorfer Maschinenfabrik | M+F Keg-Technik | MAG Plastic | Maguire | MB | Mitsubishi Corporation | Mold & Hotrunner Technology | Motan | Nemuno Banga | Netstal | Neuman & Esser | Novapet | Nuga AG | Otto Hofstetter AG | Pelliconi & C. | Piovan | Plastec | Plast Engineering Knauff | Posimat | PPS | PreSens | Pressco | Priewe | Pühler | R.P. Injection | R&D Tool | Repi | Resilux | Röders | S + S Metallsuchgeräte | Schöttli | Seaquist Löffler | Siad | Siapi | Sidel | SIG | Smart Engineering | SMF Maschinenfabrik | Starlinger | Steca | Strautmann | Umwelttechnik | Tampofl ex | Tooling Preform Systems | Viroplastic | Voridian | Welger Recycling | Wentworth Technologies | Werner Koch Maschinentechnik | Zecchetti s.r.l. | The PETplanet booth at PETpoint trade show Essen, Germany"},{"@ID":50 "EVENT PREVIEW PETplanet Insider Vol. 25 No. 05/24 www.petpla.net 48 PET recycling conference sessions & awards fi nalists confi rmed Plastics Recycling Show Europe The Plastics Recycling Show Europe, the world’s largest exhibition and conference dedicated to plastics recycling returns to the RAI Amsterdam, The Netherlands from June 19-20, 2024. The event takes place across four halls for the first time and features a record 450 exhibiting companies and organisations. The comprehensive conference programme taking place across two theatres will cover in depth all the key issues currently facing the plastic recycling value chain in Europe and beyond. Conference sessions will cover the latest political, legislative, market and technological developments in plastics recycling. Key topics will include the future of plastic recycling in Europe, market analysis and forecasts, and in-depth analysis of the EU legislative landscape. In particular, the spotlight will be on the Packaging and Packaging Waste Regulation (PPWR), alongside dedicated sessions on measures to achieve recycled content targets and explore the latest advancements in chemical recycling. Panel discussions will promote the debate on possible strategies for enhancing and harmonising collection and sorting, design for recycling, and the latest updates on the advancement of plastics circularity on a global scale. Dedicated plastic streams focus sessions will tackle the challenges, issues and opportunities in the recycling of PET, PO films, PVC, HDPE, PP and ELV & WEEE. PET recycling focus session The speaker line-up for the PET recycling focus session has been confirmed: Helen McGeough, Senior Analyst and Global Analyst Team Lead, Plastics Recycling at Icis will cover European PET recycling market: state of play and trade dynamics. Aron Damen, Director Recycling, Cirec, will address tray-to-tray recycling. Jean-Emile Potaufeux, Technical Manager at Plastics Recyclers Europe will present on: RecyClass - standardising design for recycling for PET packaging. Casper van den Dungen, Plastics Recyclers Europe’s Vice President and Group Business Development Recycling Director, Resilux, is the session moderator. Organised jointly by Crain Communications and Plastics Recyclers Europe, the free-to-attend Plastics Recycling Show Europe is designed specifically for plastics recycling professionals. It brings together key players from the plastics and recycling sectors to showcase innovative technology, share best practices, network and do business. A broad cross-section of the industry is represented at the event including plastics recycling machinery and equipment suppliers, plastic material suppliers and compounders, preprocessors, mechanical and chemical plastics recyclers, waste management specialists and industry associations. Exhibiting companies also include every part of the PET recycling value chain. In 2023, PRS Europe attracted more than 8,500 visitors from across Europe and more than 80 different countries internationally. Plastics Recycling Awards Europe 2024 The Plastics Recycling Awards Europe recognise and celebrate achievement throughout the scope of the European plastics recycling industry. The awards offer an insight into current developments in recycled material usage, product design and innovative manufacturing. Finalists will feature in a dedicated area at the Plastics Recycling Show Europe in June at the RAI in Amsterdam. The lucky winners will be announced at the awards ceremony during the event. Awards categories Automotive, Electrical or Electronic Product Building & Construction Product Household & Leisure Product Plastic Packaging Product Product Technology Innovation Recycling Machinery Innovation Plastics Recycling Ambassador The Awards are free of charge to enter. www.prseventeurope.com Award finalists will feature in a dedicated area at the PRSE which is free to enter."},{"@ID":61 "The worldwide round trip with PET world in the Middle East In a spectacular project taking us well into 2024, we will be travelling in a wide variety of ways to various countries and regions of the Middle East with different mobile editors. There we will interview machine manufacturers, the supply industry, bottle and beverage producers, as well as PET recyclers and everyone involved in the process chain. What market-specific trends are there now or will arise in the future? What developments and technologies are in vogue on the consumer and plant construction site in some of the hottest regions of the world? What special requirements are there? What role do topics such as food safety, shelf life and sustainability play in PET packaging and how are companies preparing themselves for the coming years? This, and much more we will be discussing face-to-face with all the key players and then our results will be presented to you in a series of must-read reports in PETplanet Insider. Please join on this enchanting voyage to the world of PET in the Middle East. We look forward to welcoming you on board! Our previous Road Shows at a glance 2010-2011-2012-2013-2014-2015- 2016-2017-2018-2019-2020-2022 Interested in being visited? [email protected] Autumn 2023 - 2024 6 countries numerous interviews with PET companies Sponsors to date Editour The Middle East Roadshow"},{"@ID":30 "25 YEARS ANNIVERSARY 28 PETplanet Insider Vol. 25 No. 05/24 www.petpla.net 25 YEARS ANNIVERSARY represents less than five per cent of total weight are to be exempt from those targets. The Commission is required to review the implementation of the 2030 targets, to assess the 2040 targets’ feasibility as well as, three years after the entry into force of the regulation, the state of development of bio-based plastic packaging and to lay down sustainability requirements for bio-based content in plastic packaging. The new rules would set a maximum empty space ratio of 50% in grouped, transport and e-commerce packaging. Re-use and re-fill Reuse targets will be binding for 2030 and indicative for 2040 but vary depending on the type of packaging used by operators. Cardboard is generally exempted. The new rules also exempt micro-enterprises and open the opportunity for economic operators to form pools of up five final distributors to meet beverages re-use targets. The agreement introduces a general renewable five-year derogation from the re-use targets under specific conditions, detailed in the text. Take-away businesses are to be obliged to offer customers the choice to bring their own containers to be filled with cold or hot beverages or ready-prepared food, at no additional charge. By 2030, take-away businesses must endeavour to offer 10% of products in packaging formats suitable for re-use. Deposit return systems (DRS) By 2029, member states must ensure the separate collection of at least 90% per annum of single-use plastic bottles and metal beverage containers and are required to set up DRSs for them. States will be exempt if they reach a separate collection rate above 80% in 2026 and submit an implementation plan for achieving 90%. Restrictions on certain packaging formats There will be restrictions on certain packaging formats, such as fruit and vegetables, food and beverages, condiments, sauces within the HORECA sector, for small cosmetic and toiletry products used in hospitality, and for very lightweight plastic bags (e.g. those offered at markets for bulk groceries). Next steps The proposal will be submitted to the member states’ representatives within the Council (Coreper) and to the Parliament’s environment committee. If approved, the text will then need to be formally adopted by both institutions, following revision by lawyer-linguists, before it can be published in the EU’s Official Journal and enter into force. www.consilium.europa.eu"},{"@ID":54 "25 YEARS ANNIVERSARY 8 PETplanet Insider Vol. 25 No. 05/24 www.petpla.net 25 YEARS ANNIVERSARY How it all began 25 years ago Dear readers, Today, on the occasion of our anniversary, I would like to thank all those who have made PETplanet Insider what it is today, namely an integral part of the PET industry. In addition to the team and our many other supporters, I would also like to pay particular tribute to four people who helped implement key strategic decisions during the early years of the magazine. In chronological order: Twenty-seven years ago, Gerd Liebig, then Head of Marketing at Mannesmann Demag, now CEO of Sumitomo Demag, and I were in a car together, researching an on-site article about Demag injection moulding machines at Siemens Telefone in the former GDR. The wall that used to divide Germany had fallen but the infrastructure was still very basic. It took us around five hours to cover the 200 km journey – enough time for us to think about a new idea for a trading magazine. Gerd: “I will never forget that trip and the openness and breadth of our discussions. We came up with ideas, rejected and rethought them before finally creating the PETplanet Insider concept. In fact, it continues to do very well”. Gerd and I decided to abandon the idea of the classic horizontal trade journal. With such a concept, a PET bottler needs several magazines and has to select topics of relevance to them from a mountain of information, e.g. a plastics, beverage or mechanical engineering journal etc. The new idea was to develop a vertical magazine that only picked out specific elements from the whole production chain across all the above-mentioned specialist areas. PETplanet Insider was launched twenty-five years ago in 1999 with this concept. The response from the supplier industry was enormous as they no longer had to advertise their PET machines in 30 different trade journals. The narrow target group focus of PETplanet Insider enabled them to concentrate on one publication. Processors worldwide were also enthusiastic as shown by their comments, some of which were sent by postcard I thought that Gerd and I had found the philosopher’s stone until I met Romeo Corvaglia on a fact-finding tour to Retal in Dnepropetrovsk, Ukraine in 2000. He already knew us, having seen our first issue at one of his customers in Indonesia. It covered the whole process – material, preform, stretch blow moulding, filling, drying line. “BUT” he pointed out “every bottle needs to have a closure, so why don’t you write about that as well?”. The scales fell from my eyes. Yes, of course, especially as I had completed an internship over several weeks at Alcoa in Worms during my mechanical engineering studies and had designed caps, most likely for glass bottles. Joining our project was Wolfgang von Schroeter, CEO of Mannesmann Demag, who took early retirement at 60, built a finca in Mallorca, explored the world on his motorbike and was bored at 61. That is when I got him interested in our Top Talk series. From the age of 62, he travelled around the world for us to interview all the greats. His many years of journalistic work in South Africa stood him in good stead when it came to writing and, in so doing, put PETplanet Insider into the minds of really big names. His period of boredom was over. We created a trade fair concept for the magazine. And where would be the best place for it? The Interpack fair in Düsseldorf. The project manager at the time Erhard Wienkamp, now Managing Director of Messe Düsseldorf, said that our focus on plastics meant that the K’ trade fair was a more appropriate forum for us. I said no, the readers were all going to Interpack so I rented a few rooms at Messe Essen, organised a shuttle bus service and, hey presto, PETpoint was born. This caught the attention of Petra Westphal, then new as project manager at Drinktec and now Executive Vice President Yontex, the organiser of Brau and Drinktec. Petra (affectionately written as PETra) wanted to expand the old Wolfgang von Schroeter (left) and Alexander Büchler (right) visit Volker Kronseder at the Krones premises in Neutraubling, Germany."},{"@ID":37 "EDITOUR PETplanet Insider Vol. 25 No. 05/24 www.petpla.net 35 EDITOUR 35 The company entrance of Makkah Water Krones Ergobloc L 29/25 closures from a Netstal Elion lines and one Sidel line. Three new Ergobloc systems were also part of the modernisation, so that capacities of 4x 81,000, 1x 52,000 bph, 1x 49,500 and 1x 49,000 bph are now available. “Our most popular format is the 330 ml bottle,” said Mr Kumaresh. www.sacmi.com Product design Product development Product validation Industrial production plant Process & quality control On-site and start-up assistance After-sales and Customer service SACMI 4.0 THE COMPLETE CLOSURE, PREFORM AND CONTAINER SOLUTION FOR YOUR SMART FACTORY E N D L E S S I N N O V A T I O N S I N C E 1 9 1 9"},{"@ID":46 "TRADE SHOW REVIEW PETplanet Insider Vol. 25 No. 0/24 www.petpla.net 44 Microwave assisted depolymerisation recycling technology On March 7, 2024, Gr3n invited customers and companies involved in the development of its Microwave Assisted DEpolymerisation (MADE) recycling technology to the launch of the industrial demonstration plant. The company completed the last stage before commercialisation of its new technology. Gr3n has developed a new alkaline hydrolysis process to recycle all packaging and textile PET waste into building blocks with its technology, which was installed on Gr3n’s research and manufacturing facility in Albese con Cassano, near Lake Como, Italy. “This is another step ahead for Gr3n, as it will allow us to increase our capacity and then test the material, that we can produce with our own polymerisation line, for several applications ,” said Dr Maurizio Crippa, Gr3n Founder and Chief Executive Officer. “When you develop a new process, the upscaling is a pivotal step. Being able to receive feedstock and transform it into new PET chips at scale will help us demonstrate that obtaining pure monomers is the only way to obtain virgin like PET”. The demo plant will be able to shred the input material, depolymerise it, purify TPA and MEG using a solid process, and then producing new PET chips via a dedicated 500 kg polymerisation reactor. This new industrial demonstration plant was designed as the industrial plant, with technical solution that can be easily scalable, and in some cases, like crystallisation and distillation, using “state of the art” technology. An initial hydrolysis has been successfully realised, confirming the upscaling of the process; the optimisation of the operating parameters is still underway. Maurizio Crippa, PhD, CEO of Gr3n, welcomed the audience. With Netstal’s leading preform injection molding technology. Our PET-Line impresses with broadest compatibility, maximum throughput, exceptional ĆďĆēĈĚ ĆħĄĊĆďĄĚ ĐđĕĊĎĂč đēĐĄĆĔĔĊďĈ Đć ē÷ìû Ăďą other challenging recyclates, and with its intuitive Axos control unit. Wemaximize your added value Preforms"},{"@ID":8 "PETnews 6 NEWS PETplanet Insider Vol. 25 No. 05/24 www.petpla.net Conversion of Corvaglia Closures Eschlikon’s product portfolio 90% completed The company Corvaglia, headquartered in Thurgau, Switzerland, has played a pioneering role in the development and production of tethered caps. The development of the first tethered cap models began even before the official publication of the EU directive. Since then, Corvaglia has continuously worked on solutions and has been able to convince well-known brand owners of the effectiveness of its products. As one of the first suppliers of tethered caps on the continent, Corvaglia has secured a firm place for itself in this product segment. The company’s own cap production in Eschlikon was also gradually converted to tethered products as part of this process. Since March 1, 2024, more than 80% of the closures produced in Eschlikon now meet the requirements of EU Directive 2019/904. Around 10% of the closures produced in Eschlikon are exported to non-EU countries and will remain non-tethered for the time being. The remaining 10% will be converted by July. The development of lightweight closures to reduce unnecessary plastic has always been part of Corvaglia’s work. This approach has also been consistently pursued with tethered caps. With the latest tethered caps, Corvaglia is proud to make a further contribution to reducing material and energy consumption and thus lowering CO2 emissions for beverage packaging. www.corvaglia.com Carbios celebrates the groundbreaking of its PET bio-recycling plant Carbios celebrated the groundbreaking ceremony for the world’s first PET bio-recycling plant on April 25, in the presence of representatives of local authorities, partner brands and industrial partners. Located in Longlaville, in the Grand-Est region of France, Carbios’ first commercial plant is intended to play a key role in the fight against plastic pollution, offering an industrial-scale solution for the enzymatic depolymerisation of PET waste in order to accelerate a circular economy for plastic and textiles. The plant will have a processing capacity of 50kt/a of prepared waste when operating at full capacity. Work is progressing on schedule with significant quantities to be delivered to customers in 2026. Carbios’ technology enables PET circularity and provides an alternative raw material to fossil-based monomers, giving PET producers, waste management companies, public bodies and brands a solution to meet regulatory requirements and their own commitments to sustainable development. The plant will have the capacity to process 50,000t/a of prepared PET waste (equivalent to 2 billion coloured bottles, 2.5 billion food trays or 300 million T-shirts). The plant will create 150 direct and indirect jobs in the region. In October 2023, the company secured permits to build and operate the site. Construction of the factory, situated on land acquired from Indorama Ventures on February 14, 2024, is underway. Carbios and De Smet Engineers & Contractors (DSEC) announced their collaboration in February 2024 to manage construction. Feedstock supply agreements, including with Citeo and Landbell Group, will ensure the availability of raw materials. The plant’s strategic location near the borders of Belgium, Germany, and Luxembourg provides easy access to waste supplies. www.carbios.com Repi appoints Michael Thiessenhusen as new Managing Director in Repi GmbH Repi, a manufacturer of performance additives and liquid colours for polyurethanes and thermoplastics, announces the appointment of Mr Michael Thiessenhusen as new Managing Director of Repi GmbH, based in the North of Germany. In his new role, Mr Thiessenhusen will further support the upcoming strategic development of the Repi Group in the EMEA region and globally. He joins Repi with a substantial background made up of over 40 years’ experience in the chemical industry, specifically in the colourants and additives for thermoplastic applications. Having started his career at Zipperling Kessler & Co. (Masterbatch and Compound manufacturer), he covered several operational and managemen t positions with growing responsibi l ities within Clariant, then in Avient Corporation, where he held the position of Sales Director Europe. Repi wi l l leverage his extensive know-how and network in the colourant and additive industry to boost its strategy to be a reference partner for liquid colour and performance additive solutions globally. www.repi.com"},{"@ID":5 "imprint EDITORIAL PUBLISHER Alexander Büchler, Managing Director HEAD OFFICE heidelberg business media GmbH Hubweg 15 74939 Zuzenhausen, Germany phone: +49 6221-65108-0 [email protected] EDITORIAL Kay Barton Heike Fischer Gabriele Kosmehl Michael Maruschke Ruari McCallion Anthony Withers Editorial & WikiPETia. info [email protected] MEDIA CONSULTANTS Martina Hirschmann [email protected] Johann Lange-Brock [email protected] phone: +49 6221-65108-0 LAYOUT AND PREPRESS EXPRIM Werbeagentur Matthias Gaumann www.exprim.de READER SERVICES [email protected] PRINT Chroma Druck Eine Unternehmung der Limberg-Druck GmbH Danziger Platz 6 67059 Ludwigshafen, Germany WWW www.hbmedia.net | www.petpla.net PETplanet Insider ISSN 1438-9459 is published 10 times a year. This publication is sent to qualified subscribers (1-year subscription 149 EUR, 2-year subscription 289 EUR, Young professionals’ subscription 99 EUR. Magazines will be dispatched to you by airmail). Not to be reproduced in any form without permission from the publisher. Note: The fact that product names may not be identified as trademarks is not an indication that such names are not registered trademarks. 3 PETplanet Insider Vol. 25 No. 05/24 www.petpla.net Passion for PET, but above all for you! Dear readers of PETplanet Insider, I have valued Alexander Büchler for 38 years, first as a fellow student and then as a personal friend, and as an editorial colleague for 30 years. As a publisher myself for twelve years, I have been able to follow and accompany the success story of PETplanet for the full 25 years. Publishing flair means thinking about the reader, knowing their interests and always creating new benefits for them with a medium. Publishing intuition also means knowing the markets, recognising trends and keeping an eye on the interests of the advertising industry. Publishing success, customer orientation with a clear focus on reader benefit, cannot always be achieved by the publisher alone. Even if readers and advertisers provide impulses, partnerships with industry associations, trade fair companies and conference organisers help to pick up impulses and jointly launch supplementary or completely new information formats. Publishing thrives on networking and experience, but also on the courage to try something new. The passion of the people involved is essential. Alex and his team have developed a solid feel for developments, a keen eye for the big picture, the necessary sensitivity for commercial matters and the ability to optimise every detail – consistently and with great continuity in terms of personnel. With this in mind, I have the greatest respect for the first 25 years of PETplanet Insider and for accompanying the booming PET industry. I wish Alex, his staff and the second generation at PETplanet continued success – in your interests: in the interests of our readers. Markus Lüling lueling@k-profi .de www.k-profi .world"},{"@ID":40 "BOTTLING / FILLING PETplanet Insider Vol. 25 No. 05/24 www.petpla.net 38 Kazakh mineral water bottler on expansion course with Ukrainian technology From regional to national On the southern tip of Kazakhstan, near the border with Uzbekistan, not far from the small town of Saryagash, lies the water bottler Alex Saryagash. Founded in 1993, the company has been bottling water for more than 30 years and was a pioneer in Kazakhstan in bottling in plastic. The water bottled at Alex Saryagash is a natural, mineral-rich and soft drinking water with, according to the company, a high content of active micro-constituents. The source comes from an artesian basin in the Turkestan region, the Pritashkent mineral water deposit in the Saryagash district. Here, the water is extracted from a depth of about 2,000m. Its content of active micro components and its salt content of up to 1 g/dm3. It can be consumed daily in any quantity both for medicinal purposes and as a refreshing drink. Alex Saryagash is available in transparent PET bottles of 0.5 l, 1 l and 1.5 l, both carbonated and non-carbonated. Alex Saryagash has been working at national level since 1995. Since its founding, the company, which started with 45 employees at the time, has grown immensely, employing a total of almost 130,000 people during that period and filling 2.1 billion litres of water into 1.4 billion bottles by 2022. In the course of its existence, Alex Saryagash developed new product formats and expanded its beverage portfolio for a growing population. Since 2007, the bottler has relied on the Ukrainian machine manufacturer PET Technologies. The cooperation began with a large order for a total of 18 APF- 4 blowmoulding machines, which Alex Saryagash had installed in his factory and almost all of which are still in operation today. Later came two more PET Technologies APF6004 blowmoulding machines, each equipped with four cavities like the older models in the factory and with an output of 6,000 1.5 l bottles per hour, which is almost twice as high. In 2021, the company renewed its logo and, accordingly, its bottle labels, and continued to push its growth through large-scale advertising campaigns in addition to technical investments. On the technical side, blow moulds for the redesigned 1.5 l bottles were produced and equipment supplied by PET Technologies. Since 2022, the now once regional brand has been supplying the water market on a national level. www.alexsu.kz www.pet-eu.com Blow moulding equipment from PET Technologies"},{"@ID":3 "No.5 2024 www.petpla.net D 51178; ISSN: 1438-9452 13 . 05 . 24 M A G A Z I N E F O R B O T T L E R S A N D B O T T L E - M A K E R S I N T H E A M E R I C A S , A S I A , E U R O P E A N D A L L A R O U N D T H E P L A N E T PETplanet is read in 159 countries MARKETsurvey Suppliers of preforms & inspection systems Page 29 EDITOUR LABELLINGPage 39 Page 32"}]}}
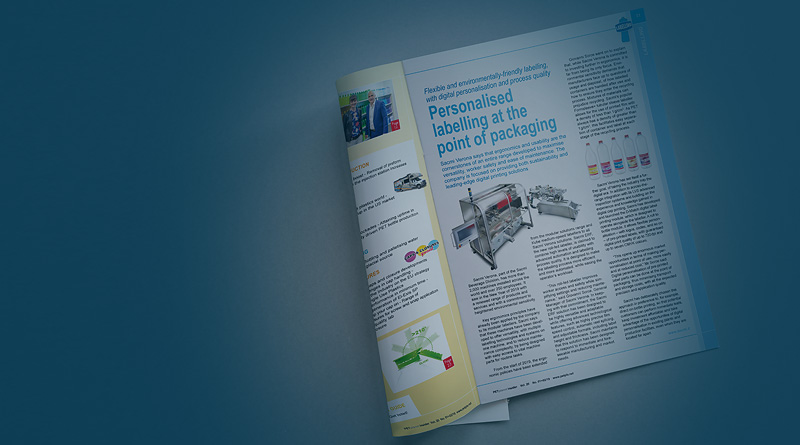