{"pages":{"page":[{"@ID":57 "The worldwide round trip with PET world in the Middle East In a spectacular project taking us well into 2024, we will be travelling in a wide variety of ways to various countries and regions of the Middle East with different mobile editors. There we will interview machine manufacturers, the supply industry, bottle and beverage producers, as well as PET recyclers and everyone involved in the process chain. What market-specific trends are there now or will arise in the future? What developments and technologies are in vogue on the consumer and plant construction site in some of the hottest regions of the world? What special requirements are there? What role do topics such as food safety, shelf life and sustainability play in PET packaging and how are companies preparing themselves for the coming years? This, and much more we will be discussing face-to-face with all the key players and then our results will be presented to you in a series of must-read reports in PETplanet Insider. Please join on this enchanting voyage to the world of PET in the Middle East. We look forward to welcoming you on board! Our previous Road Shows at a glance 2010-2011-2012-2013-2014-2015- 2016-2017-2018-2019-2020-2022 Interested in being visited? [email protected] Autumn 2023 - 2024 6 countries numerous interviews with PET companies Sponsors to date Editour The Middle East Roadshow"},{"@ID":54 "40 EVENT REVIEW PETplanet Insider Vol. 25 No. 07+08/24 www.petpla.net EVENTreview Plastics Recycling Ambassador of the Year: Erica Canaia, Fimic PETplanet: Erica, congratulations! You were honoured as Plastics Recycling Ambassador of the Year at this PRSE! What does this award mean to you personally and professionally? Erica Canaia: For me recycling is a mission. When I started many years ago in 2011, I didn’t have any idea about the efforts that all recyclers put into improving recycling and avoid waste in general in the environment. Every day, I try to speak about something other than plastic, l’m also putting my life on social media explaining the difficulties that there is to balance work and family for a woman entrepreneur with a child. I think that this is also useful because many people have reached out to me to thank me for my posts, saying they are helping them to reflect and to think deeply about certain topics. For this reason, l feel that social media and my activity can be useful for a lot of people. PETplanet: You are CEO of Fimic and co-founder of ‘Are you R’, a project to raise public awareness of the importance of plastics recycling. Can you tell us a bit about this project? Erica Canaia: Are you R is a European project aimed at increasing public awareness of the importance of plastics recycling, of the environment generally and the knowledge of the benefits associated to the recycling of plastic materials. Plastic is everywhere around us, and it’s easily available. Moreover, it has assumed a major importance over the years and it’s often unthinkable to replace it. It makes our lives easier every day in many ways. It’s really easy to use, but it’s also easy to throw it away. By using it correctly instead, we can make sure it’s recycled, so that new products can be created. Are you R was created under the auspices of a number of Italian companies, which have been operating in this sector for many years, together with Plastics Recyclers Europe (PRE). Through a variety of content, ranging from current events to technology, from economics to lifestyle, Are you R has been talking about the evolution of plastic materials and their re-use from multiple perspectives. Only if you know how it works, can you improve people’s habits. Plastic waste is a major resource. Its management and appreciating its value are the key to a more sustainable world. PETplanet: How important is public awareness and education in the success of plastics recycling initiatives? What strategies have you found effective in this area? Erica Canaia: Public awareness and education are absolutely crucial to the success of plastics recycling initiatives because when people understand the benefits of recycling and how to do it correctly, they’re more likely to participate in recycling programs. This increases the volume of recyclable materials collected, making the process more efficient and cost-effective. PETplanet: In your opinion, what are the biggest challenges currently facing the plastics recycling industry and how do you think these can be overcome? Erica Canaia: In my opinion the plastic recycling industry should be speaking louder. Because we have the information and the knowledge, we can identify when companies are applying greenwashing actions, such as producing products that are not recyclable at all but nonetheless promoting them with labels suggesting they are recyclable. We need to demonstrate to people, to the consumer whether or not a product is recyclable. Educate and tell the truth about plastic, it’s not an evil destructive material as it has been demonised. PETplanet: What are your future goals and aspirations in the field of plastics recycling? Are there any specific projects you are currently working on? Erica Canaia: I’m working every day on speaking the truth about plastics, that’s my main goal: fight all the lies about this material and demonstrate how precious it really is. PETplanet: Thank you very much Erica! PRSE 2024: Visitors increase by 32% Confirming Plastics Recycling Show Europe’s position as the world’s largest event dedicated to plastics recycling, the exhibition and conference that took place recently in Amsterdam, the Netherlands, attracted more than 10,000 attendees for the first time in its history. With more than 480 exhibiting companies and organisations (155 of which exhibiting for the first time), and over 70 expert speakers, the event’s total attendance over two days was a record 11,273. “Interest in PRS Europe continues to grow and for 2025 we are moving to the RAI’s flagship Halls 1 and 5. Exhibitors have already booked most of the additional space and we’ll have to look at how we can make even more space available to meet the demand,” said Matt Barber, Global Events Director at Crain Communications. The Plastics Recycling Show Europe brings together key players from the plastics and plastics recycling sectors to showcase innovative technology, share best practices, network and do business. Every part of the circular plastics value chain is represented at the event, including plastics recycling machinery and equipment suppliers, AI-powered sorting technology, plastic material suppliers and compounders, pre-processors, mechanical and chemical plastics recyclers, waste management specialists and industry associations. Plastics Recycling Show Europe moves to Halls 1 and 5 at RAI Amsterdam from April 1-2, 2025. Building on the growing success of PRS Europe, Plastics Recycling Shows are now being held in four global locations annually: Amsterdam, Dubai, Singapore and Mumbai. www.prseventeurope.com Erica Canaia, CEO of Fimic"},{"@ID":41 "EVENT REVIEW PETplanet Insider Vol. 25 No. 0/24 www.petpla.net 39 The series is also equipped with the company’s own Auto-Pilot control unit, which automatically adapts to material properties such as density or moisture and automatically regulates the feed pusher, cutter-compactor-extruder and pelletising speed without external intervention, which is particularly beneficial for unplanned downtimes, especially during melting processes. The supplier has also upped the ante in terms of service, advertising its new 360° service at the trade fair, which is specially tailored to the American market. The service is said to cover all aspects of the recycling process and ensure optimum machine performance and uptime through various support services, including reactive maintenance, wear and spare parts management, pre-installation support, installation, commissioning training, preventative maintenance, process and machine assessment and customised retrofit solutions. In addition to installations and maintenance, key features of the 360° service include ‘Rapid Response Support’, a 24/7 technician to respond to phone enquiries within one hour and remote access to machines for fast and effective problem resolution, a comprehensive parts inventory managed from the Atlanta location with over US$500,000 worth of parts available, and the offering of customised retrofit solutions of existing components. www.ngr-world.com Cutter-compactorextruder combination Next Generation Recyclingmaschinen GmbH (NGR) not only celebrated the tenth anniversary of its Liquid State Polycondensation (LSP) recycling technology, known under the P:React brand and with currently 60 systems installed worldwide, but also presented its further developed, modular cutter-compactor-extruder combination, ‘C:Gran’, for the production of pellets from plastic waste. The machine series is available in eight different sizes for different material throughputs from 300kg to 3t/h. According to the manufacturer, the system processes both dry, clean industrial waste as well as moist and heavily contaminated waste equally reliably, from BOPP and BOPET films, which are produced as production waste, to materials from washing plants and heavily printed films with high degassing requirements. Stefan Lehner, Product Manager for Post Consumer Recycling at NGR, explained: “The series has two independent extruder drives, which enable an optimum speed setting for both the melt and the degassing extruder. This configuration optimises the degassing and melting performance at lower melt temperatures due to the short processing unit. In addition, a clean separation between extruder and cascade with melt filtration in between ensures that no impurities get past the melt filter, resulting in a very stable process and preventing the production of off-specification pellets. Recycling and compounding is also possible in a single step when twin screw technology is part of the system.” The modular design also allows the retrofitting of additional degassing zones or the integration of a cascade with a second filtration stage. The enlarged cutter compactors of the C:Gran series are claimed to ensure high throughput values and high process stability with different input qualities. The cutter-compactor can also be equipped with a special dry boost for high input moisture levels, which increases the drying performance of the material. Another feature cited by NGR is the cascade configuration with the Power Venting Section, which was developed for more complex degassing challenges. This device is crucial for processing materials with high impurity and moisture content, as it removes volatile impurities from the polymer melt for good pellet quality, according to NGR. SB Wet Granulator Step Dryer Hydrocyclone density separation Hot Wash Step Pre-wash Drum Pre-sorting Your reliable partner for high-quality plastic recycling Modern PET washing systems from Herbold Meckesheim Herbold Meckesheim GmbH I Industriestrasse 33 I D-74909 Meckesheim I Tel: +49 6226 932-0 I [email protected] I www.herbold.com Visit us in Brussels, Belgium, at the Plastics Recycling World Expo, Booth 3.R430"},{"@ID":51 "7 NEWS PETplanet Insider Vol. 25 Krones Recycling is spun off as an independent subsidiary company With 25 years’ experience in the field of recycling, Krones has now taken the decision to pool its recycling expertise in the independent subsidiary Krones Recycling GmbH from July 2024. A logical step, as Krones CEO Christoph Klenk explains: “The spin-off will enable Krones Recycling to develop faster and in line with market requirements. Because in line with our claim ‘Solutions beyond tomorrow’, this division makes a decisive contribution to protecting the environment by returning plastic waste to the value-added cycle.” In addition, thanks to leaner processes and structures, the new company will be able to respond more quickly to changes in the constantly changing recycling market, says Michael Gotsche, Managing Director of Krones Recycling GmbH: “The newly founded company offers us the necessary flexibility and scope for action to be able to implement decisions in a customer-oriented, fast and optimised manner.” A large number of plastics such as PET, PE, PP and PS are already being processed on Krones Recycling’s lines worldwide. “Our vision is to make a daily contribution to a global circular economy for all plastics by offering our customers sustainable and profitable recycling solutions,” says Michael Gotsche, describing the overarching business objective. Consequently, Krones Recycling will continue to conduct intensive research into new innovations at its in-house Recycling Technology Centre. There, tests on the recyclability of various plastics, including adhesives and colours, can also be carried out under real conditions on behalf of customers. www.krones.com CREATING FUTURE STANDARDS Japan’s leading Aseptic PET Filling System Provider. Our website Our solution high quality reliable technology safe & secure"},{"@ID":6 "PETcontents 4 PETplanet Insider Vol. 25 No. 07+08/24 www.petpla.net 07+08/2024 EDITOUR 10 From 0 to 100 - Two Saudi water brands take off MATERIALS / RECYCLING 12 Chemical innovation supports growing rPET demand 14 PET tray packaging recycling - The CircuTray-UP project 16 Colour correction in rPET preforms 17 PET to monomer via glycolysis reaction 18 Closed-loop recycling of HDPE - Pellets for food contact 19 Additives and colour management solutions for recycled polymers CAPS & CLOSURES 21 The tethered cap story - A blessing and a curse at the same time? 24 Implementation insights - Solving tethered closure challenges 25 Ultralight neck finish debut - Sipa launches high-performance GME 30.40 LW neck finish MARKET SURVEY 27 Suppliers of 2-stage SBM machinery EVENT REVIEW 30 NPE review - part 2 37 Linear blow moulder in a compact design 38 Flexible material drying and dosing systems 39 Cutter-compactor-extruder combination 40 Review on Plastics Recycling Show Europe, PRSE Amsterdam, NL OUTER PLANET 54 Listen to Moon Music - The Ocean Cleanup & Coldplay announced LP made using recycled river plastic BUYER’S GUIDE 48 Get listed! INSIDE TRACK 3 Editorial 4 Contents 6 News 20 Recycling products 47 Patents RECYCLING Page 18 Page 24 Page 40 EDITOUR"},{"@ID":43 "41 EVENT REVIEW PETplanet Insider Vol. 25 No. 07+08/24 www.petpla.net Bottle-to-bottle recycling solutions and more Boretech highlighted its comprehensive PET bottle-to-bottle solutions including the latest advancements in equipment, engineering services, and recycl ing systems for rigid and film plastics. A key innovation featured was the upgraded ES process for PET bottle recycling. This process features an intensive washer that builds on the existing integrated module, enhancing washing efficiency whi le reducing overall equipment investment. The upgrade has also been designed to minimise the equipment’s footprint and to simplify inline process operations. Experimental comparisons have shown that the L values and b values of the washed rPET flakes remain within the original quality standards, says Boretech. In response to the growing interest in PET tray recycling, the company is developing an advanced washing process aimed at increasing the yield rate of tray recycling. Two functional units are currently undergoing lab-scale testing and have shown promising results. With the application for patents on centrifugal drying and intensive washing processes, Boretech is confident that the complete washing line will be unveiled in 2024. “While PET bottle recycling has reached saturation in regions like China and Japan, the use of PET trays is still substantial. However, due to some inherent characteristics, recycling trays can be challenging, though efforts are ongoing,” explained Alan Ou, Vice G.M. Product Director Boretech. Additionally, Boretech sees significant potential in the recycling of hard-to-recycle plastics, such as multilayer flexible films and plastic textiles, through chemical recycling technology. The PRSE exhibi t ion exceeded Boretech’s expectations in terms of the number and quality of visitors. The company noted significant interest in its complete PET bottle washing solutions, particularly the newly promoted ES washing technology and equipment, but there were also numerous inquiries about recycling HDPE and PP, and PET trays. www.bo-re-tech.com Boretech’s booth at PRSE Recycled resins portfolio EcoBlue Limited, a pioneering recycling company based in Thailand, provides rPET, rHDPE, and rPP from post-consumer and industrial waste through mechanical recycling. Key products showcased at PRSE include Efsa and US FDA-approved recycled PET resins for food applications and US FDA-approved recycled PP and HDPE resins and other value added recycled resins. “The new Packaging and Packaging Waste Regulation (PPWR) in Europe has sparked significant interest in our Efsa approved recycled PET grades. The PPWR aims to reduce packaging waste and increase sustainable material use, advancing circular economy practices. Volatile market conditions last year decreased rPET demand in Europe, but PPWR regulations have revived interest, as seen at the PRSE. The EU’s mandatory recycled content targets prompted visitors to begin qualifying recycled PET for their products. We also saw a fair bit of interest in our rPP and rHDPE grades as not many recyclers are able to provide these resins with comparable quality,” said Kirtan Pandya, Business Development Manager at EcoBlue. “We understand customer needs and are investing in advanced production technologies and quality labs to ensure top-quality recycled resins for our customers.” The company collaborates with major brands globally. Sustainability is central to EcoBlue’s mission. The “People First” program, part of this commitment, empowers participants within the plastics collection community through special incentives, driving social and economic impact. Codes of conduct and regular audits ensure compliance with social and ethical standards. www.ecoblue.co.th F.l.t.r.: Kirtan Pandya, Business Development Manager, Ruchi Jain, Head of Marketing, Pranay Jain, Founder & CEO at EcoBlue"},{"@ID":25 "CAPS & CLOSURES 23 PETplanet Insider Vol. 25 2) Manufacturing department to follow the requirements of the market and respect the time expected by the Directive. 3) Investment into the commissioning department of moulds and machines to support the start-up of the new production lines and training the operators deputed to run the machines. PETplanet: Mr Nanetti, after the discussion at this conference and of course in general, do you see a market outside the EU for the tethered cap solution? Perhaps you already have had enquiries from customers outside the EU? Mr Nanetti: Tethered closures have been requested from countries outside the EU. In this case the choice is at bottler level and we have evidence that some bottlers in some foreign countries are already delivering tethered closures to their market. The trend is increasing. PETplanet: Mr Nanetti, with your long experience in the plastic packaging business, in general, how do you see the impact of bureaucracy, regulations and obligations etc. on the plastic packaging industry? And what are the consequences? Mr Nanetti: I see an increasing lack of coordination between all the regulations and directives and the varied topics doing the rounds of the plastic beverage world. Initiatives like DRS, lightweight, bottleto-bottle and also cap-tocap, use of an increasing amount of recycled resins, PPWR, mechanical vs or in addition to chemical recycling,… and many many more have not been clarified down in a fully comprehensive system where all these activities are properly thought through with the ultimate aim of delivering the highest output. The consequence is that the industry sometimes is driven to make some moves forward and then have to reconsider this and move backwards. The open discussion between DRS and tethered closures is a clear example of this. Regulations, obligations, norms and prescriptions are needed to define a path to circularity, sustainability and finally, in simpler terms, to preserve our planet. But all these activities must play in unison like the different instruments in an orchestra. PETplanet: Many thanks to both of you for your time and your assessment! www.sacmi.com www.wisecap.eu"},{"@ID":17 "MATERIALS / RECYCLING PETplanet Insider Vol. 25 No. 07+08/24 www.petpla.net 15 With the technologies available, a recycling cycle from waste to food packaging is to be established. The aim is to provide tray packaging produced from recycled single and multilayer PET trays as early as 2026, which will replace today’s PET trays when they are ready for the market (Fig. 1). Municipal plastic waste is sorted using near-infrared sensors in the recycling centres. This results in waste fractions 328-1 to 328-5, which are heavily enriched with PET, the latter consisting mainly of PET trays. This waste is usually cut into flakes and washed for further processing. This task is tackled by ZWS Recycling. Due to the higher stiffness and brittleness of PET trays compared to PET from bottles, a large amount of fines accumulate during washing, which are often of limited use for further processing. A reduction in fines is to be achieved by developing suitable washing technologies with a design optimised to minimise material breakage. With Unisensor’s flake-based sorting technology, the flakes are sorted into a high-purity single-layer PET fraction and a multi-layer PET fraction, both of which are ready for further processing by mechanical and solvent-based recycling. The Fraunhofer IVV’s solventbased recycling aims to selectively remove the non-PET components from the multi-layer flakes to produce pure PET flakes. Previous projects have already demonstrated the applicability of such a process for mixed plastics. In an earlier project, PET flakes were obtained that are suitable for the production of films. With this film, it was also possible to produce three-dimensional trays using a thermoforming process (Fig. 2). This solvent-based recycling process, which is currently being carried out on a small technical scale, is to be scaled up to the size of a pilot plant in order to gain deeper insights for further scaling up to an industrial scale. At the same time, packaging orientated to the “Design for Recycling” guidelines is being developed that can contain a recycled content that exceeds the prescribed minimum. Such a design requires functional barrier technologies to ensure that there is no contact between the product and the rPET, as required by European legislation and necessary for modified atmosphere packaging. Suitable functional barrier technologies that prevent the migration of substances from rPET into the product during the typical storage period have already been identified and investigated prior to this project. Of the functional barrier technologies investigated, coextruded virgin PET film, PET lacquer, laminated virgin PET film and SiOx coating, both laminated virgin PET film and SiOx coating offer similar performance, although only laminated PET film can be thermoformed after application. Usually PE and EVOH are used for such barriers, but to make this packaging mechanically recyclable, a laminated PET film is chosen as the functional barrier. After washing and processing, processed and purified mono- and multilayer waste PET fractions are to be turned back into a film consisting of a sandwich structure with at least one laminated PET virgin material layer for food contact. Once Reifenhäuser has obtained the films, silverplastics will thermoform them into new trays, which can be tested on existing packaging lines. In order to prove suitability for food contact, the recyclate is analysed for non-intentionally added substances (NIAS) and the barrier is tested using a migration test in order to collect data for modelling potential storage durations. In order to demonstrate the ecological viability of the recycling chain, the processing chain is analysed and evaluated by the Öko-Institut using a life cycle assessment, whereby the recycling scheme competes with incineration with energy recovery and the production of new, modern virgin PET trays. A use case with a recyclate content of 66 per cent by weight and at least one additional life cycle is assumed. In addition, the production of the developed packaging is evaluated from an economic point of view. As the status of recycling technologies for PET trays poses a significant problem for the entire value chain involved with PET trays, cooperation is welcome. Quarterly meetings are planned for all those involved in the PET tray value chain. www.ivv.fraunhofer.de Fig. 2: From PET tray flakes to new PET trays by solvent based recycling"},{"@ID":35 "33 EVENT REVIEW PETplanet Insider Vol. 25 No. 07+08/24 www.petpla.net Inspection systems for the packaging industry The German inspection system manufacturer Intravis was represented at the NPE with several exhibits at different trade show booths. In addition to its own booth in the South Hall, where the company showcased its Labelwatcher 360° for label quality control, and its Spotwatcher for inline bottle and container inspection, interested trade show visitors were also able to get a glimpse of a Capwatcher Q-Line at Netstal, an IMLwatcher at Milacron, a Premon at Husky and an IMLwatcher Medical at Arburg ‘in action’. The Capwatcher Q-Line worked on Netstal’s world (record) innovation, a CapLine 4500 based on the Elion systems, with 128-cavity mould and a cycle time of 1.9 seconds. The Intravis machine reliably inspected up to 80 caps per second. At Milacron, Intravis’ IMLwatcher was used on a 2-cavity system for the inspection of 5-gallon buckets, integrated into the robotics of Beck Automation. At the Husky booth, the Premon monitored the preform colour, body and sealing surface directly behind an all-new HyPET 400 HPP6e. The application demonstrated a 144-cavity mould at a cycle time of 4.5 seconds and a potential output of over 100,000 preforms/h. The focus of the application, however, laid on the closed loop application for rPET colour. At the Arburg booth, the IMLwatcher Medical was integrated into a robot of Beck Automation and inspected transparent medical tubes. At Intravis’ own trade show booth, we spoke at length with company owner and CEO Dr Gerd Fuhrmann and Janina Orlowski, Head of Product Management & Marketing, about innovations, further developments, and core exhibits. According to the company, the Labelwatcher 360° is characterised above all by its 100% label inspection capability of containers in any rotational position and of any product shape – no matter whether they are round or exceptionally shaped. In addition, the Spotwatcher for inspecting stretch blow-moulded and extrusionmoulded plastic containers made of various plastics and degrees of transparency was exhibited. With its new, modular design, the system promises even more flexibility, and reliably inspects containers for production defects to ensure the correct shape, colour and neck finish. With regard to the software, we were shown a sneak preview of a brand-new intelligent production data analysis and evaluation tool. It gives detailed insights and early warnings of (potential) error sources directly within production processes of plastic packaging, which we will be discussing in detail in the near future. www.intravis.com Intravis’ booth at the NPE The Intravis team All-electric system for high-speed closure production Sumitomo Demag showed its all-electric Pac-E high-speed injection moulding machine with 350 t clamping force and 72-cavity mould from Z-Moulds in a compact design for the first time in North America. It is specifically designed to meet the needs of manufacturers of beverage caps and thin-wall packaging and, according to the company, builds on the success of the El-Exis SP packaging machine. In addition to the version on show, the Pac-E is also available with 420 t, 250 t and 300 t clamping force. In the trade fair demonstration, 2,100 26/22 beverage closures for still water were produced per minute. The HDPE copolymer, DMDC-1210 NT7, came from the material producer Dow. The dehumidification system was supplied by Eisbär, while an IMD Vista camera inspection system was used for the final inspection. A Frigel air cooler was used to cool the machine cell, which fed the machine with cold water. Sumitomo Demag emphasised that the machine would combine development know-how from Germany and Japan. The toggle levers, platens, tie bars and plasticising elements, including the screws and barrels, were developed in Germany, while the electric drives and the newly developed injection unit come from the Group’s Japanese parent company. Compared to other hybrid packaging machines from the manufacturer, the purely electrically driven axes in particular are expected to deliver energy savings of up to 50 per cent. With electricity savings of 30 cents per kilowatt hour, this could save around US$ 71,285 per year compared to a high-speed hybrid packaging machine. Lubrication of the toggle lever would also no longer cause any cleanliness problems, as it is a leak-free and completely closed circuit. Instead, the oil would be extracted, filtered and recycled. This eliminates the need to clean the toggle lever, which also saves oil. With an injection speed of 550mm/s, the series can also score points for thin-wall and lightweight food packaging with IML while using less material. www.sumitomo-shi-demag.eu"},{"@ID":20 "Omnimax recycling system with upstream single screw MATERIALS / RECYCLING PETplanet Insider Vol. 25 No. 07+08/24 www.petpla.net 18 Pellets for food contact Closed-loop recycling of HDPE High-density polyethylene (HDPE) is widely used in the manufacture of bottles, pipes and containers because of its strength and rigidity, but also in personal care products, detergents and industrial fluids because of its durability. Another major application is the manufacture of bottle caps and milk bottles. A recycle stream already exists due to changes in deposit regulations and the attachment of bottle caps to the bottle. The caps go through the same washing systems as PET, are then separated in the float-sink tank and can be further processed. As a result, they meet the high-quality requirements for bottle flakes. When treated with the Gneuss “Super Clean Process”, the company says, the regrind can be reprocessed back into bottle caps, thus closing the recycling loop. The Gneuss Omnimax recycling system, integral to this process, has undergone multiple challenge tests and has several food contact approvals and letters of no objections (LNO.) The technology does not require any upstream or downstream process steps. This is of great importance for polyethylene, as it can only be treated in other processes at very low temperatures and requires long residence times due to the slow diffusion processes involved. The Omnimax purifies the polymer through degassing using an MRSpure extruder and a robust vacuum system to remove volatile contaminants. The Multi Rotation System (MRS), preceded by a melt extruder, optimises plasticising and degassing / deodorising / decontamination steps individually. Downstream of the melt extruder, the RSFgenius filtration system removes hard contaminants through ultra-fine filtration. Its fully automatic operation with guaranteed pressure and process consistency cleans the contaminated screens directly before they re-enter the melt channel, so that the screens can be automatically reused up to 400 times. Typical filtration finenesses in HDPE recycling are 125-300μm. In addition, for milk bottle recycling, the material can optionally be fed into the extruder via a 3C rotary feeder. The recycling system is claimed to provide great flexibility: the Omnimax system compensates automatically for variations in the plastic waste to be processed in terms of moisture, contamination, viscosity, bulk density, etc. by adjusting the process para-meters so that material of consistently high quality can be produced, says Gneuss. Material changes, e.g. for batch changes, are possible within minutes due to the short residence time, so that the flexibility requirements of a new recycling plant are met, and production interruptions can be reduced to a minimum. This feature is claimed to make the Omnimax recycling system cost-effective, especially in applications where food contact or odour reduction is required. www.gneuss.com RECYCLING Regrind from HDPE bottle caps Results of the HDPE challenge tests, submitted 2024"},{"@ID":33 "31 EVENT REVIEW PETplanet Insider Vol. 25 No. 07+08/24 www.petpla.net Three questions for Alan Ou, Senior VP at Boretech PETplanet: How would you assess your overall experience at NPE this year? Alan Ou: The market is still cooling down since the end of last year. Many potential investors are postponing their projects as brand owners cut back on orders. We even set up a booth in the West Hall of NPE, but we found visitor numbers pretty much the same as the last NPE in 2018. 2024 will be a difficult year for the plastic recycling industry in my view. PETplanet: Could you please share the key exhibits or technologies showcased at your booth during NPE? What factors influenced your decision to focus on these particular offerings, and what was the response from visitors? Alan Ou: PET tray recycling was another trend a few years ago. Most recyclers are struggling to increase the yield rate in the tray washing process. Although none of the existing processes is successfully established on the market, Boretech has developed key equipment to enhance the production rate. We are planning to have our own recycling facility for demonstrating what we have achieved. Potential customers will be invited to visit our own facility for further details. PETplanet: Based on your experience at NPE and your broader industry knowledge, what developments or challenges do you observe in the American PET bottle market? Alan Ou: The main challenge for the American PET bottle recycling industry is sorting. Based on our observation, there is a lot of waste material generated during the washing process. With the same energy consumption, the low yield rate means higher production costs. We found the sorting process in the American market to be unsophisticated and needs to be improved. Recyclers are running machines that generate too much unwanted trash. www.bo-re-tech.com Boretech at the NPE with Paul Ou (right, Boretech VP Resource) and John Xu (left, Sales Engineer) (MKMXEP VEXMSREP TVSƤXEFPI ;LEX IPWI# SACMI.COM 300 4VIJSVQ MRWTIGXMSR ERH TVSGIWW IRLERGIQIRX MRGPYHIH DIGITAL (MKMXEP TVSGIWW GSRXVSP VIEGLIW TVIZMSYWP] YRXLMROEFPI PIZIPW STIRMRK YT XLI MRHYWXV] XS -S8 WGIREVMSW RATIONAL 7%'1- 4VIJSVQ :MWMSR 7]WXIQ MRGPYHIH JSV EHZERGIH GSQTVILIRWMZI TVSGIWW GSRXVSP PROFITABLE '330 TSWX GSSPMRK MRWMHI GSSPMRK W]WXIQ\r WLSVXIRW G]GPI XMQIW ERH PIEHW XS QSVI TVSƤXEFPI TVSHYGXMSR momic"},{"@ID":34 "32 EVENT REVIEW PETplanet Insider Vol. 25 No. 07+08/24 www.petpla.net Dry ice blasting unit with integrated dry ice production Surpass Industrial from Houston, the US representative for equipment from the German manufacturer Kärcher, presented the new Kärcher IB 10/15 L2P Advanced dry ice blasting machine. Compared to conventional dry ice cleaners, the special feature of the Kärcher is that it produces its own high density dry ice pellets, as we were shown. “With this model, you can clean for five minutes or five hours, no planning required. It’s always ready to use and allows to clean injection moulds in place and also while hot. No cooldown necessary,” explained Sales Manager Ottavio Cautilli. “We have customers that have cut down their mould cleaning time from 7 hours to 28 minutes by using our dry ice blasters. They love to be able to use it only when needed without wasting dry ice,” added his Sales colleague Russell Grasshoff. According to Kärcher, the simple operating concept should enable the machine to be used even without special training. In most cases, the dry ice in other dry ice blasters would often not be used or only used incompletely, as the pellets would turn into a gas after a few days and reduce the cleaning performance, whereas the IB 10/15 L2P Advanced would produce the dry ice as required, so that liquid CO2 can be stored in bottles as a raw material without loss. In addition, only a compact compressor would be required, according to the manufacturer. This new model increases the cleaning performance by using a heat exchanger that cools the supplied CO2, as the conversion rate from liquid to pellets (hence the name L2P), is greater at lower temperatures. “With this technical innovation, the new machine produces 60 per cent more dry ice compared to the smaller IB 10/8 L2P model - with the same CO2 consumption,” explained Mr Cautilli. In combination with the higher air supply the cleaning performance would be doubled. This means that sticky, encrusted accumulated contaminants could be removed just as effectively as soot and dust. If very sensitive or smaller surfaces are to be treated, the smaller 3mm nozzle can also be used with a correspondingly reduced power. An intuitive control panel and various assistance systems, e.g. for checking the minimum pressure, the correct connection of the cables or the risk of overheating, are also included. As accessories, Kärcher has a variety of quick connect nozzles, a splash guard that collects loosened dirt, a cylinder trolley and a holder for the protective cap of the gas cylinders, each compatible with the large and small dry ice blasters. www.kaercher.com www.surpassindustrial.com PET material for beverage closures The US PET material manufacturer Alpek Polyester presented its new product ‘CaPETall’ at the NPE. This PET material is aimed at a potential trend towards the production of beverage closures made from PET and is therefore of interest to the developing markets for mono-material packaging. In addition to the complete recyclability of PET bottles, where the closure can also remain in the same recycling stream, the main aim is to retain the mechanical properties familiar from conventional PE closures. In addition, there should be no visual restrictions compared to the familiar PET brilliance, as demonstrated by the product examples on display at the stand. Alpek Polyester also states that the material is a multimodal polymer technology with a high molecular weight, which improves material flowability without compromising functionality or aesthetics, a basic flowability of the polymer and could also be used for thin-walled injection moulded parts. CaPETall fulfils the requirements of PET resin identification code 1 and passes the ESCR (Environmental Stress Crack Resistance) test for closures. The sample closures shown at the trade fair stand were produced on Husky systems and were also on display at the stand. www.alpekpolyester.com The Surpass Industrial exhibition stand Different coloured PET beverage closures Ricky Lane shows the PET closure exhibits"},{"@ID":27 "CAPS & CLOSURES 25 PETplanet Insider Vol. 25 No. 07+08/24 www.petpla.net Sipa launches high-performance GME 30.40 LW neck fi nish Ultralight neck finish debut viscoZERO – processing PP, PE, PET & PS! ZERO contamination. ZERO odour. ZERO limits. foodgrade without compromise viscoZERO Upgrade your existing recycling plant with viscoZERO technology. Sipa has introduced a new lightweight GME 30.40 LW neck finish aimed at enhancing sustainability and performance within the carbonated soft drink (CSD) sector. Weighing just 2.04g, the GME 30.40 LW achieves a notable 19% reduction in weight compared to the standard GME 30.40 closure. The weight reduction of the new neck finish translates to material savings for beverage producers, contributing to cost efficiency and a diminished environmental impact. Despite its lightweight construction, the GME 30.40 LW maintains robust performance capabilities, Sipa says. The company claims it has the capacity to handle up to 4.2 volumes of CO2, ensuring optimal carbonation and consumer satisfaction. Seamless integration In terms of integration and sustainability, the GME 30.40 LW is fully tetherable to comply with current regulations, addressing concerns related to cap loss and litter while promoting responsible consumption and environmental cleanliness. Moreover, this closure seamlessly integrates with existing GME 30.40 capping lines, facilitating straightforward adoption into current production processes. Sipa says that the GME 30.40 LW neck is easily manufactured within the company’s Xform preform system and efficiently handled by the Xtra blow moulding machine. This streamlined approach is claimed to ensure efficient and high-quality production, meeting the rigorous demands of the global beverage industry. The company’s neck lightweighting solutions extend beyond the GME 30.40 LW, catering to a diverse range of applications including mineral water, CSDs, large-format containers with 55mm neck finishes, and edible oil. Notably, for hot-fillable containers, the Sipa Hotlight 28 solution offers a 40.6% reduction in weight compared to standard PCO 28mm options. www.sipasolutions.com"},{"@ID":36 "34 EVENT REVIEW PETplanet Insider Vol. 25 No. 07+08/24 www.petpla.net From high-speed leak testing to palletising Delta Engineering showcased their expertise in downstream equipment for the blow moulding industry with live demonstrations of several machines. Among the machines featured was the DP252 fully automatic palletiser. Capable of packing empty plastic bottles into trays and hoods, the DP252 can build full-height pallets up to ten feet high. With two integrated tray warehouses/dispensers that can hold up to 15 trays or hoods each, the DP252 offers flexibility in stacking patterns to meet the unique requirements of each customer. In addition to the DP252, Delta Engineering also displayed the UDK616 high-speed rotary leak tester for plastic bottles. With 16 test heads and the latest Delta Engineering leak tester software algorithms, the UDK616 is said to offer stability, low false rejection rates and easy setup. Thanks to its accurate measuring system, it safeguards the production and quality control processes of Delta Engineering’s customers. The machine is designed for quick changeovers, user-friendliness, easy access and operator safety. Furthermore, the company highlighted their expertise in conveying challenging bottles with a 45-degree vacuum conveyor with a steep incline and decline. Their conveyor seamlessly transported bottles to the UDK616 leak tester in a continuous loop, illustrating the advantages of vacuum technology. Even with the conveyor’s steep incline and decline, the vacuum system prevents the bottles from toppling over, which makes the solution suitable for highspeed transportation of unstable or difficult bottles, or in cases where high repeatability is crucial. Additionally, Delta Engineering unveiled samples of crystal clear blow-moulded squeeze tubes made of PET instead of the traditional PP. The standout feature of the new tube is that it is made by injection stretch blow moulding (ISBM) on single-step Nissei ASB machines, rather than extrusion. With the company’s new, patented process, oval-shaped blow moulded bottles are simply transformed into tubes by clipping and welding the base. This innovation opens up a new market for blow moulding companies and their bottle filling customers, says Delta Engineering. The new tubes can be filled just like regular bottles, which allows filling to a higher level than with standard tubes. Another advantage is that PET tubes can be recycled 100% in the current recycling flows, as opposed to laminated tubes. The PET tubes can also be plasma coated for enhanced oxygen barrier properties and are said to be easy to print. www.delta-engineering.be Hot runner technology for the packaging industry Global hot runner, controller and auxiliary injection unit supplier Mold-Masters exhibited at NPE, showcasing a wide selection of new products and technology. New products included the Fusion Series G3 and Eco One series hot runner systems. For the PET processing sector, Global Marketing Director Miki Bogar and Global PET Sales Director Igor Kim showed us the Axiom hot runner system for single-stage ISBM applications, which is claimed to incorporate modern technology to enhance bottle quality and reduce operating costs by extending maintenance intervals. In addition to optimised thermal properties and improved process control, Mold-Masters advertises an industry standard gate design that prevents stringing and reduces crystallinity in the gate. The system also features PET dust management, which is said to minimise material dust accumulation, reduce the frequency of maintenance and avoid downtimes. Thanks to advanced I-Flow manifold technology, colour changes are said to be up to four times faster with improved bottle-to-bottle consistency. We were also shown the Sprint Apex gate seal, which was launched on the market this year to optimise product quality in the production of caps. According to Global Sales Director Packaging and Medical Thomas Bechtel, this should improve the environmental stress crack resistance (ESCR) of CSD closures by up to 40%. Increasing safety factors improves CSD cap performance which is particularly beneficial for lowing material usage and cost savings through light weighting. Further advantages, which can be applied to any type of closure, are said to be a better appearance and quality of the closures produced, in particular the minimisation of flow lines, regardless of the colourant used. According to the company, colour changes can be made up to 65% faster. The technology, which eliminates the need for vespel insulating caps, is also said to minimise maintenance and spare parts costs. Successful case studies from customers confirm the effectiveness of the technology. Retrofitting should be possible with existing cavity inserts, which should minimise investments when changing over and shorten the ROI. www.moldmasters.com Axiom hot runner system"},{"@ID":4 "Crystal ThumpUp Our extended SportCaps range Biarritz NEW In sport, you never settle for less. That’s why we strive for the perfect closures, also when it comes to sustainability. Many closures, such as Biarritz and Monet, are made from a single material, making them easy to recycle. In addition, our sport closures are easy to handle, have integrated tamper evidence solutions and are suitable for cold, dry, or wet aseptic filling. So take the leap – and opt for more sustainability. NEW Monet Visit us at FACHPACK Hall 6, Booth 6-151 Contact us and arrange your line trials now! www.bericap.com New mono-material caps for optimized recyclability Going the extra mile for you"},{"@ID":5 "imprint EDITORIAL PUBLISHER Alexander Büchler, Managing Director HEAD OFFICE heidelberg business media GmbH Hubweg 15 74939 Zuzenhausen, Germany phone: +49 6221-65108-0 [email protected] EDITORIAL Kay Barton Heike Fischer Gabriele Kosmehl Michael Maruschke Ruari McCallion Anthony Withers Editorial & WikiPETia. info [email protected] MEDIA CONSULTANTS Martina Hirschmann [email protected] Johann Lange-Brock [email protected] phone: +49 6221-65108-0 LAYOUT AND PREPRESS EXPRIM Werbeagentur Matthias Gaumann www.exprim.de READER SERVICES [email protected] PRINT Chroma Druck Eine Unternehmung der Limberg-Druck GmbH Danziger Platz 6 67059 Ludwigshafen, Germany WWW www.hbmedia.net | www.petpla.net PETplanet Insider ISSN 1438-9459 is published 10 times a year. This publication is sent to qualified subscribers (1-year subscription 149 EUR, 2-year subscription 289 EUR, Young professionals’ subscription 99 EUR. Magazines will be dispatched to you by airmail). Not to be reproduced in any form without permission from the publisher. Note: The fact that product names may not be identified as trademarks is not an indication that such names are not registered trademarks. 3 PETplanet Insider Vol. 25 No. 07+08/24 www.petpla.net Collecting PET bottles can sometimes be a highly emotive issue. Dr Yusuf Nughraha, founder and owner of the Harapan Sehat Clinic in the small town of Cianjur, Indonesia, wishes to rid the world of plastic waste. For the 44-year old, health and the protection of the natural environment are inextricably linked and he wants to connect with poorer people in particular. Environmental protection programmes are often highly complex, which a lot of people find difficult to understand. “That is why I came up with the idea of using plastic bottles as a means of payment.” Poorer people feel confident to come to him and he is keen to help. He offers the poorest of the poor a free examination for every ten PET bottles collected. His aim is to create an understanding among the population of environmental protection, recycling and waste separation issues. Since the closure of their only landfill site, waste ends up in rivers or is burnt in front gardens, with no rubbish collection service. In the early years, he had to put his own money into the scheme to enable the clinic to continue with its work. Today, patients are able to offset payment for the cost of approximately 30-40 daily examinations by producing vouchers, which recycling dealers provide for every ten bottles collected, for their treatment. The people’s gratitude is overwhelming – watching the video brought tears to my eyes. But it is not only in the clinic that he campaigns for the need to protect the environment. He visits a school every month and talks to the pupils, explaining to the younger ones that bags and packaging simply do not belong in the environment, while he speaks to the older children about clean drinking water. This cannot be taken for granted in Indonesia which is why so many people here buy plastic bottles. Water has to be boiled or drawn from drinking water fountains. The doctor also explains to the pupils where they can start to reduce waste. With his tireless dedication to health and environmental protection, Dr Yusuf Nughraha has clearly shown how innovative ideas and personal commitment can improve the lives of so many people. His initiative, in which PET bottles are used as a means of payment for medical treatment, is not only a step towards a cleaner environment but also a significant contribution to supporting the poorest in society. Through his work, he not only inspires the inhabitants of his small town but also sets an important example for the global community: every single contribution to prevent waste and to recycle counts. Yours, Alexander Büchler Dear readers, PET bottles at the doctor’s"},{"@ID":46 "44 EVENT REVIEW PETplanet Insider Vol. 25 No. 07+08/24 www.petpla.net Catalytic upcycling process Ioniqa, a clean-tech spinoff from the Eindhoven University of Technology (NL), is specialised in creating value out of plastic waste by using its proprietary circular technology called Denua. At PRSE, the company was featuring the commercialisation of this catalytic upcycling process, aimed at achieving full circularisation of PET, in collaboration with Koch Technology Solutions (KTS). Via a licensing business model, the two firms want to further improve the sustainability of the industry. The partnership between KTS and Ioniqa addresses the growing demand for recycled content in the 30 million metric t/a PET market. Denua offers a solution to PET waste that is currently nonrecyclable, transforming it into materials suitable for high quality food grade applications such as beverage bottles. It is believed that the collaboration offers the market not only a technical solution when it comes to difficult to recycle PET waste, it also safeguards capacity of existing plants where integration is considered. KTS and Ioniqa view the technology as a disruptor in the PET industry providing a sustainable economic recycle proposition to conventional manufacturing routes. The basis of the Denua process is at Ioniqa’s current plant in Geleen, the Netherlands, where the chemical recycling process for PET has been developed and operated at kiloton scale for several years. Through their proprietary catalytic upcycling process, they break down PET to the monomer BHET, a molecule that has been shown to be directly applicable in the PET resin production processes of major players such as Indorama. www.ioniqa.com www.denuatech.com At PRSE, Ioniqa was featuring the commercialisation of its catalytic upcycling process, in collaboration with Koch Technology Solutions."},{"@ID":56 "OUTER PLANET 54 PETplanet Insider Vol. 25 No. 07+08/24 www.petpla.net OUTER PLANET The Ocean Cleanup & Coldplay announced LP made using recycled river plastic Listen to Moon Music The Ocean Cleanup project deployed Interceptor 006 in the Rio Las Vacas in 2023 to prevent plastic emissions into the Gulf of Honduras. Interceptor 006 made a significant impact and captured large quantities of plastic – which has now been sorted, blended, tested and used to produce Coldplay’s limited edition physical LP. The final product consists of 70% river plastic intercepted by The Ocean Cleanup and 30% recycled waste plastic bottles from other sources. The successful production of the Notebook Edition LP using intercepted river plastic marks an exciting new phase in Coldplay’s broad and long-standing support for The Ocean Cleanup. Coldplay provide financial support for the non-profit’s cleaning operations, sponsor Interceptor 005 in the Klang River, Malaysia (which the band named ‘Neon Moon I’) and share The Ocean Cleanup’s mission with millions of their fans during their recordbreaking Music of the Spheres tour. Coldplay and The Ocean Cleanup collaborated closely during the intensive testing and quality control process, alongside processing and manufacturing partners Biosfera GT, Compuestos y Derivados S.A., Morssinkhof and Sonopress. Having proven the potential of their partnership, The Ocean Cleanup and Coldplay will continue to explore new and innovative ways to combine their impact and accelerate progress in the largest cleanup in history. “Coldplay is an incredible partner for us, and I’m thrilled that our plastic catch has helped bring Moon Music to life.” said Boyan Slat, Founder and CEO of The Ocean Cleanup. “Ensuring the plastic we catch never re-enters the marine environment is essential to our mission, and I’m excited to see how we’ll continue innovating with Coldplay and our other partners to rid the oceans of plastic – together.” The Ocean Cleanup The Ocean Cleanup is an international non-profit that develops and scales technologies to rid the world’s oceans of plastic. They aim to achieve this goal through a dual strategy: intercepting in rivers to stop the flow and cleaning up what has already accumulated in the ocean. For the latter, The Ocean Cleanup develops and deploys large-scale systems to efficiently concentrate the plastic for periodic removal. This plastic is tracked and traced to certify claims of origin when recycling it into new products. To curb the tide via rivers, The Ocean Cleanup has developed Interceptor Solutions to halt and extract riverine plastic before it reaches the ocean. As of May 2024, the non-profit has collected over 12 million kilograms (26.4 million pounds) of trash from aquatic ecosystems around the world. Founded in 2013 by Boyan Slat, The Ocean Cleanup now employs a broadly multi-disciplined team of approximately 140. The foundation is headquartered in Rotterdam, the Netherlands, and opened its first regional office in Kuala Lumpur, Malaysia, in 2023. www.theoceancleanup.com Coldplay helped The Ocean Cleanup deploy Interceptor 005 in Malaysia. Boyan Slat, Founder & CEO of The Ocean Cleanup, holding a sample LP The Ocean Cleanup has provided PET caught by the Intercepter 006 in Guatemala for the production of Coldplay’s latest limited edition LP. In the centre Boyan Slat, Managing Director of The Ocean Cleanup, together with Coldplay (picture by Anna Lee Media)"},{"@ID":55 "MATERIALS / RECYCLING PETplanet Insider Vol. 25 No. 07+08/24 www.petpla.net 16 Colour correction in rPET preforms Intravis has announced a collaboration with Husky Technologies that integrates Intravis’ preform monitoring system, PreMon, with Husky’s HyPET6e platform. This collaboration was demonstrated at the NPE trade show in May 2024 and introduces a closed-loop application for rPET preform production that improves and enables circular economy. Closed-loop technology At the heart of this collaboration is the closed-loop application, which focuses on colour correction in rPET preform production. The solution is claimed to provide automatic colour adjustment to reduce colour variability in PET preforms made from recycled content. By using an OPC UA interface for communication, the PreMon and the Husky HyPET6e system work in tandem to monitor and adjust colour values in real-time. According to the companies, this integration ensures fast feedback and immediate corrections, with masterbatch automatically added to immediately address any significant yellowing of the preforms. The fast response capability aims for consistent quality and minimises waste, enhancing overall production efficiency without the need for operator intervention, said Intravis. Driving circular economy with rPET bottle production At NPE, the production of a lightweight preform made entirely from 100% rPET was presented to be blown into a 595ml bottle. Weighing 5.89 g, the preform supports the circular economy using recycled materials without compromising performance. The HyPET 400 HPP6e system was equipped with a 144-cavity, 45-pitch mould running at a cycle time of 4.5 s, achieving a production speed of around 120,000 preforms per hour. The companies said that both the HyPET6e system and the PreMon can handle this rapid pace, ensuring seamless integration and continuous, high-quality output. Detailed quality monitoring beyond colour In addition to colour inspection, the PreMon provides comprehensive monitoring of several other critical quality characteristics in rPET preform production. The colour inspection evaluates L*a*b* values, colour intensity, colour deviation, and yellowness effect. The monitoring system includes long gate inspection to detect any overlength at the injection point, which can affect the finish of the final product. Furthermore, it inspects the preform body for contaminations such as black spots and contrasting impurities, which can compromise the structural integrity and appearance. The sealing surface undergoes two distinct inspections: one to detect short shots, ensuring that the preform mouth is properly formed, and another to identify any defects that could affect the sealing surface and usability of the final bottle. www.intravis.com www.husky.co PreMon integrated directly behind the HyPET6e system on a small footprint RECYCLING"},{"@ID":48 "46 EVENT REVIEW PETplanet Insider Vol. 25 No. 07+08/24 www.petpla.net PET recycling management The RCS Group from Werne, Germany, presented itself as a pioneer in the recycling of packaging from the deposit system. A particular highlight was the model of the material cycle, which symbolises the RCS Group’s commitment to the circular economy. It illustrates how recycled materials can be fed back into the production process. This display attracted a lot of attention. It shows in a simplified way how the sustainable use of resources works. The RCS Group specialises in recycling packaging from the deposit system and offers processed materials and by-products for sale. The company purchases additional material for the production of PET regranulate for the food and beverage industry. www.rcs-entsorgung.de Powerfil receives Plastics Recycling Award Europe 2024 At PRSE, the DischargePro control system from Erema’s Powerfil business unit was presented with the Plastics Recycling Award Europe in the “Recycling Machinery Innovation of the Year” category. The DischargePro system automatically compensates for fluctuations in the input material, thereby ensuring uniform thickening during melt filtration and thus a consistent process. Depending on the application and contamination, Powerfil was able to reduce melt loss by up to 50 per cent with the DischargePro compared to the previous Erema laser filter control system. These facts convinced the jury, who described the technology as an intelligent technological advance in the extrusion process. With the control system, Powerfil increases the degree of automation in the filter process. The innovative discharge control system reacts to specific disruptions in the process. In this way, the speed of the scraper star is adjusted at short notice and returns to the setpoint speed as soon as the contamination peak has been discharged. Furthermore, the control system also recognises changes in throughput and adjusts the discharge rates accordingly. In the event of a higher pressure drop across the filter screen, which is caused by a higher viscosity of the melt, DischargePro adjusts the setpoint value to ensure a consistent discharge rate. Long-term changes, such as the condition of the filter screen, are also taken into account in all adjustments. www.erema-group.com The model of the material cycle, which illustrates how recycled materials can be fed back into the production process, attracted a lot of attention. “We have put a lot of effort into developing this technology. I am therefore particularly delighted to accept this award on behalf of the entire team today,” says Robert Obermayr (centre), Head of the Powerfil business unit at Erema. (Photo: PRSE 2024) MIDDLE EAST & AFRICA 10-12 September 2024 Dubai Organised by In association with ASIA 13–14 November 2024 Marina Bay Sands, Singapore INDIA 4-6 December 2024 NESCO Bombay Exhibition Center (BEC), Mumbai The Middle East & Africa’s only dedicated expo on plastics recycling returns to Dubai for its 2nd edition. Register for your FREE entry pass at: www.prseventmea.com"},{"@ID":39 "EVENT REVIEW PETplanet Insider Vol. 25 No. 07+08/24 www.petpla.net 37 Linear blow moulder in a compact design Sipa has expanded its SFL range of linear stretch blow moulding machines with the introduction of the SFL Flex, specifically designed for producing small batches. Available in two versions - one with two cavities and the other with one - the SFL Flex targets lower output segments, typically ranging from 1,0004,000 bph. This design is particularly suited for startup businesses and laboratory environments. Compact and flexible, the SFL Flex machines are designed to be user-friendly, accommodating various production needs across different industries. Despite their smaller size, they maintain the high-quality output characteristic of the larger SFL models, ensuring compliance with stringent PET bottle quality standards. These machines are versatile, supporting the production of new products in segments such as beverages, personal and home care, hot-fill applications, or refillable bottles. They are compatible with PET, rPET, HDPE, PP or other polymers used in the SBM process. Versatile & flexible The SFL Flex 2 can produce bottles of up to 3 l in volume, with necks of up to 48mm. It achieves speeds of up to 2,000bph per cavity. This capability makes them suitable for small to medium production runs. The machines can be equipped with optional features to enhance their versatility in terms of bottle shape and filling requirements, thereby meeting specific production needs. SFL Flex is designed to host any kind of existing blow mould (shell or block, from SFL, Xtra or other OEMs / mould producers). The majority of the personalised parts have the same engineering as the SFL family, allowing smooth transition to other machine sizes (scaling-up production or scaling-down blowing operations). Changeovers between moulds are quick and efficient, says Sipa, with a change time of no more than 20 minutes. This minimises downtime during production transitions, supported by simple, tool-less neck changes that enhance operational efficiency. Compact footprint In addition to their capabilities, the SFL Flex machines have a compact footprint of just 8m2, making them suitable for installations with limited space. This compact design optimises space usage while offering efficient production capabilities for small batch requirements. www.sipasolutions.com The SFL Flex 2 can produce bottles with a volume of up to 3 l and a neck of up to 48mm at speeds of up to 2,000bph per cavity. The SFL Flex has been designed for producing small batches. 2024 Training Schedule Technology&Application of PET Plastic Packaging for Hot-Fill &Aseptic Beverages Join our expert team for small group training on a variety of subjects - from materials to recycling. Scan to learn more & register for classes! ©2024 Plastic Technologies | 1440 Timberwolf Drive, Holland, Ohio USA 43528 www.pti-usa.com"},{"@ID":32 "30 EVENT REVIEW PETplanet Insider Vol. 25 No. 07+08/24 www.petpla.net EVENTreview All-electric PET EBM machine Bekum America, the US-subsidiary of Berlin-based Bekum Maschinenfabriken, showcased the US-built, all-electric Eblow 407D extrusion machine with the patented C-frame clamping and E-twin toggle system, producing a 2 l handled bottle with Indorama’s Future-PET resin EBM PET 5507-R25 with 25% rPET content in the demonstration. This mediumsized, double-sided model is a four-cavity ‘gallon machine’ with a 15 t clamping force, 520mm slide stroke and 500mm maximum mould width. Steve London, President and Chief Operating Officer, explained: “In addition to our all-electric Eblow series, we have an impressive range of traditional hydraulic machines as well as hybrid variants that can be customised to meet the different needs of our customers.” According to the company, 35 US-built Hyblow 407D (hydraulic/hybrid) machines are currently in operation in North America and there is expected to be strong market demand for the all-electric version of the 407D. Bekum also exhibited its new 3-layer spiral head technology in conjunction with its latest vertical extruders. The package presented is designed to facilitate the transition to a 3-layer system for existing customers. The company has also been working on high-performance extrusion systems with significant energy savings through optimised cylinder and screw design with direct-coupled gearboxes and high-efficiency motors. www.bekumamerica.com Ultra-thin PET food containers Canadian mould manufacturer Stackteck presented its new system for the production of round, ultra-thin 450ml PET food containers. The manufacturer relies on its proprietary ‘Thin Recess Injection Moulding’, which has been executed while incorporating seven sequentially controlled valve gates. The new mould with ISO hotrunner technology from Yudo, which is characterised by very closely spaced valves with individual controls and was developed for high-pressure injection with optimised heat management, was running as an IML system on a Netstal Elion 3200 in combination with suitable take-out robot and an inspection system from IMD Vista at the Netstal stand during the trade fair. GM PET, Rick Unterlander and VP Business Development & Marketing Jordan Robertson presented a container with 30% PET content produced using this technology. Containers with 100% recycled content are also possible and, according to Stackteck, have already been produced in practice. The containers were labelled with IML labels from the Belgian manufacturer MCC Verstraete, which, according to Stackteck, had used a PET substrate for a 100% PET content in the trade fair demonstration version. Material supplier Eastman was responsible for the PET rawmaterial with its product Eastar EN001 with an IV of 0.80dl/g and EN058 with an easier fillability (IV) of 0.58dl/g were also used. “With this mould, we can injection mould over longer lengths without having to use modified material and achieve both ultra-thinwalling and rigidity. We see great potential here in the food industry,” said Mr Unterlander. www.stackteck.com Eblow 407D Stackteck’s mould in action at Netstal Rick Unterlander, GM PET and Jordan Robertson, VP Business Development & Marketing at Stackteck Systems The final results for registration and paid exhibit space were announced: a total of 51,396 attendees or 1,106,767 square feet. NPE 2024, which took place from May 6-10 in Orlando, Florida, saw a record-breaking number of international attendees. With 15,156 international participants from 133 countries, NPE 2024 was the most global trade fair in the event’s history. There were 20,378 first-time visitors, an increase of almost 9% compared to NPE 2018. There was also a significant increase in the number of participants in the various regions, including 4,438 Latin American (LATAM) registrations, 29.3 % of international registrations and a 9.9 % increase in LATAM registrations compared to NPE 2018. Significant increases in registrations were recorded from countries such as Brazil, Colombia and Guatemala. 2,801 European participants, 18.5% of international registrations and a 23% increase in European registrations compared to NPE 2018, with the largest increase in registrations from Italy. With 2,202 exhibitors, the exhibition space has increased by 10.3% compared to NPE 2018. PETplanet’s feedback on NPE 2024 was also very positive and the dialogue with new and old acquaintances, customers and friends from the PET processing industry was extremely positive. The special live edition of the PETinar series on site at the NPE was very well received and met with a positive response. You can find exclusive content on our homepage! We look forward to seeing you at NPE 2027 in Orlando from May 3-7, 2027! www.petpla.net/category/petinars/"},{"@ID":24 "CAPS & CLOSURES 22 PETplanet Insider Vol. 25 No. 07+08/24 www.petpla.net with you a concept that we considered very carefully during the entire development. I am referring to the importance of keeping under control the efficiency that our customers expect as we convert our manufacturing processes to the tethered cap whilst also ensuring that the line operators maintain their current productivity. To get these results, our technical, automation and vision system department did a great job demonstrating considerable flexibility by adapting the range of new machines to the new requirements, but also designing upgrade kits to meet the needs of our customers. At the forefront of our minds every day is the importance of our customers’ machines and moulds. What drives Sacmi is a consultancy approach helping customers decide whether for example to replace existing equipment or the feasibility of continuing with their current machines. Another key factor that played a role has been the configuration of the Sacmi technology in respect of the scoring process, which is always done outside the mould. Not only does this make conversion easier but it makes the manufacturing process more flexible. In many cases where the customer has decided to invest in a new line, Sacmi has been able to come up with a new closure design which, coupled with a higher production output, delivers a much better ROI. PETplanet: Mr Chiozzini, do you have an overview of how many customers have already introduced the new technology? Are there any consequences for being late? Mr Chiozzini: Tethered closures are required to be on the shelves of stores and supermarkets from July 3rd and this is essentially in the hands of the beverage supply chain. The supply chain is made up of a number of players each contributing to every aspect of the process which lies behind the water or soft drink that we look forward to consuming on a summer’s day. So far as we are aware, all European customers that use our machines have been able to adapt their production on time and ready to supply closures to the beverage industry. As for the consequences of being late, every EU Member State will introduce penalties on a national level, as per article 14 of the Directive. PETplanet: Mr Chiozzini, a lot of investments have been made to realise the tethered cap technology. Is it paying off for Sacmi? Mr Chiozzini: The vital concern for Sacmi has been, from the beginning, to support in the smoothest way possible the beverage industry in this important conversion. The investment has been high in terms of people and resources, but it will not be long before the investment pays off. To give more details, the investment of Sacmi has principally been in three areas: 1) Testing equipment and laboratory resources to shorten the time from conceptual phase to piloting and testing. With Netstal’s leading preform injection molding technology. Our PET-Line impresses with broadest compatibility, maximum throughput, exceptional ĆďĆēĈĚ ĆħĄĊĆďĄĚ ĐđĕĊĎĂč đēĐĄĆĔĔĊďĈ Đć ē÷ìû Ăďą other challenging recyclates, and with its intuitive Axos control unit. Wemaximize your đēĐąĖĄĕĊĐď ĆħĄĊĆďĄĚ Preforms Fakuma I B3-3119"},{"@ID":19 "MATERIALS / RECYCLING PETplanet Insider Vol. 25 No. 07+08/24 www.petpla.net 17 PET to monomer via glycolysis reaction While plastic is an integral and indispensable part of modern life, traditional waste management methods, such as landfilling and incineration, are not sustainable solutions. As the demand for sustainable packaging solutions increases, the use of rPET has become a key focus area for industry. Recycling is overwhelmingly effected by either mechanical or chemical processes. Köksan has patented a chemical recycling process that the company describes as “the most advanced and energy efficient”. The chemical process method of depolymerisation breaks down plastic polymers into their basic monomeric building blocks that can then be used to create new plastic products or other useful chemicals. This process consists of collection and sorting, cleaning and preprocessing, chemical depolymerisation, purification, and repolymerisation. Köksan, the Turkish producer of PET resin, sheet, and PE closures, says that its patented chemical process of recycling PET to monomer (BHET) by glycolysis reaction is the most advanced and energy efficient technology. Depolymerisation can contribute to the circular economy by creating a closed-loop system for plastic production and consumption. Recycling plastic, particularly through advanced methods like depolymerisation, will reduce the carbon footprint associated with plastic production and disposal, says Köksan. It can be reused and repurposed, generating new economic opportunities and revenue streams, creating new jobs in the recycling and re-manufacturing industries, further boosting the economy. Advanced depolymerisation technologies have the potential to make plastic recycling more efficient and cost-effective. As they continue to evolve, the economic viability of plastic recycling can be enhanced, making it progressively a more attractive option for businesses and consumers alike. Köksan says that its patented process achieves high viscosity and lower than 1ppm AA level in resin. Without any SSP process, it is the most suitable technology for bottle grade application, according to the company. Its new plant will be the first of its kind for 100% rPET resin for all food grade applications. The process of recycling PET flakes through depolymerisation to BHET and subsequent threemicron microfiltration results in a resin that is comparable to virgin monomer, making it suitable for food-grade applications. The US$40 million investment in Köksan rPET plant is designed to produce up to 100% rPET content PET for food grade, textile grade, film grade and engineering applications. The plant has a capacity of 300 MTD bottle grade and 400 MTD for other grades. As of June 2024, Köksan has the capacity to produce about 240,000 metric t/a of plastic bottles and recycle 72,000 t of it. The chemical recycling project’s 110,000 t of capacity will bring the total recycling capacity to 182,000 t, which is 75% of its plastic bottle production. The recycled plastic bottles are also, themselves, recyclable. Köksan’s plastic recycling investment is set to generate more than US$ 200 million annually. www.koksan.com RECYCLING"},{"@ID":30 "MARKET SURVEY 28 PETplanet Insider Vol. 25 No. 07+08/24 www.petpla.net Company name SMI S.p.A. FlexBlow (UAB Terekas) Postal address Telephone number Web site address Contact name Function Direct telephone number E-Mail Via C.Ceresa, 10, 24015 San Giovanni Bianco (BG) ITALY +39 0345 40.111 www.smigroup.it Marketing department +39 0345 40111 [email protected] Vytauto str. 114A, Kretinga, Lithuania +370 445 514 31 www.fl exblow.com Mr Aurimas Ziausys Regional Sales Manager +370 612 429 46 az@fl exblow.com 1. Machine designation / model number EBS K Ergon EBS KL Ergon EBS E Ergon EBS KL HC Ergon FlexBlow 2 / FlexBlow 3XL / FlexBlow 4 / FlexBlow 6 Hybrid 2. Bottle volume (from/to in litres) 10ml - 20 l a) Standard machines 0.10 - 3 l 0.10 - 3 l 0.10 - 3 l up to 6 l b) Machines for large containers 0.10 - 3 l up to 20 l 3. Maximum number of stretch-blow moulds (units) a) Standard machines 4 10 16 (20 for 0.75 l bottle) 6 b) Machines for large containers 6 4 (up to 6 l) 4. Output per stretch-blow mould for: 0.5 litres CSD bottle (units per hour) 2,500 bph per cavity (*) 2,500 bph per cavity (*) 2,500 bph per cavity (*) 11,000bph 1 litre CSD bottle (units per hour) 2,500 bph per cavity (*) 2,500 bph per cavity (*) 2,500 bph per cavity (*) 10,000bph 1.5 litres still mineral water bottle (units per hour) 2,300 bph per cavity (*) 2,500 bph per cavity (*) 2,500 bph per cavity (*) 9,000bph Large capacity container 1,200bph per cavity (*) 5,000bph Other (*depending on the preform/bottle features) Various output depending on complexity, material, preform design, etc. 5. Footprint / space requirement (L x W x H in metres) 2.32 x 3.28 x 2.3 (without preforms hopper & unscrambler) 4.77 x 2.62 x 2.35 5.8 x 3.9 x 2.55 - 7.3 x 3.9 x 2.55 4.77 x 2.62 x 2.35 7.1 x 5.6 x 2.9 (FlexBlow 4) 6. Special features (short description/ keywords) SMI rotary stretch blow moulders, available both in \"stand alone\" version and in \"combi\" version, ensure high performances in the stretch blow moulding of PET, rPET and PP bottles. Heat-refl ecting and high energy-effi cient panels; air recovery system ensures up to 40% saving; ReduxAir optional kit enables to blow bottles with lower pressure compressed air; electronic processes which allow to get rid of the whole of mechanical movements and related cams and ultimately make the blower a cam-less machine; high performance, low dead volume valves system, which reduces the pre-blowing and blowing times with consequent advantages in terms of machine's effi ciency and quality of the fi nal bottles; preform heating module, compact dimensions, horizontal frame of the preform holding mandrels chain & a ventilation system optimising the preform heating process Fully electric and fully automatic, FlexBlow SBM machines are designed for producing complex containers such as hot fi ll bottles, oval containers, wide-mouth jars, large-size bottles, and more. These machines offer features like ultra-fast mould and bottle format changes, integrated quality control innovations, preferential heating, neck orientation, open architecture, and compatibility with competitor moulds. Company name Side S.A Krones AG Postal address Telephone number Web site address Contact name Function Direct telephone number E-Mail Pol.Ind. Montguit, C/Llinars s/n, 08480 L'Ametlla del Valles, Barcelona, Spain +34938463051 www.sidemachines.com Mr Josep Jiménez Sales Manager +34 677 551 928 [email protected] Boehmerwaldstr. 5 93073 Neutraubling, Germany +49 9401 70 0 www.krones.com Mr Peter Christiansen Head of Sales Plastics and Block Technology +49 9401 70 4980 [email protected] 1. Machine designation / model number 1002e - 160e/c 2006e 2003eG 5001e 3008e Contiform Speed, 15 models available Contiform, 13 models available Contiform Heatset 13 models available Contiform Preferential Heating, 10 models available Contiform BigBottle 3 models available 2. Bottle volume (from/to in litres) a) Standard machines Up to 3.5 l Up to 2.5 l Up to 2 l 0.1 - 2.0 0.1 - 3.5 0.1 - 2.0 0.1 - 3.5 b) Machines for large containers Up to 10 l Up to 50 l 3. Maximum number of stretch-blow moulds (units) a) Standard machines 2 6 8 28 28 22 b) Machines for large containers 3 1 4. Output per stretch-blow mould for: 0.5 litres CSD bottle (units per hour) 4,000 10,000 3,600 18,000 2,750 2,500 2,000 (Heatset) 2,500 1 litre CSD bottle (units per hour) 4,000 10,000 3,600 16,000 2,500 2,500 2,000 (Heatset) 2,500 1.5 litres still mineral water bottle (units per hour) 4,000 10,000 3,600 16,000 2,400 2,400 2,000 (Heatset) 2,400 Large capacity container 3,000 600 16,000 1,200 1,200 Other 300 2,500 (still water/ CSD) 5. Footprint / space requirement (L x W x H in metres) 7 x 4.75 x 3.33 6.30 x 10 x 3.65 10.48 x 6.65 x 3.65 5.80 x 5.30 x 2.88 3.00 x 12 x 3.65 Depends on machine size 6. Special features (short description/keywords) Preferential oven; neck orientation; T-handle system; PP preform blowmoulding; on-line remote device 4.0; 5 gallons returnable/ one way; beer kegs; asymetric/oval botlles; air recovery system and hot fi ll Bottle design and mould manufacturing; bottle lightweighting concepts, Nitro-hot-fi ll; air-recycling systems for standard- and heat-set machines; rapid toolless product change-over systems; automated mould change-over systems (MouldXpress robot); integrated preform- and bottle inspection; Contiform Bloc (blower-fi ller-block); Contiform Bloc BL (blower-labeller-block); Ergobloc L and LM (blower-labeller-fi ller-block); ContipureAsept Bloc with integrated preform decontamination: Preferential Heating (PH) for non-round bottle production. ContiloopAI for automated process control."},{"@ID":44 "42 EVENT REVIEW PETplanet Insider Vol. 25 No. 07+08/24 www.petpla.net PET bottle flakes and rPET pellets BIPJ’s PET bottle flakes and rPET pallets production facility in Jombang, East Java, Indonesia, has been operating smoothly since late 2022. The facility produces 24,000 t of flakes and 16,000 t of rPET pellets annually. Starting with locally sourced post-consumer PET bottle bales, BIPJ produces FDA-approved clear flakes using equipment from reputable Asian and European manufacturers. The flakes are processed into rPET pellets, known as Vega rPET, using Erema’s Vacunite extrusion line and Polymetrix SSP. Vega rPET pellets are being tested in-house and by TÜV Rheinland for benzene and limonene content, and found to be well within permissible limits. TÜV confirmed that BIPJ’s flakes and pellets do not contain any Substances of Very High Concern (SVHCs) over 0.1% by weight, per EU Reach regulations. Additionally, the products comply with EU Regulation 10/2011 for food contact materials. Also, BIPJ is in the process of obtaining Recyclass and APR certifications, expected by Q3 2024, and has completed the documentation for Efsa certification. The company is currently awaiting an audit. On delays in Efsa certification, Managing Director Gautam Rathore stated: “We obviously are facing delays in the Efsa certification, which is the case with most of the foreign PET recyclers, since the change in the regulations in October 2023. While the local recyclers in the EU seem to be well covered, it seems that the foreign recyclers find themselves in a situation where in several countries Competent Authority (CA) has still not been defined/identified and as a result there is ambiguity relating the new procedures and requirements for audits.” Looking ahead, BIPJ sees a promising future for the PET recycling industry, driven by increasing rPET demand and the emphasis on sustainability. Rathore says: “Currently the demand for rPET is primarily coming from developed markets like Europe and US where regulations are mainly driving the demand. Several multi-national brand owners have made their sustainability commitments public and are implementing them on a global level. Regional brand owners are yet to start using rPET in a meaningful way, since they are not motivated enough due to the higher price of rPET compared to vPET. Supply is still trying to catch up with the global demand and we believe this will continue to be the case for a while, while regional imbalances exist. Asian suppliers of rPET are currently focusing on selling product into developed markets until the regional markets catch up on the trend. This high demand for rPET should help improve the bottle collection rates in most Asian countries which is an important step towards a more sustainable future, not just in developed countries but across the globe.” www.bumiindus.com Gautam Rathore, Managing Director BIPJ (right) and Naman Mehta, Director BIPJ"},{"@ID":50 "MARKET SURVEY 27 PETplanet Insider Vol. 25 No. 07+08/24 www.petpla.net 07+08/2024 MARKETsurvey 2-stage SBM machinery What all types of 2-stage stretch blow moulding machines do have in common is that prior to the stretch blow moulding process, preforms must be injection moulded in a separate machine. However, there is a diverse range of models to choose from in 2-stage stretch blow moulding. Our market survey allows you to compare specific parameters of these state-of-the-art machines from leading market manufacturers: TES STM Group, 1Blow, Newamstar, KHS, SMI, Flexblow, Serac, Sipa, Sacmi, Mega Machinery, Luxber, Side and Krones. Although the publishers have made every eff ort to ensure that the information in this survey are up to date, no claims are made regarding completeness or accuracy. Resins & additives Cap producers, systems & inspection systems Preform machinery Preform production & inspection systems Preform, cap & SBM mould manufacturer SBM 2-stage Compressors Filling equipment & inspection systems Palletising & shrink film machinery Recycling machinery Company name TES STM Group 1 Blow Newamstar Packaging Machinery Co., Ltd. KHS GmbH Postal address Telephone number Web site address Contact name Function Direct telephone number E-Mail Magnacka 6, Kowale 80-180, Poland +48 58 301 71 81 www.tes.com.pl Mr Mateusz Kinda STM Group Sales and R&D Director +48 503 036 635 [email protected] 25 Chemin de Gerocourt, 95650 Boissy l' Aillerie, France +33 9800 820 70 www.1blow.com Mr Olivier Perche Sales Director +33 9800 821 80 [email protected] East Xinjing Road, Zhangjiagang Economic & Technological Development Zone, Jiangsu 215618, P.R. China +86 512 5869 1111 www.newamstar.com [email protected] Juchostraße 20, 44143 Dortmund, Germany +49 231 569 0 www.khs.com Mr Arne Andersen Product Manager SBM +49 67907 334 [email protected] 1. Machine designation / model number Blue Line Hi-Tech Series - Linear machines 1XXL / 1XXLN / 1XL / 1XL Lab / 2L / 2LN / 2LO /2LHF / 2XL / 2XLO / 4L / 4LN / 4LO / 4LHF / 5M-C / 6MO RBM2-40 InnoPET Blomax Series V 2. Bottle volume (from/to in litres) a) Standard machines 10ml - 2.5 l 0.10 - 12 l 0.06 l - 2.5 l 0.1 - 3.0 l b) Machines for large containers 0.5 l - 12 l 5 - 30 l 3 - 20 l Upon request 3. Maximum number of stretch-blow moulds (units) a) Standard machines 8 cavities 6 8-40 36 b) Machines for large containers 4 cavities 1 2\\4\\6 Upon request 4. Output per stretch-blow mould for: 0.5 litres CSD bottle (units per hour) 2,000 - up to 16,000bph 2,000 12,000 - 108,000bph Up to 2,800 1 litre CSD bottle (units per hour) 2,000 - up to 16,000bph 1,800 4,000 - 60,000bph Up to 2,600 1.5 litres still mineral water bottle (units per hour) 2,000 - up to 16,000bph 1,700 4,000 - 60,000bph Up to 2,700 Large capacity container 1,200 - up to 5,500bph 1,000 for 5 l ; 600 for 20 l 4,000 - 40,000bph Upon request Other Hot fi ll mould - 1,500 per cavity - up to 12,000bph 1,200 - 6,600bph Hotfi ll+ up to 2,250bph 5. Footprint / space requirement (L x W x H in metres) Up to 5.5 x 1.8 x 2.7 (without preform feeding system) 2.1 x 1.6 x 2.4 8.02 x 5.69 x 3.75 - 13.03 x 7.62 x 3.75 6. Special features (short description/keywords) Full electric stretch blow moulding machines from 2 to 8 cavities with: air recovery systems for reducing consuption of low and high pressure compressed air; hot air recovery system for preheating preforms in oven; multifl ex system - option of working with many bottle necks on one machine; hot fi lling version with electric mould heating; preferential heating for diffi cult shapes oval and fl at bottles; deep grip mould option; moulds moving by servomotors; NIR and IR lamps system; service connection with 24h assistance system and mould change up to 10 minutes Preferential heating (oval bottles); neck orientation (with standard preforms); hot fi ll; compatible with Sidel, Krones, KHS, Sipa, Side, Terekas moulds; recovery of blowing air; power recovery; 5M-C available as a combi in cooperation with Ermi and Synerlink; integrated ink jet coding unit; integrated bottle wall monitoring unit; Sure Grip device for blow moulded hand grip; BottleClips device available on 2 l and 4 l machines; selective access to HMI through fob reader and all machines compatible with rPET preforms Effi cient single mould capacity, perfect security system, quick-replaceable moulds, long-term continuously-running, energy-saving and lower consumption, capable for multi-type bottles, information processing system, remote monitoring and service module Clever-Loc mould hanger for larger process angle and less complexity; Double Gate NIR oven for up to 40% reduced energy consumption; Focus Heater for better material usage and bottle light weighting; DuoCooling and Eco Dry for cooling energy reduction and higher hygiene due to less mould condensation; reliable and repetitive processing of rPET; standalone and blocked solutions"},{"@ID":31 "MARKET SURVEY 29 PETplanet Insider Vol. 25 No. 07+08/24 www.petpla.net www.agrintl.com +1.724.482.2163 • Accurate. Fast. Intuitive. • Powerful, Simple Job Creation and Editing ȏ 3UH 'HȴQHG &RQWDLQHU 0HDVXUHPHQW 5RXWLQHV • AutoJob® ȃ $XWRPDWHG )HDWXUH 5HFRJQLWLRQ and Job Setup in Seconds High Precision Dimensional Measurement for Plastic Containers — 6LPSOLȴHG ® Serac Group SAS Sipa Sacmi Imola Mega Machinery Luxber, S.L.U. 12, route de Mamers, BP 46, 72402 La Ferté Bernard Cedex, France +33 2 43 60 28 28 www.serac-group.com Mr Guillaume Fayard Blowing Division Director +60 12 418 1955 [email protected] Via Caduti Del Lavoro, 3 31029 Vittorio Veneto, Italy +39 043891 1511 www.sipa.it Mr Paolo De Nardi Product Manager SBM +390438911624 [email protected] Via Selice Provinciale, 17/A 40026 Imola BO, Italy ‘+39 0542 607111 www.sacmi.com [email protected] Xia Yang’ao, Yanjiang town, Linhai city, Taizhou, Zhejiang Provice, China www.megamachinery.com Mr Simon Sales Manager +86 135 8600 2000 [email protected] Av. De Azorin, 34-36, 03440 Ibi, Spain +34 96 555 3853 www.luxber.com Mr Ricardo Sanchez Export Manager +34 606 964 907 [email protected] Serac Blow Linear Rotary blow moulders: Xtra: 6 to 24 (8 models) Xtra Big (5 -12 liters), Xtra PH (Preferential heating) Linear blow moulders: SFL Performance 3H,4H,6,7,8; SFL Flex2; SFL Dynamic 2H,3H, 4,5; SFL Big 6,4; SFL Maxi 1,2,3; SFL WM (Wide mouth) SBF Tecnopet 1000, 2000, 4000, 6000 50ml - 3 l 250ml - 3.5 l 250ml - 3.0 l 3.3 l 2 l 0,1 up to 10 l 3 - 5 l 5ml - 12 l 5 - 30 l 12 l 300 l 12 24 8 24 16 unit 1, 2, 4 and 6 4 6 3 6 4 unit 1,400 2,800 per cavity 1,800bhc 4,500 1,500 2,250 1,400 2,550 per cavity 1,600bhc 2,300 1,500 1,900 1,500 2,550 per cavity 1,800bhc 2,300 1,500 1,800 1,000 1,500 per cavity on 5 l 650bhc 1,400 1,000bph for 5 l & 10 l 12.8 x 2.2 x 4.3 - 6.9 x 2.2 x 2.7 Stand alone or in bloc with Serac fi ller for bottle or cups (Combox, Cupbox); full electrical motions, no mechanical adjustment during change-overs; signifi - cant economical savings with air recovery system & low electricity consumption; preferential heating for fl at, oval and complex shapes; mould boxing on large capacities for handle insertion; clean options to run ESL or aseptic confi guration in Bloc Output 2,800bph/cav. with process & active angle: easy to blow; reduced TCO: lower air & energy consumption. 30 sec to change blow mould (tool-less), simple use & maintenance. rPET easy process. Bottles for water, oil, CSD, heat resistant, oval symmetric and asymmetric, with preferential heating, neck orientation, with handle, wide mouth (up to 130mm NF), large size (up to 30 litres), rPET, Tritan, PE, OPP, … Deep grip bottle, heat set, PP bottle Preferential heating, air recovery system, wide neck, PP preforms"},{"@ID":21 "MATERIALS / RECYCLING PETplanet Insider Vol. 25 No. 07+08/24 www.petpla.net 19 Additives and colour management solutions for recycled polymers based on an article by Lucia Buffoni, Marketing Manager Repi Group At the NPE, Repi showcased their latest advancements in additives and colour management solutions tailored for thermoplastic polymers. Their range of additives, which facilitate the inclusion of increasing percentages of recycled polymers in final products, garnered substantial interest. The portfolio includes aesthetics additives that correct off-shade raw materials such as toners, anti-oxidants or heat stabilisers, as well as performance aids such as intrinsic viscosity enhancers that make the recycled material mechanically valid for its purpose. The company says that their anti yellow, optical brighteners and IV enhancers have represented over the years a valid aid to rPET recyclers and packaging converters. Such additives can be used at different stages of the rPET value chain, e.g., from recycling up to preform or tray manufacturing with no impact on processes, thus offering maximum flexibility even when there are variations in batches. The increasing demand for recycled percentages and the scarcity of food grade rPET flakes are presenting challenges related to quality and colour consistency between one batch and another. What both recyclers and converters particularly struggle to manage is the drop of L* of CieLab numbers while respectively recycling and moulding or extruding the final packaging. While it is possible to correct offshade rPET pellets with custom-made formulations that act both on the a* and on the b*, the darkening of material (precisely the drop of L*) is very difficult to avoid. To address this, Repi introduced StabiPlus, a liquid additive that acts as a proactive stabiliser to prevent ageing and discolouration of rPET through multiple cycles. This additive can be used both at the recycling stage and directly by converters during packaging production. StabiPlus is claimed to preserve the intrinsic viscosity (IV) of rPET, maintaining its mechanical properties and broadening the sustainable use window of rPET. Repi also showcased its IV enhancers, linear chain extenders that prevent cross-linking and increase rPET IV by over 0.05dl/g. This enhancement is claimed to improve the top load performance of rPET bottles, making them comparable to those made from virgin PET. Performance of Repi’s IV enhancers at increasing dosage on rPET in extrusion moulding and in injection moulding Colour management system A highlight of Repi’s participation at the show was the introduction of their colour management system (CMS), developed in collaboration with Krauss Maffei. The CMS, integral to Repi’s core business of liquid colours and additives for thermoplastic polymers, is claimed to meet the growing need for control and correction in processes using recycled polymers. It has shown good results in PET and rPET sheet extrusion processes, where it monitors colour consistency and provides feedback to dosing units. The system offers remote control capabilities for immediate intervention by Repi’s technical engineers, working in both transmission and reflection modes to handle coloured and transparent sheets with transparent additives. The colour management system In a live simulation at the show, virgin PP transparent preforms were injection moulded. These were then sent to a shredder, directly connected to an extruder producing rPP granules that were coloured blue by three Repi dosing units. The blue granules were conveyed to an injection moulding machine producing bottle openers, made of 100% recycled plastics. In order to better simulate a real recycling closed loop, where the incoming material is often uneven in shade, a fourth Repi dosing unit was used to inject a “disturbing colour” into the extruder. The CMS worked to neutralise the off shade by varying the dosing of the three basic colours. This was possible thanks to a spectrophotometer that after reading the Lab* values of the resulting granules sent the correct input values to the three operating units that adjusted the dosage to the set tolerances. www.repi.com RECYCLING"},{"@ID":13 "EDITOUR PETplanet Insider Vol. 25 No. 07+08/24 www.petpla.net 11"},{"@ID":15 "MATERIALS / RECYCLING PETplanet Insider Vol. 25 No. 07+08/24 www.petpla.net 13 Working with us bears a risk RI VWDUWLQJ D ORQJ WHUP SURƓWDEOH UHODWLRQVKLS IRU \\HDUV yellow.agency Swiss-engineered Preform Systems At Otto Systems we focus on solutions for special applications in PET preform production. We provide you with the most economical answers to your needs. Our unique system concept is based on smart modularity, proven performance, IXOO LQWHJUDWLRQ DQG PD[LPXP ŴH[LELOLW\\ )URP LGHD WR RSHUDWLRQ 2WWR 6\\VWHPV JLYHV \\RX D GHFLVLYH FRPSHWLWLYH HGJH with your satisfaction as our guiding principle. Jump-start your PET preform production with us. otto-systems.com"},{"@ID":3 "No.7+8 2024 www.petpla.net D 51178; ISSN: 1438-9452 29 . 07 . 24 M A G A Z I N E F O R B O T T L E R S A N D B O T T L E - M A K E R S I N T H E A M E R I C A S , A S I A , E U R O P E A N D A L L A R O U N D T H E P L A N E T PETplanet is read in 159 countries MARKETsurvey Suppliers of 2-stage SBM machinery Page 27 EDITOUR Recycling Page 12 Page 10"},{"@ID":49 "PATENTS PETpatents www.verpackungspatente.de PETplanet Insider Vol. 25 No. 07+08/24 www.petpla.net 47 An aseptic squeeze container International Patent No. WO 2023 / 232716 A1 Applicant: Société des Produits Nestlé S.A., Vevey (CH) Registration date: 26.5.2023 A specially designed squeeze container for the aseptic filling of flowable food products. Details of the preform and filling method are described in the application. A plastic bottle European Patent No. EP 3560852 B1 Applicant: Suntory Holdings Ltd., Osaka (JP) Registration date: 25.12.2017 At the end of 2023 / beginning of 2024, a plastic bottle with curved and angled compensation surfaces is to be granted a European patent. The bottle is designed for hot-filled products. Faceted side surfaces European Patent No. EP 4090601 B1 Applicant: The Procter & Gamble Company, Cincinnati (US) Registration date: 12.1.2021 A clear bottle with faceted side walls is to be awarded a European patent. A sturdy PET bottle International Patent No. WO 2023 / 235868 A1 Applicant: Abbott Laboratories, Abbott Park (US) Registration date: 2.6.2023 A lightweight, thin-walled PET bottle with circumferential reinforcing grooves and waist in the base area to ensure the container is sufficiently robust. Defined volume reduction International Patent No. WO 2023 / 243559 A1 Applicant: Suntory Holdings Ltd., Osaka (JP) Registration date: 9.6.2023 The shaping and design of a thinwalled plastic bottle which, by virtue of said design, can be compressed in a defined manner down to a small volume and secured in that state. A lightweight bottle International Patent No. WO 2022 / 177809 A1 Applicant: The Coca-Cola Company, Atlanta (US) Registration date: 11.2.2022 A lightweight bottle for holding a non-carbonated drink whose base is specially designed to be robust enough to prevent deformation."},{"@ID":40 "EVENT REVIEW PETplanet Insider Vol. 25 No. 07+08/24 www.petpla.net 38 the process variables, the XD 20 also adapts the treatment to each polymer and the CRX Mobilux has an antistress device to prevent overdrying of the granules. The VFD automatically adapts to the actual throughput and is therefore designed to guarantee perfect drying and prevent over- or under-drying of the resin. As an option, the Mobilux drying systems can also be equipped with Moretto’s inline moisture meter, which is connected directly to the drying system’s control unit and whose moisture sensor is located directly under the drying hopper. It guarantees real-time control of the drying process to minimise waste, reduce energy consumption and avoid human intervention. The manufacturer also launched the DGM 20 Gravix, the latest model in the already well-known DGM gravimetric multi-component mixer series with its proprietary Roto-Pulse technology for precise mixing and waste minimisation. It is said to be specially designed for small components where low throughput and high mixing accuracy are required. Equipped with double flap valves, the system offers precise material dosing of raw materials, masterbatches and additives. The capacity is up to 20kg/h. The demountable design is said to greatly simplify cleaning and maintenance, without the need for tools. The system is also designed for uncomplicated and rapid material changes and adjustments. Control can be systemintegrated and via a touchscreen on the device. www.moretto.com Flexible material drying and dosing systems In addition to its established products, Moretto also presented its CRX Comb series of Mobilux dryers for the first time. This compact series is based on the X Comb and is available in models with different drying. According to the manufacturer, each CRX Comb model features a honeycomb wheel of 100% zeolite desiccant and is equipped with anti-stress technology to prevent over-drying, as well as automatic drying air modulation for optimal drying performance with minimal energy consumption. Part of the anti-stress technology is the adaptation of the air flow to the drying requirements while maintaining the same drying quality. As a special feature, the parameters material type and throughput are required, while the dryer automatically regulates all other parameters such as dwell time, process temperature, air flow and anti-stress and processes all polymer types correctly. By using an exclusive zeolite desiccant, continuous dew points of -62 °C are achieved. The CRX Comb works with a single power supply, so no compressed air or water is required. The technology, based on the X Comb, includes Moretto’s OTX (Original Thermal eXchanger) hopper, whose dehumidification process and concept is said to realise a true exchange of energy and moisture with optimal energy efficiency, resulting in a 40% shorter drying time and a 40% reduction in hopper volume with the same throughput and, thanks to the internal geometry, is said to improve energy efficiency by 66%. The company offers the range of CRX Mobilux drying systems based on XD 20 dryers, which are equipped with a double tower drying system that can generate uniform -75 °C dew points. Unlike other twin tower dryers on the market, the XD 20 series features a variable frequency drive (VFD) controlled fan to modulate the airflow to the hopper to meet performance and energy reduction standards, Moretto said. Using thermodynamic simulations and automatic control of Moretto’s booth at the NPE CRX Comb DGM 20 Gravix batch gravimetric dosing unit"},{"@ID":1 "No.7+8 2024 www.petpla.net D 51178; ISSN: 1438-9452 29 . 07 . 24 M A G A Z I N E F O R B O T T L E R S A N D B O T T L E - M A K E R S I N T H E A M E R I C A S , A S I A , E U R O P E A N D A L L A R O U N D T H E P L A N E T PETplanet is read in 159 countries MARKETsurvey Suppliers of 2-stage SBM machinery Page 27 EDITOUR Recycling Page 12 Page 10"},{"@ID":12 "EDITOUR PETplanet Insider Vol. 25 No. 07+08/24 www.petpla.net 10 From 0 to 100 - Two Saudi water brands take off by Kay Barton Two water brands are virtually omnipresent in Saudi Arabia: Oska and Ival. The company behind them is Pure Beverages Industry Company, which bottles the brands in two production facilities. One of these bottling plants is located in Al-Kharj Industrial City, around 130 km south of Riyadh, near the town of Al Kharj. And although you can’t go past almost any supermarket today without coming across the water brands, the company is still very young and the brands have only been on the shelves since 2021. We asked what has led to this rapid success and met with Mr Shibin Kungaran, the Plant Manager at the Al-Kharj plant. EDITOUR Meeting with Pure Beverages Industry Company February 28, 2024 We met: Mr Shibin Kungaran, Plant Manager Al Kharj Plant Mr Shibin Kungaran welcomed us into the beautiful foyer of the bottling plant, where there is a showroom shelf displaying the various bottle formats and materials, PET and glass, and a large flat screen providing information about the production of Oska and Ival with insights into the bottling process. Shortly afterwards, we sat in a bright and very open-looking office with glass walls opposite the man who ensures that the production process runs smoothly. Mr Kungaran comes from India, holds a master’s degree in microbiology and has already worked there for a water bottler, as well as seven years for Coca-Cola Aujan in Saudi Arabia. He has been part of the team here for two years, basically since the plant was built, first as Plant Supervisor, then as Production Manager and in his current position since December 2023. Pure Beverages is part of the investment company Ajlan & Bros Group, which conceived the idea of bottling water in 2017 and began building the first plant in 2019. Mr Kungaran explained: “Here in Al-Kharj, we went live in 2021, starting with two lines and then adding a third, all PET lines. In our other plant in Jeddah, which we launched in 2022, we fill with two PET lines and an additional glass line for premium hotel and catering areas. We chose Krones as our supplier for both plants because we believe they offer the best service.” The total of five PET lines at both sites consist of four Ergobloc L and one Contiform Bloc. The glass line in Jeddah is also from Krones, as are the water treatment systems. “Here at the plant, we process around 700,000m3 of water a year. That corresponds to around 30 million cases with 40 bottles each in 2023. 420,000m3 of water is used in Jeddah and we had 23.5 million cases there in 2023. Oska and Ival are bottled in volumes of 200ml, 330ml, 600ml and 1.5 l. “The so-called drop bottle with 200ml also exists,” says Mr Kungaran. As the company does not have its own wells, the water comes from five different suppliers who extract it from wells and the municipal water supply and deliver it pre-treated to Pure Beverages. The company’s growth since it was founded has been remarkable. It started with 1.6 million cases in 2021, rising to 21 million in Riyadh in 2022 and 29.9 million together with the recently launched Jeddah plant. “We expect 83 million cases in 2024, 46 million of which will be here in Riyadh.” According to the company, this puts it among the top four water bottlers in the country, alongside Nova Water, Safa (Makkah Water) and Aquafina (Coca-Cola). 92 people are currently employed at the Al-Kharj site. www.purebeverages.com Plant Manager Shibin Kungaran with his two brands Oska and Ival Oska production Shibin Kungaran in front of the Krones Contiform"},{"@ID":28 ""},{"@ID":16 "MATERIALS / RECYCLING PETplanet Insider Vol. 25 No. 07+08/24 www.petpla.net 14 The CircuTray-UP project PET tray packaging recycling Although PET packaging is produced in large quantities and is one of the most common types of modified atmosphere packaging, it is rarely if ever recycled. Despite the established state of the art in sorting non-bottled PET packaging, the most common processing route for such packaging ends in incineration. The CircuTray-UP project, which is funded by the German Federal Ministry of Education and Research (BMBF) as part of the Plastics Recycling Technologies (KuRT) initiative, aims to close the loop for PET trays by establishing a value chain from innovative recycling strategies to the production of rPET-based tray packaging. RECYCLING The field of packaging structures encompasses a wide range of plastics, with PET being one of the most commonly used plastics for flexible food packaging after polyolefins such as PE. PET tray packaging with a production volume of 1,070 kt/a including PET film in the EU27+3 in 2022 [PET Market in Europe. State of Play. Production, collection & recycling data 2022], is used both for simple items such as fruit and vegetables and for more challenging items such as meat and cheese, which require modified atmosphere packaging. While only single-layer structures are required for low-value items, high-value items in modified atmosphere packaging usually require a multi-layer structure containing PE, EVOH, PA and adhesives. Such a conglomerate of plastics poses a problem for conventional mechanical recycling, as different processing conditions are required and the polymers do not dissolve into each other. While multi-layer structures are an obvious problem for mechanical recycling, single-layer PET is a problem in itself. The mechanical and thermal properties of PET used for trays, such as different melt viscosities, melting temperatures and intrinsic viscosities, differ significantly from bottle PET, resulting in limited compatibility with the well-established bottle PET recycling. In Germany, PET-based plastics are collected by the Dual Systems Germany (DSD) and sorted accordingly into waste fractions of non-food PET bottles and trays with different compositions and a majority tray fraction containing both single and multilayer structures. While the mixed PET fractions are partially recycled and mainly used in low-value applications, the majority tray fraction often ends up in plants for energy recovery. Pressure from legislator According to the latest revision of the European Plastic Packaging Waste Regulation (PPWR), touchsensitive packaging with PET as the main polymer, including food contact packaging, must contain at least 30 per cent recycled material by weight in 2030 and at least 50 per cent by weight in 2040. In addition, at least 70% of the packaging must be recyclable. None of the proposed minimum values can currently be achieved on an industrial scale. As the PPWR is on its way into legislation, a solution to this waste problem must be found soon, otherwise this type of packaging will have to be replaced by more recyclable packaging. Several market players have already partially addressed the problem, but not sufficiently solved it. Some have tried to take the delamination route (Repetco Spain, Linpac Packaging Ltd), others have addressed the issue of adhesives (BASF), while others have chosen the mechanical recycling route for monolayer structures only (Klöckner Pentaplast). In 2022, the recycling capacity for PET trays was 57kt/a, with the Netherlands, Spain and France contributing the most. [PET market in Europe. State of Play. Data on production, collection and recycling 2022] Advancing the recyclability one step at a time The CircuTray-UP project, which is funded by the German Federal Ministry of Education and Research (BMBF) as part of the Plastics Recycling Technology Initiative (KuRT), addresses the entire value chain by looking at sorting, waste processing, advanced recycling processes, film processing and packaging production in order to close the loop for PET trays. The strategic partners of the project committee, led by the Fraunhofer Institute for Process Engineering and Packaging IVV in Freising, are ZWS Recycling GmbH, Unisensor Sensorsysteme GmbH, Lömi GmbH, Reifenhäuser GmbH & Co. KG, Silverplastics GmbH and Öko-Institut e.V. Fig. 1: Flow chart for PET tray recycling loop"},{"@ID":58 "35 EVENT REVIEW PETplanet Insider Vol. 25 No. 07+08/24 www.petpla.net Presentation of PET circular economy and new technologies from Husky At the Husky stand, interested trade fair visitors were given a comprehensive overview of the company’s technological innovations, as well as an in-depth understanding of the importance and processes of PET bottle recycling and the circular economy. This was presented in a clear and engaging interactive, cinematic installation, created in collaboration with partnering companies. From collection, washing and grinding to blowing and filling, each step demonstrated how a circular end-to-end solution enables a bottle to be back on shop shelves and in the hands of consumers in just five days. CEO John Galt reiterated the importance of PET in the global circular economy, both in person and in prerecorded video messages shown at the stand: “PET is one of the few materials approved for use in medical devices and even for prolonged use in the human body. More than 70% of medical consumables used today are made from PET and other medical polymers.” He also cited the ecological comparisons with alternative materials: “The production of beverage containers made of aluminium and glass releases three to five times as much CO2 into the environment as the production of PET containers, and three to five times as much water is required for production. In addition, PET production avoids the unsustainable impact of deforestation associated with paper composites and the environmental impact of aluminium mining.” At the show, Husky unveiled its new HyPET6e injection moulding platform, the first of its kind. This complete machine, comprising mould, auxiliaries and realtime remote monitoring, is designed for sustainable production and processing of rPET. It is said to score particularly well with speed, energy efficiency and integrated quality control. The HyPET HPP6e system running was producing a 5.89g preform made of 100% rPET material with a cycle time of 4.5 seconds, and the company confidently stated that these can be blown into the lightest industrialisable bottles on the market (20oz/591ml). The working mould had 144 cavities with a 45-pitch and its architecture is said to double the potential output. Also on show was the high-performance Hylectric 4.0 system with UltraShot injection technology to produce a complex bioresin part. The company presented its UltraMelt technology for processing bioresins as an integral part of the system, which shall open up new possibilities for the use of alternative renewable, bio-based materials in plastics production. Of particular interest were the new design and development innovations in the area of 100% PET caps in response to growing market interest in mono-material packaging for even more targeted recycling. Husky’s optional Advantage+ Elite remote monitoring system, which analyses and evaluates all production-relevant parameters and data from the processes and makes proactive and early optimisation suggestions or points out possible upcoming problems by the Husky team in order to reduce downtimes and waste and improve the overall effectiveness of the systems, was also presented. www.husky.co Husky’s interactive, audiovisual presentation of all stages of PET bottle recycling Global Marketing Director Henry Zhang presents Husky’s new developments such as the HyPET6e injection moulding platform."},{"@ID":26 "CAPS & CLOSURES 24 PETplanet Insider Vol. 25 No. 07+08/24 www.petpla.net Solving tethered closure challenges Implementation insights The Tethered Cap Directive is in force. This means 24/7 work for Vladislav Medvedovskiy, Head of Retal Service, and his team. Following an internal survey of its customers, Retal has discovered that many customers have waited until the last possible moment to adapt their cap production lines. Retal is well positioned with its service team, which is represented at all Retal locations worldwide. At the Plastics Closures Innovations Event in Barcelona in June this year, organised by AMI, Vladislav reported on typical problems and challenges introducing the new tethered cap technology. PETplanet talked to him for some more insights. PETplanet: Vladislav, how have been the last few weeks for you and your team? Vladislav: Busy, as always! It’s now high season, so it’s important for us to make sure all our customers are ready for this time of high volumes. After the PCI presentation in Barcelona, I got straight back into visiting customers to maintain their equipment and to be ready for any urgent requirements. PETplanet: When you arrive at a customer’s plant, what are the first questions you hear regarding the implementation of the tethered cap? Vladislav: People want to be sure that they can continue production without any downtime, and that they don’t need to modify their equipment, or need any investment. I am always happy to confirm that tethered closure implementation is easy when you know how! PETplanet: What are the most common technical issues during implementation? Vladislav: The main issue I see is that the slitting of the tethered closure can create a jam in the chute. This is because they have a dual level slitted tamper evidence band and this can jam in the lower level slit as the closures stack up. My team and I can fix this by accurately adjusting the height control of the chute. PETplanet: Long machine downtimes and costly adjustments are unpleasant for your customers. How do you avoid this during the changeover? Vladislav: Keeping up with regular maintenance is key as this stops any issues before they have a chance to cause downtime. Combine this with the remote and on-site emergency offer from Retal Service and customers have the peace of mind that they’re ready for anything. PETplanet: Which tethered caps pose the greatest challenges during the changeover? Vladislav: The general transition to new closure design requires investments and high level of expertise, as not all equipment can be adapted to tethered implementation depending on the neck finish. It’s hard to highlight the specific closure which posed the greatest challenge during the changeover, as different units of the filling lines appeared more or less suited for the new closure design. So, I can say that the greatest challenge is finding an adaptation for all scenarios, that is where Retal Service comes in. PETplanet: What has been the smoothest and most complex conversion so far? Vladislav: All clients which followed following algorithm got the smoothest conversion: 1) Complete line survey for the new closure design 2) Conversion and adjustments 3) Test 4) Start production In general, if clients jumped to point #3, they experienced a more complex conversion. PETplanet: Do you also see other markets outside the EU where the tethered cap could be introduced? Vladislav: Tethered caps are not currently required by legislation in other markets, so we can work with customers in whatever markets they’re active. We think that more countries will decide to implement tethered caps after seeing the benefits tethered brings to Europe, particularly regarding litter reduction. PETplanet: Thank you very much! www.retalgroup.com"},{"@ID":11 "9 NEWS PETplanet Insider Vol. 25 No. 07+08/24 www.petpla.net Bericap opens new production facilities in Africa, South America and South East Asia Bericap is continuing its geographical expansion with new production facilities in Africa, South America and South East Asia. The closure specialist has opened new plants in Nairobi (Kenya) and Ho Chi Minh City (Vietnam) and acquired production facilities in Lima (Peru) and Durban (South Africa). The company now operates 30 production sites in 25 countries to be close to its customers in terms of project support, logistics and services. New production facility in Kenya Kenya is the driving force of economic growth in East Africa and it plays an essential role in a regional supply context. The new 3,500 m² facility in Nairobi/Kenya makes the localisation of the commercial business that has been built up over the last eight years possible. Especially closures for the lubricant industry and for food and beverage manufacturers are produced there. Bericap exports closures manufactured at the Nairobi facility to ten African countries. Operations in South Africa The company has recently invested in another plant in Africa and now has also operations in SouthAfrica. The closure business that Bericap acquired was a division of Nampak, a company with which Bericap has had a technological partnership since 1998 for the SouthAfrican market. The production facility in Durban started trading as Bericap South Africa (PTY) LTD in March 2024. Bericap SouthAfrica will be marketing the company’s entire closure portfolio, as well as the locally manufactured closures, in SouthAfrica and neighbouring countries. Production site in Peru Peru is Bericap’s fourth production site in Latin America and allows good access also to Bolivia, the northern part of Chile and Ecuador with a total of around 60 million consumers. Major companies in Peru have signalised their interest in having a closure specialist with explicit research and development expertise in the region. This prompted Bericap to acquire a 5,000m² production facility in Lima with 50 employees. The Bericap team in Peru is supported by the teams at Bericap do Brazil and Bericap Argentina. Plant in Vietnam In September 2023, Bericap chose Vietnam as another base in the prospering region of South East Asia and set up a production site there. This investment is a reflection of the region’s excellent market potential for modern closure solutions in the sectors of beverage and dairy products, food and chemical products. Production commenced in mid-October and the plant has passed all mandatory external audits. “Tamper-evident closure solutions are particularly relevant for manufacturers in the Vietnamese market who are keen to protect themselves against product piracy. Bericap has the right solutions for these manufacturers, and the fact that they are also easy to use and therefore consumerfriendly explains why they are very much in demand,” said Swee Heng Lee, Managing Director of Bericap Vietnam. www.bericap.com"},{"@ID":45 "43 EVENT REVIEW PETplanet Insider Vol. 25 No. 07+08/24 www.petpla.net organized by co-organized by 30. + 31. October 2024 Düsseldorf, Germany Maritim Airport Hotel ONLINE, Live-Stream World Congress Platinum Sponsor KOREA PACKAGING ASSOCIATION INC. Media Partner Premium Media Partner Supporter Diamond Sponsor www.pef-world-congress.com Solutions for sustainability and PCR content in packaging Avient Corporation showcased solutions to enhance the customer experience when working with post-consumer recycled (PCR) content, particularly in packaging applications. Among the highlighted technologies were advancements specifically beneficial for PET bottle applications, as Dr Jan Sültemeyer, Global Sustainability Leader at Avient, revealed. One of the key technologies introduced was the Colormatrix AAnchor Acetaldehyde Control Technology. This newly formulated acetaldehyde (AA) scavenger has been specifically developed for PET packaging to address the challenges associated with increased rPET content. AAnchor not only aims to improve the recyclability and quality of PET packaging but also to reduce risks related to regulatory compliance and the migration of the active AA scavenging component and non-intentionally added substance (NIAS) species, which are often concerns with other types of AA scavengers. Dr Sültemeyer elaborated on the rigorous testing the scavenger underwent: “We have thoroughly tested AAnchor in our Global Technology Center in Knowsley, UK. Our CycleWorks Innovation Center is also able to simulate complete material performance chains in mechanical recycling on a scale of 50-100 kg, enabling us to test for issues such as deposits in the mould, which are common with other products.” He further emphasised that even at temperatures exceeding 300 °C, the stability of the scavenger was maintained. AAnchor has been adopted by a customer in the water sector and was recognised as a finalist in the Product Technology Innovation of the Year category at the PRSE Awards. Another solution showcased was laser marking for label-less or naked bottles. “This method offers significant advantages by eliminating the need for printing inks, thus removing the necessity for de-inking during the recycling process,” explained Dr Sültemeyer. “Laser marking is a growing trend, and our additives can increase the marking speed and enhance contrast for better readability”. www.avient.com F.l.t.r.: Jan Sϋltemeyer, Global Innovation and Sustainability Manager, Mirco Groeseling, Market Development, Packaging and Sustainability Manager, John McClelland, Sales Director, Avient"},{"@ID":23 "CAPS & CLOSURES 21 PETplanet Insider Vol. 25 No. 07+08/24 www.petpla.net A blessing and a curse at the same time? The tethered cap story… Tethered caps have kept the closure and beverage industry extremely busy in recent years. Now the time has come, the EU directive is in force. Companies in the EU countries are making the change - because they have to. What are the advantages of tethered caps, what is the status of implementation? And the big question is what will happen to this type of closure outside the EU - will there be other markets? As part of the AMI’s Plastic Closure Innovation Conference in Barcelona, which took place on June 4 to 6, 2024, PETplanet spoke to Luca Nanetti, CCO at Wisecap and Stefano Chiozzini, Closures B.U. Manager at Sacmi. PETplanet: Mr Nanetti, from your perspective as a cap producer, what are three big advantages of the tethered cap solution? Mr Nanetti: Frankly, I would challenge any cap producer to come up with anything positive about tethered caps!!! The level of investments involved in this has been enormous and we are only at the beginning. But at the end of the day converters are also consumers and are themselves actively involved in the fate of our plastic beverage industry. For this reason, need coincides with opportunity to bring advantages to the industry. The three main advantages that I see are consumers becoming aware that their support is necessary to reduce littering and thereby enhance circularity. Recycling technologies have been evolving at unprecedented speed in recent years and being able to have an increasing amount of recycled plastic material (PET and now also PE used for the cap attached to the bottle) will create more opportunities to reduce crude oil consumption and make bottle-to-bottle and capto-cap more of a reality every day. Finally, the introduction of tethered caps offers an unheard-of opportunity to bring further technical innovations to the cap industry. PETplanet: Mr Chiozzini, what were the major challenges in developing the machine technology for the tethered closure? Mr Chiozzini: Let me start by replacing the word “challenges” to “opportunities”. In fact, machine technology development has certainly been a long process with many surprises on the way but it drove us to develop a new generation of machines, moulds and vision systems that nowadays enriches our range of turn-key solutions. The “tethered caps adventure” also introduced a new way of designing closures not only oriented to sealing performances but also to opening functionalities with the goal of maximising and improving the consumer experience and this has been very exciting. However, a lot of work has gone into improving the efficiency of the scoring process relating to the new way of cutting the plastic of the tamper evidence band of the tethered caps. Finally, the impact on the industry, prompted by the European SUP directive, gave producers a limited time to make the changes. Manufacturers were forced to invest heavily in the production process to reduce unnecessary delays to our lead times. This has definitely been an additional topic worthy of consideration with the final goal of avoiding delays that might have damaged the confidence and the business of our customers. PETplanet: Mr Nanetti, you offer a wide range of tethered closures. Have you identified closures that are in particularly high demand and the applications for which they are used? Mr Nanetti: In general, and in order to properly respond to national laws imposing the use of tethered closures, all families are to be delivered with a tethered cap. Thus the demand for tethered closures is spread across all the bottle families which fall within the terms of the new regulations. Additionally, and for different reasons, the first part of 2024 is showing a high level of demand in terms of volumes. PETplanet: Mr Chiozzini, what do customers have to do if they want to expand their existing Sacmi cap machine with the tethered cap solution? Can the new technology be integrated into every Sacmi cap system? Mr Chiozzini: That’s a very interesting question that helps me to share Stefano Chiozzini, Closures BU Manager at Sacmi Luca Nanetti, CCO at Wisecap"},{"@ID":10 "8 NEWS PETplanet Insider Vol. 25 No. 07+08/24 www.petpla.net Husky founder Robert Schad passes away Robert Schad, the founder of Husky Injection Molding Systems and one of the most famous entrepreneurs in Canadian plastics history, died in Toronto on July 11 at age 95. Born in Karlsruhe, Germany in 1928, Schad trained as a tool and die maker and then emigrated to Canada in 1951, arriving with $25 in his pocket and a letter of reference from family friendAlbert Einstein. He founded Husky in rented space in an Esso garage in Toronto in 1953, and the company originally built the Huskymobile snowmobile. The commercial interest in this product was limited, however – it was considered too heavy to skim over the snow – causing the business focus to change from snowmobile manufacturing to toolmaking, making tools, dies, and fixtures for others. Husky Moulds got its first piece of business when Amalgamated Electric Corp. placed an order for an electrical component mould. By 1957, Schad had moved Husky into a 12,000-square-foot facility, where it produced moulds and dies for high-production applications. Schad thought that moulding machines of the time were too slow to run his moulds at their full potential, so he designed and built his own high-speed injection moulding machine. The company had found its niche and grew rapidly, being renamed as Husky Injection Molding Systems, and supplying high-speed moulding machinery to customers in more than 100 countries from its headquarters in Bolton, Ontario. Under Schad’s guidance, Husky became one of plastics’ most dominant injection moulding machine makers, especially in the PET preform and closures market, with manufacturing plants in Canada, the U.S., Luxembourg, and China. The company eventually grew to have sales of $1 billion, 3,350 employees, and 1,600 patents. Schad also founded Husky’s hot runner division in Milton, Vt., which became an industry leader in hot runners for highcavitation injection moulds. “Robert’s leadership and foresight were instrumental in setting new standards for quality and efficiency in plastics manufacturing,” Husky’s vice president Wassim F. Labban said in a LinkedIn post. “His dedication to sustainable practices set the stage for an environmentally responsible manufacturing, long before sustainability became a global imperative. His approach based on value and customer engagement set new benchmarks in building global brand success and recognition.” Schad retired from Husky in 2005 and sold the company in 2007 but wasn’t done with the industry yet – in 2008, on the cusp of turning 80, he founded injection moulding machine maker Athena Automation, in Vaughan, Ont. Athena developed a rugged, accurate, and flexible two-platen machine platform, and then changed its name to Niigon Machines Ltd. in 2018. But the company struggled during the Covid-19 pandemic and went out of business in 2021. For his contributions to the plastics sector, Schad was inducted into the Plastics Hall of Fame in 2006 – the first Canadian to receive the honour. He also received a LifetimeAchievement Award from The Plastics Academy in 2003, and was named to the Order of Canada in 2010. “We mourn the loss of Robert. Aman who taught us that a quick decision is often better than no decision at all - this lesson remains in our hearts.” - Alexander Büchler, Publisher PETplanet Insider Schad was also a noted philanthropist, donating some $200 million to various initiatives over the course of his lifetime. He also created the Schad Foundation in 1987, which supports projects focused on solutions to environmental problems; founded Earth Rangers, a wildlife refuge and outdoor education interpretive centre for children; and was a major benefactor for the Canadian College of Naturopathic Medicine and Schad Clinic. www.canplastics.com www.plasticshof.org www.schadfoundation.com"},{"@ID":22 "20 PETplanet Insider Vol. 25 No. 07+08/24 www.petpla.net PETproducts Recycled PET drying technology Eisbär Trockentechnik GmbH has been specialising in drying systems for many years. In the last five years, the company has gradually expanded its focus to include the drying of rPET, responding to the growing demand for sustainable and efficient recycling processes. Drying rPET presents challenges due to its higher moisture content and potential contaminants compared to virgin PET. Eisbär has developed drying technologies to address these challenges, ensuring that the recycled material meets the stringent quality standards required for further processing. The company’s rPET drying systems incorporate several technological advancements. These include energy efficiency, where Eisbär utilises state-of-the-art heat recovery techniques and optimised drying processes to reduce energy consumption. Additionally, the systems are claimed to feature advanced process control, enabling precise monitoring and adjustment of drying parameters to ensure consistent and high-quality output. Scalability is another key feature, with Eisbär offering flexible solutions that can be tailored to different production volumes and specific customer requirements, making their systems versatile and adaptable. The demand for rPET drying solutions remains robust, reflecting the industry’s growing commitment to recycling and sustainability, says Eisbär. www.eisbaer.at An agglomeration unit for chemical recycling of plastics Previero N. with its Sorema division, known for highquality recycling solutions, has now redesigned its Tramu technology as a further step in closing the plastics recycling loop, especially for processing heterogeneous plastic fractions that pose a challenge for mechanical recycling. Efficient processing of the source material using a chemical recycling process is a major challenge today. The mixed plastic fraction, which consists of light, thin, flexible plastics with densities below 50-80 kg/m³ and a high moisture content, is processed in a pyrolysis process. The aim is to convert these materials into a dense, dry product with a density of over 300-350 kg/m³ while ensuring consistent quality and low energy consumption. In the context of chemical recycling, Previero has redesigned its Tramu technology, a continuous agglomerator with double degassing and calender. The main features of Tramu are its ability to agglomerate plastics at a temperature 20-30% lower than that of a standard extruder, and to remove moisture and gases at ambient pressure. By operating the machine under these conditions, the Tramu boasts low energy consumption. Wear and tear have been greatly reduced, while final density is ensured by degassing and calendering before final grinding. Tramu is available in three models, each suitable for different scales of operation, with capacities from 600 kg/h to 3,000 kg/h. www.sorema.it RECYCLING"},{"@ID":14 "MATERIALS / RECYCLING PETplanet Insider Vol. 25 No. 07+08/24 www.petpla.net 12 Chemical innovation supports growing rPET demand The growth in rPET usage is driven by a heady combination of legislation and consumer demand. The global rPET market was valued at USD 13159.36m in 2022 and is expected to see a nearly 7% CAGR, bringing it to USD 19736.88m by 2028. This, together with the recent study that shows 49% of consumers ‘feel better when they buy products with recycled packaging’, helps to explain why the upward trend for rPET usage shows no sign of slowing down. RECYCLING European Commission legislation on the requirements for recycled plastic materials for food contact is defined in EU 2022/1616. The aim of this regulation is to increase the use of recycled materials, which of course is influencing the demand for rPET for converters and packaging manufacturers, particularly in the food and beverage industries. The requirements from the EU state that 100% of plastic packaging must be recyclable by 2029, including PET packaging in separate collections, broken down into 77% by 2025 and 90% by 2030. Furthermore, PET packaging must contain 25% post-consumer recycled plastic content from 2025. However, the one potential pitfall is the unstable availability of rPET. Just because consumers want it and legislation says we must use it, doesn’t mean the industry can always get it in huge volumes. The challenge of a strong demand for rPET is showing in a lack of availability, with reliability of supply proving difficult for converters, producers and brands alike. PET resin and polyols producer Neo Group, founded in Lithuania in 2004, is proudly addressing this supply reliability issue while helping to close the loop for a circular economy. Its patented process, developed in-house by skilled chemical technologists, has created Neo PET Cycle. Food grade rPET availability Neo PET Cycle is a PET resin which includes up to 30% of rPET integrated directly into the virgin PET, so converters can use one product instead of two, while still meeting legislative requirements. Justina Volcek, PET Purchase Manager at Retal Group, explains, “They created Neo PET Cycle using a type of gentle glycolysis process and the result is a food contact grade resin that’s available at industrial volumes. With the partial replacement of fossil-based raw materials with liquified and purified rPET flakes, Neo PET Cycle supports Retal in meeting our environmental goals, as well as enabling our customers – the global brand owners of food and beverage products – to stay in line with both the EU legislation and the wishes of their consumers.” These environmental advantages include a reduction of plastic pollution, lower CO2 emissions due to the lower carbon footprint of rPET as compared to virgin PET, while reducing dependence on oil reserves. The strict filtration technology used in the Neo PET Cycle production process purifies depolymerised PET flakes from contaminants, ensuring a stable colour, intrinsic viscosity and melting point, stated Retal. With Neo Group a sister company to the multinational plastic packaging producer Retal, specialises in preforms, closures and films for the food and beverage industry, the family connection allows for a preferred supply of Neo PET Cycle, helping to overcome the challenges of rPET supply for its customers. The production process of Neo PET Cycle is based on a depolymerisation process using feedstock from postconsumer PET food packaging collections. Volcek explains, “The production consists of two raw material streams: standard raw materials and rPET flakes; Neo Group’s patented technology is a glycolysis process, chosen because it is the most efficient form of non-catalysed depolymerisation. Additionally, in Neo Group, they have a long experience in glycolysis processes producing their second product - aromatic polyester polyols - since 2011.” The technology and quality management system allow integration of flakes directly before the polymerisation stage of PET resin production, which enables part replacement of raw materials without affecting food contact approvals from state authorities for the final product. A senior Neo Group representative concludes, “We can keep control over the consistent product quality in the spherical shape of the resins, just as we can with our standard virgin Neo PET, which means that there’s no need for any changes in converters’, like Retal’s, processes. Neo PET Cycle allows customers to meet environmental legislation without any additional hassle.” www.retalgroup.com"},{"@ID":8 "PETnews 6 NEWS PETplanet Insider Vol. 25 No. 07+08/24 www.petpla.net New system concept for the production of large-volume containers Otto Systems hosted an open house event in Switzerland in midJune. Around one hundred international experts took part in the event to visit the Otto Systems Tech Centre and Otto Hofstetter’s production facilities. The hosts from Uznach presented two systems in the new Techcenter. Firstly, the PET-Series 240 3100-SP-100, which was introduced at Drinktec 2022, was shown. Secondly, the HOD-Series 160 EXT 4100TSU-100 with extended external toggles was presented to the public for the first time. This system processed Indorama Polyclear T94N on eight cavities into 330g preforms. The cycle time was 36 seconds, resulting in an output of 800 preforms per hour. The well-known 240 series was equipped with a 96-cavity mould that had cavities for a 9.8 g preform with a 26/22 neck. The cycle time here was 5.48 seconds, resulting in a production rate of 63,000 preforms per hour. The Techcenter is designed for four generously positioned systems. A central material handling system from Eisbär supplies the injection moulding machines. Thanks to this system, various PET materials as well as blends of rPET and virgin PET can be processed. As is usual at Otto Systems, the injection moulding machines come from partner BMB. The handling system is developed and built in-house. www.otto-systems.com The first PEF World Congress PEF (polyethylene furanoate) is a novel polyester, produced from 100% plant-based raw materials. It is recyclable and is regarded as a packaging material of the future, particularly in the food and beverage sector but also for textiles and more. That is why the trade magazine Renewable Carbon Plastics (previously knowns as bioplastics magazine), together with PEFerence is now organising the 1st PEF World Congress. The global conference will be held on October 30 & 31, 2024 in Düsseldorf, Germany (or online = hybrid event). It offers high-class presentations from top individuals in the industry from the complete value chain. The event will cover HMF, FDCA, and PEF, as well as applications and end-of-life solutions. There will also be excellent networking opportunities along with a table-top exhibition. Often compared to PET due to their similar chemistry, both polyesters are produced from the monomers ethylene glycol (MEG) and an aromatic diacid-furandicarboxylic acid (FDCA) for PEF and terephthalic acid for PET. Despite this similarity, PEF’s small molecular difference results in several distinct properties. PEF is claimed to have a 50% lower carbon footprint compared to PET and better barrier properties against oxygen, carbon dioxide, and water, which ensures a longer shelf life for packaged products. Additionally, PEF exhibits a lower melting temperature and a higher glass transition temperature than PET. Another advantage of PEF is its higher mechanical strength. PEF can be processed using the same equipment and methods as PET, and its recycling process is identical. Furthermore, PEF is versatile and can be used for stretch blow moulding of bottles, as well as for producing fibres, films, and even biaxially oriented (BOPEF) film. PETplanet Insider is the premium media partner of the PEF World Congress. www.pef-world-congress.com Blow Moulding 2024 International Conference, exhibition & networking event The 8th edition of the Blow Moulding Conference and exhibition will take place from December 9-11, 2024 in Brussels, Belgium. The conference brings together the entire supply chain – from brand owners to raw materials and additives, recyclers and sustainability experts as well as the regulatory authority. Presentations include market reviews and general trends as well as sessions on innovations in stretch blow moulding (Session 1), recycling, sustainability, circularity (Session 2) and advances in extrusion blow moulding (Session 3) and features keynote presentations from Coca-Cola Europacific Partners, Suntory, Asevi Home Brands & Searious Business, L’Oréal, Carrefour, Bayer, Henkel, Nestlé Waters & Leibniz Institute and the European Commission. Blow Moulding 2024 is organised by Nortal Consulting, a business consultancy specialising in the polymers and plastics industry. The conference will be chaired by Mr. Noru Tsalic, a polymers and plastics industry professional with broad expertise and experience. The full conference agenda can be found at www.blow-moulding.com The guests had the new HOD-Series 160 EXT 4100-TSU-100 explained to them."},{"@ID":7 "45 EVENT REVIEW PETplanet Insider Vol. 25 No. 07+08/24 www.petpla.net Reactive recycling technology for the circular use of plastics Nexam Chemical supply reactive additives in masterbatches (IV enhancers, MFR modifiers) that upcycle, modify and solve recycled polymer processing/property challenges for rPET, rPE and rPP. ‘Reactive Recycling’ technology is largely patented, and claimed to rebuild and restore material properties of used plastics processed in recycling centres. This claim has been scientifically verified by a team of scientists at the Politecnico di Torino, in a study published earlier this year. The technology enables plastics to return to full circulation and continued reuse. A masterbatch of active ingredients is added to the extruder of recycled feedstock. Upon reaching the activation temperature, the feedstock is chemically modified and regains properties lost during the conventional recycling process. The masterbatch is fully reacted and incorporated into the plastics. Reactive recycling rebuilds polymer chains, increasing melt strength and viscosity, thereby enabling recycled feedstocks to be used in more advanced end product applications. Processing is also more consistent and mechanical properties improved, says the company. The technology is claimed to be approved for food contact and suitable to all rPET applications, e.g. bottles, sheets, films etc. www.nexamchemical.com Exploring the Future of Advanced Recycling Uniting industry leaders and stakeholders across all plastic waste value chains. ADVANCED RECYCLING Conference 2024 20–21 November Cologne (Germany) Hybrid Event advanced-recycling.eu Topics of the Conference • Markets, Investments & Policy • Circular Economy & Ecology of Plastics • Physical Recycling • Biochemical Recycling • Chemical Recycling • Thermochemical Recycling • Other Advanced Recycling Technologies • Carbon Capture and Utilisation (CCU) • Upgrading, Pre- and Post-treatment Technologies • Digital Solutions (e.g. AI & Blockchain) Call for Posters Submit your Poster until 7 October 2024 Organiser Gold Sponsor Contact Lars Krause Program [email protected] Dominik Vogt Conference Manager [email protected] 10% Early Bird Register until 10 Sep 2024 Bronze Sponsors"},{"@ID":38 "36 EVENT REVIEW PETplanet Insider Vol. 25 No. 07+08/24 www.petpla.net PET Technologies’ NPE insights How would you assess your overall experience at NPE this year? A success. We had five days of fruitful meetings with industry professionals and newcomers. The interactive demonstrations of our APF-Max 3U blow moulder and the hands-on experience we offered were extremely well-received. Participating in NPE significantly boosted our brand visibility. We noticed a marked increase in inquiries and interest in our products post-event. Engaging directly with our target audience allowed us to gather invaluable feedback on our products and services as well as on the market in general. This direct interaction highlighted areas for new product features that could address specific customer needs. The feedback will play a crucial role in our ongoing product development and innovation strategy. Could you please share the key exhibits or technologies showcased at your booth during NPE? What factors influenced your decision to focus on these particular offerings, and what was the response from visitors? This year PETTechnologies showcased the automatic blowmoulding machineAPFMax 3U. As a new entry in our APF-Max series, it marks the progress we’ve made over recent years. With an output of up to 5,400 bph using only three cavities, it accommodated a wide range of bottle volumes from 0.1 to 10l. TheAPF-Max 3U is designed to meet customer-specific needs, including hot fill & asymmetric PET bottles, 100% rPET containers, lightweight containers, returnable & glass PET bottles, a wide range of shapes & capacities and compatibility with moulds from other PET SMB machines. The blow moulder offers flexibility with its quick-change system, allowing the use of multiple mould sets for various PET bottles with minimal changeover time. The blow mould, equipped with non-spill quick-change connections, can be replaced in one piece in just 15 minutes. Additionally, servo drives provide precise positioning, high speed, stable heater conveyor speed, and a consistent blowing process. The stretching rod position adjusts automatically based on bottle height when switching formats, and pre-blow is controlled via PLC. The blowmoulder features a short-wave near infrared heating system (NIR), uncommon in the PET blow moulding market. NIR heating offers more efficient preform heating with lower energy consumption, uniform temperature distribution, reduced heating time, compact heater size, and lower energy usage. Ceramic reflectors enhance preform heating and further reduce energy consumption, with automatic temperature regulation topping off its advanced features. Based on your experience at NPE and your broader industry knowledge, what developments or challenges do you observe in the American PET bottle market? The NorthAmerica PET bottles market size reached USD 8.20 billion in 2023 and is expected to grow at a CAGR of 4.3%, reaching USD 11.99 billion by 2032, according to EMR. The LatinAmerica PET bottles market reached over USD 2.18 billion in 2023, with a projected CAGR of 4.7%, reaching USD 3.30 billion by 2032. This positive trend matches with PET Technologies’ experience based on the projects that we are currently implementing in the Americas. Driving factors include: New applications: Growing demand for alcoholic beverages in PET containers, which are up to 80% lighter than glass. The PET bottle market for dairy products is also growing due to increased demand for convenience and single-serve options. Focus on sustainability has led to the adoption of rPET and exploration of biodegradable PET by dairy companies. North American companies are enhancing PET bottles’ barrier properties to protect dairy products from light and oxygen. Technological advancements: Rapid technological developments are improving the natural resistance of PET bottles, extending product shelf life. Portable water demand: Increasing demand for 5-gallon PET bottles due to water shortages. The US and Mexico prefer bottles with handles, while Nicaragua prefers those without. Rising use of rPET: Brands are increasing rPET use to meet sustainability goals and comply with regulations. PET Technologies has many customers in the region using 100% rPET preforms. The key challenges for PET bottles market include: Negative image of plastics: Despite studies indicating PET bottles are environmentally less impactful, the negative perception of plastic pollution persists, potentially decreasing demand. Recycled content requirements: Mandates requiring a minimum percentage of recycled content in PET bottles pose challenges due to limited high-quality rPET availability. Alternative packaging: Competition from glass, aluminium, and biodegradable plastics, perceived as more environmentally friendly, is drawing consumers away from PET bottles. www.pet-eu.com Tetiana Pronikova, Head of Marketing and Maxim Poliansky, CEO at PET Technologies A glimpse inside the APF-Max 3U blow moulder"}]}}
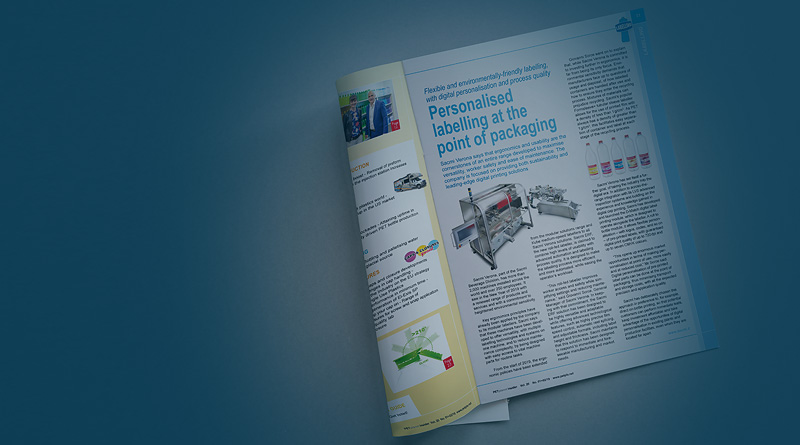