{"pages":{"page":[{"@ID":14 "EDITOUR PETplanet Insider Vol. 25 No. 11/24 www.petpla.net 12 Visit to Sarooj Water in Oman From 0 to 4 million bottles per day in 2 years by Alexander Büchler In Oman, just three years ago, a 24-pack of the favourite 250ml single-serve water bottle cost 1.60 euros in a discount supermarket. That’s not even 7 eurocents per bottle. Supermarkets are now offering the same 24-pack of 250ml Sarooj water for 0.80 euro - just half the price, or just 3.5 eurocents per bottle. What is behind it? We asked the driving force behind Sarooj Water, Mr Fahad Mohammed Riaz. Four years ago, Fahad’s world consisted primarily of trading in wood for house and furniture construction. In search of another site for his logistics operations, he was offered a site in Muladdah, near Muscat. At first he wasn’t convinced, but when he heard that it included a deep well licence for the best underground water in Oman, his ears perked up. The water is virtually sodium-free and has a tangy but balanced flavour. The two quickly came to an agreement and Fahad and his team set about developing a concept for the water from the well. What can I do better than the competition? How can I produce and sell the right quantities? A concept was quickly developed: it had to be the best bottled water in Oman, and the end consumer should only pay half as much as before. The supermarkets are supplied by full lorry loads only. The retail trade and Farad as a producer did without the usual margins and still made their money from ordinary consumers. He is enthusiastic about the concept of Niagara Water in the USA. A joint meeting with the owner family Peykoff sealed his decision: concentrate on one product, a light bottle and in bulk. What was missing was a suitable bottle and the associated production facilities. Two years ago, the moment came. After a lot of research, Fahad decided on a bottle with the relatively large 29/25 cap that is common in the region. With the Neck-Lite from Redupet, it was possible to make the bottle 8% lighter at 6.85g. After initial scepticism, blow moulding trials at Krones and Sipa showed that the bottle could be produced. Corvaglia developed a shutter weighing just 1.1g. Neither is available on the open converter market, so Fahad ordered the corresponding preform and cap systems from Netstal. A key factor in the success of the lightweight bottle was that Otto Hofstetter managed to build a 128-cavity mould for the NeckLite preform for the first time. Until now, the Neck-Lite had only been produced on small preform tools. The material advantage quickly pays for itself compared to the additional expense of in-house preform and cap production. Needless to say, Fahad also produces the film for the 24-pack himself and prints and cuts his own labels. The 128-cavity mould from Otto Hofstetter went into the Top Entry 400 t Netstal lines, the 48-cavity EDITOUR F.l.t.r.: Plant manager Ahmed Sarif, Alexander Büchler and Fahad Mohammed Riaz Fahad Mohammed Riaz (right) and Alexander Büchler in the discount supermarket, where his 24-packs of 250ml water are selling faster than the staff can stack them. The Sipa Sincro Bloc was the third system installed two years ago, with which Fahad shook up the market."},{"@ID":13 "11 NEWS PETplanet Insider Vol. 25 No. 11/24 www.petpla.net \" \"ĸrĸ ĸ ň (b- -7ࢼ 7;Ѳ -ouoĶ Ɛ ň ƐƎƍƏƔ (boubo (;m;|o Ŏ$(ŏ ň |-Ѳ ň $;Ѳĸ ƱƐƔ ƍƑƐѴ ƔƎƎƒƎƎ ň vbr-Şorr-vĸ1ol ň ĸvbr-ĸb| SIPA’sXFORMGEN4XP ru;=oulňloѲ7bm] |;1_moѲo] 7;Ѳb;uv |_; lowestconversion 1ov| -Ѳom] b|_ unmatched ;m;u] ;L1b;m1 -m7 ease of useĸ | umv b|_ loѲ7v =uol Ə |o Əƍƍ 1-bࢼ;v -v ;ѲѲ -v legacy tooling. $_; b7; HMI b|_ v;Ѳ=ňv;࣌m] ruo1;vv v;|ňr -m7 |uo0Ѳ;v_ooࢼm] ||oub-Ѳv 0ubm]v -m ;@ou|Ѳ;vv v;u ;r;ub;m1;ĸ *\r ! bv built to last ث |_bv l-1_bm; _-v 0;;m ;m]bm;;u;7 |o 1om; |_; _b]_;v| rѲ-oul uo0v|m;vv -Ѳom] b|_ less than1%of total investment om maintenancecostsĶ l-hbm] bu]bm PETandrPET ru;=oul l-m=-1|ubm] |_; 0;v| ;r;ub;m1; ;;uĸ 200 Wh/kg energy 1omvlrঞom 100% rPET pellets 1-r-0bѴbঞ;v 1 million cold half cycles guaranteed 100% 1olr-ঞ0bѴb| with legacy tooling 1% maintenance cost of total investment : an extraordinary preforming experience"},{"@ID":25 "MARKET SURVEY 23 PETplanet Insider Vol. 25 No. 11/24 www.petpla.net 11/2024 MARKETsurvey Palletising and shrink film machinery This issue is dedicated to palletising and shrink film machinery. Please refer to the machine details for the state-of-the-art solutions of the companies involved: Sidel, KHS Group, Krones AG, Jiangsu Newamstar Packaging Machinery Co. Ltd., Sipa, And & Or and SMI S.p.A. Although the publisher have made every eff ort to ensure that the information in this survey is up to date, no claims are made regarding completeness or accuracy. Company Sidel KHS Krones AG Jiangsu Newamstar Packaging Machinery Co., Ltd Postal address Telephone number Web site address Contact name Function Direct telephone number Email Rue du Commerce 67116 Reichstett, France +33 388 183 880 www.sidel.com Mr Piero Zamboni PR Manager +39 0521 999452 [email protected] Juchostraße 20 44143 Dortmund, Germany +49 231 5690 www.khs.com Mr Ernst van Wickeren & Mr Christoph Wiesenack Product Manager Packaging +49 2821 503 200 [email protected] Böhmerwaldstraße 5 93073 Neutraubling, Germany +49 9401 70 0 www.krones.com Mr Andreas Fritsch Product Mgmt Packaging Tech. +49 8031 4040 [email protected] No. 8 Xinjing East Road, Zhangjiagang Eco- and Technological Dev. Zone, Jiangsu Province, China, 215618 +86 512 5869 1111 www.newamstar.com Mr Wesley Yin Marketing Manager +86 512 56993303 [email protected] Shrink film machinery: Packaging options & output rate (packs/min) - print registered fi lm (yes/no; packs/min) Yes, up to 120 cycles/min (PET bottles), 150 cycles/min (cans) in 3 lanes Yes, max. 135 cycles/min Yes, 150 x 4 = 600packs/min Yes, 60 - nested pack (yes/no; packs/min) Yes Yes, 80 packs/min, depend on pack formation Yes, 100packs/min No - label orientation (yes/no; packs/min) Yes No No No - carry handles (yes/no; packs/min) No Yes, optional max. 80 cycles/min Yes, 80 x 2 = 160packs/min No - pad supported (yes/no; packs/min) Yes Yes, 100 packs/min Yes, 140 x 2 = 280packs/min Yes, 60 packs/min - tray supported (yes/no; packs/min) Yes Yes, 120 packs/min Yes, 120packs/min Yes, 60 packs/min - fi lm only (yes/no; packs/min) Yes Yes, max. 135 cycles/min Yes, 150 x 4 = 600packs/min Yes, 80 packs/min - tray and fi lm (yes/no; packs/min) Yes Yes,120 packs/min Yes, 120packs/min Yes, 80 packs/min - pad and fi lm (yes/no; packs/min) Yes Yes, 100 packs/min Yes, 140 x 2 = 280packs/min Yes, 80 packs/min Shrink process: - shrink tunnel with hot air or gas fi red opt. Yes Yes Yes Yes - oven Yes No No Yes - steam tunnel No No No Yes Footprint Depend on confi guration 12.6m til 28.9m depend. on machine typ and necessary speed Depends on confi guration Number of possible lanes Up to 3 1 to 4 4 With 1 or 2 lanes Packaging material and possible thickness Low-density polyethylene (LDPE) from 27-100 μm Film thickness 40 til 60 μm. Thinner fi lm up to 25 μm on request Film, min 25-120 μm 60 μm~80 μm Voltage/power/energy consumption NC Depend. on machine typ, speed and required options Depends on speed, package and material AC380V, 50Hz, about 110kW Film cutting and feeding system Yes Servo driven knife and vaccum belt transport Yes, fully automatic feeding, splicing, welding Yes Certifi cation CE certifi cation ISO 9001 certifi cation ISO 20000-1, ISO 27001, ISO 9001, ISO 50001, ISO 45001, ISO 14001, enviro, SBTi Compliant with 3c certifi cation Palletising machinery: Format changeover time Depend on confi guration Fully automatic changeover available - 0min operator time Depending on machine type, automatic changeover and manual changeover (5 to 10min) 20min Output rate (packs/min) Up to 12 layers/min Same as packaging machine 100-650lph (layers/hour) 120 Automatically intergrated: (yes/no) If necessary Yes Empty pack feeding Yes, empty pallet feeding Yes Yes Auto Insertion of interlayers Yes Yes Yes Auto Connectable to shrinkwrapper Yes Yes Yes Yes Special characteristics: i.e. low-level feed, cross conveyer barrier Available on high and low level infeed High speed with low level infeed Low-level feed, cross conveyer barrier Resins & additives Cap producers, systems & inspection systems Preform machinery Preform production & inspection systems Preform, cap & SBM mould manufacturer SBM 2-stage Compressors Filling equipment & inspection systems Palletising & shrink film machinery Recycling machinery"},{"@ID":46 "OUTER PLANET 46 PETplanet Insider Vol. 25 No. 11/24 www.petpla.net OUTER PLANET AI based sorting technology based on an article by Johannes Laier The German Würzburg-based company WeSort.AI GmbH develops advanced sorting technology using artificial intelligence (AI), enabling waste to be sorted with much greater granularity. This allows new material streams and purity levels to be achieved. Granular waste sorting involves two consecutive steps. First, waste objects are precisely captured using advanced sensor technology, and then algorithmically analysed by AI. This includes, for example, the detailed recognition of object type, material type, colour, manufacturer, and distinctions between food and non-food packaging through novel AI object recognition algorithms. Essentially, the AI not only identifies the material but also recognises the waste object itself. The AI from WeSort.AI has already been trained with several million images of various waste objects, enabling it to cover a wide range of knowledge. In the second step, the recognised waste must be sorted very precisely. For this, a compressed air nozzle bar is controlled by intelligent control software, blowing the waste into different sorting chambers. WeSort.AI’s technology covers both steps. The innovation lies primarily in the AI used to evaluate the sensor data and create a truly intelligent material stream. Current state of technology: The most advanced sorting technology currently available is primarily nearinfrared (NIR) sorters. In this process, waste on the conveyor belt is detected using NIR sensors, and the material composition is identified on a pixelby-pixel basis. NIR sensors typically penetrate a few nanometers to 1mm into the surface, and thus are only able to identify the material at the surface. This often leads to errors, especially with labelled packaging, such as paper around a yogurt cup or a PE sleeve around a PET bottle. In such cases, the yogurt cup may mistakenly be assigned to the paper fraction instead of the PS fraction, degrading the quality of the recycled material. AI technology, on the other hand, is capable of recognising packaging and other waste as a whole. Similar to the human eye, AI not only gathers material information in the form of pixel areas but also understands that it is dealing with a yogurt cup made up of materials (64% PS, 22% paper, 14% aluminium) from manufacturer “XY,” for example, in white and green colours, with a weight of 22g, classified as “food” quality, and a material value of €0.01. This new “knowledge layer” added to the material stream enables smarter detection and, in the next step, sorting. Thanks to AI, the yogurt cup can be recognised as such and correctly assigned to the PS fraction. With the technology, new fractions could be created based on food-grade quality, packaging geometry, or brand, alongside sorting by material types or new individual objects. Object-based recognition allows for both material classification and the identification of specific objects. For example, cheese packaging and yogurt cups can be sorted into the food fraction, while detergent bottles fall into the non-food fraction. Plastics originally intended for food packaging can be reused without being downcycled, reducing the need for new production. Another advantage lies in identifying disruptive and hazardous materials, allowing for their targeted removal from the process. AI material flow analysis and quality assurance Beyond the mentioned applications, this AI technology is claimed to offer a variety of other potential applications to enhance the efficiency of recycling plants. It allows for the rapid and precise collection and analysis of material flow data. Trends are immediately identified, enabling prompt responses to any issues that arise. www.wesort.ai F.l.t.r.: The brothers Johannes and Nathanael Laier founded WeSort.AI in 2021. This year, the company has been awarded this year’s prestigious Deutscher Gründerpreis [Founder’s Award] in the Start-up category."},{"@ID":39 "PETplanet Insider Vol. 25 No. 11/24 www.petpla.net 37 BOTTLES PETbottles Beverage + Liquid Food Bottle made from 100% recycled ocean-bound plastic Zen Beverage LLC from Canada sel ls i ts special ly produced water in a bottle made from 100% ocean-bound plastic - plastic that is collected before it reaches the ocean. The alkaline water used, with a pH value of 9.5, is purified by distillation and then bottled. The slightly bluish bottles are decorated with a sleeve label with a colour gradient and combined with different caps depending on the bottle size. The picture shows the 1 l bottle with a screw cap and a 700ml bottle with a sports cap. www.zenwtr.com Dosing cap for cooking oil The French agricultural group Avri l sel ls several cooking oi ls under the Lesieur brand in transparent plastic bottles with a special dosing cap. The multi-part, two-coloured cap can be twisted so that the number and size of the pouring openings can be individually adjusted to enable the product to be poured in better doses. The 1 l bottle itself is provided with spiral grooves to increase stability and grip. Two self-adhesive labels on the neck and a wrap-around foil label on the body of the bottle convey all the important information. www.lesieur-international.com New products at Valensina German juice specialist Valensina has responded to changing customer wishes and trends with two new products in summer 2024. New on the shelves are a juice soda and ice tea, which is also available in a sugarfree version. A total of three juice lemonade and four ice tea variants are on offer. The juice lemonade is filled in a 750ml waisted bottle with a sleeve label and screw cap. The Ice Tea is available in 0.5 l or 1 l bottles, also with a sleeve label and screw cap, whereby the Zero variant has a white screw cap. www.valensina.de Electrolytes in PET According to the manufacturer, the aim of the Hydr8 drink is to provide the body with sufficient electrolytes after sport, heat or nights out drinking alcohol. The drink is advertised as an alternative to electrolyte powders from the pharmacy that are mixed at home. The vegan drink is sugar-free and contains five electrolytes. The 500ml bottle is made from 100% recycled material, is decorated with a sleeve label and the large drinking opening is sealed with a screw cap that is easy to grip. www.hydr8.shop"},{"@ID":6 "PETcontents 4 PETplanet Insider Vol. 25 No. 11/24 www.petpla.net 11/2024 EDITOUR 12 From 0 to 4 million bottles per day in 2 years - Visit to Sarooj Water in Oman 14 Once local, now global: PET production in Oman BOTTLE MAKING 16 Sleek bottle base for 100% rPET - StarLite-R Premium targets high-end products 18 Doğanay’s traditional flavours find a modern home - Sipa’s sustainable packaging solutions 19 Premium-look PET for mineral water 20 The essence of purity in every drop 21 Bottle Making Products MARKET SURVEY 23 Suppliers of palletising & shrink film machinery EVENT PREVIEW 26 Brau Beviale 2024 preview, part 2 28 Petcore annual conference 2025: Pro- moting innovation, circularity & growth across the PET value chain EVENT REVIEW 30 “We need more collection, education and fines” - PET Day 2024 32 Fakuma 2024 review OUTER PLANET 46 AI based sorting technology BUYER’S GUIDE 40 Get listed! INSIDE TRACK 3 Editorial 4 Contents 6 News 37 PET bottles for beverage + liquid food 38 PET bottles for home + personal care EDITOUR Page 30 Page 16 Page 14 BOTTLE MAKING"},{"@ID":41 "PATENTS PETpatents www.verpackungspatente.de PETplanet Insider Vol. 25 No. 11/24 www.petpla.net 39 Bottle with handle Europ. Patent No. EP 4303143 A1 Applicant: Guangzhou Tech-Long Packaging Machinery Co. Ltd, Guanzhou (CN) Application date: 19.4.2021 Bottle with handle, one end of which is attached to the neck of the bottle, while the other end is not in direct contact with the bottle. Several handle and bottle variants are shown. Variable bottle Internal. Patent No. WO 2024 / 033779 A1 Applicant: Vernissage S.r.l., Trenzano (IT) Application date: 7.8.2023 A bottle is described that can be repeatedly converted from a compressed to an expanded state. This facilitates the transport of concentrate bottles or the transport volume during recycling. Improved floor moulding Internal. Patent No. WO 2022 / 185003 A1 Applicant: Société des Eaux Minerals d’Evian et en abrégé, Evian-les-Bains (FR) Application date: 1.3.2022 The registered design of the base of a lightweight PET bottle is intended to be a good compromise between stability and material savings. Bottle with grooves Internal. Patent No. WO 2022 / 182833 A1 Applicant: The Coca-Cola Company, Atlanta (US) Application date: 24.2.2022 Weight-reduced bottle with circumferential grooves and waveshaped grooves to increase stability. The grooves do not detract from the appearance of the bottle, as they are partly underneath the label. Optimised base shape Internal. Patent No. WO 2024 / 052169 A1 Applicant: Société des Produits Nestlé S.A., Vevey (CH) Application date: 29.8.2023 The application describes a lightweight plastic bottle for holding carbonated drinks. The floor shape has been optimised. Bottle for dairy products Internal. Patent No. WO 2024 / 052114 A1 Applicant: Sidel Participations, Octeville-Sur-Mer (FR) Application date: 22.8.2023 Shaping, design and process for manufacturing a bottle made of PET or rPET for holding dairy products are applied for."},{"@ID":40 "PETplanet Insider Vol. 25 No. 11/24 www.petpla.net 38 Noble bottle for shower gel The American consumer goods manufacturer Edgewell sells highquality products for body, hair and beard care in elegant and stylishly designed packaging under the ‘Cremo’ brand, whose logo is a stylised crown. The 473ml shower gel with bourbon and oak scent is filled in a clear bottle with various special features. The front of the bottle has partial longitudinal grooves, which are interrupted by a surface with a seal and crown logo. The side walls are decorated with embossed Cremo lettering. The labels are designed to match, with one of the back labels printed in the shape of a seal on the inside. A two-colour disc-top closure allows the contents of the bottle to be dispensed with one hand. www.cremocompany.com Sneaker cleaner in PET Every trend also requires accompanying new product developments to meet consumer demand. Now that sneakers have been general ly accepted for some time and are no longer only worn for sports, a market has developed around these shoes. Special cleaning and care products have been developed to clean dirty trainers. Bama GmbH from Mosbach in Germany, f or examp l e , o f f er s a sneaker cleaner under the Magix brand. 150ml of the product is filled in a PET foam dispenser. It is easy to use: shake the bottle, dispense the product via the pump dispenser, rub into the material with a soft brush, leave to work for 5 minutes and then wipe off the dirt and residual foam with a microfibre cloth. www.bama-de.com PETbottles Home + Personal Care"},{"@ID":27 "MARKET SURVEY 25 PETplanet Insider Vol. 25 No. 11/24 www.petpla.net SMI S.p.A. Via C.Ceresa, 10, 24015 San Giovanni Bianco (BG), Italy +39 0345 40 111 www.smigroup.it Ms Daniela Dadda Marketing Department +39 0345 40.318 [email protected] Automatic machines for packing plastic, metal, cardboard or glass containers; packs in fi lm only, cardboard pad + fi lm, tray only, cardboard tray + fi lm SMI designs and manufactures a wide range of fully automated machines: Shrink wrappers with in-line infeed, shrink wrappers with 90º infeed, stretch-fi lm packers with in-line infeed and combined machines (shrink wrapper + wrap-around case packer); trayformers; wrap-around case packers; pick & place case packer and cardboard multipack sleevers. The models available provide performances up to 450 packs/min (in triple lane), depending on the model chosen and on the type of product to pack. SMI shrink wrappers and case packers can be integrated with a SMI palletiser to form a “Packbloc” compact end-of-line system. Yes, up to 150 cycles/min (cans) in 3 lanes Yes No Yes Yes Yes Yes, up to 150 cycles/min (cans) in 3 lanes Yes, up to 140 ppm Yes, up to 140 ppm Thanks to the precise analysis of thermodynamic phenomena generated by the shrink process, SMI tunnel distributes hot air fl ows in an effi cient and homogeneous way on the pack, thus ensuring its good quality at the end of the process. Available tunnel methan heated Depending on the machine confi guration From 1 to 3 lanes Film: from 30 to 100 micron depending on the production speed and on the pack collation Depending on the machine model Yes CE / UL / CSA Depending on the machine confi guration 140 packs/min (according to the size of the product handled and palletisation selected) Yes Yes Yes Yes Compact and ergonomic structure, reducedmaintenance costs, lowenergy consumption, extremely simple automation andmanagement control Genius PTF - Fastlayer Genius PTF/A - Fastlayer Genius PP/PV Robby Pal Robby Pal with Fastlayer Conventional automatic palletisers steady pallet type with innovative layer preparation Conventional automatic palletisers moving pallet type with innovative layer preparation Conventional automatic palletisers steady pallet type for empty PET containers Robotic automatic palletiser Robotic automatic palletiser with layer preparation 10min 12min 15min 15min 10min Up to 330 layers/hour Up to 600 layers/hour Up to 360 layers/hour Up to 320 layers/hour Up to 320 layers/hour Yes Yes Yes Yes Yes Yes Yes Yes Yes Yes Yes Yes Yes Yes Yes - Operational fl exibility and further reduction in change-over times - Optimisation of cycle to increase performance, with improved control of the different movements using state-of-the-art electronic solutions - Customisation of the gripping systemand layer transfer according to the product to handle - Designed to accept a variable number of product infeeds - Fully automatic system requiring limited operator intervention, operating in complete safety - Possibility to handle all main pallets on themarket trouble-free, with customisable solutions - Layer preparationwith active pack orientation and arrangement with robots - Operational fl exibility and further reduction in change-over times - Optimisation of cycle to increase performance, with improved control of the different movements using state-of-the-art electronic solutions - Customisation of the gripping systemand layer transfer according to the product to handle - Vacuumhead available for widemouth containers (i.e. jars) - Designed to accept a variable number of product infeeds - Fully automatic system requiring limited operator intervention, operating in complete safety - Possibility to handle all main pallets on themarket trouble-free, with customisable solutions - Complete range to handle different types of containers and products: layer, rowandmultihead and loose product palletising systems - Flexible andmodular solutionwith reduced footprint - Customisation of the gripping systemand layer transfer according to the product to handle - Designed to accept a variable number of product infeeds - Fully automatic system requiring limited operator intervention, operating in complete safety - Possibility to handle all main pallets on the market trouble-free, with customisable solutions - Complete range to handle different types of containers and products: layer, rowandmultihead and loose product palletising systems - Flexible andmodular solutionwith reduced footprint - Customisation of the gripping systemand layer transfer according to the product to handle - Designed to accept a variable number of product infeeds - Fully automatic system requiring limited operator intervention, operating in complete safety - Possibility to handle all main pallets on themarket trouble-free, with customisable solutions - Layer preparationwith active pack orientation and arrangement with robots"},{"@ID":50 "32 EVENT REVIEW PETplanet Insider Vol. 25 No. 11/24 www.petpla.net EVENTreview Fakuma 2024 review The 29th Fakuma international trade fair for plastics processing took place in Friedrichshafen from October 15 to 19, 2024, with 1,639 exhibitors (2023: 1,636 exhibitors) presenting innovations in efficiency, sustainability, and the circular economy across twelve almost fully occupied exhibition halls and foyers. The stability in exhibitor numbers was offset by a slight dip of 7% in the number of visitors (36,675 visitors; 2023: 39,343 visitors). The trade fair has increased its international reach: 47.5% of exhibitors came from outside of Germany (2023: 44.0%). Of the 1,639 exhibitors, 170 companies were from China, 142 from Italy, 81 from Switzerland, 77 from Austria and 51 from Turkey. For manufacturers and users, topics such as increased efficiency, process stability, reproducibility and minimised setup times were at the top of the agenda. Bettina Schall, managing director of trade fair promoters P. E. Schall is optimistic about the industry’s future. “Although the current situation is challenging and we have to deal with numerous highly complex issues simultaneously, the concentrated innovative power experienced at Fakuma 2024 is a strong indication that we’re tackling the issues with determination and confidence,” says the managing director. The 30th edition of Fakuma will take place in Friedrichshafen from October 13-17, 2026. www.fakuma-messe.de Optimising the properties of PET and rPET Tosaf presented its latest developments in the field of property-enhancing masterbatches for the plastics industry. One focus was on the optimisation of products made from PET and, in particular, rPET. Tosaf offers a wide variety of solutions for PET and rPET that help to optimise quality, efficiency, sustainability and costs during processing and recycling. With regard to the aesthetics and functionality of PET packaging, additives are available that correct the colour and gloss of rPET or prevent water droplets from depositing on the inner walls of packaging. Additives for absorbing and eliminating oxygen from the headspace of packaging, UV protection additives and – especially for milk containers – ultra-lightproof white masterbatch help to extend product shelf life. Acetaldehyde scavengers prevent changes in the flavour of water in rPET bottles. Processing aid additives prevent electrostatic charging or change the surface properties of PET to prevent blocking and reduce the coefficient of friction. Special IR absorbers facilitate thermoforming with uneven wall thicknesses without impairing clarity. Additives are used to improve the properties and quality of rPET by linking shortened PET polymer chains and thus increasing the molecular weight. Compatibilisers enable the recycling of PET-PCR blends that are contaminated with polyolefins or barrier plastics such as PA and EVOH. An NIR-reflective black masterbatch facilitates sorting during recycling. www.tosaf.com"},{"@ID":29 "27 EVENT PREVIEW PETplanet Insider Vol. 25 No. 11/24 www.petpla.net Moulds and bottle design It is difficult to overestimate the role of the blow mould in making a PET bottle shine as if it were glass. And these are the moulds PET Technologies will bring to BrauBeviale. PET Technologies’ manufacturing facilities span 9,000 m² and include over 140 metalworking machines, along with two dedicated R&D departments, supporting a complete production cycle. The moulds production site is equipped with 4- and 5-axis machining centers with CNC: Deckel Maho (Germany), Doosan (South Korea), Micron MILL (Switzerland). This infrastructure permits PET Technologies to produce moulds for all European brands of rotary blow moulding machines. The company develops moulds with the help of Catia V5, a leading engineering and design tool. The company uses duralumin alloys, series 6000 of its hardness is up to 100HB. The mechanical properties of this type of aluminium has an optimum ratio of hardness and plasticity for shock loads, says the company. Depending on customer’s preference, PET Technologies can anodise moulds, applying an electrochemical coating to the surface layer. It provides additional hardness, increases wear resisting properties and protects against corrosion. In addition, PET Technologies manufactures mould cooling units. Mould base – key to innovations PET Technologies developed a new Smart Base technology. Smart Base is designed to reduce air pressure requirements and streamline material distribution by minimising friction between plastic and mould surfaces. The core of Smart Base lies in its additional air ducts in the base, which lower pressure and redirect air swiftly, reducing resistance within the mould. Testing on automatic linear blow moulding machines showed impressive results: a 30% reduction in air pressure without any compromise on bottle quality. With compressors being a primary electricity consumer in blow moulding, Smart Base offers a clear advantage in energy savings - cutting costs while maintaining top-quality output, says the company. PET bottle designs: old & new PET Technologies offers a complete, turn-key bottle design solution that includes conducting in-depth market research, following global trends, creating comprehensive branding - from product naming to logos and labels - modifying bottle shapes to meet evolving needs, and adapting new designs to fit existing filling lines. Additionally, the company provides precise 2D drawings and 3D renders of PET bottles. With a strong focus on reducing bottle weight and optimising all APF-Max series machines for rPET, visitors are invited to find the inspiration to create something new at PET Technologies booth. www.pet-eu.com PET Technologies Hall 7 | Booth 646"},{"@ID":4 "BOTTLE MAKING 18 PETplanet Insider Vol. 25 No. 11/24 www.petpla.net Sipa’s sustainable packaging solutions Doğanay’s traditional flavours find a modern home Doğanay, a name synonymous with authentic Turkish taste, has been bringing the unique flavours of Anatolian tradition to tables worldwide since the 1960s. Their journey began with Şalgam, a beloved fermented beverage, and has expanded to encompass a wide range of traditional products, from pickle juice to various vinegars and fruit juices. Doğanay’s commitment to quality is evident in every step of their process, from collaborating with local farmers to utilising state-of-the-art production facilities. This dedication to preserving heritage while embracing progress is mirrored in their partnership with Sipa. The company, renowned for its innovative approach to PET packaging technology, offers a comprehensive range of services, from design and mould production to complete bottling lines. Their expertise lies in creating packaging solutions that are visually appealing, functional and sustainable. Doğanay’s vision Recognising the need to refresh its brand image and appeal to a wider audience, Doğanay collaborated with Sipa to revamp its packaging. Sipa’s design team, leveraging their extensive knowledge of packaging trends and consumer preferences, developed four new BOTTLE MAKING Lightweighting: reduced bottle weight for a more sustainable and eco-friendly approach to packaging. Neck conversion: transitioning from a 33mm to a 28mm neck, further minimising material use and environmental impact. A successful collaboration By partnering with Sipa, Doğanay has successfully boosted its brand image while staying true to its core values. The new packaging reflects the company’s commitment to quality, sustainability, and delivering a refreshing taste of Turkish culture to the world. This collaboration is a testament to the power of combining traditional values with cutting-edge technology to create a truly impactful product experience. www.sipasolutions.com bottle formats for Doğanay’s Şalgam in 0.2 l, 0.3 l, 1 l, and 2 l sizes. These designs seamlessly blend tradition with modernity, capturing the essence of the beverage while giving it a contemporary appeal. The new shapes are produced on Sipa’s rotary blowmoulders as Doğanay’s owns existing Sipa rotary and linear blowmolders. Sipa’s contributions to the project include: Full bottle redesign: a sleek, modern aesthetic that resonates with younger consumers while honoring the brand’s heritage, translating brand identity into tangible design. Enhanced label design: eyecatching visuals that effectively communicate Doğanay’s brand identity and product quality."},{"@ID":7 "EVENT REVIEW PETplanet Insider Vol. 25 No. 11/24 www.petpla.net 30 PET Day 2024 “We need more collection, education and fines” Rain or shine, we came back to Artimino, Florence, Italy, for the 22nd PET Day. This 2024 edition was unfortunately, for the very first time, under a steady rain throughout the event, but that did not discourage the exclusive audience to be present at the iconic Villa Medicea. The event was hosted by G.S.I. Global Service International srl, Italy, and its entire team welcomed customers and suppliers, top managers and purchasers, polyesters experts and economists at the historical venue. Mr Francesco Zanchi, founder and CEO of GSI, opened the PET Day surrounded by his team introducing the new members of his international staff. The global presence of GSI is getting wider and expanding its presence in all continents, excluding only Oceania and Antarctica (for now…). The company has been on the market for more than 30 years, and it is recognised as one of the top leading player and reputable partner in the raw materials world, covering polyesters and polyolefins. The event commenced with a thought-provoking lecture presented by Paul Hodges, of New Normal Consulting, a familiar presence in the latest PET Days. He addressed the critical implications of the ageing global population, particularly in the West, where the former wealth creators, known now as the perennials (over 55 y/o) are becoming too many in comparison with the current younger population: unfortunately, this imbalance is failing to support a new cycle of new economic growth. This demographic shift poses significant challenges to the world economies and also to PET markets. These are not happy times; life is not stable anymore. All markets will change greatly in the next few years, mainly between 2027 and 2030. The EV car evolution is one example: in China already 50% of the cars are now electric. In the chemical sector, there is still an incredible number of new investments creating an even bigger overcapacity. Oil and petrochemicals will suffer: refineries will shut 30% of their capacity by 2030. Mr Hodges stated that we need some reinvention to have growth opportunities: more service orientation, provide solutions more than products, mostly addressed towards mobility, water, food, health, defence and conservation. Mr Hemant Sharma of Reliance, India, echoed the great volatility that the industry must face and must adapt to. The geopolitical tensions of the last 12 months, the rising freight costs, inflation and interest rates: he hopes the worst is behind us. At least some signals indicate that. Mr Sharma foresees oil moving down next year. Polyester producers are suffering and 2025 will be even more challenging considering the increase in capacity worldwide: “Just look at PTA where its increase of output between 2020 and 2024 is double the amount of the increase in demand. It is necessary to work on recycling and Reliance successfully is greatly committed to generate more and more awareness on recycling particularly in India,” he summarised. Philippe De Baere, managing partner of Van Bael & Bellis, Belgium, took the microphone with an overview on PET in the EU trade context, explaining how today EU trade policies are more and more linked to its environmental stance. “In any case EU trade defense measures, after having hit Chinese PET, risk now to turn towards PET of Vietnamese origin, the import of which has inevitably strongly increased. There is a possibility that the EU will use Anti-Circumvention instrument to implement new protection measures, usually a harsher tool than the usual anti-dumping.” Francesco Zanchi, GSI, started illustrating the general overcapacity in China for all polyester-related materials, from PTA to PET. “The point is that, worldwide, the demand for PET in 2025 will be dropping but capacity will keep increasing. Output is expected at around 44 million tonnes against a demand lower than 30 million. In China alone the surplus of PET nearly doubled from 2023 to 2024 (5 to 9 million tonnes) and will increase still. Eventually it is important always to watch closely what China is doing in polyesters as they have 48% of the world capacity and 75% of the world trade. In Europe, demand for virgin is getting lower, and it is moving towards rPET, whose output is increasing in line with the demand."},{"@ID":17 "EDITOUR PETplanet Insider Vol. 25 No. 11/24 www.petpla.net 15 As an innovative market player, Alpek Polyester presented closures made of PET in NPE 24. As long as it remains transparent, it can be reprocessed with the bottle in both chemical recycling and mechanical recycling which ensures recycling at its best to avoid complications in the initial separation process. With increased focus on sustainability, the plant is heavily invested in recycling capabilities including production of resin & sheets with rPET content using the chemical recycling process. Used PET bottles in the form of high-quality flakes are sourced to be made into bottle-grade again. Andrea Frigerio, Site Quality & Continuous Improvement Manager, stated: “We make sure that the quality of the flakes is as consistent as possible. Everything goes into the reactor described below, where unwanted substances like other polymers (PP/ HDPE) are removed. Another positive aspect of chemical recycling is that the material is only heated once in the reactor. As a result, it is not prone to grey or yellow haze. APME’s PET resin and single pellet technology meets FDA & EFSA standards.” www.alpekpolyester.com In the control room, Salim Ba Awain shows Alexander Büchler the process flow in the production of bottle-grade PET. Alpek Polyester, a leading global producer of PTA and PET, closed the acquisition of OCTAL Holding for US$620m on June 1, 2022, as the agreement signed was subject to regulatory approvals. OCTAL, a major producer of PET film and bottle grade PET resin with a capacity of over 1 million t/a, operates plants in Oman, Saudi Arabia, and the USA. The acquisition expands Alpek Polyester’s portfolio to include the direct-tosheet PET film segment (DPET). Alpek has an installed capacity of 5.8 million t/a and operates 32 plants in Mexico, the USA, the UK, Brazil, Argentina, Canada, Oman and Saudi Arabia. The melt-to-resin (MTR) process is a fully integrated one-step process that provides bottle-grade IV PET melt directly from the discage reactor (finisher). PET is produced from the raw materials purified terephthalic acid (PTA), isophthalic acid (PIA) and ethylene glycol (EG) using a melt polymerisation process. Conventional processes have in common that they require a second, subsequent solid condensation step (SSP) to further increase the molecular weight of the polymer. Alpek Polyester uses the MTR process, in which the IV increase takes place before the granulate is produced. This makes the material more uniform; thicker or thinner granules or dust have the same material properties. As the granulate is not subsequently heated again in the SSP, the acetaldehyde content is significantly lower, which is a decisive advantage for water bottle grades. In addition, the MTR process has a clear advantage in producing bottle-grade PET in terms of overall costs, energy consumption, plant flexibility, fixed costs, raw material utilisation and maintenance costs. www.agrintl.com +1.724.482.2163 • Accurate. Fast. Intuitive. • Powerful, Simple Job Creation and Editing • 3UH 'HȴQHG &RQWDLQHU 0HDVXUHPHQW 5RXWLQHV • AutoJob® ȃ $XWRPDWHG )HDWXUH 5HFRJQLWLRQ and Job Setup in Seconds 3DUWQHU ZLWK $JU WR DFKLHYH VLPSOLȴHG GLPHQVLRQDO PHDVXUHPHQW IRU \\RXU SODVWLF FRQWDLQHUV DQG SUHIRUPV ®"},{"@ID":10 "8 NEWS PETplanet Insider Vol. 25 No. 11/24 www.petpla.net SGR inaugurates its second PET recycling unit in France: a strong commitment to the circular economy SGR, a subsidiary of the SGT group, has officially inaugurated its second PET recycling unit located in Rezé, Loire-Atlantique, further reinforcing its commitment to the circular economy and sustainable development. The Rezé site, with a production capacity of 16,000 t/a of rPET, becomes one of the first PET recycling units in Loire-Atlantique in the west of France, as highlighted by JeanMichel Buf, Regional Councillor of Pays de la Loire. This ambitious project, supported by local and regional authorities as well as ADEME (the French agency for ecological transition), is part of a comprehensive strategy to reduce carbon footprint and promote the valorisation of post-consumer PET bottles. During the inauguration, guests were able to discover the process of transforming PET flakes into premium quality rPET pellets. This recycled material is intended for the manufacture of new preforms for food applications, adhering to the most stringent safety and quality standards. This project represents an ambitious investment of €20 million over five years, enabling SGR to achieve a total production capacity of 28,000 t/a of rPET, distributed between the Rezé and Chalon-sur-Saône sites. The recyc l i ng un i t i n Rezé i s equipped with cutting-edge technologies, ensuring efficient sorting and good rPET quality. Notable equipment includes advanced sorting systems using artificial intelligence, liquid phase decontamination technology ensuring compliance with the strictest food standards, and a highprecision control laboratory equipped with modern chromatographs to analyse recycled flakes. SGR is also equipped with the Flake Analyzer from Canadian manufacturer Eagle Vizion. This device combines infrared identification, artificial intelligence, and colour recognition to map the flow of recycled flakes with high precision. With this technology, every particle is claimed to be detected, and the different components of the flow are analysed with accuracy. The Flake Analyzer ’s constantly evolving database contains over 40 types of polymers, including multilayers, as well as materials such as wood, metal, and glass, providing good sorting and analysis capabilities. “This new facility will also help reduce our carbon footprint, with a decrease of 250 inter-site trucks per year, thus promoting more sustainable logistics,” states Frédéric Mignot, President of SGT/SGR. The inauguration concluded with a visit to the recycling unit, during which participants were able to closely observe the various stages of the process, from feeding PET flakes to producing rPET pellets intended for the agri-food market. They also had the opportunity to explore the SGT injection workshop, equipped with 21 presses dedicated to the manufacture of preforms, all integrated at the same site in Rezé. www.sgt-pet.com STEPS TO THE PERFECT BOTTLE. www.roeders.de www.roeders.de Idea & Design Technology Manufacturing Blow Mould 100% Service Y O U R PA R T N E R F O R B L OW MO U L D S ."},{"@ID":5 "imprint EDITORIAL PUBLISHER Alexander Büchler, Managing Director HEAD OFFICE heidelberg business media GmbH Hubweg 15 74939 Zuzenhausen, Germany phone: +49 6221-65108-0 [email protected] EDITORIAL Kay Barton Heike Fischer Gabriele Kosmehl Michael Maruschke Ruari McCallion Anthony Withers Editorial & WikiPETia. info [email protected] MEDIA CONSULTANTS Martina Hirschmann [email protected] Johann Lange-Brock [email protected] phone: +49 6221-65108-0 LAYOUT AND PREPRESS EXPRIM Werbeagentur Matthias Gaumann www.exprim.de READER SERVICES [email protected] PRINT Chroma Druck Eine Unternehmung der Limberg-Druck GmbH Danziger Platz 6 67059 Ludwigshafen, Germany WWW www.hbmedia.net | www.petpla.net PETplanet Insider ISSN 1438-9459 is published 10 times a year. This publication is sent to qualified subscribers (1-year subscription 149 EUR, 2-year subscription 289 EUR, Young professionals’ subscription 99 EUR. Magazines will be dispatched to you by airmail). Not to be reproduced in any form without permission from the publisher. Note: The fact that product names may not be identified as trademarks is not an indication that such names are not registered trademarks. 3 PETplanet Insider Vol. 25 No. 11/24 www.petpla.net Sometimes lateral thinking is needed Weight reduction has been the topic in the PET industry for 25 years. Generally, it is not the multinational bottlers that are pushing ahead, but the regional independent companies. This time it’s not just a regional bottler, it’s a lateral thinker who has triggered the next push for reduction. We found our lateral thinker more by chance during our Middle East roadshow in the Sultanate of Oman. Three years ago, Fahad Mohammed Riaz was still in the timber trading business when he set up a bottling business from scratch. The starting point was just a plot of land with a spring. He now produces millions of bottles a day on Krones and Sipa lines. He has commissioned a new neck finish from Redupet for both companies. It was with some scepticism that the two plant manufacturers started their initial trials. And the new development with 6.85 g (8% lighter than before) of the 250ml bottle with 29/25 neck ran through the blowing and filling systems without any modifications despite the adapted geometry. He favours mass and class and a low consumer price. Two years ago, the 24-pack cost 1.60 euros in the shop, but now it’s 0.80 euros. In Oman, with a population of just under 5 million, this has naturally triggered an earthquake among the other bottlers, who already have a high level of overcapacity. There will certainly be significant shifts here in the near future. Read more details on page 12. Yours, Alexander Büchler Dear readers,"},{"@ID":12 "10 NEWS PETplanet Insider Vol. 25 No. 11/24 www.petpla.net Coca-Cola Europacific Partners: Production line for refillable PET bottles put into operation After approximately a year of renovation, Coca-Cola Europacific Partners Deutschland (CCEP DE) has restarted a production line for 1 l reusable PET bottles at its Bad Neuenahr-Ahrweiler site in Germany. The modernised facility now fills around 36,000 bph with carbonated beverages such as CocaCola, Fanta, Sprite, and their sugar-free variants. This is about 6,000 bph more than the second reusable bottle line at the plant. The beverage manufacturer has invested around 15 million euros in modernising the existing line in the Ahr Valley and has created a total of 30 new jobs. Hannes Bessinger, who has been the plant manager at the site since May 2024, is proud of the production line now back in operation: “The modernisation of the old PET refillable line is a positive signal to our employees and the region. With this investment, we have not only increased production capacity but also secured our long-term competitiveness. The plant now has four production lines again – three for refillable glass and PET bottles and one for single-use PET bottles,” said the 38-year-old plant manager. Successful renovation during ongoing operations All components of the PET refillable line are claimed to meet the latest technological standards and operate in an energy- and water-efficient manner. The comprehensive modernisation of the previously decommissioned facility was successfully completed while the plant remained operational. While key components, such as the filler and the washing machine, were already in place, new equipment such as level meters, bottle inspectors, and packing machines had to be installed. Additionally, the connection to essential supply areas, such as the syrup room, was established. Until early 2021, the line was used to bottle Apollinaris brand mineral water. 1-litre refillable PET bottles in the market The existing production capacities for beverages in refillable PET bottles at nine of Coca-Cola’s 14 regional production sites in Germany are heavily utilised. With the additional line in Bad Neuenahr, seasonal demand peaks as well as maintenance and repair work in the German production network can now be better managed. Moreover, the newly restarted line in Bad Neuenahr enables even stronger, predominantly regional distribution of Coke classics in the Rhineland region. www.cocacolaep.com Josef Hochreiter takes over operational management of NGR GmbH Josef Hochreiter, shareholder and CEO of the Next Generation Group (NGR), is assuming the role of Managing Di rector of NGR GmbH, a key member of the group, effective immediately. Hochreiter has previously led the company and is now returning to its operational management. He takes over the position from Gerhard Ohler, who has led NGR in recent years and will be leaving the Austria-based recycling machinery manufacturer. Josef Hochreiter stated, “I would like to thank Gerhard Ohler for his dedication and contributions to NGR. Diverging perspectives on the company’s future direction have led to this decision. I will now take responsibility and, together with our strong team, help shape NGR’s future. Our mission to develop innovative plastic recycling solutions for a sustainable future remains unchanged.” Josef Hochreiter will continue in his role as CEO of the Next Generation Group, overseeing both the strategic direction of the entire group and the operational management of NGR. www.ngr-world.com"},{"@ID":1 "No.11 2024 www.petpla.net D 51178; ISSN: 1438-9452 18 . 11 . 24 M A G A Z I N E F O R B O T T L E R S A N D B O T T L E - M A K E R S I N T H E A M E R I C A S , A S I A , E U R O P E A N D A L L A R O U N D T H E P L A N E T PETplanet is read in 159 countries Palletising and shrink film machinery Page 23 MARKETsurvey Page 26 EDITOURPage 12 BOTTLE MAKING Page 16"},{"@ID":23 "21 PRODUCTS PETplanet Insider Vol. 25 No. 11/24 www.petpla.net Moulds for compression and injection presses Expertise and innovation make Sacmi a well-known provider of rigid packaging moulds. Sacmi presses - whether compression or injection - feature moulds that are precision-designed to maximse efficiency, reliability and finished product quality, says the company. Sacmi’s team of experts work in close contact with customers to develop tailor-made solutions, optimise production processes and reduce cycle times. Thermal efficiency with Cool+ Sacmi's Cool+ system is a thermal control of moulds, on both compression and injection presses. Cool+ uses a cooling system that ensures excellent heat dissipation, improving the quality of the finished product and significantly reducing cycle times, says the company. For compression press moulds: Cool+ maintains a uniform temperature across the entire surface of the mould, reducing any thermal deformations and extending the working life of the moulds. This means higher productivity and lower maintenance costs. For injection press moulds: Cool+ also provides precise thermal control for injection moulds, improving the dimensional stability of plastic parts and ensuring consistent long-term quality. Thr technology optimises cooling flows, reducing defects in produced parts and making the process more efficient. Sacmi original spare parts The use of original spare parts plays a key role in ensuring the optimal, uninterrupted operation of Sacmi systems. The company offers a broad spare parts range. Every part is designed and tested to comply with the strictest quality standards and can be seamlessly integrated into existing equipment. Using Sacmi original spare parts reduces the risk of malfunctions, minimises downtime and extends the working life of the machines, ensuring fluid, uninterrupted production. Vice versa, using non-certified spare parts can lead to serious problems such as lower finished product quality, frequent production stoppages and unforeseen breakdown/repair costs. www.sacmi.com Krones presents compact version of its Contipure AseptBloc A sterile process chain from preform sterilisation to sealing, this summarises the principle of the Contipure AseptBloc. At Krones, almost 90 per cent of aseptic fillers are currently integrated into this block solution. While this type of system was previously used primarily in the medium and high output range, there is now also a compact version that can be used to economically fill outputs as low as 8,000 containers per hour. The basis for expanding the portfolio was laid by a further development in stretch blow moulding technology: two years ago, Krones launched a new generation of its Contiform blow moulding machine, which for the first time also enabled configurations of four, six and eight cavities. Similarly, the filling technology team further developed its existing aseptic filler, also with a view to low outputs - and finally combined both systems in a compact version of the Contipure AseptBloc. The small footprint of the block is particularly noteworthy: the smallest version contains a four-cavity blow moulding machine and a filler with a pitch circle of 1,080 mm - and currently requires around 100m2 of installation space - with potential for further space savings. This small footprint can be achieved, through a revised cleanroom concept, optimised positioning of peripherals such as media supply or valve manifolds and integration of the piping directly into the system. For juice, milk or plant-based milk alternatives Apart from the space requirement, the compact version of the Contipure AseptBloc is in no way inferior to the tried-andtested standard version: only one sterilisation medium is used, namely gaseous hydrogen peroxide. Furthermore, since the preform and not the bottle is sterilised first, lightweight containers can also be used. Compared to conventional aseptic processes with container sterilisation, the Contipure AseptBloc enables material savings of around 2 g/ bottle. And as usual, the compact version of the Contipure AseptBloc is also suitable for a wide range of d i f f eren t produc t categories: Whether distributed at ambient temperature or within the cold chain, whether in the low- or high-acid range, whether with or without chunks of up to 5 x 5 x 5mm - all non-carbonated beverages such as juice or dairy products can be processed on the system, and lightweight containers, too. The smallest version of the advanced Contipure AseptBloc incorporates a Modulfill Asept filler with a pitch circle of 1,080mm, enabling up to 20,000 containers per hour to be aseptically produced, filled and sealed. The Krones filling technology team is currently working on further models of the compact version in order to close the gap between the 1,080mm version and the familiar standard lines. www.krones.com PETproducts BOTTLE MAKING"},{"@ID":37 "35 EVENT REVIEW PETplanet Insider Vol. 25 No. 11/24 www.petpla.net Digitalisation, process automation and energy efficiency Some of Moretto’s strategic development drivers - digitalisation, process automation and energy efficiency – were in the spotlight of the company’s show appearance. Among the drying solutions on display were the OTX (Original Thermal eXchanger) hopper, the compact fully electric X Comb dryer, and the Moisture Meter analyser for measuring in real time the residual moisture content of plastic granules, eliminating the need for offline sampling. To satisfy any blending requirement, Moretto exhibited the range of DGM Gravix, a gravimetric dosing unit recently updated. The improvements in the digital part, as well as the introduction of a new micro-dosing model (DGM Gravix 20), further underline Moretto’s commitment to meeting the specific needs of plastics processors. Furthermore, visitors had the opportunity to discover Dolphin, the exclusive automatic manifold for material-machine allocation in plastics conveying plants. The storage line includes SiIcontrol, the system designed and developed to control the loading of plastic granules into storage silos. All the solutions can be integrated with Mowis, a supervision and management system entirely developed in-house by Moretto. It allows connectivity between machines, processes, departments, plants and factories. A demo version was available at the stand for visitors to test the main features and benefits of this exclusive supervising system. Fakuma was also the occasion to see for the first time the new grinder Hyper Cut which is claimed to be suitable for grinding waste pieces, sprues and blown parts. The motor power is transferred to a single mobile blade, increasing cutting performance at a lower RPM (280 rpm). The cast-iron cutting chamber reduces vibrations and noise. www.moretto.com 5IF SJHIU JOTQFDUJPO TPMVUJPO GPS FBDI #055-& $0/5\"*/&3"},{"@ID":31 "No.11 2024 www.petpla.net D 51178; ISSN: 1438-9452 18 . 11 . 24 M A G A Z I N E F O R B O T T L E R S A N D B O T T L E - M A K E R S I N T H E A M E R I C A S , A S I A , E U R O P E A N D A L L A R O U N D T H E P L A N E T PETplanet is read in 159 countries Palletising and shrink film machinery Page 23 MARKETsurvey Page 26 EDITOURPage 12 BOTTLE MAKING Page 16"},{"@ID":15 "EDITOUR PETplanet Insider Vol. 25 No. 11/24 www.petpla.net 13 EDITOUR 13 cap mould from Corvaglia into the 300 t Netstal. It is important for Fahad to have production in-house, so he has a direct influence on the quality of the preforms and the caps. A simple example is the 100% in-line inspection of the caps by an IMD inspection system. After the inspection, he fills the caps into boxes that are actually intended for 5,000 to 6,000 caps. However, it only fills 4,000 caps so that the caps arrive at the capper virtually damage-free. The reject rate is in the sub-promille range. It all began with a small Krones plant in the original building. It quickly became clear that the concept was popular, and so Fahad ordered two new lines: a Sipa line and another Krones line, both in the 50,000 bph range. The Sipa system consists of an Xtra20 cavity rotary blow-moulding machine in a Sincro Bloc with a Sipa Flextronic 70-20 filler. This is followed by a labeller, a Dimac shrink wrapper and a Sipa PTF2 palletiser. The Krones is a blocked system with labelling between the stretch blow-moulding machine and the filler. Interestingly, both produce the same bottle and also use the same label and cap. The stretch blow moulds for the same bottle were produced by Sipa and Krones for their own lines. In the end, the quality of the filled bottle is indistinguishable whether it comes from the Sipa or Krones plant. In addition to the Krones plant, the same plant with 50,000 bottles is to be built, and the drying line has already been designed for this. The systems run 24 hours a day, 7 days a week, interrupted only by scheduled maintenance. Fahad could sell more if he produced more. He also has Dubai in mind as another market, just five hours away by lorry. www.saroojwater.com ? SEE HOW MUCH YOU CAN SAVE 70% LESS ENERGY MAINTENANCE COSTS 90% LESS 70% REDUCTION IN CO2e 50% MORE PRODUCTIVITY The savings will vary based on your circumstances and should be reviewed with our sales team. [email protected] www.maguire.com Discover your potential savings. With just a few clicks, you’ll gain valuable insight into how ULTRA will positively impact your bottom line. 1. Go to ultra.maguire.com 2. Input your data. 3. Receive your customized PDF report of potential savings via email. Netstal 300 t Top Entry with 128-cavity Otto Hofstetter mould next to a 400 t Netstal capping system with 48-cavity mould from Corvaglia, which feeds an IMD feeder."},{"@ID":35 "33 EVENT REVIEW PETplanet Insider Vol. 25 No. 11/24 www.petpla.net Featuring efficiency and cost savings Maguire Products, a global leader in materials handling solutions, highlighted a series of products designed to enhance efficiency, reduce costs, and deliver precision for plastics processors. Blending solutions Maguire’s Gravimetric Batch blender was a key highlight at the company’s booth. Engineered for precise dosing, material traceability, and rapid material changes, these blenders are claimed to offer the flexibility to handle small and large-scale production needs. The models WSB MB Micro and WSB 240R were presented, both of which designed to ensure quick returns on investment through operational efficiency and precise material control. Plastics drying The Ultra Vacuum dryer was also on full display. Renowned for its energy efficiency and drying speed, the Ultra dryer offers savings of up to 80% in energy costs, drying materials up to six times faster than traditional desiccant drying methods, says Maguire. Visitors to the stand could interact with the featured Ultra150 and Ultra 300 models and explore potential cost savings using Maguire’s interactive Savings Calculator. Expanded gravimetric feeder line The MGF feeder family, recently expanded to over sixty models, provides dosing accuracy for additives and masterbatch, with 20-30% savings over volumetric systems. Featured models, including the MGF and MGF+100X-3 with integrated extrusion control, demonstrated enhanced precision for both extrusion and moulding applications. FlexBus conveying control system Maguire also spotlighted its FlexBus central conveying system, designed for seamless plant-wide material handling control. Compatible with various equipment, FlexBus offers intuitive touchscreen interfaces, while the FlexBus Lite version provides a streamlined solution for smaller-scale operations. Both systems are retrofittable to third-party equipment, allowing processors to upgrade their systems without major overhauls. Tracker monitoring & reporting system The company’s new Tracker Monitoring & Reporting System has been designed to empower processors with realtime, web-based monitoring and control for blenders, feeders, dryers, and conveying systems via any web-enabled device. Fully integrated with third-party databases, Tracker delivers comprehensive reports that support smarter decision-making and improved operational efficiency. www.maguire.com Ultra Vacuum dryer The shortest cut to success With SACMI, you can convert to tethered cap production effectively without compromising productivity. This solution ensures cost-effective slitting operations. -RRSZEXI TVSƼXEFP] W[MXGL XS XIXLIVIH GETW [MXL 7%'1- sacmi.com E N D L E S S I N N O V A T I O N S I N C E 1 9 1 9"},{"@ID":30 "EVENT PREVIEW PETplanet Insider Vol. 25 No. 11/24 www.petpla.net 28 Promoting innovation, circularity & growth across the PET value chain Petcore Europe’s annual conference 2025 will take place in Brussels on February 4-5. President Antonello Ciotti sat down with us to explain what they have planned. PETplanet: Petcore’s annual conference is now in its 31st year. What is the secret to its ongoing success? Mr Ciotti: Our conference is unique as it brings together stakeholders from across the PET value chain – from polymer and machine producers to recyclers and brand owners. With a growing membership – including a new group focused on PET textiles – we offer a global perspective and networking opportunities for industry professionals. Our 2024 conference was the largest ever, with more than 330 delegates. So we have a lot to live up to! Because it takes place at the start of the year the conference sets the tone for the months ahead – particularly with major regulatory developments such as the EU Packaging and Packaging Waste Regulation (PPWR) which is still awaiting the definition of the Delegated Acts. Holding it in Brussels, at the heart of the EU, means we have the chance to dialogue with delegates and speakers from the EU institutions and to demonstrate to them how our sector is responding to various regulatory challenges. PETplanet: I understand that the Innovation Session will take place once again in 2025. What are you hoping to see this year? Mr Ciotti: The Innovation Session will showcase the latest developments and solutions taking place across the sector and highlight how we are driving innovation to meet the recommendations of Professor Draghi’s report on regaining competitiveness in Europe. It provides a platform for different players to present their latest advancements and this year we are particularly interested to highlight projects that facilitate the implementation of PET circularity. We want to show policymakers the vast potential of PET across production and recycling and demonstrate how emerging technologies are helping us adapt to societal needs. Innovation is a key driver for Petcore and we work closely alongside two innovation evaluation platforms – one for bottles and one for trays – in lending our support. The European PET Bottle Platform (EPBP) and the Trays Circularity Evaluation Platform (TCEP) both fully support a circular economy for the European PET value chain by providing design guidelines for PET bottle and tray recyclability and circularity. They evaluate packaging solutions and technologies and facilitate understanding of the effects of new PET bottle and tray innovations on recycling processes. PETplanet: So what is next for packaging and packaging waste regulation under the new 2024-2029 European Commission? Mr Ciotti: Fortunately, when it comes to packaging regulation, the PET industry has been ahead of the curve. The Single Use Plastics Directive (SUPD) meant that PET packaging already had set targets for recyclable and recycled content back in 2019. And I am happy to say that these have proven to be achievable. The challenge now is how the new PPWR regulations will be implemented across the 27 EU member states – particularly when it comes to calculating recycling rates and reuse targets. How to harmonise the SUPD and PPWR as they enter into force during the coming years will also be an important area of focus. I am concerned as to how our industry is going to be able to protect itself from the greenwashing of producers from outside of the EU who seek to place their products on the EU market. Over the past 20 years Europe’s PET value chain has taken significant steps to ensure its products meet the highest levels of food safety. We will need controls and systems to verify recycled content claims if we are to ensure a level playing field and protect the competitiveness of our sector. PETplanet: Looking to the future, what are Petcore’s priorities for the year ahead? Mr Ciotti: Aside from navigating ongoing regulation, advocacy remains a major part of our work and we have set up a new group to tackle this. Our members are very much involved in all of our working groups and bring a great deal of value and strength to our activities. With a new European Parliament and Commission, it is crucial that we introduce the new stakeholders to the value of PET and demonstrate what our sector has achieved to date in delivering circularity. We are ready to take up our responsibility but need clear regulatory guidelines – especially in areas such as chemical recycling which presents a significant opportunity. This depolymerisation recycling, as it is also known, is necessary to recycle PET textiles, but we need assurances that making the investment now will not be a waste of time and money in the future. Increasing the circularity of PET trays alongside bottles is also a priority. We are actively showcasing this to the EU institutions and held a successful Thermoforms conference in Granada last summer to highlight tray circularity. It followed the inaugural conference held in Bologna the previous year. Petcore is also recognised as leading the Functional Barrier Working Group – a consortium of thermoforming companies which is working tirelessly to get recognition for the full circularity of trays within the EU Institutions. In short, our Petcore mission remains unchanged: to represent, and be the voice of the entire PET value chain in Europe and promote market growth by showcasing PET’s unique characteristics to legislators, brand owners and consumers alike. www.petcore-europe.org"},{"@ID":42 "PETnews 6 NEWS PETplanet Insider Vol. 25 No. 11/24 www.petpla.net Alpla opens state-of-the-art recycling plant in South Africa – Production plant to supply up to 35,000 t/a of rPET material from 2025 Alpla is entering the South African PET recycling market. The international packaging and recycling specialist has just opened the state-of-the-art plant, which is located on a 90,000m2 site in the coastal town of Ballito, after a construction period of around 18 months. The company has invested 60 million euros in the new plant in the province of KwaZuluNatal and is setting the course for further growth in South Africa, providing an economic boost to the densely populated province of KwaZulu-Natal and the iLembe district. From 2025, the Alpla recycling division will produce up to 35,000 t of rPET flakes and food-safe rPET pellets annually in South Africa The high-quality material will then be processed into safe, affordable and sustainable plastic packaging at Alpla’s production plant in Lanseria. At the opening ceremony on October 31, Alpla Chairman Günther Lehner, together with Dietmar Marin, Managing Director of Alpla recycling, and Plant Manager Gerhard Meyringer, welcomed around 180 guests from the worlds of business and politics including representatives from the South African Ministries of Trade, Industry and Competition and Forestry, Fisheries and the Environment, representatives from the province of KwaZulu-Natal, the eThekwini Metropolitan Municipality and the iLembe District Municipality, as well as Austria’s Ambassador Romana Königsbrun. “South Africa is a strategically important market for us and one in which we want to continue to grow. Together with our customers and partners, our aim is to provide safe, affordable and sustainable packaging solutions to our customers and to continue improving standards of living. With our investments in Ballito and before that in Lanseria, we have laid the foundation for a successful future,” says Alpla CEO Philipp Lehner. “Alpla’s involvement does not only accelerate the industrialisation of iLembe District Municipality, but ensures investing in projects that support UN Sustainable Development Goals, attracting other companies along the value chain and creating several thousand jobs in the collection infrastructure,” says Sihle Ngcamu, CEO of Trade & Investment KwaZulu-Natal. The Ballito recycling plant will have an initial output capacity of 35,000 t of rPET flakes, of which 16,000 t will be processed into rPET pellets. A state-of-the-art extrusion line has been installed for this purpose. Once all processes have been qualified and the flakes and pellets have been approved by the customer, Alpla will start production in early 2025. www.alpla.com Avantium celebrates the official opening of its FDCA flagship plant Avantium N.V., a well-known company in renewable and circular polymers, celebrated the official opening ceremony of its FDCA Flagship Plant in Delfzijl, the Netherlands. The plant opening was officiated by Her Majesty Queen Máxima of the Netherlands, in the presence of international and local dignitaries, partners and Avantium employees. In the world’s first commercial plant, Avantium will produce 5 kt of FDCA (furandicarboxylic acid), the essential building block for 100% plant-based and circular plastic PEF (polyethylene furanoate), known under the brand name Releaf. Avantium’s Releaf is a new material set to transform the plastics industry, with versatile applications including bottles, packaging, films, and textiles. Avantium and SCGC to accelerate the market adoption for FDCA and PEF in Asia Avantium and SCGC, through SENFI Ventures, is a cornerstone investor in Avantium and furthermore collaborates with Avantium in CO2-based polymers technology. Building on their strategic intent letter from January 2024, the companies have decided to take the next step in their collaboration and accelerate the market adoption for FDCA and PEF in Asia. This is backed by Avantium’s achievement in securing global industrial-scale capacity reservations and Flagship Plant offtake agreements in key markets such as rigid packaging and apparel. A joint team will work with local and global brands to validate the market potential, further develop FDCA and PEF applications, and enhance volume commitments across the region to underpin future largescale production in Asia. www.avantium.com"},{"@ID":36 "34 EVENT REVIEW PETplanet Insider Vol. 25 No. 11/24 www.petpla.net Solutions for sustainability, precision, and efficiency across key industries At Fakuma 2024, Husky Technologies showcased the company’s latest range of technologies, solutions, and services that aim to enable food, beverage, consumer goods, consumer electronics, automotive, medical device producers and mould makers to achieve sustainability, growth, differentiation, flexibility, stability, and profitability. “We’re particularly excited this year to demonstrate how we’re supporting this goal by enabling the use of more bio and sensitive resins, designing for recyclability, and improving energy efficiency. From food and beverage containers to medical products and consumer goods, our goal is to develop solutions that promote circularity, sustainability, and help make the world a better place,” said Sean Hoy, Husky’s Vice President of Sales, Hot Runners and Controllers. The highlights on display included several advanced technologies designed to enhance efficiency, precision, and sustainability in injection moulding. Ultra SideGate Technology 2.0 offers a broader operating window and easier system maintenance, thanks to a new heater design and optimised head and tip that reduce wear and improve mould integration. Another advancement, the UltraHelix Valve Gating, delivers extended run-time cycle performance, which, according to Husky, helps reduce both production time and spare part costs. Liquid Silicone Rubber (LSR) injection moulding also showcased how it differs from traditional thermoplastic injection moulding, demonstrating the benefits of runner-less moulding and the waste reduction achieved with cold deck technology. Further innovations were evident in UltraSync Technology, which ensures consistent part filling through reduced nozzle pitch ranges and 100% valve stem synchronisation. UltraMelt Technology, an award-winning hot runner system, facilitates the efficient and sustainable moulding of bio and sensitive resins. Recognised for its contributions to sustainable practices, UltraMelt received this year’s Innovation in Bioplastics award. The Altanium family of mould controllers, featuring Husky’s Active Reasoning Technology (ART 2.0) and DataWave 2.0 Technology, is designed for highcavitation and stack tools, boosting productivity and lowering costs. Lastly, UltraShot Technology empowers moulders to improve part quality, consistency, and repeatability by integrating hot melt delivery with injection processes specifically tailored for the precise moulding of medical devices and consumables. PET for the medical market segment The company also showcased its advanced technologies designed to meet the precision, reliability, and efficiency demands of medical device production. According to Thomas Bontempi, General Manager of Husky’s Medical Business, PET remains a top material choice for medical consumables, with over 70% of today’s devices utilising PET and other medical-grade polymers. Key technologies highl ighted included Husky’s ICHOR system, which integrates mould, hot runner, controller, press, automation, and ancillary equipment to support various medical applications. Husky also demonstrated pipette tip production using up to 64-cavity moulds. For complex auto- and peninjectors, the company’s solutions are claimed to enable high-precision moulding with features such as lift, strip, or servo-driven activation to support consistent production with technical resins. Additionally, Husky’s capabilities extend to high-volume and complex stack moulds, including 192-cavity moulds and lower-cavitation options for highoutput or highly specialised applications. www.husky.co Cooling, climate and drying technologies Blue Air Systems GmbH, an Austriabased company, founded in 2010, supplies the plastics industry with technologies focusing on climate technology. This includes solutions for extremely dry and cold air for energy efficient processing in the plastics industry. In the range of material drying, the company offers an energy saving resin dryer series RD based on compressed air technology with hopper sizes from 0.5-1,300 l. In cl imate technology, the core business is focused on internal product cooling (series CAC) and dehumidification units (series DMS). This DMS system allows energy-efficient mould dehumidification without the need for cooling water and has potential for up to 85% energy savings. The Compressed Air Chiller (CAC) replaces the regular blowing air with chilled compressed air (-35 °C) inside the container during the blowing process and is claimed to guarantee as production increase up to 40%. www.blue-air.at The modular resin dryer RDL uses pre- dried compressed air for drying, either from the customer’s air system, from an integrated compressor or from the exhaust air of the blowing process of an ISBM machine. Available material capacity ranges from 24-200 kg/h. It is applicable for all resins including PET."},{"@ID":19 "BOTTLE MAKING 17 PETplanet Insider Vol. 25 No. 11/24 www.petpla.net pared to a market average premium bottle, up to 61 t/a of carbon equivalent savings can be achieved. Ready for a wide range of production setups This new premium bottle base is designed to accommodate bottle formats ranging from 0.25 l to 2 l, making it highly versatile. This base is compatible with a wide range of bottle designs and premium bottle weights, offering flexibility. It can be produced on EvoBlow, Universal, and Series 2 platforms, and is suitable for both regular and aseptic filling lines. Additionally, it is easy to retrofit into existing production lines, ensuring a smooth integration process. The premium bottle base is the latest addition to Sidel’s StarLite-R range, joining the ranks of designs like the StarLite-R Nitro and StarLite-R for carbonated soft drinks (CSD). Launched earlier in 2024, the StarLiteR Nitro is a high-resistance bottle base specifically engineered for still nitrogendosed products in 100% rPET bottles. Meanwhile, the original StarLite-R for CSD, was Sidel’s first solution dedicated to rPET, offering enhanced protection against deformation, improved stability, and increased resistance to bursting. www.sidel.com"},{"@ID":26 "MARKET SURVEY 24 PETplanet Insider Vol. 25 No. 11/24 www.petpla.net Company And & Or Postal address Telephone number Web site address Contact name Function Direct telephone number Email PI El Limon, Av. de Europa, 6, 41928 Palomares Del Rio (Sevilla), Spain +34 954 779 200 www.andyor.com Mr Caridad Ortega Suárez Sales Director +34 954 779 200 [email protected] Shrink film machinery: Packaging options & output rate (packs per minute) - print registered fi lm (yes/no; packs/min) No - nested pack (yes/no; packs/min) Yes, 15-900bpm - label orientation (yes/no; packs/min) No - carry handles (yes/no; packs/min) Yes, 15-400bpm - pad supported (yes/no; packs/min) Yes, 15-400bpm - tray supported (yes/no; packs/min) Yes, 15-400bpm - fi lm only (yes/no; packs/min) Yes, 15-900bpm - tray and fi lm (yes/no; packs/min) Yes, 15-900bpm - pad and fi lm (yes/no; packs/min) Yes, 15-900bpm Shrink process: - shrink tunnel with hot air Shrinking pistols (hot air) - oven Footprint Several models depending on speed Number of possible lanes Max. length of the pack is 1,400mm Packaging material & possible thickness LDPE + LLDPE 40-60 μm Voltage/power/energy consumption Several models depending on speed Film cutting and feeding system Yes Certifi cation CE and UL Palletising machinery: Format changeover time 15-20min Output rate (packs/min) Up to 400bpm Automatically intergrated:(yes/no) Yes Empty pack feeding Yes Insertion of interlayers Yes Connectable to shrinkwrapper Yes Special characteristics: i.e. low-level feed, cross conveyer barrier Low-level feed; tray former possible to be integrated (display palletiser) Company Sipa Postal address Telephone number Web site address Contact name Function Direct telephone number Email Via Caduti del Lavoro n. 3; 31029 Vittorio Veneto (TV) - Italy +39 0438 911511 www.sipa.it Mr Matteo Tagliaferri Marketing and Communication +39 0521 548111 [email protected] Palletising machinery: Genius PTF Genius PTF/V Genius PTF/A Genius PTF - Active Layer Conventional automatic palletisers steady pallet type Conventional automatic palletisers steady pallet type, with double platform Conventional automatic palletisers moving pallet type Conventional automatic palletisers steady pallet type with innovative layer preparation Format changeover time 15min 15min 18min 10min Output rate (packs/min) Up to 330 layers/hour Up to 420 layers/hour Up to 600 layers/hour Up to 330 layers/hour Automatically intergrated:(yes/no) Empty pallet feeding Yes Yes Yes Yes Insertion of interlayers Yes Yes Yes Yes Connectable to shrinkwrapper Yes Yes Yes Yes Special characteristics: i.e. low-level feed, cross conveyer barrier - Operational fl exibility and further reduction in change-over times - Optimisation of cycle to increase performance, with improved control of the different movements using state-of-the-art electronic solutions - Customisation of the gripping system and layer transfer according to the product to handle - Designed to accept a variable number of product infeeds - Fully automatic system requiring limited operator intervention, operating in complete safety - Possibility to handle all main pallets on the market trouble-free, with highly customisable solutions - Operational fl exibility and further reduction in change-over times - Optimisation of cycle to increase performance, with improved control of the different movements using state-of-the-art electronic solutions - Customisation of the gripping system and layer transfer according to the product to handle - Designed to accept a variable number of product infeeds - Fully automatic system requiring limited operator intervention, operating in complete safety - Possibility to handle all main pallets on the market trouble-free, with highly customisable solutions - Linear axes layer preparation with active pack orientation and arrangement"},{"@ID":44 "The worldwide round trip with PET world in the Middle East In a spectacular project taking us well into 2024, we will be travelling in a wide variety of ways to various countries and regions of the Middle East with different mobile editors. There we will interview machine manufacturers, the supply industry, bottle and beverage producers, as well as PET recyclers and everyone involved in the process chain. What market-specific trends are there now or will arise in the future? What developments and technologies are in vogue on the consumer and plant construction site in some of the hottest regions of the world? What special requirements are there? What role do topics such as food safety, shelf life and sustainability play in PET packaging and how are companies preparing themselves for the coming years? This, and much more we will be discussing face-to-face with all the key players and then our results will be presented to you in a series of must-read reports in PETplanet Insider. Please join on this enchanting voyage to the world of PET in the Middle East. We look forward to welcoming you on board! Our previous Road Shows at a glance 2010-2011-2012-2013-2014-20152016-2017-2018-2019-2020-2022 Interested in being visited? [email protected] Autumn 2023 - 2024 6 countries numerous interviews with PET companies Sponsors to date Editour The Middle East Roadshow"},{"@ID":33 "EVENT REVIEW PETplanet Insider Vol. 25 No. 11/24 www.petpla.net 31 Our continent though needs imports of recycled materials, less rules and even more controls are needed to support a quicker transition but in accordance with existing rules.” Then Zanchi made an exclusive and pivotal announcement regarding the initiation of the PET futures market in China, at the ZCE (Zhengzhou Commodity Exchange). This is an important instrument for sellers and buyers, which will allow, once accessible also to foreign operators, to fix longer term contracts on a global scale. In conclusion, the GSI founder and CEO indicated in oil rates and freight costs the two main things which will have influence on PET and raw materials prices in 2025: “Oil will maybe increase towards the 100 $ mark, but in any case, will not go below 75 $; freights will move down and possibly up again due to powerful cartels in the sector.” In the final presentation of the morning Chiara Zanchi, GSI General Manager and President of St. Lawrence Foundation, explained how the foundation is really the second heart of GSI, beating to support the community of Makeni in Sierra Leone, one of the poorest countries in Africa. From the creation of the Unimak (University of Makeni) to the courses in agriscience, to the creation of an actual company, a poultry farm (SBD) with 70 workers, raising chickens and producing eggs and feeds for the local people and farmers. The development over the past ten years has been enormous and rewarding for the Zanchi family and for all the people who offered their support to the cause. The help offered to the people in Sierra Leone to have better food and education is however just at the beginning, but the course is set. The afternoon session is opened with Prof Chris DeArmitt, connected on video from the US. He illustrated his studies reported in his (freely available) book “The Plastic Paradox”. After checking a huge number of scientific studies on plastic materials and based on his experience in polymer science, Chris gave a shocking picture of the wide misinformation on plastics. These just represent less than 1% of the materials used in the world, they are surely 13% of household waste, but just 0.3% of the ALL the waste we create! In his video “The Great Plastic Distraction” he shows how many lies on plastics have been spread around in the last years for various reason paving way to the use of other materials which are more polluting and generating bigger amounts of CO2, so contradicting the policies the mainstream policies want to implement. Mr Antonio Protopapa of Corepla introduced what his consortium is doing, in Italy, for improving circularity and sustainability. “The country has good rates in collection but must do better to reach the 90% target. Better work must be done too in separating all plastics, more accurate sorting and recycling need to be reached to have improve the quality of available recycled raw materials.” Then Zanchi opened up the three rounds of Round Table among operators of various sectors to comment on the presentation from Chris DeArmitt. In the first round, Sharma, Protopapa and De Baere agreed that it is definitely necessary to separate scientific information from all the fake news, particularly on plastic packaging. The intervention of Werner Bosman (EU Commission) from Brussels, added up some spice as he showed doubts on the actual validity of some information offered in DeArmitt’s video. In saying it is necessary not to take any step back on plastics, he considered dangerous avoiding discussing the issues that these materials create. “The American professor though is very firm in giving his study the greatest validity, confirming first the full independence of it and then his purely scientific approach in the collection of the data which were found in a long list of strictly scientific papers, without any preconceptions.” In the second round of interventions, J.L. Banos (CAIBA, Spain), fully agreed with DeArmitt and admitted there are big problems in misleading communications on plastic in general. “The main problem is the public opinion which has been influenced in the past by a lot of intentional or unintentional false claims.” Lucas Aquino and Larisa D’Otaviano (Valgroup, Brazil) think that education is fundamental: “It is necessary to properly share correct information on PET and all similar materials starting from schools, and they are trying to do so in Brazil.” Slawomir Rusocki (WIP Group, Poland) agreed that fake news must be fought: “In Poland they are spread also on television. Fighting mainstream media it is hard.” Dirk De Cuyper (Resilux, Belgium) is aware of the study from DeArmitt and would like it to be offered to greater audiences, and to convince consumers eventually. Zanchi immediately took the opportunity to stimulate the managers, and all the operators present in the PET Day room, to act and do whatever in their possibility to get the message through to people, politicians, journalists, to the broadest reachable audience, and to find ways to explain properly the truth on plastics. In the third round, Coert Michielsen (Refresco, Netherlands) was definitely interested in acting according to Zanchi suggestion. Enrico Arciuli (Frana Polifibre, Italy) is fully in line with the initiative, but likes to spend a word to remind that recycling is not just for bottlers or the packaging industry, but a major role in using up and recycling all polyester wastes has to be assigned to the fibre and the textile industry. Ferrarelle (Italy) stated that they already try their best to communicate the recyclability of PET, illustrating to their customers the importance of proper collection. Eventually littering and mismanaged waste are the problems to solve they are caused by uneducated people, not by the PET producers. “We need more collection, education and fines,” said Zanchi convincingly. “Scientifically these measures will work. All European producers must convey the message to the politicians and the public to stop blaming a material which is greener and more precious than what anyone, outside of this business, unfortunately, has been brought to think.” www.gsiplastic.com Francesco Zanchi, founder and CEO GSI and Chiara Zanchi, GSI General Manager and President of St. Lawrence Foundation"},{"@ID":11 "9 NEWS PETplanet Insider Vol. 25 No. 11/24 www.petpla.net"},{"@ID":18 "BOTTLE MAKING 16 PETplanet Insider Vol. 25 No. 11/24 www.petpla.net StarLite-R Premium targets high-end products Sleek bottle base for 100% rPET Sidel has expanded its StarLite-R range to include a new premium bottle base suitable for liquid dairy products, flavoured water as well as juices, nectars, soft drinks, isotonics and teas. “This bottle is specifically crafted for the premium market, where consumers expect exceptional performance and striking shelf appeal when purchasing a high-end product. Our new bottle is designed to endure every stage of its journey – from production through the supply chain, to the supermarket shelf, and ultimately into the consumer’s hands. The bottle quality and performance has also been rigorously tested in Sidel’s laboratories under industrial conditions,” says Pierrick Protais, Packaging Innovator Leader at Sidel. The new bottle design has been developed to meet consumers expectations of a sophisticated, streamlined appearance. The high-performing base is also claimed to minimise environmental impact. Hidden technical features Premium bottles are typically heavier than standard designs to ensure a great consumer experience through bottle rigidity and preserved beverage quality. When bottles have increased PET thickness, their bases are prone to deformation especially if manufactured at high speeds. StarLite-R Premium bottle base aims for a sleek, elegant and streamlined aesthetic. The flat-looking bottle bottom creates a high impact bottle display on supermarket shelves, and is compatible with round and squareround shaped bottles; single and multi-serve sizes; and can be used with opaque and transparent PET. The technical features allow a 100% rPET bottle to be blown at high speed while securing maximum base performance for a top bottle quality with a visually appealing look, says the company. The design uses a Sidel patented vault technology to avoid any visible ribs on the bottle base and to optimise its geometry. Made of a tall central dome, surrounded by lower radiating ridges with alternating widths and lengths, the bottle base is easy to blow, and good material distribution and a high base clearance are ensured. The base offers guaranteed bottle stability thanks to its widestanding surface. Additionally, the mould base includes an enhanced cooling circuit for efficient bottle base chilling, especially with rPET, which is processed at higher temperatures when compared with virgin sources. These technical features allow the bottle base to be highly performant when manufactured at a high speed of up to 2,500bph per mould thanks to the optimised geometry of the bottle design. Low environmental impact “Premium bottles are typically seen as less sustainable than standard versions, as they use more PET material, for increased wall thickness, and they require higher blowing pressure,” says Protais. “However, with global packaging regulations increasingly focused on environmental impact, manufacturers are now seeking exclusive product alternatives that provide carbon savings. That’s precisely what StarLite-R Premium offers.” In order to produce the new solution from 100% rPET, Sidel had to adapt its mould base technology to the material. The easy to shape base requires a lower blowing pressure. Sidel’s StarLite-R Premium bottle base offers producers carbon dioxide savings. With the switch from virgin to 100% rPET, manufacturers can save up to 3,100 t/a of carbon dioxide equivalent, and by reducing the blowing pressure of up to 25% when comBOTTLE MAKING"},{"@ID":28 "26 EVENT PREVIEW PETplanet Insider Vol. 25 No. 11/24 www.petpla.net preview part 2 ACP Ergon series: automatic compact packers SMI will showcase an ACP 22 S Ergon case packer to pack 33cl glass bottles in cardboard case in the 4x3 format, with adhesive tape closure. The cardboard case is a good solution to create a multipack and guarantees a resistant packaging that can be customised graphically for the product promotion. ACP 22 S Ergon case packers feature a pick & place packaging system with loose product top loading. This model is equipped with a double picking gripper and can reach an output up to 25 packs/minute. The ACP Ergon series consists of automatic compact packers, suitable for packing a wide range of products (glass, metal, plastic, cardboard containers and rigid bags) of several types of products, in American cardboard cases (RSC). The ACP case packers are characterised by a monobloc structure, where all machine functions are grouped: product separation, insertion into cases with product top loading, cardboard magazine and box sealing. The carton magazine, located next to the machine, allows the loading of pre-folded blanks in an easy and ergonomic way. ACP Ergon case packers are equipped with MotorNet System automation and control technology based on Sercos fieldbus, which ensures compatibility with Industry 4.0 and Internet of Things (IoT) platforms within the plant. SMI supplies a wide range of bottling and packaging machines with an innovative design, equipped with IoT technology, that offer smart solutions for productions up to 50,000bph and that meet requirements of competitiveness, efficiency, flexibility, energy saving and easy management of the production plant. www.smigroup.it Label teach-in in less than a minute The Heuft FinalView II LBL makes label inspection more adaptive. New types and designs can now be taught in within a short time. This is good for production quality and also increases the availability and overall equipment effectiveness (OEE) of entire filling plants at the same time. Individualisation is in vogue. This applies in particular to beverage packaging and its design. And what is more individual than an own image on the bottle label? Visitors to the Heuft stand will be able to create this themselves. And see how quickly and easily a new individual design can be taught in so that a personalised bottle of this kind is not rejected as a foreign type during the label inspection but recognised as good. The company says that the Heuft FinalView II LBL. can do this in less than 60 s with the intelligent Heuft reflexx A.I. image processing. The teach-in assistant of the audiovisual Heuft NaVi user guidance simplifies the learning process. It immediately and permanently memorises the modified label with all its characteristic features and design elements. This applies to a photo as well as to short-term promotional labelling, among other things. The Heuft FinalView II LBL has to go through a suitably equipped bottle once for this purpose if the container shape is unchanged – and the Heuft reflexx A.I. has permanently memorised the modified type. The modified label will no longer be evaluated as faulty from then on. The intelligent in-line inspection actually identifies foreign types of bottle as reliably as it does crooked, wrinkled or torn ones. Four Heuft reflexx A.I. highperformance cameras on two levels generate an undistorted 360° panoramic view of each individual bottle on which the smallest faults are detected and marked in real time. www.heuft.com SMI Hall 7A | Booth 503 Heuft Hall 8 | Booth 104 2024 Training Schedule Technology&Application of PET Plastic Packaging for Hot-Fill &Aseptic Beverages Join our expert team for small group training on a variety of subjects - from materials to recycling. Scan to learn more & register for classes! ©2024 Plastic Technologies | 1440 Timberwolf Drive, Holland, Ohio USA 43528 www.pti-usa.com"},{"@ID":16 "EDITOUR PETplanet Insider Vol. 25 No. 11/24 www.petpla.net 14 Once local, now global: PET production in Oman by Alexander Büchler Two years ago, Alpek Polyester acquired OCTAL, the largest PET resin and PET sheet manufacturer in the GCC, thus marking its expansion into global markets beyond the Americas and Europe. We visited the plant in Salalah and discussed bottle grade PET resin, sheet production, chemical recycling, and the Gulf market in general. The Alpek Polyester Middle East (APME) plant is a state-of-the-art modern manufacturing facility for production of bottle grade PET resin and sheets, with a combined capacity of close to 1 million t/a. With Uhde Inventa-Fischer ’s MTR technology, a differentiated, sustainable, and efficient PET resin production process, they eliminate a crucial step in conventional manufacturing, resulting in 63% less electricity consumption compared to traditional technologies, leading to a shorter cycle time for customers. The facility benefits from its strategic location, which is close to the Port of Salalah, a major hub for connecting raw materials from Asia, that allows rapid delivery of finished goods, resin and sheets, to global markets. The site can store more than 3,000 TEUs (Twentyfoot Equivalent Units) within its perimeters and includes container cleaning facilities. According to the company, the market in the GCC is dominated by the water segment which contributes to around 70% of bottle grade PET resin. APME’s WG02 grade is the most popular to service this segment and is regularly supplied to major regional and international brands. Furthermore, the use of MTR technology for PET production ensures a very low acetaldehyde content in its products, which is particularly important for water producers as it achieves the best product characteristics. APME’s strengths include just-intime (JIT) delivery in trucks by road to regional markets like the UAE, KSA, Kuwait, Qatar, Yemen, and Jordan. Their strategic location adjacent to Salalah port enables them to ship product to over 75 countries around the world from US East Coast to Japan main ports, with short transit times. The market in Oman and that of the neighbouring Gulf states is, according to the company, a stable market with the prospects of solid growth. “Offering unique products to our customers is key to our success, especially in today’s competitive market where cost optimisation is crucial. We are a preferred supplier instead of just a one-off vendor in the highly volatile commodity market.” stated Senior Sales Director - PET Resin, Prashant Boloor and he also emphasised the popularity of fast reheat grades owing to increasing energy cost globally and growing awareness among brands on reducing CO2 generation targets. As a leader in sustainability and promoting a circular economy, APME is already contributing by offering its Single Pellet Technology (SPT) which is chemically recycled PET with up to 25% recycled content to their customers in the region. Many brands have shown interest in the product due to its excellent quality and how it supports their commitment towards sustainability. Ajith Ravindranath, Sales Manager, comments: “Our aim is to ensure best quality product available to our customers, at an affordable price and on time to serve the beverage industry, FMCG and many other markets.” EDITOUR F.l.t.r.: Mustafa Deraiya, Manager - Technical Sales; Prashant Boloor, Senior Sales Director - PET Resin; Ahmed Al-Harthy, Assistant Manager - MEA and Ajith Ravindranath, Sales Manager Alexander Büchler (on the right) with the APME Sales Team, Salim Ba Awain, Continuous Improvement Process Manager & Andrea Frigerio, Site Quality & Continuous Improvement Manager. The background shows the FG Product Silos."},{"@ID":9 "7 NEWS PETplanet Insider Vol. 25 No. 11/24 Suntory introduces first commercialised PET bottles using bio-paraxylene Starting this November, Suntory Group began introducing PET bottles using paraxylene derived from used cooking oil (bio-paraxylene) for select products in Japan. This will be the first commercialised PET bottles using bio-paraxylene and will help significantly reduce CO2 emissions compared to those made from conventional virgin petroleum-based materials. The group will introduce this to approximately 45 million beverage PET bottles with consideration underway to expand its use across its product portfolio. PET resin, the raw material for PET bottles, consists of 30% monoethylene glycol and 70% terephthalic acid. Since 2013, Suntory Group has been using plant-derived materials for monoethylene glycol in its Suntory Tennensui brand PET bottles. In this new challenge, the group has succeeded in producing terephthalic acid at a commercial scale by using paraxylene derived from used cooking oil, a biomass resource. To achieve this, the group established a global supply chain in collaboration with corporations such as Eneos Corporation and Mitsubishi Corporation to procure bionaphtha derived from used cooking oil and ultimately produce PET bottles. Bionaphtha can be produced from the manufacturing process of sustainable aviation fuel (SAF), among other things, and as SAF production is expected to increase, the importance of developing a bio-naphtha supply chain is also growing. Suntory Group aims to build a more robust mass production system for bio-based PET bottles in cooperation with stakeholders. In September 2023, Suntory Holdings announced its collaboration with Eneos Corporation for the collection of used cooking oil in Japan. Suntory Group is also considering taking advantage of this collaboration to make bio-based PET bottles using bio-naphtha domestically produced at Eneos Corporation’s SAF plant which plans to start its operations after 2027. www.suntory.com CREATING FUTURE STANDARDS Japan’s leading Aseptic PET Filling System Provider. Our website Our solution high quality reliable technology safe & secure"},{"@ID":22 "BOTTLE MAKING 20 PETplanet Insider Vol. 25 No. 11/24 www.petpla.net The essence of purity in every drop The secret of the exceptionality of the still water bottled by the company Santa Vittoria Srl is an incomparable natural filter: a rock from the Ligurian Alps formed 28 million years ago, which ensures the product purity and quality. BOTTLE MAKING The peculiarity that has always distinguished the containers used by Santa Vittoria is the wonderful diamond decoration. Starting from this element, the motif was revised both in shape and size, until the achievement of an aesthetic result that enhances the purity and lightness of the water contained in them. The evolution of the study was marked by the close collaboration between SMI and Santa Vittoria, to the point of creating a customised version of the project with the decoration becoming lighter and perfectly distributed on the container. The final result is an elegant, functional bottle, easily recognisable on the market. The performance of the container was also carefully analysed and improved, especially in the part of the handle, to respond to the Ligurian company’s request to be able to use a lighter rPET preform. The weight reduction was also achieved through the choice of the 26/22 Gravity II neck, which provides a lighter thread suitable for bottling carbonated products. Starting from all these aesthetic and functional assumptions, the SMI team began to develop the new concept. The aim was to maintain the style of the existing bottle while making changes to the position and shape of the handle and the bottom, optimising the shape and proportions of the latter, in order to be able to use lighter preforms for the blowing of bottles without altering the resistance. www.smigroup.it Still or sparkling? The choice is individual, but the essence of Santa Vittoria water does not change, because it embodies the quintessence of Alpine mineral water, that stands out for its lightness and low content of mineral salts. With a fixed residue of just 180 mg/l, Santa Vittoria water can meet everyone’s needs and is suitable even for the preparation of children’s food. PET containers that enhance purity & lightness Santa Vittoria asked SMI designers to revise the existing cylindrical bottle both aesthetically and functionally, especially for the handle section. The format on which SMI staff focused for the development of the new design is the 1.5 l bottle, from which the 0.5 l bottle is derived. Both bottles are manufactured by SMI EBS 10 KL Ergon stretch-blowmoulder and bottled by Enoberg 80-15 HEVS filler."},{"@ID":38 "36 Event review PETplanet Insider Vol. 25 No. 11/24 www.petpla.net New hot runner systems, controllers and more Mold-Masters, a well-known supplier of hot runners, controllers, auxiliary injection, and co-injection systems, showcased its latest products at Fakuma 2024. These included hot runner systems, temperature and motion controllers, an auxiliary injection unit, a gate seal, and sustainable processing solutions. The new hot runner systems include the Fusion Series G3 and the EcoOne-Series. The Fusion Series G3 hot runner system comes pre-assembled and features new enhancements to optimise mould design, simplify installation, minimise downtime, and enhance overall performance. These include system installation at room temperature; reduced nozzle bore cut-outs; compound nozzles; a heated nozzle flange; compact quick release actuators; and waterless actuators featuring passive actuator cooling technology. The system on display also featured the company’s Servo Electric Valve Gate (SeVG+) system which is claimed to provide superior process control for demanding applications. It is a servo driven actuation system that provides control and precision over individual valve pin opening and closing profiles. The SeVG+ servo motor offers a compact 114mm height that minimises stack height and simplifies mould designs. The EcoOne-Series 1-16 drop hot runner system is claimed to be an economical, standardised solution suitable for processing commodity resins for simple, cost-sensitive applications. Hot runner temperature controller and mould motion controller Also on display was the new TempMaster M4 hot runner temperature controller and the M-Ax mould motion controller. The TempMaster M4 features Mold-Masters’ new HR-Connect technology, which eliminates conventional mould thermocouple and power cables and replaces them with a single cable connecting the mould to the control head unit. Featuring a new Mold Direct Mount design, the TempMaster M4 sets a new standard for temperature controller design, says Mold-Masters. The next-generation M-Ax mould motion controller features a simplified user interface with special features, including pre-programmed mode functions and energy and torque monitoring. Energy monitoring al lows moulders to measure and track the energy consumption of their motion controls, while torque monitoring can be used for a variety of purposes as determined by the user. Auxiliary injection unit Additional products featured at the show included the company’s E-Multi product line of auxiliary injection units, which now includes the E-Multi mini. A compact, lightweight unit designed for small shot weights, the E-Multi mini is affixed to the mould and can be mounted in nearly any orientation. It also has a pivoting hopper that can move from left to right to accommodate challenging installation positions and is available with a wireless display tablet interface. Gate seal The Sprint Apex gate seal minimises flow lines, improving environmental stress crack resistance (ESCR) of CSD caps by up to 40% to support light weighting. It is also designed to enhance part quality, improve colour change by up to 65% and minimise maintenance costs by eliminating the insulation cap associated with other industry standard gate seal designs. Monitoring solution Mold-Masters SmartMold mould monitoring industry 4.0 solution now has more system connection options. There is a 4G cellular option which makes connecting to SmartMold’s cloud servers simpler and keeps the manufacturing plants network separate. In addition, the company offers a local configuration set-up where data is driven directly into the facilities own ERP and MES systems. In this local configuration the cloud servers are avoided entirely, and data does not leave the facility. Co-injection multi-layer systems The company’s various processing solutions for bio-resins and recycled materials, was also on display at the booth. For example, Mold-Masters’ co-injection multi-layer systems maximise the use of recycled content. The technology allows moulders to incorporate recycled content up to 50% of total part weight as the core layer positioned between two layers of virgin resin to maintain the aesthetic look of virgin resin. The co-injection technology is compatible with small to large packaging products and a range of other applications. Mold-Masters offers both complete system solutions and a retrofit package to convert conventional single shot injection machines to co-injection. Single stage hot runner system For the specific needs of single-stage PET bottle manufacturers looking to modernise production, Mold-Masters presented theAxiom TG hot runner system. Designed as an economical, direct replacement for outdated hot runner systems, Axiom TG integrates Mold-Masters’ proven iFlow manifold technology, along with a new nozzle design and industry-standard gate seal construction. The iFlow technology ensures homogeneous melt delivery, improving bottle consistency by minimising temperature variations and reducing defects like wall thickness inconsistencies. Additionally, Axiom TG’s new thermallycontrolled nozzle design is claimed to provide precise, repeatable processing with individual temperature control and easy on-site maintenance, broadening the system’s processing window and reliability. This system is compatible with leading injection moulding machines and can be retrofitted. www.moldmasters.com Single stage hot runner system Axiom Co-injected solutions on display"},{"@ID":21 "BOTTLE MAKING 19 PETplanet Insider Vol. 25 No. 11/24 www.petpla.net Premium-look PET for mineral water The new PET bottle for the Polish mineral water brands Staropolanka and Krystynka comes in a high-quality look based on the existing glass version. demonstrating the value of plastic. The many positive reactions and high praise for the lightness and stability of the PET bottles confirm our joint approach,” says Mariusz Musiał, Alpla Country Manager Poland. Designed for recycling Unlike the disposable glass bottle, the premium PET bottle can be used in the future Polish deposit system for beverage packaging from 2025. The Alpla team is already focusing on ‘design for recycling’ in the development phase, setting the course for future recycling. After use and return, the packaging solution can be fully recycled. The potential for the Polish circular economy is enormous, as Musiał points out: “The PET bottle already meets all the requirements and criteria to be used in bottle-tobottle-recycling. With this visionary project, we want to set an exclamation point in the beverage industry and a new standard for environmentally conscious packaging.” www.alpla.com The mineral water brands Staropolanka and Krystynka are now available in a new PET bottle that mirrors the high-quality look of their existing glass versions. Developed by Alpla, this packaging solution retains the familiar shape and feel of the glass bottle but introduces advantages in terms of weight and capacity. Weighing 32g, the PET bottle is only a sixth of the weight of the glass version, while offering more content. With 380ml of water, the plastic bottle holds a whole 50ml more with the same external dimensions. In addition, the new bottle is fully recyclable. At first glance, PET and glass bottles look like two peas in a pod. The visual similarity is intentional and was also a challenge for the Alpla development team. Step by step, the premium PET bottle for Staropolanka and Krystynka mineral water in Poland came closer to the original design. About a year after the launch, the pilot phase was successfully completed in autumn 2023. The highquality plastic bottles will soon grace the shelves of Polish supermarkets. The tried-and-tested bottle shape is claimed to guarantee high quality. It can be filled on existing lines without additional investment, says Alpla. The distinctive aluminium cap matches the bottle and complements the shape and label to ensure brand recognition. Reasons for launching the PET bottle were rising glass prices, while the reduced transport weight also contribute to significant cost savings, while a potential CO2 reduction of around two-thirds compared to glass bottles aligns with broader sustainability goals. Staropolanka offers mineral water from the spa town of Uzdrowisko Kłodzkie. Krystynka is bottled in the spa town of Uzdrowisko Ciechocinek. The mineral water brands of the two traditional spas are among the most renowned in Poland. “By launching in the premium segment, we are emphasising quality and BOTTLE MAKING"}]}}
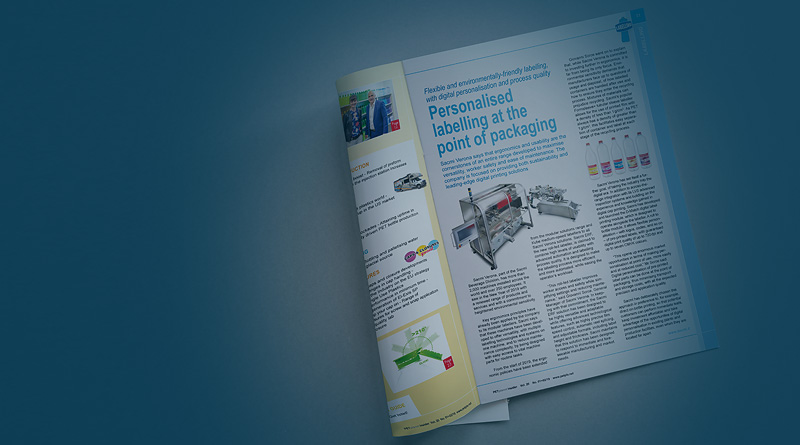