{"pages":{"page":[{"@ID":31 "BOTTLE MAKING 29 PETplanet Insider Vol. 25 No. 12/24 www.petpla.net Leading the Greek market with ketchup containers hot fi lled with Sipa’s ECS SP system Flexible hot-fill bottle production Anaplas, a Greek converter, has leveraged the power of Sipa’s ECS SP 25 machine to become the sole producer of hot-fillable ketchup containers in the Greek market. Equipped with four cavities, the machine was delivered in 2023, is now in full production, manufacturing 350ml and 520ml bottles. Anaplas not only meets local demand but also expanding its reach to neighbouring countries. In the competitive food packaging industry, the ability to produce highquality containers that meet stringent safety and performance standards is paramount. Sipa’s ECS SP ISBM machine has been designed as a versatile solution, earning recognition from prominent food industry players like Anaplas. Companies using the ECS SP system to produce hot-fillable ketchup bottles in various formats (350ml, 500ml, 1,000ml), all featuring a 38mm neck finish. These containers are specifically designed to withstand filling temperatures of 78-80 °C, ensuring both product integrity and safety. Technical features The ECS SP machine is equipped with advanced features that enhance its performance in producing hotfillable containers. One of its key attributes is its high-efficiency conditioning system, which ensures precise conditioning of preforms. This careful preparation is claimed to guarantee optimal material distribution and to The ECS SP’s flexibility allows converters to produce both hot-fill and cold-fill containers on the same machine, requiring only a mould changeover and simple adjustments to the thermo controller and air recirculation via the HMI. This translates to time and cost savings, providing converters with the agility to meet diverse customer demands. The ECS SP ISBM machine is claimed to exemplify Sipa’s commitment to providing versatile solutions for the food packaging industry. The ability to produce high-quality, hotfillable containers with a minimum of customisation, coupled with efficiency and flexibility, meets the stringent requirements of the food industry and optimises its production processes. www.sipasolutions.com enhance the strength of the resulting containers, enabling them to withstand the thermal stress associated with hot filling processes. Another feature of the machine is its electrically heated mould. This technology provides accurate temperature control during the blowing process, which prevents material degradation and ensures uniform wall thickness throughout the container. The resulting consistency in wall thickness contributes significantly to the overall strength and performance of the containers, says Sipa. Additionally, the ECS SP machine is equipped with air recirculation valves specifically designed for the blowing phase. These valves offer precise control over the blowing process, which allows for optimised material distribution. This meticulous control ensures the production of containers with consistent dimensions and robust structural integrity, meeting the high standards required for hot-fillable packaging. Hot-fill and cold-fill containers on the same machine A key differentiator of the ECS SP machine is its ability to produce hot-fillable containers with minimal customisation, using a standard machine configuration, says Sipa. This is claimed to stand in contrast to competitors who often require specialised machines for hot-fill applications, leading to increased costs and complexity for converters."},{"@ID":24 "MARKET SURVEY 22 PETplanet Insider Vol. 25 No. 12/24 www.petpla.net Company name Starlinger recycling technology Gneuss Kunststofftechnik GmbH Amut SpA Postal address Telephone number Web site address Contact name Function Direct telephone number E-Mail Furtherstrasse 47a 2564 Weissenbach, Austria +43 2674 800 3101 www.recycling.starlinger.com Mr Paul Niedl, MA Commercial Head +43 2674 800 3100 [email protected] Mönichhusen 42, 32549 Bad Oeynhausen, Germany +49 5731 5307 0 www.gneuss.com Via Cameri 16, Novara (NO), Italy +39 0321 6641 www.amut.it Mr Giovanni Cattaneo Sales Manager Director +39 0321 664943 [email protected] Frontend Sorting Section Input variable: collected pressed bottles, various colours Yes Output: sorted bottles, treated sidestreams Yes Capacity range output [t/a] Up to 150,000 Floor space [m²] Depending on design, layout Fresh water consumption per tonne output [m³/t] (if necessary) Not necessary Consumption kWh per tonne output [kWh/t] 25-55 kWh/t Grinder included When and if required Additional information Patented delabelling machine Sorting technology (NIR, laser, optical etc.), effi ciency in % From third party Washing Section Input variable: Flakes, coloured proportion max 5%, not much chlorine Yes Output: Hot washed fl akes Yes, high purity fl akes Capacity range output [t/a] From 7,000-55,000 Floor space [m²] Depending on design, layout Fresh water consumption per tonne output [m³/t] PET = 1.1 m³/t - PO 3.0 m³/t Consumption kWh per tonne output [kWh/t] 90-110 kWh/t Kind of polymer (PET, PP, PS, HD-PE, LD-PE etc.) PET, PP, HD-PE, LD-PE Additional information Patented friction washer Decontamination section Input variable: Flakes or Pellets Flake to granulate: hot-washed PET fl akes (various colours), available models: recoSTAR PET FG, recoSTAR PET FG+, recoSTAR PET art Flakes Output: Flakes or Pellets Granulate with approval, decontaminated for food contact, IV increased, AA 1ppm, lowest VOC level Pellets Capacity [t/a] 6,000-30,000 t/a rPET pellets 200-17,000 Floor space [m²] Depending on design 30-80, depending on size Approvals (FDA, Efsa, others) Several USA/FDA (C-H), Austria, Germany/BfR, Ilsi, France/AFFSSA, Finland, Australia, Canada, Egypt, Japan, Switzerland, Thailand, several Latin American countries (Bolivia, Brazil, Chile, Colombia, Ecuador, Guatemala, Peru); follows Efsa requiremens; several brand owners FDA, Efsa, Inti, brand owners (conf.) Consumption kWh per tonne output [kWh/t] Depending on design 350 Additional information Bottles to fl akes to granulate: Input variable, collected pressed bottles, various colours. Output: Granulate with approval, decontaminated for food contact, IV increased, AA 1ppm, lowest VOC level. Turn-key supply of complete plants from bottles to fl akes to rPET granulate Periphery Fresh water treatment Waste water treatment Heating systems Nitrogen generator Compressed air Chemical dosing Kind and quantity of detergents Caustic soda Yes Additives Yes Defoamer Yes Acid for neutralisation No Removal of the organic residuals up to which size [μm] Presetting residence time in the process Yes, but only continuous process, no batches Company also offers systems for Bottle-to-preform Yes Bottle-to-fi lm Yes Yes, mainly thermoforming sheet lines in direct food contact Yes Bottle-to-fi bre Yes Yes Yes Bottle-to-strapping Yes Yes No Bottle-to-tray Yes Yes Yes Tray-to-tray Yes Yes Yes"},{"@ID":16 "EDITOUR PETplanet Insider Vol. 25 No. 12/24 www.petpla.net 14 Service and sales of injection moulding systems and moulds Close to customers in the Middle East and beyond by Kay Barton The Canadian injection moulding system manufacturer Husky Technologies operates its sales and service office directly at Dubai Airport within the DAFZA (Dubai Airport Free Zone) office complex. We were able to make an appointment with the team around Mr Wassim F. Labban, Vice President, Systems & Tooling, EEMEIA, SEA, ANZ. The GM Middle East Mr Abdallah El Kharboutly, GM of Business Development Mr Philip Parubets, and Regional Manager Mr Zaher Azzam welcomed us for a brief insight into the local market and the company activities in principle, managed from this strategic hub. Interview with Husky Technologies December 8, 2023 We met: Mr Abdallah El Kharboutly, General Manager, Middle East Mr Philip Parubets, General Manager, Business Development Mr Zaher Azzam, Regional Manager, Middle East The Husky base here in Dubai has existed since 2004. Evolving from a modest start with only two employees, the machine manufacturer has grown significantly since and is currently serving as a pivotal hub in the Middle East and Africa, South and Southeast Asia, and Australia and New Zealand regions. Abdallah El Kharboutly is the General Manager of Middle East including Egypt, Turkey, the Gulf Countries and beyond. He has been with Husky since 2007 and has been instrumental in growing the business in the region. Philip Parubets has been part of the company since 2006 and brings a wealth of experience, having previously served in various technical and managerial capacities across multiple global locations. Prior to his tenure in Dubai starting in 2020, he held roles in Husky’s Shanghai and Bangkok offices as well as at the company’s global headquarters located in Bolton, Ontario, Canada. Husky is a frontrunner in injection moulding across the Middle East, but what is the secret of its success? “One key factor contributing to our success in the region is our comprehensive system offerings encompassing machines, moulds, and hot runners, all available directly from us without intermediary agents,” says Mr El Kharboutly. “Moreover, our commitment to innovation drives the continuous introduction of new solutions for preform and cap production, coupled with the proactive approach of our Advantage+Elite remote, proactive monitoring program, wherein we analyse real-time equipment performance and efficiency, promptly addressing any potential risks or concerns,” he adds. And there are also many legacy Husky systems in the market that are still running and being maintained by the local service teams, which is clearly being well received by customers. In the local UAE market, the company estimates that its own market share for preform systems is around 80% in the high-output space, with the rest being accounted for by machines from competitors Netstal and Sipa. In the UAE, there is approximately 160 kt of Husky PET processing capacity. Mr El Kharboutly anticipates an annual addition of 8 to 12 kt of additional capacity is being added to the market each year. The bestseller for preforms in the UAE is the HyPET HPP platform and for closures the HyCAP 4. The growth rate of Husky’s throughput capacity in the Middle East region has averaged 6.5% CAGR annually over the last ten years, while the PET preform unit has grown by an average of 6.2%. Due to the Covid situation, investment in new capacity fell significantly for the entire region in 2020 and 2021, but has since recovered, particularly evident in good investment growth in 2023. www.husky.co EDITOUR Interview meeting with Abdallah El Kharboutly (left), Philip Parubets (right) and Kay Barton"},{"@ID":38 "EDITOUR 13 PETplanet Insider Vol. 25 As Saudi Arabia is gradually opening up to international tourism and the annual Umrah and Hajj season, further growth is expected for water and soft drinks closures, whereas growth in the lubricating oil sector is expected to be limited and demand is likely to decline with the trend towards synthetic oils. “In recent years, a localisation process has been initiated in the foods, personal care and household goods industries at critical times,” said Mr Löffler. “Demand for these products has increased significantly and is expected to continue to grow.” Topics such as tethered caps have not yet been prioritised in local requirements, while areas such as shortneck and lightweight preforms are omnipresent, especially for margin-limited products such as water. On the other hand, higher closures that are easy to open with grip are being prioritised in certain areas. And what does the near future hold for SCCL? “We will be making investments this year to launch new closures for the food and water markets and new process equipment for labelling closures, particularly for the lubricating oil sector, We will also invest in Anti-Counterfeiting technologies, in order to protect both the product and the brands of our customers” commented Mr Alireza. “As a joint venture partner of Bericap, we can principally offer closures that meet the latest standards and environmental trends.” www.saudican.com.sa www.bericap.com The 1-pc ClipAside tethered closure with 72 knurls is equipped with an olive bore seal and provides a tight seal for PET oneway bottles with 29/25 neck finish."},{"@ID":35 "PETplanet Insider Vol. 25 No. 0/24 www.petpla.net 33 BOTTLES Christmas bath additives from tetesept Just in time for the start of the cold season and the approach of Christmas, the German company Merz Consumer Care GmbH has launched suitable bath add i t i ves under the tetesept brand on the shelves. Each of the 420ml of the nourishing additives, which smell of orange oil and cinnamon - called Winter Warmth - or winter punch and baked apple - called Bath Indulgence - are filled in white bottles with sleeve labels. The labels are designed accordingly and a shiny gold screw cap completes the look of the packaging. www.tetesept.de Loyalty size of Fairy Procter & Gamble sells its Fairy dishwashing detergent concentrate, which is designed to clean effect ively even in colder water, in a 600ml bottle advert ised under the name ‘Loyalty Size’. The concentrate is dispensed via a one-handed hinged lid cap with a dosing opening. The hinge remains fixed in the ‘open’ position and does not interfere with dispensing the contents. Several labels communicate the trade data and clearly indicate the cleaning effect against grease and in colder water. www.for-me-online.de"},{"@ID":25 "MARKET SURVEY 23 PETplanet Insider Vol. 25 No. 12/24 www.petpla.net Erema Engineering Recycling Maschinen und Anlagen Ges.m.b.H. Boretech Environmental Engineering Co.,Ltd. Sorema Div. of Previero N. SRL Unterfeldstraße 3, 4052 Ansfelden, Austria +43 732 3190 0 www.erema.com Mr Christoph Wöss Business Development Manager, Application Bottle +43 732 3190 0 [email protected] No.888, Jiuliting Avenue, Caoqiao Street, Pinghu, Zhejiang, China +86 573 85120 186 www.bo-re-tech.com Mr Alan Ou Vice General Manager +86 573 85136 190 [email protected], [email protected] Via per Cavolto, 17, 22040 Anzano del Parco (CO), Italy +39 031 63491250 www.sorema.it Mr Dario Previero General Manager +39 031 63491250 [email protected] Yes, sorting done in cooperation with long-time partners or Keycycle (Erema Group) Pre-sorted PET bottles, preferable bales Mixed loose plastics Selective & deposit collection, from blacks bags or landfi ll bottle collection Sorted bottles, colour sorting possible Sorted plastic bales Pre-sorting section with prewashing, delabelling, metal separation, fi lm separation, material and colour sorting Depending on customer requirements 5,000-10,000 Up to 20t/h Depending on the capacity of the plant 1,000-20,000 Depending on customer, multi level tower sorting line available Minimised, according to input material & water treatment design ~100 Minimised, according to input material & water treatment design Yes, by Keycycle No Yes Engineering and integration services, turnkey projects. Contact: Keycycle GmbH (Erema Group GmbH), Mr Michal Prochazka, Managing Director, +43 732 3190 545, [email protected] No Prewashing delabeller to remove lables and clean the materials before sorters Up to 99 % purity Depends on vendor's effi ciency (approx. 90 - 95%) Best technology available according to input material and output targets Pre-treated PET bottles, preferable in pressed form Collected pressed bottles, fl akes, various colours Flakes, ground from bottles pre-sorted Dried fl akes mositure content 1 % Hot washed clear fl akes Up to 10t/h 12,000-52,000 t/a 18,000-36,000-54,000 Up to 10t/h Depending on the capacity of the plant, Keycycle Depeding on design, 1,500-35,000 Depending on customer, multi level and tower washing line available Depending on contamination level approx. 1 - 2 m³/h ~1.5 Minimised, according to input material & water treatment design 150-350kWh/t ~140-190 Minimised, according to input material & water treatment design All types of common polymers possible, Keycycle PET / HDPE / LDPE/ PP / PS / ABS / PA Washing line with multiple material available: PET, PP, PS, HDPE, LDPE… System solutions for washing and drying; Lindner Washtech, Member of Erema Group GmbH; Marcel Willberg, Sales Director, +49 7148 160538-0, [email protected] State of the art washing system, full automatic for fl akes for the most demanding application Flakes and/or pellets Flakes, coloured proportion max 5%, not much chlorine Integrate sub supplier technology including decontamination section Flakes (MPR) or pellets (Vacurema or Vacunite) Upgrade fl akes or pellets According to production & supplier specifi cation Up to 48,000 8,000-40,000 According to production & supplier specifi cation Depending on through-put and technology: 50-650 300-1,500, depeding on design According to production & supplier specifi cation FDA (cat. A-H&J); Efsa (positive Efsa opinion issued); brand owners (conf.); several national approvals (Austria, CH, Zona Mercursur, etc.) Flakes and granulates with FDA approval According to production & supplier specifi cation Between 100-350 100~310 According to production & supplier specifi cation Closed loop system for water and N2, depending on application & technology type Turn key lines available on request Oon request, with external partner or Keycycle Yes, depending on design Sorema design & built water treatment Oon request, with external partner or Keycycle Yes, depending on design Sorema design & built water treatment Included Pelletising & SSP: 98kWh Sorema design & integrated heating system based on steam, electrical, cogeneration and other technologies On request Pelletising & SSP: 10-15Nm³ Integrated in case of turn key line On request Pelletising & SSP: 5m³ Integrated in case of turn key line On request NaOH (2-3kg/t output), and brand detergent (1-1.5 l/t output) Sorema design and built chemical dosing systems Chemicals use is strictly confi dential Yes for washing process, Keycycle Yes, 2-3kg/t output Yes for washing process, Keycycle CHT, 1-3 l/t fl akes output Yes for washing process, Keycycle Yes, depending on customer demand and process Yes for washing process, Keycycle Yes, 5-10 l/h, depeding on bottle bales condition 25 μm Water fi ltration up to 1 μm State of the art washing system to grant the minimum surface organic residue 1.5-15h IV 0.70→ 0.86dL/g, SSP 12-16h for pellets, 4-6h for fl akes The system is easy to set in all its parameter including the residence time in the hot washing Yes, Vacurema Inline Preform Yes, Vacurema Inline Sheet Yes, Vacurema Inline Fibre for Staple Fibre, BCF and POY Yes, one stop solution from post-consumer bottles to PSF, POY and FDY Yes, Vacurema Inline Strapping or Monofi lament Yes, with Keycycle & Vacurema Yes Yes, with Vacurema Yes"},{"@ID":42 "MATERIALS / RECYCLING PETplanet Insider Vol. 25 No. 12/24 www.petpla.net 26 Fractal graphene enhances PET bottles’ performance and sustainability And a pinch of graphene HydroGraph Clean Power Inc., a leader in sustainable commercial manufacturer of graphene, has developed Fractal Graphene powder (FGA-1), which aims to improve the performance and sustainability of PET bottles at an ultra-low loading. Tests conducted at the Graphene Engineering Innovation Centre (GEIC) in Manchester, UK, have demonstrated that HydroGraph’s FGA-1 enhances PET bottle performance with a remarkably low graphene loading of just 0.006 wt% which could lead to lightweighting and an overall reduction in plastic use. “These performance gains in PET arrive at a critical moment for the packaging industry,” said Kjirstin Breure, interim CEO and president at HydroGraph. “As manufacturers struggle with the challenge of increasing recycled content while managing costs and maintaining performance, our technology offers a solution that addresses these needs simultaneously. By enabling significant material reduction while improving performance with recycled content, we’re helping the industry meet environmental mandates without compromising product competitiveness.” When applied to a 50:50 blend of virgin PET and rPET, the technology is claimed to deliver a 23% improvement in top-load compressive strength, potential weight reduction of approximately 20% as well as an 83% decrease in water vapour transmission rate. Addressing industry pressures for sustainability According to Mordor Intelligence, the PET bottle industry produces more than 500 billion bottles annually, equivalent to 25 million tons of PET. Increasingly stringent regulations worldwide now require higher recycled content in plastic packaging. Besides the EU Directive 2019/904 on Single-Use Plastics which mandates that PET beverage bottles must contain at least 25% recycled content by 2025 and 30% by 2030, the UK Plastic Packaging Tax imposes penalties on packaging with less than 30% recycled content. In California, Assembly Bill 793 requires that beverage bottles contain a post-consumer recycled content of 15%, increasing to 25% in 2025 and 50% in 2030 and multiple other US states, including Washington, New Jersey, and Maine, have implemented or announced recycled content mandates while Canada’s Zero Plastic Waste Agenda targets 50% recycled content by 2030. Global legislation is increasingly demanding higher recycled content in plastic packaging, posing significant challenges for manufacturers. Yet, recycled PET can cost 20-30% more than virgin PET, and global supply remains limited. “Manufacturers are at a crossroads when it comes to the development of plastic packaging,” said Breure. “Given previous success we’ve seen with our graphene technology, we responded to the mounting pressure for increased sustainability and lightweighting by researching ways fractal graphene can benefit the material. We’re proud of what we’ve accomplished so far, and we’re excited to see what other breakthroughs are on the horizon as we continue our extensive research of nanomaterial technology.” Possible global impact If widely adopted, HydroGraph estimates that its FGA-1 technology could reduce plastic usage by up to 5million t/a—about 20% of current global PET bottle consumption. In an ideal scenario where FGA-1 technology is fully commercialised with PET:rPET blends of 50:50, the emissions reduction from using 20% less overall PET in bottles could represent a reduction of more than 8 million tonnes of CO2. www.hydrograph.com MATERIALS / RECYCLING"},{"@ID":43 "41 PETplanet Insider Vol. 25 No. 12/24 www.petpla.net BUYERS GUIDE Contact us Ask for your individual offer – call +49-6221-65108-0 or mail to [email protected] 1 Line = 3,2 mm Example: 1,888.– EUR/year PETplanet Insider Hubweg 15 74939 Zuzenhausen, Germany Tel. +49-6221-65108-0 Fax +49-6221-65108-28 [email protected] www.petpla.net 32 mm 6.3 Line Conversion Packaging and Preform Engineering, Moulds and Line Conversion Tel: +33 (0)5 45 36 63 50 [email protected] [email protected] 7.0 USED MACHINERY T +44 (0) 1254 584210 T +34 676 986962 (SPAIN) E [email protected] www.petmachinery.com 6.2 Design and Prototyping Locations in the US and Europe [email protected] [email protected] www.pti-usa.com Bottle and preform engineering rPET flakes and Hot fill solutions Training on Blow Moulding technologies (ISBM, SBM, EBM) www.gs4plastic.com BUYER´S GUIDE ENTRY - Print & Online Pricing Example: Placement in 10 issues plus online banner Pricing height (mm) x 5.90EUR x 10 Example 32mm = 1,888.00EUR/year Who’s Who in the PET market Stay permanently listed! Online in the corresponding news category and in the magazine’s Buyer’s Guide with your company logo and contact information."},{"@ID":13 "EDITOUR PETplanet Insider Vol. 25 No. 12/24 www.petpla.net 11 EDITOUR 11 The recyclate, around 90% of which ends up back in packaging such as PET bottles, is sold worldwide. Customers include Pepsi, Niagara, Nestlé, Coca-Cola, Retal and Alpla. The remaining material ends up in non-food applications, such as at Henkel or L’Oréal. “Our main markets are the EU and USA with over 90% exports,” explained Mr Fattah. “The rest remains in the Middle East and Egypt, where rPET is still in its infancy in bottle production. At present, recycled material in contact with food is still often perceived by the population as contaminated and therefore anything but positive. But awareness of this is gradually changing, so that we are slowly but surely seeing positive signals in the handling of recycled PET. We would like to contribute to recycling processes and the circular economy for plastics being perceived as a kind of ‘social plastic.” The company is currently building another plant in Jeddah, Saudi Arabia, which is expected to be completed in early 2025. An Erema Vacurema Prime will be used there together with an initial annual capacity of 15,000 t before plans are made to increase this to 55,000 t in the medium term, as in Egypt. www.bariq-eg.com Production Engineer Abdul Rahman (back) shows Editor Kay Barton the recycling stations at the plant All areas at Bariq are clearly marked Shall we? %X 7%'1- TEVXRIVWLMT MW JSVIZIV Choose everlasting excellence for your tethered cap production plant. With SACMI ]SYƅPP ƼRH E JYXYVI VIEH] WSPYXMSR XLEXƅW designed to stand the test of time. sacmi.com E N D L E S S I N N O V A T I O N S I N C E 1 9 1 9"},{"@ID":7 "MATERIALS / RECYCLING PETplanet Insider Vol. 25 No. 12/24 www.petpla.net 17 advancements, bio-based feedstocks and materials can contribute to a more sustainable future without compromising food security or ecosystems. PETplanet: How significant do you see the role of government policy in supporting the adoption of PEF? Dr Puente: Government policy plays a crucial role in supporting the adoption of PEF by setting clear regulations and incentives that promote sustainability. Policies that encourage the use of bio-based and recyclable materials such as regulations on eco-design and product standards, extended producer responsibility (EPR) schemes, and stricter recycling and renewable carbon content targets for materials can accelerate PEF’s market penetration. PETplanet: Thank you very much! www.nova-institute.eu PEFerence receives funding from the Bio-based Industries Joint Undertaking (JU) under the European Union’s Horizon 2020 research and innovation programme. The JU receives support from the European Union’s Horizon 2020 research and innovation programme and the Bio-based Industries Consortium. www.peference.eu"},{"@ID":45 "The worldwide round trip with PET world in the Middle East In a spectacular project taking us well into 2024, we will be travelling in a wide variety of ways to various countries and regions of the Middle East with different mobile editors. There we will interview machine manufacturers, the supply industry, bottle and beverage producers, as well as PET recyclers and everyone involved in the process chain. What market-specific trends are there now or will arise in the future? What developments and technologies are in vogue on the consumer and plant construction site in some of the hottest regions of the world? What special requirements are there? What role do topics such as food safety, shelf life and sustainability play in PET packaging and how are companies preparing themselves for the coming years? This, and much more we will be discussing face-to-face with all the key players and then our results will be presented to you in a series of must-read reports in PETplanet Insider. Please join on this enchanting voyage to the world of PET in the Middle East. We look forward to welcoming you on board! Our previous Road Shows at a glance 2010-2011-2012-2013-2014-20152016-2017-2018-2019-2020-2022 Interested in being visited? [email protected] Autumn 2023 - 2024 6 countries numerous interviews with PET companies Sponsors to date Editour The Middle East Roadshow"},{"@ID":3 "No.12 2024 www.petpla.net D 51178; ISSN: 1438-9452 09 . 12 . 24 M A G A Z I N E F O R B O T T L E R S A N D B O T T L E - M A K E R S I N T H E A M E R I C A S , A S I A , E U R O P E A N D A L L A R O U N D T H E P L A N E T PETplanet is read in 159 countries Suppliers of recycling plants and washing units MARKETsurvey MATERIALS / RECYCLING EDITOUR Page 15 Page 9 Page 21"},{"@ID":1 "imprint EDITORIAL PUBLISHER Alexander Büchler, Managing Director HEAD OFFICE heidelberg business media GmbH Hubweg 15 74939 Zuzenhausen, Germany phone: +49 6221-65108-0 [email protected] EDITORIAL Kay Barton Heike Fischer Gabriele Kosmehl Michael Maruschke Ruari McCallion Anthony Withers Editorial & WikiPETia. info [email protected] MEDIA CONSULTANTS Martina Hirschmann [email protected] Johann Lange-Brock [email protected] phone: +49 6221-65108-0 LAYOUT AND PREPRESS EXPRIM Werbeagentur Matthias Gaumann www.exprim.de READER SERVICES [email protected] PRINT Chroma Druck Eine Unternehmung der Limberg-Druck GmbH Danziger Platz 6 67059 Ludwigshafen, Germany WWW www.hbmedia.net | www.petpla.net PETplanet Insider ISSN 1438-9459 is published 10 times a year. This publication is sent to qualified subscribers (1-year subscription 149 EUR, 2-year subscription 289 EUR, Young professionals’ subscription 99 EUR. Magazines will be dispatched to you by airmail). Not to be reproduced in any form without permission from the publisher. Note: The fact that product names may not be identified as trademarks is not an indication that such names are not registered trademarks. 3 PETplanet Insider Vol. 25 No. 12/24 www.petpla.net Acetaldehyde in PET bottles: an unsolved problem? Acetaldehyde (AA) has been classified as carcinogenic by the World Health Organisation, although the human body produces small amounts of this molecule itself. Nevertheless, its presence in our environment is an issue that cannot be ignored. AA is found in relatively high concentrations in spirits in particular, such as liqueur wines - sherry or port wine. Its fruity flavour is even appreciated there, especially in sweet wines. However, AA is much less welcome in PET bottles, especially when bottling flavour-sensitive liquids such as water. The PET industry has been working for years to reduce the acetaldehyde content in bottles to a level that is not perceptible in terms of flavour. Numerous technological improvements have been developed and implemented for this purpose: from optimised plasticising processes and advanced hot runner systems in the preform injection moulding process to special AA-reduced virgin PET materials. Additives, so-called blockers, which bind the acetaldehyde in the bottle, were also introduced. These measures have led to considerable progress in the past, and for a long time the issue seemed largely resolved. Personally, I had the impression that the problem was under control in most markets - until I travelled through the Gulf States recently. In this region, where extreme temperatures of up to 45 degrees Celsius are not uncommon, I repeatedly encountered complaints about the bland taste of PET water bottles. Despite state-of-the-art plant technology, the use of so-called ‘water grade’ PET materials and the implementation of all known AA reduction methods, consumers repeatedly report flavour impairments. A local manufacturer told me in an interview: “We have found that this is the case with many water brands on the market.” To illustrate this, he handed me a bottle of water from a competitor - and indeed, the flavour was unpleasant. “As long as we have control over the storage of the bottles, everything is fine. But we can’t prevent consumers from storing the bottles in the blazing sun, for example.” Extreme conditions such as direct sunlight at high temperatures seem to push previous technical solutions to their limits. Despite intensive efforts by the industry - from the development of innovative materials to the improvement of logistical processes - the problem persists. The challenge of keeping the flavour of water in PET bottles stable even under extreme conditions is still unresolved. It remains to be seen what new approaches the industry will find to tackle this issue in the long term. Yours, Alexander Büchler Dear readers,"},{"@ID":33 "EVENT REVIEW PETplanet Insider Vol. 25 No. 12/24 www.petpla.net 31 Coperion and Herbold Meckesheim host two-day recycling conference Experience a new dimension of plastics recycling Over 180 participants from 25 nations accepted the invitation from Coperion and Herbold Meckesheim to attend the Recycling Days in the newly opened Recycling Innovation Center in Weingarten, Germany, on November 6 and 7, 2024. In keeping with the theme of “Experience A New Dimension of Plastics Recycling,” the two-day conference featured a variety of presentations and live demonstrations, allowing participants to gain insights into various technologies designed to enhance the efficiency of the plastics recycling process. Internal and external experts from the industry, including researchers, shared insights on how the right equipment can save resources and costs without compromising the quality of the recycled compound. Practical examples from successful recycling plants also significantly enhanced understanding of the topic. Achim Ebel, Head of Sales at Herbold Meckesheim, and Kürşat Başdemir, Company’s Founder and Project Director at Ekosistem Ltd., presented the latest advancements in Herbold washing lines, focusing on the impact of water treatment on the quality of the recycled compound. Martin Müller, CEO at Polymetrix, and Sabine Schönfeld, Sales Manager at Coperion, gave a joint presentation on a bottle-tobottle recycling plant. This system of Indian preform and plastic packaging manufacturer Magpet Polymer Pvt Ltd. produces rPET granulate approved for direct food contact by both the European Food Safety Administration (EFSA) and the U.S. Food and Drug Administration (FDA). Furthermore, it is brand owner approved. Spotlight on extrusion Coperion leaders Frank Mack, Head of Process Technology Engineering Plastics, and Jochen Schofer, Head of Sales Recycling, presented a lecture on the range of possible extruder types for plastics recycling, demonstrating how the choice of extruder technology can impact both the overall process efficiency as well as end product quality. Live demonstrations On both days of the conference, guests could witness the newest developments in action during live demonstrations in the Recycling Innovation Center. The added value of individual technologies was demonstrated on running systems, along with their impacts on the entire recycling process. Attendees had the opportunity to see the benefits of Coperion’s twin-screw extruders’ self-cleaning screw profiles and mixing properties by observing an STS 25 twin-screw extruder in operation. Fillers and reinforcing materials were added to the recyclate in varying quantities, demonstrating how quickly recipe changes can be implemented on Coperion extruders without cleaning effort or product loss. www.herbold.com www.coperion.com"},{"@ID":39 "An endless range of production possibilities with single-stage SIPA S.p.A. - Via Caduti del Lavoro, 3 - 31029 Vittorio Veneto (TV) - Italy - Tel. +39 0438 91151 VLSD#]Rppas.com - www.sipa.it ECS SP models stand for a guarantee of quality based on 35 years of experience in Injection Stretch-Blow Molding technologies (ISBM) technology. Their robust system, produced in Italy, allows for the production of high quality containers in a wide variety of different sizes, threads and shapes. Tooling investment can often be optimized by using one single (i.e. shared) hot runner withmultiple cold halves. ECS SPmachines have features that enable quick change-overs, accept legacy molds and are also characterized by their compact layouts and high HQHUJ\\ HIĆFLHQF\\. Injection Stretch BlowMolding System"},{"@ID":6 "PETcontents 4 PETplanet Insider Vol. 25 No. 12/24 www.petpla.net 12/2024 EDITOUR 9 Converter for water preforms and closures reaches out to Africa 10 Bottle-to-bottle recycling in Egypt - rPET pioneer from the Greater Cairo region focuses on huge capacity expansion 12 German joint venture closures in Saudi Arabia - How the growing demand for beverage, food and non-food products is being met in Jeddah 14 Close to customers in the Middle East and beyond - Service and sales of injection moulding systems and moulds MATERIALS / RECYCLING 15 PEF: A bio-based alternative to PET with lower environmental impact 18 UV protection additive for rPET packaging 20 Turning dairy PET bottle-to-bottle recycling into reality 24 Material and long-term properties in recyclates 26 And a pinch of graphene - Fractal graphene enhances PET bottles’ performance and sustainability 27 Meeting the needs of an ever-evolving sector 28 High-quality rPET granules from mixed streams - Mission PET and Next Generation Recycling GmbH collaborate on LSP PET recycling in food and non-food applications MARKET SURVEY 21 Suppliers of recycling plants and washing units BOTTLE MAKING 29 Flexible hot-fill bottle production - Leading the Greek market with ketchup containers hot filled with Sipa’s ECS SP system 30 Environmentally friendly packaging for the pharmaceutical industry - Italian company focuses on special sustainability strategy EVENT REVIEW 31 Experience a new dimension of plastics recycling - Coperion and Herbold Meckesheim host two-day recycling conference OUTER PLANET 42 Renewable carbon feedstocks - Building a net-zero chemical industry in 2050 BUYER’S GUIDE 36 Get listed! INSIDE TRACK 3 Editorial 4 Contents 6 News 32 PET bottles for home + personal care 34 On site EDITOUR Page 10 Page 29 Page 18 MATERIALS / RECYCLING"},{"@ID":14 "EDITOUR PETplanet Insider Vol. 25 No. 12/24 www.petpla.net 12 How the growing demand for beverage, food and non-food products is being met in Jeddah German joint venture closures in Saudi Arabia by Kay Barton In the well-known holiday area of Jeddah, on the west coast of Saudi Arabia, the Saudi Can Company produces cans and plastic containers for food and non-food segments, such as lubricating oils, home and personal care applications. Founded in 1979 as a manufacturer of three-piece printed lubricating oil cans, the company has undergone a steady transformation in recent years to become a supplier of packaging of all kinds. Interview with Saudi Can Closure Ltd (SCCL) April 29, 2024 A long-standing business relationship with closure manufacturer Bericap eventually led to a joint venture to meet market demand through local closure production. We spoke with Mr Muntasir Alireza, Chairman of Saudi Can Closures Co. Ltd, and Mr Peter Loffler, Operations Manager and the General Manager of Saudi Can Closures Ltd, at the Middle East Road Show about the milestones and strategy that led to the current success. According to Muntasir Alireza, the idea for the joint venture arose from the growing demand in Saudi Arabia for beverage and lubricating oil closures. The Saudi Can Company had already been purchasing closures and caps from Bericap in Germany for many years and so the company finally decided to intensify the collaboration and promote Bericap closures on the market through local production and to be able to offer customised closure designs. The result was SCCL, which is now managed by an international team. He explained: “We are now targeting a market that requires closures for water, soft drinks, lubricants, personal care, household and industrial uses, as well as food segment. Saudi Can Co. initially provided an area within its facility, which allowed for a shorter ramp-up time for production. The initial production started with three injection moulding machines as well as a cutting and printing machine.” Production initially began with the manufacture of soft drink closures, which was switched to the production of water closures due to lower demand, and significant growth potential in the water segment. A short time later, additional machines to produce new water, lubricating oil and customised closures found their way into the plant. “The market for water closures has undergone several changes over the years,” said Mr Löffler. “Initial production met the demand for 28mm closures, followed by 30/25 closures. The last change to weight-reduced 29/11 closures dates back to 2014. And recently a high-grip version of 29/11 closure has been introduced” At the end of 2017, SCCL began building a separate and future-proof site of 10,000m2, as the space available at the Saudi Can Company had been exhausted by the constant expansion. In 2022, all relevant closure production lines were finally relocated to the new site and the portfolio was expanded considerably. The company now has 85 employees. “SCCL can offer available cap designs via Bericap and, if necessary, develop new cap designs,” Peter Löffler explained further. Depending on customer requirements and application, the necessary moulds are procured from Bericap in Europe or other regions. The majority of the closures remain in Saudi Arabia, while the rest are distributed in the GCC region, via Bericap Middle East established in UAE. The annual output is over one billion closures and, as we learned, the total material input in 2023 was just under 3,500 t of HDPE and PP. The customer base in all business sectors includes a good mix of global players as well as local leading brands. Commenting on trends and markets with particular potential, Mr Löffler said: “We are seeing very good growth in the food segment, edible oil, personal care and household chemicals segments. The local market is the largest in the region with high growth opportunities and is therefore our target area.” F.l.t.r.: Mr Peter Loeffler, GM of Saudi Can Closures Ltd. and Mr Muntasir Alireza, Chairman of Saudi Can Closures Ltd. EDITOUR"},{"@ID":21 "The U2023X dosing unit The Remap UV absorber range provides several grades that cover different protection specifications set by final product needs. MATERIALS / RECYCLING PETplanet Insider Vol. 25 No. 12/24 www.petpla.net 19 real-time monitoring of UV protection and opacity in PET preforms. By correlating light intensity with additive content, it ensures consistency and provides a reliable alternative to manual inspection. These innovations reflect an ongoing dedication to enhancing performance, sustainability, and user-friendliness in the plastics industry, says Repi. www.repi.com viscoZERO – processing PP, PE, PET & PS! ZERO contamination. ZERO odour. ZERO limits. foodgrade without compromise viscoZERO Upgrade your existing recycling plant with viscoZERO technology."},{"@ID":8 "6 NEWS PETplanet Insider Vol. 25 No. 12/24 www.petpla.net Husky’s PET closure wins Packaging Europe Sustainability Award Husky Technologies, a technology provider enabling the delivery of essential needs to the global community, announces that its PET closure has won the Packaging Europe Sustainability Award in the Driving Circular Economy category. This award, presented at the Sustainable Packaging Summit that took place in Amsterdam on November 12, reflects Husky’s commitment to enabling true circularity in the beverage packaging industry. In a market traditionally dominated by two-material bottleand-closure solutions, Husky’s PET closure aims to transform industry standards. By creating a fully PET-based monomaterial solution that integrates seamlessly with existing PET recycling streams, Husky is streamlining the material sorting process, reducing environmental impact, and unlocking new efficiencies in recycling and lightweighting. “At Husky, our commitment to enabling the packaging industry to transition from a linear to a circular economy is taken seriously. Winning the Packaging Europe Sustainability Award for our PET closure reflects this commitment to delivering innovative, sustainable solutions that meet global demands for more circular packaging,” said Robert Domodossola, Husky’s President of Systems and Tooling. “Our PET closure is designed to advance the recyclability and functionality of beverage packaging by providing a mono-material solution that represents a significant step forward for the industry and consumers alike.” Unveiled earlier this year at NPE 2024 in Orlando, Florida, Husky’s PET closure has already garnered strong industry support, with select early adopters preparing for commercial production in 2025. www.husky.co PETnews ? SEE HOW MUCH YOU CAN SAVE 70% LESS ENERGY MAINTENANCE COSTS 90% LESS 70% REDUCTION IN CO2e 50% MORE PRODUCTIVITY The savings will vary based on your circumstances and should be reviewed with our sales team. [email protected] www.maguire.com Discover your potential savings. With just a few clicks, you’ll gain valuable insight into how ULTRA will positively impact your bottom line. 1. Go to ultra.maguire.com 2. Input your data. 3. Receive your customized PDF report of potential savings via email. 7 R"},{"@ID":29 "MATERIALS / RECYCLING PETplanet Insider Vol. 25 No. 12/24 www.petpla.net 27 Meeting the needs of an ever-evolving sector PET Solutions, which is part of the Pegaso Industries group, provides advanced technologies for the PET and rPET industry. It states that its range of products, including dryers, hoppers, dosing units, mould dryers, and conveyor belts, offer efficient, sustainable recycling solutions. The combination of advanced technologies, such as the DRV continuous vacuum dryers, precision gravimetric dosing units, and efficient recycling lines, provides companies in the sector with essential tools to optimise processes and ensure high product quality, says PET Solutions. Dryers The company’s latest, patented, dryer model, the DRV continuous vacuum dryer series, has been developed to optimise production processes when handling recycled PET. It has been designed for simpler maintenance and with a much faster product switching – the company claims a 66% reduction in material changeover time. Its improved efficiency, maintenance and operation are achieved by a design that eliminates residual contaminants from recycled plastic without the need for an oil condenser. Moisture is removed through a dedicated vacuum pump, so molecular sieves are not required. Hoppers The maintenance of constant temperature and uniform flow of resins to the production process are essential for quality output. PET Solutions hoppers’ thermal insulation reduces energy consumption and improves process stability. Their modular designs make them adaptable to different production needs and the construction materials have been selected to make the machines sturdy and durable. Dosing units PET Solutions offers gravimetric and volumetric dosing units that enable the accurate mixing of multiple materials. The DGB gravimetric dosing unit series can manage up to eight materials simultaneously, along with uniform mixing and constant process monitoring. Dosing precision is maintained at high levels thanks to dual load cells and automatic process control reduces scope for human error. The DGB series can be easily integrated with existing automation systems. Mould dryers The DSH series can keep moulds dry even in high humidity environments, helping to prevent condensation formation and thus reducing surface defects. Advanced refrigeration technology improves efficiency, delivering energy savings of up to 66%, compared to rotor technology. Conveyor belts and soft drop PET Solutions has developed a line of Soft Drop machines, which are designed to gently deposit preforms from the press into storage boxes, preserving their physical and aesthetic integrity while delivering preforms to the conveyor systems. Their modular design means they can be adapted to a wide range of plants, while their high efficiency motors reduce energy consumption – and therefore save costs – and wear-resistant materials used in construction offer durability. Recycling lines PET Solutions has developed a range of recycling lines and solutions for processing PET waste, enabling the reuse of material for production of high-quality recycled PET, ready for use. The company says that the lines offer high recycling systems and efficient waste management, with advanced filtration systems that ensure purity in recycled PET. They are designed to make a significant contribution to waste reduction and towards the development of the circular economy. PET Solutions continues to invest in research and development to meet new market challenges, capable of anticipating the needs of an everevolving sector. www.petsolutions.it MATERIALS / RECYCLING"},{"@ID":11 "EDITOUR PETplanet Insider Vol. 25 No. 12/24 www.petpla.net 9 Converter for water preforms and closures reaches out to Africa by Alexander Büchler Oman Industrial Investment Co. (OIIC), strategically located near Salalah port, southern Oman, stands out as a principal manufacturer in the PET preform and HDPE cap and handle. A key entity of Al-Mehdar Group, OIIC was founded by Mr Mohsen Ali Al-Mehdar, the Chairman. The company significantly expanded its capabilities five years ago post the acquisition of a major converter. OIIC’s product range encompasses preforms with 29/25 and 30/25 neck sizes, available in various sizes and colours, specifically tailored for water applications. EDITOUR F.l.t.r.: Shaik Mynuddin, Dr Omar Mohammed Bashatahil, Alexander Büchler and the Production Manager The company’s commitment to quality is underscored by its adherence to low acetaldehyde PET production, aligning with its FSSC 22000 and ISO 9001 certifications. Under the leadership of CEO Eng. Omar Mohammed Basharahil, OIIC has made remarkable advancements, increasing its production capacity by 350% within five years. This expansion has positioned the company as the largest PET converter in Oman, boasting a robust production capability and a diverse product portfolio. In the previous year, 75% of OIIC’s production was exported, highlighting its strong international market presence and competitive edge in the PET manufacturing industry. A landmark achievement in 2022 was OIIC’s evolution into a multi-national company with the establishment of several branches in Yemen and Africa, enhancing customer proximity and engagement. Pioneering sustainability and cost-efficiency, OIIC has achieved a reduction in preform weights, producing 250ml bottle preforms at 7.8 g and 500ml bottle preforms at 11.5 g, marking a first in its markets for these lower grammage sizes. To enhance production capabilities, OIIC has invested in cutting-edge technology, employing the Husky HyPET 300 system with 96 cavities, and the Sipa Xform 250 t preform system. These systems facilitate efficient handling of preform weights ranging from 7.8 g to 28 g with cycle times as low as 6.7 s, all while maintaining strict acetaldehyde content limits. Furthermore, OIIC has integrated the latest Sacmi machines for HDPE closures, specifically serving packaged drinking water companies. Mr Shaik Mynuddin, the Plant Manager, with over 25 years of industry experience, plays a vital role in maintaining production efficiency and quality. He leads a skilled technical team, dedicated to upholding high standards and ensuring customer satisfaction. OIIC is poised for further expansion, actively planning to diversify its product portfolio and enhance its regional market presence. A new, larger production hall is underway to address the growing demand for carbonated soft drink (CSD) preforms and closures. Additionally, the company plans to produce labels, offering a comprehensive packaging solution to its clients."},{"@ID":37 "PATENTS PETpatents www.verpackungspatente.de PETplanet Insider Vol. 25 No. 12/24 www.petpla.net 35 Embossed label Disclosure no. DE 102022122887 A1 Applicant: Krones AG, Neutraubling (DE) Application date: 8.9.2022 The disclosure proposes to integrate embossing into the bottle when producing a bottle from a preform, which makes an additional label superfluous. Additional grooves ensure improved stability. Coated bottle base Utility model no.: DE 202023107228 A1 Applicant: Alpla Alwin Lehner GmbH & Co. KG, Hard (AT) Application date: 6.12.2023 Stretch-blown reusable container with an outer coating in the base area that prevents cracking and thus forms a protective layer against alkalis. Container with grooves European Patent No. EP 3953262 B1 Applicant: Société Anonyme des Eaux Minérales d’Evian, Evian-Les-Bains (FR) Application date: 10.4.2020 Application is made for a structure and process for manufacturing a container made of rPET. With this design, the transparency of the container is not changed despite the use of recycled material. Plastic bottle European Patent No. EP 3889057 B1 Applicant: Yoshino Kogyosho Co. Ltd, Tokyo (JP) Application date: 7.10.2019 The European patent granted on March 6, 2024 describes the shaping of a preform and the process for producing a bottle from this preform. Aerosol container made of PET European Patent No. EP 3849920 B1 Applicant: L’Oreal, Paris (FR) Application date: 10.9.2019 A bottle for holding and dispensing an aerosol product is granted a European patent. Bottle European Patent No. EP 2821349 B1 Applicant: Yoshino Kogyosho Co. Ltd, Tokyo (JP) Application date: 27.2.2013 The European patent granted on April 3, 2024 describes the structure and shape of a bottle with equalising or reinforcing grooves."},{"@ID":22 "MATERIALS / RECYCLING PETplanet Insider Vol. 25 No. 12/24 www.petpla.net 20 Turning dairy PET bottle-to-bottle recycling into reality The chemical industry plays a key role in plastics recycling, where advancing bottle-to-bottle recyclability for rPET is crucial to closing the loop on plastic waste. Sukano, known for its commitment to sustainable plastics solutions, will support the industry with new technologies to create a circular future for plastics. MATERIALS / RECYCLING Global demand for opaque white PET bottles is rising continuously, particularly in dairy applications. As with all beverage PET bottles, these are fully recyclable. In order to maximise their recyclability and enhance waste sorting and recycling rates, it is essential that opaque PET products adhere to design for recycling guidelines provided by the European PET Bottle Platform (EPBP). Achieving enhanced bottle opacity and whiteness The Sukano White Opaque masterbatches for monolayer PET bottles were submitted for recycling trial simulations at PTI’s certified packaging performance testing labs, following the conditions specified by the EPBP protocol. The results proved that the masterbatches can be used in PET monolayer bottles, and still be processed at the same machine throughput, with no impact on colour, material properties, functionality or production rates. The melt also showed a very stable colour, with the end material remaining white at all levels, says Sukano. The integrity of the light barrier was also confirmed for extreme conditions, such as less than 0.1% light transmission at 550 nm wavelength. Sukano offers the White Opaque masterbatches to increase the whiteness of the surface while maintaining the opacity and specific light barrier properties that every brand owner needs for fresh and flavoured milk, extended shelf life (ESL) and UHT PET milk bottles. They are suitable for monolayer or multilayer/co-injection ISBM technology. In-house recyclability testing Sukano is equipped with advanced analytical and machinery capabilities to replicate essential steps of the rPET mechanical recycling process in-house. This includes flake shredding, flake drying and crystallisation, extrusion and filtration, pellet crystallisation, solid-state polymerisation (SSP) of pellets, and film extrusion. Also, analytical measurements such as yellowing, haze, and intrinsic viscosity (IV) development on pellets can be proceeded in-house to ensure all requirements are met. Stay ahead of mandatory recycling targets Sukano’s expertise and solutions support dedicated food-grade PET bottle streams for clear and light blue rPET, as well as white opaque rPET (rPETo), allowing bottles to return to their original application while enhancing the recyclate quality of each stream. When virgin PET is partially replaced with rPETo, the whiteness of the bottle surface significantly drops. Sukano addresses this by offering tailored light protection and whiteness for bottles using up to 50% rPETo. With expertise in clear rPET, rPETo, and customised solutions for light protection and whiteness, the company is committed to helping converters and brand owners realise their circularity goals with closed-loop recyclable white dairy bottles. This will help to heightened recycling rates, improved recyclate quality, and a lowered carbon footprint of packaging possible. www.sukano.com"},{"@ID":27 "MATERIALS / RECYCLING PETplanet Insider Vol. 25 No. 12/24 www.petpla.net 25 ity of the recyclate used (if reported: type and quantity of impurities) and, if applicable, its ageing condition. On the other hand, the currently known information on modes of action and mechanisms of ageing on recyclates (e.g. hydrolysis, thermo-oxidative degradation, etc.) and their influencing factors will be compiled; finally, the reported correlations to physicochemical parameters (type and amount of contained additives, chain lengths and end groups), the reported models for describing (and, if possible, predicting) the aging behaviour will be considered. The focus of this research (e.g., class and type of polymer, (un)reinforced, etc.) will be agreed upon and jointly determined among the participants. Together with the project participants, the influencing factors from the input recyclates on the mechanical properties and ageing behaviour are weighted. Taking into account individual requirement profiles, exemplary and representative formulations are produced at Fraunhofer LBF using selected recyclates and defined additives. The recyclates used are first characterised in detail regarding the molecular parameters relevant for processing and application properties. The focus is on the chemical composition (in terms of polymer content and impurities), the additives and the molecular weight distribution. Rheological properties of the compounds produced are determined and their mechanical behaviour (tensile-elongation tests, Charpy notched impact strength if necessary) is evaluated. Furnance ageing (tensile-elongation behaviour at a defined temperature as a function of time, at approx. 6 ageing times) is carried out to evaluate the ageing properties. Within the scope of the project, several compounding and injection moulding campaigns (max. total of 60 variations, divided into several campaigns) will be carried out in order to further reduce the multitude of influencing parameters and to be able to understand the underlying dependencies better and better. The detailed planning and selection of the experiments will be done in close coordination with the participants and in consideration of the respective input. After each campaign, selected material analytical investigations are carried out for better understanding of the underlying modes of action and dependencies more closely, also at the molecular level. Various thermal (e.g. TGA, DSC), microscopic (e.g. SEM, IR and Raman microscopy), spectroscopic and chromatographic methods (e.g. NMR, GPC, HPLC) are used here. Based on these findings, structure-property relationships will be derived with the intended goal of better understanding dependencies of mechanical and rheological properties as well as long-term properties (e.g. ageing behaviour) when using PCR of selected engineering thermoplastics. Furthermore, these findings should serve for an estimation or prediction of similar compositions. www.lbf.fraunhofer.de/en/ research-projects/material-and-longtime-properties-recyclates.html"},{"@ID":20 "MATERIALS / RECYCLING PETplanet Insider Vol. 25 No. 12/24 www.petpla.net 18 UV protection additive for rPET packaging Repi has introduced UV-R Remap 00561, a new UV protection additive engineered specifically for recycled PET. Designed to enhance UV resistance without compromising recyclability, this development aligns with RecyClass protocols, supporting sustainable packaging solutions. UV protection is critical for preserving the quality of products packaged in PET, as exposure to UV radiation can degrade taste, smell, colour, and biological properties. Many products contain light sensitive ingredients, and a PET barrier alone is not enough to protect them from degradation. Repi, well known in producing liquid colours and additives, addresses this challenge with its comprehensive portfolio of liquid UV additives tailored for diverse applications, including food contact and non-food sectors. As a globally active company, Repi provides products in full compliance with European directives, FDA, and regulations of other countries and regions. The Remap UV absorber range provides several grades that cover different protection specifications set by final product needs, allowing customers to select the most appropriate additive, optimising the cost/benefit ratio, while increasing shelf-life. Remap UV absorbers, benzotriazole-free, claimed to capture UV radiation from 300 to 400nm, providing different levels of protection, depending on the LDR and packaging wall thickness. In addition, they do not impact the shade of final product, allowing the user to be independent and flexible. The latest addition of UV-R Remap 00561, is optimised for the use with clear rPET bottle flakes. It fulfils RecyClass recyclability protocols as it is increasingly important to consider the impact of additives in recycling streams, with the aim of safeguarding future feedstocks characteristics for an even more intensive use of rPET. Over the years, Repi engineered high performance and reliable dosing units to support the needs of customers who use colours and additives in preform injection processes and beyond. The company’s equipment team is constantly engaged in developing new solutions to make the dosing process user-friendly and performing, to answer all technical needs, from a high dosing precision to a full bundled data collection. This last feature allows the sharing of data logs for a comprehensive control of dosing devices. Beyond additives, Repi supports precision in production with its internally engineered dosing systems. The U2023X dosing unit, their latest release, features advanced capabilities such as dosing precision at low addition rates using a gear pump and brushless motor; easy cleaning to accommodate various colours without frequent pump changes or functionality alarms and Modbus TCP/IP for data sharing and control. Repi also offers the Light Meter Plus (LMP), a patented analytical instrument that measures the intensity of the signal emitted by an RGBUvIR light allowing to correlate it to colour and additive content and giving the user the chance to monitor the consistency of preform production for MATERIALS / RECYCLING"},{"@ID":44 "OUTER PLANET 42 PETplanet Insider Vol. 25 No. 12/24 www.petpla.net OUTER PLANET Building a net-zero chemical industry in 2050 - A comprehensive analysis of 24 scenarios across 15 reports identifi es biomass, CCU and recycling as the cornerstone of the chemical industry’s feedstock in 2050 Renewable carbon feedstocks Experts from nova-Institut GmbH, on behalf of the Renewable Carbon Initiative (RCI), prepared a new report titled “Evaluation of Recent Reports on the Future of a Net-Zero Chemical Industry in 2050”. This study, which builds on RCI’s pioneering work in introducing the concepts of renewable carbon and defossilisation, provides a critical assessment of net-zero visions for the chemical and plastics industries. The now released report evaluates available studies with net-zero 2050 visions and scenarios for chemicals or plastics, with a focus on overall growth and renewable carbon shares. After rigorous quality checks of available reports, 15 studies with a total of 24 scenarios were evaluated in regards to the relative contributions of non-fossil feedstocks and pathways projected for 2050. Key findings: Industry growth projections The majority of global scenarios anticipate continued growth in the production of the chemical industry. The average annual growth rate of the global feedstock demand for the chemical or plastics industry is projected at 2.9% (range 2%-4%). This indicates a slight deceleration compared to 3-4% compound annual growth rate (CAGR) observed in recent decades. Studies differ on the extent to which this growth will be offset by efficiency gains along the value chain. Overall, this translates into an approximate 2.4-fold increase in global feedstock demand from the chemical industry by 2050 compared to 2020 levels. Notably, growth patterns show significant geographical differences: Most of the growth is expected to take place outside of Europe, and the feedstock volumes in Europe are predicted to remain stable through 2050. Renewable carbon shares The analysis reveals a clear trend toward defossilisation. All scenarios include biomass and recycling as possible alternatives to replace fossil carbon, while two thirds also include carbon capture and storage (CCU). A complete defossilisation is considered in 10 of the 24 scenarios. The remaining studies expect a residual share of fossil carbon feedstocks, and in those cases combine these processes with Carbon Capture and Storage (CCS). For the entire chemical sector, the average feedstock shares of 16 scenarios across 9 reports are 22% biomass, 33% CCU, 20% recycling and 24% fossil & CCS (see Fig. 1). For the plastics sector, 10 scenarios across 7 reports project shares of: 21% biomass, 17% CCU, 42% recycling and 19% fossil & CCS (see Fig. 2). Not surprisingly, the recycling rate for plastics is more than twice that of the chemicals sector as a whole. Plastics are easier to recycle and keep in circulation than other chemical products. Implications for the future Despite variations in modelling approaches, assumptions and scope, the results of the studies agree on a common vision: in a net-zero future, the chemical industry’s feedstock shifts dramatically away from fossil feedstocks. Biomass, CCU and recycling are consistently identified as the pillars of this transition and beyond, with recycled feedstock projected as the main source of carbon for plastics production (see Figures 1 and 2). While uncertainties remain about the volume of chemical recycling due to current low technology readiness levels, the results clearly show that maximising carbon recovery and circularity of carbon can only be achieved by including and scaling chemical recycling. This report provides invaluable insights for industry leaders, policymakers, and researchers working towards a net-zero future in the chemical sector. It highlights the urgent need for continued innovation and investment in renewable carbon technologies to meet the ambitious goals set for 2050. www.renewable-carbon-initiative.com www.nova-institute.eu Fig. 1 Fig. 2"},{"@ID":12 "EDITOUR PETplanet Insider Vol. 25 No. 12/24 www.petpla.net 10 rPET pioneer from the Greater Cairo region focuses on huge capacity expansion Bottle-to-bottle recycling in Egypt by Kay Barton The recycling plant of rPET producer Bariq is located in the west of the 6th of October City, the largest industrial and business city in Egypt and part of the Greater Cairo region. On 23,000m2 of production space, the pioneering PET recycler in the MENA region currently creates a total capacity of 35,000 t/a of food-grade rPET material, which is FDA, EFSA and Reach & Health Canada regulation compliant. And while we were still watching the whole thing live on site at the Middle East Road Show, the final adjustments were already being made to a recently acquired third line, which is also due to start production next month, increasing capacity to 55,000 t. EDITOUR Meeting with Bariq September 8, 2024 We met: Mr Ahmed Abdel Fattah, CCO Mrs Nour El Gammal, Marketing Manager Mr Abdul Rahman, Production Engineer The company was officially founded and built in 2011 as the first recycling plant for PET in the country. It began operations in 2012, at that time still as part of the Egyptian investment conglomerate Raya Holding and with a Starlinger RecoStar PET 165 iV+ with ViscoStar 150 SSP reactor. “At the time, we simply wanted to be the first on the market to tackle the issue of rPET,” explained CCO Ahmed Abdel Fattah in an interview. Having been in office for just two months, he is still very new to the company. He previously worked in the gas and oil industry for almost two decades, specifically in LPG trading and operations. The first sales markets were initially outside Egypt. Ten years its foundation, Raya Bariq sold the company in 2021 to the Egyptian Intro Group, which also invests in various industrial segments. The group includes the Intro Sustainable Resources (ISR) and Intro Resource Recovery (IRR) segments, under whose umbrella Bariq plays the central role in the closed loop: IRR’s ‘Dawar’ app, a digital waste management system, can be used to report waste for collection, for example. The ‘Environ Adapt’ business unit offers the tracking of collected waste, which ultimately ends up at Bariq for processing. Since the sale to Intro, Bariq has been aiming for massive expansion. In 2022, the plant received its second Starlinger line, a RecoStar PET art line iV+ which is the first and only art line installed in the region and the second in the world with ViscoStar 350 SSP reactor, and has now managed to triple its capacity in less than three years with the new, third recycling line, a RecoStar PET 215 iV+ with ViscoStar 350 SSP reactor. In addition to the Starlinger lines, grinders from STF, autosort systems from Tomra, washing lines from Amut and sorting equipment from Bühler and Sesotec are also in use. An estimated 60% of the PET bottles required come from the company’s own market, the rest is imported, for example from the EU, as we learn during the tour. Bariq is the only non-European recycling company that is registered with the Spanish organisation Ecoembes and is therefore part of the tendering process for bottle recycling. As in many parts of the world, the collection of PET bottle waste in Egypt is, with a few exceptions, still heavily dependent on the unorganised sector. Bottles are taken to collection centres and then end up at Bariq for processing, often with better initial quality than the imported bales. F.l.t.r.: CCO Ahmed Abdel Fattah, PETplanet Editor Kay Barton and Marketing Manager Nour El Gammal in the entrance area F.l.t.r.: Nour El Gammal, Ahmed Abdel Fattah and Kay Barton in front of the Editourmobil"},{"@ID":36 "34 PETplanet Insider Vol. 25 No. 12/24 www.petpla.net ONsite Sustainea plans investment in Indiana, advancing Agbiosciences & Circular Economy Sustainea, a company focused on sustainable chemistry, announced plans to locate its first U.S. operations in Indiana, investing USD400 million to establish its first bio-MEG (monoethylene glycol) industrial plant in Lafayette. The facility will be co-located with Primient, leveraging the company’s local supply of corn dextrose to produce a renewable, plant-based alternative to petroleum-based MEG. Sustainea is a joint venture between Brazil-based Braskem and Japan-based Sojitz created with the ambition to be the global leader in bio-MEG, which can be used as a drop-in product, delivering high quality and functionality while significantly reducing the carbon footprint. The new facility in Lafayette will produce bio-MEG from Primient’s dextrose – a carbohydrate derived from corn, providing a renewable chemical that is a key component in the manufacturing of PET. The company plans to break ground on its new Indiana operation following the finalisation of engineering and final investment decision and expects to begin production in 2028. Sustainea plans to create up to 191 new, high-wage jobs in the coming years to support its growth. Headquartered in the United States, with an office in São Paulo, Brazil, Sustainea has a team of professionals with indepth knowledge of the chemical industry and the creation and sale of sustainable solutions. The business plan envisages the construction of three industrial plants, with the first unit slated for operational startup in 2026, taking advantage of market opportunities and feedstock availability. The locations where the industrial units will be built have not been defined yet and could be in Europe, Asia, the United States or Brazil. The expectation in the business plan is that, once the technology is approved, the plants will have a combined production capacity of up to 700,000 t/a of bio-MEG. Sustainea combines Braskem’s expertise in the industrial production and sale of chemicals and plastics made from renewable sources with Sojitz’s strong presence in Asia, a region that concentrates 80% of the global MEG market and where its consumption registers the highest growth. www.sustaineabio.com MATERIALS / RECYCLING"},{"@ID":34 "PETplanet Insider Vol. 25 No. 0/24 www.petpla.net 32 PETbottles Home + Personal Care Carton replaces front label Henkel Canada sells a hand-operated pump dispenser for liquid soap in Canada under the Dial brand. The dispenser turns the liquid soap into an antibacterial foam. The bottle is set in a display-strong cardboard sleeve at the pos, which contains all the necessary information. The transparent 221ml bottle is decorated on the front only with embossed brand lettering - there is no label. This makes a ‘clean’ visual impression at the sink. A transparent foil label is stuck to the back, which serves as a refill label for this bottle designed as a refill pack. www.henkel-northamerica.com Bigger triggers in the USA Wh e n y o u wa l k through supermarkets in the USA or Canada, you notice a difference in the packaging of cleaning products compared to that in Europe. In comparison, the sprays used there are more voluminous and better integrated into the bottle design. They are also explicitly designed as reusable spray heads and are easily detachable from the bottle via a type of bayonet lock. When the bottle is empty, a bottle without a sprayer is purchased and the sprayer is placed on the new bottle. The picture shows two brands from Procter & Gamble: Mr Clean - Clean Freak as a surface cleaner and Dawn as a dishwashing liquid. The sprayer from Dawn is equipped with an actuation lock - the sprayer can only be actuated when two semicircles on the top of a rotating component have become a circle with a yellow mark by twisting it slightly. www.mrclean.com Bottle with honeycomb structure Burt’s Bees, a cosmetics company for skin care, uses ingredients from nature in its products. Bee honey is often the main ingredient. In keeping with the history of the brand, many packages are decorated with symbols from this area. Honeycomb patterns can be found on many packages. For example, the 3 in 1 micellar water for gentle skin cleansing is decorated with embossed honeycomb designs on the neck of the bottle. The clear bottle itself contains 236.5ml of micellar water with rose water. The facial cleanser is dispensed via a screw-on hinged lid with a dispensing opening. www.burtsbees.ca"},{"@ID":9 "7 NEWS PETplanet Insider Vol. 25 No. 12/24 Amcor and Berry to combine in all-stock transaction Amcor Plc has announced an USD 8.43 billion all-stock acquisition of Berry Global, creating a global leader in consumer and healthcare packaging with combined revenues of USD 24 billion. Berry shareholders will receive a fixed exchange ratio of 7.25 Amcor shares per Berry share, giving them a 37% stake in the merged entity. The boards of both companies have unanimously approved the deal, which values Berry’s stock at USD 73.59 per share, a 9.75% premium over its prior close. The merger combines complementary strengths in flexible films, containers, closures, and healthcare packaging. The combined company will invest USD 180 mi l l ion annual ly in R&D, leveraging 1,500 professionals and 10 global innovation centres. This will enhance offerings in high-growth markets, with an expanded focus on sustainable solutions such as recycled materials and lightweight designs. Amcor CEO Peter Konieczny emphasised the strategic benefits, including stronger customer focus, enhanced sustainability efforts, and improved cash flow and earnings growth. Berry CEO Kevin Kwilinski highlighted the merger’s alignment with Berry’s transformation goals, a complementary geographic coverage and shared commitment to innovation and sustainability. The merger is expected to yield USD 650 million in cost and growth synergies within three years. Financially, the combined entity targets USD 3 billion in annual cash flow and a strong balance sheet, with plans for sustained dividend growth and further portfolio optimisation. Subject to regulatory and shareholder approvals, the transaction is expected to close by mid-2025. The merged company will retain Amcor’s name, headquarters in Zurich, and primary NYSE listing while maintaining a significant presence in Evansville, Indiana, USA. Leadership will include Peter Konieczny as CEO; Graeme Liebelt will serve as Chairman and Stephen Sterrett will serve as Deputy Chairman of the combined company. www.amcor.com www.reuters.com CREATING FUTURE STANDARDS Japan’s leading Aseptic PET Filling System Provider. Our website Our solution high quality reliable technology safe & secure Repi’s UV absorbers receive RecyClass recyclability approval Repi’s UV absorber formulations ‘Remap 00395’ and ‘Remap 00561’ received a RecyClass rRecyclability approval. Independent test ing was carried out by the Institut für Kunststofftechnologie und -recycling e. V. (IKTR), following the RecyClass Recyclability Evaluation Protocol for PET bottles. The results showed no adverse effects on the recycling process, confirming its compatibility with state-of-the-art PET recycling processes in Europe. Specifically, the approval is valid as long as the amount of additive used does not exceed 0.15 wt % of the total weight of the packaging. www.repi.com"},{"@ID":30 "MATERIALS / RECYCLING PETplanet Insider Vol. 25 No. 12/24 www.petpla.net 28 Mission PET and Next Generation Recycling GmbH collaborate on LSP PET recycling in food and non-food applications High-quality rPET granules from mixed streams Mission PET and Next Generation Recyclingmaschinen GmbH (NGR) have announced the application of NGR’s Liquid State Polycondensation (LSP) technology in upcycling off-specification PET materials, such as fines, shredded lumps and mixed-coloured bottle flakes, into high-quality rPET granules. The two companies say that the successful demonstration of the technology highlights the potential for sustainable recycling solutions beyond traditional food-grade applications, paving the way for a more versatile approach to PET recycling. Mission PET, based in Austria, says that it is breaking new ground by targeting PET streams such as non-food bottles, trays, fibres, straps, agglomerates and fines, materials that were previously considered waste, into material to create valuable new products. This approach supports sustainability and meets the rising demand for highquality recycled PET (rPET) in various industrial applications. “Our collaboration with NGR and the use of LSP technology allows us to produce high-quality rPET granules from mixed streams, which significantly broadens the scope of sustainable PET recycling. We have the chance to upcycle those completely different streams and give them back a life in a valuable product,” said Markus Huemer, CEO of Mission PET. Their flagship product, “rPET BNT 75/80,” is made from a mix of coloured non-food bottle flakes, fines and lumps. It achieves a viscosity close to virgin PET, making it suitable for a wide range of applications. Production process: Leveraging LSP technology Mission PET’s process uses NGR’s LSP technology, specifically its P:React system, which enables efficient recycling of diverse PET streams through a liquid polycondensation process. Unlike conventional methods, LSP is claimed to ensure thorough decontamination in the liquid phase, which is crucial for producing high-quality rPET. NGR’s LSP is an established technology that has been used worldwide, especially for food-grade (EFSA, FDA), for over 10 years. The collaboration with Mission PET now makes it available for non-food-grade applications. The LSP process is not dependent upon or affected by material thickness. It ensures uniform quality by melting the PET before decontamination. LSP can process composites like PET/PET-G and PET/PE. The process allows precise control over the intrinsic viscosity (IV) of the PET, resulting in consistent mechanical properties in the final product. Continuous material flow and direct integration into downstream production processes reduce energy consumption and improve operational efficiency. “The LSP technology represents a significant advance in PET recycling. By decontaminating in the liquid phase we achieve a higher purity and more consistent quality, making it possible to recycle materials that were previously problematic,” David Hehenberger, Product Manager for PET Recycling at NGR explained. Mission PET says that its ability to upcycle materials traditionally destined for incineration or low-value applications into high-quality rPET granules is a game-changer. This process not only supports environmental sustainability but also reduces dependence on imported virgin PET, thus aligning with European sustainability standards. The rPET granules produced are ideal for manufacturing straps and fibres, offering good strength and durability and the consistent IV and purity of the rPET make it suitable for producing high-quality foamed PET sheets. rPET granules with higher IV values (up to 0.8dl/g) are suitable for various technical applications and thus reduce the need for virgin PET. As the demand for high-quality rPET continues to grow, the partnership between NGR and Mission PET is described as providing sustainable solutions that benefit both the environment and the economy. www.ngh.at MATERIALS / RECYCLING F.l.t.r.: Stefan Musner (NGR), Markus Huemer (Mission PET), Daniel Pichler (Mission PET), David Hehenberger (NGR)"},{"@ID":23 "MARKET SURVEY 21 PETplanet Insider Vol. 25 No. 12/24 www.petpla.net Suppliers of recycling plants and washing units Company name Krones AG Herbold Meckesheim GmbH Postal address Telephone number Web site address Contact name Function Direct telephone number E-Mail Boehmerwaldstr 5, 93073 Neutraubling, Germany +49 9401 70 0 www.krones.com Mr Peter Hartel Head of Sales - Recycling Solutions +49 9401 70 5448 [email protected] Industriestrasse 33, 74909 Meckesheim, Germany +49 6226 932 0 www.herbold.com Mr Achim Ebel Vice President Sales +49 6226 932 0 [email protected] Frontend Sorting Section Input variable: collected pressed bottles, various colours Yes, with different qualities Yes Output: sorted bottles, treated sidestreams Yes, separation in several valuable streams if necessary Yes Capacity range output [t/a] 10,000-45,000t/a; higher ranges also possible if necessary 500-6,000kg/h Floor space [m²] Starting with 1,500m² and more; will be designed to fi t the needs of the customer; depending on the scope of supply Variable Fresh water consumption per tonne output [m³/t] (if necessary) Only necessary if whole bottle washing is required 1-4m³/t Consumption kWh per tonne output [kWh/t] Designed to fi t the needs of the customer; depending on the scope of supply Variable Grinder included Yes, with high quality suppliers, mainly from Europe Yes Additional information Krones can act as turnkey-supplier and offers frontend from preferred partner Stadler Anlagenbau Equipment for bale opening, delabelling, prewash drums Sorting technology (NIR, laser, optical etc.), effi ciency in % OEM equipment, integration Washing Section MetaPure W Input variable: Flakes, coloured proportion max 5%, not much chlorine Yes Yes Output: Hot washed fl akes Yes, washed with hot caustic, rest humidity 0,8% Yes Capacity range output [t/a] 7,000-42,000t/a; higher output possible by multiplying sections Up to 6t/h Floor space [m²] 450-2,100m²; higher output reqires more space ≈ 1,800m² Fresh water consumption per tonne output [m³/t] 1.5-2.0m³, depending on input quality 1-4m³ Consumption kWh per tonne output [kWh/t] Designed to fi t the needs of the customer; depending on the scope of supply Depending on individual scope Kind of polymer (PET, PP, PS, HD-PE, LD-PE etc.) PET, PP, PS , PE-HD, PE-LD All Additional information Krones own manufacturing Hydrocyclone technology for density separation Decontamination section MetaPure S Input variable: Flakes or Pellets Flakes Output: Flakes or Pellets Flakes, pellets Capacity [t/a] 7,000-12,600t/a per decontamination unit Floor space [m²] 450-520m² per decontamination unit Approvals (FDA, Efsa, others) FDA, Efsa, various brands Consumption kWh per tonne output [kWh/t] Designed to fi t the needs of the customer; depending on the scope of supply Additional information Krones own manufacturing Periphery Fresh water treatment Yes Yes Waste water treatment Yes Yes Heating systems Yes, with partner Yes Nitrogen generator Yes, with partner Compressed air Yes, with partner Chemical dosing Yes Yes Kind and quantity of detergents Caustic soda 8.0-12.0 ml/kg output Yes Additives 0.5-1.0 ml/kg output Yes Defoamer Depending on infeed quality Yes Acid for neutralisation 1.2-1.8 ml/kg output Yes Removal of the organic residuals up to which size [μm] As needed to achieve higher fl ake quality Presetting residence time in the process Yes, according to desired fi nal product quality Yes, batch reactors with controlled residence time Company also offers systems for Yes, in cooperation with partners Bottle-to-preform Yes, with partner Yes Bottle-to-fi lm Yes, with partner Yes Bottle-to-fi bre Yes, with partner Yes Bottle-to-strapping Yes, with partner Yes Bottle-to-tray Yes Tray-to-tray Yes 12/2024 MARKETsurvey"},{"@ID":26 "MATERIALS / RECYCLING PETplanet Insider Vol. 25 No. 12/24 www.petpla.net 24 Analytics and perspectives for material fl ow-adapted melt processing by Fraunhofer LBF Material and long-term properties in recyclates The plastics industry is expected to come up with viable and practically implementable solutions that will significantly increase the share of recyclates, even in technically demanding applications.The main drivers are legal requirements at national (i.e. the German Closed Substance Cycle Waste Management Act (KrWG), including its amendments) and European level (Circular Economy Action Plan and initiatives and regulations derived from it) and legal initiatives expected in the future (e.g. the EU Single Use Plastic (SUP) Directive 2019/904). The key requirement here is the mandatory use of post-consumer recyclates in the highest possible share. While post-industrial recyclates (PIR) still have a very defined composition, the variety of possible compositions (e.g. extraneous polymers, non-plastic components, additives, adhesives, etc.) and ageing conditions of post-consumer recyclates (PCR) is very high and, not least, varies (strongly) regionally and seasonally. However, such variations of input qualities inevitably have an impact on product properties. For example, the processing and mechanical properties generally deteriorate as the proportion of PCR in the compound or the resulting product increases. The ageing resistance and thus the service life of a compound is also largely determined by its composition. The condition of the material stream used, as well as the sorting, separation and processing technologies employed, decisively determine the quality of the resulting recyclate. The compounder also has various options for further optimising the quality and properties through different measures. For example, through targeted (re-)additivation (e.g. in the case of condensation polymers such as PBT, PA, etc. through stabilisers, compatibilisers or chain extenders) or through the proportionate use of virgin material. Already the identification and evaluation of suitable extrudable secondary materials (e.g. sorted and purified flakes or regrind or regranulate) is associated with high effort. The downstream steps (e.g. characterisation or quality control, homogenisation, etc.) are also elaborate and often linked to the securing of large batches. The complexity is further increased by the variables in compounding (formulation, process). Whether the target properties (especially mechanical properties, aging resistance) are achieved as a result and whether these are also reliably controlled via other variables (such as batch-to-batch variability of the input material streams) often only becomes apparent late in the development or optimisation cycle. In many cases, this is done by the trial-and-error-method. Interdependencies between packaging, composition, compounding and application properties The joint project aims to develop and communicate extensive knowledge on the dependencies between the form of compounding (e.g. flakes, regrind, granules), the chemical composition of the input materials, influencing variables during compounding (e.g. proportion and state of recyclate, re-additives) and the resulting application properties, especially with regard to mechanical behavior and aging resistance. This is done using the example of selected condensation polymers used in technical applications, such as PA, PET, PBT or PC. The project is also intended to serve as an interdisciplinary platform of players from the entire value chain in order to develop targeted approaches to solutions for the technical problems arising around the topic of the circular economy for technical plastics. Focus & approach In the project, basic information on available (extrudable post-industrial or post-consumer) recyclates (e.g. granules, flakes, regrind, etc.) for the selected target polymers (polyamides, polyesters) will first be collected and evaluated. This includes information on availability, quality descriptions of the recyclates and sources of supply (if available). Furthermore, the main measures described in the state of the art and science (open and patent literature) for quality improvement at the compounding level (e.g. compatibilisation, chain extenders, re-stabilisation, etc.) are summarised by way of example for selected recyclates. The first project phase is rounded off by an overview of relevant and currently available additives or additive packages for optimising the mechanical properties and ageing behaviour in engineering plastics based on recyclates. The main influencing factors from the state of the art with regard to the dependencies of the mechanical properties and the ageing behaviour on the input characteristics of the recyclates are compiled and evaluated. Material and condition-specific factors are systematically considered, such as the type of polymer, the qualSamples for the analysis of additive packages to enhance the long-term properties of recyclates (Photo: Fraunhofer LBF, Raapke) MATERIALS / RECYCLING"},{"@ID":46 "An endless range of production possibilities with single-stage SIPA S.p.A. - Via Caduti del Lavoro, 3 - 31029 Vittorio Veneto (TV) - Italy - Tel. +39 0438 91151 VLSD#]Rppas.com - www.sipa.it ECS SP models stand for a guarantee of quality based on 35 years of experience in Injection Stretch-Blow Molding technologies (ISBM) technology. Their robust system, produced in Italy, allows for the production of high quality containers in a wide variety of different sizes, threads and shapes. Tooling investment can often be optimized by using one single (i.e. shared) hot runner withmultiple cold halves. ECS SPmachines have features that enable quick change-overs, accept legacy molds and are also characterized by their compact layouts and high HQHUJ\\ HIĆFLHQF\\. Injection Stretch BlowMolding System"},{"@ID":18 "MATERIALS / RECYCLING PETplanet Insider Vol. 25 No. 12/24 www.petpla.net 16 results are remarkable, since these impact potentials are two of the most relevant environmental impact categories in the current political agenda driving the transition from fossil to renewable feedstocks. PETplanet: In comparing endof-life scenarios like incineration and recycling with respect to climate impact, you project that PEF bottles could reach a similar recycling rate as PET bottles, which could offer up to an 86% advantage for PEF (Fig. 2). Given that PEF currently lacks established recycling streams, how would a comparison look between a recycled PET bottle and an incinerated PEF bottle? Dr Puente: PEF has proven fitfor-purpose with existing sorting and recycling facilities and can be recycled mechanically in a similar way using the same equipment used to recycle PET. The European PET Bottle Platform (EPBP) has provisionally approved the recyclability of PEF in the European recycling market for bottles, although in the future a separate recycling stream would have to be set up for final recycling. In this respect, PEF can easily be distinguished from PET and other plastics using nearinfrared technology. This will allow PEF to be sorted from any PCR or deposit system waste streams once the market has grown sufficiently to enable an individual PEF material recycling stream. Our study showed that a rPET bottle would need to contain approximately 85% recycled content to match the carbon footprint of a virgin PEF bottle. PETplanet: By 2030, PET bottles in Europe must have an average of 30% recycled content. How does the carbon footprint of a PET bottle with this 30% recycled content compare to a vPEF bottle? Dr Puente: Based on our assessments, a virgin PEF bottle would still have a 48% lower carbon footprint than a PET bottle with 30% recycled content. As PEF enters the market and recycling streams for PEF are further developed, its carbon footprint could decrease even further, reinforcing its role as a 100% bio-based and recyclable packaging solution. PETplanet: The production of PEF requires intermediates such as fructose and other plant-based feedstock. In 2022, EU demand for bottle-grade PET was 3.4 million tonnes. If this demand were fully met with plant-based PEF, what would that mean in terms of agricultural land requirements? Dr Puente: To make the change to a fully sustainable future we need to switch to sustainable carbon sources. With recycling alone, we will not be able to meet the full demand. Therefore, next to recycling we need to switch to plantbased materials. Materials that have a good fit with the feedstock (efficient conversion) and a performance that can, at least, compete with the current incumbent. PEF is a material that fulfils these criteria. The feedstocks required for PEF production is sourced from sustainably grown, high-efficient crops. In any case, the focus should not be solely on land use but on integrating any bio-based material production into landscapes in a way that balances environmental, social, and economic priorities. Today, plant-based plastics only make up a miniscule land use. Ultimately, there is a need to shift away from fossil feedstocks to achieve climate change mitigation and bio-based materials are part of the solution. With thoughtful planning, policy support, and technological MATERIALS / RECYCLING Fig. 1 Impact Assessment (all figures: nova-Institute) Fig. 2: Recycling rate"},{"@ID":32 "BOTTLE MAKING 30 PETplanet Insider Vol. 25 No. 12/24 www.petpla.net Italian company focuses on special sustainability strategy Environmentally friendly packaging for the pharmaceutical industry by Kay Barton Bormioli Pharma, a leading company for pharmaceutical packaging solutions, recently presented its “EcoPositive” environmentally friendly packaging portfolio, which includes over 3,000 items made of plastic and glass. According to the company, the plastic packaging segment recorded volume growth of 304% in 2021 and is part of the company’s ‘50-in-5’ strategy. This strategy aims to achieve a 50% share of sustainable materials in the products sold by 2025: in 2023, this share was already 45% and a further increase was forecast for 2024. The three company’s principles being pursued are ‘Regenerate’ (glass and plastic packaging that is recycled from first-choice waste collection, such as rPET and rHDPE bottles), ‘Renew’ (packaging made from bioplastics that are obtained from renewable sources, such as bio-PET-based or bottles and caps made from Green PE and Green PP), as well as ‘Reloop’ (products made from glass and advanced polymers, which are manufactured from materials that can be recycled indefinitely, such as carbon capture PET bottles or advanced rPET bottles). The company works with various partners to implement this, including the recycler Loop Industries, which uses depolymerisation and monomer isolation to process even heavily contaminated PET waste into high-quality recyclate for demanding applications. The EcoPositive area currently accounts for 50% of Bormioli Pharma’s standard catalogue. In-house and third-party analyses show that the company’s own rHDPE bottles have a 28% reduction in migrating compounds compared to conventional solutions made from virgin HDPE. A study on Bormioli’s rPET bottles by the specialised laboratory Lab Analysis and with a report by the Mario Veronesi Technopole Institute in Mirandola (Modena, Italy) showed that bottles made of 100% rPET from Loop Industries did not contain any toxicologically relevant extractable substances and therefore met the necessary requirements for pharmaceutical applications. The results of the study also showed that bottles produced with Loop PET outperform bottles made from untreated PET, which already fully comply with the European Pharmacopoeia limits for extractables, by around 90%. A few days ago, a new partnership was entered into with Chiesi, an international biopharmaceutical company, to produce Carbon Capture PET bottles for a drug for the prophylaxis and treatment of rhinitis, a packaging innovation in the field of pharmaceutical packaging. Compared to conventional PET, Carbon Capture PET reduces CO2 emissions by 21.9% and has comparable properties to standard PET. It is produced from CO2 emissions and converted by fermentation into bio-MEG, which is used to produce PET. The material is regularly recyclable. Two companies are significantly involved in the production of carbon capture PET: LanzaTech, which is responsible for the production of Bio-MEG, and Plastipak, a leading manufacturer of recycled resins based in Italy. Another supplier of Bio-MEG is UPM with its biorefinery based in Leuna, eastern Germany. UPM’s ‘BioPura’, bio-MEG made from sustainably collected hardwood from carefully managed forests, is used by Bormioli Pharma to produce its bio-PET bottles (see PETplanet 7+8 2023, p. 10-12). Regionally collected wood is processed at UPM, where it is converted into sugar, which in turn is used to produce bio-MEG. Bormioli currently has an annual turnover of over USD400 million. www.bormiolipharma.com Carbon Capture PET bottles Headquarters of Bormioli Pharma in Parma, Italy"},{"@ID":17 "MATERIALS / RECYCLING PETplanet Insider Vol. 25 No. 12/24 www.petpla.net 15 PEF: A bio-based alternative to PET with lower environmental impact by Gabriele Kosmehl PETplanet: At the nova-Institute you are part of the EU-funded PEFerence project. Could you briefly describe the project’s goals and your specific role within it? Dr Puente: The PEFerence project aims to establish a sustainable value chain for producing polyethene furanoate (PEF), a 100% bio-based and fully recyclable plastic developed by Avantium (NL). PEF offers a renewable carbon-based alternative to fossil-based plastics like PET in applications such as bottles, films and fibres. My role in the project is to assess the environmental advantages of PEF using the established ISO LCA methodology. PETplanet: You have assessed various products made from PEF, such as monolayer bottles and PET/ PEF multilayer bottles. Are bottle applications the primary focus for PEF? Dr Puente: PEF is indeed an excellent material for bottle applications. Its superior barrier properties — especially against oxygen and carbon dioxide — make it an ideal choice for monolayer and multilayer bottles, ensuring extended shelf life for beverages and reducing food waste. Additionally, its fully bio-based and recyclable nature aligns perfectly with the growing demand for sustainable packaging solutions. However, bottles are just one of the many applications where PEF can excel. Thanks to its remarkable mechanical strength and thermal stability, PEF can also replace traditional materials like ABS in certain application and is well-suited for films used in flexible packaging, which can replace conventional plastics in snack wrappers, pouches, and more. In textiles, PEF fibres can offer a biobased alternative to polyester, catering to industries aiming to reduce their dependence on fossil-based materials. PETplanet: How do the barrier properties of PEF compare to PET, and what other characteristics make it particularly suitable for bottle applications? Dr Puente: One of the standout features of PEF is its exceptional barrier performance. PEF offers up to 10 times better oxygen barrier and approximately 16-20 times better carbon dioxide barrier compared to PET. These properties significantly extend the shelf life of beverages, making it an ideal material for packaging sensitive products like carbonated drinks, juices, and even beer. This advantage also helps reduce food and beverage waste, aligning with global sustainability goals. Another advantage is that PEF can be processed in existing PET processing lines, therefore no additional investment is needed. PETplanet: When you compared the environmental impact of PEF to PET, what did the profiles reveal? What environmental impacts were most relevant, and how did they differ? Dr Puente: As an example, in monolayer bottles application, the LCA showed that the use of PEF would result in significant reductions (up to -73%) in greenhouse gas emissions (GHG) over the bottles’ life cycle compare to those of PET (Fig. 1). PEF bottles would also contribute to remarkably less finite resource consumption of fossil fuels (-45%), largely due to the use of 100% renewable feedstocks and the good barrier and mechanical properties of PEF enabling light-weighting designs. These MATERIALS / RECYCLING At the PEF World Congress in Düsseldorf this October, Dr Ángel Puente, Senior Expert at the nova-Institut GmbH, presented on the topic “PEF – A circular bio-based plastic with improved properties and environmental performance.” As part of the EU-funded PEFerence project, Dr Puente is evaluating the environmental impact of polyethylene furanoate (PEF). PETplanet caught up with him to discuss how PEF compares to PET and examine its potential advantages."},{"@ID":4 ""},{"@ID":41 "8 NEWS PETplanet Insider Vol. 25 No. 12/24 www.petpla.net Bericap takes full ownership of Bericap North America Bericap, a leading manufacturer of plastic and aluminium closures, has announced an agreement to acquire the 50% stake in Bericap North America (BCNA), held to date by Amcor Rigid Packaging. This means that familyowned global manufacturing company Bericap will acquire 100 per cent of the shares in BCNA. The joint venture, founded in 1997 as a 50:50 partnership between Bericap and Amcor in Burlington, Ontario, has grown to become a successful business with annual revenue of USD 200m. BCNA operates three production facilities located in the USA (Cowpens, South Carolina), Canada (Burlington) and Mexico (Mexico City) and offers the complete Bericap closures portfolio for the food, beverage and industrial markets. The acquisition of the shares in BCNA is the most significant investment in the company’s almost 100-year history and demonstrates its strong commitment to the North American market. www.bericap.com Opening of PET bottle processing plant in Latvia On October 23, the new factory of AS Iterum (formerly PET Baltija) was opened in Olaine – one of the largest in Northern Europe with a planned processing capacity of 80,000 t/a, or about 30% more than it was possible to provide at the company’s previous production facility in Jelgava. Iterum has invested more than USD 10 m (€10 m) in the creation of the new factory, while the total investment reaches more than USD 37 m (€35 m). Iterum’s newly opened factory will be one of the largest and most modern PET processing plants in Northern Europe and one of the largest industrial buildings in Latvia, with a total indoor area of approximately 30,000m2 and an outdoor area of approximately 40,000 m2. The building complies with the sustainable construction standard Breem, it will fully use energy obtained from renewable resources. Wastewater treatment equipment, unique in Latvia, has been installed in the factory, which allows the consumption of chemicals in the process of wastewater treatment to be reduced. An efficient air recuperation system has been created, which also provides for the excess thermal energy generated in the PET melting process to be used for heating the building. The new factory will provide more than 250 jobs, with a special focus on employee well-being and the sustainability of the working environment. Jūlija Zandersone, the chairman of the board of JSC Iterum, says that sustainability is one of the main pillars of the factory’s operation, while at the same time prioritising the quality of the final product, which the Latvian manufacturer can offer on the international market: “Almost 100% of our production is exported. The main sales countries are Lithuania, Germany, Finland, Poland and other regions of the world. Although Latvia is territorially small compared to other European countries, we can be proud that in terms of PET processing with high-quality production, we are able to reach up to 5% of this market share. We believe that the new Iterum factory is a new step for the further development of PET recycling, aiming to increase its market share even more.” The Eco Baltia project was implemented with the support of INVL Baltic Sea Growth Fund and in cooperation with domestic industrial park developer SIA Piche. In turn, equipment suppliers are among the distributors of the most modern solutions, one of which is the Austrian manufacturer Starlinger. www.iterum.lv www.agrintl.com +1.724.482.2163 • Accurate. Fast. Intuitive. • Powerful, Simple Job Creation and Editing • Pre-Defined Container Measurement Routines • AutoJob® — Automated Feature Recognition and Job Setup in Seconds Partner with Agr to achieve simplified, dimensional measurement for your plastic containers and preforms! ®"}]}}
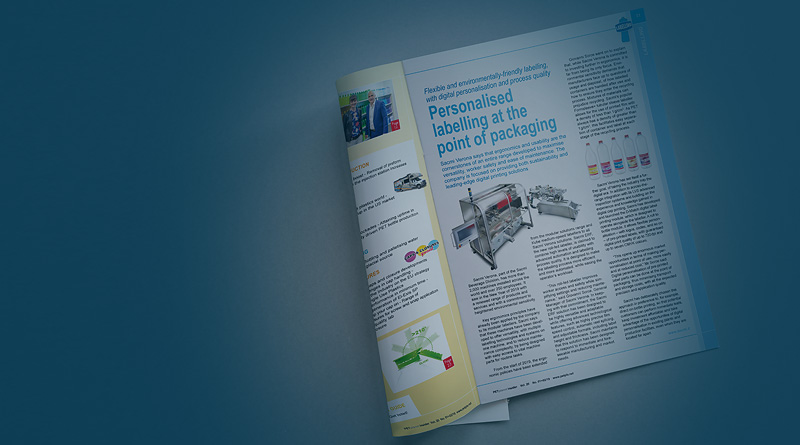