{"pages":{"page":[{"@ID":8 "PETnews 6 NEWS PETplanet Insider Vol. 26 No. 01+02/25 www.petpla.net New responsibilities at Otto Hofstetter AG and Otto Systems Effective from January 1, 2025, Reto Bamert, currently Head of Global Sales at Otto Systems, took over as Head of the PET Division at Otto Hofstetter AG. He succeeded Stefan Zatti, who has held the position on an interim basis and is now returning to focus on his roles as CEO of Otto Systems and Head of Sales and Marketing for the entire organisation. As a logical step following Reto Bamert’s appointment, the sales and after-sales services for the PET sector at Otto Hofstetter AG and Otto Systems will be more closely aligned internally. This development will benefit customers by addressing growing demands for flexibility, personalised support, swift availability, and cost efficiency even more effectively. Importantly, customers’ existing points of contact in both companies will remain unchanged and will continue to provide their reliable support worldwide. Under Reto Bamert’s leadership, the organisation will be tailored even more precisely to the needs of its global customer base. At the same time, services and solutions will continue to be developed to meet specific customer requirements and adapt to changing external conditions. His extensive experience in global sales and in-depth industry knowledge make him the ideal choice for this key role, says the company. www.otto-hofstetter.swiss 11th ICIS PET Value Chain Conference The 11th ICIS PET Value Chain Conference in Amsterdam, held March 6-7, 2025 in the Kimpton De Witt Hotel, will delve into the critical challenges and transformative shifts affecting the PET and rPET markets. Europe’s PET value chain is currently navigating significant hurdles, including logistical disruptions, pricing volatility, and uncertainties in import timelines due to global shipping issues. Additionally, the 2025 implementation of the Single Use Plastic Directive, which mandates 25% recycled content in PET beverage bottles, is accelerating the shift towards circularity and driving fundamental changes in both virgin and recycled PET markets. Conference key themes and highlights include an in-depth analysis of global PET market shifts, focusing on the interaction between virgin PET and rPET supply-demand dynamics. The conference will also explore the effects of overcapacity in Asia, evolving trade flows, and logistical challenges that are shaping the competitiveness of European players. Circularity, sustainability and technological innovation are another central focus, examining how regulatory pressures, brand owner commitments, and advancements in recycling technologies, biopolymers, and hybrid solutions are steering the industry toward a circular economy. Regional trade and procurement opportunities will also be assessed, covering market dynamics in Europe, North America, Asia, Turkey, and Africa. Discussions will address the impacts of tariffs, trade policies, certifications, and supply chain disruptions, alongside investment opportunities in both emerging and established markets. The ICIS PET Value Chain Conference provides a platform for producers, converters, and end-users to share insights, explore market trends, and understand the evolving landscape of the PET and rPET sectors amid global and regional challenges. www.icis.com Netstal establishes its own subsidiary in Mexico Netstal has founded its own subsidiary in Mexico for sales and customer service with immediate effect. The new company is based in Santiago de Querétaro. Netstal is taking over the existing employees and Netstal business operations of iTech Latinoamérica, which previously represented the brand in Mexico as an independent agency. With this step, Netstal is expanding its personnel capacities in the important Mexican market. Customers will have access to consultation and comprehensive services right from the start. The newly founded company has been operating under the name Netstal Máquinas, S. de R.L. de C.V. in the premises of the former iTech Latinoamérica since January 14, 2025. Netstal Mexico, a subsidiary of Netstal Maschinen AG, Switzerland, has successfully employed the team from iTech Mexico into its operations. Furthermore, the owners of iTech have independently decided to cease operations indefinitely by dissolving their company. The new Netstal Mexico team comprises seven employees in the areas of sales, customer service and administration. José Lelo de Lar rea has been entrusted with the management of the Mexican Netstal subsidiary. He cofounded iTech Latinoamérica in 2010 and successfully built up iTech as a managing partner. Since 2023, the company has been the official representative for Netstal in the strategically important Mexican market. iTech’s co-founding partners, Rod Selem and Irineu Scalisse will continue to play a valuable role as business and technical advisors for Netstal in the region. Renzo Davatz, CEO: “In line with our strategy, with this step we are further expanding the global Netstal organisation under the umbrella of Krones. Following the opening of Netstal Dubai earlier this year, we are establishing the next subsidiary in the growth market of Mexico. I would like to welcome all new employees in Mexico to the global Netstal team and wish José Lelo de Larrea every success in his new role as Managing Director.” www.netstal.com Looking forward to the new cooperation (f.l.t.r.): Renzo Davatz (CEO Netstal), José Lelo de Larrea (Managing Director Netstal Mexico) and Nadeem Amin (President Netstal Americas)"},{"@ID":32 "CAPS & CLOSURES 30 PETplanet Insider Vol. 26 No. 01+02/25 www.petpla.net The CapWatcher Compact by Intravis Half the space is needed... The new CapWatcher Compact from Intravis combines a sorting, feeding and inspection unit for the quality control of plastic closures in a single, compact solution. Based on many talks with customers, the system addresses one of the largest problems in modern production facilities – the availability of space! The CapWatcher Compact saves up to 50% of the floor space compared to conventional solutions and simultaneously maintains Intravis’ renowned commitment to quality. CAPS & CLOSURES Efficiency and precision in a limited space Manufacturers of plastic packaging are increasingly faced with the challenge of fitting more and more production capacity into limited space. This is where the CapWatcher Compact comes into play: It combines three previously separate elements of the plastic closure production line – sorting, feeding and inspection – in one compact housing, without compromising on functionality or inspection quality. “With the CapWatcher Compact, we have created a solution that takes our customers’ production realities into account. We offer a reliable 100% inspection with minimal space requirements,” explains Marius Pötting, Product Manager Caps & Closures at Intravis. Development in dialogue with the customer The impetus for the development of the CapWatcher Compact came from customer requests over the last year. “During the last year, some of our customers came to us and said, that in the future it will be harder for them to use our solutions, since the space in their production lines will be more and more limited. They were very sorry for that since they appreciated our sophisticated systems”, explains Marius Pötting. Intravis realised that there is a requirement to enable the proven inspection performance in a significantly smaller space. Within six months, Intravis created an initial prototype. However, it quickly became clear that simply reducing the footprint of the inspection system would not provide the necessary space savings. Only by combining several downstream elements, the necessary reduction in space requirements would be achieved. So, in a second project phase, the Aachen-based company also developed and implemented an integrated sorting and feeding technology and finally brought the system to market maturity. “Of course, it helped that we have been developing and building feeding solutions for plastic closures ourselves for many years in addition to vision inspection systems,” says An insight into the CapWatcher Compact Marius Pötting, Product Manager Caps & Closures at Intravis"},{"@ID":13 "Editour PETplanet Insider Vol. 26 No. 01+02/25 www.petpla.net 11 In Jeddah, Saudi Arabia, New Modern Plast has been operating a second production facility for several months, working with three Husky preform lines and one for closures. Another plant in Al-Kharj near Riyadh for the production of preforms on two Husky HyPET systems and closures on one Husky HyCAP system is currently being planned. “A new branch for us is the processing of rPET,” explained Khaled Elalfy. “Nestlé and Pepsi are our current customers, and we are currently in the approval process with Coca-Cola. The topic of rPET is still a nascent one in this country, but it is becoming increasingly important, which is why we are also tapping into this area.” He is referring to a US$25 million investment for the construction of a Starlinger recycling unit with a capacity of 15 t on an area of 50,000m2, which is scheduled to start in 2025. www.newmodernplast.com Khaled Elalfy (right) with Amr Mahdy in front of a Husky HyPET 300"},{"@ID":6 "PETcontents 4 PETplanet Insider Vol. 26 No. 01+02/25 www.petpla.net 01+02/2025 EDITOUR 10 Expansion course in the Middle East - Steady investment by Egyptian plastics converter 12 Label-less bottle in Oman, a first step towards b2b recycling? 14 Closures for Egypt and the entire region - Market leader from Germany in the Middle East 16 Editour, with a difference: Circular Economy Tour 2025 - Key topics: Material savings, energy efficiency, closing the loop & new EU legislation BOTTLE MAKING 18 Joint approach to packaging development and production CAPS / CLOSURES 20 “We do not feel that the market is any quieter” - Interview with Michael Fink, CEO of Z-Moulds 22 PET closures come into their own - Husky’s advances in design, manufacturing and sustainability of caps & closures 26 PET closures for 1881 and beyond - Improving performance, enhancing sustainability 28 Cap recycling takes off - Circularity for polyolefin bottle caps 29 Tethered caps assembly - Highspeed system - all processes integrated 30 Half the space is needed... The CapWatcher Compact by Intravis 32 Ready for tethered solutions - Has Plastik expands portfolio to support customers 33 Improvement of caps and closures - Towards a sustainable and lightweight packaging 34 Automated matching system - Addressing challenges and changes with the “Preforms and Closures” platform MARKET SURVEY 24 Suppliers of resins & additives EVENT PREVIEW 35 CBST 2025 preview 36 Chinaplas 2025 preview, part 1 OUTER PLANET 46 Race Eco Chain - Plastic waste management platform in India BUYER’S GUIDE 40 Get listed! INSIDE TRACK 3 Editorial 4 Contents 6 News 38 PET bottles for beverage + liquid food 39 Patents CAPS & CLOSURES EDITOUR Page 10 Page 18 Page 33 EDITOUR"},{"@ID":11 "9 NEWS PETplanet Insider Vol. 26 No. 01+02/25 www.petpla.net \r \r \r \r \r \r ! \"# \" \r \r \r ! \" \r \" \r \r \t $ \r \r % "},{"@ID":50 "Crystal Thumb‘Up Our extended SportCaps range Biarritz NEW In sport, you never settle for less. That’s why we strive for the perfect closures, also when it comes to sustainability. Many closures, such as Biarritz and Monet, are made from a single material, making them easy to recycle. In addition, our sport closures are easy to handle, have integrated tamper evidence solutions and are suitable for cold, dry, or wet aseptic filling. So take the leap – and opt for more sustainability. NEW Monet Contact us and arrange your line trials now! www.bericap.com New mono-material caps for optimized recyclability Going the extra mile for you"},{"@ID":15 "EDITOUR 13 PETplanet Insider Vol. 26 Barzman, the flagship bottled water brand of International Foods and Beverages LLC, celebrates 20 years of excellence in 2024. Production began in 2004, and Barzman quickly set industry benchmarks with its high-quality water sourced from natural underground wells rich in minerals. The company’s Al Mawaleh facility, launched in 2009, boasts a production capacity of over 130,000 bph. Barzman was the first company in the GCC to introduce 250ml bottles as a sustainable alternative to plastic cups. Committed to quality and innovation, Barzman remains at the forefront of Oman’s water industry. www.abaad.om Mr Eldho Mathew with the classic design of the 250ml bottles and the two label-less bottles. The label-less bottle features flat surfaces around the circumference, similar to hot-fill bottles, and is available in two variants—one with four panels and one with six. These structural features are added during the stretch blow-moulding process. The development took several years, requiring adjustments to preform temperature control and bottle stability. According to Mr. Alnoumani, this innovation is intended to lead the way for bottle-to-bottle recycling, incorporating recycled PET (rPET) and promoting environmental sustainability at every stage of production."},{"@ID":29 "CAPS & CLOSURES 27 PETplanet Insider Vol. 26 No. 01+02/25 www.petpla.net to produce PET caps at commercial scale,” said Origin CEO and Founder Mr John Bissell. The system has since produced caps for commercial customer qualification and has been delivered to Origin’s operations and manufacturing centre in Reed City, Michigan. There it will produce caps throughout 2025 and beyond. Additional CapFormer Systems are expected to come online during 2025 as part of commercial scale up. Announced products, partnerships, and next steps Initial products include the PCO 1881 compliant PET cap and a tethered PET cap, designed to comply with European cap tethering mandates and keep caps connected to bottles. In 2024, the company announced partnerships for the mass production of Origin PET closures with Bachmann Group for Europe and Reed City Group for North America, as well as strategic partnerships with IMDvista and PackSys Global for manufacturing. Looking ahead, Origin expects to make PET caps in a wide variety of formats for not only beverages containers but food containers and others as well, reflecting the company’s mission to enable the world’s transition to sustainable materials. “The first Origin CapFormer System has already made several million PET caps using recycled PET plastic, and we’re just getting started,” said Bissell. “We expect Origin CapFormer Systems to produce caps not only for a diverse array of beverage bottles, but food packaging, medical products – the possibilities are extensive and incredibly exciting.” www.originmaterials.com CAPS & CLOSURES 27 Shall we? %X 7%'1- TEVXRIVWLMT MW JSVIZIV Choose everlasting excellence for your tethered cap production plant. With SACMI ]SYƅPP ƼRH E JYXYVI VIEH] WSPYXMSR XLEXƅW designed to stand the test of time. sacmi.com E N D L E S S I N N O V A T I O N S I N C E 1 9 1 9"},{"@ID":40 "PETplanet Insider Vol. 26 No. 01+02/25 www.petpla.net 38 PETbottles Beverage + Liquid Food Smoothie Meal from Rewe Bio Rewe fills 250 ml of a smoothie meal with various ingredients from controlled organic farming such as apple juice, sour cherry, banana and raspberry pulp in the ‘red’ variant shown in a slim, transparent bottle decorated with a matt printed sleeve label. A slightly opaque lid allows the product colour to be seen from above. www.rewe.de Organic shots from Aldi Süd Aldi Süd is constantly expanding its range of shots with healthy ingredients and in different flavours. In addition to the organic ginger shot from the ‘rio d’oro’ own brand in a transparent bottle containing 150ml, the ‘Nur Nur Natur’ own brand launched in 2023 now also includes a drink labelled as an organic shot with apple, ginger and lemon in a smaller bottle containing 95ml. Both drinks must be kept refrigerated and the labels used indicate the origin and selection of ingredients. A number of organic seals and consumer information are also printed on the labels. www.aldi-sued.de VitaVate with less sugar Consumers are demanding a reduction in added sugar in many drinks. Manufacturers are responding to this and are increasingly offering drinks with less sugar. UniBev GmbH from Stuttgart, Germany, for example, sells several vegan tea drinks based on a strong brewed green tea with different flavours such as hibiscus, prickly pear or multi-fruit vanilla. According to the manufacturer, the drinks contain less sugar - approx. 3 g per 100ml content. The clear bottles contain 500ml, are decorated with a transparent foil label and are sealed with a screw cap with a guarantee band. www.vitavate.de High-protein meal in PET The German branch of the Huel company offers 500 ml of a proteinrich drinkable meal with 26 vitamins and minerals and little sugar under its own name. The vegan, gluten-free and kosher meal contains 35g of protein per bottle. The bottle itself is transparent and consists of 51% recycled material. It has a full-surface sleeve label and the large drinking opening is closed with a screw cap with a safety catch. The eye-catching printing makes it easy to recognise the bottle and brand. www.eu.huel.com"},{"@ID":41 "PATENTS PETpatents www.verpackungspatente.de PETplanet Insider Vol. 26 No. 01+02/25 www.petpla.net 39 Lightweight bottle European Patent No. EP 4353610 A2 Applicant: Société Anonyme des Eaux Minérales d’Evian, Evian-les-Bains (FR) Application date: 10.4.2020 Thin-walled and lightweight container with special base shape. The bottle consists of at least 50% recycled material. Plastic bottle Intern. Patent No. WO 2023 / 287662 A2 Applicant: PepsiCo. Inc., Purchase (US) Application date: 8.7.2022 A plastic bottle is provided with differently shaped grooves, constrictions and surfaces, which are intended to make the bottle more stable against deformation. Variable bottle Intern. Patent No. WO 2024 / 114842 A1 Applicant: Hernán Gomez Mejia, Medellin (CO) Application date: 29.11.2023 The outer sides of a bottle are shaped in such a way that several identical bottles can be stacked in different ways to save space - whether standing or lying down. Coupleable container Intern. Patent No. WO 2024 / 128200 A1 Applicant: Nissei ASB Machine Co. Ltd, Nagaro (JP) Application date: 11.12.2023 Two containers are equipped with features on the rear sides that allow the individual containers to be coupled by twisting them against each other. The containers can be additionally secured using corresponding features on the closure. Improved floor mould Intern. Patent No. WO 2024 / 141556 A1 Applicant: Sidel Participations, Octeville-Sur-Mer (FR) Application date: 27.12.2023 The international application describes an improved variant of the base moulding of a plastic bottle in terms of material composition, material distribution and stability. Plastic bottle with PCR content Intern. Patent No. WO 2024 / 147057 A1 Applicant: CO2PAK, Mt. Eden (NZ) Application date: 22.12.2023 The application is for a PET bottle that has various equalising surfaces in the side wall and base area to absorb the forces that occur during hot filling and subsequent cooling. The bottle has an increased PCR content."},{"@ID":22 "CAPS & CLOSURES 20 PETplanet Insider Vol. 26 No. 01+02/25 www.petpla.net Interview with Michael Fink, CEO of Z-Moulds “We do not feel that the market is any quieter” PETplanet: Dear Mr Fink, z-werkzeugbau became the Z-Group. May I ask you to recapitulate the milestones and how theses enabled Z-Moulds to achieve its leading position in the market? Mr Fink: z-werkzeugbau had three different business units in different market segments 2023: Z-Moulds, in the caps & closure market for high-performance injection moulding systems, Z-Microsystems in the medical sector, specialised in microfluidic products for lab-on-a-chip applications and Z-Prototyping as a specialist in additive manufacturing. In order to offer these three areas their full development potential, these three business units were spun off into their own independent companies. What remained was the Z-Group, as a service provider and parent company. This way the newly established z-moulds GmbH has now independency in orienting and growing in the packaging market. PETplanet: In recent years, for example, the new EU directives on tethered caps have boosted development in the caps mould sector. Since then, the market has become somewhat quieter. Where do you see future development opportunities in cap mould production? Mr Fink: Actually, we do not feel that the market is any quieter. On the one hand, there are still a lot of developments in improving the current tethered solutions and on the other hand, the new requirements came across with new standards for bottle finishes, which will now be adapted in other continents outside of Europe as well. Therefore, there is still lots of movement in the caps & closure market globally. PETplanet: The topic of sustainability plays a major role in the EU directives, as well as in a future-orientated company. What are the three most important components for sustainable business at Z-Moulds? Mr Fink: When it comes to environmental sustainability, our company can certainly be seen as one of the pioneers or early implementers. When we built our new building in 2016, we paid attention to sustainable raw materials and integration into the beautiful natural landscape of Austria from the very beginning. Our ultra-modern automated manufacturing centres fit seamlessly into a pleasant wooden facade. The electricity comes from a photovoltaic system on the roof above. Also simple things like cleverly organised waste management to reduce and recycle is key. We think each simple and small act of reducing carbon footprint counts. PETplanet: This year will once again be a particularly eventful one for the beverage industry - the Drinktec and K trade fairs are of course the big highlights in autumn. But spring will also kick off with Chinaplas for the Chinese market, for example. Where will our readers and friends of PETplanet find Z-Moulds and can you already tell us whether you have any special news in store? Mr Fink: Our exhibition year in 2025 will start with the Plastimagen in Mexico, followed by the Plastico Brasil in São Paulo and Chinaplas in Shenzhen. Then we will participate at two well-known industry conferences, the AMI Plastic Closure Innovations and the PETnology. The Autumn, as mentioned, will end the year with Drinktec, K-Show and also the Gulfood in Dubai. – And yes, of course, we will always be able to display new developments and innovations. PETplanet: Thank you very much for the interview and we are delighted to present the latest innovations from Z-Moulds now: The new 26/22mm GME 30.40 with tethered function Lightweight: Weighing only 1.7 g, the 26/22mm closure is claimed to be the lightest closure in its category on the market. Despite its lightweight design, it offers robustness and can be stored effortlessly in large containers such as octabins. This combination of low weight and high durability makes it a goodsolution for a wide range of applications, says Z-Moulds. Technical design: The sophisticated technical design of the closure ensures it is claimed to outperform comparable substitute products. With a larger opening angle than competitors - particularly compared to products from Z-Moulds - it enhances user-friendliness. Customers benefit from easier handling, providing a real advantage, especially for high-consumption products. Manufacturing technology: The closure is made from high-quality HDPE and is designed for production with moulds ranging from singlecavity up to 128-cavities. It boasts a short cycle time of around 3 s. This efficiency enables high production capacity while maintaining consistent quality. Automated manufacturing centres fit seamlessly into the wooden facade. CAPS & CLOSURES"},{"@ID":1 "No.1+2 2025 www.petpla.net D 51178; ISSN: 1438-9452 PETplanet is read in 159 countries Suppliers of resins and additives MARKETsurvey M A G A Z I N E F O R B O T T L E R S A N D B O T T L E - M A K E R S I N T H E A M E R I C A S , A S I A , E U R O P E A N D A L L A R O U N D T H E P L A N E T 03 . 02 . 25 CAPS & CLOSURES EDITOUR Page 20 Page 10 Page 24"},{"@ID":34 "CAPS & CLOSURES 32 PETplanet Insider Vol. 26 No. 01+02/25 www.petpla.net Has Plastik expands portfolio to support customers Ready for tethered solutions Has Plastik has now completed its product range with tethered solutions covering the principal sizes required by the beverage industry. Although there is no regulation requiring this practice in its home country Turkey, Has Plastik has completed its investments on tethered solutions with the idea of supporting its European business partners and customers. 29-25, 1881, 26mm GME30.40 cap types. Has Plastik is also able to supply customers with untethered as well as tethered versions of the caps. This flexibility will allow customers to switch easily to the tethered version of the cap when required by local regulations. All the sizes (29-2, 1881, GME30.40) are available as untethered, tethered (standard hinge design) or tethered (premium hinge designs). The closures are equipped with active hinge mechanisms for user-friendly opening and closing and its performance is already approved by major multinational key market players. Additionally, Has Plastik has also increased its capability to print the top of the large caps for brand identification including HOD caps, 38mm, 48mm PET bottle caps. The company has also successfully laser-marked QR codes on the interior of the closures for product offers, as well as emojis and designs inside the caps. www.hasplastik.com CAPS & CLOSURES www.prseventeurope.com 2025 Incorporating Halls 1 & 5, Rai, Amsterdam The world’s largest event dedicated to plastics recycling Organised by REGISTER TODAY for your entry badge at prseventeurope.com Registration is FREE until 1st March 2025 (€50 thereafter) Tethered caps were ready by the end of 2023 as speed has always been a key element in the company’s service to its customers. The tethered portfolio currently consists of"},{"@ID":10 "8 NEWS PETplanet Insider Vol. 26 No. 01+02/25 www.petpla.net SGT Group acquires Axium Packaging SGT Group, a leading manufacturer of PET preforms and food-grade rPET based in Rezé, Loire-Atlantique, France, announces the acquisition of Axium Packaging. This strategic move is intended to strengthen SGT’s position in the European market and to open new horizons for growth and innovation. Axium Packaging has established itself as a leading expert in the injection and blow moulding of bottles, jars, and caps. With six entities and 385 employees, the company achieved a turnover of EUR 76 million in 2024. Axium serves primarily the food and beverage sectors, as well as the health, hygiene, beauty, and household products markets. With production facilities in France, the Czech Republic, Italy, and Germany, this acquisition is claimed to provide SGT Group with enhanced industrial capabilities and a broader technological offering, all while maintaining a shared commitment to eco-responsibility. The acquisition of Axium Packaging is intended to grant SGT Group access to new expertise, particularly in injection and extrusion blow moulding, while expanding its product portfolio. This strategic complementarity is claimed to strengthen operational synergies, consolidate the group’s presence in the European market, and to create new opportunities in sectors such as cosmetics, hygiene, and beauty. In a context of increasing environmental and regulatory challenges, this alliance underscores SGT Group’s dedication to promoting rPET packaging solutions, thereby reducing its carbon footprint. Axium Packaging complements this vision with eco-designed products and a sustainability strategy aligned with international standards, such as ISO 26000 and SMETA. www.sgt-pet.com Alpla: successful 2024 financial year Alpla continued its growth trajectory in 2024 with new products, plants, business areas, acquisitions and a focus on training skilled workers. The international packaging and recycling specialist increased its turnover from EUR 4.7 billion to EUR 4.9 billion and grew its workforce to 24,350 employees. Alpla is broadening its targets for the recycling sector. The company plans to double its output recycling capacity to 700,000 t of recycled material by 2030. The annual turnover of EUR 4.9 billion represents an increase of 4 per cent compared to 2023. There has been significant growth in the number of sites and employees. Alpla has reached the 200-plant mark and created more than a thousand new jobs through new business areas, acquisitions and training programmes. A total of 24,350 employees work at 200 locations in 46 countries. Growth markets and innovation In addition to the strong growth markets in South America, Africa and the Middle East, demand in North and Central America also recovered in 2024. Alpla is also experiencing an upward trend in Europe. However, the market environment remains chal lenging. “Increasing EU regulation is creating a lot of work and weakening our international competitiveness. This is compounded by high labour costs in some countries. We are countering this with increased efficiency, new products and our leading role in recycling,” says CEO Philipp Lehner. The markets in the Asia-Pacific region offer huge potential. With the upcoming opening of a new plant in Thailand in 2025, Alpla is setting the course for the future here. Recycling: doubling capacity by 2030 The company invests at least EUR 50 million a year in recycling and is on track to achieve its goal of using at least 25 per cent recycled material in its packaging by 2025 and will significantly increase its capacity. The Alplarecycling division produces PET and HDPE recycled materials (rPET and rHDPE) at 13 plants in nine countries. The aim is to double the current installed and planned output capacity of 350,000 t by 2030. As a system provider for bottles and closures, combined with the Alplarecycling division, which has existed since 2023, the company covers numerous industries and markets. In 2024, the new Alplainject division strengthened the injection moulding line. Alplapharma was expanded in 2024 with the integration of Heinlein Plastik-Technik into the group. Alplaindustrial is another division for large-volume packaging. The portfolio was enriched with new products such as the PET wine bottle. www.alpla.com Andrea Grandi is the new General Manager of the Sacmi Group Andrea Grandi succeeds Mau r o Fenzi as General Ma n a g e r o f t h e Sacmi Group, following the conclusion of Fenz i ’s tenure on December 31, 2024. A 49-year-old electronics engineer, Grandi has been with Sacmi almost 25 years. During that time, he has displayed outstanding technical and managerial skills, most notably in mechatronics and industrial automation, says the company. His first 18 years were spent in the Special Pressing Business Unit and as the Metals PU Manager. In 2020, he became General Manager of the Advanced Technologies BU. Over the last three years he has held the key roles of Operations and Plant Director and, subsequently, Corporate Product Supply Manager, demonstrating a talent for operational management and innovation development. In addition to his positions at Sacmi, Andrea Grandi is a member of the Forming Committee of UCIMU (Association of Italian Machine Tool, Robot and Automation Manufacturers). He was also formerly on the Technical Committee of AIM, the Italian Metallurgy Association. www.sacmi.com"},{"@ID":14 "EDITOUR PETplanet Insider Vol. 26 No. 01+02/25 www.petpla.net 12 Label-less bottle in Oman, a first step towards b2b recycling? by Alexander Büchler Barzman, headquartered in Muscat, is taking a significant step toward sustainability with the introduction of its innovative “label-less bottle.” Although b2b recycling has yet to gain much traction in the region, Barzman is setting a bold example with this initiative. We spoke with Eldho Mathew, General Manager of Barzman, about this new development, their production processes, and the inhouse pallet logistics system that powers the operation. September 19, 2024 We met: Eldho Mathew, Managing Director of Barzman. Mr Saif Mohamad Khatrosh Alnoumani, Chairman of International Foods and Beverages LLC Founded in October 2003 near the village of Barzman in the Sharqiyah Governorate, about 200km from Muscat, Barzman initially focused on bottled water and other food products. The company expanded significantly with the opening of a second production facility in Muscat in 2009. Eldho Mathew, who has been with the company for over 20 years, has played a pivotal role in its success. In 2014, Barzman reached a turning point by switching to a short neck design with a 29/25mm opening, optimising bottle weight by 10-20%. The company also installed a Sidel Matrix Combi 10 production line with a capacity of 22,000 bph. Barzman’s flagship product, developed by its R&D, is the 250ml still water bottle, produced alongside formats up to 1.5 l. The production line employs a classic block system from Sidel, connecting the stretch blow-moulding machine directly to the filler. After filling, bottles are labelled and shrinkwrapped in packs of 24 and 30. Following this success, Barzman added an identical production line just a year later, boosting daily output to over 40,000 bph. The company also developed its own pallet logistics system, which allows 28 pallets to be loaded into lorry trailers in just two minutes. Barzman’s water source is a natural aquifer, rich in minerals, filtered and purified using specialised equipment. Five years ago, Barzman tripled its production capacity with the installation of a new Krones bottling line, capable of producing 81,000 bph. This line includes an integrated labelling station and inspection processes for fill levels, caps, and labels, while also expanding the pallet logistics system. Label-less bottle Despite limited waste separation and PET bottle collection initiatives in the Gulf States, Eldho Mathew has prioritised the sustainability of PET bottles. Barzman’s lightweight bottles are seen as a more energy-efficient alternative to cans or glass. Looking toward the future, Barzman has introduced the “label-less bottle,” a bottle free of labels and adhesives, simplifying the recycling process. The new bottle was unveiled on February 15, 2024 by Chairman Saif Mohamad Khatrosh Alnoumani at Barzman’s Muscat facility. EDITOUR"},{"@ID":36 "CAPS & CLOSURES 34 PETplanet Insider Vol. 26 No. 01+02/25 www.petpla.net Addressing challenges and changes with the “Preforms and Closures” platform Automated matching system The plastics industry is evolving rapidly, driven by tightening regulations and increasing demand for sustainability. Flexblow’s “Preforms and Closures” platform offers a comprehensive solution, connecting market needs with efficient and sustainable practices. “While our state-of-the-art machinery ensures efficient bottle production, customers often struggle to source compatible preforms, closures, and other components. Recognising this gap, we created the ‘Preforms and Closures’ platform to extend the value of our solutions,” says FlexBlow. The “Preforms and Closures” platform combines advanced machinery with a vast selection of raw materials to streamline the production process. Further, it provides access to a vast supplier database where products can be filtered based on specific needs, from technical specifications to sustainability criteria. The platform’s automated matching system connects preforms to bottle production needs, analysing parameters such as neck standards, wall thickness, and material composition. This system ensures that 99% of enquiries result in tailored solutions —whether selecting the right preform or finding compatible closures or handles. This approach aims to save time, reduce errors, and guarantee that clients receive optimised results for their production challenges. In a highly regulated industry, the platform also addresses regional sustainability requirements. For instance, Europe mandates PET bottles to contain at least 25% recycled plastic by 2025, increasing to 30% by 2030. Meanwhile, regulations in the U.S. and Asia present unique challenges. By actively promoting products made from rPET and other recyclable materials, the platform simplifies the transition to a circular economy. Flexblow sees one of the platform’s key strengths in its transparency and data protection: sensitive supplier information, such as company names or technical drawings, remains confidential until a client’s enquiry is confirmed. This ensures secure and trustworthy collaboration between parties. The platform also prioritises sustainability by actively promoting products made from rPET and other recyclable materials. “By integrating these solutions, it simplifies the transition to sustainable practices while helping clients meet modern market demands,” says Flexblow. www.preformsandclosures.com ABSOLUTE MEASUREMENT SOLUTIONS Access our exclusive guidebook to find out more Industrial Physics is lifting the lid on PET bottle testing techniques. How can you ensure the absolute quality of your beverage packaging? Featuring real world data CAPS & CLOSURES"},{"@ID":4 "CAPS & CLOSURES 31 PETplanet Insider Vol. 26 No. 01+02/25 www.petpla.net Marius Pötting. As a result, the system now has a footprint of just 2.4m² and therefore offers nearly the same inspection performance in half the space of a conventional setup. Technical features of the CapWatcher Compact The CapWatcher Compact offers numerous technical functions for inline plastic closure inspection: Integrated hopper and conveyor technology: The integrated hopper offers a capacity of up to 140 l. The feeder uses the familiar waterfall principle to efficiently transport closures into the inspection section. Comprehensive quality assurance: In addition to the standard modules for inner and outer closure inspection, unique and market-proven modules for micro hole inspection and cavity number reading are implemented. The top wall inspection (e.g. for inspecting prints for contamination etc.) is also available as an option. High speed: With an inspection performance of up to 40 closures per second, the system meets high-speed requirements. Second ejector: Despite the limited space, a second ejector is integrated, which can be used for sorting out quality shots or blacklisting, for example. Wide product range: The CapWatcher Compact is designed for the inspection of common CSD closures as well as tethered caps. Product-specific settings: The electrically adjustable jet height is saved for each product, and it automatically adjusts when changing products. Fault and jam detection: The system automatically recognises (by implemented sensors), when faulty moulded closures become jammed, and localises the position precisely. This ensures uninterrupted and fluent production. Ease of maintenance: Despite the compact construction, the design allows easy access to all components thanks to doors on all sides. To complete the downstream equipment, customers only need a cooling conveyor and a packaging unit in addition to the CapWatcher Compact. However, Intravis can also supply these elements as a turnkey supplier. Solution for modern production requirements With its compact design, the CapWatcher Compact addresses one of the most urgent problems in the industry: Limited space in production halls. Particularly in Europe, attempts are being made to produce more and more in the same or smaller space. With the integration of sorting, feeding and inspection in one unit, Intravis now offers a space-saving and efficient solution. “The CapWatcher Compact shows how important it is to adapt flexibly to the needs of customers. It is yet another example of how we at Intravis see ourselves as a partner to our customers. We are always ready to take on new challenges. With the CapWatcher Compact, we are proud that we have created again great value for our customers as well as our industry in general,” summarises Marius Pötting. www.intravis.com Internal accessibility"},{"@ID":45 "Crystal Thumb‘Up Our extended SportCaps range Biarritz NEW In sport, you never settle for less. That’s why we strive for the perfect closures, also when it comes to sustainability. Many closures, such as Biarritz and Monet, are made from a single material, making them easy to recycle. In addition, our sport closures are easy to handle, have integrated tamper evidence solutions and are suitable for cold, dry, or wet aseptic filling. So take the leap – and opt for more sustainability. NEW Monet Contact us and arrange your line trials now! www.bericap.com New mono-material caps for optimized recyclability Going the extra mile for you"},{"@ID":43 "EDITOUR PETplanet Insider Vol. 26 No. 01+02/25 www.petpla.net 16 Key topics: Material savings, energy effi ciency, closing the loop & new EU legislation Editour, with a difference: Circular Economy Tour 2025 A new year means a new Editour for the PETplanet Insider team. However, this year is a little different: yes, there will be market analyses, we will visit companies and report on technical innovations. But this time our Editour has a specific theme: the Circular Economy. As this topic is particularly relevant for countries connected to the European Union, these will be our Editour’s 2025 focus. The circular economy is a broad term that is easy to define at first glance, but is very multifaceted in its implementation. The PETplanet Insider team has therefore selected three parameters to serve as the cornerstones of our analyses during our on-site visits. According to our research, ‘material savings’, ‘energy efficiency’ and ‘closing the loop’ are the most important, tangible parameters that are named when it comes to the sustainable production and development of a product or to processes within a company. With our Editour 2025, we want to show how productive, creative and innovative our industry is. Beyond highlighting the economic opportunities within the circular economy, we also want to emphasise the ecological successes that can be achieved sustainably. We will be talking to our interview partners - on site at their premises - about the challenges they face, the techniques they use and their real benefits. The Editour’s focus includes: Material: Lightweighting bottles, closures, labels, and secondary packaging; exploring alternative materials; minimising production waste; and optimising supply chains. Energy: Enhancing the efficiency of compressors and heating systems, reducing CO2 footprints, and exploring renewable energy sources. Closing the Loop: Promoting B2B recycling, design for recycling, and fostering circular economy models and partnerships to increase the availability of high-quality rPET. Some courageous people are leading the way and we believe that this courage must be rewarded, especially in these times: we would like to take this opportunity to thank our sponsors, who have been with us for many years and who continue to demonstrate their innovative strength through new developments. New EU regulations In line with our Editour, 2025 will bring a number of changes for the packaging industry. Here is a small selection: In 2025, the implementation of the Single-Use Plastics Directive, which stipulates a 25% recycled content in PET beverage bottles, will accelerate the transition to a circular economy and bring about fundamental changes in the market for both new and recycled PET. The European Packaging and Packaging Waste Regulation (PPWR) is expected to come into force in mid-2026 after being formally adopted by the EU Council in December 2024. The regulation sets out new requirements for the design of packaging and the use of materials. The PPWR regulations include reducing the weight and volume of packaging, minimising hazardous substances in packaging materials and promoting the circular economy through organic recycling. But let’s take a look outside the box - there’s a lot more to come. The Corporate Sustainability Reporting Directive for example. It is one of the most important sustainability regulations in the EU. The directive, which is the successor to and extension of the Non-Financial Reporting Directive (NFRD), has applied to public interest entities since 2024. It should actually apply to all other large companies under accounting law from 2025; these are obliged to report on the 2025 financial year in 2026. Under accounting law, large companies are defined as companies that either have a turnover of more than EUR 50 million, a balance sheet total of more than EUR 25 million or employ more than 250 people (two of three criteria must be met). CBAM 2025: EU measurement method becomes mandatory and register is live The Carbon Border Adjustment Mechanism (CBAM) is an EU measure that has been in force since October 1, 2023. The aim is to minimise the risk of greenhouse gas emissions being shifted to third countries (carbon leakage). With the CBAM, the EU wants to ensure that the same CO2 price is paid for the greenhouse gas emissions of certain imported goods as in the European Emissions Trading System (EU ETS). The CBAM applies to direct production-related (grey) emissions from certain imported goods such as cement, electricity, fertilisers, hydrogen, iron and steel and aluminium, as well as other upstream and downstream products. Companies have had to submit a CBAM report to the EU every quarter since 2024. Since August 2024, the use of default values for calculating emissions is no longer permitted; since then, companies have had to collect and use primary data from the supply chain. What is new from 2025 is that the EU method for calculating emissions will be mandatory. Hitherto, companies have been allowed to determine emissions values in different ways. For example, companies were previously permitted to determine their EDITOUR Sponsors to date:"},{"@ID":39 "37 EVENT PREVIEW PETplanet Insider Vol. 26 No. 01+02/25 www.petpla.net Krones Recycling: New compact configuration available From bales to food-grade flakes: the portfolio of Krones Recycling GmbH, based in Flensburg, Germany, covers the entire plastics recycling process. The modules for grinding, washing, sorting and decontamination are available both individually and as complete recycling systems. The heart of every Krones recycling system is the washing module, which has a major influence on the quality of the flakes. In addition to gentle processing for low-fines production, the machines and lines are also designed for efficient and sustainable use of energy and resources. A new, more compact configuration of this washing module now offers customers a recycling process that is just as gentle on materials and resources. Made of the usual high-quality stainless-steel, but with a significantly smaller footprint at capacities of 2 to 3mt/h - ideal for sites with less available space or for retrofitting. This configuration produces an even lower amount of fines. As with other configurations, the module can be used flexibly for both PET and PO recycling. Thanks to consistently high wash quality standards, it can also be used for bottle-to-bottle processes. The global service and sales network of Krones Recycling and Krones AG ensures local support. At Chinaplas 2025, Krones Recycling will be showcasing this innovation for the first time, and inviting visitors to the German Pavilion to discuss the compact configuration and other innovations in plastics recycling. www.krones.com Swiss quality for PET preform production Following its successful participation in previous years, Otto Hofstetter AG will again be exhibiting at Chinaplas 2025. The Swiss family-owned company is well known in the development and manufacture of PET preform moulds. In over forty years, the company has built up extensive expertise in PET preform processes and technology. The experts at the high performance mouldmaker share their knowledge throughout the entire production process, from the initial idea, through preform design and sampling, to mould manufacture and final product quality assurance. Thanks to this process, every customer can benefit from an efficient design process, producing high-quality, cost-effective PET preforms and realising long-term savings in high-volume production, says the company. At the trade show, Otto Hofstetter AG will present its complete portfolio of high-quality injection moulds to industry professionals. This includes moulds for PET preforms from 2 to 192 cavities - for both top-entry and side-entry systems. The Swiss manufacturer also designs and builds moulds for medical applications, thin-wall packaging, cartridges and in-mould labelling solutions. Sister company Otto Systems, which specialises in special applications in the world of PET preforms, offers the PET Series and HOD Series turnkey production systems with clamping forces of 160 and 240 t. The systems are claimed to meet high requirements for quality and energy efficiency. www.otto-hofstetter.swiss Krones Hall 10 Booth W21 Otto Hofstetter Hall 10 Booth K41 144 cav. side-entry mould"},{"@ID":49 "Circular Economy Editour Europe 2025 focusing on The worldwide round trip with Editour Closing the Loop Energy Efficiency Material Savings Be part of the story. Interested in being interviewed on site? Reach out to us! Scan for more Infos Sponsors to date"},{"@ID":38 "36 EVENT PREVIEW PETplanet Insider Vol. 26 No. 01+02/25 www.petpla.net EVENTpreview Chinaplas 2025 Chinaplas, Asia’s leading trade fair for the plastics and rubber industries, is set to return from April 15–18, 2025, at the Shenzhen World Exhibition & Convention Center in Shenzhen, China. The event serves as a hub for cutting-edge solutions, technology exchanges, and business networking, offering opportunities for information and collaboration. The show is exclusively sponsored by the Europe’s Association for Plastics and Rubber Machinery Manufacturers (Euromap) in China. The 2025 edition will feature over 4,000 prominent exhibitors from around the globe, spread across an expansive exhibition area exceeding 380,000m2. Attendees wi l l have access to nine dedicated country and regional pavilions, alongside 17 specialised theme zones. These zones will showcase a wide array of technologies and materials, including injection moulding, extrusion machinery, 3D printing, recycling innovations, smart manufacturing solutions, bioplastics, composites, high-performance materials, and thermoplastic elastomers and rubber. Circular economy & smart manufacturing The concept of a circular economy will continue to be one of the key focuses of the exhibition, highlighting the industry’s commitment to sustainability and resource efficiency. By emphasising the reuse of resources to minimise waste and stimulate economic growth, the exhibition will demonstrate a clear dedication to addressing environmental challenges. Chinaplas 2025 will feature three thematic zones, namely Recycled Plastics, Bioplastics, and Recycling Technology, covering around 16,000 m2 and gathering leading material suppliers and recycling machine manufacturers. Live demonstrations of two recycling production lines, focusing on ‘Bottle-to-bottle closed-loop recycling’ and ‘Turning PE waste into treasure’ will unveil advanced equipment technology and high-value utilisation solutions within the plastic recycling sector. Chinaplas x CPRJ will host the 6th edition Plastics Recycling & Circular Economy Conference & Showcase in Shenzhen, gathering global stakeholders to delve into the latest recycling trends. Collaborating with the China Packaging Federation, Chinaplas will first introduce the Sustainable Plastics Packaging Networking Forum, connecting industry experts and exploring sustainable packaging solutions worldwide. Smart manufacturing, encompassing technologies like automation, AI and IoT integration, enhances manufacturing processes and revolutionises industries by boosting efficiency, productivity, and flexibility. At the trade fair, an extensive range of smart manufacturing solutions and machinery will be unveiled in the Injection Molding Solutions Zone and Injection Molding and Smart Manufacturing Solutions Zone, covering a substantial 53,000 m2. Leading global companies will demonstrate digitalisation, ensuring sustainable growth and competitive advantages in a rapidly evolving digital landscape. www.chinaplasonline.com Reverse dryer Pegaso Industries, the holding company based in Borgoricco, Italy, and encompassing Plastic Systems, PET Solutions, Blauwer, Ergomec, and Steel Systems will be exhibiting its latest technologies inside the Italian pavilion. PET Solutions will be highlighting onstand the DR.RE Series New Generation Reverse Dryer. The new generation dehumidifier is claimed to be a cutting-edge solution that brings significant improvements to the quality of rPET materials. It boasts a 47% increase in filtration capacity, thanks to its dual filter system, which also optimises maintenance operations. Additionally, the dehumidifier achieves a 15% reduction in energy consumption due to their new patented process design, with fans positioned after the drying towers. The larger size of the exchanger provides a 45% increase in cooling capacity. Furthermore, in rPET processing, the dehumidifier achieves an overall energy recovery of 25%. Thanks to its features, including a significant increase in the number of molecular sieves within the process towers, it is possible that the need for an oil condenser can be eliminated, resulting in additional energy savings in the overall system consumption, says the company. www.petsolutions.it Pegaso Industries Hall 10 Booth G61"},{"@ID":47 "BOTTLE MAKING 18 PETplanet Insider Vol. 26 No. 01+02/25 www.petpla.net Joint approach to packaging development and production The beverage industry is highly competitive. To succeed, companies must produce their drinks in a clean and cost-effective way. But that’s not enough. With so many brands vying for attention, standing out on the shelf is essential. That’s where Sipa comes in providing a design service that helps beverage producers achieve those goals. A recent example is their work with Beysu an important natural spring water producer in Turkey where they also installed different Sincro Bloc systems, enabling them to produce the brand new bottle family. The Beysu plant, which is operated by Konya Suki Enerji Yatirim San. VE TİC. A.Ş., was designed and built to offer high-quality natural spring water to consumers. The water is bottled at the source in the Doğanbey district of Beyşehir. Beysu sought to optimise its production line with a focus on efficiency, hygiene and sustainability, and partnered with Sipa to implement a comprehensive solution tailored to their specific needs. Sipa worked closely with Beysu to develop a range of new bottle formats that would enable them to meet their market demands while optimising material usage and performance. Three immediate objectives were identified on order to achieve the company’s goals: lightweighting, format diversification and performance optimisation. Sipa’s experience in lightweighting hepls Beysu to create bottles that minimised material consumption and consequent environmental impact, without compromising bottle strength or their aesthetics. Sipa also supported Beysu to develop a wide range of bottle formats to cater for different consumer preferences, products and market segments. It now offers water in 250, 330 and 500ml, 1l, 1.5 l and 5 l formats. Sipa’s design tools and simulations, employed over many years and across a wide range of markets, including bottled water, helped to speed up development of bottles that would meet Beysu’s performance requirements for top-load strength, carbonation retention and overall durability. Sincro Bloc: the heart of efficient and hygienic production Beysu’s new production line consists of two Sincro Bloc systems, each of which integrate blow moulding, filling and capping into a single monobloc unit. Sipa says that integrating these processes eliminates unnecessary steps and reduces bottle handling, leading to faster production speeds, lower labour costs and therefore greater efficiency and profitability. Beysu implemented two types of Sincro Blocs: the Sincro Bloc R (for rotary) and Sincro Bloc L (for linear) configurations, in order to accommodate their array of bottle formats and production needs. High-speed production for several bottle formats Beysu’s Sincro Bloc R line features the Xtra 16 rotary blow moulding machine, synchronised with a filler equipped with 60 electronic filling valves and 20 capping valves. This configuration allows for highspeed production across a range of bottle sizes. Up to 48,000 bph can be produced in 250, 330 or 500ml formats. Alternatively, the machine can produce 34,000 bph for 1 l bottles or 31,000 bph for 1.5 l bottles. Beysu’s 5 l bottles are produced on the Sincro Bloc L system, which incorporates the SFL BIG6 linear blow moulding machine synchronised with a filler equipped with 16 electronic filling valves and six capping valves. This configuration achieves a production speed of 6,600 bph for the 5 l format. Xtra rotary blow moulding machine The Xtra rotary blow moulding machine used in the Sincro Bloc R"},{"@ID":21 "BOTTLE MAKING 19 PETplanet Insider Vol. 26 No. 01+02/25 www.petpla.net system provides exceptional output, according to Sipa, as demonstrated by the productin speeds it achieves in operation. The advanced technology incorprated in the machinery help to optimise energy consumption, thus contributing to lower operating costs and reducing the environmental impact of the factory. The Xtra is designed for easy operation and maintenance, simplifying production processes for Beysu’s factory floor operators. SFL 6 performance linear blow moulding machine The SFL BIG 6 linear blow moulding machine, which is also integrated into the Sincro Bloc L system, offers real versatility. It can produce the full range of the company’s bottle sizes, including the 5 l format, with precision and efficiency. Its linear design offers a spaceefficient solution within the production facility. Sipa says that the SFL Big 6 linear blow moulding machine delivers consistent and reliable performance, leading to depeandable output of highquality bottles. The collaboration between Sipa and Beysu demonstrates how innovative technology and expert, experienced support can help beverage producers achieve their production and sales objectives. By combining Sincro Bloc systems with advanced blow moulding machines, Beysu is happy that it has created a highly efficient, hygienic and flexible production line that meets its current needs and positions it for future growth www.sipasolutions.com"},{"@ID":3 "No.1+2 2025 www.petpla.net D 51178; ISSN: 1438-9452 PETplanet is read in 159 countries Suppliers of resins and additives MARKETsurvey M A G A Z I N E F O R B O T T L E R S A N D B O T T L E - M A K E R S I N T H E A M E R I C A S , A S I A , E U R O P E A N D A L L A R O U N D T H E P L A N E T 03 . 02 . 25 CAPS & CLOSURES EDITOUR Page 20 Page 10 Page 24"},{"@ID":17 "CAPS & CLOSURES 33 PETplanet Insider Vol. 26 No. 01+02/25 www.petpla.net Towards a sustainable and lightweight packaging Improvement of caps and closures In the packaging world, innovation is the key to overcoming environmental challenges and meeting the growing market demand for sustainability. One of the most dynamic sectors is caps and closures: here, the quest for lighter solutions with lower environmental impact is transforming the manufacturing landscape. CAPS & CLOSURES Sustainable caps: The new frontier of biodegradability In recent years, industry has witnessed the emergence of cellulose caps, an alternative to traditional plastic materials: a clear response to the growing demand for eco-friendly packaging. Alongside such developments, PET caps are also gaining ground. These present some serious challenges, one being that their properties differ from those of traditional materials like HDPE. Hence Sacmi’s ongoing research to optimise PET cap performance, which involves developing technologies that improve the material’s efficiency and sealing qualities while staying committed to more sustainable packaging. Lightweighting: A strategy to reduce environmental impact Another key aspect of cap innovation is lightweighting, which allows significant savings in terms of both materials and costs. Weight reduction, in fact, means less plastic is used and, consequently, lower CO2 emissions during production and transport. This trend towards lighter caps aligns perfectly with a burgeoning demand for solutions that are ecological and sustainable. Preforms and closures: An integrated system for more efficient packaging This integration between caps and preforms isn’t just a matter of production efficiency: it’s also a response to new challenges posed by an eversharper focus on quality and sustainability. Lightweight preforms and advanced closures merge in a production cycle that aims to maximise efficiency, reduce waste, and cut energy and resource consumption. Sustainability is the future of packaging The packaging industry is undergoing far-reaching changes, with innovation driving it towards increasingly light, sustainable products. Biodegradable cellulose caps, lightweight PET caps and advanced preform manufacturing technologies are just some of the responses to the ecological issues of our time. The goal is clear: lower environmental impact, optimised production processes and a better consumer experience. In the near future, sustainability won’t just be an ‘added value’, it’ll be a must. And the caps and closures industry will be spearheading this green revolution, with cutting-edge solutions that promise to change the very concept of packaging. www.sacmi.com Leo"},{"@ID":24 "CAPS & CLOSURES 22 PETplanet Insider Vol. 26 No. 01+02/25 www.petpla.net Husky’s advances in design, manufacturing and sustainability of caps & closures PET closures come into their own Based on an article by Michael White, Director of Business Development, Beverage Closures Beverage closures are integral to the sustainability of beverage packaging, influencing material usage, recyclability, and consumer experience. Husky Technologies, known for its injection moulding systems and services, has focused on enhancing sustainability in closures through three primary strategies: material light-weighting, tethered closures, and the development of PET closures. Material light-weighting The light-weighting topic is straightforward: remove as much resin from specific closure features without negatively impacting the closure performance or the resulting user experience. A lower part weight lowers the raw material cost per piece and can enhance manufacturing productivity (lower cycle time). Husky makes extensive use of mechanical and melt flow simulation tools, known as finite element analysis (FEA), to develop its closure portfolio. The process begins by breaking the closure down into its specific elements (see Figure 1). The following step focuses on material removal from a specific feature. This light-weighting can include weight removal solely or weight removal and geometry changes. New feature proposals are then rigorously tested through running simulations to predict the performance outcome. This is an iterative approach. This methodology is applied to all closure features until the performance and flow criteria are satisfied. Husky applies this methodology to all its closure designs, achieving key benefits such as faster time-to-market, optimal balance between weight and performance, and reduced development costs. Simulation tools predict how much material can be removed from each feature without negatively impacting performance and usability. Tethered closures Husky has developed an intuitive tethering system. This solution is availCAPS & CLOSURES Figure 1: A typical 29/25 still water closure (divided into its fundamental elements) able for all industry standard (Cetie/ ISBT) neck finish types in the water, CSD, and JSDT beverage segments. To ensure a positive consumer experience, tactile and audible responses (“click”) are incorporated into the design to provide immediate consumer feedback on when the shell is locked into position. Moulding complex tethering geometry is possible with the moulded in bridge approach. The tethered features (arm, flap, and hook) are created using mould slides that form the tethering system (see Figure 2). The slides maximise design freedom and avoid any post mould operations (scoring) of the tamper evident (TE) band and"},{"@ID":26 "MARKET SURVEY 24 PETplanet Insider Vol. 26 No. 01+02/25 www.petpla.net 01+02/2025 MARKETsurvey Suppliers of resins & additives There is rapidly increasing demand for packaging materials that give even greater protection to their contents. Functional additives and resins are an important technology to fulfil this demand for more product protection and recyclability. A functional additive modifies the properties of packaging to impart desirable or beneficial functions. That is why we won’t stop a well-established tradition in opening our market surveys overview in 2025 with suppliers of resins and additives. Please find here the news of the companies: Avient, Repi Group, Sukano AG, Köksan, Neo Group, Campine, Reliance Industries and Novapet, S.A. Although the publishers have made every eff ort to ensure that the information in this survey is up to date, no claims are made regarding completeness or accuracy. Resins & additives Cap manufacturer & cap inspection Cap systems & cap moulds Preform production & inspection Preform systems & moulds Two stage SBM machinery Filling equipment Compressors Shrinkfilm & palletising machinery Recycling machinery Additives Company name Sukano AG Repi Group Avient Corporation Campine nv. Postal address Telephone number Web site address Contact name Function Direct telephone number E-Mail Chaltenbodenstrasse 23, 8834 Schindellegi, Switzerland +41 44 787 57 77 www.sukano.com +41 44 787 57 77 [email protected] Via P. Lucchini, 2, 6900 Lugano, Switzerland +39 0331 8195 11 www.repi.com +41 91 91 03 710 [email protected] 33587 Walker Road Avon Lake, 44012 OH, USA +1 440 930 1000 www.avient.com Mr Marco Schäfer Marketing EMEA +49 4102 487 158 [email protected] Nijverheidsstraat 2, 2340 Beerse, Belgium +32 14601511 www.campine.com Ms Rien Repriels Product Manager +32 1460 1624 [email protected] Additives and Colours for PET Liquid colours Yes Yes Microgranule colours Yes Yes Masterbatch colours Yes Yes UV protection additive (solid) Yes Yes UV protection additive (liquid) Yes Yes AA reduction (solid) Yes Yes AA reduction (liquid) Yes Yes Oxygen scavenger (solid) Yes Yes Oxygen scavenger (liquid) No IV Enhancer Yes Yes Yes Reheating Yes Yes Blowing additive Yes Yes Yes Slipping agent Yes Yes Yes Other PET additives: Antifog, antimicrobial, antistatic, antioxidant, compatibiliser, voiding agent, optical brightener, nucleating agent, matting agent, melt viscosity enhancer, mobility aid, mould release, slip/antiblock, light diffusor, impact modifi er, infrared, fl ame retardant, foaming agent, plasticiser, processing aid, NIR-detectable colours and blacks, light barrier for UHT and ESL milk. Sukano is a distributor of ocean-bound rPET. Anti yellow, optical brightener, heat stabiliser for PET, frost effect, PET stabilisers, recycing additives. Recycling-friendly toners, special effects, matting agent, slip additives, NIR black, light blocking additive for UHT milk bottles. Catalyst for Solid State Polycondensation; Campine CD, Campine CS, Campine CB: All products can be delivered with or without MEG (Mono Ethylene Glycol) as wetting agent. The purpose of the wetting agent is to make the catalyst powder dustfree."},{"@ID":27 "MARKET SURVEY 25 PETplanet Insider Vol. 26 No. 01+02/25 www.petpla.net Resins Company name Novapet, S.A. Köksan PET Packaging Industry Neo Group Reliance Industries Ltd Postal address Telephone number Web site address Contact name Function Direct telephone number E-Mail P° Independencia, 21, 3°, PC 50001, Zaragoza, Spain +34 976 216129 www.novapet.es Mr Ricardo Monfi l Head of Polymers Division +34 976 216129 rmonfi [email protected] 4.Organize Sanayi Böglesi 83422 Nolu Cadde No: 10 Şehitkamil, Gaziantep, Turkey +90 342 357 03 30 www.koksan.com Mr Serhat Tümer Board Member +90 532 696 55 86 [email protected] Industrijos St. 2, Rimkai, Dovilai eld., LT-95346 Klaipėda district, Lithuania +37 0464 66 710 www.neogroup.eu Mr Gediminas Paulauskas Sales Manager +37 046466 710 Building 8B, Reliance Corporate Park, Ghansoli, Navi Mumbai 400701, India +91 22 79670000 www.ril.com Mr Bharat B Mehta VP Marketing +917710022861 [email protected] RESINS 1. Brand name of the resins NovaPET K084 - K080 - K076 NeoPET Virgin PET \"Relpet\", rPET \"Relpet Green\" 2. IV Range 0.76 - 0.80, 0.84 0.56 - 0.82 0.59 - 1.00dl/gm a. of Homo-Polymers 0.58 - 0.96dl/g Homo polymers 0.76 - 0.84 0.76dl/gm b. of Co-Polymers 0.60 - 1.30dl/g 0.59 - 1.00dl/gm 3. Speciality resins No NeoPET Cycle Opaque grade for milk, Relpet OP5821 CSD LBS Soft, CR Available NeoPET 80, NeoPET 82 Relpet QH5821, Relpet G5841, Relpet Green B84 Water MW Soft, CR Available NeoPET 76, NeoPET 78 Relpet G5761, Relpet Green B76 Beer Glasstar + Sprit No NeoPET 80, NeoPET 82, NeoPET 84 Relpet B9845 (Barrier resin) Edible oil CR, Glasstar Available Relpet G5761, Relpet G5801 Wine / Liquors Glasstar, , LBS Soft No NeoPET 80, NeoPET 82 Relpet G5801, Relpet B9845, Relpet Green B80 Personal care / Pharmaceuticals Glasstar, Sprit Available NeoPET 80 Relpet G5801 Slow crystallisation Glasstar, Sprit No Relpet GL5000 Hotfi ll HF No NeoPET 82 HF Relpet H7761 Pre-coloured DCU, Luz, Polygloss No Fast reheat LB Soft Available NeoPET 82 FR, NeoPET 84 FR Relpet QH5821 Other CPET, HT, REX (for EBM), Sol (aerosol bodies), PET grades for other non-packaging applications Ultra NeoPET Relpet IM5590 for blood collection tubes 4. Increased barrier properties Light barrier: Dairy, Luz , DCU, Polygloss Gas barrier: Glasstar, Sprit No Relpet B9845 5. PEN mixes available No 6. Recycled blends available Yes, under customer requirements Yes NeoPET Cycle PET resins (25-30% PCR content) 100% rPET under Relpet Green brand 7. Special comments Focused on innovation at the service of packaging; specialised in light barrier protection; committed to create new markets for PET. MTS ( Melt-to-Resin) NeoPET Cycle - Innovation dedicated to sustainable future Customised grades can be developed"},{"@ID":12 "EDITOUR PETplanet Insider Vol. 26 No. 01+02/25 www.petpla.net 10 Steady investment by Egyptian plastics converter Expansion course in the Middle East by Kay Barton In 1998, New Modern Plast Egypt started its activities within the family-run Modern Plast Group, which is active in plastics processing. This division of the company, one of four in the group, serves the plastic packaging sector and is now one of the leading processors in preform and closure production. We met Technical Director Khaled Elalfy and Sales Manager Amr Mahdy in the industrial area of New Cairo and took a closer look at the setup. Meeting with New Modern Plast Company September 5, 2024 We met: Mr Khaled Elalfy, Technical Director Mr Amr Mahdy, Sales Manager The company originally started 26 years ago in the city of Badr and moved 2022 to the current industrial area in New Cairo. The current Chairman Mohamed Ahmed, who holds a bachelor’s degree in business administration from Cairo University, is the founder of New Modern Plast and its affiliated companies and has 30 years of experience. Vice Chairman and CEO Dr Samah has been a passionate part of the plastics industry for 13 years and has been actively involved in decision making throughout her career. She has successfully restructured the company and introduced a system that, according to the company, has significantly increased both efficiency and productivity within the organisation. A success-driven medical doctor who graduated from Ain Shams University, she is currently studying for an MBA. The facility covers a lot of space and several areas were being built on at the time of our interview visit. New Modern Plast has several production facilities located close to each other, separated by product area. There is even a technical training centre for schoolchildren to teach them about the world of plastics processing and thus lay the foundations for the potential skilled workers of tomorrow. Over the past ten years, the company has continuously invested in expansion and technology, as they explained to us. “We started with a Husky HyPET with an annual output of 120 million preforms,” explained Khaled Elalfy. “We now have eleven Husky HyPET systems ranging between 300 and 400 t with 72 to 128 cavities, as well as a Netstal PETline. Our combined preform output totals 3 billion.” In addition to the portfolio 29/25 (14 types, 7.9 g-27.5 g), PCO1881 (14 types, 15.7 g-49 g), preforms for edible oil bottles (four types, 210 g-680 g) and large format containers (three types, 19 g-26 g), 29/25, 1881, 48mm and 55mm closures are also produced. “The cap production has been around since 2021,” explained Mr Mahdy, pointing to the two Sacmi CCM48SD during the tour. A Husky 300 t Hylectric is also in operation. The company also manufactures racks for water gallons, as well as plastic pallets and transport crates. “All the plants together make up 45,000m2 of space,” says Mr Elalfy. Apart from Egypt, the products are exported to Saudi Arabia, Libya, Yemen, Morocco, Kenya and the UAE. “Outside of our portfolio, we can also plan and create customised designs,” explained Khaled Elalfy. The preform part accounts for around 50% of turnover, with closures and other plastic products such as pallets each contributing 25%. In Egypt, customers include Nestlé, PepsiCo, Dasani and Coca-Cola, as well as the water brands Wapco, Hayat and Siwa, among others. Sufficient storage facilities with around 20 warehouses, which are strategically well distributed, should ensure problem-free supply, according to the team. The Editourmobil in front of the company entrance with (from left to right) Khaled Elalfy, Kay Barton and Amr Mahdy Amr Mahdy with freshly produced Nestlé caps EDITOUR"},{"@ID":7 "EDITOUR PETplanet Insider Vol. 26 No. 01+02/25 www.petpla.net 14 Market leader from Germany in the Middle East Closures for Egypt and the entire region by Kay Barton In order to be able to adequately serve the emerging markets in Africa and the Middle East with closures, Bericap started its local representation with production near Cairo 20 years ago, more precisely in a rented property in Abou Rawash. The company remained here for nine years before relocating to owned estate of the art manufacturing facility in an industrial estate around 35 km away in the 6th of October City due to the positive development of the markets and customer situation in the region, where it then purchased land and opened a plant that is now around 20,000m2 in size. Tarek Sultan has been part of the Bericap success story for 17 years and welcomed us for an interview as part of the Middle East Road Show. EDITOUR September 10, 2024 We met: Mr Tarek Sultan, Managing Director and Board Member We sit together in Mr Sultan’s office. The 57-year-old father of three daughters has a BSc degree in Electrical Engineering and is, as he says, ‘proud to be Bericapian’. “It’s not just a job, I feel a strong emotional connection to the company,” he explained with a smile during the interview. In his first job in 1989, he worked for the oil exploration company Schlumberger and searched for oil in the North Sea. His career then took him via Procter & Gamble, where he worked for 13 years in Pampers diaper production in the UK, Germany, Argentina, Japan, Poland, Turkey and Saudi Arabia – quite a round trip. “I then came back to Egypt and worked for PepsiCo as Operations Director for three years before becoming GM for Henkel Egypt and finally GM of Bericap in 2007,” says Mr Sultan. Since 2017, he has also been a Board Member for Bericap Egypt and at the same time Director and Board Member at Bericap East Africa in Nairobi, Kenya, the new production facility of the caps and closures producer, which opened in January 2024 with 4,000m2 of space and six production lines after being a trading company for eight years. The plant in Egypt employs 130 people, around 90 of whom work in the production and tech part. 29 different closures and caps are currently in the portfolio here with an annual output of around 4 billion units. Cold halves from the in-house mould maker Bekomold are used in conjunction with a third party hotrunner systems. The Bericap closure Hexalite 29/11 UL2 (ultralight version for the neck finish 29/25) is the most popular in terms of volume. During the last year we significantly increased our capacity for this product,” explained Tarek Sultan. “And we still see growing demands in the market.” Mr Sultan has risen from the executive chair at his desk and enthusiastically goes through the map with us, which hangs on the wall behind the desk and shows the company’s activities in the individual regions. He explained that the export volume used to be 20%, today it is 40%. The Egyptian products are currently destined for 28 countries in Africa, primarily North and East Africa, and the Middle East. “We also bought a factory in Durban, South Africa, in 2024 and are now producing specifically for that region. We have also a dedicated sales office in Casablanca, Morocco.” Mr Sultan assumes that the new GME 30.40 neck finish will also be increasingly available in the Egyptian market in the near future. “When the time comes, we will be prepared in any case.” www.bericap.com Tarek Sultan at his desk Tarek Sultan (left) and Kay Barton in the Bericap Egypt production hall The Editourmobil in the yard of Bericap Egypt with Tarek Sultan (left) and Kay Barton"},{"@ID":42 "Closing the Loop Energy Efficiency Material Savings EDITOUR PETplanet Insider Vol. 26 No. 01+02/25 www.petpla.net 17 emissions data using either a CO2 pricing system at the installation site, a mandatory emissions monitoring system at the installation site or an emissions monitoring system at the installation. However, these options will no longer be permitted from 2025. From the beginning of the year, only the EU method may be used. Furthermore, companies will be allowed to estimate 20 per cent of the total grey emissions associated with complex goods. Companies will also be able to register in the CBAM register from 2025. This will become obligatory from 2026, as from next year, only companies that are registered in the EU CBAM register will be allowed to import corresponding goods (such as steel). The corresponding portal was actually due to go live on January 1 this year. Due to delays, the EU will not go live with the CBAM register until the first quarter of 2025. The CBAM will actually come into effect from January 1, 2026, when the CBAM import duties on the ‘import of emissions’ will become due. The EU supply chain law (CSDDD) The so-called EU supply chain law, the CSDDD (Corporate Sustainability Due Diligence Directive), has been in force since July 2024. With the CSDDD, the EU is imposing new due diligence obligations on companies. The aim of the directive is to prevent human rights violations and environmental pollution along the supply chain of European companies. The timetable for the CSDDD is as follows: EU member states have two years from the directive’s entry into force to transpose it into national law. The CSDDD must therefore be implemented by July 2026 at the latest. The most important information for companies is that the CSDDD will not apply before 2027, and then only for large companies with more than 3,000 employees. In the two following years, the EU supply chain law will then also apply to companies with more than 3,000 and 1,000 employees respectively. The EU Ecodesign Regulation The EU Ecodesign Regulation has been in force since July 2024. The EU wants to use it to make products recyclable and prevent products from being thrown away. Manufacturers are therefore subject to new regulations. The EU Commission wants to develop product-specific rules by March 2025. The first delegated act under the Ecodesign Regulation could come into force on July 19, 2025 at the earliest - one year after the regulation itself comes into force. Companies will then generally have 18 months from the entry into force of the respective delegated act to redesign their products in accordance with the regulation. All these directives and laws are part of the EU’s Green Deal, which is the EU’s contribution to the Paris Agreement, which the EU and all its countries ratified and which set the goal of keeping global warming to maximum +1.5 °C compared to preindustrial levels. The European Green Deal is the EU’s growth strategy. It was launched in 2019. With its package of policy initiatives, which set the EU on the path to a green transition, with the ultimate goal of reaching climate neutrality by 2050. We have summarised all these developments and explanations for you, dear readers, because we want to share them with you. On our Editour, we want to see how you specifically deal with these requirements, what they look like in practice: we will also be taking up your suggestions and reporting on them. It’s a broad field and it’s complex, but we think it’s important to report on it! We are very much looking forward to meeting you! https://petpla.net/2024/12/09/ the-circular-economy-tour-2025/"},{"@ID":46 "imprint EDITORIAL PUBLISHER Alexander Büchler, Managing Director HEAD OFFICE heidelberg business media GmbH Hubweg 15 74939 Zuzenhausen, Germany phone: +49 6221-65108-0 [email protected] EDITORIAL Kay Barton Heike Fischer Gabriele Kosmehl Michael Maruschke Ruari McCallion Anthony Withers Editorial & WikiPETia. info [email protected] MEDIA CONSULTANTS Martina Hirschmann [email protected] Johann Lange-Brock [email protected] phone: +49 6221-65108-0 LAYOUT AND PREPRESS EXPRIM Werbeagentur Matthias Gaumann www.exprim.de READER SERVICES [email protected] PRINT Chroma Druck Eine Unternehmung der Limberg-Druck GmbH Danziger Platz 6 67059 Ludwigshafen, Germany WWW www.hbmedia.net | www.petpla.net PETplanet Insider ISSN 1438-9459 is published 10 times a year. This publication is sent to qualified subscribers (1-year subscription 149 EUR, 2-year subscription 289 EUR, Young professionals’ subscription 99 EUR. Magazines will be dispatched to you by airmail). Not to be reproduced in any form without permission from the publisher. Note: The fact that product names may not be identified as trademarks is not an indication that such names are not registered trademarks. 3 PETplanet Insider Vol. 26 No. 01+02/25 www.petpla.net We have been able to admire PET closures for quite some time now. Last year, Origin Materials from West Sacramento, USA, presented two manufacturers. For North America, the Reed City Group, known for general plastic products, and for Europe, the Bachmann Group from Hochdorf, Switzerland - known for sustainable packaging. In plant engineering, this latter company cooperates with PackSys Global, also from Switzerland. The company plans to produce 1881 caps, including tethered caps, from PET and recycled PET (see article on p. 26). On page 22 there is also a report from Husky on their PET cap development. The solution is being hailed as a breakthrough in recycling circularity: bottle and cap made from one material. However, the usual polyolefin closures can be easily separated from the PET fractions in a water bath and consequently, there was never really a need for PET closure material here. On the contrary: as a closure is always a design element of the bottle, it is available in a wide variety of colours. A clean separation of cap and bottle is essential, as PET is easiest to recycle back into bottles when it is colourless. The new PET closures do not yet have an answer to this problem. They are transparent so that they do not colour the PET fraction during recycling. It remains to be seen whether bottlers will accept colourless closures. But the challenges of bottle-to-bottle recycling - which should really be called cap-and-bottle-to-cap-and-bottle recycling - start earlier. As the cap cannot simply be sorted out of the PET stream, the idea is to recycle it together with the bottle. The recycling of the closures is said to work on a laboratory scale, but we have not yet heard of a large-scale trial in a PET recycling plant, despite our enquiries. The recycling industry is asking itself whether the intrinsic viscosity (IV) of the closure material matches the IV of the bottles and whether a homogeneous rPET material is subsequently produced. It is also unclear how the PET cap manufacturers intend to avoid cold welding of the cap and bottle neck. Consumers may have difficulty removing the PET cap from the PET neck. It can be assumed that coatings or additives ensure a clean separation of neck and closure. But what influence do these additives have on rPET in cap-and-bottle-to-cap-andbottle recycling? Practice will certainly find answers to all these questions. For our part, we are looking forward to the first mass produced PET closures. Yours, Alexander Büchler Dear readers,"},{"@ID":23 "CAPS & CLOSURES 21 PETplanet Insider Vol. 26 Sustainability and cost efficiency: The 26/22 mm GME 30.40 is sustainable thanks to the patented z-slides technology; the tamper-evident (TE) band is directly moulded, eliminating the need for subsequent folding and cutting processes. This results in material savings and less production costs. This development underscores Z-Moulds’ commitment to resourceefficient manufacturing while providing a competitive advantage. Compatibility and adaptability: The closure can be easily integrated into existing filling systems. Without requiring changes to machines or processes, it can be immediately used on lines already designed for GME 30.40 closures. This saves time and costs during conversion and ensures smooth implementation. High standards: The closure’s performance has been specifically tailored to meet the stringent requirements of renowned companies like Coca-Cola and Pepsi. With a carbonation level of up to 4.5 CO2 vol%, the closure demonstrates its versatility and reliability in demanding applications. “The 26/22 mm GME 30.40 with tethered function combines lightweight design, technical sophistication, sustainability, and compatibility in an unparalleled manner. This closure makes one thing clear: innovation means not only improving existing standards but redefining them,” stated Mr Fink. www.z-moulds.com The new 26/22 mm GME 30.40 with tethered function"},{"@ID":28 "CAPS & CLOSURES 26 PETplanet Insider Vol. 26 No. 01+02/25 www.petpla.net Improving performance, enhancing sustainability PET closures for 1881 and beyond The Origin PET 1881 closure by Origin Materials introduces a versatile platform for producing rPET and PET closures, including tethered formats, across various industries. PET is not only the most recycled plastic in the world, today’s plastic recycling infrastructure is designed predominantly for PET. Closures made from PET could be transformative for packaging by designing for recycling circularity and improving the performance and sustainability of packaging. PET unlocks new design space Within the packaging industry there is strong and growing demand for solutions offering superior performance and sustainability characteristics. This is especially true for products designed for circularity, enabling the re-use and recycling of materials, as opposed to waste and downcycling. Many food and beverage companies are committed to improving recycling, expanding the use of recycled PET, and improving the performance characteristics of their products while delivering an excellent consumer experience. Origin PET closures are claimed to introduce important advantages for delivering on these goals. PET offers excellent barrier properties. Compared with other materials, this can result in less plastic needed to achieve equivalent or better performance. This can allow Origin to produce caps that can extend product shelf life, or produce the lightest caps of their kind, depending on the parameters optimised. Origin PET cap manufacturing does not require custom polymer, rather simply off-the shelf virgin or recycled PET, or blends thereof, depending on customer preference. For aesthetics and consumer experience, Origin PET caps provide a fully transparent closure to enhance product visibility. The closures allow brands to tint, print, or emboss the closure for enhanced marketing. For tamper evidence, the company’s PET cap is designed to provide a satisfying user experience, from its feel to the sound it makes when opened. The weight of the initial 1881 cap (1.5-1.8 g) is comparable or lighter than many HDPE or polypropylene caps on the market today. The light weight is afforded by the design space created by PET, with its good barrier properties - an estimated 40 times the carbon dioxide barrier, and 30 times the oxygen barrier of a similar thickness of HDPE - enabling new designs. Better recycling with non-modified mono-materials Mono-material products are made with one type of material. They are typically easier to recycle than products made from multiple materials and are highly desirable for packaging to improve recycling. For PET caps where the polymer is not modified, there is no need to separate caps from bottles during the recycling process to maintain the purity of the recycling stream, as there is with containers whose caps and bottles are made of different materials. This feature could be especially valuable for tethered cap solutions. In May 2024, Origin announced a tethered PET cap, which could become the first mass produced tethered PET closure. Many beverage brands today make claims related to recyclability and use of recycled content but often must include caveats related to caps and labels. With PET closures, the use of 100% recycled content from cap to bottom becomes possible. Manufacturing system In September 2024, the company unveiled the Origin CapFormer System, its commercial-scale manufacturing system for the production of PET caps and closures, and announced the completion of its successful factory acceptance test. “Through the novel application of thermoforming, slit-andfold technology, and proprietary design elements we have unlocked the ability CAPS & CLOSURES Origin PET 28mm 1881 showing knurls"},{"@ID":48 "OUTER PLANET 46 PETplanet Insider Vol. 26 No. 01+02/25 www.petpla.net OUTER PLANET Plastic waste management platform in India Race Eco Chain In an era where sustainability is no longer an option but a necessity, Race Eco Chain aims to redefine the future of recycling. Standing for ‘Recycling and Circular Economy’, Race Eco Chain intends to bridge the critical gaps in the PET recycling ecosystem by connecting recyclers, suppliers, and producers, importers, and brand owners (PIBOs). The platform intends to empower stakeholders with end-to-end traceability, to streamline the waste supply chain, and to ensure recyclers receive consistent quality and tonnage. With a commitment to investing in suppliers’ growth, the platform supports capacity expansion through new machinery, infrastructure, and training while assisting them with Environmental, Social und Governance (ESG) compliance audits. An ESG value chain promotes sustainable practices, all while delivering an impressive ESG score of 58. Every year, Race Eco Chain recycles over 100.000 metric tons of PET bottles, supported by a robust network of 300+ suppliers and 80+ recyclers across India. By organising the unorganised waste industry, the platform is streamlining waste collection and management in a way that minimises waste and maximises resource efficiency. With collection centers spread across various districts, Race Eco Chain is managing waste and creating a roadmap for eco-conscious practices. At the heart of this movement is PET, a material celebrated for its recyclability but plagued by underutilisation. Despite its recyclable nature, PET faces significant hurdles. Global recycling rates for PET vary, and in some regions, less than half of PET waste is recycled. Contamination, inefficient collection systems, and limited market demand for recycled PET (rPET) create a cycle of inefficiency. The result? Poor-quality rPET that struggles to meet the requirements of high-value applications. This is where Race Eco Chain aims to step in, leveraging technology-driven solutions to address these challenges head-on. Its digital platform, Race App, acts as the connective tissue of the recycling ecosystem, enabling stakeholders to collaborate seamlessly and overcome these obstacles. The digital impact of Race App: Race App streamlines the collection, sorting, and recycling of PET waste, it brings structure and efficiency to a fragmented system. Enhanced collection systems: connecting waste suppliers with certified recyclers across India, ensuring that recyclable PET waste reaches the right facilities. Real-time tracking and transparency: Race App offers real-time tracking of PET waste, giving stakeholders detailed insights into their waste streams and helping them meet regulatory requirements such as Extended Producer Responsibility (EPR). Market access for recycled materials: A key challenge for recyclers is finding consistent demand for rPET. Race App creates a direct link between recyclers and industries seeking recycled materials, fostering a circular economy where resources are reintegrated into production. Technology-driven solutions: With features like automated data management, user-friendly interfaces, and actionable analytics, Race App optimises workflows, enabling stakeholders to make informed decisions that improve operational efficiency. Redefining innovation in recycling Race Eco Chain exemplifies how technology and collaboration can transform traditional industries. Its forward-thinking approach addresses the challenges of PET recycling and sets the stage for a sustainable, circular economy. By incorporating data-driven tools, the platform enhances efficiency and transparency, inspiring a new way of managing waste. A sustainable future for PET The PET industry is at a turning point, with the potential to lead the charge in the global fight against plastic waste. Platforms like Race Eco Chain demonstrate how technology and collective action can overcome systemic challenges, paving the way for a more efficient and transparent recycling ecosystem. Improved collection systems, market access, and cutting-edge digital solutions are just the beginning. To truly maximise its impact, the PET industry must embrace innovation and collaboration while engaging consumers in the journey toward sustainability. www.raceecochain.com"},{"@ID":25 "CAPS & CLOSURES 23 PETplanet Insider Vol. 26 No. 01+02/25 www.petpla.net tethering system. This is claimed to simplify the manufacturing approach. Husky’s tethered closure designs, both standard and custom, are engineered to maintain weight neutrality compared to their non-tethered counterparts. These designs also incorporate a shelllocking mechanism to ensure secure functionality and provide an intuitive user experience, making them practical and easy to operate. A patented tethering system that enables shell locking to improve usability. This technology is available for all neck finish options. PET closure Currently, the typical beverage container features a 2-material approach: PET for the bottle and HDPE/PP for the closure. While HDPE/PP performs exceptionally well in terms of protecting/preserving the contents of the beverage, these material types are typically downcycled into other non-food contact applications (lawn furniture, buckets, etc…). Replacing the closure material with PET, creates a mono-material beverage packaging solution that can increase rPET bale yields, simplify reclamation efforts, and enhance shelf presence with its glass-like properties. Injection moulding of a PET closure has been an elusive undertaking until now. The material properties are very different than HDPE/PP thereby presenting a unique set of challenges. Leveraging all capabilities and knowledge at its disposal, Husky has developed PET closure solutions for still water applications. The design approach enables a stress-free capping performance. A patent-pending post-mould operation forms the TE band around the pilfer proof thereby creating a level of consumer security that is unmatched currently within the industry, says Husky. The roadmap also includes PET closure offerings for industry standard necks within the CSD and JSDT markets. The company’s focus on sustainable closure solutions is claimed to reflect the commitment to supporting a circular economy and meeting the evolving demands of the beverage packaging industry. By integrating advanced design methodologies with cutting-edge manufacturing technologies, the company aims to empower producers to achieve their sustainability goals. www.husky.co | www.agrintl.com | +1.724.482.2163 Featuring AutoJob® 6LPSOLȴHG DQG DXWRPDWHG MRE VHWXS LQ VHFRQGV 3DUWQHU ZLWK $JU WR DFKLHYH VLPSOLȴHG GLPHQVLRQDO PHDVXUHPHQW IRU \\RXU SODVWLF FRQWDLQHUV DQG SUHIRUPV Prepare for tomorrow... HQKDQFH HɝFLHQF\\ WRGD\\ Figure 2: Husky’s tethered solution for 180° opening Figure 3: Husky’s PET closure solution"},{"@ID":37 "35 EVENT PREVIEW PETplanet Insider Vol. 26 No. 01+02/25 www.petpla.net EVENTpreview CBST 2025 The 13th China International Beverage Industry Exhibition on Science and Technology (CBST 2025) will take place from March 5-7, 2025, at the Shanghai New International Expo Center. Hosted by the China Beverage Industry Association, CBST has grown into a premier event for the beverage industry across China and the Asia-Pacific region. Now held annually, the exhibition serves as a vital platform for showcasing cuttingedge technologies, new products, and industry trends. CBST 2025 intends to bring together stakeholders from across the beverage supply chain to promote collaboration, drive industrial upgrades, and explore sustainable solutions. With a focus on digital transformation, automation, energy efficiency, and low-carbon production, the event aims to address key challenges and opportunities in China’s rapidly evolving beverage market. Highlights include product launches, procurement discussions, and industry seminars. www.cbst.com.cn High-performance compressors for PET bottle blowing Adekom wi l l feature its KSP series screw+piston tandem highpressure compressor, a sk idmounted system that combines an advanced oil-free screw compressor for the first stage with an oil-free piston booster for the second stage. Designed for stable, energy-efficient performance, the uni t provides 5.0–30.5 m³/min of oil-free air at 40bar pressure, meeting ISO8573-1 Class 0 air quality standards. The compressor offers several significant advantages, Adekom says. Its first-stage water-injection screw compressor provides lubrication, cooling, sealing, and noise reduction, ensuring 100% oil-free air without requiring special discharge water treatment. Food-grade stainless steel is used throughout the system, including the screw air end casing and pipelines, ensuring compliance with environmental and industry standards. Corrosionresistant, these stainless steel components are also intended to enhance durability and to ensure a long service life, while the use of water as a lubricant helps absorb compression heat, maintaining low operating temperatures and minimising wear on components. To maximise energy efficiency, the system incorporates a permanent magnet frequency inverter drive, which offers a wide regulation range and reduces operational costs. Additionally, a fully automated waterchanging device allows lubrication water replacement without halting operations. Advanced digital control is provided by a PLC system, enabling centralised automation and monitoring through a single interface. With cloud-based monitoring and predictive maintenance capabilities, the compressor is ready for remote operation and management. Established in 2003, Adekom has built a strong reputation as a leading compressor manufacturer in Asia, with two decades of experience serving the food and beverage industry. The company’s expertise and commitment to innovation have positioned it as a trusted supplier in the competitive PET bottle-blowing sector. www.adekom.com.hk Support through the SMI Machinery Beijing service office Since 2001, SMI has been constantly committed to providing Chinese customers with fast and efficient local support to meet the requirements of a rapidly evolving market. SMI Machinery Beijing staff will be at the CBST trade fair to show the latest innovations of SMI machine ranges for circular packaging and sustainable development. Through the SMI Machinery Beijing Co. Ltd. Service office, the company manages the technical and sales requirements of packaging plants supplied to hundreds of companies operating in the food and beverage industry. When Chinese food and beverage manufacturers take the decision to invest in a new bottling or packaging plant, they pay great attention to the technological content and to the local presence of its partners with after-sales support. The SMI local facility is based in the district of Daxing, Beijing, a logistic and industrial point that boasts the largest airport in the world. One of SMI Machinery Beijing’s latest projects was the installation of the integrated Ecobloc Ergon blow-fill-seal system (easy-cap cap sorter) in the production plant of Huihuang United (Tianjin) Food Co. www.smigroup.it"},{"@ID":9 "7 NEWS PETplanet Insider Vol. 26 CREATING FUTURE STANDARDS Japan’s leading Aseptic PET Filling System Provider. Our website Our solution high quality reliable technology safe & secure DePoly and PTI partner to create closed loop recycled PET bottle DePoly, the Swiss CleanTech company which is specialised in advanced recycling of PET/polyester plastics, announced their collaboration with PTI (Plastic Technologies Inc) a leader in sustainable plastic packaging design and development, to create a closed loop recycled PET bottle. Using a mixed stream of feedstock, ranging from PET plastic packaging, polyester fibres and industrial waste, DePoly’s technology has broken down the PET and polyester back to its raw monomers, Purified Terephthalic Acid (PTA). From this virgin-grade quality PTA, PET pellets were produced. Finally, these PET pellets were blown into recycled PET bottles using PTI’s 40 years of expertise and technology. DePoly set out to challenge itself by using PET and polyester plastic waste from packaging and insulation. The DePoly technology produced a high-qual i ty PTA used to produce rPET that was processed into bottles by injection stretch blow moulding. This project demonstrates the strengths of bringing together the technical robustness of DePoly and PTI’s extensive expertise in plastic packaging processing and manufacturing. Both companies worked together to demonstrate a closed loop solution for plastic recycling into high grade bottles. Blowing a PET bottle is generally one of the more challenging end products to produce, highlighting the experience of PTI and maturity of DePoly’s technology, capable of bringing a universal approach to PET & Polyester recycling. Making bottles from varied PET & polyester waste DePoly’s uncompromising take on quality has been at the heart of this project. Not only did they succeed in producing a recycled PET bottle, but they did so by taking a broad spectrum of feedstock with the final product being a recycled PET bottle, one of the most difficult products to create. From a challenge point of view, this ticks off all the boxes and further demonstrates that DePoly’s technology is versatile and adaptable, enabling the company to pave the way for a new standard in the industry. In parallel to the bottle sampling, the conclusion of a preliminary screening analysis of non-intentionally added substances (NIAS) in DePoly rPET material is showing that the tested sample complies with the overall and specific migration requirements for the PET typical substances in contact with all types of food at any long-term storage at room temperature and below, including hot fill. www.depoly.co www.plastictechnologies.com"},{"@ID":31 "CAPS & CLOSURES 29 PETplanet Insider Vol. 26 No. 01+02/25 www.petpla.net Highspeed system - all processes integrated Tethered caps assembly Contexo has developed a patented all-in-one system designed to enhance the speed and efficiency of tethered cap assembly. By integrating the cutting process, the system aims to improve production reliability while also offering greater flexibility for implementing new closure designs. CAPS & CLOSURES For over 30 years, Contexo has been designing systems for complex closures and complete systems manufactured in plastic. This was the basis for the next step: the new, patented concept of the all-in-one system for single- and multi-part tethered caps. A machine platform was developed and designed that integrates all necessary processes in one system: from assembly to folding and roll slitting of the TE band to closing and packaging. The advantages of the concept are a small footprint, reduced costs and less energy consumption, says Contexo. Capacity growth The system is based on continuous-motion rotary presses to guarantee maximum output rates. This kind of speed is reached using a central tower that assembles the part, while feeder satellites guide them at a precisely controlled rate; a system that places minimal stress on the part. The integrated slitting unit eliminates the need to invest in expensive and high-maintenance injection moulds, says Contexo. Filigree in-mould operations are replaced by simple, safe processes, as material no longer has to be pressed through narrow channels. The integrated folding and roll cutting of the TE strip is claimed to be more stable in the production process: the TE bridges are not stressed or damaged during handling, the downstream process and assembly. At the same time, high speed and repeatability are guaranteed in the production process in order to reduce costs and increase safety. Inspection before and after assembly Contexo employs a quality control method where each component is inspected prior to assembly, and the finished closure is inspected afterward. To ensure efficiency, the inspection systems are integrated inline with the assembly machine and operate in synchronisation with it. The camera stations used inspect the typical elements inside and outside the closure. This results in technically flawless products which are then sent for further processing. The machine is claimed to be user-friendly with 360° accessibility, changeable slitting unit and low maintenance thanks to mechanical components. Product design Whereas previously there were restrictions in terms of shape and appearance, eye-catching designs are now possible with the Contexo system. The vulnerability of the TE bridges is eliminated, and the rotating mould axis makes unusual shapes possible. Closures without TE bridges are feasible. Contexo states that their systems offer a space-saving and effective alternative for manufacturing closures. Their machines can produce cost effectively because the company works with standardised machine concepts and a full, in-house technology spectrum. Sports Cap: Contexo´s highspeed machines show that the combination of continuous motion and inline quality control can set a new standard for high output rates and high-quality parts. Every six-hundredth of a second, a new beverage closure is assembled, folded, inspected three times, and packed. The continuous-motion rotary system enables high-performance production, achieving speeds of 920 closures per minute or approximately 1.3 million closures per day. www.contexo-automation.com"},{"@ID":30 "CAPS & CLOSURES 28 PETplanet Insider Vol. 26 No. 01+02/25 www.petpla.net Circularity for polyolefi n bottle caps Cap recycling takes off “Bottle made of 100 per cent rPET.” It’s an increasingly common message on plastic packaging, especially beverage bottles. But what about the cap? PET recycling has been an established business line for quite some time now. But demand for recycled polyolefin (PO), the material commonly used for making caps and closures, has only recently taken off, driven largely by a growing awareness of sustainability among consumers and companies alike and by tighter regulatory requirements such as mandatory recycled content laws. “The market is seven times larger” Because of their high strength and durability, PP and HDPE plastics are widely used in making containers for household cleaners and shampoo products as well as storage bins. The same properties also make them the material of choice for bottle caps and closures. Because, of course, the containers need to be stable and, most importantly, tightly sealed. When it came to recycling, though, polyolefins were long undervalued compared with PET. But they’re now gaining ground, for good reason. PET and the other polymers now each make up around 50 percent of the throughput of recycling plants. At Krones Recycling, too, a turnkey provider of recycling systems, more than half of new lines ordered are designed to process polyolefin plastics. The growing demand for PO recycling comes as no surprise to Matthias Dawartz, Head of Project Execution and Process Engineering at Krones Recycling GmbH. As he puts it, “It was only a matter of time before recyclers recognised its potential. After all, the market for PO is roughly seven times the size of the PET market. Plus, most of the processes and systems used for recycling polyolefins like rigid PP and HDPE are similar to the ones we’re already using for PET.” One process, multiple possibilities Plastics recycling entails many steps, in which the materials are sorted, shredded and washed. The process involves two product flows, which are separated based on their density, in a sink-float tank. Matthias Dawartz explains: “The density separator uses water to separate the plastic flakes into two fractions: those that sink and those that float. Depending on the desired end product, one fraction is processed and the other discharged.” If it’s PET that is to be recycled, then the sinking fraction is used. The less dense polyolefin plastics float on the surface of the water and are carried off, packaged and sold to other recyclers. If the aim is to recycle only the polyolefins, then the opposite is true. Newer recycling concepts seek to unite the two – recycling PET and polyolefin – under one roof. That is, any polyolefin materials that are discharged from a PET recycling system are passed directly, as presorted material, to a PO recycling line and processed further. Food-grade quality “In order to obtain high-quality recycled material, it’s essential that the flakes be cleaned thoroughly once they’ve been separated by density. This involves several washing stages, especially in the caustic washer that remove all contaminants and residuals,” says Dawartz. In the case of caps and closures, this step is important for another reason as well: “Most caps are made of HDPE, which is rigid but not brittle. It’s well suited for recycling, but it’s also more susceptible to picking up odours. Krones Recycling uses a hot washing process, which does a great job of reducing those odours.” Once the flakes have been washed, they are sorted once again, this time by colour and polymer type, by way of optical and sensor technologies. Additional deodorisation in a thermal-physical extraction process removes any remaining odours. The final product is claimed to meet high quality standards and has been approved for food contact by the FDA in the United States. www.krones.com CAPS & CLOSURES In the density separator, the lighter polyolefin flakes float on the water’s surface and can be drawn off for further processing."}]}}
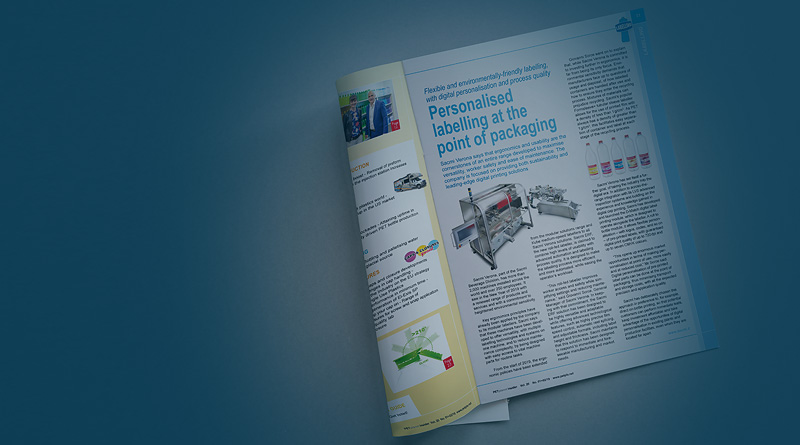