{"pages":{"page":[{"#text":"NEWS 9 PETplanet insider Vol. 12 No. 09/11 www.petpla.net Performance Filling & Capping Labelling Blowing Control PET acquires Artenius Portugal plant La Seda de Barcelona (LSB) and Control PET SGPS S.A, an investee of Imatosgil and Banco Espirito Santo, have formalised a salepurchase agreement for the Portalegre-based Artenius Portugal PET production plant. This facility, initially opened in 1966 for polyester fibre production, was later converted into a PET polymer batch production plant, with a yearly output of 70,000t. Production has been halted since the end of 2010. The agreed value for the sale is €5.6 million, to be paid between 2011 and 2015. The sales value may increase, depending on the company’s productivity during this period. It is intended that the plant should commence production, saving a number of direct and indirect jobs. The transaction continues LSB’s ongoing process of divestment of non-strategic assets, under its 2009 restructuring plan. The Potalegre plant does not conform with LSB’s future strategy in terms of technology, location and size. www.laseda.es Husky names Su Taylor Vice President, Human Resources and Organisational Development Husky Injection Molding Systems has announced the appointment of Su Taylor to the position of Vice President, Human Resources and Organisational Development. Ms. Taylor also becomes a member of Husky’s executive team. She has more than 19 years experience in senior human resources leadership roles, gained at companies such as Nortel and Xerox. Prior to joining Husky in 2009, Ms. Taylor was Principal at Mercer, a leading global human resources consulting company. She replaces Jim Reid, Husky’s Vice President of Human Resources and Organisational Development from 2008, who has left the company. www.husky.ca","@ID":11} "PREFORM PRODUCTION 22 PETplanet insider Vol. 12 No. 09/11 www.petpla.net Preform yellowing The rapid guide to perfect preforms - part 23 Troubleshooting guides have suffered in the past from being locked away in offices and not being available to the people that actually need them. Considering the high cost of machine and tools high scrap rates can be a costly proposition eating away at already tight margins. PETplanet’s “Rapid Guide to Perfect Preforms” takes a different approach. Bound in laminated paper that is easy to clean off, the small format of the book of 108mm by 151mm (4.25” by 6”) allows easy storage in back pockets or tool boxes. It has been written for the people on the floor of injection moulding companies to support their daily work in making the best preforms possible. The product of two industry experts, Rick Unterlander and Ottmar Brandau, it gives concrete advice on 35 of the most common problems in preform manufacture, most illustrated by pictures. From high AA levels to wavy bodies processors can find help when they need it. Read chapter 23 of the guide. PETplanet print vol.6 The Rapid Guide to Perfect Preforms machine no./name Vol.6 PETplanet print","@ID":24} "The inspection machines manufactured by P&S Technology are installed on the production line for inspecting preforms using for PET PET bottles. The inspection and ejection process of machines is automatic and there are variety of machine speed suitable for customer‘s production line speed. Especially PS-21GP series 3 recently having a good sales results provides lots of advantages for customers. The machine‘s maximum speed is 48,000PPH and there is no need to change parts as per changing preform‘s body size because gripper neck handling type is applied to preform handling equipment. Mold number reading or gate cutting device could be equipped as an option inside of inspection system. We say it is two in one system., so customer can save cost and space. This inspection system is mainly designed for rotary type. This system intensively inspect not only preform body but also particle and defect of preform neck external. It use the patented ‚mirror tracking system‘ for the bottle body inspected, so customer can inspect whole surface of preform body without blind spot. P&S have another solution to inspect preform. PS-21PSI Series 1 is haven’t mirror tracking system but applied “line scan camera” technology overcome the limitation by refraction of light of inspection scope. The whole surface of body inspection is guaranteed by 3 line scan cameras located 120 degree each without rotation. The gripper neck handling type on this series is applied to preform handling equipment, so there is no need to change parts. Rotary Type Whole Surface Preform Inspection System PS-21 GP Series3 Basic inspection area 1. Neck ¿nish 2. Body 3. Basement Available options 1. Gate Cutting device 2. Mold Number reading 3. Top support Ring Surface 4. Neck external surface Machine capacity 1. Low speed: ~300PPM 2. Middle speed: 300~500PPM 3. High speed: 600~800PPM Neck ¿nish Neck external Support Ring Body upper area Body lower area Basement Available options 1 Gate Cutting Device Available options 2 Mold Number Reading","@ID":9} "NEWS 8 PETplanet insider Vol. 12 No. 09/11 www.petpla.net Sacmi delivers its 1000th CCM machine The 1000th Sacmi-built CCM (Continuous Compression Moulding) machine for plastic beverage cap production of has been delivered to Taiwan’s beverage packaging giant, Taiwan Hon Chuan (THC). CCM number 1000 was officially handed over to the President of THC, Keith H. C. Dai, and the General Manager of the South-East Asia area, Jerry W.P. Pai in a special ceremony held at Sacmi’s facility in Imola, Italy. The machine, which has been specially renamed ‘1000 CCM’, will be installed at one of THC’s plants. The company operates in a number of Far Eastern countries and already has over 60 Sacmi-built production lines, totalling some 200 machines plus auxiliary equipment. THC has annual revenues in the region of €500 million. www.sacmi.com San Benedetto, Scorzè plant, selects Sacmi-RFST technology San Benedetto, the Italian mineral water, isotonic, aseptic and soft drinks company has installed a Sacmi RFST (roll-fed sleeve technology) automatic rotary labelling machine at its Italian plant in Scorzè, Venice. The machine features a laser welding system, which Sacmi says allows strong sealing and high shrink applications of wrap-around labels directly from roll-fed film and eliminates solvents, glues and other agents from sealing. Labels are created and applied directly onto the bottles in a single process that is claimed to increase efficiency and save on materials and energy. San Benedetto’s Opera 500 45T RFST machine at Scorzè applies steam-heat shrunk wrap-around plastic film labels on 250ml PET bottles for water and tea, at rates of up to 45,000bph. www.sacmi.it Final testing and commissioning for Artlant PTA plant The €500 million Artlant PTA plant in Sines, Portugal is entering its final testing and commissioning phase. The plant is one of the largest industrial projects in Portugal. It will have a production capacity of 700,000t of PTA (purified terephthalic acid), which is used as feedstock in the production of PET and in the manufacture of polyester fibres for the textile market. The commissioning process will take three months and will involve testing of 200 systems, 105 of which are for the industrial processes and the balance are infrastructural. Production is expected to commence in Q4 2011, with annual value estimated to be €400 million at current prices. The Sines plant will provide around 400 jobs, direct and indirect. Output will be 95% for export, primarily to European markets and with some production being shipped to Africa, the CIS, Baltic States, the Middle East, India and Brazil. www.artlantpta.com Colormatrix opens new global technology centre Liquid colorants and additives producer, ColorMatrix, has opened its new global technology centre at its European headquarters in Merseyside, NW England. The million GBPound investment will house a new suite of instruments for material analysis and product testing, including major expansion to the spectroscopy and microscopy analysis laboratory. An FT-IR spectrometer, X-ray fluorescence spectrometer and a colour spectrophotometer will enable the highest levels of quality control and materials characterisation. It accommodates dedicated laboratories for product development, plastic processing and testing, gas barrier evaluation, spectroscopy, microscopy and separation science and technology. The Global Technology Centre operates in tandem with a network of regional facilities to support local manufacturers in product commercialisation. This expansion follows a $250,000 upgrade of laboratory facilities with new gas barrier testing and UV spectrophotometry at the Suzhou site in China. The capacity of the Itupeva plant in Brazil has also been increased, fourfold. www.colormatrix.com Kreyenborg Group opens ASEAN office The Kreyenborg Group, of Munster, Germany, has opened a new office in Kuala Lumpur, Malaysia. The new office, which is company-owned, will focus on sales and after sales service in the ASEAN region. Focus will be directed primarily to customers in Malaysia, Singapore, Indonesia, Thailand, and Vietnam. Kreyenborg provides components and machinery for extrusion and polymerisation. Its products include screen changers, gear pumps, pelletising systems and bulk material handling components, as well as automation technology. www.kreyenborg-group.com Amcor Rigid Plastics president retires Bill Long, President of Amcor Rigid Plastics, has retired from Amcor. Mike Schmitt has been appointed the new President of Amcor Rigid Plastics, effective July 1,2011. Mike Schmitt joined Amcor through the Alcan Packaging acquisition, where he was president of the Food Americas and Global Pharmaceutical business. For the past 18 months, he has been the Senior Vice President and General Manager, North America for Amcor Rigid Plastics. www.amcor.com","@ID":10} "BOTTLE MAKING 33 PETplanet insider Vol. 12 No. 09/11 www.petpla.net Nissei ASB - globally Nissei ASB estimate that a global total of 8,600 single stage systems are installed – working with three to four moulds each. Nissei ASB participates in the market with approx. 6,000 units - i.e. with approx. 70% market share. In fiscal year 2009/2010: 445 machines and 1,030 moulds were supplied to 65 countries world wide. Market areas: 47% Asia 23% Europe 20% America 11% Japan Nissei ASB – in Europe Nissei ASB has a delivery record in Europe of over 1.000 units covering some 370 accounts/customers, 80% of which are independent converters such as RPC, APPE, M&H – PET Power, Graham Packaging, Promens, Actipack, Obeck, Sauer, Rebhan, Gerresheimer, Hanex, Masterchem - 20% of which are brand owners such as Henkel, P&G, Danone/FR, Nestle/CH, Tupperware. Karel Keersmaekers: “Single stage is pushing the technical boundaries of bottle development.” “We have positioned Nissei ASB in a market of many niche applications for PET. We are not a player focussing too much on beverages. Instead we go for the huge number of other applications. Every week together with our customers we develop yet another innovative application. Thus we have become specialists in high end cosmetic markets, beauty and health products, with very big wall containers, in pharmaceuticals, syrups, animal medicine, detergents, and others.” Karel Keersmaekers is MD of Nissei ASBs subsidiary located in the industrial zone of suburban Düsseldorf - with offices for engineering and service, store for machines await delivery and a stock of spares. He is also Executive Officer at the Head Office of the mother company in Japan. Top positions of Japanese companies are usually occupied by Japanese – Keersmaekers, Belgian by birth, being an exception. Which is reason enough to take a closer look at Keersmaekers as a person: He Nissei ASB “Rather win the market than beat the competition.” A meeting with Karel Keersmaekers, MD of Nissei ASB Europe Head Office and main factory Komoro, Nagano-Ken, Japan Manufacturing sites Komoro/Japan, Mumbai/India, Shanghai/China Sales Offices 16 Date of establishment November 8, 1978 Capital 3,860 million JPY = € 33 million Sales 2009/2020 16,822 million JPY = € 146 million Export 90% Stock Exchange Jasdaq Number of employees 1,100 Nissei ASB mould applications","@ID":35} "PETplanet is read in 150 countries imprint EDITORIAL PUBLISHER Alexander Büchler, Managing Director HEAD OFFICE heidelberg business media GmbH Landhausstr. 4 69115 Heidelberg, Germany phone: +49(0)6221-65108-0 fax: +49(0)6221-65108-28 info@hbmedia.net EDITORIAL Doris Fischer fischer@hbmedia.net Michael Maruschke Ruari McCallion Ilona Trotter Wolfgang von Schroeter Anthony Withers MEDIA CONSULTANTS Ute Andrä andrae@hbmedia.net Martina Hischmann hirschmann@hbmedia.net Ursula Wachter wachter@hbmedia.net phone: +49(0)6221-65108-0 fax: +49(0)6221-65108-28 France, Italy, Spain, UK Elisabeth Maria Köpke phone: +49(0)6201-878925 fax: +49(0)6201-878926 koepke@hbmedia.net LAYOUT AND PREPRESS Exprim Kommunikationsdesign Matthias Gaumann | www.exprim.de READER SERVICES Kay Krüger reader@hbmedia.net PRINT Chroma Druck & Verlag GmbH Werkstraße 25 67354 Römerberg Germany WWW www.petpla.net | india.petpla.net PETplanet insider ISSN 1438-9459 is published 10 times a year. This publication is sent to qualified subscribers (1-year subscription 149 EUR, 2-year subscription 289 EUR, Young professionals’ subscription 99 EUR. Magazines will be dispatched to you by airmail). Not to be reproduced in any form without permission from the publisher. Note: The fact that product names may not be identified as trade marks is not an indication that such names are not registered trademarks. 3 PETplanet insider Vol. 12 No. 09/11 www.petpla.net 150 is the Number of the Month. Not that we have been going for 150 years or that we are celebrating our 150th issue. This issue marks the despatch of PETplanet Insider to 150 countries. The most recent country to come on stream is Belize. This demonstrates that we have achieved acceptance worldwide as an information platform. The reasons are many and diverse, but one outstanding factor has to be that we visit our readers! Taking our regional reports as our guide, they showed us, in almost half of all reader countries, the extent to which the situation varies from region to region and how each of the local companies is performing on the market. There is not much difference between the machines worldwide; it’s the people locally who make the difference. On my last regional tour I was able to look closely at these individual differences: Finland is a good example. In 2008 a change in the law on disposable containers resulted in a complete turnaround in the market. Although this created a level playing field for all the bottlers, some totally different solutions nevertheless emerged. You can read all about the visit reports from Finland starting on Page 10. Yours, Alexander Büchler EDITORIAL dear readers, EDITORIAL","@ID":5} "MATERIAL / RECYCLING 15 PETplanet insider Vol. 12 No. 09/11 www.petpla.net barrier protection offered by plastics such as PET has led to the development of a number of different barrier solutions for plastic bottles. In Europe, PET blend solutions account for around half of all barrier PET solutions and multi-layer technologies represent close to one-third in terms of bottle units. Barrier coatings represent around one-fifth of the barrier technologies used for PET bottles. Barrier coatings are widely predicted to grow their share of the barrier PET bottle market over the five years to 2015 as a result of developing technologies and more competitive costs. Hot-fill and aseptic technology Bottle manufacturers have developed different versions of panel-less technology for heatset PET. Multilayer PET containers with an MXD6 nylon barrier and oxygen scavengers are used in bottles for hot-filled tea and natural fruit juices. Manufacturers of stretch blow moulding machines have increased the output of hot-fill bottles to match that of cold-fill PET. Manufacturers are also developing energy efficient PET heatsetting processes. Trends such as on-the-go consumption and healthier dietary choices for children and teenagers are reshaping the market for aseptic milk-based products. Furthermore, aseptically filled milk-based products are shelf-stable for up to a year, and can be stored until it is time to chill them for serving. Emerging categories made possible by aseptic packaging advances include low-acid soya and milk-based beverages, nutraceuticals and bioactive products. Machinery and material PET packaging market growth is being helped by the launch of new machinery that allows greater flexibility in shape and volume, faster production rates and energy saving. Sacmi Imola S.C. Via Selice Prov.le, 17/a 40026 Imola (BO) Italy Tel. +39 0542 607111 - Fax +39 0542 642354 E-mail: sacmi@sacmi.it www.sacmi.com S i ff k l i f h b acm o ers turn ey sout ons or t e everage and packaging industry: complete bottling lines for product preparation, container manufacture, filling and closing, labelling and final packaging operations. The extensive experience acquired since the company was established in 1919, in addition to its reputation for supplying advanced technology, financial solidity and a network of 70 companies throughout the world, enables Sacmi to meet all your requirements wherever youare.","@ID":17} "PRODUCTS 48 PETplanet insider Vol. 12 No. 09/11 www.petpla.net Recycling line recoSTAR PET iV+ Ongoing PET recycling innovation, quality and state-of-the-art technology, a full range of consulting services – brought to you by Starlinger. Visit us at: Fakuma 2011, Germany, Oct. 18-22, Booth A7-7403 Plast Imagen 2011, Mexico, Oct. 4-7, Booth 524A www.starlinger.com pet-recycling.com Doubled capacity of material handling control Conair’s FLX material-handling control system is now available in a larger configuration that will serve up to 64 loaders and 20 vacuum conveying pumps. This top-end capacity is double that of the original. The PLC-based system has a 5.6-inch colour touch screen operator interface on the central control box, with colour-coded icons. Alarms can be programmed as active (disabling the device being alarmed) or passive, allowing operations to continue until maintenance staff can identify the problem. Up to six remote humanmachine interface units (HMIs) can be connected to the system via Ethernet link. A built-in webserver allows any personal computer on the network to display system status as a web page. The entry-level FLX system is designed to manage eight loaders and two pumps. www.conairgroup.com ‘Eco-friendly’ labeller Krones’ recently-announced new labeller, called the Sleevematic ES, is designed for handling stretch-sleeve films. These allow an extremely high stretch rate on beverage containers of up to 55%. Based on LDPE (low-density polyethylene), these films constitute an attractive alternative to sleeves made from PVC (polyvinyl chloride). Krones claims that recyclable LDPE films are more eco-friendly and that their high stretching capability means that this new kind of sleeve is smaller and requires less material. The company also says that these stretch-sleeves are more than twice as elastic as conventional stretch-sleeves, which makes them suitable for customised containers with very prominent contours. They require neither a shrink tunnel nor a container drier, which thus offers potential savings in energy consumption. Sleevematic ES is offered in two versions. The single-carousel variant is rated at a maximum of 27,500 containers/h; the twin-carousel version is rated at 55,000 containers/h maximum. www.krones.com Light large-format water cooler bottle Siapi has recently developed a one-way 5 US Gal (19l) PET water container using a lightened 330g preform. It is 60g, or 15%, lighter than the market standard of 390g. Siapi says that this new product required extremely accurate planning and a series of software simulations and laboratory tests in order to ensure that its performance. It was also subject to practical tests, including the use of different water types, in order to fine-tune its operation. Production of a lightweight, large-capacity container requires an extremely precise blowing process because distribution of the low amount of plastic in the bottle requires precisely-controlled distribution. Siapi recommends its EA1S and EA2S machines (one and two cavities respectively) as being able to control all the parameters necessary to ensure compliance with the original design. The bottle has been registered as a design in Turkey. The company says it has raised interest from bottlers across the Gulf and Middle East region. www.siapi.it","@ID":50} "BOTTLING / FILLING 39 PETplanet insider Vol. 12 No. 09/11 www.petpla.net As the blow-moulding machine, Tirta Amarta uses a design-enhanced technology version of the Contiform. The complete valve rack, with its minimised volume of dead space, for example, consumes around 10% less compressed air than the preceding model. Unit costs downsized thanks to lightweighting Besides upgrading its technical equipment, Tirta Amarta also concentrated on cutting its unit costs through lightweighting. Tirta Amarta modelled its bottle on the weight-reduced PET container and together with Krones, the preform producer and the manufacturer for the preform moulds designed a 600-ml short-neck bottle without a support ring. The bottle, which features a neck finish customary in Indonesia, measuring 30mm outside and 25mm inside, weighs only 12.5g instead of the 16g usually found on the market. “Lightweighting demands physical compromises, of course”, concedes Rioan Silalahi. “The first and so far only placing of a lightweight bottle like this, however, secured us a competitive edge and cost advantages on the market.” Plans for more capacity upsizing Tirta Amarta is not resting on its laurels, however, and is aiming to design an even lighter water bottle. “We’re expecting annual growth of 15 to 20% in the Indonesian water market, since per capita consumption is still relatively low and per capita income is continuing to rise”, comments Plant Manager Endang Retnosusmawati. Tirta Amarta has plenty of plans up its sleeve: diversification into flavoured water, expanding the distribution network to other Indonesian islands … – and very soon now some more capacity upsizing, once again together with Krones. www.krones.com Lightweight bottle Excellent growth prospects DRYING HAS NEVER BEEN THIS EFFICIENT: ETA plus® LUXOR - now available with ETAplus® ETAplus® considerably reduces energy consumption and protects materials. When it comes to drying, saving energy is a key concern. We have developed a system that combines airflow regulation with a temperature adjustment feature – that can be disabled if required –and efficient waste heat recovery. The result? A drying system that cuts energy consumption by up to 64%: ETAplus® . motan-colortronic gmbh info@motan-colortronic.de www.motan-colortronic.com Visit us at Fakuma hall B1 booth 1111","@ID":41} "PREFORM PRODUCTION 21 PETplanet insider Vol. 12 No. 09/11 www.petpla.net The key innovation in the MHTcoolMAX is in the detail of the cooling plate, from which cooling pins protrude. It is water-cooled; air that flows through into the preforms therefore arrives significantly cooler than from uncooled plates. In the inner space of the preforms, this solution differs from other offers by its reversed coolant flow. The air initially brushes past on the preform wall toward the front and then arrives back through the inside of the cooling pins; this increases the cooling effect on the preform. In addition, the flow of coolant is divided directly after penetrating the preform and part of the air is directed to the inner space of the thread. The upgrade set is available for preforms up to a maximum water thread diameter of 30/25. MHT assumes the complete project management of the prototype production through to ramp-up to series production and guarantees a smoothrunning changeover to the new number of cavities. The upgrade set is offered within the context of a mould exchange or conversion, such as to a different preform design or weight. After installation by an MHT service engineer, the company says that it becomes a simple matter of ‘plug & play’ for the preform producer – but with output one-third higher than before. Note: Husky and HyPET are registered trademarks of Husky Injection Molding Systems, Ltd., with its headquarters in Bolton / Canada. MHT Mold & Hotrunner Technology AG has no connection to Husky. www.mht-ag.com Take-out plate","@ID":23} "CAPPING / CLOSURES 45 PETplanet insider Vol. 12 No. 09/11 www.petpla.net With these optimisations and improvements, energy consumption in the Netstal range (based on the production of a PCO 1881 closure weighing 2.3g) can be compared as follows: Compared with the SynErgy range there is a saving of up to 13% with the Evos range and up to 40% with the Elion range, following identical process parameters (see table) Continuing reduction of closure weight leads to increased output and an improvement in economic efficiency. The turning point became clear in 2009/10, when output could be significantly increased due to a substantial reduction in cycle time (see graph). Competitive advantages for closure manufacturers in this highly cost-intensive application are significant. As well as higher output per m², lower electricity consumption is a core feature of economically efficient manufacturing. The lower costs of closure manufacture that can be achieved with the measures described above, together with further improvements in closure design, mould and automation performance, are becoming apparent in series production. Specialists from Netstal’s CAP Business Unit are in the very early phases of evaluating customer requirements and needs and implementing them in complete, ready-to-use production lines. www.netstal.com (Data in kWh) Synergy Evos Elion Main Drive(s) 78 56.3 25 Screw Drive 23.5 25 25 Heaters Machine and Mould 24 27 27 Total 125.5 108.3 77 Sleevematic ES – the sensationally saving-savvy system for super-elastic sleeves. www.krones.com PACK EXPO 2011 Las Vegas, 26 – 28 Sep. South Hall, Stand 1800 Table: Comparison of energy consumption of Synergy, Evos and Elion Graph: Output and cycle time 72-cavity PCO 1881","@ID":47} "REGIONAL MARKET REPORTS 13 PETplanet insider Vol. 12 No. 09/11 www.petpla.net Over 140 years of added value through innovative technology and reliability Consultancy | Turnkey systems | Single machines | Service Pass ion for Packaging. The new shrink packer: KHS Innopack Kisters SP Focus on saving energy and resources: Next-generation, film-wrapped multipacks - Fully closed shrink packs for maximum packaging stability - Cardboard pads and trays no longer necessary Direct online printing on the shrink film for reliability and flexibility New shrink tunnel for considerably reduced energy consumption khs.com Werner A., Christian S., Ernst W. Packing technology design engineers „Our Baby – Your Benefit“ Hall 5/5–127 09.-11.11.2011 Nuremberg, Germany with all our suppliers and ultimately to arrive at these two plants”. This is how Michael describes what seems at first glance to be quite a complex approach to configuring the production lines. In all, 300 million preforms for 17 bottle geometries ranging from 0.5 to 2l per year pass through the plants. In addition, there are also different colourways available. www.sinebrychoff.fi degree of flexibility is a requirement here too, the company has integrated four Lanfranchi bottle silos between the SBM and the filler. “This means that we have up to one hour’s buffer facility between the blow moulder and the filler, more than enough time to fit in format changes. This also enables us to conveniently discharge bottles to the filler from outside”, says Project Manager Michael Slotte. A current example is the bottle from Rosti of Sweden which is used for the energy drink “Battery+“ “Converting the stretch blow moulder from a 28 to 38 mm neck is simply too complex an operation, so we are happy to accept the external bottles” says Michael. The plant has been purchased from 7 suppliers altogether – the compressors from Atlas Copco, the stretch blow moulder from Sidel, the filler along with the rinser as well from Sidel and the labelling device from Krones, the pasteuriser from Gea and the typical Finnish palletising systems from Nekos, together with the hard display from the local automation engineers. Sidel was responsible for the overall integration. “One size doesn’t fit all and so we have decided to put together the system components that are best for us in each case. We had eighteen months’ grace from the time when Parliament decided to do away with the tax on disposable bottles before the actual start. We made proper use of this time to hold discussions Michael Slotte in front of the Sidel plant for the bigger bottles (aptly named Obelix). The second (almost identical plant) is located nearby and produces the smaller bottles. This one is called Asterix. There are no plans for a third plant for very small size bottles to go by the name of Dogmatix.","@ID":15} "BOTTLE MAKING 24 PETplanet insider Vol. 12 No. 09/11 www.petpla.net Single stage feature part 3 Suppliers of single stage machinery The history of single stage has been controversial, remains controversial and is still the subject of market gossip and the object of fruitless complaints by some of the participants. But single stage is part of PET history nevertheless, when Katashi Aoki of Nissei Plastics – maker of huge number of injection moulding machines, a company still existing today, family owned and managed by members of the family – decided in the mid-1970s to develop single stage injection stretch blow moulding machines in the Aoki Techn. Lab (R&D centre) and commercially sell them via Nissei ASB. Two companies were founded, originally all on the premises of Nissei Plastics. The sons of Katashi Aoki were put in charge – Daiichi to manage Nissei ASB as Chairman and Shigeto to manage Aoki Techn. Lab. At the end of the 1970s it was decided that the companies should go their separate ways. Thereafter both companies have been rival suppliers of single stage machines. At the end of 1980s a new contender appeared on the scene of single stage, when Sipa of Italy supplied the very massive, large single stage PET moulding machines – with a design originally coming from Van Dorn of the US. Market data The three suppliers control the global markets up to the present day. We estimate that out of a total of 8.600 single stage systems installed Nissei ASB have supplied approx. 6,000 single stage systems, Aoki approx.1,800 systems and Sipa approx. 800 systems. Sipa systems are much larger in size, output and price compared with their Japanese counterparts. Although all three make single stage machines, there is a difference in design and in market policy. The Japanese Nissei ASB and Aoki cover the world market with small machines – the majority of single stage tioned that with Automa there is a No. 4 amongst the single stage machine suppliers and maybe a potential No. 5 from China, currently unknown in Europe. Husky, who also briefly took part in the single stage market mainly on exhibitions, has withdrawn from the sector under Onnex ownership. Let us now turn to the reality of the marketplace today. In the following pages we will be looking at the Big 3 Nissei ASB, Aoki as well as Sipa. We have visited the offices of Nissei ASB (Karel Keersmaekers) and Aoki Techn. Lab. (Hidenaga Nakagawe) in Düsseldorf, Germany, as application was for small machines, most of them for pharma, cosmetics and food - , in contrast to Sipa, who concentrate on the large volume single stage machines – considerable portion has in the past gone into beverages. There is fierce competition between Nissei ASB and Aoki. Sipa – manufacturing in Europe in the Euro region - consider themselves presently unable and unwilling to compete with small single stage machinery. It is true to state that Sipa starts where Nissei ASB or Aoki leave off.The biggest Nissei ASB is the smallest Sipa. For a complete picture it should be men-","@ID":26} "BOTTLE MAKING 27 PETplanet insider Vol. 12 No. 09/11 www.petpla.net 1 2 3 + 5 4 1 2 3 5 4 Aoki Nissei ASB 3 2 4 5 1 1 1 3 2 4 5 Sipa The typical Aoki series is on the basis of three stations, namely for preform injection and direct heat conditioning, stretch blow moulding and product ejection. Heat energy is retained in the preform after injection moulding and final containers are stretch blown straight away – without reheating. With the result: energy savings of between 10 and 20% and reduction of cost per container can be achieved – according to Aoki. The typical Nissei ASB series is on the basis of four stations, adding to the above three stations a preform temperature conditioning station. This fourth station, according to ASB, is to take care of varying conditions (sensitive injection filling speed and preform cooling) and thus to ensure beyond doubt consistency of the entire single stage moulding process – according to Nissei ASB. The typical Sipa single stage series – FX series for instance - has on the injection side one large plasticising unit, providing four shot pots and from there four rows of cavities – two on each sides. After injection moulding the preforms are automatically transferred into two temperature conditioning stations on each side, thereafter blown and transferred out. 1 Injection unit 2 + 3 Preform moulding / conditiong in one step 4 Stretch blow moulding 5 Bottle ejection 1 Injection unit 2 Preform moulding 3 Conditioning 4 Stretch blow moulding 5 Bottle ejection 1 Plastifying unit + 4 shot pots 2 Preform moulding 3 Conditioning 4 Stretch blow moulding 5 Bottle ejection","@ID":29} "PRODUCTS 47 PETplanet insider Vol. 12 No. 09/11 www.petpla.net For further information please contact: info@gabriel-chemie.com www.gabriel-chemie.com Innovation Don’t compromise on quality. PremiumMasterbatches for Superb Products. HALL B5 STAND B5-5204 Friedrichshafen Oct 18–22, 2011 VISIT US AT F AKUMA ! Reduced-weight closures Cargill, the US-based food company, has converted its European and Brazilian-produced 29/21 neck finish PET bottles into lighter 26/21 units, which use reduced-weight Bericap closure systems. Bericap has designed a range of closures for 26mm neck diameter bottles that are intended to save costs and material. The inner diameter of the new neck is identical to the previous 29mm diameter butweighs just 1.37g. Cargill has converted its operations in Western Europe to lighter 26/21 configuration. Since December 2010, Bericap has been supplying Cargill in Brazil with its CTC IT 26/13 closure with pourer. The new generation of closures incorporate tamper-evident tear-off band, hinge, and dripless pouring. Bericap says that its CTC IP 26/13 closures allow top embossment for brand recognition and, according to the manufacturer, are easy to fit on high-speed lines. www.bericap.com Release agent and lubricant in one US company Chem-Trend, based in Howell, Michigan, has officially released Lusin Lub O 32 F, which acts as both a release agent and lubricant for all forms of thermoplastics, with the exception of polycarbonate but including PET preforms and films. Lusin Lub O 32 F works as a release agent. When used as a lubricant, it minimizes scratching during downstream processes. It can be applied to air conveyor systems and is claimed to improve the transport efficiency of formed products, such as PET bottles. The product contains no solvents, silicone or halogens, and can be removed with water. Lusin Lub O 32 F is NSF H1 registered and EU (2002/72/ EG) certified, making it suitable for the manufacture of products that are subject to food hygiene requirements. www.chemtrend.com Hot filler for beverages with particles Sidel’s Veloce ISD, a new hot filler with integrated slurry dosing, is designed for the growing market for beverages with pulps or particles, such as pulpy juices, flavoured waters with fruit pieces, Chinese speciality drinks and aloe vera or coconutbased drinks in PET containers. The filler can dose particles up to 10x10x10mm in size and with particle quantity concentration ranges from 10 to 200ml, for bottle sizes from 200ml to 2l. The Veloce ISD in-line filler includes double-stage filling after bottle rinsing: first, dosage of a certain amount of particles in pumpable slurry; followed by filling of the bottle with liquid juice. The monobloc handles plastic bottles by the neck and is composed of a rinser, doser, filler and capper. The slurry dosing turret is equipped with contactless valves for hygienic filling. A patented volumetric dosing valve replaces the traditional filling tube. Flow cut-off is claimed to be very precise and does not cause any dripping or product wastage. The capping process eliminates microbiological risk between the neck thread and the cap. Automation allows one unique user interface (PLC) to control the entire monobloc, from rinsing to particle dosing and product filling. The Veloce ISD is available as a stand-alone filler or in Combi configuration. www.sidel.com","@ID":49} "BOTTLING / FILLING 38 PETplanet insider Vol. 12 No. 09/11 www.petpla.net In 2008, the privately owned company had progressed so well that in Bandung Barat, about two hours’ drive to the south-east of Jakarta in West Java, they commissioned its first Krones PET bottling line. Tirta Amarta produced around six million litres here in the first year. This was quickly followed by the next stage of expansion. In the summer of 2010, the second line went into production, this time as a high-speed installation rated at almost double the output of its predecessor. By the end of 2010, the output had risen to 93 million litres. The declared goal of the alliance with Krones was explained by Endang Retnosusmawati, Plant Manager of the Tirta Amarta: “We want to be operating with an efficiency of more than 85%”. Monobloc and cleanroom As with the first line, Tirta Amarta once again opted for a monobloc featuring a blow-moulder and a volumetric filler. In addition, the company enclosed the monobloc in a cleanroom, accessible only through an airlock. “The cleanroom not only provides a daily reminder to our operating staff of how important hygiene is in filling operations, but also boosts confidence in the quality of our bottling operation among our customers who visit the line”, says Endang Retnosusmawati. The PETpreforms are fed in from a room above the cleanroom through the ceiling. Outside the cleanroom, two Contiroll machines dress the 600ml and 1.5ll containers in wrap-around labels. An integrated Garantomat on each labeller applies the tamper evident proof required under statute law. The dressed containers are then packed by a Wrapapac in 12-bottle (1.5ll) or 24-bottle 600ml) cartons and palletised on a Modulpal machine. The dressed containers are then packed by a Wrapapac in 12-bottle or 24-bottle cartons. Viro water brand successfully launched","@ID":40} "MARKET SURVEY 30 PETplanet insider Vol. 12 No. 09/11 www.petpla.net Company name Nissei ASB Machine Co., Ltd. Kosme Gesellschaft mbH Luxber, S.L.U. Urola S.C. Mega Postal address Telephone number Web site address Contact name Function Direct telephone number Fax E-Mail 4586-3 Koo, Komoro-shi, Nagano-ken 384-8585, Japan +81(267)23-1565 www.nisseiasb.co.jp/en/ Mr. Katsuo Ishiguro Manager - Sales Coordination Team +81(267)23-1565 +81(267)23-1564 sales@nisseiasb.co.jp Gewerbestrasse 3 2601 Sollenau, Austria 0043-(0)2628-411-0 www.kosme-austria.com Johann Gugler Managing Director +43 2628-411-125 +43 2628-411-4125 j.gugler@kosme-austria.com Av. de Azorin, 34-36 03440 Ibi, Spain +34 965553853 www.luxber.com Mr. Ricardo Sanchez Export Executive +34 965553853 +34 965553861 luxber@luxber.con Urola Kalea s/n, PO Box 20230 Legazpi, -Spain- +34 943 737003 www.urola.com Iñaki Unanue +34 943 737144 iunanue@urola.com 47-8 # Huangzhou RD, Huangyan, Zhejiang provice, China +86-576-84020122 www.megamachinery.com Simon Cai Sales Manager +86-576-84020122 +86-576-84020107 hymega@gmail.com 1. Machine designation / model number NB Series HSB Series Linear, 6 models Rotary , 4 models TecnoPET URBI Series / 6 models 10 2. Bottle volume (from/to in litres) 25 a) Standard machines ~1.5 ~0.6 0,05 - 3,0 0,05 - 3,0 0,1 to 5 0.1 to 2 up to 2.5 b) Machines for large containers ~8 ~2 0,5 - 30,0 0,5 - 6,0 8 to 10 up to 10 up to 25 3. Maximum number of stretch-blow moulds (units) 16 a) Standard machines 4 6 1-4 6 2, 4, 8 8 up to 16 y b) Machines for large containers 2 4 2-4 6 1 4 up to 2 4. Output per stretch-blow mould for: 0.5l CSD bottle (units per hour) 900 1,000 1,700 2,000 1,600 1,500 1,500 1l CSD bottle (units per hour) 850 - 1,650 2,000 1,500 1,500 1,400 1.5l still mineral water bottle (units per hour) 900 - 1,600 2,000 1,600 1,600 1,300 Large capacity container 650 600 up to 1,250 for 5l; 350 for 30l 1,250 800 1,200 150 Other 500ml Jars 970bph/ cav** 5. Footprint / space requirement (L x W x H in metres) 5.2x2.3x2.1 6.7x2.0x3.2 min.: 4.5x .83x3.1; max.: 5.1x1.85x .1 (without preform feeding system) 6.05x3.85x3.25 (without preform feeding system) 4,5 x 5 x 2 including loading system Smallest URBI-2 (2.320x2.2x2) Largest URBI-8 (5.9x4.35x2.3) Depending on the model of the machines Company name SMI S.p.A. Siapi SRL Sipa KHS Corpoplast GmbH Postal address Telephone number Web site address Contact name Function Direct telephone number Fax E-Mail Via Piazzalunga, 30, 24015 San Giovanni , ianco (BG), ITALY 0039 0345 40.111 www.smigroup.it Mr. Pietro Volpi Marketing manager +39 0345 40.316 +39 0345 40.209 info@smigroup.it Via Ferrovia Nord, 45, 31020 San Vendemiano (TV), Italy +39 0438 4096 www.siapi.it Maico Zanco Sales Manager +39 0438 4096 +39 0438 401016 maico.zanco@siapi.it Via Caduti del Lavoro 3 31029 Vittoria Veneto (TV) Italy +390 438911511 www.sipa.it Antonio Narder Industrial Division Director +39 0438911511 +39 0438912273 sipa@zoppas.com Meiendorfer Strasse 203 22145 Hamburg, Germany +49 (40) 67907-0 www.khs.com Frank Haesendonckx Director Competence Center +49 40 679 07 475 +49 40 679 07 9475 frank.haesendonckx@khs.com 1. Machine designation / model number SR Stretch blow-moulding machines / 10 models (8 for standard capacity containers and 2 models for high capacity containers) EA series (15 models) EA-S series (8 models) EA Heat Set series (12 models) EAWM series (6 models) Rotary, SFR 6 EVO, SFR 8 EVO, SFR 12 EVO, SFR 16 EVO,SFR 20 EVO,SFR 24 EVO, SFR 9/27 (7 MODELS) Linear, SFL 2/2,SFL 2/1,SFL 4/2,SFL 4/3, SFL 4/4, SFL 6/2, SFL 6/3, SFL 6/4, SFL 6/6 (9 MODELS) KHS InnoPET Blomax Series IV, 13 models, 4 -36 stations 2. Bottle volume (from/to in litres) a) Standard machines 0.25 / 3t 0,1 - 5 l 0,1-1,5 l 0,1-1,5 l 0.25 - 3.3 0.25 - 3 0.2 - 3 b) Machines for large containers 4 / 10 5 - 40 l up to 12 l 4 - 30 up to 6 (Blomax Series III) 3. Maximum number of stretch-blow moulds (units) 20 a) Standard machines 20 from 2 to 16 from 2 to 16 from 1 to 4 27 6 36 b) Machines for large containers 6 from 1 to 6 from 1 to 3 4 8 (Series III) 4. Output per stretch-blow mould for: 0.5l CSD bottle (units per hour) 1,800 1,500-1,800 2,200 1,800 2,200 1l CSD bottle (units per hour) 1,800 1,500-1,800 2,000 1,700 2,200 1.5l still mineral water bottle (units per hour) 1,800 1,500-1,800 2,000 1,800 2,200 Large capacity container 1,100 150-600 1,250 for 5l; 800 for 30l 1,400 / 6l container, depending on geometry (Series III) Other up to 1,200 hotfill bottles up to 1,400 widemouth jars 5. Footprint / space requirement (L x W x H in metres) min 3.6x3.75x3.55(SR 4/6) / max 4.79x8.83x3.55 (SR20) 2.9x2x2.2 to 7.3x3.1x2.4 2.8x2.6x2.2 to 8.1x2.4x2.7 2.9x2x2.2 to 7.3x3.1x2.4 2.9x2x2.2 to 5.5x2.2x2.5 4,4x3,9x3,7 5,8x2,2x2,1 7,4x3,0x3,25 Blomax 4 13,3x7,0x3,25 Blomax 36","@ID":32} "MATERIAL / RECYCLING 14 PETplanet insider Vol. 12 No. 09/11 www.petpla.net Bottled water still ahead, niche beverages making their mark World trends in PET packaging Apart from its excellent performance properties, PET packaging market growth was also supported by the environmental credentials of PET as a lightweight material that can be recycled easily. However, growth in the PET packaging market has been curtailed since 2008 as a result of the world economic recession. Consumers have reduced their discretionary spending, including the purchase of some packaged beverage products. PET packaging market growth in tonnage terms has also been adversely affected by the trend to light-weight PET bottles. For example, the average weight of a single-serve PET mineral water bottle reduced by around one-third during the period 2003–08. The trend to light-weight PET bottles is set to continue. The slowdown in consumer demand for CSDs and mineral water in developed countries, and the market maturity of these key end-use sectors, is also holding back the growth of PET packaging. Furthermore, the growing use of recycled PET content in beverage bottles is displacing virgin PET material for packaging. While from 2010 to 2015 PET packaging is unlikely to register growth rates similar to those seen between 2000 and 2007, growth opportunities still remain. Barrier PET bottles and jars for juice, milk, tea, beer, wine and food are forecast to register strong growth over the period 2010–15. The developing countries of Asia Pacific, South America and eastern Europe will also show higher growth for PET packaging as a result of growing real incomes and the replacement of traditional pack formats by PET bottles. Market drivers Economic, social and demographic influences are playing a key role in driving development of the global PET packaging market. Slower economic growth in the advanced economies of Western Europe and North America will constrain future PET packaging growth in these regions. In contrast, rising real incomes in the emerging and developing markets of Asia Pacific, Eastern Europe and South America will be the main driver of growth for PET packaging over the five years to 2015. Social influences are also playing a major role in the development of the PET packaging market. Environmental concerns are driving PET packaging producers, brand owners and retail chains to adopt sustainable packaging programmes. This type of packaging addresses the growing concerns for the environment due to its ability to be light-weighted and recycled. PET packaging is lighter than its competitors such as glass bottles, and CO 2 emissions have been reduced in PET bottle production. Key demographic influences on global PET packaging growth include the fastergrowing populations in Asia Pacific, eastern Europe and South America. The development of PET bottles with enhanced gas-barrier properties presents a major market opportunity for PET preform and bottle producers over the period to 2015. Barrier PET bottles are predicted to grow at a significantly higher rate than PET packaging as a whole. Beer, wine, juices, dairy products and food all present growth opportunities for barrier PET bottles and jars. Development of the PET packaging market is being helped by continuous improvements in technology. Technological development is providing better barrier solutions, improved resin formulations, faster and more efficient PET processing machinery, and solutions for hot-filling and aseptic filling of PET packaging. PET technology developments Advances in developments barrier technologies have paved the way for PET bottles to be used for small, single-serve beverages. Barrier PET bottles have also penetrated market sectors such as juices, teas and beer and are making inroads into new enduse sectors such as wine and dairy drinks. Technology developments in hot-fill and aseptic cold-fill processes are also supporting the development of PET bottles and jars in these developing market sectors. Alongside these key technology developments, continued improvements are being made to PET resin formulation, additive technologies and processing equipment. Barrier PET bottles Plastic bottles in themselves do not provide a good barrier against oxygen and carbon dioxide for certain sensitive beverages such as beer, juice and dairy drinks. The limited Global consumption of PET packaging saw strong growth during the period 2000–07. Growth was largely driven by the replacement of glass bottles, metal cans and cartons for beverages, particularly for carbonated soft drinks (CSDs) and mineral water. While from 2010 to 2015 PET packaging is unlikely to register growth rates similar to those seen between 2000 and 2007, growth opportunities still remain, according to a recent study undertaken by Pira international*.","@ID":16} "PETpatents www.verpackungspatente.de 52 PETplanet insider Vol. 12 No. 09/11 www.petpla.net Bottle manufacture Europ. Patent Nr. EP 2248728 A1 Applicant: Yoshino Kogyosho Co. Ltd., Tokyo (JP) Application Date: 14.1.2009 A plastic bottle is equipped with surfaces facing inwards which, following hot filling and subsequent cooling, demonstrate further defined penetration into the inside so as to compensate for the negative pressure that develops. Container closure International Patent No. WO 2009 / 112752 A1 Applicant: Tetra Laval Holdings / Finance S.A., Pully (CH) Application Date: 24.2.2009 In this international patent application a number of options for improving the tamper-evident closure on a hinged lid are set out. This can be done by means of a button that changes a material bridge irreversibly so that it is readily recognisable by the consumer at the time of first opening. Stable container International Patent No. WO 2010 / 132190 A1 Applicant: Green Planet Holdings Inc., Chicago (US) Application Date: 23.4.2010 Design and stabilising characteristics of a thin-walled bottle made from bio-degradable plastic (PLA) are described Additional cover German Grant of Patent No. DE 112007001961 B4 Applicant: Gizmo Packaging Ltd., Deanpark (GB) Date of Application: 10.8.2007 Container with pouring spout and means to supply an additive to the content of the container. The products can be mixed without removing the cover for an improved mixing process. Bottle with handle International Patent No. WO 2011 / 017481 A2 Applicant: Robert Priessnitz, Dunellen (US) Date of Application: 5.8.2010 Children, the elderly or people with restricted movement in the hand find it difficult – particularly if there is an external build up of condensation – to hold a container of liquid securely and to pour out the contents. The design of this handle – moulding and integration in the neck area of the bottle – is aimed at minimising these problems. Plastic bottle International Patent No. WO 2011 / 016544 A1 Applicant: Dai Nippon Printing Co., Tokio (JP) Date of Application: 6.8.2010 The middle segment of a plastic bottle is specially moulded so as to elastically absorb any differences in pressure that may occur. Segments featuring a type of pre-tensioning can be “twisted“, thus compensating for the change in pressure by means of a change in volume.","@ID":54} "BOTTLES 51 PETplanet insider Vol. 12 No. 09/11 www.petpla.net Visible double action 125ml complexion care product, brand name “Nivea Visage“ with visible “Double Action“ is being marketed by Beiersdorf in France in a highquality PET bottle. Thanks to the clarity of the bottle and non-label-look labels to front and rear, the two product phases – blue and clear – can be clearly identified. A snap-on hinge lid that can be operated using one hand only and featuring audible clicks when opening and closing make this high-quality cosmetic packaging complete. www.nivea.com Car Care RPC Containers Llantrisant has landed a major contract to supply plastic containers for car care products manufacturer Tetrosyl, UK More than 100 distinct products in the company’s own-brand and private-label range will appear in containers manufactured at the Llantrisant factory. Tetrosyl has switched production to RPC Llantrisant from its own in-house moulding operation. The containers are being produced in PET in a range of 14 colours. They will be used for a wide variety of products including car polishes, engine oils and trigger-spray de-icers. Tetrosyl supplies ranges both under its own brands and for private labels in supermarkets and automotive outlets. www.rpc-group.com","@ID":53} "29 PETplanet insider Vol. 12 No. 09/11 www.petpla.net 2-stage SBM machinery Once again we are pleased to present our latest market survey, bigger than the 2010 edition, when 17 suppliers were taking part. This year, a total of 18 suppliers worldwide have given us comprehensive details of their products. Readers interested in obtaining further information are invited to contact the companies direct. Although the publishers have made every effort to ensure that the information in this survey is up to date, no claims are made regarding completeness or accuracy 09/11 MARKETsurvey Bottle-to-bottle recycling plants Conveyors for preforms and empty bottles Caps and closures Preforms Perform moulds and SBM moulds Single stage machinery 2-stage SBM machinery Compressors Filling equipment Resins and additives Company name TechnoPET Machineries, India W. Amsler Equipment Inc. Beutelspacher S.A. DE C.V. Postal address Telephone number Web site address Contact name Function Direct telephone number Fax E-Mail 14/15, Shree Naman Plaza,S.V.Road, Kandivali (W), Mumbai -400 067Maharashtra, INDIA. (+91) 22-28610828 www.techno-pet.com Mr. Vineet Bannore Director - Technology +91 9820346565 +91 22-28061410 sales@techno-pet.com 1245 Reid St. Unit 1, Richmond Hill ON, L4B 1G4 +1 905-707-6704 www.amslerequipment.net Heidi Amsler Sales & Marketing Manager +1 905-707-6704 +1 905-707-6707 heidi@amslerequipment.net Venados 52 Colonia Los Olivos, Tláhuac, México, D.F. C.P. 13210 +52 5840 45 62 www.beutelspacher.com Ing. Abraham Beutelspacher Engineering Manager +52 5840 45 63 +52 5845 1053 info@beutelspacher.com 1. Machine designation / model number PAuto 800/1400/2000 Auto ejection Jar 600 Semi Auto TPOL 1800/2700 Online Series TPS- 20l 5 Gallon Jar TP-Beer for beer/liquor Linear Series - 9 Models, L12, L15, L22, L25, L32, L407, L42, L515, L615 Linear Widemouth Series - 2 Models L16J, L25J Linear Convertible Series - 4 Models L32C, L42C, L515C, L615C Linear Large Format Series - 5 Models, L110, L210, M120, LM120, L120C SB 3001 2. Bottle volume (from/to in litres) a) Standard machines 0.05 to 2.0 0.2 to 5.0 0.1 to 2.0 0.2 to 2 0.05 to 5 0.1 to 6 0.05l to 5 3 b) Machines for large containers 5 to 20 4 to 23 3. Maximum number of stretch-blow moulds (units) 2 a) Standard machines One/Two/Four One Two/Four One/Two/Four 6 2 6 b) Machines for large containers One 3 4. Output per stretch-blow mould for: 0.5l CSD bottle (units per hour) 800 600 900 500 1,800 1,800 1,500 - 1,800 1l CSD bottle (units per hour) 700 500 800 600 1,400 - 1,800 1,400 - 1,800 1,500 - 1,800 1.5l still mineral water bottle (units per hour) 700 600 900 700 1,400 - 1,800 1,400 - 1,800 800 - 900 Large capacity container 100 jars/h 900(10L); 275(18.9L) Other Hot-fill and wide mouth: 450 jars Oriented Output 300 jars/h Combo filling 800 - 1,600 3,000(4L) 5. Footprint / space requirement (L x W x H in metres) 4 x 4 x 3 3 x 3 x 3 5 x 5 x 3 5 x 4 x 3.5 4 x 4 x 3 from 4.0x1.8x2.4 to 4.3x3.7x2.5 3.9x2.5x2.2 5.7x2.0x2.4 to 4.3x3.7x2.5 3.9x3.8x2.7","@ID":31} "CAPPING / CLOSURES 44 PETplanet insider Vol. 12 No. 09/11 www.petpla.net Improved injection moulding machine design helps to reduce energy consumption and improve efficiency in closure manufacturing Cutting closure production costs There is constant pressure to lower the production costs of mass-produced goods, such as beverage closures. Improved machine design, including energy-recovery systems, work with lighter weight and developing design to reduce the costs of closure systems production. Developments of the PCO 1881 closure design, launched in 2008, have continually reduced its weight. At launch, it weighed 2.45 g; it is now 2.3g when used for CSD and up to 1.8g for still water. The weight reduction has led to raw material savings of several thousand tons each year. Machine manufacturers can also contribute, through technical advances in the performance of the injection unit, clamping unit and main drive. Plasticising performance in the injection unit is a significant factor and Netstal is now furnishing its Elion and Evos series with the established barrier screw and new 1000, 2000 and 2900 unit sizes. The combination of high-performance screws and high-torque screw drives enables Netstal machines to dispense high shot weights in a very short time and with good melt quality. The PE-HD types used as standard with an MFI (Melt Flow Index) of less than two can also be processed in the same way, as shown in newly-emerging bimodal and multimodal grades. Netstal has revised its injection piston sizes, in order to achieve the same injection performance with lower oil volumes; reduced oil consumption has a direct impact on drive size and, therefore, energy consumption. The revised performance of the Evos/Elion injection moulding units allows the 2000M hybrid unit to be used, instead of the hydraulic 2150 unit. In the case of the clamping unit, the first step is selection of the right drive technology. In a hydraulic Evos clamping unit, for example, optimised internal clamping cylinders and toggle lever geometry, combined with highperformance hydraulic valves, help to save energy. The fully-electric Elion recovers accumulated braking energy – produced from closing the clamping unit, for example – and uses it to power an additional electric axle. Netstal’s 5-point toggle lever can cope with the fastest mould movements without any need for spindle drives, which are prone to wear and tear. Netstal’s spindle-free clamping unit has virtually no self-locking, so practically all braking-phase kinetic energy can be recovered. This technology has been in use since Elion was launched in 2004, years before the emergence of Formula 1’s KERS (kinetic energy recovery systems).","@ID":46} "source: Stephan Barth / pixelio.de BOTTLING / FILLING 36 PETplanet insider Vol. 12 No. 09/11 www.petpla.net From zero to 93 million litres in two years Ten years ago, in 2001, Indonesia’s water market still looked very different: about 250 vendors were producing 5.4 billion litres of water with an installed capacity of 6.7 billion litres. Only the really big producers were then offering PET bottles. Today, the installed capacity has reached almost 20 billion litres. In 2002, back in the early days of the water boom, Tirta Amarta had begun to fill gallon containers, and subsequently operated a relatively small filling line , for handling not only drinking beakers, but also PET containers. They began initiating sales in market regions outside the Jakarta conurbation. Tirta Amarta purchased the PET containers already blow-moulded, but due to the market’s rapid expansion they soon became scarce. The water brand Viro was well received: demand was rising, Tirta Amarta wanted to expand, wanted rotary technology, wanted its own in-house PET container production operation, better line availability, higher output. Gain market share by attractive pricing, minimised packaging costs plus maximised efficiency in the bottling operation: this was Tirta Amarta’s concept for tackling the Indonesian water market. And they did this firstly by means of a newly designed lightweight short-neck container, and secondly by two PET bottling lines from Krones, installed in quick succession. Accelerating growth fuels demand* Bottled water boom in Indonesia *Based on an article by Hendra Wivina, Krones AG, Indonesia Outside the cleanroom, two Contiroll machines dress the 600-ml and 1.500-ml containers in wrap-around labels. Packaged drinking water is a huge market in Indonesia. Of the approximately 14.5 billion litres packed in 2010, around 60% came from the market leader. The rest, a still-substantial 6.5 billion litres or 65 million hectolitres, is shared by an estimated 670 smaller and large bottlers. Many of them operate on only a regional or even local scale, and most of them package their water in small portion beakers with a film closure holding 200 to 300ml, or in large 5-gallon containers for home consumption. And this is precisely how Tirta Amarta got its start in the water business too.","@ID":38} "PETcontents 09/11 4 PETplanet insider Vol. 12 No. 09/11 www.petpla.net INSIDE TRACK 3 Editorial 4 Contents 6 News 46 Products 49 Bottles 50 Personal care 52 Patents BOTTLE MAKING 24 Suppliers of single stage machinery Single stage feature part 3 MARKET SURVEY 29 Suppliers of 2-stage SBM machinery BOTTLING / FILLING 36 Bottled water boom in Indonesia Accelerating growth fuels demand 40 How “dreams” come true Mineralquellen Bad Liebenwerda, Germany, invests in a KHS packing system CAPPING / CLOSURES 44 Cutting closure production costs Reduced energy consumption and improved efficiency in closure manufacturing. MATERIAL / RECYCLING 14 World trends in PET packaging Bottled water still ahead, niche beverages making their mark 18 Where the streets have no name Brazilian R-PET plant feeds own bottle collection PREFORM PRODUCTION 20 More bang for your buck MHT mould upgrade 22 Preform yellowing A rapid guide to perfect preforms part 23 Page 46 Page 18 BUYER’S GUIDE 41 Get listed! Page 24","@ID":6} "PETbottles 50 PETplanet insider Vol. 12 No. 09/11 www.petpla.net Personal Care Skin oil in PET 150 ml gentle body oil with sea buckthorn and wild rose oil is being marketed by Berlin Cosmetics under the brand name “Indra Natural Cosmetics“ in an appropriately designed PET bottle. The bottle is decorated with front and rear labels adapted to its shape; the colour of the body oil is tinged with blue and the final crowning touch to the packaging is a screw-on, green hinged lid. www.berlin-cosmetics.de Fabric softener with Kiwi fragrance The German special items retailer, Thomas Philipps of Bissendorf, is selling a litre of fabric softener with kiwi fragrance under the brand name “Ela Soft“ in a square, transparent PET bottle. This practical, space-saving packaging features an allround paper label and a white screw closure without tamper-proofing. www.proquimol.es Bath foam 950ml of bath foam scented with lavender is being marketed by Messrs. Soapland of Andernach in round PET bottle of high-quality design. The transparent packaging features an attractive, injection moulded screw cap in the shape of a diamond. Prior to initial use the bottle is tightly sealed. Colourmatched front and rear labels and a ribbon decorated with a bow are used to further emphasise the quality of the product. www.soapland.de Carrefour opts for PET The French trading group Carrefour based in Levallois is selling 500ml liquid mouthwash in a PET bottle featuring a striking design. The red product in the clear bottle has the same effect as a stop signal at the PoS. A childproof screw cap (which can also be used for dispensing) plus an innovative design in non-label-look labels to front and rear give an additional boost to the product’s appearance. www.carrefour.com","@ID":52} "BOTTLING / FILLING 43 PETplanet insider Vol. 12 No. 09/11 www.petpla.net EREMA Engineering Recycling Maschinen und Anlagen Ges.m.b.H. A-4052 Ansfelden . Austria . erema@erema.at . www.erema.at We know how. PET Extrusion System VACUREMA® Prime to produce food contact approved BTB pellets Input: Washed PET flakes Output: rPET pellets Batch process i guarantees defined decontamination time for each PET flake • FDA and brand owner approved • Efsa approval requested via customers CIC compact inline crystallisation i • lower AA ( 1 ppm possible) • higher crystallinity • space-saving equipment Permanent monitoring for direct food contact and IV i Very low energy consumption, 0.30 to 0.34 kWh/kg i The Innopal PBL operates with a combined layer/row pusher. The concept includes an integrated handling robot which uses suction elements to pick up pallet liners from a designated magazine and place each one in its specified position. At the Bad Liebenwerda mineral water bottling plant the individual layers can be palletised on half pallets or Euro pallets as required. Among other things, a fully automated system requires an articulated robot that can be instructed to steer towards up to four different pallet positions, grasp all four sides of the individual layer formations, lift them, and finally set them down on a table. From here the formations are removed row by row and the shrink packs transferred to the single-lane pack conveyors. Controlled by a support plate distributor, the shrink packs reach the conveyor belts designed to take them. Finally, the shrink packs are fed into the palletiser as described. A ReDiS (Remote Diagnostic Service) is also integrated into the line. Should problems arise within the line, a direct connection to the KHS ReDiS service centre can be made and an extensive remote analysis carried out. In the bestcase scenario, a machine problem can be solved by accessing the electronic system components online. If the problem involves mechanical components, the technicians are notified as to what action to take. Reprogramming or transferring possible updates via ReDiS is also conceivable. Perspectives on growth At present the company site measures 110,000m2 and can accommodate no further development. However, this is not necessarily a reason to rule out an increase in production at Bad Liebenwerda. As a precaution the company has already invested in land opposite, in a site on which its existing production, storage, and administration buildings could easily be duplicated. www.khs.com Horst Kuhl, Managing Director of Mineralquellen Bad Liebenwerda","@ID":45} "MARKET SURVEY 31 PETplanet insider Vol. 12 No. 09/11 www.petpla.net SMF Maschinenfabrik GmbH Krones AG Redcarstrasse 40, 53842 Troisdorf – Spich, Germany +49 2241 944 886-0 www.smfgmbh.com Przemyslaw Wojtowicz Sales Manager +49 2241 944 886-0 +49 2241 944 886-99 p.wojtowicz@smfgmbh.com Böhmerwaldstr. 5 D - 93073 Neutraubling +49 9401-70-0 www.krones.com Peter Christiansen Sales Manager +49 9401 70-4980 +49 9401 70-914980 danuta.kessler-zieroth@krones.com HS 3000 HS 6000 Stratos 10 electric Stratos 20 electric Optima7 Contiform S 9 models available Contiform M 3 models available Contiform K 4 models available Contiform H 8 models available Contiform ProShape 2 models available 0.25 – 3 0.25 – 3 3.0 – 10 5 – 20 0.25 – 2.5 0.1 - 3 0.1 - 2(1,5) 0.1 - 0,7 0.1 - 2 0.1 - 3 2 4 2 1 7 24 (28) 30 40 24 (26) 10 *per machine up to 2,750* up to 5,500* up to10,800* 2,000 2,000 2,000 2,000 up to 2,500* up to 5,000* up to10,400* 2,000 2,000 2,000 up to 2,400* up to 4,800* up to10,000* 2,000 2,000 2,000 up to 2,000*, up to 4,000*, up to 1,800* 5gal – up to 500 up to 8,700* up to 1,700* 1,700 (steel moulds) 1,600/1,800 3.5x1.4x2.2 3.5x2.8x2.2 4.1x2.43x3.42 3.3x2.23x3.95 from 6,9 x 4,4 x 3,6 to 11,6 x 6,8 x 3,6 from 7,4 x 4,4 x 3,6 to 13,9 x 6,8 x 3,6 from 10,9 x 5,2 x 3,6 to 16,6 x 6,8 x 3,6 from 6,9 x 4,4 x 4,5 to 11,2 x 6,8 x 4,5 8,1 x 6,0 x 3,6 Wei Li Plastics Machinery (H.K.) LTD. Side S.A. Mag-Plastic Machinery S.A. Sidel Group 1212, Fo Tan Ind. Centre, 26-28 Au Pui Wan St., N.T., Hong Kong +852 2690 2368 www.weiliplastics.com Peter Leung Sales Manager +852 2690 2368 +852 2690 2380 info@weiliplastics.com Pol. Ind. Monguit C/Llinars, s/n, 08480 L'Ametlla del Vallès, Barcelona - Spain +34938463051 www.side.es Josep Jimenez Global Export Manager +34 938463051 +34 902884574 josep.jimenez@side.es Rue Alfred-Pot 1 - CH – 1896 Vouvry - Switzerland 41 24 482 0820 www.magplastic.com +41 24 482 0819 sales@magplastic.com Avenue de la Patrouille de France, Octeville-sur-Mer, BP 204, 76053 LE HAVRE Cedex, France +33 2 32 85 86 87 www.sidel.com Dominique Martin Blowing & Coating Product Management Director +332.32.85.88.45 dominique.martin@sidel.com MP Easyblow (+ MaxiBlow/TMS 504/TM 1002e/TMS 2004e/TMS 2006e/TMS 2002e-G/TMS 2003e-G/TMS 5001 SSB (Synchronised stretch blow) serie: 4, LBM (Linear blow moulder) serie: 2, SLC (Super large container) serie: 1 SBO Universal & SBO Universal2 15 models (rotary) SBO Highspeed 2 models(Rotary) SBO Compact 2 models (linear) SBO Universal PH (Preferential Heating)/ 6 models available SBO Universal HR (Heat Resistant) /9 models available 10,800 to 36,000 bph 48,000 to 64,600 bph 2,400 to 6,400 bph For flat or complex packages For hot filled bottles 0.015 - 10 0.05 - 3 SSB 02 from 0.04 to 5, SSB 02 Wide Mouth & SSB 02 Hot fill 0.25 to 1.5,SSB 03 from 40 to 5, LBM 05 & LBM 10 from 0.25 to 2 0,25l to 3l 0,2 to 0,7l 0,25l to 10l 0,25l to 3,3l 0,25l to 3l 10 - 20 0.05l - 10 gallons SLC-02/25 : 11.5L to 26.5L ( 3 Gallons to 7 Gallons ) up to 10l 4 6 10 30 34 4 20 30 2 3 2 not applicable not applicable 3 not applicable not applicable *per machine 2,800~3,000* 1,500 1,200 – 1,400 2,800~3,000* 1,500 1,200 – 1,400 2,600~2,800* 1,500 1,200 – 1,400 500~600 for 5~10 1,000 400 360~400 for PP feeding bottle 4 x 3 x 2 To be determinate, depending model 6.35 x 3.0 x 3.9, Largest machine incl. elevator : 11.7 x 4.2 x 2.6","@ID":33} "BOTTLE MAKING 26 PETplanet insider Vol. 12 No. 09/11 www.petpla.net SIPA Nissei ASB Aoki + 1 4 5 2 3 + Technical specifications The Nissei ASB and Aoki machines are small machines. The difference in design between the two Japanese companies is marginal, although both companies may disagree with such a statement. (please see issue 7+8/11 for technical data sheets). 1 Plastifying unit (Sipa: extruder, Aoki + Nissei ASB: injection units 2 Preform moulding 3 Conditioning (Aoki: 2+3 in one step) 4 Stretch blow moulding 5 Bottle ejection well as the factory of Sipa in Vittorio Veneto, Italy (Roberta Gualtieri). Nissei ASB is a public company trading on the stock exchange – reasonably open with facts and figures even on finances. Aoki and Sipa are privately owned companies, where information is obviously scarcer and filtered/ screened by the owners, as can be seen from the visit reports. In this issue you can read the report about Nissei ASB (page 33). In issue 10 we will publish our reports about our visits at Aoki and Sipa. Comparison of technical specifications of single stage machinery supplied by Sipa, Nissei ASB and Aoki","@ID":28} "BOTTLE MAKING 34 PETplanet insider Vol. 12 No. 09/11 www.petpla.net studied Japanology, which centres on Japanese language, culture, all aspects of the Japanese society, but not engineering. Then he took a masters degree in export management at the EHSAL ) University in Brussels. He worked briefly for a Belgian company exporting textiles to Japan. “In 1994 I got in contact with ASB. In 1995 I joined and was stationed in Japan for four years, working one and a half years in the factory, learning the technology, assembling the machine, processing the machines. For the remainder of the time I was working in the international sales and marketing department. In 1999 I came to Germany, first active as an area sales manager. In 2002 I became Director of the company and in 2008 I became the MD of the company”. Clearly Keersmaeker’s deep knowledge of product and his European approach to the business gives his Japanese Nissei ASB a competitive advantage. Product range Nissei ASB supplies single stage machinery (ASB and PF series) as well as – in much smaller numbers – two stage systems for injection moulding preforms (PM series) as well as for stretch blow moulding same (NB series). ASB series – broad versatility, multitude of special applications ASB single stage are bestsellers - four stations, such as for preform injection, preform temperature conditioning, stretch blow moulding and container eject - for max versatility, production rates from 100 to 10,000 bph (bottles and jars). Bottle sizes vary from 2,5ml to 40l. ASB-15N/10E also available as all-electric versions. PF series – more compact, less foot print, less investment The PF series is targeting markets of two stage in small and mid-size companies. PF single stage are well positioned - six stations – such as for preform injection, secondary cooling, temperature stabilisation and pitch change, reheating, stretch blow moulding, container ejection. Production rate is between 450 up to 3,200bph. The Nissei ASB single stage machines are produced in Japan (all single stage and hot fill), in India (small ASB 50 and semi-finished ASB-70 as well as PF, which are then finished in Japan). Two step machines are made in Shanghai. (Nissei ASB’s two step machinery is not part of this presentation about single stage.) Strategic aims for implementation Asked about the strategic aims for implementation over the nexed three years, Karel Keersmaekers responds by quoting the corporate slogan “Balance and Surprise”. This means for Nissei ASB Short term planning for the future: increase in production capacity in the Indian factory. Second factory next to the first factory in Mumbai. Double output in India to be marketed and sold. Focus on moulds, which today already accounts for 23% of sales. The target is to double production capacity in India of moulds in three years, i.e. in total 1,200 moulds produced per annum for injection and blowing. Introduction of new machines into the market, firstly the ASB-150DPW with double row configuration suitable for high volume production for cosmetics and food. As we see a trend from glass to PET especially in the wide mouth formats. Development of a new generation of PF, which is a 1.5 step machine, also with a higher output, i.e. 9,000 bph in a single stage. To be launched on the market in 2012. To extend range into higher output. New potential market places: “We want to be more active in South America, also in West Africa (countries representing logistic challenges)”. New office in Nigeria. Reinforcement of staff in Sao Paolo/Brazil. (In this present issue we are not covering Nissei ASB’s developments and targets in the two step arena.) Challenges We asked Karel Keersmaekers: “You are number one. What are the challenges ahead?” And Keersmaekers answered for Nissei ASB: “We are number one in single stage, because we have learned to win the market rather than try to beat the competition. We have opened ourselves. We are looking forward. This strategy will be continued. There is room for growth in the single stage market by seeking more applications. But we have also noticed a certain amount of overlapping from single stage to two stage. There are huge numbers of small two stage manufacturers mainly in the Far East, whom we are keeping an eye on, who make two cavity, four cavity moulding machines, linear blow moulding machines, that are gaining little by little market share. That is why we develop a new generation of 1.5 stage machines, to counteract the two stepper into our single stage markets. Our response is to offer higher outputs like 10,000bph with versatile features for neck size and bottle capacity, combined with cost effectiveness. To remain on top, we must take care and progress continually.” www.nisseiasb.co.jp","@ID":36} "REGIONAL MARKET REPORTS 10 PETplanet insider Vol. 12 No. 09/11 www.petpla.net Finland Finland comes aboard In 2008, following the abolition of a tax on disposable bottles, Finland witnessed the start of the triumphal advance of the PET disposable bottle. In Part 1 we described the changes that went hand in hand with this, based on the particular type of beverage. What is remarkable about Finland is the fact that, following the change in the law, all the bottlers bought themselves new filling lines at practically the same time. And, even though the basic parameters were similar for all of them, each of the bottlers arrived at a different layout. All the bottlers need to achieve the bulk of their business within a season lasting just 3 months and at the same time produce up to 100 different products on the same equipment. You can read for yourself how the individual bottlers have risen to the challenge. The reports are about Olvi, Finn Spring, Hartwall and Sinebrychoff. by Alexander Büchler part 2 OLVI Mr. Pentti Pelttari, Technical Director Head Brewer Small is beautiful in Finland Of the three big breweries in Finland Olvi is the only one that is not owned by a multinational brand. Olvi has been brewing beer in Iisalmi since 1878 and since 1906 their bottling activities have also included soft drinks. (Cans and) PET bottles are used exclusively as containers for soft drinks. In total there are four plants bottling 137 million litres of beer and other beverages in PET, glass and cans (2010 data). Until 2008, PET, for Olvi, was synonymous with recyclable containers. However, since that time there has been a shift to disposable. To achieve this, Olvi purchased a new disposable installation from KHS with a capacity of 18,000bph. ”We envisaged the changeover as an on-going, seamless process” said Mr. Pentti Pelttari, the Technical Director and Head Brewer, however, the market took a different view. Virtually overnight the bottom fell out of the market for PET recyclable containers. It was not long before the PET recyclables plant had outlived its usefulness. It was a plant for glass and PET, with bottle handling at ground level. The Finns dismantled it and rebuilt it as a glass plant at their subsidiary Lidskoe Pivo in Lida (Belarus) where it is in building. The Finns ordered not one, but Regional market reports Finland part 2","@ID":12} "MATERIAL / RECYCLING 19 PETplanet insider Vol. 12 No. 09/11 www.petpla.net until only a short while ago. 25-ton trucks would take eight days and up to 3,300km to reach their final destination which of course implied gigantic logistic efforts. The company looked for an alternative to lower the raw material and logistics costs. The group decided to go for bottle-to bottle recycling. After consultation with various machinery manufacturers, the company finally decided to purchase the Vacurema Advanced 1716 T with a throughput performance of 1,000-1,400kg/h, which was set up in an especially constructed production hall next to the existing company. MDM Dydyo is satisfied with the results and they do benefit as the recycling operation allows them to considerably lower raw material costs. In addition, the company created more than 50 new jobs directly at the plant. Another beneficiary is Mother Nature and the Amazonian “lung of the world”, since more PET bottles are now collected and recycled. The Vacurema Advanced 1716 T system is the first expansion stage of the Vacurema Basic technology and features an additional, continuously operating upstream vacuum crystallisation dryer. The vacuum crystallisation dryer provides additional pre-drying and decontamination of the input material. The material is then transferred to the reactor of the downstream Vacurema Basic system via a discharge screw. The process is FDA approved. www.erema.at What of the future? More R-PET plants to come R-PET plants has become a hot topic in South America over the last few years, i.e. other companies such as Cabelma (Argentina) and Unnafibras (Brazil) have entered the market. At the moment the M&G Polimeros company operates a large scale PET manufacturing plant with a capacity of about 850,000t/a following material giant Braskem’s withdrawal from the PET business some two years ago. However, it is expected that the Petrobras projects Comperj and Petroquimica Suape will go on stream within the next few years with a capacity of above 1 million t/a. Would you like your products to stand out from the crowd? Thanks to the technology of Holland Colours you can turn your PET bottles into almost any colour. Our outstanding experience and efficency in producing colouring additives guarantees that your product will differ from your competitors’. Would you like to renew your PET bottles with unique shades? We can provide the solution for your business success. Holland Colours European Division Halvemaanweg 1, 7323 RW Apeldoorn, P.O.Box 720, 7300 AS Apeldoorn, The Netherlands I Tel: 31(55)368 0700 I Fax: 31(55)366 2981 I E-mail: info@hollandcolours.com SILK SCARVES? COLOURFUL BALLOONS? A MODERN STATUE PERHAPS? Or eye-catching PET bottles that are good to grab?","@ID":21} "PREFORM PRODUCTION 23 PETplanet insider Vol. 12 No. 09/11 www.petpla.net Symptom: Preforms have a yellow tint, not localized to a specific area but throughout the entire preform. Colouration may sometimes have a greenish hue. Cause: The resin has been thermally and/or oxidatively degraded, but not to the point of black specks. Solutions: 1. Check dryer for alarms and correct as necessary. A high temperature (above 175ºC (347ºF)) may cause rapid degradation especially if resin flow is idle. 2. Check condition of resin and/ or regrind quality. Remove any degraded pellets or chips from dryer hopper and in-feed line. 3. Check for excessive resin drying time in hopper (should be around 4h at 175ºC (347ºF) and up to 6h at 160ºC (320ºF)). 4. Check all temperature readings and correct if necessary. PET resin should be melted at about 280ºC (536ºF) +/- 10ºC (18ºF). 5. Check all %-controlled temperature settings and minimize if possible. %-controllers provide no temperature feedback and require fine tuning. 6. Check that all thermocouples are properly inserted and contacting the bottom of the wells. 7. Check extruder back pressure and minimize if possible. Back pressure should be sufficient to provide good melt mixing, but not too little to cause bubbles to appear. Typical range is 15 – 20 bar (200 – 300 psi). 8. Check screw rpm and minimize if possible. Screw speed should be reduced as much as possible to minimize shear heating, yet still recover within the cycle time of the machine. The stopped time at the end of recovery should be about 2sec to offset any fluctuations during screw recovery. 9. Make sure the extruder screw cushion is not excessive. This should be a minimum of 25mm to compensate for any dynamic recovery fluctuations. (Two-stage machines only) 10. Check hardware for worn, damaged or failed components, specifically the machine and mould heaters, and a misaligned shut-off nozzle. 11. For prevention, always: a.Reduce temperatures by about 40ºC (104ºF) if the machine stops for more than 15min b.Reduce %-controllers by ½ if the machine stops for more than 15min c. Shut off nozzle tip heats if the machine stops for more than 10min d.Never exceed start up temperature soak times. Machine should be started within 15min of the temperatures reaching operating settings. Nozzle tips should only be turned on 5 to 7min prior to start up. e. Always reduce the dryer temperature to about 120°C if stopped for more than 30min and 80ºC (176ºF) if stopped for more than 2h. www.petpla.net Table of Contents i........................ About the Authors ii.................................Introduction chapter 1.............................. AA Level High 2........................ Accordion Preform 3....................... Air hooks / Streaks 4............................... Black Specks 5...................................... Bubbles 6..................................Burn Marks 7...........................Colour Streaking ................................... /Peeling 8..................................Crystallinity 9.................................Drool Marks 10.......................................... Flash 11......................... Gate Depressions 12............................... Gate Peeling 13..................Gate Voids / Pin Holes 14......................... Internal Gate Sink 15................................Internal Sinks 16........................................ IV Loss 17............................ Long Gate Nub 18...............................Milky Preform 19............................ Moisture Marks 20................Neck Finish out of Round 21....................... Parting Line Crease 22.................Parting Line Deformation 23......................... Preform Yellowing 24.................................. Short Shots 25.......................................... Sinks 26......................................... Splay 27........................... Stretched Necks 28..................................... Stringing 29......................... Surface Blemishes 30......................... Thread Flow Lines 31...............TSS (Top Sealing Surface) ......................................... Sink 32.......................................Unmelts 33.................Wall Thickness Variation 34.................................Wavy Body 35.................................. Weld Lines Eisbär Material Drying PRODUCER MODEL LOW ENERGY CONSUMPTION LOW ENERGY CONSUMPTION LOWEST ENERGY CONSUMPTION ON THE MARKET RATING AAA Energy A Eisbär B C D E F G All the others A WWW.EISBAER.AT WUHRMÜHLE 22 / A-6840 GÖTZIS T +43 5523 55558-0 / COOL@EISBAER.AT","@ID":25} "MATERIAL / RECYCLING 16 PETplanet insider Vol. 12 No. 09/11 www.petpla.net Material innovation in PET has been driven by increasing demand for new products developments with advanced performance attributes including resins that offer enhanced mechanical strength and design flexibility. End-use markets CSDs are the largest end-use sector for PET packaging, accounting for a projected 35.9% share of consumption in 2010. Bottled water is the second-largest end-use sector for PET packaging with a projected 2010 share of 33.8%. All other end-use sectors command a relatively minor share of PET packaging consumption, as the joint third-largest sectors, thermoforming and food bottles, each represent 7.1% of total consumption. Bottled water is forecast to overtake CSDs as the largest end-use sector for PET packaging over the forecast period 2010–15. Other soft drinks, such as functional drinks, dairy drinks and ready-to-drink tea and coffee, are also forecast to grow at a rate higher than that of PET packaging consumption as a whole. There are also good growth opportunities for barrier food bottles and jars and thermoforming. Geographic markets Global consumption of PET packaging grew during the period 2005–10 at a and forecasts compound annual growth rate (CAGR) of 4.3% to reach 11.5 million tonnes. However, there was a sharp downturn in global consumption of PET packaging growth between 2008 and 2010. The world economic downturn and consequent reduction of consumers’ disposable incomes led to reduced demand for some key categories of packaged food and beverage products. In addition, the trend to lightweight PET bottle production and the growing use of PET recyclate for beverage bottles negatively impacted upon growth in consumption of new PET packaging. A modest upturn in consumption of PET packaging is taking place in 2010 as the world economy recovers from recession. Consumption of PET packaging is forecast to grow during the period 2010–15 at a CAGR of 4.8% to reach 14.5 million tonnes. World PET packaging market value in US dollar terms grew during the period 2005–10 at a CAGR of 4.3% to reach $29.9 billion. World PET packaging market value at constant 2009 PET prices is forecast to grow during the period 2010–15 at a CAGR of 4.8% to reach $37.8 billion. Asia Pacific overtook North America and Western Europe as the largest regional consumer of PET packaging during the period 2005–10. Asia Pacific is forecast to be the fastestgrowing world region for PET packaging, accounting for almost half of total consumption growth for the period 2010–15. In South America, eastern Europe and the Middle East and Africa consumption of PET packaging is forecast to grow at above average market rates during the forecast period. In the more mature western European and North American markets consumption of PET packaging is forecast to grow at much slower rates. These forecasts are based on a number of key assumptions, such as: the economic upturn continues and there are no major changes to the economic and financial environment; light-weighting of PET bottles will continue for water, CSDs and aseptic cold-fill bottles, especially in the developed markets of North America and western Europe; recycled PET (rPET) continues to displace new PET packaging resin over the forecast period. www.pira-international.com * Pira International: The Future of PET Packaging to 2015 - Global Market Forecasts by David Platt Global consumption of PET packaging by end-use sector, 2010 (Source: Pira International)","@ID":18} "BOTTLING / FILLING 40 PETplanet insider Vol. 12 No. 09/11 www.petpla.net Mineralquellen Bad Liebenwerda, Germany, invests in a KHS packing system* How “dreams” come true *Based on an article by Jörg Hoffmann, KHS With consumers demanding an ever wider range of products but with storage space at a premium, the retail market currently finds itself in a rather tricky situation. Faced with this dilemma, retailers think hard about which new products they should add to their purchase lists. But Horst Kuhl, managing director of the mineral water bottling plant of Bad Liebenwerda, believes that in a situation like this it is up to brand suppliers – like Bad Liebenwerda – to respond. This is why his company has invested in an automated packing and palletising line by KHS. The mineral water company Bad Liebenwerda traditionally fills high quality mineral waters. The high quality of the water has been confirmed by several very different institutions. The company was one of the first in Germany to start producing apple spritzers. Since then the company has introduced a range of spritzers: blackcurrant, cherry, light apple, and light pear. Spritzers are currently in the lead in the soft drinks segment with four million bpa, ahead of classic soda pop which accounts for 3.5 million bottles filled. Launched at the start of 2010 in three flavours, peach mented. The premise of this idea is that ‘countryside quality’ is equally in demand in both town and country – and will be increasingly popular in the future. On this assumption the company developed the Bad Liebenwerda ‘Landträume’ (=country dreams) product range. Since the beginning of April 2011 two low-calorie mineral water soft drinks have been sold under this brand name which, according to Bad Liebenwerda’s sales manager Ingo Hänßgen, contain local fruit and/or flower ingredients: Landträume apple, mallow, and hibiscus blossom and Landträume cherry, elderberry, and lime blossom. The main distribution area for these newly developed products is the same as for all other Bad Liebenwerda products, that iswithin a 200-km or 125-mile radius of the company’s site. In 1996 the company became Germany’s first mineral water plant to fill the 1.5l refillable PET bottles of the Genossenschaft Deutscher Brunnen (the Society of German Mineral Water and white tea, plum and green tea, and pomegranate and rooibos tea, the mixed tea Teeträume (tea dreams) brand is an interesting case. ‘First come, first served’ certainly seems to be true of this innovation. With 2.5 million bottles filled in 2010, sales of the Teeträume line nearly managed to draw level with those for Bad Liebenwerda soda pop in just a year. Ever faithful to the company philosophy of being happy to innovate and making a rapid response, the workforce in Bad Liebenwerda is naturally far from resting on its laurels. Only recently another very similar idea was impleMineralquellen Bad Liebenwerda, some 100 miles south of Berlin, enjoys an idyllic setting amid natural surroundings. The latest investment in KHS technology is a packing line for PET six-packs with an output of 18,000 PET bph.","@ID":42} "BOTTLING / FILLING 41 PETplanet insider Vol. 12 No. 09/11 www.petpla.net Producers), and to do so on a KHS line. The company was also among the first to introduce 1l refillable PET bottles for soft drinks and 1l refillable PET bottles for mineral water. CEO Horst Kuhl explains, “Our pioneering work was and still is rewarded with a growth in sales. At present 75% of all the bottles the company fills are refillable PET bottles, 15% are nonrefillable PET bottles, and just 10% are glass.” Ingolf Hänßgen continues “Although we prefer to use mainly refillable PET bottles as more sustainable, we recognise that for space reasons the market can scarcely accommodate any more refillable products. This is partly why we are only launching our new Landträume line to market in non-refillable PET bottles, for example.” According to Kuhl it was also partly for this reason that the company invested in the new KHS packing line. This will give them more flexibility for the needs of the retail market for both their tried-andtested range and their new products. The new KHS shrink pack line achieves an output of up to 18,000 non-refillable PET bottles in shrink packs/h. The line currently handles sixpacks of both 1.5l non-refillable PET bottles and 0.75l non-refillable PET bottles. The plan for the future is for it to pack six-packs of 0.5, 0.33, and 0.25l non-refillable PET bottles as well. The line is certainly equipped for this. ORIGINAL DESIGNS DEPENDABLE EXECUTION OPTIMIZING THE PRODUCT & THE PROCESS PET bottles are what we know and what we do. At Sidel, we design original and creative bottles as well as the tools for flexible line conversion and top performance.Weoptimizeeveryaspect of theproduct and process design so that your production is more cost-effective and your products are easy and light to transport. Based on advanced lightweighting technology, blowing and molding expertise, and material performance, we bring top quality and responsiveness to your local production site. WORK WITH US & GETA BETTER MATCH FIND US AT PACK EXPO, BOOTH C-329 FIND US AT IDFA, BOOTH #801 www.sidel.com Inline robots grasp, turn, and move the side-clamped shrink packs with millimeter accuracy, taking up only a minimum amount of space. Shrink packs are pushed directly onto the loading plate ...","@ID":43} "MATERIAL / RECYCLING 18 PETplanet insider Vol. 12 No. 09/11 www.petpla.net Brazilian R-PET plant feeds own bottle production Where the streets have no name Strong growth of Brazilian PET market The rapid economic growth in South America is generating an increasing demand for virgin PET material of about 1,300 million tons this year. South America has a mighty thirst and the prospects are bright: a growth in demand for PET is forecast to reach about 6.5% for the South American region. Water is expected to grow by an impressive 8.3%, CSD by 4.5%. The growth in demand for R-PET is expected to reach 4.4%. While the South American PET bottle recovery rate lies at only 37%, the Brazilian collection rate is, at 62%, the highest in the region, and accounts for 64% of the toal collection rate in the region. The trend is that collection volumes are set to rise due to higher recovery rates with a consequent strong growth in bottle consumption. This was the starting point for the MDM Group to make a far-reaching decision. Bottle-to-bottle recycling instead of an adventurous 3,300km trip Right in the middle of the Brazilian Rondonia Province is one of the most modern beverage companies in Latin America: MDM Dydyo, a subsidiary company of the MDM Group. The raw material used to produce the PET bottles directly in the company was delivered by an adventurous route In November 2010, an ambitious project started in the Brazilian town of Porto Velho. The MDM Group established the Amazon RCP project, a recycling company located directly in Porto Velho, collecting PET garbage from all over the region, processing it and using it to produce new bottles using Erema’s Vacurema Advanced 1716 T technology.","@ID":20} "REGIONAL MARKET REPORTS 11 PETplanet insider Vol. 12 No. 09/11 www.petpla.net two new PET installations direct. One was for the parent plant whilst the other was an additional installation for A le Coq (see Baltikum Report in forthcoming issues). The machine configuration was nearly the same; it was only the plant layout that had to be adapted to suit individual local circumstances. “The fact that we had two installations at our disposal for order processing meant that we were in a good negotiating position with our supplier. Ultimately, the reason why KHS was awarded the contract was because they succeeded in offering the right combination of quality and price.“ On the dry stretch, the displays come from the left and the bottles from the right The plant consists of a stretch blow-moulding line from Corpoplast with ten moulds and a filler which, in addition to water and drinks, can also be preloaded with CO 2 for bottling beer. Pentti has dispensed with a rinser. In 2008 there was still no question of a block installation as far as he was concerned because, at that time, the large-scale link up of blow moulding plant and fillers using star-shaped transfer mechanisms was still in its infancy worldwide. In Finland there is a need to focus on the dry component. This calls for a high level of automation because some very different types of packaging are used. A particular feature is the display – an injection moulded recyclable tray – which is loaded up along with the bottles, in addition to the classic stacks of shrink-wrapped sixpacks. The plant has a very wide range of filling volumes to process, starting at 0.45 and encompassing such exotic dimensions as 0.95 up to 2l. Under the Finnish deposits system the deposit on the PET bottle is twice as high if the volume is one or more litres; this is why it is possible, in this Land of the Lakes, to purchase 0.95l containers. Nevertheless, the bulk of sales is concentrated on the 1.5 and the 0.5l bottles. But to return to the displays. Displays are also available for recyclable glass bottles and cans. This means that one robot is able to handle any type of container. At Olvi they have taken this to the extreme, which means, with the exception of the HGV, practically the entire in-house transport system is associated with the PET installation, the 2nd can line and one glass recyclables line. All the installations are sourced from either Krones or KHS. Due to the fact that cans are increasingly in demand with the Finns, the glass line is becoming less and less used. The reaction as far as the PET bottle is concerned is stable. In total Olvi is bottling 30 million PET bottles in Iisalmi per year. The products include water, soft drinks, energy drinks, cider and beer for home consumption (a 2.2% malt beer). Up to 18,000bph are delivered to the PET disposables line by a Blomax 10 Nevertheless, the main business is beer. There is a small but exclusive museum on site which deals with beer brewing and bottling. At the entrance there is a hop garden featuring around 100 plants. At a latitude of 63 degrees and 33.2 minutes North, this has to be the most northerly hop cultivation site in the world. Only 3km further south there is the second most northerly hop plantation in the world, where Pentti tends 40 hop plants in his own garden. www.olvi.fi Finn Spring Hannu Ali-Haapala President and CEO Member of the Board; Juha-Jaakko Niemelä, Production Director From farm to filler plant It all began almost as a hobby around 20 years ago when farmer Hannu Ali-Haapala took a telephone call from his sister in London: “Hannu, the water you use for washing your laundry at home in Sykäräinen is a thousand times better than the water we have to drink here in London“. Hannu’s response was to begin bottling water from the spring on his own farm. The first big order came from Russia at a time when that market was just being opened up. “There were just two faxes and business was up and running, no marketing “, Hannu mused, looking back on how things were at that time. Since then, he has given up farming – now there are two plants bottling 50 million litres of water and soft drinks in PET bottles each year. F.l.t.r.: Juha-Jaakko Niemelä, Hannu Ali-Haapala and Alexander Büchler for the Sipa plant Most of it goes into the proprietary brand “Spring“, but Hannu is also a co-packer for a large number of external brands.","@ID":13} "PETproducts 46 PETplanet insider Vol. 12 No. 09/11 www.petpla.net Revolution in PET-extrusion! Conical co-rotating MAS-extruder | perfect solution for A-PET, G-PET, PET Co-polymer … | prime pellet / melt quality (IV, b*, AA- content) | very low energy consumption | direct extrusion into sheet | stable melt pressure build up | small foot print paired with robust design | sizes available from 200 kg/h up to 1500 kg/h | suitable for food application M-A-S Maschinen- und Anlagenbau Schulz Gmbh A-4055 Pucking, Hobelweg 1 T: +43 7229 78 999, F: +43 7229 78 999 10 info@mas-austria.com www.mas-austria.com Combination testing system Mocon Inc, of Minneapolis, Minnesota, has introduced a combination testing system for packages with one-way degassing valves. Named MultiCheck 400, the system measures oxygen (O 2 ) headspace, leak detection and seal strength, as well as one-way degassing valve performances, which is measured by the company’s new Valve Test Unit (VTU). MultiCheck 400 is based on two existing Mocon technologies: Lippke 4500 (leak detection/seal strength) and the hand-held Pac Check 302 O 2 headspace analyzer. Mocon says that its offer represents the first time that users of packages with degassing valves have had access to an accurate and repeatable way to test performance. The company also claims that combining four tests into one unit can save time and labour as well as cutting the number of samples required as a single package cycles through all of the analyses on just one unit. Applications include coffee, pet food, agricultural chemicals, resins, medical and others that require pressure relief. The VTU is also available as a standalone instrument, for operations that wish to conduct valve testing only. www.mocon.com Multi-function closure The plastics technology branch of KTW, Waidhofen/ Thaya, Austria, has developed the so-called “Simple Mix“ closure in its own innovations office. The closure was nominated for the German Packaging Prize 2010. The closure is composed of three parts with an integrated additive container; turning the cap enables metered dispensing of the contents which are added to the contents of the bottle. In addition, turning the top screw cap has the effect of lifting up an integrated insert section. This is achieved by a single turn of the upper screw cap which opens the insert section, releasing a “trapdoor“ in the insert section and dispensing the additive contained in it. This approach lends itself to situations where an additive needs to be kept in an undiluted or dry state up to the point of use because, once mixed, it would quickly degrade with a subsequent loss of quality and effectiveness. Suitable applications that deserve a mention here are the dispensing of medications or food supplements, the addition of colourants or glitter effects to party drinks or the mixing of substances in powder form or dual-component paints. The system is resistant to external manipulation by virtue of the double tamper protection installed. The patented “Simple-Mix” cap is made up of three individual parts. The main component is a screw flange which forms the connection with the bottle or the alternative container. It is fitted with tamper-proof ring and incorporates a central opening for use with the active ingredient reservoir. Above that there is a second, smaller, screw cap which is combined with the active ingredient container and is likewise fitted with a tamper-proof ring. All three components are suitable for automated assembly – including automatic filling of the reservoir. Despite its three-part construction, the “Simple Mix” cap is also suitable for sealing containers containing liquids. As mentioned initially, using it is of unrivalled simplicity by comparison to alternative products. A single turn of the small cap is sufficient to discharge the additive into the primary medium below. At the same time, the cap stays on the bottle so that the media can be mixed by means of agitation. When it comes to opening, the cap is turned further and lifted off together with the reservoir insert section to free up the pouring profile. www.ktw-group.com","@ID":48} "PREFORM PRODUCTION 20 PETplanet insider Vol. 12 No. 09/11 www.petpla.net MHT’s upgrade sets offer outputs one-third higher – on existing machines More bang for your buck* Productivity, sustainability and conservation of resources are key issues in the production of PET bottles, so who would say no to the equivalent of getting 33% more mileage from a tank of petrol in their current car? MHT Mold & Hotrunner Technology AG (Germany) says that its upgrade sets enable preform manufacturers using Husky HyPET 300 or 400 injection moulding machines to produce one-third more preforms from their existing equipment. turer in South America. The (approximately) 85mm long, 15g preform with a PCO 1881 thread is created in a cycle time of 9.0s. The control unit of the Husky HyPET 300 is designed for a maximum of 72 cavities and the upgrade adapts to it, so the injection moulding machine can continue to operate the mould. There are two options for nozzle control. Nozzles of the same thermal type are either combined, so that the machine still has a total of 72 regular positions, or an external device can assume control of all 96 nozzles. The upgrade set for HyPET 400 works in a similar manner. The second option offers customers the opportunity of running the machine in so-called single-nozzle regular operation, which means that the mould is equipped with nozzle thermal sensors. In operation, temperature is constantly monitored and regulated at each individual cavity. When preforms are produced, they need to be post-cooled in order to be dimensionally stable for further handling as bulk material. For this purpose, MHT has developed MHTcoolMax, a three-stage-post-mould cooling solution. An international patent has been applied for. MHT has developed upgrade sets that take 72-cavity machines to 96, and 96 to 128. The company says that the sets improve effectiveness, have higher cooling and energy efficiency and enable companies to get higher output from existing machines, economically and ecologically. It does this by moving the cavities slightly closer together and adding additional rows to the left and right. The MHT team has achieved higher cavitation without making the moulds much wider. The stacks, i.e. the moulds in which the preforms are created, are identical to those of the long-established 72-cavity mould technology. This space saving does not require or imply a ‘filigree’ mode of construction, which may be more susceptible to faults. A pilot project is currently running successfully with a leading preform and bottle manufacMHT has achieved higher cavitation without making the moulds much wider. Cooling pins *based on an article by Sabine Kob, MHT","@ID":22} "PETnews 6 PETplanet insider Vol. 12 No. 09/11 www.petpla.net First MTR plant in Europe starts up In the spring of 2011 Uhde Inventa-Fischer and AlcoNaphtha JSC started up the first MTR PET production plant to be built on European soil. The plant, located at AlcoNaphtha JSC’s site in Kaliningrad, has an annual capacity of 240,000t, making it currently the biggest single-train PET plant in Europe. Uhde Inventa-Fischer’s MTR process replaces the SSP (solid-state post condensation) process and is claimed to reduce energy and maintenance costs, with lower feedstock consumption and capital investment than conventional methods. The process is based on Uhde Inventa-Fischer’s 2-reactor high-viscosity technology and applies the patented Espree and Discage reactors to ensure sustained high-melt viscosity PET production. Uhde InventaFischer’s services included permit engineering, basic and detail engineering, supply of all plant equipment, supervision during construction, installation and commissioning, and operating personnel training. Sister company OOO Uhde, of Dzerzhinsk, provided local compliance services. www.uhde-inventa-fischer.com drinktec to co-organise China Brew & China Beverage Under a contract signed in Beijing on August 2, 2011, drinktec has committed to co-organising CBB (China Brew & China Beverage), the International Brew & Beverage Processing Technology and Equipment Exhibition for China, until least 2024. The contracting parties are MMG (Messe München GmbH), the organiser of drinktec, and its subsidiary MMI Shanghai, and Beijing Zhongqing Heli International Exhibition Corporation (BZHC) as the co-organisers, and the China National United Equipment Group Corporation (CNUE) as the licensee of CBB. The agreement covers a total of seven events, the first to be held from 19 to 22 September 2012 at the new China International Exhibition Centre in Beijing. MMG and MMI Shanghai will be the contact and contracting party for all international, non-Chinese exhibitors at CBB. The contract marks the provisional conclusion of talks that started in Autumn 2009 and which initially resulted in a marketing agreement covering CBB 2010. A total of 583 exhibitors took part in CBB 2010, 225 of them from outside China. www.drinktec.com Simei/Enovitis 2011 to showcase vine and olive technology Simei and Enovitis, the International Oenological and Bottling Equipment Exhibition and the Vine and Olive Growing Techniques trade show will run from November 22 -26, 2011 at the Milan Fairground in Rho. The 24th edition of Simei will present the last developments in the wine-growing and producing sector and provide an international showcase for technical innovations in production, bottling and packaging of wine and of other beverages. Labelling, packaging and bottling equipment companies will exhibit in halls 13 and 15 of Simei. Manufacturers of equipment for oil, wine and juice processing will occupy halls 9 and 11. The eighth Enovitis will exhibit vineyard equipment and the latest technologies for vine-growing. The exhibition programme includes a series of technical meetings and scientific conferences with international speakers, as well as the award of the Viticultural and Oenological Innovation Prize, organised in cooperation with Unione Italiana Vini. Up to 90% of available space had been booked by June 2011, by Italian and international companies. Online pre-registration is available and location plans will be published from October. www.simei.it www.enovitis.it Krones earnings up in H1 2011 Krones AG, the beverage filling and packaging technology company, has reported increased sales, orders and earnings before taxes (EBT) for the first half of 2011 (H1 2011). The company says that it has profited from the cyclical upturn and the initiatives it has taken to improve performance, including more efficient production methods. Sales increased by 16.8% in H1 2011 over H1 2010, to a new company record of €1257.5 million. Sales in April-June 2011 were €650.8 million, up 19.9% on 2010. H1 2011 order bookings rose by 19.8% compared to 2010, from €1104.9 to €1323.4 million. Highest growth rates in order bookings were in Africa/Near East, in Eastern Europe and the CIS nations, and in Central Europe. The highest order bookings in absolute figures came from China. At the end of June 2011, Krones had outstanding orders worth €974.6 million (2010: €917.2 million). EBT was €69.2 million, (2010: €32.0 million). EBT margin was 5.5% (2010: 3.0%). After taxes, Krones earned €49.2 million in H1 2011. Earnings per share were €1.62. The company says that the global economy remains on course for growth although uncertainty continues. Krones is confident that the situational conditions will remain favourable overall during the second half of 2011. www.krones.com","@ID":8} "REGIONAL MARKET REPORTS 12 PETplanet insider Vol. 12 No. 09/11 www.petpla.net Along with his Production Director Juha Jaakko Niemelä and the whole team, Hannu is responsible for handling production. With the changeover from PET returnable to PET non-returnable bottles, a new Sipa plant with eight moulds has found its way on to the site. The 60-valve bottler is from Procomac. This line produces up to 14,000bph. The old bottling plant for PET returnables (AMS Ferrari) has been mothballed; the switch to PET non-returnable bottles made the bottom section handling arrangement completely impractical. In the neighbouring bay a second line is currently emerging from the usable parts of the old plant, as well as a few other components. This line is expected to produce some 12,000bph. At present the plant is still being fed by an old Tetra stretch blow moulder with a capacity of only 6,000bph. As soon as the limit of capacity is reached the intention is to add a new stretch blow moulding machine to increase line capacity. So now both factories together can reach now 27,000bph with filling four lines and in the future 33,000bph. “We planned everything ourselves and we also do our own structural work, this is the only way we can be sure of knowing exactly what makes the installations tick and this enables us to do a great deal of work on the installations ourselves. Hannu is very clear about this: “If we wait around until an external engineer finally finds his way here, our short season may well be over” he says. Fortunately there were no such route-finding problems for PETplanet! Beverages are always bottled in 0.5l and 1.5l bottles only. Their own brand water also comes in light blue; the cobrands are available only in clear bottles. “Increasingly we are finding ourselves developing beverages for our customers. Whereas aromas used to come in from outside ready to use, the market has speeded up to such an extent that we actually undertake adjustments to the taste here on site.” To date Hannu has been producing almost exclusively for the Finnish market. A year ago, however, the company opened a field station in Sweden. The Finns are looking at this as a distribution point for a proportion of their products in the near future. www.finnspring.fi Hartwall Marko Rajaniemi, Technical Manager High speed and flexibility In 2001 Hartwallrelocated their entire production to Lahti,situated about an hour to the north of Helsinki. The large new factory buildings are now home to bottling plants for PET reusable glass, kegs and cans. As is the case everywhere in Finland, the reusable proportion is falling rapidly, and non-returnable cans and non-returnable PET are benefiting. The PET installations are based on Sipa stretch blow moulding installations featuring 24 moulds and a capacity of 1,800bph which load the Krones bottling plants via a rapid-delivery buffer conveyor in just a few minutes. The bottles are first of all rinsed at these filling stations before being filled. The filler plant is also capable of bottling beer, but there is as yet no call for this on the Finnish market. “The decision in favour of the Sipa plants was based on the need for very high output at the same time as high flexibility“ explained Marko Rajaniemi, Technical Manager. First the rinser, then the filler: the Krones line at Hartwall In total the company fills all types of casks with 3.2 million hectolitres of beer and soft drinks. The sizes of the PET bottles are, as is usual in Finland, 0.33, 0.5, 1.5 and 2.0l. Around one third of the soft drinks enters the market under licence to Pepsi: the remaining 2/3rds are own brands. As is the case throughout Finland, the bottles tend to be heavy: the 0.5l bottle weighs 26g, but they are currently in the process of converting to 24g. “Up to now, Finnish customers had always been used to refillable PET bottles; now they want to drink out of robust non-returnable bottles”, says Rajaniemi. Hartwall, as a 100%-owned subsidiary of Heineken, is able to fall back on its parent company’s contracts when buying in materials. The Sipa stretch blow moulder in the background, front left Marko Rajaniemi and Alexander Büchler www.hartwall.fi Sinebrychoff Michael Slotte, Project Manager “For us, change is a challenge” Sinebychoff prefers to use the last five letters of its name as an abbreviation, so it is also known as “Koff”. Like the other two big breweries, the brewery produces the entire range of water and soft drinks in addition to beer. It also operated under licence from Coca Cola. However, some of its soft drinks are actually marketed under ownbrand labels. In 2008/2009 the company also invested in 2 plants for new non-returnable PET products. Sidel with 20 moulds was chosen for the stretch blow moulder. As a high","@ID":14} "BOTTLING / FILLING 42 PETplanet insider Vol. 12 No. 09/11 www.petpla.net www.petnology.com With PET ahead: versatile, sustainable and flexible Conference Organiser PETnology/tecPET GmbH P.O. Box 120 429 D-93026 Regensburg, Germany Phone: +49 941 870 23 74 Fax: +49 941 870 23 73 conference2011@petnology.com November 7-8, 2011 Nuremberg Congress Center Nuremberg (CCN East) Prior to Brau Beviale XIV. Strategy and Technology Conference for the PET Packaging Industry How the system works At present machine operators ready the shrink packs for the four conveying segments in the line manually. The conveying segments can be filled with different items as required. For example, shrink packs of non-refillable PET bottles containing mineral water can be used on segment one, Teeträume shrink packs on segment two, soda pop shrink packs on segment three, and Landträume shrink packs on segment four. Alternatively, should a customer require only two different shrink packs to be packed, two or three conveying segments can be loaded with identical shrink packs. The layer formations required for palletising are made by a group of inline robots. It is the robots that grasp, turn, and move the side-clamped shrink packs with millimeter accuracy, taking up only a minimum amount of space. The pushing motion used for the precision positioning of the individual containers is adapted to the speed of the plastic chain mat conveyor. Once a layer formation is complete, a centering device aligns its position. … and from there onto the pallet. An integral part of the concept is a handling robot which takes the pallet liners and pallets from designated magazines.","@ID":44} "BOTTLES PETbottles 49 PETplanet insider Vol. 12 No. 09/11 www.petpla.net PET beer keg Heineken and Amstel beers are now available in The Netherlands in a new four-litre PET keg with integral tap, supplied by APPE Packaging (Artenius PET Packaging Europe), a subsidiary of La Seda de Barcelona (LSB). The new ‘Tapje’ keg is a small draft-beer system for home consumption, which Heineken and APPE say offers a cost-effective alternative to the traditional crate of beer. Tapje features APPE’s proprietary monoBLOX barrier technology with oxygen scavengers. A separately-available beer cooler can chill the contents in an hour; otherwise, Tapje is ready for use after being cooled for ten hours in a refrigerator. A colour temperature indicator on the keg shows when the beer is ready for drinking. The manufacturers claim that it will keep beer fresh for 30 days after opening. A team comprising Heineken personnel and staff from APPE’s European R&D centre in Brecht, Belgium, developed the Tapje keg over a number of months. www.appepackaging.com Pom in 710ml Pom Wonderful Europe, based in Amsterdam, is now also marketing 100% cranberry juice in a 710ml bottle which is similar to the wellknown smaller bottle but features three ball-shaped segments. The red juice in the transparent bottle gives the product its visual impact and the bottle has the required commercial and product information printed on it. A printed screw cap in a matching colour complete with tear-off tamper-proof seal completes the profile of this perfectly packaged product. www.pomwonderful.eu Handy and appetising Kraft Foods Deutschland based in Bremen/Germany have redesigned their dressings packs. The 400ml PET bottles, e.g. for balsamic dressing, have a recess in the gripping area which makes them easy to hold and are decorated with a glossy printed shrink sleeve label guaranteed to stimulate the appetite. The large screw-on dispenser cap complete with integrated self-sealing silicon membrane ensures that the bottle retains adequate stability when placed in the upright position. www.kraft.de Aluminium cap for cocktails Under the brand name “El Fuego“, Messrs. GCF of Petersbach, France are offering a range of cocktails such as “Pina Colada“ or ”Mai Tai“ in 0.2l PET bottles. The slightly waisted bottles feature decorative shrink sleeve labels and have a standard aluminium screw cap with tear-off tamper-proof seal. The production date is printed on the screw cap using an inkjet printer. www.gcfplanet.com Transparent shrink label The Dutch firm, Infra Foodbrands BV, based in Laren, is selling 1l of its tropical fruit juice Europe-wide in a transparent PET bottle under the brand name “maaza“. The bottle, which incorporates pressure compensating areas, is decorated in the belly area with a partially transparent shrink sleeve label featuring high quality printing. This gives a kind of “Non-Label Look“ effect. A matching colour screw cap with best-before date printed on it and tear-off tamper-proof seal completes the look. www.enjoymaaza.com","@ID":51}]}}
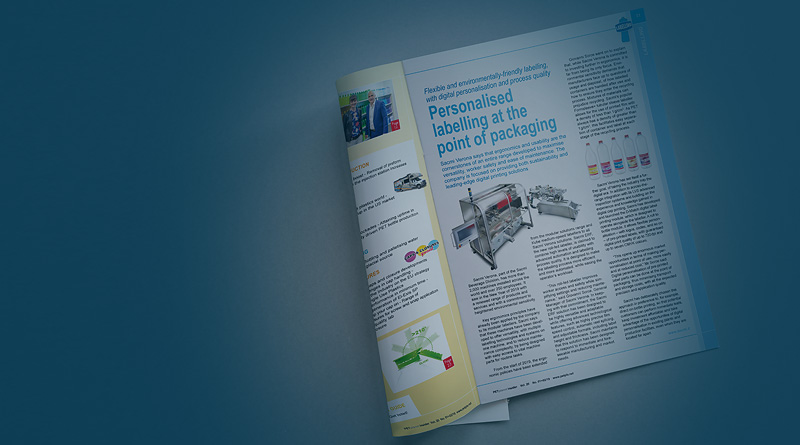