{"pages":{"page":[{"#text":"REGIONAL MARKET REPORTS 14 PETplanet insider Vol. 11 No. 12/10 www.petpla.net April 29, 2010 Artenius PET Packaging Europe (APPE) in Bierne The “new” Artenius PET Packaging Europe (APPE) “The message is: the crisis is over.” Bierne Production leaders with Manufacturing Director Guillaume Foucher (standing up on the right ) We met: Jean-Marc Rostagno, at the time BU Managing Director, APPE France, now BU Director Northern Europe. In the course of touring and investigating the French PET business one inevitably comes across the largest preform converter in France, located in Bierne - today trading under the name Artenius PET Packaging Europe (APPE) and a subsidiary of La Seda de Barcelona in Spain (LSB). APPE as well as being the largest preform converter in France, has also the longest history and longest experience in the PET business. The site in Bierne was originally constructed by Schmalbach-Lubeca in 1989 to produce refillable preforms for the German refillable PET bottle market. After a change in ownership from Schmalbach Lubeca to Amcor in 2002, APPE came under the control of the Spanish PET resin producer LSB in October 2007, and hopes were that with an integrated PET producer as a parent, that the company could expand further into the PET market with new resin developments. But instead APPE was drawn into the turmoil connected with the restructuring of LSB. What did happen and why? LSB’s financial difficulties were compounded by the steep rise in crude oil in 2008 followed by the subsequent collapse in pricing and the global economic downturn. LSB had pursued an aggressive strategy of acquisition in order to achieve a market-leading position as a vertically integrated business with reference to chemicals (PTA, MEG), PET and PET preforms. Growth was to be achieved by becoming the leading supplier in the PET resin and PET preform markets in Western Europe. This strategy was realised by acquisitions during the period between 2006 and 2008 (see table): Company Year Participation Advanca 2006 100% Selenis Portugal and Selenis Italy 2006 100% Volos 2006 100% Eastman Chemicals Iberia 2007 100% Recuperaciones Plasticos Barcelona 2007 67% Amcor PET Packaging Europe 2007 100% Begreen 2007 20% Erreplast 2008 60% Recuperaciones Plasticos Barcelona 2008 33% The implementation of this strategy combined with the global economic downturn culminated in major liquidity problems for LSB. At the end of 2008 LSB therefore found itself unable to raise the funds to meet financing obligations. Problems were further exacerbated by lower performance than had been projected by some of the acquisitions, deterioration of margins, decrease in volumes as a consequence of the financial/ economic crisis, and lack of key integration in the business, as well as delays in achieving the targeted synergies. As a consequence, and with the help of a new investor from Portugal (BA Vidro), the capital structure of LSB has been revised together with revised financing agreements from the banks. The financial “gift” however is subject to the condition that the company – parent company and all subsidiaries - will be restructured. All activities of the company will be scrutinised. The unwelcome measures under these circumstances are always the same: concentration on core business, some plants closed, work-force reduced. The ‘New’ LSB’s revised strategic direction is to become an efficient plastic packaging solution company abandoning the strategy of vertical integration into PTA and MEG. Additional opportunities are seen in the ‘Plastic Packaging’ market to grow this business by intensifying commercial activities and sustaining levels of investment in R&D. The strategic initiatives are aimed at being appropriate for the current and foreseeable market conditions, namely: Group business to be focussed on Plastic Packaging, PET and recycled PET only. The message is: the crisis is over In summary this means that APPE will emerge from the crisis thanks to their strong and consistent financial results and will come out of the LSB restructuring ready to take on many new challenges.","@ID":16} "TRADE SHOW REVIEW 29 PETplanet insider Vol. 11 No. 12/10 www.petpla.net Recycling line recoSTAR PET iV+ Ongoing PET recycling innovation, quality and state-of-the-art technology, a full range of consulting services – brought to you by Starlinger. Visit us in our laboratory for a testrun with your own material www.starlinger.com All-electric PET preform moulder Husky Injection Molding Systems is extending its product range to lower-volume producers, with the launch of its H-PET AE (all-electric) injection moulding system. The company claims that it offers lower-maintenance while still providing reliability, tight process control, accurate mould tolerances and high-quality auxiliaries. It requires lower capital investment and is available in a number of different clamp, extruder and mould cavitation combinations. It also has the facility for flexible configurations and fast changeovers. It is designed to meet the needs of customers in emerging markets as well as lower volume and custom preform and bottle producers operating in niche markets. With Husky as the single-source supplier for the complete turnkey workcell, H-PET AE includes the machine, mould, hot runner, auxiliaries, piping, electrical distribution and auxiliaries, all managed through Husky’s Polaris Control. H-PET AE workcell demonstrated at K Show produced 1l still water bottles with Alaska thread in 11.8s cycles from 22g Ecobase preforms, managed through Polaris Control. Husky will take responsibility for lifetime support for customers, including system optimisation, for H-PET AE machines as for all its systems. Husky also launched its next generation HyPETHigh Performance Package (HPP) for high output preform injection moulding. With these latest enhancements, HyPET HPP delivers industryleading cycle times and increased energy efficiency. Husky was running a 96-cavity HyPET 400 system with enhanced HPP on its booth. The system was producing an EcoBase preform, weighing 9.9g for a 500ml still water bottle application, at approximately 5s cycles. By modifying the base, EcoBase preforms are up to 2.5% lighter than other lightweight preforms, allowing moulders to reduce resin consumption. For example for a 500ml still water application it is possible to manufacture a preform with a side wall as thin as 1.5mm and thread wall of 0.8mm. www.husky.ca Modular dryers The new Somos D dry-air dryer systems from Mann + Hummel are claimed to combine improved operating ergonomics with better energy efficiency and an extended process window. The module hoppers in the range have an individual control system but based on standard concept, named MH 15. The company says that this simplifies a number of operational aspects, including expansion of the module system by one or several additional drying hoppers. The MH 25 control unit also regulates the generation of dew-point-consistent dry air with the D dryer. Mann + Hummel says that aspects of the new control systems cut energy consumption by reducing regeneration time of the drying agent and enable the D 200 dryer to be upgraded from a nominal 200m³/h dry air flow up to 500m³/h, using control engineering adjustments. The company claims that the dried material flow can be increased reliably from the previous maximum of 100kg/h to 250kg/h without additional hardware.","@ID":31} "NEWS 9 PETplanet insider Vol. 11 No. 12/10 www.petpla.net Strong fresh air for PET-bottle industry Gainnew heights in savings and energy-efficiency with the new oil-free ZD compressor Time to gain new heights. The highly energy efficient ZD compressor, with superior screw and booster technology, offers Class Zeroquality air and is extremely silent with no vibrations. Theair-cooledZD provides you anexceptional reliability, no water consumption, while driving down investment and installation cost. It all adds up to sustainable productivity for today’s challenging low carbon economy. This new ZD is The answer for all your high pressure 40 bar applications. For more information, visit www.atlascopco.com/petcompressors Eastman to sell performance polymers PET business to DAK Americas Eastman Chemical Company (NYSE:EMN) has announced that it has entered into a definitive agreement with DAK Americas, LLC, to sell the PET business and related assets and technology of its Performance Polymers segment. The sale is expected to complete during Q4 2010. The sale is expected to realise $600million, subject to the finally-agreed purchase price. A statement issued in the name of Jim Rogers, Eastman president and CEO, said that the company intended to focus on its core businesses. New PET MTR plant for Indorama AlphaPet Uhde Inventa-Fischer has announced that it successfully commissioned a second PET Resin plant in Alabama, USA, for Indorama AlphaPet, Inc. The new facility, located in Decatur, Alabama, USA, has an annual of 432,000t and came on-stream in June 2010. It is the largest plant to use Uhde Inventa-Fischer’s patented MTR technology anywhere in the world. Various grades of resin, for water and CSD bottling applications or for packaging film, may be produced at the same time. PTA is sourced from the adjacent BP facility via a direct pipeline. The MTR process is based on Uhde Inventa-Fischer’s proprietary 2 Reactor technology, which uses patented Espree and Discage reactors to obtain the desired high melt viscosities. The 2R-MTR process is claimed to reduce energy costs, through the elimination of the SSP process. In the next step, the plant will be upgraded with a flakes recycle system to further reduce the CO 2 footprint. Uhde Inventa-Fischer’s scope of supply and services included the license, the basic and detail engineering, supply of all equipment and supervision of the erection and commissioning activities. www.uhde-inventa-fischer.com New Nissei machine at PET-Power Dutch company PET-Power has acquired its first Nissei DP150 machine, which was installed in its Etten-Leur plant and began operating in May 2010. PET-Power already has two Nissei and two Aoki machines in operation but the new investment will enable it to handle larger products, up to 20l. It will also be able to meet what it says is a growing demand for wide-mouth jars; cream products in cosmetics; and large jars for sport and animal nutrition applications. The company says the range of its equipment will enable it to react quickly to changing market circumstances and unpredictable events, with all sorts of sizes, colours and styles, and across a wide range of production runs. www.petpower.nl","@ID":11} "BOTTLING / FILLING 27 PETplanet insider Vol. 11 No. 12/10 www.petpla.net Bottle lightweighting Hauser is a newcomer to the PET field, so packaging studies and development were an important phase of this project. Sidel provided support in terms of container design and technical characteristics, such as stability, as well as in the selection of preforms. Sidel’s Combi technology combines blowing, filling and capping functions for PET bottles in one machine. In combination with Predis dry decontamination of preforms, Hauser has been able to explore a range of preform lightweighting possibilities and bottle shapes. The final designs weigh just 15g and 29g, for the 500ml and 1.5l formats, respectively. Package lightweighting has been made possible by preform decontamination and the absence of conveyors between the blow moulder and the filler. Axo-Smart secondary packaging flexibility The Sidel line is also equipped with the Axo-Smart layer formation system. The completely modular and automated system handles packs by rotation and translation and can process all types of secondary packaging. Hauser’s main distribution channel is through ‘hard discount’ retailing, which requires very high levels of flexibility. The option of using software to manage any new pallet pattern is a particular advantage. The two-module Axo-Smart has a very small footprint and offers good accessibility from both sides of the conveyor belt. The Hauser line includes an Aidlin 24 cap feeder, a Rollquattro F15 labeler, a TSM2 CPL shrink wrapper, Pal-Kombi palletiser, conveyors for bottles, packs and pallets, and two AQ-Max accumulation tables. From installation to marketable bottles in three months The project was complex because of the limited space available for the line installation. Rigorous management of equipment reception schedules was required in order to achieve quick and efficient setting-up. Sidel’s expertise in space rationalisation lead to the line concept, centred around ergonomics and compactness, which means that the Combi Predis FMa and the accumulation tables have a very small footprint. Very tight deadlines for the start of marketable production placed particular demands on the project. The goal was to start shipping the first orders, for the start of the summer season, in June. Late April, two and a half months after the start of installation, saw the first aseptic validation completed. Production of tea in the 500ml format was able to begin in late May, ready for market release. The line then had to produce at the required speeds – 18,000bph for 500ml bottles and 12,000bph for the 1,500ml format – and deliver the contractually-agreed efficiency for this type of line. Combi efficiency of more than 92% and zero machine downtime for the end of line was achieved.","@ID":29} "NEWS 7 PETplanet insider Vol. 11 No. 12/10 www.petpla.net More regional expertise and 24-hour parts shipment from Husky Husky Injection Molding Systems has announced an increase in its global field support network, including more beverage packaging system specialists, faster parts shipment and enhanced global call centre capabilities, Sean Weir, Husky’s General Manager of Global Customer Support, said that the measures are intended to enable the company to respond more quickly and effectively to customer needs, around the world. It is increasing inventory levels in all regions and streamlining logistics, consolidating management of these activities into one global system. Husky plans a 20% increase in dedicated service and support technicians in the field. They will have a new global fleet of service vehicles equipped with the necessary tools to ensure they can get on site and resolve issues faster. The company says that larger regional teams will also improve responsiveness, allowing customers to achieve faster start-ups and to raise uptime levels. It aims to have a specialist is in a customer’s facility within 24 hours after a processing issue has been identified. Husky has also invested in improved technology and added resources for its call centres, which will be more regionally aligned so that customers will deal as much as possible with the same expert. www.husky.ca Siapi for jars and single serve Esterform, UK, has selected Siapi’s technology and experience for a new project, which is to offer a complete range of innovative jars in PET as an alternative to the traditional glass formats. Also due to English law, which has always imposed the development of eco-sustainable packaging, Esterform developed PET jars to minimize the impact of the materials as well as the lower transport costs. Thanks to the experience it has gathered in this sector and the constant increase in efforts by its Research and Development department, Sisai provided Esterform with support in developing the relative preforms and optimizing the profile. According to Siapi, the mechanical characteristics of the containers were improved thanks to an optimal distribution of wall thicknesses. Pepsico International selects the Siapi platform for their newAquafina container PepsiCo International has entrusted Siapi a world-wide reference for the large format market for more than 10 years, with the creation of their new Aquafina containers that will be produced using the EA2S blow-molding machine. In this way it has decided to invest in the Middle East, focusing on one way technology. Interest in one way solutions has appeared timidly recently in this emerging market, but only now thanks to Pepsi’s forward-thinking approach, signs of change are appearing, involving the entire sector. As a result, Siapi has developed for the multinational a 17.5l water container for distributors, which is distinguished by packaging that is extremely innovative, especially from the point of view of its weight (only 340g). The developed container is blown by the EA2S machine for large formats: a stretch blow-moulding, 2 cavity machine for creating large format containers up to 20l that can be configured with the automatic system for inserting the handle during or after the blowing phase, the HandleMatic 360° system. More capacity for IPP International Process Plants (IPP) has recently increased its PET holdings with the purchase of high margin speciality grade PET bottle grade resin and PET fibre and textile lines. IPP has also acquired two complete PET facilities in the USA and Germany, making it the largest company of its type and a leader in the global PET market. The company now has over 70 complete plants in its inventory, offering a range of speciality PET lines. It has seven solid state polymerisation plants, ranging from 43 to 300t/day and a further seven speciality staple fibre continuous polymerisation lines, producing from 78 to 100t/day. Eleven resin continuous polymerisation lines, producing 93 to 434 tons/day of speciality grade polyester fibre, textile and PET, 17 spinning lines (39 to 50t/day); 18 stretch-draw lines (46 to 57t/day); and six filament spinning lines (15 to 44t/day) complete its production portfolio. The plants use FII Design and various other technologies. Ancillary to their PET holdings, IPP has eight 750t Trane Absorption chillers; nine other chillers; eight hot-oil boilers; four steam boilers; and a range of air compressors. As well as complete PET manufacturing lines, IPP also has a number of PET handling equipment and systems available. The company is a worldwide buyer and seller of complete process plants and equipment. It has offices in twelve countries and over 20,000 major pieces of process equipment located worldwide. Its business model is to purchase industrial plants globally, take on site liabilities and then utilise the onsite infrastructure to restore industrial activity. Its customers include leading Fortune 500 companies. IMD Ltd. Switzerland / www.imdvista.ch Swiss Made … more than a VISION SYSTEM _Complete System Solution _INOX Line (all in stainless steel) _Vision System with COLOR cameras _Self-learn functions _Inline for 100% inspection _Easy & fast product change _Very compact Closure Testing Preform Testing","@ID":9} "REGIONAL MARKET REPORTS 11 PETplanet insider Vol. 11 No. 12/10 www.petpla.net APPE - “We are in the PET waste business and as such we must be able to convert the lowest quality post-consumer PET bottles into the highest quality PET material for new bottles.” We met: Frédéric Blanchard, Plant Director of APPE Beaune By touring France PETplanet was made to believe that the collection and sorting of PET waste and subsequent re-processing, recycling and re-use of PET bottles is a controversial and high priority issue in France, with heated discussions between the government and the beverage industry. (see previous reports in our “Focus on France”, covering the PET Story and visits to several bottlers, as well as to Valorplast). But the controversy does not stop here. After years of hesitation and reluctance, the producers of beverages and PET bottlers have finally accepted recycled PET. Food approval was achieved by APPE in 1994, however the industry was slow to accept the environmental drivers rather than the cost drivers. The percentage of blend is still a matter for discussion - 25% today, or 50% as targeted by Coca-Cola and Danone (or even 100% as requested by the demanding Alma Roxane). At the moment such volumes of recycled material are not available and as the complaints about the lack of recycled resin are increasing day by day they raise another question, and another matter of open conflict, namely “How often can recycled plastic material be reused, re-processed and re-used again? Is the usage of 100% recycled material for bottle-to-bottle a realistic approach when considering the quantities available, or is it even a sound technological solution?” And finally, the recyclers who have to purchase on open market conditions the PET waste and re-process it for bottle-to-bottle use (or any other application) face constant challenges regarding the quality of incoming waste (contaminants) and the price expectations of the finished product when compared to virgin PET. Artenius PET Packaging Europe (APPE) located in Beaune, France was the first and operates the largest PET recycling facility in Europe. In Beaune we were received by Frederic Blanchard, the Plant Director, who started the business in Beaune in 1997. Recycling at that time could be considered an idealistic whim or an eccentric indulgence. Today recycling is a pressing demand by the public and society in general, with extreme concerns about resources and the environment. It is also a priority topic for the beverage industry. The water industries in particular see recycling as a major element for sustainable business and long-term survival. Frederic Blanchard was happy to tell us the story of PET recycling in France, including his role and the role of APPE in the development of recycling. The presence of a visiting TV team from Belgium underlined the public interest in the subject of recycling. History Artenius PET Packaging Europe (APPE) was a pioneer in PET recycling in 1997 when the original owner, namely Johnson Controls, developed and subsequently produced Super Cycle PET pellets from post consumer flakes on a twin screw extruder. The APPE plant that we visited in Beaune is a smart and clean showpiece for the recycling business, which is normally associated with grime and waste, and is a strong argument in today’s discussions about the constructive role that PET and PET recycling can play in times to come. But APPE at present (APPE in Beaune as well as APPE in Bierne, the biggest converter in the country) is not in the public eye because of its technological and industrial achievements, but because of the financial turmoil of its Spanish parent and holding company La Seda. La Seda had over-invested and was forced to restructure the business with new capital and new shareholders now in place. Inevitably this has affected APPE’s expansion plans across Europe. It was decided that whilst in Beaune, PETplanet would therefore concentrate the discussions on recycling and technologies and discuss next day the rather more political matters of the company at the large APPE plant in Bierne. Recycling in Beaune Recycling was started in Beaune on a green-field site in 1997 and was producing about 5,000t of recycled resin. At that time the incoming flakes were sourced externally by the company. APPE’s first wash line to produce PET flakes was installed in 2000, followed by further expansion projects to its current 35,000t flake and rPET capacity. The APPE PET recycling process Post consumer PET beverage bottles are collected, processed and converted into food-approved PET flakes or pellets in several stages, and finally ready to be blended with virgin PET and injection moulded into new preforms. Artenius PET Packaging Europe operates the largest PET recycling facility in Europe","@ID":13} "REGIONAL MARKET REPORTS 12 PETplanet insider Vol. 11 No. 12/10 www.petpla.net Flake versus pellet Asked about the controversy of food grade flakes versus food grade pellets to be used in bottle-to-bottle operations, Frederic Blanchard replied that APPE chose to produce pellets due to the technical challenges in consuming flake 10% and also with special regards to the risk of contamination with black specks, which – as he says is under control when using pellets. Preforms production in Beaune Preform injection moulding starting in Beaune only in 2008 with an initial investment in 4 new Husky Hypet systems with cavities from 72 to 96. Two more Husky systems were added in 2009 which convert PET and nylon into multi-layer preforms. 25,000t of PET resin was converted into preforms during 2009, of which approximately 5,000t was in RPET (SuperCycle) The total plant in Beaune, i.e. recycling and injection moulding, employs over 130 people. Future expectations Frederic Blanchard comments, “There is a lot to say about recycling and bottle-to-bottle application, for example: Recycling is a young, still a commercially immature business with many inexperienced people in the market. There is a lack of feed stock resources therefore col- lection rates must be increased. Markets, including the beverage market, are demand- ing higher volumes of recycled PET. Therefore the potential for PET recycling remains very high, however customer must accept that with limited availability rPET pricing is likely to exceed that of virgin PET. The industry and governments must work together to improve the quality of the collected material (for example the banning of PVC which is a heavy contaminant in the collection stream). Suppliers must do their homework. Energy consump- tion and water consumption are still too high, despite the efforts to reduce them. Integration of a recycling process in line with injection moulding preforms must come. We have been in the recycling business for many years and overcome many challenges, however further challenges lie ahead..” And then he repeats: “I insist that we the recyclers must be able to convert the lowest quality of waste in the highest quality new granulate. Our major customers are now seriously taking ‘sustainability’ as a major board challenge. APPE Beaune with our state of the art recycling facility is best placed to assist with this strategic challenge’ APPE’s process uses mechanical recycling Post-consumer PET bottles, supplied in bales, are sorted, washed and shredded to make post consumer 1) flakes, extruded, filtered and crystallised to make NuCycle 2) (non-food grade pellets), converted in a solid state process to make SuperCycle 3) (food grade pellets). (For a technical description in detail refer to PETplanet Insider issue No. 5+6, 2003.) The Beaune plant has an intake capacity of 45,000t in bales and an output of 35,000t in finished pellet form. The difference of 10,000t (with an approximate value of some €3m Euros) is reject material (heavily contaminated PET bottles, coloured bottles, caps, labels, glue, organics and/or non-PET material such as Tetra bricks, metal cans, HDPE bottles, PVC bottles and other). “We are targeting zero waste. Even waste from PET waste collection must not go to landfill, but should find other uses”, Frederic Blanchard said. The flakes (35,000t) are converted into 35,000t of NuCycle pellets. At present 8,000t are used for non-food preforms and, after SSP processing, 27,000t as SuperCycle pellets (currently) with food approval. Production assistant Benoît Peborde and the Gneuss filter Equipment Suppliers to APPE over a period of almost 20 years: For washing: Sorema For crystallisation and extrusion: Erema, Bühler and Davis Standard For filtration: Gneuss For Solid State Process: Ohl, Stokes, Bühler Prime customers at APPE for SuperCycle Due to the high quality of APPE’s material, principal customers are usually aligned who have a high focus on sustainability such as Danone & Coca Cola. These type of customers are looking for firm commitments to reduce their carbon footprint by using SuperCycle.","@ID":14} "MATERIAL / RECYCLING 16 PETplanet insider Vol. 11 No. 12/10 www.petpla.net Zanchi attacks anti-dumping measures at PET days “Increase in duties could threaten jobs” PETday, organised by Global Service International S.R.L. (GSI) in Artimino near Florence/Italy, has been held annually since 2003 and since its inauguration it has become the major sector event for PET processors. This year 153 delegates from 26 countries and four continents found their way to Artimino. As Francesco Zanchi, CEO of GSI, which is headquartered in Rescaldina/Milan (Italy), was quick to emphasise, the delegates represented companies that purchase around eight million tonnes of PET each year. In his introduction, Francesco Zanchi informed delegates that worldwide PET requirement was set to grow by one million tonnes in 2010 and thus by around 6% by comparison to 2009. However, the requirement in Europe and the USA will see only a moderate rise due to the use of recyclates and as a result of lighter weight bottles. The picture is very different in Asia. This is due to the immense PET consumption of China, which alone accounts for 45% of the worldwide growth in PET. Nevertheless, according to Zanchi, a number of new PET facilities will be commissioned in 2011 and 2012, chiefly in Asia and the Middle East so that the increased requirement should not lead to any shortage. This is of course providing that the raw materials are readily available. Zanchi went on to highlight a particular problem resulting from the fact that the largest production capacities are already to be found in the Middle East and Asia. He pointed out that, with the proposed increase in capacity, the worldwide significance of these regions as important PET suppliers is set to increase even further. The CEO of GSI drew attention to the threat of possible anti-dumping measures which may be introduced by the EU, and the implications of this for the European market. Anti-dumping duties (AD) and compensating tariffs against subsidisation measures (so-called Antisubsidy or Countervailing Duties (CVD) are levied by the EU on PET that is produced by certain non-European countries or companies. In the short term these measures act to the disadvantage of the non-European manufacturing companies but in the long term, they form a competitive disadvantage for European PET converters who purchase PET of non-European origin. Non-European PET is subject to duties which therefore increase the price of the material. Partial success against antidumping activities In September 2009 the EU Commission examined the measures in place affecting PET originating from the United Arab Emirates (UAE), Iran and Pakistan. In the summer of 2010 duties on imports from these countries were temporarily imposed. Following this move, more than 70 EU-based PET converters which purchase a total of around 2.7million tonnes of PET each year and represent 83% of the PET market in the EU lobbied the European Commission to try to persuade them not to enforce these planned anti-dumping measures. They were supported by the Belgian law firm Van Bael & Bellis and Global Service International S.R.L. Some success was achieved through this action. Instead of anti-dumping duties, reduced countervailing duties were levied on PET from the specified countries. The result has been that, World PET demand. The worldwide requirement for PET has been characterised by continuous growth. In 2010 too the requirement will exceed that of the previous year – namely, by 1 million t or 6%. (Source: Tecnon Orbichem / GSI) World PET capacity’s new wave of investments. In 2011 and 2012 new production plants will be commissioned – especially in the Middle East and in Asia. Following a range of shutdowns of production capacity in 2009 this is very important so as to enable the demand for PET, which is continuing to increase worldwide, to be accommodated. (Source: Tecnon Orbichem / GSI)","@ID":18} "BOTTLING / FILLING 26 PETplanet insider Vol. 11 No. 12/10 www.petpla.net Small footprint for aseptic production Sidel has obtained final technical acceptance of its first complete aseptic PET line in Germany, equipped with a Combi Predis for dry decontamination of preforms and Axo-Smart secondary packaging flexibility. The line has been up and running since June at the Hauser plant, producing flavoured teas in lightweight 500ml and 1.5 litre bottles. Family-run company Hauser Weinimport GmbH specialises in vermouth, liqueurs, wine-based drinks and, more recently, fruit juices and flavoured teas. It has, historically, packaged its products in glass and cartons. In 2009, the company decided to adopt PET as the packaging material for its range of flavoured teas, branded as Eis Tee, in 0.5 and 1.5l formats. The teas are filled without preservatives and sold at room temperature, with a shelf life of about one year. Hauser wanted an aseptic solution that would ensure product sterility, without altering its organoleptic and microbiological characteristics. After investigation, it opted for Sidel’s Combi Predis FMa. Dry decontamination The Combi Predis uses hydrogen peroxide (H 2 O 2 ) to ensure 100% decontamination of the preforms, which also means there is no water consumption and minimal chemical use. In producing 100% sterile bottles, TCO (total cost of ownership) optimisation and environmental aspects were important factors in Hauser’s choice. The Predis system is wellestablished; lower chemical and water consumption of dry decontamination technology, when compared with conventional technology, significantly lowers costs and reduces waste water.","@ID":28} "NEWS 8 PETplanet insider Vol. 11 No. 12/10 www.petpla.net DöhlerGroup and PureCircle ally for Stevia development PureCircle, headquartered in Kuala Lumpur, Malaysia, and DöhlerGroup, of Darmstadt, Germany, have announced a global strategic partnership for the development of Stevia-based ingredients and formulations. PureCircle has a large portfolio of Stevia ingredients; DöhlerGroup has established expertise in sweetening, sweetening flavour and application. The companies have, together, 21 application centres around the world. PureCircle is a global leader in the production and marketing of natural high-purity Stevia sweeteners. It has invested around $200 million in its supply chain and infrastructure, which gives it control across plant breeding, harvesting, extraction, purification and application. It holds a number of US patents and has over 50 patent applications. Döhler is a global producer, marketer and provider of technology-based natural ingredients, ingredient systems and integrated solutions for the food and beverage industry. Its product portfolio ranges from flavours and emulsions, natural colours and health ingredients, compounds, fruit preparations, alcoholic and non-alcoholic bases, dairy bases, malt and cereal bases to sweetening systems. www.purecircle.com www.doehler.com AGR International and PET Engineering agreement on development Italian company PET Engineering and American AGR International have signed an agreement in order to achieve a technological development of the PET bottle, intended to provide bottlers with constant quality monitoring of the containers being blown. The greater complexity of the blowing processes and the reduction of the process windows imposed by lightweighting require monitoring systems and automatic feedback in order to assure constant quality of PET containers. PET Engineering says that this agreement is representative of its ongoing processes of development of lightweighting, including the development of ultra-light bottle projects finalized for raw material savings, savings in energy consumption and ongoing quality improvement, constantly monitored by AGR systems. Birkner’s Beverage World 2010/2011 The 15th edition of Birkner’s Beverage World, 2010/2011, contains more than 22,000 company profiles from 199 countries, in the book and the internet database. Information on over 5,600 breweries, 6,100 producers of mineral water, juices and refreshing drinks and bottlers, 2,600 distilleries, 1,200 hop, malt and raw material suppliers, 5,900 suppliers and 450 associations and institutions are included. The new edition features names and addresses, over 12,000 e-mail addresses, internet addresses and data regarding management, services, products and brands, machines and capacities, capital and turnover. The hardcopy edition is complemented by a regularly updated Internet database at www.beverage-world.com, which offers unlimited multilingual researches within the subscription period. The book is available at €251 and access to the complete internet database at €284 p.a, directly from Birkner GmbH & Co. KG, Winsbergring 38, 22525 Hamburg, Germany. Fax: +49-40-800 80 1902; e-mail [email protected]. www.beverage-world.com KTW opens new test and application technology centre KTW (Kunststofftechnik Waidhofen an der Thaya GmbH) of Austria, which specialises in closure moulds, has almost doubled its application technology capacity and, on November 1, commissioned a new, 1,400m² test centre. The new centre is designed for performance optimisation of multi-cavity moulds, mostly for mineral water and soft drinks - more than 5,000 cavity sets per year are allotted to this product group. There is also a significant focus on ‘personal care’ applications – flap and flip-top closures for shampoos and lotions, in multi-colour and multi-component design. KTW currently has eight injection moulding systems currently available for test operation, with clamping forces ranging from 500 to 5,500kN. The primary focus is currently on the trend towards multi-component applications, with multiple materials or multiple colours. Four of the eight systems are equipped with either two or three injection units; additional injection units equipped with individual drive systems that can communicate the process cycle in the corresponding machine control through the Euromap 67 interface are available. KTW believes that the key to performance optimisation lies in ‘fine-tuning’, to the analysis and optimization of the de-moulding process in particular. The company has a high-speed camera available to study the trajectory of finished parts and the performance of the demoulding system. Thermal imaging cameras are used in the optimisation of flow rates in the multi-channel cooling systems. The layout within the test centre allows the individual regulation of flow rate to each machine, which enables optimum cycle times as well as accurate simulation of conditions in operation at the customer’s production location. In addition to the performance tests of the injection moulds in their own test machines, the KTW applications centre offers sufficient space and the necessary infrastructure to additionally accommodate three to five customer-machines, which can be combined with the KTW manufactured injection moulds into production cells. www.ktw-group.com","@ID":10} "PETbottles 34 PETplanet insider Vol. 11 No. 12/10 www.petpla.net Personal Care FoodBevcom A world of food and drink www.beverageawards.com functionaldrinks The only global awards scheme dedicated to the global functional drinks industry 6 categories – 24 awards Awards will be presented at the InnoBev Global Beverages Summit in Washington, DC, US March 2011 ENTER NOW PET for Poliboy The manufacturer Brandt + Walter based in Lilienthal, Germany, is offering its Poliboy range of furniture care products in 200ml PET bottles in various designs. For intensive furniture care applications, the bottle is coloured red whilst, for teak oil, it is transparent. Both bottles have a red, screw-on hinged cap and sport an additional sticker with the advertising slogan “Quality made in Germany”. A common feature of the bottles is their innovative, easy to handle shape and the fact that the labels are adapted to this format. www.poliboy.de Clear and simple 150ml soothing cleansing lotion in the “Active Sensitive“ brand range is being offered by Yves Rocher of La Gacilly , France, in a transparent and simple PET bottle. The lotion is a light pink colour and as such ensures some interesting colour effects at the POS, depending on the light. Non-label-look labels to front and rear as well as a silver plastic screw cap secured by means of an adhesive sticker complete the look of this unusual cosmetics packaging. www.yves-rocher.com Fruit Shampoo in red 300ml shampoo with scent of the cranberry fruit is being offered by Garnier France in a red PET bottle. A high quality, printed non-label-look label on the front and a red, hinged lid ensure that the product attracts attention on the cosmetics shelf as well investing it with a high quality rating. The snap lid can be easily opened and closed using one hand only. The lid is held in the “open position” by means of a spring mechanism. www.garnier.com Carefree with aloe The cosmetics manufacturer Johnson & Johnson in Düsseldorf is offering, under the “Carefree“ brand name, sensitive and soapfree intimate washing lotion with aloe in an oval PET bottle with a 2-section, red pressure cap. The front and rear labels are matched to the shape of the packaging, printed with details about the product and give all the required trading information. www.carefree.de","@ID":36} "TRADE SHOW REVIEW 31 PETplanet insider Vol. 11 No. 12/10 www.petpla.net DEUTSCHE EDELSTAHLWERKE, Obere Kaiserstr., D-57078 Siegen / Auestr. 4, D-58452 Witten Who knocks PET bottles into shape? CorroPlast® – the ultimate steel for all-stainless mould sets. Recycling solutions Amut SpA’s North American business has been finding consistent demand for sustainable solutions in PET production. A leading contender for the biggest smile at the K Show 2010 was Anthony Georges, North America sales manager for Amut SpA, who is based in Richmond Hill, Ontario, Canada. “We have just signed a large contract, at the show, for a total bottle to bottle recycling plant,” he said. “It will have an output of 2,000kg/h for clear PET. The contract is a good sign the recession is over.” He also talked about a second washing plant to be built in the Middle East in 2011, which would follow another that is coming online in early 2011. “The Middle East offers excellent opportunities for sustainable technologies but we are finding sustainability is a key word in North America. We have seen a number of companies, from multinationals to small enterprises, grasp the idea of reducing their effect on the environment. Five years ago, hardly anyone was listening but having seen, for example, Global PET, Inc., grow from a small operation to $25 million a year with a grinding business has opened the eyes of the industry in North America.” Key to acceptance is always going to be the bottom line and potential savings of 50-60% on resin prices, simply by knowing how to recycle, are going to catch the eye of anyone interested in operating profitably. “We have seen a number of installations for bottle-to-bottle recycling during September,” said Georges. “The Ice River project, for example, is producing 3000kg/h of clear PET and 500kg/h of green from two washing lines operating in parallel. It’s a total closed-loop solution, which is capable of producing 4 billion bottles/year.” Amut SpA will be installing a 4,000kg/h plant for Custom Polymers, Inc., in Athens, Alabama. It will come on line in late 2010/early 2011. Another plant has been installed at Global PET’s recycling plant in Perris, California. “They took delivery of a 180mm single-screw sheet line, which can produce 2000kg/hr from 100%rPET flake, which it supplies to the local thermoforming market,” Georges continued. “It has also installed two FFG 980 Quad thermoforming machines – it is on the way to becoming the first totally in-house recycled bottle to thermoforming company west of the Mississippi.” The low environmental impact of recycled PET is clearly becoming a big benefit in the USA and other parts of the world. www.amut.it","@ID":33} "TRADE SHOW REVIEW 32 PETplanet insider Vol. 11 No. 12/10 www.petpla.net Heat and light In a year that has been one of evolution, rather than revolution in the field of PET bottle production, Krones AG unveiled some innovations designed to customers improve efficiency, and productivity and flexibility. The company stand featured operating Contiform S8 machines, which demonstrated developments available from model year 2011. Energy consumption in heating and blowing air have been particularly addressed but the overall effect is to improve performance in other areas, also. One of the challenges to producing multiple forms and colours on a single line is consistency. If a line has dark and light preforms running one after the other, conventional heating systems will produce inconsistent results. Light-coloured preforms will reflect heat while dark-coloured models absorb it. The result is that the lighter units are not heated as effectively as the darker ones, which will lead to varying finishes and unreliable quality. Krones has addressed this issue with Flex-Wave, a microwave heating technology that consumes significantly less energy than conventional infra-red solutions. But energy saving is only part of the story. The company says that Flex-Wave is particularly well suited for Contiform/filler monoblocs, as the very short heating time needed by the microwave system reduces the number of preforms that have to be inside the oven to a fraction of the former figure. according to Krones, this means very few losses in the event of an emergency stop. But there is another benefit that flows from the heating characteristics of microwaves: Significant penetration depth. Each microwave station is fitted with an enclosed cavity resonator, which ensures that the microwave energy is properly deposited in the preform. The penetration depth enables the preform to be evenly warmed up without surface cooling or equalisation time. As each heating station can be separately controlled, this offers a wide variety of process variability options which can cope with different preform colours, PET material and varied proportions of recyclate. A second Contiform S8 machine demonstrated Krones ProShape technology, which is designed to produce oval-section or asymmetrical containers. It uses the Contiform series’ existing heat-up and stretch blow-moulding technology in combination with a new module for preform orientation and selective temperature control. The ProShape module is integrated into the machine between the standard linear oven and blowing wheel. Temperature-controlled aluminium moulds, specifically designed for the required bottle, are used to apply the appropriate temperature profile to the preforms. This ensures optimised material distribution for the downstream stretch blow-moulding process, which in turn enables very accurate profiles with sharply defined temperature boundaries. Krones says that this permits stable thick-walled areas to be located directly alongside thin-walled segments. An optical camera system is able to recognise and correctly position preforms by orientation marks. The company says that a huge range of different orientations can be processed and that station outputs of up to 2,000 containers/h are achievable. www.krones.com Kreyenborg and Seebach announce new filterdisc Extrusion and polymerisation company Kreyenborg and filtration specialists Seebach have jointly developed a new ‘filterdisc’, which is designed for depth filtration tasks in polymer filtration. It offers increased filtration area but, at the same time, takes up less space. Standard wire mesh screens are only suitable for surface filtration, for removing solid particles from fluid. The new screen goes somewhat further. It is designed to separate and filter out short-chain polymer molecules – gels – from the main polymer. The differentiation between the two, the main polymer and the gel, is only the different viscosity. The Kreyenborg and Seebach filter uses filterdisc elements that utilise a special fleece as the core layer of the filter element. ‘Viscoelastic’ particles are captured and held within the fleece cells, rather than being held on the surface, as in wire mesh filters. This both greatly increases surface and enables melt quality to be improved, which makes the final product suitable for more demanding applications. The filterdisc was demonstrated in piston screen changers by both companies at K Show 2010. www.kreyenborg.de www.seebach.com Cleaner colours PolyOne, which is headquartered near Cleveland, Ohio, has announced the European launch of its OnColor Complete Liquid Colour Solutions, a liquid colorant system that is designed to help converters and OEMs reduce costs and eliminate waste by optimising colorant use, handling and management. The system has been developed in association with Maguire companies, including Maguire Products, Inc., which is headquartered in Aston, Pa, USA, Clearfield Color, LLC, and Riverdale Color Company, in which Maguire Products is a stockholder. Maguire, which supplies liquid colour pumps, material management systems and other auxiliary equipment for plastics moulding, extrusion, and compounding, believes that the new equipment addresses the major disadvantages of liquid colours, compared with masterbatches; namely, that liquid has, historically, been messy and difficult to handle. The containers are fully self-contained and ship with their own pump. As a liquid, colour dosing can be undertaken in very small quantities. Dispensing is immediate, Maguire says, and the sealed unit ensures that the liquid remains within the container, rather than spilling, dripping or oozing onto the floor. The pump and drum are recyclable and can actually be used up to five times before recycling in what is claimed by the companies to be a first-of-its-kind, closed-loop system. The company says that the system will eliminate waste and storage associated with unused colorant, as well as disposal of discarded containers. By eliminating spillage and mess while, at the same time, simplifying material changeovers and clean-ups, the system is claimed to reducing operating costs. The pre-packaged and sealed-unit drums may also assist with inventory management. The metering system integrates feed, the dosing pump. Single dispersed pigment colorants are supplied through an exclusive arrangement with Riverdale Color Co Ltd. the OnColor delivery service provides colorant delivery and replenishment, collecting emptydrums for re-use. The OnColor Complete system is currently available in North America and Europe; availability in Asia is scheduled for early 2011. www.polyone.com www.clearfieldcolor.com www.maguire.com www.riverdalecolor.com","@ID":34} "PREFORM PRODUCTION 25 PETplanet insider Vol. 11 No. 12/10 www.petpla.net 11. Check that the decompression (pullback) time and position is not excessive. This should be set as low as possible to minimize the risk of poor nub formation, yet enough to eliminate drooling into the cavity from excess melt pressure. Typical settings for valve gated moulds are: Time = 0 – 1sec; Distance = 0 – 10mm. 12. Check to ensure that the valve gate compressed air pressure is sufficient to close the valve stems properly. Typical pressures are in the range of 8 – 12bar (120 – 145psi). 13. Check hardware for worn, damaged or failed components, specifically the mould gate inserts, valve stems, valve stem seals, nozzle tips, tip insulators, and clogged core / cavity cooling channels. name ................................................................................................................ company ........................................................................................................... function ............................................................................................................. street................................................................................................................. city ................................................................................................................... country .............................................................................................................. phone ............................................................................................................... fax.................................................................................................................... e-mail................................................................................................................ credit card ......................................................................................................... expiration date.................................................................................................... name on card ..................................................................................................... PETplanet print Vol. 6: The Rapid Guide to Perfect Preforms by Rick Unterlander and Ottmar Brandau fax: +49 (0) 6221-65108-28 [email protected] www.petpla.net Order your copy now! 7. Check that the cooling time isn’t excessive for the preform being moulded. This typically ranges from about 1 to 3sec depending upon the preform wall thickness. Reduce time if necessary to minimize the nub solidifying and adhering to the gate. This may improve nub release during initial mould opening. 8. Check that the hold (packing) pressure isn’t too high to cause excessive swelling, especially in the last zone. Reduce as necessary. 9. Check that the valve gate close timing is adjusted properly. This is typically 0 – 0.5sec for valve gate close delay. Minimize to improve nub formation. 10. Check that the hold (packing) time isn’t too little for the preform being moulded. Increase as necessary to improve gate formation. Table of Contents i..................................... About the Authors ii............................................. Introduction chapter 1.......................................... AA Level High 2..................................... Accordion Preform 3....................................Air hooks / Streaks 4............................................ Black Specks 5................................................... Bubbles 6.............................................. Burn Marks 7..........................Colour Streaking / Peeling 8.............................................. Crystallinity 9............................................. Drool Marks 10.......................................................Flash 11......................................Gate Depressions 12............................................ Gate Peeling 13.............................. Gate Voids / Pin Holes 14......................................Internal Gate Sink 15............................................ Internal Sinks 16.....................................................IV Loss 17........................................ Long Gate Nub 18........................................... Milky Preform 19.........................................Moisture Marks 20............................ Neck Finish out of Round 21....................................Parting Line Crease 22............................. Parting Line Deformation 23......................................Preform Yellowing 24...............................................Short Shots 25.......................................................Sinks 26......................................................Splay 27........................................Stretched Necks 28..................................................Stringing 29......................................Surface Blemishes 30......................................Thread Flow Lines 31.....................TSS (Top Sealing Surface) Sink 32................................................... Unmelts 33............................. Wall Thickness Variation 34..............................................Wavy Body 35...............................................Weld Lines prices in EUR + VAT. 1- 3 exemplar each 129,- € 4 - 10 exemplar each 99,- € 10 exemplar each 69,- € PETplanet print vol.6 The Rapid Guide to Perfect Preforms machine no./name","@ID":27} "zoom zoom fax: +49-6221-65108-28 [email protected] www.petpla.net ANA LY S I S OF A L L E S S ENT I A L P E T BOT T L E COMPONENT S WOR L DWI D E PETpla.net Zoom sheds light on the mysteries surrounding the manufacturing processes of leading PET bottle manufacturers and provides a comprehensive analysis of the PET bottles of this world. Get the results online. Professional. Precise. Up-to-date. Global. Join the inner circle and become a real insider! Why not give it a try, and download some sample data? Go to zoom.petpla.net ! It’s sure to impress! PETpla.net Zoom Analysis of all essential PET bottle components worldwide Photo: ©suzannmeer - Fotolia.com NEW Why PETpla.net Zoom? ~ Comprehensive market information on bottles and closures ~ Benchmark information for focused product development ~ Technology input on container performance and perform information","@ID":26} "MATERIAL / RECYCLING 18 PETplanet insider Vol. 11 No. 12/10 www.petpla.net since 29th September 2010, the price of every tonne of PET from the UAE sold in the EU has increased by €42.34, PET from Pakistan costs €44.02 more. Iranian PET has since increased in price by €139.70 per tonne also. (For other current ADs and CVDs see Fig. 3). Long term consequences of the AD and CVD measures using PSF as an example Francesco Zanchi went on: “Although we were not successful in having the levies on PET from the three countries totally abolished, we can nevertheless claim a partial success. The fact is that at present most production capacity is already to be found in the Middle East and Asia. In two years the proportion will be even greater. That is why it is important for us to take a stand against measures of this kind – especially if we keep in mind the ever-increasing requirement for PET“. Zanchi then went on to explain what he thought would be the devastating effects levies of this kind may have specifically on the economy in the EU. Ironically, at first sight, they are designed to protect Europe’s PET producers, but, he continued, “if we take polyester staple fibre (PSF) as an example, anti-dumping measures against PSF are intended to protect European fibre manufacturers from low cost imports from countries outside the EU. However, the European textile industry is thereby deprived of the opportunity to buy cheaper and more competitive products from lower-cost producers. And what has been the ultimate result of this? The European textile industry effectively no longer exists.” Even worse, Zanchi concluded, “only very few of the European fibre producers have survived.” The theme was taken up by Philippe De Baere from the law firm Van Bael & Bellis, who enlarged upon the reasons that may be applied by the EU Commission for imposing anti-dumping levies. He made three points: “If price dumping Anti-dumping levies and countervailing duties at a glance In order to prevent any damage being done to producers in the European Union, the Community uses a system of anti-dumping and anti-subsidy measures against countries that supply the Community, at the same time taking advantage of competition-distorting dumping and/or banned subsidies. Based on the directive relating to protection against subsidised imports the Community may, in principle, levy anti-dumping and/or countervailing duties on any goods the import of which into the Community causes damage. Countervailing duties may then be levied if it is proven that a subsidy is granted for the goods in the exporting country in respect of the manufacture, production, export or transport thereof. should in fact take place i.e. that PET is sold at a higher price in the country of origin than in the EU, if there is a perceived threat to indigenous European producers, or if the measures are in the interests of the EU (a reason being cited more and more frequently). But to cite the argument that PET producers in the EU need to be protected from imports from outside Europe is to take a very short-term view. In Europe PET producers employ around 3,000 people, but if imported goods are to be increasingly the subject of onerous anti-dumping and anti-subsidy measures, we run the risk of jeopardising around 50,000 European jobs in related industries. The reason is that European processors will be obliged to purchase under conditions that are not, globallyspeaking, competitive” he concluded. Price of cotton - a key driver Francesco Zanchi then considered trends in the price of PET. As already mentioned at the 2009 PET day (and reported in PETplanet at the time), careful attention should be paid not only to the price of crude oil and PET raw materials - Paraxylene, PTA and MEG, but also, and perhaps more significantly, on the price of cotton. The reason given for the very high demand for polyester fibre over the past few months is primarily the shortage of its competitive product, namely cotton. Adverse weather conditions in China and the catastrophic floods in Pakistan resulted in a failure of the harvest which in turn meant a scarcity of cotton. Hence the price of cotton has risen to an all-time high. The consequence is a strong demand for polyester fibre whose principal raw materials are PTA and MEG. These could become scarce and / or more expensive which in turn will have an impact not only on the supply of polyester fibre but also in PET bottle production, where they are also used. Against this background, Zanchi went on to suggest that the price of cotton would be one of the key drivers of future PET price increases. The next few months, he was convinced, will see a further rise in the price of PET. Cotton price vs. polyester raw materials. This diagram shows how the prices for the polyester raw materials PTA and MEG are adjusted to the price of cotton. (Source: GSI) Summary of AD/CVD currently applicable to imports of PET. The EU has levied anti-dumping duties (AD) or countervailing duties and/ or anti-subsidy duties (CVD or AS as applicable) on PET from the countries of origin listed. The table shows the framework within which these levies fluctuate and the date up to which they are valid. (Source: van Bael & Bellis)","@ID":20} "36 PETplanet insider Vol. 11 No. 12/10 www.petpla.net PETpatents www.verpackungspatente.de Automatic lid opening system European Grant of Patent No. EP 2024248 B1 Applicant: Seaquist Closures Spain S.A, Torello Barcelona (ES) Date of Application: 15.5.2007 This European Grant of Patent describes a closure with a hinged lid for bottles or similar. A type of pre-stressed holding device is integrated in the lid. The lid springs open automatically as soon as downward pressure is exerted on a specified point. Non-removable cap International patent No. WO 2008 / 150831 A1 Applicant: Graham Packaging Comp., York (US) Date of application: 29.5.2008 A closure is fitted to a container such that once it has been screwed on it can no longer be unscrewed without causing irreversible changes to the fixture. The cap, which also has a hinged lid, is designed as a dispensing cap for use on a container that stands in the inverted position. Variable dispenser cap European Patent No. EP 2184235 A1 Applicant: Yoshino Kogyosho Co. Ltd., Tokyo (JP) Date of Application: 26.8.2008 Cap for screwing on to a container. The cap can be opened at a number of different levels, depending on the amount to be dispensed, by folding back the individual cap segments. Relocatable pourer International Patent No. WO 2010 / 066926 A1 Applicant: Capsulas Torrent S.A., Jerez de la frontera (ES) Date of Application: 12.11.2009 Pourer with lid for installing in a container opening. When the lid is removed the spout is “automatically“ extended to facilitate the subsequent pouring operation. Design and operation registered internationally. Bottle moulding International Patent No. WO 2010 / 064749 A1 Applicant: Kyung Il Jung, Gyeongi-do (KR) Date of Application: 9.12.2008 A plastic bottle is fitted in the area of the bottle neck or across the entire bottle form with spiral-shaped mouldings; the intention with these is to make possible improved pouring behaviour and to facilitate disposal. Turning the bottle is supposed to reduce its volume. Lids for different diameters International Patent No. WO 2009 / 014351 A1 Applicant: Jeong-Min Lee, Seoul (KR) Date of Application: 18.7.2008 This international patent application describes a closure for screwing on to containers with an opening diameter of 26.78 and 28mm. Integrated in the lid is a chamber which will accommodate an additive in either liquid or powder form.","@ID":38} "TRADE SHOW REVIEW 28 PETplanet insider Vol. 11 No. 12/10 www.petpla.net K2010 Review Visitors and exhibitors in positive mood at K Show 2010 While the K Show 2010, which ran from October 27 to November 3, had fewer visitors than the previous edition, in 2007, the overall attendance gave exhibitors and the organisers grounds for satisfaction and for optimism, going forward. Three years ago, the industry was in ‘boom mode’ – but that was before the financial crisis and the global industrial downturn. The exhibitor and delegate attendances this year indicate that the recession is definitely over. Around 220,000 trade visitors, 9% less that in 2007, attended the eight days of the trade fair, which filled all 20 main and sub-halls at the Dusseldorf showground and hosted over 3,100 exhibitors. PETplanet Insider’s staff learned that the visitors were not just looking at exhibits; they were enquiring about and signing papers for real orders. While some manufacturers, after two years of downturn and cancellations, held to the cautious path and were not prepared to count anything as final until deposits were received, there was an undercurrent of guarded optimism. Nearly 60% of the total visitor numbers came from outside Germany, with nearly half of that from outside Europe. The largest group came from Asia, with approximately 30,000, followed by India, with around 11,000. Turkey and Israel were represented by 4,100 and 3,600, respectively – both figures were up around 50% since 2007. Representation from the Americas remained pretty much static, with 10,500 from Latin America and 6,800 from the USA and Canada. Machinery was the major reason for attendance, followed by raw materials and auxiliaries, semi-finished products, technical plastics and rubber components. After a period in which the PET industry has been promoting faster, bigger and more complex machinery, the trend this year is to smaller, more flexible equipment and a continuing emphasis on after-sales service. China is getting to be the largest and remains the fastest-growing major market in the world but activity in India, Brazil, SE Asia, North Africa and other developing countries is also accelerating. Exhibitors from China and India at K’2010 could have populated a reasonable exhibition on their own, with a number of small stands, joint exhibits and national pavilions. However, smaller operators in emerging markets are interested in machinery that is more flexible and more attuned to their needs – which seem to be for smaller runs, or for line expansions that do not require big capital commitment. What is clear from this year’s show is that the manufacturers of mould machines, hotrunners and ancillary equipment have picked up on that demand and are intent on serving it. The drive for ever-higher cavitation numbers and ever-faster output may resume in the future but a noticeable theme at K Show 2010 was for smaller machines, which are more affordable but still receive mainstream support and are easier to handle. Single-minute exchange of dies (SMED) was demonstrated as a reality. Modular moulds that can accommodate bottle shape changes without a complete refit were also in evidence. Contaminant detectors and separators S+S Separation and Sorting Technology GmbH’s stand at the K Show featured its range of separation and sorting solutions for the complete life cycle of plastics. The systems comprise metal detectors and separators, magnet systems for all production stages and conveying types in plastics processing, and contaminant separators for plastics recycling. S+S makes two solutions for the protection of high-performance injection moulds for preforms or caps and closures against metal contaminations, which are also intended improve efficiency and productivity. The Protector-XHT is a metal separator for processing temperatures of up to 200ºC. The separator is installed directly at the inlet of the injection-moulding machine or after the drier and inspects all the fed materials at the last-chance control point. The Protector-HR metal separator is designed for high-performance moulds, such as bottle cap equipment with up to 96 cavities. The company says that its systems are ideal for PET flake sorting because their high standard of effectiveness allows use of recycled material in the food segment. www.sesotec.com","@ID":30} "MARKET SURVEY 22 MARKETsurvey12/10 Company name Atlas Copco Crépelle Arizaga, Bastarrica y Cía, S.A. Postal address Telephone number Web site address Contact name Function Direct telephone number Fax E-Mail 2 place Guy de Dampierre 59008 Lille Cedex, France +33 3 20 52 47 11 www.atlascopco.com Sabine Wagnon Communications 33 3 59 01 05 02 [email protected] Pol. Ind. Azitain 6, 20600 Eibar, Spain +34 943 820 400 www.abc-compressors.com Ignacio Azcuna Product Manager +34 630 751 355 +34 943 820 235 [email protected] 1. Machine designation / model number ZD ZD VSD X-booster SX 4X H-Booster 3THA-3-LT 3HA-4-LT 2. Number of models in range 23 6 6 1 12 3 4 14 3 4 3. Output in m³/h 792 - 4,108 FAD 792 - 1,177 FAD 529-1,152 FAD up to 1,5833,957 FAD 576 to 1,030 FAD up to 400 125 330 10,000 535 1,050 4. Compressor type Low pressure air Screw Screw Variable speed drive screw Variable speed drive screw High pressure blowing air (up to 40bar) Piston Piston Variable speed drive piston Variable speed drive piston Reciprocating Reciprocating Integrated system Reciprocating Reciprocating 5. Lubricated or Oil-free Low pressure compressor Oil-free Oil-free Oil-free Oil-free Booster compressor Oil-free Oil-free Oil-free Oil-free Lubricated Oil-free Integrated system Lubricated Oil-free 6. Machine layout Horizontal Horizontal Horizontal Horizontal 7. Number of compressor stages 2 and 2 2 and 2 2 and 2 2 and 2 1 or 2 2 4 1 or 2 3 3 8. Are special foundations required ? No No No No No No No No No No 9. Cooling system Water Air Water Air Air Water 10. Belt or direct drive Low pressure compressor Drect drive Direct drive Direct drive Direct drive Booster compressor Belt drive Belt drive Belt drive Belt drive Belt or direct Belt Integrated system Belt or direct Belt or direct Belt Belt Company name Boge Kompressoren Postal address Telephone number Web site address Contact name Function Direct telephone number Fax E-Mail Otto-Boge-Straße 1-7 33739 Bielefeld, Germany +49 5206 601-0 www.boge.com Matthias Eichler Head of Marketing +49 5206 601-159 +49 5206 601-200 [email protected] 1. Machine designation / model number BFP - minimum model BFP - maximum model BS Line minimum model 2. Number of models in range BOGE Flex Pet 100 BOGE Flex Pet 1080 BS Line 14-0 3. Output in m³/h 93 1076 1150 4. Compressor type Low pressure air screw screw Screw High pressure blowing air (up to 40bar) piston piston Piston Integrated system - - - 5. Lubricated or Oil-free Low pressure compressor Lubricated Lubricated Oil-free Booster compressor Lubricated Lubricated Oil-free Integrated system - - - 6. Machine layout Screw compressor separate; screw compressure, low pressure vessel, adsorption dryer, filters, piston booster compressor, high pressure vessel and switch cabinet are mounted on on skid screw compressor separate; screw compressure, low pressure vessel, adsorption dryer, filters, piston booster compressor, high pressure vessel and switch cabinet are mounted on on skid Screw compressure, low pressure vessel, piston booster compressor, refrigeration dryer, filter, high pressure vessel and water cooling tower 7. Number of compressor stages screw: 1 - piston: 1 screw: 1 - piston: 1 Screw: 2 - piston: 2 8. Are special foundations required ? No No No 9. Cooling system Air Air Water (cooling tower inkl.) 10. Belt or direct drive Low pressure compressor Booster compressor Belt drive Belt drive Direct drive Integrated system Belt drive Belt drive Belt drive","@ID":24} "imprint EDITORIAL PUBLISHER Alexander Büchler, Managing Director HEAD OFFICE heidelberg business media GmbH Landhausstr. 4 69115 Heidelberg, Germany phone: +49(0)6221-65108-0 fax: +49(0)6221-65108-28 [email protected] EDITORIAL Doris Fischer [email protected] Michael Maruschke Ruari McCallion Tony O´Neill Ilona Trotter Wolfgang von Schroeter Anthony Withers MEDIA CONSULTANTS Ute Andrä [email protected] Miriam Kiesler [email protected] phone: +49(0)6221-65108-0 fax: +49(0)6221-65108-28 France, Italy, Spain, UK Elisabeth Maria Köpke phone: +49(0)6201-878925 fax: +49(0)6201-878926 [email protected] LAYOUT AND PREPRESS Exprim Kommunikationsdesign Matthias Gaumann | www.exprim.de READER SERVICES Kay Krüger [email protected] PRINT WDW Druck GmbH Gustav-Throm-Straße 1 69181 Leimen-St.Ilgen Germany WWW www.petpla.net | india.petpla.net PETplanet insider ISSN 1438-9459 is published 10 times a year. This publication is sent to qualified subscribers (1-year subscription 149 EUR, 2-year subscription 289 EUR, Young professionals’ subscription 99 EUR. Magazines will be dispatched to you by airmail). Not to be reproduced in any form without permission from the publisher. Note: The fact that product names may not be identified as trade marks is not an indication that such names are not registered trademarks. 3 PETplanet insider Vol. 11 No. 12/10 www.petpla.net News round-up from the preform production scene For those PET-experts strolling round the K-Fair, Evolution rather than Revolution will have been uppermost in their thoughts. Only amongst the preformers were we able to discover the any mechanical engineering content. It is amazing how Husky, as a world market leader, continues to be able to further exploit the technological and economic potential inherent in preform manufacture. “Output/ Capital“ is the guiding theme as far as the Canadians are concerned. Today, it’s the all-electric machines (H-PET AE 180) and we also find the theme being taken up for smaller moulds (32 times over) too. John Galt, Husky CEO, said in a PETplanet interview that integral components (clamping unit and injection unit) were based on components from the Japanese injection moulding machine manufacturer Toyo, although the system integration is still 100% Husky as before. A 22g EcoBase preform for a 1l (still) water bottle represents a new benchmark with a cycle time of 11.8s. Husky’s fiercest competitor in the hot runner field, Mold Masters, has now also turned its attentions to the preform sector. Having acquired a 100% stake in the stack manufacturer Abba, mould production is now entirely in the hands of the Canadians. However, the real showpiece was the MasterPET system in which the mould change can be carried out within 18mi instead of the usual 4h. Bruce Catoen said in the PETplanet interview that, because of the articulated robot, the cycle time is some 2/10ths of a second slower than with a linear robot but where frequent tool changes are the norm, the system quickly pays for itself. This makes the system ideal for high-flexibility production. In the coming year Mold Masters will be a full-line supplier, that is, they will be offering a mix of mould and machine in their range. Olicorp, who are looking to reinvent the compression moulding of performs, are trying out a new “old” approach. Although Sacmi has already been working on a technology of this kind, Olicorp is hoping to win over customers for themselves, with practically the same technical approach and adopting the business model “Pay as you sell“. Payment will be made for each preform sold. In this the marketing concept is similar to the concept of converter Dynoplast back in the 80’s,.Since that time the market has undergone a radical change. Whereas the converters at the time were still selling bottles to the bottler, these days many bottlers manufacture the bottles themselves. Perhaps today the time is riper than it was 30 years ago for a leasing model such as the one offered by Olicorp. We are looking forward eagerly to the first reports from customers. The interviews with John Galt, Husky and Bruce Catoen, Mold-Masters as well as other reports on significant developments found at K’ 2010 will be appearing in forthcoming issues. Some of the highlights can be found on pages 28-32. Yours, Alexander Büchler EDITORIAL dear readers, EDITORIAL","@ID":5} "21 PET bottle-to-bottle recycling plants Caps and closures Conveyers for preforms and empty bottles Preforms Preform moulds and SBM moulds Two-stage SBM machinery Preform and single stage machinery Resins and additives Filling equipment Compressors Compressors for PET bottle blowing Traditionally at this time of year, in the last issue of the year, our market overview of compressor manufacturers heralds our detailed reports on suppliers to the PET sector. Participants in this year’s report are the well known providers to the sector. CompAir is now part of Gardner Denver and therefore does not feature separately. A compressor is of course a complex piece of equipment, and a host of parameters influence performance. Changes and developments in the compressor area are not so immediately apparent or spectacular, yet they are vital in stretch blow moulding. The information in this article has been provided by the companies themselves. Inevitably, we cannot compare in detail the machines of the various providers but instead we limit ourselves to describing a few parameters. For fuller information please contact the appropriate specialist in individual companies. Whilst the publishers have made every effort to ensure that the information is up to date, no claims are made regarding completeness or accuracy. 12/10 MARKETsurvey Company name Kaeser Kompressoren GmbH Neuman & Esser Deutschland GmbH &Co.KG Leobersdorfer Maschinenfabrik GmbH & Co.KG Gardner Denver Ltd - Belliss & Morcom Postal address Telephone number Web site address Contact name Function Direct telephone number Fax E-Mail Carl-Kaeser-Str. 26, 96450 Coburg, Germany +49 9561/640-0 www.kaeser.com Wolfgang Hartmann Marketing Manager +49 9561/640-252 +49 9561/640-890 [email protected] D-52531 Übach-Palenberg Germany +49 2451-481-01 www.neuman-esser.com Siegfried Meyer Sales Manager +49 2451481121 +49 2451481139 [email protected] Suedbahnstrasse 28 2544 Leobersdorf, Austria +43 2256 9001 www. Lmf.at Damir Pilipovic Sales Manager +43 2256 9001 339 +43 2256 9002 [email protected] Claybrook Drive Redditch B98 0DS England +44 1527 838600 www.gardnerdenver.com Trevor Perry Director, Sales & Marketing +44 1527 838606 +44 1527 838630 [email protected] 1. Machine designation / model number Sigma PETAir Oilfree piston / V1 / V63 VC / VC-B / VCL-BBS Line minimum model VH & WH Range 2. Number of models in range 25 3 10BS Line 38-0 12 3. Output in m³/h 336 - 2772 1,000-2500 600 - 3,200 420 - 3,200 FAD 4. Compressor type Low pressure air Screw Screw High pressure blowing air (up to 40bar) Piston 2V1-3V1-3TEV63 Xpiston 3 Stage, oil-free, water cooled, reciprocating Integrated system - 5. Lubricated or Oil-free Oil-free Oil-free Oil-free Low pressure compressor Lubricated Oil-free Booster compressor Lubricated Oil-free Integrated system - 6. Machine layout \"V\" (2 cylinder), \"W\" (3 cylinder) Piston Screw compressure, low pressure vessel, pistion booster compressor, refrigeration dryer, filter, high pressure vessel and water cooling tower Single machine V and W configuration 7. Number of compressor stages 1+1 2/3 3 and 4; screw: 2 - piston: 2 3 8. Are special foundations required ? No No No No 9. Cooling system Air (water option) Closed cooling water system Water cooled; water (cooling tower inkl.) Yes 10. Belt or direct drive Belt Belt and direct drive Direct drive Low pressure compressor Direct Booster compressor Belt Direct drive Integrated system Belt","@ID":23} "TRADE SHOW REVIEW 30 PETplanet insider Vol. 11 No. 12/10 www.petpla.net Faster mould changeovers A modular mould design from Sidel has made SMED (single minute exchange of dies) a reality. At the same time, the company has unveiled a new blow-moulder that achieves energy savings of up to 45%. With market demands for individuality and instantly-identifiable bottle shapes, the pressure has been on mould manufacturing companies to deliver ever-faster changeovers. Sidel used the opportunity of K Show to present a single mould that can cater for various different bottle shapes. Sidel says that Modulomold enables several bottles of the same size (up to 700ml) to be produced in a single mould. It uses removable mould inserts, designed in accordance with Smed methodology so that they can be assembled and disassembled without tools. The units cannot be laterally mixed up; for ease of identification, they are colour coded - red for the insert to be placed in the left half-mould, green for the right. Each numbered insert is kept in a specially designed box, for safety in transport and storage as well as good workstation ergonomics. Bottles produced in Modulomold have two shared parts: the labelling area and the base. Either one or both of the shoulder and the body can be customised with the inserts. The company claims that the mould actually beats the single-minute target: changeovers can be achieved in less than 30s. Sidel also demonstrated its new SBO Universal2 Eco blow moulder, which reduces energy consumption in the oven by up to 45%. The company says that it has changed the oven configuration, cutting the number of lamps per module as well as the number of heating modules. Eco has a 40mm pitch (distance between two spindles) instead of 50mm, eleven oven modules instead of 14, and eight lamps per module rather than nine. As a result, installed electrical power has been decreased by more than 40%. Optimisation of oven efficiency has helped to reduce heating time by up to 15%. At the same time, greater precision in preform heat treatment is claimed to ensure that technical characteristics and bottle quality are maintained at the same levels as the rest of the SBO Universal blow moulder range. Lower installed power also helps to reduce the oven’s footprint. Sidel ran an SBO 14 Universal2 Eco blow moulder (28,000bph) equipped with the new oven design machine at K Show, producing 1.5l EcoLoop sparkling water bottles. electricity consumption was 2.6Wh per bottle, 44.7% lower than the SBO Universal2 demonstration machine achieved at drinktec 2009. The new system can be adapted to existing machines. PETplanet has already reported on other Sidel developments present at K Show, including Bottle Switch. www.sidel.com Rotary blowmoulder Italian company Sipa SpA introduced a new addition to its SFR Evo series of rotary blowmoulders at K Show, which it demonstrated at 2,300b/h/c. The SFR 6 Evo has just six cavities but its output capacity is up to 13,800 bph. Among the technologies carried forward from the SFL linear range are the preform alignment system, which is located inside the machine and contributes to its small footprint; a technopolymer transport chain; and the heating oven.The SFR Rotary’s traditional blowing unit has vertical mould opening. It is built into the new model, as are blowing units and relative electronic control, which have been developed in the SFR 6 Evo to ensure process consistency at up to 2,300bph per cavity. Sipa’s ARS and ARS-Plus air recovery systems are designed to achieve significant savings in compressed air and electricity. SFR 6 Evo, can, optionally, be equipped with an electrical stretch unit, which allows containers to be manufactured at different speeds. The company says that extremely lightweight and particularly complex containers can be produced on the new equipment, a recent example being a one-litre container that weighs just 16g and can be made at up to 2,200 bph per cavity. Sipa further claims that this is the first rotary machine that can be equipped with preferential heating. For CSD containers, blowing speed can be changed depending on filling capacity – e.g., high speeds for small formats and low speeds for larger. www.sipa.it","@ID":32} "REGIONAL MARKET REPORTS 10 PETplanet insider Vol. 11 No. 12/10 www.petpla.net Part 4 France by Wolfgang von Schroeter Part 4 of our series “Focus on France” is devoted to a company whose significance in the PET market, past, present and future, is difficult to overestimate: Artenius PET Packaging Europe (APPE). Although the company has faced a number of problems recently, Jean-Marc Rostagno, Managing Director, was anxious to give a clear message to the market about the company’s prospects and invited PETplanet to share his thoughts with our readers. The message is clear: APPE was drawn into the turmoil connected with the re-structuring of the Spanish parent company La Seda Barcelona (LSB), but the disruptions, both internal and external, caused by this restructuring are now firmly in the past. The company is now looking forward to resuming its major role in the French PET market. APPE has facilities in Beaune, the first and largest PET recycling operation in Europe, and also in Bierne, which is the biggest PET converter in France. In the next, and concluding, part of our Focus on France” series, we will be looking at Retal France and Bericap France. April 28, 2010 Artenius PET Packaging Europe (APPE) recycling plant in Beaune Frédéric Blanchard, Plant Director of APPE Beaune Regional market reports France Part 4","@ID":12} "BOTTLES PETbottles 35 PETplanet insider Vol. 11 No. 12/10 www.petpla.net Liquid food Double-pack PET jar The Campbell Soup Company has launched a new 38 fl oz (1.12l) double-pack PET jar for its Pace salsa line, which has been specifically designed for the ‘club store’ or ‘warehouse club’ retail channel. The ‘dog bone’ double-pack is intended to replace the company’s previous 64oz PP jug packaging. Campbell developed the new multi-layer, hot-fill PET jar in partnership with Graham Packaging Company, L.P., York, PA, a specialist design and manufacturer of custom blow-moulded plastic containers for branded consumer products. The smaller jars are designed to provide consumers with greater convenience and flexibility and have been developed in order to be easy to grip, handle and store. While the new container replaces a well-established ‘hourglass’ shape of the PP jar, the Pace brand’s visual traits have been maintained in the shatterproof PET package. The move from PP to PET makes the container more recyclable. The jar is manufactured with Graham Packaging’s proprietary vacuum absorption system, which produces virtually invisible vacuum panels. The company’s barrier technology may extend shelf life to 18 months, compared to six to nine months without it. The development process, from conception to market, took nine months. Design work took only a few hours, during a creative session held at Graham Packaging’s Design Center and involving personnel from both companies. www.grahampackaging.com www.campbellsoup.com Busy bees at PET-Power PET-Power has introduced a PET bottle, specially designed for honey, with what the company says is a unique and specific look. It is a round bottle with a 38 SP400 neck finish and a volume of 325ml. At its top part the bottle has a honeycomb decoration and the bottom part is corrugated. In the middle is a recessed smooth surface area, which is suited for labelling. The company can supply suitable caps in different colours. www.petpower.nl Jim Beam in PET Various American products such as, for example, mustard with Jim Beam Whiskey or spicy flavourings in Whiskey have also been sold by the CMC The Food Company GmbH based in Mühlheim, Germany, in a range of PET bottles or cans. The 263ml mustard bottle is shaped like a small whiskey bottle and is closed by means of a secure screw cap with a hinge. The round PET spice package (contents 99g) features wraparound labelling and also has a screw-on container shaker closure with two flap openings of different sizes. Both packages are firmly sealed – under the screw cap – with a laminate die-cut lid prior to initial use. www.food-company.com China soya in PET The Danish company O. Kavli AS based in Hvidovre is offering 300 l real Chinese soy sauce in a round, special shape PET bottle. The clear bottle features a label printed with information and a red, screw-on hinged cap. In the PET bottle the soy sauce has a shelf life unopened of approximately 1 year. www.kavli.dk Natural coconut water The first 20oz stock PowerFlexT PET container from Amcor Rigid Plastics has been selected for specialist beverage company GreaterThan’s new sports/hydration drink, which is based on coconut water. Amcor’s stock PowerFlex bottle features a patented panel-less design, specially developed for hot fill (185° F) bottle options, which provides a large, completely smooth rib-less label panel. It absorbs vacuum through a specially designed base, which has a diaphragm within that draws upwards as the liquid cools. Its geometric characteristics enable the inverted cone-shaped diaphragm to deflect upward as the vacuum is created. Amcor says that the absence of sidewall vacuum panels makes the PowerFlex bottles easier to label, which removes any concerns about mislabelling – missing the vertical bars when applying labels – and eliminates the ‘ripple effect’ that occurs when labelling over panels. The company claims performance and cost advantages for its product, including portability, light weight, recyclability, and reduced transportation costs. The stock PowerFlex bottle has a 38mm finish and features a screw-top closure and a coated paper label.","@ID":37} "REGIONAL MARKET REPORTS 15 PETplanet insider Vol. 11 No. 12/10 www.petpla.net Despite the apparent problems faced by the company Jean Marc Rostagno had invited PETplanet because he wanted to give a clear message to the market via PETplanet - a positive message to the many customers of APPE, who have always received the best products and the best service from the largest converter in France. the message is that the crisis is over now. Jean Marc Rostagno insisted that the scenario of plant closures and manpower reductions does not apply to APPE France, since the plants in Bierne and Beaune are profitable and should be extended rather than reduced. “We are growing the business despite the internal and external crises. Now we also have cash at our disposal to pay our patient suppliers.” Preform production in Bierne After this introductory explanation we turned our attention to APPE, the preform manufacturer in Bierne. La Seda acquired 7 preform plants and 1 recycling plant from Amcor Europe At APPE in Bierne we found: The production area covers 33,000m 2, plus 870m2 for offices. PET resin annual usage: 72,000t Production of 2 billion preforms annually, moulded on 19 injection moulding systems and 42 moulds (all Husky) Workforce: 92 people The plant supplies 50% of its output to French customers and 50% to Benelux and other European customers, and for virtually all brands – the largest being Coca-Cola, Colgate, Unilever, Refresco, etc. Filled products include CSDs and water, sensitive juices, even beer, wine and liquors, as well as detergents, edible oil and sauces, etc. April 29, 2010 Coca-Cola Enterprises in Bierne PET line at Coca-Cola, Bierne Coca-Cola beverage filling plants are prime destinations for those interested in PET packaging. Coca-Cola Enterprises operate 5 filling plants in France, one in Toulouse, one in Marseille, two near Paris and one in Dunkerque. Our visit was arranged by Jean-Marc Rostagno, Managing Director of APPE France. The APPE Bierne plant was built next door to the Coca-Cola plant, specifically to supply Coca-Cola with preforms. We met Philippe Lechantre, Supplier Development Manager. He guided us freely through the very modern and impressive factory, full of high-tech equipment. Philippe Lechantre’s responsibility is quality assurance of all incoming materials including PET preforms. He runs trials on RPET (APPE’s SuperCycle) to evaluate light weighting and neck changes. The weight of the 2.0l PET bottle (made from a 25% RPET blend) was successfully reduced from 45gto 41.5g. Philippe Lechantre commented, “Our head office in Brussels validates bottle design in principle. We adapt and optimise for our manufacturing conditions here in Bierne. It’s the same procedure when selecting equipment and suppliers.” In the very impressive Bierne plant we saw: 4 filling lines for cans each with 96,000cph. capacity 1 integrated PET line blowing/filling with 36,000bph capacity at 1.5/2.0l 1 aseptic PET blocked blower/filler with 36,000bhp capacity at 0.5l The “large” PET line, i.e for large for large bottles, is a Krones/KHS combination. The aseptic line was supplied by Krones. The plant was started in 1989 with one single can line. In 1990 three more canning lines were added. The so-called “large” PET line came early in 2000. The aseptic blocked blower/filler line has been running for 3 years. Coca-Cola Bierne employs, during the winter, 352 people and 458 people during the summer. Following the French market trend, Coke’s CSD business is growing. Reg i ona l mar ke t repor t France part 5 - Issue 01/2011 Last Part: Retal France and Bericap France","@ID":17} "6 PETplanet insider Vol. 11 No. 12/10 www.petpla.net PETnews drinktec and Brau Beviale agree to make PETpoint annual The organizers of drinktec and Brau Beviale, Messe München GmbH and NürnbergMesse GmbH, have concluded an agreement under which PETpoint, the PET segment at drinktec, will also take place at Brau Beviale in Nürnberg, starting November 2011. PETpoint focuses on the presentation of technologies and accessories for the manufacture and recycling of drink bottles made of PET. PLA (polylactide) and other plastics for beverage containers are also represented at PETpoint, which has been an integral part of drinktec since 2005 and operates under its own label. At the last drinktec in September 2009, some 120 exhibitors showed their products at the PETpoint on a gross area of 11,000m², which was 50% more space than in 2005. The faster innovation cycle in the PET segment compared with other sectors of the beverage and liquid food industry is not adequately reflected in a four-year cycle. The agreement means that PETpoint will now take place annually; Nürnberg will host it every year except during drinktec years, in which Brau Beviale does not take place. The next PETpoint at drinktec will be in 2013; in 2011, it will be marketed as part of visitor promotion for Brau Beviale and occupy a pavilion in hall 2. Organisation remains in the hands of the drinktec team at Messe München, which acquired the rights to the PETpoint brand from heidelberg business media GmbH (hbmedia) on October 1, 2009. A record number of more than 400billion plastic containers, the majority of PET, were used for filling beverages worldwide in 2009. PET now leads glass containers, cans and cartons in beverage packaging across the world. Arabian filling company chooses Corvaglia cap solution The Masafi company, of Dubai, United Arab Emirates, is an established supplier in the Gulf region of natural mineral water, fresh and natural fruit juices and other products. It has been using its own-manufactured standard closures for cold-fill products and imported two-piece caps for hot-fill from Australia. After the conclusion of a successful trial period, Masafi is now using onepiece hotfill caps it produces itself on a 16-cavity tool supplied by Corvaglia, of Eschlikon, Switzerland. Corvaglia has been selling the one-piece concept to companies in several Latin American companies. After the market launch of the cap by an international beverage filler in Mexico, Corvaglia presented the one-piece hot-fill cap to Masafi. Initial trials used 38mm caps; following minor modifications to the filling equipment, the concept was accepted and Masafi has now become the first beverage filler in the Middle East to produce its own hot-fill caps, using a 16-cavity tool supplied by Corvaglia. Corvaglia reports that other beverage fillers in the Middle East have also declared an interest in its hot-fill cap system. www.corvaglia.ch 50 years of Assocomaplast Assocomaplast – the Italian plastics and rubber processing machinery and moulds manufacturers’ association – has recently celebrated its 50th anniversary. Founded in Milan on September 28, 1960, by just eight companies, the association now has 143 active members, representing around 90% of the Italian sector’s turnover. Together with French and German national associations, it promoted the creation of the European association, Euromap. On October 9 the association held a celbratory gala dinner at the Leonardo da Vinci Museum of Science and Technology, which has a section devoted to plastics and rubber. The founders and other personalities were awarded special prizes for their commitment in the sector. Simei Exhibition 2011 The 24th International Oenological and Bottling Equipment Exhibition Simei is confirmed for November 22 - 26, 2011 in Milan, Italy. It will be held in halls 9, 11, 13 and 15 of Fiera Milano. The exhibition has been running for 40 years; the 2009 edition attracted 705 exhibitors from 25 countries and 51,545 trade visitors from 100 countries. Simei 2011 will feature exhibitions of machinery, equipment, products and services for drinks preparation, bottling and packaging. The organisers say that it will provide both a display window and, with a number of meetings, seminars and presentations during the exhibition, opportunities for discussions on current themes affecting the sector. www.simei.it Krones enjoys continued upturn Krones, the beverage filling and packaging company, has reported that its sales in the period January-September 2010 rose by 16.1%, to €1,583.0million. The company has seen particularly strong performance in markets outside Europe, where sales were almost 30% higher than in the same period of 2009. New orders over the nine months totaled €1617.7 million, 14.4% higher than 2009. Outstanding orders at the end of September totaled €932 million, €35.4million up on 2009, like-for-like. Earnings before taxes (EBT) rose to €47million, a recovery of €73.9million from the previous year’s loss of €29.6million. The company’s equity ratio stood at almost 39% as at September 30, with €60.4million net liquidity. Earnings have recovered to €1.05 per share, compared to a net loss of €0.85 per share in 2009. Krones says that it remains confident for the business year and expects to achieve its target of 15% sales growth for 2010. Looking to 2011, the company remains confident of further improvements in sales and earnings, assuming no radical changes in general conditions. The full Q3/2010 report can be retrieved at: www.krones.com/downloads/Q3_2010_d.pdf","@ID":8} "MARKET SURVEY 23 Siad Macchine Impianti Aeroflon Engineers Private Limited Via Canovine, 2/4 24126 Bergamo, Italy +39 035 327611 www.siadmi.com Ing. Luigi Beducci Standard Compressor Director +39 035 327618 +39 035 327694 [email protected] B-505 Premium House, Ahmedabad 380 009, Gujarat, India 079 26589712 www.aeroflon.com Mitul Choksi Chief Operations Officer - International Business 079 40069715 079 26586954 [email protected] 3THP-3-LT 3HP-4-LT 4HA-4-TER-LT 4HA-6-TER-LT 4HP-4-LT 4HP-6-LT Tempo2 BS Line Actbo42 Series 4 5 4 5 4 4 20 19 8 Models 1,965 4,210 875 1,730 3,135 6,080 90 – 5,550 Nm3/h* (*) suction conditions : 0°C – on sea level - R.H. 0% 1,000 – 6,000 Nm3/h (*) suction conditions : 0°C – on sea level - R.H. 0% Up to 722 m3/hr High pressure blowing air (up to 40 bar) High pressure Low pressure screw 5 r High pressure piston (booster) 15 42 Oil free Oil-free Oil-free Oil-free Oil-free Oil-free Oil-free W V Rectangular Layout 3 3 4 4 4 4 3 2 Screw + 2 booster= 4 total 3 No No No No No No No No Yes, Cement foundation required as per specification Water Water Water cooled system Belt drive Direct drive V-Belt drive Belt drive V-Belt drive Belt Belt Belt Belt Belt Belt V-Belt drive Ingersoll Rand Company 800 D Beaty Street, Davidson, North Carolina, USA 704 655-4000 www.air.ingersollrand.com George Mankos Global Portfolio Manager +1 704 655-4311 +1 704 655-4039 [email protected] PETStar –4 Models – 1500, 1700, 1900, 2100, 2300, 2500, 2800, 3000, 3300 Centac C750-18, C750-20, C750-21, C1050-36 PETStar – Booster / PS-2B 1250, 1470, 1980, 2290, 2840, 3340, 3850. 9 Models 4 models 7 Models 1497-3298] 3,085-6,360 Based on an inlet pressure of 8 bar-g, output range is the following: 1,195-3,696. 4-stage from atmosphere reciprocating to 40 Bar Centrifugal design – 4-stages from atmosphere to 40 bar Primary booster system Available oil free 2-stage Screw or 3-stage Centrifugal Two stage reciprocating booster Oil-free. Oil- free Oil-free Horizontally opposed layout Horizontal layout. Horizontal layout. 4 / double acting. 4-stage from atmosphere design. Petstar Primary + Booster is a 4 or 5 stage design. 2-3 stages Primary + 2-stage booster No special foundations are required. Unit can be mounted using typical practice of grouting & anchoring or on anti vibration mounts on standard factory floor No special foundations are required. Unit can be mounted using typical practice of grouting & anchoring or on anti vibration mounts coupled to standard factory floor. No special foundations are required. Unit can be mounted using typical practice of grouting & anchoring or on anti vibration mounts on standard factory floor Water cooled. Water cooled Water cooled Direct driven primary. Booster is belt driven. Belt drive Direct drive","@ID":25} "Vol.6 PETplanet print PREFORM PRODUCTION 20 PETplanet insider Vol. 11 No. 12/10 www.petpla.net Long Gate Nub Chapter 17 of the “Rapid Guide to Perfect Preforms” by Rick Unterlander and Ottmar Brandau Troubleshooting guides have suffered in the past from being locked away in offices and not being available to the people that actually need them. Considering the high cost of machine and tools high scrap rates can be a costly proposition eating away at already tight margins. PETplanet’s “Rapid Guide to Perfect Preforms” takes a different approach. Bound in laminated paper that is easy to clean off, the small format of the book of 108mm by 151mm (4.25” by 6”) allows easy storage in back pockets or tool boxes. It has been written for the people on the floor of injection moulding companies to support their daily work in making the best preforms possible. The product of two industry experts, Rick Unterlander and Ottmar Brandau, it gives concrete advice on 35 of the most common problems in preform manufacture, most illustrated by pictures. From high AA levels to wavy bodies processors can find help when they need it. Read chapter 17 of the guide. Symptom: The projected gate nub has extended beyond its normal length. Cause: The preform gate nub is deformed either during the initial mould opening sequence (core side separating from cavity side) due to the nub not releasing freely from the gate (photo A), or from poor formation due to the valve stem not closing properly (photo B). Solutions: 1. Check water cooling temperature. This should be 7 – 10ºC (45 - 50ºF) for optimum cooling. 2. Check water cooling flow to mould. This should be at the mould manufacturers rating (for a given preform size and cavitation). 3. Check dryer for alarms and correct as necessary. A high dewpoint (above –40ºC (-40ºF)) may cause extrusion problems, leading to downstream melt strength problems and must be rectified. The resin must be dried below 50ppm of water to minimize IV loss and melt strength issues. 4. Check for adequate resin drying time in hopper (should be around 4h at 175ºC (347ºF) and up to 6h at 160ºC (320ºF)) 5. Check all temperature readings and correct if necessary. PET resin should be melted at about 280ºC (536ºF) +/- 10ºC (18ºF). 6. Check nozzle tip heat settings. This area has a major impact on gate nub quality. Settings too high may cause the dome and gate nub area to remain hot and easily deformable. The settings should be adjusted low enough to improve nub strength yet not too low to cause crystallinity to form. A: Holland Continued on page 25","@ID":22} "PRODUCTS PETproducts 33 PETplanet insider Vol. 11 No. 12/10 www.petpla.net Full-body sleeves for organic vodka Galatea Spirits’ ‘Good ol’ Sailor’ organic vodka has been launched in recyclable PET bottles with full body sleeves supplied by CCL Decorative Sleeves. The colourful sleeves are manufactured in 50 micron high-shrink PET and gravure printed in six colours. The design features illustrations of classic sailor tattoos, including a large sail ship; they cover the entire sleeve from the neck of the bottle to the base. The decorative effect features tactile qualities and is intended to create strong brand differentiation on the shelf. The sleeves are hotair shrunk onto empty PET bottles by Petainer in Lidköping. The material has to ensure a tight fit around the bottle. CCL Decorative Sleeves provided full technical support throughout the project and provided a complete package to Galatea and Petainer, including supply of the change parts for the machine to run the sleeves. The choice of PET offers a significantly lower carbon footprint than the equivalent glass packaging and creates a mono-material pack for recycling. Galatea is a leading beer importer in Sweden and also offers a range of wines, spirits and ciders. The new 70cl bottles will be supplied to all 410 Systembolaget shops. www.ccl-label.com Modular linear labelling system Swiss company Pago International AG has launched a new range of modular linear labelling systems.The company says that the modular design makes the machines more flexible, user-friendly in operation and more secure. The standard base frame accepts all modular configurations. Pago is offering a wide range of extension and add-on modules with its new system. Users can choose between a wide range of modules for product transfer and also for product isolation and centring. The systems offer a wide range of front and back labelling, complete or partial all-round labelling and labelling from top or bottom, for large and heavy objects through to shaped bottles. The choice of control and operating variants is also claimed to be wide and to offer opportunities for roll-changing without interrupting the process. A particular variant is available for the pharmaceutical industry. Barrier food packaging in PET M&H Plastics, a supplier of plastic components and bottles, jars, flexible tubes and closures for the personal care, pharmaceutical, health and nutrition markets, has announced the launch of an oxygen-scavenger in PET containers. The company says this barrier development limits exposure to oxygen and maintains product quality, helping to extending shelf life. The product is manufactured from a blend of PET and an oxygen-scavenging concentrate. It creates an active barrier against the ingress of oxygen through the packaging walls, which enables PET containers to keep products fresher and maintain colour and taste for longer. It is an appropriate application for tomato-based goods, fruit juices and citrus items and is fully compliant with both European and US Food Standards. The first products to be launched with M&H’s new PET barrier packaging are among the range of British company Fire Foods’ chilli-based foods. www.mhplastics.com www.firefoods.co.uk Hot stuff – 3,500kg/h infrared dryer for PET bottle flakes Kreyenborg Plant Technology has delivered an infrared drum (IRD) with a throughput capacity of 3l500 kg/h of PET bottle flakes. With a diameter of 2,500mm, length of 5400mm and 540kW of installed radiator output, it is the largest IRD ever brought to production. The machine is designed to dry PET bottle flakes with a bulk density of about 0.35kg/dm³, from max. 1% initial moisture to 0.05% and to crystallize it at the same time. Achieving a homogeneous residual moisture of the flakes is very important, although the reality is that this can be subject to significant variations, due to the treatment process and the storage of the material. However, as material in the IRD has a short residence time of 10-15min, there is significantly less material in the drying process than in conventional systems. This advantage of the IRD means that bulky drying vessels are not needed. Kreyenborg has been offering infrared drying technology since 2005. Its range includes machine sizes from 20 – 4,000kg/h throughput rates, in both continuous and batch operation. www.kreyenborg.de Pressure-sensitive labelling system Moduline is a compact, rugged, yet economically-priced pressure sensitive labelling system for front/back, side panel or full wrap applications. The system was designed to compete with low cost Asian imported systems and is configurated for packaging lines with a production rate of 150ppm or less. www.quadrel.com","@ID":35}]}}
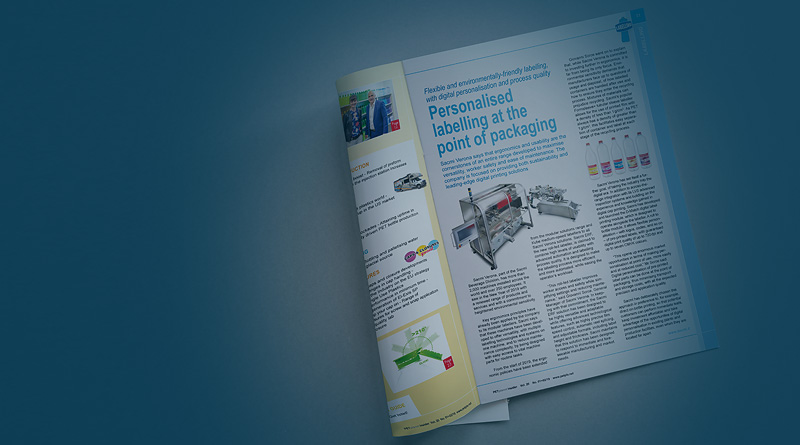