"PREFORM PRODUCTION 18 PETplanet insider Vol. 12 No. 04/11 www.petpla.net sumer bottles in Ukraine is not up to the mark. Yuriy would invest in a bottle-to-bottle programme if it were more developed and supported. Importing recycled material is not feasible due to the high prices and the lengthy transport distances. In order to cut the number of cardboard octabins for preform transport on wooden pallets Retal Dnipro is working on replacing these cartons with multiuse metal boxes, which, in its turn, will allow to eliminate pallets and achieve significant savings on packaging and preserve natural resources. There has been a further change during the last few years. Ever since the early days, Yuriy and his team have been cultivating a very good partnership with Husky for injection moulding machines and Corvaglia for capping tools. In auxiliary equipment supply sector Retal Dnipro is marked by long-lasting and friendly relations with Piovan. This cooperation began from the very first machine. “Their support is first rate, their reaction is immediate and there is always a possibility to make coordinated decision“. In the final analysis, this system of cooperation with teams on the basis of trust is Yuriy’s recipe for success. This not only applies to suppliers but also especially to his customers. His friendship with Felix Nosov of Biola goes back decades, but his management style is based on this system of trust and cooperation. He shares all his successes with his team. “In the final analysis we can only move the company forward by working together“ is the maxim that enshrines his corporate philosophy. 10-year cooperation between Corvaglia and Retal (former Uniplast) Long-term customer relationships foster mutual growth – a key factor for success. Uniplast – today part of the Retal Group – and Corvaglia have been connected by a close cooperation for over 10 years. Both companies have grown from local enterprises to global players in the last decade. Mr. Romeo Corvaglia, CEO and owner of the Corvaglia Group, based in Eschlikon, Switzerland, remembers his first journey to Dnipropetrovsk in 1999: “At that time, we had already been working with Husky for several years. They invited us to a meeting with Uniplast at short notice.” The cooperation between Mr. Corvaglia and the CEO of Uniplast, Mr. Yuriy Khmara, was excellent from the very beginning. Corvaglia’s focus on research and development and Uniplast’s need for economical cap solutions in the Ukraine and later also in Russia were the basis for this success story. Together with Uniplast’s technicians, Mr. Corvaglia visited bottling plants in the Ukraine. His goal was to convince them of one-component closures for carbonated soft drinks. The efforts of both companies were successful. Today, Retal Dnipro is a major player in the Ukrainian market in both the production of preforms and one-component closures. The Retal Group will supply well-known brand owners with the new 1881 closure solution, replacing the 1810 closures. This replacement was engineered by Corvaglia. The Swiss company will spearhead the launch of 1881 emphasising the lightweighting and cost-saving aspects of the new cap both to converters and to multinational companies. As a first step, Uniplast’s two 1810 injections moulds were converted into 1881 moulds last year. Thanks to the modular system of all Corvaglia moulds, the conversion of the 10-year-old injection moulds went smoothly, and proved more economical than buying new moulds. In 2011, Corvaglia also installed two new injection moulds with 96 cavities each at Retal Dnipro. Aseptic closure production Romeo Corvaglia, CEO and owner of the Corvaglia Group. The Retal Group will supply customers with the 28mm PCO 1881 closure solution.","@ID":20} "CAPPING / CLOSURES 40 PETplanet insider Vol. 12 No. 04/11 www.petpla.net Injection moulds for the production of caps with a tamper-evident band (TE) are compact high-performance systems with exacting requirements in terms of output, production safety, quality, and reliability. The decision of a manufacturer for one concept is essentially influenced by the fact that they are familiar with one particular mould concept. Regional safety requirements can also influence the decision for or against one particular removal concept. Traditional sliding split moulds Many cap producers use slider systems. This most traditional of removal methods is preferred by the majority of mould makers and widely used in many mould-operating facilities, numerous production sites and among most operators. Sliding split moulds remove the tamper-evident band by opening the sliders. Slider systems are available with different geometries and are popularly used for demoulding undercuts of moulded parts. Removal with collet chucks Collet chuck moulds are considered rare and they represent a smaller market segment, as only very few suppliers are able to manufacture them. Nonetheless, the market segment for this removal method is growing steadily. Schöttli claim that their collet chuck moulds offer to a high extent freedom in cap design and geometry combined with a particularly compact cavity arrangement in the mould and low space requirements. This method allows production on relatively small injection moulding machines. Collet chucks ensure that all bridges that connect to the tamperevident band (TE) are demoulded in a geometrically identical manner because of the opening of the collet chuck in six directions. This approach is beneficial for contract bottling companies as well as for consumers. The constant and even geometry of bridges across the diameter of screw caps allows an uninterrupted capping operation at the bottling filling line as the tamper-evident band is evenly distended during capping. During this process, all connecting bridges are subjected to an identical load, so that weak connections are not torn during capping. Schöttli claims a lifecycle guarantee for its collet chucks of 5 million cycles, despite the fact that they are under high mechanical stress due to frequently changing loads. Processors using smaller collet chuck injection moulds have recently taken to ordering new moulds with a higher number of cavities. Accordingly, the Swiss company has built collet chuck moulds with a total of more than 8,000 cavities over the past years and almost all recently supplied moulds were equipped with 96 cavities. Post-slitting of the tamper-evident band Bottling specialists in the US, Europe and in China prefer caps with continuously gated tamper-evident bands that become operable by means of folding or slitting in downstream stations. These screw caps provide consumers with maximum safety from manipulation. This mould concept does not require any further movement for demoulding by sliders or collet chucks. Nonetheless, demoulding of small undercuts also has to be ensured. The core must withstand the forces applied during stripping. Schöttli adapts the forced ejection method to product and customer requirements. After injecOne-stop shop for cap moulds with various ejection systems A feather in their caps Schöttli AG is a manufacturer of injection moulds for the production of caps, offering all standard mould concepts from one single source. 96 bottle caps, the current maximum number of caps produced in one single mould, can be removed by slider systems, collet chucks or without either of these two, in cases where the tamper-evident bands are slit after moulding. 32-cavity Schöttli cap mould with slider system","@ID":42} "MATERIAL / RECYCLING 10 PETplanet insider Vol. 12 No. 04/11 www.petpla.net New conical technology boosts rPET processing* Conical and co-rotating The use of co-rotating twin-screw extruders is common in compounding. The conical design offers a very wide performance spectrum, especially in PET scrap processing. The range of applications varies, from production of high quality pellets or direct extrusion to sheet and fibres made from PET re-grind or pellets, A-PET, C-PET, G-PET, washed PET flakes or URRC-PET flakes, PET flakes or pellets with pigments, fillers etc. Approved products comply with FDA standards for food applications. *based on an article by Dipl.-Ing Gunther Klammer, Managing Director of M-A-S Maschinen und Anlagenbau Schulz GmbH. Pucking, Austria, with: Prof Dr Mont. Clemens Holzer; Dipl.-Ing Stephan Schuschnigg; and Dipl.-Ing Ramesh Kumar Selvasankar, all of the Chair of Plastics Processing, Montanuniversitat Leoben. Twin-screw extruders with intermeshing, co-rotating screws are the leading processing technology in compounding and fulfil an essential function in plastic production and processing. The New Conical Technology (NCT) developed by MAS combines the benefits of conical extruders with those of parallel co-rotating twinscrew extruders. Compared with conventional extruders, the conical design offers substantially higher filling volumes and material intake. This results in a higher screw filling level, which gives the highest possible output with comparatively high pressure ratios and low melt temperatures. The corotating design provides total homogenization. Generously dimensioned screw shafts, paired with strong backpressure bearings, lead to a robust design, long service life, and thus provide efficient PET compounding and processing. The machine also has low energy consumption. A project with the Chair of Plastics Processing at the Montanuniversität Leoben, Austria, was initiated in order to put the experiences already gained with conical, co-rotating twin-screw extruders on a firm theoretical foundation and establish the framework for further development. In the first part of the project, the discharge zone was closely analyzed. Beginning with conservation laws and geometric conditions, appropriate equations were developed for different screw channel geometries to describe the volumetric flow in relation to back pressure. The changing geometric data in the case of the conical twin-screw extruder meant that calculations had to be performed iteratively, using a computer program. With the slightly modified Erdmenger profile, the dimensions of the outer screw and root diameters, tip width, number of flights, and shape of the channel formed by the flights are geometrically dependent on each another. These dependencies are a result of the ‘co-rotating’ and ‘intermeshing’ aspects of the two screws, and are thus attributable to the principle of motion. These relationships have a key influence, not only on the screw profiles that can be cre-","@ID":12} "PRODUCTS 51 PETplanet insider Vol. 12 No. 04/11 www.petpla.net Preforms and bottles Parle Agro’s PET division was India’s first manufacturer of PET preforms for the beverage and water industry and is one of the country’s largest producers today. It operates production processes to international quality control standards and offers single-source, end-to-end packaging development solutions. The company operates two facilities, located at Silvassa and Khurda (Orissa) and equipped with Husky and KraussMaffei machinery. Parle Agro produces its own range of beverages but also supplies PET preforms to competitors in its consumer markets. Parle Agro’s PET preform manufacturing operation is established as a separate division within the group, supplying preforms to customers in the bottled water, ready-to-drink beverages, carbonated drinks, edible oil, confectionery and pharmaceutical segments. It supplies products with both 30/25mm and short necks for water applications, and PCO necks for carbonated and juice products. The PET division of Parle Agro also provides technical advice on blowing, bottle moulds, bottle design, closures, capping, filling, and other issues. The team works closely with customers to develop light-weight bottles that bring down packaging costs and help to keep final product prices under control. Parle Agro history PET was introduced to India in the 1990s, at a time when products were packaged in either PVC or glass bottles. PET technology was, initially, not very popular. Parle Agro decided to enter the plastic packaging segment as a backward integration process and became the first beverage producer in the country to launch a flagship brand – named Frooti – in a PET bottle. Considerations included the facts that PET is odorless, with clear transparency, superior strength and better overall quality. Other companies followed suit and launched their products in PET packaging, thus widening the PET market in India. The arrival of PET bottles in the country provided consumers with convenience and improved aesthetics. Sales of the Frooti brand increased after it was launched in a PET bottle, and was followed by the company’s ‘Appy’ still apple drink, which began sales in PET in 2010. Parle Agro’s first blown bottle was for its 1l packaged drinking water brand, Bailley, in 1996. It was blown in a 21.8g, 30-25 neck in Tri start, neck preform in 1996. The product was previously packaged in PVC. Products like beer, wine, liquor, and natural fruit juices are also being packaged in PET bottles. The attractions to the market are the increased shelf life of PET bottles and the products’ compatibility with PET. www.parleagro.com","@ID":53} "TRADE SHOW PREVIEW 45 PETplanet insider Vol. 12 No. 04/11 www.petpla.net Delivering solutions, shaping the future. Light 1881 Original Aptar Food+Beverage introduces the 1881 light Original sport closure : less plastic and no compromise on performance 25% Less Weight [email protected] - www.aptar.com Unscrambler systems and delicate or awkward-shape bottle handling Posimat, which is based in Barcelona, Spain, will be showing a Posiflex unscrambler with automatic, instant changeover, which allows push-button addition of new formats without extra change parts. The Posisilo in-built silo on the unscrambler has a special discharge flap system, which is designed handle very delicate bottles without damage. The Posijet air conveyor, with its Vertijet system, is claimed to be the first and only vertical air conveyor capable of going up (or down) at any inclination from 0 to 90º with or without accumulation. This circuit will run a flat/oval PET bottle. The stand will also feature a BTU (Bottle Transfer Unit), which sends even very unstable bottles from the unscrambler to the filler in pucks; a rotary OR orienter; a Giramat-D linear turning device that handles asymmetrical bottles in pucks and presents bottles oriented in the same position; and a Posipharma unscrambler, which handles containers with wide openings and large-diameter caps, used mainly in the pharmaceutical industry. www.posimat.com Posimat Hall 16 Booth B46 New generation shrink tunnels, shrink packaging and online printing The KHS GmbH stand will feature a new, modular shrink tunnel design that has been developed as a basic platform and can be extended as required to incorporate additional functions in the future. The system uses individual hot air nozzles, which enable airflow to be set to suit individual pack formats and can be positioned manually or electronically, and can be individually configured. The new shrink tunnel also features optimised heating chambers. KHS maintains that the new design will achieve energy savings of up to 20%. The shrink packer manipulating unit, also on the stand, is claimed to wrap containers in shrink film without the formation of shrinkage holes. KHS says this will enable the elimination of trays or cardboard pads. The online film printing system that will be displayed, applies print to the inside of the packaging, which can greatly reduce damage or manipulation of printed coding information. www.khs.com KHS GmbH Hall 14 Booth A14/B15","@ID":47} "REFERENCES 1 Kohlgrüber, K.: Der gleichläufige Doppelschneckenextruder - Grundlagen, Technologie, Anwendungen. Hanser, München 2007 MATERIAL / RECYCLING 12 PETplanet insider Vol. 12 No. 04/11 www.petpla.net Experimental investigations and results In addition to the theoretical investigations, practical trials were conducted on an M-A-S 55 conical corotating twin-screw extruder. The trials were conducted at four to five different rotational speeds, using a die with an adjustable discharge opening height. The throughput for the individual measurements varied between about 300 and 560kg/hr. This figure clearly shows that the pressure and mass flow have a linear function of speed. Pressures achieved with this die opening varied between 90 and 110bar. The FEM program is used to calculate the volume flow and pressure at the end of the screw as well as the pressure along the screw. The screws have the ability to build up a pressure of 180bar. Viscosity and shear rate have a major effect on processing. The Erdmenger profile requires shear rate and viscosity to be calculated for many positions in the channel in order to findt he dissipated energy. At a higher shear rate, the amount of energy dissipated also increases ( ) - a desirable effect at the beginning of the extrusion process, as this provides a major part of the heating and facilitates melting. On the other hand, when melt flow alone is involved, the requirement is for the lowest possible temperature increase. ln the case of the conical system, the speed in the front region of the barrel is lower because of the smaller outside diameter and, as a result, the shear rate and dissipation decrease (Fig. 1). In this case, the energy density decreases by 50% over the length of the discharge zone, which can be attributed to the quadratic term for the shear rate. Therefore the MAS extruder provides ‘low shear’ processing. Use for PET recycling Processing of PET bottle regrind provides the ideal processing prerequisites for conical twin-screw extruders. The processing unit has a large feed-in volume, with unusually high torque being transmitted because the screw diameters are so large. This mechanical strength leads to the high load capacity of the thrust bearings, which are designed to be correspondingly robust in response to the increasing distance between screw centre lines. As the investigations demonstrated, the equipment has not only the processing capability to build up the pressure but also the mechanical ability to absorb the pressure, so that a melt pump is not necessary, even when employing a 30μm melt filter. The slowly rotating extruder screws operate at high fill levels and pick up the material with little shear. A small amount of friction is introduced into the material only in the front zone of the screw, which is where only the pressure build-up occurs. This translates into what is, overall, gentle and energy-saving polymer processing, in the case of PET, in particular. It was also found to be possible, under appropriate conditions, to achieve the parameters needed for further processing, such as IV degradation of less than 0.02dl/g; ideal colour value b* and extremely low acetaldehyde (AA) content. The fill level of the screw was found to be an essential parameter, one that permits very fine adjustment of the plasticising capacity. The stock temperature is almost inversely proportional to the fill level. This enables the achievement of stock temperature from 275°C to 295°C, without difficulty and using the same screws. The plasticizsing unit of the extruder is further characterised by two-fold venting, which (compared to conventional systems) provides twice the venting area and completely independent venting through the use of a dam element (Fig. 2). If necessary, a high-performance vacuum can also be connected. The throughput spectrum from 150kg/h (M-A-S 45) to 2,000kg/h (M-A-S 90) is covered by the four extruder sizes 45, 55, 75 and 90. As it is common in compounders, the screws are made in segments, in order to ensure the greatest possible flexibility. www.mas-austria.com Figure 2: Processing unit with two-fold venting","@ID":14} "PREFORM PRODUCTION 22 PETplanet insider Vol. 12 No. 04/11 www.petpla.net ‘Best Supplier’ award for Manjushree Technopack Bangalore-based packaging manufacturer, Manjushree Technopack Ltd, was presented with the ‘Best Supplier Performance Gold Award’ by Hindustan Coca Cola Beverages Ltd (HCCB), the bottling arm of Coca Cola India, at HCCB’s Second Strategic Supplier Summit, in New Delhi. The award was presented to Mr. Vimal Kedia, Managing Director, Manjushree Technopack Ltd, by Mr. Patrick Yadauga, Senior Vice President - Supply Chain CocaCola, India. Manjushree is involved in the manufacture of speciality plastic packaging products for domestic and export markets, in FMCG, CSD, pharma, alcoholic beverage and food processing sectors. The company has been a preferred supplier to HCCB for over three years. www.manjushreeindia.com ment, more than half of this is to be built on. Husky will assume responsibility for process planning. The amount of investment will be 15 million US$. Despite all the euphoria about the rapidly growing beverages business, the company has still not neglected its roots in the jars and non-food sector. In the meantime the company supplies more than 400 different products. These are manufactured chiefly using single level equipment from Nissei ASB. Something else that has also grown out of this environment is PET bottles for hot/warm filling. Whereas Coca Cola and Pepsi Cola do actually bottle at high temperatures (85 °C) the regional bottling plants carry out their bottling activities at 72°C, plus they add a dash of preservative. This enables them to save themselves a few grams of PET in the neck finish area. Currently their mango juice is particularly trendy and the enquiries are rolling in at Manjushree. And there was one very special highlight that fascinated me at Manjushree way back on my last visit and that was their Museum of Packaging. On the ground floor there are packaging exhibits covering practically every topic imaginable and the 1st floor is given over to matters relating to PET. More than 10,000 bottles – sorted by subject areas – provide an inexhaustible fund of new and creative ideas. In the same way that PET production is growing, the museum is also growing. At preFrom the museum - a veritable rarity: a 250ml Coca Cola bottle in PET complete with Crown Cork dating from around the year 1990. Behind it is a 200ml aluminium bottle vintage 2007, a reusable 200ml glass bottle and a present-day 500ml PET bottle still with the PCO 28 In front of the entrance to the museum: F.l.t.r.: Ankit Kedia, Alexander Büchler, Surendra Kedia and Rajat Kedia. The Husky installations are still encapsulated in the old factory. Not night life but instead night light in the factory. The company operates round the clock. sent they are working on the 2nd floor. Bangalore is well worth a trip if only for the Museum.","@ID":24} "MARKET SURVEY 33 mouldtec Kunststoff GmbH SBECM EKG Group Aptar F ood + Beverage Viroplastic CZ Gulf Packaging system Co Weener Plastik AG Wiesenstraße 22, 87600 Kaufbeuren, Germany +49 8341 670-0 www.mouldtec.de Eric Peil Sales Manager +49 8341 670-229 +49 8341 670-217 [email protected] Rue de la plaine 47230 Lavardac, France +33 5 53 97 41 00 www.sbecm.com Jean-Luc Didouan Manager +33 5 53 65 85 97 [email protected] Njegoseva 10 34220 Lapovo, Serbia +381 34 61 000 11 Dragan Miljkovic Manager +381 34 61 000 11 +381 34 61 000 12 [email protected] Löfflerstrasse 1 D 94078 Freyung +49 8551975234 www.aptar.com Silvia Christoph Director Sales Beverage Europe +49 8551975175 [email protected] CZ-73801 Frýdek-Místek, Lískovec 405 +420 558412440 www.viroplastic.cz Radovan Vesely Sales Representative +420 603169232 [email protected] Post Box 20266, Jeddah 21455, Saudi Arabia +96626360099 www.gulf-pack.com Bader Abdullah Sales Manager +96626360099 x 107 +96626352111 [email protected] Industriestraße 1, 26826 Weener, Germany +49 4951/306-0 www.wppg.com Manfred van Essen Sales +49 4951/306202 +49 4951/30615202 [email protected] Closures Plastic Closures Sports Caps and dispensing closures for beverage. Caps for soft drinks, milk, oils Caps for non-returnable PET bottles Yes, HDPE, LDPE Yes - HDPE, LDPE or PP Yes - HDPE, LDPE or PP Yes, one piece sports cap in PE or PP Yes Yes, HDPE for low carbonation Yes, HDPE closures No No No Yes, two piece sports cap, body in PP, spout in PE No Yes, PP+ non PVC Liner for CSD No CSD, still beverages, water, fruit drinks, milk, oil Water, CSD, juices, dairy products, any liquid or non liquid products CSD, Dairy Products, Juices, Water, Beer Bottled water, juices, functional drinks, RTD tea, dairy, other CSD, water, juice, milk, beer Pepsi / Coca-Cola approved Non-carbonated and carbonated beverages, mineral water, isotonic beverages, fruit juice beverages, 28mm PCO 1810 and BPF, 28mm PCO 1881, 37mm 2-start, 38mm 30/25 high and low, 29/25, PCO 28 (1810, 1881, BPF), 38mm, 48/41 PCO 28 1881, 38mm, 48/41, 30/25 high and low 28mm 1810 PCO/BPF, 28mm 1881 PCO, 30/25 high, 38mm 2 start, 38mm 3 start BPF-PCO, 1881, 38 Europe 28 mm PCO, 28mm BPF, 30/25 HNF 45 mm PCO 28 (1810) and PCO 28 (1881) Yes No, but embossed Yes Custom Yes Yes Yes, one or two colour printing possible Yes Yes Yes Yes Yes Yes Yes Yes On request No No No Yes No Yes (twist and pull). On request Yes Flip-top sports caps No Yes Yes Handles for 5l, overcaps On request Several patents Philo cap Bender GmbH CCT - Creative Closure Technology GmbH Affaba & Ferrari S.r.l. Krallmann Kunststoffverarbeitung GmbH Georg Menshen GmbH & Co. KG Frankenstr. 12-14 67227 Frankenthal, Germany 06233-441-0 www.gcs.com Katja Huck Management Assistant 06233-441-212 06233-44138212 [email protected] Idsteiner Strasse 74 D-65527 Niedernhausen +49 6127 8954 or 8850 www.cct-gmbh.com Alexander Schmitz Managing Director +49 6127 8954 +49 6127 78189 [email protected] Via Don L. Sturzo, 2, 26851 Borgo San Giovanni (LO) - Italy 0039 0371 2130321 www.affabaferrari.com Ms. Silvia Ferrari Sales & Marketing Director +39 0371 213030 +39 0371 97031 [email protected] Siemensstraße 24 32120 Hiddenhausen, Germany +49 5223 989-0 www.krallmann.de Mr. Alexander Knipp Sales Manager +49 5223 989-262 +49 5223 989-201 [email protected] Industriestrasse 26, 57413 Finnentrop, Germany +49 2721 518 0 www.menshen.com Carsten Lurz Director Sales & Marketing +49 2721 518 114 +49 2721 518 115 [email protected] Beverage plastic closures Development of closures; closure turnkey projects Caps and closures for the food & beverage industry, agrochemical products, oil & lubricant sector Injection moulding of caps and closures, rigid packaging, R&D for individual customer needs Development and production of caps and closures Yes, HDPE Yes / HDPE und PP 38mm and 48mm flat caps made in HDPE and PP Yes, customized solutions / designs Yes, HDPE and PP Yes, PP +HDPE Yes 38mm flat caps with IHS liner and Oxygen Scavenging liner - 2-pc flip top caps available, as well No Yes, plastic closures with aluminium liner CSD, water, juice CSD, still water, juice, beer, medical care, etc. water, juices, CDS, flavoured water, smoothies Food, beverages, cosmetics, etc. dairy drinks, juices, water,cosmetics, detergents 1810 and 1881 Ø26, Ø27, PCO1810, PCO1881, 29/25, 30/25, Ø38-3start, Ø38-2start, Ø48, handles etc. 28mm: PCO1810, BPF, BPF light, 1881, 3-start (Alaska) - 38mm: 1-start, 2-start (aseptic), 2-start/ hot fill, 3-start pitch 8 (A&F), 3-start pitch 9 PCO 28, 38/400, 33/400, 25 snap, and many more PCO28 Yes Yes Yes Yes Yes Yes No Yes Yes Yes No No Yes Yes Yes Yes No Yes No Yes Lightweighting cap for 28mmPCO, 26mm for water etc. including non-beverage closures Customized solutions are offered Closures with dosing valves; closures with double tamper evidence feature; Non drip closures with valve; closures with special customized design Flip-top caps, sports caps, wide range of weldspouts for flexible packagings CCT 29/25, PCO1810 and PCO1881 double seal version A&F owns many patents and utility models Closures with dispensing valves for sauces, honey, shower gel, etc. Cool cap: reclosable drinking cap for carbonated beverages","@ID":35} "PRODUCTS 49 PETplanet insider Vol. 12 No. 04/11 www.petpla.net Lightweight closure systems Closure Systems International (CSI) has added new closure profiles to its portfolio of short-height mini closures. The new products are intended to deliver high-performing, light-weight solutions for the non-carbonated beverage segment. Sports-Lok mini is an ultra-lightweight product designed to improve bottlers’ economics as well as offering better environmental sensitivity, while continuing to meet consumers’ requirements. The closure is available in short-height 28mm and 26mm sizes. The easy-open pushpull design provides bottle finish and closure resin savings of approximately 20%. Non-carbonated beverages, such as juices, sport drinks, teas, and enhanced waters, have particular requirements related to sealing, safety, removal torques, and application. CSI’s offer in these market segments is a family of light-weight caps in 28mm and 38mm sizes, including Asepti-Lok V38 3S. The company’s one-piece aseptic closures incorporate a distinctive safety venting feature and tamper evidence system. The closures are claimed to help prevent product spoilage and eliminate risks to consumers from improper storage or handling throughout the entire supply chain. CSI’s Extra-Lok 38mm OD closure is designed for hot-fill applications and is one of the lightest twopiece 38mm closures on the market. Its liner profile enables customers to reduce their bottle finish thickness without compromising performance. The cap design maintains the seal with hot-fill vacuum packages, but allows excess pressure caused by fermentation to vent, which provides the product with improved consumer safety. www.csiclosures.com ABC COMPRESSORS NEW 40 BAR RANGE THE MOST PROFITABLE AIR Safe Investment Total energy savings over 50% Efficient Consumption MinimumMaintenance RELIABLE BEYOND LIMITS www.abc-compressors.com · 3 year guarantee. · Special financial terms. · Plug&Play. Complete set on base frame. · Up to 6.080 m3/h with a single compressor. · Built-in quality. The only manufacturer machining, mounting and testing the 100% of its bare compressors in Europe. · Proximity. Whole packages delivered through our sites in Europe, America, Asia and Africa. · ABC guaranteesup to 15% saving thanks to our efficient design. · Save 50% of compression energy thanks to air reinjection in our 4 stage machines. · Additional 15% savingscoming from perfect adaptation to frequency converters. · Energy-audits to demonstrate it. · 8.000 hours of operationwithout any additional maintenance. · Life cycle services. From express spare parts delivery to special maintenance contracts and machine refurbishing. · 24Hx365D available worldwide for any service through our web platform. · More than 25 technical service hubs around the world to be closer. FISPAL: Sao Paulo (Brazil), 7th-10th June, STAND K203 PROPAK ASIA: Bangkok (Thailand), 15th-18th June, STAND C19 EXPOPACK: Mexico City (Mexico), 21st-24th June, STAND 1006 CBST: Shanghai (China), 6th-8th November, STAND F2-2 EXHIBITIONS GOING ON 2011. Visit our stand at: Multiple label applications Quadrel has announced the launch of a programmable platform rotary labelling system. The company says that its pressure sensitive product offers efficient product handling with technically advanced label applicators and controls. The machine has programmable bottle platforms, can accommodate up to four label applicators and is capable of applying front/back, wraparound, neck and spot labels at up to 250 products per minute. www.quadrel.com","@ID":51} "TRADE SHOW PREVIEW 44 PETplanet insider Vol. 12 No. 04/11 www.petpla.net Revolution in PET-extrusion! Conical co-rotating MAS-extruder | perfect solution for A-PET, G-PET, PET Co-polymer … | prime pellet / melt quality (IV, b*, AA- content) | very low energy consumption | direct extrusion into sheet | stable melt pressure build up | small foot print paired with robust design | sizes available from 200 kg/h up to 1500 kg/h | suitable for food application M-A-S Maschinen- und Anlagenbau Schulz Gmbh A-4055 Pucking, Hobelweg 1 T: +43 7229 78 999, F: +43 7229 78 999 10 [email protected] www.mas-austria.com Integrated blow moulding, labelling, filling & capping Sipa’s new Sincro TriBloc is incorporates reheat blow moulding, labelling, filling & capping. The company says that the system offers savings in space, capital investment, running costs and energy. The design eliminates a number of elements found in traditional lines and uses up to 55% less space as a result. The SFR EVO preform blow moulding unit can produce up to 2000 bottles/cavity/hr. The labelling station incorporates ‘Adhesleeve’ technology from P.E. Labellers SPA, which uses pressure-sensitive adhesives instead of hot-melts and is claimed to be highly energy efficient. Label cutting and application operations are carried out on a single cylinder, eliminating several quality problems associated with traditional roll-fed machines. Sincro TriBloc can be equipped with gravimetric, volumetric and isobaric fillling systems, capable of handling still and carbonated soft drinks, juices and hot filled products. Sipa’s row preparation system, designed to optimize average and low speed palletisation plants, is composed of a clamp type head installed on linear axes, suitable to up to six packs at the same time. Packs slide on a modular chain conveyor and impact pack turning devices, row spacers and rollers of the traditional solutions have been eliminated. The active layer module can be installed on existing plants, offering output increase and space saving. Reflecting the trend towards ‘green’ packaging, a wide range of preforms and containers with different percentages of recycled PET will be on the stand, as well as a display of lightweighted neck finishes and containers for various different applications, from mineral water bottles to oval containers for food and detergents and large size containers for watercoolers. www.sipa.it Sipa Hall XX Booth XXXX Krones AG Hall 14 Booth D14/E29 Eco-compatible and resourceconscious secondary packaging Krones AG, Neutraubling will be introducing its new packaging design, which has been developed using a different approach from conventional shrink-wrap packages. Krones says that its new design is a response to trends for PET container secondary packaging to be eco-compatible and to save on resources and energy. The company claims that users will be able to achieve cost savings, compared to shrink-film. The complete pack system to be exhibited at the show includes the packaging and associated machinery. www.krones.com","@ID":46} "BOTTLE MAKING 35 PETplanet insider Vol. 12 No. 04/11 www.petpla.net Optimising compressor system design can achieve energy savings of up to 35% Design to perform ABC Compressors has been working with clients across the world to design compressor systems that save energy, reduce waste and improve productivity. Whatever an organisation’s activities and whatever its size, engineers designing PET blowing lines face similar challenges in the generation of high-pressure air. As the PET market has matured, plant engineers have become increasingly aware of the importance of their high pressure compressor central units, participating in and guiding selection of compressors for their blowing lines. Plant production and, ultimately, company profitability will be affected by their decisions. A compressor may represent just 10% of overall line investment but might be responsible for 50% of energy consumption during production. Operating costs over 10 years will actually be higher than the initial capital investment. Installing one compressor per blowing line increases overall energy consumption in medium to large plants by more than 10%. All of this means that energy consumption is the key parameter to be controlled, as it represents over 80% of the compressor’s total operating cost. Different lines are frequently installed sequentially, as individual units, with each compressor designed and installed for a particular blower’s needs. ABC Compressors works on savings in compressor central units and makes recommendations to guide distribution line set-up. Coordinating the work done by all the compressors together will help to provide energy savings in a number of ways. It will minimise the number of compressors running idle and the number of startups. It helps to stop machines that are not required and identify which compressors should be adapted to total air demand at any time; and considers and covers possible compressor stoppages due to maintenance requirements or breakdowns. ABC Compressors maintains that the familiar picture of several compressors, working for one blower each, must be changed into a high pressure air production central unit, which will supply air to a complete array of blowers’ demands. Fig. 3: Compressor 4HP-6-LT for 6.000m3/h Fig. 1:Compressor package from ABC","@ID":37} "CAPPING / CLOSURES 38 PETplanet insider Vol. 12 No. 04/11 www.petpla.net Asian soft drinks consumption continues to drive future closure demand It’s closure’s time In spite of the economic slowdown in many markets over the last two years, beverage closure demand has continued to grow strongly, driven partly by the sustained shift towards pre-packaged beverage consumption in many developing markets and partly by the continuing growth in popularity of the plastic ‘bottle plus cap’ format – especially PET bottles in smaller ‘on-the-go’ sizes. Understandably perhaps in the more austere commercial climate, the overwhelming theme has been improved efficiency and cost/weight reduction, linked to growing environmental awareness and marketing focused on more efficient use of increasingly scarce and expensive resources. This does not mean that the market has lacked innovation however. Rising use of sports caps, dosing caps and similar ‘added value’ features is testament to the fact that the underlying demographic changes that are driving demand for greater convenience in closure design remain in place; it means that these ‘added value’ technical and performance features now need to be achieved at similar or lower price and reduced closure weight, creating ever more pressure on beverage closures manufacturers to come up with creative solutions. Looking at the global beverage closures market in detail, total demand across the soft drinks, dairy drinks and beer markets under review amounted to around 1055 billion closures in 2010. Of this, ring-pull can ends (which unusually for this study are treated as closures) accounted for 24% or about 250 billion closures, plastic closures took a 42% share at 440 billion units and metal closures 31% or 325 billion). All other beverage closures totalled a little below 40 billion, while there are still an estimated 210 billion beverage containers sold each year without dedicated closures (e.g. sachets and perforated cartons). In the years between 2003 and 2010, plastic closures saw their volumes increase at around 6.5% per annum, a combination of rising beverage consumption (in the 2003-2008 particularly), more beverages being sold in plastic bottles and the conversion from other closures to plastic. Since 2008 the growth rate of plastic closures has dropped but remained positive and they are still forecast to remain fairly robust in the years to 2015. Metal closure usage on the other hand is only expected to increase by a single percentage in coming years to maintain growth of 3% and 4% throughout the period to 2015. On a regional basis, Asia already accounts for the largest share of total annual closure volumes at 36%, equivalent to around 375 billion units. Collectively, the Americas combine for just under 400 billion, Europe for around 250 billion, the rest of the world around one tenth of that. Global beverage closures by type /% share by volume 2010 Global beverage closures by region 2010 - % share by volume","@ID":40} "PETbottles 54 PETplanet insider Vol. 12 No. 04/11 www.petpla.net Personal Care Optimum design options The French cosmetics manufacturer Laboratoires Vendome in Dijon has packaged its “Le Petit Marseillais“ brand products almost exclusively in PET bottles. Vendome is making full use of the options offered by this variant. High-visibility, coloured gels, the impact afforded by the printing on the inside of the rear labels and the transparent non-label-look front labelling means that the article at POS is assured of an eye-catching unique status. Metallic colours and snap-on caps also enhance the quality rating and complement the presentation. Footcare Healthcare Deutschland GmbH in Maintal is selling a 275g vitalising footcare bath in a handy, transparent PET bottle. This features colourful printing on front and rear labels as well as a colour-matched, white screw cap. The transparency of the bottle accentuates the orange-coloured product (with mint and orange oil) particularly well. www.scholl-footcare.com Plax ice for teeth Colgate-Palmolive’s new mouth rinse “Plax Ice“ (which offers 12 hours of protection) is being marketed Europe-wide in a blue 500ml PET bottle. The shiny metallic front label invests the product with a high quality rating and catches the eye immediately at the POS. The back is designed with a non-label-look sticker and incorporates all the necessary product and retail information. The white screw dispensing cap is secured by means of a printed shrink label perforated for ease of opening. www.colgate.eu.com Rossmann opts for PET in the laundry For its “domol“ brand rose-scented de-ionised water, the discount drugstore Rossmann of Burgwedel has gone for a litre-capacity PET bottle with attractive and modern styling. The use of the “non-label look” label on the front provides a view of the rear label featuring a rose printed on the inside. Depending on the way the light falls, some striking effects can be created. A one-hand operation, twocolour screw cap facilitates content removal and re-closure www.rossmann.de Starlight magic from a discounter The German discount drugstore dm of Karlsruhe are selling 200 ml packs of “Priness Starlight” easycomb shampoo in a pink coloured PET bottle. “No label” look labels on the front and back complement the design, aimed at youngsters, and contain all of the necessary product and commercial data. A screw-on hinged cap with a crown-shaped top nicely finishes off the pack. www.dm-drogeriemarkt.de Blue PET for fabric fragrancer The German company Noelle Industrielle Umwelttechnik GmbH of Rheinberg are marketing a whole range of laundry aids, including some in PET bottles. There is, for example, “Summer Breeze” in a blue 125ml PET bottle with spray insert and a white screw-on cap. According to the manufacturer 2 or 3 squirts of the product, based on natural ingredients, in each wash cycle is sufficient to fragrance the linen. A metallic finish “no label” look label on the front of the pack and an informative rear label complete this attractive PET bottle. www.waescheduft.de","@ID":56} "MARKET SURVEY 32 MARKETsurvey 04/11 Company name Idee + Form Viscose Closures Ltd Euro-Plast JV ltd. Postal address Telephone number Web site address Contact name Function Direct telephone number Fax E-Mail Via Leoncavallo 31, 6614 Brissago, Switzerland +41 917809648 Gerhard Priewe Director +41 7809648 + 41917809650 [email protected] Unit 1, Royce Rd Bus. Park, Fleming Way, Crawley, West Sussex, RH10 9JY, United Kingdom +1 1293 519251 www.viscose.co.uk Ian Coster Technical Services Manager - Caps & Closures +1 1293 596815 +1 1293 540005 [email protected] Gorkogo str., 95, loc. 1, Grodno 230005 Belarus +375 152 45 04 51 www.euro-plast.by Katherine Tolkach +375 152 45 04 51 +375 152 45 07 59 [email protected] Product range sport-caps Do you produce one-piece closures for beverages (Yes /No -If Yes, please specify material No Yes - HDPE yes, HDPE Do you produce two-piece closures for beverages (with liner) (Yes / No -If yes, please specify material No Yes - PP/EVQ Yes, PP Applications relevant to PET containers, e.g. CSD, water, juice, beer, etc.) CSD, water, juices CSD/water CSD, water, juice, milk, tea, beer Neck finishes available as standard PSO 28mm PCO, BPF, MCA, 1881, Corvaglia 28mm (BPF, PCO), 38mm (3start) Printed caps available (Yes / No) No Yes Yes, 2-color Colour matching service (Yes / No) Yes Yes Yes Child-proof closures (Yes /No) No No No Push-pull / sports caps (Yes / No) Yes Yes No Special comments/special closures (e.g. flip-tops, drinking spouts, lightest cap for 28 mm PCO, 26 mm for water etc including non-beverage closures...) Twist sport-caps for still, carbonated 6bar and 10bar 1881 & 1881 Sports Special patented closures or marketing features Fullytop AF6-PNE cap Company name Finn-Korkki Oy Corvaglia Closures Eschlikon AG Injectoplast KunststoffverarbeitungsgmbH Postal address Telephone number Web site address Contact name Function Direct telephone number Fax E-Mail Konepajantie 10, 13300 Hämeenlinna, Finland +358 3 628 641 www.finn-korkki.com Robert Jeynes Export Sales +358 36286428 +358 36197294 [email protected] Hörnlistrasse 14, 8360 Eschlikon, Switzerland +41 71 973 77 77 www.corvaglia.ch Peter Schkoda Chief Sales Officer +41 71 973 77 77 +41 71 973 77 01 [email protected] Brunner Straße 40 A-3830 Waidhofen a. d. Thaya, Germany +43 2842 52572-0 www.injectoplast.at Mr. Erwin Mayer, Mr. Reinhard Toepfl General Manager, Sales Manager +43 2842 52572-300 / 311 +43 2842 52572-330 [email protected] Product range RingCrown & RipCap closures PCO 1881, PCO 1810, 38mm, two-start, threestart, Alaska, MCA2 Do you produce one-piece closures for beverages (Yes /No -If Yes, please specify material No Yes, HDPE Yes, HDPE Do you produce two-piece closures for beverages (with liner) (Yes / No -If YES, please specify material Yes, steel or aluminium cap with liner No No Applications relevant to PET containers, e.g. CSD, water, juice, beer, etc.) CSD, water, juice, beer, energy drinks, wine, functional drinks, dairy drinks All beverage sectors CSD, water, juice, beer, soft-drinks and milk products Neck finishes available as standard pry-off crown cap & 42mm RipCap All corresponding neck finishes PCO 1881, PCO 1810, 38mm, two-start, threestart, Alaska, MCA2 Printed caps available (Yes / No) Yes No Yes, single and two coloured Colour matching service (Yes / No) Yes Yes Yes Child-proof closures (Yes /No) No No No Push-pull / sports caps (Yes / No) No Yes No Special comments/special closures (e.g. flip-tops, drinking spouts, lightest cap for 28mm PCO, 26mm for water etc including non-beverage closures...) Ring crown caps of different sizes for pasteurisation, sterilisation, hot fill and cold fill applications. Lightweight closures; push-pull sports closures; hot fill; aseptic filling Lightweighting cap for 28mm PCO+ lightweighting cap for 26mm PCO Special patented closures or marketing features Finn-Korkki ring crown caps & ring crown equipment. CSN 26mm BTL; 29/25; PCO Corvaglia; 38mm hotfill; 5 gallon cap No","@ID":34} "CAPPING / CLOSURES 39 PETplanet insider Vol. 12 No. 04/11 www.petpla.net Not only is Asia already the largest market for closure sales, but it is also the fastest growing, with the annual growth rate for the period 2003 to 2015 put at above 7% - double the global average. The mature markets of North America and West Europe have eked out growth, the former adding around 1% per year to annual volumes, the latter only 0.2% to 2010, as demand, particularly for bottled water, has decelerated. North America is expected to contract to the CAGR achieved in West Europe (0.2%), while a modest upturn in annual volume growth will be evident in West Europe, even if far from spectacular at 0.8% in the years to 2015. Latin America, Eastern Europe and the rest of the world will see solid growth in the region of 3% per year, but in each case this will represent a decline on average annual advances posted in the year to 2010. Finally looking at end-use sectors, of the 1055 billion beverage closures sold in 2010, 58% were for soft drinks, 31% for beer and just 11% for dairy drinks. In each sector, a significant proportion of product is sold without a closure – in soft drinks and beer, on-trade dispense plays an important role and in dairy, sachets and the informal milk are prominent in the developing world. In terms of closures demand, each sector has exhibited positive overall “Innovation in Beverage Closures, 2011” is a new special-interest report published by Canadean which provides a summary of global market trends and developments in the beverage closures as well as a review of recent new product development and innovations in beverage closure design within the global beer, dairy and soft drink markets. The report is an update of Canadean’s 2008 study, focusing particularly upon developments over the last 2 years. www.canadean.com growth in the period 2003 to 2010 and is expected to continue to do so going forward, beer at the same rate, a CAGR of 2.7%, dairy at a slightly reduced average – 4.1% per year against 4.7% in the years to 2010 – and soft drinks at a slightly enhanced rate – 4.1% against 3.9%. While it is difficult to generalise at the macro level because of regional and even national distinctions, for each sector the factors underpinning these trends are different. In milk, a conversion of pouch to carton and plastic bottle has an impact in creating a shift to larger sizes, in soft drinks a continuing desire for greater convenience will see more smaller packs appear, whilst in beer the bottle and can size expectations are well understood by consumers – 330ml, 500ml, 660ml being the most common - and changes to closure demand may be more associated with conversion between pack types than changes in the pack sizes offered to consumers. Development Plastics-compatible design and injection-moulding simulation High Cavity Moulds The patented z-slidesTM-closure-mould-technology breaks the sound barriers of conventional cycle times and puts - as a modular system - new scales in ease of maintenance and operation of moulds. Multi-component Injection Moulds In the high-performance sector Technology Centre Plastics technology Production Support After Sales Service z-moulds a brand of z-werkzeugbau-gmbh Competent – professional – inspiring Hoechster Strasse 8 · 6850 Dornbirn, Austria · T +43 5572 7272-720 · www.z-moulds.com Brasilplast May, 9 to 13, 2011 Hope to see you at our booth! NEW: Global beverage closures by sector 2010 %share by volume ( Source: Canadean)","@ID":41} "PREFORM PRODUCTION 17 PETplanet insider Vol. 12 No. 04/11 www.petpla.net This is quite a surprising move, considering that usually the material is purchased centrally by the Colas of this world, with the converter only receiving a processing fee. Any dramatic savings in materials would, in consequence, flow directly into the coffers of the big concerns. Nevertheless, Yuriy thinks that the CSD manufacturers will soon be working with the new 1881, and this includes Ukraine. In any event, Retal Dnipro is still able to process 11,000t of PET each month. The fact that it is impossible to forecast prices for the material has meant that lightweighting has very much come into its own. The topic is even proving to be a driving force for small bottlers and Yuriy and his teams are offering local bottlers every imaginable piece of advice and support. The use of recycled material is also part of this topic. Overall the Ukrainian market consumes 150,000t of PET bottles. 10% of this tonnage are going into the edible oil sector, 10% into the juice sector and 80% into the major carbonated beverages such as water, CSD and beer. Unfortunately, only a small quantity of these bottles is recycled because the collection facility for post-conVisit line up. Another new feature since our last visit are the materials silos. A line-up we have become very familiar with over the past ten years (from left to right: Alexander Konnov, Alexander Buechler, Yuriy Khmara, Igor Kim and Alexander Kachanov Enjoy completeness Sacmi Imola S.C. Via Selice Prov.le, 17/a 40026 Imola (BO) Italy Tel. +39 0542 607111 - Fax +39 0542 642354 E-mail: [email protected] www.sacmi.com Sacmi offers turnkey solutions for the beverage and packaging industry: complete bottling lines for product preparation, container manufacture, filling and closing, labelling and final packaging operations. The extensive experience acquired since the company was established in 1919, in addition to its reputation for supplying advanced technology, financial solidity and a network of 70 companies throughout the world, enables Sacmi to meet all your requirements wherever you are. 17","@ID":19} "BOTTLE MAKING 26 PETplanet insider Vol. 12 No. 04/11 www.petpla.net the neck of the bottle. Although, as regards the 0.5l bottles, Kenya was still on a similar level to Germany, the error ratio for the 1l bottles was more than 5 times as high. Only South Africa offers a constant level of quality across all volume categories, at what is a comparatively low level. (Fig. 3) The label may be rated as the outstanding visual characteristic of any bottle. Here too, apart from the printing, a wealth of different characteristics may be observed. The characteristics of “Label Type” and “Label Material” (cat.) are set out by way of examples in the following diagram. What is to be deduced from this is very clear, i.e. that, as far as abels are concerned, the preference is for wraparounds made from plastic; one qualified exception here is Kenya, where paper in relatively large quantities is also used. In addition to the body label which, depending on the process, is produced from plastic film, glued labels made from paper as well as from plastic are also used to a minor extent (Fig.4). 26 Fig. 3: Average weight [g] and height [mm] of lid and by volume and country of origin Fig. 4: Orange Peel by volume and country of origin","@ID":28} "BOTTLES 53 PETplanet insider Vol. 12 No. 04/11 www.petpla.net Valensina on an upwind The one-time brand classic “Valensina“ is well on the way to winning back the leading position that it enjoyed in the 1980’s. However, there are now also various Valensina Smoothies available in 250ml PET bottles as well as ”Mild Breakfast”, a mixture of orange, mango, pineapple, banana and apple in a 1l PET bottle and guarantee of purity without any additional sugar. The bottles have a 32mm screw cap with tear-off tamper-proof facility and an all-round body label made from paper. PET with a handle Cholimex Foods of Vietnam is selling 2l sweet and sour chilli sauce throughout Europe in a transparent PET bottle complete with handle. The injection moulded yellow handle is firmly snapped into place in a suitably configured recess in the bottle and is enormously helpful in facilitating metered pouring. An informative front label and a screw cap secured by means of a perforated shrink label round off the packaging. Importer of the product is Messrs. Kreyenhop + Kluge of Oyten, Germany. www.cholimexfood.com Stability in the groove Vals Mineral Springs of Vals in Switzerland are marketing 1.5 litres of natural mineral water under the brand name of “Valser Naturell“, featuring a high mineral content and without additional carbon dioxide, in a PET bottle with circumferential grooves to improve stability. This reinforced version is necessary because the product does not generate any internal pressure. The grooves also ensure improved handling of the packaging whilst a narrow, all-round label in the upper section and a printed screw cap with tear-off anti-tamper guarantee complete the overall picture. www.valser.ch Coloured PET for Loëlla Under the label Marque Repère, which stands for a balanced diet, the French retail company Leclerc of IvrySur-Seine is selling various low-calorie fruit drinks in the “Loëlla“ brand range in1l content packaging. The round and handy bottles are of slim and transparent design and are relatively tall. The necessary product and retail information is supplied by an all-round body label made from plastic film and the bottles are sealed by means of colour-matched screw closures with tear-off anti-tamper seals. www.marquerepere.com","@ID":55} "TRADE SHOW PREVIEW 43 PETplanet insider Vol. 12 No. 04/11 www.petpla.net interpack 2011 Düsseldorf, 12 – 18 May Hall 14, Stand D14/E29 A seductively attractive way to economise: the newkronesLitePac. www.krones.com Magplastic Hall 11 Booth C20 Bottle blowing flexibility Magplastic (Switzerland), part of the SIH Group, and supplier of linear mid output machines with particular expertise in the production of PET beverage containers will be presenting a newly developed PET bottle blowing machine capable of producing bottles in sizes from 40ml to 2l. The new SSB03i was developed specifically for the demands of the Indian market, where Magplastic established a dedicated facility in Pune in 2004 in order to be able to respond quickly to the needs of this emerging sector. The machine offers a speed up to 3,800bph in a 3 cavity configuration blowing bottles from 40ml to 1l, and 1,800bph for bottles from 1.25 to 2l as a 2 cavity machine. The SSB03i has been developed in conjunction with Bisleri, India. Traditionally Bisleri sold mineral water in small bottles but its growing popularity combined with higher disposable incomes among many consumers led to increasing demand for larger sizes from 250ml up to 2l. While volumes are relatively low at present, Bisleri wanted a machine that was capable of producing a variety of sizes, both small and large, in order to be able to meet both current and future needs. www.magplastic.com Clarifying and nucleating agents for caps and closures Plastics additives producer Milliken will be exhibiting its Millad clarifying agents and Hyperform HPN nucleating agents, which can be used with injection or extrusioncompression moulding processes. Millad NX8000 helps produce clear PP parts with optical properties intended to enable processors to switch from ‘glass clear’ plastics. In combination with Milliken’s ClearTint colorants, Millad NX8000 allows the production of caps and closures with highly transparent, bright colours. There are two grades of Hyperform HPN for PP grades for caps and closures: Hyperform HPN-20E; and Hyperform HPN-68L for applications where ‘pigment levelling’ is important. Milliken says that the additive raises the crystallisation temperature of the polymer to override any nucleating effect created by the pigment, making part shrinkage the same whatever the compound’s colour. Processors can use the same mould and processing conditions for production of caps and closures across the colour spectrum. www.millikenchemical.com Milliken Hall 10 Booth C32","@ID":45} "BOTTLE MAKING 36 PETplanet insider Vol. 12 No. 04/11 www.petpla.net Compressor coordination The central unit is made up of a battery of compressor packages, each one usually with its motor-compressor, air receiver and dryer. ABC Compressors’ normal practice is to form self-contained and centralised packages on a skid (Fig. 1). Outlets are taken from each of the compressors to a common pipe, thus forming a central air production unit, run by PLC-controlled management systems to select the optimum combination of compressors. Installation of check valves on the compressor’s outlet will help ensure that pressurised air from the line does not affect the final-stage exhaust valves of an idling compressor. Fitting a cut-off valve on the unit outlet makes isolation from the high-pressure line easier when, for example, swapping compressor units or undertaking maintenance. Where compressor units are cooled by common water systems, installing a solenoid valve in the water inlet pipe will prevent cold water from circulating when the compressor has stopped, thus avoiding unnecessary costs, losses and internal condensations. The compressor unit, made up of a complete and automated package, possibly built on to the chassis, will simplify entry or exit from the central unit. Compressor regulation Each compressor in the centralised system will be working at full load or stopped, with the exception of a single, regulating unit. This will minimise energy losses and also help to minimise energy consumed in blowing air. A further important factor should be considered in order to reduce energy consumption by the regulating compressor. This motor-compressor should have a VSD (variable speed drive or frequency converter), in order to Fig. 5: ABC project with a bottler in 2010 ensure that it idles for the shortest time possible. ABC Compressors’ units claim speed reductiond of up to 50% without compromising lubrication and smooth operation. (Fig. 2) Distribution pipes As compressed air travels through the pipe to the blower, it loses pressure. As the pipe diameter gets smaller, the pressure loss increases. If several blowers are connected along the pipe, the high demand for air from any of them could destabilise the line pressure and have a harmful affect on the blowing pressure for downstream machines. The pipe distribution design is fundamental to prevent pressure losses and consequent energy cost. Pipes optimised for the flow and working pressure, with a pressure drop target of 0.5 bar, should be fitted. Future extensions to the circulating flow should be anticipated by incorporating new blowers and new compressors. The pipe should be arranged into a closed ring, from which blowers are hung. This arrangement allows more air flow to be distributed with the same diameter of pipes, while stabilising the pressure. Best practice experience In 2010 ABC Compressors and a world-class bottler developed and installed a very large compressor for use in a PET bottle production plant. The factory’s high-pressure system was redesigned according to the key aspects previously outlined. An ABC 4HP-6-LT compressor works as a base compressor unit, with two ABC 4HP-4-LT machines of 3,000m3/h each, totalling 12,000 m3/h 40 bar high-pressure air. The four-stage compressors have horizontally-opposed, double acting cylinders and have long running times (around 8.000 hours) between services. The machines are PLC coordinated and regulated with a VSD in one of them. The factory’s high pressure line is in a closed loop and provides air to more than five blowing lines, producing different container sizes and with highly variable air demand throughout the year. This installation demonstrated that it is possible to make progressive improvements, as time and resources become available, and to obtain immediate savings when implemented. Adapted from a speech on energy saving in central compressor units, by Ignacio Azcuna. www.abc-compressors.com Fig. 2: VSD. 50% of regulation Fig. 4: Three compressors produce 12,000m³/h 40 bar","@ID":38} "NEWS 8 PETplanet insider Vol. 12 No. 04/11 www.petpla.net Indorama Ventures approves plans to expand capacity in Europe Indorama Ventures board on April 5,2011 has approved a brownfield expansion of PET polymers production in Europe with a capacity increase of 220,000t/a. This expansion, completion expected in 2013, will increase the total capacity of IVL in Europe to 1,300,000t/a of PET Polymers with five locations strategically placed to serve all countries in the EU competitively. In addition, IVL has 2 PTA plants in Europe, located at Rotterdam, Netherlands and Ottana, Italy. The company had earlier announced on February 7,2011 that it was entering into a binding agreement to acquire Trevira GmbH, the Polyester company in Germany. The decision to grow was motivated by the supply/ demand dynamics within the EU and the need for competitive assets to better serve customers. Indorama has been in the forefront of investing in state of the art production across the world. The last time a new plant was built in the EU was also by Indorama, back in 2006 in Lithuania. IVL also identified the benefits of a “brownfield” expansion at this time as being more cost effective solution than developing a “new greenfield” site. www.indoramapolymers.com Happy anniversary for Buhler Buhler Technology Group has reported a rise in orders, increased sales and growth in profits for 2010, its 150th anniversary. Order levels exceeded CHF 2 billion for the first time in its history; at CHF 2160 million, they were 21% higher than the previous year. Strongest growth, at 48%, was achieved by Advanced Materials division, followed by Food Processing (+27%) and Grain Processing (+15%). The company said that the performance of the Food Processing division was affected by the delayed market recovery. The highest rises in orders were received from emerging markets in Asia (+39%), North and South America (+19%), and the Middle East (+96%), while turnover in the mature markets of Europe contracted. Sales grew by 11% (13% currency-adjusted) to CHF 1907 million. The Customer Service business (services, spare parts, expendable materials) has seen its share of total Group sales rise steadily over the past years. Structural costs increased at a lower-than-proportional rate relative to sales. It invested over CHF 80 million in research and development in 2010. The development of new midmarket customer segments contributed substantially, and discussion about safe and healthy foods also stimulated demand for its technologies. Order backlog of CHF 1238 million at the end of 2010 was almost 30% above the level of 2009. Turnover is expected to continue to rise in the current fiscal year. www.buhlergroup.com","@ID":10} "Vol.6 PETplanet print PREFORM PRODUCTION 14 PETplanet insider Vol. 12 No. 04/11 www.petpla.net Moisture Marks Chapter 19 of the “Rapid Guide to Perfect Preforms” by Rick Unterlander and Ottmar Brandau Troubleshooting guides have suffered in the past from being locked away in offices and not being available to the people that actually need them. Considering the high cost of machine and tools high scrap rates can be a costly proposition eating away at already tight margins. PETplanet’s “Rapid Guide to Perfect Preforms” takes a different approach. Bound in laminated paper that is easy to clean off, the small format of the book of 108mm by 151mm (4.25” by 6”) allows easy storage in back pockets or tool boxes. It has been written for the people on the floor of injection moulding companies to support their daily work in making the best preforms possible. The product of two industry experts, Rick Unterlander and Ottmar Brandau, it gives concrete advice on 35 of the most common problems in preform manufacture, most illustrated by pictures. From high AA levels to wavy bodies processors can find help when they need it. Read chapter 19 of the guide. fax: +49 (0) 6221-65108-28 [email protected] www.petpla.net Order your copy now! PETplanet print vol.6 The Rapid Guide to Perfect Preforms machine no./name","@ID":16} "PETbottles 52 PETplanet insider Vol. 12 No. 04/11 www.petpla.net Children’s drink easy-to-open Schwollener Sprudel, based in SW Germany, has recently launched a new drink for children, in partnership with Mainzbased Sonic Drink Marketing. Based on mineral water with natural fruit juice and available in apple, orange and cola flavours, the new line is packaged in a 0.5l yellow PET bottle, featuring popular cartoon character SpongeBob Square Pants on the label. The bottle is capped with a bi-colour 28mm Original Sport Cap with matching yellow spout from Aptar Food + Beverage. Schwollener Sprudel chose the Original Sport cap for its combination of technical performance and colour flexibility. The tight seal of the closure and easy opening and closing are essential factors when designing a product for children. www.aptar.com Blauer Bock in a PET Bottle 1.5l of “Blauer Bock“ apple wine spritzer is being marketed by Landkellerei Höhl of Maintal in a clear, no-deposit PET bottle. According to the manufacturer, the drink has a low alcohol content (3.5% alcohol) and very few calories (23 kcal per 100ml). The tall bottle features a printed all-round body label made from paper and a colour-coordinated screw cap complete with tear-off anti-tamper guarantee. www.hoehl-hochstadt.de Shot in PET “Shot“ is what Coca Cola Spain calls its low calorie beverage in a transparent 0.5l PET bottle with all-round “non-label look” label. The handy, round bottle sports a printed, red screw cap with a tear-off anti-tamper seal. www.cocacola.es Perfect by Penny The German discount retailer “Penny“ is marketing a 250ml 9-vitamin drink, with the brand name “Paradiso“ under licence to Jan Bicks Bar-Bolz-Bande in a perfectly designed PET bottle. The packaging is easy for children to grab hold of and is decorated with a child-friendly design sleeve label. By way of a closure there is a 2-section push-pull arrangement with additional safety cap and integrated anti-tamper seal. www.barbolzbande.de","@ID":54} "PETpatents www.verpackungspatente.de 56 PETplanet insider Vol. 12 No. 04/11 www.petpla.net Hot fill container International Patent No.WO 2010 / 075001 A2 Applicant: Amcor Ltd., Abbotsford (AU) Date of Application: 11.12.2009 PET container moulded so as to facilitate gripping which absorbs vacuum forces generated during hot filling and subsequent cooling without any visible deformation. Particular attention is paid to describing the tapered grip area. Pressure compensation International Patent No. WO 2010 / 081081 A2 Applicant: Porex Corp., Fairburn (US) Date of Application: 11.1.2010 An opening is made in the lid of a container intended for hot fill products through which air can penetrate so as to compensate for the vacuum created by the air during cooling. A capsule made from porous material acts as a filter for the air. Container International Patent No.WO 2010 / 075252 A2 Applicant: Amcor Ltd., Victoria (AU) Date of Application: 21.12.2009 Container with compensating areas that, in the case of hot fill, absorb the expanding heat and on cooling return to their original form by means of elastic deformation. Dispenser International Patent No.WO 2010 / 079023 A1 Applicant: Unilever Plc., London (GB) Date of Application: 4.12.2009 Container with flexible side wall and dispensing device for metered dispensing of the product (here a detergent additive) into a chamber in the lid. As a result of pressure on the side wall the dispensing chamber in the lid is filled and the content can then be deployed. Hinged cap Europ. Patent Nr. EP 12204333 A1 Applicant: Weener Plastik AG, Weener (D) Date of Application: 5.1.2010 Hinged cap for a drinking bottle. When open the lid is fixed in this position by means of two holding sections. The procedure for manufacturing a container with this particular type of closure using injection moulding is described. Plastic container International Patent No.WO 2010 / 085610 A1 Applicant: Graham Packaging Comp., York (US) Date of Application: 22.1.2010 Plastic container with special reinforcing ribs and compensating areas for hot filling. In addition, areas are provided where labels can be attached.","@ID":58} "PREFORM PRODUCTION 15 PETplanet insider Vol. 12 No. 04/11 Table of Contents i..............About the Authors ii...................... Introduction chapter 1................... AA Level High 2..............Accordion Preform 3............ Air hooks / Streaks 4.....................Black Specks 5............................Bubbles 6....................... Burn Marks 7.. Colour Streaking / Peeling 8....................... Crystallinity 9......................Drool Marks 10............................... Flash 11...............Gate Depressions 12.....................Gate Peeling 13....... Gate Voids / Pin Holes 14.............. Internal Gate Sink 15..................... Internal Sinks 16............................. IV Loss 17................. Long Gate Nub 18.................... Milky Preform 19..................Moisture Marks 20..... Neck Finish out of Round 21............ Parting Line Crease 22...... Parting Line Deformation 23...............Preform Yellowing 24....................... Short Shots 25............................... Sinks 26...............................Splay 27.................Stretched Necks 28.......................... Stringing 29.............. Surface Blemishes 30...............Thread Flow Lines 31.... TSS (Top Sealing Surface) ...............................Sink 32............................ Unmelts 33......Wall Thickness Variation 34...................... Wavy Body 35....................... Weld Lines Symptom: Grooves formed around the circumference of the preform. Cause: The melt front has made contact with moisture on the moulding surfaces. The moisture is pushed along the length of the preform until enough water has built up to interfere with the melt flow, causing the melt front to buckle and form improperly. Y O U R PA R T N E R F O R B L O W M O U L D S . Sidel • SIG • Krones • SIPA • MAG • ADS • Kosme • Nissei a. o. Röders GmbH / Scheibenstr. 6 / 29614 Soltau / Germany / www.roeders.de Telephone +49 5191-603-53 / Fax +49 5191-603-36 / E-Mail [email protected] For our subsidiaries in China, USA and Latin America please check our website. PET STRETCH BLOW MOULDS Benef i t of 30 Years of Exper ience in Blow Mould Manufactur ing! Solutions: 1. Check to ensure that no moisture exists on the moulding surfaces, either from water leaks or condensation. This may obstruct normal melt flow and cause filling problems. The environmental dewpoint should be below the chilled water temperature to eliminate the risk of condensation. 2. Check hardware for worn, damaged or failed components, specifically the cavity / gate insert o-rings, mould neck insert o-rings, core o-rings, and stripper plate hoses.","@ID":17} "PET - THE NEXT GENERATION 55 PETplanet insider Vol. 12 No. 04/11 www.petpla.net PET bottle artistically transformed into Chinese lucky fish PET art objects There hare not only the two options for old PET bottles: recycling or landfill. Thai inspiration and creativity, for example, has found a third way: the “artistic upgrading” of PET bottles. For six years now the young Thai couple Nana and Naed have been converting old discarded PET bottles into wonderful looking flowers, lamps and Chinese lucky fishes. Within the space of two or three days an empty 1.5l bottle can be transformed into a handcrafted and colourful lamp. A discarded 450ml Coke bottle takes on a new life as a Chinese lucky fish. The silver version of the Chinese lucky fish is the best seller of the moment. Currently some 200-300 bottles (450ml, 1.5l and 5l) per month are being artistically converted. The two young artists from Bangkok are not content simply to create PET art objects, but are keen to spread the word to others. For the modest fee of US$35, potential PET sculptors can have a go themselves, suitably equipped with soldering iron, paper templates, and a range of different colours. Thus a cottage industry is created which can help boost the local economy. The PET bottle lightweighting does not particularly please the young artist Naed, who still prefers the thicker and heavier CSD bottles. But his business will survive. He has just opened a second outlet in Bangkok.","@ID":57} "31 Bottle-to-bottle recycling plants Conveyors for preforms and empty bottles Caps and closures Preforms Perform moulds and SBM moulds Preform and single stage machinery 2-stage SBM machinery Compressors Filling equipment Resins and additives Suppliers of caps and closures for PET bottles It’s closure time. No fewer than 21 suppliers feature in the latest of our regular annual market surveys. With so many participants, this is without doubt the most comprehensive of our market overviews. Lightweighting, the subject that five years ago ushered in a general trend, is increasingly and consistently the topic of the moment, although in certain sectors classical closures are still holding their own. A number of suppliers have launched new products on the market, and on pages 46, 49, 50 we take a closer look at them. *Whilst the publishers have made every effort to ensure that the information is up to date, no claims are made regarding completeness or accuracy. 04/11 MARKETsurvey Company name Bericap GmbH & Co.KG Closure Systems International Has Plastik San. TIC A.S. Silgan White Cap Postal address Telephone number Web site address Contact name Function Direct telephone number Fax E-Mail Kirchstrasse 5, 55257 Budenheim, Germany 49 6139 2902-0 www.bericap.com Volker Spiesmacher Director +49 6169 2902-0 +49 6139 2902-188 [email protected] HQ: 7702 Woodland Drive, Indianapolis, IN 46278 USA +34 93 891 62 49 www.csiclosures.com Neus Piloneta European General Manager Assistant +34 93 891 62 49 +34 93 891 78 00 [email protected] Esenyurt Yolu No 50 Avcilar Istanbul, Turkey + 90 212 695 50 00 www.hasplastik.com, www.hascap.com KerimAtas Sales Executive +90 212 695 50 00 +90 212 694 97 24 [email protected] Wijdbos 33 2440 Geel, Belgium www.silganwhitecap.com Hans van Baekel Business Development Manager +32 475 81 64 85 [email protected] Product range Caps and closures Plastic and aluminium closures Plastic closures 38mm closures Do you produce one-piece closures for beverages (Yes /No -If Yes, please specify material Yes, DoubleSeal Super Shorty for PCO 1881, HexaLite for PET 29/25 and PET 28/22, Double Seal 38 for 38mm 2-start and 3-start neck finish Yes (HDPE, PP, Copolymers) Yes HDPE Yes , PE Do you produce two-piece closures for beverages (with liner) (Yes / No -If yes, please specify material Yes, Liner Seal, SuperShorty for PCO 1881 Yes, plastic and aluminum closures. (PP primarily) Yes with liner, PP Yes, PP Applications relevant to PET containers, e.g. CSD, water, juice, beer, etc.) CSD, still mineral ater, HOD and bottled water, beer, juices, energy drinks, RTD, teas, syrups), for hotfill and aseptic application, edible oil, sauces and dressings, dairy CSD, water, isotonics, juice, beer, teas, food, distilled spirits, wine and automotive fluids CSD, water, beer, juice, shampoo, household All NCB with 38mm hotfill, aseptic and coldfill applications Neck finishes available as standard PCO 1881, PCO 16, PCO 1810, PET 26/22, PET 29/25, PET 26/21 Short-height 28mm (1881 & 1873), short-height 26mm, standard height 28mm (1810 & 1716), standard Height 26.7 (1844), 30/25 haute, 33mm (1851), 29/25 finish, 2-Lead 38mm (1874), 3-Lead 38mm (1876 & 1875), 38mm (1842, 1843, & 1845), and 43mm (1799, 1814, & 1841), etc. 28mm 1810, 28mm 1881, 30-25mm, 29-25mm, 26-22mm, 48-41mm , 38mm three lead, 38mm two lead, aseptic and hot fill. Yes, all 38mm standards , hotfill , cold & aseptic 2 and 3 thread Printed caps available (Yes / No) Yes, up to 3 colours Yes Yes Yes, photo quality Colour matching service (Yes / No) Yes Yes Yes Yes, on sample of label, brochure, botle, cap or against PMS Child-proof closures (Yes /No) Yes No Yes No Push-pull / sports caps (Yes / No) Yes, 3-piece push-pull and 2-piece thumb-up Yes Yes No Special comments/special closures (e.g. flip-tops, drinking spouts, lightest cap for 28 mm PCO, 26 mm for water etc including non-beverage closures...) 3-piece push-pull for aseptic filling without aluminium foil with high flow rate Integrated closure & capping solutions Also 43, 48, 63mm closures Special patented closures or marketing features Thumb screw for easy dispensing Lightweighting solutions Patented finger loop design for 5 gallon caps, triple barrier technology for CSD, non solvent printing system for cap decoration Static and dynamic venting features Laser UTC printing, Coke approved closures for both aseptic and hotfill, Oxygen scavenger pad inserts","@ID":33} "TRADE SHOW PREVIEW 47 PETplanet insider Vol. 12 No. 04/11 www.petpla.net Sacmi Hall 8A Booth E03 Plastic cap compression press The Team Sacmi stand will have as its centrepiece the company’s new CCM48SB press. The machine, which sits at the top of its range, has been designed for the lightweight single-piece HDPE cap market and produces caps for water, hot filling and CAF (cold aseptic filling). Sacmi says that cycle times have been reduced to 2s (from 2.4s) and has energy consumption of 0.4 kWh/kg. All parts on the CCM48SB have been redesigned to reduce maintenance times, with the number of necessary tasks minimised and parts optimised to reduce the required task times. The machine on the stand will be equipped with a mould suitable for the production of single-piece HDPE S29W-3 caps, with a 29mm diameter and a weight of 1.25g. Online quality control will be by Sacmi’s CVS vision system. Sacmi has observed that the focus in the beverage industry is no longer on individual machines but tends, rather, to complete ‘turnkey’ solutions. The company’s stand will include other machines and equipment in a display intended to demonstrate its overall ‘bottle analysis and optimisation’ strategy. Visitors will have the opportunity to examine roll-fed sleeve Technology in labelling; filling machines, featuring exclusive patented Solo-Mas technology that allows the dozens of filler valves to be managed via a single flow meter controlling a master valve; and SBF blowers, which allow two bottles (of 1l or less) to be produced at a time. www.sacmi.com Increased flexibility The Sidel Group will be presenting its latest technology for each stage of the bottling process. Its emphasis is on increased flexibility and reliability, from high-tech packaging machinery and line engineering to beverage protection, packaging design and technical training. The company will be demonstrating its new SP 1000 HS low-level palletiser. During layer formation the machine rotates and positions the packs into a perfectly shaped layer to be stacked and transferred precisely onto the pallet. Sidel’s patent-pending ‘pusher’ guides layers alternately to the right or to the left while optimizing ‘return stroke’ time. The process is supported by Place (Pallet and Layer Automated Configuration Editor), Sidel’s new software program, which is particularly suitable for short-batch runs. The software is compatible with Sidel’s Robo-Smart and Axo-Smart layer-preparation systems. The new SP 1000 HS palletiser is also compatible with Robo-Kombi and Robo-Column, which pick up and place the packs. www.sidel.com Sidel Hall 13 Booth C35/E46","@ID":49} "Machine Vision Inspection System High Quality! Your Best Choice! History P&S Technology company was established in 1997. And our company is professional corporation in the manufacturing of image processing inspection machine for all of beverage and food containers. Also, P&S is invested by The Korea Development bank, the government-funded company, and the image-processing technology as well as the total solution has been regarded by the government. The future value of investments in P&S has been very highly regarded. Solution Most of P&S inspection machine are connected directly to the client‘s production lines, the On-line system, which inspect without interrupting Client‘s production ef¿ciency. And the system accurately ejecting defective products are receiving a favorable evaluation from many clients. In fact, the suppliers that provides total solution for inspection machine are not so much in the world Food & Beverage market. So far, exclusive suppliers of inspection machine do not provide the perfect solution for a long time, because the rate of development and acceptance for new technology is very slow. Despite in the rapidly developing the image-processing technology, some supplier still provide the old technology beyond ten years for clients. Concept The inspection machines manufactured by P&S Technology are designed with the concept focus on ‚Professional & Simple‘ and both of all the hardware and software have been designed and developed by P&S its own. The main inspection machine of P&S has done a complete inspection for Preform and PET Bottle. It has been developed an effective and economical method for Glass bottle as well as Plastic Closure, Metal Can End, Metal Can Body, Instant noodle cup, and Food container. To design the inspection system, P&S has many solutions and alternatives for answering client‘s requirements and the condition of the production line. With the various models and Series, P&S provides many times optimal condition on the client‘s budget and requirements. For example, P&S‘s Empty bottle Inspection system is mainly designed for Rotary type. It use the patented ‚mirror tracking system‘ for the bottle body inspected, this is perfect inspection system as secured many overlap sections. However, all Clients are not able to equip the Rotary type, relatively expensive, so the Linear type that is suitable for the customer‘s production line and the most ef¿cient at the same time also has supplied. Most of manufacturers provide their own standard models and force for the clients to choose among their models, while P&S provides the most effective standard models as well as various models that the clients are able to choose according to their own requirements. Flexibility is the main advantage. Powerful On the contrary to this, the most employers of P&S are young and have fast developing skills, so we can respond quickly to client needs. P&S can provide superior technology more than other inspection machine supplier of long-standing in only 14 years by virtue of these young men. Currently, P&S enter into the world market beyond Korea Food & Beverage market since 2005, now is exporting to eight countries, including Japan, China, Taiwan, Malaysia, Thailand, India, Myanmar, Vietnam. Each year, approximately 20% of the exports are increasing. P&S does not concentrate on the sales only, by training agents in each country on a regular basis, the policy of ‚after sales service‘ is ¿rmly established, and we make preparation for a system that can respond within 24 hours. E-mail: [email protected]","@ID":23} "CAPPING / CLOSURES 41 PETplanet insider Vol. 12 No. 04/11 www.petpla.net 96-cavity Schöttli cap mould with collet chuck demoulding 96-cavity Schöttli cap mould with forced ejection tion moulding, the individual screw caps are routed past cutting knives that are rotating at high speed, in order to partially cut open the closed TE band. Up until recently, a part of the cap producers have been using compression moulding as their preferred production technique, which required post-folding and -slitting. Many of these manufacturers are currently changing to injection moulding, but retained the existing closure geometry. Accordingly, they still prefer forced ejection in order to be able to still use their existing downstream equipment for folding and slitting. This twotier strategy allows facility operators to flexibly change to injection moulding without problem and prevents the risk of potential maintenance requirements, which may otherwise occur with unknown demoulding technology. All Schöttli cap moulds can be maintained while installed on the injection moulding machine. The mass production of light-weighting, thin-wall caps calls for a high degree of precision of machines and moulds. Integrated camera monitoring systems used for optical inspection prevent the supply of defective caps, which are produced with a reject rate of virtually nil. www.schoettli.com IMD Ltd. Switzerland / www.imdvista.ch Swiss Made … more than a VISION SYSTEM _Complete System Solution _INOX Line (all in stainless steel) _Vision System with COLOR cameras _Self-learn functions _Inline for 100% inspection _Easy & fast product change _Very compact Closure Testing Preform Testing 41","@ID":43} "PETnews 6 PETplanet insider Vol. 12 No. 04/11 www.petpla.net Silgan acquires Graham Packaging Silgan Holdings Inc., a supplier of rigid consumer goods packaging products, announced that it has entered into a definitive merger agreement to acquire Graham Packaging Company Inc., a global supplier of value-added rigid plastic containers for the food, specialty beverage and consumer products markets. The combined company has annual sales of over $6.2 billion, and its over 17,000 employees will operate 180 manufacturing facilities in 19 countries. Following the transaction, Silgan is expecting to achieve combined revenues of approximately $4.6 billion.Following the acquisition, on a pro forma basis Silgan expects to generate approximately $500 million in free cash flow, or approximately $5 per share, in the first full year of operations. Silgan expects to realize operational cost synergies of $50 million by the third year following the combination. The acquisition is currently expected to close in the third quarter of 2011, subject to the approval of the transaction by Silgan’s shareholders and Graham’s shareholders, receipt of applicable regulatory approvals and the satisfaction of customary closing conditions. www.silgan.com Plastic Technologies and Cetea partnership for training Plastic Technologies, Inc. (PTI), which engages in PET design, development and engineering services, partnered with Brazil’s Centro de Tecnologia de Embalagem (Cetea) to produce a three-day training course entitled PET Packaging for Hot- and Aseptic Filling of Sensitive Beverages, held during April 2011. Cetea is a State of São Paulo packaging technology research institution, which is part of Ital, the Food Technology Institute. The course, which featured modules on PET Technology, Hot-Fill and Aseptic Technology, and PET Recycling and Sustainability, was held at Ital’s headquarters in Campinas. A training agreement between PTI and Cetea was signed in 2010. www.cetea.ital.cp.gov.br www.plasticstechnologies.com Invista reports improved performance in 2010 Invista Resins & Fibers GmbH has reported improved sales volumes and increased market share in speciality segments, following its 2009 restructuring and implementation of its new business strategy. The company’s Polymer & Resins business strategy involves a diversified product portfolio and new developments. In 2010, the business launched low-melt Type 7001 resin and Oxyclear barrier resin products, and continued to supply Polyshield resin. In the first quarter of 2011, the Polymer & Resins business undertook a complete overhaul of one of its polymer production lines, which had been temporarily shut down. The third quarter is scheduled to see a comprehensive overhaul of Invista’s DMT plant in Gersthofen. www.polymers.invista.com Full FDA approval for Gneuss PET recycling Gneuss Kunststofftechnik GmbH has received unrestricted FDA approval for food packaging products of all types (classes C – G) for its extrusion process, following last year’s receipt of a Letter of Non Objection for a complete PET recycling system including an SSP system. The company’s MRS extruder, its devolatilising system and the Rotary Melt Filtrations system are approved for the processing of up to 100% unwashed PET bottle flakes for food contact containers, without any pre- or post-extrusion treatment of the material, including drying, drying under vacuum, crystallizing etc. The company says that the approval is because of the devolatilising performance of the MRS extruder. It uses a very large polymer melt surface area in the multiple rotation section of the extruder, together with a rapid melt exchange and optimised venting. Gneuss has sold more than 20 extruders since its market launch, less than four years ago. www.gneuss.com New Sidel training lab in Italy From January 28, Sidel has a new training lab at its Parma site, which extends classroom and hands-on training services for customers and Group experts on its range of standard or aseptic fillers, all the way through to end-ofline equipment. The centre holds nearly 200 multilingual sessions for more than 1,000 customer-trainees each year. The site already offers classrooms, theoretical learning and a ‘virtual reality’ room. The new lab is equipped with the latest generation of standard or aseptic sub-assemblies for hands-on operations. One room houses two automation training stations, including a Fanuc robot model for the training of robot operators and maintenance technicians, and a teaching carrousel and test tables for the configuration of filler and mixer sub-assemblies. A second room is dedicated to training on Sensofill FMa and FMm aseptic fillers, as well as aseptic instruments and components. The third space is given over to different types of filling technologies and valves. Sidel is also investing in the expansion of its Beijing Training Centre, which is scheduled to open in the second half of 2011. www.sidel.com","@ID":8} "PREFORM PRODUCTION 16 PETplanet insider Vol. 12 No. 04/11 www.petpla.net From commodities to custom-made items Ukraine is always worth a visit, in particular for people who are keen to experience at firsthand what is probably THE success story in the PET preform sector. When we visited Dnepropetrovsk in 2003 Uniplast had 12 Husky lines; by 2005 the number had risen to 29. Since then Uniplast has been absorbed into the Retal Group. At the location itself there are now 25 preform lines and 7 cap systems. A total of 196 machines are in service at Retal worldwide. This makes Retal Dnipro the biggest production location in the Group today, with 4.2 billion preforms and a 2.5 billion cap production capability. The worldwide economic crisis hit Ukraine very hard; all sectors went into decline, even the beverages industry. But despite the fact that the team around Yuriy Khmara had known nothing but a growth scenario, it has succeeded in surmounting the downturn too. In the meantime, the crisis seems to have been overcome; the consumption of beverages is back to its former high level. Nevertheless, there have been changes at Retal Dnipro. In the course of our visits over the last decade, Yuriy’s key focus was on the production of commodities which he could sell to virtually anyone in the sector. Now, custom-made preforms are making a significant contribution to turnover. Lightweighting in particular has made this possible for the company. “Millions more preforms from fewer tonnes of material“ is the company’s mission statement. This has not only been the case since the price of PET has been on a relentless upward trend, - no, for exactly one year now the company has been producing the 1881 neck finish at a rate of around 600 million pieces p/a for its neighbour Biola. They have managed to reduce the weight of the 2-litre CSD bottle from 52 to 37g. For the 0.5l bottle, the preform has been slimmed down from 26 to 15.7g. This has meant that the material used to make 2 old preforms now produces 3 – more caps, less plastic. As is the case everywhere in the world, here in Ukraine too the regional bottler Biola has been much quicker off the mark than established brands like Coca Cola and Pepsi Colas in taking advantage of the Lightweight Bottles. Retal is, however, also in talks with the two Cs with a view to introducing the 1881. Alexander Büchler and Yuriy Khmara: Regardless of preform and colour, Retal Dnipro has developed from being a supplier of commodities to a provider of custom-made items. by Alexander Büchler","@ID":18} "BOTTLE MAKING 24 PETplanet insider Vol. 12 No. 04/11 www.petpla.net PETplanet Zoom - Bottle analysis and comparison by PETplanet Insider in collaboration with the Technical University of Ilmenau- Part II Africa A great diversity In the introductory section of our Zoom Study the overall project together with results were presented with special reference to Germany. Part II is intended to provide you with a few insights into the African database. The study focused on Egypt, Kenya and South Africa. Although, by contrast to Germany data, the database is more restricted, even just a random sample of the bottles in the survey enables us to appreciate that in the comparison Egypt demonstrates a considerably greater degree of diversity as far as the various bottle volumes are concerned. Concentrating on the categories 0.5l, 1 L as well as 1.5l as already defined in the first Zoom Report and looking at the average values for the different bottle weights, it will be observed that the African bottles consistently turn out to be heavier than in Germany, whilst at the same time the Kenyan bottles come very close to the German values; however, it is not possible to identify a fundamental trend here. The low weight of the 1.5l bottles from Egypt deserves particular mention. This anomaly may be attributed to the fact that the mineral water here is non-carbonated and the preferred shape of the bottle used for it tends to be cylindrical with a flat, unstructured base. Interestingly, where the African bottles in the 1.5l category are concerned, these also comprise non-carbonated beverages, Fig. 1: Number of bottles recorded for Africa by country and volume","@ID":26} "BOTTLE MAKING 29 PETplanet insider Vol. 12 No. 04/11 the calculation when computing the amount of PET to be processed. The InnoPET Blomax Series III has a heater module that operates with classic infrared radiation. Within the project, the temperature profile generated in the preform wall during heating was analysed and optimised. The variables used to asses the heating process were the energy content of the preform and its axial temperature profile. An optimum thermal profile for a preform can be achieved by applying various doses of infrared thermal radiation and an adjustable flow of air to cool the outer surface. Tests have revealed that the consumption of energy in the preform preheating process can be optimised by between 15 and 20%. Application of this information means that the amount of electricity needed to preheat preforms would drop from 0.15kWh/kg PET to 0.12kWh/kg PET. On the assumption that electricity costs €0.10 per kWh, this would yield an annual saving of €7,800. Further energy savings could be achieved by using near-infrared (NIR) technology for preform heating. The use of only shortwave or near-infrared leads to a substantially higher energy density. With NIR, the penetration of the preform wall is extremely intense – a feature further increased by feeding the preform through a closed heating chamber with all-round reflection. Application of NIR heating technology leads to a further potential saving in electricity of up to 30%, compared to classic infrared radiation. The project also takes completely new heating technologies for preforms into account, such as, for example, laser power. Heating with diode lasers would possibly provide new ways of profiling temperature both in the axial preform direction and across its entire circumference. Compressed air: reduced consumption through intelligent ventilation and recycling The third criterion was the amount of compressed air needed to inflate the PET bottles. This was to split into two areas: firstly, the amount of compressed air needed to blow mould the PET container itself, and secondly, the quantity of compressed air supplying what are known as dead space volumes. E modulus increase as a function of the stretch speed","@ID":31} "PRODUCTS 50 PETplanet insider Vol. 12 No. 04/11 www.petpla.net Aseptic linerless closure technology Portola Packaging, Inc., of Illinois, USA, has announced the commercial launch of a new linerless plug closure technology that meets the standards required for aseptic beverage packages. The product, named Steri-Shield, is compression moulded in a proprietary resin blend that includes HDPE. Portola claims that the lightweight closure does not crack or back off during the sterilisation and/or distribution process and can withstand an aseptic sterilization environment of up to 140°F. The plug closures can be made in sizes ranging from 38 to 43mm, with or without a tamper-evident band. The cap is suitable for a wide variety of aseptically-filled beverages, including juices, isotonics, dairy, energy drinks, milk, vitamin waters, drinkable yogurt and teas. Aseptic products have traditionally used closures with thermoplastic elastomer (TPE) or foil liners to achieve seal integrity for both low- and high-acid beverages. By eliminating the liners, Portola says that the plug design helps minimise package cost and contributes to material source reduction. Commercialisation is being backed by internally-developed shelf-life testing protocols to predict the performance of the plug closure over time. Computer modelling was used to accurately project shelf life and other performance attributes. www.portpack.com Faster detection of microbiological contamination Döhler, which produces additives, ingredients and technologies for the food and beverage industries, has announced the launch of a new analysis system for yeast, moulds and bacteria in water, the company claims its Trans-Fast system can cut analysis and detection times by 75%, from 96 to 24h. TransFast Gel, which is supplied ready-to use, eliminates the need to liquefy agar or to keep it warm. The liquid gel promotes the flow of nutrients to possible contamination sources, allowing contamination to be spotted early. The TransFast system includes a back-lit incubation lightbox, in which the sample tubes are lined up next to each other in front of the light source. The direct lighting of the transparent samples allows any possible contamination to be identified immediately. There is no need for Petri dishes, allowing the evaluation time to be reduced by up to 90%. Trans-Fast is an addition to Döhler’s range of microbiologically selective nutrient media, which are marketed under the Döhler Microsafety Design brand and are intended for quality assurance in production of beer, water and non-alcoholic beverages. www.doehler.com Recycling line recoSTAR PET iV+ Ongoing PET recycling innovation, quality and state-of-the-art technology, a full range of consulting services – brought to you by Starlinger. Visit us at: Brasilplast May 9 – 13, São Paulo, Brazil Plastpol May 24 – 27, Kielce, Poland www.recycling.starlinger.com Upgraded granulators Nuga AG Kunststoffschneidmühlen, Germany, has launched an updated range of CentriCut granulators, designed for grinding plastics and rubber. Available as standalone or in-line systems, the range extends from the Type 33r for small- and mediumsized parts, sprues and hollow items with a maximum throughput of 500kg/h, through to the Type 44slr, which has a maximum throughput of 2,500kg/h. A major focus of the upgrade is wear protection. Nuga has developed its own wear-tester; the company says that application of the results of tests have enabled it to raise the service life of typical wear parts across the entire range of CentriCut granulators substantially. The new range is claimed to offer users low maintenance, long uptimes and reduction of costs in recycling rubber and plastics. In addition, the machines do not require a cooling agent, which further helps to save costs in recycling rubber. www.nuga.ch","@ID":52} "TRADE SHOW PREVIEW 46 PETplanet insider Vol. 12 No. 04/11 www.petpla.net Developments in drying, crystallisation and condensate separation Mann+Hummel ProTec will feature its new Somos D 200 dry-air dryer with its new MH 25controller, which controls the triggering of the dew point-constant dry air and, with other features, is claimed to offer more flexible operation. The dryer can be expanded from 200 u.m/h up to 500m³/h by adjustment to control technology; dried material throughput can be increased up to 250kg/h, without extra hardware. The redesigned rotary desiccant container process control reduces time needed for drying agent regeneration. The modular design allows flexible expansion, with drying hoppers from 50 to 300l. For PET processing, material throughputs from 500 to 2,000kg/h are available, with larger sized dryers and dryer hoppers. The company’s new modular condensate separator enables return air to be cleaned of all volatile material, including monomers and dust particles. The condensate separator consists of three serially connected units. All are readily accessible and can be cleaned quickly and easily. Mann+Hummel ProTec Hall 9 Booth G10 Bericap Hall 10 Booth E67 Lightweighting in closure design Bericap will be showcasing developments in closure technology across a range of markets, including the beverage and food industries. The theme is lightweighting in closure design, with a particular emphasis on aseptic filling and hot-filling processes, but including new developments for the food market; specifically for edible oil and squeezable products, and technical applications that protect contents from counterfeiting and product piracy. In partnership with Egyptian juice processor Juhanya, Bericap recently introduced a one-piece 38mm closure for hot filling in PET. Bottlenecks are set to become lighter in future for both the 38mm and 28mm PET bottles currently on the market. A 33mm neck size will shortly complement the product range. In 2010, Bericap launched a 33mm closure, with a bottle neck co-designed with Sidel, which offers weight saving of approximately 30% on a 38mm neck. The closure is fitted with a folded and pre-cut tamper-evident band, which breaks when first opened. Bericap’s ‘pushpull next generation sports closure, fitted with DoubleSeal technology, is suitable for aseptic filling and for both wet and dry sterilisation. N2 dosing of the bottle is possible in aseptic filling processes. It requires no aluminium foil seal and offers a 30% higher flow rate compared to conventional products. The company’s new valve design for products such as ketchup and mayonnaise, a segment dominated by silicon valves, consists of two parts, both manufactured from the same material. This offers advantages with recycling. Bericap will also be showing a new range of closures for a 26mm bottle neck diameter to support the move towards saving on costs and materials in the edible oil industry. The new closure neck weighs 1.37g but has an inner diameter identical to the previous 29mm diameter closure. www.bericap.com SMI Hall 14 Booth D06/16 Integrated and energy-saving PET packaging Italian company SMI SpA will be presenting its new Ecobloc Plus system, an integrated solution for stretch-blowing, filling/capping and labelling of PET containers of capacities from 0.2 to 3.0l, running up to 36,000bph. The system on its stand will feature an eight-cavity stretch-blowmoulder, producing 0.5l PET bottles from 11g preforms. The bottles will be filled and capped by a 66-valve electronic filler using ‘baseless’ technology and labelled with adhesive sleeves. Bottle transfer by direct ‘starwheel-to-starwheel’ handover eliminates the need for conveyors between the blower, filler/ capper and labeller. All Ecobloc Plus models are equipped with an air recovery system, which SMI says is an ecofriendly technology that cuts energy costs and provides up to 40% saving on high-pressure air consumption. The company will also be exhibiting a Smiflexi SK 350 F shrinkwrapper, running up to 35 packs/minute, combined with a Smipack’s HA40 handle applicator. Smiflexi packers are automated and controlled by Smitec division’s MotorNet System, based on a Sercos fieldbus. www.smigroup.it","@ID":48} "PREFORM PRODUCTION 20 PETplanet insider Vol. 12 No. 04/11 www.petpla.net Stars old and new in the heavens When we visited Manjushree in Bangalore India in 2008 the company belonged to the leading PET processors in the jars and non-food items sector (see PETplanet Insider 09/08). By way of a highlight, the Kedia family, the proprietors, have installed a multi-level plant for ketchup bottles. In those days there was no sign anywhere of PET for beverages. Today – a mere five years later - Manjushree is the largest manufacturer in India of preforms for the beverages industry. They have outshone all their competitors by far with what currently amounts to an overall consumption of PET of 36,000t/a. “We invest first and then get the orders in from the big multi-brands, Coca Cola and Pepsi Cola, whereas our competitors would rather have an order in the bag before making any investment“, is how Rajat Kedia, the son of the founder of the company Vimal Kedia, explains his company’s success. They were the first company to put pressure on Coca Cola in Bangalore to introduce the weight-saving Neckfinish PCO 1881. “We have funded the investment in the new moulds out of our own pocket; we didn’t receive any subsidy from Coca Cola“ Rajat went on. “Don’t go out looking for more money, look to enhance your sales volume“ is Kedia’s secret. They are the first and only company in India to have their own preform tools. Coca Cola in Bangalore converted in June 2010 and are very satisfied. As Coca Cola in India featured slightly higher levels of carbonisation, it was not clear whether other countries’ experiences with the 1881 could be transferred without any problems. Now, however, Coca Cola is looking to convert 3-4 plants in India each year. Beer packed in PET is no longer just a remote possibility in India and because the bottler has also adopted the weightsaving neck finish PCO 1881, beer is also poised to become a major topic as far as the Kedia family is concerned. In order to be able to manufacture preforms in these quantities, Manjushree has opted for Husky HyPET 96– cavity systems. “When we started out, two years ago, with the 96-compartment, everyone thought we were mad, today Coca Cola prefers to concentrate its enquiries solely on suppliers with 96-cavity moulds“ says Rajat. If the market continues to develop at this rapid pace, the first 144-cavity machines will be springing up in Bangalore. But not on the old premises any more. Manjushree is planning a new building close to Coca-Cola in the suburb of Bidad. A 40,000m² tract of land has been earmarked for develop-","@ID":22} "PETproducts 48 PETplanet insider Vol. 12 No. 04/11 www.petpla.net Upgraded design adds features on capper New England Machinery, Inc. (NEM), of Bradenton, Florida, USA, has introduced new design features of its rotary chuck cappers that are intended to make changeovers easier, reduce the machines’ footprint and cut dust-collecting areas. The new modular design upgrades include a compact frame, frameless guarding and tool-free changeovers. New machines also incorporate a high efficiency main drive motor, which is intended to save energy, a re-designed lift drive, an option for corrosive products, and an FDA lube option. Frameless guarding is designed to eliminate dust-collecting areas and is appropriate for pharmaceutical and clean-room operations. Similar machines can have interchangeable change parts, which allows operators to run the same product on multiple machines. The cappers now have electronic programmability, designed for easier setup and changeover. www.neminc.com Dry aseptics take step forward with non-objection from FDA Krones AG, of Neutraubling, Germany, has received a letter of non-objection from the FDA for a rotary dryaseptic PET-bottle filling system featuring H 2 O 2 (hydrogen peroxide) as the sterilising agent. The American Food and Drug Administration (FDA) test includes verifying microbiological safety when filling low-acid aseptic products in the range from pH 4.6 to pH 7. Krones’ process undertook a required validation procedure carried out by an FDAapproved ‘process authority’ with a rotary aseptic filling system in the low output category for one of Nestlé’s research centres in the USA, which led to the issue of the FDA non-objection letter. Krones is the first bottling line manufacturer able to provide a complete dry process featuring H 2 O 2 in compliance with the stringent stipulations applying in terms of sterilisation performance, residual concentration and shrinkage. The bottle and closure sterilisation process is completely dry and a seal sterilisation feature is also based on H 2 O 2 . The isolator, after it has been cleaned with caustic and rinsing water and then dried, is sterilised in a dry process using evaporated H 2 O 2 . This process corresponds approximately to the procedure adopted in the pharmaceutical industry. The machine has been validated for 48h of continuous operation. Subsequent cleaning and sterilisation takes 3.5h. www.krones.com OptiCheck sidewall and label inspection system Agr International, Inc., of Butler, PA, USA, has announced the introduction of its OptiCheck sidewall/label quality management system for plastic container production. The vision-based inspection and measurement system uses multiple high-resolution cameras in conjunction with long-lasting LED lighting, for 360° inspection on bottles that are translucent or opaque. It is designed to take into consideration day-to-day variations in the production of plastic containers, including product changeovers, colour changes and limited line space. Defects that can be detected by the system include folds, contamination, foreign materials, opaque spots, holes, missing or distorted features, flash and label defects. It is designed specifically for bottle measurement and inspection applications, as well as process control. It is presented as a ‘drop-in-place’, ready to operate inspection system, using established bottlespecific test and measurement routines, so does not need custom programming. Modules are available for high-accuracy on-line finish gauging, seal surface defect management, and sidewall and label inspection, which can be performed at the same time as general sidewall defect detection. Agr says that the OptiCheck is appropriate for in-mould labelling processes, as bottles and labels can be inspected as a complete unit. The system is designed for use in tabletop conveyor applications and features a high-resolution touch-screen user interface. www.agrintl.com Label removing machine Herbold Meckesheim USA, a subsidiary of Herbold Meckesheim Germany, has announced the launch of a new Label Remover machine, which is designed to remove wraparound polyvinyl chloride (PVC) labels from PET bottles. The machine achieves complete removal of labels and adhesives from bottles through friction between exchangeable rip-off elements bolted to the rotor and exchangeable pins fitted to stator elements. The design of the chamber has no spaces where bottles might pass through without undergoing full frictional contact and there are no surfaces to constrict the bottle flow, which reduces the possibility of damage to bottles. The design ensures even loads and dwell times as bottles are advanced by the rotor. The machine enables need for extra steam generation. The label remover is available with two different capacities - 4,500 or 8,000 kg/hr. it has been designed for ease of access for parts exchange, the self-aligning roller bearings are mounted outside the housing to minimize contamination and anti-vibration mounting pads are standard. Herbold Meckesheim USA says that the removal of almost all wraparound labels early in the recycling process saves money downstream, where cutting blades will stay sharp for longer because they won’t be dulled by label residues. www.herbold.com","@ID":50} "BOTTLE MAKING 30 PETplanet insider Vol. 12 No. 04/11 www.petpla.net New bottle designs and integration of intelligent ventilation systems could help to reduce the amount of compressed air used. Tests also focused on the aspect of compressed air recycling through Airback systems. The Okertaler mineral water bottling plant uses two air recycling systems. Some of the compressed air in the newly inflated bottles in Airback System 1 is extracted and used to blow mould new bottles in Energy-saving potential of the InnoPET Blomax Series IV as opposed to Series III technology other stations. Airback System 2 regulates the recirculation of residual compressed air back into the compressed air system itself. A reduction in compressed air consumption of 31% is estimated. An additional 5% saving can be predicted if the there is a change in the shape of the bottle; in total, this would result in 36% less compressed air consumption, which, in turn, generates a yearly cost cut of €26,000 at €0.10 per kWh. Results First results show that considerable savings in materials, electricity, and compressed air can be made.criteria and characteristics have been defined and the current state of the stretch blow moulder, which is equipped with state-ofthe-art measurement systems, has been recorded and consumption has been minimised. The remaining project objectives are to continue to assess and optimise the amount of material, energy, and compressed air, and also to research new heating technologies. Final results will be published at the end of 2011. www.khs.com PET bottles undergoing a top load test using finite element analysis For further information please contact: [email protected] www.gabriel-chemie.com Innovation Don’t compromise on quality. PremiumMasterbatches for Superb Products. Kielce, 24–27 May 2011 VISIT US AT P LASTPOL !","@ID":32} "TRADE SHOW PREVIEW 42 PETplanet insider Vol. 12 No. 04/11 www.petpla.net interpack 2011 Interpack 2011 will take place from May 12 to 182011, in Düsseldorf, Germany. About 2,700 exhibitors from roughly 60 countries are expected, who, with a good 174,000m² of net space, will again be occupying all 19 halls of the Düsseldorf exhibition centre. Interpack 2011 is presenting packaging and process solutions for companies in numerous sectors including food and beverages, confectionery and bakery products, pharmaceuticals and cosmetics, non-food consumer goods, industrial goods and related services plus packaging materials and their manufacture. You can read below details of some of the exhibitors involved in PET packaging. www.interpack.com Aseptic blow fill system GEA Procomac has developed ABF (Aseptic Blow Fill system), a rotary aseptic blow moulding machine with an integrated aseptic filler and capper. The ABF will be officially launched at Interpack. ABF can blow and fill up to 48,000bph and operate at different levels of decontamination. This allows the filling of products with different shelf lives to be produced on the same system. ABF can be used for ambient or cold-fill operations. Preforms are being sterilised with hydrogen peroxide at the exit of the oven; This sterility is maintained throughout the whole blowing capping and filling process. This minimises the use of chemicals, requires no bottle rinsing, enables a simpler and smaller layout and reduces energy consumption. The Airstar, a sterile and aseptic blow moulder, is an integral part of the ABF system. ABF has integrated GEA Procomac’s Fillstar volumetric electronic filler fitted with magnetic flow meters. The Fillstar can fill any beverage including products with pulp, fibres or fruit pieces. The bottles are neck handled throughout filling and capping. The first GEA Procomac Airstar 10 integrated with a Fillstar FX mod. 100.15.113 will be started up in Poland within a few months on a production line for still drinks, fruit-based products and flavoured water.. The line has an output of up to 17,000bph for 1.5l, 1.75l and 2.0l PET bottles. www.procomac.com Oval shape with single stage Nissei ASB will be showing its one-step stretch blow moulding machine ASB-12N/10 for the fully automatic production of medium and small sized plastic bottles. Nissei will be demonstrating the production of a 250ml oval PET bottle with an extremely short neck finish to fit a low profile snap on flip-top cap. The ASB-12N/10 one step stage injection stretch blow moulding machine has been designed to mould a variety of bottles such as cosmetics, health care products, medicines and food stuff in relatively small quantities. Throughout the entire duration of the exhibition Nissei ASB GmbH will also have an open house during which it will demonstrate the double blow re-heat blow moulding machine HSB-6M producing a 350 ml wide mouth hot fill jar, ideal for jams, marmalade, pickles and a wide range of sauces. www.nisseiasb.co.jp GEA Procomac Hall 13 Booth 13 E78/E90 Nissei ASB Hall 11 Booth E56 Gernep GmbH Hall 13 Booth A45 Latest offers in labelling Gernep, from Southern Germany, will be showing two different machines for wraparound labelling: the Rollina model for contact-free application of pre-cut paper or plastic labels from label magazines; and the Rollfed model, for labelling of OPP labels from label roll. End gluing is undertaken by a continuous adjustable end-gluing ledge at the end of the label magazine. Closed gluing systems mean that the entry of any foreign matter is effectively prevented, reducing cleaning and maintenance. The Labetta SK labelling machine uses servo drives located at the dispenser to transfer labels precisely and smoothly. It is suitable for exclusive label designs, the ‘no-label’ look, and for water resistant plastic labels. A sister machine, the Labetta, offers wet-glue labelling. Labetta Combi offers a combination of wet glue, hot glue and selfadhesive labelling. www.gernep.de","@ID":44} "BOTTLE MAKING 27 PETplanet insider Vol. 12 No. 04/11 www.petpla.net Use PETpla.net Zoom to pinpoint the machines and tools used in the manufacturing process and enjoy the first scientific analysis of PET bottles, wherever they are produced, worldwide. PETpla.net Zoom uses around 75 criteria for the detailed evaluation of weight, geometry, caps, preform manufacturers and the preform employed. All data, facts and figures on PET bottles are prepared for you in bite-sized chunks. Select all countries important to your PET business from the database and get our best offer today. www.zoom.petpla.net The findings from the study are consistently being refined. In addition, methods of analysis are being developed with a view to making it possible to tap into further data of relevance to the industry. Any suggestions as regards the study will be welcomed. Similarly, the potential also exists for analyses that are topic-related and tailored to company-specific problems (Fig. 5). 27 See our expertise for yourself at Interpack 2011 Düsseldorf – Hall 9 / Stand G10 MANN+HUMMEL ProTec GmbH Stubenwald-Allee 9, 64625 Bensheim/Germany Tel. +49 6251 77061-0 E-Mail: [email protected], www.mh-protec.com Injection moulding or extrusion: Superior materials processing will add more value to your operation! supply capability – for everything from individual parts to complete handling systems: Conveying Drying Crystallization Dosing Cutting SOMOS® Fig. 5: Breakdown of the different types of labels by country, type of label and label material","@ID":29} "MATERIAL / RECYCLING 11 PETplanet insider Vol. 12 No. 04/11 www.petpla.net ated, but also on the self-wiping capability, conveying characteristics and stress applied to the material [1]. Volume flow calculation The volume flow rate has an important role in the calculation of the pressure at the tip of the screw and the power requirement of the system. The appropriate equations were developed, based on the conservation laws and the respective geometric conditions. In the case of the Erdmenger profile, the equation could no longer be solved analytically and it was necessary to use computational methods. The use of a computer program for the calculation is always necessary for a conical system, since the geometric and processing conditions change with the axial position. Back pressure length The back pressure length is a critical design parameter for the pressure build-up zone. If there is insufficient length in the pressure build-up zone, the preceding zone (frequently a venting/degassing zone) experiences an overflow. The back pressure length can be determined by transforming the pressure equation [1]. The length required for the conical system is defined by the maximum pressure at the tip of the screw for a specific volume flow. If this length is not provided, the discharge zone can no longer accommodate the material being conveyed, and material is forced out of the vent opening. Over 140 years of added value through innovative technology and reliability Consultancy | Turnkey systems | Single machines | Service Hall 14, Booth A14/B15 May 12–18, 2011, Düsseldorf Pass ion for Packaging. The new shrink packer: KHS Innopack Kisters SP Focus on saving energy and resources: Next-generation, film-wrapped multipacks - Fully closed shrink packs for maximum packaging stability - Cardboard pads and trays no longer necessary Direct online printing on the shrink film for reliability and flexibility New shrink tunnel for considerably reduced energy consumption khs.com Werner A., Christian S., Ernst W. Packing technology design engineers „Our Baby – Your Benefit“ Figure 1: Shear rate and dissipation in the discharge zone","@ID":13} "NEWS 9 PETplanet insider Vol. 12 No. 04/11 www.petpla.net Colormatrix receives industry recognition for recyclability in PET additives The European PET Bottle Platform (EPBP) has recognised the recyclability of ColorMatrix’s oxygen scavenging HyGuard and light blocking Ultimate UV technologies by concluding that they will have “no negative impact on current European PET recycling”. The EPBP aims to evaluate technologies and products and to enable new PET packaging innovations. It also looks to optimise the economic and environmental consequences for the European PET recycling industry. HyGuard is not based on an oxidisable polymer like conventional oxygen scavengers. A catalytic barrier system, it works in conjunction with the bottle closure system, leaving the container wall free of any additive material which may have a negative effect on container clarity and limit its recyclability. Based on current market knowledge and assuming a market penetration of 10%, the EPBP concluded that the HyGuard catalyst formulation HyCat-1 would have no negative impact on current European PET recycling at its maximum use level of 0.1%. In addition, closures containing the activator portion of the HyGuard technology were found to float on the washing water and are therefore removed as normal during the sink/float step of the recycle process. Ultimate UV390 provides an effective UV barrier allowing less than ten per cent UV light transmission up to 395nm - the edge of the visible spectrum. . The EPBP’s evaluation concluded no negative impact on recyclability for Ultimate UV 390-1 and Ultimate UV390.CC-1 at addition rates of 0.15%. This endorsement follows APR (Association of Post Consumer Plastic Recyclers) recognition for HyGuard and Ultimate UV technologies as fully recyclable under its strict Critical Guidance guidelines. www.colormatrix.com La Seda de Barcelona, S.A. sells stake in Evertis, SGPS, S.A. Spanish PET producer La Seda de Barcelona has announced that it has transferred its 20% shareholding in Evertis, the barrier film company, to Moura Consulting S.L. A minimum price of €3 million has been agreed; the final price will be based on five times Evertis EBITDA for financial year 2013. The sale is part of the company’s strategy for disposal of non-core assets, in accordance with the restructuring plan agreed at the shareholders’ general meeting held on December 17, 2009. www.laseda.es Think about it. Is your hot runner supplier just a supplier, or your partner? moldmasters.com/thinkaboutit [email protected] Mold-Mastersand theMold-Masters logoare trademarksofMold-Masters (2007)Limited. ©2011Mold-Masters (2007)Limited.All rights reserved. Large or small, complicated or simple, Mold-Masters has the depth, breadth and innovative problem solving to bring all your designs to production. As the world’s leading hot runner manufacturer with the most responsive customer service in the industry today, Mold-Masters offers a level of harmony you know you can trust.","@ID":11} "BOTTLE MAKING 28 PETplanet insider Vol. 12 No. 04/11 www.petpla.net Research into energy-optimised stretch blow moulder Faster stretching, lighter bottle Improving energy efficiency in production processes is of great interest to bottlers and PET bottle makers alike. Every year the German Federal Ministry of Education and Research (BMBF) sponsors industrial projects in this field. In 2009, a group of stretch blow moulding experts jointly submitted a grant application under the title “Increasing Energy and Resource Efficiency in the Manufacture of PET Bottles”. The team consists of KHS Corpoplast, the Institute for Plastics Processing (IKV), AdPhos Innovative Technologies, and Okertaler Mineralbrunnen, a mineral water bottling plant. The project is schedule for completion in 2011. Weight, electricity, and compressed air Each year, around 25 billion PET bottles are made in Germany alone, and around 500 billion worldwide. The manufacture of 1kg of PET requires approximately 1.9kg (4.2 lbs) of oil and 23kWh of energy. In light of these facts the team focused on three main fields where the highest energy savings could be expected: weight of the preform/bottle; energy consumption during preform heating; and compressed air. Practical tests have been performed, analysed, and optimised on a KHS Corpoplast InnoPET Blomax Series III, with 14 blow stations and up to 25,000 PET bph capacity. The machine is installed at Okertaler Mineralbrunnen. Fast stretching increases strength, allows weight reduction The material content offers the greatest potential for energy savings and cost reductions. As a rule of thumb, 70% of the costs of a PET bottle can be attributed to the amount of material used. Preform production and actual production of the PET bottle account for a further 15% of costs. Reducing the weight of a PET bottle is important both for its economic competitiveness and in reducing its energy consumption. Prduction of a PET bottle involves stretching in both axial and radial directions. The team analysed the way that the properties of the PET bottle changed when the biaxial stretch of the PET material was altered. The result: the material’s orientation is the highest when stretched at the highest possible speed, i.e. the strength of the PET material increases when it is stretched rapidly. In this particular case, the faster stretching results in an improved PET strength of around 10% for the Okertaler bottle. This greater strength and higher orientation allows the design of lighter PET bottles. If stretching at speed results in 10% increase in strength, then this would mean that future 1.5-litre PET bottles could become 3% lighter. The weight of each PET bottle would thus drop from the current 31g to 30g. 1g less material per bottle would lead to a considerable saving of 100,000kg (roughly 220,500lb) of material per annum, assuming approximately 100 million bottles are produced per year. At a market price of €1.20 for 1kg (2.2 lb) of PET, the annual amount saved would be €120,000. The design of the PET bottle is also important, as the specific shape can help to use less material. During the course of the project, the shape of the Okertaler PET bottle was redesigned with the help of KHS Corpoplast ‘Bottles & Shapes’ program . To date, the company has optimised around 9,000 PET bottles using this program. Optimised preform heating can reduce energy consumption 15 to 20% The second decisive factor was the amount of energy required to heat 1kg (about two pounds) of PET. An important consideration is the fact that the preform mouth is not heated in the stretch blow moulder and thus not altered, meaning its weight can be deducted from the weight of the overall preform when calculating the total weight to be heated. Thus if a preform weighs 25g and its mouth 5g, only 20g needs to be included in Development in the weight of 1.5l PET bottles over the last ten years Development in the amount of energy used for preform heating over the last ten years Development in the inflation pressure used to manufacture PET bottles over the last ten years.","@ID":30} "NEWS 7 PETplanet insider Vol. 12 No. 04/11 www.petpla.net ‘60 not out’ for CCL CCL Label Gmbh, founded in 1951, is celebrating its 60th anniversary this year. It currently operates 60 production facilities worldwide and has approximately 5,800 employees, CCL is the largest converter of pressure sensitive and film material for label applications and also produces aluminium aerosol bottles, cans and extruded plastic tubes. www.cclbeverage.com Sidel creates South Africa subsidiary The Sidel Group has established Sidel South Africa, a new subsidiary company, which is based in Johannesburg and will serve customers in all countries in southern Africa, as far north as Tanzania. The company has had an agency presence in the country for 30 years and has an installed base of more than 400 pieces of equipment. Sidel’s presence is mainly in the CSD, beer and converters segments. The beer market is forecast to grow by 5.4% a year from 2010 to 2014, and carbonated beverages to expand at 1.6% annually. Sidel marked the establishment of its new subsidiary with a one-day event in October 2010, held at its offices in Johannesburg, entitled ‘Sustainability in Packaging’. www.sidel.com Resilux increases profits and raises dividend Resilux, the Belgian manufacturer of PET preforms and bottles, has announced rises in sales volumes, turnover (revenues) and profits in 2010. Sales volumes increased by 10.3% compared to 2009, with the strongest growth being seen in Spain, Central Europe and Russia. Turnover rose by 15.9% to €233.6 million, attributed to both increased sales volumes and to rises in raw material costs. Resilux is able to pass on fluctuations in raw material prices to its customers. The total number of employees has also increased, by 47 full-time equivalents. Total cash costs are reported to have increased by 4.2%. Pre-tax profit was €14.8 million, €1.4 million higher than 2009; profits after tax were €12.8 million. The company increased investment in fixed assets in 2010, to €12 million (2009: €11 million). Major investments included increased machinery and mould capacity, and start-up costs for the Air0Pack joint venture with Air0Lux AG. Resilux expects deliveries of Air0Pack to commence in 2011. Net financial debt rose to €30.5 million at December 31, 2010 (2009: €22.7 million) which the company attributes to increased working capital. A dividend €1.65/share is proposed, up 10% over 2009. Resilux expects 2011 results to be in line with those of 2010. www.resilux.com Visit us: Hall 13 Stand B73/C74 Performance www.sipa.it","@ID":9} "imprint EDITORIAL PUBLISHER Alexander Büchler, Managing Director HEAD OFFICE heidelberg business media GmbH Landhausstr. 4 69115 Heidelberg, Germany phone: +49(0)6221-65108-0 fax: +49(0)6221-65108-28 [email protected] EDITORIAL Doris Fischer [email protected] Michael Maruschke Ruari McCallion Ilona Trotter Wolfgang von Schroeter Anthony Withers MEDIA CONSULTANTS Ute Andrä [email protected] Martina Hischmann [email protected] Ursula Wachter [email protected] phone: +49(0)6221-65108-0 fax: +49(0)6221-65108-28 France, Italy, Spain, UK Elisabeth Maria Köpke phone: +49(0)6201-878925 fax: +49(0)6201-878926 [email protected] LAYOUT AND PREPRESS Exprim Kommunikationsdesign Matthias Gaumann | www.exprim.de READER SERVICES Kay Krüger [email protected] PRINT Chroma Druck & Verlag GmbH Werkstraße 25 67354 Römerberg Germany WWW www.petpla.net | india.petpla.net PETplanet insider ISSN 1438-9459 is published 10 times a year. This publication is sent to qualified subscribers (1-year subscription 149 EUR, 2-year subscription 289 EUR, Young professionals’ subscription 99 EUR. Magazines will be dispatched to you by airmail). Not to be reproduced in any form without permission from the publisher. Note: The fact that product names may not be identified as trade marks is not an indication that such names are not registered trademarks. 3 PETplanet insider Vol. 12 No. 04/11 www.petpla.net Material savings are everywhere. Here is the automotive industry repeatedly insisting that it wants to build lighter cars and thus reduce fuel consumption, yet research by our sister publication polymotive - polymers in the automotive industry – reveals that in the past ten years there has been no reduction in the weight of the automobile. Very different from the situation in the beverages industry. No promises here about reducing the weight of PET bottles, weight is continually being reduced. The key factor in accelerating this trend in recent years has been the caps. With the introduction of lightweight closures for CSD and still water, new neck geometries have taken the market by storm. Assuming conservatively a weight saving of 5g per bottle, this means some 2,000t less plastic is being used. The process is in full swing, regional suppliers with their flexible structures have recognized their advantage and are moving quickly. The multinationals meanwhile are following slowly. In addition to the more complex internal decision-making, another reason for their lagging behind may be that Coca Cola bottlers may be unwilling to pay their preform and cap producers for the high tooling cost of the new neck geometries. A preform producer told us: „Don’t ask Coca Cola for a higher price, higher volume is their aim.” This raises the question whether such a policy does the brands more harm than good. First: From a financial perspective, material savings would cover new tooling costs many times over. Second: The end user will vote with their wallet. On the supermarket shelf, a PCO 1881 looks elegant with its sleek design, in stark contrast to the PCO 28 with its square, chunky shape. Added to this, using an unnecessarily large amount of material is damaging to the environment not only during manufacture, but also transportation and, ultimately, when the bottle is consumed. This is diametrically opposed to a number of bottlers who have nailed their colours to the environmental mast. The major Coca Cola bottlers have all acknowledged this, and have made the change or will shortly do so. For many small regional bottlers of the multinational brands there is as yet no sign of a re-think. Let’s hope for a change of heart. Yours Alexander Büchler EDITORIAL dear readers, EDITORIAL","@ID":5} "BOTTLE MAKING 25 PETplanet insider Vol. 12 No. 04/11 www.petpla.net mixed drinks and mineral water in equal parts, however these bottles are on average 2/3rds heavier than the Kenyan ones (Fig. 1.) By contrast to the bottle weights, when it comes to the caps we find ourselves looking at a considerably more homogeneous picture, the slight deviation in the case of Kenya 0.5l is due to a few beverage caps. Particularly where 1.5l bottles are concerned, Egypt, like Germany, demonstrates the phenomenon whereby the weight of the lid has been optimized to a greater extent than is the case with the 0.5l and 1l bottles. Here too a correlation between the heights and weights of the caps is also discernible. By contrast to this, where the South African bottles are concerned, the fact that the caps are not so tall on the 1.5l bottles is not reflected in lower weight ratios (Fig. 2). It is interesting to undertake a quality-based study of the African bottles by comparison to Germany. Here we have used orange peel on the neck and base of the bottle as a basis for comparison. Whereas, in the area of the base, relatively high error margins were identified universally, a very mixed picture emerged in the visual area at Fig. 2: Average weight of bottles based on volume and country of origin [g]","@ID":27}]}}
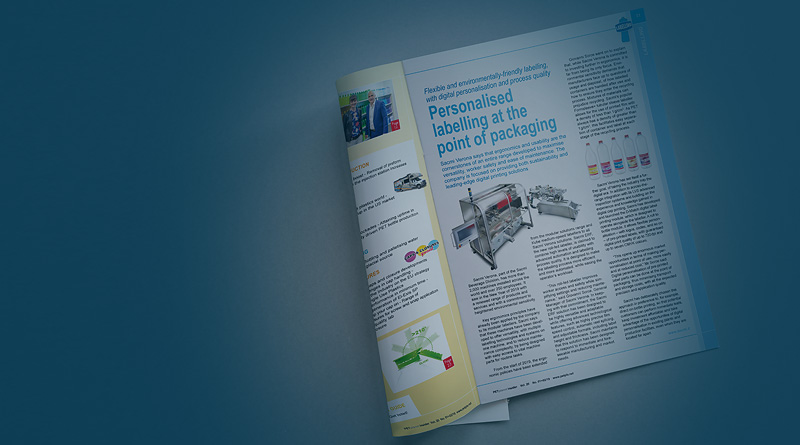