{"pages":{"page":[{"#text":"BOTTLING / FILLING 36 PETplanet insider Vol. 12 No. 11/11 www.petpla.net Worldwide beer consumption rising Global beer consumption is set to rise by approx. 3% a year by 2015. If this comes about, worldwide beer consumption could top the 2 billion hectolitre mark as early as 2013. Growth rates are expected to be highest in Asia and Africa, where an increase of some 5% per year is anticipated in each case. Asia would then have a share of 38% of world beer sales by 2015. Annual growth of 3% is expected in Latin America and 1.5% in Eastern Europe. The West European beer market is the only market that is forecast to stagnate by 2015. Although declining beer consumption is on the cards for Germany, the Netherlands, France and Great Britain, beer still has potential in Finland, Italy, Norway, Portugal and Spain (source: Canadean). A closer look at sales figures for worldwide beer consumption broken down by brewing groups shows that the four largest brewing concerns, Anheuser-Busch InBev, SABMiller, Heineken and Carlsberg, alone account for about 42% of worldwide beer consumption. According to Grupo Modelo, the most important beer brands in the world are Budweiser, Snow, Skol, Miller and Corona. Within Europe, the Czech drinker holds first place for per capita consumption with 142.4l ahead of Austria with 108.1l and Germany. An interesting feature of the Polish market (87.3l per head) is a packaging phenomenon unique in Europe. Hard to believe it may be, but 40 % of beer in Poland is sold to consumers in cans; a percentage unparalleled in any other European country . Reason: the can scores in Poland with its high convenience level and is simply “in” among young people. Meanwhile in Russia, beer consumption in Russia dropped to 73l per head in 2010 (source: Canadean). Vodka – the most popular spirit internationally A study by the British International Wine and Spirit Research (IWSR), expects worldwide consumption of spirits to rise by approx. 2.2% from 2010 to 2014. About 4.8% growth is expected from Asia, which already enjoys a 44.6% share of the worldwide spirits market today. Vodka was the most frequently drunk spirit around the globe in 2010. Growing popularity of wine The three leading wine nations, France, Italy and Spain, accounted for around half of the wine produced worldwide in 2010. China occupiedseventh place among the world’s biggest wine nations. Chinese wine production is expected to grow by another 77% from 2010 to 2014. Up to now, however, high quality wines are lacking in China. Worldwide wine consumption can be expected to increase by about 3.2% by 2014. Approx. three quarters of the increased consumption of still wine, which makes up 92.6% of worldwide wine consumption, is expected to be shared among the USA, China and Russia. The USA is forecast to be the biggest market for still wines in 2012 – still ahead of Italy and France. Sparkling wines held a 7.4% share of worldwide wine consumption. With approx. 5.6% more by 2014, they are expected to grow at an even stronger rate than still wines. Germany currently occupies ninth place among the world’s wine-producing countries – although the 2010 crop was poor in terms of quantity. German wine consumption is forecast to grow by approx. 0.5% by 2014 (source: IWSR study).","@ID":38} "BOTTLE MAKING 18 PETplanet insider Vol. 12 No. 11/11 www.petpla.net to the attention of mainstream brand owners. The first commercialisation was a ball-shaped bottle used by Ohio Wesleyan University to help commemorate the signing of baseball legend Jackie Robinson by Branch Rickey (OWU ’04) of the Brooklyn Dodgers. Target markets Emergent envisions a wide variety of applications for the Smiler concept. In addition to vended snack and drink combos, after-the-game treats for youth sports, fund-raising tools and other promotional products, the bottle can be used to promote health and wellness, and even humanitarian causes. It is possible, for example, to insert a twoweek supply of water purification tablets in the bottom cavity and air drop bottles into disaster areas even when roads are impassable and it’s not possible to land aircraft. The top cavity can be used to collect locally-available water, while one of the purification tablets from the bottom cavity can create first-response, drinkable water. *Emergent Technologies is a business incubation services company that takes ideas from concept to commercialisation. The company partners globally with subject matter experts and firms to assist its clients in bringing products to commercialisation. www.emergent-technologies-us.com www.plastictechnologies.com Interview with Scott Steele PETplanet: How does the Smiler concept compare to other dual chamber packages? What are the differences or similarities? Scott Steele: The Smiler concept allows for packaging dissimilar amounts of the products easily. The forming technology is essentially standard with little or no impact on production speeds. No secondary forming is needed for the package. PETplanet: What kind of specialized filling and sealing systems are required for this package? Scott Steele: None is anticipated for the main chamber, assuming it’s filled with a still beverage of some type. And Emergent can tell you about the filling and sealing systems required for products going into the secondary cavity. They’ve done an extensive amount of research on the systems needed, and every piece of equipment needed for high production runs is already available on the market. PETplanet: Does this technology also require a unique preform design or can a stock preform be used? Scott Steele: There is nothing to rule out stock-preform use. A stock production preform was used for the ball-shaped concept bottle. There are some additional restrictions on sizing the preform compared to standard bottles. PETplanet: Can you use standard PET resins with this technology? Scott Steele: Standard PET resins have been used in producing sample containers so far. PETplanet: Does it work for barrier (multilayer) packages? Scott Steele: Yes, barrier additives or multilayer preforms could be used in the bottle. PETplanet: Is there a secondary operation which forms the base? Scott Steele: No, it’s formed with the rest of the bottle. PETplanet: As regards the bottle shape, are there any variations possible? Scott Steele: The blow moulded container could also have a noncylindrical footprint. It doesn’t necessarily have to have a ball or spherical shape. Moreover, vertical, contoured or tapered wall designs can be made. PETplanet: If the machinery to blow mold/thermoform the two components is new, who developed the equipment? Scott Steele: We produce the package on Standard Sidel SBOseries blowmoulding machines. The thermoforming equipment is also not a specifically developed machine. PETplanet: If the machinery isn’t new, but only modified, can any PET blow moulding equipment be used to blow the bulb? Scott Steele: We produce the package on Standard Sidel SBOseries blowmoulding machines and would depend on the bottle design.","@ID":20} "BOTTLES 51 PETplanet insider Vol. 12 No. 11/11 www.petpla.net Shower gel for kids The health and beauty discount store Müller of UlmJungingen, Germany, has put 300ml shower gel for kids in a PET bottle on its shelves. The bottle features printed Nolabel-look labels designed to appeal to kids and is closed by means of a snap-on, colour-coordinated hinged lever lid that can be operated using one hand only. www.mueller.de Oil for the muscles Under the brand name ”aptonia“, the sports goods specialist Decathlon headquartered in Villeneuve D’Ascq is marketing 150ml of warm-up oil with a slight pink tinge in a PET bottle characterised by its distinctive shape. The bottle has two information labels which are adapted to the shape of the pack and a white hinged lid that can be operated using one hand only. www.aptonia.com Gentle care Under the brand name “Vichy“, Vichy France based in Asnières is offering 200ml of gentle shower gel with extract of rosebuds in an elegant-design, 200ml PET bottle. At the front the bottle features a No-labellook label and a 2-colour snap-on hinged lid complementing the shape of the pack rounds off the “Facing“ at the POS. The one-hand operation lid is easy to operate and indicates the respective closure status by means of a “clicking sound”. www.vichyconsult.com","@ID":53} "BOTTLING / FILLING 34 PETplanet insider Vol. 12 No. 11/11 www.petpla.net The driving force behind the rising consumption of soft drinks remains Asia with a quarter of world consumption. India excelled in 2010 with growth rates of 16%, followed closely by China with 14%. North America accounts for one fifth of worldwide sales – with slightly declining consumption in 2010. Also growing extremely strongly, but from a low level is the African market and the Middle East with under 10% of world consumption. Whereas 35l/per head of soft drinks are currently bought in Asia, the figure in Africa and the Middle East is still fewer than 10l per head. People in Latin America also enjoyed soft drinks in 2010. The overall 5% growth there is driven by the Brazilian market, which accounts for 30% of sales in Latin America. Brazil achieved 7% growth in 2010. The East European market has made a significant recovery, especially Russia. Sales in the West European market for soft drinks fell by less than 1%, but from the very high level of 18% of worldwide sales. From an overall viewpoint, the BRIC countries particularly are likely to be the soft drink markets of the future. Whereas they accounted for just 12% of global sales of soft drinks at the turn of the millennium, their share had already risen to more than 20% by 2010. Another rise to up to 25% is forecast by 2015 (source: Canadean). If global sales of soft drinks are broken down by drink categories, fruit juices, fruit juice drinks, sport drinks and carbonated drinks achieved slight growth in 2010, and bottled water a more appreciable rise of approx. 4%, which means bottled water accounts for 30% of the worldwide consumption of soft drinks. Energy drinks excelled with double-digit growth rates. The markets in Western Europe with the strongest growth in this segment are Denmark, France and Norway. Water with added benefits is becoming increasingly popular and sales have more than doubled since 2005. The focus is on primarily three markets with a share of 80% of the global volume: Germany, the USA and Japan. Whether added vitamins, minerals, fruit or oxygen, water with added benefits is available in a wide variety of formulations – completely adapted to consumers’ wishes in the different regions of the world. Around 30 billion litres of RTD (ready-to-drink) tea drinks were consumed worldwide in 2010. The four markets of China, Japan, the USA and Indonesia accounted for three quarters of total worldwide sales. More growth is expected in the next few years (source: Euromonitor International). The world beverage market for soft drinks, beer, wine and spirits The world of drinks In the run-up to Brau beviale, the organisers, Messe Nürnberg, published some figures about worldwide beverage consumption. The global consumption of soft drinks in 2010 was more than 550 billion litres, with a global per capita consumption of around 80 litres. After the rather lean year of 2009, sales of soft drinks increased by just under 4%. About one third of all drinks sold worldwide are soft drinks, and approx. another third are hot drinks. The remaining one third is divided almost equally between milk and alcoholic drinks.","@ID":36} "PETproducts 46 PETplanet insider Vol. 12 No. 11/11 www.petpla.net Moretto S.p.A. Via dell’Artigianato 3 - 35010 Massanzago (PD) ITALY Tel. +39 049 93 96 711 - Fax +39 049 93 96 710 www.moretto.com The innovative shape of the OTX hopper solves the falling flow problems of the granules and permits to keep the drying process under control. designed by Moretto Drying Revolution Stand 7A - 431 PETsleeve recycling solution ratified Sleever International’s PETsleeve solution for recycling biodegradable plastic films has been ratified by four leading waste collection and recycling companies: Cleanaway in the UK, Unisort in Germany, Returpack in Sweden and Visy in Australia. PETsleeve is based on TPE-G and -S films and was developed after 24 months of research. Trials conducted on standard bottles for carbonated and pasteurised drinks in the recycling circuits of these four countries showed that, thanks to a density lower than 1 (compared to an average of 1.3 for PET), the PETsleeve comes off the container by gravitation, automatically and completely. Sleever International says that this makes it possible to recuperate a 100% recyclable PET resin, which can be used to manufacture new bottles of identical quality. PETsleeve is currently the only PET decorative solution in the world holding recylcability ratification. The approval is valid for all its markets. The solution is being used for Aquarius, Coca Cola’s energy drink, in Belgium; Carlsberg Festis in Sweden; and Fruitval fruit juice for Andros in France. PETsleeve is adapted to helio-engraving and UV flexography printing in up to ten colours on both sides. With low density (solvent free) inks, PETsleeve can be implemented automatically on steam shrink Powersteam or infrared Powerskinner machines at speeds of between 15,000 and 30,000 bottles/hour. www.sleever.com High-speed, low-level palletising system Sidel says that its new high-speed SP 1000 HS palletiser offers the same level of performance in a low-level palletiser as operators have previously experienced only from high-level machines. The company says that it has adjusted and upgraded its existing machines and processes and integrated intelligent software for improved productivity. The core of the improvement is in making the layer preparation and palletisation functions work together faster and more effectively. Sidel’s new patent-pending ‘pusher’ is able to guide the layers alternatively to the right or to the left, while optimising the ‘return stroke’ time, traditionally an’empty’ movement. The process is supported by a new software program, named Place (Pallet and Layer Automated Configuration Editor). It creates and manages diverse pattern configurations before the layer-formation phase. Sidel says this is particularly useful for short-batch runs. The software can be installed either on the touch screen operator panel or on a PC and is compatible with Sidel’s Robo-Smart and Axo-Smart layer-preparation systems. Sidel’s Robo-Smart and Axo-Smart form and prepare the layers as the packs come off the production line onto the conveyor belts. Layer, bottle and pack format changeovers are entirely automatic and software-managed; the operator simply chooses the required format on the operator panel controls and there is no need to stop the line. Any danger of packs falling due to oscillation has been minimised, as the device handling the pack travels at exactly the same speed as the surface on which the product travels. The SP 1000 HS palletiser permits use of either Robo-Kombi or Robo-Column, which physically picks up the packs and places them on the pallets. Sidel says that both solutions offer highspeed operation, integration with existing solutions, and versatile gripping for working with different formats, including shrink-wrapped packs and empty PET bottles. www.sidel.com","@ID":48} "BOTTLES 49 PETplanet insider Vol. 12 No. 11/11 Banjo bottles The Private Label Foods, Inc, filling line for Savory Collection Dressings and Marinades is achieving faster running speeds since TricorBraun sourced new banjo bottles for the company. Private Label had been experiencing up to 25% deficiency on the line because of crushed bottles and panelled shoulders. The new 16-ounce, clear PET banjo bottle has a more even wall distribution and is closed with a polypropylene continuous-thread 38-490 closure that is both two grams lighter and costs less than the previous system. costly. The bottle is finished with a paper label with a shrink neckband. www.tricorbraun.org Vinaigrette in two phases 450ml red wine vinaigrette brand name “Isio 4“ is being sold by Lesieur France in an easy to handle PET bottle. The product content substances separate once more after standing for a certain period of time and this results in a kind of 2-phase product. In the lower part of the bottle the red wine vinegar settles out with the onions whilst, in the high visibility top section, the clear ingredients collect. Prior to each use the bottles must be shaken thoroughly. Two belly labels in the upper and lower section and a firmly attached snap-on, 2-colour hinged cap with a tear-off tamper-proof guarantee make the package complete. www.lesieur.com T E CHN O L O G Y T O OL I N G L IFE CY C L E P A C K A G I N G FLEXIBLE SOLUTIONS RELIABLE SUPPORT THINKING OF THE BIG PICTURE & THE MINOR DETAILS We don’t believe in delivering on one thing and not the other. At Sidel, we offer you the complete package of solutions for your business and the 24/7 support of a strong partner. From packaging development through filling right up to end of line, we bring everything to the table making sure that you receive the highest level of reliability and flexibility matched to the unique needs of your production line. WORK WITH US & GETA BETTER MATCH www.sidel.com","@ID":51} "The inspection machines manufactured by P&S Technology are installed on the production line for inspecting preforms using for PET PET bottles. The inspection and ejection process of machines is automatic and there are variety of machine speed suitable for customer‘s production line speed. Especially PS-21GP series 3 recently having a good sales results provides lots of advantages for customers. The machine‘s maximum speed is 48,000PPH and there is no need to change parts as per changing preform‘s body size because gripper neck handling type is applied to preform handling equipment. Mold number reading or gate cutting device could be equipped as an option inside of inspection system. We say it is two in one system., so customer can save cost and space. This inspection system is mainly designed for rotary type. This system intensively inspect not only preform body but also particle and defect of preform neck external. It use the patented ‚mirror tracking system‘ for the bottle body inspected, so customer can inspect whole surface of preform body without blind spot. P&S have another solution to inspect preform. PS21PSI Series 1 is haven’t mirror tracking system but applied “line scan camera” technology overcome the limitation by refraction of light of inspection scope. The whole surface of body inspection is guaranteed by 3 line scan cameras located 120 degree each without rotation. The gripper neck handling type on this series is applied to preform handling equipment, so there is no need to change parts. Rotary Type Preform Whole Surface Inspection System PS-21 GP Series3 Basic inspection area 1. Neck ¿nish 2. Body 3. Basement Available options 1. Gate Cutting device 2. Mold Number reading 3. Top support Ring Surface 4. Neck external surface Machine capacity 1. Low speed: ~300PPM 2. Middle speed: 300~500PPM 3. High speed: 600~800PPM Neck ¿nish Neck external Support Ring Body upper area Body lower area Basement Available options 1 Gate Cutting Device Available options 2 Mold Number Reading Screw Thread","@ID":34} "TRADE SHOW PREVIEW 45 PETplanet insider Vol. 12 No. 11/11 www.petpla.net B&W Solutions Hall 7 | Booth 841 Handles on multi-packs Messrs. B&W Solutions GmbH, Böblingen, Germany, will be presenting their handle mounting machine HDE 70/1. It is nine years now since the company started marketing machines which are supplied by the Italian manufacturer Comag and more than 200 installations have been installed worldwide. Now the company has developed its own machines. The first items of equipment have been supplied and installed to companies in the beverages sector. The models 35/45/60/70 and 100 cycles/min (both single and twin-track) cover the entire performance spectrum. These machines are used for attaching plastic handles to shrinkwrapped multi-packs. They are also targeting PET containers with their new machines. Around 40 to 50% of the PET bottling plants have a handle mounting device – these are the people we want to get through to with our machines“ says Managing Director Giovanni Berardi. B&W Solutions GmbH produces handle mounting machines and also markets Mosca products (vertical and horizontal pallet strapping machines) and special solutions associated with scanner applications from Leuze Electronics. At the beginning of 2012 B&W Solutions of Böblingen will be moving to Bietigheim, Germany, where they will commence operations on a production area of more than 1000m². www.b-w-solutions.com Doehler Hall 1 | Booth 303 A range of different tastes As a global producer, marketer and provider of technology-based natural ingredients, ingredient systems and integrated solutions for the food and beverage industry, Doehler will be showcasing around 100 new product applications. This includes for example a range of sweetening systems in the MultiSweet Plus product range, under the natural sweetening system MultiSweet Stevia. Moreover Doehler has developed lifestyle-oriented and cloudy beer mix concepts. The company will be introducing cider concepts with milder taste profiles and fruity, natural flavours, which meet the tastes of a wider range of customers. Doehler offers a comprehensive portfolio of alcoholic and non-alcoholic cider bases, in addition to innovative fruity wine bases. In the malt beverages sector, it will be presenting malt beverages that taste like beer, fruity-flavoured malt beverages, “Malta con Leche” and Kvass. Apart from these Doehler has developed energy drink concepts geared for success, such as new taste, juicy and coffee energy drinks. A portfolio of directly-brewed “Strong Tea Infusions” is presented together with the company “Plantextrakt”. The product concepts span from brewed iced teas and premium iced teas through to true teas. Orange, blood orange and grapefruit carbonate products with higher fruit juice content and optimised lemonades are also part of the extended portfolio. New concepts developments for Water plus beverages such as flavoured waters and aqua plus, providing the market with natural, fruity refreshment will also be on show. The focus in flavoured water concepts is on new fruit combinations. The new aqua plus beverages are based on the recent EU health claims. Visitors to the Doehler stand will have the opportunity to see and taste the new product applications themselves. www.doehler.com IN EVERY BOTTLE THERE IS ALL OUR KNOW HOW. RESEARCH & DEVELOPMENT A constant projection towards the future oriented to search not only for new materials but also new PET technologies of transformation and innovative materials. CONSULTANCY A concrete answer to all your questions. We put at your disposal all our know-how for every single requirement. PROTOTYPATION Prototypes of containers and innovative preforms in record times: you will be able to touch with your hands the bottles within a short time after approval of the design. DESIGN Creativity in search of elegance and refinement. Innovative designs, ergonomic structures, eye-catching and functional containers. We give a true shape to your product! HALL 7 - STAND 236/337 09-11 NOVEMBER BRAU BEVIALE 2011 NUREMBERG - GERMANY","@ID":47} "TRADE SHOW PREVIEW 44 PETplanet insider Vol. 12 No. 11/11 www.petpla.net Revolution in PET-extrusion! Conical co-rotating MAS-extruder | perfect solution for A-PET, G-PET, PET Co-polymer … | prime pellet / melt quality (IV, b*, AA- content) | very low energy consumption | direct extrusion into sheet | stable melt pressure build up | small foot print paired with robust design | sizes available from 200 kg/h up to 1500 kg/h | suitable for food application M-A-S Maschinen- und Anlagenbau Schulz Gmbh A-4055 Pucking, Hobelweg 1 T: +43 7229 78 999, F: +43 7229 78 999 10 [email protected] www.mas-austria.com Siapi Hall 7A | Booth 529 / 628 Blow-trimming of wide-mouth jars Siapi will be presenting their “blow-trimming” technique for the production of wide-mouth jars and containers. The development of this technology stems from the specific requirements of a client who needed to produce two different containers on the same machine and from the same preform: jars (with a neck diameter from 60 to 85mm) and bottles (with a neck from 30 - 38mm) and to maintain a high level of productivity, from 8,000 to 9,000bph. The Italian manufacturer has developed a system of blowing which allows the use of the same machine to obtain both bottles (with a neck from 30 - 38 mm and wide-mouth bottles and jars (60-85mm) from the same preform. The company calls this process “blow-trimming”. In a first blowing phase the neck is made wide-mouth in a second phase a cut is made at the top of the container (dome) with the narrow neck. A detailed study of the preform and of the process is required in order to: minimise the weight of the neck and the “dome”; facilitate the cutting phase and reduce the amount of material cut obtain a good formation of the thread in order to ensure the seal with the cap ensure high consistency of the thread with the appropriate weight of the neck for a perfect grip and neck resistance. The new technique allows the production of containers from 250ml to 1000ml with neck finishes from 30 to 85mm. www.siapi.it Bottles - , container - and case drying equipment Gesete GmbH, Germany, will be presenting drying equipment for packs; the bottle drying plant Compaktline LK for the small to medium-sized performance range; the Highline bottle and container drying plant for the discerning user as well as for the higher performance range and the Compaktline K for drying boxes and other types of end packaging. In addition to the energy-efficient blower technology and bottle drying facilities the company will also be presenting the new Labelblow blow-off system. According to Gesete, during blow-off of plastic sleeve labels on PET deposit bottles energy savings of up to 85% can be achieved by comparison to other systems can be achieved due to the special nozzles. www.gesete.de Gesete Hall 7 | Booth 320","@ID":46} "imprint EDITORIAL PUBLISHER Alexander Büchler, Managing Director HEAD OFFICE heidelberg business media GmbH Landhausstr. 4 69115 Heidelberg, Germany phone: +49(0)6221-65108-0 fax: +49(0)6221-65108-28 [email protected] EDITORIAL Doris Fischer [email protected] Michael Maruschke Ruari McCallion Ilona Trotter Wolfgang von Schroeter Anthony Withers MEDIA CONSULTANTS Ute Andrä [email protected] Martina Hischmann [email protected] Ursula Wachter [email protected] phone: +49(0)6221-65108-0 fax: +49(0)6221-65108-28 France, Italy, Spain, UK Elisabeth Maria Köpke phone: +49(0)6201-878925 fax: +49(0)6201-878926 [email protected] LAYOUT AND PREPRESS Exprim Kommunikationsdesign Matthias Gaumann | www.exprim.de READER SERVICES Kay Krüger [email protected] PRINT Chroma Druck & Verlag GmbH Werkstraße 25 67354 Römerberg Germany WWW www.petpla.net | india.petpla.net PETplanet insider ISSN 1438-9459 is published 10 times a year. This publication is sent to qualified subscribers (1-year subscription 149 EUR, 2-year subscription 289 EUR, Young professionals’ subscription 99 EUR. Magazines will be dispatched to you by airmail). Not to be reproduced in any form without permission from the publisher. Note: The fact that product names may not be identified as trade marks is not an indication that such names are not registered trademarks. 3 PETplanet insider Vol. 12 No. 11/11 www.petpla.net Go to Brau Beviale The Editourmobil is now well and truly “on the road“, which is a picturesque way of putting it. From our starting point in Nuremberg we are making steady progress towards Azerbaijan. The regional report for Slovenia is safely in the bag and we are now setting our sights on Turkey and Serbia, having surmounted some hurdles with flying colours. Our blog at www.petpla.net is attracting a huge interest. There have been of course the inevitable hitches and glitches that have sometimes got in the way of making our visits. The windscreen went, but the Iveco service station in Sofia came to the rescue with immediate help. They actually had the correct windscreen in stock. Then just outside Sofia, in Saedinenie, the camera gave up the ghost when we were on a visit to Gotmar. However, our small compact camera was able to fill the breach; two days later and we had a new camera body so no more worries about not getting reasonable quality pictures. Luckily we have not yet had to call on our big box of spares which contains a range of filters, fan belts and spare wheels. Most of our time is spent arranging, and in some cases re-arranging, our programme of visits as the Editourmobil whisks us from city to city and through a variety of different countries. Things would not be as smooth without the tireless efforts of our colleague Heike Fischer back at the office in Heidelberg. The Internet connection to the Editourmobil is only up and running once a day, so much of the associated to-ing and fro-ing takes place by text and – of course – directly via our mobile phone, which means that Heike has her hands full just keeping up. As for me, when you read this editorial, I will have taken over the reins of the Editourmobil. Before, I still had much to cram into my busy schedule: I was spending time in the States, having a look at plastic parts for our automotive magazine ‘Polymotive’. With barely a pause for breath, I was then off to an electric cars trade fair in Munich. Finally, I was boarding the plane to Turkey where the regional reports for Turkey and Serbia were awaiting my attention. At the time of my departure we still had to set up some of the dates for meetings in Turkey. Once we arrive in Serbia, I shall be pretty much up to my neck in appointments. I am already looking forward to finding out to what actually makes Serbia different from Slovenia. If you would like to share our experiences in the Editourmobil, simply visit www.petpla.net to find out just what we are up to or visit us at the Brau Beviale where you will be able to experience the Editourmobil directly. It will be parked in Hall 7A Stand 720 right at the transition point to Entrance East. Yours, Alexander Büchler EDITORIAL dear readers, EDITORIAL","@ID":5} "MARKET SURVEY 31 PETplanet insider Vol. 12 No. 11/11 www.petpla.net Sipa vVa Caduti del Lavoro 3, 31029 Vittorio Veneto (TV) Italy 0039 0438 911511 Matteo Tagliaferri Marketing and Communication +39 0521 548111 +39 0438 912273 [email protected] Rotary Weigh Filler (R) NV, computer conntrolled volumetric filling machine, for still water and juice (cold and hot) Isofill P Isotronic SC Stillfill S Stillfill R\\HR UNITRONIC SC 8 - 90 36 - 144 20-160 50-160 20-140 20-140 20-160 Up to 48,000 up to 68,000 bph 60,000 63.000 67,600 No 63,000 No 51,000 (CMW) 60000 (CMW) No No No Up to 48,000 No No No No 53,000 Up to 48,000 up to 44,000 bph 53,000 55.000 67,600 55000 53,000 Gravimetric filling tank Yes Yes Yes Yes Yes No No Yes Yes Gravimetric filling tank Yes Yes Yes Yes Gravimetric filling tank No Gravimetric filling tank Up to 10% Yes Yes Nozzles with valve and net weigh Non contact, free flow filling valve with MID ( magnetic inductive flowmeter ) Isobaric mechanical level filling valve Isobaric volumetric filling valve Mechanical gravity filling valve Mechanical gravity filling valve with recirculation Gravity volumetric filling valve GEA Procomac KHS GmbH Via Fedolfi 2, 43038 Sala Baganza (PR), Italy +39 0521 839411 www.procomac.com Flavio Salvadori Sales Director +39 0521 839411 +39 0521 833879 [email protected] Juchostrasse 20 44143 Dortmund, Germany +49 231 569-0 www.khs.com Heinz Hillmann Produktmanager +49 671 852 2714 [email protected] Cold chain, Combi Predis FMm Traditional filling: Fillstar SF, Fillstar HF Fillstar FX Traditional filling: Fillstar CX Aseptic filling: Fillstar FX Fillstar CX DRV: computer conntrolled volumetric filling machine for carbonated softdrink NV: computer conntrolled volumetric filling machine for still water and juice (cold and hot) 24 to 72 Fillstar FX 50 - 140 Fillstar SF 50 - 120 Fillstar HF 50 - 140 70 - 160 Fillstar FX 15 - 140 Fillstar CX 24 - 140 48 - 180 36 - 144 8,000 -4 5,000 FX up to 84,000, SF up to 62,000 up to 72.000 bph up to 68.000 bph Up to 60,000 CX 5,000 - 40,000 up to 55.000 bph 8,000 - 40,000 FX up to 64,000, SF up 37.000 FX 6,000 - 64,000 8,000 - 40,000 HF up 40,000 FX 6,000 - 64,000 CX 5,000 - 40,000 up to 55.000 bph up to 44.000 bph 4°C Yes Yes Yes (Fillstar FX) yes yes Yes Yes (Fillstar CX) yes no Yes (Fillstar HF) No yes yes Yes no no Yes Yes (with dimensional limits) Yes (with dimensional limits) Yes with specific filling valve (with dimensional limits) no up to 10% Contact less filling with inductive flowmeter FX electronic / flow meter, SF gravity level filler: mechanical filling head, HF pneumatical filling valve Electronic / flow meter, Electronic volumetric filler flow meter valve with swirl modul for foam free filling, volumetric system with MID non contact, free flow filling valve with MID ( magnetic inductive flowmeter )","@ID":33} "BOTTLE MAKING 22 PETplanet insider Vol. 12 No. 11/11 www.petpla.net New ISBM process by Cypet Where injection moulding meets stretch blow moulding The Cypet process is a new patented single stage injection stretch blow moulding (ISBM) process to produce a wide range of PET bottles and jars. A standard injection moulding machine is converted into a PET ISBM machine by adding injection and blow moulds as well as a blowing station. Invention and challenges The inventor and driving force behind the Cypet process is Constantinos Sideris, a former Technical Director of the Interplast/Harwal Group. The reason for developing such a system was the high investment costs related to conventional single stage PET injection stretch blow moulding machines, especially for countries with small market sizes. This led to the idea of using a normal injection moulding machine as a base to achieve the same result at substantially lower investment costs Two main challenges were faced during the development phase. First was the mechanical design of the blowing station, which was originally executed in a horizontal arrangement and later had to be changed to a vertical arrangement, for a smaller footprint, and a more practical and operator friendly operation. The second main challenge was the optimisation of the preform design to suit the process. All challenges were faced successfully. Design and process The Cypet process is based on a composite injection-blow mould set, mounted in the clamping unit of a standard injection moulding machine. What makes the Cypet process special is the arrangement of the injection and blow cavities in relation to each other and in relation to the machine clamping plates. The opening and closing of the clamping plates opens and closes the injection and the blow cavities simultaneously (no need for two separate clamping units). The machine’s clamping force is used to keep all injection and blow cavities securely closed against both the injection pressure and blowing pressure. In a typical production cycle, when the Various containers produced on Cypet machines","@ID":24} "BOTTLE MAKING 23 PETplanet insider Vol. 12 No. 11/11 www.petpla.net clamping unit of the machine opens, there are ready containers in the blow moulds that are removed and there are also ready preforms, which are transferred from the injection cavities to the right position in the blow cavities ready to be stretch-blown into containers in the next cycle. Then the clamping unit closes and while the next set of preforms is being injected, the preforms just placed in the blow cavities are being stretch-blown into containers The Cypet system can also be equipped with a (temperature) conditioning device between injection and stretch-blowing, with modes for round, oval and square containers. This feature allows the temperature fine-tuning of the preforms, thus widening the processing window, especially with respect to preform design tolerances. Reasons for using an “injection moulding machine” The use of a standard injection moulding machine provides technical advantages such as a comfortable clamping area which allows the use of two or even three rows of cavities. The clamping force of the machines is high enough to allow a higher number of cavities to be employed, even for wide mouth jars. These characteristics and the fact that moulds are used which do not require any duplication of mould parts (only 1 set of neck rings needed), leads to lower machine and tooling costs with the use of many cavities for higher productivity. The hot runners apply the traditional and proven design of the 2-stage process preform moulds, with the same spare parts. A fast product changeover is another feature of the Cypet system. According to the company it takes only about 1 ½ hours for a complete configuration change. The Cypet machines are available in three models, K-16 (160t clamping force), K-28 (280t) and K-53 (530t), with up to 24 cavities. It is possible to produce a variety of different containers on the same machine. For example, the smallest Cypet machine (model K-16) can produce 120mm neck jars in one cavity or 300ml bottles in twelve cavities. With the two bigger Cypet machines, bottles up to 30l and jars up to 145mm neck diameter can be produced. The Cypet process is protected by patents that have been granted in the USA, Canada, Europe, Russia, China, Mexico, Taiwan and Israel, and patents are pending in many other countries. Machines are currently in the final stages of beta testing operation in the Middle East and Asia or under test production in Cyprus. As an example, 10l bottles produced on the K-28 model with two cavities are cycling at 29s. www.cypet.eu Cypet Technologies is a branch of M. Sideris & Son Ltd, established by Constantinos Sideris to develop and commercialize the Cypet process.","@ID":25} "PETnews 6 PETplanet insider Vol. 12 No. 11/11 www.petpla.net Bericap in Argentina Bericap founded Bericap Argentina SA in Buenos Aires. The new plant will cooperate with Bericap Brazil Ltda and will increase the companie’s presence in South America where Bericap produces since 1998. Production start for manufacturing the DoubleSeal Supershorty suitable to PCO 1881 is planned for January 2012. www.bericap.com More PET with fewer Watts As part of of an industrial research project the SKZ (South German Plastics Centre, Würzburg, Germany) is comparing the energy consumed by a range of recycling processes in preparing ground stock for PET bottles. The individually measured consumption figures are handled on a confidential basis, whilst the spectrum of results provides the participating companies with a sector-based comparison and promotes the closer consideration of strengths and pinpoints the potential for optimisation. Interested companies are still able to join in the recently launched project.During PET processing, manufacturing costs as well as profit are significantly influenced by the cost of raw materials. Reducing material usage where PET bottles are concerned is largely irrelevant toda ; there are only a few available options concerning cost reduction. One of the most promising of these is energy efficiency. The manufacturers of PET recycling systems have already achieved energy savings using case-specific technological approaches. The resulting savings potential is comprehensively portrayed in product information literature and trade articles. An independent energy-based comparison of the procedures used to achieve an objective and reproducible measuring scheme has as yet, however, not been forthcoming. The primary aim of the project now initiated by SKZ is the energy-based analysis of different PET recycling processes. With this the system manufacturers will, for the first time, have access to an independent, objective data and assessment principle. It will enable each participating company to classify its own process within the branch spectrum on the basis of energy usage. The detailed measuring results may also be used as a basis for further optimisation in terms of energy efficiency. In the first phase of the project, agreement is reached with all participants on the control room and the specifications for ground stock and/or PET qualities for the processes to be examined. The subsequent measurements consist of the incorporation of electrical, thermal and pneumatic energy in the industrial production cycle. One method of guaranteeing process comparability is by analysing the material samples in accordance with the agreed specifications. The assessment is individually prepared and presented for each company. The SKZ is inviting interested companies to join the recently launched project. www.skz.de Petainer’s prize-winning keg The Petainer Keg, a family of lightweight beverage containers manufactured in recyclable PET and designed for one-way use, has received ‘Obal Roku 2011’, the packaging award in a competition organised by Syba, the Czech Packaging Institute. The keg has also been shortlisted for a special prize to be awarded by Ing. Jana Lukešová, the head of the competition judging panel. The winner will be announced on November 23, 2011 at Packaging Gala evening in Prague. The Obal Roku award was given to the Petainer Keg in the ‘transport and packaging technology’ category. The keg is designed to be an environmentally-friendly and cost-effective alternative to metal kegs for draught beverages. Once empty and de-pressurised, it can be easily crushed and put into the recycling bin with other recyclable plastics containers. It is available in 15l, 20l, 30l and 40l sizes. www.petainer.com Krones targets record in 2011 and increased turnover in 2012 Krones AG, the global beverage filling and packaging technology manufacturer, has reported that its sales rose by 14.6% in the first three quarters of 2011 compared to the same period in 2010, to €1,814.2million. Demand rose in all major sales regions, with the highest rates of increase in Asia, South America and Russia. Order bookings rose by 17.0%, from 2010’s €1,617.7million to €1,892.7million and order backlog at the end of September stood at €987.3m (2010: €923.2m). Profitability in the period under review showed a significant improvement, reflecting market growth in the newly industrialising countries. Earnings before taxes (EBT) in the first nine months of 2011 rose from €47.0million in 2010 to €84.1million, making the EBT margin 4.6 % (2010: 3.0 %). Krones earned €59.3million (2010: 31.9 m) from January to September. Earnings per share were €1.97, against 2010’s €1.05. Krones’ business has not, so far, been affected by the deterioration in economic prospects, in Europe and the USA in particular; it is approaching its target of increasing sales by more than 10% over 2010 and exceeding 2008’s record figure of around €2,381million. In order to help it achieve its medium-term targets the company has expanded its workforce, including significant hiring of skilled temporary staff. While this is expected to impact earnings in the short term, Krones AG’s Executive Board anticipates that results in 2011 as a whole will show significant improvement over the preceding year, with pretax return on sales of about 5%. The company maintains that its business is not heavily dependent upon on economic cycles. It expects to increase earnings in all business segments in 2012 and to generate pre-tax total return on sales of around 7%. www.krones.com","@ID":8} "PETcontents 11/11 4 PETplanet insider Vol. 12 No. 11/11 www.petpla.net INSIDE TRACK 3 Editorial 4 Contents 6 News 46 Products 48 Bottles: Beverages 50 Bottles: Personal care 52 Patents MARKET SURVEY 29 Suppliers of filling equipment for beverages in PET BOTTLING / FILLING 28 The world of drinks The world beverage market for soft drinks, beer, wine and spirits TRADESHOW REVIEW 38 Brau Beviale Nuremberg, November 9- 11, 2011 REGIONAL REPORT 10 The Baltic States: Lithuania / Estonia Part 2 PREFORM PRODUCTION 18 Sinks A rapid guide to perfect preforms - part 25 BOTTLE MAKING 16 A winning smile Emergent Technologies and PTI create two-compartment container 20 The conversion factor Sidel’s one-stop line conversion 22 Where injection moulding meets stretch blow moulding New ISBM process by CyPET 24 Bigger is better From idea to reality in large containers 26 Reducing weight, increasing benefits PET bottle light-weighting initiative offers energy and raw material savings Page 38 Page 16 BUYER’S GUIDE 53 Get listed! Page 46","@ID":6} "REGIONAL MARKET REPORTS 10 PETplanet insider Vol. 12 No. 11/11 www.petpla.net Lithuania / Estonia The second and last part of our regional report on Lithuania and Estonia is dedicated to the reports on Senderlen, Estonia. and Retal Industries, Lithuania, by Alexander Büchler Gustav Poola at the supermarket with his fresh milk PET bottle from Farmi. Senderlen The Trailblazer Stretch blow moulding bottles and then selling them is what Senderlen of Tallinn do. The difficult thing about this business model is the fact that, as soon as the customer finds that he needs more than approximately 1/3rd of a million bottles each month, he installs his own stretch blow moulding machine at his own plant. This means that company proprietor Gustav Poola always has to be looking over his shoulder to make sure that new customers are coming up behind. And here he is doing spadework on behalf of the entire PET industry. First of all he builds up contacts with potential companies and then tries to persuade them to change from glass, cardboard or HDPE to PET. “Eight years ago I invested in the company purely as a financial investment as an adjunct to my activities as an IT specialist and it is only now that I realise that the spadework has proved insufficient, this is why I am now doing it myself“ is what Gustav has to say. Meanwhile, he has been enjoying increasing success and is holding discussions with a manufacturer of carrot juice who has, up to now, been using cartons for his filling operations. He is particularly pleased with his order from the milk sector; here he is now supplying 1 litre and 0.5l coloured bottles for fresh milk and other fresh dairy products to Farmi and Airan (www.farmi. ee, www.airan.ee). Another speciality is mayonnaise in a wide necked pot. Among the classic beverages bottles for Regional market reports Lithuania Part 2","@ID":12} "29 PETplanet insider Vol. 12 No. 11/11 www.petpla.net Bottle-to-bottle recycling plants Conveyors for preforms and empty bottles Caps and closures Preforms Perform moulds and SBM moulds Single stage machinery 2-stage SBM machinery Compressors Filling equipment Resins and additives Suppliers of filling equipment for beverages in PET To coincide with the opening of the Brau Beviale, we will be publishing our overview of filling equipment suppliers. In addition to all the familiar names such as Gea Procomac, Sacmi, Sidel and Sipa from Italy, Krones and KHS from Germany, and fogg fom the United States, Eastern Europe now enters the ring with Vipoll (Slovenia) and Nate (Czech Republic). Each of the systems boast many special features which for reasons of space are impossible for us to describe here. For further details contact the relevant person shown in the table. Although the publishers have made every effort to ensure that the information in this survey is up to date, no claims are made regarding completeness or accuracy 11/11 MARKETsurvey Company name Krones AG Sacmi Filling S.p.A. Postal address Telephone number Web site address Contact name Function Direct telephone number Fax E-Mail Böhmerwaldstr. 5 D - 93073 Neutraubling +49 9401 70-0 www.krones.com Stefan Kraus Product Manager Filling Division +49 9401 3144 +49 9401 3056 [email protected] Via E. Ferrari, 1 - 43058 Ramoscello di Sorbolo (PR) - Italy +39 0521 695411 www.sacmifilling.it Matteo Quaini Sales General Manager +39 0521 695411 +39 0521 695400 [email protected] 1. Machine designation / model number Modulfill Solo-Mas Volo-Mas Alfa Vega 2. Number of filling heads (range: from/to) 16 up to 216 16/168 32/192 32/168 32/192 3. Filling speed/output - based on 1l bph a. Still water (1 litre bottles per hour) up to 72,000 10,000/72,000 10,000/72,000 10,000/72,000 10,000/72,000 b. Carbonated drinks with 8 g CO² (1l bph) up to 65,000 10,000/60,000 10,000/60,000 c. Milk (1 litre bottles per hour) up to 60,000 7,000 / 40.000 7,000 / 40,000 d. Fresh fruit juice (1l bph) up to 60,000 10,000 / 60,000 10,000 / 60,000 10,000 / 60,000 10,000 / 60,000 4. Filling process Pressureless (still drinks) Volumetric filling system; net weight filling system; heigh filling system Contactless filling system; short tube or long tube filling system Yes Yes Yes yes Pressure filling (carbonated drinks) Volumetric filling system; net weight filling system; heigh filling system Contactless filling system; short tube or long tube filling system No Yes No yes Hot filling Volumetric filling system; net weight filling system; heigh filling system Contactless filling system; short tube or long tube filling system Yes Yes Yes yes Cold aseptic filling PETAsept L / PET Asept D Contactless filling systems No No No no Juices with high pulp content Heigh filling system; pre-dosing system Long tube filling system; full bore / contactless / for pulp, fibres or fruit pieces Yes Yes Yes yes 5. Type of filling valve and metering system Volumetric filling system; net weight filling system; heigh filling system Magnetic flow meter; weighing cell; electronic fill height measuring Electronic volumetric / flowmeter Electronic volumetric / flowmeter Mechanical / vent tube Mechanical or electropneumatic / vent tube","@ID":31} "BOTTLE MAKING 33 PETplanet insider Vol. 12 No. 11/11 www.petpla.net narrowed process variation window and lower standard deviation assured the company that it could continue its aggressive light-weighting program while maintaining identical package performance. Moving forward Commenting on the Process Pilot a few months after its deployment, Deputy General Manager Kobayashi listed “reduced process optimisation time at startup, improved bottle performances, reduced influence of operators on blowmoulder settings, and a decrease in rejected packages” as its primary benefits. Before the system was installed, bottle and preform rejects averaged about 1%/a. Reject totals were reduced by 80%. The beverage producer has also successfully reduced the bottle weight. The 44g 2l tea bottle shed an additional 7g. Its current weight is now down to just 37g, a 16% reduction. Assuming resin pricing for bottle-grade PET of $1.00 per lb, the subsequent reduction works out at roughly $0.015 per bottle. With Haruna’s production of millions of bottles per month, the savings are considerable. Equally important, the company has made the move to lighter-weight preforms with no loss in bottle performance. Now that the first Process Pilot has been fully approved, Suntory intends to extend deployment to additional blowmoulding lines, bringing it increasingly closer to the light-weighting goals of its sustainability campaign. Further light-weighting will produce significant savings in raw material costs as well, even more so with rising PET prices. www.agrintl.com To quantify the benefits of the AGR Process Pilot, Suntory gathered data over two 10-hour production periods, with and without the process control system enabled. The test showed that swings in the brimful volume were significantly reduced and the overall average standard deviation was more consistent with the Process Pilot turned on. (Courtesy of AGR International) Figure 1: Brimful Figure 2: Topload When the same testing scenario was repeated to measure topload, similar results were obtained. With the Process Pilot enabled, Suntory found more consistent topload resistance and lower overall standard deviation. (Courtesy of AGR International)","@ID":35} "MARKET SURVEY 30 PETplanet insider Vol. 12 No. 11/11 www.petpla.net MARKET survey 11/11 Company name Serac Postal address Telephone number Web site address Contact name Function Direct telephone number Fax E-Mail 12 route de Mamers - BP 46 F-72400 La Ferte Bernard / France +33 2 43 60 28 28 www.serac-group.com Roland NICOLAS Dairy & Aseptic Business Development Director +33 2 43 60 28 32 +33 2 43 60 28 37 [email protected] 1. Machine designation / model number Serac Aseptic System (SAS) Highly Hygienic Filler (H2F) 2. Number of filling heads (range: from/to) 8 - 90 12- 42 3. Filling speed/output - based on 1l PET bottles a. Still water (1l bph) Up to 48,000 No b. Carbonated drinks with 8 g CO² (1l bph) No No c. Milk (1l bph) Up to 48,000 Up to 24,500 d. Fresh fruit juice Up to 48,000 Up to 24,500 4. Filling process Pressureless (still drinks) Gravimetric filling tank Gravimetric filling tank Pressure filling (carbonated drinks) No Hot filling Gravimetric filling tank Gravimetric filling tank Cold aseptic filling Gravimetric filling tank Gravimetric filling tank Juices with high pulp content Gravimetric filling tank Gravimetric filling tank 5. Type of filling valve and metering system Magnetic valves and net weigh (Multiflow) Magnetic valves and net weigh Company name Nate - nápojová technika a.s. Vipoll d.o.o. Fogg Filler Sidel Group Postal address Telephone number Web site address Contact name Function Direct telephone number Fax E-Mail Žižkova 1520, 583 01 Chotěboř, Czech Republic +420 569 551 235 www.nate.cz Michal Tecl Technical Director +420 569 551 238 +420 569 623 305 [email protected] 9242 Križevci pri Ljutomeru, Slovenia +386(0)25888450 www.vipoll.si Stanko Zver Director +386 25888450 +386 25888460 [email protected] 3455 John F Donnelly Dr Holland MI 49424 USA 616-786-3644 www.foggfiller.com Mike Raczynski Sales Representative +616-738-0263 [email protected] Via La Spezia 241 A 43100 Parma Italy +39 0521 9991 www.sidel.com Gero von Stackelberg Product Manager Sensitive Products +49 172 7114982 [email protected] 1. Machine designation / model number PETBlock Visitron Fogg Filler Models, F4.1, F6.2, F8 and F9 Aseptic , Sensofill FMa / Combi Predis Fma Hotfill , Veloce FM Ultra Clean for CSD, Combi Predis FMc 2. Number of filling heads (range: from/to) 12 - 144 6 - 140 12 - 90 32 - 120 40 to 108 70 to 130 3. Filling speed/output - based on 1 litre PET bottles a. Still water (1l bph) 1,000 to 50,000 No information provided 3,600 - 36,000 b. Carbonated drinks with 8 g CO² (1l bph) 1,000 to 50,000 No information provided none 18,000 - 36,000 c. Milk (1l bph) 1,000 to 15,000 No information provided 3,600 - 37,800 10,000 - 60,000 d. Fresh fruit juice (1l bph) 1,000 to 25,000 No information provided 3,600 - 37,800 10,000 - 60,000 10,000 - 48,000 4. Filling process Pressureless (still drinks) Volumetric with flowmeters Volumetrical/isobaric filling Gravity fill Pressure filling (carbonated drinks) Volumetric with flowmeters Volumetrical/isobaric filling None 18°C Hot filling No Volumetrical/isobaric filling Gravity fill - hot fill Up to 94°C Cold aseptic filling Volumetric with flowmeters Volumetrical/isobaric filling None Yes Juices with high pulp content Volumetric with flowmeters Mass flow mesuarement Gravity fill with extended shelf life filling options Yes Yes, up to 10x10x10mm No 5. Type of filling valve and metering system Volumetric, mass flow measurement Tri-line valves (contact) for gravity, mass, or mag flow meters for metered filling Magnetic filling valve with flowmetering control Contactless filling with inductive flowmeter Contact filling with inductive flowmeter","@ID":32} "TRADE SHOW PREVIEW 42 PETplanet insider Vol. 12 No. 11/11 www.petpla.net Bottle testing Heuft Systemtechnik GmbH, Burgbrohl, Germany, will be presenting three of its very latest new products for the in-line quality testing of empty and full containers. In addition, the company will be showcasing systems for checking cases and sorting empty bottles, detecting foreign objects and leaks, labelling and the final inspection of full bottles as well as optimising the efficiency of complete filling lines. Whether inspecting empty containers or checking the fill level, tightness, closure and labels of full containers, the new developments combine the maximum amount of operating and detecting reliability with a particularly simple and convenient operation. The systems remove faulty bottles and cans before they reach the market. Also featured on the stand will be a range of complementary equipment: the LGX empty case inspector, the SX empty bottle sorting unit, the eXaminer XO X-ray foreign object inspection, the squeezer QS leakage check for plastic bottles, the VX fill management system, the Tornado R wrap-around labeller and the FinalView FO for an extensive label and closure inspection. Heuft will also be presenting solutions for an interferencefree bottle flow and increased line efficiency with, among other things, the beetec, a servo direct drive for conveyors and the Strategy Gate database server for the central acquisition of operating and production data. www.heuft.com Heuft Systemtechnik GmbH Hall 5 | Booth 309 Microbiological safety of filling lines Since 2004, the French company Claranor has offered a range of dry and non-chemical solutions for cap decontamination for sensitive beverage filling lines. The company will present its technology on the booth of German company Loehrke, the German distributor of Claranor equipment. Using the technology of pulsed light, Claranor designs compact equipment to be integrated on new or existing lines, to prevent the development of moulds or bacteria due to packaging contamination. Applications are flavoured waters, fruit-based beverages, carbonated soft drinks and drinkable dairy products. Nestlé Waters was the first important industrial actor to invest into the technology on several plants worldwide. In 2011, Claranor has sold its 40th machine and improved the performance of the technology to be able to comply with the constraints of extended shelf life production. A recent project of the German company Vilsa has seen the installation of a cap sterilisation unit on a Krones packaging line of flavoured water. This installation by Loehrke was part of a global project of cleaning maintenance system installation, including a permanent spraying around sensitive areas and an automated cleaning system, supplied by Loehrke themselves. www.claranor.com Claranor c/o Loehrke Hall 4 | Booth 413 Recycling line recoSTAR PET iV+ Ongoing PET recycling innovation, quality and state-of-the-art technology, a full range of consulting services – brought to you by Starlinger. Visit us at: Interplastica Moskau 2012, 24.-27.01.2012 Plastindia New Delhi 2012, 01.-05.02.2012, Booth B14, Hall 12 www.recycling.starlinger.com pet-recycling.com","@ID":44} "BOTTLING / FILLING 20 PETplanet insider Vol. 12 No. 11/11 www.petpla.net Sidel’s one-stop line conversion service enhances bottlers’ market responsiveness The conversion factor The stakes are always high in the beverage industry, whether it’s about lightweighting bottles or launching a new product in time for the high season. New products have to reach the market at the right time and under the best conditions, in terms of both production and distribution. Consequently, bottlers are challenged to adapt their lines as quickly and efficiently as possible. Sidel supports its customers in their efforts with centralised project management, both as an original equipment manufacturer and as a package designer. This integrated approach offers bottlers immediate equipment efficiency, short times to market and low costs for optimal Total Cost of Ownership (TCO). Customers usually have one of three reasons for converting their beverage packaging lines – lightweighting, format or design change, or change of the product. Project management is a key factor in successfully achieving necessary line adaptations and Sidel’s senior project managers help bottlers to ensure optimised and secured conversion of their line. The managers’ profound engineering knowledge enables them to take all industrial considerations into account in preparing the production line in advance, and in determining the exact parts that need to be adapted. This centralised project management helps bottlers to ensure that their products are released on time. Shorter necks – significant savings As raw materials account for 70-80% of a bottle’s price, lightweighted preforms and caps, along with shorter necks, can lead to substantial savings in weight and costs. These features deliver quick return on investment and a smaller carbon footprint, factors that are increasingly important for customers’ purchase decisions. This is why more and more bottlers worldwide are adapting their lines accordingly. In 2010 French food and mineral water company Danone’s Polish water brand, Zywiec Zdroj was helped by Sidel to switch its lines to short necks. After a close analysis of various contractors, Zywiec Zdroj decided that Sidel could best suit their needs for quality, reactivity and close support during implementation. The order involved two lines at its Northern Plant, in Miroslawiec. Sidel undertook to work very closely with the company during the whole process. Each line was stopped for only four days for conversion to short-neck production. Quick new product launch Sidel does not just provide central project management for line conversion; it also assists customers in designing bottles for new products.","@ID":22} "PREFORM PRODUCTION 15 PETplanet insider Vol. 12 moulded. Increase as necessary to optimize part weight. 6. Check water cooling temperature. This should be 7 – 10ºC (45 – 50ºF) for optimum cooling. 7. Check water cooling flow to mould. This should be at the mould manufacturers rating (for a given preform size and cavitation). 8. Check that the valve stems are opening properly. A partially open valve stem may restrict melt flow. 9. Check to ensure that the valve gate compressed air pressure is sufficient to open the valve stems properly. Typical pressures are in the range of 8 – 12bar (120 – 145psi). 10. Check that the valve gate open timing is adjusted properly. This is typically 0sec. Minimize to allow more time to open. 11. Check all temperature readings and adjust as necessary. PET resin should be melted at about 280ºC (536ºF) +/- 10ºC (18ºF). 12. Check that transition position is set to about 13% of shotsize + cushion. Higher values may result in under-filling. 13. Check that the decompression (pullback) time and position is not excessive. This should be set as low as possible to minimize the risk of melt backflow into the nozzle tips, yet enough to eliminate drooling into the cavity from excess melt pressure. Typical settings for valve gated moulds are: Time = 0 – 1sec; Distance = 0 – 10mm. Non-valve gated moulds may require higher values to minimize gate stringing. Are your standard PET preform molds making you as much money as they should? Ask how MPET with iFlow technology improves production and achieves greater quality results. Innovation doesn’t happen in isolation. It happens when blue-sky thinking meets down to earth knowhow and exceptional supply chain execution. The sort of innovation that Mold-Masters is known for, now applied to PET tooling for industry-leading results. Introducing MPET – the new PET preform tooling solution designed for the standards of tomorrow. Mold-Masters and theMold-Masters logoare trademarks ofMold-Masters (2007) Limited. ©2011Mold-Masters (2007) Limited.All rights reserved. Think about it. moldmasters.com/thinkaboutit [email protected] 14. Ensure the mould neck insert and lock ring vents are clean. This will minimize gas entrapment at the neck finish. 15. Check to ensure that no moisture exists on the moulding surfaces, either from water leaks or condensation. This may obstruct normal melt flow and cause filling problems. The environmental dewpoint should be below the chilled water temperature to eliminate the risk of condensation. 16. Check hardware for worn, damaged or failed components, specifically the valve stems, valve stem seals, nozzle tips, shut-off nozzle plunger alignment, shooting pot motion, extruder screw check valve leakage (single-stage machine only), and clogged core / cavity cooling channels. www.petpla.net","@ID":17} "56 PETplanet insider Vol. 12 No. 11/11 www.petpla.net Buyer’sguide Entries from 5,70 Euro/mm, Call +49-6221-65108-0 3.1 Preform moulds www.wtbvc.com Preform Moulds, Components, Refurbishments and Conversions. Highest Quality, Fastest Delivery, Lowest Cost. United States - 937-898-8460 [email protected] Poland - 48-17-860-1020 [email protected] UK - 44-1623-658-416 [email protected] Argentina - 54-11-4753-1111 [email protected] PET Preform and Blow Molds for Different Application Guang Dong Xing Lian Precise Machinery Co., Ltd. Baoshi Rd, Xiabei, Pingzhou, Nanhai, Foshan, Guangdong, China Tel: (86-757) 8677 7168 Fax:(86-757) 8623 3168 E-mail: [email protected] Website: www.gdxl.com Huayan Huayan PET Preform Injection Molding Systems Guangzhou, China Manufacturer of High Precision High Performance PET Preform Injection Molds and Machines; Tel. +86 20 8226 6148 ext. 8215 Email: [email protected] Website: www.gzhuayan.com Single & Two Stage PET Molds 33-4, Wonmi-Dong, Wonmi-Gu Bucheon City, Kyunggi-Do Korea 420-110 Tel.: +82-32-663-6377 [email protected] www. ksmold.com Production of blow moulds and PET mould parts tel.: +359 32 606 821 fax: +359 32 606 888 [email protected] www.itd.bg KHS Corpoplast GmbH Meiendorfer Str. 203 22145 Hamburg Deutschland T +49 40 67907-0 F +49 40 67907-100 E-Mail: [email protected] www.khscorpoplast.com Specialist for PET Preform Injection Mold, Injection Stretch Blow Mold & PET Blow Mold www.moltechkorea.com Tel : + 82-11-224-1571 / + 82-32-684-0153 Fax: + 82-32-684-0139 [email protected] for North American market [email protected] for International market No.1517, Sec.8, Huanjhong Rd, Wurih Township, Taichung 414, Taiwan Tel: +886-4-2335-9689 [email protected] www.passcard.com.tw via Caduti del Lavoro,3 31029 Vittorio Veneto, Italy Tel. +390438911511 Fax +390438912273 [email protected] www.sipamolds.com R&D -Integrated Solutions In Plastics Leverage - Integrated Industrial Design Hamilton Road Sutton-in-Ashfield Nottinghamshire, NG17 5LD England Tel: +44 1623 556287 Fax: +44 1623 552240 www.rdleverage.com 1009 SE Browning Avenue Lee’s Summit, Missouri MO. 64081, USA Tel: +1 816 525 0353 Fax: +1 816 524 5068 www.rdleverage.com PREFORM MOULDS / STRETCH BLOW MOULDS Tel: 0039 071 7500214 Fax: 0039 071 7501958 [email protected] · www.simexitaly.it TOOLING PREFORM SYSTEMS BV Moulds & Robotics PET-related Services & Technologies C. Houtmanstraat 42 Emmen, The Netherlands Tel +31 (0) 591 679768 Fax +31 (0) 591 630616 [email protected] · www.tps.nl www.wtbvc.com Blow Molds for All Technologies, All Machine Types, All Sizes. Highest Quality, Fastest Delivery, Lowest Cost. Canada - 905-574-0010 [email protected] Poland - 48-81-820-5730 [email protected] UK - 44-1623-658-416 [email protected] China - 86-137-646-05384 [email protected] Argentina - 54-11-4753-1111 [email protected] Mold-Masters Europa GmbH Postfach/P.O. Box 19 01 45 76503 Baden-Baden, Germany Neumattring 1 Tel: +49 7221 50990 Fax: +49 7221 53093 [email protected] www.moldmasters.com MHT MOLD & HOTRUNNER TECHNOLOGY AG www.mht-ag.de Otto Hofstetter AG Zürcherstrasse 73 8730 Uznach, Switzerland Tel. +41 55 285 22 11 Fax +41 55 285 22 44 [email protected] www.otto-hofstetter.com www.petkamold.com [email protected] Single Step ISBM Moulds, Reheat Blow Moulds Preform Moulds - Hot & Cold Half Pet Moulds Pvt Ltd, India +91 9884390999, 9884390666 [email protected] [email protected] www.petmoulds.com 50 Galaxy Blvd. #13 Toronto, Ontario M9W 4Y5, CANADA P- (+1) 416 213 9400 F- (+1) 416 213 9379 [email protected] www.rnaprecision.com","@ID":58} "REGIONAL MARKET REPORTS 13 PETplanet insider Vol. 12 No. 11/11 www.petpla.net preforms for very special customers. We didn’t have any of these customers on our books” Raimundas explained. And so the HGVs continue to roar off to Germany laden with preforms. Particularly for the western markets and the big Colas, they offer the 1881 preforms for 0.5, 1.5 and 2.0l. “Unfortunately, here in our home market of the Baltics, no-one has yet jumped on to the material saving bandwagon. Maybe we shall soon be seeing the lighter bottle in Finland in spite of the hard tray discussion (see PP Finland Report)“ is Raimundas’ comment. The preforms are already there anyway. Retal Baltic Giedrius Viederis (right) and Alexander Büchler taking a look at the new cap production facility at Retal Baltic Making a virtue of necessity is part of the tools of the trade of every businessman. In 2003 the former owners of Retal Baltic built a production facility for preform installations in the Klaipeda Freetrade Zone. Initially, there were two plants in operation there but these were soon moved to Retal Dnipro. Retal then installed a Kuhne PET film plant in the empty 7,000m². production hall. At 6,000t/a it is more of a smaller installation. However, plans for a further plant are already afoot. As a further refinement, there is an aluminising plant available. The remaining Retal works, meanwhile, are full of injection moulding machines, with the result that once again two plants have found their way to Retal Baltic. This time, however, the guys from Klaipeda are concentrating on cap production. The PCO 28 customary in the region is fabricated using one large and one small Husky plant. The moulds produce the caps in every conceivable colour. A further refinement is the availability of a 3-colour Tampoprint system. “ When it comes to caps the competition is disproportionately high by comparison to preforms. Here we predominantly notice the manufacturers from Poland. Nevertheless, we are very satisfied with the start“ is the verdict of Director Giedrius Viederis. A major part of production is sold to customers of the Retal Europe subsidiary, but nurturing the delicate little cap plantlet has enabled it to succeed in creating its own customer base outside the existing preform contacts. The Retal Industries Subsidiaries Retal CIS, Collected under this heading are preform and cap production in the former CIS States excluding the EU. Here we visited Retal Dnipro, formerly Uniplast (see PP 4/11)., Retal Russia (see PP6+7/06 ) and Retal Kasatan (see PP 10/08). A newcomer to the list of subsidiaries is Retal Georgia. Retal Europe Retal has gathered together all plants in the EU under this umbrella that produce preforms and caps. There are visited Retal in Vilnus (see above) Retal Germany (see PP 1+2/10) Retal France (see PP 1+2/11) , Retal Iberia (see PP 10/07), Retal Czech Republic and Retal Italy. Retal Baltic PET film production. In March 2011 the company started an additional activity - production of HDPE bottle caps. Neo Group There is only one plant and that is in Klaipeda, here the group produces 300,000t/a of bottle material and will soon be producing around 7,000t/a of Polyol (see above).","@ID":15} "PETbottles 50 PETplanet insider Vol. 12 No. 11/11 www.petpla.net Personal Care Anti-Callus bath Scholl-Footcare Deutschland (ReckittBenckiser) are marketing a 150ml creme bath with an anti-callus effect in a handy PET bottle. The bottle has informative printed labels at front and back and a white screw cap that also serves as an aid to dispensing. www.scholl-footcare.com Dead Sea salt 250ml of slightly bluish coloured dissolved salts from the Dead Sea incorporating sea buckthorn oil is being marketed as a shower bath by the cosmetics manufacturer Kuehn of Haiger in a transparent PET bottle. Front and rear labels featuring informative printed text plus a white, one-hand operation hinged screw cap complement the packaging. www.kuehn-kosmetik.de Rose fragrance for the bath 75ml of bath and shower gel is being marketed by the French company L’Occitane of Manosque in a small PET bottle under the brand name “Rose 4 Reines“. This product has a dual section, gold-coloured plastic cap which fosters the impression of high quality and an all-round paper label. In addition, parts of the label also feature gold-coloured lettering to match the cap, and in this way product appeal and quality rating are emphasised. www.loccitane.com Mouthwash in red The French retail chain Cora based in Marne-la-Vallée is marketing its mouthwash in a handy 500ml PET bottle. The bottle is decorated with a No-label-look label at the front. The high contrast white screw cap which can also be used as a measuring container is secured against tampering by means of a pull-off ring. www.cora.fr Easy comb spray for kids The cosmetics manufacturer Mann & Schröder from Siegelsbach is marketing150 ml Easy Comb Spray with extract of cherry and magic formula to combat head lice in a handy PET bottle under the brand name of ”dulgon kids“. The bottle incorporates an informative all-round belly label and a screw-on spray pump. www.dulgon.de","@ID":52} "BOTTLE MAKING 16 PETplanet insider Vol. 12 No. 11/11 www.petpla.net Emergent Technologies teams with PTI to create two-compartment PET container A winning smile Emergent Technologies, LLC*, Chanhassen, Minn., has teamed up with Plastic Technologies, Inc. (PTI) to commercialise a two-compartment PET container, called the Smiler. Having done extensive research, Emergent saw a dual-compartment container as a way to help meet multiple consumer objectives. However, they needed to partner with a technology expert in order to transform their vision into a commercially-viable package. That’s when Emergent turned to PTI for assistance. The driving force behind the concept was to give brand owners the opportunity to market a single-serving of two compatible products - such as milk and biscuits - within one portable container, according to Bill Weber, President and General Manager, Emergent. “Every time we showed the concept, people smiled and that’s how we came up with the brand name. We spent a lot of time looking for ways to push PET design and processing boundaries beyond what had previously been done.” The proprietary Smiler technology enables bottles/containers to be injection blow moulded into different shapes and sizes. The larger, top compartment holds the liquid, while the bottom holds the snack item. Additionally, both can be used for dry products and/or non-food items. The second or bottom compartment is created by drawing the base upwards which forms a small cavity into which a heat-sealed portion cup, containing solid, granular or powdered products, can be inserted and held by friction. The base opening can then be closed using a variety of heatseal or pressure-sensitive materials/ methods. The top compartment relies on a traditional finish and closure. The biggest challenge was figuring out how to make a base cavity that was deep enough to house a second product. “We went through multiple iterations over a year-plus to make sure that both the design elements and the blow moulding process would meet performance objectives,” explained Scott Steele, Vice president, PTI. For example, in early iterations, the depth of the base cavity would cause the bottle to get hung up in the mould. An additional piece of hardware had to be designed to positively extract the bottle from the mould. “On the material side of the fence, the objective was to get monolayer PET to work. We did not want to blend in additives to achieve performance attributes because that would negatively impact container prices, as well as have a potential negative effect on the recycling stream,” Steele said. “The key was determining the optimum ratios between the bottom and top cavities, coupled with the finish diameter.” Containers have already been successfully produced for promotional events, but Emergent and PTI are now looking to bring the concept","@ID":18} "REGIONAL MARKET REPORTS 11 PETplanet insider Vol. 12 No. 11/11 www.petpla.net a range of naturally carbonated spring waters the ”Voluvesi“ brand from Wisewater is one that stands out (www. wisewater.ee) in terms of its design. The squared off corner design and the 1.25l volume large bottle are especially eye-catching. Senderlen’s existing capacity leaves plenty of scope for further orders and Gustav Poola is looking at being able to supply additional bottles for bottling plants in the high season. He has set his sights on the Nordic countries as his export markets. “The standard of living here is higher which also means that customers are willing to pay higher prices for their bottles“ is Gustav’s credo. Once the competitors of Farmi or the carrot juice manufacturer notice that their sales will increase more quickly than those of their competitors as a result of changing from cartons to PET bottles, they too will be queuing up on Gustav’s doorstep. www.senderlen.ee Square for water, round for mayo(nnaise) and white for milk – all the PET containers come from Senderlen. Retal Industries Pellets, preforms, caps Precisely three of Retal’s plants lie in Lithuania: one for PET production, one for preform production and one for PET films. Although all three production workshops belong to different Retal subsidiaries, they nevertheless work closely together. The following is an overview of the different Retal branches and more detailed reports on the three sites in Lithuania. What initially looked like a glorious hotch-potch of different preform manufacturers in Europe purchased by Uniplast has developed into a powerful preform group. With the backward integration of the supply of raw materials, the group remained in a position to deliver even during the years of crisis. Turnover in 2010 was of the order of €1.2million. Production has now reached 15 billion preforms per year and 300,000t of PET material for preforms. Around 30% of material production goes into producing their own preforms, the rest is sold outside the group. Retal Industries have split up what now amounts to 14 production locations into four subsidiaries, Retal Europe, Retal CIS, Retal Baltic and NEO Group (see box). Giedrius Viederis shows off the two extruders in the film line. Recycling Of interest to our readers will be the loop that has been constructed for production waste in Klaipeda. This can be used for the subsequent building of a fully-fledged recycling facility which can also be employed for postconsumer waste. The central element is the production of PET film in Retal Baltic. The demands made on PET for PET thermoforming sheets are not as high as they are for bottle material. As a result, the majority of production residues enter the films in the form of an intermediate layer. Currently these include the crushed film residue from their own production, punching scrap from film customers, crushed preforms from preform production and low quality PET granulate from their own PET manufacturing activities. The extruders for the film production are capable of processing up to 60% flakes without the output of 1,200kg/h giving way under the strain. If a sufficient number of PET postconsumers could be identified in the region, the company would be ready to invest in corresponding treatment plants here. Alexandr Grynko, new business development chief, is talking of a requirement of 15,000t before 10,000t of recyclable flakes can be achieved. In Lithuania , out of an approximate 16,000t of bottles, only 3,000t have been collected up. Too few to set the ball rolling. The intermediate layer is covered top and bottom with new material. “Our current capacity of 6000t/a is already exhausted“ says Director Griedrius Viederis. They are thinking about a second plant with a capacity of 10,000t for the medium term. But even that does not mean an end to recycling. The production waste and the PET residue (which is expensive to shred) is now being processed into Polyol, a component for PUR manufacture, by Neogroup. For this they are looking at 7,000t/a. So, to conclude, it is only new PET material, preforms, caps and PET films that pass through the plant gates at Retal.","@ID":13} "NEWS 7 PETplanet insider Vol. 12 No. 11/11 Order placed for 100th KHS Corpoplast InnoPET Blomax Series IV stretch blow moulder A very special moment for KHS Corpoplast came when the contract was signed for delivery of the 100th InnoPET Blomax Series IV stretch blow moulder. The order was placed by Western Container Corporation, USA. KHS will supply an InnoPET Blomax Series IV with 24 blow stations. The machine has a maximum capacity of 52,800bph. According to KHS, the response to the InnoPET Blomax Series IV in the beverage industry has been extremely positive, particularly in the soft drinks, mineral water and fruit juice sectors. The popularity of these machines has continued to increase right up to the present day. Reduced energy, compressed air and material consumption, enhanced performance and flexibility and a smaller footprint are highly impressive advantages which differentiate the InnoPET Blomax Series IV from the previous generation. A wide variety of PET bottles ranging in size from 120ml to 3l can be produced on the InnoPET Blomax Series IV which has a maximum capacity of 72,000bph. Featuring an uncompromising modular design, the InnoPET Blomax Series IV comes with between 4 and 36 blow stations, each with a capacity of up to 2,200bph. The new heater, which uses NIR (near infrared) radiation to bring the preforms up to temperature, consumes up to 25% less energy than the previous generation. Moreover, the heating zone only takes up half the original space. Because the stretching process on the InnoPET Blomax Series IV is controlled by servo motor, the stretching motion can now be perfectly matched to the varying speed of the filler section. As a direct benefit, the process is more stable and the scrap rate is lower. In addition, the preforms can be optimized down to the last tenth of a gram of PET material. www.khs.com KraussMaffei Group brings all PET activities under Netstal The definition of a PET strategy for the entire KraussMaffei Group has led to the unification of its PET divisions at Näfels (Switzerland) and Munich (Germany) under the responsibility of Netstal, with effect from October 1, 2011. Thomas Anderegg assumes the responsibility for the new business unit in addition to his existing tasks. He has been in charge of Netstal’s sales, marketing and applications departments with the Cap, Med, Pac and Tec business units since 2009. Netstal and KraussMaffei PET products will be marketed under the names of PET-Line and PETForm, respectively. www.netstal.com www.sipa.it SIPA’s experience and expertise in PET bottle production extends throughout the entire process to include blow moulds as well as machines. And it’s all about helping the customer make a better bottle, more cost effectively. SIPA produces aluminum and stainless steel moulds for any application and any shape of container (round, oval, square, complex shaped), and with a wide variety of engravings and decorations. Reducing your packaging weight at the minimum. Hall 7 stand 637 500 ml 8.8 g 1500 ml 21 g 2000 ml 26 g Some examples of mineral water bottles in production:","@ID":9} "NEWS 9 PETplanet insider Vol. 12 No. 11/11 Seminar on PET for alcoholic beverages in India Meeting at Westin Hotel, Pune, 18 November 2011 brings together end-users and producers to discuss opportunities for growth While PET bottles are well-established globally for alcoholic beverages in sizes ranging up to 3 L, packages in India are largely limited to 750 ml, with some larger sizes in southern Indian states. Total usage of PET resin in the alcoholic beverages sector has grown, from 23kT/yr in 2007-8 to 38 kT/yr in 2010-11, and is projected to continue growth at 20% pa. The Indian PET industry has identified alcoholic beverages as one of the key focus areas for promotion & development. PET usage in liquor for both country liquor and Indianmade foreign liquor (IMFL) is growing, is being used for a wider range of products and is gaining approval across more states. Reliance Industries Limited (RIL), in association with other companies, is organising a seminar that is intended to inform end-users on all aspects of PET usage and development and to address their technological and commercial concerns. It will be the first of its kind in India and the objective is to increase PET usage in the liquor sector and to bring providers together with end-users, by providing and developing comprehensive and innovative solutions. A similar exercise for the pharma and edible oil sectors received a good response from both end-users and converters. The PET Packaging Trends and Technologies for the Liquor Business seminar is scheduled for November 18, 2011 at the Westin Pune Hotel, 36/3-B Koregaon Park Annexe, Mundhawa Road, Ghorpadi, Pune, Maharashtra, India. Country liquor and IMFL manufacturers will be in attendance, as well as representatives of statutory bodies in the Western region. The half-day programme begins at 4pm and will be followed by dinner. The seminar will cover PET advantages; filling line solutions; printing innovations; process cost reduction by shrink-wrapping; and developments and trends in liquor labels. Allied Blenders, Distillers Pvt Ltd and G M Breweries Ltd Mumbai will share their PET experiences. The forum will highlight new PET packaging variants for liquor, as well as opportunities for cost-reduction at different stages. There is no registration fee and the structure of the seminar is designed to encourage all stakeholders to brainstorm and share ideas and experiences. Contacts for further details: M R K Gera ([email protected]) and Anand Sunka (9967033107 & 9987022404), Reliance Industries Ltd;","@ID":11} "BOTTLE MAKING 26 PETplanet insider Vol. 12 No. 11/11 www.petpla.net PET bottle light-weighting initiative offers energy and raw material savings Reducing weight, increasing benefits Founded over a century ago, Suntory Holdings Ltd, produces beverages in Japan and has more than a 20% share of the domestic market. In addition to a strong wine and spirits business, the company produces or markets a wide line-up of soft drinks, teas, juices, and bottled water. Suntory recently launched an enterprise-wide campaign to shrink its carbon footprint. Part of the sustainability strategy was aimed at lightweighting PET bottles. The benefits of this initiative range from decreased plant energy and raw material consumption to reduced carbon emissions and transportation costs. Weight and performance targets PET bottles have slimmed down over the past decade. By 2010, Suntory had already managed to trim 11g from its 2l tea bottle, from a weight of 55g to 44g, but the company wanted to achieve even further reductions. However, it takes considerable effort and expertise to develop a lightweighting program. The mandates of Suntory’s initiative included the need to reach aggressive light-weighting targets without compromising bottle performance criteria or the extremely stringent quality standards demanded by the Japanese market. Thorough investigation of available light-weighting tools led Suntory to the Process Pilot automated blow moulder management system manufactured by AGR International. The Process Pilot works in conjunction with AGR’s PETWall Profiler material distribution measurement system to automate the management of blow moulding production. Analysing the relationship between the material distribution in the container and the blow moulder, the Process Pilot’s software algorithms and thickness measurement capabilities interact with blow moulder controls. The Process Pilot simultaneously manages all aspects of blow moulder operation to maintain proper thickness distribution during bottle production. On sensing changes in processing conditions - such as cooler than normal preforms or a draft of warm air, for instance - the Process Pilot software responds automatically to keep the blow moulder on track, making the requisite adjustments much more quickly and reliably than a human operator. Three stages of testing According to Japanese protocol, new measurement equipment must undergo a thorough evaluation process before commissioning and adoption. Suntory’s Haruna plant, which produces tea and juice filled in PET bottles manufactured on site, was designated as the test bed for the AGR technology. The PETWall Profiler system with Process Pilot control was installed on a KHS Blomax 18 Series III blowmoulder. Running at 18,000bph, the line is dedicated to producing newly designed, lightweighted 2l bottles. Together the two companies formulated a rigorous three-stage program to validate the new equipment. Mr. Toshiya Kobayashi, Deputy General ManagerEngineering Department at Suntory, described the testing regimen as “extensive”. The first stage validated the accuracy of the system measureSuntory Holdings Ltd., Japan, chose AGR as a partner for their sustainability strategy. The initiative led to significant weight reductions of their 2l tea bottle","@ID":28} "Vol.6 PETplanet print PREFORM PRODUCTION 14 PETplanet insider Vol. 12 No. 11/11 www.petpla.net Sinks The rapid guide to perfect preforms - part 25 Troubleshooting guides have suffered in the past from being locked away in offices and not being available to the people that actually need them. Considering the high cost of machine and tools high scrap rates can be a costly proposition eating away at already tight margins. PETplanet’s “Rapid Guide to Perfect Preforms” takes a different approach. It has been written for the people on the floor of injection moulding companies to support their daily work in making the best preforms possible. The product of two industry experts, Rick Unterlander and Ottmar Brandau, it gives concrete advice on 35 of the most common problems in preform manufacture, most illustrated by pictures. From high AA levels to wavy bodies processors can find help when they need it. Read chapter 25 of the guide. Symptom: Depressions of various shapes and sizes that occur randomly on the preform surface. Cause: Excessive shrinkage has occurred while the preform is contained within the mould. Table of Contents i........................ About the Authors ii.................................Introduction chapter 1.............................. AA Level High 2........................ Accordion Preform 3....................... Air hooks / Streaks 4............................... Black Specks 5...................................... Bubbles 6..................................Burn Marks 7...........................Colour Streaking ................................... /Peeling 8..................................Crystallinity 9.................................Drool Marks 10.......................................... Flash 11......................... Gate Depressions 12............................... Gate Peeling 13..................Gate Voids / Pin Holes 14......................... Internal Gate Sink 15................................Internal Sinks 16........................................ IV Loss Solutions: 1. Check for correct shotsize setting. The injection cushion should be about 3 – 5mm to compensate for any melt process fluctuations. 2. Check injection time isn’t too low (injection rate too fast) and adjust if necessary. Injection rate should be about 10 – 12g/sec/cavity. 3. Check that the cooling time isn’t excessive for the preform being moulded. This typically ranges from about 1 to 3sec depending upon the preform wall thickness. Reduce time if necessary to minimize the risk of nonuniform shrinkage while contained in the mould. 4. Check to ensure hold (packing) pressure isn’t too low, especially near the beginning of hold time. Adjust higher if necessary to fully fill out the preform. 5. Check that the hold (packing) time isn’t too little for the preform being 17............................ Long Gate Nub 18...............................Milky Preform 19............................ Moisture Marks 20................Neck Finish out of Round 21....................... Parting Line Crease 22.................Parting Line Deformation 23......................... Preform Yellowing 24.................................. Short Shots 25.......................................... Sinks 26......................................... Splay 27........................... Stretched Necks 28..................................... Stringing 29......................... Surface Blemishes 30......................... Thread Flow Lines 31...............TSS (Top Sealing Surface) ......................................... Sink 32.......................................Unmelts 33.................Wall Thickness Variation 34.................................Wavy Body 35.................................. Weld Lines","@ID":16} "TRADE SHOW PREVIEW 39 PETplanet insider Vol. 12 No. 11/11 www.petpla.net Natural flavours and sweeteners Rudolf Wild GmbH & Co KG will focus its spotlight on natural sweeteners such as Fruit Up and stevia, as well as drink creations like coconut water, beer mixes and malt drinks. New additions to the Wild range include ice teas, lemonades and fruit nectars, all sweetened with stevia, for which official European approval is expected at the beginning of 2012. Wild staff on the stand will be providing information on stevia and its uses. The company has also developed new concepts for cloudy beer mixes, in reaction to consumers’ growing preference for cloudy varieties with juice content and a natural image. Wild will also be showcasing a wide range of malt drink concepts: pure; fruit-flavoured; or in combination with juices. The company says that coconut water is a new trend from the USA and it will be presenting coconut as a basis for non-alcoholic drinks. Premium and ‘adult’ taste profile soft drinks will also be represented. www.wild.de Wild Hall 1 | Booth 119 Gernep Hall 7 | Booth 222 Rollfed, self-adhesive and wet glue labelling Gernep, the labelling machine manufacturer from southern Germany, is using the show to present its latest developments in all areas of labelling. The Gernep Rollfed can handle wraparound labelling of different container formats, with OPP labels. The rotary labelling machine’s glue application is by a closed hot melt system that, the company says, prevents entry of contaminants and reduces cleaning and maintenance time. A recently-developed glueing head applies hot melt contactfree; the machines can, alternatively, be equipped with an end-glueing head for a continuous end-glued strip. Gernep’s Labetta SK self-adhesive rotary labelling machine has servo drives at the self adhesive dispenser to transfer labels precisely and smoothly, including into recesses and larger label fields. It can also process ‘no-label’ look and water-resistant plastic labels. The Labetta wet-glue labeller features a new overlay gear for precise label adjustment, and glue segments are individually adjustable. Gernep’s Labetta Combi incorporates wet glue, self adhesive and hot melt labelling. www.gernep.com","@ID":41} "TRADE SHOW PREVIEW 41 PETplanet insider Vol. 12 No. 11/11 www.petpla.net Low profile sports closures Aptar Food + Beverage, part of Aptargroup, will be showing 1881 Light Original, the latest addition to its ‘Original’ range of sports closures. The 1881 Light Original has a lowprofile neck finish that offers a weight reduction of 25%, with the same performance and aesthetics of the Original Sports Closure range. Aptar’s team at Brau Beviale will be available to discuss both its standard range of products and solutions tailored to particular needs. www.aptar.com Aptar Food + Beverage Hall 4 | Booth 336 New production methods for new markets Visitors to Sacmi’s stand will find an analysis and discussion of how to adapt to particular market needs in beverage packaging. The Russian market is relatively new to Western companies and has its own distinct characteristics. Key to success in Russia has been the challenge of maintaining the quality of beer stored in PET bottles. Sacmi has developed a compelte turnkey plant solution covering the entire production process, from PET preform injection for 1.5l bottles, to filling and on to compression manufacture of one-piece plastic imitation crown caps and final labelling. Sacmi says this is the first time such an end-to-end solution has been available to this market segment. www.sacmi.it Sacmi Hall 5 | Booth 343 Cap and closure manufacuturing Engel Austria will be using video presentations to demonstrate shorter cycle times, higher production levels and potential energy savings available from various types of electric injection moulding equipment for cap and closure manufacturing. The Engel e-cap 420 is claimed to use energy and water very efficiently. It has a 96-cavity mould, a cycle time of 2.7s and a capacity approaching 130,000 caps and closures per hour. Engel says that the e-cap consumes 40% less energy than an equivalent hydraulic machine and features injection speeds of 450mm/s. The company will also highlight the production of beverage crates on its duo pico injection moulding machine, with particular emphasis on multi-component technologies combined with in-mould labelling for high quality surface finishes for sales packaging. www.engelglobal.com Engel Austria Hall 6 | Booth 437","@ID":43} "BOTTLE MAKING 27 PETplanet insider Vol. 12 No. 11/11 ments. Next came testing to confirm the optimum Process Pilot settings. The third stage, over a longer term, compared bottles produced on the KHS Blomax with Process Pilot ON and OFF to quantify the benefits derived from its use. Accuracy validation Because the Process Pilot control software relies on precise thickness data to operate successfully, the first step in the evaluation program was to validate the PETWall Profiler’s measurement capabilities. Suntory conducted multiple tests to compare the accuracy of the on-line measurement system with traditional off-line measurements, which are typically thought to generate a higher degree of accuracy. Several sets of bottle samples were taken during production runs, and on-line measurements were recorded for individual bottles in each set. The same bottles were subsequently measured by a high accuracy laboratory device. After thorough analysis of both sets of data, Suntory concluded that the PETWall Profiler possessed the highly accurate measurement functionality necessary for its lightweighting initiative. Blowmoulder control The second stage of testing evaluated the Process Pilot’s ability to actually control the blowmoulder to maintain desired bottle thickness distribution consistently over a period of time. This series of tests included varying oven settings, pre-blow pressure and timing, preform temperature, and oven ventilation with the Process Pilot system enabled to prove its ability to control and stabilise the process, regardless of changes in environmental conditions. Results showed that the Process Pilot system quickly responded to the various control input changes and maintained the process with little variation. Suntory then moved into more extensive production testing. Multiple production runs were conducted, each with a different set of Process Pilot configuration settings, incrementally tightening the tolerances. From these, the ideal configuration was determined, resulting in an extremely stable process with little variation. Confirming Process Pilot value Utilising the blowmolder configuration developed during the earlier tests, the third phase of tests analysed bottles produced with and without Process Pilot control to assess the effects on bottle quality and performance. Over several weeks, the physical bottle parameters - thickness distribution at critical locations, topload, and volume - were documented for bottles produced with Process Pilot turned OFF and ON. Bottles produced with the system showed a marked improvement in the form of reduced standard deviation of sidewall thickness, increased topload strength, and greater consistency in brimful volume (see figures 1 and 2). The","@ID":29} "TRADE SHOW PREVIEW 43 PETplanet insider Vol. 12 No. 11/11 Liquid colours, additives and dosing systems for PET packaging Repi, Italy, manufacturer of high performance liquid colours and additives for plastics, will be showcasing their full product portfolio for the PET packaging industry: Remap Liquid Colours with a broad range of colour shades and effects, improving packaging aesthetics Remap Additives for protection of the packaging content, greater operational performance and improved recyclability. The latest developments in Remap Colour Barriers will also be explained. With Repi BS Colour Barriers customers are free to adopt any kind of PET barrier systems whatever the preferred barrier technology adopted: barrier resin, barrier additives or multi-layer technologies. A special presentation will be given to the LS Colour Barriers, suitable for monolayer packaging for ESL and UHT milk, and other light sensitive materials. www.repi.com Repi Hall 7A | Booth 620 Pre-glued, roll-fed labelling Italian company P.E.Labellers SpA will be exhibiting a range of its labelling machines, including its Adhesleeve system, which uses white or clear pre-glued roll-fed films, which are thicker than those normally used on classic roll-fed labellers. The company says that the elimination of hot melt in its preglued film system offers a number of attractions, including a more sanitary and ecologically friendly working environment; the elimination of fumes; and complete recyclability. It is available with a thermal shrinking system and is claimed to be user-friendly in operation. It is also able to create a sleeve-type packaging with one labelling machine, by simply changing the type of film being used. www.pelabellers.it P.E. Labellers S.p.A. Hall 7 | Booth 716 Terboven GmbH Cryogenic Technology Hubert-Underberg-Allee 14 47495 Rheinberg Germany P.O. Box 1331 47478 Rheinberg Germany Phone: +49 (0) 2843 9727-0 Fax: +49 (0) 2843 9727-20 E-mail: [email protected] www.terboven.net Terboven GmbH – THE experts for innovative and effective liquid and gaseous nitrogen applications! Several hundred units, including more than 250 STERILE LIN 'RVLQJ 6\\VWHPV IRU FROG DVHSWLF ¿OOLQJ VROG DQG LQ RSHUDWLRQ worldwide - FDA approved versions available, too! Liquid Nitrogen Dosing Systems Coating Tumblers, Cryogenic Precoolers, Cryo-Pelletizers, Highvacuum-Superinsulated Piping - with accessories such as valves, phase separators and line degassers On-site STERILE LIN Production Units Individual machines and equipment for the Cryogenic Application Technology Soft LIN outlet for Hot Fill, CAF, Standard Units","@ID":45} "TRADE SHOW PREVIEW 40 PETplanet insider Vol. 12 No. 11/11 www.petpla.net Closure Systems International Deutschland GmbH Hall 4A | Booth 317 Flexible maintenance Closure design and manufacturing organisation Closure Systems International (CSI) has introduced a customised preventative maintenance program, called PM Select. It includes four scheduled CSI technical service visits per year, at each of which the company’s technical service experts perform services, selected by the bottler from a menu of CSI’s preventive maintenance offerings. Popular choices include capper audits, capper rebuild/set-up, line capability studies, headset/spindle exchange, capper assessments, and PlasTech application training. CSI says that advantages include overall cost savings from multiple services per visit, as well as the scheduling of capping line maintenance several months in advance, which helps to minimise downtime. The company serves customers in carbonated soft drinks, bottled water, juices, isotonics, teas, adult beverages, dairy, foods, and automotive fluids sectors. www.csiclosures.com Stretch blow-moulders on display With over 4,000 machines installed worldwide, Italian company SMI S.p.A. has over 4,000 machines installed worldwide, with capacities of up to 36,000 bph. The company’s stand will feature its SR6 rotary stretch blow-moulders, which it says offer reduced maintenance and operation costs and are suitable for plastic containers covering a range of capacities, and for detergents, cosmetics, pharmaceuticals and chemicals, as well as food and beverage. SMI claims that the SR6 series is capable of producing quality 500ml PET water bottles weighing just 9.94g. Among SMI’s installed estate are twelve CNC machining centres connected in FMS line, which can run without an operator by following pre-set CAM production programmes. www.smigroup.com SMI S.p.A. Hall 7 | Booth 716 Beverage oxygen measurement Berlin-based company Dr. Thiedig +Co KG will present Digox 6.1, its latest beverages oxygen analyser, which is used for measuring oxygen in laboratories and in-line at the storage tank, after filtration, and at the filler, or for inspection of tank deliveries. It is available in both stationary and portable versions. TPO (total packaging oxygen) can be integrated into the device as an option. Thiedig says that the Digox 6.1 features intuitive menus that are adjustable to daily operational procedures and that calculation of total oxygen in bottles and cans is available after 10min. Up to 500 data sets can be saved and directly loaded into a PC for documentation and evaluation. The Digox 6.1 features direct measurement of oxygen by means of a membrane-free Thiedig sensor and built-in automatic Thiedig Active Calibration. The measuring electrode is in direct contact with the measuring medium, which enables the system to respond to changes in oxygen concentration in less than 10s. www.thiedig.de Dr. Thiedig + Co. KG Hall 4 | Booth 322","@ID":42} "REGIONAL MARKET REPORTS 12 PETplanet insider Vol. 12 No. 11/11 www.petpla.net Neo Group Neo Group is the PET production line for Retal Industries. In Klaipeda it produces 308,000t of bottle material. The company started in 2007 with their first delivery of granulate. After what was generally a difficult 2008 and 2009 , the plant has now been running at full capacity since 2010. It produces primarily NEOpet 82 with fast reheat additive and standard material NEOpet 80. The plant is made up of two blocks, each of 150,000t. A third block is still being mothballed due to the former difficult economic situation and Neogroup is considering whether to build it up in the short term so that, from 2014, capacity can be further extended. Up to 2009 the company had focussed on the big customers; now that the plant is operating at full capacity their active customer base has risen to around 100 firms. From Klaipeda the Neo Group can, commercially speaking, reach pretty well any point in Europe. Portugal, in particular, has made this possible for the Lithuanians. Here a competitor’s plant has recently been closed. They are keen to achieve strong growth in this market which lies practically at the other end of Europe. For some years now consumption within the EU has remained stable at around 2.9 million tonnes. Although the PET sector is currently registering growth in the east, higher levels of consumption are not coming about. One possible reason for this, in the opinion of Linas Bulzgys, CEO of the NEO Group, is the increase in the use of the lightweight preform / bottle design. Standing on the right is Linas Bulzgys explaining the PET plant to Alexander Büchler in the control room. Retal Europe Raimundas Luneckas CEO Retal Europe proudly showing off the new control of the Genesis dryer from Piovan. He is looking forward to energy savings of 30% as a result of this new concept. The second largest injection moulding location operated by Retal industries after Retal Dnipro is situated in Lentvaris/Lithuania. Waiting for us there was a factory bay packed with 22 preform installations. “We have an installed capacity of 2.5 billion preforms and we actually manage up to 2.3 billion preforms each year“ says Technical Manager Janus Maculskis. The company would dearly love to put more machines in there; Raimundas Luneckas, the CEO, is thinking about two to three additional machines. However, there is unfortunately no space left for them. So the Lithuanians have moved a multi-layer plant to France and installed it on the premises of their associate company, thus enabling a new Husky Monolayer plant to be installed. In view of their previous good experiences with Piovan, this is the first plant to feature Piovan’s new material drying system, Genesis. “We anticipate an energy consumption of 74Watt/kg PET during drying, this would be around 30% less than with material dryers up to now“ says Raimundas and he goes on “as the plant is still under construction we cannot, however, yet confirm the value for us, but we are quite confident”. The second largest injection moulding location operated by Retal is situated in lentvaris/Lithuania, with a capacity of 2.5 billion prefroms per year. Even the crisis which shook eastern Europe more significantly than other regions was unable to do much damage to the company. “ I believe we were able to keep up full production, even during the period of crisis, because we in our group have our PET production with our NEO Group subsidiary as well and have always been able to guarantee our customers full supply capability” says Janus. The supply area means pretty well any region within a radius of 2,000km, with the exception of the non-EU countries. The expansion of the Retal Group with the plant at Merseburg in Germany (see PETplanet insider issue 1+2/10) could only enhance the success of the Lithuanians. “The Germans produce only a few different types of","@ID":14} "BOTTLE MAKING 24 PETplanet insider Vol. 12 No. 11/11 www.petpla.net From idea to reality in large containers Bigger gets better Sipa says that it has the capacity to develop applications in PET containers right across the size range and that it has the equipment, automation, technology, design expertise and materials knowledge to take an idea from initial concept through to production. It claims that this applies whether the product is a single-serve package or a 40l container, regardless of contents – water, beer, vegetable oils, mineral oils, detergents, chemicals, and so on. Attention to the container itself is not enough; the way it is handled and packed affects efficiency as well. The company has, for example, suggested changes that enable more containers to fit onto a pallet – vertically as well as horizontally – to make the best use of space and so help to reduce logistics costs. Large containers require attention to aesthetics but good looks are not enough if a design has insufficient top load strength or cannot be blown; all the variables have to be considered. Sipa provides advice on the best resin to use and it can design the optimum preform - or act as a partner in fine-tuning and producing and testing prototypes. 25l for edible oil Sipa recently helped Able Perfect, a Malaysian producer of palm oil, to develop square, stackable containers in 10, 20 and 25l formats, compatible with the entire existing production system. Sipa designed preforms to optimise both the blowing process and container base cooling, which was critical to on-pallet stackability. HODs Omorika, a Bosnian converter, uses a linear SFL 2/2 for production of 680g PET containers, completely engineered by Sipa from the preform to replace an existing polycarbonate container. A Chinese customer asked for a new five US gallon PET bottle to replace an existing PC container, at lower weight but still tough enough to cope with the Chinese road network and arrive safely. Sipa delivered a solution for design and production of 350g one-way HOD 18l water bottles, Large, stackable containers for edible oil Large PET containers for water, edible oil, beer, detergents etc.","@ID":26} "PRODUCTS 47 PETplanet insider Vol. 12 No. 11/11 Multi-product weight filler Hema, part of the Sidel Group, has announced its new GW weight filler for dairy products and vegetable oil packaging. Its stainless steel weight sensors can be used for volumes up to 5l. The filler is equipped with an offset valve allowing it to process both liquid and more viscous products and a small chamber helps to save on water and cleaning products, the company claims. Output speeds are up to 60,000bph. The GWm model is adapted to fresh or ESL liquid dairy products, including drinkable yogurt. The nozzle can handle foamy liquids like milk or more viscous products, such as drinkable yogurt with fruit bits or soft cereals up to 5x5x5mm, without the need to change the nozzle tip. The nozzle is available for volumes ranging from 80ml to 1 US gallon (3.78l). The GWm complies with 3A, EHEDG and FDA standards and enables laminar flow layout. Post-production cleaning cycles (CIP– COP) and sterilisation cycles at 115°C (SIP–SOP) are fully automated. The GW weight filler is also available in an integrated Combi version, for blow moulding, filling and capping of liquid foods and household products in PET containers and can be used for sensitive products, with Predis dry decontamination technology for preforms. Gravimetric technology Hema proposes fillers in which one turret is used for a thick product and a second turret for a thinner one. This design meets the needs for two-phase products, which are now a high-growth market. This synchrobloc has four turrets: first, rinsing and volumetric filling for the viscous phase with fruit bits up to 20x20x20mm in size, then weight filling for the liquid phase with pulp up to 5x5x5mm in size and finally capping. Package sterilization is done with peracetic acid (PAA) and capsule decontamination with pulsed light. The filling chamber is under filtered air. depending on the chosen recipe and the volume to dose on each carrousel, machine speed can range from 150 to 500 packages per minute. This configuration enables the filling of a multitude of dairy products such as yogurts, two-phase foods, cream desserts and fruit sauces The first synchrobloc in ultra-clean configuration was recently delivered to a major European dairy group. www.hema-filler.com","@ID":49} "BOTTLE MAKING 25 PETplanet insider Vol. 12 No. 11/11 www.petpla.net using a PPS 300/12 L preform injection moulding machine and SFL 2/2 stretch-blow moulder producing over 900bph. 10l for hot fill In just eight months, Sipa recently delivered a complete solution to a South Asian company for the production of 270g, 10l hotfill soy sauce containers. It developed the preform and bottle designs, with production by a PPS 300/12 L preform injection moulding machine and an 1100 b/h SFL 2/2 stretchblow moulder. 6,000 5l bph for water and edible oil The company introduced new systems for large containers at Yihai Kerry, part of Wilmar International. It now uses several dozen 26 SFL linear stretch blow moulding machines to produce 5l cooking oil bottles, with a new SFL 6/6 XXL linear stretch-blow moulder capable of running at 6,000bph. Another SFL 6/6 XXL is producing 6000 68g 5 L water b/h at a multinational beverage company’s operation in Spain. The bottle resists a top load of 100kg by using nitrogen during the filling phase. Sipa says that its approach is to work collaboratively with customers, rather than just as a supplier in handling all aspects of mechanically demanding products like large PET containers. It can undertake moulding trials as well as all types of relevant mechanical tests on prototype containers. www.sipa.it Sipa supplies solutions for the production of large containers.","@ID":27} "PETbottles 48 PETplanet insider Vol. 12 No. 11/11 www.petpla.net Black PET for stock The Danish company Oscar from Rønnede is also marketing various concentrated stocks in Germany for convenient use in preparing dishes, such as in this case, for example, Veal Stock concentrate in a black 200ml PET bottle. The bottles are decorated with informative front and rear labels and the closure consists of a screw-on dispenser cap with an integrated snap-on lid. The packs also feature a sealed attachment plate underneath the screw cap which provides security against tampering prior to opening. www.oscar.dk PlantBottle for Vio Under the slogan “The bottle that thinks about tomorrow“ CocaCola Deutschland is advertising its new ”PlantBottle“, which among others will be used in Germany for the ”Vio“ mineral water. According to Coca-Cola, the new PET bottle is made up of 14% sustainable raw materials, 35% of recycled plastic, it is 100 % recyclable and thus saves valuable resources. A belly label made from plastic foil and an elaborate push-pull drinking cap with tear-off tamper-proof ring and additional tamper-proof cap make the innovation complete. www.vio.de Robust and with maximum grip The French foodstuffs manufacturer Melfor of Mulhouse is selling a litre of Citrona lemon juice for refining foods in a yellow PET bottle. On the outside the bottle features – in addition to the area provided for affixing the label – a stabilising, maximum grip honeycomb structure. A printed, snap-on dispensing screw cap with an integrated, tear-off tamper-proof strip rounds off the unusual appearance of this product. www.melfor.com Premium in blue Sylter Quelle, a company from Rantum, is now offering its natural mineral water with added carbonation in premium bottles in a shapely design with a one litre content. The blue coloured bottles featuring a black screw cap with tamper-proof strip have No-label–look adhesive labell affixed to the front and rear. The front label features silver printing so as to emphasise the quality of the product. www.sylt-quelle.de Neat and convenient dispensing Unilever France is offering 490g Barbecue Sauce in France under the brand name “Aurora“ in a handy PET upside down bottle. The function of the self-closing silicone membrane is precisely explained on the labels which are adapted to the shape of the packaging. Prior to initial use the complete lid must be unscrewed and a sealing membrane sealed on to the closure removed. The high restoring force of PET is positively ideal for packaging variations of this type. www.amora.com","@ID":50} "BOTTLING / FILLING 21 PETplanet insider Vol. 12 No. 11/11 www.petpla.net Both strengths were in demand at Norwegian bottler Isklar. It decided to launch a sparkling water for several reasons: to tap a huge market potential; to better meet the needs of the gastronomy industry; and to address individual customers who increasingly prefer sparkling water over still water. Isklar’s existing water bottle had to be completely redesigned in order to withstand the pressure of added carbonation. Sidel supported Isklar’s design engineers in their efforts and helped to create a bottle that still had brand-specific facets but was stable enough to contain sparkling water. Tight time frame was a further mission-critical project aspect. The new product had to be launched before the trade’s ‘shelf review’, which is when wholesalers undertake major changes in their assortments and planograms. Iskar’s production line required an optical detection system, the first time one had ever to be installed in a high speed PET line, but Sidel was able to complete the line conversion within only two weeks of complete stoppage. Sidel enabled Isklar to launch its new sparkling water as scheduled. “If you fail to launch by a market’s shelf review date, you can miss the full year,” says Helge G. Valeur, Chief Operating Officer at Isklar. “In Norway, the trade’s shelf review date is the 1st of February. If you are late for that date, it is more difficult to get into the trade later in the year. We had a tight schedule to meet but Sidel succeeded. At the end of July, Isklar officially confirmed its intention to launch the new product. It was required that the first bottles were produced by December, in order for a scheduled taste panel to finalise the carbonation level of the product. That target was achieved and we were very pleased with that. We have to credit Sidel for staying on the project’s schedule.” www.sidel.com Sacmi Labelling S.p.A. Via dell’Industria 237060 Mozzecane (VR) Italy Tel. + 39 045 6347511 - Fax +39 045 6347559 [email protected] www.sacmilabelling.com SACMI presents its Modular Opera R.F.S.T. - Roll Fed Sleeve Technology: the answer to all of your labelling flexibility needs. Developed around a cutting edge process, this labeler applies wrap-around thermo-shrink plastic film labels from machine direction oriented rolls, by means of laser welding technology. Following the creation and application of the sleeves within the machine, the containers travel through a heat tunnel to complete the process. This Technology from SACMI is the only modular labelling machine on the World market that can accept full body/partial sleeve, rollfed, pressure sensitive, cut & stack labelling modules. It allows an inexpensive, easy and clean labelling process. The SACMI Labelling Opera R.F.S.T. offers flexibility, efficiency, cost savings and environmental friendliness. Modular Opera R.F.S.T.: the all-in-one unique solution. Flexibility lies in the label.","@ID":23} "PETpatents www.verpackungspatente.de 52 PETplanet insider Vol. 12 No. 11/11 www.petpla.net Hot filling International Patent No. WO 2011 / 014759 A2 Applicant: Amcor Ltd., Hawthorn (AU) Date of Application: 30.7.2010 A thin-walled plastic bottle for hot filling is designed to enable a major part of the reduction in volume that occurs during cooling to be absorbed via the base area. Variable bottle Intern. Patent No. WO 2011 / 023833 A1 Applicant : Rodolfo Enrique Munoz, Fuengirola (ES) Date of application: 10.6.2010 The side wall of a plastic bottle made from PET is constructed to resemble a concertina in order to make it possible, if part of the content is removed, to compress the bottle or to ensure low volume disposal of the bottle once it has been completely emptied. Safe and easy mixing Intern. Patent No. WO 2011 / 025745 A1 Applicant : JPRO Dairy International Inc., Oceanside (US) Date of application: 23.8.2010 Two products that, in order to guarantee that the product will have the best possible effect, must not be mixed together until shortly before application or consumption, are accommodated in two containers that are “coupled“ with one another by means of threads. This means that none of the product can be spilt, thus altering the required mixing ratio. Containers with elastic handle recesses Intern. Patent No. WO 2009 / 126712 A1 Applicant : Colgate-Palmolive Comp., New York (US) Date of application: 8.4.2009 The preform for manufacturing a container is partially combined / coated on the outside with a second material. This means that, on extrusion of the container from the mould, the result is a container that features a softer, grip-friendly material in the area required. Plastic container Intern. Patent No. WO 2011 / 027049 A1 Applicant : Sidel Participations, Octeville sur Mer (FR) Date of application: 31.8.2010 This international patent application describes the forming operation for a plastic bottle suitable for hot filling. For this it is fitted with special, elastically deformable segments that absorb any change in volume that may occur on cooling. Container pack Disclosure No. DE 102009044067 A1 Applicant : Krones AG, Neutraubling (D) Date of application: 21.9.2009 Elements featuring different modes of construction are integrated in the top surface of a bottle closure. A common holding frame is clipped into this so as to give a positive fit and to create a firm container pack.","@ID":54} "TRADE SHOW PREVIEW 38 PETplanet insider Vol. 12 No. 11/11 www.petpla.net Brau Beviale will be opening its doors again on Wednesday, November 9, 2011 in Nuremberg, Germany. The exhibition covers all aspects of the beverage sector. A total of 1,300 exhibitors will be presenting their latest developments to an anticipated 32,000 visitors. In our second preview for Brau Beviale, we have gathered information from exhibitors which is sure to be of interest to every company in the PET bottling sector. PETplanet insider will be there and we hope that you will look out for us as you make your way through the halls. Do visit us in Hall 7A / Stand 720 and share PETplanet’s experiences on the ‘Go-to-Brau Beviale’ round trip with the Editourmobil. Bigger PET bottles and new barrier technology Appe will be showcasing its latest designs and developments in PET containers for beer, wines, juice, CSD and mineral waters. Its Deep Grip bottles are represented as an alternative to extrusion blow moulded HDPE bottles with integrated handles. Recesses of up to 25mm each side are intended to create effective hand-holds in containers up to 7l. Typical applications will include juice and dairy. Appe’s new barrier technology is particularly aimed at juice and wine applications and is claimed to offer improvements over existing barrier technologies in terms of performance, clarity of material and recycling potential. The company’s testing programme has shown good results in prevention of vitamin C loss and oxygen ingress. The stand will have individual sections focusing on capabilities in beer, wines, juice, CSD and mineral water, including its recentlylaunched Heineken keg, a small draft beer system for home use. Visitors will be able to discuss various initiatives in recycled PET production and its 100% remanufacture into packaging applications, as well as Appe’s in-house energy reduction programmes. www.appepackaging.com www.sacmi.com PET Verpackungen Hall 4A | Booth 413 Wide-ranging preforms, bottles and jars PET-Verpackungen GmbH Deutschland will be presenting its full range of standard and bespoke services. The company designs, develops and manufactures PET preforms, bottles and jars for standard, tailormade and specialised applications in the food & beverage industry. PETVerpackungen will also be talking to visitors about bioplastics, reflecting the increasing demand from the market to become ‘greener’. www.pet-verpackungen.de Appe Hall 4 | Booth 409 Sidel Hall 5 | Booth 121 New developments in beer bottling Sidel’s main focus will be on beer bottling, a sector to which it has delivered more than 7,000 pieces of equipment in over 100 countries over the past 40 years. Its new pasteurisation system called Swing is claimed to reduce energy consumption. It uses a single heat exchanger for all pasteurization zones, rather than one for each. Its ‘rain deviation’ system ensures that hot and cold water never mix. The company says that very precise control of the pasteurising units, by its Prince (Prediction In Control Equations) system, optimises the process and enables close monitoring of the quality of heat treatment of the product and protection of flavour and aroma. The Prince software system is now offered as an option and upgrade on Sidel’s entire pasteuriser portfolio. Visitors to the stand will also be able to discuss the company’s installed machinery estate and tools such as its integrated data acquisition and production management systems, and its customisable MES (manufacturing enterprise system). The company’s new bottling and packaging technologies are available as part of the new generation of equipment and can also be retrofitted on existing machinery. www.sidel.com","@ID":40} "NEWS 8 PETplanet insider Vol. 12 No. 11/11 www.petpla.net PET + Drink Tech Asia The fifth PET + Drink Tech Asia International Exhibition, held at Milan Mela Exhibition Center, Kolkata, West Bengal (India) from August 27 - 29, 2011, attracted over 50 exhibitors and more than 5,000 visitors from across the country. Participants from Nepal, Germany and China made the trade fair an international show. Exhibitor stands included PET injection moulding machines; blow moulding machines; PET bottle filling; capping and labelling equipment; PET moulds and dies, PET compressors; masterbatch, colorants and additives; PET preforms, bottles and jars; PET film, sheets and strapping rolls; hoppers, loaders and dehumidifiers; chilling plants and cooling towers; caps, closures, lids and handles; shrink sleeves and labels; drinking water tanks, cabinets and equipment; process automation and control; and fruit processing. Kesari Media and Events Pvt. Ltd. will be organising the sixth PET and Drink Tech International Exhibition & Seminar 2012 at Coimbatore, Hyderabad or Mumbai in September, 2011. Husky appoints new Vice President, Hot Runners Husky Injection Molding Systems has appointed Dave Whiffen to the position of Vice President, Hot Runners, in which role he becomes a member of Husky’s executive team and will head a dedicated hot runner group. Mr. Whiffen has been with Husky since 1986 and has held a number of senior positions, most recently in the company’s global Sales Support organization. He holds a degree in Chemical Engineering from McMaster University in Canada. www.husky.ca NürnbergMesse North America acquires InterBev Organisation of the next InterBev, to be held in October 2012 in Las Vegas, Nevada, is being undertaken by NürnbergMesse North America, a subsidiary of NürnbergMesse GmbH. Some 300 exhibitors are expected to attend InterBev 2012, including manufacturers and bottlers of refreshment drinks, juices, waters and energy drinks, as well as beverage raw materials, packaging, logistics, and marketing companies. Tea and mixed milk beverages are planned to be added to the scope of the trade fair. The organisers expect around 3,000 visitors from the North American beverage industry in the areas of purchasing, production and sales. NürnbergMesse North America, headquartered in Atlanta, Georgia, acquired InterBev from the American Beverage Association (ABA), who will continue to support the event and have largely designed the accompanying congress programme. The event will host the InterBev Beverage Innovation Awards and special presentations for such as beverage innovations, sustainability, logistics and storage. The first InterBev took place in 1920 in the middle of Prohibition, showcasing alcohol-free beverages. It is held every two years at various different locations and has been most successful in Las Vegas. Initial contact between ABA and NürnbergMesse North America was made by Wolfgang Schellkes, CEO of Fair Relations GmbH. NürnbergMesse Group organises Brau Beviale in Nuremberg and has been involved with the beverage market since the late 70s. www.nürnbergmesse-north-america.com Petainer opens corporate HQ in UK Specialist plastics packaging technology business Petainer has opened a new corporate head office in Peterborough, UK. The new facility has been established to support the company’s future business growth and international expansion, particularly in the development of new large PET containers for beverages and other applications. Petainer has manufacturing plants in Sweden, the Czech Republic and Germany. The holding company is a UK-registered business and its major investors are UK businesses or individuals. Petainer is aiming to build the business worldwide, through organic growth and by acquisition, with new manufacturing and sales operations. It is increasing its product range, particularly with large containers such as its new Petainer Keg and it is also developing its capability to deliver complete turnkey packaging solutions. www.petainer.com R&D Leverage sees continued growth in Europe R+D Leverage has enjoyed four consecutive years of double-digit growth in Europe and saw a 40% increase in production capacity in 2010. The company has announced further investment in plant capacity, technical material, and human capital. The workforce has expanded by 13% and the sales team has added language and engineering expertise suitable for a growing presence in Germany, Poland, Russia and the Middle East. Investment at the Nottinghamshire, England facility includes new design software for the engineering department, which has been developed in accordance with the company’s established best practices. 3D software has also been installed in the Quality Assurance department. Capacity in plate-line surface grinding equipment has been increased by 50%, while energy management systems have simultaneously increased electrical power supply to the UK facility and maintained lowest possible demand. A closed-loop system for compressed air supply has been installed in both the manufacturing facility and Product Solutions Laboratory, and machine capacity in the steel plate-line CNC milling department has been increased by half. The laser engraving department’s machine capacity is up by 25%. A second Nissei ASB70DPH version 4 machine in the Product Solutions Laboratory (PSL) allows for unit tool testing, production tool approvals and material and colour trials on site. R+D Leverage has also extended its apprenticeship programmes. www.rdleverage.com","@ID":10}]}}
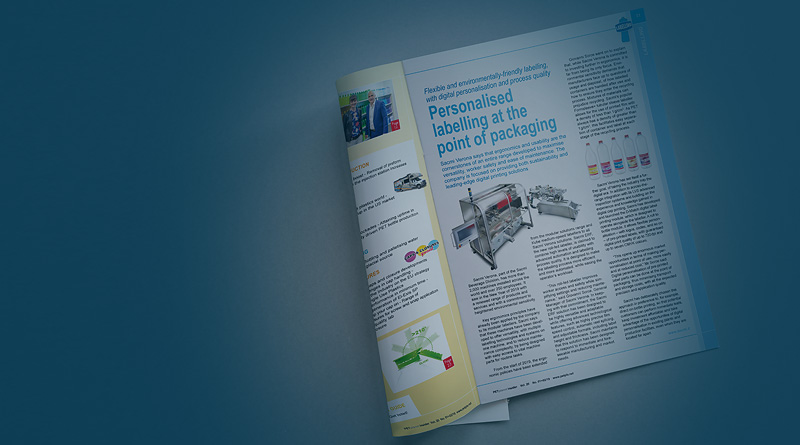