{"pages":{"page":[{"#text":"PETpatents www.verpackungspatente.de 32 PETplanet insider Vol. 12 No. 12/11 www.petpla.net Plastic bottle Intern. Patent No. WO 2011 / 024694 A1 Applicant: Yoshino Kogyosho Co. Ltd., Tokyo (JP) Date of application: 19.8.2010 The design and procedure for manufacturing a PET bottle are described. The bottle, which is manufactured using the biaxial stretch blow moulding process has defined strength / material values at the container opening. Plastic bottle Disclosure No. DE 102009038608 A1 Applicant: Krones AG, Neutraubling (D) Date of application: 26.8.2009 Thin-walled plastic bottle with sufficient stability to absorb the different pressures that occur during hot filling and the subsequent cooling process. In addition, this bottle has a sufficiently large surface to enable labels to be applied. Stackable bottle Europ. Patent No. EP 2292519 A1 Applicant: August Gysen, Gent (BE) Date of application: 8.9.2010 Set – consisting of at least two bottles which can be safely stacked thanks to top and bottom faces which fit into each other. For lighter weight and enhanced comfort when carrying, a folding handle is attached to the neck of the bottle. Optimised labelling Intern. Patent No. WO 2011 / 037762 A1 Applicant: Graham Packaging Comp., York (US) Date of application: 10.9.2010 A plastic bottle for hot filling with a corresponding compensating area to absorb the change in volume during cooling is specially shaped in the labelling area in order to improve the application and the appearance of the label. Indentation for drinking straw Intern. Patent No. WO 2011 / 023586 A1 Applicant: Innoprax AG, Meggen (CH) Date of application: 17.8.2010 This international application describes a plastic bottle featuring indentations which are incorporated in its curved surface area and which are designed as a zone for holding drinking straws. This enables a drinking straw to be sold along with the bottle so that it is secure and impossible to lose. Simple closure Intern. Patent No. WO 2011 / 026736 A1 Applicant: Nestec S.A., Vevey (CH) Date of application: 19.8.2010 Closure simply superimposed and placed directly on top of the container opening using high frequency, complete with tamper-proof seal and reclosable lid. The constructive closure can be manufactured at a favourable price.","@ID":34} "MATERIAL / RECYCLING 11 PETplanet insider Vol. 12 No. 12/11 www.petpla.net tal issues, energy and water supply and waste water treatment, among others. Dan said that the new rules are supporting improvement in flake quality. Dr. Shell Huang, of The Coca Cola Company, USA, reported that, as well as mechanical recycling, Coke is working to produce plant-based PET. Its aim is to produce polyester raw materials that are currently crude-oil based, such as mono-ethylene glycol and terephthalic acid, from biomass by 2020. Dr. Thomas Friedlaender of Krones AG, Germany, introduced the company’s new bottle flake washing technology. Key to its new process is the intensive removal of impurities by thermal treatment in the presence of chemicals and counter-flow of process water. Dr Friedlander said that the washing process provides flakes that fulfil FDA approval standards and are suitable for high-end applications. Anti-dumping: impact and opportunities Sun Ma of Cixi Jiangnan Chemical Fiber Co. Ltd., China, explained the impact of the EU-antidumping policy for recycled polyester staple fibre producers. While the policy has had a negative economic impact on Chinese fibre producers, it has also forced them to enter new markets, in developing countries especially, and to improve product quality. Waste collection for economic liberation; flexible food packaging production PetStar SA De CV, Mexico, has established a successful PET bottle collection system and bottle flake production – without governmental support – in a challenging social and economical environment, Jamie Camara reported. The primary factors include the intensive education of the people and their children, who collect the bottles from waste dumps. The company also made efforts to provide better work and living conditions for the bottle pickers. Feng Fenghua introduced Buehler China’s capabilities in plastic sorting and demonstrated the ACCEP-sorter, which has a range of applications and is not limited to polyester bottle and flake sorting. Ralf Altepeter, of Gneuss Kunststofftechnik GmbH, Germany, made a presentation on new opportunities for the production of food packaging from recycled PET material. Key points of the Gneuss process are the combination of MRS extruder, moderate vacuum treatment, continuous filtration and online viscosity control. He said that the Gneuss system is a flexible application, suitable for recycling processes in both bottle flake and fibre processing. The presentation by Peter Mayer of Sesotech (S+S Separation and Sorting Technology GmbH), Germany, compared conventional bottle and flake sorting with a new concept, which collects all sorting steps like bottle sorting, metal separation, colour sorting and material sorting within a single machine. A significant advantage of the new technology is the elimination of presorting, he said. Recycling in China and worldwide Helen McGough, senior consultant with PCI Ltd., UK, reported on global trends in bottle collection and reuse. A total of 6.7 million tons of bottles were collected in 2010. Asia’s share of the total was 52.4%; Europe had 21%; and North America collected 15,1%. The lowest collection rates are in Eastern Europe and the Middle East, followed by the Americas. China has the highest collection rate: nearly 85%. The main end-use application is fibres (71%), followed by blowmoulding (11%) and rPET sheet, with about 10%. Her presentation also analysed the situation and trends in Europe, the USA and China. The situation of the rPET industry in China was analysed in detail by Cao Wenting, consultant with CCFEI (China Chemical & Fiber Economic Information Network). His presentation included China’s production capacities for virgin and recycled staple fibre, filling fibre and filaments, as well as the output of virgin bottle grade PET. The impact of the debt crisis in Europe and the USA on the Chinese economy was also the subject of detailed analysis. A case study about the effect of bottle flake quality on the investment cost of high-end flake conversion processes was presented by Dr Ulrich Thiele, Polyester Technology Consulting Service, Germany. He concluded that vertical integration from baled bottles to end product provides the best prospects for successful operations. A deeper look at pelletizing technology and its optimal use in polyester recycling was provided by Xu Jianlei of MaagAutomatic Group, China, and Huang Weijang, of Shaoyang Textile Machinery Co Ltd., China, gave a report on experiences with energy-efficient recycling equipment. Future plans Initial participant feedback was that there should be more space for technical and business communication alongside the main conference. In planning for the future, the conference organisers will consider combining the conference with an exhibition focusing particularly on technical aspects of the recycling industry. Publications and papers from the conference are available as a CD from drthiele@polyester-technology. com (handling fee applicable). www.ce-pip.com. *Based on a report by Dr Ulrich Thiele, Polyester Technology Consulting Service, Germany.","@ID":13} "NEWS 8 PETplanet insider Vol. 12 No. 12/11 www.petpla.net PET recycling up again in N America The 2010 Report on Post Consumer PET Container Recycling Activity, the latest report from Napcor (National Association for PET Container Resources), the Association of Postconsumer Plastic Recyclers (APPR), and the PET Resin Association (Petra) finds that the rate for recycling of PET in the USA has increased again. 2010 is the seventh consecutive year of growth and was achieved despite a reduction in publicly-funded collection programs in California and some other states. PETplanet Issue 10/2011 carried figures for 2009, as comparison with Europe’s data. The release of the Napcor/APR/Petra report brings the transatlantic figures up to date with Europe’s. Total PET collected for recycling was the highest to date in the USA, as was the use of recycled PET in end-use applications, at over 1.5 and 1 billion pounds (678,000t and 452,000t) respectively. The 2010 Report also details the end uses for a record 1,002 million pounds of recycled PET utilised in manufacturing applications. Applications in sheet & film, food & beverage bottles, strapping, and fibre end-use categories all showed increases over 2009. After two years of decline, sales of PET bottles and jars rebounded during 2010 across all sectors, although carbonated beverage saw growth tailing off during the last two months of the year. Increases in bottle and jar numbers did not directly translate to increase in quantity of PET produced and used, and the drive for lighter weight continued in 2010 and will continue for at least the next few years as every fraction of a gram used in a bottle is scrutinised. Napcor determined that the total weight of PET bottles and jars available in the United States for recycling in 2010 was 5.350 billion pounds (2,420t), which includes resin used by bottle manufacturers from US, foreign, and recycled sources, less scrap generated and not reused, exported bottles and preforms, and bottles less than 8oz in size. A total of 1,557 million pounds (703,000t) of postconsumer PET bottles was collected for recycling and sold in the USA during 2010. Of this, just under half was purchased by US reclaimers and a little less by export markets. Just over 4% of the total PET bottle components were included in mixed bales for export. The full report is available for download at www.napcor.com/ PET/pet_reports.html. Napcor, the National Association for PET Container Resources, is the trade association for the PET plastic packaging industry in the United States and Canada. www.napcor.com APPR, the Association of Postconsumer Plastic Recycling, represents companies involved in acquisition, reprocessing and sale of more than 90% of post-consumer plastic processing in the USA, Canada and Mexico. www.plasticsrecycling.org Recycling line recoSTAR PET iV+ Ongoing PET recycling innovation, quality and state-of-the-art technology, a full range of consulting services – brought to you by Starlinger. Visit us at: Interplastica Moskau 2012, 24.-27.01.2012 Plastindia New Delhi 2012, 01.-05.02.2012, Booth B14, Hall 12 www.recycling.starlinger.com","@ID":10} "PETnews 6 PETplanet insider Vol. 12 No. 12/11 www.petpla.net EU support Krones PET recycling The European Commission, under the aegis of the EU’s programme for competitiveness and innovation, is subsidising Krones’ introduction of an FDA-compliant flake recycling process. The objective of the scheme is to successfully establish eco-compatible processes and environmentfriendly products on the European market, and to upgrade the competitive capabilities of companies in the EU. Krones’ SuperPET recycling process has been adjudged to offer cost-efficient operation and significant market potential in the 27 EU nations. The process, which is fully developed, produces food-quality flakes from used PET bottles for use in the manufacture of new PET containers, and is claimed to offer substantial energy, CO 2 and other savings. www.krones.com Registration for drink technology India/PackTech India now open Online registration is now open for drink technology India (dti) and PackTech India, the international exhibitions for the packaging, packaging printing, processing, beverage and liquid food industries. They will be running concurrently in Mumbai, India, from 6-8 November 2012. The venue is the Bombay Convention & Exhibition Centre, where over 260 exhibitor companies are expected. India is one of the fastest-growing markets in the world for beverages and packaged food products, with double-digit growth forecast for the next few years. Demand is high for machinery, equipment and accessories from western Europe, the US and China. The exhibitions will be supplemented by speaker presentations and a packaging conference. More than 6,000 trade visitors attended the previous event, in November 2010. The 2012 edition will be the second time that the trade fairs have been jointly organised by Messe München, Messe Düsseldorf and their Indian subsidiaries. www.drinktechnology-india.com www.packtech-india.com PET Engineering launches Polaris project PET Engineering has launched the Polaris project, a refurbishing and modernisation service to update old blowing machines, and bring them to the same level of productive performance as current modern machines. The company claims that significant energy savings can be achieved by changing the pitch between the lamps, meaning fewer lamps are required. This results in a lower consumption of energy when heating the preform inside the oven. Compressed air is also recovered and this is used to feed the primary functions of the blowing machine. According to the company, Polaris also permits the blowing of ultra-light containers, thanks to its five modules which can be applied separately or together, and this improves the efficiency of the machine and reduces the number of maintenance operations on the blowing components. www.petengineering.com Coca-Cola and Eco Plastics unveil recycling joint venture Coca-Cola Enterprises Ltd (CCE) and Eco Plastics have announced that Continuum Recycling Limited, their joint venture for recycling, will be located in Lincolnshire, in the east of England. The companies say that the name is reflective of the new company’s continuous process for re-processing plastic bottles. Eco Plastics received planning permission for a £15 million expansion of its plant in May 2011 and groundworks, foundations and a new road have already been completed. The new facility will increase the amount of high-quality bottle-grade rPET currently produced in the UK to more than 75,000t/a, more than double the current total. Once transformed into foodgrade rPET pellet by Continuum Recycling the material will be used in Coca-Cola bottles, enabling CCE to meet its target of including 25% recycled PET in all its plastics packaging by 2012. Eco Plastics began reprocessing post-consumer plastics in 2006. It has quadrupled its processing capacity and tripled the factory footprint since then. In early 2009 it became the first UK company to receive food grade accreditation for its rPET resin. www.ecoplasticsltd.com IVL to acquire Wellman International recycling and fibre business Indorama Ventures Public Company Limited has signed an agreement to acquire Wellman International Ltd and its related company, MJR Recycling BV, from Aurelius AG. The acquisition is expected to be completed before the end of 2011, subject to necessary regulatory approvals. It will provide access to proven recycling technology and the potential for a technology transfer to the Company’s Asian assets. IVL is seeking to become a ‘zero waste’ company with a low carbon footprint and the acquisition will help it to serve both the beverage and fibre segments of its customer base. Wellman International is Europe’s largest recycler of PET bottles and also produces polyester staple fibre products and rPET. It has three production facilities in Europe producing over 153,000t/a. These are: a polyester fibre plant in Mullagh, Republic of Ireland; and recycling plants at Spijk, Netherlands, and Verdun, France. IVL’s main products are PTA, PET and Polyester fibre. It employs approximately 7,996 people worldwide and its latest annual figures show consolidated revenue of $4.6 billion. www.indorama.net","@ID":8} "MARKET SURVEY 21 PETplanet insider Vol. 12 No. 12/11 www.petpla.net Neo Group Reliance Industries Limited. DAK Americas LLC Rimkai LT-95346 Dovilai eldership Klaipeda District ,Lithuania 37046466700 www.neogroup.eu Tadas Bernatonis Sales Manager +37062067507 +37046466711 [email protected] Reliance Industries Ltd, Building No. 8, B Wing, 1st Floor, Thane Belapur Road, Reliance Corporate Park (RCP), Ghansoli, Navi Mumbai, 400701 , India +91-22-44770000 www.ril.com Mr B. Arun Sr Executive Vice President +912244781239 (D) +9122 44779107 [email protected] 223 Wilmington West Chester Pike, Suite 210, Chadds Ford, PA 19317, USA +1 610-558-7380 or 888-738-2002 www.dakamericas.com George Rollend Senior Technical Manager +1 603-672-6403 +1 866-833-5069 [email protected] NeoPET Relpet Laser+ PET Resin 0.76 - 0.84 No 0,76 Yes 0.76-0.84 0.73-0.86 Yes G5841 Laser+ Yes G5761 Laser+W Yes B9845 Yes Yes G5801 No H7761 Laser+HS No Yes QH5821 Laser+W, Laser+, Laser+ HS B-2-B resin Laser+ EBM, Laser+C B9845 No No Suitable for wide variety of beverage and juice, water and CSD, milk, edible oil and soy sauce containers.Also recommended for thermoformable sheets, cosmetics and household packaging.Available at different viscosities of 0.76 up to 0.84, with fast reheat or non fast reheat properties, depending on customer requirements. Valspar Clariant SE Americhem Europe Ltd ColorMatrix Gabriel-Chemie Gesellschaft m.b.H. 2001 Tracy St. Pittsburgh, PA 15233 USA +1412-734-8544 www.valsparpackaging.com Lynn Spataro Market Manager +1 412-734-8544 +1 412-766-8953 [email protected] Am Unisys Park 1 65843 Sulzbach am Taunus, Germany +49 6196 757-60 www.clariant.com Severine Wild Marketing Support +49 61 96 757 6276 +49 61 96 757-8856 [email protected] Cawdor Street, Eccles Manchester M30 0QF, UK +44 1617897832 www.americhem.com Pierre Vandekerckhove +44 7825 419086 +44 161 7877832 [email protected] Unity Grove, Knowsley Business Park, Knowsley, Merseyside L34 9GT, UK +44 151 632 8800 www.colormatrix.com Claudia Finamore Marketing Manager - EMEA +44 151 632 8821 [email protected] Industriestraße 1, 2352 Gumpoldskirchen, Austria +43 2252 636 30-0 www.gabriel-chemie.com Ing. Thomas Ankowitsch Unit Manager Food Brand Packaging +43 2252 636 30 1653 +43 2252 627 25 1653 [email protected] Yes Yes Yes Yes Yes Yes Yes Yes Yes Yes Yes Yes Yes Yes Yes Yes Yes valOR Activ and valOR ActivBloc Yes Yes Yes Yes No Yes valOR ActivBloc and valOR Bloc for passive barrier Yes Yes Yes","@ID":23} "BOTTLES PETbottles 31 PETplanet insider Vol. 12 No. 12/11 www.petpla.net Aje Thai launches new water brand in Thailand Thailand is battling against the flood waters, 30% of the country is inundated. The shelves in Bangkok and over much of the country are bare with one of the most important goods missing: drinking water. Broken supply chains, a lack of plastic bottles (especially closures) and panic buying are the main reasons. Major discounters such as Tesco Lotus and Big C have ordered bottled water from Malaysia to restore the supply chain, leading to criticisms and objections from established water suppliers in Thailand. It was at this precise moment that Aje Thai Co., the bottler of Big Cola soft drinks, entered the Thai market with the launch of its its new water brand. For the first time in many weeks consumers can find 600ml water bottles on the shelves once more, but this time in the unfamiliar livery of the unfamiliar “Cielo” brand. At the launch, there were no fanfares and no big marketing campaigns, but the timing, tragically inopportune as it was, did help alleviate the serious lack of bottled water in the affected areas. The factory of AjeThai is located in Chon Buri (South-East of Bangkok) and is not directly affected by the flooding. Responding to the crisis, the company modified two soft drink production lines and can produce 200,000 bottles of water per day. And due to the high demand, the company is already in the process of converting further production lines to bring the total capacity to 400,000 bottles per day. Aje Thai is highly successful in the Thai market. In just five years, Big Cola has gained a 27% market share in cola drinks in Bangkok, and 22% for the whole country. Currently, Aje operates four factories in Asia: in Chon Buri, Ho Chi Minh City, Jakarta, and Pune, near Mumbai. All in good spirit… RPC Containers Llantrisant, Wales, is supplying an industry-standard PET bottle for the packaging of an environmentally-friendly paint cleaner. The manufacturer, EG, claims that its Spirit Green solvent-free alternative to the commonly-used white spirit is safe on skin and can be poured down the sink after use. EG says that it sought to create a product with strong images of environmentalism as well as professionalism, which would fit within the company’s existing market offering. Spirit Green is a totally non-toxic, non-flammable and nonsmelly paint cleaner that works on all paint types. The bottles are injection stretch blowmoulded in clear plastic, with a large labeling area and a child-resistant closure. www.rpc-llantrisant.co.uk Czech brewery selects Petainer keg Nachod Brewery has selected the Petainer Keg for the packaging and supply of its Primátor brand beer to its customers worldwide. It is the first Czech brewer to use Petainer Kegs, which are available with one-way fittings that allow it to be connected to existing tapping systems for draught beer. Nachod said that the Petainer-packaged product is aimed particularly at seasonal customers, restaurants and bars with limited storage space, as well as other outlets that sell beer on tap. No advances are charged for the Petainer kegs and return costs are eliminated completely, as empty kegs can be crushed and put into the recycling bin. Nachod uses a KHS Innokeg Till PETboy F2 machine for filling. Primátor beer is now supplied in 20l Petainer kegs in branded cardboard cartons to markets across the world including Hong Kong, Italy and Russia. The kegs are available in 15, 20, 30 and 40l sizes. www.petainer.com www.primator.cz Children’s sports drinks Minerálne Vody a.s., a Slovakian bottled water company, has recently launched a new format 0.33L bottle in their Drobček range, which is aimed at the children’s market. The Drobček range comprises four water varieties, three of which are flavoured. All four are equipped with a standard transparent 28mm Original Sport Cap. The closure manufacturer, Aptar, says that the Original range offers a number of features in the areas of safety and hygiene. It has no risk of either the lid or spout detaching; the recloseable lid and tight seal keeps the spout clean and prevents spills and elaks; it is easy for children themselves to open and reclose; and it is easy for even small children to use. A SimpliSqueeze silicone flow control valve option is also available. The Original sport caps are available in a range of standard colours and in different colours for spout and body. www.aptar.com","@ID":33} "PREFORM PRODUCTION 24 PETplanet insider Vol. 12 No. 12/11 www.petpla.net Interview with Thomas Anderegg* Netstal takes over PET activities from Krauss-Maffei Healthy competition within your own group lends wings to business – this has for years been the maxim as regards the PET activities of Holding KraussMaffei AG. Its two subsidiaries, Krauss Maffei Technologies GmbH and NetstalMaschinen AG, have set out their stall with their own preform machine concepts. Whilst Krauss Maffei has, in its PETform series, opted for the vertical clamping, Netstal has built the classic horizontal clamping into the PET-Line series. Since October 1, 2011 both series have been running under the Netstal umbrella. We spoke with the new divisional director at Netstal, Thomas Anderegg. PETplanet: Mr Anderegg, just under 20 years ago KraussMaffei bought into Netstal. Since then we have been waiting for the announcement that the PET divisions would join together. Why specifically now? Mr Anderegg: It’s not quite as easy as that. Although KraussMaffei acquired a share in Netstal 19 years ago, it was not until 1998 that it launched its own PETform line at the NPE in Chicago. So the maximum time you could have waited for this announcement is 13 years. PETplanet: Conversely, that means that PETform, which has been pronounced dead and buried on a number of occasions, is still alive? Mr Anderegg: PETform has never been pronounced “dead and buried” as you put it. At most, you could say it had an uneventful life, but year on year, it has sold in respectable quantities. For my part, I have a clear commitment to PETform. This also means that we need to further develop the machine. The series will now run under the name of “Netstal PETform“, alongside the well-known ”Netstal PET-Line“ series. PETplanet: As far as the machinery range is concerned there is an overlap; the largest of the Netstal PETform machines is clearly, in terms of its capacity, getting close to the smallest Netstal PET-Line? Mr Anderegg: We will always offer the customer the best commercial solution, tailored to suit his product. Depending on the requirement, that may be the PET-Line or the PETform. But you are right, the 2000 series Netstal PET-Line displays a distinct overlap with the PETform. Here we will, in the course of updating our models, be replacing the 2000 series with the 2400 series. This means that the processor can have 72-cavaties moulds running on it without any problems. In the end what counts as far as the processor is concerned is not the clamping force categories but the transformation costs and output per investment and it is here that we consider that our strength lies. PETplanet: KraussMaffei and Netstal are both marketing manufacturing plants for closures on beverage bottles. Will these two sectors also be combined? Mr Anderegg: The closing caps market is different in structure to the preform market. Each company has its customers and its focal points. For this reason we do not at the present time anticipate combining these two sectors. Already today the Netstal business unit Cap is fully focused on high volume commodity closures for beverages in PET bottles. We are market leader in this sector with more than half of the total installed capacity. PETplanet: OK. So it’s 13 years... Mr Anderegg: Netstal has been operating independently since KraussMaffei came on board, with its own technology and its own team. In the meantime it has, however, become apparent that we need to pool our resources specifically in the PET sector. PETform has enjoyed great success in the developing countries and for widemouth bottles, PET-Line supplies the high end markets. Thus, together, we can offer the optimum solution for practically every application, both in small as well as in larger quantities.","@ID":26} "imprint EDITORIAL PUBLISHER Alexander Büchler, Managing Director HEAD OFFICE heidelberg business media GmbH Häusserstr. 36 69115 Heidelberg, Germany phone: +49(0)6221-65108-0 fax: +49(0)6221-65108-28 [email protected] EDITORIAL Doris Fischer [email protected] Michael Maruschke Ruari McCallion Ilona Trotter Wolfgang von Schroeter Anthony Withers MEDIA CONSULTANTS Ute Andrä [email protected] Martina Hischmann [email protected] Ursula Wachter [email protected] phone: +49(0)6221-65108-0 fax: +49(0)6221-65108-28 France, Italy, Spain, UK Elisabeth Maria Köpke phone: +49(0)6201-878925 fax: +49(0)6201-878926 [email protected] LAYOUT AND PREPRESS Exprim Kommunikationsdesign Matthias Gaumann | www.exprim.de READER SERVICES Kay Krüger [email protected] PRINT Chroma Druck & Verlag GmbH Werkstraße 25 67354 Römerberg Germany WWW www.petpla.net | india.petpla.net PETplanet insider ISSN 1438-9459 is published 10 times a year. This publication is sent to qualified subscribers (1-year subscription 149 EUR, 2-year subscription 289 EUR, Young professionals’ subscription 99 EUR. Magazines will be dispatched to you by airmail). Not to be reproduced in any form without permission from the publisher. Note: The fact that product names may not be identified as trade marks is not an indication that such names are not registered trademarks. 3 PETplanet insider Vol. 12 No. 12/11 www.petpla.net EDITORIAL dear readers, EDITORIAL What has been happening these past few weeks? Well, Brau Beviale has just closed its doors, so let’s start by looking at some numbers. Footfall this year was down by around 1,000, compared to last year. 31,693 visitors came through the door, (Source: Auma) and stayed a surprisingly long time considering it was a three day event: on average 1.4 days in 2010, almost half the duration of the Fair. If the average were to be maintained for 2011 too that would mean that more than 22,600 people visited the Fair. have to say I’m surprised that the sector is reckoned to be as big as 22,600. I think this might require a little more investigation... Let’s take another thread for a moment by looking at the Drinktec 2009 figures (Source: Auma again). Hmm – similar visitor numbers for Germany. There has to be something in that, but the question remains: just how big is the sector? Meat and drink for the editorial. Here’s Volker Kronseder, Krones CEO, a man with the facts at his fingertips, but in his opening speech at Brau Beviale, he gave figures from the VDMA only, and nothing about visitor numbers. Step forward Gerhard Ilgenfritz, CEO of Private Breweries Bavaria e.V. who quotes an initial figure of 1,325 breweries, not counting the micro-breweries. Is it just coincidence that there are 1,400 exhibitors and 1,325 breweries in Germany? The plot thickens. Here’s another thread in the story. Let’s consider the non-alcoholic sector where the situation is looking as clear as mud. The commercial units are either spread all over the place in the statistics or have not been included because of a lack of information on minimum size. I found this surprising, so let’s see if we can match up the size of the sector with the numbers of visitors. My maths isn’t up to it, sadly. The highlight for me is Gunnar Sprinkmann’s security strategy (see picture). No longer can anyone tamper with the PET bottle undetected. Neither can I if I forget the code. My dodgy maths tells me that, with three rings to turn, there are 1,000 possible combinations, slightly fewer than the number of breweries in Germany! Yours Alexander Büchler","@ID":5} "NEWS 9 PETplanet insider Vol. 12 No. 12/11 www.petpla.net MHT MOLD & HOTRUNNER TECHNOLOGY Dr. Ruben-Rausing-Str. 7 | D-65239 Hochheim/Main Tel. +49(0) 6146-906-0 | www.mht-ag.de Make the most of your machine – with a mold from MHT! For many machine types, we supply the mold with the highest cavitation, thereby enabling optimum preform output. For the Husky HyPET machine, we offer an upgrade set for 33% more preforms, without refitting on the machine! • 60 cavities for Netstal PETline 2000 • 96 cavities for Husky HyPET 300 • 112 cavities for KraussMaffei 350 Engineering made in Germany Patent pending: MHTcoolMAX® post mold cooling KHS Erratum Unfortunately, in the Market Survey covering the suppliers of filling equipment which featured in our last issue 11/1, the data for KHS was omitted by mistake. We apologise for this omission. The data has now been added to the online version of the Market Survey of issue 11/11. Please refer to this to view a printed version of the supplementary data. Company name KHS GmbH Postal address Telephone number Web site address Contact name Function Direct telephone number Fax E-Mail Juchostrasse 20 44143 Dortmund, Germany +49 231 569-0 www.khs.com Heinz Hillmann Product Manager +49 671 852 2714 [email protected] 1. Machine designation / model number DRV: computer controlled volumetric filling machine for carbonated softdrink NV: computer controlled volumetric filling machine for still water and juice (cold and hot) 2. Number of filling heads (range: from/to) 48 - 180 36 - 144 3. Filling speed/output - based on 1l PETbottles a. Still water (1l bph) up to 72,000 up to 68,000 b. Carbonated drinks with 8 g CO² (1l bph) up to 55,000 c. Milk (1l bph) d. Fresh fruit juice (1l bph) up to 55,000 up to 44,000 4. Filling process Pressureless (still drinks) yes yes Pressure filling (carbonated drinks) yes no Hot filling yes yes Cold aseptic filling no no Juices with high pulp content no up to 10% 5. Type of filling valve and metering system valve with swirl modul for foam free filling, volumetric system with MID non contact, free flow filling valve with MID ( magnetic inductive flowmeter ) NPE2012 registration opens Online registration for NPE2012, the National Plastics Exhibition is now available at www.npe.org. Organised by SPI, The Plastics Industry Trade Association, the 2012 edition of the triennial NPE will run from April 1-5, 2012, at the Orange County Convention Center, Orlando, Florida, USA, after 40 years in Chicago. Visitors can use the online facility to select from various registration packages and fees for the NPE trade show, as well as co-located events such as conferences. For international visitors who require a visa to enter the US, registration includes the option of requesting an official invitation letter from SPI, which must be presented for visa interviews at US embassies and consulates. The site can also be used for hotel reservations through a link to the official housing contractor, Expovision. The main NPE show will feature 2,000 exhibitors in 93,000m². Space sold so far exceeds total space occupied at NPE2009, according to SPI. At least a dozen multi-exhibitor pavilions will be dedicated to specific industry sectors like elastomers and thermoforming, plus emerging technologies like bioplastics and nanocomposites. Product entries to the Second International Plastics Design Competition will be on display and winners announced in a special presentation. Special programmes include Plastics in Sports; a Technology Theatre presenting product demonstrations and exhibitor seminars; and Recycling at NPE2012. A complete schedule is available at the website. www.npe.org New STF PET recycling plant starts up STF Recycling, headquartered in Aicha vorm Wald, started up a second Erema Prime extrusion plant in August 2011. The new plant has a capacity of 14,000t of PET regrind, which raises the company’s total food-grade PET regrind capacity to approximately 25,000t. STF Recycling owns 10 PET recycling plants with a total capacity of 130,000t of PET bottles, across three different sites: Aicha vorm Wald, Gelsenkirchen and Bremerhaven. It produced 114,000t of PET flakes in 2010, which were used in foil, fibre, strapping and bottles. www.stf-group.de","@ID":11} "PETcontents 12/11 4 PETplanet insider Vol. 12 No. 12/11 www.petpla.net INSIDE TRACK 3 Editorial 4 Contents 6 News 29 Products 31 Bottles 32 Patents MARKET SURVEY 19 Suppliers of resins, colours and functional additives for PET bottle production PREFORM PRODUCTION 23 Splay A rapid guide to perfect preforms - part 26 24 Netstal takes over PET activities from Krauss-Maffei Interview with Thomas Anderegg BOTTLING / FILLING 28 Water from the desert Installation of SMI PET line at the Siwa Oasis, Egypt RECYCLING SPECIAL MATERIAL / RECYCLING 10 Recycled polyester on the rise Conference report on 7th China International Polyester forum Shanghai 12 A flexible plant concept Erema’s plant concept offers three different operating modes in rPET production. 14 Food packaging from recycled PET Gneuss Kunststofftechnik offers recycling system for PET with full FDA approval 16 Recycling the flower of Africa PET recycling organisation in South Africa PET - THE NEXT GENERATION 28 A light comes shining PET bottle bottoms into inpressive chandeliers Page 27 Page 16 BUYER’S GUIDE 33 Get listed! Page 24","@ID":6} "BOTTLING / FILLING 26 PETplanet insider Vol. 12 No. 12/11 www.petpla.net Installation of SMI PET line at Egyptian “National Company for Producing and Bottling natural water & olive oils” Water from the desert At the western end of the Egyptian desert, on the border with Libya, around 300km southwest of Marsa Matruh, the Siwa Oasis offers its visitors an almost unique experience. The presence of water in the oasis encourages agricultural activities, related food processing businesses and a small number of factories specializing in the production of mineral water. Among these, the “National Company for Producing and Bottling natural water & olive oils” stands out. Owned by the Egyptian army and controlled by the NSPO (National Service Products Organization), it produces and markets Safi mineral water. NSPO chose SMI as a partner for the engineering study and the final installation of a complete 6,000bph PET SBM line. The Siwa Oasis The fertile lands of the oasis have enabled the development of agricultural production based mainly on olives, date palms and alfalfa which are flanked by small crops of other kinds of vegetables and fruit, mainly intended for local use. As well as its agricultural activities and food processing (dates and olives) companies, Siwa is also a prestigious industrial centre. Tourism is the second most important economic sector in the area, attracting around 10,000 visitors per year. The Siwa Oasis springs up out of nowhere with its palms and trees which extends, at 50km from the border with Libya, between the Qattara Depression and the Egyptian Sand Sea. In the oasis, located on the ancient trade route for dates which terminates at Memphis, there are over 300 freshwater springs which water thousands of date palms and large olive plantations. Between Siwa and the capital Cairo, nothingness reigns, or rather 550km of sand. During the course of its long history, it has remained largely isolated from events which took place on the banks of the Nile and has developed independently from the rest of Egypt. Until the 1980s, the most common means of transport was carts pulled by donkeys. The new asphalt road connects Siwa to the city of Marsa Matruh, to the North-East. The oasis is located in a depression, whose depth reaches 60m below sea level, which stretches for around 82 km. The Siwa depression and its lakes, one of the most spectacular places in Egypt, are the remains of an ancient sea which later evaporated and which extended up to here.","@ID":28} "PET - THE NEXT GENERATION 28 PETplanet insider Vol. 12 No. 12/11 www.petpla.net PET bottle bottoms into impressive chandeliers A light comes shining For more than ten years Cornelia Pitschi has been exploring the realm of recycling design. The take up and incorporation of recycling and recyclable materials is an important guiding principle of her design process. The fascination for materials ranges from electronic waste found on wheel covers to PET bottles. PET bottle material, with its glass-like character, especially the moulded base, inspired her to develop one of her favourite subjects - light objects. Apart from the light object “Pulpo”, which consists of PET bottle necks, the artist mainly works with PET bottle bottoms which are converted into different sized balls using a selfdeveloped plug-in system. As one of her first creations (2005) she developed the “Petobjektvase”, followed by the ball of light objects “Medusa1, 2 & 3”. Still some way from completion is an impressive chandelier, made up of 150 PET bottle bottoms in an impressive array of shapes! In order to get the raw material, discarded PET bottles bottoms, she cooperates with the social institution “Marktlücke” in Zurich. The institution collects the PET bottles from its canteen and prepares them as semi-finished products for the artist. For light objects which are made of new PET bottles, the material is sent to the social institution “Werkstätte Drahtzug“. There, the PET bottle bottoms are processed into semi-finished products which are then transformed into fascinating objects in her art studio in Zurich. For her new project Cornelia Pitschi is proposing a new campaign “Recycling - get involved” on her website. Here participants, who are interested in a Josefine PET-Object, can actively take part by collecting and sending the pre-processed bottle bottoms to Josefine, in the process saving a useful 30% off the standard sales price. www.josefine.ch The “Petobjektvase” is one of the first PET creations by Swiss artist Cornelia Pitschi The PET chandelier “Medusa” is made up of 150 PEt botle bottoms","@ID":30} "MATERIAL / RECYCLING 10 PETplanet insider Vol. 12 No. 12/11 www.petpla.net Conference report on 7th China International Polyester forum Shanghai* Recycled polyester on the rise Recycling companies and major end-users discussed the global market, economic factors and technological developments at the 7th China International Recycled Polyester Forum Shanghai 2011. The rapidly growing importance of the polyester industry in China and worldwide was reflected at the 7th China International Recycled Polyester Forum Shanghai 2011, which attracted 280 participants from 15 countries. Representatives attended from 38 international companies, including global majors such as Coca Cola, Pepsi Cola, Reliance, Eastman, LG International, BP, Unifi, Nike, Kolon and DuPont. Conference content was a mix of technical innovation, economic background and Chinese economic policy. In his address on polyester post consumer clothing recycling, Li Shidong, Secretary General of CCFA (the China Chain Store and Franchise Association), emphasised the segment’s huge potential. He presented an analysis of the current situation in the US, Japan, EU and China, and how factors such as fashion, design, production and usage of textiles make successful clothing recycling highly complex, compared to bottle recycling. He reported on current clothing recycling projects, such as Ecocorcle of Teijin, and the Zhejiang Furun Recycling Company, which is processing post-consumer army uniforms back to military supplies like tarpaulins, socks, camouflage net, and so on. Li pointed out that the huge amount of global textile military supply offers potential for government savings and opportunities for entrepreneurs entering textile recycling. Imports, biomass PET and flake washing Dan Hanliang, Lunnex Chemical Fibre Co. Ltd., China, explained the new rules for importing baled bottles. While only shredded bottles were formerly allowed to be imported, the Chinese government now issues broader import licenses under certain legal constraints, related to environmen-","@ID":12} "MATERIAL / RECYCLING 17 PETplanet insider Vol. 12 No. 12/11 www.petpla.net separated PET flakes are then dried and extruded into small, clear pellets. These are delivered to end-users for manufacture of a number of items in everyday use, such as fibre for polyester carpets; fabric for T-shirts; and – most importantly – back into new PET containers for both food and non-food products. The venture has created over 18,000 jobs in the informal collector segment. Investment in recycling infrastructure Petco also supports projects with a strong focus on public and consumerbased education and awareness programmes and these initiatives and activities have contributed to the visible recycling of PET. Many of these programmes, such as beach cleanups, trade shows, baling equipment, and bulk bag collections, as well as training, have been introduced with support from Plastics SA. Workshops for members on topics aimed to reduce contamination, such as designing PET bottles and containers with recycling, are hosted by Petco around South Africa. Along with major retailers Woolworths and Pick’n’Pay, Petco has established the Retailers for Recycling Forum. It aims to minimise the environmental impact of post-consumer packaging on the South African landscape by creating awareness among consumers of recycling issues, and by supporting retailers as they work with their own suppliers to ensure that packaging is designed with reduction, re-use and recycling in mind. Petco hopes this initiative will ultimately include all retailers and all packaging materials, as well. Polypet (Polyoak Packaging Pty), a specialist in the manufacture of PET preforms and containers for the beverage, food and wine markets, recently won the Best Recycled Product of the Year competition, hosted by The South African Recycling Organisation (Sapro), for their 1.5l recycled PET (rPET) juice bottle sold at Woolworths. Developing a common vision “This bottle is an excellent example of the way major retailers can influence an industry when they make a commitment towards environmental responsibility and sustainability”, said Cheri Scholtz, Chair of Plastics SA’s Sustainability Council and CEO of Petco. She reported that, in 2010 alone, 99,400t of PET was used in beverage bottles in South Africa and continued to say that collective efforts and a common vision of reducing the industry’s impact on the environment has enabled the industry to develop the most sustainable use for resources and to achieve the ability to ‘close the loop’ – recycle a bottle back into a bottle. At the same time, a vital new end-use market for the millions of PET bottles currently being recycled daily in South Africa has been created. “Using rPET in the Woolworth’s 1.5l juice bottle paves the way for other brand-owners and converters to utilise the growing percentage of recycled post-consumer PET bottles available in our country, instead of relying on virgin PET,” she said. Recycling saves money Petco received a special commendation at The Mail and Guardian’s ‘Green the Future’ Awards for the work it has been doing to promote recycling of PET in South Africa. The awards are designed to inspire innovation and action to address the causes of climate change, reduce impacts on resources and improve eco-efficiency. Recycling 1t of PET plastic bottles saves 1.5t of carbon, as well as reducing the need for raw materials and saving energy. Recycling a single plastic bottle can conserve enough energy to light a 60W light bulb for up to 6h. Petco is working with the Department of Environmental Affairs (DEA) and the two organisations have set stiff collection targets for 2015. The goal is for the public and private sector to put in place a cost-effective separation-at-source strategy. Objectives include the wider implement of kerbside collection, to reduce, reuse, recycle and recover plastics much more efficiently, and to completely eliminate the disposal of plastics to landfill. Low recycling rates adversely affect the ability to supply markets and will not encourage new projects. About Petco Petco is a member of the Recovery Action Group (RAG), which represents the packaging waste stream and has put together a draft Industry Paper and Packaging Waste Management Plan. This plan will ultimately be used to improve the collection of recyclables from the municipal solid waste stream prior to landfill. Petco actively urges all businesses involved in the PET packaging industry chain to become members, in order to protect and promote PET growth, awareness, recycling and reuse. It maintains that a strong membership base helps the PET industry to influence national environmental authorities. www.Petco.co.za Recycling 1t of PET bottles saves 1.5t of carbon","@ID":19} "MARKET SURVEY 20 PETplanet insider Vol. 12 No. 12/11 www.petpla.net Resins Additives MARKETsurvey12/11 Company name M&G Polimeri Italia SpA ExpoPET Green INTL LTD Invista Resins & Fibers GmbH NovaPET, S.A. Postal address Telephone number Web site address Contact name Function Direct telephone number Fax E-Mail Via Morolense Km 10 03010 Patrica (FR) - Italy +39 0775 84.221 www.gruppomg.com Marilena Grecchi Area Sales Export and Marketing Intelligence Support +39 02 82.273.242 +39 02 82.273.314 [email protected] 125 Shenley Road, Clarendon House WD6 1AG, London, United Kingdom +44 208 207 7356 www.expopetgreen.com Richard Kennedy Business Manager +44 208 207 7389 +44 207 183 5276 [email protected] D-65795 Hattersheim Philipp-Reis-Strasse 2, Germany +49 69 305 84655 www.polymers.invista.com Sebastien Casterman Sales Manager +49 69 305 85582 [email protected] P° Independencia, 21, 3°, PC 50001 Zaragoza, Spain + 34 976 216129 www.novapet.es Mr Miguel Angel Arto Business Development Director +34 976 216129 +34 901 021138 [email protected] RESINS 1. Brand name of the resins Cleartuf EXPO PolyShield; OxyClear; Polyclear NovaPET 2. IV Range a. of Homo-Polymers === 0,62 to 0,96 b. of Co-Polymers 0.76 ÷ 0,95 0.75 - 0.87 dl/g 0,72 to 0,82 3. Speciality resins CSD Cleartuf Ultra/Ultra Plus Expo A8, Expo A8+ Lbs Soft, Cr Water Cleartuf P76 / P82 Expo A7, Expo A8 Mw Soft, Cr, Glasstar and X_treme Beer Poliprotect PolyShield Glasstar Wine / Liquors Poliprotect OxyClear Glasstar Personal care /Pharmaceuticals Cleartuf P82 Glasstar, Sprit H 11, Sprit L01, Kera Slow crystallisation Cleartuf Aqua D Polyclear T94N Glasstar, X_treme Hotfill Cleartuf P85 HF HF Pre-coloured Dairy, Luz Fast reheat Cleartuf Ultra Expo A8FR Lbs Other Barrier resin (i.e. Poliprotect), for different applications (juices, beer, wine, dairy/milk based products…) CPET, HT 4. Increased barrier properties Yes, with Poliprotect Yes (UV for ultraviolet protection) PolyShield; OxyClear Dairy, Luz (Light barrier) 5. PEN mixes available No Yes, under customer requirements 6. Recycled blends available On request Yes, under customer requirements 7. Special comments Light barrier protection for long shelf life milk products (UHT, ESK, milk shakes, yogurt) Company name BASF Color Solutions Germany GmbH Holland Colours Europe BV Chroma Corporaion Repi S.p.A. Postal address Telephone number Web site address Contact name Function Direct telephone number Fax E-Mail Clevischer Ring 180 51063 Cologne (Germany) +49 221 96498-0 www.basf.com/masterbatch Anna Herbst Marketing Manager +49 221 96498-515 +49 221 96498-520 [email protected] Halvemaanweg 1, 7323 RWApeldoorn, P.O. Box 720 7300 AS Apeldoorn, The Netherlands +31 55 3680700 www.hollandcolours.com Florian Balogh Sales Manager EMEA +36 56 420644 +36 56 424/895 [email protected] 3900 W. Dayton Street McHenry, IL 60050, USA 815-385-8777 www.ChromaColors.com Stuart D. Swain Director of Sales and Marketing +1815-759-2110 +1815-385-1518 [email protected] Via B. Franklin 2 21050 Lonate Ceppino VA, Italia +39 0331 819511 www.repi.com Maurizio Amicabile Market Development Manager - Packaging +39 0331 819511 +39 0331 819581 [email protected] Additives and Colours for PET Liquid colours Yes Yes Yes Yes Microgranule colours Yes Yes Yes Yes Masterbatch colours Yes No Yes Yes UV protection additive (solid) Yes Yes Yes Yes UV protection additive (liquid) Yes Yes Yes Yes AA reduction (solid) No Yes No Yes - SenzAA- AA reduction (liquid) No No No Yes - SenzAA Oxygen scavenger (solid) No No No No Oxygen scavenger (liquid) No No No No Other PET additives in liquid or solid form Yes High opaque white for light protection (solid), frost additive (solid), slip agent (solid), oxygen barrier neutral colourant, tintmask for recycled PET, Frosted PET Colours Anti yellow (liquid), process aid (liquid), IV enhancer (solid), blowing additive (liquid), optical brightener (liquid), colour toners (liquid), In addition to liquid colours and additives, Repi supply Remap Colour Barriers for protection of the packaging content.","@ID":22} "MATERIAL / RECYCLING 16 PETplanet insider Vol. 12 No. 12/11 www.petpla.net South Africa’s PET recycling efforts are being driven Petco, a non-profit industry body. The country’s recycling rates have nearly quadrupled since it was established in 2004. The ‘flower of Africa’ is the ironic name given to discarded plastic waste, including bags and bottles, which litter the countryside and has reached a critical level in parts of the continent. South Africa’s PET waste consists mainly of plastic bottles and the country’s PET industry established Petco seven years ago as a non-profit organisation. It is charged with the responsibility for the facilitation and recycling of PET, and to minimise its impact on the landscape. Since 2004, PET plastic recycling has grown from 9,840t to 37,842t in 2010, and 3 million PET bottles are now recycled each day. These recycling rates have been achieved by Petco in partnership with service providers Extrupet, Kaymac and Sen Li Da, who combine collection, recycling and end-use in their PET value chain. Local reuse and recycling South Africa has an advantage over other African countries because almost all of the post consumer PET bottles collected are recycled within the country for end-use, rather than being exported to China. The consequence of the growing collection of post-consumer PET bottles is that end-use markets have the opportunity to expand and develop. The largest end-use market for post consumer PET bottles in South African is currently the fibre market (bottle-to-fibre). More recently, there is installed capacity for post consumer PET bottles, to be recycled into new PET containers (bottle-to-foodgrade). B2FG resin take-up is, however, currently relatively slow and Petco is working with retailers and brand owners to increase the demand for PET recyclate. Discarded post consumer PET bottles are collected, baled and delivered to the recycler – unfortunately, however, many of these are still collected from landfill. In the recycling plant, PP bottle tops are removed and the bottles are inspected and sorted according to colour, with any non-PET items being removed. The sorted bottles are then granulated into flakes, which go through numerous hot and cold washes before ultimately arriving in a flotation basin for final separation of non-PET material. PET has a higher density than other plastics, except PVC, and will sink while other materials, such as paper from labels, rises to the top and floats. The Products made of recycled PET","@ID":18} "MATERIAL / RECYCLING 14 PETplanet insider Vol. 12 No. 12/11 www.petpla.net Gneuss Kunststofftechnik offers recycling system for PET with full FDA approval Food packaging from recycled PET With the introduction of its MRS technology, approximately four years ago, Gneuss established itself as a specialist in PET recycling equipment. The company’s extrusion process, consisting of the MRS multi rotation system devolatilising extruder together with a rotary melt filtration system, has now been approved for reprocessing of PET post consumer waste (flakes) to direct food contact packaging products, without pre- or post-extrusion treatment of the flakes or pellets. It enables the manufacture – from up to 100 % PET post consumer bottle flakes – of sheet and food containers of all types for direct food contact. Systems for recycling post-consumer PET reclaim to high quality (and value) products for the food packaging industry, with unrestricted FDA approval, are already well established on the market. Gneuss Kunststofftechnik offers a system for high quality food standard results without thermal treatment of the flakes, either before or after to the extrusion process. The Gneuss processing system consists of the MRS extruder with its devolatilising system, a processconstant rotary melt filtration system for efficient purification of the melt, and an online viscometer for automatic regulation of viscosity in response to variations in the viscosity and/or residual moisture level of the input material. The specific energy consumption of the MRS extrusion unit is approximately 20% lower than that for conventional single or twin-screw extrusion systems, as neither pre-drying nor crystallisation of the material is necessary. In addition, maintenance requirements are significantly because neither pre-drying equipment nor a maintenance- intensive high vacuum system are needed. Additional material treatment steps are eliminated by the MRS patented design. The MRS extruder is based on a single screw extruder equipped with a special devolatilising section: the Multi Rotation System, which gives the extruder its name. MRS Multi Rotation Section with plasticising and discharge screw sections","@ID":16} "19 PETplanet insider Vol. 12 No. 12/11 www.petpla.net Bottle-to-bottle recycling plants Conveyors for preforms and empty bottles Caps and closures Preforms Perform moulds and SBM moulds Single stage machinery 2-stage SBM machinery Compressors Filling equipment Resins and additives Suppliers of resins, colours and functional additives We end the year with a Market Survey covering the suppliers of PET bottle resins and additives. The additives available include barrier improvement additives for sensitive beverages, UV blocker, brighteners and many other performance enhancers. The following resin manufacturers are included (in alphabetical order): DAK Americas, ExpoPET, Invista, Indorama, M&G, NEO Group, NovaPET and Reliance. In the additives sector, nine global players have come on board: (in alphabetical order) Americhem, BASF, Chroma, Clariant, Colormatrix, Gabriel-Chemie, Holland Colors, Repi and Valspar. Whilst the publishers have made every effort to ensure that the information is up to date, no claims are made regarding completeness or accuracy. 12/11 MARKETsurvey Resins Company name Indorama Ventures Ltd Postal address Telephone number Web site address Contact name Function Direct telephone number Fax E-Mail 75/102 Ocean Tower 2, 37th Floor Soi Sukhumvit 19 (Wattana), Bangkok 10110, Thailand +662 661 6661 www.indoramaventures.com W.G. Hoenderdaal Technical Services Manager +31 6 51809942 [email protected] Europe USA Mexico Asia 1. Brand name of the resins RamaPET Preformance PET, Polyclear PET Polyclear RamaPET 2. IV Range a. of Homo-Polymers 0.58-0.95 0,80 b. of Co-Polymers 0.70 - 0.84 0.58 - 0.84; 1.0+ 0.74 - 0.86 0.76-0.86 3. Speciality resins CSD R1/ R1L/ R182/ R180 ES11, 1101 Refresh 1101 and 1111 S1/S2/BL8050 Water N1/ N1(S)/ N2/ N180/ W170 N2R, 3301 Splash 3301 N2/N1/BL8050 Beer N1/ N1(S)/ N180 1708CC, 3302 Wine/liquors N1/ N1(S)/ N180 1708CC, 3302 Personal care/pharmaceuticals N180/ N1(S) 1708CC, 3302 N1 Slow crystallisation P184 Type 94 PET T-94 Hotfill R1/ HF 1708HS, 2201 Preserve 2201 H1/BB Pre-coloured Fast reheat R1/ R1L/ R182/ R180 ES11, 1101 R1/ES11 Other R182 PlantPET ES11Eb Semi-dull, film grade, superbright, high IV chips (0.95-1.08) 4. Increased barrier properties Oxyclear Barrier Resin 5. PEN mixes available Yes 6. Recycled blends available Polyclear Conserve PET; FuTuRe-PET 7. Special comments RamaET W170 Easyflow, low IV (0.70) for thin-wall applications, preforms and other injection moulded articles. Polyclear EBM PET for extrusion blow moulded containers, Low IV and functionalized PET and copolYester polymers also available","@ID":21} "PRODUCTS PETproducts 29 PETplanet insider Vol. 12 No. 12/11 www.petpla.net pet-recycling.com New S+S sorting systems S+S has developed solutions that separate contaminants from PET material flows and sorts them into unmixed fractions. Polymer separators with multi-spectral sensors are used to detect contaminants and plastic types. The fully-automatic systems separate unwanted plastic from the PET material by infrared absorption. S+S claims that its systems remove PVC contents or bioplastics such as PLA, which compromise recycled material quality and can make high-quality recycling impossible. S+S says that this is a valuable feature, given the increasing use of ‘bio bottles’, made of up to 100% vegetable raw materials, which cannot be distinguished from conventional PET bottles from the outside. www.sesotec.com Removing full-wrap labels before recycling Herbold Meckesheim has announced the commercial launch of its new label remover, which it claims is the first machine that can remove and separate PVC wraparound labels at the prewash stages of PET bottle recycling. It removes tightly-wrapped labels in a single step, early in the process and without the generation of extra steam. Herbold Meckesheim says that the new machine helps to save money downstream in the recycling process, as cutting blades will stay sharp longer without the dulling effect of label remnants. Removal of labels and adhesives from bottles is achieved through friction between exchangeable rip-off elements bolted to the rotor and exchangeable pins fitted to stator elements. All rip-off elements and pins are made of wear-resistant steel. The chamber is designed to achieve even loads and dwell times as bottles are advanced by the rotor, and it has no spaces where bottles might pass through the machine without undergoing full frictional contact. The new machine is also able to separates bottles that are stuck together. Access for part replacement is through a hinged cover and additional service openings and the rotor’s dual selfaligning roller bearings are mounted within the housing, to minimise contamination. Anti-vibration mounting pads are standard. The label remover is available in 4,500 or 8,000kg/h capacities. www.herboldusa.net SPHERO® underwater pelletizers Beautiful things are formed underwater. Your single source for comprehensive pelletizing solutions. Expert pre-sales advice and post-sales service included. www.maag.com Meet us at Interplastica Forum booth FE55","@ID":31} "PRODUCTS 30 PETplanet insider Vol. 12 No. 12/11 www.petpla.net Mann+Hummel launches new monitoring software Mann+Hummel ProTec has announced the launch of microprocessorcontrolled visualisation software for the new generation of stationary material drying facilities. The company says that it enables the energy-efficient Somos D dry air dryer and its associated drying hoppers to be centrally monitored and administered. It allows easy access and alignment of individual controls from a central location in response to changes in processing parameters, for example. Mann+Hummel says that the software has been designed for the monitoring of a modular hopper installation consisting of up to ten drying hoppers whose controls can each operate two conveyor machines – one for filling and one on the processing machine – making it possible to control up to 31 individual machines. The central visualisation software enables expansion of drying facilities, from less than 31. www.mann-hummel.com Holland extends UV protection range While the UV spectrum relevant to PET packaging extends from 200 to 400nm, PET itself only absorbs up to 320nm. Additional UV protection must be added to packaging of products such as beer, juices , energy drinks and vitamin-enhanced beverages, as well as household cleaners and dish washing liquids. Most commercially available UV absorbers extend the level of coverage to 370nm, which is sufficient for many products including some commonly used ingredients. However, some food colorants and vitamins, when used in complex formulations, show an increased sensitivity and can have an unexpected negative influence on others, leading to decreased product integrity, losses in functionality and colour and shorter product shelf life. Extensive, timeconsuming and costly testing can be required to determine exact protection requirements. Holland Colours says that a PET package with UV protection optimised in the container wall can provide increased flexibility in formulating with components that are known to be somewhat UV sensitive but for which the matrix effects are unknown. The need to use stabilisers in the product itself may also be eliminated, enabling the use of more natural components. Holland Colours has introduced a series of absorbers that can provide UV protection in a specific range. Calculation models are available to determine the required dosing level and resulting additive cost as a function of container wall thickness and UV protection requirements. www.hollandcolours.com KHS preform sterilisation method for ultra-clean applications A new method for sterilising preforms from KHS eliminates the need for traditional upstream PET bottle sterilising and rinsing, by sterilising at preform stage. The company says this saves the costs of a rinser and rinse water. Sterilising the preform involves a significantly smaller area than a finished PET bottle and reduces the amount of sterilising agent needed. KHS claims that the method is suitable for ultra-clean applications. It is intended for use in the company’s InnoPET BloFill stretch blow moulder/filler monoblock. A newly-developed sterile chamber module is installed in the heater area, following the initial preform heating process. A sterile air airlock separates the chamber at both preform feed and discharge ends from the remaining heater area. This prevents germs from entering, while containing the hydrogen peroxide (H 2 O 2 ) sterilising agent. The risk of corrosion in adjacent machine areas is eliminated, as well as hazards to machine operators from discharged H 2 O 2 . Preforms are sterilised inside the chamber module by a mixture of hot air and H 2 O 2 and are subsequently flooded with sterile air, to remove any surface remnants of H 2 O 2 . The preforms then travel to another heating chamber for precise preheating, which KHS says enables the optimal distribution of materials throughout the PET bottles during the stretch blowing process, enabling very lightweight bottles. The preforms are transferred to the blowing process through a housing containing sterile air, to eliminate any risk of contamination. The freshly-blown bottles pass through a similar housing at the discharge end, to ensure that materials are sterile when they ultimately reach the ultra-clean filling area through a sterile air airlock. www.khs.com New Moretto hopper helps dehumidification Moretto’s new OTX Spyro hopper features a novel shape that, the company says, helps to solve ‘falling flow’ problems and allows more efficient management and control of the drying process inside the hopper. The configuration provides an homogeneous airflow and temperature, which provides optimal treatment of the granules. It is also claimed to reduce energy costs, compared with conventional hoppers. Moretto says that the new hopper’s shockproof Spyro finishing makes it more resistant to damage. www.moretto.com","@ID":32} "PREFORM PRODUCTION 23 PETplanet insider Vol. 12 No. 12/11 PETplanet print Vol.6 The rapid guide to perfect preforms - part 26 Splay Troubleshooting guides have suffered in the past from being locked away in offices and not being available to the people that actually need them. Considering the high cost of machine and tools high scrap rates can be a costly proposition eating away at already tight margins. PETplanet’s “Rapid Guide to Perfect Preforms” takes a different approach. It has been written for the people on the floor of injection moulding companies to support their daily work in making the best preforms possible. The product of two industry experts, Rick Unterlander and Ottmar Brandau, it gives concrete advice on 35 of the most common problems in preform manufacture, most illustrated by pictures. From high AA levels to wavy bodies processors can find help when they need it. Read chapter 26 of the guide. Symptom: Numerous translucent streaks on the surface of the preform. Usually localized in one area of the preform. They are shaped as U’s and/or V’s with the closed ends towards the preform gate. Cause: Air / gas has merged with the melt and was drawn to the surface of the preform during injection. Solutions: 1. Check dryer for alarms and correct as necessary. A high dewpoint (above –40ºC (-40ºF)) or low inlet resin temperature (should be minimum of 160ºC (320ºF)) may cause extrusion problems and must be rectified. 2. Check for adequate resin drying time in hopper (should be around 4h at 175ºC (347ºF) and up to 6h at 160ºC (320ºF)) 3. Check all temperature readings and correct if necessary. PET resin should be melted at about 280ºC (536ºF) +/- 10ºC (18ºF). Decrease as necessary. 4. Check nozzle tip heat settings. This area has a major impact on splay in the gate area. Settings too high may cause the melt in the nozzle tip to overheat resulting in gases to be mixed and conveyed into the cavity. Settings too low may cause plastic to build up in the nozzle tip and gate area, interfering with the melt flow, resulting in air being trapped in the melt. The settings should be adjusted to optimize melt quality and minimize the risk of air / gas entrapment. 5. Check injection time isn’t too low (injection rate too fast) and adjust if necessary. Injection rate should be about 10 – 12g/sec/cavity. 6. Check that the valve stems are opening properly. A partially open valve stem may restrict melt flow. 7. Check to ensure that the valve gate compressed air pressure is sufficient to open the valve stems properly. Typical pressures are in the range of 8 – 12bar (120 – 145psi). 8. Check throughput of plastic in system doesn’t exceed output of extruder screw. The processed kg/h of plastic should be below the manufacturers rating of the screw. Contact manufacturer for spec, and if exceeded, raise extruder temperatures and/or increase cycle time to compensate. 9. Check extruder throat cooling isn’t cooling resin pellets too much (should be minimum 160ºC (320ºF) inlet temperature). Restrict cooling as necessary. NOTE: Do not restrict when using colorants that are susceptible to jelling or coagulation. 10. Make sure no bridging (clogging) has occurred in the extruder barrel and if necessary clean out the plastic bridged material. WARNING: When preparing to release bridged material, you must completely cover your body with protective gear including facemask, safety helmet and thermal gloves. Gases may build up inside the barrel and may release when the bridged material is removed, causing molten plastic to be sprayed out. 11. Check for adequate extruder back pressure. This must be high enough to squeeze out gases as the plastic is being melted and compressed. Typical range is 15 – 20 bar (200 – 300 psi). 12. Make sure the extruder screw cushion is sufficient to prevent the screw from bottoming out. This should be a minimum of 25mm to compensate for any dynamic recovery fluctuations. (Two-stage machines only) 13. Check for proper resin flow at extruder throat. If interrupted, air pockets may be drawn into extruder. 14. Check that the decompression (pullback) time and position is not excessive. This should be set as low as possible to minimize the risk of drawing in air, yet enough to eliminate drooling into the cavity from excess melt pressure. Typical settings for valve gated moulds are: Time = 0 – 1sec; Distance = 0 – 10mm. Non-valve gated moulds may require higher values to minimize gate stringing. 15. If using regrind, check that the chip size is fairly uniform and not too large. 16. Check for any colorant build up in the extruder throat and remove if necessary. 17. Check hardware for worn, damaged or failed components, specifically the mould nozzle tips, tip insulators or PET filled space at tips, the resin in-feed line, and misaligned shut-off nozzle. www.petpla.net","@ID":25} "BOTTLING / FILLING 27 PETplanet insider Vol. 12 No. 12/11 www.petpla.net Natural par excellence Safi natural mineral water is known throughout Egypt for its high quality and many beneficial properties. Thanks to modern and sophisticated systems, water is extracted from a spring in the Siwa Oasis at a depth of 1,000m, from which it reaches the surface in a pure and uncontaminated state. As evidence of these characteristics, the National Company for Producing and Bottling natural water & olive oils obtained the ISO 9001: 2008 certification for its quality management system. In addition, production takes place under the direct supervision of the Ministry for Health and in accordance with international quality standards. Safi water is particularly recommended for diets that are lacking in sodium and is free from iron and manganese. Its high fluorine content helps to protect the teeth. In all stages of production, the Egyptian company uses fully automated machinery, to which, in response to growing market demand, a new bottling line has recently been added. Engineering study and implementation Asked about the main factors that led Safi – National Co. for Producing and Bottling to invest in a new 6,000bph bottling line, Gen. M. Moawad of Safi Bottling Water responds: “Primarily, the strong increase in demand for Safi water. In order to bring our production capacity in line with market demand, it was absolutely essential to purchase a new 6,000bph PET line, which included a four cavity Smiform stretch-blow moulder for producing containers of 0.2/0.66/1.5l. The new facility will allow Safi to increase sales in Egypt and also to satisfy demand coming from abroad.” The engineering study of the line for the new 6,000bph system was entrusted to SMI. The SMI project managers looked very closely into the production requirements of the National Co. for Producing and Bottling water & oils. Following a preliminary study, several inspection visits to the Sawi Oasis and careful evaluation of all logistical aspects, they drew up a technical solution which was in line with the company’s requirements, both in terms of production and finance. In order to guarantee maximum operating efficiency of the line, SMI also presented the customer with an accurate analysis of the cost dynamics (Total Cost of Operation), a 3D graphical simulation of the new system and a detailed study of the interactions between the different machines which co-exist on the line. All the Smiline conveyors were designed to respond appropriately to requests for fluidity and flexibility. The SMI systems allow, among other things, for optimal management of product flows, thanks to a careful study of the dynamics of accumulation, distribution and movement of the loose containers and packaged products. The modular structure of the Smiline conveyors easily adapts to various types of bottles and product flows, with format changeover times reduced to a minimum, which allows for the rapid switch from one type of production to another. A Smiform SR 4 rotary stretch-blow moulder has been placed at the “head” of the bottling line, which is capable of producing up to 7,200bph. M. Moawad comments: “During the process of growth of any company it is absolutely essential to have at your side an established and well-organised supplier, which guarantees that our company achieves maximum production efficiency in the quickest possible time. The technical solutions adopted by SMI for this project were designed with our requirements for rapid returns on investment and maximum energy saving in mind.” Bottle design The design and creation of the new PET containers of 0.25l / 0.66l / 1.5l, created by the Smiform designers, took account of the functional, economical and aesthetical requirements of the customer. The “design” of the new Safi water PET bottles is actually inspired by the Egyptian company’s image and its logo, which includes the symbols for the sun, water and palm trees. In addition to their “design”, the ”appeal” of the new PET containers results from the accuracy and precision with which Smiform has created the moulds used to produce them. www.smigroup.it","@ID":29} "MATERIAL / RECYCLING 15 PETplanet insider Vol. 12 No. 12/11 www.petpla.net In the devolatilising section, the polymer melt flows onto a rotating drum. This contains eight smaller satellite screws, which rotate in opposing directions. In this way, an extremely large polymer melt surface and a disproportionately large surface area exchange rate are delivered. The polymer melt can be devolatilised so efficiently at a vacuum of only 20 to 40mbar that PET with a residual moisture level of as high as 1 % can be processed without problems. At the same time, volatile contaminants are efficiently extracted. Flexibilty The MRS extrusion unit is very flexible, allowing the use of input material with varying residual moisture levels. The elimination of pre-treatment steps means that changing between different colour feedstocks is quick and simple. The IV of the output material can be selected via the Online Viscometer and is automatically held at the selected level. The gentle processing of the MRS extruder and the avoidance of thermal pre-treatment means that yellowing of the material is kept to an absolute minimum. In the case of bottle-to-bottle processes, the pellets can be processed in amorphous condition or subsequently crystallised and a short SSP process can be used to raise the IV value to the required level. Proven in practice Sheets A Brazilian manufacturer of thermoforming sheet currently operates a smaller line with an MRS 110 and a throughput rate of approx. 600 kg/h. It processes PET bottle flakes and flakes from reground skeletal waste and edge trim to high quality sheet, without pre-drying and with simple vacuum technology. Bottle-to-bottle Gneuss systems are also in use on bottle-to-bottle recycling applications. A supplier of PET bottle flakes with sorting and washing expanded its process by processing these flakes into chip/ pellets and thus increased its margin. It dispensed with the time-consuming and costly pre-drying and crystallising of post consumer PET bottle flakes. High quality bottle grade chip/pellets are manufactured at a throughput rate of up to 2,000 kg/h with a vacuum of 25 to 30 mbar. Its MRS extruder keeps the dwell time of the chip/pellets in the solid state polymerisation to a minimum. The RSFgenius enables reliable filtration, and the Online Viscometer VIS provides accurate real-time viscosity monitoring and control of the vacuum system. www.gneuss.de Holland Colours European Division Halvemaanweg 1, 7323 RW Apeldoorn, P.O.Box 720, 7300 AS Apeldoorn, The Netherlands I Tel: 31(55)368 0700 I Fax: 31(55)366 2981 I E-mail: [email protected] Why would you hide your product behind dark and thick wall bottles? Holland Colours can offer a solution which can preserve any UV sensitive product from the negative impacts of UV light while keeping the PET bottle transparent – or give it a light colour if you wish. Holland Colours UV 370 and UV 390 range offers optimized protection in a cost effective way. BECAUSE ORANGE JUICE IS ANORANGE JUICE Invisible UV protection","@ID":17} "Machine Vision Inspection System The inspection machines manufactured by P&S Technology are installed on the production line for inspecting preforms using for PET PET bottles. The inspection and ejection process of machines is automatic and there are variety of machine speed suitable for customer‘s production line speed. Especially PS-21GP series 3 recently having a good sales results provides lots of advantages for customers. The machine‘s maximum speed is 48,000PPH and there is no need to change parts as per changing preform‘s body size because gripper neck handling type is applied to preform handling equipment. Mold number reading or gate cutting device could be equipped as an option inside of inspection system. We say it is two in one system., so customer can save cost and space. This inspection system is mainly designed for rotary type. This system intensively inspect not only preform body but also particle and defect of preform neck external. It use the patented ‚mirror tracking system‘ for the bottle body inspected, so customer can inspect whole surface of preform body without blind spot. P&S have another solution to inspect preform. PS21PSI Series 1 is haven’t mirror tracking system but applied “line scan camera” technology overcome the limitation by refraction of light of inspection scope. The whole surface of body inspection is guaranteed by 3 line scan cameras located 120 degree each without rotation. The gripper neck handling type on this series is applied to preform handling equipment, so there is no need to change parts. Rotary Type Preform Whole Surface Inspection System PS-21 GP Series3 Basic inspection area 1. Neck ¿nish 2. Body 3. Basement Available options 1. Gate Cutting device 2. Mold Number reading 3. Top support Ring Surface 4. Neck external surface Machine capacity 1. Low speed: ~300PPM 2. Middle speed: 300~500PPM 3. High speed: 600~800PPM Neck Finish Neck External Support Ring Body Upper Area Body Lower Area Basement Available Options 1 Gate Cutting Device Available Options 2 Mold Number Reading Screw Thread","@ID":24} "MATERIAL / RECYCLING 12 PETplanet insider Vol. 12 No. 12/11 www.petpla.net Erema’s new plant concept offers three different operating modes in rPET production. A flexible plant concept Vacurema technology Since it was launched the patented process for recycling postconsumer PET bottle flakes and in-house PET waste, over 130 systems have been installed around the world. Erema offers Vacurema technology in three different system designs, according to the field of application and the requirements placed on the end product – Vacurema Basic, Advanced and Prime. www.erema.at Austrian company Erema, which specialises in the development, manufacture and distribution of plastic recycling systems and technologies for the plastics processing industry, has developed what it describes as a ‘flexible plant concept’ for its established Vacurema Prime technology. The company says that the concept enables users to produce both rPET flakes and pellets, at food grade. Erema designed and developed the new technology in response to the results of a market survey conducted in the USA and Europe. The report showed a clear desire on the part of recycling companies for a system that allows them to determine themselves the form of the processed rPET they produce at any time – in short, to choose between flakes and pellets. There are a number of reasons for this customer demand. Extreme price fluctuations for PET flakes means that production of rPET pellets alone does not always make sense; its difference compared to virgin material can be so low that there is no market for them and in those circumstances it is more advantageous to sell processed flakes directly. In addition, the demand for food-contact grade flakes – PET sheet especially – is also increasing; research by PCI PET Packaging, Resin & Recycling Ltd., shows market demand rose from 176,000t of rPET flakes in 2008 to over 220,000t in 2010. Furthermore, prices of rPET bales in the USA and Europe are subject to severe fluctuations, as does the price differential between rPET and virgin PET. Three-in-one solution Erema’s new concept for its Vacurema Prime technology allows the user to choose from three different operating modes, according to requirements. The company says that this means that plant operators can generate processed rPET in different physical forms, enabling it to adjust flexibly to meet market demands. Mode 1 is production of 100% rPET pellets; Mode 2 is production of 100% rPET flakes; and Mode 3 allows the simultaneous production of both rPET flakes and rPET pellets. The concept allows the production of both decontaminated, pre-dried and crystallised rPET flakes and melt-filtered rPET pellets. Both products are suitable for direct food contact and exceed all minimum quality and purity requirements. Batch operation of the Vacurema Prime technology allows preciselydefined minimum treatment duration for each thin-walled PET flake. Individually-adjustable batch times enable the individual specification of the degree of purity and the required IV value, regardless of the operating mode selected. In addition, Erema claims that its ecoSave design reduces CO2 emissions and energy consumption, while lowering production costs at the same time. The new plant concept has been developed by Erema in collaboration with its customers, and has already achieved three sales in the USA.","@ID":14} "PREFORM PRODUCTION 25 PETplanet insider Vol. 12 No. 12/11 PETplanet: You have set yourselves some ambitious goals. You are looking at 40% more machines by 2014. How do you envisage achieving these aims so quickly with your Netstal team? Mr Anderegg: We have consistently marketed the Netstal PET-Line worldwide. As far as sales and service is concerned, we will be looking at making greater efforts into establishing more KraussMaffei Group sales and service branches. PETform will continue to be built in Munich. The Näfels team will specify the direction development is to take, but the actual development work will be carried out in Munich as before. Thus we will be able to build on an experienced core team that will also be able to bolt together more machines than ever before. PETplanet: And maybe a quick word about your new developments? Mr Anderegg: Here at Brau Beviale we are for the first time presenting a definite improvement in material distribution in the base area of the preform. Even as regards the weightoptimised base geometries presented over the past few years, we are still getting up to 2g out of it. The secret lies in the fact that we apply internal pressure to the preform in the cooling station and thus pre-blow the base area so that the preform becomes thinner at that point. This additional process stage is integrated in the cooling station and can be retrofitted very easily, in particular for those customers who have already kitted their plant out with our cooling system with preform internal pressure. PETplanet: Many thanks, Mr Anderegg PS: The detailed article about saving material in the base area by pre-blowing the preform will be published in PETplanet Insider 1+2/2012 * by Alexander Büchler www.netstal.com EREMA Engineering Recycling Maschinen und Anlagen Ges.m.b.H. A-4052 Ansfelden . Austria . [email protected] . www.erema.at We know how. PET Extrusion System VACUREMA® Prime to produce food contact approved BTB pellets Input: Washed PET flakes Output: rPET pellets Batch process i guarantees defined decontamination time for each PET flake • FDA and brand owner approved • Efsa approval requested via customers CIC compact inline crystallisation i • lower AA ( 1 ppm possible) • higher crystallinity • space-saving equipment Permanent monitoring for direct food contact and IV i Very low energy consumption, 0.30 to 0.34 kWh/kg i","@ID":27}]}}
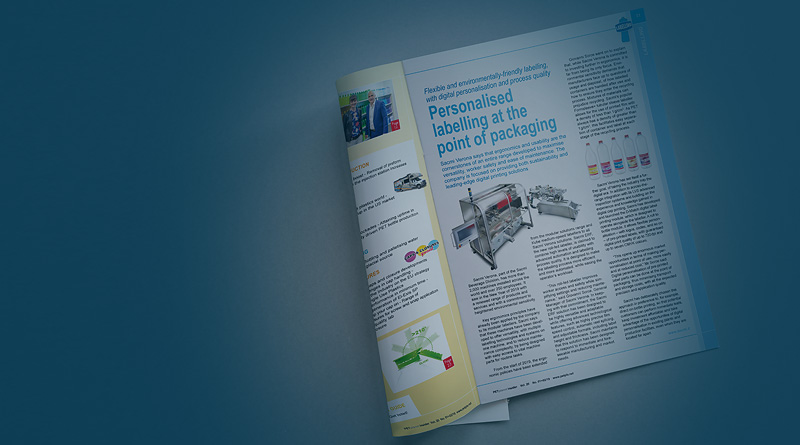