{"pages":{"page":[{"#text":"TRADE SHOW REVIEW 32 PETplanet insider Vol. 13 No. 04/12 www.petpla.net Hot filling and aseptic filling with original pulp at Anuga Foodtec The whole fruit inside The sixth Anuga FoodTec 2012 closed its doors after four intensive trade fair days in Cologne. Anuga FoodTec’s visitor numbers grew by around 25, totalling more than 42,000 trade visitors from 131 countries. PETplanet was on site and identified a major trend towards beverages containing “bits” of various kinds. This trend is becoming established in the juice and dairy segments in particular. As far as the bottling technology side is concerned, three companies at Anuga FoodTec have provided a response as regards the bottling of beverages containing “bits” in PET. The following is a brief introduction to the concepts and technologies used by Krones, Sidel and Procomacin Cologne. Krones: Twin-flow concept Krones presented a twin-flow concept for the hot filling of juices and milk-based mixed drinks which integrates both process and filling technology for producing and bottling beverages containing fruit chunks and fruit fibres. In order to preserve the structure of the fruit chunks and avoid costly product losses, there has to be stringent separation between the juice or milk-based mixed drink and the fruit chunks in the process technology as well. This means the juice or the milk-based mixed drink is treated in its own dedicated process, while the fruit chunks, measuring up to 10x10x10mm, are pasteurised in a separate shell-and-tube heat exchanger with interior cross-corrugated tubes. Rigorous separation and gentle product treatment are continued in the filling process, featuring Krones’ new FlexiFruit pre-dosing equipment for fruit chunks or pulp. In the predosing system, the fruit chunks are inserted into the bottles, and then the juice or the milk-based mixed drink is added in the main filler. The filling process is to run hot pre-dosing into the containers of a fruit-fibre or fruitchunk mixture with a fruit content of around 50% in chunks measuring up to 10x10x10mm in size into the container plus 50% juice, before the actual free-jet hot-filler is reached. Krones has developed a simple, hygienic system that is easy to clean, featuring diaphragm valves. The dosing filler itself does not possess an additional measuring instrument. The entire fill quantity is measured in the downstream weighing-cell filler, where the juice without any fruit cells is bottled. High priority was also given to ensuring operator-friendly maintenance. The juice can be pasteurised in the conventional way using plate heat exchangers (on request, of course, also with shell-and-tube heat exchangers, with concomitantly reduced wear and tear). The crucial factor claimed here is that in the juice flow more affordable standard components can be used, like centrifugal pumps, valves with a standard stroke, etc. The fruit flow, by contrast, mixed with a small quantity of juice, is treated in specially dimensioned shell-andtube heat exchangers, which enables the cost-intensive fruit preparation to be very gently pasteurised. Product losses and damage to the valuable fruit chunks are significantly reduced. In its concept, Krones deploys de-aeration only for the juice, but not for the fruit preparation. The thermally treated fruit preparation is then first pre-dosed into the containers using a pre-filler, after which the main filler adds the flashpasteurised juice at the same temperature. Krones has in addition already developed a single-stream aseptic filling process for beverages with chunks in cartons. www.krones.com Sidel: Hot-fill and aseptic Sidel presented its new solutions which are based on the Veloce ISD (see PETplanet issue 9/2011, page 47) and Sensofill FMa. The new fillers are suited for both hot-fill and aseptic. The Veloce ISD is suited for hot-fill production, while Sensofill FMa fillers are used for aseptic particle filling. The new Veloce ISD filler can dose particles up to 10x10x10mm in size. The inKrones’ Flexi-fruit pre-dosing system for fruit chunk or pulp","@ID":34} "TRADE SHOW REVIEW 39 PETplanet insider Vol. 13 No. 04/12 www.petpla.net The specialists inplastic recycling systems. VACUREMA® – PETextrusion technologies Sacmi: increased productivity, lower energy and better quality Sacmi’s CCM48SB is an evolution from the company’s CCM48SA model and is capable of producing up to 1,600 caps per minute, with lower energy consumption than its predecessor. Cycle times and energy consumption have both been reduced. Sacmi says that this machine is suitable for light single-piece caps for water bottles with moulding diameters up to 33 mm, as well as for single and double piece caps for CSD (Carbonated Soft Drinks). Energy savings are delivered by its CCM (continuous compressing moulding) technology, whose consumption is equal to 0.75 kWh/kg at its maximum production speed. The company says this is 25% less than the best values found for injection technology. The machine has a CVS 052 (CVS 3000) optical inspection system integrated on the CCM exit belt. The Sacmi stand also featured a number of other quality control inspection systems. The CHS 003 “stand-alone” visual inspection unit can control both plastic and aluminium screw caps. Its three-camera system, which can be increased to four, uses two vacuum belts. The two sides are controlled first by the internal cameras, followed by an external colour camera. Together, they provide data that “explodes” the cap and checks the surface condition point by point. It can inspect up to 120,000 pieces per hour. The four-camera CVS 360 is designed to provide total control of lateral wall cap development, including searches for burrs on the cap jumpers with injection-moulded safety bands. “Cavity Recognition” can identify and read the number of cavities moulded in the caps, using an illuminator and dedicated software that collates defect statistics. The “Spark Tester” can identify invisible micro-holes or cracks by using ‘electric rigidity’ principles. The CHS range can either be integrated into the line or deployed for post-production batch checking. The Sacmi SBF range of rotary stretch blow moulding machines, with six to 24 blow moulding stations, can produce more than 64,000 500ml bph. www.sacmi.com Microgel RCP water chillers from Frigel North America NPE 2012 saw the introduction of a range of twelve new water chiller models by Frigel North America. The Microgel RCP line of selfcontained, water-cooled chillers are single-zone units that have been designed to meet the special demands of PET, closure moulds, multi-cavity moulding and other applications that need refrigerated high pressure/high flow coolant. The Microgel RCPs are available in sizes ranging from 9.2 to 126.7t. They are equipped with shell-and-tube condensers and can operate with a Frigel Ecodry closed-loop clean water cooling system or a conventional, evaporative cooling tower system, with or without heat exchanger. When used with a closed-loop system, the RCP units can be equipped with a “free cooling” option, which automatically shuts down the compressor when the Ecodry or closed-loop cooling tower system can produce coolant at the chiller set point. This is claimed to help achieve significant electrical energy savings during cold weather operation, with fans providing coolant to the process rather than the refrigeration compressors. www.frigel.com","@ID":41} "NEWS 8 PETplanet insider Vol. 13 No. 04/12 www.petpla.net Innovation Don’t compromise on quality. For further information please contact: [email protected] www.gabriel-chemie.com PremiumMasterbatches for Superb Products. Kielce 29.5–1.6.2012 VISIT US AT P LASTPOL ! PETCO increases South African recycling South African recycling company Petco, which was established in 2004 by Coca-Cola and other brand owners, bottlers, resin manufacturers, converters and retailers, has reported that over 1.4 billion PET bottles were recycled during 2011 – nearly 4 million bottles each day. It recycled 42% of post consumer beverage PET and 29% of total PET; total weight was 42,651t of PET collected and recycled out of a 145,000t 2011 resin market. This exceeded the 2010 PET plastic recycling rate by 5,290t – a 14% increase. Petco members contribute voluntary financial support and other income sources include the recycling levy and grants-in-aid. Petco works in partnership with contracted service providers, Extrupet, Kaymac and Sen Li Da, who combine collection, recycling and end-use in their PET value chain. Petco has assisted in the establishment of over 430 plastic recovery stations throughout South Africa and supported training of staff at these drop-off sites, and has been involved with separation at source and school education projects. The organisation has helped to generate almost 26,000 indirect jobs; total CO2 saved via PET recycling is in excess of 63,000t. Petco has also provided millions of SA Rand worth of financial support to PET recycling companies and helped to expand both bottle-to-fibre and bottle-to-foodgrade recycling. However, 2012 will be the first year that the local bottle-to-fibre market has reached saturation and local recyclers have reached capacity. Almost all recycled post-consumer PET bottles in South Africa are used locally, rather than being exported to China. The largest market is currently fibre, with the recent addition of installed capacity for Bottle-2-Bottle. The “Retailers for Recycling Forum” aims to create awareness amongst consumers of recycling issues and to drive reuse and recycling among retailers and their suppliers. The 2012 target for recycled post consumer beverage PET is 48,356t. www.petco.co.za Erema’s best year ever The Linz, Austria manufacturer of plastic recycling systems for both in-house recycling of production waste and strongly contaminated post-consumer waste, Erema Engineering Recycling Maschinen und Anlagen Ges.m.b.H., has reported its best-ever fiscal results. Turnover for April 2011 to March 2012 was €115 million, which exceed its previous record year (2007/8) by 25% and its 2010/11 performance by 40%. During the 2011/12 fiscal year, the company produced 200 recycling systems and 100 individual components, such as screen changers and pelletisers. Consolidated group turnover for 2011/12, including its subsidiaries Erema North America Inc., Ipswich, MA, and 3S GmbH of Roitham near Gmunden, was approximately €127 million. The company’s products include TVEplus for recycling severely contaminated postconsumer plastic waste and heavily printed and laminated film packaging in-house; the Vacurema process; and the environmentaloriented ecoSAVE recycling systems design. www.erema.at","@ID":10} "NEWS 10 PETplanet insider Vol. 13 No. 04/12 www.petpla.net Engel and Plastisud create Green Cap Mould manufacturer Plastisud and injection moulding machine producer Engel Austria have established Green Cap, a joint venture company that is offering turnkey solutions for the production of sealing caps for water and soft drinks containers in China, the world’s largest market for caps and closures, in terms of volume. China is imposing increasingly stringent requirements on packaging products and their manufacture. Packaging weight has to be reduced, quality has to be raised and demanding performance levels have to be delivered with energy efficiency. The two partners claim to have analysed the Chinese market and the demands of Chinese manufacturers in great detail and their aim is to offer an economically viable solution to plastics processing companies in China. Plastisud and Engel were launching the new company at the Chinaplas 2012 trade fair in Shanghai. The Green Cap stand (F41 in hall W1) will feature an all-electric Engel e-cap 3440/420 injection moulding machine with a 96-cavity mould made by Plastisud that will make nearly 130,000 sealing caps per hour, reaching a cycle time faster than 2.8s. Green Cap is promising energy consumption of just 0.75kWh per kilogram of granules and efficient use of cooling water. Green Cap solutions come with 32 to 96 cavities moulds as standard along with machine clamping force of 200 to 420t, with 500t machines also available. Plastisud has a sales office in Shanghai; Engel has a production plant in Shanghai as well as three sales and service offices. www.engel.at €400 million Artlant plant starts production The new €400 million Artlant PTA plant, located at Sines, Portugal, began production of PTA (purified terephtalic acid) in March 2012. PTA is used in the manufacture of PET and is 100% recyclable. Construction of the plant commenced in 2008 and has an installed capacity of 700,000t of PTA annually. It is projected to become one of the world’s major strategic production plants and is expected to have a European market share of 17%. The facility has been equipped with state-of-the-art PTA production equipment and is expected to be 25% more energyefficient than existing equivalent factories. Artlant will create 400 new jobs, both directly and indirectly. The plant was deemed to be of national interest for the Portuguese government. Revenues at Artlant PTA are anticipated to exceed €600 million Euros annually, with 95% of its production destined for international markets, such as Brazil, the Middle East and India. www.artlantpta.com Krones grows in 2011 Beverage filling and packaging technology manufacturer Krones reported that its sales revenues in 2011 were 14.1% up on 2010’s figures, rising from €2,173.3 to €2,480.3 million, which is ahead of growth target. Booked orders were 14.6% higher, at €2,514.0 million. Earnings before taxes rose from €70.8 to €74.6 million. These results are affected by a provision in the financial statements for 2011 relating to potential settlements arising from litigation in the USA*. Earnings after taxes fell in 2011 by comparison with the preceding year, from €50.9 to €43.7 million. Due to the abovementioned one-off effect and the expenses entailed by a tax audit, the company’s tax rate rose significantly in comparison to the preceding year. The Supervisory and Executive Boards will be proposing the AGM a dividend of €0.60 per share, 50% up on the preceding year. As at December 31, 2011, Krones had no debts with banks and net cash totalled more than €125 million and the equity ratio was 38.5 %. Krones expects a positive development for the 2012 business year, and is anticipating a significant strengthening of its profitability. *Krones is currently engaged in mediation with US plaintiffs with respect to the Le-Nature’s case. The legal disputes are related to the financial scandal involving the bankruptcy of the US company, whose former directors have been convicted of fraud. In 2005/2006, Krones produced, delivered and commissioned filling lines representing a contract volume of approximately US$100 million for the Le-Nature’s facility in Phoenix, Arizona. www.krones.com IVL captures Old World Indorama Ventures Public Company Limited (IVL), the Thailand-listed producer of PTA, PET and polyester fibre, has completed its US$795 million acquisition of the USbased Old World Industries I, Ltd., and Old World Transportation Ltd. Based in Clear Lake, near Houston, Texas, Old World operates the largest single ethylene oxide (EO) and ethylene glycol (EG) production facility in the U.S. with crude EO capacity of 435,000t/a. Old World will continue to serve the US’ purified EO merchant market in addition to its glycol customer base. Old World Industries, LLC will continue to own and operate its Consumer Products Group business. Indorama Ventures will continue to supply Ethylene Glycol to Old World’s Consumer Products Group for its coolant business under a long-term contract that was part of the purchase agreement. IVL has 9,000 employees worldwide and generated consolidated revenues of US$6.1 billion 2011. www.indorama.net Sidel honoured in India At the annual Hindustan Coca-Cola Beverages Strategic Supplier Summit in Gurgaon, India, Sidel was presented with the Supplier Performance Silver Award 2011 in the Production Equipment category. On February 1, 2012, Plastindia Foundation, the Indian industry association, awarded Sidel the silver trophy in the Innovative Plastics Processing Machinery & Ancillary Equipment category. The prize was awarded at the Plastindia tradeshow in New Delhi. Sidel highlighted its Synergy Combi linear PET stretch blow moulder at the show. www.sidel.com Appe opens factory in Poland Appe, the packaging division of LSB, has announced the establishment of Appe Polska in Poland, which will serve emerging Eastern European markets. The company is investing in excess of €15 million in a new factory in Katowice in South Poland, which will offer its full range of services, including preforms and bottles, advanced technologies, barrier bottles, bespoke container designs and the capabilities to provide dedicated Through-The-Wall operations at customer sites. The factory is due to open later in 2012 and Appe says that it has already secured two major new contracts with leading companies for the Polish facility. www.appepackaging.com","@ID":12} "TRADE SHOW REVIEW 37 PETplanet insider Vol. 13 No. 04/12 www.petpla.net Siapi: Bigger containers and better orientation Siapi’s new EA4 and EA7 linear stretch-blow moulders range in size from two to ten cavities and offer additional capabilities through options and kits created specifically for production of custom containers for markets such cosmetics and household chemicals. All of the machines in the range can be equipped with advanced infra-red (IR) oven banks, which are claimed to offer reduced energy consumption and optimised material distribution, and additional weight savings and precision material distribution on oval and oblong bottles with a preferential heating option. The company says that this option does not incur a cycle time penalty. Maintenance and access has been improved by reducing the type and quantity of change parts; installation of a tool-less release system; and the employment of mould changeover cart systems. Complete machine format changeover is now claimed to be achievable in 30min. IndexMatic, a new neck orientation system, is available with or without preferential heating and with a bottle exit orientation system for consistent orientation of oval and oblong containers. The company’s stretchblow-moulding machines for large capacity containers include the EA1S monocavity and the EA2S, which can produce with five, three or two cavities 5, 10 and 20l containers, respectively, by replacing just the mould and selecting the correct software configurations on the monitor. The machines can produce up to 5,500 5l bph or 1,500 20l bph. The EA1S and EA2S can be equipped with the HandleMatic system, which allows the automatic insertion of the handle during the blowing phase. Siapi continues to develop ‘wide-mouth’ technology with openings up to 180mm diameter and capacities up to 12l. www.siapi.it","@ID":39} "MARKET SURVEY 27 PETplanet insider Vol. 13 No. 04/12 www.petpla.net EKG Group SBECM Viroplastic CZ Viscose Closures Ltd Corvaglia Group Retal Baltic, JSC Njegoseva 10 34220 Lapovo, Serbia +381 34 61 000 11 Dragan Miljkovic Manager +381 34 61 000 11 +381 34 61 000 12 [email protected] Rue de la plaine 47230 Lavardac, France +33 5 53 97 41 00 www.sbecm.com Jean-Luc Didouan Manager +33 5 53 65 85 97 [email protected] Lískovec 405, CZ-73801 Frýdek-Místek,Czechia +420 558412440 www.viroplastic.cz Mr. Vesely Sales Representative +420 603169232 +420 558412459 [email protected] Unit 1, Royce Road Bus. Park, Fleming Way, Crawley, West Sussex, RH10 9JY, England +44 1293 519251 www.viscose.co.uk Ian Coster Technical Services Manager - Caps & Closures +441293 596815 +44 1293 540005 [email protected] Hörnlistrasse 14, 83860 Eschlikon, Switzerland +41 71 973 77 77 www.corvaglia.ch Peter Schkoda Chief Sales Officer +41 71 973 77 77 +41 71 973 77 01 [email protected] Pramones str. 14, LT-94102, Klaipeda,Lithuania +370 46 492360 www.retalbaltic.lt Mr. Vaidotas Bucevicius Project Manager +370 614 31139 +370 46 492361 [email protected] Yes HDPE, LDPE or PP Yes HDPE, LDPE or PP Yes, HDPE Yes HDPE Yes HDPE yes, HDPE No No No Yes PP/EVQ No No CSD, dairy products, juices, water, beer Water, CSD, juices, dairy products,any liquid or non liquid products CSD, water, juice, milk, beer CSD, water All beverage sectors CSD, beer, juice, water PCO 28 1881, 38mm, 48/41, 30/25 high and low 30/25 high and low, 29/25, PCO 28 (1810, 1881, BPF), 38mm, 48/41 PCO/BPF, 28mm 3 starts, 28mm 1881, 38mm 3 starts, 38mm AF PCO, BPF, MCA, 1881, Corvaglia All corresponding neck finishes PCO 1810/BPF; PCO 1881 Yes No, but embossed Yes Yes No Yes, up to 3 colours Yes Yes Yes Yes Yes Yes No On request No No No No Yes On request No Yes Yes No On request Handles for 5l, overcaps 1881 & 1881 Sports Several patents No CSN 26 m BTL; 29/25; PCO Corvaglia; 38mm hotfill; 5 gallon cap Aptar Food + Beverage Euro-Plast JV ltd. Affaba & Ferrari S.r.l. Gulf Packaging Systems Co. Löfflerstrasse, 1 D 94078 Freyung, Germany +49 4985 519750 www.aptar.com Nathalie Jude Regional Marketing Director - Europe +33 1 60 41 13 25 [email protected] Gorkogo str., 95, loc. 1, Grodno 230005 Belarus +375 152 45 04 51 www.euro-plast.by Katherine Tolkach Foreign Language Assistant +375 152 45 04 51 +375 152 45 07 59 [email protected] Via Don L. Sturzo, 2, 26851 Borgo San SAN Giovanni (LO), Italy +39 0371 213021 www.affabaferrari.com Silvia Ferrari Sales & Marketing Director +39 0371 213030 +39 0371 97031 [email protected] P. O. Box 20266, IndustrialArea Phase V, Jeddah - 21455, Saudi Arabia +966-26360099 www.gulf-pack.com Engr. Bader Abdullah Sales Manager +966-26360099 Ex. 107 +966-2-6082170 [email protected] Yes PP or PE Yes, HDPE Yes, HDPE and PP Yes Yes PP + PE Yes, PP Yes Yes Yes, all soft drinks CSD, water, juice, beer, milk, tea, beer Still water, carbonated water, juice, CSD, flavoured water, smoothies Yes (except beer) 28mm PCO 1810, 28mm PCO 1881, 30-25 high, 38mm 2 start and 3 start 28 mm (BPF, PCO), 38 mm (3start) 28mm : PCO 1810, BPF, BPF light, 1881, Corvaglia, 3-start (Alaska) - 38mm : 1-start, 2-start (Aseptic), 2-start (hot fill), 3-start (pitch 8), 3-start (pitch 9) 28mm PCO 1810, 28mm PCO 1881, 30/25, 28mm Oprist & 38mm Yes, on specific request Yes, 2-colour Yes Yes Yes and a wide range of standard colours Yes Yes Yes Original flip-top closures meet BSDA child safety requirements No Yes No Yes, flip-top sports caps, valve capable for optimal flow control No Yes Yes (push-pull only) The Original range of flip-top sports closures, also foilpiercing closures, pouring closures with and without liner, closures with pull-ring TE. Bi-injected flip-tops. Special patented closures or marketing features Flip top caps for water and soft drinks, flex spout caps for lubricants, caps and seals for technical gases. A&F offer customized solutions Patented dispensing, spraying and dosing solutions. For optimal flow control, ‘SimpliSqueeze’valve system in swimming silicone for compatibility with PET recycling stream. Fullytop af6-pne cap Yes","@ID":29} "PETnews 6 PETplanet insider Vol. 13 No. 04/12 www.petpla.net Bernhard Merki leaves Netstal KraussMaffei Group has appointed Dr. Hans Ulrich Golz as “President” of a common Group-wide Injection Molding Machinery Segment. Bernhard Merki, CEO of Netstal Maschinen AG, decided to step down from his position and to leave the company. “The new “President” of the Group-wide Injection Molding Machinery Segment, Dr. Hans Ulrich Golz has served the company to date as President of the Extrusion Technology Segment and Chairman of the Management Board of KraussMaffei Berstorff. Dr. Karlheinz Bourdon and Frank Peters, previously responsible for Injection Molding Machinery and Reaction Process Machinery at KraussMaffei, will take up new posts as part of the reorganization measures at the injection moulding machinery segment. Dr. Karlheinz Bourdon will take up the post of “Vice President Technologies” and will be amongst others responsible for the common segment activities in Research and Development, Product Management and Process Engineering Development. As “Vice President Sales KraussMaffei” Frank Peters will have sole responsibility for sales of injection molding machinery bearing the KraussMaffei brand. “We will increase our injection moulding activities throughout the Group. We will therefore maintain the independent market presence of the Netstal and KraussMaffei brands with a clearly defined product portfolio and separately operating sales organizations for both brands”, said Jan Olaf Siebert, Chairman of the Board of Management of KraussMaffei AG. www.krauss-maffei.com www.netstal.com Unifi using Starlinger for Repreve yarn Unifi, the US-based producer of multifilament polyester and nylon textured yarns has installed two Starlinger recycling lines at its Repreve Recycling Center in Yadkinville, North Carolina. The Starlinger recycling lines have been designed to recycle PET flakes from plastic bottles, fibre waste and polyester fabrics. The post-consumer product is produced on the recoStar PET machine while a recoStar universal machine is used for the hybrid product. At Unifi’s request, Starlinger custom-designed the equipment with a focus on colour, IV (intrinsic viscosity) and POY(preoriented yarn) spinning and texturing performance. The recoStar PET recycling line converts 100% PCR flakes into chip, which is then processed on a special spinning line. It is designed to ensure constant IV in the recycled chip. It has an integrated energy recovery kit that reuses heat from the granulation process for preheating the PCR flakes. In-house waste, combined with a share of PCRflakes, is recycled on a Starlinger recoStar universal line. Both lines use a specially designed cascade filtration system that enables filtration down to 25μm, to meet the high requirements in the fibre industry. Repreve is used by a range of brands and retailers, including Polartec, Patagonia, The North Face, Hon and Steelcase. As reported in PETplanet (issue 3/2012, page 36), Ford Motor Company has chosen the Repreve product for its new Focus Electric car. www.starlinger.com Industry standard optical measurement of permeation published The Industrievereinigung fur Lebensmitteltechnologie und Verpackung e.V. (IVLV) has published a standard entitled “Testing plastic materials - optical method for determination of the oxygen permeability of packaging systems (films and moulded parts)”. The Fraunhofer Institute for Process Engineering and Packaging IVV was involved in the development of the testing method and prepared the technical bulletin. The oxygen permeability of a packaging system is one of the most important criteria determining whether that packaging system can be used for foods and pharmaceuticals. Oxygen permeability has most commonly been measured using the manometric or the oxygen-specific carrier gas method with an electrochemical sensor. Oxygen sensors that can be read optically are also now available and have become established in biotechnology and beverage technology. They are currently primarily used for barrier measurements on filled beverage bottles but there have been no accredited standards and measurement procedures for them, until now. The Fraunhofer IVV has developed and validated a permeation test procedure in collaboration with an industrial partner, which can be downloaded free of charge as Technical Bulletin no. 108/2011 in either English or German at http://ivlv.de/de/Veroeffent.html. The standard will serve as the basis for DIN, CEN, and ISO standards, which will be drawn up in collaboration with analytical equipment manufacturers, research institutes, and users starting in 2012 or 2013. http://ivlv.de/de/Veroeffent.html The 8th China International Recycled Polyester Forum Shanghai 2012 CCFEI and PRF have announced that they are jointly organizing the 8th China International Recycled Polyester Forum 2012, September 13 -14 at the Jin Jang Rainbow Hotel Shanghai, Yan’an West Road, Changning District, Shanghai, PRC. The conference will cover the latest market trends in mainland China and provide in-depth information of technology development in the polyester recycling industry chain. China now accounts for a quarter of the world’s PET capacity and a similar proportion of the PET recycling market. Details of the polyester recycling industry chain and the results of CCFEI’s market research focus on polyester recycling will be presented during the event. www.ccfei.com www.ce-pip.com www.polyester-recycling.com","@ID":8} "TRADE SHOW REVIEW 33 PETplanet insider Vol. 13 No. 04/12 www.petpla.net line filler works on a double-stage filling basis: First, a certain amount of particles is dosed in a “pumpable” slurry, followed by the filling of the bottle with liquid juice. The Sensofill FMa filler is based on the aseptic Predis technology and uses dry preform decontamination, thus eliminating the use of water and the creation of effluents. Both technologies are able to dose particle concentration from 10 to 200mm, depending on the recipe and the bottle size, which can range from 200ml to 2l. The accurate dosage of the fillers ensures a steady and exact particle quantity in the final beverage, while minimising waste of raw material. The physical integrity of the particles is maintained and the concentration of particles in the liquid meets product specifications. According to Sidel, the flow cutoff is precise and does not cause any dripping or product waste. Contactless valves improve hygienic filling. Both particle filling technologies are available as stand-alone fillers and in the Combi configuration. The Combi Veloce ISD is the combined technology for hot-filling requirements. When it comes to aseptic filling, the Combi Predis/Capdis FMa, an integrated blow-fill-cap solution operating with dry preforms and caps decontamination, is the technology of choice. www.sidel.com GEA Procomac: Aseptic dual filling system GEA Procomac showed its new aseptic dual filling system for the filling of PET bottles with products containing particulates. The new system is composed of two separate filling carousels: the new aseptic piston doser PX for solid particles with set volume from 30 to 150ml and the volumetric electronic filler Fillstar FX, an industry standard for aseptic beverages filling. Filling of the bottles takes place in two operations: first the dosing of the solid particles; then the addition of the liquid phase. The dual fill system requires a two-stream process line: one dedicated to the thermal treatment of the pieces and the other to the thermal treatment of the clear liquid. The new aseptic dual filling system is designed for the bottling of still beverages, both high acid and low acid, containing pulps, fibres, and pieces of fruit or cereals with dimensions up to 10x10x10mm, or products whose density does not allow the consistent distribution of the pieces. In the aseptic process the juice/drink and the particulates have to be handled in two separate processing plants, with pasteuriser / UHT and aseptic buffer tank. The advantage is to achieve specific parameters for each product and to achieve the highest product quality (incl. PU control, homogenisation , de-aeration…. where applicable) combined with long production runs, controlled heat load, efficient use of energy and low product loss. GEA Procomac can offer the whole system in cooperation with GEA TDS. www.procomac.it Sidel’s Veloce ISD is configurated for hot-filling and the dosing of particles GEA Procomac’s aseptic piston doser PX for the filling of particles","@ID":35} "PREFORM PRODUCTION 17 PETplanet insider Vol. 13 No. 04/12 www.petpla.net PETplanet print vol.6 The Rapid Guide to Perfect Preforms machine no./name 1- 3 exemplar each 129,- € 4 - 10 exemplar each 99,- € 10 exemplar each 69,- € prices in EUR + VAT. 6. Check that the hold (packing) pressure isn’t too high to cause excessive swelling at the gate area, especially in the last zone. Reduce as necessary. 7. Check that the valve gate close timing is adjusted properly. This is typically 0 – 0.5s for valve gate close delay. Minimize to improve nub solidification. 8. Check to ensure that the valve gate compressed air pressure is sufficient to close the valve stems properly. Typical pressures are in the range of 8 – 10bar (120 – 145psi). 9. In non-valve gated moulds, check that the decompression (pullback) time and position is not too little. This should be set to provide full decompression of the hot runner and minimize the risk of drooling from excess melt pressure. Typical settings for non-valve gated moulds are: Time = 1 – 3s; Distance = 10 – 50mm. NOTE: The positive suckback coupling should be installed when nonvalve gated moulds are used. 10. Check hardware for worn, damaged or failed components, specifically the mould gate inserts, valve stems, valve stem seals, nozzle tips, tip insulators, and clogged core / cavity cooling channels. www.petpla.net PETplanet print Vol. 6: The Rapid Guide to Perfect Preforms by Rick Unterlander and Ottmar Brandau fax: +49 (0) 6221-65108-28 [email protected] www.petpla.net Order your copy now! Maag Group is the innovative solution provider for pump, pelletizing and filtration systems. We deliver high-quality components and complete systems, from extruder tips to pelletizers. In addition to our primary locations in Switzerland and Germany, we have eight sales and service offices around the globe to provide our customers with full service par excellence. Automatik Plastics Machinery GmbH Ostring 19 ß 63762 Grossostheim ß Germany ßT +49 6026 503 0 ß [email protected] brands of maag group Maag Pump Systems AG Aspstrasse 12ß8154 Oberglatt ßSwitzerlandßT +41 44 278 82 00ß[email protected] www.maag.com","@ID":19} "PETbottles 42 PETplanet insider Vol. 13 No. 04/12 www.petpla.net Beverages Shadow and GNC bring in CSI GNC, speciality retailers of a variety of health and wellness supplements, including diet and sports nutrition products, has selected the CSI (Closure Systems International) lightweight Extra-Lok V 38mm OD cap for use on a new line of GNC Advanced Nutrition Beverages. With its licensee partner, Shadow Beverages LLC, GNC has entered the ready-to-drink beverage category in new markets with a range of nutritional waters, sport nutrition, and protein nutrition beverages. The beverage line includes “XP” / Extreme Performance drinks, targeted towards performance athletes, and “Active” drinks, formulated for more mainstream active consumers. The products are packaged in 20oz. and 14oz PET bottles by Graham Packaging. The XP beverage lines have black labels and black closures; the Active bottles have white labels and clear closures. CSI also provided technical services and support. Distribution of the new line of GNC beverages, currently consisting of 14 SKUs, is through various channels in the USA. www.csiclosures.com “Greenest ever” refillable bottle Specialist plastics packaging technology business Petainer has developed what it describes as its ‘greenest ever’ refillable bottle, which is manufactured using more than 25% post-consumer ‘one-way’ recycled PET. The company claims that it has the same performance characteristics as a refillable bottle made entirely from virgin material. Petainer maintains that the bottles are more ‘eco-friendly’ because they use up to 90% less virgin material per filling, and that the introduction of post-consumer recyclate leads to consumption of less energy and other resources in manufacturing. As the cost of virgin PET resins rise, the use of recycled material becomes more economic. Petainer is now working with bottled water companies, carbonated drinks producers and brewers across Europe to put its new ‘greener’ refillable bottles into use. Petainer has demonstrated that one-way bottles can be manufactured from 100% recycled material; its latest developments in manufacturing technology allow more than 25% of post-consumer waste from used PET bottles to be included in refillable bottles. The ‘greener’ bottle’s performance is identical to the performance of conventional refillable bottles. It gives the same number of ‘round trips’ and has the same top-load strength, which allows it to be stacked in the same way as other refillable bottles. The company asserts that it provides the same level of retention of CO 2 in carbonated soft drinks. The technology can be applied both to bottles manufactured in its own plants and to bottles blown from Petainer-supplied preforms. www.petainer.com Old Jamaica Ginger Beer 500ml Old Jamaica Ginger Beer is being sold in England by Messrs. Cott Beverages Ltd. based in Kegworth in a slightly tinted PET bottle with waisting in the label zone and surface embossing in the neck area. The whole package is emblazoned with a paper label featuring gold-coloured printing. The tamper-evident screw closure is colour-matched. www.oldjamaicagingerbeer.com Cult beverage from the Caribbean The English drinks specialist A.G.Barr plc is marketing a soft drink that has its roots in recipes from the Caribbean and is intended to provide a taste of the area. Under the KA brand name, 500ml of “Black Grape“ (ingredients: blackcurrant, carrot), a carbonated beverage, are being bottled in a PET bottle with a black screw cap. Colorants are added to give the product a purple tinge. A paper label which has been kept dark rounds off the product’s appearance. www.agbarr.co.uk","@ID":44} "TRADE SHOW REVIEW 34 PETplanet insider Vol. 13 No. 04/12 www.petpla.net A success by many measures This year’s NPE saw a significant increase of 26% in visitor numbers from 43,125 at the most recent event in 2009 to the current total of 55,359. Also setting a new record for international participation was the number of exhibiting companies from outside the United States, approximately 40% of the total. PETplanet was there to visit companies with PET-related exhibits. We also seized the opportunity to interview some of the leading lights of the PET world. In this and in the next issue of PETplanet insider, there will be a full round-up of all the new products we saw in Orlando. Penn Color debuts PET Essentials American company Penn Color introduced its line of PET Essentials at the National Plastics Expo in Orlando, alongside its existing range of Pennacle colorants. Penn Color says that its Pennacle range, which was launched in the mid-2000s, offers a number of features that make it easier to use than traditional additives. It features a proprietary and commercially confidential technology, a modified carrier resin package, that does not need to be pre-dried, even in bottle grade. The company’s novel technology, which was originally developed for polyester fibre and has been adjusted to be suitable for single-stage and two-stage blow-moulding applications, is claimed to eliminate problems of delamination and screw slippage, maximises IV retention and is compatible with all PET resins. It is already being used for water, beer, milk and dairy, and CSD products. Penn Color further states that, while Pennacle colorants do not have oxygen barrier quality themselves, they are completely compatible with oxygen barriers and do not detract from their effectiveness. Its white PET masterbatches have high TiO2 content and no carbon. The PET Essentials line includes several standard products, suitable for nutraceuticals, pharmaceuticals, wines and spirits, food and beverage markets, and special effect colours for cosmetic and personal care packaging. Its current customer base is primarily in North America but it also has an operation in The Netherlands, which started offering PET products and masterbatches in 2011. Penn Color is based in Doylestown, Pennsylvania and has been a producer of colour concentrates and pigment dispersions for plastics for nearly half a century www.penncolor.com Agr provides an inside view Agr International introduced its Pilot Vision in-theblowmoulder vision-based inspection and quality management system for PET containers. The system is designed to work in conjunction with high-speed reheat stretch blowmoulding equipment to provide detection of randomly occurring defects during the production of PET bottles. The company says that the increased use of non-virgin materials has contributed to growing incidences of contaminants, black specs and un-melted material and have led to the need for 100% inspection to keep them out of the production stream. It has an operating speed of up to 100,000 b/h and it is compatible with a wide variety of models and brands. Open architecture allows for simultaneous management of up to six cameras in multiple locations, typically: preform inspection in the oven area; bottle seal surface; bottle base; and complete sidewall inspection of bottles up to 16 inches tall. Camera and imaging components are sealed to prevent damage from fluids and moisture and active cooling is also available for high temperature operation. The system has multiple adjustable ROI tools, digital image filtering, zone scaling and the ability to capture and hold a large set of images for evaluation or setup purposes. Operation, monitoring and control is by high-resolution touch screen user interface. Pilot Vision is available either as a standalone system or as part of Agr’s Process Pilot automated blowmoulder management system. www.agrintl.com Alps launches new leak tester The new Speed-Glider from Air Logic Power Systems LLC (Alps) is a multiple-station continuous-motion linear container leak tester intended for inspection speeds up to 250/300c/m (15,000 to 18,000c/h). The company says that its new machine offers hole size sensitivity comparable to a four-station rotary leak tester, and speed capacity similar to an eight-station rotary unit but at lower cost. Positive container handling and control is achieved by the use of a precision timing screw for each container type. Alps asserts that this method means that the equipment can be used on customers’ existing tabletop conveyors, that it minimises jams and false rejects, and prevents untested containers from being passed due to sensor errors or fallen bottles. www.alpsleak.com","@ID":36} "PETpatents www.verpackungspatente.de 44 PETplanet insider Vol. 13 No. 04/12 www.petpla.net Outer packaging and labelling Intern. Patent No. WO 2011 / 116851 A1 Applicant: Lemo Maschinenbau GmbH, Niederkassel-Mondorf (D) Date of Application: 1.2.2011 Multi-layer plastic film which is welded in such a way as to produce compartments for holding a container. The outcome following set up of the container and shrinkage of the film is the emergence of outer packaging for a number of containers. With this arrangement, on removal of the container part of the film is left behind on the container as a label. Coated PET container Intern. Patent No. WO 2011 / 112775 A2 Applicant: Amcor Ltd., Hawthorn (AU) Date of Application: 10.3.2011 A container made from PET incorporates features that are integrated in the container and serve as carbon dioxide dispensers and as oxygen scavengers. This means that product quality is maintained over a long period. Should these features be integrated into the wall of the container, this will not lead to any ‘clouding’ of the colour of the container. Individually scented shower gels Intern. Patent No. WO 2011 / 106539 A1 Applicant: Colgate Palmolive Comp., New York (US) Date of Application: 24.2.2011 The dispenser head enables the storage and addition of a substance to a basic personal hygiene product. This enables the user to vary (e.g.) his shower gel to his heart’s content whilst having only one container in use at a time. PET / PTT container Intern. Patent No. WO 2011 / 110890 A1 Applicant: SA des Eaux Minerales D’Evian Saeme, Evian-les-bains (FR) Date of Application: 11.3.2010 Design and method of manufacturing a preform from a PET / PTT mixture. This mixture makes an efficient, inexpensive manufacturing process possible in spite of a high container with a small diameter opening. Ease of refilling Intern. Patent No. WO 2011 / 108729 A1 Applicant: Kao Corp., Tokyo (JP) Date of Application: 4.3.2011 A container used for refilling a second container is formed so as to display at the top, following removal of one segment or a sealing membrane, an inclined spout that can be coupled easily and without mess with the opening of the container to be refilled. Variable base Europ. Patent No. EP 2368804 A1 Applicant: Yoshino Kogyosho Co. Ltd., Tokio (JP) Date of Application: 18.11.2009 A plastic bottle (PET) is fitted with a base which, when the contents are heated and in response to the associated change in volume, will absorb this deformation energy elastically and on cooling return to its initial position.","@ID":46} "imprint EDITORIAL PUBLISHER Alexander Büchler, Managing Director HEAD OFFICE heidelberg business media GmbH Häusserstr. 36 69115 Heidelberg, Germany phone: +49(0)6221-65108-0 fax: +49(0)6221-65108-28 [email protected] EDITORIAL Doris Fischer: [email protected] Michael Maruschke Ruari McCallion Ilona Trotter Wolfgang von Schroeter Anthony Withers MEDIA CONSULTANTS Ute Andrä [email protected] Martina Hischmann [email protected] Ursula Wachter [email protected] phone: +49(0)6221-65108-0 fax: +49(0)6221-65108-28 France, Italy, Spain, UK Elisabeth Maria Köpke phone: +49(0)6201-878925 fax: +49(0)6201-878926 [email protected] LAYOUT AND PREPRESS Exprim Kommunikationsdesign Matthias Gaumann | www.exprim.de READER SERVICES Kay Krüger [email protected] PRINT Chroma Druck & Verlag GmbH Werkstr.25 67454 Römerberg Germany WWW www.petpla.net | india.petpla.net PETplanet insider ISSN 1438-9459 is published 10 times a year. This publication is sent to qualified subscribers (1-year subscription 149 EUR, 2-year subscription 289 EUR, Young professionals’ subscription 99 EUR. Magazines will be dispatched to you by airmail). Not to be reproduced in any form without permission from the publisher. Note: The fact that product names may not be identified as trade marks is not an indication that such names are not registered trademarks. 3 PETplanet insider Vol. 13 No. 04/12 www.petpla.net EDITORIAL dear readers, EDITORIAL At the NPE in North America we saw only one PET installation - Sipa was making its debut with its Xform preform system. Instead, the machine builders appear to have re-discovered the closure systems for themselves. Anybody with any reputation to maintain had a fast-running system on the stand. Particular eye-catchers were Husky – who were now exhibiting in the wake of their acquisition of KTW – and Engel, where the fourth generation of owners has now taken over management of the closure caps sector and has every intention of becoming market leaders in this sector. In addition to the high spots in relation to content, the NPE has given itself a complete makeover. The decision to move the event from Chicago to Orland in Florida, which raised eyebrows at the time, seems to have come good. Visitor numbers speak for themselves, from 43,125 at the most recent event in 2009 to the current total of 55,359 visitors. The comparison is a bit misleading because, in 2009, North America was still going through one of the most severe recessions it had ever experienced. Nevertheless, despite everything, the NPE has garnered a wave of new visitors. Never before had so many visitors from Central and South America been counted at an NPE! The exhibition layout featuring two large halls turned out to be a success, with visitors seemingly finding them quite acceptable. True, the marginal areas (West Hall F and Nord Hall) were more sparsely visited but overall, visitor appreciation was high. Even the long walk between the halls subsequently turned out to be not quite so daunting; it took me twelve minutes to get from Engel’s stand in one of the two halls to Sabic’s stand in the other hall. Going from one hall to the other at the K Fair in Düsseldorf can take considerably longer. Something else worth pointing out is also the proximity of the hotels and restaurants to the fair, a large proportion of the visitors were able to dispense with the bus service and walk to the exhibition centre. The bars and restaurants were also located within walking distance. Despite all the excellent preparations on the part of the organisers of the fair and the city of Orlando, the only fly in the ointment was the fact that the number of visitors to the NPE had meant that certain speciality dishes were off the menu, and some restaurants actually ran out of beer! Probably a clear sign that the NPE was considerably better than some had thought it would be. Yours Alexander Büchler","@ID":5} "EDITOUR REPORTS 29 PETplanet insider Vol. 13 No. 04/12 www.petpla.net Altintas Ambalaj Sanayi ve Ticaret A.S. (Goldcap) We met: Mr Cem Altintas, Commercial Director Tin plate, aluminium and polyolefin closures - all under one roof* Altinas in Ankara came to plastic caps from operating a classic closure business. Today the company produces 2 billion PET closures. In view of their origins in crown bottle caps and taking into account their established association with Sacmi, it is quite natural that the plastic closures should be manufactured on Sacmi machines. Mr Cem Altintas is the second generation of his family to manage Altintas. This family concern was set up in 1963 to produce bottles and closures and has succeeded in making a name for itself over the following years. With the move into the first Industrial Area of Ankara in 1990, the company expanded into premises with a total floor area of 15,000m². Today it employs 80 people and operates a 3-shift system. Later, Mr Altinas goes on, the company changed its production strategy and, based on experiences in previous years, they concentrated exclusively on closures that they have since been able to offer in the variants PCO 1810, aluminium twist-off caps, crown caps, and aluminium lids for foodstuffs in glass jars, in any colour and, on request, with individual print. These are produced on machines from Sacmi. Altintas today ranks as one of the most important manufacturers of closures in Turkey and exports to 20 European countries, the Caucasus and the Middle East. With its “Goldcap” brand introduced in 2000 (the name comes from Altintas’ name which means “golden stone“) the company generates an output of around two million closures per year Much has happened since that memorable day in May, d PETplanet special correspondent Kay Krüger was fortunate indeed to catch up with Ell (or as he is known in real life, Eldar Gasimov) to discover just how winning the contest has changed his life. In a wide-ranging interview Ell talked about the Eurovision Song Contest, and about how he got together with Nikki, as well as his plans for the future. Touring to far-flung places, living out of suitcases, and the stressful schedules can take a heavy toll and it can be difficult to keep a sense of perspective. This is just one reason why Kay was keen to talk about non-musical things, including such important topics as what is Ell’s favourite beverages packaged in PET bottles. Sadly, Nikki (real name Nigar Camal) wasn’t able to join us for the interview due to family commitments. She currently lives in London with her husband and two daughters. At the appointed hour of 10.30pm, we met at the Opera lounge, one of Baku’s fashionable nightspots, and our chosen venue. Like the star he has now become, Ell had just stepped off the London flight and had dashed into town for our interview. Ell has creativity in his blood, like his great-grandfather and his grandmother before him (they were distinguished Azerbaijani actors and stage directors). So where did Nikki come in? They first met and formed a duo in February 2011, after each of them had to be continued on page 30","@ID":31} "MATERIAL / RECYCLING 12 PETplanet insider Vol. 13 No. 04/12 www.petpla.net Comparing PET bottle-to-bottle recycle testing protocols: US and Europe What happens down the recycling stream? by Julianne Brown, Recycling & Material Evaluation Specialist, Plastic Technologies, Inc. Brand owners are continuing to push performance boundaries by working with new resins, additives and multilayer structures to achieve longer shelf life and other attributes. The downside is that very little is known about what happens to the recycling stream when many of these innovative materials enter it. For example, will products containing barrier or high-recycle content worsen the current stream? Do additives play a big part in impacting the recycle stream? To obtain answers to some of these questions, suppliers and brand owners are turning to experienced organisations to better understand the impact of PET bottle and thermoform recycling on the next generation of bottle quality. The Association of Postconsumer Plastic Recyclers (APR) in the United States and the European PET Bottle Platform (EPBP) in Europe promote recycling. Each has established testing protocols for resins, multilayer structures, coatings, additives, adhesives and labels used in PET applications. Why is there a need for two separate testing protocols? While there are a vast number of PET resin grades in the United States, they are not necessarily the most widely used in Europe and vice versa. For example, the European protocol does not allow the use of resins containing “heat-up” additives to be used as test controls. Conversely, since heat-up resins are widely used in the United States they are the preferred control resin for carbonated soft drink testing protocols there. Unfortunately, there is currently no common base resin that can be used for both of these protocols. Therefore, these differences can make it difficult if not impossible to perform one study The primary steps of the US and European recycle protocols","@ID":14} "CAPPING / CLOSURES 19 PETplanet insider Vol. 13 No. 04/12 www.petpla.net Doubled output MHS’ new stack mould technology allows plastic closure manufacturers to double production of valve-gated parts, without having to run additional or larger injection moulding machines. This advance in technology exploits the untapped potential of smaller, more efficient machines by adding a second parting line to the closure mould. The patented internal valvegate design of the new Rheo-Pro iVG hot runner system is what allows MHS to build back-to-back “short stacks”, which are compact enough to fit into smaller 180-300t machines. A standard 48+48 iVG stack mould running in a small 200t machine can produce 96 lightweight bottle closures every 3s, or almost 3 million parts per day, making it 30% more costeffective than a conventional 96-cavity single-face hot runner system. Easier maintenance Stack moulds that inject parts in both directions using two parting lines are being used by a number of moulders to increase output of their existing equipment: there are no new or unknown processing factors. iVG hot runner systems do not require larger injection moulding machines, because of their extremely compact size. They have also been made maintenancefree by doing away with wear items such as seals and lubricants. Moulds can run millions of cycles and parts continuously, without interruption. Valve-gating delivers better part quality and consistency, compared to hottip or thermal gate systems, as well as significantly increasing mould uptime. This consideration is particularly important when moulding stronger parts with thinner walls, using highviscosity polyolefins. Over 50% energy savings Rheo-Pro internal valve-gates offer a reduced carbon footprint of the moulding cell, through increased energy efficiency in the heating of the hot runner system, as well as the operation and production of smaller moulds and machines. For example, reduced energy consumption in a 48+48 iVG closure stack mould has resulted in total cost savings of over $23,000 annually, or 56%, compared to a single-face mould with the same number of cavities. This does not include the additional savings in productivity gains and capital equipment; altogether, up to 30% lower production costs can be achieved. www.moldhotrunnersolutions.com Standard 48 + 48 RheoPro iVG stack hot half New iVG internal valve gate hot runner nozzles in back-to-back formation CCT Creative Competence Technology GmbH Idsteiner Strasse 74 D-65527 Niedernhausen, Germany [email protected] www.cct-systems.com PET Molds Design and Patents Closure Molds Developments PET Systems Closure Systems Price: from 830.000 € Closure Systems +Y +Z + Y + Z f 72 Cav. Turn Key System consisting of: O Injection MC (Hybrid or Full-E) O 72 Cav. Closure Mold CCTsystems® 1881 SST O Conveyer System Unit O Cap Cooler Unit O Video Inspection Unit O Dehumidification Unit O Vacuum Packaging Unit O Installation O Training O Start Up Support O Product Development O All equipment made in Europe","@ID":21} "PRODUCTS 41 PETplanet insider Vol. 13 No. 04/12 www.petpla.net Adhesleeve labellers for Waldquelle Austro-Czech bottler Waldquelle has installed two Adhesleeve labellers at the company’s plant in Kobersdorf, which are intended to handle its two PET lines, which run at 15,000 and 30,000bph. The Adhesleeve labellers can handle films 20μ thick, which is 30% thinner than the 30μ standard used for roll-fed labelling. Reels with the thinner film have 70% more labels than standard. The preglued labels do not require special storage conditions and have longer shelf-life than standard roll-fed equivalents. Manufacturer P E Labellers claims that Adhesleeve can be classified as a variant of a self-adhesive labelling machine, although it is roll-fed. It is a linerless labelling machine and is suitable for application of wrap-around preglued white or clear film labels. The company says that application is eased by the elimination of hot melt glue and a new cutting system, and does not require skilled labeller operators. www.pelabellers.it New PET packaging material Artenius FastFlow+, a new PET packaging materials from Artenius, the PET & Recycling Division of LSB, represents the latest generation of “fast-reheat” PET resins. Artenius says that the new material captures the heat energy of the blowing process more efficiently, leading to potential energy savings in excess of 20% compared to standard PET resins, and to the potential for higher production output. Together, these factors are claimed to help reduce users’ carbon footprint. The new formulation includes a new additive for absorbing Near Infra-Red (NIR) radiation, leading to faster heat absorption. The formulation of FastFlow+ has been optimised to offer wider injection stretch blow moulding (ISBM) and stretch blow moulding (SBM) windows, as well as the ability to blow thinner walled preforms into more complex bottle shapes. The company claims that its intrinsic viscosity is particularly suitable for lightweighting initiatives and the material can be used on older blow-moulding machines, as well as the latest equipment. Artenius’ internal testing has found that its luminescence has a minimal impact on the final product, has good clarity and very low haze. FastFlow+ is approved for use in plastics intended to come into contact with foodstuffs. It is in compliance with Regulation (EC) No 10/2011 and approved by both the US FDA and EFSA. www.artenius.com","@ID":43} "EDITOUR REPORTS 21 PETplanet insider Vol. 13 No. 04/12 www.petpla.net definitely include Kötsan and Sunpet in Gaziantep. But Eskapet, a processor from Bursa (until recently regarded as one of the smaller fry) made some massive investments last year. Things are looking different on the caps market where all brands buy on the free market. The family-managed company Hasplastik in Istanbul has taken up a good position, but Altinas in Ankara also play an important role. A newcomer in this hotly contested market, Köksan is currently coming on-stream. Whilst Hasplastik supplies the market with its own designs, Köksan relies on Corvaglia. One thing that is common to all converters is the fact that they work with a large number of Netstal lines. Murat Aner, Technical Director of Hasplastik, knows the reason for this too: “Netstal’s service here in Turkey is outstanding“. Sipa is also a force to be reckoned with in Turkey. Husky have only gained a significant foothold during the last year. They have been able to supply some new machines to Eskapet. All three sectors, that is, water, CSD and oil are so strong that the 2-stage process is almost exclusively used for these products. Where water is concerned it is not an issue, here the quality requirements for the preform and the cap have increased dramatically. The entire water sector in Turkey has gone over completely from 30/25 to the Shortneck 29/25 over the past three years. In addition, high performance bottling plants have come on to the market which incorporate a distinctly narrower process window than the bottling lines to date. In the CSD sector nobody is thinking aloud about reducing weight. Coca Cola is happily continuing to produce the heavy 1810. It seems that here none of the other CSD bottlers is keen to engage with top dog Coca Cola. There is no doubt that, as regards this consideration, the enormous transport distances in Turkey have a role to play. The distance from the eastern to the western frontier is 2,500km and Coca Cola has its bottling plant close to the western border. Which brings us to Turkey’s geographical position. Contingent on its southerly location, the summer season from February to October pans out at just under nine months. In addition there is a further peak in December. Accordingly, the converters have planned their production capacities to suit the season. In practice no stockpiling for the summer takes place. Within Turkey some 150,000t of PET are currently being produced; the sector has to import the remaining 200,000t. Here Köksan, in its capacity as the largest of the preform manufacturers, sees its chance. At present the company is building a plant with an annual capacity of 216,000t. 2015 will see the addition of an equivalent capacity. This will make Turkey self-sufficient. Alexander Büchler Eskapet The Eskapet team line-up before the Editourmobile We met: Ramazan Akar, Factory Manager Kadir Fota, Service Engineer Breakthrough Eskapet has tripled its capacity in 2011 to a current 50,000t throughput of PET. This tremendous step forward has been made possible thanks to a new building located in Inegöl near Bursa. We asked Factory Manager Ramazan Akar for details. To begin at the beginning, Eskapet is situated between Istanbul and Izmir which puts it right at the centre of the water bottling industry in Western Turkey. And it’s not too far either to the capital city of Ankara. This puts the company in a favourable strategic location for its customer base. Whereas these had, until recently, been predominantly small and medium-sized bottling plants, they were now in a position to approach major brand names and to generate enthusiasm for their preforms. These bulk orders are actually the reason why the company has not only ramped up capacity but is also managing to sell the products they manufacture. Preform production started in 2002 with two Sipa lines, which were subsequently augmented in 2006 by a Netstal with 144 cavities. At that time it was only the fourth Netstal line with such a high number of cavities.","@ID":23} "PETproducts 40 PETplanet insider Vol. 13 No. 04/12 www.petpla.net Profiler gauges American company Agr, Inc.’s new generation of measurement devices, the “T” series laboratory Profiler Gauges (PG9800T and PG9810T), are presented as an alternative to section weight cutting for monitoring material distribution during the production of PET bottles. The T-series gauges are designed for use on the plant floor or in the laboratory. Agr says that measurement can be performed in less than 10s, without destroying the subject bottle. The gauges use the same infrared measurement technology as Agr’s PETWall Profiler to scan the sidewall of the bottle and produce a visual representation of wall thickness, material distribution and bottle height. Graphs are superimposed over a graph of a baseline bottle, in order to allow immediate identification of shifts in distribution. Information can be captured and saved to a database for future reference or exported for use in plant-wide process management systems. PG9800T is intended for use with mono-layer containers. It can enable operators to perform vertical scans in up to eight sectors around the container and horizontal scans at multiple height locations. PG9810T has the same capabilities as the PG9800 but can also identify the presence and/or thickness of barrier materials on multi-layer containers. Both models have an LCD touch-panel operator interface and system display; a new main system processor and operating system; additional USB ports for job backup, data connectivity and printer interface; graphic or numerical display of test data; integrated section average calculations; and auto-learn for easier setup. www.agrintl.com Pressure-sensitive labels CCL Label says that PSL (Pressure Sensitive Labels) promote significantly cleaner labelling operations, as there are no glue delivery lines that need to be warmed up at start-up – shutdown and start-up is immediate – and there is no need for periodic clean up, as required with wet glue lines. The company also asserts that PSLs offer greater flexibility in terms of rapid changes between variants. Downtime for set-ups, startups, end of shift clean-ups, removal of misapplied labels, jams and changeovers is claimed to be less than with wet glue labels. PSLs do not require controlled temperature and humidity and are not greatly affected by variances in storage conditions. PSL maintains that average line efficiency can be increased by approximately 15% and has sustainability advantages, compared with wet glue labels. PSLs can be used on PET bottles, as well as glass. www.cclbeverage.com Coding at the speed of light The Solaris e-SolarMark HD is a laser coding device developed developed by German company Bluhm. The system uses water as a cooling medium and for increasing the IP protection category. A complex design concept ensures that no condensate can form in the print head. The compact construction system is designed for high speed labelling of materials such as paper, foils, glass, plastic or coated metals. The typeface with the e-SolarMark HD features particular impact and is easily legible. One typical application area is the lettering on bottle labels or PET bottles. Depending on the application, belt speeds of up to 300m per minute or 1,500 product coding operations per minute are possible. The e-SolarMark HD can also be fitted with two marking devices to enable it to handle (e.g.) front and rear labels. www.bluhmsysteme.com Lanco crystallizers for smaller throughputs German manufacturer has launched a new range of stainless steel crystallizers, intended for laboratory applications and smaller throughputs for manufacturers and processors of PET and PET additives. The company says that the machines offer lowerprice alternatives to large, higher-end solutions intended for production of tons per hour. The first examples are already in commercial use. Fast cleaning of the crystalliser hopper is facilitated by a hydraulic system that raises the cover carrying the gear motor and the agitator. Crystallising tank covers are equipped with vision panels and flange connections, which enable Lanco loaders to bring in amorphous PET for continuous operation. Process fan speed is controlled by converters; the process air heating chamber is directly connected to the crystallising tank and controlled by SSRs, as well as temperature limiters and air stream surveillance. The units are equipped with touch screen controllers. Long-distance remote control and support is available via Ethernet connection and VPN router, if required. www.lanco.de","@ID":42} "BOTTLES 43 PETplanet insider Vol. 13 No. 04/12 www.petpla.net PETbottles Personal Care Clear shine Schwarzkopf, with their “glanz Styling Spray” (“Shiny Styling Spray“) from the got2b product range, gives the hair an endless shine. A transparent PET bottle is filled with 200 ml of clear product. Pump dispenser, protective cap and a rear label – all in pink – create accents of colour. There is direct printing on the front section and a pink-coloured dot acts as an eye-catcher. www.got2b.de Window with a view Under its own brand name “Denk mit“, the German dm Drugstore Market chain is marketing a transparent PET bottle containing 1l of de-ionised water for use in ironing. This water, which is enriched with fragrances, can be poured into the iron, either undiluted or mixed with distilled water in any mixing ratio. The rear label is printed on the inside and provides, along with the front label, some interesting perspectives. www.dm-drogeriemarkt.de Foam bath The Italian company Mirato is marketing, under the brand name “Malizia“, a relaxing foam bath scented with ”White Musk“ in a 1-litre content bulbous bottle. The material from which the bottle is made was changed from PE to PET which gave a simultaneous 20 % reduction in weight. The milky bottle is decorated with a lime green sleeve label and a screw cap matching the colour and the shape of the container completes the packaging. www.mirato.it Cares for hairs Procter & Gamble took advantage of the opportunity presented by the re-alignment of the Pantene Pro-V hair care product range to revise the packaging. One example of the new design is the shampoo which cares for and strengthens fine hair. The transparent PET bottle, which is flattened at the sides and has a content of 250ml, has a non-label-look label at the front and a paper label at the rear which gives the commercial information. A snap-on, translucent hinged lid in PP with an opening segment coloured black makes it easier to open the pack. www.pantene.de","@ID":45} "NEWS 7 PETplanet insider Vol. 13 No. 04/12 www.petpla.net SMI is 25 SMI, a worldwide manufacturer of hi-tech packaging machines and bottling plants for markets including food & beverage, chemical and pharmaceutical products, detergents and cosmetics, is celebrating its 25th anniversary during 2012. The company has delivered more than 35,000 packaging machines worldwide and its estimated sales revenues in 2011 were €101.2million. The SMI Group’s current focus is on energy saving and system integration. Recent launches include its Ecobloc integrated system for blow-moulding, filling/capping and labelling of PET containers from 0.25 to 10l. The Ecobloc range can achieve a maximum output of 36,000bph www.smigroup.it Sacmi holds open house for IPS Sacmi built a new preform press using injection technology: the IPS – injection preform system and is now the world’s only supplier able to offer the market two alternative technologies – injection and compression and will be presenting all the latest at the Plast fair in Milan from May 8 -12, 2012. Every day of the Plast Fair in Milan (May 8 - 12, 2012) Sacmi will be presenting its new IPS (injection preform system) technology in the form of a fully-functioning 48-cavity model with a clamping force of 220t. The company will be providing a special shuttle service to the parent company’s factory in Imola, where visitors can get a first-hand look at it in action. A second special demonstration area in the factory will host a CCM compression cap-making machine. PETplanet insider reported on the IPS machine in Issue 3, page 18 www.sacmi.com Appe and Nissei strike DoubleBlow deal LSB’s packaging division, Appe, and Nissei ASB GmbH (Europe) the European subsidiary of Nissei ASB Machine Co., Ltd. (Nagano, Japan), have formed a strategic partnership for the development and supply of hot-fill and pasteurisable wide-mouth plastic jars for the food market in Europe and Turkey. The partners will seek to develop capabilities for production of plastic jars and bottles with lighter weight, better safety and improved environmental impacts compared to existing formats, for products such as sauces, tomato-based foods, jams, pickles and vegetables. Nissei ASB will work exclusively with Appe in Europe and Turkey in the continuing development of the DoubleBlow wide neck system. Appe will take delivery of two systems in Europe during 2012 and expects to launch the first DoubleBlow products to the market later in 2012. www.appepackaging.com What does the standard closure hot runner system and SPRINT have in common? Ask how SPRINT with iFlow technology improves fill balance while reducing pressure loss. Mold-Masters and theMold-Masters logo are trademarks ofMold-Masters (2007) Limited. © 2012Mold-Masters (2007) Limited.All rights reserved. .ti tuoba knihT moldmasters.com/thinkaboutit [email protected] Nothing. In today’s business climate, you have to continually innovate and change to stay ahead of the competition. Which is why Mold-Masters is the new choice for closure hot runner technology. SPRINT gives you lightning-fast colour changes, optimal part quality and greater durability for maximum uptime, while dramatically reducing overhead. Choose SPRINT by Mold-Masters, the world’s only full-service hot runner partner.","@ID":9} "MATERIAL / RECYCLING 13 PETplanet insider Vol. 13 No. 04/12 www.petpla.net that simultaneously meets the requirements of both organisations. Protocol specifics The APR calls its series of primary testing protocols the Critical Guidance and Applications Guidance Documents. The EPBP’s version is called the PET Recycling Test Protocol. (Additionally, both organisations provide design guidelines to help minimise future recycle stream impact.) Materials to be evaluated in these studies can include a new PET resin, an additive, bottle coating, barrier resin, or even a label adhesive for a package. To start the process, blown bottles, also referred to as the “innovation bottles,” are ground. Primary steps of the protocols The flow chart below outlines the primary steps that are performed in each of the recycle protocols. Bottle grinding / flaking The simple task of grinding the bottle flake for each study is slightly different due to the allowable grind size for each protocol. Although some might think that this makes very little difference, a smaller flake grind size can increase the amount of fines produced. In a multilayer structure, it can result in more separation. When evaluating a multilayer bottle, the smaller flake grind (which is suggested in the APR protocol) can aid in the separation of the middle layer from the PET. These requirements allow for a ground flake size that can range from a nominal 6.35mm to 12.7mm, while the EPBP protocol simply calls for a 12mm screen size. Pre-wash air elutriation Air elutriation is the next suggested step in the U.S. protocol. Performed before washing, air elutriation will remove “lights” (labels) or thin multilayer materials. Depending on the type of innovation being studied, this step may not be relevant and can be skipped if the application warrants it. However its inclusion can be important in studies evaluating multilayer resins or even labels. The European test protocol does not call for this first elutriation of the ground flake materials. Flake washing Washing the flake is an important and critical step in both protocols. There are a wide variety of wash systems in use today, and one may believe the differences are not crucial but in fact they can be significant. A laboratory wash process has been developed that simulates what is currently in commercial use. Both the APR and the EPBP wash protocols are similar when both use aggressive hot caustic washes. Testing the solution intrinsic viscosity of ","@ID":15} "EDITOUR REPORTS 20 PETplanet insider Vol. 13 No. 04/12 www.petpla.net Turkey At the time of our last visit in 2005, preform manufacturers in Turkey were processing around 130,000t. When we visited again in 2011 it was 350,000t. Even if around 20% of this goes for export as preforms, that still leaves just under 300,000t in the country today. This is used to cater essentially for just 3 segments – ahead of everything else comes water, then the CSD sector and, last of all the variables worthy of note, the edible oil sector. If we reckon with 20g as the average weight, this works out at 15 billion bottles or 200 PET bottles per inhabitant. By comparison to other, more western European countries, it can be seen that, despite the progress in terms of growth, there is a lot more potential. In the edible oil sector PET is ubiquitous, as it is for the water sector. It is only where the big 19 litre containers are concerned that a proportion of PC reusable containers can still be identified. PC has, however, had problems from a health point of view, so PET disposable has been gaining in popularity for the past two years. This would seem to indicate that, in the near future, the big water containers will all be PET. It is only in the CSD sector that the can is bravely hanging on; nevertheless, here the big brand names have introduced the 0.2l PET bottle on a large scale. The juice and milk products sector seem to be practically free of PET. Here there are tentative attempts being made to counteract the reinforced carton and the HDPE bottle but so far these have not met with any major degree of success. Coca Cola basically produces its preforms itself, Pepsi Cola has chosen Alpla as its preferred supplier. Danone and Nestlé purchase on the free market. Hence the independent converters have to make do without the large CSD volumes. Two of the biggest A market opens up Five years ago, the Turks would only reach for the PET bottle something like twice a week. Today they empty a bottle every second day. This rapid growth is, of course, having an effect on the overall PET chain. We paid a visit to Turkey on the occasion of our Go to Brau Beviale Tour and asked around. Nuremberg Ljubljana Saedinenie Istanbul Yerevan Baku Beograd Novi Sad Subotica Cegled Dulo Selo Mirna Peˇc Radenci Gorica Svetojansk Plovdiv Gaziantep Ingöl Ploiesti Ankara","@ID":22} "EDITOURS REPORTS 30 PETplanet insider Vol. 13 No. 04/12 www.petpla.net for the PET bottle sector alone. This sector corresponds to around 40% of the overall production volume. In addition to selling the caps and closures, Altintas also places a high degree of importance to its after-sales customer service. The use of PCO 1810 means that the closures attract customers both in the CSD sector (more than 50%) and in the non-CSD sector. One key Altintas customer that deserves a mention here is Coca-Cola. Depending on whether the PET market develops further to encompass the trend towards using PCO 1881, Mr Altintas is assuming that a corresponding rapid adaptation of his closure caps may well be necessary. PET is set to grow further because the difference in price from glass plays a significant role. Glass is very expensive in Turkey. *by Kay Krüger www.altintas-goldcap.com.tr Hasplastik Ayhan Haspaylan and Murat Aner in front of the Editourmobil We met: Ayhan Haspaylan, President Murat Aner, Technical Director emerged as winners of the 2011 Milli Seçim Turu talent contest. There was immediate chemistry between the two of them and they lost no time in seeking a platform to launch their careers internationally. The Eurovision Song Contest provided the ideal opportunity and they quickly teamed up with Swedish producers Stefan Örn and Sandra Bjurman who penned what was to be the winning song ‘Running Scared’. 22-year old Ell said he fell in love with the title straight away, not only because of the very harmonious duet with Nikki, but also because he felt that the world needed a love song in these universally critical times. There is no doubt that the voting countries shared his opinion; the couple’s victory is evidence of this. The singer does not particularly consider himself a natural solo artist, but he could well imagine his career taking that direction. The thought of solo status and making studio recordings would represent a challenge which Ell would not shy away from. Singing is not the only string to his bow. He has very recently made a film which features his acting as well as singing talents. The film is scheduled for release in 2012. Just how important the 2012 Eurovision Song Contest 2012 is for Baku in particular and Azerbaijan in general is revealed everywhere PETplanet went in the country: euphoria and enthusiasm of course but also a genuine desire to ensure that the country’s infrastructure is well prepared for the event. Azerbaijan is a highly hospitable country and this is precisely the impression its people are anxious to convey to the world in 2012. Already underway is a superb modern 30,000 seater stadium, and new hotels and restaurants are springing up throughout the city. And, according to Ell, plans are afoot which will make it easier to enter Azerbaijan so that large numbers of international visitors can be accommodated. We will be keeping our fingers crossed and looking forward together to the Eurovision Song Contest 2012 in Baku. And finally, what was Ell’s favourite PET packaged drink? The answer is ………………………. FANTA! And that, appropriately, is a FANTAstic way to conclude our interview with a modest, but very talented guy. - Kay Krüger -","@ID":32} "TRADE SHOW REVIEW 38 PETplanet insider Vol. 13 No. 04/12 www.petpla.net Engel strives for market leadership status in closure cap plants Interview with Dr. Christoph Steger At the NPE, CEO Dr. Peter Neumann made clear that Engel’s intention with its e-cap was to become one of the major players in the cap market. The highly ambitious challenge to achieve this goal will be one of the tasks for the new Vice President of Engel’s business unit Packaging, Dr Christoph Steger,* who recently joined Engel, making him the fourth generation of the Engel family to play an active role in the business. PETplanet: Dr. Steger, you have been in charge of Business Unit Packaging at Engel since February. In so doing you have become the second member of the 4th generation of the family to take an executive role in the business. What drove your decision to take up this challenge? Steger: Basically, my decision to accept Engel’s offer to join the company was very easy. Not because I married into the family but because Engel is one of the world’s leading injection moulding machine manufacturers, with a considerable number of obvious strengths. The active involvement of the owning family in the daily operation of the company and and its strategic objectives are adequate testimony to the company’s long-term vision. Hence, it is an honour for me to join my brother-in-law and great-grandson of the company founder Ludwig Engel, Dr Stefan Engleder, who as technical executive has contributed significantly to the success of Engel for many years, as second member of the fourth generation of the Engel family being active in the business. PETplanet: Dr Neumann has just stated at the press conference at the NPE that, in the shape of the Engel e-cap, you have one of the most efficient and powerful closure cap plant on the market and your intention is to become market leader with it within a short space of time. Looking at the strong competition in this field, it seems to me that this is not going to be that easy. Could this not be said to be an ambitious goal that you have set yourselves? Steger: We think that ambitious goals are one of the main drivers for success. This goal is certainly one of our bigger challenges but I still think it is achievable. We estimate the global market demand – excluding China – to be around 100 heavy duty plants per year and aim to gain a market share of about 1/3rd within the next couple of years. And our all-electric e-cap series is definitely a great solution with outstanding features, be it in the area of efficiency, speed, precision or reliability. PETplanet: Husky has now brought KTW on board as a cap toolmaker and is therefore able to offer a complete system that is very, very fast. By contrast, you are looking at achieving your goals using external toolmakers. Steger: As Dr Neumann said previously, our all-electric Engel e-cap plant is one of the most efficient and powerful on the market. Anyone who says anything to the contrary will have to prove it first. Our approach for offering complete systems is to cooperate with the best possible partners depending on the desired end product. It is well known that customers in different regions have different requirements concerning product specifications and demand different solution characteristics. By establishing partnerships with several of the best specialists we in each case can guarantee a very high level of efficiency and the best solution for the individual demand. PETplanet: On one occasion you challenged Husky, when Engel brought preform systems on to the market. Steger: We didn’t challenge Husky, we identified an interesting market segment and introduced a preform system but realised that due to the fact the we did not have the necessary mould competence in house we did not have a proper solution for that particular market segment. PETplanet: Could you then envisage acquiring another established preform machine manufacturer in order to close this loophole in your range? Steger: “Never say never“ is what they say, but at the moment I can definitively rule this out. So far Engel has grown organically and I think this situation will go on for a bit longer yet. PETplanet: Many thanks, Dr Steger, I can see that the 4th generation is making just as foresighted and dynamic a start as we have become accustomed to with the three previous generations at Engel. www.engel.at *Dr Christoph Steger joined Engel in February as Vice President of the business unit Packaging. He studied business administration at the Vienna University of Economics and Business with majors in Innovation and Strategic Management. Initially starting in the consulting business, Christoph Steger has worked for several years in the plastics machinery industry being in charge of Marketing, Product Management and Processing for the battenfeldcincinnati group of companies before recently accepting the new challenge at Engel. He is married to the great-granddaughter of the company founder Ludwig Engel and together with his brother-inlaw Dr. Stefan Engleder represents the fourth generation of family members to be actively involved in the company’s business. Dr Christoph Steger(left) and Alexander Büchler in front of the e-cap","@ID":40} "EDITOURS REPORTS 22 PETplanet insider Vol. 13 No. 04/12 www.petpla.net Then as now the preforms for water represented the main product. After 2006 things were quiet for some time, the old premises were no longer sufficient. The breakthrough happened in 2010 when the management decided to locate a new building on a green field site. This meant more space for new machines. Other Sipa and Husky lines found their way onto the new shop floor. Now there are five Sipas, one Netstal and four Husky lines standing next to each other and producing preforms. This combination of all three leading preform machine manufacturers has – in my opinion – got to be a one-off. The shop floor incorporates 15 bays which means that another five lines can be fitted in. But Akar has been thinking ahead. Extending the machine shop will give him the room for siting another ten machines. The floor to ceiling height on one side means that the driers can be accommodated; the crane lines are already installed on the other side of the shop floor. At present Eskapet are using the bays as a store. Once the extension has been built there will new storage bays linked to the production building. In addition to the water preforms mentioned, Eskapet also manufacture CSDs and edible oil preforms. By way of a field of activity they have been on the lookout for the 19l container for water. Here they are now fabricating 3 gram weights on 16-fold cavities. Over the past two years the classic PC disposable containers have come to replace the PET single-usage bulk container. The reason for this is the health issue that goes hand in hand with PC. Ramazan Akar sees weight optimisation as a general trend in Turkey, the conversion of almost all water preforms to shortneck happened in only three years. As regards the CSD market he is anticipating the arrival shortly of the first 1881 lightweight machine. “But here the conversion of the entire branch will take longer than was the case with water because bottlers here and there still have emotional reservations“ says Akar. www.eskapet.com Ell & Nikki – the Eurovision Song Contest comes to Azerbaijan As part of the Go to Brau Beviale tour 2011, PETplanet Insider took time off to meet singer and musician Ell, one half of the Ell and Nikki Duo. They triumphed at the 2011 Eurovision Song Contest in Germany and as a result the 2012 contest will take place in Baku, Azerbaijan, starting on May 22. Baku was the turning point of PETplanet Insider’s grand tour, and we marked the occasion by talking to Ell about his career as an artist. We also had an important question for him: what is the favourite drink in a PET bottle for celebrated singers like him? Having garnered a massive 221 points, the duo Ell & Nikki swept the board at last year’s Eurovision Song Contest held in Düsseldorf, Germany on 14th May, 2011, well ahead of runners-up Italy (189 points) and third-placed Sweden (185 points). Their victory was a double celebration: Ell & Nikki won the coveted trophy ahead of 25 participating countries, and ensured that the next contest would be held in Baku, Azerbaijan, for the very first time. Previous winner Lena (2010 song: Satellite, 2011: Taken by a Stranger) had to be content this time round with 10th place, but was happy to join with Ell & Nikki in celebrating their magnificent victory. to be continued on page 29 The market in Turkey opens up","@ID":24} "Vol.6 PETplanet print PREFORM PRODUCTION 16 PETplanet insider Vol. 13 No. 04/12 www.petpla.net Stringing The rapid guide to perfect preforms - part 28 Troubleshooting guides have suffered in the past from being locked away in offices and not being available to the people that actually need them. Considering the high cost of machine and tools high scrap rates can be a costly proposition eating away at already tight margins. PETplanet’s “Rapid Guide to Perfect Preforms” takes a different approach. It has been written for the people on the floor of injection moulding companies to support their daily work in making the best preforms possible. The product of two industry experts, Rick Unterlander and Ottmar Brandau, it gives concrete advice on 35 of the most common problems in preform manufacture, most illustrated by pictures. From high AA levels to wavy bodies processors can find help when they need it. Read chapter 28 of the guide. Symptom Hair-like strands of plastic are emerging from the preform gate nub. Cause The preform gate is too hot, causing the nub to draw out. Typically observed on non valve gated moulds, but can also be found with valve gated moulds as caused by the valve stem not closing properly. Table of Contents i........................ About the Authors ii.................................Introduction chapter 1.............................. AA Level High 2........................ Accordion Preform 3....................... Air hooks / Streaks 4............................... Black Specks 5...................................... Bubbles 6..................................Burn Marks 7...........................Colour Streaking ................................... /Peeling 8..................................Crystallinity 9.................................Drool Marks 10.......................................... Flash 11......................... Gate Depressions 12............................... Gate Peeling 13..................Gate Voids / Pin Holes 14......................... Internal Gate Sink 15................................Internal Sinks 16........................................ IV Loss Solutions 1. Check water cooling temperature. This should be 7 – 10ºC (45 – 50ºF) for optimum cooling. 2. Check water cooling flow to mould. This should be at the mould manufacturers rating (for a given preform size and cavitation). 3. Check all temperature readings and correct if necessary. PET resin should be melted at about 280ºC (536ºF) +/- 10ºC (18ºF). 4. Check nozzle tip heat settings. This area has a major impact on gate nub stringing. Settings too high may cause the dome and gate nub area to remain hot. The settings should be adjusted low enough to solidify the nub yet not too low to cause crystallinity to form. 5. Check that the cooling time is sufficient for the preform being moulded. This typically ranges from about 1 - 3sec depending upon the preform wall thickness. Increase time if necessary to improve nub solidification. 17............................ Long Gate Nub 18...............................Milky Preform 19............................ Moisture Marks 20................Neck Finish out of Round 21....................... Parting Line Crease 22.................Parting Line Deformation 23......................... Preform Yellowing 24.................................. Short Shots 25.......................................... Sinks 26......................................... Splay 27........................... Stretched Necks 28..................................... Stringing 29......................... Surface Blemishes 30......................... Thread Flow Lines 31...............TSS (Top Sealing Surface) ......................................... Sink 32.......................................Unmelts 33.................Wall Thickness Variation 34.................................Wavy Body 35.................................. Weld Lines","@ID":18} "MARKET SURVEY 26 PETplanet insider Vol. 13 No. 04/12 www.petpla.net MARKETsurvey 04/2012 Company name Weener Plastik AG Hasplastik SAN.TIC.A.S. Postal address Telephone number Web site address Contact name Function Direct telephone number Fax E-Mail Industriestraße 1, 26826 Weener, Germany +49 4951 3060 www.wppg.com Manfred van Essen Sales Manager +49 4951 3060 [email protected] Esenyurt Yolu, Firizkoy Bulvari, No 50 Avcilar Istanbul, Turkey + 90 212 695 5000 www.hasplastik.com A.KerimAtas Sales executive +90 212 695 50 00 +90 212 694 97 24 [email protected] Product Range One-piece closures for beverages Yes, HDPE Yes , HDPE Two-piece closures for beverages (with liner) No Yes with EPE liner, LDPE Applications relevant to PET containers (e.g. CSD, water, juice, beer, etc.) Csd, water, beer, juice, shampoo, household, cosmetics Neck finishes available as standard PCO 28/1810 and PCO 28/1881 28Mm 1810, 28mm 1881, 30-25mm ,29-25mm ,26-22mm , 48-41mm , 38mm three lead , 38mm two lead, aseptic and hot fill aplications, 55mm hod, …etc Printed caps available Yes Yes Colour matching service Yes Yes Child-proof closures No Yes Push-Pull / sports caps Yes Yes Special comments/special closures (e.g. flipt-tops, drinking spouts, lightest cap for 28 mm PCO, 26 mm for water etc including non-beverage closures...) Various weights are available for the same closure type Special patented closures or marketing features 1D and 2D barcode application (for promotion security), patented finger loop design for 5 gallon caps, triple barrier technology for CSD, non solvent (UV) printing system for cap decoration, automatic video inspection for QA Company name Finn-Korkki Oy Closure Systems International Krallmann Kunststoffverarbeitung GmbH Postal address Telephone number Web site address Contact name Function Direct telephone number Fax E-Mail Konepajantie 10, 13300 Hämeenlinna, Finland +358 3 628 641 www.finn-korkki.com Robert Jeynes Export marketing +358 3 628 6428 +358 3 619 7294 [email protected] World Headquarters: 7702 Woodland Drive, Indianapolis, IN 46278 USA +34 93 891 62 49 www.csiclosures.com Neus Piloneta European General Manager Assistant +34 93 891 62 49 +34 93 891 78 00 [email protected] Siemensstraße 24 32120 Hiddenhausen, Germany +49 5223 989-0 www.krallmann.de Alexander Knipp Director Sales & Marketing +49 5223 989-262 +49 5223 989-201 [email protected] Product Range One-piece closures for beverages (Yes /No -If Yes, please specify material No Yes (HDPE, PP, Copolymers, Etc.) Yes, PE, PP Two-piece closures for beverages (with liner) (Yes / No -If YES, please specify material Yes, steel and aluminium cap with liner Yes - plastic and aluminum closures (PP primarily) Yes, PE, PP, TPE Applications relevant to PET containers (e.g. CSD, water, juice, beer, etc.) Beer, wine, water, CSD, juice, functional, cider, energy drinks CSD, bottled water, sport drinks, juices, teas, beer, distilled spirits, wine, food, automotive fluids All beverage sectors Neck finishes available as standard standard pry-off crown cap and RipCap 42mm Short height: 28mm (1881 & 1873), 26mm (1914, 1901, Etc.) Standard height :28mm (1810 & 1716), 26.7 (1844); 30/25 Haute, 33mm (1851), 29/25 Finish, 2-Lead 38mm (1874), 3-Lead 38mm (1876 & 1875), 38mm (1842, 1843, & 1845), and 43mm (1799, 1814, & 1841)... All corresponding neck finishes Printed caps available (Yes / No) Yes, in 6 plus colours Yes Yes Colour matching service (Yes / No) Yes Yes Yes Child-proof closures (Yes /No) No No Yes Push-Pull / sports caps (Yes / No) NO Yes (short-height and standard height) Yes, individual solutions Special comments/special closures (e.g. flipt-tops, drinking spouts, lightest cap for 28 mm PCO, 26 mm for water etc including non-beverage closures...) Ring crown caps of different sizes for pasteurisation, sterilisation, hot fill and cold fill applications. FinnKorkki is a leader in ring pull bottle closures with over 30 years experience being shared with customers. Range of food / non food caps, ‘K-Squeeze’ closure range with patented technologie, multi component injection moulding, non refillable closures, own tool-shop Special patented closures or marketing features RingCrown and RipCap closures Short-height beverage closures and lightweight 38mm closures which incorporate patented safety and design features IML solution for caps, patented K-squeeze valve technologie, R&D departement and toolmaking for individual solutions.","@ID":28} "CAPPING / CLOSURES 18 PETplanet insider Vol. 13 No. 04/12 www.petpla.net Mold Hot Runner Solutions claim 30% savings for injection moulded plastic closures production Stack, mould, save How can plastic closure manufacturers increase output without investing in additional or larger injection moulding machines? Mold Hotrunner Solutions (MHS), a global supplier of hotrunner systems and engineering services, offers a new stack mould technology that can double production of valve-gated parts. Harald Schmidt, President of MHS, explains the new technology. World demand for caps and closures is projected to grow by 4.6% annually, to in excess of US$40 billion in 2014. While beverages will remain the main consumers of caps and closures, rapid gains are expected in other markets, such as food and pharmaceuticals. Technological advances that address this growing market potential have been significantly led by manufacturers of all-electric and hybrid injection moulding machines and control equipment. Mould-makers and hotrunner manufacturers have been slower to produce substantial contributions to improved energy savings and cycle time reductions. However, new hotrunner technology is aimed at precisely these issues, while lowering production costs and improving part quality. Small, compact stack-mould systems with internal valve-gate components offer a number of advantages compared with their large, single face predecessors. For example, they can produce parts with much more efficiency, inside significantly smaller injection moulding machines. A rising number of moulders are expected to employ back-to-back valve-gate stack moulds, in order to gain a competitive advantage in the marketplace. How to break the cycle time barrier In order to lower the production cost of injection moulded caps and closures, moulders must increase productivity. Without investing in additional equipment, greater production output can only be achieved by reducing cycle times – but it is impossible to cut cycle times in half on a single face mould, given the high degree of efficiency already in place. However, doubling the number of parts produced by implementing a stack mould solution makes a step-change in productivity possible. The cost of purchasing and operating additional or larger injection moulding machines, moulds and controllers is substantial. An end user in the packaging business, relying on plastic closures for its product, will pay that additional cost through higher prices for each part; moulders will simply become less competitive. Three ways to injection mould 96 closures per shot: A small stack mould shows better performance than a bigger single face mould Annual production of plastic closures (million of parts)","@ID":20} "EDITOUR REPORTS 31 PETplanet insider Vol. 13 No. 04/12 www.petpla.net Focus on closures Hasplastik produces predominantly water and CSD closures. The company focuses on its own designs that are very well adapted to customer requirements. In the meantime there are just under 40 cap lines operating in Istanbul, chiefly on Netstal and Husky lines. Bottlers using Hasplastik caps are to be found in 45 countries worldwide. The company is older than 32 years now and more than 16 years ago the family-owned company Hasplastik made the decision to give up its activities in the bottle blowing sector and to concentrate instead on beverage closures. Murat Aner, Technical Director explains the move: “We were keen to export; closures are easier to transport than empty bottles“. Today there are 39 closure lines in Istanbul processing 15,000t of Polyolefin. (With the additional four new lines it will be around 18.000 t within 2012.) It is mainly single-piece closures but a small number are fitted with a liner. All the closures come from injection moulding machines. Here the short neck closures for water (29/25) and CSD closures (PCO 28) dominate the picture on the shop floor. In addition a few other technical closures and caps are still being manufactured for the 19l containers. This trend in closures is being driven by Hasplastik itself in cooperation with toolmakers. “We came from 30/25 for water with a weight of 2.4g; then we went down to 1.75g gradually. Following the change to 29/25 we are now down to around 1.3g“ says Aner. The standard European designs do not extend to everywhere on the markets in which Hasplastik is active; therefore they are working on improvements to their own closures. View of one of the injection moulding halls with the big Netstal lines In addition to the lightweighting trend, the bottling speed is increasingly coming into play. The faster a bottling plant runs, the greater the degree of precision needed for the closures. So all the closures go through camera inspection systems. Hasplastik has even applied the cavity number internally so that it is almost invisible. In the event of repeated errors in a particular cavity, this can undergo specific machining in the tool. The reason why the engraving needs to be so small is because Hasplastik also offers inside laser marking for promotional campaigns. If there were differences in height due to engravings the laser process would not function satisfactorily. When it comes to printing on the closures Hasplastik has its own reasons for treading an additional path. Whereas the conventional route as regards CSD closures involves printing with inks containing solvents, they print the water closures with UV-drying inks. This eliminates any possibility of an adverse effect on the taste of the water due to solvents. One particularly striking example of in-house closure development is the 19l container sector. Here, one customer asked the company if they could please fit a pull ring because the pull tab that had been standard up to then was not user-friendly. No sooner said than done. But it was not long before a second generation developed where the pull ring (which not only protruded vertically so that you didn’t know whether opening involved pulling to the right or the left) subsequently became slightly tapered, thus ensuring that users were clear about which direction to pull in so as to open up the container. 19l container cap with tear off ring But Hasplastik is not only investing in new developments; as far as the company is concerned, it is also important for them to offer value for money. And this is the reason why they are also investing in higher numbers of cavities wherever they find that they are no longer able to achieve the market price using the tool they have always used because of low numbers of cavities. As a result of having regularly invested in new tools Hasplastik has some tools where, although the closures are technologically-speaking OK, the small number of cavities nevertheless puts pressure on commercial viability. They are now considering, along with these tools, a few machines and local partners, relocating their initial ownproduction outside Turkey in order to circumvent the relevant import duties. www.hasplastik.com Read Editour reports: Turkey PETplanet insider issue 5/2012: Köksan Sunpet Coca-Cola Icecek","@ID":33} "PETcontents 04/12 4 PETplanet insider Vol. 13 No. 04/12 www.petpla.net INSIDE TRACK 3 Editorial 4 Contents 6 News 40 Products 42 PET bottles: Beverages 43 PET bottles: Personal care 44 Patents MARKET SURVEY 25 Supplliers of caps and closures for PET bottles TRADESHOW REVIEW 34 The whole fruit inside Anuga Foodtec, Cologne, Germany, March 27-29, 2012 38 A success by many measures NPE, Orlando Florida, April 1 -5, 2012 MATERIAL / RECYCLING 10 What happens down the recycling stream? Comparing PET bottle-to-bottle recycle testing protocols: US and Europe PREFORM PRODUCTION 16 Stringing The rapid guide to perfect preforms - part 28 CAPPING / CLOSURES 18 Stack, mould, save 30% savings for injection moulded plastic closures production EDITOUR REPORTS 20 A market opens up Turkey Part 1 Page 12 Page 19 BUYER’S GUIDE 45 Get listed! Page 32 Page 34","@ID":6} "TRADE SHOW REVIEW 36 PETplanet insider Vol. 13 No. 04/12 www.petpla.net Husky: More productive HyCap, efficiency upgrades Husky Injection Molding Systems announced various new developments of its technologies for the beverage packaging, closures, medical and hot runner markets at NPE 2012. The principle exhibit on its stand was the global unveiling of the latest version of its HyCap fully integrated injection moulding system for beverage closure manufacturing. Husky says that the new systems offer two performance levels, each with improved cycle times along with high levels of reliability, repeatability and part quality. The HyCap 300 system that was running at NPE 2012 was producing a 0.95g 26/22 lightweight water closure at a 2.2s cycle, using a 96-cavity KTW beverage closure mould. The latest version offers a 45% productivity improvement over the 300 model, which debuted at NPE 2009 with a 72-cavity system running a similar application at a 2.4s cycle. New features include direct drive technology, which Husky claims helps to improve plasticizing speed and control, leading to improved shot-to-shot repeatability and better quality parts. Elements of the system, such as the plasticizing screw and check valve, have been adapted to suit the characteristics of direct drive technology. The clamp lock function has been electrified, with the intention of improving efficiency and cycle potential. The new HyCap has a single interface for central control of the entire system, including hot runner temperature control and auxiliary equipment. The design and development of the new HyCap system had input from both Husky and KTW. The company says that the new mould concept offers cycle time improvements and faster and easier maintenance, as well as specific features such as SmartStart and SmartStop for faster startup and shutdown; simplified set-up; improved mould longevity; and the elimination of the need for sensors to monitor sensitive components. The latest generation of Polaris Control offers high levels of precision and repeatability and a greater degree of fine tuning, which may be of particular interest to faster-cycling lightweight applications. Husky further asserts that its Mold ID feature improves integration between machine and mould, allowing access to specific mould setup and maintenance information. Husky’s EcoBase preform design was also featured on the stand. It provides weight savings of up to 2.5% while maintaining the bottle’s mechanical integrity. www.husky.ca KTW integrated at Husky Interview with Jeff MacDonald, Vice-President Marketing, Husky injection Molding Systems As 2011 drew to a close, Husky enjoyed one of the best years in its history. The Canadians have an estimated market share of 80% in manufacturing solutions for preforms. And they made big moves in the cap sector by leveraging their May 2011 acquisition of mouldmaker KTW to develop not one, but two new systems for closure production, the first of which was introduced at NPE. We spoke with Jeff MacDonald at the NPE. PETplanet: At your stand here at the NPE we are looking at the newest generation of your HyCap. MacDonald: Yes. It is important for us to show that we are not standing still as far as our efforts in the closure sector and in the preform sector are concerned. The new HyCap 3.0 brings together the best of KTW and Husky to introduce the first true system for injection moulded closures. Compared to the HyCap we showed at the last NPE we have been able to increase the output of the system by 45%. PETplanet: It is just under a year since you acquired the toolmaker KTW. Is this machine fitted with a KTW tool? MacDonald: Yes. The tool comes from the KTW operation in Austria but it is a complete re-design, bringing together the best know-how of both companies. Now that we’ve added KTW’s mouldmaking capability we are able to take the same systems approach that we do in PET, where we engineer all elements to work together as a system. We’re able to achieve levels of performance not possible by simply integrating different components, and our customers get the benefit of single source support for the entire system. PETplanet: Up to now you have worked together with external toolmakers in the cap sector. How is your further strategy shaping up as far as this is concerned ? MacDonald: While this new HyCap system already benefits from our approach to engineering the complete system as one, it also offers the flexibility to use existing tooling. Flexibility is a very important consideration for us. As we continue to develop our HyCap product line we expect that each element of the system will be dependent on the rest of the system to achieve leading performance and quality. PETplanet: As regards the preform sector, what you are focusing on at this Fair is optimising existing systems? MacDonald: First of all, new systems business is very important to us as we continue to have a successful and growing customer base. In particular the small H-PET AE systems introduced eighteen months ago has been a nice surprise in reaching new customers and new applications with existing converter customers. Our line-up of systems and tooling solutions has allowed us to again approach 80% market share in the past year. But, in the meantime, there are around 4,000 preform systems operating throughout the world which means that it is extremely important to help our customers to achieve the best performance from their installed base of assets. Today’s systems offer significant economic benefits over older systems but with our Encore upgrade packages, even an older X-line system is capable of a significant improvement in performance. The typical payback on upgrades to X and G-line systems can be in as little as twelve months. PETplanet: Two new suppliers of preform systems have appeared on the market in the shape of Sacmi and Sipa. Does this mean that your 80% share of the market is in danger? MacDonald: Neither Sipa nor Sacmi is actually a “newcomer“ to PET. Both have introduced new concepts. The market will ultimately decide based on the value of the solution and support. We continue to have an exciting portfolio of new developments for both PET and closures and we’re assuming that we will continue to grow with our customers, too. PETplanet: Thank you very much. Jeff MacDonald (right) and Alexander Büchler at NPE 2012","@ID":38} "MATERIAL / RECYCLING 14 PETplanet insider Vol. 13 No. 04/12 www.petpla.net Post-wash air elutriation The next testing step is elutriation. While both the APR and EPBP call for this step, the APR allows for a higher elutriation loss rate than the EPBP which will aid in more thin multilayer material and /or label removal. Therefore, studies involving multilayer materials or labels can be impacted by which protocol is used. Study blend compositions This is an area where the two studies have similarities but also differ. The U.S. protocol calls for compositions of 0, 25 and 50% innovation flake blended with control flake. The European protocol allows for additional percentages of 2, 5 and 10% to cover lower levels of innovation flake content. Extrusion / palletisation Extrusion of the various flake blends to pellets creating a second melt heat history is next. The temperatures can be different in each protocol with Europe calling for a higher extrusion temperature. The U.S. protocol does not specify a particular extrusion temperature and allows for optimisation on the smaller laboratory equipment being used for the extrusion/ palletisation step. The result is that while the higher extrusion temperatures may cause increased yellowing, they are considered closer to actual production scale conditions. The U.S. protocol, with its lower temperatures, may not show problems with an innovation material that is prone to yellowing at higher temperatures. Solid-state processing Solid stating of the crystallised extruded pellets is the next testing phase called for in both protocols. Both set specific parameters for material that will be moulded into preforms and plaques. The European protocol sets a specific time of eight hours for solid starting. This is sampled at various times to determine the IV build rate for each variable being studied. The United States protocol requires longer solid stating with measurements taken at 8 and 15h. (The 15h is to make sure the material will meet an IV requirement of 0.95 for strapping applications.) This test is also intended to measure the solid stating rate of each variable. However, both protocols specify that each variable must be solid stated to produce a quantity of material that has a final IV 0.80(+/-.02)dL/g for use in plaque melding and preform melding. Plaque melding Plaque melding simulates the third melt heat history of each of the 0.80(+/-.02)dL/g variables. In the United States, plaque melding is done with 100% of each extruded material variable. This can accentuate the co lour and haze issues in the moulded plaque. The European protocol uses a 50% blend of each variable along with virgin resin to meld the plaques, which can improve on the yellow colour. This could be considered more “real world” as the innovation material will normally not be found in high concentrations in the rPET recycle stream. Preform and bottle testing Both protocols are very similar from this point on. Each of the 0.80(+/-.02)dL/g variables are diluted with virgin resin at 50 per cent, injection moulded into preforms and then blown into bottles for testing. Both organisations use a typical generic bottle and similar test protocol for bottle evaluation. Innovation recognition Because the European protocol looks at testing levels of 2, 5, 10, 25 and 50%, the innovation material can be granted approval for meeting the protocol requirements based on the anticipated market penetration at any of these lower levels. This aids in better defining the impact it may have on the recycle stream based on limited introduction into the market. The United States views this differently. A recycler may receive a concentrated amount of innovation material bottles that may cause his rPET product to temporarily worsen. If that product goes on to become a commercial success, it may end up becoming a larger component of the recycle stream. Then, its effect on quality could become more noticeable. For this reason, the APR uses only 25 and 50% blend rates and does not consider the lower percentages for innovation recognition. Conclusion Although there are differences between the test protocols, a common goal remains. Both the U.S. and European testing approaches help maintain the current rPET recycle stream quality. They also guide bottle manufacturers and brand owners in producing PET bottles that can maintain the flow of good usable material back into the supply chain. The nagging questions that remain include: What will comprise future feedstocks? How can we produce better rPET to improve the recycle stream? How can we collect a wider variety of high performance PET bottles and thermoforms? Plastic Technologies, Inc. (PTI) is one of only two U.S. companies approved by APR to provide testing services in conjunction with the organisation’s critical guidance documents. The APR and PTI are embarking on a recycle monitoring program which will evaluate current recycled PET materials, meld them into plaques and track their colour on a regular basis. This monitoring program will aid in determining the quality of what is currently being produced and how the quality may change over time. There is no shortage of applications for high quality rPET. PET recycling in the United States and Europe can increase and prosper if the quality of the bottles being recycled can be kept high. Organisations such as the APR and the EPBP will be instrumental in assisting PET bottle manufacturers to improve the quality of their products. www.plastictechnologies.com","@ID":16} "25 PETplanet insider Vol. 13 No. 04/12 www.petpla.net Conveyors Bottle-to-bottle recycling plants Caps and closures Preform moulds and SBM moulds Preforms Preform and single stage machinery SBM machinery Compressors Filling equipment Resins and additives Suppliers of caps and closures 19 companies once again bear witness to the still-growing beverage industry. Their names and product ranges will be found in our annual review of global and local providers of caps and closures. In alphabetical order they are: Affaba & Ferrari, Aptar, Bericap, Corvaglia, CSI, Europlast, EKG, Finn-Korki, Georg Menshen, Gulf Packaging, Hasplastik, Idee + Form, Krallmann, Retal, SBECM, Silgan White Cap, Viroplastic, Viscose Closures and Weener. In the survey itself, the companies are listed in the order in which they were received by the editors. Although the publishers have made every effort to ensure that the information in this survey is up to date, no claims are made regarding completeness or accuracy. 04/2012 MARKETsurvey Company name Georg Menshen GmbH & Co. KG Idee + Form Silgan White Cap Bericap GmbH & Co.KG Postal address Telephone number Web site address Contact name Function Direct telephone number Fax E-Mail Industriestraße 26 57413 Finnentrop, Germany +49 2721 518 0 www.menshen.com Christian Nöh Marketing Manager +49 2721 518 113 +49 2721 518 115 [email protected] Via Leoncavallo 31, 6614 Brissago, Switzerland +41 91 780 9648 Gerhard Priewe Director +41 91 7809648 +41 91 7809650 idee-form@bluewinch Hansastrasse 4 30419 Hannover, Germany www.silganwhitecap.com Hans Van Baekel Business Development Manager +32 475 81 64 85 [email protected] Kirchstrasse 5, D–55257 Budenheim, Germany 49 6139 2902-0 www.bericap.com Volker Spiesmacher Director +49 6169 2902-0 +49 6139 2902-188 [email protected] Product Range One-piece closures for beverages Yes - PP / PE No Yes Yes Two-piece closures for beverages (with liner) l Yes - PP / PE No Yes Yes Applications relevant to PET containers (e.g. CSD, water, juice, beer, etc.) Yes Yes CSD, still mineral water, HOD and bottled water, beer, juices, energy drinks, RTD, teas, syrups), for hotfill and aseptic application, edible oil, sauces and dressings, dairy Neck finishes available as standard Yes Yes PCO 1881, PCO 16, PCO 1810, PET 26/22, PET 29/25, PET 26/21, 38mm 2-start, 38mm 3-start, 33mm 2-start aseptic, 33mm 2-start HF Printed caps available Yes Yes , full photo quality cap toppanel printing / inside cap laser coding Yes, up to 3 colours Colour matching service Yes Yes Yes Yes Child-proof closures) Yes No No Yes Push-Pull / sports caps Yes Yes No Yes Special comments/special closures (e.g. flipt-tops, drinking spouts, lightest cap for 28 mm PCO, 26 mm for water etc including non-beverage closures...) Flip-top caps; sports caps; special sports closures for CSD; weldspouts; sponge applicators; chemical closures Flip-Top 30/25 And 28 Mm, 1810 And 1825 O2 scavenging features available 3-piece Push-Pull for aseptic filling without aluminium foil with high flow rate Special patented closures or marketing features \"one2dose\" - special dosing cap e.g. for concentrates Twist sport-closure up to 10 bar pressure, dosing-caps for vitamin included into the cap 28mm and 38mm Thumb screw for easy dispensing hot fill sports closure without aluminiuim foil, aseptic sports closure without aluminiuim foil","@ID":27} "NEWS 9 PETplanet insider Vol. 13 No. 04/12 www.petpla.net Engel expands Schwertberg site Engel Austria is investing some €12 million in the expansion of its headquarters at Schwertberg in Upper Austria. The manufacturer of injection moulding machines and automation specialist is taking the step to handle the rising volume of orders world-wide, improve working conditions on the site and underline its commitment to company premises in Austria. An additional 6,000m² of floor space will be created at the southern end of the factory. The shipping, incoming goods and storage areas will be the main beneficiaries of the expansion; the assembly area will also increase in size. There will be more loading and unloading spaces for lorries and containers, and trucks will be able to drive straight into the building. This means that staff working in the logistics division will no longer be exposed to the weather. Workstations in the assembly and warehouse areas will also be ergonomically redesigned. Construction work adjacent to Schwertberg railway station is scheduled for completion by the end of the year. Schwertberg is both the headquarters and the largest site of the Engel group. More than two thirds of the group’s 3,900 employees are based in Austria; the company also has factories in St.Valentin and Dietach. www.engel.at Gneuss nets four lines in Brazil Brazilian recycling companies Unnafibras Textil S.A. and Nova Pack Embalagens Ltda have installed a total of four recycling lines produced by Gneuss Kunststofftechnik GmbH, of Bad Oeynhausen, Germany. Unnafibras has purchased two lines for textile fibre production and a third for bottle-to-bottle recycling. The two machines at its headquarters in Santo André produce co-extruded polyester fibres from recycled material, with a total capacity of 1,500kg/h. The third line, located at the company’s factory in Paraiba, has a capacity of 2,000 kg/h and produces pellets from PET bottle flakes for use by local injection moulding companies in bottle preform production. Nova Pack, which manufactures thermoforming sheet made of PET, PP and PS, has bought an extrusion line with a Multi Rotation System (MRS) Extruder. It undertakes dehumidification of recycled material without pre-treatment, includes a rotary filtration system for removal of contaminated particles and has an online viscometer for automatic control of melt viscosity. The line enables Nova Pack to produce packaging from 100% recycled material. www.gneuss.com Schoeller subsidiary takes over ProTec Ohl Engineering GmbH PET Recycling Technologies, a subsidiary of Schoeller Industries, of Pullach near Munich, will complete the acquisition of ProTec, the Mann+Hummel subsidiary, on April 30, 2012. This acquisition leads to the expansion of the new owners’ Schoeller Plast Industries division, which operates in the field of plastics processing and recycling. Schoeller has also taken on all employees from ProTec. Schoeller Plast Industries operates worldwide and provides reusable packaging systems, caps for drinks bottles, and systems for processing and recycling of plastics. Ohl Engineering designs and promotes turnkey PET bottle-to-bottle recycling units. ProTec is a vendor of devices and systems for material handling in the plastics industry. Its turnover in 2011 was around €22 million. www.ohl-eng.com","@ID":11}]}}
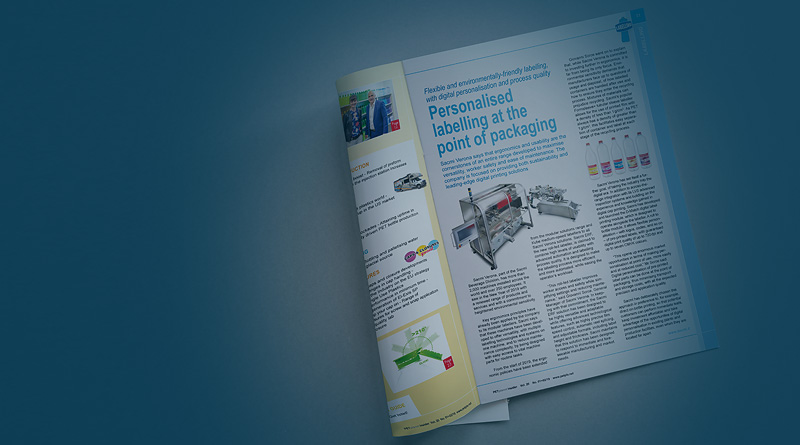