"BOTTLE MAKING 38 PETplanet insider Vol. 14 No. 09/13 petpla.net Bottles, performs and closures, 2nd Edition – part 5 Verification of the 3D design through finite-element simulation Simulation of the mechanical behaviour of a bottle, e.g., under top load or internal pressure, can avoid costly mould modifications, shorten the overall time to market, and allow qualitative comparisons of design variants. Such simulations are possible using the FEM. In this part we look at how the simulation of mechanical behaviour of the bottle can support the bottle design process. Ottmar Brandau has newly revised his book, “Bottles, Preforms and Closures” first published by hbmedia, and now to be re-issued under the Elsevier imprint. PETplanet insider is publishing extracts from successive chapters in a series of articles in forthcoming issues. Modern high-end CAD systems already include a finite-element (FE) module for simple, or in some cases even complex, simulations. This means that the FE simulation can be made simultaneously with the CAD design of the bottle described in the previous section. For more accurate computations and special tasks such as the simulation of the barrier properties, higher-value stand-alone FE expert systems are available, such as Ansys and B-Sim.","@ID":40}, "EDITOURS REPORTS 16 PETplanet insider Vol. 14 No. 09/13 petpla.net Peru February 18, 2013 San Miguel Industrias PET, Lima We met: Sven Brodersen, CEO Everything from a single source The privately owned company SMI in Lima belongs to one of the largest manufacturers of preforms and bottles for Lima and southern Latin America. With 2.4 billion preforms p.a., they have a market share of 80%. For the past two years SMI have also been regenerating PET bottles from consumer waste. We spoke with Sven Broderson, CEO for the PET side of the business. Sven Broderson CEO PET SMI and Alex Büchler in the 30,000m² empty bottle plant For producers of preforms, things are relatively straightforward. They produce commodities that are clearly defined by material and dimensions. What subsequently happens to them is as a rule up to the bottle blowers, i.e. the bottlers. Under this definition, SMI are not one of the classic preform producers, since 80% of their preform production goes into their own stretch blow moulding equipment. About half of this is blow moulded in the main plant in Lima whilst the other half goes for in-house production at the bottlers. The plants are located in Ecuador, Panama, Salvador, Columbia and, of course, Peru. Overall there are 33 plants involved in blow moulding operations at all locations. Most of the machinery has been supplied by Sidel and Sipa. In addition, depending on customer requirements, there is also the labelling of the empty bottles, although Sven Broderson actually prefers to sell bottles only. An inline labelling operation prior to bottling can have a negative effect on the overall efficiency of a plant. The in-house plants are each tailored to the individual customer, sometimes producing directly in-line, sometimes in silos but also on pallets. Using this system, SMI are able to ensure full utilisation of their plants. In the high season, from December to May, 80 % of production stays in the country, in the low season it is still a healthy 60%. One particular speciality is the hot fill bottles for Gatorade, which they produce in the main plant on Sipa equipment. In La Paz, we have three interesting appointments. First off we meet the waste separation organisation Ecovecindarios/Swisscontact followed by label producer Industrias Lara Bisch and finally Pepsi licensee CBN. After the visits we sally forth to the next stage, Santa Cruz, through the rain forest. Leaving the Andes behind we reach Santa Cruz, located in the lush tropical rain forest. Here we have an appointment with Coca Cola licensee Embol. The preforms for Embol’s PET bottles come from Empacar, which is where we are heading for our next appointment. Later at Empacar we learn that the preforms supplied to Coca Cola are made from 10% recycled material which the company produces in-house on a bottle to bottle line. Before driving finally to Santiago de Chile for handing-over the Editourmobil to the second team consisting of Kay and Shiraz there’s still another interview to conduct in Bolivia’s constitutional capital, Sucre. But, how to get there? Major roads will involve a huge detour, and so we opt for the minor roads instead. Moments later we find ourselves bumping along for 300km over sand and gravel. Poor Editourmobil! And just to make life more interesting, we manage to get stuck in a mud hole, from which a kindly truck driver drags us out. In Sucre, we instantly despatch the vehicle to the local car wash, where a diligent team of 4 spend a good four hours giving the Editourmobil a thorough springclean inside and out. Our final appointment with the small brewery Surena is situated at a height of 3,300m. After an interesting meeting and numerous small serpentine roads we are ready to leave Bolivia, but surprise, surprise, there is no direct route to our destination. We again opt for a challenging road and find ourselves crossing the beautiful landscape of the National Park in southwest Bolivia… and reaching finally the customs office at an altitude of 5,020m, where we get an official customs stamp allowing us to leave Bolivia with the vehicle. by Alexander Büchler 360°","@ID":18}, "BEVERAGES / INGREDIENTS 61 PETplanet insider Vol. 14 No. 09/13 petpla.net the Döhler R & D include a new range of “brown” flavours. These range from chocolate, cocoa, nut, nougat and coffee through to caramel and vanilla, each available in what the company describes as a “diverse range of nuances”. As well as extracts and natural flavours, the company also offers a number of compositional flavours. At the flavours sector Döhler seizes the current consumers trend to the taste of honey in extensive varieties. The taste notes of honey provide the finishing touch to many fruity and spicy taste nuances. Another important trend is ginger. While the fruity and spicy root was used mostly in Asian cuisine in the past, it is jazzing up supermarket shelves around the world today. The company has developed a broad portfolio of ginger flavours, in line with this “hot” trend. Geographically speaking, Döhler has 50 sales offices around the globe and business activities in more than 130 countries. Among other regions the BRIC states are a relevant focus. Low-cal sweeteners The worldwide trend to low calorie drinks here is Stevia, for example, a sweetener that acknowledges the trend towards naturalness and low calorie products. Döhler has developed products sweetened with MultiSweet Stevia for all relevant categories of beverages and milk products. The range extends to soft drinks, still drinks, sports drinks, tea drinks, nectars, beer mixes, drinking yoghurts, spoonable yoghurts and desserts. The Döhler product MultiSweet Stevia allows us, depending on the product, to achieve a reduction of 5-6 Brix sugar. Stevia, however, although it has significantly fewer calories, instead features an innate bitter taste similar to liquorice which the majority of people find unpleasant. The aroma technology “Sweetness Improving Technology“ (SIT) is intended to mask the liquorice after-taste and thus improve the sensory characteristics of Stevia. Its collaboration with PureCircle, the company that manufactures and markets natural Stevia sweeteners, gives Döhler access to the raw ingredients used in Stevia. In the natural low calorie sweeteners sector, Döhler also opts for de-acidified apple or pear juice in addition to Stevia and the classic sweeteners. Sustainability With the increasing demand for mixed drinks the topic of raw materials shortages can no longer be disregarded, even in the sector of beverage ingredients. This is why the company sites its production locations almost directly under the fruit trees of the world. The trend is moving in the direction of regional juices, unmixed for small bottling plants, but also towards low fruit content drinks. Furthermore Döhler has committed itself to a “Code of Conduct“ SGF / Global G.A.P., and is pressing ahead with the implementation of this code among its suppliers. In addition, the ingredients manufacturer is having comprehensive raw materials analyses (contaminants, residues) carried out in cooperation with the leading institutes. Olaf Biedekarken, Head of Sensory and Consumer Science at Döhler, (left) and Alexander Büchler","@ID":63}, "PETplanet insider Vol. 14 No. 09/13 petpla.net BOTTLE MAKING 46 More than 100 delegates experience PET expertise KHS PET event More than 100 international KHS customers visited the KHS PET event which started with a series of talks and finished with a tour of the new production shop at the KHS Corpoplast plant in Hamburg, Germany. The latest innovations to be highlighted during the PET event were a new ultraclean concept with an integral mini hygiene housing, the direct digital printing of PET bottles, which can be seen at drinktec, and the newly developed FreshSafe PET marketing concept which documents the further improved Plasmax coating technology from the consumer’s point of view. The event also focused on the KHS Service department with its wide range of services from the supply of spare parts to individually tailored maintenance contracts. Toshihiro Ueki, General Manager of Shonan Plant Kirin Beverage Company Limited, and Thomas Reise, Technical Director of Hansa-Heemann AG, reported on many years of successful cooperation with KHS. Technical highlights The latest technical developments to individually tailored maintenance contracts. Ultraclean monoblocks The newly developed ultraclean technology monoblocks the InnoPET Blomax Series IV stretch blow moulder with the filler/capper section which is incorporated into what is known as a mini hygiene housing. The advantages of this concept are the system’s small footprint, improved sustainability and reduced costs while providing maximum microbiological safety. to be highlighted during the PET event were the ultraclean concept with an integral mini hygiene housing, the direct digital printing of PET bottles, and the newly developed FreshSafe PET marketing concept which documents, from the consumer’s point of view, the advantages of further improved Plasmax coating technology (a more extended article about this subject will be published in PETplanet insider issue10).The event also focused on the KHS Service department with its wide range of services from the fast supply of spare parts The KHS PET event in Hamburg, Germany, focused on the presentation of KHS innovations as well as a tour of the newly erected production shop.","@ID":48}, "EDITOURS REPORTS 24 PETplanet insider Vol. 14 No. 09/13 petpla.net February 27, 2013 Industrias Lara Bisch S.A., La Paz We met: Roberto Renjel Doria Medina, CEO; Felipe Villarroel, Finance During further processing operations where a high proportion of manual involvement is called for, the terminals take care of input to the production planning system. Next to them is Roberto Renjel Doria Medina, Managing Director of ILB. Specialists in packaging Industrias Lara Bisch (ILB) are Bolivia’s packaging specialists. In addition to a wide range of paper and cardboard products, the company primarily produces printed sheets for sectors such as flow-pack packaging (beverages and food), advertising and labels for the beverages industry. They have an annual turnover of around US $20million. One speciality here is sheets for flow-pack beverages. It is here that the 3-ply foil sheets for the flow-pack beverages are printed. ILB was established by German immigrants in the late 1920s. Today the company is still in family ownership. Three years ago a new, young team embarked on turning the company around and putting it on a profitable path. CEO Roberto Renjel Doria Medina, 36 years of age, is assisted by a management team not one of whom is over 40. Previously the company was very much product-led, now the focus is on meeting specific customer requirements. In addition, Roberto and his team have built up service teams who make a point of investigating the machinery at the customer’s premises, evaluating how ILB’s products best fit requirements, and coming up with appropriate proposals. Today ILB process 80t of plastic into sheets. The latest installation is a Novagraf flexo-printing system. In front of it, to the left, Felipe Villaroel, in the middle Roberto Renjel Doria Medina and Alexander Büchler on the right. In the background the single-ply blow machinery. One example is the flow pack used for packaging soft drinks and milk products. The state gives every school-age pupil a serving of milk in a flow-pack bag. The sheet used for this is three-ply in structure and is produced by ILB inhouse. Inside there is a black layer to prevent the ingress of light and oxygen, then the actual backing layer, likewise made from the same material but in white. After this comes the printing. The final layer is a transparent layer covering the pack. Hitherto, manufacturers of this type of packaging have been demanding 100μm thick sheets; using new additives, ILB has developed a type of foil sheeting with a thickness of 60μm. The advantages from a packing point of view are clear: You get more packaging from one kg of foil No need to change the foil rolls on the machine quite so often Logistics expenditure is less because fewer rolls are needed Possibility of processing the foil on the existing installations Lower costs whilst maintaining same quality Nevertheless, the processors stopped short of taking on the 60μm foil. Some of them have now converted to 80μm. A compromise between gut feeling and technical feasibility. 360° 360° 360°","@ID":26}, "BOTTLING / FILLING 54 PETplanet insider Vol. 14 No. 09/13 petpla.net With the Innosept Asbofill ASR KHS is now plugging the final gap in the area of aseptic fillers for bottlers of liquid dairy products and non-alcoholic beverages. With its range of linear and rotary systems the company now offers the industry a full aseptic programme, just in time for drinktec 2013. own. The Innosept Asbofill ASR can process filling volumes from 250ml to 1.5l with two different capacities available. The two Innosept Asbofill ASR 24 machines output of 24,000bph for volumes up to 500ml or 1l; the three Innosept Asbofill ASR 36 models are able to process 36,000bph for the above two volumes plus a third bottle size of 1.5l maximum. Linear aseptic filling machines generally cover a low to medium output range, with rotary aseptic machines catering for the higher capacities. To take a typical example: a fruit juice company tends to fill the same type of bottle at rates of at least 24,000bph with very few product changeovers, and in this case a rotary machine would be the aseptic system of choice. However, if bottle types are changed several times a day, a linear aseptic machine would be better. The reason is that changeovers are faster and easier on linear machines than on rotary machines. On the Innosept Asbofill ABF, for instance, the bottles are fed through the entire machine in one single holder. All conversions and replacements take place in the nonsterile area outside the aseptic zone, with the bottle neck conveyed solely in the sterile zone. As in the linear technology the new generation of Innosept Asbofill ASR rotary machines has an integrated valve manifold with identical functions which is installed on the machine to save space. Development has focused on aseptic safety, with the new rotary technology based on the room-within-a-room concept implemented in the ABF series. Specific measures protect the minimally dimensioned aseptic zone from the surrounding machine area which in turn forms a mechanical barrier to the production shop. The surrounding machine area can be opened for any necessary work even during production without endangering the sterile conditions prevalent in the integrated aseptic zone. To ensure maximum microbiological safety the necessary regular cleaning process is fully automatic. Sterilisation with H 2 O 2 aerosol The Innosept Asbofill ASR adopts the same principle of sterilisation as The Innosept Asbofill ABF 611 and Innosept Asbofill ABF 711 linear aseptic filling machines are designed for bottling capacities of up to 12,000bph and a bottle surface hygienisation of up to log6. In the extended shelf life segment, the Innosept Asbofill ESL 611 and Innosept Asbofill ESL 711 models offer bottlers a surface hygienisation of up to log5. The difference between the 611 and 711 series lies in the type of bottle to be processed; the 611 model handles plastic bottles holding between 100 and 750ml, whilst the 711 is designed for volumes of 0.25 to 2l as standard. The original machine output of both the Innosept Asbofill ABF and the Innosept Asbofill ESL can be doubled by the addition of the Twin option, raising the capacity to up to 24,000bph. Increasing capacities With outputs like these, the new Innosept Asbofill ASR rotary aseptic technology really comes into its Plugging the gap Based on an article by Thomas Niehr, Head of Aseptic Filling Technology, and PaulUwe Winterhoff Head of Aseptic Filling Technology Design Engineering, both KHS GmbH, Bad Kreuznach, Germany The Innosept Asbofill ASR aseptic rotary machines are based on the room-within-a-room concept of the Innosept Asbofill ABF linear aseptic filling machines. The Innosept Asbofill ASR fills up to 36,000bph.","@ID":56}, "Sidel has introduced Sidel Matrix, its modular generation of PET bottling equipment. The company says that its latest equipment offering is “a broad, proven and upgradeable system” and offers improvements over previous generation machinery in terms of performance, flexibility, cost savings and sustainability. Sidel makes a number of claims in relation to its new Matrix product, including improved hygienic compliance, environmental friendliness, lower energy and material usage, and adaptability. It features some tried-and-trusted technology, along with some distinctly new developments: the Ecoven oven is made to optimise energy consumption; electrical stretching improves material distribution; assisted changeovers cut downtime; and compressed air consumption is also cut. Grease-free components and fewer moving parts through the system are claimed to save on maintenance costs. The modular concept of Matrix is designed to interrelate with standard interfaces for “plug and play” operability that can be configured according to customer needs. The modular approach is to integrate changes arising from both technological and market developments. A selection of options and upgrades are already available. The components are: the Matrix blower; Matrix fillers; Matrix Combi; and Matrix Rollfed labeller. Matrix Blower The Blower has a capacity of up to 2,250bph per mould and its modular architecture allows flexible configuration. Its three sizes of blowing station facilitate production of a variety of different bottle shapes, in sizes ranging from 100mm to 3.5l. The blower’s electrical stretching provides a better material distribution and a more consistent process to ensure package integrity and consistency. In the blowing process, special neck protection, combined with an “embedded intelligence” for bottle quality control and self-regulation, minimise the standard deviation of blown bottles and thus automatically reduces scrap. Assisted mould changeover between formats on a 20-cavity machine can take a single operator less than 15 minutes bottle-to-bottle with Sidel’s Bottle Switch system, helping to reduce downtime and manual labour costs and increase productivity and output. The installed Ecoven, a development that is designed for energy efficiency, requires fewer heating modules and lamps reduces preform-heating time and cuts electrical consumption by up to 45%. It has an oven-top reflector made of Sidel’s modular system approach Entering the Matrix PETplanet insider Vol. 14 No. 09/13 petpla.net BOTTLE MAKING 44","@ID":46}, "CAPPING / CLOSURES 59 PETplanet insider Vol. 14 No. 09/13 petpla.net part by their extension into new markets, and plastics are set to increase their market share from 46.2 to 49.3% (Fig. 3/4). Drivers of Change Population growth, the rise in the number and proportion of smaller households (especially in the developed world), growing income in emerging markets, individualisation of consumption and increasing ‘on the go’ consumption, as well as other factors, all have a bearing on market demand. Longer-term technical drivers include the development of new materials, especially plastics; improved performance in existing materials; new processing and filling technologies; rising influence of developing markets; light weighting and materials reduction; and the ever-increasing drive for higher technical performance but at lower cost. Since 2008, stagnating demand in mature markets has led to intensification of competition, leading to a shift in emphasis from added value and convenience to cost reduction and light weighting. R&D in closure design therefore continues to focus to some extent on other value-added features, such as single-piece hot-fill and ‘new generation’ sports closures; and active, non-spill, dosing and dispensing closures. The market will see an increase in the variety, types and sizes of closures on offer, as well as growth in the share of simpler, single-piece and single-polymer closures, with a balancing decline in complex, multipart and multi-material types. Liner-less closures are expected to become more widespread and PP is expected to decline in the face of increasing use of HDPE. Canadean says that light weighting is by far the most important technical trend in beverage closures in recent years and virtually every major beverage closure manufacturer has a lightweight range. Improved designs and processes have helped to serve the need to reduce costs and improve resource efficiency. Plastics’ rising share of the market reflects their greater ability to adapt to demands for lighter weight, improved performance and lower costs. www.canadean.com Global beverage closure market 2009-11 - by type Volume - thousands of units Closure Type 2009 2010 2011 CAGR 2009-10 CAGR 2010-11 Carton Closures 32,068 33,993 34,482 6.00% 1.44% Metal Crowns 258.753 262,853 263,165 1.58% 0.12% Metal RO/ROPP 46,456 47,403 47,523 2.04% 0.25% Metal Twist-Off 13,378 13,767 14,031 2.91% 1.92% Other Closures 35,358 386,17 40,121 9.22% 3.89% Plastic screws 367.237 381,258 394,914 3.82% 3.58% Ring-Pulls 248,483 250,988 253,212 1.01% 0.89% Sports Caps 21,006 24,609 27,153 17.15% 10.34% TOTAL 753,250 777,891 794.236 3.27% 2.10% Plastics' Share 44.60% 45.40% 46.20% Fig. 2 Forecast of global beverage closure market - by region Volume - thousands of units Region 2011 2015 CAGR 2011-15 Tot Grth 2011-15 % Shr of grth Asia 400,513 518,271 6.70% 117,758 29.40% 65.25% East Europe 73,169 8,1234 2.60% 8,065 11.02% 4.47% Latin America 159,608 186,141 3.90% 26,533 16.62% 14.70% North America 239,119 251,821 1.30% 1,2702 5.31% 7.04% Rest of World 26,534 30,450 3.50% 3,916 14.76% 2.17% West Europe 175,658 187,144 1.60% 1,1486 6.54% 6.36% TOTAL 1.074.601 1.255.061 4.00% 180.460 Fig. 3 Forecast of global beverage closure market - category 2011-15 Volume - thousands of units Category 2011 2015 CAGR 2011-15 Tot Grth 2011-15 % Shr of grth Beer 326,518 366,655 2.90% 40,137 12.29% 22.24% Carbonates 258,875 269,137 1.00% 10,262 3.96% 5.69% Drinking Yoghurt 56,912 71,814 6.00% 14,902 26.18% 8.26% Energy Drinks 23,021 30,092 6.90% 7,071 30.72% 3.92% Flavoured Milk 11,721 14,136 4.80% 2,415 20.60% 1.34% Iced/RTD Coffee 18,351 19,164 1.10% 813 4.43% 0.45% Iced/RTD Tea Drinks 48,921 72,606 10.40% 23,685 29.40% 13.12% Juice 20,313 22,593 2.70% 2,280 11.02% 1.26% Nectars 12,353 14,575 4.20% 2,222 16.62% 1.23% Packaged water 174,403 220,671 6.10% 46,268 5.31% 25.64% Soymilk 3,127 4,010 6.40% 883 14.76% 0.49% Sports Drinks 15,432 19,425 5.90% 3,993 6.54% 2.21% Still Drinks 57,362 79,816 8.60% 22,454 14.76% 12.44% White Milk 47,292 50,364 1.60% 3072 6.54% 1.70% TOTAL 1.074.601 1.255.058 180.460 Fig. 4 Forecast of global beverage closure market - type 2011-15 Volume - thousands of units Category 2011 2015 CAGR 2011-15 Tot Grth 2011-15 % Shr of grth Carton Closures 34,482 40,393 4.00% 5911 17.14% 3.28% Metal Crowns 263,165 293,789 2.80% 30,624 11.64% 16.97% Metal RO/ROPP 47,523 52,455 2.50% 4932 10.38% 2.73% Metal Twist-Off 14,031 16,486 4.10% 2455 17.50% 1.36% Other Closures 40,121 57,830 9.60% 17,709 44.14% 9.81% Plastic Screws 394,914 485,357 5.30% 90,443 22.90% 50.12% Ring-Pulls 253,212 272,980 1.90% 19,768 29.40% 10.95% Sports Caps 27,153 35,772 7.10% 8619 11.02% 4.78% TOTAL 1,074,601 1,255,062 180,460 Plastics' Share 46.20% 49.30% 68% Fig. 5","@ID":61}, "EDITOURS REPORTS 20 PETplanet insider Vol. 14 No. 09/13 petpla.net Coca Cola were able to resume their full range of deliveries – they stayed with Backus’ own brands. This generated increased growth for the company of the order of 40% per year in the water and CSD sectors. Production now stands at around 1200 million litres of CSD and 800 million litres of water per year. The main size for water is the 600ml bottle and, for CSD, the 500ml bottle. All the plants are operating at full capacity with these. This contributed to the company achieving a 14% market share in Peru in 2012. The controlling factors in this success story are not only external ones either; the rapid growth has been possible solely due to a good on-site team. And this is something that Jorge Ayestas, who is responsible for water and CSD production, is working at intensively. “Everyone in the operation, from the operative to the director, must try, within his own sphere of activity, to optimise quality, quantity and cost and not just focus on one of the three targets“ is his stated objective. For this reason, the company regularly passes on the target and actual figures to its employees. In turn, the employees work to a continuous improvement process that is also displayed on charts so as to ensure transparency for everyone concerned. At the end of the line is the shrink packer. To the immediate right of this is the beginning of the line, the labeller and, still further to the right, the mixer. In the plant the maxim is “A place for everything and everything in its place“. From the largest machine right through to the smallest dustpan everything is documented, where it is and how it is to be used / set up. This means that even new employees have no problem finding their way about the installations with no adverse effect on any one of the three target areas of quality, quantity and costs. Although there are plenty of other plants all over the world that adopt a similar approach, Jorge Ayestas and his team seem to implement the system more consistently and with a greater degree of success. They regularly scoop first place for the most efficient CSD plant and second place for the water plant. He is justly proud of having achieved this accolade and, most of all, of being able to maintain it. And he does not work with the latest or, technicallyspeaking, the most lavish equipment either. The water plant that achieved the distinction is more than ten years old (supplied by KHS) and the CSD plant that took the award is from Sipa (three years old). As is standard practice in Peru, the bottles come from an external supplier. In this case, SMI Peru have installed an in-house production facility with two Sipa stretch blow moulders (12- and 8-cavities). Having received the empty bottle from SMI, Backus first of all label it ready to go into the rinser/filler/capper block with 135 valves. An SMI (Italy) shrink packer groups the bottles into 6-packs or larger packs. In the middle of the installation is the mixing area. Intelligent logistics ensure that a change of format takes place only once every two days. Various CSD drinks and alcohol-free beverages are bottled. With its focus on quality, quantity and cost optimisation, Backus was the first in Peru to opt for the lightweight 1881 closure. The conversion took place in September 2011. The water plant in San Mateo was converted by the team there themselves; in the case of the CSD plant in Lima, the Sipa service personnel were enlisted to help. www.backus.com.pe Bolivia February 26 Ecovecindarios La Paz We met: Mrs. Ximena Ayo, Anna Apel Collecting PET in Bolivia Where and how are PET bottles collected in Bolivia? Indeed, are they collected at all? For answers to these questions, we sought out an organisation based in La Paz called swisscontact (the not-for-profit Swiss Foundation for Technical Cooperation), who, since 2009, have been Right in the heart of the bottling plant is the team responsible for ensuring that the CDS plant in the SAB Miller Group is the No. 1 world-wide. Behind the team is the labelling operation for the empty bottles, further to the right is the bottling area and, even further to the right, the mixer. 360° 360°","@ID":22}, "EDITOUR REPORTS 19 PETplanet insider Vol. 14 No. 09/13 February 25, 2013 UCP Backus y Johnston, S.A., Lima We met: Jorge Ayestas, Maria Contreras The best of a good bunch The most efficient CSD plant in the worldwide SAB Miller Group is in Lima; the Group’s second most efficient water plant in Peru. Both are part of the Backus Brewery. Here we met Jorge Ayestas and Maria Contreras who let us into some of the secrets of their success. One thing needs to be made clear from the start: Backus’ main business is beer. With a market share of more than 95% in Peru, it is difficult to ignore them and their product. Eleven years ago, in the course of implementing their beer expansion strategy, Backus also bought up a smaller brewer. Included in the package was a water and CSD operation in San Mateo (located at a height of 3300m above sea level and around two hours by car from Lima). Here optimum quality mineral water comes out of the ground. This subsequently helped Backus walk off with the international Golden Water Award from Brussels. In Peru, there is only one mineral water and that is the one trading under the San Mateo brand name. All the competitors operate with treated water. From the first tender shoots, two bottling plants have now emerged: the water continues to be bottled at source and CSD bottling takes place in Lima. Backus installed its new CSD plant in Lima in 2010 and it was then that the totally unforeseen boom began. Triggered by a lengthy strike at Coca Cola in 2011 and the ensuing delivery bottlenecks, many consumers switched to the Backus brands. It seems that they liked the taste so much that – even once Jorge Ayestas and Maria Contreras, both from Backus, standing on the zebra stripe. The zebra stripe separates the hall into SMI’s area (left) which is responsible for bottle production and the right hand side in which the actual bottling operation is located. 360°","@ID":21}, "PRODUCTS 85 PETplanet insider Vol. 14 No. 09/13 petpla.net ProTec Polymer Processing GmbH Headquarters Stubenwald-Allee 9 64625 Bensheim/Germany Phone: +49 6251 77061-0 E-mail: [email protected] Web: www.sp-protec.com Trendsetting solutions to upgrade your virgin and post-consumer polymers! Munich, Sept 16-20, 2013 Hall B3, Booth 127 Saves space SMI has developed a stackable PET container it calls “neck-in bottle”, which is designed to save space, cut costs, optimise transport effectiveness and reduce waste. The new design features a much deeper hollow on the bottle base, which allows several layers of bottles to be directly stacked on each other, without any space between them. The necks on the lower bottles fully insert into the base hollow in those in the overlying layer. The standard design for 5l bottles allows three layers per pallet; the ‘neck-in bottle” allows four layers. The new design eliminates the need for interlayer cardboard pads, which saves material costs and also reduces production waste caused by neck breakages during palletisation. SMI even claims that the visual appeal of the pallets is improved. The new container can be produced on either Smiform’s stand-alone stretch-blow moulding machines or on Ecobloc compact blow/fill/cap machines. www.smigroup.it Biodegradable caps Thermoplastic compound specialist API Spa and Sacmi, the Italian packaging machine company, have jointly developed and produced a 100% biodegradable mineral water bottle cap. The product, which will be on show at drinktec and K 2013, was developed from a compound belonging to the Apinat bio range. Their chemical structure and versatility allow these compounds to be processed using widely available technology; they are already in use in footwear, agriculture and packaging applications. Sacmi’s cap-making compression technology is able to adapt fully to the rheology and behaviour of the molten Apinat material. www.sacmi.com The new caps developed by API Spa and Sacmi are biodegradable and compostable","@ID":87}, "imprint EDITORIAL PUBLISHER Alexander Büchler, Managing Director HEAD OFFICE heidelberg business media GmbH Häusserstr. 36 69115 Heidelberg, Germany phone: +49(0)6221-65108-0 fax: +49(0)6221-65108-28 [email protected] EDITORIAL Doris Fischer: [email protected] Michael Maruschke Ruari McCallion Waldemar Schmitke Ilona Trotter Wolfgang von Schroeter Anthony Withers MEDIA CONSULTANTS Martina Hischmann [email protected] Roland Loch [email protected] phone: +49(0)6221-65108-0 fax: +49(0)6221-65108-28 France, Italy, Spain, UK Elisabeth Maria Köpke phone: +49(0)6201-878925 fax: +49(0)6201-878926 [email protected] LAYOUT AND PREPRESS Exprim Kommunikationsdesign Matthias Gaumann | www.exprim.de READER SERVICES Heike Fischer [email protected] PRINT Chroma Druck & Verlag GmbH Werkstr. 25 67454 Römerberg Germany WWW www.hbmedia.net | petpla.net PETplanet insider ISSN 1438-9459 is published 10 times a year. This publication is sent to qualified subscribers (1-year subscription 149 EUR, 2-year subscription 289 EUR, Young professionals’ subscription 99 EUR. Magazines will be dispatched to you by airmail). Not to be reproduced in any form without permission from the publisher. Note: The fact that product names may not be identified as trade marks is not an indication that such names are not registered trademarks. 3 PETplanet insider Vol. 14 No. 09/13 petpla.net dear readers, Lies, damned lies, and ...? Sometimes it is the simplest questions that fox us the most. Here’s one: “How many preforms are produced worldwide each year?“ The more I have to do with PET – and I’ve been involved with the sector now for more than 15 years – the more I realise that there is no way of reaching a reliable conclusion. If we go on from there and ask “How many PET bottles?” or “What is the number of injection moulding machines or filler lines”, we are increasingly tempted to believe that old saw about “lies, damned lies, and …” Nowhere was this dilemma more striking than in reading the reports from our editors following the Editourmobil tour of Latin America. We were analysing the figures for Bolivia produced by two of the most respected market research organisations in the business. Their figures differ by a staggering 100%. And that’s not all: when they consider trends over the past five years, they still cannot agree. For one, growth is at 5%, whilst the other sees 12% in the same year. The following year sees the figures reversed. If these “fully paid up experts” are unable to agree on the figures for a relatively small country, what hope have the rest of us ordinary mortals got in producing valid figures for the entire world? As Churchill is alleged to have said: “The only statistics I can rely on are those I have made up myself…” So what are we to do? Perhaps our best hope is to see if we can discern some nugget of truth from this veritable fog of figures. We can of course always ask the people at the chalkface. During our visit to them, Coca Cola gave their own production figures for Bolivia which conveniently lay between the two “expert” values. Question is: does the truth always steer a middle course? We have no hesitation this time in leaving this question unanswered, for you, our readers, to build up for yourselves a picture of the size of the market in South America. Truth, and accuracy, can sometimes be a moveable feast. The saying attributed to Churchill above, for example, was loftily dismissed by the London Times with the words: “…we have never heard of this quotation …”. Let us make amends by quoting something that Churchill actually did say, in 1925: “You must look at the facts before they look at you!” Which is exactly what our editors did in their Latin American reports. So, without further ado, let’s go down to the shop floor and check what is happening in the real world. Yours Alexander Büchler","@ID":5}, "PREFORM PRODUCTION 34 PETplanet insider Vol. 14 No. 09/13 petpla.net KraussMaffei and Netstal’s PET Business join forces Under one roof In October 2011 KraussMaffei Group bundled the PET activities of KraussMaffei and Netstal under the Netstal banner. One and a half years ago the Group also strengthened their injection moulding business by creating one group-wide segment. We spoke with Dr Hans Ulrich Golz, President of KraussMaffei and Netstal’s group-wide integrated injection moulding machinery segment and CEO of Netstal, while the KraussMaffei PET activities has apparently been consolidated under the Netstal umbrella for K and drinktec/PETpoint. range of machinery to Näfels in Switzerland. PETplanet: The product range has always offered excellent value for money. Can you continue to maintain this at the relatively expensive Swiss location? Golz: The moulds used to come from Switzerland as a rule anyway and many parts of the line come from outside Switzerland. So the cost structure at the production site in Switzerland should remain much the same. The important factor was to bring together at a single location the PET competencies of the group, which had hitherto been spread over two locations. PETplanet: Are you considering producing the PET lines in China? Golz: Yes. The KraussMaffei Group has a production facility for injection moulding and reaction moulding machines and extrusion lines operating over in Haiyan. While we want to serve the Asian market better, we want to provide our PET portfolio and better services from a local base in the future. PETplanet: Let’s talk about the PET portfolio. Will we see anything new in next year? Golz: Yes. We are strengthening our leading market position worldwide by presenting the new Netstal PETLine 2400 for the first time at drinktec 2013 in Munich. With this product we now have an extensive product range as well as comprehensive application and system expertise for beverage bottles and caps. At the same time, the new Netstal PET-Line 4000 will be available for individual inspection at works in Näfels. We are very confident that the new products will serve the needs of our customers perfectly. They will be able to improve their production and energy efficiency as well as their productivity. Great emphasis is also placed on material, and hence, cost savings. Hydromechanically driven axes with state-of-the-art valve and control technology as well as a further increase in throughput performance of the injection unit make it possible for Netstal to reduce cycle times again, hence massively increasing output capacity. Thanks to the use of the innovative “Eco Powerunit” drive technology and the possibility of recovery in the intermediate circuit, energy savings of up to 10% can be achieved at the same time. PETplanet: And one last question: your major competitor has declined to participate either in the K-Fair or in drinktec/PETpoint. Are you anticipating fewer visitors with an interest in PET at your stand? Golz: All the customers I have spoken to are coming to these important fairs. I believe we can look forward to holding more intensive talks and perhaps more of them. www.kraussmaffei.com PETplanet: Mr Golz, over a year ago the announcement that Netstal was being integrated into KraussMaffei generated some disquiet. Pessimists were already forecasting the end of Netstal. Golz: I would like to mention that Netstal became part of the KraussMaffei Group in 1992. Last year we bundled our group-wide injection moulding activities to strengthen our position in key markets and deliberately extend our presence on growth markets. Therefore we maintained the independent market presence of the Netstal and KraussMaffei brands with a clearly defined product portfolio and separately operating sales organisations for both brands. PETplanet: Netstal continues to exist not only in terms of its own logo but also as an own-brand with its own development section. Golz: Yes, Netstal will act independently in the market. We have optimised the product portfolio and our services we offer and eliminated any unnecessary overlaps. Netstal has a clear focus on PET and fast-moving types of thinwall packaging as well as caps and closures. During the course of the reorganisation, we decided that it would make sense to relocate production of the KraussMaffei PETForm Dr Hans Ulrich Golz, President of KraussMaffei and Netstal’s group-wide integrated injection moulding machinery segment and CEO of Netstal Here they are side by side rather than apart - the three independent brands of KraussMaffei, Netstal and KraussMaffei Berstorff 360°","@ID":36}, "BEVERAGES / INGREDIENTS 64 PETplanet insider Vol. 14 No. 09/13 petpla.net Change as a constant – focusing on health The global beverage markets The markets in beverages are subject to constant change, consumers are always yearning for new taste trends and varieties. For the industry, this development has led to a high demand for diversification of product lines and new products. drinktec 2013 is presenting the current developments, plus the latest technologies in the highly-automated production and packaging sector. Soft drinks are the leading growth category in the global beverage market, as shown by studies carried out by the market research institute Canadean. Energy drinks and iced teas are expanding strongly, with high growth rates forecast for readyto-drink teas in particular. The trend is for high-quality tea concepts with a less sweet, authentic tea flavour. Milk-based drinks are also experiencing positive growth worldwide, and the global market volume of malt drinks has increased noticeably. However rising prices in raw materials for juice concentrates are having an adverse effect on soft drinks containing fruit. Fruit juice and energy drinks The fruit juice market appears to be split in two: while Asia, South America and North Africa are recording strong growth rates, consumer requirement for juices seems to be","@ID":66}, "MARKET SURVEY 50 PETplanet insider Vol. 14 No. 09/13 petpla.net 9/2013 MARKETsurvey Company name GEA Procomac Postal address Telephone number Web site address Contact name Function Direct telephone number Fax E-Mail Via Fedolfi 2, 43038 Sala Baganza (PR); Italy +39 0521 839411 www.procomac.com Flavio Salvadori Sales Director +39 0521 839490 +39 0521 833879 [email protected] Standard filling Standard filling Aseptic filling 1. Machine designation / model number Fillstar SF Fillstar HF; Fillstar LX Fillstar LXi Fillstar FX; Fillstar CX 2. Number of filling heads Fillstar LX: 50 - 140 Fillstar SF: 50 - 120 Fillstar HF: 50 - 140 50 - 160 Fillstar FX: 15 - 140 Fillstar CX: 24 - 140 3. Min to max bottle contents (in litres) 0.06 -3 0.2 -3 0.06 -3 4. Filling speed: output (bph) 1l bottle / still water (bph) LX: 6,000 - 72,000 SF: 6,000 - 60,000 1l bottle / CSD (bph) 6,000 - 60,000 CX: 5,000 - 40,000 1l bottle / Milk (bph) LX: 6,000 - 60,000 SF: 6,000 - 36,000 FX: 6,000 - 64,000 1l bottle / Juice (bph) LX (in ESL): 6,000 - 60,000 HF: 6,000 - 40,000 FX: 6,000 - 64,000 CX: 5,000 - 40,000 5. Filling process Pressureless (still drinks) Yes Yes Yes (Fillstar FX) Pressure filling (carbonated drinks) Yes Yes (Fillstar CX) Hot filling Yes (Fillstar HF) Cold aseptic filling Yes Juices with high pulp content Yes (with dimensional limits) Yes (with dimensional limits) Yes with specific filling valve (with dimensional limits) 6. Type of filling valve and metering system LX: volumetric electronic / flow meter; SF: gravity level filler: mechanical filling head; HF: pneumatical filling valve Volumetric electronic / flow meter Electronic volumetric / flow meter Company name Sacmi Sidel Group Postal address Telephone number Web site address Contact name Function Direct telephone number Fax E-Mail Via Selice Prov.le 17/a 40026 Imola (BO), Italy +39 0521 695411 www.sacmi.com Luca Bernazzoli Filling Sales Director +39 0521 695411 +39 0521 695401 [email protected] Avenue de la Patrouille de France,Octeville-sur-Mer BP 204, 76053 Le Havre Cedex, France 33 2 32 85 86 87 www.sidel.com Jennifer Cariou Public Relations Coordinator 33 2 32 85 89 47 33 2 32 85 81 34 [email protected] 1. Machine designation / model number E-Series/A-Series/V-Series Matrix SF 300 FM Matrix SF 100 FM 2. Number of filling heads 24 - 216 32 - 216 32 -144 3. Min to max bottle contents (in liters) 0,125 - 12 0.2 - 3 0.2 - 3 4. Filling speed: output (bph) (min to max): 8,000 - 55,000 at 18°C 15,000 - 75,000 1l bottle / still water (bph) 72,000 72,000 75,000 1l bottle / CSD (bph) 60,000 55,000 at 18°C 1l bottle / Milk (bph) 60,000 1l bottle / Juice (bph) 50,000 5. Filling process Pressureless (still drinks) Yes Yes Yes Pressure filling (carbonated drinks) Yes Yes Hot filling Yes Cold aseptic filling Juices with high pulp content Yes Yes 6. Type of filling valve and metering system Mechanical and electronic filling system, with and without contact Electropneumatic volumetric with flowmeter volume control Electropneumatic volumetric with flowmeter volume control, with NO bottle/valve contact","@ID":52}, "BEVERAGES / INGREDIENTS 66 PETplanet insider Vol. 14 No. 09/13 petpla.net satisfied in the industrial countries, with figures remaining static, although at a high level. In these countries premium quality, NFC juices and lowacid products are currently particularly in demand. The wellness and health trend is as strong as ever; and market researchers are noting a further shift towards high-quality products with added benefit through functional ingredients or organic features. Euromonitor sees the global per capita consumption of fruit and vegetable juices rising from the current 10.5l (2012) to 12.4l by 2016 (total volume from 73 billion l to 90 billion liters by 2016) This corresponds to an average annual growth of 5.3%. The market for energy drinks is characterised by its ongoing dynamic development and is currently diversifying rapidly. drinktec 2013 is showcasing the new generation of energy drinks, featuring fruit, natural malt components and tea and coffee flavours. Milk Market surveys undertaken by Euromonitor underline the globally very positive picture for the dairy industry. Worldwide milk production is expected to increase from the current level of 126 billion litres to around 137 billion by 2015. The trend leaders, with the biggest rates of increase, will be Asia and the Pacific Region. Here Euromonitor sees volumes growing from 31 billion litres today to 37 billion, while consumption in Europe and North America is set to stagnate at a high level. In many of these stronggrowth countries milk is consumed mainly as a beverage. In China, for example, the milk drinking proportion of the overall volume of milk processed is over 90%. In Germany, by comparison, it is at around 20%. Beer Growth in volumes will continue to be a feature of the global beer market for many, many years to come, according to the market researchers. The simple reason is that worldwide per-capita consumption is still below 30l. Canadean, for example, is predicting that between 2009 and 2015 the world beer market will have grown by 2.8% per year on average. For Asia, Canadean is forecasting an annual average increase of 5% for the same period. These British market researchers also predict an annual rise of 5% for the African beer market, 3% for South America and 5.5% for the Middle East. For Eastern Europe their forecast is a rise of only around 1.5%, and, for North America, even lower, at only 0.5%. For Western Europe, Canadean is even predicting a small decline. As growth hot spots, they have identified Kazakhstan, Vietnam, Angola and India, some of which will see double-digit increases. Special area “New Beverage Concepts”Innovative beverage concepts with new blends have led to unusual flavours being developed. Ingredients such as ginger, fresh coconut water, mint flavourings and Chinese red date are lending an exotic touch. Coconut flesh feels remarkable in the mouth as does “bubble tea” with its toppings in a wide variety of flavours. Fruits such as elderberry and rhubarb are currently causing a stir in the beverage sections in European stores, and newly developed flavour technologies are supporting this trend. In the Special Area “New Beverage Concepts” in Hall B1 at drinktec 2013, product managers and marketing experts are demonstrating the latest concepts in sweetening, flavour and colour. Special events Marketing and marketing ideas come under the spotlight at the new Innovation Flow Lounge (IFL) at the West Entrance. On Wednesday, September 18, 2013, IFL partner Krones is presenting new packaging concepts and ideas. Also on this day visitors will get the chance to find out more about examples of best practics, e.g. of Coca Cola and Carlsberg. In the IFL on the Monday and Tuesday of the show, soft-drinks executives will be able to pick up ideas on successful marketing: IFL partner Krones is addressing the question of “What raw materials are needed for successful marketing?” drinktec has hosted the presentation of the “Beverage Innovation Awards” before, in 2009. Prizes are being awarded in categories such as fruit juice, functional drinks, energy drinks, best additives and ingredients and best marketing campaign, but there are also awards for the best initiatives in areas such as sustainability and health. In conjunction with FoodBev Media, 27 prizes are being awarded in six categories, and for the first time there will be an award for innovative beverage technology. The winners will be announced on Thursday, September 19, 2013. www.drinktec.com","@ID":68}, "BOTTLE MAKING 40 PETplanet insider Vol. 14 No. 09/13 petpla.net Meeting Serac in La Ferté-Bernard, France to see their new Combox H2F An integrated line solution to blowing-filling-capping by Wolfgang von Schroeter The company PETplanet Insider had previously visited Serac in 2010 – as part of our series of regional reports on the French PET market. The development of the company since that time merited a much closer look at their operation. In 2013, we talked to the key managers (in alphabetical order): Auvray, Sylvain: Industrial Director - Filling and Blowing – Serac Asia Binet, Marc: Managing Director– Serac France Chériaux, Fabienne: Marketing Manager – Food, Dairy and Beverages – Serac Shared Services Chevreteau, Ollivier: Sales Director – Serac France Tilloy, Jean-Paul: Design & Production Manager – Food & Dairy – Serac France Vague, Aymeric: Product Marketing Manager – Blowing – Serac Shared Services Founded in 1969 by the French engineer Jean-Jacques Graffin, Serac supplies rotary filling machines for the food and non-food markets, mainly for dairy products (38% of turnover), home care & personal care (22% of turnover) and for edible oil (9% of turnover) to be filled and packaged in glass, metal and plastics. Capacities of Serac machines reach up to 45,000 containers per hour. Serac’s target market is an international midsize, demanding, quality-conscious clientele. A comparatively high proporchallenges facing the company. The company has 490 employees in six manufacturing facilities, in France (3), the USA (1), Brazil (1) and Malaysia (1). Filling and capping machines are assembled in all sites. Aseptic filling and ultra clean are handled in France only, whilst blowing is confined to Malaysia. Sales turnover is on the rise (financial year April 1 - March 31): 2010-2011 €80 million 2011-2012 €90 million 2012-2013 €120 million The sales target in two years’ time – i.e. for 2014-2015 – is for €140 million and this is already within reach today. 5,200 machines are installed world-wide in 100 countries, 60% in Europe, the Middle East and Africa, 15% in North America, 15% in the Asia, 10% in North America. Growth is expected particularly in Asia and North America. Variety of machines on shop floor in La Ferté-Bernard Full order books (as at our visit in July 2013) means that production is already running at over-capacity. Temporary facilities were needed to extend the assembly and testing tion of total sales (over 30%) are for customer services, which include life cycle services beyond the normal warranty periods. The objective behind this policy is to promote communication between company and client, to maintain the efficiency of installed machinery and to maintain or improve productivity. The Serac product portfolio was supplemented by the acquisition of Nova in France in 2004 – they manufacture machines for food product filling in pre-formed cups. The purchase of shares in Agami followed in 2010 – they design and develop production lines for plastic bottles using thermoforming technology with reels of plastics. In 2013 Serac introduced the first PET bottle blowing machine, designed and assembled in-house, which, on the eve of Drinktec, has become a vital part of the Combox H2F. The ownership of the Serac Group has remained unchanged since its foundation: 63.5% Graffin family, 18.8% managers, 17.7% investors. At Serac in La FertéBernard the pioneering atmosphere is still very much present. On tour through the factory what stands out are the many different designs with individual extras and options for as many different applications, customers and markets. There is a lot (too much perhaps) going on in the factory, and Serac are quick to acknowledge that the layout is less than rational, but is a symbol of the Sylvain Auvray, Industrial Director, presenting the blower section Serac makes a bold claim for their new line for mid-sized dairy products manufacturers. Petplanet went over to their factory in La Ferté-Bernard, France, to investigate, as well as to witness trials of the new machine, learn about the design and understand the strategy of the company. Combox H2F will be presented to the public on this year’s Drinktec in Munich.","@ID":42}, "PRODUCTS 86 PETplanet insider Vol. 14 No. 09/13 petpla.net Fit to shrink KHS has announced two new shrink packer developments intended to respond to industry demands for economy and sustainability. Before it actually wraps packaging units, shrink film is unwound from the reel, spread, and then cut to the specified length. KHS’ new Innopack Kisters packaging machines spread packaging film with the help of air-covered diverter rails, which reduce compressed air consumption by as much as 90%, the company claims. The air itself acts as a lubricating film so that the wrapping film is conveyed with as little friction as possible, minimising the possibility of damage. Compressed air is, traditionally, supplied through a number of 1mm holes in the rails, a process that consumes a lot of air. The new development uses diverter rails made of a microporous material, which allows air to flow through very fine hairline cracks. The resulting lubricating effect is much more evenly spread than formerly, which means that less air is needed – up to 90% less, in testing. At the same time, potentially damaging friction is also greatly reduced and, as the new diverter rails prevent crease formation, there is no need to respool the film to meet different process requirements, which helps to shorten changeover time. KHS says that the system can be retrofitted on existing machinery and ROI is in about 18 months. KHS’ new distance sensor helps to maximise film use and minimise wastage, which it says leads to significant material savings. The sensor is calibrated to the size of the reel centre before the machine is started. It contains a laser which enables film to be processed until a layer only about two millimetres thick remains. It has, until now, been common for around a centimetre thickness of film – weighing about a kilogram – to remain on each reel. Assuming two-shift production runs for 300days/a, a single-lane machine working at 80 cycles a minute and equipped with the new sensor can save up to 12t of material. Assuming printed film costs €3.20/kg, KHS says that it can help to save more than €38,000/a. The new distance sensor can also be quickly and easily retrofitted into existing machinery. www.khs.com","@ID":88}, "PREFORM PRODUCTION 36 PETplanet insider Vol. 14 No. 09/13 petpla.net Coca Cola Amatil: preform and closure systems equipped with quality inspection systems from Intravis Continuous quality inspection of preforms & closures Intravis Hall 11 Booth A58 A dedicated mimic consisting of T-conveyor and refeed-conveyor enables the Intravis Sample-PreWatcher to continuously “sample” of the production stream of preforms, inspecting the item thoroughly before finally delivering it to the correct transport bins. Coca Cola Amatil (CCA) is one of the largest bottlers in the Asia-Pacific region and one of the top five Coca-Cola bottlers in the world.It has operations in Australia, New Zealand, Fiji, Indonesia, Samoa and Papua New Guinea. The company recently equipped all eight of its Husky injection moulding machines at its Eastern Creek, Australia, plant with quality inspection systems from Intravis. This contemporary approach was intended to enable CCA to become an established producer of preforms and closures within a very short time. system inspects the top sealing surface (short shot, ovality, diameter, scratches), end cap (contamination, pin holes, bubbles, crystallisation, offcentre gates), preform body (coreshift, wall thickness, diameter, ovality, length, contamination) and weight. Colour deviations are checked by a highly accurate spectrometer. Combined CapWatcher and PrintWatcher CCA also installed three CapWatcher systems for the inspection of closures at its facility. Every closure is measured in real time through the CapWatcher. The integrated PrintWatcher inspects at the same time the print on top of the closures, automatically sorting out those with an imperfect decoration. Due to the automated quality inspection system CCA gets the fastest possible response time in any case of a systematic error during production and therefore could reduce significantly offline measurements. The share of recyclate can also be increased while all quality parameters are checked, including the average number of contaminations per preform. CCA now plans to equip other preform manufacturing sites with the Intravis inspection systems. www.intravis.com Sample-Prewatcher Every ten minutes, preforms of a shot are checked and are returned to the transport bins after inspection. Intravis Sample-PreWatcher system is connected via Shotscope, Husky’s process and production monitoring software, to CCA’s central ERP (Enterprise Resource Planning) system. The continuous longterm recording of quality data makes production efficiency and quality transparent. The Sample-PreWatcher Coca Cola Amatil recently equipped its Husky injection moulding machines with quality inspection systems from Intravis","@ID":38}, "BOTTLES 91 PETplanet insider Vol. 14 No. 09/13 petpla.net Want the real secret to bottle light weighting? Measurement and process control systems for the packaging industry Process Pilot® automated blowmolder control system can make the difference between a modest attempt at light weighting and a truly successful program. Process Pilot works with your blowmolder to continually monitor and maintain material distribution on every bottle to an unmatched degree of accuracy. Featuring automatic adjustment and 24/7 control, Process Pilot can facilitate even the most aggressive light weighting program while ensuring the highest quality and performance! Not convinced? See us at the drinktec and K shows to set-up a trial. BOOTH: B3/332 BOOTH: 11B40 Shower oil Under its “Marque repére“ label, which stands for good quality at a sensible price, the French hypermarket group Leclerc is marketing a range of diverse products under various additional brand names. In the cosmetics sector, for instance, there is a shower oil made by “Manava“ with honey and argan oil in a PET bottle with a content of 250ml. The transparent bottle is closed by means of a snap-on 2-colour hinged cap. The proportion of recycled PET is 25%. Two non-label-look labels transmit the retail information and give an unrestricted view of the honey-coloured product. www.marquerepere.com Body oil with vanilla 150ml of body oil complete with Monoi oil and vanilla additives to pamper the skin is being packed by the French company Interlac Laboratoires under the brand name ”Soleil des Iles“ in a PET bottle tinted in a bronze to brownish shade. The bottle features a stamp which points to Tahiti as the country of origin of the Monoi oil which gives the skin a special sheen. Labels to match this are used to transmit the retail data. The oil, is applied by means of a screw-on pump dispenser complete with a protective cap. www.soleil-iles.com High-stability washing up liquid Method, a company that embraces ecological ideas, is also embarking on new approaches as regards the packaging for its products. The packaging is made from 100% recycled PET and is optimised in terms of both form and function. One example of this is the high- stability bottle for 532ml washing up liquid for use when washing up by hand. The greenish, shimmering concentrate with its aroma of cucumber harnesses the cleansing power of natural substances. The pump dispenser, which is activated by turning, is of adequate size, easy to operate and is secured by means of a sleeve hood prior to initial opening. www.methodhome.com","@ID":93}, "TRADE SHOW PREVIEW 78 PETplanet insider Vol. 14 No. 09/13 petpla.net It’s K time again At K 2013, which takes place every three years in Düsseldorf, Germany, about 3,100 exhibitors from 60 countries will present their latest developments in machinery and equipment for the plastics and rubber industry. A total of 200,000 specialists from all over the world are expected to visit the trade show, which will be open from October 16 to 23. A new Science Campus, will be launched at K 2013. Presented by a number of scientific organisations, the event is intended to intensify the discourse between science and industry. For the first time, 16 universities, institutes and agencies will present pioneering technologies and solutions for the key challenges faced by the plastics and rubber industry. At the communication and discussion forum, the hosts will discuss topical issues of interest and concern to the entire industry such as Surfaces (functional scope and processes), Functional integration (materials and processes), Light-weight engineering (structural materials and processes), Material cycles (renewable resources, biopolymers, recycling), Scientific education. To guide you through the immense world of plastics to the PET focused companies, we have brought together a wealth of information provided by the suppliers to the PET bottle industry. The doors will open from 10a.m. to 6.30p.m. www.k-online.de Additive for PE Caps Milliken’s additive solutions on-show at K 2013 embrace the performance and productivity requirements of plastics processors, including caps and closure manufacturers. Its Hyperform HPN-20E is suitable for high barrier high-density polyethylene (HDPE) blown film, industrial blow moulded containers, caps and closures, and extruded tubes, as well as in linear low density PE (LLDPE) and is claimed to increase the crystallisation temperature of the polymer, allowing earlier de-moulding of parts, cutting cycle times and increasing productivity up to 10% and in some cases by 20% www.milliken.com Milliken Hall 6 Booth A27 Precise dosing and better distribution Koch-Technik’s Graviko, a gravimetric dosing and mixing system, provides the user with a range of products for dosing material for injection moulding, extrusion and blow moulding. Depending on the particular Graviko device, throughput ranges from 3 to 2,000kg/h. GK 65, the latest addition to the series, provides a throughput of up to 70 kg of plastic an hour and can weigh up to three volumetrically added material components in its internal weighing container. GK65 is the first Graviko product to have two synchronous precision load cells; Koch-Technik says that its new product offers the user absolutely correct dosing, regardless of the bulk materials used. All dosing parameters are set and monitored on the Mcm-g Touch control unit touchscreen’s graphic user interface. Also on the stand will be the company’s fully-automated Navigator material feed system. The system is claimed to deliver accurate material distribution with zero residue in central conveyor systems. Pneumatic sliders automatically move the required material and machine lines together and connect them; Kock-Technik says that this offers very high levels of protection against contamination and undesired mixing. Navigator can distribute up to 40 different plastics to the processing machines in a single material supply system. A number of new features will also be presented on other conveying solutions on the stand. www.koch-technik.com Koch-Technik Hall 10 Booth A21","@ID":80}, "BEVERAGES / INGREDIENTS 63 PETplanet insider Vol. 14 No. 09/13 petpla.net 175 years - a long history The company was set up in Erfurt in 1838 by Lorenz Döhler as a spice mill selling spices and spice mixtures throughout Germany. From 1924 onwards strong brands of baking ingredients such as “Backfein“ (“Fine Baking“) and “Backstolz“ (“Baker’s Pride“) as well as the “Döhler-Pudding“ were developed. In 1948, following expropriation of the business, the Gemmer family moved over to West Germany and set up operations in Frankfurt and Bad Wildungen. Flavourings and baking agents along with flavourings for the confectionery and spirits industries were its first products in the West. From 1952 onwards raw materials, flavourings and additives on a fruit base grew into a new production sector for the rapidly growing soft drinks industry. Since 1957 the company’s head office has been in Darmstadt. With the acquisition of the Belgian firm Citrusco in 1982, Döhler took its first steps on to the international stage. The years from 1990 onwards saw the subsequent establishment of subsidiaries in Russia, Poland and the Czech Republic. In 1995 Döhler acquired Euro-Citrus, a Dutch manufacturer of fruit juice concentrates with an international operation.1996 was the year when the production location Döhler China was established; in 1997 the company added Brazil to its portfolio (a joint venture with orange juice concentrate manufacturer Fischer, today Döhler América Latina). Since 2001 there have been numerous take-overs, plant openings worldwide such as the acquisition of Dinter, a producer of fruit juice in Neuenkirchen (Altes Land), Alko in Roggel/The Netherlands (now called Döhler Roggel B.V.), Jahnke with production sites in Poland and Ukraine, Bonjuice in Schwalmtal/Germany and the fruit juice producer Sanchuan in Rizaho/China. Döhler made a continuously investment in modern production sites such as the biggest facility in Oosterhout/The Netherlands, new and extended plants in Pune/India, Limeira/Brazil, Shanghai, Denizli and Karaman in Turkey as well as the commissioning of a production facility for cereal & malt extracts in Neuss/Germany. In 2011/2012 a state-of-the-art flavour plant was built in Darmstadt. The latest investments are the integration of King Bee, a leading producer of cereal ingredients in Jinshan/China and the acquisition of the juice and flavour business of Delro in Cairo/Egypt. Headquartered in Darmstadt, Germany, Döhler today boasts 23 production and 24 application centres, 50 sales offices and sales activities in over 130 countries and more than 3,000 employees, including 350 in R&D. Today the company produces and provides technology-based natural ingredients, ingredient systems and integrated solutions for the food and beverage industry. The product portfolio ranges from flavours and emulsions, natural colours and health ingredients, compounds, fruit preparations, to alcoholic and non-alcoholic beverage bases, dairy bases, malt and cereal bases, sweetening systems to fruit and vegetable juices, purees, concentrates and blends. www.doehler.com Scan & Measure Oxygen Ingress & Transmission Rates www.PreSens.de/ Fibox4 Fibox 4 Stand-alone fiber optic oxygen transmitter Visit Us at Drinktec: Hall B3, Booth 406","@ID":65}, "TRADE SHOW PREVIEW 72 PETplanet insider Vol. 14 No. 09/13 petpla.net 72 cavities Otto Hofstetter will be exhibiting a new generation 72-cavity PET mould. In the forefront of this new development are, primarily, improved energy efficiency and a maintenance-friendly mould. The insert group components are also compatible with moulds with different numbers of cavities. This generation of moulds, developed by Otto Hofstetter AG in collaboration with Netstal, has been coordinated with the new development PETLine 2400 injection moulding machine. At drinktec a 0.5l thin wall preform is to be produced on this in a total cycle time of 5.4s. www.otto-hofstetter.ch Otto Hofstetter AG Hall B3 Booth 341 Light caps Engel, will feature an E-cap 3440/380 with a 72-cavity mould by the Austrian mould supplier specialist z-moulds from Dornbirn producing 1.8g closure caps for still water (UCL Design 28mm PCO 1881). Cristalpet in Montevideo (Uruguay) already runs this application in high-volume. The all-electric series is available with clamping forces of between 100 and 420t. Engel and its partners will present a fully automated production cell based on a 380t machine with integrated quality control. The system features the patented z-slides technology from z moulds. The cap cooler is provided by Eisbär (Götzis/Austria) and the camera-based control system, by Intravis www.engelglobal.com Engel Hall B3 Booth 326 SGT Hall B3 Booth 342 Preform performance Societé Général des Techniques (SGT) will be exhibiting its range of PET preforms, which extends to 200 models, 14 neck finishes and two ranges of caps. SGT was certified to FSSC 22000 in July 2013 and says that it can reduce the weight of the bottles without compromising quality, food security or performance. www.sgt-pet.com New developments in preforms PDG Plastiques will have a variety of new and recently-developed preforms on display, including examples with Ø38mm necks for juices and milk. The trend towards weight reduction will be represented by products with 29/25 light necks for mineral water and flat beverages and units weighing from 2.4g to 8g, designed for dairy products. PDG’s Preblow technology allows prform weight reduction by reducing the wall thickness of the bottom. Prelactia preforms feature a 100% light barrier for sterilised longlife milk. Its range now includes a 24g 1l bottle. www.pdg-plastiques.com PDG Hall B3 Booth 336 Closure Systems International Hall B3 Booth 331 Consistent changeovers CSI will present its new FlexChuck capping chuck design and system. It uses an internal array of multiple and independent grippers, which are designed to adapt instantly to a wide range of knurl patterns and varying closure dimensional tolerances. CSI asserts that the system reduces the need for changeovers and reduces capping chuck inventory requirements. The company claims that Flex-Chuck reduces maintenance costs by up to 50%; its hardened steel grippers have shown no signs of wear after more than a full year of continuous use. It is currently available in 28mm size, with larger diameter 33mm, 38mm and 43mm variants currently under development. www.csiclosures.com","@ID":74}, "BOTTLE MAKING 41 PETplanet insider Vol. 14 No. 09/13 petpla.net areas. We saw a variety of machines on the shop floor, such as Aseptic filler for UHT milk in HDPE bottles Dairy filler connected to Urola blower for pasteurised milk, juice and yoghurt in PET bottles Dairy filler with a PAA (platic acid for flavoured milk in PS bottles Aseptic filler for whipped cream in metal aerosol Corrosive products filler (where plastic, hastelloy and titanium materials are used instead of stainless steel as they do not corrode) for toilet cleaner in HDPE bottles Combox H2F integrated blowing/ filling/capping for chilled drinks in PET bottles Combox H2F The Combox H2F, the latest member of Serac’s product portfolio for packaging in PET bottles is the ultra clean blow moulding-fillingcapping line for dairy PET bottle production at up to 12,000bph. The integrated line solution consists of the SBL blower (Serac Blow Linear) linked to the H2F rotary filler (Highly Hygienic Filler). The blower and the filler are new developments for Serac. In fact the design and manufacture of the machine, as well as its competitive positioning of Combox H2F was a joint effort by all departments within the company. Jean-Paul Tilloy in front of the filler section Fabienne Chériaux, Marketing Manager (left) and Aymeric Vague, Product Marketing Manager Marc Binet, Managing Director, Serac, France (r.) and Wolfgang von Schroeter Serac’s marketing team – namely Aymeric Vague and Fabienne Cheriaux from Serac Shared Services – presented the company’s strategy behind the new development. Sylvain Auvray demonstrated the SBL blower in the test area, Jean-Paul Tilloy explained the innovations of the H2F rotary filler: the blower comes from Malaysia, the filler from La Ferté. The factory here integrates the two machines mechanically and electronically. Strategic considerations For 40 years, Serac’s focus has been and remains to this day their","@ID":43}, "EDITOURS REPORTS 18 PETplanet insider Vol. 14 No. 09/13 petpla.net Sven Broderson started using the lightweight 1881 for the first time in February 2010. The blow moulding equipment for this was manufactured in Panama. They even ventured to have a go at the neck for the 3l bottle which was still awaiting a final decision at the time. Today some 80% of the total preform production has been converted. A special closure is also running on the 1881 for still waters. This has not yet been introduced in this region. However, because still water is growing faster than CSD, the advent of proprietary water closures is surely only a matter of time. The 500t Hypet from Husky produce preforms for 0.33l bottles on 144-cavity moulds Sven Broderson manufactures all preforms centrally at the main plant. 15 Husky systems are working on this round the clock. The machinery installed goes up to 500t. There are 144-cavity moulds running on the two largest systems. Piovan is the material supplier. Before the material arrives in the dryer there are two dispensing systems located upstream of each system. “This allows us to process any mixing ratio of virgin and regranulate“, is his comment. Unfortunately, Peruvian legislation still does not permit regranulate in bottles which means that preforms with a proportion of recycled material only go abroad. But it is confidently expected that even Peru’s FDA will soon permit authorised material in beverages bottles. The Sipa blower SFR 12 EVO is specially designed for the production of hot fill bottles Which brings us to Sven Broderson’s new baby - bottle to bottle recycling. Until two years ago in Peru all bottles were compressed and shipped off to China by a very wide range of privately organised (and sometimes unregulated) PET collectors. Now, however, the main plant contains the first recycling system to be installed in northern and western Latin America - and this is still the largest, even today. Producing at the rate of around 1t/h, they generate over 10,000t of FDA inspected regranulate. With a total annual consumption of more than 60,000t, this represents a considerable proportion. In addition to obtaining the permit, they have also had to work hard on the collecting side. Bearing in mind that collection has tended up to now to be in the hands of unregulated organisations, Sven Broderson feels that it is important that the collecting operations should, among other things, pay social security contributions, not employ child labour and, of course, observe safety regulations. Although this has made the collection process more expensive, it has despite this become more reliable. Smaller partners supply up to 40t/a whilst larger companies collect up to 400t/a for SMI. “The smaller the collecting operation, the cleaner and better sorted the material will be. However, the most important thing about recycling is washing“, says Broderson. The Tecnofer washing plant therefore features three consecutive washes and, even at the end, there will still be minute remains of labels coming out of the plant. The Gatorade bottle labels cause particular problems. They are made from PTG, a plastic that has similar characteristics to PET. As a result, the label cannot be discharged in the normal way via the sink-or-swim fraction. It has proved necessary to install a cyclone in addition. Even in the recycling hall maximum cleanliness and tidiness predominates, as is the case everywhere in the plant. The Starlinger plant produces 1t/h virgin material. The flakes, now clean and uniform in colour, are then fed to the Starlinger plant which will turn them into FDA material from them. As the flakes come straight out of the washing plant, no de-dusting is required. At the heart of this process is the Recostar 165 extruder which has a throughput of 1t/h. The material spends six hours in the vacuum reactor before subsequently exiting the plant as finished bottle material. The material is accommodated in 70t silos. SMI is not willing to address the topic of closures; it sees itself as a producer of preforms and bottles. www.smi.com.pe www.clearpet.com.pe 360° 360° 360°","@ID":20}, "ceramic, along with an optimised profile th ceramic wall replacing lamps with a back coating. Savings on compressed air consumption can be up to 35%, compared with previous Sidel generations. The blower’s grease-free components and fewer mechanical parts are claimed to require less maintenance. Matrix fillers The Matrix fillers have been designed with a particular focus on hygiene for both still and carbonated beverages. Their enclosures are designed for better control of the filling environment, which can be operated under a positive overall pressure to avoid contamination from external sources. Integrated electro-pneumatic components, the absence of vertical movement of the bottles, no ring bowl or carousel and no contact between bottle and filling valve for still beverages are intended to eliminate cross-contamination risk. Their testing program included simulations extending far beyond normal working life or conditions. Each is operated by brushless motors. Neck bottle handling by gripper enable fast format changeovers are very fast; the option of fully automatic changeover can help to achieve greater productivity and greater overall equipment efficiency (OEE). Improved cleaning technology reduces water and chemical use and the use of servomotors contributes to savings in electricity consumption of as much as 30%. Matrix Combi Sidel’s Matrix Combi blow-fill-cap solution is intended to bring the company’s new generation of blowing and filling into a single solution. It has a single, hygienic enclosure with no intermediate equipment. It features improved commonality between the blowing and filling functions and a single operator interface. Its low-maintenance design contributes to increased uptime. Rollfed labelling The company says that Matrix Rollfed allows customers to produce bottles with labels at a reasonable cost and holds out the potential of using labels that are one-third thinner. Its new features enable it to speed up the application of labels and cut costs on other aspects, from materials to maintenance. It uses direct-drive technology to replace gearboxes and mechanical transmission, which leads to 40% less maintenance and a 30% reduction in energy consumption. Fewer moving parts connected to the motor reduces breakdowns and extends operational life. It can handle bottle diameters from 45 to 160mm, as well as different types of materials and ultra-lightweight bottles. All essential areas of are accessible and simpler changeovers reduce the risk of injury. All main modules can be replaced without dismantling the unit. www.sidel.com The Matrix approach is a modular system approach from the blower to the filler, labeller and capper... ..., including a Combi version. PETplanet insider Vol. 14 No. 09/13 petpla.net BOTTLE MAKING 45","@ID":47}, "EDITOUR REPORTS 29 PETplanet insider Vol. 14 No. 09/13 Creating value with powerful solutions www.krones.com February 28, 2013 Empacar Santa Cruz We met: Ivo Kuljies, proprietor Carlos Limpias , (Plant Manager), From preforms to recycling Empacar Santa Cruz’s preform production started in 2004 with an order from Coca Cola. By 2007 the company had embarked on recycling of post-consumer PET bottles. This was followed in the same year by the processing of closures and labels. The company is considerably older than this; it was way back in the 70s that the proprietor, Ivo Kuljis, made a start with paper processing. This quickly developed to encompass the processing of various hygiene products as well. However, Ivo soon sold this branch to a multi-national brand. Today his PET business is just one of his many interests; also in the ownership of his family are supermarkets, restaurants and a bank. As far as the PET sector is concerned, recycling now represents the cornerstone. In the Santa Cruz area Empacar collects the bottles from the regional collecting points and takes them to the plant uncompressed. Bottles from the rest of Bolivia arrive in the classic pressed bale format. Initially, Empacar started with a Brazilian washing installation from Seibt, with a view to producing flakes. Carlos Limpias, (Plant Manager), had to undertake a number of adaptations to the equipment before the flakes were of the desired quality. Last year a second washing plant was added, this time from Tecnofer. It was tailored precisely to Carlos’s requirements. The basic components here came from Italy, some were made by the Bolivians themselves and a third group was bought in from China at a bargain price. Despite all the automation, careful preliminary sorting by hand is the secret which guarantees clean flakes. Although PET does not represent proprietor Ivo Kuljis’s main business, he is nevertheless very proud of it, saying: “At this moment, we are recycling 60% of PET bottles in Bolivia” 360°","@ID":31}, "EDITOUR REPORTS 21 PETplanet insider Vol. 14 No. 09/13 patiently and persistently attempting to persuade the residents of the major Bolivian cities of the virtues of waste separation. To get the message across they have established an initiative known as Ecovecindarios. We spoke with Mrs Ximena Ayo and Anna Apel about how the project is progressing. The scale of the problem of waste in Bolivia is daunting. The majority of Bolivians live in poverty and disposing of household rubbish is the least of their concerns. Organised waste collection has been rudimentary and unreliable, so Bolivians dispose of their rubbish either by simply dumping it by the wayside, or burning it, throwing into the nearest river or even burying it in the garden. The consequences for health, hygiene and the environment are not hard to imagine. Over the past four years or so, swisscontact has been providing advice to rural communities with a view to creating a comprehensive and sustainable waste management system. The current system is that municipalities have had their rubbish collected by private sector organisations which are paid 246 Bolivianos (roughly €27) per tonne of waste. In La Paz this amounts to around 0.5kg per inhabitant, per day. Sorting out and separating the recyclables from the waste is carried out entirely (and illegally) by the black economy. The incentive to do this is the humble PET bottle, one of the most highly sought-after commodities in the piles of rubbish, and the reason it is so highly prized is that its resale value is 2 to 3 Bolivianos (around €0.220.33) per kg. Swisscontact starts with the smallest unit, the neighbourhood zone. Typically, between 2,000 and 5,000 people live in such zones. They elect a President charged with the administration of the zone. With the support of these Presidents, Ecovecindarios has been able in certain of the zones to set up sysThis is how informal recyclables collections have looked up to now: collectors sifting through the waste on the side of the road.","@ID":23}, "TRADE SHOW PREVIEW 77 PETplanet insider Vol. 14 No. 09/13 petpla.net drinktec Munich, hall B3, stand 339 K 2013, hall 15, stand B27/C24/C27/D24 Heuft Hall B4 Booth 315 Optimising bottle flow Heuft Systemtechnik Gmbh will be showcasing new developments that are intended to make the management of highly complex high-speed processes for a bottle flow optimisation and a precise in-line quality inspection much simpler. The company says that its new product features a high degree of automation, and that new user guidance provides real support during operation, maintenance and brand changeovers. Heuft says that it has turned the human machine interface (HMI) into a machine human interface (MHI) and the operator into a user, enabling the handling of the new systems easily and safe operation even without any previous knowledge. It claims that it reduces to a minimum the risk of unintentional misadjustments and consequent compromise of product safety and line efficiency. www.heuft.com Till Gmbh Hall B5 Booth 320 Direct digital print Till GmbH, pioneer in direct digital print on containers, will present live prints with its easy to use, fully integrated smartprint system for test runs or small scale production. The system consists of a single smartprint module for printing onto cylindrical objects such as bottles or cans. Till machines enable bottling companies to directly print decoration on any container at industrial speed. The product range includes modular smartprint machines starting at 10 up to 600 containers/min. Till offers certified UV curing inks. According to Till, direct digital decoration offers new marketing opportunities such as reduced time-tomarket to include up-to-the-minute information or limited editions up to individualised packaging. Minimum order quantities can be reduced to lot size one without additional costs. (see PETplanet insider 3/2013, page 32). www.till-tech.com","@ID":79}, "NEWS 10 PETplanet insider Vol. 14 No. 09/13 petpla.net “Threepeat” for drink technology India and Pack Technology India drink technology India and International PackTech India are teaming up for the third time in succession in the Indian city of Mumbai. Their joint event will take place between September 25 and 27, 2014 at the Bombay Convention & Exhibition Centre. The show will include products and solutions from and for the international packaging, packaging print, processing, beverages and food industries. Hall 1 at the Bombay Convention & Exhibition Centre, which offers 11,000m² of space, has been exclusively reserved for these two trade events. The organisers are inviting applications from companies interested in exhibiting at these two events. Online applications for drink technology India can be sent to the addresses below. The show organisers are expecting a total of at least 260 exhibitors (2012: 220) in 2014 along with an increase in the number of visitors, from 2012’s 7,500 trade professionals to 8,500 in 2014. International PackTech India will again feature an accompanying conference. The Exhibitor Forum at drink technology India will feature roundtable talks with experts from India and around the world. In 2012 India imported food processing and packaging machinery to the value of €662 million and over 60% of all the machinery and systems delivered are of European manufacture. The most important trading partner is Italy, accounting for 19% of the business, followed by Germany, with 16%. www.drinktechnology-india.com www.packtech-india.com Sidel helps Erikli to shorter necks When Turkey’s Erikli mineral water brand decided to switch to PET bottles with shorter necks, it tasked Sidel with carrying out the conversion of three bottling lines at the company’s Bursa plant. The project took seven months from the planning phase through to full completion. Sidel provided a complete solution from the technical specifications through validation of the preform drawings with the customer, to project management on the complete line and adapted parts for the new neck (blow moulder, filler, rinser, cap feeder, capper and bottle inspection). It also managed the technical and operating warranty. The plant now has three complete lines each equipped with a Sidel SBO 20 blow moulder, a Combi 20 and a Combi 34, as well as two Series1 blow moulders. After conversion, the 1.5, 0.5 and 0.33l format bottles have neck heights typically decreased from 18.5mm to 12.6mm. Weight reductions of 1.42g on the preform neck and 0.6g on the cap have been achieved. Erikli plans to release further lightweighted bottles for its smaller 0.33 and 0.5l formats and for the 1 and 1.5l sizes. It is part of Nestlé Waters Turkey, a subsidiary of Nestlé Waters, and has its own distribution network www.sidel.com PMMI and Koelnmesse get together The Association for Packaging & Processing Technologies (PMMI), which owns and produces the PackExpo family of trade shows, is joining forces with Koelnmesse GmbH, the organiser of Anuga FoodTec and other trade fairs, to jointly promote their packaging and processing industry events. The agreement allows for promotional support and exhibiting at selected events for and by each group. Koelnmesse will add to marketing efforts for PMMI’s PackExpo International, PackExpo Las Vegas and ExpoPack México; PMMI will do the same for Koelnmesse’s Anuga FoodTec, ProSweets Cologne and International FoodTec India. The agreement will be in place through to the end of 2018 and will include the next Anuga FoodTec event, running from 24-27 March 2015. www.packexpo.com www.anugafoodtec.com www.koelnmesse.de Kreyenborg goes diamond Family-owned Kreyenborg GmbH celebrated its Diamond Jubilee – 60 years – in April 20013. It began life in 1953, with the trade of tubular grounding busses for lightning conductors. In 1957 it switched its focus to the construction of mixers for concentrates and hammer mills, before turning its attention to the nascent plastics industry in 1965. Its product portfolio today includes melt filters, polymer melt pumps and valves. It now has locations in Germany, USA, China and Malaysia. www.kreyenborg.com","@ID":12}, "EDITOUR REPORTS 15 PETplanet insider Vol. 14 No. 09/13 petpla.net as bottle to bottle material. Depending on the source, two thirds to three quarters of all soft drinks in Peru and Bolivia are bottled in PET. The remainder goes into glass. Cans are only of any significance as far as the beer segment is concerned. We have visited recyclers, preform producers, suppliers and bottlers in both countries on your behalf. A special personal highlight was a visit to the Surena brewery, located at the dizzying altitude of 3,300m above sea level! These reports will certainly be something for you to look forward to! Soft drinks Bolivia and Peru Market Sizes | Historic | Softdrinks in mn litres Mio. litres 2007 2008 2009 2010 2011 2012 Off-trade Vol. 422.4 472.3 509.3 556.4 620.6 673.7 On-trade Vol. 138.2 153.6 164.6 179.8 199.1 219.9 Off-trade Vol. 1,593.4 1,867.1 1,982.6 2,176.0 2,328.7 2,477.8 On-trade Vol. 252.9 269.8 283.9 298.4 314.0 330.9 =Bolivia =Peru © Euromonitor International Blog Summary Peru/Bolivia We are back on the road. Our Editourmobil spent from Christmas right up to the beginning of February in the belly of a ship before reaching South America. Rolf and I are the first team on this huge tour. After a long flight, we took over the vehicle in Lima. Our part of the tour starts with a meeting at SMI, manufacturer of preforms and bottles in the region, with a market share of 80%. Our next appointment takes us to the Backus brewery, part of the SABMiller group, before heading off to La Paz, Bolivia with the Andes in between. The Editourmobil faces the daunting challenge of a 4,600m high pass. Will it make it? I can feel my strength and powers of concentration ebbing away as we pass the 4,000m mark. How good to come down to 3,000m again later, when we could start thinking about where we might park up for the night. At an altitude of between 3,100 to 4,100m above sea level lies La Paz city. Before we reach La Paz itself we have to negotiate the centre of El Alto, where we come to a grinding halt, because of a strike organised by the transport union. They have blocked all the roads with huge boulders. So we use Plan B and head off over the fields, bumping our way over unpaved side roads. 360° In the CSD sector Coca Cola is the dominant player. Picture shows the Coca Cola truck winding its way up the pass in the Andes and overtaking our Editourmobil","@ID":17}, "TRADE SHOW PREVIEW 81 PETplanet insider Vol. 14 No. 09/13 petpla.net HOLLAND COLOURSEurope BV | Halvemaanweg 1 | 7323 RW Apeldoorn | P.O. Box 720 7300 AS Apeldoorn | The Netherlands | T +31(0)55 368 07 00 | F +31(0)55 366 29 81 [email protected] | www.hollandcolours.com Thousands of colour shades, a variety of product forms and a dedicated team at YOUR SERVICE to assist toYOUR SUCCESS. é Protective colourants with specific light and UV absorbance é Functional colourants for Oxygen Scavengers é High opaque white for dairy é AA Reducer é Tintmask-neutralising off-colour regrind é Blowing Aid é Optical Brighteners é Slip Additives é Matting Agents Visit us at: Hall B3 / Stand: 103 In-mould labelling, barrier injection and cubes Ferromatik Milacron, which is part of the Milacron Group, will present two system designs for cap manufacture. The company’s stand at K 2013 will feature the highspeed F 350 hybrid with a clamping force of 3500kN which uses a size 70 Advanced Performance (APh) hydraulic injection unit. Driving a 64-cavity Corvaglia mould, it will produce 2.6g 33mm beverage closures every 4.5s. The F 270 Cube, is claimed to be the first all-electric cube machine of its type on the market. The fourth machine in the exhibition lineup is a 1600kN F 160, which incorporates a hydraulic Advanced Performance (APh) size 45 injection unit in combination with a vertically mounted E-Multi injection unit from Mold-Masters. With a 16-cavity mould from F&S Tool (USA), it will demonstrate production of two-component closures using barrier injection. www.ferromatik.com Ferromatik Hall 15 Booth C06","@ID":83}, "EDITOURS REPORTS 26 PETplanet insider Vol. 14 No. 09/13 petpla.net MHT MOLD & HOTRUNNER TECHNOLOGY Dr. Ruben-Rausing-Str. 7 | D-65239 Hochheim/Main Tel. +49(0) 6146-906-0 | www.mht-ag.de Make the most of your machine – with a mold from MHT! For many machine types, we supply the mold with the highest cavitation, thereby enabling optimum preform output. For the Husky HyPET machines, we offer upgrade sets for up to 50% more preforms, without refitting on the machine! • 60 cavities for Netstal PETline 2000 • 96 cavities for Husky HyPET 300, • 112 cavities for KraussMaffei 350 Engineering made in Germany 128 for HyPET 400 + 1/C35 Booth B3/441 A glimpse of the new installation; at the moment running the sleeve-type labels for PET bottles. But it is not only the school milk packaging that represents an important market segment, almost all milk delivered to the man or woman in the street is via flow-pack. In the labels sector, Big Boys Coca Cola and Pepsi Cola switched some three years ago from sleeve-type labels to roll feed labels. ILB has, of course, gone down the same route and adapted its production accordingly. In the case of the printing sector particularly, this involves a large number of printing rollers in a very wide range of diameters. Roberto: “Because each supplier will have bottles with widely differing diameters, they are likely to need labels of appropriate length. This has meant our having to invest in printing rollers to ensure that we can offer each and every format to our customers”. However, sleeve-type labels are continuing to be processed by local suppliers. Around 24 t of labels leave the plant stores each year and the trend is rising. ILB blows the major part of the foils themselves. Several single-ply installations and a three-ply system are used exclusively for own-usage production. Nevertheless, the focus is on the printing technology. Here there are three technologies available: classic offset printing for paper and cardboard, flexo-printing for up to eight colours is reserved particularly for foils and labels and other printing processes. ILB subsequently assembles the foils and carton. These could, for example, be cut-outs, roll feed rollers or even pouches welded on three sides. In addition to enhanced customer priority, Roberto also needed to get things moving internally. In addition to team rejuvenation, the internal flow of information in particular was the major priority. ILB decided to switch to a supplier from Brazil, who offers a production planning and monitoring software specially developed for printshops. The majority of machines also manage their data automatically but, in locations where this is not possible, the workforce operate terminals and enter data manually. www.ilbsa.com 360°","@ID":28}, "TRADE SHOW PREVIEW 69 PETplanet insider Vol. 14 No. 09/13 petpla.net Federspiel GmbH Hall A5 Booth 544 Grab head with no change parts Federspiel Maschinenbau GmbH, Germany, will be exhibiting a multi-grab head along with its application in the “Multipak“ packer, the packing and unpacking system for bottles which has no change magazine. In order to dispense with the need to change container and the ensuing inevitable production stoppages in packaging beverages in glass or PET bottles, Federspiel have developed a grab head that operates in accordance with a new principle. There is no longer any need for conversion and adjustment work or a grab head magazine. The grab head, as well as the supply lanes, is activated by touchscreen; these traverse into the programmed positions with millimetre precision. Any pick-up head bladders not required move to one side to occupy a home position inside the packing head. So “changing the container” only takes a few minutes with the “Multipak“ and the space that used to be needed for the magazine is now available for other purposes. “Multipak“ is a freely programmable portal packer with a stainless steel frame. The drive system has been completely re-worked by Federspiel and is claimed to be low-maintenance and low-wear. The motors are servo controlled drives with wear-resistant linear rack units. The packer can be supplied for two and up to as many as ten crates per stroke and with single or dual track inlet / outlet. Depending on the type and size of package, the “Multipak“ can carry out a packing or unpacking operation at a rate of 6 strokes/h (up to 3,600 crates/h). It is capable of processing bottles (glass or PET) from 0.33 to 1l. www.federspiel-maschinenbau.de Gernep Hall A5 Booth 302 All sorts of labelling Gernep, from southern Germany, will be exhibiting its range of labelling machines. Its Labetta SK self-adhesive unit has been completely revised and features a new appearance and new technological developments, particularly in optical orientation. Wet glue machines are at the heart of Gernep’s business, in the brewery segment in particular. Rollfed and Rollina hot melt wraparound machines use roll-fed plastic and magazine-fed paper labels, respectively. Glue application for both systems is by closed hot melt unit. The Gernep Combi combines wet glue, self adhesive and hot melt labelling, with short changeover times. www.gernep.de Precise measurement The Berlin, Germany, based family-run company, Dr. Thiedig GmbH & Co KG, will be presenting its Digox 6.1 latest-generation analyser for oxygen measurement in beverages, in both stationary and portable versions. The machines and their proven technology were fully described in PETplanet Insider issue 11/12. www.thiedig.com Dr Thiedig Hall A5 Booth 500","@ID":71}, "PETbottles 88 PETplanet insider Vol. 14 No. 09/13 petpla.net Beverages & Liquid Food PET goes sporty PET Power has added two more ‘sports-themed’ standard models to its range: Foot Ball 1000ml and Tennis Ball 500 ml. Both are produced with a 63 RTS neck finish. The company says that these types of packaging are highly suitable for promotional campaigns by sports clubs, for example, as well as providing eye-catching on-shelf presence with links to specific sports. The jars can be filled with sweets and other food products, and also offer opportunities for the toy sector. The two types can be provided with sleeve labels and thus finished in, for example, club colours. PET Power says that the 63 RTS neck enables it to draw and produce virtually any desired shape. www.petpower.eu Got that Mojo working Mojo beverage company in Switzerland has launched its third line of natural beverages. The first product line, launched at start-up in 2005, included Mojo Sparkling Fruit Drink (in three flavours); the second was the functional, vitamin-added Mojo Vitamin Waters. The newest is the Mojo energy Drinks. They are available in three flavours: Exotic, Pomegranate and Classic, and each contains 10% to 25% pure fruit juice. The Mojo Energy Drinks are described as an exclusive alternative to conventional, very sweet tasting energy drinks. They contain the usual energy drink ingredients along with gingko and gurana. All Mojo beverages are produced without preservatives and contain no artificial ingredients or colours. The new Mojo Vitamin Waters are packaged in 38g PET hot-fill bottles with a weight of 38g. The Sparkling Fruit Drinks are filled on a cold-aseptic filling line, using standard 23g PET bottles. www.mojo-drink.ch PET goes for Origami Goya Foods Inc., based in Secaucus, N.J., is the largest Hispanic-owned food company in the U.S. It has recently undertaken a major redesign of its marinade product line and converted its 12oz (355ml) and 24.5oz (725ml) product packages from glass to lightweight PET bottles supplied by Amcor Rigid Plastics. Amcor’s “Latin America” custom-designed hot fill containers are made in a distinctive shape and also feature a new shrink wrap label. The package was developed to promote a clean, modern and elegant style. Compared with the previous glass packaging, the hot fill bottle delivers cost and other advantages including portability, reduced breakage, lighter weight, recyclability, lower transportation costs, and over 60% reduction in greenhouse gas emissions, compared to glass. Amcor calculates that the lighter weight and thinner package walls enable 52% more product per truckload to be shipped. Goya has also increased package contents in the new PET bottle from 705ml to 750ml. The two PET bottles are the first to feature Amcor’s new Origami hot fill technology, which incorporates six flat panels to counteract the vacuum that develops in hot filled containers. The vacuum panels are designed to collapse and compensate for shrinkage during cooling, in order to maintain structural strength and integrity. The bottles are designed for both ambient fill (up to 60°C) and hot fill (up to 85°C) applications. They have a 38mm finish and have been seamlessly integrated into its existing glass filling lines with minimal adjustment, according to Goya. The marinade products are available in three varieties - Chipotle, Mojo, and Naranja Agria - and are sold in supermarkets and club stores in the U.S., Puerto Rico, and the Dominican Republic. Goya Foods also plans to replace glass with PET in an existing 12oz juice beverage line, during summer 2013. www.amcor.com www.goya.com","@ID":90}, "TRADE SHOW PREVIEW 74 PETplanet insider Vol. 14 No. 09/13 petpla.net Cubist revolution Arburg, the German injection moulding machine manufacturer, will be demonstrating electric cube-mould production in action, along with its partner, Foboha. The machine on the stand will be an electric two-component Allrounder 720 A, which will produce 12 juice container closures in a cycle time of 6s. In this application, both rotation of the cube and the linear mould movement are powered electrically. Arburg says that cube-mould technology enables high-quality moulded parts to be manufactured in very short cycle times, because four sides of the cube mould can be used for production. This means that individual manufacturing steps such as mould filling, cooling or part removal can run simultaneously, resulting in increases in in productivity of up to 100%. The Allrounder 720 A on the stand will be a two-component version with a clamping force of 3,200kN and a 12+12-cavity cube mould processing PP and HDPE juice container closures from Adval Tech-Foboha. The larger 800 injection unit operates horizontally as does the smaller 400 injection unit, which is mounted on the machine’s moving mounting platen. Cube rotation and linear mould movement are electrically driven. The entire cube system together with the servo-electric rotary units on the central block are controlled and monitored by the Selogica control system, including subsequences. According to Arburg, cube-mould technology offers many more cavities over the same clamping surface than conventional moulds, enabling specific levels of production to be achieved with fewer or smaller machines, which increases the efficiency of production overall and reduces machine floor space. www.arburg.com Arburg Hall B3 Booth 420 Upgrade sets MHT Mould & Hotrunner Technology AG will be presenting its upgrade sets for Husky’s HyPET injection moulding machines. Now the upgrade family comprises upgrade sets for the HyPET 120 and 225 in addition to the sets for HyPET 300, 400, 500 and GL 600. MHT says that its equipment enables manufacturers to produce up to 50% more preforms per HyPET, without any need for expensive changes to the machines. MHT has achieved this by moving the cavities slightly closer together and adding an additional row on either side. The boost to cavitation comes without making the moulds much wider but the saving in space does not imply a more filigree and less reliable mode of construction. The upgrade set also includes a new, three-stage post-mould cooling solution, developed by MHT. The upgrade set is available for preforms up to a maximum water thread diameter of 30/25 and is offered within the context of a mould exchange or conversion, such as to a different preform design or weight. www.mht-ag.de MHT Hall B3 Booth 441 Repi Hall B3 Booth 500 Lighting and colour Italian company Repi S.p.A. will be showcasing its complete product portfolio for packaging. Remap colours and additives are developed to improve packaging aesthetics and product performance. Personnel will be on hand to explain the performance of Repi U2011 dosing equipment and its Light Meter. www.repi.com PreSens Hall B3 Booth 406 Easier inspection PreSens will be introducing its new optical oxygen measurement device. The company says that Fibox 4 trace is designed for easy handling and fast multiple sample work flow. The oxygen meter can be used with different chemical optical sensors, which allow non-invasive measurements in a range of 1 ppb up to 100% oxygen. The new Sensor Management System and integrated barcode reader enables sensors to be calibrated and measurements started with a single scan. www.PreSens.de","@ID":76}, "PETbottles 90 PETplanet insider Vol. 14 No. 09/13 petpla.net Home + Personal Care Bottle comes with refill You, a brand name of the French company Laboratoires Salveco, is selling its environmentally friendly household cleaner with an innovative re-fill pack. The clear, 500ml content bottles made from PET are sealed with a screwon pump dispenser.Once the product has been used up the dispenser is unscrewed, the bottle filled with water and refill pack complete with concentrate (contents 12ml, separate purchase) is screwed on. At the same time the concentrate is released and mixed with the water by repeated shaking. Unscrew concentrate container, screw on dispensing pump again and the product is thoroughly mixed and ready for use. www.youpuissantnaturellement.fr/la-gamme Viss with cardboard slip case When it comes to the re-introduction or re-launch of a product with an improved formula it is important to identify a bold yet simple way of making it stand out so as to attract the attention of the customer. The display surface of the familiar Viss bottle made from PET with a content of 750ml has been changed to such an extent by means of a cardboard slip case that it is possible to summarise the advantages of the product in such a way that they are readily visible and readable. The slip case is pushed over the pump dispenser and at the same time secured in position. www.unilever.com Precision-engraved bottle Mitra Ltd, Minsk, Belarus, recently introduced a precision-engraved 500ml personal care product PET bottle in Russia. The new b is the result of the latest collaboration between R&D/Leverage Europe and Mitra Ltd., “According to Magdalena Villate, Account Manager, R&D/Leverage Europe, the region represents significant growth opportunities. “The Russian cosmetics market, now estimated at € 10.8 billion and the fifthlargest in Europe, is expected to grow to € 15.6 billion by 2015,” she said. In addition, she noted that the demand for premium type consumer packaging – such as the clarity of engraving evidenced in this particular bottle, used in Clever Company-branded personal care products – is growing fast throughout the region. www.rdleverage.com","@ID":92}, "PETplanet insider Vol. 14 No. 09/13 petpla.net BOTTLE MAKING 47 Direct printing The Innoprint generation of labelling machines makes it possible to print digital images directly onto PET bottles. Here, plastic bottles are printed with food-grade UV inks which ensure a brilliant colour image. One particular advantage of direct printing is the rapid response. For a sporting event, for example, direct printing allows bottlers to offer the consumer a filled PET bottle bearing a picture of the winning team shortly after the end of an event. The required print image can be transmitted directly from the computer to the control unit of the labelling machine. This enables international beverage companies to send print files to all of their plants which can then immediately start printing at the same time – wherever they are in the world. Plasmax coating How can the advantages of PET bottles with an internal Plasmax coating (an ultrathin film of SiO x or pure glass) be communicated to the end user? KHS Plasmax went into this question in great detail, commissioning a consumer study on the subject. The result was that 76% of those surveyed would choose this option, they said, and believe it is a good idea to decorate bottles like these with a FreshSafe logo which stands for quality protection, a long shelf life, a fresh taste and 100% recyclability. It is interesting to note that nearly all of those who took part in the study and were impressed by the new Plasmax technology were prepared to pay more than usual for a beverage in the FreshSafe PET bottle. Plant tour Following the highly interesting presentations the next item on the agenda was a tour of the KHS Hamburg plant. Prof. Dr.-Ing. Matthias Niemeyer, CEO/CTO of KHS GmbH, welcomed the delegates in the new production shop. with an additional assembly area of 2,300 m² which was erected at the end of 2012. The plant therefore now has about 11,000m² of assembly space, around 3,500m² for logistics use and an office area of approximately 6,500m². Thomas Karell, Managing Director of KHS Corpoplast GmbH, says, “There are now over 1,500 KHS Corpoplast stretch blow moulders in use around the world, including approximately 220 InnoPET Blomax Series IV stretch blow moulding machines.” As a result of the global success of the InnoPET Blomax Series IV KHS plans to increase the assembly space by a further 2,300m² for 2015. www.khs.com","@ID":49}, "TRADE SHOW PREVIEW 83 PETplanet insider Vol. 14 No. 09/13 petpla.net Nothing up the sleeve… Amut’s DLB delabeller removes heatshrink sleeves, making more PET bottles available for recycling. The delabeller unit is designed for for post-consumer PET bottle washing plants is and will be on show at K 2013. The DLB was unveiled last June as the solution to the problem of full-bottle shrink sleeves, which were convenient for bottlers but have been so problematic to remove that they effectively rendered bottles unrecyclable. Amut says that the DLB enables recovery of PET bottles with PVC or PETG full-body sleeves, with a more than 80% efficiency level. The machine overcomes the fast expansion associated with heat-shrink sleeves, when recycling has been attempted. The machine uses friction to remove the labels, in a completely dry process that treats the flow of bottles continuously. They are fed by a conveyor belt and the selected residence period within the machine ensures the high efficiency of separation of the label, while maintaining the integrity of the bottles and necks. After treatment the tattered labels are collected in a hopper under the machine and are discharged with a screw-feed extractor. Final separation of any remaining free labels is undertaken downstream through a “rotary ballistic screen” blown-air system. The recovery and valorisation of the dry labels helps to reduce disposal costs; polymer and colour recognition is undertaken by electronic detectors. The DLB available in three models, depending on the customer needs, with a continuous working process and the assurance of almost total recovery of both bottles and labels, delivering greater PET flake purity. DLB 30 and DLB 60 are designed for high flow rates and are able to treat the entire bottle flow at the beginning of the washing line. The third type, DLB10, is installed downstream of the washing line and is designed to treat bottles rejected by the main NIR sorter. DLB 10 can process 1000kg/hr; DLB is rated at 3,000kg/h and DLB 60 at 6000kg/h. www.amut.it Amut Hall 16 Booth D43","@ID":85}, "EDITOURS REPORTS 30 PETplanet insider Vol. 14 No. 09/13 petpla.net It is only once they get to the second washing plant that Empacar can deal with the stragglers. At the moment there are 1,000t awaiting recycling Currently Empacar boasts a capacity of 12,000t/a flakes. A proportion of these goes into direct sales, but the majority ends up in the company’s own Starlinger bottle-tobottle plant. Installed in 2009, the installation now produces 7,000t/a under the Ecopet brand name. At the time the decision to opt for Starlinger brooked no argument, although they did need the approval of Coca Cola, who did not have any comparable equipment at the time. And again, Coca Cola is one of the driving forces as far as Ivo is concerned. They are keen to have at least 10% r-PET in their preforms. Something which poses no problem for Carlos. He is tending to focus on incorporating more bottleto-bottle material in his preforms. He has customers who are anxious to have up to 60% Ecopet. The Starlinger bottle-to-bottle plant in classic construction Preforms are produced on 6 Husky injection moulding systems featuring 56 to 72 cavities. The injection moulding machines are fed from the dryers and, in particular, the Piovan blenders. Carlos is able, via the blenders, to feed r- and virgin PET in a fixed ratio. Each machine is fed directly from big bags. Carlos is not keen on central silos; with the big bags he can be sure that he always has the correct material at the correct machine. The preform bay is constructed the opposite way round. The injection moulding side is located in the middle of the bay, in front of this is the Piovan blender which draws on an R-PET and a virgin PET Big Bag alternately. Empacar is now retrofitting its Piovan dryers with gas heating. Gas is available in Bolivia and has the advantage of being reasonably priced. The electric heaters are nevertheless retained at the plant as a standby. www.empacar.com.bo Empacar collects the PET bottles direct from the collection companies in Santa Cruz. One Big Bag holds 120kg of bottles 360° 360° 360° 360°","@ID":32}, "BEVERAGES / INGREDIENTS 60 PETplanet insider Vol. 14 No. 09/13 petpla.net Döhler goes for Sensory and Consumer Science Savour and flavour Once a beverage becomes established in the marketplace, it’s not only external values, like the packaging, that count but of course what’s inside the packaging as well. So taste assumes significant importance when assessing the success of the overall concept. This year the company will be celebrating its 175th anniversary. A good enough excuse for us at PETplanet to make our way to Döhler’s HQ in Darmstadt, Germany. Talking to Herbert Eickmeier (Senior Marketing Manager), Olaf Biedekarken (Head of Sensory and Consumer Science) and Nathalie Laqua (Senior Product Manager) has given us a detailed insight into production workshop kitchens where not only tried and tested recipes are conjured up but new products are also sampled and tested. With a view to ensuring that it is thoroughly in control when it comes to the success of its new products Döhler has adopted a proactive approach to its operations by setting up its Sensory and Consumer Science division. Main trends in the beverage ingredients industry In matters of taste Döhler has gone with a number of trends. According to Herbert Eickmeier, an upcoming area is that of products made from malt and cereals and the company’s new tea concepts (TrueTea). Malt beverages are on the way to becoming a big trend worldwide. With a broad product portfolio of gently processed, filtered and concentrated malt extracts and malt compounds, Döhler makes it possible to produce malt beverages cost-efficiently. Beverage producers can enter this interesting market without the necessity of investing in additional filtration technology and production steps. And the still drink products continue to make up a sustained trend and growth sector. In the long term the trend is moving towards fruit juice beverages containing less juice while maintaining the same particularly fruit taste sensation. Herbert Eickmeier also mentions the factor of enhanced mouth feel, as well as drinks containing pulp or chunks, by way of a new and important trend. Döhler has a toolbox of multi-faceted ingredients such as fruit juice concentrates, purees, cells & pieces as well as flavours, colours, health ingredients and emulsions at its disposal for the creation of innovative still drinks. Further examples of innovations from Malt beverages are on the way to becoming a trend worldwide.","@ID":62}, "EDITOURS REPORTS 22 PETplanet insider Vol. 14 No. 09/13 petpla.net tems for the collection of recyclables such as cardboard, paper, aluminium, glass and PET. Subsequently, organic waste, electrical waste and batteries have been added. Collection of the waste is carried out within the zones using a part-time workforce who can earn up to 500 Bolivianos (€55) a month. As a benchmark, the minimum wage in Bolivia is currently around 1,000 Bolivianos (approx. €110 euros) per month. Every year around 450,000t of waste arrives unsorted at the landfill site in La Paz alone. It is by educating the public, and by highlighting successful neighbourhood projects that entrepreneurs hope to be able to convince municipalities and ultimately the country as a whole that collecting and separating waste is infinitely preferable to dumping it in landfill. Unsurprisingly, not everyone agrees. Private waste collection companies are unhappy. They have been netting more than 100 million Bolivianos (around €11million) for collecting and transporting the waste to landfill sites from La Paz alone. If local entrepreneurs succeed in establishing a waste collection and recycling system, the private companies stand to lose 77% of their income (see graph). The stakes are high. Collecting recyclables in the neighbourhood zones. The collector goes from door to door and picks up the recyclables. The swisscontact initiative doesn’t stop there. In addition to their ongoing discussions with administrative bodies, the organisation is also keen to support individuals and companies who re-use recyclables by providing benefits in kind. Thus printer cartridges recyclers or construction waste treatment companies are beginning to emerge. One interesting result of these developments is the processing of PET bottles into brooms for sweeping the streets. Ecovecindarios has also set up waste collection points for PET bottles at central locations. After four years, Phase 1 of the project has now been completed and Ecovecindarios is launching Phase 2. Phase 1 concentrated on actually getting the waste collected and separated, now, in Phase 2, they are placing more emphasis on educating senior managers in both municipalities and state government on the virtues of waste separation. The overriding aim as part of the project is to support and give encouragement to those entrepreneurs who exert a major influence on the environment. In prosaic terms, collecting batteries is a lot more important than making jewellery out of crown caps. Working at grass roots level will also enable swisscontact to extend the scope of the project. For example, they are fostering initiatives as diverse as the importance of saving water to promoting the health benefits of cycling. Total amount of refuse collected in La Paz: 450,000t 23% residual waste 2% PET 3% glass 7% paper 8% plastic 55% organic 2% metals","@ID":24}, "BOTTLING / FILLING 56 PETplanet insider Vol. 14 No. 09/13 petpla.net Further options The ASR series can be equipped with a servo capper where each capping element has a servo drive for capping. These servo-controlled motors are capable of generating any desired speed and any desired capping torque regardless of the machine speed. The filler can be fitted with a number of additional monitoring options and with the KHS remote diagnosis system ReDiS. Nitrogen Another possible option is to place a drop of liquid nitrogen in the head space of the filled plastic bottles. This procedure is recommended where very lightweight plastic bottles are to be filled. Adding liquid nitrogen causes the pressure inside the plastic bottle to build up, thus giving the bottle greater stability. It also displaces the oxygen in the bottle head space. Neck conversion package A neck conversion package is also being planned. Customers who opt for the neck conversion package will be able to fill bottles with both a 38mm neck and those with a 28mm neck along with rapid changeover times. Establishing two sterilisation units with an integrated switch for different types of closure is also feasible. Monoblocking with a stretch blow moulder The Innosept Asbofill ASR program is to include a monoblock version of the filler with the InnoPET Blomax Series IV stretch blow moulder. In the monoblock version the air conveying segment is replaced by a transfer module which combines the stretch blow moulder with the rotary aseptic machine. Customer services KHS pursues a strategy of familiarising employees with the aseptic line equipment at a very early stage. Those responsible for the line are usually already on board during the final assembly phase at the plant. This is when a basic course on microbiology is also held and operators are taught about the individual components and how to work ‘their’ machine. In an ideal situation operators are also present at the installation and commissioning of aseptic systems. After production startup KHS stays on site for several more days to help and train up the operating personnel to work on the aseptic line. www.khs.com The Innosept Asbofill ASR has a compact design with integrated valve manifold on the machine.","@ID":58}, "TRADE SHOW PREVIEW 71 Stacking it up R&D/Leverage and Eastman will be presenting its new, stackable bottle, which was developed in R&D/Leverage Product Solutions Laboratory and produced on a Nissei ASB 70DPH Injection Stretch Blow Moulding Machine. The bottle has been specially produced for drinktec in order to demonstrate the possibilities of Eastman’s recently-launched range of glass-like polymers. This development is particularly aimed at the cosmetic industry but R+D/Leverage says that it could also have uses in the drinks industry. www.rdleverage.com Dispensing solutions Aptar Beverage will be introducing two new flip-top sports closures: Asepta and Contender. Asepta was designed especially for wet and dry aseptic filling and is intended to allow more access to flip-top linerless closures to producers of sensitive beverage. Asepta features a patented technology that prevents any ingress during sterilisation and its design includes an opening with nondetachable tamper evidence. Contender is a hot-fill compatible 38mm linerless flip-top closure designed to be easily manipulated with one hand. Two new products will make their debuts at drinktec. The latest Tropicana multi-serve pack, launched in the U.S. in transparent PET, uses a new Aptar flip-top pouring closure and Kraft uses Aptar SimpliSqueeze silicone valve dispensing in Mio, their new liquid concentrate. www.aptar.com Aptar Hall B3 Booth 206 PETplanet insider Vol. 14 No. 07+08 China connection Chum Power Machinery Corporation, from Taiwan, will be showing its latest CPSB-LSS12C PET stretch blower and connector. The company says that it can produce up 18,000 600ml water bph. The blower is a 12-cavity unit and the connector transfers bottles directly into the filling machine. www.chumpower.com Chum Power Hall B3 Booth 214 Pet_Planet_Insider_Settembre.eps 1 30/07/2013 10.26.59 R+D/Leverage Hall B3 Booth 303","@ID":73}, "TRADE SHOW PREVIEW 82 PETplanet insider Vol. 14 No. 09/13 petpla.net Prepare for Life! Visit our booth 11/A58 at the K-Show and see our brand new preform inspection system PreWatcher III Netstal Hall 15 Booth B27/C24/C27/D24 Hybrid drive concept for cap manufacture Netstal is expanding the Elion product range by two new models. At the K 2013 in Dusseldorf, the company will be launching the Elion 4200 with hybrid drive concept. Netstal will be demonstrating the manufacture of a 29/25 water cap on a new Elion 4200. Mould partner is the Swiss company Schöttli. The HDPE moulded part will be produced in a total cycle time of 2.0s using a 96-cavity mould. Closure cooling and air drying will be carried out using equipment provided by Austrian company Eisbär and ef-cooling from Switzerland, while the German company Intravis is responsible for comprehensive inspection. Netstal is showing the Elion 4200 for the first time already at drinktec 2013 (September 16 to 20, Hall B3, Stand 339). www.netstal.com Cypet Hall 14 Booth C58 Electrifying single-stage processing Cypriot company Cypet Technologies Ltd will have examples of its single-stage PET processing technologies on its stand at the K Show. The newest additions to its range are two all-electric machines, which can process PET bottles up to 20l and PET jars with neck sizes up to 145mm. The electric machines are in addition to Cypet’s existing range of three servo-hydraulic units. An article on Cypet Technologies was published in PETplanet Insider in April 2011 and the new all-electric machines were announced earlier in 2013. www.cypet.eu","@ID":84}, "EDITOURS REPORTS 32 PETplanet insider Vol. 14 No. 09/13 petpla.net March 4, 2013 Surena, Sucre We met: Paola Alverez Banzer, Marketing Brewing beer at a height of 3,300m above sea level In Sucre, the constitutional capital of Bolivia, Surena brews beer at a height of 3,300m above sea level. It is a small brewery that is successfully competing against the all-powerful CBN brewing group. Surena is, incidentally, also the only producer of malt in Bolivia. The barley that grows all around Sucre is the reason why the Surena brewery opened up here in 1951. This means that the brewery is able to obtain one of its most important ingredients direct. Four different malts are produced in its own maltings, three light and a darker variety. Four bottom-fermented beers are produced from these malts. Surena also sells the malt to other small breweries who likewise make beers from it which they sell over the counter to their own customers. The 80,000hl are brewed in the classic tradition and matured for six to eight weeks in the conditioning tanks. In the plant there are two brewing lines, an older one made from copper and a newer one parallel to it in stainless steel. The brewpots need to have pressure applied to them as otherwise, at this altitude, the water will boil before it reaches the required boiling temperature of 100°C. The water is supplied by the municipality. “It’s on tap, and it’s top quality“ says Marketing Manager Paola Alverez Banzer who shows me round the plant. At the time of our visit Surena was busy filling cans. In the background is the tunnel pasteuriser through which the bottling operation also passes. 360°","@ID":34}, "BOTTLE MAKING 39 PETplanet insider Vol. 14 No. 09/13 petpla.net What is FEM? An FE system will first divide the bottle shape into separate triangular or square elements (FEs). The smaller these individual elements are, the finer the resulting mesh will be. The finer the mesh, the more exact the computed results, but computation will also take much longer. With a view to increase the accuracy and/ or meaningfulness of the results while reducing the required computation time, the mesh is designed so as to be finer in certain areas of the bottle, e.g., in the shoulder, in the base zone, near the special design elements such as grooves, and in the lateral area. In addition to the data on the contour geometry of the bottle, each mesh element is assigned data on the wall thickness. Also, information on mechanical characteristics, such as modulus of elasticity, strength, and other material properties, as well as the laws governing the material, is entered into the FE system for the description of the behaviour of the bottle under mechanical and heat load. Entering and maintaining these data, rules, and tolerances in the FE system requires a qualified specialist in each company. What FEM can do FE systems permit the following statements: For the demonstration of the required top-load properties, an FE system will, in its most simple version, supply qualitative information based on a “red/green” (fail/pass) statement. In case of a failure, the position of any weak spots in the bottle can be identified. The FE simulation of the top-load properties is also very well suited for a qualitative comparison of various shoulder geometries or the effect of grooves or beads in the lateral surface. FE simulations of the behaviour of a container under internal pressure will provide both qualitative and quantitative statements on the widening of the container, also near grooves or beads, as well as on the increase in the bottle height in excess pressure computations. In the case of hot-fill bottles, the deformation of the Please order your copy at the PETplanet insider book shop: https://petpla.net/books Bottles, Preforms and Closures A Design Guide for PET Packaging Second Edition by Ottmar Brandau 115,00 € 180 pages © Copyright Elsevier 2012 bottle caused by the vacuum that is produced when the hot contents cool down can also be simulated (see also Part 4). FEM also allows simulations of the behaviour of a bottle at higher temperatures. Apart from the top load and the internal pressure behaviour at elevated temperatures, the deformation of the base near the gate is of particular interest. These simulations will also reveal whether the gate will protrude from the bottom to such an extent that the bottle is not stable when standing upright. If one or several of these FE simulations show that the bottle does not yet meet the requirements, iterations involving changes in design elements, such as the number, position, and geometry of grooves or beads, can be used to simulate the required measures until the bottle conforms to the specifications. Sometimes the FE simulation may show that a heavier preform is required. Within limits, a shifting of wall thickness values across the contour of the bottle is also possible. If the integrated FE system gives the go-ahead for the mechanical characteristics such as top load and internal pressure, this means that the wall thickness and the wall thickness distribution have been selected such that the bottle will withstand the anticipated loads. Optimisation of these wall thicknesses with a view to generating lightweight bottles will require the above-mentioned FE expert systems or at least consultation with the FE specialist of the company. Such high-value FE expert systems also permit a simulation of the shelf life of bottles for carbonated products. If bottle geometry, wall thickness, and – in the case of multilayer bottles – the thickness of the individual layers are given, statements such as X% CO 2 loss after 90 days or 5% CO 2 loss after X days can be calculated. Such simulations usually take two to three days, whereas measurements on real bottles would take at least four weeks. What FEM cannot do Despite the impressive capabilities of high-end FE systems, the temperature-dependent, nonlinear, elastic– viscous behaviour of thermoplastics such as PET has not yet permitted us to predict the exact wall thickness distribution in a bottle based on the input of preform, bottle geometry, and heating conditions. Nor is this input sufficient to determine the optimum adjustment of the heating panels in the oven system of the blow moulder. Yet, science and industry are already working on development projects to address these challenges. *This article was published in Bottles, Preforms and Closures, Ottmar Brandau, Chapter 1.5., Copyright Elsevier 2012","@ID":41}, "EDITOUR REPORTS 14 PETplanet insider Vol. 14 No. 09/13 petpla.net Bolivia and Peru are the countries where our South America report starts. Two countries that could hardly be more different but which are nevertheless linked by a number of factors. Peru with its location on the Pacific coast skirting the Andes where the mountain pass roads rise to a height of 5,000m above sea level. But it is precisely the Andes that link both countries. Bolivia’s access to the sea is via the mountain range, the seat of the government of Bolivia at La Paz lies in the Andes at a height of 4,000m above sea level, the main city of Sucre at 3,000m above sea level. Prosperity thrives in Santa Cruz in the tropical part of Bolivia. The 10.5 million inhabitants are spread around the country in and around these three centres. The roads between these centres are long, dusty and not infrequently bumpy. The country has only around 9 million telephone connections and only one in every ten inhabitants uses the internet. Things are quite different in Peru. Here everything is concentrated on the main city, almost a third of all 30 million Peruvians live in the Greater Lima area. The other locations on the coast and in the Andes can be reached quickly via well-constructed roads. The telecommunications network has been extensively developed: there are more telephone connections than inhabitants and every 3rd inhabitant is an internet user. In Peru, the GDP per head is, at 10,900US$, double that in Bolivia. An expanse of coastline, the Andes rising to a height of 7,000m above sea level and tropical zones – all these we have crossed for the Peru and Bolivia Editour Report. However diverse the regions may be, everyone drinks something like 50l of CSD per year. We identified even more factors in common, but also a number of differences. And moving now to the factors in common: Both countries exhibit restrained population growth of just over 1% per year; between 85 and 88% of the population in both countries have access to clean drinking water. Depending on the basis for the data, in both nations each inhabitant drinks around 50l of CSD and approx. 10l of packaged water per person. Exact figures are not actually available because the two market research companies, Canadean and Euromonitor, present very different statistics. The data from Coca Cola lies somewhere between the two values. In Bolivia the pent-up demand was probably greater than in Peru; here growth in the beverages industry has been of the order of some 10%/a whilst Peru is registering growth of around 5-7%/a. Also similar is the PET recycling sector. In both countries there were unregulated street collections with all the associated negative phenomena such as child labour and exploitation. The situation has undergone a distinct improvement here in the last few years, contingent on the processing of the bottles collected in each of the countries from large industrial processing operations - SMI in Peru and Empacar in Bolivia – the companies have managed to bring about the gradual legalisation of the collecting sector. A consistent rise in the rate of returns is their reward for their trouble. The quality of separation is so good that, in Peru, every sixth kilogram of PET is already being used Lima Santiago La Paz Buenos Aires Montevideo Progresso São José dos Pinhais São Paulo Rio de Janeiro Lindóia Santa Cruz Sucre Quilmes Pilar Jaú Concepción Santa Fe Barueri Jundiai Sorocaba Amparoa Limeira Peru, Bolivia by Alexander Büchler","@ID":16}, "CAPPING / CLOSURES 58 PETplanet insider Vol. 14 No. 09/13 petpla.net Canadean predicts growth in the closure market to be led by newer markets, beer, packaged water, iced tea and still drinks The shape of things to come Global beverage closure market 2009-11 - by region Volume - thousands of units Region 2009 2010 2011 CAGR 2009-10 CAGR 2010-11 Asia 348,911 375,716 400,513 7.68% 6.60% East Europe 76,413 76,059 73,169 -0.46% -3.80% Latin America 147,884 153,322 159,608 3.68% 4.10% North America 244,349 242,761 239,119 -0.65% -1.50% Rest of World 25,058 25,836 26,534 3.10% 2.70% West Europe 180,125 179,793 175,658 -0.18% -2.30% TOTAL 1,022,740 1,053,487 1,074,601 3.01% 2.00% Fig. 1 Canadean, the research company that specialises in analysis of the beverage packaging and soft drink and alcoholic beverage industries, says that growth in the period 2011-15 will be led by the developing markets, particularly Asia and Latin America, and that beer, water, iced tea and still drinks will have the largest physical share of growth. The segments expected to show the highest year-on-year growth rates will be iced tea, still drinks, energy drinks and soymilk. The total global beverage closure market in 2011 amounted to 1,075 billion units, which was 2% more than the previous year and just over 5% higher than 2009. Asia remains the fastest-growing region with a 6.6% uplift, slightly slower than the previous year. Latin America follows with 4.1% and the Rest of the World (Africa, Middle East, Australasia, etc) was also in positive territory, with a 2.7% increase. As to sales in Western Europe, North America and Eastern Europe these regions are still below 2009 levels although Canadean reports some signs of pickup in Western Europe and North America in Q3 2012 but emphasised that the situation remains very mixed (Fig.1). Beer, carbonates and packaged water together accounted for 71% of the total volume of closure sales in 2011 but Canadean identifies energy drinks, iced tea, still drinks and soymilk as key growth categories. Packaging and closures actually grew slightly faster than beverage consumption, which reflects the global trend towards packaged products. In terms of closures, plastic screwtops (37%), metal crown corks (24%) and ring-pulls (24%) lead but it is again the categories with smaller market shares that lead the growth statistics; in the case of sports closures, by a long way at over 17% CAGR from 2009-10 and 10% from 2010-11 (Fig. 2). The current core trend towards lightweight, single-piece closures is expected to continue; enhanced features and functionality, with little on-cost, will appear. There is also the expectation of further polarisation between high-volume, including economy and private label, and well-established premium brands. This is expected to lead to further diversity in the variety and types of closures available. Asia is expected to maintain its position as the fastest-growing market in the period 2011-15 with a total increase of 29.4%. Latin America, the Rest of the World and Eastern Europe will also show strongly. Western Europe and N America remain large and important but continue to be slow to throw off the economic consequences of the banking crisis of 2007-8. Packaged water, beer, still drinks and iced tea, in that order, are forecast to lead growth to 2015. In terms of growth rates, energy drinks are expected to see the highest levels (30.7%), followed by iced tea (29.4%), drinking yoghurt and flavoured milk. Sports caps and other plastic closures are expected to show strong growth through to 2015, led in","@ID":60}, "BOTTLE MAKING 42 PETplanet insider Vol. 14 No. 09/13 petpla.net historical markets, i.e. filling food such as dairy products, sauces, edible oil, but also non-food, i.e. home care, personal care and chemicals. Bottles/containers/cups to be filled can be glass, metal and plastics. In liquid dairy packaging future global market growth is expected especially for flavoured milk, drinking yoghurt and buttermilk – particularly packaged in PET. Among packaging materials worldwide, growth is predicted for PET. PET will continue to be a substitute for glass, carton and metal, and is expected to show above average growth in the emerging countries. Serac’s target markets for 40 years and to this day are fillers with low to medium production output, i.e. from 2,000bph to max. 45,000bph. Competition with high output machine makers for commodity products such as water and CSD is deliberately avoided. Customer preferences are for integrated blowing-filling-capping in volume production. Serac has already met this current trend by matching their fillers with blowers from Sipa or Urola and will continue doing so on request. Combox H2F is a complete Serac in-house solution. For Serac, the Combox H2F represents the logical outcome of their strategic aspirations, combining as it does not only design and development but their entire engineering expertise and experience. SBL blower (Serac blow linear) The SBL range includes six models with blowing cavitations ranging from two to eight, volumes from 50ml to 8l and an output between 2,400bph and 12,000bph. Technical features: A patented transfer system converts the sequential motion of the linear blower into a continuous motion of the rotary filler, thus ensuring transfer of bottles free of contact and damage. Energy consumption is optimised due to all electric drives. A perfect toggle closing of the mould – 50t force – ensures limited parting lines appear on the bottles. Mould change assistance. Ergonomic design with sliding doors over the entire length of blower to provide total visibility and access to the inner parts. The SBL blower is assembled in Serac’s lean manufacturing production facility in Malaysia under the professional management of Sylvain Auvray. He can call on 15 years’ experience, when he managed Sidel Malaysia and subsequently was instrumental in the construction of Sidel Bejing, where complete blowing-filling lines are manufactured. His services and also his local knowledge are available for Serac. Our hosts were keen to point out that quality is key issue in the Malaysia production. The SBL is manufactured in preassemblies, controlled, tested and tried, before final assembly. 85% of materials are of local Malaysian origin, 15% of materials are imported from Europe – i.e. components such as the B&R control panel, the servo motors, power regulator by Olicorp, the Seitz valves for blowing. H2F rotary filler (Highly Hygienic Filler) Inspired by the aseptic milk filling Serac developed this ultra clean filler. H2F is available in various categories depending on product quality, shelf life, cold chain, hygiene of container, storage, etc. Jean-Paul Tilloy presented design features such as the clean surfaces in the working zone, the machine sealing quality, a simplified neck transfer, the multi-flow nozzles and with reference to the integrated new capper TCS4 the screw monitoring of the tightening torque and the decontamination with pulsed light. Aymeric Vague summed up: “Without question, the Combox H2F is a dramatic step forward in our product development. The development is based on existing technical knowledge and will add to the existing core business and open new markets.” He went on to claim: “The Combox H2F is the affordable solution for mid-sized dairy products manufacturers – very much in the Serac tradition. No oversizing, no over-investment.” www.serac-group.com The ultra clean blow moulding-filling-capping line for dairy PET bottle production at up to 12,000bph is being assembled at the Serac plant in La Ferté-Bernard. The Combox H2F is the latest member of Serac’s product portfolio.","@ID":44}, "BEVERAGES / INGREDIENTS 62 PETplanet insider Vol. 14 No. 09/13 petpla.net Nutrient media Döhler offers its customers a very wide range of services e.g. for validating aseptic bottling plants (AVM – Aseptic Validation Medium) and for analysing weak points in the bottling sector (NBB-B- enrichment medium). All nutrient media are easy to use and achieve fast and reliable results. A matter of good taste The department of Sensory and Consumer Science, headed by Olaf Biedekarken, is an important part of the Döhler enterprise and undertakes consumer tests and sensory services on behalf of the foodstuffs and beverages sector. The study of products from a sensory perspective is an essential feature in ensuring the sustained market success of consumer goods. Döhler Sensory & Consumer Science SCS has extensive proprietary resources at its disposal: Consumer panel (n=2,000, available for focus groups, studio tests and online surveys) Pool of around 100 experts with training in matters relating to sensory perception Premises for conducting extensive consumer surveys (up to n=300) Resources for the programming and administration of online studies (Sawtooth SSI Web) Database with results from more than 250 consumer studies with acceptance data relating to approx. 1,100 concepts and products. With the help of these resources the Döhler Sensory & Consumer Science Team carries out numerous projects on behalf of customers both at home and abroad as part of its focus on innovative developments and benchmark studies. One important factor in product development CCT Creative Competence Technology GmbH Idsteiner Strasse 74 . D-65527 Niedernhausen, Germany [email protected] www.cct-systems.com PET Molds Closure Molds Developments PET Systems Closure Systems ComPETCap® Designs Design and Patents CCTSystems®BPF for CSD (carbonated soft drinks) current design CCT design 6,26g 4,32g CCTSystems®3025 for still water 3,92g 3,05g current design CCT design CCTSystems®38-2-3S for non CSD, Milk or Juice 4,38g 3,83g current design CCT design CCTSystems®1810 for CSD (carbonated soft drinks) current design CCT design 5,05g 4,10g at the drinktec in Munich (Sept. 16-20), booth B3/414 at the K in Düsseldorf (Oct. 16-23), booth 1/1A40 is, according to Olaf Biedekarken, a grasp and an understanding of consumer behaviour. Typically, 70% of newly introduced products flop and as a result tests of this nature are gaining in importance. In carrying them out, Döhler makes use of a full range of methods and resources - quantitative consumer tests, face-to-face interviews, focus group and telephone interviews, in-house tests, online studies and lots more. They have, for example, discovered what it is that persuades consumers to purchase a new product. The decisive factors when it comes to persuading people to buy are: advertising, recommendation, brand name, label, tastings, and packaging. Some key criteria on the likelihood of the customer purchasing again are taste, effect – for example, in the case of energy drinks and practical handling (convenience). A new tool at Döhler, which has been developed for malt beverages, is ‘sensory emotional profiling’ as it is called. By means of this tool certain concepts relating to the taste of the beverage are applied with a view to identifying something that, despite the fact that it has been tasted, cannot be given a specific name. To meet regional taste preferences, all products for the local markets are developed locally. The company is passing on the wealth of experience acquired by Döhler Sensory & Consumer Science in the form of tailor-made customer seminars and sensory training courses. PETplanet is invited to join such a Training Course experience acquired by Döhler Sensory & Consumer Science in the form of tailor-made customer seminars and sensory training courses and will be reporting on it. Döhler has a pool of around 100 experts with training in matters relating to sensory perception.","@ID":64}, "PETcontents 09/13 4 PETplanet insider Vol. 14 No. 09/13 petpla.net INSIDE TRACK 3 Editorial 4 Contents 9 News 84 Products 88 PET bottles for beverages and liquid food 90 PET bottles in health and beauty care packaging 92 Patents BOTTLING / FILLING 54 Plugging the gap KHS Innosept Asbofill ASR aseptic filler for liquid dairy products CAPPING / CLOSURES 58 The shape of things to come! Canadean predicts growth in the closure market BEVERAGES / INGREDIENTS 60 Savour and flavour Döhler goes for sensory and consumer science 64 The global beverage markets Change as a constant - focusing on health TRADESHOW PREVIEWS 68 Drinktec ahead Munich, Germany, September 16 - 20, 2013 78 It’s K’ time again Düsseldorf, Germany October 16 - 23, 2013 EDITOUR REPORT 13 Peru and Bolivia Go with the flow tour 2013 - Part 1 PREFORM PRODUCTION 34 Under one roof KraussMaffei and Netstal’s PET Business join forces 36 Continuous quality inspection of preforms and closures Coca Cola Amatil: preform and closure systems equipped with quality inspection systems from Intravis BOTTLE MAKING 38 Verification of the 3D design through finite-element simulation Bottles, preforms and closures - part 5 40 An integrated line solution Meeting Serac in La Ferté-Bernard, France, to see their new Combox H2F integrated line solution to blowing-filling-capping 44 Entering the Matrix Sidel’s modular system approach 46 KHS PET event More than 100 delegates experience PET expertise 53 Pillars of Power Amcor Powerblock 3.0 lightweight hot fill container MARKET SURVEY 49 Filling equipment BUYER’S GUIDE 93 Get listed! Page 40 Page 60 Page 53","@ID":6}, "TRADE SHOW PREVIEW 70 PETplanet insider Vol. 14 No. 09/13 petpla.net Drying solution Piovan’s Gensys system offers users the opportunity to have a specific drying solution configured for their particular needs. Low, intermediate and high volume PET perform production lines have their own distinct requirements: Genesys is aimed at adapting to them. Piovan says that the management of different PET grades and typologies is emerging as a major factor to be managed by producers and that Genesys’ automatic adaptability function allows any PET to be properly treated before it hits the extruder barrel. The company says that it also foresees the need for additional processing variables in meeting demand for complex container formats and performance requirements and that the new machine will be able to adapt to them. www.piovan.com Piovan Hall B3 Booth 119 Empty bottles inspection and PET leakage monitoring BBull Technology, Germany, will be showcasing numerous new developments. First of all, in the shape of its Multikon EBI, BBull will be presenting an empty bottles inspection machine, together with Pulse – a special leakage monitoring system for flexible packaging which eliminates crushing, pressing or stress as far as the packaging is concerned. “Multikon EBI“ is characterised by its hygienic design and its hydraulic adjustment facility – no more handwheels or spindles. Up to 70,000bph can be inspected and defective bottles separated out. Pulse is an inspection system for controlling the pressure of flexible containers (cans, PET, plastic containers). This involves the use of the telekinetic impact procedure which delivers highly precise information regarding the internal pressure (and with it the tightness) of the container. Any container that falls outside a previously defined standard is identified and separated out at a speed of up to 60,000bph. The procedure can be used as a stand-alone solution or in combination with Compact Vision level control (the compact monitoring system based on cameras for filling level and closure) or a BBull Image data control system. Also exhibited will be Protecx, the system for identifying foreign bodies in glass bottles featuring a combination of X-ray and image processing technology as well as the sorting and distribution of containers: with servo motor (”Brush Off“), with static (”Flex“) or dynamic multi-segment rejection “Snake“ www.bbull.de All about caps Corvaglia’s stand will host displays presenting its four business areas, which range from product development, through mould manufacture and cap production, up to capping. www.corvaglia.ch BBull Technology Hall A5 Booth 544 Making the mould Kiefer Werkzeugbau GmbH makes moulds for all rotary stretch-blow moulding machines and for linear stretch-blow machines. The company offers customer support from research and design through to pilot blowmould and series production, in the beverage, cosmetic and chemical industries. www.kiefer-mold.de Kiefer Hall B3 Booth 108 Corvaglia Hall B3 Booth 201 Labelling systems Markem-Imaje, manufacturers of industrial coding and labelling systems, will be presenting a complete range specially geared to the requirements of the beverages industry and including two innovative items. SmartLase C, is a CO2 SmartLase encoder with touch screen, with an output of up to 100,000bph and featuring up to 120 characters per code as well as improved print quality. There are several models available in the new series. One model has been developed to prevent any damage to very thin-walled PET bottles. 9232S is an ink jet printer capable of delivering 2 lines of text at around 160m/ minute, i.e. a labelling capacity of 120,000bph. The 9232S will label all the materials for beverages packaging with just one ink. The availability rate has been increased to 99.9 % with the Smile-All-in-Program. Markem-Imaje will also be showcasing a number of labelling solutions for secondary packaging and pallets (ink jet printers, labelling systems) together with their CoLOS software solution (centralised data management, pooling of print orders). www.markem-imaje.com Markem-Imaje GmbH Hall A6 Booth 339","@ID":72}, "TRADE SHOW PREVIEW 68 PETplanet insider Vol. 14 No. 09/13 petpla.net drinktec + PETpoint, September 16 -20, Munich, Germany Drinktec ahead Drinktec PETpoint is about to embark on a further round; from September 16 to 20, 2013 some 1,400 exhibitors together with approx. 60,000 visitors from more than 70 countries are expected. The gates will be open from 9 am to 6 pm each day. This preview again highlights exhibitors that are of particular interest to manufacturers and fillers of PET bottles. www.drinktec.com Stretching the point PDC Europe will be presenting its R-450, a small-footprint shrink-sleeve applicator with a capacity of up to 400ppm on a 300 mm height shrink sleeve, and up to 600ppm on smaller sleeves, both from a single applicator head. PDC says that the PDC R-450 has already been installed on a selection of operating lines. Also on the stand will be a tamper-evidence applicator designed specifically for beer keg taps, which features a diestacker for small cardboard tags, which can be used for branding, promotion, bar code ID, etc. In addition, PDC will be showing the technology for decorating both metal and plastic kegs using a non-heat PE sleeve, which is already being used by Heineken. www.pdceurope.com PDC Hall A2 Booth 126 GEA Procomac Hall A4 Booth 314 Sensitive handling GEA Procomac will be exhibiting its range of filling machines. Its ABF (Aseptic Blow Fill) system consists of an aseptic blow-moulding machine – claimed to be the market’s first for PET bottles with an integrated aseptic filler and capper. The system sterilises the preform with vapourised hydrogen peroxide (VHP). A 48,000 500ml bph format ABF system will be on the stand, as will a new 12g PET bottle, specifically designed by GEA Procomac for the aseptic filling market. The Sterilcap VHP machine for plastic caps sterilisation has been developed to allow a single sterilising agent to be used for an entire system. It can now treat both flat and sport caps without the need for a change of format. Artis EVO low-level, infeed palletisation technology incorporates a layer management system that eliminates the need for a pusher. The stand will host GEA Procomac’s Aseptic Dual Filling System for PET bottles with products containing particulates (up to 10mm³) and a new range of filling machines for PE and HDPE bottles for fresh and ESL liquid dairy products. Its sixth generation PAA sterilisation system is claimed to enable a further reduction in water, steam and PAA consumption and has a smaller footprint. It can reach six log reductions (log6) with a speed range from 6,500 to 72,000 bph, with no need of intermediate sterilisation cycles www.gea.com Lightweight label Austrian company Brigl & Bergmeister GmbH will be presenting a new, lightweight reel-fed label, named the NiklaPET Web 55. The numbers stand for its weight; 55g. Brigl & Bergmeister says that it has developed the lighter label specifically for reel-fed labelling. It can run on the same machinery as film labels. www.brigl-bergmeister.com Brigl & Bergmeister GmbH Hall A2 Booth 314 Shine a light French company Claranor says that it has now over 80 pulsed light sterilisation units installed worldwide. It will be exhibiting its extended range of solutions for the beverages sector including a new generation electronic cabinet, which has been developed in accordance with hygienic design practices. On show will be its system for ESL and acid aseptic filling lines, which enables sterilisation of entire caps, inside and out. Other sterilisation solutions to be displayed at the Claranor stand will include 5 gallon caps; double-chute equipment; preform necks; a chemical-free system for a combined preform/cap treatment, and a new system for aluminium foil sterilisation. www.claranor.com Claranor Hall A4 Booth 315","@ID":70}, "TRADE SHOW PREVIEW 79 PETplanet insider Vol. 14 No. 09/13 petpla.net MRS extruders put to work A complete extrusion line and an MRS 160 Extruder with a throughput of 1.4t/h will represent Gneuss’ Multi Rotation System (MRS) extrusion technology. The extrusion line consists of an MRS 130 Extruder, and RSFgenius 200 and an RSFgenius 250 fully automatic filtration system. The line has a tandem filtration system to enable it to process up to 1,000kg/h of PET bottle flake directly into continuous filament, which requires 25 micron filtration. Also on the stand will be an RSFgenius M, which has been developed especially for highly contaminated materials. The SFXmagnus R includes integrated self-cleaning of the filter elements for the first time in the series. www.gneuss.com Gneuss Hall 9 Booth A38 Cost reduction in PET production As the price for PET continues to fall, the production cost pressure for PET polymerisation and PET recycling continues to grow. BKG Bruckmann and Kreyenborg claims that with its the CrystallCut pelletising system (Münster, Germany) offers an effective way to reduce these costs. At an average energy cost of 12 cents/kWh, energy savings of up to €15/t can be achieved. Today’s PET polymerisation plants can achieve a production capacity of 600t/day.With a throughput of 600t/day annual savings of approximately 26,000MWh can be achieved. Extrusion lines which recycle PET bottle flakes and have a production capacity of 1,500kg/h can achieve savings of more than 180kWh. Furthermore, due to the crystallisation of the pellets from the inside to the outside, a better crystalline structure is achieved which in turn will save on the costs/ energy to remelt the material. The CrystallCut system utilises the thermal energy of the melt for crystallisation. The melt is granulated by means of an underwater pelletiser and reduces the residence time in the water to a minimum. The outlet temperature of the pellets after the dryer is already at required crystallisation temperature of 160-180°C. With this temperature, the pellets can be fed directly to the subsequent process. www.kreyenborg.de/en/ BKG Bruckmann & Kreyenborg Granuliertechnik GmbH Hall 9 Booth A44 A48 / 55 / A57","@ID":81}, "PRODUCTS 87 PETplanet insider Vol. 14 No. 09/13 petpla.net Top gear Kreyenborg GmbH has provided a customised GPE 140/140-03 gear pump, along with a K-SWE-280-4K75-V/RS screen changer with a filtration fineness of 40μm and the associated adapter for an extrusion line that will process four tons/h of recycled PET. The pump has a specific volume of 1,482cm/rev, flow rate of 4,000kg/h of recycled PET material, and 11,100Nm driving torque. While separate support carts are normally used for each machine component, a particular customer asked that the two machines should be mounted on a single support cart. Kreyenborg was able to comply with the request by integrating linear guiding on the cart, which stands on fixed castors and can be moved in the direction of the extrusion along floormounted rails. This arrangement also made it easy to pull the equipment away from the line for maintenance. Drives for the company’s gear pumps are typically installed horizontally, so the pump will be mounted with gears parallel to the cart frame. However, in order to provide enough space for machine operators to make screen changes, a more compact system design was achieved by installing the pump on its side and mounting the drive underneath. This particular extrusion line processes a material with a viscosity of 240-290Pas. The self-lubricating gear pumps are sealed by thread shaft seals. The materials to be processed are pseudoplastic and tend to degrade due to the shearing in the slide bearing and also in the thread shaft seal. As product viscosity is highly dependent on temperature, additional cooling has a positive influence on the sealing effect of the thread shaft seal; for this reason, it was designed with an adjustable cooling system that removes heat energy from both the seal and the material itself. Cooling can be with either air or demineralised water. Kreyenborg says that, if a shear-sensitive material is to be processed, residence time in the pump should be absolutely minimised and the company consequently recommends a type 03 gear pump. The gear pump type 03 was developed several years ago and since then has proven successful through reduced flow channels which reduce residence time. www.kreyenborg.com","@ID":89}, "TRADE SHOW PREVIEW 80 PETplanet insider Vol. 14 No. 09/13 petpla.net Agr International Hall 11 Booth B40 Better management Agr International, Inc. will exhibit its range of products designed for the measurement and quality management of plastic containers and packaging. Its Process Pilot automated management system interfaces with the PET bottle blowmoulder to provide precise material thickness distribution management and defect detection, with hands-off blowmoulder control. Agr says that the system offers bottle producers the ability to aggressively pursue bottle lightweighting strategies. Its OptiCheck multi-camera inspection system offers a vision-based inspection solution for bottles and similar containers transported on a conveyor line. It checks seal surface, sidewall, base and label defect detection as well as precision finish gauging. Versions of the modular OptiCheck system are available for both opaque and transparent containers. www.agrintl.com More efficient PET recycling ProTec Polymer Processing will be exhibiting a range of services for material handling, including the planning and construction of complete plants from silos up to processing machines, along with its technologically established and energyefficient Somos brand devices and systems for drying, conveying and dosing pellets and regrind. Premiered at the K show will be Somos BB 500, a new gravimetric batch dosing system for up to four components with throughput rates up to 500kg/h. The Ohl process will be shown for the first time at the K. It enables washed flakes reclaimed from used PET bottles to be reprocessed into rPET, with an acetaldehyde content of ≤ 1ppm and overall material properties akin to virgin PET material, as certified by a “Non-Objection Letter” from the FDA (Food and Drug Administration) for direct contact with food. www.sp-protec.com ProTec Hall 9 Booth D60 Washing, drying and agglomeration Herbold Meckesheim GmbH’s stand will feature a range of machines, from shredders and granulators through to washing and separation lines. The company says that its new HVT mechanical dryer’s vertical rotor construction saves space and offers lower energy consumption than its predecessors. The show will see the launch of a new range of friction washers including the FA 60/300, which is designed to deal with 2 to 3t/hns/hr of film or four to 6t/h of rigid plastics. The companies granulators will be represented by two items: the SML 45/60 SB with forced feeding; and an example of the heavyduty SMS series. Visitors will also be able to see an HV 50 series Plastcompactor, which is designed for continuous agglomeration of films, fibres, foams and dust, and a medium-range, vertical shaft PU 650 pulveriser. www.herbold.com Herbold Meckesheim GmbH Hall 9 Booth B42 Moretto Hall 11 Booth H57 Air control Italian company Moretto SpA will be exhibiting a range of control, management and monitoring systems. Of particular interest to the PET field will be a dedicated variant of its Eureka dehumidification system, which is designed to use and monitor only the precise amount of process air required and thus optimise energy use. In the PET variant, the Flowmatik integrated automatic process air distributor, OTX thermal exchanger and Xmax dryers are calibrated to reduce airflow by over one-third, compared with standard systems, with consequent savings in process and heating energy usage. www.moretto.com","@ID":82}, "PETpatents www.verpackungspatente.de 92 PETplanet insider Vol. 14 No. 09/13 petpla.net Stabilising sleeve Utility Model DE 202012007933 U1 Applicant: Karl-Heinz Schön, Rastatt (D) Date of Application: 18.8.2012 One drawback of thin-walled PET bottles is the risk of the bottles becoming slightly distorted during gripping and lifting so that product is accidentally discharged or the bottle slips out of the user’s hands. In order to prevent this, a re-usable sleeve is proposed which can be mounted on the top of the bottle. Drip-free closure Intern. Patent No. WO 2013 / 011581 A1 Applicant: Zenshin Co. Ltd., Fukuoka (JP) Date of Application: 20.7.2011 Construction of a 2-section container closure which is opened by pressing the top section down and is of “drip-free” construction. Sliding Lid Intern. Patent No. WO 2013 / 010934 A1 Applicant: Nestec S.A., Vevey (CH) Date of Application: 13.7.2012 Cup-type packaging with an elongated lid complete with opening. The lid is so constructed that it can be pushed along on the edge of the cup until the discharge opening appears inside the cup opening. Pushing the lid back closes the cup again. Engagement keyway European Grant of Patent No. EP 2173623 B1 Applicant: Krones AG, Neutraubling (D) Date of Application: 16.7.2008 A plastic bottle manufactured from a preform incorporates a support ring which enables the bottle to be gripped mechanically. In order to make this ring smaller (saving material) a proposal has been made to incorporate a keyway in the preform which acts as a new ”gripping point“ for machinery. Container closure International Patent No. WO 2013 / 017810 A1 Applicant: Obrist Closures Switzerland GmbH, Reinach (CH) Date of Application: 11.7.2012 Multiple-section closure for dispensing a free-flowing product. Openings in the area of the top surface simplify the manufacture of the lid and make it easier to incorporate retention features that enable the lid to be securely fixed on to the container opening. Container shapes International Patent No. WO 2013 / 025464 A1 Applicant: Graham Packaging Comp., York (US) Date of Application: 10.8.2012 This international application describes a number of ways of designing a container and the base of a container so as to ensure that the deformation forces that are absorbed during hot filling and subsequent cooling can be absorbed to best possible effect.","@ID":94}, "BOTTLE MAKING 53 PETplanet insider Vol. 14 No. 09/13 petpla.net Amcor developed Powerblock 3.0 container, a lightweight 64oz hot fill PET bottle Pillars of power Amcor Rigid Plastics has developed a lightweight 64oz hot fill PET bottle for juices and teas and slashed 9g, or 13.2%, from the typical 68g PET bottle. The hot fill container also boasts a 38mm lightweight finish which saves material compared to the standard 43mm finish for 64oz PET bottles. Amcor‘s Innovation Group, consisting of a cross-functional design team of 20-year packaging veterans, developed Powerblock 3.0 technology to provide a lightweight and strong hot-fill stock PET bottle with superior filling and stacking performance. Multiple utility and design patents are pending for this novel container. One patent covers an optimised conical base pushup with special diameter and height ratios and relationships. Another patent covers a round or rectangular base with strap-like features that are added to create a footed-style base. Packaging details The segmented standing surface consists of four standing one-inch columns, which are lightweight, strong, and rigid. Together, these technologies work synergistically to unlock material normally trapped in the base area. This allows for better material distribution in the container body, resulting in a lighter weight container without sacrificing performance. Angles, ratios, and other bottle geometry are optimised to obtain a balanced response to vacuum, pressure, and top load forces. Powerblock 3.0 provides multiple fill contact points and flat sides for added stability; optimised footprint (width and depth) for improved pallet pattern and corrugate savings; and secure consumer handling with three intuitive areas for single-hand pouring. Virtual modelling A number of virtual modelling techniques were utilised to effectively predict key performance parameters like quantified hot-fill characteristics and warehouse stack performance. While the new hot-fill container is initially targeted for 64oz hot fill containers, Amcor expects to adapt the technology to other hot-fill bottles. Amcor has completed all development and the stock bottle is already commercially available in several locations across the U.S. www.amcor.com","@ID":55}, "NEWS 13 PETplanet insider Vol. 14 No. 09/13 petpla.net Clarification drinktec preview issue 7+8/13: PET Engineering’s EvoLight bottles are available only in 0.5l (for still water and still with nitrogen filling) and 1.5l (for still and sparkling water) formats. The 1l and 75cl bottles, for milk and juices respectively, are different projects. We are happy to provide this clarification. NGR on the up NGR, the Austrian recycling machinery manufacturer, reported increased sales in financial year 2012/13 compared with the previous year. The improvement was in excess of 20%, rising from €24 to €29 million. The company says that the improvement was because ongoing expansion of its product portfolio, along with technical enhancements of NGR equipment, led to new recycling applications. The modular design of the equipment platforms and the use of standardised components has shortened the steps in the development process, allowing the company to increase the speed of implementation of new recycling applications and speed up its response to special requests from customers. NGR says that demand has in part increased dramatically for integrated recycling systems that take up and treat process-related production waste and re-introduce the recycled material into the plastics stream. The company says that it will present the first results of its acquisition of Britas, the filter manufacturer, at the K 2013 trade show in Dusseldorf. www.ngr.at Separate recycling for PET trays vital Plastics Recyclers Europe says that PET trays must have their own recycling stream in order to ensure resource efficiency. Casper van den Dungen, Plastics Recyclers Europe PET Chairman, said that “trays and bottles cannot be recycled in the same line. Their designs and chemical compositions are not the same and can create quality problems for existing PET recyclers.” The 700,000t of PET trays consumed in Europe each year can be recycled effectively if they are properly separated from other streams such as PET bottles or polyolefins. Plastics Recyclers Europe has called for a joint value chain approach and warned that unilateral actions could endanger recycling of this material. www.plasticsrecyclers.eu","@ID":15}, "TRADE SHOW PREVIEW 73 PETplanet insider Vol. 14 No. 09/13 petpla.net Bottle-to-bottle recycling Starlinger will be showcasing various equipment and technologies designed to enable processors to satisfy the rising demand for recycled material. The rPET produced on Starlinger recoSTAR PET iV+ lines is food-safe and conforms to the standards of various national and international authorities such as FDA and EFSA, and has been approved for use in food applications by many brand owners. The company says that total installed bottle-to-bottle recycling capacity will be 400,000t/a by the end of 2013. The recoStar PET machine range has been expanded with the launch of the recoStar PET 330iV+. It processes 2,900kg/h (or 3,600 kg/h as HC version) of washed PET flakes for bottle-to-bottle applications. The first unit was sold to a joint venture between the largest recycler in the UK and Coca-Cola Enterprises and has been in operation since May 2012. www.starlinger.com SGT, naturally innovative The leading manufacturer of PET preforms, focused on customized and innovative solutions for packaging liquids. Meet us at Drinktec 2013 Hall B3 Booth 342 Tel. + 33 (0)2 40 05 09 37 - www.sgt-pet.com Starlinger Hall B3 Booth 412 Hit for four 1 Blow will be presenting 4L, its new four-cavity machine, which can produce bottles from 0.2 up to 2.5l at rates up to 8,000bph. The company says the machine has a very small space requirement, possesses universal compatibility with electricity standards, and that it accepts existing moulds from Sidel, Sipa, Krones and Side. Air recovery and power recuperation are fitted as standard, in order to improve energy efficiency. It can be specified or subsequently upgraded with a hot fill option. 1 Blow will also exhibit at K’ (Hall 13 / Booth D 92). www.1blow.com 1Blow Hall B3 Booth 344","@ID":75}, "PETproducts 84 PETplanet insider Vol. 14 No. 09/13 petpla.net Ending the squeeze Filtec, which is based in Torrance, California, specialises in inspection and laser coding equipment. Its new Pressure/Leak Detector (PLD) for PET and HDPE containers is claimed to be a “revolutionary” step forward in inspection technology. The system has a single moving part, a feature that is claimed to increase reliability, reduce maintenance and lower the cost of ownership. It uses precision guide rails to support bottles during inspection, rather than belts, which reduces maintenance needs as there are no belts that will require replacement. The system also eliminates damage, spillage and contamination during inspection as it does not squeeze bottles while testing them. Each bottle is inspected by an intelligent sensor, which utilises a proprietary algorithm and enables the PLD to give an immediate and reliable read. When the pressure is unacceptable a defect is indicated and the bottle is rejected from the line. The system has a quick disconnect feature that allows for changeovers of less than 1min. PVC change parts are colour-coded and precision-pinned, in order to provide for accurate alignment for different bottle diameters. The PLD connects to any existing filtec Fill Level Inspection system using the same rejector. An SPT colour touch screen display is standard equipment with the PLD and is also compatible with most filtec machines. As well as monitoring of rejects by type, it provides the normal range of management functions including problem detection, data management and access control. www.filtec.com Through the pinhole Amsler Equipment manufactures empty bottle inspection systems for all plastic containers, which test for pinholes, cracks, short shot neck finishes, abnormal wall thickness and choked necks. Stationary-head, flying-head, multi-head and custom-designed systems are available. The company’s leak detectors can detect holes as small as 0.006 of an inch (less than 0.03/mm) and are supplied with a 2m conveyor. Inspection can be performed on bottles up to 5l on the standard machine, with larger sizes available on special request; 500ml bottles can be checked at throughputs up to 6,000/h, 5l up to 1,000bph. Holes as small as 0.012/inch (0.05mm) in standard N American 16.9 oz bottles can be detected at up to 8570bph. Optional features enable wall thickness checking on four different sections and/or colour and density checking. The machines can be installed on existing conveyor lines or as free standing units and are available in N American voltage, with others available on request. www.amslerequipment.net Meet us at 16~20 September 2013 drinktec Booth: A3507 Magnetic Bottle Thickness Gauge Secure Seal Tester PET Bottle Pressure Tester ( Burst ) Hot Wire Bottle Cutter CanNeed Instrument HK Limited Tel: +86-758-2788469 Fax: 758-2782729 E-mail: [email protected] Web: www.canneed.com ( ) +86-","@ID":86}, "EDITOUR REPORTS 23 PETplanet insider Vol. 14 No. 09/13 Once collected, there is still plenty to do before … …the PET bottles have been separated out. In a second stage, the strips are turned into brooms for street sweeping (All photos ecovecindarios) Swisscontact, a nongovernmental organisation, operates worldwide and is concerned with Vocational Education and Training, SME Promotion, Financial Services, and Resource Efficiency, principally in Third World countries. It is mainly financed through monetary donations by industry and the municipalities in Switzerland. www.swisscontact.bo Not all the PET bottles collected are melted down. Here Ecovecindarios have helped small business Recojo by providing a machine that transforms the PET bottle by cutting it into a long strip of PET. PROVEN COST SAVINGS PERFORMANCE moldmasters.com Mold-Mastersand theMold-Masters logoare trademarksofMold-Masters (2007) Limited. ©2013Mold-Masters (2007) Limited.All rights reserved. Rely on our global support network for fast service and parts. North America 1-800-387-2483 | Europe 49 (0) 7221 5099-0 Asia 86 512 86162882 ALWAYS INNOVATING. + More efficient use of platen real estate increases the cavitation for a given machine size + Proprietary iFLOW and iCOOL technology reduces cycle times while improving balance, lowering injection pressure and increasing dimensional repeatability + Tooling solutions to revitalize, recapitalize and rev up existing systems + Take advantage of global sales, service and manufacturing locations Get 50% more output from the same machine 96-CAVITY MICRO PITCH MOLD FOR 300T MACHINES Visit us at Hall 1 / A39 Contact us today at: [email protected]","@ID":25}, "PETplanet insider Vol. 14 No. 09/13 petpla.net BOTTLES 89 On-the-go wine glasses The wine producer Fetzer from the USA is selling red and white wine in PET containers shaped like a wine glass, each containing 187ml. The clear glasses, which are designed for use at functions, picnics or outdoor events, are already filled and securely sealed by means of a sleeve label so as to be leakproof. After opening and complete removal of the label, the demountable slip lid on the top is slid over the base of the glass and used as a stabiliser. There is also a sealing membrane at the top that needs to be removed prior to drinking. www.candqwines.com Proactive and reactive Natural mineral water with extra benefits due to the addition of vitamins is a trend that nearly all drinks manufacturers are turning to their advantage. One example of this are two drinks currently being marketed under the brand name Rosbacher which is part of Hassia Mineralquellen GmbH & Co. KG, “proactive“ with an apple flavour and a “reactive” variety flavoured with orange. “Reactive“ is claimed to reduce tiredness and fatigue, whilst “proactive“ is reputed to assist with energy metabolism. A rectangular PET bottle with rounded corners and with 1.5 litre content serves as packaging. Reinforcing grooves, an all-round label and a tamper-proof lid complete the packaging. www.rosbacher.com Lemon-ade The well-known juice producer Granini recently launched its newest product innovation “The Limo“ on the market. The three types, Limette-andLemon, Pink Grapefruit + Cranberry and Orange + Lemongrass feature a fruit content of between 10 and 18% and are free of artificial aromas, colourants and preservatives. The lemonades are bottled in PET bottles with a content of 0.5 / 1l. The transparent bottles incorporate an embossed brand name logo in the area of the neck and in the shoulder area the indentations typical of the brand in the form of bubbles. Matching self-adhesive labels demonstrating the non-label look plus a screw cap with a tamperproof strip ensure that the bottles draw attention to themselves at the PoS. www.granini.de Badoit with taste In collaboration with the top French chef, Thierry Marx, Danone Waters have expanded their range of “Badoit“ mineral waters characterised by their fine bubbles by two further products featuring a fruity taste. The sugar-free beverages taste of raspberries and passion fruit. The round body PET bottles containing 1l of product are lightly green-tinged and include a self-adhesive label and screw cap to match each of the different types. For the market launch slip cases with information about a discount promotion were slid over the neck of the bottle. www.danoneaunaturel.fr BERICAP the plastic closure company committed to your success www.bericap.com Research and Development Developing closure solutions to meet your specific requirements Mould Technology A detailed understanding of mould design with in-house mould making facilities in Hungary and Germany Global Presence Local production in 21 strategically located factories. An on-going strategy of stregthening our global presence Capping Technology and Know-How Special advice on capping technology with on-going technical support Innovation and Flexibility Our broad range of plastic closures is the basis for generating new innovation. Our expertise covers aseptic, hot fill, barrier, anti-counter- feiting TE-systems, consumer convenience and child resistance","@ID":91}, "EDITOUR REPORTS 33 PETplanet insider Vol. 14 No. 09/13 petpla.net substituting virgin resin at up to 100% A month ago Surena updated its website – new labels, new advertising - and its sales have risen by 40%. Now, in the low season, Surena is able to run additional production (ultimately the brewery is designed for 100,000hl) but should the 40% growth continue until the start of the season in November, things could be a little tight. “This is the sort of problem we don’t mind worrying about”, says Paola. The heart of the brewery. We are standing in the new brewhouse, behind us you can see the older brewing kettles 360°","@ID":35}, "NEWS 12 PETplanet insider Vol. 14 No. 09/13 petpla.net Krones reports strong Q2 Krones AG has reported that its revenues for the first six months (H1) of 2013 was up 6.8% over H1 2012, to €1,377.5 million. Earnings before taxes (EBT) rose even more sharply, by 24.5%, to €79.7 million, and EBT margin improved from 5.0 to 5.8%. Net income improved 25.8% to €55.6 million, with earnings per share up from €1.47 to €1.81. Second quarter (Q2) performance saw revenues rise 8.3%, to €694.1 million, with a strong position in emerging markets helping to drive growth. Total revenue in H1 was €1,377.5 million, with the steepest increases in the Western Europe, Middle East/Africa, and Asia-Pacific sales regions. New orders were up 4.1% year-on-year to €1,382.8 million, with the biggest growth coming from Asia and Africa/Middle East. Demand from the USA stabilised. As at 30 June 2013, the company had an orders backlog of €1,004.6 million (2012: €980.4 million). The company said that price quality remained satisfactory overall. Equity ratio was 43.5% at the end of H1 (31 December 2012: 37.8%); Krones had no bank debt at the end of June and held net cash and cash equivalents of €128.6 million. The Executive Board has raised its forecast for EBT margin for 2013 to between 5.8% and 6.0%. The company says that it has made good progress towards its medium-term target of 7%. The forecast for revenue growth for 2013 remains at 4%, with no support expected from price levels. Krones is confident that it will achieve ROCE of 15%, its third strategy target, in 2013, with free cash flow for the year as a whole to be improved. The overall economic picture is expected to improve in 2014. www.krones.com Eco Plastics gets double hit Eco Plastics, of Lincolnshire, England, picked up awards from two different organisations during one busy evening in July 2013. In naming the company as the National Recycling Awards Materials Recycler of the Year, the judging panel mentioned the scale and strength of Eco Plastics’ recycling operation and its use of key partners to “…close the recycling circles”. Its Continuum Recycling joint venture with Coca-Cola Enterprises, which was awarded the prize of Business Green Leaders Recycling Project of the Year, was recognised both for the partnership’s impact on the local economy and for its broader contribution to domestic rPET production. Nick Brown, Associate Director for Recycling at Coca-Cola Enterprises, noted that Continuum had sorted more than half a billion bottles in just a year. James Murray, editor of Business Green, said that the project had a major impact on the UK’s recycling capacity and ensured that CocaCola was able to recycle all the bottles collected from the London 2012 Olympic Games, as well as providing an example of how closed loop manufacturing can slash environmental impacts and greenhouse gas emissions. www.ecoplasticsltd.com","@ID":14}, "TRADE SHOW PREVIEW 76 PETplanet insider Vol. 14 No. 09/13 petpla.net HSM Hall B4 Booth 106 Baling out HSM, the manufacturer of baling presses and PET solutions from southern Germany, will be showing its latest machine, the HSM PET FluidEx 600. It is designed to empty full PET bottles and other packages that have, for example, been incorrectly filled, wrongly labelled, or have exceeded the expiry date. The liquid is purified of small plastic fragments by a filter system and labels are cleaned and removed. Up to 10,000 1l bph can be processed. The HSM PET CP 4988 crusher and baling press combination will also make its show debut at drinktec. It is claimed to reduce the volume of empty PET bottles by up to 90% in one cycle and produces compact raw material bales of up to 100kg, at a rate of up to 4,000bph. The busy stand will, in addition, feature the HSM V-Press 860 P vertical baling press, which is designed for compressing opened or perforated PET bottles, and two machines from Pühler-HSM GmbH + Co. KG, HSM’s subsidiary. One of these is the Pühler-HSM URP-S 300 disposable packaging press, which empties, compresses and conveys incorrectly filled or past-date disposable packaging. www.hsm.eu Mold-Masters Mold-Masters will be unveiling the latest developments in its PET mould program. It will be demonstrating a 96 cavity MPET system running on a 300t machine setup; the current market standard for such systems is 400t. The MPET team at MoldMasters has also managed to run 128 cavity systems on a standard 400t machine, which will enable higher output volumes with lower capital investment. A recent MPET case study on a 96 cavity system for a 9.8g water preform demonstrated increased productivity and savings in various areas, based on replacement with the new micro pitch technology. The replacement resulted in shorter fill, cooling and cycle times. Alongside the MPET product showcase will be its hot runner solution for beverage closure systems,named Sprint. The exhibition will demonstrate a range of features, including sub-two second cycle times, fast colour changes and optimised gate cooling. The new nozzle design is claimed to run below 1.9s cycle time. Mold-Masters includes its PurgeWizard system, a semi-automated process for chemical and mechanical purging, into all TempMaster M2 controllers, as found on the Sprint. The Iris co-injection technology for barrier moulding provides a proven solution to mould multilayer preforms to accommodate requirements such as higher shelf life. www.moldmasters.com Mold-Masters Hall B3 Booth 526 Petainer Hall B3 Booth 530 Kegs Petainer’s PET plastic kegs will be on display at the drinktec trade show, in Munich in September. The lightweight kegs are available in 15, 20 and 30l capacities for drinks including beer, cider, wine, concentrates and low pressure carbonated soft drinks. The kegs are also available in preforms, which can be distributed, blown and filled locally. Additional products include small container preforms, refillable and one way bottles, and water coolers (BPA free. www.petainer.com Please visit us Hall B3, Stand 501","@ID":78}, "EDITOURS REPORTS 28 PETplanet insider Vol. 14 No. 09/13 petpla.net this is that they have now also found a way to treat waste derived from concentrates. In the plants extra spaces have been earmarked for the collection of production waste. It is chiefly companies licensed by the Bolivian State that take care of the recyclables. Part of this strategy is a social project where young people who are recovering from addictions to alcohol or other drugs can find themselves a new job. The project involves processing empty PET bottles and turning them into brushes for street sweepers. www.cbn.bo February 28, 2013 Embol S.A., Santa Cruz We met: Roberto Francina, Technical Director Coca Cola Bolivia Refillable, disposable, recyclable When it comes to filling operations, Embol, Coca Cola’s licensee in Bolivia, is not just using glass and one-way PET. They are also using refillable PET. Ever since 2002, Roberto Francina, Technical Director of Embol, has been consistently building up his plants. Roberto Francino in his office from which he controls all four plants in Bolivia. In his hand he is holding the 190ml Coca Cola bottle. With a total of 260 million bpa, Coca Cola Bolivia is the largest producer of PET bottles in Bolivia. Coca Cola produces its brand name products in four plants across the country. Its headquarters are located in Santa Cruz. What is special about Bolivia is the refillable PET bottle. The 2l bottle, weighing in at 107g, is reasonably stable and can be re-used a number of times. Roberto has the refillable bottle printed directly. This means less rubbish in the washing line and, most importantly, he knows what product was previously in the bottle. Nevertheless, he still has to make use of a specialist “sniffer” who checks every returned bottle for prohibited substances. There is no deposit on the refillable bottles but 93 % of the bottles sold still come back. Despite the fact that the system is working, around 60% of the filling operations fall into the one-way category, 30% consists of recyclable glass and a mere 10 % recyclable PET. A few years ago things were different; in those days the recyclable system was dominant. This was reflected in the filling lines. Recyclable glass and refillable PET and later also the one-way PET were being processed on the same filling line. These lines are still running today, although the real growth is in the PET refillables sector. In 2003, PET refillables amounted to 180 million litres, today, in 2013, Roberto’s filling operations account for 675 million litres of CSD. The associated lines have also developed correspondingly; essentially these are Sidel stretch blow moulders in block format for PET one-way plus Krones fillers. Only now can they look forward to a new PET refill line for the plant at the end of the year –the first for many, many years. Although the plant in Santa Cruz has shown consistent growth, Roberto Francino has succeeded in maintaining a rational production structure. The materials for all four lines installed (two refill, two one way) come from one side of the plant; the wet sections are located next to and parallel to one another (see photo) and the packing lines follow, likewise parallel to them. It is only the 40,000m² stores that he has had to banish to a site three kilometres away; had he not done so, the situation here could have become confusing. The mix of refill and one-way is also the reason why Roberto has waited so long before introducing the lightweight PCO 1881. The combined glass/PET lines cannot be converted. However, he is now looking at converting all the one-way bottles to the lightweight closure at the end of the year. Since the 2l bottle accounts for some 50% of filling operations, Roberto is paying special attention to this bottle; before embarking on the closure conversion, he is keen to optimise the 2l bottle from a weight point of view, getting it down from 56g to 48g. He has already changed the labels. One or two exceptions apart, he has since last year managed to get away from the sleeve labels and is now working exclusively with roll feed labels. They offer a sharper printed image, and they are also better suited to his high speed lines. Roberto has a host of glass formats to cope with – 1l, 1.25l, 1l, 0.6l and 0.19l. Here the 190ml bottle is the lynchpin of the marketing strategy. For the past 18 years this has cost the customer one Boliviano. Roberto has made every effort to maintain the price at this level but in the end cost pressures caused a re-think and the price is now 1.5 Bolivianos.Up to now he has been able to keep up with fast pace of growth, however he would like to have more lines. In the season all the filling lines operate round the clock and in the off-season he likes to get on with maintenance jobs. He is hoping, with the new PET refill line, to at least take some of the pressure off as far as the refill lines are concerned. 360° 360°","@ID":30}, "NEWS PETnews 9 PETplanet insider Vol. 14 No. 09/13 petpla.net Change of management at Corvaglia Closures Eschlikon AG Dr. Peter Schkoda, General Manager of Corvaglia Closures Eschlikon AG, has left the company with effect from August 2013. The Board of Directors and management regret his departure and at the same time would like to thank him for his commitment and contribution. In the interim, Franco Bischof, member of the Corvaglia Group’s Board of Directors, will manage operational matters at the Eschlikon site. Overall responsibility for the global closure business and the two production sites in Mexico and Eschlikon has been transferred to Mr. Bernardo Osés. Mr. Osés has been General Manager of Corvaglia Closures S.A. de C.V. in Mexico since 2003. He will continue to pursue the direction of the direct closure business with his international growth strategy. www.corvaglia.ch Silgan to acquire Portola packaging Silgan Holdings Inc. announced that it has entered into a definitive agreement to purchase Portola Packaging Inc., manufacturer of plastic closures. This business, with sales of approximately $200 million in 2012, operates eight facilities in North America and Europe. The purchase price for this transaction is $266 million. The transaction is expected to close as early as September 2013, subject to certain customary conditions and regulatory approvals. Silgan expects to fund the purchase price for this acquisition from a combination of cash on hand and borrowings under the Company’s senior secured credit facility. Silgan Holdings is a supplier of rigid packaging for shelf-stable food and other consumer goods products with annual net sales of approximately $3.6 billion in 2012. Silgan operates 81 manufacturing facilities in North and South America, Europe and Asia. The company is also a supplier of metal containers in North America and Europe, a worldwide supplier of metal, composite and plastic vacuum closures for food and beverage products, and a leading supplier of plastic containers for shelf-stable food and personal care products in North America. www.silgan.com European Pet bottle recycling 2012 According to a report by PCI for Petcore Europe and Plastics recyclers Europe, PET is the largest plastic material recycled in Europe, with the equivalent of more than 60 billion bottles recycled in 2012. PETcore Europe Chairman Roberto Bertaggia said: “Despite the poor economic situation in the European region, the consumption of PET bottles is still showing clear trends of penetration into new market segments through innovative packaging and the recognised capability of PET to be recycled. From a sustainability perspective, our industry is thrilled to have achieved an overall collection rate in 2012 of more than 52% of all post-consumer PET bottles available in the region. “With the exception of two members, all EU Member States managed to achieve PET recycling rates above the Packaging & Packaging Waste Directive target of 22.5% for plastics.” he added. Casper van den Dungen, PET Chairman at Plastics Recyclers Europe, underlined that “The overall European collection of PET bottles to 1.68Mt reflects an increase of 5.6% compared to the previous year. This has helped to ease the overcapacity situation of recyclers with an average plant utilisation of 80%.” In 2012 the fibres market was still the single largest end-market for recycled PET, but strong growth in the sheet and bottle market is putting these three markets at similar levels.” said Casper van den Dungen. www.petcore-europe.org Amsler drives sales with GMK Canadian company Amsler Equipment Inc., the sole North American manufacturer of all-electric reheat stretchblow moulding machines, appointed GMK Advisors Inc. to manage sales in the USA & Caribbean early in 2012. The appointment followed Mag-Plastic Machinery’s announcement of its withdrawal from the PET stretch-blow moulding machinery market. Tom Schneider and Bill O’Day, the owners of GMK Advisors, both have executive experience with blow moulding machinery manufacturers, including Mag-Plastic. Amsler says that GMK has helped it to promote and sell its PET stretch-blow moulding machinery and leak testers into new accounts in the USA and Caribbean, including a four-cavity machine to Containers Plus in Barbados and four machines to Consolidated Container Corporation in the USA. www.amslerequipment.net","@ID":11}, "BOTTLING / FILLING 55 PETplanet insider Vol. 14 No. 09/13 petpla.net its linear aseptic counterparts and also has an identical aerosol and heating system to the Innosept Asbofill ABF. In the steriliser, H 2 O 2 aerosol enters each plastic bottle through a lance inserted in the bottle that ends just below the neck. The bottle exterior is sterilised by H 2 O 2 being directly sprayed onto the bottle wall. The special sterilisation principle is applied within a single drying carousel. Filling method A non-contact filling system is used in the ASR series, with operators able to choose between two different types of filling valve. The filling carousel is much smaller. KHS claims that the new system enables around 30% fewer valves to be utilised at the same filler speed. Capper area It is usual for rotary aseptic equipment to have the entire capper unit contained in the aseptic zone. On the new KHS rotary setup, however, only the cone of the capper heads is now in the aseptic area – as in the ABF series. All other components are in a separate sanitary room which is separated from the main aseptic zone by an airlock. This keeps major interfering elements out of the sterile zone, with the safety aspects of linear machines now applied to rotary technology. Additionally, the cap steriliser has been completely redesigned. The compact unit is incorporated into the machine as a fixed component. The plastic caps travel straight from the sorter into a feed chute. The caps are sterilised with H 2 O 2 aerosol. The Innosept Asbofill ASR can also process sports caps as an option. Specific measures protect the minimally dimensioned aseptic zone from the surrounding machine area which in turn forms a mechanical barrier to the production shop.","@ID":57}, "TRADE SHOW PREVIEW 75 www.drinktec.petpla.net Supported by: Go With The Flow Tour Our successful South America tour is behind us! Our PETplanet Insider team, ever thirsty for knowledge, has been off on another tour of exploration. Starting in Lima, our longest tour so far in the Editourmobil took our editors, split into in four teams, through six countries in South America: from Peru via Bolivia, stop-off point. Three and a half months‘ travelling time, a distance of more than 12,000 kilometres and any amount of exciting interviews with the Great and the Good of the PET sector – the results of this year’s tour are once again an absolute highlight. Read all about the thrilling moments of the trip in our tour blog www.drinktec.petpla.net and experience the tour and all the companies interviewed for yourself on our exhibition stand at drinktec from16th to 20th September 2013, Hall B3, Stand 501! Looking forward to meeting you! ¡Hemos dejado atrás nuestro exitoso Tour a Sudamérica! Nuestro equipo PETplanet Insider, cada vez más ansioso de conocimiento, ha salido en otro Tour de descubrimiento. El viaje comenzó en Lima, siendo el más largo hasta el momento en nuestro Editourmobil que llevó a nuestros editores, divididos en cuatro equipos, a través de seis países de América del Sur: de Perú a Uruguay, pasando por Bolivia, Chile y Argentina, para duración de tres meses y medio, un recorrido de más de 12.000 kilómetros y una gran cantidad de entrevistas fascinantes con la elite del sector PET: los resultados del recorrido de este año son una vez más de lo más destacado. Lea todo acerca de los emocionantes momentos vividos en el viaje en nuestro blog del Tour www.drinktec.petpla.net y ¡viva la experiencia del Tour y de todas las empresas entrevistadas para usted en nuestro puesto en la feria en el drinktec desde el 16 al 20 de septiembre de 2013, Hall B3, Puesto 501! ¡Esperamos conocerle allí ansiosamente! Nossa excursão de sucesso pela América do Sul terminou! Nossa equipe PETplanet Insider, sempre em busca de mais conhecimento, saiu para outra excursão de exploração. Partindo de Lima, nossa excursão mais longa até o momento na Editourmobil levou nossos editores, divididos em quatro equipes, por seis países da América do Sul: saindo do Peru, passando pela Bolívia, pelo Chile e pela Argentina, chegando ao Uruguai de viagem, mais de 12 mil quilômetros percorridos e uma quantidade enorme de empolgantes entrevistas com os Notáveis e os Talentos do setor PET foram o resultado da excursão deste ano e, mais uma vez, um sucesso absoluto. Leia tudo sobre os emocionantes momentos da viagem no nosso blog da excursão (www.drinktec.petpla.net) e conheça a excursão e todas as empresas entrevistadas em nosso estande de exposição na drinktec, de 16 a 20 de setembro de 2013, salão B3, estande 501Go with the flow The South-America round trip with 18th February - 24th May, 2013 18 de febrero - 24 de mayo de 2013 De 18 de fevereiro a 24 de maio de 2013","@ID":77}, "EDITOUR REPORTS 27 PETplanet insider Vol. 14 No. 09/13 petpla.net EDITOUR REPORTS 27 February 27, 2013 CBN Cerveceria Boliviana Nacionales S.A., La Paz We met Ibo Blazicevic, General Director, Cristina Montilla, Director CSD, Laura Ugalde Marketing Assistant Ibo Blazicevic, General Director CBN (right), Cristina Montilla, Director CSD (left) and Laura Ugalde Marketing Assistant (far left) discussing the soft drinks market in Bolivia with Alexander Büchler and Rolf Sinkovec (both from PETplanet). Pepsi in Bolivia The CBN brewery is 126 years young. In addition to beer they also bottle Pepsi products. We looked in on the CSD people and encountered a motivated team. In Bolivia the Pepsi licence is held by CBN - Cerveceria Boliviana Nacionales – a 100% owned subsidiary of Ambev. CBN is not only the Number 1 beer producer in Bolivia; it is also one of the largest companies in the country. With a 20 % share of the market, the soft drinks division is Number 2 after the all-powerful Coca Cola. Nevertheless, the CSD division is putting on a brave show. It is registering a 5% growth rate each year on the Bolivian market. In Santa Cruz the level of growth is higher; here it is around 10%. Bottling takes place at 2 locations; one is El Alto, the sister city of La Paz, situated at a height of just under 4,000 metres above sea level. 40 million PET bottles leave the plants each year. It is mainly family sizes in 2 or 2.5 litre volumes. This also helps to explain the high quantity bottled of just under 100 million litres. The single serve bottle with a content of 500 ml hardly registers on the market. CBN are still using the 2-section PCO 1810 closure to seal their bottles. They are holding internal discussions on converting to the lightweight PCO 1881. Their other competitors in Bolivia are also still manufacturing the heavy PCO 1810. The plant structure is classic, the bought-in preforms are blow moulded and filled, labelling takes place at the end of the line. The bottles are constructed to the familiar Carolina design.CBN is keeping out of the pure water sector; this is dominated by local suppliers and Coca Cola. CBN do not ignore their responsibilities as regards the environment and social issues. In-plant the company is proud of having sent 88 % of its internal waste for recycling last year; this year they have their sights set on 96 %. The reason for 360°","@ID":29}, "MARKET SURVEY 49 PETplanet insider Vol. 14 No. 09/13 petpla.net Caps and closures Bottle-to-bottle recycling plants Preform and single stage machinery Preforms Preform / Stretch blow moulds Two-stage SBM machinery Filling equipment Resins / Additives Compressors Closure systems Suppliers of filling equipment Our market survey for filling equipment for the drinktec issue is coming up featuring all the usual suspects: listed in alphabetical order below are the global players. GEA Procomac, KHS, Krones, Sacmi, Serac, Sidel, Sipa, SMI. It is well worth taking a closer look because some of the major players will be standing by with one or two innovations just in time for drinktec. Featured in this issue are detailed reports on these from KHS, Serac, and Sidel. The companies are shown in the table in the order in which their details were received by the editors. Although the publishers have made every effort to ensure that the survey is up to date, no claims are made regarding completeness or accuracy. 09/2013 MARKETsurvey Company name Krones AG Sipa Postal address Telephone number Web site address Contact name Function Direct telephone number Fax E-Mail Böhmerwaldstr. 5 93073 Neutraubling, Germany +49 9401 70-0 www.krones.com Stefan Kraus Product Manager Filling Division +49 9401 3144 +49 9401 3056 [email protected] via Caduti del Lavoro n. 3 31029 Vittorio Veneto (TV) Italy +39 0438 911511 / +39 0438 912273 Matteo Tagliaferri Marketing and Communication +39 0521 548111 [email protected] 1. Machine designation / model number Modulfill Isofill P Stillfill S Stillfill R\\HR Flextronic C Flextronic SE 2. Number of filling heads 16 - 216 20-160 20-140 20-140 50-160 20-160 3. Min to max bottle contents (in litres) 0.125 - 12 4. Filling speed: output (bph) (min to max): specifiy: 1l bottle / still water (bph) 72,000 60,000 67,600 68,000 63,000 1l bottle / CSD (bph) 65,000 51,000 (CMW) 65,000 (CMW) 1l bottle / Milk (bph) 60,000 53,000 1l bottle / Juice (bph) 60,000 53,000 67,600 55,000 59,000 53,000 5. Filling process Pressureless (still drinks) Volumetric Net weight Height Contactless Contactless Short tube or long tube Yes Yes Yes Yes Yes Pressure filling (carbonated drinks) Volumetric Net weight Height Contactless Contactless Short tube or long tube Yes Yes Hot filling Volumetric Net weight Height Contactless Contactless Short tube or long tube Yes Yes Yes Cold aseptic filling PETAsept L / PETAsept D Contactless Juices with high pulp content Height, Pre-dosing system / aseptic Pre dosing system / hot Long tube Dosing into filling valve Full bore filling / contactless / for pulp, fibers or fruit pieces Yes Yes Yes 6. Type of filling valve and metering system Volumetric Volumetric Net weight Height Inductive flow meter Mass-flow meter Weighing cell Electronic fill height measuring Isobaric mechanical level filling valve Mechanical gravity filling valve Mechanical gravity filling valve with recirculation Isoaric volumetric filling valve Gravity volumetric filling valve","@ID":51}, "MARKET SURVEY 51 PETplanet insider Vol. 14 No. 09/13 petpla.net SMI S.p.A. Serac I-24015 San Giovanni Bianco Via Piazzalunga 30, Italy +39 0345 40111 www.smigroup.it Pietro Volpi Marketing Dept. Manager +39 0345 40316 +39 0345 40209 [email protected] 12 route de Mamers - BP 46 F-72400 La Ferte Bernard / France +33 2 43 60 28 28 www.serac-group.com Aymeric Vague Marketing Manager Home/Pers. Care +33 2 43 60 29 55 +33 2 43 60 28 37 [email protected] Roland Nicolas Dairy & Aseptic Business Development Director +33 2 43 60 28 32 +33 2 43 60 28 37 [email protected] Standard filling Ultra-clean filling Aseptic filling Baseless: electronic volumetric fillers Rotary Weigh Filler (R) Highly Hygienic Filler (H2F) Serac Aseptic System 4 (SAS 4) From 18 to 126 6- 90 6-90 8 - 90 0.25 - 10 0,05 - 20 0,60 - 2 0,05 - 2 4,800 - 36,000 3,000 - 48 000 6,000 - 38,000 6,000 - 48,000 4,800 - 36,000 3,000 to 48,000 4,800 - 36,000 4,800 - 36,000 36,000 up to 25,000 36,000 4,800 - 36,000 36,000 up to 25,000 36,000 Yes Electronic net weigh filling Electronic net weigh filling Electronic net weigh filling Yes Electronic net weigh filling Electronic net weigh filling Electronic net weigh filling Electronic net weigh filling Electronic net weigh filling Electronic net weigh filling Electronic net weigh filling Electronic net weigh filling Electronic net weigh filling Electronic volumetric filling valves. Electronic net weigh filling, pneumatic valves Electronic net weigh filling Electronic net weigh filling KHS GmbH Juchostr. 20 44143 Dortmund, Germany +49 231 569-0 www.khs.com Heinz Hillmann Product Management +49 671 852 2714 [email protected] Europa WM Matrix SF 700 FM Sensofill FMa KHS Innofill DRV KHS Innofill NV 32 - 120 32 to 108 32 -100 48 - 180 40 - 144 0.2 to 3,0 0.2 - 2 From 0.2 to 2,0 0,1 - 3 0,1 - 5 15,000 - 65,000 6,000 - 60,000 6,000 - 60,000 65,000 70,000 60,000 45,000 60,000 48,000 36,000 45,000 50,000 50,000 Yes Yes Yes Yes Yes Yes Yes Yes Yes Yes Yes Yes Mechanical level Electronic volumetric filler, with electropneumatic system with magnetic flowmeter volume control, without bottle/valve contact Electronic volumetric filler Short tube filling valve, volumetric Free flow filling valve, volumetric","@ID":53}]}}
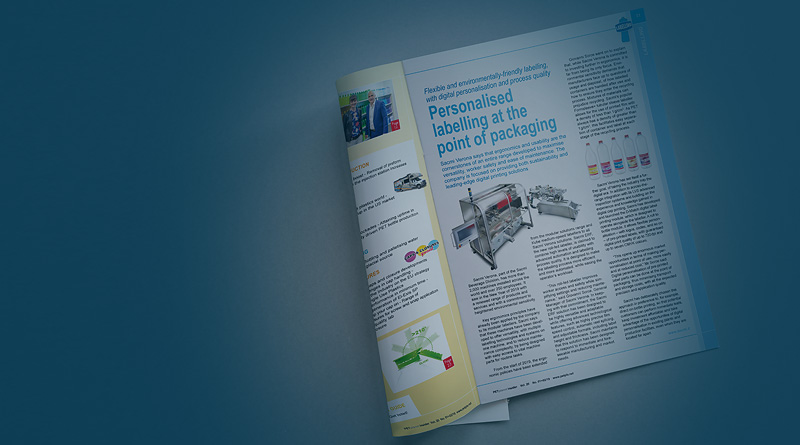