"BOTTLE MAKING 22 PETplanet insider Vol. 15 No. 03/14 petpla.net Spreading the word Italian EBM and ISBM machinery supplier Automa S.p.a. has upgraded its new product development function and operates in 75 countries worldwide. PETplanet insider visited Automa during K 2013. iLab raises standards One of the subjects that Automa is most eager to highlight is iLab, its recently-opened centre of excellence for product improvement and new project development. iLab is made up of a team of experts who are dedicated to implementing the company’s approach to providing economic solutions for container development projects. iLab has machines on-site in the European plant and Automa intends to open a similar, mould-making facility in North America. iLab uses specialised and internally-developed software to support the development of our moulds and related bottle designs. It is designed to enable Automa to achieve better results in terms of container shapes and weight reduction. The company works with mould makers in various regions across the world in developing final products that, after laboratory testing, will meet all customer specifications as required, including CP/CPK analysis. ISBM series for PET Automa’s PET single-stage solution has been continuously updated throughout the years it has been in production. It now offers reduced energy consumption, increased production output compared to comparable products, and a reduced machine footprint. Automa considers the most critical elements of this technology to be the mould components: blow moulds, injection hot runners and cold halves. The main features of its ISBM technology are: hybrid technology, which leads to low energy consumption; fast dry cycle and faster tooling changeover; smaller footprint; higher output per cavity free mould legacy Automa’s ISBM machinery is used in the production of PET containers for food, pharmaceutical, detergents and personal care markets. Specifications include: narrow neck finishes (20mm), including amenity and sample bottles traditional finishes (20 to 48mm) for, e.g., beverages, personal care, and household cleaners wide mouth finishes ( 53mm) for food products like peanut butter, mayonnaise and nuts Automa upgrades its single stage machinery","@ID":24}, "41 PETplanet insider Vol. 15 No. 03/14 petpla.net BEVERAGES / INGREDIENTS systems dedicated to monitoring line status and events, improves production traceability and can even be used to improve line efficiency. The role of PET packaging Packaging plays a vital role in protecting the safety of our food and drink. When in direct contact with its contents, packaging needs to meet the very highest standards of safety, hygiene and legislative requirements in order to maintain product quality and safety. Whether the beverage is packaged in can, glass, carton or PET, every component of the production line that comes into contact with the contents to be consumed has to be carefully designed to meet these high standards. This also applies to the packaging itself for which the choices of material and barriers are equally important and usually determined by the required shelf life and consumer expectations of the finished drink. As a material of choice for primary packaging for drinks, PET has been successfully in use for over 30 years with no reported adverse effects. This is because it is a biologically inert plastic, for which the constituent materials are well defined, needing no additives for enhanced performance and for which the manufacturing process is equally standardised. It has been thoroughly reviewed as a primary packaging material and fully approved by international safety agencies such as the US Food & Drug Administration (FDA), Health Canada and the European Food Safety Authority (EFSA). Suppliers of PET resin are required to produce two different certificates demonstrating approval of use for their material in direct contact with food: the Material Safety Data Sheet (MSDS) which provides information regarding the actual plastic resin, its constituent parts and its compliance with food regulations; and the Technical Data Sheet (TDS) related to the performance characteristics of the plastic. The regulations covering the use of recycled PET (RPET) are somewhat different. Unlike the virgin material, a list of possible recycling processes is published by EFSA. Yet no list of approved RPET material exists, neither does a list of approved RPET material suppliers. PET protects the sensitive Used to protect sensitive beverages such as beer, juice and milk products from light and oxygen, ‘barrier’ PET can extend the shelf life of products and improve their look and taste. Regulations and legislation Experience the Limits! Inspection Systems for Barrier Enhanced Containers www.intravis.com Booth E1T09","@ID":43}, "imprint EDITORIAL PUBLISHER Alexander Büchler, Managing Director HEAD OFFICE heidelberg business media GmbH Häusserstr. 36 69115 Heidelberg, Germany phone: +49 6221-65108-0 fax: +49 6221-65108-28 [email protected] EDITORIAL Doris Fischer: [email protected] Gabriele Kosmehl Michael Maruschke Ruari McCallion Waldemar Schmitke Ilona Trotter Wolfgang von Schroeter Anthony Withers MEDIA CONSULTANTS Martina Hirschmann [email protected] Roland Loch [email protected] phone: +49 6221-65108-0 fax: +49 6221-65108-28 France, Italy, Spain, UK Elisabeth Maria Köpke phone: +49 6201-878925 fax: +49 6201-878926 [email protected] LAYOUT AND PREPRESS Exprim Kommunikationsdesign Matthias Gaumann | www.exprim.de READER SERVICES Heike Fischer [email protected] PRINT Chroma Druck & Verlag GmbH Werkstr. 25 67354 Römerberg Germany WWW www.hbmedia.net | petpla.net PETplanet insider ISSN 1438-9459 is published 10 times a year. This publication is sent to qualified subscribers (1-year subscription 149 EUR, 2-year subscription 289 EUR, Young professionals’ subscription 99 EUR. Magazines will be dispatched to you by airmail). Not to be reproduced in any form without permission from the publisher. Note: The fact that product names may not be identified as trade marks is not an indication that such names are not registered trademarks. 3 PETplanet insider Vol. 15 No. 03/14 petpla.net dear readers, Mediterranean here we come! At long last the time has come for the Editourmobil to set off on tour again. Following brief stops in Austria and Switzerland, our itinerary will begin in Italy where we are looking forward to visiting companies both large and small in the weeks leading up to Easter. The next stage of the tour will see us in North Africa and Spain. As usual you will be able to follow our progress from the end of March via our online blog. You will recall that we were undecided about the vehicle livery. After much deliberation, we have opted for the big green spaces option. This nearly caused a major upset to the timetable. Instead of two days as planned, our films man took nearly a week to apply the film neatly to all the windows and flaps all around the vehicle. We almost had to postpone the start of the tour! The livery was not the only thing that has changed. The Editourmobil itself has been transformed into a new (old) vehicle. The Laica on an Iveco base served us splendidly during our tours to Russia and the East and the arduous trip through Latin America. It has now gone to a good home in Chile. For our new vehicle we were hoping for a bit more floor space and, primarily, a vehicle without any electronics. Eventually, we came down in favour of a Mercedes Benz 814, built in 1990. The only electronic item in the vehicle is the radio. To put it through its paces and check everything was in order, we took it on a 5,000km trip. We made a couple of minor changes, the first being to fit a large roof light to ensure we had plenty of light. Next we re-worked the electrics, fitted new batteries, inverters and a patch panel which ensures we will have a reliable power supply. Another vital element was the router to supply us with WLAN whenever possible and enable us to upload the photographs on to the blog promptly. The pièce de résistance, however, has got to be our own beer and it’s on tap! This is all part of an in-depth experiment we shall be conducting to establish whether PET kegs are suitable for beer. There were several systems to choose from (see article in issue 4/13), and in the end we decided on the Keykeg system, which seemed to us to be the most suitable for our requirements. The system requires no carbon dioxide and a small compressor ensures that adequate pressure is maintained between the beer bag and the PET keg. When we are on the move, we have a filler valve available, which means that we can also take a keg with us on site. In the second stage in the configuration the air pressure for the 2-circuit air braking system comes from the chassis. It is only when the compressed air tanks are empty that the small compressor swings into action. We will report back once we get to this stage. In the meantime, you will be more than welcome to join us in a glass or two of the amber liquid. Yours Alexander Büchler","@ID":5}, "CAPPING / CLOSURES 38 PETplanet insider Vol. 15 No. 03/14 petpla.net advaltech Foboha specialise in moulds for 2-component closures. With patented developments Foboha have played a decisive role in the field stack turning technology and/or cube technologies for manufacturing multi component parts in plastic. Over a period of 30 years Foboha have developed around 2,000 multi-component injection moulds. Foboha service the international premium niche markets, in particular closures for energy drinks and/or food supplements. Hansjörg Keusgen quote: “In instances where the design is coordinated with the process and is right for the process, the advantages of cube technology are clear; complex components with just one machine – machine clamping force halved – cavities doubled – production cycles significantly shortened. Numereous ptoduct ideas are generated by this technology.“ Mold-Masters We met: Michael Feltes, Director Business Development Iris & E-Multi Claudiu Bolovan, Program Manager, New Products Mold-Masters hot runners are to be found on a large number of injection moulding machines being exhibited and demonstrated at the K 2013 Fair, for example on the Engel, Netstal, Stork, Sumitomo Demag and Ferromatik Milacron stands. On their own stand, Mold-Masters were showcasing their electric E-Multi injection unit in a multi-component application – on an all-electric Ferromatik Milacron F160 with F&S mould. The items for injection moulding were 38mm closures in HDPE for hot fill, into which a barrier made from EVOH was co-injected – using the so-called Iris co-injection process. Michael Feltes quote: “The new type of process (coinjection) offers a revolutionary alternative to traditional packaging methods. As far as we are concerned there is no doubt that there is a market for multi-component closures, especially - and in particular in the case of large closures - where the penetration of oxygen to the inside and/or nitrogen to the outside is greater than it is with PET bottles”. The product The E-Multi is a compact, allelectric injection unit that is directly mounted on the mould. E-Multi and Iris co-injection can be installed on standard injection moulding machines, lowering overall capital costs compared to other systems while providing 100% process control with a fully integrated control system. Features The E-Multi combines five Mold-Masters core technologies: Iris the compact co-injections nozzle (two materials flow in parallel) iFlow the distribution technology for a balanced infeed of melt and homogenous cavity filling E-Drive checking the needle opening and closing movement by means of the precision E-Drive Servo System TempMaster M2 hot runner temperature control system E-Multi all-electric additional injection unit mounted on the mould side (direct servo drive for injection, belt drive for barrel). Claudiu Bolovan quote: “These five core elements are integrated and interlinked on a single control system. The electronics of the controls are the brains of the system – controlling the E-Multi (barrel and needle movements) as well as the hot runner temperatures.” MHS We met: Harald Schmitt, President Jörg Schmidt, Managing Director Founded in 2002, with headquarters in Ontario, Canada, the company specialises in high performance, runnerless injection moulding systems. At K 2013, MHS showcased its Rheo-Pro iVG stack mould hot runner system in a stack mould for double part output – in an application for caps and closures. The new MHS stack mould technology - injecting parts in both directions using two parting lines - allows plastic closure manufacturer to double production of valve gated parts without having to run additional or larger moulding machines. A standard 48+48 iVG stack mould in a small 200t injection moulding machine can produce 96 light weight bottle closures every 3s and thus is claimed to be over 30% more cost efficient than the conventional 96 cavity single face hot runner system. Major savings are in lower capital investment for smaller moulding machines with less clamp tonnage required, in energy savings, reduced space requirement and a lower carbon footprint. Harald Schmidt quote: “The moulder benefits from the ability to produce more plastic parts in smaller machines with less clamp tonnage - which means better operating cost, significantly higher production outputs and most importantly, better profitability.” Mold-Masters techonology at K 2013 MHS stand at K 2013","@ID":40}, "NEWS 11 PETplanet insider Vol. 15 No. 03/14 petpla.net IMAGINE FILLING MULTIPLE PRODUCTS ON THE SAME LINE…NOW YOU CAN! Water, juice and soft drinks, all on a single machine? The Flextronic modular platform adapts effortlessly to still or sparkling, clear or pulpy and hot or cold-fill, and easily switches from one bottle neck-size to the other. A revolutionary filling technology that gives you extreme operational flexibility with minimal product loss and downtime at flavor switch. Clean, safe and versatile. Welcome to the new generation of fillers. carbonated still hot-fill cold-fill pulp non-pulp water juice soft drink SIPA S.p.A. - Via Caduti del Lavoro, 3 - 31029 Vittorio Veneto (TV) - Italy Tel. +39 0438 911511 - Fax +39 0438 912273 - e-mail: [email protected] www.sipa.it Change at the top of Brigl & Bergmeister The Brigl & Bergmeister Group, Niklasdorf, Austria, a manufacturer of speciality paper for labels and flexible packaging, has announced that Mr Ahmad Porkar has replaced Mr Martin Ruopp as Managing Director of the company, effective January 31, 2014. Mr Porkar has owned the group since 2011. www.brigl-bergmeister.com Krones spins out valves to Evoguard Beverage filling and packaging technology company Krones AG has announced that it has established a new totally-owned subsidiary company, Evoguard GmbH, located in Nittenau, Germany. It will operate Krones’ valve technology business as a stand-alone business. Operations began in January 2014 and it is intended that it will be able to develop sales in sectors outside the food and beverage industry. Krones said that, as an independent and autonomous company, Evoguard will benefit from a favourable cost structure, high flexibility, and a streamlined management structure. Evoguard valves are produced in a 4,000m2 facility in Nittenau, which houses R&D, design, sales and assembly operations. www.krones.com Pro Mach acquires André Zalkin US packaging machinery and integrated system provider Pro Mach, Inc., has announced the completion of its acquisition of Ets. André Zalkin & Cie, the global capping machinery manufacturer. Financial terms of the transaction were not disclosed. Zalkin’s management team and employees will continue to operate from existing facilities in Montreuil L’Argillé and RueilMalmaison, France. Pro Mach owned a minority stake in Zalkin before acquiring the remaining shares. The two companies have worked together for over 40 years, since the 1972 initiation of a partnership between Pro Mach’s Fowler Products division and Zalkin, which has delivered capping solutions to customers in the food, beverage, pharmaceutical, and consumer goods markets. www.promachinc.com","@ID":13}, "PRODUCTS 45 PETplanet insider Vol. 15 No. 03/14 Optical sorting station for flake processors The Bühler Group, a global supplier of optical sorting solutions, has unveiled its Optical Sorting Station (OSS) system, at K. The optical sorting station brings together the key elements of successful optical sorting, including plant engineering, sorting technology, pneumatic conveyors, pre-conditioners and auxiliary equipment. For flake processing, an optical sorting station features a purifying, refining, sizing and grading stage which can include one or more Sortex optical sorters. These are linked by all the necessary equipment to convey the product between stages and, if required, to re-introduce it into the system for resorting. Flakes can be fed into one end of the station and collected at the other end - ready for bagging or further processing. Bühler says they have already installed the full optical sorting station for several of their plastics customers, including Deceuninck and ITW Poly Recycling. www.buhlergroup.com/optical PET and glass with Galileo The new long skirt LSK EV Galileo II 29/44 closure system from Bericap, which is designed to fit on 30-2921mm PET and glass bottle neck finishes, is configured with a flexible hinge and is available in both single and two-colour versions. It is designed with double tamper evidence; tabs break on first opening and a tear-off membrane has to be opened. After opening, pouring is controlled by a flow regulator and the pourer is of a nondrip design. The large printing area on the side of the closure provides opportunity for brand advertising. The new long skirt closure system is already on the market and is being used by a number of bottlers. www.bericap.com","@ID":47}, "PETpatents www.verpackungspatente.de 52 PETplanet insider Vol. 15 No. 03/14 petpla.net Fixed open position European Grant of Patent No. EP 2427387 B1 Applicant: Obrist Closures Switzerland GmbH, Reinach (CH) Date of Application: 4.5.2010 A hinged lid for closing a container incorporates snap-in features that fix the lid in the open position. Optimised container European Grant of Patent No. EP 2316740 B1 Applicant: Yoshino Kogyosho Co., Tokyo (JP) Date of Application: 28.2.2000 This European Grant of Patent describes a number of options for mounting reinforcing grooves, ribs or recesses in order to make a container more stable. The container is nevertheless “lightweight” and can be easily compressed for low volume disposal. Base design International Patent No. WO 2012 / 038075 A1 Applicant: Red Bull GmbH, Fuschl am See (AT) Date of Application: 21.9.2011 The design of the base of a plastic bottle specially adapted to the needs of a drink containing carbonic acid is outlined. Dispensing closure International Patent No. WO 2013 / 113640 A1 Applicant: Obrist Closures Switzerland GmbH, Reinach (CH) Date of Application: 25.1.2013 Single or multi-section container closure with pouring spout and hinged lid is described. The lower section can be adjusted to the shape of the container. Plastic bottle International Patent No. WO 2013 / 114760 A1 Applicant: Yoshino Kogyosho Co., Tokio (JP) Date of Application: 20.12.2012 A plastic bottle is specially designed in the areas of the base, shoulder and side wall to guarantee adequate stability along with simultaneous low weight. The shape of the all-round, wavy grooves is irregular. Multipack International Patent No. WO 2013 / 117849 A1 Applicant: Sidel Participations, Octeville-Sur-Mer (FR) Date of Application: 4.2.2013 The film for holding a number of individual bottles together in a multipack is specially formed in the area of the shoulder and the base and/or incorporates openings that allow a number of multipacks to be stacked together without the base of the top bottle touching / destroying the film.","@ID":54}, "EDITOUR REPORTS 14 PETplanet insider Vol. 15 No. 03/14 petpla.net A pioneer in the Brazilian PET market Initially, PET bottles were bought in from the market in Sao Paulo. It was not until 1994 that the company purchased its own blow moulding machine from Messrs MAG Plastic Switzerland with four blow moulding stations installed and the preforms bought in from all over the world. As we toured the factory, we noted a Krones Contiform S8 stretch blow moulding machine and a KHS bottling machine with a bottling capacity of 14,000bph. In each case the bottler is modified to suit the bottle sizes required. 80% of the preforms are purchased from Plastipak Packaging do Brasil and the plastic closures from CSI Closures Brazil in the 1881 lightweight version with a weight of 2.7g. The change-over to this closure took place in 2012. As far as the bottle sizes are concerned, the 2l PET bottle accounts for 80% of production, followed by the 0.6l with 7%, 1.5l with 6% and 290ml with 7%. Two particular areas of growth are the 1.5l and 2l bottles. A special requirement of consumers in the Parana and Santa Catarina regions is the “family size” bottle” and Hugo Cini take pride in catering for this market. The total bottling capacity is 14 million litres a year in PET bottles. The portfolio also comprises Cini soft drinks bottled in reusable glass bottles as well as mineral water (carbonated and non-carbonated) bottled in PET bottles (some of which are recyclable) and plastic tumblers marketed under the Cini brandname but filled by partner companies. The share of the market for recyclable beverages packaging in the region continues to be stable at 15%. According to Nilo Cini Jr, having a large portfolio is important for generating customer loyalty. This brings us to the sales structure.Transport costs are high here, and this is why the company focuses on a sales radius of some 200km using their own transport fleet and personnel. According to Nilo Cini Jr, “this is also a way of taking on the big boys. We have an easy and direct access to the market, and it facilitates the introduction of new products for smaller bottlers. The majority of our 200 direct employees are sales people. Anything over and above this is handled via trade organisations.” The company’s philosophy has been to ignore the traditional beverages market focusing instead on the requirements of a particular group of purchasers by exploiting differences in taste. An example of this is sugar-free drinks, which Hugo Cini was one of the first beverage bottling companies to be able to offer as far back as the 1990s. The years 2005/6 saw the launch of soft drinks based on juices from Brazilian fruits and tea was also introduced. According to Nilo Cini Jr, there is nothing currently on the market that is similar to their Swiss Lemonade (Limonada Suica), a beverage which appeals to a large number of people in the region. The various flavours are devised in-house, and the concentrates are bought in and blended. The fruit concentrates, for example, come from other companies within the family who own factories in Manaus and produce fruit extracts from regional fruits. The market strategy is positive. According to Nilo Cini Jr, in 20012 they registered growth of 10% and are anticipating a similar figure for 2013 which means they are above average for Brazil. May 7, 2013 Industria Zugliani de Refrigerantes e Bebidas Ltda. We met: Sidney Angelo Zugliani, Director Industrial Jose Guilherme Zugliani, Finance Manager From left to right: Well Bueno, Dept. Marketing, Lady member of staff, Sidney Angelo Zugliani, Director Industrial In the background a Brazilian bottling machine for bottling Soda soft drinks in 250ml PET bottles Step by step This family-run enterprise, founded and still run by the descendants of Italian immigrants, has been producing beverages for more than a century. Even before waves of Italian immigrants arrived in Brazil in between 1877 and 1900, the family was already active in the wine business. However, it was not until 1941 when the family acquired a controlling stake in a soft drinks producer that the company really took off. Over subsequent years the company was Nilo Cini, Junior Director / Bottling of Cini Laranjinha soft drinks in 600ml PET bottles on a KHS bottling machine","@ID":16}, "BOTTLE MAKING 20 PETplanet insider Vol. 15 No. 03/14 petpla.net Nissei ASB Machine CO., LTD.: Four new machines at K 2013 Live on the stage Nissei ASB Machine Co., Ltd. showcased four machines at K2013. and was also celebrating its 35th anniversary at the forefront of the PET container industry. exhibition a 500ml, 26mm neck diameter (light-weight neck), 9.8g water bottle was moulded at an output of 9,000bph. PF24-8B 12 cavities: High output 1.5-stage machine for up to 5l bottles One of the key features of the new PF24-8B is that it is capable of being converted to mould in two configurations. Either 24 injection plus eight blow cavities, or twelve injection plus four blow cavities can be utilised for up to 1.5l and up to 5l bottles respectively. In this second PF24 machine, the cavitation has been set to mould 5l containers in 12 cavities. With additional factory options, this model can also mould bottles with 1 E-tech (Retain-Heat Equalising Process Technology). ASB’s patented technology is able to adjust the temperature of injected preforms to maximise the quality of finished containers, the handles being inserted prior to blowing. As such, this machine enables a wide range of container designs making it suitable for users who are thinking about a future expansion of production. During the exhibition a 5l, 48mm neck diameter, 83g PET edible oil bottle was moulded at an output of 2,400bph. PF24-8B 24 cavity: High output 1.5-stage machine for up to 1.5l bottles The PF24-8B is a high-end addition to ASB’s PF Series, 1.5-stage machines, which produce finished containers directly from PET resin in a compact space. It is developed as a high-speed mass production machine with productivity of 9,000bph (lightweight 500ml water bottle); currently the highest output machine in ASB’s product range. It boasts particularly small space requirements with respect to its high output, hydraulicelectric hybrid systems for greater energy efficiency and an E-tech*1 for stable moulding. The new PF24-8B global model high-speedmachine made its international debut at K2013. Its productivity step-up from ASB’s existing PF8-4B machine is three times higher, while only requiring 1.5 times the floor space. During the PF24 1.5 stage machine","@ID":22}, "NEWS 9 PETplanet insider Vol. 15 No. 03/14 petpla.net First South African-European colloquium on recycling Petco, the PET Recycling Company (Pty) Ltd of South Africa, hosted the first-ever South African-European forum on the subject of recycling, in December 2013 from Cape Town, S Africa. The forum, entitled “Global Partnerships for a Sustainable Recycling Sector: Sharing. Dialogue. Action”, was dubbed a colloquium – an informal meeting or discussion. It attracted more than 200 delegates, from Africa, Europe and N America, the majority attending via videofeed. Six plenary sessions saw 15 members of the European Association of Plastic Recycling and Recovery Organisation (Epro), and 15 of South Africa’s experts on recycling, waste management, recovery and sustainability, deliver papers on the challenges, opportunities, latest trends and innovations. Panel debates involved the audience to pose questions and comments to local and international experts. Janez Potočnik, European Union Commissioner on the Environment, highlighted the value of waste as a resource that should not be landfilled or burned, as well as the need for a transition to a circular economy as a more sustainable economic growth model. He encouraged joint efforts and initiatives aimed at increasing material recovery and reducing the impact of litter on the environment on a global scale. Cheri Scholtz, CEO of Petco, said that S Africa is the leading country in Africa in plastics recycling and is not far behind European countries in recycling and waste recovery solutions. Part of the intention of inviting Epro to South Africa to have their first ever General Meeting on African soil and to participate in the colloquium was to create a platform for the sharing of ideas and set the stage for future global partnerships. According to Scholtz, the international delegation was eager to share with South African audiences their knowledge and experience from activities in Europe and the United States, and was also keen to learn from experiences across all packaging streams in Southern Africa, the BRICS and other developing countries represented on the programme. Waste management is an important element of the South African economy and places a strong emphasis on job creation and service delivery. www.petco.co.za www.epro-plasticsrecycling.org Chinaplas 2014 “to be biggest ever” The organisers of the 28th International Exhibition on Plastics and Rubber – better known as Chinaplas 2014 – which will be staged at Shanghai New International Expo Centre, China, April 23-26 2014, say that this year’s edition will be the largest in the event’s history. It is expected to attract more than 2,900 exhibitors and will occupy an exhibition area of over 220,000m2, and will feature international pavilions from countries in Europe, the Far East, Turkey and the USA. Bayer MaterialScience, Dow, Kolon Plastics, and Sunshow, Uniplas have confirmed their attendance. In order to help delegates to find their way around the large exhibition area, some products will be classified into particular zones; Chemicals and Raw Materials, Colour Pigment and Masterbatch will be located at additional exhibition hall C10, with Additives in hall C11. The exhibitor list and app has been launched and can be found online at the address below. www.ChinaPlasOnline.com Milacron buys IMSI and PPM US company Milacron LLC has announced that it has completed the acquisition of Industrial Machine Sales, Inc. (IMSI) and its sister company, Precise Plastics Machinery (PPM). IMSI specialises in the application engineering of primary plastics processing and support systems for operations including injection moulding, extrusion and blow moulding. PPM was established in 1994 as a full service support company for the plastics industry, including offering pre-owned equipment and turnkey services. Imsi and PPM and their staff will continue to be based in Southlake, Texas, which will serve as a High Impact Technical (H.I.T.) centre in the region providing machinery support, training, and aftermarket parts and service. Their customer base includes major manufacturers in the plastics industry located in Texas, Louisiana, Oklahoma, Arkansas, Mississippi, New Mexico and the northern border of Mexico. Larry Burchett, the president and owner of IMSI and PPM, will serve as Vice President of Sales and General Manager of the Milacron Certified Pre-Owned Machinery division. Burchett began his career at Milacron, leaving on his purchase of IMSI in 1991 but maintaining a connection through a 20-year agent association between IMSI, PPM and Milacron. www.milacron.com","@ID":11}, "13 marzo – 15 agosto 2014 Giro dell’Europa sudoccidentale e del Nord Africa con PETplanet Go to Brau Beviale – Esplorazione della regione del Mediterraneo occidentale Si parte per nuove avventure! Il nostro team di reporter di PETplanet Insider è di nuovo in partenza. L’Editourmobil è più grande e abbonda lo spirito di scoperta; questa volta il team esplorerà l’area del Mediterraneo occidentale. I nostri impavidi specialisti Alexander Büchler, Waldemar Schmitke, Kay Barton e Rolf analizzeranno i mercati PET di Italia, Tunisia, Algeria, Marocco, Spagna, Portogallo e Andorra. Il loro viaggio epico durerà 5 mesi, e comprenderà un arduo itinerario di 7.000 chilometri che attraverserà due continenti, durante il quale tre team di PETplanet incontreranno i principali esponenti del settore. E ancora una volta ci auguriamo di porgervi il benvenuto a bordo per condividere il viaggio con noi: seguite il blog del viaggio a www.braubeviale.petpla.net E potrete leggere le interviste con le aziende che visiteremo sul nostro stand alla Fiera Brau Beviale dall’11 al 13 novembre 2014 e successivamente in PETplanet Insider. www.braubeviale.petpla.net Supported by: Del 13 de marzo al 15 de agosto de 2014 Gira del Sudoeste de Europa y Norte de África con PETplanet Go to Brau Beviale – Explorando la región del Mediterráneo occidental ¡Nuevas aventuras a la vista! Nuestro equipo de reporteros de PETplanet Insider vuelve a poner rumbo hacia nuevos mares. Con un Editourmobil más grande y abundante espíritu aventurero, la gira explorará la región del Mediterráneo occidental. Nuestros intrépidos especialistas, Alexander Büchler, Waldemar Schmitke, Kay Barton y Rolf analizarán los mercados de PET de Italia, Túnez, Argelia, Marruecos, España, Portugal y Andorra. Ante ellos se abre un épico viaje de 5 meses con un extenuante recorrido de 7.000 kilómetros que les llevará a través de dos continentes. A lo largo del camino, tres entusiastas equipos de PETplanet entrevistarán a los principales jugadores del sector. Una vez más esperamos darles la bienvenida a bordo para que compartan el viaje con nosotros: siga la gira en el blog del viaje en www.braubeviale.petpla.net Descubra todas las entrevistas con las empresas que visitamos en el stand de la exhibición Brau Beviale del 11 al 13 de noviembre de 2014 y después en PETplanet Insider. 13 March - 15 August, 2014 Circular tour of South West Europe and North Africa with PETplanet Go to Brau Beviale – Exploring the western Mediterranean region Up and away on new adventures! Our team of reporters from PETplanet Insider are off on their travels again. Featuring a larger Editourmobil and the spirit of discovery in abundance, the tour this time is centred on and around the area of the western Mediterranean. Our intrepid specialists Alexander Büchler, Waldemar Schmitke, Kay Barton and Rolf will be analysing the PET markets of Italy, Tunisia, Algeria, Morocco, Spain, Portugal and Andorra. Before them is an epic journey of 5 months, involving a gruelling 7,000 kilometre itinerary covering two continents, during which three PETplanet teams will be talking with the major players. And once again we look forward to welcoming you on board to share in the trip with us: follow the tour by travel blog on www.braubeviale.petpla.net And you can find out all about the interviews with the companies we visit on our exhibition stand at Brau Beviale from 11 to 13 November 2014 and afterwards in PETplanet Insider. 13 mars – 15 août 2014 Tour de l’Europe du Sudouest et de l’Afrique du Nord avec PETplanet Go to Brau Beviale – À la découverte de la région méditerranéenne occidentale En avant vers de nouvelles aventures ! Notre équipe de reporters de PETplanet Insider reprend la route. Avec une édition de l’Editourmobil plus importante et une soif de découverte sans fin, le tour sera cette fois-ci centrée sur la partie occidentale de la région méditerranéenne. Nos intrépides experts, Alexander Büchler, Waldemar Schmitke, Kay Barton et Rolf , analyseront les marchés du PET en Italie, en Tunisie, en Algérie, au Maroc, en Espagne, au Portugal et en Andorre. Un voyage épique de 5 mois les attend, avec un éprouvant trajet de 7000 kilomètres couvrant deux continents tout au long duquel les trois équipes de PETplanet s’adresseront aux principaux acteurs du marché. Nous sommes là encore impatients de vous recevoir à bord pour faire ensemble un bout de chemin: suivez le tour sur notre journal en ligne www.braubeviale.petpla.net: vous trouverez tout ce qu’il faut savoir sur nos interviews avec les entreprises que nous rencontrerons sur notre stand d’exposition de Brau Beviale de 11 au 13 novembre 2014 et, après cela, à PETplanet Insider. Go to BrauBeviale The Western Mediterranean round trip","@ID":45}, "BOTTLE MAKING 24 PETplanet insider Vol. 15 No. 03/14 petpla.net Coca-Cola in Northern New England embraces PET Bottle-blowing on-site The Coca-Cola Bottling Company of Northern New England (CCNNE) has begun producing PET bottles on-site for the first time ever, with a KHS Innopet Blomax Series IV machine. The Coca-Cola Bottling Company of Northern New England (CCNNE) recently invested in the installation of a KHS InnoPET Blomax Series IV stretch blow moulder, which enabled it to produce PET bottles on-site for the first time in its history. This does not mean that CCNNE was not using PET bottles – it has been, for several years, but it sourced all of its PET containers exclusively from converter company Southeastern Container. Perhaps paradoxically, John Palermo, the former vice-president of Operations at CCNNE and now chairman of the supervisory board at Southeastern Container, is partly responsible for this decision. “To date, the majority of PET bottles have been procured by the beverage industry in the USA from converters. However, I believe the future is in producing PET bottles on-site, buying the preforms from the converters,” he said, and went on to explain that the economics of the InnoPET Blomax machine, including the energy and material savings it offers, helped to reduce on-site PET bottle production costs. There Neal visited a number of beverage operations in Europe and gathered valuable impressions and experience. They saw the newly-developed Series IV on display on the KHS stand at drinktec 2009 and came to believe that it had the ability to change the attitude to inline PET bottle production on the US market. is an environmental impact as well, as the 28-cavity machine eliminates approximately 1,800 truck deliveries each year. CCNNE first took note of the trend towards inline PET bottle production on the European market about ten years ago, when Palermo and CCNNE bottles the full range of Coca-Cola brand beverages. The bestseller is still Coca-Cola Classic with a share of about 22%, followed by Diet Coke (18%) and Dasani bottled water (9%). The products bottled at CCNNE are sent out from nine distribution centres in New England and New York State. The products bottled at CCNNE are sent out from nine distribution centres in New England and New York State","@ID":26}, "EDITOUR REPORTS 12 PETplanet insider Vol. 15 No. 03/14 petpla.net March 30, 2013 Mineracao Campo Branco Ltda., Progresso We met: Erminio Vivian, General Director Nestor Jose da Silva, Production Manager Diego Pellenz, Finance Manager Direct from spring to bottle In the midst of the hilly landscape of the Sirra Gaucha, 150 kilometres north-west of Porto Alegre, we find the management team of Mineracao Campo Branco, the mineral water spring and associated bottling operation, waiting for us at the end of a gravel road. This family business was set up in 2006 to bottle mineral water directly from their own spring. Filling operations take place as follows: PET bottles 0.5 – 1.5 – 2.0l carbonated, 0.5 -1.5 - 2.0l non-carbonated. PET water dispensers, 5l, non-carbonated PP water dispensers, 10l and 20l, non-carbonated PP tumblers, 200ml non-carbonated The 20l PP water dispensers account for the highest bottling volume in terms of litres per year. The highest quantities in terms of units are achieved by the 0.5l PET bottles. Total bottling capacity is at 9.6 million litres of mineral water per year. Of this 40% is carbonated and 60% still. The sales territory covers Greater Porto Alegre Rio Grande do Sul. Campo Barnco products are to be found predominantly in supermarkets, including the Carrefour chain. Interviews in Brazil in this issue: Mineracao Campo Branco Ltda. Hugo Cini S.A. Industria Zugliani de Refrigerantes e Bebidas Ltda. to follow: Coca Cola Brasil Ltda. Andina Rio de Janeiro Refrescos Ltda. Lindoyana de Aguas Minerais Ltda. Grupo Ravi Amcor Rigid Plastics South America Husky Injection Molding Systems Bericap do Brasil Ltda. Ambev Logoplaste Shefa Döhler América Latina Ecoplaca (by Florian Roscheck) Krauss Maffei do Brasil Ltda Otto Hofstetter AG Lima Santiago La Paz Buenos Aires Montevideo Progresso São José dos Pinhais São Paulo Rio de Janeiro Lindóia Santa Cruz Sucre Quilmes Pilar Jaú Concepción Santa Fe Barueri Jundiai Sorocaba Amparoa Limeira Brazil Part 2 by Waldemar Schmitke","@ID":14}, "MARKET SURVEY 30 PETplanet insider Vol. 15 No. 03/14 petpla.net 3/2014 MARKETsurvey Company name Krones Starlinger Tecnofer Ecoimpianti Erema Engineering Recycling Maschinen und Anlagen Gneuss Kunststofftechnik Postal address Telephone number Web site address Contact name Function Direct telephone number Fax E-Mail Böhmerwaldstraße 5 93073 Neutraubling, Germany +49 9401 70-0 www.krones.com Peter Hartel Sales Dept. PET-Recycling +49 9401 70-5448 +49 9401 70-91-5448 [email protected] Sonnenuhrgasse 4 1060 Wien, Austria +43 1 59955-0 http://recycling.starlinger.com Elfriede Hell General Manager recycling technology +43 1 599 55 1300 +43 1 599 55 180 [email protected] Via Calto 409 45030 Ceneselli (Ro) Italy +39 0425 849090 www.tecnofer.biz Mauro Garbellini Sales Manager +39 0425 849090 [email protected] Unterfeldstraße 3, 4052 Ansfelden, Austria +43 732 3190-0 www.erema.at Christoph Wöss Vacurema Product Manager +43 732 3190-352 +43 732 3190-23 [email protected] Mönichhusen 42, 32549 Bad Oeynhausen, Germany +49 5731 5307 0 www.gneuss.com Andrea Kossmann Marketing +49 5731 5307 10 +49 5731 5307 77 [email protected] Bottles to granulate Four models: recoStar PET FG, recoStar PET FG+, recoStar PET iV+, recoStar PET iV+ Superior Input variable: collected pressed bottles, various colours Engineering of washing lines and / or a turn-key project with components and technologies available in the market Yes, in cooperation with long-time partners Engineering of washing lines with long term partners Output: Granulate with approval Yes Yes (decontaminated for food-contact, IV increased, AA 1ppm, lowest VOC level) Yes Capacity [t/a] 3,500 - 21,000 6,000 - 26,000 Up to 17,000 Floor space [m²] 800 - 2,000 Depending on design Which approvals FDA - LNO, EFSA, various others Several USA / FDA (C-H), EFSA, Austria, Germany BfR, Ilsi, France / AFSSA, Finland, Australia, Bolivia, Canada, Switzerland, Peru (pending); brand owners FDA, ESFA (pending), INTI, brand owners (conf.) Fresh water consumption per tonne output [m³/t] 1,0 - 2,5 Depending on design Depending on bottle contamination Consumption kWh per tonne output [kWh/t] Depending on design Depending on input material Flakes to granulate Input variable: Flakes, coloured proportion max 5%, not much chlorine Four models: recoStar PET FG, recoStar PET FG+, recoStar PET iV+, recoStar PET iV+ Superior Basic flakes specifications: Higher contamination can influence pellet quality but are basically possible to process, after discussion and agreed by Erema Output: Granulate with Approval Yes Yes (decontaminated for food-contact, IV increased, AA 1ppm, lowest VOC level) FDA, efsa (postive opinion issued), ANVISA, ilsi, BGBI, brand owners FDA, ESFA (pending), brand owners (conf.) Capacity[ t/a] 3,500 - 21,000 1,500 - 26,000 (5 extruder sizes) up to 32,000 200 -17,000 Floor space [m²] 800 - 2,000 130 - 540 Depending on through-put and technology: 8-200 30 - 80, depending on size Which approvals FDA - LNO, EFSA, various others Several USA / FDA (C-H), EFSA, Austria, Germany BfR, Ilsi, France / AFSSA, Finland, Australia, Bolivia, Canada, Switzerland, Peru (pending); brand owners FDA [cat. A-H&J]; efsa (pending); brand owners (conf.); several national approvals (Austria, CH, Zona Mercursur, etc.) FDA, ESFA (pending), INTI, brand owners (conf.) Fresh water consumption per tonne output [m³/t] 1,0 - 2,5 approx. 0,15 Depending on application and technology type but we have a closed loop system No fresh water needed Consumption kWh per tonne output [kWh/t] approx. 410 (depending on design) 250 - 350 350 Bottles to flakes Input variable: collected pressed bottles, various colours Yes (decontaminated for food-contact, IV increased, AA 1ppm, lowest VOC level) Yes, in cooperation with long-time partners Output: Flakes with/without approval with/without approval FDA [cat. A-H&J]; efsa (pending); with Multi Purpose Reactor (MPR) Capacity [t/a] 3,500 - 21,000 3,700 - 10,500 (5 sizes) 3,000 - 25,000 up to 15,000 Floor space [m²] 800 - 2,000 m² approx. 150 500-1500 between 20-40 Which approvals FDA - LNO, EFSA, various others FDA (hot-fill), follows EFSA requirements not applicable FDA, efsa (postive opinion issued) Fresh water consumption per tonne output [m³/t] 1,0 - 2,5 1,5-3 Closed loop system Consumption kWh per tonne output [kWh/t] k.A. 120 - 250 (incl. bottle washing to SSP) 280-320 100 Miscellaneous Engineering of washing lines and / or a turn-key project with components and technologies available in the market Company also offers systems for Super- PET process from bale to preform Bottle-to-non-wovens systems Bottle-to-film Yes Yes Yes Bottle-to-fibre Yes Yes Yes Bottle-to-strapping Yes Yes Yes","@ID":32}, "BOTTLES 51 PETplanet insider Vol. 15 No. 03/14 petpla.net Crystal oil for the hair With their new product in the ‘Gliss Kur Range’, Schwarzkopf & Henkel are promising a shimmering shine and light reflections by the million. The promise of shine is reflected both in the bottle and in the surface of the cardboard packaging. The bluish-tinged PET bottle, which tapers slightly towards the base, has a content of 75ml and is decorated on the front with a non-label-look label whilst the rear label features printing with a 3-dimensional effect on the inside. The pump dispenser for applying the content is golden coloured. At the PoS the bottle is presented in a fold-down box which features identical printed text. www.glisskur.de On Broadway… Spectra Packaging have added six new PET packs to their Broadway range of oval containers. Following customer demand, Spectra decided to release six new containers in PET, expanding the entire Broadway oval range to twelve packs in total. In addition , there are also three PET tottle packs to choose from. As with existing Broadway containers, the new packs feature integral snap neck closures offering a complete oval packaging solution. The four new PET Broadway ovals are available in 200ml, 250ml and 300ml capacities. Additionally, the new tottle versions are also available in 200ml, 250ml and 300ml capacity options. www.spectra-packaging.co.uk Hand gel hygiene Under their own “Balea“ brand name, the drugstore discounters dm are offering an anti-bacterial hygiene hand gel. The product, which eliminates 99% of all bacteria, can be used without the need for additional soap and water. The 300ml contents are bottled in a bulbous, stand-alone bottle made from PET. The product, which is similar to a gel and incorporates air bubbles, is discharged by means of a screw-on, lockable and transparent pump dispenser. An all-round selfadhesive label ensures product visibility the product and gives a ”clean“ look to the packaging. www.dm-drogeriemarkt.de product development caps & closures design high cavitation moulds multi-component moulds closure production systems after sales service competent – professional – inspiring Hoechster Strasse 8· 6850 Dornbirn, Austria· T +43 5572 7272-720· www.z-moulds.com CHINAPLAS 2014 April 23rd-26th meet us at booth W1-T05","@ID":53}, "PETproducts 44 PETplanet insider Vol. 15 No. 03/14 petpla.net Nordson Kreyenborg’s single support cart Nordson Kreyenborg has announced the launch of a concept that combines screen changer and gear pump on a single movable cart. The company claims that the new product takes up less floor space than separately mounted machines, simplifies deployment in an extrusion line, and provides easier access for replacement of filter media. The concept was originally developed at the request of one of its customers but it can be applied with equipment custom designed by Nordson Kreyenborg for other companies, including extrusion processors, compounders, and recyclers. The cart is mounted on fixed casters that permit transversedirection movement into and out of the extrusion line, while precisely aligned movement in the extrusion direction is provided by floor-installed rails. Linear guides on the cart permit independent extrusion-direction movement of the gear pump and screen changer. In order to save space facilitate access for changing screens, the gear pump has effectively been turned onto its side so that its drive can be mounted below the pump. Coolant can be either air or demineralised water and its rate of flow is adjustable. www.nordson.com www.kreyenborg.com Precision without barriers Intravis, Germany, supplier of quality inspection systems for the plastic packaging industry, presents a new development for its Sample PreWatcher. This system, first introduced to the market in 2009, is by today the standard system for high precision preform inspection and measurement in the plastic packaging industry. Optionally, the Sample PreWatcher is now able to visualize and determine barrier layers in preforms helping to optimize packages for sensitive beverages. The device is in use already in the market. www.intravis.com End of the line Sipa’s new generation of Digipac pallet stretch-wrapping equipment is designed to provide a compact, flexible, and cost-efficient solution on bottle packaging lines, the company says. The range, which comprises the Orbiter rotating pallet and Cinetic rotating arm, is claimed to be easily installed on lines running with conventional or robot palletisers. Cinetic’s film unwinding arms are mounted on a rotating platform that is anchored to the ground and turns around the fixed pallet. It is available either with one or two rotating arms, and is capable of wrapping up to 120 pallets/h. The Orbiter stretch-wrapping units, which rotate the pallet, are capable of handling up to 50 pallets/h. Sipa’s “Matrix” system, in which the film unwinding arms are mounted, is claimed to be robust and stable, with a rigid and balanced construction. Finished pallets exit at 90° to the line, without the need for a turntable. An impermeable top sheet can be positioned by the optional Fast-cover. The Pre-cover option can be used for special requirements or to achieve a double pallet cover. The Stunit device pre-stretches the film by as much as 320%, depending on the speed of the operation and product needs. Cutting and welding of the end of the film is performed by Cs-unit. www.sipa.it LSP PET recycling process After an R&D period of more than 30 months, NGR (Next generation recycling maschinen) GmbH, of Feldkirchen, Austria, has launched a new process for PET recycling which focuses on increasing the IV value and decontamination of the material. The decontamination service is carried out impartially by a third party in a challenge test. The test results form the basis for approvals in the food industry. NGR’s LSP process aims to use the higher rate of reaction in the melt phase to save energy and time during PET processing. The processing unit used in lab testing had an output rate of only 70kg/h. A production unit with an output rate of 380kg/h was designed and put into operation in Autumn 2013. The processing method was the subject of frequent discussions with a number of European and American PET processors, and the concept was well received, according to NGR. The new process has been developed for processing PET from industrial waste, fibres, bottles, preforms, films and washed post-consumer-flakes. www.ngr.at","@ID":46}, "CAPPING / CLOSURES 36 PETplanet insider Vol. 15 No. 03/14 petpla.net BMB We met: Nigel Baker, Managing Director UK & Ireland Stewart Leng, Area Sales Manager UK & Ireland Among the Italian machine manufacturers, BMB is the upmarket address when it comes to packaging, including the injection moulding of caps and closures. The company (400 employees, annual turnover approx. € 90 million) is privately owned by the Marco Bugatti family, who was doing the honours on the BMB stand with his resplendent machine. At the same time the British BMB representatives did the utmost to explain the technology of the equipment as well as the glamour and glory of the company – in the motivated and enthusiastic manner that we have come to expect from the Italian company. A PETplanet study at K 2013 Caps and closures In part 2 of our study we continue to describe the state-of-the art technology and the developments, strategies and competitive differentiation of the companies involved in the market of suppliers of systems and moulds for the production of caps and closures. Stewart Leng quote: “We sell what our customers want to buy. Every machine is tailor made to our customers’ requirements. The prime consideration of BMB engineering is that the machine performs perfectly for the application whilst at the same time ensuring that the lifetime performance of the mould is not detrimentally affected. For clean Stewart Leng","@ID":38}, "NEWS 10 PETplanet insider Vol. 15 No. 03/14 petpla.net Döhler snaps up Mexican subsidiary Innoval Döhler, based in Mexico City, became a 100%- owned Döhler subsidiary in January 2014 and will be fully integrated in the Döhler group, a manufacturer of technology-based natural ingredients, ingredient systems and integrated solutions for the food and beverage industry headquartered in Darmstadt, Germany. Mexican ingredient specialist Innovación Alimentaria was founded in 1992, by Gustavo León. Döhler acquired nearly 40% of the company in 2006. The new subsidiary, renamed Döhler Mexico S.A. de C.V., is planned to be increasingly active in the United States and Canada markets. Juan Maldonado, previously Commercial Director at Grupo Altex, has been appointed General Manager. Gustavo León and his son Ricardo will remain with the company. www.doehler.com G’s Fresh and Amcor pick up prizes at UK Packaging Awards The UK Packaging Awards 2013, held in London, England, saw G’s Fresh M&S (Marks & Spencer) beetroot range sealed with Amcor ReClose win First Prize in the ‘Consumer Convenience’ category, along with a Highly Commended prize in the ‘Flexible Plastic Pack of the Year’ category. The G’s Fresh M&S Beetroot range is packed in a punnet, sealed with Amcor’s ReClose lidding film. Amcor ReClose technology allows film-lidded trays to be opened and reclosed up to 15 times; it seals to PE, PS, PP or directly to APET trays. Amcor Flexibles Europe & Americas, a division of Amcor, is the world’s largest supplier of flexible packaging. G’s Freshis a vertically-integrated supplier of produce that operates farms and production facilities throughout the UK. www.amcor.com www.gs-fresh.com Autoneum appoints new CFO Autoneum Holding Ltd has appointed Dr. Martin Zwyssig as Chief Financial Officer (CFO) and member of the Group Executive Board. Martin Zwyssig, 48 and a Swiss national, will take up his duties on April 1, 2014. He was previously Group CFO of Schaffner Holding Ltd (2003-8) and Group CFO of Ascom Holding Ltd (2008-13). Urs Leinhäuser, currently CFO and Deputy CEO, has decided to leave the company for personal reasons and to focus on his external mandates and entrepreneurial activities. www.autoneum.com Coke wins awards with Krones design Coca-Cola Amatil CCA has won the 2013 Australian Packaging Design “Best of Show” Award with the NitroHotfill bottle, designed by Krones. The 600ml Powerade Sports bottle is an extremely lightweight, eco-friendly hotfill bottle with a 38mm wide-neck closure. The container’s weight has been cut from 33 to 24g and the filling process was changed over from hotfill to warmfill, which led to substantial energy savings. All of the bottle’s constituents can be fully recycled. Bottles made with Krones’ NitroHotfill process can be produced with a minimised weight, without vacuum panels and with flatter bases, the company says. The design was also recognised by the World Packaging Organisation, which chose the container as the 2013-2014 Worldstar Winner in its packaging competition. www.krones.com Milacron buying Kortec US company Milacron LLC has continued on the acquisition trail with the purchase of Kortec, a supplier of co-injection technology solutions to the packaging industry. Milacron CEO Tom Goeke described the addition of Kortec as a “perfect” accompaniment to the company’s 2013 acquisition of Mold-Masters, the hot runner manufacturer. Paul Swenson, Kortec’s President and CEO, said that the acquisition would enable his company to reach a larger customer base and to supply a wider variety of solutions. The acquisition was scheduled to complete before the end of February 2014. www.milacron.com","@ID":12}, "EDITOUR REPORTS 15 PETplanet insider Vol. 15 No. 03/14 petpla.net gradually expanded and the move to Jau in the Federal State of Sao Paulo in 1950 saw the foundation stone for the present-day factory being laid. The proclamation of the Republic of Brazil on November 15, 1889 was, commercially-speaking, so important for the Zugliani family that the number 15 was adopted as a brand name for the beverages and is still in existence today. Change to PET bottles Originally glass bottles were used for packaging all drinks. Then, in 2000, they gradually went over to disposable PET. However, there still remains a substantial market for re-usable glass bottles and Zugliani has been kept consistently busy over the years to meet market requirements which currently amount to 10% of production.The overall bottling capacity is 800,000l/ month of carbonated soft drinks. The flavours range from Guarana (a native fruit widely used in S American soft drinks. Its seeds contain more caffeine than coffee beans!), Soda Lemonade, Orange, Cola right through to Crazycat energy drinks. The most popular flavour by far is Guarana, at 50%, followed by Soda Lemonade at 13% and Cola, which has over the years moved from the shadows to take a 16% share, and this is rising. The bottle sizes in PET range from 250ml, 600ml, 1l right through to 2l, which accounts for over 75% of the market. The reason is that for the Brazilian consumer, the 2l PET bottle is “family size”, and very typical of the region. Bottling operation In the bottling operation we saw a PET bottler of the Brazilian brand Zegla. A capacity of 3,000 6-pack trays is achieved in an 8h a day, single shift operation. The PET bottles come from the region covered by Blow PET and the plastic closures (BPF) from Aro in Rio de Janeiro. However, the design of the bottle is owned by Zugliani. The investment is still too high to think about lightweighting in the area of the closure and neck finish. There is one remaining bottling line available with washing machine and crown cork closing device for bottling four drinks in 600ml recyclable glass bottles. Fruit concentrates and aromatic flavourings are ordered from Brazilian fruit processors, mixed here in the factory and fed to the bottling machine together with the carbonic acid.The PET filling line made in Brasilia undergoes appropriate modifications for the different bottle sizes. 2014","@ID":17}, "EDITOUR REPORTS 13 PETplanet insider Vol. 15 No. 03/14 petpla.net In front of the Brazilian bottling plant Mesal Maquinas, from left to right. Nestor Jose da Silva, Production Manager, Erminio Vivian, General Director, Diego Pellenz, Finance Manager, Waldemar Schmitke PETplanet. Erminio Vivian, General Director of Campo Branco and himself a member of the family proudly shows us the water tanks behind the factory which collect the mineral water directly from the spring via a system of pipes. The output from the spring is between 3,000 and 14,000l/h. According to Erminio Virian, the mineral water in this region is known for its good quality and has a pH value of 7.1. This is the reason why mineral water is extracted from a total of 26 mineral water springs in this region, spread over 23 bottling plants. The 0.5, 1.5 and 2.0l bottles are made in-house on a Multipet ESM 2/6 linear stretch blow moulding machine with a capacity of 1,800-2,000 0.5l PET bottles. Preforms and closures are bought-in, preforms from Cristal PET Uruguay and the closures from one of the production facilities situated in the vicinity. The water dispenser containers are ordered by Campo Branco on the open market. For bottling the 0.5-2.0 litre PET bottles there is a Mesal Maquinass Best Fill 30.30.10 bottling line with a capacity of 13,000bph. Placing the 6-packs on pallets is a manual operation and, should the labelling machine break down, the labels can also be applied by hand. “We like to be flexible”, says Erminio Virian. Asked about what the prospects are for the immediate future, Erminio Vivian answered: “For smallish operations such as ours there is always the danger of predators waiting to snap us up”, he said, “so it’s important for us to maintain our growth objectives. That apart”, he went on, “we are now thinking of manufacturing our own preforms in-house. This would mean our investing in a preform system with a number of injection moulding machines.” Should a machine break down, labels can be attached by hand. May 3, 2013 Hugo Cini S.A. Industral de bebidas e conexos We met: Nilo Cini, Junior Director Ana Mamore, Marketing Manager Catering to the region’s tastebuds The story of Hugo Cini began 109 years ago. Italian immigrants were looking for a new home in Brazil. The Cini family, with long experience as wine-growers, were seeking a new beginning in Brazil’s beverages industry. A successful start was made with the manufacture and sale of alcoholic drinks and this led in 1920 to the establishment of a brewery splendidly named “Cervejararia Esperanca” (“Hope Brewery”) producing “Schwarzbier” (“black beer”) using the bottle conditioning process. This was the foundation for the present-day factory that was named after one of the founder’s sons, Hugo Cini. From left to right: Nilo Cini, Junior Director and Waldemar Schmitke, PETplanet 1990 was a milestone in the history of Hugo Cini. By this time the beer business had been definitively abandoned in favour of carbonated soft drinks and reusable glass bottles had given way to disposable PET bottles. Nilo Cini fondly recalls these turbulent times when the structure of the company was completely overhauled. It was still the era of recyclable glass, and it was thus possible to fully utilise the bottling capacity of 28,000bph. However, demand for soft drinks in disposable PET bottles was burgeoning and this led to a breakthrough for the company. Alongside the changeover to PET disposable bottles, there were changes coming in the market place. Increased competition grew with the arrival of the big multinationals such as Coca Cola. In 1990, there were still 50 soft drinks manufacturers in the Federal State of Parana. Today, by contrast, there are fewer than half that number. “Smaller companies have been gobbled up by the majors”, which, according to Nilo Cini, “led to further major changes in the company’s structure to meet these new challenges.” “Undeterred”, he went on, “we continue to go our own way, knowing that we were and are one of the pioneers in the Brazilian market. “","@ID":15}, "MATERIAL / RECYCLING 19 PETplanet insider Vol. 15 No. 03/14 petpla.net Control (FCC) feature supervises the stored recipe data. This enables users to switch to the process parameters required for the production of the respective recyclate simply by pressing a button. If levels go beyond defined limits an alarm is triggered automatically and (optionally) material flow is diverted away from the production line. This guarantees traceability Efficiency performance A total of eight different PET recycling technologies available on the market were tested by an independent institute for electrical and thermal performance. The Vacurema Inline Sheet system (used to produce food contact grade thermoforming sheet) of a customer in Germany came out on top in an energy comparison with other systems available on the market, recording the lowest specific total energy consumption (including sheet downstream) of 0.29kWh/kg (Fig. 2). Vacurema technology proved to be 40% more energy efficient than other systems also in the bottle-to-bottle field with a rating of 0.295 kWh/kg. This is due on the one hand to the decontamination before extrusion which – unlike other systems on the market – requires only a single energy input for processing. Plus, on the other hand, no additional pre-drying is required as materials with input moisture of up to around 1.5% can be processed. The very large active filter areas of the Erema filter systems likewise contribute to The plastic closure company committed to your success BERICAP Technology Research and Development Mould Technology | Global Presence Capping Technology and Know-How Innovation and Flexibility www.bericap.com the system’s remarkable efficiency performance. The patented partial surface backflush screen changers from the RTF series feature a fully automatic self-cleaning system which, despite extremely fine filtration (32μm screen mesh), allows low pressure losses, high filter capacity and long filter service life. The result is highly clean repellets. Users are also spared from having to buy expensive special filters which are often necessary with other manufacturers. Erema’s highperformance filters can be connected directly to the extruder outlet. They have been successful for large area ultrafine melt filtration in the production of flat film and as a consequence other manufacturers of film plants now use the Erema piston screen changer as standard. These are available in a variety of sizes and output levels, up to the six-piston system with twelve parallel filter screens. Inline crystallised strand pellets Vacurema technology is based on Compact Inline Crystallisation (CIC). According to Erema, this technology makes Vacurema the only system on the market which is able to produce strand pellets. As around 80% of virgin material is produced in strand form, mixtures of repellets made using Vacurema and virgin material are now easier and actually possible. www.erema.at Fig. 3: Vacurema Basic energy efficiency","@ID":21}, "29 PETplanet insider Vol. 15 No. 03/14 petpla.net Caps and closures Bottle-to-bottle recycling plants Preforms Preform and single stage machinery Preform / stretch blow moulds Two-stage SBM machinery Compressors Resins / additives Filling equipment Closure systems Bottle-to-bottle recycling plants Contributions to this year’s market survey for bottleto-bottle PET recycling plants come from ten companies: In alphabetical order they are: Amut (Italy), Erema (Austria), Gneuss (Germany), Herbold (Germany), Krones (Germany), Protec Polymer Processing (Germany), Sorema (Italy), Starlinger (Austria), Tecnofer (Italy) and Zheijiang Boretech (China). The companies are listed in the order in which their details were received by the editors. Although the publishers have made every effort to ensure that the information in this survey is up to date, no claims are made regarding completeness or accuracy. 3/2014 MARKETsurvey","@ID":31}, "PETbottles 50 PETplanet insider Vol. 15 No. 03/14 petpla.net Home + Personal Care This is the one Superdrug has selected M&H Plastics for the packaging of its new range This One – a collection of haircare products. The range includes shampoos and conditioners, a replenishing treatment, curl and wave crème, hair oil and a blow dry spray. All products carry the Cruelty Free International symbol. The shampoos and conditioners use M&H’s 250ml PET tubular bottle with a double-wall X-Press cap whilst the replenishing treatment uses M&H’s 150ml double walled spirit jar. In addition the hair oil is packaged in a 100ml PET tubular shape topped off with a serum pump, whilst the 150ml curl and wave crème comes in a 35mm diameter tube. The product range has been manufactured in a shade of purple with flashes of bright colours, and all the closures have been colour coordinated in purple, ensuring the range stands out in PoS displays. www.mhplastics.com Listerine sensitive Johnson & Johnson has launched on the market a variant of their Listerine mouthwash product range with a milder taste for people with sensitive teeth. The mouthwash is intended to combat the many and diverse causes of painful sensitive teeth. The product is packaged in a transparent, angular PET bottle with a content of 500ml which sits comfortably in the hand. Three labels transmit the retail information and a childproof screw cap with a dispensing function and tamper proof guarantee add the finishing touches to the appearance. www.listerine.de Surface haptics The Italian company Deco Industries is marketing, under its “Scala“ brand name, a range of hand washing up detergents packaged in a transparent PET bottle with a content of 750ml. The bottle incorporates recesses in the area of the base and the top which are reminiscent of bubbles of foam and make it possible to grasp the bottle with wet or sticky hands. A screwon, silver-coloured hinged lid with a dispensing aid and two shaped self-adhesive labels completes the packaging. www.decoindustrie.it Premium fabric softener from dm The brand manufacturers lead the way using various exotic fragrances in colourful bottles and the discount stores follow suit. The German drugstore discounters dm are selling, under their own brand name of “Denk mit”, 1l of fabric softener complete with the tag “Oriental Dream“, which is calculated to transport the consumer and carry them away into the sensuous world of oriental fragrances. The waisted PET bottle is tinted to shine like gold, designed so as to be easy-to-handle, decorated with two self-adhesive labels and sealed with a colourmatched screw cap complete with dispensing aid. www.dm.de/denkmit","@ID":52}, "BOTTLE MAKING 25 PETplanet insider Vol. 15 No. 03/14 petpla.net Ressources It is usual in the USA for CocaCola bottlers to source their PET bottles or preforms from Southeastern Container or Western Container, depending on their location. Both companies were founded by a conglomerate of several Coca-Cola companies, with Western Container launched in 1979 and Southeastern Container in 1982. Western Container now has five production sites and Southeastern Container ten. CCNNE originated in 1977 when Japanese company Kirin Holdings bought shares in a small Coca-Cola bottling plant in New Hampshire. After a number of acquisitions, CCNNE is now fully owned by Kirin Holdings and part of its Overseas Beverages operation. It is the largest independent bottler of Coca-Cola in the USA. The company is also involved in the production of alcoholic and non-alcoholic beverages for the Japanese market, and pharmaceuticals and biochemical. CCNNE’s facility in Londonderry, NH, now produces 28 million crates (around 266 million litres) of alcoholfree beverages a year. It is currently the fifth-largest Coca-Cola bottler in the USA, producing the full range of the company’s products, which it sends to nine distribution centres throughout New England (Maine, New Hampshire, Vermont, Massachusetts, Rhode Island and Connecticut) and in the state of New York. The sales area covers about 85,000 square miles and is home to around 4.5 million people. About half of all sales are in low and zero-calorie soft drinks and water. Coca-Cola brand beverages are only filled into PET bottles (40%) and cans (60%); there are no glass containers. The range of PET bottles includes the 300ml, 12, 16, 20 and 24-oz, and on to the 0.5, 1.0, 1.25 and 2l bottles. The 20-oz and 2l bottles are especially popular in the PET The InnoPET Blomax Series IV at CCNNE has 28 blow stations, each of which outputs up to 2,250 PET bottles per hour. Its distinguishing features include savings in energy, compressed air and materials and the production of top-quality bottles.","@ID":27}, "40 PETplanet insider Vol. 15 No. 03/14 petpla.net BEVERAGES / INGREDIENTS Food safety: The ‘sine qua non’ of food and beverage production Let’s play it safe By Sid Johari, Executive Vice President for Industrial Operations, Sidel Scandals involving product safety still have the capacity to shock the food and beverage industry and, more importantly, badly affect consumer confidence all over the world. Various incidents, widely reported around the globe, have made consumers more aware than ever of food safety issues and the potential for food production to go wrong. With social media playing an increasingly powerful role, consumers also have the means to communicate any failings immediately to a waiting and responsive audience. However, this has resulted in a significantly increased focus within Europe on traceability throughout the industry. Sid Johari casts an inquiring eye on the measures which can be taken by the food and beverage industry and their suppliers to guarantee food safety. Safety throughout the supply chain Food and beverage manufacturers are, of course, highly aware of the level of damage that can be caused by any product safety scandal that results in the breakdown of consumer trust in their brands. Most now work more closely than ever with all stakeholders in their own particular supply chains to ensure quality, traceability and the achievement of the appropriate standards. This collaboration generally covers every aspect, from the sourcing of raw materials and basic ingredients, through the whole manufacturing process, to the filling and packaging of products and the eventual distribution and transporting of the finished product to the consumer. This is because all stakeholders at every level have a shared responsibility to ensure complete food safety. Traceability practices Within the beverage industry, traceability practices are equally vital. Drinks companies must be able to understand everything that occurs on their production lines. They should be able to trace any batch of drinks from the raw ingredients stage throughout the whole production process through distribution and storage. In the event of any incident of contamination, only real traceability provides access to critical plant information, either in real time or after the occurrence. These days, of course, there are tracking solutions readily available that can be implemented on any beverage production line. The data acquired by these","@ID":42}, "BOTTLES 49 PETplanet insider Vol. 15 No. 03/14 petpla.net Molasses in headstand bottle The German company Eurovera is marketing 300 grams of sugar cane molasses in a headstand bottle made from PET. The molasses are extracted in the form of juice or syrup during pressing of the sugar cane, they are a mineral concentrate and also act as a sweetener. The PET bottle has a honeycomb-type surface structure and is sealed with a snap-on hinged lid. Self-adhesive labels to front and rear convey the retail information. www.medicus.de Smoothies from Lidl The discounter Lidl is marketing its “naturis“ smoothies with 100 % fruit in two different shape PET bottles. One is slim, slightly waisted and tall, the other tends to be squat with a distinct waist in the middle and incorporating reinforcement grooves. Sleeve labels and a tamper-proof screw cap are an additional feature in both. The major difference lies in the haptics of the bottles. The shorter bottle provides enhanced handling reassurance when lifting, opening and drinking, whereas the slim bottle appears “unstable”. petengineering.com [email protected] P.E.T. Engineering: the one-stop shop for beverage packaging. Technology excellence, captivating design, ergonomic shapes: a product developed by P.E.T. Engineering is easily recognizable. Its technical know-how and experience have made of it a leader brand in the sector of PET containers. Design, prototyping, laboratory tests and the production of blow moulds: P.E.T. Engineering is the perfect partner, holding itself all the possible solutions. PACKAGING. EVERYTHING YOU NEED DESIGN The perfect shape for an easy handling. PROTOTYPING Bottles available just a few hours DIWHU WKH ȴQDO GHVLJQ RESEARCH AND DEVELOPMENT New materials, innovative solutions and cutting edge technologies. PRODUCTION AND CUSTOMISING OF THE MOULDS High quality blow moulds for every kind of container and any type of blowing machine. STARTUPASSISTANCE AND TRAINING Supporting the client during the whole project. Deluxe with screw cap Right on cue for the holidays at the end of 2013 the German discounter Lidl increased the assortment in its deluxe range to 150 different products in attractive packaging. For example, salad dressings were packed in slim, transparent PET bottles each with a content of 250ml. The photograph shows the variants Balsamico with Fruits of the Forest and Honey with Mustard. The bottles are closed by means of an aluminium screw closure which also features an adhesive paper strip which acts as a tamper-proof seal prior to initial opening.","@ID":51}, "MARKET SURVEY 31 PETplanet insider Vol. 15 No. 03/14 petpla.net Zheijiang Boretech Herbold Meckesheim GmbH Sorema division of Previero Amut ProTec Polymer Processing GmbH Phoenix Technologies International Pinghu, Economic Development Zone, Pinghu, Zhejiang, China. 314214 +86-573-85120186 www.bo-re-tech.com Chris Chen Sales Manager +86-573-85120186 +86-573-85113959 [email protected] Industriestrasse 33 74909 Meckesheim +49 / 6226 / 932 0 www.herbold.com Siegfried Engel Vice President Sales +49/ 6226 / 932 133 +49/ 6226 / 932 495 [email protected] Via per Cavolto 17 22040Anzano del Parco, Italy +39 031 63491250 www.sorema.it Dario Previero Sales Manager +39 031 63491250 +39 031 63491217 [email protected] 28100 Novara, Italy Via Cameri, 16 +39 0321 6641 www.amut.it Piergianni Milani President Recycling Division +39 0321 664941 +39 0321 474200 [email protected] Stubenwald-Allee 9, 64625 Bensheim, Germany +49 6251 77061 - 0 www.sp-protec.com Hans Schnell Senior Techn. Expert Projects & Processing +49 6251 77061 142 +49 6251 77061 580 [email protected] 1098 Fairview Ave, Bowling Green, OH 43402 USA +1 419 353 7738/419 353-rPET www.phoenixtechnologies.net Lori Carson Director Commercial Operations +1 419 353 7738 +1 419 354 7738 [email protected] Yes No own plants, but cooperation with established washing system manufacturer (Agglomerate) up to 36,000 3,000 to 45,000 1,000 0,5 - 1 depends on stream quality 545 300-600 Yes Yes - standardized process for production of foodgrade pellets; special feature is a flexible process which enables the reliable adjustability of customer specific values of viscosity Flakes, clear, blue, green Yes - for direct food contact. Including iV increase and lowest VOC levels, AA 1 ppm Pellets, both bottle grade and food contact grade up to 13,000 (1unit) 3,000 to 15,000 4,000 - 15,000 (bigger sizes are also available) 40,000 64 300 - 500 depending on capacity 900 EFSA, FDA, Anvisa, brand owners FDA, Health Canada, ANZI, EFSA pending 0,5 0.5 negligible approx. 125 Depending on design 0.35 - 0.4 (depending on plant size and humidity of incoming flakes it may vary) 450 Yes No own plants, but cooperation with established washing system manufacturer 3,960 - 47,520 6,000 - 30,000 5.000 - 45.000 3,600 - 45,000 500 - 1,500 1,000 - 3,000 800 - 5,000 2 to 3 1 - 3 1 90 - 140 approx. 250-300 0,22 - 0,27 250-300 PET bottle washing plants, turnkey systems, single components, size reduction components Pre-sorting system for mixed plastics. De-labeller machine for complete removal of sleeves Yes Yes Yes Yes Yes Yes","@ID":33}, "BOTTLE MAKING 35 PETplanet insider Vol. 15 No. 03/14 petpla.net stress cracking resistance is the time period until the bottle starts to leak or burst. The fill level is marked, and the time is noted when it falls. Specifications usually include a time before which no bottle may fail, and then a time at which a percentage of failures is acceptable (e.g., no bottle fails for 20min, then a maximum 50% failure rate after a further 20min). Fillability In laboratories equipped with the appropriate filling valves, tests are carried out to find out whether the bottles are suitable for trouble-free filling with the proposed filler. Although this is not so critical for long-tube fillers, the filling behaviour is more important in the case of fillers where the contents flow down the inside of the container wall, especially if a strongly foaming product is being bottled. Crystallinity For hot-fill bottles, the degree of crystallinity, which is a measure of the temperature resistance, is determined. The crystallinity is usually determined by measuring the density of the PET in the container wall. For this purpose hydrostatic balances based on the Archimedes principle can be used. The cheapest solution is a density gradient column in which fluids of various densities are layered on top of each other. Depending on how deep the PET sample sinks, its density can be read from a scale on the vessel. A relatively quick method, which unfortunately requires significant investment, is the Fourier transform infrared crystallinity index measurement in which the crystallinity can be directly derived from an infrared spectrum. Droptest In this test filled and closed bottles are dropped onto the floor in free fall from a height of 2m. The bottle must not burst. A variant is the drop test on an inclined plane in which the bottle hits the plane with one of its feet. Drop tests are usually performed at ambient temperature but may also be carried out at 4 or 6°C, depending on the specification. Please order your copy at the PETplanet insider book shop: https://petpla.net/books Bottles, Preforms and Closures A Design Guide for PET Packaging Second Edition by Ottmar Brandau € 115,00 180 pages © Copyright Elsevier 2012 Barrier Various methods are used to determine the barrier properties depending on whether a barrier against the ingress of oxygen or against CO 2 loss is specified. Barrier against oxygen As a rule, the tested bottles are filled with the intended contents and are stored at higher temperatures to accelerate the diffusion processes. This yields faster results than realtime shelf life. One of the possible O 2 barrier test methods (available from PreSens, Germany) comprises a low-cost sensor spot that is placed on the inner wall of the PET bottle. This sensor spot is then excited with blue light from the outside and sends an optical signal back through the PET wall. The captured signal is proportional to the oxygen content. Barrier against loss of CO 2 There are also several possible test methods for measuring CO 2 retention. In one of these tests a sample bottle is pressurized with pure CO 2 an internal pressure that is maintained constant. The bottle is placed within a measuring chamber. This may be a gas-phase chromatograph, and in this case, the CO 2 increase in the measuring chamber outside the bottle will be measured directly. Another possibility would be to use a pressure measurement chamber in which the pressure increase outside the bottle is measured. Both measurements allow statements on the amount of CO 2 diffusing through the container wall. There are also measuring methods involving bottles filled with carbonated water or product. The bottles are filled, closed, and stored. Special instruments permit the determination of the residual CO 2 in the bottle. Segment weight distribution As a preparation of a subsequent online quality assurance or a subsequent determination of the machine capability, sample bottles conforming to all specifications are cut with a hot wire into three segments at exactly defined positions (bottom, label or lateral area, and shoulder); hot-fill bottles may even be cut into as many as five segments. These segments are weighed and the results are recorded. This approach permits a good approximation to the material weight distribution in production bottles by comparing these benchmark values with the easily determined segment weights of sample bottles from production runs. If the segment weight distribution is identical, then it is assumed that all other specifications are met as well. This method also allows an easy identification of excessive variations or fluctuations in the production process. * This article was published in Bottles, Preforms and Closures, Ottmar Brandau, Chapter 1.8.3.1. to 1.8.3.4., Copyright Elsevier 2012","@ID":37}, "CAPPING / CLOSURES 37 PETplanet insider Vol. 15 No. 03/14 petpla.net and energy efficient running all drives are direct fully electric. All moulds are welcome on BMB machine, subject to mould makers being validated by our engineers. Here at K 2013 we are working together with Corvaglia.” Exhibit at K 2013 eKW 450 – 5500, fully electric, 350t clamping force, 96 cavities Standard beverage closure 1810 for CSD, 2.1g, cycle time approx. 4.0s Power requirement: not specified Mould: Corvaglia Hot runner: Moldmaster Quality control: IMD Vista USP in their own words All drives fully electric using SKF roller bearing technology. Roller screw working in oil bath. Patented 5-point external toggle clamp. Outwards moving mechanical linkage system to enable clamp force uniformly distributed over mould surface. Recycling line recoSTAR PET iV+ Offices in: Brazil, China, India, Indonesia, Russia, South Africa, USA, Uzbekistan, and agents in over 130 countries worldwide textile packaging consumer bags BMB clamping eliminates platens deflection, ensures perfect parallelism and enables long opening stroke. Control of clamp ensures that clamping pressure is released prior to expiration of cooling phase, mould faces stay together for a fraction of seconds before opening – with the consequence of shorter cycles. Looking ahead Stewart Leng reflects on perspectives for the future: “The benchmark for us is the central European specialists with their hybrid machines, the Netstals, as well as the Huskys. BMB injection moulding machines are, despite expensive technology, are the only ones to consistently feature all-electric drives – with the same power density and performance as the market leaders. At the present time, as far as we are concerned, we see no weakness and no instances suggesting room for technical improvements“. Foboha We met: Hansjörg Keusgen, Head Sales & Marketing, Executive Management","@ID":39}, "MATERIAL / RECYCLING 18 PETplanet insider Vol. 15 No. 03/14 petpla.net Vacurema: efsa-approved and energy consumption tested rPET for direct food contact Around 779,000t of PET are collected in the USA every year and in the region of 514,000t remain in the country. Of this total, approximately 295,000t are processed to make rPET for direct food contact. Erema claims that half of the US rPET is produced with its Vacurema technology; in Europe the market share in this segment has reached 30%. According to the company more than 150 Vacurema systems are in use around the world, with an overall annual capacity of around 1 million tonnes. Vacurema technology for the recycling of post consumer PET bottle flakes, PET in-house waste as well as PE-HD bottle flakes was launched in 1998. In this process, food contact compliant decontamination takes place before the extrusion process. The patented pre-treatment of PET flakes at raised temperature and in high vacuum before the extrusion process removes moisture and migration materials from the feedstock very effectively and in a stable process environment. Thanks to the vacuum treatment, stable IV values can be achieved even in the case of varying moisture levels and different IV values in the input material. As input materials with up to 1.5% moisture can be processed, no expensive pre-drying is necessary, unlike other processes available on the market. Extruder degassing is not required either, meaning that a short extruder screw can be used and the thermal stress on the material is reduced as a result. Additionally, the unique, patented configuration means considerably less maintenance compared to other systems. efsa approved and tested The repellets/end products produced with Vacurema technology for direct food contact fulfill the purity requirements of major brand owners and, besides country-specific approvals, also has internationally recognised certification from the North American FDA and efsa, the European Food Safety Authority. Some 347,000t of rPET for direct food contact are produced every year with Vacurema systems. “Our customers use up to 100% of the recycled pellets for the production of bottles and food contact grade thermoforming sheet in accordance with efsa guidelines,” explains Christoph Wöss, Vacurema Product Manager. An automatic operating mode with FCC – Food Contact Control keeps the process stable. The parameters for direct food contact compliance are monitored and archived continuously in the recycling process on all Vacurema systems. The Food Contact Erema’s Vacurema Prime system Fig. 2: Erema Vacurema efsa test values","@ID":20}, "PETnews 6 PETplanet insider Vol. 15 No. 03/14 petpla.net Avery Dennison launches PET liner recycling Avery Dennison has expanded its PET recycling program with the addition of two new collection facilities in Europe. Waste PET liners can now be sold directly to Morssinkhof Rymoplast, Avery Dennison’s recycling partner, at its main plant in Zeewolde, Netherlands, or at collection facilities in Lichtenvoorde (Ned) and Przeczno, Poland. Recycled liner material is converted to rPET granules, which are then used in applications such as textile production and manufacturing. The company claims that the expansion of its recycling program offers brand owners the opportunity to generate additional income from liner recycling and to avoid the need to pay for landfill or incineration. It says that 5 million m² of release liner waste is currently worth €16,000 to €26,000. Quantities as low as 500kg are accepted, well below the current 5t minimum quantity for waste pickup. Morssinkhof Rymoplast will reimburse brand owners directly with the material’s value. www.averydennison.com Fabian Neumann new Chairman of the PET Forum On the occasion of the last meeting of the PET Forum on September 11,2013 in Munich, Fabian Neumann of Mitteldeutsche Erfrischungsgetränke GmbH & Co. KG (MEG), Germany, was elected Chairman. In assuming this position he took over from Karl-Heinz Achhammer of Krones AG who has now retired. Fabian Neumann is the Divisional Leader responsible for Publicity and Sustainability in the Mitteldeutsche Erfrischungsgetränke (MEG) Group of Companies and has been with MEG since 2008. The company is a subsidiary of the Schwarz Group and has specialised in the production of high quality commercial brands for the retail foodstuffs trade. In addition to the Chairman, Fabian Neumann, who represents the beverages bottlers, the following were also appointed to the Board: André Graichen (Equipolymers) for the PET processors, Dr. Thomas Friedlaender (Krones) for the machine manufacturers, Oliver Wiegand (PET packaging) and Uwe Röhn (Vogtland PET) for the PET recyclers. As a packaging manufacturer, Oliver Wiegand will continue to represent the PET Forum on the IK Board. www.kunststoffverpackungen.de Krones acquires upgraded technology Krones AG has announced that it has acquired a 100% holding in HST Maschinenbau GmbH, a German company that designs and manufactures homogenisers and reciprocating pumps for the food and beverage industries. The acquisition price was not specified but was described as being “in the mid-single-figure-million range”. HST employs around 25 people and has been trading profitably; turnover in 2012 was reported at nearly €5 million. With this acquisition Krones intends to upgrade its future corporate capabilities in process technology designed for producing juices and milk, and to expand its global service and maintenance business in this sector. The agreement is subject to approval by antitrust regulators. www.krones.com Petainer rushes in Petainer, the British plastic container supplier, has opened a new site in Russia that is producing recyclable PET beer kegs and water cooler bottles for the local market. The factory, which is in Klin, 40 miles from Moscow, is equipped with a Side blowing machine that is capable of manufacturing 700 kegs/h, up to a maximum size of 50kg. The facility is currently supplying 20 and 30l Petainer kegs to customers in Russia, Belarus and Ukraine. The kegs are lightweight beverage containers manufactured in recyclable PET. They are available with one-way, low cost fittings that enable them to be connected to existing tapping systems for draught beer. PetainerCoolers are also made out of PET and contain zero bisphenol-A (BPA). Petainer says that they are environmentally friendly, returnable and refillable, and designed to be compatible with major water cooler dispensers or dispensing systems. www.petainer.com","@ID":8}, "BOTTLE MAKING 23 PETplanet insider Vol. 15 No. 03/14 ISBM-AT080SR at K show Cavity 6 cavity mould Neck finish 28x400 Capacity 500ml Bottle weight 30g Cycle time 14.3s Output 1510bph Material RamaPET BL 8050 Energy consumption 21.5 Kwh www.automaspa.com hot fill bottles with fill temperatures up to 205°C for food and beverages oval shapes different neck orientations colours and additives Automa is now working on a new machine size, named ISBM-AT150SR, a 150t, fully electric machine, designed to produce wide mouth jars for the food market. The same model will also feature double row moulds, which are intended to deliver significant cost and commercial benefits in small bottle production. The comapny is considering developing double row application on the ISBM-AT80 platform as well but the final decision will be taken based on market response. Automa is a family-owned company that was founded almost 42 years ago in Bologna, Italy, and has sold over 3,000 units to over more than 400 customers around the world. In 2010 Automa joined the TMC Network, a group of companies located in Bologna, which together have branch offices and agencies in 75 countries worldwide. TMC has its own network of representative branches in the United States and Brazil. Technical service is available from all branches related to the territory and via agents’ technicians, who have been fully trained in Europe, South America & Australia. Along with AMS, another company in the TMC network, Automa can provide after-sales service for EBM and ISBM Tech in Italy and across the world.","@ID":25}, "PETbottles 48 PETplanet insider Vol. 15 No. 03/14 petpla.net Beverages & Liquid Food A saucy taste Marks & Spencer, one of the UK’s leading high street retailers, is being supplied with a range of own-label pickles packed in Appe’s ThermaLite pasteurisable PET jar. Food manufacturer G’s selected the wide-mouth jar because it offers the same clarity as glass, as well as improved production line efficiencies and less environmental impact. Anthony Gardiner, G’s marketing director, said that the company’s research found that consumers understand the benefits of a plastic container but they expect the same clarity as glass as they want to see the product. He explained that Appe’s pasteurisable PET jar allowed G’s to overcome the challenges that had previously prevented the company from using a clear PET jar with hotfill products, such as pickles. ThermaLite jars can be hot-filled and/or pasteurised at temperatures up to 95°C. They are fully recyclable, are up to 85% lighter than glass equivalents and are claimed to provide efficiencies during transportation and filling, as well as offering safety and convenience benefits. The jars can incorporate a metal closure, which means that they can be used on existing glass filling lines. Appe says that the containers can be used for cooking sauces, pesto, tomato-based products, relishes, chutneys, fruit purées, jams and spreads, as well as for pickles. The new jar received two Highly Commended certifications in the Food, and Environment & Sustainability categories in the recent Starpack Awards, and received the Horners Bottlemakers Award for 2013. www.appe.com Vöslauer with waves Clear water in transparent bottles in long rows on the shelves; how is the consumer expected to find their own “personal” water rather than just grabbing the nearest bottle? In order to distinguish themselves from the competition, manufacturers are, in addition to the different variations in taste, going their own ways when it comes to design. One example is the Vöslauer Balance bottles made from PET with a recycled proportion of 100%. The containers, with a content of 750ml, can be distinguished by means of peripheral, wave-shaped grooves in which the light is diffused to maximum effect, thus attracting attention at the PoS. An easy-to-handle screw cap with a downward taper plus tamper-proofing and a wraparound label in the top section complete the packaging. The neck area features the name Vöslauer in embossed script in two locations. www.voeslauer.com Brightly-coloured yoghurt drinks Milbona – an own-label brand name of Lidl – are marketing their range of yoghurt drinks with a content of 750g / 711ml in an easy-tohandle, shaped bottle made from PET. This is tinted white and features peripheral reinforcement grooves in the waisted area. The conspicuous, bright design sleeve labels ensure that the goods get noticed on the cooler shelf. The bottles are sealed by means of blue screw closures with tamper proofing. BOOTH NO:E5G31","@ID":50}, "BOTTLE MAKING 21 PETplanet insider Vol. 15 No. 03/14 petpla.net HSB-2M The HSB-2M is a two stage blow moulding machine with double blow which can mould heat- resistant jars of up to 4l capacity, with a 110mm neck diameter. It was making its global debut at K2013.The heatresistant PET jars moulded by this machine enable either hot-filling or incontainer pasteurisation of a variety of foodstuffs such as jams, pickles and pasta sauce, etc. With this machine, it is possible to produce heat-resistant PET jars with even the largest neck sizes required by the industry. Together with the existing HSB-6M model (six cavity production of heatresistant jars up to 350ml capacity, 63mm neck size), ASB can offer machinery for the production of various sizes of jars from small to medium and large. During the exhibition a 950ml, 82mm neck diameter, 66g PET heat-resistant jar was moulded at an output of 1,440bph. ASB-12M The ASB-12M is a small versatile one-stage injection stretch blow machine which is capable of moulding a full range of container designs for products such as pharmaceuticals, cosmetics, liquor, foodstuffs etc., in PET and a variety of other materials such as PP, PC, PEN, PS, PPSU, PLA and recycled PET. The ASB-12M utilizes two servo-driven hydraulic pumps thereby reducing actual energy consumption by about 20% over similar class, hydraulically operated machines. Besides energy reduction, noise and vibration are also reduced. Moulds made for the existing ASB-50MBv3 and ASB-12N/10 can be mounted on the ASB-12M using some optional parts for full compatibility. Nissei says that this compatibility enables an easy upgrade path for ASB’s customers who are already using these existing machines. During the exhibition, to help celebrate Halloween a 350ml, 61mm neck diameter, 25g PET jack-o’-Lantern container was moulded at an output of 600bph. www.nisseiasb.co.jp HSB-2M 2-stage machine ASB-12M 1-stage machine","@ID":23}, "ONsite 46 PETplanet insider Vol. 15 No. 03/14 petpla.net Nampak opts for Sipa’s XForm 500 preform system Nampak, headquartered in Sandton, South Africa, and Africa’s largest packaging company, has chosen Sipa XForm 500 preform production system to make juice and CSD bottle preforms for major beverages players on the South African market. The system was installed during 2013. Sipa supplied Nampak with a complete preform system that included the XForm 500 injection moulding machine equipped with a 72-cavity mould, together with another two 72-cavity cold halves, to produce preforms in various weights for production of bottles between 500ml and 2l in volume. Nampak’s history dates back to 1920, when it began making cartons. It now offers a comprehensive product range across multiple industries, manufacturing in metal, glass, paper and plastics. As well as South Africa, the company has presence in Zimbabwe, Botswana, Kenya, Malawi, Mozambique, Nigeria, Swaziland, Tanzania and Zambia. It also operates in Europe, from nine sites in the UK. “Nampak was looking for a reliable partner who understands packaging development,” said Giovanni De Rosa, Southern African Area Manager at Sipa. “We have our own office in South Africa too, so we can stay on top of things here.” The two companies are working together on a number of other projects, covering stretch-blow moulding as well as injection moulding. Nampak has declared itself very satisfied with both the XForm 500 and the relationship it has developed with Sipa. “The system has been running smoothly since the day we first switched it on, achieving excellent preform quality,” said Mthandeni Mkhize, Technical Director at Nampak Petpak. “Sipa has done a good job with know-how transfer to our people, and on-site service is available with all the right skills, which helped provide a smooth transition. We are happy to have found a partner that can support us in both technology and packaging development.” Sipa says that the XForm 500 has the capability to handle moulds with up to 144 cavities. It will accept moulds from any supplier and the moulds can also be changed over quickly: Sipa quotes a downtime of just 3.5h. Energy efficiency has also been a focus in the system’s design. Moulds can be cooled with water at 14°C rather than the traditional 8°C, for example. Post-mould cooling is carried out in six stages. Continuous low speed screw rotation minimizes the stress on the PET to ensure minimal generation of acetaldehyde. Sipa further claims that XForm 500 performs very well with rPET flakes: throughput drop is less than 10% with 50% flakes. www.sipa.it Sacmi doubles output in Venezuela Empresas Solar, which has been involved in the beverage, food and packaging industries in Venezuela for over 70 years, recently commenced operations on an all-new made in Sacmi production line at its Bodegas Pomar plant. It is designed to produce around 6,900 filled 1.75l PET bottles of Sangrìa Caroreña/h. The line includes a filler – and associated conveyor belts – manufactured by Sacmi Filling; a new labeller-sealer from Sacmi Verona; and a bundler and palletiser made by Sacmi Packaging. The new line, which was implemented under the auspices of Sacmi Beverage, has enabled Empresas Polar to double its output capacity. The plant’s high degree of automation will allow the company to boost its monthly production of Sangrìa Caroreña alone from 160,000 to 240,000 bottles. www.sacmi.it Coca-Cola Brazil launches award-winning Crystal Eco Spaipa, the third largest bottler of the Coca-Cola brand in the Brazilian territory, was recently acquired by Coca-Cola Femsa Mexico. Spaipa’s four factories, in Curitaba, Mariingá, Marilia and Bauru, operate a total of 14 bottling lines producing CocaCola, Fanta, Sprite, fruit juices, Powerade, mineral water, and beer. The latest addition to the range, Crystal Eco mineral water, is packaged in a bottle that contains 20% less PET. PE Labellers has recently supplied an Adhesleeve N810/18T linerless labelling machine for the application of wrap-around labels on 500ml and 1,500ml cylindrical bottles. A pressurisation system for empty bottles, with a speed of 36,000bph, is installed below the blower. This installation can apply labels to empty bottles and the company says that requirement for adjustment of the height of the air conveyor belts for different size bottles is no longer necessary. PE Labellers says that this particular version of the Adhesleeve was designed with an ergonomic machine body, circular guards and a double labelling station on the peninsula, in order to improve safety and make replacement of the empty roll easier. It is also claimed to be 28% more efficient than a traditional hot melt labeller. In November 2013, Agua Crystal (Crystal Eco) was confirmed as the winner of the Grandes Cases de Embalagem 2013 award. www.pelabellers.com","@ID":48}, "PETcontents 3/14 4 PETplanet insider Vol. 15 No. 03/14 petpla.net INSIDE TRACK 3 Editorial 4 Contents 6 News 44 Products 46 On site 48 PET bottles for beverages and liquid food 50 PET bottles in health and beauty care packaging 52 Patents MARKET SURVEY 29 Bottle-to-bottle PET recycling systems CAPPING / CLOSURES 36 Caps and closures A PETplanet study at K2013 - part 3 BEVERAGES / INGREDIENTS 40 Let’s play it safe Food safety: The ‘sine qua non’ of food and beverage production EDITOUR REPORT 12 Brazil- Part 2 Go with the flow tour 2013 MATERIAL / RECYCLING 18 rPET for direct food contact Vacurema: efsa approved and energy consumptiontested BOTTLE MAKING 20 Jive on the stages Nissei ASB: Four new machines at K2013 22 Spreading the word Automa at K2013 24 Bottle-blowing on-site Coca-Cola in Northern New England embraces PET 33 Triple the light fantastic Kortec and Sidel develop 3-layer light-blocking technology for milk bottles 34 Mould trials and examination of sample bottles Bottles, preforms and closures, part 9 BUYER’S GUIDE 53 Get listed! Page 24 Page 36 Page 33 Page 46","@ID":6}, "BOTTLE MAKING 26 PETplanet insider Vol. 15 No. 03/14 petpla.net segment. CCNNE’s InnoPET Blomax Series IV currently manufactures 12, 16 and 20-oz and 0.5l bottles, supplying both PET lines and currently covering about 60% of the company’s PET bottle requirements. CCNNE has been using KHS equipment since 1989, when one KHS filler and one KHS blender began operation on both of the then new lines (one for cans and one for PET bottles) at the newlyopened Londonderry plant. Both fillers and the blending equipment are still working - as are their other KHS Promix systems, ordered almost ten years ago. The equipment is kept busy with full three-shift operation. The company has embraced a policy of keeping line personnel closely identified with ‘their’ machines “The same operator has been responsible for the canner from day one and he really looks after it. Identifying with a machine like this is crucial if you want excellent performance and a long life cycle, I think.” This experience led to CCNNE’s decision to have all those who would be jointly responsible for the new investment intensively trained by KHS before the new InnoPET Blomax Series IV was installed at the plant. CCNNE sent a team of seven to KHS Corpoplast in Hamburg, Germany, where they were acquainted with the features of the InnoPET Blomax Series IV in both theory and practice. When the new machine arrived on site, the team was actively involved in helping the KHS service engineers install and commission the stretch blow moulder. Performance The InnoPET Blomax Series IV at CCNNE has 28 blow stations, each of which produces up to 2,250bph. The stretch blow moulder has the flexibility to produce bottles holding between 0.2 and 2l. One of the features that was most striking was in the heater area, which just about halves heating times, compared with the Series III machines. It also takes up less than half the space of its predecessor. Series IV stretch blow moulders use near infra-red (NIR) or shortwave infra-red radiation. Preforms are heated by near infrared (NIR) or shortwave infrared radiation, which delivers extremely intense heat penetration of the preform walls. This effect is heightened by the preforms being conveyed through an enclosed heating chamber with all-round reflection and the mandrels being very tightly spaced at just 37.7mm (minimum pitch). This heating technology achieves energy savings of up to 40%, compared with traditional heating technology. “The short heater also ensures that only very few preforms have to be discarded if there’s an emergency stop,” said Russ Brunner, plant engineer at CCNNE. Compressed air usage by the InnoPET Blomax Series IV is also improved, by up to 15%, depending on bottle size. The staggered array of the blow stations on the new generation of KHS stretch blow moulders also saves on space, which means that the blow wheel diameter is smaller. Only one half of the mould on each blow station is opened, with a toggle mechanism to open and close the blow stations. The mould carrier no longer has to be locked, which leads to less mechanical susceptibility and consequent higher machine efficiency. Another significant aspect for CCNNE is the short time needed for changeovers, when swapping from one bottle variant to another. The use of servotechnology means that the stretch die does not have to be changed or mechanically adjusted; new settings are communicated to the system by on-screen entry. Moulds are replaced in the blow stations very quickly thanks to their new design and the Speed-Loc quick-change system. Changeovers on the Series IV are around 50% shorter than those on the previous machine generation. As the company’s plan involves the manufacture of more types of bottle, rather than fewer, quick changeovers are extremely important. It is also worth noting that start-up time is extremely short, thanks to the very quick preform heating process, which takes only 15s. Bottle quality is a particular consideration to CCNNE and to all companies belonging to Kirin Holdings, which has been recognised with no fewer than eight Coca-Cola President’s Awards, the annual prize presented to the most quality-conscious Coca-Cola bottler in the USA. “What’s also important for us is that this machine gives us a return on investment in just three years,” said Rick Neal, head of the CCNNE production site in Londonderry. www.ccnne.com www.khs.com Rick Neal, head of the CCNNE production site in Londonderry (right), and Russ Brunner, Plant Engineer at CCNNE (left)","@ID":28}, "42 PETplanet insider Vol. 15 No. 03/14 petpla.net BEVERAGES / INGREDIENTS regarding the different barrier solutions vary between solutions and from country to country. In Europe, all the constituent parts of the different layers have to be food-approved materials - even if they are isolated between other layers - whereas in America, the FDA has granted a ‘Non-Object’ for multi-layer PET technologies which offer a functional barrier. This requires an inner layer of virgin PET material of a minimum 0.025mm thickness to separate the outer ‘barrier’ material from direct contact with the contents. Barrier technologies such as additives or blends, directly incorporated into the composition of the basic PET material, as well as employed as a coating, have the potential to affect the composition of the PET resin and may cause some degradation of the beverage. That is the reason many leading figures within the industry, particularly in Europe, are required to have all components individually approved for direct contact with food. Blow moulding and lightweighting EFSA and the FDA correctly identify that the potential threat to food safety linked to today’s packaging material mainly arises from the possible degradation of the material during transformation. This could lead to the creation of ‘by-products’, however there are no by-products that impact food safety during preform injection processing. They are instead, colourless gases at normal room temperature that may migrate to bottled water causing a harmless but mildly unpleasant taste. The blow moulding process itself within the production and filling of the PET bottles has no impact on the features of the packaging material. It is a neutral process involving a preform in which the plastic material has already been transformed. The oven temperature that heats the preform is below the fusion temperature and does not cause any risk in terms of degradation of the resin. The actual blow moulding process stretches the material, changing its state from amorphous PET to semi-crystalline. The finished bottle has superior strength and greater barrier properties as a result. The current drive towards ever more lightweighting of bottles does not have an effect on the properties of PET regarding food safety. Although the thinner bottle walls do have a decreasing effect on the performance of the PET barrier, it requires accurate testing of material permeability to ensure the required shelf life of the beverage is achieved - and to ensure that migration of external components into the product does not take place and cause contamination. All manufacturers also need to be aware of other potential risks such as the migration of inks required for bottle marking or glues from the bottle labelling process through the thinner PET walls. Hygienic design is essential The hygienic design of all food production equipment is, of course, vital. Mostly, the general principle of hygiene within machinery is related to the materials used to construct that machinery. The surface finish, the construction and fabrication details, the installation, operation and maintenance are all crucial elements and must be considered from the outset for the entire operating life of the equipment. Surfaces that come into contact with any food or drink product at any point in the production process must be made from materials that are smooth, non-toxic, non-absorbent, corrosion-resistant and easily cleanable under normal operating conditions. As much as is possible, interior surfaces of the equipment should be devoid of joints, sharp angles, pitched to a drainable port and self-draining. Maintaining food safety Even when bottling lines have been developed, manufactured, installed and commissioned, correct and regular maintenance is essential in maintaining safe and profitable production. Leading manufacturers will, of course, provide a thorough aftersales service of routine maintenance. Most will pass on maintenance manuals and advice on procedures for the operating personnel. As food standards continue to change and evolve, the collaboration between equipment supplier and operator is vital in ensuring safe and reliable production that meets the requirements of international standards. Operators will naturally be supplied with HACCP (Hazard Analysis and Critical Control Points) plans along with suggestions on laboratory and quality analysis. Having learned from each customer, each installation and years of experience, leading equipment suppliers are eager to communicate all recommendations concerning the food safety of their equipment. Achieving Good Manufacturing Practices (GMP) is not about meeting legislative requirements, but relaying simple recommended ideas that can help operators to maintain complete beverage safety and quality throughout the entire production life of the machinery. In that way, suppliers will know that they have done everything they can to contribute to the safety of the world’s food and beverages. www.sidel.com In Europe, all the constituent parts of the different bottle layers have to be food-approved materials - whereas in America, the FDA has granted a ‘NonObject’ for multi-layer PET technologies which offer a functional barrier.","@ID":44}, "EDITOUR REPORTS 16 PETplanet insider Vol. 15 No. 03/14 petpla.net In response to the question, why is there no mineral water bottling, Angelo Zugliani responded; “Space problems and the statutory regulation in Brazil that only permits the operation of bottling lines specifically designated for mineral water and thus markedly restricts the flexibility of a smallish company such as ours“. Distribution structure With 12 HGVs of its own, the company is able to supply the market within a radius of 100km directly with beverages. This includes 18 - 20 towns with a total of 2,200 sales points such as supermarkets and restaurants. The company also has a network of dealers and many of the drinks sporting the “15” label find their way as far as Sao Paulo City. The next stage as far as the 60 members of staff strong company is concerned is to relocate the sales operation from the factory into a region with its own branches. “We’ll take it step by step,” says Angelo Zugliani, “Slowly but surely”. From left to right: Sidney Angelo Zugliani, Director Industrial, Jose Guilherme Zugliani, Gerente Administrativo, Waldemar Schmitke, PETplanet, in front of the Editourmobil at the factory in Jau Touring the length and breadth of Brazil (by Waldemar Schmitke) Team 3 led by Waldemar Schmitke and Florian Roscheck is complete.We start off from Porto Alegre. The Editourmobil is chock-full of food and drink, so we are ready to go. Our first appointment takes us through some beautiful mountain scenery to Campo Branco to Mineracao Campo Branco . Here we are greeted by Erminio Viran , General Director and a member of the founding family. The company uses its own spring to fill 0.5 litre PET bottles up to 20 or so PP / PET water dispensers. After finishing our meeting, we take the same route back and continue our journey to the coast. It is May 1, a public holiday in Brazil, and we take the opportunity of relaxing before setting off on the next stage of our journey, an appointment in the state of Parana. On the motorway, we suddenly become aware of an ominous rattling sound coming from the roof of the Editourmobil. A rapid inspection quickly identifies the cause: there is a loose cable is flapping around. Someone has apparently stolen the solar panel which supplies the vehicle with additional electricity. It’s very annoying, but we have to push on regardless. We have an appointment with the soft drink bottler Hugo Cini in Sao Jose dos Pinhais, a PET pioneer in Brazil. Director Nilo Cini Jr. takes us on a tour of the company. By the time we leave, it is already late, and we need to find somewhere to park for the night. It seemed a sensible idea to use the weekend to tackle the 700 km haul to our next interview. We are supposed to be heading for Manaira but for some reason, we have somehow managed to muddle up Manaira with Maringa, a rather unfortunate error which has cast us 2,500 km adrift of where we should be! Jaú to Rio de Janeiro (by Florian Roscheck) It’s Monday evening and Waldemar and I have just enjoyed an excellent repast at a Churrascaria, a typical Brazilian grill on the outskirts of Jaú, a city in the state of Sao Paulo. Before it gets dark we need to find a secure overnight parking place for the Editourmobil. By a stroke of good fortune, we manage to find a petrol station which is not only open but also supervised by security guards. On the following day we meet the bottler Indústria de Zugliani Refrigerantes e Bebidas. Director Sidney Angelo Zugliani and Administration Manager José Guilherme Zugliani go to a lot of time and trouble to answer all our questions.","@ID":18}, "BOTTLE MAKING 33 PETplanet insider Vol. 15 No. 03/14 petpla.net Kortec and Sidel develop 3-layer light-blocking technology for milk bottles Triple the light fantastic A new multi-layer co-injection technology from Kortec, Inc., developed in association with Sidel, is claimed to enable production of PET bottles for milk with 100% light-blocking capability. The new Kortec LB technology facilitates the moulding of a threelayer preform, which is then blown to make the milk bottle. The preforms, developed in cooperation with Sidel, consist of three layers of PET: white on the outside, black in the middle, and white on the inside. This design ensures that the light-blocking black PET layer covers the whole of the bottle, including the base, completely exclude light from the container’s contents. The finished bottles offer a package suitable for delivering lightsensitive beverages safely to retail shelves and to consumers. The black layer provides complete protection to the contents – typically milk, but the technology is suitable for a range of sensitive products – and the white external appearance retains the look that consumers expect. Naima Boutroy, Sidel Packaging Project Manager, commented: “Kortec LB protects the product throughout its lifecycle in the bottle, from production through the supply chain to the consumer. By combining Kortec’s preform with Sidel’s bottle design expertise, we have a solution that ensures product safety while also addressing the consumer-driven demand for a uniform look to the packaging.” Kortec has many years of experience in designing and producing high-barrier packages. Barrier-layer material placement and dispersion is critical to blocking the correct wavelengths of light from the package. The first fruits of this technological collaboration between Sidel and Kortec are 25g preforms for 1l bottles and 22g preforms are currently in development. Kortec claims that additional benefits of its new LB technology include moulds of up to 128 cavities; fast cycle times; and minimum use of materials while, at the same time, achieving 100% light blocking. The company further asserts that the new product offers the lowest overall total cost light-blocking packaging technology currently available on the market. Russell Bennett, Vice President of Sales and Marketing with Kortec, maintained that the new technology offers competitive advantage to converters and end users, as well as addressing the issue of sustainability through low material usage. Vincent Le Guen, Sidel Vice President for Packaging & Tooling, added that Sidel is continually looking at opportunities to partner with suppliers up and down the supply chain, to develop innovations that deliver value to customers and end consumers. www.sidel.com www.kortec.com","@ID":35}, "BOTTLE MAKING 34 PETplanet insider Vol. 15 No. 03/14 petpla.net Laboratory tests on sample bottles – Bottles, preforms and closures, part 9 Mould trials and examination of sample bottles Normally the finalised mould design is used to make a single cavity for the production of sample bottles in a laboratory machine. These sample bottles are then tested comprehensively to see whether they meet the defined requirements. This article will cover the next steps in bottle examination from strass cracking resistance to segment weight distribution. PETplanet insider is publishing extracts from successive chapters of Ottmar Brandau’s “Bottles, Preforms and Closures”, which was first published by hbmedia. A newly revised version is reissued under the Elsevier imprint. Stress cracking resistance Failure in the base area under the influence of alkaline solutions (stress cracking resistance) is especially important for bottles intended for carbonated products. Although today many conveyor systems are lubricated with acid lubricants, this test is still demanded by a number of customers. The bottles are tested in freshly blown condition and/or after a defined ageing period. The test bottles are pressurized at up to 5.3 bar by either filling them with carbonated water or connecting them to compressed air hoses. They are then placed in separate dishes with diluted soda lye. The criterion for the","@ID":36}]}}
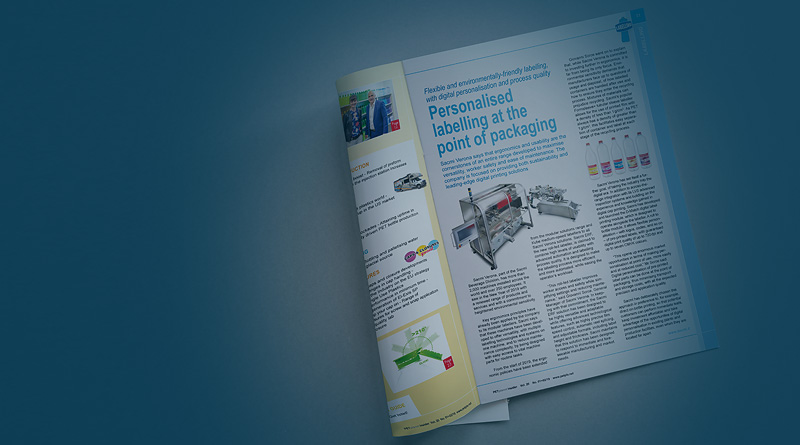