"BOTTLES 33 PETplanet insider Vol. 15 No. 08/14 petpla.net Beauty care bottles in two-step process PDG Plastiques have developed two new bottles for beauty care products. The challenge was to use the two-steps process for a 500ml and a 1l oval and flat top shoulder bottle. It took more than nine months to find the right design and process to obtain the customer’s desired bottles. According to PDG Plastiques, there is a growing demand for PET bottles and jars in the field of health, beauty, body care liquids and creams in France, due to the materials’ characteristics related to unbreakability, crystallinity and competitiveness compared to glass. www.pdg-plastiques.com Bio-mango & bio avocado for the hair Laverana GmbH & Co. KG of Wennigsen in Germany is marketing 200ml of silicone-free Color Glanz Shampoo with BioMango & Bio Avocado under the trade name ”lavera Naturkosmetik“ in a slim, white PET bottle. The product contains 100% natural fragrances and aromas, surfactants on a vegetable base and is free of paraffins and mineral oil. A snap-on hinged lid closure complete with dispensing opening and two self-adhesive labels in natural colours emphasise the natural nature of the product. www.lavera.de Body spray from alverde The own label side - “alverde natural cosmetics” - of the German drugstore discounter dm recently launched a summer edition of its body spray on the market. The green-tinted PET bottle holds 100ml of the spray which is scented with cucumber and water melon. This is dispensed via a similarly green-coloured, handoperated pump dispenser secured by means of a protective cap. There is a paper label which draws attention to the natural ingredients and explains all about the product. www.dm.de/alverde Cream Soap with karite butter 30ml cream soap with the brand name “alverde natural cosmetics” is being bottled by dm in an easy-to-handle, stable and tinted PET container. This nurturing product for gentle hand cleansing which is scented with pomegranates and karite butter is dispensed duly measured out via a lockable, opaque pump dispenser. Two labels to front and rear complete the packaging. www.dm.de/alverde","@ID":35}, "CAPPING / CLOSURES 14 PETplanet insider Vol. 15 No. 08/14 petpla.net New frontiers Permeation testing on caps *based on an article by Peter Heumueller, Business Friends Market Entry Consultants, Wachtberg, Germany Graham Jennings, Systech Illinois, Thame, UK Recent years have seen tremendous improvements in the oxygen barrier properties of packaging materials. A 1l PET bottle’s barrier properties can be as low as 0,015cm³/b/day. At the same time as packaging is being lightweighted by downgauging, with material content being reduced, barrier properties are being improved in order to extend product shelf life. As packages become more sophisticated, specific area analysis is recommended, in order to understand where oxygen permeation occurs. While caps and closures amount to just 0.5 to 6% of the total package, it is worth checking their vulnerability to oxygen ingress. This article offers some ideas and guidelines for the testing of the oxygen transmission rate of caps and closures. A PET bottle cap has to perform several tasks simultaneously. It must be: easy to open tamper proof tight under all conditions of transport and storage integrated into the complete package. Oxygen permeation testing is a well-established method of assessing barrier properties of films and packages. Systech have performed a number of permeation tests in order to identify the contribution of the closure to the total oxygen transmission of the complete package. Testing regimes should ensure that the closure will be examined and Fig 1. : False-colour photo","@ID":16}, "PRODUCTS 35 PETplanet insider Vol. 15 No. 08/14 petpla.net PETproducts A gentle touch KHS says that its new Feedflow feed unit offers reliable and gentle conveying of lightweight PET preforms to the InnoPET Blomax stretch blow moulder, even at high speeds. Its maximum output is 84,000 preforms/hr. The preforms are fed into a silo, which can be equipped with a protective lid. If the machine is going to handle sensitive products, including those with high hygiene needs, it can be fully enclosed. Preforms travel from the silo along an inclined conveyor to an interim conveyor, which discharges into the preform sorter. They are then fed in one lane to a discharge rail or, depending on the application, onto the active, horizontal conveying segment. In contrast to a traditional, gravity-fed discharge rail, the Feedflow method actively conveys the preforms along the horizontal feed segment in a targeted flow of air. Frequency-controlled blower motors are claimed to ensure a constant and reliable flow of materials, which also helps to ensure high levels of line availability, KHS maintains. The system is also designed to be compact, to offer easy access and to be easy to operate and service. The combined Feedmax/Feedflow feed system has a controller included in the blow moulder. The KHS ClearLine HMI controls the process centrally, reduces machine complexity and simplifies operations, KHS claims. www.khs.com Soft yellow joins the spectrum New addition to Döhler range Döhler has extended its spectrum of successful Crystal Clear Colours with a new soft yellow shade alongside the vibrant orange and yellow tones. In the past, the only way to achieve a ‘warm orange’, ‘shining yellow’ or ‘soft yellow’ in clear beverages without affecting the taste and stability was by using artificial colours. All colour tones in the Crystal Clear Colours range display optimum stability and a particularly balanced sensory profile in transparent beverages, without the use of any artificial ingredients at all. The Clear Colours range is based on natural colouring principles such as paprika extract, beta-carotene and lutein. Thanks to this use of exclusively plant-based raw materials, the colours are also suitable for vegetarian and vegan products. The range of natural, crystal clear orange and yellow tones is therefore opening up new options for the beverage industry in the development of natural beverages. The colours are characterised by outstanding stability under the influence of light, heat and different pH values. These properties and their colour intensity make the range ideal for a wide range of beverage applications, such as still drinks, water plus beverages and clear lemonades. This new range allows clear beverages to stand out with a colour spectrum ranging from intense, warm orange tones to bright, shining or soft yellow tones. The company also offers the food and beverage industry a whole spectrum of products on the theme of colours: from colouring concentrates and natural colours to colour and cloud emulsions. www.doehler.com French honey gets the squeeze treatment - BericapValve dosing valve made of TPE Several squeezable valves are now used for squeezable food products, most of them made of silicone. The Bericap Valve is different because it is made of TPE, which has the advantage, that – unlike the commercial silicone valves – it prevents contamination in the recycling process. Bericaps bi-injected dosing valve closures offer a perfect product security and support controlled dosing of products such as honey. Honey is traditionally packed in glass jars closed with aluminium twist-off closures as well as in squeezable PET bottles using FlipTop closures with silicone valves. Now it seems that French honey bottlers are showing considerable interest in the TPE valve. The reason is twofold: it is easy to recycle without contaminating the recycling stream and, in addition, the taxes payable for a TPE valve are lower than those for a silicone valve. The BericapValve is available in various shore hardness and cut lengths in order to suit various products other than honey, such as ketchup, chocolate syrup, body lotion and pharmaceutical products, all having individual viscosities. Even products containing pieces, such as cocktail sauces, are easy to dose with the valve. Bericap offers a wide range of hinged closures in which the bi-injected Bericap Valve can be inserted. Customised designs can be developed in the company’s R&D centres. www.bericap.com","@ID":37}, "ITALIAN SUPPLIER 13 opment in this field is the solution – with the acronym S.U.P.E.R. – that features a special combination of preform neck finish (developed by Sipa) and light weighted caps (made on Sacmi machines) that solves several key problems associated with the operation of a cap on the neck of a PET. Finally, we meet Gianfranco Zoppas, President of Zoppas Industries, who is happy to have his photograph taken with the new xform series bearing the words “we are right on track“. Zoppas firmly believes that Sipa is well down the right track with its strategy of providing customers with complete solutions that go even beyond the proverbial “pellet to pallet,” since the company also has a very strong concept and design service for PET packaging. “People want total solutions now, not just the container or the machine to make the container, and we are very strong in that department,” he says. “They also want new ways to produce lightweight containers for economic and ecological reasons, and Sipa has all sorts of technology and know-how to help them there too. So I am quite confident for the future.” www.sipa.it PETplanet insider Vol. 15 PROVEN COST SAVINGS PERFORMANCE moldmasters.com Mold-Mastersand theMold-Masters logoare trademarksofMold-Masters (2007) Limited. ©2014Mold-Masters (2007) Limited -AMilacronCompany.All rights reserved. Rely on our global support network for fast service and parts. North America 1-800-387-2483 | Europe 49 (0) 7221 5099-0 Asia 86 512 86162882 ALWAYS INNOVATING. + More efficient use of platen real estate increases the cavitation for a given machine size: s 72 vs. 48 Cavity with a 28mm finish in a 225T s 72 vs. 48 Cavity with a 38mm finish in a 300T s 96 vs. 72 Cavity with a 28mm finish in a 300T s 128 vs. 96 Cavity with a 28mm finish in a 400T + Proprietary iFLOW and iCOOL technology reduces cycle times while improving balance, lowering injection pressure and increasing dimensional repeatability + Tooling solutions to revitalize, recapitalize and rev up existing systems Get 50% more output from the same machine 96-CAVITY MICRO PITCH MOLD FOR 300T MACHINES Contact us today at: [email protected]","@ID":15}, "PETnews 6 PETplanet insider Vol. 15 No. 08/14 petpla.net Mexican subsidiary of Corvaglia celebrates 10th anniversary The Mexican subsidiary of Swiss Corvaglia Holding AG celebrates ten years of operating in Mexico. Back in 2004 on the July 24th at 14:47 hours, the first closure left the conveyor belt. Today, more than 10 million closures per day are produced. Corvaglia Closures S.A. de C.V. located in Ixtlahuaca, State of Mexico, has over 100 employees and is meanwhile the third largest closure producer in Mexico. For the 10th anniversary event various activities for customers, suppliers and employees are planned. www.corvaglia.ch KHS receives ISO 14001 and ISO 50001 certification Protection of the environment, sustainability in the use of natural resources and social responsibility are major corporate objectives of KHS GmbH and KHS Corpoplast GmbH. This accommodates the wishes of customers in the beverage, food and non-food industries worldwide, as they often consider attaining these goals across their entire supplier chain and within their own companies to be part of their brand policy. Such customers therefore attach great importance to certification which confirms that their suppliers are acting responsibly. It is for this reason that in 2011 KHS had its Innofill Glass DRS/ZMS glass filler certified by Germany’s TÜV SÜD as energy-efficient plant technology. In the same year, KHS was certified in keeping with OHSAS 18001 (the Occupational Health and Safety Assessment Series). With a currency in over 80 countries OHSAS 18001 is one of the best-known standards for occupational health and safety management systems in the world. The next machines to be certified according to TÜV SÜD’s energy and media efficiency standard in 2012 were the InnoPET Blomax Series IV stretch blow moulder with its AirbackPlus system and the gas shrink tunnel for packing machines. Furthermore, in 2012 and 2013 KHS carried out ethical audits at various national and international production sites and was granted the appropriate certification. KHS customers can view the results of the KHS ethical audit on the Sedex database. At the beginning of 2014 the company was certified according to ISO 14001, the environmental management standard, and ISO 50001, the standard for energy management valid worldwide, for all of its German production sites. www.khs.com Expansion of production capacity at Gneuss in Bad Oeynhausen In recent years, Gneuss has consistently transformed itself from a component supplier to a supplier of complete compounding and extrusion systems for recycling, fibre and sheet manufacturing. An important market is polyester processing where recycled material is used. Earlier this year, Gneuss purchased an additional 13,000m² of land adjacent to the existing site to expand capacity. In addition to another 700m² storey to the administration building, a completely new building will be erected on the former car park which will increase the current production area for the extruders, filtration systems and measurement sensors by 50%. Gneuss plans to have the new building completed by the end of this year. www.gneuss.com Realignment of KraussMaffei and Netstal brands in France Since January 1, 2014, the KraussMaffei and Netstal brands in France has been brought together under one roof. According to the company, the reorganization of the two brands has been positively received by the customers as they are now able to buy from a broader product range from a single source. Both brands will continue to have an independent market presence. Responsibility for the subsidiary KraussMaffei Group France is now with the former General Manager of Netstal France, Jacques Socquet. Faredh Djaziri, the former president of KraussMaffei France, is responsible for expanding business development of the KraussMaffei and Netstal brands within the injection moulding technology segment outside of France, primarily in French-speaking Africa, including the Maghreb countries. www.kraussmaffeigroup.com","@ID":8}, "ON SITE 31 PETplanet insider Vol. 15 No. 08/14 petpla.net ONsite Satisfying the booming African demand for cola Coca-Cola Sabco needed a new PET production line to capitalise on a growing domestic market for cola carbonates. Total annual sales in the country recently reached 1,800 million litres and the popularity of the drinks currently shows no sign of slowing down. The line Coca-Cola Sabco installed was needed to enable the company to increase both product supply and quality in order to increase its market share. It was also looking to reduce the environmental impact of its production. The company decided to invest in the Sidel Matrix solution for its Polokwane plant. Established in 1940 in Port Elizabeth in South Africa, the South African Bottling Company has since gone on to become a major player in the carbonated soft drinks (CSD) bottling industry. With 21 production sites throughout a total of nine countries, the company currently supplies some 240 million consumers. The company has five manufacturing sites located throughout South Africa in Port Elizabeth, Bloemfontein, Polokwane, Nelspruit and Port Shepstone. The Sidel Matrix system, which includes blowers, fillers, Combi and labellers, can be installed in any complete-line configuration required. It is said to offer fast changeover times, oven efficiency and improved uptime with reduced environmental impact. Designed to minimise the resources used, it is intended to use less energy, water and chemicals compared to other systems while offering the possibility to produce ultra-lightweighted bottles. Coca-Cola Sabco’s investment in the complete production line for the plant in Polokwane featured a Sidel Matrix Combi, equipped with 20 blowing stations and 165 filling valves, as well as a Starblend mixer, a Sidel Rollquattro roll-fed labeller and a palletiser. The new Polokwane line is used to produce several of the company’s larger formats, including its 2l version, and is capable of achieving production rates of 32,500bph. www.sidel.com Amut chosen for Carbon Lite plastics recycling facility Carbon Lite Recycling LLC has chosen Amut equipment as part of a new 20,000m² recycling plant that will process post-consumer bottles into PET (PCR-PET) pellets which are used to make new bottles. Carbon Lite is specialized in bottle-to-bottle recycling, producing PCRPET bottles and serving major beverage brands. The output will be about 45,000t per year of finished products. With this investment Carbon Lite doubles its capacity at its new plastic recycling facility in Abilene, Texas which will also supply Nestlé’s bottling facilities near Dallas. Total investment in equipment and infrastructure exceeds USD 60 million. Another plant of Carbon Lite is operating in Riverside, California. The Amut equipment will be used in several processing steps for the cleaning of the PET bottles. The scope of supply includes a delabeller (DLB-60 model – patentpending) full-body shrink sleeve label-removal system and the patented PW-180/5 high friction washing system which will be incorporated for the cleaning of the whole bottles prior to the wet grinding process. For the final cleaning of the PET flakes the patented hot flake friction washing system AX 150/5 will be used. The delabeller (launched in 2013) is able to remove full-body shrink sleeve labels, other labels and general dirt using a complete dry prewashing system (water free). For the food-grade purification and pelletizing, Carbon Lite will use technology from Erema North America Inc. The new plant’s front-end, bale-opening and bottle-sorting will be built by Bulk Handling Systems of Eugene, or using sorting modules from its subsidiary NRT of Nashville, TN. www.amut.it","@ID":33}, "CAPPING / CLOSURES 25 PETplanet insider Vol. 15 No. 08/14 petpla.net Caps produced on Netstal line Efficiently energetic Netstal says that its Evos injection moulding machine offers efficient, high performance moulding but with lower energy consumption than previous models. Netstal’s Evos range of injection moulding machines is available in four versions: 3000, 3500, 4500, and 5500. The numeral designations refer to their clamping forces, in kN. Although it stands as an integrated unit it is designed as a modular system, which means that the clamping unit, plasticizing unit and drive are all individually selectable this makes the machine customisable for a wide range of applications. As the clamping and injection units are in two separate machine modules, manufacturing and assembly processes can be run in parallel. The Evos series features hybrid drive technology, which is designed for lower energy consumption. Netstal identifies the benefits of the Evos machines are that they are energy-efficient; user-oriented; precise and fast; and flexible. It says that the machines are well-suited for manufacturing of closures; it claims that its large clamping surfaces provide sufficient space for moulds with a high number of cavities. The Evos clamping unit is based on Netstal’s well-established fivepoint toggle lever system. The doubletoggle lever is designed to ensure optimal transfer of force to the centre of the mould mounting area and even distribution of the clamping force; at the same time, its strong construction prevents deformation of the clamping plates. The inward-facing closing cylinder inside the toggle lever area is designed to save space. Movement sequences starting positions are managed by digital clamping unit control. Pneumatic valves facilitate fast response times. Netstal says that the Evos series can be customised for a range of different application areas. Connections for hydraulic auxiliary mould controls can be installed on the operating or non-operating side of the machine, as required. Multiple socket outlets with integrated circuit breakers can be installed in various positions on the machine, for peripheral devices connection. Depending on the mould, appropriate cooling water distributors can be placed in any position on the mould plates. The distributors are protected from corrosion and ball valves are used in order to achieve optimal flow rates. The company says that the machines are designed to offer high levels of accessibility, to be easy to use, and very easy to maintain. The Evos machines have also been designed to meet the growing demand for in-mould labelling, a feature that offers the potential for cost saving as well as functional benefits. The closedloop lubrication system and completely sealed drive unit mean that the Evos series is suitable for use in clean rooms as well as conventional production floors. It also incorporates technology for embossing processes and both gas and water injection. The modular concept is not just limited to the main components – the clamping and injection units. Additional equipment packages are also modular in design and can be individually configured. www.netstal.com","@ID":27}, "MARKET SURVEY 22 PETplanet insider Vol. 15 No. 08/14 petpla.net 08/2014 MARKETsurvey Company name Amsler Equipment Inc. Serac group KHS Corpoplast GmbH Kosme Gesellschaft mbH Postal address Telephone number Web site address Contact name Function Direct telephone number Fax E-Mail 1245 Reid St., Unit 1, Richmond Hill, Ontario Canada L4B1G4 +1 905 707 6704 www.amslerequipment.net Ms Heidi Amsler Sales and Marketing Manager +1 905 707 6704 +1 905 707 6707 [email protected] 12, route de Mamers, BP 46, 72402 La Ferté Bernard Cedex, France www.serac-group.com Mr Philippe de Sarrazin Managing Director - Serac Asia Pacific +60 37847 2228 [email protected] Meiendorfer Strasse 203 22145 Hamburg, Germany +49 40 67907 0 www.khs-corpoplast.com Mr Marco Böhnke Product Manager +49 40 67907 0 +49 40 67907 100 Marco.Bö[email protected] Gewerbestrasse 3 2601 Sollenau, Austria +43 2628 411 0 www.kosme-austria.com Mr Johann Gugler Managing Director +43 2628 411 125 +43 2628 411 4125 [email protected] 1. Machine designation / model number Linear Series - 6 Models: L12, L15, L22, L32, L407, L42 Linear Widemouth JAR Series - 2 Models: L16J, L25J Linear Convertible Series - 2 Models: L32C, L42C Linear Large Format Series - 3 Models: L110, LM120, L120C Rotary Series - 2 Models: APT10, APT16 SBL Series (Linear) InnoPET Blomax Series IV Linear Machines (5 models) 2. Bottle volume (from/to in litres) a) Standard machines 50ml to 5l 100ml to 6l 50ml to 5l 50ml to 3l 0,05 to 8l 0,2-3,0 0,05 - 3,0 b) Machines for large containers 4l to 23l up to 5,0l 0,5 - 30,0 3. Maximum number of stretchblow moulds (units) a) Standard machines 4 2 16 8 36 4 b) Machines for large containers 6 2 2 8 2 4. Output per stretch-blow mould for: 0.5 litres CSD bottle (units per hour) 1,800 1,800 1,500 1,800 2,250 1,700 1 litre CSD bottle (units per hour) 1,400-1,800 1,400-1,800 1,250 - 1,500 1,800 2,200 1,650 1.5 litres still mineral water bottle (units per hour) 1,400-1,800 1,400-1,800 1,300 - 1,500 1,800 2,200 1,600 Large capacity container 300 (18,9l) 1,000 800 up to 1250 for 5,0l; 350 for 30,0l Other 800 -1,600 3,000 (4l) 5. Footprint / space requirement (L x W x H in metres) from 4,0 x 1,8 x 2,4 to 4,3 x 3,7 x 2,5 3,9 x 2,5 x 2,2 from 5,7 x 2,0 x 2,4 to 4,3 x 3,7 x 2,5 3,9 x 3,8 x 2,7 2,7 x 2,2 x 3,1 to 4,2 x 3,0 x 3,2 5,2 x 2,2 x 2,7 13,3 x 7 x 3,2 m (Blomax 36S) 4,5 x 1,83 x 3,1 to 5,1 x 1,85 x 3,1 (without preform feeding system) Company name Luxber, S.L.U. Wei Li Plastics Machinery (HK) Ltd. Mega Machinery Mould Sidel Group Postal address Telephone number Web site address Contact name Function Direct telephone number Fax E-Mail Av. de Azorin, 34-36 03440 Ibi, Spain +34 965 55 3853 www.luxber.com Mr Vicente Mira General Manager +34 965 55 3853 +34 965 55 3861 [email protected] Room 1212, Fo Tan Industrial Centre, 26-28 Au Pui Wan St., Fo Tan, N.T., Hong Kong +852 2690 2368 www.weiliplastics.com Ms Christine Kwan Senior Marketing Executive +852 2690 2368 +852 2690 2380 [email protected] 47-8 # Huangzhou Rd., Huangyan, Zhejiang provice, China +86 576 840 20 122 www.MegaMachinery.com Simon Sales Manager +86 576 840 20 122 +86 576 840 20 107 [email protected] 4, Avenue de la Patrouille de France, Octeville-sur-mer, BP 204, 76053 Le Havre Cedex, France +33 2 3285 8687 www.sidel.com Mr Damien Fournier Blowing & Coating Product Management Director +33 2 3285 8815 [email protected] 1. Machine designation / model number Tecnopet MP Series / AP03 Series / PX Series MG Sidel Matrix Blower: 61 models Sdiel SBO Universal 2eco: 20 models Sidel SBO Highspeed eco: 2 models Sidel SBO Universal 2eco PH: 8 models 2. Bottle volume (from/to in litres) a) Standard machines 0,1 to 2,5 1,5l up to 2,5l 0,25l to 3,5l 0,25l to 3l 0,20l to 0,71l 0,25l to 2l b) Machines for large containers 0,5 to 12 10l-20l 30l 3. Maximum number of stretchblow moulds (units) a) Standard machines 6 16 16 34 30 34 20 b) Machines for large containers 4 2 5l up to 6, 10l up to 4, 20l up to 2l 4. Output per stretch-blow mould for: 0.5 litres CSD bottle (units per hour) 1,800 1,000 1,600 2,200-2,300 2,200 2,000 SBO 24 / 1,950 SBO 34 1,400 1 litre CSD bottle (units per hour) 1,400 1,000 1,500 2,200-2,250 2,200 1,400 1.5 litres still mineral water bottle (units per hour) 1,600 1,000 1,400 2,200-2,250 2,200 1,400 Large capacity container 1,000 500-800 5l 1,000; 10l 800; 18,9l 500 Other 500-800 2,000 Sidel Matrix HR blower 5. Footprint / space requirement (L x W x H in metres) 5,8 x 4,2 x 3,1 3,12 x 1,62 x 1,6 to 4,26 x 2,72 x 2,15 depend on the machine model M model: 7,9 x 4,6 x 3,7 - G model: 9 x 5 x 3,7 - L model: 13,7 x 7 x 3,7 11,3 x 4,9 x 3,9 to 13,1 x 4,9 x 3,8 6,7 x 3,3 x 3,8 to 10,6 x 4,9 x 3,9","@ID":24}, "MATERIAL / RECYCLING 17 PETplanet insider Vol. 15 Short cycle times, high shot-to-shot quality, low energy consumption and maximum flexibility. The new XFORM 300 with its unique 6-position post-mold cooling system boosts your output performance for the widest range of preforms. Cooling preforms faster and better, the 96-cavity platform is ideal for large runs and quick mold changes. And it lets you run any mold you want, old or new, OEM-built or not, in total freedom. From ultra-thin walled (with proprietary XMould™ technology) to wide mouth. XFORM 300, low transformation cost, high value. SIPA S.p.A. - Via Caduti del Lavoro, 3 - 31029 Vittorio Veneto (TV) - Italy Tel. +39 0438 911511 - Fax +39 0438 912273 - e-mail: [email protected] www.sipa-xform.com Designed to adapt. Built to last. The new XFORM 300 IMAGINE THE LOWEST TRANSFORMATION COST. IN TOTAL FREEDOM. Bottle Platform have been promoting Design for Recycle Guidelines for PET Bottles. These recommendations encourage designers, converters and brands to consider PET recycling in the earliest stages of their product design process by integrating technologies and additives that do not negatively affect the potential to recycle PET back into higher end applications such as new bottle, film and sheet manufacturing. By specifying an AA scavenger that meets performance requirements and maintains polymer clarity and quality, brands and converters are in a better position to meet the environmental demands of the industry. AA scavenging solutions: Meeting performance and quality criteria A comparative moulding study of an anthranilamide versus a polyamidebased AA scavenging system was carried out. Figures 1 and 2 (see page 19) represent the chemical reaction of both solutions with AA. The ring closing reaction of the anthranilamide formulation in Figure 1 creates a stable adduct to help prevent the migration of AA. Test method and results Samples were prepared on an 80-ton injection moulding machine fitted with a four-impression test plaque mould. The machine was run under standard laboratory conditions for PET. The process was allowed to run with virgin, bottle grade PET resin for 30min in order to purge degraded material from the machine barrel and to allow the machine to approach equilibrium conditions for AA generation. Parts were sampled at this point to form an initial control. The polyamide formulation was added to the process at 0.1%, 0.2% and 0.3%. The anthranilamide formulation was then added at various addition rates up to 0.3%. Between each test, the machine was purged with virgin PET, without stopping the machine cycle. A series of control samples was taken to confirm that the machine was running at equilibrium. AA Scavenging performance Sample mouldings were reduced to a powder by freezing them with liquid nitrogen before milling them in a rotary cutting mill. The powder samples were analysed for AA using headspace gas chromatography. The methodology is based on that described in ASTM 2013-1.","@ID":19}, "NEWS 8 PETplanet insider Vol. 15 No. 08/14 petpla.net gwk acquires former HQ of Battenfeld in Kierspe gwk have been designing and manufacturing their cooling and temperature control units in central Kierspe since 1967. Historically, the structure of the buildings has grown with the company. Not all the processes are in line with the logical flow of materials. The site and the factory premises have undergone further development. Partner Patrik Zeppenfeld explains: “As soon as the former Battenfeld plant in Meinerzhagen – just round the corner from us – came up for sale, we seized our opportunity”. Helmut Gries, Managing Director, continues: “We are doubling our production area and in this way are doing everything possible to ensure future growth so that we can expand further to meet the needs of the market. For us, it’s more than simply moving offices, – it’s a step into the future“. The factory bays and the administration building meet the requirements of the Kierspe people. To go back to Zeppenfeld again: “At the end of the year the 13 production bays came up for sale. We had a preliminary look round, investigated more deeply and soon came to the conclusion that this would be a perfect fit. The big straight long bays, along with the offices and administration buildings, were exactly what we were looking for. In addition, the premises are extremely well equipped with all supply facilities and there are even a large number of cranes with very high load-bearing capacities. Battenfeld’s production activities there also featured a very high level of in-house manufacturing. This, of course, is in line with our requirements”. The company is also making use of the move to optimise its processes and to introduce new manufacturing technologies. Gries: “We are modernising the site, and as plant engineers we know quite a lot about what’s involved in that. We are also looking at ways of re-organising our procedures generally, from the supply and flow of materials, to the introduction of new production processes, information channels, in short, we are looking at a complete overhaul of what we do and how we do it. This necessitates considerable investment, for example in a new paint line set up which will be energy-saving and environmentally friendly. We will be bringing in 5-axis machining centres, a palletiser, a plasma cutting machine and we are also developing a new test concept for quality assurance. Some of the acquisitions have already been put in hand”. www.gwk.com Sidel presents low-output aseptic technology at Aseptipak Europe 2014 Sidel took part at this year’s Aseptipak Europe Global Forum from 18 to 19 June 2014 in Warsaw, Poland and presented a case history on Fonti di Posina, the Italian co-packer who recently installed Sidel Combi Predis FMa with dry preform decontamination. Title of the presentation: “Recently Launched Breakthrough Technology for Low-Output Aseptic Production of PET Bottles: A Customer Case Study”. The introduction of the Combi Predis FMa technology in 2014 at Fonti di Posina has removed the need for any bottle rinsing, eliminating the need for water and has enabled lightweighting of the company’s 1,5l bottles, with material savings of 20%. The aseptic PET Combi achieves 95% efficiency while allowing the doubling of the current aseptic production capacity. Fitted with an ecological oven, the system also features energy savings of 43% at the blowing stage. www.sidel.com Krones ranks among Western Europe’s 50 most trustworthy companies The prestigious US business magazine Forbes lists Krones, the global supplier of beverage filling and packaging systems, among the 50 most trustworthy companies in Western Europe. With 98 points out of a possible 100, Krones AG, Neutraubling, Germany, received the best rating of all companies analysed. The list is based on a study conducted by GMI Ratings, a provider of analyses and ratings, evaluating risks in connection with business management and balance sheet probity. GMI analysed more than 4,000 companies listed on Western Europe’s stock exchanges against around 60 different criteria, and arrived at an “Accounting and Governance Risk” (AGR) rating. www.krones.com","@ID":10}, "PREFORM PRODUCTION 28 PETplanet insider Vol. 15 No. 08/14 petpla.net Drying of PET- Bottles, preforms and closures, part 13 Manufacture of PET Preforms Although this book will not detail every aspect of the injection moulding of PET preforms, we will give an overview of some aspects that are critical to designers. PETplanet insider is publishing extracts from successive chapters of Ottmar Brandau’s “Bottles, Preforms and Closures”, which was first published by hbmedia. A newly revised version is reissued under the Elsevier imprint. Because PET is hygroscopic, it must be dried before it can be injected. The maximum amount of water that can be in the resin when it is in the extruder throat is 50ppm. This residual moisture will react with the PET in the extruder and lead to an acceptable drop of 0.03–0.04 in IV. Higher moisture levels will lead to much higher IV drops, rendering the material unsuitable for the application (Fig. 2.10). The correct drying parameters are a combination of time and temperature at a certain airflow. Modern dryers are able to generate the required airflow of 4m3/h/kg h (1 cfm/lb h). Under these conditions, processors must calculate or determine by practical experiment what the residence time of the resin in the hopper is for a given job. To do this practically, a handful of colour pellets is placed on top of the resin in the 0 50 100 150 200 250 300 350 400 1.2 1.0 0.8 0.7 0.6 1.2 1.0 0.9 0.8 PPM Water Final IV Initial IV Fig. 2.10","@ID":30}, "MATERIAL / RECYCLING 18 PETplanet insider Vol. 15 No. 08/14 petpla.net The level of AA (ppm) was reduced by both formulations, but results demonstrate that the anthranilamide solution performed significantly better, particularly at lower addition rates up to 0.15%. Comparing percentage reduction performance, it is clear that the use rate of the polyamide solution is around three times higher than the anthranilamide product to achieve a comparable reduced AA level. For brand owners and manufacturers, using an anthranilamide product could translate into lower inventory levels. Plaque colour Plaque colour was measured in transmission, at selected addition rates, using a spectrophotometer. Five plaques were measured from each sample set, to help gauge part-to-part variability. Container aesthetics and clarity play an important role in shelf impact and maintaining brand integrity. One of the obvious signs of PET polymer degradation is yellowing, and the ability to control and minimise this polymer yellowing is fundamental to increasing its acceptability for recycling. The comparative data reveal the plaques manufactured with polyamide are yellower than those incorporating the anthranilamide solution. Additional toner or colorant may need to be added to the polyamide process to achieve improved aesthetics and counteract the yellowing, which adds further complexity to the process and the overall formulation. The box plots also indicate that part-to-part variance is greater in the polyamide samples. The colour test results demonstrate potential commercial value for brand owners in two ways: 1) Aesthetic quality is critical for brands to make their products appealing on supermarket shelves. Incorporating an effective AA scavenging technology that also minimises polymer yellowing helps maintain bottle clarity, aesthetic appeal and ultimately brand integrity. 2) Reducing the rate of variance helps manufacturing teams reduce scrap, improve quality consistency and streamline overall production efficiency. Recycled PET bottles","@ID":20}, "ITALIAN SUPPLIER 12 PETplanet insider Vol. 15 No. 08/14 petpla.net tory for all machine areas at this site are also housed here, conveniently close to one another. Mould construction capacity here in Italy is 25,000 mould inserts/blow moulds per year. A further capacity expansion of 20% is scheduled for 2014. A similar moulds capacity is available in the Chinese operation. Plant No.2 In Plant 2 we find production lines operating on “lean” principals for all linear and rotary stretch blow moulding machines ranging from two to 24 blow moulding stations. In a ratio of approx. 30/70%, rotary/linear, stretch blow moulding machines that have undergone acceptance testing leave the plant in accordance with the specified moulding cycle. In the case of the rotary machines, the principal areas of application are the beverages sector, whilst for the linear machines, the range of applications is considerably greater, taking in sectors such as edible oils, body and health care, household and foodstuffs packaging right through to detergents and wide-mouth applications. Also worthy of note here is the particularly strong market for PET large size containers (up to 5 gallons), according to Roberta Gualtieri, be it stackable containers, kegs, from 5l up to 5 gallons with handles or special large size self-collapsible containers for water coolers. Plant No.3 Here we see the assembly and acceptance of the preform systems for all the range of machines. These include the xform range based on three machine sizes with a locking force of 150/300/500t and up to 144 cavities. The two smaller “hybrid” units, with their hydraulic injection units and electrically operated twoplaten clamp units, were developed in collaboration with Athena in Canada, while Sipa partnered with Engel in Austria on the xform 500 to accept moulds from any supplier. Also seen here are such in-house developments as ECS Integrated Systems for injection-stretch-blow moulding and the xtreme series. As for assembly, of the almost 50 xform machines so far sold (the range has been on the market for just 18 months) the majority are 96-cavity. Machines have been supplied to Asia, Japan, the Middle East, North, Central and Latin America, Europe and Africa. The ECS series is continuing to be marketed only for special applications e.g. wide-mouth or hot fill. We were fortunate in being able to view another machine for an American customer at the assembly stage. According to Sipa, there are already three customers for the A first glance of EDITOUR 2014 latest development of the xtreme construction series, although details of the ultimate end users remained firmly under wraps. Bottling machinery plant in Parma The plant in Parma has been taken over by bottling machinery manufacturer Berchi. With 130 employees, Sipa is today concentrating on PET bottling systems featuring up to 160 filler valves with subsequent automatic packaging and palletising. These multi-production lines, as they are known, represent a special area here. Customers are able, using relatively simple re-tooling, to bottle still water and CSD as well as tackle hot fill applications. There is also the trend towards block lines with a preference for operating these with their own stretch blow moulding machines. According to Matteo Tagliaferri, 50% of the bottling lines supplied are already block or triblock lines and the tendency is increasing. Machines for closure One item still missing from the company portfolio is machinery for closure manufacture. According to Roberta Gualtieri, collaborative relationships already exist here with major manufacturers and there are no plans to invest in this product range. A new devel-","@ID":14}, "MATERIAL / RECYCLING 16 PETplanet insider Vol. 15 No. 08/14 petpla.net Achieving product protection and maintaining aesthetic quality Acetaldehyde migration in PET water bottles: Based on an article by Matt Jackson, R&D Lead Technologist PolyOne ColorMatrix Acetaldehyde (AA), a degradation product of PET polymer, is generated during the PET preform injection moulding process and becomes trapped within the preform walls during cooling. AA subsequently migrates into the water after filling and during storage, which can affect the taste and smell of carbonated and still mineral waters. Two currently used AA scavenging additives help reduce the negative taste and odour effects of AA migration to maintain product quality and ultimately preserve brand integrity. This article explores their effects on PET polymer colour and performance. One is an anthranilamide-based formulation, dispersed in a PET liquid carrier system; the second is a solid granule polyamide-based additive. AA scavenging performance and container aesthetics are important for brand owners. In addition, today’s eco-conscious plastics industry demands that the effect of additives on polymer quality and clarity be a key consideration because this factor helps determine recyclability. As a result, an additive’s effect on clarity can be a deciding factor in specifying one product over the other. A series of laboratory tests were carried out to gauge scavenging performance, and more specifically, to measure the effects each additive has on polymer colour and clarity, both after initial processing and after a second heat process following a simulated recycling study. Global PET bottled water market The global PET bottled water market is the largest for PET containers. This market, while growing at a slightly slower rate compared with growth in the last decade, is forecast to manufacture over 250 billion bottles of water in 2015. (see Table 1 and 2) There is growing pressure on the plastics industry to increase the rate of recycling. In Europe, more than 60 million PET beverage bottles were recycled in 20122 and while most of these would be re-used in fibre applications, using more recycled PET in new bottle and sheet manufacturing is a growing trend. In North America, the second largest regional consumer market for bottled water, 276 MM lbs (over 125,000t) of recycled PET was used in food and beverage bottle End-use 2005 2010 CAGR 2015 CAGR Beer 5.9 8.4 7.2% 11.9 7.2% Carbonated soft drinks 116.1 138.5 3.6% 163.9 3.4% Juice beverages 26.4 32.5 4.2% 43.1 5.8% Milk and dairy drinks 10.3 12.3 3.5% 15.4 4.6% Ready-to-drink-tea 20.5 37.8 13.0% 61.2 10.1% Sport and energy drinks 19.5 28.4 7.8% 44.7 9.4% Water 143.1 195.5 6.4% 251.4 5.2% Wine and spirits 14.3 17.4 4.0% 22.4 5.2% Other beverages 3 3.8 5.1% 4.9 4.9% Total 359.1 474.6 5.7% 618.8 5.4% Table 1: Global PET Bottle volume consumption (billion units) Geographic region 2005 2010 CAGR 2015 CAGR Asia 32.9 55.7 11.1% 82.4 8.1% Europe 44.9 50.8 2.5% 54.6 1.5% North America 35.7 46.7 5.5% 52.8 2.5% Rest of world 29.6 42.2 7.4% 61.5 7.8% Total 143.1 195.5 6.4% 251.4 5.2% Table 2: Global PET Bottle volume consumption – water (billion units) manufacturing in 20123. This represents an increase of 14% over 2011 and a clear indication of the accelerating growth market for recycled PET in new bottle production. For brand owners, the use of recycled materials strengthens their environmental profile, and companies like Nestlé, Mountain Valley and Eldorado already use from 25% to 100% recycled content for certain water brands. PET recycling bodies like Napcor in North America and The European PET","@ID":18}, "PETpatents www.verpackungspatente.de 36 PETplanet insider Vol. 15 No. 08/14 petpla.net Drinking aperture International Patent No.WO 2012 / ß95491 A1 Applicant: SA des Eaux Minerales D’Evian Saeme, Evian-les-Bains (FR) Application Date: 12.1.2012 The application proposes including one or more drinking caps with a removable spout in a multipack for water bottles that are closed by means of a “normal” screw closure. This will enable consumers to screw on their preferred closure. Shape of bottom section of a Plastic Bottle International Patent No.WO 2013 / 180032 A1 Applicant: Yoshino Kogyosho Co. Ltd., Tokyo (JP) Application Date: 24.5.2013 As bottles become ever lighter, the bottom section also needs to be specially shaped so as to satisfy the requirements in terms of elastic distortion as a result of hot filling and the associated change in volume. Screw closure International Patent No. WO 2013 / 178665 A1 Applicant: IM Production, Pressiat (FR) Application Date: 29.5.2013 The screw closure on a container incorporates a number of sealing edges and a small opening. This means, for example, that any overpressure present can escape or can be removed from or added to the free space using an “air” device. Bottom section with grooves International Patent No. WO 2013 / 178905 A1 Applicant: Sidel Participations, Octeville Sur Mer (FR) Application Date: 15.5.2013 The bottom section of a plastic bottle made from PET incorporates reinforcement grooves and two concentric graduations for improving stability. Bottle with handle International Patent No. WO 2013 / 182541 A1 Applicant: S.A. des Eaux Minerales D’Evian, Evian-les-Bains (FR) Application Date: 4.6.2013 The application describes the shape, selection of materials, manufacture and surface design of a refillable plastic bottle that is placed upside down in a water dispenser. The bottle is fitted with a separately manufactured handle to promote better handling. Fragrance-conducting membrane International Patent No. WO 2013 / 192428 A1 Applicant: Juan E. Bruna, Miami (US) Application Date: 20.6.2013 A sealing membrane for a scented product is tamper-proofed by means of a membrane. This membrane incorporates openings that allow fragrances to permeate to the outside but which at the same time keep back the contents of the container.","@ID":38}, "imprint EDITORIAL PUBLISHER Alexander Büchler, Managing Director HEAD OFFICE heidelberg business media GmbH Häusserstr. 36 69115 Heidelberg, Germany phone: +49 6221-65108-0 fax: +49 6221-65108-28 [email protected] EDITORIAL Heike Fischer Gabriele Kosmehl Michael Maruschke Ruari McCallion Waldemar Schmitke Ilona Trotter Wolfgang von Schroeter Anthony Withers MEDIA CONSULTANTS Martina Hirschmann [email protected] Roland Loch [email protected] phone: +49 6221-65108-0 fax: +49 6221-65108-28 France, Italy, Spain, UK Elisabeth Maria Köpke phone: +49 6201-878925 fax: +49 6201-878926 [email protected] LAYOUT AND PREPRESS Exprim Kommunikationsdesign Matthias Gaumann | www.exprim.de READER SERVICES Till Kretner [email protected] PRINT Chroma Druck & Verlag GmbH Werkstr. 25 67354 Römerberg Germany WWW www.hbmedia.net | petpla.net PETplanet insider ISSN 1438-9459 is published 10 times a year. This publication is sent to qualified subscribers (1-year subscription 149 EUR, 2-year subscription 289 EUR, Young professionals’ subscription 99 EUR. Magazines will be dispatched to you by airmail). Not to be reproduced in any form without permission from the publisher. Note: The fact that product names may not be identified as trademarks is not an indication that such names are not registered trademarks. 3 PETplanet insider Vol. 15 No. 08/14 petpla.net dear readers, Water, water, water... everywhere… ...this element, vital to life, may indeed be everywhere, as the poet sings, but not necessarily in adequate quantities everywhere, and very often not of potable quality. Currently, it is calculated that something like one billion people do not have access to clean drinking water. Hitherto, the most widely used method of purifying water was simply to boil it, thereby killing off all the bacteria, but in many wilderness areas, finding readily combustible material was difficult, not to say impractical. Bottling water in PET, at first sight an expensive solution, may however prove to be the first step in the provision of potable water, and in many of the world’s poorest regions this initiative is being put to the test. How can PET bottles help? A more sophisticated option to kill off harmful bacteria is to subject the water to UV radiation, and this is where the PET bottle comes in. Project Sodis – Solar Water Disinfection – is an ingenious method of subjecting the water to solar radiation by using the PET bottle as the water tank, and the sun as the source of radiation. In 6 hours, 2 litres of water in a PET bottle can be treated. (see page 26) The beauty of this solution lies in the fact that both the sun and PET bottles are plentifully available, making this an effective and cheap way of making water drinkable. The Who (World Health Organisation), Unicef and the Red Cross are therefore recommending the Sodis method as one option for providing potable water in developing countries. As the project was rolled out, follow-up scientific studies were undertaken and these provided evidence of the efficiency of Sodis. Regional awareness campaigns were conducted amongst target populations by means of flyers, brochures and TV advertising. To date, more than 5 million people now have access to pure drinking water thanks to Project Sodis. Encouraging these figures may be, but it should not be forgotten that there are still almost one billion people in the world without access to clean drinking water. There is a lot of work still to do. Yours Alexander Büchler","@ID":5}, "PETbottles 34 PETplanet insider Vol. 15 No. 08/14 petpla.net Home Care Fabric softener concentrate in PET In Italy the Unilever subsidiary Coccolino is marketing 750ml of fabric softener concentrate with a long-lasting spring fragrance in an elegant, bulbous bottle made from PET. The contents of the transparent bottle are designed for 30 washes. Once unscrewed and up-ended, the cover lid also serves as a dispensing cup for the fabric softener. www.unilever.it Liquid feed for orchids 200ml of liquid feed for orchids in concentrate form is being marketed by the Italian company Flowers from Piacanza in a green PET bottle with a dispenser cap. Screwed on to the bottle is a cap which makes contact with the product via an opening at the bottom and a riser. On removal of a protective cap and by exerting slight pressure on the bottle, product is conveyed upwards into the transparent dispensing chamber which incorporates markings. After that the contents are transferred into a watering can and mixed with the corresponding amount of water. The bottle is tinted green, decorated with two labels and secured by means of an adhesive sticker prior to initial opening. www.blumen.it Fishing for plastic Ecological cleaning company Ecover has launched its first ever bottle made from waste plastic fished out of the ocean. The Ecover Ocean Bottle, which holds Ecover’s washing-up liquid, is made entirely from recycled plastic, with 10% of that plastic coming from the sea – a huge amount of PET bottles but also plastic bags or canisters. The washing-up liquid itself has been developed with a special ‘sea lavender and eucalyptus’ fragrance. The bottle represents a joint initiative between Ecover and some leading innovators in the marine conservation and packaging worlds. Using existing fishing boats kitted out with clever new technology, Waste Free Oceans’ ‘catch of the day’ project enables European fishermen to earn money by collecting between 2 and 8t of waste plastic per catch for cleaning and recycling. As part of a trial project, this waste has been sent to Closed Loop Recycling’s plant where it was processed and turned into plastic, which was used by Logoplaste to make the new Ecover bottles. This year, Ecover will be using 1t of ocean plastic, which it aims to increase to 3t next year. However, the main goal is to develop the infrastructure and a wider network of fishermen, recycling facilities and manufacturers, for to start using recycled ocean plastic on a global scale. As part of the project, the ocean waste has been sent to Closed Loop Recycling’s plant where it was processed and turned into plastic, which was used by Logoplaste to make the Ecover bottles. Logoplaste created a showcase in Leixoes Port, Portugal, on how to collect plastic waste from the oceans. www.ecover.com www.logoplaste.com The distinct design of the new Ecover Ocean bottle is inspired by the skeletons of unicellular aquatic organisms Diatoms and Radiolarians, whose design principles helped optimise the mechanical performance of the container.","@ID":36}, "MARKET SURVEY 23 PETplanet insider Vol. 15 No. 08/14 petpla.net Urola S.C. Sacmi Imola Sipa S.p.A. 1 Blow Urola Kalea s/n, PO Box 20230 Legazpi, Spain +34 943 737003 www.urola.com Mr Iñaki Unanue +34 943 737144 [email protected] Via Provinciale Selice 17/a 40026 Imola (Bo), Italy +39 0542 607111 www.sacmi.com Mr Moraldo Masi B.U.PET - Beverage Division +39 0542 607888 +39 0542 642354 [email protected] Via Caduti del Lavoro, 3 31029 Vittorio Veneto (TV), Italy +39 04389 115 11 www.sipa.it Mr Pietro Marcati Stretch Blow Molders Sales Director +39 04389 11 67 +39 04389 12 273 [email protected] 35 rue de la Ravine de Glatigny 95280 Jouy Le Moutier, France +33 9800 820 70 www.1blow.com Mr Olivier Perche Sales Director +33 9800 820 75 +33 9800 820 71 [email protected] Rotary Machines (8 models) Linear, URBI-2, URBI-4, URBI-6, URBI-8, URBI2L, URBI-4L Rotary, SBM-6S, SBM-10S, SBM-14S, SBM-20S,SBM-6, SBM-8, SBM-10,SBM-14, SBM-20 SBF Linear Systems SFL 6: 6/6, 6/6 XXL, 6/4 XL, 6/4 XXL , 6/3 XL (5 Models); SFL 4: 4/4, 4/3 XL, 4/2 XL (3 Models); SFL 4 WM: 4/4 WM, 4/3 WM, 4/2 WM (3 Models); SFL 2/2 & SFL 1 (2 Models) Rotary SFR EVO CUBE: 6 - 8 - 10 - 12 - 16 - 20 -24 cavity (7 Models) 1XL / 1XL Lab / 2L / 2LO / 4L / 4LO / 1XXL / 2XXL / 3XXL 3,1l 0,05 - 3,0 100 ml up to 2 l 100-700ml yes 250ml to 3l 250ml to 3l 0,15 to 12l 0,5 - 6,0 up to 10 l 100-2500ml 5 to 30l 5 to 30l 18 (in double cavity - 61.600bph up to 0,6L) 8 8 20 6 24 4 6 4 20 2 3 2,000 1,600 1,800 3,400 1,700 2,250 2,000 2,000 1,600 1,800 1,800 1,600 2,250 1,800 2,000 1,700 1,700 1,800 1,650 2,250 1,700 1,250 1,250 1,600 650 1000 for 5l ; 600 for 20l 6,05 x 3,85 x 3,25 (without preform feeding system) 2,32 x 2,20 x 2 to 5,90 x 4,35 x 2,30 2,4 x 1,6 x 3 to 4,5 x 3,5 x 3,24 12 x 5,5 x 3,8 (SBF618) 2,1 x 1,6 x 2,4 Side S.A PET Technologies Krones AG Siapi srl Pol. Ind. Montguit, C/ Llinars, s/n 08480 L'Ametlla del Vallès (Barcelona), Spain +34 938 46 3051 www.sidemachines.com Mr Oriol Vives Bages Sales Manager +34 938 46 3051 +34 938 49 2211 [email protected] Prof. Dr.Stephan Koren Strasse 10 2700 Wr.Neustadt, Austria +43 720 902 169 www.pet-eu.com Mr Maxim Poliansky Commercial Director +43 720 902 169 [email protected] Böhmerwaldstr. 5 93073 Neutraubling, Germany +49 9401 70 0 www.krones.com Mr Peter Christiansen Sales Director +49 9401 70 4980 +49 9401 70 914980 [email protected] Via Ferrovia Nord, 45, I 31020 San Vendemiano (TV), Italy +39 0438 4096 www.siapi.it Mr Fabio Firmani Sales & Marketing Director +39 0438 401016 [email protected] Sidel SBO Universal 2eco HR: 11 models Easyblow Maxiblow 1002e/2004e/2006e 2002eG/2003eG 5001e APF-6004,APF3002, APF-4 APF-30, APF10, APF-5 Contiform 3: 11 models Contiform 3 SC: 4 models Contiform 3 H: 8 models S, SC, SE ranges: Standard & Special Cnt; SX range: X-Large Cnt up to 40 l.;SW range: wm container 180mm 0,25l to 3l 0,1 - 2,5 0,1 - 10 0,2 - 3 0,1 - 10 0,2 to 2l 80ml to 12l 5 -10 5 - 10 5-30 3,0 to 30l 0,1 - 3,0 0,1 - 0,7 0,1 - 2,0 40 l ,30 l (2 cavities), 20 l (3 cavities) 4 2 30 1 1 2 / 4 / 6 2 / 3 10 (SE 10) 1 1 1 28 36 26 5 (SX 5) 1,800 / 1,700 for SBO 30 1700 1350 1500 1250 1500 1,800 1,800 / 1,700 for SBO 30 1700 1350 1500 1250 1500 2,250 2,250 2,000 1,700 1,800 / 1,700 for SBO 30 1700 1350 1500 1250 1500 2,250 2,000 1,800 1350 1250 950 1250 2,250 1,800 1,500 for 5l 120 for 30l 800 for 30l 7,1 x 3,3 x 3,8 to 18,8 x 6,6 x 3,9 Depending on machines models 8,6 x 3,2 x 2,5 to 6,4 x 2,8 x 2,3 9,2 x 2,2 x 2,7 to 9,2 x 2,4 x 2,7 6,5 x 5,4 x 4,6 to 11,7 x 7,6 x 4,6 10,7 x 6,2 x 4,6 to 14,4 x 7,6 x 4,6 6,9 x 4,4 x 4,5 to 11,2 x 6,8 x 4,5 SC: 4,1 x2 x 2,5; SE: 6 x 2,2 x 2,4; SX: 3 x 2,1 x 3,4; SW: 2,9 x 2,1 x 2,2","@ID":25}, "PETplanet insider Vol. 15 No. 08/14 petpla.net PET - THE NEXT GENERATION 26 Water disinfection in PET bottles Sunlight + PET = formula for disinfecting water Solar water disinfection - the Sodis method - is a simple procedure to disinfect drinking water. Contaminated water is filled in a transparent PET-bottle and exposed to the sun for 6 hours. During this time, the UV-radiation of the sun kills diarrhoea-causing pathogens such as viruses, bacteria and parasites (Giardia and Cryptosporidium). This makes the convenient method ideal for treating water for drinking in developing countries. A method which, by all accounts, also works at low air and water temperatures. Nepalese woman preparing drinking water using the Sodis method As early as the 1980s, Lebanese scientists found out that sunlight can disinfect water. However, this revolutionary discovery did not receive the attention it deserved. Systematic scientific studies or adaptations to users’ needs were lacking. So, in the 1990s, the water research institute Eawag, the Swiss Federal Institute of Aquatic Sciences and Technology, decided to investigate the idea and create a safe, simple method that can be used in developing countries. An interdisciplinary research team consisting of microbiologists, virologists, engineers and drinking water specialists then worked out a method that only needs PET bottles and sunlight: the Sodis method. To see how effective and how applicable this method was, Eawag ran tests in the laboratory and under field conditions in developing countries. In these tests, the Sodis method was shown to be effective and userfriendly, and also cost-effective. In order to confirm the effectiveness of the technique, it was necessary to carry out microbiological tests. The studies investigated the effective-","@ID":28}, "PREFORM PRODUCTION 30 PETplanet insider Vol. 15 No. 08/14 petpla.net Please order your copy at the PETplanet insider book shop: https://petpla.net/books Bottles, Preforms and Closures A Design Guide for PET Packaging Second Edition by Ottmar Brandau € 115,00 180 pages © Copyright Elsevier 2012 purpose the neck inserts are mounted on slides that are often cam driven. Cores and cavities are always watercooled, whereas neck inserts may or may not be water-cooled. Injection moulding of preforms is different from other forms of injection moulding as the preform wall is relatively thick, injection pressures are relatively low, and the injection speed is low to prevent shearing of the material. We begin injection with the tool closed, forming an empty cavity as in Fig. 2.13. Fig. 2.13: Empty cavity The material enters the cavity through the gate. Despite the relatively low injection pressure, the material pressure may bend the injection core to one side and cause what is known as “core shift” with the resulting preform wall thickness becoming uneven. This is especially true for thin cores (below 17mm) but may also happen for standard ones when guide bushings are worn out, for example (Fig. 2.14). Fig. 2.14: Start of injection As the hot material hits the cold mould walls, the resin in direct contact with the wall freezes off and forms a boundary layer. The material in this layer will not change during injection. Its thickness restricts the mold channel and is one reason why a minimum wall thickness must be maintained in the preform gate area (Fig. 2.15). Fig. 2.15 Boundary layer builds As more material enters the cavity the boundary layer expands along the length of the preform. Its thickness stays the same as long as hot material is flowing through. The air that is present in the mould cavity must have an escape path. Otherwise, trapped air would lead to sink marks in the preforms. Four to eight vents approximately 0.001–0.0015mm deep are machined into the face area of the preform neck, allowing air to vent to the outside. Sink marks are also prevented, and the flow of material is improved by giving cores a finish in the direction of material flow rather than radially. This is achieved by special machinery that turns the cores while moving a polishing stone back and forth on the longitudinal axis of the core (Fig. 2.16). Fig. 2.16: Injection continues At this point in the injection process the cavity has been filled (Fig. 2.17). The added resistance causes the hydraulic pressure to increase, and it is here that the machine needs to be switched from injection to hold or packing pressure. This can be done by using the actual pressure as the setting to trigger the hold pressure, but for PET a position-based trigger has proven to be more consistent and is therefore used almost exclusively. The point at which this occurs is called the transition or switchover point and can be dialed in on the screen. During the hold phase, material that is now starting to shrink as it cools is replaced through the still open centre of the melt stream. This is necessary to avoid sink marks (Fig. 2.17). Fig. 2.17: Injection cavity full During cooling time, the material cools quickly and shrinks onto the core in the process. It is noteworthy that the gate area of the preform always stays warmest as it is the last part of the preform to receive hot material. Most preform defects such as cloudiness are located here for this reason. In single-stage stretch blow moulding the warmer gate area limits the processability of the preform as the temperature is a result of wall thickness and injection parameters and therefore not directly controllable. (Fig. 2.18) Fig. 2.18: Cooling time When problems with a particular preform arise, designers should be aware of the various aspects of the injection moulding process and drying parameters and should first ensure that preforms were processed correctly before making changes to the shape of the preform. * This article was published in Bottles, Preforms and Closures, Ottmar Brandau, Chapter 2.4. Copyright Elsevier 2012","@ID":32}, "NEWS 9 PETplanet insider Vol. 15 No. 08/14 petpla.net Engel supplies gas injection technology module to Haidlmair Engel Austria and Bauer Kompressoren have delivered a gas injection technology cell to Austrian Haidlmair, a mould maker specialized in moulds for drink crates, large containers and pallets. The three partner companies expect the new cell to strengthen their joint development work. Bauer Kompressoren is Engel Austria’s exclusive partner in the field of gas injection technology (GIT). Under the name Engel gasmelt, the injection moulding machine manufacturer offers complete integrated solutions for injection moulding with gas injection technology. The project with Haidlmair also demonstrates that older systems can be easily upgraded. The new GIT module was integrated into a large existing Engel machine. The gasmelt process and the individual gas feeds can be controlled and monitored via the injection moulding machine’s display. During mould trials, Haidlmair particularly benefits from the leakage monitoring system integrated as a standard in the Engel gasmelt cell. Especially in the case of large moulds with several gas injectors, being able to map the alarm messages to the control loop facilitates troubleshooting in the event of leakages and increase the availability of the system. In general, with key patent protection rights for the gas injection technology having expired, the process is now being given a fresh boost. In view of the ever increasing cost pressure and the demand for more process stability, there is an increasing demand to employ gas injection technology, according to Engel Austria. www.engelglobal.com Full inspected! PVS-2 in line or off-line Sampling Quality Inspection System for PET preform PVS-2 is capable to detect all the possible defects that could appear during preforms production, reading the cavity number and weight all the preforms. All the data are filed in a SQL data base that can be shared over a LAN. PVS-2 can be connected to any type of injection moulder or used as a standalonemachine for the quality lab. The system can run at the speed of 1.100 preforms/hour. f.l.t.r.: Klaus Mittmannsgruber, Engel Austria, Mario Haidlmair, Haidlmair, Raffael Kurz, Bauer Kompressoren, Christian Wolfsberger, Engel Austria, with the new compressor that was integrated into a large existing Engel machine","@ID":11}, "ITALIAN SUPPLIER 11 PETplanet insider Vol. 15 No. 08/14 petpla.net From preform to bottle, everything from a single source by Waldemar Schmitke This slogan, from Sipa, neatly encapsulates the philosophy that drives the company’s PET container production and development strategy. The company, headquartered in Italy, also operates a workshop for moulds in China enshrining Sipa’s dedication to its range of machinery and development focus. Included in the range, alongside traditional preform injection moulding machines, we find new developments in the xtreme series using rotary injection and compression technology. Alexander Büchler and Gianfranco Zoppas in conversation in front of an xform 500 with 96 cavities In the stretch blow moulding sector, there are single-stage and two-stage machines in the range, in both linear and rotary construction. The injection and blow moulds come from the company’s own capacity, manufactured for its own machinery projects as well as for third party products. Rounding off the range are complete bottling lines that can incorporate filling, capping, labelling, wrapping and palletising. On the next stage of our editorial tour we have the opportunity to visit the main workshops in Vittorio Veneto and here we meet Gianfranco Zoppas, President of Zoppas Industries, to which Sipa belongs and Roberta Gualtieri, Marketing Manager and Matteo Tagliaferri, Marketing and Communication, Sipa Filling & Packaging Division. With the exception of the assembly plant for bottling lines and palletisers in Parma, all the other Italy-based activities are to be found here on site, spread over three plants. Plant No.1 This houses the mould construction facility. Preform moulds from one to 144 cavities, incorporating the company’s own hot runner technology, are manufactured and assembled here for own machine projects as well as for third party machine manufacturers. This also applies to blow moulds in the 2-stages sector. Only the complete mould sets for the 1-stage machines are manufactured exclusively for Sipa’s own lines. Prototyping and testing facilities and the laboraA first glance of EDITOUR 2014","@ID":13}, "CAPPING / CLOSURES 15 PETplanet insider Vol. 15 No. 08/14 petpla.net Welcome to visit TECH-LONG CHINA BREW CHINA BEVERAGE 2014 No. 23 Yunpu 1 Road, Luogang District, Guangzhou, 510530, China Tel: +86 20 62956800 Fax: +86 20 82266913 www.tech-long.com E-mail: [email protected] TECH-LONG PACKAGING MACHINERY CO., LTD. BEVERAGES HOUSEHOLDS CONDIMENTS DAIRY BEER Booth: E2C67 Date: 2014 10.13-16 Add: New China International Exhibition Center, Beijing,China analysed under the same or very similar conditions to those in which it will be deployed. The false-colour photo of the cap’s cross-section (Fig 1) reveals that oxygen permeation through the closure is occurring solely through its flat region (highlighted in the oval area). In the threaded area (identified by the green arrow), where the cap mates to the bottle neck, air has an almost free access to the neck itself. It is, consequently, the bottle’s PET material that allows permeation in this region. The transition between the bottle and the cap’s sealing is a particularly sensitive area and it is essential that a cap should be tested on the thread of the bottle. The program therefore undertook testing with a closure fitted to a preform neck that had been cut from the rest of the bottle. It is also important to measure the performance of a preform neck fitted with an impermeable aluminium top. The results enable determination of the permeation rate of the cap independently of the preform’s threaded area. A preform with a suitable thread from any supplier can usually be used as a standard for testing cap modifications. For a final permeation result, however, it is better to test the cap with the preform that is to be blown into the bottle on which it will be fitted. This eliminates variations in the selection of the PET master batch. The interface between the closure and the package is highly sophisticated and it is best to include this area in the test. Systech’s advanced oxygen permeation analysers are capable of testing the oxygen barrier properties of packages with a detection threshold of 4E-05cm³/pack/day. All the cap samples and preforms tested have been collected from recent packaging industry shows and exhibitions. In the case of bottle caps, the bottle necks, caps and preform threads with the aluminium shims are glued directly on the platen of the permeation analyser. A rapid setting epoxy resin seals the caps and preforms onto the platen, quickly and easily. Pairing of caps to preforms has been done randomly. In this case study, it is the test principle and procedure which is of interest. The variety of available cap systems in the market cannot be measured in the frame of an application report. Oxygen transmission rates for this random selection of caps have been measured between 8.3 E-02 and 1.47E-02 cm³/cap/day, including a contribution from the preform neck. The contribution of the neck itself is in the range of 2.6 to 2.16 E-03cm³/ neck day and has to be deducted from the values in the diagram. www.systechillinois.com","@ID":17}, "PET - THE NEXT GENERATION 27 PETplanet insider Vol. 15 Respecting values in effective dialogue www.krones.com drink technology India 2014 Mumbay, 25 – 27 September Hall 01 H21 Water disinfection project in Vietnam ness of Sodis against a wide range of germs such as bacteria (cholera, typhus, dysentery, etc.), viruses (polio, hepatitis, etc.) and parasites (giardia, cryptosporidium, amoeba, etc.). Research into the question of why the germs die revealed that bacteria die because membrane proteins as well as enzymes of the respiration are being damaged by UV-A radiation. This damage is evidently so severe that the bacteria can no longer repair it. The role of PET The PET bottle plays a key role in the Sodis method. PET is recommended because the bottles are light, do not break and are easy to obtain in many regions of the world. However, clear glass bottles or special bags can also be used. Reports regarding substances in PET bottles that may be a risk to health are worrying users of the Sodis method. Therefore, a number of research institutions tested the scientific accuracy of these reports and carried out their own analyses of substances such as antimony, adipates, phthalates, acetaldehydes and formaldehydes. One focus was the question of whether formaldehydes and acetaldehydes are transferred from the PET bottles to the water when the Sodis method is applied, and if so, in what quantities. It was found that exposure to the sun has no effect on the concentration of acetaldehydes, though the concentration of formaldehydes does increase with the length of exposure. However the concentrations of aliphatic aldehydes remained far below the state regulatory limit for drinking water in all samples. These studies show that when the Sodis method is applied correctly with PET bottles, there is no danger to human health. Eawag set up projects in developing countries to make sure that the method was made available to the people who needed it most urgently. At the moment more then 5 million people in 24 countries in Africa, Asia and Latin America use the Sodis technique to disinfect the drinking water. www.sodis.ch","@ID":29}, "MATERIAL / RECYCLING 19 PETplanet insider Vol. 15 No. 08/14 petpla.net An efficient barrier is essential for us. We inspect it. www.intravis.com Figure 1: Anthranilamide reaction Figure 2: Polyamide reaction Simulated recycling study Further, plaques were moulded at equivalent AA reduction performance (0.1% anthranilamide vs 0.3% polyamide). Samples of plaques were retained for subsequent colour measurement, while the rest were cryogenically milled into granules. These granules were re-crystallised in a vacuum oven set to 190°C, with vacuum and nitrogen purge. Re-crystallised material was again moulded into plaques and the colour compared to the first mouldings. The same re-crystallised material was used to mould preforms on a Husky GL-160 machine, fitted with a twin cavity mould. The significantly reduced b* (yellow) colour variation of the anthranilamide process versus the polyamide process suggests the anthranilamide-based formulation not only provides more clarity and aesthetic quality through one heat process, but suggests polymer clarity can be maintained after recycling and at least one further heat process. The haze measurements (ASTM D1003)","@ID":21}, "PETbottles 32 PETplanet insider Vol. 15 No. 08/14 petpla.net Health + Beauty Care Natural packing solution Adding an unusual touch to the beauty and health market, the blow moulding machine manufacturer PET Technologies has introduced a delicate fruit aroma into a unique fruit-like PET bottle design for the Alliance of Beauty and Pharmaceutical Products Scientific Research Centre. The distinctive shape became an original solution for shower-gel and liquid soap packing in a 500ml PET bottle. The bright self-adhesive labels depicting a juicy apple or sweet melon, a sunny orange and fiery pomegranate ensure these bottles stand out on the shelf. Colourful snap top caps and lotion pumps are said to make this kind of packing easy-to-use in everyday life. www.pet-eu.com PET aerosol PET packaging specialist Appe has launched a PET aerosol that is said to provide a lower cost alternative to tinplate or aluminium cans. The new pack called ‘SprayPET’ is intended for a variety of personal care and home care products, such as creams, shaving gels, sun tan lotion, hair care products, polishes and surface cleaners. The 335ml PET aerosol offers a lightweight construction ensuring a lower total cost of ownership compared to metal equivalents as well as delivering a lower carbon footprint of up to 65% (calculated using the Bilan Carbon method). The container is also recyclable, adding to its sustainability benefits. Other pack sizes will follow shortly. SprayPET can be delivered in white or transparent PET, with printing and sleeving options available. The material’s design flexibility means a variety of different shapes and styles can be created to enhance brand image and offer effective product differentiation on-shelf. The aerosol also offers durability and will not dent or rust. SprayPET can be specified with any standard actuator and Appe is pleased to be working with Plasticum, a supplier of aerosol over caps, spray caps and actuators, to provide these. A 57mm gel actuator is currently available and the range will be extended with both foam actuators and spray caps, tailored to the specific dispensing requirements of different product applications. www.appe.com","@ID":34}, "PETcontents 8/14 4 PETplanet insider Vol. 15 No. 08/14 petpla.net INSIDE TRACK 3 Editorial 4 Contents 6 News 31 On site 32 PET bottles for health and beauty care products 34 PET bottles for home care products 35 Products 36 Patents PET - THE NEXT GENERATION 26 Sunlight + PET = formula for disinfecting water MARKET SURVEY 21 Suppliers of two-stage stretch blow moulding machinery PREFORM PRODUCTION 28 Manufacture of PET Preforms Bottles, preforms and closures, part 13 BUYER’S GUIDE 37 Get listed! Page 11 Page 25 ITALIAN SUPPLIERS 10 Three ratings, two cylinders A visit in Bergamo 11 From preform to bottle Everything from a single source CAPPING / CLOSURES 14 New frontiers Permeation testing on caps 25 Efficiently energetic Lower energy consumption MATERIAL / RECYCLING 16 Acetaldehyde migration in PET water bottles: achieving product protection and maintaining aesthetic quality Page 32 A first glance of EDITOUR 2014","@ID":6}, "PREFORM PRODUCTION 29 PETplanet insider Vol. 15 No. 08/14 petpla.net PREFORM PRODUCTION 29 hopper with the time noted. The coloured pellets will eventually show up in the preforms, and the time can then be measured. Depending on the position of the resin in the hopper, drying times differ with the resin in the centre of the hopper travelling up to 20% faster. Therefore, a median residence time must be chosen. Once this residence time has been established, the proper drying temperature can be chosen from the graph toward the left (Fig. 2.11). Maximum drying temperature is 171°C (340°F). Higher temperatures lead to oxidation, which shows up as yellowing of the resin. Improper drying and the resultant drop in IV change the inflation behavior of the preform in that the preform will inflate under lower pressure because the NSR is greater. In turn, this will lead to less orientation and weaker bottles. Preform designers should know this connection in case problems arise during production, which are all too easily blamed on the preform design. The theory of Injection moulding of preforms We will not discuss the melting and viscoelastic flow of the material in the extruder barrel as they do not pertain as much to the preform design. However, the injection part is important for designers to understand because of the particular opportunities and process limits as well as the possible defects that will then affect the blown bottles (Fig. 2.12). Injection moulds consist of the male core, the female cavity, and the neck insert. The last has to move during ejection of the part to release the undercuts created by the thread beads. For this 4 5 6 7 8 9 10 11 350 340 330 320 310 300 290 280 171°C 160°C 149°C Peller Dwell Time. Hr Fig. 2.11 Fig. 2.12 The various components of a typical injection mould.","@ID":31}, "MATERIAL / RECYCLING 20 PETplanet insider Vol. 15 No. 08/14 petpla.net MATERIAL / RECYCLING 20 The plastic closure company committed to your success BERICAP Technology Research and Development Mould Technology | Global Presence Capping Technology and Know-How Innovation and Flexibility www.bericap.com Description Colour coordinates Colour change on recycling L* a* b* ∆L* ∆a* ∆b* ∆E Bottle grade PET 95.54 -0.10 0.63 Bottle grade PET Recycled 95.28 -0.29 1.40 -0.26 -0.18 0,76 0.83 anthranilamide 0.1% 94.52 -0.51 1.55 Anthranilamide 0.1% recycled 94.03 -0.85 2.96 -0.48 -0.34 1.41 1.53 Polyamide 0.3% 94.93 -0.48 2.47 Polyamide 0.3% recycled 93.89 -0.56 4.69 -1.05 -0.08 2.22 2.45 Table 3: Colour changes following recycling simulation Name % Haze ∆%Haze Bottle grade PET 1.99 Bottle grade PET Recycled 1.59 -0.41 Anthranilamide 0.1% 2.23 Anthranilamide 0.1% recycled 2.20 -0.03 Polyamide 0.3% 4.45 Polyamide 0.3% recycled 7.15 2.70 Table 4: Variation in haze levels following recycling simulation in Table 4 provide further evidence of this clearer polymer aesthetic. The combined test data suggest that of these two additive solutions, the PET processed with anthranilamide would contribute more effectively to the recycling stream. www.colormatrix.com Preforms moulded with re-crystalized material f.l.t.r.: Bottle grade PET, anthranilamide, polyamide","@ID":22}, "MARKET SURVEY 21 PETplanet insider Vol. 15 No. 08/14 petpla.net Caps and closures Bottle-to-bottle recycling plants Preforms Preform and single stage machinery Preform / stretch blow moulds Two-stage SBM machinery Compressors Resins / additives Filling equipment Closure systems Suppliers of two-stage stretch blow moulding machinery The companies are listed below in alphabetical order; in the table they appear in the order in which their details were received by editors. Amsler Equipment Inc., 1 Blow, KHS Corpoplast GmbH, Kosme Gesellschaft mbH, Krones AG, Luxber S.L.U., Mega Machinery Mould, Nissei ASB Machine Co., PET Technologies, Sacmi Imola, Serac Group, Siapi srl, Side S.A., Sidel Group, Sipa S.p.A., SMI S.p.A., Technopet Machineries, Urola S.C., Wei Li Plastics Machinery (HK) Ltd. Although the publishers have made every effort to ensure that the information in this survey is up to date, no claims are made regarding completeness or accuracy. 08/2014 MARKETsurvey Company name Technopet Machineries Nissei ASB Machine Co., Ltd. SMI S.p.A. Postal address Telephone number Web site address Contact name Function Direct telephone number Fax E-Mail 14/15, Shree Naman Plaza, S.V.Road Kandivali(W), Mumbai- 400 067, India +91 22 2861 0828 www.technopet.in Mr Vineet Bannore / Mr Sunil Bharkada Director +91 982034 6565 / +91 982104 0637 +91 22 2806 1410 [email protected]; [email protected] 4586-3 Koo, Komoro-shi, Nagano-ken 384-8585, Japan +81 267 23 1565 www.nisseiasb.co.jp/en Mr Katsuo Ishiguro Manager - Sales Coordination Team +81 267 23 1565 +81 267 23 1564 [email protected] Via C.Ceresa, 10, 24015 San Giovanni Bianco (BG), Italy +39 0345 40 111 www.smigroup.it Mr Pietro Volpi Marketing Dept. Manager +39 0345 40 316 +39 0345 40209 [email protected]; 1. Machine designation / model number Pauto 1200/1600 Auto 1800 Auto TSBM 2200 Pauto 2X2X5 TPS 20L 5 Gallon Jar TP-Beer For Beer/ Liquore/ Hotfill HSB-4N, HSB-6N, HSB-6M SR series / 9 models (7 for standard capacity containers and 2 for high capacity containers) 2. Bottle volume (from/to in litres) 0,25 to 10l a) Standard machines 100ml to 2l 100ml to 2l 100ml to 2l 100ml to 5l 5l to 20l 200ml to 2l up to 0,6l 0,25 to 3l b) Machines for large containers up to 2l 4l to 10l 3. Maximum number of stretch-blow moulds (units) 20 a) Standard machines 2 2 2 2 1 1,2,4 6 20 b) Machines for large containers 1 1 4 6 4. Output per stretch-blow mould for: 0.5 litres CSD bottle (units per hour) 1,200/1,600 2,000 2,200 1,000 500 1,000 1,800 -2,000 1 litre CSD bottle (units per hour) 1,200/1,600 2,000 2,200 800 600 1,800 -2,000 1.5 litres still mineral water bottle (units per hour) 800 1,600 1,800 600 700 1,800 -2,000 Large capacity container 500 100 600 1,100 -1,200 Other 1,600 800 300 combo filling 500ml jars at 970bph/cav 5. Footprint / space requirement (L x W x H in metres) 0,90 x 0,60 x 1,75 0,91 x 0,65 x 1,10 1,5 x 1,2 x 2,25 1,50 x 1,2 x 2,25 1,5 x 0,90 x 1,80 80 0,90 x 0,80 x 1,20 2,20 x 1,20 x 2,50 1,10 x 1,10 x 2,00 6,7 x 2,0 x 3,2 3,7 x 4,4 x 3,5 (SR 4HP /SR 6HP) to 4,8 x 8,8 x 3,5 (SR20)","@ID":23}, "ITALIAN SUPPLIER 10 PETplanet insider Vol. 15 No. 08/14 petpla.net Three ratings, two cylinders by Waldemar Schmitke The first visit of our Go to Brau Beviale 2014 tour in Italy takes us to Siad Macchine Impianti in Bergamo. The company, founded in 1927, is active throughout the world with plants for the manufacturing and separation of industrial gases; it has 34 service centres and 40 country-specific sales agencies spread across the globe. In total the Group has some 1500 employees and recorded a turnover of approximate € 470 million in 2013. We find 228 people working here at the site in Bergamo. The Vito team complete with Head of Company f.l.t.r: Giovanni Brignoli, Luigi Manenti, Compressor Division Technical Office Manager, Manuela Teocchi, Market Analyst & Projects Development Leader, Paolo Ferrario, President & CEO, Alexander Büchler, PETplanet, Anna Roggeri, Compressor Division Executive Assistant, Paola Piccinelli, Marketing Communication & Public Relations Vito One of the Group’s business units is involved in the development and manufacture of piston compressors for PET stretch blow moulding machines, based on Siad’s industrial gas plant concept. A new generation of compressors is now being specially developed under the Vito brand name for use in conjunction with PET stretch blow moulding machines. Particular features of the new oil-free air PET compressor generation include two pressure cylinder lines with three pressure ratings and an elegant design. According to Giovanni Brignoli, Product Leader Compressor Division Food&Beverage,“ this has enabled us to cut our energy usage by 16%. The first model covers five capacity ratings from 1,210 up to 1,920m3/h at 42bar. Having said that, the actual basic compressor is always the same. The individual capacity ratings are achieved solely by replacing the drives“. The model is thus able to cater for 60% of PET applications. Two further models are planned, both up and down the scale, one of which will handle capacities of 300 to 1000m3/h (20% of the market) whilst the other will address capacities ranging from 2000 to 3000m3/h (20% of the market). The first prototype supplied following 1500h of testing at the plant in Bergamo is already installed at Fonti Pineta in Clusone (an hour away from Bergamo in the Editourmobil). A further prototype is being prepared for delivery to the Sem Group in Italy. Today’s target markets are the Far East, China, Mexico and Russia. According to Giovanni Brignoli “it is here that the growth markets are to be identified and we are very well placed with our service centres. In addition, it is our aim, with the new Vito models, to get more involved with the PET line manufacturers than has been the case in the past. Up to now the proportion of direct customers has been between 60 and 70%“. After a tour of the plant we take our leave of the company, intending to visit Fonte Pineta in Clusone (Bg) the following day. The Ladies Power Team from Vito will be accompanying us at this meeting. This is made up of: Manuela Teocchi (Market Analyst & Projects Development Leader), Anna Roggeri (Compressor Division Executive Assistant) and Silvia Sangiorgi (Customer Relation Manager). We are looking forward to this occasion. www.siadmi.com A first glance of EDITOUR 2014","@ID":12}]}}
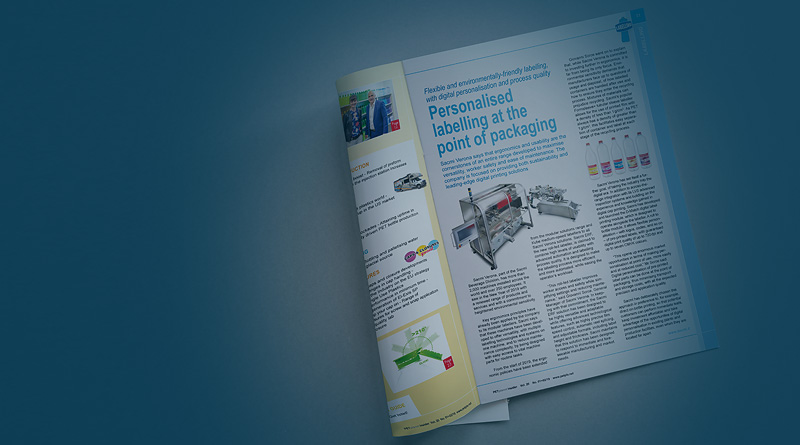