"EDITOUR REPORT 17 PETplanet insider Vol. 15 No. 10/14 petpla.net There are various approaches when it comes to developing preforms and bottles. The first one is the Nestlé’s Product Technology Centre (PTC) at Vittel in France. However, the primary interest here is theoretical fundamentals. Italy, with its focus on carbonated mineral water, CSDs and iced tea has specifications that often differ from France and the USA, for example. This is where the work begins as far as Chimetto’s team is concerned. Observing the market and responding to it. Devising and implementing proposals for solutions with their own ideas or in collaboration with the PTC or with suppliers as P.E.T. Engineering. Potential topics include weight reduction, the improvement of preform and bottle geometries, labels, closures and much more. The premium status claimed by the brand name is always to the fore. For instance, where further weight reductions are concerned, Fabio Chimetto sees the limiting factor as lying not in what is feasible but in what is convenient for the customer. Another project is the installation of a process pilot on two stretch blow moulding machines. The Agr system measures the wall thickness of each individual bottle at different points and automatically changes the machine settings if there are any variations. How the machine reacts to changes permits conclusions to be drawn not only as regards the technical status of individual components of the machine, for example, the stretcher rod and blow station, but also about preform quality. By isolating individual problems or by pointing out the need for optimisation and action an effective quality control system can be established. Armed with the knowledge gained, the process pilot gradually arrives at an optimum automatic process parameters setting for the blow process. The result is a narrower process window with enhanced effectiveness, especially important for critical bottle moulding, and this reduces dependency on qualified personnel at any time of the day or night, says Fabio Chimetto. As far as the Italian market is concerned, the forecast is low or slow growth for soft drinks, mineral water and also iced tea in the foreseeable future. This is another reason why Sanpellegrino is also continuing to go for export and innovative product add-ons, says Fabio Chimetto.We extend our thanks for the illuminating discussions. www.sanpellegrino.com Alexander Büchler, PETplanet, with a selection of San Pellegrino beverages.","@ID":19}, "TRADE SHOW PREVIEW 48 PETplanet insider Vol. 15 No. 10/14 petpla.net Line-end efficiency SMI’s stand will feature energy-saving line-end solutions including its integrated Packbloc system, which brings together a Smiflexi wraparound LWP 30 machine with a Smipal APS 1550 P Plus palletiser. It is equipped with brushless motors and has eliminated geared motors; SMI says that this contributes to greater efficiency and, consequently, less energy usage in operation. The company further claims that the compact design of the Smipal APS Plus palletisers enable operators to concentrate the use of forklifts, transpalleters and similar equipment into a well-defined zone. Pallets and interlayers are handled on the same side of the palletiser, which means that they do not interfere with other production line activities. The APS 1550 P PLUS palletising system has a 50 packs/minute (about 150 layers/ hr) capacity and can handle both 800x1200mm euro-pallets and 1000x1200mm pallets. www.smigroup.it SMI Hall 7A | Booth 503 PET Arena and Passion for PET The first “PET Passion Week” will combine the PETnology Conference November 10-11, 2014 and PETarena exhibition at Brau Beviale 2014. Presented by PETnology/tecPET GmbH, the inductry meeting is aimed at all suppliers and customers involved with PET value chain. www.petpassionweek.com PET arena Hall 4A | Booth 233 Acetaldehyde analysis ten years on Piovan will be commemorating ten years of its AA analyser, which measures acetaldehyde. More than 150 PET preform and bottle production locations have installed at least one of its PETes units, which enable the simple, rapid, reliable and repeatable measurement of acetaldehyde content in PET preforms by the use of gaschromatography. The PETes AA Analyzer, which in a single desktop-type cabinet, incorporates a de-adsorption cell, gaschromatograph, microprocessor control and colour LCD screen and has an automatic process for gaschromatograph calibration, performed with either acetaldehyde solution or ethanol. Two versions will be on show: Lab, for use in a laboratory environment; and Turret, which can be used on the production floor. www.piovan.com Piovan Hall 4A | Booth 233","@ID":50}, "MARKET SURVEY 34 PETplanet insider Vol. 15 No. 10/14 petpla.net Resins Additives 10/2014 MARKETsurvey Company name Novapet, S.A. Gabriel-Chemie Gesellschaft m.b.H. Repi S.p.A. Penn Color International B.V. Postal address Telephone number Web site address Contact name Function Direct telephone number Fax E-Mail P° Independencia, 21, 3°, PC 50001, Spain + 34 976 216129 www.novapet.es Mr Miguel Angel Arto Head of LB&Concentrates division + 34 976 216129 + 34 901 021138 [email protected] Industriestrasse 1, 2352 Gumpoldskirchen, Austria +43 2252 636 30 0 www.gabriel-chemie.com Mr Manuel Hakel Key Account Manager Caps & Closures +43 2252 636 30 1641 +43 2252 627 25 1641 [email protected] Via B. Franklin 2 - 21050 Lonate Ceppino VA, Italy +39 0331 819511 www.repi.com Mr Maurizio Amicabile Market Development Manager - Packaging +39 0331 819511 +39 0331 819581 [email protected] Smakterweg 31, 5804 AE Venray, Netherlands +31 478 554000 www.penncolor.com Mr Scott Stamback Business Director Thermoplastics +31 478 554000 +31 478 554009 [email protected] Additives and Colours for PET Liquid colours no yes yes Microgranule colours yes no yes Masterbatch colours yes no yes UV protection additive (solid) yes no yes UV protection additive (liquid) no yes yes AA reduction (solid) no yes - SenzAA no AA reduction (liquid) no yes - SenzAA no Oxygen scavenger (solid) yes no no Oxygen scavenger (liquid) no no no Other PET additives in liquid or solid form DCU, LUZ & Polygloss, the new generation of PET concentrates for (opaque and transparent) light barrier and metal gloss effects yes Anti yellow (liquid), process aid (liquid), IV enhancer (solid), blowing additive (liquid), optical brightener (liquid), colours for barrier solutions (liquid), white for monolayer UHT milk (liquid) yes Company name NEO Group M&G Polimeri Italia SpA Postal address Telephone number Web site address Contact name Function Direct telephone number Fax E-Mail Industrijos str. 2, Rimkai LT-95346, Klaipeda district, Lithuania +370 464 667 10 www.neogroup.eu Mr Gediminas Paulauskas Sales Manager +370 686 73401 +370 464 667 11 [email protected] Via Morolense Km 10 03010 Patrica (FR), Italy +39 0775 84 221 www.mg-chemicals.com Ms Marilena Grecchi Area Sales Export and Marketing Intelligence support +39 02 82 273 242 +39 02 82 273 314 [email protected] RESINS 1. Brand name of the resins NeoPET Cleartuf 2. IV Range a. of homo-polymers 0.56 - 0.82 b. of co-polymers 0.76 - 0.84 0.76 ÷ 0.95 3. Speciality resins CSD NeoPET 80, NeoPET 82 Cleartuf Ultra Water Aqua NeoPET 76, NeoPET 78 Cleartuf P76 - Cleartuf P82 Beer NeoPET 80, NeoPET 82 Wine / liquors NeoPET 80, NeoPET 82 Poliprotect Personal care /pharmaceuticals NeoPET 80 Poliprotect Slow crystallisation Hotfill NeoPET 82 HF Cleartuf P85HF Pre-coloured Fast reheat NeoPET 82 FR, NeoPET 84 FR Cleartuf Ultra Other Ultra NeoPET 1) Barrier resins (i.e. Poliprotect), for diffrent application (juice, beer, wine, dairy/milk based products, ketchup, mayonnaise…) 2) Cleartuf T95 (high viscosity).Main application trays 4. Increased barrier properties yes, with Poliprotect 5. PEN mixes available 6. Recycled blends available 7. Special comments","@ID":36}, "PETbottles 58 PETplanet insider Vol. 15 No. 10/14 petpla.net Home + Personal Care Head & shoulders tackles hair loss Head & shoulders, synonymous with anti-dandruff hair shampoo, is increasingly building up its product range to include a range of agents that act on thinning hair or hair which is falling out. One example of this is Anti-Hairloss Tonic which is packaged in a 125ml bottle made from white coloured PET and which is applied to the hair when still damp and/or to the crown of the head and massaged in. The slimline, waisted bottle fits snugly in the hand and the screw-on pump sprayer makes for easier dispensing. A clip-on sleeve protects the dispenser from faulty operation and this prevents any downward pressure on the pump. The directly printed bottle is enclosed at the PoS in a cardboard box with an automatic base and an internal, separate chamber for the detailed application instructions. www.headandshoulders.com Air freshener in PET “Denk mit“, one of the own label brand names of the German discounter dm, is selling various air fresheners in a PET bottle with a content of 150ml. The stand-alone, transparent bottle is equipped with a closure which has a sponge on its underside. This conveys the volatile product upwards where it “vaporises”. The fragrancing strength is set by twisting / screwing the closure anticlockwise. The bottle is decorated by means of a sleeve label that is pulled over the closure. This not only acts as a tamper evident seal, but also protects the product from evaporating during transport and storage. www.dm.de","@ID":60}, "BOTTLES 59 PETplanet insider Vol. 15 No. 10/14 petpla.net Scented foam soap from Palmolive Palmolive is selling its new raspberry-scented foam soap under the name of “Magic Softness“ in a transparent PET bottle with a non-symmetrical shape and a content of 250ml. Echoing the shape is a front label which is also curved and has a shiny metallic finish. Screwed on to the bottle is an opaque pump dispenser which, in a chamber, generates a foam which is pleasant to the touch from the basic liquid product. A locking function activated by rotating the pump head through 90° prevents accidental activation during transport and storage. www.colgate.com The brightly coloured world of cleaning at Aldi Adopting the slogan Design Cleaner, Aldi Süd had six different cleaners in its range in August 2014. The various cleaners sport different colours and are packed in transparent bottles made from PET and decorated only with no-label look labels. The same bottle featuring a lockable, opaque trigger and with a content of 500ml is used for glass cleaners, bath cleaners and all-purpose cleaners. The WC cleaner bottle is appropriately shaped for its purpose, the dishwashing liquid is fitted with a lockable pump dispenser and the room freshener likewise provided with a lockable trigger closure. Each individual product has a further tag attached to its name to match the colour, such as, for example, “Strong Green“, “Strong Lavender“ or ”Shiny Red“ on the label. www.aldi.com The plastic closure company committed to your success BERICAP Technology Research and Development Mould Technology | Global Presence Capping Technology and Know-How Innovation and Flexibility www.bericap.com","@ID":61}, "PREFORM PRODUCTION 44 PETplanet insider Vol. 15 No. 10/14 petpla.net Please order your copy at the PETplanet insider book shop: https://petpla.net/books Bottles, Preforms and Closures A Design Guide for PET Packaging Second Edition by Ottmar Brandau € 115,00 180 pages © Copyright Elsevier 2012 * This article was published in Bottles, Preforms and Closures, Ottmar Brandau, Chapter 2.6. Copyright Elsevier 2012 A display of a temperature without set point is the temperature of the incoming resin as measured just above the extruder throat. A temperature of about 165°C (329°F) is optimal for PET processing Practical Guide to Injection Moulding of Preforms The percentage of power the controller puts out to the heater band. For example, if this value is 40%, the heater band is on for 4s and then off for 6s. The controller will use a value that is best suited to keep the heater band at the set point. This is regulated by a so-called proportional, integral, and derivative (PID) loop, and all controllers use some form of this control programme (fig. 3.7). A typical temperature profile starts at 270°C (518°F) at the feed zone and increases to 285°C (545°F) toward the extruder nozzle. This can be used for most PET applications. Temperatures over 300°C (572 °F) are not recommended as they will lead to burning the material if the residence time becomes too long. The extruder cannot be started until all heaters are at the set point and the soak timer has timed out. Most machines have a protection against this “cold-start” condition. Screw rpm should be chosen at the lowest level that still guarantees that the extruder is not holding the machine back from cycling. This can be checked by watching the end of screw turning (called recovery) and stopping the time until transfer or injection occurs. If it is more than 1 or 2s, screw rpm can be lowered. On machines with “short” screws, i.e. with L/D ratios below 22, a higher screw speed may be required to assure proper melting. Back pressure is hydraulic pressure that is acting against the return movement of a recovering screw. Without it the screw may slip under the material without melting it. Because PET is so shear sensitive, selected adjustments should be below 20 bar (300 psi). If it is too low, bubbles may appear. These are made up of air. Air is of course present inside the material pellets and must be pushed out of the extruder throat as the material moves forward. Too low a back pressure may make it too easy for the material to move forward without squeezing out the air. Figure 3.6 Mixing in stages is the advantage of barrier screws. (Diagram courtesy of Barr Inc). Figure 3.7 A variety of parameters are available for temperature control. Numbers in white are for display only. (Picture courtesy of Netstal-Maschinen AG).","@ID":46}, "PETproducts 50 PETplanet insider Vol. 15 No. 10/14 petpla.net No more foreign bodies Avoiding breakdowns in recycling Every now and then there is breakdown caused by foreign bodies that enter the recycling machines with the feeding material. In simple cases there is “only” excessive wear at the grinding tools; massive foreign bodies, however, can cause a breakdown of the machine. There are different approaches of how to solve this problem and how to avoid a breakdown. All of them, however, have detrimental effects: inductive metal separators are only appropriate for detecting metals – but often foreign bodies are not metal parts but stones, shoes, wooden pieces. Alternative solutions are often too expensive or need too much room. For the separation of foreign bodies Herbold Meckesheim GmbH has developed a simple, efficient solution that is part of a pneumatic conveyor. Heavy materials are separated and evacuated from the product flow in an ascending pipe via a discharge chute. The advantage is twofold: firstly, the foreign bodies are separated and, secondly, any further transport is no longer necessary. The underlying principle is that materials with a considerably higher flying speed in the conveying pipe of the pneumatic system are separated out. A first plant has been sold for a PET bottle recycling line: entire bottles, not yet size-reduced, are separated from foreign bodies and at the same time conveyed to the next processing step. The line is suitable for processing bottles that have not yet been sizereduced, but it is also appropriate for separating foreign bodies from preshredded thick-walled parts. Not only metal parts but also mineral foreign bodies – generally all heavy parts are separated. www.herbold.com CCT – SYS GmbH Idsteiner Strasse 74 D-65527 Niedernhausen, Germany [email protected] www.cct-systems.com Portfolio Caps • Closure molds beverage field (produced under the brand “CCT Systems®)” - Completely new constructed and optimized molds for closures with slitted tamper evident band (SBT) - Completely new constructed and optimized molds for closures with slitted and folded tamper evident band (SFBT) • Devices and equipment for closure production Portfolio Preforms • Preform molds and preform molds cold halves • Conversion parts and spare parts for preform molds (here especially conversion parts for the weight reduction according to “ComPetCap®” construction) • Devices and equipment for preform production Consulting and supporting possibilities for • Closure development • Closure production • Closure processing • Preform development • Preform production PET Molds and Accessories Developments PET - Devices and Equipment Closure – Devices and Equipment New Range of Services Consulting und Support Closure molds and Accessories","@ID":52}, "BOTTLES 57 PETplanet insider Vol. 15 No. 10/14 petpla.net Premium milkshakes get RPC PET packaging Mr Sherick’s Shakes, a new range of premium milk shakes, are packaged in PET bottles supplied by RPC Containers Ltd, of Llantrisant, Wales. The company says that the “elegant and simple” bottle design is intended to help convey a quality image on the shelf. Mr Sherick’s Shakes, created by former retail buyer Andrew Sherick, are aimed at a market opportunity for a range of branded adult milk shakes and are already being listed at premier retailers such as Selfridges, Harrods and Waitrose. They are intended to enable both retailers and caterers to offer their customers a new “pure indulgence treat”. The range currently extends to five flavours: Pot au Choc; Strawberry Pavlova; Softly Banoffee; A Hint of Mint; and Cookies & Cream. The Lightweight PET bottles from RPC Llantrisant enable the consumer to see the contents clearly and are designed to be suitable for both at home and on-the-go consumption. www.rpc-group.com A sip of crystal clear water Devin, the well-known mineral water brand from Bulgaria, has chosen the company P.E.T. Engineering to develop its new packaging for the launch of its Devin-Crystal Line, a water intended for the HO.RE.CA sector. The idea behind the packaging was to give premium value to a low cost material by means of a sophisticated design and a glass effect finish capable of combining the unbreakability, lightweight and low cost advantages of PET with concepts of elegance and refined simplicity. Regular forms of crystal glass were used as a starting point. The bottle’s three dimensional decoration and the use of Novapet’s Glasstar, reproducing the transparency of glass, produces an interesting refraction effect and the bottle shines like a crystal in the light. The blue and silver label matches the colour of the cap. www.petengineering.com product development caps & closures design high cavitation moulds multi-component moulds closure production systems after sales service competent – professional – inspiring Hoechster Strasse 8· 6850 Dornbirn, Austria· T +43 5572 7272-720· www.z-moulds.com FAKUMA 2014 October 14th-18th meet us at booth A7-7502","@ID":59}, "MATERIAL / RECYCLING 20 PETplanet insider Vol. 15 No. 10/14 petpla.net Scan & Measure Oxygen Ingress & Transmission Rates www.PreSens.de/ Fibox4 Fibox 4 Stand-alone fiber optic oxygen transmitter PET to PET Recycling Österreich GmbH – one of the companies in the Coca-Cola Hellenic Österreich, Radlberger Getränke, Rauch Fruchtsäfte, Spitz and Vöslauer Mineralwasser Group, is the sole PET recycling plant in the country and has been in operation since 2007. In the autumn of 2010 the plant was extended, a granulation line was added and the plant underwent a complete conversion to the manufacture of foodstuffs-compatible PET recyclate (PET flakes and PET granulate). The next move was for PET to PET to invest €550,000 in a fully operational packaging cycle to complete the next stage of the expansion project. In August, exactly five years after the foundation stone of PET to PET Recycling Österreich GmbH was laid, the new bottle sorting line became operational. Currently €130,000 is being invested in the installation and commissioning of an injection moulding machine. In the future, this will enable the PET to PET team to carry out all quality testing in-house directly on site. At PET to PET Recycling Österreich GmbH around 570 million PET bottles – i.e. 20,000 tonnes – are processed and supplied for re-use in foodstuffs packaging every year. This represents a total of 70,000 tonnes since the line came into existence. Consumers at home send 82% of PET bottles for recycling (source: ARA May 2011). PET 2 PET Recycling Österreich GmbH expands its plant and invests more than €500,000 A boost in PET 2 PET Recycling “We are delighted at the consistent rise in collective morale and the awareness of recycling among Austrians which has enabled us to break through the “20,000 tonne barrier” for the first time in 2013 with a total record quantity of 20,167 tonnes’ worth of PET bottles”, says Christian Strasser MD of PET 2 PET. As far as director Christian Strasser is concerned, this is sufficient mandate for them to continue to invest in meaningful and resource-saving “bottle-to-bottle” recycling activities. Strasser states that their showcase plant is growing with the recycling awareness of their consumers. According to Strasser, only in this way PET 2 PET can do justice to its role as an international pioneer in efficient PET recycling. Dipl. Ing. Christian Strasser, PET 2 PET Managing Director","@ID":22}, "EDITOUR REPORT 16 PETplanet insider Vol. 15 No. 10/14 petpla.net Strong brand, declining market by Waldemar Schmitke Sanpellegrino S.p.A. Having heard from a number of sources that the market for water in Italy somewhat stagnant, yet private labels seem to be in full spate, there has to be a loser somewhere: in this case, it is the traditional brands. We visited the strongest brand in the mineral water sector that Italy has to offer, Sanpellegrino, a Nestlé Group company, where we spoke with Fabio Chimetto, Application Group Manager. Basically, he corroborates the trend of the price-sensitive customer who is turning more and more to value brands in the supermarket. Sanpellegrino has not escaped entirely unscathed, but this value trend is most likely to affect the middle price segment. Here losses have been dramatic. As far as Sanpellegrino is concerned, Nestlé are displaying an increasing focus on export. Today the carbonated mineral water is available all over the world. The proportion that goes for export is 60%. “Depending on the target market,” explains Fabio Chimetto, “Sanpellegrino’s bottling operations may involve the use of some fairly expensive containers. In addition to the glass bottle we supply to export markets, there are also PET multilayer 0.5l and 1l bottles in the filler, enabling us to meet high quality requirements and also to withstand the rigours of lengthy shipment times.\" For the local market, however, Nestlé use the classic monolayer bottle under the brands name Nestlé Vera, Levissima, Recoaro, San Bernardo as well as Sanpellegrino and Acqua Panna which are mainly the two international flagships. In addition to pure mineral water, Nestlé have also established their Sanpellegrino brand name as a CSD brand name. Here they sell, in the premium range, not only the traditional flavours but also those featuring an innovative combination of aromas not previously seen on the market. The Italians launched a new range of products with juices and flavour, named Incontri on a specific 75cl PET bottle. Another international mineral water brand from Sanpellegrino Company is their Acqua “Panna\" brand. This is the still companion on the best tables in the world of the sparkling Sanpellegrino. Fabio Chimetto reported that Acqua Panna is highly suitable for wine tasting. Acqua Panna water enables the mouth to be neutralised from a taste point of view between one wine tasting session and the next and is therefore also very popular with professional wine tasters. Due to the size of the company, getting new bottles, flavours or even brand names established calls for considerably more internal coordination within Sanpellegrino than is the case with smaller companies that are mainly family-owned. Nevertheless, specifically due to their size and position in the marketplace, Sanpellegrino are able to achieve a level of penetration that is all the more intensive. In order to get the beverages into the bottles, Sanpellegrino produce a proportion of their preforms themselves on ten 48-cavity and one 96-cavity Husky line at their San Giorgio di Bosco site. The company produces further preforms in Levissima. There are three further 48-cavity and two 60-cavity Index preform systems in production. Full capacity utilisation of a mould right round the clock invariably means incorporating the preform into in-house production. In addition, colour changes are allowed. “We always have to use outside competitors as a yardstick; for this reason an important proportion of our preforms (20%) are sourced on the market,“ says Fabio Chimetto. For example, specialities such as multilayer preforms are basically bought in, such as in this case from Resilux and Retal. Fabio Chimetto is quick to emphasise that “preform manufacture is not our core business; we are bottlers and invest in stretch blow moulding and bottling lines”. On we go to the bottling lines. Here at the facility there are two PET lines in block construction and further blow moulding machines, two aseptic lines and very recently a can filling line has been added (no glass). The PET lines are from Sidel. The fillers are from Sidel, while in other plants also Krones and KHS are installed, the labellers predominantly from Krones. Iced tea is run exclusively on the Gea Procomac aseptic line. On the other lines it is water and soft drinks. As regards labels, paper, plastic and shrink labels are used (the plastic labels are dominant, especially where lines in block format are concerned). When it comes to the packaging, cardboard boxes are used for export, for the domestic market it is chiefly shrink film and trays. The closure caps are bought in from Obrist and recently also from Bericap. There is no question of manufacturing closure caps themselves; closure cap manufacture is too far removed from their core business, according to Fabio Chimetto. The PET raw material is negotiated centrally and ordered as required by the individual processors in the Sanpellegrino Group. f.l.t.r. : Waldemar Schmitke, PETplanet insider and Fabio Chimetto, Application Group Manager, at Nestlé Vera in San Giorgio in Bosco.","@ID":18}, "AFTER SALES SERVICE 38 PETplanet insider Vol. 15 No. 10/14 petpla.net Service performance – Key measure for equipment sourcing Investments in machinery are frequently made on the basis of a whole spectrum of decision criteria. In addition to the price/performance ratio, however, ‘soft’ factors such as the sound nature of the supplier relationship, operational reliability of the plant/lines and the supplier’s performance in terms of service are often of crucial importance too. Hitherto there have been very few solid insights paving the way to understanding the decision to purchase machinery against the background of the specified ‘soft’ criteria. Reason enough for PETPlanet to undertake a more in-depth examination of the drinks packaging market in the form of a questionnaire. The plastics technology team at the Technical University of Ilmenau, Germany, whose members have a wide range of experience of the machine / plastics packaging and beverages industries, carried out the study which is described below. The focal point of the survey was to assess the quality of the service provided by the machine manufacturers in the PET packaging technology sector. The questionnaire was addressed to approx. 1,000 participants in 334 companies. Packaging materials manufacturers (bottles, preforms, closure caps) were also included, as were bottling/filling companies and beverages companies (Fig. 1). Fig. 1 Primary focus of business Special attention was paid to 102 countries with rapidly growing markets but which are not classified as major industrial nations of the western world. The objective of one online questionnaire was to assess customer preferences in respect of the after sales service policies of machinery suppliers and to appraise the level of service provided by PET packaging systems manufacturers. Various detailed questions were asked about these aspects in particular. The following contains a summary and explanation of the results. Fig. 2 Magagement levels Various levels of management and employees were addressed within the companies questioned (Fig.2). The questionnaire was distributed in seven languages (English, French, Spanish, Portuguese, Chinese, Russian and Arabic) with the aim of covering different levels of employment within the company. This enabled those participating in the questionnaire to select their preferred language right from the start. 65% opted for English, after that came Spanish at around 12%, followed by Russian, Chinese and Portuguese with 7% each. The share of Arabic and French questionnaires amounted to only 1%. The data was collected in the period from January to February 2014. Taking part were a total of 233 companies. The response rate of approx. 70% enables us to draw meaningful conclusions from the questionnaire. It has to be said that there were numerous instances where the responses might usefully have been more comprehensive, but the online dwell time of 18min spent on average by participants completing the survey was encouraging. In terms of job function within the company (Fig. 2), 42% of responses came from operations managers followed by technical managers on 32%. Both these categories play a major role in investment decisions. A further 16% of responses were from supply managers who are also heavily involved in decision-making. The participants in the study cannot be assigned directly to a specific branch and/or a specific field of technology and this increases the general applicability of the statements. The question about the category of the equipment and suppliers also covered PET preform manufacture (Fig. 4.1.1), drinks closure cap manufacture (Fig. 4.2.1), PET bottle manufacture (Fig. 4.3.1) and filler/bottling plants (Fig. 4.4.1). The distribution of the various brands is certainly representative, although the same cannot necessarily be said about claims of market share. A f t e r S a l e s Service","@ID":40}, "imprint EDITORIAL PUBLISHER Alexander Büchler, Managing Director HEAD OFFICE heidelberg business media GmbH Häusserstr. 36 69115 Heidelberg, Germany phone: +49 6221-65108-0 fax: +49 6221-65108-28 [email protected] EDITORIAL Heike Fischer Gabriele Kosmehl Kay Barton Michael Maruschke Ruari McCallion Waldemar Schmitke Ilona Trotter Wolfgang von Schroeter Anthony Withers MEDIA CONSULTANTS Martina Hirschmann [email protected] Johann Lange-Brock [email protected] phone: +49 6221-65108-0 fax: +49 6221-65108-28 France, Italy, Spain, UK Elisabeth Maria Köpke phone: +49 6201-878925 fax: +49 6201-878926 [email protected] LAYOUT AND PREPRESS Exprim Kommunikationsdesign Matthias Gaumann | www.exprim.de READER SERVICES Till Kretner [email protected] PRINT Chroma Druck & Verlag GmbH Werkstr. 25 67354 Römerberg Germany WWW www.hbmedia.net | petpla.net PETplanet insider ISSN 1438-9459 is published 10 times a year. This publication is sent to qualified subscribers (1-year subscription 149 EUR, 2-year subscription 289 EUR, Young professionals’ subscription 99 EUR. Magazines will be dispatched to you by airmail). Not to be reproduced in any form without permission from the publisher. Note: The fact that product names may not be identified as trademarks is not an indication that such names are not registered trademarks. 3 PETplanet insider Vol. 15 No. 10/14 petpla.net Many factors come into play when decisions are being made about whether or not to invest in a new line. In the majority of cases, it boils down to the specification. This establishes the key factors: the desired output range of the equipment, the products to be produced, whether the line is compatible with existing machinery and so on. These are the “hard” facts, but “soft” factors increasingly have a part to play. What about servicing? Are spares easily available? Is the quality of training up to scratch? Every supplier will, of course, offer reassurance on such issues, but does the reality match the rhetoric? In our on-site reports we are used to hearing all sides of the discussion, but for us, it is never clear whether it is simply an individual viewpoint we are hearing, or whether there is actually something amiss in the sector. In the Western European orientated countries (efficient infrastructure, stagnating economies), complaints are considerably fewer than in the rapidly growing countries. In many cases on-site knowhow – especially for new market participants – is not as great as would be the case with a manufacturer with 50 years acquired experience in the market. All the more important, then, for suppliers to tailor their after-sales service to the particular features of these rapidly growing markets. We wanted to examine these aspects systematically, and we therefore asked Prof. Dr Dipl.-Ing. Michael Koch of the Technical University of Ilmenau, Germany, to carry out an in-depth investigation covering no fewer than 102 countries. These countries may not necessarily be classified as major industrial nations of the western world, but they are growing rapidly. Taking part in the survey were just under 200 companies with more than 900 machines between them, and equipment from the preform, stretch blow moulding and bottling systems. We are deeply grateful for their participation and cooperation. The results of this extensive survey will be presented in a three-part series. We begin today with the first part – a look at the current state of play. Enjoy reading! Yours Alexander Büchler dear readers,","@ID":5}, "MARKET SURVEY 35 PETplanet insider Vol. 15 No. 10/14 petpla.net Valspar Clariant Masterbatches Europe Sukano AG Holland Colours Europe BV Invista Resins & Fibers GmbH PolyOne ColorMatrix 2000 Georgetowne Drive Sewickley, PA 15143 USA +1 800 873 5575 www.valsparpackaging.com Mr Will Hoffman Market Manager +1 724 940 3137 [email protected] Am Unisys Park 1 65843 Sulzbach (Taunus), Germany +49 6196 757 6276 www.clariant.com/masterbatches Ms Severine Wild Marketing Europe +49 6196 757 6276 +49 6196 757 6113 [email protected] Chaltenbodenstrasse 23 8834 Schindellegi, Switzerland +41 447 875 777 www.sukano.com Mr Michael de Braaf Ceo +41 447 875 777 +41 447 875 778 [email protected] Halvemaanweg 1, Apeldoorn 7323 RW, Netherlands +31 55 368 0700 www.hollandcolours.com Mr Wilfried Grob Sales and Marketing Director +31 55 368 0700 +31 55 366 2981 [email protected] Philipp-Reis-Strasse 2, 65795 Hattersheim, Germany +49 69 305 85550 www.polymers.invista.com Mr Karsten Fritsch Business Manager PET Resins +49 821 479 3257 +49 821 479 2721 [email protected] Unity Grove, Knowsley Bus. Park, Knowsley, Merseyside, L34 9GT, Great Britian +44 151 632 8800 www.colormatrix.com Ms Faye Freeman Sales Director, Europe +44 151 547 6652 +44 151 632 8807 [email protected] yes yes yes yes yes yes yes yes yes yes yes yes Ultimate UV yes yes yes Triple A valOR Activ and valOR ActivBloc yes Functional colourants for oxygen scavengers OxyClear barrier resin, PolyShield masterbatch Amosorb Plus no Functional colourants for oxygen scavengers valOR ActivBloc and valOR Bloc for passive barrier Slipping agent, reheating, matting agent and specai effect yes slipping additive, tintmask, blowing aid, optical brighteners, matting agents, protective colourants with specific light and UV absorbance yes Reliance Industries Limited Invista Resins & Fibers GmbH DAK Americas LLC DAK Americas LLC Specialty Polymers RCP, Building 8B, First Floor, Thane Belapur Road, Ghansoli, Navi Mumbai , Maharashtra, India +91 22 4477 0000 www.ril.com Mr Methil B. Menon Exports +91 22 44781 241 / +91 9967623810 [email protected] Philipp-Reis-Strasse 2, 65795 Hattersheim, Germany +49 69 305 85550 www.polymers.invista.com Mr Karsten Fritsch Business Manager PET Resins +49 821 479 3257 +49 821 479 2721 [email protected] 5925 Carnegie Blvd. Suite 500 Charlotte, NC 28209, USA +1 704 940 7500 www.dakamericas.com Mr George Rollend Senior Technical Manager +1 603 672 6403 +1 866 833 5069 [email protected] 223 Wilmington West Chester Pike, Suite 210 Chadds Ford, PA 19317, USA +1 610 558 7380 www.dakamericas.com Mr John W. Jones Senior Account Manager +1 215 794 7727 +1 215 794 7399 [email protected] RelPET Polyclear PET, PolyShield resin, XPURE Polyester Laser + DAK Array 9921M 0.60 - 0.90 56 to 1.3 0.76-0.84 0.81 - 0.87 Laser+ 0.72 - 0.84 (dL/g) 56 to 1.3 RelPET G5841 Polyclear PET 1101 Laser + RelPET G5761 Polyclear PET 1101 Laser + W RelPET B9845 PolyShield resin 2300K Laser + RelPET B9845/RelPET G5801 OxyClear barrier resin Laser + RelPET G5801 Polyclear PET T94N Laser + C Blow Fill Seal (BFS) Polyclear PET T94N, XPURE Polyester Laser + C RelPET H7761 Laser + H RelPET QH5821 Polyclear PET 1101 Laser+, Laser+ W, Laser+ HS Relpet Green (Recycled PET) Polyclear EBM resin 5505 (extrusion blow moulding) Array 1.0 - 1.3 (dL/g) 9921 - non-medical; PETG RelPET B9845 PolyShield resin 2300K, OxyClear barrier resin IPAmodified PETs yes yes Relpet B9845 barrier resin has both active oxygen barrier and passive CO2 barrier. Batch processed specialty polymers available","@ID":37}, "BOTTLING / FILLING 25 PETplanet insider Vol. 15 No. 10/14 Hotfilling in Mongolia The line that came in from the cold Mongolian soft drink producer Vitafit now has its first purpose-built bottling line, for which Krones AG was the main contractor. Vitafit’s solutions to challenges of hot-fill bottling and finishedproduct transportation in sub-zero temperatures are both innovative and advanced. Vitafit, which was established in 1997 by three siblings and a German investor, has come a long way in a short time. Starting with a second-hand glass bottling line imported from Germany, it has grown to become a major player in the market for carbonated beverages and soft drinks in Mongolia. When it was faced with the need for additional capacity it commissioned Krones for a new hot-fill bottling line to handle still beverages with a fruit-juice content, squashes and juices, with milk-based mixed beverages planned for the near future. Vitafit is now entirely owned by the Bolorsaikhan family, who have focused on providing quality solutions to niche opportunities and reinvested much of its profits in technology and marketing, based around its motto of “Quality smiles”. “Multi”, its best-selling product in its beverage portfolio, is a multi-vitamin drink featuring twelve different fruits and with a juice content of 20%. It accounts for around a third of the company’s 80 million fills a year. It now has a share of approximately one-third of the market, roughly the same as the regional The Acetaldehyde Reducer Additive High Performance Liquid Colours and Additives repi.com SenzAATM is a trademark of INVISTA Coca-Cola operation. The balance is shared between several smaller, domestic vendors. When Vitafit was","@ID":27}, "TRADE SHOW PREVIEW 46 PETplanet insider Vol. 15 No. 10/14 petpla.net Perfect Cooling and Temperature Control Gesellschaft Wärme Kältetechnik mbH Scherl 10 · D-58540 Meinerzhagen Tel. +49 2354 7060-0 · www.gwk.com You will feel better having made the right decision. Reduce your energy consumption. Tailor made solutions Energy saving cooling systems Temperature controllers Chillers System solutions Water treatment Cooling technology Mould inserts Temperature control technology 14.-18. Oct. ’14 Hall B 1 Stand B1 - 1205 In-line inspection solutions A cross-system platform, a common machine human interface and three smart devices that have just entered series production form the main attractions on Heuft’s stand. The Heuft Spectrum II is made up of modular devices that can function and operate independently. Automatic functions include the positioning of the detection units, which adapt to container formats without any need for human intervention. The audiovisual Heuft NaVi user guidance application is designed to explain clearly to operators has to be done, when and where, and provides support through each step of the process. Heuft claims that the new Spectrum platform’s increased processing capacity increases precision in tracking, inspecting and rejecting empty and full bottles, transmitting data in real-time. The three devices ready for series production that will be shown on the stand are Heuft’s InLineII IXS X-ray assisted empty bottle inspector; the Spectrum II VX fill management system; and the eXaminer II XOS for foreign object detection in full containers. www.heuft.com Standard and special bottles and jars PET-Verpackungen GmbH Deutschland develops and manufactures PET preforms, bottles and jars for standard, tailor-made and specialised applications in the food & beverage industry. Its full range will be on display, including the latest addition to its range: hot fill bottles and customised preforms for large containers, up to 30l. www.pet-verpackungen.de PET Verpackungen Hall 4A | Booth 417 Heuft Hall 5 | Booth 311","@ID":48}, "EDITOUR REPORT 14 PETplanet insider Vol. 15 No. 10/14 petpla.net preform converter market in Italy is approximately 10 billion preforms.” Amos Tonoli went on: “Just to maintain our market share of 18% among the converters demands regular investment in machinery optimisation, energy-reducing measures such as, for example, implementing gas heating for the dryers and possible reductions in preform weights. And we need to do all this as quickly as possible. As we say here, invest or lose out.” Tonoli continued: “This is precisely why we have invested in a further preform system with a higher number of cavities (144) for 0.5l preforms which will come into service later this year. From the point of view of applications, we envisage further growth in the sectors of detergents, household goods, foodstuffs and cosmetics, as well as in PET milk packaging. This will be the focus of our attention in the future.” Amos Tonoli gave us a brief financial summary: “In 2013 we succeeded in registering 15% growth. This year, we are once again looking at 10%, which is an ambitious goal. We are assuming the market will remain stable and that we will gain market share.” We from PETplanet wish them every success with their undertaking and move on. www.gardaplast.it Focus on private labels Fonte Ilaria S.p.A. & Fonti di Posina S.p.A. In 2011, MonteCristo based in Tuscany, made its debut in the beverages sector. The company, owned by the Biella and Colombo families, was formed following the acquisition of Fonte Ilaria in Lucca and Fonti di Posina in the Dolomites. Both were seriously underperforming before the take over, each producing only slightly more than 10 million litres of water per year. Antonio Biella (right), General Manager, and Alexander Büchler - PETplanet in front of the Editourmobil in Posina. MonteCristo concentrated on private labels right from the start. This is what Mr Antonio Biella, GM, has to say about the focus on the third party brands: “Although the beverages markets are stagnating, the proportion of private label bottling within the various segments is growing. This enables us to grow, even though, overall, the market is at a virtual standstill “. The few items bottled under their own brand name from their own “LISSA“ springs in Posina go mainly for export. The Ilaria water is destined for the regional market. The proportion of private labels / own label is 80% / 20%. The Group’s export rates are around 20%, the Posina location accounting for the lion’s share. 50% of production in Posina goes for export. Countries to which products are exported include Germany, Switzerland, Slovenia, Australia, Algeria, Libya and Japan. Following the takeover, a Krones line for CSD was installed at Ilaria alongside the existing Sidel line. In Lucca, 2014 production amounts to some 150 million litres, the product split being approximately 40% water and 60% CSD. As regards bottle sizes, the 1.5l dominates, followed by 0.5 und 2l. The facility is working at full capacity; in addition, the CSD sector is promising improved margins, according to information provided by Marketing Manager Emanuele Biella. At Fonti di Posina, the parent company has also invested in two new PET lines from Sidel. The first, for mineral water and CSD, went into production in October 2013, the second line (aseptics, combi predis) started up in January 2014. The special thing about this aseptic line is that the preform is sterilised with H 2 O 2 , and not just the blow moulded bottle. As the company does not run a filling operation in pH-critical sectors (as is the case with milk), the line represents an optimum as far as price and performance are concerned. 50 million litres were bottled in Posina in 2013. Of these 10 million litres were aseptic beverages such as juices and teas, otherwise mineral water was dominant. With the two new PET lines and the three remaining lines (two glass lines and an aseptic bottling line dating back to 2000) they are looking at bottling more than 100 million litres at the facility this year. The company’s mission statement also incorporates sustainability in all its aspects. Posina is striving to operate its production facilities as energy efficiently as possible and with very little production waste. However, even where the products are concerned, the Italians are putting ever greater emphasis on sustainability. This is why they are offering the private label bottles made from recycled PET. This is also the direction in which they are moving on the product side. Organic beverages form part of their range. In addition to juices, the organic ice tea “Infusion“ is a best seller here. And the filling process for all of these is, of course, aseptic. If the brand name owners do not wish to join them in moving in this direction, they create their own label for the foreseeable future and, if the sales figures are good, they transfer the new brand name to the private labels.","@ID":16}, "NEWS 10 PETplanet insider Vol. 15 No. 10/14 petpla.net Milacron to invest USD30 million to expand India production capacity Milacron LLC, the manufacturer of plastic processing equipment and control systems, announced its plans to further invest USD30 million (EUR23 million) in its India operations. The firm plans to invest USD20 million in Ferromatik Milacron India’s Ahmedabad facility to double its manufacturing capacity of injection moulding and blow moulding machines as well as commence the production of extrusion lines. The expansion will increase the production capacity from 1,500 to 2,100 injection moulding and blow moulding machines a year. The company is also planning to double the workforce from the current 1,200 employees in various Indian locations to 2,400 in line with the expansion. The company will invest another USD10 million in Mold Masters (a subsidiary of Milacron LLC), manufacturer of hot runners and controls, for expansion at its Coimbatore facility to meet the growing customer needs. www.milacronindia.com Resilux reports positive half-year Resilux NV, the Dutch producer of PET preforms and bottles, reported a positive trading pattern in the first half (H1) of 2014. The volume of preforms and bottles sold increased by 3.3% compared to H1 2013. West Europe, Russia and The United States were all positive but there was a decrease of sales in East and Central Europe. The growth was the result of diversification in the customers base and products. Turnover was EUR147.7m, down 3.3% on H1 2013. The company says this arose from increased volumes, lower average prices of raw materials and a slight decrease of the average weight of the preforms. Resilux can pass on fluctuations in raw material prices to customers. Gross profit (“added value”) was up 6.5% (€2.1m) to €33.7m. EBITDA rose by 8.0% to €18.0m. Depreciations and amortisations increased €0.4m, to €6.6m, which was ascribed to lower reversals of depreciations of stocks compared to the first half of 2013. Total personnel cost rose by €1.0m. “Operating result” for H1 2014 amounted to €11.4m (2013: €10.5m), an increase of 9.1%. Pre-tax net profit amounted to €9.6m, a decline of €0.3m compared to H1 2013. Post-tax profit has been declared at €7.7m, up 2.7% over the previous year. Resilux expects that operating results for H2 2014 will be in line with the equivalent period in 2014. www.resilux.com New senior appointment at Petainer Petainer, the Czech-based container manufacturer and supplier of plastic packaging for beverages, has appointed Herman Green as Global Sales Director Large Containers. He has joined Petainer from Libbey Inc., a leading producer of glass tableware products, where he served as Sales Manager, Sales Director and Commercial Director for Libbey Portugal. Prior to this he worked for Hunter Douglas, a manufacturer of window coverings and architectural products. He will be speaking on behalf of Petainer at Canadean’s Beverage Packaging Conference, 28-29 October 2014, Brussels, Belgium. www.petainer.com Petcore announces PET recycling figures PET is by far the most recycled plastic material recycled in Europe, with the equivalent of around 65 billion bottles recycled in 2013, according to findings by Petcore Europe. This represents around 56% of all PET containers in circulation but the report found that there are still huge disparities in collection rates among EU Member States. Petcore Europe Chairman Roberto Bertaggia said that all stakeholders need to work together to align the collection processes, in order to deliver the increased recycling objectives recently announced by the European Commission. The total collection of PET bottles in Europe at 1.64Mt represents a 7% increase on the previous year. One of the challenges to utilisation of existing spare recycling capacity was highlighted as the increasing complexity of some collected baled bottles. Petcore said that improved and standardised collection and sorting processes would help to address that issue. The full findings will be presented during the PET Network Day 2014 conference in Brussels, Belgium, 9 October. www.petcore-europe.org PTI aiming to cut energy costs Plastic Technologies, Inc. (PTI) has announced that it is embarking on an initiative to help bottle producers reduce energy costs. The initiative is building on the success of a project that has already seen a small number of North American brand owners cut costs of bottle manufacture by up to USD500,000/yr. PTI says that it is aiming to expand the initiative to other companies and internationally. Donald Miller, Vice-President, technical services, with PTI said that the key to reducing energy consumption is to think of air delivery and air demand [blow moulding equipment] requirements together, rather than as separate areas. PTI designs bespoke energy savings plans after undertaking a multistep analysis of the entire bottle production process, from preform to discharge. The entire process, including machine capabilities, blowing cycle, oven control and validation are examined. PTI says that its review and recommendations could help multi-site bottle producers to save millions of dollars annually. www.plastictechnologies.com","@ID":12}, "PETpatents www.verpackungspatente.de 60 PETplanet insider Vol. 15 No. 10/14 petpla.net Dual chamber vessel Utility model DE 202007009670 U1 Applicant: Gunther Froehlich, Hamburg (D) Application Date 24.1.2011 Dual chamber vessel consisting of two containers, one internal, the other external. The containers are coordinated with one another in such a way that the contents of the inner container also show through / become visible at a number of points. The result is visually attractive product packaging. Improved preform International Patent No. WO 2014 / 019936 A1 Applicant: Nestec S.A., Vevey (CH) Application Date 25.7.2013 This international application describes the concept and the procedure for manufacturing a preform which is split up into several segments / production stages. In this way individual preforms can be manufactured which fully satisfy the requirements relating to the bottle. Closure cap Utility model DE 202012007857 U1 Applicant: Incap International Ltd., Hong Kong (HK) Application Date 9.8.2012 Closure cap for a container. A chamber to accommodate an additional product is integrated in the simply constructed cap which can be manufactured inexpensively. Rotating and pushing down destroys a membrane and this releases the product. Integrated handle International Patent No. WO 2014 / 035616 A1 Applicant: Edward Robbins, Muscle Shoals (US) Application Date 6.8.2013 One disadvantage of many thin-walled plastic bottles is their (lack of) stability when lifting and pouring out the liquid. The application proposes the integration of recesses on the outside of a bottle into which a separately produced, fold-down handle is inserted. The bottle can be lifted without exerting pressure on the walls. Bottle base Disclosure No. DE 102012107656 A1 Applicant: Herta Schmid, Martino (IT) Application Date 21.8.2012 The base section of a thin-walled plastic bottle is made up of five sections in spiral form which ensure adequate bottle stability. Preform European Patent No. EP 2698321 A1 Applicant: Inotech Kunststofftechnik GmbH, Nabburg (D) Application Date 4.7.2013 The preform used in the manufacture of a container is made up of a number of segments / components which are in contact with one another. The container is reinforced in the outlet area so as to enable savings in material to be made in the remainder of the area, but still ensuring that adequate stability is maintained.","@ID":62}, "MATERIAL / RECYCLING 18 PETplanet insider Vol. 15 No. 10/14 petpla.net Alpla on growth strategies and the role of recycled PET R-PET for own use by Waldemar Schmitke To kick off our Go to Brau Beviale Editourmobil Tour 2014, we pay a visit to the plastics packaging specialist Alpla in Austria. The company, founded by Messrs Alwin and Helmut Lehner in 1955, is still in private ownership today and run by members of the family. Today the company, which has its main office in the Austrian town of Hard, employs more than 15,000 people worldwide and has a turnover of more than 3 billion euros spread over 150 production workshops in 40 countries. And the indications are that the trend is rising. The company’s external profile is surprisingly low within the sector for an enterprise of this magnitude and, as far as end users are concerned, remains something of an unknown; the family places a great deal of emphasis on maintaining its privacy. At the company head office, I meet Hermann Riedlsperger, Head of Corporate Sales PET. Alpla is split up into three divisions which, in terms of turnover, can be broken down as follows: 10% manufacture of closures and caps 45% PET preforms and stretch blow moulding 45% extrusion blow moulding PET applications The largest PET markets for Alpla are Western and Eastern Europe together with Central and South America. However, the biggest growth in the beverages sector today is to be found in South America, Asia and India. In China and the USA, business is concentrated exclusively on the non-beverages sector. The production range is divided up as follows: ¾ for beverages applications and ¼ for household applications, food and other packaged goods. At the same time, where the non-beverage packs are concerned, growth is kept within limits, due to the large number of different specific requirements in relation to packaging. In the beverages sector, growth is a hot topic, although this is limited depending on the specific country. In the majority of markets, preform systems incorporating 72 and 96 cavities are used. However, in large markets such as Mexico or Brazil, it goes without saying that systems with up to 144 cavities will also feature in production. According to Riedlsperger, in the European market however there is more call for flexibility than for higher numbers of cavities. 50% of the companies already work on the basis of the wall-to-wall concept, and the trend is rising. This involves setting up PET bottle manufacturing facilities in an adjacent room or a neighbouring building within a bottling plant. This consequently enables the PET bottles to be delivered directly to the bottler’s filling machine via conveyor lines through a “hole in the wall”. This means that no transport or storage costs are incurred for the PET bottles. Hence the PET bottle manufacturing operation lies within the responsibility of the bottle supplier. UHT milk in PET bottles represents a smaller area of beverages packaging and is a feature mainly in Poland and Italy. The technology used here involves the processing of a high-concentration light barrier in the preform machine using the mono process. Recycling Within the Group a high priority is set on the processing of recycled PET. One aspect is the processing of food-safe recycled PET in flake form in proportions of up to 50% in the preform machine. Another feature is up to 100% processing of food-safe PET in the form of pellets from the company’s own recycling lines in order to produce preforms and bottles. In addition, Alpla has established its own recycling plants in Poland and Austria, with a capacity of 50,000t/a. These plants supply mainly bottleto-bottle quality for their own use. In addition, as Hermann Riedlsperger Hermann Riedlsperger, Head of Corporate Sales PET, Alpla","@ID":20}, "BOTTLE MAKING 22 PETplanet insider Vol. 15 No. 10/14 petpla.net PET bottles extend milk shelf life and offer greater freedom in dairy packaging It is estimated that 34bn litres of milk and dairy drinks were packaged in Europe in 2013; only 8% of those packages were PET bottles. This market has been identified offering one of the highest potential growth opportunities for PET bottles in the coming years. HDPE (High Density Polyethylene) bottles and cartons (often called ‘bricks’) have dominated the packaging of long life and extended shelf life milk for many years. Compared with their ‘clear glass’ forerunners these materials have proved successful, performing their primary functions of containing and protecting the milk during long storage and ambient distribution, as well as preventing light damage. The instability of vitamins, particularly B2 (riboflavin), B6 and B12, during processing and storage can contribute to losses in the nutritional quality of foods. Light, between 320nm – 520nm spectrum, has the effect of degrading these vitamins through photo oxidation, and they are essential for normal growth in the human body. In addition, the secondary degradation of lipids through oxidation causes flavour deterioration, often referred to as creating a ‘light taste’. The balance that manufacturers need to achieve is to provide the required level of light protection while minimising cost, weight and material usage. Today’s PET market offers many options for providing a light barrier, including multilayer materials, the addition of colorants, or TiO 2 (titanium dioxide) additives dispersed directly during PET polymerisation. And it is embracing this last technology that GEA Procomac opted for the last of these options in ‘White & Safe’, its bottle for the UHT dairy market. The company partnered with PET Engineering and with Novapet for the bottle design, development and optimisation. Its objective was to demonstrate that it is now possible to combine the highest level of hygiene and safety of aseptic filling, with packaging that provides a ‘total light barrier’ (over 99.5% of the visible light spectrum), together with guaranteed shelf life of over nine months for UHT milk. GEA Procomac claims that its bottle delivers significant advantages over earlier materials. Barrier PET goes beyond flexible and modular light barrier functionality and offers the potential for light-weighting, in exactly way as ordinary PET, which will enable significant reduction of material costs along with the same bottle to bottle recyclability potential as normal PET. In 2007, in partnership with Novapet and Leche Pascual (now Calidad Pascual, Spain), the first PET bottles for UHT milk entered the market. Since then, many other important bottlers across Europe have chosen","@ID":24}, "PRODUCTS 53 PETplanet insider Vol. 15 No. 10/14 petpla.net PROVEN COST SAVINGS PERFORMANCE moldmasters.com Mold-Mastersand theMold-Masters logoare trademarksofMold-Masters (2007) Limited. ©2014Mold-Masters (2007) Limited -AMilacronCompany.All rights reserved. Rely on our global support network for fast service and parts. North America 1-800-387-2483 | Europe 49 (0) 7221 5099-0 Asia 86 512 86162882 ALWAYS INNOVATING. + More efficient use of platen real estate increases the cavitation for a given machine size: s 72 vs. 48 Cavity with a 28mm finish in a 225T s 72 vs. 48 Cavity with a 38mm finish in a 300T s 96 vs. 72 Cavity with a 28mm finish in a 300T s 128vs. 96 Cavity with a 28mm finish in a 400T + Proprietary iFLOW and iCOOL technology reduces cycle times while improving balance, lowering injection pressure and increasing dimensional repeatability + Tooling solutions to revitalize, recapitalize and rev up existing systems Get 50% more output from the same machine 96-CAVITY MICRO PITCH MOLD FOR 300T MACHINES Contact us today at: [email protected] Active oxygen absorbers for PET- longer shelf-life, less food waste, less packaging material New Cesa-absorb for active oxygen barriers in PET packaging and advanced Hydrocerol nucleating agents for new-generation construction insulation have been launched to meet market trends and customers’ needs by the specialty chemicals producer clariant. Cesa-absorb responds to the global need of securing food supplies for the world’s growing population by providing effective oxygen barrier solutions for plastic packaging, particularly lightweight, thin and mono-layer packaging – chosen for their environmental benefits – where food needs greater protection from permeating oxygen. Cesa-absorb is a masterbatch with an integrated active oxygen barrier that optimally protects sensitive packaged goods from oxygen-induced degradation. According to the company, it provides long-term oxygen barrier performance to PET packaging such as bottles and films without impacting on transparency or the recyclability of PET. Based on proprietary and patent protected Clariant chemistries, the oxygen scavenging units consist of a catalyst and an oxidisable substrate, which are uniformly dispersed in the polymeric matrix of the packaging wall. Cesa-absorb and the advanced Hydrocerol nucleating solutions are scheduled for commercial launch at the end of 2014/beginning 2015, respectively. www.clariant.com To cap it all Spectra Packaging announce 24/410 Shallow Cap. Spectra already supplies a wide selection of closures that feature a variety of thread fitment options and the new 24/410 cap is aimed at giving customers even greater flexibility when choosing a closure to complement the company’s range of bottles. Although the company continues to launch new products, they are aware that quality is equally as important as choice. The company reports that the 24/410 flip top has proved extremely popular with customers looking for a 410 option. It appears that there is a limited choice of 24/410 fitments on the market and the company is keen to capitalise on what it believes is an ever increasing demand. www.spectra-packaging.co.uk","@ID":55}, "BOTTLE MAKING 31 PETplanet insider Vol. 15 No. 10/14 petpla.net The biggest drying system for plastic materials ever installed in the world, 6,000 kg/h PET. www.moretto.com Drying Revolution designed by Moretto STAND 3208 HALL B3 ovens and reflectors were also studied during the design stage to ensure optimum heating environment is maintained for the preforms while allowing other components to stay within the targeted temperature range. The LSS16 is the first machine from Chumpower to feature the quick change sealer design, and since the mould change and stretch rod setting are relatively straight forward, thus helps in shortening the production changeover period. Recovery system is standard for this machine, featuring European based blow valve system with fast responding time and low dead space volume. This system was also well tested within the industry. The estimated air consumption rate for producing 600cc bottles with 11.5g preforms at 24,000bph is 16.8m³/min, and the total energy consumption rate is 45.6kWh. The most important aspect for Chumpower to create this high output machine is to offer the possibility to couple the blowing machine to high-output rotary filler and formed a combi system, which illuminate the need for expensive air conveyors and saves precious floor space. By linking the LSS16 to bottle-handler system, the finishing bottles are precisely carried from the blower and feed into the star wheel of the filler. CCD camera system can also be installed in the downstream conveyor belt to monitor the output bottle from the combi system for proper filling level and closure capping. Traditional combi line uses a rotary blow moulding machine as the blower, however, this setup would pose a higher entry barrier for new comers in the PET bottle industry. Therefore Chumpower’s combi system concept or the LSS16 machine is very suitable for clients who are looking to setup a medium to high production capacity line. www.chumpower.com Chumpower’s combi systemwith filling-and-capping machine","@ID":33}, "BOTTLE MAKING 30 PETplanet insider Vol. 15 No. 10/14 petpla.net BOTTLE MAKING 30 Linear stretch blow moulding machine goes together with rotary filler Chumpower LSS16 A nice couple Since 2008, the Taiwanese stretch blow manufacturer Chumpower has been putting lots of resource in refining their linear blow moulding machines. From the beginning of 6,000bph for the six cavities machine back in 2008 to today’s massive 24,000bph (600cc bottle production) from the 16 cavities machine, Chumpower has set the bench mark for all high-speed linear machine within the industry. The LSS16 stretch blower is a fully electric machine driven by ten servo motors, from the heavy-duty clamping system to fast-responding sealer or preform-eject actuation, precise servo synchronization and high mould cavity count are the two key factors making high output capacity possible. This platform has been well-tested within the industry for years, so it is a suitable candidate for Chumpower to design the LSS16 based on that platform. Since this model has nearly the twice production capacity, robust clamping and fastresponding subsystems were essential in making the machine stable during production. The clamping system was driven by two servo motors actuating each side of mould, since the mould has long horizontal span to house sixteen 500cc bottles, strong cam-driven indexer were used to transfer the high torque from servo motor to the swing arm and push-rod system which subsequently also drive another cam to actuate the base mould. Two sets of servo motors drive the stretching system via rack-and-pinion mechanism. Also sealers were servo driven actuated by cams. Ten modules of heating ovens were fitted on the machine to heat 24,000 preforms per hour, and Chumpower’s narrow pitched preform chain (38mm) allows more preforms to be heated at one time. Each oven is controlled by advanced IR heating-control system from Olicorp to regulate the electrical current and ensure stable IR lamp output. The estimated average power consumption of the LSS16 for producing a single bottle would be1.9Watts. The fluid-dynamics for heating","@ID":32}, "PETcontents 10/14 4 PETplanet insider Vol. 15 No. 10/14 petpla.net INSIDE TRACK 3 Editorial 4 Contents 6 News 50 Products 54 On site 56 PET bottles for Beverages +Liquid food 58 PET bottles for Home + Personal care 60 Patents MARKET SURVEY 33 Suppliers of resins and functional additives for PET bottle production CAPPING / CLOSURES 36 Bottling of sensitive products A special challenge AFTER SALES SERVICE 38 Service performance Key measure for equipment sourcing Part 1 TRADESHOW PREVIEW 45 Brau Beviale 2014 November 11-13, 2014 Nuremberg, Germany BUYER’S GUIDE 61 Get listed! Page 16 Page 26 EDITOUR REPORT 12 Invest, or lose out Garda Plast S.p.A. 14 Focus on private labels Fonte Ilaria & Fonti di Posina S.p.A. 16 Strong brand, declining market Sanpellegrino S.p.A. MATERIAL / RECYCLING 18 R-Pet for own use Alpla on growth strategies and the role of recycled PET 20 A boost in PET 2 PET Recycling Pet 2 Pet Recycling Österreich GmbH BOTTLE MAKING 22 PET bottles extend milk shelf life 30 A nice couple Linear SBM machine goes together with rotary filler 41 Practical Guide to Injection Moulding of Preforms Bottles, preforms and closures, part 15 BOTTLING / FILLING 25 The line that came in from the cold Hotfilling in Mongolia Page 57 A f t e r S a l e s Service","@ID":6}, "PREFORM PRODUCTION 41 PETplanet insider Vol. 15 No. 10/14 petpla.net Extrusion and Screw Control, part 15 Practical Guide to Injection Moulding of Preforms Quite a number of parameters need to be adjusted on a typical injection moulding machine, which may seem at first somewhat intimidating. After reading through Chapter 2, the reader should have a good understanding of what the process should be to yield acceptable preforms. Putting this into practice is of course another matter. This chapter aims to translate the discussed theoretical concepts into concrete advice to run a machine on the floor. There will be some more theory to make concepts more understandable. PETplanet insider is publishing extracts from successive chapters of Ottmar Brandau’s “Bottles, Preforms and Closures”, which was first published by hbmedia. A newly revised version is reissued under the Elsevier imprint.","@ID":43}, "ONsite 54 PETplanet insider Vol. 15 No. 10/14 petpla.net Cabreiroá water is revitalised with Spear’s reverse printed labels Cabreiroá is a mineral water derived from springs in the Galicia region of Spain. Being one of the leading brands in the North West region for over 100 years, Cabreiroá, owned by Hijos de Rivera is setting its sights on a national market The traditional brand is being revitalised, with a new PET bottle range and collection of six pressure sensitive labels, printed by Spear. Aimed at the premium market, each of the six back labels were printed with a different scenery design in mirror fashion. Spear then applied a solid white to conceal it before printing the back label design (promoting their sponsorship of the Spanish national football team). The Cabreiroálogo on the front label had to be a strong, clean white to stand out against the photographic back label image. In line with requirements for a premium look pack, Spear chose a hi-reflectance silver, printed sub-surface, to create a foil effect on which to display the beverage description. The result is an aquatic scene magnified through the bottle, complimenting the energetic silhouette on the front label. “The new labels represent a turning point into the world of PET containers. Thanks to our collaboration with Spear, we have achieved optimal synchrony between the front and back label. In our opinion, this is a fantastic method of conveying a message of vitality and Galician origin in a simple and natural way.” Juan Paz García, Hijos de Rivera. www.cflex.com/Labels.1668.0.html www.spearsystem.com HSM channel baling presses feed by Euro Pool Systems In neatly lined-up wire cage carts, cardboard, PET bottles and cans from 175 post consumer waste of a supermarket chain in Hungary were carried via chain conveyors into two parallel channel baling presses and tightly compacted. Two shifts a day, six days a week. Euro Pool has decided to build a new hall in Hungary which will accommodate the recycling of materials from the food industry. Two fully automatic channel baling presses from HSM will enable the volume of packaging to be drastically reduced and returned to the recycling loop in the form of bales of material. The system at Euro Pool System comprises two HSM VK 8818 FU channel baling presses and materials handling. VK 8818 means: a fully automatic channel baling press with a press capacity of 880kN and a feed opening of 1,000 x 1,800mm. The presses are each equipped with a frequency converter (FC) and thus save around 40% in energy compared with conventional power units. The facility was planned and built together with a new hall. The operating personnel continuously load the chain conveyors with the materials to be compressed, which have been supplied correctly sorted. One of the two presses is equipped with a PET perforator so that the PET bottles are perforated before being compressed and thus their volume can be substantially reduced. The HSM channel baling presses produce solid bales with five straps measuring 1,100 x 750mm, weighing between 500 and 700kg and between 1 and 2m in length. The bales are correctly sorted and therefore bring in a high level of sales revenue. www.europoolsystem.com www.hsm.eu VISIT US AT: Fakuma Friedrichshafen, Germany Hall A7, Stand 7312","@ID":56}, "MARKET SURVEY 33 PETplanet insider Vol. 15 No. 10/14 petpla.net Caps and closures Bottle-to-bottle recycling plants Preforms Preform and single stage machinery Preform / stretch blow moulds Two-stage SBM machinery Compressors Resins / additives Filling equipment Closure systems PET bottle resins / colours and functional additives PETplanet insider presenting the suppliers of PET bottle resins and the supplier of colours/functional additives in this market survey. The additives available include barrier improvement additives for sensitive beverages, UV blocker, brighteners and many other performance enhancers. Also included among the resin manufacturers, in alphabetical order, are: DAK Americas, Indorama, Invista, M & G, Neo Goup, Novapet and Reliance Industries. In the additive range, there are ten global players among the suppliers, in alphabetical order: Clariant, Colormatrix, Gabriel Chemie, Holland Colours, Invista, Novapet, Penn Color, Repi, Sukano and Valspar. The suppliers are listed in the order in which their details were received by the editors. Although the publishers have made every effort to ensure that the information in this survey is up to date, no claims are made regarding completeness or accuracy. 10/2014 MARKETsurvey Resins Company name Novapet, S.A. Indorama Ventures Ltd Postal address Telephone number Web site address Contact name Function Direct telephone number Fax E-Mail P° Independencia, 21, 3°, PC 50001, Spain +34 976 216129 www.novapet.es Mr Miguel Angel Arto Head of LB&Concentrates division +34 976 216129 +34 901 021138 [email protected] 75/102 Ocean Tower 2, 37th Floor Bangkok 10110, Thailand +662 661 6661 www.indoramaventures.com Mr W.G. Hoenderdaal Technical Marketing Manager +316 518 099 42 [email protected] RESINS Europe USA Mexico Asia 1. Brand name of the resins NovaPET RamaPET Preformance PET, Polyclear PET Polyclear RamaPET, Afron for antomony free batch products 2. IV Range a. of homo-polymers 0.62 to 0.96 IV 0.71 to 0.95 IV 0.58 to 0.95 IV 0.50 to 1.08 b. of co-polymers 0.60 to 1.10 IV 0.70 - 0.84 IV 0.58 to 0.84 IV 0.74 to 0.86 IV 0.58 to 1.08 3. Speciality resins CSD Lbs Soft, Cr R1, R182, R180 ES11, ES11 (A)-R10, 1101 1101, 1111 S1, S2, R1, N1S Water Mw Soft, Cr, Glasstar and X_treme N1, N1(S), N2, N180, W170 N2R, N2R (A)-R10, N2R-Ti, 3301 3301 N2, N1 Beer Glasstar N1, N1(S), N180 1708CC, 3302 N1 Wine / liquors Glasstar N1, N1(S), N180 1708CC, 3302 N1 Personal care /pharmaceuticals Glasstar, Sprit H 11, Sprit L01, Kera N1, N1(S), N180 1708CC, 3302 N1 Slow crystallisation Glasstar, X_treme,CLP (Sheet) P184 T-94, T-94-Ti T-94 G1, G1AS (scratch resistant), SG1 Hotfill HF R1, HF 1708HS, 2201 2201 H1 Pre-coloured Dairy, Luz Fast reheat Lbs R1, R182, R180 ES11, 1101 R1, R2, ES11 Other CPET, HT, REX (for EBM) Other non packaging applications R182 PlantPET, high IPA modified resins 1110 (10% PCR) PlantPET L1 (High flow blood tubes), film grades, low melting resins and silica masterbatches, HV 3008, HV3012, NR00N 4. Increased barrier properties Dairy, LUZ , DCU, Polygloss (light barrier). Glasstar (gas barrier) Oxyclear barrier resin 5. PEN mixes available yes 6. Recycled blends available Yes, under customer requirements Polyclear Conserve PET, FuTuRe-PET 7. Special comments Specialised in light barrier protection for long shelf life milk products (UHT, ESK, Milk shakes, yogurt) Polyclear EBM PET for extrusion blow moulded containers, low IV and functionalised PET and copolyester polymers N2G (Germanium based PET) for crystal clear bottles/articles, Titanium catalysed grades, BioPET","@ID":35}, "42 PETplanet insider Vol. 15 No. 10/14 petpla.net Screens on injection machines of different manufacturers differ greatly in their representation of basically the same parameters. Some are more text based, whereas others use graphics to display relationships. The experienced processor will intuitively be able to make sense of different displays, whereas a novice may have difficulties in understanding an unfamiliar operator interface (OI) to another. The concepts explained in this chapter are usable on all machines, from the crudest single-line OI to the most sophisticated graphical interface. It will be up to the reader to recognise them in the various formats. (Fig.3.1) 3.1 Extrusion and screw control The first task of the injection machine is to transform the dried resin pellets into a homogeneous melt that can be injected into the tool. Three extrusion systems are used for the production of PET preforms: Standard reciprocating screw whereby the screw recovers, then pushes the material out Two-stage (“P”) system, that consists of a top-mounted screw that recovers and then transfers the molten material into a shooting pot that subsequently injects the material Two extruders feeding a common shooting pot The advantage of systems with a shooting pot is that the screw has a longer portion of the cycle time to recover. With reciprocating screws the screw can only recover after hold and decompression times as it is the screw that injects and holds the pressure. In a shooting pot system the screw transfers molten material to the shooting pot under low transfer pressure, and then immediately starts recovering. This allows the use of smaller screws for the same overall output, which is beneficial for PET because shear stress increases with the square of the screw diameter and is therefore harder to control with larger-diameter screws. The resin that enters the extruder throat is a mix of crystals and amorphous parts. In order to melt the resin the extruder must heat and soften the amorphous fraction and melt the crystalline fraction. All crystals must be melted because unmelted crystals would act as nuclei (starting points) of crystallisation in the preforms. This has to be avoided as the goal is to have the preform completely amorphous (see Chapter 2.2). The melting of the resin is accomplished mainly by transferring the mechanical energy of the rotating screw into shear energy. By rubbing the spherulites against each other and against barrel and screw, the extruder brings on the necessary shear heat for melting. Heat transfer from barrel through heater bands is only about 30% – may even be negative in some zones! Negative heat transfer would be the case when the temperature readout of an extruder zone is higher than the set point. In this case the friction inside the barrel is so high that it actually overheats the barrel and must be cooled down to maintain the temperature that is selected. This usually happens at the end of the barrel in the so-called metering zone of the screw. Most of the heat (about 70%) comes from pellet inlet temperature (dryer) and friction (screw and barrel). Most screws used in PET processing are called barrier screws. Like all screws, barrier screws are manufactured with three distinct areas (fig. 3.2): Feeding Compression or transition Metering Each screw consists of a number of flights that are organised around a changing root diameter. The L/D ratio is calculated by dividing the flighted length by the screw diameter (fig. 3.2). This parameter allows easy classification of a screw in terms of residence time. Short L/D ratios are for materials that are sensitive to degradation when exposed to heat for a long time, whereas long ratios are for materials that need the extra residence time to completely melt. Typical ratios for PET screw are 22:1 to 24:1 with shorter screws being used in some singlestage machines. The compression ratio is calculated by dividing the flight metering height by the flight feeding height. The compression rate is calculated by dividing length of the transition zone by the value that arises when the metering root depth is subtracted from the feed root depth. Figure 3.1 Only thorough understanding of the moulding process allows operators to continually mould high-quality preforms. Figure 3.2 Standard screws are common for many injection-moulded parts. (Diagram courtesy of Barr Inc)","@ID":44}, "ON SITE 55 PETplanet insider Vol. 15 No. 10/14 Sidel Combi for CSD achieves 17% reduction in energy consumption at Refres Now The Argentinian beverage producer Refres Now has invested in the biggest Sidel Combi ever built for filling carbonated soft drinks and has achieved a reduction in energy consumption of 17%. As part of a complete line, the Sidel Combi was installed at the company’s bottling plant in La Matanza for the bottling of family pack sizes, which are in great demand in Argentina at the moment. The La Matanza plant of Refres Now, located in the Greater Buenos Aires province of Argentina, is one of the largest soft drinks production facilities in the world. The plant produces more than ten different products each day, bottling a total of over 3.5 million litres. The company’s working relationship with Sidel first began back in 2005 when Refres Now was originally founded. The recently installed complete line features a Sidel Combi Eurotronica FMc and a Sidel Starblend mixer. The line is presently achieving production output rates of 30,000bph for the larger 2,5l bottles of carbonated soft drinks. The Combi is equipped with 20 blow moulding stations, 162 electronic flowmeter filling valves and 18 capping heads. Brushless motors and an interface between blowing and filling functions contribute to energy savings and improved security. In addition to the energy savings, the bottles now feature an increased base stability. These higher quality bottles are therefore better suited to withstand the forces of transportation and handling throughout the entire supply chain. The higher stability also avoids costly bottle deformation which may occur due to the increased internal pressure of the carbonated drinks resulting from the ambient conditions in Argentina: temperatures can reach up to 45°C with humidity levels climbing to 78%. In order to keep up with Sidel’s very latest developments, the company owners Orlando and Walter Canido recently visited several Sidel production sites in France and Italy to witness the Sidel Matrix system in operation and to see first-hand the latest technology. www.sidel.com IMAGINE FILLING MULTIPLE PRODUCTS ON THE SAME LINE…NOW YOU CAN! Water, juice and soft drinks, all on a single machine? The Flextronic modular platform adapts effortlessly to still or sparkling, clear or pulpy and hot or cold-fill, and easily switches from one bottle neck-size to the other. A revolutionary filling technology that gives you extreme operational flexibility with minimal product loss and downtime at flavor switch. Clean, safe and versatile. Welcome to the new generation of fillers. carbonated still hot-fill cold-fill pulp non-pulp water juice soft drink SIPA S.p.A. - Via Caduti del Lavoro, 3 - 31029 Vittorio Veneto (TV) - Italy Tel. +39 0438 911511 - Fax +39 0438 912273 - e-mail: [email protected] www.sipa.it","@ID":57}, "PRODUCTS 51 PETplanet insider Vol. 15 No. 10/14 petpla.net Precise inspection for a good coffee It was developed in 1986 and for years only used in gastronomy. In the last few years it has become a global trend that gains more and more fans: the coffee pod. Since 2007, the global sales growth of the pods has expanded by more than 20% annually. The Swiss company Nestlé alone has sold about 8 billion pods worldwide in 2013, thanks to its affiliated company and leading brand Nespresso. While Nespresso is still considered as the biggest player, many competitors have entered the market and gained ground during the last few years, especially in the lower price segment. The pods are usually made from aluminium, PET and other plastic materials. This makes an efficient quality control inevitable. Due to its specific function, the coffee pods feature an extremely complex design. A special challenge is to reproduce the fine structures with thin flow channels inside the pods. A trouble-free functioning is crucial for moistening, infusing and rinsing the coffee inside and to produce the quality and taste expected by the customer. However some of these flow channels may be locked by malfunctions during the plastic moulding process like under- or over-filling. To avoid delivering products of low quality, vision inspection systems by Intravis have proven to be helpful being included in the quality control. The German producer has gathered much experience in inspecting coffee pods over many years and for different worldwide operating customers. A close and detailed vision inspection guarantees flawless end products. www.intravis.de","@ID":53}, "CAPPING / CLOSURES 37 PETplanet insider Vol. 15 Respecting values in effective dialogue www.krones.com BrauBeviale 2014 Nuremberg, 11 – 13 November Stand 7A-514 side seal. This technology has been tested for hotfill already ten years ago. Nowadays many companies are using this technology industrially for hotfill in all parts of the world. This exposure in the field under different climatic conditions and by companies valuing highly a safe and a high quality level makes linerless DoubleSeal technology for hotfill a proven solution. Advantages are: Lower application torques because the DoubleSeal system does not rely on top seal but on side seal. Very convenient and consistent removal torques. No risk of deformation of the PET neck when exposed to heat. The side seal is not sensible to a small back-off, less risk to contaminate the product. Lower wall thickness – 1.5mm - of the PET neck due to the fact that the upper rim of the PET neck is supported inside and outside by sealing elements of the closure. Lower production cost of the closure due to elimination of the lining process. The predominant neck finish in hotfilling is as for aseptic filling the 38mm neck finish. There exist numerous neck finish designs which differ in neck height and wall thickness. At least per country neck designs seem to be identical for 38mm hotfill but there are differences from country to country or region to region. Bericap offers screw cap solutions to many of the neck variants existing in the market. As in aseptic filling there exists a 33mm neck for hotfilling. The neck finish recommended by Bericap has like for aseptic filling a neck height of 15mm. The Bericap linerless DoubleSeal technology has proven safe hotfilling for the 28m neck with the standard neck finish PCO 1881 and a standard PCO 1881 closure from Bericap. This combination simplifies the availability of performs for hotfilling in 28mm. The product range of screw caps is like for aseptic filling complemented by push-pull sportscaps which do not require an aluminum seal but resist the heat exposure during filling. www.bericap.com","@ID":39}, "EDITOUR REPORT 15 PETplanet insider Vol. 15 No. 10/14 petpla.net Currently Fonte di Posina carries out filling operations for some 170 private labels. This implies a very high level of flexibility in production, given bottle sizes of 0.2 to 2l. Antonio Biella describes the issues they face: “We produce significant quantities of labels for the highly pricesensitive discounters and we have to balance this with the relatively small volumes for the speciality markets which of course offer bigger margins.\" He concluded: “This balancing act between discounters and niche markets comes up on a daily basis.” Flexibility was a key reason for opting for the new aseptic filling line. “In contrast to the existing wet aseptic line (bottle sterilisation) the new Sidel line features dry decontamination for both preforms and caps,” explained Antonio Biella. “The time required for cleaning and sterilisation is significantly shorter which means that changing formats, vital especially for the small production batches, is also greatly reduced. There are environmental benefits: peracetic acid is no longer used and water savings are even achieved in the rinsing process. The capacity is double by comparison to the wet aseptic line.” The production capacity of the new line is typically 12,000 0.5l bottles of tea per hour. For mineral water, a Sidel blow moulding and filling line in block format with ten blow stations and bottle bottom cooling is available during transfer of the blow moulded PET bottles to the filler module. Depending on the filler module, the capacity of the line is 18.000bph. The blow moulding temperature is set to 100° and the blow moulding pressure to 24 bar. As regards aseptic filling, there are two types of closure available, all with a diameter of 38mm. Flat closer Sport caps For mineral water filling, there are two models available, each with a diameter of 28mm Covallia for CO 2 Alaska for still mineral water The business has its own sales and marketing department, currently employing six staff. We extend our thanks for the interview and leave the beautiful valley in the Dolomites and head off in the direction of Venice. www.lissa.it www.fonteilaria.it CHOOSE THE NUMBER ONE. BACK TO LIFE. VACUREMA® –FoodContact Approved Recycling With highly efficient decontamination BEFORE the extrusion process. Bottle-to-bottle Pelletising Inline Applications From left: Emanuele Biella, Marketing Manager, Giuliano Nelli, Managing Director, and Alexander Büchler, PETplanet Insider in front of the Editourmobil at Fonte Ilaria in Lucca.","@ID":17}, "BOTTLING / FILLING 26 PETplanet insider Vol. 15 No. 10/14 petpla.net Vitafit makes more than 40 different products under seven individual brands founded, over 80% of juice-based beverages were imported into the Mongolian market. The equivalent figure today is well below 10%. Growing with PET Vitafit first adopted PET packages in 2002, when it began bottling its Vita brand table water in PET containers. That particular line, which uses Chinese equipment, now operates at 10,000bph. Aseptic production is concentrated on filling 1l carton packages with juices and milk at 11,000bph. A Chinese-manufactured hotfill line was installed in 2005 and bottles iced tea, juices and pulpy drinks in 600ml wide-neck PET containers at 6,500 to 8,000bph. It introduced dry-aseptic filling of PET bottles with juices in 2005. Vitafit is now the exclusive Pepsi-Cola licensee in Mongolia and operates its CSD line at 15,000bph. Kefir, a fermented milk product, is filled in 1l and 1,5l PET and HDPE containers and small tubs. Vitafit now sells more than 40 different lines under seven individual brands including Multi added-vitamin juice; Goy fruit juice-based beverages; Goy iced tea and Superfruits; and Anar 100% fruit juice. Demand continues to rise and Vitafit continues to invest to meet it. New for Mongolia: Krones hotfill line In the summer of 2013 Vitafit expanded its equipment portfolio to include an 18,000bph hotfill PET line from Krones AG, which was the first of this kind that the company had installed in Mongolia. As lead contractor, Krones was also tasked to manage the project’s installation and integration. Its machines serve as signal generators for all other machines upstream, including in the new syrup kitchen, which is equipped with Chinese-manufactured reverseosmosis water treatment system, container conveyors, labeller and bottle cooler. The kitchen features a Krones deaerator and VarioFlash shell-and-tube heat exchanger as a flash pasteuriser. The bottling line incorporates a Contiform H12 blowmoulding machine with a hopper, preform feed and preform interior cleaning, which is monobloc-synchronised with a Modulfill VP-GL-PET filler, where the beverages are filled at a temperature of 88°C. A Checkmat 731 FM-X+L inspector monitors output, inluding fill levels. End-ofthe-line packaging is handled by a Krones Variopac Pro FS non-returnables packer from Krones. Vitafit opted for a hotfill line instead of a second aseptic line because the hotfill line is less complex and thus easier to operate; aseptic specialists are both rare and expensive in Mongolia. Vitafit preferred a monobloc configuration for the blowmoulding machine and the filler. The new line had to be integrated into an existing section of the hall, which favoured the reduced footprint of the monobloc. Getting lighter The first delivery package included four mould sets, for containers with volumes of 250, 480, 500 and 1,250ml. These are used to bottle eleven different still products, including the Multi and Anar 20% fruit-juice beverages, in hotfill bottles with paneltype sidewalls and a 28mm narrowneck design. Beverages are filled into PET bottles at 88°C on the Modulfill VP-GL-PET filler.","@ID":28}, "TRADE SHOW PREVIEW 47 PETplanet insider Vol. 15 No. 10/14 petpla.net Next steps in PET preforms Italian company Sipa will be revealing the latest developments in its PET preform and packaging production machinery, in which sustainability is a notable common thread. Sipa has been involved in a two-year development program that will help industry save energy and reduce emissions of carbon dioxide. According to General Manager Enrico Gribaudo, the program and its results “…maximise the potential for synergies throughout the total process of conception, design, and production of containers.” www.sipa.it Sipa Hall 7 | Booth 657","@ID":49}, "BOTTLE MAKING 24 PETplanet insider Vol. 15 No. 10/14 petpla.net the PET bottle as an alternative to the more traditional multi-layer cardboard and HDPE containers, or as an effective way to open new sales channels. Building on the experience accumulated in these years with “Dairy” PET resins, Novapet has developed a DCU concentrate (TiO 2 based). DCU provides greater flexibility to its offer by means of an adjustable light barrier, which has a range of barrier properties from lesser to total. These qualities are achieved by the addition of the product to conventional bottlegrade PET, when this is injected to produce the preform. The level of light protection provided can be customised by adjusting the concentration of DCU in the preform, according to the needs of each individual product. Tests have shown that DCU concentrations between 16% and 18% have the ability to provide a virtually complete light barrier. Concentration can be reduced to 14% with little difference in effectiveness and cutting it to 9% still provides a level of protection that is acceptable for ESL operations of up to 95%. This enables control of production costs. There is no need for dedicated technology for the injection process. With little investment, and in a very short time, preforms can be produced by a standard high-speed mono-layer injection machine at whatever TiO 2 concentration is required. The singlelayer process eliminates the risk of delamination during blow moulding. Because the process uses GEA Procomac ABF (Aseptic Blow Fill) technology, which sterilises the preform rather than the blown bottle, it is possible to reduce package significantly, without any risk of deformation during heat treatment. P.E.T. Engineering and Novapet, in collaboration with Husky Injection Molding Systems, developed the 1l ‘White & Safe’ bottle, designed specifically for ABF technology. The result of this cooperation is a 19.5g, ultra-light bottle for milk that provides extended shelf life. The UHT version weighs 21.5g. The two versions deliver 15.2% and 10.4% (respectively) weight savings, compared to the lightest containers currently on the market. The 1l milk bottle with DCU was among the finalists in the Best Packaging innovation category in the 2014 World Dairy Innovation Awards. www.gea.com www.husky.ca www.petengineering.com www.novapet.com","@ID":26}, "CAPPING / CLOSURES 36 PETplanet insider Vol. 15 No. 10/14 petpla.net A special challenge or closure design and application Bottling of sensitive products Sensitive products can be bottled in an aseptic filling or hotfilling process. Aseptic filling of sensitive products If sensitive products like dairy products or juices are bottled in an aseptic filling process closures have to pass a washing process for decontamination of the closures. This washing process takes off slip agent and changes the application properties of the closure. These changes must be counterbalanced by closure design. Bericap has developed a tamper evidence design which allows in the aseptic filling process easy application despite washed off slip agent and which allows rinsing of the tamper evidence band. The sealing design provides a safe seal and does not worsen application. The screw cap range for aseptic filling is complemented with push-pull sportscaps which do not require an aluminium seal but pass the washing process safely and still offer an easy application. The predominant diameter in aseptic filling is 38mm. There exist a 3-start neck finish and a 2-start neck finish both having a good geographical spread and preforms in the market with necks following these 2 standards. The latest development is the move to a 33mm neck finish. The 33mm neck finish offers a substantial weight saving compared to a 38mm neck finish but still offers the necessary distinction on the shelf. In addition researches have shown that consumers appreciate the good comfort when drinking from a 33mm neck finish compared to other neck diameters. The 33mm neck finish recommended by Bericap has a height of 15mm from top of neck to the support ring. This neck height provides safe application and at the same time good consumer convenience due to sufficient grip height. Hotfilling of sensitive products The alternative process to aseptic filling is hotfilling. The hotfill process remains a popular process since it is a safe process, less complex and requiring less attention of people running the filling line compared to aseptic filling. Closures and PET bottle necks used in a hotfill process are exposed to significant heat after capping and risk to get deformed when they become softened by filling temperatures around 80°C. Traditionally closures used in hotfilling are made from polypropylen and have an additional liner of resilient compound to achieve a good seal after the exposure to heat. These 2-piece closures require a high application torque resulting in high removal torque and have a risk of back-off. In addition 2-piece closures require PET necks with high wall thicknesses of 2,1 – 2,5mm in order to avoid neck deformation during exposure to heat. Bericap had developed the linerless DoubleSeal technology for carbonated beverages long ago. This technology is as of today state-of-theart and has been successfully used globally in hundreds of billions. This technology does not rely on a top seal. It relies on an inner and outer","@ID":38}, "PETbottles 56 PETplanet insider Vol. 15 No. 10/14 petpla.net Beverage + Liquid Food Coloured bottles for still spring water Following the trend towards reduced sugar or sugar-free drinks for small children, Hipp launched its latest product on the market in time to coincide with summer. Hipp bottles 300ml of low-natrium spring water into a PET bottle designed for children aged from one year upwards which is easy to grasp and hold. In order to awaken the interest of the children in the “boring” tasting drink, the bottles are coloured and thus arousing children’s curiosity. The bottles are embossed with the word “Hipp”, sealed with a tamper-proof push-pull and decorated with a brightly coloured paper label. www.hipp.de Hohes C as tea with a deposit Eckes-Granini have reviewed their “hohes C Naturelle“ range, streamlined it and added new products to it. Since summer 2014 a soft drink that is more than 60% white tea and which boasts an enhanced taste due to fruit juice additives has been available at retail outlets. The product contains no additional sugar, artificial additives or preservatives. The 0.75l bottle has been replaced by a re-designed PET bottle with content of 500ml. The bottle features embossed brand logos, a 2-colour sports cap closure, a foil label and is subject to a deposit. Prior to initial opening the bottle, on which a deposit is now payable, needs to have its closure unscrewed and a sealing membrane removed. www.hohesc.de Exotic mix for children The German discounter dm is marketing a limited edition fruit juice drink with a particular composition of fruits under its ”babylove“ brand name. The drink, which incorporates a bio-seal, is more than 40% made up of apple, mandarin and acerola juice and still mineral water. The product, which is free of added sugar, is packaged in a PET bottle with reinforcement grooves. The bottle is also shaped so that it can also be grasped easily by small hands and has a content of 330ml. A screwon, tamper-proof sports cap with a blue drinking spout serves as a closure. www.dm.de Aromatic spice spray from Aldi A 150ml spice spray incorporating a range of aromas such as for example “Curry Style“ or ”Smoky American Style“ is one item in the range offered by the German discounter Aldi Süd. Slimline PET bottles, coloured black with a screw-on pump spray similarly in black are the packaging format for the product. The bottles have been labelled with self-adhesive labels in various colours. The shaped label has been stretched across the transparent snap lid made from plastic. Removing the lid for the first time destroys a tab, thus making it evident that the bottle has been opened. www.aldi.com","@ID":58}, "AFTER SALES SERVICE 39 PETplanet insider Vol. 15 No. 10/14 Fig. 4.1.2 Other suppliers of preform injection machines Fig. 4.2.1 Injection moulding equipment for bottle caps Fig. 4.2.2 Other suppliers of cap making equipment Fig. 4.3.1 PET blow moulding equipment Fig. 4.1.1 Injection moulding equipment for preforms","@ID":41}, "MATERIAL / RECYCLING 19 PETplanet insider Vol. 15 No. 10/14 petpla.net also informs us, Alpla also operates a PET recycling plant in Mexico together with Coca-Cola and Coca-Cola FEMSA. Closures and caps The manufacture of closures and caps is 40% oriented towards Europe. The injection moulding process is used exclusively in manufacturing and involves one-piece caps for the beverages sector. For reasons of flexibility, 48/72 cavity moulds tend to dominate; however, depending on the customer, there are also 96-cavity applications. In contrast to the PET business, here there are quite some converter businesses where it is more often the customer who provides the product-related tooling and Alpla produces the closures on its own injection moulding machine. Depending on turnover, the beverages closures tend to be the dominant factor here. 30% beverages closures incl. cartonised applications 70% others With the acquisition of Injectoplast, the production operation for plastic closures in Waidhofen, Austria, the company is now also expanding within the standard closure caps business; up to this point in time, the focus has been more on customer-specific solutions. Operations focusing purely on closures and caps are only to be found in Germany, Austria and the USA, otherwise the capacities form an integral part of the individual business operations in the individual countries. www.alpla.com Q Preform sterilization in the heating tunnel Q Protected conveying of preforms and bottles Q %QORNGVGN[ J[IKGPKE ƂNNKPI CPF ECRRKPI RTQEGUU The UCF BloFill monoblock from KHS – with fully enclosed hygiene housing Give your sensitive beverages more private space. Learn more at www.khs.com or scan the QR code. Brau Beviale 2014 November 11–13 | Hall 5 | Booth 147","@ID":21}, "BOTTLING / FILLING 29 PETplanet insider Vol. 15 No. 10/14 petpla.net BOTTLING / FILLING 29 With Sacmi, the beverage specialists are always at your side. With our unbeatable technological know-how and continuous research we are creating new containers and closures designed to ensure outstanding performance. The new IPS injection system for preforms and the CCM compression press for caps, fully designed and built by Sacmi, allows for large-scale production with considerable advantages in terms of efficiency and flexibility. The outcome? Reduced plastic volumes, less energy consumption and lower running costs. All in a bottle: the one you’ll soon be making. Preform & Closure technologically together Save RAW MATERIALS reduced plastic volumes Save ENERGY less energy consumption Save TROUBLE more quality and higher performance, guaranteed by a sole supplier Full INSPECTED online quality control / stand alone Since the end of 2013, the line has also been filling milk-based mixed drinks in 250mm. The trend – in Mongolia as elsewhere – is towards narrower necks and lightweighting. The Krones line is already using 23.5 to 25g bottles, which are lighter than Vitafit’s competition. The line went operational, on time, in July 2013. Cool running Vitafit undertakes its own distribution. Its fleet of around 50 trucks cover the whole country, delivering even in the depths of minus 40°C winter. Over the longer journeys, the beverages arrive frozen but this has been taken into account; they thaw out without any loss of quality. The new Krones line is now operating in three shifts. Its peak demand season is the four-month summer, when the company sells between 50 and 60% of its annual output. Vitafit currently employs around 700 people and is intending to increase its annual sales with the introduction of new niche-oriented products, such as strawberry-flavoured milkbased drink, which will be bottled on the Krones line; a near-water beverage called “Vitaplus” in lime, apple and pomegranate flavours; plus a vitamin-enriched water. It intends to launch smoothies onto the market towards the end of 2014. The Mongolian fondness for black tea and Georgian green tea is something else that Vitafit intends to translate into a technically viable product. The capacity of the new Krones hotfill line will be exploited with the launch of to or three new products each year. www.krones.com End-of-the-line packaging by a Krones Variopac Pro FS non-returnables packer.","@ID":31}, "EDITOUR REPORT 13 PETplanet insider Vol. 15 No. 10/14 petpla.net Tonoli explains: “Because of the relatively low price of virgin PET, recycled PET is too expensive, regardless of what form it comes in.” A noticeable factor is the frequent use of colour concentrates. At the time of our visit all the preform machines in production were using liquid colouring. 90% of preforms finish up in the beverages industry and only 10% in PET containers for detergents, foodstuffs and cosmetics. Preform production programme Mineral water: Neck finish 28mm BPF, PCO, 267 Novembal and PCO Corvallis 16.8 Soft drinks: Neck finish 28mm BPF, PCO and PCO Corvallis 16.8 Juices/teas: Neck finish 38mm Affaba Ferrari and Bericap Milk: Neck finish 38mm Affaba Ferrari and Bericap Edible oil: Neck finish 29/21 und 30/29 Cleaning materials: Neck finish DET 29/410 The company’s five largest customers are as follows: Refresco, Pineta, Bracca, Norda and Tavina- responsible for purchasing 50/60% of the preforms. Manufacturing takes place all the year round; i.e. in the winter months a stock is built up which is used up in the peak summer months. To do this raw material has to be purchased in advance and stored possibly for several months. A delicate balancing act, demonstrating that preform production is not without risk. The crucial thing is to buy the raw material at the right time and to agree the right conditions with the supplier and the preform customer. As Amos Tonoli puts it: “We operate like a bank when it comes to financial operations”. Raw material is stored in silos and bags, depending on the supplier. Preform storage and shipment, on the other hand, is in an Octabin on a pallet. The packaging components are recycled in different ways. The Octabin 5 cycles Lid and base 2 cycles The pallet 10 cycles Market According to Amos Tonoli: “The Italian preform market is stable in terms of its volume, but the consumption of material is constantly falling. The reason is of course the focus on reducing preform weight. For us, this means regular investments in moulds. This is something that has been a particular feature over the past few years. The fact that the market is stable but not seeing any growth in terms of its volume does not really help us. The size of the Welcome to visit TECH-LONG PACKEXPO 2014 CHICAGO 6817 E GAGE AVE COMMERCE, CA,90040 USA TEL:+15629287755 FAX:+1 562 928 4499 www.tech-longusa.com Email: [email protected] TECHLONG INC BEVERAGES HOUSEHOLDS CONDIMENTS DAIRY BEER Booth: N4975 Date: 2014 11.2-5 Add: McCormick Place North Building (Upper) Chicago, IL","@ID":15}, "NEWS 9 PETplanet insider Vol. 15 No. 10/14 petpla.net US demand for caps and closures to exceed USD11 billion in 2018 US demand for caps and closures is projected to advance 4% per year to USD11.1 billion in 2018, with unit demand exceeding 300 billion. Gains will be driven by an acceleration in container unit growth relative to that of the 2008-2013 period, the continued popularity of single serving containers, and greater use of costlier product types, such as dispensing and child-resistant closures (CRCs). Preventing faster growth will be the maturity of several large beverage applications and competition from closureless packaging options such as aluminium cans, most standup pouches, blister packs and peelable lidding. These and other trends are presented in Caps & Closures, a new study from The Freedonia Group, Inc., a Cleveland-based market research firm. Beverages are the single largest cap and closure market, representing 33% of total value demand and 54% of total units in 2013. Pharmaceuticals, the second largest cap and closure market in value terms, will see the fastest growth through 2018, aided by the expansion of older segments of the population and the need to comply with government regulations and industry standards. Plastic caps and closures, which comprised 81% of unit demand in 2013, will post unit and value advances in line with the overall averages through 2018. The outlook for plastic closures will be constrained by the already high penetration of plastic containers in most markets and a lack of new large volume applications. Dispensing closures will enjoy the fastest growth based on convenience and functionality. Metal cap and closure demand is expected to rise 2.4% per year through 2018. Despite ongoing losses due to inroads by plastic closures and the resurgence of aluminium cans in the beer market, units will increase modestly based on greater use of roll-on closures with wine and opportunities for screw and lug closures with ready-to-drink beverages such as iced tea and coffee. www.freedoniagroup.com Octal becomes member in the National Association for PET Container Resources (NAPCOR) Octal is taking steps toward their goal of increasing visibility within the PET packaging industry through its recent membership in the National Association for PET Container Resources (Napcor). Founded in 1987, Napcor is a trade association for the PET packaging industry that advocates for the use of recycling and re-use of PET packaging, promoting the features that make it an environmentally sustainable packaging material. Octal views the membership in Napcor as a way to become involved with other PET industry leaders, collaborating to find new ways to expand PET’s competitiveness. Through a combined effort of leaders in the PET packaging industry, the implementation of innovative ideas and recycling practices will have a positive impact on the future of PET resin and sheets for clear rigid packaging. www.napcor.com/PET/index.html www.octal.com Full range of automatic labelling machines on display at Pack Expo 2014 The company P.E. USA will present six different types of labelling machine at the upcoming Pack Expo 2014 in Chicago. The Compact model, a pressure sensitive linear labelling machine, is suitable for those with space restrictions. This labeling machine is characterised by the absence of safety doors, thus reducing overall dimensions. A high-tech optical barrier system is said to guarentee safety to operators. The labelling machine for low production speeds, the Modular Plus 540 model, features three labelling stations installed on the peninsula, claimed maximum accessibility to operators. The company will also show the labelling machine Modular Top 1120 for the front and back application of labells combined with the Maya model, a linear sleeve labell applicator for Bi-Pack promotional packaging and the Modular Plus 810 labeling machine with Ergo Seal cachet applicator. Also on display is the made-in-USA Roll-Line model which consists of a roll-fed linear labelling machine. www.pelabellers.it Al Ahlia Gulf Line achieves 20% energy savings with Sidel Al Ahlia Gulf Line, which is the licensed bottler and distributor of Coca-Cola brands in the United Arab Emirates (UAE) and Oman, has announced savings of 20% in energy after upgrading its water production line with solutions from Sidel Services. Al Ahlia made use of Sidel’s Eco Booster service, which provides measurement, advice and continuous improvement of Sidel production equipment. Improvement in the performance of its blow moulder enabled a reduction in energy consumption, the company said. Al Ahlia is ISO 14001:2004 (environmental management system) certified and has set what it describes as ambitious plans to reduce its carbon footprint and energy consumption, in line with government ecological initiatives. It started operations at its Al Ain Plant in 1990 and now produces Arwa Water, as well as bottling and distributing Coca-Cola brands including Fanta and Sprite. The plant uses two Sidel SBO8 Universal blow moulders for CSD production, along with a PET water line fitted with a Combi SBO 20 blow moulder, Eurotronica filler and Rollquatro labeller. www.sidel.com","@ID":11}, "TRADE SHOW PREVIEW 45 PETplanet insider Vol. 15 No. 10/14 petpla.net Brau Beviale 2014, 11-13 November: Tradition turns to innovation... Now in its 36th year, Brau Beviale in the historic town of Nuremberg, Germany, is one of the most important exhibitions in the international beverage industry. Small and medium enterprises as well as global players from Europe and the rest of the world use the creative atmosphere at Brau Beviale to find and develop solutions to their unique challenges year by year. We at PETplanet are proud to have partnered with Messe Nürnberg for our latest Editour, and are equally proud to bring you comprehensive coverage before, during and after the event! On the following pages we have put together a first selection from many exhibits of interest to producers and fillers of PET bottles. Rotary labelling systems for various applications Gernep GmbH, from southern Germany, will be exhibiting its range of rotary labelling systems, including the latest version of its Labetta SK self-adhesive machine, which now uses servo motor technology on the self-adhesive dispenser in order to ensure precise and smooth label transfer. The Labetta wet glue labelling range includes Gernep’s patented overlay gearbox, which is designed to facilitate easy positioning. Rollfed and Rollina hot melt machines will also be on display. These machines use a closed hot melt system, which minimises contamination as well as cleaning and maintenance. The Gernep Combi system combines several different labelling processes on the same machine platform, within a compact footprint. www.gernep.de Gernep GmbH Hall 7 | Booth 331 Energy performance, labelling and aftersales support Krones will be showcasing its latest developments for both large companies and small and mid-tier bottlers. It will be showing how it helps clients to identify potential savings at existing breweries and to translate the potential into reality. It will also be highlighting its labelling systems. It describes its Ergomatic labeller as “comprehensively versatile” and capable of being modified to accommodate fixed stations and subsequent replaceable stations. Its e-business platform, Krones.shop, is a central portal where customers can access spares, upgrades, training courses and service support. www.krones.com Krones Hall 7A | Booth 206","@ID":47}, "MATERIAL / RECYCLING 21 PETplanet insider Vol. 15 Short cycle times, high shot-to-shot quality, low energy consumption and maximum flexibility. The new XFORM 300 with its unique 6-position post-mold cooling system boosts your output performance for the widest range of preforms. Cooling preforms faster and better, the 96-cavity platform is ideal for large runs and quick mold changes. And it lets you run any mold you want, old or new, OEM-built or not, in total freedom. From ultra-thin walled (with proprietary XMould™ technology) to wide mouth. XFORM 300, low transformation cost, high value. SIPA S.p.A. - Via Caduti del Lavoro, 3 - 31029 Vittorio Veneto (TV) - Italy Tel. +39 0438 911511 - Fax +39 0438 912273 - e-mail: [email protected] www.sipa-xform.com Designed to adapt. Built to last. The new XFORM 300 IMAGINE THE LOWEST TRANSFORMATION COST. IN TOTAL FREEDOM. On delivery the bottles are examined and non-PET components are sorted out manually. Having established that only PET bottles are present in the process these are crushed in a mill to form flakes. The flakes now go through not only a dry but also a wet cleaning process. Contaminants and dirt are removed using a chemical treatment. The PET flakes can now be separated from one another on the basis of differences in their specific weight and then dried. In the United Resource Recovery Corporation (URRC) process the flakes again undergo thorough gentle cleaning. Since the flakes are required to conform to very high food safety standards, it is important that any flavouring agents are removed. For this reason the top layer of the flakes is removed. The manufacture of the recyclate in the recoStar PET granulating line is carried out in the following sequence. The washed flakes are first of all dried, then melted, filtered using a fine filter, pressed through a nozzle plate and finally cooled under water and cut into spherical pellets. After this, the granulate is crystallised and subjected to in-depth cleaning using Solid State Polycondensation (SSP). The mechanical characteristics are being improved, and today the recycled PET granulate has to all intents and purposes the characteristics of new material. The combined processing of both these forms of recyclate in the future will bring together the advantages of maximum purity and colour quality with optimum processing conditions – in terms of a further increase in the use of recyclate in the PET beverage bottle. The PET recyclate is packed into big bags and added at the premises of the preform and bottle producers during the manufacture of new PET bottles. The proportion of recycled PET is on average 30%, depending on the size and shape of the bottles. It can also be more. PET to PET in Müllendorf work round the clock in four shifts. Production is shut down on one day a month only to enable cleaning and maintenance works to be carried out. The time from delivery of the bales consisting of collected PET bottles to delivery of the PET flakes in big bags is a mere seven to eight hours. www.pet2pet.at PET to PET Recycling Österreich GmbH plant","@ID":23}, "EDITOUR REPORT 12 PETplanet insider Vol. 15 No. 10/14 petpla.net Invest, or lose out by Waldemar Schmitke Amos Tonoli, General Manager, in front of the control panel of a Husky 96-cavity preform machine The company manufactures 365 days a year / 24 hours a day, with a plant efficiency of 82%. The Sacmi preform system is used for low volume production and tests and this means that it is only 50% utilised. The drying and air curtain equipment comes exclusively from Messrs. Plastic-Systems Italy (today Husky). It is primarily virgin material that is processed; recycled material is seldom used, solely for reasons of cost. Amos Garda Plast S.p.A. After a weekend spent in the beautiful old town of Sirmione on Lake Garda, we head off in the direction of Popenazze (BS) where we visit Garda Plast, manufacturers of PET preforms. The company, which was set up in 1996, is wholly owned by the family of Amos Tonoli, General Manager of Garda Plast, whom we meet here on site. Geographically, the company is at the heart of Italy’s PET industry. Within a radius of 200km, 70% of Italy’s PET companies are concentrated. This location was not only chosen because it was where the family had settled, but so as to keep the transport costs as low as possible. Compared to other states in Europe, transport costs in Italy are extremely high and therefore make up a significant proportion of the costings for any converter. By the end of 2014, Garda Plast’s overall capacity will amount to approx. 1.8 billion PET preforms with a workforce of 37 employees, one of whom, Lucas, is also the brother of Amos Tonoli. Preform Machines The fleet of machines is made up of a total of nine preform machines. 4 x Husky 72-cavity 4 x Husky 96-cavity 1 x Sacmi 48-cavity Nuremberg Milan Rome Naples Palermo Tunis Algiers Rabat Casablanca Marrakech Seville Madrid Lisbon Bologna Monastir Agadir Tangier Valencia Cordoba Bilbao Oporto Andorra La Vella Venice Turin Florence Messina Barcelona Zaragoza ITALY Part 2","@ID":14}, "PETnews 6 PETplanet insider Vol. 15 No. 10/14 petpla.net Former Husky Vice President joins NPE 2015 sales team Former Husky VP Michael Urquhart joins the NPE 2015 sales team and will work in cooperation with Mr Gunther Hoyt Associates, a key international sales agent for the NPE 2015. It was announced by SPI, The Plastics Industry Trade Association, which produces the triennial NPE shows. Mr Urquhart will focus on sales of NPE 2015 exhibit space to the packaging industries, in particular the PET segments. Mr Michael Urquhart retired last year after a 33-year career with the global plastics equipment manufacturer Husky Injection Molding Systems Ltd. One of his responsibilities was to organise the company’s exhibits at numerous trade shows. At his retirement, he was Husky’s Vice President of global sales for packaging systems. www.npe.org Pernod Ricard UK’s personalisation campaign The advent of personalisation in different fields of marketing has not just brought many positive brand experiences, but also caused a notable rise in purchases. Just lately, Pernod Ricard UK launched its “Your Signature Spirit campaign”. The idea behind this campaign is that Pernod Ricard UK gives customers the possibility to create their unique and personalised message which is then printed on labels of “Chivas Regal 12 Year Old”, “The Glenlivet 12 Year Old” or “Aberlour 10 Year Old”. The whole process from the label draft by the customer to the delivery of it is quite simple and quick: firstly, the consumer purchases the bottle in-store or online and, as proof of purchase, enters the barcode from the original bottle label. Then, the consumer personalises the label with a personal message which is then printed and delivered to the consumer within seven days. CCL Label UK played a major role when it came to the realisation of these self-created, personalised labels, using CCL’s digital printing capabilities. The CCL seven colour process of digital printing plus the application of hot foil, flexo print, embossing and high build silk screen as embellishments are intended to let the product labels become unique, and a very close representation of the current branded label. www.cclbeverage.com American Starlinger-Sahm: ground breaking for North American headquarters Greenville-based American Starlinger-Sahm, Inc. is expanding and held the ground breaking ceremony for construction of the North American Headquarters on August 26, 2014. The new facility will be located in the South Chase Business Park in Fountain Inn, South Carolina, and comprises a total of 23,000sq.ft (9,140sq.m). The facility consists of a machine exhibition area, spare parts warehouse, and office space for sales and technical support throughout North America. At the new location the company will offer the full range of their products and services. Machinery from Starlinger textile packaging, Starlinger recycling technology, Starlinger viscotec and Sahm will be installed and available for demonstration runs and customer trials. The grand opening is scheduled for late spring 2015. The two European companies Starlinger and Sahm are major technology suppliers to the woven plastic packaging, plastics recycling and textile industries. American Starlinger Sahm, Inc. (ASSI) is owned by Starlinger Export GmbH and handles sales activities and spare parts supply for the divisions Starlinger textile packaging, Starlinger recycling technology, and Starlinger viscotec, as well as for the winder specialist Georg Sahm GmbH & Co. KG. www.starlingersahm.com Amut delabeller frees ‘sleeved’ PET bottles for recycling Italian company Amut says that its new de-Labeller system can deal with heat-shrunk PVC or PETG sleeves that completely cover PET bottles and have made them difficult or impossible to recycle. The new system is available in three models, depending on customer needs, and are claimed to provide almost total recovery of both bottles and at least 80% of sleeves. Operators can set and control the treatment and dwell time within the machine, although they flow through the delabeller in a continuous process. Amut says that the integrity of bottles and necks is preserved, which enables downstream detectors to be used and reduces material loss. The recovery, retention and verification of the dry labels is designed to reduce disposal costs and material and colour recognition by electronic detectors is intended to increase productivity and ensure improved PET flake purity. Bottles are fed into the machine by conveyor, where labels are dry-removed by friction, then discharged by a screw-feed extractor. The shredded labels are collected in a hopper mounted under the machine and conveyed to a compacting press or storage container. Any remaining label material is removed downstream of the machine, through an air system or a sieve. www.amut.it","@ID":8}, "PREFORM PRODUCTION 43 PETplanet insider Vol. 15 No. 10/14 petpla.net In the feeding section, resin is only transported and not meant to melt. Usually the surrounding area in the extruder housing is water-cooled with tower water to avoid “bridging”, a situation where partly melted material clumps together and prohibits new material from entering the extruder. In the feeding zone the root diameter of the screw is the smallest and the material is given room to enter and to be pushed forward (figs 3.3 and 3.4). Resin transport is accomplished by manufacturing the barrel surface slightly rougher than the screw surface. This allows the screw to turn under the material (slipping), whereas the outer layer of the material sticks to the barrel. As a result the material is pushed forward. When burned material accumulates on the screw the screw may become “sticky”, and this process does not work as well any more. This shows up as decreased screw output, and the screw needs to be cleaned. In the compression or transition section the root diameter of the screw increases, leaving less and less room for the material, thereby forcing the pellets against each other and the barrel and screw. At the end of this section most of the material has been melted. The metering section’s task is to melt any remaining unmelted material and force it to become a homogeneous mix. The root diameter of the screw is the largest here but does not change any more. A screw may differ in how the screw ends are shaped with some screws having special adaptors that are especially useful to mix color or other additives (fig. 3.5). In a standard type, screw melting and mixing happen gradually and there is a chance that not all material has undergone the complete process by the time it leaves the extruder. PET is shear sensitive, i.e. it starts to burn when too much shear heat is generated by too steep a compression zone or when screw revolutions per minute (rpm) or injection speed is too high. Therefore, screws must melt the material gently but this may lead to un-melts. To overcome these problems, designers have developed the socalled barrier screws (see fig. 3.6). There are a number of designs in the market that deliver outstanding results not just for PET. In this design there are two threads going along the screw diameter at different depths. Material flows back and forth between the two channels, thereby mixing more vigorously. A disadvantage of this design is that improved mixing can lead to higher shear heat. Increased clearance between the channels seems to be the most successful way of reducing this. Machine control of the operator is mainly through adjustment of the Heats Screw rpm Back pressure Although heater screens differ from machine to machine, they all convey the same information. They may show: The location of the heater band (usually going right to left) Degrees centigrade or fahrenheit The set point The actual temperature Figure 3.3 All screws feature a small root diameter in the feed section. (Diagram courtesy of Barr Inc). Figure 3.4 Clean screws are important to allow material to be conveyed forward. (Diagram courtesy of Barr Inc). Figure 3.5 Standard screw designs may lead to incomplete melting for shear-sensitive materials like PET. (Diagram courtesy of Barr Inc).","@ID":45}, "PRODUCTS 52 PETplanet insider Vol. 15 No. 10/14 petpla.net Perfect products. Inspected by INTRAVIS. Systems for any requirements. ww .intravis.com BOOTH 7839 Lightweight parachute closure The parachute closure, designed by Global Closure Systems (GCS) is a lightweight concept of a flip top closure system. The base part of the closure has a clip design which enables the angle neck finish to be light weighted by incorporating the patented “feather snap” system. The intention of the designers was to maintain the brand identity on the shelf; the customer is not aware of the weight saving until the closure is first opened, and this enhances brand value. The closure weighs approximately 3.65g and has been designed in PET and PP versions. The system is said to be easy to apply to a bottle and may be used with a standard preform. The parachute closure system is intended for personal care, food and household markets. www.gcs.com Automatic blank magazine Easy-Load Among new opportunities offered by Smiflexi division there is the Easy-Load cardboard blanks magazine, an accessory device (available both for the wrap-around case packers of the WP series and the heat-shrinkwrappers of the SK series) which is said to feature advantages from an operating and functional point of view. With Easy-Load the operator is also said to be able to easily load cardboard blanks stacked horizontally in uniform groups - because the feeding belt of the magazine is positioned at the same working height as the packer’s infeed belt, rather than under it. The solution devised by SMI eliminates the disadvantages related to the manual loading of the cardboard blanks magazine, which force the operator to bend their body continuously to place the blanks in the bottom part of the machine. The operator simply places the cardboard blank stacks on the outermost roller conveyor so that the automatic control system can perform all the subsequent steps. Thanks to specific sensors, the layout and feed of the cardboard blanks on the conveyor belts fitted with the motorised roller and their loading into the packer’s magazine is fully automated. The unloading of cardboard blanks is also performed automatically. The technology used in the Easy-Load magazine is said to ensure fluid and constant picking operations with a wide range of cardboard blanks having a thickness between 0.5mm and 5mm. www.smigroup.it","@ID":54}, "TRADE SHOW PREVIEW 49 PETplanet insider Vol. 15 No. 10/14 petpla.net Multi-sensory ingredients Döhler will be exhibiting ingredients and ingredient systems for food and beverages in what it describes as a “multi-sensory experience”. Its stand will showcase a diverse range of ingredients aimed at providing a variety of taste sensations, product colour and full organoleptic experience, along with ingredient solutions that are intended to allow consumers to experience “indulgence with no regrets”. The product portfolio includes flavours, colours, health & nutrition ingredients, cereal ingredients, dairy ingredients, speciality ingredients, fruit & vegetable ingredients and ingredient systems. Product concepts on display will include carbonated beverages, energy drinks, aqua plus beverages, juices, nectars, and malt, beer and wine mix beverages. www.doehler.com Döhler Hall 1 | Booth 303 LEADING TECHNOLOGIES Messehinweise etc. www.gneuss.com FOR POLYESTER RECYCLING • Unmatched Devolatilizing Efficiency with Gneuss MRS Extrusion Technology • Reliable Melt Filtration and True Process Consistency with Gneuss Rotary Filtration Technology • Permanent Accuracy and Quality Assurance with Gneuss Measurement Technology Naturally with up to 100 % Recycled Material and for Direct Food Contact Applications. See you there! Fakuma Friedrichshafen, Germany Hall A6, Stand 6501","@ID":51}]}}
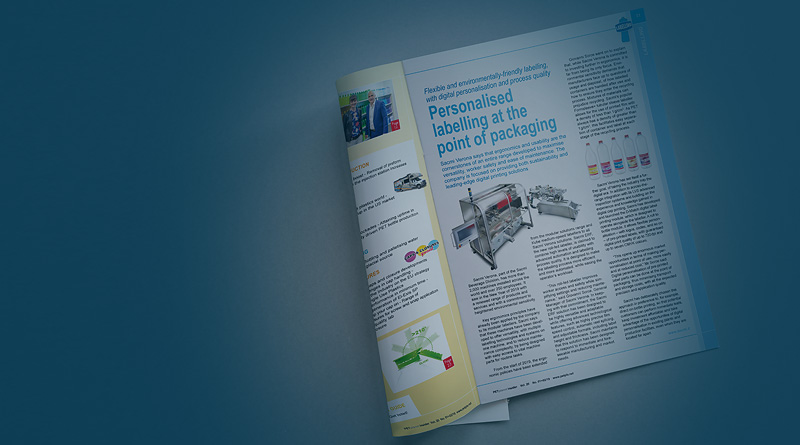