"Toronto Québec New York Atlanta Orlando Chicago Denver Las Vegas Seattle Calgary Montréal Los Angeles San Francisco Vancouver Dallas Houston Phoenix Washington, D.C. Boston Detroit Halifax Kansas City Oklahoma City Albuquerque www.npe.petpla.net , / 0 Premium Sponsor Sponsors NPE 2015 - The North American Road Show The first leg of our latest trip has been successfully concluded! From the busy harbour of the NPE 2015 our expedition crew has been reviewing all the meetings with the key players of the Canadian and US PET industries on the PETplanet exhibition stand in the South Hall. After resting at anchor awhile in Florida’s tranquil waters, our team of PET bottling Columbuses, consisting of Captain Alexander Büchler, Helmsmen Kay Barton and Waldemar Schmitke, together with Helmsman’s Mate and Able Seaman Rolf, is now steering a course towards the markets of Central USA. Wafted along by gentle zephyrs, the team is embarking on the second part of their voyage of discovery in Texas and will be sailing in a wide arc in the direction of Phoenix, before ultimately cresting the waves along the west coast of the USA, proceeding thence to the west coast of Canada. This is a tour where figures speak louder than words: a total travel distance of around 17,000 km and roughly six months of this thrilling adventure are out there just waiting for you! And, as always, you have the opportunity to accompany the crew interactively by following the entire tour on our weekly travel blog at npe.petpla. net. Please contact us if you would like our editors to make a detour to your own bottling, PET processing, closure cap, material manufacturing or recycling plant. YOU are our story. All aboard! Part 2 The worldwide round trip with","@ID":44}, "BOTTLES 45 PETplanet insider Vol. 16 No. 06/15 petpla.net Mini Volvic in Germany With the launch of “Mini-Volvic“, 0.33l of natural mineral water, Danone Waters aims to offer parents a healthy drink for children. The product, which has already been available for some time in other countries, is packaged in a transparent PET bottle that is easy for children’s small hands to grasp. For the launch the bottles have been fitted with labels printed with Astérix, Obélix and Idéfix motifs. A resealable 2-colour screw-on sports closure featuring a made-to-measure dispenser opening facilitates handling and keeping qualities. At the POS six bottles are packed together using a shrink sleeve to form a multipack. www.volvic.de Bio Range from dm Since May 2015 the German drugstore discounter dm has been bringing various food products with a bio-certificate to store shelves under its own brand name “dm Bio“. The aim of this is to increase the selection in its own markets and to respond to increasing demand. As far as possible they have complied with the wishes of critical consumers and dispensed with undesirable additions of colorants, flavourings and preservatives. One example from the “dm Bio“ range is a number of fruit juice spritzers in PET bottles with a content of 500ml. The drinks are made from natural mineral water and a proportion of juice and / or vegetables which together account for approx. 50%. The waisted bottles feature horizontal reinforcing grooves and diamondshaped embossing in the neck area. To round off the appearance of the package at the POS, a paper label and a green screw cap with tamper-proof guarantee are used. www.dm.de/dmBio","@ID":47}, "MATERIAL / RECYCLING 18 PETplanet insider Vol. 16 No. 06/15 petpla.net Recycling machine manufacturers who are also recyclers themselves by Kay Barton KSM 800 STF Maschinen- und Anlagenbau GmbH is making an appearance at the NPE as a supplier of integrated solutions. STF Maschinen- und Anlagenbau is part of the STF group of companies of Aicha vom Wald, Germany. The divisions STF Recycling and STF Thermoforming Foils are also part of the Group. At the exhibition STF are showcasing their grinder KSM 800 that can be used either as a dry or wet grinder. The machine is used for wet grinding of post-consumer plastics and can reach 90 to 160KW. Prior to the actual washing process, an initial rough clean is carried out by adding water during the grinding process. As a result, 95% of bottle labels made from paper are destroyed. Available options include ten rotor blades on five or 14 on 7 rows of cutters, as well as four stator blades on two rows of cutters with a rotor diameter of 800mm and a working width of 1200mm / 1530mm. The inside of the KSM 800 is lined with the low-wear material Hardox. As one of its follow-up aims in terms of global expansion, the company is expanding its presence in North American marketplace and with Zimmer America Recycling Solutions has identified a suitable sales partner to represent STF locally. Currently there are 4 plants installed in North America. “Companies that decide to go with us can expect an influx of knowhow because we are users ourselves. I am not sure whether this combination exists in quite the same way anywhere else in the recycling sector”, says Roland Zimmer, CEO at Zimmer America Recycling Solutions. Markus Ingenpass agrees and adds: “Over and above this, our in-house manufacturing capability is in excess of 90%, because we have the full complement of product development and manufacturing facilities on our own premises. All that we buy in are smaller components like optical sorters or electronic metal separation equipment”. We enquired which other features make the STF lines stand out in use. “The systems use only a very small quantity of water, power and chemical consumption per tonne of material for processing. Maintenance expenditure is also low. Looking at the procurement costs and level of efficiency, we are offering a good price/performance ratio here”. Technical support, together with consultancy services and service facilities, are provided both by the main branch in Germany and the local representatives on-site, who, in addition to service, are also self-sufficient in the supply of spares. “There is extensive potential for recycling in the USA because the country is keen to develop the issue over the coming years. At present we have a rate of perhaps 25-30% when it comes to used PET bottles, but there is still plenty of space left to fill”, says Mr Zimmer. www.stf-aicha.de The company was founded 35 years ago. In 1980 the present group launched the corporate thermofoil manufacturing division. “At the time, we had compounds within Industrial Waste that it made sense to separate out“ said Markus Ingenpass, Sales Manager at STF. “It was this that triggered the development of our own in-house washing technology. We subsequently used our wealth of experience in these applications to become a recycler ourselves. Starting with foil recycling, we moved on into the PET recycling sector with the boom in PET bottles in the mid-1990s and have developed the washing lines further. From this came the transition into the grinding sector. Each machine is tested directly on our premises”. Today STF is one of the largest postconsumer waste recyclers in Europe with a focus on PET recycling and handels around 130,000 tonnes annually. At the same time, STF builds machinery for complete turnkey plastic recycling lines that cover the entire process right through to the flake. Another branch of the company is active in the construction of special machines for turbine housings and construction machine accessories.","@ID":20}, "BOTTLING / FILLING 33 PETplanet insider Vol. 16 No. 06/15 petpla.net Sidel Rollquattro at Jussara plant Jussara has extensive experience in milk and is extremely knowledgeable about carton packaging. When it considered switching to PET bottles it needed to learn the full range of factors and skills involved in a new production operation. Sidel helped the company through the process, from concept and design through evaluating the right protective opaque PET material to use and on to bottle production and filling. On the shelf, Jussara Max is differentiated simply by being packaged in a PET bottle and its visual styling and presentation further helps build brand awareness. New equipment, training and skills The choice of PET material was also linked to the choice of the specific Sidel aseptic bottling technology. This includes blowing, filling and capping functions in a single production enclosure and utilises Combi Predis FMa and Capdis, Sidel’s patented dry preform and cap decontamination solutions. Senior Jussara management visited a French dairy company to see the aseptic technology in action and how lightweighting was achieved. The dry preform decontamination technology does not require chemicals or warm water to rinse the bottles, which helped sustainability. Jussara’s current one-litre PET bottle weighs 29g, is 100% recyclable and does not require aluminium foil. The complete Sidel line includes an aseptic Combi Predis FMa, a Rollquatro Evolution rollfed labeller, a shrinkwrapper, mechanical conveyors for bottles and packs, a palletiser and an overwrapper. Sidel provided support for implementation and training in equipment operations, cleaning and sterilisation programmes, and maintenance procedures. The aseptic line was installed in the second half of 2014 and is currently running at 18,000 bph, producing over 3 million bottles/month. “The line has already reached an average of 95% efficiency, reaching up to 98%,” says Mr Odorico Alexandre Barbosa. “As consumer response is very positive we are targeting line production capacity of 10 million bottles per month by mid-year. We expect to increase our turnover by the end of 2015 to one billion Reales Brasileiros”. www.sidel.com","@ID":35}, "PETcontents 06/15 4 PETplanet insider Vol. 16 No. 06/15 petpla.net INSIDE TRACK 3 Editorial 4 Contents 6 News 40 Products 43 On site 44 PET bottles for Beverage + Liquid Food 46 PET bottles for Home + Personal Care 48 Patents CAPPING / CLOSURES 30 Bottles, preform, closures Closure history and closure function, part 1 MARKET SURVEY 27 Suppliers of preform moulds / stretch blow moulds BOTTLING / FILLING 32 Standing out from the crowd - Jussara packages UHT milk in PET bottles LABELLING 34 Rapid conversion, flexible and extremely robust PACKAGING / PALLETISING 36 The compact end of line INSPECTION SYSTEMS 38 Inspection systems for preforms BUYER’S GUIDE 49 Get listed! Page 17 EDITOUR REPORT 10 North Africa, part 3 SPECIAL WATER TREATMENT 17 New technology of online mineral-adding MATERIAL / RECYCLING 18 Recycling machine manufacturers who are also recyclers themselves 20 Bottler, recycler or producer? 22 PET bottle-to-bottle recycling in the Andes BOTTLE MAKING 24 Linear and rotary functions on new PET bottle machine 25 Adiabatic cooling towers cut energy consumption Page 45 Page 23","@ID":6}, "PRODUCTS 41 PETplanet insider Vol. 16 No. 06/15 petpla.net Greiner takes a single step forward Greiner Packaging’s new Kavoblow technology is designed for the singlestep manufacture of packaging in a wide range of material, including PET and PP, with non-round and off-center mouths as well as individual colours. The more common method is the two-step process, in which preforms are cooled and stored after the injection procedure, to be reheated and inflated subsequently. Greiner Packaging asserts that the two-step process can give rise to damage, such as ‘stroke marks’, and is one of the pioneers of the one-step method. In this, the preforms are inflated immediately after the injection process while still warm. It has been collaborating since 2009 with Mould & Matic, part of the Haidlmair Group, on refining the method and making it more efficient. The result of the collaboration is a completely new machine called “Kavoblow”. The range of mouth diameters extends from very small, for applications such as liquor, to very large wide-neck containers for the food industry, for example. Greiner’s Kavo division maintains that the one-step method offers improved efficiency and lower production costs, compared with existing machine concepts. Preforms are line-produced in multiple rows, which means that several production pieces can be made within a shorter period, the company asserts. Kavoblow technology is aimed particularly at the 5 - 20 million units segment and combines the claimed characteristics of quality and efficiency of the one-step production process with levels of efficiency previously associated with two-step systems. To date, Kavoblow products have been found primarily in the ketchup, honey, marmalade, sauce, mouth rinse, and household cleaner markets, but Greiner says that customers from the chemical, cosmetic, and healthcare industries, are expressing interest in packaging concepts based on Kavoblow technology. www.greiner-gpi.com","@ID":43}, "LABELLING 34 PETplanet insider Vol. 16 No. 06/15 petpla.net Jütro Feinkost & Konserven install new Gernep labeller Rapid conversion, flexible and extremely robust At Jütro Feinkost & Konserven GmbH & Co.KG, Jüterbog there are nine different packaging lines operating around the clock five days a week (or six if they really have to during the high season). The company employs 200 who pack every imaginable type of preserve, mustard, ketchup and mayonnaise, not to mention innumerable sauces, into tubs, jars, tubes, cartons and plastic containers. A new wet glue labelling machine supplied by specialist manufacturers Gernep GmbH of Barbing is the latest addition to the line with a production capacity of up to 10,000 containers per hour. Success is also a matter of labelling This is one of the guiding principles of the company which has been in production in the small Brandenburg town of Jüterbog (population 12,000) since 1911. For almost 50 years, up to 1994, the town, situated to the south of Berlin, was a garrison town firmly in the hands of the Russians. In the vast forested areas along the Fläming ridge where the Russian army trained for decades, there are now wind turbines. Jütro was founded 104 years ago as a business concentrating on packaging gherkins pickled in vinegar; it developed into a pickled preserves specialist and is today an expert in delicatessen products – mayonnaises, ketchup, sauces, salsas. The volume of containers packed annually amounts to 76 million and production takes the form of retail goods destined for all the big German food chains, only a small proportion under the company’s own “Jütro” label. “However, regardless of what we package and who we package it for – not only the product itself must be of the highest possible quality, but the packaging as well as the label must always be excellent. This is also a reason for our decision to go to Gernep for the plastics line” reports Jütro’s Technical Director, Rico Retzke. “The manufacture of our products is characterised by the fact that we attend lovingly to every detail. Anything that fails to meet our high standards will not be packaged. The labels on our products are subject to a regular re-launch so as to enable us to present our customers with a design that has consistently undergone adaptation to suit the times. And they must always be perfectly attached!“ Vast customer warehouse Since 1911 the preservation of foodstuffs has determined the everyday activities at Jütro. A very wide range of methods distilled from a wealth of experience going back several generations is employed. Here it goes without saying that work is carried out on a high-tech basis using the most modern preservation and bottling lines, focusing on conserving the valuable content substances and vitamins to the maximum possible extent. Fully assembled and securely packaged, the goods are put into interim storage in the company’s own warehouses with space for more than 10,000 pallets before being marshalled punctually to meet the desired delivery date. First it was gherkins, then it was sauces One of Jütro’s focal points in production is fruit and vegetable preserves. Respect for tradition has resulted in the emergence of a specialist interest in the processing The Labetta is presented at Jütro in a new design format incorporating protective guarding complete with corner pillars and safety doors constructed in the form of lift guards on all four sides","@ID":36}, "PETbottles 46 PETplanet insider Vol. 16 No. 06/15 petpla.net Home + Personal Care MHT MOLD & HOTRUNNER TECHNOLOGY AG Your Machine - Our Solution German Technology Orange help with cleaning The natural cleansing power of the orange has been harnessed by Erdal Rex for its “Orange Multi-Surface Cleaner“ which ensures streak-free cleaning on most surfaces. The cleaner is said to offer particular advantages on smooth surfaces. 500ml of the slightly tinted product are packaged in a transparent PET bottle consisting of 65% recycled material. A lockable screwon trigger is used for spraying on the product. For purposes of advertising and in order to draw attention to the advantages of the product the bottle is also fitted with a plastic sticker which is only partially coated with adhesive and which is attached to the trigger and bottle neck. www.frosch.de Footbath in PET Scholl, the well-known manufacturer of footcare products, is marketing 150ml of a cleansing and relaxing footbath in a slightly waisted PET bottle. The active ingredients of the “Velvet Smooth“ footbath include the active ingredients green caviar, sea serum and vitamin E. The bottle is closed by means of a snap-on, 2-colour hinged lid that can be opened with one hand and remains in the open position. Two likewise slightly waisted self-adhesive labels enable a direct view of the greenish shimmering product. www.scholl-fusspflege.de","@ID":48}, "INSPECTION SYSTEMS 38 PETplanet insider Vol. 16 No. 06/15 petpla.net Inspection systems for preforms With the PVS family, Sacmi offers a range of preform quality control solutions that join the tried and tested CHS systems for caps and the innovative Cube Eye, capable of producing a 3-D ‘CAT scan’ of the entire cap-bottle system. Thanks to its modularity, the machine can be enhanced with additional functions such as weight and body checks by using a patented grid method that allows identification of defects which would normally only be visible with polarised light. All checks are performed by a system of HD cameras that executes accurate analysis of the entire product, eliminating the risk of residual defects and warning the operator every time production moves outside the optimal pre-set quality range. All machine-calculated datas are saved on statistical databases that can be consulted remotely and/ or after lengthy periods of time and exported towards other corporate management applications. The PVS002 Plus is flanked by the PVS003 and PVS024 models for high-speed preform quality control; they can be installed on lines with the moulding press, upstream from stretch-blow moulding, or off line. The PVS003 is particularly suitable for quality control of 100% of line output, downstream from the press or before stretch-blow moulding. The system has 8 modules which perform quality control on all preform parts. In addition to the standard checks, it has a module for in-depth inspection of neck and thread. Capable of inspection rates as high as 50.000pph, this machine allows continuous monitoring of output, guaranteeing all-round inspection of preforms and thus eliminating the risk of lots with faulty preforms, a possible source of customer complaints. This precision, speed and reliability also allow a general increase in production process efficiency, thus minimising any need for line downtimes. Sacmi offers a range of solutions, expanded and improved in recent years, that ensure quality control on both, the production line and in the test lab. Established in 1987, Sacmi’s Automation & Inspection Systems Division has been operating not only as a service to the various other group businesses but also, as an independent provider of quality control machines and plants, high performance solutions that have reached widespread market acceptance. One of Sacmi’s solutions for PET manufacturing is the PVS (preform vision system) range for inspection of performs, both on line and off line. One of the latest innovations in that range is the PVS002 Plus for the inspection of PET preforms; this further development of the PVS 2 series can test, with maximum precision, up to 1.100pph. Designed to help quality control staff rapidly complete all their routine lab tests, the PVS002 Plus system is able to carry out, with a cycle time of 3sec., a broad range of checks: identification of visual defects on the opening, finish, thread, body and bottom measurement of dimensions reading of cavity numbers The PVS 002 +","@ID":40}, "MARKET SURVEY 29 PETplanet insider Vol. 16 No. 06/15 petpla.net Wentworth Mold Ltd. Sipa Molds Awanti Polymoulds PVT. LTD. Krones AG Hallink RSB Inc. Sacmi 566 Arvin Ave., Units 3&4., Stoney Creek, ON, Canada. L8E 5P1 +1 905 643 9044 www.wentworthmold.com Mr Tar Tsau General Manager +1 905 643 9044 ext 311 +1 905 643 5406 [email protected] Via Caduti del Lavoro 3 31029 Vittorio Veneto,Italy +39 0438911 511 www.sipa.it Mr Franco Porracin Molds & Hot Runner Division Manager +39 043891 1511 +39 043891 1694 [email protected] 25/5A/1/2, Nanded,near Sawali Dhaba, Sinhagad Road, Pune - 411 041, India +91 20 24392225 www.awantipolymoulds.com Mr Shirish Kshirsagar Managing Director +91 20 24392225 +91 98220 40771 [email protected] Böhmerwaldstrasse 5 93073 Neutraubling, GERMANY +49 9401 70 0 www.krones.com Mr Jürgen Werner Sales LCS Retrofits Products +49 9401 70 3491 +49 9401 70 913491 [email protected] 284 Pinebush Road, Cambridge, OntariO, Canada N1T 1Z6 +1 519 624 9720 www.hallink.com Mr Jason Warmington General Manager +1 519 624 9720 ext. 258 +1 519 624 9721 [email protected] Via Selice PROV.LE 17/A 40026 Imola BO, Italy +39 0542 607 111 WWW.SACMI.COM Mr Iacopo Bianconcini Marketing Manager +39 0542 607 111 +39 0542 642 354 [email protected] 10l 30l 20l 3,5l 120ml to 19l 3,3l Yes. No Sidel, MAG, Cypet, Shyam plastic Machinery, Electropneumetics Yes Yes No Yes, also manufacture multiplatform compatible mould systems Yes Yes Yes Yes Yes For all blow moulding machine platforms. e.g.Sidel, Krones, KHS, Sipa, etc. Sidel, Krones, KHS/SIG/Krupp, SMI, Siapi, Kosme, Side Cocacola, Sprite, Fanta, ThumsUp, Limca, Kinley, Aquafina, Maaza, Bisleri, Bailley water, Bailley soda, Oxyrich, Frooti, Appy Fizz and others Krones, Kosme, Sidel, Sipa, KHS (SIG) Corpoplast etc. Sidel, Krones, KHS, SIPA, Kosme, SIAPI, Urola, SIDE, W. Amsler Yes, also prototype sampling and bottle performance tests. Yes, brandbuilding, product repositioning, marketing design, packaging engineering, lightwiegtening of exhisting bottles, etc… Yes Yes Yes Yes Hot-Fill/Heat-Set moulds with energy efficient system and multiplatform interchangeable quick mould systems. Wide mouth,large sizes (up to 30l), asymmetrical, Nitrogen hot fill, containers with handles, HDPE to PET conversions. Functional laboratory for conducting over 15 different quality tests on bottle Packaging development customised to filling- & packaging lines with performance commitments. Preform-/bottle light weighting for standard- and heat-set process. Mould quick change systems. Blow moulds, preform and bottle personalisation parts for any brand/model of 2 stage stretch blow moulder Double cavity moulds for small sizes (up to 600ml) Specialised in refurbishment and reconditioning of blow moulds of Sidel, Krones, SIG, SIPA, MAG etc. Simex Srl TPS - Tooling Preform Systems Steelmades MHT Mold & Hotrunner Technology AG Sipa Molds Sacmi Via M.Biagi e M.D'Antona ,5 60025 Loreto (AN) Italy +39 071 7500214 www.simexitaly.it Mr Graziano Giuggiolini Sales Manager +39 071 7500214 +39 071 7501958 [email protected] C Houtmanstraat 42 7825VG Emmen, The Netherlands +31 591 679768 www.tps.nl Mr Richard Tempel Account Manager +31 6 25041136 +31 591 630616 [email protected] B/14, Ghatkopar Ind. Estate, LBS Road, Ghatkopar (W), Mumbai - 400086, INDIA +91 22 2500 7774 www.steelmades.com Mr Vipul Mehta CEO +91 932390 7774 +91 22 67969001 [email protected] Dr. Ruben-Rausing-Str. 7, 65239 Hochheim/Main, Germany +49 (0) 6146-906-0 www.mht-ag.com Mr Carsten Lurz Head of Sales and Service +49 6146 906 122 +49 6146 906 399 [email protected] Via Caduti del Lavoro 3 - 31029 Vittorio Veneto, Italy +39 043891 1511 www.sipa.it Mr Franco Porracin Molds & Hot Runner Division Man. +39 043891 1511 +39 043891 1694 [email protected] Via Selice PROV.LE 17/A 40026 Imola BO, Italy +39 0542 607 111 WWW.SACMI.COM Mr Iacopo Bianconcini Marketing Manager +39 0542 607 111 +39 0542 642 354 [email protected] Up to 144 cavity 96 06 to 72 2-192 Up to 192 16,24,32,48,72,96 All sizes and all finish Up to 50l Yes Up to 600g, for bottles up to 30l Up to 30l Up to 48mm neck finish and 140g weight Mineral water, milk, oil, beer, etc. Husky, Netstal, Engel, Battenfeld, Demag and others KM, ASB (Cold Half) Netstal, Husky, Engel, Arburg, Cincinnati, SIG, BMB; Sumitomo Husky, Netstal, Krauss-Maffei, krupp, BMB 96 06 to 72 2-112 up to 96 up to 50l Yes up to 600g, for bottles up to 30l up to 10l Krauss Maffei MHT, Husky (Cold Half) KraussMaffei Standard and custom Yes No No No Yes, for SIPAmachines No Injection Preform moulds for PE/PP Specialized in large Preforms, also double wall We offer Spares (Stacks) level support for all reputed moulds Wide mouth, high performance molds, up to 8 gallon, trigger molds, molds for vacuum blood test tubes Air recovery Systems, Rotary blowmolder and filling lines spare parts","@ID":31}, "ON SITE 43 PETplanet insider Vol. 16 No. 06/15 petpla.net ONsite 24th Fakuma International trade fair for plastics processing Injection moulding machines Thermal shaping technology Extrusion plants Tool systems Materials and components 13.–17. OCT. 2015 FRIEDRICHSHAFEN www.fakuma-messe.de First Swiss sorting centre for plastic bottles opened Not all plastics are equal; new PET can only be extracted from old PET. The same goes for all the different kinds of plastic found in the new range of plastic bottles. Müller Recycling AG have invested SF10m in a new sorting line, making it now possible for plastic bottles used for shampoos, washing and cleaning materials and made from completely different types of plastic to be mechanically sorted and sent for recycling and all whilst maintaining a high level of quality. It is essential, however, to keep the various items separate during collection. Despite these mechanical innovations, the two material flows of PET beverages bottles and other plastic bottles need to be kept separate for reasons of food hygiene. The aim for the foreseeable future is to create new plastic bottles from old ones, as has been the standard for 15 years now in the recycling of PET beverage bottles. Bottle-to-bottle processing, as it is known, is the main reason why PET recycling today is twice as environmentally friendly as landfill disposal. The traditional family concern Müller Recycling AG has been in operation since 1957 and is now run by members of the second and third generation of the family. In the last few years more and more materials have come to be recycled, from a mere 500 tonnes in 1991, to almost 20.000 tonnes last year. Since earlier this year it has also been possible to sort plastic bottles mechanically, thanks to the company’s rapid reaction to news that retailer Migros, followed by the Co-op, had also begun to collect plastic bottles. Positive influence on PET recycling quota Studies have shown that PET beverages bottles which could be of relevance for calculating quotas are frequently to be found in PET bottle collections. With the sorting facilities in the new plant, even these can now be «salvaged» and recycled, something which will have a positive effect on recycling quotas. www.mueller-recycling.ch","@ID":45}, "MATERIAL / RECYCLING 23 PETplanet insider Vol. 16 No. 06/15 petpla.net f.l.t.r. Elfriede Hell, General Manager recycling technology at Starlinger and Celis Carvajal, Group coordinator for Integral Management and Processes at Enka Production flexibility The Starlinger recoSTAR PET 330 iV+ recycling line for Enka is designed for an output capacity of 2.4 tonnes per hour and features two 165mm single-screw extruders and adequately sized upstream and downstream equipment. The input material is cleaned in a Sorema washing line; two viscoSTAR 120 solid state polycondensation reactors ensure constant IV level increase according to product specifications. The recoSTAR PET 330 recycling line has a flexible production output: it can be adjusted between 1.1 and 2.4 tonnes per hour. The newly developed Single Mode Operation Package enables Enka to operate the recycling line at 45% of its nominal production capacity. In this case only one extruder is used and production of smaller quantities is possible without losses in pellet quality or a disproportional increase in energy consumption. This gives Enka flexibility in adjusting their production according to raw material availability and rPET demand. Accurate IV control, energy efficiency This installation at Enka is the first to be equipped with a newly developed automatic IV control system that is integrated in the process. After setting the desired IV level the recycling line automatically adjusts operation parameters to reach it. During production the IV level is constantly monitored and parameters readjusted if necessary. This avoids IV variations after the extruder and ensures very constant IV values already during pellet production. In compliance with Enka’s sustainability strategy, energy efficiency plays an important role in this installation. Enka operates its own electric plant, and the steam generated during electricity production is used to supply the predrying unit and the SSP reactor of the recycling line. Together with the included energy recovery kit (ERK) used for the hot air dryer, this helps to reduce electrical energy consumption by more than 40%. About Enka de Colombia S.A. Founded in 1964, Enka de Colombia S.A. started out as a producer of resin as well as polyamide and polyester synthetic fibers and filaments for the textile, tyre and plastics industries. Today, Enka is the largest synthetic fiber producer in the Andean region. The company’s production plant is located 28 kilometres north of the city of Medellín. In 1993 Enka opened its first recycling plant to process PET waste from the production of filaments and fibers, adding a project for recycling PET bottles for fiber production in 2009. With the new PET recycling line from Starlinger, Enka de Colombia has now entered the bottle-to-bottle market. www.enka.com.co www.recycling.starlinger.com The recoSTAR PET 300","@ID":25}, "MATERIAL / RECYCLING 22 PETplanet insider Vol. 16 No. 06/15 petpla.net PET bottle-to-bottle recycling in the Andes Starlinger recycling technology installed a recoSTAR PET 330 iV+ recycling lines, operating at 1,300m above sea level. An established producer of fibers, filaments, yarns and resins for the textile industry based in Medellín, Enka de Colombia S. A. recognised the great potential of bottle-to-bottle recycling and decided to move into this application. rPET for up to 100% recycled content “After we started to recycle post-consumer PET bottles for fiber production in 2009 we saw PET recycling both as a new challenge and an opportunity for a new line of business that aligns perfectly with our sustainability strategy”, said Aníbal Celis Carvajal, Group Coordinator for Integral Management and Processes at Enka. “With PET consumption in Latin America steadily growing and PET recycling gaining a foothold, we began to study the various recycling technologies in different continents of the world, especially in the area of bottle-to-bottle recycling.” Having looked at the various technologies available on the market, Enka opted for the Starlinger superclean process and purchased a recoSTAR PET 330 iV+ PET recycling line in 2013. “Approvals of FDA and EFSA as well as of major brand-owners, decontamination efficiency, viscosity increase, compliance with product specifications and pellet shape were the criteria we were looking for in the equipment”, Celis explained. “But also global recognition, the quality of equipment, machine footprint, technical support and the price played a significant role.” The PET recycling plant took up production in December 2013. Enka’s experiences with the produced rPET on the Colombian market are promising: Evaluations of the recycled PET resin made by Enka customers showed very satisfying results – both as raw material and in bottles produced with different mixing ratios. “Tests were carried out with bottles that have been produced with a recycled content ranging from 25% to up to 100%. All of them received very good acceptance from our customers”, said Aníbal Celis. In December 2013 Enka obtained the approval of the Colombian health authority INVIMA (National Institute of Surveillance of Drugs and Food) for four years. Enka de Colombia S.A. based in Medellin","@ID":24}, "LABELLING 35 PETplanet insider Vol. 16 No. 06/15 petpla.net and refining of gherkins. The range extends from the use of cranberries and raspberries right through to creations involving other varieties of fruit. These are harvested at the peak of their ripeness, processed carefully and packaged when they are aromafresh. As far as Jütro is concerned, sauces and dressings which used to act as a weighty “top-off” ingredient are becoming ever more important. Today they are presented in a guise that stimulates the appetite, in a tasty and fresh, one might almost say “cheeky” format. On offer are noodle, rice and barbecue sauces, as well as dressings and stocks, and even classic Bolognese or exotic curry sauces offering a taste of Thailand, gherkin relish for steak or a fresh Italian dressing to go with your salad. These speciality sauces are also available in practical cardboard packaging as well as in plastic bottles. Labatta with new design On one of these plastics lines 120 PP and PET bottles with volumes of 250ml, 300ml and 500ml are filled every minute and fitted with two each pre-cut paper wet glue labels which are attached to the front and rear of the bottle. This line has now been equipped with a new labelling machine from Gernep, a Labetta 4/3/12 784 2A. Machines in the Labetta series have been proving themselves in all sectors over many years and are undergoing further technical development. Due to the use of brand name components in drive and control applications, the customer are assured of a high level of machine availability. The space-saving, compact rotary construction with precision bottle feed, together with the tried-andtested wet glue labelling in high end technology, ensures meticulous label presentation. The table control cam is maintenance-free and divided up into segments, a special overlay gearbox handles the precise positioning of the label. The multifaceted machine with in-situ label magazines ticks all the right boxes when it comes to traditional requirements in terms of features. The combination of tried-and -tested techniques makes this labelling machine stand out in its performance class. The entire complement of electrics for drive, servos, photoelectronic alignment and camera systems is clearly arranged and integrated in a maintenance-friendly way. Separate, space-intensive switch cabinets and control cabinets are not necessary. The machine at Jütro is presented in the new design incorporating protective encapsulation with corner pillars and safety doors which, in this project, are featured on all 4 sides to act as a lift guard. Cold glue labelling With the newly developed wet glue unit, the people at Gernep are setting standards in compactness, ease of maintenance and operator comfort. As always, the adhesive glue pallets are resistant to wear, individually interchangeable and readily adjustable for optimum adhesive action. The stainless steel gluing roller and the split glue scraping knife have shown themselves over a number of years to be ideal for glue metering and the gearbox which is encased in oil has likewise proved itself. The “No bottle – no label – no glue” automatic system is standard on the machine as is the maintenance-free, heated glue pump. Now this unit has been new designed, is hermetically sealed so that it is splash-resistant as well as being constructed to be more operator- and maintenance friendly. Possible equipment Thanks to the fact that the dimensions of the magazine have been kept to a minimum and due to a perfected system of connectors it is possible to achieve very small intermediate distances as regards the positioning of the labels – the precondition for meeting sophisticated design requirements. This represents a flexible approach to attaching labels to the body, shoulder and rear of the bottle, full neck labels, champagne bows, clip-lock closure and closure safety label. Currently only one shoulder and one rear label are being applied at Jütro but “we are already planning to affix self-adhesive labels. From a technical viewpoint, the machine is perfectly set up for this already”, says Retzke. Operation / Maintenance The console is ergonomically integrated in the upper section of the machine at a distance which makes it easy for the operator to view and make any necessary interventions. The entire machine is controlled by means of a touch screen incorporating up-to-the-minute microelectronics. The data relating to the current operation is displayed constantly. Performance information, parameter settings and the causes of any faults are displayed in a text box. Robust and flexible The technical specialists at Jütro had been looking for a machine that featured reliability and, primarily, flexibility in terms of format changes. “Then, a year ago, we came across the Gernep Labetta at the Anuga FoodTech. The servicing aspect helped convince us, as well as the fact that it was realistically possible to carry out a format change within ten or 15 minutes. The machine also impressed us with its robustness, solidity and reliability.”, explains Technical Director Retzke. Although the bottle formats are changed only every three or four days “we nevertheless have specialists in production and bottling machine technology who know exactly how to go about manufacturing and packaging a delicate mayonnaise or sensitive sauce hollandaise. We also have a special three man team that is responsible for upgrading the lines whenever we have format changes. If, with nine lines, every change of format were to take hours, the line would be at standstill for far too long. With the Gernep Labetta this can be done quickly: the equipment features a number of integrated innovative technologies such as the fact that the format components can be replaced very quickly but still without any compromises as regards precision adjustment. And nothing bends or goes out of shape because everything is designed to be robust. We are really very satisfied with the machine“. www.gernep.de/en","@ID":37}, "MATERIAL / RECYCLING 21 PETplanet insider Vol. 16 No. 06/15 petpla.net Short cycle times, high shot-to-shot quality, low energy consumption and maximum flexibility. The new XFORM 300 with its unique 6-position post-mold cooling system boosts your output performance for the widest range of preforms. Cooling preforms faster and better, the 96-cavity platform is ideal for large runs and quick mold changes. And it lets you run any mold you want, old or new, OEM-built or not, in total freedom. From ultra-thin walled (with proprietary XMould™ technology) to wide mouth. XFORM 300, low transformation cost, high value. SIPA S.p.A. - Via Caduti del Lavoro, 3 - 31029 Vittorio Veneto (TV) - Italy Tel. +39 0438 911511 - Fax +39 0438 912273 - e-mail: [email protected] www.sipa-xform.com Designed to adapt. Built to last. The new XFORM 300 IMAGINE THE LOWEST TRANSFORMATION COST. IN TOTAL FREEDOM. At Ice River Springs, the 500ml bottle accounts for the lion’s share of the bottles that are produced by several Husky Injection Molding systems, which have up to 144 cavities. No additives are added to the rPET; a few blue flakes in the transparent flake batch mean that the bottles have a slight blue tinge but they help to ensure yellowing does not occur. The 500ml bottle preform currently weighs in at around 8.6g. Ice River Springs also makes its own proprietary 26mm 0.92g closures, which it developed in-house and are manufactured at several of its plants on Husky systems. The company’s bottling lines use equipment from various manufacturers and operate at rates up to 72,000 b/hr. A large percentage of production is private label; the balance is marketed under its own brand name. Its own-brand production has enabled the Ice River Springs team to highlight its key differentiator. As the bottles are made up of 100% rPET, Jamie Gott, CEO of Ice River Springs, created the idea of green rPET for the bottle. Up till now the green-coloured portion of waste has not been processed into PET bottles but it is now appearing on retailers’ shelves under the Ice River Green brand. As far as customers are concerned the concept is not unfamiliar, as green-coloured bottles are already associated with carbonated water from, e.g., San Pellegrino, Perrier, and others. Awareness is now dawning that green can also mean environmentallyfriendly, because these bottles are made from 100% rPET. The company transports the packaged bottles on its own fleet of trucks to customer distribution centre, bringing back used bottle bales on their return journey. This has established an efficient “virtuous circle”, covering both the flow of materials and the logistics cycle. With so much meticulous attention to closed-loop recycling, the success of the company’s bottling operation is almost secondary but the Gott family has demonstrated significant success in this aspect as well. In the past 10 years the company has undergone significant expansion and now maintains 12 bottling plants in North America. Although the Canadian plants bottle spring water, the US consumer demands both spring and purified water. The Gott family’s heart remains close to the land. They recently established Osprey Organics, an accredited organic producer, very close to the company’s Feversham plant. The Gotts would not be true Canadians if they did not produce maple syrup, and - something of an innovation – a maple beverage. They strongly maintain their commitment to conducting all their operationss in an environmentally- friendly and ecological way – which prompts the: is the Gott family business a bottler, recycler or organic producer? www.iceriversprings.com","@ID":23}, "EDITOUR REPORT 15 PETplanet insider Vol. 16 of PET. The conveyor and metered dispensing units come from Piovan. “HSB has in its time achieved some real pioneering work”, says Mr Houssine. The introduction of the standard also signified the arrival of the first Husky PET injection line in the whole of Morocco and that was back at the beginning of the 1990s”. Although a proportion of the preforms are used in the company’s own edible oil bottling operation, the remaining proportion goes to SBGS for bottling CSDs. The excellent partnership with Coca-Cola, which goes back 40 years, ultimately gave the company the impetus it needed to be in the PET sector right from the very start. The manufacture of closure caps includes types 48 and 50mm for oil, 33mm for milk and 28mm for CSDs fabricated from (LD/HD-) PE at a rate of 150mill. units per year. The quantity of handles and margarine tubs stands at around 45mill. and 25mill. All preforms are used within the Belhassan Group, the same applies to the other products. And something else as well. As of 2015 HSB is poised to open up the market as a supplier for other bottling enterprises too. “The level to which PET is deployed in the edible oils market in Morocco is in excess of 90%”, says Mr Houssine. Coming to the edible oils bottling side: this is split between two plants, one in Agadir and the other in Meknes 700km to the north. Here in Agadir, some 20 minutes away from the Plastics Division, are the business premises for the brand names “Lousra” and “Lio”, both soya edible oils, together with the “Oued Souss” brand of olive oil which is named after the Moroccan river of the same name. The latter has just celebrated its 60th birthday and was Belhassan’s very first product after the group was established. The premises here occupies 30.000m2. The production, transport and labelling units come","@ID":17}, "MARKET SURVEY 28 PETplanet insider Vol. 16 No. 06/15 petpla.net 06/2015 MARKETsurvey SBM moulds Company name Nissei ASB Machine Co., Ltd. Simex Srl Solent Mould Tools Ltd COMEP TPS-Tooling Preforms Systems Postal address Telephone number Web site address Contact name Function Direct telephone number Fax E-Mail 4586-3 Koo, Komoro-shi, Nagano-ken 384-8585, Japan +81 26723 1565 www.nisseiasb.co.jp/en/ Mr Katsuo Ishiguro Manager, Sales Coordination Team +81 267 23 1565 +81 267 23 1564 [email protected] Via M.Biagi e M.D'Antona ,5 60025 Loreto (AN) Italy +39 071 7500214 www.simexitaly.it Mr Graziano Giuggiolini Sales Manager +39 071 7500214 +39 071 7501958 [email protected] Relay Road, Waterlooville, Hampshire, PO7 7SB UK +44 23 9223 9950 www.solentmouldtools.com Mr Mark Sim Managing Director +44 23 9223 9950 +44 23 9223 9951 [email protected] ZAE du Pont Neuf - 11 rue de la Bonne Fin - 16130 Salles D'Angles (Cognac), France +33 5 45 36 63 50 www.sa-comep.fr Mr Frédéric Mandin Sales Manager/Marketing +33 5 45 36 63 50 +33 5 45 32 08 08 [email protected] C. Houtmanstraat 42 7825VG Emmen, The Netherlands +31 591 679768 www.tps.nl Mr Richard Tempel Account Manager +31 6 25041136 +31 591 630616 [email protected] Stretch blow moulds Bottle size (max.) (in litres) 22l 20l (5 gallon) 5l 0,03l to 30 l 50l Moulds supplied directly to blowing machine manufacturers No, for our own machines only Yes Yes Krones, KHS, Sacmi, Bosch packaging, Side, Urola, One Blow... No Do you supply retrofit moulds for existing SBM machines? Only for own machines Yes Yes, all platforms Krones, KHS, Sacmi, Bosch packaging, Side, Urola, One Blow… Yes For which makes of bottle makes have you already produced moulds Mould designs are customised on a per customer basis. Yes Sidel, Krones, KHS, Sig, Siapi, AOKI, Nissei, Krupp, Mag, etc All types in PET, Still water bottle, CSD bottle, home care product, oil, alcool,sauce... Various Bottle design service Yes, complete design service from concept to finished moulds and machines. Yes Yes, full bottle design capability and rapid prototyping of marketing mock-ups Team of 3 people Yes Specialities Handled, non-round, wide-neck, hot fill, non-round neck, offset neck, heavy weight cosmetic, PET, PP, PC, PES, PEN, PLA, etc. Pet Containers for Mineral water,CSD, milk, edible oil, wine, beer, cosmetics and other Interface parts & carriers to allow different OEM moulds to be fitted in other machine platforms All kind of moulds for high speed machines (rotary and linear) with short lead times Large containers Other Processing support available across N - America and Europe for pilot and production runs 2 patents for energy savings during the phase of blowing In house production equipment for preforms and containers up to 50l Preform moulds Company name Milacron c/o Mold-Masters Europa GmbH R&D Leverage Nissei ASB Machine Co., Ltd. Postal address Telephone number Web site address Contact name Function Direct telephone number Fax E-Mail Neumattring 1, 76532 Baden-Baden, Germany +49 7221 5099 0 www.moldmasters.com Mr Jeremie Cuny Sales Manager MPET Europe +49 7221 5099 0 +49 7221 53093 [email protected] Leverage House, Hamilton Road, Sutton inAshfield, Nottinghamshire, United Kingdom, NG175LD +44 1623 556287 www.rdleverage.com Mr Alan Tolley Managing Director +44 1623 556287 +44 1623 552240 [email protected] 4586-3 Koo, Komoro-shi, Nagano-ken 384-8585, Japan +81 26723 1565 www.nisseiasb.co.jp/en/ Mr Katsuo Ishiguro Manager, Sales Coordination Team +81 267 23 1565 +81 267 23 1564 [email protected] Horizontal opening Number of cavities Up to 144 Up to 96 Preform sizes Up to 5 gal / 20 l 24mm - 63mm neck, 12gram - 350gram weight moulds already built for (makes) all major brands of PET systems Husky, BM Biraghi, Milacron, Engel, Krupp, Krauss-Maffei Vertical opening Number of cavities Up to 96 6 - 48 Preform sizes Up to 5 gal / 20 l Up to 241g, necks up to 120mm diameter Moulds already built for (makes) All major brands of PET systems Supply for our own machines only Do you produce single stage tooling sets? (Preform moulds AND blow moulds) Axiom Hot Runners for Single Stage IBM & ISBM Yes Yes, main business is single stage. Preforms up to 800g, bottles up to 20l Other M-PET 300, a new servo-hydraulic PET system; 96 drop molds for 300t machines; iFLOW hotrunner systems; Rapide system (fast tool changes); iCOOL conformal mold stack cooling technology; iFLOW inside hot runner manifold upgrade program; Hot Runner refurbishing program; Hot Runner upgrade programs for all brands (for higher longevity & improved system performance); Co-Injection systems; Full range of PET preform molds, conversions, refurbishments and replacement stacks R&D Leverage is a supplier for the single stage, Injection Stretch Blow Moulding ISBM industry.","@ID":30}, "EDITOUR REPORT 16 PETplanet insider Vol. 16 No. 06/15 petpla.net Supported by: Next... In the upcoming issue you will read about our appointments in Spain and Portugal! The Sample - PreWatcher. Game - changing inspec t ion per formance. W W W . I N T R A V I S . C O M from Krones, HSB uses Sacmi in the subsequent palletising operation. The annual quantities are, for Lousra and Lio around 65 million litres and for Oued Souss around 25 million litres. “At the moment we are exporting about 10% of our finished products to Canada, USA, France, and Belgium, for example, and shortly to Senegal as well. It is our intention to expand exports to 30% in the future and we shall be extending our fleet of machines in order to accommodate this” predicts Mr Houssine. “One delegation also recently paid a visit to the Ivory Coast with Mr Belhassan. Here we also envisage some good opportunities”. www.gbhmaroc.com www.husky.co","@ID":18}, "EDITOUR REPORT 11 PETplanet insider Vol. 16 No. 06/15 petpla.net Morocco Water for the North Chaouen Water | June 16, 2014 We met: Mr Ahmed Amziane, Plant Director f.r.t.l.: Ahmed Amziane with Kay Barton Mundane, with no information signs or a company logo immediately apparent, the production centre for the two brands of mineral water, Chaouen and Rif, looms into view on a slope just 11km north of the town of Chefchaouen, in the rural province of El Ouedin. Here we meet Mr Ahmed Amziane, the Plant Director. After the founding of the company in late 2004 and its subsequent establishment Chaouen Water began production in April 2008. The equally modern production lines date from this time. “We have opted for Krones for our entire production operation”, explains Mr Amziane, indicating the proportion of work which has already been completed on a pie chart. The Krones line has a capacity of 12.000 1.5l bph. With company premises extending to 9 hectares, of which 6.000m2 is currently in use, and a total of 20 employees. Chaouen Water is still a fairly compact enterprise, but the ambition is evident. “Today we cover around 6% of the market and our next goal is to achieve 10%”. The biggest competitors of Chaouen Water are the Oulmes and Sidi Ali brands, which between them account for 75% of the market. Preforms for West Africa PET Preforms Morocco Sarl | June 17, 2014 We met: Mr.R.Nourredine, Managing Director In Benslimane, located not far from Casablanca, we meet preform manufacturers PET Preforms Morocco who realised their ambition to enter preform production in 2008. Managing Director, Mr Nourredine made his decision to go in for preform manufacture as a result of visiting customers in West Africa. He had previously spent a number of years in Switzerland and in Germany; he began his career as a Production Manager in a dairy, then worked for Procter & Gamble before finally moving to a major ingredients supplier in Germany as Head of Sales for Africa, “Over Chaouen Water obtains its two waters from two different springs. Both for “Chaouen” and the second product “Rif” are located a mere 400m opposite the production facility with one large and several smaller collecting tanks. Both springs are situated just 80m from each other. Both waters are different in terms of their mineral content and are obtainable exclusively in 0.5l and 1.5l bottles. 20.5g and 30g preforms from APPE with a BPF neck finish are used, together with closures supplied by Allplast. Touring the production facility we spot a water purification unit from Chriwa, alongside a Krones Contiform S8, the Volumetic und SynCo and a wrapping unit. There is an Atlas Copco compressor for use in the blow moulding process. “The line currently produces 3.200bph but we already have a fairly full warehouse as well as limited sales outlets and so the plant is only operating 100 days a year”. The markets for Chaouen and Rif are currently restricted to the North of Morocco but the intention in the medium term is to extend them to the entire country. “As things stand at the moment, export is not high on our list of priorities, but our immediate aim is to have our two products available throughout the whole of Morocco”. Capping of Chaouen Water and over again in the course of my meetings with customers, the topic of the booming PET market kept cropping up, and this is what inspired me to enter the business” Mr Nourredine explained. At K fair he made his first contact with Netstal and the entrepreneur decided to purchase a 48 cavity PET line. In what was, for this country, an incredibly short period of only eight months, not only was building work on the 1500m2 site completed but the equipment had also been successfully installed, with the result that production was already underway shortly after. Disaster nearly struck the company","@ID":13}, "NEWS 9 PETplanet insider Vol. 16 No. 06/15 petpla.net EXPOPACKMEXICO,16/19.06.15-#2636- CiudaddeMéxicoMEXICO PROPAK ASIA, 17/20.06.15 - HALL 106 6G26 - Bangkok THAILAND ROSUPACK, 16/19.06.2015 - A205 - Moscow RUSSIA PROPAK WEST AFRICA, 1/3.09.2015 - Lagos NIGERIA SCANPACK, 20/23.10.2015 - B02:09 - Gothenburg SWEDEN With Sacmi, the beverage specialists are always at your side. With our unbeatable technological know-how and continuous research we are creating new containers and closures designed to ensure outstanding performance. The new IPS injection system for preforms and the CCM compression press for caps, fully designed and built by Sacmi, allows for large-scale production with considerable advantages in terms of efficiency and flexibility. The outcome? Reduced plastic volumes, less energy consumption and lower running costs. All in a bottle: the one you’ll soon be making. Preform & Closure technologically together Save RAW MATERIALS reduced plastic volumes Save ENERGY less energy consumption Save TROUBLE more quality and higher performance, guaranteed by a sole supplier Full INSPECTED online quality control / stand alone Amcor Rigid Plastics wins Brazilian packaging design award for innovative PET containers Amcor Rigid Plastics has been recognized by the Grandes Cases de Embalagem, a Brazilian packaging award competition sponsored by Embalagem e Marca magazine, a leading trade magazine based in São Paulo. Amcor received the packaging award for its designs for Coca-Cola (carbonated soft drink bottle), Unilever (condiment bottle), and Johnson & Johnson (shampoo container). The award ceremony brought together more than 450 attendees, including representatives of the user industry, converters, design agencies, and raw material manufacturers and equipment makers. Amcor was recognized for its development of a 15g polyethylene terephthalate (PET) preform for CocaCola’s 200ml Contour carbonated soft drink (CSD) bottle. Compared to the previous 20.6g preform, the new preform is approximately 33% lighter and exceeds CO2 loss requirements, maintaining a minimum shelf life of 63 days. Through design enhancements, Amcor was able to optimize stress ratios and molecular orientation. Despite the weight reduction, functionality and performance were maintained. The material reduction also increases the bottle’s recyclability and reduces the energy needed for its production, significantly decreasing the package’s environmental footprint. Cradle-to-gate greenhouse gas emissions and energy use are cut by over 25%, according to calculations performed using Amcor’s ASSET streamline life cycle assessment software. Amcor was also honored for its development of ergonomically designed upside-down condiment containers for Unilever’s Hellmann’s brand products. The ambientfilled 350ml (21g preform) and 175ml (17g preform) bottles underwent preferential heating and indexing to optimize finish orientation. A major challenge was aligning the elliptical closure to the bottle shape. Amcor used finite element analysis (FEA) to adjust the preform and the overall design to enhance blowing and adaptability to the filling line. The bottles, which are targeted for ketchup, salad dressing, and mustard, are manufactured in-line at Unilever’s filling operation in Goiania, Goias. Amcor was also cited for its conversion of Johnson & Johnson’s baby shampoo product to 50% post-consumer recycled (PCR) polyethylene terephthalate (PET) bottles. The 200ml bottles, originally in virgin resin, are the first PCR containers for J&J, which gained sustainability benefits with the switch to PCR resin. By converting to 50% PCR resin, J&J reduced its PET packaging carbon footprint by 27%. www.amcor.com","@ID":11}, "CAPPING CLOSURES 30 PETplanet insider Vol. 16 No. 06/15 petpla.net Introduction, closure history and closure function, part 1 Closures for PET bottles PETplanet Insider is publishing extracts from successive chapters of Ottmar Brandau’s “Bottle, Preforms, Closures”, which was published by hbmedia. A newly revised version is reissued under the Elsevier imprint. Introduction Closures usually are the least expensive part of a container. On the other hand, they are the primary interface between the product and the customer. Today’s closures have to offer high-performance functions such as resistance to gas pressures up to 12 bar and temperatures up to 65°C. This is necessary if we consider that these containers have to be transported and stored in countries where temperatures reach 55°C with even higher temperatures in truck trailers. Also, a modern closure has to provide easy processability at capping speeds of up to 70.000bph without breaking the tamper evidence. It has to be opened easily by elderly people and children, showing clear tamper evidence, and it has to reseal the container perfectly after first use. Closures also carry decorations like four colour printing on the outside and promotional engravings or printings showing an instant win on the inside. Considering that such closures are sold between 0.5 and 0.9 US cents per piece, it is clear that the production has to be more than only efficient. A highperformance injection moulding (IM) or compression moulding (CM) machine can provide more than 1000 closures per minute. Offset printing machines can print up to 4000 closures in 1 minute with decorations in four colours. The investment for such a closure production line today is well over 1 million USD. If we consider that 67% of the closure cost is for raw materials and the second factor with 7% is energy, we can understand why there are only a few companies worldwide that can exist in this highly competitive market of plastic closures (Fig. 4.1). 4.1.1 Closure History The first mass-produced closure able to keep up with CSDs was a metal closure with a crown-shaped flange, lined with natural cork. This goes back to 1892 when William Painter invented the crown cork. It took almost 80 years until a young man named Albert Obrist from Switzerland introduced a onecomponent high-density polyethylene (HDPE) closure for returnable glass bottles in Switzerland. The advantage of prethreaded plastic closures was obvious, but it took 15 years for other companies to introduce plastic closures that were able to compete with the solution of Obrist. These closures were based on the design of aluminum closures mostly with shell and liner and in some cases also with an inserted tamper evident band. The two different backgrounds of the developing companies were the reason for the development of injection moulded closures from Obrist and the compressionmolded closures from HC Industries together with Alcoa. Still today there is only a handful of companies able to produce plastic closures for soft drinks with constant quality and high performance. This","@ID":32}, "BOTTLING / FILLING 32 PETplanet insider Vol. 16 No. 06/15 petpla.net Strategic expansion in the milk sector Brazil is the largest consumer of UHT milk in the world. In 2013, the Brazilian market consumed 6.3 billion litres of it. UHT milk has a 60% share of the drinking market; pasteurised has 13% and milk powder, 27%. UHT consumption grew four per cent last year and is still gaining market share, with over 90% penetration in Brazilian homes. Jussara, a family-owned company, is the ninth-largest producer of dairy products in Brazil overall and is currently ranked fifth in its UHT milk market. When it decided to extend its product portfolio the company sought to meet consumers’ demands with novel products with special formulation and function and with more practical, user-friendly packages. Brazil’s first ‘dry’ aseptic production line The adoption of a PET bottle was an important step in a domestic market dominated by carton packaging, and helps Jussara to differentiate itself and its brands. The new PET production line, which is located in the Patrocínio Paulista plant in São Paulo State, is equipped with Latin America’s firstever aseptic blow-fill-cap production line with dry preform decontamination technology, supplied by Sidel. “Our company presents one of the most modern PET bottle packaging technologies in Latin America,” said Mr Odorico Alexandre Barbosa, Superintendent Director of Jussara. As a packaging material PET offers flexible design opportunities, in keeping with the company’s drive for greater brand recognition. The Jussara Max range for long-life milk with added calcium and vitamin D is packaged in an eyecatching PET bottle and is available in full-fat, skimmed and semi-skimmed versions. On-shelf differentiation Brazil’s UHT dairy and milk products are, overwhelmingly packaged in cartons; they have 99% market share. However, PET has already demonstrated its benefits in the beverages market and producers are increasingly becoming aware of its advantages in bottling. The package itself provides protection and product integrity and meets stringent global food safety standards, while offering opportunities for brand differentiation of liquid dairy products stored and distributed at ambient temperatures or in refrigerators. New materials, new ideas “We were convinced by the marketing opportunity the PET bottle could offer to our UHT premium milk,” said Mr Laercio Barbosa, Commercial Director and owner of Jussara. “Our challenge was to create innovative and functional packaging which was cost-efficient and sustainable to produce. PET bottles have all the qualities necessary to meet our expectations. They give a freedom in package design to differentiate our products on the supermarket shelves. They match consumers’ expectations, they are user-friendly, tough and resealable. They also offer great physical product and food barrier protection, retaining the milk’s fresh taste and vitamin content.” Jussara packages UHT milk in PET bottles Standing out from the crowd Brazilian company Jussara has become Latin America’s first dairy producer to adopt an aseptic blow-fill-cap solution equipped with dry preform decontamination. The new line, manufactured and installed by Sidel, has enabled Jussara to expand its portfolio and raise its on-shelf visual profile. Its new PET bottle is a strong differentiator in a market dominated by cartons. The first milk to be bottled by the Sidel line is Jussara Max a long shelf life UHT milk enriched with added calcium and vitamins.","@ID":34}, "EDITOUR REPORT 13 PETplanet insider Vol. 16 f.l.t.r.: Rachid Afelad, Houssam Slimi and Kay Barton in front of the Editourmobil Today APPE supplies market leaders Coca-Cola via the NABC plants with four associated plants in Casablanca, Marrakech, Fes and also ABC in Tangier & SGBS in Agadir plus a number of CSD and water bottlers. A recent addition to the company portfolio is Pepsi that has come on stream via a company called Varun Beverages; originating from India and owned by RJ Corp. APPE Morocco is managed by APPE Spain which, in turn, reports to the main company in the UK. The company’s premises extend to 6000m2 and it has 20 employees. “Today”, says Mr Afelad, Plant Manager at APPE, “our production operation runs on five Husky machines and we produce around 350 million preforms a year”. A new machine is already budgeted for and with this they are looking to increase the output to 400 million units. APPE produces preforms for the CSD, mineral water, edible oils, juices and, more recently, also for the Health, Beauty and Personal Care sectors. The PET material (naturally dependent on the price of resin) comes from the Emirates and the Far East. “However, we are currently ordering mainly from the Emirates, since trade agreements mean that we do not incur any import duties here”, says Mr Afelad. The company portfolio includes not only PCO 1810 but also PCO 1881 neck finish. In the PCO 1810 sector 18g, 21g, 24g, 27g, 28g, 31g, 35g, 37g, 49g and 52g are available for bottle sizes from 0.5l to 5l. In the PCO 1881 sector the company offers 19g, 25g, 35.5g, 46.7g and 48.5g for CSD, bottle sizes 0.33 litres to 2l”. “We manufacture the 19g preform with barrier especially for the 0.33l Pepsi bottles”. A further special feature is the fact that, in principal, the same preforms that are used for the CSD Sector can also be used for personal care products. “As far as this goes, we have already carried out a number of trials aimed at convincing the customer that it is worthwhile using these preforms and so we do not need to invest in new types”. Ignoring the “self-manufacturers” in the There is no challenge we will say no to. Because we know that with the widest range of products, technologies, expertise and services, there is no solution we can’t conceive. Contact us to see how our philosophy of Yes has reshaped the very fabric of our brand. Explore all that’s possible with injection, extrusion, blow molding, co-injection, hot runner systems, mold technologies, process control equipment and fluids. Visit www.milacron.com","@ID":15}, "BOTTLES 47 PETplanet insider Vol. 16 No. 06/15 petpla.net [email protected] Tel: +90 212 695 50 00 Fax: +90 212 694 97 24 .com Caps & Closures New shape for rinse aid The German drugstore discounter dm is using an unusually shaped bottle for its own brand “Denk mit“. A litre of rinse aid is packaged in a blue-tinged and curved PET bottle. The product is supplemented by a relatively bitter additive which is intended to prevent the contents being swallowed accidentally by small children. For stabilisation purposes the bottle also incorporates horizontal recesses and/or notches. The rinse aid is poured into the dishwasher via a screw-on dispensing closure with push/pull function. The particular shape of the outlet channel makes it easy to adopt a specifically targeted approach to pouring the rinse aid into the rinse aid chamber. www.dm.de/denkmit Soft oil in PET Beiersdorf are marketing 250ml of their new soft oil product with avocado oil in a slightly tinted PET bottle for caring for dry skin. The oil is reported to smooth the skin and protect it from drying out. The slimline bottle is closed with a screw cap and the bottle opening incorporating a dispensing aid in the form a small hole in the opening of the bottle. The upper edge of the lid is on a slant and features a shiny brand logo. The addition of a transparent self-adhesive label at the front and a colour-matched label at the back makes the pack ready for sale. www.nivea.de Beach look on demand As part of its “Studio Line“ range L’Oréal are marketing a salt spray with a matting action that is intended to give the hair a tousled beach look. On display at the POS is a 150ml pack consisting of a spherical PET bottle with a pump spray. The striking container features a shrink sleeve label that incorporates the instructions for use and the retail information. Despite its unusual shape the container sits comfortably in the palm of the hand and the product can be dispensed easily. A plastic cap protects the spray pump from dirt and accidental operation. www.lorealparis.de","@ID":49}, "PETpatents www.verpackungspatente.de 48 PETplanet insider Vol. 16 No. 06/15 petpla.net Tamper-proof ng International Patent No. WO 2014 / 129485 A1 Applicant: Toppan Printing Co. Ltd., Tokyo (JP) Date of Application: 19.2.2014 The closure on a container is fitted with an IC chip with antenna. Should the container be opened, the antenna is “destroyed“ and the chip can no longer be selected or modified. This ensures that any attempt at opening can be easily identified. Aerosol container in plastic US Patent No. US 2013 / 0082074 A1 Applicant: Graham Packaging Comp., York (US) Date of Application: 3.10.2011 Structure and process for manufacturing a plastic container in PET which is used as a pressurised aerosol container. In order to achieve adequate stability at certain points, an additional heat treatment is required. Improved sleeve label International Patent No. WO 2014 / 146899 A1 Applicant: Sleever International Comp., Morangis (FR) Date of Application: 4.3.2014 A sleeve label is designed so as to feature a multi-layer arrangement in the area of the seam and fitted with security characteristics such as a barcode, QR-Code or characters that are no longer legible or identifiable once opened. Dock-on closure International Patent No. WO 2014 / 154718 A1 Applicant: Obrist Closures Switzerland GmbH, Reinach (CH) Date of Application: 25.3.2014 Hinged lid closure for a container. The closure is specially designed for product concentrates and enables a straightforward and convenient link-up with / docking on to the opening of a further container. Laminated plastic bottle International Patent No. WO 2014 / 157258 A1 Applicant: Yoshino Kogyosho Co. Ltd., Tokyo (JP) Date of Application: 25.3.2014 A plastic bottle is fitted on the inside with a second, flexible layer of material. As the container is emptied, the inside layer becomes detached, it contracts and air flows via an opening between the outside and inside layers. Gas-tight plastic bottle International Patent No. WO 2014 / 161652 A1 Applicant: Cedar Advanced Technology Group Ltd., Zug (CH) Date of Application: 1.4.2014 In order to improve the gas tightness / permeability of a thin-walled plastic bottle, it is proposed that the bottle be fitted with a comprehensive sleeve label. The characteristics of this label can be adapted to suit the relevant requirements.","@ID":50}, "PETbottles 44 PETplanet insider Vol. 16 No. 06/15 petpla.net Beverage + Liquid Food Coca-Cola with Stevia Responding to consumer demand for a lower sugar content, preferring light products with artificial sweeteners, Coca-Cola has developed a Coke featuring a proportion of stevia. This first appeared on the market in South America, the home of the stevia plant, and was then successively introduced and marketed in the other countries, most recently in Europe / Germany. In the case of “Coca-Cola Life“, 37% of the sugar is replaced by stevia extract. In this way it has been possible to reduce the calorie content from 42 to 27 kilocalories per 100ml. In order to emphasise the natural origins of the sweetener and to make Coca-Cola “greener“, the well-known transparent PET bottle has been combined with a green paper label and a green screw closure complete with tamper-proof guarantee strip. www.coca-cola.com Punica Saft-Limo Under the name of “Punica SaftLimo“, Pepsi-Co Deutschland GmbH is marketing three different carbonated Saft-Limos with a juice content of 15%. The varieties (orange and passion fruit, lemon and raspberry and red fruits) contain less sugar than traditional lemonades and are free of any preservatives. In each case 1.25l are packaged in a returnable bottle with an attractive shape made from transparent PET. In the neck area the bottle is fitted with two embossed brand logos and an allround plastic label and closed with a screw cap incorporating a tamperevident strip. www.punica.de Spanish mineral water in blue PET bottle Spanish beverages purveyor Aquas de Solán de Cabras is bottling its natural mineral water in a blue - tinged PET bottle with a content of 500ml. The water boasts a long tradition and it used to be available in chemists‘ shops as a medicinal water. The shape of the bottle is also reminiscent of this time. Even today health-promoting qualities are still attributed to the water. On the front is the name of the spring and a coat of arms, while the back contains information in braille. A paper label in the vicinity of the neck and a tamper-proof, white screw closure for the bottle opening with a diameter of approx. 35mm complete the packaging. www.solandecabras.com New brand and new bottle Two years after introducing Volvic Juicy to the market in a 0.5l bottle, Danone Waters Deutschland is continuing to add to its range of flavours and container sizes. Following the introduction of the 1.5l bottle, the latest variation is the deployment of a transparent PET bottle with a content of one litre. The bottle has all-round reinforcement grooving and 3-dimensional recesses protruding inwards that increase stability and grip whilst enabling the weight of the bottle to be reduced. The bottle is decorated with a transparent plastic label and closed by means of a screw closure with embossed brand logo and guarantee strip. The picture shows the 0.5l bottle with pineapple and the 1l bottle with orange/mango flavour. www.volvic.de","@ID":46}, "EDITOUR REPORT 12 PETplanet insider Vol. 16 No. 06/15 petpla.net right at the start when a crane toppled over, nearly hit Mr Nourredine’s father who also works in the company. He himself also runs another small PET recycling for producing flakes. Fortunately, father and machine escaped without damage. f.r.t.l.: Haj Nourredine, Si Mohammed, Rachid Nourredine and Kay Barton “This was something of a shock for us all which we shall never forget”, says Mr Nourredine reflectively. “At that time we started with three employees, manufacturing around 20 million preforms; now we employ 18 people in a 3 shift operation and run the line to the limits of its capacity with 100 million units”. Currently in operation are four moulds supplied by Otto Hofstetter. In the CSD sector, the preform types produced are the 28mm PCO 1810, 38g for 1l and 28g for 0.5l, plus, in the still water sector, 32g and 18g for 1.5l and 0.5l with 30/25 neck finish. “It was only a few months ago that Coca-Cola introduced the PCO 1881 Standard into Morocco, and preform manufacturers will soon be gradually moving over to them” says Mr Nourredine. f.l.t.r.: Rachid Nourredine, showing his PET Morocco logo on the Editourmobil, and Kay Barton Currently, PET Preforms Morocco keeps back less than 10% of its products for the local market. Its direct competitor here is APPE. The remainder (in excess of 90%) is made up of exports, e.g. to Mauretania, Senegal, Nigeria and Burkina Faso. As far as possible, the company obtains the necessary PET material from Asia. There are plans for a major expansion before the end of 2014. A new 3000m2 workshop facility has already been constructed not far away and is waiting to be equipped. “We shall also be getting involved in closure cap production and be offering our customers complete packages in the future” explains Mr Nourredine. For this the company will be opting for a Netstal Synergy machine in the future. In the preforms sector, too, the vision for the future is to build up the output rates with the help of new machines. “Our aim is to become a leading supplier for preforms and caps in West Africa, this is our ultimate goal”. www.petmorocco.com Multifunctional preforms APPE Morocco | June 18, 2014 We met: Mr Rachid Afelad, Plant Manager & Mr Houssam Slimi, Husky North Africa Representative f.r.t.l.: Rachid Afelad, Houssam Slimi and Kay Barton APPE Morocco has already succeeded in carving out a dynamic history for itself within the space of just a few years. Following an enquiry from Coca Cola Bottlers (Atlas Bottling Cie & SBGS), the German packaging company Schmalbach-Lubeca via its subsidiary in Spain Pet Containers Iberia set up a facility in El Jadida in 1999 with the aim of manufacturing preforms locally. The reason for this was Coca-Cola’s desire to be closer to the Moroccan bottlers, because until then, Coca-Cola was being forced to import its PET preforms from Europe and PET was slowly overtaking glass as the predominant material. Following a construction period of eighteen months and commissioning of two Husky XL300 preform machines initial deliveries commenced in 2001. In 2003 Schmalbach-Lubeca sold its PET Division to Amcor where it remained until, finally in 2007, when La Seda de Barcelona LSB Group in turn purchased Amcor’s PET unit.","@ID":14}, "imprint EDITORIAL PUBLISHER Alexander Büchler, Managing Director HEAD OFFICE heidelberg business media GmbH Häusserstr. 36 69115 Heidelberg, Germany phone: +49 6221-65108-0 fax: +49 6221-65108-28 [email protected] EDITORIAL Heike Fischer Gabriele Kosmehl Kay Barton Michael Maruschke Ruari McCallion Waldemar Schmitke Wolfgang von Schroeter Anthony Withers MEDIA CONSULTANTS Martina Hirschmann [email protected] Johann Lange-Brock [email protected] phone: +49 6221-65108-0 fax: +49 6221-65108-28 FRANCE, ITALY, UK Elisabeth Maria Köpke phone: +49 6201-878925 fax: +49 6201-878926 [email protected] LAYOUT AND PREPRESS EXPRIM Werbeagentur Matthias Gaumann | www.exprim.de READER SERVICES Till Kretner [email protected] PRINT Chroma Druck & Verlag GmbH Werkstr. 25 67354 Römerberg Germany WWW www.hbmedia.net | petpla.net PETplanet insider ISSN 1438-9459 is published 10 times a year. This publication is sent to qualified subscribers (1-year subscription 149 EUR, 2-year subscription 289 EUR, Young professionals’ subscription 99 EUR. Magazines will be dispatched to you by airmail). Not to be reproduced in any form without permission from the publisher. Note: The fact that product names may not be identified as trademarks is not an indication that such names are not registered trademarks. 3 PETplanet insider Vol. 16 No. 06/15 petpla.net dear readers, Chinaplas 2015, held this year in Guangzhou, closed its doors a few days ago, having registered 128.000 visitors. This is slightly fewer than the previous year’s 130.000 day visitors when Shanghai hosted the exhibition. The number can be interpreted in various ways. Viewed in a positive light, the number of visitors increased by 14.000 or 11%, compared with the previous occasion two years ago that the event was held at this venue. However, compared to last year’s figures, numbers were down by 1.5%. Whatever gloss is put on the figures, the fact remains that, as far as the PET industry is concerned, this was undoubtedly a successful exhibition. From discussions with exhibitors and visitors it was clear that Chinese suppliers are seeking new horizons in world markets. In mould technology, companies are now offering levels of quality that can be utilised throughout the world. Building a worldwide presence means a long haul, calling not only for quality in technology but also for a first rate on-site service. In addition to these companies hoping to make their mark worldwide, we encountered a number of new companies in the PET sector who seemed to be mushrooming wherever we looked. For the moment, these companies are focusing on the domestic market, but, depending on how things develop, they are likely to be looking eventually to spread their wings beyond China’s borders. All in all, it is clear that China remains not only an exciting consumer country for PET machinery and moulds, but its reputation as an innovative supplier country will continue to grow. At PETplanet we recognise the need to gain a more secure foothold here, to explore the plastics sector in China in greater depth. To do this, we are already busy kitting out our new Editourmobil in which we intend to visit our readers in China in 2016. Yours Alexander Büchler","@ID":5}, "WATER TREATMENT 17 PETplanet insider Vol. 16 No. 06/15 petpla.net New technology of online mineral-adding A new generation of inline mineral-adding technology developed by Newamstar has recently been approved by Coca-Cola. The assessment process included testing the quality of the water four hours after minerals were added. Newamstar says that Coca-Cola’s approval recognises that it has reached an advanced, global level in mineral water production. Accumulating knowledge, overcoming challenges Newamstar has years of experience in water production, but the addition of minerals was a new subject when it began this project in early 2013. The company assessed various different kinds of mineral-adding technology as it sought to build understanding. After several rounds of discussion, testing and development, Newamstar designed the systems shown in f g.1. The design then underwent a laboratory test to determine whether the conductivity of mineral salts at different concentrations has a linear functional relationship. The conclusion was that this is indeed the case, as shown in f g. 2. Newamstar maintains that the biggest advantage of its inline mineral-adding technology over traditional methods is that material flow and mineral adding quantity is stable and well mixed, and that very small adjustments can be achieved and slight variations can be identified by the flow detector and conductivity meter. The operator needs only to turn the valve in order to dissolve the main mineral agent every 6-8 hours. It is well-known that pure water becomes progressively darker as more and more ink is added to it. Even just a drop will affect the purity and concentration of the liquid and Newamstar says that its mineral-adding technology is the same. Mineral concentration must be precisely controlled during the design process as just a single excess drop may lead to the required product concentration being exceeded. It is therefore vital that every drop of product is controlled and the right mixture is maintained. Newamstar says that good products must satisfy customers and help them to increase efficiency, while delivering benefits in terms of safe and sustainable production. After completing the Coca-Cola project the company installed a two mineral water production line for Panpan group. As living standards continue to increase, the environment and healthy lifestyles rise in importance. Drinking water is closely identified with a healthy lifestyle and mineral water improves people’s acceptance of water generally. Newamstar asserts that progressively more consumers are going to enjoy the convenience in their healthy drinks that are brought by its advanced technology. www.newamstar.com RO tank supercharge pump f owmeter pipeline mixer conductivity meter mixing tank water supply metering pump premix tank factitial mixing conductivity meter Fig 1: Dosing and regulator f owmeter (RO water) set to adjust the dosage of metering pump (mother liquor). Mixing and additive proportions are monitored by conductivity meter","@ID":19}, "PACKING / PALLETISING 36 PETplanet insider Vol. 16 No. 06/15 petpla.net The compact end of line The efficiency of a bottling and packaging plant whose daily output reaches millions of bottles depends also on end-of-line operations which need to be perfectly synchronised one another. Smipal, a SMI division specialised in the production of automatic palletising systems, offers reliable cuttingedge solutions with the APS P series. The APS P model features a SCARA arm and integrates in its central column the operations of palletising, empty pallet feeding and pad insertion - three different operations usually performed by separate machines inside their own dedicated space. The new Smipal palletisers of the APS P series, besides the standalone version, can be integrated in a Packbloc Neo compact system, gathering in a unique, small sized plant the operations of an automatic packer, together with an automatic fixed-column palletiser and a turnplate pallet wrapper. The integration of multiple machines offers considerable advantages from the standpoint of operational flexibility and reduction of costs and energy consumption, as it reduces the need to install long stretches of conveyor belts - usually required to connect various stand alone units to one another – and allows a single operator manage the entire system. An example of Packbloc Neo system includes a Smiflexi model LWP 30 wrap-around case packer together with a palletiser Smipal model APS 1550 P and a turntable wrapping machine. Sturdy and elegant packages with the LWP 30 case packer The automatic LWP 30 wrap-around case packers produced by SMI, suitable for production speeds up to 30 packs per minute, stand out in the packaging machine market for a number of technical features which place them at the top of the reference range. Machine adjustments in these systems are made by means of convenient cranks and useful numeric counters, which allow the operator to switch from one pack format to another simply, quickly and accurately without having to use any tools. The cardboard blanks are picked up by a mechanical system that ensures precise synchronisation with the other operations performed by the packaging machine. The blanks used to make the finished boxes are transferred from the cardboard blanks magazine to the main work surface smoothly and uninterruptedly by an up-going, slightly curved system that significantly improves continuity in the feeding of the packaging material. Smiflexi’s LWP series new wraparound case packers have a compact and solid frame, are able to adapt easily to any logistic condition and also mount brushless motors that drive the axes, reducing their energy consumption. A more efficient production thanks to new control systems The LWP series of packaging machines can be equipped with accessory devices that increase their level of efficiency such as, for example, a control device based on video camera. This is mounted at packer outfeed to inspect every single pack produced to detect its size characteristics and correct closing. In case a pack does not comply with the quality parameters entered in the production program, it is rejected automatically. This control system can be further automated by installing a new device to eject and unload defective packs: a conveyor belt that runs on free ball bearings. This belt carries the nonconforming pack to the outside of the production line by gently acting on the bottom of the pack instead of pushing it abruptly on the sides, as occurs in traditional ejection systems. The APS 1550 P automatic palletiser The heart of the compact and integrated Packbloc Neo system is the new Smipal APS 1550 P palletiser. All movable mechanical components are housed within the fixed central column. First there is a cross-member that supports the layer-loading head that moves up and down on the","@ID":38}, "PETproducts 40 PETplanet insider Vol. 16 No. 06/15 petpla.net PET Engineering develops new bottle for Heineken’s Bulgarian beer Zagorka, part of the Heineken Group, is based in Bulgaria and makes a beer that is claimed to be distinguished by a particular bitterness, aroma and flavour by a recipe that includes the combination of two different types of hops. Its main target market is the 20 to 30-year-old segment. It commissioned PET Engineering to design a package that would strengthen the beer’s on-shelf visual impact and align the 1 and 2l PET bottles to the product’s smaller glass and aluminium containers. PET Engioneering says that the new Zagorka PET bottle gives the brand a “more distinctly masculine” image through a robust shape and the inclusion of two lions on the body of the bottle. The lions are symbolic of Bulgaria. The labels have been deliberately located in the upper part of the container in order to achieve immediate recognition, when the bottles are placed within a range of other brands; the normal practice is to have large labels in the central part or thinner ones in the lower area. The location provides the bottle with an extensive gripping area, which is meant to make it easier to handle. It is also intended to create a physical connection between the brand and the consumer, as well as aligning the PET bottle with the glass and aluminium packages. www.petengineering.com Semo Packaging launches Fresh’Closure recloseable food packaging solution Semo Packaging’s Fresh’Closure system utilises a new mono-material solution and is designed for easy opening and closure of food packs. The company says that Fresh’Closure has been developed in response to what it says are unsatisfactory performance aspects of existing food packaging solutions, including poor user-friendliness; time-consuming opening and closing; inadequate product preservation; broken films and lost ties. Semo further asserts that a badly-closed product is more at risk from humidity, dirt or mould and will end up as waste, more quickly, and can also present a risk to health, because of food poisoning. The Fresh’Closure film and packaging incorporates a drawstring system and is intended to offer better preservation of products, for longer, as well as easier opening and closing. The product is claimed to enable the packaged contents to retain most of their freshness and nutritional properties, even with repeated use. The Fresh’Closure film has been designed to be 100% recyclable and reusable and its production process requires less material than current, competitor solutions; the company says that this enables reduced CO 2 emissions. Semo Packaging says that this product has also been designed for high on-shelf recognition. www.semoflex.com","@ID":42}, "MARKET SURVEY 27 PETplanet insider Vol. 16 No. 06/15 petpla.net Caps and closures Bottle-to-bottle recycling plants Preform and single stage machinery Preforms Preform / stretch blow moulds Closure systems Two stage SBM machinery Compressors Resins / additives Filling equipment Suppliers of preform moulds / stretch blow moulds Our annual overview of the market on the topic of mould tools for PET bottle production introduces you to the manufacturers of perform moulds and stretch blow moulds. The companies are listed above in alphabetic order; in the tables they appear in the order in which their details were received by the editors. 20 companies participated: ASB, Awanti Polymoulds, Comep, Demo, Hallink, KHS, Kosme, Krones, MHT, Milacron, PET Technologies, R&D Leverage, Sacmi, Simex, Sipa Mold, Solent Mould Tools, Steelmades, Tooling Preform Systems, Vitalii and Son and Wentworth Mold. Although the publishers have made every effort to ensure that the information in this survey is up to date, no claims are made regarding completeness or accuracy. 06/2015 MARKETsurvey SBM moulds Company name DEMO Design and Moulds KHS Corpoplast GmbH Vitalii and Son Kosme GmbH R&D Leverage PET Technologies Postal address Telephone number Web site address Contact name Function Direct telephone number Fax E-Mail Via Olivera, 48, 31020 San Vendemiano (TV), Italy +39 0438 409048 www.designandmoulds.com Mr Alberto Castellan General Manager +39 0438 409046 [email protected] MeiendorferStr. 203, 22145 Hamburg, Germany +49 40 679 07 0 www.khs.com Mr Arne Wiese Manager Bottles +49 40679 07 113 [email protected] 276, bul. Vladislav Varnenchik, Bulgaria; 9009 Varna +359 8885 18782 www.vitaliiandson.eu Mr Vitaly Marinyak Executive Manager +359 8885187 82 +359 525101 68 [email protected] Gewerbestr. 3, 2601 Sollenau, Austria +43 2628 411 0 www.kosme.at Mr Johann Gugler Managing Director +43 2628 411 125 +43 2628 411 4125 [email protected] Leverage House, Hamilton Road, Sutton in Ashfield, Nottinghamshire, United Kingdom, NG175LD +44 1623 556287 www.rdleverage.com Mr Alan Tolley Managing Director +44 1623 556287 +44 1623 552240 [email protected] 2 Shirokaya St., Chernigov, 14021, Ukraine +43 720 902 169 www.pet-eu.com Mr Maxim Poliansky Commercial Director +43 720 902 169 [email protected] Stretch blow moulds Bottle size (max.) (in litres) Up to 20l Up to 3,125l Up to 20l 30l 5l 30l Moulds supplied directly to blowing machine manufacturers Yes, as well as bottlers Yes Yes No Yes Do you supply retrofit moulds for existing SBM machines? Yes Yes Yes Yes Yes Yes For which makes of bottle makes have you already produced moulds Rauch, SA Damm, Norda, Vinadio Mainly for KHS Corpoplast InnoPET Blomax SBM; Krones Contiform Sidel,SIG, 1Blow, MAG, Sipa, ADS, Kosme, Krones, Siapi Kosme, Krones, Sidel, KHS Sidel, Krones, Sipa, Side, Chumpower ADS, Dynablow, KHS, Kosme, Krones, Siapi, Sidel, SIPA, SMIForm, etc. Bottle design service New PET bottle design and modification of existing containers for improvement purposes (eg. Lightweighting) Yes (bottles & shapes) Yes Yes Yes Specialities Complete service carried out entirely within one production plant reducing costs and lead times Light-weight design and special applications Bottle designing, prototyping, parts enegineering Bottle development service free of charge, if blowmoulds are ordered Bottle design, prototyping, laboratory tests, blow moulds production, auxiliary parts and mould repair Other Prototyping, laboratory tests, mould installation, machine start-up Researches on weight and material distribution R&D Leverage is a supplier for the single stage, Injection Stretch BlowMoulding ISBM industry.","@ID":29}, "CAPPING CLOSURES 31 PETplanet insider Vol. 16 No. 06/15 petpla.net shows how delicate and professional closure production still is. 1885 – Already 150 patents applied in the USA for closures and lids 1892 – William Painter invented crown cork 1900 – Ceramic stoppers with rubber washer 1940 – Aluminum roll-on 1970 – Albert Obrist introduced the first prethreaded plastic closures 1985 – Albert Obrist became part of Crown Cork and Seal Company 1985 – HC Industries, today Alcoa, introduced the first compressionmoulded closures 2005 – More than 90% of all closures are produced in plastic 4.1.2 Closure Functions Closures are often overlooked when we discuss about bottle packages. However, they form an important part of the overall functionality. In this chapter we are discussing all the important details of closure design, process and tool selection, and operational considerations. Most plastic caps are threaded, allowing consumers to easily open the package without the use of tools (such as a bottle opener for crown corks), and then reseal it to finish the product at their convenience. This easy resealing is maybe the biggest advantage that threaded caps have over other forms of closures. Other packages have incorporated this feature often at considerable cost. Examples are necks with caps fastened to cartonated drinks and rotating crown corks that can be opened without a tool. The main function of the cap is of course to prevent leakage of the product from the bottle and to protect it from contamination, and it must do so under all conditions that the package was designed for. Caps for carbonated beverages, for example, must withstand significant internal pressure, whereas caps for contents that could suffer from microbial contamination must be sterilised before or after filling. But most modern caps also have tamper evident bands that assure customers that the seal has not been broken since the bottle was filled. These are designed to either stay on the cap in the unscrewed position or stay on the bottle instead. Caps may also provide proof of purchase or inform the consumer of an instant win. They may be printed or may carry the logo or some other identification of the brand owner. Besides protecting the contents, caps also must be consumer friendly in terms of unscrewing and resealing. Other caps must be designed for the opposite function, i.e., prevent children from getting access to the contents of the bottle. Child resistant closures are not part of the beverage industry but may be used for medication and similar products. Another group of closures are sports caps. These closures feature a lower member that is in firm contact with the bottle, usually by means of a thread, and an upper member that features some way to open access to the drink in the bottle. These are popular with sports enthusiasts because they allow drinking by using one hand only, a nice feature for consumers involved in some activity. Caps may be produced in IM or CM in 1 or up to 192 cavities. Chapter 4.6 provides an overview of both methods and compares the important elements. There is also a significant difference in tooling design. Tamper evident bands may be formed right in the tool or slit as a secondary operation. Some tools use unthreading devices to strip closures off the injection cores where others “bump” them off. Lowcost tools save initial capital outlay but may run at slower cycles, produce inferior quality, and have higher maintenance costs associated with them. It can be seen from the above considerations that a variety of closure designs is necessary to fulfill the various requirements. It should also be obvious that closure as well as tooling design play an important role in the design of the overall package. Please order your copy at the PETplanet insider book shop: https://petpla.net/books Bottles, Preforms and Closures A Design Guide for PET Packaging Second Edition by Ottmar Brandau € 115,00 180 pages © Copyright Elsevier 2012 * This article was published in Bottles, Preforms and Closures, Ottmar Brandau, Chapter 3.8. Copyright Elsevier 2012 Figure 4.1 Raw material is by far the most important cost component. (Graph courtesy of Corvaglia Ltd).","@ID":33}, "EDITOUR REPORT 10 PETplanet insider Vol. 16 No. 06/15 petpla.net Nuremberg Milan Rome Naples Palermo Tunis Algiers Rabat Casablanca Marrakech Seville Madrid Lisbon Bologna Monastir Agadir Tangier Valencia Cordoba Bilbao Oporto Andorra La Vella Venice Turin Florence Messina Barcelona Zaragoza North Africa Part 3 by Kay Barton The PET market of Morocco The Go to Brau Beviale Tour moves on to the next stage. Following our reports on the PET sector in Tunisia and Algeria, our highlight in this issue is the Moroccan market. Industry experts see significant growth in the packaged water sector, driven by increasing demand for good quality drinking water. Hotfill is another hot topic, as consumers increasingly favour healthy drinks like juices. Our journalistic voyage of discovery took us from Tangier in the north to Agadir in southern Morocco. As we traversed the country, we met the water bottler Chaouen Waters, PET preform manufacturers Preformer Morocco and APPE, as well as injection moulders and bottlers of cooking oil Les Huileries du Souss.","@ID":12}, "PACKING / PALLETISING 37 PETplanet insider Vol. 16 No. 06/15 petpla.net Securing value for a strong future www.krones.com EXPO PACK México 2015 Mexico City, 16 – 19 June Center Banamex, Stand 3100 ProPak Asia 2015 Bangkok, 17 – 20 June Hall 101, Stand 1F01 column. The layer-loading head itself performs fast and accurate horizontal movements along the cross-member thanks to a telescopic guidance system. Finally, an articulated arm based on SCARA technology performs both vertical and horizontal movements to feed the empty pallets and to insert the cardboard pads between layers. All the vertical and horizontal movements of the mechanical components of this SMI palletising system are managed by the machine’s automation and control system, which establishes precise and coordinated trajectories for each one. This happens in synch with the operations performed by the layer-loading head so that the machine’s various components will never touch or interfere with one another. Continuous-flow layer formation Among the features of the new Smipal APS 1550 P palletiser is the machine’s infeed section with the layer pre-composition system. It consists of a pack rotation device equipped with belts running on free ball bearings, a row-formation belt and a layer-formation belt. In the new system proposed by Smipal, packs are, before the row is formed, rotated in the palletiser’s infeed section through a conveyor belt fitted with free ball bearings. By setting this function in the palletising pattern, these bearings impart rotary motion to the bottom of the pack in transit. This feature avoids the drawbacks linked to traditional pack-turning systems in which the pack is turned by making it collide against a fixed blocking element located above the sliding belt. Efficient end of line with the integrated turnplate pallet wrapper The compactness and efficiency of the Packbloc solution proposed by SMI were further enhanced by the Neo version, integrating a turnplate pallet wrapper in the palletiser’s structure, which wraps the individual layers as soon as they are placed on the pallet. In fact, the configuration of the Packbloc Neo packaging system featured the wrapping of the pallet in wrap-around film simultaneously with the formation of its layers, thereby eliminating dead time typical of other solutions in which the wrapping takes place once the pallet is finished. This solution is especially suited to the palletising of unstable containers such as, for example, loose 5 to 10l bottles not packaged in cardboard trays. These remain firmly placed on the pallet as it advances on the machine’s conveyor belts, thanks to the wrapping of the single layer. www.smigroup.it","@ID":39}, "EDITOUR REPORT 14 PETplanet insider Vol. 16 No. 06/15 petpla.net Independent supplier and regional solidarity preform sector, APPE Morocco has an estimated market share of around 56%. The company also uses preforms from its own group from time to time in order to cope with capacity bottlenecks and these preforms are subsequently imported into Morocco. “We have a clear vision of what we want to do”, says Mr Afelad. “In the future we are looking to expand our export business in Africa to gain a foothold in that market”. Market studies being carried out by APPE Spain are already underway in the regions of interest and a factory in Algeria is also planned for 2015/2016. www.appe.com www.husky.co Les Huileries du Souss | June 23, 2014 We met: Mr Nabil Houssine, Technical Director, Mr Belhassan, CEO and Mr Houssam Slimi, Husky Representative North Africa f.l.t.r.: Houssam Slimi and Nabil Houssine In Agadir we visit not only the plastics division but also the edible oil production facility operated by Les Huileries du Souss (HSB), a company based not far from the sea. We were welcomed to the Plastics Division by Mr Nabil Houssine, the Technical Director, who was formerly with Tetra Pak for a number of years, as well as the CEO of the parent group Belhassan, Mr Belhassan himself. According to Mr Houssine, the Plastics Division more or less represents the headquarters of HSB from an operational point of view. The history of the Belhassan Group begins more than 60 years ago with the production of olive oil. Today the company has around 5000 employees and is still under family management. Nowadays Belhassan comprises, in addition to HSB, the companies SBGS, licensed bottlers for Coca-Cola and covering the south of Morocco, Cibel, active in the production of canned fish, Domaine Nora, responsible for the cultivation of oranges as well as two real estate companies and one marketing company. But let’s stay with HSB, which was set up in 1976. Today, in addition to the production of various types of edible oil, packaging / production and marketing activities are carried out in the coffee, tea and margarine sectors. “It has always been particularly important to us to affirm our commitment to the local area, the southern Moroccan region of Souss, and the Belhassan family which has its roots here and to reflect this in the way we go about our lives, hence the name “Huileries du Souss’”, explains Mr Houssine. Let’s concentrate initially on the Plastics Division, some 10km outside the centre of Agadir. The site is still relatively new. Until three years ago the Plastics Division was to be found at a different location in Agadir. It has since relocated to the new facility during a series of expansion exercises. Nowadays the company employs 250 people in a 3-shift operation on a plot measuring around 30.000m2. In addition to PET preforms, the portfolio also comprises closures and handles together with margarine tubs. Container with freshly produced HSB preforms There are two type G300 Husky machines in operation that were taken over from the previous site and six Netstal Synergy 2400s for caps, handles and margarine tubs. In the preforming area the belt width accommodates 18g, 25.5g, 35.5g, 48g, 60g, 75g, 91g and 125g of PCO 1810 and PCO 1881. The current output for PCO 1881 is 380mill. preforms annually. This equates to roughly 10,000t","@ID":16}, "PETnews 6 PETplanet insider Vol. 16 No. 06/15 petpla.net Phoenix Technologies invests USD18 million to expand rPET production Phoenix Technologies International, a global producer of recycled polyethylene terephthalate (rPET), is announcing an USD18 million expansion to enable upstream production integration. The company will be adding a proprietary new wash line, expected to be operational by the end of 2015, so that it can self-manufacture clean flake. The company uses clean flake as in feed material to create rPET, which is used to produce packaging for applications such as beverages, food, personal care and household cleaners. Up until now, Phoenix has either purchased clean flake directly or sourced baled bottles, which have been reclaimed from curbside collection, and then tolled through a third-party wash operation to create clean flake. The wash line has a projected output of 25,000 tons (50 million pounds) of clean flake per year. The new line will be housed in a leased 6,130 square meter (66,000 square foot) facility located in close proximity to Phoenix’ existing manufacturing plant. When the operation is in full production, the new facility is expected to employ approximately 30 associates. This is in addition to the 53 employed at the main plant. www.phoenixtechnologies.net 16th GEPET in France covers low crude prices, PET markets and packaging innovations The sixteenth edition of GEPET (Greater Europe PET Resin Trade, Applications & Recycling) on 10 -12 June, 2015 in Lyon, France, will cover discussions over the impact of low crude prices on the PET market, RPET industry vis-à-vis low virgin PET prices and bring a fresh perspective on cost optimisation, lightweight developments and conversions from HDPE to PET. David Swift, Managing Director, PCI PET Packaging, Resin & Recycling Ltd will open the event and give his views on the burgeoning question ‘Low oil price: Opportunity or threat to polyester packaging?’. Packaging majors including Nestle Waters MT and APPE will share key perspectives on ‘Packaging Sustainability: Why we should look at the entire product life cycle’, ‘Revolutionary ThermaLite PET jars - for hot/cold fill and all methods of pasteurisation’ as well as French converter PDG Plastiques with an insightful update on ‘PET packaging for milk and dairy products’. Futher topics covered by executives from Anellotech Inc, Reliance Technology Group, Reliance Industries Ltd and Sorepla will include bio-based paraxylene from non-food biomass, PX competitiveness, competitiveness in the rPET business, among others. In addition, a pre-conference site visit to the state-ofthe-art PET recycling plant of APPE in Beaune is scheduled on 10 June. A post-conference workshop on ‘Improving RPET Quality for Food Contact Applications & New Developments in PET (bottles /trays/ sheets) Recycling’ will round off the programme. www.cmtevents.com Flying start: the Evoguard valve series Krones AG’s series of valves, produced by subsidiary Evoguard GmbH and unveiled at the recent BrauBeviale in Nuremberg, can be considered as a success. So far, more than 150,000 valves have been produced: disk valves, seat valves, double-seat valves, aseptic seat valves and aseptic double-seat valves. “The Evoguard series of valves has been optimally tailored to the needs of the food and beverage industries, and of the dairy sector too,” explains Martin Zierer, Managing Director of Evoguard GmbH. “The most important requirement applying when we were designing the valves was excellent functionality in actual use, incorporating high-performance seal systems that meet all the hygienerelated stipulations involved.” The use of the latest materials available for producing the seals has proved to be a good choice for both the disk valves and for the seat and double-seat valves, creating several advantages in process applications. In addition, the parts can be precisely traced and identified using a matrix code. The Evoguard valves are produced in the Upper Palatinate town of Nittenau, where the 4,000 square meter production and administrative building accommodates the R&D, design, sales, manufacturing and assembly departments. www.krones.com Polymetrix EcoSphere SSP for new mega scale PET plant Polymetrix AG, the former Bühler Thermal Processes AG, has been awarded a contract for the delivery of two mega scale EcoSphere SSP lines for a bottle grade PET production facility in Jiangsu Province, P.R. China. The plant is scheduled to be commissioned in the second quarter of 2016. The integration of the Polymetrix EcoSphereTM PET SSP technology and the latest generation of melt phase technology built by Chemtex, is setting new standards for PET manufacturing in terms of size, product quality, conversion costs and capital costs. The CP and SSP sections are directly coupled in order to avoid investment in intermediate storage silos. Special attention has been paid to keep the operational robustness of the new PET production concept at a comparable level to conventional PET manufacturing processes. www.polymetrix.com","@ID":8}, "NEWS 8 PETplanet insider Vol. 16 No. 06/15 petpla.net The plastic closure company committed to your success BERICAP Technology Research and Development Mould Technology | Global Presence Capping Technology and Know-How Innovation and Flexibility www.bericap.com SPI restructures its marketing and business development group The plastics industry trade association SPI has restructured its marketing group to centralize the branding and messaging of all of its products, member services, and event offerings, and has added business development roles to further develop its portfolio of expositions, conferences and meetings. Reflecting the change is the appointment of Brad Williams as vice president of marketing and business development. He will continue to oversee marketing and sales for SPI’s triennial NPE trade show, but will also be responsible for overall SPI marketing and the development of new SPI offerings. Kristen Petersen is now marketing director and will oversee day to day activities of SPI’s marketing program. Reporting to her will be Angie Tran, now promoted to senior marketing manager for all SPI properties. And Adam Cromark, SPI’s marketing specialist will expand his role of supporting marketing efforts across all SPI properties, expanding SPI’s online, mobile, and social media presence. The restructured marketing group will report to Gene Sanders, senior vice president at SPI. www.npe.org Doehler Multi-Sensory Design for colours In addition to a good taste, the product colour is largely responsible for a product’s success. Consumers associate the colour of a food or beverage with certain taste and product attributes, stirring senses and subconsciously triggering emotions. Based on its broad portfolio of natural colours and colouring concentrates, as well as the findings of a consumer study, the company Doehler has developed the so-called Multi-Sensory Design for colours. As part of its in-house consumer research, Doehler investigated the reasons behind consumers’ colour associations in a global study. The study concluded that selecting the right colour supports the product positioning of food and beverages in a targeted manner. This makes it possible for producers from the food and beverage industry to find the right, natural colour tone that matches the desired product positioning. The methods developed can be applied to all segments of the food and beverage industry and tailored to meet specific customer issues, market requirements and applications. www.doehler.com The future in PET preform base lightweighting Smart Base is a new preform base lightweighting technology. Compared to other existing preform base lightweighting systems available in the market, Smart Base is different in the way that the design changes: it involves exclusively the outside of the preform tip without changing the standard geometry of the injection core, while obtaining the same weight saving of other comparable solutions. In order to implement Smart Base in an existing injection mould, the only part that needs to be changed is the gate pad in the cavity. There is no need for a new injection core or for new gates in the take off plates/cooling tubes. This alone, on top of the weight saving benefits, can significantly reduce the conversion costs. The substitution of a standard gate pad in the cavity with a Smart Base gate pad is also a very fast and simple procedure which has very little impact on production time both during in house testing and during the actual conversion of the entire mould. www.smartbasepreform.com","@ID":10}, "MATERIAL / RECYCLING 20 PETplanet insider Vol. 16 No. 06/15 petpla.net Bottler, recycler or organic producer? It’s not just PET bottles that make their way to the plant. Aluminium cans, plastic packaging and other impurities are separated out by Blue Mountain Plastics Ice River Springs Water Company Inc. of Feversham, Ontario, is a bottler of water – as the name implies. The company gets its supplies from springs on the lands owned by the Gott family and it is the leading private-label bottler in Canada. It holds a large share of the Canadian bottled water market and enjoys a growing presence in the USA. Sustainable operations rank high in the company’s priorities; this focus helps to explain why it can recycle up to 85% of all consumer PET plastics generated in the Province of Ontario into new bottles for their own needs, thus minimising the use of new material. Ice River Springs, together with its subsidiary, Blue Mountain Plastics, Shelburne, is one of the largest PET processors in Canada. The plant, which is situated to the north of Toronto, ON, has a capacity of over 22,600 metric tons of pressed PET bales a year. One of its challenges is the fact that the bales it receives are not as well differentiated as is the case in other parts of the world. They are only 65% PET, with the balance made up of closures, labels, aluminium cans and other plastic packaging. To cope with this, Blue Mountain Plastics, together with Amut SpA, has built up a complex sorting operation. Every portion of a bale is sorted and recycled with only a small percentage of the bale residual materials ending up in landfill. Individual types of containers and colours are separated out in the conditioning plant, which helps it to achieve a very high degree of purity. In this system, the bottle undergoes total shredding only at the end of the process. Sorting of the various elements begins with the baling wire that keeps the bales together. This is chipped and sold to metal recyclers. Aluminium cans exit via a metal separator, where they subsequently undergo post-sorting and baling. The pure aluminium cans themselves will attract higher prices than the per kg price of the original bale. Next, the used labels are collected and the PET bottles split up into clear and blue and green streams. At the end of the process the flakes go through a colour separator again, thus delivering a very high level of purity. Ice River Springs has recently expanded its use of the other recovered mixed plastics with the acquisition of a share of CR Plastics — a company that manufactures outdoor furniture from 100% recycled HDPE and PP. As a result of this partnership the company has found a valuable use for the post-consumer plastics bundled in with the PET bales; all the recovered HDPE and PP chips go to CR Plastics for its 100% recycled chairs. After this process, the washed PET flakes go down two different routes in-plant before they become reborn in bottles. Ice River operates both Starlinger and Krones bottle to bottle recycling systems and can process up to 3000kg/h. The purified PET materials comply with both CFIA and FDA requirements and can be used directly in beverage applications. Ice River processes these materials into preforms at injection moulding machines located in each of its plants. It is unique in Canada in being able to manufacture bottles with up to 100% rPET. In the traditional conditioning operation, the PET needs to be heated 3 times (melt filtration, decontamination, and subsequently injection moulding) to make a preform. Ice River is working actively with both Starlinger and Krones to develop new processing methods to minimise these steps, which will lead to savings in both energy and processing costs. Premium Sponsor Sponsors Plastics furniture made from recovered HDPE and PP chips collected and washed at Blue Mountain plastics.","@ID":22}, "PREFORM PRODUCTION 25 PETplanet insider Vol. 16 No. 06/15 petpla.net Adiabatic cooling towers cut energy consumption EarthSmart adiabatic cooling towers from Conair can reduce water and energy consumption and prevent contamination of process f uid, while maintaining stable leaving f uid temperatures even in hot weather Plastics processors who use EarthSmart adiabatic cooling towers of Conair can reduce water and energy consumption and prevent contamination of process fluid, while maintaining stable leaving fluid temperatures even in hot weather. Process fluid circulates in a closed loop through tubing in the tower, so it is isolated from contamination and evaporation. Eleven models are available to handle nominal flow rates from as little as 170 l/ min (45 gal/min) up to 1,930 l/ min (510 gal/min) of process fluid (35% ethylene glycol). Lower process water temperature than conventional tower The adiabatic part of the system is what reduces the temperature of the air flowing through the tower. The evaporation of moisture from the adiabatic pads causes it to cool the air so that it can remove heat from the process water circulating through coils in the tower. The cooled air allows the tower to achieve a lower process water temperature than can be reached with only ambient air flowing through conventional towers. In addition, the adiabatic design saves water and energy by keeping the process fluid separate from the water evaporated during the adiabatic process. Cooling tower can be operated with or without using adiabatic process Adiabatic wetted panels are mounted so that they are in front of the cooling tower coil through which process water flows. As ambient air passes through the wetted panels, water evaporates, reducing the temperature of the air flowing into the unit so that it cools the process fluid. The cooling towers can be operated without using the adiabatic process (relying on ambient air to cool the coils) when air temperatures are low. This saves water and energy. By using the adiabatic process only when it is absolutely required during periods when outdoor temperatures are high, the unit reduces water consumption to just a fraction of what conventional towers use. The process circuit is a closedloop. All of the evaporation and water consumed in the adiabatic process is external to the process loop, so process-fluid contamination, and unwanted build-up in mould-cooling channels, is eliminated. The closed process loop also allows an ethyleneglycol mix to be used in place of water, which helps prevent freezing during cold weather. PLC precisely controls when the adiabatic process is required An application-specific programmable logic controller (PLC) and electronically commutated (EC) motors, standard on the EarthSmart towers, ensure minimal electrical power is used during the process. Smart-fan technology varies speed to minimise energy consumption when the tower is under partial load. The PLC also precisely controls when the adiabatic process is required to maintain accurate leaving fluid temperature and reducing water use. Further features contributing to stress-free maintenance include: Motor-repair switches that allow individual fans to be shut down for service while other fans continue to operate. The adiabatic wetted panels that slide out easily for cleaning with no special tools required. EarthSmart tower coils that are supported independently of the frame allow for natural expansion and contraction, which eliminates wear points and extends the lifespan of the coil. www.conairgroup.com","@ID":27}, "INSPECTION SYSTEMS 39 PETplanet insider Vol. 16 No. 06/15 Alongside the PVS003, Sacmi proposes the PVS024 inspection machine, specifically developed for the control and review of preform lots on which defects have been detected. This solution can automatically read the cavity number of each preform; this information, in addition to being used to produce detailed statistical reports, lets operators select the numbers of those preform cavities to be eliminated with ease via a user-friendly interface. The machine can inspect preforms of various sizes at rates of up to 36.000pph. The PVS range features the latest version of the CVS3000 2.0 64bit software, which allows a simple and intuitive manmachine interaction. One of the advantages of the CVS3000 is the standardisation and compatibility with all automated inspection systems produced by Sacmi, including the CHS (closures handling system). Since 2013 Sacmi completely redesigned to raise inspection rates to new, high-speed levels. Sacmi has, over recent months, developed a potentially innovation for in-lab quality control not only of the cap or the container, but also the entire cap-bottle system. That solution is called Cube Eye. It executes complete X-ray tomography analysis of plastic or aluminium caps and the bottle, highlighting all the sealing characteristics quickly in a non-destructive manner. The far-reaching network of sales and assistance centres of Sacmi covering five continents and provides close support for customers by local technical assistance services. www.sacmi.it The Cube Eye","@ID":41}, "BOTTLE MAKING 24 PETplanet insider Vol. 16 No. 06/15 petpla.net The 1Blow PET reheat stretch blow moulding machine design combines rotary and linear functions for process flexibility and high production. Linear and rotary functions on new PET bottle machine The 1Blow PET blow moulding machine 2L shown at the NPE 2015 The two common types of PET reheat stretch blow moulding machines - rotary and linear - are cost- and/or performance-prohibitive at production rates of about 4.000 to 8.000bph, according to 1Blow, of Boissy-l’Aillerie, France. It offers a range of compact, all-electric stretch blow moulding machines that use both linear and rotary functions to produce PET bottles ranging in size from 200ml to 20l (5.3 US gallons), and with neck finishes from 20mm to 70mm. Production rates extend from 500 to 8000bph. It can use blow moulds from manufacturers such as KHS Corpoplast, Krones AG, Sidel and Sipa SpA. The rotary blow moulding units are offered with six technology kits, to expand bottle design and functional possibilities. The rotary wheel design’s efficiency claims are based on the continuous preform-to-bottle operation. The primary mechanical component is the rotary union or blow wheel, which supports and indexes the blow moulds around its circumference. 1Blow says that it is a highly complex, high-precision component that houses critical utilities such as low-pressure air, highpressure air, cooling water, electriWhen the preform exits the oven it is transferred to a proprietary gripper and pitch-changer. Inside the oven the preforms rotate on spindles and have a pitch (centre to centre) spacing of 60mm; in the mould the pitch distance is typically 120mm to 160mm, depending on machine brand. The pincers on 1Blow’s grippers can open up 180 degrees, which allows them to completely clear the preform’s neck finish. They traverse a servo-driven linear system to transfer the preform from the pitch-change unit to the mould. 1Blow has offered one-cavity and two-cavity units for several years and added a four-cavity model in 2013. A six-cavity standard unit and a model for production of wide-mouth bottles are in development. Other standard features include a high-pressure airrecovery system, Internet-ready connectivity, an on-board technical and maintenance manual, and an internal voltage modulation/regulation system that eliminates the need for an electrical transformer. www.1blow.com cal controls, recovery air and hot oil. It becomes less efficient and more expensive at lower production levels and has to rotate without leaking. The potential inefficiencies of linear-type reheat stretch blow units lie in their operating motion, which includes a non-productive return stroke. 1Blow’s in-line rotary machine uses 11 key motions to move the process from PET preform to finished bottle; 16/17 production steps are required in competing SBM units. Nine of the 11 functions use rotary devices; the final two steps of the process, preform into the mould and blown bottle out of the mould, are linear. The 1Blow design does not include a rotary union so the moulds do not move through the machine; they are stationed at the clamping/ blowing point. PET preforms enter the system by elevating conveyor and are moved to the preform orientation device and static-rail preform feeder. A star-shaped in-feed wheel transfers the preform to a carouselstyle rotary reheat oven; its three banks of adjustable infrared (IR) heating lamps are claimed to provide capacity 50% greater than competing machines.","@ID":26},
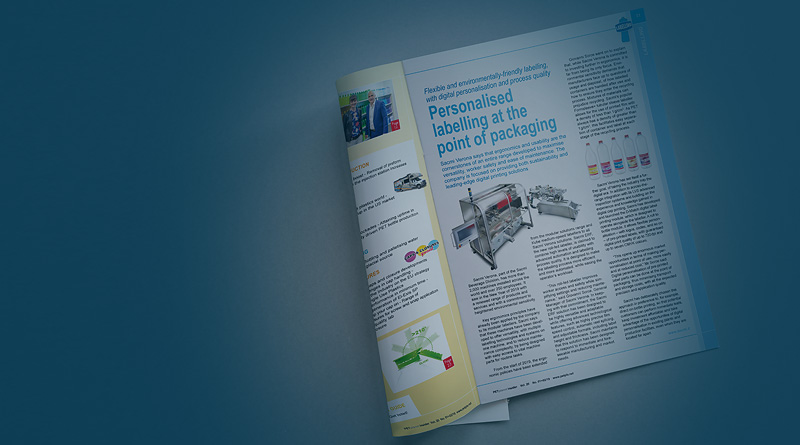