"PACKAGING 32 PETplanet Insider Vol. 17 No. 11/16 petpla.net PET packaging of ready-to-drink teas and more Hot-filled – cold-chilled Based on an article by Dominik Appoltshauser, Krones AG Hot-filled ice tea – a definite success story for Leão Alimentos e Bebidas. As part of Coca-Cola Brasil and its regional producers, the company is responsible for administering the entire production chain of the national line with still beverages, teas and energy drinks from the domestic Coca-Cola portfolio. In order to upgrade the quality and natural goodness of the ready-to-drink teas and soft drinks being produced, and to upsize the filling capacities, the company has since 2010 installed three new complete lines and a syrup kitchen from Krones at its facility in Linhares. As a market leader, Leão is actively involved in the Brazilian economy, creates jobs, and thus invests in several of the country’s regions. The production facilities in Linhares (Espiritu Santo), Americana (São Paulo), plus Fazenda Rio Grande and Fernandes Pinheiro, both of them in the Paraná region, make numerous highly disparate products that refreshingly quench the thirst of millions of Brazilians all over the country with a huge choice of squashes, mixed drinks, juices, soft drinks, teas, chocolate and wellness beverages, plus energy drinks. Ready-to-drink tea in PET At the two production facilities in Paraná State, Yerba Mate is refined and roasted, the concentrates for the ready-to-drink tea line are prepared and in addition the tea brands Leão Fuze and Matte Leão for self-brewing are produced. Another plant in Espiritu Santo produces fruit purees from passion-fruit, mango and guava for two filling facilities, in which subsequently the squashes, fruit juices and fruit-based mixed drinks are filled in beverage carton packs and in cans. In Linhares, Leão also produces readyto-drink teas and soft drinks, which are then bottled in PET containers. Linhares is located on the Atlantic coast in the state of Espiritu Santo, about 700km north-east of Rio de Janeiro. The plant there accommodates beverage cartoning lines, canning lines and now three PET lines from Krones. Since the company attaches high priority to producing and filling its drinks in as natural a state as possible, and above all without any preservatives, the group changed over its filling modalities for readyto-drink teas to PET containers: from cold-filling with preservatives to hot-filling without them. The plant in Linhares was an obvious choice for this. “We’ve always aimed to install innovations and high-tech in our facilities,” explains Dirk Schneider, Leão’s German-born Industrial Director, whose remit covers all of the company’s production plants. He has lived in Brazil for 15 years, and since 2013 has been responsible for technology, engineering, innovations, safety and operational quality. In 2010, Leão was already operating a PET hotfill line from Krones in Linhares. The first product bottled there was Powerade. For making some of its products, two more hotfill PET lines were ordered from Krones. Due to what were back then high levels of demand for beverages in this category, Leão swiftly upped the production output by 50%. When the new lines were installed, there were two challenges that had to be mastered: firstly, the hall area selected, The DecoBloc’s technology enables the containers to be dressed in either sleeves or wraparound labels.","@ID":34}, "TRADE SHOW PREVIEW 54 PETplanet Insider Vol. 17 No. 11/16 petpla.net The main difference - compared to injection technology - is the heightened efficiency that stems from single-stage technology (i.e. synchronised production of preforms and their subsequent stretch-blowing). Minimum levels of potential preform contamination (thanks to high machine outlet temperatures and immediate transition to subsequent blow-moulding and bottling) make it ideal for the dairy industry and other fields where even low-level preform and container contamination can affect product integrity. In addition to considerable savings on the preform cleaning and decontamination fronts, there are energy savings as there is no need to cool, store and subsequently reheat preforms prior to blowing. Elimination of the preform storage unit, now transformed into the dynamic Sacmi CPB Link buffer which intervenes, only as necessary, to make up for the different “average efficiency” of the two processes and acts in a controlled ultra-clean environment eradicates preform cleaning and heating-cooling costs. This is intended to allow manufacturers to cut average bottle costs by 5-15% while keeping energy consumption (including all preform production and blow moulding) below 1kWh per kg of processed PET. This result is also achieved thanks to net savings on the use of raw material (preform weight is reduced by 0.2-0.4g, about 4%, container characteristics remaining equal, thanks to absence of the gate; this technology also allows flat-bottomed preforms to be produced). Container quality and healthiness: acetaldehyde formation is directly proportional to PET processing temperature and pressure and is thus minimised thanks to compression, a process which acts at lower temperatures and pressures, providing manufacturers with considerable savings vis-à-vis the additives needed to prevent the formation of this harmful substance; because high-viscosity PET can be used (not possible in the injection process, as it needs to transit very narrow channels) it is possible to obtain stronger, longer-lasting containers. Moreover, the moisture absorption that typically affects traditional PET manufacturing processes is virtually eliminated thanks to synchronisation of preform production and blow-moulding. There is an evident boost to logistical efficiency (no internal preform transport and storage facilities required). “Sacmi heroPET 4.0”, explains Iacopo Bianconcini, Marketing Manager of the Sacmi Group Beverage and Closures&Containers Division, “represents the culmination of that PET revolution which began in 1973 when plastic bottles first started replacing glass ones. For years, neither traditionalpreEntire integration for the beverage industry Sacmi will present heroPET 4.0, the first comprehensive, integrated platform for “one-step” production of preforms, stretch-blow moulding and filling that shows all the advantages of compression technology. Sacmi has developed a completely new system that allows preform production to be synchronised with stretchblow moulding of the preform using a rotary blow moulder. This result was achieved thanks to the flexibility of the process which, in the event of stretch-blow moulder stoppage, allows production and handling of cold preforms within an automated ultraclean storage environment. Sacmi Hall 7A | Booth 319 / 323","@ID":56}, "PETpatents www.verpackungspatente.de 64 PETplanet Insider Vol. 17 No. 11/16 petpla.net Indent to level out pressure Intern. Patent No. WO 2016 / 016372 A1 Applicant: S.I.P.A., Vittorio Veneto (IT) Application date: 30/7/2015 To reach the necessary stability (specific internal pressure) after cooling a light PET bottle conceived for hot filling, it is suggested to integrate an all-round notch / indentation in the shoulder region. This adapts to the internal pressure in a flexible way and provides the necessary change of volume. Plastic bottle Intern. Patent No. WO 2016 / 021009 A1 Applicant: Suntory Holdings Ltd., Osaka (JP) Application date: 6/8/2014 The design of a plastic bottle with especially developed pressure balance surface is described. Collapsible floor Intern. Patent No. WO 2016 / 029016 A1 Applicant: Amcor Ltd., Victoria (AU) Application date: 20/8/2015 The floor of a PET bottle intended for hot filling is designed in such a way that it can be pushed inwards after the manufacture, filling and cooling of the bottle, in order to increase the internal pressure inside the container and in so doing the stability of the bottle. Light container Intern. Patent No. WO 2016 / 028393 A1 Applicant: Amcor Ltd., Victoria (AU) Application date: 29/6/2015 The design of the bottle and floor of a lightweight PET bottle are announced. The bottle sufficiently possesses balance surfaces to be able to register pressure differences through elastic deformation. Movable floor Intern. Patent No. WO 2016 / 029023 A1 Applicant: Amcor Ltd., Victoria (AU) Application date: 20/8/2015 Design and manufacture of the bottle and floor of a lightweight plastic PET bottle are announced. Particular reference is made to floor deformability and the change in the plastic structure. Bundle with binding elements Intern. Patent No. WO 2016 / 037748 A1 Applicant: Krones AG, Neutraubling (DE) Application date: 22/7/2015 The application proposes connecting several / at least two bottles with doublesided adhesive binding elements. Single bottles can be removed from the bundle without “destroying” the bundle as a whole.","@ID":66}, "60 PETplanet Insider Vol. 17 No. 11/16 petpla.net BOTTLES PETbottles Beverage + Liquid Food Organic tomato ketchup in PET The German Frusano GmbH, specialist in fructosefree foodstuffs, is selling 550g of organic tomato ketchup, which is free from gluten, lactose and granulated sugar, in a clear squeeze bottle. Fructosefree organic glucose syrup is used as a sweetening agent. It is therefore particularly suited to people who have fructose intolerance. Under the screw-on hinged lid clasp with a silicone valve there is a seal membrane which must be removed before first use. www.frusano.com Fruity by Aldi Aldi Süd is selling several soft drinks under its own water label “Aqua Culinaria” and the product name “Fruity” with a fruit content of up to 8% in non-circular, clear bottles with 500ml and revolving reinforcing grooves in the label area. The disposable bottles are sealed with suitably coloured, lightweight screw caps and a seal of warranty. www.aldi-sued.de Isotonic after activity drink The United Soft Drinks GmbH from Cologne, Germany, is selling several assorted drinks, especially catered to athletes’ needs before, during and after sport, with the name AA Drink – After Activity Drink – in an extremely thin-walled bottle with 500ml content. The surface has a non-grip design and is equipped with imprints in the shape of runners. The cap is a resealable sports cap with detachable firstuse safety clasp. The bottle is decorated with a sleeve label. www.aa-drink.com Yogurt drink by Rewe Rewe is selling several yogurt drinks under its own label “ja” with a fat content of 0.1% of milk in a gripfriendly and white-coloured PET bottle with 500g content. In the handle area, the bottle is stable enough not to collapse while holding, opening and drinking. The screw cap combined with a seal of warranty allows for straightforward drinking directly from the bottle and easy pouring, thanks to its large opening. The colourfully printed sleeve label makes the flavours immediately visible. www.rewe.de","@ID":62}, "TRADE SHOW PREVIEW 41 PETplanet Insider Vol. 17 No. 11/16 petpla.net SSB03 (three cavities) are in use. Manjushree Technopack also purchased a three-layer Collation Shrink Film Line from Reiffenhäuser, which is also in operation here and represents something of a new area of business. Around 70 specialist employees and 200 additional members of staff work on production operations 24/7, all year around. The company produces over 65 different preforms in ten different neck types, from 10g for 160ml bottles, to 770g for 19l PET containers. The actual production output of the factory is currently 70% of capacity, a rate that is increasing all the time. A further expansion has not yet been planned, however. Rajat Kedia observed that the company has doubled its output since the beginning of 2013, and has probably reached its limit for the moment. In 2015, Manjushree’s total turnover was €72m; the new factory accounted for approximately €44m. It is forecasting an increase of at least 10% for 2016. Projects for the immediate future are focussed on business improvement and environmental performance. It intends to implement TQM and QatS (Quality at Source) – the latter in cooperation with a CSD customer. The company also has a variety of commitments in the production of clean, green energy. “We are installing wind and solar power plants here. Our goal is to obtain 80% of our requirements for electricity from renewable sources by 2018,” Rajat Kedia explains. “We already have concepts for delivering our products in reusable boxes as well. Our company is also a key participant of a team working on experiments with barrier preforms and recycled PET flakes in the R&D department of the Directorate of Science and Research. We may be able to offer these new technologies to the market from 2018 onwards.” Manjushree’s “old” home location in Bommasandra, which is now used as a blow moulding facility, processes around 10,000t of PET each year, F.l.t.r.: Sanjay Balakrishna and Kay Barton in Manjushree’s material storage area along with approximately 6,000t of PP and HDPE. More than 150 machines are currently in use at the original site, including EBM and injection moulding lines. Its main product lines are packaging for the food sector but packaging for spirits and alcoholic drinks, the pharmaceuticals sector and the home and personal care industry are also manufactured there. www.manjushreeindia.com Engineering Excellence Efficiency at the highest level PET-LINE machines www.netstal.com The best values for cycle times and output, combined with energy savings of up to 10%: the PET-LINE sets standards in efficiency. The state-of-the-art production system for PET preforms proves its value with: – Hydromechanically driven axes – State-of-the-art valve and control engineering – A consistently increased injection unit throughput – Innovative drive technology with energy recovery in the intermediate circuit PET-LINE – continuously further developed for maximum efficiency! BrauBeviale 2016, hall 4A, booth 233","@ID":43}, "TRADE SHOW PREVIEW 49 Labelling machines in modular block building system The well-established labelling machine manufacturer Gernep from Barbing in southern Germany presents the latest developments of its rotary labelling machines in modular block building system. Due to the flexibility of the Gernep rotary labelling machines to be equipped with different glueing systems and the possibility of designing the labelling machine in accordance with different equipment requirements - Gernep labellers are on duty in breweries, wine, spirits, water and soft drink bottling plants as well as in the chemical, pharmaceutical and cosmetics industries worldwide. Features of the Gernep rotary labelling machines are firstly, the modular design of the basic machine with the opportunity of varying, different container orientation processes, label control units and bottle plate drives. Secondly, Gernep rotary labelling machines provide the flexibility to use different glueing processes such as: cold glue labelling from the magazine, hot melt wrap-around labelling from the magazine, hot melt labelling from the roll and self-adhesive labelling with all its individual advantages in combination on one flexible platform. To meet all decoration demands in different industries, the Gernep Labetta rotary labelling machine is specialised in universal cold glue labelling, Gernep Rollina in affordable hot melt wrap-around labelling out of the magazine and the Gernep Rollfeld in efficient wrap-around labelling with hot melt from the roll. The newly developed Gernep Soluta - in an optimised control and security design – has been developed to meet the constantly increasing demand for flexible and diverse container decoration in self-adhesive labelling. www.gernep.de Gernep GmbH Hall 7 | Booth 331 PETplanet Insider Vol. 17 No. 11/16 We do more. Contiform AseptBloc #GermanBlingBling #ContiformAseptBloc BrauBeviale 2016 Nuremberg, 8 – 10 November Stand 7A-520","@ID":51}, "TRADE SHOW PREVIEW 53 PETplanet Insider Vol. 17 No. 11/16 Lightweight yet user-friendly closure solutions The emphasis in the past was on reducing the weight of closures, particularly in the food and beverage sector. Cost savings and an improved carbon footprint were a priority, while user-friendliness tended to take a back seat. Bericap developed lightweight closures to cater for market demand. Combined with a 29/25 thread, the HexaLite 29/11 allowed a 33% weight reduction compared with its predecessor neck finish 30/25. While the bottlers were happy with this lightweight product measuring just 11mm, some customers struggled with the small closure and found it rather awkward to handle. The focus was therefore switched from “lightweight” to “user-friendly” and the HexaLite 26/13 and 29/13 closures were designed with an extra 2mm of height. The new caps are virtually the same weight but look more substantial and are now easier for customers to handle. All HexaLite closures have a cut and folded security strip that breaks easily the first time the bottle is opened. N2 dosing is possible. The 29/25 and 26/22 neck types are approved by CETIE. www.bericap.com Bericap Hall 4 | Booth 515 P.E. Labellers P.E. Labellers will exhibit two of their labelling machines. The first will be a roll fed model Rollmatic 540, with hot melt labelling system for big containers, suitable for labelling round plastic bottles up to 20l. The roll-fed labelling machines by P.E. Labellers have been completely updated achieving a greater versatility for the user, a guarantee of better glue distribution with greater savings and is equipped with a new film tensioning system. It also has a new transmission system to guarantee lower noise and zero maintenance and is provided by the latest generation electronic software. The second one, the latest model launched by P.E. Labellers, will be the Maya sleever, for the application of sleeve labels on containers, empty or full, of any material, shape and size, with shrinkage percentage up to 80%. The advantage of the label sleeve is that it allows the use of the entire surface of the container to present the features of the product, in addition to making the packaging thoroughly modern and appealing. The new sleever is available for full-body, halfbody, tamper-evident, bi-pack promotional applications. www.pelabellers.com P.E. Labellers Hall 7 | Booth 337","@ID":55}, "PACKAGING 29 PETplanet Insider Vol. 17 No. 11/16 petpla.net equipped by Krones. In 2015, at its Ödemiş site in Izmir, the Turkish company commissioned a NitroHotfill line from Krones with an output of 22,500 containers per hour. A year after installation, a Krones team on site at the line launched tests to improve the compressed air system. After an upgrade and simple optimisation of the Contiform 3 blow moulding machine, the line went back into normal operation. A test run has achieved extraordinary results, the company claims. With unchanged container quality, this modification has achieved 44% savings in compressed air consumption. The upgrade yields cash savings amounting to some EUR 40,000 per year based on a calculated machine running time of 6,000 hours per year. The company KHS is also showing that the potential of production equipment is still far from fully exploited. The company Mineralbrunnen Teinach GmbH has been using the KHS stretch blow moulding machine InnoPET Blomax Series III for the production of PET bottles since 2007. To cut the line’s energy consumption, the KHS experts have modified its heater box in which the PET preforms are heated for subsequent stretch blowing. For Mineralbrunnen Teinach GmbH, this has yielded over 40% energy savings – savings made possible essentially by the use of new, advanced ceramic reflectors and precision-adapted geometry in the heater boxes, explains Frank Goebel, Head of Service Engineering at KHS. (See PETplanet 5/2016 page 28) Thanks to the special design, the physical properties of the ceramic elements have had a markedly beneficial effect on energy distribution, so less energy is needed to heat the preforms. In addition, the reflectors and infrared radiators have been conPhotod in such a way that the bottle’s delicate thread zone is not unnecessarily heated. The cooling of this area can be reduced, says Goebel, thus saving further energy in Teinach. “Thanks to greater efficiency, it is often possible to shorten the heating section,” he adds. If fewer heating elements are necessary in the oven, energy consumption by the infrared radiators also drops as a consequence. www.khs.com www.krones.com www.interpack.com NitroHotfill line from Krones with an output of 22,500 containers per hour.","@ID":31}, "Congresses PET symposiums and lectures WikiPETia.info PET knowledge management system Pulse The monthly PET price index Worldwide PET magazine Social Media Connecting worldwide Events Fairs, open houses, on-site sessions ... No.4 2016 ZZZSHWSODQHW ' ,661 25.04.16 PETplanet Page 27 petpla.net D 51178; ISSN: 1438-9452 No. 9 2016 PETplanet is read inmore than 140 countries MAGAZINE FOR BOTTLERS AND BOTTLE-MAKERS IN THEAMERICAS,ASIA, EUROPEANDALLAROUND THE PLANET 07.09.16 MARKETsurvey Bottle-to-bottle recycling plants Page 41 TheChinaRoadShow Page 12 bottlemaking Page 21 Page 52 PETplanet is read in more than 140 countries petpla.net News Daily PET business news Editours Worldwide editorial reporting The whole world of","@ID":25}, "MATERIAL / RECYCLING 14 PETplanet Insider Vol. 17 No. 11/16 petpla.net BP PTAir launch: more sustainable solution to the polyester chain Tackling environmental challenges By Anthony Withers On the hottest September day in England for a century, the luxuriant setting of Kew Gardens was the exotic backdrop for the launch of BP’s PTAir, which the company claims will be a sustainable solution for all the major players in the polyester chain from users themselves to brand owners and retailers. It forms an integral part of the company’s Target Neutral strategy. Some seventy industry professionals, consultants and representatives from media outlets attended the launch. The main themes of the presentation were outlined at the start of the presentation by senior BP executives notably Rita Griffin, COO Petrochemicals, Andrea Abrahams, Global Director of BP’s Target Neutral strategy and Luis Sierra, CEO BP Global Aromatics. These themes included: sustainability, climate change, reducing CO 2 emissions, recycling, more efficient use of resources and much else besides. Speakers focused on how producers, industry leaders and consumers can come together to meet the environmental challenges faced by the planet. Andrea Abrahams, Global Director BP Target Neutral Three guest speakers delivered their own take on the problems and challenges faced by all the principal actors in the polyester chain. First on the podium was Mark Kenber of Mongoose Energy, an expert on climate change and international climate policy. In a wide-ranging speech, he delivered a comprehensive review of the current situation, from the disappointments of the 2009 Copenhagen Accord on climate change, which promised much but achieved little, to the 2016 Paris Agreement, which by general consent, represented a step change in securing international agreement on reducing carbon emissions. Mark Kenber, Mongoose Energy From this global perspective, the next speaker, Mike Barry, Director of Sustainable Business at Marks & Spencer, offered the sometimes conflicting views of the typical M & S customer. Some, he said, were deeply committed to “saving the planet”, others couldn’t care less, and in between were what Barry called the “swing voters” whose views were mostly favourable but could be swayed by changes in their personal economic circumstances. He emphasised how much the individual consumer is the driver behind M & S’s commitment to sustainability, suggesting that this is why the M & S brand is known for its high quality offer, and is an industry leader in delivering environmental initiatives. Mike Barry, Director of Sustainable Business Marks & Spencer The final speaker, Dr Pieterjan van Uytvanck, Consultant, PCI Wood Mackenzie, analysed the polyester lifecycle, stressing how important the material was in everybody’s everyday lives. Reducing the carbon footprint has now become a priority as the previous speakers had demonstrated and Dr van Uytvanck went through the various processes that could lead not only to a reduction in carbon emissions, but could save energy and boost cost-efficiency. Lightweighting and more efficient recycling were examined as well as innovative ideas that enable heat to be recovered and returned to the grid. Dr Pieterjan van Uytvanck, PCI Wood Mackenzie As Luis Sierra pointed out in his concluding remarks, there is still a long way to go, in particular balancing environmental sustainability with competitive forces in the market. Carbon Rita Griffin, COO BP Petrochemicals","@ID":16}, "imprint EDITORIAL PUBLISHER Alexander Büchler, Managing Director HEAD OFFICE heidelberg business media GmbH Bunsenstr. 14 69115 Heidelberg, Germany phone: +49 6221-65108-0 fax: +49 6221-65108-28 [email protected] EDITORIAL Kay Barton Heike Fischer Gabriele Kosmehl Michael Maruschke Ruari McCallion Waldemar Schmitke Anthony Withers WikiPETia.info Doris Fischer [email protected] MEDIA CONSULTANTS Martina Hirschmann [email protected] Johann Lange-Brock [email protected] phone: +49 6221-65108-0 fax: +49 6221-65108-28 LAYOUT AND PREPRESS EXPRIM Werbeagentur Matthias Gaumann | www.exprim.de READER SERVICES Till Kretner [email protected] PRINT Chroma Druck & Verlag GmbH Werkstr. 25 67354 Römerberg Germany WWW www.hbmedia.net | petpla.net PETplanet Insider ISSN 1438-9459 is published 10 times a year. This publication is sent to qualified subscribers (1-year subscription 149 EUR, 2-year subscription 289 EUR, Young professionals’ subscription 99 EUR. Magazines will be dispatched to you by airmail). Not to be reproduced in any form without permission from the publisher. Note: The fact that product names may not be identified as trademarks is not an indication that such names are not registered trademarks. 3 PETplanet Insider Vol. 17 No. 11/16 petpla.net Dear friends of PETplanet Insider, A short pause between the autum trade fairs I’m in Shanghai, sitting on my packed bags. The China Brew and Beverage exhibition is over, and with it our China road tour. Our Editourmobil occupied centre stage on our stand, next to the photographs taken during our visit. The tour gave us a great deal of insight into China’s PET industry, which is currently in a consolidation phase. The talks at the exhibition indicated that this is probably a temporary situation. While most exhibitors at the fair expressed caution, some companies reported growth rates typical for China. I can’t judge the extent to which that is a matter of wishful thinking as opposed to real numbers. What is certain, though, is that looking forward, everyone takes a positive view of the future. That is true of both foreign and Chinese exhibitors. The local exhibitors in particular used the China Brew and China Beverage fair to present new machine designs to visitors for the first time. These designs were entirely their own. The days when the Chinese just copied others’ work seem to be over. The successful Chinese suppliers are now showcasing their own technology. The new exhibition grounds are impressive for the quality of their infrastructure and their excellent connections to Shanghai. The city itself is worth a visit, and it does not cost much to get there. I wonder how my impressions from China will compare with those at K 2016. I don’t have to completely unpack my bag, as BrauBeviale starts in Nuremberg in just a few days. See you at our booth 7A 203. Yours, Alexander Büchler","@ID":5}, "TRADE SHOW REVIEW 57 PETplanet Insider Vol. 17 No. 11/16 petpla.net real time is correlated both with quality and key business operating figures and analysed in a variety of ways. It then becomes particularly exciting if not only the production cells of an individual site but of a global production network are integrated using Engel e-factory. The processes can be optimised from the company headquarters, and colleagues are better supported locally. The new energy module allows the detailed presentation, analysis and optimisation of energy consumers. Energy enables Engel e-factory to control the start-up of the injection moulding machines and production cells automatically and reliably avoid any energy peaks. The electricity costs of the machinery are therefore reduced. smart service To increase the machine availability of injection moulding machines and manufacturing cells, smart service relies on short routes, remote maintenance and a view into the future. The Engel e-connect.monitor is said to make it possible to analyse the condition of process-critical machine core components in the live operation and reliably predict the risk of default. The condition-based, predictive maintenance makes it possible to exploit the service life of critical machine parts to the full and avoid any unplanned equipment stoppages that occur in spite of this. The regular condition monitoring supports process optimisation in the long term. Critical process settings that accelerate the wear of certain components are identified by analysing the wear parameters and are then subsequently avoided through process changes. The Engel e-connect.monitor is particularly beneficial for process-critical machine components that maintenance staff do not constantly keep in focus. These include the spindles that actuate the axial movements in electrical injection moulding machines. Since there are multiple spindles operating in each machine and the failure of only one brings the entire production cell to a standstill, the condition monitoring of the ball screw drives is done continuously. In future, the data captured by the sensors is transmitted in real time to the Engel e-connect customer portal where it is automatically analysed with the help of mathematical and physical models. The operator can then call up the current condition of the individual spindles at any time and is immediately notified in the case that a spindle reaches a critical condition. If desired, the software can be programmed so that the alarm notification automatically initiates an order for spare parts and books an appointment for a service technician. As far as the packaging industry is concerned, Feltes points another advantage out: “Process data at the point of sale is another contribution of Industry 4.0 to the packaging industry. In future, consumers will not only find information on the ingredients of foods and cosmetics in the supermarket, but also on how and from what materials the packaging was made.” www.engelglobal.com NOCONSTRAINTS LABELINGMACHINE Interchangeable modules with or without cart. Free to decide how to fit your labeler at any time: before, during and after purchasing. Models for all speeds. CHOOSE THE SPECIALIST PH. +39 0376 389311 MAIL: [email protected] WEB: www.pelabellers.com Hall 6–Stand #G029 Stand 7-337 Booth #S-2520","@ID":59}, "TRADE SHOW PREVIEW 39 PETplanet Insider Vol. 17 No. 11/16 petpla.net drink technology India 2016 drink technology India (dti) will bring together the national and international beverage and food industry in the Bombay Convention & Exhibition Centre in Mumbai between December 15 and 17, 2016. This year’s event is registering record interest: On over 7,000m2 of exhibition space (2014: 4,500m2), the visitors to dti 2016 can gather information on all the latest developments from the most important companies in the sector. As well as the classic areas relevant to the beverage industry, the now expanded section on milk and dairy products and liquid food is contributing strongly to the high level of bookings in the hall: “Currently India is the world´s biggest producer of dairy products, and the forecasts are for further growth (up to +28% by 2018) in the coming years,” explained Markus Kosak, Exhibition Director of drink technology India. Added value for visitors to dti also comes from the high-calibre supporting programme that accompanies the exhibition; it features an Exhibitor Forum and Round Table Talks. Exhibitor Forum The Exhibitor Forum at dti is a knowledge platform that focuses on the challenges and needs of the Indian market. In 2016 the forum will provide information on the following trade themes: Innovative equipment for bottle manufacturing processes Preform and closure manufacturing – lightweight vs stability vs design India’s beverage, beer and spirits industry – trends and technologies in manufacturing and packaging Milk and dairy in India – processing, packaging and product trends New developments in beverage flavours and ingredients Round Table Talks In addition to the Exhibitor Forum dti is also putting on the Round Table Talks as an additional platform to discuss the future of the beverage and liquid food industry in India. Under the main theme of “Beverage manufacturing, food processing and product packaging in India: lifestyle, trends, challenges and future concepts” the following topics will be covered: Liquid food and beverage safety in India Ensuring broad appeal for India´s young and older people Packaging for India’s rural market (small quantities at lower cost to attract the large rural population) Manufacturing possibilities for India´s (future) markets of milk and dairy products Different processing and packaging requirements for various climates The challenges of transport over large distances In 2016 drink technology India is again taking place in conjunction with PackTech India and - new this year - is being supplemented by FoodPex India. www.drinktechnology-india.com www.packtech-india.com www.foodpex-india.com Beverage technology at drink technology India With a quarter of the world’s population and one of the world’s most dynamic economies, India is a strategic market for the industry’s top global players. Sacmi responds to this need with advanced, customised solutions and of far-reaching service. A single production, sales and assistance centre is serving the entire Indian market. Sacmi Engineering is based in Ahmedabad, the thriving industrial centre in Gujarat State. Sacmi Engineering brings together the various manufacturing, sales and service facilities working in India, providing a clear reference point for the ceramics and beverage & packaging industries. More than thirty years of doing business on this market and strong local manufacturing roots provide a solid foundation for the Sacmi Group’s participation in dti, Mumbai; the last edition of this event, which focuses on industry-related technology, enjoyed 37% growth in terms of both visitors and specialised operators from all over South-East Asia. The constant dynamism in terms of fast-evolving consumer habits, India is a not-to-be-ignored strategic market for the world’s leading beverage players. Sacmi Group is pivotal for the design and the production of the complete manufacturing lines that handle everything from cap and preform production to filling, labelling and quality control. www.sacmi.it","@ID":41}, "BOTTLING / FILLING 22 PETplanet Insider Vol. 17 No. 11/16 petpla.net F.l.t.r.: Michael Chen, Managing Director of Bericap China and Alexander Büchler, PETplanet Insider in front of the Editourmobil Aseptic Dual Fill technology From beverages to liquid food Technology for the aseptic dosing of fruit or cereal pieces into beverages offers new opportunities for manufacturers to capitalise on developing trends. Technology can actually drive trends; it can provide the means for manufacturers and suppliers to make advances in processing that then enable the creation of genuinely new products. Gea Group, the process technology company headquartered in Düsseldorf, Germany, claims that its new Dual Fill equipment, which features its recently-developed Piston Doser, is this kind of innovative technology. Beverage to liquid food Recent developments in the food and beverage markets have blurred the distinction between ‘drinks’ and ‘food’. In the Far East especially, a trend has developed for beverages to have ‘solid’ pieces included, such as fruit, fibres, and cereals, which turn a drink into a meal in itself. The concept of the “liquid breakfast”, for example, is now widely familiar. Milk and fruit drinks can be dosed with fruit, coconut, nuts, aloe vera pieces, even berries and cereals, to make foods that are perceived as being of higher quality than liquids alone. The inclusion of fruit pulps and fibres enable fruit beverages to mimic freshly-squeezed juice more closely. Process Gea has run extensive tests for the filling and dosing of drinks bottles using products such as peaches, chestnuts and even walnut kernels. It has experimented with different carrier liquids of various viscosities for both processing and filling elements. The process of preparation and thermal treatment is a critical phase in terms of sterilisation and handling. The proportion of particles, their dimensions, the density and viscosity of the liquid carrier, all contribute to the product’s final taste. Two-stream process lines are needed for some applications, in order to optimise quality. One is dedicated to the thermal treatment of the pieces and the other to the thermal treatment of the liquid. Aseptic dual filling Gea’s Aseptic Dual Filling system provides a means of filling drinks that include solid pieces of up 10x10x10mm. The system uses two different fillers: the Aseptic Piston Doser PX for solid particles and the well-established Fillstar FX volumetric electronic filler. The cam-driven piston draws the prescribed volume of solid particles into a cylinder, then injects it into a waiting PET bottle. It then moves to the Fillstar FX, which adds juice and completes the aseptic filling process. Aseptic integrity is maintained by a hygienic seal around the piston, which prevents product leaking through to the non-aseptic side. There is no contact between the filling nozzle and the bottle neck, so filling is ‘clean’. Dosing volume can be regulated from 30ml to 150ml by changing the dosing value on the HMI (Human Machine Interface) system. This technology is suitable for HA (high acid) or LA (low acid) products and conforms to the most demanding microbiological validation protocol specifications. All sanitation and sterilisation cycles are automatically controlled in all critical locations. The system has a small footprint and can maintain a production level of 800bpm (48,000bph). Filling accuracy is +/-5% of dosed volume. Gea says that it has run extensive tests using a range of products with different carrier liquids of various viscosities in both the processing and filling phases. Validation of the sterilisation and cleaning-cycle of the machine has been performed under the scrutiny of the US Process Authority that is overseeing the FDA validation path. Four aseptic filling lines equipped with the Piston Doser for HA drinks with fruit chunks have been in operation in SE Asia since 2013, and two lines have recently been installed in North America, for both HA and LA drinks. Two more lines are soon to be installed for customers in the Middle East. www.gea.com","@ID":24}, "TRADE SHOW PREVIEW 47 From filling to packaging: produce flexibly and sustainably Both medium-sized and large breweries are increasingly relying on flexible secondary packaging systems. The partnership between KHS and Gerhard Schubert GmbH is now generating some particularly individual and flexible packaging options. At BrauBeviale both companies will be exhibiting a blocked system for the first time which already has a taker; Brauerei Schützengarten AG is now to take delivery of the new combination of a KHS packer blocked with a Schubert erecting and closing module. Merging the technologies of both companies brings about an increase in flexibility, quality and efficiency. Further details will be revealed by KHS at BrauBeviale. NMP Systems GmbH will also be represented in Nuremberg. The KHS subsidiary is responsible for the marketing of the pioneering, innovative Nature MultiPack and Direct Print Powered by KHS plant engineering. At BrauBeviale visitors can take a close look at the first implementation of Nature MultiPack worldwide by Evian in 2016. Live demonstrations of the Direct Print software platform for the digital printing of PET bottles also give visitors an insight into the future of packaging design. www.khs.com KHS Hall 5 | Booth 147 PETplanet Insider Vol. 17 No. 11/16 You make a great product – why hide it? We’ve seen the future of canning and it’s Klear. Milacron’s Klear Can technology gives manufacturers a cutting-edge, cost-competitive alternative to metal cans for fruits, vegetables, soups, meats and other products – and it’s transparent, so you can show off your goods. Using the same machinery as metal cans, going Klear requires minimal investment. With the option to use colored plastic cans, in-mold labels, or standard labels, the possibilities are endless. Ready to see what you can do? Contact us or visit www.Milacron.com to learn more.","@ID":49}, "MATERIAL / RECYCLING 13 PETplanet Insider Vol. 17 No. 11/16 petpla.net found to be due to the lesser thickness in that area, compared to the other variables. However, the results were still well within performance requirements. The only significant deviations from virgin PET performance were in their appearances. Yellowing (b*) and haze both increase as the recycled content rose. Bottles made from rPET A yellowed more than rPET B, at all levels and as the rPET level increased (fig. 2). However, bottles made from rPET B had, on average, higher haze levels than rPET A, as the percentages increased – although rPET A showed higher levels of haze at 100% concentration (fig. 3). The yellowing and haze are both aesthetic factors; they do not affect physical performance in practice. Conclusions All of the samples passed the standard performance specifications for hot fill bottles, even at high percentages of rPET. Measured shrinkage increased slightly at recycled content levels above 50%, but the bottles remained within the specification. Top load performance for one of the rPET variables slightly improved as the recycled content increased. However, the analysis led to the conclusion that the performance increase can be correlated to wall thickness differences, more than the rPET content. The only significant drawbacks of high rPET content are increased yellowing and higher haze levels. However, these are aesthetic issues and do not impact performance. www.plastictechnologies.com Figure 1: Hot-fill performance with rPET content Figure 3: % RPET vs. haze Figure 2: % RPET vs. yellowing (b*) MHT MOLD & HOTRUNNER TECHNOLOGY AG Your Machine - Our Solution 1996-2016 20YEARS Mumbai, Dec 15-17 Booth 1-F38","@ID":15}, "PREFORM PRODUCTION 19 PETplanet Insider Vol. 17 No. 11/16 petpla.net New preform design & prototyping service The quality of a bottle, its aesthetic appearance and its mechanical performance is also the result of a correct preform design and of the quality of materials with which it was made. Often, a good design can be affected by the selection of a wrong preform or by the improper use of materials. PET Engineering created a new preform design & prototyping service that is said to ensure the right preform for every application and the perfect bottle for every preform. The service offers a perfect result thanks to the up to date technologies, e.g. HyPET Husky injection machine. The production of small and big batches is possible. The testing of material, additives and closures are realised separately. There is a guaranteed quality thanks to the application quality tests during all production steps. Preform design The development of an ad hoc preform starts with the characterisation of a current preform and container, but also with the mechanical and barrier performance levels that need to be achieved. The characterisation activities make it possible to have an overall picture of the current quality of the preform and bottle, thus to understand the improvements that can be achieved by implementing a new preform. Prototyping Once the stack has been created or modified PET Engineering will install it on a machine to prototype the preform. The prototype phase is designed to test the project by evaluating the performance of the container or containers that will be created with this preform. Manufacturing In this phase, PET Engineering designs and implements new stacks consisting of gate insert, grips, tap holder and cooling EOAT cups. Also the cavity, cooling tube and the tap were creating. Testing Once injected, the preforms are tested in the lab to verify their suitability with regards to required parameters. www.petengineering.com","@ID":21}, "PACKAGING 30 PETplanet Insider Vol. 17 No. 11/16 petpla.net Technology for wrap-around case packaging Sturdy packages When it comes to beverage packaging cases, switching quickly from one pack format to another is essential. The automatic LWP Ergon packers from Italian company SMI are promising an easy and fast changeover for packing containers in corrugated cardboard cases and/or trays without film. Depending on the product handled and on the packing pattern, the wraparound packers run at up to 30 packs per minute. For the design of the new LWP Ergon case-packer, SMI engineers have built on the solutions introduced by the Ergon platform, applied two years ago for the first time to the automatic packers of the SK series and then to the other primary and tertiary packaging machines manufactured by SMI. The features of the platform include a compact structure and ergonomic design, intended to simplify general operations such as cleaning and machine maintenance and ensuring space saving within the packaging line. The machine guards have a curved design to enable the external mounting of the motors to the mechanical groups, facilitating easy access for maintenance. Sliding doors are equipped with a slow-down hydraulic closer, avoiding any sort of hazards when closing the doors and preventing any structural damage of the machine. In addition, the new secondary packaging machines are equipped with almost exclusively brush-less motors. Sturdy and elegant packages The automatic LWP 30 wraparound case-packers are suitable for production speeds of up to 30 packs per minute. Machine adjustments in these systems are made by means of convenient cranks and useful numeric counters, which allow the operator to switch from one pack format to another simply, quickly and accurately without having to use any tools. At the machine infeed, a group of guides lines up loose containers along a conveyor belt featuring low-friction chains made of thermoplastic material. Afterwards products are grouped in the pack-forming unit in the chosen packing pattern by means of an alternate-motion pneumatic device. Then, a sheet of corrugated cardboard is picked from the blank magazine by an alternate-motion picker with vacuum suction cups that ensures precise synchronisation with the other operations performed by the packaging machine. The cardboard blank is then carried up along the blank ramp and positioned under the incoming pack collation with short leading side. The box/tray former operates in continuous motion with wrap-around system. Subsequently, flap-folding devices fold first side flaps and then upper/ lower flaps on both the front and the back of the pack. A gun sprays a thin layer of hotmelt glue on the flaps to ensure a perfect adhesion of the box/ tray. At the machine outlet the case walls are pressed by special guides to ensure durable pack squaring. SMI’s LWP Ergon series’ new wrap-around casepackers have a compact and robust frame, capable of adapting easily to any logistic condition, and are equipped with brushless motors to drive machine axes and reduce energy consumption. The new LWP 30 Ergon will be exhibited at BrauBeviale in Nuremberg (hall 7A booth 503). The machine on display will be packing 0.33l beer bottles in 3x4 wrap-around cardboard cases. www.smigroup.it","@ID":32}, "TRADE SHOW PREVIEW 55 form and container production methods nor the subsequent bottling stage underwent any major changes: even after the launch, in 1997, of the first stretch-blow moulding machines integrated with the bottling line, the three phases remained largely distinct. With heroPET4.0, we’ve overcome all the problems that previously hindered full integration of these processes, doing so by making full use of compression technology, a field in which Sacmi has worldbeating skills that stem from decades of experience and thousands of systems installed all over the world.” Tested with a leading Italian bottler who has validated its performance (the plant produced 30,000 half-litre still water bottles an hour for a year, using preforms weighing just 9g, with energy savings of between 1.3 and 1.5kWh per kg of PET), the new Sacmi heroPET 4.0 platform is now presented to the market. It uses both the advantages of compression technology and Sacmi process automationintegration solutions. It can also be supplied complete with the full array of direct in-line inspection and quality control systems developed by the Group’s Automation&Service Division. www.sacmi.it","@ID":57}, "PACKAGING 31 PETplanet Insider Vol. 17 No. 11/16 petpla.net During BrauBeviale 2016, Italian company OCME will present its secondary packaging solution Packetto which is achieved by OCME’s Vega Shrinkwrapper. Born out of the fierce competition in the beverage industry, this solution is intended to allow customers to improve the aesthetics of their shrinkwrapped packs, raising the impact for the final consumer. The Packetto shrinkwrapping solution has the same characteristics as a traditional shrinkwrapped pack, except that it has been improved by small changes giving a greater impact. Thanks to the application of tiny dots of glue on the bottles onto which the film is applied, the pack does not wrinkle but is said to remain perfectly formed. Ocme claims that Packetto offers not only an upgrade of the brand image by increasing the area for branding artwork but thanks to the method of fixing the film, the amount of film can be reduced by up to 30%. The solution comes in three different options: Smart Packetto is said to offer wrinkle-free packs whilst saving on film and increasing the print area for branding artwork and the pack aesthetics. During the shrinking process, the film remains in position, to allow the pack to be perfectly formed. The unique feature of Eco Packetto is the comfort carry handle which runs right around the pack, adding strength to it. Packetto Eco also uses very thin but solid film (down to 25μm). Thanks to this concept, the amount of film used is also reduced by up to 30%. With a “sharing-friendly” design, Party Packetto allows the final customer to chill their cans or bottles, making parties indoors or out that much more enjoyable. This concept is intended to allow the pack to become a marketing support for multi-brand promotions and merchandising. www.ocme.it One of OCME’s customers, Coca-Cola Oricola (part of the Hellenic Bottling Company) has integrated the module into their Vega shrinkwrapper. Shrink-wrapping to improve on-shelf impact of bundles Wrinkle-free wrapped","@ID":33}, "ON SITE 59 PETplanet insider Vol. 17 No. 11/16 petpla.net ONsite Labelling for the US market The roll-fed technology by Sacmi labelling has been chosen by a key US-based multinational to renew a major facility producing several renowned soft drink brands. The two Opera 300 24T labellers are the latest in a series of orders this US Group has placed with Sacmi after several dozen Sacmi solutions have so far been installed by this American multinational. Capable of providing a response to the far-reaching plant renewal and reorganisation plan being enacted by this US firm, Sacmi has again won the customer’s trust by combining the high productivity of the supplied solutions – the two labellers can handle 30,000-60,000bph – with user-friendliness and design features that are intended to ensure reliability. For example, cleaning tasks only need to be done once per shift, thus optimising productivity and cutting maintenance costs to the bone. Like the other machines in the Opera series, the two labellers are equipped with the automatic reel splicing system, ensuring smooth, downtime-free operation. In addition, both supplied solutions are UL certified (the most widely recognised non-compulsory international safety hallmark in the USA and Canada) and, of course, comply with the American multinational’s strict policies concerning the mechanical, electronic and electro-mechanical standards that must be met by all the automated systems installed on its lines. For Sacmi, this order represents another step along the path towards growth and development on the strategic US market. www.sacmi.com","@ID":61}, "MARKET SURVEY 35 PETplanet Insider Vol. 17 No. 11/16 petpla.net 11/2016 MARKETsurvey Preforms Filling equipment Resins / additives Preform / stretch blow moulds Caps and closures Preform and single stage machinery Bottle-to-bottle recycling plants Compressors Closure systems Two stage SBM machinery Suppliers of systems and moulds for the production of caps and closures for PET bottles For this issue 11/2016 of PETplanet Insider interviewed the market participants in the system for the production of closures sector. These include both: The machine manufacturers and the mould suppliers! We received feedback from the following companies (in alphabetical order): Arburg GmbH & Co KG, Corvaglia Mould AG, Engel Austria GmbH, Husky Injection Molding Systems, Milacron c/o Mold-Masters Europa GmbH, Sumitomo (SHI) Demag Plastics Machinery GmbH and z-werkzeugbau-gmbh. Although the publishers have made every effort to ensure that the information in this survey is up to date, no claims are made regarding completeness or accuracy. Systems for cap/closure production Company name Ferromatik Milacron GmbH Sumitomo (SHI) Demag Plastics Machinery GmbH Postal address Telephone number Web site address Contact name Function Direct telephone number Fax E-mail Riegeler Str. 4 79364 Malterdingen, Germany +49 7644 78 0 www.milacron.com Mr Stéphane Grossnickel Director International Accounts & Intercompany +49 7644 78 0 +49 7644 6885 [email protected] Altdorfer Str. 15 90571 Schwaig, Germany +49 911 5061 0 www.sumitomo-shi-demag.eu Mr Arnaud Nomblot Director - Business Development Packaging +49 911 5061 625 +49 911 5061 96 625 [email protected] Systems for cap/closure production 1 Model Ferromatik Electric El-Exis SP 2 Procession technology Injection moulding Injection Moulding 3 Clamp force 1,500 - 6,500kN 150 - 750t 4 Cycle time (guaranteed 98% closure system efficiency for): 26 mm: 2,800 caps/min a_High speed production: closure type/weight/cavities: caps/min 1881/1.6 - 1.9 g/ 2.9 seconds +/- 5% 29 mm: 2,300 caps/min b_Individual cap solution: closure type/weight/cavities: caps/min PCO 1881: 1,650 caps/min 5 Drive concept Electrical Hybrid 6 Energy consumption (kwh/kg) Under 0.20kWh/kg (based Ferromatik Electric with 48 cavity mould ) 0,40 - 0,50 7 Preferred mould makers z-moulds / Plastisud; StackTeck / Corvaglia 8 Special features Special ejector design dedicated for caps, modular machine concept, high level of customisation","@ID":37}, "TRADE SHOW PREVIEW 48 PETplanet Insider Vol. 17 No. 11/16 petpla.net www.bericap.com Unique range of light weight screw and sports closures for light weight PET neck standards for water • Closures for all common neck sizes 26/22, 28mm (PCO 1810, PCO 1881), 29/25, 30/25 • Light weight Hexalite range allowing light weight neck • Still water closures suitable for N 2 dosing • Sports closures fulfill BSDA requirements • Boreseal systems for excellent tightness • Consumer friendly opening forces BERICAP Technology for still water Fast-growing micro and craft brewer market Petainer, a leader in PET packaging, is focusing on the fast-growing micro and craft brewer market as part of its global expansion plans. The business has made a significant investment to ensure that it can support this key market effectively and efficiently. Petainer has developed a highly tailored craft brewery proposition, which will be showcased at this year’s BrauBeviale. Using its expertise in advanced polymer engineering, Petainer has developed the highly successful one-way 20 or 30l petainerKeg, which is increasingly being used as a low-cost alternative to traditional steel kegs, reducing the cost of entering new markets and launching new products. In addition to significant cost of ownership and sustainability benefits, it provides enhanced product protection, making sure that the beer is as good as the day it was brewed for up to a year. Petainer will be hosting a series of inspiring talks by successful craft brewers from around the world on its stand including the Steamworks Brewery from Canada, Ale Browar from Poland and German brewery Pfungstädter Brauerei. They will be sharing their first-hand experiences of setting up their operations, the challenges they have faced along the way and the key to their success. www.petainer.com Solutions, components and services for greater process efficiency Gea will present components and solutions for breweries, wineries, beverage production as well as to beverage industry experts. Gea’s innovations and improvements offer a wide range of possibilities to make processes more efficient and hygienic, and improve product quality. Gea will present the HopstarTA Dry for hop treatment in the cold process area of breweries. It is available as a skid-mounted standardised plug & play unit for dosing rates from 200g/hl to 600g/hl. Gea offers batch processing using reverse-osmosis/ membrane filtration with a capacity of 2.5hl/h up to 10hl/h to produce high-quality non-alcoholic beer along with evaporation technology. The technology uses filtration temperatures below 10°C and reduces alcohol levels 5 to 0.5 Vol. %. Gea rotoramic Membrane Disc Filters help with the concentration of valuable products. They can, for example, be used to recover beer from surplus yeast or retentate in the fruit juice industry. Membrane Disc Filters have 75% lower energy consumption when compared to cross flow filtration systems. Gea D-tec stem diaphragm valves are perfect for dairy and beverage industry applications requiring elevated hygiene standards. They help extend product shelf life and reduce the use of preservatives. www.gea.com/en Petainer Hall 4 | Booth 236 Gea Hall 7 | Booth 602","@ID":50}, "TRADE SHOW PREVIEW 40 PETplanet Insider Vol. 17 No. 11/16 petpla.net Sustainable preform production in India By Kay Barton March 9, 2016, Manjushree Technopack Ltd. We met: Mr Rajat Kedia, Director Mr Ankit Kedia, Director Mr Sanjay Balakrishna, Assistant General Manager (Operations) Manjushree Technopack, one of the biggest PET processing companies in India, opened a new facility for preform production in 2013. The plant, which is located around 30km towards Mysore from the centre of Bangalore, was a major project for the company. It wasn’t just a simple move; it was a relocation and expansion of its entire preform division, whose long-time home had been in Bommasandra, near the Electronic City district; it is now based in Bidadi, from where it serves customers in the water, fruit juice and soft drinks bottling segments, including major brands such as CocaCola, PepsiCo and Bisleri. The new building is not only special from the technological and ecological points of view. Directors Rajat Kedia and his brother Ankit Kedia explain their strategy and goals. “In 2010 and 2011 it became increasingly apparent to us that our PET processing on 96 cavity systems at our home location in Bommasandra, as well as the storage options available there, would no longer be sufficient for us to respond to the strongly growing market,” says Director Rajat Kedia. “That is why we decided to divide our company into a blow moulding factory in Bommasandra and an injection moulding division at a brand new location. We were offered a plot at the Bidadi industrial estate by the Government of Karnataka, which happened to be in direct proximity to two Coca-Cola bottling plants. In addition to the available space, an excellent water supply and the proximity to Bangalore made the decision to take the plot was a very easy one. It enabled us to become a strategic partner to Coca-Cola.” The total area of the approximately €30 million project is around 60,000m². The factory building accounts for roughly 42,000m²; the storage area is in the region of 32,500m². The complete factory concept was constructed together with Husky with the intention of creating a highly automated facility. In addition to the technical dimension, a key focus was on the environmental friendliness and sustainability of the building itself. To this end the factory features rainwater collection and biodegradable waste recycling, the use of sunlight as a source of light, sprinkler systems, disabled-friendly building access and more besides. The building earned Manjushree Technopack the Gold Award from the IGBC (Indian Green Building Management). Rajat Kedia estimates that its novel design enables it to save 1,500 units of power each day, compared with conventional production. The innovative design of the storage facility also creates and uses space, very efficiently. Materials containers are stored next to and above each other in individual cage segments, which has enabled the facility to reach a capacity of 7,200t on the plot, which is 2,500t more than conventional design would have allowed. The capacity of the overall installation totals 90,000t of processed material per annum for preforms and finished PET bottles, which translates to 2.1 billion preforms and 40 million bottles, in 2015. This year is forecast to see a 14% increase in preform production and a 50% increase in bottle production. The company uses two Husky HyPET 4.0 (144 and 96 cavities), two HyPET HPP (96 and 48 cavities), one H-PET AE (40 cavities) and one ASB PMI NII (24 cavities) in its production operations. Part of the building is also available for blow moulding. Here, four two-stage systems, one Sidel Synergy 06 (six cavities), Synergy 04 (four cavities) and one Mag Plastic Manjushree’s plant in Bidadi with Sanjay Balakrishna (right) and Kay Barton","@ID":42}, "BOTTLES 61 PETplanet Insider Vol. 17 No. 11/16 petpla.net DRYING HAS NEVER BEEN THIS EFFICIENT: ETA plus® LUXOR A 80-2400 Now available with ETA plus ® ETA plus ® considerably reduces energy consumption and protects materials. When it comes to drying, saving energy is a key concern. We have developed a system that combines airflow regulation with a temperature adjustment feature – that can be disabled if required – and efficient waste heat recovery. The result? A drying system that cuts energy consumption by up to 64%: ETA plus ® . motan-colortronic gmbh [email protected] www.motan-colortronic.com Sweetener without calories 100g of Truvia nectar – a product with a stevia glycoside basis which has been additionally refined with erythritol and natural aromatic substances – fill a slim, contoured and transparent PET bottle under the protected trademark Truvia by the American corporation Cargill. The viscous, honey-coloured product is served via a hinged lid clasp with selfclosing silicone valve. By pressing the bottle, a dosed quantity of the product is released. The bottle is labelled with a sleeve label which covers the snap cap as a first opening safety measure. Before first use, part of the label must be perforated and removed. www.truvia.com Topping for popcorn For popcorn fans, the American company Kernel Season‘s offers various additions to perk up the popcorn made at home, so that it tastes like the buttery popcorn “from the cinema”, for example. With this is mind, the company fills a transparent bottle with screw-on hinged lid and dosage opening with 417ml of the liquid consisting of several edible oils and flavourings. The product is to be used following instructions and poured onto the prepared popcorn. A colourful sleeve label gives information on usage and application tips. www.kernelseasons.com","@ID":63}, "MATERIAL / RECYCLING 11 PETplanet Insider Vol. 17 No. 11/16 petpla.net Fully automatic disposal concept of empty PET bottles The mineral well Teinach GmbH is a company of Mineralbrunnen Überkingen-Teinach GmbH & Co KGaA. The regional brand company produces mineral water and sweet drinks. More than 160 million bottles a year are filled on a production area of about 2,500m². These are sold to beverage wholesale trade or food retail. The company now compacts the PET bottles with three machines of Strautmann Umwelttechnik GmbH, manufacturer of bale- and briquetting presses. “We looked for a partner that automates our disposal solution and guarantees us reliability,” says Michael Schanz, plant manager, Mineralbrunnen Teinach GmbH. In the production of Mineralbrunnen Teinach GmbH, just slightly damaged bottles are automatically removed from the production process. These bottles are transported on a conveyor belt which passes through a slot in the adjacent hall. In this hall the three Strautmann machines are positioned. Through the conveyor belts the empty PET bottles are directly transported into the two redundant briquetting presses. Disposal of full PET bottles Full PET bottles are disposed of with the LiquiDrainer. Full PET bottles, which are after the best of date, are collected in small containers and lifted by truck into the LiquiDrainer. The PET bottles are emptied and savely devaluated. The now empty PET bottles are transported via the ejection onto the conveyor belt of the BrikPress and then compressed into briquettes. BrikPress channel system The highly compacted briquettes are pushed through channels outside to the triple distributor. The transport of the briquettes is made without additional energy consumption, as the briquettes are automatically pushed by the strong pressing force of BrikPress. This saves energy and time. Via the triple distributor the briquettes then pass into the container. When a container is full, the logistic department gets a message and can order the collection. Disposal previously Before the PET bottles were disposed of with Strautmann, they have been disposed of by a perforator and a channel baler. The two systems were very far away from the production, thus the Mineralbrunnen Teinach GmbH had long transport ways and a high in-house handling. Emissions of filler and blowing machine was collected in containers and driven by a truck outside to the disposal site. The bottles were then thrown in the perforator and thus pre-compressed and emptied. The presorted emptied bottles were blown into the ejector via an air transport in a channel baler. The PET bottles were pressed into large bales. The bales then had to be stored. If enough bales had been accumulated for a truck, the bales had to be picked up from the disposer. This was also a time-consuming step, because the bales had to be charged. For the Mineralbrunnen Teinach GmbH it was important to obtain a reliable and fully automated disposal solution that can be integrated into the production. The use of two redundant BrikPress machines ensures also a high reliability. Through the installation of LiquiDrainer, the two BrikPress and briquette channel system the internal handling has been reduced to a minimum. Schanz says: “We chose the Strautmann machines, because we wanted to reduce time and energy effort. Since then we have significantly less transport routes – we don’t even need to load anything anymore.” www.strautmann-umwelt.de Triple distributer at the Mineralbrunnen Teinach GmbH Filling the BrikPress channel system","@ID":13}, "MATERIAL / RECYCLING 16 PETplanet Insider Vol. 17 No. 11/16 petpla.net Pens to be made from bottle caps in a joint recycling project between Stabilo, Coca-Cola and Interseroh Reborn as a marker pen The writing instruments manufacturer Stabilo has begun a joint plastic recycling project with soft-drink manufacturer Coca-Cola and the recycling service provider Interseroh, which could be a marker for the future. In the project, Stabilo will, for the first time ever, manufacture highlighters from Coca-Cola bottle caps. Stabilo will market the highlighters made from 83% recycled plastic Procyclen under the brand name Stabilo Green Boss. The recycled plastic Procyclen was developed by Interseroh Dienstleistungs GmbH, a sister company of the international recycling specialists and raw material provider Alba Group. Coca-Cola bottle caps are particularly well suited as the starting material for the production of highlighters as their plastic meets the special Stabilo health and safety requirements due to its original approval for foodstuffs. During preparation of its PET reusable bottles for refilling, Coca-Cola is collecting bottle caps throughout Germany as a separate recyclable material and can thus provide them unmixed for the production of highlighters. “For this reason it quickly became clear to us that we had found a source of plastic here that is perfectly suited for us”, explained Peter Satzinger, Global Engineering Manager, Stabilo International GmbH. Interseroh manufactures the multiple award-winning recycled plastic Procyclen from Coca-Cola bottle caps through a specifically developed recycled resource process. “What’s special about Procyclen is that through its individual composition this recycling plastic meets all the expectations of a high-quality product and is absolutely equal to new products made from crude oil. An added bonus is that it has a significantly better balance of conservation of raw materials, energy and climate,” stated Dr Manica Ulcnik-Krump, Head of Recycled Resource Research and Development at Interseroh. Scientists from the Fraunhofer-Institute have estimated that greenhouse emissions resulting from production can be reduced by up to 50% if Procyclen is used instead of virgin materials. Interseroh is one of the brands under the Alba Group umbrella. The Alba Group is active with both of their brands Alba and Interseroh in Germany and Europe, as well as Asia with around 7,500 employees in total. “With respect to innovative packaging solutions, we are continuously working on making our bottles lighter, and we are capitalising on the use of recycled materials and plant-based raw materials and, of course, on the multiple use of materials through reuse and recycling. We are more than excited that together with our partners we have found a way of highquality processing for our bottle caps,” explained Sanam Moayedi-Stummer, Procurement Director, Coca-Cola European Partners Deutschland GmbH. The refillable highlighters will be sold in four colours as part of Stabilo’s “Green Range”. It is the first product made from the collaboration between Stabilo, Coca-Cola and Interseroh. Further products are expected to follow. www.albagroup.de www.coca-colacompany.com www.recyclingnews.info In a joint recycling project, Coca-Cola bottle caps are turned into highlighters (photo: Coca-Cola) Highlighters made from bottle caps (photo: Alba Group)","@ID":18}, "PETcontents 11/16 4 PETplanet Insider Vol. 17 No. 11/16 petpla.net INSIDE TRACK 3 Editorial 4 Contents 6 News 58 Products 59 On site 60 PET bottles for Beverage + Liquid Food 62 PET bottles for Home + Personal Care 64 Patents MATERIAL / RECYCLING 11 Fully automatic disposal concept of empty PET bottles 12 A clearer view 14 Tackling environmental challenges 16 Reborn as a marker pen PREFORM PRODUCTION 18 Preform dedusting boosts product safety at Gerolsteiner 19 Preform design & prototyping service BOTTLING / FILLING 20 Maintaining healthy properties 22 From beverages to liquid food INSPECTION 24 Optical sensors for oxygen permeability PACKAGING 28 To kill tow birds with one stone 30 Sturdy packages 31 Wrinkle-free wrapped 32 Hot-filled - cold-chilled MARKET SURVEY 35 Suppliers of closure systems TRADE SHOW PREVIEW 38 drink technology India (dti) exhibitors 39 dti preview 40 Sustainable preform production in India 42 Country Liquor: the PET Pioneer from West Bengal 43 New flavours for trend-conscious consumers 44 BrauBeviale preview 54 Entire integration for the beverage industry TRADE SHOW REVIEW 56 Self-optimising factory BUYER’S GUIDE 65 Get listed! Page 18 Page 52 Page 43","@ID":6}, "BOTTLING / FILLING 20 PETplanet Insider Vol. 17 No. 11/16 petpla.net F.l.t.r.: Michael Chen, Managing Director of Bericap China and Alexander Büchler, PETplanet Insider in front of the Editourmobil Complete line solution for Serbian mineral water producer Maintaining healthy properties To increase the capacity of its Prolom mineral water production facility, the Serbian spa resort owner and bottler Planinka is turning to Sidel, a leading provider of production equipment and services for liquids in PET, in establishing a new complete line. Maintaining the healthy properties of Prolom water was key for this customer. Planinka is a joint-stock company founded in 1964. They began bottling Prolom water at their bottling facility in 1990 in response to continuing local demand and the growing global trend for healthier drinks. At the time, there were only sparkling waters available in the former state of Yugoslavia, with no still waters on the domestic market at all. The average unit price of bottled water in Serbia increased by 4% above the country’s inflation rate in 2015. Domestic producers remain in a much better overall position in Serbia, despite the growing popularity of imported bottled water from countries such as Croatia and Slovenia. With numerous natural springs in the area offering very high quality water, local bottlers are able to provide the optimum combination of quality and cost which international companies find difficult to match, according to Euromonitor. Prolom spring water is claimed to ensure optimal rehydration with its natural diuretic and bacteriostatic effects. Additionally, the high alkalinity of Prolom water is said to make it ideal for stablishing the body’s pH balance and, due to its low mineralisation, it can be consumed in quantities. Collaboration since 2007 Planinka has worked with Sidel since 2007, when it purchased its first blower, a Universal SBO 6, for its water bottling line at its facility in Prolom Banja, and reverted also to Sidel when the decision for an investment in a complete new production line was made to meet the demands of its domestic and export markets. “As top producers in the beverage business, we are looking for great performance and the lowest possible total cost of ownership (TCO) from all our production lines,” says Mr Dragoslav Ilic, Head of Prolom Voda. “The main challenge of this particular project related to space constraints. However, Sidel’s line project team was able to offer the solution to fit all the component machinery needed for the line into the available space in a safe and functional way.” As this is the first occasion that Planinka has purchased a complete mineral water production line - including a Combi solution comprising blowing, filling and capping processes in a single system - the company conducted some investigative trips in both Serbia and Italy before finalising its decision.","@ID":22}, "NEWS 10 PETplanet Insider Vol. 17 No. 11/16 petpla.net Verstraete IML opens production site in USA In-mould labels company Verstraete will, in the coming months, start preparing the construction work for the new production site in Clarksville, Tennessee, USA, together with its parent company Constantia Flexibles. The new site is intended to allow Belgium-based Verstraete IML to get closer to its customers in the largest growth market for IML labels outside Europe. The site will begin production in the second half of 2017 and will have multiple printing press and finishing lines. Some 55 jobs will be created. Verstraete IML expects to invest EUR 18 million (USD 20 million) in its new US plant within a period of three years. The two Belgium-based plants in Maldegem and Ursel will continue to operate at the same capacity levels. Verstraete IML is part of Constantia Flexibles, one of the world’s leading manufacturers of flexible packaging and labels. Mike Henry, EVP Constantia Flexibles’ Labels division: “The new site is located in Clarksville, Tennessee, where Constantia Flexibles already has a paper and pressure sensitive labels plant serving the American beverage and food market. This has many benefits. Constantia has the management, legal and technical experience we need to operate successfully and rapidly in the North American region.” www.verstraete-iml.com The new site will be located in Clarksville, Tennessee, where Constantia Flexibles already has this paper and pressure sensitive labels plant serving the American beverage and food market. SGT, NATURALLY INNOVATIVE “ ” CHECK OUT OUR NEW PET PREFORMS CATALOG + 33 (0)2 40 05 09 37 SGT FRANCE 3 RUE DE L’ÎLE MACÉ 44 412 REZÉ - FRANCE WWW.SGT-PET.COM [email protected] COME & MEET US ATALL4PACK 2016 HALL 6 STAND 6D 048 Neck 27/31 for packaging syrups 14 -17 NOVEMBER 2016 - PARIS-NORD VILLEPINTE Preforms for big containers Preforms for UHT milk with full light barrier Lightweight preforms","@ID":12}, "NEWS 9 Development of the Italian plastics machinery market before K 2016 The Italian Plastics and Rubber Processing Machinery and Moulds Manufacturers’ Association Assocomaplast reported that foreign trade data for plastics and rubber machinery, equipment and moulds, in the first half of 2016 compared to those for the same period in 2015, show imports at nearly EUR 390 million, with a new peak (+9.7%) (source: ISTAT). This would seem to reaffirm the signs of recovery in the domestic market that had shown up on the radar last year. The trend in exports this year, on the other hand, was much less impressive: the bottom of the trough was seen precisely last June at -2.3%, following months of foreign sales dropping by 0.5% to -1.0%. Regarding the key geographical macro-areas for sales abroad – which are again the strong point for the sector – particular increases were seen in sales to the NAFTA countries. Specifically, there was a strong increase in exports to Mexico. Asia is also said to be a bright spot, thanks to increased sales in the Far East – China, India, South Korea and Vietnam – and, as regards the Middle East, to the much anticipated recovery of sales in Iran. The ISTAT data are confirmed also by the recent Assocomaplast sentiment survey of a sample of processors, who report a recovery in domestic and a slowdown in foreign demand, and among its members, where there is a trend toward stability in orders, especially from foreign markets, a situation that is expected to continue to the end of the current year. In parallel, they observed that competing German manufacturers closed out the first half of 2016 with substantial stability in imports and exports, recording positive variations in the order of tenths of percent. In effect, for years various Italian and German manufacturers have been recording a slowdown in orders in the months leading up to K trade fair in Düsseldorf, Germany. Interested buyers probably prefer to get an idea of the new technologies exhibited at the fair before planning and committing to their investments. www.assocomaplast.org PET 2020 - The future of the PET industry Petcore Europe has announced that its next annual conference will be held in Brussels on February 1, 2017. Building on the success of its 2016 edition, this major event will bring together around 200 experts and leaders from the complete PET value chain in Europe and beyond. The conference will include two interactive sessions on the future of PET packaging and sustainability. Each session will consist of key note presentations, followed by an extended panel debate with experts from the PET value chain, the EU institutions and other leading organisations. www.petcore-europe.org ","@ID":11}, "MATERIAL / RECYCLING 12 PETplanet Insider Vol. 17 No. 11/16 petpla.net rPET can be safely used with hot-fill packaging. A clearer view A study by Plastic Technologies, Inc, has determined that the use of rPET in hot-fill packaging has no significant impact on bottle performance at concentrations up to 50%. Above that level, the major impact is some haze or yellowing. Companies across the packaging industry are constantly seeking ways to improve the performance of their product. The focus in recent years as far as PET is concerned has been to include a higher proportion of rPET (recycled PET). As recyclate recovery and purification methods have improved, the potential for raising the percentage of rPET in food and beverage packaging has grown. The advantage is that packagers will benefit from being seen to be environmentally sensitive, and legislative and financial impacts will be reduced by the increased use of recycled materials. The concern is that higher concentrations of PET will see decline in performance. A recent study by Plastic Technologies, Inc (PTI), the American company known for its expertise in preform and package design and development, has produced results that will raise confidence in packaging containing quite high proportions of recycled material. It found that rPET content up to 50% has no significant effect on material performance at all. The objective While there is quite a lot of relevant information already available in the marketplace, PTI wanted to help provide brand owners with additional, relevant data and knowledge, which would help to facilitate the decisionmaking processes. Its research considered and analysed the use of rPET in a range of percentages, from fairly low (25%) to total (100%), and to determine the commercial viability of the range of recipes. The study - parameters This study was focused on evaluating virgin PET and two different rPET resins, which were added to virgin PET at 25%, 50% and 100% levels. The study focused on the production and performance of a 27g commercial 500ml six-panel hot-fill bottle and preform. Bottles containing recycledcontent variables were processed similarly, in order to maintain equivalent bottle wall thicknesses and maximise preform temperatures. In this way, the study could focus on the performance of rPET at various concentrations, as it would then be the only variable. The bottles were tested to determine hot-fill and top load performance, wall thickness, colour, haze, crystallinity and acetaldehyde (AA) content. The hot-fill testing regime the study subjected the bottles to is indicative of how the packages will perform under commercial hot-filling conditions. A vacuum is formed as the hot product cools inside the enclosed containers and this has the effect of increasing the chances of the occurrence of ovality or bottle denting. The heat of the product with which the package is being filled also causes the PET to shrink, through relaxation of the stresses created during the blow moulding process. Ovality and shrinkage were measured in order to ensure that they met standard performance specifications (fig. 1). The study - results Table 1 summarises the results of the key performance tests. The results show that, in all of the formulations - the virgin, 25% and 50% - and for both recycle resins, the materials and packages performed similarly. In terms of minimum peak top load results, rPET A performed at least as well as virgin PET. Ovality results were within acceptable levels at all concentrations. The bottles measured actually showed less ovality at 25% rPET than virgin PET, in both formulations. With the proportion of rPET at 100%, the bottles experienced shrinkage at the bell that reached levels that almost exceeded specification. The 100% rPET A resin also showed increased shrinkage at the lower bumper. This latter result was Spec Virgin 25% rPET A 50% rPET A 100% rPET A 25% rPET B 50% rPET B 100% rPET B Min. peak top load (lbf) ≥ 44 86 87 86 91 79 79 77 Max. ovality (mm) ≤ 3 0.53 0.42 0.6 0.93 0.47 0.6 0.81 Max. diameter shrinkage (%) ≤ 2% -1.43% -1.39% -1.42% -1.99% -1.27% -1.37% -1.95% Max. volume shrinkage (%) ≤ 2% -0.91% -0.87% -0.90% -1.55% -1.08% -1.12% -1.34% Table 1: Testing summary","@ID":14}, "BOTTLES 63 PETplanet Insider Vol. 17 No. 11/16 petpla.net Autumnal bubble bath by Tetesept Under the brand “t: by tetesept”, Tetesept Pharma GmbH has launched a new bubble bath series in packaging with an attractive and high-quality design. Just in time for autumn, another variant has arrived on the market as a limited art edition with the addition of Kuschelzeit (cuddle time). Along with macadamia nut oil, the product also contains orange, cinnamon and cardamom and provides a wintery fragrance in the bath. 420ml – sufficient for about nine full baths – fill a steady bottle with a metallic-looking screw-on cap. An artist designed the wintery sleeve label, which matches the product and the fragrance. www.tetesept.de Beauty shower gel by Nonique The German natural cosmetics manufacturer Yeauty GmbH has launched under the brand “Nonique” a new vegan product line on the German market. An example from the product range is the beauty shower gel with organic argan oil and organic pomegranate for demanding skin. According to the manufacturer, it has the fragrance of raspberries, cassis and vanilla. 250ml fill an almost opaque bottle which is decorated with a wrap-around self-adhesive label. A screw-on tilting lid clasp, which can be operated with one hand, facilitates use in the shower. www.nonique.de","@ID":65}, "PREFORM PRODUCTION 18 PETplanet Insider Vol. 17 No. 11/16 petpla.net Preform dedusting boosts product safety at Gerolsteiner Gerolsteiner Brunnen GmbH & Co. KG boosts its product safety in the manufacture of PET containers with the help of a preform deduster from KHS. By cleaning its PET preforms the company cuts costs and improves quality in the production process. Any foreign bodies are gently and reliably removed prior to the stretch blow molding process. PET preforms can be soiled for a number of reasons. Sometimes particles such as PET dust or foreign bodies, including splinters of wood or fragments of PET, can enter preforms during production, transportation or storage. “If foreign bodies like these are detected during preform inspection, the preform is rejected,” explains Marco Böhnke, product manager at KHS Corpoplast. Although the rejection rate for soiling of this kind is usually under half a percent, even this very slight amount is soon noticeable at a high production volume. A preform may only cost a few cents but by dedusting preforms and thus preventing unnecessary rejections annual savings into five figures can be made. The mineral water bottling plant in Gerolstein in Germany has now opted for this system. To save costs for preforms which would otherwise be lost, Gerolsteiner has placed a dedusting unit from KHS upstream of its inspection system. After six months in operation Dieter Kuhl, production manager for one-way containers at the bottling plant, is very pleased with the new extra. “We’re constantly working on improving the quality of our products. Further developments in inline quality control also help us here. We’re one step nearer to this goal with our dedusting unit and in addition we’re cutting our costs in the long term.” By using a compressed air lance specifically inserted into each preform the compact system removes unwanted particles at a rate of up to 81,000 preforms per hour. As a result not only are considerably fewer PET preforms lost; the risk posed by contaminated preforms is minimised further in combination with an inspection unit. “KHS preform dedusting is a prudent addition to any quality assurance setup,” says Böhnke. The deduster is upstream of the stretch blow moulder and compactly integrated into the machine layout. The cleaning system is supported by an effective extraction unit which reliably ejects all particles into an easy-to-clean collection vessel. The cleaning module has been designed so that it can be retrofitted for all customers with InnoPET Blomax stretch blow moulders in series III and IV. Gerolsteiner Brunnen was founded in 1888 in the Volcanic Eifel, Germany. Gerolsteiner’s unique mineral composition and its subsequent neutral and refreshing taste quickly made it a popular mineral water. Within a year, the mineral water was exported to the Benelux countries. Gerolsteiner was first shipped to the USA in 1890 and 1895 marked the start of international trade with Australia. More than 125 years after its foundation, Gerolsteiner is just as rooted in its home country and is even more widely enjoyed around the globe. The export to more than 35 countries, including the USA, Canada, Australia, Taiwan and the Benelux countries. Exports account for five percent of total turnover, which corresponds to sales of almost 31 million bottles. International trade focuses on Gerolsteiner Sparkling Mineral Water, which is available in both the optimised high-quality glass bottles, as well as in the light PET bottle. The sizes vary between 0.33l and 0.75l for glass and 0.5l, 1.0l and 1.5l for PET. Gerolsteiner Naturell and Apple Spritzer are also available in selected countries. These products are also available in the glass or PET bottle in different sizes. Due to the proximity, the range of products available in the Benelux countries is broader. www.khs.com www.gerolsteiner.de","@ID":20}, "MATERIAL / RECYCLING 15 PETplanet Insider Vol. 17 No. 11/16 petpla.net emissions are expected to increase to 40bn tonnes by 2035, and much of this will come from non-OECD countries. How far will westernised economies be obliged to carry the burden of emissions from the less developed countries? Will population growth hinder widespread acceptance of climate change accords? Luis Sierra, CEO BP Global Aromatics The overall conclusion from the conference was that there is still a huge amount to be done, and every member of the polyester chain, every government and consumers at the front line of climate change will have to play their part. www.bp.com PTA solution PTAir PTAir is claimed to be a new low carbon and carbon neutral PTA brand with three products that offers a more sustainable solution for the polyester value chain (purified terephthalic acid PTA is widely used to manufacture PET). It seamlessly fits into the current supply chain as a ‘drop in’ substitute for higher carbon, conventional PTA. A feature of PTAir is its use of proprietary PX and PTA technology which is claimed to support a 29% lower global warming potential than the average European PTA production. This low carbon benefit has been independently assured by ERM CVS. In addition to this BP will also be launching PTAir Neutral, the world’s first certified carbon neutral PTA. PTAir Neutral is intended to offer customers the opportunity to purchase a carbon neutral product where associated CO 2 equivalent emissions are mitigated through the investment in carbon projects providing equivalent CO 2 benefits and delivering a net zero position. Furthermore, through PTAir Neutral products customers have the opportunity to offset all of their product footprint - over and above their PTA use - to achieve full carbon neutrality across their product portfolio. This unique offer is made possible through BP Target Neutral, BP’s longstanding, not-for-profit carbon management programme. PTAir is available in Europe, and BP plans to roll out in the US and Asia in due course.","@ID":17}, "TRADE SHOW PREVIEW 50 PETplanet Insider Vol. 17 No. 11/16 petpla.net Innovations for drinks processing HSM GmbH Co. KG, a German manufacturer of baling presses, PET solutions and document shredders, will be exhibiting its new product solutions “Made in Germany” at the BrauBeviale trade fair. By means of a continuous feed, the HSM BRP 4810 briquetting press quickly and automatically compresses large amounts of PET bottles and beverage cans to up to a thirtieth of their original volume. A drive with a press force of 477kN is achieved via an efficient and low-maintenance PowerPack. It is not necessary to strap the briquettes. Thanks to the multilevel compression, the machine spits out briquettes with a density of up to 400kg/m³ with PET and up to 760kg/ m³ with aluminium cans. The robust construction made of wear-resistant steel is maintenance-friendly, since the third compression stage, the primary pressing stage, and thus the most wear-intensive part, can be completely replaced. The HSM PET FluidEx 600 quickly and reliably empties full PET bottles, cans and Tetra Paks, which were, for example, incorrectly filled or labelled or whose shelf life has expired. Using a filter system, small plastic chips and labels are cleaned from the liquid and removed. Up to 10,000 one-litre bottles per hour can be processed. This high performance, as well as the low space requirement and possibility of direct integration into existing recycling processes, are the key factors of the HSM PET FluidEx 600. www.hsm.eu HSM Hall 7 | Booth 640 www.PreSens.de Scan & Measure Oxygen Ingress & Transmission Rates Fibox 4 Stand-alone fiber optic oxygen transmitter BrauBeviale 2016: Hall 4, Booth 411 Revolution to the storage and transport of preforms and closures In order to be competitive on the global market, industrial preform and closure manufacturers are constantly striving to organise their logistics in the most cost effective manner. Their end customers are large bottling and filling companies, who need to receive their preforms and closures in a returnable packaging container that is fully hygienic, easy to fold down when empty, and efficient to store in the warehouse. DS Smith has integrated all these elements in their Stackabox product range, that offers a plastic alternative to the cardboard or metal solutions used today. The Stackabox series come in three different sizes to offer the best volume for each application, whether it’s closures, preforms or blown bottles. A standard trailer will hold 52 full Stackaboxes, while a return load can take no less than 156 folded containers, thanks to the good fold ratio. Furthermore, the patented bottom chute offers the possibility to empty the contents directly on the lines via the bottom, reducing neck breakage of the preforms. Of course the Stackabox is fully compatible with existing conveying and tipping equipment in the factories. The pallet and the sealable lids are all integrated into this one-piece container, in order to avoid loss of detachable components. True to its recycling policy, DS Smith closes the loop by offering a product that is fully recyclable at the end of its life, as the polypropylene raw material can be reused over again for the production of new containers. www.dwplastics.be DS Smith Hall 4A | Booth 207","@ID":52}, "TRADE SHOW PREVIEW 52 PETplanet Insider Vol. 17 No. 11/16 petpla.net Stretching the Limits of PET Processing to50 Ltrs Visit us in Hall 7 Booth 451 Product safety and efficiency on small and large filling lines Compact and flexible solutions for quality check At BrauBeviale, Heuft will clarify how to reduce product recalls effectively without thwarting line efficiency using SMEs by way of example in a special enlightenment area. You can even be treated to a beer created by Heuft at a rotary system with Heuft devices for an easy full container check, conveyor control system and fault rejector in a confined space. Furthermore compact and flexible solutions for a reliable empty bottle inspection will be presented for small filling plants in the new enlightenment area. Leakage check and closure inspection of the new generation The Heuft Spectrum device generation which offers more performance can also be experienced. The new additions are: The Heuft FinalViewI Cap for a complete all-around inspection of closures and the Heuft squeezeI QS a leakage check for filled plastic bottles. They combine maximum automation and a self-explanatory audiovisual user guidance with an unprecedented precision when inspecting, tracking and rejecting containers as do all the systems based on the new platform. This is intended to provide maximum product safety, to reduce the false rejection rate and at the same time to save valuable human resources. www.heuft.com Premium decoration Responding to the growing trend, CCL has created its own Craft Beer Unit. Thanks to a tightly woven network as well as limitless press capabilities, CCL is able to offer the needed technology and flexibility required for the craft beer segment. The EcoStream technology is the ideal solution for bottle-to-bottle recycling of PET bottles decorated with PS labels. Thanks to its composition it helps maximise both yield and quality of the bottle-to-bottle recycling stream. www.cclbeverage.com Heuft Hall 5 | Booth 311 CCL Hall 7A | Booth 510","@ID":54}, "MARKET SURVEY 37 PETplanet Insider Vol. 17 No. 11/16 petpla.net Husky Injection Molding Systems Ltd. 500 Queen Street South Bolton ON Canada L7E 5S5 +1 905 951 5000 www.husky.co Mr Henry Zhang Director of Business Development, Medical and Specialty Packaging +1 905 951 5000 +1 905 951 5337 [email protected] Mr Michael White Business Manager - Beverage Closures +1 905 951 2913 ext. 2913 +1 905 951 5337 [email protected] Sports drinks, water, aseptic, hot fill, CSD Threaded beverage closures Personal care, edible oil, spice jars, carton closures, pouch fitments Individual closure solution Flip top Screw on cap with tamper evidence band PP HDPE Variety of weights to meet customer specifications ≥0.7g 300t - high-cavitation available 4-96 cavities (25mm-48mm neck finishes) Husky Husky Hot Runners In-Mould closing; eIMC technology; Fully integrated; Reflex platen Optional front mounted cavity design for quick tip access/unblocking; Horn-pin less design for faster cycles; Robust design with integrated pillar supports; Ultra hot runner design for leak proof operation & rapid colour change; Optional moulding intelligence feature that when bundled with the HyCAP4 machine unlocks a variety of functions/features that maximise uptime, promote part quality, and simplify operation (Mould Alignment, Eject Assist, Auto Colour Change, & Smart Start/Stop) ENGEL AUSTRIA GmbH Ludwig-Engel-Straße 1 A-4311 Schwertberg, Austria +43 50 620 0 www.engelglobal.com Mr Michael Feltes Manager Business Unit Packaging +43 50 620 3100 +43 50 620 13100 [email protected] ENGEL e-cap 220 ENGEL e-cap 280 ENGEL e-cap 380 ENGEL e-cap 420 ENGEL e-cap 280 ENGEL e-cap 380 ENGEL e-cap 420 injection moulding injection moulding injection moulding injection moulding injection moulding injection moulding injection moulding 2,200 kN 2,800 kN 3 3 3 3 3 3 3 3 3 3 3 3 4,7 4,8 4,7 4,8 4,7 4,8 4,7 4,8 Closure type 26 29/25 30/25 26 29/25 30/25 26 29/25 30/25 26 29/25 30/25 1881 1810 1881 1810 1881 1810 1881 1810 weight 1 1,3 1,7 1 1,3 1,7 1 1,3 1,7 1 1,3 1,7 2,3 2,6 2,3 2,6 2,3 2,6 2,3 2,6 cavities 48 48 48 64 64 64 72 72 72 96 96 96 48 48 64 64 72 72 96 96 caps/min 960 960 960 1280 1280 1280 1440 1440 1440 1920 1920 1920 610 600 816 800 918 900 1224 1200","@ID":39}, "NEWS 7 PETplanet Insider Vol. 17 No. 11/16 petpla.net i IMAGINE FILLING MULTIPLE PRODUCTS ON THE SAME LINE…NOW YOU CAN! Water, juice and soft drinks, all on a single machine? The Flextronic modular platform adapts effortlessly to still or sparkling, clear or pulpy and hot or cold-fill, and easily switches from one bottle neck-size to the other. A revolutionary filling technology that gives you extreme operational flexibility with minimal product loss and downtime at flavor switch. Clean, safe and versatile. Welcome to the new generation of fillers. carbonated still hot-fill cold-fill pulp non-pulp water juice soft drink SIPA S.p.A. - Via Caduti del Lavoro, 3 - 31029 Vittorio Veneto (TV) - Italy Tel. +39 0438 91151 - Fax +39 0438 912273 - e-mail: [email protected] www.sipa.it PROCESSES AND PACKAGING LEADING TRADE FAIR DÜSSELDORF, GERMANY 08 14 MAY 2014 INTERPACK.COM TO JOIN US AT INTERPACK HALL 13 BOOTH B73","@ID":9}, "INSPECTION 24 PETplanet Insider Vol. 17 No. 11/16 petpla.net Chemical optical sensors determine oxygen permeability of barrier and breathable packaging material Optical sensors for oxygen permeability Based on an article by Christian Huber, PreSens Precision Sensing GmbH; Kajetan Müller, Fraunhofer IVV; Gernot John, PreSens Precision Sensing GmbH The barrier requirements of synthetic materials towards oxygen can differ widely, depending on their later use. Unwanted oxygen in packaging, taken up while filling or by permeation through the packaging material, can lead to oxidative deterioration of food, and shorten the shelf-life of certain products. Different methods are currently applied to determine oxygen permeation in packaging materials such as the barometric method or the use of carrier gas. However, these traditional analysing techniques do not guarantee realistic conditions, as they are only applicable for empty packaging. A new technique is permeation measurement with chemical optical sensors with a detection limit of 1ppb of dissolved oxygen. They can measure oxygen ingress continuously, non-destructively and noninvasively under real conditions over long time periods. The PreSens PSt6 sensor can be applied to measure packaging material for most food applications. It enables the analysis of both barrier and breathable packaging materials. A recently developed measurement device together with the new low oxygen sensor PSt9, with a detection limit of 0.5ppm and a dynamic range of 0 to 1,000ppm gaseous oxygen, fulfill the requirements of measuring high barrier materials which are needed for technical applications. Measurement principle Chemical optical sensors consist of a thin layer containing an analyte sensitive dye. These sensor spots are excited by light of a certain wavelength and emit fluorescence. If the indicator dye in the sensor encounters an oxygen molecule, the excess energy is transferred to oxygen in a non-radiative way; the indicator molecule does not show luminescence and the total measurable luminescence signal decreases or is quenched. This principle of decay time measurement is used to determine the oxygen concentration in the sample. An optical fibre transfers light to the sensor and the fluorescence signal back to a photodiode integrated in It is very important to determine the barrier properties of packaging and other synthetic materials to protect oxygen sensitive foods, pharmaceuticals and technical applications. New methods in material research are therefore required for oxygen permeation measurements to characterise special synthetic films. A novel approach is the non-invasive, non-destructive measurement of oxygen permeability with chemical optical sensor technology. Oxygen ingress in filled or empty packaging for most food applications can be determined. Another advantage is that these sensors can be used to measure breathable as well as high barrier films. Fig. 1: Measurement system set-up: The new measurement cell with two gas connectors for each of the two chambers; the sensor spot is integrated in the upper chamber and read out via polymer optical fibre by the fibre optic transmitter (source: Fraunhofer IVV).","@ID":26}, "PACKAGING 28 PETplanet Insider Vol. 17 No. 11/16 petpla.net To kill two birds with one stone In the beverage sector, the packaging industry has to kill two birds with one stone. Firstly, consumers expect individually designed packages, if possible with supplementary functions. And secondly, increasingly eco-minded drinks consumers are showing a growing thirst for resource-conserving containers manufactured with environmentally compatible methods. The industry achieves this balancing act with new packaging strategies and efficient production equipment. For example, the mineral water brand evian, which is owned by Danone Waters, goes to huge lengths to highlight the uniqueness of its products. For its prestigious plastic bottles, it exploits the new Nature MultiPack technology, a packaging innovation that uses specialised adhesives to join the individual PET bottles together in such a way that they can be individually positioned and later released from the others with ease. (See PETplanet 4/2016 page 34) In the design field, Danone is also going unusual ways. Since 2008, evian has issued nine Limited Editions of mineral water bottles styled by well-known fashion designers. In 2016, the American couturier Alexander Wang has taken up the barcode as a package theme and rendered it with black-and-white stripes on the glass bottles. The spaces between the stripes and the purist design are intended to express evian’s natural purity. But individuality and differentiation are highly popular not only among upmarket brands, as a growing throng of drinks manufacturers are marketing their mineral water and lemonade additionally in smaller, 0.5l returnable bottles to appeal to smaller households. Or they sell their product in elegant faceted bottles to improve their chances of selection by high-class restaurants, for example. The benefits notwithstanding, lavish packages do have their drawbacks. The greater the individuality and complexity of the product’s packaging, the more elaborate and expensive is its production. The higher production costs are ultimately passed on to the customer in higher prices – a point that consumer activists often criticise. What is more, elaborate production methods and disposable bottles burden the environment. To minimise the impact, some countries have set in some cases ambitious targets for bottle reuse. Germany, for example, wants to achieve an 80% reuse rate, although this has fallen since 2004 from two thirds to 45%. At the same time, the quantity of waste from oneway drinks packages has since increased by 30%. According to current statistics from the German Federal Government, package consumption rose from roughly 465,000t to 600,300t in 2014. Retailers and manufacturers are regarded as the instigators of this singleuse boom. Packaging manufacturers are also under an obligation. They have to achieve the balancing act of spectacularly presenting the package with a consumer-friendly design while conserving raw materials and thus easing the burden on the environment. The requirements that have to be met by packaging machines are therefore becoming more exacting as well. “Treating natural resources responsibly and doing business in an environmentfriendly way have high priority among manufacturers of food processing machines and packaging machines. They know that sustainable production processes are hugely important for their customers,” says Vera Fritsche, expert at the VDMA (Mechanical Engineering Industry Association) association for food processing machines and packaging machines. Intelligent control and automation technology and energy-saving drives, compressors, fans and pumps rank, she claims, rank among the classic solutions for saving power and other resources and boosting energy efficiency. Efficient motors perfectly adapted to the machine’s motions and acceleration processes reduce power consumption. In addition, Fritsche continues, innovative and improved processes lower the consumption of energy and water while innovative machine strategies extend service and maintenance intervals and service life and thus save energy. Innovation potential in production All the same, big potential for cost savings can be found not only in the materials sector, but also in production equipment. Industry is therefore doing all it can to improve production methods. An example of this is the Doğuş Çay tea factory in Izmir The heater boxes are distinguished by new reflectors made of modern ceramics and a precisely adjusted geometry.","@ID":30}, "NEWS 8 PETplanet Insider Vol. 17 No. 11/16 petpla.net Gerd Liebig new CEO at Sumitomo (SHI) Demag Gerd Liebig (55) has been appointed CEO at Sumitomo (SHI) Demag. Starting January 1, 2017 he will succeed Dr Tetsuya Okamura (60) who will take over a new responsible position at Sumitomo Heavy Industries Ltd. Gerd Liebig has been working in responsible positions in Sales and Marketing in the injection moulding industry for more than 25 years. From April 2015 to date he was the Chief Sales Officer at Sumitomo (SHI) Demag Plastics Machinery GmbH. Together with CSO Gerd Liebig and CTO Andreas Schramm, Dr Tetsuya Okamura managed the company as CEO from March 2008 until December 2016. In that time, Dr Okamura developed Sumitomo (SHI) Demag into a financially strong company with a clear strategic focus on the company’s core competences in production and product portfolio. The company invested significantly in its production sites and subsidiaries, most recently in a huge number of machines for the Schwaig production facility. Currently, considerable resources are being devoted to supporting “eService” and to expanding the subsidiaries. Gerd Liebig joined Sumitomo (SHI) Demag on April 1, 2015 as CSO. From 1990 until 2005 he was Head of Marketing with Sumitomo (SHI) part of the Demag Plastics Group before moving to an Austrian competitor. With Sumitomo (SHI) Demag’s new subsidiaries in Hungary, Austria and Spain, Gerd Liebig strengthened the company’s advisory skills as well as its problem solving competence; he also put customer service on an international footing. “Since joining the company Gerd Liebig has made innovation his priority. He motivated employees and customers with his competence, enthusiasm and conviction. Gerd Liebig has played a hugely important role in the company’s distinctive growth during the last year. The market shares in all strategic market segments have increased considerably,” says Dr Tetsuya Okamura: “I am confident that Sumitomo (SHI) Demag will continue to be in very good hands when the new Managing Board takes over responsibility.” Sumitomo (SHI) Demag expects to see considerable potential to develop synergies in the production strategy and in sales and service. With CTO Andreas Schramm we will continue to set the company on the way to internationalism and to further incorporate our activities with Sumitomo’s Plastics Machinery Division and Headquarters in Japan,” says Gerd Liebig. www.sumitomo-shi-demag.eu CEO Dr Tetsuya Okamura (centre), with Sumitomo (SHI) Demag‘s new CEO Gerd Liebig (left) and CTO Andreas Schramm (right) Säntis AG transfers PET packaging business unit to Bonapack The Swiss Säntis AG is transferring its PET packaging business unit at the end of 2016 to Bonapack AG also located in Switzerland. Bonapack will be managing the business in the PET blow moulding unit in cooperation with Biplast AG, particularly in the Development, Production and Service divisions. Bonapack will ensure a seamless transition for Säntis clients. With the expanded product range and the additional services, for instance with regard to bottle decoration, new packaging options are provided. Säntis will still produce its products until the end of November of this year. In December, the relevant machines, tools and documentations will be handed over to Bonapack AG, which will begin production in the new manufacturing facility in January 2017. The separation from the PET packaging business unit is viewed by Säntis as a further stage in its business strategy. www.saentis-ips.com www.biplast.ch The innovative packaging company Damstraat 4, 9230 Wetteren, Belgium T +32 (0) 9 365 7474 www.resilux.com, [email protected] Considering PET Preforms and Bottles? Monolayer, Barrier, Refill and Hotfill? Let’s meet up at: BrauBeviale2016, Nuremberg, Germany: Hall 4A, stand 233 All4Pack, Paris, France: Hall 7L, stand 130","@ID":10}, "PACKAGING 34 PETplanet Insider Vol. 17 No. 11/16 petpla.net onto pallets by a Modulpal in each line. Downstream, both lines share a stretch wrapper, in which the pallets’ loads are stabilised for transport. In order to ensure optimum protection for its kit, Leão purchases lubricants from KIC Krones. Syrup kitchen Krones was also responsible for the concept and installation of the entire syrup kitchen, which has been accommodated on two floors: the ground floor houses the product formulation system where suction pipe end pieces extract the tea concentrates from the drums and place them in mixing tanks. The kit can also process powders. On the same level, two product tanks are accommodated for each of the two lines, which through apertures in the ceiling rise up to the floor above. It is on this top level that the two VarioFlash H flash pasteurisers with shell-and-tube heat exchangers, and the two Contiflow two-component mixers have likewise been erected. Installation work for the lines and the process section began in mid2013, and the lines had already been acceptance-tested in September. Water treatment In parallel with the installation work, Leão also had to substantially upgrade the infrastructure in the plant, and to revamp some of the utilities like water supply and treatment, electricity, superheated steam and pressure. Leão equipped its wastewater treatment process with a reverse-osmosis system, so that the treated wastewater can be re-used in the plant as process water. This is because in Brazil, too, water consumption is an increasingly exigent focus. Rather like in California, suffering from an almost total drought, the metropolis of São Paulo, for example, with its 21 million people, has for some years now found water scarce, so that the city council has had to optimise consumption per household: using too much is punishable by a fine. Sustainable utilisation of water is thus a mandatory principle for Leão. “The frequent product change-overs in the bottling lines, particularly, consume a bit more water for cleaning,” explains Dirk Schneider. Usually a product is run for not more than 15 hours at a time before a product change-over is scheduled – once or twice a day. This is a challenge faced by almost every beverage producer,” explains Dirk Schneider. www.krones.com Dressed and packed A Linadry dries the containers, which are then dressed in full-body sleeves by the two DecoBloc labellers, whose technology enables them to be dressed in either sleeves or wrap-around labels. Leão is at present using the machines solely for the sleeve technology, but there is also an option for linking up stations of the Contiroll HS for wrap-around labelling. The first PET line installed by Krones in 2010 likewise already incorporates a DecoBloc. Once the PET containers have been dressed in sleeves, these are snugly shrink-fitted to the container’s shape in a Shrinkmat shrink tunnel, thus constituting an attractive sales package amenable to multiple design variants. A specially dimensioned Checkmat FM-G then uses a 360-degree monitoring unit to inspect the containers for correct positioning of the sleeves. After that, two Variopac Pro packers installed in parallel group the bottles into sixpacks, which are arranged in the appropriate layer pattern by a Robobox grouping system. The finished layers are then stacked Dirk Schneider, Industrial Director at Leão Alimentos e Bebidas The two lines are, with the exception of the fillers, almost identical. They each begin with a Contiform Bloc, comprising a heatset Contiform H blow-moulder and a filler. Reel change at the DecoBloc labeller The shrink-packs are arranged in the appropriate layer pattern by a Robobox grouping system.","@ID":36}, "PETnews 6 PETplanet Insider Vol. 17 No. 11/16 petpla.net Sidel Matrix Blowers awarded certification for energy efficiency Sidel has been awarded certification for the efficiency of its Sidel Matrix blower by a leading technical service organisation, TÜV SÜD. The new certification is an international stamp of approval for the energy consumption efficiency of Sidel equipment. It is claimed to provide objective validation of the blower’s performance by an independent organisation and demonstrates that the Sidel Matrix blower complies with very high standards, is safe and sustainable and has minimal impact on the environment. The certification experts began the procedure with an audit, then assessed the energy efficiency of the complete machine, its design and all its components, inspecting all relevant documentation and engineering procedures. They looked at how developments to improve energy efficiency of the equipment can be demonstrated, also comparing the machine with the best available technology in the market using benchmark data. Once the requirements of the TÜV SÜD certification have been met, the certificate is valid for three years, with an annual audit to ensure continued compliance. www.sidel.com Packaging design to reach over $1 trillion by 2026 According to market research experts from Smithers Pira the total value of the packaging market is set to rise at a CAGR of 3.8% from $806.3 billion in 2016 to $1,162.1 billion in 2026 – and packaging design will have a major part to play in facilitating this growth. “The Future of Packaging Design: Long-Term Strategic Forecasts to 2026” states the future of the packaging industry, as any other, will be shaped by general political, economic, social and technological factors. Meanwhile, the specific future of packaging design to 2021 and 2026 is forecast to be determined by supply side technological trends and demand side consumer trends. The report looks at the influence of factors such as convenience, consumer income, health and wellness, and single-person households on market demand, and on resulting packaging design trends. Ashley Gange, report author states: “The political environment will affect the packaging industry and packaging design via initiatives, legislation and regulation affecting environmental affairs such as sustainability, food packaging labelling and packaging safety. Sustainability has become a particularly important consideration in many areas over the past decade. “This is especially true in packaging where it is a major issue since packaging materials are extremely visible to the consumer. This is because packaging as a single-use product faces intense and growing pressures from consumers, retailers, suppliers, governments, regulators, NGOs, environmental groups and others for the development of environmentally friendly solutions.” For the first time the European labour market witnessed more workers retiring than joining in 2010. The impact of this trend on the printing industry will become more evident with time, as the gap is predicted to increase substantially. In a decade, more large counties including Canada, China and South Korea will have more people at retirement than working age. Emerging markets such as Brazil, Mexico and India are seeing more than people ever joining the labour markets. If these counties provide their youth with adequate education and opportunities to develop their skills, this demographic trend will benefit local printing industries. www.smitherspira.com The PETplanet Collection All you need to know about caps and closures Filled PET bottles be without their caps? Unthinkable! Systematically arranged in WikiPETia, we have compiled a list of some of the major suppliers in the caps and closures sector. You will find companies in the following areas: Suppliers of caps and closures Suppliers of closure moulds Suppliers of machinery for the production of caps and closures Suppliers of ancillary equipment https://petpla.net/wiki?title=Capping If your company is active in this sector but not yet included in our WikiPETia directory, you are cordially invited to submit your details. Please contact us at: [email protected] Suppliers of moulds for closures and of equipment for manufacturing caps can also be found with specific production data in our Market Survey on page 35. Clicking on the company names will take you to the relevant WikiPETia page where you will find out more about what they can offer in the cap sector. www.wikipetia.info","@ID":8}, "TRADE SHOW PREVIEW 51 Vipoll can filler This year, Vipoll, the Slovenian specialist for filling plants, is presenting the new Vistron VK-EID-DN 30 can filler. The volumetric filling plant features 30 filling valves and is ideal for the production of all kinds of still beverages (with or without pulp) and carbonated drinks. The second focus lies on filling systems and solutions for nonalcoholic drinks without preservatives in PET bottles. A simple and automated conversion mechanism enables the Vistron can filler to use the same filling valve for a multitude of can types, thus offering maximum flexibility when filling different can and cap diameters. Carbonated drinks are processed under counterpressure, still drinks, such as juices, without overpressure. A blocked capper with four heads located in the filler housing is linked to and in sync with the filler. The servo drives are also synchronised. The entire cable guide is installed in the housing and piping. An automated CIP bell application is standard in Vipoll can fillers with the filler technically adapted for the connection with a CIP or foam cleaning system. In addition, the company produces systems and solutions for filling alcoholic drinks without preservatives in PET bottles (natural juices, smoothies, dairy products, tea, etc). This is possible thanks to special filling blocks with multi-chamber housings and controlled overpressure zones as well as state-of-the-art machine cleaning in connection with sophisticated process plants. www.vipoll.si Vipoll Hall 7 | Booth 233 PETplanet Insider Vol. 17 No. 11/16","@ID":53}, "PACKAGING 33 PETplanet Insider Vol. 17 No. 11/16 petpla.net measuring 3,500m2, had actually been planned for the smaller line ratings originally ordered, and secondly both lines were to be installed within a timeframe of only about four months. Dirk Schneider remembers: “Over a period of eight months before installation began, we had an intensive planning phase with Krones. Since the ready-to-drink teas Leão Fuze and Matte Leão exhibit an entirely different formulation to Powerade, the project also demanded a rethink.” In order nevertheless to accommodate twice the output on the same area, the two lines U and V were put together like a kit in an exceptionally compact layout. On two decks Both lines hot-fill the products at 85°C. After that, a Checkmat FM-G inspects the containers for proper fill level and closures. Directly downstream, there is in each line a heatholding section on which the filled containers are transported lying on their sides, so as to also enable their necks and closures to be thermally decontaminated with the requisite dependability. Now comes the first interface between the two lines: both of them utilise a double-deck cooling unit, which reduces the bottles’ temperature from filling to room temperature. Here, the bottles from the one line are passed through the bottom deck while those from the second line travel along the top deck. The cooling water, which is being warmed up in the process, is used as warm water for flash pasteurisation in the two VarioFlash H shell-and-tube heat exchangers, which are located in the separate syrup kitchen. One Accutable buffer table has been integrated for each line, with the two of them space-savingly installed one above the other. Each provides sufficient buffering and accumulation space between the blow-moulder/filler block and the labeller. PROCESS PILOT® makes producing a better PET bottle as easy as 2 3 1 MEASURE CONTROL OPTIMIZE every bottle for changes in material distribution process variation, inside the blowmolder material utilization and orientation to achieve maximum bottle performance CONTACT US TODAY TO LEARN MORE! AGRINTL.COM | +1.724.482.2163 | [email protected] VISIT US IN HALL 4A BOOTH 233 Retrofit option for the FlexiFruit process The two lines are, with the exception of the fillers, almost identical. They each begin with a Contiform Bloc. The heatset Contiform H blow-moulder is supplied with preforms from a preform feeder, which first of all are passed through a linear preform rinser. An inspector checks the preforms in the feeder for any damage. The downstream filler is directly block-synchronised, and accommodated in a cleanroom with HEPA filters and overpressure air control. In what is called Line U, the filler provided is a volumetric Modulfill VFS with flow metering. For Line V, Leão has kept an option open for retrofitting the filler at a later date with the Krones FlexiFruit process. This enables the client to ensure product-friendly predosing of fruit chunks into the containers. Line U was originally designed to handle six different container shapes and sizes. At present, it is being used almost solely for filling the 300ml bottle with Leão Fuze and Matte Leão. Line V with the FlexiFruit option has been initially equipped with five different moulds for 300ml, 500ml and 1.5l containers. This line, too, is currently specialising in a single product – it is filling the two ready-to-drink teas in the 1.5l bottle. Put together from Coca-Cola Brasil and its regional producers, Leão Alimentos e Bebidas is responsible for administering the entire production chain of the national line with still, teas and energy drinks from the domestic Coca-Cola portfolio.","@ID":35}, "INSPECTION 25 PETplanet Insider Vol. 17 No. 11/16 petpla.net the measurement device. Measuring luminescence lifetime as the oxygen dependent parameter avoids common problems with intensity based measurements, particularly with the decay time which can depend on fluctuations in the intensity of the light source, or by signal loss and other factors involving the indicator dye. Chemical optical sensor systems allow non-invasive and non-destructive measurement in containers, as the sensor is integrated inside the vessel, while the opto-electronic device is placed outside. The sensors are read out through the transparent vessel wall or through an optical window without piercing or damaging the material. The systems perform through transparent materials up to a thickness of 10mm and even through turbid packaging. The sensors can measure both in liquid and in gaseous (headspace) phase. This way the interior oxygen concentration of closed, filled packaging and permeability in parts per million to parts per billion ranges can be determined. Measuring oxygen permeability PreSens offers a complete system for permeation measurement in packaging materials like PET bottles. The set-up for oxygen ingress measurement with chemical optical sensors is very simple (fig. 2). A trace oxygen sensor spot type PSt6 can be attached directly to the inside vessel wall, if the material is transparent or only slightly coloured, and the bottle is closed with a standard closure. For darker materials that can act like a filter for the excitation and emission light, special transparent, oxygen tight closures were designed which contain the sensor and can be attached to PET bottles with a safety screw. This safety screw is adapted to standard bottle threads. The sensor signal is read from the outside and transferred to a trace oxygen meter with a polymer optical fibre. Single-channel but also multi-channel oxygen meters are available that allow for simultaneous characterisation of several bottles. It is recommended to perform oxygen ingress measurements under realistic conditions, so reliable results can be obtained. Ideally, PET bottles filled with the final product should be measured, but for products such as beer, oxygen-free carbonated water is used to ensure the barrier properties of the bottle are accurately investigated. For oxygen ingress measurements PET bottles are filled inside a nitrogen-flushed glove box, so the oxygen content in the environment is 0.1% oxygen. Nitrogen-saturated water with a dissolved oxygen concentration of 100ppb is carbonised with a pressure tablet, which contains sodium carbonate, sodium hydrogen carbonate and citric acid. In addition silver nitrate (0.2mmol/L) is added to the water to avoid growth of bacteria that might consume oxygen and falsify the measurements. The bottles are filled and sealed with the standard closure or the oxygen sensitive cap with the integrated PSt6 sensor. After filling, the bottles are removed from the glove box, put into a climate chamber and shaken for half an hour. This way the temperature of the liquid inside the bottle can adjust to the measurement temperature. As oxygen permeation is dependent on temperature and humidity the permeation measurements are performed in a controlled environment, in these experiments 30°C and 50% relative humidity. Continuous shaking of the bottles throughout the measurements guarantees equilibrium state of headspace and liquid. Permeation measurements were performed in different PET bottle types. Test 1: Outside coated PET bottles filled with oxygen-free water In a first experiment an externally coated bottle was compared to an identical non-coated bottle over a period of 30 days. Both bottles had a weight of 38g, a filling volume of 500ml and 20ml headspace. They were filled with nitrogen-saturated water that was not carbonised. During the first 48 hours both bottle types show a high and non-linear increase in oxygen concentration (fig. 3). There are two reasons for this strong increase: first, the matrix oxygen, dissolved in the PET bottle wall migrates into the liquid inside the bottle. The second reason is the so called “steady state” permeation where oxygen molecules move from the high concentration side (atmosphere) to the low concentrations side (product inside the bottle) through the PET bottle wall. At the beginning of the Fig. 2: Illustration of non-invasive and non-destructive measurement of oxygen ingress into PET bottles Fig. 3: Oxygen ingress into an externally LC2 coated PET bottle compared to the respective non-coated reference bottle","@ID":27}, "INSPECTION 27 PETplanet Insider Vol. 17 No. 11/16 petpla.net remains active even after 180 days. Reducing the scavenger content in the inner PET layer to 0.5% leads to an increased oxygen ingress over 180 days compared to the bottle with 1% oxygen scavenger. But still the total oxygen after 180 days is below 1ppm. This shows that there is the possibility of reducing the amount of scavenger used in this type of PET bottles. Interior coating in PET bottles Inorganic coatings can be applied to the inside of the bottle after blowing. The Sidel Actis coating technology produces a thin layer of amorphous carbon, typically with 100 to 200nm layer thickness, on the inside surface of the bottle. This is deposited from high-energy plasma of acetylene gas within a high vacuum environment. Oxygen ingress curves of an Actis coated bottle compared to an identical non-coated bottle are shown in fig. 5. For both bottle types the sampling rate was adjusted to 30 seconds and the mean value was taken from seven bottles. The inner coating prevents oxygen desorption from the bottle wall into the product for the first few days of storage, which cannot be observed in externally coated bottles. A BIF of 9.9 was calculated by comparing the slopes of oxygen ingress of coated and non-coated bottles. Determining OTR in empty PET bottles The oxygen transmission rate of PET bottles filled with nitrogen can also be determined with the chemical optical oxygen ingress measurement system. Two types of 0.5l PET beverage bottles from Sidel with interior coatings Actis Lite and Actis A were tested. Measurements were performed for 27 days at 23 ± 1°C and 50 ± 2% relative humidity. A special stainless steel closure with integrated trace oxygen sensor type PSt6 and a PCO28 threading was used to seal the bottles. The OTR of this special closure was determined, and amounted to 0.0023cc / (pack * day). With the PreSens system an OTR of 0.0070 for Actis L and 0.0031 for Actis A was determined deducting the OTR of the bottle closure from the obtained GOTR value, while with the Oxtran method values of 0.0068 for Actis L and 0.0027 for Actis A were measured. The standard deviation for Sidel L was 0.0004 with both measurement systems while for Sidel A the optical system showed 0.0004 and Oxtran 0.0008. The mean values obtained with the optical measurement are very close to those obtained with the reference Oxtran method. OTR measurement device The Permeation Measurement Device consists of a measurement cell, which is divided into two chambers and made of stainless steel. The cell has improved leak tightness. Test materials are fixed between the upper and lower chamber of the measurement cell (fig. 1). Each chamber has two gas connectors and first both chambers are flushed with nitrogen to determine the leakage of the chamber. The lower chamber is then flushed with oxygen. A chemical optical sensor spot is fixed in an optical window in the upper chamber and connected to a Fibox 3 LCD trace oxygen meter to conduct the oxygen measurements. A well characterised 100μm PET film whose permeation rate is well known was used for reference measurements. During zero measurement the oxygen partial pressure increased by 0 to 0.01hPa after five days. This corresponds with a zero value for the permeation of 0 to 0.03cm3 / (m2 d bar). The increase of oxygen partial pressure over time showed a quasi linear scope up to 40hPa. Adapting the ideal gas law the permeation is then calculated. Conclusion With the oxygen ingress measurement system by PreSens it was shown - under conditions very close to reality - that the amount of oxygen that will enter the product inside PET bottles depends on the location of the coating and whether an oxygen scavenger is used or not. A shelf-life of 180 days was not achieved with externally coated bottles due to oxygen desorption of the matrix material. The best performance is shown by those bottles which use an active barrier additional to the passive barrier which is also acting as protection layer to prevent the reaction of the scavenger with atmospheric oxygen. The system allows measurement in packages filled with gas but also liquids, and investigation of complete packages - empty as well as filled – is possible. Moreover sequential measurements can be conducted which means that the equipment is not blocked for the complete measurement time. The oxygen transmission rate for all food packaging materials can be measured with the PSt6 sensor type, with a measuring range between 10-2 to 107 cm3 (STP) / (m2 d bar). With the new low oxygen sensor PSt9 an expected range between 10-3 and 100cm3 (STP) / (m2 d bar) can be achieved. www.presens.de All external sources on which this article is based on as well as the long version of the article can be requested at PreSens Precision Sensing GmbH (www.presens.de).","@ID":29}, "TRADE SHOW PREVIEW 43 PETplanet Insider Vol. 17 No. 11/16 petpla.net Bisleri launches its Pop range New flavours for trend-conscious consumers By Kay Barton April 12, 2016, Bisleri International Pvt. Ltd. We met: Ms Anjana Ghosh, Director With a national production volume of around over 150 million bottles per year, Bisleri has a justifiable claim to be the undisputed leader of the market for bottled water on the Indian subcontinent. Almost 23 years after its last development in the CSD sector, the company has surprised the market with the launch of “Pop”, a completely new range of products, currently comprising four new flavours of drinks, packaged in PET and cans. Just a few days after the initial launch of Pop and in 35°C heat, we meet with one of the people behind the idea: Director Anjana Ghosh, who spoke to us at the plant in Mumbai. “Our research showed that, in the current market, buyers view existing CSDs as offering too little variety. This was the basis for the development of the Pop range; the idea of making something brand new in terms of flavour,” Ghosh explains. And she’s right: all four products, namely “Spyci”, “Limonata”, “Pina Colada” and “Fonzo” taste completely different from conventional products on the market. “In principle, every variety has its own particular attribute, which makes it stand out from the soft drinks competition. We deliberately oriented ourselves to the requirements of the Indian consumers.” This deliberate decision to present a particularly Indian character is manifested in the flavours. Spyci has a hint of Indian spices; Limonata has an enhanced lemonade taste; Pina Colada is the first drink of its kind in India; and Fonzo represents a “first”, in its combination of mango, orange and peach for the first time. Bisleri has consciously created a product that has not been conceived as an export. Pop is currently available in the PET bottle sizes of 200ml and 300ml and as a 250ml can, all at a comparatively low retail price. In this way, Bisleri is focusing primarily on the strongly growing trend for single-serve buyers aged from 16 to 35. The CSDs are currently being bottled in the company’s own factories in Bangalore and Rudrapur; at franchise holders Oriental Beverages and Asianlac; and at co-packers Pushpam and Tethyst. PET bottles are currently leaving the production line at an 85% capacity. Current output is 6.4 million batches, or around 650 million bottles per year. PET amounts to 70% of production, with cans accounting for the balance. Equipment from Shyam and Sidel is used for bottle blowing, while technology from Hymec and Hilden is used for bottling. Preforms are supplied by Chemco, the large scale processor, with necks conforming to the PCO 1881 standard. Finished bottle weight is 21.5g; Bisleri buys closure caps from Aglo Polymers and Secure. Looking to additional projects, Ms Ghosh adds: “We’ll have to see how the Pop range does on the market. As soon as long term results are evident, we will make decisions regarding further investments.” www.bisleri.com Director Anjana Gosh at Bisleri office","@ID":45}, "PETproducts 58 PETplanet Insider Vol. 17 No. 11/16 petpla.net Two-container snap-fit PET package The Clasper blow moulded bottle technology is being made available to brand owners who want to market a product in a package with two separate containers. It provides a packaging solution for boundary-pushing food, beverage, pharmaceutical, nutraceutical, industrial and household chemical products. The Clasper concept enables two different products to be consumed in sequence or mixed together and then consumed. The first commercialisation of this new technology was the recent introduction of Yumix portable, shelf-stable line of cocktails (see PETplanet 10/2016). The Clasper technology combines two PET containers, with the bottom container snapping into the base of the larger top bottle. The Clasper package concept is the brainchild of Yumix founder Alex Garner and was engineered by Plastic Technologies, Inc. (PTI). The challenge for PTI was to find the right geometry and bottle weight to keep the dimensions within the appropriate tolerances so that the snap fit was consistently achieved, but yet have the containers be easily separable by the consumer. “With brand owners continuing to develop new products and create new sub-categories, we wanted to create a disruptive package type that pushes traditional boundaries. It gives companies a way to market companion products - such as two liquids or a liquid and a powder - that, for whatever reason, cannot be premixed,” explained Ron Puvak, director of marketing and new business development, Plastic Technologies, Inc. Although the Clasper package was original designed for a hot-fill application, modifications can be made to accommodate other process types. The containers can also be decorated via a shrink sleeve which provides added visual appeal and usage instructions. www.plastictechnologies.com Official launch of the industry’s first single operation Top Load & Volume Gauge Torus Measurement Systems have announced the launch of the B304 Top Load & Volume Gauge. The system showcases a single operation Top Load & Volume Test to the plastic bottle market. Once the bottle is loaded by the operator all functions can be carried out in sequence without the need for operator interference to move the bottle between tests. The gauge will allow bottle manufacturers and fillers the ability to verify mould designs, dimensions and geometry, providing the customer with a solution to carry out precise volumetric measurement in accordance with export laws and safeguarding bottle strength during transport for stacking and palletising. The key benefit of the B304 Top Load & Volume Gauge is the ability to perform two tests in one system. By combining the two tests (Top Load and Volume), it negates the need for operator intervention thus eradicating laborious manual inspection and saving time. Carrying out time-consuming manual volume tests often results in inaccuracies. The average time to perform a manual volume test is approximately 8-10m per bottle with the quality of results being susceptible to human error. The Top Load results are traceable to UKAS standards and the system adheres to ASTM D2659 standard test method for Column Crush properties of blown thermoplastic containers. The user selects the part and test mode, loads the bottle into a centralised location and waits for the results. Standard selectable measurement features of the gauge are: brim-full volume, fill height volume, dry top load force, wet top load force (filled bottle), and empty bottle weight and bottle deflection point. An example of the B304 volume test would be, recording the empty bottle weight, filling the bottle to brim-full or fill height set point, measuring the weight of the filled bottle and automatically calculating the volume using the weight and temperature data. B304 Top Load & Volume Gauges are currently installed in large industry bottle manufacturers. Due to the enclosed self-contained cabinet the system is suitable for shop-floor or laboratory environments and is commonly used in research & development or production. Torus gauges are installed around the world and are supported by a global dedicated service team. www.torus-group.com","@ID":60}, "62 PETplanet Insider Vol. 17 No. 11/16 petpla.net PETbottles Home + Personal Care Blue tea and lotus for dishwashing Aldi Süd is selling in limited edition a litre of dishwashing liquid with added blue tea & lotus under its own label “alio” brand. The product, advertised on the label as having a high grease-dissolving power, is of a light blue colour and fills a transparent, grip-friendly shaped bottle. Two self-adhesive labels and a screw-on, two-colour push-pull cap complete the eye-catching packaging with its colourful content. www.aldi-sued.de Tautening body oil by Dove Under its Dove brand, Unilever has launched a skin care series “DermaSpa straffend +”. Among its products there is also a body oil which should make the skin more elastic and taut from its first application. It has the fragrance of water lily, cucumber and violet. 150ml fill a light blue-coloured, slim bottle made of PET, which is equipped with a screw-on cap and a dosage dispenser pressed in the outlet opening. The front label is unusually shaped and printed with the required information. www.dove.com Shower gel with grape seed oil Lacura – an Aldi own label – has a shower gel with organic grape seed oil on offer. The oil comes from controlled organic cultivation and the shower gel does not contain any parabens, silicones or mineral oils. The light green shower gel fills a transparent 300ml bottle which is equipped with a hinged lid clasp with dosage dispenser. The nonlook label is supplied with a large barcode on the front to improve machine readability, while on the back label a barcode is imprinted near the trade information in normal size. Shower gel with chocolate fragrance The drugstore discounter dm is selling a 250ml chocolate-scented shower gel with the name Schoko Love under its own label range balea. The slim bottle is decorated with a colourfully designed sleeve label. A screw-on tilting lid clasp with a defined pressure point for intake of the fingertip allows one-handed use in the shower. www.dm.de","@ID":64}, "TRADE SHOW PREVIEW 42 PETplanet Insider Vol. 17 No. 11/16 petpla.net Country Liquor: the PET Pioneer from West Bengal By Kay Barton March 10, 2016, Alpha Malts Pvt. Ltd. We met: Mr Nishu Nigam, Director When Indian spirits bottling company Alpha Malts opened its plant in Kolkata in September 2012, it became the first bottler to PET as well as glass packaging in its field: the “country liquors” market. The packaging concept has proven to be popular with consumers and the bottling firm says that the use of PET enables it to provide a customer-friendly service in the low price segment. The pioneer of the entire project is Director Nishu Nigam. Country Liquors offers six different brands in volumes of 180ml, 300ml and 600ml, and fills around 80,000 PET bottles per day. It certainly seems to have struck the right note in its market. In 2013, its glass to PET ratio was 50/50; by 2015 the PET share had increased to 80%. The PET bottles have, to date, been blow-moulded and supplied externally but Mr Nigam tells us that the company now intends to collaborate with a local preform supplier and to undertake blowmoulding itself. “Currently, we have two PET lines and one glass line for our products,” Mr Nigam says. “PET has accounted for 80% of our production. A third PET line is already on site and is going to be set up soon. In order to maintain our higher output, we are also considering investing in our own blowmoulding machine in the future.” The base alcohol, which is 96% proof, is purchased in the West Bengal region and from the states of Uttar Pradesh and Punjab. It is mixed with different natural flavours and blended with oils and water, on-site. The finished products, which come in flavours such as mango and orange, contain 22% alcohol and are all colourless, in accordance with official regulations. Aluminium caps and glue-paper labels are used, exclusively, and all of the products from the Kolkata plant are solely for the local market in West Bengal; tax considerations mean that there is no point in selling to any other Indian states. The key sales periods, which align with state-wide festivities and/or stockbuilding by retailers, are October, December and March. “Our direct competitor is IFB Agro, the spirits bottling firm, which is also from Kolkata. Funnily enough, we actually buy products from them for processing!” Nigam explains. Alpha Malts estimates the total volume currently in the local market to be around 46 million bottles per month - 60% PET and rest in glass; most sales are in 600ml sized bottles. Across the whole of India, Alpha Malts estimates that the consumption of country liquors totals around 600-700 million litres per month. TRADE SHOW PREVIEW 42 PET bottle filling in action with (f.l.t.r.) Rajesh Nath, VDMA India, Nishu Nigam. Alpha Malts, and Kay Barton .com 100815dmyL","@ID":44}, "INSPECTION 26 PETplanet Insider Vol. 17 No. 11/16 petpla.net measurements externally coated bottles show similar oxygen ingress rates as non-coated bottles, because the outside partial pressure is in equilibrium with air and considerably higher than the inside partial pressure. This is the case until a new equilibrium within the polymer is established. After an equilibrium state between matrix oxygen in the PET and the product is reached a linear increase of oxygen ingress over time can be measured. As long as the saturation level is not reached the increase of oxygen is expected to follow a straight line. The slope of the curve gives the oxygen ingress in ppb/day. Also the total oxygen can be calculated from the slope of the curve. Knowing the maximum allowed concentration of O 2 in the product, 1mg/l in the case of beer, and dividing it by the slope of oxygen increase the theoretical shelf-life can be calculated. The externally coated bottle shows a reduced oxygen permeation rate but a shelf-life of approx. 53 days is not sufficient since usually a shelf-life of at least six months is demanded. This proves that even the externally coated PET bottle would need improvement using oxygen scavengers in the material to protect the product. Test 2: Oxygen scavengers in PET bottles In a second test different amounts of oxygen scavenger were used in the bottle material. Desorption of oxygen from the PET bottle wall into the product is one of the main disadvantages of externally coated bottles. The matrix oxygen dissolved in the PET bottle can be removed by adding an oxygen scavenger into the PET material. Measurements in a non-coated bottle containing 2% oxygen scavenger were compared to an identical bottle without scavenger. Furthermore, LC2 externally coated PET bottles with either 1% and 0.5% oxygen scavenger were tested. In the non-coated PET bottle containing 2% oxygen scavenger the matrix oxygen is removed by the scavenger and therefore the measurements show no initial increase in oxygen at the beginning (fig. 4). After eight days though, a strong increase in oxygen concentration is detected. This indicates that the scavenger is being consumed. After 20 days, the graph of the PET bottle with scavenger shows an identical slope to the non-coated PET bottle, as the scavenger is completely consumed by then. The LC2 external coated bottle without scavenger shows a strong oxygen increase over the first 48 hours as described in test 1. When the equilibrium between matrix oxygen and dissolved oxygen in the liquid is reached the graph again displays the linear slope. After 40 days the curve of the LC2 external coated bottle without scavenger intersects the graph of the non-coated bottle with 2% scavenger. The oxygen ingress in both of these bottle types is too high and the maximum oxygen pick up of 1,000ppb at 30°C is reached before a 180 days period. These bottles would not guarantee a long enough shelf-life of products. Bottles with a combination of LC2 external coating and 1% or 0.5% scavenger were also measured. The scavenger is located in the inner PET layer and protected from ambient oxygen by the external barrier coating. The inner-layer scavenger reacts with oxygen molecules permeating through the outside coating and is also available to decrease oxygen in headspace and liquid, which is integrated during the filling process. The combination of external coating and scavenger results in a significantly reduced oxygen ingress rate, below 1,000ppb over six months. As the scavenger is protected by the outer barrier layer from ambient oxygen and only reacts with molecules permeating through the barrier its lifetime is longer, and it Fig. 4: Oxygen ingress into different treated PET bottles of the same type; (A) noncoated PET bottle with 2% scavenger, (B) LC2 coated PET bottle with no scavenger, (C) LC2 coated PET bottle with 1% scavenger, (D) LC2 coated PET bottle with 0.5% scavenger Fig. 5: Comparison of oxygen ingress into an Actis coated bottle and the respective non-coated reference bottle","@ID":28}, "MARKET SURVEY 36 PETplanet Insider Vol. 17 No. 11/16 petpla.net Moulds for caps/closure production 11/2016 MARKETsurvey Systems for cap/closure production Company name z-werkzeugbau-gmbh Corvaglia Mould AG Postal address Telephone number Web site address Contact name Function Direct telephone number Fax E-mail Dr. Walter Zumtobel Str. 9 6850 Dornbirn, Austria +43 5572 7272 720 www.z-moulds.com Mr Michael Fink VP Sales & Marketing +43 5572 7272 721 +43 5572 7272 8621 [email protected] Hörnlistrasse 14 8360 Eschlikon, Switzerland +41 71 973 77 77 www.corvaglia.ch Mr Albert Brunner Director Sales & Service +41 71 973 77 52 +41 71 973 77 78 [email protected] 1) Filling good beverages Carbonated and non-carbonated drinks, water, juices, etc. Carbonated soft drinks & non-carbonated pressurised & non-pressurised beverages including water, juices, teas, milk/dairy, coffee, beer, isotonics, energy drinks, etc. other Edible oil, dairy, beer, etc. Edible oil, detergents, other filling goods possible upon request individial cap solutions Personal care and household products Possible, upon request 2) Closure: type All single-piece standard closure dimensions for all neck finishes, sports closures, flip-tops, push-pulls, multi-component closures. Flat top & sports closures for 26-29, 30, 31, 33, 37, 38, 48mm neck finishes, e.g. Alaska, 1810, 1881, 29/25, 30/25, 33 HF, 33 ACF, 38 HF, 38 ACF material HDPE, LDPE, PP, TPE, … HDPE (PP for transparent parts) weight Lowest from 0.8g starting from 0.8g 3) Moulds: a Clamping dimensions/Cavities 16 to 128 cavities 24 - 96 cavities b Preferred hot runner suppliers Mold Masters Corvaglia and others 4) Special features Several patented technologies for most efficient closure production Closure design approvals from all major beverage brand owners Postal address Husky Injection Molding Systems Ltd. Arburg GmbH + Co KG Postal address Telephone number Web site address Contact name Function Direct telephone number Fax E-mail 500 Queen Street South Bolton, ON, Canada L7E 5S5 +1 905 951 5000 www.husky.co Mr Michael White Business Manager - Beverage Closures +1 905 951 2913 ext. 2913 +1 905 951 5337 [email protected] Arthur-Hehl-Strasse 72290 Lossburg, Germany +49 7446 33 0 www.arburg.com Mr Andreas Reich Senior Sales Manager Packaging +49 7446 33 3240 +49 7446 33 3185 [email protected] Systems for cap/closure production 1 Model HyCAP4 System Hidrive Packaging 2 Procession technology Injection moulding system with reciprocating screw. Shot capacity (197g - 404g), throughput capacity (125kg/h - 225kg/h). Injection Moulding 3 Clamp force 225t - 500t (2,250kN - 500kN) 130 - 460t 4 Cycle time (guaranteed 98% closure system efficiency for): Cycle times as fast as 2.2s | ~ 2,500 caps/min ~ 3.7 - 4.0s ~ 4.0 - 4.3s ~ 2.8 - 3.2s ~ 2.5 - 2.8s ~ 4.2 - 4.5s a_High speed production: closure type/weight/cavities: caps/min PCO 1881; 2.35g PCO 1810; 2.65g 29/25; 1.2g 26 mm; 1.0g 38 mm; 2.9g b_Individual cap solution: closure type/weight/cavities: caps/min 5 Drive concept Clamp Motion is a belt driven ball screw (electrically driven) Hybrid machine technology, servo-electric axes for clamp, ejection and dosing, hydraulic accumulator for injection 6 Energy consumption (kwh/kg) Application dependent. Among industry best in terms of energy consumption. 7 Preferred mould makers Husky & HyCAP tooling platform z-moulds, Wiro, and others depending on customer's demand 8 Special features Reflex Platen design for industry's most even force distribution; Simplified Operator Control (Intuitive 19\" touch screen interface); Full control over Husky auxiliary equipment via single HMI; Direct Drive injection unit for high speed injection & robust operation; Simultaneous operation of clamp, ejector, cores and plasticising functions; Leveraging synergies generated by Mold ID technology to further: Simplify operation & Improve part quality; Improved energy performance leveraging following technologies: Electric Mold Stroke (ELMS). Servo Variable Pumping (SVP) System. Hybrid machine with 3 servo-electric axes; Electric ejector with booster function for demoulding of tapped parts; Synchroneous ejection for smoother demoulding; Position regulated screw for highest process repeatability","@ID":38}, "BOTTLING / FILLING 21 PETplanet Insider Vol. 17 No. 11/16 petpla.net Maintaining water properties The complete new line installation began in October 2016, at the Prolom Voda facility, and will operate in addition to the existing PET bottling line. It will include a compact Sidel Matrix Combi, featuring a Sidel Matrix blower SBO 6 and a Sidel Matrix Filler SF100 FM with 36 valves. The Sidel Matrix Combi is based on the most cost effective technology of the latest generation of Sidel Matrix systems. The Combi system integrates the blow-fill-cap functions in a single unit - with neckhandling transfer of bottles enabling potential for lightweight bottles - occupying up to 30% less floor space and requiring only one operator, due to its single and simple control interface. Sidel Matrix SBO blowers are claimed to create high PET bottle quality and performance. They offer the flexibility to pick and choose a size and shape that best fit specific production needs. With three sizes of blowing stations and up to 200 possible blower configurations, a great variety of distinctive light or ultra-lightweight bottle shapes are possible in sizes ranging from 0.1-3.5l. Additionally, the new 13,200bph Prolom PET bottling line will feature the contactless Sidel Matrix Filler SF100 FM, suitably developed to handle with high precision the filling of beverages with little or no conductivity. For high accuracy and improved efficiency, it minimises product losses and its external tank holding the beverage is easy to clean. All parts that come into contact with the water are made from stainless steel AISI (American Iron and Steel Institute) 316L. A tight enclosure, featuring HEPA (high-efficiency particulate air) filters on the roof, keeps the filling environment safe, preventing risk of contamination and further increasing the already high standards of hygiene. The health properties of natural Prolom water are vital to the appeal of the brand so maintaining these through a fully hygienic bottling process is central to the brand’s ongoing success. The complete line will also include equipment from the Sidel Group, such as a cap feeder, an automatic shrinkwrapper and bottle and pack conveyors. www.sidel.com BOTTLING / FILLING 21","@ID":23}, "TRADE SHOW PREVIEW 44 PETplanet Insider Vol. 17 No. 11/16 petpla.net BrauBeviale November 8-10, 2016: The table is set – for BrauBeviale 2016 All good things come in threes – and so it is for BrauBeviale 2016, opening once again after two successful events, before it closes its doors for the scheduled break next year. The participants are: European specialist beverage world with almost 1,100 exhibitors and over 37,000 visitors at the last event. From November 8 to 10, the sector’s regular table at this year’s important equipment show for the beverage industry will cover all aspects of the beverage production process chain; the menu features high-quality raw materials, efficient technologies, effective logistics solutions and creative marketing ideas. Among others, once again in the Craft Beer Corner, beverage experts will be presenting special tasting sessions for specialist retailers, caterers, producers and all other interested trade fair guests. We would like to introduce you some more exhibitors relevant for the PET industry. You are cordially invited to stop by at our booth in hall 7A / 7A-203 in Nuremberg and meet the PETplanet team. We look forward to your visit! BrauBeviale2016 Future-fit compressed air As Industry 4.0 becomes ever more present in all industrial sectors, the Sigma Air Manager 4.0 (SAM 4.0) helps compressed air systems to keep up with the rapidly evolving associated technologies and services. Through connection to a centralised control system and real-time data transmission, it constantly keeps the operator up to date regarding every aspect of the compressed air supply system. It assures energy cost savings together with dependable and efficient compressed air production. It provides the basis for the use of advanced services such as Predictive Maintenance. Operators requiring higher pressures need look no further than Kaeser’s new booster compressors. With available motor powers from 22 to 45kW and flow rates from 2.9 to 19.6m³/min and a discharge pressure up to 45 bar (with an initial pressure of 13 bar), the new DN C series models are the first all-in-one booster packages. They feature a new design with a footprint half the size of previous models, which gives these compact boosters a refreshing clean look both inside and out. The new component layout not only ensures optimised cooling air flow, but also provides improved maintenance access. Furthermore, thanks to the integrated Sigma Control 2 controller, DN C systems are ready for immediate operation and are self-monitoring. Connection to, and control via the Sigma Air Manager 4.0 is also possible. The recently introduced DBS series screw blowers are saving energy especially when it comes to wastewater treatment systems. The powers ranging from 15 to 37kW and flow rates from 4 to 22.5m³/min. The blowers are quiet and operate with a maximum sound level of 72dB(A) in their main field of use, which means that they are no louder than a modern vacuum cleaner. www.kaeser.com Kaeser Hall 4 | Booth 441 For all beverage needs For cans, PET or glass containers alike, and irrespective of the particular production step involved: on Krones’ stand at this year’s fair, one can find plenty of solutions covering the entire multifaceted spectrum of the beverage industry’s needs. Kosme’s KSB 6R blow-moulder, for example, supports you in producing PET bottles in a highly disparate range of sizes, at maximised cost-efficiency even in small batches. When it comes to precision and dependability, the Krones Ergomatic Pro scores very highly with its perfect label placement, and the Krones Linatronic 735 with its eagle eyes for inspecting empty bottles. For the first time, System Logistics will be showcasing its corporate capabilities together with Krones at the BrauBeviale. As the name BrauBeviale implies, Krones will focuse primarily on beer – with solutions for small and large breweries. www.brau.krones.com Krones Hall 7A | Booth 520","@ID":46}, "TRADE SHOW PREVIEW 38 PETplanet Insider Vol. 17 No. 11/16 petpla.net Company name # 99 Food & Processing A A.G. Belting Pvt Ltd Abachem Speciality Chemicals Pvt Ltd Ace Hygenic Products Ace Technologies AdvanceInfo Media & Events - Beverages and Food Processing Times AdvanceInfo Media & Events - Oil & Food Journal Agaram Industries Aguapuro Equipments Pvt Ltd Ahimsa Industries Ltd AJ Compressors LLP AlTIOS CONSULTING PVT LTD Annapurna Pet Pvt Ltd Anton Paar India Pvt Ltd Arol India & Apac Pvt Ltd Ashirwad Carbonics (India) Pvt Ltd Ashtavinayaka Technocrafts Pvt Ltd Ateliers Francois SA B Bb Brewmaster Ventures Pvt Ltd Beijing Y.C.T.D Packaging Machinery Co Ltd Beltecno India Pvt Ltd Bericap India Pvt Ltd Brewforce Technologies Burkert Contromatics Pvt Ltd C Canadian Crystalline Water India Ltd Centec RRR Systems & Sensors Pvt Ltd Chembond Chemicals Limited Chemco Plastics Industries Pvt Ltd Chlorophyll Technologies Cipriani Harrison Valves Pvt Ltd Constantia Haendler& Natermann GmbH D DAPL Della Toffola Della Toffola Dongguan Longsun Machinery Co Ltd DVKSP Impex Pvt Ltd Company name E EasyBrew Ecokrin Hygiene Pvt Ltd Elephas Engineering Endress + Hauser (India) Pvt Ltd Enprosyst Solutions Pvt Ltd F Fill Pack Technology Filmatic Systems Food & Beverage News Food Beverages and Hospitality Fresh Pet Private Limited Fristam Pumps (I) Pvt Ltd G GEA Process Engg (India ) Pvt Ltd Goma Engineering Pvt Ltd Gruppo Bertolaso Spa Guangzhou Jeepine Intelligent Compression Molding Machine Co Ltd H Hilden Packaging Machines Pvt Ltd Hypro Engineers Private Limited I Indo-Air Compressors Pvt Ltd Infocom Network Limited Intralox (India) Private Ltd ION Exchange (India ) Ltd J Jiangsu Newamstar Packaging Machinery Co Ltd Jiaxing Haoneng Science and Technology Corp Ltd K KHS Krome Dispense Pvt Ltd Krones AG L Lechler (India) Pvt Ltd Lehui International Lombardyne Industries Pvt Ltd Lunarmech Machinefabrik Ltd M Magic Special Purpose Machinery Pvt Ltd Malik Polychem Ltd Manjushree Technopack Ltd Membrane Group India Pvt Ltd Meritt Transmissions Metrodispenser Iniciativas y proyectos hosteleros S.L. MHT Mold & Hotrunner Technology AG Modern Plastics India Magazine N National Polyplast India Limited Neelkant Engineers Nexgen Drying Systems Pvt Ltd Nilkamal Limited NPM Machinery Pvt Ltd NuFFooDS Company name O Orient Enterprises P Paques Envorimental Technology India Pvt Ltd Pentair Praj Industries Limited Processed Food Industry R R J Brewing Solutions Rahul Ferromet & Engg Pvt Ltd Rapid Bevtech Pvt Ltd Repute Engineers Pvt Ltd Royal Industries S Saarc Oils And Fats Today Magazine Sacmi Sanky Technical Consulting Pvt Ltd Schubert & Salzer Representative Office India Shyam Plastic Industries Sidel India Pvt Ltd SNS Overseas Pvt ltd Spectraa Technology Solutions Pvt Ltd Spraying Systems (India) Pvt Ltd SRJ Engg Pvt Ltd T Talos Holding Ltd Tech-Long Packaging Machinery Co Ltd Tender Tiger TMC Padovan Spa Transline Conveyors Pvt Ltd U Udyogprerana Unipack Machines Pvt Ltd V Versuchs- und Lehranstalt für Brauerei in Berlin (VLB) Vibgyor International Pvt Ltd Vijay Engineering Corporation Vishal Beverages Pvt Ltd W Wenzhou Kequan Equipment Co Ltd Wenzhou Wurong Science n Technology Co Ltd Weyermann Specialty Malts Z Zhangjiagang Sunwell Machinery Co Ltd Zhejiang Zhangda Light Industry Machinery Co Ltd Zoren Hops Breweries Exhibitors dti 2016","@ID":40}, "TRADE SHOW REVIEW 56 PETplanet Insider Vol. 17 No. 11/16 petpla.net Industry 4.0 and its advantages for the packaging industry Self-optimising factory The injection moulding machine manufacturer and systems expert Engel presented all three areas of its smart factory programme – smart machine, smart production and smart service – at K 2016. With the help of the networking and integration of production systems, the systematic exploitation of machines, process and production data and the use of decentralised, intelligent assistance systems, the manufacturing processes in a smart factory will be able to continuously optimise themselves. Industry 4.0 is different for every undertaking, and there are also differences from industry to industry. “For the packaging industry, Industry 4.0 primarily means two things: networking and integration.” explains Michael Feltes, Head of Engel’s Business Unit Packaging. “The aim is to control the complete manufacturing cell including the moulds, hot runners, IML automation and quality control systems, from the display of the injection moulding machine.” The pooling of all process data along the complete product creation process then offers the opportunity to find optimisation potentials and to exhaust the capabilities of all components in the manufacturing cell. smart machine The human-machine interface will play an increasingly important role in the factory of tomorrow. As the processes become increasingly complex because of greater integration and automation, its management and control needs to become simpler and more intuitive. Self-adapting, decentralised systems increase process capability and quality, without the machine operator having to assimilate additional specialist knowledge. For example, the iQ software products from Engel continually analyse critical process parameters in order to identify and immediately compensate for deviations even before rejects are produced. While iQ weight control keeps the injected melt volume and the viscosity constant throughout the entire injection moulding process, including the holding pressure phase, the new iQ clamp control software determines the mould breathing to continually readjust the clamping force. Even if the environmental conditions change, or the granulate quality fluctuates, the software solutions keep the process constant and consistently ensure high product quality. As mould temperature control also affects efficiency and quality, Engel had already introduced an electronic temperature-control water manifold system at K 2010 and has continuously developed this further since then. Engel e-flomo monitors and documents all cooling and temperature control circuits of injection moulds and independently regulates either the flow volumes or differences in temperature. Today, Engel e-flomo and temperature control unit merge at controller level to form a single unit. With the help of the new iQ flow control software, the pump speed is adapted automatically to current requirements based on the measurement values determined by Engel e-flomo. The Engel e-flomo increases the process stability and therefore lowers the reject risk, whilst the automatic speed adjustment ensures that temperature control requires less energy. smart production Engel’s exhibition stand was already a regular small business with seven highly integrated and automated production cells plus the iQ demonstration injection moulding machine. All production cells were networked together using Engel e-factory to be able to view and analyse the current condition of the individual injection moulding machines, their utilisation and output from a central computer. With e-factory, Engel has its own MES (manufacturing execution system) in its product portfolio that is specifically tailored to the requirements of the plastics processing industry and achieves a high level of vertical data integration. It even takes account of the number of cavities in the mould. In addition, e-factory is claimed to ensure greater transparency. Bottlenecks and downtime are localised at a glance. Only in this way is it possible to optimally utilise the overall available capacity of machinery. The condition and process data transferred in Engel e-factory enables the processor to have a view of the entire production process from the central computer.","@ID":58}, "TRADE SHOW PREVIEW 46 PETplanet Insider Vol. 17 No. 11/16 petpla.net Tailored solutions Individual customer requirements in the beverage industry - Procme GmbH from Bad Kreuznach shows how it works. This year, the company specialising in filling, labelling and packaging technology is showing machines from TMG and P.E. in its portfolio. At BrauBeviale 2016 the label specialist P.E. will be showcasing its MODULAR Plus labelling machine. TMG, professionals in the field of packaging, is presenting a partial line consisting of the Combi 8H packaging machine, cardboard weighing machine and the Master 500 robot palletiser for a German customer. www.procme-gmbh.de Conveying and pressing Strautmann Umwelttechnik GmbH presents a number of disposal solutions: The LiquiDrainer: With the LiquiDrainer problems of faulty batches and residual liquids are addressed whether in cans, PET bottles or Tetra Brik. Through the special rotor technology and a throughput capacity of up to 10,000 1l bottles per hour around 150 bottles can be emptied in one minute. Using a hopper full beverage containers or beverage containers with residual liquids can be inserted manually or automatically. A pendulum plate then transports the material into the rotor, which pierces the beverage containers. In this way, the bottles are emptied and pre-compressed. At this stage the beverage containers will be devalued and possible abuse is prevented. In the last step the liquids flow through a filter box and are efficiently drained. With the LiquiDrainer emptying works automatically and without any manpower. The disposal remains in-house and prevents faulty batches from getting into circulation. In addition, remarketing of liquids and compaction of beverage containers into bales or briquettes achieve high revenues. The Strautmann BrikPress compacts fully automatic recyclables such as cans, Tetra Brik and PET bottles. It compresses the collected accruing material into briquettes. The BrikPress can be integrated into the product running. For over 20 years BrikPress has been working for the beverage industry. Via conveyors or lift trucks, the press can be filled around the clock. With a throughput of up to 50,000bph, the material inside the press chamber is compressed with a pressing force of 380kN. The highly compacted briquettes are then pushed out through the channel systems automatically and can be stored in containers. With GPS the operator receives a message when the container is full, enabling the operator to dispose of it quickly and in timely fashion. The compact design of the BrikPress enables installation directly at source. Moreover no pretreatment of the material is necessary, the bottles and cans can be inserted directly with and without caps. Due to the strong compression of the briquettes a high sales revenues can be generated. www.strautmann-umwelt.de Strautmann Hall 6 | Booth 203 Procme Hall 7 | Booth 539","@ID":48}]}}
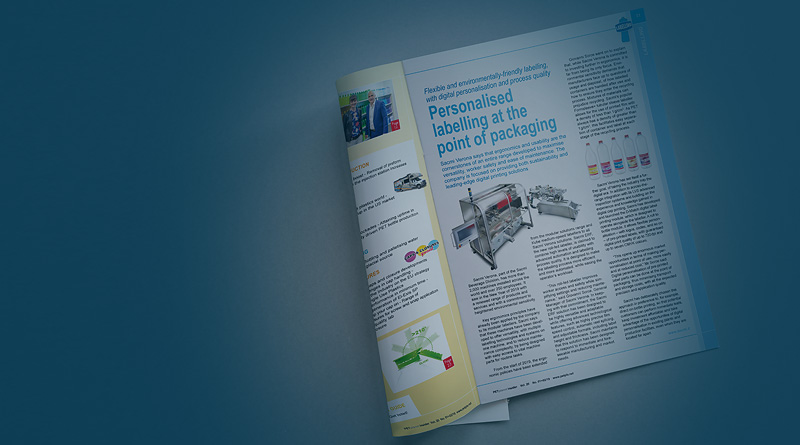