"PETpatents www.verpackungspatente.de PETplanet Insider Vol. 18 No. 04/17 petpla.net 72 Bottle bases Intern. Patent no. WO 2016 / 100483 A1 Applicant: The Coca-Cola Comp., Atlanta (US) Application date: 16.12.2015 Various shapes for the base of a PET bottle containing a carbonated content are described. The shape has a major influence on non-breakability and the use of material this therefore requires. Aerosol cans made from plastic US - Patent no. US 2015 / 0001256 A1 Applicant: Oxygon Technologies, St. Thomas (CA) Application date: 26.6.2014 A plastic bottle under pressure is “coated” or surrounded on the base and upper side with adapters to protect the bottle, as protection against bursting, for improved handling and for optical reasons with separate additions. The parts are joined and fixed with a sleeve label. Coloured code surface Intern. Patent no. WO 2016 / 110546 A1 Applicant: Sicpa Holding S.A., Prilly (CH) Application date: 7.1.2016 The application proposes a re-usable, large-volume water bottle which is fitted with a coded label, coloured in this area in order to improve legibility. Bottles whose label is not “legible” can no longer be filled in some countries. Large actuator button Intern. Patent no. WO 2015 / 017306 A1 Applicant: MSD Consumer Care Inc., Memphis (US) Application date: 28.7.2014 The application describes the construction of a sufficiently large actuator button for an aerosol product filled into a pressurised PET bottle. Compensation surfaces for PET bottles Europ. Patent no. EP 3028951 A1 Applicant: Yoshino Kogyosho Co. Ltd., Tokyo (JP) Application date: 10.7.2014 A PET bottle has many part areas with elastic formable surfaces. The bottle is made narrower in the gripping area in order to make gripping easier and to improve the bottle’s aesthetic. This will also make it more difficult to overturn the bottle accidentally. Easily removable guarantee band Europ. Patent no. EP 3037362 A1 Applicant: Nishiaki Kousakusho Co. Ltd., Yokohama-shi Kanagawa (JP) Application date: 31.1.2014 Removing the separate guarantee band from a bottle during recycling or re-use is a problem with closing devices with a guarantee. This describes a bottle neck which makes this work easier.","@ID":74}, "BOTTLE MAKING 32 PETplanet Insider Vol. 18 No. 04/17 petpla.net MHT Vulcan II - faster and more efficient Hotrunner components High material throughput, even filling, quick cooling. When it comes to high-performance tools with up to 192 cavities, as they are used for PET preforms, the hotrunner has its work cut out for it. It decides performance. The tool manufacturing MHT Mold & Hotrunner Technology AG (MHT) has updated its hotrunner components and offers now three advantages with its new Vulcan II series: longer operating times and quicker maintenance combined with lower energy consumption. To achieve this, the development team completely redesigned the piston package. Overall, the piston package of the Vulcan II is somewhat thinner, longer and based on a totally different setup, consequently increasing durability and ease of maintenance. Here, the pistons and piston housing have exchanged the number of their parts: the piston itself is now made from two components (previously one) and the piston housing is now made from one piece (previously two), which results in stability advantages. The central goal of the redesigning process was the tightness of the system. While so far a metallic sealing between the valve bushing and the backing plate was only created by the contact pressure when the processing temperature was reached, this task is now carried out by an elastic O-ring. The latter already closes the valve bushing in cold conditions and prevents the escape of compressed air. Further wear and tear-optimised piston seals can be replaced without any stretching and thus without any material damage, thanks to the two-part construction of the piston. One simply opens the piston casing, removes the upper part of the piston, inserts a new seal and closes the entire system again. A special focus of the Vulcan II is the resistance against PET dust. For this purpose, the valve stem guidance of the reversing device was lengthened considerably. This prevents PET dust from getting into the piston housing, where it would have an abrasive effect and limit the precise function of the piston. Just in case, the piston package still has an emergency reservoir, where the PET dust is able to be collected temporarily. All measures combined result in the maintenance interval increasing to up to six million cycles, and when maintenance is needed, it is completed quickly because all piston packages are very easily accessible. Also removing the valve stem is no longer required with the Vulcan II. Changes as extensive as those now implemented for the sub-assembly piston housing had already been made to the nozzle tip of the Vulcan I – and these were optimised even further. Now, the nozzle tip is screwed into the base of the nozzle with an internal screw thread, resulting in the heating band being in direct contact with the nozzle. Formerly, the tip had had an exterior screw thread, so that the metal layer of the nozzle base was located between it and the heating band. As a result, the heat transfer is now considerably better and more efficient. In plastic injection moulding, the transition from the nozzle to the cavity is the meeting place of hot and cold. While the material in the hotrunner has to be gently and evenly kept at processing temperature, the material in the cavity is supposed to cool down very quickly. On the one hand to keep cycle times as low as possible and to allow for a high throughput, but on the Installed Vulcan II nozzles and piston casing","@ID":34}, "LABELLING PETplanet Insider Vol. 18 No. 04/17 petpla.net 35 LABELLING 35 specifically in this context: “The industrial implementation of a digital printing process with low migration and UV-curing inks, which provide a food-safe solution for PET bottles, is very interesting in this area. Bottlers save material with the direct printing method and can flexibly implement a new look for a container at short notice.” A new trend: serialisation Another trend in the beverage industry supports labelling technology, i.e. serialisation. Strictly speaking, this is the transformation of an object into a byte stream. This term from computer science combines two requests from the industry: the customisation of products on one hand and the traceability of product paths on the other. “For example, labelling technology makes it possible with the application of a QR code on a container to individualise it and trace the product path via use of the code by a consumer,” Richter explained. The customer in turn has the option of checking the originality and authenticity of the product using a smartphone to scan the QR code. At the same time, his action is forwarded to the manufacturer who can then enter into the desired interaction with the consumer. RFID technology, the “identification with the aid of electromagnetic waves”, has already been introduced in the beverage industry. It acts as authenticity protection on one hand and anti-theft protection on the other. In a southern European country, for example, a well-known whisky distiller consistently employs RFID technology in its high-quality products. An RFID transponder is hidden in the back label, which can trigger an alarm at an attempted theft, for example. “Using RFID technology is very easy with modern labelling technology. However, transponder costs remain an issue,” Richter added. Despite all the new developments, there is continuity in the labelling segment: the good old paper label definitely still has a future. It can be processed at high speeds, looks good and will remain in the market for the foreseeable future. www.drinktec.com Labelling trends at drinktec 2017 Packaging and labelling technology will occupy considerable space at drinktec. Approx. 50% of exhibitors will be presenting packaging solutions. In addition, drinktec has created a dedicated area (hall A2) with the World of Labels specifically for manufacturers of labelling technology and labels. The supporting programme is also addressing this issue. The top issues of the future in the packaging area are dealt with in the Innovation Flow Lounge and in the field of packaging technology at the drinktec forum.","@ID":37}, "42 TRADE SHOW PREVIEW PETplanet Insider Vol. 18 No. 04/17 petpla.net TRADE SHOWpreview Pick and place box packer And&Or’s EPAbox packer will be displayed at interpack. It is able to pack in boxes either empty or filled bottles. It counts with an arranging table to prepare the bottle layer previous bottle insertion into box. The picking head is designed according to bottle formats, being able to pack bottles with no neck ring, heavy bottles and empty light ones. Benefits of EPA box packer are: The machine can pack several levels of bottles in the same box. Machine is flexible to work also with cardboard trays in case of need. Easy change over to adapt to several formats and different layer`s configuration. Servo-motorised movements. Layer indexation for round formats. And&Or also offers a wide range of palletisers to fully automate the end of the line process. www.andyor.com And&Or Hall 13 - Booth E46 “Smart machine” Gebo Cermex, part of the Sidel Group, is introducing its latest advanced performance systems and packaging line solutions at interpack. the company is demonstrating its portfolio for the beverage and food, home and personal care (FHPC) customers based on its Agility 4.0 program. ‘Smart’ equipment is the focus at this year’s exhibition, with a comprehensive packing solution at the company’s booth. Marc Aury, President & Managing Director of Gebo Cermex, explains: “As a key player in the ‘Factory of the Future’ movement with our Agility 4.0 program, at interpack this year we are excited to give visitors a preview of our vision of the ‘Smart machine’, with a comprehensive robotic/cobotic case packing solution embedding advanced and connected systems.” A ‘Smart machine’ is so much more than a piece of machinery. Featuring the latest motion technology, robotics and cobotics, auto adjustment and auto feeding, as well as being a connected machine, it establishes itself as a forward looking comprehensive solution. Aury continues: “It is no longer a case packer simply putting products in a case. It’s a 360° integrated approach using the latest technologies to deliver all functionalities.” www.gebocermex.com Interpack 2017 is recording the highest demand among exhibitors in its history of over 55 years. By the official closing date of this international event for the packaging industry and related processing industries, exhibitors had booked about 20% more space than was available at the exhibition centre with its 262,400m2 in 19 halls. Around 2,700 exhibitors can therefore be expected again from May 4-10, 2017, coming from about 60 different countries. Save Food will play a role at interpack 2017. A special show called innovationparc will be held, with packaging ideas and solutions designed to reduce food losses and waste. interpack is a unique platform for businesses offering products and solutions in packaging technology and related processes as well as packaging media and materials for the various segments of this industry: food, beverages, confectionery and baked goods, pharmaceuticals, cosmetics, non-food consumer goods and industrial goods. The products and services presented here will be supplemented by several specialist areas. Working together wi th the German Engineering Federation (VDMA), interpack 2017 will put the focus on Industry 4.0, in particular. The special show will take the form of a technology lounge at the VDMA stand, featuring examples of solutions in packaging machinery and process engineering and opening up new opportunities for applications in security, traceability, copying and counterfeit protection as well as in customised packaging. We from PETplanet Insider have piched on the PET relevant themes and companies in our preview! Gebo Cermex Hall 13 - Booth C47","@ID":44}, "MARKET SURVEY 41 PETplanet Insider Vol. 18 No. 04/17 petpla.net Company Sipa Sacmi Packaging S.p.A. Postal address Telephone number Web site address Contact name Function Direct telephone number Fax Email Via Caduti del Lavoro Nr. 3 31029 Vittorio Veneto (TV) Italy +39 0438 911511 www.sipa.it Mr Matteo Tagliaferri Marketing and Communication +39 0521 548111 [email protected] Via Brodolini,10/A 40026 Imola (BO) Italy +39 0542 649811 www.sacmipackaging.com Mr Matteo Modenese Technical Director +39 0542 649811 +39 0542 640783 [email protected] Palletising machinery: Palletising machinery: Genius PTF (conventional automatic palletisers steady pallet type) Genius PTF/V (with double platform) Genius PTF/A (moving pallet type) Genius PTF - Active Layer (with layer preparation) Genius PTF - Fastlayer (with layer preparation) Genius PTF/A - Fastlayer (with layer preparation) Robby Pal (Robotic automatic palletiser) Robby Pal with Fastlayer (with layer preparation) Format changeover time 15 min 15 min 18 min 10 min 10 min 12 min 15 min 10 min 15 min Output rate (packs per minute) Up to 330 layers/ hour Up to 420 layers/hour Up to 700 layers/hour Up to 330 layers/hour Up to 330 layers/hour Up to 700 layers/hour Up to 320 layers/hour Up to 320 layers/hour 150 packs/min Automatically intergrated: (yes/no) Empty pack feeding Yes (pallet) Yes (pallet) Yes (pallet) Yes (pallet) Yes (pallet) Yes (pallet) Yes (pallet) Yes (pallet) Yes Insertion of interlayers Yes Yes Yes Yes Yes Yes Yes Yes Yes Connectable to shrinkwrapper Yes Yes Yes Yes Yes Yes Yes Yes Yes Special chracteristics: i.e. lowlevel feed, cross conveyer barrier Optimisation of cycle to increase performance using electronic solutions; customisation of the gripping system & layer transfer according to the product to handle; possibility to handle all main pallets on the market trouble-free, with customisable solutions Complete range to handle different types of containers & products: layer, row and multihead & loose product palletising systems; flexible and modular solution with reduced footprint; automatic system requiring limited operator intervention, operating in complete safety Able to take care of the buffer between shrinkwrapper and palletiser Company SMI S.p.A. GEA Procomac Postal address Telephone number Web site address Contact name Function Direct telephone number Fax Email Via C.Ceresa, 10 24015 San Giovanni Bianco (BG) - ITALY +39 0345 40 111 www.smigroup.it Ms Daniela Dadda Marketing Department +39 0345 40 318 +39 0345 40 209 [email protected] Via Fedolfi 29, 43038 Sala Baganza, Parma, Italy +390521839411 www.gea.com Mr Paolo Ventrelli Product manager +39 0521 333705 [email protected] Shrink film machinery: Machines for packing plastic, metal, cardboard or glass containers Packaging options & output rate (packs per minute) From 30 to 450 packs/min (in triple lane), depending on the model chosen; shrinkwrappers and casepackers can be integrated with a SMI palletiser to form a \"Packbloc\" compact end-of-line system - print registered film (yes/no; packs/min) Yes - nested pack (yes/no; packs/min) Yes - label orientation (yes/no; packs/min) Yes - carry handles (yes/no; packs/min) Yes - pad supported (yes/no; packs/min) Yes - tray supported (yes/no; packs/min) Yes - film only (yes/no; packs/min) Yes - tray and film (yes/no; packs/min) Yes - pad and film (yes/no; packs/min) Yes shrink process: - shrink tunnel with hot air or gas fired option Smiflexi tunnel distributes hot air flows in an efficient and homogeneous way on the pack - oven Available tunnel methan heated - steam tunnel No Footprint Single lane machine: AFW serie ( 10,060 x 1,774 x 2,450mm) till the bigger size SK 1200 HS (18,752.5 x 1,774 x 2,450mm); double lane machine: machine LSK 32 (9,820 x 1,974 x 2,450mm) till SK 1202 HS (18,752.5 x 1,974 x 2,450mm) Number of possible lanes From 1 to 3 lanes Packaging material and possible thickness film: 30-100 micron depending on the production speed & on pack collation; cardboard: low wave corrugated cardboard blanks: 3mm Voltage/power/energy consumption Depending on the machine model Film cutting and feeding system Manual sealing bar joins the films, equipped with a dedicated reel truck. The mandrels feature a pneumatic blocking system, special device stops for film ending. Cutting knife with motorised blade. Adjustment of the film length is electronic. There is device for centering the printed film provided with reference mark. Certification CE Palletising machinery: Format changeover time Sercos Fieldbus technology, user interface for quick & easy management of end-of-line palletising operations. A touch-screen display for real-time machine diagnosis & technical support additionally machine control features. The HMI displays all possible palletisation patterns by entering the pack size & specifications, and the number of layers required. 1 minute (from HMI panel) Output rate (packs per minute) 35 to 100 packs/minute (according to the size of the product handled & to the palletisation cheme selected) Up to 150 packs per minute Automatically intergrated:(yes/no) Yes Empty pack feeding Yes Yes Insertion of interlayers Yes Yes Connectable to shrinkwrapper Yes Yes Special chracteristics: i.e. low-level feed, cross conveyer barrier Swift & precise movements: The central column is actuated by brushless motors, which guarantee highly dynamic, reliable & precise movements of all axes of operation. The employment of this technology within palletisation systems, which are characterised by repetitive actions, turns into higher reliability, fewer maintenance operations & lower operating costs. Possible low or up level infeed","@ID":43}, "46 TRADE SHOW PREVIEW PETplanet Insider Vol. 18 No. 04/17 petpla.net Flexible packaging virtuosity in the “House of Krones” The “House of Krones” will be built at interpack in Düsseldorf - virtually at least. It will constitute the five core sections of Krones AG: digitisation as the roof and superstructure, process, filling and packaging technologies, plus intralogistics, as the functional premises, and Lifecycle Service as the base, the solid foundation. In terms of machinery, the principal focus will be the Varioline packaging system, which has proved successful in gaining widespread acceptance among bottling and canning companies. The firms are frequently tasked with first placing individual containers in multipacks, and then packing these in suitable sales or secondary packaging. So by developing the Varioline as a responsively flexible solution, Krones has found an answer for this profile: here, a single machine replaces up to six conventional individual machines with conveyors. With the Varioline, up to three-stage packaging processes can be implemented with a single machine. Space savings in the layout, reduced maintenance outlay and fewer operators are the results. The modular Varioline kit consists of three units: cartoning module, feed module, and basic module, which can be combined to form a customised packaging system. This modularised construction offers flexibility. The machine handles up to 52,000 containers per hour. The Belgian speciality brewery De Brabandere is one of more than 30 bottlers who have benefited from the Varioline’s versatility. It bottles 23 different beers, and thanks to the Varioline produces up to 34 different packages. www.krones.com Flexible and compact: KHS presents new InnoDry Block With its integrated buffer system the newly developed KHS InnoDry Block permits accumulation-free, gentle pack conveying without the side guides otherwise required. The KHS InnoDry Block combines a packaging machine with a palletiser and has a handle dispenser integrated into the packer. This setup is made possible by especially flexible buffer areas and the use of a highly dynamic handling system for layer formation which is being used in the blocked machine concept for the first time. Shorter conveying segments and, as a result, a reduction in maintenance effort speak for the compact block. Format changeover times are shorter as side guides are no longer needed on the conveying segment. KHS also retrofits conversions into older packers and palletisers so that these can also produce FullyEnclosed film packs, for example, helping to save on tray material. Another new service on offer is gas burner maintenance which permits KHS packaging machines to be operated efficiently for many years. Maintenance is supported by standardised maintenance plans and certified, specially trained personnel, thus reducing the amount of planning required by the customer. NMP Systems GmbH will also be exhibiting trendsetting packaging systems at the KHS booth in the form of Direct Print powered by KHS and Nature MultiPack, for which NMP is responsible. KHS is also displaying a high-performance system in the context of its partnership with packaging manufacturer Gerhard Schubert. www.khs.com KHS Hall 13 - Booth A31 IML in thermoforming and packaging development Illig, the systems provider for thermoforming solutions will be demonstrating the potential provided by in-mould labelling in thermoforming (IML-T) combined with clean and hygienic filling and packaging of dairy products. In live demonstrations Illig will show the production of rectangular cups out of PP on the IML-T production line IC-RDM 70K, forming area 680 mm x 300 mm, together with the compact IML unit RDML 70b. The 18-up mould produces cups with three different labels at the same time with an hourly output of 17,280 cups. Decoration is performed in brilliant photo quality on all four side walls of the pack and also on the bottom directly during forming. Currently, Illig is the only machine manufacturer from which IML-T can be obtained from one source with all required and optimally synchronised technology modules. IML-T lines integrated in form fill and seal lines (FFS, FSL lines) are also realised for clean and hygienic production, especially in the dairy industry. FSL 48 combined with IML-T: Variable dairy packs The FSL 48 form, fill and seal line developed by Illig is suitable for requirements by the food and especially the dairy industry. The filler with CIP (cleaning in place) and SIP (sterilisation in place) functions can be equipped technically in such a way that it meets the different hygienic demands by the food industry, even through to hygiene class IV according to VDMA (hygienic filling machines). All standard materials suitable for FFS lines can be processed on FSL 48, such as PS, PP, multilayer materials (e. g. PS/EVOH/PE), APET and even materials made of the biopolymer PLA (polylactic acid). www.illig.de Krones Hall 14 - Booth E33 Illig Hall 6 - Booth E02","@ID":48}, "45 TRADE SHOW PREVIEW PETplanet Insider Vol. 18 No. 04/17 petpla.net Sacmi excellence for food & beverage packaging The Sacmi booth at will be showcasing the new technology from modular labellers to Packaging robots. Pride of place on the stand will go to the new CCM application for the manufacture of coffee pods and confectionery packaging (the stand will be shared with C&M Holding). The application exhibited at the fair is a 32-cavity CCM press. This offers a cycle time of 2.4-3.2 seconds as opposed to 3.8-5 seconds with injection technology, while the special plastic extrusion process which, with compression, occurs at lower temperatures, gives energy savings of up to 30%. In addition, there is a complete guarantee of process repeatability as it is possible to manage each cavity independently and incorporate the advanced vision systems produced by the Group’s Automation & Service Division. Applicable to both systems and the manufacture of compatible pods, the system ensures lower running costs. Further applications have been developed for the production of eco-compatible and self-seal pods. From coffee pods to labelling solutions, the renowned Kube range (Sacmi’s new modular labellers) offer markets versatility and have won over a growing number of key bottling customers, especially in the wine sector. Kube “plug&play” technology lets manufacturers work efficiently across multiple labelling technologies and systems - hot, cold, self-adhesive - with one machine and with minimum label and/or format changeover times. When it comes to automated handling and end-line solutions, Sacmi will, at Düsseldorf, be exhibiting a 4-axis pick&place “spider” robot with an integrated vision system for the insertion of flexible packages (pouches, pillow bags etc.) in American RSC boxes. www.sacmi.com Sukano’s new additions to its matting agent masterbatch portfolio enable converters to make uncoated BOPET films appear very similar to coated flexible packaging, in terms of visual aesthetics and low gloss effect. Benefit fromSukano's expertise and proprietary formulations, to reach unprecedented performance levels both during manufacturing and on the shelf. Thinking of coating replacement? Talk to Sukano! w.sukano.com Sacmi Hall 4 - Booth G20","@ID":47}, "PETplanet Insider Vol. 18 No. 04/17 petpla.net 65 TRADE SHOW REVIEW related issues outlined in the strategy: the high dependence on fossil feedstocks, the low rate of recycling and reuse of plastics in general, and the significant leakage of plastics into the environment. Stéphane Arditi from the European Environmental Bureau insisted on the implementation of deposit systems to encourage consumers to pull together with the industry. “If you want to put responsibility on the consumers, you have to raise awareness by touching their wallets and consider a deposit system,” Arditi outlined. Sander Defruyt from the Ellen MacArthur Foundation concluded the session with his presentation on the New Plastics Economy, which had been recently presented during the World Economic Forum at Davos, where 40+ business and government leaders endorsed a global action plan on plastic packaging. “Three strategies are needed to transform the global plastic packaging market: fundamental packaging re-design and innovation, reuse systems and recycling with radically better economics and quality,” he pointed out. “59% of PET bottles were collected and recycled in Europe in 2015,” outlinedAn Vossen from Epro/Plarebel in her presentation. “But what about other PET applications, like trays or stf·sorting line stf·washing line professional plastic recycling solutions – made in germany The stf· group is the leading manufacturer of plastic sorting and washing machinery, especially for PET post-consumer bottles, with more than 60 turn-key plants and several single machines delivered worldwide. stf·group Industriestr. 1-3 94529 Aicha v. Wald – Germany fon +49 8544 960-110 mail [email protected] web www.stf-group.de scan for vCard stf ·group F.l.t.r.: Helen McGeough, Eric Liégeois, An Vossen, Sander Defruyt, Stéphane Arditi and Casper van den Dungen F.l.t.r.: Francoise Poulat, Gian de Belder, Johannes Burghaus, Antonello Ciotti and Carsten Lauridsen opaque and difficult to recycle containers that represent significant recycling challenges?” She further emphasised that the common practice of “cherry picking” the most recyclable fraction from the complete plastic waste has to stop. “We have to adapt our collection and recycling systems, and have to make sure that all plastics waste is recycled,” said Vossen further. “In order to implement such a Circular Economy, packaging and recycling cannot be looked at in isolation, you need to combine innovation and recycling.” From the recyclers’ perspective, Casper van den Dungen, Vice President of the Plastics Recyclers in Europe (PRE), clearly emphasised that a lot has to be still implemented to meet the European Commission’s 2025 target proposal of 55% recycling rate for the complete plastic waste stream in the EU. PET bottle recycling is best in class today with more than 55% recycling rates. “However, for achieving these overall targets for all plastics and packaging, the most important thing is that the right infrastructure is in place, which is not yet the case,” he stated during his presentation. The next Petcore Europe Conference will take place in the first quarter of 2018. The exact date and place will be announced in the second half of 2017. www.petcore-europe.org","@ID":67}, "TRADE SHOW REVIEW PETplanet Insider Vol. 18 No. 04/17 petpla.net 64 Petcore Europe Conference 2017 on “PET 2020 - The future of the PET industry” Opportunities and challenges of PET packaging “In all its ongoing activities, Petcore Europe is already well engaged as a significant contributor to the Circular Economy,” emphasised Patrick Peuch, Executive Director of Petcore Europe, who moderated the event. “PET is one of brand owners’ packaging materials of choice due to its outstanding performance in safely delivering products and its recyclability.” However, the PET value chain is also facing major challenges that were reflected in the conference debates. PET packaging 2020 From the PET producers’ side, Antonello Ciotti, Vice President of CPME (Committee of PET Manufacturers in Europe) started with a business overview on PET global demand and the European market. He also emphasised the reasons why PET is one of the most sustainable packaging materials: beverages and food protection avoiding wastage, resource savings due to light weight, outstanding LCA and carbon footprint and its full recyclability. He also presented the challenges posed by the Circular Economy, including shifting from fossil to bio-based PET. These challenges will require innovation from all actors and the PET producers are committed to take part in this effort. Nicolas Rivollet from Huskyand Carsten Lauridsen from Faerch Plast focused their respective presentations on the trends in PET packaging and design, while illustrating past and future developments. “In 2020 we expect to see 5% more bottles per ton of PET in a bale of recycled bottles: this results from the combination of the slow to negative growth of Carbonates Soft Drinks, an increased share of low volume formats and resin efficiency gains for a given format,” explained Rivollet. “Small CSD, juice sport drinks & teas, liquid dairy, home, personal care and food packaging currently represent the next frontier for PET: these applications require more engineered PET packages and the number of those packages could double by 2020.” Lauridsen showed a spectacular vacuum skin packed sirloin with a shelf life increase from 6 to 16 days and a food waste reduction from 34% to 18% in stores. Finally, leading brand owners outlined their perspective on PET packaging and sustainability. Gian de Belder and Johannes Burghaus from Procter & Gambleas well asFrançoise Poulat from Danoneexplained their respective companies’ sustainability packaging solutions and innovations. P&G presented a range of new packaging such a PET aerosols and its new Head and Shoulders shampoo bottle made from recycled plastics collected from beach clean-ups. Danone emphasised their efforts in using recycled PET, while insuring food safety compliance, using eco-design tools in new projects, and considering bioplastics in the future. PET sustainability 2020 During the afternoon session, speakers from the European Commission, the European Environmental Bureau and the Ellen MacArthur Foundation were invited to give an outlook on the future environment in which the PET industry will operate. Focusing on the implementation of a Circular Economy, they emphasised the need for increasing recycling rates and also discussed critical environmental challenges such as marine litter. In this context, Eric Liégeois from the European Commissionpresented the recently published roadmap for the Strategy on Plastics in a Circular Economy, currently open for public feedback. He emphasised the three critical interIn February, 160 delegates from the entire PET value chain from Europe and beyond convened in Brussels, Belgium, for the annual Petcore Europe Conference 2017. Under the theme “PET 2020 – The future of the PET industry” visions were presented and exchanged. Additionally, speakers from the European Commission, the European Environmental Bureau and the Ellen MacArthur Foundation gave an outlook on the development of the Circular Economy and other environmental challenges ahead.","@ID":66}, "PREFORM PRODUCTION PETplanet Insider Vol. 18 No. 04/17 petpla.net 18 Polyoak opts for Sipa preform systems PET container for cold drinks Recently, Cape Town based Polyoak Packaging bought two additional latest generation preforms systems and two stretch-blow moulding systems for the production of various sizes of containers for cold drinks. The blow moulders are able to produce a wide range of bottle sizes and shapes. The South African company picked the systems for high reliability and low cost of maintenance and energy efficiency, backed up by Sipa’s capability to support it in the development of special containers. Polyoak now has numerous Sipa injection moulding systems for the production of PET preforms, as well as stretch-blow moulding systems. Sipa equipment fits well with Polyoak’s philosophy of producing small lots of containers for many customers. This means that it needs to be able to change moulds very quickly – something that Sipa preform injection moulding and bottle stretch-blow moulding equipment is suited for. “This latest order from our longstanding customer Polyoak Packaging is further confirmation of the company’s confidence in Sipa,” says Sipa’s Giovanni De Rosa. Polyoak is the biggest packaging converter in South Africa, with over 30 manufacturing plants around the country (as well as in neighbouring Namibia). Its PET bottle production operations are handled by its Polypet division, which has been using Sipa equipment for ten years. Sipa has also been given the job of converting some existing preform tooling for the production of new preforms. Four years ago, Sipa strengthened its position in southern Africa with the establishment of a sales and assistance centre in Cape Town. From there, qualified technicians make regular visits to Polyoak operations in Cape Town itself, as well as in Johannesburg, Durban and in neighbouring countries. Privately-owned Polyoak Packaging has been in business for over forty years, producing a wide range of rigid plastics packaging. With manufacturing and distribution operations in several countries across southern Africa, it has divisions specialising in the design and manufacture of blow moulded, injection moulded, compression moulded, and thermoformed plastic packaging for the dairy, beverage, food and industrial markets. The company prides itself on excellent product quality with international certification for food safety and quality management. www.sipa.it www.polyoakpackaging.co.za Sipa’s XForm machinery system at Polyoak at Cape Town, South Africa One of southern Africa’s top rigid plastics packaging suppliers has once again chosen PET processing technology specialist Sipa for an investment in equipment for the production of preforms and bottles.","@ID":20}, "44 TRADE SHOW PREVIEW PETplanet Insider Vol. 18 No. 04/17 petpla.net News about baling press series HSM V-Press HSM GmbH + Co. KG, a German manufacturer of baling presses, PET solutions and document shredders, will be exhibiting three new machines from the vertical baling press series HSM V-Press. Their performance and longevity make them an economical waste management solution. The HSM V-Press series is said to reduce costs at the usually underestimated waste disposal cost centre. The smallest, the HSM V-Press 60, is a mobile collection container with an assembled manual press for voluminous packaging materials such as plastic films, plastic and paper bags, as well as packaging paper and light cardboard packaging. Due to the leverage, the machine produces well-compacted, stackable bales with a bale weight of up to 40kg for reducing the volume of waste. The bales produced by the HSM V-Press 60 can be pressed into hydraulic HSM bale presses and pressed to larger and higher-density bales. The HSM V-Press 825 is characterised by its low transport height. The pressing process runs automatically. A text display provides detailed information on the current state of affairs. The sliding door automatically opens at the end of the pressing process. It is easy to remove the bales; the bales weighing up to 280kg can be conveniently transported on a pallet. The HSM V-Press 860 is equipped with the fast-speed technology that was specially developed at HSM for the V-Press series. This reduces power consumption and drive output while increasing throughput at the same time. Compared to conventional drives, this technology reduces the cycle time by up to 40%. Due to the special pump technology, the machines are particularly quiet. With a press force of 548kN and the stable press guiding plate, it effortlessly presses used packaging material such as cardboard and plastic film. The bales reach a weight of up to 480kg and are held together by a 4-fold wire strapping. Polyester strapping is also available as an option. www.hsm.eu HSM Hall 11 - Booth A32 New blow-moulder EBS K Ergon: SMI solution devoted to Industry 4.0 Since 1987 SMI has been developing cutting-edge projects and technologies, in order to offer turn-key bottling lines and flexible, ergonomic, efficient packaging machines, inspired by the concepts of Industry 4.0 and Internet of Things (IoT). On booth 14D12, SMI will exhibit the world premiere of the new compact blow-moulder EBS K Ergon (Electronic Blowing System) in Ecobloc version (model Ecobloc Ergon 4-12-4 K EV) as well as an electronic volumetric filler. Based on the technical developments of the stretch blow-moulders of the EBS Ergon series, SMI engineers have developed a new series of compact rotary machines, called EBS K Ergon (“K” refers to the German word “Kompakt”), suitable for outputs up to 8,800bph. The new models, available in 2-, 3- and 4-cavity versions, offer all advantages of rotary technology, with an output range traditionally controlled by linear blow-moulders (from 3-4,000 to 8-9,000bph); thanks to the state-of-the-art solutions, the EBS K Ergon series can produce PET containers up to 30l with a maximum output of 2,200bph per cavity for the 0.5l format. Some benefits of the new EBS K Ergon series are: the preform heating section (tunnel) is integrated with the stretch blow-moulding section (blowing wheel) in a single, compact module, which can be installed even in small bottling lines. The tunnel features a horizontal preform feeder chain and an optimised ventilation and aeration system. The infrared lamp units responsible for heating the preforms in transit are equipped with a system of thermo-reflective panels made of an energy-efficient composite material, and are situated both in front of and behind the lamps. The structure that contains the tunnel and the blowing-wheel is equipped with safety doors that are slightly rounded, providing more space inside the machine to perform cleaning and maintenance tasks easily and safely. The stretch-blowing wheel is equipped with motorised stretch rods controlled by electronic drives and do not require mechanical cams; this innovative solution ensures control of the stretch rod’s travel and position, as well as energy savings. www.smigroup.it SMI Hall 14 - Booth D12","@ID":46}, "imprint EDITORIAL PUBLISHER Alexander Büchler, Managing Director HEAD OFFICE heidelberg business media GmbH Bunsenstr. 14 69115 Heidelberg, Germany phone: +49 6221-65108-0 fax: +49 6221-65108-28 [email protected] EDITORIAL Kay Barton Heike Fischer Gabriele Kosmehl Michael Maruschke Ruari McCallion Waldemar Schmitke Anthony Withers WikiPETia.info [email protected] MEDIA CONSULTANTS Martina Hirschmann [email protected] Johann Lange-Brock [email protected] phone: +49 6221-65108-0 fax: +49 6221-65108-28 LAYOUT AND PREPRESS EXPRIM Werbeagentur Matthias Gaumann | www.exprim.de READER SERVICES Till Kretner [email protected] PRINT Chroma Druck & Verlag GmbH Werkstr. 25 67354 Römerberg Germany WWW www.hbmedia.net | petpla.net PETplanet Insider ISSN 1438-9459 is published 10 times a year. This publication is sent to qualified subscribers (1-year subscription 149 EUR, 2-year subscription 289 EUR, Young professionals’ subscription 99 EUR. Magazines will be dispatched to you by airmail). Not to be reproduced in any form without permission from the publisher. Note: The fact that product names may not be identified as trademarks is not an indication that such names are not registered trademarks. 3 PETplanet Insider Vol. 18 No. 04/17 petpla.net Dear friends of PETplaner Insider, Exciting things are in prospect at the NPE next year. Here are some highlights. On May 7–11 2018, in Orlando, FL, USA , “the bottle zone“ (www.npe.org/bottlezone) will be taking place, for the first time at the trade fair. With joint support from the SPI, drinktec and PETplanet Insider, all exhibitors will be focusing on the theme of plastic bottles. Previously, bottles were spread out over the entire site, but now the visitor interested in this sector will be able to find everything under one roof. Highlighting this fresh approach, the NPE has now published, together with the Plastics Association, a market analysis entitled “Plastic bottles today - Innovating to reach today’s consumer”. It is an interesting brochure, which gives a good overview of the market and technology in North America for ambitious newcomers. But the professional will also find highlights here and there which are certainly interesting. The analysis assumes an average growth in the plastic bottle sector across the world of 5.2% to 6% a year. An important part of the analysis is the environmental concern about a smaller carbon footprint. The analysis was published before the election of the new President. It remains to be seen whether new protectionist politics will be implemented, and whether, under such circumstances, this level of growth can be achieved whilst meeting environmental targets in North America. Only time will tell. What is certain is that PET will not be able to pull out of the political climate. The analysis describes very well individual packaging segments, such as drinks, pharma etc. It also gives a concise picture of the market players in the supplier and users areas. Brief statements from Coca-Cola, Pepsi Cola and MillerCoors enhance the brochure. What is particularly interesting is the latter’s contribution, considering that beer is an emerging market for plastics bottling. MillerCoors saw a spike in sales of its 40-ounce and 32-ounce bottles when it moved from glass to plastic containers. While only one percent of the company’s total sales are made with plastic bottles, Jonah Smith, sustainability manager for policy and reporting at MillerCoors, predicts the use of PET bottles is only going to increase in the years to come. “I’d say within 10 to 15 years you’re going to start to see more and more of the packaging product mix switch over to more environmentally sustainable choices. Is PET going to increase? Probably. It’s also going to increase as more MRFs, material recovery facilities, improve their technologies in how to best recycle PET,” said Smith. With a recycling rate of just a third in the USA, there is still room for improvement. Yours Alexander Büchler","@ID":5}, "BOTTLE MAKING 33 PETplanet Insider Vol. 18 No. 04/17 other hand also to prevent the PET from crystallising. This would otherwise cause the preform – and therefore later the bottle – to not being completely transparent at this point. To better split the two temperature areas of nozzle and cavity, the insulation performance was enhanced by a titanium ring. The result was a reduced energy requirement thanks to the more efficient separation between the hot and cold areas. When comparing the – apart from the hotrunner – identical tools, power consumption of the Vulcan model was higher by a double-digit percentage. Further power savings can be achieved by using a HP gate insert, which directs the cooling to the mould contour and prevents unnecessary dissipation of heat from the hotrunner nozzle. This allows for double savings: less heating required at the nozzle tip and lower cooling performance of the cooling water system. Also the owners of an existing MHT tool can benefit from this savings potential, simply by replacing the existing nozzles with the Vulcan variety. With the change, they simultaneously gain an increased amount of flexibility. The two-part nozzle with tip inlay makes the exchange particularly easy – be it in case of wear and tear or if a new diameter, a new design or different materials are required. Pre-alignment of the valve stem is possible as well. To summarise, the Vulcan hotrunner components of MHT combine tightness with easy maintenance and energy efficiency. www.mht-ag.de 3 YE ARS NBĔ H?Q ;AĔ I@ J;=E;ACHĴ HIGH FLEXIBILITY... LOW ENERGY CONSUMPTION The all-new Ergon product range stands out for an innovative ergonomic design that further improves the economic efficiency, the operational flexibility and the environmental performance of SMI’s packaging machines and that brings together the very latest in process automation, advanced technologies and energy saving. ERGON packers are the ideal choice for the secondary packaging up to 450 packs/minute (in triple lane configuration). NEW ERGON PACKERS LCMERGON PACKERVIDEO ...scan & discover it! I COMPLETE LINES I ROTARY STRETCH-BLOW MOULDERS & FILLERS I I PACKERS I PALLETISERS I www.smigroup.it May 04 - 10 | Hall 14 | Booth D12 Nozzle cases of different lengths with heating and thermal sensor","@ID":35}, "PACKAGING / PALLETISING PETplanet Insider Vol. 18 No. 04/17 petpla.net 36 Decentralised packing machine processes beer bottles made of glass and PET without the need for changes One machine does it all Based on an articly be Gunthart Mau, trade press officer SEW-Eurodrive The speciality beer “Mohren Pfiff” is, alongside the traditionally brewed “Mohren Spezial”, one of the flagships of the Austrian Mohren brewery. With its sparkling “Pfiff” [Whistle] in the eye-catching rustic glass bottle, in 1990 the Mohren brewery went down a new route as one of the first fillers in Austria. Around 20 years later, the brewery decided to offer “Pfiff” in a lightweight, unbreakable PET bottle as well, with a closing device which, unlike a crown cap, has no sharp edges and can be opened without a bottle opener. To produce this advantage in the packaging with precision however represented a challenge for head brewer Ralf Freitag. The so-called “Easy Open Cap” from the Austrian packing specialist Alpla has a really long flap on the side. From a handling point of view, this is a challenge, because the bottle neck differs significantly from the usual glass bottles because of this “attachment”. The specifications for modernising parts of the equipment therefore went to the engineers at RST Automatisierungstechnik GmbH in Barbing, Germany: the packing clamps had to be able to handle bottles with the PET closing device as well as all other types of bottle at the brewery, including glass bottles which have a swing-top closing device. “We had to design the packing clamps in such a way that they can go further down the bottle neck than usual” is how head brewer Ralf Freitag describes the task they passed on to RST. For their part, RST Automatisierungstechnik, under the leadership of managing director Rupert Hadersbeck, designed the appropriate vacuum gripping clamps and delivered a four-head packer which can handle various bottle shapes without any modifications. Using vacuum technology, each individual pack is lifted into the crates carefully and safely. 4 x 20 bottles are moved in one operation – with a drive technology which meets the Austrian clients’ ecologically-orientated energy management. Energy-efficient motors The decentralised packing machine in the “Europac” line is appropriately fitted with efficient Movigear drive motors from SEWEurodrive. Massive modular belts for moving the crates in and out are moved by the compact mechatronic units. The enclosed and improved overall system of motor, drives and control electronics achieves a high level of efficiency so the drives in the whole series meet efficiency class IE4. Up to 50% of energy can be saved compared to other drive solutions. Other electro-motors and drives from SEW-Eurodrive operate in the decentralised packing machine. A bevel-wheel geared motor with integrated encoder moves the centring frame, which fixes the drinks crates during filling and centres the bottles on the box compartments. The twoaxle robot portal is positioned precisely and quickly by CMP servo-drive motors. Over 32,000 bottles per hour can pass through the four-head packThe Mohren brewery in Dornbirn, Austria, produces many types of beer which are filled into multi-use, one-off, swingtop and PET bottles. Four years ago, the brewery ordered a decentralised packing machine from RST Automatisierungstechnik in Barbing, Germany. It has improved gripping clamps and can process the widest variety of beer bottles. The compact Movigear drive units from SEW-Eurodrive form the backbone of the plant’s transport areas. The long flap on the side, the “Easy Open Cap” represents a challenge for handling. (Photo: Mohren Brewery)","@ID":38}, "57 TRADE SHOW PREVIEW PETplanet Insider Vol. 18 No. 04/17 petpla.net Amut Group debuts the ACF Series The ACF 820 mode l wi l l be i n operation during the Chinaplas exhibition. This model is configured in three stations (forming - cutting - stacking), with forming mould size of 820 x 650mm and clamping force of 240kN. The cutting station has an area of 800 x 630mm and clamping force of 600kN. The heating oven is a new development with 5-step length or 3,250mm, and permits the processing of thick PP sheets without any need of a pre-heater. The visitors will see the machine deliver PET punnets starting from 350μ foil and reach a production speed up to 60 wet cycles per minute in the configuration with 15-cavity mould. The ACF series assures a flexible production for a wide range of articles, handling different materials, such as PET, APET, rPET, CPET, OPS, HIPS, PS, EPS, PP, PLA, PVC, has a modular concept and can be supplied in different configurations. Inline solutions are also available. The forming and cutting presses are purposely equipped with counterbalanced platens. All Amut Comi thermoforming machines are driven by Easy, the smart HDMI that understands the data set by the operator and processes them proposing optimised solutions. Amut Comi is keeping up with advances in technology, complying with the smart manufacturing and Industry 4.0 trends. www.amutgroup.com Newamstar intelligent factory solutions for food beverage In May 2017, Newamstar will show two core sections at interpack (13E57) and Chinaplas: servo motor stretch-blowing technology and the intelligent factory controlling system. No matter how the bottle types change, an optimum stretch-blow speed and angle can be achieved, reducing equipment parts change and loss. In addition, the Newamstar intelligent factory controlling system helps to monitor and manage equipment as long as there is a mobile platform available. By remote data acquisition and diagnosis, the system provides reports to show how the line is operating, thus helping to reduce costs and improve efficiency. www.newamstar.com 2017 Hall 4.1 - Booth C45 Hall 11.1 - Booth K41","@ID":59}, "PETnews 6 NEWS PETplanet Insider Vol. 18 No. 04/17 petpla.net New Executive Director at Petcore Europe appointed On March 31, 2017, Patrick Peuch stepped down from his role as Executive Director at Petcore Europe. Christian Crépet has been appointed as his successor by the Petcore Europe Board. “It has been a real pleasure for me to run Petcore Europe for the last four years since the start. With the continuous trust, support and contribution of our members, we have grown Petcore Europe to a reference model and a well-respected European organisation, acknowledging our open-minded approach and pro-active activities, our partnerships and relationships. It is now time for me to step down and to thank you all, and to express my best wishes to my successor,” outlined Patrick Peuch during the annual general meeting of Petcore Europe. “Patrick played a key role in the growth of Petcore Europe and delivered outstanding performance not only to the Petcore Europe association but to the benefit of the whole PET value chain. I wish him all the best for his future activities,” stated Roberto Bertaggia, Petcore Europe President. “I welcome Christian, one of the founders and board members even before Petcore Europe, whose in-depth knowledge of the PET world, his motivation and skills, I am sure, will further foster Petcore Europe activity along the path traced by Patrick.” With a commercial and business management background, Christian Crépet started his career with Dow Chemical and went on with Enichem both in France and other European countries. Before running Petcore Europe, he has been the Managing Director of French recycling company Sorepla Industrie for the last 21 years. He is very familiar with the PET industry, having been a member of Petcore, the pre-Petcore Europe association, for a long time, a Vice-President of PRE and Vice-Chairman of their PET WG, and more recently a Board member and Treasurer of Petcore Europe. www.petcore-europe.org Logoplaste Innovation Lab wins iF Design Award for its Vimágua water bottle The Logoplaste Vimágua water bottle has been awarded with the iF Design Award in the category “Packaging Design / Beverages”. Each year, Germany’s oldest independent design organisation, Hannover-based iF International Forum Design GmbH, organises the iF Design Award. This year’s award ceremony took place in the BMW Welt in Munich, Germany, on March 10, 2017. Vimágua is a reusable, eco-friendly, 100% recyclable and lightweight water bottle, created to be offered to the local school communities. The bottle is said to be a mission to promote the consumption of tap water and raise awareness among the young, on the importance of water to the environment and health. The design, inspired by both the drop and the water surface ripple effect, is ergonomic for children and is meant to fit in a small lunch bag. The 450ml PET bottle weights 25g, and its manufacturing process uses less energy, when compared to reusable bottles produced in other materials. The PP cap is also optimised and weights 1.3g. www.logoplaste.com www.ifworlddesignguide.com NPE 2018 Bottle Zone The demand for plastic bottles continues to grow across numerous products and sectors, including home goods, personal care, beverages, food and pharmaceuticals. With the industry slated to grow 4.6% annually over the next five years, bottling has become one of the fastest growing industry segments in plastics manufacturing. Plastics Industry Association (Plastics) recognised this trend and is adding a new exhibit space - the Bottle Zone - at NPE2018, taking place May 7-11, 2018 at the Orange County Convention Center in Orlando, Florida, USA. The area will feature more than 40 industry leaders presenting the latest advancements, technologies and supplies in bottling manufacturing. Innovative ideas that will be shared include: limiting overhead costs, increasing automation, reducing material waste per unit, streamlining production, lowering energy consumption and PET drying technologies. “Devoting more than 50,000 square feet to the new Bottle Zone at NPE2018 speaks to the importance of this growing segment,” says Bill Carteaux, president and CEO of Plastics, the non-profit organisation representing the entire plastics supply chain and organiser of NPE2018. “It will showcase the latest state-of-the art machinery, equipment, supplies, innovations and strategies driving bottling manufacturing.” Bottling ranks in the top quarter of all plastics product manufacturing segments in terms of employment numbers, dollar value of shipments and capital expenditures. With that rapid rise, it is important for manufactures to stay on top of key issues and advances affecting bottling so they stay competitive and keep growing. The Bottle Zone will offer concentrated education sessions hosted by PETplanet Insider and ISBT that address those very topics to keep this important segment on the cutting edge. www.npe.org/bottlezone WikiPETia.info New contents at wikipetia.info","@ID":8}, "MARKET SURVEY 40 PETplanet Insider Vol. 18 No. 04/17 petpla.net 04/2017 MARKETsurvey Preforms & preform inspection Recycling plants & washing units Palletising & shrink film machinery Caps & closure systems & CC inspection Labelling & marking systems Recycling: Cutting plants Filling equipment & filling inspection Resins, additives Compressors SBM machinery & quality inspection Palletising & shrink film machinery For the first time PETplanet Insider will focus on palletising and shrink film machinery to mark the occasion of Chinaplas and Interpack trade fairs 2017. Please have a look at the new and innovative developments on palletising and shrink film machinery of following companies: SMI S.p.A., Sipa S.p.A., Sacmi Packaging S.p.A., Newamstar Packaging Machinery Co., Ltd., Gebo Cermex, And & Or, S.A. and Krones AG. Although the publisher have made every effort to ensure that the information in this survey is up to date, no claims are made regarding completeness or accuracy. Company Newamstar Packaging Machinery Co., Ltd. Gebo Cermex AND & OR, S.A. Postal address Telephone number Web site address Contact name Function Direct telephone number Fax Email East Xinjing Road, Zhangjiagang Economic & Technological Dev. Zone, Jiangsu 215618, P.R. China +86 512 5869 1111 www.newamstar.com +86 512 5867 3920 [email protected] 5-7 Rue du Commerce 67116 Reichstett, France +33 388 183 850 www.gebocermex.com Ms Valerie Cattenoz Shrink-wrapping product manager +33 612 324 103 [email protected] PI el Limon, AV. de Europa, 6 41928 Palomares del Rio (Sevilla), Spain +34 954 779200 www.andyor.com Ms Caridad Ortega Suárez Sales Director +34 954 779200 +34 954 774244 [email protected] Shrink film machinery: Packaging options & output rate (packs per minute) - print registered film (yes/no; packs/min) Yes, 45-120 Yes, 150 cycles/min No - nested pack (yes/no; packs/min) Yes, 150 cycles/min Yes (from 15 to 900bpm) - label orientation (yes/no; packs/min) Yes, 50 cycles/min (can/glass) No - carry handles (yes/no; packs/min) Yes (from 15 to 400bph) - pad supported (yes/no; packs/min) Yes Yes, 85 cycles/min Yes (from 15 to 400bph) - tray supported (yes/no; packs/min) Yes Yes, 85 cycles/min Yes (from 15 to 400bph) - film only (yes/no; packs/min) Yes Yes, 150 cycles/min Yes (from 15 to 900bpm) - tray and film (yes/no; packs/min) Yes Yes, 85 cycles/min Yes (from 15 to 900bpm) - pad and film (yes/no; packs/min) Yes Yes, 85 cycles/min Yes (from 15 to 900bpm) shrink process: - shrink tunnel with hot air or gas fired option Hot air Yes Shrinking pistols (hot air) - oven Yes - steam tunnel No Footprint 20-32m2 Several models depending on speed Number of possible lanes 1 and 2 1 to 3 and soon to be 4 Max. length of the pack is 1,200mm Packaging material and possible thickness PE, 0.04-0.08mm Film from 27 to 100 microns LDPE + LLDPE 40 to 60 micron Voltage/power/energy consumption 380V/50Hz 140kW/h for a VersaFilm 5MF SFR running 150 cycles/min Several models depending on speed Film cutting and feeding system Vacuum or injection table in lane or at 90°C Yes Certification CE/ ISO/ ATEX/UL CE and UL Palletising machinery: Format changeover time Possibility of zero changeover time when palletiser equipped with automatic changeover 15-20 minutes Output rate (packs per minute) 45-120 Wide range of solutions, up to more than 300 packs/minute Up to 400 bpm Automatically intergrated: (yes/no) Yes Empty pack feeding Yes Yes Yes Insertion of interlayers Yes Yes Yes Connectable to shrinkwrapper Yes Yes Yes Special chracteristics: i.e. low-level feed, cross conveyer barrier Robot palletiser, low-level palletiser, single-arm palletiser Low & high level infeed range available, capability to be integrated with LGVs, full range of pallet conveyors for pallet handling, pallet inspection & rejection systems, pallet elevator lowerator Low-level feed Tray former possible to be integrated (display palletiser)","@ID":42}, "BOTTLE MAKING 22 PETplanet Insider Vol. 18 No. 04/17 petpla.net on the market for connecting kegs to draft dispensing systems. Particular attention was given to accommodating Dolium’s plastic valves to the variations in tolerance of the metal couplers from different manufacturers. The system uses glass reinforced polyamide. www.dolium.eu Sometimes yes, sometimes no: the bag A yes for the bag comes from the keg system of Lightweight Containers from Den Helder, the Netherlands. The bag separates the beer from the compressed gas, so that it cannot come into contact with the oxygen. The lightweight one-way kegs meet the very strictest safety requirements. The Keykegs with double wall technology are tested to 7 bar during manufacturing. The Keykeg coupler is also the only system in the world fitted with a special safety valve. Filling can take place manually or by machine. Individual printing ensures good branding. Keykeg is available as slimline in 10, 20 and 30l kegs. A no for the bag applies to UniKeg, also by Lightweight Containers, introduced two years ago. The new 20l keg uses the Double Wall technology and integrates an American Sankey D fitting. Jan Veenendaal, CEO of Lightweight Containers says, “UniKeg was developed to offer a successful product-price-market combination.” The system will be manufactured in the US and will only be sold there initially. The main difference between the new UniKeg and Lightweight Containers’ well established product, the Keykeg, is that the UniKeg lacks the laminated inner bag. Lightweight Containers produces their kegs on a fully automated production line in Den Helder, the Netherlands. The line is based around two Sipa SFL2/2 linear stretch-blow moulding units, one for the inner bottle, and one for the outer. It has a capacity of 400 kegs per hour. Sipa has not only supplied Lightweight Containers with the stretch-blow moulding equipment, but also collaborated in research, prototyping and development of the containers. As well Sipa has been chosen by major multinationals beer producers (AB-Inbev, Heineken, etc) as the blow moulding machines manufacturer to blow patented solutions beer kegs. www.keykeg.com www.unikeg.com www.sipa.it The bag separates the beer from the compressed gas. (photo: Sipa) Outside HDPE, inside PET Ecokeg uses a stable outer shell of HDPE which provides mechanical protection for the PET bladder. Suitable for gravity filling, valves can be connected and reconnected multiple times. The PET ball is reportedly the strongest on the market: with 490g virgin PET preform, it provides durability for long-distance exports. Heat tested up to 60° Celsius in a dormant state. Pressure tested to up to 10 bar, 32l capacity, allowing for 2l of headspace heat expansion. The PET features an oxygen scavenger and thus allows for shelf lives of up to nine months. The outer HDPE skin weighs 2.5kg in Europe and 1.8kg in Australia. Ecokeg’s patented technology was originally developed in collaboration with the Foster’s Group on One-WayKegs (OWK). Closely replicating a steel keg, Ecokegs are compatible with the tap / dispensing systems used by pubs and bars. The design combats issues such as Fobbing and allows Livening through the valve. www.ecokeg.com PET bladder in a stable outer HDPE shell (photo: Ecokeg) Mechanical engineering Lines for racking beer in non-refillable kegs KHS and Petainer jointly developed the Petainer keg system. The system is designed for multi-shift operation, for racking beer in standard 20 or 30l kegs made of PET. This system is designed for a capacity of up to 420 kegs per hour. The system components can include stretch blow moulding, filling, encoding, packaging, and palletising and the necessary inspection equipment. The process precision of the stretch blow moulder ensures that the disposable kegs are reliably fed to the subsequent production process. The Innokeg PETBoy F2 non-refillable keg system with two independently operating filling heads. (Photo: KHS)","@ID":24}, "EDITOUR PETplanet Insider Vol. 18 No. 04/17 petpla.net 11 Indonesian rupees (IDR) – around 40 euro cents. Newcomers to the market should be stocked on supermarket shelves for less than 3,000 IDR and water should only cost 1,000 IDR (7 cents) for 240ml. Yet water is not sold in PET bottles, rather in deep-drawn polypropylene cups with a sealing lid. It is clear that the PET industry has to stretch itself so that there is still something left at the end of the day. The solution for almost all suppliers is to invest in the latest western technology, whether it be preforming equipment or cold aseptic. Additionally, reducing the number of formats used in production means products can be manufactured in very high quantities. We have visited all production stages in the PET industry, from recycling plants to bottling factories, but it was difficult to form a comprehensive picture of the size of the market, as whoever you asked, you got different, often contradictory answers in return. What we do know is that Indonesia has a population of more than 260 million, and more than half live in the cities. Yet only 25% have an internet connection. If you take this figure and use it as an indicator of income, 65 million people can be considered as middle class (fig. 1). Bottled water and other beverages This distinction is especially important with water. The Indonesian drinking water organisation Aspadin boasts bottled water production figures of 27.17 billion litres for 2016. 207 of the 700 concession bottled water companies in Indonesia are currently part of Aspadin. The largest global bottled water company Danone Aqua finds itself within this segment, producing 13 billion litres/a. That is almost 50% of the market. This share would have been even larger a few years ago, but regional brand names have grown faster than Aqua, particularly the Indonesian food corporation Mayora. They have penetrated the water market with their branded water Le Mineral, supported by a large advertising budget. If we shared 27.17 billion litres among the 260 million inhabitants, it would work out at more than 100 litres per head. That looks good, but it is misleading. Even though 88% of the Indonesian population have access to communal drinking water, health-conscious Indonesians do not use this tap water for cooking, never mind drinking. The bulk goes into 5 gallon containers (19litre) made from polycarbonate. Around 30 million are produced per year. During their 2-year lifespan, they recirculate around 40 times, meaning water bottling companies fill these containers an average of 20 times within one year. That alone equates to 20 x 19 litres x 60 million units = 22.8 billion litres, just for this segment (fig. 2). That is around 87 litres per head (260 million). Around 4.4 billion litres of remaining water is bottled in higher-priced packaging. There are now 65 million wealthy Indonesians, corresponding to a consumption of around 68l per head of water in small bottles. such as preforms and caps also work from multiple main factories, however they are not quite as dispersed. Another aspect which influences the drinks industry is that the Indonesian consumers are particularly conscious of their health and the environment, something which is not necessarily common in emerging nations. A product has to be healthy and environmentally-friendly in one way or another. Packaged spring water counts as healthy, tea and juice too, but sugary drinks like lemonade have a low approval rating in the eyes of the consumer. In Indonesia, PET bottles have a positive image, especially since a small yet distinguished recycling sector has established itself here. Large-scale companies like Danone Aqua use 10% rPET in their bottles, and this is welcomed by the consumer. The water market remains relatively stable throughout the year, suffering only minor fluctuations, while other kinds of beverages are subject to major variations according to the season. Sales figures take the biggest hit during monsoon season and Ramadan, soaring once again in the subsequent festival period and summer time. High costs – low retail price The consumer is extremely pricesensitive, however they are up against high transport costs and high health and environmental standards. The threshold between defining a product as affordable or luxury is 6,000 Fig. 2 Share of water [mio l] in PET bottles and 5-gallons containers, total 27,200 mio liter Fig. 3 Beverages filled in PET [mio l], total 6,200 mio liter Fig. 4 PET bottles used for water, CSD and RTD aseptic beverages [mio], total 9,000 mio bottles 22,800 4,400 4,400 1,500 300 5,600 2,500 900","@ID":13}, "60 TRADE SHOW PREVIEW PETplanet Insider Vol. 18 No. 04/17 petpla.net The new Zhuli underwater pelletising system Maag, a Dover company and leading manufacturer of gear pumps, pelletising and filtration systems and pulverisers for demanding applications in the plastics, chemical, pharmaceutical and food industries will be displaying a number of its technologies. The highlight of the show for Maag will come when the company unveils its new Zhuli underwater pelletising system. The Zhuli system combines Maag’s best existing pelletiser, waterbox bypass, process water and dryer technologies. Other Maag products that will be on display at Chinaplas 2017 include: Pearlo underwater pelletiser: Designed to process spherical pellets for raw materials, compounds, masterbatches, engineering plastics, wood and nature filler-filled polymer composites, thermoplastics elastomers, hot-melt adhesives and gum bases at capacities that can reach 36,000kg (79,200lbs.) an hour. CSC series screen changers: Features a double-piston design that allows tailormade adjustment of the filtration unit per the user’s specific process requirements while allowing the use of five different filter-cavity shapes within the same screen-changer housing: circular, oval, arched, leaf-disc and candle. x6 class gear pump: Offers improved volumetric efficiency and pressure capabilities that allow it to be operated at reduced rpms, shear rates and temperatures, resulting in reduced residence time and energy consumption with improved production rates, polymer quality and pump life cycle. Baoli S strand pelletiser: The Baoli S builds on the standard-setting Baoli pelletiser model with its automated cutting chamber interlock system able to deliver increased performance, higher productivity and reliability, improved handling, greater flexibility and an optimised cost/benefit ratio in critical strand-pelletising applications. www.maag.com Hall 5.1 - Booth S61 High quality injection moulds Following the successful trade fairs in 2015 and 2016, the Swiss firm company Otto Hofstetter AG will be present with its own booth. Otto Hofstetter AG will show customers the complete portfolio of high quality injection moulds. Besides these well-known high quality injection moulds, the company will also be giving information about the full portfolio of services, which start from a basic idea of the project, continue with a consultation process and finally conclude with the design of the actual product. Once the injection mould is built, the after sales service will round up the complete package. Otto Hofstetter AG is well known for PET preform moulds from 2 up to 192 cavities, as well as for injection moulds for thin walled packaging application and in mould labelling solutions. Otto Hofstetter AG will present products for the thin-walled packaging industry as well as demonstrating the company’s technical competence in complete systems for producing silicone cartridges with IML. www.otto-hofstetter.ch Hall 4.2 - Booth E45","@ID":62}, "BOTTLING / FILLING PETplanet Insider Vol. 18 No. 04/17 petpla.net 28 of ensuring product integrity without the need for preservative additives, which would contradict lifestyle statements that are important to various market segments. While UHT milk has traditionally been sold in in tetra pack in India, PET has been introduced by the dairy company Amul, which is managed by GCMMF. Big players, like Amul, have gone for high capex (capital investment) aseptic packaging, because of their need for high capacity filling and automation. But medium level players can also now consider PET opportunities, as “low to medium capex” aseptic lines have now become available. The low capacity aseptic lines are now available with capacities as little as 2,000bph. UHT treated milk is traditionally filled in sterilised bottles and one of the trends is now use of preform decontamination and sterilisation as an alternative to bottle decontamination. The enclosed stretchblow-mould-fill systems ensure that contamination is avoided and sterility maintained until the container is capped. The product is cooled down to room temperature immediately prior to bottling, which guarantees minimal vitamin degradation and flavour variation. It also helps to maintain organoleptic qualities, which are believed to be superior in cold-filled dairy products. Flavoured milk and ESL (extended shelf life) products, aseptically packaged in PET bottles, can also be transported and stored at room temperature. As detailed above, cold aseptic filling maintains product integrity without the need for the addition of preservatives. Reliance Industries Limited - PET Division has developed Relpet OP5821 resin (Opaque White) for UHT milk which is packaged in an aseptic filling line by Amul in India. Buttermilk and lassi milk variants are now being filled in PET packs ranging from 200ml to 1l. Indian Ghee can be found in PET jars across India, being used widely by companies such as Gowardhan Dairy, one of the major producers in the western region among others. PET CANS are also available in the market, suitable for ghee and other VADP’s. Producers have found that PET packaging readily lends itself to security measures, which helps in the fight against counterfeiting. In addition, thermoformed APET trays, glasses, cups and lids are slowly gaining acceptance in Indian Dairy sector due to enhanced clarity, improved physicals and also lowest embrittlement temperature. There are a number of reasons why dairy majors are today evaluating PET aseptic packaging for flavoured milk. They include: product quality, because of short time heat treatment for UHT milk consistently high safety performance single use, eliminating cleaning and contamination risks light weight, easy to transport over long distance, lower transportation cost more options for bottle shapes and capacities; attractive design/aesthetics productivity – high speed aseptic lines high oxygen barrier bottle clarity easy to handle, re-sealable and shock resistant easy to recycle Relpet, the PET division of Reliance, has been working with the Chemours Ti-Pure protect system for the dairy PET bottle range. The system is designed on the principle that ‘changes in riboflavin levels determine the Light Protection Factor (LPF) for the milk packaging’. The ‘Ti-Pure Protect’ solutions help in the design of PET milk packages with enhanced light protection. Indian PET market The PET packaging market in India has been growing in recent years and continues to expand into new application areas. In 2007/2008, PET consumption for non-alcoholic beverages, including dairies, was at 76kta, it now stands at 510kta (1617) – a growth of 500 % plus in nine years. This growth has been based particularly on expanding application areas of PET in the packaging of beverages, milk variants, edible oil, mineral water and bulk water. Reliance has been supporting brand-owners in packaging solutions including their niche resins for dairy and other enduse markets. Mr Sodhi, the Managing Director of GCMMF, has said that ‘value-added diary products will drive Indian dairy growth’. The industry estimate is that the ‘organised dairy’ segment will more than double in size by 2020. www.ril.com www.india.vdma.org The Pride of Cows brand from Parag Dairy received encouraging market response for its fresh milk bottled in PET (photo: Parag Dairy)","@ID":30}, "BOTTLING / FILLING PETplanet Insider Vol. 18 No. 04/17 petpla.net 26 India’s dairy industry grows – with PET White revolution Fifteen years ago India was responsible for one-tenth of the world’s total milk production; it now accounts for one-sixth of total global milk output. Current milk production in India is 116 million tonnes a year; the country’s 12th five-year plan aims at lifting that output to 150 million tonnes or so by 2017. According to figures from VDMA India (German Engineering Federation, India), milk production in the country is growing at 4% per annum, which is well ahead of the world average of 2.1%. PET has now established itself as the packaging material of choice, ahead of traditional solutions including HDPE, pouches, Tetrapack and glass. At the 45th India International Dairy Conference, held in February 2017 in Mumbai, Mr RK Gera, AVP – Business Development for the PET Division of Reliance Industries Ltd, one of India’s largest private-sector companies, gave a presentation to explain how that shift had happened. The story begins with the launch of India’s “White Revolution”, which was also known as “Operation Flood”. This was a three-phase plan, operated by the National Dairy Development Board, to revitalise India’s dairy production and make it self-sufficient in milk. The program was so successful that, by 1998, India was the world’s largest milk producer. The project attracted international attention and India is expected to continue to play a major role in the world’s dairy industry in coming years. It is expected that global milk production will rise to 867 MMT (million metric tonnes) – up 26% from the current level of 714 MMT. India’s milk production is currently growing at a CAGR (compound annual growth rate) of 4%; at a projected rate of 4.5%, it is expected to reach 180 MMT by 2020. This will increase its share of world milk production from 16% to 21%; in line with the country’s population, which is approximately one-fifth of the world’s total (VDMA).","@ID":28}, "PACKAGING / PALLETISING PETplanet Insider Vol. 18 No. 04/17 petpla.net 37 ing machine thanks to these hightorque drives – and this figure has been maintained for four years now. Modern brewing technology has tradition “To date we have not had any breakdowns” electrician Hubert Strobl states happily – and head brewer Ralf Freitag keeps fingers crossed. “Drives from SEW-Eurodrive are practically standard in all filling plants” says the qualified engineer and beer sommelier. SEW motors can therefore be found in abundance in pack transport as in the handling plants for pallets and containers. In 1997, as one of the first beer producers in Europe, the Mohren brewery automated the palleting of the casks with a 6-axle robot. The Kuka machine was fitted out and programmed to be ideal for its purpose by RST Automatisierungstec The Mohren brewery has been in the centre of Dornbirn since the mid-19th century. (Photo: SEW-Eurodrive) The “Europac” decentralised packing machine from RST Automatisierungstechnik is fitted with efficient Movigear drive units and other electro-motors and drives from SEW-Eurodrive. (Photo: SEW-Eurodrive) The packing clamps must be able to handle the PET closing device and all other types of bottle in the brewery in the same way, including glass bottles with a swingtop cap. (Photo: SEW-Eurodrive)","@ID":39}, "EDITOUR PETplanet Insider Vol. 18 No. 04/17 petpla.net 12 Tour Sponsors: That corresponds with other figures claiming around 9 billion caps are produced per year. Around 900 million bottles go into the aseptic sector (mainly 0.33l bottles, which equals 300 million litres, or 4.6l per head) 2,500 million bottles go into the CSD sector (mainly 0.600l bottles, meaning 1.5 billion litres, or 23l per head) and 5,600 million bottles go into the water sector (an average of around 0.79l equals 4.4 billion litres, or 68l per head) (fig. 3 & 4). As such, the total market for PET bottles amounts to around 6.2 billion litres for 65 million people, or 94 litres per head. If you also count water from the 5 gallon containers (87l/head), the middle class consume around 181 litres per head. These figures are good considering the country’s population drinks a lot of hot tea and coffee. These numbers were a result of comparing different sources to create a kind of mean value from all the assertions we were given. However, some, even official, figures diverged dramatically from our results. It would seem clear that the growth of the PET world is essentially generated by the growth of the middle class, considering the high per capita consumption of 181 litres per head for the middle class population. Other PET bottles In the Muslim country of Indonesia, the alcohol market is heavily taxed and as such not relevant in gaining an overall view of the PET world. Another large market is the edible oil market in Asia, where cooking traditionally involves using lots of oil. However, we were unable to evaluate any figures from this sector. It was equally not possible to find any reliable figures regarding household cleaning and personal hygiene products. We saw a number of one-stage and two-stage PET bottles in the supermarket, however shelves were dominated by HDPE bottles. We were unable to find any PET bottles in the milk sector. DOUBLE ACTING DIRECT COUPLED MOTOR HEAT RECOVERY SYSTEM HORIZONTAL OPPOSED MARKET BENCHMARK PROPAK ASIA (Bangkok) 14th – 17th June DRINK JAPAN (Tokyo) 28th – 30 June DRINKTEC (Munich) 11th – 15th September PACK EXPO (Las Vegas) 25th – 27th September CBST (Shanghai) 22nd – 24th November PLAST PRINT PACK (Accra) 5th – 7th December","@ID":14}, "56 TRADE SHOW PREVIEW PETplanet Insider Vol. 18 No. 04/17 petpla.net TRADE SHOWpreview Chinaplas 2017 will be held in China Import & Export Fair Complex, Pazhou, Guangzhou, PR China on May 16-19, 2017. It will feature “intelligent manufacturing, high-tech materials and green solutions” with advanced plastics machinery, materials and technologies all found in a 250,000m2 exhibition area from over 3,300 renowned suppliers. As awareness and understanding of sustainability become ever more prevalent, the packaging industry is turning its focus towards sustainable packaging. Lightweight and green packaging has become the bandwagon for the packaging industry to get on in order to balance ecological, economic and social needs. To cater for the demand of the packaging industry’s development, Chinaplas 2017 will bring to packaging professionals new technologies, materials and solutions from over the world to facilitate the migration towards lightweighting and sustainability. Come around and visit the PETplanet Insider team at hall 11.1, booth T25! ASB-70DPH v4 one-step injection stretch blow moulding machine Nissei ASB Machine Co., Ltd. will once again be exhibiting at Chinaplas with twice-daily live moulding demonstrations. This year the featured model is the company’s versatile ASB70DPH one-step injection stretch blow moulding machine. The ASB-70DPH is a medium sized machine which can produce containers from PET and a wide range of other resins direct from raw material to finished product in one machine. It is also available with a range of options that allow users to further adapt its capabilities to cater to their local market needs. The key facts of this model are: From raw material to finished product in one compact machine, there is the ability to process more than 15 resin types in addition to PET. Moulds containers from 50ml or less all the way up to 10l capacity are available. Additionally a variable cavitation from 18mm neck diameter small bottles in 12 cavities through to 149mm neck diameter jars in a single cavity. There are no hydraulic components above the moulding area to eliminate the risk of product contamination. The machine will be demonstrated moulding a 700ml copolyester (Tritan) re-usable drinking flask in a four cavity family mould at a cycle of 14.4s. This product is currently enjoying a boom in popularity in China and the simple container design being moulded has been selected to demonstrate the superior visual moulding quality of the ASB-70DPH model. www.nisseiasb.co.jp Unique Injection Molding Systems Co., Ltd. PETplanet corner of the world, and in recent years has been enhanced by its Editourmobil project, meeting with the major players in the industry and sharing information about companies, markets, and developments affecting the sector world-wide. This year the Editourmobil is touring China and South East Asia and will be highlighting Guangzhou Unique. www.unique-pet.com Hall 9.1 - Booth R21 Hall 11.1 - Booth R21","@ID":58}, "PETproducts 66 PETplanet Insider Vol. 18 No. 04/17 petpla.net Revitalised water range PET Engineering has collaborated with Swedish Stockholm-based agency Nine to develop the new packaging for the Swedish mineral water brand Ramlösa, the Carlsberg Group. The purpose of the project was to develop 33cl, 50cl and 150cl containers that could, on the one hand, meet the strict technical requirements of the customer’s production department and, on the other, use a single 3D object to express the brand’s values, namely natural purity, quality and refreshing enjoyment. The concept was developed by Nine and engineered by PET Engineering’s technical team of PET experts, who developed a high performance packaging solution that’s also easy to handle, easy to grip and that remains stable on the production line, on the shelf and during use. PET Engineering was also involved with the manufacturing of the container, providing six series of moulds for the production of the packaging. www.petengineering.com Infrared lamps for PET manufacturing The industrial lamp manufacturer, Victory, Hemel Hempstead, Hertfordshire, UK, says its infrared lamps for PET manufacturing reduce energy consumption, resulting in savings in production costs. Tested against major competitors, the heat output of its PET lamps is proven to be higher than competitors’ equivalents, Victory claims, so during their lifetime the lamps will consume less energy, decreasing the cost of each unit produced. With a longer service life than the market equivalents, they also offer a reduction of replacement costs and down time, the company says. Lamps are available with or without Victory’s ceramic reflector coating and are compatible with all blow moulding equipment including Sidel, Krones, Sipa, SMI, ADS, Side & KHS. Victory also offers several other product ranges for industrial processing. Its Contour infrared lamps can be formed to match the shape of the object to be heated – useful in industries such as automotive where items such as vehicle lights need precise heat applying. The company also offers medium wave infrared modules and ceramic elements; these can be assembled into panels to heat larger items or areas. www.victorylighting.co.uk Brau Union Austria launched Desperados PET event bottles with CCL Label’s Eco Stream technology CCL has created a low-density label for Desperados at Brau Union Austria which enables bottle-to-bottle recycling for PET bottles with pressure sensitive label decoration without loss in quality. The Eco Stream labels shrink in hot washing baths and detach from the PET flakes without leaving traces of ink or adhesive behind, says CCL. While the label flakes float to the surface the PET flakes sink, which enables an easy separation of materials. Since inks and adhesive stay on the labels neither washing bath nor PET flakes are contaminated or discoloured. Furthermore Eco Stream labels meet the guidance of the recycling associations EPBP (Europe) and APR (U.S.). Due to the clean separation of the lowdensity material from the PET flakes, valuable raw materials can be returned seamlessly into the recycling stream ensuring complete reuse. No limitations or alterations had to be made for the Desperados Eco Stream version. The label design was transferred completely and the tactile varnish gives it a 3D look and feel. Eco Stream labels with this kind of embellishments were approved separately by EPBP and APR as Eco Stream+ to verify that their functionality is not affected. www.ccllabel.com www.brauunion.at","@ID":68}, "LABELLING PETplanet Insider Vol. 18 No. 04/17 petpla.net 34 Trends in labelling and equipment technology Breakthrough in direct printing? The beer bottle or the soft drink container is on the shelf and waiting for its buyer. In addition to the price and type of container or the sales package, the label is the only selection criterion. It serves to produce a direct sales approach at the point of sale and creates the recognition effect of a brand. Modular machines and self-adhesive labels “Marketing departments in the beverage world want maximum flexibility,” Stefan Richter, Head of Inspection and Labelling Technology at Krones AG, stated. “Bottle design is advertising, and that is highly individual. Consumers like to rely on the first appearance of a product when they make purchases, and manufacturers can support this with the appropriate design. As a producer of labelling machines, we experience first-hand that the quantity of ordered module equipment is increasing steadily year on year.” With module machines bottlers can keep all options open. Different labelling units of almost any kind can be docked, regardless of whether for cold glue, hot glue or self-adhesive labels. As a result, beverage manufacturers remain flexible in their choice of designs even years after a large investment decision. The trend in labelling plastic containers is toward increasingly thinner foil in the PET segment. Another interesting development is represented by pre-glued sleeve labels. Special selfadhesive labels offer many customisation options. The self-adhesive label is removed in the bottle washer, and then the container can be refilled and labelled anew. Individual solutions thanks to direct printing This trend is also in line with direct printing. It can be applied almost anywhere and provides highly customised solutions. It is all a matter of chemistry between ink and container material. “The print quality of direct printing is getting better all the time, and the speed is increasingly faster,” according to Richter. In addition to the general trend to reduce packaging material and toward increased sustainability, the market is also changing in the area of labelling and design technology. “The trend toward individual bottle design is continuing and will grow even more,” Prof. Matthias Niemeyer, CEO of KHS AG, stated and emphasised direct printing Labelling and equipment technology can sometimes be the cause of tension between marketing experts, designers, paper and foil manufacturers as well as technicians in bottling plants. Their individual demands are not always congruent, but they must be brought together if the desired result is to be achieved. If one element is lacking, the others cannot succeed, and vice versa. The reason is that a label is the “brand ambassador” at the point of sales. The digital Krones DecoType ink-jet system applies ink in a direct-print method onto the bottle. This enables the realisation of structures which could not be processed before. The UV inks directly printed onto each individual bottle have a good opacity and brilliance and are set on the containers within a few milliseconds.","@ID":36}, "PETplanet Insider Vol. 18 No. 04/17 petpla.net 63 TRADE SHOW REVIEW Another presentation targeted the Russian PET film and sheets industry. Marsel Khanukaev, Commercial Director of SafPlast said that the annual growth rate in this area was about 6%, meaning particularly that PET-G films has seen difficult times, whereas PET-A films have clearly increased. At 55%, SafPlast holds pole position in the manufacture of PET films, followed by Lada-List with 29%. PET projects Two talks threw light on current major projects in the PET field. Askhat Battalov, Managing Director of SafPet explained the current status of the planned PET and PTA production in Tartastan. The large plant for there should, according to today’s planning, be in operation by the third quarter of 2019 and by 2020 be running at full capacity (210,000t/a PTA; 250.000t/a PET). Bottle-, food- and fibre-grade PET as well as PTA will be produced by the petrochemical company Nizhnekamskneftekhim and with Taneco as the supplier of raw materials. The Russian market should thus be independent of imports, in particular from China, as the on-site production brings with it logistical advantages. According to the current status, all planning has been completed and licence agreements signed. Federal approval for construction is still awaited but the project is under way. 70km away from the former Russian textile centre, Ivanovo, a new PET production factory is being built. Igor Sabaev, Commercial Director of Polyester Plant Ivanovo spoke about the current state of play of the greenfield project. Contractual talks are coming to an end and 550 new jobs should be created. The polyester fibres produced there should cover the high demand from the growing home market, for which the import level lies at 60%. The factory’s capacity should be around 175,000t and start in 2020. Technologies Other presentations on the day were concerned with technologies. Stefan Bartz, Vice President Sales at Uhde Inventa-Fischer explained the cost advantages which can develop for polyester producers from using the 2-reactor mega-scale polycondensation technology. According to Bartz their technology offers a determining factor for reducing the producers’ high pressure from costs. Drying solutions for PET treatment were presented by Pavel Andrushchuk, Eurasia Head of Sales, Moretto. Using the Moretto drying system, particular mention was made of a homogenous material flow through the hopper at constant speed, to guarantee the same amount of air and heat for each granule. This should also prevent faults in the product from over-dried granules. Viacheslaw Maschke, Area Sales Manager for Nordson BKG introduced the system solution in underwater pelletising. The company’s fully continuous CrystallCut process is said to provide substantial energy savings in comparison with standard PET polymerisation systems by using the thermal energy of the molten polymer in PET pelletising for subsequent crystallisation. The CrystallCut system integrates underwater pelletising, drying, water filtration and direct crystallising and can be used for the recycling of PET as well. Granulating virgin PET with direct crystallisation technology was the theme of the presentation from Ralf Herbert, Sales Manager at Maag Automatik. In particular he introduced their underwater pelletising system, Sphero, with its components for the entire process from plastic melt to the finished pellet, with special mention of the latest generation of gear driven pumps and the thought-through designs for the “moulds”. Conclusion The economic situation in Russia is seeing a turn-around in the areas of stability and growth and also offers prospects for the PET industry. Fibres and film are clearly important but the food packaging area is the main sales market for PET. There is a temporary lull in the filling of beer into PET – traditionally a market for large PET bottles in Russia. Following the hotlydiscussed plan from the government, to ban the filling of alcoholic drinks over 0.5l into PET, at the start of the year a compromise solution came into force. According to this, pack sizes in PET up to 1.5l can be used for filling low alcohol drinks, at least initially. www.creonenergy.ru","@ID":65}, "PACKAGING / PALLETISING PETplanet Insider Vol. 18 No. 04/17 petpla.net 38 The legacy of innkeeper Josef Mohr The origins of the Mohren Brewery lie in the Vorarlberg region in 1784: in that year a certain Josef Mohr opened a brewery restaurant in the Austrian town of Dornbirn. 50 years later, Franz-Anton Huber bought the business, including its hop garden. The water for brewing came from the hills around Ebnit, the mountainous area of Dornbirn, which bordered a protected nature area. Twelve types of beer are brewed in accordance with the German Purity Law – in addition to the fashionable “Pfiff” there were also natural types like unfiltered cellar beer, bock beer and Munich-type beer but also trendy beer mix drinks (also available in the unbreakable PET bottle) and a particular speciality, the fruity “Pale Ale“. In addition, the business offers numerous refreshing drinks as well as wine and various international beers. The business employs about 120 staff today and over a year produces more than 220,000 hectolitres of drinks. By comparison, in the foundation year under the leadership of Josef Mohr, the modest quantity of “300 pails” was supplied. Compact mechatronic Movigear units move the massive modular belts both in and out. (Photo: SEW-Eurodrive) nik. In total, the Vorarlberg drinks producer has been in the forefront of computer-controlled processes in many areas of production. This delight in innovation has almost become a tradition in this family business: as early as the mid1980s the brewery developed and patented its own automated beer cask change-over machine for the dispensers in restaurants. www.sew-eurodrive.de A bevel-wheel geared motor with integrated encoder moves the centring frame, which fixes the drinks crates during filling and centres the bottles on the box compartments. Head brewer Ralf Freitag (photo: SEW-Eurodrive)","@ID":40}, "BOTTLE MAKING 31 PETplanet Insider Vol. 18 Please order your copy at the PETplanet Insider book shop: petpla.net/book3 Stretch Blow Molding Second Edition by Ottmar Brandau € 130,00 320 pages © Copyright Elsevier 2012 molecules are long and entangled, however, the amorphous state can be ‘frozen in’ by rapidly cooling the PET melt. Crystallisation can occur at any temperature at which the polymer chains have sufficient mobility to rearrange themselves. The rate of crystallisation is a function of the temperature, the IV of the polymer, and any co-monomer content. Very rarely, polymers are able to crystallise completely. The temperature range for crystallisation is between the glass transition temperature (Tg) and the melt temperature (Tm). Below Tg, the resin is described as being “glassy,” because the mobility of the polymer chains is greatly reduced and is essentially locked in place irrespective of whether they are in an amorphous or crystalline state. Above Tm, the polymer chains have too much energy to form stable ordered structures, and the molten resin is amorphous. Between Tg and Tm, the polymer chains have enough energy to rearrange themselves into the most thermodynamically favoured structure, so the resin crystallises. Thermally induced crystals are arranged in structures called “spherulites,” since they start from a point source (nucleation site) and grow, radiating outward, in a spherical pattern. This must be avoided since the crystallised regions cause haze, destroying the clarity of the preform, and prevent proper stretch-blow moulding. The mould cooling becomes essential and determines the quality of the preform at this stage. An increase in IV reduces the rate of crystallisation by lengthening the polymer chains, making it more difficult for a given chain to disentangle itself from other chains and form an ordered crystal. Copolymer content changes the molecular structure of the chains, inhibiting crystallisation by essentially introducing a unit into the chain which may not easily form crystals due to structural differences, or disrupts the crystalline pattern.","@ID":33}, "TRADE SHOW PREVIEW PETplanet Insider Vol. 18 No. 04/17 petpla.net 53 Layer preparation for single packages offers flexibility for palletisation systems Simplifying the handling of difficult packages Gea will be showing its Polaris F layer preparation for single packages, built around an anthropomorphic robot. Polaris F represents a consolidated solution specifically designed to simplify palletisation systems for the beverage, food, dairy, bakery and pharma industries. It is said to offer advantages in terms of total cost of ownership. Smooth handling and switching With variable speed operation, the Polaris F layer preparation system flexibly handles single packs, with a dedicated gripping head, and prepares an entire layer of product for palletisation. Polaris F automatically rotates and moves the packs on a preparation table so that they can be prepared in a smooth, gentle way. The gentle movement allows a wide range of complicated and unstable packs to be handled simply and efficiently in a continuous process without any interruption in the preparation of each layer. Products can be switched quickly and easily without the need for any mechanical intervention. Simplifying the handling of difficult packages Polaris F has been developed by Gea to work with its Omnia palletising and de-palletising system. The use of the anthropomorphic industrial robot gives the Omnia system flexibility allowing it to comply with a wide range of different requirements and simplify the handling of difficult packages. It can operate at variable production speeds, up to medium capacity, to suit the application and be equipped with a range of accessories such as gripping heads for loose containers or for palletising single rows or complete layers of packed product. The system also inserts an interlayer divider as part of the process. The Omnia anthropomorphic industrial robot features include simultaneous palletisation from multiple lines; simultaneous palletisation of packages of different types and dimensions; simultaneous palletisation and de-palletisations; fast gripping and automatic head change for east product switchover, as well as small footprint to optimise the use of floor space. Omnia is available with a range of gripping heads to meet the needs of each application. This allows the system to be easily adapted to handle different sizes of loose bottles up to five gallon capacity and shrink-wrap packs, cartons and crates, loose jars and cans. There is also a magnetic head for handling canned goods. Market needs No two applications are the same so Gea uses its engineering know-how to design systems that match precisely each customer’s needs. This has allowed Gea to meet the growing trend for the palletisation and de-palletisation of aseptic beverages and powder products that are growing in popularity worldwide. For example Gea has recently installed a high-speed aseptic filling line equipped with Polaris F in the Middle East and a new packaging system for dairy powder containers in Latin America. Total cost of ownership (TCO) is a key factor in any cost/benefit analysis. Gea has brought together its many years of experience and the skills of its engineers to create a palletisation and de-palletisation system that provides true cost benefits over time. The company has achieved this through a process of continual improvement that has minimised the footprint of the equipment thereby releasing free space within the plant for other uses, reduced energy consumption, and made its equipment as easy as possible to operate and maintain. Combined, these factors provide the user with advantages in terms of TCO and a fast return on investment. www.gea.com Themed “Packed with Inspiration”, the Gea stand will demonstrate engineering solutions for the packaging and processing industries. The company will be exhibiting beyond the food package industry and displaying process equipment, solutions and services for the beverage, bakery, confectionery, dairy and pharma sectors. Polaris F represents a consolidated solution to simplify palletisation systems. Hall 7a - Booth B09/B31","@ID":55}, "47 TRADE SHOW PREVIEW PETplanet Insider Vol. 18 No. 04/17 petpla.net 100% chemical free packaging sterilisation Claranor is this year showcasing the latest chemical-free developments to sterilise packaging. Two systems have been designed with the beverage industry in mind. The first is the Claranor Essential, a very compact and cost-attractive cap sterilisation solution, designed for low and medium speed lines. The second is the Full cap sterilisation, a solution to address the cross-contamination issue for the ESL products ( 60 days). The Puls’Combi FS, which is a combined decontamination of cups and lids, is specifically for the dairy industry. On the Claranor’s booth, visitors will have the opportunity to see two cup sterilisers already sold to dairies in France (four lanes) and in Turkey (12 lanes), to be installed on Doselec filling lines. The compactness of the unit makes it easy to integrate on an existing line. Using no water and no chemicals, the decontamination solutions meet the expectations of the industry in terms of germicidal effects without the drawbacks of chemical and the irradiation solutions. With over 250 production lines equipped worldwide, pulsed light solutions for caps, preforms, cups and lid sterilisers are now acknowledged by the major food and beverage companies as well as the main equipment manufacturers. This exhibition is intended to offer opportunities for food and beverage manufacturers as well as for OEMs to discuss their packaging sterilisation projects with Claranor and Löhrke, its exclusive distributor in Germany. www.claranor.com Claranor Hall 13 - Booth A37","@ID":49}, "TRADE SHOW PREVIEW PETplanet Insider Vol. 18 No. 04/17 petpla.net 61 Tour Sponsors: From preform design to bottle blowing – Andy, Chairman of Demark Holding, talks to PETplanet about his company’s past and future projects Entrepreneur with a vision by Alexander Büchler There are still young entrepreneurs who, with fresh ideas and vision, can transform a small machine manufacturing business into a major international company and then grow it over the decades. The PET industry counts a number of such people in its ranks. Amongst this cohort of entrepreneurs, mention must be made of Robert Schad, who turned Husky into a major player, Franco Zoppas, who developed Sipa into a full service provider or Volker Kronseder, who made Krones a market leader. In China we have discovered someone else, who - we believe - may come to be mentioned in the same breath as these pioneers: Andy. Just Andy, nothing else. 13 years ago Andy set up Demark China, with the vision of becoming a high-tech provider of tools and machines for the PET industry. Even more, he aimed to offer the full range from preforms via bottles to the closing device. The thirty five year old is now sitting opposite me. He has invited me to join him in the traditional Chinese tea ceremony to talk about how the company developed. His first job was working for his uncle. The company manufactured manual blowing machines. It was quickly clear to Andy that the future lay elsewhere and this prompted him to set up his own company. In 2001 China joined the WTO and western machines came into China. Andy learned a lot from these foreign-made machines and began to build his own. For him, automation is key. And similarly, a full and clear commitment to the two-stage process. Moulds and rotary blowing machines came next, in 2008. The 10-cavity machine was capable of 16.000b/h. At the time, he restricted himself to 48-cavity preform moulds. Today, the blow-moulding machine runs at 1,900 b/h/cavity with 16 cavities. In the preform area, his machines can accommodate moulds of up to 128 cavities. He produces his own moulds, and has cooperated with MHT at the China Brew and Beverage exhibition. The preformline was running at 128 cavities with an MHT tool. Two robots handle the removal stage. The first takes the preform out of the mould and the second one is responsible for cooling. His clients can now choose either the Demark moulds or in the higher cavities area, the MHT mould. “The fact that we offer European tools on our machines should create confidence in our technology,” is how Andy explains this rather unusual step. 60% of sales are exported. Andy assesses the inland market currently as quiet. However, he sees the current situation has a good side to it as well: “The market needs times like these, so that weak companies disappear from the market and the strong ones will come out of it stronger”. Andy is investing further in his production. Next year he would like to acquire another factory with a production surface area of 20,000m² for moulds, 30,000m² for injection moulding machines and 15,000m² for stretch-blow moulding machines. In order to strengthen sales, he is building up a Sales and Service network in various countries. Initially he is restricting himself to the rapidly growing markets in Asia, Africa and South America. He is excluding the industrialised nations from his strategy. In answer to my question as to what we will be talking about were we to meet in ten years’ time, he does not hesitate: “Well, obviously about moulds, preform machines and stretch-blow machines”. A man who not only possesses vision but also staying power. www.demark-pet.com Booth 9.1 R41 Andy, Chairman of Demark Holding","@ID":63}, "PETplanet Insider Vol. 18 No. 04/17 petpla.net 70 PETbottles Home + Personal Care Scented washing pearls from Aldi The German discount chain Aldi has brought its own brand “Tandil” scented washing pearls onto its shelves. The washing pearls, offered in scent varieties “Purple Lotus”, “Aqua Touch” and “Sunshine Moments” and the wording “Tandil Premium Scent”, are put directly into the washing machine drum before washing. A particular dosage is recommended but which the user can individualise – depending on the scent level wanted. 480 grams of the granular product are packed into a tapered, clear bottle which is decorated with a sleeve label. A transparent, slightly coloured dosing cap is placed over the metallic shiny screw cap. www.aldi-sued.de 5 in 1 shower gel for after sport L’Oréal has expanded its Men Expert shower gel range with a “5 in 1” shower gel, which is specially designed for a sportsperson’s needs. The Camphor Shower Gel After Sport – Vitalising is said to clean and be perfectly gentle on the body, face and hair, have a soothing effect and revitalise the body. 300ml of the citrus-scented product are filled into a yellow-ish coloured upside-down bottle. It is closed using a two-coloured closing device. The hinged area to be opened is in a contrasting colour. Transparent, self-adhesive labels explain how to use the shower gel and its advantages. www.menexpert.de Sponsors January – July 2017 The worldwide round trip with Go with the flow. South East Asia Road Show Cambodia Laos Thailand Indonesia Vietnam Malaysia Singapore Follow us on blog.drinktec.com powered by asia.petpla.net 2017 is Drinktec year! All over the world, the beverage and liquid food industry is preparing for the next edition of the great event, held once again in Germany. A new year also means a new road show - and a very special one. PETplanet is again partnering with Drinktec and we will be bringing our crew to South East Asia, under our new slogan: Go with the flow – South East Asia Road Show. From the end of January our editors Kay Barton and Alexander Büchler, along with “Flowy“, the Drinktec mascot, will be investigating the latest market-specific characteristics of distant countries as well as following well-trodden oaths, as always. With various “Editourmobil” vans we will travel to Thailand, Vietnam, Cambodia, Malaysia, Singapore and Indonesia. As our valued reader, you will once again get insider information and insights from the PET beverage and supplier industries, published regularly in PETplanet Insider. You can get even closer to the Tour experience by following us live on our travel blog at asia.petpla.net. Drinktec awaits us at journey‘s end. When we get there we will be presenting factsheets and product samples of all the companies we visited. We hope you enjoy “keeping up with the PETplanetarians“. We look forward to welcoming you on board once again!","@ID":72}, "9 NEWS PETplanet Insider Vol. 18 No. 04/17 petpla.net Bottle alliance to develop 100% bio-based bottles Danone and Nestlé Waters have joined forces with Origin Materials, a startup based in Sacramento, California, USA, to form the NaturALL Bottle Alliance. Together, the three partners aim to develop and launch at commercial scale a PET plastic bottle made from bio-based material, i.e. 100% sustainable and renewable resources. The project uses biomass feedstocks, such as previously used cardboard and sawdust, so it does not divert resources or land from food production for human or animal consumption. “Our goal is to establish a circular economy for packaging by sourcing sustainable materials and creating a second life for all plastics,” declared Frédéric Jouin, head of R&D for plastic materials at Danone. “We believe it’s possible to replace traditional fossil materials with biobased packaging materials. By teaming up and bringing together our complementary expertise and resources, the Alliance can move faster in developing 100% renewable and recyclable PET plastic at commercial scale.” Danone and Nestlé Waters are providing expertise and teams, as well as financial support, to help Origin Materials make this technology available to the entire food and beverage industry in record time. This next-generation PET is intended to be as light in weight, transparent, recyclable and protective of the product as virgin PET. The exclusive use of renewable feedstocks which do not divert resources or land from food production is the Alliance’s main focus area. The R&D will focus initially on cardboard, sawdust and wood chips but other biomass materials, such as rice hulls, straw and agricultural residue could be explored. “Current technology on the market makes it possible to have 30% bio-PET,” noted John Bissell, Chief Executive Officer of Origin Materials. “Our breakthrough technology aims to reach 100% bio-based bottles at commercial scale. With the help of our Alliance partners, Origin Materials will be able to scale up a technology which has already been proven at the pilot level.” The NaturALL Bottle Alliance partners consider that everyone should benefit from this new material, so the technology will be accessible for the entire beverage industry. This unique approach demonstrates the allies’ commitment to open innovation and sustainable business. Origin Materials has already produced samples of 80% bio-based PET in its pilot plant in Sacramento. Construction of a “pioneer plant” will begin in 2017, with production of the first samples of 60+% bio-based PET to start in 2018. The initial volume goal for this first step is to bring 5,000 metric tons of bio-based PET to the market. Thanks to their complementary skills and shared vision, the NaturALL BottleAlliance aims to develop the process for producing at least 75% bio-based PET plastic bottles at commercial scale as early as in 2020, scaling up to 95% in 2022. The partners will continue to conduct research to increase the level of bio-based content, with the objective of reaching 100%. www.danone.com www.nestle-waters.com www.originmaterials.com Chinaplas 2018 on the move After year-long evaluation and analysis, Adsale Exhibition Services Ltd. has decided that Chinaplas 2018 will move to a new venue – the National Exhibition and Convention Center (NECC) in Hongqiao district, Shanghai. Chinaplas 2018 is confirmed to take place at NECC from April 24-27. Growing hand in hand with the Chinese plastics industry, the trade show has kept on expanding in recent years, from 180,000m2 of total exhibition area and 2,400+ exhibitors in 2011 to an estimated 250,000m2 and 3,300+ exhibitors in 2017. “We really ran out of space in Shanghai New International Exhibition Center (SNIEC),” said Ada Leung, General Manager of Adsale. “Evaluation and analysis on moving to NECC began in early 2016, and considering the long term development of the show, we made the decision in the fourth quarter,” she explained. SNIEC had been a very good venue for Chinaplas, Ada said, but all the indoor halls were fully occupied in each edition in Shanghai since 2012. More and more outdoor tents and exhibition suites were built to cater for the space demand. That was not the most convenient solution for exhibitors and visitors, especially when the rain comes, Leung admitted. Show scale to reach 300,000m2 Opened in 2015, NECC offers 400,000m2 of indoor exhibition space and 100,000m2 of outdoor display areas. Despite a much bigger capacity, Leung said the expansion of Chinaplas 2018 will be done in a well-planned and controlled manner. The targeted exhibition space is 300,000m2. Exhibitors have already been informed of the news and many of them were excited about the move, Leung said, noting that prolonged move-in and move-out time will be provided to help exhibitors adapt to the new venue. Chinaplas will continue to alternate between Guangzhou and Shanghai. This year, the show will take place from May 16-19 in Guangzhou, China. www.adsalecprj.com","@ID":11}, "PETcontents 04/17 4 PETplanet Insider Vol. 18 No. 04/17 petpla.net Page 70 Page 20 INSIDE TRACK 3 Editorial 4 Contents 6 News 66 Products 68 PET bottles for Beverage + Liquid Food 70 PET bottles for Home + Personal Care 72 Patents GO WITH THE FLOW SOUTH EAST ASIA ROAD SHOW 10 Indonesia - The underestimated islands 13 From pellet to shelf MATERIAL / RECYCLING 14 UK to block bottle deposit proposal? 16 Opening up a new market - Food grade pellets from Egypt 17 25 bottles make a door PREFORM PRODUCTION 18 PET container for cold drinks BOTTLE MAKING 19 PET to push away the competitors 29 Material basics - Strech Blow Moulding, part 2 32 Hotrunner components KEG SPECIAL 20 Sell and forget keg - Disposable PET kegs - an overview 25 Italian-made PET kegs BOTTLING / FILLING 26 White revolution - India’s dairy industry grows with PET LABELLING 34 Breakthrough in direct printing? Trends in labelling and equipment technology PACKAGING / PALLETISING 36 One machine does it all MARKET SURVEY 40 Palletising and shrink film machinery TRADE SHOW PREVIEW 42 Interpack 2017 50 Industrial waste and post-consumer recycling 52 Safely capped - Closure solutions for product protection 53 Simplifying the handling of difficult packages 54 On-trend beverage compositions 56 Chinaplas 2017 61 Entrepreneur with a vision TRADE SHOW REVIEW 62 Bottles remain the key to Russian PET industry 64 Opportunities and challenges of PET packaging BUYER’S GUIDE 73 Get listed! Page 13","@ID":6}, "59 TRADE SHOW PREVIEW PETplanet Insider Vol. 18 No. 04/17 petpla.net Varioline #GermanBlingBling #Varioline We do more. interpack 2017 Düsseldorf, 4 – 10 May Hall 14, Stand E33 Efficiency in post-consumer recycling Erema will have an Intarema TVEplus 1108 with Laserfilter live in action. This combination enables the highly efficient recycling of heavily contaminated materials with different bulk densities. These range from film to regrind with cellulose contaminants such as paper, rubber or silicones which is processed to make high-quality recyclates. Post-consumer material, especially household packaging waste, was previously considered to be plastic which is difficult to recycle due to the fluctuations in quality of the materials, including for example the type of contaminant and the respective different degree of contamination. Erema developed the Intarema TVEplus system especially for this type of plastics processing which, with a market share of over 80% in Europe, has managed to gain a clear edge over its competitors. Manfred Hackl, CEO of the Erema Group, explains the benefits of the interplay of the TVEplus with the Laserfilter as follows: “This unique combination is particularly suitable for material with a high degree of contamination when conventional melt filters are no longer able to deliver the necessary cleaning efficiency. The Intarema TVEplus and Laserfilter open up new sales markets for our customers in the post-consumer sector for their high-quality recyclates and products.” James Qiu, CEO of Erema China, is convinced that the potential of plastics recycling in China can be tapped even further: “The amount of unwashed scrap film with paper labels, for example from commercial waste, HDPE from household waste or WEEE waste in China is high. Current developments in terms of increased investment in the expansion of sorting and collection systems are also encouraging. With regard to cost-effectiveness and sustainability it makes sense – parallel to this – to use high-performance recycling technologies which can make valuable secondary raw material, i.e. recyclates, even out of heavily contaminated input.” www.erema.com Hall 9.2 - Booth A41","@ID":61}, "67 PRODUCTS PETplanet Insider Vol. 18 No. 04/17 petpla.net Forced feed granulators For the grinding of PET bottles, Herbold’s SBGranulators with forced feeding are available for capacities of 500 to 10,000kg/hr, depending on machine size and screen size. In comparison with standard gravity feed granulators, Herbold sees the advantages of their SB-Granulators with forced feeding in that fewer fines are created during size reduction because bottles are not bouncing on top of the rotor and that the positive feeding into the cutting chamber ensures minimum dwell time in the cutting zone. In addition, the granulators possess 30-50% more capacity compared to standard gravity feed machines and smaller machines can be used for the same amount of material, according to the company. That the forced feeder is a buffer helps to balance uneven feed, for example from a sorting line. Depending on customer requirements, dry or wet grinding operation is possible. Design features: double cross cutting action: the machine cuts like a scissor, because rotor and stator blades are both inclined, in opposite direction. outboard bearing arrangement: no fines can enter the bearings, no grease can contaminate the flakes. hydraulic opening device for easy access. pre-adjustment of the blades outside of the machine in a jig to reduce downtime to a minimum, because spare blades can be adjusted while the machine is still in operation. The machines are equipped with a standard wear protection package: all inner areas affected can be replaced, because there are bolted wear plates fitted. Also rotors with replaceable, bolted blade supports are available, so there is no need to take out the rotor for refurbishment. Wet grinding is the preferred way to handle size reduction of post-consumer PET bottles: the friction created during the cutting process helps to release the contamination from the surface of the bottles. In wet operation, a higher lifetime of the blades can be expected than with dry grinding. www.herbold.com RECYCLING LINE recoSTAR PET iV+ l l l consumer bags textile packaging recycling Visit us at: Interpack Düsseldorf, May 4 – 10, Hall 11, Booth C20 Chinaplas Guangzhou, May 16 – 19, Hall 9.2, Booth C41 drinktec Munich, September 11 – 15, Hall A4, Booth 520 Recycling at the highest level, substituting virgin resin at up to 100% in various types of food packaging. 6WDUOLQJHU +HDG 2IßFH Sonnenuhrgasse 4, A 1060 Vienna 7 ) [email protected] www.recycling.starlinger.com A member of Starlinger Group rECO EXCELLENT food grade rPET PELLETS","@ID":69}, "BOTTLE MAKING 19 PETplanet Insider Vol. 18 No. 04/17 petpla.net Blown handle application for different sizes of PET containers PET to push away the competitors Following a strategy to expand PET into high technical demanding market and niche products, during 2016 the companies have dedicated significant resources to expand PET containers in the areas of stackable and mediumlarge size handed bottles. Based on the joint experience to develop stackable containers and handed bottles with the handle applied along the vertical parting line of the blow cavity, the engineers have pushed PET material and process boundaries enabling PET to replace other substrates such as metal or HDPE. The HDPE jerry can is relatively standardised with horizontal handle feature as well as stackability from medium to large size. Dethapak, who owns the intellectual property rights, in collaboration with IPC, has designed and developed the new bottle concept combining the style and the targeted performance and sampled a 10l container thanks to the Lanfranchi unit cavity blow moulder which has been updated with the handle implementation module. IPC, Lanfranchi and Dethapack have successfully converted these containers into PET and have produced bottles with a horizontal incorporated handle that can stack one up the other 3-4 levels depending on the volume of the container. The handle application is produced while blowing. This is a remarkable development in this project because the handle was horizontally applied into the blowing cavity just before the blow mould closing so that PET encapsulates the handle while forming the container. In other more common applications, the handle is applied vertically along the blow cavity parting line with the anchoring points that are almost parallel to the preform. This module opens and closes synchronised with the blow mould cycle and it has been designed as a separate entity of the blow mould activated by pneumatic cylinder and a spring for the closing action. The container was tested in Lanfranchi’s laboratory and specific tests have been developed to verify the specification and legal requirements even for the transportation of dangerous products according to the EU instructions. The newly designed preform as well as the container and the blow mould features are patent pending. To complete the scenario, Lanfranchi gives a high flexible way to produce containers with a wide range of handle application. For example Lanfranchi’s linear blow moulder can produce round bottles, square bottles or oval bottles with a handle applied vertically along the parting line of the blow mould. The evolution of systems completes the range of applications with a container handed horizontally. www.lanfranchi.it IPC and Lanfranchi have just celebrated their first anniversary of collaboration, as pioneers of new developments in the PET packaging sector. In close cooperation with Dethapak, they have launched a new packaging that fully replaces the metal or HDPE jerry can and its main features. The main features of the container are the robust handle encapsulation and the stackability. The new container is handed horizontally in the upper part of the container and a special module of the blow mould has been designed to reach this target.","@ID":21}, "49 TRADE SHOW PREVIEW PETplanet Insider Vol. 18 No. 04/17 petpla.net Nissei ASB to demonstrate one-step ISBM cosmetic container moulding Nissei ASB Machine Co., Ltd., manufacturer of PET and plastic bottle stretch blow moulding machines, will be conducting daily live moulding demonstration of its ASB-12M model, the latest iteration of the smallest class of machines produced by the company, that can trace their ancestry back to the early 1980s. Despite the small size of the machine, it has a vast range of capabilities for production of all types of PET containers including efficient light-weight bottles, all the way through to premium brand heavy-weight cosmetic containers of the highest quality. The ASB-12M’s popularity is further enhanced by its ability to process a wide range of non-PET resins combined with very low total cost of ownership. Key features include: ability to process more than 15 resin types in addition to PET moulds containers from 5ml or less up to 2,500ml capacity variable cavitation from 15mm neck diameter eye drop bottles in eight cavities through to 83mm neck diameter jars in a single cavity servo driven hydraulic pumps installed as standard, contributing to major energy savings and offering smooth and quiet operation backwardly compatible with existing class mould tooling with minimal modifications small size allows fast mould changeovers will minimal manpower, and minimal / no special lifting equipment In addition, the model displayed on-site will be fitted with the optional long stroke injection unit that provides a 50% increases in available shot-size, expanding the scope for large containers, heavy-weight cosmetic bottles, or materials such as polypropylene that have lower density. All of these benefits make it an ideal platform for a start-up company looking to make future-proof investments in an ever-changing market. ASB-12M with its full featured specification also makes an ideal laboratory machine for R&D work and pilot moulding before committing to much larger multicavity systems for major projects. At the show, the machine will be demonstrated moulding a 100ml thick walled cosmetic type bottle in four cavities with a substantially improved production rate. www.nisseiasb.co.jp Nissei Hall 11 - Booth D40","@ID":51}, "BOTTLE MAKING 29 PETplanet Insider Vol. 18 No. 04/17 petpla.net Stretch Blow Molding, part 2 Material Basics by Ottmar Brandau Ottmar Brandau has newly revised his book “Stretch Blow Molding”, first published by hbmedia / PETplanet Publisher, and now re-issued in a second edition under the Elsevier imprint. PETplanet Insider is publishing extracts from successive chapters in a series of articles. weights or chain lengths. As far as end users are concerned, the result is that the chemical structure of a grade of PET can be described by only two measures: IV (intrinsic viscosity), which is a measure of molecular weight, and the co-polymer content. In contrast, a polymer such as polyethylene can have unique molecular weight distributions and widely varying degrees and types of branching, which affect processing and performance profoundly. Intrinsic Viscosity The properties of the PET polymer are largely dependent upon the average molecular weight or the average number of repeat units of the polymer chains. This is usually determined by the measurement of intrinsic viscosity (IV). The relationship between molecular weight and IV is fairly linear. High IV PET has a higher molecular weight than low IV PET. The longer chains give the resin better properties in the final product and also affect the processing in predictable ways. IVs used for PET bottle manufacturing are in the range of about 0.73–0.86. Co-polymer Content PET co-polymers are made by replacing a few percent of one of the starting components with a different monomer. Eastman uses CHDM (cyclohexane dimethanol) to replace part of the DEG. Most other resin manufacturers use IPA (Isophthalic Acid), which is also called PIA (puriManufacture of PET There are a few chemical routes to manufacturing PET. A compound with two acids, such as terephthalic acid (TPA), is esterified with a compound with two alcohols, such as ethylene glycol (EG) (see fig. 2.2). Since there are two functional groups on each component, they can continue to link up to form long chains. Water is a by-product of this process. This esterification reaction is reversible, and this is the key to understanding much of the behaviour of PET. Commercially, the polymerisation is done in two stages. Melt-phase condensation results in molten polymer with about 100 repeat units (intrinsic viscosity, as explained below, is about 0.6). The melt is pelletised and can be used for some applications such as fibre production at this point. To continue the polymerisation, a process called “solid stating” is used. Solid stating produces high-molecularweight PET needed for fabricating bottles. Catalysts Different catalysts are required for the two main chemical routes to manufacture PET. Special catalyst combinations can be used to influence the side reactions, to reduce he amount of diethylene glycol or allyl alcohol, or to improve the colour. Since the catalyst residues remain in the PET, they are still present during drying and processing. Therefore, different grades of PET from different manufacturers react differently if not processed at optimum conditions. For example, the DMT process (used chiefly by Eastman) requires an additional catalyst, which may result in a greater tendency for the resin to oxidise or ‘yellow’ when over-dried. PET is a Linear Condensation Polymer PET does not branch: each molecule is a long “linear” chain. In addition, because it is formed by a reversible condensation reaction, it has a very simple distribution of molecular","@ID":31}, "TRADE SHOW PREVIEW PETplanet Insider Vol. 18 No. 04/17 petpla.net 52 Closure solutions for product protection Safely capped Depending on the area of use, closures must not only ensure that the container is closed and tightly sealed, but also protect its contents against product piracy whilst complying with high official technical safety standards. On that note, on over the more than 180m² of its stand, the global manufacturer of plastic closures Bericap will be showcasing new packaging, alongside advances in its tried-and-tested closure solutions. A new development showcased at the Bericap booth is the e-smoCap, a childproof closure that makes it easier to refill e-cigarettes. The closure has ISO 8317 CRC certification from the Laboratoire National d’Essais, which is supervised by the French government. A sealing strip ensures that it is tamper-proof, thus providing protection and security for end consumers. There is a long, narrow drip nozzle inside the closure for easy refills. It is also possible to conceive of other applications for this product in which precision dosing is of paramount importance. Protection against product piracy Product piracy and the accompanying product counterfeiting are sensitive problems when it comes to chemicals of high value. In order to protect refills from being adulterated or tampered with, all closures have a folded and slit tamper evidence band (TE) which is difficult to manipulate and provides visual evidence in the form of broken bridges if the closure has been opened. Other safety options are customerspecific closure designs, possibly complemented by an additional security label fixed across the closure body and TE band, or the use of laser technology enabling, for example, the company name to be lasered across the TE band and closure, even on uneven surfaces. Bericap has further developed a special counterfeit protection system using a laser print where e.g. a logo can be printed on the side of the closure. Also on uneven surfaces. As soon as the closure is opened, the security strip breaks and the logo is “destroyed”, making it obvious that the bottle has already been opened. Closure with side laser print for counterfeit protection Closures for beverages Bericap will be introducing types of closure that are intended to surpass the usual standards. Examples include closures that combine the desire for consumer satisfaction – such as good grip – with optimised material usage. This is particularly true for closures for aseptic fill and hot fill applications. New closures for the carbonated beverage market will be presented as well. When it comes to closures for still water, the emphasis in the past has been on reducing the weight. Cost savings and an improved carbon footprint were a priority, whilst consumer convenience has been neglected so far. Developing new closures for a new light 29/25 or 26/22 PET neck resulted in weight savings for closure and neck of 33% compared to their predecessors. However, the new closures were low in (grip) height – only 11 and 10.5mm – making it awkward for the consumer to open the closures. As a consequence Bericap developed closures for the 26mm and 29mm PET neck which are higher and allow convenient opening due to a good grip height. In addition, the lightweight necks were maintained and the little added weight to achieve a higher closure was insignificant. The new caps are virtually the same weight but look more substantial and are now easier for customers to handle. All HexaLite closures have a cut and folded TE band rip that breaks easily the first time the bottle is opened. N2 dosing is feasible.The 29/25 and 26/22 neck types are approved by CETIE. HexaLite 26/13 SFB 3T featuring greater grip height for easier handling A 2-piece closure, allowing a 2-colour look with a transparent PP shell and a coloured HDPE pourer section has been developed for sports drinks. Thumb’Up Crystal is designed with a tear strip, offering tamper evidence functionality for the over-cap, but will also be available in bridgeonly form. The reactive Double Galileo hinge allows an opening angle of 180°, so that the over-cap no longer comes into contact with the cheeks. The hinge is compliant with BSDA safety standards, available for the PCO 1881 and the 29/25 neck. www.bericap.com Hall 10 - Booth E67 e-smoCap closure for refilling e-cigarettes","@ID":54}, "TRADE SHOW REVIEW PETplanet Insider Vol. 18 No. 04/17 petpla.net 62 Helen McGeough, Consultant of PCI Wood Mackenzie, opened proceedings with an overview of the worldwide PET market. According to her presentation, PET resin consumption worldwide is expected to grow in all regions with a growth at the end of 2016 of 4.7% compared to the previous year and an expected growth in 2017 of 5.3%. The highest proportion is in bottle-grade resins for water bottles, CSD and other beverage applications. The fact that in addition to a low oil price and per capita also technology has an impact on the use of PET, was demonstrated by McGeough using examples from other sectors, such as an increased demand for PET for aerosols, for personal care products or - apart from bottle making - PET in sheets for wind turbines. The Asian market is the worldwide leader in PET resin consumption, in 2016, having 40% of the world’s share, with a leading position to be given in particular to the Chinese market, followed by the USA (19.4%) and the western European market with 15%. The Russian PET market Detailed numbers for the Russian market were provided by Dr Victor Kernitskiy, President of Arpet, a nonprofit partnership for development of the PET industry. In the last year, Russia has produced 534,000t of PET domestically, which corresponds to a rise of 7% compared to the previous year. In addition, there were 108,000t of imports. Although these figures relate to the entire PET market, there is particularly some growth in the bottle-grade segment, which Kernitskiy put down to a hot summer and the associated high consumption of packaged drinks and to a change in society, where the taste for alcoholic drinks is falling and the consumption of water and CSDs is rising. With an annual bottled water consumption of 39l, Russia is still a long way behind the European average of over 100l per head and offers further scope for growth. Filling beer into PET has, in the last few years, provided rich pickings for discussion. Large packs were a classic market for the Russian PET sector. After the Ministry of Natural Resources and Environment first questioned whether beer and other alcoholic drinks should be filled into PET, as a compromise solution, this has been limited since the start of the year to pack sizes of up to 1.5l. The smaller breweries in particular have found financial disadvantages in this. By contrast, Kernitskiy is expecting growth in the PET kegs area. Kernitskiy named Polief, AlcoNafta, Senezh and Sibur as major players in PET manufacture. He sees coming to grips with trends in the packaging area and further development as the most important aims for the PET industry and mentioned reducing the weight of the bottles and a higher proportion of rPET, filling dairy products into PET and driving the beer kegs market as examples. 13th conference “PET 2017” in Moscow Bottles remain the key to the Russian PET industry by Gabriele Kosmehl Part 1 On February 16 and 17, the conferences “PET 2017” and “RPET and recycled plastics 2017” were once again organised by Inventra, part of the Creon Group, in Moscow, Russia. During these annual meeting point of experts from the Russian PET industry, major trends and projects provoked lively discussion for the worldwide market and for the Russian market in particular. The latter shows a promising development for PET while there is still a lot to do as far as the recycling business is concerned. Some interesting extracts from the conference of the PET bottle industry are set out below, whilst an article on the recycling industry in Russia will follow in a forthcoming issue of PETplanet. Helen McGeough, Consultant of PCI Wood Mackenzie Dr Victor Kernitskiy, President of Arpet","@ID":64}, "BEVERAGE INGREDIENTS PETplanet Insider Vol. 18 No. 04/17 petpla.net 55 Coffee: totally different New and innovative beverage concepts that offer completely unknown taste experiences are always popular. One great current example is cold brew coffee, a trend that started in the US and is now travelling around the globe. And there are other coffee innovations, too. Coffee cherry, for instance, serves as a base for a new type of coffee indulgence called brewed coffee cherry – a light beverage with a fruity-dry note that is more like a refreshing drink than coffee. Doehler has taken these trends and developed its cold brew coffee and brewed coffee cherry concepts. Available as all-in-one solutions and as single ingredients, these enable potential consumer concepts such as ready-to-drink products and strong cold brew coffee infusions as well as coffee cherry infusions. Creativity can run riot here, and additional ideas could use these ingredients in their pure form or with additional ingredients such as natural flavours, juices, regular milk and dairy alternative ingredients made of oat, coconut, rice or almond. Multi-sensory experiences with nutritional value Less sugar, fewer animal products, but more vegetables and protein: more and more people around the world are making efforts to pursue a healthier, more sustainable and more natural lifestyle. As well as the overall multi-sensory impression, a product’s healthy nutritional values and the sources of its ingredients also need to convince the customer. That is why, when developing a product, Doehler pays attention to delivering both a unique multisensory experience and ensuring that the product contributes to a healthy diet – with optimum nutritional value. The broad spectrum here ranges from integrated solutions for vegan products to ingredients for gluten-free and dairy/ lactose-free products, to name just a few examples. Less sugar With media coverage highlighting the downsides of sugar, consumers all over the globe are looking for alternatives – and the more natural, the better. Doehler’s portfolio of classic and natural solutions allow sugar and calories to be reduced without sacrificing taste. For instance, the MultiSweet Classic range combines carefully balanced blends of high-intensity sweeteners for good taste experiences. Doehler’s expert team also utilises its vast knowledge of natural sweeteners for the calorie-free and natural MultiSweet Stevia range, as well as for MultiSweet Fruit solutions, which derive 100% of their sweetness from fruit. Enhancing the perception of sweetness is also the aim of Doehler’s MultiSense flavours. This range of natural flavours can be used to achieve sugar reduction without the need for sweeteners, as well as to mask the aftertaste of high intensity sweeteners and/or to improve the mouthfeel of reducedsugar products. In reduced-sugar carbonated soft drinks and still drinks in particular, MultiSense Flavours is intended to create a good overall multisensory impression, while MultiSense Mouthfeel delivers an extraordinary mouthfeel. Less is more: free-from Alongside sugar reduction, “free-from” products such as “dairyfree” and “gluten-free” also became increasingly popular. Doehler’s range of application-specific gluten-free malt extracts can be used to add natural taste, colour or sweetness, as well as to produce tasty gluten-free beer. Good growth is also being seen in the “lactose-free” sector, with product choices now stretching from soy and rice-based beverages to almond ice cream. With its diverse portfolio of natural, dairy-free ingredients based on almonds, rice, oats and soy, Doehler paves the way for the development of foods and beverages that are free from lactose and cows’ milk. Growing numbers of consumers are also opting for vegetarian and vegan foods. Using high-quality plant-based “green” proteins, Doehler can give vegan products added nutritional value. A carefully crafted mixture of plant-based proteins can, for example, be adapted to suit any recipe and achieve end products with sensory appeal. www.doehler.com MHT MOLD & HOTRUNNER TECHNOLOGY AG Your Machine - Our Solution 5.1 C15 QUALITY MADE IN GERMANY","@ID":57}, "48 TRADE SHOW PREVIEW PETplanet Insider Vol. 18 No. 04/17 petpla.net P.E. Labellers and Packlab to showcase a wide range of technological innovations On the booth, the labelling machine model Modular Top 112016 SMwill be on display, equipped with: a trolley with self-adhesive module 140mt, a trolley with self-adhesive module 140mt featuring an automatic joiner, a trolley with a cold glue unit and five pallets for seal application and with new up and down safety guards; equipped with a hot melt reinforcement system and finally with a multi-format grippers’ starwheels and augmented reality (a system using an iPad application that allows to “frame” the machine, monitor its operation, display alarms, signals or maintenance). The sleever Maya will also be present, available for full-body, half-body, tamper-evident and bi-pack promotional applications: a compact, powerful, versatile machine, fully customisable with accessories to meet varied marketing needs, able to pack containers, empty or full, of any shape, size and material and to work sleeves with reduced thickness compared to the standard, with a consequent reduction in the cost of rolls. Packlab will showcase the linear labelling machine Easy REP FB 40 SL, a compact model of the Wing version with full cover sliding safety guards, even at the top. It ensures reduced bulk and is as flexible as a Wing with a production speed up to 7,200pph. The Packlab labelling machines are constantly evolving in order to better satisfy customer demand. The machine is equipped with a thermal transfer printer for variable data. www.pelabellers.com Sipa to highlight evolution of SFL For the first time, as a world preview, Sipa will present a newmodel of its best in class linear blowmolding systems, the SFL 6/8 EVO. The SFL 6/8 EVOwill carry all the technological advantages of the successful system, plus it will be even more performing: the output is increased by 10%, it will reach now the 2000 b/h/c while having further reduced consumption on both preform heating and bottle blowing. Another feature is the new clamp opening and closing system: directly driven by brushless motor reducer, the clamp can adjust the width of the opening accordingly with the container to be blown in order to expand production flexibility. In addition to its capability in two-stage systems (Sipa also makes several sizes of XForm preform injection moulding units), Sipa will highlight its ECS range of single-stage ISBM equipment at the show. This range was extended several months ago with the addition of two smaller models when Sipa acquiredAutoma’s ISBM business. These ECS ‘SP’ units, which were recently upgraded, have enabled Sipa to improve its ability to provide a full service to companies producing specialty containers in all shapes and sizes, whatever the output requirement. ECS SP machines are ideal for production of containers as small as 20ml in small to medium-sized lots, for such markets as detergents, pharmaceuticals, personal care, cosmetics and beauty care, and also foods. They can also make the miniature drinks bottles used by airlines for their light weight and break resistance. Sipa’s product design and development expertise will also be showcases at Interpack.Sipa bottling lines allows bottlers to fill multiple products on the same line like water, CSD and hot filled juices enhancing the value of the investment. www.sipa.it A market launch, exhibition firsts and bestsellers Interpack 2017 will see the launch of Hapa’s Industry 4.0–ready UV digital system printing two colours on blister foil. At home in a digital Industry 4.0 factory, the in-house printing solution demonstrates experience-driven design and function. As part of an Industry 4.0 production line with Coesia sister companies, a redcube digital print-module will print QR codes on promotional cartons, the “Coesia Box”. The boxes are manufactured by Emmeci and filled with tea bags from Acma, hand cream tubes from Norden, and power banks personalised for registered visitors by a Hapa BlisterJet CMYK printing system. Hapa’s bestselling UV flexo/UV digital Hybrid will demonstrate two-colour printing on blister foils. At the ACG booth, an integrated WebJet M will print on blister foils. At IMA, a “redcube plus” integrated in a POD blister line will print in a late stage customisation solution. Hapa Ink will also be in Düsseldorf. The division manufactures pharma-compliant inks designed for Hapa systems and applications. It also manufactures inks designed to exact client specifications for all foil substrates, plastic, aluminium, or labelling material of any kind. Orders for any volume of ink, no matter how small, are catered for. www.hapa.ch P.E. Labellers and Packlab Hall 14 - Booth D09 Sipa Hall 13 - Booth B73 HapaHall 6 - Booth D+E31 / D+E57","@ID":50}, "BEVERAGE INGREDIENTS PETplanet Insider Vol. 18 No. 04/17 petpla.net 54 This year’s beverage trends will be dominated by naturalness, nutritional value and new taste experiences On-trend beverage compositions During the upcoming months, the major food trends of nutritional excellence and naturalness will undergo further development. Consumers are increasingly looking for products with extraordinary, multi-sensory experiences, as well as for foods and drinks that provide naturalness and support a healthy lifestyle. The producer, marketer and provider of technology-driven natural ingredients, ingredient systems and integrated solutions for the food and beverage industry, Doehler is tracking, developing and playing with these trends on a global scale. Almost homemade Craft beers, craft beer mixes, craft sodas - born out of the American brewing industry, the trend for “craft” products has spread into various beverage sectors around the world. Consumers are drawn to craft products because they offer an attractive blend of authenticity, premium natural ingredients and production methods that seem almost homemade. Over and above this, “craft” represents something extra. Craft beer, for instance, is far more than just a special type of beer: it is a way of life, and a stance taken by brewers who want to distance themselves from the mainstream. Doehler has developed a range of new concepts for the craft brewing and non-alcoholic beverage industries. These include “double brew” beer mixes and craft colas and lemonades made with specially selected spices and premium fruit juices that deliver a glass of pure, “homemade” tradition. In addition, Doehler has responded to this trend by offering a variety of solutions for unique craft beers. Its sour wort and wort concentrates, for instance, are intended to facilitate the production of premium beers and beer specialities with distinct and authentic taste profiles – available with or without gluten. Simple and tasty This desire for authenticity and tradition is also reflected in today’s booming organic movement. The younger generation in particular is keen to buy products with organic provenance as this fits well with their healthy and sustainable lifestyle ideals. But for manufacturers, it is no longer enough to offer something as simple as cloudy organic apple juice. Consumers want variety and choice. “Organic superfruit”, “organic herb soda” and “organic still juice drinks” for children are just a selection of concepts developed by Doehler who offers a portfolio of organic fruit and vegetable ingredients. From NFC juices and juice concentrates to purees made from traditional as well as exotic fruits, Doehler’s organic spectrum allows the creation of new taste experiences with a huge “plus” on health. Consumer demand for all things authentic and pure is the main reason why NFC juices are more successful now than they have ever been before. Doehler is capturing this trend by developing solutions with premium quality NFC ingredients such as juices, nectars, smoothies and fruit splashes that not only impress thanks to their outstanding, naturally fresh tastes, but also provide inspiration for healthy, on-trend product positionings. Hall 3 - Booth F07","@ID":56}, "PETplanet Insider Vol. 18 No. 04/17 petpla.net 71 BOTTLES Spray for removing dog hairs The German firm Trixie Heimtierbedarf [Pet Needs] sells a spray to make caring for a dog’s coat easier and it should make combing easier. The spray, which has no smell is claims to smooth the hair structure and have the effect of repelling dust, dirt and water. The PET bottle contains 175ml and has a screw-on pump dispenser. A clear protective cap prevents accidental usage when it is stored and transported. www.trixie.de Body spray with lychee scent Treacle Moon, a brand started up in 2007 in England, has surprised the trendaware users yet again with new scent experiences. The latest example is the body spray “exotic lychee sorbet”, which smells of lychee and, according to the manufacturer, is “a spray-on good mood”. A slightly pink coloured bottle with 200ml contents, an all-round non-label-look label and a black pump dispenser with a protective cap complete the offer. As is customary with the brand, the text and descriptions are written in a humorous manner. www.treaclemoon.de","@ID":73}, "BOTTLING / FILLING 27 PETplanet Insider Vol. 18 No. 04/17 PET bottles for all milk variants The move to PET packaging in India began in the mid 80s, with the introduction of PET bottles for household containers (jars) and edible oil (EO). The market expanded to include bottled water, CSD, alcoholic beverages, fruit drinks, wellness drinks, personal care, agro-chemicals etc. in the 1990s. The next decade saw energy drinks, fortified water, RTDs etc. added to the PET packaging portfolio. The PET bottle for fresh milk by Gowardhan was launched more than a decade back and PET for other milk variants and dairy products have been added in recent years, and this segment has shown particularly strong growth. Reliance makes Relpet grade PET resin used for making PET bottles which finds application with the full range of milk variants available on the market. This includes fresh milk, flavoured milk, buttermilk, UHT milk and these milk variants are filled in more than ten locations across India. PET is catching up fast for “Farm Fresh” milk in India. While it was milk majors like GCMMF Ltd (Gujarat Co-operative Milk Marketing Federation) that initially offered milk variants such as flavoured milk and lassi (a yoghurt-based drink) packaged in PET in 2013, the positive market response has triggered interest in PET in small and medium dairy companies across the country. This trend would be encouraged and strengthened by machine suppliers addressing the need for “low capacity” aseptic filling equipment, suitable for the requirements of small or medium-sized dairy companies. Such developments would enable a broad range of aseptically filled products. The aseptic process has the specific advantage ChemTrend.com PROTECT YOUR ASSETS. Team up with Lusin® and Ultra Purge™ Lusin® and Ultra Purge™ form a winning combination Ultra Purge™ and Lusin®purging compounds, release agents andmold maintenanceproducts protect your assets by reducing downtime, increasing efficiency and extending the life of your tooling. Milk and dairy products in India are currently packaged in: Fresh milk: PE pouches, HDPE and PET Flavoured milk: Tetrapack, glass, PP and PET Buttermilk: PE pouches, Tetrapack and PET UHT milk: Tetrapack, BOPET and PET Emerging trends include growth in the use of PET for fresh, flavoured, UHT and buttermilk. Gowardhan Dairy packs fresh milk in 1l/28g transparent PET bottles. It has a 4-day shelf life. Amul Dairy offers A2 milk in 500ml transparent PET bottles, with 4-day shelf life. Amul launched a 200ml PETpackaged flavoured milk range in May 2013 and has started two more ‘PET aseptic’ filling lines. UHT milk is sold by Amul Dairy in opaque white 200ml PET bottles, with a shelf life of six months.","@ID":29}, "BOTTLE MAKING PETplanet Insider Vol. 18 No. 04/17 petpla.net 25 Disposable kegs for beer, wine and CSD Italian-made PET kegs by Kay Barton Polykeg manufactures containers in four ranges. Premium Line (BT), Smart Line (HS Plus), and Basic Line (H Plus) are each available in four sizes, ranging from 16 to 30l. Slim Line HS and H kegs come in 20l capacities; they are primarily differentiated by their handle designs. “Our customers don’t just come from the beer and CSD sectors; they come from the wine industry as well, so our kegs are used across a wide range,” Erica Tenconi explains. “We offer them in four different colours and with five different connections, for different markets and systems.” She used a 24l container from the HS Plus series to illustrate her points. With the exception of the Slim Line kegs, all the different types of kegs have PP reinforcement in the base section. Depending on the model line, the top part of Polykeg kegs feature a carrying ring with or without a second reinforcement, as well as carry handles. Although inner bags can be integrated if requested, the company says that the kegs don’t actually need them in most circumstances. “The containers all work with a nominal pressure of 3.5 bar, as required by the market,” Walton says. “During our regular quality assurance pressure tests, the PET containers actually burst under approximately 10 bar of pressure. This means that our kegs – across all four ranges - are among the most resistant currently available in the market. In terms of the logistics, we wanted to create an infrastructure for our products similar to that used with steel kegs. The BT and HS Plus and Slimline, in particular, are ideal for stacking, due to their PP reinforcement and their carry ring systems.” Four different preform types for the kegs are manufactured by Polykeg in-house. The company also offers the possibility for production at customers’ own facilities, by means of an integrated Polykeg production line. “Business is going very well,” Tenconi says. “Since 2015, we have doubled our capacity.” Today a large proportion of this capacity is exported. www.polykeg.com During our PET keg tour we visited Italian manufacturer Polykeg, which is based near the city of Bergamo. The company, which claims to be the only manufacturer in its field currently active in Italy, produces four ranges of disposable PET kegs. Polykeg was founded in 2012 by CEO and inventor Sergio Sonzogni, as a division of his existing corporate group. Sonzgoni, who originally came from the water cooler market, has more than 25 years of professional experience in the PET field. We weren’t able to speak to Sergio Sonzogni himself; his colleagues, Philip Walton, Technical Director, and Erica Tenconi, Management Assistant, related facts and background information about the company. The innovative packaging company PET PREFORMS & BOTTLES MONOLAYER, BARRIER, REFILL, HOTFILL VISIT US AT INTERPACK DÜSSELDORF 4 TO 10 MAY 2017 | HALL 7, LEVEL 1 / B21 www.resilux.com | [email protected]","@ID":27}, "BOTTLE MAKING 21 PETplanet Insider Vol. 18 No. 04/17 petpla.net PET kegs PET-a-Draft mini beer keg system Hendrik Lombard builds his own beer tap using PET bottles. His version of a mini keg set-up to serve home-made beer from 2l PET bottles. It solves a few issues for lovers of home-made and craft beer: Beer going flat once the growler has been opened. Having to clean and fill 48 bottles to store your batch of home brewed beer. It allows the use of 2l PET bottles which is cheap. Also possible are 3l PET bottles in the US. Or 6l PET bottles from Tap-a-draft. They use 38mm caps, the same as beer growlers. He points out that one should not exceed 2.7 bar. The construction plan can be downloaded at: www.instructables.com/id/PET-aDraft-mini-beer-keg-system Hendrik Lombard’s PET-a-Draft mini beer keg system Petainer The manufacturer said the improved one-way PET keg, which was launched at BrauBeviale 2015 features a solid and robust external casing that is designed to run on most steel keg filling lines. According to Petainer, the new product introduces benefits such as increased resilience throughout the supply chain, lightweight, an ergonomic design and a 2,800cm² surface area for branding opportunities. “For brewers petainerKeg Linestar fits on most existing steel keg filling lines and is strong enough for robotic handling and palletisation. The classic range includes containers in 20 or 30l sizes, while an active oxygen scavenger ingredient is incorporated within the PET material which keeps the contents fresher and prolongs shelf life. www.petainer.com Petainer sells their kegs ready for filling or as preforms for in-house blowmoulding. One-way keg for four different couplers Three years ago, Dispack Projects and Quadrant CMS (Quadrant Creative Molding & Systems) developed a one-way PET beer keg with a recyclable valve system as a cost-effective and easy-to-transport alternative to traditional multi-trip stainless steel kegs. The one-way Dolium 20- and 30-litre kegs incorporate valve systems injection moulded in glass reinforced polyamide, as well as protective, stability-adding external keg rings for improved handling and storage. To develop a cost-effective and more environmentally friendly option for the beer industry, Dispack’s founder Albert Wauters, a draught and keg expert, had to ensure that product integrity, food safety regulations and an extensive list of performance requirements would be met by the keg and its various accessories, including an integrated pressure relief valve system. At the same time, priority was also given to limiting the operational impact versus the traditional keg by achieving compatibility with existing filling lines and draught equipment. In line with these factors, the two companies chose the market’s four most popular metal valves and their corresponding couplers as the main reference points for the development. For the final Dolium PET kegs, the two companies developed new valves in four different versions that can be used with the most common couplers","@ID":23}, "43 TRADE SHOW PREVIEW PETplanet Insider Vol. 18 No. 04/17 petpla.net CHOOSE THE SPECIALIST ALL INONESOLUTION TOKEEP YOURPRODUCT SAFE Labeller+Sleever+Shrinking tunnel Available for speed from4.000 to24.000 bph APPLICATION LABELS +TAMPER EVIDENT PH. +39 0376 389311 MAIL: [email protected] WEB: www.pelabellers.com Stand 14D09 Producing all types of PET bottles 1Blow will present its 2-cavity machine type 2LO that is capable of producing all types of PET bottles between 150ml and 2.5l: round, square, oval, offcentred, with or without neck orientation, for cold and hot fill applications. All options are directly available on a new machine or as an upgrade at a later stage. Consequently, 1Blow customers are free to adapt their equipment and their investment to the real needs of their markets. Most of the existing standard moulds in the market may be re-used on 1Blow machines thanks to the specific mould holder that is installed in the press. All main functions are servo-driven, providing high accuracy and extreme high outputs. 1Blow machines maybe directly connected to an air conveyor or to a chain conveyor to exit the bottles to the filling line or to a palletiser. Despite its footprint limited to only 2 x 2 metres, the 2LO offers a full access to all components thanks to its internal floor, enabling easy and quick changeovers. www.1blow.com 1blow Hall 14 - Booth D03 All around rotary labelling The labelling machine manufacturer Gernep presents the latest developments of its rotary labelling machines. To meet all decoration demands in different industries, the rotary labelling machine Soluta, in the optimised control and security design, is for selfadhesive labelling. The Labetta is specialised in universal cold glue labelling and the Rollfed and Rollina machines in efficient hot melt wrap-around labelling. It is also possible to combine all labelling systems, cold-glue, hot melt and self-adhesive. Thanks to the possible combination there are hardly any boundaries in any kind of compilation. For flexible use of different container formats, Gernep provides for all labelling machines alternatively servo driven bottle plates. The company’s rotary labelling machines are characterised by their flexibility in the equipment, precision and quality workmanship. www.gernep.de Gernep Hall 14 - Booth D29","@ID":45}, "BOTTLE MAKING 24 PETplanet Insider Vol. 18 No. 04/17 petpla.net The heart of the filling line is the Innokeg PETBoy F2 non-refillable keg system with two independently operating filling heads. The multiple-axiscontrolled robot with a 360-degree working radius conveys the disposable kegs fully automatically to the racking system and from there into the respective packaging. www.khs.com Bevkeg The Bevkeg from Krones is a complete solution for the market of disposable PET beverage kegs. Depending on the performance class, the Bevkeg can be supplied in two varieties, one a preform and the other a container that was rolled after the blowing process and thus compressed. The option for container compression optimises the transport to the filler. Moreover, CO 2 cleaning before filling also becomes less resource-demanding due to the lower internal volume. The required machine and equipment technology for filling, labelling and palletising is supplied by Krones. The brewery or restauranteur receives the dispensing technology for Bevmate from Micro Matic, the specialist for dispensing systems. www.bevkeg.com Bevkeg (photo: Krones) Filling line for Pet kegs Capacity is up to 60 kegs/hour. Semi-automatic and automatic machines for pet keg-filling, utilise filling and CO 2 heads (to pressurise the keg). The pressurising/filling heads provided with magnetic sensor for the control of a correct opening of the fitting and dummy keg to install during the CIP phase. The parts in contact with the product are stainless steel with EPDM gaskets. Series of AISI 316L N.C. pneumatic valves for the control of flows related to the washing/ filling cycle. The valves are supplied with external position indicator. www.gbo-group.com Assembly equipment for Keykegs Schulz Systemtechnik, Visbek, Germany, manufactures the assembly equipment for Keykegs. Performance is 14 seconds/keg or 250 kegs/h. The facility starts by extracting two PET balls from the output rail of the blow ing machine and handing them over to the conveyor belt. Simultaneously, the aluminium bag is taken from a depot. The bag is put into the balls. Subsequently, the seal cover and compressed air system is pressed in between the ball and the aluminium bag. All kegs are tested for tightness and are then placed in a box. In a last step, the cartons are covered in film and palletised. www.schulz.st Small fillers The Czech brewery system Opava, Czech Republic, offers a filler for plastic kegs. The PKF-50 is a machine for the automated filling of 45 to 55 kegs per hour, suitable for almost all PET kegs. Using the same machine, via the simple keying in on the operator panel, various types of plastic kegs can be filled. The work phases are managed automatically. The only manual step is the loading and unloading of the keg at the processing point. Keg-filling range 10-30l, hourly production 45/55kegs. www.czechminibreweries.com And another small filler Machinery & Technology from Minsk, Belarus, supplies new and rebuilt keg/keggy racking and filling equipment for 30 to 40 kegs per hour, keg straightening machines, CO 2 fillers, palletising systems, and for fitting tighteners. www.tma1992.ru Mould making Kiefer Werkzeugbau GmbH, Schwaigern, Germany has been active in the field of tool and mould making for the plastics processing industry for almost 30 years. As an independent mould maker, blow moulds are produced for all current rotary blowing machines and for linear blow-moulding machines. The company now offers big container design - up to 30l, as well as prototyping and test runs at the companyspecific competition centre. Large moulds for the innovative PET barrels are currently in high demand. Here, an optimum selection of materials with a special aluminium alloy are as important as a well thought-out and optimised arrangement of the mould cooling. These specifications of the 30l keg are adapted for all common blowing machines. www.kiefer-mold.de 30l keg mould (photo: Kiefer Mold technologies)","@ID":26}, "EDITOUR PETplanet Insider Vol. 18 No. 04/17 petpla.net 13 Tour Sponsors: From pellet to shelf by Alexander Büchler February 14, 2017 We met: Mr Bambang Mujianto, Production Manager Indofood is a comprehensive food manufacturing company and also operates supermarkets. Thanks to help from Asahi from Japan, they have now broken into the beverage sector. Using aseptic bottling technology, they are penetrating the market. One example is RTD coffee which they can offer in their own store for half the price of the other competitors. Over the last two decades, Indofood has progressively transformed itself into a total food solutions company with operations in all stages of food manufacturing, from the production of raw materials and their processing, to consumer products for the market. 2013 Indofood entered the beverage business through joint venture (JV) companies with Asahi Group Holdings Southeast Asia Pte. Ltd., established in 2012. In 2014 Indofood expanded its beverage business by entering the packaged water business, with the acquisition of packaged water assets including the Club brand. The Beverages Division offers a wide variety of beverage products from ready-to-drink (RTD) tea and coffee to packaged water, carbonated soft drinks and fruit flavoured drinks. The business is conducted through two JV companies with Asahi – PT Asahi Indofood Beverage Makmur (AIBM), which handles manufacturing; and PT Indofood Asahi Sukses Beverage (IASB), which handles the commercial operations of non-alcoholic beverages. The division has an annual production capacity of around three billion litres. The division’s products are marketed under Ichi Ocha, Tekita, Caféla, Club, Pepsi, 7Up and Fruitamin brands. We visited the plant in Sukabumi, which is operated as part of a JV with Asahi. An aseptic bottling plant for teas, coffee and coconut juice was built here on a greenfield site in 2014. We were greeted by Mr Bambang Mujianto, the production manager. We went out onto a gallery from which we could see the manufacturing areas. The tour started in the “kitchen” where the raw ingredients for the tea, coffee and coconut juice are mixed together and processed. After the UHT, the products are transported to the bottling room which has a clean room class of 100,000, and the actual aseptic area a class of 100. The dry aseptic bottling line with 800b/min was made by Sidel. Two SMI facilities pack the bottles in cartons of 12 or 24 at a rate of 40 times per minute. Overall, 1,500,000 cases are made in one month. An automatic storage system takes the completed pallets. Internally alone, 3,000 plastic pallets are in operation. High-bay storage is provided for 1,200 pallets. The fully automatised plant has a capacity for two more lines. The aseptic facilities only have to be deep cleaned every 120 hours making it possible for the employees to produce products five days a week in three shifts. “It’s important to have solid training on the machines” says Mr Bambang. “Aseptic doesn’t just need good machines, it also needs good staff.” Ichi Ocha RTD Green Tea is one of Indofood Asahi’s products. It is a green tea made from Ichiban tea in 350ml & 500ml sized bottles. The coconut juice with desiccated coconut and Caféla is a RTD coffee made from coffee beans, crafted with mixture of cream milk and creamer, in 250ml bottles. At 3,000 IDR (some 0.21 Euro) the coffee is extremely good value in the shop. “We can only get the good price because of the aseptic technology,” says Mr Bambang, adding “The reason is the lighter bottles which are therefore better value, have a better aroma and are faster in comparison with hot fill.” With these prices, Indofood is about 50% cheaper than the competitors. While Asahi has a 51% say in the manufacturing and all of the designs and beverage development comes from Japan, Indofood has a 51% say in sales. So the company stocks its own supermarket chain with the aseptic products. www.indofood.com www.sidel.com www.smigroup.it The aseptic bottled coffee only costs 21 euro cent, 50% less than the hot filled competitor. The SMI facilities make 1,500,000 cases per month. Mr Bambang Mujianto, Production Manager gives a tour of the plant","@ID":15}, "PREFORM PRODUCTION PETplanet Insider Vol. 18 No. 04/17 petpla.net 16 MATERIALS / RECYCLING 16 Food grade PET pellets from Egypt Opening up a new market BariQ Egypt, a subsidiary of Raya Holding, is the biggest bottle-to-bottle recycler in the MEA region. It was established in 2010, has been in operation since 2012 and currently has 200 employees. The company reprocesses postconsumer plastic PET bottles into food grade FDA, EFSA & Health Canada compliant PET pellets on the foundation of the sustainability pillars of being economically justified and environmentally sound. These bottles would otherwise have likely become part of the landfill or burnt. BariQ incorporates state-of-theart cutting edge green technology from major European suppliers with the washing line from Amut and an upgrading SSP line from Starlinger, in addition to automatic sorters from Tomra, Sesotec & Buhler targeting major international bottle and food container makers and major fibre producers throughout Europe and North America. BariQ holds a number of industry related certifications that are concerned with quality (ISO9001:2008), environment (ISO14001:2004) occupational, health and safety (OHSAS18001:2007), and food safety (ISO22000:2005), while establishing an integrated management system that complies with these international standards. The company is aware of today’s businesses needs to play a pivotal role in promoting sustainability development goals (SDG’s) and as part of Raya that is a UN Global Compact active participant BariQ is committed to contribute to these goals and be a local SDG pioneer through the continued efforts in fostering innovation and economic growth. In 2016, BariQ expanded its operations and product portfolio by adding the recycling of HDPE and PP containers into resin suitable for various non-food applications such as outdoor furniture, crates, pallets, pipes and insulation sheets. Egypt is a prosperous market because of the geographic location that allows access to different regional markets. The country has various free trade agreements with most of the global markets that facilitate importing like free trade agreement with Europe, GSP with USA and COMESA with African countries. BariQ exports accounted for 96% of its total revenue in 2016, where it caters its customers in countries such as the USA, Belgium, France, Greece, Italy, Romania, Spain, Switzerland, Turkey and UK in Europe. Serving various PET packaging applications such as plastic bottles (water, CSD, edible oil, cosmetics & detergents), sheet rolls and food containers. Additionally it produces staple fibre grade resin suitable for textiles and carpets. As part of BariQ’s strategic objectives for the coming years, BariQ began to implement the Lean Supply Chain principles in Q1-2016 in partnership with one of the leading service providers. This project will enable the elimination of the different wastes that might occur throughout the value chain in order to improve the quality of the final product with fewer defects and rework. In terms of operations, this means fewer breakdowns, organised workplace, higher efficiencies and more output. Additionally, achieving lower levels of inventory and on-time delivery of orders will lead to greater customer satisfaction and improved employee morale, together with higher profits. www.bariq-eg.com","@ID":18}, "MATERIALS / RECYCLING PETplanet Insider Vol. 18 No. 04/17 petpla.net 17 The Swedish furniture retailer Ikea is relying increasingly on recycled PET bottles. 25 bottles make a door At the start of this year, Ikea introduced Kungsbacka - a range of kitchen cabinets made from recycled PET bottles and reclaimed wood. The furniture company has worked together with its Italian Purchasing Operation Team to develop a plastic film for this purpose - made entirely from recycled PET bottles. 25 PET bottles (0.5l) are needed in order to make enough plastic film for one 40x80cm Kungsbacka kitchen cabinet door. The project’s PET bottles are collected in Japan, the same location where the plastic film is produced. This film then begins its journey across the sea to Italy, where it’s glued onto kitchen doors. 25 half-litre PET bottles are needed in order to make plastic film for the front of one 40x80cm Kungsbacka black kitchen cabinet, meaning almost 1,000 bottles would be required to manufacture an entire kitchen (in the standard measurements) with 20 doors and the corresponding amount of panels. “What we do here at Ikea has major consequences for the environment, as we work on a large scale with large quantities. If we use recycled material, it means production becomes more sustainable,” explains Anna Granath, Ikea product designer and project manager of the team who worked to develop the Kungsbacka range. A project with a vision: two years previously, in March 2015, the wheels of the plan to design kitchen cabinets that were both sustainable and affordable were set in motion. Together with an Italian Ikea supplier, the product development team began to explore the possibilities that recycled materials had to offer, leading to a new material being developed – a plastic film made from PET bottles that had been thrown away. These bottles are collected and processed into a film in Japan. This film then begins its journey across the sea to Italy, where it is laminated onto kitchen doors. “Of course we’d like all the stages of production to be in one place, but unfortunately we’re not there just yet,” outlines Anna Granath. Even the wood used as a base material in the Kungsbacka range is 100% reclaimed and FSC-certified, obtained from old furniture or packaging material, for example. This means that both main materials used to manufacture Kungsbacka kitchen cabinets (wood and plastic) are 100% recycled, and it is only the adhesive material used in the chipboard, and colour pigment used in the plastic film, that are in fact new. “Our biggest challenge in making a film from recycled material is trying to achieve the same quality standards as attained by film made from new material. We have now accomplished this without having to compromise on quality or price,” explains Marco Bergamo, manager of the development team at the Italian Ikea supplier 3B. Ikea has forecast that using recycled films instead of those containing oil results in 20l less oil being used to manufacture a kitchen. If every kitchen cabinet door made by Ikea was coated with a plastic film like that used in the Kungsbacka range, 9.6 million litres of oil could be saved in 2017 alone. “We want to use recycled materials for all plastic films applied to our doors in the future. In doing so, we’ll use other recycled plastics and not just PET bottles,” outlines product designer Anna Granath. www.ikea.com","@ID":19}, "PETplanet Insider Vol. 18 No. 04/17 petpla.net 68 PETbottles Beverage + Liquid Food New bottle shape for mineral water In Canada, under the brand name “Riva”, the Okinshaw Water Company sells 500ml alkaline mineral water, which is brought to the surface under artesian principles and is thus enriched with minerals. The water is put into an unusually shaped bottle which is curved front and back and which tapers towards the back. An all-round non-label-look sleeve label and a positive-locking cap give the bottle an almost “cosmetic” appearance. www.okinshaw.com Alkaline water This water, with a pH of 8.8 and which can revitalise the body after sporting activities, comes from several natural sources in Canada. The “alkiss” water is filtered via reverse osmosis, is “remineralised“ and is a blend from several sources. 500ml are filled into a slightly blue-coloured slim bottle. An irregular, sideways on, continuous self-adhesive label and a blue screw cap with a tamper band complete the packaging. www.alkiss.ca Olive oil in PET The French discount chain Auchan fills 250ml of olive oil from Spain into a slim, transparent PET bottle. There are two grooves on the sides which improve both picking up and pouring out as well as stability. The closing device is a green screw cap, with an integrated ring-pull making it tamper-proof, and a specially shaped edge to guard against dribbles when pouring. www.auchan.fr Smoothie as a shot The Dutch company Hoogesteger sells various smoothies in German supermarkets as so-called “shots” – small amounts as a one-off portion for a quick boost. The “Clear Green” and “Hello Yellow” smoothies seen in the image must be shaken before use and, according to the manufacturer, remain fresh for longer because of the production process. In each case, 60ml are filled into easy-to-handle transparent bottles with a tamper-proof screw cap and a paper label. The products distributed in the Netherlands have different names and other varieties. More varieties are also available there. www.hoogesteger.nl PROCESS PILOT® makes producing a better PET bottle as easy as 2 3 1 MEASURE CONTROL OPTIMIZE every bottle for changes in material distribution process variation, inside the blowmolder material utilization and orientation to achieve maximum bottle performance CONTACT US TODAY TO LEARN MORE! AGRINTL.COM | +1.724.482.2163 | [email protected]","@ID":70}, "MATERIALS / RECYCLING PETplanet Insider Vol. 18 No. 04/17 petpla.net 14 MATERIALS / RECYCLING 14 UK to block bottle deposit proposal? by Anthony Withers Despite widespread public concern at the litter blight disfiguring much of the UK’s towns and countryside, the government looks set to reject proposals for a bottle deposit scheme. By imposing a 10p or 20p levy on plastic bottles ministers hoped to encourage recycling and crack down on the substantial amount of waste clogging up landfill sites. However, the proposal is likely to be rejected, according to sources in the Department for Environment Food and Rural Affairs (Defra). The Deposit Return Scheme (DRS) has had a chequered history in the UK, with the big drinks companies, such as Coca-Cola and others, being adamantly opposed to the scheme. In 2015, Scotland produced a report into the trial deposit scheme then underway, which raised concerns about the amount of money it could cost to set up the deposit return system and about whether consumers would embrace the idea. However officials working for Environment Secretary Andrea Leadsom were said to be “unimpressed” with the scheme, citing ‘significant uncertainties’ over the evidence, saying the proposal was ‘unlikely’ but ‘not off the table’. The scale of the problem in the UK can be seen from the figures. The average UK consumer recycles little over half of the 470 plastic bottles they use each year. These 16m plastic bottles end up littering towns and cities and are a problem in the world’s oceans. Why would DRS not work in the UK when it has been adopted successfully in other countries such as Germany, Sweden, Denmark, the Netherlands and Estonia, and by the same companies? Opponents say it would discourage people who already recycle who would see the 20p levy as simply a stealth tax. In addition, local authorities have put in place efficient recycling schemes for plastic bottles, and improved kerbside waste collections would, it is claimed, provide the best solution. The main opposition to DRS came from drinks manufacturers such as Coca-Cola, Pepsi, Nestle and others. Their trade association, the British Soft Drinks Association (BSDA), waded into the fray, arguing that consumers wouldn’t want it, that DRS would be ineffective, and that no cost benefit analysis has been produced. Supporters of the scheme countered by pointing out that in Germany, the introduction of a DRS led to 98.5% of refillable bottles being returned by consumers. Similar success was reported elsewhere: Estonia for example, with a population of only 1.3 million people, has collected and recycled 3.2bn “deposit packages” in the last 12 years. Last year, the return rate was 75% for cans, and 87% for both PET bottles and one-way glass. Intense lobbying by the companies ensured that the project stalled. Then, in February 2017, came a U-turn, when, to general astonishment, Coca-Cola announced that it was prepared to support DRS. It is anticipated that other companies will swiftly follow suit. This change of heart may have been brought about by public concern about plastic waste, backed up by the success of DRS schemes elsewhere in Europe. This encouraging move meant that the ball was now firmly back in the government’s court, but sadly, the response was not encouraging. Andrea Leadsom said that although she is alarmed about plastic bottle litter, she is sceptical about introducing a deposit scheme. But with Coca-Cola’s backing, and the mounting evidence of economic benefits, ministers might rethink their positions. The story is far from over. www.bericap.com Unique range of light weight screw and sports closures for light weight PET neck standards for water • Closures for all common neck sizes 26/22, 28mm (PCO 1810, PCO 1881), 29/25, 30/25 • Light weight Hexalite range allowing light weight neck • Still water closures suitable for N 2 dosing • Sports closures fulfill BSDA requirements • Boreseal systems for excellent tightness • Consumer friendly opening forces BERICAP Technology for still water","@ID":16}, "TRADE SHOW PREVIEW PETplanet Insider Vol. 18 No. 04/17 petpla.net 50 In additional to Multi Rotation System (MRS) design optimisation over the past year, Gneuss has developed the new Jump system. This is installed directly downstream of the Gneuss Processing Unit and thanks to its ingenious process ensures an accurate and controllable IV boost of the PET in the melt phase. The Jump system is a compact alternative to conventional SSP (solid state) systems and enables direct reintroduction of the polymer into the production process without the need to re-melt the PET. With the Gneuss industrial waste concept, industrial waste is first fed through a shredder or a knife mill until the size is reduced so that it can be fed into the extruder. This can mean either compaction of the size reduced waste or a crammer feeder fitted directly to the extruder. The first important processing stage: melt decontamination takes place in the extruder. With its devolatilisation capacity, the MRS extruder can process PET waste with high residual moisture levels and/or contamination (such as spin finish oils) without the need for any pre-treatment of the waste. In the Multi Rotation (MRS) section of the extruder a huge polymer surface area and rapid surface exchange rate under vacuum ensure that all these volatile contaminants are reliably extracted. Solid contamination is extracted with the fully-automatic and process-constant Gneuss Rotary Melt Filtration System. With filtration finenesses of down to 20μm and below, a pure and particle-free polymer melt is guaranteed. During the second stage of the process, the purified and homogenised polymer is fed by means of a melt pump into the Jump. A large surface area of the polymer melt and optimum residence time of the polymer under vacuum are decisive factors. The purified and homogenised polymer is fed by means of a melt pump into the Jump. Here, too, a large surface area of the polymer melt and optimum residence time of the polymer under vacuum are decisive factors. The polymer melt is kept under vacuum as it passes over slowly rotating elements. Through control of the residence time and the speed of the rotating elements, controlled polycondensation takes place whereby controlled IV boosting takes place of typically 0.02 to maximum 0.3dl/g. The design of the Jump system avoids the ingress of oxygen so that the yellowing effect encountered during the recycling of PET is reduced to an absolute minimum. After the PET melt has passed through a stilling chamber in the Jump system, the polymer is pumped directly into the production process (for example direct extrusion spinning, strapping) or to a pelletising (chip cutting) system. With the complete system consisting of the Gneuss Processing Unit with the MRS Extruder and a Jump system, The Gneuss Processing Unit (GPU) has been available for several years and has proven itself on the reprocessing of bulky PET waste such as post-consumer bottle flake and industrial waste from fibre and film manufacture. This Gneuss Processing Unit consists of the Gneuss MRS extruder with its unmatched devolatilisation and decontamination performance together with the highly-efficient Gneuss Rotary Disc melt filtration systems and the Gneuss Online Viscometer for intelligent dynamic viscosity control, monitoring and logging. Gneuss Processing Unit with Jump North entrance - Booth C03 Reprocessing of PET industrial and post-consumer waste Industrial waste and post-consumer recycling","@ID":52}, "58 TRADE SHOW PREVIEW PETplanet Insider Vol. 18 No. 04/17 petpla.net Sacmi’s response to food & beverage market trends in China Sacmi will host the best the group has to offer the closures industry, such as the new CCM24CS compression press, being showcased for the first time on this market. Key improvements to mechanics, hydraulics and automation have given the new 24-head version of the press higher output (cycle time 1.44s), without penalising the cooling time; moreover, consumption has been reduced further and cap quality has been raised. The machine on show will produce an HDPE single-piece 30mm water bottle cap weighing 85g, with an output of 800 caps/minute with just 24 heads (cycle time 1.8s). Sacmi provides alongside individual technological and plant engineering solutions, advanced quality control systems. All Sacmi vision systems (developed by the Group’s Automation & Service Division) are designed to operate in line with the machines at ultra-high speeds: from the CVS 052, the cap vision system integrated downstream from the CCM, to the PVS002 Plus, capable of testing no less than 1100pph; the latter also has optional weight and body control features. Fully aware of the far-reaching changes affecting both the market and the manufacturing methods, Sacmi will also be taking part in the Industry 4.0 conference, an event linked to the fair itself. Here, Sacmi will give a talk on the Sacmi 4.0 and H.E.R.E. (Human Expertise for Reactive Engineering) projects. The latter is a solution set that networks production processes, supervising and exchanging information with interconnected machines to provide production process advantages and sharpen smart factory growth strategies. www.sacmi.com Hall 4.1 - Booth C41 Moretto’s Moisture Meter Moretto will be showcasing its latest development in the PET area: Moisture Meter is an instrument designed to measure, in line, the residual moisture content of the plastic granule. Installed directly on the processing machine, thanks to the patented “Power Peak” technology, the system measures the actual moisture content (real time control) of the plastic granules assuring a certified production. No calibration is needed. It is necessary to select the polymer to be treated and Moisture Meter provides control of the process with sampling every 2s. The system is being targeted for technical applications where precision in confirming the residual moisture content of the production resin is paramount. Moisture Meter Plus allows the control of the dryer performance by comparing the humidity from the initial part of the process to the end, automatically adjusting the dryer parameters to ensure optimal drying. This concept creates a closed loop connecting material, dryer, process quality, and plastic processing machine, which represents the condition to move straight ahead towards Industry 4.0. Moisture Meter is equipped with USB, Ethernet and RS485 Modbus communication ports and is compatible with the Moretto Mowis supervising system. The system has 40 material profiles among the most common technopolymers as PET, ABS, PMMA, PA6, PA66, PEEK and many others. It will be possible to select the material to be treated and Moisture Meter assures that all the transformed pieces match the quality standards required. It is also possible to create the profile of specific or custom materials. Once the new ones have been created, no other calibration is required. The material profile could be connecting through the USB port while the Ethernet port assures the remote assistance. The touch view controller allows up to six devices to be managed. The exhibition will be the occasion to show other innovative Moretto’s solutions for the plastic processing industry, for example, Gramixo, continuous loss-in-weight dosing system; X-Comb, a high-performance mini-dryer solution for small polymers batches; X DRY AIR series with a stable -70°C Dew Point; TE-KO, a full optional temperature controller series. www.moretto.com Hall 4.1 - Booth B41","@ID":60}, "BOTTLE MAKING 30 PETplanet Insider Vol. 18 No. 04/17 petpla.net .com 100815dmyL fied isophthalic acid), to replace part of the TPA. The co-polymers therefore have structures such as this: PET TETETE… PET-co-CHDM TETCTE… PET-co-IPA TEIETE… DEG, a by-product of the polymerization reaction, is another comonomer which lowers the melt temperature but is not as effective at slowing down crystallization rates. DEG takes the place of EG in the chain. Several advantages are gained by using the co-polymer, especially in preform moulding applications: 1) Co-polymers crystallise more slowly than homopolymers, making it easier to fabricate clear preforms (see Crystallisation). 2) Co-polymers are easier to melt in the extruder as a result of the lower melting point and lower maximum degree of crystallinity. 3) Co-polymers impart better stresscrack resistance to the bottle (see Embrittlement and Stress Cracking). Some of the generalised effects of IV and co-polymer content are outlined in table 2.1. Process/ Performance parameter Effect of increased IV Effect of increased co-polymer content Crystallisation rate Extruder motor load Natural stretch ratio Orientation Side wall thickness AA generating potential Aging rate Stress crack resistance Table 2.1 The generalised effects of IV and co-polymer content 2.2 Crystallisation of PET PET is a semi-crystalline resin. The word ‘crystalline’ refers to a region of ordered chain arrangement, as opposed to ‘amorphous’ where the polymer chains lack order (fig. 2.3). Melted PET, by definition, is amorphous. Fig. 2.3 Rendering of a PET chain When polymers are in an amorphous state, the molecular chains can be compared to a tangled web of spaghetti or springs. The analogy to tangled, stretched springs is particularly suitable for semi-crystalline polymers, because, under certain conditions, the polymer chains tend to coil into ordered structures, forming crystalline regions. The repeating units of the homopolymer chain fit together neatly, forming a close-packed array, which has a higher density than the amorphous state. Density measurement is commonly used to determine the degree of crystallinity. At room temperature, amorphous PET has a density of 1.335g/cc. The calculated density of perfect PET crystal is 1.455 g/cc. The density of a semi-crystalline sample with x fraction crystallinity is: 1 x (1-x) p 1.455 1.335 + = The crystal structure has a lower energy state than the amorphous arrangement, so it is the favoured arrangement. Because polymer Figure 2.2 An alcohol and an acid form the ester groups of PET that make it a polyester. 30 BOTTLE MAKING","@ID":32}, "TRADE SHOW PREVIEW PETplanet Insider Vol. 18 No. 04/17 petpla.net 51 industrial waste can be quickly and efficiently reprocessed in one processing step to a high quality polymer melt which can be directly processed to a finished product. With the MRS Extruder, Gneuss has developed an extruder specifically designed not only with the material PET in mind, but with the reprocessing of PET. Thereby Gneuss offers a processing unit which enables PET to be extruded without any pre-drying or crystallisation. This applies both to the processing of both virgin and post- consumer bottle flake with a residual moisture level of 1% and in some cases more. The extruder will easily handle PET / PE scrap (laminated sheet) and mixtures of PET and PETG. Thanks to the high polymer surface exchange rate under vacuum in the MRS section, a vacuum level of only 25 bar is required in order to achieve 100% moisture extraction. Another effect of the high polymer surface area exchange rate under vacuum is the extraction of volatile contaminants. The system achieves the requirements of the FDA, EFSA and Invima without restrictions. PET sheet made on the MRS extruder is therefore suitable for food contact applications whatever input material is used and without any pre-treatment of the input material. The Gneuss Processing Unit includes also the unique Gneuss Rotary Melt Filtration System for the efficient removal of solid contaminants with fine filter elements even on post-consumer bottle flake. The Gneuss Online Viscometer ensures a consistent, defined IV value of the polymer thanks to the intelligent control system and is a useful tool for quality monitoring and control. Gneuss offers complete lines including the up- and downstream components from the material dosing system to the die, roller stack and to the winder, which are all tailored to the exact requirements of the individual customer. www.genuß.com W W W . I N T R A V I S . C O M LDPE, PET, HDPE, PE and PP bottle inspection L I V E A T B O O T H 5 . 1 J 1 1 SpotWatcher® Bottle Inspection Today. Non-destructive layer inspection Label inspection at up to 50 objects per second OptoSonix® LabelWatcher® Gneuss Sheet-Line","@ID":53}, "PETplanet Insider Vol. 18 No. 04/17 petpla.net 69 BOTTLES Yoghurt + smoothie Under its own brand, “Desira”, Aldi Süd has a drink made from yoghurt and smoothie on its shelves. The proportion of juice in each variety is 43%, which is made from the different fruit juices. Each of the white-coloured bottles contains 250ml, has a white screw cap with a tamper band and a sleeve label to match the particular flavours. www.aldi-sued.de “high 2” – the cool sister of high C When introducing his direct juices and smoothies found in the chill cabinet into a growing market segment, Eckes-Granini created the brand name “hoch 2” [“high 2”]. This stands for the Eckes-Granini juices – not to be confused with “high C” which are direct juices and smoothies which have to be kept cool – as these do not require cooling whilst unopened. Currently the market offers three juices and three smoothies. All are 100% natural, vegan, free of sugar additives, free from colourings and preservatives and t he r e a r e no genetically modified ingredients. The bottles, made from 25% recycled PET, contain 250ml smoothie, whilst the direct juices contain 800ml. An easily visible note about the brand sister is on the fresh seal on the screw cap with a tamper band. www.deinhoch2.de Société Générale des Techniques 3 rue de l’Île Macé - 44 412 Rezé - France www.sgt-pet.com [email protected] + 33 (0)2 40 05 09 37","@ID":71}, "BOTTLE MAKING 20 PETplanet Insider Vol. 18 No. 04/17 petpla.net Disposable PET kegs - an overview Sell and forget keg by Alexander Büchler A steel keg is expensive, heavy and difficult to clean. No surprise that brewers are looking for alternatives. With disposable PET kegs, they can save weight, do not have to clean them and, especially, since the kegs do not have to be returned, they can expand their distribution area. Global shipping of draft beer is now no longer a problem, which was impossible with steel kegs. In addition to all economic and ecological aspects, the idea of “Sell and forget keg” is the most important. Our last overview of PET kegs is now three years old already (PETplanet Insider 05/14), so it is time to check what is new. Two main strains have developed. The majority of suppliers of disposable PET kegs decided to incorporate as much as possible from the existing waste and dispensing systems of the steel kegs. These are usually characterised by featuring classic connectors for keg couplers. One exception in this regard is Keykeg, who have developed their own coupler with safety valve. The systems are very popular. Especially the driving idea ‘sell and forget keg’ is at its most obvious here. The user does not have to invest in new dispensing technology. These systems include: Petainer Keykeg Unikeg Polykeg Dolium Ecokeg In addition, two independent systems, which require special keg compression technology in the bar, are trying to establish a foothold. One was developed by Carlsberg. It compresses the keg from the outside using compressed air; the other – Bevkeg - was developed by Krones, which uses a mechanical stamp to squeeze the keg. But there are more stories on the subject of PET kegs; for example, Heineken/Amstler has been offering a small PET keg for the end consumer for years, and of course the hobby brewer community has been dealing with this topic on a smaller scale. We can point to the system of Hendrik Lombard as an example (see p21). Users Carlsberg rethinks draught beer dispense for bars Carlsberg UK has launched November 2016 a convenient beer dispensing solution for bars and food-led outlets, called DraughtMaster. It requires only water, a power supply, drainage and space for installation, usually within the bar or drinks service area. The advanced technology, designed and refined by Carlsberg over ten years, uses 20l PET kegs, replacing CO 2 with an in-built air compressor. The system features an easy self-cleaning system and a simple modular structure to stock or rotate up to six draught beers, delivering a consistent, quality and cost-effective serve every time. The system is a proven Carlsberg initiative and is currently operating in 16 countries around Europe including Italy – a market where 90% of Carlsberg products poured in the on-trade now uses the technology. Added benefits of DraughtMaster include significantly increased beer shelf-life of 31 days compared to 5-7 days for a traditional steel keg; a specialist air compression system meaning every pour delivers on the quality and consistency intended by the brew master, with no contact with oxygen throughout the process; reduced waste, a semi-automatic cleaning system and reduced need for space. www.draughtmaster.com Carlsberg fills speciality products for the taproom into PET kegs Heineken has been using 4l PET beer kegs for 5 years Heineken and Amstel fill beer into a 4l PET keg with an integral tap supplied by Appe, now part of the Plastipak group. The “Tapje” keg is a small draft-beer system, which consumers can use at home. It has been launched in the Netherlands prior to introduction into other markets. The Tapje features Appe’s proprietary monoBlox barrier technology with oxygen scavengers, resulting in a robust container with superior barrier performance that protects the integrity of the beer by keeping out oxygen whilst keeping in the carbonation. Once open the beer remains fresh for 30 days and so is ideal for occasional drinking or for parties The Tapje is ready for use after being cooled for ten hours in a refrigerator. A separate beer cooler is available which reduces this time to an hour. A coloured indicator on the front of the keg shows when the beer has reached the correct temperature for consumption. www.plastipakeurope.com","@ID":22}, "EDITOUR PETplanet Insider Vol. 18 No. 04/17 petpla.net 10 Tour Sponsors: Go with the flow South East Asia: Indonesia The underestimated islands by Alexander Büchler Indonesia is a superlative country, often underestimated; it is the fourth most populated country on the planet and, with a population of 30 million in Greater Jakarta, this is also the second largest metropolitan area in the world behind Tokyo. Indonesia also boasts the world’s largest Muslim population; on a commercial level, it has the biggest water brand in the world – by volume – and finally, and what the country is quite possibly best known for – it has 17,000 islands and heavenly beaches. Unfortunately, I was unable to enjoy these beaches in mid-February, as my tour around Jakarta, Bogor and Tangerang was limited to the island of Java. As mentioned above, this is the second largest metropolitan area in the world and it is the hub of Indonesian industry. Indonesia’s economy seems to be strong and robust, growing at a rate of more than 6% each year, in spite of upheavals in the global economy. As a result, it is the third fastest growing economy in the world after China and India. Inflation is around 5%. One reason why the economy continues to grow steadily may be due to its relatively minor involvement in the global economy compared to domestic demand which has firmly established itself. High levels of political stability are an advantage for the economic climate and economic indicators appear to be largely positive. The GDP is currently $11,700/person. President Joko Widodo Elected in 2014, the new president Joko Widodo has further improved the general conditions for economic growth. He abolished government subsidies for fuel and electricity, instead using these funds to expand and develop infrastructure. This strategy initially had negative impacts for the drinks sector, as increased energy costs dampened the domestic demand at first. Nonetheless, the drinks market has grown, particularly propelled by the high levels of water consumption. Despite all these positive reports, the country suffers from the problems typically encountered by an emerging nation, such as poverty and unemployment, inadequate infrastructure, corruption, a complex regulatory environment, and unequal resource distribution among its regions. Transport is particularly expensive due to overcrowded streets in the metropolitan areas and, on a larger scale, due to the segmented structure of the islands. And so drinks companies have spread their factory locations across Indonesia in order to be able to reach their consumers using the shortest routes possible. Suppliers for products Fig. 1 Population of Indonesia [mio] Key facts Indonesia: 260 million inhabitants 1,811,569km2 land 17,000 islands $ 11,700 per person GDP 5% inflation 6% economy growing a year 195 65","@ID":12}]}}
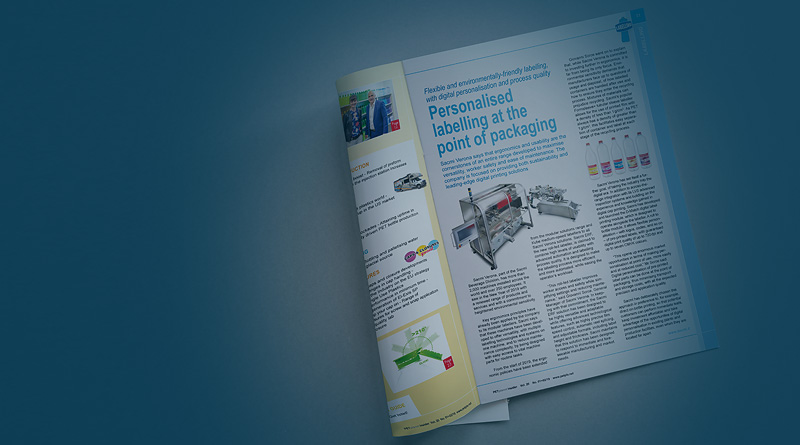