"PREFORM PRODUCTION PETplanet Insider Vol. 18 No. 09/17 petpla.net 14 Interview with Stefan Zatti, CEO, Otto Systems AG Joint forces for the perfect preform system by Alexander Büchler Otto Hofstetter AG and Yudo are founding a joint venture to enable them to offer complete preform systems. To do this they are relying on machinery and components from providers already on the market to enable them to offer customers the perfect system for their preform. Stefan Zatti, CEO of Otto Systems, Uznach, Switzerland is presenting the new concept in the BMB factory in Brescia, Italy. As a first proof of concept, Otto Systems together with BMB reveals the BMB320 (clamping force 3200kN) with an Otto Hofstetter 96-cav system. This produces an 8g preform with a 29/25 neck. Output is 60,650 items per hour (1.4 million/day). With a micropitch of 50*84mm, the mould is very compact in construction. It can therefore be removed both laterally and also upwards from the cavity between the spurs. The machine moves the moveable platen and plasticising is also effected using electricity. The result out of this is an excellent electricity consumption balance. The shooting pot and the ejector work hydraulically. The robot is supplied by JV partner Yudo. Because of the low pitch, the extraction arm has only two cooling stations, making this machine design more suitable for lighter preforms. The system is supplied by a Piovan Genesys system. We asked Stefan Zatti about the background behind why the Otto Hofstetter AG wants to gain a foothold in the preform machinery market. PETplanet: Mr Zatti, with Otto Systems you are entering the fiercely competitive market for complete preform systems. Many powerful companies have tried it and subsequently withdrawn. What makes you think you’ll be successful? Zatti: For our parent company Otto Hofstetter AG, every customer project begins with the preform. The customer has certain ideas here. But which mould design or machine to use is very often a secondary consideration. And this is where we see our expertise; we have over 40 years of experience in the implementation of specific customer requirements. We would like to pull this expertise together with our JV partner Yudo. PETplanet: So you do not want to build machines yourself, but merge available components into an overall system? Zatti: Depending on the requirements of the preform and the situation of the customer, different components from different manufacturers can be the best solution. We are not committed to any one preform system manufacturer or on any one kiln provider. PETplanet: Does this ultimately mean that Otto Systems also offers moulds that have not been built by the Otto Hofstetter AG? Zatti: Our main concern is to build systems uncompromisingly tailored to the needs of the customer. If an Otto Hofstetter mould is the right solution – fine. But if another mould proves more suitable, we will also offer the option of third-party moulds. PETplanet: If you combine all brands with one another, there will be an unbelievable mountain of interfaces. How will you control this? Zatti: As I have already mentioned, we have been building moulds for the widest variety of systems for over 40 years now. So the machine-mould interface is no problem for us. New for us is the robot-machine interface, and that is Yudo’s area of responsibility. PETplanet: Your workshops in Uznach are working to capacity so how do you plan to build a complete system before delivery so as to guarantee a functioning unit for the customer? Stefan Zatti from Otto Systems is passionate about the new concept. The extraction side is from JV partner Yudo","@ID":16}, "TRADE SHOW PREVIEW PETplanet Insider Vol. 18 No. 09/17 petpla.net 68 Swiss partnership comes up with upgrades and new solutions Preform & closure inspection solutions IMD Ltd. and M. Tanner Ltd. are presenting preform and closure innovations as the complete upgrade of the IMDvista Peco V3 preform inspection system, the new IMDvista Digital Printer CLDP and the IMDvista Portal, which links all the systems together. Inspection solutions get more and more important for the fully automated and optimised preform production process in the plastic industry. Factory layouts are optimised to the limits and no square meter stays “unused”. Driven by the need to use recycled material, using UV blocker etc., defect detection is becoming a must. Problems like black spots, colour deviations, crystallisations etc. happen during production, appear and go away again. The IMDvista Portal links all the systems together offering the production people a fast and easy overview of the monitored production. Problems are displayed and alerted immediately when they happen and corrective actions can be initiated immediately. IMDvista Peco V3 Upgrade of a well proven inspection system: The target was better accessibilty, a smaller footprint and an artificial intelligence to read the cavity number. The Tanner roller sorter was lowered to the floor to gain accessibility. With two easy to open swing doors, operators get the perfect acces to the inspection systems. IMDvista V5 Vision Control Center with its new and unique artificial intelligence module is used to read the cavity number of your preform. The statistics are well presented to the operator based on the defects per cavity. The proven Tanner sorting system combined with a new connection to the IMDvista Peco V3 inspection system makes the system even more reliable and easy to use. The concept of preforms sorting was kept with roller system because the tests have proven that this is still the most gentle way compared to the rotary sorters. The layout has a wide range of configuration possibilities to flexibly adapt to the production area. A unique “double conveyor” feeds the good and the bad parts to half octabins, again to perfectly adapt to the production aiming for the best possible logistics in production. IMDvista CLDP Closure Digital Print (CLDP) is printing 1,500 closures per minute in high quality and full flexibility in format and print. For the first time the IMDvista CLDP will be shown in operation. Starting with the “clean and save” concept conveying the closures on a stainless steel conveyor, the closure is pre-treated and then conveyed through the RedCube Plus from Hapa. CMYK printing up to 720dpi can be combined with a white print head to be as flexible as possible with almost no limitations in artwork and colour. The unique ink handling makes the system easy to use for the operator. By using the same calibrated ink artwork is always in the same quality. An automated cleaning and conserving system is the base of a robust and clean industry proven digital printing system. Hapa low migration ink, specially developed and optimised for this application, makes the system reaching unseen adhesions. Specific migration is compliant with EU 10/2011. As a perfect combination, the digital printer does not require specially skilled people and by principle can not damage a closure. For final inspection, an IMDvista print inspection system is part of the system to make sure 100% conforming print is reaching the customer. V5 Vision Control Center is the controlling HMI to make it as easy to use as the known vision inspection systems. IMDvista Portal connects the vision systems The IMDvista Portal became a proven data center. Based on an SQL database there is easy access to all the connected vision systems. Compact and well organised product screen provides a simple and fast production overview. Quality monitoring comes as easy as using an app by a simple event log. SPC charts for easy and fast trend analysis is the base for preventive actions: act before something goes wrong. A simple click connects the user with their vision system. Industrie 4.0 is in everybodys to do list to improve efficiency. Also “closed loop control” becomes possible feeding back the data from the vision system. www.imdvista.ch Hall B5 - Booth 115 at PackSys Global Booth Hall A4 - Booth 514 at Arburg Booth Hall A4 - Booth 323 at Engel Booth Hall A4 - Booth 324","@ID":70}, "BOTTLING / FILLING PETplanet Insider Vol. 18 No. 09/17 petpla.net 39 Bottleneck filling capacity Following these investments, the filling capacity was now the bottleneck in the production operation. NT was running a total of three rather elderly bottling lines: a 12,000bph line for 1l bottles, featuring a Krones Contiform blowmoulder a 6,000bph line for 2l bottles a line for 5 and 10l containers Together, these lines handle 500,000l a day – not enough for NT. Which is why under its new management the company decided to double its capacity, and concentrate on a single line the filling operation for the 1l container, for which demand is highest. Following a transitional phase, all premium products, plus mixtures of rapeseed and sunflower oils, will also be bottled here in future. By block-synchronising the blow-moulder and the filler, NT has managed to downsize the weight of the 1l container to 16.5 or 18.5g – depending on the brand of oil involved.","@ID":41}, "82 PRODUCTS PETplanet Insider Vol. 18 No. 09/17 petpla.net New hot fill options Fogg Filler is a market leader in the design and manufacture of rotary filling systems for the liquids industry. Temperature management for hot-fill applications has been made simple with using the Fogg recovery trough, says the company. The built-in sensor allow to manage product temperature in the bowl and filling valve tip temperatures, when line stops occur. The operator can easily send the trough into position to purge the cooled product in the valves until production can be resumed, sending only a small amount of product back to rework. When customers have specifications that will not allow the product to encounter the atmosphere by using the trough system, Fogg has developed another option. This new system recirculates the product within the bowl including the product in the valve tips. This virtually eliminates the product loss associated with other hot fill methods. To switch from cold-filling to hot-fill on a new Fogg, it can be as easy as warming up the product and go, according to the company. Fogg’s proven technology is intended to lower operating costs and to provide reliability for the production lines. www.foggfiller.com Time saving by fast conveying mandrel changeovers In developing a new fast changeover concept KHS has greatly reduced changeover times on its InnoPET Blomax stretch blow moulders. The optimised active mandrel now enables format changeover times to be reduced by more than half for all standard neck designs. This new option is of interest to all beverage producers who bottle products with different types of neck. During a format changeover operators not only switch over the blow moulds but other components as well. The conveying mandrel in particular is of especial significance in this process as a full changeover of these format parts was extremely time-consuming to date. “Depending on its size a high-performance Blomax stretch blow moulder can have around 280 conveying mandrels,” explains Marco Böhnke, product manager for stretch blow moulding technology at KHS. When a product is changed over during beverage production and requires a change in the type of bottle neck, to date each individual mandrel had to be exchanged in its entirety. KHS has now developed a variant which is much quicker to replace, making changeovers ergonomic and tool free without any great force being required. Besides the conveying mandrels the shields, grippers and other parts can now also be easily switched over using quick-change mechanisms; in some cases these can be adjusted without any installation work being required by simply rotating the part. Thanks to the above measures formats can be changed over in less than half of the time operators used to need. In its new development KHS has retained its tried-and-tested active mandrel design. “The optimised changeover process is distinguished by the fact that only the actual format part, i.e. the mandrel head itself, is replaced, with the entire mandrel mechanism left untouched. This enables customers to save money and gain valuable production time,” states Böhnke, as a mandrel can now be replaced in about 5s. The new procedure can be easily retrofitted on any InnoPET Blomax Series IV stretch blow moulder as following one-time adjustment of the conveying mandrels no further mechanical or electrical conversion of the machine is required. One KHS customer has already subjected the quickchange process to successful long-term testing. The system is also to be installed at a company on the German market in the near future. www.khs.com .com 100815dmyL Go with the flow. September 11-15, 2017 Messe München Hall: A4 Booth #232","@ID":84}, "58 TRADE SHOW PREVIEW PETplanet Insider Vol. 18 No. 09/17 petpla.net PROCESS PILOT® makes producing a better PET bottle as easy as 2 3 1 MEASURE CONTROL OPTIMIZE every bottle for changes in material distribution process variation, inside the blowmolder material utilization and orientation to achieve maximum bottle performance CONTACT US TODAY TO LEARN MORE! AGRINTL.COM | +1.724.482.2163 | [email protected] see us at Booth A4-336 Now its Drinktec time! To conclude our summery of the PET relevant exhibitors we invite you to enjoy reading our third part of the Drinktec preview! At this point we would like to advise you to one further event at the trade fair: The BevTech Europe technical conference. The theme of the 14th BevTech Europe is “Innovation and Technology in the Beverage Industry” and the program will be packed with interesting topics, delivered by subject matter experts in the different areas of interest in the industry. It addresses all beverage manufacturers and suppliers and promotes dialogue on the scientific and process-oriented aspects of manufacturing non-alcoholic beverages. That includes beverage recipes, production processes, packaging, operating materials and distribution. The conference is a genuine highlight, and not just for technicians. BevTech Europe is part of the International Society of Beverage Technologists (ISBT). ISBT is a technical society for the Beverage industry and is an originator of critical technical methods, standards and guidelines adopted by major corporations, other societies and governments around the globe. The topics are: Research and development for beverages and ingredients/ additives Equipment for retailers/specialty retailers and fountain technology Beverage gases Hygiene and microbiological control Beverage handling and processing Sweeteners Packaging technologies Water quality and treatment Quality assurance Packaging technologies Water quality and treatment Quality assurance We wish all of you an exciting and successful Drinktec 2017! We cordially invite you to visit our booth (Hall 4A, booth 501) to have some nice talks with the PETplanet Insider team! TRADE SHOWpreview Preform range PDG Plastiques is specialised in PET preforms and bottles with a focus on dairy and UHT milk. During Drinktec the company will propose new packagings for UHT milk, drinks and other liquids. In particular, light weighting of PET preforms and bottles and also new designs. The new technology Prelactia 2.0 allows to decrease opaque component in material in order to improve recycling of UHT milk bottles, says PDG Plastiques. The new technology Mint-Tec is claimed to allow decreasing of weight of PET preforms without decreasing the mechanical strength of the bottle. An increased range of PET preforms for standard products will also be on display. www.pdg-plastiques.com Hall A4 - Booth 349","@ID":60}, "PETpatents www.verpackungspatente.de PETplanet Insider Vol. 18 No. 09/17 petpla.net 88 Improved opening Internal Patent No. WO 2017 / 013226 A1 Applicant: Nestec S.A., Vevey (CH) Application date: 21.7.2016 A problem with popular hinged lid closures is the limited angle of opening, which hampers direct extraction of the product. The application describes a closure with an “extended” hinge, which simplifies extraction but does not protrude beyond the outer shape when the bottle is closed. Bottle and container Internal Patent No. WO 2015 / 121560 A1 Applicant: Sidel Participations, Octeville-sur-Mer (FR) Application date: 28.1.2015 Unusually shaped PET bottle, which can be dovetailed together with several similarly shaped bottles to make an attractive and “small-volume” display. Stackable container Europ. Patent issue No. EP 2640646 B1 Applicant: Pet Engineering & Services Srl., Grassobbio (IT) Application date: 27.10.2011 The design and structure of an easily stackable plastic keg is awarded a European patent. Movable base Europ. Patent No. EP 3109176 A1 Applicant: Sidel Participations, Octeville-sur-Mer (FR) Application date: 23.6.2015 On a hot-filled PET bottle, which cools/is cooled after filling, the base shape must absorb the forces arising from cooling so as to prevent any excessive and visually negative distortion of the bottle body. Bottle Europ. Patent issue No. EP 2752369 B1 Applicant: Yoshino Kogyosho Co. Ltd., Tokio (JP) Application date: 29.8.2012 The shaping and manufacturing procedure for a hot-filled, lightweight plastic bottle with a base that absorbs vacuum forces is awarded a European patent. Aerosol canister Internal Patent No. WO 2017 / 021038 A1 Applicant: Coster Tecnologie Speciali S.p.A., Calceranica al Lago (IT) Application date: 14.6.2016 PET aerosol canister with improved closure plate and valve seat for a liquid, pressurised product. The performance of the canister has been optimised for water tightness and manufacturing.","@ID":90}, "PETnews 6 NEWS PETplanet Insider Vol. 18 No. 09/17 petpla.net Gabriel-Chemie increases production capacity in Russia The Austrian Gabriel-Chemie Group has been operating successfully with its own subsidiary in Russia since 2007. Due to the steadily growing business and the increasing demand for masterbatch in the Russian region and the neighbouring countries of Azerbaijan, Kazakhstan and Belarus, it was necessary to adjust the production capacity of Gabriel-Chemie Russia to the future requirements. On August 3, 2017, Gabriel-Chemie CFO Andreas Berger and the Governor of the Kaluga oblast Anatoly Artamonov signed an investment agreement concerning the construction and operation of a masterbatch plant in the Vorino industrial park in the Kaluga oblast. On the 27,000m2 grounds in the Vorino industrial park, a modern masterbatch production facility is to be built in four construction phases. The completion of the first section and the relocation from the existing location in Dorokhovo (Moscow region) are planned by the end of 2018. During the first stage, around 260 million roubles will be invested in the new location and modern, environmentally friendly production technology with a capacity of 2,000t/a. The maximum production capacity can be increased step by step to 20,000t/a until after completion of all construction phases. The 2,000-hectare industrial park Vorsino is about 90km southwest of Moscow city centre and attracts numerous Russian and international corporations, due to its good infrastructure and transport connections. www.gabriel-chemie.com U.S. imports of plastic bottles topped $937.9 million last year The U.S. exports of plastic bottles nearly doubled from $387.2 million in 2003 to $766.1 million in 2012. On average, the annual growth of plastic bottles exports from the U.S. was 8%. In the last four years, however, it started to decrease in sync with the overall decline in U.S. total exports due primarily to the weaker economic environment of U.S. trading partners and the strengthening of the U.S. dollar. A strong dollar makes U.S. goods more expensive - a bane for U.S. exports, but a boon for imports into the U.S. Early this year, however, the U.S. dollar began moving slowly below its prior high, after it started appreciating from 2014 to 2016, to a stable rate vis-à-vis major foreign currencies. Rising imports of plastic bottles into the U.S. and falling exports means the trade deficit in plastic bottles is growing. As of June this year, the U.S. trade deficit in plastic bottles was $151.6 million - already more than half of last year’s total deficit. In 2003, the U.S. trade surplus in plastic bottles was $2.4 million. In earlier years prior to 2003 it was even higher, ranging to a high of $89.1 million between 1992 and 2002. The U.S. imports of plastic bottles last year topped $937.9 million - more than doubled from $441.2 million when U.S. began experiencing a trade deficit in plastic bottles in 2004. Such a dramatic increase in imports over time can be attributed to higher demand for bottled beverages in the U.S. which is nicely complemented more recently by the U.S. ability to import more due to the stronger U.S. dollar in recent years. The popularity of bottled water, the demand of which has surpassed the demand for carbonated drinks, and the influx of fruit juices into the U.S. market have contributed to higher plastic bottles imports into the U.S. Both imports and exports of plastic bottles into, and from, the U.S. are expected to stay positive as part of an increasing trend of global production of plastics containers that is estimated to reach 67.9 million metric tons by 2020 according to Research and Markets. As the U.S. continues to experience a demographic shift - ageing baby boomers and a rising number of health conscious millennials who appreciate portable products - the production volume of plastic bottles, particularly for beverages, can be expected to increase. The positive growth in bottling manufacturing and imports is part of why NPE2018 will feature the Bottle Zone, a dedicated section of the trade show floor full of supply chain solutions for the bottling industry. The Plastics Show returns to the Orange County Convention Center in Orlando, Florida, USA May 7-11, 2018. www.NPE.org/Bottle-Zone Gabriel-Chemie CFO Andreas Berger and Governor Anatoly Artamonov signing the investment agreement","@ID":8}, "PACKAGING / PALLETISING PETplanet Insider Vol. 18 No. 09/17 petpla.net 53 according to the desired cycles and the size of the system. “For this, the various keg processing times have to be taken precisely into account in each of the processing steps,” Daum explains. Keg stoppers ahead of the processing machine space the containers required distance apart before they enter the machine. The conveyors also play an important role in this fine-tuning: the length of the conveying segment is adapted according to the exposure time specified by the customer for the kegs filled with caustic solution between pre-washing and main washing steps. The KHS Innokeg AF-C is suitable not only for returnable kegs: one-way kegs, also PET kegs, can optionally be racked without changing over the line. The user does this by switching off the keg washers so that the kegs pass through the machine to the racker. “This is ingeniously simple,” remarks Daum while emphasising that this kind of flexibility has not been offered on the market to date. The system has been designed for medium-sized companies be operated by a tablet or smartphone using the latest in control technology. Changes to the production process, such as changeover to a different keg type or product are thus easily completed. It is also possible to shut down the line at the end of production and to start CIP cleaning. www.khs.com The conveying segment of the Innokeg AF-C from KHS is centred between the processing stations. and larger bottling plants. In addition to beer, it is also possible to rack wine and carbonated beverages. The IO-link technology used in the Innokeg AF-C reduces the cost of installing the wiring by up to 50%. This also noticeably shortens the time required for installation. The AF-C can SGT Dairy products Syrups Carbonated drinks Wines Naturally Innovative Meet us at September 11 - 15, 2017 Messe Munchen Hall A4 Stand 330 New range of multilayer PET preforms to maximize beverage shelf live. Société Générale des Techniques 3 rue de l’Île Macé - 44 412 Rezé - France www.sgt-pet.com [email protected] + 33 (0)2 40 05 09 37","@ID":55}, "TRADE SHOW PREVIEW PETplanet Insider Vol. 18 No. 09/17 petpla.net 70 Handling technology with a new approach on conveying and accumulation Product handling all-in-one The packaging industry is increasingly facing sophisticated consumption trends that present various challenges to the production and distribution of goods. Gebo Cermex is responding to these ever-changing complex needs with the introduction of the product handling technology AQFlex. Packaging line performance of this new system is offered together with agility and contactless product conveying and accumulation, in a compact space. With packaging quality playing a key role in brand recognition and ever-increasing production diversity, a growing number of stock keeping units (SKUs) and even product and secondary packaging personalisation now possible, manufacturers are looking for improved flexibility and responsiveness from their existing packaging systems. Easy re-engineering of existing lines is also important if producers are to easily adapt to big changes in demand. Producers and brand owners are therefore becoming increasingly demanding when it comes to their line requirements. They look for packaging solutions that are space-saving, easy to maintain, ergonomic in design, simple to use and sustainable. In face of these ever changing demands, Gebo Cermex claims that the product handling system AQFlex would help manufacturers meet all their current performance objectives, as well as prepare for the challenges of tomorrow. According to Gebo Cermex, AQFlex is designed as a new concept in packaging solutions that accommodates any product, whatever the application, whatever the market, in all container materials, formats and shapes, full or empty while also enabling automatic changeovers via an intuitive and user-friendly Human Machine Interface (HMI). Care of product integrity is ensured by the single-lane, contactfree product handling and accumulation system that is able to process even fragile, unstable or premium containers. First-in, first-out operating principle The system is able to operate at any speed, from 1,000 to 100,000 containers per hour, delivering energy savings of up to 60%, without compromising high efficiency (99.5% even at high speeds) or sustainability, says the company. This is ensured by high line performance regulation, together with a high accumulation performance to maintain continuous product flow - at any speed with the use of advanced robotics based on a proven logic motion technology. A centralised system architecture ensures the accurate synchronisation of motion control for all the servo axes of the equipment. Ludovic Tanchou, Vice President Strategy, Products and Innovation at Gebo Cermex says: “Moreover, for greater product traceability and continuous control of production quality, the solution works according to a ‘first-in, first-out’ (FIFO) operating principle.” Up to 40% space saving All the conveying functions of AQFlex, including contactless accumulation and multilane machine infeed, are regrouped into this single handling solution. As all conveying and accumulation is carried out as a single-file process, the usual peripheral conveying functions associated with mass accumulation - such as deceleration, de-grouping, combining and laning - are eliminated. Its compact design provides up to 40% space savings compared to traditional solutions and can be easily integrated into existing production lines. The solution has a clear and open design that gives full accessibility at floor level for enhanced ergonomics and easy cleaning. Having only a few added mechanical parts compared to a conveyor, maintenance of AQFlex can be compared to that of a standard conveyor - without the need for any lubrication. www.gebocermex.com Hall A6 - Booth 330","@ID":72}, "83 PRODUCTS PETplanet Insider Vol. 18 No. 09/17 petpla.net Shoe care for Adidas Originals in rPET A new shoe care range has been launched by the brand Adidas Originals in collaboration with Gizeh PET: the plastic packaging specialist developed two new PET containers featuring a high-end design for the new range. The target group: sneakerheads. The development work on the two bottles focused on the quest to create a high-end design that was consistent with the brand’s image. “The product’s target group is very urban, trend-focused and fashion-conscious”, said Daniel Rüth, Head of the PET Division at Gizeh. “As a result, the containers had to meet high standards in terms of appearance and function.” The clear and streamlined design of the two bottles is a real eye-catcher. The semi-transparent brown colour creates a medicinal look that adds an additional element to the high-end design. The corporate philosophy of the customer, BNS Bergal, attaches particular importance to environmentally friendly packaging. Consequently, both containers consist of 100% rPET. Gizeh PET is producing a 100ml and a 200ml container for the Adidas Originals shoe care range. The 100ml bottle contains “Suede Liquid”, a product used to treat suede shoes, and features an integrated sponge applicator. The cap is attached to the bottle using a blow-moulded clip mechanism. This posed the challenge of designing a reliably secure clip mechanism, in spite of the production tolerances of the cap, that was also user-friendly in terms of how easy it was to open and close again. The crimped 200ml container holds a waterproofing spray and features a pump element covered with a cap. The pump element is fixed using a snap-on mechanism, i.e. is slid over a clip mechanism and clicks into place. Once again, the clip mechanism had to be designed so as to ensure that the combination of the bottle and the cap would be completely sealed while ensuring that putting the cap on the container would not require too much force and that the pump could not end up coming off the container during use. The new care products in the Gizeh PET bottles were unveiled in July 2017 and have been exclusively available in sneaker stores stocking Adidas Originals ever since. The care products are produced by BNS Bergal, a company in the Werner & Mertz Group, which also includes the Erdal and Frosch brands, among others. Gizeh PET has already been working withWerner &Mertz for some time now. The company developed containers for the market launch of the cosmetics range “Frosch reine Pflege” and the designer washing-up liquid range “Frosch Aloe Vera”. www.gizeh-pet.de","@ID":85}, "CAPS & CLOSURES 51 PETplanet Insider Vol. 18 No. 09/17 petpla.net have to be securely attached to the closure base to prevent pollution and choking on the cap. The closure cap used in this example already conforms to coming EU requirements: the hinge is securely welded to the body by laser. Production: First, the overcaps have to be fed in and oriented. Contexo uses servo technology to align the caps according to the hinge’s location, and position them over the body-spout module. At the same time, the hinge pin is precisely inserted into the body and welded in place by laser. A final check for captivity completes production of this closure. Product life cycle: modular platform system Because today complex closures frequently come to market with new beverage products, a beverage’s success leads to a sudden increase in the number of complex closures demanded. A flexible platform that can adapt to the new required output is therefore critical. For this reason, Contexo has developed a modular platform system capable of widely different output rates within a short period of time. It also handles the various phases of the product’s life cycle: Market launch: Contexo builds its machines for this phase primarily around the highly economical rotary indexing system. European market: Should the product start to become successful on the European market, multi-lane linear indexing machines are the best choice. Global market: If a small installation Continuous-motion assembly machine: the technology allows high output rates on a small footprint. Scan QR code for more information: Scan & Measure Oxygen Ingress & Transmission Rates Fibox 4 Stand-alone fiber optic oxygen transmitter footprint is required for global production, Contexo switches to continuous-motion technologies. The modular platform system allows existing stations and tools to be transferred to new machines. This enables economical adaptation to changing output amounts. The key to success: innovative technology combined with a flexible platform system This overview of the assembly process shows how the number of automation tasks increases in the production of complex closures. New technologies are a requirement. But to bring closures to market successfully, it is also important to develop a platform system that enables quick adaptation to changing output needs. www.contexo-automation.com","@ID":53}, "PETplanet Insider Vol. 18 No. 09/17 petpla.net 86 PETbottles Home + Personal Care Spray to braid the hair Hair care specialists are introducing new products onto the market in keeping with current trends in hairstyling. The most recent example is a “long-lasting braid spray” that hairdressers can apply to hair that is fixed in braids or in a bun. The product, which is marketed under the dm brand “Balea”, can be sprayed on damp and dry hair before braiding and comes in a lightly coloured 150ml bottle with a screwed-on pump dispenser and protective cap. www.dm.de Blue Lotus for long-term volume The Guhl brand which forms part of the Kao group is selling a special Vitamin Complex 150ml Fohn Active styling spray as part of their “Long-term volume” Blue Lotus range. It comes in a slim, clear, light-blue coloured and easy-to-grip 150ml PET bottle with a screwed-on silver pump dispenser and transparent protective top. The product can be applied to the hair before being blow-dried, strengthening the hair with each application. www.guhl.com Shampoo with bamboo Ogx is continually expanding its product range in Germany with new varieties of an already brand-typical bottle shape. One example of this is a shampoo that contains bamboo and soya ingredients. It strengthens the hair, making it more voluminous and full-bodied. It comes in a familiar, bulbous 385ml green coloured bottle with a useable gold-hinged cap. A non-look label on the front and a fold out label on the back contain the necessary product information. www.ogxbeauty.com","@ID":88}, "INSPECTION 42 PETplanet Insider Vol. 18 No. 09/17 petpla.net Agr system takes sting out of producing the Cisowianka ‘Wasp-waist’ bottle by: Ewa Prokulewicz, Sales Coordinator, Agr Europe, Aleksander Broda, Regional Director CE Europe & UK, Agr Europe, David Dineff, Global Marketing Director, Agr International, Inc. A three-year collaboration with Agr has helped Nałęczów Zdrój S.A. take a proactive approach towards their quality management program with the integration of Agr’s Process Pilot automated process control system. With Agr’s assistance, Nałęczów Zdrój S.A. was able to overcome the environmental and quality issues that challenged the production of their unique ‘wasp-waist’ bottle for the Cisowianka product line. Nałęczów Zdrój S.A. is a company with a tradition that extends more than 35 years in the business of bottling water. The plant is located in southeastern Poland in the village of Drzewce, approximately 6 kilometers from the spa town of Nałęczów noted for its “healing waters”. Waters from the Nałęczów aquifers are exceptionally pure and have very low sodium content. The Nałęczów Zdrój plant sits atop these same aquifers and draws from five locations to produce its three brands: Poland’s most popular mineral water Cisowianka (together with Cisowianka Perlage), export brand Perlage and Nałęczów Zdrój. The mineral water is sold not only in Poland, but also all around the world – USA, France, Italy, Japan, China and many others. Demand for products of Nałęczów Zdrój has been growing rapidly. At the same time, the challenge of meeting production while maintaining the quality of their packaging has grown along with this demand. Facing these challenges, the company turned to Agr International to provide a solution to managing the quality and, at the same time, production efficiency of their bottle blowing operation for the Cisowianka product. Bottling operations Nałęczów Zdrój operates one glass filling line for non carbonated Cisowianka and seven PET lines for a production capacity of 2,800,000 bottles per day across a broad volume range. Five PET lines are used for filling 1.5l bottles, the remaining two for the 0.5l, 0.3l and 0.7l ‘sport cap’ bottles, and for the 0.7l Perlage bottles, respectively. All PET bottles are produced in house, blown on the spot from preforms sourced from thirdparty suppliers, including those produced on two KHS Blowmax Series IV blow-moulding machines, the newest editions to their production operation. Quality is of prime importance With such large production volumes, regular and accurate quality control procedures performed at all stages of the production process are the key to maintaining the high quality standards that Nałęczów Zdrój is famous for. This includes not only the purity and quality of the water but also the packaging that protects the product, which must maintain its pristine appearance through the chain of distribution into the hands of the consumer. Grzechorz Nachowicz, Head of Technical Department at Nałęczów Zdrój, explains that they take quality seriously with rigid quality control routines applied in the production of Cisowianka. “In a nutshell, our quality control is a three-step process. Stage one is the operator’s self-check. Stage two takes place at the quality control department, where the quality control personnel conduct an end-to-end check, including preforms, caps and labels to verify that they are suitable for production purposes. And stage three, which takes place either simultaneously with the production process Cisowianka 1.5 l ‘wasp-waist’ bottle for lightly carbonated water – made from a 30.5g preform","@ID":44}, "TRADE SHOW PREVIEW 75 PETplanet Insider Vol. 18 No. 09/17 award at the 2017 Motion Control Industry Awards, Robuschi’s Robox triple-impact energy screw compressor is claimed to be ideal for energy-intensive wastewater treatment and processing plants, offering savings of up to 30%. The smart process control tool with HMI interface optimises airflow and is essential in achieving the energy savings so important in reducing life cycle costs. The new machine has a smaller footprint than comparable equipment and can installed easily in existing compressor rooms, helping to avoid additional capital expenditure, says the company. Vacuum pump, side channel blower and liquid ring pump Elmo Rietschle will be exhibiting three key products: the S-VSI 300 screw vacuum pump, G-2BH1600 side channel blower and L-SV 2SVT liquid ring pump. Driven by two parallel screw rotors, the oil-free S-VSI range can achieve an ultimate vacuum of 0.1mbar, while its low rotational speed ensures low noise and vibration throughout operation. The S-VSI range’s contact-free technology ensures constant vacuum performance, while minimising maintenance and the associated downtime and costs, delivering greater productivity as a result. Robust yet lightweight, the G-Series side channel blower range is available in a range of performances up to 3,000m3/h, with differential pressures offered up to 1,000mbar. Suitable for even extreme conditions, the L-SV 2SVT liquid ring pump uses highquality materials such as stainless steel and ceramics to resist corrosion and abrasion, offering a reliable pump solution for the beverage and liquid food market. www.gardnerdenver.com www.sukano.com AdditiveMasterbatch Solutions for Recycled PET Enhance appearance and performance with color correction, density reduction, improved impact and melt strength. Products available with food contact approved PCR carrier to help meet PCR content goals. The Ultima compressor is part of the PureAir series from GardnerDenver.","@ID":77}, "81 PRODUCTS PETplanet Insider Vol. 18 No. 09/17 petpla.net PETproducts Disruptive PET container with integrated handle Pretium Packaging, a North American manufacturer of plastic containers and closures, using technology from Practically Impossible Labs, Houston, Texas, has developed a 64-ounce, 38-400mm finish, stock PET container with an integrated handle. Trademarked, the SureHandle PET container, this disruptive commercialisation is intended to give brand owners shelf differentiation, handling convenience and aesthetics. SureHandle containers create multiple marketing opportunities for brand owners seeking to appeal to a wider audience. The container is claimed to be easy to handle for both younger children and older adults, and those with physical challenges, compared to pinch grip or straight-sided alternatives. The handle not only provides carrying advantages, but also improved pouring control. It has been engineered for products needing fill temperatures up to 120° Fahrenheit (48.9°C) and can accommodate an induction seal or foam liner. Additionally, the container has been designed with enhanced top load capabilities. This enables the use of a shrink wrapped tray pack (vs. a corrugated case) which can withstand stacking of five layers to a pallet, four pallets high. Using a tray pack can potentially reduce secondary packaging costs by up to 80%. This also means easier unloading at the retail level, as well as retail-ready displays for big box stores. The end result is a cost-competitive container alternative, with convenience benefits and reduced secondary packaging. “There have been a variety of attempts over the years to develop handled PET containers, but most have fallen short of the mark. This new technology creates all sorts of possibilities for products - including beverages, foods and household and industrial chemicals - that could benefit from a monolayer container with an ergonomic handleware solution” said Paul Kayser, president and chief executive officer, Pretium. The container combines preform technology developed by Practically Impossible Labs, and Pretium’s injection and blow moulding manufacturing expertise. The capability begins with the preform which is structurally different than traditional straight-sided, injection moulded preforms used to blow mould PET containers. This preform features an injection moulded handle attached to the side wall. The integrated-handle preform is loaded in the same manner as a conventional preform. Proprietary enhancements have been made to standard blow cavities to accept and position the handle during the blowing process. Because no secondary operation is required to add the handle to the container, the end result is increased structural integrity. Pretium will be producing the preforms and bottles at its Walterboro, South Carolina facility on Husky Injection Molding Systems and Sidel reheat stretch blow moulding equipment, respectively. www.pretiumpkg.com","@ID":83}, "INSPECTION 43 PETplanet Insider Vol. 18 No. 09/17 petpla.net INSPECTION 43 or afterward for the quality control of finished goods. This is to make sure that the client receives a thoroughly tested product, so that we can rest assured that our products are of great quality and will cause no harm to consumers.” Proper material distribution – key to consistent production The company’s biggest quality-related achievement to date – and, at the same time, the greatest challenge – has been maintaining the consistent quality of bottles. Even the slightest variation in temperature between two sections in the production facility will change the conditions significantly affecting material distribution, and the overall quality of the bottles. And, depending on the time of day or season of the year, the temperature variation of the preforms can be significant. The company came to a conclusion that correct distribution of the PET material is the key to optimum bottle performance as well as downstream production efficiency. As a result, they decided to invest in equipment to help manage the fluctuations in material distribution that affects the quality of its products. This came into play when the two newest production lines were installed to meet the growing demand for the Cisowianka product. When the decision was made to invest in these lines, the ability to proactively manage material distribution was a key criterion. With Sacmi, the beverage specialists are always at your side. With our unbeatable technological know-how and continuous research we are creating new containers and closures designed to ensure outstanding performance. The new IPS injection system for preforms, the CCM compression press for caps and the quality control systems fully designed and built by Sacmi, allows for large-scale production with considerable advantages in terms of efficiency and flexibility. The outcome? Reduced plastic volumes, less energy consumption and lower running costs.All in a bottle: the one you’ll soon be making. DRINKTEC,11/15.09.17 |HALLB5 -302|MunchenGermany SIMEI,11/15.09.17 |HALLC3 -209|MunchenGermany PROPAKMYAMAR,21/23.09.17 |Yangon,Myanmar PACKEXPOVEGAS,25/27.09.17 | LasVegas,USA SINGLE-SERVECAPSULES2017 |10/11.10.17 |Cologne,Germany HOST,20/24.10.17 |Milan, Italy IPF JAPAN,24/28.10.17 | Tokyo, Japan GULFOOD,31.10-2.11.17 |Dubai,UAE THEPLASTICCAPS&CLOSURES,8.11.17 |AmsterdamCity, TheNetherlands CBST,22/24.11.17 |Shanghai,China ‘Wasp-waist’ bottle for still water – made from a 27g preform Cisowianka 1.5l production line","@ID":45}, "61 TRADE SHOW PREVIEW PETplanet Insider Vol. 18 No. 09/17 Hall A4 - Booth 500 Colour explorers Repi, multinational producer of liquid colours and additives for plastics, will present its focus on plastic packaging applications. If flexibility, product safety, sustainability and ease of operation are the key words for the packaging industry, then Repi claims to be on track. Flexibility because liquid colours and additives allow for quick colour change making it possible to run small production batches in a limited timeframe. Additives can be added to PET when necessary (to give protection as well as enhanced performance to the product) without limiting nor affecting production schedules. Moreover liquids are normally dosed at so low LDR that with a limited amount is enough for large productions. Safety because each step of Repi’s production process is controlled and monitored according to the international requirements. A risk assessment procedure is implemented for a 360 degree quality insurance. Sustainability because having the freedom to switch from a colour or an additive to another in a very short time reducing to the minimum material and time waste is synonymous of a more efficient and economical way to produce on the long run. Ease of operation because besides liquids, Repi also offers reliable dosing equipment which have a total control on the dosing process and the Light Meter, an analysis instrument which ensures the product has the right colour and performance properties before going to the blowing stage. It’s with these preconditions that the barrier line for long life (UHT and ESL) dairy product applications was developed allowing monolayer containers to extend products’ shelf life by providing the right protection from light degradation. The same care is behind the UV additive ranges, formulated to meet customers’ specific protection requirements, enabling them to avoid over specified and expensive solutions. As a result the packaging solution is cost efficient and provides exactly the right protection every time, says Repi. And it’s having a particular attention for customers’ needs and future that the Light Meter upgraded version has been designed. www.repi.com","@ID":63}, "TRADE SHOW PREVIEW PETplanet Insider Vol. 18 No. 09/17 petpla.net 69 Husky to feature its Multi-Layer Technology with a system running on its booth Multi-Layer live on stage Husky Injection Molding Systems will be featuring its Multi-Layer Technology and will be running a system with this technology for the first time at a tradeshow. Since its introduction in 2015, the company has sold more than 20 Multi-Layer systems around the world for a breadth of applications including CSD, juice, sparkling water, beer, tea, dairy, food and personal care. As the momentum for this technology continues to grow, the company anticipates an increased demand from customers looking to explore new applications. Husky’s Multi-Layer co-injection technology at Drinktec will be running on the company’s proven HyPET HPP5 fully integrated preform manufacturing system. The system will be producing a 17g carbonated soft drink application using a 72-cavity mould and running at an 8.7s cycle time. Also on display will be many new solutions related to Multi-Layer, including a fully integrated solution for preform inspection that Husky developed in partnership with Intravis Vision Systems. The integrated LayerWatcher preform inspection system automates the assurance of barrier protection and package security. The Husky system will also demonstrate the company’s automated Mold Alignment feature, as well as the awardwinning self-cleaning Mold Technology, which is claimed to significantly reduce downtime by eliminating hundreds of hours of mould maintenance per year. Live demonstrations of the system are set to take place every day of the show. Understanding consumer trends and being the first to deliver novel innovations that, through close partnerships with its customers, allows the company to respond to shifts in the market that create opportunities for packaging growth is something significant for Husky. “What is different today, is that consumers are demanding more variety. They are more health conscious and are quick to respond to trends. They expect increasingly higher quality,” said John Galt, President and CEO of Husky. “We are evolving the way we do business to get ahead of these trends and help our customers make plastic packaging more cost effective, more functional and more attractive. Our Multi-Layer Technology is a prime example of how we do this.” Complete package Husky is the industry’s only supplier of complete manufacturing solutions for both PET preforms and closures. This position allows Husky to work closely with customers to deliver closures and preforms that are precisely engineered to work together as an integrated, high-performing package. To demonstrate its capability, Husky will be showcasing industryleading manufacturing technologies and its global packaging development capabilities, along with an extensive range of proactive services aimed at optimising performance and extending the life of its manufacturing equipment. Husky will also showcase solutions that promote improved package sustainability, having been developed though collaboration with key industry partners. www.husky.co Hall A4 - Booth 338","@ID":71}, "PREFORM PRODUCTION PETplanet Insider Vol. 18 No. 09/17 petpla.net 15 Zatti: To start with, we are building systems completely at the machine manufacturer site and running it in. For future development, Mr Hofstetter has bought a 20,000m² site in Uznach. We will see. PETplanet: Already two years ago, Yudo presented preform hot runners and moulds on the NPE 2015. Are you not concerned that as a small Swiss company, you will be crushed by the Asian giant? Zatti: I don’t think so. The JV is a 50:50 arrangement so both partners are on an equal footing. First of all, we will integrate the robots from YudoSuns and we combine the best of the Hofstetter Hotrunner technology with the Yudo technology in one system. PETplanet: A personal question to finish: you have been working for the Hofstetter family for more than 20 years and are now yourself a CEO. How does that fit together? Zatti: I am currently wearing two hats. On the one side I am responsible for sales for Otto Hofstetter and The machinery base from BMB with Piovan dryer, Yudo extraction robot and an Otto Hofstetter tool And a picture to remind us of the control system display on the other side for the establishment of Otto Systems. It works very well, although I sometimes wish there was more time for Otto Systems. PETplanet: I wish you every success. www.otto-systems.com","@ID":17}, "BOTTLE MAKING 27 PETplanet Insider Vol. 18 No. 09/17 petpla.net Management has decided to put additional investment into its Taiping plant where in-house manufacture of preforms is achieved by using HuskyHypet injection moulding machine. In all, fifteen bottle lines are filled by Spritzer. At the beginning, there were Western manufactured stretch and blow systems, followed by Asian bottling systems and stretch wrap made by various Western manufacturers. Each bottle is tested inline to ensure nothing goes wrong with the mix. Spritzer has introduced a small, yet excellent, portfolio of beverages other than water, ranging from soda and flavoured water to more functional drinks. Two years ago Spritzer Management Team decided to bring in large recyclable PET containers as an alternative to PC five-gallon ones – indeed, PC is no longer used in Malaysia. Ms Chong Mee Yoong, Spritzer’s Deputy General Manager, is considering expanding into aseptics. “That would allow us to broaden our portfolio in areas where we have not hitherto been active”, she says. Perhaps aseptic bottling will be the next big step for Spritzer Berhad. www.goldenpet.com.my www.spritzer.com.my mer’s disease. Consequently, Spritzer is now also sold as a health drink in the UK. Although Golden PET continues to earn money from preform bottles and caps that are manufactured for a variety of different uses, Spritzer Berhad During a visit of manufacturers to the bottling plant, the number of flawless products are counted at the end of the process.","@ID":29}, "MARKET SURVEY 48 PETplanet Insider Vol. 18 No. 09/17 petpla.net Resins 09/2017 MARKETsurvey Company name Neo Group Indorama Ventures Ltd Postal address Telephone number Web site address Contact name Function Direct telephone number Fax E-Mail Industrijos str. 2, Rimkai LT-95346, Klaipeda district, Lithuania + 370 46466 710 www.neogroup.eu Mr Gediminas Paulauskas Sales Manager +370 686 73401 +37046466711 [email protected] 75/102 Ocean Tower 2, 37th Floor Bangkok 10110, Thailand +662 661 6661 www.indoramaventures.com Mr W.G. Hoenderdaal Technical Marketing Manager +316 51809942 [email protected] RESINS Europe USA/Canada 1. Brand name of the resins NEOPET RAMAPET Polyclear PET Oxyclear Barrier PET Oxyclear Shield PET Preformance PET 2. IV range a. of homo-polymers 0.56 - 0.82 IV 0.58 - 0.95 IV 0.58 - 0.95 b. of co-polymers 0.76 - 0.84 IV 0.58 - 0.84 IV 0.58 - 1.08 3. Speciality resins CSD NEOPET 80, NEOPET 82 R1, R182C, R180 ES11, ES11 (A)-R10, 1101 Water Aqua NEOPET 76, NEOPET 78 N180, W176, W170, N1, N1(S) N2R, N2R (A)-R10, N2R-Ti, 3301 Beer NEOPET 80, NEOPET 82, NEOPET 84 N1, N1(S), N180 Oxyclear Shield PET 2310 Wine / liquors NEOPET 80, NEOPET 82 N1, N1(S), N180 1708CC, 3302, Polyclear EBM PET 5505 and 5507; Oxyclear Barrier PET (3500, 2700 2510) Personal care / pharmaceuticals NEOPET 80 N1, N1(S), N180 1708CC, 3302; Polyclear EBM PET Slow crystallisation P184 T-94-Ti Hotfill NEOPET 82 HF R1, HF 1708HS, 2201 Pre-coloured Fast reheat NEOPET 82 FR, NEOPET 84 FR R1, R182C, R180 ES11, 1101 Other Ultra NEOPET R182C PlantPET (bio) PlantPET resin (Bio-MEG) 4. Increased barrier properties Oxyclear Barrier PET ( 3500, 2700 2510) OxyClear Shield PET 2310 5. PEN mixes available Yes PolyClear Heat 2222, 2224, 2226 6. Recycled blends available r-PET flake and granulate FuTuRe-PET Resin PolyClear Conserve PET 7. Special comments","@ID":50}, "The whole world of Congresses PET symposiums and lectures WikiPETia.info PET knowledge management system Pulse The monthly PET price index Worldwide PET magazine Social Media Connecting worldwide No.4 2016 ZZZSHWSODQHW ' ,661 25.04.16 PETplanet LVUHDGLQPRUHWKDQ 140FRXQWULHV MAGAZINE FOR BOTTLERS AND BOTTLE-MAKERS IN THEAMERICAS,ASIA, EUROPEANDALLAROUND THE PLANET BEVERAGE +ingredients Page 10 MARKETVXUYH\\ 6XSSOLHUVRI UHVLQVDGGLWLYHV Page 27 ZZZSHWSODQHW petpla.net D 51178; ISSN: 1438-9452 No. 9 2016 PETplanet is read inmore than 140 countries MAGAZINE FOR BOTTLERS AND BOTTLE-MAKERS IN THEAMERICAS,ASIA, EUROPEANDALLAROUND THE PLANET 07.09.16 MARKETsurvey Bottle-to-bottle recycling plants Page 41 TheChinaRoadShow Page 12 bottlemaking Page 21 Page 52 PETplanet is read in more than 140 countries News Daily PET business news Editours Worldwide editorial reporting petpla.net WHY PETPLANET? For more than 17 years, PETplanet Insider has been the world’s leading magazine for the PET bottling and bottle-making industry, bringing together machine manufacturers and their customers – directly, with up to date on-site reports at customer plants, providing first hand information on the latest developments and trends. Our market reports and surveys, along with interviews with the major players in the industry give our readers an excellent overview of what is happening in the world of PET. PETplanet Insider continues to be the highly specialised source of information for more than 10,000 readers in over 140 countries and the ideal publication for advertisers who wish to target decision makers in this sector. Events Fairs, open houses, on-site sessions ...","@ID":58}, "INSPECTION 45 PETplanet Insider Vol. 18 No. 09/17 petpla.net We do more. Bottling on demand drinktec 2017 Munich, 11 – 15 September Hall B6 Agr Process Pilot systems are an important component to control the production of the very challenging wasp-waist feature of the bottle. “The sensors measure bottle thickness over practically its entire body. As a result, we get a model of a perfectly dimensioned bottle in terms of material distribution in specific parts of the bottle. Correct thickness distribution for the wasp-waist bottle depends on whether we stick to that model. While setting up a job in the system, we saved a perfect thickness distribution model, which is a best fit for our purposes. Now we only need to reproduce it with the Pilot system in place” comments Mr Banaśkiewicz. This is done automatically with the Process Pilot system. The material distribution model is saved with the blowmoulder recipe for the specific bottle. Once the model is defined on the Agr system, the material distribution is automatically maintained according to the model. When the Agr systems were installed at the Cisowianka production facility, the height of the bottle was also reduced by 5mm along with the bottle weight. As Mr Banaśkiewicz recalls, it posed quite a challenge: “It was a brand new product for us – a new bottle design, a new blow-moulding machine, and a new preform. And the Agr Pilot system helped us optimise the bottle and its thickness based on continuous monitoring, segment by segment. Otherwise, we would be forced to rely on traditional cross-section measurements that are labor intensive and require considerable trial and error, a very time consuming process. Now, with Agr equipment in place, we can control thickness distribution in a continuous manner, on two blow-moulding machines; as a result, we are able to blow a lighter preform into a container with a more uniform thickness distribution. Production of the Wasp bottle at this weight is very difficult without the Process Pilot.” Vision inspection to manage preform defects Compounding the challenges of light weighting with the wasp-waist bottle were on-going preform quality issues. All of the preforms used in this plant are purchased from outside sources bringing additional quality and production issues. One of the problems they faced was the presence of sealing surface defects that resulted in product leakage that compromised quality and the customer experience. This was another important justification for the purchase of the Agr system. In addition to material distribution management, the system also incorporated cameras to inspect the preform sealing surface for scratches and damage that may compromise the seal. With the seal inspection in place on the 2 KHS lines, the company was able to eliminate the downstream problem by identifying the defective preforms and rejecting them before they were processed further.","@ID":47}, "TRADE SHOW PREVIEW PETplanet Insider Vol. 18 No. 09/17 petpla.net 78 Silgan Closures presents caps and closures for all types of containers Sealing solutions Hall A4 - Booth 531 The Silgan Closures stand at Drinktec aims to underline the company’s capabilities in the development of both metal and plastic closure solutions for the drink and food markets. In its plastic closure ranges, the company will be demonstrating its pioneering technology for the bottled water market with a new sealing system for five gallon containers that improves hygiene levels while delivering sustainability benefits, as well as a new flip top sports cap for on-the-go beverages. Latest metal closure innovations include a new next-generation design for baby food jars. Also on display will be a new capping system specifically designed for lower speed filling operations. In addition, Silgan Closures will outline the availability of its comprehensive ‘one-stop solution’ to meet all customer requirements through its ‘Total System Approach’ service. K-Seal closure The new K-Seal closure for 5 gallon water bottles features Silgan Closures’ Probe+ system, suitable for a wide range of water coolers, which ensures full plug engagement to the cooler spike with minimal risk of misapplication and detached plugs. The reformulated Flow Seal material intends to reduce the ability for microbes to attach themselves to the material surface and survive, while a reduction in pigment usage substantially reduces the risk of taste or odour issues. At the same time, use of the latest manufacturing techniques, along with a new resin and low-power consumption during production, reduces the closure’s carbon footprint. Equally important, the closure retains the overall height of a traditional five gallon closure, meaning it can run on existing lines with little or no adjustment to filling or capping equipment. Flip top The latest flip top sports cap combines ease of application for fillers with end-user convenience. The robust design incorporates a tamper-evident spout for consumer safety and the one-handed opening ensures ease of use. It has been designed for maximum line efficiency and complies with the BSDA code of practice for sports closures. Metal closure The new metal closure solutions on display for the food industry demonstrate Silgan’s ability to meet current market trends and requirements. Its new 54mm and 60mm PRH PT (press-on, twist-off) closures for baby food jars enable larger size neck finishes to be achieved in order to facilitate easier access and spooning out of the product. This has been achieved through a redesigned glass finish that allows the height of the closure to be reduced at the edge so that less material is needed, while enabling the closure diameter to be increased to 54mm and 60mm from the more traditional 51mm. New capper For lower-speed capping operations, Silgan has launched a new system. The SWC 150 capper is capable of around 100-150 jars per minute and is suitable for all twist-off diameters from 38mm to 82mm. The stainless steel design meets the latest hygiene standards and the machine is CE compliant. Total system approach For all its solutions on display, Silgan’s ‘Total System Approach’ provides customers with a complete service in the creation of a closure, comprising design, choice of decoration, advice and supply of suitable filling and capping equipment and support in the meeting of relevant food and drink standards and regulations. www.silgan-closures.com","@ID":80}, "67 TRADE SHOW PREVIEW PETplanet Insider Vol. 18 Visit us inhall A4 - booth 124C Website: www.hymega.com Email: [email protected] High speed machines for sports caps and complex closures German machine builder Contexo is presenting its continuous motion technology for fast assembly of sports caps and complex closures. The machine on show has an output rate of over 1,300,000 parts a day - while at the same time the footprint is low. Contexo’s engineers have integrated comprehensive quality-control and TE-proof feeders into a compact continuous-motion system. The machine can be directly chained with an injection-moulding machine, and moments later pack the finished and fully inspected cap. This means extremely high output rates are now possible on a very small installation area. You could literally operate a production site in your living room, says Contexo. Contexo attains these high output rates on a small footprint through a handful of technological developments. Firstly, Contexo chains injectionmoulding machines directly to the assembly unit. For this, Contexo developed its own TE-proof feeding technology that processes warm parts. It feeds the assembly unit without human intervention and contamination. Another important part of the technological concept is Contexo’s continuous motion technology. It allows high productivity on a small space. Contexo has been developing its system for over a decade and became a technological leader in the market. Finally, Contexo uses inline vision control systems that are integrated into the machine workflow and perform over a dozen quality checks to guarantee 100% reliability. Even with output rates of more than a million parts a day, the company’s promise is that not a single defective part leaves the factory. www.contexo-automation.com Hall A4 - Booth 236","@ID":69}, "9 NEWS PETplanet Insider Vol. 18 No. 09/17 petpla.net Drinktec @ WikiPETia Are you fully prepared yet for Drinktec? In WikiPETia you will now find many exhibitors who are active in the PET sector - clearly listed in the events section under “Drinktec”. petpla.net/wiki?title=Events The companies can be sorted alphabetically, by booth number at the fair or by product category. A link to the respective company page on WikiPETia provides everything you need to know about the companies and their portfolio. So it’s quick and easy to find the exhibitors you want to see and plan your visit to Drinktec! In the online news section of the PETplanet homepage, we are also bringing together the Drinktec exhibitors who are active in the PET sector. Simply click on the news category “Drinktec”, and you will discover numerous exhibits connected to PET. The companies involved are also linked directly to their WikiPETia entries. petpla.net/news.php Krones and Erema are joining forces to progress PET recycling Krones AG, Neutraubling, Germany, and Erema Engineering Recycling Maschinen und Anlagen GmbH, Ansfelden, Austria, have agreed to collaborate in the field of PET plastic recycling. The aim of this alliance is to incorporate the technical expertise of both companies into the planning and design of PET recycling lines and complete factories, so as to be able to offer clients from both the beverage and PET recycling industries an optimal line or an entire factory. Erema contributes the expertise required for PET processing, and Krones the expertise as a leading manufacturer and vendor of filling and packaging technology. Krones’ product portfolio, however, comprises not only machines and lines for filling and packaging beverages and liquid foods, but also machines for producing PET bottles, plus modules and lines for the recycling process. The collaborative arrangement will also focus significantly on planning entire factories, which Krones is already offering to beverage bottlers and PET recyclers from the feasibility study stage all the way through to the finished factory. Krones’ product range, particularly the MetaPure W hot-wash technology developed specifically for PET and validated by performance in the field, combined with Erema’s Vacurema technology developed for PET, will enable the two companies in future to offer responsively customised job sections - for washing and/or decontamination technology all the way through to complete factories for PET plastics recycling, and handle them as a turnkey vendor. This means that the clients will soon be able to close the entire PET cycle, from manufacture of the PET plastic products all the way through to their recovery, and thus make a sustainable contribution towards the “circular economy”, with concomitantly reduced resource consumption and environmental impact. www.krones.com www.erema-group.com Plastic Technologies appoints Thierry Fabozzi president of global operations Thierry Fabozzi has been appointed president of Plastic Technologies, Inc. (PTI), a leader in package development and design, rapid prototyping, and material evaluation engineering for plastic packaging. Effective immediately, Fabozzi will be responsible for global operations and will report to the company’s board of directors. In 2012, he joined the company as managing director of PTI Europe S.a.r.l., Yverdon, Switzerland. Fabozzi will report to Betsy Brady, chairwoman of the board, Plastic Technologies. Fabozzi has a 30-year track record of significant packaging technology and business development achievements. For the past five years, he has helped major European brand owners achieve their packaging objectives. Before joining PTI, he was the business stream packaging leader and rigid packaging specialist for Nestlé’s Nestec Product Technology Center Orbe, Vevey, Switzerland. Before that, he spent seven years in technical and business development positions with Milacron Plastic Technology Group. This included the Ferromatik injection moulding machine operation in Germany, as well as the Uniloy blow moulding business unit in Michigan, USA. His experience also includes eight years as a technical and research and development manager with Tetra Pak Plastics, Inc., Geneva, Switzerland. “Thierry’s multidiscipline experience in the packaging sector makes him uniquely qualified to lead PTI’s global initiatives,” said Brady. “Having spearheaded projects for brand owners, machinery manufacturers and material suppliers his entire career, he is ideally suited to take our business to the next level.” www.plastictechnologies.com","@ID":11}, "EDITOUR PETplanet Insider Vol. 18 No. 09/17 petpla.net 23 Gathering at Alpla’s entrance area with (f.r.t.l.) Thomas Ahrer (Alpla), Kay Barton (PETplanet), Jorge Martinez Hernandez (Coca-Cola Femsa), Romano Reyes (Husky), John Willauer (Alpla), Mervin Tuquib (Coca-Cola Femsa) The shared history and partnership between Alpla and Femsa dates back to the 1990s. Femsa, which is originally from Mexico and is now the second-largest bottler of Coca-Cola products in the world, acquired CocaCola Bottlers Philippines Inc. in 2013. That takeover also laid the foundations for Alpla production to be established in the country. Alpla began its in-house installation just one year later and, since then, it has met CocaCola’s huge demand for preforms and bottles with outputs of approximately 1.5bn preforms and around the same volume of finished PET bottles. The range of production here at the factory includes around 20 different preform types, ranging from 9.5g to 94g and including PCO 1881, 29/25, 28mm reinforced and 38mm necks. 70% of the preforms are used by Femsa for CSD; roughly 25% for water; and 5% for hot and/or cold fill applications. In addition to this production facility, Alpla has an additional in-house facility at the Coca-Cola factory in Santa Rosa, approximately 10km away. The company employs approximately 230 people across the two locations; 130 of them at the Canlubang plant. “We operate in shifts, on a 24/7 basis,” Thomas Ahrer explains. “In the near future we will be upgrading our installation here in Calunbang with a further Husky HyPET 400 4.0 injection moulding machine.” Among other sources, Alpla and Femsa obtain materials from the Taiwan-based Far Eastern Group. The use of rPET will start in 2017, with a target rate of around 25%. www.alpla.com","@ID":25}, "TRADE SHOW PREVIEW 73 PETplanet Insider Vol. 18 No. 09/17 lasting closure, with the possibility of using different types of cardboard. The SMI MP Ergon cluster packers are intended to be an ideal solution for creating packs with appealing graphics and a strong visual impact, able to capture the consumer’s attention. In addition, cardboard blanks are resistant to hits and easy to manage, open and store. The model, which will be shown at the exhibition in Munich packs 0.33l beer bottles in 2 x 2 OTT packs with flap inside. The clusters produced are then packed in cardboard boxes, completely closed by the new CWP Ergon casepacker in the 4 x 4 pack format. The CWP Ergon project arose from SMI’s desire to launch on the market a compact version of the WP packer featuring the same design and manufacturing principles as CSK Ergon shrinkwrappers. Adopting some of the main features of the CSK series, the new CWP series has been designed as a technologically advanced packaging machine, which stands out for automation, flexibility, energy savings and environmental safeguard. The series currently includes just one model for the packaging in wrap-around cases or in only tray packs a wide range of rigid containers at the maximum output of 40 packs/ minute (depending to the container dimensions and the package format). www.smigroup.it EBS Ergon stretch blow moulder","@ID":75}, "MARKET SURVEY 47 PETplanet Insider Vol. 18 No. 09/17 petpla.net Additives 09/2017 MARKETsurvey Preforms & preform inspection Recycling plants & washing units Palletising & shrink film machinery Caps & closure systems & CC inspection Labelling & marking systems Recycling: Cutting plants Filling equipment & filling inspection Resins, additives Compressors SBM machinery & quality inspection PET bottle resins / colours and functional additives PETplanet Insider is presenting the suppliers of PET bottle resins and the suppliers of colour and functional additives in this market survey. The additives available include barrier improvement, additives for sensitive beverages, UV blocker, brighteners and many other performance enhancers, up to date! The companies are: Invista, Clariant, Repi, Penn Color, M&G, Neo Group and Indorama. Although the publishers have made every effort to ensure that the information in this survey is up to date, no claims are made regarding completeness or accurancy. Company name INVISTA Resins & Fibers GmbH Clariant Plastics & Coatings (Deutschland) GmbH, BU Masterbatches REPI S.p.A. Penn Color International B.V. Postal address Telephone number Web site address Contact name Function Direct telephone number Fax E-Mail Philipp-Reis-Strasse 2, 65795 Hattersheim, Germany +49 69 305 6025 www.polymers.invista.com Mr Achim Heyer Business Director PET Resins +49 69 305 6025 [email protected] Am Unisys-Park 1 65843 Sulzbach am Taunus, Germany +49 6196 757 60 www.clariant.com/masterbatches Ms Severine Wild Marketing Europe +49 6196 757 6276 +49 6196 757 6113 [email protected] Via B. Franklin 2 - 21050 Lonate Ceppino VA, Italy +39 0331 819511 www.repi.com Ms Lucia Buffoni Marketing Manager +39 0331 819511 +39 0331 819581 [email protected] Smakterweg 31 5804 AE Venray The Netherlands +31 478-554000 www.penncolor.com Mr Scott Stamback Business Director +31 478-554000 +31 478-554009 [email protected] Additives and colours for PET Liquid colours Yes Yes Pennacle - L Microgranule colours Yes Pennacle Masterbatch colours Yes Pennacle UV protection additive (solid) Yes Yes UV protection additive (liquid) Yes Yes Yes AA reduction (solid) Yes Yes - SenzAA No AA reduction (liquid) Yes Yes - SenzAA No Oxygen scavenger (solid) OxyClear additive, PolyShield masterbatch Yes No Oxygen scavenger (liquid) No No Other PET additives in liquid or solid form Slipping agent, reheating, matting agent and special effect Anti yellow (liquid), process aid (liquid), IV enhancer (solid), blowing additive (liquid), optical brightener (liquid), colours for barrier solutions (liquid), white for monolayer UHT milk (liquid) Slip, AntiBlock, high opacity dairy, laser marking, frost, mold release, IV enhancer, flow modifier, re-heat","@ID":49}, "PREFORM PRODUCTION PETplanet Insider Vol. 18 No. 09/17 petpla.net 16 Interview with Robert Schad, Chairman of Athena Automation Working closely together with mould makers by Alexander Büchler & Mike Urquhart This 150t PET preform system serves as a Lightsout demonstration site for unattended moulding PETplanet: Robert, how does your strategy set you apart from your competition? Schad: First, we only build injection moulding machines and work with a variety of mould makers and auxiliary equipment suppliers. We focus on technology – a rigid base, a twoplaten clamp with market-leading tie bar spacing, servo-driven pumps and ball screws for accuracy and energy efficiency. Then we have pre-engineered options including PET, stack/cube, two material, robotics and integrated mould servo functions to provide significant advantages for different moulding applications. Also, we are customer focused. Athena operates without sales people. Instead, we build relationships through our regional technical support and by working with mould makers to ensure their moulds run optimally. With the machines now in production, we have learned so much that we can offer a 5 year parts and labor warranty and allow customers to buy parts directly from our suppliers. PETplanet: What is unique about your new NIIGON line of PET preform machines? Schad: Athena PET machines have the lowest cost of ownership from 2 to 192 cavities. With up to 6 stages of post mould cooling, we achieve industry leading cycle times while maintaining preform exit temperatures below 55°C to ensure the highest quality and get the lowest energy consumption (0.21kWh/kg). We work with various mould makers, dryers and dehumidification suppliers to optimise customers’ systems. PETplanet: What feedback are you getting from your customers? Schad: Both the customers and the mould makers we are working with have been very pleased. Some customers have already placed repeat orders. As part of our Lightsout development program, we are now supplying preforms to a local customer from our facility and have shipped over four million preforms in four different products and numerous colours without a single reject. PETplanet: What are you doing to expand your customer support network? Schad: There are now machines operating in 11 countries on 5 continents, and we have regional technical support in the USA, Canada, and Europe. Latin America is next. PETplanet: What are you doing to ensure Athena will prosper post Robert Schad? Schad: We have built a company and a facility capable today of building 300 machines per year and have land for expansion. Athena is a familyowned company with employee shareholders. We have a long-term outlook and are debt-free after an investment of $150 million. Our management team is dedicated to carrying this vision forward and growing the company. I welcome your readers to visit us and see for themselves that this is a very different company that offers unique advantages. PETplanet: Robert what has been your greatest success? Your biggest failure? Schad: My greatest success is Athena, and my biggest failure was following my major competitors’ lead in setting up component manufacturing in-house, instead of focusing only on what we did best. PETplanet: What do you see as the major trends affecting the preform (or moulding) industry in the next 10 years? Schad: We see more diversification – customers tend to have their own preform designs requiring more flexibility – quicker mould and tooling changes – and smaller systems. There is also an increasing demand for automated operations that can run unattended. With improvements in communication – commonly referred to as Industry 4.0 – between machine, mould, hot runner controller, robot, and other auxiliary equipment there is no need to have one supplier for the entire system. The moulder will be able to take advantage of improvements from suppliers of each of these components to optimise their moulding system’s performance. www.athenaautomation.com F.l.t.r.: Robert Schad, Chairman, Liz Schad, Member of the Board, Rob Sicilia, Business Manager PET, and Harold Luttmann, CEO","@ID":18}, "TRADE SHOW PREVIEW PETplanet Insider Vol. 18 No. 09/17 petpla.net 79 All about closures For Corvaglia’s expert team, Drinktec is one of the highlights of the year because the company looks forward to the opportunity to have many interesting conversations about closure solutions. Digital cap printing as well as an ‘Aqua 2522’ injection mould can be witnessed in live action in Munich. Hall A4 - Booth 302 A Corvaglia ‘Aqua 2522’ injection mould can be witnessed in live action. Together with the company’s partners Engel (Stand 324, Hall A4) and HRSflow Corvaglia will have an injection mould in use at the fair, which is operated in exactly the same way at the Corvaglia Closures plant in Switzerland. Corvaglia claims that there are not many other closure companies who produce four million closures a day out of one mould - using less than 3.5t of resin while still meeting the most stringent requirements of bottlers. Some of the caps are printed during the exhibition using a digital printer from IMDvista (Stand 115, Hall B5). Corvaglia is glad to be the first beverage closure manufacturer that uses a digital printing solution which is able to match the high speed of its own mould technology. This will enable limitless, yet economic options for printing caps in the future. The company’s ‘Aqua 2522’ mould is operated at the Engel stand (Stand 324, Hall A4). Printed cap samples are available on Corvaglia’s stand. At Drinktec sales managers for all regions of the world will be present at Corvaglia’s booth to discuss any topic around beverage closures. Among them will be representatives that are able to provide visitors with firsthand information about the upcoming market launch of Corvaglia Closures USA, Inc. with a closure manufacturing facility in the Southeastern USA. www.corvaglia.ch MHT MOLD & HOTRUNNER TECHNOLOGY AG Your Machine - Our Solution Hall 4A, Booth 416 QUALITY MADE IN GERMANY","@ID":81}, "BOTTLE MAKING 28 PETplanet Insider Vol. 18 No. 09/17 petpla.net is a deformation, or a difference in strength in the PET, sections become weak and they can pop out or deform. The new spiral Fanta bottle isn’t symmetrical at all. Inspired by the twisting of an orange to release the juice and flavour, it has a series of ‘ribs’, with a torsion in the bottom half. The concept of incorporating the ‘twist’ or ‘squeeze’ came about in the very first kick-off session hosted by design agency Drink Works. This new design process began in 2012. Some markets had found that the previous ‘splash’ bottle had become something of a category standard and Fanta was no longer standing out. The twisted design was an early front-runner, but it completely contradicted the brief – to be in any way practical, it had to be symmetrical. Gregory Bentley and Leyton Hardwick – the heads behind the new design - say they went through hundreds of iterations, making foam models, developing structural drawings and hollow models. “The reality from the start was that we all knew which one we wanted. We all had the same favourite. The problem was, there were just so many layers of people who said it couldn’t work,” admits Bentley. A pivotal moment came in 2013. Despite producing thousands and thousands of images for consumer testing, with artwork for small and large bottles in all the different countries, in eye-tracking trials (where consumers are monitored for where they look first) the new design in 2D wasn’t sufficiently attractive – people looked to the current design shape first. But, like all great dramas that come back from a cliff hanger, this story does, of course, continue. By chance in 2015, an Italian colleague of Bentley’s, Marco Beggiora, packaging manager, was looking for a new bottle design and the market was willing to do a small-scale, isolated market test. Within eight months, the Spiral design was resurrected and on the filling line in Sicily. During a like-for-like sales volume comparison, the new bottle excelled. Consumers loved it. Since that very first pilot programme, the design continued to progress, both from a brand marketing perspective, led by Delia Maloney and from a packaging point-of-view, with expert Roger Moore working closely with local teams and bottlers to review the technicalities. The new bottle also has an updated label which has been moved further up towards the neck of the bottle, taking it someway to align with Coke and Sprite. It has the added advantage of no longer being placed where shelves or stacking units end up covering it. Today, the bottle is sold in Italy, Poland, Malta, Serbia, Finland, Romania and Great Britain, with plans to expand production globally in the coming months. www.coca-cola.co.uk After almost two years in the making, Fanta now comes with a new bottle design Twistin’ time First appearing on shelves in the 1940s, Fanta is The CocaCola Company’s biggest brand after Coke itself. It has evolved over the years, with a few bottle re-designs under its belt; but, until now, the bottles have always had one thing in common – they have been symmetrical. Inspired by the twisting of an orange to release the juice and flavour, it has a series of ‘ribs’, with a torsion in the bottom half. There is more pressure in a carbonated drinks bottle than there is in your car tyre. As soon as there","@ID":30}, "Compressors PETplanet Insider Vol. 18 No. 09/17 petpla.net 36 Efficient high pressure blow air production at Hansa-Heemann plant in Loehne, Germany with ABC compressor technology A Horizon-3000 for Hansa-Heemann After having launched its new Horizon for the PET industry in 2015, the Spanish high pressure compressors manufacturer ABC Compressors has celebrated the 200th installation of this new range. The company’s main technical developments were the combination of the optimised design of the horizontal-boxer type with double acting compressors and the directly coupled transmission. This compressor range can be upgraded with two energy saving features, the Variable Speed Drive (VSD) and the Heat Recovery System, with noticeable impact on the energy TCO category and environment care. The VSD adapts, by means of a pressure transmitter, the compressor rotational speed to the real high pressure air consumption needed, maintaining at the same time the required working pressure in the pipe line. This reduces or even eliminates the compressor idle operation and the resultant wasteful energy consumption. On average, it saves 20% of the consumed energy when running at half of the nominal air flow capacity, says ABC Compressors. This achievement is feasible thanks to the balanced operational torques and the absence of vibrations. The Heat Recovery System recycles the heat generated during compression to provide hot water (above 80°C) for the operation, allows extra savings and reduces the CO 2 footprint. The system is said to recover up to 45% of the energy consumed by the compressor. After each compression stage, hot air enters a first phase cooling chamber where it is cooled down to 80-90°C. From the chamber, ABC provides hot water to the customer while the air continues to the next cooling phase. Using double circuits-phase in all the compressor coolers not only provides water flow at high temperatures but delivers overall Δt of 6-8°C for optimum compressor set thermodynamic efficiency. According to ABC, this is the only system on the market adapted to all the compressor inter- and after-coolers. Being vibration free, due to the well balanced torques distribution, the skid is placed directly on the floor, avoiding vibration pads. The compressor achieves efficiency below 0,16kW/m³ at full capacity without considering the VSD impact, thanks to the balanced compression ratios between the stages, large cooling capacity and low transmission power requirements. Compressor installation at Hansa-Heemann Since the commercial launch of the Horizon at the Brau Show in Nuremberg in November 2015, many key players worldwide have trusted this technology, either for new installations or to replace old machinery. One of them, HansaHeemann, a supplier of mineral water and soft drinks in Germany, installed the Horizon-3000 for Loehne, one of their five plants, at the end of 2016. Horizon-3000 installation at Hansa-Heemann’s plant Loehne. Throughout the enquiry, selection, purchasing, installing and commissioning process and during the initial approx. 4,000 production hours, the cooperation between Hansa-Heemann and ABC Compressors has been faultless and beneficial to both parties. ABC Compressors delivered the Horizon-3000 initially to the Brau Show. Hansa-Heemann and ABC Compressors group photo at the Brau Exhibition in Nuremberg, 2016. Since Hansa-Heemann provided an internet access, ABC monitors the Horizon-3000 online via its ‘Ability’ Eye-surveillance system. ABC Compressors’ First and Second Level Support can access the compressor and visualise all the operational parameters in real time. This includes the historical data for a predictive diagnosis. Thanks to the weekly report, ABC Compressors provides reliability and a good performance guarantee to Hansa-Heemann where the new compressor is working 90% of the time, adapting perfectly to the plant’s high pressure requirements. The compressor operates loading 90% of the time due to VSD. www.abc-compressors.com","@ID":38}, "BOTTLE MAKING 32 PETplanet Insider Vol. 18 No. 09/17 petpla.net Figure 3.9 Linear ovens and blowing wheels have become standard in the design of rotary machines. Photo courtesy of KHS Corpoplast GmbH. The main difference to other machine types is in the design of the blow clamp. In a rotary machine each preform travels to its own blow clamp that is arranged on a blow wheel. All services to these clamps come through the centre of the blow wheel by means of rotary distributors. A massive drive gear sits underneath the wheel and a variable-speed motor drives it. The time between the end of oven section and the start of blowing is identical for each preform and this feature, combined with cam-controlled motions, allows rotary machines to deliver excellent quality, on a consistent basis. To familiarise the reader with the main machine components, the layout in Fig. 3.10 should prove to be helpful. Figure 3.10 Layout of typical rotary blow-moulding machine. Diagram courtesy of Krones AG. Preforms enter the machine at position #20. Injection moulders often pack their preforms in the so-called ‘gaylords’ (cardboard storage boxes of roughly 1m3 volume). Resin companies use these gaylords to ship resin and they are widely available. The unloading station might have a ‘gaylord tipper’ that enables personnel to easily tilt gaylords to empty them (see Fig. 3.11). Position #19 is the storage bin, a simple metal enclosure open to the top. Figure 3.11 Storage bin and incline conveyor to unscramble. Photo courtesy of Krones AG. Position #18 is the incline conveyor that takes the preforms to the unscrambler. Incline conveyors are controlled by downstream switches that detect the amount of preforms in the line and only feed preforms when needed. Position #17 is the unscrambler. It orients the preforms onto the in-feed rails at position #16 with flexible paddles and the support of gravity. The preforms hang from their neck-support ring between two stainless steel rails (Fig. 3.12) and travel this way again by gravity to the in-feed star wheel at position #5. Figure 3.12 Preforms hanging from their neck-support rings on rails (upper left of the picture) on their way to the infeed of the machine. Photo courtesy of Krones AG. In the in-feed section, preforms are transferred by various means onto mandrels (see Fig. 3.13). Figure 3.13 Machine using a star wheel to transfer preforms onto mandrels. Photo courtesy of KHS Corpoplast. These mandrels feature various spring-loaded devices to hold the preform in place and guarantee both alignment and secure assembly (Fig. 3.14). Most mandrels ride in tracks (position #6) and feature a sprocket on the top (in oven systems where the preforms ride upside down, the sprocket is at the underside). The sprocket engages with a chain that spins the mandrels and may also move the mandrels through the oven section at position #2. Spacing between mandrels on the track ranges from 38mm to about 50mm (1.5″–2″) and can be increased to double that figure for wide-mouth applications. The majority of soft drink and water bottles use necks of 28-33mm diameter, easily accommodated by the standard spacing. Figure 3.14 Mandrel using an innovative design with two rows of balls holding preforms firmly in place. Photo courtesy of KHS Corpoplast. Spinning with the mandrels, the preforms are exposed to infrared radiation. The machine shown in Fig. 3.15 has 14 heating ovens (position #12), ten on the way away from the blowing wheel position #1 and four on the return route. In the turnaround section as well as in between the last oven in the line and the blowing wheel, preforms undergo equilibration, i.e., a balancing of temperature differences inside the preform wall (see Chapter 6). Figure 3.15 In this machine preforms passing through the ovens upside down. Photo Courtesy of Sidel Inc.","@ID":34}, "PETplanet Insider Vol. 18 No. 09/17 petpla.net 87 BOTTLES Washing-up balsam as a monster edition As part of a promotional campaign, the German discount pharmacy, dm, is selling its liquid dish washer detergent as part of its “Let us think” brand as a monster edition, which has a removable adhesive sticker as well as having an appropriate choice of name for the detergent monster “Willi Wisch” or “Susi Sauber”. The washing-up balsam and dishwashing liquid Ultra contain bitter substances in order to protect children. The liquid comes in clear 500ml bottles with a screwed-on and selected push and pull closure. Embossed selfadhesive labels have been placed in the recesses of the bottle which make it easy to grip with wet hands. www.dm.de ‘2 in 1’ wash gel for men The German firm, Jean and Len Ltd, specialising in products which are free from substances that can harm the body such as parabens, silicones etc., has recently introduced a series of especially for men care products onto the shelves. One of these is a ‘2 in 1’ wash gel that cleans and looks after the face and beard. The socalled “brd” gel refreshes the skin with peppermint water and moisturises it with glycerine. The gel comes in a 250ml brown coloured bottle with a screwed-on and lockable pump dispenser. A jet black label provides information for the consumer and gives the packaging an appearance which is similar to pharmacy bottles. www.jeanlen.de Note the date! 27February – 1March2018 beviale-moscow.com Local success. Global solutions.","@ID":89}, "PACKAGING / PALLETISING PETplanet Insider Vol. 18 No. 09/17 petpla.net 52 Innokeg AF-C comes with inverse relationship between conveying and processing stations Single-lane keg racking With its new concept KHS now offers several advantages for keg racking. The transversal Innokeg AF-C Transversal (TR) is an efficient and modular solution that can expand together with increasing user requirements. The decisive difference from conventional systems is the inverse relationship between the conveying and processing stations. This special development has been designed especially for the 250 to 700 keg-per-hour capacity range and is also suitable for a wide range of PET kegs. Conventional transversal keg systems are characterised by a module ratio of one processing station to two conveying stations. The processing stations of these systems are located between the infeed and discharge conveyors. The discharge conveyor of KHS’ Innokeg AF-C by contrast is positioned between the processing stations. The kegs are pushed sideways from this conveyor to these stations and back. Breweries benefit from this innovative concept. In addition to optimising space utilisation, this design also considerably improves the accessibility to the racking and washing stations. Modular design meets increasing requirements A new feature of the modular and material-saving design is that it reduces acquisition costs on the one hand and allows the KHS Innokeg AF-C to grow correspondingly with increasing production volumes on the other. “We group up to four processing stations together in one module frame. Thanks to the compact design, this group fits into one shipping container,” says Roger Daum, Keg Product Manager, explaining the design of the new system. All conceivable cycles are possible within these frames. “Up to four module groups can be combined to create a processing machine that operates as a pre-washer, main or combined washer, or as a racker,” Daum adds. In addition to a high level of flexibility, this special design is also said to ensure increased efficiency during on-going operation. Processing modules can be easily added and removed from the group. This makes it easy to expand the system with additional modules. This is made possible by the centrally located conveying segment that also improves machine accessibility. The ergonomic design provides operators direct access to the processing modules without the access-blocking external conveyors of the common transversal systems to date. Intelligent control system for high machine availability Intelligent keg conveying logistics is of particular importance in view of the compact design and high capacity. The processing sequences are simulated and optimised in advance In light of the compact design and the high capacity of the Innokeg AF-C, intelligent keg conveying logistics is of particular importance. The flexible design of the Innokeg AF-C makes it possible to combine up to four module groups in one processing machine. These groups can be operated as a pre-washer, main or combined washer, or as a racker.","@ID":54}, "10 NEWS PETplanet Insider Vol. 18 No. 09/17 petpla.net Currier Plastics awarded patent for tamper evident cap Currier Plastics has been granted a United States Patent for their new design of a Tamper Evident (TE) closure. The Research and Development (R&D) Team at Currier has spent the last three years in the design, development and testing of their TE closure design of which the Currier team expects to cross over into multiple markets including medical, healthcare and personal care. One of the positive features that Currier designed into their TE closure includes a confirmation window which provides an immediate indication that the lid has been opened. The TE closure design includes a frangible TE finger that keeps the lid in the closed position. When the lid is lifted, the finger becomes separated from the lid and is captive between the lid and the bottle neck. When Currier built the prototype closure, they also designed a bottle and built prototype samples of both the closure and the bottle to complete testing. The team received their United States Patent on May 16, 2017. The TE closure is intended to be beneficial to multiple industries such as in vitro diagnostics and medical packaging, where there is a focus on health safety and reliability. www.currierplastics.com Sesotec has a new managing director in Italy With Andrea Festelli, the Sesotec group, with effect from April 1, 2017, has recruited a new managing director for the two Italian subsidiaries. The Genoese-born Festelli studied electrical engineering at the university of Genoa. Before he moved to Sesotec, Festelli had worked for seven years for the Italian subsidiary of the GEA group, where he held the position of managing director, and before that headed up the service department. In the course of his professional career he has held positions in international sales, marketing, and R&D departments. One of the major tasks of Andrea Festelli (47) will be to merge the two Italian companies Sesotec Italy, specialised in product inspection, and ASM, who focus on food sorting. www.sesotec.com","@ID":12}, "TRADE SHOW PREVIEW PETplanet Insider Vol. 18 No. 09/17 petpla.net 76 Patent-pending pneumatic blow moulding process optimises bottle formation Adjustments in real time With Aventics’ new patent-pending solution, a world first, users can monitor the pre-blow moulding process in the production of PET bottles online, in real time, and immediately make any necessary adjustments. This results in reduced material and energy consumption during high-throughput PET bottle production. For the first time, PET bottle formation can now be controlled and adjusted during the blow moulding process. Aventics will present this new solution to the professional public for the first time at Drinktec. With this new solution based on proportional technology, Aventics is entering uncharted technological territory. In collaboration with a major filling company, the pneumatics specialists performed extensive research on the blow moulding process. By combining a proportional valve, control electronics, and software, the patent-pending solution records the actual values occurring during the process and compares them with the set points. Precise control The new solution is intended for applications in the pre-blowing process. The set points for this step can either be stored in the electronics or transmitted via all common real-time Ethernet protocols and fieldbuses. During a blowing period of around 200 milliseconds, enough control cycles are available to precisely control bottle formation. This allows process technicians to intervene as needed, for Hall A3 - Booth 327 example to reduce material consumption and fine-tune the formation of the bottle wall. Additional energy savings are possible by lowering the pressure level or reducing the furnace temperature. Process data taken from the analysis can be used to derive continual improvements. At the same time, quality documentation is carried out in order to safeguard and track the process. In addition, trend analyses of the data enable the detection of wear before a failure can occur. Condition monitoring notifies maintenance early on to be able to carry out the necessary work in planned maintenance breaks. The electro-pneumatic solution also meets new requirements in bottle production resulting from the trend towards more and more complex PET bottle shapes and smaller batches. As a software-based solution, the bottle formation process can be changed easily, without any mechanical alterations, and specific to each blowing station on the machine. The software can also automatically control process events, for example reaching the yield point and target bottle volume, according to specifications and keep them constant provided no wear limits have been reached. Once saved, parameters for a bottle type or specific material can be opened and activated at any time, significantly reducing waste during start of production. In close collaboration with product designers, the developers at Aventics validated numerous sample settings during the pilot production phase of new bottles. www.aventics.com The power of the New Generation WWW.SIDEMACHINES.COM Hall A4 - Booth 543 Pol. Ind. Monguit, Llinars s/n 08480 »L’Ametlla del Vallès Barcelona-Spain fon +34 93 846 30 51 » fax +34 93 849 22 11 e.mail post venta: [email protected] »e.mail comercial: [email protected]","@ID":78}, "BOTTLE MAKING 30 PETplanet Insider Vol. 18 No. 09/17 petpla.net Stretch Blow Molding, part 6 Reheat Stretch Blow Moulding Machines by Ottmar Brandau Ottmar Brandau has newly revised his book “Stretch Blow Molding”, first published by hbmedia/ PETplanet Publisher, and now re-issued in a second edition under the Elsevier imprint. PETplanet Insider is publishing extracts from successive chapters in a series of articles. Figure 3.5 Linear continuous motion machines increased in popularity, as they combine excellent quality with a lower price tag compared to rotary machines. Diagram courtesy of Siapi. 3.4 Linear continuous motion machines To improve the performance and quality of low-to medium-output machines, companies have developed new type of machine, borrowing some proven concepts from the rotary line of blow-moulding machines (Fig. 3.5). This starts with the in-feed section. On these machines, only a single rail is mounted and preforms flow continuously into a star wheel (Fig. 3.6). They are right side up at this point and will stay this way throughout their journey through the machine. Figure 3.6 The in-feed section of these linear continuous motion machines is very similar to rotary machines. Picture courtesy of Sipa. As the star wheel turns, mandrels move down into the neck opening of the preforms and pick them up via a spring-loaded mechanism. Spacing of the mandrels is around 38mm or 50mm, allowing necks with maximum transfer rings of 36.5mm and 48.5mm diameter, respectively. There are a few machines for preforms with wider necks that I will describe later. Close preform spacing improves oven efficiency and the continuous motion guarantees even preform heat. Once preforms leave the oven section, they are grouped in the appropriate number of cavities (up to 12 at the time of writing) and shuttled into the blow moulds where they are stretched and blown together (Fig. 3.7). While they travel into the mould area, the pitch is increased to the cavity pitch by a pitch-changing device, which is proprietary to each manufacturer. Each cavity has its own set of blow","@ID":32}, "MARKET SURVEY 49 PETplanet Insider Vol. 18 No. 09/17 petpla.net INVISTA Resins & Fibers GmbH M&G Polimeri Italia SpA Philipp-Reis-Strasse 2, 65795 Hattersheim, Germany +49 69 305 6025 www.polymers.INVISTA.com Mr Achim Heyer Business Director PET Resins +49 69 305 6025 [email protected] Via Morolense Km 10, Italy +39 0775 84 221 www.mg-chemicals.com/en Ms Marilena Grecchi Area Sales Export and Marketing Intelligence support +39 02 82 273 242 +39 02 82 273 314 [email protected] Mexico/Latin America Asia Polyclear PET Preformance PET RAMAPET ASPET AFRON for Antimony Free Batch products Polyclear PET, PolyShield Resin, XPURE Polyester CLEARTUF IV 0.50 - 1.08 0.60 - 1.0 IV 0.74 to 1.25 IV 0.58 - 1.08 0.81 - 0.87 0.76 ÷ 0.95 1101, 1111 S1, S2, R1, N1S, AS21C, AS21CF Polyclear PET 1101 CLEARTUF ULTRA 3301 N2, N1,N2R, AS19C, AS19CF, AS20C, AS20CF Polyclear PET 1101 CLEARTUF P76 - CLEARTUF P82 N1 PolyShield resin 2300 and masterbatch POLIPROTECT Polyclear EBM PET 5507 N1 OxyClear barrier resin POLIPROTECT Polyclear EBM PET N1, G1, L1, AS22CJ Polyclear PET T94N CLEARTUF P82 T-94 G1, AS22CJ Polyclear PET T94N, XPURE polyester 2201 H1, H1S, N2G, HPC grades BB8055, AS20HF CLEARTUF P85HF R1, R2, N2R, AS19CF, AS20CF, AS21CF Polyclear PET 1101 CLEARTUF ULTRA PlantPET resin (Bio-MEG) L1 (High flow blood tubes), E1 (extrusion blow moulding) 1) Barrier resins (i.e. POLIPROTECT) 2) CLEARTUF T95 (high viscosity). Main application: trays Oxyclear Barrier PET ( 3500, 2700 2510) PolyShield Resin 2300, OxyClear barrier resin Yes, with Poliprotect PolyClear Heat 2222, 2224, 2226 PolyClear Heat 2222, 2224, 2226 FuTuRe-PET Resin PolyClear Conserve PET FuTuRe-PET Resin R1-20, N1-100 Next generation catalyst series XPURE","@ID":51}, "BOTTLE MAKING 31 PETplanet Insider Vol. 18 No. 09/17 petpla.net valves, allowing fine-tuning and reducing dead-air volume. The same device that shuttles preforms in also takes the blown bottles out, either on standup or on air conveyors. Figure 3.7 This machine uses a camdriven blow clamp and base insert mechanism controlled by a servo motor. Picture courtesy of Chumpower Machinery Corp. Machines of this type use servo motors to achieve proper synchronisation between the continuously moving mandrels and the pick-up devices (see Fig. 3.8). Low energy consumption and minimal maintenance are resulting benefits. While the time between the end of oven section and the start of blowing is slightly different for each preform (the first preform may exit the oven section up to 3s before the last), the author has not found this to be of any consequence to the bottle wall distribution and has never had to use individual blow air control. Figure 3.8 Some of these machines use a gripper system that is very similar to that used on rotary machines. Picture courtesy of Kosme GmbH. The great advantage to these machines is that they deliver nearly identical quality to rotary machines at outputs ranging from 1,700 to 2,200 b/c/h (bottles/cavity/hour) but at a much reduced capital cost. Rotary machines are more expensive because of the costly distributor systems that are in the centre of the blow wheel. The excellent quality of the linear continuous motion machines stems from the fact that all preforms receive the same heat and can be blown into bottles with identical wall thickness distribution. One caveat for owners of rotary machines may be that moulds of those will not fit into some linear machines. 3.5 Rotary machines Rotary machines are the stars of the blow-moulding world and produce most the world’s soft drinks and water bottles. This market segment consumes up to 80% of all PET converted into bottles, and the resulting income stream has enabled manufacturers to pour significant amounts of money into research and development efforts. This, in turn, has resulted in massive innovation intended to drive outputs up. Output is usually measured in bottles/cavity/hour and this number has increased from 800b/c/h in the 1990s to 2,200b/c/h today on some machines. Machines up to 40 cavities and with output of up to 80,000 b/h are on the market today. The enormous progress was possible by increasing mechanical speeds and fine-tuning process time. One major obstacle to running at the highest output rates is the thicker wall thickness in the base of a bottle that needs cooling time. Readers should note that published output numbers always refer to lightweight water bottles that feature completely stretched-out bases. Custom and carbonated soft drinks (CSD) bottles require longer process time and thus result in a reduced machine output. The oven sections of rotary machines are very similar to those of other machine types and each manufacturer has a particular design to effectively heat preforms and avoid undue temperature increase in the preform necks and at the connections of the infrared lamps (Fig. 3.9). This is discussed further in the section on oven design.","@ID":33}, "63 TRADE SHOW PREVIEW PETplanet Insider Vol. 18 No. 09/17 petpla.net Hall A4 - Booth 330 Engineering Excellence www.netstal.com Maximum output No defects At Netstal our aim is to help you manufacture the perfect drinks closures: minimum cycle times combined with maximum quality yield the lowest unit costs and best possible production. And that’s no coincidence: our team of experts are specialised exclusively in closures – and machines made to perform. Drinktec, hall A4, booth 321 Preform range expansion Société Générale des Techniques (SGT), a French family firm, has consolidated its expertise in the manufacture of PET preforms with the recent acquisition of an injection press exclusively dedicated to multilayer applications. This new Husky HPP5 state-of-the-art machine is intended to not only give the company more flexibility but also more freedom in the design of new barrier solutions. In developing such applications, SGT will also be able to intensify its presence in packaging sectors for sensitive products like wines, syrups, milk and carbonated soft drinks. With this multilayer process, SGT aims to offer preforms featuring stronger barriers (oxygen, CO2 , light, UV, etc.) while at the same time offering lighter packaging that was not conceivable until now. With a standard range of 220 preforms designed for a great variety of applications, SGT claims to meet the requirements of all bottlers by henceforth offering monolayer and multilayer solutions for cold, hot or aseptic filling processes that thereby guarantee the shelf life and quality of their products. www.sgt-pet.com Thread, body & thickness gauge Torus Measurement Systems will be exhibiting a fully automated B302 Thread, Body & Thickness gauge for plastic bottles and preforms which will incorporate the use of a robot to automatically load. Torus’ newly developed B302 can be supplied as a semiautomatic manually loaded or robot automated system and utilises the most recent camera and lighting technology with incorporated start of thread alignment routines, removing operator influence from the neck finish measurement. Torus’ automated B302 TBT offers improved measurement repeatability and absolute thickness capability by using the latest high resolution sensing technologies, allowing features such as base clearance, thread, body & height dimensions to be taken without any operator influence. The intelligent robot loader removes the need for time-consuming, manual processes and consequently improves efficiency. As with all Torus gauges, the B302 is fully traceable to UKAS standards and is supplied with calibrated masters which are measured in Torus’ own accredited laboratory. www.torus-group.com Hall A4 - Booth 146","@ID":65}, "60 TRADE SHOW PREVIEW PETplanet Insider Vol. 18 No. 09/17 petpla.net Hall A4 - Booth 321 motan-colortronic gmbh - [email protected] www.motan-colortronic.com LUXOR A 80-2400 ETA plus® considerably reduces energy consumption and protects materials. Drying has never been this efficient: ETA plus ® Shoot & cap The Swiss injection moulding system provider Netstal will be producing 38mm single-piece closures for milk bottles on an Elion 2200-1000. Shoot and cap: the HDPE closures, which weigh just 2.8g, are produced in a 32 cavity mould from z-moulds and, thanks to the patented z-slides, they receive a fully-functioning tamper evident band in the mould. The cycle time is 4.0 seconds. Piovan provides the systems for drying the material and dehumidification. The water cooling is made available by EF Cooling. The PET granulate and the colour master batches are supplied by Total Polymers. The CapWatcher III from Intravis is used for the optical inspection that concludes the process. Together with Intravis, Netstal will, for the first time, present the integration of external peripheral data into the aXos machine controller. The most important product characteristics of the 38mm closures that are being produced live at the trade fair stand will be constantly analysed by the Intravis CapWatcher III. They will then be transmitted via Euromap 82/OPC-UA to the machine controller of the Elion 2200-1000 in the form of data packages and displayed immediately in the aXos machine controller. If needed, individual characteristics, such as the diameter of the closures, can also be displayed on the individually configurable dashboard, which allows machine operators to always keep an eye on them. That means corrective measures can be taken quickly. If implemented according to Industry 4.0, the operator will no longer have to actively take action since the injection moulding machine in a control circuit can self-regulate. Minimal changes to a product characteristic can be performed automatically within a defined process window. This allows for the sustained production of closures with the exactly defined product characteristic. www.netstal.com Bigger blow-moulding machines French manufacturer 1Blow will be exhibiting its full range of blow-moulding machines, including its latest 1XXL, which is specifically designed for the production of large containers. The single-cavity machine can produce bottles from five to 30 litres. It employs servo drives as standard on mould movement and on the stretching system, and also incorporates, as standard, systems to recover power and blowing air, in order to reduce costs. Its heating system has the capacity to handle thick preforms (10mm) for both oneway and returnable containers. A neck orientation system is available as an option. Visitors to the stand will also be able to see demonstrations of preform blowing, utilising newAventics HP valves. www.1blow.com Hall A4 - Booth 350","@ID":62}, "BOTTLE MAKING 34 PETplanet Insider Vol. 18 No. 09/17 petpla.net Please order your copy at the PETplanet Insider book shop: petpla.net/book3 Stretch Blow Molding Second Edition by Ottmar Brandau € 130,00 320 pages © Copyright Elsevier 2012 product development caps & closures design high cavitation moulds multi-component moulds closure production systems after sales service competent – professional – inspiring Hoechster Strasse 8 | 6850 Dornbirn | Austria | www.z-moulds.com drinktec 2017 September 11th-15th meet us at booth A4.417 Moulds at Drinktec Cap 29/25mm 3-start water @Arburg in A4.323 Cap 38mm 3-start aseptic @Netstal in A4.321 Cap 26mm water @Sumitomo Demag in A4.123 At the end of the oven track, preforms enter a star wheel or other transfer device and are moved one by one onto the blowing wheel position #1. The machine described has 18 blow cavities (position #3). Each cavity has its own blow mould, stretch rod, water connection, and three blowing valves for pre-blow, blow, and exhaust. Air and water connections as well as electrical lines for sensors and switches come from a feeding unit located in the centre of the blowing wheel. These central distributors are one of the reasons that rotary machines are more expensive compared to linear machines of the same capacity. Figure 3.16 One of the two blow-mould halves with bottle and bottom insert. Photo courtesy of KHS Corpoplast. Blown bottles leave the mould via grippers or star wheels onto conveyors at position #11 (see Figs 3.16 and 3.17). These grippers are very different from the ones used on linear machines and transfer preforms between ovens and blow moulds and bottles between blow moulds and discharge unit. They are cam-controlled and rotate on shaped tracks. Instead of having cylinders that open and close them, they are actually just pushed and pulled into and from preforms that are securely held in star wheel pockets or the blow moulds in the case of finished bottles. This saves time and maintenance. However, it does require a particular preform neck design. Figure 3.17 One of many gripper designs. Diagram courtesy of KHS Corpoplast. To facilitate the handshake between star wheel and gripper, there must be room for the gripper to engage the preform above the transfer ring as the preform is hanging from it in the star wheel (Fig. 3.18). This requires the preform to have a straight section underneath the thread beads for the gripper and another section underneath the transfer ring for the star wheel. Figure 3.18 During handshakes between various parts of the machine the area on to and underneath, the transfer ring is used for grippers. Brand owners in industries such as cosmetics may find transfer rings unappealing for their customers and it is possible to run preforms without a transfer ring through an RSBM machine, albeit at a slower speed. High-speed machines generally use air conveyors where bottles hang from their neck support ring, gently pushed by air blowers. Anti-slip agents in the resin help reduce any friction in the conveyor lines.","@ID":36}, "62 TRADE SHOW PREVIEW PETplanet Insider Vol. 18 No. 09/17 petpla.net Hall A4 - Booth 546 All-electric stretch blowing India-based Shyam manufactures stretch blow moulding machines, ranging from 600 B/H to 12,000 B/H. The company will be demonstrating a seven cavity all electric Pristine series linear blowing machine, with a speed of 10,000 B/H. The preform loading system and heating conveyor is based on continuous movement without the pneumatic reciprocating movements, eliminating abnormal wear & tear of moving parts and also reduces air consumption. The machine is based on Neck Hold system, right from preform entry to bottle ejection, thereby reducing the number of change parts, and change-over time. A servo stretching system with individual blowing valves is claimed to allow precise stretch blow process control. Blow Air Recovery being an integral part of the equipment further reduces power consumption. The use of servo motors allow for smooth and controlled movement that help in reducing abnormal wear and tear of parts. Reduced pitch in the oven allows a higher number of preforms in the given heating area, and hence efficiently heat preforms using less heat, with minimal heat loss.In addition to live reports, live user manual, the Online Remote monitoring provided in the machine makes it easy to provide After Sales support to the customer. www.shyamplastic.com Stackabox for the supply chain of preforms and closures There is a tendency in today’s circular economy to pack, transport, and dispense preforms and closures in a returnable packaging container that is fully hygienic, easy to fold down when empty and efficient to store in the warehouse. DS Smith has integrated all these elements in their Stackabox product range. The base dispensing offers the possibility to empty the contents directly onto the lines via the bottom, reducing neck breakage of the preforms. Stackabox is fully compatible with existing conveying and tipping equipment. The pallet and the sealable lids are all integrated into this one-piece container, to avoid loss of detachable components. DS Smith recently launched a version with an integrated sliding door for the optimal dispensing of caps & closures.The product is fully recyclable at the end of its life, the material can be reused to produce new Stackaboxes. www.dssmith.com Hall A2 - Booth 324","@ID":64}, "PETplanet Insider Vol. 18 No. 09/17 petpla.net 85 BOTTLES Power drink from Rewe As part of their “Rewe to Go” range, the German company, Rewe, is selling more Power Smoothies called “Power Drinks” which contain health enhancing additives such as chia, activated carbon and flax seeds/oat flakes. The drinks come in 250ml bottles, while the fruits and additives that give the product its colour are easily recognisable through the transparent bottle and on semi-transparent labels. The black screw tops have an additional security adhesive strip which can easily be read with the appropriate accessory. www.rewe.de International trade fair for the beverage and liquid food industry processing+filling+packaging+ logistics ANNUAL SHOWCASE First time ever in Delhi [email protected] Contact","@ID":87}, "MOULD MAKING PETplanet Insider Vol. 18 No. 09/17 petpla.net 24 z-moulds is building its new headquarters in Dornbirn, Austria More space for creative mould making With its new built headquarters in Dornbirn, Austria, z-moulds is launching a new and innovative creative-centre: clear, cubic structure, light and wood in perfect symbiosis complement each other to form a highly attractive spatial structure. The production hall is centrally arranged in its heart; the building itself is modelled on a Roman atrium, the centre of where the family came together to talk, work and think. In this case, the family consists of four departments, which have been brought together under the umbrella of z-werkzeugbau-gmbh, a privatelyowned company since 2005: z-automation, z-microsystems, z-moulds and z-prototyping. PETplanet Insider met Michael Fink, Vice President of Sales and Marketing, and spoke to him about the new headquarters and the development of z-moulds. PETplanet: Mr Fink, this is a very impressive building. What would z-moulds like this building to represent? Fink: This building is not just the home of our company, its expressing also our culture. With its open structure, we wanted our employees to know that we are all under one roof. It doesn’t matter if on the shop floor or in the CEO’s office, all rooms are opened. Our customers can watch their moulds while they are assembled and tested in the technology centre. – This openness endorses the quality of production at z-moulds. PETplanet: This quality is known all over the world. What makes you different from your competitors? Fink: That’s right. Our z-moulds customers are spread out all over the world, from Australia to Tahiti, from Argentina to Russia or South Africa to the US. Of course, we also have many customers in the European market. For example, our beverage moulds feature the patented z-slides system. z-moulds has several smart technologies with patents. One of these is the world-wide proven z-slides technology. This technology is used for all beverage screw caps with moulded tamper evident band. Compared to common lateral slider moulds these sliders are mounted on the inside of the mould, moving only in the machine direction. Thus, the sliders and all necessary guiding elements need less force and preventing stress to the steel by re-directing force. This results in a longer life-time of the mould and the overall maintenance time is reduced dramatically. PETplanet: The entire design of the mould consists of individual components which can be easily replaced and operated. What do you attach importance to, what are the advantages? Fink: This technology is easier to be operated and maintained and that’s the major key to cost saving and at the same time increasing the output. Beside that fact, this modular concept allows a very flexible use and change of the cavities. For example, these moulds can also easily be changed to a z-folded mould for folded and sliced tamper evident bands. In general, the concepts grant a maximum of productivity and cost-effectiveness. PETplanet: Where do you see your future customers? How do you estimate the market for cap mould manufacturing? Fink: Most growth, in my opinion, is still in the water sector, especially on the Asian market. The Chinese market is particularly characterised by using lightweight closures, compared to the more traditional European market. Speciality closures are also a rising field, they allow to diversify, for example elaborate sports closures in developing markets. The CSD market is so far stable for us. PETplanet: Here in Dornbirn on the newly created production area of 7,000m2, customers can plan and implement their ideas with state of the art technologies. If it’s a problem to get to your offices in the beautiful country of Austria, one can visit you at Drinktec. Fink: Yes, we will be there on our booth in hall A4/417, but also showing multiple moulds with our machinery partners. Netstal is running a 32-cavity mould for an 38mm closure to fit their pre-form application, Sumitomo Demag is running a 72-cavity mould for a 26mm closure at very fast cycle time and Arburg is running a z-moulds application with the patented z-slides system for a Cap29/25mm water closure. PETplanet: We are very much looking forward to seeing you at the trade fair and thank you very much for your invitation to Dornbirn. www.z-moulds.com Detail of the z-slides mould F.l.t.r.: Heike Fischer and Michael Fink at the new relaxing area for the staff of z-werkzeugbau","@ID":26}, "EDITOUR PETplanet Insider Vol. 18 No. 09/17 petpla.net 19 foreign investors, maintain the positive growth trend and create new jobs, large investments are being made for the development of infrastructure, reducing bureaucracy, fighting against corruption, and reformation of the fiscal system. In addition to China and Japan, the USA is the most important trade partner and is where almost three of the total of eight million OFWs (Overseas Filipino Workers) live and work. An economic rapprochement with China is leading the Philippines to expect high levels of inward investment. The service sector is booming; call centres and online support, accounting and software development combine to make up 59% of total GDP. This sector is helping to fuel the growth of the middle class working in the country. The Philippines has now replaced India as the top country for outsourced telephone services. It is a founding member of ASEAN and one-third of its exports are electronic goods; 75% of which them are semiconductor electronics. The government is aiming to achieve a yearly growth of 3% in the renewable energy sector by 2030, with the Philippine Energy Plan, by which means it is seeking to provide one-third of total energy generation with renewable power. The Philippines‘ primary energy sources are coal and natural gas, although hydropower and geothermal energy plants are becoming more and more significant. Get in touch with… PET and local trends The Filipino population loves soft drinks: that much is clear. With 60% of the market by sales, the soft drinks industry is leaving other drink types behind; bottled water, for example, which accounts for only 10% of market sales. Returnable glass is still often used for soft drinks bottles, mainly for competitive pricing reasons; despite strong growth in recent years, PET sales have not yet overtaken glass bottles. Since Coca-Cola Femsa acquired Coca-Cola Bottlers Philippines from Coke Bottling Investment Group (BIG) in 2013, sales of PET bottles have risen by 75%. Glass bottle sales have declined over the same period, by three per cent, but still just lead in total sales. Flexible aluminium/plastic packaging, in third place, has seen a small marginal growth in sales. This could change soon, as CocaCola Femsa looks to expand in the popular PET single serve sector, over the medium term. It has already successfully introduced 300ml and, more recently, 250ml packages – sizes that have previously been used with reusable glass bottles. Pepsi, too, is experimenting with the single-serve trend, with the launch of individual 300ml and 345ml PET bottles. The growth in this sector is challenged restricted by the Philippines’ geographical situation. Transport – and, consequently, shelf life – is faced with major hurdles that it has to cope with; first and foremost, by the huge number and spread of inhabited islands. They all need to be served with food and beverages, which leads to complex logistics in preserving and conveying goods. However, CocaCola is planning to tackle this problem by constructing new plants in a number of different locations. The water market, which is small in comparison to that of soft drinks, is expected to see double-digit growth rates over the next five years. PET bottles have been the main choice of packaging in this sector and have enjoyed a constant market share of approximately 93%. Bottling companies are focusing tightly on smaller bottles here as well: 350ml and 500ml sizes in particular. Philippine Spring Water Resources is expanding, in order to react effectively to forecast growth and in pursuit of a strategy to supply the local market with more of its own water products. Asia Brewery Inc. has expanded its “Absolute” distilled water brand portfolio with the launch of a 250ml bottle for children; in so doing it has capitalised on the ban on the sale of sugary drinks in schools. Canned soft drink distributors had the lowest percentage of sales in the country in 2016, with approximately 3%. According to expert information, Coca-Cola Femsa’s estimated 50-60% market share makes it the largest soft drink manufacturer in the country. Filipinos are among the largest consumers of Coca-Cola products worldwide. With almost 30% market share PepsiCola Products Philippines (PCPPI) sits in second place; RC Cola from AsiaWide is in third. Smaller bottling companies have expanded the market with additional water brands, a trend that is set to continue in 2017. Asia Brewery Inc.‘s “Summit” mineral water and “Absolute” distilled water are the most significant local brands. The Philippine Spring Water Resources bottling company is the market leader in terms of production capacity; its main product, Macro-economic data the Philippines Population 2016 104.2 million Population growth 2016 1.56% p.a. GDP 2016) US$ 304.9 billion GDP growth rate 2016 6.9% GDP per capita 2016 US$ 2,753 Import / export 2015 (2014) US$ 70.2 (67.7) bn US$ 58.6 (61.8) bn National debt 2016 42.1% of GDP Unemployment 2016 5.7% Inflation 2016 1.8% Sources: Federal Foreign Office, AHK (Chamber of Foreign Commerce), GTAI, WKO (Austrian Chamber of Commerce), World Bank","@ID":21}, "EDITOUR PETplanet Insider Vol. 18 No. 09/17 petpla.net 22 Tour Sponsors: EDITOUR 22 Tour Sponsors: In-house preform manufacturing at Coca-Cola Austria meets the Philippines By Kay Barton At the Coca-Cola Femsa Canlubang Bottling Plant, we met Thomas Ahrer, local General Manager of the in-house representation of packaging manufacturer Alpla. Thirty-eight-yearold Mr. Ahrer from Austria has been working at the company for eight years and previously worked at Alpla’s locations in China and Thailand, before ending up in the Philippines. Alpla Philippines Inc. May 23, 2017 We met: Mr Thomas Ahrer, General Manager Mr John Willauer, Packaging Engineer Mr Jorge Martinez Hernandez, Coca-Cola Femsa Plant Manager Mr Mervin Tuquib, Coca-Cola Femsa Packaging Manager Mr Romano Gulinao Reyes, Husky Business Manager Beverage Packaging PhilippinesThomas Ahrer (right) with Romano Reyes from Husky","@ID":24}, "PACKAGING / PALLETISING 55 PETplanet Insider Vol. 18 The company has two plants in Karnataka. The unit in Bidadi, which is the crown jewel of the packaging industry, is a LEED Gold Certified Green factory. Unit 2 in Bommasandra manufactures PET, PP and HDPE bottles and jars for customers across various consumer and healthcare verticals. The unit also manufactures closures and carries out labelling (shrink sleeves, adhesive labels, in-mould labelling and screen printing). The company’s in-house technical design centre specialises in the design development, engineering and deployment of rigid packaging solutions for its customers. They focus on practical, manufacturable designs which can be realised with maximum cost benefits for customers. Manjushree’s R&D department is recognised by the Department of Scientific & Industrial Research, Govt. of India. Manjushree was the first in India to introduce shortneck PCO 1881 preforms for single and multi-serve soft drink packaging. These ‘green engineered’ marvels save both on plastic weight and cost per preform as well as cap. In 2016, Manjushree forayed into flexible packaging with the installation of a multilayer blown film line for the production of LD shrink film. This is being used as a substitute for paper carton primarily for the packaging of plastic bottles, metal cans, glass packages, paper composites and Tetra Pak cases. Equipped with new generation machines from Reifenhäuser, Germany, one of the leaders for shrink film, the plant is capable of extruding 650kg of plastic blown film every hour. As new technologies scale the frontiers of rigid plastic packaging, Manjushree Technopack is committed to making innovation practical and relevant for consumers. www.manjushreeindia.com Interior of the Manjushree Technopack Areal of the Bidadi factory","@ID":57}, "INSPECTION 46 PETplanet Insider Vol. 18 No. 09/17 petpla.net In one particular instance, the Agr system, and specifically the visionbased sealing surface control, helped identify a problem on the part of a supplier of preforms. It turned out that a third-party supplier provided a batch of preforms with damaged surfaces. The preforms, still fresh and soft, were not handled properly in their production facility. When Nałęczów Zdrój began to process them, the defects became quickly evident when they began producing an above average number of bottles that did not seal properly. According to Mr Nachowicz they contacted the supplier and requested them to correct the problem with the preform quality. However, as the situation had it, Nałęczów Zdrój had a large stock of these preforms that would have to be returned and scrapped, and at the same time they needed preforms to continue production. In order to continue production, some preforms were kept and the Agr system was adjusted to accept ‘borderline’ containers. There were more rejects than usual, but the Agr system made it possible to use some of them. This was a win-win situation. They had the preforms to produce bottles, and the supplier was not forced to rework the entire batch. The value of the preform inspection capability is evidenced in the recent addition of another module for the system, a camera for identification of defects on the preform body. This has helped improve quality control even further by making it possible to identify and reject defective preforms from the blow-moulding machine before the bottle is blown. In addition to optimising the production process, the system will give the company an additional advantage – it will provide an absolute proof that preforms were defective before they were blown into bottles, which means that the filler’s involvement was minimum at that point. The monitoring of preforms at a pre-blow stage of the process will identify the party responsible for a given defect in nearly all cases. Further, with the Agr system, the company is able to present concrete data concerning, for example, a defective batch of preforms, which gave it a strong position in negotiations. “The system gives an additional back-up for the company – the specific measurement data. As such, it has earned the trust of the company’s employees,” Mr Nachowicz admits. Providing value to the production process For more than two years, Nałęczów Zdrój has been using Agr’s Process Pilot systems to control material distribution, increase process and filling line efficiency, and manage the quality of their preform supply for the Cisowianka bottles. All of these functionalities and capabilities have helped to optimise their production process and bring value to their operations let alone on-going financial savings resulting from the light weighting efforts on the Cisowianka bottles. And the value of producing a high quality product with lower customer complaints also has a financial dimension. Competition in the water market is stiff. In order to get competitive advantage, producers are doing their best to drive down costs. The policy at Nałęczów Zdrój is to optimise costs based on the economies of scale. “This is where we are looking for returns and Process Pilot has helped us” explained Mr Banaśkiewicz. An example of this is the elimination of short periods of downtime and faster reaction time. “When we see that something is wrong, the alarm goes off immediately. We don’t have to wait and cut bottles into cross-sections to find the source of the problem, losing a couple thousand bottles in the meantime,” cited Mr Banaśkiewicz. In the event that the blowmoulder is shut down to correct a problem, because the Process Pilot manages the distribution, usable bottles are available almost immediately, improving production output. In the name of productivity, the Agr Process Pilot system has had a positive effect. In addition to identifying problems with production bottles, it is also a diagnostic tool for the blowmoulder maintenance, making it possible to identify the cavity where the defects originate. This gives added value to the technical department, as they get a preliminary diagnosis of the situation allowing them to pinpoint the exact location of the problem, quickly address the issue and return to production with minimal downtime. The use of the Process Pilot system has also led to an increase in filling line efficiency and reduced downtime by ensuring that only commercial grade bottles reach the filler. Furthermore, the filling lines are able to run at higher speeds. “What I appreciate about the Agr system the most is the quality control function. It gives us assurance that consumers will buy a safe product. Thanks to Agr, we are looking closely at every single bottle and we are sure that it is 100% safe after filling and capping – both in terms of possible damage to sealing surface, which could harm the consumer and in terms of consistent bottle quality” explained Mr Banaśkiewicz. Mr Banaśkiewicz also stated that sometimes it is hard to quantify benefits, such as the ability to produce and fill a challenging bottle like the 1.5l Cisowianka bottle with minimal issues, increased efficiency and less downtime. With the demand for the Cisowianka product, every advantage that increases production is critical. And with less downtime during container production and filling operations, production yield is increased, improving profitability and competitive advantage. www.agrintl.com www.cisowianka.pl Agr’s Pilot Profiler measures every bottle at the mould out take and provides the feedback for Agr’s Process Pilot automated blowmoulder control.","@ID":48}, "11 NEWS PETplanet Insider Vol. 18 No. 09/17 petpla.net IS STILL 50% TOO MUCH. The KHS solution for more sustainability: New avenues in packaging technology. We are continuously improving our packaging. By applying innovative technologies and swit Carbon footprint of recycled PET Recycled PET (rPET) from PET Recycling Team GmbH, a wholly owned subsidiary of Alpla based in Wöllersdorf/ Lower Austria, results in 79% lower CO 2 emissions compared to new material. This is a significantly higher saving than previously assumed. A study conducted by denkstatt GmbH on behalf of Alpla came to this conclusion. Alpla, an international producer of plastic packaging solutions, has been working on PET recycling for over 20 years. Although the economic conditions for the recycling of plastic are currently difficult due to the low price of oil, Alpla continues to follow this development of its sustainability strategy. To highlight the value of recycling PET plastic, Alpla commissioned denkstatt GmbH to calculate the carbon footprint for rPET. The result of the study exceeds previous assumptions. The rPET produced by PET Recycling Team GmbH in Wöllersdorf has a carbon footprint of 0.45kg CO 2 equivalent per kilogram of rPET. Virgin PET, or new material, accounts for a CO 2 equivalent of 2.15kg per kilogram. This corresponds to a CO 2 equivalent of 1.7kg or 79% lower greenhouse gas emissions for rPET. Plant manager Peter Fröschel explains: ‘The savings for a single kilogram of rPET are enough to power a 13-watt bulb continuously for twenty days in the Austrian power mix.’ The carbon footprint was calculated in accordance with ISO 14044, starting with the collection and sorting of used PET bottles, covering transportation to the recycling plant in Wöllersdorf, through to washing, processing and granulating. The analysis is based on the mass and energy balance (electricity and gas consumption) for 2016 at the Wöllersdorf recycling plant in Austria. Alpla has decades of experience in the recycling of PET, as well as in the processing of recycled plastics. Alpla operates recycling enterprises at three sites – a joint venture in Mexico, the wholly owned subsidiary PET Recycling Team in Wöllersdorf and a new recycling plant built in southern Poland in 2013. The annual capacity of these plants is around 65,000t of food-grade rPET. ‘We are witnessing a clear trend towards PET packaging. And not just in summer, when the beverage industry enjoys a boom due to hot weather,’ says Fröschel. This makes it all the more important to collect used packaging and return recyclable materials to the production process. ‘Our recycling plants play a key role in this regard,’ the plant manager concludes. www.alpla.com","@ID":13}, "TRADE SHOW PREVIEW PETplanet Insider Vol. 18 No. 09/17 petpla.net 74 Solutions from the Gardner Denver group of companies for the beverage industry Oil-free compressors centre stage CompAir’s oil-free Ultima and scroll compressors Available as part of the company’s compare PureAir brand, the oil-free compressor Ultima offers up to 12% improved energy efficiency compared with a conventional twostage machine, with a roughly 37% smaller footprint. The new compressor is available in models from 75kW to 160kW and is designed for applications that demand high levels of air quality and purity. The 160kW model will be available on the stand for visitors to see. In addition, Ultima supports iConn, a new cloud-based, air management platform that enables operators to manage, optimise and improve compressed air-based services. With Industry 4.0 driving manufacturers to share and analyse asset data, iConn has been developed to deliver advanced analytics, enabling operators to stay in control of their compressed air system. Gardner Denver will also be exhibiting the new S-series of oil-free scroll compressors from CompAir. With compressed air purity absolutely crucial for the beverage and food sector, the range is certified to ISO 8573-1 Class 0 and silicone free, ensuring high standards of air quality. VH21 oil-free compressor In PET bottle blowing, optimum efficiency and performance is key, as any issues with the transfer of power from the compressor motor can result in significant energy loss. In fact, it is estimated that belt drive system inefficiencies can result in an additional 12% on energy bills. Gardner Denver will be exhibiting Belliss & Morcom’s VH21 oil-free compressor, which incorporates a unique shaftless motor to deliver assured drive efficiency, and requires no drive system maintenance. Visitors to Gardner Denver’s stand will be able to find out more about the VH21 model and Belliss & Morcom’s other highly efficient oil-free compressors for the PET bottle blowing market. Energy screw compressor With the food and beverage sector dependent on wastewater treatment plants to provide clean water for processes such as bottle washing, the industry requires a proven and assured compressor solution to meet these stringent demands. The oil-free Robox energy screw compressors from Robuschi are a new development whose use in sewage treatment are intended to offer significant advantages, especially in economic terms. Up to 1,000mbar pressure and flow rates up to 4,100m³/h are achieved with an economical use of energy. The efficient demand-controlled power is achieved by the drive with the speed-controlled permanent magnet motor. The communicable compressors are delivered ready for operation with an integrated control cabinet and frequency converter. Having recently won the prestigious Environmental and Energy Efficiency Hall A4 - Booth 107 The Robox “Triple Impact energy” screw compressor from Robuschi has recently won the Environmental and Energy Efficiency Award at the 2017 Motion Control Industry Awards. CompAir’s S-series oil-free scroll compressor","@ID":76}, "BOTTLING / FILLING PETplanet Insider Vol. 18 No. 09/17 petpla.net 38 In Hungary, one of Europe’s fastest bottling lines for edible oil has recently gone into operation High-speed oil “The new line from Krones has enabled us to double our bottling capacities at a stroke – to what is now almost one million litres a day,” says Milan Kunciř, Managing Director of the Hungarian company NT GmbH, which produces sunflower oil for the international markets. The installation of this line, with a comparatively high rating for edible oil of 22,000 containers per hour, was the highlight so far of NT’s corporate thrust for expansion. Hungary is the world’s eighthlargest producer of sunflowers, and in terms of yield per hectare it even comes top. In European Union, Hungary has since 2016 ranked first, with a harvest of well above 1.8 million tons. So for the Agrofert Group, acquiring a stake in NT GmbH was a strategic decision: in 2014, it began to build a rapeseed edible oil refinery in Lovosice, the north of the Czech Republic next to existing rape seed crushing plant. Most of the oil produced there is used to make biodiesel, though part of it is also targeted to edible oil production. In order to establish a second source of revenue in this sector, Agrofert then decided in mid-2014 to take over the Hungarian sunflower oil producer. NT was then already supplying about 20% of the country’s edible oil market. Following the capacity expansion of the refinery, NT together with Agrofert was able to increase sales principally through various sales channels. Currently the company is holding a market share above 50%. The parent company: Agrofert The Czech Agrofert Group was founded in 1993, back then with four staff members. Today, it consists of more than 250 firms, has a total workforce of around 34,000 people, and is thus the largest privately owned employer in the Czech Republic. There, and in Slovakia as well, Agrofert claims to be the most important conglomerate in the agricultural and food sectors. The company is also investing substantial sums in Slovakia, in Germany and Hungary. In 2014, it took over NT GmbH. The subsidiary: NT In the Hungarian city of Kiskunfélegyháza, in the particularly prosperous southeast of the country, NT GmbH is at home. The company buys sunflower seeds from around 1,000 farmers in the region - storage capacities for 120,000t are available for this purpose. Thus, the production site is in operation all year round, where NT processes the sunflower seeds to high-quality, refined sunflower oil. Its products … “Kunsági Éden” is the premium sunflower oil of NT GmbH. It is bottled in a 1l PET container, with a striking closure in the Hungarian national colours, and sold through Hungary’s food and beverage retailers. NT bottles its own secondary brands and merchandise in container sizes ranging from 0.9-10l. … and sales channels Besides food and beverage retailers, the HoReCa market (hotels, restaurants, catering) is the second-most-important sales channel, followed by industrial customers like mayonnaise producers, who receive the sunflower oil in tanker trucks. NT uses the by-products from vegetable oil processing to make animal feed, or utilises them to supply its own energy. Milan Kunciř, Managing Director of the Hungarian company NT GmbH During this period, the company also invested purposefully at its facility in the south-east of Hungary, in both oil mill and refining technologies. This has enabled its capacity to be upsized to 250,000t of sunflower seeds processed per annum.","@ID":40}, "TRADE SHOW PREVIEW PETplanet Insider Vol. 18 No. 09/17 petpla.net 72 Inspired by Industry 4.0 Within the framework of Industry 4.0 and under the mottos “new age of packaging” and “new age of bottling”, Italian SMI will be presenting the Ecobloc Ergon integrated system, the CWP Ergon casepacker and the MP Ergon overlapping cardboard sleeve packer. The new market solutions aim to ensure more flexibility, efficiency, eco-compatibility, management and monitoring simplicity within the production lines. “New age of bottling” Among the solutions for the blowing and bottling processes, SMI will be exhibiting the EBS (Electronic Blowing System) Ergon stretch-blow moulder in an Ecobloc version with an electronic filler. The new EBS Ergon is the result of an intensive research and development project, which has introduced concepts for the design and manufacturing of the new SMI rotary blow moulders. The stretch-blowing module of the EBS Ergon series is equipped with motorised stretch rods, whose functioning is controlled by electronic drives requiring no mechanical cams; this is claimed to ensure a precise control of the stretch rod’s path and position, as well as bringing energy savings. The EBS Ergon series also uses high-performance, low dead-volume valves that reduce pre-blowing and blowing times, thereby improving machine efficiency and the quality of the bottles produced. The motorisation of the mould mechanical assembly is integrated with the electronic stretch rod, making the EBS Ergon stretch-blow moulders a “cam-free” system, with considerable advantages in terms of greater kinematic accuracy, less maintenance, less vibration, less noise and increased system longevity. The stretch blow-moulders of the EBS Ergon series is equipped with a newly designed preform-heating tunnel, featuring compact dimensions, with a horizontal preform-holding mandrel chain and with optimised ventilation and aeration systems. The new heating module is equipped with a system of thermoreflective panels made from a highly energy-efficient ceramic material, situated both in front and behind the infrared lamps units responsible for heating the preforms; this innovative solution ensures a high reflection of the heat generated by the lamps and consequently a more uniform distribution of the heat over the entire surface of the preforms, says SMI. “New age of packaging” The secondary packaging solutions on the show include a new overlapping cardboard sleeve packer of the MP Ergon series and a new casepacker of the CWP Ergon series. The packers of the MP Ergon series are suitable for packing a wide range of containers in numerous different configurations. The continuous cycle packaging system aims to ensure a fluid production process, without jerking movements, which protects the containers from damage, ensuring integrity of the product, high-quality of the package and reduced mechanical wear of the machine components. The pack bottom sealing with hot melt glue ensures a precise and longHall A6 - Booth 302","@ID":74}, "INSPECTION 44 PETplanet Insider Vol. 18 No. 09/17 petpla.net Managing variation simplified As part of the project, the company installed the Agr Process Pilot automated blowmoulder management system with vision in both of the new KHS series IV blowmoulders that produce bottles for these lines. The Agr system incorporates three components; the Pilot Profiler (PET material distribution measurement), Pilot Vision (visual defect detection), and the Process Pilot closed-loop control software, providing the link between the bottle measurements and blow-moulding machine controls. The Pilot Profiler measurement component relies on an array of sensors, located at the mould out-take, that measure material distribution on every bottle. These measurements provide continuous feedback to the Process Pilot controls which use this data to continuously adjust the blowmoulder to maintain desired material distribution regardless of even minor plant temperature changes or other variations that may impact material distribution. This configuration enables the control and operation of the blowmoulding system with simultaneous measurements of bottle thickness and control of the sealing surface. According to Kamil Banaśkiewicz, Technical Project Coordinator, it proved very beneficial in terms of dealing with the long-standing problem of material distribution variability due to the temperature fluctuations of the preforms. The Process Pilot system’s reaction to temperature variations of materials (preforms) is quite useful. Previously, any change in preform temperature forced the operator to adjust machine parameters and to evaluate the bottle. Currently, the adjustment is carried out automatically through the Process Pilot. The Agr system, with target models saved in the memory, reacts flexibly in two ways. It either adjusts the machine parameters automatically, if necessary, or rejects non-compliant bottles which exceed certain dimension ranges (in other words, have much, too much or not enough material). Those bottles never make it to the market. Addressing the challenges of the wasp-waist bottle ‘Wasp-waist’ - Distinct bottle shape for a unique brand The Cisowianka bottle has a very special shape, the ‘wasp-waist’ in the middle. It was designed to permit consumers to hold the bottle firmly but comfortably and pour the water in a safe manner. The need to manage material distribution with precision became even more critical with an effort to reduce the weight of the wasp-waist bottles for the Cisowianka brand. The wasp-waist feature did not come without challenges. While going through the light weighting process on this bottle, the company discovered that there was a certain weight limit they had reached with the preforms that they were unable to cross. When the weight of the preforms was reduced beyond this point, the bottle would bend when held by the label panel due to limitations in material in the waist region. It became evident that with the light weighted bottle, the material that was available had to be in the right place to avoid these problems, and the waist section was especially critical. The Process Pilot systems, installed on the new lines, were a critical component in the light weighting effort on this bottle. As experiments were performed with a number of different preform weights, the Process Pilot system was able to profile the material distribution, telling them precisely where the material would flow when the bottle was blown. This was particularly valuable in order to understand how the material in the critical areas of the waist region would be distributed. After considerable experimentation, they settled on new weights for the product that were lighter yet would preserve the feel and support the wasp-waist design, without compromising the quality. This current Cisowianka bottle is produced in three 1.5l formats, using a 30.5g preform for carbonated product, a 28.5g for the lightly carbonated product, and 27g for the non-carbonated version. Agr Pilot Profiler with Process Pilot automated blowmoulder control manages material distribution for the production of the Cisowianka ‘wasp-waist’ bottle on KHS series IV blowmoulder","@ID":46}, "TRADE SHOW PREVIEW PETplanet Insider Vol. 18 No. 09/17 petpla.net 77 Integrated production of beverage caps Precision and process consistency In collaboration with partner companies, the injection moulding machine manufacturer and systems provider Engel, based in Schwertberg, Austria, will present a complete system solution in the highly integrated production of beverage caps. During the five days of Drinktec, under actual production conditions and at a cycle time of under 2.5s, the production cell will deliver 26mm caps made of HDPE and including tamper-proof bands. At the core of the energy efficient integrated solution is an Engel e-cap 2440/380 injection moulding machine with a clamping force of 3,800kN. A 96-cavity mould by Corvaglia from Eschlikon in Switzerland will be used. Engel has integrated additional peripherals into the system including a DMS dry-air system by Blue Air Systems (Kundl, Austria), a TWIN model cap inspection system by IMDvista (Brügg, Switzerland), and material handling units by Piovan (S. Maria di Sala VE, Italy). The hot-runner temperature control is made by S.i.S.e. (Oyonnax, France), and partners for the raw materials are Borealis, (Vienna, Austria) and Gabriel Chemicals (Gumpoldskirchen, Austria). All-electric e-cap “In terms of geometry, beverage caps have reached their lightweighting minimum. This means that the demands on the precision and repeatability of injection moulding machines are higher than ever before”, says Frank Schuster, Sales Director of Engel packaging, describing a trend that is often decisive in the design of injection moulding machines and production cells for cap production. In addition, the sensitivity of producers to energy efficiency continues to increase. In order to meet both challenges, Engel is focusing on all-electric high performance machines for cap production. With clamping forces of 1,100 to 4,200kN, the Engel e-cap series was developed specifically for this market segment. Among other things, the highperformance servo direct drives are responsible for the process stability and precision of the e-cap injection moulding machines. They ensure the required plasticising capacity and a maximum of usable parts even when using the new high-strength HDPE materials with a MFI significantly lower than 2 or even 1g/10min. In addition, the increased ejection and clamping forces help to achieve very short cycle times. In spite of its performance, the e-cap is claimed to require little energy and cooling water, even at constant high-speed. Fast project planning As a complete system, the production cell represents the state-of-theart in efficient cap production. Both Blue Air Systems and IMDvista will be presenting their latest innovations at the Engel booth. The DMS series devices by Blue Air Systems allow for higher product quality and energy savings of up to 85% as compared to conventional mould dehumidifiers. What makes this series special is that it works without water. Without precooling, it guarantees condensationfree production conditions regardless of the weather and the climate zone. With its TWIN flying closure system, IMDvista has solved one of the biggest challenges in the inlineinspection of beverage caps. Usually, the freshly produced caps undergo camera inspection while lying on a conveyor belt. This means that the top side of the caps cannot be viewed by the cameras. With the new technology, caps are lifted by a stream of air, and can thus be inspected from above and below without extending processing time. From a single source, Engel delivers highly integrated and automated system solutions for the production of bottle caps worldwide. Advantages for the producer are that for one thing, efficiency and quality potentials can only be fully utilised when the individual components of the production cell have been precisely synchronised from the start, says Engel. Apart from that, the systems solution accelerates project planning and commissioning due to the fact that the producer does not need to coordinate various suppliers. www.engelglobal.com Hall A4 - Booth 324 During Drinktec, a fully automated e-cap injection moulding machine, equipped with a 96-cavity mould, will be producing 26mm caps including tamper-proof bands at a cycle time of under 2.5s.","@ID":79}, "PETplanet Insider Vol. 18 No. 09/17 petpla.net 84 PETbottles Beverage + Liquid Food Skyr drink from Desira Just as Greek yoghurt products were in public demand some time ago, so the current trend is for so-called Skyr products, milk products made the Icelandic way. Following on from brand owners or small and regional manufacturers, Aldi South has started to introduce more and more Skyr drinks under the “Desira” brand onto the market. The drinks come in tapered, white coloured 250ml bottles that contain lots of protein but very little fat. Suitably designed sleeve labels for each variety of drink, together with a screw top to protect the product prior to opening, complete the packaging at point of sale. www.aldi-sued.de Mixed fruit juices from Solevita Various mixed 100% fruit content juices displayed in a refrigerated unit are on offer as part of a Lidl promotion under their own “Solevita” brand. Along with apple juice, pineapple juice, grapefruit juice, lime, banana and mango pulp, the “green” variety also contains 0.2% kiwi seeds. The “orange” variety contains different fruit juices including 20% carrot juice in response to customer demand for mixed juices made from various fruits and vegetables. The clear 500ml bottles were decorated with corresponding sleeve labels, with a transparent area for product presentation. The sleeve label has been placed over the screw top as an additional security feature which has to partially removed along defined perforations prior to opening for the first time. www.lidl.de Fruit shots from rio d’oro “Hero of the Day” is part of Aldi South’s rio d’oro brand which comes in a 4-pack of fruit shots as a small volume alternative to smoothies. The drinks consist of three types of fruit; apple-orange-passion fruit, or grape-banana-chokeberry, both with added acai. Each clear 125ml bottle has a decorative sleeve label and is secured by a screw top and tamperproof strip. The four bottles are packed together as a sales unit in colourful printed cardboard packaging, with recesses into which the individual bottles can be secured. www.aldi-sued.de Smoothie with natural yoghurt The Austrian firm, Berglandmilch, is selling its Smoojo, a Smoothie with natural yoghurt, in Germany under the Schaerdinger brand. The Smoojo comes in four flavours: raspberry-strawberryblackberry and acai; strawberrybanana-pineapple-banana-coconut and mango-passion fruit. They come in a 250ml, white PET bottle which has a screw top and security strip. Full length, subtly designed sleeve labels with adhesive stickers on the lid ensure each variety is easily recognisable at point of sale. www.schaerdinger.at","@ID":86}, "BOTTLE MAKING 26 PETplanet Insider Vol. 18 No. 09/17 petpla.net Tour Sponsors: Over 30 years of PET in Malaysia by Alexander Büchler Golden PET, Chemor, Spritzer Taiping, April 10, 2017 We met: Ms Tan Poh Fah, General Manager, Golden PET Mr Yap Mou Kar, Production Manager, Golden PET Mr Lam Sang, Managing Director, Golden PET Ms Chong Mee Yoong, Deputy General Manager, Spritzer Ms Winnie Chin, Group PR Manager, Spritzer Mr Sow Yeng Chong, Group Financial Controller, Spritzer In 1983, a small plastic manufacturer had the idea of filling bottles with cooking oil. Until then, it was common practice to use metal cans. Initially with PVC, the business founder, Mr Lam, joined Golden PET in 1986. Ten years later, Mr Lam introduced the first large PET bottles to replace the big 3 and 5kg cans used in the Malaysian cooking oil industry. From these early beginnings, Golden PET factories have expanded their scope of supply to include water bottles, preforms and closures. Today, Mr Lam is the Managing Director of Golden PET, which is a wholly owned subsidiary of Spritzer Bhd, a public listed company on the Main Market of Bursa Malaysia Securities Bhd. Spritzer Berhad owned Spritzer premium brand which, to this day, is the only bottled mineral water filled from its own springs in Malaysia. tles into the cooking oil sector has brought Mr Lam many plaudits. Thirty years ago, he extended his company’s range to include water bottles, preforms and closures. It was started with the 32-cavity preform Husky machine. At the time, preform production equipment was used to manufacture 17g for 500ml and 35g for 1.5l bottles. There was another Husky cap line with a Corvaglia tool to fashion the seals and an approximately 3g PCO 1810. Today, Golden PET’s portfolio comprises eight preform facilities with an output of 210 million preform/ annum and five Huskys producing 600 million caps/annum. They also have seven blowing machines producing various types of bottles for oil, water and juices packaging. Spritzer Berhad, Taiping Bottling under the “Spritzer” brand name began in 1987 in Taiping, about an hour’s drive from Golden PET which used the best quality mineral water extracted from a spring from a depth of around 128m (420ft). The spring is surrounded by protected tropical rainforest which forms part of Spritzer’s 330 acres (134ha) operational site. Two more water bottling plants later opened in the area around Shah Alam, Selangor and Yong Peng, Johor to the south. In 2012, Professor C. Exley from Keele University in the UK discovered that Spritzer’s 35mg/l mineral water was rich in silicon content and useful in the prevention of AlzheiGolden PET (GPI) produces preforms and the necessary caps. On the left, Mr Lam Sang, Golden PET’s Managing Director; on the right, Mr Yap Mou Kar, Golden PET’s Production Manager. There is a wider range of beverages other than water – soda, flavoured water and functional drinks. Mr Lam and Ms Tan Poh Fah, Golden PET’s General Manager, explain their portfolio. Mr Lam has a team who have been working with him for many years. Ms Tan Poh Fah is Golden PET’s General Manager and Mr Yap Mou Kar, is in charge of production. It began with the injection moulding of household utensils. Golden PET still makes toothbrushes for export to Japan as well as for the domestic market. The introduction of PET bot-","@ID":28}, "CAPS & CLOSURES 50 PETplanet Insider Vol. 18 No. 09/17 petpla.net Complex sports cap: the closure’s interior may contain powder, fluid or pills. Assembly machine innovation brings new opportunities Complex closures One manufacturer in this market is the assembly-machine builder Contexo, who has been building turnkeyready machines for beverage closures for 15 years. The company became well known for its solutions in the medical-devices sector. Contexo has successfully transferred this expertise to the beverages market. Today, the family-run firm is one of the leading providers of machines for complex beverage closures. The portfolio of Contexo includes machines for complex-closure designs (e.g., non-rotationally symmetrical), closures with additives (e.g., powders or fluids integrated into the cap), and for special seals for highly carbonated beverages. The assembly steps for a complex closure with a chamber for a powder are presented below. Spout: the heart of the closure The spout is important to the user primarily for its haptic qualities. It is the part of the bottle users touch with their mouth. With complex closures, it is especially the internal structure that is important. It can contain powder, fluid or pills. Production: First the parts have to be fed in. This is a particularly gentle procedure that uses vibrationfeeding devices to prevent pearlescence and damage to the seal elements. Contexo developed its own feeding technology that guarantees gentle handling of the parts even at high speeds. If the closure type is not rotationally symmetrical, the part must also be correctly oriented. A dosing unit integrated into the assembly machine fills the chamber. Powders and fluids are dosed in the ml range. Tabs and pills are also frequently used. Finally, a foil seal is used to close the chamber. The Contexo assembly machine stamps the foil inline immediately prior to assembly. This saves time, minimises production area and avoids contamination. The chamber is then closed and sealed with the foil. To guarantee the seal’s tightness, inline vision inspection is used to check around half a dozen criteria. Only 100% perfect parts may continue to the next stages of the production process. The checked parts are then turned around prior to the assembly process so that they can later be correctly mounted to the body. Body: the base of the closure The body’s main role is to connect bottleneck and spout. In the case of the present closure with powder chamber, the body contains cutting teeth. By turning the spout, the cutting teeth open the foil seal and empty the chamber’s contents. Increasingly complex closures dominate the beverages market in the middle- and high-price ranges: innovative machine designs can today manufacture closures that were not profitable just a few years ago. The following overview shows you the typical assembly steps involved in the production of a complex sports cap. Active ingredients: a twisting action perforates the lower foil and releases the ingredients. Production: First, the bodies are fed in and oriented according to their visual features. Visual-inspection systems check the quality of the cutting teeth. This ensures that the foil seal is cleanly opened. Here too, Contexo uses inline vision inspection. Now comes the “wedding”. The filled spout is united with the body – the two parts are mounted together. Finally, the TE band is folded and activated. Overcap: the closure’s protective jacket The closure’s cap mainly performs a protective role: it guarantees that the beverage is uncontaminated at point of sale and enables secure re-closing. An EU regulation is currently being planned for this functionality. Overcaps will soon","@ID":52}, "PACKAGING / PALLETISING PETplanet Insider Vol. 18 No. 09/17 petpla.net 54 PACKAGING / PALLETISING 54 State-of-the-art facilities pack excellence Globalisation is typically reflected in product packaging. This is particularly true for consumer goods which fuel maximum demand for packaging worldwide. Globally, the consumer goods market will leap from $8 trillion in 2014 to $14 trillion by 2025, while in India it will grow at a CAGR of 14.7% to reach US$ 110.4 billion by 2020. Consumer goods companies in India are focusing on specialisation and superiority in packaging technologies. The Indian packaging industry constitutes about 4% of the global landscape. Bangalorebased Manjushree Technopack is the bellwether of the industry as South Asia’s largest rigid packaging solutions provider. It offers 360° packaging solutions to 200+ companies across industry verticals. Manjushree’s expertise lies in delivering innovative solutions using its state-of-the-art facilities and advanced technologies. Manjushree has given traditional products fresh design, amplifying their convenience factor for consumers. The company works with renowned brands including Coca-Cola, Pepsi, Nestlé, Mondelez, Dabur, Reckitt Benckiser, Unilever, GlaxoSmithKline, L’Oréal, Himalaya, Diageo, and Tata Tea among others. From humble beginnings in 1977, as a packaging supplier for tea estates in Assam, it has become an Indian packaging giant in 2017. Late last year, the company acquired the packaging business of Varahi, which included its four production facilities in North India. Additionally, it also established a greenfield facility in Assam. Now, Manjushree boasts a pan-India presence with eight strategically located manufacturing facilities, to cater to the discerning needs of its customers. Today, the company has an installed capacity of 125,000 MTPA and revenue of US$ 125 million making it a leader in rigid plastic packaging. The Bommasandra clean room • 28mm, 33mm and 38mm screw closures • Robust and trouble free capping • Established DoubleSeal™ technology - for secure sealing performance - for better protection against micro-organisms • Slit FLEXBAND® band technology for enhanced tamper evidence • O 2 barrier and scavenging options for screw flat caps supporting longer shelf life and fresher taste • Sports closures for aseptic filling and hot filling without aluminum foil • Special closures for syrups and carton packaging Unique range of screw and sports closures designed for cold fill and aseptic application BERICAP Technology for juices, RTD teas, health drinks www.bericap.com","@ID":56}, "Materials / Recycling PETplanet Insider Vol. 18 No. 09/17 petpla.net 12 The add-on Multi Purpose Reactor (MPR) technology of Erema – one year after the re-launch rPET packaging with food contact compatibility PETplanet: Mr Wöss, first of all I have to compliment Erema. In the past 15 months, Erema has sold 24 Vacurema Inline systems. What are the reasons for such a really good result? Wöss: The trend in the PET recycling sector is clearly in the direction of food-grade direct processing. This means that granulate production is not required as an intermediate step, and post-consumer PET flakes or even PET production waste are treated directly and without being reheated in a heater to final product. At the moment, 1.3 million tonnes of PET are recycled worldwide using Vacurema technology. End products are for example food-grade preforms for the beverage industry, thermoforming films, fibres or strapping. PETplanet: The MPR is an add-on technology within the Vacurema system. How flexibly can the MPR be used in existing extrusion lines? Wöss: The MPR is installed in front of the existing extrusion line. It replaces conventional crystallisers and pre-dryers. In one step, the product is decontaminated, dried, de-dusted and crystallised giving a guaranteed foodgrade material. Long process times and high energy costs are thus already eliminated. The average pre-drying and crystallisation takes about 6-8 hours with a modular design, whereas our compact system takes 1-1.5 hours. PETplanet: What is the energy consumption of the MPR and what material can be used in the reactor? Wöss: The extremely low overall energy consumption of only 0.1kWh/kg is a really good argument for the MPR. The entire process takes place at a temperature of about 190°C. Due to the steady rise in temperature, the polymer structure opens and the process of removal of the migration substances as well as the internal moisture from the flakes begins. The input material used can be either washed PET bottle flakes, ground PET flat film waste, as well as PET virgin material and mixtures thereof. The bulk density of 200-350kg/ m3 has been increased by the Reactor to 450-480kg/m3. This promotes a uniform and higher output of the extrusion line. This ensures the customer a guaranteed increase in performance of their system. PETplanet: In conventional processes there are always problems with the colour quality of the material - how does the MPR cope? Wöss: Polyamide oxygen barrier or PVC for example has negative impact on colour quality. The vacuum processing of flakes avoids discolouring due to absence of oxygen. In addition, thanks to the frictional heat of the MPR, the effect on bridging and staining of materials with low melting points is reduced. Over and above the viscosity can be increased slightly. PETplanet: After these very interesting details, I come back to the beginning - for our readers particularly interesting of course is how often this plant is used in the beverage sector? For example, how many systems do you have installed recently in the bottle to bottles area? Wöss: In the past months, Erema has been able to record some deals. This is interesting because the price of virgin PET is still low. It is evident that a rethink will be required in this area to get things moving. PETplanet: With Sipa, Erema has the best possible partner for the Xtreme Renew project presented at the Discovery Day last year, combining the Vacurema technology directly linked to the Xtreme for preform production from 100% recycled material. What is the current situation? Wöss: On September 4-6, so before the Drinktec trade fair, Erema and Sipa together issued an invitation to come to Italy where the completed prototype is to be presented to our customers. A first live demonstration of the plant and first process results will be presented. Over three days, customers and the trade press will be coming to Italy and we will be available to answer questions. PETplanet: We are delighted, because we are also invited to enjoy the beauty of Italy and will report on these first results. Now you have just mentioned this yourself: Drinktec is just around the corner. What can we expect at the Erema booth? Wöss: We will be in the PETpoint Hall A4 to welcome visitors at booth 346. We cordially invite all visitors to our booth to exchange views about current recycling topics and are greatly looking forward to this trade fair, so important for us! PETplanet: Mr Wöss thank you very much for your time and for a pleasant and informative conversation. www.erema.com One year has elapsed since Erema invited their customers to the Discovery Day 2016 at Ansfelden, Austria, to present the optimised MPR technology. A good reason to ask Mr Christoph Wöss, Business Development Manager for the bottle division at Erema about business developments. Christoph Wöss in front of the MPR of Sky-Light at Erema’s production facility by Heike Fischer","@ID":14}, "TRADE SHOW PREVIEW PETplanet Insider Vol. 18 No. 09/17 petpla.net 71 Inspection and coding systems Hall B5 - Booth 344 DRINKTEC (Munich) 11th – 15th September PACK EXPO (Las Vegas) 25th – 27th September CBST (Shanghai) 22nd – 24th November PLAST PRINT PACK (Accra) 5th – 7th December MARKET BENCHMARK PET-HIGH PRESSURE LOW PRESSURE DOUBLE ACTING DIRECT COUPLED MOTOR HEAT RECOVERY SYSTEM HORIZONTAL OPPOSED Filtec will be presenting the latest generation of its systems: New Filtec OMNIvision 3: At 1,400bpm this machine is said to be the fastest empty bottle inspector in the market. With high resolution cameras and rapid image processing, returnable glass and RefPET inspection is claimed to be more secure. The new design offers easy access to the machine for faster change over and cleaning. High performance at a low cost of ownership is another advantage of the system. VISIONtec: This modular vision inspector is designed to be both compact and easily scalable, condensing many inspection features like fill level, closure, and label inspection, into a single housing. VISIONtec also includes Filtec’s filler valve monitor system, which allows technicians to monitor the individual performance of filler valves and capper heads to increase line efficiencies and reduce maintenance costs. The Fill Level Inspector: With its compact design, this comprehensive fill level inspection system can be installed in any filling line. Large icons on the new graphic user interface make it easy to work with the product, and “widgets” explain directly on the screen how to conduct product changeovers or typical maintenance tasks, simplifying operation. The user interface also allows networking with other Filtec inspection systems. The system is upgradable to a Filler Valve Monitor. www.filtec.com","@ID":73}, "imprint EDITORIAL PUBLISHER Alexander Büchler, Managing Director HEAD OFFICE heidelberg business media GmbH Bunsenstr. 14 69115 Heidelberg, Germany phone: +49 6221-65108-0 fax: +49 6221-65108-28 [email protected] EDITORIAL Kay Barton Heike Fischer Gabriele Kosmehl Michael Maruschke Ruari McCallion Waldemar Schmitke Anthony Withers WikiPETia.info [email protected] MEDIA CONSULTANTS Martina Hirschmann [email protected] Johann Lange-Brock [email protected] phone: +49 6221-65108-0 fax: +49 6221-65108-28 LAYOUT AND PREPRESS EXPRIM Werbeagentur Matthias Gaumann | www.exprim.de READER SERVICES Till Kretner [email protected] PRINT Chroma Druck & Verlag GmbH Werkstr. 25 67354 Römerberg Germany WWW www.hbmedia.net | petpla.net PETplanet Insider ISSN 1438-9459 is published 10 times a year. This publication is sent to qualified subscribers (1-year subscription 149 EUR, 2-year subscription 289 EUR, Young professionals’ subscription 99 EUR. Magazines will be dispatched to you by airmail). Not to be reproduced in any form without permission from the publisher. Note: The fact that product names may not be identified as trademarks is not an indication that such names are not registered trademarks. 3 PETplanet Insider Vol. 18 No. 09/17 petpla.net It’s that time again. Drinktec time. Even if it seems like it’s all about the exhibitors, in fact everything revolves round you. You are there to look at the exhibits, to exchange views with other like-minded people and finally to enjoy this 4 yearly spectacle in Munich. So make sure you visit us at the PETpoint hall A4, booth 501; immortalise yourself with a photo, and stick your picture here on page 3! In addition to PETplanet, enjoy one or two delicious home-brewed beers or other beverages every evening from 17.00 to 22.00h. See you there! Yours Alexander Büchler Dear friends of PETplaner Insider, Visit us at Drinktec Hall A4 Booth No. 501 and have your photograph taken to paste it in here! Live in Munich!","@ID":5}, "BOTTLING / FILLING PETplanet Insider Vol. 18 No. 09/17 petpla.net 40 22,000 containers per hour Installed in its entirety by Krones, the line handles 22,000 containers per hour, and comprises: Blow-moulder/filler block, consisting of a Contifeed preform roller sorter, a Contiform 3 Pro blow-moulder, and a Modulfill NWJ weighing filler with 55 filling valves Checkmat inspector for verifying the fill level Modularised Prontomodul labeller with a Canmatic module for precut paper labels and a Contiroll module for wrap-around labels made of OPP (oriented polypropylene) Checkmat inspector for verifying correct label placement Variopac Pro WTS for end-ofthe-line packaging in trays with film or wrap-around cartons Modulpal 2AC palletiser for stacking the packs on europallets or Düsseldorfer halfpallets Weighing cell technology For bottling edible oils, maximised accuracy in the filling operation is a crucial criterion for decision-making. For the first time, NT is using a weighing filler instead of a volumetric model. “We believe this will give us higher filling accuracy, irrespective of the product’s filling temperature and viscosity,” says Milan Kunciř. The Modulfill NWJ assures these precise fill quantities specified, since its weighing cells monitor the inflowing oil during the entire filling operation. Once the desired weight has been reached, the valve closes and the product can briefly settle. Then the weight is checked again. labeller there is an option for using OPP labels in the future, particularly for exports. “We want to have a rapidresponse capability for the market’s changing requirements.” Installation of the new line was a well-nigh perfect job, says Milan Kunciř: “Krones was right on schedule. So far we’ve been extremely satisfied,” he avers. Now that the new high-speed oil line has eliminated the bottleneck in the firm’s filling capacities, NT can tackle some new projects: the tank farm is to be upsized, the output of the oil mill increased yet again, and the processing of the byproducts upgraded. So the thrust for expansion is set to continue for quite a while yet. www.krones.com www.ntkft.hu “Kunsági Éden” is the premium sunflower oil of NT GmbH. It is bottled in a 1l PET container, with a striking closure in the Hungarian national colours. Milan Kunciř singles out several points that influenced the choice of Krones: “The crucial factors for us were the good performance of the Contiform technology in the existing line. Krones’ high profile, particularly in Czechia’s brewing industry and the local expertise provided by Krones’ agency in Hungary. Another advantage is the producing and bottling of 480,000l in round-the-clock operation – with all of the kit single-sourced. The quality and reliability of German engineering and the acceptable price are important points as well.” 20% less weight And there was something else, too. “We wanted to offer to our clients an additional advantage in terms of costs and ecological footprint, by producing lighter bottles,” explains Milan Kunciř. “By block-synchronising the blow-moulder and the filler, we’ve managed to downsize the weight of the 1l container to 16.5 or 18.5g – depending on the brand of oil involved. What’s more, we use a short neck, which means we can also fit a lighter closure. Overall, redesigning the bottle has saved us up to 20% in terms of plastic consumption.” For the first time, NT is using a weighing filler instead of a volumetric model for higher filling accuracy. The two different filling speeds ensure perfect flow behaviour. Flow straighteners in the valve produce a filling operation with minimised foaming and turbulence. Milan Kunciř has an almost personal preference for plastic labels, too: “I believe this will make it easier to recycle the entire container, since the paper labels don’t need to be disposed of separately,” is his firm conviction. The bottles are still being dressed in wrap-around paper labels, because “the Hungarian market, especially, is conservative in this regard,” he remarks. But with the modularised","@ID":42}, "PETcontents 09/17 4 PETplanet Insider Vol. 18 No. 09/17 petpla.net Page 58 Page 22 Page 12 INSIDE TRACK 3 Editorial 4 Contents 6 News 81 Products 84 PET bottles for Beverage + Liquid Food 86 PET bottles for Home + Personal Care 88 Patents MATERIAL / RECYCLING 12 rPET packaging with food contact compatibility 13 rPET made in New Zealand PREFORM PRODUCTION 14 Joint forces for the perfect preform system 16 Working closely together with mould makers EDITOUR 18 PET in the Philippines 22 Austria meets the Philippines MOULD MAKING 24 More space for creative mould making BOTTLE MAKING 26 Over 30 years of PET in Malaysia 28 Twistin’ time 30 Reheat Stretch Blow Moulding machines - Stretch Blow Moulding, part 6 COMPRESSORS 36 A Horizon-3000 for Hansa-Heemann BOTTLING / FILLING 38 High-speed oil INSPECTION 42 ‘Wasp-waist’ bottle MARKET SURVEY 47 Suppliers of resins & additives CAPS AND CLOSURES 50 Complex closures PACKAGING / PALLETISING 52 Single-lane keg racking 54 State-of-the-art facilities pack excellence TRADE SHOW PREVIEW 57 Drinktec A4 hall plan 58 Drinktec 2017 preview 68 Preform & closure inspection solutions 69 Multi-Layer live on stage 70 Product handling all-in-one 71 Inspection and coding systems 72 Inspired by Industry 4.0 74 Oil-free compressors centre stage 76 Adjustments in real time 77 Precision and process consistency 78 Sealing solutions 79 All about closures 80 Ready to be recycled BUYER’S GUIDE 89 Get listed!","@ID":6}, "EDITOUR PETplanet Insider Vol. 18 No. 09/17 petpla.net 20 Tour Sponsors: “Nature’s Spring” purified water, is also available in four different flavours. The company is also undertaking lot of copacking with other brands. Coca-Cola Femsa and its “Wilkins” water brand has also been involved in local markets for flavoured water for some time, with “Wilkins Delight”. Universal Robina Corporation leads the RTD tea market, with its “C2” brand. Drink trends that are expected to continue to gain market presence in the future are flavoured and functional water products, along with RTD coffee and milk-based drinks. As there is set to be new taxation on sugar, several brands are already reacting with various flavoured water products and waters with additives (vitamins). Milk-based products are currently still imported from overseas as they have better production conditions, including aseptic filling capacity, although it can be assumed that the first new filling plants for on-site production in the Philippines could soon be established. Preform production is now predominantly handled locally, meaning there is almost no need for imports. This is due to either local processors technically improving the necessary equipment to take on production over a number of years, or established foreign processors opening their own branches in the Philippines. Pepsi, who used to rely on imports from China and other South East Asian countries of preforms for hot fill and CSD, is now supplied by Manly Plastics from the Manila region, which also supplies several local brands for various applications. Alpla Philippines Inc., Coca-Cola Femsa’s in-house preform producer, and Indorama Ventures Packaging Philippines Inc., the local branch of the Thai PET giant, have made huge investments in machinery and tools for manufacturing preforms in recent years. While Alpla produces exclusively for Coca-Cola, Indorama has a dedicated plant for Coca-Cola and a separate plant for other local brands. All graphs retail/off-trade unit volume in million units (Source: Euromonitor) Thin Wall Plastic Containers, HDPE Bottles, Brick Liquid Cartons 80.0 Metal Beverage Cans, Glass Bottles, Brick Liquid Cartons, Flexible Aluminium/Plastic 4.0","@ID":22}, "66 TRADE SHOW PREVIEW PETplanet Insider Vol. 18 No. 09/17 petpla.net l l l consumer bags textile packaging recycling rECO Vision inspection solutions Pressco Technology Inc. will showcase their newest vision inspection solutions for companies that manufacture and fill food and beverage containers.The scalable, modular platform delivers a wide range of inspection options across an entire blow-fill line. In the blowmoulder, Pressco offers a combination of camera modules which detect defects on the preform and/or the empty bottle, including virtual section weight measurement which is vital to process control. On the filling side, the company’s solutions include a multi-camera system for filled bottle inspection to detect misapplied closures, tamperband defects and under/ over-filled bottles. Additional inspection options may be deployed at the cap feeder, labeller, date coder and case-packer. These inspection capabilities are controlled via a single centralised processor with one or more HMIs, which eliminates the inefficiency of multiple platforms from different suppliers. Pressco’s integrated system of distributed inspection means that one vendor can provide sales & service, training, technical support, spare parts, etc. on an entire vision system. Pressco Technology’s booth at Drinktec will have live demonstrations of their “up-and-down-the-line” inspection capabilities for H2 O, CSD, hot fill and aseptic lines. www.pressco.com New generation of SBM machines Side S.A. will introduce the new generation of PET blowmoulding machines. This new generation promises a step forward to supply solutions and cost savings to the company’s customers. One of the main objectives of the engineers at Side has been to design a new preform loading system that will include a recovery line for poorly positioned bottles to enable their return to the loading chute, thereby eliminating losses at this point. Also, the new generation has updated its design. The new casing is claimed to provide more space and greater accessibility to all the operational areas of the blower, thanks also to the combination of sliding doors. In addition, the new design makes handling and maintenance easier. Anew mobile support for the control touch screen of the blower has also been added, which gives the operator greater mobility and improved ergonomics during the PET bottle production process. Every product needs a good solution when it comes to wrapping and packaging. And when the product requires specific technical features, the correct container choice is essential for the product’s market success. The beverage industry is the perfect example of this kind of requirements. On site at Drinktec, the commercial team of Side will explain and answer questions about the new generation of PET stretch blow moulding machines. Also, Side will show the most new bottles design of Thandle and the lastest developments for big containers, like the 30l for beer kegs from Petainer. www.sidemachines.com Hall A4 - Booth 402 Hall A4 - Booth 543","@ID":68}, "TRADE SHOW PREVIEW PETplanet Insider Vol. 18 No. 09/17 petpla.net 80 Emptying and compacting of PET bottles Ready to be recycled With the strapline `fast and economical compaction´ Strautmann will be presenting different waste disposal solutions. The dewaterer LiquiDrainer and the baler BaleTainer will be the principal focus of the company’s exhibits. The emptying of PET bottles will be demonstrated live at Strautmann’s booth. With the dewaterer `LiquiDrainer´ beverage containers like PET bottles can be emptied and devalued. The LiquiDrainer pricks the beverage containers so that the liquids flow out. The material is perforated and not shredded. Thus there is no wear on the rotor. The residual liquids pass through a coarse filter and can be subsequently sold for example to biogas plants. Thanks to the separation of liquid and packaging no particles enter the wastewater. In the next step the material is compacted with bale or briquetting presses. The fully automatic compaction of the beverage containers into high compacted bales und briquettes saves space and costs. Recyclable materials can be sold profitably. Disposal solution at Hansa-Heemann Hansa-Heemann AG, manufacturer of non-alcoholic soft drinks with several production locations in Germany, offers a complete disposal solution for PET, cardboard and film. At their Löhne site 400 million beverage cans are filled in a three-shift operation. Prior to their decision to use Strautmann Umwelttechnik for PET bottle disposal, Hansa-Heemann had already been compacting film and cardboard with Strautmann presses for more than seven years. “While producing mineral water and sweet beverages residual liquids need to be disposed of economically and ecologically. Our PET bottles are now drained and compressed economically by using the Strautmann LiquiDrainer and BaleTainer” says Thomas Hartsieker, Plant Manager, Hansa-Heemann AG. Disposal process The now compressed PET bottles are collected in Hansa-Heemann containers and lattice boxes and then brought to the outside waste disposal area. Here, using a forklift an employee lifts the boxes and empties them into the hopper of the LiquiDrainer. Via a conveyor belt, the PET bottles are transported into the LiquiDrainer, which empties and devalues them. The emptied and already pre-compressed PET bottles are transported from the LiquiDrainer directly into the fully automatic baler BaleTainer, prior to being compacted directly into marketable bales. Before installing the LiquiDrainer solution, the process was handled by a disposal company. Emptying of 120 bottles/min With the LiquiDrainer, the manual emptying of PET bottles is eliminated. Employees are able to focus on the core business and work faster and more efficiently. Thanks to special rotor technology and a throughput of up to 7,000l/h, approximately 120 bottles can be emptied in one minute. The beverage containers are emptied and devalued to prevent fraudulent re-use. Baler compacted “Cardboard, film and PET were previously stored in troughs with a filling capacity of 7-30m³. Up to 15 troughs were positioned inside the production area and warehouse. The material collected was inserted manually. Because the material was inefficiently collected, the troughs were filled very rapidly, and they needed to be placed outside to be picked up constantly.” remembers Ender Yilmaz, Disposal, Hansa-Heemann AG. “In one trough about 500kg of loose film was accumulated.” With compaction by a baler now about 8-10t can fit in one trough. In production three multi-chamber balers now give an impression of cleanliness and order. The presses enable sorted compaction of cardboard and film. The high-compacted bales of the presses are then taken to a hopper by a forklift truck and picked up by the disposal company. The installation of the balers directly at source eliminated a lot of unnecessary walkways and made the work more efficient. www.strautmann-umwelt.com Hall B4 - Booth 512 Filling of the dewaterer LiquiDrainer The LiquiDrainer pricks the PET containers so that the liquids flow out. PET bottles waiting to be emptied and compacted. Marketable bales of compacted PET bottles","@ID":82}, "64 TRADE SHOW PREVIEW PETplanet Insider Vol. 18 No. 09/17 petpla.net Hall B5 - Booth 115 (IMD) & Hall B5 - Booth 302 (Sacmi) Hall A4 - Booth 306 Hall B5.115 Drinktec München, 11. – 15. September 2017, visit IMD @ Inspection Systems for the Plastic Packaging Industry Swiss Made | www.imdvista.ch IMDvista CLDP Closure Digital Print. Flexible in format & design. Up to 1’500 ppmin. IMDvista PECO V3 Preform Inspection. Less than 7mƹ and up to 90’000 pph. Cavity reading. IMDvista TWIN Closure Inspection. «Flying Closure» for true, 100% inspection. PET flake sorting station At the Drinktec, Sesotec GmbH presents itself for the first time as a supplier of complete sorting stations for PET flake recycling. The revised Flake Purifier+ multisensor sorting system will be the company’s highlight. A complete PET flake sorting line from Sesotec offers advantages such as fewer interfaces and contact persons, and uniform operation of all the line components, says the company. Mechanical sorting is claimed to be perfectly matched to sensor sorting, and both ensure optimal performance. The Flake Purifier+ multi-sensor sorting system was comprehensively modified and features optimised material infeeding for a more evenly distributed material flow and increased material throughput. It also allows easier maintenance and integration. The system’s dust-proof design and integrated dust and label extraction connections provide increased efficiency in the recycling process. All Sesotec multi-sensor sorting systems - and of course also the new Flake Purifier+ - are available with all sensor combinations and in various working widths. www.sesotec.com Integrated “redcube plus” modules printing on self-adhesive labels and beverage closures In partnership with two partners, Sacmi (Hall B5, Stand 302) and IMD (Hall B5, Stand 115), two Hapa “redcube plus” UV DOD digital printing modules will be showcased. Integrated into a Sacmi bottle-labelling line, a “redcube plus” will CMYK print on labels which afterwards will be applied on bottles. The flexible printing module supports design customisation for even short production runs. The UV inks used on the bottle-labelling line are designed and produced by Hapa Ink, out of the Aposta series. A further “redcube plus” is included in an IMD Closure Direct Print line and will print full-colour (W-CMYK) onto beverage closures. The Hapa inks used by the line are out of the series Enserra. www.hapa.ch","@ID":66}, "59 TRADE SHOW PREVIEW PETplanet Insider Vol. 18 No. 09/17 petpla.net NBĔ H?Q ;AĔ I@ INNFCHĴ GREAT TECHNOLOGY ...IN A SMALL BODY NEW EBS ERGON BLOWERS EBS ERGON VIDEO ...scan & discover it! Compact and ergonomic design, cutting-edge technical solutions, top performances, high energy saving: that’s the new EBS ERGON series of fully electronic rotary stretch-blow moulders for manufacturing PET containers from 0.10 to 10 L up to 35,200 bottles/hour (0.5 L format). Available as stand-alone equipment or integrated into an ECOBLOC® ERGON compact systemof bottle blowing, filling and capping. I COMPLETE LINES I ROTARY STRETCH-BLOW MOULDERS & FILLERS I I PACKERS I PALLETISERS I www.smigroup.it Efficient use of water in the beverage industry Water in all its facets: this is the specific aspect chosen by the VDMA Food Process Machinery and Packaging Machinery Association to look at one of the branch’s key topics during Drinktec. The 34 lectures presented at the water-technology@drinktec symposium will be featuring the extensive portfolio of solutions available from the branch’s suppliers and vendors. The topics cover issues involved in water treatment, wastewater treatment, process optimisation and quality control for process and product water. Technical solutions, practical examples and concepts for restructuring the cleaning processes as well as saving water cover the broad range of interests shown by visitors. A few examples: Reverse osmosis is one of the common methods for producing product and process water. The investment and operating costs are defined not just by volume flow, raw water quality and yield. Here an essential role is also played by customer quality requirements, such as hygienic design, CIP and sanitising capability. Water treatment methods with new mineral adsorbents are used for effective, low-cost removal of semimetals and heavy metals from drinking water. Reducing water consumption rates by integrating recuperation solutions in water systems is a highly promising approach for saving water and energy in the markets of the emerging countries with their extreme water shortages. In addition to lectures by technology providers, the symposium also features scientific projects: benchmarking to save water in the beverage industry, simulation methods for process optimisation in the fruit juice industry and smart, self-learning cleaning systems are just a few examples. The symposium can be attended by Drinktec visitors free of charge without prior registration. http://nuv.vdma.org/drinktec dSpace - a new way of developing PET containers Italian Demo Design and Moulds will be introducing dSpace. The digital platform is intended to bring people digitally together who are involved in a new project. dSpace is the place to share thoughts and information, be creative and stay productive, share project roadmap and activities, get the solution online. The idea behind dSpace is to coordinate a team at separate locations and to speed up the work process and decisions. Via the digital platform, the Demo team supports their customers in outlining a bottle project, in designing a new bottle, or in delivering the expertise of producing a nicely designed bottle efficiently with a skilled industrial approach. www.designandmoulds.com Hall A4 - Booth 303","@ID":61}, "EDITOUR PETplanet Insider Vol. 18 No. 09/17 petpla.net 18 Tour Sponsors: Soft drinks on the up; the issue of logistics PET in the Philippines by Kay Barton When you think about the Philippines, you can’t help but think of sunny islands and palmlined, idyllic beaches and, indeed, some of the most luxurious resorts in the world can be found here. While tourism is an important part of the economy it is not the most prominent one; this country of many islands is undergoing an exciting economic transformation. Continuous growth, increasing per capita income, ambitious plans to improve infrastructure and simplification of bureaucracy are leading the Philippines’ drive to entice both domestic and foreign investors to an attractive location in South East Asia. Positive results can be seen in the machine and systems industry, including the world of PET-bottled beverages. Although the Philippines had not been on the original plan for our South East Asia Tour, we decided to make a detour to Manila and Cebu and to talk with some market experts about recent developments. Get in touch with… economy & infrastructure With 7,107 islands, the Philippines is the fifth largest island nation in the world. The country is divided into 81 provinces, over 18 regions. The archipelago stretches 1,850km from north to south and almost 1,130km from west to east, making a total surface area of over 300,000km2. Broadly, the country is divided into three groups, with Luzon in the north, Visayas in the middle and Mindanao in the south. Luzon and Mindanao are the two largest island groups. The eleven largest islands make up around 94% of the total land mass; their combined coastline amounts to 35,000km – the longest of any nation in the world. The 320km wide Luzon Strait in the north joins the South China Sea in the west to the Philippine Sea in the east, and to Taiwan to the north. In the south-west, the Sulu Sea separates the Philippines from Malaysia. Mindanao is on the northern shore of the Celebes Sea, with Sulawesi and the Indonesian Malaku Islands on the south. Papua New Guinea lies further away, to the south-east. The entire territory of the Philippines is located in the northern tropics, between the equator to the south and the tropic of Cancer to the north; its average temperature across the year is over 26°C. The population reached approximately 104.2 million people in 2016; it is resident on only the largest one-fifth of the islands, according to current estimates. The larger proportion of the population is spread across the northern islands; more than one-tenth live in the greater Manila metropolitan area, on the main island of Luzon. It includes both the capital, Manila City, and Quezon, the largest city. As in many South East Asian countries, the population is predominantly young; its average age is 23.4 years. The Ethnologue lists no fewer than 184 current spoken languages in the Philippines; Filipino – a standardised version of Tagalog – and English are the official languages, used in government, education, print, broadcast media, and business. However, English is not spoken widely outside the cities. The influence of the USA, since the country formally declared independence from Spain in 1898, is responsible for both the extent of English as and for the hint of American accent in speech. Economic growth of almost 6.5% in recent years makes the Philippines one of the most exciting markets in South East Asia. This rapid growth is fuelling a high demand for investment and consumer goods, leading to growth in imported goods. Purchasing power is supported and expanded by transfers from Filipinos working abroad, who sent home over US$25bn in 2015. This trend is forecast to continue in coming years. This emerging nation remains strongly split into poor and rich populations. The northern island of Luzon is relatively advanced and boasts a modern electronics industry; the southern island of Mindanao, by contrast, is primarily agricultural and very poor. Over one-quarter of the population works in the countryside but agriculture contributes only around one-tenth of the whole economy. Approximately 30 million people – nearly a third of the population – are classed as living in poverty. The government has taken various steps to counteract this inequality and stimulate growth. In order to make the market particularly appealing for","@ID":20}, "MATERIALS / RECYCLING PETplanet Insider Vol. 18 No. 09/17 petpla.net 13 MATERIALS / RECYCLING 13 New Zealand’s first integrated rPET plant rPET made in New Zealand The opening of Flight Plastics’ new washplant in New Zealand marks the completion of Australasia’s first complete rPET treatment and manufacturing facility of its kind. Flight Plastics, a family-owned company based in Wellington, New Zealand, has been manufacturing plastics for over 40 years and began producing PET in the 1970s, in the form of rollstock and thermoformed plastic containers. Its UK factory, in Romsey, Hampshire, uses 75% recycled PET (rPET) in its packaging products, which are used in supermarkets across the country. The company installed similar technology in its New Zealand plant in 2013 and started taking in rPET flakes and turning them into new products the following year. The source of the rPET flakes was outside the country, which meant that New Zealand was importing washed and processed rPET, while whatever used PET the country was collecting was being bundled up and sent overseas for processing. Each year it imports 20,000 tonnes of virgin PET, which is used primarily for making bottles but also in the production of food trays. Around 8,000 tonnes of PET, mostly from bottles, is collected annually for recycling. Flight Plastics initiated a five-year programme in 2012 to research, introduce and install the most up-to-date extrusion and thermoforming capability and capacity available. The NZ$12m investment was co-funded by the Waste Minimisation Fund, which is managed by New Zealand’s Ministry for the Environment. As well as the economic advantages, the Fund’s objectives include reduction of environmental harm and increasing benefits by recovering waste and preventing dumping or loss of control. The Waste Minimisation Fund’s conditions state that it is not intended to provide ongoing support for existing activities; as Flight’s reprocessing facility is totally new, the washplant clearly qualified for support and was the final piece in the first complete PET reprocessing plant in Australasia. It has capacity for up to 6,000tpa, which is more than the current volume of clear PET currently being collected in New Zealand, and can be expanded as “Kiwis” (New Zealanders) recycle more. Flight Plastics points out that making packaging from recycled rPET is not a “one shot exercise” – it is not something that can never be repeated. A single tonne of virgin PET can be completely recycled into a tonne of rPET, and then recycled again and again. The challenge has been to establish an end-use for the recycled material. The company’s experience of using rPET extensively in the UK means that it already has the experience and expertise to make food-grade containers. With the completion of its integrated plant, Flight Plastics can now supply customers with rigid containers and trays for meat, produce and manufactured foods, such as biscuits and confectionery, entirely from PET waste sourced within New Zealand itself. It is the only company in the country currently able to do so. www.flight.co.nz","@ID":15}, "65 TRADE SHOW PREVIEW PETplanet Insider Vol. 18 No. 09/17 UV absorbers for clear, transparent PET bottles Milliken Chemical will demonstrate how its ClearShield Colorless UV Absorbers can bring value to PET packaging by protecting UV-sensitive contents from degradation while maintaining the material’s clarity and transparency. ClearShield is intended to protect beverages and other UV-sensitive contents against harmful light exposure by incorporating the UV blocker into the PET package itself. These absorbers filter 95% of UV light at up to 390 nanometers and are effective at low loadings, enabling the use of more highly UV-sensitive natural colourants in the packaged products. At Drinktec, Milliken will use real-life examples and case studies to highlight how these additives create a new UV protection performance standard for PET bottles and containers, including for such products as juices and energy drinks. Due to the photooxidation effect, most vitamins are sensitive to light, heat and oxygen in the presence of light. Vitamin degradation can lead to off-flavour and colour shift in the beverage formulation. Milliken says that studies have shown that vitamin A’s shelf life, for example, is 30 times better when protected in a ClearShield-modified bottle than when packaged in standard PET. Vitamin B6 shows a better than 70 times improvement, riboflavin seven times, folic acid 3.5 times and vitamin B12 double the shelf life. ClearShiels is approved for foodcontact applications by the European Food Safety Authority (EFSA). www.millikenchemical.com Hall A2 - Booth 108","@ID":67},
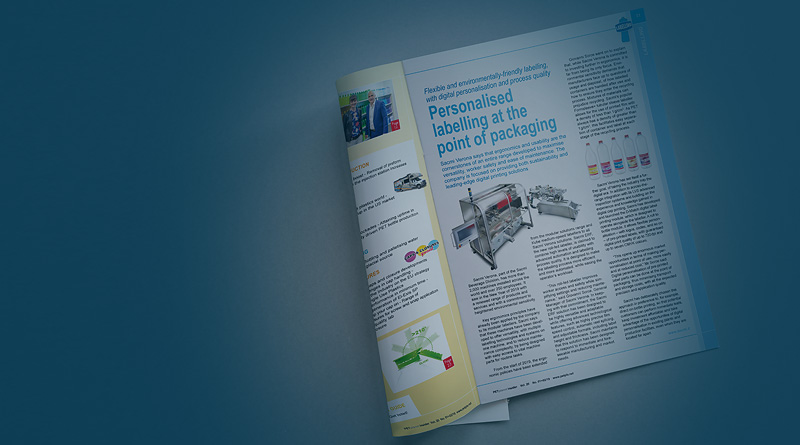