MATERIALS / RECYCLING PETplanet Insider Vol. 18 No. 11+12/17 petpla.net 14 Key issue: “Made in China 2025” The PET recycling industry in China: Between fire and ice by Ulrich Thiele The thirteenth issue of the ”Recycled Polyester and PET Packaging Conference and Exhibition”, organised by the China Chemical & Fiber Economic Information Network and Dr Thiele Polyester Technology took place this year September 6th – 8th in Shanghai, China. Despite severe hurdles, such as the ongoing low polyester virgin prices, low facilitation rates and increasing governmental activities toward stringent regulation of plastic waste import, some 300 participants and exhibition visitors from China and abroad expressed their unbroken interest in our industry. Besides technical presentations, the conference program of this year was dominated by the key issue “Made in China 2025” followed by reports about progress in polyester textile recycling and several market analyses. Li Hongliang, Researcher, Energy Saving and Comprehensive Utilisation Department of the Ministry of Industry and Information Technology (MIIT) spoke about “Interpretation on related policies for comprehensive utilisation of waste textiles in China”. With the slogan “Made in China 2025” the Chinese government is implementing and supporting a bundle of activities to renew development of the industry. After years of intensive investigation the Chinese government is to release stringent rules to improve the industry development in general, focusing especially on solving the environmental problems of the country. “Made in China 2025” includes green processes, technologies, products and applications. On the subject of waste treatment and recycling, the MIIT defined development goals for eight areas, namely paper, plastics, rubber, steel, cars, electronics, waste mineral oils and textile products. Within these waste categories, the MIIT has formulated the following development targets: a standardisation of production technologies, an improvement in facilitation rates/running rates, an implementation of green developments and an emphasis on energy saving and environmental protection. One important part of “Made in China 2025” is expected to be a general and complete ban on the import of all kind of waste materials. As far as PET recycling is concerned this general ban will include waste bottles, PET bottle flakes and all other kinds of PET waste. The Chinese government will publish detailed implementing regulations by the end of 2017. It was indicated that the government might grant, for a transition period, a limited number of import licences to companies which still fulfil the above listed development goals. During the entire conference, it was apparent how seriously this new movement was being taken because all internal discussions revolved around the impact of the new policy on the industry and market participants. The possible practical consequences of the new waste import rules were graphically outlined by Cao Weidong, Chairman of the Board, Zhejiang Huafei Recycling Resources Co. Ltd. with his presentation: “Winwin Cooperation for the rPET Industry in the era of significant change.” He laid out a series of ideas and possible practical actions to resist or overcome the effects of the new import policy. He defined the current situation of the PET recycling industry in China “between fire and ice”. At present no clear guidelines have been released, his proposals covered a wide range including the following: Increase in sales, production capacity and speciality products Integration of the whole recycling cycle from bottle collection, via flake production to production of filaments, fibres and final apparel goods within one enterprise Business optimisation by lean management Differentiation in specialities Or: abandon completely the Chinese market and seek other Asian markets such as Japan, Malaysia, Thailand or Philippines – in other words any Asian country with a stable political and economic system. Putting to one side all possible negative impacts to the single entrepreneur or recycling company, Cao Weidong liked the idea that the government will strengthen the rPET industry to force market participants into cooperation, deeper integration, specialisation and intelligent waste collection. And, obviously, he hoped that the struggle of the recycling industry will help change sentiment in the government. Kurt Pichelmann, Sales Manager of Erema GmbH and David Hehenberger, Product Manager of Next Generation Recycling Machinery GmbH reported on their companies’ further developments of re-pelletising RECYCLING S P E C I A L,@ID:16}, BOTTLING / FILLING PETplanet Insider Vol. 18 No. 11+12/17 petpla.net 28 Pere Ocean supplies Singapore from Malaysia Two factories in one place by Alexander Büchler Father Jerry T.H. Tan (right) and son Eugene Tan in the Pere Ocean warehouse in Singapore. Wanin Industries, Singapore April 17, 2017 Pere Ocean, Ulu Tiram April 13, 2017 We met: Mr Jerry T.H. Tan, Director Mr Eugene Tan, Son Mr Foo Suan Wan, Factory Manager With two factories in Ulu Tiram, Pere Ocean produces still water in bottles, the majority of which goes to Singapore. The parent company Wanin Industries is located there, managing not only sales but also administration. The company is run by founders Mr Jerry T.H. Tan and his son Mr Eugene Tan. The father began in 1986 in Indonesia with the production of water bottles for Singapore. But as early as 1991, he opened facilities in Ulu Tiram in Malaysia. There he was able to secure the licence for a well, which has provided the company with water to this day. Primarily, he bottles water for household use in Singapore. This includes refillable PC containers, as well as 1.5l and 0.5l bottles. Alongside this, the Tans have also developed several flavoured waters, preferably with a sugar content under 6 Brix, the magic limit under which it can be sold to schools in Singapore. A year ago, the Tans converted the filling system from PCO 1810 to the lighter PCO 1881. They are not convinced by the 29/25. “We believe that the market in Singapore isn’t yet ready for this easy closure; we will continue to run the 1881,” says Mr Tan senior. Filling in Ulu Tiram was soon too small so the second factory was constructed a couple of blocks away. Here, Pere Ocean mainly produced its preforms and one of the large-volume bottles, and these are then brought to the original factory for filling. “Not only space but also the high energy needs of the plastic machine made a division of production necessary,” says Mr Foo Suan Wan, Factory Manager. www.pereocean.com Tour Sponsors:,@ID:30}, TRADE SHOW REVIEW PETplanet Insider Vol. 18 No. 11+12/17 petpla.net 48 TRADE SHOW REVIEW 48 Even the most advanced PET bottle blow-moulding system experiences variations in bottle material distribution from mould to mould; each one performs slightly differently, even in the same region. Such variations can result in inconsistent performance even from bottles in the same production run, leading to potential downstream problems. In a collaborative effort between Agr and KHS, work was performed to develop a means to reduce or eliminate mould-tomould variation, resulting in Individual Mould Control. Built on the foundation of Agr’s Process Pilot automated blow moulder control system, Individual Mould Control provides the ability to optimise the blow-moulding process by controlling the blow parameters for each individual mould station, in addition to the global parameters set for all moulds. This makes it possible to proactively manage the process down to the individual mould level to finely control material distribution and minimise mould-to-mould variation. The Process Pilot system captures high-precision thickness distribution measurements on every bottle. It manages material distribution to a base-line thickness established on an overall average of all mould stations by controlling the oven parameters and P1 pressure, as well as start time. These parameters are common to all the moulds and move the material distribution close to baseline, to produce a consistent quality of bottles. The Individual Mould Control option takes distribution management to a new level by identifying the distribution variance from mould to mould. It uses an advanced control algorithm to reduce individual mould station variability by proactively adjusting the pre-blow start time of each one, through individual mould offsets. By doing this, the material distribution can be controlled on a per mould basis. This makes it possible to achieve an overall tighter distribution model over the entire mould set one that is much closer to the baseline than can be provided using the global approach. The level of trend analysis incorporated by Process Pilot on a mould station by station approach proAgr introduces “Individual Mould Control” for the Process Pilot automated blow moulder control system Mould Control Agr International, Inc., has announced the launch of Individual Mould Control, the latest addition to its systems. The company says that this technology expands the capabilities of Agr’s Process Pilot product group to include the management of thickness distribution during PET bottle production, at the individual mould level. .com 100815dmyL Individual Mould Control option for Agr’s Process Pilot system optimise the blow-moulding process by controlling the blow para-meters for each individual mould station,@ID:50}, MAINTENANCE PETplanet Insider Vol. 18 No. 11+12/17 petpla.net 36 PET preform mould cleaning and maintenance with dry ice Smart, smooth, speedy and safe by Gabriele Kosmehl Preform mould cleaning is an important part of the production process in order to maintain the quality of the moulded parts and the service life of the moulds. There are various methods on the market, often including a combination of chemicals/solvents, mechanical means and/or ultrasonic baths. Dry ice cleaning is another one which stands out for various reasons, claims provider Cold Jet. PETplanet visited the company’s German headquarters and technology centre in Weinsheim to find out why. Usually it is on a Friday that the injection moulding systems fall silent to allow the cavities to be given a thorough cleaning. In the preform moulds, it is at the taper where deposits tend to build up due to the emission of plastic. The air vents at the neck ring and the air holes are other typical places where dust and debris are deposited. The greater the increase in cycle times, the quicker the impurities build up. If not removed promptly, they lead to blemishes and unwanted flashes on the final product, creating more rejects and contributing to a shortened lifespan for the tool. Previously, workers sometimes undertook the painstaking manual task of cleaning the system cavity by cavity; today the dry ice cleaning procedure offers a much quicker, cleaner and gentler method. “I’ve seen it myself how sometimes two men in the company would set about cleaning out the system using cloths and cotton buds,” remembers Dietmar Juchmes, General Manager Europe. “Where previously a 72 cavity preform mould would be cleaned manually in 2-3 hours, today this is possible with our system in three quarters of an hour or less – and with significantly better results.” Key Account Manager Europe Steffen Kalisch explains why: “The Cold Jet procedure is efficient because places on the tool that are hard to access manually are also reached very effectively. Cleaning is also contactless. Manual process, as happens for example with a cleaning cloth, always affects the material surface. Our procedure is gentle on the material and after cleaning, the system is ready for use again right from the very first shot.” Cleaning with pressurised dry ice uses rice grain sized 3mm dry ice particles that are blasted onto the tool, which does not need to be dismantled beforehand. The combination of dry ice blast cleaning’s kinetic energy and thermal effects breaks the connection between dirt and the surface, lifting away contaminants. Because the dry ice, which is nothing but CO 2 at a temperature of minus 78.3°C, sublimates on contact back into CO 2 gas, there is no run off, rinsing or drying of any liquids required. There is likewise no secondary waste to be disposed of, so the procedure’s neutral CO 2 footprint is a winner from an ecological point of view too. As regards employee safety, there are further positives for the odourless environmentally friendly dry ice procedure. There are no toxic cleanCold Jet Aero 80FP PET mould cleaning system with Tight Access applicator and nozzle 312v2 Dietmar Juchmes, General Manager Europe Cold Jet, Christiane Rach, Marketing Manager Germany Cold Jet, Gabriele Kosmehl, PETplanet, Steffen Kalisch, Key Account Manager Europe Cold Jet (from left),@ID:38}, MATERIALS / RECYCLING PETplanet Insider Vol. 18 No. 11+12/17 petpla.net 15 or direct spinning of pre-purified polyester textile waste applying extrusion, melt filtration, re-polycondensation and pelletising/spinning. Yu Zheng, Sales Engineer of Sorema div. of Previero N. SRL introduced the new delabelling technology either situated as a pre-washing stage or prior washing as a dry delabeller. The new technology promises an optimisation in pre-washing and in downstream sorting stages. Stewart Hardy, Global Manager – Petrochemical Market Dynamics of Nexant Inc. summarised his view on the market development with his contribution “Upstream Developments and the effect on rPET”. He characterised the PX-situation as “China’s PX import requirement will remain a significant element of demand, but does not leave room for new exporters in other regions” and “The proposed build is enormous, but proportionally less than what occurred on PTA” and the conclusion “The scale of the build in China is stifling developments in other regions”. The PTA situation is summarised as “China became the most challenging PTA market, and saw the greatest volume of closures”, by which he was referring to small, uneconomical production units. On the development of MEG, Nexant stated “Operating rates and margin outlook on MEG is relatively healthy despite the planned new plants” and “Asia and US have replaced the drop in new capacity growth in the Middle East”. The development of the rPET industry under the new regulations is summarised in the following headlines: Import restrictions such as “Green Fence” and “National Sword” will continue to restrict availability. Draft legislation suggests raw PET waste (bale) imports may be outlawed altogether. Clampdown on recyclers without adequate water treatment etc. pushes up the cost of rPET flakes in China. The lack of Chinese buying interest pushes down rPET bale prices in Europe, Japan, and the US etc. supporting local demand. Growth in the Chinese PET market and therefore domestic rPET supply has slowed. Lower PX costs will support PET selection against other materials, but growth in the beverage market will remain slow. In Conclusion: rPET availability will remain short in China. The ongoing pressure on prices as loss of PX and ethylene margin feeds through PTA and MEG to virgin fibre. The raw bale prices supported by restrictions on imports results in slow growth in the domestic PET market. The Revival of interest in garment production in developed regions (Zara etc.) could stimulate flake demand for rPET in other regions to support “closed loop” initiatives in the West. The rPET industry will need to adapt to a further significant drop in virgin polymer prices. Cao Wenting, product manager of CCFEI outlined in her contribution “rPET Market Structure under New South Hall · S21085 German Technology Policies” the expected severe impact of import policy changes. But her analysis began by speculating that: “The market is abuzz with rumours ranging from a ban on imports of post-consumer bottles all the way to a complete ban on all solid wastes” and she gave a list of some of the currently officially published statements, announcements and policies. She summarised the development of rPET industry thus: Capacity shrinking: The limitation on imports, the squeeze on margins and low profits will certainly lead to a shrinking of the capacity of rPET fibre. Extend the industrial chain and move to other production: Extend the industrial chain upward to lower the costs for enterprises. Elimination, integration, relocation: Low-profit products will be eliminated, and high-profit products are likely to face consolidation. Partial enterprises will probably go abroad. Industrial upgrading: High-priced raw materials need to be transformed into high-value products. In the 13 years of the existence of this conference, never before had discussions revolved so completely round the issues of the likely impact for the industry of the proposal to prohibit the import of foreign waste and the reform of the solid waste management system. This will certainly provide food for thought which we will be exploring in our next conference in 2018. www.polyester-technology.com,@ID:17}, MAINTENANCE PETplanet Insider Vol. 18 No. 11+12/17 petpla.net 37 ing substances or harmful gases for employees to be exposed to - and also no direct contact with the sharpedged tool. Tailored application solutions With the Aero 80FP model designed specifically for the PET sector, Cold Jet offers a cleaning solution to which different nozzles can be applied using a quick change system. The selection of specially designed nozzles for PET processors, for example for cavity tamper, hot runner, neck ring vents or inner side cavity, simplifies the cleaning of hard to access parts of the tool. Depending on the type and degree of soiling, the patented MERN nozzles can be adjusted variably as regards the size of the dry ice particles; while tough contaminants are handled with pellet-sized particles, precise cleaning methods with delicate fragmentation of the ice can be used on delicate substrates. A 360° round cavity nozzle has likewise been developed for delicate areas such as the lock ring taper and cavity taper, air vents and air holes, which are affected particularly quickly during production. Compared with manual cleaning, the efficient dry ice cleaning procedure quickly shows its worth economically over a year, as Kalisch indicates: “If we take a 96 cavity on a basis of 360 mould cycles, this adds up with a weekly saved cleaning time of 2 hours to 3,594,240 preforms per year that would not otherwise have been produced. Even if the savings in labour costs or the extended equipment life time are taken out of the picture, the purchasing costs for our system are swiftly paid off – for a system of 5 IMM (Injection Moulding Machines) with 96 cavities in just 6 months!” In response to the question of where the dry ice used for cleaning actually comes from, Kalisch says: “The dry ice itself is no problem to procure and keeps for up to seven days in the tank it is delivered in. The requirements are easy to plan for, based on the assumption that a tool can be cleaned completely with 40-60kg.” Any dry ice loaded into the system but not yet needed, is simply drained out via a tilt-out hopper for later re-use. And for companies with very high usage requirements, Cold Jet also offers dry ice production systems adapted to capacity needs. www.coldjet.com The Coldjet company was founded in the USA in 1986 and has its global headquarters in Loveland, Ohio. Subsidiaries are in Zellik, Belgium, where today’s European headquarters are located, as well as in Denmark, France, Germany, Spain and Poland. In Denmark and Poland, there are also engineering, assembly and manufacturing facilities for the Cold Jet line of dry ice cleaning and production equipment. Dry ice cleaning solutions from Cold Jet are used in the widest variety of industry sectors in more than 85 countries and more than 35 industries, for example in the food, automotive and tyre industries. With around 70% of the turnover, the plastics industry represents the largest purchasing industry. Dry ice is an approved media by the EPA, FDA and USDA. Areas to clean in a preform mould PET mould cleaning with dry ice PET mould cleaning ROI for 5 injection moulding machines Lock ring cleaning,@ID:39}, PETplanet Insider Vol. 18 No. 11+12/17 petpla.net 53 BOTTLES A winter edition from Innocent The smoothie and juice specialists, Innocent, have created a new “winter edition” of a fresh juice made from clementines and mandarins which stands out on the refrigerated shelf with its almost glowing and unique colour compared with the mostly yellow orange juices made by other manufacturers. The product’s orange colour is quite striking. The juice, which is made from 20 clementines and five mandarins, comes in a brand-typical, easy to handle 900ml bottle which has an embossed product label and a positive-locking, hinged pressdown lid with freshness seal. A wrap-round paper label that follows the contours of the bottle shape includes product information as well as lottery details. www.innocentdrinks.de An acai juice from Sambazon An American company, Sambazon, which has long since recognised the health enhancing benefits of the acai berry, as well as having produced fruit-based products that respect organic farming practices and fair trade with suppliers, also has a 100% fruit juice on offer. The drink comes in a 10.5 fluid ounce or 310ml, firm, transparent bottle, decorated with a sleeve label and secured by a screw top prior to being opened for the first time. www.sambazon.com,@ID:55}, MATERIALS / RECYCLING PETplanet Insider Vol. 18 No. 11+12/17 petpla.net 19 MATERIALS / RECYCLING 19 continuous cleaning in the Water Treatment Box (WTB). Filtration units and a two-stage floatation system ensure, that even the finest impurities are removed from the process water. This results in PET flakes with impurities of 10ppm, which are suitable for immediate solid-phase condensation by the final processor. Hofmann states how the idea already had an enormous response from the market by tipping point: “Our business model has been confirmed by all the big players, whether they are at feedstock level or are recycling companies.” Hofmann is convinced that the model will quickly become established, as long as economic efficiency is guaranteed for each participant in the process chain. Then, the necessary collection hubs will arise of their own accord. The company also hopes for an uplift triggered by the restrictions on the imports of plastics from China, as Hofmann explains: “The sector is now under tremendous pressure to do something to tackle the enormous quantities of plastic waste, and this is where our compact technology comes in. If I may express a personal wish, it would be to successfully build up a standardised process chain where the end user can be certain that the PET bottles they have purchased will find their way as a fixed rPET proportion as part of a new bottle - a real cradleto-cradle operation.” www.hydrodyn.de Michael Hofmann, Managing Director HydroDyn Systems GmbH (on the right) and Gabriele Kosmehl, PETplanet in front of an Universal Compact Cleaner (UCC) at Fakuma Save RAW MATERIALS reduced plastic volumes Save ENERGY less energy consumption Save TROUBLE more quality and higher performance, guaranteed by a sole supplier Full INSPECTED online quality control / stand alone With Sacmi, the beverage specialists are always at your side. With our unbeatable technological know-how and continuous research we are creating new containers and closures designed to ensure outstanding performance. The new IPS injection system for preforms and the CCM compression press for caps, fully designed and built by Sacmi, allows for large-scale production with considerable advantages in terms of efficiency and flexibility. The outcome? Reduced plastic volumes, less energy consumption and lower running costs. All in a bottle: the one you’ll soon be making. Preform & Closure technologically together,@ID:21}, PETplanet Insider Vol. 18 No. 11+12/17 petpla.net 45 TRADE SHOW REVIEW tools chosen by the customer can then be built here”, said Perche. The system that was demonstrated in Munich also highlighted another special feature. “The pneumatic systems’ manufacturer, Aventics was approaching us with a special valve that they have developed as a means of controlling volume more effectively during pre-blowing “, Perche explained. “With their electro-pneumatic solution, the moulding during pre-blowing can be directly re-adjusted as well as monitored”. Perche sees advantages in energy savings achieved by lowering furnace temperature and adapting pressure levels to a specific bottle wall thickness mould that can result in reduced consumption of material. Perche continues “This solution is of particular interest to manufacturers who are looking for a complex bottle design or those who often switch between different designs. Adjustments can be achieved without any mechanical procedures while individual setpoints can be created for each blowing station”. One such system has been trialled over the past year at the Danone Research Centre in Evian where the laboratory machine has been well received. A new test centre opened in France As a new service outlet, 1Blow has recently established a new test centre in Boissy l’Aillerie situated to the north-west of Paris where the company’s product range can be rigorously tested with or without the controlled preblowing compressed air system. “We have decided to take this step in response to lively customer interest. This shows that there is also a market for small machines!” enthused Perche and he is inviting interested customers to test the system with their own tools and preforms. Here, interested parties can also see the 1XXL single cavity system which is a new 1 Blow product range. This has been specially designed for the manufacture of large 5-30l containers. It employs servo drives as standard in mould movement as well as on the stretching system. Recovery systems are also basically provided (power + blowing air) in order to reduce the bottles’ production costs. The heating capacity may handle thick preforms (10mm) for one-way and returnable containers. The 1XXL bottle machine produces bottles with neck orientation, hot fill bottles and oval bottles. www.1blow.com From left: Gabriele Kosmehl, PETplanet, Benoit Sanchez, Chairman 1 Blow, Olivier Perche, Sales Manager 1Blow and Heike Fischer, PETplanet Scan QR code for more information: Scan & Measure Oxygen Ingress & Transmission Rates Fibox 4 Stand-alone fiber optic oxygen transmitter,@ID:47}, TRADE SHOW REVIEW PETplanet Insider Vol. 18 No. 11+12/17 petpla.net 42 Sidel presents concept SBM oven with laser diodes Precise heating of preform to widen packaging opportunities by Alexander Büchler By replacing the currently used infrared heating element, laser diodes can supply the preform with a precise temperature profile, enabling significantly better material distribution in the blown bottle. The temperature profile allows the manufacturing of geometrics which were not possible to blow hitherto. This could also result in potential material savings: as the solution is currently in development phase, the team at Sidel is still evaluating the exact figure. In an interview, Vice President for Packaging at Sidel Vincent Le Guen shows us a wine glass stretch-blown from a PET preform. Have you ever seen any PET bottle similar to the Sidel PET wine glass? This type of profile is not achievable with the current SBM technology. Why? The radiation emission of the IR halogen lamps is diffused and cannot be precise enough on heating zones. With laser instead, Sidel achieve a narrowly focused radiation, allowing a very precise heating profile without any interaction among the heating zones. So, packaging producers can play with the material distribution and allocate it where it is needed. As a result, the wider process window unlocks innovative packaging design opportunities. At drinktec 2017, Sidel has shown how the upcoming laser oven technology can achieve new bottle shapes like the wine glass. Near infrared laser diodes are used in the SBM heating function. This allows the preforms to be heated more precisely individually, with three times more layered zones. This enables a great material stretching during the bottle blowing, from the shoulder to the bottom zone. Sidel demonstrated how flexible the new process can be by stretch-blowing a wine glass. The laser oven technology builds on the solid-state emitter trend for LED to perform accurate preform heating with infrared. As an alternative to the currently used infrared solution, VCSEL laser diode extends the process capability and flexibility of the existing blower, for improved bottle quality and greater packaging opportunities. Emitting a more focused narrow spectrum selected to optimise in-depth interaction with polymers, such as PET, laser diodes irradiate at a low temperature (less than 30 to 40°C) with no need of oven ventilation. Compared to a halogen oven, there are three times as many heating zones in the new solution from Sidel. Also, the reduced oven pitch enables a higher number of preforms to be accommodated in two rows in a shorter heating zone: heating time is reduced to just a few seconds. These shorter heating modules make it possible to create a compact machine, with the potential to reduce the oven footprint by up to 60% for optimised line layout. The extensive process window increases packaging opportunities with greater freedom in bottle shape design. The heating process is incredibly accurate and stable, allowing consistent material distribution for greater efficiency and top bottle quality from the very outset of production. Needing no ventilation, it provides heating independent of ambient, environmental conditions. This means that the same set-up is used for the same bottle quality regardless of time of day or seasonal conditions. Changeover is fast and efficient with minimal manual intervention, a reduced number of spindles to change and quick machine startup after stoppage. Needing less maintenance because of the long lifetime of the diodes, Sidel’s new laser heating solution is also highly user-friendly, with very few parameters to set up. We spoke to Vincent Le Guen, Vice President for Packaging at Sidel. Since 2011, he has been responsible for all areas of packaging development, such as packaging and preform design, packaging optimisation and qualification as well as liquid-package interaction analysis. His career path has come full circle: Sidel, Coca-Cola, Plastic Technologies Inc. Europe (PTIEurope) and in 2011, Vincent re-joined Sidel as Vice President for Packaging. www.sidel.com Heike Fischer, PETplanet Insider, Vincent Le Guen, VP Packaging at Sidel and Alexander Büchler, PETplanet Insider,@ID:44}, BOTTLING / FILLING PETplanet Insider Vol. 18 No. 11+12/17 petpla.net 24 New product launch The fact that the beverage producer is making so many different types of beverage so soon after commissioning is also down to both partners’ fast reaction times. The Butsifal Group actually wanted to start out by merely filling its mineral waters on the new KHS line. A seasonal characteristic of the Uzbek beverage market precipitated the launch of several completely new products, however. In this country in Central Asia there is practically a fixed season for mineral water, with the remainder of the year set aside for carbonated beverages. Whereas March to September are the bestselling months for mineral water, iced tea and CSDs have their high season at the end of the year. As the KHS line went into operation in June 2016 in the middle of the water season, Khalilov decided to immediately create more variety in his portfolio. Besides the quality mineral water segment, which Butsifal has been serving right from the start with its Sayhun water brand, the company also developed a low price range by introducing its new Gazalkent mineral water brand and iced tea products and CSDs under the name of SIFA-T. “Despite the huge time pressure this was exactly the right decision to make. We immediately found a very successful niche for our new products,” Khalilov resumes. KHS developed the new bottle designs for the additional products within its Bottles & Shapes program in Hamburg, Germany. Development centered on both lightweighting and handling rigidity. “The design technologists’ expertise enabled us to come up with the required high-quality design very quickly,” says Khalilov. The round bottle formats now weigh 12.1g for the 0.5-litre bottle, 21g for the 1.0-litre receptacle and 25g for the 1.5-litre container. KHS had optimised the design of the available square PET bottles in advance. The engineers in Hamburg were able to reduce the bottle weight here, too: the square 0.5-litre PET bottle for Sayhun mineral water now weighs 17g instead of the previous 20g. ReDiS remote diagnostics system for fast troubleshooting The two partners are still working closely together with a local service engineer giving the Butsifal team support whenever needed. He advises the company on line control and pays the site a visit on an ad hoc basis. Using the ReDiS remote diagnostics tool, which is free of charge during the warranty phase, on request KHS can access the plant equipment externally through a safe VPN connection. The Butsifal Group logs the KHS engineers into its system as and when required. “With this we solve possible operating problems or errors within the shortest possible time and can upload new software updates to the system,” explains Oliver Schneider, vice president for Eastern Europe at KHS GmbH. “This does away with the necessity for elaborate, costly and above all lengthy on-site installation assignments.” The Butsifal Group is achieving its goals thanks to the new line, states Khalilov. He stresses that “The new line technology enables us to produce a wide range of high-quality beverages.” The company now already has an approximately 10% share of the Uzbek water market and is also forcing its international expansion. Following commissioning, a number of export agreements were signed with business partners in bordering countries. It has been decided to further expand production. KHS will continue this working progress with Butsifal Group with further investments. “Our After visiting the customer’s site KHS engineers planned the production layout for the Butsifal Group, taking all local conditions into account. The Butsifal Group saves on resources and energy costs by using the KHS Innopack Kisters SP. Affirmation of a long-term partnership: the Butsifal Group advertises KHS on some of its bottle labels – an usual ploy for a beverage producer.,@ID:26}, PETplanet Insider Vol. 18 No. 11+12/17 petpla.net 52 PETbottles Beverage + Liquid Food A pomegranate juice from Aldi South Aldi South has brought out a freshly pressed 100% natural and gently heat-treated pomegranate juice onto the retail shelves under its own “rio d’oro” brand. A clear, shapely 500ml bottle was the chosen packaging. In order to draw attention to this new product on the retail shelf, the bottle is decorated with a distinctively coloured sleeve label which allows a direct view of the product through a circular, wave-shaped transparent window and iconic picture of a pomegranate. www.aldi-sued.de An organic soft drink from Christinen The German drinks’ manufacturer, Teutoburger Mineralbrunnel Ltd and Co. KG, is selling an organic soft drink with lime concentrate called “Bio Limette Medium” under the Christinen brand name. The drink is made from organically farmed limes with added natural citrus flavour. The light bluish 1-litre PET bottle has a firm grip area and is made from 55% recycled material which is appropriate for an organic drink. A wrap-round paper label and green screw top with a tamper-proof strip complete the packaging. www.christinen.de [email protected] TRADE SHOW REVIEW PETplanet Insider Vol. 18 No. 11+12/17 petpla.net 46 The big Xs of Sipa at the Drinktec 2017 in Munich Towards a sustainable, daily production process L to R: Roberta Gulatieri, Marketing Manager Sipa, Alexander Büchler, PETplanet, Martina Bottarel, Communication Management Sipa, Enrico Gribaudo, General Manager Sipa and Heike Fischer, PETplanet, in front of the Xtra stretch-blow system On the Sipa booth, the specialist in PET processing technology, the new generation of the Xtra stretch-blow system, the Xtreme Renew and the Xform were presented. In addition, the new Flextronic, a modular platform of volumetric fillers, was shown. The new Xtra is capable of producing 2,550bpc. This is the result of an R&D process putting particular emphasis on kinematics and mechanical movements. Such a high figure enables the number of blow moulds to be reduced for any given total output requirement, accelerating changeover times and lowering investment costs. The process angle on the new Xtra is 200 degrees- such a wide process angle makes it possible to apply high pressure air for up to 0.8s, enabling production of containers, even the most complex ones, with extreme accuracy. Xtra can produce bottles from 0.2 up to 3.5l in volume and also accommodate different neck sizes (28/38 mm). The clamp stroke has two settings: short, to produce bottles of up to 1.5l at a maximum speed of 2,550bhc; and long, for containers up to 3l and an output of up to 2,400bhc. This mechanical flexibility is complemented by the ability of the machine to produce hot- and cold-fill containers, without any changes to the system. It is combinable with other machines upstream and downstream. It can for example be directly connected to a filler to create a standard system for production and filling of PET containers; equally, it can be integrated with Sipa’s Xtreme rotary injectioncompression platform for preform production. Finally, Xtra can interface with Xtreme Renew, which produces preforms directly from recycled bottles, Xtreme Renew Sincro. With a live video demonstration, visitors were invited to participate at the production of a fully sustainable PET bottle-to-bottle production, fit for the circular economy. This process is possible with Xtreme Renew from Erema and Sipa. Together, the two companies have created an integrated system that uses up to 100% recycled post-consumer PET to produce preforms with properties on a par with those made from virgin polymer. The new Xform 350, a preform injection moulding platform, now sits alongside its well-established bigger brother, the Xform 500. Both are built on the same platform, but as the numbers make clear, the Xform 350 has a smaller clamp unit, with a clamp force of 3,500kN rather than 5,000kN. It has been optimised to accept moulds with between 72 and 128 cavities. Just like the Xform 500 though, the new Xform 350 has a low cost of maintenance, and accepts all legacy moulds, as well as legacy end-of-arm tooling (EOAT) for preform handling. The toggles on the Xform 350 are powered by servoelectric motors. This makes it fast as well as highly energy-efficient. Lock-tolock time is below 2.4s. Flextronic is the new name of the new modular platform of volumetric fillers. New filling valves in EVO versions have been integrated and are interchangeable on this platform. By taking full advantage of the modular design and by combining suitable filling valves, solutions can be designed to meet the diverse requirements in the bottling world. One of the key guidelines in designing the Flextronic platform was the ability to fill multiple products on the same line. www.sipa.com,@ID:48}, TRADE SHOW REVIEW PETplanet Insider Vol. 18 No. 11+12/17 petpla.net 44 Systems for small and medium-sized operations with a variety of clever options “There is also a market for small machines” by Gabriele Kosmehl A world innovation has been promised by the French manufacturer of PET blow-moulding machines 1 Blow. Reason enough for PETplanet to pay a visit to Olivier Perche, Sales Manager 1 Blow, and witness the preforming of a PET bottle live on stage at Drinktec. “In blowing a bottle, the preblowing stage is the most important step of the process because this is where the material distribution happens. And for the first time ever at a trade show, we made this process step visible” enthused Olivier Perche. A 1XL blow-moulding machine was modified for Drinktec in a way that enabled visitors to follow the pre-blowing process as it happened through a specially designed viewing window. With a standard preform having been briefly heated, the bottle was transformed into a phial-like shape during the pre-blowing stage using a cylindrical mandrel to stretch it to the desired length. This would normally be followed by the final inflation process using compressed air to mould it into the required shape. In this respect, 1 Blow usually values compatibility above all else. “We would rather provide the mould carrier than introduce any new mould standards. Companies’ Pre-blowing process live on stage at the Drinktec 1Blow booth TRADE SHOW REVIEW 44 • 28mm, 33mm and 38mm screw closures • Robust and trouble free capping • Established DoubleSeal™ technology - for secure sealing performance - for better protection against micro-organisms • Slit FLEXBAND® band technology for enhanced tamper evidence • O 2 barrier and scavenging options for screw flat caps supporting longer shelf life and fresher taste • Sports closures for aseptic filling and hot filling without aluminum foil • Special closures for syrups and carton packaging Unique range of screw and sports closures designed for cold fill and aseptic application BERICAP Technology for juices, RTD teas, health drinks www.bericap.com,@ID:46}, MATERIALS / RECYCLING PETplanet Insider Vol. 18 No. 11+12/17 petpla.net 18 Michael Hofmann’s maxim is straight and to the point: “Bring technology to the feedstock”. The Managing Director of HydroDyn, which was founded five years ago, is convinced that this is the only way to tackle many of the problems that arise in the recycling circulation system. “The aim is to build a system which results in recycling materials that are in no way inferior to primary goods - but at a fraction of the price. This is what we aim to achieve by establishing the first added value step with the retailer or the sorting facility. Most problems arise only during subsequent logistics, so it is important to get our hands on the feedstock as early as possible.” The model constructed by HydroDyn works with 20-foot containers that hold the entire technological system needed to generate flakes that can be further processed into recycled granulate in final finishing systems operated by specialised companies. These UCCs (Universal Compact Cleaners) can be configured to meet requirements and constructed to save space – from the one or two-stage Turbo Washing Box to a granulator attachment or a Thermal Drying Unit and Water Treatment Unit. These components make the system suitable either for new installation in an industrial washing plant or for retrofitting in an existing system. The model is based on the idea that clean plastic flakes are already available at the retailer sorting hubs, long before weathering or the baling press can take their toll on the goods to be recycled. Hofmann continues: “We are offering the sector a tailored business model, which is economically rewarding for all participants in the process chain.” The compact construction of the system also facilitates its incorporation even into small businesses. The HydroDyn process The HydroDyn process is based on the principle of hydrodynamic friction cleaning. In combination with a high-turbulence water current, the HydroCleaner removes adherent organic dirt particles or adhesives from up to 3t of plastic waste per hour. The patented procedure even releases particles that conventional hot washing with caustic soda cannot shift, but can be added also by a smart hot postwash treatment with very low needs of energy and caustic soda. In a preliminary stage before cleaning, the model crushes the source material and separates other matter. In the PET bottle sector, the ValueSeparator can adjust this material separation precisely to suit the degree of soiling of the source feedstock. Density Separation is carried out by using a laminar flow procedure combined with final flushing to achieve a pH 7 value. The end result is separation with 100% discriminatory power; as regards PET bottles, even of PP or HDPE lids without PET impurities. After the flakes have been separated from the contaminated process water, they are dried by dewatering with a PhaseSeparator and finally using the Mechanical Agitation Dryer (MAD) working with vacuum exhausting. The process water can be reused in the circulatory system; it undergoes Compact technology for recycling facilities offers competent washing directly at sorting and collecting hubs Bringing technology to feedstock by Gabriele Kosmehl Heavily soiled source materials, composites with other polymers or aluminium cans that have been wedged firmly together with PET bottles in the baling press, complex logistics, varied-origin flakes – the recycling sector faces any number of challenges. The Hamburg company HydroDyn offers one solution that features much earlier in the process than other technologies on the market. It is applied directly where recyclables are collected: at the retailer or the sorting and collecting hub. Heart of the HydroDyn UCC System is the HydroCleaner with HydroFlush Feeder and Venturi Discharge. The cleaning efficiency is the highest available by lowest energy consumption and need of installation space. The HydroCleaner can be operated as cold or hot wash even in caustic conditions. RECYCLING S P E C I A L,@ID:20}, MARKET SURVEY 34 PETplanet Insider Vol. 18 No. 11+12/17 petpla.net SBM moulds Company name FlexBlow Hallink RSB Inc. Wentworth Mold Ltd. Kiefer Werkzeugbau GmbH Sacmi PET Engineering Postal address Telephone number Web site address Contact name Function Direct telephone number E-Mail Vytauto g. 114A, Kretinga, Lithuania +370 445 51431 www.flexblow.com Mr Gytis Sirvinskas Head of Export Department +370 62011 528 [email protected] 284 Pinebush Road, Cambridge, Ontario N1T 1Z6, Canada +1 519 624 9720 www.hallink.com Mr Jason Warmington General Manager +1 519 624 9720 ext. 258 [email protected] 156 Adams Blvd Brantford, ON, Canada +1 519 754 5400 www.wentworthmold.com Mr Tar Tsau General Manager +1 519 754 5400 ext 611 [email protected] Steinhäldenstraße 11 74193 Schwaigern, Germany +49 7138 97320 www.kiefer-mold.de Mr Maik Weber Sales & Project Manager +49 7138 973270 [email protected] Via E. Ferrari 1, 43058 Sorbolo PR, Italy +39 0542 607 111 www.sacmi.com Via Celtica 26/28 San Vendemiano, Italy +39 043 840 3069 www.petengineering.com Ms Elisa Zanellato Marketing & Communication Mgr. [email protected] Stretch blow moulds Bottle size (max.) (in litres) 20 19 10 30 3.0 10 Moulds supplied directly to blowing machine manufacturers No Yes Yes Independent mould maker No Yes Do you supply retrofit moulds for existing SBM machines? Yes Yes Yes, also manufacture multi-platform compatible mould systems Yes No Yes For which bottle makers do you already have produced moulds? All rotary and linear mould machines 1Blow,ADS,Aoli, Böhm, ChiaMing, Cincinnati-Milacron, EFI/ Autotec, Kosme, Krones, Krupp/ SIG/KHS, MAG, Siapi, Side, Sidel, Sipa, SMI, Tetra Plast/ Dynaplast, Urola, W.Amsler For all blow moulding machine platforms e.g. Sidel, Krones, KHS, Sipa, etc. Kosme, Krones, Sipa, Sidel, ADS, Sacmi, KHS, Bekum, Tetra Pak, Side, SMI, MAG Bottle design service Yes Yes Yes. Container design, prototype sampling and bottle performance tests. Yes Yes Yes Specialities Hot-fill, oval shaped, wide-mouth, light weight, large size 2-stage stretch blow moulds and personalisation parts Hot-fill / Heat-Set moulds with energy efficient system and Multi-Platform Interchangeable Quick Mold systems Lightweightdesign,specialdesign for functional drinks, juices, oil and vinegar, household chemistry, dairy products, cosmetic industry, petrochemical industry Bottle design tests in internal lab. Design bottle, preform and cap Company name Röders TEC Krones AG SMI S.p.A. PETform Taizhou Huangyan MEGA Machinery Mould Co. Ltd. Kosme Gesellschaft mbH Postal address Telephone number Web site address Contact name Function Direct telephone number E-Mail Scheibenstrasse 6, 29614 Soltau, Germany +49 5191 603 53 www.roeders.de Mr Friedo Böhling Sales Manager +49 5191 603 53 [email protected] Böhmerwaldstrasse 5 93073 Neutraubling, Germany +49 9401 70 0 www.krones.com Mr Peter Christiansen Head of Sales Blow Moulding +49 9401 70 4980 [email protected] Via C.Ceresa, 10, 24015 San Giovanni Bianco (BG) Italy +39 0345 40 111 www.smigroup.it Mr Pietro Volpi Marketing Dept. Manager +39 0345 40 316 [email protected] 502Topiwala Center, Goregaon W-Mumbai 400062, India +91 22 2877 6984 www.PETform.net Mr Shurid Mody CEO +91 976 9748 634 [email protected] 47-8 Huang Zhou Road, Huangyan, Zhejiang Province, China +86 576 840 201 22 www.megamachinery.com Mr Cai Jiahan (Simon) Sales Manager +86 576 840 201 22 [email protected] Gewerbestr. 3, 2601 Sollenau, Austria +43 2628 411 0 www.kosme.at Mr Johann Gugler Managing Director +43 2628 411 125 [email protected] Stretch blow moulds Bottle size (max.) (in litres) 10 3.5 10 50 30 30 Moulds supplied directly to blowing machine manufacturers Yes Yes Inhouse production of moulds and mechanical components Yes Yes No Do you supply retrofit moulds for existing SBM machines? Yes Yes Yes Yes Yes Yes For which bottle makers do you already have produced moulds? Sidel, KHS Corpoplast, Krones, Sipa, Kosme, ADS, Nissei Krones, Kosme, Sidel, Sipa, KHS (SIG) Corpoplast etc. Up to now, SMI has designed about 1,700 containers Sidel, Krones, Sipa, KHS, Side, Siapi, Aoki, Nissei ASB, CyPET Kosme, Krones, Sidel, KHS Bottle design service Bottle design & development & test blowing & full certified laboratory available Yes 3D CAD Department for the design and graphic processing of the bottles Yes Yes Yes Specialities Solutions for compatibility of moulds between different machine types Bottle development customised to filling- and packaging lines with performance commitments Large Bottles & jars Large size blow mould, heat set mould Bottle development service free of charge, if blowmoulds are ordered Company name Sipa SpA R&D/Leverage Moldintec Brasil Moldintec Argentina Side S.A Postal address Telephone number Web site address Contact name Function Direct telephone number E-Mail Via Caduti del Lavoro 3 31029 Vittorio Veneto, Italy +39 043 8911 511 www.sipa.it Mr Franco Porracin Molds & Hot Runner Division Man. +39 043 8911 511 [email protected] Leverage House, Hamilton Road, Sutton in Ashfield, Nottinghamshire UK, NG175LD +44 1623 556287 www.rdleverage.com Mr Alan Tolley Managing Director +44 1623 552240 [email protected] Rua Dr. Marcos Pentenado de Ulhoa Rodrigues 939, torre Jacaranda 8° andar, Barueri, SP, Brasil +55 11 2844 2330 www.moldintec.com Mr Eng. Thiago Tullio Country Manager +55 11 98815 3333 [email protected] Lamadrid 501, Los Troncos del Talar, Tigre, BA, Argentina +54 11 6632 9999 www.moldintec.com Mr D.I. Jorge Pucci Commercial Director +55 911 4146 9894 [email protected] Pol.Ind. Montguit, C/Llinars, s/n, 08480 - L'Ametlla del Valles (Barcelona), Spain +34 93846 3051 www.sidemachines.com Mr Josep Jiménez Sales Manager +34 677 551 928 [email protected] Stretch blow moulds Bottle size (max.) (in litres) 30 5 20 20 50 Moulds supplied directly to blowing machine manufacturers No No Yes Yes Mould and designs Do you supply retrofit moulds for existing SBM machines? Yes Yes Yes Yes Yes For which bottle makers do you already have produced moulds? Sidel, Krones, KHS, SIG, Krupp, SMI, Siapi, Kosme, Side Sidel, Krones, Sipa, Side, Chumpower CSD, NCB, juice, edible oil CSD, NCB, juice, edible oil Bottle design service Yes: brandbuilding, product repositioning, marketing design, packaging engineering, lightweighting of existing bottles, etc. Yes Yes Yes Specialities Wide mouth, large sizes (up to 30l), asymmetrical, nitrogen hot fill, containers with handles, HDPE to PET conversions supplier for single stage and ISBM, Product solution laboratory Ultra low pressure blow moulding Ultra low pressure blow moulding T-handle,@ID:36}, MATERIALS / RECYCLING PETplanet Insider Vol. 18 No. 11+12/17 petpla.net 12 Tour Sponsors: Their local market share is about 18% which is better than that achieved by TCK and Precision Plastic. A large quantity of preforms are exported from Thailand to other parts of the world such as Australia, Indonesia, the Philippines, Mongolia, Fiji, Laos, Cambodia, Myanmar, etc. PET is exported throughout the world, including the Middle East and Latin America. What do the Thai people drink? “We are seeing a steadily increasing consumption of packaged water and a trend towards healthy drinks,” Mr Chandrasekar added. “In terms of packaged water, the Crystal comes out on top, followed by Singha then Nestlé,” says Vipin Kumar. “In the ready-to-drink teas category, Oishi and Ichitan are the strongest market brands. Japanese brands have always had an excellent reputation in this part of the world, although in this instance they are not from Japan but use a Japanese sounding name. Sports drinks have started becoming more popular in Thailand. Traditionally these have been in glass but recently there is a trend of new brands being launched in PET with larger serve sizes.” When asked about other applications such as milk and alcoholic drinks, the team answers in the negative. “This is very unpopular here. Milk products can come along at any time but here the market is determined by PE bottles and cartons. Beer and spirits are and will continue to be glass dominated for the foreseeable future.” The whole Lopburi plant covers a total area of 40,000m2. Around 1,000 people work there including 200 employed in PET. We are now sitting in Indorama Ventures’ headquarters’ offices on the 35th Floor of Ocean Tower II in the centre of Bangkok, near the well-known Sukhumvit Road where the hustle and bustle of city life continues day and night. We are met by Mr Sunil Marwah, Senior Vice President, Packaging Business (he has been with Indorama Ventures for five years) and his colleague, Mr Weerasawat Chindanon, Sales and Marketing Assistant Vice President, Thailand (he has been with Indorama Ventures for nine years). He starts the discussions by quoting some very impressive key facts. “In Thailand, we produce 400,000t of PET each year, 85% of which goes into PET packaging for beverages, food and non-food items with the remainder used for PET sheets. Indorama Ventures’ PET sales growth in Thailand is 10% per year and is mainly driven by water. This growth has remained relatively stable over the years.” However, if you look at cooking oil in the food sector, below 5% growth is not so strong when compared with other South East Asian Countries. According to Mr Marwah, Indorama Ventures, along with Preci-sion Plastic, TCK Propet, Hon Chuan and Srithai, are active in PET packaging in Thailand’s competitive market, while Thai Shinkong and Thai PET Resin are involved in the materials sector. www.indoramaventures.com Vipin Kumar next to the South East Asia Road Show banner F.l.t.r.: Kulprabhassorn Kritapongseth, Krishnaswamy Chandrasekar, Vipin Kumar, Govind K. Narkar and Manus Sornsa-Ard Taking a “closure“ look - freshly produced,@ID:14}, MATERIALS / RECYCLING PETplanet Insider Vol. 18 No. 11+12/17 petpla.net 10 Tour Sponsors: Thailand’s PET giant by Kay Barton At the beginning of 2009, PETplanet’s editor Michael Maruschke went to meet the management of Indorama Ventures’ subsidiary, Indorama Polymers, a materials manufacturer and processor at its Lopburi plant in Thailand (see PETplanet Insider 08/2009). Since then, the company has become the world’s largest PET manufacturer, having increased its material production rate more than tenfold, as well as significantly extending its influence to 24 countries. The company’s average growth rate of core EBITDA over the past five years has been 18% per annum while its production output has grown 14% on average per annum, which puts Indorama Ventures ahead of its global competitors such as Alpek, JBF and Formosa internationally. During the South East Asia Roadshow, we readily accepted an invitation from Mr Vipin Kumar, Senior Vice President, Asia PET Business at Indorama Ventures, to discuss the current state of play and entrepreneurial challenges with his management team, with particular emphasis on the Thailand market. Indorama Ventures Public Company Ltd., June 19/20, 2017 We met: Mr Vipin Kumar, Senior Vice President, Asia PET Business, Indorama Ventures Global Services Ltd. Mr Sunil Marwah, Senior Vice President, Packaging Business Mr Krishnaswamy Chandrasekar, Vice President Manufacturing, Indorama Polymers Public Company Ltd. Mr Nitin B Bopardikar, Senior Vice President Manufacturing Head (Asia), Indorama Polymers Public Company Ltd. Mr Govind K. Narkar, Joint Vice President Operations, Petform (Thailand) Ltd. Mr Weerasawat Chindanon, Sales and Marketing Assistant Vice President, Thailand Depending on the traffic, it takes around two to two and a half hours to travel the 120km from Bangkok to the Lopburi plant where Indorama Ventures manages one of its countless materials manufacturing sites, Indorama Polymers Public, as well as Petform processing. 2003 and 2010 through acquisitions, site constructions and expansions which included the USA, Lithuania, the Netherlands and the UK. In addition, purified terephthalic acid (PTA) assets were added to the portfolio. Between 2010 and 2014, additional sites were established, mainly in growth markets in Africa, North America, Europe and Asia, with a focus on R&D and HVA products. Furthermore, production of monoethylene glycol (MEG) was integrated within its operations in North America. Since 2015, Indorama Ventures has been concentrating its efforts on sustainability, increased vertical integration to further optimise the value-added chain, as well as continuing to enhance their global know-how through more worldwide takeovers. Indorama Ventures currently has 70 manufacturing sites on four continents, including 31 PET material production plants in 16 countries, seven of which are being further developed. Comparative figures from 2007 and 2016 show that the company increased its total materials output from 0.7 to 10.5 million tons, its workforce from 2,000 to around 15,000 employees and pre-tax profits from US$76 million to US$775 million. Their current client base includes Coca-Cola, Pepsi, Nestlé, Danone, Suntory, Kirin, Asahi, ThaiBev, Oishi, Guinness, Procter and Gamble, Unilever, Zara, Bayer, BMW, Bridgestone, 3M, General Motors and Volkswagen. For PET in particular, the Company has around 800 Asian clients, with 150 in North America, 50 in Africa and a further 200 in Europe. In 2016, F.r.t.l.: Govind K. Narkar, Krishnaswamy Chandrasekar, Nitin B Bopardikar, Vipin Kumar and Kay Barton A brief outline of the company’s history. The company began operating in Thailand in 1995 and from here achieved world leader status in its field. In the years up to 2003, it worked exclusively in PET and polyester production before strategic overseas markets opened up between,@ID:12}, BOTTLING / FILLING PETplanet Insider Vol. 18 No. 11+12/17 petpla.net 22 Modern filling technology for the Uzbek water market Aiming for the top The water market is growing worldwide. How beverage producers are meeting the increasing demand and preparing themselves for future growth in this segment can be illustrated by an example of the Butsifal Group in Uzbekistan. With a high-performance KHS filling and packaging line for PET bottles the newcomer is challenging the supremacy of local market leaders and doing business beyond its own national boundaries. The times when water was drunk from public supply lines have long gone in Uzbekistan. Prior to independence the inhabitants of the Central Asian country still drew their water from taps found in public areas. At the end of the Cold War there was no much-needed investment in the country’s drinking water systems, causing the water quality to suffer. People then had to think anew. Since setting up the Republic of Uzbekistan the government has paid great attention to its citizens’ water supply – and still does – yet the Uzbeks increasingly turned to bottled water, thus triggering the boom in mineral water. The market is still growing fast today: in 2010 the Uzbeks consumed about 1.6 million hectolitres of water from the bottle. In 2015 the output reached more than 2.5 million hectolitres. By 2020 this figure is expected to increase to over four million hectolitres according to surveys by Euromonitor. Four out of five consumers drink their water out of PET bottles – preferably one-way PET. The Butsifal Group entered this growth segment less than ten years ago, with the company’s business developing just as dynamically as the entire Uzbek water market. Founded in 2009, the beverage producer aimed to close the gap on the market leaders, establishing the Sayhun water brand after just a short time in operation. The brand name is a reference to the old word for the longest river in Central Asia, the Syr Darya. Thanks to its natural origins, balanced mineral composition and low sodium content Sayhun water is becoming ever more popular. From one million litres of water in 2010, within five years the company boosted its output of mineral water forty times over. This rapid growth soon reached its limits, however. The capacity of the two lines by Chinese manufacturers was no longer sufficient. The low level of automation prevented efficient processes; time and again longer downtimes compromised filling. The Butsifal Group thus decided to renew its processes, with filling and packaging equipment by KHS. After a short planning and production phase the new line went into operation in the middle of 2016. High-performance technology processes up to 26,400bph “Thanks to KHS technology we’ve strengthened our position on the market and even already improved on it,” says Abdumalik Khalilov, director of the Butsifal Group. Since commisHigh-performance technology for the Butsifal Group: the KHS InnoPET Blomax Series IV stretch blow moulder and KHS Innofill DRV filling machine form the beginning of the KHS turnkey line. Premium water for Uzbekistan: Sayhun, the Butsifal Group’s flagship brand, is sold in both round and square bottles in still and carbonated versions.,@ID:24}, PETplanet Insider Vol. 18 No. 11+12/17 petpla.net 49 TRADE SHOW REVIEW vides valuable data for condition-based mould station maintenance. There are several benefits to controlling thickness distribution on the individual mould basis. These include: Reduced production variation Increased production days due to targeted maintenance Elimination of “outlier” mould-specific containers that may cause downstream issues Opportunities for further light-weighting The Process Pilot with the Individual Mould Control option is compatible with rotary stretch blow-moulding systems that incorporate independent mould station management. The Individual Mould Control option is currently available for KHS Series IV and V blow moulders. A retrofit version is also available for Process Pilot systems currently operating in the field. Agr’s Process Pilot Automated Blowmoulder Control system has proven to be a vital tool in the production of light weight bottles, while improving overall bottle performance and quality. It is unique in that it manages the blow moulder based on direct bottle measurements, on every bottle produced. Agr says that, by basing control on direct feedback from bottle measurements rather than just blow moulder performance indicators, its system can ensure that the final product has the desired quality and performance attributes regardless of environmental, blow moulder or material variations that occur during the production process. The addition of Individual Mould Control further complements this. www.agrintl.com motan-colortronic gmbh - [email protected] www.motan-colortronic.com Better than ever before Probably the most flexible loader system on the market METRO G Individual Mould Control screen on Process Pilot user interface,@ID:51}, PETnews 6 NEWS PETplanet Insider Vol. 18 No. 11+12/17 petpla.net Sustainability and Recycling at NPE2018 Around the world, the demand for plastic bottles continues to rise, fuelled by the growing bottled water market. In the United States alone, demand for beverage containers is expected to increase 1.9%/a to 283 billion units in 2019. But, with this growth, consumers are also increasingly looking to manufacturers and suppliers to move toward incorporating more environmentally-friendly products and processes. Whether its energy output from machinery or material lightweighting, equipment manufacturers are at the forefront of finding solutions to help brands employ more green practices. Beverage packaging manufacturers will lead the charge in bottle manufacturing as they look to optimise their assembly lines, reduce their carbon footprint, incorporate faster machines, and offer lightweight, recyclable containers and innovative packaging design. Coca-Cola serves as an example of manufacturers making process improvements to reduce the impact. Producing its partially bio-based PlantBottle packaging since 2009, they’re pioneering the use of bioplastics and are focused on achieving their goal of creating 100% bio-based bottles. Currently, the PET in Coca-Cola’s PlantBottle package is 30% plant-based; the company has reduced its use of fossil fuels without impacting the recyclability of the bottle. Given the role plastics play in today’s society, there is a heightened awareness of end-of-life issues regarding their recycling and disposal. The plastics industry has responded with sustainability efforts and educational endeavours. Two Technology Zones at NPE2018 will put greater emphasis on the technology, ideas and innovations that bottling and beverage packaging manufacturers will need to further greater sustainability and recyclability in their operations. The Bottle Zone is a new sector-specific area of the NPE 2018 program and show floor where event attendees can explore all the innovations in bottling manufacturing, including sustainability and recycling. This area will feature more than 6,000m2 packed with new machinery, equipment and sustainable materials from 80+ suppliers, giving bottling professionals unprecedented access to solutions designed to maximise efficiency and reduce their carbon footprint. In addition, the Bottle Zone Technical Forum will give engineers and designers access to in-depth sessions focused on the latest information and processes surrounding bottle manufacturing, including recyclability and sustainability, to strengthen their position in this $12.6 billion sector of the U.S plastics industry. Similarly, the Re|focus Zone at NPE2018 and the Re|focus Sustainability & Recycling Summit will address manufacturers’ real-world challenges with recycling and sustainable processes. The Summit will feature three half-days of plenary and breakout sessions dedicated to solutions and challenges around opportunities in sustainable manufacturing. The Zone will feature materials, machinery and solutions focused on allowing brand owners and manufacturers to meet their green goals. www.npe.org R&D/Leverage Open House The R&D/Leverage open house event included presentations on trends and developments in packaging design and mould manufacturing. Almost 50 attendees from global converters to brand owners attended the three day event, ran from September 20-22, 2017. The theme was “Breaking Down the Silos in Plastic Packaging” where R&D demonstrated that working with design, engineering, and manufacturing early in the planning process, fosters innovation and cost efficiency. The keynote speaker, Gerry O’Brion, brought a powerhouse presentation that demonstrated from his extensive experience on the benefits of making packaging stand out and bring on innovation by working together. He gave examples from working with big brands such as Procter & Gamble, Coors Light, Quiznos, and Red Robin. A stop of interest was the hall of fame wall where 103 pictures of employees are shown who have worked at the company for more than 20 years. Other stops included manufacturing value streams, quality control, laser, Leverage, repair and refurbish, polish, prototype, blow moulding, quality assurance, and welding departments. www.rdleverage.com Birkner’s Beverage World 2017/2018 The new updated edition of Birkner’s Beverage World 2017/2018 provides in reliable manner professional company and trade information on companies in the international beverage industry. In structured manner 20,000 company profiles from 197 countries are listed with more than 5,400 breweries, 5,500 producers of mineral water, juices and soft drinks, 2,400 distilleries, 1,300 hop, malt and raw material suppliers, 6,200 suppliers und 480 associations and institutions. Apart from names and addresses including websites the new edition also offers information regarding management, services, products and brands, machines and capacities, capital and turnover. In addition to the 12,600 e-mail and web addresses in the print edition there are also QR Codes for direct contacts and offers at your disposal. With the updated book edition and the internet database, users have two sources of information available to follow their business interests against the backdrop of the current market situation. www.beverage-world.com,@ID:8}, MATERIALS / RECYCLING 11 PETplanet Insider Vol. 18 PET gained the biggest sales share of 38%, followed by fibres (35%) and other raw materials such as PTA, MEG and isophthalic acid (IPA). Most of the 80% profit is generated in Western countries. Indorama Ventures’ current global PET market share is 20% which puts the company ahead of DAK and M&G. Conversion of raw materials into in-house preforms is about 125,000t/a. “When you see how far Indorama Ventures has grown, particularly over the last decade, a key factor has been the acquisition of existing companies”, says Mr Vipin Kumar, Senior Vice President of the Asian PET Business at Indorama Ventures. “This form of continuous growth is part of the company’s strategy,” he says. Mr Kumar lives in Bangkok and has worked for Indorama Ventures for 20 years, 12 of which have been in PET. The 49 year-old is a qualified textile engineer, as well as having an MBA Marketing Degree and a Foreign Trade Diploma. Mr Kumar previously worked for the Indian textile giant Raymond and for Reliance industries. As well as the Lopburi plant in Thailand, Indorama Ventures has other factories in Rayong, Pathum Thani and Nakhon Ratchasima that produce materials as well as preforms, closures, bottles and fibres. “In Thailand, we produce over 2.0 billion preforms every year for supply to ThaiBev, Oishi, Pepsi and other customers at our plants in Lopburi and Rayong”, says Mr Govind K. Narkar, Joint Vice President of Operations, Petform (Thailand). These preforms are for use in the beverage industry, for aseptic green tea bottles and for water bottles. Indorama Ventures relies heavily on Husky equipment for their injection moulding production. Outside the PETform facilities repi.com A NONCOLOUR TECHNOLOGY ANTI YELLOW ADDITIVES TO IMPROVE AESTHETICS OF RECYCLED PET NPE - Orlando, FL - South Hall - Level 1 - Booth S19103,@ID:13}, 38 TRADE SHOW REVIEW PETplanet Insider Vol. 18 No. 11+12/17 petpla.net TRADE SHOWreview Well T-handled The company Side, located in Barcelona, Spain, presented the new generation of machine and innovation of its T-handle concept for PET containers. In this system for producing containers with handles, the handle is formed during the blowing process itself. “The big advantage is that there is no need for subsequent modification to the containers”, says Josep Jimenez. The system is suitable for producing bottles of up to 4l in a variety of design options, such as oval, square or round containers, coloured or transparent and opaque with a flexible handle position. What they all have in common is that the starting product is a standard preform. “After one year of development, we were able to offer the market a solution to produce handled products using our range of SBM machines with a significant reduction in costs compared to other solutions. Besides the use of standard preforms, the production time is very fast. On a 4-cavity machine, we can produce 4,000bph. And as there is no need for any further changes to the container, labour-intensive post-processing can be omitted”, says Jimenez. When asked for his estimation for this market, he stated: “The beverage market is looking for big PET containers with handles, and other industries such as detergents are also registering an increased demand from their customers.” Besides the handle solution, Side was featuring the new generation of its PET blow moulding machinery, the 2006e model, as well as blowing solutions for highcapacity containers up to 50l such as PET kegs. www.sidemachines.com Advanced pad printing technology for bottle closures German printing equipment manufacturer Tampoprint AG chose the Drinktec trade show to present its “Continuous Circular” system, which it has just registered for a patent. The machine, which has a compact footprint, delivers 360° printing of closures in a continuous process. This latest development of rotational pad printing can be equipped with several printing modules and used for single- or multi-colour printing of cylindrical closures. It can be also used as a combined automation solution with printing on top ends, if required. “The machine prints to the highest accuracy on cylindrical parts such as metal closures for wine bottles and spirits,” Sales Manager Thilo Reichelt said. “Depending on the type of closure, it can produce up to 15,000 units per hour. In addition to the standard colour range, metallic finishes such as gold and silver can also be printed”, Tampoprint asserts that its machines are easy to operate and offer users the potential for new print designs. www.tampoprint.de Best-ever result at drinktec 2017 With over 76,000 visitors from more than 170 countries, drinktec has chalked up the best-ever result in its 66-year history. The number of visitors rose by 10,000 over the previous event in 2013. In particular at the international level, the trade fair was able to grow attendance again, this time by 12%. The ratio of visitors from outside Germany thus rose to 67%. The number of exhibitors increased to 1,749 from 80 countries. That is mainly attributable to the wine technology trade fair Simei, which was held as part of drinktec for the first time, as well as further growth in the number of exhibitors at drinktec itself. The number of visitors from China was more than 2,000, an increase of 65%. That means China already occupies second spot in the rankings of the top 10 countries of origin for visitors - behind Italy, which likewise recorded a sharp increase thanks to Simei: by around 45% to 5,240 visitors. There was also a striking rise in attendance from South America. Simei apparently helped boost the number of visitors from Argentina to 545 (an increase of 165%). 1,100 visitors came from Brazil, a rise of 40%. France, likewise a wine country, came fourth this year with 1,800 visitors. Apart from Italy, China and France, other countries in the top ten were Russia (1,857 visitors), the UK (1,619), the U.S. (1,570), Austria (1,567), Spain (1,254) and the Netherlands (1,221). A few of those exhibitors related to PET can be found in our PETplanet Insider Drinktec review. www.drinktec.com,@ID:40}, MARKET SURVEY 32 PETplanet Insider Vol. 18 No. 11+12/17 petpla.net 2-stage SBM machinery 2-stage SBM machinery Company name FlexBlow Amsler Equipment Inc. Serac Group Postal address Telephone number Web site address Contact name Function Direct telephone number E-Mail Vytauto g. 114A, Kretinga, Lithuania +370 445 51431 www.flexblow.com Mr Gytis Sirvinskas Head of Export Dep. +370 62011 528 [email protected] 1245 Reid St., Unit 1 Richmond Hill, Ontario, Canada L4B1G4 +1 905 707 6704 www.amslerequipment.net Ms Heidi Amsler Sales and Marketing Manager +1 905 707 6704 [email protected] 12, route de Mamers, BP 46, 72402 La Ferté Bernard, Cedex, France +33 243 6028 28 www.serac-group.com Mr Vincent Friart Blow Molding Division Manager +60 3 7847 2228 [email protected] 1. Machine designation / model number FlexBlow Linear Series - 6 Models (L12, L15, L22, L32, L407, L42, L42X) Linear Widemouth JAR Series - 2 Models (L16J, L25J) Linear Convertible Series - 2 Models (L32C, L42C) Linear Large Format Series - 3 Models (L110, LM120, L120C) Rotary Series - 2 Models (APT10, APT16) Serac Blow Linear 2. Bottle volume (from/to in litres) a) Standard machines 0.05 - 2 0.05 - 5 0.1 - 6 0.05 - 5 0.05 - 3 Up to 5 b) Machines for large containers 0.05 - 6 4 - 23 3. Maximum number of stretch-blow moulds (units) a) Standard machines 6 4 2 16 12 b) Machines for large containers 4 6 2 4 4. Output per stretch-blow mould for: 0.5 litres CSD bottle (units per hour) 1,600 1,800 1,800 1,500 1,200 1 litre CSD bottle (units per hour) 1,500 1,400 - 1,800 1,400 - 1,800 1,250 - 1,500 1,200 1.5 litres still mineral water bottle (units per hour) 1,300 1,400 - 1,800 1,400 - 1,800 1,300 - 1,500 1,500 Large capacity container 1,100 300 (18.9l) 1,000 Other 800 - 1,600 3,000 (4l) 5. Footprint / space requirement (L x W x H in metres) 2.7 x 1.8 x 2.6 4.0 x 1.8 x 2.4 to 4.3 x 3.7 x 2.5 3.9 x 2.5 x 2.2 5.7 x 2.0 x 2.4 to 4.3 x 3.7 x 2.5 3.9 x 3.8 x 2.7 2.7 x 2.2 x 3.1 to 4.2 x 3.0 x 3.2 6.9 x 2.2 x 2.7 6. Special features (short description / keywords) Ultra-fast mould change, quick neck change, high versatility: hot-fill, wide mouth, oval shaped, deep grip, large size bottle production possibility on 1 machine accepts MAG & other moulds Hotfill, polypropelene Fully integrated with Serac fillers (Combox solution); no mechanical adjustement in change-overs; significant economical savings with air recovery system and low electricity consumption; preferential heating for flat, oval and complex shapes. Company name Sipa SpA Sacmi Kosme Gesellschaft mbH Postal address Telephone number Web site address Contact name Function Direct telephone number E-Mail Via Caduti del Lavoro 3 31029 Vittorio Veneto, Italy +39 043 8911 511 www.sipa.it Mr Paolo De Nardi Project leader/Stretch- Blow Molders Development +39 043 8911 624 [email protected] Via E. Ferrari 1 43058 Sorbolo PR, Italy +39 0542 607 111 www.sacmi.com Gewerbestr. 3, 2601 Sollenau, Austria +43 2628 411 0 www.kosme.at Mr Johann Gugler Managing Director +43 2628 411 125 [email protected] 1. Machine designation / model number Rotary Blowmoulders XTRA: 6 - 8 - 10 - 12 (4 models), SFR EVO Cube: 16 - 20 -24 (3 models) Linear Blowmoulder SFL 6 (5 models), SFL4 (3 models), SFL 4 wide mouth (4 models), SFL 2/2 & SFL 1 (2 models) sbf Rotary machines (8 models) 2. Bottle volume (from/to in litres) a) Standard machines 0.25 - 3.5 0.25 - 3.5 3 0.05 - 3.0 b) Machines for large containers 5 - 30 0.5 - 6.0 3. Maximum number of stretch-blow moulds (units) a) Standard machines 24 8 18 8 b) Machines for large containers 2 6 4. Output per stretch-blow mould for: 0.5 litres CSD bottle (units per hour) 2,550 per cavity - up to 54,000 bph 1,800 bhc 4,500bph/mould 2,300 1 litre CSD bottle (units per hour) 2,550 per cavity 1,600 bhc 2,250bph/mould 2,300 1.5 litres still mineral water bottle (units per hour) 2,550 per cavity 1,650 bhc 2,250bph/mould 2,200 Large capacity container 650 bhc 1,250 Other 5. Footprint / space requirement (L x W x H in metres) 10.8 x 5.6 x 3.3 6.05 x 3.85 x 3.25 (without preform feeding system) 6. Special features (short description/keywords) Best output 2,550 bph/cav. with process angle: easy to blow. Reduced TCO: lower air & energy consumption (-25%). Quick mould changeover time, simple use & maintenance. Bottles for water, oil, csd, heat resistant, oval symmetric & asymmetric, with preferential heating, neck orientation, with handle, wide mouth (up to 130mm NF), large size (up to 30l), OPP and PLA Double cavity technology up to 70mm bottle diameter Active neck cooling; patented modular oven (low evergy consumption); block version with fillers for all sizes avbl.; ProShape technology available for oval bottles with an output of up to 2,000bph/cavity,@ID:34}, BOTTLING / FILLING PETplanet Insider Vol. 18 No. 11+12/17 petpla.net 26 Tour Sponsors: Father and son working hand in hand New bottling plant opening soon by Alexander Büchler La Boost, Shah Alam, April 12, 2017 We met: Tan Chee Chung, Director (Son) Tan Chin Wee, Managing Director (Father) The La Boost bottling plant is situated in Shah Alam near Kuala Lumpur. The father, Tan Chin Wee, has led his company successfully for many years, in good times and bad. Now his son has stepped up to the plate and, together, they are turning everything around. In a few weeks, a new bottling plant will open which will eliminate delays in the production process. Mr Tan has been in the drinks’ business since 1985 having imported Carlsberg beer to Malaysia for many years. However, in 2009, he decided to give this up and build a bottling plant himself as it was vital for him not to be solely dependent on one large company. So, in 2009, the La Boost plant started operating. Two difficult years followed as his bank was not too happy that he had switched from high beer sales to low revenues from water production. The economic crisis did not help either. However, La Boost was able to gain a foothold in the market and establish steady growth. Today, six bottling lines stand next to one another in this pristine facility, three for 0.5l and 1.5l bottles, one for large disposable PET containers and two for water in cups - that fill around 12 million bottles a month. All this was achieved working at full capacity over a two-year period. Father and son then decided to invest in a new system. In order to create more space, the warehouse was reduced to half of its original size by introducing a semi-automatic pallet system. In the coming weeks, construction on a new (blocking) Techlong plant can begin. Its capacity will be 27,000 1.5l bph or 48,000 0.5l bph which will create some breathing space that allows more bottles to be sold. The father, Tan, is clear on what the thinks of Western production. No matter how good the technology, costs and delivery times for spare parts are enormous and lengthy. He also has to pay for business class flights and premium hotels whenever he needs the services of a technician which is quite different from dealing with Asian manufacturers. In the end, he decided in favour of the European shrink tunnel manufacturer SMI. Justifying his decision, Tan said: “SMI can transport packages stacked together, which allows me to get on with production using the tunnel. And besides, SMI’s service point isn’t all that far from here”. He had no reservations in choosing a shrink tunnel as this is an innovation for the Malaysian market. PET bottles are traditionally packed and transported in cardboard boxes in Malaysia. Cardboard boxes can be stacked better, particularly as large numbers are always transported without pallets. The son, Tan, says that “cardboard prices have risen by over 20% during the past six months with the closure of a large paper mill in China. This proves that our decision to choose foil was the right one”. La Boost is already carrying out smallscale trials using a 12-pack of 0.5l bottles. www.laboost.com.my Mr Tan Chin Wee invites me to taste a Durian fruit which is not allowed on Malaysian trains given its pungent smell. I found you could eat them! La Boost produces its preforms on a Husky Hypet injection moulding system. They are placed in small plastic boxes for internal transport. As with preform, the company produces its caps on an HyCap 225 using a 48-cavity tool.,@ID:28}, PETcontents 11+12/17 4 PETplanet Insider Vol. 18 No. 11+12/17 petpla.net Page 52 Page 46 Page 18 INSIDE TRACK 3 Editorial 4 Contents 6 News 52 PET bottles for Beverage + Liquid Food 54 PET bottles for Home + Personal Care 56 Patents MATERIAL / RECYCLING 10 Thailand’s PET giant 14 The PET recycling industry in China: Between fire and ice 16 Bottles to fibres PET recycling in Malaysia 17 Prepared for the future Bottles turned back into bottles 18 Bringing technology to feedstock 20 Intelligent recycling in passenger aviation Emptying and compacting of containers BOTTLING / FILLING 22 Aiming for the top Modern filling technology for the Uzbek water market 26 New bottling plant opening soon Father and son working hand in hand 28 Two factories in one place Pere Ocean supplies Singapore from Malaysia MARKET SURVEY 31 Suppliers of SBM machinery, moulds & quality inspection MAINTENANCE 36 Smart, smooth, speedy and safe PET preform mould cleaning and maintenance with dry ice TRADE SHOW REVIEW 38 Drinktec 2017 review 42 Precise heating of preform to widen packaging opportunities 43 Green light in South East Asia 44 “There is also a market for small machines” 46 Towards a sustainable, daily production process 47 Benchmark for energy efficiency 48 Mould Control BUYER’S GUIDE 57 Get listed! RECYCLING S P E C I A L,@ID:6}, Industrial Solutions for Polymer Plants MTR® Melt-To-Resin PET resin technology developed by Uhde Inventa-Fischer for all your packaging needs Opt for superior quality resin with our proven MTR® technology that eliminates SSP (solid-state processing). The MTR® process is based on our advanced, proprietary 2-Reactor high i.V. melt technology. Reduced thermal stress and soft reaction conditions, combined with minimum raw material consumption and an economical investment will highly improve your profitability – 30% less conversion cost is feasible. www.uhde-inventa-fischer.com,@ID:23}, BOTTLING / FILLING PETplanet Insider Vol. 18 No. 11+12/17 petpla.net 23 sioning the output has significantly increased, he continues. “With our short production and delivery times we can now offer fast solutions to requests for offers we couldn’t satisfy in the past.” This is thanks to the high performance of the line. Instead of processing 4,000bph on each of the previous machines, the KHS filling system can fill up to 26,400bph. Following a format changeover the InnoPET Blomax Series IV stretch blow moulder, KHS Innofill DRV filler and KHS Innopack Kisters SP shrink packer automatically realign themselves with one another according to the given values in the software. The labelling machine upstream of the packaging process has been adapted by KHS, too. The KHS Innopro Paramix C sends the finished product to the filler depending on the beverage type. The elementary ingredients are prepared in accordance with the relevant beverage in the KHS Innopro syrup room which consists of a sugar dissolver, mixing tanks, a Batchmix unit for batch production of finished syrup and a filtration unit for the beverage blends, among other things. The machine operators reset the recipes on the touchscreen. In order to adapt its processes to meet the demands of modern production the Butsifal Group simultaneously converted and expanded its site. According to specifications and taking the prevalent local conditions into account KHS then planned the line design. The particular challenge here was to enable both round and square PET bottles to be filled on one line. The conveyors and labelling machine were specifically adjusted to satisfy this customer requirement. KHS integrated special servodrives into the labeller which permit wrap-around labelling of rectangular bottles. Fast format changeovers from round to square bottles The special line design plays a significant role when it comes to regular format changeovers: from still mineral water in square bottles through carbonated waters to CSDs and iced tea a total of nine products are filled on the line in 0.5-, 1.0- and 1.5-l formats. If the bottle shape and format stay the same, the KHS line allows products to be switched over in five minutes. A categorical reduction in the number of change parts on the line enables the Butsifal Group to change over from round bottle formats to rectangular ones in 15 minutes. “Thanks to the automation of our filling processes it’s a lot easier for our engineers to operate the line,” says Khalilov. “This helps us to avoid human error which in turn boosts process quality.” In the past up to 15 employees managed the outmoded systems. Just a few operators now control the automated processes – at a capacity which is six times higher than before. Other positive outcomes are that a vast amount of time is saved during filling, resources are used sustainably and less energy is consumed. The cost of filling each bottle has also dropped by about 40% through savings in the use of materials, energy and air, among other factors. Products are fully blended and fed to the filling process by KHS Innopro Paramic C.,@ID:25}, MATERIALS / RECYCLING PETplanet Insider Vol. 18 No. 11+12/17 petpla.net 16 stf·sorting line stf·washing line professional plastic recycling solutions – made in germany The stf· group is the leading manufacturer of plastic sorting and washing machinery, especially for PET post-consumer bottles, with more than 60 turn-key plants and several single machines delivered worldwide. stf·group Industriestr. 1-3 94529 Aicha v. Wald – Germany fon +49 8544 960-110 mail [email protected] web www.stf-group.de scan for vCard stf ·group PET recycling in Malaysia Bottles to fibres by Alexander Büchler Diyou Fibre, Nilau, April 11, 2017 We met: Mr Nick Lim, General Manager Only Diyou Fibre recycles PET bottles in Malaysia, limiting themselves to the processing of clear PET bottles. All other kinds go to China. PET recycling is not all that common in many South East Asian countries. No waste separation takes place in Malaysia either, which means used bottles for recycling are collected by rubbish collectors. Mr Nick Lim, Diyou Fibre’s General Manager, is compressing around 30,000t into flakes and fibres in Nilau. Explaining his position, Lim said: “Unfortunately, I don’t get enough bottles here so I have to buy them from Europe. In addition, the amount collected seems to vary widely for no apparent reason which, in turn, affects the number I need to get from abroad”. He mainly compresses water bottles into bales. At least 90% of bottles received from local collectors need to be of good quality otherwise he does not use the bales. He accepts lower grade purity levels from abroad in the knowledge that high purity content is not available there. He produces fibres which are principally converted into bedding. He has to guarantee the highest purity levels given the filling material is routinely used in hygiene items. This can only be achieved by using water bottles made from raw materials and this places considerable demands on the collector. Given the bottles are only filled with water, he does not have any restrictions on the type of detergent used for double hot washed flakes. The fibres are exported almost exclusively to Turkey, the Middle East and Europe. He hopes that in perhaps 10 years’ time, the Malays will have come to realise the benefits of waste separation as for him it is an easy way of separating recyclable, compost and residual waste material. Then we would have made a giant leap forward. www.diyoufibre.com Tour Sponsors: RECYCLING S P E C I A L,@ID:18}, BOTTLING / FILLING 25 PETplanet Insider Vol. 18 No. 11+12 first joint project creates the foundation for a strategic, long-term partnership. We see a promising, far-reaching partnership for the future – both for KHS and for ourselves,” stresses Khalilov. Butsifal’s appreciation of its German partner is also being visibly reflected to its end consumers. In an unusual move for a beverage producer the Butsifal Group advertises KHS on some of its bottle labels. This is probably pleasing to one customer of the up-and-coming beverage producer in particular: for many years the German Embassy in Tashkent has been one of the group’s most renowned customers. www.khs.com Looking ahead: Abdumalik Khalilov, director of the Butsifal Group, aims to challenge the major beverage producers on the mineral water market. Butsifal Group The Butsifal Group is a producer of beverage products located in the foothills of the Tian Shan Mountains not far from the capital of Tashkent. Founded in 2009, the company has established itself in Uzbekistan with mineral water – and especially the Sayhun premium brand. The company now also produces mineral water for the low price range and carbonated soft drinks and iced tea. Besides the usual 0.5-, 1.0- and 1.5-litre bottle formats the Butsifal Group also processes larger containers holding between 5- and 18.9-litres. In the peak season the company employs up to 80 people.,@ID:27}, MARKET SURVEY 35 PETplanet Insider Vol. 18 No. 11+12/17 petpla.net The North American Road Show Toronto New York Atlanta Orlando Denver Las Vegas Seattle Los Angeles San Francisco Vancouver Dallas New Orleans Phoenix Washington, D.C. Boston Detroit Kansas City Oklahoma City Albuquerque Milwaukee Chicago Minneapolis Charlotte Ottawa Montreal Quebec www.npe.petpla.net March – August 2018 The North American Road Show - Bottle Zone on tour PETplanet has successfully deployed its “Editourmobil” Road Shows across the world for seven years now. This is in addition to traditional forms of reporting; we have found that travelling by road enables deeper insights into markets; interviews with bottlers, suppliers and manufacturers can be conducted with greater flexibility, both in cities and in more rural areas. The appearance of the Editourmobil has created quite a stir in several countries - in addition to the impact of the interviews and meetings themselves. The Editourmobil is to return to North America once again, in cooperation with the NPE trade show (May 7 – 11, 2018 in Orlando, Florida). From March through August 2018 - three years after our last tour in 2015, which proved to be very successful - the PETplanet team will, once again, visit a variety of locations across the USA and Canada. The “Editour“ journeys will take in professional discussions and interviews with market leaders from the West to the East Coast. We will be stopping off at the NPE show itself, where the PETplanet and Editourmobil team will present initial reports of our visits and interviews. We will be part of the new Bottle Zone, which will be a first for us as well! Make sure you’re on board with us when we set off again. Get ready for in-depth analyses of the special features and trends in the bottles and beverages sectors of North America! All aboard! The worldwide round trip with,@ID:37}, imprint EDITORIAL PUBLISHER Alexander Büchler, Managing Director HEAD OFFICE heidelberg business media GmbH Bunsenstr. 14 69115 Heidelberg, Germany phone: +49 6221-65108-0 fax: +49 6221-65108-28 [email protected] EDITORIAL Kay Barton Heike Fischer Gabriele Kosmehl Michael Maruschke Ruari McCallion Waldemar Schmitke Anthony Withers WikiPETia.info [email protected] MEDIA CONSULTANTS Martina Hirschmann [email protected] Johann Lange-Brock [email protected] phone: +49 6221-65108-0 fax: +49 6221-65108-28 LAYOUT AND PREPRESS EXPRIM Werbeagentur Matthias Gaumann | www.exprim.de READER SERVICES Till Kretner [email protected] PRINT Chroma Druck & Verlag GmbH Werkstr. 25 67354 Römerberg Germany WWW www.hbmedia.net | petpla.net PETplanet Insider ISSN 1438-9459 is published 10 times a year. This publication is sent to qualified subscribers (1-year subscription 149 EUR, 2-year subscription 289 EUR, Young professionals’ subscription 99 EUR. Magazines will be dispatched to you by airmail). Not to be reproduced in any form without permission from the publisher. Note: The fact that product names may not be identified as trademarks is not an indication that such names are not registered trademarks. 3 PETplanet Insider Vol. 18 No. 11+12/17 petpla.net China bans imported waste, including PET waste China is serious about clamping down on environmental pollution. The closure of a large number of “dirty” industries in and around large urban areas is now being followed by a ban on the importation of recyclable waste. For the most part, this relates to the very environmentally damaging recycling of electronic waste but it has also affected plastics – and therefore PET. Mr Xie Zhenhua, leader of the Chinese delegation at the annual climate conference, explained somewhat self-critically what it was all about in an interview with Der Spiegel on 15.11.2017: “For China, economic development is the key to solving all of our problems. But at the same time, we must tackle poverty, ensure social equality, create more jobs, improve people’s health – and therefore protect the environment. There is quite a lot for us to do! In some areas, we have driven the economy forward but neglected to protect the environment. Our relatively rough development model and our technical backwardness have led to heavier environmental pollution and caused ecological damage.” Just as the Chinese are energetically building an enormous highspeed train network or constructing new airports throughout the entire country, so now environmental pollution, and primarily air pollution, is to be prioritised. For every nation around the world, this now means that the recyclable waste mountains must be processed somewhere else, ideally within each nation itself. For PET there is surely sufficient capacity; all our on-site research shows that recyclers are lamenting the shortage of PET bottles. However, the legal provisions must also be clear and of course relevant to the situation in the real-world. What use is legislation that is hard to comply with - which stipulates that only a small proportion of bottles from the non-food sector may be recycled - if modern recycling technology can process even non-food bottles into food grade material? The lack of legal provisions to divert flows of PET from China to individual countries is a greater barrier than a lack of recycling capacity. Yours, Alexander Büchler Dear friends of PETplaner Insider,,@ID:5}, MATERIALS / RECYCLING PETplanet Insider Vol. 18 No. 11+12/17 petpla.net 20 Emptying and compacting of containers Intelligent recycling in passenger aviation LSG First Catering, the Swiss airline catering specialist from Bassersdorf, near Zurich airport, produces around 19,000 meals and sandwiches for the aviation industry every day. Its 230 employees are totally engaged enabling airlines such as Edelweiss Air, Helvetic Airways, Swiss International, Etihad Airways, Qatar Airways, Oman Air, American Airlines and United Airlines to provide their passengers with food and drinks. Every piece of packaging carried onto the plane is returned after the flight and must be disposed of. Owing to the high cost of disposal and the lack of options for recycling the materials themselves, the company decided to acquire a “Liquidrainer” dewatering press and a semi-automatic “Autoloadbaler” baling press from German recycling plant manufacturer Strautmann Umwelttechnik, based in Glandorf. LSG now empties all full and half-full bottles that come back from the airport, compacts 350kg of packaging per day for baling and, as a result, now saves around US$41,000 a year. “We put the liquids directly into the wastewater disposal and from there into the water treatment plant,” Operations Manager Mr Marcel Schneider explains. “Before the new disposal process was installed, everything was cleaned at the wastewater treatment plant.” The empty PET bottles, together with glass bottles, are collected by Kibag Entsorgungstechnik AG, a waste disposal company located just two kilometres from the LSG facility, and sent for recycling. According to Mr Schneider, LSG First Catering itself produces very little waste on site. But everything which arrives and is required for production of the meals is packaged and must be unpacked. This outer packaging is collected, pressed into bales with the semi-automatic baling press, and disposed of. Around 127t of cardboard packaging is collected in this way and sent for recycling each year. In the case of PET, LSG used to simply throw the bottles – including their liquid contents – into the residual waste. This turned out to be a significant expense, and it meant that the company could not send the PET bottles for recycling. After switching to the Strautmann equipment, the caterer now disposes of its waste more efficiently and in a more environmentally friendly manner, and the raw materials can be sent for appropriate recycling. Thanks to the massive reduction in the weight of the K1 waste (catering and food waste from means of transport operating internationally) and the additional remuneration for the cardboard bales, the company saves around US $41,000 per year. www.strautmann-umwelt.de All of the food and drinks prepared at the Bassendorf site are taken directly onto the aeroplanes at Zurich airport. When the planes are unloaded, every single item of packaging, from dishes through chewing gum, to full and empty PET bottles, is removed. The trolleys are restocked and everything that needs to be, is disposed of. All PET bottles are collected in plastic boxes and then tipped into the Liquidrainer, which empties the bottles completely and shoots the empty outer packaging into a large box. Marcel Schneider, Operations Manager LSG First Catering RECYCLING S P E C I A L,@ID:22}, 39 TRADE SHOW REVIEW PETplanet Insider Vol. 18 No. 11+12 Compressed air control and Industry 4.0 At Drinktec 2017, compressor manufacturer Kaeser continued to focus on intelligent control, in response to the demands and needs of industry 4.0 applications. The German company, which is based in Coburg in Bavaria, has more than 100 representative branches or trade partners worldwide. It introduced its Sigma Air Manager 4.0 on a huge touch screen at the trade fair. The software, which is an integrated element within the compressed air system, takes over control tasks and manages safe transmission of process data from the system during operation and in real time, including “Sigma Smart Air”, its latest service, which is available as an option. This facilitates the analysis of usage parameters via remote diagnostics; in response to the results, it sets up preventative, needs-based maintenance intervals, which will help to extend the machine’s life. Kaeser predicts a reduction in service costs of up to 30%, as well as reduced down time and increased reliability of supply. The system intelligently connects available components and sends all transmitted compressor data to the operator in numerical and graphic form. Energy consumption and exact cost details for individual processes can be produced, and required changes to system-specific functions can be carried out in real time. The energy report is produced by Air Manager 4.0 in accordance with ISO 50001. The system controls four compressors in the basic version; optional software upgrades can scale it up to manage up to 16 compressors. The interface, following the current trend to portray highly complex systems in easy to understand and transparent ways and make operating them easier, offers an easy-to-use reduced layout. The same interface can be accessed as an HTML site on end devices such as laptops, tablets or smartphones. www.kaeser.de,@ID:41}, 41 TRADE SHOW REVIEW PETplanet Insider Vol. 18 No. 11+12/17 petpla.net Polymetrix, a former Buhler GroupCompany, continues to bea successful technology supplier in thepolymer market. We serve customers worldwide with customized plant solutions, advanced process technology and high quality service in the field of virgin bottle grade PET, virgin technical yarn, recycled PET, polyamide and other polymers. www.polymetrix.com BEYOND THE HORIZON 20 MILLION TONS PER YEAR OF BOTTLE-GRADE PET SSP CAPACITY INSTALLED SINCE 1984 a former Bühler Group Company DACHCOM,@ID:43}, PETplanet Insider Vol. 18 No. 11+12/17 petpla.net 54 PETbottles Home + Personal Care Cardboard sleeve for a plastic bottle The Italian manufacturer of pet products, Conagit SPA, has developed new packaging for a granulated product designed to improve litter box hygiene as part of “Giuntini’s” “Hygiene Plus” series. The granulate, which is mixed in small quantities in normal cat litter, has an antibacterial effect as well as preventing odours. The product comes in a thinwalled, transparent plastic bottle with a properly sized cardboard sleeve. The face side of the packaging on the shelf has been improved, with product information printed on the solid card easier to read than, say, on a sleeve label. There is a sealed membrane under the screwed-on screw top and two dispensing spouts which must be removed prior to its initial opening. www.giuntinipet.com A foam bath from Dresdner Essenz The s t i l l re l a t i ve l y young German company, Li-Ih Ltd from Dresden, whose commitment is to 100% certified vegan natural cosmetics with 100% plant-based detergents and 100% natural fragrances, is continually expanding its product range. Their latest series’ creation is a foam bath with special fragrances such as organic mango/kumquat/ and organic vanilla. The product, which the manufacturer says produces a lot of foam, also contains organic aloe vera and organic sesame oil ingredients. It comes in a 300ml beige coloured bottle and is enough for approximately nine full baths. A dispensing aid has been inserted into the bottle opening. The screw top is decorated with an extra sticker to match the colour of the bottle label. www.dresdner-essenz.com,@ID:56}, PETplanet Insider Vol. 18 No. 11+12/17 petpla.net 47 TRADE SHOW REVIEW Engel all-electric e-cap operates with short cycle times and a maximum of good parts Benchmark for energy efficiency by Gabriele Kosmehl At Drinktec, a fully automated e-cap injection moulding machine was producing 26mm HDPE caps including tamper-proof bands. The cycle time was 2.2s. Michael Feltes, Vice President Business Unit Packaging and Frank Schuster, Sales Director Packaging spoke about this machinery in particular and trends in caps & closures in general. PETplanet: At the last Drinktec in 2013, an e-cap 3440/380 with a 72-cavity mould was presented, which produced a 28mm closure. At that time, the cycle time for the 1.8g cap was 3s. What further developments have contributed to the e-cap 2440/380 model that we see here today? Feltes: Here, we are presenting a production cell as it could be found in manufacturing operations. Our intention is that a specialist sees the system and discovers his every need reflected in the tiniest detail. Since the last Drinktec, we have received lots of feedback from our customers and this has also contributed to further developments. An example here is the topic of plasticising. Thanks to our high-performance servo direct drive, the new high-strength HDPE materials can be processed with an MFI significantly lower than 2 or 1g/10 min with a high degree of performance and precision to produce good parts – with very short cycle times. PETplanet: Material developments aim for low part weights. However, many closure manufacturers are meanwhile reporting that they are placing more value on the convenience aspect. But the inevitable question is: in terms of possible material savings, are we now at the outer limits? Feltes: The trend is still heading towards ever lighter closures. Weight savings of course mean greater savings in terms of material, energy and ultimately cost. On the other hand, the requirements for closure geometry and convenience and hence material selection are growing because the physical properties must be fulfilled and the final product must be usable for the consumer Schuster: Regarded in a purely physical light, still more can yet be gained but in our opinion the limits of lightweighting, with regards to convenience, have been reached. However, this is perceived very differently in different regions. For example in Asia, easy handling takes first place for customers and weight plays a rather subordinate role. In the USA however, lightweight remains a significant topic – particularly focusing on CO 2 reduction, which is very important to American customers. As a rough estimate, another 1/10 can be saved in weight in the closure market there. And here in Europe, both requirements – lightweighting and convenience – are somewhat in balance. PETplanet: What do the energy needs look like for this fully electric system, based on the current cycle time of 2.2s? Schuster: The specific energy consumption of just the machine is 0.42kwh/kg. The overall system including the chiller is 0.7kwh/kg. These values are setting the benchmark worldwide. If we accelerate the process, the energy requirements fall per item produced but of course this raises the overall energy costs. Squeezing more out of the cycle time also could result in increased ejector power and clamp force requirements needed for very short cycle times, which will ultimsately also increase the energy requirements. Feltes:Another of our innovations is crucial here: the integrated kinetic energy recovery system! Based on the flywheel principle, braking energy from plate movements is stored in a special configured servo motor and then returned to the system when required for next acceleration. This is primarily an advantage to cut power peaks and reduce overall energy and power consumption . PETplanet: Many thanks for the interesting insights! www.engelglobal.com F.l.t.r.: Gabriele Kosmehl and Heike Fischer, PETplanet, with Frank Schuster, Sales Director Packaging and Michael Feltes, Vice President Business Unit Packaging, Engel, at the Engel Drinktec booth,@ID:49}, 40 TRADE SHOW REVIEW PETplanet Insider Vol. 18 No. 11+12/17 petpla.net Developments for a turnkey solution Newamstar, Chinese liquid (beverage) packaging solution and smart factory supplier, based around 120km north-west of Shanghai in Jiangsu Province, has regularly impressed over recent years with additions to its machine portfolio in the beverage and food production segment. The company now covers the entire process chain from water and beverage pretreatment to blow moulding production lines; filling, capping and conveying system, and downstream equipment for processing goods for despatch. Its customer base includes names such as Danone, Coca-Cola, PepsiCo., Nestlé, Wahaha, Nongfu Spring, Ganten and Otsuka. At Drinktec 2017, Newamstar presented a turnkey system model to demonstrate that it has now reached a level at which it can provide drinks manufacturers with comprehensive solutions, in line with full plant layout planning. A special focus for the company at the trade fair was its “Intelligent Warehouse System”. Launched in 2015, this is a logistics solution designed to complete the downstream portfolio. After products are transferred by the palletiser, they are then placed in the stereoscopic racks by computer-operated robots using an automated, three-dimensional FIFO process. The company also supplies a range of autonomous transport robots, with or without rail systems, as an automated solution to additional transport requirements in the downstream segment. “Our storage system is designed to offer effective and efficient logistics management right up to transfer to the AGV/RGV,” said Wesley Yin, Head of Marketing. “The aim is to optimise the use of storage space and minimise picking times. We are also seeking to minimise any sources of error with automation and save energy costs too.” The company offers a comprehensive product tracking system for food safety throughout the production and packaging process, in addition. The individualised storage system structure is designed to save (building) space, as well. Planning services for customers can include complete facility construction and the necessary technical installations. Like Newamster’s equipment for other process areas, the warehouse can also be integrated as a module into existing systems from other manufacturers. www.newamstar.com Mould temperature control The Japanese company Osaka Reiken presented its temperature control equipment and resin treatment systems. “While our clients include several key players from the Japanese PET bottle and beverage industry, we do also serve other plastic manufacturing processes,” explains Yoshiki Kanaoka, President of Osaka Reiken. “Our solutions for the plastics industry include mould chilling units, water or oil based temperature controllers, PET solid-state polymerisation systems, crystallising dryers, as well as preform neck and bottle neck crystallisation systems, among others.” In Munich, the company presented its latest innovation, a CO2 -based mould chiller. Additional features such as proportional inverter control permit energy savings, and a large flow rate ensures stable mould temperatures to increase production efficiency. The Japanese company was the first to offer a chiller using CO2 as a refrigerant for the plastics industry: “This is the next logical step in the refrigeration business,” Kanaoka points out. “We see more and more F-gases being phased out in the near future, because their global warming potentials can be several thousand times that of CO2 . We are not just considering to make our products as future-proof as possible; we are really hoping to contribute to the responsible production of plastics.” www.reiken.co.jp Sports closures for short necks 28mm PCO 1881 and 29/25mm At Drinktec, Aptar presented a variety of new products for beverage dispensing, including two new fliptop hinged sport closures for “on-the-go” PET bottles. “ G u a r d i a n ” , a two-piece bi-injected closure for 29/25mm neck finish, features a comp l e t e l y new tamper-evident system that the company points out is very visible, intuitive and non detachable. When the closure is first opened – by pushing up the large one-hand finger recess – a small white ‘indicator’ component automatically drops down into a pocket that is clearly visible through the transparent PP bi-colored body, which also allows a clear view of the internal, coloured, 7mm spout. The spout itself is customisable and available with or without Aptar’s “Simply Squeeze” swimming silicone valve. “Avantage”, a one-piece flip-top 28mm PCO 1881 valvecapable closure, is also equipped with a new, non detachable tamper evident seal. Users press a point in the front area and the closure mechanically opens when the lid is pushed up. The company says that Avantage is the first closure to be equipped with the “Stay-with” ring, which keeps the closure with the bottle, even when it has been unscrewed from the neck. Aptar says that, with these closures, it is especially targeting on-the-go bottled water, sports or functional drinks and juice applications. www.aptar.com Guardian two-piece bi-injected closure,@ID:42}, MARKET SURVEY 33 PETplanet Insider Vol. 18 No. 11+12/17 petpla.net KHS Corpoplast GmbH Krones AG SMI S.p.A. Taizhou Huangyan MEGA Machinery Mould Co. Ltd. Meiendorfer Strasse 203, 22145 Hamburg, Germany +49 40 67907 0 www.khscorpoplast.com Mr Marco Böhnke Product Manager +49 40 67907 483 [email protected] Boehmerwaldstr. 5 93073 Neutraubling, Germany +49 9401 700 www.krones.com Mr Peter Christiansen Head of Sales Blow Moulding Technology/Block Technology +49 9401 70 4980 [email protected] Via C.Ceresa, 10, 24015 San Giovanni Bianco (BG), Italy +39 0345 40 111 www.smigroup.it Mr Pietro Volpi Marketing Dept. Manager +39 0345 40 316 [email protected] 47-8 Huang Zhou Road, Huangyan, Zhejiang Province, China +86 576 840 201 22 www.megamachinery.com Mr Cai Jiahan (Simon) Sales Manager +86 576 840 201 22 [email protected] KHS InnoPET Series IV Contiform 3 Pro 11 models available Contiform 3 Pro SC 4 models available Contiform 3 Pro H 11 models available The EBS (Electronic Blowing System) Ergon serie (10 models) & EBS K RB, EB, SS, E 0.1 - 3.0 0.1 - 3.5 0.1 - 0.7 0.1 - 2.0 0.10 - 3 2.5 5.5 3.5 - 10 30 4 - 36 cavities 28 36 28 16 Up to 16 cavity 4 - 8 cavities 6 Up to 2 cavity 2,500 2,500 2,500 2,000 2,100/2,200bph per cavity 1,200bph 2,500 2,500 2,000 2,000/2,100bph per cavity 1,000bph 2,250 2,400 1,800 2,000/2,100bph per cavity 900bph 1,500 1,100/1,200bph per cavity 500bph for one time use; 200bph for returnable bottle 2,000 In Multiprocess config. max. 2,500 6.1 x 4.7 - 11.1 x 7.1 from 6.5 x 5.4 x 4.6 to 11.7 x 7.6 x 4.6 from 10.7 x 6.2 x 4.6 to 14.4 x 7.6 x 4.6 from 6.9 x 4.4 x 4.5 to 11.2 x 6.8 x 4.5 Standard models: min 4.2 x 3.5 x 2.75 / max 6.8 x 3.9 x 2.75; HC - high capacity models: min 4.45 x 3.46 x 2.57 / max 5.55 x 3.46 x 2.57 InnoPET Silent TipTainer: efficient noise and preform protection; SpeedLoc: fast mould change over system; airback air recovery system; NIR heating technology; efficient external preform dedusting, inspection and rejection system; widemouth-option for food applications; preferential heating: perfect bottle quality for oval containers; standardised and open block interface Bottle design and mould manufacturing; nitro-hotfill; air-recycling systems for standard- and heat-set machines; rapid product change-over systems (MouldXpress); integrated preform- and bottle inspection; Contiform Bloc (blower-filler-block); Contiform Bloc BL (blower-labeler-block); Ergobloc L (blower-labeler-filler-block); Contipure Asept Bloc with integrated preform decontamination, ProShape (non-round bottle production) Compact frame, ergonomic and functional design, new preform-heating module Oval bottle, handle bottle, large keg Side S.A 1 Blow Urola S.C. Pol.Ind. Montguit, C/Llinars, s/n 08480 - L'Ametlla del Valles (Barcelona), Spain +34 93846 3051 www.sidemachines.com Mr Josep Jiménez Sales Manager +34 677 551 928 [email protected] 23 Chemin de Gerocourt 95650 Boissy L'Aillerie, France +33 9800 820 70 www.1blow.com Mr Olivier Perche Sales Director +33 9800 820 75 [email protected] Urola Kalea s/n, PO Box 20230, Legazpi, Spain +34 943 737003 www.urolasolutions.com Mr Iñaki Unanue Commercial Director +34 943 737144 [email protected] Linear machines (7 models) Maxiblow 1002e 2004e 2006e 2002eG 2003eG 5001e XL 1XXL / 1XXLN / 1XL / 1XL Lab / 2L / 2LN / 2LO /2LHF / 2XLS / 4L / 4LN / 4LO / 4LHF / 6MO Linear (URBI-2, URBI-4, URBI-6, URBI-8, URBI-2l, URBI-4l) 0.05 - 3.0 10 2.5 3 2.5 10 10 30 0.10 - 12 0.10 - 2 0.5 - 30.0 15 50 5 - 30 Up to 10 4 1 2 4 6 2 3 1 6 8 3 1 2 4 6 2 3 1 1 4 1,700 1,500 3,000 7,000 10,000 3,000 4,500 950 2,000 1,600 1,650 1,500 3,000 7,000 10,000 3,000 4,500 950 1,800 1,600 1,600 1,500 3,000 7,000 10,000 3,000 4,500 950 1,700 1,700 up to 1,250 for 5.0l; 750 for 15.0l; 700 for 20.0l; 350 for 30.0l 1,200 2,800 7,000 10,000 2,600 3,600 700 1,000 for 5l; 600 for 20l 1,250 min.: 4.50 x 1.83 x 3.10; max.: 5.10 x1.85 x 3.10 (without preform feeding system) To be determinated. Taylored solutions for small areas 2.1 x 1.6 x 2.4 Smallest URBI-2: 2.32 x 2.2 x 2.0; largest URBI-8: 5.9 x 4.35 x 2.3 (dimensions without hopper-loader) Air recycling system; mould shells of linear machines are compatible with rotary machines; fast semiautomatic mould change within 10min; preferential heating T-handle, preferential oven, neck orientation, recovery air system Preferential heating (oval bottles); neck orientation (standard preforms); hot fill; compatible with Sidel, Krones, KHS, Sipa, Side moulds; recovery of blowing air; power recovery Fully electric, very compact, low energy consumption; same residence time of all preforms in the oven; transfer of preforms to press wit fixed pitch,@ID:35}, 8 NEWS PETplanet Insider Vol. 18 No. 11+12/17 petpla.net WikiPETia.info New contents at wikipetia.info Erema North America Discovery Day 2017 Erema’s Discovery Day - already established in Europe - has now been held for the first time at Erema North America in Ipswich, Massachusetts, under the title “Circular Economy In Action”. Over 100 customers and interested attendees were given an insight into the latest technical developments emerging at Erema and discussed the current upswing of recycling in the North American plastics industry. Martin Baumann, Vice President Sales at Erema North America (ENA), opened the Discovery Day 2017 with the words: “Not only the recycling industry, the entire plastics industry as a whole is experiencing drastic change.” This statement corresponds with the remarks made by Patty Long, Executive Vice President of the Plastics Industry Association (PLASTICS), who, as keynote speaker, elaborated on the increasing relevance of recycling in the North American plastics industry. “Members of the entire plastics industry are calling for more sustainable management of plastics through innovation and the creation of products that are designed for recycling, from inception to end use”, says Patty Long. With a total of over 650 Erema systems in operation, the USA and Canada rank among the most important sales markets for Erema recycling technology. “There is one aspect, however, which sets the USA and Canada aside from other markets – and that is their enormous growth potential. The change of thinking in the industry will without doubt be intensified by China no longer being an international customer for post-consumer waste plastic. As, unlike waste plastic, high-quality recycled pellets can still be exported to China, this represents a great opportunity for plastics recycling in North America,” says Martin Baumann, summing up. The focus of the technical presentations was above all on the recycling of clean production waste and post-consumer recycling (PCR). The filter system is crucial, especially when recycling municipal PCR, to process heavily contaminated plastic to make high-quality recycled pellets. In connection with this, the new Erema business unit Powerfil was presented for the first time. The proven melt filters are now also available as individual components for existing extrusion plants. ENA Technical Center expansion Participants were given an insight into the recycling solutions presented in the form of live demonstrations on four Erema systems. Thanks to the addition of an Intarema TVEplus RegrindPro at the Technical Center, existing and potential customers from the USA and Canada now have a total of five recycling machines at their disposal for material trials. The new addition to the machines which make up the Technical Center is a brand new RegrindPro, with top technology for the efficient processing of regrind material. It features a high-performance Erema Laserfilter with which unwanted impurities even from heavily contaminated materials can be removed, including contaminants such as rubber, silicone, paper or aluminium which are otherwise difficult to filter out. www.erema.com Otto Hofstetter AG opens branch in Luxembourg On November 1, 2017, Otto Hofstetter AG, the manufacturer of moulds for PET preforms and the packaging industry, opened a branch office in Luxembourg. With this new office, the family-owned company from Uznach, Switzerland, is expanding its international presence and increasing its proximity to its customers in the EU. Otto Hofstetter Luxembourg SA will start out with a team of six specialists. The core competences of the branch will be design and consulting. The team consists of highly skilled specialists with decades of experience in the PET industry. With the new location in Luxembourg, Otto Hofstetter AG is now much closer to its numerous customers in the Benelux countries, in France and in Germany. The experienced design engineers in Luxembourg will support the team at Otto Hofstetter’s headquarters. Regarding the expansion, Otto Hofstetter, owner and CEO of the Swiss mould manufacturer, said the following: “Our new location allows our customers and ourselves to benefit in three ways.” The market is moving increasingly towards individual solutions, while the speed of innovation continues to increase and the amount of time available for projects continues to decrease. “Today, the goal is to increase flexibility while maintaining quality and reliability.” Otto Hofstetter is sure that Otto Hofstetter Luxembourg SA will allow the company to meet this need at any time. Management at Otto Hofstetter AG wants to fully integrate the specialists in Luxembourg in three months at most. www.otto-hofstetter.swiss From left: Mike Horrocks (CEO, Erema North America), Patty Long (Executive Vice President, Plastics Industry Association), Martin Baumann (Vice President Sales, Erema North America),@ID:10}, PETproducts 50 PETplanet Insider Vol. 18 No. 11+12/17 petpla.net Penn Color develops Pennacle barrier model for dairies Penn Color has developed its Pennacle Barrier model to meet the specific needs of the dairy industry. The company says that it is designed to predict various unknown variables during the package development process and thus enable dairies seeking to package their liquid dairy products in rigid packaging to preserve nutritional quality and taste. Penn Color, which is a leading global producer of colour and additives masterbatches, has been co-developing solutions with their converter and brand owner customers in support of Ultra High Temperature (UHT) sterilised and Extended Shelf Life (ESL) liquid dairy markets in Europe, South America, China, Middle East and the U.S. Dairies are looking for innovative ways to package their products and extend shelf life, and rigid bottles and containers have proven to be an effective solution. However, many unknown variables are encountered when designing a light sensitive package; the company says that the Pennacle Barrier model provides accurate packaging recommendations and predictive cost modelling ahead of the expensive blow-moulding and filling lines experimentation phase. Solutions can be customised to meet nutritional quality and taste expectations in addition to extending shelf life, for both mono and multilayer structures. In conjunction with the predictive model, customisable Pennacle Opaque masterbatch technologies for PET, PE and PP are available, which Penn Color claims that can enhance the container’s light barrier at low LDR’s, without negatively impacting the conversion process. Penn Color’s Pennacle Barrier model can be applied to dairy applications and any rigid packaging application that is sensitive to light degradation, including: vitamins; supplements; nutrition drinks; and enhanced beverages. The company also emphasises that it has the ability to measure the effectiveness of oxygen barrier resins and additives to assure that its colour masterbatches do not affect O 2 ingress or CO 2 digress. www.penncolor.com The one-camera solution: IntraOne Intravis GmbH, known for vision inspection systems for the plastic packaging industry, launched IntraOne, a onecamera solution combining the advantages of a smart camera with Intravis’s IntraVision software at Drinktec 2017. IntraOne can be used for various inspections on preforms, closures, bottles, containers, labels or decorations and can be integrated into any production line. Intravis can use its powerful IntraVision software due to the industrial PC integrated into the camera. The user-friendly software is pre-installed, ready for operation, and does not have to be configured separately. The system inspects for typical defects such as contamination, colour or contour deviation or even any types of damages with inspection speeds up to 30 pc./sec. By entering the smart-camera market, Intravis now offers its customers a cost-effective turn-key solution in combination with its proprietary software. www.intravis.de Dosing cap UK Plastic Packa g i n g S u p p l i e r & Ma n u f a c t u r e r Raepak introduces its new dosing cap. It has been engineered to measure out the exact amount of liquid. The dosing cap can work with a range of liquid viscosities. This bottle cap makes it easier for the consumer to squeeze the correct amount of liquid every time. Andrew Paterson, Director and company and owner of Raepak explains: “We wanted to offer a simple solution that can make a huge change in the packaging industry. The ‘one dose squeeze cap’ is a new innovating idea that makes it easy for brands to get involved. Everyone can benefit towards reducing packaging size and liquid contents. It makes it easier for consumers to recycle and manufactures to produce”. The new cap will roll out by 2018. www.raepak.com,@ID:52}, PETplanet Insider Vol. 18 No. 11+12/17 petpla.net 43 TRADE SHOW REVIEW Green light in South East Asia by Kay Barton “A major part of our production is foreseen to be supplied to customers in the ASEAN region; closures for food products, especially. This is a field in which we are able to fulfil some highly sensitive product requirements,” Henckes said. “We currently have definite plans for South East Asia with four major brand manufacturers with whom we are already working in Europe. We will further seek to develop new products and markets.” Mr Henckes maintains that competition is quite scarce, so the company plans to gradually develop its customers in Southeast Asia. It is worth noting that, currently, approximately 25% of nutritional products in South East Asia are sold online. Four fully electric Engel injection moulding machines will be used at the new plant. When the company expands into beverages, it is to be assumed that the company would opt for a solution with focus on fast cycle times. Closure solutions United Caps showed some of its standard closure solutions for the beverages industry at Drinktec, including two newly revised 29/25 caps: the 1.3g Progrip; and the 3g Prospring onepiece sports closure, which is designed on the same basis. Both are to feature an improved finger-grip and easier opening. The new 28-1881 Prospring, weighing 3g, is set for launch in 2018, along with the company’s CC Flex 28-1881, weighing 1.9g. These two closures are designed for applications on the PCO 1881 neckfinish. Currently undergoing testing is the slightly shortened 26/22 Flat Premium closure, weighing 1.8g; United Caps is currently awaiting customer feedback on this new development. www.unitedcaps.com Luxembourg-based closure manufacturer United Caps will soon officially launch its new plant in Malaysia. The company currently has seven plants in Europe; the new facility will be its first to be established outside the borders of the EU. We met CEO Benoit Henckes at Drinktec and discussed with him why the markets of South East Asia are looking so exciting for the company, today and in the future, as well as its new product innovations that were presented at the trade show. “We have managed projects in the nutritional segment in Singapore from Europe in the past and we have already gained considerable experience with the local markets. It was on the basis of this work that the idea of having our own plant in the region emerged,” Mr Henckes explained. “We looked in detail into various possibilities and finally decided to build a plant in the Kulim district in northern Malaysia. This will provide us with an adequate starting point for our activities at every level, in terms of potential customers, demand, transport infrastructure, skilled staff and governmental support. The proximity of other injection moulders in the north also contributed to our decision. The port of Penang, which is an important shipping hub, is nearby, as well.” At the launch of its production operations, the company will initially be serving the nutrition and chemicals only. An expansion into the beverages sector is quite possible over the long term and makes sense in the light of the growing markets. There is a widespread and considerable requirement for food safety in the region, a requirement that United Caps wants to tap into. In discussions with CEO Benoit Henckes United Caps meeting with (f.l.t.r.) CEO Benoit Henckes, Astrid Hoffmann-Leist (Chief Marketing and Innovation Officer) and Kay Barton, PETplanet Insider,@ID:45}, 9 NEWS PETplanet Insider Vol. 18 No. 11+12/17 petpla.net W W W . I N T R A V I S . C O M Sample-PreWatcher® PreWatcher® III ColorWatcher® Integrated Fast inspection on eight square meters. It offers the most elaborated cavity number reading on the market: the PreWatcher® III. It feeds the preforms gently to the inspection stations by centrifugal force. The result: space-saving and unique preform inspection. Detailed inspection. The Sample-PreWatcher® inspects samples of preforms for numerous defect criteria right behind the injection molding machine – down to the last detail. The system is also suitable as fast and objective measuring and inspection machine in the quality lab. Quick and precise color inspection. The ColorWatcher® Integrated inspects transparent and translucent preforms right after their production and gives instant feedback. It inspects every shot and does not need floorspace through its integration into the injection molding machine. Preform Inspection today. Launch of the new European project on chemical recycling Demeto The new European project on chemical recycling Demeto is officially launched. Demeto aims at enabling chemical depolymerisation of PET at industrial scale based on its microwave-based process intensification, focusing as a start on coloured bottles waste. The project has received funding from the European Union’s Horizon 2020 research and innovation programme under grant agreement no 768573. During its kick-off event at the end of September in Brussels, the consortium welcomed around 60 experts from the PET packaging and polyester industry and gave an insight into the project, its technical foundation, economical aspects and role in a circular economy. “Demeto proposes the industrialisation and demonstration at full-scale of a new industrial process which allows to chemically recycle PET bottles, food containers and even textiles in a highly profitable and environmentally sustainable way,” explained Maurizio Crippa, CEO of gr3n, during the event. The core technology of Demeto has been invented by his company gr3n to enable an effective process intensification of the depolymerisation reaction (hydrolysis) of plastic, from bottles as much as from any other source, leading it back to its building blocks (EG and PTA) and, consequently, allowing their full re-introduction directly at the virgin-grade production stage. “Demeto’s technology, once successfully implemented, would allow to close the recycling loop for PET, with a potential impact on environment and society at large that would be enormous, introducing the concept of full circular economy in the plastic domain,” added Franco Cavadini, CTO of Synesis. The business exploitation strategy of Demeto is based on a synergistic relationship between two industrial stakeholders: gr3n, as the manufacturer of the Reactive Units, and Processi Innovativi, as EPC contractor that builds the full-scale de-polymerisation plants. gr3n will supply Processi Innovativi with all the reactors needed to realise these plants required to cover progressively the total available market. www.spire2030.eu,@ID:11}, MATERIALS / RECYCLING PETplanet Insider Vol. 18 No. 11+12/17 petpla.net 17 Bottles turned back into bottles Prepared for the future For many years this is a common practice at BTB PET-Recycling GmbH & Co. KG based in Bad Salzuflen, Germany: At BTB PET-Recycling, 20,000 tons of PET input material from the German bottle return system PETcycle are processed every year. The owner-managed company was founded in 2006 and has operated a Starlinger PET recycling line type recoStar PET 165 iV+ since 2007, presently with six SSP reactors. Long-term cooperation (f.l.t.r.): Richard Wüllner (BTB), Christian Lovranich (Starlinger) and Andrzej Zajontz (BTB) At the moment, BTB PET-Recycling has 30-35 employees and produces food-safe PET regranulate for reuse in the production of beverage bottles. The company is in possession of a positive EFSA opinion concerning the food safety of its rPET; an extended EFSAsubmission has been filed. In addition, BTB PET-Recycling is certified according to ISO 9001:2008 as well as ISO 50001:2011. A factor worth highlighting is its first-rate life cycle assessment: The geographical proximity of preformer, bottler and recycler reduces the carbon footprint to a minimum. BTB PET-Recycling has fixed customers for its regranulate; an internet presence is therefore not necessary. Changing market requirements call for flexibility and constant adaptations on the part of the recycler. Over the course of the last 10 years, there have been massive changes in the design of PET bottles, e.g., the bottles have become lighter and/or their walls have become thinner (causing the bulk density to change significantly), and they may contain additives (acetaldehyde and oxygen blockers). According to one of the managing directors of BTB PET-Recycling, Andrzej Zajontz, the Starlinger recycling line is insensitive to variations in input material. These can be compensated by parameter adjustments alone, thereby ensuring consistent regranulate quality. To keep the machine up to date from a technical point of view, upgrades are provided on a regular basis. The recycler emphasises the machine’s ease of operation – allowing for swift training of new personnel – as well as Starlinger’s uncomplicated service. Christian Lovranich, Head of Process Engineering of the division recycling technology, has provided support to BTB PET-Recycling from Ease of operation: the colour touch panel of the PET recycling line A Starlinger recoStar PET 165 iV+ with SSP 1800 the very beginning and is clearly proud of the line’s high uptime: „The machine achieves an uptime of 95%. This means that the output has far exceeded the client’s expectations.” Service of the machine has been optimised to minimise downtime; the line has to be stopped only for certain maintenance work such as a knife change. An advantage is the modular design of the Starlinger line at BTB PET-Recycling. By adding an additional vacuum SSP reactor, the capacity can be extended very easily, allowing for continuous growth. Company owner Richard Wüllner reports that the capacity was increased through adding one SSP reactor in 2013 as well as in 2015 to meet the growing demand for food-safe regranulate. In addition, upgrades were made in the areas of washing, bottle sorting, and flake sorting. A further increase in capacity is planned for the near future. The regular investment in the recycling line shows that the recoStar PET at BTB PET-Recycling is far from being outdated, on the contrary: It is well equipped for the next 10 years. www.starlinger.com RECYCLING S P E C I A L,@ID:19}, PETpatents www.verpackungspatente.de PETplanet Insider Vol. 18 No. 11+12/17 petpla.net 56 A PET carafe Internal Patent Application No. WO 2017/ 064532 A1 Applicant: Societé Anonyme des Eaux Minerales D’Evian et en Abrege, Evian-les Bains (FR) Registration date: 16.10.2016 Design and method for the production of an optically eye-catching, oval PET bottle for drinking and mineral water that differs from others on the market. The preform required for production needs to be designed accordingly. A superior PET container European Patent Application No. EP 2663498 B1 Applicant: Graham Packaging PET Technologies Inc., Lancaster (US) Registration date: 15.12.2011 This application describes a PET container with advanced thermal properties and is designed for higher filling and pasteurisation temperatures. Petaloid base of a container European Patent Application No. EP 2643225 B1 Applicant: Sidel Participations, Octeville-sur-Mer (FR) Registration date: 22.01.2011 This application describes a plastic bottle with a petaloid base that lengthens the bottle, as well as explaining the geometric shapes, angles and contours of the bottle’s base. A base with a recessed curve European Patent Application No. EP 2981474 B1 Applicant: Sidel Participations, Octeville-sur-Mer (FR) Registration date: 31.03.2014 A plastic bottle with a base stabilised by strengthened and intermediate reinforcement grooves. The design and arrangement of the grooves are explained in the application. A stable bottle European Patent Application No. EP 2580133 B1 Applicant: Sidel Participations, Octeville-sur-Mer (FR) Registration date: 14.06.2011 A firm bottle with a flexible contact surface and special bottom design for flexible absorption of pressure differences. A plastic bottle European Patent Application No. EP 2853501 B1 Applicant: Yoshino Kogyosho Co. Ltd, Tokyo (JP) Registration date: 18.11.2009 A thin-walled plastic bottle with a flexibly adjustable base. The bottle remains stable even when the base is shifted more to the inside of the container.,@ID:58}, MARKET SURVEY 31 PETplanet Insider Vol. 18 No. 11+12/17 petpla.net 11+12/2017 MARKETsurvey Preforms & preform inspection Recycling plants & washing units Palletising & shrink film machinery Caps & closure systems & CC inspection Labelling & marking systems Recycling: Cutting plants Filling equipment & filling inspection Resins, additives Compressors SBM machinery & quality inspection SBM machinery, SBM moulds & quality inspection For this year PETplanet Insider concludes its market surveys with an overview of 2-stage SBM machinery and manufacturers of SBM moulds for the bottles. In addition we present inspection systems for bottles, state of the art! SBM machinery and moulds: Terekas, Hallink, Amsler, KHS, Sipa, Wentworth Mold, Serac, Kiefer Mold, Röders GmbH, Krones, SMI, PETform, MEGA Maschinery, Sacmi, Kosme, Moldintec, Side, 1Blow, Urola, PET Engineering and R&D/Leverage. For inspection: Intravis, AGR, Sacmi, ALPS, Pressco Technology and IMD. Although the publishers have made every effort to ensure that the information in this survey is up to date, no claims are made regarding completeness or accuracy. Quality inspection Company name Intravis GmbH Agr International Inc. Sacmi Imola S.C. Postal address Telephone number Web site address Contact name Function Direct telephone number E-Mail Rotter Bruch 26a, 52068 Aachen, Germany +49 241 9126 0 www.intravis.de Mr Markus Juppe Chief Marketing Officer +49 241 9126 0 [email protected] 615 Whitestown Road Butler, PA 16001, USA +1 724 482 2163 www.agrintl.com Via Selice Prov.le 17/A 40026 Imola (BO), Italy +39 054 2607 111 www.sacmi.com Mr Stefano Severi Sales Area Manager +39 335 6594 236 [email protected] Bottle inspection system SpotWatcher PETWatcher IntraOne! Agr Pilot Vision The Pilot Vision BVS Type of system Stand-alone, multicamera system Integrated, multi- camera system Integrated, singlecamera system Integrated Modular vision-based inspection system Both, stand-alone or integrated in Sacmi SBM Body inspection Holes; contamination (e.g. material defects, burn marks); colour smears; deformations & contour; thin wall inspection Sidewall inspection; neck folds; clarity and consistency; areas of crystallinity; contamination; foreign materials; dark spots Thin wall management as an option; comprehensive sidewall thickness monitoring; on every bottle Yes; holes, contamination, colour, deformation, thin wall inspection Bottle base Foreign debris; contamination (e.g. material defects, burn marks); holes; injection gate position; cristallisation at injection gate; thin wall inspection Holes in base, foot region and gate; opaque spots; foreign particles; unmelted material; crystallisation detection and management, with CrystalView option Under-blown & improperly formed feet and base characteristics; gate position; folds in base region; off-center gate; gate size; gate ovality/tears Yes; foreign debris, contamination, injection gate position, holes, crystallisation Sealing surface Scratches & notches; short shots; diameter / ovality Surface irregularities; seal surface width; inner/ outer diameter; ovality Blown finish; seal surface integrity Yes; scratches, notches, short shots, diameter Thread Dimensional characteristics; contamination; flash; short shots Dimensional characteristics; contamination; flash; short shots Short shots Yes; dimensional characteristics, flash, contamination, short shots Inspection performance Up to 72,000 objects / hour Up to 72,000 objects / hour Up to 108,000 objects / hour Throughput up to 100,000bph; additional details regarding specific inspection performance provided upon request Up to 60,000bph Company name Air Logic Power Systems LLC (ALPS) Pressco Technology Inc IMD Ltd Postal address Telephone number Web site address Contact name Function Direct telephone number E-Mail 2440 W Corporate Preserve Drive, Unit 600, Oak Creek, WI 53154, USA +1 414 574 4151 www.alpsleak.com Mr Mike Lawson Sales Manager +1 414-574 4151 [email protected] 29200 Aurora Road, Cleveland, OH, USA +1 440 498 2600 www.pressco.com Mr Tom O'Brien VP, Marketing, Sales & New Business Dev. +1 440 498-2600 [email protected] Moosweg 1, 2555 Brügg, Switzerland +41 32 366 80 66 www.imdvista.ch Mr Martin Gerber Sales Director IMD Ltd. +41 32 366 80 66 [email protected] Bottle inspection system Flexpitch Intellispec IMDvista BOCO - Bottle Inspection System Type of system Stand-alone Stand-alone; conveyor-mounted or blowmoulder-integrated Inline system solution integrated into customers production line Body inspection Holes; seal surface; bottle height; thin wall Underblown; folds; pearling / hazing / clarity; contamination; incorrect colour container; malformed containers; holes; choked necks & crooked necks; light or heavy panel / neck / base sections; changing mass distributions Swirls and scratches; contamination and black dots; colour, deformation; holes; label inspection; crystallisation; wall thickness to confirm upon request; thermographic inspection – panel and bottom; other defects to be confirmed by IMD Bottle base Holes Contamination / foreign debris; cracked gates; folds / slugs; holes in gate or feet; off-center gates; pearling / hazing / clarity Injection point; injection point and gate position; deformation points; holes in base; dots on bottom; damages bottom side; thermographic inspection – panel and bottom; other defects to be confirmed by IMD Sealing surface Scratches; notches; short shots Damaged / nicked seal surfaces; cuts, dips / saddling, oval finishes; short shots; blown finishes; seal surface flashing; contamination; rolled surface Contamination on sealing surface and on neck; damages / short shots on neck; diameter; ovality; other defects to be confirmed by IMD Thread None Gross damage; finish dimensional measurements; contamination Flashes, contamination, other defects to be confirmed by IMD Inspection performance Up to 72,000bph Container size ranges from 50-150mm diameter, 150-365mm height; container materials including PET, LDPE, HDPE, PE, PP; defect detection down to 0.2mm depending on inspection FOV; false reject rate 0.05% PET and HDPE inspection possible; other materials to be confirmed by IMD,@ID:33}, PETplanet Insider Vol. 18 No. 11+12/17 petpla.net 55 BOTTLES A glitter spray from Schwarzkopf Schwarzkopf and Henkel are selling an enchanting glitter spray called #Instashine under the Schwarzkopf got2b brand which, according to the manufacturer, is designed to give the hair a glitter boost, a sparkling finish and longlasting fragrance. The glitter product comes in a 75ml oval, clear bottle with a pink screwed-on pump dispenser and fitted with a protective cap. The label on the bottle and sticker on the protective cap are slightly reflective in order to reflect the light, as well as attracting the buyer’s attention. www.schwarzkopf.de 96% natural ingredients Garnier is advertising its soothing facial tonic containing 96% natural ingredients and part rose water. According to the manufacturer, the facial toner has a mixture of 96% purified water and naturally derived ingredients. The remaining 4% is for ease of use and long-lasting effect. The used transparent bottle is 100% recyclable which is in keeping with the product’s ethos. A screwed-on hinged top with dispensing spout, a non-look label on the front and a back label printed with a rose blossom on the inside complete the packaging. www.garnier.de,@ID:57},
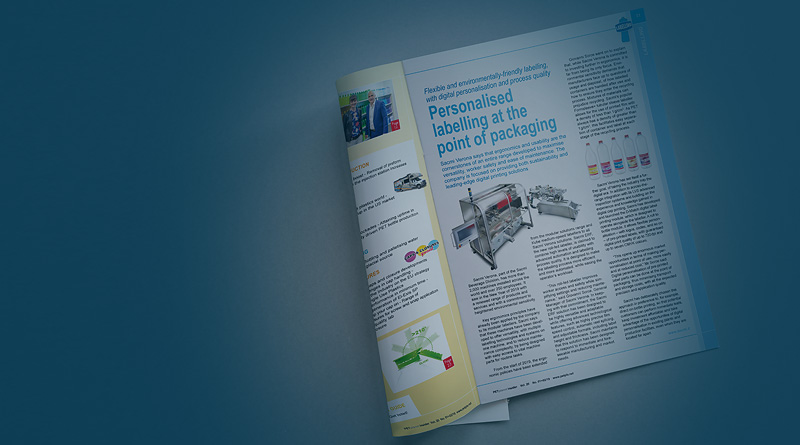