"PACKAGING / PALLETISING PETplanet Insider Vol. 19 No. 11/18 petpla.net 31 DS Smith Hall 4A booth 207 DS Smith introduces Stackabox Hybrid and Stackabox C&C to their line of dispensing containers Storing and dispensing solutions Stackabox bulk dispensing containers have become a common name in the world of PET preforms. Stackabox was already available in compact, medium, and maxi formats and is suitable for an optimum truckload in the UK and mainland Europe. At Brau Beviale, the company introduces two new special versions. The most important aspect of Stackabox is that it fits perfectly in the fully automated dispensing systems of beverage, filling and caps & closures companies. The patented design is the only bulk container that allows for both top-as bottom dispensing in a wide variety of existing dispensing frames. Bottom dispensing is becoming the overall preferred system because it has the unique advantage of decreasing damage to the bottleneck of the preforms, by smoothly sliding the preforms in the hopper of the filling line, but the flexibility of the Stackabox allows integration in every imaginable automated system. DS Smith is expanding their Stackabox line of bulk dispensing containers with two special versions: The Stackabox Hybrid and the Stackabox C&C. The new Stackabox Hybrid can further optimise the supply chain by adapting the container’s height to the optimal size for content or transportation. The new bulk-dispensing container has the same base as Stackabox. The height can be easily adapted to customer requirements thanks to the AkyPack corrugated plastics sleeve in the middle section. Stackabox Hybrid is a lighter version of the original Stackabox in weight but equally durable offering long life cycles, says the company. – ONE for ALL STAND E-11019 STAND D05:20 STAND: 6 D 055 The smooth surface of the AkyPack sleeve is washable and suitable for printing. Stackabox C&C was designed especially for handling caps & closures with a dispensing ‘sliding door’ located at the base of the bulk-container. The base dispensing system makes them the ideal solution that can be easily utilised throughout the entire production process of bottle packaging. Optimising customers’ supply cycle logistics needs is the key innovation driver offered by DS Smiths Plastics Stackabox line of dispensing bulkcontainers. Stackabox has a lifespan of 8-10 years and can be recycled entirely at the end of its life. www.dssmith.com Like the traditional Stackabox bulk dispensing container, both Stackabox hybrid and the Stackabox C&C have an ideal fold-down ratio, no need of a pallet and a unique base dispensing system or is compatible with all other dispensing systems.","@ID":33}, "TRADE SHOW PREVIEW PETplanet Insider Vol. 19 No. 11/18 petpla.net 39 SMI Hall 6 booth S068 Smart packaging machine to be more competitive SMI designs and manufactures bottling and packaging machine with an innovative design, equipped with IoT technology, in order to provide customers all over the world with smart solutions, able to satisfy their needs of competitiveness, production efficiency, operational flexibility, energy savings and management and monitoring simplicity of the whole production plant. The LSK SF Ergon series arises from the need to provide an ad hoc machine for packing rigid containers in film only and consequently have available an extremely compact machine, easy to control and monitor. A model of the new LSK 30 SF Ergon will be showcased on the booth. The machine is equipped with rounded safety doors made of anodised aluminum, which let all the motors, featuring low-energy consumption, be placed externally compared to the mechanical groups they activate. The door closing system is equipped with a slow-down device and accompanies the door smoothly in its final phase of closure. The process of packing in film is extremely fluid: on the machine infeed conveyor, equipped with low-friction chains made of thermoplastic material, loose containers are clustered in the desired format by a pneumatic device and electronically synchronised separating bars before accessing the film wrapping section and the shrink tunnel. SMI offers a wide range of shrink tunnels, with technology to limit energy costs and guarantee maximum environmental compatibility. For instance, the new version of ST Ergon tunnels manage the distribution of hot air flow on all the surface of the forming pack efficiently and consistently, guaranteeing a high level of shrinking. Furthermore, at the tunnel outfeed, the pack undergoes an immediate cooling process, by means of an advanced ventilation system, this sets the shape, the appearance and rigidity to prevent deformation or breakage during the following packing stages. SMI shrink tunnels are designed to allow the operator to have easy access, in complete safety, to the internal parts of the system during maintenance and cleaning, which, compared to other traditional systems are much smaller. The ovens of the ST Ergon series are available fuelled by electricity or by methane gas, where the necessary heat for shrinking the transiting packs is obtained by the combustion of methane rather than the special electrical resistances. The tunnels fuelled by electricity can be equipped with fibre glass chains (standard supply) or with metal chains (standard supply or optional according to the model of machine). Fibreglass hold the heat more efficiently, therefore, reducing energy consumption. Also, the film rarely leaves residue on this kind of chain.The metal chain releases more heat, therefore consumption is slightly higher, but at the same time it guarantees improved film sealing under the pack. Laboratory tests show that, in countries where natural gas is available at convenient prices, the use of a methane fed shrink tunnel guarantees a saving of 60% compared to energy consumption of a traditional tunnel fuelled by electricity. The development of this new range of ST Ergon tunnels fuelled by gas began with this consideration, to offer innovative technology with low environmental impact, to customers who have a supply of methane gas at advantageous prices. This pack shrinking solution, which is highly technological, eco-sustainable and with a reduced environmental impact, can be combined with all the shrink wrappers and combined packers produced by SMI. www.smigroup.it","@ID":41}, "MATERIALS / RECYCLING PETplanet Insider Vol. 19 No. 11/18 petpla.net 12 Post-consumer PET into food-grade finished packaging products Totally closed-loop recycling rPlanet Earth, a new company dedicated to closed-loop recycling of post-consumer plastics, has started up a large grassroots facility completely vertically integrated plant for converting PET packaging waste into finished rPET products with properties comparable to those made from virgin PET. The new rPlanet Earth facility sorts, cleans, and purifies rPET to produce high quality rollstock, thermoformed containers, and moulded bottle preforms. The 302,000 sq.ft (28,060m2) facility in Vernon, CA takes in bottles, clamshell containers, and other packaging waste from kerbside collection, puts it through an extensive series of sorting and cleaning procedures, grinds it into flake and subjects it to rigorous wash and decontamination. It raises the intrinsic viscosity (IV) of the material in accordance with end-use requirements and processes it into food-grade sheet, thermoformed containers, and injection moulded preforms for bottles. The new rPlanet Earth plant has an annual capacity of 80,000,000lb. (36,290 metric tons). The total investment at Vernon thus far is around US$ 100m. According to rPlanet Earth co-CEO Robert Daviduk, plans are in the works to add a second bales-to-end-product production line in the facility within the next two years. Beyond recycling PET, rPlanet Earth meets other sustainability goals, noted co-CEO Joseph Ross. “While our rPET packaging provides appearance, purity and physical properties comparable to those of virgin PET, our carbon footprint is 60% less than that of packaging made from virgin resin and in fact is 20% less than that for rPET products from other companies,” said Mr Ross. He added that the figures take into account kerbside collection, baling, and transportation as well as the operation in the Vernon plant. “In addition, our recycling operation uses 90% less water, per quantity of output, than a PET resin plant.” Comprehensive process for reclamation and re-use After bales entering the rPlanet Earth facility have been broken into a single stream of bottles and thermoforms, the material is subjected to multiple sorting procedures. Magnetised sorters remove foreign matter such as wire; near-infrared scanners identify PET and separate it from other polymers. Another sorting step separates PET materials by colour. Next comes a dry system for grinding the material into flake; water is avoided because it is a carrier for inks and adhesives that can negatively affect the quality of the finished rPET. The first encounter with water is in the wash line, where the material is cleaned before it moves to a tank where PET, which is heavier than water, sinks, while labels, adhesives, and other matter are skimmed off. Subsequently the flake enters a Krones MetaPure reactor where ~200°C heat and vacuum are used in a final decontamination process; solid state polymerisation (SSP) raises the IV of the rPET to various levels, depending on the target application. rPlanet Earth bypasses the pelletising step in favour of adding value to flake by using it in its own in-house plastics processing lines. “By skipping the pelletising of rPET we potentially avoid degrading our products’ appearance, since a melting step that can negatively affect colour is completely eliminated,” said Mr Daviduk. “Our customers are looking for products that come from a truly closed-loop recycling system.” He noted that rPlanet Earth can supply sheet, thermoformed packaging, or preforms whose rPET content can range up to 100%, depending on whether or not a customer requires some percentage of virgin PET. The company currently operates seven plastics processing lines: Two Husky injection moulding systems are for the production of preforms; three Welex extrusion lines produce sheet for sale as rollstock to the merchant market or for use in-house on two large Lyle thermoforming machines. The thermoformed products manufactured by rPlanet Earth may include drinking cups, produce packaging, clamshell containers, and virtually any other food-grade thermoformed packaging currently made from PET. The three Welex sheet lines supplied by Graham Engineering include extruders that yield widths up to 75 in. (190cm) and can be configured for coextrusion, the XSL Navigator controls capable of integrating with plant-wide automation systems. Nordson’s BKG HiCon screen changers, BlueFlow gear pumps, and static mixers and Nordson’s EDI Ultraflex sheet dies. Graham Engineering also supplied thickness scanners, edge trim systems, winders, and other equipment. “We spent an enormous amount of time researching plastics processing equipment suppliers and chose Graham Engineering because of their technical capabilities, their engineering and design support, and their Converge Conical Twin Screw (CTS) technology, which is more compact and streamlined in comparison with conventional twinscrew systems,” said Mr Ross. “It was a joint decision between us and Graham Engineering to include Nordson components. The in-line backflush capability of the BKG screen changers was particularly attractive because this self-cleaning feature enables us to avoid shutdowns due to screen buildup. In addition, Nordson backed their EDI die with extensive experience in PET sheet processing, exceeding that of other die suppliers.” www.rplanetearth.com F.l.t.r.: The co-CEOs of rPlanet Earth, Joseph Ross and Robert Daviduk","@ID":14}, "PETplanet Insider Vol. 19 No. 11/18 petpla.net 62 PETbottles Home + Personal Care Colourful bottles for cleaner With its own-brand “Zekol” cleaners, Aldi Süd is injecting some colour into the world of household cleaners. The limescale cleaner comes in a vibrant orange bottle holding 750ml of product, while the degreaser with soda comes in a green bottle. Both bottles feature ridges in the grip area for a more secure hold and better activation of the trigger. The lockable trigger is designed to spray without foam build-up. Self-adhesive labels describe application and usage. www.aldi-sued.de Wash foam with glitter effect The German discount pharmacy chain dm has a magical, swirling wash foam for little girls on its shelves under its own brand “Prinzessin Sternenzauber”. The raspberry-scented cleaner for face and hands must be shaken before use to mix the sparkling glitter with the product. A lockable pump dispenser dispenses the glittering wash foam. www.dm.de Laundry scent in an eye-catching bottle Laundry and clothing that smell fresh for a long time and release this scent when they are worn are the result of special laundry scents that are placed in the drum during the laundry cycle and attach themselves to the clothing fibres. The newest representative of this category in Germany is the “Kuschelweich” brand belonging to fit GmbH. The bottle contains 275 g of scent pearls and stands out from its competitors on the market because of the interplay between its bottle shape and lid construction. The bottle is decorated with a sleeve label with a transparent area that allows a direct view of the scent pearls. www.fit.de","@ID":64}, "BOTTLE MAKING 16 PETplanet Insider Vol. 19 No. 11/18 petpla.net Both Sidel and Krones use standard clamping devices with both mould sides opening. KHS has moved to one stationary and one moving side, reducing blow-wheel footprint. Sipa uses what they call the “crocodile” mould movement, with one side being stationary while the other opens to the front instead of to the side (Fig. 4.17). It is also a space-saving measure. Figure 4.17 Instead of opening sideways, this clamp opens one side vertically. Picture courtesy of Sipa. Changeover times Changeover times are important for those factories that do not have the luxury of running the same product 365 days/year but have to change 2–5 times per week. When the same necks are used, the steps involved are as follows: Disconnect water hoses Replace blow moulds Replace bottom inserts Replace stretch rod stops or dial in new stop values Change PLC recipe Change preform supply. All blow machine manufacturers have now quick-change systems (Fig. 4.18 that make this task much less time consuming. Water hoses are equipped with quick-disconnects or eliminate the disconnection completely by feeding water through the carriers with the molds being outfitted with O-rings that do not require anything to be disconnected. Blow moulds used are mounted with two screws holding each half. Modern systems feature locking mechanisms that allow mould removal with one twist of a special tool or no tool at all. Same for the bottom inserts. Stretch rod stops are also easily replaced or not necessary when servomotors are used instead of cam-driven pneumatic cylinders. An overview of the various parameters of rotary machines Parameter KHS Krones Sidel Sipa Max. b/c per h (small water) 2,250 2,250 2,300 2,250 Max. bottle size (l) 3 3.5 3.5 3 Cavitation 0.7 l max. 4–36 8–36 6–34 6–24 Maximum transfer ring 36/48 38/48 38/48.5 38/43 Preform orientation Up Up Down/up Down/up Stretch rod movement Servo Electromagnetic Cam/air Cam/air Max. output (b/h) 81,000 81,000 78,200 50,400 Table 4.4 Depending on the machine speed different degrees of machine rotation take different times Bottles per cavities per hour Degrees 1500 1600 1700 1800 1900 2000 2100 2200 15 0.100 0.094 0.088 0.083 0.079 0.075 0.071 0.068 30 0.200 0.188 0.176 0.167 0.158 0.150 0.143 0.136 45 0.300 0.281 0.265 0.250 0.237 0.225 0.214 0.205 60 0.400 0.375 0.353 0.333 0.316 0.300 0.286 0.273 75 0.500 0.469 0.441 0.417 0.395 0.375 0.357 0.341 90 0.600 0.563 0.529 0.500 0.474 0.450 0.429 0.409 105 0.700 0.656 0.618 0.583 0.553 0.525 0.500 0.477 120 0.800 0.750 0.706 0.667 0.632 0.600 0.571 0.545 135 0.900 0.844 0.794 0.750 0.711 0.675 0.643 0.614 150 1.000 0.938 0.882 0.833 0.789 0.750 0.714 0.682 165 1.100 1.031 0.971 0.917 0.868 0.825 0.786 0.750 180 1.200 1.125 1.059 1.000 0.947 0.900 0.857 0.818 195 1.300 1.219 1.147 1.083 1.026 0.975 0.929 0.886 210 1.400 1.313 1.235 1.167 1.105 1.050 1.000 0.955 225 1.500 1.406 1.324 1.250 1.184 1.125 1.071 1.023 240 1.600 1.500 1.412 1.333 1.263 1.200 1.143 1.091 255 1.700 1.594 1.500 1.417 1.342 1.275 1.214 1.159 270 1.800 1.688 1.588 1.500 1.421 1.350 1.286 1.227 285 1.900 1.781 1.676 1.583 1.500 1.425 1.357 1.295 300 2.000 1.875 1.765 1.667 1.579 1.500 1.429 1.364 315 2.100 1.969 1.853 1.750 1.658 1.575 1.500 1.432 330 2.200 2.063 1.941 1.833 1.737 1.650 1.571 1.500 345 2.300 2.156 2.029 1.917 1.816 1.725 1.643 1.568 360 2.400 2.250 2.118 2.000 1.895 1.800 1.714 1.636 Table 4.3 Depending on the speed of the machine the same time leads to different angle displacements Time (s) Bottles per cavities per hour (degree) 1500 1600 1700 1800 1900 2000 2100 2200 0.1 15 16 17 18 19 20 21 22 0.15 22.5 24 25.5 27 28.5 30 31.5 33 0.2 30 32 34 36 38 40 42 44 0.25 37.5 40 42.5 45 47.5 50 52.5 55 0.3 45 48 51 54 57 60 63 66 0.35 52.5 56 59.5 63 66.5 70 73.5 77 0.4 60 64 68 72 76 80 84 88 0.45 67.5 72 76.5 81 85.5 90 94.5 99 0.5 75 80 85 90 95 100 105 110 0.55 82.5 88 93.5 99 104.5 110 115.5 121 0.6 90 96 102 108 114 120 126 132 0.65 97.5 104 110.5 117 123.5 130 136.5 143 0.7 105 112 119 126 133 140 147 154 0.75 112.5 120 127.5 135 142.5 150 157.5 165 0.8 120 128 136 144 152 160 168 176 0.85 127.5 136 144.5 153 161.5 170 178.5 187 0.9 135 144 153 162 171 180 189 198 0.95 142.5 152 161.5 171 180.5 190 199.5 209 1 150 160 170 180 190 200 210 220 Table 4.2","@ID":18}, "TRADE SHOW PREVIEW PETplanet Insider Vol. 19 No. 11/18 petpla.net 49 the base mould and the other for stretched drive units, as well as cabinet cooling if required. This effective cooling process also prevents condensation on the mould’s outer shell, thereby achieving additional energy savings of up to 15%. The patented AirbackPlus air recycling system which provides up to 40% energy savings complements the KHS Series Five with its new EcoDry air management system. It uses air left over after the blow and recycling process to replace a separate air dryer in the base mould area and blowing wheel. This means that, in combination with DuoCooling, the entire blow mould remains free from condensation and corrosion even under adverse climatic conditions. Consequently, EcoDry users are able to save around 50,000 Euros per year on 5,000 production hours. Beyond blow moulding In addition to the Blofill Series V, KHS will be highlighting more solutions which are of interest to the PET industry. The Nature MultiPack marketed by NMP Systems, a wholly-owned subsidiary of KHS GmbH, groups beverage containers into a stable, easily ‘openable’ or separable pack using dots of adhesive rather than shrink film. The packaging solution is suitable for both PET bottles and cans. Compared to containers classically packed in film DoGa 2 heating concept: In the oven, the preforms are positioned to the left and right of centrally fixed radiant heaters. the Nature MultiPack not only saves on packaging materials but also on energy; the KHS packaging system requires up to 85% less material than the conventional multipack and reduces energy consumption during production by a maximum of 67%. Also in the spotlight will be the FreshSafe technology, a wafer-thin glass coating which is applied to the inner wall of a PET bottle to protect the sensitive content. Unlike multilayer solutions, the glass-coated PET bottles are completely recyclable, as the coating is washed off in the recycling process and the PET is then homogenous. KHS offers the FreshSafe-PET technology not only for juices and nectars, but also for other sensitive beverages such as milk, by combining the barrier solution with their aseptic fillers Innosept Asbofill. www.khs.com Tech-Long offers a complete line of high-speed packaging solutions to deliver "BOTTLE MAKING 20 PETplanet Insider Vol. 19 No. 11/18 petpla.net Please order your copy at the PETplanet Insider book shop: petpla.net/book3 Stretch Blow Molding Third Edition by Ottmar Brandau € 130,00 374 pages © Copyright Elsevier 2017, 2012 5.2 Base mould Today, all base moulds feature a small recess like a well in the center. This allows some room for the protruding injection gate on the preform. Keeping the gate in the center of the mould is probably the most important task in the blow process because any deviation from the center leads to uneven wall thickness variation. The well catches the injection gate and prevents it from slipping as long as there is enough pressure from the stretch rod. In many custom applications the bottle bottom is thicker than is really needed but because of preform design or machine insufficiencies it ends up like that. In these cases it is often the cooling of the bottle bottom that controls the cycle time. Proper cooling is therefore crucial to come to a cost-effective solution with fast cycles. Cooling lines should not be smaller than 6mm in diameter (unless of course there is no room in very small bottles) and the flow path should have no restrictions. High water supply pressure with low water return pressure are also helpful (Chapter 13, Section 13.2). 5.3 Making a mould Today’s mould-making process starts with a three-dimensional (3D) computer model of the container itself. Physical models may be made by a variety of processes, the most popular still being stereo lithography with 3D printing catching up quickly because of the availability of low-cost printers. The model may be used to give marketing people a better “feeling” for a new container. Once approved, data of the computer model are then fitted in a new or existing mould base. At this point, shrinkage has to be added to the container dimensions. Polyethylene terephthalate (PET) shrinks approximately 0.08% but shrinkage is not uniform and it is the experience of the mould maker that determines how closely the capacity of the container matches specification. A variety of computer-aided design (CAD) / computer-aided manufacture (CAM) programs allow the creation of machine cutter paths that are downloaded directly into high-speed machining centers. Machine operators load and center blocks of aluminum of suitable size and special cutters, spinning at up to 30,000 r.p.m., move at a speed of up to 20m/min. The resulting cavity surface is already smooth to the eye but most mould makers add a high, mirror-like polish, which still requires skilled, manual labor. The use of sandblasted surfaces that are common in other plastic processes has gained some ground as there is little difference in the appearance of the containers. Some mould makers then coat the cavity surfaces with various materials, often containing nickel and Teflon, to give it abrasion resistance. 5.4 Venting Venting is another area where the experience of the mould maker becomes extremely important. Because PET fills the mould cavity during blowing, the air inside the cavity must be exhausted. For this purpose mould makers add a variety of vents. Compared to other processes, such as injection moulding or extrusion blow moulding, PET is processed at a relatively low temperature in the RSBM process. Vent sizes are limited to 0.04mm (0.0015in.) in injection moulding but vents of up to 0.5mm (0.020in.) are used in RSBM with hole vents up to 1mm (0.040in.). All moulds have vents on the contact surface of the cavities. One mould half is typically completely recessed against the mould base by up to 0.20mm (0.08in.) or more commonly by 0.15mm (0.006in.). Base vents are also common and are accomplished by leaving the base insert to move 0.25–0.3mm (0.010–0.012in.) downward under the force of the stretch rod. The resulting ring-shaped gap between base insert and mold cavity allows air to escape. Hole vents up to 1mm are used in areas where air entrapment is suspected. Vents of this diameter may not show in areas where the material has stretched and consequentially strainhardened but will show as small dimples where this is not the case. A common example of highly stretched material is the foot of a petaloid base for carbonated soft drinks (CSD) containers. Two small holes in each foot let air escape that might otherwise be trapped by the material flowing around it (Fig. 5.4). Figure 5.4: Hole vents up to 1mm in diameter can be successfully used as shown here in the panel area of a hot-fill bottle. Photo courtesy of Garrtech Inc. Another use of venting is to direct PET into hard-to-blow areas. In a highly oval bottle, for example, there is always the possibility of a ridge of higher wall thickness forming at the center of the narrow side of the container. Vent holes at the far side of the mould can attract PET to flow more quickly into these areas, thereby stretching out the preform walls close to the narrow side. A fine sandblast finish instead of the mirrorfinish also helps to let the air move out of the mould. Due to low temperature in the RSBM process compared with uses in other processes, PET does not flow easily into small mould crevices. Minimum dimensions for female radii might be given as 0.8mm (1/32in.) but it will depend on the stretch ratio of the PET flowing toward it whether it will fill out or form a greater radius instead. Male radii should be double that amount especially when used in bases. Here a sharp radius may cause a crease in the material and open the door to stress cracking. Venting in these areas can be attempted to reduce the risk of air entrapment stopping the advance of the parison but more often than not they do not seem to have much effect. We will simply have to live with the fact that PET benefits from more generous radii in this process.","@ID":22}, "TRADE SHOW PREVIEW PETplanet Insider Vol. 19 No. 11/18 petpla.net 41 PET Engineering was commissioned to design the new packaging by Ferrarelle SpA following the success of the other two packaging solutions that the company developed for the group group: Fonte Essenziale and Acqua Vitasnella. Parmalat’s first PET bottle for the Canadian market Parmalat Canada’s first PET range of milk bottles, available in 237 ml, 473 ml, 1 l and 1.5 l formats, was created to meet the company’s need to offer its customers a bottle with three key features: it had to be resealable; be easy to carry around and use; and be 100 % recyclable. Milk bags and cartons are currently the only packaging solutions available in Canada. PET Engineering’s concept had to adapt to the different positioning of the two brands, Lactantia Cream (premium) and Beatrice (mainstream), while appealing at the same time to both millennials and baby boomers. The new 1.5 l bottle also had to be the right size to fit on refrigerator shelves. PET Engineering’s design is an easy-to-hold and light packaging solution with a ribbing system that makes the bottle rigid, robust and easy to pour. Marco De Palma, General Manager, Fluid, at Parmalat Canada revealed that the new bottles were the result of a three year project involving Parmalat’s Research and Development, Marketing and Operations teams. www.petengineering.com","@ID":43}, "TRADE SHOW PREVIEW PETplanet Insider Vol. 19 No. 11/18 petpla.net 40 PET Engineering Hall 6 booth R 039 PET Engineering delivers solutions for water, light wellness beverages and Canada’s milk market Dressed in PET Packaging is the key interface between producer and consumer. First impressions last, and a visual message has to be conveyed to the purchaser in an instant, before their attention is drawn elsewhere. Lurisia: the image and the message PET Engineering was tasked to transfer values and shapes from Lurisia’s iconic glass bottles for both Stille, its still mineral water brand, and Bolle, its sparkling water product with carbon dioxide from a natural deposit. The 0.5 l bottle presented a complex challenge for PET Engineering’s technical team, which was briefed to imitate the champagne base used in the current glass bottle. While the use of a dedicated preform would have allowed a perfect distribution of material on the base and easily avoided the “rocker bottom” effect, the designers were briefed to use a preform already in the market. The two versions – for still and sparkling water – had to be morphologically identical in order, both to preserve Lurisia’s distinctive packaging and to enable it to use the same series of moulds for both lines’ production. The design started from the more complex container: the sparkling water bottle. The team decided to modify the existing market preforms to make them more suitable for the purpose and, at the same time, to redesign the lower area of the container and its planned, controlled deformation caused by internal pressure. The deformation itself gives rise to a profile that reproduces the glass version and enables it to imitate the existing sinuous and elegant shape. The new Bolle and Stille bottles in PET fit consistently into the Lurisia portfolio, maintaining the iconic style and identity orginally designed by Sottsass Associati. Le Linfe: the new range from Acqua Vitasnella Ferrarelle SpA’s Acqua Vitasnella brand has launched a three new sugar-free and zero-calorie functional waters. The “Le Linfe” range are promoted as combining the lightness of Vitasnella with the purifying qualities of aloe vera, the draining properties of birch sap and the hydrating benefits of coconut water. Le Linfe is designed for active, health-conscious consumers, with a particular focus on a female target audience. The range required a product identity that can convey both the lightness of the water and the functional benefit of each variant, while remaining aligned with the Acqua Vitasnella brand. The Le Linfe packaging’s decoration is taken from Acqua Vitasnella. The artwork runs sinuously down the bottle, symbolising the water entering the body and excess liquids and toxins being eliminated. The packaging therefoe provides continuity in terms of appearance with existing Acqua Vitasnella products while defining Le Linfe as a product in its own right, highlighted by the bottle’s different yet equally as attractive shape. The bottle has a full-sleeve with a simple and effective iconographic style that highlights the plus points of each variant and its ingredients.","@ID":42}, "BOTTLING / FILLING PETplanet Insider Vol. 19 No. 11/18 petpla.net 23 and vertically driven into the bowl of a rotary unscrambler. Positioned at the edge of a rotating table and supported by the neck flange, the preforms are moved onto a rail by a filtered airflow. Instead of traditional gravimetric infeed rails, the preforms are driven by two motorised, food-grade brush belts up to the infeed blowing wheel, contributing to keep the level of preform integrity very high. This patented technology is claimed to ensure operators’ safety and overall easier operations by reducing the footprint and the height for preform infeed. Bill Hall, Executive Vice President of Manufacturing at Niagara Bottling LLC, comments, “As a result, we have seen OEE (Overall Equipment Effectiveness) improvements, which are worth about 2% more produced bottles per year according to our estimations. In a line like the one embedding EasyFeed and the Sidel Super Combis, this translates to 2 million cases per year of extra productivity. That would not have been possible with a traditional preform feeder, so we are really happy with this achievement.” With output speeds up to 82,000 bph, the solution installed suits PET water bottle producers like Niagara Bottling LLC, who need to combine high-speed production lines with ultra-light PET bottles handling, while increasing the availability of their lines. Enhancing PET packaging quality The right preform feeder is crucial in reducing total cost of ownership (TCO) and maintaining a high level of efficiency. The team at Niagara Bottling LLC recognises that the tight layout of the Super Combi, a good utilisation of the integrated labeller and the redesign of the labeller itself are beneficial for their production targets. Niagara is one of the first companies running the brand-new Roll-Fed labeller, which can handle lightweight containers and ultra-thin labels, yet allowing for better glue control and distribution, together with reduced consumption. While developing this labelling solution, which uses hot glue to apply wrap-around plastic labels, ease of operations has been high on the Sidel engineers’ agenda. The vacuum drum is built in light-weight sectors for easy and quick replacement and features newly patented adjustable pads for longer production time and minimal maintenance time. The ergonomics of the solution have been optimised for top productivity and a sustainable footprint, with all main components fully visible and accessible during production or maintenance, without having to disengage the station. The whole solution performance is controlled by an integrated vision system. It is able to capture even minor defects on the bottle’s surface, body, and base, while duly checking the correct label application, filling level and cap positioning, states the company. With EasyFeed as the safe and easy-to-operate entry point to the line and Super Combis showing their performance in blowing, filling, labelling, and capping, the end-of-line production needed to be optimised for footprint, efficiency at very high speeds, and overall lower capital expenditure. This is where engineers at Gebo Cermex, part of the Sidel Group, stepped in. The Gebo Cermex high speed shrink-wrapping system, which is part of the end-of-line at Niagara, delivers high quality packs. The fully accessible low-level palletiser with robotic layer preparation at the infeed is laid out to ensure reliable, non-stop production. www.sidel.com www.gebocermex.com Niagara Bottling LLC plant with Sidel PET line and Gebo Cermex conveying and end-of-line equipment Starting point of the new complete line at Niagara’s plant is Sidel’s EasyFeed, a compact and safe ground-level preform feeder for PET lines.","@ID":25}, "BOTTLE MAKING 17 PETplanet Insider Vol. 19 No. 11/18 petpla.net BOTTLE MAKING 17 Figure 4.18 This tool-less system allows mould changeover in less than 1min/cavity. Picture courtesy of Sidel Inc. Taken all measures together may reduce changeover time from 5min/cavity to less than 1min/cavity. On a 20-cavity system, this would result in time savings of 80min/changeover, allowing an additional production of over 53,000 bottles if the machine runs at a speed of 2,000 bottles/ cavity per h (b/c per h). Even if the margin was only 0.5 cents/bottle, an additional revenue of $250 per changeover could be achieved. Air consumption Another important feature is air consumption and more specifically the so-called dead air volume. Air is the single-most costly part of blowing bottles besides the preforms and users do well to pay close attention to this issue. Air consumption is driven by the air pressure, the actual volume of the bottles produced, and the air that is not used in the blow process but needs to be exhausted every blow cycle. This air “hides” in the connection pieces between the blow valves and the cavity. When the exhaust valve is energised, all air that is between it and the cavity must be exhausted besides the actual bottle volume to make sure there is no pressure left in the blown bottle. Many manufacturers of blow machines do not publish this important information but users can calculate it by looking at the machine specifications. Let us assume a manufacturer specifies blow air consumption of 1300Nm3/h for the production of 20,000 b/h of 1.5 l volume at 35 bar. The volume that is actually inside the bottles is 20,000 b/h × 1.5 l × 35 bar/1,000 l/m3 = 1,050Nm3/h. The difference of 1300 − 1050 = 250Nm3/h is the dead air volume. This in turn is 367ml/bottle (250Nm3/h × 1000 l/Nm3/h/20,000 b/h/35 bar). It is important to calculate this as a fixed number rather than a percentage as this lost air is present for bottles of each size. A 500ml bottle has the same losses as a 1.5 l bottle; however, in the case of the smaller bottle 73% more blow air is needed than would be if just the bottle needed to be supplied. Smaller dead air volumes will save significant money over the lifetime of the machine. Small machines particularly often feature high dead air losses and users should carefully examine manufacturers’ offerings (Fig. 4.19). "10 NEWS PETplanet Insider Vol. 19 No. 11/18 petpla.net Cott announces acquisition of Mountain Valley Spring Company Cott Corporation announced that DS Services, a Cott Corporation subsidiary, acquired The Mountain Valley Spring Company for $78.5 million in cash from Great Range Capital. Mountain Valley is a fast-growing American brand of spring and sparkling water and a recognized home and office distribution brands in the United States. It has been bottling continuously since 1871, with one production facility in Hot Springs, Arkansas, and four protected and owned springs in the Ouachita Mountains with excess capacity to supply long-term demand. Channels of business include HOD, the natural food channel, on-premise, E-commerce and strategic contract packing. Mountain Valley focuses on spring water bottled in a variety of glass bottle sizes ranging from five-gallon bottles to single serve sizes such as 1 l, 500ml and 333ml. Over the years Mountain Valley has added sparkling and flavored sparkling water in glass bottles as well as PET offerings for its sparkling and spring water lines. Mountain Valley is positioned as the premium American water brand and is a leader in the high growth premium bottled water branded category as well as the sparkling and flavoured water categories. Mountain Valley has grown revenue from approximately $ 39 million in 2015 to over $ 50 million in estimated sales for 2018, with high single digit growth expectations for 2019. The purchase price was $78.5 million, on a debt and cash free basis, representing approximately 8x estimated year 2 post-synergy adjusted EBITDA. Cott financed the transaction through a combination of cash on hand and drawing on its asset based lending facility. The transaction closed on October 15, 2018. Additional financial and integration information relating to the acquisition of Mountain Valley will be provided during Cott’s third quarter earnings release conference call scheduled for November 8, 2018. www.cott.com Chinaplas 2019 will highlight Circular Economy After “Industry 4.0” “Circular Economy” will be the next megatrend highlighted at Chinaplas. This has been announced by the organisers Adsale Exhibition Services Ltd. “We’ve been aware of the concept of the circular economy for some time. As early as 2011, we launched the ‘Bioplastics Zone’, introducing biodegradable plastics and bio-based plastics. We have also set up a ‘Recycling Technology Zone’ since 2016 in Shanghai. The show line-up continues to grow. In the upcoming Chinaplas, the circular economy will be promoted to a prime position, leading exhibitors and visitors to explore the enormous potential.” says Ada Leung, General Manager of Adsale Exhibition Services. The core of circular economy is the efficient use and recycling of resources, and plastic waste recycling is an indispensable part. It is predicted that by 2025, China, one of the world’s largest waste plastics recycling countries, will produce urban solid waste amounting to nearly a quarter of the world’s total. In addition to circular economy, new market trends and demands, new business opportunities, changes in the world economic situation, opportunities and challenges for plastics innovations resulting from Sino-US trade debate will be in the focus of the show. A ‘Belt and Road Initiative’ has therefore been launched, in the course of which staff will be sent overseas to invite local associations and enterprises to visit Chinaplas. The aim is to help exhibitors explore new business opportunities so as to increase return on their investment. Chinaplas 2019 will be returning to the China Import and Export Complex, Pazhou, Guangzhou and run from May 21- 24, 2019. An estimated total of more than 3,400 industrial leaders from around the world will be showcasing their products and solutions in more than 250,000m2 of exhibition space to at least 180,000 professional visitors from 150 countries and regions. www.chinaplasonline.com Illig expands production capacity outside Germany Illig, a German machinery manufacturerwill build a new production site in Romania. During the next few years Illig Maschinenbau SRL will develop into a further production site outside Germany located in Sura Mica industrial park in the Sibiu region. „At the new site Illig will be manufacturing thermoforming lines from its product range to ensure increasing market demands can be met“, Dr Heinrich Sielemann, Illig managing director, substantiates the expansion. In 2019, the first office buildings and production halls will be constructed in a first construction phase on a surface of 60,000 square meters. On-site personnel recruitment was started with the intent to prepare the new staff members at the Heilbronn central site for their new tasks. Moreover, Illig intends to sustainably become involved in the training of qualified staff on site. The existing Romanian dual vocational training system and a cooperation with the Sibiu University are suitable options to achieve this goal. During the last few years the Sibiu region developed into one of the fastest growing economic centers of Romania. Many German and Austrian companies have settled in Sibiu, the former Hermannstadt. The city has a population of around 150,000 inhabitants and it is optimally linked to the most important longdistance connections by road, railroad and air. www.illig.de/en","@ID":12}, "33 TRADE SHOW PREVIEW PETplanet Insider Vol. 19 No. 11/18 petpla.net Introducing the latest development: the 4LO blow-moulding machine Since commencing production in 2010, 1Blow has been producing next-generation stretch blow-moulding machines suited for PET bottle converters. In 2018, these limits are said to be pushed further with the commercial launch of the new 4LO stretch blow-moulder. The 4LO is built upon the same, efficient virtual-rotary platform that has been commercialised in numerous applications over the last six years. The 4LO possesses all of the superior 1Blow machines features and benefits. Rotary motion is the key to achieving high-speed and low energy consumption in machinery through its unique virtual rotary concept. Over 90% of the 4LO machine motions are rotary with a maximum mechanical output of 2,000 bph. All of the main machine motions on the 4LO are driven by servo-motors. Known for their repeatability and reliability, servo-motors are most energy efficient motion system. 1Blow says that comparative operational testing to similar sized competitive machines has demonstrated that their machines can use up to 60% less energy. The 1Blow clamp format and stretch rod pitch were designed for all blow moulds from virtually all other competitive SBM machines on the market. This ability allows customers to utilise existing blow moulds on a 1Blow machine; some of the company’s customers are already using two or three different types of blow moulds. The 4LO was designed to minimise the number and quantity of change parts with the goal of reducing format costs for converting customers. Another benefit of minimising the number and quantity of change parts is that it takes less time to do a machine changeover: in some cases the machine has 50% fewer change parts. Despite its compact footprint, the 4LO has superior internal accessibility for technicians. The virtual rotary concept is spatially efficient and provides many open areas inside the machine large enough to comfortably accommodate a technician. Furthermore, the 4LO machine can accommodate several options, providing more possibilities for various applications and markets: Preferential and offset neck heating: with this additional specific heating system, selected longitudinal areas of the preform may be specifically heated in order to produce oval bottles. These longitudinal areas may also be moved off-axis from the preform centreline, so that offset neck bottles can be produced. Neck orientation: this mechanical system puts all the neck finishes on each and every bottle to be in the same orientation. This is invaluable for containers that use a flip-top cap so that is aligns in the proper position for opening and pouring. 1Blow can do this alignment without the need of a specific tab or V-notch on the preform. The system relies on the thread start and thus can use standard preforms, opening us the spectrum of preforms that can be used. Heat set: this set combines heated blow-moulds with recirculating high pressure air cooling to induce higher cristallinity into the bottles. This higher cristallinity allows the resultant bottles to have heat set resistance for the hot fill process. www.1blow.com Looking for a challenge A specialist in PET packaging for over 30 years, the Société Générale des Techniques has been offering high performance solutions for packaging liquids. SGT has invested in new HDPE injection moulding machines for caps in a new site in Setif, Algeria. This latestgeneration equipment will enable the SGT Group to increase its production capacity from 800 million to 2 billion caps per year, with new references for the necks: 29/25, 30/25 high ring, 33mm, 38mm, 38mm hot fill, 28mm, 48 mm and 28 PCO 1881 and 1810. SGT proposes a complete and varied range of 260 PET preforms, 6 types of HDPE caps and 2 lightweight handles for 38MM and 40/48 necks. All these new products will be presented at the All4Pack exhibition on the SGT booth. www.sgt-pet.com SGT Hall 7 booth E 219 1Blow Hall 6 booth F040","@ID":35}, "BOTTLE MAKING 18 PETplanet Insider Vol. 19 No. 11/18 petpla.net Figure 4.19: During the “airback” phase, blow air is redirected to a distributor panel instead of exhausted to the atmosphere. Diagram courtesy of KHS Corpoplast GmbH. There is one more source of needed air volume that is not mentioned yet. On some machines that use pneumatic cylinders for stretch rod activation, this air is actually highpressure blow air that is reduced to the 8 bar or so that the stretch rod cylinders are using. While compressing air to 35 or 40 bar and then reducing it to 8 or 10 bar is an expensive undertaking, this is done to avoid adding another line to the distributor inside the blow machine as this distributor for air, water, and electrical power is one of the most expensive parts of the blow moulding machine. The newest machines with servo or electromechanically controlled stretch rods do of course not use any air and will save money in the long run. Because of the cost of air consumption, most companies now offer air-recycling systems. These systems, instead of exhausting blow air into the atmosphere, pipe it back to a storage tank where it can then be used for preblow and stretch rod air, the machine air circuit, or other plant air requirements. Of course, pressure reducers in the systems allow the proper pressure for the various uses. In this manner, savings of 25–50% can be achieved. This not only reduces operational costs but also helps with capital expenses as fewer or smaller compressors may be needed. A small cycle time penalty is unavoidable because the air does not move as fast to the pressurised storage tank as it does to the lower atmospheric pressure. 5. Blow moulds Blow moulds play a large part in making high-quality bottles. While the machine has to deliver preforms at the right temperature, it is the blow moulds that give containers repeatable features and a brilliant appearance (Fig. 5.1). Figure 5.1 Blow mould halves in and out of mold base and base insert. Highly polished aluminum is the most commonly used material for standard bottles. Photo courtesy of Sipa. 5.1 Design Neck and thread finish are already formed in the preform; so blow moulds form only the body and base of the bottle. In the reheat stretch blow moulding (RSBM) process they consist of three parts: two mould halves and one base insert (also called push-up). The base insert is necessary because the walls at the base of the concave container could not slide over the mould halves during mould opening if these were forming them. Instead, the vertically moving base insert is drawn out of the way before, or as, the mould opens (Fig. 5.2). Figure 5.2 Typical mould design for linear RSBM machine. The given details are followed by their descriptions: 1, Preform retainer insert; 2, S.S. insert; 3, Mould body; 4, Back plate; 5, Base insert/push-up; 6, Locating ring; 7, Push-up holder; 8, Taper lock pins and bushings; 9, Guide finger. Drawing courtesy of Hallink Molds Ltd. While the three-piece design is common to all moulds, they are manufactured quite differently depending on the type of machine to which they will be fitted. Linear machines have all mould cavities mounted within two blocks where the cavities sit side by side. In rotary machines each blow mould is mounted to a separate carrier, opening and closing individually. Modern machines use so-called shell moulds whereby the actual mould halves are only 5-mm thick and are assembled onto bases that are all the same for a family of containers. These bases carry all water connections and need not be touched during a changeover, thus reducing valuable time. Moulds are usually built from aluminum, which is chosen for its high heat transfer rate, easy machinability, and lightweight. The types of aluminum used are typically those used in the aircraft industry. AL 7075 T6, T-2024, or Alumenec 89 are some of the grades used worldwide for this application. Base inserts may be of the same material or made from beryllium–copper. Another material in use is stainless steel for hot-fill applications. While a polish to mirror-like quality is still the norm, some companies have quite successfully tried to leave moulds at a much rougher polishing state. This saves cost because the mirror polish is still applied manually while detracting only very slightly from the expected bottle surface appearance. The internal pressure of the blow air results in a considerable force against the closing mechanism of the blow mould. Blow moulds have guide pins and bushings as well as taper locks in the base insert that keep the mould in position during the blow process. Mould carriers feature locking mechanisms that keep them closed against the blow pressure. To alleviate these stresses and also make everlighter frames possible, “pancake” cylinders have become increasingly popular. These cylinders are very thin shells behind the blow moulds and are filled with the same air that blows the bottle. Since pressure is equal both inside and outside the mold there is no resultant force acting against the mold halves (Fig. 5.3). Figure 5.3: Blow mould with locking mechanism mounted inside a rotary machine. Photo courtesy of Sipa.","@ID":20}, "45 TRADE SHOW PREVIEW PETplanet Insider Vol. 19 No. 11/18 petpla.net Solutions for the beer planet Technological developments for filling and labelling beer will be in the spotlight of Sacmi’s presence at Brau Beviale. This includes latest-generation fillers specifically developed for this field. In addition to a combined filler for bottles and cans, Sacmi is also presenting a wide range of labelling solutions and LVS positioning systems; an Opera 400 Modul 33T – high-speed and featuring modular plug & play technology - will be on show to highlight the enormous flexibility and extensive application range. These include LabelCheck-360, with a renewed structure (light alloy in place of the traditional stainless steel) and consolidated CVS360-3D software, allowing total quality control both of the label (presenceabsence, orientation, faulty or mixed application, colour characteristics, etc.) and of the entire bottle body, including the cap. The capacity of the system to identify all types of defects and to operate perfectly in line with the labeller. Capable of operating as a leader in various sectors and technologies, Sacmi completes its offer with the IPS (injection preform moulding) range, the PET preform production platform with good characteristics in terms of usability, versatility and automation. www.sacmi.it Sacmi Hall 7A | Booth 323 We do more. Contipure AseptBloc #GermanBlingBling #ContipureAseptBloc BrauBeviale 2018 Nuremberg, 13 – 15 November Stand 7A-510","@ID":47}, "BOTTLE MAKING 15 PETplanet Insider Vol. 19 No. 11/18 petpla.net whereas at 1,500b/cph it is already up to 0.72s or an almost 50% increase, although small in real numbers. Most linear machines use a higher percentage of overall time for unproductive time as it takes longer to shuttle the preforms and bottles in and out of the mould, and open and close of the mould. However, there is no change in this whether the machine runs at maximum speed or not; these movements always take the same amount of time. Potential buyers should always ask what the process time is for a given output and then judge from their range of applications which type of machine fits best. 4.5 Rotary machines comparison While there are many suppliers of linear machines, the rotary machine market is dominated by four suppliers: KHS Corpoplast, Germany (Blowmax series IV) Krones, Germany (Contiform Generation 3) Sidel, France (Matrix) Sipa, Italy Since this market produces the vast percentage of all PET bottles, it is worth to compare the different machine characteristics so the reader can better understand what is different about them. I will examine the latest offerings in Table 4.4. One should note that only bottles with stretched-out bases, such as lightweight water bottles, can be moulded at these speeds. Thicker bases require longer cooling time to avoid the creeping out of the base center, which can lead to an additional “leg” causing the bottle to rock (the so-called rocker bottom). In carbonated soft drinks (CSD) bottle production, this is especially important as the center disk is stressed significantly and must stay rather thick. This in turn is required by the pressure cycles inside the bottle that may reach up to 5bar (70psi) when the bottle contents are agitated as happens during a bumpy truck ride. One of the parameters that quality control has to monitor is the so called base clearance to make sure this does not happen. All machines show decreased output as the number of cavities increases. This is because the centrifugal forces become rather large with the larger blow wheel diameters. A COLOUR IDENT I TY LIQUID COLOURS AND ADDITIVES FOR PACKAGING repi.com The trend in blow moulding machines has been to eliminate the turning of preforms and/or mandrels, which reduces handling and wear issues that have plagued some of the systems. Only Sidel turns the preforms after the oven section up, whereas Sipa uses what is referred to as a “caterpillar” oven where preforms travel upward and downward on their mandrels but there is no actual turning.","@ID":17}, "PACKAGING / PALLETISING PETplanet Insider Vol. 19 No. 11/18 petpla.net 26 allows the Movigear to be used very flexibly without having to oversize the drive. Moreover, synchronous motors used in the MGF..-DSM geared motor have a higher overload capacity and lower losses over the whole operational range compared to asynchronous three-phase AC motors. The drive systems of the Movigear product range have even lower losses than those specified for IE4 (Super Premium Efficiency) motors. Energy advantages Compared to classic asynchronous motors, the savings potential is up to 50% of the industry average. As a result, operating costs in bottling plants can be reduced on a sustainable basis. If this information is fed into system planning, the feed-in current and thus the installed feed-in capacity of the entire transport system can often be reduced. Drive units from the SEW-Eurodrive Movigear product range ensure reliability of bottle transport (Photo: Hell Energy) The system’s overall efficiency is a key factor in the energy performance of an entire transport facility in the drinks sector. Drive technology including sophisticated process control is particularly important here. Flexible tuning of the rotational speeds over a wide adjustment range enables changes to the conveyor system to be made quickly and, above all, in a way that does not affect the product too much. Possible downtimes and subsequent start-up situations are therefore avoided. In addition, standardised control and drive concepts result in a sustainable reduction in on-going operational costs. The amortisation of investments is limited to a relatively short two-year period. Hygienic design Additional features are the high level of protection and the potential for easy cleaning of the drives. The surface design that meets appropriate hygiene standards predestines the mechatronic SEW-Eurodrive systems for use in drink bottling plants. Another advantage to the low noise mechatronic drive systems is reduced noise pollution in the workplace. The Hungarian drinks’ manufacturer was nominated for the prestigious Strategic Manufacturing Award for its new factory building. The bottling plant was nominated as one of the top three factories in Europe in the “World Class Manufacturing Globale” category. The award recognises excellence and innovation in manufacturing and logistics, as well as for outstanding production strategies, business growth and proven cost savings. www.sew-eurodrive.de/home.html Hell Energy’s PET bottle filling facility can fill bottles of various sizes: 330ml, 500ml, 750ml, 1,500ml and 2,500ml. (Photo: Hell Energy) The processes involved in the drinks’ industry places special demands on conveyor systems and their drives. (Photo: Hell Energy) Nov. 6-8,2018, Dubai Hall 2, Booth D2-24 German Technology","@ID":28}, "59 PRODUCTS PETplanet Insider Vol. 19 No. 11/18 Compact accumulation table Spanish company And&Or, which is headquartered in Seville, specialises in the design, development and manufacture of ancillary and support machinery and solutions for blow-moulding, bottling and packaging. The company says that the latest additions to its accumulation systems are designed to guarantee production efficiency and uninterrupted operation and of plastic bottle manufacturing or filling lines in reduced spaces. Its latest table operates on a FIFO “First In First Out” basis and is capable of working with empty or filled bottles. During normal line operation the desk is empty. In the event of a downstream stop, upstream production interruption is avoided by the table being used as a buffer, with bottles fed into it by the input gripper. When downstream flow resumes the desk will empty the bottles into the main line sequentially, without stopping the nominal bottle flow coming from the upstream machines. In the case of an interruption at the blow moulder, the accumulation table allows the performs in the oven to be emptied into the line, thus avoiding the waste of having to eject them. The table frame is made of stainless steel. The operating area can be completely surrounded by a safety frame. And&Or claims that the dimensions of its latest model accumulation table offer significant space savings, compared to traditional accumulation systems, while eliminating the risk of causing a jam. It is also designed for easy maintenance and service. www.andyor.com","@ID":61}, "PETpatents www.verpackungspatente.de PETplanet Insider Vol. 19 No. 11/18 petpla.net 64 Increased internal pressure Intern. Patent No. WO 2016 / 161338 A1 Applicant: Graham Packaging Comp., L.P., York (US) Application date: 1.4.2015 The application describes the shaping and the procedure for fixing a seal on a PET bottle used as a pressurised aerosol can. Plastic container Disclosure No. DE 102016118495 A1 Applicant: Krones AG, Neutraubling (DE) Application date: 29.9.2016 Shown here is the special base shaping of a plastic bottle. The “feet” of the bottle feature specially shaped ridges and grooves. Optimised compensation areas Europ. Patent No. EP 3290345 A1 Applicant: Yoshino Kogyosho Co. Ltd., Tokyo (JP) Application date: 8.4.2016 For plastic bottles intended for hot filling with slanted compensation areas to compensate for the vacuum forces arising during cooling. The outer shape of the bottle does not change. Plastic bottle with necking Europ. Patent No. EP 3290356 A1 Applicant: Bernard Fafournoux, Louveciennes (FR) Application date: 5.9.2016 The application describes a PET bottle with stark contouring and/or necking so that only a small aperture remains open. A small ball should seal this aperture to impair / prevent degassing of the content. Plastic for aseptic filling Europ. Patent No. EP 3299306 A1 Applicant: Suntory Holdings Ltd., Osaka (JP) Application date: 19.5.2016 Thin-walled, light plastic bottle for filling under aseptic conditions but sufficiently stable – especially at the base – to absorb any pressure differences, e.g. with carbonated products. Bottle without support ring Intern. Patent No. WO 2018 / 075093 A1 Applicant: Amcor Group GmbH, Zürich (CH) Application date: 31.3.2017 The application describes the shaping of a plastic bottle, which is designed specially in the neck and/or threaded area without a support ring. This reduces the weight of the bottle and simultaneously improves the appearance of the bottle.","@ID":66}, "MARKET SURVEY 36 PETplanet Insider Vol. 19 No. 11/18 petpla.net Company Sipa Postal address Telephone number Web site address Contact name Function Direct telephone number Email Via Caduti del Lavoro n. 3 31029 Vittorio Veneto (TV) Italy +39 0438 911511 www.sipa.it Mr Matteo Tagliaferri Marketing and Communication +39 0521 548111 [email protected] Palletising machinery: Genius PTF Genius PTF/V Genius PTF/A Genius PTF - Active Layer Conventional Automatic palletisers steady pallet type. Conventional Automatic palletisers steady pallet type, with double platform Conventional Automatic palletisers moving pallet type. Conventional Automatic palletisers steady pallet type with innovative layer preparation. Format changeover time 15min 15min 18min 10min Output rate (packs per minute) Up to 330 layers/hour Up to 420 layers/hour Up to 700 layers/hour Up to 330 layers/hour Automatically intergrated:(yes/no) Empty pack feeding Yes, empty pallat feeding Yes Yes Yes Insertion of interlayers Yes Yes Yes Yes Connectable to shrinkwrapper Yes Yes Yes Yes Special characteristics: i.e. low-level feed, cross conveyer barrier - Operational flexibility and further reduction in change-over times - Optimisation of cycle to increase performance, with improved control of the different movements using state-of-the-art electronic solutions - Customisation of the gripping system and layer transfer according to the product to handle - Designed to accept a variable number of product infeeds - Fully automatic system requiring limited operator intervention, operating in complete safety - Possibility to handle all main pallets on the market trouble-free, with highly customizable solutions - Operational flexibility and further reduction in change-over times - Optimisation of cycle to increase performance, with improved control of the different movements using state-of-the-art electronic solutions - Customisation of the gripping system and layer transfer according to the product to handle - Designed to accept a variable number of product infeeds - Fully automatic system requiring limited operator intervention, operating in complete safety - Possibility to handle all main pallets on the market trouble-free, with highly customisable solutions - Operational flexibility and further reduction in change-over times - Optimisation of cycle to increase performance, with improved control of the different movements using state-of-the-art electronic solutions - Customisation of the gripping system and layer transfer according to the product to handle - Designed to accept a variable number of product infeeds - Fully automatic system requiring limited operator intervention, operating in complete safety - Possibility to handle all main pallets on the market trouble-free, with highly customisable solutions - Operational flexibility and further reduction in change-over times - Optimisation of cycle to increase performance, with improved control of the different movements using state-of-the-art electronic solutions - Customisation of the gripping system and layer transfer according to the product to handle - Designed to accept a variable number of product infeeds - Fully automatic system requiring limited operator intervention, operating in complete safety - Possibility to handle all main pallets on the market trouble-free, with highly customisable solutions - Linear axes layer preparation with active pack orientation and arrangement Company SMI S.p.A. Postal address Telephone number Web site address Contact name Function Direct telephone number Email Via C.Ceresa, 10, 24015 San Giovanni Bianco (BG) - Italy +39 0345 40 111 www.smigroup.it Ms Daniela Dadda Marketing Department +39 0345 40.318 [email protected] Shrink film machinery: Automatic machines for packing plastic, metal, cardboard or glass containers. Packs in film only, cardboard pad + film, tray only, cardboard tray + film. Packaging options & output rate (packs per minute) Shrinkwrappers machines ; trayformers; overlapping cardboard sleeve multipackers; wrap-around casepackers and combined machines, provide performances from 30 to 450 packs/minute (in triple lane), depending on the model or product to pack. - print registered film (yes/no; packs/min) Yes - nested pack (yes/no; packs/min) Yes - label orientation (yes/no; packs/min) Yes - carry handles (yes/no; packs/min) Yes - pad supported (yes/no; packs/min) Yes - tray supported (yes/no; packs/min) Yes - film only (yes/no; packs/min) Yes - tray and film (yes/no; packs/min) Yes - pad and film (yes/no; packs/min) Yes shrink process: - shrink tunnel with hot air Smiflexi tunnel distributes hot air flows in an efficient and homogeneous way on the pack, thus ensuring its excellent quality at the end of the process. - oven Available tunnel methan heated Footprint Single lane: smallest AFW serie (10060 x 1774 x 2450mm) till the bigger size SK 1200 HS (18752,5 x 1774 x 2450mm) Double lane: smallest LSK 32 (9820 x 1974 x 2450mm) till SK 1202 HS (18752,5 x 1974 x 2450mm) Number of possible lanes From 1 to 3 lanes Packaging material & possible thickness film: 30 - 100 micron depending on the production speed and pack collation, Cardboard: Low wave corrugated cardboard blanks: 3mm thickness. Voltage/power/energy consumption Depending on the machine model Film cutting and feeding system Manual sealing bar joins the films, film reelsthe machine is equipped with a dedicated reel truck, pneumatic blocking system and when the film ends, the machine stops, adjustment of the film length is electronic, equipped with a device for centering the printed film provided with reference mark. Certification CE Palletising machinery: Format changeover time The machine automation and control are entrusted to the Sercos Fieldbus technology,intuitive user interface for quick and easy management of end-of-line palletising operations, real-time machine diagnosis and technical support further enhance the machine control features. Output rate (packs per minute) 35 to 100 packs/minute (according to the size of the product handled and palletisation selected) Automatically intergrated:(yes/no) Yes Empty pack feeding Yes Insertion of interlayers Yes Connectable to shrinkwrapper Yes Special characteristics: i.e. low-level feed, cross conveyer barrier Swiftandprecisemovements:Thecentralcolumn isactuatedbybrushlessmotors,whichguaranteehighlydynamic,reliableandprecisemovementsofallaxesofoperation.Machine automationandcontrolareentrusted to the innovativeSercosFieldbus technology, featuringan intuitiveuser interface forquickandeasymanagementofend-of-linepalletisingoperations.","@ID":38}, "MARKET SURVEY 37 PETplanet Insider Vol. 19 No. 11/18 petpla.net Genius PTF - Fastlayer Genius PTF/A - Fastlayer Genius PP/PV Robby Pal Robby Pal with Fastlayer ConventionalAutomatic palletisers steady pallet type with innovative layer preparation. ConventionalAutomatic palletisers moving pallet type with innovative layer preparation. Conventional Automatic palletisers steady pallet type for empty PET containers Robotic automatic palletiser Robotic automatic palletiser with innovative layer preparation. 10min 12min 15min 15min 10min Up to 330 layers/hour Up to 700 layers/hour Up to 330 layers/hour Up to 320 layers/hour Up to 320 layers/hour Yes Yes Yes Yes Yes Yes Yes Yes Yes Yes Yes Yes Yes Yes Yes -Operationalflexibilityand furtherreduction in change-over times -Optimisationofcycle to increaseperformance, with improvedcontrolof thedifferentmovements usingstate-of-the-artelectronicsolutions -Customisationof thegrippingsystemand layer transferaccording to theproduct tohandle -Designed toacceptavariablenumberof product infeeds -Fullyautomaticsystemrequiring limitedoperator intervention,operating incompletesafety -Possibility tohandleallmainpalletson the market trouble-free,withhighlycustomizable solutions -Layerpreparationwithactivepackorientation andarrangementwithrobots -Operationalflexibilityand furtherreduction in change-over times -Optimisationofcycle to increaseperformance, with improvedcontrolof thedifferentmovements usingstate-of-the-artelectronicsolutions -Customisationof thegrippingsystemand layer transferaccording to theproduct tohandle -Designed toacceptavariablenumberof product infeeds -Fullyautomaticsystemrequiring limitedoperator intervention,operating incompletesafety -Possibility tohandleallmainpalletson the market trouble-free,withhighlycustomisable solutions -Layerpreparationwithactivepackorientation andarrangementwithrobots -Operationalflexibilityand furtherreduction in change-over times -Optimisationofcycle to increaseperformance, with improvedcontrolof thedifferentmovements usingstate-of-the-artelectronicsolutions -Customisationof thegrippingsystemand layer transferaccording to theproduct tohandle Vacummheadavailble forwide mouthcontainers(ie jars). -Designed toacceptavariablenumberof product infeeds -Fullyautomaticsystemrequiring limitedoperator intervention,operating incompletesafety -Possibility tohandleallmainpalletson the market trouble-free,withhighlycustomisable solutions -Anextremelycompleterange to handledifferent typesofcontainersand products: layer,rowandmultiheadand looseproductpalletizingsystems -Extremelyflexibleandmodularsolutionwithreduced footprint. -Customisationof thegrippingsystem and layer transferaccording to the product tohandle -Designed toacceptavariablenumber ofproduct infeeds -Fullyautomaticsystemrequiring limitedoperator intervention,operating incompletesafety -Possibility tohandleallmainpallets on themarket trouble-free,withhighly customisablesolutions -An extremely complete range to handle different types of containers and products: layer, row and multihead and loose product palletising systems - Extremely flexible and modular solution with reduced footprint. - Customisation of the gripping system and layer transfer according to the product to handle - Designed to accept a variable number of product infeeds - Fully automatic system requiring limited operator intervention, operating in complete safety - Possibility to handle all main pallets on the market trouble-free, with highly customisable solutions - Layer preparation with active pack orientation and arrangement with robots Company Productive Systems (Pty)Ltd GEA Group Postal address Telephone number Web site address Contact name Function Direct telephone number Email PO Box 7643, Centurion, 0046 South Africa +27 12 661 1250 www.productivesystem.com Mr Stefan Schonfeldt Marketing Director +27 12 661 1250 [email protected] Via Fedolfi 29, 43038 Sala Baganza, Parma, Italy +39 0521 839 0 www.gea.com Mr Alessandro Bello Vice President Head of Blowing, Filling & Packaging +39 0521 839 411 [email protected] Palletising machinery: Semi automatic & Automatic Yes Format changeover time 10 – 20min depending on differences in formats 5' (completle automatic) Output rate (packs per minute) 25,000bph (empty plastic bottles) 6 layer/min Automatically intergrated:(yes/no) Empty pack feeding Yes Yes Insertion of interlayers Yes Yes Connectable to shrinkwrapper Yes Yes Special characteristics: i.e. low-level feed, cross conveyer barrier Yes Low level, high level, manipulator pack infeed","@ID":39}, "TRADE SHOW PREVIEW PETplanet Insider Vol. 19 No. 11/18 petpla.net 54 SMI Hall 7A booth 503 “Smart” bottling and packaging systems incorporating Internet of Things and Industry 4.0 technology Compact rotary combi SMI will be presenting its latest range of ‘smart’ machines, including the new EBS K Ergon rotary stretch-blow moulders and the EcoBloc K Ergon integrated systems. SMI says that these machines are compact, ergonomic, eco-friendly machines can be installed even on small bottling plants. An example of the new EBS K Ergon range will be also showcased at the Brau Beviale exhibition. Global solutions. Local success. Welcome to a market on the rise! Highly attractive in presenting the latest beverage technology for the industry, Beviale Moscow also focuses on education, packaging, liquid processing, marketing, and raw materials, offering important networking opportunities in a constantly growing market. Be part of it! Inquiries/Learn more: T +49 9118606-86 84 | [email protected] beviale-moscow.com The EBS K Ergon stretch-blow moulder is available in 2, 3 and 4-cavity versions. It is claimed to offer the advantages of rotary technology in a speed range (from 1,000 to 9,000 bph) that is traditionally served by linear stretch-blow moulders. The machine’s compact dimensions have been achieved by integrating the preform heating and stretch-blow moulding sections within a single, modular structure. It incorporates Internet of Things connective technology, making it suitable for Industry 4.0 “smart” operation and features a completely electronic production process, with a transmission system that uses brushless motors equipped with integrated digital servodrivers. SMI says that users will benefit from low operating costs and low","@ID":56}, "MATERIALS / RECYCLING PETplanet Insider Vol. 19 No. 11/18 petpla.net 13 MATERIALS / RECYCLING 13 Bottle-to-bottle recycling at Ferrarelle SpA The rPET project The long-established Ferrarelle SpA company, well known throughout Italy, has been bottling its naturally effervescent water since 1893, and is now taking the next major step in its development by installing a new recycling plant. In pursuing an ambitious strategy of improving its production processes and at the same time developing its goal of ecosustainability, the Italian mineral water bottler Ferrarelle SpA has invested in recycling technology by Amut to run the whole process of bottle making, filling and recycling in-house. With Amut’s washing technology, Ferrarelle will produce up to 3,000 kg/h of flakes recycled from post-consumer PET bottles, and thanks to a re-gradation process, the flakes will be suitable for food applications. The rPET flakes, of high quality and purity, will be processed directly to produce preforms and final bottles. After the bottling process, the newly produced bottles will finally reach the supermarket shelves. “Under full production process, we expect to exceed our annually preform in-house requirement – actually around 700 million/year. The flakes we will be producing with the Amut plant are of high quality, and may thus be an additional source of income for us. “By selling recycled PET to third parties, we will be part of a virtuous circle that benefits everyone,” comments Pietro Bortone, Plant Manager of Ferrarelle SpA. He continues “With our new recycling plant in Presenzano, Caserta, we are taking a further step in our eco-friendly stance that we have been adopting over recent years. Already involved in a number of social and cultural international projects, Ferrarelle is also conscious of its own local environment, increasing productivity and providing employment, whilst also reducing waste volume and pollution.” Functioning of the plant Once the bottle bales are opened and sent to the constant feeder, a detector performs an initial positive selection to separate bottles from any contaminants before the washing phase. The upfront part of the line allows the treatment of PET bottles bales not properly sorted which may contain a significant quantity of pollutants. The bottles are conveyed to the Delabeller-PreWasher, a patented machine working in a dry process to remove any labels and initiate the first cleaning action. The dry process reduces energy consumption. Two NIR detectors for colour/metal separation handle the final sorting and purify the stream from any nonPET material. The flakes are then washed with Amut patented technology: Turbo washer and friction washer carry out a strong cleaning action to remove all fine pollutants and glue. The combination of these machines allows the treatment even in the case of highly polluted bottles, achieving the desired results in term of final product quality and output. www.amut.it","@ID":15}, "69 PETplanet Insider Vol. 19 No. 11/18 petpla.net BUYERS GUIDE 5.0 RECYCLING Bühler Thermal Processes AG As of April 2015, the company is renamed to Polymetrix > see Polymetrix Highly efficient process chemicals, tailor-made process solutions and an unique technical support. CHT Germany GmbH Tel +49 7071 154 - 233 [email protected] www.cht.com Performance Products for PET and Plastics Recycling Applications. Via Vigevano 61 28069 - San Martino di Trecate Novara - Italy Phone. +39.0321.789710 [email protected] Macdermidenthone.com/industrial Polymetrix AG a former Bühler Group Company Sandackerstr. 24 9245 Oberbüren, Switzerland Direct +41 71 552 10 00 www.polymetrix.com PET-Recycling Plants Consulting & Engineering Complete Solutions 5.8 Complete recycling plants Tel: +86-573-85120186 [email protected] www.bo-re-tech.com - Complete PET Bottle Washing Plant - Bottle to Fiber Project Engineering - Bottle to Bottle Project Engineering - PET Pelletizing Plant Complete PET recycling plants, FDA approved, integrated IV increase without Pellet-SSP, process features lowest overall energy consumption, more than 140 plants supplied to industry. EREMA GMBH Unterfeldstr. 3, A-4052 Ansfelden Tel. 0043-732-3190-0 [email protected] · www.erema.at Herbold Meckesheim GmbH PET Granulators, Agglomerators, Shredders, Complete PET washing and recycling lines Industriestrasse 33 74909 Meckesheim Tel.: 06226 - 932 – 0 Fax: 06226 - 932 – 495 [email protected] www.herbold.com “PET washing and recycling plants, turnkey and modules for B2B, fiber, sheet” SOREMA division of PREVIERO N.srl Via per Cavolto 17, 22040 Anzano del Parco (Co) -Italy Tel:+39 031 63491250 [email protected] · www.sorema.it Starlinger recycling PET recycling equipment www.recycling.starlinger.com Blow moulding, filling, packaging lines North America: (1) 630 510 9343 South America: (55) 11 3611 2400 Europe: (33) 0243 60 28 28 Asia: (60) 3 8605 3690 [email protected] www.serac-group.com 4.4.1 Labelling machinery Finpac Italia srl tel +39 02 89775524 [email protected] – www.finpac.it P.E. LABELLERS S.p.A. Via Industria 56 46047 Porto Mantovano (MN), Italy Tel.: +39 0376 389311 [email protected] www.pelabellers.com 4.5 Downstream equipment Tel: +34 954779200 [email protected] www.andyor.com 4.6 Liquid Nitrogen Dosing Phone: +1-781-933-3570 Fax: +1-781-932-9428 Email: [email protected] Web: www.vacuumbarrier.com Turnkey solutions and modules for plastic recycling and washing plants (PET, PE, PP, PS); more than 60 plants supplied worldwide; “made in Germany” STF Maschinen- und Anlagenbau GmbH Industriestr. 2, D-94529 Aicha v. Wald Tel: +49 (0) 8544 960-110 Mail: [email protected] Web: www.stf-group.de Complete washing lines for PET recycling, for fibre, sheet, B-t-B applications TECNOFER ECOIMPIANTI SRL Via Calto, 409/28 45030 Ceneselli (RO) - Italy Tel: +39 0425 849090 [email protected] www.tecnofer.biz 6.0 OTHER 6.1 Laboratory equipment CANNEED INSTRUMENT GROUP LIMITED Tel: +86 758 2788469 Fax: +86 758 2782729 Email: [email protected] Web: www.canneed.com 6.1.2 O 2 barrier measurement 6.1.4 Bottle, Preform and Cap inspection equipment [email protected] www.agrintl.com","@ID":71}, "44 TRADE SHOW PREVIEW PETplanet Insider Vol. 19 No. 11/18 petpla.net Automated quality control on beverages and beverage packages The specialist in electromechanical measuring systems Steinfurth sets this year’s focus in the improved and extended product line for combined monitoring of quality parameters on beverages, closures and packages. The non-destructive CO2 tester CDA-OST is an optical instrument with a standardised calibration and validation strategy. Together with the well-established and robust CDA family the complete range of CO2 measurement on packaged beverages is covered. The Compact Package Analyzer (CPA) as extendable combination of the CO2 , torque, brix, fill level, pH and conductivity measurement is meanwhile well-established as a customised Mini Lab for time optimised and complete QA monitoring directly at the filling line. The TMS family known worldwide as unsurpassed in the torque measurement has been extended with the patented sensor technology for measurement of application angle. A full range of instruments for a packaging laboratory (all offered by one supplier) and the continuously growing number of creative solutions for single and multiple sample handling in various applications perfect the Steinfurth innovation package. www.steinfurth.com Unique decoration To give visitors a good idea of the limitless printing possibilities, CCL Label created a promotional self-adhesive label exclusively for BrauBeviale. By combining various special effect inks, functional- and promotional-features – all in one – it illustrates the invaluable impact a label can have on brand perception. CCL Label will present solutions from high-quality self-adhesive labels embracing the latest packaging trends to outstanding sleeve decorations. www.ccllabel.com Steinfurth Hall 6 | Booth 131 CCL Hall 7A | Booth 523 ADHESLEEVE® TECHNOLOGY THE BEST SOLUTION FOR ROLL-FED LABELLING EVEN ON CANS! BRAU BEVIALE NOVEMBER 13 - 15, 2018 NUREMBERG, GERMANY BOOTH # 7-315 ProMachBuilt.com | PELabellers.com LABELS APPLICATION WITHOUT HOT MELT GLUE. EASY LIKE SCOTCH-TAPE! EVEN MORE! The first eco-friendly linerless labeller using pre-glued films. 100% ecologic and recyclable product. Also for empty containers. Adhesleeve + thermal-shrinking system. More than a valid alternative to the sleeve application. HALL 6 - STAND G027 ALL4PACK NOVEMBER 26 - 29, 2018 PARIS, FRANCE","@ID":46}, "32 TRADE SHOW PREVIEW PETplanet Insider Vol. 19 No. 11/18 petpla.net All4Pack Paris preview The All4Pack will bring together 87,000 professionals for four days of exchange, demonstrations, innovation and presentations from sectors such as food, beverages and liquids, cosmetics and toiletries, healthcare and pharmaceuticals, retail, e-commerce, consumer goods and capital goods. The All4Pack Startup Lab will be shown in hall 7 for the first time. 15 startups will present themselves and demonstrate over four days their innovation during live pitch sessions. Also in hall 7, the Creativ Lounge, with awarded company in the packaging and intralogistic area, will entertain the visitors. This fairground is in addition to the new communication space with conferences, debates, key-note speeches and awards. All4Pack Paris offers a comprehensive range which perfectly addresses the integration strategy witnessed by the market, raw materials, process, packaging and packing machines, marking and coding, packaging solutions and containers, pack printing and labels, secondary, tertiary and shipping packaging machines. It also addresses the intralogistics sector: continuous handling, automated systems, logistics services and IT systems, storage and warehouse facilities, lifting, and forklifts. Exhibitors are expected from all over the wolrd. 44% working in the packaging industry, 39% acting in processing, 11% in logistics and 6% in printing. PETplanet is looking forward to exploring this promising event! www.all4pack.fr Liquid assets Global packaging solutions company Retal will be presenting its complete range of PET preforms, closures, containers and films, including its market-leading multilayer technology. Retal’s multilingual team is looking forward to meeting customers and industry experts to discuss the ever-changing trends and the all-important demands of consumers, including the need for more sustainable solutions. Protect with multilayer Emilie Chassagnard-Perreau, Commercial Manager at Retal France, says, “one example where we have been meeting consumer demands and leading is in the multilayer preforms market across our active European markets since 2003. We have considerable experience in what is a relatively new technology. Multilayer is the technology to protect the product and the environment. The objective is to compete with the performance of glass bottles while keeping the advantages of plastic: lighter weight and reduced carbon footprint.” Retal understands that the beverage industry is in an exciting yet challenging phase, with the environmental concerns of brands and consumers needing to be balanced with the performance and practicalities of packaging. Its cost-effective multilayer preforms excel across all categories, with all Retal solutions carefully considered for market appeal. Chassagnard-Perreau concludes, “We offer a broad range of complete solutions that allow us to develop, create and supply packaging that meet the strict demands of our global beverage and food brand customers. We look forward to sharing our offer at All4Pack.” Retal develops and manufactures high quality polyethylene terephthalate (PET) packaging solutions, including preforms, closures, containers and films. Retal employs around 2800 people in Europe, Russia, the Middle East and the USA, and supplies customers worldwide. Strongly focused on quality and flexibility, Retal is ISO 9001, ISO 14001 and ISO 22000 accredited. Parent company Retal Industries Ltd is owned by Anatoly Martynov and is headquartered in Limassol, Cyprus. www.retalgroup.com Discussing hot topics for the upcoming show in Paris. F.l.t.r.: Eva Passmann (Marketing & Communication imf Promosalons), Claudia Josephs (General Manager, epda), Séverine Dageville (Elipso), Inga Kelkenberg (Manager Communication IK), Dominique Cherpin (Director Promosalons Germany), Véronique Sestrières (Business Unit Director Comexposium), Barbara Appel & Prof Dr Otto Appel (Director PETnology), Aurélie Jouve (Communication Director Comexposium), Cécile Robinet (Marketing & Communication imf Promosalons) and Fabrice Peltier (DesignPackaging Expert) Retal Hall 7 booth E184","@ID":34}, "34 TRADE SHOW PREVIEW PETplanet Insider Vol. 19 No. 11/18 petpla.net Sumitomo (SHI) Demag to showcase the new IntElect2 S The production cell designed as a complete solution around the IntElect S 180 produces decorative lids for food containers. Sumitomo (SHI) Demag is presenting this exhibit in a joint project with Rouxel as the injection compression mould manufacturer, Machines Pagès as a specialist for high-speed extraction robots and downstream moulded part handling, Verstraete as experts for decorative labels. During injection compression moulding, plasticised material is already introduced into the cavity prior to complete locking of the mould. The machine closing movement aids distribution of plasticised material in the cavity, reduces the injection pressure requirement and the required clamping force, ensures that the pressure is distributed evenly and, as a consequence, reduces residual stress in the finished part. Warping 3 due to shrinkage is less pronounced as a result, reducing the wall thicknesses and weight of the moulded part. Compression at the highest mould and injection movement velocity, termed speed compression, is a particular challenge for the injection moulding machine and its sensors, control and drive technology. Despite the high speeds involved, the machine guarantees to deliver a high degree of precision and exact reproducibility from cycle to cycle. www.rouxel-sa.com www.machinespages.net www.verstraete-iml.com www.sumitomo-shi-demag.eu Sacmi beverage 4.0 - all inclusive line The Group stand will be placing particular emphasis on the wide range of valves designed by Sacmi Beverage for still beverage and CSD filling. The key elements of this Sacmi technology are high quality materials and the precision and hygiene of the contactless filling process, making it the perfect response to the needs of today’s global beverage industry. Complete and versatile, Sacmi filling solutions, highly sophisticated electronic fillers that ensure outstanding flexibility, hygiene and performance. Their applications range from water to soft drinks, beer, dairy products and other “sensitive” drinks and can be combined with upstream solutions that ensure maximum versatility with all format types. Hence the growing market success of SBF, the Sacmi stretch-blow moulder that, thanks to the dual cavity system, provides double the speed with medium-small formats. Container closure and labelling operations complete the new Sacmi HeroLine, an all-inclusive line that, through integration and synchronisation of all processes, now brings ‘smart industry’ principles to the beverage world. Producers can thus look forward to an array of new opportunities, such as the ability to integrate bottling lines - including an all-in-one version with the new Sacmi Heroblock – with upstream cap (CCM) and preform (IPS range) production solutions. Automation and fewer handling requirements maximise the manufacturing and energy efficiency of what is a true pellet-to-pallet PET line. Since Sacmi machines are able to communicate both with each other and the Sacmi H.E.R.E. line supervisor, customers can unite excellent technological performance with advanced monitoring and diagnostics. All topped off with the broad, comprehensive range of inspection systems, developed by the Group’s Automation & Inspection Systems Division, ensuring total quality control at every stage of production. www.sacmi.com Sumitomo Hall 7 booth D059 Sacmi Hall 6 booth D059","@ID":36}, "47 TRADE SHOW PREVIEW PETplanet Insider Vol. 19 No. 11/18 Flexibility on 4-cavity machine 1Blow keeps developing its range of stretch blow-moulding machines so that customers can enjoy more possibilities on their machines: from one to four cavities, all 1Blow machines are capable of producing all types of bottles (round, square, oval, off-centred, with neck orientation, using standard necks, with a deep grip for easy handling, hot fill) and a wide variety of applications, such as water, soft drinks, edible oil, sauces, juices, teas, honey, detergents or cosmetics. All these options are avaiable as options with a new machine as well as upgrades. Thanks to this, customers are adapting their investment to the market’s needs; meanwhile they are aware their machine may evolve and produce bottles with even more added value. 1B l ow c l a ims t ha t t he i r machines are of high flexibility thanks to easy and quick changeovers - all components are directly accessible. With a few rapid transfers inside the machine, the energy demand is low. The operator monitors all functions via the easy-to-use touch screen, thanks to servo drives that make these machines reliable, highperformance and low-energy consuming. Moreover, all 1Blow machines are equipped with an air recovery system that further reduces the total power demand of the system. www.1blow.com Sustainability, safety and new markets Petainer will be launching new Petainer keg products which have been specifically developed using circular economy designs, focused on recycling and reuse. According to the company, they provide a more cost-effective and sustainable alternative to traditional stainless-steel kegs, and a low-cost way of entering new domestic and international markets. Improved features include puncture and drop resistance. As a global business, Petainer will also be announcing new manufacturing facilities at the show, as it seeks to reduce the impact of its operations by bringing the supply chain to new markets, making its products even more cost-effective and more environmentally-friendly. www.petainer.com 1Blow Hall 7A | Booth 527 Petainer Hall 4 | Booth 137","@ID":49}, "TRADE SHOW PREVIEW PETplanet Insider Vol. 19 No. 11/18 petpla.net 50 Sipa Hall 7 booth 659 Sipa showcases linear and rotary options for inline blowing, filling & capping of PET bottles Debut of the 3-in-1 system Visitors to the Sipa stand at Brau Beviale will be able to see the company’s latest technologies on preform production equipment, such as Xtreme and the fourth generation of Xforms, the Xtra high-speed production machine, and the ECS SP 25, the latest addition to the Sipa ISBM range in the range. Making its Brau Beviale debut will be the SincroBloc fully integrated PET bottle blowing / filling / capping systems. These machines, which were officially launched some months ago, are based on SFL linear stretch-blow moulding units. Sipa says that the range enables beverage companies to choose the line that best fits their production requirement for formats of all sizes. High speed and a wide range of sizes Rotary versions can work at speeds of up to 54,000 small and medium-sized bottles per hour, while an SFL system for large formats with a BigFill volumetric gravity-filling monobloc can push out 4,000 12 l containers over the same period. SFL SincroBloc units can produce and fill small and large containers, in various formats, including bottles with handles. They can work with all types of ready for wrapping, the bottles are totally protected from the external environment. The high levels of cleanliness mean that customers can use them for CSDs that contain no artificial preservatives. A variety of mechanical and electronic fillers Sipa produces various types of fillers that can be coupled with the linear and rotary blow moulders for small formats. These include the Stillfill Evo mechanical gravity filler for hot- and cold-filled non-carbonated drinks; the mechanical Isofill isobaric level filler for carbonated soft drinks and mineral waters; the Flextronic S and SE electronic volumetric fillers for various types of still liquids and hot-fill products respectively; and the Flextronic W electronic weight filler for products with extra added value. www.sipasolutions.com liquids, including still water, CSDs, milk, hot-filled products, or products with high added value such as oils, detergents and personal care. Compact dimensions and lower cost of ownership The linear format has further important advantages. It is very compact, for example, and mechanical movements are simpler than with a rotary stretchblow section. Total cost of Ownership (TCO) is reduced, thanks to lower initial investment cost and reduced maintenance requirements. Cleaning and hygiene Neither the linear nor the rotary systems require rinsing between blowing and filling. As monobloc units they have no need for external conveying systems. From the moment the preform enters the feed shoot until the filled and sealed product emerges,","@ID":52}, "PACKAGING / PALLETISING PETplanet Insider Vol. 19 No. 11/18 petpla.net 27 The Movigear product range of mechatronic drive systems The Movigear mechatronic drive system The Movigear mechatronic drive system combines motor, gear and drive electronics into a single system. It is designed to be used flexibly in various communication infrastructures. This makes it suitable for all decentralised applications on-site, particularly in general conveyor technology. All the components – the permanently energised Efficiency Class IE4 synchronous motor, the high-quality gearbox and integrated electronics, have been optimally matched with one another and the overall system optimally energised. As a result, the Movigear has a high level of system efficiency which means that energy savings of up to 50% (compared to conventional, older drives) can be achieved on a regular basis. The MGF..-DSM drive unit For central installations, the integrated MGF..-DSM geared motor, combined with the Movigear LTP-B control cabinet inverter, is a highly efficient IE4 solution. Plant manufacturers and operators can also use the Movigear mechatronic drive system’s many advantages for central installations. These features make the system ideal for use in products, containers and container transport systems in the food and drink industries and are therefore mainly used for retrofit projects with emphasis on high energy efficiency. It is equally suitable for new installations that require a central control cabinet installation of the frequency inverter. The DRC.. electronic motor The DRC electronic motor extends the range of mechatronic drive systems for decentralised applications more widely. Its compact design combines a permanently energised Efficiency Class IE4 motor with integrated drive electronics. As for the gearbox, it offers maximum flexibility. In combination with an efficient bevel, spur or flat gear from SEW-Eurodrive’s extensive gear portfolio, the electronic DRC motor forms a powerful decentralised drive unit. For this, there are identical communication versions as with Movigear. IS STILL 50% TOO MUCH. 50% L SS P CK G NG The KHS solution for more sustainability: New avenues in packaging technology. We are continuously improving our packaging. By applying innovative technologies and ","@ID":29}, "PETcontents 11/18 4 PETplanet Insider Vol. 19 No. 11/18 petpla.net Page 48 Page 36 Page 61 24 INSIDE TRACK 3 Editorial 4 Contents 6 News 58 Products 60 PET bottles for Beverage + Liquid Food 62 PET bottles for Home + Personal Care 64 Patents MATERIAL / RECYCLING 12 Totally closed-loop recycling - Post-consumer PET into food-grade finished packaging products 13 The rPET project - Bottle-to-bottle recycling at Ferrarelle S.p.A. BOTTLE MAKING 14 Machine details - Blow wheel / blow clamp Strech Blow Molding, part 10 BOTTLING / FILLING 22 2 million cases of extra productivity - Niagara Bottling LLC invests in line efficiency PACKAGING / PALLETISING 24 Smooth flow of energy - Drinks’ conveyer technology with mechatronic drives 28 Filling and packing of PET kegs - from preform moulding to transport-ready product 31 Storing and dispensing solutions - DS Smith introduces Stackabox Hybrid and Stackabox C&C MARKET SURVEY 35 Suppliers of palletising and shrink film machinery TRADE SHOW PREVIEW 32 All4Pack Paris 2018 39 Smart packaging machine to be more competitive 40 Dressed in PET - PET Engineering delivers solutions for water, light wellness beverages and Canada’s milk market 43 Brau Beviale 2018 48 Higher output, lower energy consumption - The fifth generation InnoPET Blomax stretch-blow moulding machine 50 Debut of 3-in-1 system - Sipa showcases linear and rotary options for inline blowing, filling & capping of PET bottles 51 Filling matters - Flexible rinsing, filling, seaming and capping with one filler 52 Raising the rPET bar - Average recyclate content of 50 percent in disposable PET bottles by 2022 53 Adapting consumer demands - Flexible production process will meet consumer trends in beverage packaging 54 Compact rotary combi - “Smart” bottling and packaging systems incorporating Internet of Things and Industry 4.0 technology TRADE SHOW REVIEW 56 Fakuma 2018 BUYER’S GUIDE 65 Get listed! 3628","@ID":6}, "57 TRADE SHOW REVIEW PETplanet Insider Vol. 19 No. 11/18 petpla.net Advancing applications based on new Victrex FG food grade portfolio To help OEMs to meet the stringent regulatory and quality demands affecting the food equipment industry, Victrex has introduced a dedicated Peek food grade portfolio at the Fakuma show. Compared to metals, the new Victrex FG family of high-performing thermoplastics offers additional benefits in terms of cost-effectiveness, productivity and performance and the neutral taste expected by consumers. Applications range from cookware and beverage dispensers for commercial and domestic use to industrial applications involving food-contact components in conveyor systems, aseptic processing, sensors, gears and nozzles. www.victrex.com Innovation ABMF PET – perfectly adapted to processing parameters of thermoplastic plastics “With the ABMF PET, we have increased our range of products again. Both, temperature control and heating capacity are designed for higher processing temperatures. Furthermore, for the lower viscosities, the filter sealing is optimised by a die guiding. Of course, also the filter surface and the channel guiding are designed for throughputs with PET “, emphasised DI Dr Friedrich Kastner, CEO Britas and Thomas Lehner, Director Sales Britas. “At the moment, the ABMF PET is available with a filter surface of 570cm2. ABMF 1600 has been a very well established and proven technology with 50% more output. The Automatic Belt Melt Filter ABMF 1600 is very successfully accepted by the market. The advantage of this Britas melt filter is that it ensures even more throughput and improved filtration. With the ABMF 1600, we have increased the filter surfaces by 50% and meet the requirements of our customers. “ Britas filters are used in the post-consumer sector and for agricultural films but also for post-industrial waste. Britas test centre – plastic waste can be tested under real conditions One more piece of good news: Britas has recently open a new test centre in Hanau,Germany,– there, recycling and compounding companies can perform test runs with their materials. “For customers, it is an advantage that now, with the test line, we can test any plastic waste. The line can be installed either with the Britas ABMF-0750-09 or the Britas ABMF-0750-09-C. With that possibility, our range of service is increased even more and our position in the market is strengthened “, explains DI Dr. Friedrich Kastner, CEO Britas. “Moreover, our customers can test materials under real conditions, no matter whether it is post-consumer or postindustrial material. “Additional components of the line are a NGR C-Gran 85-110 VV HD with double degassing (cutter compactor) with a throughput of up to approx. 420 kg/h as well as a die face pelletiser. www.britas.de Digital application for colour matching including virtual assistant To guide customers through the world of masterbatch and the product discovery process Gabriel Chemie has developed a browser-based and mobile application Master of Colours, it is the first tool to be released as part of the Master of Batch platform by Gabriel-Chemie. At this year‘s Fakuma, the digital tool was presented, which enable many daily colour requests to be answered within a very short time. With GABi the users also have a virtual assistant at their side. The intelligent search-algorithm finds suitable products based on common colour systems or standardised colour references such as RAL and is able to recognise colours and propose appropriate products using the X-Rite Color-Eye System via a smartphone camera. The Color-Eye calibration card enables accurate colour measurement on Apple and selected Android phones, removing variation caused by lighting and camera differences. Dosage, temperature stability and light-authenticity are processing parameters that can be filtered. “Master of Batch provides quick digitised access to our masterbatch world. Customers can quickly and easily select their products to shorten product development and time to market. The fact that we can demonstrate long-term cooperations with established global companies such as X-Rite speaks for the pioneering direction of Gabriel-Chemie.“ said Lukas Houska, project manager Digital Colours. “We are excited to work with Gabriel-Chemie, addressing their customer challenges to find colour match‘s across their product ranges.“ stated Matthew Adby X-Rite Portfolio Manager. www.gabriel-chemie.com","@ID":59}, "imprint EDITORIAL PUBLISHER Alexander Büchler, Managing Director HEAD OFFICE heidelberg business media GmbH Bunsenstr. 14 69115 Heidelberg, Germany phone: +49 6221-65108-0 fax: +49 6221-65108-28 [email protected] EDITORIAL Kay Barton Heike Fischer Gabriele Kosmehl Michael Maruschke Ruari McCallion Waldemar Schmitke Anthony Withers WikiPETia.info [email protected] MEDIA CONSULTANTS Martina Hirschmann [email protected] Johann Lange-Brock [email protected] phone: +49 6221-65108-0 fax: +49 6221-65108-28 LAYOUT AND PREPRESS EXPRIM Werbeagentur | exprim.de Matthias Gaumann READER SERVICES Till Kretner [email protected] PRINT Chroma Druck & Verlag GmbH Werkstr. 25 67354 Römerberg Germany WWW www.hbmedia.net | petpla.net PETplanet Insider ISSN 1438-9459 is published 10 times a year. This publication is sent to qualified subscribers (1-year subscription 149 EUR, 2-year subscription 289 EUR, Young professionals’ subscription 99 EUR. Magazines will be dispatched to you by airmail). Not to be reproduced in any form without permission from the publisher. Note: The fact that product names may not be identified as trademarks is not an indication that such names are not registered trademarks. 3 PETplanet Insider Vol. 19 No. 11/18 petpla.net In all areas of beverage production and packaging, acquisitions are making the headlines. On one side of the coin, the process of concentration in the industry is continuing, on the other, acquisitions are being almost exclusively being made by strategic investors with a long-term vision, where the portfolio is meaningfully supplemented or strengthened. The “wild west” spending spree in the PET sector is over. We are now in the era of normality. In the sector of natural food and beverage ingredients, Döhler has acquired the Swiss company Passina, noted for its passion fruits. In the area of packaging, Alpla has taken over the Greek company Argo. As a result, Alpla is strengthening its presence in Central and Eastern Europe in areas such as pharmaceutical and personal care. From India comes the news that private equity fund Advent International is set to acquire a controlling interest in packaging solutions company Manjushree Technopack, promising that Manjushree will be a major player in the fast-growing Indian market for rigid plastic packaging, with growth rates of 15% being forecast. Sidel, manufacturers of turnkey systems, has acquired PET Engineering. The Italian company is known for its innovative bottle design and mould making. Krones is strengthening its microbrew division with two acquisitions. First in China, the Neutraubling-based company are taking over their former supplier Xiantong and in the States, the Wisconsinbased Sprinkman company, manufacturers of beverage processing equipment and also a manufacturer of microbrew systems. And yet another acquisition, this time from the US beverage sector, where Cott has recently acquired Mountain Valley Spring Co. Yours, Alexander Büchler Dear readers,","@ID":5}, "PACKAGING / PALLETISING PETplanet Insider Vol. 19 No. 11/18 petpla.net 24 Drinks’ conveyor technology with mechatronic drives Smooth flow of energy As the name suggests, the Hungarian drinks’ manufacturer, Hell Energy, promises its customers a hell of a lot of energy. Seven years ago, it built a state-of-the art factory on a greenfield site. Today, the company has become a market leader in this drinks sector across many countries. Krones bottle filling lines, together with mechatronic drive units from SEW-Eurodrive’s Movigear product range, ensure a continuous and smooth flow of energy. It only took Hell Energy Hungary Limited 12 years to become the market leader in energy drinks at home. The company is now operating in Romania, Bulgaria, Slovakia, Cyprus and Azerbaijan. Hell Energy is currently achieving annual doubledigit growth which is stronger than the market average. At present, the drink is sold in nearly 50 countries around the world. The product range extends from the classic energy drink to Cola, Hell Strong with extra caffeine in different varieties and also a “zero” drink which does not contain any sugar, calories or carbohydrates. State-of-the art filling facilities for cans and PET bottles Due to their increasing popularity and correspondingly higher demand at home and abroad, Hell Energy Hungary Limited decided in 2011 to build a new, larger factory with adjoining warehouse in Szikszó, just 200 km north-east of Budapest. Hell Energy has invested the equivalent of 15 million Euros in a new can filling plant and buildings here. 1500 million cans can be produced in Szikszó each year. Just one year after the can filling facility was completed, more than seven million Euros were invested in another PET bottle filling plant. After a good experience with can filling lines from Krones, Hell Energy collaborated with the plant manufacturer from Neutraubling again in this new investment venture. The decisive factor here was their high-quality performance. With a total of 27 trucks, Krones supplies one of the most modern PET bottle filling facilities in Europe. It can fill bottles of all sizes: 330ml, 500ml, 750ml, 1,500ml and 2,500ml. The Hell Energy’s bright red factory in Szikszó, northern Hungary (Photo: Hell Energy) Movigear product range: Movigear Mechatronic Drive System, DRC.. Electronic motor, MGF..-DSM drive unit (from left), Movitrac LTP-B control cabinet inverter above. (Photo: SEW Eurodrive)","@ID":26}, "9 NEWS PETplanet Insider Vol. 19 No. 11/18 petpla.net Survey on recycling behaviour in the USA While traditionally the effort to increase recycling rates has focused on education and awareness, a new study among over 2,000 Americans conducted by The Harris Poll on behalf of The Institute of Scrap Recycling Industries (ISRI) suggests action by brands and government may play a significant role as well. The poll revealed two-thirds (66 %) of Americans agree that “if a product is not easy/convenient for me to recycle, I probably would not recycle it.” The poll also provides insights into ways these two sectors can better drive recycling. “Understanding what is recyclable and what is not, can be confusing,” said Robin Wiener, president of ISRI. “The easier it is for people to understand if a product is recyclable, the more likely it is to make its way to the recycling stream. This includes not only making products that are easy to recycle through design for recycling and product labeling, but making recycling convenient through collection efforts.” In addition to finding significance in the ease and convenience of recycling an item, the survey provided the following takeaways for brand owners. The vast majority of Americans would like to see manufacturers and/or retailers display a “Recycling Guide” label on products that would detail the parts and percentage of the product that could be recycled and how (81 %). Having this information more prominent may help Americans consider these aspects of their product when making a purchase – or it could also encourage recycling of the product or package when disposing of it. Younger Americans (aged 18-34) are more likely to consider the products packaging than older Americans (over 34) – including whether or not the packaging can be recycled (17%/11%), what the package is made of (16%/9%) and whether the package is made from recycled materials (16%/8%). This could be an important aspect for brands targeting the purchasing power of millennials. The survey also found government can also set an example for Americans by prioritising recyclable materials. In fact, four in fiveAmericans (80%) agree that governments at all levels should prioritise the use of recyclable products/material when making purchasing decisions. Recycling is demand driven, and thus increasing the use of recyclable materials in manufacturing is critical to the success of recycling. This is also an important takeaway for brands participating in the government procurement process. The study also found 86 % of U.S. adults agree recycling collection sites need to be more readily accessible to consumers. The survey also looked at American’s attitudes towards curbside collection programs. Detailed results are available online. This survey was conducted online within the United States by The Harris Poll on behalf of ISRI from September 17-19, 2018 among 2,003 U.S. adults. This online survey is not based on a probability sample and therefore no estimate of theoretical sampling error can be calculated. www.isri.org Sidel Group acquires PET Engineering On October 11, the Sidel Group concluded the acquisition of PET Engineering Srl, further expanding the company’s portfolio of packaging solutions. PET Engineering is expected to help Sidel expand its packaging offering – especially regarding the design of containers for water, soft drinks, liquid dairy products and beer. Founded in 1999 and based in San Vendemiano, Italy, PET Engineering has 40 employees. An agile company with a strong name in creative packaging design, PET Engineering has solid blowing process knowledge and expertise and enjoys a loyal global customer base. Their integrated approach between design, engineering and industrialisation and the capacity to create a delicate balance between technical feasibility and creativity helped PET Engineering win prestigious packaging awards. www.sidel.com United Caps seeks to build new manufacturing plant in France The manufacturer of caps and closures United Caps will build a new plant in Normandy, France, in addition to the eight existing plants in Europe and the two future extensions in Malaysia and in the UK. The site chosen is located in the Valframbert Business Park of Alençon, France. United Caps is currently working with the Communauté Urbaine d’Alençon (CUA - Urban Community of Alençon) and with Orne Développement (a service of the Orne Department Council) to negotiate the purchase of 25,000m2 of land upon which a purpose-built factory will be constructed, with a first construction phase of 4,000m2. This project represents an investment of €12 million and is expected to employ 15 staff in two years. Benoit Henckes, CEO of United Caps states “With our ‘Close to You’ strategy, we seek to place our factories as close to our customers as possible, as shown by the two new factories that will open next year, in Malaysia and the UK. We are especially interested in building a factory in Alençon because of its proximity to customers, who will have access to our full portfolio of solutions, and will also benefit from the proximity to our R&D centre in Messia (Jura, France) if customisation or bespoke development is required. We also like the fact that the Institut Supérieur de Plasturgie d’Alençon (ISPA - Institute of Plastics and Composites) is located nearby, ensuring a source of highly skilled staff.” www.unitedcaps.com","@ID":11}, "56 TRADE SHOW REVIEW PETplanet Insider Vol. 19 No. 11/18 petpla.net Fakuma 2018 TRADE SHOWreview More intuitive, more safety Engel has redefined the humanmachine interface w i t h i t s CC3 0 0 . Engel said that the control unit makes it more efficient, userfriendly and safe to use injection moulding machines and integrated system solutions. For its fifth anniversary, the Engel control unit showcased along with an upgraded control concept and new features at the Fakuma 2018 trade fair. Tutorials, which play directly on the display, keep the machine operator up-to-date and highlight areas of potential for optimisation. The increasing complexity of the production process poses increasingly tough challenges for control technology. The clearer and more intuitive the control unit, the more safely and efficiently the machines and production cells can be operated. For this reason, when it comes to the CC300 control unit’s ongoing improvement, ‘keep it simple’ is a key guiding principle for injection moulding machine manufacturer and system solutions provider Engel. The design and operating philosophy are the essential elements for truly intuitive operation without restricting the scope of the machine or system solution. Visitors to the Engel stand at Fakuma clicked through the tutorials live and learned more about the CC300 control unit’s new features. Along with the control panels at the machinery exhibited, there was a dedicated Expert Corner to provide assistance. In addition, all the tutorials will be available to the users of Engel machines and systems solutions at any time and in any location via the Engel customer portal e-connect. www.engelglobal.com Laser marking in different colours The Finke laser enables high-contrast marking of many common polymers, especially PE, PP, PET or ABS. At Fakuma, Finke has presented a comprehensive additive batch and masterbatch program for coloured laser markings. It ranges from additive batches for functional modification of existing colour concentrates to FibaPlast combination batches which offer both colour and function. Colour laser markings have been shown on extruded HD-PE sheets in postcard size, which have been coloured with various FibaPlast combination batches: free-flowing polyolefin-based colour concentrates (concentration: 7 % or 8 % in HD-PE). The sheets are manufactured by the German extrusion specialist CS-Plastik. Laser marking is carried out at Finke’s laser laboratory. Laser marking is the method of choice when it comes to permanent marking for labelling, graphic design or functionalisation of plastics surfaces. A laser works quickly and efficiently. The marking is applied permanently, shows a good contrast, can neither blur nor fade and is individualised easily. Applications range from imprinting expiration dates and conveying information (e.g. as QR codes) to the individual design of products. www.finke-colors.eu Plastics processing in digitalisation mode Everyone who’s anyone in the field of plastics processing came together at the once again fully booked out Fakuma international trade fair for plastics processing on Lake Constance where Germany, Austria and Switzerland meet for the 26th the time from the 16th through the 20th of October. The international exhibitors were pleased once more this year with the great demand for this pioneering event in the field of plastics technology: 1,933 market and technology leaders from 40 countries presented their companies to 47,650 expert visitors from all over the world! The proactive technology transformation appears to be succeeding in the field of plastics processing: new materials, more efficient manufacturing processes, 3D and 4D printing alternatives, digitalised and automated production solutions, reduced energy consumption for machines and systems – these are just a few of the regulating screws that need to be tweaked by today’s plastics processors. The issue of sustainability, including aspects such a plastics recycling, material savings and biomaterials, was the subject of more discussion than ever before at this year’s Fakuma, because the demands of plastics users such as the automotive industry and the consumer goods and packaging manufacturers are becoming more and more complex. Fakuma 2018 very impressively verified the fact that the plastics industry is up to the challenge, and that it has the most up-to-date tools at its disposal in every regard, in order to work economically with efficient use of materials and resources. The production of affordable, and at the same time rugged lightweight design structures was presented at the event to just as great an extent as a broad-based portfolio of new materials. New machines, adapted tooling, integrated quality assurance, controllable hydraulic and to an ever greater extent electric drives, and last but not least networkable and thus communicative controllers complete with software – the plastics industry is becoming more and more digital, which is not least of all made apparent by great demand for Industry 4.0-capable equipment and systems. www.fakuma-messe.de/en","@ID":58}, "43 TRADE SHOW PREVIEW PETplanet Insider Vol. 19 No. 11/18 petpla.net TRADE SHOWpreview Brau Beviale 2018 Brau Beviale will open the exhibition halls in Nuremberg from November 13-15, 2018. Due to moderate growth, an extra hall has been added this year. This results in a new hall configuration, positioning exhibitors in the order of the beverage production process chain around the exhibition park. Supporting programme The three-day supporting programme includes the Export Forum German Beverages. With high-calibre speakers and networking opportunities, the Forum is intended to help manufacturers to make decisions about exporting their products. The European MicroBrew Symposium hosted by the Berlin-based research and teaching institute for brewing (Versuchs- und Lehranstalt für Brauerei, VLB) is intended for international craft brewers and brewpub operators. Another hot topic among brewers worldwide is heirloom brewer’s barley. This will be the focus of the Heirloom & Terroir Barley and Malt Symposium hosted by RMI Analytics. The BrauBeviale Forum will once again take place on all three days of the exhibition. The proven blend of talks, presentations, panel discussions and award ceremonies invites visitors to become informed about raw materials, technologies, entrepreneurship and marketing. The diversity of beverage specialities can be experienced in the Craft Drinks Area. The European Beer Star, which has been part of Brau Beviale since it was “born” in 2004, will also be awarded again at the event. In 65 categories, breweries from all over the world can submit their beers for inclusion in one of the most important beer competitions worldwide. Various themed pavilions will present themselves as the focal point for certain issues tailored to specific groups of visitors, as the Artisan and Craft Beer Equipment and brau@home for micro-breweries and hobby brewers, or the “Sustainable Water Management in the Beverage Industry” pavilion. At the Special Show Innovative Beverage Packaging interesting examples of packaging innovations will be provided by the winners of the World Packaging Awards that will be presented by the World Packaging Organisation. The reasons why these products won their awards will be explained clearly to visitors. PET continues to be a topical and important issue. The quality association Wertstoffkette PET-Getränkeverpackungen e. V. will cover various approaches and present ideas and solutions for PET recycling. Of course, PETplanet will also be on site again with an own stand. We look forward to your visit at our booth 8-302 in Hall 8. www.braubeviale.de PET keg technology PET Technologies emphasises that its latest developments for the brewery industry are not limited to PET stretch blow moulders and blow moulds. For the first time ever at the PET Technologies booth, visitors will find a complete system for preparing PET kegs, suitable for breweries as well as wine, cider or cold brew coffee manufactures. The keg preparation complex is a complete line for blow moulding the amber container, assemble a fitting with spear, seal the container, add gas and check for pressure leakage. A conveyor connects all the units. Ready to pack kegs are accumulated at the collecting table. The company points out that the usage of various fitting types is possible. Capping unit heads are claimed to be easy to change. The fittings storage tank capacity guarantees 2 hours of continuous line running. TheAPF-30 PET keg blow moulder highlighted at Brau has two modifications with output 120bph and 250bph. Both PET kegs and PET watercooler bottles can be produced at the same machine! www.pet-eu.com PET Technologies Hall 7 | Booth 749","@ID":45}, "PACKAGING / PALLETISING PETplanet Insider Vol. 19 No. 11/18 petpla.net 28 From preform moulding to transport-ready product Filling and packing of PET kegs The Danish Carlsberg Brewery has at its facility in Fredericia commissioned a complete line from Krones for filling beer in 20 litre kegs. Carlsberg brews more than 60% of its entire beer volume for the Danish market in Fredericia. Besides the Jacobsen speciality-beer and showcase brewery in the centre of Copenhagen, the Fredericia facility is the only Carlsberg brewing plant in Denmark. The company produces here for the whole nation, and for export to European countries. “In the craft beer and speciality-beer segment, we achieved volume growth of 29% in 2017,” says Plant Manager Martin Bjeld. “Draught Master is a super instrument for supporting the concomitant premiumisation of the brands.” In order to provide the catering trade with an option for offering beerlovers a maximally broad spectrum of different beers, Carlsberg has developed Draught Master. The system ensures that beer filled in PET kegs remains fresh for up to 30 days after first tapping. For filling these 20 litre disposable PET kegs, Carlsberg has invested in a line from Krones which has been dimensioned for an output of 500 containers per hour. Special machine from Krones The PET preforms are moulded in the line by a stretch blow-moulding machine into 20 litre containers, and fed to the filler via AirCo conveyors. The filler is a special machine from the Modulfill VFS series, with 18 specially modified large-size filling valves. Since PET containers cannot be pre-evacuated, a blowing starwheel is inserted, through which the air in the containers is flushed out by means of carbon dioxide, thus preventing the filled beer from coming into contact with oxygen. This is already the third time that Krones has built this special filler for Carlsberg. Together with the upstream container rinser and the downstream six-head closer, it is accommodated in a cleanroom. In this case, the kegs are sealed with a pressure closure, which is pressed on, not screwed. After being filled, the containers are transported in carriers suspended on belts. A Variocart carton erector feeds in the cartons, and after the beverage kegs have been date-coded and labelled, the Linapac II packer inserts four containers at a time in a carton. After a downstream weight check, a Variocol closes and seals the boxes, which are then labelled. Next, a robot places 15 cartons at a time on a pallet, which is subsequently stabilised for transport with a net. Currently, Carlsberg is producing 48 different SKUs on the new Krones line. From the Carlsberg Group’s breweries abroad, too, tank beer is filled here in large PET containers. This means that well-known brands like Feldschlösschen, Kronenbourg or Holsten can likewise be seen on the cartons, but also, of course, craft beer brands like Jacobsen Yakima IPA or Jacobsen Wheat Beer. The high output of the Krones line enables a large number of different products to be filled. Changing over the line to a new beer type – including cleaning – takes just one hour. The PET preforms are moulded in the line by a stretch blow-moulding machine into 20 litre containers, and fed to the filler via AirCo conveyors. Carlsberg is already producing 48 different SKUs on the new Krones line. From the Carlsberg Group’s breweries abroad, too, tank beer is filled in Fredericia on the line in large PET containers. Jeppe Holm-Jørgensen, responsible for the kegging operation as Senior Line Manager","@ID":30}, "BOTTLE MAKING 14 PETplanet Insider Vol. 19 No. 11/18 petpla.net Strech Blow Molding, part 10 - Blow wheel / blow clamp, blow moulds Machine details by Ottmar Brandau Ottmar Brandau has newly revised his book “Strech Blow Molding”, first published by hbmedia / PETplanet Publisher, and now re-issued in a third edition under the Elsevier Imprint. PETplanet Insider is publishing extracts from successive chaperts in a serie of articles. 4.3 Blow wheel / blow clamp Rotary machines Blow clamps are highly engineered, complex devices contributing significantly to the rather large price premiums that rotary machines demand when compared with linear machines of the same cavitation. Each clamp has its own valves, water, and electrical connections supplied from the center of the blow wheel. As mentioned before cams control all blow mould movements. While the blow wheel turns carrying the blow clamps, stationary cams engage through rollers and levers guiding the linkages into the desired movements. Figure 4.15: Drawing numbers and their respective functions: 1. cam “opening/ closing of the mould”; 2. cam “lifting the base mold”; 3. cam “locking the mould”; 4. cam “unlocking the mould”; 5. cam “lifting/lowering the stretch rod.” Moveable mechanisms deflect cams and levers in the case of a malfunction. Blow clamps are built to accept the most common bottle sizes ranging from about 200ml to 2.5 or 3l in volume. There are also minimum and maximum preform and bottle dimensions that must be respected. Over the years engineers have significantly lightweighted blow clamp components. This in turn has allowed the increase in throughput of the machines. To achieve this the closing mechanisms do not themselves hold the moulds closed, which would require them to resist the large forces created by the high pressure. Instead, locking mechanisms of various designs engage after mould closing. To reduce the stress on these, blow air in small quantities acts on the outside of the mold thus balancing the forces inside and outside of the blow clamp (Figs. 4.15 and 4.16). Figure 4.16: Blow clamp and components. Diagram courtesy of Krones AG. 4.4 Machine timing In rotary machines the control of the various machine functions is facilitated by using the 360 degrees of the turning wheel as trigger points rather than timers. Typically, timing starts when the mould is fully open. Each movement then happens with a start and end degree. For example, the mould may close between 14 and 44 degrees. How long this actually is depends on the machine speed. Table 4.2 lists the converting times in degrees. Table 4.3 is the reverse table, converting degrees into times. This now has the peculiar effect that process time cannot be simply calculated. Here is an example to demonstrate the following. Assuming that a machine runs at 2,200b/cph for a lightweight water bottle and the mould closing takes 30 degrees. It would therefore take 0.136s to complete. When the machine is then slowed down to 1500b/cph to make a thicker-walled bottle the same movement now takes 0.2s. In most rotary machines process time (preblow, blow, and exhaust) is about 70% with 30% necessary to complete the mechanical machine functions. A 30% dead time or unproductive time translates into 108 degrees and at 2,200b/cph into 0.49s","@ID":16}, "TRADE SHOW PREVIEW PETplanet Insider Vol. 19 No. 11/18 petpla.net 51 TRADE SHOW PREVIEW 51 Gea Hall 7 booth 602 Flexible rinsing, filling, seaming and capping with one filler Filling matters Gea’s focus at this year’s trade fair is their newly acquired subsidiary, Gea Vipoll from Slovenia, which develops and produces filling technologies for hot and cold fill drinks. Together, Gea and Gea Vipoll will present their highly flexible, multifunctional beverage lines which provide added value to their 360° approach for the brewing industry. Filling experts will be on-site to demonstrate Gea’s All In One monoblock filler, which can switch between bottle, cans and PET filling. The system can handle a wide variety of forms and can accommodate various lid shapes for non-carbonated and carbonated beverages with hot and cold filling techniques. After the trade fair, the exhibit will be sent to Norway: the client is the traditional brewery Mack, which will be filling their products such as beer, cider, carbonated soft drinks on the 8,000 bph line. Joint network Since the acquisition, the company has recorded numerous project successes: during 2018, it supplied customers in Croatia and Sweden with its All In One rinser /filler / capper block. It is currently building an All In One filler for beer, soft drinks and water for craft brewer East Coast Brewing from South Africa, which placed a follow-up order after the installation of a Gea Craftstar brew house. In October 2018, Gea Vipoll will also deliver the first multifunctional filler to partner Foodmach in Australia. In the coming months, the plant will be commissioned at the site of Lion, one of the largest food and beverage producers on the Australian continent. Via the acquisition of the Slovenian mechanical engineering company Vipoll d.o.o. in January 2018, Gea has strengthened its market position as a full-range supplier to the beverage industry. Gea can now also fill beverages in glass and PET bottles as well as cans that do not require sterile processing. This segment now complements aseptic filling, in which the company already claims to be a leader for blow moulding and filling processes, especially for PET and HDPE bottles. “Last year at drinktec, we presented the ‘Brewery 4.0’ concept. This includes continuous production and the late-differentiation approach. Our technologies are now being enhanced by highly flexible, multifunctional filling lines from Gea Vipoll, which meet the demand for complete solutions,” says Paddy Kenna, Head of Application Centre Beverage at Gea. www.gea.com www.bericap.com Unique range of light weight screw and sports closures for light weight PET neck standards for water • Closures for all common neck sizes 26/22, 28mm (PCO 1810, PCO 1881), 29/25, 30/25 • Light weight Hexalite range allowing light weight neck • Still water closures suitable for N 2 dosing • Sports closures fulfill BSDA requirements • Boreseal systems for excellent tightness • Consumer friendly opening forces BERICAP Technology for still water","@ID":53}, "PETplanet Insider Vol. 19 No. 11/18 petpla.net 61 BOTTLES PET can with window The American company Performix, foods manufacturer for active sports enthusiasts, is selling various products under its own brand including energy drinks in PET drinks cans. The cans contain 334ml of the differently coloured liquids. These aim to increase performance and stamina during sport or to support recovery after activity – depending on the selection of contents. The transparent cans are decorated with full sleeve labels with transparent windows to make the content of the product visible to consumers. The seal is a metal lid with ring-pull. www.performixdriven.com Halloween Smoothie from Aldi In time for Halloween, Aldi Süd brought several smoothies made from various fruits and/or juices onto its own chiller shelves in a time-limited promotion. The base was always bloodorange juice, which was then complemented with pear, cranberry and pomegranate or peach and raspberry. The vegan juices are 100% pure fruit. The transparent bottles each contain 250ml, are decorated with a rough, matt-printed label and are sealed with a screw cap with guarantee band. www.aldi-sued.de CakeLove in a jar Whether at room temperature, chilled or frozen, cakelove is a ready-to-eat batter or cake mix with cream cheese for immediate consumption or as a small snack. 96 g of the sweet temptation is packaged in a small, transparent PET container with a screw cap and a clear shrink-foil cover as a tamper-evident seal. The product can be found on the chiller shelves and must be kept cool; it is available in a variety of flavours and fits into any pocket or bag. www.cakelove.com Just dressing in PET Just for all, a relatively young company aiming to supply healthy, sustainablyproduced and reasonablypriced products for everyone, is selling under the “Just” label several dressings with recipes that meet the following requirements - non-GM, egg-free, glutenfree, dairy-free, Kosher, no artificial flavours. The transparent bottles contain 356ml of dressing – shown here is the “Ranch” variety. A transparent self-adhesive label on the front and a printed paper label on the back describe the product. The bottle is sealed with a hinged cap. For first opening, the cap must be removed and the freshness seal underneath removed. www.justforall.com","@ID":63}, "PETnews 6 NEWS PETplanet Insider Vol. 19 No. 11/18 petpla.net Passina sells Dutch operations to Döhler Group Döhler Group and Passina Group have reached an agreement on the acquisition of Concentra Europe BV with its Dutch and German subsidiaries by Döhler Group. The proposed transaction has now been filed with the relevant antitrust authorities and is conditional upon their approval. This transaction marks a step where customers will benefit from a more complete offering and improved efficiency of the combined businesses in a global market that is characterised by volatility, as well as the challenges and opportunities of supply and demand. Döhler Group and Passina Group believe that this step has created a path towards further growth in the market, while simultaneously strengthening their respective positions, specifically as reliable suppliers of tropical and natural plant-based ingredients for the global food & beverage industry. Concentra Holding AG, owner of the brand name Passina, will focus its future activities on its core business; the production and commercialisation of passion fruit products, including passion fruit juices, concentrates and derivatives. Maintaining its high-quality standards, it will place additional focus on the development of innovative new products and solutions. www.doehler.com Advent International invests in Manjushree Technopack Private equity investors Advent has invested in Manjushree Technopack Ltd., India’s largest rigid plastic packaging solution provider, in partnership with the founding Kedia family. As part of the transaction, Advent purchased all the shares owned by Kedaara Capital and a portion of the Kedia family’s stake in Manjushree Technopack. Manjushree’s Founder and Managing Director, Vimal Kedia, and the rest of the company’s senior management team will remain closely involved in the business. Financial terms of the transaction were not disclosed. Manjushree Technopack is the No.1 manufacturer of rigid plastic packaging for the fast-moving consumer goods (FMCG) industry in India. With world-class facilities and technologies, the Bengaluru-based company serves a wide range of FMCG vertical markets, including home care and personal care products, food and beverages, pharmaceuticals, dairy and edible oil. Advent International has been investing in India for 11 years and opened a Mumbai office in 2009. The transaction is Advent’s fifth investment in India in three years and third investment in the consumer packaging sector globally in less than two years. Including Manjushree, Advent has invested approximately 60 billion rupees (nearly US$1 billion) in seven companies with headquarters or operations in India. Advent also has significant experience in the industrial sector, including recent investments in two other consumer packaging businesses: Færch Plast, a Danish producer of rigid plastic packaging for the food industry, and Fort Dearborn, a leading North American supplier of high-impact decorative labels for the consumer goods marketplace. Kedaara Capital is an operationally oriented private equity firm pursuing control and minority investment opportunities in India. The firm has made 10 investments since 2014 across diversified verticals, including consumer and consumer derivatives, financial services, industrial and healthcare. Kedaara has strong expertise in the packaging sector with its investments in Manjushree Technopack and Parksons Packaging. www.adventinternational.com PepsiCo and Loop sign rPET agreement Loop Industries, Inc., a leading technology innovator in sustainable plastic and PepsiCo, Inc. announced that they have entered into a multi-year supply agreement that will enable PepsiCo to purchase production capacity from Loop’s joint venture facility in the United States and incorporate Loop PET plastic, which is 100% recycled material, into its product packaging by early 2020. Loop Industries has emerged with technology that allows no and low value plastics to be diverted, recovered and recycled endlessly into new, virgin-quality Loop PET plastic. This solution allows plastic bottles and packaging of any colour, transparency or condition, carpet, clothing and other polyester textiles that may contain colours, dyes or additives, and even ocean plastics that have been degraded by sun and salt to meet FDA requirements for use in food-grade packaging. As one of the largest purchasers of recycled PET plastic in the consumer goods space, PepsiCo has identified Loop PET as a commercially viable technology to expand the amount of recycled content in its product packaging and help meet its sustainability ambitions and consumer needs. The deal will also include a marketing and communications plan to raise awareness of the importance of recycling, sustainability and the circular economy. www.loopindustries.com","@ID":8}, "PACKAGING / PALLETISING PETplanet Insider Vol. 19 No. 11/18 petpla.net 30 Draught Master Draught Master is the 20-litre PET container from Carlsberg with a special tapping system, which guarantees longer-lasting freshness of the beer even after it has been first tapped. In a normal steel keg the freshness will already begin to deteriorate about seven days after first tapping, whereas in the PET keg the beer remains fresh for up to 30 days. This is a crucial consideration when it comes to underlining the premium character of a beer, because the guest in a pub or restaurant also expects a maximally wide diversity of beers. Thanks to Draught Master, restaurateurs are able to offer a broad choice of speciality beers without them getting stale, even if the volumes concerned are not large. And diversity is definitely much in demand in Denmark: the country’s inhabitants number a mere 5.8 million people, for whom more than 250 microbreweries are currently brewing over 2,500 craft beer varieties. “We would like to convert many more hotels, restaurants and catering outlets from aluminium kegs to the containers of the Draught-Master system, because they’re much easier to handle,” says Jeppe Holm-Jørgensen, who is in charge of the four shifts with two operators each. “Aluminium kegs are returnable containers, you see, you need water and chemicals to clean them, the empty kegs require storage space and they’re heavier.” The weight of the filled 20 litre PET kegs is significantly lower than that of aluminium kegs. And the fact that the PET kegs are used as disposable packs makes handling and logistics a whole lot easier. www.krones.com The filler is a special machine from the Modulfill VFS series, with 18 specially modified large-size filling valves. Since PET containers cannot be preevacuated, a blowing starwheel is inserted, through which the air in the containers is flushed out by means of carbon dioxide, thus preventing the filled beer from coming into contact with oxygen. After being filled, the containers are transported in carriers suspended on belts. C O N V E Y O R F O R C L O S U R E S Cross conveying Cooling","@ID":32}, "TRADE SHOW PREVIEW PETplanet Insider Vol. 19 No. 11/18 petpla.net 55 energy consumption, as well as an eco-friendly process. The stretch-blow moulding carousel is equipped with motorised stretch rods, controlled by electronic drives which do not require mechanical cams. This arrangement is designed to deliver precise control of the path of the stretch rod, significant energy savings and require less maintenance. The stretch-blow moulding system uses high-performance, low-dead volume valves, which help to reduce pre-blowing and blowing times, improve machine efficiency and boost product quality. SMI describes its Ecobloc Ergon K series as an ultra-compact system for stretch-blow moulding, filling and capping PET containers up to 3 l. It uses the same rotary technology and is suitable for production requirements from 1,000 to 9,000 bph. The EV models are designed to be suitable for milk and still water bottling lines; the EV versions are intended for edible oils. The Ecobloc version does not require rinser and the conveyor belts between the stretch-blow moulder and the filler. Electronic control and flow metercontrolled high-efficiency valves are designed to provide a precise and fast filling and capping process. False bottles integrated in the valve itself contributes to reduced preparation and cleaning time. The newly designed, unwelded modular frame incorporates safety doors made of tempered, highly resistant, long-lasting glass. SMI says that the “combi” solution of the Ecobloc Ergon K Series offers attractive value for money and is an innovative solution for even small bottling lines. www.smigroup.it Via Scodoncello n° 41/E - 43044 Collecchio (PR) - Italy - Tel.: +39 0521 541011 Everything and more... cooperating together global solutions for containers in PET and other plastic materials Design, construction & installation of: • Systems for handling & storing all types of plastic containers • Linear blow molders for PET bottles LANFRANCHI S.r.l. www.lanfranchi.it innovation plastic container Design, industrialization, blow molds & prototype sampling for PET containers IPC S.r.l. www.ipcsolution.it","@ID":57}, "11 NEWS PETplanet Insider Vol. 19 No. 11/18 petpla.net Bottled water overtake all other soft drinks worldwide Zenith Global launches new Globaldrinks Database “Bottled water consumption is set to overtake all other soft drinks worldwide this year,” according to Richard Hall, Chairman of Zenith Global, the global food and drink experts, speaking at the 15 th Global Bottled Water Congress in Evian. “This is all the more remarkable because other soft drinks include carbonates, juices, energy, sports, concentrates, ready to drink teas and coffees, some of which are also growing strongly.” Bottled water consumption reached 418 billion litres in 2017, up 92% since 2007, an average approaching 7% a year and a 10 year increase of 200 billion litres. All other soft drinks totalled 438 billion litres in 2017, up 24% since 2007, an average of 2% a year and a 10 year increase of 84 billion litres. “We are therefore forecasting 2018 will be the year when bottled water exceeds the total for all other non-alcoholic beverages. It covers 24 non-alcoholic beverage categories and segments across 86 countries in both volume and value, with figures going back to 2006 and forecasts up to 2022.” The globaldrinks.com database was originally introduced in 2000 and has become the definitive business planning reference for many companies in the beverage industry as well as others seeking to understand and compare national market characteristics against regional or global trends. The database is fully interactive and can be used to generate charts as well as tables. Richard Hall demonstrated the power of the database by comparing bottled water prices for five market segments over the past 10 years. “This shows that the vast majority of bottled water is not only healthy, convenient and local, it is also very affordably priced with virtually no increase in average prices during the past ten years.The price of bulk water in packs over 10 litres has consistently averaged out at US$0.15 or less per litre and the average for smaller packs of still water has not risen above US$0.65 per litre. Nevertheless, there is a strong premium for other waters, with sparkling water averaging up to US$0.97 per litre, flavoured water up to US$1.49 per litre and functional water up to US$1.95 per litre. In dynamic and constantly changing markets, it is essential for producers and suppliers to keep on top of the latest consumption trends. This database underpins and informs much of our work around the world across the full range of beverage categories,” he concluded. www.globaldrinks.com","@ID":13}, "PACKAGING / PALLETISING PETplanet Insider Vol. 19 No. 11/18 petpla.net 25 PACKAGING / PALLETISING 25 filling capacity for 1.5 litre bottles is 18,000 bph. Mechatronic drives for conveyor technology The processes involved in the drinks’ industry place particular demands on conveyor systems and their drives. All movements and speeds must be adapted to the filling process. SEW-Eurodrive has many years of experience in mechanical and electrical drive technology for the drinks industry. Whether as a mechatronic drive unit, as a geared motor with integrated electronics or as a compact gear motor in combination with the control cabinet inverter, the SEWEurodrive Movigear product range is claimed to be an effective solution for the particular demands of conveyor systems. SEWEurodrive has been able to minimise system losses and make the drive units extremely compact, thereby meeting customer requirements, even with limited installation space. Thanks to optimally matched components, these drive solutions have a very high system efficiency. Synchronous rather than asynchronous motors are used. The higher power density makes the drives smaller and the permanently energised motors have a higher overload torque. They operate in an optimised energised manner and enable the drive solutions to be standardised. This [email protected] Tel: +90 212 695 50 00 Fax: +90 212 694 97 24 100815dmyR .com The processes involved in the drinks’ industry places special demands on conveyor systems and their drives. All movements and speeds must be adapted to the bottle-filling process. (Photo: Hell Energy) Hell Energy has invested more than seven million Euros in a PET bottling filling facility. (Photo: Hell Energy)","@ID":27}, "MARKET SURVEY 35 PETplanet Insider Vol. 19 No. 11/18 petpla.net 11/2018 MARKETsurvey Palletising and shrink film machinery For the second time PETplanet Insider focuses on palletising and shrink film machinery to mark the occasion of Brau Beviale and All4Pack trade fairs 2018. Here you find the machine details of state of the art technology from participating companies: SMI S.p.A., Krones AG, Productive Systems (Pty) Ltd, Gebo Cermex, Jiangsu Newamstar Packaging Machinery Co., Ltd., GEA Group, And&Or and Sipa S.p.A. Although the publisher have made every effort to ensure that the information in this survey is up to date, no claims are made regarding completeness or accuracy. Resins & additives Preform machinery Preform production Preform inspection SBM 2-stage Compressors Filling equipment & filling inspection Caps & closures and inspection Palletising & shrink film machinery Recycling Company Krones AG Gebo Cermex Jiangsu Newamstar Packaging Machinery Co., Ltd AND & OR Postal address Telephone number Web site address Contact name Function Direct telephone number Email Böhmerwaldstraße 5 93073 Neutraubling, Germany +49 9401 70 0 www.krones.com Mr Andreas Fritsch Product Man. Packaging Techn. +49 8031 404-516 [email protected] Rue du Commerce, 67116 Reichstett, France +33 388 183 880 www.gebocermex.com Ms Lucia Freschi PR Manager +39 0521 9991 [email protected] No. 8 Xinjing East Road, Zhangjiagang Eco- and Technological Dev.-Zone, Jiangsu Province, China, 215618 +86 512 5869 1111 www.newamstar.com Mr Gang Yin Marketing Manager +86 512 56993303 [email protected] PI El Limon, Av. de Europa, 6, 41928 Palomares Del Rio (Sevilla) - Spain +34 954 779 200 www.andyor.com Mr Caridad Ortega Suárez Sales Director +34 954 779 200 [email protected] Shrink film machinery: Packaging options & output rate (packs per minute) Up to 120 cycles per minute (PETbottles), 150 cycles per minute (cans) in 3 lanes - print registered film (yes/no; packs/min) Yes, up to 150ppm, 4-lane è 600ppm Yes Yes, 60 No - nested pack (yes/no; packs/min) Yes, up to 100ppm Yes No Yes, from 15 up to 900bpm - label orientation (yes/no; packs/min) Yes, up to 200ppm Yes No No - carry handles (yes/no; packs/min) Yes, up to 80ppm, 2-lane è 160ppm No No Yes, from 15 up to 400bpm - pad supported (yes/no; packs/min) Yes, up to 120ppm Yes Yes, 60 Yes, from 15 up to 400bpm - tray supported (yes/no; packs/min) Yes, up to 120ppm Yes Yes, 60 Yes, from 15 up to 400bpm - film only (yes/no; packs/min) Yes, up to 150ppm, 4-lane è 600ppm Yes Yes, 80 Yes, from 15 up to 900bpm - tray and film (yes/no; packs/min) Yes, up to 120ppm Yes Yes, 80 Yes, from 15 up to 900bpm - pad and film (yes/no; packs/min) Yes, up to 120ppm Yes Yes, 80 Yes, from 15 up to 900bpm shrink process: - shrink tunnel with hot air or gas fired option Yes Yes Yes Shrinking pistols (hot air) - oven Yes Yes Yes - steam tunnel No No Yes Footprint Depends on speed Depends on configuration Several models depending on speed Number of possible lanes 4 Up to 3 lanes Max. length of the pack is 1400mm Packaging material and possible thickness LDPE + ( LLPDE, MDPE, HDPE, PP) Printed …., 25μm-120μm Low-density polyethylene (LDPE) from 27 to 100 microns LDPE + LLDPE 40 to 60 microns Voltage/power/energy consumption Depends on speed, package and material NC Several models depending on speed Film cutting and feeding system Yes Yes Yes Certification CE / UL CE certification CE and UL Palletising machinery: Format changeover time Depending on machine type from 0 to 10min Depends on configuration 20min 15-20min Output rate (packs per minute) Depending on machine type up to 600 layers/h; output rate of packs additionally depending on pack type and layer formation; example: 600 layer/h and 10 packs per layer: 6000 packs/h Up to 12 layers/min 140 Up to 400bpm Automatically intergrated:(yes/no) Yes Yes Empty pack feeding Depends on type of pack, technical request necessary Empty pallet feeding Auto Yes Insertion of interlayers Yes Yes Auto Yes Connectable to shrinkwrapper Yes Yes Yes Yes Special characteristics: i.e. low-level feed, cross conveyer barrier Single and double column machines, groundframe,earthquakesafety,highand low level infeed depending on machine type, pallet hoist systems possible Available on high and low level infeed Low-level feed, cross conveyer barrier Low-level feed Tray former possible to be integrated (display palletiser)","@ID":37}, "PETproducts 58 PETplanet Insider Vol. 19 No. 11/18 petpla.net Connected caps Closure Systems International (CSI) and Talkin’ Things, a leading company in product communication platforms, have collaborated to integrate smart packaging technology into CSI’s global platform of closures. CSI and Talkin’ Things have developed a new packaging solution named Talkin’ Cap, which uses embedded Near Field Communication (NFC) tags, for application on the inside of closures. This technology introduces a powerful platform to support a brand owner’s mobile marketing activities right from the package itself, with just a simple tap. Brand trustworthiness and product reliability are paramount for consumer loyalty. Talkin’ Caps ensure product safety and reduce brand owners’ liability by protecting against counterfeiting and “grey market” activities throughout the distribution stream. CSI’s Talkin’ Caps allow for real-time consumer interconnectivity at the point of consumption, giving brand owners the unique ability to have dynamic interaction and gather actionable insights based on consumer location and usage history. Talkin’ Caps are an app-less way to drive marketing content, brand and product information, gamification, loyalty programs, awards and coupons to connected consumers. www.csiclosures.com www.talkinthings.com Because fresh drinking water is worth its weight - in Gold Around the world, Ujeta Care is helping ensure that people can obtain clean drinking water for themselves, quickly and easily. Schneider Kunststofftechnik, based in Kirchheim, Germany, and the parent company of Ujeta GmbH, has now been honoured with the German Innovation Award, in recognition of its unique water filter system. Ujeta Care won the Gold Award in the “Business to Consumer” category. The innovative water filter system has already impressively demonstrated its value-added for others. For example, 10 Ujeta Care units are in use in Haiti, supplying around 300 children there daily with fresh drinking water since hurricane “Matthew” in October 2016. Ujeta stands for water (Kosovan “uje”) and life (Kosovan “jeta”). The Ujeta water filter is one of the smallest and most effective water treatment systems in the world, with a filter output of up to 5,000 litres per unit. As a portable, lightweight system (weighing about 3000g), it is quickly ready to use and filters the water in the place where it is needed, not where it is extracted. That enables the Ujeta Care to deliver a lasting improvement in drinking water supply worldwide. Thanks to combined ultra-filtration using activated carbon and membrane filters (LOG 6 classification), the Ujeta Care removes 99.99% of all bacteria and germs, along with heavy metals, drug residues, chlorine products and chlorine decomposition products, pesticides, organic compounds and asbestos fibres. The high-quality activated carbon filter operates with a filter fineness of up to 0.45μm, and also exploits the high absorption effect of the activated carbon, as a pure natural product. The membrane filter, with its high-tech hollow-fibre membrane, has a filter fineness of up to 0.1μm. Bacteria, germs, moulds, metal particles and microorganisms are thus retained in the membrane filter, while valuable minerals remain intact in the water. Energising bio-crystals and a special turbulence technique gives the filtered water a spring-water quality. The effectiveness of the Ujeta Care was confirmed by the well-known drinking-water laboratory of Dr. Staber & Kollegen. Scientific ‘before and after’ examinations using brackish pond water have shown that the Ujeta Care is ultraefficient in filtering out coliform bacteria, intestinal enterococci and E. coli. Where the brackish pond water exhibited 200.5 MPN/100ml E.coli, after filtration using the Ujeta filter this was 0 MPN/100ml. www.ujeta.com www.sk-tech.de","@ID":60}, "TRADE SHOW PREVIEW PETplanet Insider Vol. 19 No. 11/18 petpla.net 52 RAL Hall 4A booth 511 Average recyclate content of 50 percent in disposable PET bottles by 2022 Raising the rPET bar RAL quality association “Wertstoffkette PET-Getränkeverpackungen e.V.”, founded in 2014, has set itself the goal of promoting further development of PET beverage bottles from an ecological point of view. The RAL quality association spans supply chains and sectors. Its 30 plus members include PET recyclers that manufacture recyclates which come into contact with food (food-grade), preform producers and beverage producers of mineral waters and soft drinks. At Brau Beviale, the RAL quality association will present the special show PET Recycling. With its technical requirements, the RAL quality association sets the benchmark for the process stages of the PET beverage packaging recycling chain. Manufacturers of PET recyclates, preform manufacturers and beverage bottlers took the initiative in 2014 to ensure a virtually closed material cycle within the framework of current and future quality assurance. The aim is to increase the amount of recycled material in PET beverage bottles in accordance with high quality standards. This will ensure a high level of consumer protection and optimised interfaces across all stages of the supply chain. In order to be able to carry the uniform RAL quality mark, it has been necessary to manufacture new PET bottles containing at least 25 percent recycled PET material. According to the latest GVM study, an average of 26 percent PET recyclate is currently used in German non-refillable PET bottles. This value is to be significantly increased. The RAL quality association has set itself the goal of achieving an average recyclate content of 50 percent in the qualityassured products by 2022. The members are endeavouring to include further relevant links in the recyclables chain in the quality association in order to achieve this goal. “We are aware that the various stages are not yet represented in the quality association. We are open to innovation and, together with the beverage industry and above all the retail trade, would like to cover the entire value chain of PET beverage packaging in the future”, says managing director Irina Bremerstein. “The public’s and consumers’ desire for more sustainability affects all sectors of the beverage industry. That’s why a voluntary commitment for a sustainable cycle is the right response,” continues Bremerstein. At Brau Beviale the RAL quality association presents its goals to the visitors. It is supported by the “Arbeitsgemeinschaft konsumenten- und ökologieorientierte Getränkeverpackungen e.V.” (Consumers’ and Ecology-Oriented Beverage Packaging Association) and the “IK Industrievereinigung Kunststoffverpackungen e.V.” (IK Industrial Association for Plastic Packaging). The Industrial Association for Plastic Packaging represents the interests of plastic packaging and film manufacturers in Germany and Europe. The Beverage Packaging Association and the companies it represents are committed to sustainability and continuous optimisation of the PET disposable system. www.wertstoff-pet.de","@ID":54}, "TRADE SHOW PREVIEW PETplanet Insider Vol. 19 No. 11/18 petpla.net 53 Sidel Group Hall 7A booth 223 Flexible production process will meet consumer trends in beverage packaging Adapting consumer demands The beverage market in Europe is set to experience a number of considerable changes within the next three years: the industry is anticipating a trend towards smaller size containers coupled with an overall movement towards the multiplication of SKUs and a premiumisation of the package. These trends require flexibility in the production process while simultaneously reducing the Total Cost of Ownership (TCO). The Sidel Group’s answers to these upcoming challenges can be appraised at Brau Beviale. Sidel and Gebo Cermex will be showcasing their flexibility to adapt to changing consumer demands with their latest solutions. Among them are the new Sidel EvoDeco labelling solutions: designed for total flexibility and optimised for unmatched performance, it gives producers the ability to choose technologies based on their specific labelling needs and output levels. Additionally, Sidel will highlight Sidel Actis, the plasma coating soluAs proof points of the company’s secondary packaging expertise, visitors to the Sidel Group stand will have the opportunity to get a handson experience of the Gebo Cermex’s WB46 - a wrap-around case packer that is claimed to offer good performance in terms of flexibility, hygiene and ergonomics – and of the company’s EvoFilm shrink-wrapping system. The latter one is a robust, versatile, compact and energy-efficient solution that is drawing on the company’s 50 years of experience in this field. Maintain and improve performance over time EIT (Efficiency Improvement Tool) is a solution established to maintain and improve packaging lines’ performance throughout their lifecycle. This data acquisition and plant intelligence system is designed to decrease unplanned downtime, reducing waste and costs, and increasing the plant’s output, as it gives employees at all levels real-time access to relevant and actionable information on productionrelated issues. www.sidel.com www.gebocermex.com tion extending the shelf life of beverages bottled in PET, while enabling package lightweighting. New approach of conveying and accumulation Gebo Cermex, long-time expert in the beer processing market, will focus on AQFlex, an all-in-one product handling technology, able to accommodate any product, whatever the application, whatever the market, in all container materials, formats and shapes, full or empty, while also enabling automatic changeovers and ensuring total care of product integrity.","@ID":55}, "46 TRADE SHOW PREVIEW PETplanet Insider Vol. 19 No. 11/18 petpla.net The Zeg keg Cypet Technologies will showcase its new, one-way beer PET keg. The ‘Zeg’ features a top chime and handles that are integrated with the rest of the keg body (patent pending). Having the top chime, handles and keg body formed as one piece significantly reduces the production cost of the keg, since there is no need to separately produce the top chime and assemble it onto the keg, states the company. Furthermore, the strong mechanical properties of PET allow for the top chime to be lighter in weight than conventional chimes yet still able to handle the loads that the Zeg will face through its life cycle. On the safety side, apart from having a high burst pressure (four times higher than the normal beer dispensing pressure), the Zeg features a patent pending pressure relief valve that is incorporated on the neck of the keg. In case of internal pressure build-up, the valve will be triggered automatically to release the excess pressure. The valve protects the keg all through its life cycle, even while it is coupled to a dispensing system. Once the keg is empty, it can be easily de-pressurised manually using no tools, ready for recycling. Advantages of the Zeg include no cleaning, return or theft costs. Coming to the brewery pre-purged with Nitrogen, pristinely clean and with excellent O2 , CO2 and UV barrier properties, it keeps the beer fresh and intact with a year-long shelf life. The Zeg has been built using Cypet’s patented injection stretch blowmoulding process. www.cypet.eu Permanent inline quality control of cap and fill volume To avoid regular customer reclamation because of over- or under-torqued screw caps, or such that are tilted or even leaking, BBull Technology developed Image APA FQM. What happened previously with random samples in the laboratory can be done now inline or in a bypass by a special optics which detects the cap application angle (APA) of every sample. This gives feedback to the torque of the closure and allows the detection of tilted caps or leaking closures. Additionally, a calibrated checkweigher can be installed in the bypass to determine the filling volume to a legally confirmed precision. In combination with BBull Image FQM software the faults are immediately visualised, in relation to the filling or closing head. A permanent real-time quality control happens now directly at the “point-of interest”, with documented results - and not hours late in the laboratory. Other new inspection systems exhibited include Pulse for missing pressure on flexible containers like PET and cans. Additionally, the latest generation of empties inspection as well as sorting and distribution system will be on the display. www.bbull.de Full-range supplier to the beverage industry Together with its subsidiaries Kosme, Syskron, Evoguard, KIC Krones, Milkron and System Logistics, Krones will be showcasing its comprehensive corporate capabilities as a complete-system vendor for filling and packaging technology in the brewing and beverage industries. When it comes to beer production, filter systems and Krones Dynafill filling concept will be on display. Filling and capping comes up with further innovations: The Modulfill HES, specifically designed for beer, carbonated soft drinks and wine, has been design-enhanced from the infeed, then filling and closing, all the way through to the discharge, focusing particularly on the issues of safety, operator-friendliness, space savings and hygiene. The Varioline packer from Krones AG, which has established itself very successfully in the brewing and beverage industries, will also be showing its latest innovations at the Brau Beviale. Krones’ portfolio at the Brau Beviale will be supplemented by products from its subsidiaries. Kosme will be spotlighting new systems for the compact class. One highlight here is the new KSB 3R Compact stretch blow-moulding machine. With its three cavities, it extends Kosme’s portfolio of rotary machines, scoring particularly highly in terms of minimised footprint and energy savings. System Logistics’s laser-controlled Automated Guided Vehicles and Syskron’s Connected Line are handling the logistics within the production and Syskron’s Connected Line not only provides plant operators valuable information on production. Storing production data in the cloud renders them accessible at all times to everyone involved. The advantage is manifest: the better the communication between machines, processes and staff, the more efficient the production process will be. www.krones.com Krones Hall 7A | Booth 510 Cypet Hall 7 | Booth 820 BBull Hall 7 | Booth 546/647","@ID":48}, "PETplanet Insider Vol. 19 No. 11/18 petpla.net 63 BOTTLES Dual function snap-on lid The question of where to put the shower gel in the shower is answered by the manufacturer in many ways. Under its own brand “PJC”, the Canadian pharmacy chain Jean Coutu is selling 395ml of shower gel with lemon scent and tea-tree extracts in a slightly contoured bottle with a specially shaped snap-on lid. When removed from the upper end, it can be attached securely to the base. The bottle can now be suspended as an upturned bottle and the product can be dispensed through the silicone valve in the cap by squeezing with one hand. When the pressure is released, the valve cuts off the flow of product. www.jeancoutu.com Aloe Vera gel for after-sun skincare The Canadian retail chain Sobeys is selling 480 ml of moisturising Aloe Vera gel under the brand “Compliments” in a clear bottle with a screw-on disc-top cap. The cap has a surface to guide finger positioning to open the cap even with wet hands. The thick, almost rigid liquid is extracted by squeezing the bottle. A self-adhesive label around the bottle provides product and retail information. www.compliments.ca/en Melon and cucumber washing-up assistance The cleaning powers and aromas of melon and cucumber are used by the Canadian retail chain Sobeys in their Ultra Dishwashing Liquid for handwashing crockery. The symmetrical, transparent bottle holds 739ml and has indented areas for its shaped self-adhesive labels. The seal is a screw-on, push-pull cap. www.iga.net/en www.compliments.ca/en/","@ID":65}, "BOTTLING / FILLING PETplanet Insider Vol. 19 No. 11/18 petpla.net 22 BOTTLING / FILLING 22 Niagara Bottling LLC invests in line efficiency 2 million cases of extra productivity The private label bottled water supplier, Niagara Bottling LLC, with its many plants throughout the US and Mexico, has recently upgraded its Salt Lake City facility with a Sidel complete PET line. The line features two Super Combis, equipped with the compact ground-level preform feeder, EasyFeed, along with Gebo Cermex conveying and end-of-line equipment. This investment has enabled the bottler to increase its productivity to +2million cases per year. Niagara Bottling LLC has more than 50 years of business experience in the water market, offering its customers products of more than 40 different brands. Grounded on the fact that the PET bottled water market in the US is expected to grow by acompound annual growth rate (CAGR) of 3% year on year between 2016 and 2020 (according to Euromonitor data), the company decided to rely on its long-standing business relationship with Sidel and install a new complete PET line to enlarge its production capacity to answer consumers’ demand. Starting point of the new complete line at Niagara’s plant is Sidel’s EasyFeed, a compact and safe ground-level preform feeder for PET lines. From the hopper, the preforms are lifted by an elevator column to only 2,5m. They are then sorted mmm$he[Z[hi$Z[ Y O U R PA R T N E R F O R B L OW MO U L D S . STEPS TO THE PERFECT BOTTLE. >YZV 9Zh^\\c IZX]cdad\\n BVcj[VXijg^c\\ 8bem CekbZ &%% HZgk^XZ Meet us at Brau Beviale in Nuremberg - Hall 7A / 7A - 301","@ID":24}, "PETplanet Insider Vol. 19 No. 11/18 petpla.net 60 PETbottles Beverage + Liquid Food Summer juice from Aldi Süd For a short time, Aldi Süd had in its own-brand Rio d’Oro range, two NFC juices made especially from summer fruits. The chilled juices, “Surfing in the peach!” with apple, peach, strawberry and blackcurrant juice and “Summer Berries!” with apple, raspberry and rhubarb juice were 100 % not from concentrate and gently pasteurised. The 750ml bottle, slightly contoured in the neck area, was decorated with a partially transparent foil label and sealed with a screw cap with a guarantee band. www.aldi-sued.de Protein drink from Canada In Canada and the USA, protein drinks have already become classics for retailers. An example of suitable bottle shapes for this category is the contoured, stable bottle from the brand “Core Power” from fairlife, a federation of smaller milk producers, who sell their products in collaboration with Coca Cola. The milk is specially filtered and gently treated to create the best possible product quality. The bottles contain 340ml of drink with a protein proportion of 26 grams per bottle. The informatively printed sleeve label is drawn up over the screw cap as a tamper-evident seal and is perforated for easy removal. www.fairlifecanada.ca/en Brewed ice tea in PET The Canadian manufacturer Compliments, is selling 1.75 l of Brewed Ice Tea with a raspberry flavour under the brand “Sensations” in a carafe-shaped, multi-surface bottle with an easy-grip neck area. The body of the bottle features horizontal embossing to stabilise it during handling. Two opposingly positioned self-adhesive labels and a screw cap with guarantee band complete the packaging. www.compliments.ca/en","@ID":62}, "TRADE SHOW PREVIEW PETplanet Insider Vol. 19 No. 11/18 petpla.net 48 KHS Hall 8 booth 418 The fifth generation InnoPET Blomax stretch-blow moulding machine Higher output, lower energy consumption The mechanical engineering company KHS can look back on over 40 years’ experience in PET processing, particularly in the development of stretch-blow moulding machinery. High speed and energy performance could further be boosted at its InnoPET Blomax whose Series V will celebrate its world premiere at this year’s BrauBeviale. This and other new developments will be presented for the first time by Kai Acker, the new Chairman of the KHS Group Executive Management Board. KHS promotes the fifth generation of its stretch-blow machine as the most sustainable and best performing InnoPET Blomax machine ever produced. “The views of customers are very important to us and inform on-going efforts to improve our stretch-blow moulding machinery. However, such a technological advance has only been possible with the completion of a new heating concept development. With the introduction of the new Series Five generation of machines, we want to show people what a stretch-blow moulder is really capable of”, says Marco Böhnke, Product Manager of Block and Stretch-Blow Moulding Technology at KHS. The Fifth Series of InnoPET Blomaxis designed to produce up to 90,000 0.2-3.0 l bottles per hour, as well as making lightweight and premium bottle types just as efficiently as individual bottles and containers. Depending on requirements, 6-36 blowing stations are available, each with a capacity for producing up to 2,500 bph. Thanks to the quickchange system, changes in sizes can be undertaken smoothly and quickly ensuring constant high system availability. The new generation of stretch-blow moulders is claimed to fit seamlessly within the KHS Group’s blocking strategy and can be operated in tandem with fillers and labellers, Plasmax barrier technology and many other modules at the same time. A new heating concept Compared with its predecessor, Series Five can achieve energy savings of up to 40% thanks to a brand new heating concept, one of the key developments in the latest generation of technology. The focus here is on Near Infrared (NIR) emitters which are centrally mounted in the closed reflector tunnel. Preforms in the oven are placed to the left and right of centrally fixed radiant heaters, resulting in very small spacing between the preforms of 18mm (compared to the previous 37mm). Consequently, KHS has been able to reduce the number of heating boxes which also cuts down radiation losses, have contributed bring about these huge energy savings. Two cooling cycles The new DuoCooling concept involves an external cooler which supplies two cooling cycles operating under different temperatures; one for The KHS InnoPET Blofill series five: the fifth generation InnoPET Blomax is the most sustainable and best performing machine of its kind thanks to a range of different innovations. DoGa 1 heating concept: Series Five achieves energy savings of up to 40% compared to its predecessor due to a completely redesigned heating concept.","@ID":50}, "The whole world of Congresses PET symposiums and lectures WikiPETia.info PET knowledge management system Pulse The monthly PET price index Worldwide PET magazine Social Media Connecting worldwide ISSN: 1438-9452 No. 9 2016 PETplanet is read inmore than 140 countries MAGAZINE FOR BOTTLERS AND BOTTLE-MAKERS IN THEAMERICAS,ASIA, EUROPEANDALLAROUND THE PLANET 07.09.16 MARKETsurvey Bottle-to-bottle recyclingplants Page 41 TheChinaRoadShow Page 12 bottlemaking Page 21 Page 52 PETplanet is read in more than 140 countries News Daily PET business news Editours Worldwide editorial reporting petpla.net WHY PETPLANET? For more than 19 years, PETplanet Insider has been the world’s leading magazine for the PET bottling and bottle-making industry, bringing together machine manufacturers and their customers – directly, with up to date on-site reports at customer plants, providing first hand information on the latest developments and trends. Our market reports and surveys, along with interviews with the major players in the industry give our readers an excellent overview of what is happening in the world of PET. PETplanet Insider continues to be the highly specialised source of information for more than 10,000 readers in over 140 countries and the ideal publication for advertisers who wish to target decision makers in this sector. Events Fairs, open houses, on-site sessions ... 1999 19 YEARS o f PE T l p ane t","@ID":31}]}}
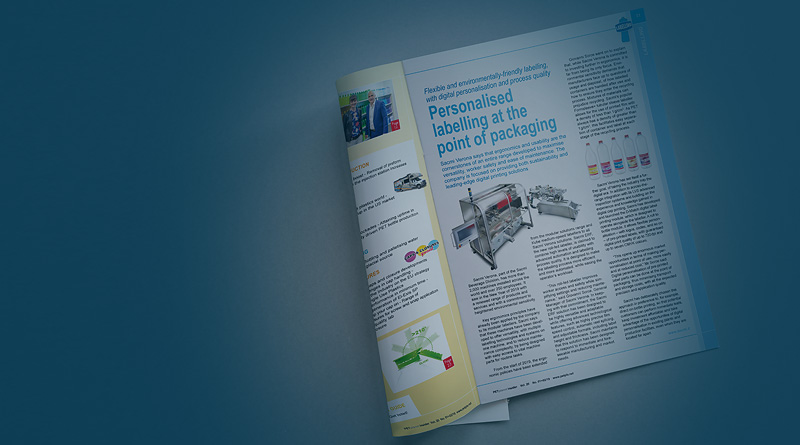