38 TRADE SHOW REVIEW PETplanet Insider Vol. 19 No. 12/18 petpla.net CBB Impressions - Chinese exhibitors of PET Filling & Combibloc solutions Guangzhou Vanta Intelligent Equipment (Mr Daniel Tao) www.vanta.cn Filling, sealing, packaging Hefei Zhongchen Light Industrial Machinery Co Ltd (Mr Aaron Zheng) www.hfqj.com Combibloc up to 30,000bph Jiangsu Zhongyin Machinery Co Ltd (Mr Wu Han) www.china-beverage.com Filling 3,000 up to 36,000bph, aseptic, CSD, edible oil Sushou Puqia Blowing Technology Co Ltd // Zhangjiagang Hy-Fill Machinery Co Ltd (Mr Winco Lui) www.puqiapet.com Aseptic line PET 8-18 cav. 15,000-30,000bph (500ml) Hangzhou Youngsun Intelligent Equipment Co Ltd (Mr Jared) www.youngsunpack.com Filler up to 40,000bph water, CSD Jiang ASG Packaging Machinery Group (Mr John Chen) www.asgmachinery.com Combibloc up to 45,000bph, water, CSD, aseptic Langfang BestCrown Packaging Machinery Co Ltd (Ms Sarah) www.bestcrownchina.com Combibloc up to 81,000bph, water, aseptic Zhangjagang Fillex Machinery Co Ltd (Ms Anna Yang) www.fillex-packer.com Filler 1,800 up to 32,000bph, non-carbonated Hangzhou Zhongya Machinery Co Ltd (Mr Niel Zhang) www.zhongyagroup.com Combi 14 to 20 cav. 24,000-36,000bph Sunrise Intelligent Equipment Co Ltf www.kqsbz.com Aseptic filling 8,000-24,000bph Zhangjiagang Asiastar beverage Machinery Co Ltd (Ms Una Li) www.asiastarewa.en.alibaba.com Rotary filler for 4.5 and 15 l 12 valves Zhangjiagang City Wanjin Machinery Co Ltd (Ms Bella Wang) www.wanjinjx.cn Complete lines for water, CSD and hot filling from 1,000bph up to 32,000bph,@ID:40}, TRADE SHOW REVIEW PETplanet Insider Vol. 19 No. 12/18 petpla.net 40 Sidel presents solutions for a fast-changing market environment at CBB – PETplanet in talk with Clive Smith, Executive Vice President of Sales, Sidel “Modularity and service are key“ PETplanet: To what extent does Sidel’s presence here at CBB reflect the requirements of the Chinese beverage technology market? Clive Smith: The focus in China is currently on aseptic filling. This is why we are establishing aseptic lines into the Chinese supply chain. Our Aseptic Combi Predis FMa blow fill seal filler is one example. Our patented technology is 100% safe for the packaging of UHT milk, soymilk, coconut water, or teas in PET bottles. And it is FDAapproved following tests run at a dairy customer in North America last year. The Sidel Aseptic Combi Predis is one of our highlights here, merging dry preform sterilisation with aseptic blowing, filling and sealing functions within a single production enclosure. It differs from traditional aseptic technology because the package sterilisation takes place at the preform rather than at the bottle phase. PETplanet: When we talk about aseptic - which drinks are currently trending in China? Clive Smith:The water market is on the rise but the liquid dairy market is growing as well – drinkable yogurts for example are very promising. The juice market is also growing but this is not so obvious. And even in traditional beverage segments, such as tea, there is the potential for new creations. A relatively new beverage trend for example is carbonated tea. PETplanet: Aside from aseptic filling, what other trends regarding filling in PET are you observing in China? Clive Smith: Here, premiumisation is a big trend. It is quite the opposite from the lightweighting trend other countries are facing. Premiumisation means a rather thick glass-like appearance whereas thin packaging formats have lost share. As regards packaging materials, this results in a switch to PET, often from HDPE, for premium products. In the premium segment, we can win with our StiffPrime packaging solution. Featuring a “champagne base” and the possibility of closing the bottle with a crown cap, this PET bottle design resembles glass containers, thus contributing to brand image, while offering great resistance to high carbonation and pasteurisation. This is why, besides adding value to the product, it is particularly suitable for carbonated soft drinks and beer. by Gabriele Kosmehl Clive Smith, Executive Vice President of Sales, Sidel,@ID:42}, PREFORM PRODUCTION PETplanet Insider Vol. 19 No. 12/18 petpla.net 14 Interview with Gianfranco Zoppas at Sipa’s Open House in Vittorio Veneto Boundaries becoming blurred by Alexander Büchler Up until now, the PET world has been characterised by recyclers and processors. The pioneering Gianfranco Zoppas, the owner and founder of Sipa, has been blurring the lines that have existed for decades. In addition to its “Xtreme Renew” injection-compression preform line starting from flakes, the processor can bring the vital phases involved in PET processing in-house, while the recycler can also become a preform producer. At the in-house exhibition in Vittorio Veneto, Italy, Sipa showcased their latest development in Xtreme, blocked with a stretch blow mould and filling line: Xtreme Sincro Cube. The idea is as simple as it is brilliant. The process from flakes to bottles takes place directly in one single thermal cycle instead of via granulation as has been the case previously. Many companies have attempted this but with varying levels of success - these have always resulted in specks and burned dark spots appearing in the bottle wall. Sipa has taken a new approach and is processing washed and sorted flakes which first pass through the Erema upstream food-approved decontamination system Vacurema Advanced or equivalent system to get the IV to the required level. From there, it goes via an extruder directly into the Xtreme’s hot runner. As the preforms are produced one after another in individual cavities – arranged on a carousel – the melt flow is continuous. The Xtreme system can produce preforms that are up to 8% lighter than even the lightest injection moulded preform - but without compromising on any key properties. Injection-compression moulding overcomes the issue of filling moulds with very thin walls, by floating core. This means lower injection pressure can be used, lower clamp force is needed and there is less stress on the melt. Xtreme is a clean machine too: it is the first totally oil-free high-output preform production system. Preforms are 100% controlled in-line by cameras to assure the best quality. The hot preform leaves the Xtreme and is transferred to a conditioning unit by means of transmission stars. This is where Sipa can demonstrate all of its 40 years of know-how in single-stage systems where conditioning is vital for a uniform stretch blowmoulding process. Once the blowing phase is complete, the filling process takes place without a rinser or bottom cooling. The entire system has a number of distinct advantages: Up to 8% of material can be saved by using the injection-compression moulding process; The energy input in the preform processing is sufficient to produce the finished bottle. No infrared heating of the stretch blow mould is required; The space needed for the integrated plant is significantly smaller than for a facility that has individual machines as preform handling, for example, is not required. “My dream: The Xtreme” PETplanet: When it comes to preform production equipment, we have seen many well-known machine builders come and go. Sipa has been very successful in this field for more than 20 years. What is the secret of your success? Zoppas: There is no secret. My vision is from pellet to pallet. Our focus is on the entire process chain for producing a PET bottle. This knowhow is built in to all our preform systems and moulds. PREFORM special Xtreme Sincro Cube Gianfranco Zoppas welcomes Alexander Büchler at the Sipa Open House.,@ID:16}, BOTTLING / FILLING PETplanet Insider Vol. 19 No. 12/18 petpla.net 26 will make a significant contribution towards growing exports, and towards exerting a beneficial influence on our country’s economic development as well,” is Irina Gaprindashvili’s firm conviction. “Our aim is to supply these products, and our own, to the entire region comprising our neighbouring countries, and to the Near East.” This makes the new plant a strategic location as a regional producer for Rauch’s beverage portfolio and for the Nabeghlavi articles. The second important aspect for Healthy Water was to be also able to fill dealer’s brands in the future. “Producing private labels in cans is a particularly attractive option. Some inquiries in this regard have already reached us from neighbouring countries,” explains Irina Gaprindashvili. The multiple options for filling available at Healthy Water and its closeness to the port can be expected to translate this concept into marketing reality quite soon. “The mediumterm goal is to increase the number of fills from its present 76 million to 200 million by 2023,” she says. “And even that would not be the end of the story for us. We could erect the warehouse a bit further upstream, at the place where the old factory used to be, and accommodate further filling lines on the ground floor of the new plant.” These plans augur extremely well for a highly promising future at Healthy Water. www.krones.com The plant has been generously dimensioned for an annual capacity of up to 300 million fills. For this, Krones prepared the layout for and installed the following process-engineering kit: A complete syrup kitchen with sugar preparation and CIP system; Two Hydronomic water treatment systems: one Hydronomic MF (micro filtration) (installed since 2010 in the old facility) for mineral water, and a new Hydronomic UF (ultra filtration) for spring water. Six lines are available for filling; amongst them, two PET lines with outputs of 8,000 bph and 14,000 bph. The Krones PET line from 2007, likewise originally installed in the old plant, was equipped with new machines as from the labeller. A new PET line for soft drinks is composed of machines from Kosme (SynchroBloc comprising a KSB 6R blow-moulder and a Barifill filler) and Krones (Contiroll wrap-around labeller interlinked with a Sleevematic labeller; Pressant Universal 1N palletiser; Contiflow mixer). In the soft-drink PET line, the Contiroll wrap-around labeller is interlinked with a Sleevematic labeller. It is not least production under license of fruit drinks from the Austrian Rauch company that constitutes a guarantor of Healthy Water’s future-viability. Healthy Water today produces more than 40 different beverages of various brands, primarily mineral and spring water as before. May 21-24, 2019, Guangzhou German Technology,@ID:28}, 37 TRADE SHOW REVIEW PETplanet Insider Vol. 19 No. 12/18 petpla.net Seven generations of aseptic filling technology In recent years Newamstar has developed the aseptic combiblock that integrates blowing, packaging sterilisation, filling and capping solutions. It is claimed to provide the perfect packaging service for both high-acid and low-acid products. From the debut of 24,000bph aseptic line to the extension of 36,000bph aseptic filling line, the aseptic combibloc highlighted at CBB produces 48,000bph. Wesley Yin, Head of Marketing Newamstar, states “With the improvement of living standards, people are paying more and more attention to food safety, health and nutrition. Since the successful development of aseptic filling technology by Newamstar, Newamstar’s technology research and development team has carried out many upgrades and innovations, and has realised the high speed of equipment production (24,00048,000bph) and the combiblock of aseptic blowing filling and capping. And the full coverage of sterilisation technology (PAA, H2 O2 and electron beam).” Facing new changes, demands and opportunities in the era of Industry 4.0, Newamstar also continues to upgrade smart logistic system: the intelligent ASRS, rail shuttle RGV, material handling AGV and warehouse management system (WMS) according to the production characteristics of beverage enterprises. It has created a new automatic management system including product life cycle management, process management and information management to improve quality and create more value for customers. Newamstar’s intelligent plant management platform is intended to help beverage manufacturers to strengthen the real-time monitoring and management during the production processes. The platform automatically collects real-time data and the condition of energy consumption from the production line, on which basis, it can provide Overall Equipment Effectiveness (OEE) analysis, as well as other performance indicators to help companies constantly optimise production. The company’s Smart Retailing Solution, the provision of multiple payment methods, fast and convenient delivery of goods and the improvement of the consumer’s shopping experience, start the full service of Newamstar liquid packaging solution from the production, packaging, warehousing, logistics and retailing. www.newamstar.com Société Générale des Techniques 3 rue de l’Île Macé 44412 Rezé - France SPECIALIST, FOR OVER 37 YEARS, OF PET PREFORMS FOR EVERY LIQUID PRODUCT [email protected] + 33 (0)2 40 05 09 37 www.sgt-pet.com CUSTOMIZED PREFORMS (wide variety of weights, colors and sizes) MADE FROM RECYCLED PET (up to 100%) LIGHTENED MONO OR MULTI-LAYER Wesley Yin, Head of Marketing Newamstar and Alexander Büchler (left),@ID:39}, MARKET SURVEY 27 PETplanet Insider Vol. 19 No. 12/18 petpla.net 12/2018 MARKETsurvey Suppliers of recycling machinery For the first time this year PETplanet focuses on recycling plants and washing units. Please have a look at the detailed information supported by: Tecnofer Recycling Equipment & Machinery, Amut S.p.A., Reciclat S.A., Erema Engineering Ges.m.b.H., Empacar S.A., Gneuss Kunststofftechnik GmbH, Starlinger & Co. Ges.m.b.H. and STF Maschinen- und Anlagenbau GmbH. Although the publisher have made every effort to ensure that the information in this survey is up to date, no claims are made regarding completeness or accuracy. Resins & additives Preform machinery Preform production Preform inspection SBM 2-stage Compressors Filling equipment & filling inspection Caps & closures and inspection Palletising & shrink film machinery Recycling Company name Tecnofer Ecoimpianti SRL Amut SPA Reciclar S.A. Postal address Telephone number Web site address Contact name Function Direct telephone number Fax E-Mail Via Calto 409 45030 Ceneselli (Ro), Italy +39 0425 849090 www.tecnofer.biz Mr Mauro Garbellini Sales manager +39 0425 849090 +39 0425 849066 [email protected] Via Cameri 16, 28100 Novara, Italy +39 0321 6641 www.amutgroup.com Mr Piergianni Milani President +39 0321 664941 [email protected] Heredia 3220, Sarandi, Provincia de Buenos Aires, Argentina (CP 1872) +54 11 4205 0102 www.reciclarsa.com.ar Mr Nicolás Pell Richards Director +54 11 4205 0102 +54 11 4205 1086 [email protected] Bottle to Granulate Input variable: collected pressed bottles, various colours Yes Output: Granulate with approval No Capacity [t/a] 3,000-45,000 Floor space [m²] In function of size and stream quality Which approvals Fresh water consumption per tonne output [m³/t] Depends on stream quality Consumption kWh per tonne output [kWh/t] 300-600 Flakes to Granulate Input variable: flakes, coloured proportion max 5%, not much chlorine Yes Output: Granulate with Approval No 24t/d food grade Capacity [t/a] 3,000-45,000 6,900t/a Floor space [m²] In function of size and stream quality 1,500 Which approvals FDA, MSBsAs Fresh water consumption per tonne output [m³/t] 1m³/t NA Consumption kWh per tonne output [kWh/t] 100-400 346kWh/t Bottles to Flakes Input variable: collected pressed bottles, various colours Loose or bales, collected pressed bottles, various colours Yes Output: Flakes with/without approval Flakes with approval (EFSA/FDA) Yes 90t/d Capacity [t/a] 500-4,000kg/h 3,600-45,000 21,600t/a Floor space [m²] In function of plant configuration according to material quality In function of size and stream quality 19,000 with storage area Which approvals Flakes with approval (EFSA/FDA) MSBsAs Fresh water consumption per tonne output [m³/t] In function of plant configuration according to material contamination 1m³/t 5 Consumption kWh per tonne output [kWh/t] In function of plant configuration 250-300 310 Kind and quantity of detergents Detergent of different suppliers; quantity in function of the detergent Non disclose Liquid detergent 0.9l/t Removal of the organic residuals up to which size [μm] 50ppm NA Presetting residence time in the process Non disclose 15min Company also offers systems for Bottle-to-film Yes Bottle-to-fibre Yes Bottle-to-strapping Yes,@ID:29}, Preform production PETplanet Insider Vol. 19 No. 12/18 petpla.net 19 20% larger container but keeping the same weight Turn up the volume The quest for the perfect preform continues: with smart collaboration between PET packaging solutions provider Retal and one of its global beverage brand customers to create a bigger, lighter, easier-to-pour container that performs better in every way. It started with a conversation between a Retal expert and one of their customers. The customer, a multinational beverage brand owner, wanted a larger alternative to its current 5 l container without increasing its weight, and needed to further address the ever-important issue of sustainability in its packaging. With Retal’s competence to create PET and rPET packaging solutions, this conversation started a chain reaction that included technically-advanced designers, the latest CAD software and true dedication to finding an answer. Retal’s technical director Alexandr Kachanov led the project. He explains how his team worked together to create a lighter, brighter preform. “This was a great opportunity to bring real value to our customer and show our preform design capabilities. Working together right from the start meant that every element of the project was focused on the solution they needed. The customer explained to us how their current 5 l container needed to evolve; they wanted a PET container that was 20% larger but still kept the same weight of 64 g. Retal rose to the challenge!” Retal senior designer Andzejus Buinovskis played an integral role in this project, with technical knowledge able to get the best out of the Dassault Systemes’ Abaqus software plugin. Andzejus tells PETplanet, “We took the original container and reversed engineered it; analysing the bottle top load, different pouring situations, stretch ratios... we redefined the packaging completely, including the closure. I worked with the team to redesign the 48mm opening on the 5 l container to make it just 38mm for the 6 l preform prototype, which gives the consumer more pouring control and made it easier to open.” Preform special Andzejus notes how the analysis phase was crucial in understanding how the existing 5 l preform worked and how such impressive changes could be made in the new 6 l ‘Karavan’ container. He adds, “We looked deeply into how we could make improvements, with many bottle drawings, visualisations, images with bottle SBM (stretch blow moulding) and top load simulations.” “Our Retal reengineering team has done a great job with this project,” adds Aleksandr “To have successfully increased the PET container volume without increasing its weight highlights the future possibilities of lightweighting and our on-going dedication to collaborating on commercially advantageous innovations.” With this light yet strong and easy to pour 6 l container already in production, Retal is pleased to share its technical advancement to highlight how its latest PET packaging solution can support beverage brands in their ongoing focus on lighter preforms that meet the strictest performance and sustainability demands. www.retalgroup.com,@ID:21}, PETcontents 12/18 4 PETplanet Insider Vol. 19 No. 12/18 petpla.net INSIDE TRACK 3 Editorial 4 Contents 6 News 45 Products 46 PET bottles for Beverage + Liquid Food 46 PET bottles for Home + Personal Care 48 Patents TOP TALK 10 Structure and order - Interview with Kai Acker, Chairman of the Executive Management Board at KHS GmbH EDITOUR 12 Knowing how to grow - Retal’s expansion into the US market PREFORM PRODUCTION 14 Boundaries becoming blurred - Interview with Gianfranco Zoppas at Sipa’s Open House 17 Step up investment in preform technology 18 Safe and hygienic storage 19 Turn up the volume - 20% larger container but keeping the same weight CAPS AND CLOSURES 20 UV light barrier caps in all colours - Closure solutions for the dairy industry BOTTLE MAKING 21 Starting from scratch - German start-up Share launches 100% recyclate water bottle 22 Virtually engineering bottles of the future BOTTLING / FILLING 24 From hand bottling to 76 million fills 31 Booming juice market in Saudi Arabia MARKET SURVEY 27 Suppliers of recycling machinery INSPECTION 33 Vision systems for the US market MOULD MAKING 35 Keep up with your customer needs - Moldintec has developed an App for their PET customers TRADE SHOW REVIEW 36 China Brew China Beverage 2018 40 “Modularity and service are key” - Sidel presents solutions for a fast-changing market environment 42 “Large emerging markets with large potential” - Petra Westphal, Exhibition Group Director for Messe München, on DTI India and FDT Africa exhibitions BUYER’S GUIDE 49 Get listed! PREFORM special Page 36 Page 14 243621 Page 36,@ID:6}, MOULD MAKING PETplanet Insider Vol. 19 No. 12/18 petpla.net 35 implement industry 4.0 technologies across our company. We modernise, the customer wins. Creating craft innovative customer interactions by adding specialised features and services boost brand loyalty and we feel a closer connection with our customers around the world, becoming an enterprise powered by a rich flow of data in our core,” Eng. Thiago Tullio Mouldintec’s, Brazil Country Manager is convinced. Based on Unity, a mobile games programming platform, the Mouldintec App takes advantage of the strong programming capabilities to create an easy to use interface and “lightweight” software. A PC version runs on the company’s computers also. The app is a 10 stages timeline of a standard PET blow mould manufacturing process. Starting with a P.O. every stage is linked with the confirmed delivery time. The app shows when a stage must be accomplished , - from Moldintec’s side. The inner customer process is exposed, including the limit date for a customer task to keep the project on track. Receiving moulds on time is mandatory in the industry. Many stages are usually out of the control of the mould manufacturer as are bottle drawing approval, blower technical specs, tooling definitions, as well commercial terms. “With the new app, all the players are on the same page. One can track more accurately the information flow and how bottlers around the world interact with Moldintec. In addition one sees online the project timeline, if any data is missing from one side or if the project is on time or delayed. We prefer working in confidence with our supplier even if we’re not on track. That minimises uninformed delays that are dangerous when we are launching a new product to market,” explains Eng. Demis Verastegui, AJE Group Global Packaging and Innovation Director. Mouldintec delivers a unique username and password for every customer with the start-up of a new project. That will be the ID for the next projects too. With the company working with a customer’s confidential information each project has to be given a codename to avoid data leakage. The internet is a hard environment; even the most protected database can be hacked, so the app information does not show the final beverage, shape or other sensible commercial material. The app is operating a system language adapted to English, Spanish and Portuguese, following Moldintec’s major markets. For non-customers, the company offers a demo user/pass for PETplanet readers: User: PetPlanet Password: Industry4 www.moldintec.com.ar,@ID:37}, BOTTLING / FILLING PETplanet Insider Vol. 19 No. 12/18 petpla.net 31 Two new Sidel PET lines for Almarai Booming juice market in Saudi Arabia Almarai, the leading producer of liquid dairy and juice products in the Middle East, approached the Sidel Group to increase its production capacities around orange juice distributed via cold chain. With high speed and reliability of the line coupled with great product quality among the top requirements from this customer, the global provider of equipment and services for the liquid packaging industry was a qualified partner for the job. Since its founding in 1977, Almarai has grown via strategic investments, becoming the largest producer and distributor of food and drink in the Middle East with a market capitalisation exceeding $12,5bn. Almarai’s production, marketing, and distribution structure enables the daily distribution of products to over 110,000 retail outlets across the six Gulf Cooperation Council (GCC) countries, plus Egypt and Jordan. Bold consumer preference for juice drinks When Almarai recently reached out to Sidel, they needed to increase the production capacity around the single-serve format of its orange juice, 200ml, bottled in PET and handled under cold chain distribution. This opportunity was especially driven by the consumer preference around it: part of a range offering twenty taste possibilities, as such perfectly reflecting the major trends impacting the beverage market in Saudi Arabia. There, the search for more healthy and natural formulations is expected to influence juice sales considerably. With the leading position in the juice market, Almarai decided to install two Sidel PET complete lines, each one handling 54,000bph, in the Al Kharj central processing plant (CPP). State-of-the-art packaging solutions For Almarai, quality is the founding principle, upholding the company’s commitment to achieving the highest standards on behalf of its consumers and hence its motto: ‘Quality you can trust’. With Sidel PET production for more than 35 years and leveraging a longstanding expertise as a complete line provider, they looked perfectly established to partner with Almarai in the quest for exceptional manufacturing and processing capabilities. The largest food manufacturer and distributor in the Middle East strives to operate to the highest standards of international best practice, starting from the processing step: the two new PET complete lines installed at the Al Kharj production site – the first ones Almarai awarded to Sidel – employ the processing equipment and capabilities of Tetra Pak Processing Systems (TPPS). This represents a further testament of a successful cooperation, benefitting from experience and learnings gained in nearly 100 joint complete line projects from around the world. The TPPS process equipment captures the natural taste of the product and ensures it is safe to drink. Anurag Sharma, Sidel Sales Manager in Saudi Arabia, explains, “The key challenge was to find a solution able to ensure greater efficiency, so as to strengthen profitability and optimise Total Cost of Ownership (TCO). All of this without compromising top product quality, a must-have for Almarai considering the great sales performance of its orange juice. To address this within the two complete lines, Almarai opted for the Sidel Combi. Integrating blow moulding, filling and capping processes into a single system, the Combi reduces operating costs and uses up to 30% less floor space compared to traditional standalone equipment. Using fewer component machines, the solution offers up to 4% higher efficiency levels than standalone machines, on top of lower energy consumption and faster format changeovers. This results in a reduction of operating costs by up to 12%, saving labour, raw materials, and spare parts.” The two Combis supplied to the Al Kharj site are equipped with a Sidel SF100 filler, ensuring optimum uptime and the highest productivity. Its ‘dual speed’ valve allows consistent performance and the best drink quality, especially when handling beverages with pulps. Additionally, both magnetic flowmeters and filling valves are equipped with plungers, leading to higher accuracy and more efficient filling and cleaning. In fact, the system allows for no clogging and an easier removal of pulp residual. For greater product safety and ease of operations, the tight enclosure with HEPA filter allows for top hygiene, while Cleaning In Place (CIP) requires no intervention from operators thanks to the automatic dummy bottles. Sidel’s proven and versatile RollQuattro Evo labeller complements the Combi. Primarily using wrap-around rollfed technology to apply either paper or plastic labels with hot glue, it delivers all the flexibility needed to match Almarai’s needs when processing lightweighted containers and extremely thin labels at very high speed. End-of-line system for greater flexibility and pack quality Benefitting from Sidel Group’s expertise as a full solution partner, Almarai went for Gebo Cermex’s solutions to optimise its end-of-line performance. Two shrink-wrapping systems have been installed to manage three different pack configurations: 6x4, 2x3 and 2x3 bottles as clusters. For additional flexibility at a very high speed (67,500bph in overspeed), a shrink-wrapper is handling single squared bottles in mass flow, putting them in tray plus film, while the other one is managing both single bottles and cluster packs of bottles through special selection fingers with rollers identifying the clusters according to product grouping or batch. To ensure a consistent and,@ID:33}, 36 TRADE SHOW REVIEW PETplanet Insider Vol. 19 No. 12/18 petpla.net TRADE SHOWreview PART1 China Brew China Beverage 2018 - review part 1 One of the major trends in Asia’s beverage and liquid food market is: “quality, not quantity.” As incomes rise, people prefer to consume better products instead of more products. At the same time, demand for production systems and machines remains high. As a leading trade fair for the industry, China Brew China Beverage (CBB) provided a far-reaching overview of the market with the exhibitors’ presentations and its comprehensive supporting programme. The number of exhibitors and visitors showed an increase: A total of 869 exhibitors meant an increase of 9%. The trade fair used eight fully booked halls, including two that were used by 256 international exhibitors. That represents a growth rate of 6%. Of the approximately 56,000 participants, a large number came from abroad, from countries as Indonesia, Myanmar, the Philippines, Thailand and Vietnam to inform themselves about trends of the entire process chain for all areas of the beverage and liquid food industry (last trade fair 2016: 53,183 participants). The next CBB will be held in October 2020 at the Shanghai New International Exhibition Centre (SNIEC). www.cbb.drinktec.com Continuous trend towards premiumisation and new brands proliferation in China PETplanet: Mr Bastien: Which topics have most interested your customers at this fair? Bastien: For us at Husky, we are seeing two conflicting trends in the market. On the one hand, we see a need for high performing plants and machinery for the ever-growing water business, and on the other hand, smaller more flexible facilities for emerging sectors such as household goods, sauces and emerging beverage brands. Additionally, we see the dairy market as having a large potential for conversion to PET. PETplanet: What systems are you using in the water market? Bastien: At the moment, we often use a 128 or 144 cavity mould in China. In the future, we anticipate even larger cavitation will be used more frequently. These larger platforms are already proven and in production in some other areas of the world, and we believe they are now ready to enter the Chinese market. The trend towards right-weighting and premiumisation is continuing, with 15-19g half-litre bottles being common in the market. PETplanet: And what about household and dairy products? Bastien: The competition is pushing brand owners to drive on-the-shelves differentiation and PET packaging is a great solution for this need. We are already seeing the switch from cartons and HDPE in the dairy market, while in the household market we see a strong potential for PET to replace HDPE packaging. In the personal care segment we have already sold three Multi-Layer systems, with those applications making the switch from HDPE to PET. In this case the manufacturer is using our technology to give the bottle an eye-catching colour to further increase shelf differentiation. PETplanet: How will the Chinese market develop over the next five years? Bastien: We anticipate both trends to continue, i.e. the growth of water driving the need for high-efficiency, high-output systems, and more flexible, lower-output plants to drive growth for emerging brands in local/remote areas . In parallel, Multi-Layer Technology will help to support a market that seeks more food safety through better package protection. What will change and what we are already seeing today is the speed and the quantity of new brands coming on to the market without a long life-time, requiring more agility and responsiveness to the market. The competition for market share is quite fierce, which is why we offer a variety of solutions for any application in order to help our customers’ products stand out on store shelves, while maintaining the lowest cost to produce. www.husky.co Blow moulds and preform moulds PETplanet: How was CBB for you? Au-Yeung: It was a great event for us to strengthen our bonds with partners and meeting new customers. PETplanet: Which of your products highlighted here in Shanghai was of most interest to the visitors at your booth? Au-Yeung: Our precise blow mould and preform mould products had been the highlights to visitors. PETplanet: How much has the Chinese market changed in recent years? Au-Yeung: There has been an increasing and sustainable demand on healthy, innovative and user-friendly products in the beverage market. www.gdxl.com Aurelien Bastien (right), VP Beverage Packaging Sales Husky and Alexander Büchler Billy Au-Yeung, Marketing Specialist GDXL (left) with Aleander Büchler,@ID:38}, BOTTLE MAKING 23 PETplanet Insider Vol. 19 No. 12/18 petpla.net BOTTLE MAKING 23 This proven process ensures there are no prototyping difficulties or ‘trialand-error’ guess work. The software algorithms draw on validated scientific data, the vast experience in accurately predicting material performance, and the unique material model to accurately represent the PET behaviour in SBM. Key outputs of the simulation include 3-D and axisymmetric simulation, bottle section weights and thickness distribution which provide a detailed analysis of the effects of processing conditions on material distribution. Finally, using all of the validated data in previous steps, Step 6 involves using the simulation to explore the process window and produce an optimum preform to meet the in-service performance requirements of the bottle. With deep understanding of this science behind polymers, BMT claim that they can engineer, test, simulate and design the new plastic bottles and preforms of the future with confidence, be it from PET resins, PET blends, recycled PET, additives, bio-plastics or bio-materials. With the experience, knowledge and tools, they can help facilitate this seismic shift in the industry, creating environmental, economic and social benefits for all, states the company. www.bmt-ni.com Visual Simulation Output,@ID:25}, BOTTLING / FILLING PETplanet Insider Vol. 19 No. 12/18 petpla.net 32 reliable output for greater pack quality – a challenging objective considering the small diameter of the bottle – the machine has been suitably equipped with a 3D inspection camera, detecting missing containers in the tray before shrink-wrapping them. Moreover, the shrink-wrapper’s extractable injection table allows for easy maintenance and stable film handling. To guarantee greater energy savings and up to 10% TCO reduction, the shrink-wrapping systems are combined with two Gebo Cermex EvoFlex palletisers, offering unparalleled flexibility and efficiency even with high-speed applications. The only palletising system with a low-level infeed capable of running at up to 12 layers per minute, EvoFlex offers significant advantages in terms of ergonomics, energy consumption, and safety. The solution is equipped with AxoSmart, the layer preparation system designed by Gebo Cermex to meet the need for more eco-friendly packaging (lightweight bottles and less secondary packaging) and a wide product portfolio. With a modular design allowing for smooth adaptation to various line speed requirements, AxoSmart offers the possibility to handle a high number of pack types in the same cycle; all of that, without compromising on optimal stability and reliability. Operational intelligence to support continuous improvement The two PET complete lines installed at the Al Kharj plant are featuring Sidel Group’s EIT (Efficiency Improvement Tool), a data acquisition and plant intelligence system. It automatically records 24/7 raw production data, calculates a wide array of KPIs to help measure performance, analyses production issues, detects efficiency loss sources, and performs root cause analyses. Currently installed in more than 70 countries, it is designed to ultimately decrease unplanned downtime, reduce waste and costs, and increase the plant’s output as it gives employees at all levels of the organisation real-time access to relevant and actionable information on productionrelated issues. As an additional bonus feature, the EIT version leveraged by Almarai comes with the ECO module, monitoring and measuring energy and utilities consumption at equipment and line level. On top of providing energy cost per produced unit, the system establishes correlations between consumptions trends (including power, water, steam or compressed air) and line events or production phases for improving performance over time. The two lines started to work in the last quarter of 2017, both beyond 98% of efficiency, with products available in the market as of the same period. Given the remote location where the Al Kharj plant is based, Almarai benefitted from Sidel’s reaction time and expertise, key for replacing spare parts and solving technical issues. Based on this positive experience, Almarai recently established monthly technical visits to properly control and monitor the line’s performance. www.sidel.com BOTTLING / FILLING 32,@ID:34}, INSPECTION 33 PETplanet Insider Vol. 19 No. 12/18 petpla.net Solving problems before they occur Vision systems for the US market by Heike Fischer May 22, 2018 Intravis Inc, Atlanta, USA We met: Andreas Mueller, CEO, Scott Heins, Director of Sale & Marketing and Winta Patterson, Sales & Marketing Coordinator Since the founding of Intravis GmbH by Dr Gerd Fuhrmann near Aachen, Germany in 1993 the company has become one of the world market leaders for vision inspection systems for the plastic packaging industry. Intravis develops, manufactures and delivers turnkey inspection systems for manufacturers of closures, bottles, preforms, thin-wall containers and decoration. Tour Sponsors: In 2004 the first subsidiary was founded in Atlanta, GA, USA in the heart of the American beverage and plastic packaging industry. In 2012 the second subsidiary followed in Shanghai, China. Sales and service centres are located worldwide e.g. in Mexico City, Moscow, Sydney and Bangalore. After the NPE show in Orlando, FL, PETplanet continues its Editour north and take the opportunity to stop by at Norcross close to Atlanta where Andreas Mueller, Scott Heins and Winta Patterson welcomes the Editourmobil at the Intravis Inc. facility. Andreas was the first man on the ground at the Norcross facility. As a field service engineer he worked for Intravis in Germany and moved to Norcross in 2006. Here he started as Executive Vice President with his wife Vera managing accounting and administration. At this time the facility had a footprint of 800 square feet. In 2007/2008 he hired more technicians and a sales manager to build up a service department. When he became CEO in 2011, Andreas doubled the turnover of the business. To build up their team, Intravis Inc. came to rely on people with a military background, because of their technical education, field experiences and trustworthiness. Today in 2018, 20 employees work in a 10,000 square foot facility. “From Norcross we serve all of the North, Central and South American markets,” explains Andreas. “We specialise in bottle, preform, closure, and in-mould label (IML) inspection. The American market has some different requirements than the European market, for example we do more thread dimension inspections, and the speed demands are commonly the highest here due to the high volume demands for plastic packaging. Europe and North America are very important markets for us, as well as China. We are seeing general growth in all markets, with some variations due to the regional economies,” says Andreas. “With our latest product introduction, the new PreWatcher 4, we have shown once more that Intravis is very much a specialist in complete turnkey design. With innovative engineering, we offer solutions based on cutting edge technology for the plastic packaging inspection industry,” emphasises Scott Heins. Scott joined Intravis Inc. as Sales & Marketing Director two years ago. “The PreWatcher4 is designed for inspection speeds up to 100,000 preforms per hour and can handle clear, opaque or semi-transparent preforms. It is a linear system, offering great flexibility while avoiding the need for change parts. The handling system presents the preforms so there are no blind spots. A complete changeover can be done in 5 minutes. With 17 cameras the PreWatcher 4 is doing a full array of inspections,“ Scott continues. “At the NPE show we have had enquiries for eight systems, and the system presented on the booth has already been sold.” After a tour through the offices and plant, we ask Andreas what is so special about Intravis, what makes it unique, he says: “We are a true specialist for plastic packaging manufacturers, we continue to push the leading edge of technology, and our company is service focused.” www.intravis.de From left: Andreas Mueller, Heike Fischer (PETplanet), Scott Heins and Winta Patterson The Intravis Inc. team in front of the Editourmobil,@ID:35}, BOTTLING / FILLING PETplanet Insider Vol. 19 No. 12/18 petpla.net 25 So as to meet the rising levels of demand, the company decided to completely refurbish its existing plant and to build a new factory right next to it. This latter was inaugurated in June 2017. Erection of the lines went wellnigh without a hitch: installation work began in late 2016, by the following April production had already started, and in September of that same year 2017 all the filling lines were up and running. Nearly all of the firm’s 150 staff come from the surrounding region, and are taken to the plant each day with the company’s own buses. With the commissioning of the new plant, the number of SKUs (stock-keeping units) rose from twelve to siginificantly more than 100. This is primarily attributable to the cooperative alliance the firm has entered into with the Austrian fruit-juice producer Rauch, coinciding with an expansion of its own portfolio: whereas the old plant was used to fill only water until 2017, Healthy Water today produces more than 40 different beverages of various brands. The portfolio includes: Nabeghlavi: natural, carbonated mineral water and flavoured water, filled in green glass bottles, PET containers and cans Bakhmaro: still spring water, since 2002 filled in blue glass bottles and PET containers Buga: an energy drink in cans Geo Natura: flavoured carbonated soft drinks, filled in PET containers and glass bottles, plus non-alcoholic Mojito in cans Licensed filling of products from Rauch: fruit juices, ice teas, flavoured carbonated soft drinks, plus other soft drinks, in PET containers, cartons and cans. “Our cooperative alliance with Rauch, one of Europe’s leading producers of fruit juices and other soft drinks, SynchroBloc comprising a KSB 6R blow-moulder and a Barifill filler. SIPA S.p.A. - Via Caduti del Lavoro, 3 - 31029 Vittorio Veneto (TV) - Italy Tel. +39 0438 911511 - Fax +39 0438 912273 - email: [email protected] We make it happen. www.sipa.it Imagine a totally new operator experience. Designed to adapt. Built to last. Preform Systems THEMOST ENERGY EFFICIENT SYSTEM below 195W/kg,@ID:27}, BOTTLING / FILLING PETplanet Insider Vol. 19 No. 12/18 petpla.net 24 Versatile beverage factory From hand bottling to 76 million fills In mid-2017, Healthy Water’s new production facility started operation. Krones was responsible for large portions of the plant engineering involved, supplied new lines, and integrated new machines into existing ones. The production under licence of fruit drinks from the Austrian Rauch is not the least of the developments that constitutes a guarantor of Healthy Water’s future-viability. The small hamlet of Nabeghlavi in the west-Georgian region of Guria has no village centre you could recognise as such. The few houses and farmsteads are scattered over the hills, the village sign is the only indicator denoting that a settlement is actually located here. A wild stream has cut a small valley into the landscape, a valley so narrow that the architect who planned the new building for Healthy Water’s beverage factory had to opt for a multi-storey design. The kit is installed on two floors so as to utilise the entire height of the building, with the ground floor accommodating the warehouse, and the first floor the filling lines and utilities. The office buildings each comprise four storeys, with the building complex rounded off by a section featuring 14 guest rooms, both for visitors and the company’s own staff. The company’s history started back in the early 1990s, when a Swiss businessman privately invested 40,000US$. In 1997, together with two Georgian families he had befriended, he was able to purchase the Nabeghlavi mineral water spring and plant, unused at that time. 200 million fills planned by 2023 In 1997, the Swiss-Georgian group of investors revived the bottling operations, this time under the name of JSC Healthy Water. In its first year, the firm filled 600 bottles by hand. But after that, things really took off. A mere three short years later, production output had risen to one million fills. In 2003, the first Krones line was installed, for glass bottles. Two years later, sales had already reached 15 million fills. The market share of Healthy Water in Georgia soared, from its former 6% to over 50%, with the Nabeghlavi brand evolving into the market leader. In the following years, the company also channelled some capital into other sectors, but the Healthy Water mineral water operation remained the holding’s keystone. After consolidating its domestic sales, from 2010 the mineral water division’s export grew strongly, and currently supplies 28 different countries. The logistical conditions might seem at first unhelpful, because the plant is located right in the very heart of nature, in the foothills of the Caucasian mountains, yet is only an hour’s drive away from the port of Poti on the Black Sea. In terms of process technology, Krones planned and installed a complete syrup kitchen. Irina Gaprindashvili, Head of Operations, with Plant Manager Vakhtang Megrelishvili,@ID:26}, MOULD MAKING PETplanet Insider Vol. 19 No. 12/18 petpla.net 34 Moldintec has developed an app for their PET customers Keep up with your customer needs The manufacturing 4.0 is changing the rules of the industry. From the CAD systems integrating platforms for moulds configuration according to customer requirements, CNC controls connected, robots, and ERPs. The PET blow moulds manufacturer Moldintec has developed an exclusive mobile app for their customers. The R&D+I team is not just working on petaloid bases, laser advanced decoration or mould cooling. Taylormade in-house software and plugins programming push the company to step forward into IoT. The app presents online updated 24/7 info of every running moulds project to put customer needs ahead of the game. Every day the market moves forward at an ever-increasing pace. The new generation of young engineers are arising who were born with the internet at home and the internet of things (IoT) as part of their everyday lifes. This blow moulds manufacturer company got the message coming from the market: keep abreast of customer needs moving to the smart factory concept: respond quickly to customer feedback and market trends with specialised solutions. Today searches are made by voice; mobile devices are the standard as well wearable. Information was always king, but today the way that information flows is more important than any tangible that a company can deliver to the market, states the company. “Moldintec has evolved in many ways during its 20 years of business. Founded in 1998 the company started up with a fax machine in the office, now mobile phones are a thing of the past here, instead pop-up alerts show incoming messages. Our customers expect us to respond at google speed!” says D.I. Jorge Pucci, Moldintec CCO. Moldintec asked itself how to keep a moulds manufacturing business growing in a market where intangibles are more valuable than tangibles? Is bottle design or mould engineering enough for the future of the business? After internal meetings about how to keep the customer service and innovation as the company focus for the next coming years, the answer comes from the young programmers putting the customer’s project at their fingertips, on a mobile screen, online 24/7. The bottle and mould technology are fields where the company leads thanks to a strong R&D budget, so the software point of view will change the rules and the way that company and customer are connected. The development of an app inside the walls of an industrial company was challenging. Without previous experience, the obvious solution was to hire a mobile software company to get the app for a price, but that’s not in the company DNA so the management took the long route programming it internally to keep the knowledge in the company. Creating an agile supply chain through IoT With a focus on personalised customer service as a key to the success of the business model, Moldintec App puts the customer at the centre of the company’s operation. Streamlining the commercial, engineering and manufacturing process give the company the capability to discover actionable insight in real time with an end-to-end point of view that softens the impact of issues and gets products to market faster. Both sides of the supply chain now are connected due to an app which not only demonstrates Mouldintec’s inner process, but customer related milestones (purchasing, financial, technical, international trade, etc) are also integrated as part of the moulds manufacturing to keep the company’s competitive edge. “What we’re talking about is delivering a degree of visibility and collaboration unseen before in the blow mould industry. We were working to,@ID:36}, PETnews 6 NEWS PETplanet Insider Vol. 19 No. 12/18 petpla.net And & Or new facilities opening On November 16, And & Or officially opened its new 2,000m2 plant in the Parque Empresarial Guadalquivir, Seville, Spain. This expansion intends to meet And & Or’s machinery and solutions growing demand for all the markets where the company currently operates. The specialisation and subdivision of the production phase depending on the product type has been the key force to achieve an efficient and sustainable growth in the past years, with the aim of improving the quality of the service provided to our customers, states the company. The facility will be specialised in the manufacture of machines for assembly and quality control: linear and rotative handles applicators, liner cap insertion, rotative leak testers, taps lines and other special machines. With this expansion, And & Or will result in a total surface area of 11,500m2 between both production plants, the spare parts storehouse and the offices. www.andyor.com 50% rPET: new target for bottles with the RAL quality mark The use of recycled material in disposable PET bottles is expected to increase significantly in the coming years. This has been decided unanimously by the RAL quality association for the recycling of recyclable PET drinks packaging e.V. By 2022, PET beverage packaging with the RAL quality mark will consist of an average of 50% recycled PET material. As a result, the organisation wants to further close the recycling cycle and increase the sustainability of beverage packaging. The minimum recyclate rate of 25% to obtain the quality label will remain. After the weight and material consumption of disposable PET bottles has steadily dropped in recent years, the Gütegemeinschaft sees the increase in the recycling percentage in PET bottles as the key to sustainable development. Against this background, it has formulated the goal that all bottles bearing the RAL quality seal should have an average of half recycled PET by 2022. The members of the Gütegemeinschaft, including preform manufacturers, beverage producers and recyclers, unanimously supported the implementation. With the target, the RAL Quality Association complies with the requirements of the German Packaging Act, which comes into force on January 1, 2019. This aims to promote the recycling of beverage packaging in closed circuits. www.wertstoff-pet.de Nestlé Waters North America signs agreement with recycled PET supplier CarbonLite Nestlé Waters North America announced that it has signed an agreement with recycled PET plastic (rPET) supplier CarbonLite, and that CarbonLite will expand its U.S. operations by building a third facility in the Lehigh Valley area of Pennsylvania. The new contract builds upon Nestlé Waters’ existing relationship with CarbonLite, one of the largest producers of food-grade, post-consumer rPET, and allow the beverage company to further expand use of recycled materials in its packaging. The company currently purchases rPET from CarbonLite’s existing facilities in California and Texas. CarbonLite anticipates the facility will be in full production by early 2020, and will have the ability to recycle over 2 billion post-consumer bottles a year. The new 200,000-square-foot processing facility is anticipated to save 60,000 t of carbon annually by using post-consumer materials and produce 80 million pounds per year of food-grade rPET pellets. Nestlé Waters, which has two bottling facilities in the Lehigh Valley, uses recycled plastic in a number of its brands including Nestlé Pure Life and Deer Park which are bottled locally. The company has been increasing the amount of rPET it uses in its packaging since 2011, and in February 2018, Nestlé Waters launched a 700ml Nestlé Pure Life bottle made of 100% rPET. In California, all of the company’s singleserve sizes of Arrowhead Brand Mountain Spring Water and Nestlé Pure Life bottles produced in the state are made with 50% rPET. Nestlé Waters’ parent company, Nestlé SA, is a signatory of the recently announced New Plastics Economy Global Commitment. An initiative of The Ellen MacArthur Foundation and UN Environment, the “Global Commitment” is an agreement to ensure that 100% of plastic packaging can be reused, recycled or composted by 2025. www.nestle.com Athena changes name to Niigon Machines Ltd. Athena Automation Ltd., a company manufacturing injection moulding machines near Toronto, Ontario, announced that it is changing its name to Niigon Machines Ltd. “This allows us to emphasise our business objective of becoming a global leader in customised injection moulding machines” said Robert Schad, Chairman. “Niigon is an Ojibwa word that means ‘for the future’.” www.niigonmachines.com,@ID:8}, 39 TRADE SHOW REVIEW PETplanet Insider Vol. 19 No. 12/18 petpla.net P R E F O R M I N S P E C T I O N Solutions for microbreweries Since 2016, Enoberg, the producer of filling machines, has been part of the SMI Group. At CBB, SMI and Enoberg presented solutions especially for microbreweries. “The microbrewery business in China is going up”, explained Giacomo Cirillo, Managing Director Assistant Smi Machinery Beijing. Specially targeted for this customer segment, Enoberg offers compact rinsing/filling/capping machinery to fill beer in PET or glass bottles. The ELC 5-5-1 C Microbloc comes complete with a rinser, isobaric electro-pneumatic filler with double-pre-evacuation system and single head crown capper. The valve allows flexibility in adjusting the filling cycle by adapting the vacuum and filling timings via PLC. The ELC 5-5-1 isobaric filler stands out for its “stepby-step” operation principle. To maintain a compact structure, the machine has been designed based on a linear type machine, with every phase of the machine positioned around a central star. This way, for the rinsing and filling procedures, the bottles are handled in groups of five. The capper is not tied to this concept, so the capping head applies the crown cap to every bottle that passes. The key advantage of a step-by-step machine is the short time required for the changeover procedure compared to the linear or rotating machines. The central star and the guides are the only components that need to be replaced, plus the adjustment of the height of the different devices. All motors and mechanical transmissions of the machine are installed below the machine base, to avoid any contact with the wet part of the machine. The output for 330ml bottles is 1,000 bph. www.enoberg.it www.smigroup.it From left: Giacomo Cirillo, Managing Director Assistant SMI Machinery Beijing and Matteo Gambarini, Sales Department - Area Manager Enoberg Srl,@ID:41}, PREFORM PRODUCTION PETplanet Insider Vol. 19 No. 12/18 petpla.net 18 Esterform opts for Stackabox for PET preforms logistics Safe and hygienic storage British PET converter Esterform has been among the first to adopt Stackabox, initially for handling its Purity Soft drinks lines. It subsequently presented the system to customers as its standard primary packaging. The challenge Esterform was looking for a better solution for storage, dispensing and transportation of preforms because its incumbent system was presenting a range of problems. Capacity restrictions meant that some containers could hold only a maximum of two thousand preforms, for example. The packaging was not collapsible, so returning trucks were effectively carrying air, with no opportunity to carry alternative cargoes. In its search for a solution to these issues, Esterform sought a bigger, foldable container, with multiple dispensing possibilities, which would guarantee safe and hygienic storage and prevent damage, such as neck breakage. The approach The capacity issue was overcome by utilising a large Stackabox container, which can hold around 10,000 38 g preforms. It is fully collapsible but can be erected, ready for filling by a single operator in just 30 s. The integrated lids mean that there is no requirement for an extra wooden pallet underneath. If required, liners can be easily placed and removed. Smooth internal surfaces are purpose-made for easy cleaning. The Stackabox polypropylene construction was chosen for its extended life, for hundreds of journeys between producers and customers. The dispensing container’s design prioritises recyclability, reusability and reparability; all parts are replaceable. The result Replacing the previous packaging with Stackabox and integrating it into its production lines enabled Esterform to improve efficiency. The large container is readily adaptable to the latest current robotic systems. Esterforms’ clients, which are all in food and beverage, are able to meet the sector’s higher hygienic standards with its new packaging system. The absence of wooden pallet eliminates risks of odour, wood splinters or similar contamination. With no centre skid at the base, damage from fork lifting is also a thing of the past. The ease of erecting and collapsing, means fewer people are needed for handling, further reducing costs. At the customer’s site, the bottom dispensing method smoothly slides preforms into the hopper of the filling line and decreases damage to bottlenecks. CO 2 transport emissions are significantly reduced. A standard trailer can hold 52 full Stackaboxes, stacked two high and 182 empty, folded boxes on the return journey, stacked seven high. This is 3.5 times more efficient than the previous type of packaging, states the company. www.dssmith.com PREFORM special,@ID:20}, PETplanet Insider Vol. 19 No. 12/18 petpla.net 46 PETbottles Beverage + Liquid Food A solid bottle for olive oil US company Gourmet Factory is selling 100% pure olive oil under its “Capatriti” brand which comes in a 473ml tapered, clear bottle with a square base. The waist of this new round bottle starts above its base. The olive oil’s quality is monitored according to strict “USDA” rules. The bottle is covered with a Mediterranean printed sleeve label. Two transparent windows incorporated into the side of the label allow a clear view of the product and to see how much of it has been used. A screw top with built-in dispensing aid makes it easy to hold. www.capatriti.com A melon drink in PET There are several watermelon and watermelon juices on the USA market under the name “WTRMLNWTR”. Slightly damaged melons which cannot be sold as whole fruit are converted from waste to raw material to produce a refreshing drink of different fruit additive tastes. The juice is cold-pressed and must be cooled. It comes in a slim, clear 355ml (12 fl. oz.) bottle with sleeve label and screw top with tamper-proof strip. www.wtrmlnwtr.com An energy drink with caffeine American Body Building is selling a high caffeine (250mg), sugar-free, low in calories drink under their “A.B.B. Speed Stack” brand. It is specially aimed at power athletes and comes in an easy to hold, grey-coloured 532ml bottle which has several circular grooves. The plastic covered base area has a special surface quality and shape. The “Fruit Punch” flavour variety is easily recognisable by the red label in the shoulder area. A tamper-proof screw top is covered by the A.B.B. logo. www.americanbodybuilding.com Organic lemonade from Aldi-South Organic multi-fruit lemonade with pear/lemon and raspberry/ peach flavours containing 10% fruit is being sold by Aldi-South in a clear 500ml bottle. According to the manufacturer, the fruity, sparkling lemonade needs to be kept in a cool place and away from the light. The non-returnable bottle has paper labels and is secured by a shiny, silver screw top whose shape is similar to a crown cork. www.aldi-sued.de Home + Personal Care Pop-art label In a special campaign, Aldi-South has come up with a cardboard display of a number of variously scented dishwashing detergents in their checkout areas. The liquids, which smell of berries, aloe vera, cucumbers and other fragrancies, are appropriately coloured and come in clear 500 ml bottles. The main coloured labels printed with comic drawings, funny slogans and pop-art are also in keeping with the product. The overall effect is completed by an appropriately coloured push-pull lid. www.aldi-sued.de,@ID:48}, PREFORM PRODUCTION PETplanet Insider Vol. 19 No. 12/18 petpla.net 17 PREFORM PRODUCTION 17 Step up investment in preform technology [email protected] Tel: +90 212 695 50 00 Fax: +90 212 694 97 24 100815dmyR .com PREFORM special Sacmi’s IPS (injection preform moulding) range has been further improved and expanded to provide a broader, more complete response to numerous possible needs within the beverage industry. Offering high performance and low consumption, the IPS platform complements an all-round line range that extends from pellet to pallet. Following good market feedback, the Group is making further investments in the platform to extend the range and meet the manufacturing needs in the beverage industry. Sacmi has widened the available machine range and raised productivity, which can reach 60,000 preforms per hour. First-rate performance in terms of cycle time and energy consumption form the cornerstone of the range. This has been achieved thanks to – especially as regards consumption – the application of major technical innovations to both the hydraulic system and handling in the post-cooling area. The mould range from 24 to 128 cavities meets possible sizing and production requirement. Sacmi has redoubled its efforts to provide customers with maximum flexibility of use by ensuring presses can easily be adapted to most commercially available moulds. Moreover, Sacmi has – alongside its development of a higher-performing machine – invested heavily in production plants to accelerate prototyping and testing of complete (machine + mould) industrial systems. This has already resulted in improved lightweighting, with preform weights of 4.5 g (25mm neck), and the additional added value customers gain from receiving constant support right from the design stage and throughout the working life of the machine and plant. Other key platform features include defect reduction (all Sacmi IPS solutions can be fitted with the PVS preform inspection system, developed by the Quality & Process Control Division) and the elimination of contamination, the latter being achieved through the implementation of specific technical features (e.g. unloading of preforms in the postcooling area, performed directly in a controlled environment by special picking grippers). The preform production range developed by Sacmi stands alongside a comprehensive range of cutting-edge technologies for cap manufacturing (CCM, continuous compression moulding) and stretch moulding (SBF, stretch blow forming). This aspect – thanks also to further downstream integration with container filling and labelling solutions – confirms Sacmi’s status as a player capable of providing all the technologies needed to transform raw materials (PET and HDPE) into filled, palletised bottles. www.sacmi.it,@ID:19}, 7 NEWS PETplanet Insider Vol. 19 No. 12/18 petpla.net Acquisition of MHT - Krones strengthens its PET capabilities Krones, a leading manufacturer of filling and packaging solutions, has acquired MHT Holding AG (MHT). MHT, based in Hochheim, Germany, together with its subsidiaries provides injecting moulding tools and services to the PET industry. The company generates approximately €25 million revenues with 125 employees. The acquisition of MHT represents an extension of the Krones PET product portfolio into tooling for PET preform manufacturing and thus closes a gap in the Krones PET value chain. Krones can now offer a broader portfolio of PET capabilities for customers in the beverage industry, who increasingly demand integrated solutions. Acquiring MHT enables Krones to close the PET cycle, from PET preform manufacturing and stretch blow moulding all the way through to PET recycling – and then back to the manufacture of a new preform. MHT’s headquarters will remain at Hochheim with the current management to continue to run the business. In April 2018, Krones acquired 70% in Integrated Plastics Systems AG, Switzerland. Integrated Plastics Systems AG is focussing on providing turnkey PET injection moulding solutions for the beverage industry. The acquisitions of MHT and Integrated Plastics Systems AG are intended to enhance the Krones PET competence and portfolio. www.krones.com BrauBeviale 2018 After three days of exhibition, BrauBeviale closed its doors on a record high note. Over 40,000 trade visitors (2016: 37,923) – over 18,000 of them international – travelled to Nuremberg to attend this year’s capital goods exhibition for the beverage industry from 13 to 15 November 2018. While there, 1,094 exhibitors – 53% of them international – presented their products and solutions related to the entire beverage production process chain, with offerings ranging from raw materials to technologies and components all the way to packaging, as well as accessories and marketing ideas. A varied supporting programme rounded out the three days. Statements confirm the results of a survey by an independent institute: some 90% of visitors are involved in their companies’ investment decisions. The trade visitors came from many different parts of the beverage industry: breweries; malthouses; the areas of mineral springs, soft drinks, juice, and wine; and mechanical engineering and plant construction, as well as the trade and catering. Attendees travelled in from Germany and other countries, primarily Italy, the Czech Republic, Switzerland, Austria, the UK, Russia, Belgium, the Netherlands, and France. Some 98% of the surveyed trade visitors were satisfied with what they found at the exhibition. And 95% said they would also like to return to BrauBeviale next year. www.braubeviale.de Petainer expands manufacturing footprint to Latin America and China Petainer, a global leader in one-way kegs, is partnering with Great Leap Brewing in China to start manufacturing petainerKeg in 2019. This is in response to rapidly growing demand for draught beer in China and the suitability of one-way PET kegs in a country where logistics are complex. The announcement follows the commencement of Brazilian manufacturing in September with partner Blue PET, marking key steps in Petainer’s growth strategy and commitment to bringing the supply chain closer to the market. Petainer also manufactures in Europe, the US and Australia. The blow moulding plant in Tianjin, which has a PET Technologies APF-30 machine, will serve the domestic market as well as becoming the manufacturing hub for Petainer’s Asia region. Great Leap Brewing will also self-manufacture kegs at the facility to support their own business development strategy. The plant will produce Petainer’s 20l Hybrid keg, the oneway PET keg to use a circular economy design, focused on recycling and reuse. Designed for drinks producers such as breweries as a more cost-effective and sustainable alternative to traditional stainless-steel kegs, the keg is claimed to provide a low-cost way of entering new domestic and international markets. Petainer’s Classic and USD keg will also be manufactured at the site. www.petainer.com PTI and Big 3 enter into business alliance PTI has entered into a business alliance with Big 3 Precision Products, Inc., Centralia, Illinois, to help brand owners achieve quality and speed-to-market goals for products sold in PET bottles. For the past three decades, PTI has been the confidential development engine behind many well-known PET bottle commercialisations. Big 3’s Mold Services Group has been a leader in producing moulds for single-stage PET blow moulding machines, as well as injection blow moulding equipment. “With this alliance in place, we will now be able to seamlessly pair our PET bottle development services with the mould making capability necessary to run production quantities. Integrating the mould supplier into the early stages of the development process eliminates compatibility issues. It also removes another responsibility from the brand owner task list, truly reinforcing our ability to provide concept to commercialisation services,” explains Craig Robinson, vice president of business development and innovation, PTI. Big 3 brings three-plus decades of mould building expertise to the alliance. The company’s precision approach to creating tools enable it to meet the demanding production needs of leading brand owners. www.big3precision.com,@ID:9}, 9 NEWS PETplanet Insider Vol. 19 No. 12/18 petpla.net Global premium water growing 8% a year Global sales of premium bottled water reached US$ 16.5 billion at consumer prices in 2017, 48% more than five years ago, according to a new report from Zenith Global. Consumption volume also rose strongly by 26% over the five years to 11.2 billion litres. Zenith Global Chairman Richard Hall states “The most popular premium waters are high quality, differentiated and inspirational brands, often with distinctive, natural heritage.” The overall bottled water market, including flavoured and functional waters, has been growing strongly in recent years. The main drivers have been healthy hydration, convenience, affordability and reliability. Premium water perceptions can be subjective and may differ from one market to another. Zenith Global uses a combination of criteria including price, design, distribution, target audience, brand story, provenance, purity, water type and purchase frequency. Consumers may value provenance over purity in one country and the opposite in another. The 2018 Zenith Global Premium Water Report highlights the dominance of Europe in both volume and value, as well as exploring the development of emerging markets, with a deep-dive into five key countries: China, Japan, United Arab Emirates, United Kingdom and United States. It also assesses the relative importance of still or sparkling, along with water provenance and health claims. The report concludes with estimates for the segment’s future outlook. Full details of the 2018 Zenith Global Premium Bottled Water Report are available online. www.zenithglobal.com Recycling Technologies returns to crowdfunding to launch its recycling machine Recycling Technologies opened its second campaign to raise a minimum of £ 1.3m with Crowdcube as it seeks to build and open its first commercial plant in Scotland. This follows its successful debut Crowdcube funding round in February this year which closed at £ 3.7m, well ahead of its scheduled completion date. Recycling Technologies has developed and patented a plastics recycling machine, the RT7000, that is claimed to turn plastic waste back into oil called Plaxx from which new plastics can be made. The machine heats up the plastic in the absence of oxygen to break the waste plastic down into Plaxx. This process allows the RT7000 to recycle also plastics commonly considered unrecyclable such as plastic film, and laminated plastics such as food pouches. Furthermore, the RT7000s are modular allowing them to be transported and installed within existing waste management facilities where the majority of the residual plastic waste already arises. The company is now about to embark on the commercial manufacturing of the RT7000. This starts the next stage of its business, to develop its first full scale RT7000 and then assemble and deliver an initial fleet of twelve RT7000s to meet the anticipated demand for urgently-needed plastics recycling capacity. After the initial build of the company’s fleet, Recycling Technologies plan to grow the sales of RT7000s and drive further expansion into the UK, and global export markets. The aim is to install capacity to recycle 10 million tonnes of plastic by 2027, producing 7 million tonnes of Plaxx annually to replace fossil oils. This target will more than triple Europe’s current waste plastic recycling capacity. www.recyclingtechnologies.co.uk Tomra strengthens set-ups in China Tomra, a global leader in sensor-based sorting technology, is committed to its long-term development in China and has further strengthened its set-up in this fast-growing market. Since establishing the first subsidiary in China in 2010, Tomra has been actively increasing its investment and business activities in this dynamic market. Currently Tomra has three businesses operating in China: recycling sorting, food sorting and grading as well as beverage container collection. Tomra’s business activity in China ranges from business development, product management, R&D, assembly, sales, service and application validation in the local test centers. After expanding Tomra’s fresh fruit and vegetable grading manufacturing site in Kunshan, Tomra further reinforced its engineering team in China and expanded its technology center in Xiamen. With the “Made in China 2025” strategy, blueprinted by the nation’s top decision makers, there has been a national consensus that China should make a transition to sustainable development. In the coming years, priority will be given to innovation, manufacturing quality, environmental protection and structural change in the economy. Tomra’s vision of building a circular economy and a sustainable future with the aid of cuttingedge technology resonates with China’s top-level strategy. To prepare for the new opportunities created by China’s transformation, Tomra has been strengthening its organisational base in this vibrant country. Envisioning Tomra’s contribution in China’s shift to sustainable development, Jacob Rognhaug, general manager at Tomra China, says, “During China’s transformative development, more innovative technologies are needed to address the challenges of efficient use of resources, environmental protection and the provision of high-quality food. At Tomra, we are dedicated to optimising resource productivity with sensor-based technology, and our solutions can answer some of the main challenges that China is facing today. That’s why we have been increasing our financial investment in China while also investing a considerable amount of time in achieving a better understanding of the local market. I’m confident our technology can contribute significantly to China’s goal of sustainable development.” www.tomra.com,@ID:11}, PETplanet Insider Vol. 19 No. 12/18 petpla.net 41 TRADE SHOW REVIEW PETplanet: What about labelling? Do you have any ambitions to implement digital printing or any other new technologies in labelling? Clive Smith: Digital printing is a technique we are not pursuing right now as it still presents recycling-related issues. Our concept is to bring modularity and flexibility into labelling. To meet the growing variety of beverage types and bottle formats, our solution handles several kinds of labels, such as roll-fed or self-adhesive. Our EvoDeco labelling solutions enable producers to deliver different stock keeping units, with no impact on performance. They might either include several labelling applications in one multi-technology machine or work as a single labelling application through dedicated equipment, for optimised uptime, reduced footprint and low total cost of ownership. In addition, we are working on a new direct printing technology. Teased in occurrence of Drinktec 2017 and currently under development, our EvoBrand Active can differentiate bottles by activating part of the label design directly in the plant. One advantage is the personalisation aspect which is easy to achieve with it. The printer overcomes any possible quality issues by using laser activation. Not only is this cleaner than traditional inkjet printing, it also reduces environmental impact because it uses no ink – a real benefit in the food industry – and no solvent to clean the equipment. We are endeavouring to take this process up to recycling now. PETplanet: What other new projects are currently in your pipeline? Clive Smith: Generally speaking, modularity and service are becoming key. Talking services, for instance, it is worth to notice that we have the capabilities to test our customers’ products in our facilities in Europe. Additionally, through the PET Engineering acquisition, we have recently expanded our capabilities to support our customers in every aspect of packaging development, further strengthening our partnership with them when it comes to packaging design. This is an aspect that is growing in importance, especially when considering the critical impact packaging plays in terms of brand experience. PETplanet: Thank you very much. Via Scodoncello n° 41/E - 43044 Collecchio (PR) - Italy - Tel.: +39 0521 541011 Everything and more... cooperating together global solutions for containers in PET and other plastic materials Design, construction & installation of: • Systems for handling & storing all types of plastic containers • Linear blow molders for PET bottles LANFRANCHI S.r.l. www.lanfranchi.it innovation plastic container Design, industrialization, blow molds & prototype sampling for PET containers IPC S.r.l. www.ipcsolution.it,@ID:43}, Preform Production PETplanet Insider Vol. 19 No. 12/18 petpla.net 12 Retal’s expansion into the US market Knowing how to grow by Heike Fischer In Donora, Washington County, Pennsylvania, 20 miles south of Pittsburgh we visit the first Retal facility in the US. The building is located in a very pleasant valley. While driving over an old industrial bridge we saw the five big blue-shining letters of Retal ahead of us. We met Admir Dobraca, President and CEO of Retal PA, LLC. Tour Sponsors: June 4, 2018 We met: Admir Dobraca, President and CEO of Retal Pa, LLC Admir Dobraca, a formerly with Husky, told us about Retal’s promising start in the US with the building of its first facility. “At the end of 2015 the decision was made to enter the US market. We were attracted to the idea by our customers with high volume expectations with us. The former Polyone plant offered the space we needed, power was already available, and there was a rail connection. Geographically, the location was ideal with 65% of the US population within a 500 mile radius. Our aim is to build production hubs. ” After six months’ hectic activity, the work was completed. “On April 22, 2016 we received the keys of the facility and by the end of October the first packed trucks left the plant. The 14.000m2 area is currently mostly occupied with the production area, and is capable of further growth. Prospects are looking healthy in the long term for our operations in the US. “A centre of excellence for R&D is planned. At the moment we have a hybrid operation with a small team, but we are currently building it up right.” We have a former PTI person with a lot of experience in analytical testing.” With a total investment of US$30m the newest generation of chillers and dryers have been installed. “We also work with Kaeser Compressors and blenders from Conair,” Admir explained. The US plant is the 24th plant Retal has built up. “Every division of Retal worldwide produce preforms, roughly ten divisions are producing closures and preforms, four produce containers and bottles, some with single-stage, some two-stage machinery. Film is produced by three divisions in Russia, Ukraine and Lithuania. At the moment Retal has a € 900m, US$ 1 bn turnover, with 32,000 employees globally. We deliver 18 billion preforms a year. We have 800 different preform designs, different neck finishes; Retal is also a leader in multilayer. With 11.5 billion closures we are the largest PCO1881 producer in Europe by far.” “Here in Donora we are set up to produce three billion preforms on 400 or 500 t machines and up to six billion closures in the building as it is today. By the middle of next year staff numbers will grow from 65 to over 100. This division has a turnover of US$ 30m. A realistic market share of Retal in the US is at the moment 5%. We are working with global multi nationals in different CSD and water segments while developing local markets, with the smaller producers of water, dairy and similar beverages. The next big expansion will be to install the blowing capacity for cold fill and hot fill.” In the field of bottle production Retal has two new high-quality proRetal President and CEO Admir Dobraca (on the right) with PETplanet editor Heike Fischer High output, low energy consumption: Engel’s e-cap 420 based at the production hall of Retal,@ID:14}, BOTTLE MAKING 22 PETplanet Insider Vol. 19 No. 12/18 petpla.net Virtually engineering bottles of the future Something big is happening in a small corner of Northern Ireland which is making a global impact among its Fortune 500 clients. Blow Moulding Technologies (BMT), who envision ‘a scientific approach to Stretch Blow Moulding’ has emerged as a market leader in virtual engineering and testing bottles of the future. As the world scrambles in its search for the optimum bottle with the least material, yet with the same performance and at a lower cost, BMT provides a missing tools and the knowledge required to test these applications that a confident and seamless shift towards more sustainable and alternative polymer containers can be made. Using advanced data-driven tools and validated techniques, BMT’s team of qualified doctorate engineers from Queen’s University Belfast are enriching the SBM industry with the much-needed insight data which allows its clients to accurately predict the characteristics of new and recycled materials, preforms and bottles. Whereas the industry is predominately vested in PET, the seismic global shift towards new materials has created an intense focus on the application of recycled materials, new additives, bio-blends and bio-materials to the mass production of polymer containers. In light of the negative global trends against plastic, BMT’s highly optimised solutions have rapidly emerged into the limelight with what is, quite simply, the right solution at the right time. BMT offer a suite of technologies which facilitate this scientific approach to bottle engineering. The solution involves a consolidated stepped process which has been refined and optimised with over 20 years of research from leading experts in this field. Step 1 involves the characterisation of the material by using a stateof-the-art bi-axial machine which is specifically designed to replicate the processing conditions and understand its behaviour during stretch blow moulding. It generates data by bi-axially stretching the material to breaking point using different temperatures, strain rates and stretch ratios. Figure 1: 6-step process Figure 2: Bi-axial characterisation Step 2 involves measuring the temperature dependent mechanical properties post deformation using DMA and tensile testing. This creates a database of elastic modulus, for different processing histories, which is used in the design process. Step 3 involves the use of a stateof-the-art instrumented free-blow machine. This provides data for validating the material model for simulation by enabling critical outputs from the free-blow process to be measured and compared. Free-blow experiments are conducted over a large process window, where the cavity pressure, stretch rod force, surface strain, the evolving bottle shape and material behaviour (stress / strain) are measured. Figure 3: Preform characterisation using free-blow and digital image correlation to give stretch ratio map over time for various conditions Step 4 involves analysing the biaxial test data and free blow data to generate material parameters for the user material model of PET for the stretch blow moulding simulation. This will include simulation of the freeblow tests from Step 3 which will validate the material model for the resin. As well as fitting the material parameters for the PET material model, the linear viscoelastic parameters need to be derived from the DMTA data. This will include the generation of the master curves assuming time temperature superpostion along with Prony series parameters. Figure 4: Free-blow validation - strain results and process results Step 5 involves working with clients to produce validated simulations of their manufacturing process.,@ID:24}, PETpatents www.verpackungspatente.de PETplanet Insider Vol. 19 No. 12/18 petpla.net 48 Marketable bottles European Patent no. EP 3309084 A1 Applicant: Elite S. R. L., Fontaniva (IT) Registration date: 12.10.2017 In order to improve the labelling of a large number of identical bottles at bigger sporting events, it is suggested that the outer part of the bottle should have deeper embossments. Individual letters, numbers or symbols can be added by colouring the fields with a pen. Bottom shape International Patent No. WO 2018/085092 A1 Applicant: PepsiCo Inc., New York (US) Registration date: 25.10.2017 The application explains the specially designed shape of the bottom of a plastic bottle that contains a carbonated drink. Bottom shape of a light bottle International Patent No. WO 2018/089908 A1 Applicant: Amcor Group Ltd, Zurich (CH) Registration date: 13.11.2017 The bottom of a weightreduced bottle needs to be specially shaped to be able to absorb the forces generated by fluctuations in pressure. Several designs and manufacturing processes are described. Base-moulded light bottles International Patent No. WO 2018/09545 A1 Applicant: Jiangping Tang, Liaoning (CN) Registration date: 25.11.2017 It is proposed that several small-volume individual bottles be put together to form a standard large bottle. Both the bottom and the closure need to be designed accordingly. The contents are always fresher and more germ-free than if the consumer drinks from a large bottle for a longer period of time. Special surfaces European Patent No. EP 3152117 B1 Applicant: The Procter and Gamble Company, Cincinnati (US) Registration date: 03.06.2015 The European Patent application describes the appearance and process for manufacturing a plastic bottle with a multi-faceted surface. A bottle designed in such a way will immediately stand out on the shelves. Improved squeeze bottle European Patent No. EP 3321199 A1 Applicant: Kewpie Corporation, Tokyo (JP) Registration date: 23.06.2016 A squeeze bottle made from PET or HDPE for, among other things, mayonnaise and ketchup. It is designed as a headstand bottle and specifically shaped to reflect its squeezability, elastic shape and restoring force.,@ID:50}, PETplanet Insider Vol. 19 No. 12/18 petpla.net 47 BOTTLES Room scent beads in a PET container US company Bright Air has come up with a visually attractive product that neutralises bad odours and replaces them with pleasant fragrancies. 283 g of shimmering blue and slightly moist scented beads come in a clear PET container with well-rounded corners and edges. The beads are activated by unscrewing the recessed lid, removing the sealing membrane, then replacing the cover. Two labels provide product information, while the front one can be easily removed so that the container can be used as a decorative feature that can be put anywhere in the room. www.bright-air.com Mild 2 in 1 shampoo for children Garnier has extended its “Real Treasure” range with a mild 2 in 1 shampoo for children which does not sting their eyes or irritate the hair making it easy to comb. The product has been medically tested, smells of cherries and uses the soothing effect of sweet almonds for gentle hair and scalp care. The clear product comes in a lightly-coloured 300ml bottle with a hinged lid in matching colour. A leafshaped embossing enables the top to be easily opened, even with wet hands. A transparent label on the front and a printed self-adhesive label with product information inside complete the item’s packaging. www.garnier.de Body lotion in a pump dispenser Dm’s own Alverde natural cosmetics brand is selling body lotion from olive derived natural ingredients in a brown-coloured 200ml bottle under its “Naturally beautiful” label. Its colour and shape are very much like a pharmacist’s bottle. A lockable, black pump dispenser is screwed on to the mouth of the bottle, while a black and white label divided by several lines provides information about the product and how it should be used. www.dm.de Home + Personal Care,@ID:49}, TOP TALK PETplanet Insider Vol. 19 No. 12/18 petpla.net 10 Interview with Kai Acker, Chairman of the Executive Management Board at KHS GmbH at Brau Beviale Nuremberg, Germany Structure and order by Alexander Büchler Kai Acker has been Chairman of the Executive Management Board at KHS GmbH for a few weeks now. We spoke to him about his first impressions, his management style and the stimuli he wants to create within the company. Top of his agenda are “structure and order” for the benefit of customers and the company. CV Kai Acker Since 10/15/2018 Chairman of the Executive Management Board at KHS GmbH, Dortmund 2012 to 2018 Management roles at Leoni Special Cables GmbH 2006 to 2012 Management roles at Krones AG 1997 to 2006 various activities in industry and research Until 1997 training as an Energy Electronics Engineer, General Electrical Engineering at RWTH Aachen MBA at TU Munich Born in 1968 PETplanet: Mr Acker, for a few days now you have been Chairman of the Executive Management Board at KHS GmbH. Prof. Dr.-Ing. Heinz Jörg Fuhrmann, Chairman of the Executive Board at Salzgitter AG said: “I am sure that Mr Acker will create vital stimuli for the growth-oriented development of the KHS Group.” What kind of stimuli did he mean? Acker: There will certainly be a few. First and foremost, I have used these first days for a great deal of observation. Previously, I attended the in-house exhibition at KHS Corpoplast, and I was also able to gather some impressions of our customers, employees and suppliers at China Brew China Beverage. I think that structure and order do a company a lot of good. But we will also be looking to close some gaps in our full range of services. Furthermore, we have several projects already on the go that have not been completed yet. We will continue to develop these in a targeted way or make the decision not to pursue them further. PETplanet: What are you thinking of here? Acker: In our full portfolio, I’m thinking of the aseptic rotary block. It will be with us as soon as possible. In the labelling sector, there are still gaps and in the full line range there is still room for expansion. The technology will be thrilling. PETplanet: You are talking about the stimuli of structure and order. You worked for many years for a provider of beverage systems, which has basically increased in size through organic growth. Now you are managing a company that has been created through mergers and acquisitions. Is that a challenge for you or do you see it as an opportunity? Acker: It’s quite clearly an opportunity! If we channel these different cultures and bring them together in one direction, that is surely a benefit to customers and the entire company. For the last six years, I worked at Leoni Special Cables. There, we had German engineering, Chinese production and American customers. There is plenty to transfer to KHS from this mix. PETplanet: What management style will you use to implement these objectives? Acker: I have a cooperative management style; I give employees plenty of trust, delegate responsibility and so build individual motivation. But I absolutely draw the line at telling lies. PETplanet: For many consumers, plastic packaging is seen in a poor light and is a synonym for increasing environmental pollution. Legal regulations are increasingly restricting the use of plastic. How do you see the responsibility of KHS with regard to this topical issue? Acker: Of course, as a consumer I see the mountains of plastic, too. Many plastics can certainly be replaced, but I see no alternative to the PET bottle. It’s different for secondary packaging and here we have developed the Nature MultiPack which Carlsberg introduced to the market under the name Snap Pack, for example. Instead of film around multiple cans, we stick the cans together. Danone Waters used our solution for PET bottles under the name Evian Prestige. Here too, we stick the PET bottles together and do without film entirely. PETplanet: Mr Acker, in the past you often spent 6 years at the same company; where will you stand with KHS in 6 years? Acker: It is my aim to think in the long term, so KHS and I will hopefully work together for the coming 6 years or even longer. Through strengthened customer service, a full-range portfolio and simultaneously improving the company structure, we will generate profitable growth for the benefit of customers and the company. PETplanet: Many thanks, Mr Acker. Effective October 15, Kay Acker has become the new KHS GmbH Executive Management Board Chairman.,@ID:12}, CAPS & CLOSURES 20 PETplanet Insider Vol. 19 No. 12/18 petpla.net Closure solutions for the dairy industry UV light barrier caps in all colours Dairy products belong to a growing product group in global food consumption. Liquid dairy products are forecasted to grow by 30% between the years 2010 and 2020 to reach 350 billion liters. What will be essential for a sustainable growth of the industry will be a light, economic, environmentalfriendly packaging of the products – while at the same time convenience demands increase continuously. In the fast-growing product segment of dairy goods, the protection of the products through the packaging is crucial, since milk and dairy products are expected to keep their preferred taste, vitamin content, and colour. Especially for long-life dairy products with a longer shelf life, this poses great challenges to the industry. The packaging must meet optimum aseptic and hygienic standards and protect its contents from external influences for at least the promised shelf-life. At the same time, however, consumers in the “to-go” era attach great importance to ensuring that the products, respectively their packaging, are handy, lightweight, easy to transport and, above all, reclosable. In this context, the closure is just as crucial as the PET bottle itself. Special requirements are placed on closures for long life dairy products. “While closures for fresh milk must be primarily liquid-impermeable because of their short shelf life, in aseptically filled products additional protection against the ingress of microorganisms and impact of light is crucial”, says Christoph Thünemann, Group Director Communication and Marketing at Bericap. For a long time, this greatly restricted the design of the packaging and thus the differentiation of the products at the POS. To achieve maximum opacity, special-coloured masterbatches that provide a UV barrier should be used. However, these limited the possible colour variations. Bericap has succeeded in developing an optimal UV light barrier solution, which enables the production of screw caps in all colours. The product range encompasses light weight screw caps for 38mm neck and the 33mm neck and provides numerous customised closure solutions to this market. The 33mm size has now become established as a new, user-friendly, weight-optimised closure – also for dairy products – in several European countries. Closure specifications for premium products like oxygen reduction or aseptic filling are not a challenge for the packaging experts from Budenheim in Germany. “Our closure solutions with incorporated oxygen scavenger – O 2 reduced headspace bottles – provide maximum quality standards. And based on our vast experience in closure solutions for aseptic filling, we offer the necessary technical customer service, as well”, Thünemann explains. Overcaps, decoration and custom design Bericap supplies both customised closure designs and overcaps which can be used for small volume promotions or for long-term customisation of the package. They can be clipped onto almost all screw caps available in the company’s portfolio. “One of the most significant recognitions from market research and marketing theory is that a product’s customisation strongly influences consumer behaviour. It is a matter of course that we offer our customers a broad range of personalised and customised features so that their products stand out at the point of sale. Our solutions include top printing, embossing, debossing, laser coding and pad printing”, Thünemann concludes. www.bericap.com,@ID:22}, imprint EDITORIAL PUBLISHER Alexander Büchler, Managing Director HEAD OFFICE heidelberg business media GmbH Bunsenstr. 14 69115 Heidelberg, Germany phone: +49 6221-65108-0 fax: +49 6221-65108-28 [email protected] EDITORIAL Kay Barton Heike Fischer Gabriele Kosmehl Michael Maruschke Ruari McCallion Waldemar Schmitke Anthony Withers WikiPETia.info [email protected] MEDIA CONSULTANTS Martina Hirschmann [email protected] Johann Lange-Brock [email protected] phone: +49 6221-65108-0 fax: +49 6221-65108-28 LAYOUT AND PREPRESS EXPRIM Werbeagentur | exprim.de Matthias Gaumann READER SERVICES Till Kretner [email protected] PRINT Chroma Druck & Verlag GmbH Werkstr. 25 67354 Römerberg Germany WWW www.hbmedia.net | petpla.net PETplanet Insider ISSN 1438-9459 is published 10 times a year. This publication is sent to qualified subscribers (1-year subscription 149 EUR, 2-year subscription 289 EUR, Young professionals’ subscription 99 EUR. Magazines will be dispatched to you by airmail). Not to be reproduced in any form without permission from the publisher. Note: The fact that product names may not be identified as trademarks is not an indication that such names are not registered trademarks. 3 PETplanet Insider Vol. 19 No. 12/18 petpla.net If we talk about size in the preform sector, we are talking about Husky. For years, the company has held a market share of around 80%. Other well-known machine manufacturers have tried time and again to gain a foothold in the sector. Many just came and went after a short time. Too high are the demands on the machine, tool and above all service. Netstal has always put itself forward as a small but second provider over the years. However, it has also taken a breather in Naefels. Otto Systems offer an interesting concept, buying in parts and melding them into a complete system. Niigon, formerly Athena, is building preform plants in Canada under the experienced eye of Husky company founder Robert Schad. And let us not forget, in this context, the Italian contribution, especially Sipa. Two years ago, the company introduced the Xtreme preform compression system. Viewed somewhat sceptically by the experts initially, the first systems are now up and running at customers. Corporate visionary Gianfranco Zoppas has now built a flake processor, stretch blow moulding machine and filler around the preform plant. Thus, the complete process can now be achieved from flake processing through to finished bottle. A giant step forward. His analysis of the position of the preform converter: “tough competition, low margins”, hence his Xtreme dream. But read about it for yourself on page 14. Yours, Alexander Büchler Dear readers, Movement at preforming plants,@ID:5}, 45 PRODUCTS PETplanet Insider Vol. 18 No. 0/17 petpla.net PETproducts The prefect preform size Eskapet PET Product Ltd was found in Bursa, Turkey in 2000. Staring with PET bottle production, the range has been expanded by the production of PET preforms in 2003 and by jar production in 2013. When moving the factory to Nilüfer, Sanayi Bolgesi Eskapet started to produce also PET preforms for PET water and beverage bottles, as well as edible oil. Now Eskapet developed a new preform with Husky and KHS with a 25/22 opening in five sizes, 6.2 g, 7.55 g, 8.5 g, 12 g and 22 g. Since the end of November this water preform is being produced by the Turkey Company Gumus Water. www.eskapet.com PREFORM special Title 25/22 mm neck detail Revision 24.10.2018 Drawing NR Eskapet-Ç11 Scale 1/1 (mm) Material PET Weight 1.13g ± %5g Quality ISO EN 9001,@ID:47}, PETplanet Insider Vol. 19 No. 12/18 petpla.net 43 Trade Show review PETplanet: And now Africa: Why the decision to hold FDT Africa alongside the two other trade fairs? Westphal: With the new concept of holding analytica Lab Africa, FDT Africa and IFAT Africa in parallel, we are creating a common platform for exhibitors and visitors to gather crosstopic information about trends and innovations from the analysis, drinks, foods and environment industries. The combination of three trade fairs offers tailored and cross-sector solutions and therefore added value on all sides. PETplanet: Do you have a concrete example of how the three events create added value for exhibitors and visitors? Westphal: Yes, let’s take water as an example: the food and drink sector in southern Africa relies on a comprehensive and robust water provision and processing system. One of the most important topics at FDT Africa is the efficient use of water, whether as a raw material, as process water or for cleaning facilities and machines. This interconnects with IFAT Africa, which illuminates the issues around water in all its facets, including drinking water production, preparation of process water and treatment of waste water. Accordingly, an important role is played here by analysis and quality control. At analytica Lab Africa, visitors can see solutions for taking samples, for different analysis methods and for assessment procedures. PETplanet: How would you describe growth in the drinks sector in general and the development for investment goods for drinks and packaging producers in Africa and India? Westphal: I’ll start with India: according to VDMA Food Processing and Packaging Machinery Association, the demand for drinks is set to increase by 89% by 2022. Local drinks production rose in the period from 2012 to 2017 by 63% and further growth of around 9% is expected in the coming years. The growing production is reflected accordingly in an increasing demand for processing and packaging machinery. This makes India one of the most important sales markets in Asia for companies that produce machinery for manufacturing, processing and packaging drinks and liquid food products. In South Africa too, the market is developing dramatically. It is interesting that there, consumption behaviours are changing, and consumers are reaching increasingly for modern processed and packaged drinks, liquid food and foods. This trend is arising from increasing urbanisation and a very young but growing population with an average age of 27. According to VDMA, the demand for packaged food is to increase by 11% by 2022. Also according to VDMA information, drinks sales should increase by around 18% by 2022. In turn, this stimulates an increasing need for modern manufacturing, processing and packaging machinery. So in coming years, South Africa will continue to offer great potential for international companies to supply food and packaging machinery. PETplanet: To what extent is the omnipresent topic of PET recycling brought further into focus and how is the industry responding? Westphal: PET and PET recycling is already a major issue in these countries, and it will increase in importance in the future. PET is the most widely used packaging material. Accordingly, in India and South Africa, recycling, PET from renewable resources, bottle-to-bottle recycling and biodegradable materials are hot topics in the industry. We see this at trade fairs too, particularly through the great interest in fringe events about this sector. PETplanet: Which other markets in Africa and among India and its neighbouring countries currently direct their attention to FDT Africa and DTI but could in future become new international locations for drinktec? Westphal: Currently, we are wellplaced for the regions with our locations in Johannesburg in South Africa and Mumbai, New Delhi and Bangalore in India. In addition to these is China Brew China Beverage in Shanghai, China. Basically, we keep an eye on market trends and respond accordingly after consultation with the industry. It is entirely possible that there will be additions to the Drinktec family. PETplanet: Thank you very much!,@ID:45}, MARKET SURVEY 28 PETplanet Insider Vol. 19 No. 12/18 petpla.net Company name Erema Engineering Recycling Maschinen und Anlagen Ges.m.b.H. Empacar S.A Gneuss Kunststofftechnik GmbH Postal address Telephone number Web site address Contact name Function Direct telephone number Fax E-Mail Unterfeldstraße 3, 4052 Ansfelden, Austria +43 732 3190-0 www.erema.at Mr Christoph Wöss Business Development Manager, Application Bottle +43 732 3190 352 +43 732 3190 23 [email protected] Parque Industrial 45, Santa Cruz de la Sierra, Bolivia +591 3 34655 25 www.empacar.com.bo Mr Carlos Limpias Elío General Manager +591 3 34655 25 +591 3 34618 83 [email protected] Mönichhusen 42, 32549 Bad Oeynhausen, Germany +49 5731 5307 0 www.gneuss.com Bottle to Granulate Input variable: collected pressed bottles, various colours Yes, washing done in cooperation with long-time partners Engineering of washing lines with long term partners Output: Granulate with approval Yes Capacity [t/a] Up to 17,000 Floor space [m²] Which approvals FDA, ESFA, INTI, brand owners (conf.) Fresh water consumption per tonne output [m³/t] Depending on bottle contamination Consumption kWh per tonne output [kWh/t] Depending on input material Flakes to Granulate Input variable: flakes, coloured proportion max 5%, not much chlorine VACUNITE- and VACUREMA-Technology. Specification of input flakes: higher contamination can influence pellet quality but are basically possible to process, after discussion and agreed by Erema PET flakes 10ppm, PVC max content Output: Granulate with Approval FDA, EFSA (positive opinion issued), ANVISA, ilsi, BGBI, brand owners Yes: EFSA and FDA approved technology FDA, ESFA(pending), brand owners (conf.) Capacity [t/a] Up to 32,000 8,000 200-17,000 Floor space [m²] Depending on through-put and technology: 50-600 3,000 30-80, depending on size Which approvals FDA [cat. A-H&J]; EFSA (pending); brand owners (conf.); several national approvals (Austria, CH, Zona Mercursur, etc.) Coca Cola , Pepsico , Local Government FDA, ESFA (pending), INTI, brand owners (conf.) Fresh water consumption per tonne output [m³/t] Depending on application & technology type, there is a closed loop system 1.5 no fresh water needed Consumption kWh per tonne output [kWh/t] Between 250-350 333 350 Bottles to Flakes Input variable: collected pressed bottles, various colours Specification of input flakes for MPR: Higher contamination can influence flake quality but are basically possible to process, after discussion and agreed by Erema Pressed and loose bottles, clear, green and blue Output: Flakes with/without approval FDA [cat. A-H&J]; EFSA (pending); with Multi Purpose Reactor (MPR) Capacity [t/a] Up to 20,000 12,000 Floor space [m²] Between 20-60 3,000 Which approvals FDA, EFSA (positive opinion issued) Coca Cola , Pepsico , Local Government Fresh water consumption per tonne output [m³/t] Closed loop system 1.8 Consumption kWh per tonne output [kWh/t] 100 350 Kind and quantity of detergents 0.4kgrs/t Removal of the organic residuals up to which size [μm] 1,000μm or 30 Mesh Presetting residence time in the process 360-400min in SSP @ 200-210°C Company also offers systems for Bottle-to-film Yes, Vacurema Inline preform (Xtreme Renew) Yes Yes, mainly thermoforming sheet lines in direct food contact Bottle-to-fibre Yes, Vacurema Inline sheet No Yes, several lines under operation worldwide Bottle-to-strapping Yes, Vacurema Inline fibre; Yes, Vacurema Inline strapping Yes, 100% rPET strap 8 -20mm width; yes, 700mm width, 0.1-1.5mm thickness Yes, several lines under operation worldwide 12/2018 MARKETsurvey,@ID:30}, Bottle making 21 PETplanet Insider Vol. 19 No. 12/18 petpla.net German start-up Share launches 100% recyclate water bottle Starting from scratch Berlin start-up Share is the first beverage producer in Germany to sell its water in PET bottles made of 100% recyclate. With its expertise from the Bottles & Shapes consultancy program the KHS group supported the company by helping to design and develop the bottle in a very short time indeed. The plans are ambitious: in 2019 Share is hoping to fill water into about a million bottles a month made entirely of recycled PET and thus save over 200 t of plastic waste per year. “The plastic problem is of concern to more and more people, because they now encounter plastic every day and even on the beach on holiday. Despite this, most drinks continue to be sold in plastic bottles, which are mostly made from crude oil and too often end up as plastic waste in the environment. Our share bottle does not require any new raw materials, thus closing the cycle of production and recycling. That way, we avoid over 200 t of plastic waste per year,” says Share founder Dr Sebastian Stricker. For several weeks now the product has been on sale at Germany’s supermarket chain Rewe and drug store dm and has caused quite a stir in the media. “It took a long time for the original idea to be implemented,” says Iris Braun, head of Product and Social Projects at Share. “Finalising the technology and obtaining certification are both lengthy processes. Your partners are thus crucial.” Besides the two aforementioned retailers Share’s other partners are bottler Mineralbrunnen Allgäuer Alpenwasser and preform manufacturer Plastipack, which is also the world’s biggest converter. KHS Corpoplast was also largely instrumental in the implementation of the project. Easy handling of rPET preforms The German engineering company KHS supported the start-up in several ways, including in the development of the bottle design. Thanks to its holistic Bottles & Shapes consultancy program the systems supplier was able to contribute to the Share project experience drawn from over 4,000 designed bottles. Marc Eysel, who is responsible for sales in Northern Europe at KHS Corpoplast states that there were no unusual hurdles or challenges to be overcome through the use of 100% recyclate. “Manufacture is actually simpler as the material’s darker colour makes the preforms easier to heat than PET bottles made of virgin material.” Besides providing advice on the bottle design KHS also helps with production. Share’s still and carbonated water is bottled at the Allgäuer Alpenwasser bottling plant in Oberstaufen using KHS technology. The bottles are blown on an InnoPET Blomax stretch blow moulder, with no special adaptations to the system necessary, according to Eysel. Following the market launch of the recyclate bottle, interest is now also growing among other beverage producers, emphasise Braun and Eysel. “A number of bottlers wishing to increase the amount of recycled PET they use have now contacted us,” claims Eysel. www.khs.com www.share.eu Share founders (from left) Sebastian Stricker, Ben Unterkofler, Iris Braun and Tobias Reiner (photo: Gene Glover) For each purchased product Share provides people in need with a similar product on the basis of the 1+1 principle. According to the company, one bottle of water provides enough drinking water for a day through the construction or repair of wells in crisis regions such as Senegal (photo: Victor Strasse).,@ID:23}, Trade Show review PETplanet Insider Vol. 19 No. 12/18 petpla.net 42 Petra Westphal, Exhibition Group Director for Messe München, on DTI India and FDT Africa exhibitions “Large emerging markets with great potential” PETplanet: In the drinks sector, how would you describe the local trade fair situation and the need for events in India and southern Africa? Westphal: I think this can be shown very clearly by the numbers from the last events: 111 national and international companies (2016: 86) and around 1,600 participants (2016: 1,550) from 81 countries took part in Food & Drink Technology (FDT) Africa. At Drink Technology India (DTI), we likewise had an increase in the number of exhibitors: 201 exhibitors (2016: 146) from 17 countries showcased their products and solutions and occupied around 23% more net exhibition space than at the last trade fair in Mumbai. Visitor numbers remained at the same very high level as at the last event in Mumbai. We are extremely delighted with the unabated interest in the trade fairs and see this as a clear endorsement of the focus and design of our events. PETplanet: In your view, why is a DTI/FDT Africa important? Westphal: India and South Africa, these are large emerging markets with great potential. As organiser of Drinktec, the world’s leading trade fair for the beverage and liquid food industry, we want to offer precisely suited local platforms for the sector. Our impetus was to bring the expertise of Drinktec exhibitors into these emerging markets – and even to combine this with local sector expertise. Connecting global and local expertise provides inspiration for the entire industry; ‘learning from one another’ creates exchange and networking opportunities. This perfects the range of services and makes the local events into tailored platforms. PETplanet: What are the significant changes since the last DTI/FDT Africa? Westphal: Actually, we have several special features planned for 2019. Firstly, DTI is taking place twice. The trade fair will take place in Bangalore in spring and in New Delhi in December. Secondly, FDT Africa is taking place in July and for the first time will be a co-location event together with analytica Lab Africa (International Trade Fair for Laboratory Technology, Analysis, Biotechnology and Diagnostics) and IFAT Africa (International Trade Fair for Water, Sewage, Refuse and Recycling). PETplanet: Let’s begin with India. What led to the decision to hold DTI twice next year? Westphal: India is an enormous country! Each region works differently, and the drinks sector accordingly has different requirements. To do this justice, there is a yearly rotation. In even years, Mumbai is the meeting point for the sector; in odd years, we decided to hold the trade fair in Bangalore and in New Delhi. With this approach, we reach more targeted visitor groups in the individual regions. PETplanet: Are there differences in content, depending on the event location? Westphal: As regards the attendance of the individual sectors in the regions, the focus is on different segments. In the metropolis region of New Delhi, the focus is on beer, soft drinks and dairy products. Bangalore deals more with juices, beer, spirits, wine and liquid food. Mumbai is the international hub for the drinks and liquid food industry. There, visitors see innovations in the fields of manufacturing, filling and packaging of drinks of all types, as well as liquid food and dairy products, oils and fats.,@ID:44}, MARKET SURVEY 29 PETplanet Insider Vol. 19 No. 12/18 petpla.net • 28mm, 33mm and 38mm screw closures • Robust and trouble free capping • Established DoubleSeal™ technology - for secure sealing performance - for better protection against micro-organisms • Slit FLEXBAND® band technology for enhanced tamper evidence • O 2 barrier and scavenging options for screw flat caps supporting longer shelf life and fresher taste • Sports closures for aseptic filling and hot filling without aluminum foil • Special closures for syrups and carton packaging Unique range of screw and sports closures designed for cold fill and aseptic application BERICAP Technology for juices, RTD teas, health drinks www.bericap.com Starlinger & Co. Ges.m.b.H. STF Maschinen- und Anlagenbau GmbH Sonnenuhrgasse 4, 1060 Wien, Autria +43 1 59955 0 www.recycling.starlinger.com Mr Paul Niedl Commercial Head Division Recycling Technology +43 2674 800 3100 [email protected] Industriestr. 2, 94529 Aicha v. Wald, Germany +49 8544 960 110 www.stf-group.de Mr Erwin Forstner Sales Manager +49 8544 960 110 +49 8544 960 130 [email protected] Four models: recoStar PET FG, recoStar PET FG+, recoStar PET iV+, recoStar PET iV+ Superior Starlinger offers the engineering of washing lines and / or a turn-key project with components and technologies available in the market Yes (decontaminated for food-contact, IV increased, AA 1ppm, lowest VOC level) 6,000-26,000t/a rPET pellets Depending on design Several USA/FDA (C-H), Austria, Germany/BfR, Ilsi, France/AFFSSA, Finland, Australia, Canada, Egypt, Japan, Switzerland, several Latin American Countries; follows EFSA requiremens; several brand owners Depending on design Depending on design Four models: recoStar PET FG, recoStar PET FG+, recoStar PET iV+, recoStar PET iV+ Superior Yes (decontaminated for food-contact, IV increased, AA 1ppm, lowest VOC level) 1,500 t/a-26,000 t/a (6 extruder sizes) 130 - 540 Several USA/FDA (C-H), Austria, Germany/BfR, Ilsi, France/AFFSSA, Finland, Australia, Canada, Egypt, Japan, Switzerland, several Latin American Countries; follows EFSA requiremens; several brand owners Approx. 0.15 Approx. 410 (depending on design) Starlinger offers the engineering of washing lines and / or a turn-key project with components and technologies available in the market Deposit, curbside, MRF/PRF-collection, loose or baled, all kind of colours, other plastics, other contaminations Yes (decontaminated for food-contact, IV increased, AA 1ppm, lowest VOC level) Flakes with/without approval: PET flakes with approval (FDA, EFSA) 3,700-10,500 (5 sizes) 1t/h up to 6t/h Approx. 150 1,000-2,000 FDA (hot-fill), follows EFSA requirements FDA, EFSA, brand-approvals Different water circulation & treatment systems, from 1-0.1 fresh water (zero discharge) 120-250 (incl. bottle washing to SSP) 200-250 sorting, grinding & washing line total Caustic soda, detergent from various brands. The quantity of detergent depends on the brand, approx. 0.5-1l/t Total removal of residual organics on flakes, filtration of water 0.015μm possible 45-60 minutes, continuous fall system Yes Yes Yes,@ID:31}, PREFORM PRODUCTION PETplanet Insider Vol. 19 No. 12/18 petpla.net 15 PETplanet: Nevertheless, even your business is not immune from setbacks. Your large single-stage plant has virtually disappeared from the market. This was once your showcase project. Zoppas: The market has changed. In the past, single-stage plants were required. Today, it has become a two-stage technology to produce large quantities. Xtreme Sincro is the natural technological development to a “dynamic one-stage system” combining the advantages of both one and two stage equipments, with full control of all process steps. Also, since PET is the ideal material for cosmetic, pharmaceutical and food market, we are rapidly expanding our traditional single-stage range and are able to satisfy these markets with the required flexibility and output. PETplanet: You now have the first three Xtreme (injection-compression preform systems) on the market: two in Japan and here at the in-house exhibition, we can see a third plant for Brazil. Why injection-compression moulding? Zoppas: We must offer added value to the market. I think the preform injection-moulding sector is at its very limits. There is fierce competition for the converter with low margins. Hence my dream of the Xtreme. We are in front of a real technological breakthrough in preform production, similar to what happened in the electronic market in recent year. PETplanet: Did you ever consider abandoning the project while it was still being developed? Zoppas: If you want to be successful, you first have to invest a lot of money so as not to lose. It’s up to you to determine your pain threshold. But the greater the initial loss, ultimately the bigger the profits. And for the customer, the Xtreme could be the system with the best TCO. We are in front of a real revolution and we are very confident of its success after the extremely positive comments from our customers that could visit our system during the Open House. PETplanet: Thank you very much, Mr Zoppas! Moving to the next generation Sipa’s new XForm Gen4 XP system, unveiled in November, incorporates the latest generation of preform injection moulding technology to deliver lowest conversion cost alongside, unmatched speed, flexibility and ease of use. New technology incorporated into both the 350 and 500t system, capable of running with moulds holding up to 128 cavities and 180 respectively, has been designed to handle demanding applications. It is claimed to have short cycle times, to offer state of the art energy efficiency and to have low maintenance cost. As with all other XForms, the XForm Gen4 XP accepts virtually all legacy tooling produced by any major mould maker. A large 21.5-inch touch screen provides a new HMI operator experience, with high-definition graphics, swipe functions just like a smartphone, a multi-function control knob for onehanded operation. In addition it has fast response times unaffected by processor load. The HMI incorporates an advanced automatic process set-up and an in-depth part quality troubleshooting tutorial. This helps users improving machine up-time, to reach lower scrap rates, and depend less on highly skilled machine operators. Powered by servo-driven hydraulic pumps, the new preform production system has a low L2L (lock to lock) time, paired with an increased injection rate. Total energy efficiency has been increased by a similar amount: in a typical set-up with the machine set-up to full screw utilisation and PET with an IV of 0.80, the XForm Gen4 XP consumes 0.195kW of energy for one kilogram of material processed. One of the reasons for the improvements in dry cycle time and energy efficiency is the introduction of a kinetic energy recovery system acting on the toggle drive. Sipa’s XForm platform has gained a reputation for its ease of maintenance,on the Gen4 XP, it was pushed further, Sipa says. For example, the company has modified the accumulator area layout that the accumulators are now mounted on a pull-out rack inside the machine frame. In addition, the oil tank has been redesigned that it does not need to be emptied in case of maintenance (it can also be used at altitudes of up to 3,000m without modifications). The net result of all these improvements is that Sipa customers will be able to operate more consistently, at higher speeds, spending less on energy and maintenance, using a machine that will reduce conversion cost at recordlow levels. www.sipasolutions.com www.erema.com Preform production system XForm Gen4 XP,@ID:17}, Preform production PETplanet Insider Vol. 19 No. 12/18 petpla.net 13 jects: the company is the partner of choice for Nestlé, producing a 100% rPET preforms for them. The second project is an innovative six panel design bottle for hot fill. It involves lightweighting and a dedicated onepiece closure. The company believes it marks a significant advancement, with a 27.5 g total bottle weight. He continues: “Once the US operation is fully up and running we will no longer be so dependent on Europe. We plan to grow further in the US: over the next 3 years we want to build up 3-5 plants throughout the US, but maybe not the same application. We will be looking at blowing. We will be responding to market demands, and brand owners are looking for more diversity in the offering.” This success story will continue, Admir emphasises: “Retal is a global company working in the market since the 90s. Because it is privately held company, we still try to act as a small company, reacting quickly to customer requirements, thinking the impossible. Ours is a holistic approach: we offer cap, preform and bottle, and we can also supply the label too. In the preplanning stage, we can offer design, development and even marketing strategy. We see ourselves as facilitators, making our customers’ wishes reality. We identify ourselves as drivers, delivering solutions that may not even have been thought of, we think ahead.” www.retalgroup.com www.husky.co www.engelglobal.com www.imdvista.ch A 100% reliable machine-combination: Husky’s HyCap 300 with IMD Closure Testing System,@ID:15}]}}
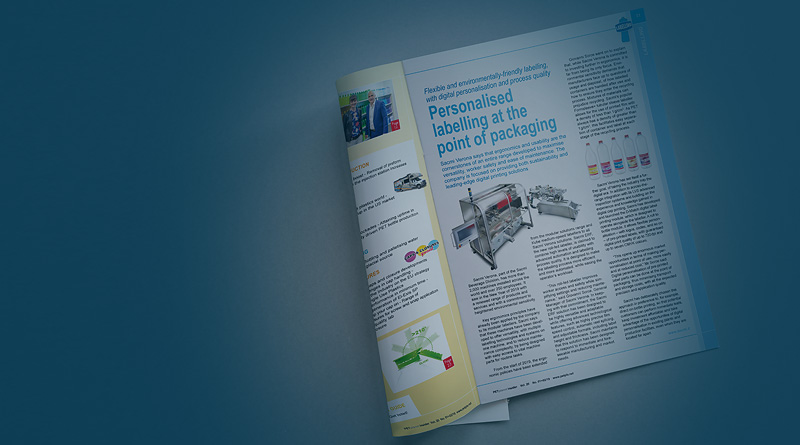