"MARKET SURVEY 29 PETplanet Insider Vol. 20 No. 01+02/19 petpla.net Resins Company name Indorama Ventures Ltd Postal address Telephone number Web site address Contact name Function Direct telephone number E-Mail 75/102 Ocean Tower 2, 37th Floor Bangkok 10110, Thailand +662 661 6661 www.indoramaventures.com Mr W.G. Hoenderdaal Technical Marketing Manager +316 51809942 [email protected] Resins Europe USA/Canada Latin America Asia 1. Brand name of the resins RamaPET, PlantPET Polyclear PET, Oxyclear Barrier PET, Oxyclear Shield PET, Performance PET, FuTuRe-PET Resin, PlantPET Resin Polyclear PET, Oxyclear Barrier PET, Oxyclear Shield PET, Performance PET, FuTuRe-PET Resin, PlantPET Resin RamaPET, Afron 2. IV Range a. of homo-polymers IV 0.58 - 0.95 IV 0.58 - 0.95 IV 0.74 - 1.25 IV 0.50 - 1.08 b. of co-polymers IV 0.58 - 0.84 IV 0.58 - 1.25 0.58 - 1.25 IV 0.58 - 1.08 3. Speciality resins CSD R1, R182C, R180 ES11, ES11 (A)-R10, 1101 1101, 1111 S1, S2, R1, N1S Water N180, W176, W170, N1, N1(S) N2R, N2R (A)-R10, N2R-Ti, 3301 3301 N2, N1 Beer N1, N1(S), N180 Oxyclear Shield PET 2310 Oxyclear Shield PET 2310 N1 Edible oil Wine / Liquors N1, N1(S), N180 Oxyclear Barrier PET 3500, PolyClear EBM PET 5505, 5507; 1708CC, 3302 Oxyclear Barrier PET 3500, Polyclear EBM PET 5505 and 5507 N1 Personal care / Pharmaceuticals N1, N1(S), N180 Polyclear EBM PET 5505/5507 Polyclear EBM PET 5505/5507 N1, G1 Clear Slow crystallisation P184 T-94 T-94 G1, G1AS (scratch resistant version) Hotfill R1, HF 2201, 1708HS 2201 H1 Pre-coloured None Fast reheat R1, R182C, R180 ES11, 1101 R1, R2, ES11 Other PlantPET R182C PlantPET Resin (Bio-MEG), High IPAmodified resins, BOPET Grades PlantPET resin (Bio-MEG) L1 (high flow blood tubes), film grades, low melting resins & silica masterbatches 4. Increased barrier properties Oxyclear Barrier PET 3500, OxyClear Shield PET 2310 Oxyclear Barrier PET 3500, OxyClear Shield PET 2310 5. PEN mixes available Co-polymers; Homo Polymer PolyClear Heat 2222, 2224, 2226, PEN PolyClear Heat 2222, 2224, 2226, PEN 6. Recycled blends available rPET flake and granulate FuTuRe-PET Resin, PolyClear Conserve PET FuTuRe-PET resin, PolyClear Conserve PET 7. Special comments RamaPET L1 for injection thin walled articles Polyclear EBM PET for extrusion blow moulding; low IV and functionalised copolyester N2G (Germanium based PET); HPC Grades for crystal clear bottles/articles, BioPET based on BioMEG Company name Invista Resins & Fibers NEO Group Reliance Industries Limited Postal address Telephone number Web site address Contact name Function Direct telephone number E-Mail Philipp Reis Strasse 2 65795 Hattersheim, Germany +49 172 614 6425 www.invista.com Mr Achim Heyer Business Dir. Polymer & PET Resin +49 172 614 6425 [email protected] Industrijos str. 2, Rimkai LT-95346 Klaipeda district, Lithuania + 37046466710 www.neogroup.eu Mr Gediminas Paulauskas Sales Manager +370 46466710 [email protected] PET BU, Build. No. 8, B Wing, 1st floor, Thane Belapur Road, RCP, Ghansoli, Navi Mumbai, 400701, Maharastra, India +91 22 7967 0000 www.ril.com Mr Rajesh K Gera Asst. Vice President - Business Development +91 2279681426 (D), +99 67033107, +91 22 79679107 [email protected] Resins 1. Brand name of the resins Polyclear PET, PolyShield Resin, XPure Polyester NEOPET Relpet and Relpet Green 2. IV Range a. of homo-polymers 0.60 - 1.0 0.56 - 0.82 0.76 b. of co-polymers 0.81 - 0.87 0.76 - 0.84 0.59 - 1.00 3. Speciality resins CSD Polyclear PET 1101 NEOPET 80, NEOPET 82 Relpet G5841 Water Polyclear PET 1101, T94N Aqua NEOPET 76, NEOPET 78 Relpet G5761 Beer PolyShield Resin 2300 and Masterbatch 2520 NEOPET 80, NEOPET 82, NEOPET 84 Relpet B9845 Edible oil Polyclear PET T94N Wine / Liquors PolyShield Resin 2300,2520; OxyClear Barrier Resin NEOPET 80, NEOPET 82 Relpet B9845/ Relpet G5801 Personal care / Pharmaceuticals Polyclear PET T94N, XPure Polyester NEOPET 80 Relpet G5801 Slow crystallisation Polyclear PET T94N, XPure Polyester Relpet S5841 (5 gallon returnable, thick sheet and thick moulded articles) Hotfill NEOPET 82 HF Relpet H7761 Pre-coloured Fast reheat Polyclear PET 1101 NEOPET 82 FR, NEOPET 84 FR Relpet QH5821 Other Next generation catalyst series Xpure Ultra NEOPET Relpet C1000 (CPET trays, high tenacity straps), Relpet IM5590 (thin wall products and injection moulded articles), Relept OP5821 (UHTmilk on aseptic filling line) 4. Increased barrier properties PolyShield Resin 2300, OxyClear Barrier Resin Relpet B9845 barrier grade has both active oxygen barrier and passive carbon dioxide barrier 5. PEN mixes available 6. Recycled blends available Relpet Green (100% PCR) 7. Special comments Grades have been developed based on finer requirements of end-use; customised grades (like EBM) are available on request.","@ID":31}, "CAPS & CLOSURES 23 PETplanet Insider Vol. 18 No. 0/17 petpla.net Both regulations have the goal of increasing the amount of bottles being collected and recycled, consequently reducing marine litter. To support the new demands of the market, Aptar’s Flip Lid closure and Stay-With technology were both designed to promote post-use recycling, as the bands remain attached to the bottle, enabling the closure to go through the correct recycling stream. Flip Lid In addition to its sustainability benefits, Flip Lid is a uniquely simple, consumer friendly closure, intended to create a convenient and enjoyable experience, as consumers no longer need to unscrew the cap, but simply flip it open to drink or pour the product. Consumers will also benefit from the patented, wide-opening hinged lid, and the audible “click” when reclosing. Flip Lid has been developed in partnership with Krones to increase filling line efficiency in a 26/22 neck finish. Other standard neck finishes are currently in development. Stay-With In addition to helping to promote recycling of the cap, Stay-With is a unique, patented, multipurpose techCAPS & CLOSURES ADHESLEEVE® TECHNOLOGY THE BEST SOLUTION FOR ROLL-FED LABELLING EVEN ON CANS! ProMachBuilt.com | PELabellers.com LABELS APPLICATION WITHOUT HOT MELT GLUE. EASY LIKE SCOTCH-TAPE! EVEN MORE! The first eco-friendly linerless labeller using pre-glued films. 100% ecologic and recyclable product. Also for empty containers. Adhesleeve + thermal-shrinking system. More than a valid alternative to the sleeve application. BOOTH #L1 MARCH 19 - 21, 2019 HO CHI MINH, VIETNAM Range of tethered closures for screw and snap application You can leave your cap on Aptar’s new tethered closures have been designed to meet the requirements of the new European regulation called “Single Use Plastics” (SUP), recently agreed on by the European Parliament, as well as the AB 319 California legislation in the USA. nology which provides improved consumer convenience, as they no longer need to worry about the closure being misplaced. This innovative technology aligns with the Association of Plastic Recyclers “Caps-On” initiative to raise awareness of the importance of recycling the closure with the bottle. Stay-With is transferable to almost any application, including sports caps and flat caps. www.aptar.com","@ID":25}, "imprint EDITORIAL PUBLISHER Alexander Büchler, Managing Director HEAD OFFICE heidelberg business media GmbH Bunsenstr. 14 69115 Heidelberg, Germany phone: +49 6221-65108-0 fax: +49 6221-65108-28 [email protected] EDITORIAL Kay Barton Heike Fischer Gabriele Kosmehl Michael Maruschke Ruari McCallion Waldemar Schmitke Anthony Withers WikiPETia.info [email protected] MEDIA CONSULTANTS Martina Hirschmann [email protected] Johann Lange-Brock [email protected] phone: +49 6221-65108-0 fax: +49 6221-65108-28 LAYOUT AND PREPRESS EXPRIM Werbeagentur | exprim.de Matthias Gaumann READER SERVICES Till Kretner [email protected] PRINT Chroma Druck & Verlag GmbH Werkstr. 25 67354 Römerberg Germany WWW www.hbmedia.net | petpla.net PETplanet Insider ISSN 1438-9459 is published 10 times a year. This publication is sent to qualified subscribers (1-year subscription 149 EUR, 2-year subscription 289 EUR, Young professionals’ subscription 99 EUR. Magazines will be dispatched to you by airmail). Not to be reproduced in any form without permission from the publisher. Note: The fact that product names may not be identified as trademarks is not an indication that such names are not registered trademarks. 3 PETplanet Insider Vol. 20 No. 01+02/19 petpla.net The planned EU-wide planned ban on the most common disposable plastic packaging continues to create shockwaves throughout the sector. Following the major corporations CocaCola, Danone, Pepsi and Nestlé’s rejection, in a joint statement, of the introduction of the mandatory tethered caps on certain beverage containers and instead rely on an upgraded withdrawal policy, the Verband Deutscher Mineralbrunnen (VDM) has even commissioned a legal opinion. According to this legal opinion, the Brussels design rule violates EU law. Plant manufacturers and fastener producers are still preparing for the fight and working on solutions to ensure that the cap remains firmly attached to the bottle. We have captured some of the current thinking of closure and mould manufacturers for you on pages 18-21. A retrospective of successful developments in the caps and closures segment also marks the start of our series of anniversary contributions, with which we are intending to celebrate our 20th anniversary! In each issue, a technological area is put under the microscope, questions asked about its development and commented on by up to date industry voices. Our Jubilee Year is already upon us! Over more than 10,000 pages, we have reported continuously on innovations, procedures and players in the PET sector since 1999. But we are also looking forward, for example to an update on the EU plastic strategy at the Petcore conference in Brussels (February 6-7 2019). The Drink Technology India trade shows in Bangalore (April) and New Delhi (December) provide the setting for this year’s India Road Show roundtrip. In May we will be meeting you at Chinaplas and the year will be rounded off with the K fair in Düsseldorf and the BrauBeviale in Nuremberg. We look forward to sharing an exciting 2019 with you, and take this opportunity of thanking you for 20 years of loyal support and encouragement, and for the trust you have continued to place in us! Yours, Alexander Büchler Dear readers,","@ID":5}, "40 TRADE SHOW REVIEW PETplanet Insider Vol. 20 No. 01+02/19 petpla.net Tradeshow confirms that packaging has begun its revolution! After a few years of absence the PETplanet Insider team visited Paris exploring the new All4Pack trade fair and was impressed by the well working marketing strategies the organisers worked on long time before. The market change driven by regulatory and environmental requirements, the new needs of b2b and consumer multichannel trade and the opportunities arising from industry 4.0 were among the many topical issues addressed from November 26 - 29, in Paris at the All4Pack 2018. For its 2018 edition, All4Pack Paris laid on an extensive array of show features and a content-rich programme which further enhanced the dynamism of meetings between exhibitors and visitors. This edition received positive reviews for the quality of its presentation and more particularly in terms of the professionals in attendance, with their planned projects and investments. In figures, All4Pack Paris 2018 drew a total of 79,000 professionals, in line with its forecasts, including 1,350 exhibitors and their teams. The show welcomed a sizeable international visitor contingent during the first two days, with nearly 35% of visitors from abroad, 21% of whom from Africa. A total of more than 60 countries were represented, together with foreign delegations from nations that included Cuba, Germany, Israel, Japan, Taiwan and Turkey. With regard to French visitors, 35% came from the Paris region and 65% from other regions in France. The programme of talks and round tables, purposefully more selective this year with 25 talks and more than 80 speakers, addressed leading issues faced by the industry today and looking towards the future. Taking place before a packed auditorium, these talks included: A presentation of the double European survey conducted by All4Pack and its white paper “Packaging ready for its revolution” The Awards ceremony of Pack The Future, Sustainable Plastic Packaging Award 2018, coordinated by Elipso, the French plastic and flexible packaging association, and its German counterpart Industrievereinigung Kunststoffverpackungen e.V. (IK) The latest innovations in plastic and flexible packaging (European competition Pack The Future) The packaging of the future: Pack Odyssey, the recycling of packaging of the future, specific issues for plastics; Sustainable packaging: fulfilling consumer expectations. Another premiere for All4Pack Paris 2018 was the organisation of the 22nd edition of the international polyethylene terephthalate (PET) summit, held in Paris for the first time. The issues addressed ranged from the circular and supportive economy to eco-design and technical developments in thermoforming and pre-stretching. From suppliers of raw materials and recyclers to packaging manufacturers and clients, the PETnology European Conference gathered together the stakeholders in the sector. There was positive feedback from organisers Barbara and Otto Appel and attendees. www.all4pack.com Best practice for the food, home and personal care industry Sidel and Gebo Cermex presented advanced systems and innovative packaging solutions suitably developed for the food, home and personal care industries. PETplanet talked to Cécile Alexandre, Director of Food, Home and Personal Care at Sidel and Jean-Marc Passemard, Marketing Communications for FHPC Markets, about the presented PET packaging solutions. Cécile said “Packaging is a key component of any marketing mix: it must be eye-catching to differentiate brands in the marketplace with dependable performance all the way from concept to consumer. The advantages of PET as a packaging material are numerous: it is strong, unbreakable, light, transparent, safe, and above all 100% recyclable. As a lightweight material, PET offers also considerable environmental benefits in the form of lower transport costs and reduced fuel emissions. Its unique geometric properties and inherent barrier properties, together with its design flexibility, have enabled food, home and personal care manufacturers to use less and less material in the packaging process, while optimising energy use. These processes also help reduce waste and improve sustainability measures.” At the booth we saw the proven Sidel Matrix blowers, overcoming the challenge of complex shapes by using preferential heating. This system benefits from the company’s twenty-year expertise in producing complete PET lines for the most demanding FMCG producers. Thanks to preferential heating the production of lightweight bottles in a variety of asymmetrical shapes across a wide range of packaging applications with an optimal material distribution is no longer a challenge. Very interesting was the unique SteadyEdge patented base solution, which offers FHPC producers enhanced brand differentiation options together with high production efficiency. In the FHPC markets, traditionally dominated by HDPE (High Density Polyethylene) and PP (Polypropylene) Sidel’s SteadyEdge base offers chances to accelerate the take-up of PET containers. Along with innovative and attractive PET package design variants, it ensures stable and cost-efficient production. Sidel and Gebo Cermex showcased attractive solutions across packaging and end-of-line systems. www.sidel.com www.gebocermex.com","@ID":42}, "45 PRODUCTS PETplanet Insider Vol. 20 No. 01+02/19 petpla.net PETproducts From Greece to Saudi Arabia: the journey of a premium water A water with superior flavour, winner of a Taste Award, deserves to become w e l l - k n o w n f a r beyond the borders of its country of origin. That’s why Eurowaterland decided to send its brand Epirus Kostilatas Springs on a long journey, taking it from the green Athamanian Mountains to the hot terrains of Saudi Arabia. The market that the brand has decided to take on is therefore a demanding one, where international brands such as Evian are already battling it out. In order to face such tough competition, Eurowaterland asked PET Engineering to design a premium bottle with as few strengthening ribs as possible, despite the lower weight requested, and with few decorative features. PET Engineering came up with a cylinder-shaped packaging solution with a mountain motif on the shoulder and a series of small vertical grooves. These grooves not only stiffen the bottle against the vertical load and prevent it from losing its radial shape, but also represent the narrow ravines of the Athamanian Mountains through which the water runs before reaching the end consumer, enriched with precious mineral salts. As well as designing the packaging, this project also involved making the container lighter by implementing a new 29/25 thread: PET Engineering handled the conversion of the Krones bottling line and supplied the set of moulds. www.petengineering.com Cap feeding and sorting systems technology NII Laser Technology has developed a new compact feeding unit for 28-38mm caps, the Gravity Sorter Compact (GS-C). Fully stainless-steel design provides various advantages including elimination of unwanted static current. Various closure design and dimensions can be handled in the same feeding unit with a simple and quick re-setup process with only few parts needing to be readjusted to work with closures of different diameter and height. The universal belt does not need any readjustments to run caps of different diameter. The productivity of the system is increasing to 200,000pcs/h. Moreover, the GS-C system does not need a compressed air connection that may be an advantage to certain production layouts. Its compact design together with a number of speed options combines efficiency and robustness, states the company. The sorting system can be used with various equipment to feed closures and caps to video inspection, printing machines, laser systems, closure counters and others. The feeding unit can be optionally equipped with a flow splitter or other device to divide closures on the belt. www.niilt.com New multi-module quality control – Torus’ TQ-Lab Torus Measurement Systems released the latest systems for plastic containers. After 5 years developing Torus integrated the latest measurement modules into a single system – The TQ-Lab. This development offers customers multiple quality control tests which can be selected by module to suit each customer requirement. Offering non-contact and destructive tests on both empty and filled containers or preforms, this portable machine delivers reliable data to the network with no operator influence. This offers users multi-module gauging all controlled by one interface, simplifying the quality control process. The requirement of the TQ-Lab is to place batches of containers onto a turnaround conveyor and select the relevant program. A vision-system locates the position of the neck and with little programming, an intelligent force feedback gripper and multi-axis pick and place system transfers the product from the conveyor to the first measurement module. Here non-contact thickness and dimension measurements can be taken. Once the first module measurements are complete, the gripper transfers the container into the second module where non-contact internal diameter measurements are taken using miniature white light confocal technology. Finally, top load, volume capacity & container weight are measured in the third station before a final transfer to dedicated pass or fail bins. This multi-station concept, TQ-LAB, can be supplied as a manually loaded or fully automated package. As with all the Torus range, measurements are fully traceable and certified to UKAS standards and come with CE certification. The gauge utilises Torus’ own windowsbased software GaugeXplorer, allowing customers to take control of their quality at a single control station. www.torus-group.com","@ID":47}, "41 TRADE SHOW REVIEW PETplanet Insider Vol. 20 No. 01+02/19 petpla.net Nitrogen injection PETplanet met Thomay Buys, Project Manager and Philip Kerckx, Managing Partner at Vacuum Barrier Systems, presenting their Vacuum Barrier’s Nitrodose liquid. These nitrogen injection systems are used to pressurise and/or inert delicate packages, like cans and PET bottles. A precise drop of rapidly expanding liquid nitrogen into hot and cold fill lightweight PET packages and aluminium cans allows for consistent pressure from package to package and eliminates paneling and palletising problems. While efforts to reduce the amount of plastic used in each bottle have resulted in more environmentally friendly packaging, these lightweight bottles are less stable. Dosing the headspace of the filled bottles with liquid nitrogen pressurizes the container and adds rigidity, which helps during packaging and handling. www.vbseurope.com Blow moulds and more We t a l k e d w i t h Eyüp Sivri Marketing Manager at Petka Mold about their leadership in Turkey and the Middle East. Eyüp caused it because of on-time delivery, product warranty and a very well after sale and technical service. At All4Pack Petka Mold showed some PET blow moulds and highlighted their 96 cavaties cold half preform mould which is suitable for machines e.g. from Husky, Netstal, Sipa or Demag. www.petkamold.com Volumetrical filling Pierre Ronvel, Commercial Director at ezs easy solutions talked about their portfolio of PET bottle conveying systems and the partnership with Vipool. On the booth the companies presented a Visitron VKR-EI-DN. This filling machine is designed for filling beer, sparkling or still wines, high viscosity products, carbonated or non-carbonated water, carbonated and non-carbonated juices, and still tea. The filling valves are mounted to the filling ring from outside, are electro-pneumatically controlled and made with the latest technology for volumetrical filling. www.ezsolutions.fr www.vipoll.si Reduced friction The Spanish company Posimat presented a Posijet air conveying system. Miriam Ciriano, Commercial and Marketing Department, explained the double guide profile that envelops the bottle above and below the neck ring, preventing marks from being made on the bottle and reducing air turbulence and thereby providing greater bottle stability at very high line speed. The precisely directed airflow reduces levels of contamination, increases bottle speed, and considerably diminishes bottle jams while keeping bottles more vertical at speed over 1,200 bpm. The efficient performance is also provided with short-neck bottles. She continues explaining that the guides are only in contact with the neckring. The airflow generates a cushion between the guides and the neckring, thereby reducing friction significantly, resulting in lower air pressure during operation and lower energy consumption of the fan. Miriam ended that the air flow is controlled automatically by sensors that adjust fan rotation speeds according to the conditions of bottle accumulation on the line. Each type of bottle saves its own parameters so the operator does not have to make adjustments after changeovers. www.posimat.com F.l.t.r.: Thomay Buys, Project Manager and Philip Kerckx, Managing Partner at Vacuum Barrier Systems in front of their liquid nitrogen dosing systems","@ID":43}, "BOTTLING / FILLING PETplanet Insider Vol. 20 No. 01+02/19 petpla.net 15 air conveyor between the blower and the filler. SMI says that it is a compact and flexible solution for creating bottles with either flat or sports caps. The blower has lower energy consumption than comparable previous models because its preform heater module is equipped with high efficiency IR lamps. The stretch-blow moulding module features a double-stage air recovery reduces energy costs associated with high air compression. Wrapping and palletising Downstream of the production unit, the LSK 25T shrink wrapper wraps 500ml bottles in 4x3, 5x4 and 6x4 film-only, in double lane 3x2 filmonly, and in 4x3 and 6x4 tray plus film collations. The larger, 1,500ml bottles are collated in 4x3 and 3x2 film-only, and 4x3 tray plus film arrangements. SMI says that it is designed for easy format changeovers, within a compact but ergonomic structure that allows installation even in restricted spaces, while remaining easily accessible even to less skilled operators. An LWP 30 wrap-around packer also handles 500ml and 1,500ml with either flat or sports cap in filmonly collations arriving from the LSK 25T shrink wrapper. Already packed 3x2 (500ml and 1,500ml) bottles are packed in wrap-around corrugated cardboard boxes in 4x3 and 4x6 formats. 1,500ml loose bottles are packed in wrap-around corrugated cardboard in 3x4 and 4x6 layouts. The wrap-around packaging system is equipped with a mechanical device that groups products and forms the cardboard box around the transiting bottles without having to stop the machine. The solution is suitable for a package that is resistant to impacts and can protect the product during transport. The cardboard boxes can be graphically personalised to capture consumers’ attention, offering greater opportunities for marketing and promotion. The APS 1550P palletising system provides fully automatic loading of 1,016x1,219mm USA pallets. Ice Age Glacial Water Company says that increases in demand and sales put unsustainable pressure on its previous system. When it decided to invest in upgrading its production processes, technologies and capacity, it determined that it required a solution that would be able to work with functional efficiently of at least 95%, across a range of different containers and formats. Flexibility was also a key feature, in order that it could react immediately to even the earliest and slightest signal in the fast-changing water industry. The company expects that the trend away from sugary and carbonated drinks and towards healthier alternatives will continue, and that minimally-processed glacier water is well placed to meet this demand. www.smigroup.it C L O S U R E I N S P E C T I O N The new CapWatcher® Q-Line Brings the quality lab to the production line","@ID":17}, "BOTTLE MAKING 13 PETplanet Insider Vol. 20 No. 01+02/19 petpla.net Attaining uptime in a sustainability-driven PET bottle production world Minimising blockades In PET bottle manufacturing lines, downtime amounting to just minutes reduces output by thousands of products. And, in our ever-more environmentally-conscious world, strategies to increase uptime can clash with increasingly stringent sustainability touchpoints. A lubricant applied on the outside of preforms or bottles is said to optimise the slipping zone between blow moulded bottles and to act as a mould release at the same time - in an environmentally-conscious way. Blockades are a particular problem in PET stretch blow moulding plants. A post-moulding issue, blockades arise as bottles are transported via air conveyor systems when bottle-to-bottle friction triggers a line block. It is coefficient of friction that causes moulded bottles to move with instability through conveyor systems, and then stick together. This causes a ‘fan-like formation’ of bottles on the line, which is generally spotted only when production stops. Production process aid It’s vital that bottles rotate freely as they pass through the transport conveyor or their forced rotation will lead to a blockade. Common at the curves and ascents of conveyor systems, that is where blockade prevention strategies prove critical. Chem-Trend offers a product that is claimed to improve the transport efficiency of formed PET products through air conveyor systems. The product is applied as a lubricant on the outside of preforms or bottles at key points along the PET bottle production process. It can be added at preform or post blow mould stage. It is applied by spraying the product on preforms or bottles by any spray equipment. A proven and very efficient system is in Process Integrated Coating (PIC) from company Steidle GmbH, based in Leverkusen, Germany. General Manager of this company Rolf Lamers said “Coating the surface with the extremely thin sliding film – Lusin Lub O 32 F – allows the PET bottles to rotate against each other freely. This minimises blockades and facilitates the transport of the PET bottles more smoothly.” Optimising the so-called slipping zone between blow moulded bottles boosts productivity by reducing the potential for blockades along transport conveyors. The coating also provides a protective layer for preforms that continues to function well beyond blow moulding process and transportation stages. Mould release optimisation Another advantage of this lubricant is that it acts as a mould release agent, reducing the potential for defects. Bottles sticking to the mould also negatively affect cycle times, meaning higher cost per bottle or more bottles in the scrap bin. During mould ejection, this lubricant ensures a quick and clean release of bottles. Applied directly on the preform before blowing, the lubricant lays evenly into the blow moulds’ surfaces, ensuring a smooth and even repartition of lubricant on the blown bottles. As the lubricant stays fluid, there is no risk of a hardened build-up. A sustainable PET bottle production aid which reduces imperfections Sometimes preforms are dropped into octabins before warehousing. Despite every effort during their handling, this might lead to scratches and other imperfections on the preforms. These defects will have a significant impact on the heat absorption of PET preforms when passing though the blow moulding line as well as on the appearance of the finished goods. The lubricant significantly improves the scratch-resistance of the plastic surfaces during transport and handling. Its lubricating properties also prevent contamination by providing a barrier against dust and enhance the gloss of blown bottles. An added advantage of using Lusin Lub O32F is the optimisation of bulk box filling levels, which can reduce the transport cost significantly. It does not contain any solvents, silicones or halogens and can be removed with water. It is therefore an environmentally-conscious solution for solving many of the problems that arise in PET preform production and blow moulding processes. www.chemtrend.com Coating the bottles’ surface with a thin sliding film allows them to rotate against each other freely. (Illustration by Steidle)","@ID":15}, "CAPS & CLOSURES 18 PETplanet Insider Vol. 20 No. 01+02/19 petpla.net Voices from the industry on the EU strategy paper on Single Use Plastics Future challenges in cap handling Dr Michael Krüger, CEO Corvaglia Group “Marine littering is a severe problem that requires action urgently. So I definitely welcome that the EU has taken action by proposing and passing a directive on the topic. It seems as if a lot of the changes that will be enforced make a lot of sense to help reduce marine littering. Unfortunately, the article that enforces caps to remain attached to the container does not make sense – neither ecologically nor economically. We estimate that in the worst case this requirement will increase CO 2 emissions from beverage packages by as much as 400,000 tons CO 2 equivalent per year in the EU with minimal to zero positive impact on marine littering. The EU commission seems to expect such minimal impact themselves, if I interpret their impact assessment correctly. With the vast amount of money industry – and finally consumers – will have to spend on implementing the required changes, I am sure much better options could have been realised to reduce marine littering. It will be painful for a lot of stakeholders and distract companies from other valuable developments, but of course the directive can be implemented.” “The most impactful development in my opinion was when multimodal resin technology was introduced to organoleptic HDPEs for use in caps and closure applications. It just helped everyone in the industry to accelerate the speed of lightweighting at same or better closure performance, particularly for CSD applications. While introduction took place already several years ago, we only experience the full benefits on a broad scale since recent years.” www.corvaglia.com Michael Fink, Vice President z-moulds “The fact itself that the EU is working on such a guideline is important and absolutely positive, but the outcome itself is not totally uncontroversial. Tethering the caps to the bottles to ensure that they find their way to the recycling station is trying to solve the issue without involving the people. Education might be a better way to ensure the proper handling. Technological there are different ways on the one hand we have some simple solutions available to ensure that the bottler fulfils the requirements of the law, but most of them are not really convenient for the end-users and therefore will mostly be used as a interims solution. In my opinion the implementation is possible, but the final impact is not clear today. For example so far we just know the cap needs to be tethered to the bottle, but nothing describes how strong!” “As a mould supplier I tend to focus on the mould technologies when answering such a question, therefore I think our patented z-slides system is definitely one of the biggest game changers in the past years for the beverage closure manufacturers. On the closure side itself I would say the trend of lowering opening torques as well as improving the haptic properties for better grip, while opening, brought some good changes.” www.z-moulds.com As a regular reader of PETplanet Insider you will know that our editors travel around the world keeping their eyes and ears on the ground to pick up all the relevant, hot topics of the day: for nearly six months discussions on the EU strategy paper on Single Use Plastics, which includes the handling of caps in a circular economy, has been causing shock waves in the sector, -culminating in a written statement from October 2018 in which the major players, Coca-Cola, Nestle, Danone and Pepsico expressed the view that,: “investments should be directed into technology and infrastructure that will achieve a collection rate of 90% of bottles and their caps by 2025.” In a widespread deposit return system, a higher level of responsibility from producers, and a pan-European consumer education program, these key players see a more effective means of preventing the littering of beverage caps. Prior to the EU vote on Article 6, it is the moment for us to ask caps- and mould producers about their assessment of the proposed EU regulation and the consequences that might ensue if it is passed into law. We have therefore collected the views of producers such as Bericap, Corvaglia, Sacmi, United Caps and z-moulds, and we are grateful to Husky for adding their comments reflecting the Canadian and US point of view!","@ID":20}, "CAPS & CLOSURES 16 PETplanet Insider Vol. 20 No. 01+02/19 petpla.net A review of caps and closures developments It was a Swiss designer named Albert Obrist who in 1970 developed the first plastic top for CSD drinks bottles with the injection-moulded onepiece HDPE cap. Originally intended for use with returnable glass bottles, his idea quickly attracted the interest of the PET bottle industry which increased sharply at the end of the 1970s. The key advantages of the HDPE cap over its aluminium counterpart were considered to be, firstly that damage to the bottle mouth caused by rolling the aluminium caps onto the neck finish could be avoided, and secondly that the HDPE caps were more compatible with the precise geometries of the PET thread. Obrist’s innovations were subsequently incorporated into the Crown Cork and Seal Company’s operations during the mid1980s. At the same point in the 20th century, the Alcoa CSI acquired H-C Industries decided to approach the problem from a different perspective and patented the compression moulding process for plastic CSD caps, resulting in the H-C Wing-Lok design. Compared with injection moulding, compression moulding output in those days sometimes was more than double. In 1986, when CSI acquired H-C Industries, its rotary compression-moulded process for making closures was an industry first. The H-C Wing-Lok closure is regarded as the beverage industry’s first successful mechanical tamper-evident closure. Since then, changing consumer needs, along with new trends in drinks, regulations and technological advances, have led to ever new innovations and improvements being made in the design of caps and closures. What has not changed, however, is the need for tight closures (under a variety of conditions) that protect a bottle’s contents, and which are easy to open and re-seal, can be incorporated within the package design and are cost effective to produce. PETplanet has been covering the developments in closures technology in over 10,000 of its magazine’s pages since 1999. And while a survey like the following can never account for completeness, we hope you enjoy our selection of 20 years of achievements in caps and closures for PET bottles, as reported in PETplanet! Caps and closures – some highlights 1999 to 2019 2000 In issue 8 KHS and CCT presented a cap with a moving liner for capping oxygen-sensitive products such as beer. 2001 In issue 11+12 we reported that Bericap had won a “Packaging Oscar” for their BO2S beer closure. 2003Bericap launches the onepiece hot fill closure in the Chinese market (issue 2). Products packed were mainly juices and energy drinks. 2005At PETpoint, Bericap presented the “Shorty” for beer. The door was open for anyone to submit designs for lightweight caps and neck forms. Also at PETpoint, and reported in issue 12, Romeo Corvaglia enters the discussion on lightweight caps for both still drinks and CSDs. 2006PETplanet and Sacmi organised the first joint cap forum with an intense discussion on the advantages and disadvantages of injection moulded and compression moulded caps in issue 11. Alcoa summed it up with the comment “it all depends...”. In the same issue Bericap presented their Supershorty, a range of closures in line with the new 28mm light weight neck finish ISBT standard PCO 1881 for CSD. 2007The first commercial application of the 1881 neck finish (Martens brewery in Belgium) was reported in issue 12. 2009Romeo Corvaglia reported in issue in 2+3, that the 0.99g cap for still water was on the market in North America. Issue 9 reported that Coca-Cola China had decided to universally adopt the PCO 1881 by the end of 2009. 2010Lightweight is still a hot topic: In issue 5 we report on Bericap’s new hot fill initiative, resulting in newly modified one-piece DoubleSeal 38mm closures together with neck wall thicknesses of 2mm - as a first step. In issue 6, MHT Mold & Hotrunner Technologies presents savings from lighter caps and threads, launching with the MHT-21Light thread family a lightweight alternative to the PCO 1810. CCT has been designing the cap for the new thread. 2011 In issue 4 we report on the launch of a push-pull closure for hot fill packages without aluminium foil, developed by Bericap in 2010. 2012A lightweight combination cap for the 1881 short neck format for both, carbonated drinks as well as still water, is close to launch (Corvaglia, issue 1+2). A 26mm closure range for edible oil, superseding the standard 29/21 neck finish has been developed by Bericap, as we are covering in issue 1+2, generating weight savings. In issue 6, the company announces the launch of the DoubleSeal one-piece hot fill closure in the North American market, with reduced wall thicknesses. 2013Following the K trade fair, PETplanet is publishing a study of the caps and closures markets to describe the state-of-the art technology, starting with issue no. 12/2013 and the developments, strategies and competitive differentiation of the companies involved in the market of suppliers of systems and moulds for the production of caps and closures. CAPS & CLOSURES","@ID":18}, "CAPS & CLOSURES 20 PETplanet Insider Vol. 20 No. 01+02/19 petpla.net Christoph Thünemann, Group Director Communications and Marketing at Bericap “The SUP directive will prescribe that caps are tethered to the neck of single use plastic beverage bottles. The scope of beverages subject to this prescription is still unclear. The prescription of tethered caps represents a major challenge for the entire beverage industry involving massive cost in all levels of the supply chain – more than 100 bln packages need to be redesigned. The PWC impact study estimates change over cost of 4-14 bln EUR depending whether neck finishes need to be changed or not. Bericap has developed a system which maintains design of most neck finishes or requires only small changes to the closure design.” Significant neck and closure weight reduction Bericap has developed the 26mm CSD closure – DS 26/14 SFB CSD (7046) The 7046 closure is an alternative product to PCO 1881 closures. There is a significant weight saving of ~30 % in total due to the dimensional neck and closure reductions compared to the PCO 1881 closure and neck solution. The achievable weight savings are higher comparing with the previous change from PCO 1810 to 1881. For the bottlers, this results in a faster payback of their filling line conversion costs incurred in changing their filling line to the new system. It is interesting to note that, in addition to its aesthetic appearance, the closure offers a comfortable grip, is equipped with the well-proven double seal system, as well as a slit flex band for proper application and offers a user-friendly opening torques. The closure is usable for bottles up to 2 l with a CO 2 carbonisation of 8 g/l. The weight reduction comes purely from a decrease in height and a reduction of the T-diameter / thread diameter of the neck, which results in a smaller outer diameter. The inner diameter is exactly the same as for PCO 1881. For the end-consumer there is no compromise on drinking performance and quality and there is no change for the filling nozzles on the bottlers’ side. Bericap has started production, installing new line in its European plants. The product has now been introduced at various major brands. Due to the increasing demand, Bericap has invested in additional production capacity. The new Bericap 7046 is an attractive offer, in order to save costs for bottler and brand owners. www.bericap.com Sacmi’s approach and strategy in relation to the new EU directive on single use plastics Over the last 10-15 years, the focus of the beverage industry has been light-weighting: that is, reducing packaging weight (bottles and caps) without affecting performance or the consumer experience. The industry collectively spent millions and managed to reduce energy consumption and CO 2 emissions to levels unthinkable at the time the whole process was begun. We are the unsung heroes of the environment, as the combined efforts of all industry players allowed the market to grow, while keeping environmental impact stable. At present, the challenges faced by plastic cap manufacturers and their mould suppliers and the efforts they need to make are intrinsically bound up with new EU regulations. During the next few weeks, the European Parliament is to vote on the directive 2018/0172 (COD) “Reduction of the impact of certain plastic products on the environment”. For cap manufacturers and OEMs, the most relevant part of the directive is Article 6, which states the following: 1) Member States shall ensure that single-use plastic products listed in Part C of the Annex that have caps and lids made of plastic may be placed on the market only if the caps and lids remain attached to the container during the product’s intended use stage. 2) For the purposes of this Article, metal caps or lids with plastic seals shall not be considered to be made of plastic. Glass and metal beverage containers that have caps and lids made of plastic shall not be covered by this Article. 3) By ... [3 months after the date of entry into force of this Directive], the Commission shall request the European standardisation organisations to develop harmonised standards relating to the requirement referred to in paragraph 1. Those standards shall in particular address the need to ensure the necessary strength, reliability and safety of beverage container closures, including those for carbonated drinks. Since it has not yet been clearly established when a cap can be considered attached to the container, market players shall need to wait for the harmonised standards. Sacmi will support its partners in every possible outcome of this period of change and has initiated developments and activities as follows: 1) new light weight caps for returnable plastic bottles, both with and without liner, should a bottler decides to move from single use bottles to returnable bottles; 2) light weight metal crown caps, in case the bottler decides to use a metal cap on a plastic bottle; 3) new slitting patterns together with the partner company to let the cap stay “attached” to the bottle; 4) ongoing testing for new mould layouts dedicated to hinged flip top caps. www.sacmi.it","@ID":22}, "MARKET SURVEY 28 PETplanet Insider Vol. 20 No. 01+02/19 petpla.net 01+02/2019 MARKETsurvey Resins & additives Preform machinery Preform production & inspection Preform & SBM mould manufacturer SBM 2 stage Compressors Filling equipment & inspection Caps & closures & inspection Palletising & shrink film machinery Recycling Additives Suppliers of resins & additives There is rapidly increasing demand for packaging materials that give even greater protection to their contents. Functional additives and resins are an important technology in meeting this demand for greater product protection in the plastic packaging market. A functional additive modifies the properties of packaging to impart desirable or beneficial functions. That is why we won’t stop a well-established tradition in opening our market surveys overview in 2019 with suppliers of resins and additives. These companies participated: Addform Limited, Invista Resins & Fibers, Clariant Plastics & Coatings GmbH - BU Masterbatches Germany, Repi S.p.A, Indorama Ventures Ltd, Sukano AG, indorama Ventures, Neo Group and Reliance Industries. Although the publishers have made every effort to ensure that the information in this survey is up to date, no claims are made regarding completeness or accuracy. Company name Addform Limited Clariant Plastics & Coatings GmbH, BU Masterbatches Repi S.p.A. Sukano AG Invista Resins & Fibers Postal address Telephone number Web site address Contact name Function Direct telephone number E-Mail Unit 21, Skypark Industrial Estate Liverpool, L24 1YL, Great Britain +44 151 659 1102 www.addform.co.uk Mr Richard Glen Sales Manager +44 151 659 1102 [email protected] Am Unisys-Park 1 65843 Sulzbach am Taunus, Germany +49 6196 757 60 / +49 6196 757 6276 www.clariant.com/masterbatches Ms Severine Wild Marketing Europe +49 6196 757 6276 [email protected] Via B. Franklin 2, 21050 Lonate Ceppino VA - Italy +39 0331 819511 www.repi.com Ms Lucia Buffoni Marketing Manager [email protected] Chaltenbodenstrasse 23 8834 Schindellegi, Switzerland + 41 44 787 57 77 www.sukano.com +41 44 787 57 77 [email protected] Philipp Reis Strasse 2 65795 Hattersheim, Germany +49 172 614 6425 www.invista.com Mr Achim Heyer Business Director Polymer & PET Resin +49 172 614 6425 [email protected] Additives and Colours for PET Liquid colours Yes Yes Yes No Microgranule colours No Yes Yes Masterbatch colours Yes Yes Yes UV protection additive (solid) Yes Yes Yes UV protection additive (liquid) Yes Yes Yes No AA reduction (solid) Yes Yes - SenzAA No AA reduction (liquid) Yes Yes - SenzAA No Oxygen scavenger (solid) Yes No OxyClear Additive, PolyShield Masterbatch Oxygen scavenger (liquid) No No IV Enhancer Yes Yes Yes (solid) Yes Reheating Yes Yes No Blowing additive Yes No Yes (liquid) Yes Slipping agent Yes Yes Yes (liquid) Yes Other PET additives: Anti Yellow, Antiblock Matting Agent, Surface Modifier and Special Effect Anti Yellow (liquid), Process Aid (liquid) Optical Brightener (liquid) Colours for Barrier Solutions (liquid) Whites for monolayer UHT Milk (liquid) Antioxidants, Antistatics, Melt Enhancer, Voiding Agent, Optical Brightener, Nucleating Agent, Mould Release, Matting Agent, Slip/Antiblock, Light Diffusor, Light Barrier, Impact Modifier, Flame Retardant, Antimicrobial, Plasticizer, Pinning Agent, Foaming Agent","@ID":30}, "CAPS & CLOSURES 21 PETplanet Insider Vol. 20 No. 01+02/19 petpla.net Tethered closures in the USA A new bill was proposed in the state of California (AB-2779) in February 2018. This bill (if passed into law) would prohibit a retailer from selling or offering for sale a single-use plastic beverage container that does not feature a closure that is contiguously affixed (connected) to the beverage container containing water (≤ 1liter). The primary driver for this bill is the belief that closures on single use plastic bottles contribute to environmental pollution. The bill was ordered inactive at the request of the author on June 4, 2018. It remains to be seen whether the approved European SUP directive will result in a reactivation of this specific bill or a variant thereof. Regardless of these laws (enacted or proposed), Husky is developing solutions to ensure full compliance without compromising usability and the drinking experience. The lowest cost to produce and simplifying tooling conversions are dominant value drivers for Husky’s entire tethered closure portfolio and available closure manufacturing solutions. Matching new closure products to consumer trends/needs Water: The water segment continues to demonstrate extremely strong growth globally as healthy beverage options dominate consumer preferences. Global unit demand expects to remain strong through 2023 with a forecasted CAGR of 4.1% (Source: Global Data). 29/25 family Within the water segment, premiumisation is a dominant trend. Water brands looking to position their product as a premium offering can leverage the closure as a means to differentiate. Husky’s 29/25 portfolio offers various grip heights to communicate product positioning and enhance user experience. For the brand owner, there are weight savings to be realised on the entire dispensing system without compromising the user experience. Carbonated Soft Drink (CSD) While the CSD market segment has not enjoyed the robust growth of water, it remains a very relevant beverage category. Global unit demand is positive through 2023 with a forecast CAGR of 1.3%.(Source: Global Data). 26mm CSD Brand owners have introduced smaller format sizes to correspond with changing consumer preferences around sugar content. These smaller format sizes provide a cost savings opportunity for brand owners to light weight the dispensing system (PET neck finish + closure). Husky’s 26mm CSD dispensing solution (neck + closure) offering satisfies the strict test criteria of many brand owners while rated to a high level of carbonation (4.7% vol). This design has minimal impacts on the grip height vs 1881 (~4mm) and no impact on the drinking experience. Juices, sports drinks & teas (JSDT) As consumer preferences shift towards healthier beverage alternatives, the JSDT market segment is well positioned to lure consumers seeking beverages with natural ingredients. Global unit demand is positive through 2023 with a forecasted CAGR of 2.5% (Source: Global Data). 32mm Aseptic The 32mm neck finishes have been developed as alternatives to the widely used 38mm necks for material and cost savings opportunities. Compared to the 38mm dispensing system, material weight savings up to 30% can be realised on the neck finish and closure. Compared to the 38mm bottle, the consumer can enjoy a more pleasant drinking experience thanks to the smaller neck finish. The 32mm closure offers an industry leading weight at 1.75g and passes Sidel’s strict B180 test for sealing robustness. A slightly heavier 2.35g option offers improved robustness with B180 and Capdis compliance for aseptic filling. www.husky.co","@ID":23}, "CAPS & CLOSURES 17 PETplanet Insider Vol. 20 No. 01+02/19 petpla.net 2014Caps with benefits: Vicap Systems launches sports caps with a dosing chamber with which consumers can freshly supplement their drinks with flavours or vitamin shots (issues 4+9). In issue no. 9, we talk about DTI India: Bericap unveils its new lightweight closure, HexaLite 29/11, whose weight saving compared with a 30mm/25mm neck and closure combination is as much as 33%. As well as this lightweight trend, the spotlight is increasingly on interest groups with difficulties in opening operations. Brazilian Clever Pack is one example for capping solutions for those who suffer from reduced grip strength, developing reusable building block closures (as reported in 9/14). 2015Dispensing caps go further: an international project team from Hähl and Teamplast, Incap and Sumitomo developed caps suitable for liquid additives and granules, sellable in combination with a beverage or as an independent refill product (issue 5). 2017 Developed for aseptic filling of wide mouth bottles, RPC Obrist Madrid launched its 38mm closure, as we report in issue 1+2. At Interpack, United Caps presented, amongst other things, its 1881 petal flower cap. Developed for Wattwiller Mineral Waters, the unusual shape of the closure allows end-users to open bottles with minimum effort. 1881 petal flower cap For the 26 mm and 29 mm neck, Bericap developed higher closures with a better grip (issue 4). In the same article, product piracy and counterfeiting are being encountered with closures with a folded and slit tamper evidence band or with laser printing across the TE band and closure. In our Drinktec preview in issue 8, Bericap introduces an extremely light 28 mm PCO 1881 flat closure for non-carbonated beverages. Israeli company Water.IO is turning caps into smart devices, as we report in issue 8: The caps not only remind the consumers of keeping hydrated but turn the complete container in a connected device with many benefits such as re-ordering. Corvaglia presents the digital printing of caps at Drinktec, matching the high speed of its own mould technology (issue 9). Aptar launches sports closures for the on the go bottles market, a one-piece flip-top 28 mm PCO 1881 as well as the two-piece bi-injected closure for 29/25 mm neck finish (issue 11+12). 2018 We report in issue 1+2 on Bericap’s Neo 30/17 weight optimised version for the neck finish 30/25; the SnapCap 26: a hinge cap pressed on a lightweight 26/21 neck and the 33mm neck closure for cold-aseptic or hot-filling recipes. SnapCap 26 Silgan Closures develop a plug and play system: The K-Seal ensures full plug engagement to the water cooler spike (issue 1+2). In the run-up to NPE 2018, Corvaglia announces a 188 slitted/folded closure with a better grip. The closure features a 25% weight reduction compared to other 1881 closures while returning to the consumer comfort of 20 years ago! Continuous growth of aseptically processed beverages and an increase of on-the-go beverage formats are reasons for Aptar to launch a new sportscap in a wide mouth neck finish. The 38mm 1-piece closure is described in issue 5. 38mm 1-piece flip-top PP closure For issue 10 we fly downunder, visiting Coca-Cola Amatil’s plant opening of their new sports cap production line. Being made entirely of HDPE, it is easier to recycle than the traditional mix of HDPE and PP. Also for on-the-go customers, the dispensing solution Guardian Light by Aptar is presented in the same issue. In issue 12 Bericap highlights UV light barrier screw caps. The product range encompasses 33mm neck caps and light weight 38mm neck caps in all colours. UV barrier closure, developed for the dairy industry Year Total 2017 563.98 bn 2018 593.31 bn 2019 624.16 bn 2020 656.62 bn Global caps and closures market, based on beverage container units filled and an estimated annual growth of 5.2% (source: Krones Group Annual Report 2017) CSD: 1-piece cap for Late nineties Late 2Ks Today PCO1810 neck 3.1 g 2.8 g 2.5 g PCO1881 neck 2.5 g 2.0 g 26/22mm neck 1.6 g Water: 1-piece cap for 30/25mm neck 2.4 g 2.0 g 1.6 g 29/25mm neck 1.3 g 1.2 g 26/22mm neck 1 g 0.9 g 25/22mm neck 0.7 g Caps & Closures weight developments over the past 20 years for still water and and CSD (source: Sacmi) The Vicap sports cap comes with a dosing chamber","@ID":19}, "PREFORM PRODUCTION PETplanet Insider Vol. 20 No. 01+02/19 petpla.net 10 Removal of preform cooling from the injection station to the conditioning station increases productivity Productivity boost With the Zero Cooling technology, Nissei ASB Machine Co., Ltd. intends to push PET moulding efficiency one step further. The technology has been developed to increase productivity and to improve container quality. The company is now applying Zero Cooling as a new standard technology to models in the company’s four-station, one-step ASB Series line-up. The four stations of the ASB Series machines seen in fig.1 operate simultaneously within each cycle. Standard one-step moulding works on the principle that a customdesigned preform is injection moulded and cooled to the point where the PET resin is still above its glass transition temperate (Tg), so it is still flexible as it is transferred to the following stations. The residual heat in the preform is then used to allow blow moulding into the finished container shape at the stretch-blow station. Because injection and cooling of the preforms always requires the longest time of these four processes, the injection station dictates the overall cycle time of the moulding machine, and therefore productivity. Nissei ASB sees the advantage of its ASB Series in the second of its four stations, known as the preform conditioning station. It is used to apply a variety of adjustments to the temperature profile and/or the shape of the preform, providing greater flexibility and stability over moulding systems lacking this feature. Improved productivity Now, ASB has reviewed the role of the preform conditioning station to develop an advanced cooling technique called “Zero Cooling”. In standard moulding, preform cooling occupies a significant portion of the total cycle time. By shifting the necessary preform cooling from the injection station to the conditioning station (fig.2) it can be combined with the appropriate temperature profile adjustment. The injection station is now available to start filling the cavity for the next injection cycle while cooling of the previous shot continues simultaneously in the conditioning station. It is this removal of cooling from the injection station that enables average productivity increases of 1.5x and gives rise to the name of “Zero Cooling” for the process, states the company. Physical properties Since the cooling rate of PET resin is a fixed property, in standard moulding the only way to shorten cooling time is to make the preform thinner, which for a given container weight means the preform also becomes larger (fig.3). Doing this reduces the overall stretch ratio from preform to finished container so the positive effects of strain hardening from biaxial orientation, that increase the stiffness and tensile strength of PET, are significantly reduced. Nissei ASB claims that smaller preforms have the advantage of providing higher stretch ratios resulting in a good material distribution and topload strength around 15% higher than standard moulding or that of competitor’s products (fig.4). With standard moulding, thicker preforms would require longer cooling resulted in reduced productivity. Fig.1 One-step moulding in 4 stations allows for zero cooling. Fig.2 Cycle reduction with Zero Cooling","@ID":12}, "PETcontents 01+02/19 4 PETplanet Insider Vol. 20 No. 01+02/19 petpla.net INSIDE TRACK 3 Editorial 4 Contents 6 News 45 Products 46 PET bottles for Home + Personal Care 47 PET bottles for Beverage + Liquid Food 48 Patents PREFORM PRODUCTION 10 Productivity boost - Removal of preform cooling from the injection station increases productivity EDITOUR 12 Colouring the plastics world - Repi’s rising up in the US market BOTTLE MAKING 13 Minimising blockades - Attaining uptime in a sustainability driven PET bottle production world BOTTLING / FILLING 14 Cool filling - Bottling and palletising water right from its glacial source CAPS AND CLOSURES 16 A review of caps and closure developments 18 Future challenges in cap handling - Voices from the industry on the EU strategy paper on Single Use Plastics 22 Maximum performance in minimum time - The fourth generation of El-Exis SP 23 You can keep your cap on - Range of tethered closures for screw and snap application 24 The inline quality lab 26 Time for closure MARKET SURVEY 28 Suppliers of resins and additives LABELLING 31 Personalised labelling at the point of packaging - Flexible and environmentally-friendly labelling 32 Western style BBQ bottles - Rotary labeller for flexible self-adhesive labelling 33 Dynamic labelling - Heuft launches ‘Tornado II Dynamic’ 34 Connected labelling - Packaging and decoration stepping into the virtual world 35 A second skin for PET containers - Sleeving PET detergents and body care products TRADE SHOW REVIEW 37 China Brew China Beverage 2018 40 All4Pack Paris 2018 42 BrauBeviale Nuremberg 2018 44 The key to sustainability - Increased use of rPET in disposable PET bottles in Germany BUYER’S GUIDE 49 Get listed! CAPS & CLOSURES Page 36 Page 23 243612 Page 31","@ID":6}, "9 NEWS PETplanet Insider Vol. 20 No. 01+02/19 petpla.net Increased manpower MHT USA strengthens customer support, engages new partners and commits investments into 2019 MHT USA enjoyed a very strong and successful year in 2018. Order volume was double that of the year before and, with new partners joining the international team, it is looking forward to 2019 with optimism. Customers in the Americas are now being supported and serviced by four agencies, operating in the local languages and in the same timezones. AMZ Resulting / Marcio Amazonas has been announced as the new business agent for Canada and the US. Marcio Amazonas, former Coke and PTI business development executive, recently joined MHT in its efforts to reach out more directly into the US market. “There are still many Canadian and US bottle and preform manufacturers, with whom we are not in touch. Even though the overall market growth is low, with our service and customer dedication we can grow and win many more projects and customers here,” said Andreas Krampe, CEO of MHT USA. In Central America, Plasgrom joined the team at the beginning of 2018. Two key accounts have already been developed and supported by Enrique Estrada – Plasgrom’s main PET representative – and David Felix. MHT will join Plasgrom in early April 2019 at the Plasimagen exhibition in Mexico City. “Mr Estrada is well known and respected in the industry for his customer dedication and reliability. He sold several projects into HPP5 and other machines in 2018 and predicts more deliveries for 2019,” said Mr Krampe. In Brazil, another key market for PET moulds, MHT is represented by Fabio Franco of Globalplast. Franco was one of MHT’s first agents in the Americas. He provides refurbishment and conversion support in Brazil and surrounding countries, as well as technical services on site and from his facilities in Sao Paulo. In other South American countries, MHT is represented by Lateral Hint. Sergio Freire and Pablo Almazan provide technical services and customer support from Panama to Argentina, from their base in Chile. Andreas Krampe said that the recent connection of MHT USA to its parent company’s global ERP system, along with the imminent provision of engineering, preform design support and CAD services from its offices in Atlanta means that it will provide better service and faster feedback to its growing North and South American customer base. During 2018, MHT USA undertook several projects with inhouse assembly of new moulds in its home territory. With partners in Mexico, it can provide refurbishment and conversion services domestically there, and Globalplast is the third full service and refurbishment centre in the Americas. MHT was recently acquired by Krones AG, Germany; its North American centre is in Franklin, Wisconsin. www.krones.com www.mht-ag.com 9 NEWS Team Plasgrom / Central America with (f.l.t.r.) Enrique Estrada, Andreas Krampe, David Felix in front of MHT’s HQs in Hochheim, Germany [email protected] Tel: +90 212 695 50 00 Fax: +90 212 694 97 24 100815dmyR .com","@ID":11}, "37 TRADE SHOW REVIEW PETplanet Insider Vol. 20 No. 01+02/19 petpla.net TRADE SHOWreview PART2 Strong growth in PET We caught up with the Managing Director, KHS Greater China Christian Schwarzmann, at the CBB trade event in Shanghai and spoke to him about KHS’s China Strategy. PETplanet: Mr Schwarzmann: What have your customers been talking to you about here in Shanghai? Schwarzmann: The main topics have been water in PET bottles and beer in cans. The Chinese market has seen very strong growth in PET for water (around +7%) and for beer in cans (around +5%). PETplanet: Can you as a western technology provider compete with Chinese production suppliers in terms of prices? Schwarzmann: We have noticed that upward of a certain capacity level, inquiries tend to only be sent to Europe’s three main integrated plant constructors. PETplanet: Even if time is tight and the facility has to be up and running quickly? Schwarzmann: Delivery times are always an issue, particularly here in Asia. Once the machines have been built, we have to ship them from Europe to China which has a knock-on effect on delivery times. Using our local production allows us to respond quickly to the market demands. PETplanet: Was that the reason for your intention to build a production facility here? Schwarzmann: We are producing already machines here in China since year 2013. Now we look for a new facility with bigger space to be able to bring our premium technology faster and in a more economical way to the market. PETplanet: One of your competitors also has large production plants in China but cannot operate them at full capacity. What makes you sure that yours can? Schwarzmann: I cannot speak for our competitors but our market analysis indicates that there is demand here in China and in South-East Asia. We prefer to have the space and flexibility to operate in today rather than waiting until tomorrow. www.khs.com Demand for self-adhesive labels PETplanet: Mr Hammerschmid: Is China a popular market for you? Hammerschmid: We have been manufacturing and supplying labelling machines worldwide since 1986. In 1992 we succeeded in entering the Chinese market. Since then, a huge number of Gernep labelling machines was installed over the years. China will remain a very important business for us also for the future. PETplanet: In your opinion, how much has the Chinese market changed in recent years? Hammerschmid: From a technological point of view, the competition in wet glue machinery increased the last years. We focus now more and more on equipment for individual self-adhesive labels and do provide a customised solution for our customer. Demands for packaging design, particularly for cosmetics, are also increasing all the time. We enjoy dealing with challenging problems and coming up with tailor-made solutions. www.gernep.de Full bottle inspection Since 1966, Pressco Technology has grown into a worldwide supplier of machine vision systems for the food and beverage packaging industry, with rapid expansion in China over the past few years. “China is a very important market especially for inspection systems for filled bottles”, said Michael Coy, Director of Marketing at Pressco. That is why the company decided to showcase their FHCP-3X full bottle inspection module, designed to be integrated onto existing conveyors at the exit of the filler to monitor >72,000 bph. “The most critical inspection criterion is the placement of the closure on the bottle,” stated Coy, explaining the advantages of the system. “Our system uses multiple cameras to guarantee a 360° inspection of the cap, including the tamperband. Fill level accuracy, closure damage or colour changes are captured as well”. www.pressco.com Christian Schwarzmann, Managing Director, KHS Greater China Martin Hammerschmid (left), Managing Director Gernep, talking to Alexander Büchler Michael Coy, Director of Marketing (third from left) and the Pressco team","@ID":39}, "7 NEWS PETplanet Insider Vol. 20 No. 01+02/19 petpla.net DAK Americas to acquire PET recycling facility DAK Americas LLC, an Alpek Polyester business, announces that it has signed an Asset Purchase Agreement with Perpetual Recycling Solutions, LLC to acquire the Perpetual PET recycling facility in Richmond, IN, USA. The Perpetual PET recycling operations have an approximate annual capacity of 100 million lbs/a (~45,000 t/a) of high quality rPET flake. This facility will complement Alpek Polyester’s current food-grade PET recycling capacity in Pacheco, Argentina and its fibre-grade recycling joint venture facility in Fayetteville, NC, USA. The terms of the agreement have not been disclosed and the acquisition is expected to be completed in the first quarter of 2019. www.dakamericas.com Alpla: Philipp Lehner appointed CFO Philipp Lehner is the new Chief Financial Officer (CFO) of the international packaging specialist Alpla as of January 1, 2019. He takes over the role from Georg Früh, who will now focus on Family Office responsibilities. Philipp Lehner has been active in the family company since June 2014 and has worked in several areas of the company. The 34-year-old son of CEO Günther Lehner most recently served as Regional Manager for North America. He takes the place of Georg Früh as CFO and will be responsible for Finance, IT, Digitisation and Human Resources. Philipp Lehner studied at Nanjing University in China, at the European Business School London and at Harvard Business School in Boston. Prior to joining Alpla, his career led him to the finance and consulting industry, including positions at McKinsey (Hamburg) and H.I.G. European Capital Partners LLP (London). As Project Manager, Plant Manager and Regional Manager in North America, he has gained a deep understanding of the world of Alpla over the last five years. Georg Früh has held numerous management positions at Alpla in over thirty years at the company. He joined Alpla Germany in 1987 and was appointed CFO in 1999. Georg Früh contributed greatly to the international success of the group, states the company. www.alpla.com Philipp Lehner (Photo: Alpla; Photographer: Matthias Weissengruber)","@ID":9}, "PREFORM PRODUCTION 11 PETplanet Insider Vol. 20 Zero Cooling however is said to allow for the use of smaller, thicker preforms that can be moulded much faster than previously possible because cooling is conducted in the conditioning station simultaneously with the next injection cycle. Furthermore, since the material strength has been improved by better orientation, more scope is available to apply additional lightweighting to a container’s specification. Visual quality & stability Large, thin preforms with low stretch ratios are prone to produce visual defects in the finished container, most notably “fisheye”, “body ring” and “orange peel”, all of which are undesirable. The increased material orientation achieved by the smaller, thicker preforms of Zero Cooling eliminates any risk of these faults resulting in high visual quality. The advanced cooling method also enables the moulding of heavy-weight premium cosmetic containers in very short cycle times using standard PET grades while exhibiting no haziness, says Nissei ASB. www.nisseiasb.co.jp Fig.4 Comparison Zero Cooling and standard moulding Fig.3 Smaller preforms provide higher stretch ratios. SIPA S.p.A. - Via Caduti del Lavoro, 3 - 31029 Vittorio Veneto (TV) - Italy Tel. +39 0438 911511 - Fax +39 0438 912273 - email: [email protected] We make it happen. www.sipa.it Imagine a totally new operator experience. Designed to adapt. Built to last. Preform Systems THEMOST ENERGY EFFICIENT SYSTEM below 195W/kg","@ID":13}, "PETplanet Insider Vol. 20 No. 01+02/19 petpla.net 46 PETbottles Home + Personal Care Pop-art label In a special campaign, Aldi-South has come up with a cardboard display of a number of variously scented dishwashing detergents in their check-out areas. The liquids, which smell of berr i e s , a l oe v e r a , c u c umb e r s a n d other fragrancies, are appropriately coloured and come in clear 500 ml bottles. The main coloured labels printed with comic drawings, funny slogans and pop-art are also in keeping with the product. The overall effect is completed by an appropriately coloured push-pull lid. www.aldi-sued.de A metallic look for PET bottles “Düring AG”, the Swiss specialists in limescale removal, is now selling a Universal Bio version of its fast-acting descaler, “Durgol”. According to the manufacturer, the descaler is more than 99.5% biodegradable and acts five-times quicker than citric acid. The product comes in a shiny, metallic 750ml bottle with a shoulder embossing that depicts a mountain range. The shape of the base of the bottle is quite striking, resembling a stand-up pouch with a fold or centre line raised towards the inside of the container. The screw top is difficult to remove from the container, while two self-adhesive labels provide information about the product. www.dueringag.ch A shaped bottle for a mouth rinse Act, a Sanofi brand of dental care products, is marketing a mouthwash in a wavy-shaped, side-line bottle aimed at improving children’s dental hygiene (6-years and over). This alcohol-free product is designed to prevent tooth decay, mineralise teeth and rinse away small food particles. The liquid comes in a clear 500ml bottle, coloured according to taste. A chamber under the screw top is built into the bottle, which is filled by applying pressure to the bottle and a vertical tube reaching to the bottom. The screw top is secured with a pre-perforated, colour-coordinated, tamper-proof shrink-wrap. The two self-adhesive labels are also wave-shaped. www.actoralcare.com 10 -11April 2019 Organisers Event supporters established 1987 CO","@ID":48}, "PETpatents www.verpackungspatente.de PETplanet Insider Vol. 20 No. 01+02/19 petpla.net 48 Plastic container European Patent No. EP 3323746 A1 Applicant: Suntory Holdings Ltd., Osaka (JP) Registration date: 14.07.2016 A PET plastic bottle in the surface area to which a label is attached is designed in such a way that the label can be affixed properly and correctly even when the bottle is slightly “bulged” by its contents when being filled. Bottle packing International Patent No. WO 2018/118041 A1 Applicant: Tommy Patton, Oak Glen (US) Registration date: 21.12.2016 In order to be able to transport large quantities of bottles in as little room as possible, the proposal is to put a cardboard tray on a number of standing bottles and place another set upside down in the space between the two. Plastic bottle European Patent No. EP 3342723 A1 Applicant: Yoshino Kogyosho Company Ltd., Tokyo (JP) Registration date: 15.07.2016 An application is being made for the design and process for manufacturing a plastic bottle with compensatory surfaces for accommodating differences in pressure. Plastic containers European Patent No. EP 2927143 B1 Applicant: Suntory Beverage and Food Ltd., Tokyo (JP) Registration date: 25.11.2013 The European Patent application outlines the design of a larger bottle (approx. 2 l), which has been improved in terms of stability, shape and resistance to pressure. Plastic bottle with compensatory surfaces US Patent No. US 2017/0073137 A1 Applicant: PepsiCo Inc., Purchase (US) Registration date: 08.09.2016 A plastic bottle with differently aligned and shaped compensatory surfaces that allow for changes in pressure. The bottle is shaped in a predetermined way and method, but is always easy to hold. Container base European Patent No. EP 2697125 B1 Applicant: Sidel Participations, Octeville-sur-Mer (FR) Registration date: 10.04.2012 This European Patent application describes the shaping and process for producing a specially formed container base with twin recess.","@ID":50}, "CAPS & CLOSURES 19 PETplanet Insider Vol. 20 No. 01+02/19 petpla.net The Leader in Dispensing Innovation Delivering solutions, shaping the future. Drinking www.aptar.com Pouring Squeezing United Caps’ position statement on the tethering of closures by Benoit Henckes, Chief Executive Officer “In keeping with our long held principles of openness and transparency, I wish to make you aware of United Caps perspective on the EU Directive on Singe-Use Plastic and the actions we are already taking in anticipation of them. At United Caps, we bring to market, innovative solutions that meet the outstanding performance requirements of our customers in the regulatory environments in which they operate. We possess a firmly-held belief that our closures should differentiate today and sustain tomorrow, it is a key ethos that underpins our design principles and is in complete alignment with the Commission’s proposals. In May 2018 the EU commission published a proposal for ‘single use’ plastics directive, currently approved by the parliament, in plenary voting process. The political negotiation process has concluded. The Directive is expected to enter into force in Q2 2019. Member States has then to transpose it into national law by 2021. From Q2 2024 there will be a new requirement for the tethering of closures to PET beverage containers (bottles) with all existing neck finishes and Bricks with all existing neck finishes. Still beverages and carbonated beverages are included in this Directive. United Caps has anticipated this regulatory environment and is innovating accordingly. Time and time again, throughout our proud 80 year history, we have demonstrated an ability to set clear targets and deliver on our promises. Our sights remain fixed on our long term partnerships and those partners can be assured that we are taking the necessary decisions today that help them prepare for the future.” Position Statement on Circular Economy (summarised) United Caps endorses the EU vision and strategy as stated in the EU Circular Economy Package (CEP). United Caps believe that the Circular economy is an important tool to challenge energy consumption, resource depletion and environmental pollution. Maintaining the value of products, resources and materials within the economy for as long as possible is vital for future generations. Currently almost 100% of the plastic waste accumulating during our production process is recycled either internally or externally. Plastic products have an important role to play in more environmentally friendly and resource efficient Europe for their intrinsic characteristics. They are lightweight, durable, versatile and recyclable as such they are important in helping to reduce emission and lower energy consumption. United Caps is aware of, and embraces the challenges of transitioning towards the EU circular economy and fully acknowledges the new guidelines of the EU directive 2018/850 on the landfill of waste, EU directive 2018/851 on waste and EU directive 2018/852 on packaging and packaging waste as part of the EU Action Plan for the Circular Economy (2015) which contains new targets for the increased recycling of plastics. With regards to the use of recycled plastics in food-contact applications, United Caps prioritises high food safety standards following Directive 2018/852 (article 5). No compromises on food hygiene, health and safety should be made. United Caps recognises that the EU CEP vision requires collective action on recycling streams within the Member States. Today’s recycling rates are variable between Member States. Actions allied to modifying consumer behaviour, coupled with improved sourcing like bio-sourced plastics, better characterisation of contaminants and a safety recycling material plan will aid the creation of a vibrant and rewarding circular economy. It is appropriate that United Caps, a company with a proud heritage takes an active role in this process by setting out to meet today’s needs without compromising the future. www.unitedcaps.com","@ID":21}, "LABELLING PETplanet Insider Vol. 20 No. 01+02/19 petpla.net 31 Flexible and environmentally-friendly labelling, with digital personalisation and process quality Personalised labelling at the point of packaging Sacmi Verona says that ergonomics and usability are the cornerstones of an entire range developed to maximise versatility, worker safety and ease of maintenance. The company is focused on providing both sustainability and leading-edge digital printing solutions Sacmi Verona, part of the Sacmi Beverage Division, has more than 2,000 machines installed across the world and over 250 employees. It saw in the New Year of 2019 with a renewed range of products and services and with a commitment to heightened environmental sensitivity. Key ergonomics principles have already been applied by the company to its modular labellers. Sacmi says that these machines have been developed to offer versatility, with multiple labelling technologies and systems on one machine, and to reduce maintenance complexity, by being designed with easy access to vital machine parts for routine tasks. From the start of 2019, the ergonomic policies have been extended Giovanni Sorce went on to explain that, while Sacmi Verona is committed to investing further in ergonomics, it is far from being its only focus. Environmental sensitivity demands that manufacturers face up to questions of usage and disposal, of how labelled containers are handled after use and how to ensure they enter the recycling process. Mixtures of materials can prejudice recycling. Sacmi’s popular Formsleeve+ tubular sleeve labeller allows for the use of printed film with a density of less than 1 g/cm3. As PET always has a density of greater than 1 g/cm3, this facilitates easy separation of container and label at each stage of the recycling process. Sacmi Verona has set itself a further goal, of taking the industry into the digital era. In addition to across-therange integration with its LVS advanced inspection systems and building on the experience and knowledge gained in digital cap printing, Sacmi has developed and launched the D-Match digital label printing module, which is designed to operate alongside the labeller. A roll to bottle module, it allows flexible personalisation – with logos, codes, and so on – of pre-printed labels, with guaranteed digital print quality of up to 720dpi and up to seven CMYK colours. “This opens up enormous market opportunities in terms of making personalisation at point of use, more easily and at reduced cost,” Mr Sorce said. Digital personalisation of pre-printed label parts can be done at the point of packaging, thus minimising transport and storage costs, with all the expected precision and application quality. Sacmi has deliberately chosen this approach in preference to, for example, direct on-bottle printing, so that potential customers can perform immediate tests, keep investment affordable and take advantage of the opportunities of digital personalisation in existing plants and production facilities, even when they are located far apart. www.sacmi.it from the modular solutions range and Kube medium-speed labellers to all Sacmi Verona solutions. Sacmi ERF, the new roll-fed labeller, is claimed to combine high levels of usability with advanced automation and labelling process quality. It is designed to make the labelling process more efficient and more automated, while easing the operator’s workload. “This roll-fed labeller improves worker access and safety while simplifying settings and reducing maintenance,” said Giovanni Sorce, General Manager of Sacmi Verona. In keeping with that commitment, the Sacmi ERF solution has been designed to be highly versatile and adaptable while offering advanced technological features, such as highly precise film speed control, automatic reel splicing, and adjustable formats, including label height and thickness. Sacmi maintains that this solution has been designed to respond to immediate and foreseeable manufacturing and market needs.","@ID":33}, "EDITOUR PETplanet Insider Vol. 20 No. 01+02/19 petpla.net 12 Repi’s rising up in the US market Colouring the plastics world From Atlanta we went up north to our next appointment in North Carolina, Charlotte. There we were welcomed by Giuseppe Lombardo, Commercial Director for Thermoplastics at Repi LLC, who is developing the US Thermoplastics business for Repi. The entrance hall of this new 45,000 square feet big factory is a remake of the Italian Headquarters, a special tribute to US customers. Tour Sponsors: May 25, 2018 We met: Giuseppe Lombardo Commercial Director for Thermoplastic Repi LLC Repi entered the American market with sales activity through a distributor back in the 90’s with products dedicated to the polyurethane industries. The business activity grew rapidly and in 2003 the decision to open a whollyowned subsidiary, namely Repi LLC was taken. This represented the first ingress into the country, followed soon after by the decision to start a production facility serving US customers. In 2012 Repi LLC moved to Dallas-NC becoming a full-service company, with manufacturing facilities, laboratories and offices, for both business units (thermoplastics and polyurethanes). The thermoplastics business unit has its core business in the packaging field (preforms, bottles, PET sheets, caps, etc.) as well as in industrial applications such as the building and construction industry, the furniture sector and the world of the injection moulded parts. “Today Repi LLC has a team of around 25 people and a double digit turnover thanks to commercial activities in the Americas,” Giuseppe Lombardo told us. In 2014 Giuseppe with a 20 years’ experience in the liquid colour industry, joined Repi LLC. “The recognition of the Repi brand in PET packaging industry worldwide helped us in the US market. But of course, we are newcomers in the continent and have to compete with already well established competitors. We have a lot of opportunities in the packaging market, which is steadily growing. Packaging design and state of the art R&D apartments are important areas for us. We are pretty proud to be able to offer to our customers not just a product, but a complete support, which begins with the identification of the specific need and results in the formulation of the required colour (which implies lab tests and sometimes R&D support) and in packaging prototyping. A skilled technical team is available for trials on customers’ sites, start of industrial productions, training and extraordinary maintenance. This gives partners the opportunity to run special development projects, from the initial concept to final item. Infront of the colour portfolio at Repi’s showroom (f.l.t.r.): Heike Fischer and Giuseppe Lombardo From here we serve the whole North, Central and Latin American markets.” Repi is among the top liquid colour producers in the North American market. “Additives are the segment where we see great development opportunities; it is the area where we are growing significantly. The PET colour market here is not as big as in Europe; we have a lot of clear preforms.” “We are growing in UV blockers and anti-yellowing for the PET recycling market as a result of a high volume of enquiries.” Giuseppe spoke about the challenge of the rPET market in the US in general. Repi is part of the Napcor society in the US. “We are in close contact with them to see where the rPET market is heading. The holy and protected treasure: a view in the state of the art production lab There are concerns about volume, the collection rate and the cost. Producing rPET is a big challenge because you have to compete against virgin PET - in total it is a challenge here in North America.” Giuseppe summarises “After more than 45 years of activity worldwide, Repi has become a leading supplier with direct presence in 5 geographical areas, but still independent and privately owned. This allows the Group to be flexible and near to the customer who feels to deal with a trustworthy partner. The future goals are challenging, but the right vision and business plan are there, so we are really excited for next results to come.” www.repi.com by Heike Fischer","@ID":14}, "LABELLING PETplanet Insider Vol. 20 No. 01+02/19 petpla.net 32 Rotary labeller for flexible self-adhesive labelling Western style BBQ bottles Founded in the Netherlands in 1925, Remia is a leading manufacturer in the international food industry of margarine, mayonnaise, tomato ketchup, salad dressings and sauces, and produces both for retail and in large containers for the catering industry. To ensure its American BBQ sauces range also stand out on the supermarket shelf, each 450ml PET bottle is equipped with self-adhesive labels in eye-catching designs. The labels, carrying names like Black Jack, Big Chief or Wild Bill should sit very precisely on the bottles to underline the high quality of the products. This is what Remia requested and why Hilko van der Linde, project manager at the company, chose the Bavarian manufacturer Gernep for labelling. The rotary labelling machine Soluta, distributed by the Dutch trading partner De Koningh Coding & Labeling for Gernep, is claimed to be the ideal labelling solution for the requirements that Remia insists on for its products. Since its first installation in 2015, two more labellers have been added to the factory in Den Dolder, and a fourth machine was recently commissioned by Gernep, another Soluta with three self-adhesive labelling dispensers for six different plastic bottle formats. The Soluta 12-784 3SK SD was followed by a Soluta 10-640 2SK SD and a Soluta 12-784 2SK SD, all three equipped with bottle-top servomotors and a non-stop function for changing label rolls without downtime in current production. The three rotary machines label glass and plastic bottles in the range of 125ml to 1,000ml, including the BBQ sauces, with body, back and neck ring label. The performance of each machine is up to 15,000 bottles per hour. Hilko van der Linde quickly saw the advantages of self-adhesive labels: “The label should emphasise the ‘hard Western look’ of the bottles. With the Gernep Soluta, which uses the latest servo technology, we can accurately and flexibly position the labels on the bottles. Also neck ring labels are labelled very rapidly and above all, with absolute precision,” and he adds “Of course, the special advantages of the self-adhesive technology compared to the conventional wet glue technology, which we have used for years, are no glue residues on the bottle, no cleaning times on the machine and format parts, small format part circumference and thus very short changeover times with format change. The non-stop function on the self-adhesive dispensers also have great advantages here as regards downtime. Previously, the machine was changing labels, now we save a lot of time by the tandem function on the label dispensers.” When “label roll empty” is signalled at one dispenser, it stops and the second dispenser starts fully automatically, with no downtime in production. www.gernep.de The Gernep Soluta Last label test run before delivery in one of the three selfadhesive dispensers","@ID":34}, "LABELLING PETplanet Insider Vol. 18 No. 0/17 petpla.net 35 Sleeving PET detergents and body care products A second skin for PET containers Detergents and body care brands are demanding more and more sophisticated container shapes and new styles of decoration, making the packaging industry face new challenges. Finpac Italia has developed a machine capable of applying sleeves on special bottle shapes, on filled or empty bottles at speeds of up to 70,000 bph. Sleeving can be tricky on any shape which is not round: it is vital to maintain the artwork on bottle panels correctly with minimum positioning tolerance. The correct sleeve position is given by a combination of factors during the application and shrinking process. The Finpac system is capable of bottle and sleeve orientation at the same time, ensuring the sleeve is applied in the best possible condition. A progressive positioner fine-tunes the application of the sleeve without any shock or rotation. Before or after filling? Sleeving after filling is easier: bottles are more stable, rigid, resistant to high shrink temperatures. Sleeving before filling is more difficult but can be an advantage for a number of reasons: the cap can cover the top part of the sleeve, hiding any ‘’empty gap’’ between sleeve and cap; different bottles blown by different lines can be conveyed to a single sleeving line; a stand-alone sleeving line may ease blown bottles stock keeping bottles blowers can deliver already decorated bottles, offering end users a lean manufacturing process Underlap There are shapes which require underlapping to achieve the most attractive result: the sleeve can shrink a few millimetres under the bottle base to hide any ‘’smiling effect’’. The bottle is lifted and vacuumed (if empty) at the same time, to allow the sleeve shrink under its base and to keep it stable. In Finpac’s new system, application and underlapping operations take place in the same frame, which is a very compact solution. Shrinkage Body sleeve shrinkage is executed by low-pressure and low-temperature steam, saving energy, with no risk of destabilising / damaging empty plastic containers and with no sleeve rotation. ","@ID":37}, "PETplanet Insider Vol. 20 No. 01+02/19 petpla.net 47 BOTTLES Beverage + Liquid Food A large cap for a small bo ttle The US juice specialists, Tropicana, have produced a 100% pure, natural orange juice involving very little pulp. It comes in a 355ml (12 fl.oz.), clear, easy to hold bottle. Its striking feature is the screw top which is huge compared to its bottle size, making it easy to hold. On the outside, the cap has extra grooves which make it difficult for the fingers to slip off when opening. Two adhesive labels provide information on the product. www.tropicana.com Bottle with Stickpack The German start-up company, 2KIQ Beverages Ltd, is selling a new kind of energy drink under their “Energieliebe!” brand which has two elements to it. The first is a liquid, slightly pink-coloured component with coconut water, lime juice, marula and baobab, together with a stick of foil that ensures the vitamins and minerals are fully protected from light, moisture, heat and oxygen. The bag is attached securely to the bottle by means of a pre-perforated adhesive strip. Prior to consumption, the bag is carefully removed from the bottle, opened, the contents poured into the bottle and the ingredients mixed and activated by shaking together well. According to the manufacturer, keeping the elements separate does not alter the taste due to storage and the interaction of the products with one another. The bottle is covered with a sleeve label and secured by a screw top. www.2kiq.de Almond smoothie from Rewe In creating new flavour experiences or adopting new trends, competing smoothie manufacturers are constantly in competition for the patronage of consumers. Following on from smoothies with vegetables and smoothies with coconut, a smoothie with almonds has recently come onto chiller shelves. Rewe is selling the drink containing apple, banana, coconut and chai spices in a transparent bottle that holds 250ml. The container is labelled with a foil label colour-matched to the product and a paper strip label, which is affixed over the screw seal as an additional tamper-evident seal. www.rewe.de","@ID":49}, "CAPS & CLOSURES 22 PETplanet Insider Vol. 20 No. 01+02/19 petpla.net The fourth generation of El-Exis SP Maximum performance in minimum time With a market share exceeding 20%, Sumitomo (SHI) Demag claims to be the leading manufacturer of injection moulding machinery for plastic packaging. Launched twenty years ago, the hybrid El-Exis SP is the main contributor to this success. Its fourth generation is quicker and one of the advanced machinery on the market. Located in Schwaig near Nuremberg, Germany, the injection moulding machine manufacturer has adapted the high-speed machine from version to version to meet the increasingly exacting demands of packaging producers. The fourth generation was introduced in 2016 and is primarily distinguished by its optimised use of energy and resources – one of the most pressing challenges in engineering given the global increase of production volumes. Depending on production parameters, it requires up to 20% less energy when compared to its predecessor. The hydraulic accumulator enables the achievement of injection speeds of up to 1,000 mm/s and accelerations of up to 4g. Intelligent accumulator control simultaneously ensures process-dependent, variable accumulator allocation. More than 172,000 closing caps per hour To produce standardised closing systems, maximum mould speeds with short strokes and optimal dosing performance have to be possible. ElExis SP meets these requirements and has a reliable and safe operation with cycles far below 2.5s over many years. Thanks to the fast clamping unit and the dynamic ejector, maximum production output can be achieved. Special solutions have been optimised specifically for this application, such as the water distribution for mould cooling. Clamping force of 8,000kN The hybrid concept combines the high speed demanded by the customer with availability and reliability in a single machine.“Right from the outset, development of the El-Exis focused on the demand that performance, service life and energy consumption should play equally important roles and that no sacrifices should be made in this respect,” explained Arnaud Nomblot, Director Business Development Packaging at Sumitomo (SHI) Demag. The dynamic hybrid drive ensures a maximum level of performance and excellent process consistency and accuracy, both during acceleration and braking. “In the area of packaging, we primarily benefit from two facts. First of these is our specific experience in this sector, for example during the design of mould clamping plates which, thanks to finite element analysis, exhibit considerably superior rigidity to conventional plates and, secondly, the high vertical range of manufacturing in our company. Crucial machine elements such as screws, plates or columns are manufactured by us rather than being purchased outside”, continues Nomblot. “This direct control of manufacturing precision is a decisive factor in ensuring that the machine meets all requirements in the high-speed range and works reliably and accurately over the years.” Sumitomo (SHI) Demag meets the growing demand for large machinery for multiple cavities by expanding the clamping force range of the El-Exis SP series. With maximum clamping forces of 8,000kN, the machine impresses through a dry cycle time of 2.05s during daily operation. Cycle times of less than 4s for the production of milk product containers (500g) in an 8-cavity IML mould underline the aspiration of the machine manufacturer to set the highspeed benchmark on the market with the El-Exis SP. Broad application spectrum as standard feature Next to the ejection rate, repeatability, availability, efficiency and sustainability, versatility has since become an equally important development driver. The El-Exis SP opens up a wide process window to the user when it comes to cycle times and process parameters such as injection speed. IML, twocomponent and injection compression moulding are also standard. Injection compression moulding in particular is one of the technologies at Sumitomo (SHI) Demag that is suitable for more sustainable, higher quality and, simultaneously, more cost-effective packaging production. A high precision level and the injection speed of El-Exis SP machines transform injection compression moulding into speed compression, even in the standard version. For example, trays made of a PP Mfi 20 with a flow path wall density ratio of 450:1 are produced in a cycle time of 3.5s in a 2+2 cavity level mould developed and patented by Plastisud. This technique achieves wall thicknesses up to 25% thinner and, consequently, a lower part weight with comparable product characteristics. In addition, the customer can run processes with around 30% lower clamping forces. www.sumitomo-shi-demag.eu CAPS & CLOSURES Over 172,000 closing caps (29/25mm) per hour possible with Sumitomo (SHI) Demag’s high-speed El-Exis machine","@ID":24}, "42 TRADE SHOW REVIEW PETplanet Insider Vol. 20 No. 01+02/19 petpla.net BrauBeviale2018 TRADE SHOWreview Brau Beviale 2018 Over 40,000 trade visitors travelled to Nuremberg to the 2018 edition of Brau Beviale. 1,094 exhibitors – 53 percent of them international – presented their products and solutions related to the entire beverage production process chain, with offerings ranging from raw materials to technologies and components all the way to packaging, as well as accessories and marketing ideas. A varied supporting programme rounded out the three days. The next Brau Beviale will be held from November 12-14, 2019. www.braubeviale.de ABC Compressors: New Sales Area Manager ABC Compressors took advantage of the Brau Beviale exhibition not only to show one of their latest Horizon 3000 machines sold in Germany, but also to present Marcos Arteaga, their new Sales Area Manager for DACH. Among his responsibilities are the management of blowers and the development of the CO2 business area, which has been experiencing double-digit growth in recent years. Born in Spanish San Sebastián, but since the beginning very close to Germany, he brings a new energy and dynamism to ABC, states the company. www.abc-compressors.com New closure for lighter weight PCO1881, compatible with PCO1810 F.l.t.r. PCO1881 High Grip, PCO1881 Standard, PCO1810 Among the products that packaging manufacturer Retal exhibited on its stand at Brau Beviale 2018 was its new High Grip closure. This system, which was presented for the first time at the trade fair, features a taller overall design and continuous slats, which are intended to provide an optimised, non-slip opening and closing of beverage bottles. The closure height is at the same level as the classic PCO1810 closures and also fits PCO1881 bottle necks, but only at a weight of 2.45 g. “The closure is already on the shelves in Europe with a multinational CSD brand. It is also to be found on some local beverage brand bottles,” said Maria Ushakova, Senior Marketing Manager EU at the Retal trade fair stand. The closure aims to enable co-packers to continue using the existing PCO1810 secondary packaging for stores but, at the same time, to enjoy the benefits of a bottle that is 1.3g lighter in weight. By the end of the year, Retal forecasts that approximately 140 million of its High Grip closures will have been manufactured and distributed. PET jars for milk products Retal has also been active in the liquid food segment, as demonstrated by its new, thermostatic 160ml PET jar, which is already available in the Russian market. Danone, the milk processing giant, is using it for a traditional, long-standing yoghurt product. This yoghurt is aimed to link into the established Russian family tradition. Retal’s press department says that the company is already Danone’s biggest supplier of preforms and closures in Russia. The 160ml jar aims to continue with the success achieved by the 250 ml jar, for which Retal was presented with the Danone “Best Innovative Partner” supplier award in the year 2016. www.retalgroup.com Marcos Arteaga, ABC Compressors’ new Sales Area Manager for DACH","@ID":44}, "LABELLING PETplanet Insider Vol. 20 No. 01+02/19 petpla.net 33 LABELLING 33 Heuft launches ‘Tornado II Dynamic’ Dynamic labelling Announcing the launch of its Tornado II Dynamic – the first semi-modular labeller to be based on its highly automated Heuft Spectrum II platform – Heuft Systemtechnik GmbH said that the new machine offers higher levels of performance, precision and dynamics during wet glue, self-adhesive and wrap-around labelling processes, along with its integrated quality inspection. The machine’s voice-controlled machine analysis and process monitoring is intended to deliver more efficiency and productivity along the entire line. Heuft says that the Spectrum II features higher levels of automation, computing power and accuracy than predecessors, as well as multiprocessing capabilities for tracking containers, applying labels, checking quality and rejecting faults. Up to four electrically-coupled labelling stations, designed to be replaced quickly and easily at changeover, have been incorporated in order to increase flexibility. Operators can, for example, use three wet-glue units for collar, back and neck labelling of up to 60,000 containers/h, or a combination of wet-glue, self-adhesive and wrap-around labelling, all in the same machine. Heuft says that its established camera-based, servocontrolled “flex” technology for fine alignment ensures that all labels are applied tidily and without creases, with millimetre precision. Integrated inspection modules for label, fill level and closure detection check quality features, also during the process, and reliably reject faulty bottles, incorrectly marked or nonbrand containers, as well as verifying best before dates and microcodes. This is designed to enable effective overview and quality control to be maintained even with a large variety of brands and equipment variants. This NaVi user interface is displayed on the terminal of the compact machine and on four flat screens positioned around its upper level, enabling the operator to monitor the Tornado’s II status wherever he or she is during operation. The machine’s control system features audiovisual user guidance with individual step-by-step assistance. The new hands-free voice control is also designed as an added-value feature. The new generation labeller can be operated by voice alone and without manual intervention in a real dialogue with “Amanda” the virtual assistant. It listens to the user, answers questions and speaks as soon as something needs to be done, giving verbal alerts in good time for the remaining quantity of labels in the magazine, or how long a particular program still needs to run. Verbal instructions for actions such as brand changes or test bottle programs are implemented directly. The automatic magazine feed for label stock during wet glue labelling is asserted to be another efficiency boost. Heuft says that it can be easily integrated into the semi-modular labelling machine of the new generation, the same as with the different labelling stations. The Heuft Tornado II Dynamic which has practically no machine table, facilitating optimum accessibility for cleaning, maintenance, changeovers and retrofitting. www.heuft.com NG Beverages Discover one of the biggest ranges of closures in the beverage market. www.bericap.com/capfinder","@ID":35}, "TRADE SHOW REVIEW PETplanet Insider Vol. 20 No. 01+02/19 petpla.net 44 Increased use of rPET in disposable PET bottles in Germany The key to sustainability Germany’s RAL Gütegemeinschaft Wertstoffkette PET-Getränkeverpackungen e.V. (RAL Quality Association for the Recycling of PET Beverages Packaging) has determined that the use of recycled PET material in disposable PET bottles is to increase significantly. By 2022, PET beverage packaging carrying the RAL quality seal will incorporate 50 percent recycled PET material, on average; the minimum proportion of 25 percent required for the quality seal will remain. Irina Bremerstein, Managing Director of the RAL Quality Association for the Recycling of PET Beverages Packaging, emphasised that this decision demonstrates the Association’s commitment to the guiding principles of the ‘circular economy’ for synthetic packaging. “We are making a clear statement about sustainability. With a high percentage of recycled material, the eco-balance of PET packaging will be even more favourable,” she said. Following a steady fall in weight and materials used in recent years, the Association considers the increase in the percentage of recycled materials in PET bottles to be key to sustainable development. The RAL Quality Association’s new target is in compliance with the requirements of the German Packaging Act, which came into effect on 1st January 2019. RAL’s minimum recycled materials requirement remains in place. In order to be certified in accordance with its test specifications, PET bottles must consist of at least 25% recycled PET material. According to Germany’s Gesellschaft für Verpackungsmarktforschung (Association of Packaging Market Research), non-refillable PET bottles in Germany currently include an average of more than 26% recycled materials. A large share of used bottle material bypasses the bottle-to-bottle recycling loop and is used in, among other areas, the textile-fibre and plastic films industry. At the RAL Quality Association’s press conference at Brau Beviale 2018, Dr Isabell Schmidt, Director of the “Forum PET” and Managing Director of IK Industrievereinigung Kunststoffverpackungen e.V. (German Association for Plastics, Packaging and Films), and Jonas Harth of the ifeu Institute for Energy and Environmental Research Heidelberg, provided up-to-date facts and figures concerning current recycling levels. Germany recycled 93% of all used PET beverage bottles in 2017; the proportion with compulsory deposits exceeded 97%, Dr Schmidt announced. PET bottles manufactured in Germany in 2017 contained an average of 26.2% rPET, compared with 24% in 2013. Of the 93% of PET that was recycled, new beverage bottles accounted for 32.6%; PET plastic films, 29.4%; and the textile-fibre industry, 21.8%. Some 16.2% of recycled material found its way into other applications. The remaining 2-4% PET loss is accounted for by the recycling process. Mr Jonas Harth provided an insight into the eco-balance of PET recycling. This looked at the parameters of the choice of packaging materials (glass, PET, bioplastics, etc.), the ratio of packaging weight to contents, the proportion of recycled materials, the trippage rate, the structure of distribution and the end-of-life parameters (recycling rate, proportion of waste incineration, etc.). He envisaged a clear benefit to closed-loop, bottle-tobottle manufacturing, in which 100% rPET could, in principle, be used. When comparing reusable PET and glass bottles with disposable PET deposit bottles, disposable bottles in the water and CSD category demonstrate better results in terms of greenhouse gas emissions, assuming that the proportion of rPET is high, bottle weight is low, and distribution is local. Mr Harth explained that various well-known brand name manufacturers, NGOs and industry associations intend to focus increasingly on ensuring the use of rPET in the future, in both the EU and worldwide. www.wertstoff-pet.de www.forum-pet.de www.kunststoffverpackungen.de www.ifeu.de Jonas Harth (Ifeu) analyses the ecobalance of different packaging types. Dr Isabell Schmidt (Forum PET) shares details on the current recycling situation.","@ID":46}, "43 TRADE SHOW REVIEW PETplanet Insider Vol. 20 All-electric bottle blowers for medium-sized outputs German machine manufacturer SMF Maschinenfabrik, from ToisdorfSpich, has a history that stretches back 25 years. It specialises in the construction of bottle blowing and filling systems, as well as unscramblers for a wide variety of applications, from 200ml to 20 l PET bottles. SMF serves and supplies customers in more than 80 different countries. Its Optima 4 NT model, the latest addition to its Optima Turbo PET bottle blower series, was presented for the first time at the Brau Beviale 2018 trade fair. The l i nea r eng i nee r ed Optima Turbo Series includes a four-cavity machine with an output of 7,200 bph; an e i gh t - cav i t y ve r s i on w i t h 14,000 bph capacity; and the biggest, which has 16 cavities and is capable of producing 28,800 bph. “The series is designed to be fully electric and is effectively supported by PLC and nine servo drives,” Key Account Ma n a g e r A g n e s P l a s k a explained. While the standard versions of all three machines in the Optima Turbo series are designed to produce bottles in the 500 ml to 5 l range at rates up to 35,000 bph, in the case of 500 ml bottles. However, she explained that the special Optima 1-2-3 v e r s i o n , wh i c h i s a n ew machine available in the series, allows the number of cavities to be intelligently adapted to the product to be manufactured. In practice, this means that 200ml containers and big-volume bottles up to 7 l could also be produced on this machine. SMF says that the blowing pressure for the series extends up to 40 bar. At the same time, the series strives to be energy-efficient, with a specially-designed NIR heating process in place of conventional IR ovens. In addition, the oven’s compact design is intended to minimise space requirements at the production level. Mrs Plaska refers also to a reduced air consumption for the blowing. Finished bottles are transported by air conveyor directly to the filling machine. Maintenance is also designed for ease of use and user-friendliness. The Optima Turbo Series features a central system for lubricant provision, and facilitates rapid mould changeover, to minimise downtime. www.smfgmbh.com SMF’s Optima 4 NT at Brau Beviale","@ID":45}, "CAPS & CLOSURES 24 PETplanet Insider Vol. 20 No. 01+02/19 petpla.net The inline quality lab “We bring the quality lab to the production line!” Gerd Fuhrmann, CEO of Intravis GmbH, announces as he introduces his company’s future strategy for Industry 4.0 in the field of cap inspection. The reason for this was the product presentation of the new CapWatcher Q-Line, where visitors also were introduced to the CapFeeder, the first in- house at Intravis manufactured cap sorter system. Industry 4.0 is and will remain the dominant topic in the industry. According to a survey conducted in 2018 among more than 300 companies in the industry, the goals pursued by Industry 4.0 applications are above all the improvement of processes, higher capacity utilisation and faster implementation of individual customer requirements. If Industry 4.0 should mainly achieve the optimisation of processes in manufacturing companies, vision quality inspection is currently the main focus of the process. By constantly inspecting and measuring the produced objects, the quality of the processes can be determined in the end. Only good processes lead to good quality. And if you succeed in deriving recommendations for actions from the measurement results, then we are on a quick path to the “Smart Factory”. In quality labs, the various characteristics of an object are often measured partly-mechanically or by hand in extensive but laborious work. After a certain time, relevant data is collected and can be back tracked to a single object which then enables conclusions about the entire process to be drawn. Wouldn’t it be better to gain large amounts of data from innumerable produced objects within a very short time and then be able to directly draw conclusions about the process? This thought triggered the development of the inline quality control, which is playing an increasingly important role today. The aim was to collect meaningful measured values quickly, comprehensively and across all produced objects in order to be able to draw well-founded conclusions about the quality of the process. Intravis GmbH, supplier of inspection solutions for the plastic packaging industry has always gone beyond solely sorting faulty products with its systems. Rather, it has always gathered extensive measurement data, which, provided at the right time, helps to increase the Overall Equipment Effectiveness (OEE) of the production plant. Gerd Fuhrmann says: “We don’t want to just collect data with our systems. We also want to detect even minimal trends directly.” Based on these data and trends, an experienced machine operator or even a self-regulating injection moulding machine can adjust the processes so that defective parts are virtually eliminated. “Intravis has already shown how a self-regulating process, also known as closed loop, can look like at Drinktec 2017 in a showcase together with Netstal Maschinen-AG (see also PETplanet Insider 4/18). Thanks to different interfaces such as OPC-UA, Profibus, Shotscope or even MQTT, the inspection system measurement data can be made available to all parties involved in the process, from machine control center to any other systems on the production line. Furthermore, thanks to the data connection, it is also possible to transmit test orders from the Manufacturing Execution System (MES) to the inspection system. This saves time, optimises processes and minimises potential sources of error. The Intravis systems therefore represent an interface in their own right, namely between planning and process data. The CapWatcher Q-Line The new CapWatcher Q-Line is an important piece to the puzzle in Intravis’ future Industry 4.0 strategy. The newest system in this line was launched on November 2018 at a major premiere for around 60 invited guests from the plastics industry, politics and press. Thanks to many new developments, it is claimed to meet the demand for highprecision measurements. “For good, high-precision measurement, a stable positioning of the closure is helpful. Belt transport is currently the best choice, which is why we have been using our double track belt technology for a long time,” explains Klaus Schönhoff, CTO of Intravis when describing the importance of positioning. But Intravis offers even more. “For the first time in the new generation of the CapWatcher Q-Line, we have installed our new, positivelocking singularisation system. This way, we can guarantee positioning that is accurate to the millimeter and even more precise measurements later on,” says Schönhoff. A positive side effect here: due to the form-fitting handling of the closure from the side, an even more gentle treatment of closures of all tamper evident band variants is possible. In addition to improving positioning, the CapWatcher Q-Line offers even more innovations. The focus has been on the testing of functional elements, to always enable faultless and fully functional closures reach the consumer. For example, to prevent closures from being processed with incompletely ejected or damaged threads, the system checks the complete thread area with a special inhouse developed imaging. The testing of the sealing elements has also been improved. Smallest notches or missing material – regardless of one or twopiece closures – can lead to uncontrolled degassing or the ingress of foreign substances. To prevent this, two independent inspection stations check the sealing elements for their functionality. An essential element of the functionality of closures is a perfect tamper evident band. On one hand, it has to make sure that a closure hasn’t been opened already; on the other hand, the end user should be able to open the closure Intravis’ new CapFeeder with a capacity of up to 288,000 cph CAPS & CLOSURES","@ID":26}, "CAPS & CLOSURES 25 PETplanet Insider Vol. 20 No. 01+02/19 petpla.net easily. For the first time the CapWatcher Q-Line also checks the quality of the tamper evident band. For folded bands, additional attention is paid to the quality of the slit. This makes it possible to detect worn knives or problems with the temperature of the blade at an early stage. In the case of injection-moulded tamper evident bands, inspections are in place for long and short shots between the bars, which would question the functionality of the closure. Another technical highlight is the measurement with a temperature sensor. This sensor makes it possible to give each closure a timestamp. Closures, which obviously have been on the road for a longer time than the average of the last tested closures, are indeed inspected and their results included in the summary. However, the measurement results do not have any influence on possible changes to the process because they are not further processed for this case. This ensures that closures from the past have no influence on current line optimisations. Another value of the temperature sensor is that one is able to make a prediction about the shrinkage behaviour of the closures. This means that a closure manufacturer can ensure that the closure at the planned time of the application has exactly the dimension that he assures to its customers. With eight high-resolution cameras, accuracies in the hundredth of a millimeter range and more than 40 inspection criteria per cap, the CapWatcher Q-Line collects, visualises and reports on quantitative statistical data at a rate of 60 closures/s in just 1min evaluation. Due to the efficiency, the system already offers the security of high quality closures on the production line - not after being checked by a quality lab. High line output Increasing the capacity utilisation of a production line is another of the goals when using Industry 4.0 applications. An essential component of this is that you get as many elements of a production line as possible from a single source. Dr Fuhrmann states “Although we do not produce injection moulding systems, in the future all customers will be able to source from Intravis production. From now on, aside from our cooling and cross conveyors as well as our CapWatcher product family we also offer our own cap sorter, the Intravis CapFeeder.” With a capacity of up to 288,000cph, the sorter is also a powerful infeed system and, in combination with the CapWatcher S-Line, the fastest closure inspection system line in the plastics industry, states Intravis. Extended product family In the area of standard beverage closures, Intravis brings the quality lab into the production line with the CapWatcher Q-Line described above. In contrast, the enhanced CapWatcher S-Line focuses entirely on the reliable high-speed inspection of beverage closures. At test speeds of up to 80, six cameras provide all the information needed to sort the closures with the highest precision. With the CapWatcher Slitter, Intravis offers a compact system for closure inspection after the slitting process. In addition to reliable cavity readings, this system is equipped with a comprehensive range of spindle statistics, so that seals and error types can be clearly assigned and traced. Furthermore, the system offers the improved high-voltage test for non-contact control of the microhole closures around the injection point and inspection of the slit quality. The fourth member of the product family is the CapWatcher SC. It serves the entire range of closures outside the standard beverage closures such as sports caps, flip-top caps or large oil closures. The product portfolio is rounded off by integrated systems for the inspection of single or multipart closures in assembly handling systems or in feeding systems of large filling lines. Industry 4.0 applications are and will remain a current topic. Intravis GmbH has used its experience of recent years to be able to offer its customers the best possible solutions in the future. Not only that the new CapWatcher Q-Line now offers an even more powerful system for cap testing, which supports industry 4.0 applications such as self-regulating injection moulding machines with its high-precision testing. By expanding the product range with its own sorter, they now have another important element of the downstream equipment of a closure production in their portfolio. www.intravis.de","@ID":27}, "LABELLING PETplanet Insider Vol. 18 No. 0/17 petpla.net 34 Packaging and decoration stepping into the virtual world Connected packaging Combining print with other media such as online is nothing new but the latest developments enable a whole new dimension of connection. CCL Label’s Arilyn app provides the means to offer customers a wide range of immersive experiences, through their smartphones. Packaging is one of the most essential components for presenting a brand’s identity. As the only medium (besides the product itself) in direct contact with the consumer, it plays a crucial role in carrying the brand message out into the world. Visual identity is a decisive factor for success at the point of sale. By modernising their brand identity, CCL Labels says that its customers see increased sales. Pressure sensitive labels, 360° decorative shrink and stretch sleeves offer original and powerful ways to attract new consumers across all demographic segments. In a world of “mass customisation”, interaction and a personal approach are key. Augmented reality solutions enable brand owners to offer individual customers their own unique experiences – a trip around the world; a concert; creation of their own game avatar; or even their personal version of the packaging, by means of scanning labels with their smartphones. Immersive 360° videos and games, using cloud-based technology, can be accessed within seconds. Producers’ product labels can be brought to life and even the customers’ surroundings can merged with virtual reality. The technology to enable such interaction with customers is actually available now. CCL Label says it has the capabilities and experience to provide advanced decoration solution and technologies. It says that its Arilyn App not only provides convenient creation and usage of the content for an augmented reality experience; it offers analysis and easy adjustments to maximise the potential of sales campaigns. Packaging and decoration has stepped into the digital world by integrating tiny antennas and electrical circuits (RFID & NFC). Digital printing technology opens up a whole new world of possibilities, including offering each consumer a unique product. Each product can be outfitted with an individual design and variable data can be integrated easily. Mosaic software allows personalisation of any print run with images, text and designs for maximum impact. It automatically generates hundreds, thousands and even millions of unique graphics. CCL’s digital hybrid technology enables varnishes to be integrated, allowing individuallyapplied special effects; fluorescent ink on each label and sleeve, for example. Printing from a digital-based image directly to a substrate reduces cost for tools and lead times, while offering high levels of flexibility. Embracing labelling trends There are many different situations consumers go through when deciding on what to buy. Whether it is in front of a supermarket shelf or at a bar, surprising features and outstanding product appearance have immense impact on what the decision will be. Creating unique brand experiences has therefore become one of the top goals for leading brands worldwide. CCL Label says that it helps create the desired brand image by actively supporting global and local companies in the consumer goods industry with latest technologies and innovations, as well as vast printing capabilities. www.ccllabel.com","@ID":36}, "38 TRADE SHOW REVIEW PETplanet Insider Vol. 20 No. 12/19 petpla.net German Technology May 21-24, 2019, Guangzhou Hall 5.1, Booth S27 Audiovisual user guidance PETplanet: Unlike many other exhibitors here at the CBB, Heuft is showing its systems live on the stand. How has that been received? Kurz: That’s right, we have a number of systems on the stand. The Heuft One can be used to perform simple quality control tasks, with the Heuft Prime standard tasks in full-product inspection. The Heuft Spectrum II, our filling management system in a new product generation, can be seen for the first time at a show in China. For empty bottle inspection, we have our InLine II IR and IS lines on site. The number of visitors may be slightly lower than in previous years, but we had very specific requests, especially from important visitors from the brewing industry. PETplanet: What role does PET play in the Chinese beer sector? Kurz: So far not too big but that will perhaps change. For environmental reasons, the Chinese government is investing a lot in sustainability and therefore also in PET recycling, and so I believe that beer in PET can come in China. PET is already very strong used in softdrinks of any kind. PETplanet: To what extent do Heuft systems make life easier for the user? Kurz: Instead of our former Heuft pilot, we now offer a new navigation interface NaVi with intuitive controls. Via an audio interface which we already showed on the Drinctec last year in Germany, the operator can connect in future to it via voice control and get exactly the support tailored to his needs. www.heuft.com CBB Impressions - Chinese exhibitors of Caps/Closures, Labelling, Inspection Bejing Centigram Technology (Mr Wang Shuang) www.xidima.com Inspection: inline caps and bottles Canneed www.canneed.com Inspection: Instruments of analysing, measuring, testing AT2E China Limited www.at2e.com.cn Inspection: analysing & measuring instruments Jürgen Kurz, Managing Director of Heuft Systems Technology Shanghai (fourth from right) with his team at CBB","@ID":40}, "PETnews 6 NEWS PETplanet Insider Vol. 20 No. 01+02/19 petpla.net New study on the world market for plastic caps and closures Changing consumer patterns are revolutionising the packaging industry. The trend towards on-the-go products, for example, is driving demand for resealable packaging. The current, second study on the world market for plastic caps and closures by the market research institute Ceresana examines in detail the demand for the different types of closures: screw caps, flip-top closures, disc-top closures, dispensers, spays, lids, and overcaps. In the next eight years, analysts at Ceresana expect – based on the number of units – worldwide demand for plastic closures to increase by about 3.2% per year. According to Ceresana’s CEO Oliver Kutsch, in 2017, screw caps accounted for more than two thirds of the global market for plastic caps and closures. Their market share, however, is expected to decrease as competition from other types of closures increases significantly. The growing demands of consumers are increasing the demand for closures that allow easier handling and accurate dosing of package contents. The different requirements for closures within the individual application areas as well as the different designs of the types of closures have an effect on the choice of the types of plastics used. The study on the worldwide closures market offers separate figures for the market leaders polypropylene (PP) and polyethylene (HDPE and LDPE) as well as for polyethylene terephthalate (PET), Polystyrene (PS), and the aggregate of “other plastics”. Other factors which are influencing the demand for plastic closures include consumer health concerns and government taxes on beverages containing sugar which are inhibiting demand for carbonated soft drinks or juices in many countries. By contrast, demand for bottled water is likely to continue to account for high growth rates over the next few years. However, the individual factors and the resulting market dynamics can vary considerably from region to region. www.ceresana.com/en/market-studies/packaging/plastic-caps-world Drink Technology India in Bengaluru: Event date postponed Drink Technology India (DTI) Bangalore has been postponed at the request of the exhibitors. The trade fair will now take place from April 10 to 12, 2019. The Bangalore International Expo Centre will remain the exhibition venue. The second event date of DTI in 2019 in New Delhi remains unchanged. The fair had been planned for the end of February (February 28 to March 3) in Bengaluru and is mainly aimed at Indian exhibitors and visitors. The premiere of DTI in the metropolis has now been postponed following close consultation with the industry. Numerous Indian exhibitors had requested that the event not be held at the planned date. The background to this is the production cycles and the annual statement of accounts of the companies that tie up the workforce during this period. Accordingly, the number of registrations for the new date has remained virtually unchanged: around 95% of the Indian exhibitors who had already registered will also attend the new date. The international companies will also remain loyal to the event in April. In view of the varying presence of the sectors in the Indian regions, the focus in Bengaluru is on fruit juices, beer, spirits, wine and liquid food. In 2019, DTI will take place twice. After the premiere in Bengaluru, the event will be launched in New Delhi from December 5 to 7 as a combined fair with Pacprocess India, Indiapack and Food Pex India by Messe Düsseldorf. Mumbai remains the international hub for the beverage and liquid food industry in India, and the next event there will take place from December 9 to 11, 2020. www.drinktechnology-india.com SGT launched its own plastics recycling unit Société Générale des Techniques (SGT) has decided to speed up its transition to a circular model. This is coming to fruition with the creation of a recycled PET production unit at its Chalon-sur-Saône site in France under the name “SGR”. The rPET produced by SGR is intended to enable SGT to respond to current market demands by assisting its customers with their own commitments to a circular and responsible economy. SGR’s rPET production will have EFSA (European Food Safety Authority) and FDA (Food and Drug Administration) approval for food contact. This means that thanks to its preform production SGT will provide its customers with guaranteed supply and quality in the “bottle-to-bottle” principle. SGR has invested €7m in its decontamination line which has been recognised and validated by the food safety authorities. This recycling unit will have an initial processing capacity of 12,000 t/a and will directly supply the preform production unit located at the same site, creating around ten jobs. It is scheduled to start operations in September 2019. With this new project which has the support of the ADMEME and the Burgundy Franche Comté Region, SGT states to make an active contribution to the collective objective of developing a fairer and more environmentally-friendly economy. It provides used bottles with a second life so that they are seen as reusable resources. www.sgt-pet.com","@ID":8}, "BOTTLING / FILLING PETplanet Insider Vol. 20 No. 01+02/19 petpla.net 14 Bottling and palletising water right from its glacial source Cool filling When the Ice Age Glacial Water Company in Vancouver, Canada, decided to invest in upgrading its production processes, technologies and capacity, it determined that it required a solution that would be able to work with functional efficiency of at least 95%, across a range of different containers and formats. It was also expected to maintain the company’s position as one of the most automated bottling companies in North America and the world. Flexibility was also a key feature, in order that it could react immediately to even the earliest and slightest signal in the fast-changing water industry. A compact and flexible solution has been installed by Italian SMI Group. As its name suggests, Ice Age Glacial Water Company, based in British Columbia (BC), Canada, bottles water exclusively from glacier sources on its doorstep, in the mountain ranges of western North America. It recently invested in a new, integrated SMI Ergon system for the bottling and packaging of its 100% natural water, using advanced technologies in order to ensure that it reaches the tables of millions of consumers in North America and meet rising demand with its purity and freshness maintained. Ice Age Glacial Water Company, which was founded in 1992 as Watermark Beverages Inc., has grown rapidly in the bottled water sector and has earned a leading position in the North American premium segment. Ice Age Premium Glacial Water, the main company brand, has won many awards for its design and packaging quality, as well as the American Tasting Institute Gold Medal for its taste and the quality of its composition, in both 2002 and 2003. Ice Age water is sold in a range of different formats. Its bottling plant is located in Delta, a township within the metropolitan area of Vancouver, the principal city of BC. The company collects, bottles, transports and sells its product, which is kept scrupulously uncontaminated and pure during the production phase and is claimed to be 100% free of bacteria. Unpolluted source The water itself is collected from the Alpine Creek torrent in the Toba fjord, BC. The creek is fed by ice from the Hat Mountains in the Coastal Glacier Range mountain chain, about 200 miles north-west of Vancouver, far from houses and industry. The area receives over 175 cm (69 inches) precipitation a year. The water that flows from its glaciers has very low mineral content, a characteristic associated primarily with snow or melted ice; the freezing of water vapour is itself a purification process. As a precaution, however, the bottling uses UV and ozone processes so that the unique structure and character of the water remain pure. Everything bottled at the Ice Age Glacial Water Company originates from glacier sources and are 100% natural; they are not subjected to any working process and have minimum filtration. The company’s Vortex 9.5 brand, introduced in April 2005 while it was still known Watermark Beverages Inc, is a premium alkaline water with a PH of 9.5 – hence the name. It is claimed to provide important benefits and contain natural antioxidants and electrolytes. New plant installed 2016 Ice Age Glacial Water Company’s cutting edge bottling plant has been operating since summer 2016. It complies with the most severe production standards and is claimed to allow consumers to drink bottled water as pure as if it had come straight from its glacier source. The solution installed for Ice Age and Vortex water packages in 0.5 l and 1.5 l PET bottles by Italian SMI is equipped with a latest generation automation and control system incorporating ‘smart factory’ technologies. The integrated Ecobloc Ergon 6-24-6 HP VMAG stretch-blow moulds, fills with still water and caps both 500ml and 1,500ml PET bottles, at up to 12,000bph in the 500ml format. As a monobloc, it doesn’t need a rinser or","@ID":16}, "CAPS & CLOSURES 26 PETplanet Insider Vol. 20 No. 01+02/19 petpla.net Time for closure Leading global packaging manufacturer Retal develops and produces a range of closures as part of its varied portfolio, alongside preforms, containers and films. Offering PET and, increasingly, rPET, Retal provides standard and bespoke solutions to its large roster of global food and beverage brand customers. Jean-Noel Boursiez is Retal’s director of closures, with his expertise gained from decades of working to solve the specific demands of global customers. Boursiez tells PETplanet, “Retal has long been considered a strong player in the global closures sector, particularly for beverage brands in both still and carbonated drinks. We are currently in the process of expanding our portfolio even further, with a focus on the ‘premium standard’ products. This is a great way for us to utilise our experience and our technical capacity; we’re not pioneering for its own sake, we’re introducing closures that really add value.” reliable closure solutions that are versatile for different liquids and neck sizes. We have had great success in Europe particularly over the last few years, with the market demanding more aseptic solutions, such as our 38ml closure that is a key product for us in Eastern Europe. We have vast experience in quickly delivering complete solutions.” Retal is driven by the desire to develop and manufacture closures that perform. The company is proud of its high level of service and ability to successfully collaborate with customers, which, when married with a long history of producing closures that meet the strict expectations of many of the world’s largest bottlers, means that Retal is already perfectly in tune with the next generation of closures. www.retalgroup.com The latest example of a Retal closure that adds value is its High Grip. A clever closure that is easy to open thanks to distinctive grooves and good rigidity due to its added height. High Grip is now in mass production, with over 200 million units already manufactured. Boursiez says, “We have gained vast expertise over the last 20 years, developing, producing and servicing single-piece closure solutions. Our High Grip uses the new lighter 1881 PCO standard, saving about 1.3 g per bottle, yet retains the convenient overall height of the 1810 because of the taller cap. A great benefit of the High Grip is that copackers can continue to use their existing stacking trays designed for 1810 specifications; High Grip eliminates the height difference and it’s just 2.45 g.” Premium standard Boursiez explains how many of the issues that face global beverage brands due to the increasingly in-demand lightweighting of closures can be solved through product design, strict quality control and tight tolerances on production, as well as playing close attention to material selection. He says, “A key driver for us is the consistent ability to develop responsible, CAPS & CLOSURES","@ID":28}]}}
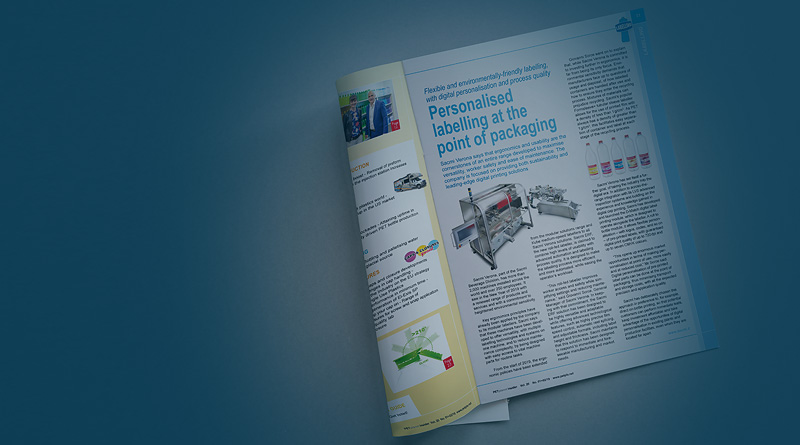