"34 TRADE SHOW REVIEW PETplanet Insider Vol. 19 No. 07+08/19 petpla.net Tritan bottle production on PET single-stage machine Chumpower demonstrated its single-stage allrounder CPSBSS10 and its extensive range of capabilities beyond conventional PET processing, with the production of Tritan-Copolyester bottles, which it first launched onto the market in autumn 2018. During the live presentation at the trade fair, the CPSB-SS10, which Chumpower has now had in its portfolio for eight years, used two of a possible total of four cavities. Although the manufacturer promised a maximum of 200 bottles per cavity per hour, the heavier Tritan preforms used in the demonstration achieved top speeds of about 15% less. The system was operating at 25 bar and 47 kW/h. Two servo systems independently control material quantity and clamp; the objective is to contribute to an optimised control and energy consumption. The Chumpower clamping system is of the toggle type, with actuation by a hydraulic cylinder. “We currently have five customers for this application in particular, all from non-food market sectors,” Michael Lee, Sales Department Manager, explained. “This technology is of primary interest in the areas of beauty care and cosmetics, and is an appropriate addition to the PET portfolio. The machine is also appropriate for the expanding pharmaceuticals products packaging market.” Tools are manufactured in-house, like the machine. The CPSB-SS10 can be shipped in a sealed container, with the objective of minimising the transport costs. “On average, we are around 20% cheaper than the known competition in this segment,” Mr Lee concluded. www.chumpower.com Rotary blower for up to 2.5 l PET bottles Turnkey PET bottle and beverage system manufacturer Tech-Long, which is headquartered in Guangzhou, the home of the Chinaplas trade fair, presented its CPX10 rotary SBM system. The machine is especially designed for applications in the standard bottle segment, ranging from 0.25 l to 2.5 l. It is expected to achieve an hourly output of 24,000 water bottles, 20,000 for CSD and hot-fill bottles, in 10-cavity format. The CPX series is equipped with 4 to 26 cavities, depending on the model. Tech-Long also offers applications outside the beverages segment, such as liquid food and non-food. The company says that complete changeover of the moulds in the CPX10 in approximately 20-30 minutes. According to Tech-Long, the concept of quick change-over for tooling and parts is to be pursued consistently in its machines, with the objective of simplifying any maintenance work. With the CPX10, the manufacturer also delivers low consumption of electricity and compressed air: approximately 80 kW/h and 20 bar on the model shown. www.tech-long-intl.com Chumpower’s booth at Chinaplas with Michael Lee (right) and Hanna Hsu F.r.t.l.: Frankie Pan, Yang Liu and Kay Barton at Tech-Long’s Chinaplas booth","@ID":36}, "INSPECTION 30 PETplanet Insider Vol. 19 No. 07+08/19 petpla.net Acti Pack’s approach to production and supply of high-end containers Exceeding expectations Acti Pack PET Packaging, based in AndrézieuxBouthéon, Auvergne-RhôneAlpes, France, specialises in premium containers particularly for food, cosmetics, and health and beauty products markets. It is a subsidiary of Groupe Axium, which is comprised of five ISO9001 certified plants serving the European packaging market. Acti Pack itself was founded in 1992 and focused on the production of PET jars and bottles. In the years since its foundation it has expanded its European operations to include three plants; the main plant and headquarters in France; Acti Pack Czech, which opened in 2000 in the Czech Republic; and KKT Germany, which was acquired in 2016. Each plant has its own speciality but, overall, the Acti Pack plants are all engaged in the production of high-end PET jars and bottles, using the stretch blowmoulding process. Two other plants within the Axium organisation – Loire Plastics Industrie and LAPAC – supply caps and closures that complement Acti Pack containers, alongside their own range of injected packaging. Acti Pack claims to differentiate itself by its ability to provide a total package to its customers. While some manufacturers are dedicated to bottle production and others focus on closures, Acti Pack provides design and production of both container and closure and is able to incorporate innovative design and labelling solutions. “We propose a standard or customised closure for every bottle and jar in a complete package solution,” Acti Pack Management and Export Assistant, Corinne Reynaud-Rival, explained. As part of this complete solution, the company prides itself on high standards of quality and an agile approach to production. Meeting quality demands Given its location, it is not an accident that the list of Acti Pack’s major customers includes giants of the cosmetic and personal care industry. “These customers are very demanding about quality,” said Sandra Maillet, Head of Operations. “They continually push for higher precision and tighter tolerances on the containers we produce.” Keeping demanding customers means that Acti Pack must produce containers that not only meet, but exceed quality expectations. In order to ensure exceptional product quality, strict quality standards and procedures have been put in place throughout production. However, in order to fully achieve their goals, the quality team determined that it was necessary to procure a quality management tool that would provide very precise dimensional measurements. This tool would be used to support production, verify dimensional accuracy and confirm that their products fully met customer specifications. This is where the Gawis system from Agr came into play. Sandra Maillet explained that the quest for a measurement device started several years ago. She and her team visited an exhibition and met with several measurement equipment vendors but none of them fully met their needs. That is when they turned to Agr and the Gawis measurement system. As well as confirming dimensional accuracy, they also needed to measure material distribution or thickness, at many points on the container - typically a very time-consuming job when performed manually. The Gawis system can perform comprehensive non-contact material distribution measurement and profiling as well as dimensional gauging of the body and finish of a container, with high accuracy and repeatability, all in a single operation. It has the flexibility to perform very simple measurements for basic quality management work or very detailed combinations of dimensional and thickness measurements to aid in the design and qualification processes. As part of the machine evaluation process, Sandra provided Agr with a wide array of samples with defects and examples of the attributes that Acti Pack PET Packaging specialises in premium containers with a focus on cosmetics, health and beauty products. Acti Pack PET Packaging is based in Andrézieux-Bouthéon, in the French Region of Auvergne-Rhône-Alpes. INSPECTION","@ID":32}, "INSPECTION 28 PETplanet Insider Vol. 19 No. 07+08/19 petpla.net Agr’s patented automated blowmolder control technology helps youV that contain an increased percentage of recycled PET. PROCESS PILOT® front. For example, we were the first to offer a high speed cavity number reading for preforms. At K 2013, we presented the PreWatcher Inline (formerly PreWatcher III), which offers sorting, feeding and inspection of preforms on just 8m². In 2017, we presented a closed loop for the production of beverage closures together with Netstal at Drinktec and thus for the first time demonstrated the influence and importance of inspection systems in the production process of the future. Last year, our increasing protectionism are not conducive to industry. But there is another issue that specifically affects the plastics industry and will be prevalent in the coming years: how will we deal with plastic packaging in the future? I think there needs to be a discussion about the benefits of plastic packaging, because I do not think that everything will be better if we stop making plastic packaging.” www.intravis.de Torus Technology Group, Spencer Whale, Global Sales Manager (BILD) (I) “After 20 successful years as a global leader of inspection equipment in the metal packaging industry, Torus first ventured into the PET market in 2013. Having already got the specialist metrology skills and transferrable technologies required for manufacturing world-class quality control inspection equipment, applying them to the PET Fig.1: Multi-module measurement CapWatcher Q-Line, the inline quality lab, celebrated its world premiere. It is the first inline inspection system for beverage closures with integrated temperature measurement. And this year too, we have prepared two absolute world firsts that will join this group - one in the preform sector and the other in the area of Industry 4.0 solutions.” (III) “At the moment we see a changing world. Of course, the currently prevailing trade conflicts and industry seemed an obvious choice. Industry competitors were, at the time, using outdated technology and hadn’t got the innovation or customer centricity that Torus pride themselves on, providing an opening for Torus. Torus have since developed an entire line of quality control equipment for plastic containers and preforms, all utilising the latest technology sensors and intelligent vision systems. As a UKAS accredited company, all of Torus’ equipment is provided with measurements traceable to UKAS standard via Torus’ own temperature controlled UKAS certified laboratory.” (II) “As the plastic packaging industry evolves and industry 4.0 intensifies, the need for large sets of more consistent and reliable quality control data to be provided in the most efficient manner as well as the demand for automating processes are providing potential growth areas for Torus. Torus’ latest, exciting innovation, the TQ-Lab, offers a solution that meets these changing industry demands.” “The TQ-Lab involves the automation of multi-module quality control checks for PET and other rigid plastic packaging. Customers can choose up to four inspection modules to be included in a single cabinet and controlled via a single operator interface. The system, which is the first of its kind, uses multiple noncontact and contact sensor types. Bene-","@ID":30}, "INSPECTION 27 PETplanet Insider Vol. 19 No. 07+08/19 petpla.net be thought away from the industry. As the technology is “very simple” this IP is internationally patent protected. With our unique preform factory concept 4.0 we offer the PET industry a complete inspection platform. Last but not least, one of the most exciting developments is clearly our closure digital printing machine, IMDvista CLDP. We see the way and the reason why our customers printed closures will come to change in the short future. However, stay up to date and in the lead of the industry, we have some new developments to come very soon.” (III) “The pressure to user recycled materials is going up tremendously and will even require more inline vision inspection systems. We are a fast, organic growing company and it is not always easy to keep up with the growing demand. We did move to bigger production facilities last summer and do also move the operations into an optimised office space to fulfil this needs. We feel ready for the future.” www.imdvista.ch our most important development. A very simple to use monitoring system, adding no floor space to existing preform production lines, enables all preform producers monitoring their preform production. Especially with the fast moving trend into the usage of recycling PET, this tool can no more Initravis GmbH, Gerd Fuhrmann, CEO (I) “I founded Intravis in 1993 and initially focused on the development of computer tomography systems. Since 1995, Intravis has focused on inspection solutions for the plastic packaging industry. The trigger for this was a request from Alpla for a bottle inspection system using our ideas and technology. Over the years, this request has led to a specialisation in complete solutions for the plastic packaging industry. Today we offer turnkey systems and equipment for quality control of preforms, closures, bottles and containers as well as decorations (e.g. IML label). An increasingly growing part of our business is analysis software. Today, ten of ten major global converters are using our systems.” (II) “We are fortunate that we have several strong markets where we each belong to the world market and innovation leaders. These are above all the preform, closure and bottle area. Also our solutions for IML inspection are unique on the market. A growth market is analysis software. In recent years, we’ve seen a lot of change in our industry: our systems are no longer just used to sort out poor quality. Today’s customers claim that the results of the quality inspections must help them to improve the production processes and thus prevent them from producing any bad parts at all. We have dedicated ourselves to this topic since the very beginning and with today’s computer technology it is possible to implement our ideas profitably for our customers. As far as developments are concerned, of course there have been many exciting projects in the last 25 years. It has always been our goal to be technologically in the very fore-","@ID":29}, "MARKET SURVEY 25 PETplanet Insider Vol. 20 No. 07+08/19 petpla.net German Technology Oct 16-23, 2019 Hall 1, Booth C42 Company name ABC Compressors Nanjing Shangair Machinery Manufacturing Co.,Ltd. Hertz Kompressoren GmbH Postal address Telephone number Web site address Contact name Function Direct telephone number E-Mail Pol. Ind. Azitain 6, 20600 Eibar, Spain +34 943 820 400 www.abc-compressors.com Mr Gonzalo Gabarain Sales & Marketing Manager +34 647 413 760 [email protected] No.1,Xiyan Road, Binjiang Economic Development Zone Jiangning District, Nanjing, China +86 25 86408239 www.shangair.com Mr Edward Zhou Overseas Sales Manager +86 1519595 1347 [email protected] Kronacherstr. 60 96052 Bamberg, Germany +49 951 96 43 13 88 www.hertz-kompressoren.com Mr Ercan Asmaz Sales Manager / Europe +49 533 962 64 22 [email protected] 1. Machine designation / model number Horizon | Horizon LP WM PET Master & PET Master VSD Series 2. Number of models in range 30+ models 2 PET Master 50/75/100/125/150/180/220/270/300 PET Master VSD 75/125/180/220/300 3. Output in m³/hour 250-6,000 60~72 810 (PET Master VSD 180) 4. Compressor type Oil-free reciprocating piston compressor \"all-in-one\" skid High pressure blowing air (up to 40bar ) Low pressure air Low pressure piston compressor High pressure blowing air (up to 40 bar) High pressure piston compressor (atmospheric up to 40bar) Reciprocating Integrated system Atmospheric compressor including VSD with huge regulation range from 20% to 100% of the capacity 60m3/min, 72m3/min, air tank 150l 5. Lubricated or oil-free 100% Oil-free compressor class 0 Oil splash lubricate Oil-free (high pressure compressor) Low pressure compressor 100% Oil-free compressor class 0 30bar (None of these options) Booster compressor Not needed Integrated system Atmospheric 100% Oil-free compressor class 0 6. Machine layout Horizontal opposed cylinders, forces balanced and virtually no vibrations 4,192 x 1,977 x 2,814 7. Number of compressor stages 2 for LP and 3-4 for HP 2 3 8. Are special foundations required? No, virtually no vibrations No Yes 9. Cooling system Water cooled (closed cooling tower or aerocooler) Air cooling Water-cooled 10. Belt or direct drive Direct drive Belt Low pressure compressor Direct drive Belt Booster compressor Not needed Integrated system Direct drive","@ID":27}, "INSPECTION 31 PETplanet Insider Vol. 19 No. 07+08/19 petpla.net they needed to measure. The result of the analysis showed that the system could measure most of those attributes but possibly not all. “Essentially, Agr told us what we could and could not measure. They were very honest about capabilities,” she explained. “In the end, we found that the Gawis would meet the majority of our measurement needs.” As this device was a major investment and would be central to their quality program, Agr made arrangements for the Acti Pack team to visit a local company that was using the Gawis as part of their quality program. It was helpful to talk to actual users and get the benefit of their hands-on experience. The feedback was that programming might take time but the results were worth it – near perfect, every time. After the visit, Sandra approached Acti Pack’s CEO with the recommendation to purchase. The business case was ultimately made, successfully. The arrival of the Gawis system was quite timely, as Acti Pack was just starting work with one of the world’s largest cosmetic companies. This equipment supported the jobs at hand and offered an advantage when soliciting future business. Big cosmetic companies demand very high quality packaging, which must present a premier appearance, have correct and consistent colour, and exact physical dimensions, every time, to ensure proper closure fit. A different approach to manage production Integrating the Gawis system prompted Acti Pack to totally change their approach to first article and new bottle production. Originally, the company prepared a control range prior to production, using bottle drawings only, and then managed production accordingly. Following the Gawis purchase, the process was changed to first create a “temporary or draft control range”, produce the first bottle, and then program the Gawis for creating the final control range to manage production bottles. Measurement of the actual bottle is critical to this process as the drawings are not enough. Gawis is then used continuously to verify dimensional and thickness distribution specifications. Samples are taken at regular intervals of each production run. Each bottle is measured for key dimensional and thickness attributes, including up to 15 levels for thickness, bottle height and a range of critical neck/finish dimensions. A final test report, documenting dimensional and thickness conformity, is provided with each customer shipment. Testing takes approximately 1.5 minutes per bottle; manual testing would take a lot longer and be less accurate. In addition to the Gawis system, the Acti Pack lab includes a number of other essential devices for managing quality, including a topload tester, vacuum chamber, test ovens, viscosity and colour measurement equipment. Agility Acti Pack, which has under 100 employees and over 500 SKUs in its catalogue, runs a very lean operation with a level of agility that other producers cannot match. On average, the plants change the production mix at least 700 times per year. Changes often include mould and colour. “Agility means spending minimal time in meetings and making decisions quickly,” according to Sandra Maillet. “Having the same kind of machines in each of our three plants means we can interchange moulds and adjust production to meet the needs of a particular customer or market.” All plants have the ability to provide back-up. In the event of capacity or other issues, critical production can be scheduled at another facility, or even moved within a day or two. This flexibility is very important for safety and continuous production. Acti Pack recently placed an order for two additional Gawis systems, destined for the Czech and German plants. Matching quality Acti Pack, along with the entire Groupe Axium, maintains a permanent drive for improvement, quality and customer satisfaction. The Gawis system is used to aid in managing production, qualifications of new designs and the verification of container specifications. www.agrintl.com With less than 100 employees, Acti Pack runs a very lean operation. The Agr Gawis dimensional and thickness measurement system is used continuously to verify that production runs meet dimensional and thickness distribution specifications. Agr’s Gawis all-in-one measurement station plays a vital role in Acti Pack’s strive for quality excellence.","@ID":33}, "BOTTLING / FILLING PETplanet Insider Vol. 19 No. 07+08/19 petpla.net 20 Slovak beverage producer Slovenské pramene a žriedla modernises its production facilities Boosting efficiency The water market in Slovakia is serviced by many small, regional suppliers and, accordingly, the competition is fierce. Market leader Slovenské pramene a žriedla holds its own over its strong rivals by continuously developing new products. In doing so, the Slovakian beverage producer relies heavily on technology from KHS. For its plant in Lúka the bottler recently procured an InnoPET BloFill stretch blow moulder/filler block and an Innopro Paramix C blending system from the Dortmund systems supplier. The water market in Slovakia is dominated by a large number of bottlers. Consequently pressure from the competition is high. Market leader Slovenské pramene a žriedla, which also exports to the Czech Republic and Hungary, among other countries, faces down its strong rivals by constantly developing new products. “Here, it is especially important to recognise new trends early on and to gear the product portfolio accordingly”, explains Michal Harajda, technical director for the Slovak beverage producer. “The Slovaks are paying more and more attention to their health. Natural mineral water and beverages with added minerals and vitamins are currently very much in demand.” In addition, it is forecast that the home market share for water in PET bottles will rapidly increase by 2022. Particularly high growth rates of 13% and 11% are expected for flavoured and still bottled water respectively. In an attempt to successfully satisfy customer requirements they now have an increasingly complex product range, which has meant heavy investment in KHS machines for their water bottling operations. Slovenské pramene a žriedla has relied on technology engineered by KHS since the early 1990s. At the start of the cooperation between these two companies the Slovak beverage producer purchased only used machines. “Most of this machinery is still up and running today and still economically viable,” states Harajda. The beverage producer now operates KHS machines at four of its five production sites, investing in a blocked InnoPET BloFill at the plant in Tornaľa two years ago. During the same period the bottler initially also acquired two single KHS machines for stretch blow moulding and filling for its Budiš production site. However, the Slovaks were so convinced by the block system that they subsequently also had their existing KHS machines in Budiš blocked. In 2018 Slovenské pramene a žriedla then invested in a further InnoPET BloFill for its new bottling plant in Lúka. Latest procurements boost efficiency The latest investment was sparked by the move of one of the company’s old facilities to the village of Lúka. The previous bottling plant was in the mountains which proved difficult for some of the trucks, especially in the winter. The bottler therefore had to decide whether to relocate the machines from its old site to Lúka or to replace them. “Our positive experience with the KHS stretch blow moulder block prompted us to purchase a BloFill for Lúka as well,” Harajda states. The impact the KHS machine had on the beverage producer’s electricity consumption alone was huge: this was halved following the installation of the new stretch blow moulder/filler block. “The sales figures for water in Slovakia have continuously risen over the last few years. At 14,000 bottles an hour, the production capacity of our old line was no longer sufficient,” says Haradja, giving another reason for the recent investment. By using the InnoPET BloFill the output has increased considerably, with up to 26,000 0.33- to 1.5-litre bottles and a maximum of 22,000 2.0-litre containers now being produced per hour. In the course of the recent investment drive, the bottle caps were also changed over from the old PCO 1810 standard to the PCO 1881, which is 4mm shorter. This, along with various other factors, cuts down on the use of materials and therefore on the weight of the bottles. On the 2.0-litre variant the bottler now saves 4 g of material per bottle, with the 1.5-litre container weighing as much as 6 g less. At the Lúka site, Slovenské pramene a žriedla not only bottles natural waters but also soft drinks and vinegar. At its five bottling plants, Slovenské pramene a žriedla produce 300 million litres of water, soft drinks and syrups per year.","@ID":22}, "PETproducts 22 PETplanet Insider Vol. 19 No. 07+08/19 petpla.net BluStream sterilisation technology Chemical sterilisation of caps can be an issue. It often employs work at high temperatures that can distort the cap. To eliminate these issues, Serac offers an alternative to chemical sterilisation. Serac’s new BluStream is a lowenergy e-beam treatment that can be administered at room temperature. It’s capable of ensuring a 6 log bacteriological reduction in 1 second without any chemicals. This module is intended for use on bottling lines of nonrefrigerated and ESL 90 day beverages. Ebeam is a physical dry treatment. To sterilise the surface, Ebeam dispenses a beam of electrons over the surface of the product. The electrons quickly destroy the microorganisms by breaking their DNA chains. BluStream offers manufacturers a safe, real-time monitored and environmentally friendly solution. The BluStream technology can be integrated on new Serac lines as well as existing machines, whatever their OEM. Serac’s BluStream module stands out in the aseptic packaging market. It uses low-energy electron beams which do not penetrate the treated material and it will not affect the internal structure of the cap. www.serac-group.com Sidel introduces 6.5g bottle for 500ml still water Sidel states that its new solution Sidel X-Lite Still is, with 6.5 g of weight and a height of 195mm, the lightest 500ml PET bottle in the world for non-pressurised still water. This bottle is featuring a Novembal Novaqua RightCAP26 closure. Thanks to its extremely light industrial bottle design, it is claimed to be the most cost-effective and sustainable packaging available on the market. The new bottle integrates the proven StarLite Still base solution, already implemented worldwide due to its stability and stress resistance through the value chain, its design flexibility and the lightweighting possibilities it offers. Moreover, the energy savings enabled by StarLite Still – mainly achieved through a reduction in blowing pressure and heating power – are claimed to be significant, with no compromises on the packaging performances. This base design can be adapted to all Sidel blowing platforms and applied to existing production lines to reduce the Total Cost of Ownership (TCO). X-Lite Still has been optimised by the company’s engineers for the Sidel Super Combi, the single smart solution integrating five process steps: preform feeding, blowing, labelling, filling/capping and cap feeding. “Based on a dedicated preform design for optimal mechanical performances, this latest addition to our packaging portfolio is able to withstand label application on the empty bottle, in spite of its extremely light weight. It allows for the ideal bottle shape design for nested packs and enables an optimum top load resistance of 34 kg, able to match the supply chain requirements in terms of pallet stability”, explains Laurent Naveau, Sidel Packaging Expert. As the lightest bottle in the world for still water, Sidel X-Lite Still reduces the consumption of PET resin: for example, when compared to bottles weighing 12 g, the new solution can save a 1,485 t of PET per year while generating energy savings of up to 335,000 kWh/year (based on Sidel Matrix Combi handling 2,700 bph/mould). The company stated that by switching from a 12 g PET bottle to the X-Lite Still 6.5 g bottle, the payback time for a line upgrade would be between two to four months. www.sidel.com","@ID":24}, "8 NEWS PETplanet Insider Vol. 19 No. 07+08/19 petpla.net Hillenbrand, Inc. to acquire Milacron Holdings Corp. Hillenbrand, Inc. and Milacron Holdings Corp. announced that they have entered into a definitive agreement under which Hillenbrand will acquire Milacron in a cash and stock transaction valued at approximately $2 billion, including net debt of approximately $686 million as of March 31, 2019. Under the terms of the agreement, which has been unanimously approved by the Boards of Directors of both companies, Milacron stockholders will receive $11.80 in cash and a fixed exchange ratio of 0.1612 shares of Hillenbrand common stock for each share of Milacron common stock they own. Based on Hillenbrand’s closing stock price on July 11, 2019, the last trading day prior to the announcement, the implied cash and stock consideration to be received by Milacron stockholders is $18.07 per share, representing a premium of approximately 34% to Milacron’s closing stock price on July 11, 2019, and a premium of approximately 38% to Milacron’s 30-day volumeweighted average price as of the close on July 11, 2019. Upon closing, Hillenbrand shareholders will own approximately 84% of the combined company, and Milacron stockholders will own approximately 16%. Milacron manufactures, distributes, and services engineered and customised systems in the approximately $30 billion plastics technology and processing industry, as well as fluid technologies and processing systems. Milacron operates in three segments: Melt Delivery & Control Systems, which designs and manufactures technically advanced hot runner and process control systems, mould bases, and components; Advanced Plastics Processing Technologies, which designs and manufactures plastics processing equipment and systems, including injection moulding, extrusion, and auxiliary systems; and Fluid Technologies, which manufactures products that are used in a variety of metalworking processes. This transaction is stated to represent a pivotal step in Hillenbrand’s vision to become a world-class global diversified industrial company by adding new strategic businesses in hot runner systems and injection moulding to its portfolio through Milacron’s leading brands, including Mold-Masters and Milacron injection moulding. Together, the combined company will have increased scale and meaningful product diversification, enhancing its ability to serve customers through complementary technologies across the plastics value chain, including plastic base resins production, compounding, processing both extruded and injection-moulded products, and recycling. The transaction, which is expected to close in the first calendar quarter of 2020, is subject to customary closing conditions and regulatory approvals, including the approval of stockholders of Milacron. Hillenbrand intends to fund the cash portion of the transaction through debt financing and has secured a committed bridge financing facility led by J.P. Morgan. www.milacron.com Berry Global Group, Inc. completes acquisition of RPC Group Plc Berry Global Group, Inc. announced the completion of its acquisition of RPC Group Plc for a purchase price of approximately $6.5 billion, which includes approximately $4.3 billion of cash paid for the equity interest in RPC and $2.2 of net debt and estimated transaction related costs, subject to closing adjustments. The combination of Berry and RPC creates a leading global supplier of valued-added protective solutions and one of the world’s largest plastic packaging companies. Berry’s combined global footprint will consist of over 290 locations worldwide, including locations in North and South America, Europe, Asia, Africa, and Australia. The pro forma combined business will employ over 48,000 people across six continents with sales of approximately $13 billion based on the latest published financial statements of Berry and RPC. The acquisition of RPC was financed with a portion of the proceeds of Berry’s May 2019 sale of $1.25 billion of 4.875% first priority senior secured notes due 2026 and $500 million of 5.625% second priority senior secured notes due 2026 and a $4.25 billion incremental term loan and a €1.075 billion incremental term loan, which also served to refinance an existing Berry term loan. Berry is scheduled to announce its third fiscal quarter earnings on August 7, 2019, and will provide an update on its progress at that time. Goldman Sachs International, Wells Fargo Securities, and J.P. Morgan Securities acted as financial advisors and Freshfields, Bruckhaus Deringer LLP and Bryan Cave Leighton Paisner LLP acted as legal advisors for Berry. www.berryglobal.com","@ID":10}, "BOTTLING / FILLING PETplanet Insider Vol. 19 No. 07+08/19 petpla.net 21 Bottling of vinegar At the Lúka site Slovenské pramene a žriedla not only bottles natural waters but also soft drinks and vinegar. The market leader for water therefore also decided to invest in a KHS Innopro Paramix C blending system. The company is very proud of the outstanding quality of its beverages. All of its eight KHS machines have subsequently been equipped with ultraclean technology supplied by the Dortmund systems manufacturer. For its new site in Lúka, Slovakia’s market leader in the water bottling segment has procured an InnoPET BloFill and an Innopro Paramix C from KHS. Initially the processing of vinegar proved to be a challenging undertaking as a number of modifications were necessary before the machines could bottle vinegar. The customer’s requirement – an unusual one for KHS – was ultimately achieved by using special sealing materials, among other features, which demonstrated long-lasting resistance to the acid. With its new procurements Slovenské pramene a žriedla is now able to expand its product portfolio. “We hope that in the future we can bottle all kinds of sensitive beverages in order to cater for the individual needs of our clients,” Haradja explains. www.khs.com","@ID":23}, "PETnews 6 NEWS PETplanet Insider Vol. 19 No. 07+08/19 petpla.net Husky World Tour in Mexico Husky Injection Molding Systems, a leading technology provider to the plastics processing community, hosted a one-day Husky World Tour event in Santa Fe, Mexico. The event was attended by more than 70 business leaders from throughout Mexico and included insightful presentations delivered by Husky and industry experts, engaging discussions, and networking opportunities that armed attendees with the latest information about technology enabling a circular economy and the importance of effectively responding to changing trends in the consumer packaging market. Over the last several years the market in Mexico has changed rapidly, with consumers demanding more diverse, sustainable, premium packaging. In response, Husky has been developing flexible, digital solutions that help its customers to be more competitive by enabling differentiated packages, with a reduced environmental footprint, that are brought to market faster. Recent technologies introduced by Husky to satisfy this need include its HyPET HPP5e system, Next Generation Operating Model and NexPET mould. www.husky.co Alpla and PTT Global Chemical announce partnership Alpla and PTT Global Chemical (GC) will collaborate on a feasibility study for the construction of a recycling plant in Thailand. The companies announced the plan at the “Circular Living Symposium 2019 – Upcycling Our Planet” in Bangkok at the end of June. Alpla develops and produces plastic packaging solutions worldwide and has been active in recycling for more than 25 years. With two of its own recycling plants in Austria and Poland and joint ventures in Germany and Mexico, the plastics converter has since become a preferred partner for PET recycling. Now, Alpla and PTT Global Chemical (GC) are currently investigating the prospects of further activities in Thailand. GC serves as PTT Group’s chemical flagship. The company has committed to the principles of the circular economy with the aim of always optimising the use of resources. Examples of its commitment include the development of bioplastics as an alternative type of plastic and the implementation of effective waste management systems. “GC will work with Alpla to conduct a study on investing in the first high-quality circular plastic recycling plant in Thailand, including materials such as rPET and rHDPE. We will make a decision in the third quarter of this year after reviewing the results of the study,” said Supattanapong Punmeechaow, President and CEO of GC. www.alpla.com Alpla and PTT Global Chemical (GC) will collaborate on a feasibility study for the construction of a recycling plant in Thailand. On the right: Alpla Regional Manager Bernd Wachter; and on the left: Supattanapong Punmeechaow, President and CEO of GC. BrauBeviale 2019 spotlights future viability of the beverage sector From 12 to 14 November 2019, Nuremberg will be the hub for the international beverage industry, when the sector gathers for this year’s capital goods fair for beverage production and marketing Brau Beviale. The products and solutions on display by the around 1,100 exhibitors, 53 percent of which are from outside Germany, covers the entire process chain for beverage production, from raw materials, technology and components to packaging, accessories and marketing ideas. This year too, the main theme is the future viability of the beverage industry. What are challenges being faced by both equipment suppliers and beverage manufacturers? Through its product range and supporting programme, BrauBeviale states to offer the platform for knowledge-sharing and innovation, while creating momentum and providing inspiration. The new route around the displays that was introduced for visitors in 2018 has proven effective and offers visitors ease of navigation in an atmosphere that is as constructive and welcoming as usual. The various halls around the perimeter of the central lawn are grouped into thematic focus areas: raw materials and sensory attributes in Hall 1, technologies in Halls 6, 7A, 7, 8, 9, water treatment, analysis and components in Hall 6, packaging in Halls 4A and 4, and accessories and marketing in Halls 5 and 6. The main theme of BrauBeviale, the future viability of the beverage sector, focuses on the issues and challenges currently confronting beverage producers, which are generally the same across borders. Efficient and flexible technologies, diverse and high-quality raw materials and ingredients and sustainability in production are just as important as digitalisation and automation, future strategies for companies, packaging, marketing messages and communicating with consumers and end clients. BrauBeviale not only covers these topics through the product range on display but also in the supporting programme. It is intended to appeal to all beverage producers, whether they are brewers, mineral water operations, winemakers or manufacturers of spirits or alcohol-free drinks. www.braubeviale.de","@ID":8}, "BOTTLING / FILLING PETplanet Insider Vol. 19 No. 07+08/19 petpla.net 16 Investment in state of the art technology is the key Filling at its best We met: Bernie Zarda, Sr Vice President Premium Waters, Inc. Premium Waters is a consortium of bottling plants in the North of the US. It has a long history in the bottled water business. The company was incorporated by the Chesterman Company in 1994. That same year, it was purchased the Kandiyohi Bottled Water Company, signalling the reentry into the bottled water industry. In 1997, Premium purchased Chippewa Springs, a company that has been in the spring water business for more than a century. Tour Sponsors: In 1999 Bernie Zarda, Sr. VP, joined the company; at this time they have three plants in operation. “In 2004 we started making our own bottles and preforms. We aggressively go in self production until 2007. At this time we bought a lot of Sipa and Husky equipment. In 2012 we built this facility here in Missouri, and started buying Krones Ergo Bloc three times, as well as the Contiform BlowFill Blocks. We also bought an Athena injection machine. For injection we also have Sipa and a Husky HyCap as well.” The corporate offices are located in Minneapolis, MN and Kansas City, MO. Through the growing network of bottling plants and distribution centers, Premium serve customers throughout the United States. In spite of continued growth, Premium made a decision not to be a national producer, preferring to perform well in the regions they serve. All of the plants have state of the art blowing and filling equipment, most is not older than five to six years. “The injection equipment is a little bit older but still works fine”, Bernie added. In total they have 16 PET lines, in this facility in Missouri there are three PET lines. “This equipment puts us in a pretty good spot: especially the energy savings, the production speed as well as the much quicker changeover are significant advantages. Also controlling and processing are much better. The payback of the technology is very fast.” Premium fills around 4 billion bottles a year, only Niagara and Nestlé fills more. The range of bottle design in shape and size is amazing. The bottles were produced out of virgin PET. Acquisitions complemented natural growth and allowed to scale the business. Geographic expansion followed acquisitions of plants. They fill spring and drinking water. Premium combined branded- and private-label production as part of its strategy. By producing 5-gallon, gallons and PET packages, the company provides a broader service for the customers. “We do a lot of gallons, in six plants. It also enabled Premium to reach more consumers with their offerings,” Bernie concluded. In addition to innovation, cost reduction and competitive pricing are ways to keep products and services going strong in the marketplace. “Today our bottle weighs 8.47 g, there is still the possibility to lightweight it, but at the moment it is a best seller”, Bernie explained, and continued: “Resin and transportation are big costs here in the North US. It is hard to control. We see a lot of resin increase; this drives us to put some more weight out of the bottle. In the last two years we have an increase of 20% in resin costs.” Bernie sees still room for growth in the bottle water market. “We have to be aware of our responsibility as water fillers, in terms of handling the springs and recycling. We gain every year a percentage of consumers changing from tap water to bottled water. Do you remember a few years ago the situation in Flint?” (see PETplanet 04/16) Premium Waters is proud to be a member of the International Bottled Water Association (IBWA). The membership means for them subject to strict standards of quality that ensure continually meeting the promises of reliability and satisfaction. www.premiumwaters.com Heike Fischer and Bernie Zarda in front of the Premium Waters plant in Missouri The Krones Equipment was bought in 2012.","@ID":18}, "PETpatents www.verpackungspatente.de PETplanet Insider Vol. 19 No. 07+08/19 petpla.net 40 PET bottle Intern. Patent No. WO 2017 / 103467 A1 Applicant: Sidel Participations, Octeville-sur-Mer (FR) Application date: 14.12.2016 Application is made for the shaping and base construction of a weight-reduced PET bottle. The feet of the bottle are furnished with special ridges and steps to make it sufficiently stable. Plastic bottle Europ. Pat.issue No. EP 3112280 B1 Applicant: Yoshino Kogyosho Co. Ltd., Tokyo (JP) Application date: 10.12.2012 European patent issue describes a slightly contoured plastic bottle with reinforcement ridges and special shaping in the shoulder area. Cap for plastic bottle Intern. Patent No. WO 2018 / 203146 A1 Applicant: Resilux N.V., Wetteren (BE) Application date: 2.5.2018 Proposed in the side wall of a plastic bottle is the integration of a groove to snap a cap onto the base, which protects the base and makes the bottle visually more appealing, e.g. for bottling higher value products. Bottle for hot filling Intern. Patent No. WO 2018 / 208903 A1 Applicant: The Coca Cola Comp., Atlanta (US) Application date: 9.5.2018 A plastic bottle designed for hot filling with compensation areas and reinforced and/or stabilising longitudinal edges. Curving compensation areas Intern. Patent No. WO 2018 / 208906 A1 Applicant: The Coca Cola Comp., Atlanta (US) Application date: 9.5.2018 A contoured plastic bottle designed for hot filling and/or carbonated product with curving, z-shaped compensation areas. Slanted contouring Intern. Patent No. WO 2017 / 102111 A1 Applicant: Compagnie Gervais Danone, Paris (FR) Application date: 26.6.2016 A plastic bottle is manufactured with slanted contouring. Alongside the look and feel of the bottle, it also has greater stability when stacked.","@ID":42}, "BOTTLING / FILLING PETplanet Insider Vol. 19 No. 07+08/19 petpla.net 19 BOTTLING / FILLING 19 glass bottle. This means the transportation of our products results in less green house gases (CO 2 emissions). And the production in glass would also have been much more expensive. For example the mould costs of PET were much more attractive.” The preforms are supplied by a small local manufacturer and additionally by Resilux. Black Fly bottles are strong and unbreakable, making these bottles a safe choice in environments where broken glass poses a problem, explains Rob. Recycable The bottles are also much easier to break down during recycling requiring less energy to shred PET then to melt glass. Black Fly’s single use bottles are not necessarily single use. The bottles actually have a much longer life span as recycled materials then as Black Fly bottles. The deposit programs implemented by their retail partners ensures a high rate of customer return and therefore recycling than other bottles and plastics that have no return monetary value to consumers. Black Fly bottles work their way through The Beer Store’s recycling system in Ontario, ending up at a Canadian recycling business where they are then sold to companies that make car parts, clothing and other plastics. Reduced corrugate Reduced packaging designs: Black Fly’s 4 pack carriers were designed to reduced packaging using the least amount of corrugate possible while remaining compliant with industry packaging standards for crush testing and tamperproof packaging. The open sided carriers allow consumers to easily see the products, while providing a sturdy consumer carrying container. Black Fly uses less corrugate then traditional top-open and closed containers. Black Fly 4-packs have a unique locking design which utilises a glue-less closure system. Black Fly’s team is committed to reducing waste at all levels, from staff sorting and recycling any business materials that do not have bins within their industrial area, to larger initiatives that involve large recycling companies. Bottles, corrugate and shipping containers at Black Fly are all recyclable after use. Black Fly uses a local recycling business to support its programs, and commends its staff for initiating and committing to these green programs. We thank Rob for an interesting presentation of his unique company. www.blackflybooze.com Visit us: www.bericap.com In addition to quality closures, BERICAP provides capping equipment and unique customer and technical service, globally. Experience from global business New product introduction Line / capping efficiency improvement Training for customers Troubleshooting on site (capper) Technical Service An advantage of PET: non-breakable, resealable bottles","@ID":21}, "33 TRADE SHOW REVIEW PETplanet Insider Vol. 19 No. 07+08/19 petpla.net TRADE SHOWreview Chinaplas 2019 closed with attendence record Chinaplas 2019 closed its four-day run in Guangzhou on May 24. The annual show – held this year at the China Import & Export Fair Complex, Pazhou, in Southern China – attracted 3,622 exhibitors and 163,314 professional visitors from all over the world. More than a quarter of attendees (42,005) were overseas visitors from over 150 countries and regions. The top 15 countries, in terms of visitors, were Brazil, India, Indonesia, Iran, Japan, South Korea, Malaysia, Pakistan, the Philippines, Russia, Singapore, Thailand, Turkey, Vietnam, and the United States. The unstoppable trend of the circular economy was apparent at the show, as an abundance of high-performance, environmentally friendly and recyclable solutions were on display. The theme zones that focused on the circular economy –– namely, the “Recycled Plastics Zone”, the “Recycling Technology Zone” and the “Bioplastics Zone” –– proved hugely popular with visitors. The next edition of the show will return to Shanghai next spring, with the show set to take place again in the National Exhibition and Convention Center (NECC), in Hongqiao, Shanghai, PR China, from April 21-24, 2020. www.chinaplasonline.com Relocating cooling achieves shorter cycle times in ISBM In launching its “Zero Cooling” technology, at the end of 2018, Nissei ASB laid down a genuine challenge in the singlestage industry and took the conventional technology to a new level in terms of productivity (see PETplanet 1+2/2019, p.10 et seq.). At Chinaplas 2019, we spoke with Managing Director Karel Keersmaekers-Michiels and Haruo Sakato, Section Manager International Section Sales and Marketing, about what they refer to as a “game changer” in the single stage segment, its areas of use, and what the technology can mean for the user. To briefly recap: instead of placing the cooling phase in the usual position, in the first step immediately following the injection phase, ASB uses Zero Cooling to shift preform cooling to the second step; the conditioning stage. According to them, relocating the process away from the first phase means that a 30-40% improvement in cycle time can be achieved, as both stations can now work at the same time. A second advantage is that the conventional achievement of shorter cycle times through the adaptation of wall thickness and/or preform size has been omitted, while the positive attributes of the shorter, thick-walled preforms with respect to the stretch ratios and the material distribution have been retained. “We thought about ways of shortening the cycle but maintaining or improving the container quality until we hit upon the idea that this can only be achieved with a shift of the cooling phase,” Karel Keersmaekers-Michiels explained. “We started in the cosmetics packaging sector and then received successive enquiries from other sectors, including numerous enquiries from the pharmaceuticals, health and beauty care sectors, for bottles for example, but also for jars from the food segment.” Zero Cooling was demonstrated at ASB’s stand at Chinaplas 2019 in the form of the ASB-70DPH. It achieved a closing speed of 4.5 seconds during the bottle production demonstration. “With PET jars, for example, we achieve a cycle time of 10 seconds whereas conventional arrangements took 16 seconds. In principle, the application is ideal for thick-walled containers of all kinds,” Haruo Sakato added, showing us some sample jars and bottles with a glass-like appearance. In terms of energy consumption, Nissei ASB explained that, with higher output rates, the overall rates of consumption are likely to decrease significantly. www.nisseiasb.co.jp Nissei ASB’s Chairman and CEO Daiichi Aoki (right) and Managing Director Karel Keersmaekers-Michiels (left) with Kay Barton","@ID":35}, "MATERIALS / RECYCLING PETplanet Insider Vol. 19 No. 07+08/19 petpla.net 11 The buzzword: circular economy These days, everyone is talking about the “circular economy”. The term may not yet have an entry in many dictionaries, but an internet query yields over five million results, not counting translations into other languages. But what does this buzzword – which is used in many fields besides the plastics industry – actually mean? Mostly, people talk about recycling, about collection and reprocessing instead of single usage and disposal. Vöslauer is heading for the 100% mark For beverage producer Vöslauer Mineralwasser in Bad Vöslau, Austria, circular economy is not just a buzzword, but a company philosophy. Although Vöslauer PET bottles already consist of “rePET” (that’s what the company calls the recovered secondary raw materials) to a large extent, this is not enough for the manufacturer: no less than 100% in all of its bottles is the ambitious target, with its implementation planned as quickly as possible. Like many other brand owners, Vöslauer has registered a voluntary self-commitment with the EU that pledges to raise the usage of rePET from 3,300 to 5,500 metric tons within the next years. “We aspire to become better and better, to continue to develop our products, bottles, and packaging including labels and tray films – our principle is to design each product in a more sustainable way than its predecessor”, says CEO Birgit Aichinger. “In the last decade, we have repeatedly optimised Vöslauer bottles, labels and caps in view of their recyclability (“design for recycling”)”, adds CEO Herbert Schlossnikl. As recently as October 2018, the family business called attention to itself as it was the first Austrian company to introduce a bottle made from 100% rePET on the Austrian market; in Germany, the entire product range (except for Vöslauer Balance) was already changed to 100% rePET beginning of 2019. To support these efforts, Vöslauer monitors the amount of material used in production, as a low transport weight ensures a lower carbon footprint. The wholesome concept extends to the entire spectrum: Latest by 2025, all films and labels will consist of 100% recycled material, and beverage crates will enter a recycling loop to 100%. Vöslauer obtains the recycled material from PET to PET Recycling Österreich GmbH located in the Austrian. In the previous year, this recycling site, which Vöslauer has founded jointly with Coca-Cola, Egger, Rauch and Spitz, has processed around 25,400t of PET which is equivalent to one billion PET bottles. Since 2010, PET to PET has been operating a Starlinger recoStar PET 125 HC iV+ for the recycling of washed and sorted PET flakes. This line raises the molecular weight of rPET to the original level of virgin PET via a process known as polycondensation; as a result, the material maintains its intrinsic viscosity and is therefore suitable for a 100% closed recycling loop. The process also provides extensive decontamination of the material, rendering it suitable for food contact. The individual process steps of the PET to PET recycling line, e.g. drying, extrusion, filtration, and energy recovery, are being optimised continuously in order to achieve the highest possible capacity. Through these measures, the company hopes to better meet the increasing demand for high-quality regranulate. www.recycling.starlinger.com To achieve a 100% closed circle, a number of obstacles have to be overcome. Companies see availability of material as the biggest challenge; for the continuous production with secondary raw materials, the supply needs to be ensured in sufficient quantities. This starts with an area-wide collection system, since everything that is not collected can also not be recycled. Also, materials that are collected, but turned into different kinds of products fall out of the closed loop. Yet another obstacle is the attitude of the population towards recycled goods; in the past, recycled materials have often been dismissed as inferior. This image influences the collection morale of each individual as well as the willingness of brand owners to replace primary with secondary raw materials. On the part of the recyclers, there are technical limitations such as material losses through washing and grinding of the PET bottles. An example is PET fines; these are small particles of 1-3mm in size that occur in the amount of up to 5%. Quite often, recyclers lack the equipment to process these fines into high-quality material, causing it to be used in inferior applications. This situation prompted Starlinger to develop recycling lines for PET fines that take the special characteristics of this material stream into account. Two solutions are possible: processing PET fines jointly with PET flakes, or processing them separately on a special recycling line for fines.","@ID":13}, "35 TRADE SHOW REVIEW PETplanet Insider Vol. 19 No. 07+08/19 petpla.net Seminar on multilayer and co-injection A day prior to the official start of Chinaplas 2019, the Chinese mould manufacturer GDXL Precise Machinery from Foshan near Guangzhou hosted a technical seminar on co-injection, multilayer and barriers. The company, which celebrated its 25th anniversary last year, invited over 300 guests to the Hilton Hotel Foshan to share and discuss technologies and trends in preform and packaging manufacturing with the industry. The invited guests, of whom around 100 came from abroad, represented companies in mechanical and plant engineering, converters, beverage brand manufacturers, and the supply industry. In addition, representatives of local authorities, the National Standardisation Committee and industry associations attended the full-day event, which included a large-scale on-site tour of GDXL’s new premises. Companies making presentations at the seminar, alongside GDXL itself, were (in chronological order) Milacron Co-Injection (Kortec), Mitsubishi Gas Chemical (MGC), Valspar, Kuraray, Polyone, Netstal and Mocon. The main focus of the seminar was the limitation of external influences on the shelf life, stability and appearance of drinks and food by incorporation of barrier layers in the injection moulding process, as well as the successful verification of the same. Topics included the use and exploitation of gas barriers such as MX Nylon (MGC), Valor (Valspar), and Amosorb (Polyone), as well as light / UV barriers such as Lactra and Ultimate UV (Polyone) and Eval for thin wall applications (Kuraray). These presentations were complemented by a presentation on current and future projects by GDXL for Beverage, Food and Non-Food applications in cooperation with partners such as Mold Masters. www.gdxl.com Approaching 29,000 preforms per hour production, and a standalone inspection system At the Chinaplas 2019 trade fair, plant manufacturer Demark, headquartered in Huzhou, presented its Eco machine series once again but including the latest additions to the range. When we met Jason Xue, GM Assistant Sales and Marketing, the Eco 400/3500 Preform Injection System presented this time was so new that it had not yet been listed in the in-house portfolio brochures. The latest machine is positioned between the Eco 300/3500 and Eco 400/4300 systems. “Essentially, we have expanded the cavities and clamp force,” said Mr Xue as he demonstrated the interior of the machine. An in-house 72-cavity mould was applied with the use of a clamp force of 400 t - a 33% increase in force, compared with the 48-cavity system Demark presented in 2018. The single screw with pressure holding valve aims to convey 4,300g PET per shot, with a cycle time of 9 seconds. “Maximum outputs of 28,800 units per hour can be achieved,” Xue continued. Although it was demonstrated with an in-house mould, the Eco is also designed for moulds from Husky. Stated hourly energy consumption is approximately 430kW. With a size of 1,250x210x250 (LxWxH), the system has identical dimensions to the adjacent, larger model: the Eco 400/4300. Demark demonstrated the production of 12.3g preforms on the system at the trade fair. On the other side of the stand the company presented the JP, its compact standalone preform inspection system, which completes a visual inspection for irregularities, defects and soiling at up to 300 preforms/min, with a consumption of 4kWh. The focus here is on classic attributes such as the neck, body and injection point. Preforms with a diameter of 20-40mm and a height of 60-140mm are processed with the use of eight high-resolution CCD cameras. Demark guarantees identification and removal of 99.5% of faulty preforms, with an error rate of 0.1%. www.demark-pet.com More than 300 guests attended GDXL’s technical seminar in Foshan. Jason Xue (right) with Kay Barton in front of Demark’s JP1300 preform inspection system [email protected] Tel: +90 212 695 50 00 Fax: +90 212 694 97 24 100815dmyR .com","@ID":37}, "imprint EDITORIAL PUBLISHER Alexander Büchler, Managing Director HEAD OFFICE heidelberg business media GmbH Bunsenstr. 14 69115 Heidelberg, Germany phone: +49 6221-65108-0 fax: +49 6221-65108-28 [email protected] EDITORIAL Kay Barton Heike Fischer Gabriele Kosmehl Michael Maruschke Ruari McCallion Waldemar Schmitke Anthony Withers WikiPETia.info [email protected] MEDIA CONSULTANTS Martina Hirschmann [email protected] Johann Lange-Brock [email protected] phone: +49 6221-65108-0 fax: +49 6221-65108-28 LAYOUT AND PREPRESS EXPRIM Werbeagentur | exprim.de Matthias Gaumann READER SERVICES Till Kretner [email protected] PRINT Chroma Druck & Verlag GmbH Werkstr. 25 67354 Römerberg Germany WWW www.hbmedia.net | petpla.net PETplanet Insider ISSN 1438-9459 is published 10 times a year. This publication is sent to qualified subscribers (1-year subscription 149 EUR, 2-year subscription 289 EUR, Young professionals’ subscription 99 EUR. Magazines will be dispatched to you by airmail). Not to be reproduced in any form without permission from the publisher. Note: The fact that product names may not be identified as trademarks is not an indication that such names are not registered trademarks. 3 PETplanet Insider Vol. 20 No. 07+08/19 petpla.net The Editourmobil roadshow rolls on from Mumbai via Bangalore, Chennay, Kolkatta, Delhi back to Mumbai. In Rajastan we are sweating in 50 °C heat in the shade! It is unusually hot even for this desert area; which brings us nicely onto the subject of water in India. In recent days, the city of Chennai with its population of 10 million has found itself completely without water. At the moment, it is being brought in by train from nearby Kerala. What is the reason for this? Is it down to global warming? This year’s rather late monsoon has exacerbated the problem but ultimately the cause is self-inflicted. The former 200 km2 wetland area outside the city gates had been reduced “slightly” by 1980 to an area of 186.3 km2. However, today, according to a study undertaken by the Care Earth charity, it is only 15% of its original size. The main reasons for this are the rapid growth of IT companies to the south of Chennai, coupled with an overall increase in the real estate market. 35% of the water for Chennai’s increasing population is now being pumped from Lake Veeranam, some 235 km away. In addition, huge amounts of groundwater are being extracted. Chennai needs 1,200 million litres of water every day but at present the Government is only able to supply 550 million litres. By 2030, Chennai will require as much as 2,100 million litres a day. However, it is not only in Tamil Nadu where those in positions of authority have been turning a blind eye to the climate change problem over the years: 21 Indian cities, including the capital, New Delhi, are expected to run out of groundwater by 2020, according to research conducted by the Government think-tank, Niti Aayog. Their study predicts that 40% of the Indian population will no longer have access to drinking water by the year 2030. The Ministry of Water plans to develop the world’s largest irrigation infrastructure programme involving interconnecting rivers and water reservoirs throughout India. This will create an additional 3,000 dams and 15,000 km of new canals connecting 30 major rivers in order to supply water to large Indian cities. You do not need to be a clairvoyant to realise that such a project will inevitably lead to water shortages elsewhere. Perhaps in India too there will be a heightened awareness of the need to use water wisely at some point. Your PETplanet Insider Roadshow Team Dear readers, INDIA’S WATER CRISIS","@ID":5}, "PETplanet Insider Vol. 19 No. 07+08/19 petpla.net 39 BOTTLES Micellar shampoo from Nivea Micelles are small particles that improve cleaning effects and are longestablished in the facial cleaning sector; these are now also being used by the manufacturer for nourishing and gentle hair cleaning. Under its Nivea brand, the German company Beiersdorf AG has added a moisturising micellar shampoo with lotus extract for daily use to its range. The transparent product does not contain silicone and is available in a clear 400ml bottle. A disc-top cap with indentations to aid opening makes it easy to handle and dispense. www.nivea.de Garnier Fructis with argan oil The variety on the hair shampoo shelves is ever increasing; there seems to be a suitable shampoo for every hair type and every problem. In its Garnier Fructis range, Garnier promises help with dry and unmanageable hair with the addition of “Argan Silky & Shiny”. Plant-based keratin proteins and argan oil provide intensive care for the hair, giving it longlasting sleekness, a silky shine and no frizz. The slightly green-coloured bottle with a colour-matched and easyto-operate hinged cap holds 300ml of shampoo. Two self-adhesive labels complete the packaging and indicate that the proportion of recycled material in the bottle is 25%. www.garnier.de Good conversations. braubeviale.de CONNECT WITH THE FUTURE Over 1,000 exhibitors and more than 40,000 trade visitors all have exactly one goal in mind: To drive progress for the beverage production of tomorrow, so that new solutions can be used to market better products. Sound exciting? Find out more: braubeviale.de/next Good business. Nuremberg, Germany | 12–14 November","@ID":41}, "PETplanet Insider Vol. 19 No. 07+08/19 petpla.net 38 PETbottles Home + Personal Care Wash gel from new dm own brand In the stores of the discount pharmacy chain dm, there is a specially marked and newly laid out area for men’s products for skincare, styling and shaving. This continually growing segment is supported by the new dm own-brand “Seinz.”, which offers products for men in suitable packaging. An example is a wash gel with microalgae for thorough cleaning of the face and beard. The container is made from 98% recycled material, is coloured grey and contains 250ml of product. It has a self-adhesive label and supports the Plastic Bank. The gel is dispensed via a screwed-on pump dispenser with a lock function. www.seinz.dm.de The growing “Share” product family “Share” is an initiative and/or social brand that is promoted on the basis that for every product bought by a consumer, a similar product is donated to a person in need. The range of products is growing. The most recent examples are a sports shower gel with lime & lemongrass and a relaxing shower gel with blood orange & cedarwood oil. The vegan shower gels come in browncoloured 100% recycled PET bottles holding 250 ml of product. The gel is dispensed via a disc-top cap. There is a QR code printed on the self-adhesive label via which each donation can be tracked. www.share.eu Listerine Fresh Forest With its latest product development in its mouthwash range, Johnson & Johnson is relying on the power of the forest. According to the manufacturer, the addition of extracts of salvadora persica and eucalyptus should remind the consumer of a refreshing stroll through the forest. The 6 in 1 Total Care product with a mild flavour comes in the familiar Listerine 500ml bottle; contrary to the other varieties, the sleeve label is pictorial and printed completely with a forest panorama. The childproof push-and-twist cap is also secured with a shrinkwrapped sleeve label with easytear perforations. www.listerine.de Garnier Bio wash gel with lemongrass Garnier is selling 150ml of invigorating face wash gel with fresh lemongrass cultivated organically in Sri Lanka in a slim, tall and slightly green-coloured bottle. The lemongrass oil and the organic cornflower water is claimed to offer an even more intensive washing experience. There is a screwed-on pump dispenser with a lock function and a transparent, circulating self-adhesive label to describe application and ingredients. www.garnier.de","@ID":40}, "7 NEWS PETplanet Insider Vol. 19 No. 07+08 New Engel technology centre Engel Austria has launched its new “Engel Technology Centre. Innovation at heart” at its headquarters in Schwertberg, Austria, featuring 1,700m² of machine floor space. The new customer technology centre is the heart of the latest expansion at headquarters. Engel already bundles a large number of its products and solutions for the smart factory under the inject 4.0 banner. The portfolio is continually being expanded. Vertical integration describes the integration of all machines, systems and manufacturing processes within a company or manufacturing network into a superordinate control system. The Engel technology centre provides practical demonstrations of integration beyond the boundaries of a single location, as it is connected to the technology centres at Engel’s plants and subsidiaries worldwide. Key products for this are the Engel e-connect customer portal and TIG authentig. The MES by Engel subsidiary TIG uses a cloud solution to make all machine parks within the production network transparent. In addition to transparency, intelligent assistance systems make a major contribution towards boosting production efficiency in the smart factory. All the machines in the new Engel technology centre are equipped with a wide variety of assistance systems from Engel’s iQ product family. In addition to iQ weight control, iQ clamp control and iQ flow control, which have been very successfully established in injection moulding companies for some time now, the brand-new iQ systems, which Engel will be presenting at K 2019 in Düsseldorf in October, are deployed at the technology centre at a particularly early stage. Digital transformation is another forward-looking topic. The individual vertical platform solutions are connected with each other horizontally along the value chain. Where vertical networking is about function-related and mostly domain-specific optimisation of the individual stages in the value chain within a company, horizontal networking allows processes to be optimised across functions along the entire value chain. A pilot factory for this was opened in Linz at the beginning of June. The aim of the LIT Factory is to use digital system models to research and further develop product creation processes along the value chain – from materials to product development, and from production to recycling. www.engelglobal.com","@ID":9}, "INSPECTION 29 PETplanet Insider Vol. 19 No. 07+08/19 petpla.net Swiss Made | www.imdvista.ch Inspection Systems for the Plastic Packaging Industry Closure Inspection – 100% Inline “IMDvista INOX Line” Robust, compact and very flexible. One control center (HMI) for the whole line. Preform Inspection – Inline or Offline “IMDvista PECO V3” Less than 7mƹ and up to 90’000 pph. Cavity reading. Preform Monitoring – Shot by Shot “IMDvista PECO LUX” Requires no additional floor space. No preform orientation. The new TQ-Lab provided by Torus Measurement Systems Finding new innovative ways to bring improvements to the quality control aspect of the plastics industry has been Torus Measurement Systems’ focus since launching their first plastic packaging inspection systems in 2013. The customer-centric philosophy together with the technical expertise within the Torus Group has led to the latest development, the TQ-Lab. Historically, bottles and preforms have been collected from production, brought into the laboratory and checked for their conformance. Whilst there are systems used to provide faster or even line speed checks, unfortunately their accuracy is limited. Torus specialise in offering quick and efficient batch testing, where measurements can be taken quickly but do not compromise on the accuracy and reliability of results delivered by laboratory level tests. The philosophy of modularity has proved to be successful for Torus Group for over 25 years. The TQ-Lab provides an enhancement of Torus’ trademark modular approach to plastic packaging quality control. Customers can specify the most critical measurement modules and incorporate their needs into one automated system, see. Fig 1. This could be used for qualification of new moulds or production of existing containers and preforms. Fig. 2: Intelligent neck-find system on the TQ-Lab fits include removing laborious testing and data handling processes, saving factory floor space and selectable modules to suit bespoke customer requirements. The TQ-Lab also produces large measurement data sets which customers may use to analyse and reveal trends. These measurements are transferred automatically to the customer network, removing any operator influence from measurement data whilst increasing throughput and freeing up quality personnel to perform important data analysis. Through bringing customers specialist solutions by utilising unique expertise, Torus expect to grow further in this area.” (III) “The main challenge for Torus is developing equipment that can maintain world class accuracy and repeatability whilst offering industry leading flexibity for the demanding container shapes available today. Round, oval, square and custom shaped containers must all be handled, automated and measured accurately without any operator influence.” The design of such a system is the first of its kind. Currently this total quality solution is available with up to three modules, including – Thickness, neck and body dimensions, internal diameter and top load & volume capacity. In total, the TQ-Lab can offer more than 40 different measurement features without any interventions from the operator. The operator loads batches of containers onto a flexible puck system which cycles on a turnaround conveyor, the relevant program is then selected from a single centralised interface. The operator is then able to walk away and allow the TQ-Lab to take care of the rest. Programming time has been reduced to a minimum by use of a custom, neck-find vision system at the pick-up area of the conveyor, see Fig. 2. The vision system locates the neck and passes coordinates to the handling gantry which will automatically drive to the required pickup position. Torus’ B302 TBT Gauge which will carry out wall thickness, base thickness, neck finish, body diameter and perpendicularity measurements. Once complete the handling system transfers the container to the second module, the B309 Internal Diameter Gauge measuring internal diameter using a unique white light sensor. The TQ-Lab produces large measurement data sets which customers can use to analyse and reveal patterns or trends to make quick decisions relating to the validation of new designs or maintaining production quality. www.torus-group.com","@ID":31}, "MOULD MAKING PETplanet Insider Vol. 19 No. 07+08/19 petpla.net 13 Driving for better service in an increasingly saturated market Adapting to China’s new circumstances by Kay Barton Almost three years after our last site visit to mould and machine builder Guangdong Guozhu Group (see PETplanet Insider No. 10/16), we returned to Fogang County, which is about an hour away from the Cantonese capital Guangzhou. In the years since our last meeting, the company has been obliged to adapt its strategy to intensifying local competition and to find new ways to retain customers over the long term. The team, managed by Sales Director Heidi Cao, is now focusing increasingly on services. Particular attention is being paid to the planning process with customers and on after-sales, in order to stand out from the crowd. Guangdong Guozhu Precision Mold’s customer base is balanced between small businesses and largescale customers. Its market share, which, according to the company’s own data was 50% for moulds, has now shrunk to 35-40%. The reason for this is an increasing saturation of the market due to new, smaller toolmakers in China. “We were forced to realign ourselves in certain areas in order to stay ahead. We want to achieve this on a permanent basis with new products but, above all else, through service,” said Mrs Laura Cai, interpreting for Heidi Cao. What the company understands by service, however, is set to extend far beyond the classic area of after-sales service. The new approach is intended to provide a turnkey service, including full customer support, from the idea through to market commercialisation. “We regard this to be essential, if we are to remain economically secure over the long term. In principle, until the market launch, all of the R&D should take place with the consistent involvement of the customer,” Mrs Cai continued. “We also want to become stronger in the fields of hot runners.” The company identified the production of injection moulds of closures and handles, along with medical packaging moulds (since 2014), to be increasingly important markets. “We believe that there is considerable market potential in these three areas,” she explained. “Between a third to a half of our total mould production is for the manufacture of closures and handles. In the area of medical applications, the approval process that is necessary due to the exacting requirements is in progress and it is foreseeable that the approvals will be issued in good time.” Generally, the company has seen a noticeable increase in enquiries from the non-food sector, for the production of packaging for beauty care products and cosmetics, for example. The expansion of international customers and markets represents another step forwards. “This year, we are expecting growth in markets outside China of approximately 20%. Last year, our export share for moulds and machines was 20%,” Mrs Heidi Cao concluded. The total turnover of the Guozhu Group in 2018 was US$ 34 million. Striving for a bright future, Guozhu intends to stay in this industry and maintain its promised, ongoing support to its customers. www.guozhu-pet.com Moulds for production of handles Excursion with the Guozhu Team (f.l.t.r.): Kay Barton, Heidi Cao, Till Kretner (PETplanet Marketing Executive), Laura Cai and Johann Lange-Brock","@ID":15}, "PREFORM PRODUCTION PETplanet Insider Vol. 19 No. 07+08/19 petpla.net 14 Investment in new preform moulding machines Flexibility is key Electra Form Industries (EFI) is a division of Wentworth Technologies, a global business focusing on tooling and processing for the plastics’ industry. EFI has been a provider of PET preform moulds for over 40 years operating out of their 65,000 square foot facility near Dayton, Ohio. Over the last decade, the business has transformed from PET tooling to preform production + tooling. With the growth of their moulding business, EFI bought new preform moulding machines. Rob Sicilia, VP PET Preforms, Niigon Machines and Brian Karns, General Manager, EFI in front of EFI’s Niigon preform machines “We now offer a more complete service for our customers” says Brian Karns, General Manager. “EFI specialises in preforms - capabilities include, unit cavity tooling and delivering moulded preforms in as little as three weeks. In house tooling recuts allow multiple prototype weights within a couple of days enabling customers to review a number of options quickly to confirm optimum design for production”. EFI has two small tonnage injection machines for running prototype preforms and an SBO1 to blow sample bottles in house Moulding preforms for their customers has grown to be the largest part of EFI’s business. Flexibility is key to the operation with capabilities to run customer tooling, make and run new tooling (up to 72 cavities) and a program to handle lower volumes by installing stack components into an EFI 24 cavity mould base. “Many of our customers work in test markets or with niche applications where there is not sufficient business today to justify a new tooling investment” says Max Buchanan, Senior Account manager. “We enable customers to accelerate time to market with an affordable solution involving by converting a 24 cavity cold half & EOAT”. With the growth of their moulding business, EFI bought new preform moulding machines. “We had three preform moulding machines in house, and last year we needed to add a 300 t machine” says Karns. “We chose Niigon, and we are so pleased with it that we just received our second Niigon and we have added one at the Wentworth Monarch plant in Oakville, Ontario. The Niigon machines are a great fit for our business because they are flexible and efficient. They run legacy tooling from any preform mould maker and we get fast cycles with very low energy consumption compared to competitive machines.” In addition, Karns also appreciates Niigon’s customer service and the five year machine warranty, and states: “A unique advantage is access to machine component information that allows us to buy parts directly from their suppliers without a markup”. Room for expansion EFI has room on their existing property to add an expansion that would contain up to six more preform systems to keep pace with customer demands. PET tool building capabilities allow EFI to offer flexible solutions to companies with blow / blow & fill operations “As our customers grow their businesses, some will want to take their preform moulding in house” says Buchanan. “Working with Niigon, we can now offer a complete PET system that allows them to enjoy capacity management flexibility and optimise capital investment. We are very excited about this new opportunity to better serve our customers”. www.electraform.com www.niigonmachines.com","@ID":16}, "BOTTLING / FILLING PETplanet Insider Vol. 19 No. 07+08/19 petpla.net 18 PET is the material of choice for rtd alcoholic drinks The Black Fly of Canada We met Rob Kelly, Co-Founder of Black Fly Beverage Co. Black Fly Beverage Company, Ontario’s first micro-distillery was founded in 2005 by husband & wife Rob Kelly and Cathy Siskind-Kelly after being awarded the first Distillery License granted in Ontario in over 100 years. “It was a real start-up” Rob explained. “We have not been in the beverage business before; we came from very different working areas.” Tour Sponsors: “We originally planned a micro brewery 15 years ago. But because of the growing in this business we shifted our plans to produce a kind like a ‘cool craft alcohol, ready-to-drink’ which was very unique at this time,” Rob continued. “Even if there has been some other products on the market, in Europe they call them Alcopops, they mostly have been mass production, we would like to focus on specialties”. The vision was to create more natural and less sweet premium spirit beverages using quality ingredients and innovative packaging. Like the iconic Canadian insect after which the company is named, Black Fly started small with determination to fly under the radar and deliver a mighty bite. Since that time, Black Fly has successfully developed and launched a line-up of unique premium spirit beverages that speak to what today’s consumers are looking for; innovative “Not to sweet” quality ready to drink. Originally housed in an historic bank building in the heart of downtown London, Ontario, Black Fly Beverage Company moved its operation in May of 2008 to a state-of-the-art production facility located in the city’s leading industrial quarter. Black Fly strives to work with as many local suppliers and trade partners as possible in an effort to support Ontario and Canadian businesses and reduce our environmental footprint by shopping local. Green initiatives “At Black Fly we understand that as we continue to grow so will our environmental footprint. Reducing that environmental footprint through good business practices and a host of green initiatives is a key value of Black Fly Beverage Company. That is why we started to produce our own bottles at a certain point in time. For a small craft alcohol producer it is unique to do so. The decision was made in favour of Sipa equipment in 2016. My production manager was previously at trade fairs and had the opportunity to get to know Sipa. We were invited to see Sipa machines during production. We will continue to grow, so we will buy more equipment from Sipa.” Rob explained. Bottles Black Fly bottles are made locally in Ontario. These bottles are made from PET, the most recyclable plastic currently used in this industry. “These drinks are characterised as convenient drinks, glass was no option. The consumer takes the drink with him everywhere, so the packaging must be light and easy to handle. There were no bad experiences with drinking cocktail from a PET bottle, with wine or beer it wouldn’t work. Our bottles are only 40 grams when empty which is six times lighter than a traditional “We are very happy with the Sipa machine, it is an impressive, simple and elegant machine. It makes sure that we have a maximum output,” Rob Kelly stated. 4x400ml pure lime juices and genuine Mexican tequila in PET bottles","@ID":20}, "PETplanet Insider Vol. 19 No. 07+08/19 petpla.net 37 BOTTLES Coffee drink from Rauch The company Rauch is actually known as a juice manufacturer but it has expanded its range under the brand “Cafe mio” to include several mixed milk drinks with coffee. There are three varieties with varying caffeine levels and a vanillanut variety. The drinks are advertised as iced coffees and are found on chiller shelves; they should be shaken vigorously into a creamy drink before being enjoyed ice cold. The contoured bottles contain 250ml of product, are decorated with a sleeve label and sealed with a colour-matched screw cap. www.rauch.cc Kefir in a conical bottle Under the newly introduced brand “All I Want”, Danone is launching different products based on cream cheese and kefir, which are completely without added sugar. The kefir products are available in three varieties – Natural, Blueberry & Pomegrana t e and Cucumbe r & Lime. They are packaged in a conical bottle holding 260 ml of product. The neck area and/or the area around the neck ring is specially shaped so that visually, the transition from neck to cap is more effective. This is supported by the coloured design of the opaque sleeve label. A nutritional values score is printed on the label. www.alliwant-de.com","@ID":39}, "PREFORM PRODUCTION 15 PETplanet Insider Vol. 19 No. 07+08/19 petpla.net PREFORM PRODUCTION 15 Preform storage length / conditions can cause PET bottle performance issues An issue of age www.sacmi.com SACMI manufacturing technology: the advanced solution,from single machines to complete lines Product design Product development Product validation Industrial production plant Process & quality control On-site and start-up assistance After-sales and Customer service SACMI 4.0 THE COMPLETE CLOSURE, PREFORM AND CONTAINER SOLUTION FOR YOUR SMART FACTORY Your Smart Factory will be child’s play. sculpture by Antoine Geoffrion / bottlerobot.com Products created using SACMI compression technology can be made from PCR polymers too. Proprietary research from PTI shows that PET bottle performance issues may have their root cause in how long preforms are stored and in what environment. “Our plant support personnel were frequently being asked what storage duration was acceptable for preforms and what problems can present themselves during longer storage periods,” explains Sumit Mukherjee, chief technology officer, PTI. “With almost 40 years of experience in this area, we knew that the longer the preform is stored, the greater the impact on performance—particularly if that preform was stored in a high-humidity environment.” To get specific answers to the question, PTI studied 2 liter and 20-ounce preforms that were more than a year old. These preforms were dried under vacuum at 40 °C to get them back to a condition similar to when they were first moulded. The short answer is that preforms stored three, six or 12 months, respectively, will each process differently. The older the preform, the more difficult it will be to processing so that the container meets performance criteria. The time of year the preforms were injection moulded, along with the environmental conditions in which they are kept, will also impact performance. Additionally the study found a diminishing moisture egress rate with time from a drying perspective, that wet preforms absorb more heat under the same process conditions, that moisture is more impactful on the properties of larger diameter preforms, and that drier preforms stretch less. The finding also include that moisture acts as a plasticiser, allowing for more stretching and lesser strain hardening. www.pti-usa.com","@ID":17}, "PETplanet Insider Vol. 19 No. 07+08/19 petpla.net 36 PETbottles Beverage + Liquid Food Bio Iso in PET Under the name “Bio Iso”, German company Acáo GmbH from Wiesbaden is selling low-calorie, isotonic, organic and refreshing drinks in transparent bottles holding 600ml of product. So far, two of the three first-mentioned flavours, Cranberry-Raspberry, Maracuja-Orange and Grapefruit-Lemon, are available on the shelves. According to the manufacturer, Bio Iso consists only of natural ingredients and is the first isotonic drink in Germany that is certified organic. The bottle consists of 100% recyclate, is decorated with a colour-matched foil label and is sealed with a screwed-on drinking cap with a tamper-evident seal. www.bio-iso.de Moodwater from Canada A variety of funny faces to explain or show off an individual’s frame of mind are printed by Canadian Moodwater Company on the labels of their 591ml natural spring water bottles. The idea behind the amusing “emojis” is the manufacturer’s wish to raise a smile among consumers. The slim bottles are sealed with a screw seal with guarantee band. www.mymoodwater.com Easy-grip bottle for pineapple-lemongrass drink Under its brand name “Skipper”, Italian fruit juice specialist Zuegg is offering 1,000ml of a mixed fruit juice drink in a bottle furnished with circulating reinforcement ridges. It contains 20% pineapple juice, 12% white grape juice, approx. 2% lemon juice and no added sugar. A particular feature of the bottle is the sleeve label with matt surface, which also improves grip on the bottle, even with wet hands. A green screw cap with tamper-evident seal makes the appearance typical of the brand. www.skipperzuegg.it New varieties for Müllermilch Shake Range Right on time for the summer season, the Müller dairy has brought new varieties of its Müllermilch Shake Range onto chiller shelves. The new variety is “White Choc & Almond”. According to the manufacturer, the product should be shaken to a creamy foam and consumed ice cold. The product is available in 400ml / 421g bottles, which have the slight contouring typical of the brand, and are decorated with a sleeve label suitably designed for the product. The Shake Range is sealed with a white screw cap printed with the brand logo and a tamper-evident seal. www.muellermilch.de","@ID":38}, "MATERIALS / RECYCLING PETplanet Insider Vol. 19 No. 07+08/19 petpla.net 10 “There is no alternative to plastic recycling” F.l.t.r.: Mr Günther Lehner, CEO Alpla and Mr K. Ralf Schneider, CEO Werner & Mertz on the opening day of the new Werner and Mertz production hall in Mainz, Germany PETplanet spoke with Mr Günther Lehner, CEO of Alpla, on the occasion of the opening in May 2019 of Werner & Mertz’s new production building. It is characterised by a sophisticated sustainability concept in line with the company’s sustainable philosophy. Together with its long-standing partner, Alpla has implemented a common vision in Mainz, Germany. “We have been working together for over 20 years”, Günther Lehner laughed, “probably for 30 years already. Since 1996 we have been here in Mainz at Werner & Merz. Before the opening of the new hall we produced in a different building, now we are fully integrated into the production flow”, he explained. In Mainz the bottles for the detergent manufacturer Werner & Merz, known for its brand Frosch, are produced on Alpla machines. Production has been growing steadily ever since. In the last ten years this was achieved with the focus on the Frosch brand, where the product range was expanded. The preforms are delivered from the nearby Alpla site in Kaiserslautern and consist of 100% rPET. Up to 20% of the recycled PET for the rPET preforms comes from the German yellow bag, which means that it is 100% post consumer PET. This is due to the reycyling initiative of K. Reinhard Schneider, CEO of Werner & Mertz (see PETplanet 4/2019). “Especially detergents and shampoo bottles from the yellow bag are recycled. PET beverage bottles are recycled in Germany via a deposit system. The challenge is sorting and processing of post consumer material out of the yellow bag”, Lehner continued. For the new production hall, there was a renewed machine park, special attention was paid to energy efficiency. There are now four PET and four polyolefine lines. Together with Werner Mertz, Alpla designed the entire production line from filling to logistics. In addition to flexibility, the avoidance of secondary packaging was an important factor. “In any case, we proved that it is possible to use 100% rPET material, we have the know-how and know what the material has to be able to do. We run it with the same efficiency as virgin PET, without losses during production or filling”, Lehner proudly reported. PETplanet asks for his opinion on the subject of EU directives and the problem of material procurement. “In the next 1-2 years it will be exciting to see how the individual countries position themselves in relation to how each country meets the requirements! There is a European dilemma, which means each country has its own procedures and waste management system. This makes it difficult to find enough PET material that can be recycled again.” Alpla invested in its own recycling plants at an early stage in order to have the knowledge of the challenges posed by post consumer material. “This knowledge has now helped us here at Werner and Mertz. Even though Europe is fragmented, there is a clear trend towards collecting the important material flows to make them available for recycling, but it is still a big challenge not to lose the high quality material to other processing industries, such as the fibre or sheet industry - to be truly circular“, Lehner stated. Therefore Lehner wanted longterm supply contracts to get away from the spot market. “The German deposit scheme is unfortunately not a 100% a good example either, the material ends up in retail and the one that offers the most gets it. The material is publically auctioned in Italy and Spain. The idea of recycling has to be focused more strongly so that bottle to bottle can be realised – so in a fact really closing the loop. The used plastic bottles are no waste, they are a valueable material that must go back into bottle packaging again. In recent years we have also had to struggle with our two recycling sites, where customers were only interested in the recycled material if it was cheaper than the virgin material. Since the last two years we are sold out, so we see that something has changed. Mechanical recycling is a much optimised process, a good basis. Chemical recycling also has its advantages and could possibly complement the mechanical recycling to fulfil the EU targets. Of course the price will always play a role; you can’t be blue-eyed. But already many of our big customers follow what we see here at Werner & Merz in absolute consistency. We believe that recycling is the solution, and our attitude is the same as that of Werner & Mertz. Our packaging is mainly made from plastic so we continue to invest in bottle to bottle recycling. For plastics, recycling is the solution,” summarised Lehner in conclusion. www.alpla.com","@ID":12}, "INSPECTION 32 PETplanet Insider Vol. 19 No. 07+08/19 petpla.net The in-line quality lab CapWatcher Q-Line Killing two birds with one stone The CapWatcher Q-Line was recenly rated as one of the top ten innovations at Plastimagen in Mexico City. The high inspection speed of up to 70 closures per second was impressive and convincing. The CapWatcher Q-Line, referred to by Intravis as the in-line quality lab, checks for typical features such as diameter, ovality or contamination. For the first time, an in-line inspection system records the temperature of the closures. Why? “With the help of temperature we can kill two birds with one stone,” says Dr Gerd Fuhrmann, CEO of Intravis. “Firstly, we can help the operator make an accurate prediction of the shrinkage behaviour of his closures. The operator can then determine if the promised sizes are precisely met or if something should be switched around the system to be on the safe side.“ He continues: “On the other hand, the temperature measurement allows our system to detect how long ago the production time of the closure approximately goes back. For statistical evaluations and trend determinations, which are nowadays regularly used to optimise the production line, it would be fatal if an older closure that “hid” in the bunker for some time would have the same influence on selected trend statistics as a newly produced closure under new settings. By determining the temperature, we can weigh the influence of the individual closure accordingly.” Industry 4.0 For many years, the company has been committed to offering more than just sorting out bad parts. Extensive data is collected from each individual object produced. If they are prepared in statistics and condensed into trends, this provides a unique insight into the production processes. And that’s exactly what Intravis systems have been doing for a long period of time, states Dr Fuhrmann: “Back in 1996, I came up with the idea that the quality of previous batches needed to be able to influence and optimise the quality of future batches. Unfortunately, at that time the technology was simply not ready to return the data to the producing machine in a timely manner”. Today, with the computing technology available, it is easy to collect all the important information and prepare it in a timely manner. This makes it easy for an operator to make better decisions when setting up the production line. A first example of the practical application of this idea was shown in 2017 at the Drinktec together with Netstal. The two global players jointly presented a closed loop solution. Netstal’s injection moulding machine regulated the operation, fully automatically, based on the feedback provided by an Intravis CapWatcher. Targeted deviations from the desired standard were detected immediately and the injection moulding machine responded immediately with appropriate countermeasures. Within minutes, the closure was back within the desired tolerance ranges. Cooperation with Henkel Intravis provides another example of the possible influence of trends and statistics provided by its inspection systems in cooperation with Henkel AG. Recently, they were part of a comprehensive information campaign on the digitisation strategy for the supply chain of the Düsseldorf-based company. An important element in this: the inspection systems which have been in use in Henkel’s production lines worldwide for over 15 years now. The spectrum ranges from bottle to label to closure inspection systems. Dr Dirk Holbach, Managing Director, Global Supply Chain, says: “The Intravis systems take a picture of each bottle and its label. For example, they check whether the right label is on the bottle, whether it is in the right position or whether there are wrinkles in the label.“ The data of the inspection systems are decisive in the optimisation of the production line. “In addition to inspecting, the systems help us to set machine parameters correctly to get the perfect result,” Dr Holbach continues. The team behind it And who is behind all these innovative ideas? Dr Gerd Fuhrmann, who was named one of the Leading Lights in the PET world in the last issue of PETplanet 6/2019. He says, “I could never handle it all alone. Surely I give one or the other thought-provoking idea, but without my staff none of this would be feasible. More than 50 engineers as well as skilled employees and trained technicians work here in Aachen. Each one of them contributes to the innovative power of this company.“ www.intravis.de INSPECTION","@ID":34}, "INSPECTION 26 PETplanet Insider Vol. 19 No. 07+08/19 petpla.net INSPECTION A review of inspection systems In this issue we focus on the manufacturers of inspection systems. We have asked them since when their company deals with inspection in the PET area (I), in which area of inspection they are active and where they see potential for further growth (II). We also asked them about their most exciting project and the challenges they face. (III) IMD Ltd., Matthias Hermle, CEO (I) “In 1998, we were approached by Obrist, a Swiss drinks closure manufacturer. I was immediately intrigued by this field, saw the potential and set out to develop the first industrial closure testing system with colour cameras and a speed up to 1,500 cpm. In 2000, we had a pivotal meeting with one of the leading closure manufacturer at a trade fair in Munich. That was the start of a business partnership, which is still very active today. And IMD has developed into a leading manufacturer of testing systems for the closure inspection systems industry. All our equipment carries out a very complete set of controls, including the possibility to read the cavity number, measure dimensions and detect visual defects. But above all, our patented “grid inspection” carries out an outstanding Quality Control that other competitors cannot offer. (II) Sacmi have produced Vision Systems for Quality Control for over 30 years (the first unit was designed and sold in 1987!). Part of our production is directed to control quality in caps produced both with plastic or metal. We consider the quality control of PET preforms an important market still in growth. We will soon unveil a new PVS machine with outstanding technologies.” (III) “The PET preform is a complex object both to inspect and manipulate. The future is to design smart machines to ease the life of operators: fast changeover, easy interaction with the software, possibility to connect the equipment with the ERP and/or plant supervisor.” www.sacmi.com Sacmi Imola S.C. (I) “Sacmi sold its first PVS machine in 2005. This equipment was called PVS-1 and it was capable to inspect up to 30,000 preforms/hour for the following criteria: top seal, bottom and body. At this time we also introduced our patented “Grid inspection“ to identify defects usually visible with polarised light. The reason for which we decided to invest in PET preform inspection came from the consideration that we already controlled the plastic caps at 360° and each cap is then paired to a bottle, so for sure inspecting the preform would have become an industrial need. Moreover, other factors push up our decision: the increased production speed, the introduction of big moulds (144 cavities), the use of rPET, the weight reduction. All these factors would have increased the possibility to create defects in big quantities.” “Today we count on a wide range of machines for quality control of PET preforms that spans from the QC Lab (PVS-2) to the off-line inspection (PVS-3) or in-line (PVS-5) with a very compact equipment that can be easily integrated with any new or existing injection moulding machine of any producer. Again driven by the market, we developed to a complete system provider starting by a cross conveyor throughout the cooling system, sorter and of course still the vision system controlled by one vision control center. Because others followed our way we see us as “trendsetter”, not only introducing the first stainless steel system but also using colour cameras or high speed vision inspection. Still unique is, that we develop and assemble the whole system ourselves, all made in Switzerland. As every closure has “its bottle respectively its preform” it was obvious that we also developed a system for inspecting preforms. In 2007 we introduced our first preform testing system where the preform was hanging on an overhead vacuum conveyor. Realising that this was not a “robust” way of doing it we followed with version 2 and 3. Concerning the sorting system, we collaborate with M.Tanner AG and did always rely on the roll sorter technology because we did not see rotational feeder as the appropriate technology to sort preform (spinning around parts like preforms…). As we see the market is also tending towards the “linear line” as well, we feel confirmed in our decision made in the past.” (II) “The preform monitoring system Peco Lux we see as one of","@ID":28}, "MARKET SURVEY 24 PETplanet Insider Vol. 20 No. 07+08/19 petpla.net 07+08/2019 MARKETsurvey Resins & additives Preform machinery Preform production & inspection Preform & SBM mould manufacturer SBM 2 stage Compressors Filling equipment & inspection Caps & closures & inspection Palletising & shrink film machinery Recycling Compressors Compressors – not often in the spotlight perhaps, yet a vitally important component of PET production, and with significant potential of energy saving. Our annual market survey takes a closer look at these unsung heroes of the PET industry, featuring six compressor manufacturers and their product range: Siad Macchine Impianti, AF Compressors - Ateliers François S.A., Kaeser Kompressoren SE, ABC Compressors, Nanjing Shangair Machinery Manufacturing Co.,Ltd., and Hertz Kompressoren GmbH. Although the publishers have made every effort to ensure that the information in this survey are up to date, no claims are made regarding completeness or accuracy. Company name Siad Macchine Impianti AF Compressors-Ateliers François S.A. Kaeser Kompressoren SE Postal address Telephone number Web site address Contact name Function Direct telephone number Fax E-Mail Via Canovine, 2/4 24126 Bergamo, Italy +39 035 327611 www.siadmi.com Mr Giovanni Brignoli Compressors Division, Food & Beverage Product Leader +39 035 327609 +39 035 327694 [email protected] Ateliers François, Rue Côte d'Or 274 Liège B-4000, Belgium +32 4 229 70 10 www.afcompressors.com Mr Pascal Heyden Marketing Manager +352 26 95 66 28 [email protected] Carl-Kaeser-Str. 26 96450 Coburg +49 9561 640 0 www.kaeser.com Mr Henry Beyer Produkt Manager Kolbenkompressoren +49 9561 640 5017 [email protected] 1. Machine designation / model number BS Line Vito CE & L (high pressure), OPC (low pressure) Sigma PETAir 2. Number of models in range 19 models 32 30 (high pressure), 22 (low pressure) 25 3. Output in m³/hour 1,000 – 6,000 100 - 6,000 150-3,300m³/h (high pressure); 4323,480m³/h (low pressure) 336 - 2,772m³/h 4. Compressor type High pressure blowing air (up to 40 bar) Low pressure air Low pressure screw 7-10 bar Screw type High pressure blowing air (up to 40 bar) High pressure piston (booster) piston 20-40 bar Piston type Integrated system All in One System; high & low pressure simultaneously 5. Lubricated or oil-free Oil free Low pressure compressor Oil free Oil-free 6-15bar Lubricated Booster compressor Oil free Oil-free 0-40bar Lubricated Integrated system Yes Yes 6. Machine layout V V and H (horizontal) L shape \"V\" (2 cylinder), \"W\" (3 cylinder) 7. Number of compressor stages 2 screw + 2 booster = 4 total 3 3 1+1 8. Are special foundations required? No No No No 9. Cooling system Water Water Evaporative or radiator system Air (water option) 10. Belt or direct drive Belt drive V-belt transmission Low pressure compressor Direct drive V-belt transmission Direct Booster compressor Belt drive 0-40bar, V-belt transmission Belt Integrated system","@ID":26}, "PETcontents 4 PETplanet Insider Vol. 20 No. 07+08/19 petpla.net 07+08/19 INSIDE TRACK 3 Editorial 4 Contents 6 News 22 Products 36 PET bottles for Beverage + Liquid Food 38 PET bottles for Home + Personal Care 40 Patents MATERIALS / RECYCLING 10 “There is no alternative to plastic recycling” 11 The buzzword: circular economy MOULD MAKING 13 Adapting to China’s new circumstances - Driving for better service in an increasingly saturated market PREFORM PRODUCTION 14 Flexibility is key - Investment in new preform moulding machines 15 An issue of age - Preform storage length/con- ditions can cause PET bottle performance issues BOTTLING / FILLING 16 Filling at its best - Investment in state of the art technology is the key 18 The Black Fly of Canada - PET is the material of choice for rtd alcoholic drinks 20 Boosting efficiency - Slovak beverage producer Slovenské pramene a žriedla modernises its production facilities MARKET SURVEY 24 Suppliers of compressors INSPECTION 26 A review of inspection systems 30 Exceeding expectations - Acti Pack’s approach to production and supply of high-end containers 32 Killing two birds with one stone - The in-line quality lab CapWatcher Q-Line TRADE SHOW REVIEW 33 Chinaplas 2019 BUYER’S GUIDE 41 Get listed! Page 15 Page 36243610 Page 36 INSPECTION","@ID":6}]}}
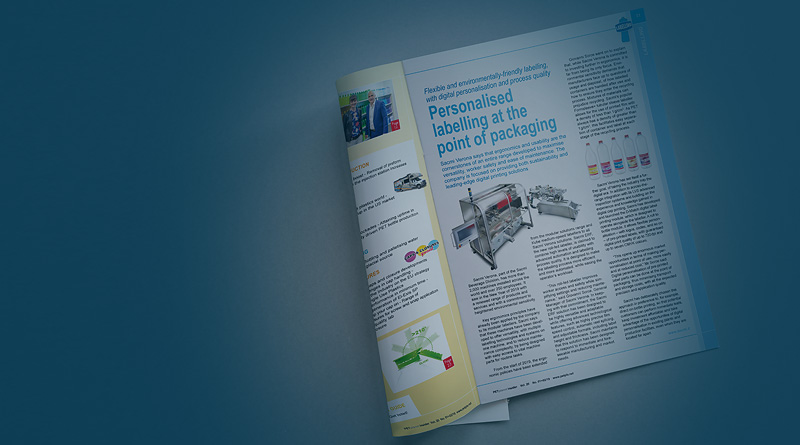