"120 l PET drum next to 1.5 l bottle TRADE SHOW PREVIEW PETplanet Insider Vol. 20 No. 10/19 petpla.net 60 120 l open-mouth PET drum with 400mm neck diameter World’s biggest PET container Drums are used for the storage and transport of a wide variety of products. Traditionally metal has been the material of choice, however plastic drums made from HDPE have become very popular as well as fibre drums to a lesser extent. Sizes vary from 30-220 l and various types are available according to the size of opening (open top, wide mouth, closed top). The tendency of metal drums to rust and the sensitivity of fibre drums to wet conditions, have resulted in the popularity of HDPE plastic drums, manufactured using Extrusion Blow Moulding. By using PET, Cypet are now adding another new material into the mix. The only other plastic raw material besides HDPE that exhibits high mechanical strength and is suitable for processing into hollow containers is PET. In addition to its very good mechanical properties, PET also offers transparency and a smooth, glossy surface finish, making PET containers easy to clean. It is also easily recyclable and can be upgraded during the recycling process to bring its properties back to their original levels, including the suitability for food contact applications after recycling. PET containers have very successfully replaced other materials such as metal, other plastics, glass and paper in many applications typically in sizes up to 2 l, but more recently also for applications in the 5-30 l size range. PET processing technology for large containers Machines for PET processing have been commercially available for the production of PET containers up to a maximum size of 30 l. As a result of the non-availability of machines for PET containers larger than 30 l, this market segment had not been developed for PET, despite the fact that large PET containers offer a cost efficient and attractive alternative to other materials for large containers. Cypet Technologies states that its single-stage PET processing technology has been proven to be able to produce very large PET containers, up to 150 l. The Cypet production system has the capability to injection mould the preforms and directly stretch-blow mould them into containers on the same machine, in such a way that enables large container production with minimal energy consumption. In Cypet’s history of success, the world’s first 50 l PET container, a beer keg, was produced in Australia in 2015 on a Cypet machine. The world’s second 50 l PET container, a milk drum with built-in rigid handles, was produced in 2016 in Kenya, also on a Cypet machine. In 2018, finally breaking the 50 l size barrier, Cypet Technologies’ engineering team, succeeded in producing a 60 l PET container, the world’s first transparent, stackable crate for fruit and vegetables, with a large, rectangular 570 x 370mm neck opening. 50 l milk container with built-in handles Hall 14 Cypet Booth C58","@ID":62}, "TRADE SHOW PREVIEW PETplanet Insider Vol. 20 No. 10/19 petpla.net 63 specific additional equipment and in an energy-efficient manner, but also the material cycle it closes and which preserves resources without any loss in quality, both represent a sustainable solution. Not only for masterbatch crystallisation and drying Kreyenborg will also be showing an IR-Batch 90/100-30. Exactly like the continuously working infrared rotary drums, the discontinuously working IR-Batch is claimed to ensure a gentle while efficient treatment of the material. Whether the task is heating-up, crystallising, drying or coating of plastics pellets, the IR-Batch is flexible and versatile. It is not only suitable for processing plastic materials, but also chemical products and foodstuff. The IR-Batch has become established worldwide in PET masterbatch drying processes, says Kreyenborg. This is due to its two key features of convenient process control and flexibility. Drying of PET masterbatch is only possible if the polymer crystallises simultaneously, because otherwise undesired pellets agglomerations could form. Therefore, the drum of the drying unit is equipped with incorporated mixing elements. Owing to a very precisely and individually adjustable temperature control, the pellets can be crystallised gently, as well as safely. The heat input by the infrared radiation is direct, so that short process times of just 15 to 20 minutes are guaranteed. As cleaning of the process unit is of major importance, the company ensured easy accessibility and quick material changes. The IR-Batch can be opened completely and the infrared module can be moved out of the rotary drum on an extraction unit. processing times of 10 to 20 minutes. The IR-Batch 90/100-30 will be exhibited at K’2019; it will be equipped with a big sight glass for demonstration purposes. It has a diameter of 90 cm, a length of 100 cm and is suited for a filling quantity of 40 kg. www.kreyenborg.com Due to its simple structure, the drum does not have any concealed or poorly accessible areas and is therefore very simple to clean by means of a suction device or compressed air. After cleaning, the system can be used again immediately without any pre-heating. IR-Batch units are available with filling volumes in the range of 60 to 300 dm³, which cover a throughput range between 150 and 500 kg/h in","@ID":65}, "PETpatents www.verpackungspatente.de PETplanet Insider Vol. 20 No. 10/19 petpla.net 80 Pivotable bottle Intern. Patent No. WO 2019 / 030333 A1 Applicant: Maura Oerding, Berlin (DE) Application date: 9.8.2018 Drink bottle consisting of lower and upper part, which can be connected with each other to pivot and twist to enable a comfortable drinking position. Stackable bottle Europ. Patent No. EP 3431408 A1 Applicant: Brian Leonard Lodge, Milton Keynes (GB) Application date: 18.7.2017 A PET bottle with more than two litres of content is shaped so that two different handles can be slid over the bottle neck – depending on consumer wishes – but a good stackability is still guaranteed with both handles. Coated PET container Europ. Pat.issue No. EP 3218276 B1 Applicant: Graham Packaging Comp., Lancaster (US) Application date: 10.9.2015 Procedure for manufacturing PET containers with improved silicon dioxide coating. Divided container Intern. Patent No. WO 2019 / 030758 A1 Applicant: Johny Belah, Ramla (IL) Application date: 8.8.2018 To achieve sufficient freshness in a carbonated drink, it is proposed to divide the bottle into several areas / chambers that can be opened separately. Hot f lling Intern. Patent No. WO 2019 / 040749 A1 Applicant: Graham Packaging Company L.P., Lancaster (US) Application date: 23.8.2018 Container for filling with hot products. The base is specially shaped to be able to absorb in a certain way the forces that arise during cooling. Small-volume wine bottle Intern. Patent No. WO 2019 / 054866 A1 Applicant: Creative Cloud Company B.V., Hilversum (NL) Application date: 13.9.2018 Small-volume, compact bottle made of plastic (PET) with screw cap for intake of wine. Preferred usage area is the catering sector in aeroplanes, trains or similar. One bottle is designed to fill one glass.","@ID":82}, "59 TRADE SHOW PREVIEW PETplanet Insider Vol. 20 No. 10/19 petpla.net Relevant sustainability aspects combined in one bottle KHS presents a new PET concept based on the juice bottle as an example. It combines individual e n v i r o nme n t a l l y friendly packaging solutions in one container and thereby supports the theory of circular economy. Kai Acker, CEO of KHS, emphasises the continuously growing demand in the food and beverage industry for packaging solutions that support efficient production processes and at the same time contribute to the protection of the environment while maintaining a high level of product protection. With this in mind, a new PET bottle was developed, which will be presented for the first time at the K show. The company combines various disciplines of its know-how to create a unique container. With this concept, KHS is pursuing its strategy of reduction, recycling and reuse and for this purpose has concluded a partnership with an environmental service provider. Compared to conventional PET containers, the system provider’s new approach is claimed to ensure a high level of product protection and a longer shelf life, in particular for sensitive beverages. Moreover, these bottles are completely recyclable and conserve on additional resources. The fact that system provider KHS at the same time designs the entire process chain efficiently and sustainably is also demonstrated by its line solutions for PET processing. These systems are not only able to effectively process recycled plastic, they are also hallmarked by energy and resource efficiency - from the stretch blow moulder to palletiser. With the Bottles & Shapes program, KHS is also furthering its developments along the entire production chain. Not only the initial ideas, drawings and 3D animations are developed for the desired bottle, but also prototypes, individual sample bottles and durable blow moulds. www.khs.com Hall 13 KHS Booth A75 Colour, care, clarity and performance Milliken’s stated goal is to assist in “enabling plastics to improve people’s lives and transform the impact plastics have on the environment for the better.” In aligning itself with the chemical industry’s long-standing Responsible Care initiative, Milliken is committed to being a good corporate citizen through its products, processes and partnerships. In addition to constantly working to advance the sustainability of its entire product portfolio, Milliken is also helping customers to lower their carbon footprint, reduce dependence on single-use plastics with more durable and recyclable alternatives, and reduce overall waste. Milliken has partnered with Chicago-based PureCycle Technologies to advance closed-loop recycling of polypropylene (PP) resin. Using technology developed and licensed by Procter & Gamble Co., PureCycle plans to open its first plant in Ohio by 2021, employing a patented recycling method that restores virgin-like quality to waste PP resin. This will enable the recycled material to become truly circular and be reused in its original application, as opposed to having to be downcycled into lower-value products. One example of the extensive product range of Milliken is the KeyPlast colourants for plastics. These are versatile products that can be used by liquid and solid masterbatch producers, resin producers and compounders, and are suitable for use with a wide range of polymer and resins systems. These include PET in transparent, food-contact applications, as well as other transparent amorphous polymers such as polystyrene (PS), polycarbonate (PC), acrylic (PMMA) and polysulphone (PSU). These KeyPlast colourants which enhance the visual appearance of virgin polymers deliver stable, reproducible colours. Milliken’s ClearTint colourants will also be on display. www.milliken.com Hall 6 Milliken Booth A27","@ID":61}, "TRADE SHOW PREVIEW PETplanet Insider Vol. 20 No. 10/19 petpla.net 70 Zero Cooling, multiple benef ts Nissei ASB Machine Co., Ltd., a leading manufacturer of machines and moulds for injection stretch blow moulding of PET and other plastics, intends to be making a strong impact with the target audience with live moulding demonstrations of five ASB-Series machines strongly showcasing ASB’s recently introduced “Zero Cooling” moulding process at its 712m2 booth. The major sectors of the PET container market that utilise one-step injection stretch blow moulding (ISBM) process are commonly those where containers are designed for market appeal and brand quality. This is particularly true for cosmetics, personal care, pharmaceutical, household or general food packaging. Zero Cooling - ASB’s advance in preform cooling technology - is claimed to suit the needs of these industries as it enables increased product quality at short moulding cycles. Taking full advantage of ASB’s proprietary 4-station, 1-step moulding method, the required preform cooling is now shifted away from the injection station and into the second, conditioning station to reduce injection cycle times. Crucially, the Zero Cooling moulding method, first announced in 2018, enables short cycle times while avoiding the need for thin, compromised design preforms that are susceptible to several quality related problems, most notably the undesirable ‘fisheye’, ‘body ring’ and ‘orange peel’. Now, with the preform designer able to freely focus on a shorter preform design with a thicker wall section that optimises stretch ratios, the result is improved quality as well as increased productivity, states the company, and continues: Actual results from typical Zero Cooling moulds have shown 15% or greater increase in stiffness and topload strength, improved control of material distribution and an average of 1.5 times productivity increases while improving on visual quality. In addition, since the container strength has now been improved by better orientation, more scope is available to apply additional light-weighting to the container’s specification. The advanced cooling method also enables the moulding of heavyweight premium cosmetic containers in dramatically shortened cycle times exhibiting no haziness even when using standard, lower cost PET grades, rather than the higher priced specialised, low-crystallisation grades that are normally required. All this is intended to result in visual quality while saving cost and boosting productivity by 2-3 times over conventional moulding of these glass-like, premium designs. ASB-12M - small size with vast capability The model ASB-12M has established itself in the class of small, fully automated 1-step stretch blow moulding machines. Its Version 2 specification is intended to bring great performance and utility to the table. The Vision1 control system ensures that response & communication speed is 2.5 times faster than dedicated PLC systems enhancing machine cycle efficiency and control precision. The PC based system makes it flexible in use and compatible with Industry 4.0 for enhanced factory networking. Also, a larger, easy to read panel provides easier access to relevant information without changing pages. Other advantages include touchscreen operation, improved operator feedback Hall 14 Nissei ASB Booth B38","@ID":72}, "MATERIALS / RECYCLING PETplanet Insider Vol. 20 No. 10/19 petpla.net 23 MATERIAL DRIER AS ALL IN ONE UNIT FOR 50 TO 200 KG/H VISIT US AT K 2019 BOOTH 10H48 been taken in account: The flow of cooling water required is managed by an automatic system. Small particles of metal can be another source of contamination, typically resulting from grinding, from blades or knives. Metal separators can be installed on the material lines during the pneumatic conveying: the dilute phase during the conveying combines with a reliable sensor mounted on the metal separator, recognising the metal parts with a minimum waste of good plastic material. Using recycled materials means returning into the main production stream the internal scraps, non-compliant or rejected final products or intrinsic production scraps i.e. from production change and start-up phases. Piovan has designed a complete package consisting of a tilter to empty the preform octabins, conveyor belt and grinder suitable for grinding preform and bottle. From the granulator the material is conveyed to a de-dusting unit and then it can be re-introduced into the process. In the case of low percentage even a simple proportional valve can be enough to mix virgin chips and regrind before the drying step, but market demand is going in the opposite direction, for a higher and higher percentage of regrind. So it can be necessary to provide an additional step to crystallise the material, or a dedicated drying system with a special geometry to process flakes or dosing systems to manage the proportion between virgin PET, rPET, regrind as flakes, additive and masterbatch. www.piovangroup.com","@ID":25}, "BOTTLING / FILLING PETplanet Insider Vol. 20 No. 10/19 petpla.net 37 Rounded, anodised aluminium, sliding, protection doors, which allow all the motors (with low energy consumption) to be placed on the outside of the mechanical groups that they run. Infeed conveyor with a thermoplastic, low friction belt and a motorised system of oscillating separator guides. Film reel unwrapping controlled by a brushless motor which guarantees precise, constant film tensioning. Machine equipped with a system of film splicing with a heated blade, this allows the ends of the two reels of shrink film to be spliced without stopping production. Reduced energy consumption and low maintenance costs. Compact knife group with film cutting blade run by a brushless “direct-drive” motor. Shrink tunnel with cutting edge technology to contain energy consumption and guarantee environmental compatibility. High quality of final pack, thanks to the uniform distribution of hot air flow on all the pack surface inside the tunnel. Automatic palletising system APS 1550 P Packed products: packs in film only in format 6x4 and 4x3 (0.33 l and 0.5 l bottles) and 3x2 (1.5 l bottles) coming from the shrink-wrapper SK 600 F Pallets worked: 1,000 x 1,200mm and 800 x 1,200mm Advantages: Single column with two Cartesian axes with SCARA technology, flexible and easily adapted to any end of line logistic condition within multiple industrial sectors. Reduction of maintenance and energy costs, as well as lengthening the life cycle of the installation, thanks to the machine’s mechanical simplicity and the use of components derived from robots. The automation and onboard management of the APS system is entrusted to technology based on sercos fieldbus, thanks to which the operator, using a simple, intuitive, man-machine interface can quickly and easily manage all the end of line, palletising operations. Conveyors Function: carrying loose and packed bottles in PET, in particular: Moving bottles from the outfeed of the integrated system Ecobloc Ergon, moving in infeed/outfeed to the shrink-wrapper SK 600 F Ergon and moving in infeed to the palletiser APS 1550 P Ergon. Main advantages: constant, fluid no-hitch movement of loose and packed bottles in PET; format changeover times reduced for the quick switch from one batch to another; modular, ergonomic structure, which can easily be adapted to different sizes of containers or production flows; energy consumption and running costs among the lowest on the market; low running and maintenance costs; product guides made from stainless steel and anti-friction UHMW plastic, which maintain the quality of the container.","@ID":39}, "TRADE SHOW PREVIEW PETplanet Insider Vol. 20 No. 10/19 petpla.net 72 Versatile ASB-70DPH v4 model With the ability to mould PET and up to 20 other resin types, combined with the capacity to mould up to 10 l capacity jars in a single cavity all the way through to sub-100ml bottles in up to 12 cavities, the ASB-70DPH is a best-seller model of Nissei ASB. The ASB-70DPHv4 is a mid-range one-step injection stretch blow moulding machine that is claimed to offer moulding versatility in a “just-right” size with competitive investment costs and low cost of ownership. It utilises ASB’s renown 4-station moulding process to achieve moulding efficiency and stability of a wide range of moulding materials. Key features include: Ability to process up to 20 resin types in addition to PET Moulds containers from 50ml or less all the way up to 10 l capacity Variable cavitation from 18mm neck diameter small bottles in 12 cavities through to 149mm neck diameter jars in a single cavity A wide array of factory options to tailor the machine to project-specific needs With no hydraulic components above the moulding area the risk of product contamination is eliminated At the K exhibition, this version 4 model will be demonstrated moulding a 250ml cylindrical shampoo / cosmetic container at a cycle of 13.4s with 10 cavities producing over 2,600bph. The demonstrated container design falls into a category that is often difficult to mould with perfect visual quality. Its small neck to body diameter ratio and a higher-than-normal weight as per the client’s requirement for a “quality feel” would cause moulding compromises with a standard mould. However, with the added benefits that Zero Cooling provides, not only is the productivity increased over a standard mould, the visual quality of the container becomes flawless, states the company. Advanced version of ASB-70DPH Although its external appearance is similar to the standard version on display, the ASB-70DPH Advanced Version has been fully re-engineered to demonstrate a variety of techniques to achieve reduced indexing time that fully complements the Zero Cooling process and to provide enhanced output, especially for smaller containers. Key points being demonstrated on this concept machine include: Revised hydraulic circuit for faster, smoother motion of clamping Adjustable stroke in all clamping stations reduces machine indexing time for shorter preforms, while adjustable daylight also allows longer preforms - a feature especially useful for many non-PET moulding resins Fully revised blow station to reduces index time, to simplify blow mould changeover and to reduce maintenance Compatibility with existing ASB70DPH moulds Height adjustment system for injection unit reduces mould changeover times in high product mix moulding scenarios With this Advanced Version machine giving a 40% reduction in indexing time, the demonstrated container using a short preform can ASB-12M v2 1-step ISBM machine with optional take-out unit ASB-70DPH v4 1-step ISBM machine with optional take-out unit German Technology Oct 16-23, 2019 Hall 1, Booth C42","@ID":74}, "MATERIALS / RECYCLING PETplanet Insider Vol. 20 No. 10/19 petpla.net 25 Recycling rates for aluminium cans vary worldwide. In the UK, the recycling rate has reportedly risen to 75%, its highest ever level. In the US, a 2017 report showed the consumer recycling rate had seen a decline, to 49.4%. In Brazil, it’s more than 90%. In some countries rates are increased by income disparity, as the value of aluminium creates an economic impetus for collection. Durability and flexibility When it comes to durability, plastic bottles have an inherent advantage. While dented cans often end up on retailers’ discount shelves, plastic is less likely to deform in transit. Flexibility is another advantage for PET. While supermarket shelves are stacked with resealable bottles of water in convenient different sizes, a 2 l can of water is much less practical. Shelf life Shelf life is often defined more by contents than packaging, but it is a consideration. Drinks in cans generally have a longer shelf life than those in PET bottles. Additives can improve the barrier properties of PET to extend shelf life, but there is often an environmental impact. Some are introduced in small enough quantities that recyclability is not affected. Others, such as colourants, mean the bottle cannot be recycled for food grade applications. The food grade factor Not all PET can be recycled back into new water bottles. Contamination, polymer degradation and additives can all affect suitability for food grade applications. New technologies could help to resolve this. Chemical recycling shows promise as a way to upgrade lower-quality PET back into virgin-grade resin. This is a mid-term trend in the experts’ view, with significant volumes of chemically recycled material at least 5-10 years away. So, while 3 million tonnes of PET bottles will be mechanically recycled back into food and beverage bottles by 2029, the total will climb to 4.6 million tonnes with chemical recycling volumes. In the case of aluminium, the recycling process itself has a sanitising effect. Cost of materials Aluminium is currently around US$ 1,750-1,800 / tonne. A 330ml can weigh around 16 g. The polyester for PET is around US$ 1,000-1,200/ tonne. A PET water bottle weighs about 8-10 g for 500ml. However, as carbonated drinks need a stronger bottle the average weight will be around 22-25 g for 500ml. Plastic material does cost less and go further. On a per-litre basis a beverage will cost less to distribute, with less energy needed to transport it. If the product is water, rather than a higher value beverage such as beer, the cost impact is amplified. Additional costs are typically pushed along the value chain to the customer. Price sensitive consumers may not tolerate the increase, so brand owners may be forced to absorb the additional cost. Availability of stock In the UK alone, 7.7 billion plastic water bottles are used each year. WoodMac estimate that replacing that with 7.7 billion cans would require 99,000t of additional aluminium sheet stock. For some years, the aluminium rolling industry has been switching away from producing can stock to more profitable sheet for automotive applications. To trigger a reversal of that investment the conversion margin would need to shift. Rolling mills would have to be incentivised by a significant increase in the price of can stock. Such a radical shift wouldn’t happen overnight. But regulation could drive a step change in polymer demand, with an impact on investment cycles as a result. So, will aluminium cans replace plastic bottles? Brands offering cans of water could find a receptive market, and it will be interesting to see how consumers respond over time. However, Wood Mackenzie’s data shows a trend decline in the consumption of aluminium beverage packaging over the next ten years, except for a few emerging markets in Southeast Asia. Meanwhile, PET bottle consumption is increasing, at a global level and in most regionals. Healthy living is one important driver. Put simply, people are choosing a bottle of water over a can of fizzy drink. And the industry is changing. Targets are being set across the value chain to improve collection and recyclability and maintain more of a closed loop. Is there a better alternative to PET? The analysts’ finding is that there’s no easy answer. Each material brings its own challenges. Paper or card options typically have a polymer coating that can be challenging to recycle. Glass is heavy, and inefficient to transport. Bioplastics have been criticised for diverting arable land from food crops, amongst other potential trade-offs to the environment. And will consumers pay for greener, but costlier alternatives for water on the go? www.woodmac.com Chemical recyling growth forecast","@ID":27}, "BOTTLE MAKING 31 PETplanet Insider Vol. 20 No. 10/19 petpla.net Middle East and Africa but to a total of 40 countries worldwide. Sunpet in India runs at about 90% of maximum capacity, producing over 3 billion units a year. The company Thai Plaspac as a whole has a total installed capacity of 80,000 t across all its ten plants, including those in Thailand. “For the fiscal year 2019, we are expecting an increase in revenues of around 25%, around USD70 million,” explained Shrinath Kasi. “We have seen 15% growth in PET alone in TPAC India.” TPAC India employs more than 300 staff across its total production space of approximately 80,000m2. With over three decades of experience, the company claims a history of innovation in the pharmaceutical, edible oil and dairy segments. Its client list includes several of India’s leading brands in the milk and fresh juice markets, which were previously dominated by glass bottle and pouch packaging; the trend is now towards PET bottles. The attractions of PET include increased food safety, better quality, longer shelf life, improved product hygiene, reduced environmental impact compared to traditional packaging materials like glass or paper, innovative packaging options – and, of course: consumer convenience. TPAC and one of its customers developed 200ml and 500ml PET bottles to provide these benefits in dairy segment; they are now widely in use across the country. Sunpet is also the exclusive manufacturer of PET cans for Hershey’s chocolate spreads. The team around Chitaranjan Swain (on the right) manages the three plants Umbergaon, Silvassa & Dadra. On the left are the Umbergaon team members: plant manager Nagar Patel; production manager Arun Chaudhari; and maintenance manager Ramesh Kadam Mr Kasi mentioned that Sunpet is widely known as a packaging solution provider to the Food & Beverage industry, a position that was recognised by its recent award of “Best Brand – 2018” by the Economic Times Food Processing & Packaging. “TPAC Packaging’s speciality is hygienic consumer packaging,” he added. “Our The Editourmobil in front of Sunpet’s gates in Umbergaon, south of Silvassa core strength is stringent hygiene standards, maintained for critical sectors such as pharma, food and personal care. I would also emphasise our portfolio of blue-chip brand customers, where our relationships have been built up and span multiple decades.” www.sunpet.in","@ID":33}, "TRADE SHOW PREVIEW PETplanet Insider Vol. 20 No. 10/19 petpla.net 61 PET drums become reality In 2019, the Cypriot company broke its own record in large PET containers, by producing an open-mouth PET drum of 120 l, with a 400mm neck diameter, providing the PET processing industry with the opportunity to enter new applications, with a unique and value-adding PET container. The main advantage of PET drums is their lower weight, typically being about one-third less than for an equivalent HDPE drum. This is made possible by the superior mechanical properties of PET and generates substantial savings in raw material cost. The resulting important economic, logistical and environmental benefits, especially for exportoriented applications, makes the shift to PET drums an attractive option. In addition to the weight reduction, PET drums can be made transparent, which may be preferable for specific applications. Furthermore, due to the orientation of the PET molecules during the stretch blow moulding process, PET drums provide very good barrier properties for alcohol and essential oils products. Finally, the smooth, glossy surface finish provides an attractive appearance and also allows for easy cleaning when required. Tailored drum dimensions for export Many products are exported in drums, like active pharmaceutical ingredients, pigments, fish oil, chemicals etc., for which logistics efficiency is very important. Drum dimensions can be optimised to container loading, saving freight costs. For example, a 100 l PET drum speciallydesigned by Cypet for the bulk drug industry, fits nine drums per pallet, allowing the loading of 360 drums per 40 ft container. This compares to five HDPE drums per pallet currently used, resulting in an increase of container loading from 200 to 360 drums, representing a 44% reduction in shipping costs. There is additionally a significant saving to be made on the drum cost, which would have a weight of about 1.8 kg, compared to 2.4 kg for HDPE. This is a saving of 25% on raw materials in addition to a saving on electricity due to the Cypet machine’s low energy consumption. An additional benefit of PET drums for all applications, including for exports to environmentally sensitive countries, is the fact that the PET drums are easily recyclable repeatedly at the end of their service life and re-used in various applications, thus completely closing the loop and enabling a fully circular PET economy. www.cypet.eu IS STILL 50% TOO MUCH. 50% L SS P CK G NG The KHS solution for more sustainability: New avenues in packaging technology. We are continuously improving our packaging. By applying innovative technologies and switching over to mono-material khs.com/packing-systems Hall 13 | Booth A75 K-Show 2019 October 16 - 23","@ID":63}, "56 TRADE SHOW PREVIEW PETplanet Insider Vol. 20 No. 10/19 petpla.net +44 (0) 1254 584210 [email protected] petmachinery.com Active for over 25 years, our global network and specialist knowledge makes us the go-to company for the sale or purchase of a PET machine. Commercially savvy, we work closely with our customers and our global network, to make sure everyone gets the best deal. Providing comprehensive advice throughout your sale or purchase; we can arrange dismantling, loading, packing, shipping, specialist insurance and commissioning. If you have amachine to sell or you’re looking to purchase, please get in touch. THE INDUSTRY EXPERTS High quality injection moulds and PET systems Following the successful trade fairs of previous years, the Swiss company Otto Hofstetter wil have their own booth showcasing their latest products and services. Otto Hofstetter is a producer of PET Preform moulds from 2 up to 192 cavities, as well as for injection moulds for thin walled packaging applications and IML solutions. Otto Hofstetter intends to enlighten customers on their complete portfolio of high quality injection moulds. Besides the well-known high quality injection moulds, Otto Hofstetter‘s strength is their extensive portfolio for plastics, which starts with the initial idea for a product, followed by their consultancy and design services to produce the end product. Once the injection mould is built, their after sales support will round up the complete package. Otto Systems AG specialises in conceiving, planning and implementing first-class systems to produce PET preforms. Experienced experts in tailoring high-quality components to specific customer needs to create optimal, top-performing systems. They will be available at the same stand. www.otto-hofstetter.swiss www.otto-systems.com Hall 1 Otto Hofstetter Booth C12 Material handling meets circular economy Motan is focusing on two topics while at K‘2019: along with the new products Spectroplus, Metroflow, Luxor CA A and the new material loader range Metro SG, the company is also addressing the core topic of this year’s K show – circular economy. The Spectroplus is a dosing system for all applications in extrusion and compounding. The modular design is suitable for a large range of different materials, from powders, granulates and regrinds to liquids and flakes. The synchronous dosing unit can be augmented with the Spectroflex dosing modules, which are also available as gravimetric or volumetric versions. It is controlled by the new Spectronet control, which can control both dosing modules as well as external dosing units. Metroflow is a gravimetric vacuum conveying system for precise material throughput control. These gravimetric material loaders are used in pneumatic conveying systems, for example to convey material from a silo to a drying bin or to the processing machine. It is suited for monitoring material consumption in real time, which means that the units are predestined for use in an Industry 4.0 environment. Luxor CA A, a compressed air dryer for small to medium throughputs with optimised control and integrated ETAplus technology is designed for small to medium material throughputs. The dryer operates in a temperature range from 30- 180 °C. It can be installed directly on top of the processing machine or on a mobile frame. The dryer is available in four sizes with bin volumes of 8, 15, 30 and 60 l respectively. Motan has reworked and expanded the Metro range of system individual material loaders. The new material loaders Metro G (Granulate) for large material throughputs is now available in three sizes with 60, 100 and 150 l capacities respectively. As part of the central K’ topic circular economy, Motan is involved in the presentation of a closed material and processing cycle at the KrausMaffei stand (Hall 15, Stand C24) with a drying system incorporating energy saving technology and a new residual moisture sensor, with material loaders, and with a Gravicolor 30 gravimetric dosing and mixing unit. All components within this production cell, including the ancillary equipment provided by motan, are connected via the interface standard OPC-UA with a central data collection point. www.kshow.motan-colortronic.com Hall 9 Motan Booth C64","@ID":58}, "PACKAGING PETplanet Insider Vol. 20 No. 10/19 petpla.net 14 In the same year (issue 08/01), we discussed a series of PET-packaged vehicle care products from Sonax, produced in cooperation with Rosti Verpackungen GmbH, which withstood chemical substances in tests with temperatures as low as -20 °C, in the container development phase. Sonax’ vehicle care products Also in 2001, as detailed in a report (issue 10/01), RPC Containers from the UK envisaged a growth market for non-food PET packaging. At that time, RPC was already manufacturing hair gel containers and cans for household products and considered the material, then new in this area, to be an asset. A little later, in 2003, the words: “unimagined ten years ago - today a reality” heralded the introduction of a new 200ml PET shampoo bottle from Kunze (issue 07/03). At the end of the same year (issue 12/03), moulds manufacturer MHT announced an increased degree of interest in the research and development of new preform sizes and bespoke preform necks for special closures, such as those used in cosmetics and pharmaceuticals packaging. MHT envisaged potential growth for PET outside the straightforward beverages industry, due to attractive packaging appearance and the resulting customer appeal. However, the company also said that a considerable amount of research into the manufacturing of moulds to achieve complex or textured surfaces, for example, was still required. New preforms and closure developments for non-food packaging In 2004 (PP 03/04), Astron Communications tapped into the area of household goods with the “wow” factor by developing small PET side tables for children’s bedrooms or picnic activities. The then highlight was a PET table top placed on either empty or full PET bottles, which form the table legs. Colourful PET table, placed on full or empty bottles Procter & Gamble is a manufacturer we have encountered time and again during the lifetime of PETplanet. In our April issue we reported that the Ohio, USA-based multinational group had just switched its 1 l Lenor fabric softener from carton to PET. At launch, the preforms originated from Austrian converter Alpla. Fabric softener in PET by Procter & Gamble A month later (issue 05/04), we reported on German company Sauer, which manufactured containers exclusively for household cleaners and beauty care products, had added two of the then new Ecomax single-stage ISBM machines from SIG Blowtec to its fleet, in order to expand its portfolio to include PET packaging. Sauer described the look and feel of PET products as “close to glass, which remains standard in the cosmetics industry.” Products packed by Sauer Germany 2005 - 2010 In the summer of 2005 (issue 06+07), toy manufacturer Lego launched a series of PET cans, the design of which addressed their respective contents – such as the tower of a castle including battlements and the corresponding Lego bricks, as we reported in our magazine. Two years later, in 2007 (issue 10/07), Impressions Packaging Georgia, USA, presented its frosted and sandblasted look containers. This appearance of the thick-walled containers with glass optics was achieved with a masterbatch from Ampacet, and was available in filling volumes of 100-240ml. In 2008 (issue 09), Italian converter Stropol presented its one-piece snap-on closures, which, in contrast to the screw-on closures for PCO and BPF preform necks then available on the market, could click easily onto a standard preform – the first time in the market. This enabled standard preforms to be used without much effort, for body care packaging, for example (see photo on page 15).","@ID":16}, "TRADE SHOW PREVIEW PETplanet Insider Vol. 20 No. 10/19 petpla.net 73 be moulded at up to 2.4 s faster compared to a standard model. This saving is in addition to the reduced cycle time obtained from the use of Zero Cooling technology in the mould design. Combining the aforementioned machine revisions with ASB’s Zero Cooling mould technology, the 8-cavity, single row mould producing a 30ml, 3.8 g, 19mm screw neck container for medical or toiletry use will cycle at 4.4 s to provide over 6,500 bph. The double-row moulding equivalent to the ASB-70DPH is optimised for production of smaller bottles in moulding configurations from 8 to 24 cavities for high productivity of containers up to 1l capacity. Assisting with energy saving, the servo hydraulic system provides power consumption savings of 30-40% compared to the same mould and cycle time running in a conventional machine, while an optional blow air recycle system has the capability to take exhausted blowing air back into the machine system for air cylinder operation. Now fitted as standard, an enhanced mould changing system in all stations permits reductions in overall mould change time. For a blow mould change, just 30% of the previous time is required while for a total and complete preform and blow mould change, around 50% of the previous time is required. At K, the machine will be moulding an oval 300ml shampoo container in 14 cavities at a cycle time of 13.6 s to generate over 3,700 bph using a 100% recycled rPET. ASB-150DPW: for small & medium bottles & jars The largest model on display is part of the ASB-150 Series that operate using single, double or triple row moulding. Despite being a high productivity machine for small to medium sized containers, the double row layout of the ASB-150DPW also has the versatility to mould a wide variety of bottles and jars in PET and other resins. Output is typically around 2.5 times that of the smaller ASB-70DPW. With its design based on the shared ASB-150DP / ASB-150DPX mechanical architecture, operation, maintenance and spare parts share many common features, thereby reducing total cost of ownership where its “siblings” are also in use. Energy consumption is maintained low due to the adoption of standard variable displacement or optional servo driven hydraulic pumps. The ASB-150DPW is capable to mould containers from 1.5 l jars with 94mm necks to sub-150ml bottles ranging from 8 to 36 cavities. At K, the machine will be demonstrated moulding a 900ml, 70mm neck diameter general food jar in 14 cavities. The adoption of Zero Cooling offering a cycle of 9.4 s means that productivity will exceed 5,300 bph while moulding strong containers in 100% rPET. www.nisseiasb.co.jp ASB-70DPW v4 1-step ISBM machine ASB-150DPW 1-step ISBM machine","@ID":75}, "52 TRADE SHOW PREVIEW PETplanet Insider Vol. 20 No. 10/19 petpla.net motan-colortronic gmbh - [email protected] www.motan-colortronic.com ETA plus® considerably reduces energy consumption and protects materials. Drying has never been this efficient: ETA plus® LUXOR A Please visit us: Hall 9, Stand C64 16 - 23 October 2019 Plug & Dry - material drying all-in-one-solution In the field of auxiliary equipment, Eisbär manufactures systems to improve quality and productivity for the plastics industry, specialising in products to avoid condensation on the moulds, drying of plastic resin and the process of PET flakes. Manufacturers are aware of the insufficient or incorrect drying. The results are the production of scrap and impair the quality of the product which leads to costly complaints. The production of high-quality products are the top priority objectives of the plastics processor. For these reasons, it demands a controlled drying process with operational reliability. The continuous and energysaving drying from Eisbär intends to satisfy these demands. Space for installing material drying systems is expensive and often limited. Eisbär Plug & Dry is an all-in-one-solution for efficient material drying. Power connection and material supply line is all that is requested to start the process as this system is running without cooling water. The energy-efficient compact module Plug & Dry for drying PET granules and flakes consisting of material dryer, drying hopper and material conveyance is characterised by compact design and offers a multitude of advantages. Highest efficiency for low throughputs (25-200 kg/h) combined with lower space requirement compared to conventional drying systems. The system offers conditions using a closed circuit for continuous and rapid material drying. The adsorption drying technology offers user-optimised design and easy maintenance. The continuous drying process, lowest energy consumption and long life are basic advantages of the system to ensure optimal material drying. The heart of the continuous material drying process is the slowly rotating adsorption wheel with its multitude of honeycombed, axially aligned tunnels. The inner walls of the tunnels are lined with a desiccant. As it flows through the lower half of the adsorption wheel, the process air is dehumidified by the dessiccant. During the next quarter-turn, hot regeneration air flows through the tunnel and in turn dehumidifies the desiccant. In the next quarter-turn, the adsoprtion wheel is cooled to operating temperature and is then able to dehumidify process air again. To operate the interface system there is a touch panel with graphics capabilites. On a series of monitor pages, the operator can call up operating parameters in different languages, such as for instance process-air dew point, filling level in the drying hopper, delivery capacities, valve status or process temperatures. On this monitor pages one can adjust process set points and alarm settings. After selecting with the cursor, the monitor displays the type of error, the time at which it occurred and a fault signal number. www.eisbaer.at Hall 10 Eisbär Booth H48","@ID":54}, "PACKAGING PETplanet Insider Vol. 20 No. 10/19 petpla.net 19 greatest challenge in the creation of the moulds was the correct representation of the rib design in the upper third of the bottle. Detergents by Amir, Algeria What’s happening now, and where is the journey going? Mr. Giovanni Milesi, OEM Key Account Manager SMI S.p.A. We talked to industry expert Giovanni Milesi, OEM Key Account Manager at Italian company SMI Group, one of the world’s largest bottling and packaging equipment manufacturers. Globally represented with local machine production in San Giovanni Bianco and annual sales of € 145 million in 2018, the turnkey supplier for beverage, food and non-food is well aware of the trends and potential of PET packaging in the latter segment. “The fact that PET has significant advantages as a preferred material in cosmetics and beauty care, household products and other non-food areas is reflected on every supermarket shelf,” Milesi explained. “In addition to the low cost, ease of process, positive mechanical properties, high availability of raw materials worldwide and an annual growth rate of over 6%, the excellent visuals of the packaging and the material throughput also speak in favour of its use in these areas. This is joined by the high recycling capability of PET. Compared with the outputs of HDPE extrusion equipment, for example, PET stretch blow moulding equipment is able to manufacture significantly higher quantities. A key challenge for non-food processors is to make the right choice of closure. Ideally, these should correspond to uniform preform necks, so as to avoid having to invest in new preform moulds for each type of neck.” Mr Milesi is confident that “if influential companies in the industry further develop the closure design to a standard, this could unify the preform market for non-food conversion, globally improve the availability of preforms for these segments and, in the best case scenario, render the neck issue obsolete.” The fact that there has not, so far, been a standard for necks explains the success of both technologies, whether single-stage or two-stage. What used to be a single-stage attribute can now also be used in two-stage processes, thanks to selective or differential heating technology for PET preforms. This means that stretch-blown, non-cylindrical containers, such as rectangular, oval and additional designs with a completely uniform material distribution are now possible. According to SMI, the message that the product on the shelf sends to the customer is now more important than ever before and a key factor for success and sales, which is why huge efforts are now being made in packaging and design. “PET’s attributes enable it to fulfil these requirements in the non-food sector,” Mr Milesi explained. Despite this, it is difficult to predict how the market will develop, whether there will be a uniform neck standard or innovation in the handling of different neck finishes, which will make the equipment more flexible. DNC boosters Turnkey all-in-one system ","@ID":21}, "PACKAGING PETplanet Insider Vol. 20 No. 10/19 petpla.net 18 The Clariant Team in front of the lab In the middle of the year (issue 06/16), French manufacturer Serac offered its new heating module for the selective heating of preforms in its Blow Linear machines. The module was designed to make the in-house SBL system series suitable for the manufacture of containers for home and personal care applications with special bottle shape and flexibility requirements, using lightweight preforms. The SBL system was able to achieve up to 18,000 bottles with containers with a volume of up to 5 l. Non-food bottles moulded on Serac equipment In September (issue 09/16), we announced as a matter of “certainty” that Amcor had developed the firstever liquid detergent bottle made from 100% recycled PET material for Method, the American “eco” detergent manufacturer. The challenges in the segment, which was dominated by HDPE, were the crystal clear transparency of the bottle to flawlessly express the colour of the contents, a handfriendly format, and a covered neck geometry, as the PP closure was originally developed for HDPE bottle necks. Detergent bottle made from 100% rPET In the same issue (09/16), Tricor Braun’s US-based packaging experts solved the problem of a series of containers for sealants, each with three different chambers for different contents. The company developed a three-chamber PET and PP package for Prestone, a manufacturer of automotive chemicals, for which Tricor Braun was later presented with DuPont’s Silver Award. It was possible for each of the separate chambers of the series to be filled with two liquid chemicals in the container body and solid pellets in the overcap cover. The main container was made of PET, with a filling volume of roughly 530ml. Inside it was a separate PP container, with a capacity of nearly 90ml. Despite a tight development schedule, the complex product was launched onto the market in record time. Tricor Braun’s three-chamber containers for Prestone A year later (issue 09/17), in the “Products” category, we reported on Adidas’ collaboration with German packaging manufacturer Gizeh PET. The occasion was the launch of a new premium series of shoe care products from the sportswear manufacturer. In addition to the medically-inspired look of the brown 100ml and 200ml containers, they were also designed to reflect the concept of sustainability, so that Gizeh opted for the use of 100% rPET during the development. Adidas shoe care developed by Gizeh PET In the summer of 2018 (issue 07+08), an interview was published with Liquiform, a business unit of US company Amcor, in Michigan, which had succeeded in bypassing the blow moulding process during bottle shaping and to shape the preform directly with the final contents. The first product to be shaped using this technique made its way onto the shelves at the beginning of 2018: a liquid soap from the brand “Nature’s Promise”, which was created in partnership with co-packer Greenblendz, also from Michigan. The PET bottle with dosing system had a filling volume of approximately 355ml, and contained 50% rPET. In addition to the omission of a complete process step and the associated energy and space savings in the factory, the technology also achieved a more detailed, finer resolution structure for graphic and texture applications on the container surface in tests, compared with conventionally shaped PET containers. Container formed with Liquiform technology One magazine issue later (issue 09/18), we addressed Sarl Amir 2000’s acquisition of a KHS InnoPET Blowmax Series IV. The Algerian company manufactured cleaning agents for home use, with a sales volume of 21,000 t of cleaning products in 2017 (see photo on page 19). The background for the investment was a planned expansion into additional countries in Africa, with the generation of higher capacities. The KHS system was designed for up to 12,000 bph, with both a round and oval design, using preferential heating technology. In the same issue, “People Against Dirty” presented plans for new packaging for their detergents in HDPE bottles from European brand Ecover. Together with developers R&D Leverage, a series of transparent washingup liquid bottles made of 100% rPET was developed in six months. The","@ID":20}, "MARKET SURVEY 45 PETplanet Insider Vol. 20 No. 10/19 petpla.net Sacmi Imola S.C. Intravis GmbH Via Selice Prov. Le 17/A 40026 Imola (BO) - Italy +39 0542 607111 www.sacmi.com Mr Stefano Severi Sales Area Manager +39 3356 594 236 [email protected] Rotter Bruch 26a, 52068 Aachen Germany +49-241-9126-0 www.intravis.de Mr Christoph Wynands Product Manager Caps and Closures +49 241 9126 0 [email protected] IMDvista CLDP, Closure Digital Print System CHS200 CapWatcher Q-Line CapWatcher S-Line CapWatcher SC (Specialty Closures) IntraOne Up to1,500ppmin-90,000pph (oncustomersrequest) Up to 4,000cpm 60cps / 3,600cpm / 216,000cph 80 cps / 4,800 cpm / 288,000 cph 80 cps / 4,800 cpm / 288,000cph 50 cps / 3,000 cpm / 180,000 cph A complete solution for digital closure printing in high print quality (up to 720dpi) with integrated inspection system Artificial computer vision, spark tester 3 cameras for inner inspection (sealing elements, thread, tamper evident), 4 cameras for shell inspection, 1 camera for topwall inspection, contactless microhole inspection, temperature measurement, cavity reading 1 camera for inner inspection, 4 cameras for shell inspection, 1 camera for cavity reading, microhole inspection Fully customised inspection systems that are tailored to the needs and wishes of our customers System for OEM-integration into capper-, filler-, assembly-, laser- or printing-systems Various closure upon request Plastic, sport-, hinge caps and multi component caps Tethered caps, standard one-piece beverage closures, standard two-piece beverage closures Standard one-piece beverage closures, standard twopiece beverage closures Tethered caps, carton fitment, flip-top, sports cap, push-pull, 3-piece closures, screw top cap, spout & dosing, beauty & home-care, food & beverage, pharma, automotive, inserts, cutters, lids, dustcover Tethered caps, standard one-piece beverage closures, standard two-piece beverage closures, carton fitment, flip-top, sports cap, push-pull, 3-piece closures, screw top cap, spout & dosing, beauty & home-care, food & beverage, pharma, automotive, inserts, cutters, lids, dustcover Yes Measurement of inner seal cone diameter (σ=0.02mm), pulled thread inspection, TE band, black specks, contamination, colour deviation, inner seal cone, outer seal cone, QR-codes Black specks, contamination, colour, inner seal, outer seal, liner, QR-codes Pulled thread, TE-band, plug eal, constant distance between inner seal & outer seal, homogeneity between inner seal and outer seal, liner, laser engraving Ovality, up-side-down-caps, liner, missing TE band, flashes, short shots, black specks, contamination, colour, QR-codes Yes Long gate, slit quality, flashes between bridges, colour deviation, black specks, contamination, short shots, flashes, flow lines at the injection gate, cracks at the injection gate, prints, temperature measurement Flashes between bridges, colour deviation, black specks, contamination, ovality, short shots, flashes Long gate, slit quality, broken bridges, flashes between bridges, colour deviation, black specks, contamination, ovality, short shots Colour deviation, black specks, contamination, short shots, prints on the head plate Yes Measurement of outer closure diameter (σ=0.02 mm), inner seal cone diameter (σ=0.02 mm), closure height (σ=0.02 mm) Measurement of outer closure diameter, closure height, inner seal cone Diameter, closure height, assembly faults, missing components, damaged components diameter, Closure height, assembly faults, missing components, damaged components Yes Unique, robust cavity reading with specially developed illumination technology, cap-oriented imaging and machine-learning algorithms for outstanding cavity recognition; no time-consuming teaching or learning procedure necessary Unique, robust cavity reading with specially developed illumination technology, cap-oriented imaging and machine-learning algorithms for outstanding cavity recognition Unique, robust cavity reading with specially developed illumination technology, cap-oriented imaging and machine-learning algorithms for outstanding cavity recognition Unique, robust cavity reading with machine-learning algorithms for outstanding cavity recognition Yes, using spark tester New contactless microhole inspection - no need to dip into the closure Microholes in the area of the injection gate New contactless microhole inspection - no need to dip into the closure Yes Missing components, closure height, diameter and ovality, flow lines Print inspection directly integrated in the digital closure printing system Sidewall inspection through CVS360-3Dmodule for sidewall reconstruction out of 4 images by 4 side cameras, an algorithm allows compensation of any deformation of the image that might stem from perspective, optical deformation and spatial position. Precise decoration inspection including colour registration, colour shades, stains, contamination, mixed decoration, wrong colour, missed colour planes etc. Flexible in-line or off-line system solution available Yes Yes Yes Yes Yes Flexible in-line or off-line system solution available Yes Yes Yes Yes Yes IMDvista V5 VCC - Vision Control Center with newest intelligent software technology, IMDvista Portal, connects all system on one central data base (HMI for fast and transparent production overview) Latest release of CVS3000 software platform, common to all Sacmi vision systems, CVS3000 can be connected to a production machine to monitor the process, allowing auto-tuning and records a wide range of statistical information in SQLdatabase, can be connected to LAN so the information can be visible to all external devices (PC, tablet, smart phone) for a proper access to the network & equipment, connection to ERPsystem for automatic production change or to download information. IntraVisualizer - for the analysis of the entire production process, all process and production data of different production machines can be integrated with a robust OPC-UA interface according to EUROMAP standard; in addition, they can integrate order data from MES/ERP systems; IntraOptimizer - production assistent (please look at IntraOne) IntraVisualizer & IntraOptimizer IntraVisualizer & IntraOptimizer IntraOptimizer - production assistent. Extensive knowledge database specialised on processes; using machine learning algorithms, the IntraOptimizer will suggest the machine operator recommended actions to solve production issues & simplify daily work of production employees; increases overall equipment effectiveness (OEE) and avoids time-consuming downtimes","@ID":47}, "TRADE SHOW PREVIEW PETplanet Insider Vol. 20 No. 10/19 petpla.net 68 Process solutions for the treatment of plastic waste Size reducing, washing, separating, drying and agglomeration The machine and plant manufacturer Herbold Meckesheim GmbH will be presenting tried and tested process solutions for the treatment of plastic waste in Düsseldorf in addition to its wide range of machines. Pre-shredding Pre-shredding is an essential process step when the feed material is too bulky to process or when it has to be coarsely broken up before sorting, visual inspection, or testing. Herbold uses shredders, granulators, guillotines, and hammer mills for pre-crushing. For example: EWS 60/210 Shredder The demand for high-performance shredders that can process entire bales is increasing, especially when used in washing lines. Herbold will present the EWS 60/210 for the first time at the K 2019 trade fair. This shredder was developed for dry operation as well as for wet operation and has a maintenance-friendly design in addition to its high capacity. The machine is designed to be very robust and durable. In many plants, the crusher is the first stage in the process. In this stage, foreign bodies are often impossible to avoid. For this reason, some of the special features of this stage have been taken into account during its development that the company claims are unavailable in any other machines on the market. The company focuses on making a perfect wear-protected rotor that, in addition to custom knife configurations, is equipped in particular with bolted armour plating and a special grinding chamber seal. The timeconsuming hard-facing of rotors is therefore unnecessary. The two-sided belt drive is lowmaintenance, and to safeguard against foreign bodies, there is a clutch that prevents damage to the machine when uncrushable feed material is encountered. The maintenance concept is tailored to ensure optimal accessibility based on ergonomic considerations. The first machines are already in use at customers in Europe, and the official product launch will take place at the K 2019 trade fair. Easy accessibility ensured DWS two-shaft shredder A new two-shaft shredder with the stator positioned in the middle will be presented as a new innovation at the fair. Due to the large surface area of the rotor, the machine is stated to have a good feed performance and to be suitable for materials that can only be fed in doses using conventional shredders such as big bags or highvolume containers. Size reduction Herbold granulators grind all plastic waste materials. SB granulators with force feeding The Herbold SB series granulators with force feeding have been used successfully worldwide for many years. “We have consciously redesigned this series of machines to enable complete horizontal charging”, stated Karlheinz Herbold, who is responsible for the technology as the Executive Director. The feed material is not fed into the grinding chamber from the top through the force of gravity as in the case of standard granulators, but by even feeding the material into the grinding chamber horizontally at the height of the rotor using screw conveyors. To accomplish this, the machine housing and feed system were completely redesigned to meet all requirements in terms of size-reduction performance as well as ease of access for maintenance purposes. Herbold SB granulator with force feeding (trade fair exhibit SMS 80/160 SB) Washing, separating, and drying The treatment of process water also plays a decisive role, especially for washing lines. Herbold now offers solutions covering this area as well. Hall 9 Herbold Booth B42","@ID":70}, "TRADE SHOW PREVIEW PETplanet Insider Vol. 20 No. 10/19 petpla.net 69 Film washing lines with hot washing Achim Ebel, Division Manager for washing lines states: “We look closely at the planned input quantities and compositions, but at the same time keep an eye on the desired applications for the washed end products. We do not offer washing lines off the shelf – designing a solution that meets the particular requirements is a more intensive individual process performed together with the customer.” Herbold offers tried and tested solutions for many applications including PET bottles, post-industrial and postconsumer films, post-consumer hard plastics, big bags and other monofilaments, Tetra paks and pulp waste. The following new developments from the washing line product area will be presented. VWE 700 prewashing unit An important component in a Herbold film washing line is the multi-stage prewashing unit, which captures coarse foreign bodies and reduces the mineral fraction, both to protect the subsequent machines. The remainder is also gently pre-washed. The type of pre-washing developed by Herbold Meckesheim has been a proven technology. Now this process step has been further optimised by increasing the throughput performance for films, optimising the flow of water, and integrating a baffle plate thickener into the unit to clean the process water. Contaminants are removed directly on the unit. Hot washing Increasing quality requirements in the plastic recycling industry also require optimised cleaning stages when building a plastics recycling plant. An important step in plastics recycling is the hot washing step, which has been a major one in the PET bottle recycling process. Herbold Meckesheim has advanced this step of the process for PO films and can offer optimised temperatures and appropriate dwell times, as well as optimal cleaning results and end material quality through the use of suitable additives. Mechanical drying The dryers from Herbold Meckesheim are claimed to meet high quality requirements in terms of high drying efficiency and performance, good accessibility, wear-protected parts, and automatic cleaning systems. Now, the company has also implemented the principles of multistage vertical drying in their horizontal dryers. This improves the product output rate and the lifespans of the wear parts. Furthermore, the thermal drying process has been optimised. Thermal drying The two-stage thermal dryer is completely new. The flow through the coils was optimised and the heating temperature was improved in terms of energy consumption. This design is used especially in the recycling of increasingly thinner films. It is used to reach low residual moisture contents and ensure the material can be processed afterwards with as little energy as possible. Label remover Herbold has made numerous minor improvements, and therefore introduced a new and improved generation to the market. Based on a proven basic principle, the Herbold HLR label removers are now much more variable, states the company. This applies to the removal process as well as to the integrated separation using a classifier. They are now able to control the dwell times and intensities of the label removal process much better. To accomplish this, a series of adjustable machine parameters is used. Hot washing, also for f lms www.herbold.com","@ID":71}, "MATERIALS / RECYCLING PETplanet Insider Vol. 20 No. 10/19 petpla.net 22 Getting the best from recycled materials The impact of plastic is a topic that has been recently under unprecedented pressure. It is unquestionable that one of the main challenges for the plastics industry is to reduce its environmental impact by moving towards a circular economy. For 13 years, Piovan Group has been designing and producing complete systems to promote the use of recycled materials, investing in research in order to devise processes that will ensure the responsible transformation of raw materials, sustainable production and low environmental impact, in order to move towards a circular economy. The use of recycled material, both as re-pelletised PET and PCR flakes, is something that is already a common practice in the industry. Using recycled materials means facing different challenges all along the process from the storage to the injection moulding machine inlet, from the dosing to the feeding systems. What are the factors to be considered in processing recycled material? Piovan identifies some of the most relevant: The possible high amount of humidity especially for PET flakes, the presence of dust, difficult handling due to an irregular shape and the tendency of making bridges. Other relevant factors are the light weight, the possible presence of contaminants and the fact that the raw material is amorphous and cannot be simply dried without a preliminary process that increases the crystallinity grade. In order to provide high reliable turnkey systems, Piovan has developed solutions making the bottle-to-bottle process stable. Dust removal The presence of dust can have a negative impact on the quality of the final product and affects the reliability and performance at the feeding system. To solve this problem, it is necessary to manage the dust already present in the raw material to prevent it causing any problem. The generation of additional dust is to be avoided and of course it is essential to remove the dust from the raw material. A complete range of filtering units can be provided to convey heavy dusty materials. The features of these filtering devices are: wide filtering surface, obtained with a kit consisting of multiple cartridges; device for the automatic cleaning of the cartridges by means of compressed air; bins for collecting the separated dust designed for an easy handling and with the possibility of disposing of the dust without stopping the system. In many cases, recycled material has a bigger content of dust, but in addition dust can be created during the feeding phase. In order to minimise this, it is important to evaluate the sizing parameters, in order to find the right balance between air flow rate, pipe diameter, speed of the material and of the air inside the pipe. To further adjust actual running conditions, Piovan has introduced the control system Varyo, that, combined with a frequency converter of the process blower, enables the setting of the material speed inside the pipe. Another area of possible intervention is removing dust from the raw material. This can be done with de-dusting units. The principle of these devices is to create two contrary flows: the material falling down meets a flow of de-dusting air according to the counter-current principle. In the case of flakes from bottle grinding, the most critical point is the handling, due to the fact that flakes are light, thin and with a tendency to create bridges. For this reason, there are some areas that require a particular care and dedicate features. One cross characteristic is the geometry of all the equipment involved, from the drying hopper to the vacuum receivers, from the blender buffer hopper to the storage bins. The most evident factor is the steeper internal walls, but this is just what can be seen at first glance; there is more, and this makes a difference: from the specific design of the slide gates of the blenders to a different criterion in the selection of the diameters of the conveying pipes. In some cases, even the design of the static parts is not enough, and so bridge breakers and a pneumatically operated flap completes the package, helping the flow of the critical materials. No details are neglected to guarantee the reliability of the system: for example, the presence of dust can give a false reading, misleading a capacitive level sensor or very light material can float making it impossible for a mechanical sensor to detect the level. Contaminated material For post-consumer flakes it means that the material was a bottle and has been in contact with a beverage and a label; the bottle was then ground and washed - often with cold and warm water and with different cleaning agents. During the crystallising and drying processes, material is heated up to 160170°C. This can cause the evaporation of residual oils, glues, solvents and oligo-polymers. All these substances are collected by the flow of dried air and carried into the circuit. This can affect the life-cycle and performance of many components. There is, for example, the risk of obstruction of the drying air circuit or of a rapid degradation of the molecular sieves. Piovan has developed a range of fume condensers, thus providing an additional step of filtration and increasing the general reliability. As for the design of the other entire machine, also for fume condensers, operational costs and efficiency have","@ID":24}, "PETplanet Insider Vol. 20 No. 10/19 petpla.net 66 Inspection systems at a glance at Intravis booth Preform inspection: a world f rst Intravis GmbH, one of the world market leaders of vision inspection solutions for the plastic packaging industry, will have the largest trade show presence of its more than 25-year history at this year’s K show. In addition to improvements to its well-known products, the Aachen, Germanybased company will present innovations in the field of preform inspection and analysis software. Hall 11 Intravis Booth A58 stf·sorting line stf·washing line professional plastic recycling solutions – made in germany The stf· group is the leading manufacturer of plastic sorting and washing machinery, especially for PET post-consumer bottles, with more than 60 turn-key plants and several single machines delivered worldwide. stf·group Industriestr. 1-3 94529 Aicha v. Wald – Germany fon +49 8544 960-110 mail [email protected] web www.stf-group.de scan for vCard stf ·group Hall 12 Booth F56 Intravis will present eight systems and two additional new software developments. The fair appearance is thus the largest in the history of the company. Managing Director Dr Gerd Fuhrmann is visibly delighted: “We are delighted to be able to show products at so many other partner booths this year in addition to our own booth and thus present our wide range of solutions for the plastic packaging industry”. A world first at the Intravis booth Intravis is still holding back information about the exhibit at its own booth. Dr Fuhrmann only reveals: “We will present an absolute world novelty at our booth. The solution concerns the preform area and may be called truly revolutionary. We have worked for a long time to overcome the bottleneck in preform quality inspection; the result is spectacular and must be seen”. In addition to its own booth, Intravis will also present the new preform innovation at the booth of its longtime partner Husky Injection Molding Systems S.A. (13 A61). The inline quality lab One of the highlights already announced will be the CapWatcher Q-Line, which will be presented for the first time at","@ID":68}, "55 TRADE SHOW PREVIEW PETplanet Insider Vol. 20 No. 10/19 petpla.net Work together on a “clean” future Plastics have become an indispensable part of our everyday lives, since their low specific weight and special versatility allow us to improve our quality of life. However, what happens to the synthetic materials after they have been used? At present, almost the entire population is concerned with this question, and solutions are urgently sought. We must learn to use these materials in such a way that they do not harm the environment, especially after use. For some thermoplastics, such as PET and HDPE, recycling methods are already available which enable the recovery of the plastics. The CHT Group states to take responsibility worldwide and to be supporting the mechanical recycling process for years using sustainable innovations. An efficient use of the limited resources is the positive consequence. Further possibilities for optimising recycling processes can be found. In this way, CHT intends to enable its customers to explore new paths and set trends, even apart from bottle recycling. With the optimal coordination of processes and chemical auxiliaries, the best possible further processing of the recycled materials can be guaranteed. The CHT cleaning agents of the efficient Tubiwash series remove impurities and organic residual substances, adhesives and printing inks. Solutions and application fields of Tubiwash are versatile, and it can be applied in a wide range of most different applications and convince by improving the quality. A further approach taken by the CHT Group is to ensure that different materials are processed separately within the recycling processes. With its Tubiwet range, CHT provides solutions for numerous types of plastics and applications. During product development, the CHT Recycling Solutions already pays attention to sustainability in the recycling process. First of all, process auxiliaries minimise the use of resources such as energy and water, and they can be removed from the wastewater so that there is no negative impact on the environment. The CHT Group intends to continue to play an active and sustainable part in the further development of plastics recycling in the future; as a globally active partner with good services, clever solutions and profound know-how. www.cht.com Hall 8a CHT Booth D50 Delivering white opaque PET with 50% less TiO2 Penn Color’s pennaHolt brings the benefits of high opacity – low TiO2 to mono- and multi-layer PET packages. Bottles with pennaHolt are more materialefficient, faster and more energy-efficient to manufacture and are recyclable at higher rates in the non-clear rPET stream. Penn Color’s penneffex has special effect pigments to deliver unique colour effects that make engineered PET packages stand out. The penneffex team has overcome critical challenges usually associated with special effects pigments. The results are special effects concepts for mono- and multi-layer PET and HDPE extrusion blow moulded bottles. Just some of the special effects that can be achieved include bicolour, thermo chromatic, phosphorescent effects and metallic-themed options. www.penncolor.com Hall 7 Level 2 Penn Color Booth B13","@ID":57}, "PETplanet Insider Vol. 20 No. 10/19 petpla.net 78 PETbottles Home + Personal Care pure97 shampoo in PET Exclusively available from German discount pharmacy dm, New Flag GmbH from Munich is selling its hair care products under the brand name “pure97”; they are 97% from natural ingredients. An example from the Jasmine & Coconut Range is the moisturising shampoo, which is 100% vegan, 0% silicone and gluten-free. The shampoo is manufactured in Great Britain and comes in a handy 250ml bottle, which is slightly flattened and green-coloured with a screwed on hinged cap with dosage opening. Two self-adhesive labels provide the necessary data and ingredients. www.pure-97.com Attractively shaped bottle for active shower gel Traditional German company Kneipp recently brought a product range of several active shower gels onto the market. With active ingredients Sandalwood & Tonka Bean, Mandarin & Vetiver and Mint & Rosemary and names like “Be relaxed”, “Be happy” and “Free your mind”, the active shower gels are available in specially shaped bottles. These are subtly coloured and are tapered in the neck area, making them easy to grip and giving them a nostalgic look. They are reminiscent of old, almost antique glass bottles. The active shower gels are dispensed via a screwed-on, disc-top seal. According to the manufacturer, the bottles are up to 100% from recyclate and the labels are made from stone paper. www.kneipp.com Good conversations. braubeviale.de CONNECT WITH THE FUTURE Over 1,000 exhibitors and more than 40,000 trade visitors all have exactly one goal in mind: To drive progress for the beverage production of tomorrow, so that new solutions can be used to market better products. Sound exciting? Find out more: braubeviale.de/next Good business. Nuremberg, Germany | 12–14 November","@ID":80}, "PACKAGING PETplanet Insider Vol. 20 No. 10/19 petpla.net 15 Stropol’s snap-on closures We are now approaching the year in which PETplanet celebrated its tenth anniversary. At the start of the anniversary year of 2009 (issue 01/09), Editorin-Chief Alexander Büchler devoted his editorial to the topic of Personal Care packaging. He took the global economic crisis as an opportunity for the PET industry to break new ground and focus more strongly on PET packaging for non-beverage products, as the new mainstay of the industry. He explained that technological developments in the two-stage segment were sufficiently advanced (and that the “neck ring” hurdle had been overcome) for this technology to be usable in the Health and Beauty Care segment with high output rates, a market that had traditionally been dominated by polyolefin and glass bottles. To herald the start of the year, a new editorial category named Personal Care made its way into the magazine, with the brief of providing summary information and illustrations about new products. Later in the year (issue 07/09), an article was published about US-based company Novapak, which acquired its first Sidel SBO 4 blow moulder at the end of 2008 and was manufacturing HDPE and PVC packaging, as well as two different bottle formats for detergents at 4,800 units/hour. Novapak envisaged a strong trend and development opportunities for PET in the cosmetics and household products markets, as replacements for glass and PVC. At that time, PET already accounted for some 60% of its annual packaging volume, or approximately 1 billion packages. Sidel SBO 4 at Novapak’s shop f oor At the beginning of 2010 (issue 01+02), PTI (Plastic Technologies Inc.) launched a foamed PET bottle, then known as oPTI, in cooperation with Coca-Cola, which went onto shelves in Denmark. The bottles were recyclable in the conventional PET recycling stream and offered barrier properties without additional additives. The same technology was used in the test for the manufacturing of shampoo bottles that were designed not to slip out of users’ fingers, even when in the shower. NO. ONE-WAY PRODUCTION. YES. TOP QUALITY RECYCLING. How can your recycled product meet permanently increasing demands? With the CHT range of high performance process solutions with environmental relief for the wet chemical cleaning. We support you directly on site and ensure your quality controls in our laboratories with state-of-the-art equipment. Thus, your strong position in the growing market is confirmed day by day. More about us at www.cht.com K | October 16–23 2019 Dusseldorf | hall 8A | booth D50","@ID":17}, "BOTTLE MAKING 30 PETplanet Insider Vol. 20 No. 10/19 petpla.net The journey of the Sunpet brand From Thailand to India by Kay Barton TPAC (Thai Plaspac) Packaging established a major manufacturing bridgehead in India in 2018, when it acquired six sites of Sunrise Containers; they are now operating under the Sunpet brand. The Thai company, whose history stretches back to 36 years, has been the principal shareholder of its local representative in India since 1989. Sunrise Containers Ltd merged with TPAC in 2018, was rechristened TPAC Packaging India Pvt Ltd, and Sunpet is now their flagship brand. We spoke to Mr Shrinath Kasi, CEO, and Mr V. Subramanian, Vice President, Marketing, and visited two plants, at Silvassa and Umbergaon, with Mr Chitaranjan Swain, Assistant Vice President Operation. Tour Sponsors: March 2019 We met: Mr Shrinath Kasi, CEO of TPAC Packaging India Pvt. Ltd. Mr V. Subramanian, Vice President Marketing Mr Chitaranjan Swain, Assistant Vice President Operation TPAC was founded in Thailand in 1983, where it is listed on the stock exchange. Its current headquarters are in the metropolis of Bangkok. Having enjoyed continuous growth and invested in a steady increase in capacity since its foundation, the converter has succeeded in becoming a key market leader. TPAC now has 10 production locations, six in India and branded as Sunpet, and four in Thailand. The Indian plants are scattered across the west and north of the country. The Silvassa plant is in the Union Territory of Dadra and Nagar Haveli, about 200 km North of Mumbai, on the west coast. Its operations began in 1989, with the production of PVC containers. Today, the facility manufactures 5 g to 125 g weight bottles and containers, on Japanese technology single-stage systems. All the units are located in a Class 1 (100,000 ppm) clean chamber. Bottles are packed and then pass through a shrink tunnel, with no additional processing. The facility in Haridwar, Uttarakhand, 200km north of New Delhi, has machines that produce preforms from injection moulding processes and bottles from single stage process.The Umbergaon Gujarat plant, located south of Silvassa, specialises in wide-mouth preforms and containers and is the largest facility in the group. The containers are produced on two-stage systems. Preforms are produced on state-of-theart machines from global brands, then blown into bottles in a stretch-blow unit on semi-automatic SBMs. The most popular is a 90ml bottle; 20-25 million examples are produced per month. The plant hosts a modern injection-moulding production facility, located within an air-conditioned environment. The workhorses are host of Japanese technology machines, which mainly produce preforms for widemouth containers, but the key feature of the plant is undoubtedly the Class 1 clean chamber, where large capacity German-origin machines produce preforms for aseptic filling lines. Sunpet believes in continuous improvements and its operations team endeavours to improve product quality, machine efficiency, reliability and energy consumption under the company’s Manufacturing Excellence initiative. It has seen some significant investments – such as a 560kW roof-mounted solar system – but it also sees small, incremental improvements that make a difference: such as a tray located next to a machine to hold tools; or excellent logistical planning, right down to each carton having its own defined space; or threads tied to a ventilation outlet so that people can see at a glance that all the fans are working. Fifty per cent of its plastic material production is accounted for by the processing of preforms across all its facilities; 35% is dedicated to bottles and 15% to PET jars for food applications. TPAC exports 15% of its output by revenue value, primarily to the F.r.t.l.: Mr Kasi and Mr Subramanian in discussions with Kay Barton","@ID":32}, "imprint EDITORIAL PUBLISHER Alexander Büchler, Managing Director HEAD OFFICE heidelberg business media GmbH Bunsenstr. 14 69115 Heidelberg, Germany phone: +49 6221-65108-0 fax: +49 6221-65108-28 [email protected] EDITORIAL Kay Barton Heike Fischer Gabriele Kosmehl Michael Maruschke Ruari McCallion Waldemar Schmitke Anthony Withers WikiPETia.info [email protected] MEDIA CONSULTANTS Martina Hirschmann [email protected] Johann Lange-Brock [email protected] phone: +49 6221-65108-0 fax: +49 6221-65108-28 LAYOUT AND PREPRESS EXPRIM Werbeagentur | exprim.de Matthias Gaumann READER SERVICES Till Kretner [email protected] PRINT Chroma Druck & Verlag GmbH Werkstr. 25 67354 Römerberg Germany WWW www.hbmedia.net | petpla.net PETplanet Insider ISSN 1438-9459 is published 10 times a year. This publication is sent to qualified subscribers (1-year subscription 149 EUR, 2-year subscription 289 EUR, Young professionals’ subscription 99 EUR. Magazines will be dispatched to you by airmail). Not to be reproduced in any form without permission from the publisher. Note: The fact that product names may not be identified as trademarks is not an indication that such names are not registered trademarks. 3 PETplanet Insider Vol. 20 No. 10/19 petpla.net Dear readers, While politics is entangling itself in half-baked plastic bans and pseudo-recycling regulations that environmental activists consider to be somewhat last-ditch, the plastics industry has long been working on sustainable concepts. In the PET industry in particular, we have been focusing for decades on saving weight and energy. Admittedly, it was initially the cost savings that spurred on this trend. However, companies today are even more prepared to invest in material and energy savings. The origins were an optimisation of bottle design, in particular wall construction, so as to achieve the same mechanical properties using less material. The material accumulations at the neck and base of the preform that arise from the injection moulding process fell by the wayside in the next step. The first to trigger this size trend was definitely Corvaglia, which invested very early on in the development of weightsaving neck geometries. Today, the heavy PCO 1810 is hardly in use; the PCO 1881 is the latest technology. Neck-Lite is breaking new ground by reducing the material accumulation beneath the neck ring using crosspieces. The next big step was reducing the material use at the injection point on the Cappello, Ecobase and Mint-Tec bases. Not forgetting Sipa with the injection-compression moulding system for preforms, which made redundant many material accumulations arising from injection moulding processes. At SBM too, ever more sophisticated preform heating options came into use. These basically increased heating efficiency, and also enabled ever more precise heating of parts of the preform so as to optimise material distribution during the stretch blowing process. The peak of achievement was surely when heating was done using laser diodes, as presented by Sidel in 2017. In our interview on page 9, Stefan Bock identifies an even greater potential within companies besides material and energy savings. Untrained employees or poor machine maintenance lead to high scrap rates; material and energy waste that finds no mention in official statistics. There is still a great deal to do. Your PETplanet Insider Editorial Team","@ID":5}, "PREFORM PRODUCTION PETplanet Insider Vol. 20 No. 10/19 petpla.net 26 How market giant Chemco is continually adapting to the market New f elds of activity and closer cooperation with suppliers by Kay Barton In 2016, we visited plastics processing company Chemco in their offices in Goregaon, Mumbai (see PETplanet 05/16). As this visit took place three years ago, we decided that it was high time that we took another look at the company, which has seen its market profile and presence grow significantly in the intervening period. Tour Sponsors: Chemco off ce meeting with (f.r.t.l.) Vaibhav Ram Saraogi and Amitabh Agrawal (Chemco), Rohan Shahane and Yves Rebert (Husky Injection Molding Systems) and Kay Barton March 2019 We met: Mr Vaibhav Ram Saraogi, Managing Director Chemco Group Mr Amitabh Agrawal, Executive Director We wanted to find out how Chemco has positioned itself in the fast-growing Indian market since then and how it is meeting the changing needs of its customers. The India Road Show offered the ideal opportunity to do so. Once again, we met with Managing Director Vaibhav Saraogi but, this time, it took place in his new office in Nariman Point in the south of the city, where we also met Executive Director Amitabh Agrawal, who has only recently joined the company. Also at the meeting were Husky Injection Molding Systems representatives Yves Rebert, General Manager for the regions SAARC and Central Asia, and his colleague Rohan Shahane, PET Account Manager SAARC. Chemco’s office in Nariman Point is located not far from the Ocean itself; the coastline and the sea are clearly visible from the managing director’s corner office. Vaibhav Saraogi cut a relaxed figure as he sat at his desk. To his left was recent appointee as Executive Director, Amitabh Agrawal. The Chemco group has enjoyed an average growth of 35% in the injection moulding sector over the past few years, manufacturing preforms, bottles, PET containers and closures. “Nowadays, we have to respond to customer wishes in a more individual manner than ever before,” Mr Saraogi explained. “In doing so, even closer cooperation with our machine suppliers was and continues to be extremely important. This is something that makes a considerable contribution towards our success. Alongside our fleet of over 200 machines from ASB, Milacron, Krauss Maffei, Reifenhauser and many others, we currently use 15 machines from Husky; we’re planning to increase this to 30 in the near future.” Chemco claims to be a market leader, in terms of preform diversity. “Our many years of experience in the beverage segment help us when it comes to new applications,” Mr Saraogi continued. “Since our last meeting, our activities have continued to grow in the beverage sector as well as straying more and more into nonfood areas and into hygiene article packaging. In those areas, Husky’s strategic step to adapt itself to the needs of the Indian market in a more targeted manner has undoubtedly played into our hands and helped to strengthen our cooperation. Each customer is different and quick, custom solutions are more in demand than ever.” Product development processes have been improved in collaboration with machine suppliers, helping to raise levels of customer expectations and satisfaction that have come about as a result. Keeping products lightweight and high-performing while keeping costs low continues to be a topic of huge importance. Sixty-five per cent of Chemco’s products are in the food and beverage segments which, in figures, amounts to 50,000 t. PET makes up around 85% of this. The company also processes around 25,000 t of plastics for non-food and non-beverage applications annually, with PET accounting for 50%. This means that, across all segments, the PET share of Chemco’s Indian market remains one of the largest. “Indian business is actually highly emotionally driven. This undoubtedly","@ID":28}, "57 TRADE SHOW PREVIEW PETplanet Insider Vol. 20 No. 10/19 petpla.net www.intravis.com/K2019 Vision Inspection Systems at hall 11 booth A58. Be the first to know. 100% blown & inspected bottles on 1Blow machines rPET is more than just a trend, it is a reality for all companies who have put sustainability in their daily rules. Thanks to their advanced features, all 1Blow machines are suitable for the production of PET bottles with up to 100% rPET. However, due to the varying quality of rPET material, even with an accurate blowing process, a small number of bottles are leaking. This phenomenon gets bigger with the increasing proportion of recycled PET (rPET) in preforms. Consequently, this turns into a problem on the filling lines with more downtime due to fouling and subsequent cleaning work. To prevent this from happening, 1 Blow is introducing an innovation on K show: each blown bottle is tested within the blow-moulding machine before being taken by a downstream conveyor. Bad bottles are automatically ejected, only good bottles are conveyed. Thanks to a patented technology, the tiniest cracks are detected instantaneously. Due to the very short response times of this additional function, the output of the 1Blow machine is not slowed down. Furthermore, no parts need to be removed for changeovers so the changeover time of the machine remains as short as before. 1 Blow is going to introduce another innovation at their booth: in response to customer demand, th company has introduced the Tiered Access System. This User Control Option is a Multi-Coloured Key Fob System combined with a SensorReader at the HMI. Each fob can be programmed to allow the user to access as much or as little of the machine’s controls corresponding to the need of the user. Machine operators can have as little as on-off and screen viewing access; while senior technicians can have full parameter access. These new features are available on the entire 1Blow range of PET stretch-blow moulding machines. A 2-cavity machine with preferential heating and integrating are also amongst the developments being exhibited at the booth. www.1blow.com Hall 14 1Blow Booth B70","@ID":59}, "PREFORM PRODUCTION PETplanet Insider Vol. 20 No. 10/19 petpla.net 27 PREFORM PRODUCTION 27 makes it difficult to compare with other continents. Trust – which begins with the initial conversation – and subsequent reliability are essential aspects of a successful deal. And we can only achieve this with the continuous involvement of our partners,” Mr Saraogi explained. “The ubiquitous trend towards small packaging sizes means that total output is generally declining, which ultimately also has an effect on our pricing. The challenge is to proactively involve the customers in the situation from an early stage, thus allowing for agreements to be made on pricing which are based on longterm, close business relationships and mutual reliability.” As well as securing its existing markets, Chemco has expanded into new areas, such as shrink film for beverages, for example. It is also planning expansions in the field of flexible packaging, and new projects and developments in the field of multilayer preforms are also under way. The company has also begun manufacturing the preforms for Coca-Cola’s 250ml popular products for the first time and it is playing an active role when it comes to the issue of recycling. “As one of the co-founders of PACE (PET Packaging Association for Clean Environment), we are in constant contact with the authorities in order to implement recycling more strongly across the market. Compared with just a few years ago, this issue is being given much higher priority by the authorities”, said Mr Saraogi. www.chemcogroup.com www.paceindia.org The Husky team (left) with the Chemco team (right) and Kay Barton (middle) in front of the Editourmobil","@ID":29}, "PETnews 6 NEWS PETplanet Insider Vol. 20 No. 10/19 petpla.net Nestlé inaugurates packaging research institute Nestlé officially inaugurated the Institute of Packaging Sciences. The new Institute is intended to enable Nestlé to accelerate its efforts to bring functional, safe and environmentally friendly packaging solutions to the market and to address the global challenge of plastic packaging waste. The Nestlé Institute of Packaging Sciences focuses on a number of science and technology areas, such as refillable or reusable packaging, simplified packaging materials, recycled packaging materials, high-performance barrier papers as well as bio-based, compostable and biodegradable materials. Stefan Palzer, Nestlé CTO said, “Reducing plastic waste and mitigating climate change effects through cutting-edge technology and product design are a priority for us. Nestlé experts are co-developing and testing new environmentally friendly packaging materials and systems together with our development centres, suppliers, research institutions and startups. Located at our Nestlé Research facilities in Lausanne, Switzerland, the Institute also leverages our existing research capabilities in food safety, analytics and food science.” The Institute is part of the company’s fundamental research entity Nestlé Research in Switzerland, reaffirming Nestlé’s commitment to further strengthen the unique Swiss innovation ecosystem. www.nestle.com Aptar announces partnership with TerraCycle’s Loop platform AptarGroup, Inc., a global leader in dispensing, drug delivery and active packaging solutions, announced that the company has entered into a partnership with Loop, a global circular shopping platform from TerraCycle that delivers consumer products in reusable containers. As part of the partnership agreement, Aptar’s President of Food + Beverage, Marc Prieur, will sit on Loop’s advisory board. Loop is a shopping platform that allows customers to purchase their favourite products in reusable packaging and have them delivered to their home in a Loop tote that eliminates the need for disposable, single-use shipping materials. Once consumers are finished using their products, they simply put them back in the tote and schedule a pick up. All containers are cleaned, refilled and readied to ship again, creating a hassle-free, sustainable and circular product experience. Aptar currently provides lotion pumps for several of the products found in Loop’s online shopping platform. www.aptar.com Change at Otto Systems AG – Otto Hofstetter Holding now holds 100% of the shares According to the company, Otto Hofstetter Holding has bought back the 50% shares of the Yudo Group and becomes a sole share holder of Otto Systems AG. The change in the shareholder structure is by mutual agreement and has no influence on further partnership in the field of robotics and hot runner systems. Otto Systems AG, which was launched in spring 2017, is based in Switzerland. The company concentrates on consulting and engineering of turnkey systems for the production of PET preforms. It was founded as a joint venture between the Korean Yudo Group and the Swiss Otto Hofstetter AG. At the end of July, representatives of the two family companies agreed to appoint Otto Hofstetter Holding as the sole owner. Those responsible have not yet commented on the reasons. However, they stated that the cooperation in the areas of robotics and hot runner systems will be continued as before in a spirit of partnership. Otto System AG configures systems entirely according to the needs of its customers. The focus here is on the total costs over the service life and the production efficiency as well as the expenditure for maintenance and the durability of the system. The experts at the Swiss consulting and engineering company have an extensive portfolio of high-quality components from well-known manufacturers at their disposal. Top and side entry systems are available with injection moulds from 2-192 cavities for containers of up to 10l. Otto Systems AG’s systems are already in operation at well-known European bottle manufacturers. In some cases, higher performance could be achieved during operation, as in the system manufacturer’s Tech Center. www.otto-systems.com","@ID":8}, "8 NEWS PETplanet Insider Vol. 20 No. 10/19 petpla.net Circularity for Polymers: The ICIS Recycling Conference The polymer industry is facing an unprecedented moment brought on by a global shift towards circularity and sustainability. The European Commission’s Strategy for Plastics and increasing brand-owner commitments for recycled content in packaging puts pressure on an industry challenged already by supply constraints and market uncertainty. With the full value chain impacted by these challenges, the importance of industry collaboration is emphasised more than ever before. In response to this changing industry, Berlin will play host to the first ‘Circularity for Polymers: The ICIS Recycling Conference’ (5 November 2019, Radisson Blu Hotel), an event specifically designed to promote collaboration, solution finding and real change within the polymer industry. The launch of the event is being supported by key industry players, including: Lush Fresh Handmade Cosmetics, The North Face, Electrolux, Borealis, Sabic, SUEZ and LyondellBasell. Isabelle Karpinski, Conference Producer, Circularity for Polymers: The ICIS Recycling Conference, said: “The polymer industry is experiencing a period of rapid change; this event was launched to provide a space for the value chain to interact and share knowledge.” “This industry has highlighted the importance of collaboration and full value chain engagement in solving the challenges present in this sector. Our conference serves as a platform for discussion, to enable those active in recycling and circularity to find real solutions and achieve real change from within the industry.” The conference will include interactive roundtable sessions and Q&As with thought leaders in the space, offering a unique opportunity to stay on the cutting edge of recycling. www.icisevents.com Sumitomo (SHI) Demag announces new Managing Director in China Effective September 9, 2019, Mr. Stephan Greif was handing over the leadership responsibilities of Demag Plastics Machinery Ningbo Co. Ltd to incoming Managing Director Mr. Pietro Scattarreggia. For close to two decades, Stephan Greif has led the Chinese subsidiary of the Sumitomo (SHI) Demag Plastics Machinery Group. The impact of Stephan Greif’s contribution, comprising the merger with Sumitomo Heavy Industries Ltd. in March 2008 and the expansion of production capabilities in Ningbo in April 2015 have all been critical in cementing the company’s domestic market presence and global reputation as an machinery innovator, states the company. Reflecting on the importance of the Chinese market and the significance of Sumitomo (SHI) Demag being the first European injection moulding machine manufacturer to establish its presence there, CEO Gerd Liebig hailed Stephan Greif’s entrepreneurial spirit as being the pillar of the company’s deep rooted success. The team at Ningbo, China with their incoming and outgoing Managing Directors Mr. Stephan Greif (in the middle on the left) and Mr. Pietro Scattarreggia (in the middle on the right) At the start, the company’s production area in Ningbo measured 3,500 m². In 2015, driven by rapidly growing demand for technically advanced injection moulding machines, Ningbo’s production footprint increased more than fivefold. Having realised his ambition, creating a prospering enterprise and paving the way for future growth in China and South East Asia, Stephan hands over the reigns to successor Pietro Scattarreggia. Returning to Germany, Stephan Greif will continue to consult with Sumitomo (SHI) Demag, sharing his extensive service and sales experiences. For more than 18 years, Pietro Scattarreggia has worked at Sumitomo (SHI) Demag Plastics Machinery GmbH in numerous sales and service management posts. As the former business development director for the company’s electronics and medical segment at the Group’s European headquarters, Mr. Scattarreggia is expected to bring a fresh service and consultancy perspective when he relocates to China, effective September 9, 2019. www.sumitomo-shi-demag.eu Milliken invests in Asia with new manufacturing facility in Singapore Expected to begin operations in Q1 2021, the facility expands Milliken’s chemical manufacturing footprint to support increasing demand across Asia, including rapidly growing markets in India and China. The company currently operates an applications lab and technical service and sales office in Singapore, and recently celebrated its 20-year presence in the region. “Milliken’s commitment to our growing markets in Asia is unwavering. With this investment, we hope to expand the positive impact innovative chemical manufacturing can contribute to the region and to the world,” said Allen Jacoby, senior vice president of the Plastics Additives business within Milliken’s Chemical division. The new plant will have the capability to manufacture several integral Milliken plastic additives that bring sustainability and production benefits to the global plastics industry. Primarily, the location will produce the company’s Hyperform family of nucleating agents for polypropylene (PP) and polyethylene (PE); as well as specialty colourants for a broad range of product applications, including home and laundry care, personal care, industrial and institutional cleaners, and polyurethane foams. www.milliken.com WikiPETia.info More than 300 companies at","@ID":10}, "TRADE SHOW PREVIEW PETplanet Insider Vol. 20 No. 10/19 petpla.net 64 Sustainability and recyclability The common thread running through all the new Sacmi products at the K show is sustainability. The solutions on display demonstrate means of reducing the amount of virgin resin used in processes and augmenting opportunities for complete recycling, in accordance with circular economy principles. It will be showing how the use of larger quantities of recycled resins, to the point that they constitute the bulk of materials employed to produce containers is already a reality. Sacmi will be showing its IPS220 injection preform system, which can make 100% rPET preforms and use up to 50% recycled PET flakes, using standard machines and hot runners. Both the IPS220 and IPS400, with 96 and 128 cavities respectively, are designed for fast size changeovers and, on the larger version, compatibility with most commercially available resins. The solution showcased at the fair is an intrinsically sustainable ‘native’ solution that requires no modifications to the machine. Artificial Intelligence (AI) The company will be presenting Computer Vision, which it says is the first complete system for the on-line identification of abnormal stress on preforms via a combination of polarised light and advanced AI algorithms. Polarised light inspection has been impossible to perform directly on-line because traditional algorithms were not up to the task. Sacmi says it has succeeded in replacing traditional, manual sampling checks with a fully automated control system. The PVS10L on the stand will demonstrate how the new control system enables ‘self-learning’ required checks. This simplifies QC procedures and enables operators to work directly on the line without having to manually set complex and changing inspection recipes. Sacmi says that developments of AI algorithms, used in conjunction with traditional video camera inspection techniques, are being driven by the need to simplify the system. The possibility of fielding new checks and, at the same time, simplifying the checks themselves with systems that can self-learn, address the most complex inspection needs of the plastics and metal graphics industries, while minimising waste and optimising process costs. The ultimate goal is to extend QC from inspection of every product to government of the entire production process, maximising line efficiency by objectively identifying problem types and origins. Multilayer compression CCMM (Continuous Compression Multilayer Moulding), developed and marketed since early 2019, is designed to combine established Sacmi compression with user-friendliness, process consistency and shorter cycle times. Initially focused on the manufacture of single serve capsules for coffee, tea and other foods and drinks, development projects have resulted in the capacity to manage a broad range of materials and minimise rejects, through improved process consistency. Compression Blow Forming Sacmi CBF (Compression Blow Forming) is designed to enable manufacturers to precisely produce plastic containers directly from pellets, helping to lower average raw material consumption and augment the humidity barrier effect by up to 40%. First prototyped by Sacmi in 2004, the single-stage CBF method consists of a continuous plastic extrusion process in which the outflowing material is cut into pellets. These are then inserted in an open mould and compressed to make a preform. It is not cooled completely but regulated to a temperature that allows immediate blow-moulding. CBF offers weight reduction of up to 10% and, therefore, less raw material consumption and containers that augment the humidity barrier effect by 30-40%, for the pharmaceutical packaging industry. The possibility of replacing traditional PS and PE resins with PET, especially in the dairy field, lets customers take a step towards the circular economy without having to do any further work on production lines. Solutions on the Sacmi stand will be an application for the pharma sector, alongside some PET dairy container samplings. CBF is equipped with a video camera container inspection system. It has been designed as an open system, suitable for installation on the line with other Sacmi or third party machines, and has a greatly reduced footprint. Compression works at lower temperatures than other technologies, lowering energy and raw material consumption requirements. EVOH barrier film can be inserted between the different layers, sealing in the organoleptic qualities of products like coffee without any need to act on secondary packaging. Sacmi says that its CCM multilayer compression allows producers to choose the number and type of layers to insert, according to the specific product being packaged. The tie layer can be managed separately in dedicated layers, reducing required quantities and thus preserving the purity of the polypropylene, at lower cost. www.sacmi.com Hall 13 Sacmi Booth A63 CCMM Continuous Compression Moulding Machine","@ID":66}, "MARKET SURVEY 44 PETplanet Insider Vol. 20 No. 10/19 petpla.net Closure inspection Company name Pressco Technology Inc IMD Ltd. Postal address Telephone number Web site address Contact name Function Direct telephone number E-Mail 29200 Aurora Road, Cleveland, OH, USA +1 440 498 2600 www.pressco.com Mr Tom O'Brien VP, Marketing, Sales & New Bus. Dev. +1 440 498 2600 [email protected] Industriestrasse 37A, 2555 Brügg Switzerland +41 32 366 80 66 www.imdvista.ch Mr Martin Gerber Sales Director IMD Ltd. +41 32 366 80 66 [email protected] Inspection system High-speed Vision System IMDvista Closure Vision Inspection Standard Closure Inspection Line IMDvista CLCO OEM Closure Vision Inspection IMDvista SPIX Pinhole Detection System IMDvista SDL Slitting & Folding System Inspection speed Up to 3,600ppm Up to 4,000ppm - 240,000pph Up to 4,000ppmin-240,000pph (on customers request) Up to 2,000ppmin-120,000pph (on customers request) Inspection method Non-destructive, In- or off-line solution as a downstream solution, from undermould conveyor (UMC) to cooling conveyor (CCS) in the feeding system (WFS) up to the vision inspection (CLCO) and packaging station (BS), integrated as OEM systems in any kind of machine Integrated in any kind of external OEM systems such as sssembly machines, folding- and slitting machines, robot-systems, labelling machines Non-destructive in-line solution as a complete downstream solution, new high voltage source with password protection Slitting & folding, inspection & complete downstream equipment for closure production Inspected objects Food, beverage, pharma, specialty, dispensing, sport, plug seal or liner, injection or compression moulded One piece closures, assembled closures, doy pack closures, oil closures, sport caps, aluminium (longskirt) closures, rubber parts, coffee cups, coffee filters, shampoo- and medical closures, lens- and food containers, pouches One piece closures, assembled closures, doy pack closures, oil closures, sport caps, coffee cups, shampoo- and medical closures, food containers One piece closures, assembled closures, oil closures, sport caps, shampoo closures, medical closures Inspected parameters: - Inner inspection Yes Short shots, overfill & flashes, contamination, seal defects, colour & colour changes, deformations, diameter & ovality , laser marking inspection Short shots, overfill and flashs, contamination, seal defects, colour & colour changes, deformations, diameter and ovality, laser marking inspection - Outer inspection Yes 360° outside view, colour & colour changes, contamination, height measurement 360° outside view, colour & colour changes, contamination, height measurement - Geometry Yes Upon request Upon request - Cavity number reading No Easy teach in function, cavity recognition, cavity related statistics and alarm Easy teach in function, cavity recognition, cavity related statistics and alarm - Microhole inspection No Upon request - Additional inspection criteria for inserts Wide range of insert types and materials Upon request Further inspection options Colour, UV, print/deco, liner/wad, caps on filled containers IMDvista CLDP Closure Digital Print System, SDL Slitting & Folding System, BTIX Barrier Testing System - Closure Barrier Inspection System Complete closure Inspection after slitting and folding Installation: Stand-alone (offline) Yes Flexible in-line or off-line system solution Inline Yes Flexible in-line or off-line system solution Software features: Real-time trend data, last 100 images, defective image database/ archive, remote access, biometric user login, customisable reports, OPC connectivity IMDvista V5 VCC - Vision Control Center with newest intelligent software technology IMDvista Portal, connects all system on one central data base (HMI for fast and transparent production overview) IMDvista Portal, connects all system on one central data base (HMI for fast and transparent production overview) IMDvista V5 VCC - Vision Control Center with newest intelligent software technology; IMDvista Portal, connects all system on one central data base (HMI for fast and transparent production overview)","@ID":46}, "BOTTLE MAKING 28 PETplanet Insider Vol. 20 No. 10/19 petpla.net German technology with Indian engineering artistry Blow moulding machines for medium-scale outputs by Kay Barton The neighborhoods of Waliv, 40 km north of Mumbai, is home to Global PET Industries Pvt. Ltd., a manufacturer of semi- and fully automatic blow moulding machines. It has been building systems for beverage bottling businesses in the small- and medium-sized performance segment, as well as for food and non-food packaging businesses, for 20 years. The family-operated company also operates Dynamic PET Mould, a wholly-owned subsidiary, as a separate division. It designs custom and bespoke blow moulds according to customer requirements, for both Global PET and third-party operators. March 2019 We met: Jugal Panchal, Head of Business Development, Global PET Industries Bipin Panchal, Managing Director, Global PET Industries Milan G. Kotadia, Partner, Dynamic PET Mould A hydraulic elevator took me directly to Global PET’s reception area, where I was greeted by the sight of copies of PETplanet magazine on display. Head Business Development Jugal Panchal, relaxed in his air-conditioned office on a typically baking hot Indian day, showed me a range of PET bottles that have been manufactured using his systems. Also in the office was his uncle, Director Bipin Panchal, who founded and established the company in 1996. Initially, it constructed only semi-automatic blow moulding machines. “Our first machines manufactured 600bph. We reached 1,000bph in the early 2000s, and then 2,000bph followed,” he explained. “We subsequently brought our fully automatic machines onto the market, first with two cavities and then with four. This enabled us to make 5,600bph. Our next step was the fully electric servocontrolled blow moulding machines, with capacities of 6,000-9,000 bottles.” Global PET constructs approximately 150 semi-automatic and 36 fully automatic systems per year. The demand for cost-effective systems has increased steadily, so the newer models of semi-automatic systems respond appropriately. “A key attribute of our systems is the components that we install,” Mr Jugal continued. They use components from Festo and Schneider. “Quite simply, we believe in German technology and durability”. In addition to customers in India, Global PET sells 30-40% of its products to African countries and 10% to Gulf states, and its equipment is also to be found in Nepal and Bhutan. Its Indian customers include Bisleri, Parle Agro, Sab Miller (Foster’s) Group, Xotik Bev., Sunpet, Hamilton and the ITC Vendor. Around 60% of its machines are used in beverages and liquid food packaging; food items (such as cans) account for 25-30%, and non-food products for approximately 5%. Water bottlers form the largest proportion of beverage bottle converters, followed by producers of CSD and fruit juice. Edible oil is an increasingly important market with innovation of online as well as offline handle type jars as a competitive replacement for HDPE containers in the 2-3l segment. In 2019, the company has forecast that its combined turnover will be approximately US$4.8 million. Blow mould manufacturing We visited Dynamic PET Mould’s premises, which are just a short walk away from Global PET. It manufactures blow moulds on seven CNC machines supplied by Californian Tour Sponsors: Head Business Development, Jugal Panchal in his off ce Bottles produced on Dynamic PET Mould equipment","@ID":30}, "TRADE SHOW PREVIEW PETplanet Insider Vol. 20 No. 10/19 petpla.net 62 Infrared-rotary drums for various applications in plastics processing and recycling Gentle PET decontamination At its exhibition stand, Kreyenborg GmbH & Co. KG from Senden, Germany, will be showing its IRD B 180/270-135, thus representing all kinds of infrared applications in the plastics processing and recycling industry. Individual, tailor-made infrared rotary drums are available for pre-heating, crystallisation, drying and coating of virgin materials. The company has developed the IR-Clean especially for de-gassing and decontamination processes of PET post-consumer bottle flakes. This economical solution for the treatment of recycling material, which has already been awarded a letter of non-objection by FDA and positive results by EFSA, will be one of this year’s highlights at Kreyenborg’s booth. Apart from complete production lines for bulk material handling processes, infrared rotary drums are the key competences of Kreyenborg GmbH. Several hundreds of these systems have already been installed world-wide in the plastics processing industry alone. Their fields of application are as manifold as the designs selected by each specific customer individually. But the one thing they all have in common is their functional principle: the PET post-consumer bottle flakes are poured into the rotary drum through a volumetric dosing system. Inside the drum, an in-welded helix and the continuous rotation ensure a homogenous material flow at a pre-defined residence time (first-in/ first-out principle). At the same time, the material is mixed and a revolution of the surface takes place permanently, which causes the infrared elements tailor-made geometry, the targeted process control and a special control unit make the IR-Clean an ideal drying and decontamination unit for PET recycling material. This has been confirmed by a Letter of Non-Objection issued by the American FDA Authority and by several challenge tests, which have proven conformity with the criteria of the European EFSA. PET recycling material, which has been dried and decontaminated in the IR-Clean, can be used for packaging that comes directly into contact with the foodstuff. Consequently, the IRClean itself, which works without any Hall 9 Kreyenborg Booth A55 positioned above the material bed to achieve a quick and even heatup result. Infrared rotary drums work without any expensive vacuum technology and are designed according to each customer’s individual requirements as to their size and length. They can be designed either as a stand-alone solution or as a unit to be incorporated into a new or an existing extrusion line. The IRD B 180/270-135 that will be exhibited has a diameter of 180 cm, a length of 2.7m and is perfectly suited for material flows of up to 800 kg/h. Kreyenborg’s IR-Clean is a very specific development of an infrared rotary drum especially for the treatment of PET recycling material. Its IR-Batch for PET masterbatch drying processes The IR-Clean is a drying and decontamination unit for PET recycling material","@ID":64}, "TRADE SHOW PREVIEW PETplanet Insider Vol. 20 No. 10/19 petpla.net 71 and standardised interface across the model range assisting in operator training. Major machine functions can be added or updated via software installation only. The revised ASB-12M expands the capabilities for production of a vast range of PET containers, including efficient lightweight bottles and wide mouthed jars. Key features include: Ability to process more than 20 resin types in addition to PET Moulds containers from 5ml or less all the way up to 2.5 l capacity Variable cavitation for up to 15mm neck diameter bottles in eight cavities through to 83mm neck diameter jars in a single cavity Servo driven hydraulic pumps installed as standard, contributing to major energy savings and offering smooth and quiet operation Backwardly compatible with existing class mould tooling with minimal modifications Small size allows fast mould changeovers will minimal manpower, and minimal lifting equipment. The model displayed at K’ will be fitted with the optional IU-10L long stroke injection unit that provides a 50% increase in available shot-size, expanding the scope for large containers, heavy-weight cosmetic bottles, or materials with lower density. At the trade show, this machine will be moulding a 4-cavity “family” mould featuring two separate premium grades, glass-like cosmetic container designs of 80ml and 45ml fill capacity sharing a common preform design. Thanks to the use of Zero Cooling, the cycle has been reduced from a typical previous time of up to 40 s down to just 12.5 s to achieve greater than 3 times increase in productivity. This revised cycle is being achieved using standard bottle grade PET. Overview of Zero Cooling (patented)","@ID":73}, "51 TRADE SHOW PREVIEW PETplanet Insider Vol. 20 No. 10/19 petpla.net Hall 14 And&Or Booth B03 Compact machines for higher productivity per unit area At K 2019 the Engel e-mac 280 is taking to the packaging floor, allowing for a more granular performance gradation for the packaging industry in all-electric use cases. The Engel e-mac machines are exclusively equipped with particularly powerful servomotors, including the ejector and nozzle movement. This is intended to ensure maximum precision and process stability, and an optimum overall efficiency level. The series covers a wide spectrum of applications. Featuring clamping forces of 500, 750, 1,000, 1,800 and 2,800 kN, the e-mac machines have become very well established in the teletronics and technical moulding industries. Two series for even shorter cycle times In the high-speed, all-electric high-performance range, with cycle times of less than 6s, Engel’s e-motion series and e-cap machines, which are tailored to caps and closures applications, meet a wide range of market requirements with high precision and cost-effectiveness. Together, the two series cover a clamping force range from 300-6,500kN and achieve cycle times of less than 2s. Both the e-motion and e-cap machines are equipped with encapsulated toggle levers and a clean linear platen guide; this makes them ideal for strictly regulated production areas and cleanrooms in the foods and medical technology industries. www.engelglobal.com AGV - Automatic Guided Vehicle for the plastic industry TheAnd&Or AGV is specially designed for flexible blow moulding line automation, which requires intensive work and complex production flows. It can easily be integrated in existing production plants, with no need for machine movements or civil works. It allows the transport of pallets, boxes, bottle layers, etc. The navigation system and the mechanical solution are designed as per specific project needs. The navigation is incorporated and is safe and silent as well as having an energy regeneration system. The AGV minimises plant movements and reduces cost of indoor transportation. Several vehicles working together can recognise each other. Set-up time is very short and the system can be up and running from day one. www.andyor.com Hall 15 Engel Booth B42-C58","@ID":53}, "MARKET SURVEY 43 PETplanet Insider Vol. 20 No. 10/19 petpla.net 10/2019 MARKETsurvey Supplier for caps & closure and inspection systems For issue 10/2019 PETplanet asked machine manufacturers and mould makers of caps and closures to share their state of the art equipment details with us. In addition we asked for closure inspection systems. We thank all participants: z-Werkzeugbau GmbH, Sumitomo Demag, IMD Ltd., Sacmi Imola S.C., Intravis GmbH, Pressco, Corvaglia Mould AG and Husky Injection Molding Systems Ltd. Although the publisher has made every effort to make sure that the information in this survey is up to date, no claims are made regarding accuracy and completeness. Moulds for caps & closure production Company name z-moulds Corvaglia Mould AG Postal address Telephone number Web site address Contact name Function Direct telephone number E-mail z-werkzeugbau Gmbh, Dr.-Walter-ZumtobelStrasse 9, 6850 Dornbirn, Austria +43 5572 7272 0 www.z-moulds.com Mr Michael Fink VP Sales & Marketing +43 5572 7272 610 [email protected] Hörnlistr. 14 8360 Eschlikon, Switzerland +41 71 973 77 77 www.corvaglia.ch Mr Albert Brunner Director Sales & Service +41 71 973 77 52 [email protected] Filling good: - beverages Carbonated and non-carbonated drinks, water, juices, beer, coffee & teas, dairy, etc. Carbonated soft drinks and non-carbonated pressurised & non-pressurised beverages including water, juices, teas, milk/dairy, coffee, beer, isotonics, energy drinks, etc. - other Edible oil, soy sauces and other filling goods possible on request Edible oil, detergents, other contents/applications possible upon request - individial cap solutions Possible on request Possible, upon request Closure: - type All single-piece standard closure dimensions for all neck finishes, sports closures, flip-tops, push-pulls, multi-component closures… Flat top & sports closures for beverages for 25, 26, 27, 28, 29, 30, 31, 33, 37, 38, 43, 48mm neck finishes, e.g. Alaska, 1810, 1881, 29/25, 30/25, 33 HF, 33 ACF, 38 HF, 38 ACF - material HDPE, LDPE, PP, TPE, … HDPE (PP for transparent parts) - weight Lowest from 0.7g Starting from 0.8g Moulds: Clamping dimensions/ cavities 16 - 128 cavities 24 - 96 cavities Preferred hot runner suppliers Mold Masters and others Various Special features Several patented technologies for most efficient closure production, with lowest downtimes and spare parts usage Closure design approvals from all major beverage brand owners; most economical closure designs for private labels; tethered cap solutions for carbonated and non-carbonated drinks according to requirements of EU Directive 2019/904 Systems for caps Company name Sumitomo (SHI) Demag Plastics Machinery GmbH Husky Injection Molding Systems Ltd. Postal address Telephone number Web site address Contact name Function Direct telephone number E-mail Altdorferstr.15 90571 Schwaig Nürnberg, Germany +49 911 5061 0 www.sumitomo-shi-demag.eu Mr Arnaud Nomblot Director - Business Dev. Packaging +49 911 5061 625 [email protected] 500 Queen St S Bolton, ON, CAN L7E 5S5 +1 905 951 5000 www.husky.co Mr Michael White Business Manager, Beverage Closures +1 905 951 5000 ext. 2913 [email protected] 500 Queen St S Bolton, ON, CAN L7E 5S5 +1 905 951 5000 www.husky.co Mr Henry Zhang, Dir. Busin. Dev., Medical and Specialty Packaging +1 905 951 5000 ext 5196 [email protected] Systems for cap/closure production Model El-Exis SP HyCAP4 225t RS50/50; RS60/60, HyCAP4 300t RS50/50; RS60/60; RS70/70, HyCAP4 400t RS60/60; RS70/70, HyCAP4 500t RS70/70 HyperSync Procession technology Injection Moulding Injection achieved by a direct drive reciprocating screw Injection achieved by a direct drive reciprocating screw Clamp force 150 - 1,000t 225t (2,250kN); 300t (3,000kN); 400t (4,000kN); 500t (5,000kN) Cycle time (guaranteed 98% closure system efficiency for): 26mm: 2,800 caps/min Varies depending upon application Varies depending upon application - High speed production: closure type/weight/cavities: caps/min 29mm: 2,300 caps/min - Individual cap solution: closure type/weight/cavities: caps/min PCO 1881: 1,650 caps/min Drive concept Hybrid Clamp stroke achieved by a servo driven ball screw Energy consumption (kwh/kg) 0.40 - 0.50 Varies depending upon application Varies depending upon application Preferred mould makers z-moulds / Plastisud Husky Husky Special features Mould Identification (ID) ready; Mould Alignment ready large 19\" intuitive touch screen HMI for simple operation eIMC servo-driven in-mould closing technology Mould Identification (ID) ready; Mould Alignment ready","@ID":45}, "USED MACHINERY PETplanet Insider Vol. 20 No. 10/19 petpla.net 38 Trading with used PET machines A new life for old machinery For almost three decades it’s been a success story for PET Machinery, the first to market, identifying the opportunity to sell used PET machinery. PET machinery’s founder, Anthony Thompson, recaps the story of the first PET machine he sold back in the early 1990s. Anthony Thompson, founder of PET machinery at his daily work: inspecting used machinery. “It was a Nissei ASB650 – an old contact relay machine being sold by Constar at their UK plant in Sherburnin-Elmet. I was told the machine had been stored outside but under tarps at what was ominously called the ‘scrap yard’. It was a typical August morning, raining heavily, and as I came around the main building was greeted with the sight of several ducks happily paddling around in the pool made by the collapsed tarpaulin. A base cup applicator stood rusting a few yards away, perch for another duck which promptly flew off, annoyed by our intrusion. Such was the demand back then for affordable PET bottle making equipment that I immediately agreed the purchase, ducks and all! The machine itself was cleaned up, tested and subsequently shipped off to Kampala, Uganda.” Since that first venture Thompson and his co-director since 2008, Erik Van Bommel, have sold machines to around 135 countries. Thompson continues: “We have had the satisfaction of helping many start-ups off the ground and many of these are now national or internationally recognised players in the business. Our relationship with these companies has come full circle as they have now become our suppliers of used equipment. To assist sales where local knowledge is essential, we have appointed agents or on occasion, set up offices in different regions, most notably PETAnker Chile Ltda.” The internet has definitely changed things for the PET Machinery Industry. It has become easier for buyers and sellers to connect and many manufacturers, particularly larger multinationals with lots of potential equipment, have tried to exploit this by posting their own equipment online. However, as many have discovered, listing the equipment is the easy bit. Responding to the many (often fruitless) requests for information takes time, especially as many potential buyers require costs for dismantling, loading, packing, shipping, insurance, and subsequent start-up and training. Then comes price negotiation – often very convoluted and finally, many overseas buyers need to pay via letter of credit or other fiscal means due to exchange rate controls. “This is where we come in,” says Van Bommel, “we have been doing this for almost three decades now and have learned a tremendous amount in that time. We can usually weed out the tyre kickers from the ‘real’ buyers and we can establish the ground rules to manage a smooth sale. Unfortunately, sales margins aren’t what they used to be and typically we work on a tight percentage in order to move machines quickly for the sellers. We still see many brokers hiking up the prices on equipment, including our own offerings, in the hope that a buyer will come along and pay a premium. That is not our style. Our suppliers appreciate that we are actively selling the equipment at close to base cost and of course this also benefits our buyers. We can be very competitive because we run a very lean business and try in so far as possible to broker machines from seller to buyer.” To positioning themselves as a uniquely PET reseller, the company has recently invested in the launch of a new website. This extends their services to other dealers or direct sellers via a dedicated area of the site where dealers can add their equipment for sale, for free and take advantage of their digital marketing tools to showcase their machines to a wider market. Van Bommel comments, “Our database is comprised of customers who have actually dealt with us in one way or another over the years and is constantly updated to ensure all the data is real. So, it is a very valuable resource to us. The recent GDPR requirements allowed us to re-engage with clients old and new to establish whether they wished to remain on our database and as such receive our regular emails flyers. Nearly all respondents confirmed to remain which was very pleasing.” It’s a win-win situation with the sellers benefiting from a professional marketing process and customers being assured they are dealing with an established and reputable brand in terms of reliability, investment control and logistics to ensure as safe a transaction as possible. The directors will be attending the upcoming K’ show via Sipa stand hall 13, booth B11. www.petmachinery.com","@ID":40}, "48 TRADE SHOW PREVIEW PETplanet Insider Vol. 20 No. 10/19 petpla.net product development caps & closures design high cavitation moulds multi-component moulds closure production systems after sales service competent – professional – inspiring Dr.-Walter-Zumtobel-Strasse 9 | 6850 Dornbirn | Austria | www.z-moulds.com K-SHOW 2019 October 16th-23rd meet us in hall 10-H48 Mould at K-Show 26mm 3-start water 72-cavity with patented z-slides @Sumitomo Demag, Hall 15-D22 Solutions for sustainable manufacturing Among t he exhibits of SMI will be the compac t EBS 4 K ERGON series of compact fully electronic stretchblow moulders. Capable of satisfying production demands of up to 9,200bph, the EBS K models are available in 2, 3 and 4-cavity versions, and offer all the advantages of rotary technology in a “speed” range traditionally controlled by linear stretch-blow moulders, states the company. Among these advantages are a compact modular design; high technological content, inspired by Industry 4.0 and IoT concepts; easy management and control of the production cycle; an electronic machine with transmission systems employing brushless motors; low operating and maintenance costs as well as low energy consumption and eco-friendly processes. To achieve the latter, the stretch-blow moulding carousel is equipped with motorised stretch rods, controlled by electronic drives which do not require mechanical cams; this solution is claimed to ensure precise control of the path of the stretch rod, energy savings and reduced mechanical interventions. The EBS 4 K Ergon stretch-blow moulder showcased at K is equipped with preferential heating, that is suited to the production of non-cylindrical containers for detergents, cleaners, cosmetics, pharmaceutical products, sauces, condiments and some alcoholic beverages, with the ratio of the long and short side exceeding 2. It uses a differentiated/dedicated temperature profile, ensuring a good material distribution and the elimination of zones with an excessive thickness. It also claims to facilitate labelling and to optimise the weight of a particularly complex container. www.smigroup.it Hall 14 SMI S.p.A. Booth B69 Recycling technology: a new life for PET bottles PET bottle flakes are a valuable secondary resource. At K show, Starlinger recycling technology will be presenting recycling solutions for three different applications: bottle-tobottle, bottle-to-fibre, and bottle-to-bag. Bottle-to-bottle: Starlinger has installed more than 55 PET bottle-to-bottle recycling lines worldwide with a total installed capacity of 550,000 metric tons/year. The lines are available for a throughput of 150 up to 3,600 kg/h. The cleaning efficiency of Starlinger’s recoStar iV+ PET recycling lines meets the strict criteria of various national and international authorities (e.g. EFSA, FDA) with regard to food contact as well as the quality requirements of major brand owners. Bottle-to-fibre: The biggest challenge nowadays lies in material quality. If bottle flakes are mixed with polyester fibres, the material may require high-end filtration and/or an increase in intrinsic viscosity (IV). Starlinger has the entire technology in-house: solid-state polycondensation plants for IV increase, and a continuous polymer filter, the Rapid Sleeve Changer, for finest filtration down to 15 μm. Bottle-to-bag: Post-consumer bottle flakes are turned into polyester tape fabric for bags or big bags / FIBCs that are in turn recyclable. The production of packaging from waste (i.e. PET flakes) saves valuable resources and allows for a closed loop production. The first rPET FIBC projects have just been installed in Europe and Asia. www.starlinger.com Hall 9 Starlinger Booth D22","@ID":50}, "54 TRADE SHOW PREVIEW PETplanet Insider Vol. 20 No. 10/19 petpla.net Sukano - Your Specialist in additive and color Masterbatches for PET, PLAand specialty resins. www.sukano.com Meet us at K 2019 - Hall 8A, H28 and join our daily presentations Scan QR-Code to find out more. New IBM model designed to produce small PET containers Jomar Corp. manufacturer of injection blow moulding (IBM) machinery for the pharmaceutical, healthcare, and household products industries will launch the TechnoDrive 65 PET machine at the K show. The newly designed IBM machine is specifically designed to run PET resins but can easily switch back to other materials for injection blow moulding such as polypropylene (PP) and polyethylene (PE). The TechnoDrive 65 PET machine is a high-speed IBM production machine first unveiled in 2017. It has a dry cycle time of only 1.7 s. At K it will run 50ml perfume bottles in clear PET on a six-cavity mould. Using the original TechnoDrive platform as the base, Jomar engineers expanded its capabilities by adding a more robust plastifier motor, high-pressure valves, as well as built-in nozzle heaters to aid in the processing of PET. Some IBM machines require a fourth station to process PET. This “extra” station is used to condition the core rods and ensure the correct temperature before enveloping the rod in PET. The Jomar TechnoDrive 65 PET accomplishes this task in the ejection station, thereby merging the third and fourth stations. This gives Jomar the ability to manipulate the core rod temperature and create the optimal processing conditions within a super-fast cycle time. The TechnoDrive 65 PET can mould a variety of shapes and sizes in PET. The average wall thickness for a TechnoDrive 65 PET bottle in PET is about 1mm, so it is more suitable to mould jars, vials, and bottles for the pharmaceutical or cosmetic industries rather than the beverage industry. All PET projects for the TechnoDrive 65 PET would be accepted as a turnkey project where Jomar would build both the machine and mould. This allows Jomar to tailor the equipment to provide the widest processing window and ensure the project’s overall success. At the K show, Jomar will continue to demonstrate its ability to work with different materials in projects that are considered unusual for IBM. Such was the case at NPE 2018 when the company moulded polycarbonate lamp covers for LED bulbs. www.jomarcorp.com Hall 14 Jomar Booth A32 Hall 9 Tecnofer Booth C76 Hot treatment unit Mod.MTC1 Flexibility, compactness, water and energy saving: these are the strong points of the new hot treatment unit MTC1 that Tecnofer will show at K’ 2019. The scope of this machine is to remove contaminants like glue and oil from the PE-PP-PET flakes using a hot washing process with or without the use of detergents. The whole process is controlled by a dedicated management programme with the aim to streamline all the phases of the process that can be customisable according to the treated material. This unit has been designed with the possibility to add a second module to double productivity. www.tecnofer.biz","@ID":56}, "INSPECTION 41 PETplanet Insider Vol. 20 During the guided tour through the production hall, the voice control was demonstrated to the visitors on a Tornado II dynamic. These create full transparency and genuine know-how automatically with large touchscreens and the Heuft NaVi user guidance including Heuft checkPoints and audiovisual step-bystep assistance. Heuft brought the very first systems with monitors to the bottling hall for a better overview. Soon followed its own graphic user interface, then the audiovisual Heuft NaVi user guidance and finally even a real voice control for full operational reliability and productivity. The audiovisual Heuft NaVi user guidance makes the operator a competent user. On the rare occasions when he has to take action it is explained to him in words, pictures and sound step by step and shown in detail what has to be done where and how. He can therefore restore full operational reliability without a great deal of prior knowledge. This marks the provisional peak of the second basic developmental concept which Heuft has promoted from the very beginning: as much overview, assistance and support for the operator as possible. Not only forward drive with countless technological pioneering achievements of the last 40 years has brought the medium-sized family-owned company on a sustainable course for success, but also the resulting continuous growth in the company’s area, international sales and service locations as well as competent employees in research and development, production, project planning and support. Today, Heuft Systemtechnik GmbH, which produces exclusively in Germany, is a globally active manufacturer of modular systems for sustainable quality control and inspection in the filling and packaging of beverages, foodstuffs and pharmaceuticals. www.heuft.com We do more. KRONES Recycling Solutions #GermanBlingBling #KronesMetaPure K 2019 Düsseldorf, 16 – 23 October OA Hall 15/15.1","@ID":43}, "PETplanet Insider Vol. 20 No. 10/19 petpla.net 76 PETbottles Beverage + Liquid Food Cereals for drinking Under the name “Landliebe Mein Morgen”, German company Landliebe Molkereiprodukte GmbH has created four different drinkable yoghurts combined with a preparation of fruit and cereals. The contoured 350 g/330 ml bottles have sleeve labels with printing appropriate to the variety and are easy to distinguish from one another by colour differences. Like with many products, the sleeve label has perforations for sorted recycling. For market launch and to attract new customers, the white screw cap has a sticker with information about a free trial promotion. www.landliebe.de Smoothie with healthy additive Under the name “Innocent plus”, smoothie pioneer Innocent Alps GmbH has launched a new range onto chiller shelves. The four varieties – Berry Set Go, Blue Break, Citrus Shield and Wonder Green – contain additional vitamins alongside freshly pressed juices and pureed fruits and, depending on the variety, goji berries, ginger, matcha or blue spirulina algae. They come in 750ml transparent bottles typical of the brand with a screw cap fitting the shape and a freshness seal that goes over the cap as a tamperevident seal. www.innocentdrinks.de","@ID":78}, "TOP TALK PETplanet Insider Vol. 20 No. 10/19 petpla.net 11 for the reheating process before the stretch blowing – the smaller mass of PET material can be heated much more easily. A side effect is that NeckLite is visible at the bottle neck and can therefore be advantageous from a marketing perspective. PETplanet: Where do you see development opportunities for ReduPET GmbH? Stefan Bock: The training sessions and system evaluations are currently establishing themselves well on the market. Practical specialised training sessions for production staff are more in demand than I expected. This also applies to refresher courses. This is definitely because the efforts pay off in many ways in production. Furthermore, we are also active in implementing individual measures for system optimisation, working closely with component manufacturers for these systems and thus developing innovative technical approaches. The main focus however is MintTec and Neck-Lite. We are convinced that with the ongoing discussions about plastics among processers and through the pressure on legislators and machine manufacturers, innovations like these will be implemented. The PET bottle is a plastic product that hardly any other product can replace. But we must deal with the PET bottle more responsibly. And it is exactly here that ReduPET GmbH can offer further development opportunities, when we take on this responsibility. PETplanet: In your opinion, what are the greatest challenges for the plastics industry over the next ten years or so? Stefan Bock: Plastics are generally better than their reputation. The main problem is that they are not always in the right place, or are used wastefully or not in the right composition. After fulfilling their task, they are seldom seen as recyclable, i.e. as an important resource. And this is precisely where the tasks of the plastics industry lie in the next ten years. But I am convinced that here too, global legislators have a great responsibility and task to tackle. Because the plastics industry, and primarily the packaging industry, lives on low margins but on mass production, it is comparatively sluggish and inflexible in terms of changes to products or processes through innovation. As changes are almost always very cost intensive, there must be reconsideration to avoid the risks that are hindering the plastics industry. This is why new guiding principles and support measures applied by legislators to whole countries are so important. Unnecessary, resource-guzzling products must disappear from the market and the focus must be on guiding the material flows to after use and recycling. In my opinion, the focus doesn’t necessarily have to be on making plastic available again at the same quality level, as this also brings up the question on whether premium recycling also has a negative impact on the environment. It is also the responsibility of the suppliers of production systems to be encouraged to supply systems that take all of this into consideration and reflect on the future in a holistic and responsible way. Often, highperformance systems are delivered to developing countries with great pride, possibly even in exchange for financial incentives. But these high-performance systems ultimately produce rubbish on a grand scale, such as single use ice cream spoons – individually wrapped in foil – and the receiving country simply cannot deal with this. And it is here that there is little consideration. In short, for the next ten years, the challenges for the plastics industry are very varied, not only in our own back yard but globally. www.redupet.com www.mint-tec.com Compared to standard, with Mint-Tec is a 20% weightsaving on the base a common average. Mint-Tec left: minted preform with 1mm wall thickness / right: same preform not minted with 2.3mm wall thickness","@ID":13}, "BOTTLING / FILLING PETplanet Insider Vol. 20 No. 10/19 petpla.net 36 Solutions from stretch blow moulding to conveying Bottled water from Cappadocia A maze of towers, crevices, canyons, pinnacles and rugged castles; this is the fairy-tale landscape in the magical region of Turkey, in central Anatolia. It is in this region, rich with stone mines and marble quarries, that Badem Pinari, leader in the mining sector, decided to branch out and invest in the bottled water sector. To compete and diversify itself among other companies present in this market, Badem Pinari aims at high quality products and excellent service. To carry out these aims, the bottler turned to SMI for the project, creation and installation of a new production line of 22.500 bottles/hour to bottle and pack 0.33 l, 0.5 l and 1.5 l PET bottles with natural mineral water. The Badem Pinari company is part of the Bademler group, and was founded after an idea of the owner Murat Badem, who wanted to expand his business activities in the mining sector by investing in a new sector: bottled water. Despite the large number of soft drink and water bottling companies present in Turkey, the founder of Badem Pinari decided to become part of this sector thanks to the results of in-depth market research which highlighted a great opportunity for growth. The bottling and packaging line at Badem Pinari was designed and created to satisfy the specific requirements of flexibility, control and management of a modern “smart factory”. The installations supplied by SMI can be easily and automatically adapted to market demand for production flow and to switch quickly from one bottle format to another. The proposed solution includes an integrated system from the Ecobloc range, an automatic labeller, a shrinkwrapper from the SK 600F range and an automatic palletising system, which fulfil the requirements of this Turkish company to have a functional production line which is able to produce high quality products for a demanding market. “The suppliers must be able to provide the best technical solutions that satisfy our requirements in terms of operational efficiency, energy savings and controlled production costs,” says Murat Bardem. He chose an installation that was suitable to meet his aims, and today he is pleased to create water bottles in PET for still water that weigh only 9g. “They are very light containers that consumers are beginning to appreciate for their practicality, recycling and ecocompatibility and which will slowly take the place of the heavier, more rigid bottles that Badem Pinari are still using to bottle water,” Murat Bardem believes. www.smigroup.it Integrated system Ecobloc Ergon 12-36-12 EV Functions: stretch-blow moulding, filling and capping of 0.33 l/0.5 l/1.5 l bottles in PET with natural mineral water Badem Pinari, and a production capacity of up to 22,500 bph (0.5 l). Zafer Ozcan (third from left) SMI agent in Turkey with the staff of Badem Pinari Main advantages: The primary packing is carried out in an efficient and flexible way thanks to the integrated compact solution for stretch-blow moulding, filling and capping bottles in PET. Production of simple, light-weight bottles. Dual air recovery system, which allows to reduce costs tied to the production of high pressure compressed air. IR lamps mounted on the preform heating module to guarantee high energy efficiency. Shrink-wrapper SK 600 F Ergon Packed products: 0.33 l/0.5 l/1.5 l bottles in PET Packs worked: the 0.33 l and 0.5 l bottles in PET are packed in 4x3 and 6x4 film only; the 1.5 l bottles are packed in 3x2 film only Main advantages: Automatic machine suitable for packing different types of rigid containers.","@ID":38}, "PETplanet Insider Vol. 20 No. 10/19 petpla.net 67 67 a European trade show. The inspection system, which is optimised for the quality inspection of standard beverage closures, convinces above all with its innovative inspection solutions and the abundance of high-quality information it supplies about each inspected closure. The CapWatcher Q-Line checks up to 60 closures per second on typical features, such as sealing elements, threads and the tamper evident band, and for the first time an inline inspection system measures the temperature of the closures. “Especially in connection with our reliable and robust cavity reading, temperature measurement generates real added value through the accurate prediction of the shrinkage behavior,” says Christoph Wynands, Product Manager Caps & Closures. Software development in combination with CapWatcher Q-Line In combination with the CapWatcher Q-Line, the new IntraOptimizer software is introduced, which is intended to take the idea of the closed loop of Drinktec 2017 to a new level. During ongoing production the system takes high-precision measurements, collects extensive product data, and feeds this information into the newly developed software in real time. The correlation and analysis of the product and process data now offers the unique possibility of process optimisation, controlled by the inspection system. With the help of a well-founded database and machine learning algorithms, the operator at the production line receives a weighted selection of recommendations for action, and can work through them according to prioritisation. The CapWatcher Q-Line’s continuous BERICAP TetheredCap Easy Handling Safe application No Change to • Neck finish • Capper • Filling line For more information about BERICAP TetheredCaps: production monitoring ensures that success is monitored immediately, and leads to complete automation of the optimisation process in the subsequent steps. Performance in the IML segment Intravis will be presenting the IMLWatcher at four booths with a dedicated version of the inspection software IntraVision which is completely focused on IML defects. The new inspection software is characterised above all by a simplified setup of new products on the inspection system. The new comprehensive statistical functions enable an optimal analysis of the production line. The inspections have been improved so that the IMLWatcher can now cope with the most difficult applications. All IMLWatchers are now equipped with the IntraVisualizer trend and analysis software. It evaluates the machine and process data of all the Intravis systems used by the customer and other machines connected to the production lines simultaneously. Furthermore, the IntraVisualizer visualises all data graphically and reveals trends and serial defects before they arise. Interested parties can view and test the IntraVisualizer on their mobile phone. Smart camera solution for printing system The smallest system in the long list of Intravis inspection systems is the IntraOne single-camera solution. Integrated into a printing system of the partner Tampoprint, the system inspects for the presence and accuracy of a laser engraving on the inner top plate of standard beverage closures. www.intravis.com TRADE SHOW PREVIEW Hall Booth Exhibitor Product 11 A58 Intravis GmbH World first for preform inspection 13 A61 Husky Injection Molding Systems S.A World first for preform inspection 15 D22 Sumitomo (SHI) Demag Plastics Machinery GmbH CapWatcher Q-Line incl. CapFeeder & world first IntraOptimizer 12 A51-03 Beck Automation AG IMLWatcher & IntraVisualizer 13 A33 BMB S.P.A IMLWatcher & IntraVisualizer 15 D24 KraussMaffei High Performance AG IMLWatcher & IntraVisualizer 12 A36 Enelkon IMLWatcher & IntraVisualizer 4 C46 Tampoprint IntraOne","@ID":69}, "PACKAGING PETplanet Insider Vol. 20 No. 10/19 petpla.net 16 Different types of foamed bottles by PTI In the early summer (issue 06/10), Henkel in Vienna used a KHS Corpolast InnoPET Blomax8 CL PH to manufacture PET bottles of 1-3 l, with recessed grips for detergents and cleaning products. The bottles were destined for the Austrian market and another 18 markets in Eastern Europe. The long-standing cooperation between Henkel and KHS in determining the right designs and usability led to increased sales in certain countries, such as the Czech Republic, especially with large-volume bottles. A little later in the year (issue 10/10), PTI-Europa, Sidel and P&G presented the results of their collaboration in developing “Deep Grip Packaging”, an ISBM-moulded bottle with up to 25mm deep grip recesses, and challenged the extrusion blow moulding process previously used for this purpose. The bottles could have a diameter of up to 220mm. This allowed for a higher output per cavity – the target was up to 1,200bph – at the same time as lower material input in the manufacturing process, while the geometry of the recessed grip provided additional stability. The design made it possible for production to take place directly in-line within the filling line. Design of a deep grip bottle 2011 - 2015 In an interview in mid-2011 (issue 6/11), Procter & Gamble praised the possible material savings and higher outputs of PET ISBM bottles with comparable mechanical characteristics to HDPE bottles in home care products. In the long term, the proportion of ISBM – roughly 20% at the time of the interview – was to increase significantly. For this purpose, the company worked closely with Sidel to develop new packaging strategies. In the next issue of PETplanet Insider (7+8/11) we visited top ten European single-stage converter, PET Power. They were then serving only the pharmaceutical (clean room), cosmetics and food packaging sectors, with pharmaceuticals as their main area of business. At that time, the company had 52 single-stage systems from Nissei-ASB and Aoki and was able to manufacture 1,200 different products, with an annual output of up to 500 million containers. PET Power’s Managing Director Marcel Schröder A step forward to 2015 (issue 07+08/15) took us to Farmaplás in Madrid, Spain. The visit shed some light on the consumer behaviour in the country where, according to company statements, changes in packaging required a longer acceptance period. Despite this, the PET trend arrived in the southern European country as an alternative to other plastics and glass, with the processor adding PET to its portfolio from then on. At that time, Farmaplás already processed 50% PET for food applications and 25% for non-food on two-stage machines from Sidel, and single-stage machines from Aoki and Nissei ASB. F.l.t.r.: Waldemar Schmitke, PETplanet and Justo Antonio Yanez Vega, General Manager Farmaplás Towards the end of the year (issue 11/15), we visited PTI (Plastic Technologies Inc.) in Ohio. The meeting provided us with information about the market developments in the USA. The company, which accompanied customers through the entire product development process of beverages, food and non-food packaging, was able to closely follow PET packaging trends. Although there were already a number of applications in the nonfood segment at the time, we were told that change would only take place very slowly, as the US market was still too strongly based on PP and HDPE in the extrusion sector and, in most cases, the price of the raw materials, compared with PET, would not make a technical change worthwhile. The trends for these areas included the in-house development of the foamed oPTI bottle. Scott Steele, President and COO at PTI 2016 - today In an interview with masterbatcher Clariant in West Chicago in early 2016 (issue 1+2/16), the company revealed that it saw its growth market for PET applications lay clearly in the cosmetics sector. The company and its team had researched the current colour trends, created sample packaging on site using local equipment for beverages, food and non-food, and tested it for effectiveness under typical supermarket conditions.","@ID":18}, "BOTTLING / FILLING PETplanet Insider Vol. 20 No. 10/19 petpla.net 34 BOTTLING / FILLING 34 lute determination to innovate and their flexibility in finding solutions when special challenges sometimes have to be met.” This often goes hand in hand with the launch of new technologies. That was also true of the installation of the first InnoPET TriBlock at the RealPure Bottling Company in Magee, Mississippi, acquired by the family in 2017. The new pre-glued method used here prevents open bottles from coming into contact with hot melt vapours as in conventional labelling as the prepared labels are already coated in adhesive. The operators were at first sceptical of the new process yet were quickly convinced by the stable procedure – and by the fact that there was no longer any need for regular maintenance involving the arduous removal of residue adhesive. Kane Richmond of course also has the key economic figures in focus, such as his return on investment and overall operating costs. “Every cent counts – especially for us as a supplier to the major sales markets,” he emphasises. “And for a company which produces 24/7 our priority is how reliably the system can be operated with the least cost and effort. In this respect all of our KHS lines are distinguished by their enormously high degree of availability.” This also considerably eases the work of plant manager John Bickerstaff who for 13 years now has worked for the RealPure Bottling Company, founded in 1917. “The labelling process is a composite part of the TriBlock and must run at the absolute highest level of availability, effectiveness and quality,” he states. “Also, regarding ease of maintenance and production reliability along the entire line we’ve had top results right from day one with the pre-glued technology.” He puts this down not just to the innovative labelling method but also primarily to the continuous neck handling of the lightweight bottles which protects them from mechanical stress during production. The Silver Springs facility in Ocala in the heart of Florida is the Richmonds’ control centre: from here they also manage three other water bottling plants. The pre-glued labelling method used here for the f rst time prevents adhesive vapours from entering the bottles and reduces the maintenance effort. Your recycling needs. Our grinding solutions. +49 2154-94390 [email protected] triaplastics.de Hall B3 Booth 3118 all 9 t E05","@ID":36}, "MATERIALS / RECYCLING PETplanet Insider Vol. 20 No. 10/19 petpla.net 20 In the future, we will use more plastics – and why this is good news Physicist Michael Carus (MSc), founder and managing director of the nova Institute, has been working for over 20 years in the field of the bio- and CO 2 -based economy. He is considered to be one of the leading experts and market researchers in Europe in this field, and his expertise is valued in many societies, associations and international organisations. Bio-based News, the “Portal for the bio-based economy and industrial biotechnology” by the nova-Institut GmbH provided an interview to share with our readers, conducted by their Chief Editor Linda Engel. We hope that Michael’s answers to today’s challenges in the plastics industry are as interesting for you as they were for us. Linda: Currently, the plastics industry is coming under a lot of pressure. But you don’t seem to be too worried? Michael: Absolutely. There are no other materials that have such a broad spectrum of properties and they can be brought into any conceivable form with the greatest efficiency. In addition, plastics perform better than other materials under most sustainability criteria. This is due on the one hand to the high production efficiency already mentioned and, on the other, to their low density with which they can score points in transport. In addition, product properties can often be achieved with much less material input. Linda: So, there’s nothing to worry about at the moment and the current hysteria about plastics is unfounded? Michael: Not at all! There are significant problems, but all of them can be solved and must be solved urgently. It is estimated that around 20% of the plastics produced worldwide end up in the environment uncontrolled, that is 60 million tonnes per year, of which around 8 million tonnes end up in the sea. The rest remains on land in the soil, lakes and rivers. This is completely unacceptable. The other problem is the use of fossil carbon as a raw material that escapes into the atmosphere as CO 2 at the end of life. This also has no future, the entire chemical industry must switch to renewable carbon – which can come from recycling, biomass or CO 2 . “The age of plastics has only just begun” Linda: According to a recent survey, almost 80% of Germans consider plastics to be harmful rather than indispensable. Can we really solve these problems or should we not switch to other materials? Michael: But to which ones? The reserves of metals are limited and mining often takes place under inhumane conditions. And minerals? Sand for cement is already becoming a scarce commodity worldwide. In the future, we will no longer be able to build our houses from reinforced concrete, as we do today, but rather from plastics. Because their raw material carbon is practically unlimited: As CO 2 in the atmosphere, which we can make usable with the help of renewable energies or as biomass. That is enough raw material for the next millennia. This is the reason why plastics will gain in importance and the age of plastics has only just begun. And this is precisely why plastics must become sustainable as quickly as possible and win back a positive image. Linda: And who bears the main blame for the whole dilemma? Michael: The chemical and plastics industry, which has systematically tried to sweep problems under the carpet and sit out instead of actively pointing out and solving the problems. As one should expect from a crucial future industry! Linda: What are the mistakes that were made? Michael: The microplastic problem has been well known for at least ten years, which was when the Austrian documentary film “Plastic Planet” was first shown. But the industry acts according to the motto: ignore it, do not talk or write about it, just sit out the problem. The considerable quantities of plastic waste, which are also released into the environment in an","@ID":22}, "47 TRADE SHOW PREVIEW PETplanet Insider Vol. 20 No. 10/19 petpla.net TRADE SHOWpreview www.sise-plastics.com - e-mail: [email protected] HOT RUNNER CONTROL MOLD TEMPERATURE CONTROL VALVE GATE CONTROL PRODUCTION & PROCESS MONITORING PLASTICS TECHNOLOGY UNDER CONTROL INTERNATIONAL SPECIALIST IN TEMPERATURE AND PROCESS CONTROL FOR PLASTICS AND COMPOSITES Hall 1 / D06 Tethered caps for carbonated and non-carbonated beverages Corvaglia will be de-monstrating designs for closures that are attached to bottles (known as “tethered caps”). These conform to the requirements set down in EU Directive 2019/904 on the reduction of the impact of certain plastic products on the environment. Corvaglia has developed solutions for carbonated and non-carbonated drinks. The company states that it has always been their goal to reduce the consumption of materials and energy (and therefore also CO2 emissions) required to create packaging while keeping the specifications for each type of packaging the same or better. This goal will remain in place for tethered closures as well. The global bottle cap manufacturer Corvaglia is a highly specialised provider of closure solutions for the beverage industry. Founded in 1991, the company now has four production facilities in Switzerland, Mexico and the USA. www.corvaglia.com Automated modular intelligence Torus Measurement Systems will be demonstrating automated modular intelligence at their first ever K show appearance. Their latest development, the TQ Lab, is intended to expand on Torus’ unique modular philosophy and to offer customers a new approach to quality control whilst maintaining the most critical industry standard tests. The system is available as either manual loader or as a fully automated package that comes equipped with conveyor loading and intelligent container handling. Both solutions include a centrally controlled windows-based software package that offers customers faster, more reliable data with reduced operator influence. Measurements are fully traceable and certified to UKAS standards and data can be automatically transferred to all varieties of SPC and ERP factory network systems. The TQ-Lab offers customers unrivalled flexibility with selectable modules including automatic burst testing, non-contact internal diameter measurement, top loading, volume capacity, neck finish, body dimensions and thickness feature selections. Blank modules can also be included for future upgrades. www.torus-group.com Hall 12 Corvaglia Booth A51-10 Hall 14 Torus Booth B64 Biopolymers, collaborations for sustainable projects and products designed for recycling For a long time the reuse of PET was limited to application like fibre or often downcycling its original use. Times have changed and calls for innovative products and functionalities that address the poor quality and lack of standardisation of the current bale profiles as well as waste stream technology requirements. One focus is on upcycling PET mixed bottle flakes into thermally stable rCPET food trays. Sukano’s rPET masterbatch portfolio allows for higher rPET content and creates new recycling streams via additive and colour masterbatches. Sukano’s novel masterbatch allows bottle makers to run conveyer belts and robots at mixed speed increasing productivity and yields. Thanks to this mobility aid masterbatch, problems like release, scuffing and sticking are eliminated. There will also UV enhancers and biopolymer innovations exhibited at Sukano. www.sukano.com Hall 8a Sukano Booth H28 K show 2019 - Preview part 2","@ID":49}, "PETplanet Insider Vol. 20 No. 10/19 petpla.net 79 BOTTLES Two-phase make-up remover L’Oréal is selling make-up remover specially for long-lasting and waterproof make-up in a transparent 125 ml bottle. The product consists of a transparent and a blue liquid, which must be mixed by shaking before use. Placed on the bottle is a twocoloured hinged cap seal with an extended cap body. The fill level ends at the white cap edge. Semi-transparent self-adhesive labels provide retail information and enable a direct view of the two-phase product. www.loreal-paris.de biff pro nature in recyclate bottle “99.9% natural ingredients in a bottle of 100% recycled plastic” is how Henkel is advertising the biff pro nature bathroom cleaner, which contains sustainably cultivated ingredients. The transparent, easy-grip bottle holds 750ml of the likewise transparent product, which is dispensed through an adjustable trigger. Two labels describe the product, which has been awarded the blue environmental angel. www.henkel-reiniger.de ORGANISED BY: SILVER SPONSOR: SUPPORTING PARTNER MEDIA PARTNERS: BOOK NOW! Early bird rates available until 4 October 2019 Plastics Caps and Closures 2019 Conference 18-19 November 2019 • Beurs van Berlage, Amsterdam PROGRAMME ANNOUNCED! Key topics include innovation drivers, sustainability, the circular economy and tethered cap solutions. KEYNOTE SPEAKER: Hans van Bochove Vice-President Public Affairs Europe Coca-Cola European Partners Filip Vangeel Manager Circular Economy Valipac Augustin De Tilly Global Business Development Director Beverage Aptar Food + Beverage SPEAKERS INCLUDE: VIEW THE PROGRAMME AND REGISTER AT: PLASTICSCAPSANDCLOSURES.COM","@ID":81}, "58 TRADE SHOW PREVIEW PETplanet Insider Vol. 20 No. 10/19 petpla.net Circularity for Polymers: The ICIS Recycling Conference 5HGHȴQLQJ WKH GLVFXVVLRQ RQ FLUFXODULW\\ WR ȴQG VXVWDLQDEOH VROXWLRQV 5 November 2019 // Berlin, Germany NEW FOR 2019! As brand-owners continue to support and introduce circularity initiatives, the plastics industry looks for ways to support those targets to advance global commitments to the circular economy. The FMCG Panel: Maintaining brand values while supporting circularity KEY ATTENDING COMPANIES To check out the full agenda, speakers, attending company list and fees information Visit www.icisevents.com/recycling and book your place now for just €999! SESSION HIGHLIGHT Speakers from: Borealis &RFD &ROD Endress+Hauser (YRQLN Fater SpA -)& *URXS LyondellBasell 02/ *URXS PepsiCo 5HPRQGLV 3(7 RITTEC 6DEHUW TechnipFMC 8$% 5HWDO Veolia PET Hall 3 Packsys Booth D90 capLAB PackSys Global manufactures high speed machines for creating tamper evident bands by folding and slitting plastic caps. Until now the most important quality control test, known as the pull-off test, which checks the strength and consistency of the tamper evident band, has been done periodically offline in a remote laboratory. At the K show PackSys Global will introduce their latest development in this field, “capLAB” at their own booth as well as at the Engel booth (hall 15 booth B42-C58). capLAB is a fully automatic in-line pull-off tester for quality supervision of cap production. The system can select caps at random or caps which meet specific requirements, for example caps from each cavity on an injection or compression mould or caps which were processed on a specific mandrel on the folding and slitting machine. Because the testing is done on an ongoing basis the time to get the results is measured in seconds. In addition capLAB can use the test results to automatically change the settings on the folding and slitting machine so that caps never go outside the approved limits. Because the testing is done automatically capLAB helps to reduce labour costs. The lower labour costs can mean that cap production can be performed at a location closer to the site where the caps are applied to the filled bottles, thereby saving transportation costs and reducing the transportation carbon footprint. www.packsysglobal.com Maag enhances systems expertise For the first time in its history, all the Maag Group’s companies will be showing together at the K show, featuring all their system solutions together on their joint booth. Maag will also be represented in hall 16 in the VDMA’s Circular Economy Pavilion. The experience within the Maag Group extends across virgin polymer production, compounding, extrusion, mechanical end-of-life recycling of plastic products, and highly engineered industrial pump applications. Maag concentrates on melt pump and filtration technology, automatik on strand pelletising technology, and Gala on underwater pelletiser and dryer technology. The Group’s pulverisers are manufactured at the Center of Excellence in Kent, Ohio, USA. The Ettlinger product range now also offers high-performance filters for post-consumer recycling as well as solution packages downstream of the extruder. Maag’s Centers of Excellence in Oberglatt, Switzerland, Grossostheim and Xanten in Germany, Eagle Rock, Virginia, and Kent, Ohio in the USA, as well as Maag Italy and the subsidiary in Shanghai, China, offer the engineering expertise to combine global know-how in custom systems. Maags portfolio extends from small machines and systems for throughputs up to 100kg/h to machine and plant components capable of handling more than 100 t/h (centrifugal dryers, polymer pumps and custom solutions in industrial applications). At K’, trade visitors to the Maag stand will be served by an international team from all over the world, presenting new and upgraded machinery in pump, filtration, pelletisation and pulverising technology. www.maag.com Hall 9 Maag Booth A04","@ID":60}, "53 TRADE SHOW PREVIEW PETplanet Insider Vol. 20 No. 10/19 petpla.net BOTTLE INSPECTION SOLUTIONS K 2019 – 16 -23 October in Düsseldorf IMD Booth Hall 10 /A03 Swiss Made | www.imdvista.ch ALPS | www.alpsleak.com Vision Inspection Leak Testing Handling material the right way Suited to the big stage, Moretto, supplier of automation and auxiliary equipment for the plastic industry, will exhibit systems and products for injection moulding, blow moulding and extrusion. There are two exhibition areas in Hall 11, one specifically dedicated to the extrusion sector, with Contrex brand products, the group brand specialising in the supply of automation and control systems for blown film extrusion (Moretto Hall 11, Booth H 57, Contrex Hall 11, Booth E65). Particular attention is paid to the drying of PET granules, a delicate phase especially for large productions, typical of the rigid packaging and beverage sectors. In a dedicated area, Moretto will present a drying system consisting of an XD 800X series dryer combined with the OTX hopper and Moisture Meter Manager. This solution is able to guarantee certifiable results, energy efficiency for any type of material and a completely automatic system of the drying process. The turbo-compressors system of the XD 800X series dryer, together with the OTX hoppers, is stated to offer high levels of energy efficiency. The XD 800X dryers do not use cooling water or compressed air, being this another advantage in the treatment of PET and ensuring energy saving compared to conventional dryers. The use of the exclusive OTX hopper allows a homogeneous flow of the material inside the hopper during the process, an effective and controlled drying, with an energy efficiency of + 66% and a reduced material treatment time. In the treatment of PET in the beverage sector, one of the aspects to which Moretto customers are most loyal, is the constant treatment of OTX which ensures a stable process and an improvement in machine cycle times, in the order of half a second. This is equivalent to producing up to 17 million additional preforms per year. The Moisture Meter Manager application integrates the dryer into a responsive system as required by the 4.0 intelligent factory projects. It measures the initial moisture of the granule and based on this, knowing the precise behaviour of each material, it performs the appropriate drying cycle to obtain the result requested by the customer in terms of final moisture, which is then monitored at the hopper’s outlet. www.moretto.com Hall 11 Moretto Booth H57","@ID":55}, "BOTTLE MAKING 29 PETplanet Insider Vol. 20 No. 10/19 petpla.net BOTTLE MAKING 29 company, Haas. The equipment here is pretty new; all the machines were purchased within the last five years. The partners Mr Bipin Panchal and Mr Milan Kotadia, showed us a range of bottles based on Dynamic PET Mould Designs. Over the past few years, the share of moulds for third-party machines has become a genuine driving force for the company. “Our moulds are also used in Sidel or ASB machines,” Mr Milan Kotadia explained. “It’s a long time since we manufactured moulds only for our own machines; we offer a more cost-effective alternative for use in third-party equipment and we have acquired a large international market here.” Dynamic PET develops its products in accordance with customer requirements and specifications. It offers a very fast turn round time. “Including design and prototyping, we are able to deliver within five days,” he said. Together with Global PET, the family business employs approximately 155 workers, most of whom come from nearby villages, on shift bases. The plant covers a compact 2,000m2, with another 500m2 for Dynamic PET Mould. This is soon going to be extended to 1,300m2. The company has local offices for customer relationship management in Delhi, Hyderabad and Ahmedabad. Mr Jugal Panchal goes on to explain that, as the issue of recycling and environmental protection also gains ground in India, they want to become more involved. In the meantime, local authorities are also set to implement respective concepts with companies that integrate companies in the plastics segment more strongly. “As regards our products, in the future, it will be important for us to further develop and improve the energy efficiency of our machines,” he added. www.globalpetind.com The Global PET team in the factory hall The executive tier in front of the Editourmobil www.sacmi.com Product design Product development Product validation Industrial production plant Process & quality control On-site and start-up assistance After-sales and Customer service SACMI 4.0 THE COMPLETE CLOSURE, PREFORM AND CONTAINER SOLUTION FOR YOUR SMART FACTORY Compression goes multilayer. Enjoy SACMI innovation. The new SACMI CCMMTM applies all the advantages of continuous compression technology to multilayer capsules, creating a barrier effect that protects aromas and makes production processes more and more sustainable. Barrier layer Tie layer Tie layer Main layer Continuous Compression Moulding with Multilayer technology. TM Main layer","@ID":31}, "50 TRADE SHOW PREVIEW PETplanet Insider Vol. 20 No. 10/19 petpla.net .com 100815dmyL Hall 14 Urola S.C. Booth B14 New full electric linear blowers The Urbi Series of Urola linear blowers,100% electric, have a compact, solid and ergonomic design that guarantees high performance for the manufacture of PET containers with a capacity of up to 10 l and speeds between 2,500 and 13,600 bph. Because of the high technology and the low total cost of ownership Urbi Series offers the opportunity to produce PET containers with a variety of forms that range from the simplest to the most complicated. The main character of the Urbi Series machines, are: Unique (“L” form) linear architecture divided in modules: integrated preform feeding, linear oven, direct transfer system, blowing block press. Multi-module oven, with eight or nine IR lamps. Air flow within the oven homogenises the heat through the whole preform wall. Neck cooling via cooled air. Direct transfer system: simultaneous transfer of the heated preforms from the oven to the mould, and of the blown bottles to the bottle exit. No need to space out the preforms for their transfer to the press. Stretching system driven by servomotors and blowing system. Stretcher movement in two phases: approximation and stretching. Isobaric blowing in the neck area to prevent any possible deformation. Shell-type moulds that are fitted to the cooling block. This shell figure structure allows for very fast format change, without adjustment during the individual mouldshell change or during the change of the mould’s base support. (Moulds above 2 l are of one piece, including cooling circuit). Pneumatic compensation of mould closing to ensure a perfect clamping and to avoid “parting lines”. Easy-to-use control station: touch screen integrated to the frame to control blower controls and settings. Perfect access to the primary machine parts for maintenance, adjustments and mould replacements. The Urbi 8 and Urbi 4 l models consist of two presses that take the preforms that come from the ovens, with a single feed hopper of preforms and a single outlet of containers. www.urolasolutions.com Resource-saving solutions for the packaging industry In cooperation based on partnership Kiefer mold technologies bring 30 years of know-how as an independent tool maker into the customer’s ideas, across the fields of thermoforming, PET blow moulding and injection moulding. The company states to be a leading partner for the plastics processing industry meeting complex demands placed on medical, packaging and food technology tools. Kiefer presents tool technology such as mould-stamping thermoforming tool with extreme side pushers, IML in thermoforming with small invest, „skew“-products with new mould-technology, notched band steel and finally a new plug-assist material: Form X, Form 2X and Form LX. www.kiefer-mold.de Hall 3 Kiefer Booth C94","@ID":52}, "TOP TALK PETplanet Insider Vol. 20 No. 10/19 petpla.net 10 and put them into reality. However, with greater experience, my global network and my innovative efforts, I was encouraged to take action and so I founded ReduPET GmbH. PETplanet: Have you achieved your ambitious objectives from that time? Stefan Bock: My activities were divided into two focal points. I started by writing down all of my experiences in a logical and practical way so that I could work out practicable solutions for conserving resources. These were documented and translated into several languages. I then presented these to the PET processor industry as a package, whereby their operational employees could do a workshop and together work out the potential new measures that they could adopt in their production facilities. I would be on hand as a consultant throughout implementation so that these projects did not grind to a halt. This works well in the processing industry because it is realistic, understandable for all participants and the measures always lead to a noticeable success. My customers and I are very happy with this development. I brought to market maturity the material saving innovations Mint-Tec and Neck-Lite in partnership with company CPS (Creative Packaging Solution) as holder of the patents. Even when we have experienced enormous support, as experienced with the blow moulding machine manufacturers, the market reaction is very varied. Drinks manufacturers in particular, who are among world market leaders, are especially taken with the technologies. Some have already issued market releases for their products. The technologies Mint-Tec and Neck-Lite are revolutionary and provide a bridge between established injection moulding and blow moulding – therefore calling into question the previous interaction of these technologies. And this is all kept relatively far away from the end customer. There are some hurdles to overcome as acceptance is not easy to obtain and each individual wants to benefit from a technology like this. Without profit, interest is usually almost nothing. This is why CPS has been working on this development for over seven years and has brought in enormous resources in terms of finance and time. ReduPET GmbH is doing this in the same style to guarantee longevity. Of course, motivation comes from our successes. Today, we are very proud that Mint-Tec is now running industrially. PETplanet: With ReduPET GmbH, you are trying, for example in the product process for preforms, to save up to 8% of material consumption and costs; at the base of the bottle it is up to almost 20%. What kind of technology is behind this? What are Mint-Tec and Neck-Lite all about? Stefan Bock: Mint-Tec and Neck-Lite are two material-saving innovations for PET bottles. In the manufacturing of a PET bottle, two processes usually come into play – injection moulding and stretch-blowing. However, the two processes do not fit optimally together, as each is subject to the laws of physics. In the injection moulding process, the preform is manufactured. This preform is then reheated in a further process and stretch blown into the finished bottle, where the plastic undergoes high-grade hardening. To achieve optimum hardening, the preform would have to demonstrate a geometry which cannot be manufactured purely through injection moulding technology. For example, the preform base would have to demonstrate a much lower wall strength to enable the optimal stretch blowing of the subsequent bottle base. But this is not possible with injection moulding. With thin walls, the material would freeze too quickly and the unavoidable shrinking process caused by cooling, primarily in the seal area, could no longer be compensated. This would result in leaky bottles. By contrast, the blowing machine is not really capable of stretching out the material accumulation in the base to a satisfactory level. So the material remains unnecessarily in the base area of the bottle – a not inconsiderable waste. If you cut the bases off PET bottles in the supermarket, this waste can more or less be observed on almost all bottles. It must also be noted that the blowing process benefits a great deal from the light base. It enables a blowing machine to produce products more quickly with lower energy consumption in the heater oven. The shorter cooling time in the base enables a faster production run. The blowing pressure can also be reduced, as the base can now be formed more gently, which means another significant energy saving. The same idea is the basis of the Neck-Lite innovation. In the neck area, beneath the transport ring, the melt channel is shaped in a way that is just as unnecessarily thickened, so that the PET material does not freeze too quickly and the shrinkage, again caused by the cooling process, can also be counteracted. The idea here is to leave only small channels to supply the compensating material at the neck during the shrinking process, while the rest of the material can be omitted. This leads not only to a material saving but also the blowing process requires significantly less energy Neck-Lite left: Here you can see that the amount of material under the transport ring has been greatly reduced compared to the standard product (on the right). Left: Cross section through a Mint-Tec preform with reduced bottom wall thickness in comparison to the standard (on the right).","@ID":12}, "Kane Richmond, CEO Silver Springs BOTTLING / FILLING PETplanet Insider Vol. 20 No. 10/19 petpla.net 33 Two block systems for Silver Springs and RealPure Bottling Making every penny count Driven by the market’s demand for water as a beverage, Silver Springs Bottled Water Company has become Florida’s largest privately held bottled water company. The company attributes this success particularly to the equipment in which they have invested: pleased with their first KHS InnoPET TriBlock, they immediately purchased a second one for another plant. The Richmonds from Florida are real pioneers: when in 1991 Karl and his wife Margaret acquired the Silver Springs Bottled Water Company, founded six years previously in Ocala, Florida, bottled water in the United States was still a total niche market. The Richmonds firmly believed in the future potential of Nature’s very own thirst-quencher, however – at a time when the favoured refreshment of the regular consumer in the land of Pepsi and Coke was the sweetened soda pop. The couple’s boldness was rewarded: water may not have topped sugary soft drinks in popularity in the USA until 2016 yet in the many years en route to this success the Richmonds have enjoyed growth rates of 20% and more. At the outset they managed to meet demand with just six employees, now several hundred people work for the company at its now four sites dotted along the east coast. The business keeps the whole family busy: father Karl turns up for work every day at the ripe old age of 85 and sons Kirk, Keith and Kane share the tasks of executive management and responsibility for the various production facilities. With grandsons Kiel and Mason, the third generation of the family has also long been bottling water, with them now running one of the biggest independent bottling operations in the United States. Technical foresight The Richmonds’ instinct for market opportunities isn’t the only factor which has paved the way for their success; they have also demonstrated plenty of technical foresight. Alcides Vieira, Vice President of Sales & Marketing KHS USA, has close ties to the Richmonds: “For as long as we’ve known each other, the Richmonds have always been among the very first to opt for our new technologies.” In 2008, for instance, they invested in KHS’ latest InnoPET BloFill stretch blow moulder/filler block. And in 2017 they were the first to commission the KHS InnoPET TriBlock with a labeller integrated between the stretch blow moulder and filler. Besides a certain amount of the aforementioned pioneering spirit, this also requires a high degree of trust on the part of the customer – and a convincing performance by the line supplier. This is confirmed by Kane Richmond, CEO of Silver Springs. “We of course work in a people’s business where mutual trust and long-term relations play a central role. What we especially value in KHS above and beyond this, however, is their absoThe f rst of the two InnoPET TriBlocks with a stretch blow moulder, labelling module and f ller is installed at the RealPure Bottling Company in Magee, Mississippi.","@ID":35}, "TRADE SHOW PREVIEW PETplanet Insider Vol. 20 No. 10/19 petpla.net 65 The new TEM machine offers new possibilities for slitting or slitting and folding of tamper evident bands for specialty caps. The TEM, a highly versatile machine for beverage, food, beauty & home, chemical and other products. Modular design machine for slitting/folding or folding/slitting of tamper evident band Large variety of cap dimensions, including sport caps All size parts located in the outside for easy adjustment and changeover Heating system for the blade. Blade position sensor Servo-driven infeed star wheel, integrated cap stop and sensor controlled upside down closure detection Operator friendly interface Match the output of associated moulding and downstream machines Easily integrated into any production line due to independent control and optional vision inspection system PackSys Global and its affiliated companies offer a wide product portfolio: Complete lines for laminate, extruded and aluminum tubes Plastic closures slitting and folding machines Cap printing lines Monobloc aerosol can lines Hot stamping solutions from Madag Printing Systems Tube, aerosol can and cartridge packing solutions from Texa Packaging Highly skilled R&D and production teams ensure constant development and integration of the latest technology on our equipment. We stand for Swiss engineered innovation and performance. Creating Packaging Technology. PackSys Global AG T +41 55 253 38 31 [email protected] www.packsysglobal.com A Member of Brückner Group SPECIALTY CLOSURES TAMPER EVIDENCE","@ID":67}, "TOP TALK PETplanet Insider Vol. 20 No. 10/19 petpla.net 9 “The challenges for the plastics industry are varied” In the run up to the K’ trade fair in Düsseldorf, excitement is in the air in the plastics industry. The topics of sustainable production and recycling are on everyone’s lips and they are high up on the K trade fair agenda this year. PETplanet spoke to Stefan Bock, CEO and founder of company ReduPET GmbH and an old hand in the field of blow moulding and preform injection moulding. He shared his strategy for conscious production and discussed the future challenges for the PET sector. PETplanet: You have worked in the plastics industry for over 30 years. Plastic has never before been so controversially discussed in society. What do you make of this discussion? Are there aspects that you think are being missed? Stefan Bock: The current discussion is crucial to the survival of the plastics industry. Of course, we all know that we cannot continue like this with a material that is so important to our living standards. This means that the pressure building up from the current discussions is a driver for rethinking the industry and becoming more innovative and responsible. First and foremost I think what is missing is legislators in more countries adopting sensible and well thought out laws. For example, as far as I know, plastic waste from Germany is exported by ship. Once the plastic is loaded onto the ship, it is considered in Germany to be recycled, even if it is then disposed of improperly in Asia. The consumers themselves must have a much greater awareness of plastic as a recyclable material and act accordingly, whether voluntarily or through incentives or legal enforcement. There is a clear need for global action here. PETplanet: In your opinion, what does this discussion hold in terms of effects on the plastics industry and the PET industry in particular? Stefan Bock: Plastic is regarded more critically and so is receiving significantly more attention and is unfortunately getting a negative reputation. This pulls plastic products into the focus and calls them into question, which is surely a positive effect. Basically, awareness is being raised around the world; it is just a shame that this is often done in a sensational and therefore media-attracting way instead of it being constructively explained and handled. This is urgently needed - wake up calls are no longer enough. Especially in my sector, the beverage industry, we can see that containers have become increasingly “convenient”, i.e. smaller. This means that more and more plastic is used. This also happens in hot countries, where these small packages bear no relation to people’s needs. Meanwhile, packages are so small – and therefore so large in proportion to their content – that they now have to have a multilayer construction to increase the barrier effect. This means that the valuable recyclable PET material is now contaminated with an incompatible barrier material and this makes recycling much more difficult. Surely it would be more appropriate to divert discussion to these absurd developments that are no longer in keeping with the times and to ask ourselves why the EU is clutching at plastic straws - in the face of these absurdities. PETplanet: You founded ReduPET GmbH two years ago. What was the deciding reason for this? Stefan Bock: As you said, I have been working in the plastics industry for over 30 years, primarily in the packaging industry. Most of the time, I was employed in engineering but I was also able to make a contribution around the world in production operations for different applications and in different cultures and to get to know and assess these. Because of mass production, the plastic industry is extremely resource intensive in terms of both energy and raw materials. As already mentioned, the industry works with narrow margins, meaning that operating staff are not always well educated or do not have deeply held expertise to understand the processes in great detail – robust production with good products is the objective. Often, it is not recognised that the machines are not running efficiently and both raw materials and energy are wasted unknowingly in huge quantities. Once I had settled on the idea of acting in a resource-friendly way in my own environment, especially at home, I could see in my work environment a much greater potential and also therefore the responsibility to support the plastic processing industry in saving energy and raw material resources. At that time, I was not in a position to act upon these convictions Stefan Bock, CEO and founder of ReduPET GmbH, was previously with Bekum, Krupp Kautex and SIG for ISBM Systems and Netstal. by Heike Fischer","@ID":11}, "PETcontents 4 PETplanet Insider Vol. 20 No. 10/19 petpla.net 10/19 INSIDE TRACK 3 Editorial 4 Contents 6 News 75 On site 76 PET bottles for Beverage + Liquid Food 78 PET bottles for Home + Personal Care 80 Patents TOP TALK 9 “The challenges for the plastics industry are varied” - Interview with Stefan Bock, ReduPET PACKAGING 12 PET packaging in non-food areas - A review of developments over the last 20 years MATERIALS / RECYCLING 20 In the future, we will use more plastics - and why this is good news 22 Getting the best from recycled materials 24 The bottle battle - The pros and cons of PET bottles and aluminium cans PREFORM PRODUCTION 26 New fields of activity and closer cooperation with suppliers - How market giant Chemco is continually adapting to the market BOTTLE MAKING 28 Blow moulding machines for medium-scale outputs - German technology with Indian engineering artistry 30 From Thailand to India - The journey of the Sunpet brand BOTTLING / FILLING 33 Making every penny count - Two block sys- tems for Silver Springs and RealPure Bottling 36 Bottled water from Cappadocia - Solutions from stretch blow moulding to conveying USED MACHINERY 38 A new life for old machinery - Trading with used PET machines INSPECTION 40 Striving forwards for 40 years - Company jubilee at Heuft Systemtechnik MARKET SURVEY 43 Suppliers of caps & closures and inspection systems TRADE SHOW PREVIEW 52 K’ show 2019 - Preview part 2 60 World’s biggest PET container - 120 l open-mouth PET drum with 400mm neck diameter 62 Gentle PET decontamination - Infrared rotary drums for various applications 64 Sustainability and recyclability 66 Preform inspection: a world first 68 Size reducing, washing, separating, drying and agglomeration 70 Zero Cooling, multiple benefits BUYER’S GUIDE 81 Get listed! Page 3624367 Page 30","@ID":6}, "PETplanet Insider Vol. 20 No. 10/19 petpla.net 77 BOTTLES Lemonade from Roots & Goods German business group Rewe has placed several products on chiller shelves from company Roots & Goods, which belongs to Netherlands juice manufacturer Hoogesteger. These include fresh juices and fresh lemonades. The cold pressed and gently processed juices are available in slim, transparent 250ml bottles; the equally gently manufactured lemonades are available in 500 ml bottles. All bottles are labelled with self-adhesive, transparent foil labels. www.roots-goods.com Bulbous bottle for almond drink In the USA, company Califia Farms is selling 1.4 l of a vanilla-flavoured almond drink in a bulbous, easy-grip bottle. The product is kosher, vegan and free from gluten, soya and milk constituents and carrageen. The transparent bottle is BPA free and is decorated with a milky sleeve label with a design typical of the brand. It is sealed with an opaque screw cap with detailing that also enables a secure hold on the bottle when unscrewing. www.califiafarms.com","@ID":79}, "MATERIALS / RECYCLING PETplanet Insider Vol. 20 No. 10/19 petpla.net 24 The pros and cons of PET bottles and aluminium cans The bottle battle Is there an alternative to PET water bottles? One which is even more eco-friendly and economical at the same time? Are aluminium cans the answer? Uday Patel, Senior Research Manager for Global Aluminium Markets at Wood Mackenzie and Pieterjan Van Uytvanck, Principal Analyst for Chemicals at Wood Mackenzie, consider key points of comparison. The humble single-use PET water bottle has become a powerful symbol at the heart of the debate on plastics and packaging material. According to a European Commission study, PET bottles and their lids are some of the most commonly found items among ocean debris. Meanwhile, PET bottle consumption is increasing. As shown in Wood Mackenzie’s report on the EU’s single use plastic directive, in Europe it’s now around 140 units per person, per year. In the US it’s 290 units. Globally, around 57% of these are collected, according to the latest figures from Wood Mackenzie’s rPET Global Supply Demand Analytics Service. Political pressure will see that figure rise. One of the most ambitious targets of the EU directive is the call for 90% of PET beverage bottles to be collected by 2029. Significant investment in new waste management infrastructure is needed to meet this goal. But collection doesn’t guarantee recycling. In the US, 70% of the plastic collected for recycling goes to landfill. It’s 30% in the EU. Many argue that the real mission is to find a cleaner, greener alternative. Aluminium is one contender. The Coca-Cola Company’s Dasani water brand, for example, will soon be available in cans in the US as part of its efforts to reduce plastic waste. The environmental impact - how does a can compare to a plastic bottle? The experts find that on a first-use basis, neither material scores highly. Plastics rely on crude oil extraction. It’s an energy-intensive process, from drilling and refining to extrusion and moulding. A 2017 life cycle assessment study on PET resin from the CPME showed that producing virgin material requires 69.6GJ/tonne. Aluminium is extracted and refined from mined bauxite ore. It’s complicated, costly and energy-intensive. Wood Mackenzie calculate that it takes an average of 14,000kWh of electricity to produce one tonne of aluminium. Life cycle assessment studies from the Aluminum Association indicate that the total primary demand for aluminium production is 138GJ/tonne. Electrolysis accounts for the majority of the total primary energy requirements and it has also been shown that 36% (depending on location and value chain) of this energy demand can be sourced from renewable sources, often hydro. In terms of temperatures, polymer can be produced and extruded at around 250300°C. Aluminium smelting requires temperatures over 1,000°C. Recyclability: PET PET has the highest recycling levels of any of the six most common resins used in packaging. By 2029 WoodMac forecast that 68% of PET bottles will be collected globally. There will be some disparity in regional collection rates, however: 30% in the US, 57% in Europe and 82% in China. Some go into closed loop recycling, creating new food grade bottles. Others go into open loop recycling, destined for sheet or fibre applications. The environmental impact varies. Fibres that end up in duvet filling will probably stay out of landfill much longer than a poor quality “fast fashion” t-shirt. In 2018, 19.7 million tonnes of food and beverage PET bottles were produced, with 845,000 t mechanically recycled back into food and beverage bottles. By 2029 WoodMac predict that will reach 30.4 million tonnes, with more than 3 million tonnes mechanically recycled. Demand for recycled PET (rPET) is growing. The EU directive includes a target to incorporate 25% of recycled content in all PET beverage bottles from 2025, increasing to 30% from 2030. Leading brands such as CocaCola, Danone and PepsiCo have all called for a 50% use of rPET in their bottles by 2030. The analysts thus forecast a six-fold increase in demand for rPET in Europe by 2030 as a result. Recyclability: aluminium Aluminium recycling is a true closed loop. According to the Aluminum Association, it’s one of the most recycled materials on the market. Recycling it saves more than 90% of the energy required to produce new metal.","@ID":26}, "INSPECTION 40 PETplanet Insider Vol. 20 No. 10/19 petpla.net Company jubilee at Heuft Systemtechnick Striving forwards for 40 years What began more than 40 years ago has since developed into a global manufacturer of innovative control, inspection, rejection and labelling systems for continuous inline quality assurance in the filling and packaging of beverages, foodstuffs and pharmaceuticals: Heuft Systemtechnik GmbH was founded on April 1st in 1979. On this occasion, Heuft invited its customers, friends and politicians to take a look into the future and to review the successful history of the company. With just twelve confidants, Bernhard Heuft started operations in Burgbrohl in the Volcanic Eifel, Germany. The fact that the strength of his highly motivated team has increased a hundredfold in the last 40 years to over 1,200 employees worldwide impressively illustrates that the right course was set at that time to put the young family business on the road to success in the long term. In the truest sense of the word: Heuft received the first patent for a truly ingenious invention by the company’s founder, which still defines the state of the art today in the accurate standing high-speed rejection of faulty empty and full containers: the Heuft Delta-FW multi-segment flow rejector. Several rejection fingers which can be pneumatically retracted and extended individually form a curve which removes each faulty bottle from the line upright and without wobbling but leaves the adjacent good containers there. It has only been slightly modified but it still defines the state of the art today regarding the automatic high-speed rejection of faulty empty and full containers. It was also important to uncover the causes of the quality defects detected at an early stage and without human intervention: a specially developed locator function already carried out something similar in 1980 by automatically determining the filler valve responsible for the filling error detected. Therefore what others are only turning into a trend today was already possible at that time: preventive maintenance. Over 500 further patents have been added since then - and thus genuine technological unique selling points that not only sustainably optimise inline quality assurance in the filling and packaging of beverages, food and pharmaceuticals, but also the efficiency of entire lines. From the first optical fill level check to the multi-processing filling management system, from the first empty bottle inspector in efficient straight-line operation to the all-surface empty container inspection on a footprint of less than one square metre, from the unique pulsed X-ray to the company’s own real-time image processing, from clean labelling to precise labelling inspection, from harmonious conveyor control to comprehensive line analysis: a broad spectrum of innovative technologies from the modular Heuft modular system has been setting standards for efficient inline quality assurance for 40 years. Right from the start, basic research and solution development focused not only on maximum automation in precise product tracking, reliable defect detection and targeted defect rejection, but also on consistent user support. The systems from the modular Heuft Spectrum series available since the early 1990s already had screens as standard. The Heuft Pilot, a self programmed graphical user interface, offering the operator even more overview and orientation is added less than ten years later with the Heuft Spectrum TX. And the network interface which has been integrated since then reduces the effort required for line analysis and maintenance: essential operating, production and quality data are automatically recorded and evaluated with the Heuft Profiler introduced in 2002. In addition remote diagnosis and maintenance is possible for the first time with the Heuft TeleService. It was also possible to centrally manage and convert the brands and recipes to be processed by Heuft Spectrum II devices as from 2015. In the third generation, Alexandra Heuft (right) and Bastian Heuft (left) take over the company. The Prime Minister of the Rhineland-Pfalz Mrs Malu Dreyer (middle) was also invited. “The family business Heuft is exemplary for our strong middle class and an excellent visiting card for the economic and employment location RhinelandPfalz”, said the Minister President.","@ID":42}, "MATERIALS / RECYCLING PETplanet Insider Vol. 20 No. 10/19 petpla.net 21 uncontrolled manner in the European Union, are systematically missing from the plastic statistics. For decades, bans on hormone-active plasticisers were prevented. Eyes were closed on the large-volume of plastic waste exports to developing countries, which count as material recycling. Every expert knew what really happened to the plastics. In the European Union, less than 10% of waste plastics are recycled into new plastics. Thermoplastics can be recycled very well if collected in their pure form, better than most other materials. Instead of tackling the actual problems, it was perceived only as a “communication problem”. And when the plastics industry is asleep, they should not be surprised if the EU Commission and the national environment ministries now take matters into their own hands. The recently adopted plastics strategy, including restrictions and bans on certain disposable plastic products, is the consequence of this behaviour. Linda: And are politicians doing better than the industry now in tackling the problem? Michael: I’m afraid not. Of course, there are some sensible measures being taken, such as the ban on oxodegradable plastics, which decompose particularly quickly into microplastics. However, the “single-use ban” is a purely symbolic policy and a bad one at that, which will have little effect, but will inflame the hysteria about plastics, introduce unnecessary product bans and leave the field to worse materials – without affecting the real problems at all! There are a number of measures that would make a real difference on a large scale: a ban on the export of plastic waste, curtailing the use of landfill, mandatory deposit for all plastic bottles for all types of beverages, a ban on the intentional use of microplastics and increased use of high-quality polymers instead of composite systems, as these are easier to recycle (Design for Recycling). Plastic waste could be systematically collected and recycled worldwide. A global standard for the biodegradation of certain polymers could reduce risks in cases where leakage into the environment is unavoidable. And finally, a clear concept is needed on how to move from fossil to renewable carbon by 2050. Or would the plastics industry like to be pilloried in 2050 as one of the largest and last emitters of fossil carbon? As an industry of the future? A photovoltaic area of only 1% of that of the Sahara would suffice to supply the entire chemical industry with renewable carbon – via solar hydrogen and CO 2 from the air. “The single-use ban fuels the hysteria about plastics, but it’s not plastics we should be doing without” Linda: What is so bad about the single-use ban, aren’t many products really pointless or can they be better substituted by other materials? Michael: Why is a coffee plastic stirrer worse than a wooden stirrer if it is properly rinsed or disposed of? Nothing. On the contrary. Due to its efficient production, the plastic stirrer should have a lower carbon footprint and can be materially recycled. The plastic stirrer can thus be turned into a plastic stirrer again. This will not be possible with the wooden stirrer – unless plastic helps to bind the wood particles. This is just one example among many. If one does not want to switch to ecologically worse materials, the single-use ban of plastics is practically equivalent to product bans. Do we want an eco-dictatorship? A race for bans? One person thinks straws, the other balloon holder or coffee capsules are unnecessary – in the end we will all miss many products. Wouldn’t it make more sense to respect the needs of the people and find the best materials and end-of-life options that have the least environmental impact? In many cases, these are already plastics today – whether PET bottles, shopping bags or packaging that protect food – and this will increasingly be the case for future plastics based on renewable carbon, either from mechanical and chemical recycling, biomass or direct CO 2 use. The single-use ban fuels the hysteria about plastics, but it’s not plastics we should be doing without. The aim is to quickly turn plastics into a truly sustainable material solution and set up comprehensive disposal and recycling systems that minimise the risk of plastics entering the environment and causing microparticles. Given the raw material situation, we have no other option. And consumers will learn that more sustainable plastics will be more expensive, but already today almost half of German consumers are willing to spend more money on sustainable products. Linda: And will this be successful? Michael: I’m an optimist. The plastics industry can emerge from the current crisis renewed and strengthened like the Phoenix from the ashes – if it does its homework now and consistently tackles and solves the problems, and finally understands that they are not communication problems! In the meantime, the first, long overdue steps have been taken: around 30 leading chemical companies that operate along the value chain worldwide have organised themselves in the “Alliance to End Plastic Waste (AEPW)” and intend to invest around 1.5 billion dollars over the next five years to promote projects for waste management, the circular economy and new recycling technologies. Manufacturers of consumer products are finally beginning to produce their packaging from 100% recycled material and make it fully recyclable. The targeted collection of plastic waste is also starting with its first projects. In Haiti, for example, the inhabitants collect plastic waste, and this year the amount is expected to reach 300 t. In return, Henkel provides benefits in kind such as charcoal for cooking, vouchers for children attending school and the opportunity to recharge their mobile phones, or simply cash. A valuable scheme to buy collected plastic waste as a raw material. That should set a precedent all over the world. Linda: Thank you for the enlightening conversation. www.nova-institute.eu","@ID":23}, "49 TRADE SHOW PREVIEW PETplanet Insider Vol. 20 No. 10/19 PET: the closed plastics cycle under one roof Holistic recycling of packaging Millions of bottles are recycled using Krones’ MetaPure systems, handling different material qualities, all the way up to food-grade PET. Since Krones apply a holistic approach to recycling, they are expanding their technology step-by-step to include other types of plastics. The MetaPure W washing modules are designed to process both PET and polyolefins (PO). At the K 2019, customers will able to view the interior of the module’s pre-wash components. Krones cooperates closely with Stadler Anlagenbau GmbH to equip its customers’ factories with customised turnkey equipment. The company is one of the market leaders in the field of sorting systems and has sold around 350 turnkey systems and 2,000 individual components worldwide. At the Krones booth, experts from both cooperation partners will be available to discuss the synergistic effects of their partnership and the overall solutions that will result from the collaboration. Energy-saving container stretch blow moulding The Contiform stretch blow moulder processes preforms comprising of 100% recyclate. The Contiform 3 Speed, the highspeed version of the series, will be exhibited at the show with one blowing station. At a station output of up to 2,750 containers per hour, it produces custom-fit packaging solutions for still water, carbonated soft drinks and sensitive products. As with all of the machines in the Contiform series, it is designed to have high energy and media efficiency. It can improve on the very low energy and compressed-air consumption of the Contiform 3 Pro by an additional 15%. The cap and container as a single unit Flip Lid is stated to be a completely innovative packaging system developed by Krones and Aptar. Due to the fact that the lid and the bottle are permanently joined together, the lid is prevented from being discarded into the environment – and ensures that the entire beverage bottle is sent back for recycling. www.krones.com Hall 15 Krones Booth 15.1","@ID":51}, "John Bickerstaff, production manager for the RealPure Bottling Company BOTTLING / FILLING PETplanet Insider Vol. 20 No. 10/19 petpla.net 35 Lightweighting record The Richmonds are also eager to attain further pioneering status when it comes to sustainability. One of their chief concerns is that they reduce their bottle weights and thus the amount of PET used. “With the help of the experts from KHS’ Bottles & Shapes program and our preform manufacturer Plastipak we’re setting a new lightweighting record with practically every new product we introduce,” smiles Kane Richmond. “In Magee we’ve been using 500ml PET bottles which weigh just 7.8 g since 2017 and on the brand new TriBlock in Ocala the containers only clock up 7 g on the scales.” Kane admits that with a recycling rate of a mere 30% the USA is no trailblazer when it comes to cutting down on plastic waste. However, the growing health awareness of his fellow countrymen and women, who are turning to bottled water with ever greater frequency, is being echoed by an increased sensitivity to the issue of sustainability. Of this he is convinced. He even suspects that the recycling rate among people who buy water is already much higher than among those who purchase sweetened beverages. At his company Kane does what he can. This includes recycling his own PET waste – where he’s soon to achieve a quota of 100%. www.khs.com PET BOTTLE RECYCLING LINE SUPER CLEAN PROCESS (SCP) Micro Denier Filament Grade www.bo-re-tech.com Modular Design for Flexible Layout Next Generation VISIT US 8BE31","@ID":37}, "PACKAGING PETplanet Insider Vol. 20 No. 10/19 petpla.net 12 A review of developments over the last 20 years PET packaging in non-food areas by Kay Barton Although we are primarily a magazine for the beverage industry, it was only a matter of time before the triumphal march of PET would prevail in other areas of packaging. Depending on the intended use, significant advantages such as lower manufacturing or material costs, userfriendly properties – such as precision dosing of contents by pressure on flexible containers and high recycling capability, together with brilliant appearance in the end product – are attractive. Consequently, we began reporting on the growing food and non-food markets for PET at an early stage. This field has developed from being covered by individual articles in the early 2000s, to an extra section in PETplanet Insider magazine, through to reports on newly-launched products in these areas along with news from the industry, covering both suppliers and users. As in the beverages sector, the change from other packaging materials to PET for household goods, personal care and beauty care, cleaning agents and chemicals, etc., presents new challenges in terms of production, appearance and feel. An extreme example is the contrast between PET cosmetic containers and beverage bottles. These segments could hardly be more different in terms of technical requirements, production speed and material costs. Today, new and incredible designs, which were unthinkable until a few years ago, appear in both areas almost every week. The technical starting points are completely different, however. In the modern two-stage process for beverages, lightweights, minimum cycle times and highly automated workshops are the norm. In short: a highly efficient use of materials and energy with the maximum output of containers, with customer-specific designs, which should maximise appeal to the consumer in terms of appearance and haptics, must be achieved. This is the case in all price segments. Even in highly price-sensitive areas, such as the popular singleserve area for water from smaller, local bottlers, where manufacturer margins are naturally small, the individual product should not be lost in the variety of the market. In the highly-priced cosmetics sector, which is dominated by single-stage systems, the same aspiration of the manufacturers prevails, even though the costs of manufacturing and the use of materials are in completely different leagues. Customers purchasing a cosmetic product costing around € 100, for example, expect premium packaging which, in terms of its design, has a period of home use lasting months and. in some cases: years. For such customers, luxury takes centre stage, a factor that is reflected in the contents, as well as the packaging. Completely individualised neck finishes are one such example. With the migration of several world brands in cosmetics and beauty care from glass to PET and PETG, the demands and expectations placed on the end product have been, and remain, correspondingly high. In addition to the identification of the brand, the premium feel of a glass container in this segment should not be neglected under any circumstances. Ideally, buyers should not be able to detect any significant difference from a glass container, or whatever packaging preceded it. Technically, this requires not only a complex moulding process but also a high quality material input, with the elimination of unwanted crystallisation during conversion, often paired with sophisticated shapes, colours and surface textures, using sophisticated masterbatches. The technical requirements for single-stage PET have developed in this direction in recent years and the associated PET market is growing steadily. While writing this report, I am looking at a high-gloss thick-walled box with an extra-thick base, which I was given at a meeting with Nissei ASB at the Chinaplas trade fair in 2015. It weighs in at 60 g, with a filling volume of 100ml, manufactured on a two-cavity system in a cycle time of 42 s. In technical terms, standard nonfood consumer goods, such as household cleaners and body care products, are both dependent on quantity, wall thickness and neck diameter. Here, too, the best possible customer experience in terms of the packaging and user satisfaction is required. Over the years, the use of additives or barriers to prevent unwanted changes to or deterioration of products has been continuously improved, especially so in the case of transparent containers in which the content takes centre stage, as with the beverages segment. There is plenty to discover on these topics in the PETplanet Insider archive, and we have compiled some of them for you here. 1999 - 2004 The USA has certainly played a pioneering role in the adoption of PET in the non-beverages sector, with cosmetics and even perfumes with spray caps in PET first appearing in America as long ago as the early 2000s. In 2001, an advertisement from extrusion blow mould manufacturer Bekum demonstrated production of a shampoo bottle in its two-cavity Reheat Stretch Blow Moulder, which was designed for the processing of PET and PP bottles of up to 1 l.","@ID":14}, "75 ON SITE PETplanet Insider Vol. 18 No. 0/17 petpla.net Beyond recycling ..! Food grade rPET from Egypt’s BariQ Egyptian company BariQ, a Raya Holding subsidiary, is the first food-grade bottle-to-bottle rPET producer in the Middle east North Africa (MENA). It is located in Giza, just under 5km SW of Cairo. Founded in 2012, it specialises in processing post-consumer bottles into food grade PET pellets, compliant with FDA, EFSA, Reach & Health Canada regulations. BariQ exports to global bottle and food container producers and major fibre producers across Europe and North America. Its annual capacity of 15,000 t means that it transforms 1.6 billion PET bottles a year into food grade rPET. Its operations incorporate advanced green technology, sourced from major European suppliers. The company’s portfolio includes food and non-food grade PET in both clear and green colours, plus injection grade rPP and rHDPE. BariQ is the only non-European PET recycler registered in Ecoembalajes Espana. This registration enables it to purchase PET bottle bales through the established periodic tendering system, for final recycling in its Egypt plant where it recently installed a STF grinder with V-cut technology, intended to minimise washing line downtime. The company recently installed a Tomra Autosort Flakes Sorter 2.0. This upgrade in equipment helps to maintain the quality levels needed for the conversion of flakes to higher end PET pellets, to meet customers’ evolving requirements and enable BariQ to deliver sustained output quality, regardless of input source. The upgrades also increased output capacity by 30%, while reducing contamination. The company intends to install an extra Tomra Bottle sorter, which will help to strengthen quality control of bales and eliminate contamination. BariQ is also planning to double capacity, in order to satisfy the increasing need for food grade rPET. As the only recycler in Egypt, BariQ embraces the responsibility to raise general awareness on waste management issues. It has cooperated in a number of initiatives with global players in different sectors, including Nile river clean-up projects, Protectorate Natural waste collection, student education and supporting young entrepreneurs in their green projects, with field experience and financial support. BariQ joined the United Nations Development Organization’s MED TEST II project, which identified opportunities to decrease energy consumption by up to 20% per tonne. www.bariq-eg.com","@ID":77}]}}
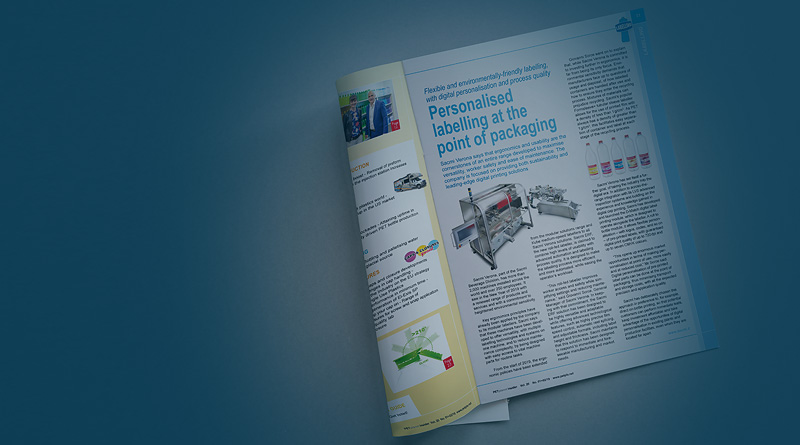