"MAINTENANCE PETplanet Insider Vol. 21 No. 01+02/20 petpla.net 30 New cleaning system boosts production time and productivity Cutting cleaning costs Silgan Plastics’ use of Cold Jet i3MicroClean and Aero System for cleaning injection moulds, blow moulds and stretch blow moulds cut cleaning time from 2-3 hours to 45 minutes. Cleaning moulds hot and in-place significantly cut cleaning time and equipment damage caused by assembly and disassembly. Operator safety has been improved by reducing work undertaken close to hot equipment. Silgan Plastics is a leading supplier of metal containers for food products in North America and of plastic containers for personal care products. It is also a producer of metal, composite and plastic vacuum closures for food and beverage products worldwide. With more than 22 production plants, it is one of the top 10 blow moulders in North America. Silgan’s Toronto, Canada, manufacturing facility uses injection moulding, injection blow moulding and injection stretch blow moulding systems to produces a variety of plastic containers, lids and caps, many using 72-cavity PET preform moulds. Its preventive maintenance program was developed to meet customers’ special product quality needs in the pharmaceutical and PET segments. Scheduled downtime for routine cleaning Silgan’s manufacturing software generates a work order based upon cycles for each mould. Cleaning cycles are set-up with each customer to ensure that their moulds are well maintained and in good working condition. This approach has become a standard for all Silgan moulds and customers’ moulds. The 72-cavity moulds, which run 10 s production cycles, are cleaned by hand after every 15,000 cycles, using chemical and citrus cleaners, degreasers, wire brushes, drills and pipe cleaners, a process that took 2-3 hours per mould. After 60,000 cycles, the moulds were removed from the presses and given a more thorough cleaning. Despite the amount of time spent maintaining them, it was difficult to get the moulds completely clean. “Not only is it time consuming, it is difficult to get behind every slide and neck ring,” said Joe Pond, Setup Supervisor for Silgan Plastics. “The coatings and plastics we use tend to get on other parts of the equipment, which also adds to the challenge.” Moulds before cleaning... ...and after dry ice blast cleaning After a Husky Injection Molding Systems seminar, Pond asked Husky representatives what was the best method for cleaning high-cavitation moulds; they recommended Cold Jet dry ice blast cleaning systems. Cutting downtime and improving machine care Dry ice blasting uses non-abrasive, recycled CO 2 pellets that won’t damage surfaces or equipment or compromise part quality consistency.","@ID":32}, "CAPS & CLOSURES 9 PETplanet Insider Vol. 21 No. 01+02/20 petpla.net 9 been developed for a multitude of closures, including the next-generation lightweight 26/22 neck. PETplanet: So, what is the secret enabling all these tethered closure solutions to be designed for standard necks? Reimann: The secret lies in the material. The design has to be precisely fine-tuned, there is not much safety space left. If you look for example at the active hinge design, these are much easier to realise with more material. For a fine-tuned solution, the material has to be sturdy but with good flow characteristics. PETplanet: The lasso design is a double-slotted TE-band design. When looking at this flexible solution, one could easily imagine that the closure could annoy the consumer while drinking, which could result in it being torn off. Hoffmann-Leist: Bringing together standards and user-friendly design with integration into the supply chain is actually a balancing act. We are therefore carrying out several consumer studies and have had the three tethered versions tested. Each alteration is difficult because consumers will open the bottle in the way they are used to opening bottles. There are also significant regional differences here. In some countries, screw-tops are preferred, and consumers are skeptical about using hinge caps; in other countries these caps are much more common. But from the feedback, we understood that userfriendliness has been certified for all three solutions. Reimann: What’s special about the lasso cap is that we designed it in such a way that it does not dangle in the consumer’s face during drinking. Alongside safety, intuitive use and reliability, “convenience” is one of the four standards that the brand owner stipulated for the caps. But here too, the material side is enormously important because there must be a guarantee that the cap cannot simply be ripped off. The great advantage of the lasso design is that existing moulds could still be used. PETplanet: Besides these tethered caps, you have also designed a tethered closure concept from recycled material. What is this about? Trocherie: In the cap sector, incorporating the use of recycled material has long been difficult because of the contact with food. What we have designed for K fair is a prototype to demonstrate the feasibility of the production chain from mixed plastic waste to an end application. We used feedstock made from post-consumer plastic waste. Using our proprietary molecular recycling technology MoReTec, we converted this waste to oil to produce ethylene and then polyethylene in one of our production assets. This product has the same physical properties as conventional plastics derived from petrochemicals. PETplanet: Thank you for the interesting discussion!","@ID":11}, "CAPS & CLOSURES 16 PETplanet Insider Vol. 21 No. 01+02/20 petpla.net Solutions for attaching caps to single-use bottles for the duration of their use Till recycling do them part by Gabriele Kosmehl As far as tethered closures go, Aptar Food + Beverage may have the edge over others, as already five years ago, the manufacturer of sports closures and dispensing systems introduced the first sports closure solution with a tethered feature. At the BrauBeviale trade fair, the company presented several of their latest developments that conform to EU Directive 2019/904 Article 6. Ryan Kenny, Aptar’s President Food+Beverage EMEA, explained these solutions in more detail to PETplanet. “It was approximately six years ago that we undertook a new development of tethered closures on the assumption that the future could lie here,” says Ryan Kenny, explaining Aptar’s development history in this field. He continues: “By the end of 2020, every new Aptar sports closure will be developed and commercialised integrating some form of tethering feature.” During BrauBeviale, the company presented three tethering solutions: Stay-With, Flip Lid and StrapBand. The Stay-With solution, originally developed and patented for Aptar’s first tethered sport closure, is primarily intended for sports closures where drinking is done from the closure spout and not the bottle neck. StayWith features a band that allows unscrewing of the closure from the bottle neck, yet maintains a connection point to prevent complete removal from the bottle. The “lasso” type of ring as Kenny describes it, ultimately prevents the closure from being fully detached where the consumer could lose the closure, while also allowing the consumer to fold the closure down and out of the way when drinking directly from the bottle. “The advantage of Stay-With is that it is a versatile and proven solution, capable of being integrated within existing products and assets, ultimately reducing the level of investment required and time to bring solutions to market. For sports closures, where drinking is primarily done from the closure spout and not the bottle neck, Stay-With can be an excellent solution to meet new tethered regulations.” explains Kenny. Aptar is addressing the challenge that currently faces all manufacturers wanting to bring tethered caps into their range, by bringing intuitive handling and user-friendliness into harmony with functional and regulatory attributes. “The EU rules and tethered caps were developed almost in parallel, so currently a variety of different solutions are being introduced in the market that may not offer a user friendly or convenient experience for the consumer.” Aptar considers its recently developed StrapBand solution as a product that addresses such a challenge, and one that is particularly intuitive to operate. The solution has come from a partnership with Nippon Closures Co., Ltd. (NCC), a leading company in Japan for bottle closures. NCC’s patented StrapBand feature represents a market proven tethered solution available for today’s flat caps. Aptar and NCC continue collaborating to bring StrapBand to market for a broader range of flat cap sizes in various product categories. Benefits of StrapBand include having a hinging functionality in a flat cap format, a wide opening angle and an audible click when articulating the closure down and away from the bottle opening; it can be adapted for both flat and sport caps for still and carbonated beverages. “StrapBand features a very intuitive locking mechanism. After unscrewing, just open the cap to the point you hear a click sound, and the closure will CAPS & CLOSURES StrapBand provides a hinge functionality with a wide opening angle and a click sound when tethered. Ryan Kenny, President Food+Beverage EMEA explaining Aptar’s tethered solutions at Brau Beviale","@ID":18}, "TRADE SHOW REVIEW PETplanet Insider Vol. 21 No. 01+02/20 petpla.net 38 Focus on efficiency and circular economy ABC Compressors made use of the platform presented by Brau Beviale to make clear its belief that PET is the best alternative currently available for the production of beverage industry packaging, in terms of CO 2 emissions. “It is not correct to claim that PET is more harmful than glass for the environment and there is no other solution that can outperform either of the two materials,” said Nacho Urbistondo de Leiva, ABC’s sales manager for Eastern Europe and Russia. He emphasised that there is an increasing trend towards the use of 100% recycled PET (rPET) in lighter preforms. However, recycling on its own is not the complete solution. Telmo Sexmilo, ABC’s sales area manager for the Middle East and the CIS, made the point that moving to a circular PET production cycle is a challenge to and the responsibility of everyone in the industry. “There is no alternative to PET in bottling,” Gonzalo Gabarain, the company’s sales area manager for the Francophone countries, Southern and Western Africa and Italy Key Account Manager added. “The trend will be to recycle PET and to educate society to do so. The preforms will tend to weigh less, so the compressors will tend to be smaller and sized for lower pressure. Energy consumption will, consequently, be much lower, and reduce TCO (total cost of ownership) as a result.” The ABC sales area manager for East Africa, Central Europe and the United Kingdom, Marcos Arteaga, confidently claimed that the concentration of customers and suppliers in the PET market will intensify and new formulas will be sought to avoid losing market share. Delivery deadlines and local services in the CO 2 market will become increasingly important. The war against plastic will centre on recycling and the reluctance to make new PET investments will disappear. Horizon and Ecoo ranges highlighted ABC sought to support its points by showcasing its Horizon and Ecoo compressor ranges, which it claims are market leaders in efficiency and robustness. The PET blowing Horizon range’s horizontal design is intended to minimise vibration, which reduces heat generation and component wear, and increases compressor service life and efficiency loss. Its built-in frequency converter or variable speed drive (VSD) is claimed to reduce unload times and save energy with a large regulation range. ABC says that its Ecoo range, which is designed for CO 2 compression, offers reliability and flexibility. It also features a horizontal structure. It offers compression solutions for a range suction pressures and up to 20 bar, and can handle flows from 600 kg/h to 4,000 kg/h. The company also exhibited its recently-launched ROI Gauge, which helps companies ascertain the return on investment (ROI) of their machines that derives from less consumption and lower maintenance costs. The sector’s future: recycling to boost PET investment ABC sales and service director Xabier Noguera said that he expects the coming years to see fewer players in the compressors market. “This higher concentration means that 2020 will be a key year for a major push in the company’s worldwide expansion,” he concluded. www.abc-compressors.com The ABC team in Nuremberg (from left): Telmo Sexmilo Olasagasti, Sales Area Manager, Marcos Arteaga, Sales Area Manager, Nacho Urbistondo de Leiva, Sales Area Manager, Xabier Noguera, Sales & Service Director, and Lucio Arizaga, Oil & Gas Business Unit Director","@ID":40}, "PETnews 6 NEWS PETplanet Insider Vol. 21 No. 01+02/20 petpla.net ICIS Asian Recycling & Sustainability Conference 2019 has been a defining moment for the plastics industry as the drive towards a sustainable future becomes the main agenda of multinational corporations, governments and even consumers. While there is no single formula at the moment to end the problem on plastic waste, collaboration plays a critical role in bringing change to what is already a worrying trend. Next month, ICIS is bringing the Asian Recycling & Sustainability Conference for the first time to Bangkok, Thailand. This one day event will focus on the theme “Seeking paths and working collaboratively to establish a circular economy road map in Asia” and aims get to the bottom of the issues related to the immensity of the plastic waste crisis, the strategies of producers and long-standing brand owners to explore and promote solutions and many more. As industry news confirms noteworthy and ground-breaking projects of local governments, plastic manufacturers, recyclers, producers, waste management companies and brand owners, it is critical to be in the know about these important headlines allowing you to remain competitive amidst changes and challenges within the plastics industry. This inaugural conference will be taking place at the Hyatt Regency Sukhumvit Hotel in Bangkok on 19 February 2020. Companies in attendance include: Alliance to End Plastic Waste, Asahi Group, Borealis, Chevron Phillips, Clariant Plastics & Coatings, The CocaCola Company, Dow, Dynapack, Eastman Chemical, ExxonMobil, Henkel, Indorama Ventures, Milliken, Nu Pure Beverages, SCG Chemicals, Thai Griptech, Union Petrochemical PCL and more. www.icisevents.com/asianrecycling Vimal Kedia, MD & CMD Manjushree Technopack, declared as one of ‘Asia’s Most Promising Business Leaders’ by The Economic Times Mr Vimal Kedia, Chairman & Managing Director Manjushree Technopack, a leading rigid plastic packaging company in India, has been declared one of Asia’s Most Promising Business Leaders by The Economic Times. This title was conferred on Mr Kedia at the 4th edition of Asian Business Leader conclave held in Singapore recently. The conclave saw leading thought leaders and businessmen across Asia discuss pertinent issues facing the Asian region, particularly India and Singapore. The award is an acknowledgement to pioneers who play a significant role in shaping business demographics around the world. Mr Kedia was recognised for his outstanding achievement and contribution to the packaging industry in India. On winning the award, Mr Kedia commented “I am honoured to be one of Asia’s Most Promising Business Leader by The Economic Times. It has been a phenomenal journey with Manjushree Technopack these last 40 years. Manjushree stands for integrity, customer centricity, innovation and environment sustainability. These core values have helped us stay ahead of our peers and steer the rigid packaging industry. This award is a testament to our unwavering commitment to design and to delivering world-class and thoughtful packaging solutions. www.manjushreeindia.com Husky appoints Tony Black to lead Customer Success Management organisation Husky Injection Molding Systems announced the appointment of Tony Black to the position of President, Customer Success Management (CSM). Mr Black joins Husky’s senior leadership team leading the company’s global CSM organisation. “Since forming our consolidated CSM organisation in 2017, our goal has been to provide the industry’s most exceptional service and support to help customers elevate their Husky investments, as well as protect and improve their bottom lines,” said John Galt, Husky’s President and CEO. “I am excited to have Tony join our team and am confident he has the experience, skills and expertise to take our CSM organisation to the next level, especially as we move to accelerate development innovation around evolving consumer and market demands.” “Husky is a company with a strong team clearly dedicated to providing the industry’s most responsive and effective customer service and support,” said Tony Black. “The organisation is poised for innovative change and I look forward to applying my existing knowledge to help strengthen our capability to deliver proactive, optimised support to all customers around the world.” Mr Black brings more than 25 years of experience in global business development and operations and has a record of accomplishment for consistently improving customer satisfaction and service-oriented performance. www.husky.co","@ID":8}, "CAPS & CLOSURES 18 PETplanet Insider Vol. 21 No. 01+02/20 petpla.net Sacmi proposal with the option of the tethered feature Sustainable trends in caps Ten years ago, the beverage industries adopted the light weigh PCO1881 neck finish, in order to reduce package weight and reduce plastic consumption.The efforts for further light weighting and better sustainability never stopped and times are ready for a new lighter neck finish, which might replace PCO1881. The Cetie worked on a new 26/22mm neck finish, which is named GME30.37. It is currently used for medium and high carbonated soft drinks (CSD) across Europe. (Fig.1) On top of being manufacturer of continuous compression moulding machines and related moulds with about 2000 units installed worldwide, Sacmi’s core lies in the R&D lab, which so far developed more than 1,000 caps design. Sacmi’s proposal for the GME30.37 neck weighs 1.65 g in the version for CSD. The neck/cap finish combination allows saving up to 1.8 g per package compared to current PCO1881, and it is already on the market, produced by a leading global player. Considering both the weight and energy savings, Sacmi claims that it is another big step forward for the environment. On the same sustainability topic, the Sacmi 26/22mm cap can feature a tethered function (Fig. 2), with a separation force higher than 25 Newton, in order to already comply with the EU Directive 2019/904. The directive, in fact, states that beverage containers with a capacity of up to three liters that have caps and lids made of plastic may be placed on the market only if the caps and lids remain attached to the containers during the products’ intended use stage, starting from 2024. Therefore, new investments can be done without the need to worry for future legal requirements. www.sacmi.com Fig.1: PCO1810 - 5.06g PCO1881 - 3.81g GME30.37 - 2.4g Fig.2: Sacmi 26/22mm cap can feature a tethered function with a separation force higher than 25 Newton. Easy opening ... ... staying and finally closing. CAPS & CLOSURES","@ID":20}, "LABELLING PETplanet Insider Vol. 21 No. 01+02/20 petpla.net 28 Sustainable labelling – using PET by Liselotte den Ouden (Product Manager Film) and Jenny Wassenaar (Compliance & Sustainability Director), Avery Dennison There is no doubt that sustainable packaging and waste reduction have become key business priorities. The search for solutions that can boost a brand’s eco-credentials is gathering pace. Major gains are possible when brands get things right. Consumers pay particularly close attention to packaging, and there are significant environmental improvements to be made and communicated. Useful brand messages emerge from initiatives that create a truly circular economy. Labels are a highly visible part of packaging, so they play a key role. The label recycling challenge Recycling waste from different stages of the labelling process is complex, especially when seeking to create useful by-products or closing the loop entirely. Even the word ‘recyclable’ is sometimes misleading because some recyclable products will end up in landfill, as things stand. A viable end-to-end recycling solution has to look at real-world performance of all the different components of a package. This means considering sourcing of materials, how much is being used, and the actual end-oflife destination. The ultimate goal, of course, is zero waste. Better label materials A standard self-adhesive label, once it has been dispensed onto a package or product, comprises a facestock and an adhesive. Before dispensing, it is also held on a release liner. Sustainability considerations often start with the facestock, as the most visible element for consumers. Certification is helpful here, showing that materials are from renewable resources. Materials can also be shown to contain recycled material, and to be recyclable themselves. 95%+ of Avery Dennison’s paper facestock volume within the EU is already FSC-certified, and some of the more specialised products include facestocks made from grape or sugar cane waste – a great way to promote brand messaging in particular segments, such as wine and spirits.","@ID":30}, "imprint EDITORIAL PUBLISHER Alexander Büchler, Managing Director HEAD OFFICE heidelberg business media GmbH Bunsenstr. 14 69115 Heidelberg, Germany phone: +49 6221-65108-0 fax: +49 6221-65108-28 [email protected] EDITORIAL Kay Barton Heike Fischer Gabriele Kosmehl Michael Maruschke Ruari McCallion Waldemar Schmitke Anthony Withers WikiPETia.info [email protected] MEDIA CONSULTANTS Martina Hirschmann [email protected] Johann Lange-Brock [email protected] phone: +49 6221-65108-0 fax: +49 6221-65108-28 LAYOUT AND PREPRESS EXPRIM Werbeagentur | exprim.de Matthias Gaumann READER SERVICES Till Kretner [email protected] PRINT Chroma Druck & Verlag GmbH Werkstr. 25 67354 Römerberg Germany WWW www.hbmedia.net | petpla.net PETplanet Insider ISSN 1438-9459 is published 10 times a year. This publication is sent to qualified subscribers (1-year subscription 149 EUR, 2-year subscription 289 EUR, Young professionals’ subscription 99 EUR. Magazines will be dispatched to you by airmail). Not to be reproduced in any form without permission from the publisher. Note: The fact that product names may not be identified as trademarks is not an indication that such names are not registered trademarks. 3 PETplanet Insider Vol. 21 No. 01+02/20 petpla.net It is now clear to most of us that “environmental pollution from plastic waste” will ultimately have a major bearing on the uptake of PET bottles. So it is always interesting to take a look at how high-growth countries are dealing with the issue of “plastic”. Today, the focus is on Malaysia and China. Malaysia is once again returning a large amount of illegally imported plastic waste back to their countries of origin. 150 container ships with 3,737 tonnes of waste on board are on their way back to France, Great Britain, the USA and Canada. A further 110 tonnes are due to follow shortly, 60 of which will be sent to the USA, according to Malaysia’s Environment Minister, Yeo Bee Yin. Imports of plastic into Malaysia tripled between 2016 and 2019 which is why container vessels were sent back several times last year and is one reason for the significant increase which other Asian countries such as Indonesia and the Philippines are also experiencing. In 2018, China announced it would no longer process used plastic from other countries, citing the need to improve its environmental footprint. The country had previously imported large quantities of waste for recycling. Now, the People’s Republic has gone one step further in its fight against the flood of plastic with its Government’s imposition of a ban on plastic bags in supermarkets, as well as on the use of single-use plastic products such as cutlery, toothbrushes and combs in hotels and restaurants. Strict rules are also to apply to courier services. These measures will come into effect in major cities from the end of 2020 and in smaller cities from the end of 2022. A nationwide ban on plastic straws will also be imposed from the end of 2020. With this plan, the Chinese Government hopes to “effectively control” environmental pollution from plastic by 2025 and to “significantly reduce” the amount of plastic waste held at disposal sites in major cities. We will see what all this means for the PET bottle. Your Alexander Büchler Dear readers,","@ID":5}, "PETplanet Insider Vol. 21 No. 01+02/20 petpla.net 33 TRADE SHOW REVIEW discussed availability shortages - particularly of food-grade material - and how this combined with the growing anti-plastic consumer backlash, an increasingly hostile legislative environment and rising competition for waste volumes - including fresh competition for chemical recycling pilot plants - is driving players to consider alternative materials. Victory also discussed the increasingly two-tier market for recycled polyolefins prices between grades used in packaging applications, which are largely sustainability target driven, and grades used in other industries, which are largely cost-driven, and how this is weakening the traditional relationship between recycled polyolefin and virgin prices. Rising demand from the packaging industry saw rHDPE and rPP natural pellet prices trade above virgin prices for the first time in the second half of 2019. The presentation “The status of the recycled PET market today” by Helen McGeough, Senior Analyst, Plastics Recycling, ICIS, dealt with the discrepancy between the high price of rPET on the one hand and the pressure on the other hand to allow this to pass into the packaging. She ascribed her own figures to this: according to her analysis, 2.1 million tons of PET bottles were collected in Europe in 2018, which corresponds to a bottle collection rate of 63%. McGeough acknowledged: “There is great variation between countries. The collection rates vary between 21% (Bulgaria) and 96% (Germany).” A lack of infrastructure explains low collection rates, while the top seven highest rates were found in countries operating deposit return schemes. Helen McGeough Against this 2.1 million tons of PET collected in 2018, McGeough set 1.4 million tons of rPET that was available to the industry that same year. This corresponds to a recycling rate of 44%. “We are losing a great deal of material in the process,” stated McGeough, suggesting poor sorting and high contamination as the cause for this. However, analysts are also finding a great willingness in the industry to do more. rPET capacity expansions and projects are already in place and should provide at least 250,000+ tons of food grade rPET in the next two years. It was agreed that four large groups had a possible influence on geopolitical factors relating to rPET: Circular Economy China and Trade of Waste Resources “Plasti-phobia” Investment “The EU Directive is a driver,” explains McGeough, “and the manda-","@ID":35}, "PETplanet Insider Vol. 21 No. 01+02/20 petpla.net 39 TRADE SHOW REVIEW Hand-held CO2 measuring device for sealed containers and carbonated beverages Made to measure by Kay Barton We met: Mr Johannes Angres, Director New Business Development and Technical Support The traditional approach of “tapping” the cap is a widely-used method for measuring the carbon dioxide content of beverages bottles, such as those which have been transported or stored for long periods of time. At this year’s Brau Beviale trade fair in Nuremberg, Steinfurth, a company based in Essen, Germany, presented a brand new method for taking measurements, which can be carried out without damaging the beverages’ packaging. It consists of a compact hand-held wireless measuring device that weighs just 1.2 kg, which is placed on the head of the bottle to be measured. With gentle hand movements along the X-axis, the CO 2 pressure and temperature of the beverage are relayed to a small touch screen or archived internally in less than 15 seconds. “The ‘NicO2’ collects the data using Steinfurth’s patented laser technology,” Johannes Angres, Director of New Business Development and Technical Support, explained. “A laser beam is sent through the neck of the bottle before being evaluated on the opposite side of the device. The measuring device can flexibly store a bunch of measurements taken depending on its memory size and can transmit the data collected to a PC or smartphone, wirelessly. The measuring accuracy of this non-invasive system is within two per cent. This new method and the machine’s compact design makes possible completely new areas of use.” In the PET sector, this applies in particular to product impairment due to material-related bidirectional gas diffusion for extended periods of time. “This means, for example, that reproducible CO 2 values could be measured for beverages that are subject to longer transport or storage times, or, in theory, the question of how the CO 2 content changes over time in certain situations can be answered. Therefore, we not only consider the device to be of use for laboratory and quality tests, but also in the transport chain, with distributing companies, for example,” Mr Angres added. “The device is already being used at Coca-Cola in Atlanta.” According to Steinfurth, the NicO2 takes measurements in a range of 1-6 bar and a temperature of 5-35 °C. The battery is replaceable. Tabletop measurement Steinfurth also presented an additional measuring device for even more accurate CO 2 measurement at its stand. The CDA-OST, a fixed tabletop instrument, is designed to combine the high-precision destructive measurement method, which entails the piercing of the bottle being analysed, with the advantages of non-destructive optical measurement. An exact measurement is taken by destroying a single sample that is also measured optically at the same time. “With this combination it is possible to extrapolate the influence on the optical sensor for a wide range of carbonated beverages,” Johannes Angres explained. It should then be possible to complete all subsequent measurements of the same type or from the same production batch on a non-destructive basis and just as accurately. It should also be possible to calibrate the device intuitively and to detect individual neck diameters automatically. Its measurement capability ranges from 1-10 bar and temperatures of 5-35 °C. www.steinfurth.de Hand-held wireless solution to measure CO 2 and temperature of bottled beverages","@ID":41}, "BOTTLING / FILLING PETplanet Insider Vol. 18 No. 0/17 petpla.net 21 Edible oil in PET: East India holds out by Michael Maruschke May 2019 We met: Mr Raj Kumar Gupta (FCA), Associate Vice President-Procurement Emami Agrotech Limited is the edible oil business unit of Emami Group of companies, a business conglomerate headquartered in Kolkata, West Bengal. It is a market leader in diversified industries including FMCG (Fast Moving Consumer Goods), biodiesel and edible oil, paper, writing instruments, real estate, healthcare, retail, cement, solar power and contemporary art. Its edible oil business employs approximately 2,500 people in three plants: at Haldia, West Bengal; Krishnapatnam, Andhra Pradesh; and Jaipur, Rajasthan. With the exception of mustard, the company imports all its oil supplies for processing at these three plants. Tour Sponsors: Raj Kumar Gupta (right) and Michael Maruschke While Eastern India is the fastest growing region in India for PET packaging in general, it has not yet penetrated its edible oil market. In contrast to most other parts of India and Asian markets more widely, edible oils in the East are still packed in tins, pouches and in rather old-fashioned and unappealing HDPE containers. Of Emami’s total oil production of around 6,000 tonnes per day, about half is destined for further processing and half is packed by the company: around 50% in tins, 35% in pouches, 5% in HDPE jars (42mm neck 5 l jars, and also 15 l) and cans; and only 10% in PET. Emami ships all over India: pouches are mainly destined for the North; PET and HDPE to other parts of the country. Bottles and caps are very price sensitive when it comes to the packaging of edible oil. The production department PET production capacity is around 125 million bottles per year: 20% of the total in 200ml; half in 500ml and the remaining 30% in 1 l format. Preforms, which weigh from 10 g (0.2 l) and 14.5 g (0.5 l) to 19.5 g (1 l), are currently sourced externally. A new, 2 l PET bottle is to be launched soon. Two hundred bottles a minute are blown on a Techlong SBM (stretchblow moulder). Bericap supplies all of Emami’s 29/21 HDPE caps. A locally produced Jagmohan blow-moulding machine makes HDPE jars at the rate of 3,000 a day; an AKEI unit produces 14,000 a day. Total HDPE processing capacity around 200 tonnes per month. Personal care division Emami also has a personal and healthcare division, which packs Navratna Oil, its flagship product. This therapeutic cooling oil is formulated to provide relief from daily mental and physical stress, is filled exclusively into PET bottles, of 50ml, 100ml and 200ml capacity, the majority of the company’s PP butterfly hinge flip-top caps are supplied by Alpla. www.emamiagrotech.in","@ID":23}, "7 NEWS PETplanet Insider Vol. 21 No. 01+02/20 petpla.net drink technology India (dti) final report 9,925 visitors, 201 exhibitors and a total floorspace of 11,400m2 (30% increase) – these are the figures achieved by dti drink technology India (Messe München), co-located with pacprocess and food pex India (Messe Düsseldorf). Richard Clemens, Managing Director of the VDMA’s Food Processing and Packaging MachineryAssociation, confirms the importance of the event: “Demand amongst Indian consumers is growing across all segments of the beverage and liquid food industry and is expected to have risen by around 89 per cent by 2022 according to market researchers. Indian suppliers are therefore importing systems and machinery in order to be able to meet this demand. This represents a great opportunity for international companies wishing to gain a foothold in the Indian market.” At drink technology India, international exhibitors accounted for 12%, with China being the most represented country, followed by other international exhibitors from Germany, Italy, Spain and Turkey. The Packaging Design Innovation & Technology Conference was held for the first time at the trade fair. Companies operating in the consumer goods industry presented interesting solutions and thought-provoking impulses relating to packaging design, sustainability, food safety and smart packaging. The supporting program also included the Indian DairyAssociation’s Conference, which showcased packaging solutions for the dairy industry, as well as the FSSAI seminar, which highlighted regulations and initiatives as part of India’s “Eat Right Movement”. The Oil Technologists’ Association of India (OTAI) hosted a seminar on oils and fats. Special focus was given to food and non-food-related uses of palm oil. The place2beer and the Buyer Seller Meetings with more than 400 business talks are now firm fixtures of drink technology India. drink technology India alternates every year between Mumbai and New Delhi. The next drink technology India will take place in Mumbai from December 9 to 11, 2020. www.drinktechnology-india.com Chinaplas 2020 focuses on tapping into potential in Asian markets As the global economy faces mounting downward pressure and factors of uncertainties, the global plastics and rubber industries are at crossroads. The challenges are steering investments to become more conservative as companies adjust their strategies. However, growth outlook remains strong for Asian markets that are not new to economic ups and downs, especially the emerging economies in the region. Chinaplas 2020 takes a “local + regional + global” approach and intends to provide a platform of highly cost-effective and technologically advanced solutions that fit the needs of new markets for both upstream and downstream players. Asia currently represents more than a third of the global economy, and its self-reliance continues to strengthen – trade within Asia far exceeds the total of Asia’s trade with other regions such as North America and Eurozone. Attracted by the region’s momentum, foreign investment continues to grow in Asia. China’s Ministry of Commerce announced in November 2019 that China is gaining more foreign investment, not less, despite the sluggish global investment scene. During the first three quarters of 2019, China established more than 30,000 new foreign-invested enterprises and utilised 683.2 billion yuan of foreign investment – up 6.5% year over year. Chinaplas has deep roots in China but has tasked itself with serving the Asian markets to the fullest. Regardless of their region and business scale, visitors are stated to gain a lot, find suitable products and solutions to tackle business growth challenges, reduce production costs, reach breakthroughs in new product development, and accomplish environmentally friendly and sustainable growth. Chinaplas is scheduled to return to the National Exhibition and Convention Center, in Hongqiao, Shanghai, PR China on April 21-24, 2020. The industry event is expected to present 340,000 square meters of exhibition space, and to bring together 3,900+ global exhibitors (more than 2,500 exhibitors from China) and 180,000+ visitors, 11 country/region pavilions including Germany, Italy, U.S., and Japan, as well as 19 theme zones, centering around innovative solutions in plastics and rubber machinery, materials and processes. www.chinaplasonline.com 30th International Colloquium Plastics Technology and 70 years of IKV RWTH Aachen University celebrates its 150th anniversary, IKV will celebrate its 70th birthday and it will be the 30th time it stages the International Colloquium Plastics Technology – on 11-12 March 2020 in the Eurogress Aachen, Germany. The day before the Colloquium, on 10 March, IKV will mark its anniversary by holding the International Symposium on Plastics Technology in the VIP area of the Tivoli soccer stadium. While the IKV Colloquium will present the broad range of IKV research and will target primarily the plastics industry with its practiceoriented research, the Symposium will feature papers from scientists from 14 countries, and aims to arouse lively discussion between scientists and industry. The main highlight of the Colloquium will be the plenary papers on the circular economy, digitalisation/Plastics Industry 4.0, and additive manufacturing. The research topics at the Colloquium will be covered in 15 lecture sessions, each consisting of two presentations from IKV scientists plus a keynote paper from an industry expert: Process-setup in injection moulding by Human-Machine-Interfaces and AI; Throughput increase and quality assurance in packaging technology; Advanced fluid modelling in rubber processing; Precise, reproducible process control for injection moulding; Simulative optimisation of mixing and die technology in extrusion; New methods for testing and quality assurance of high-performance FRP; New injection moulding products using melts loaded with blowing agents; Integrative simulation methods for optimised injection moulding products; Plasma modified barriers and membranes; Digital shadows for data based material and process characterisation; Multi-scale material modelling for predicting part properties; Developments for the resource-efficient production of PET bottles; Process and design optimisation in additive manufacturing; Increasing precision in injection moulding by controlled solidification; and finally Quality features of UD tape-based laminates for forming simulation. www.ikv-colloquium.com www.ikv-symposium.com","@ID":9}, "37 TRADE SHOW REVIEW PETplanet Insider Vol. 21 No. 01+02/20 petpla.net New inline preform monitoring system Inravis presented it’s PreMon, a new system for inline preform monitoring in Düsseldorf. The supplier of vision inspection systems for the plastic packaging industry thereby supports the growing trend to use recycled material in the production of preforms. The PreMon is Intravis’ new inline monitoring system for producers of transparent, translucent and opaque preforms. Integrated into the transport process between the injection moulding machine and the packaging of the preforms, the system inspects up to 70% of the preform flow for typical defects. In concrete terms, this includes: Colour deviations, contaminations, ovality of the muzzle, injections, defects on the surface of the muzzle and length of the injection point. The operator receives monitoring results for each octabin and can use the data to decide on further measures for the respective container, e.g. re-sorting. With the PreMon Plus, which also has an ejector, customers can eject faulty preforms directly. The user can hereby actively improve the quality of his octabin. Future trend recycling Dr Gerd Fuhrmann, Managing Director of Intravis GmbH, sees the PreMon as indispensable for all preform production lines in the future: “Today more and more preforms are produced with recycled material. The resulting problems in the production process, such as contamination or yellowing of preforms, cannot be predicted. Constant monitoring of the preform flow is therefore indispensable. If a manufacturer wants to get a good overview of the quality of his products, then a monitoring system like the PreMon is the perfect solution at a moderate price.” At the K show Intravis was able to announce several sales of the new system. www.intravis.de Swiss engineered innovations, performance and reliability PackSys Global and its subsidiaries Madag Decoration, Combitool Solutions and Texa Packing presented their new highlights at the K show. The capLab: PackSys Global manufactured a high speed machine for creating tamper evident bands by folding and slitting plastic caps. Until now the most important quality control test, the pull-off test, checks the strength and consistency of the tamper evident band, has been done periodically offline in a remote laboratory. The capLab is the first fully automatic in-line pull-off tester for quality supervision of cap production. It selects caps at random or caps which meet specific requirements, for example caps from each cavity on an injection or compression mould or caps which were processed on a specific mandrel on the folding and slitting machine. Because the testing is done on an ongoing basis the time to get the results is measured in seconds. The capLab uses the test results to automatically change the settings on the folding and slitting machine that caps never go outside the approved limits. Because the testing is done automatically it helps to reduce labour costs. Madag Decoration manufactures hot foil stamping machines for different industries, especially for cosmetics packaging. The machines allow metal foil to be embedded in the packaging in an environmentally friendly process. Madag Decoration presented its DecoRoll-XC machine. The machine is well adapted to the needs of small orders. By using the hot foil stamping technique, the customer can choose between a high-gloss gold and silver appearance or even a brushed or textured look in the product’s packaging. This option is not possible with other techniques. NEOSeam is PackSys Global’s new side-seam technology for 360° printed appearance showing no visible overlap to the consumer. This new technique was demonstrated on PackSys Global’s LTR2 side-seamer. The NEOSeam produces decorated cosmetic laminate tubes. NEOSeam was combined with PackSys Global’s focus on the use of large diameter tubes to replace extrusion blow moulded plastic bottles. Many brand owners use plastic bottles for larger volume packs however these come with an environmental cost. Plastic bottles commonly use between 12 and 40% more plastic than a tube which holds the same volume. PackSys demonstrated production of 60 mm diameter tubes using NEOSeam (suitable for pack size of 250 ml to 400 ml). www.packsysglobal.com","@ID":39}, "CAPS & CLOSURES 10 PETplanet Insider Vol. 21 No. 01+02/20 petpla.net Range compatible with existing bottling lines Checking all the boxes on tethered caps CEO Dr Michael Krueger summed up the challenges for Corvaglia: “During the development of our concepts, we focused on ensuring 100% compatibility with existing bottling lines and improving the drinking experience for the consumer.” There is a lot to consider when planning and designing these new solutions: Most importantly, the requirements of the EU Directive have to be met. These will be laid out in more detail in a CEN standard that is currently being drafted. Tethered caps also have to offer customers the same physical performance as standard closures. Last but not least, tethered caps ideally need to be implementable without the need for modifications to the neck finish and filling systems and without any loss of efficiency in the handling and filling processes. The tethered cap solutions from Corvaglia are claimed to check all the abovementioned boxes. Film hinge caps, lasso caps, shift caps The experience of designing closures using different types of tamperevident bands and manufacturing technologies has enabled Corvaglia to develop a wide range of tethered cap solutions. Three concepts are worthy of special mention here: film hinge caps, lasso caps, and shift caps. Film hinge caps have an opening angle of 180 degrees and can be locked easily. This means that liquids can be drunk or poured without the lid part of the cap getting in the way at all. For most neck finishes, the weight of the film hinge caps is the same as that of standard caps. Lasso caps have an opening angle of more than 180 degrees without a lock. This concept features a particularly user-friendly reseal option. There is also no material added for most CAPS & CLOSURES ‘Lasso’ caps feature a wide opening angle and a user-friendly reseal option. Film hinge caps offer a 180° opening angle. The patent-pending shift cap can be used for all drink types. In May 2018, the EU announced a new Directive on how to deal with single-use plastic products. Under this Directive, in the future, drinks will only be allowed to be sold in plastic containers if the cap remains attached to the container. This has made the subject of tethered caps omnipresent in the beverage industry. Since the announcement, the specialists at Corvaglia have been working hard to find solutions for beverage caps that not only meet the requirements but improve also consumers’ drinking experiences. In the autumn of 2019, the Corvaglia group presented its current generation of tethered cap solutions at K 2019 in Düsseldorf. cap types for this solution. As a result, these two solutions profit entirely from the progress that Corvaglia has made in lightweighting their cap portfolio over the last three decades, states the company. The film hinge and lasso caps are set to be gradually introduced for various kinds of neck finish during the next few years. With the shift cap concept, Corvaglia has already developed what they call the next step in the evolution of tethered caps. Shift caps can simply be tucked away on the container after opening. The advantage of this is that the cap does not get in the way despite staying on the bottle. The solution can be used for all drink types. A patent is pending for the concept. www.corvaglia.com","@ID":12}, "TRADE SHOW REVIEW PETplanet Insider Vol. 21 No. 01+02/20 petpla.net 34 tory recycled content in PET bottles will be the biggest game changer!” To fulfil the target of 25% rPET content in 2025, use of food grade rPET must more than triple. Across Europe, 37 further food grade rPET units with an output capacity of 20kt/y are required to provide enough rPET to meet bottle market demands, but this assumes the bottle sector has complete access to total rPET supplies where other packaging markets compete for those supplies. To fulfil the ambitious target of 30% by 2030, a 4.5-fold increase must be achieved. Work must also be done providing post-consumer bottles, as the analyst explained further: meeting the SUP targets requires an annual increase in collection of 4-7%. McGeough summarised that these numbers reflect the differences in systems, consumer participation and government ability to prioritise investment in waste management. The lack of standardisation in everything from waste infrastructure to final rPET product specifications continues to present as many challenges as opportunities for one of the most developed recycled markets in the plastic industry. In her presentation, Tristanne Davis from the Sustainable Packaging Coalition presented design considerations for packaging to improve recycling rates. She addressed the questions ‘How are brands evolving packaging design to support recyclability?’, ‘How might we improve the recovery system with recycling marker systems?’ and ‘How can effective labelling help to improve consumer recycling habits?’. As a general formula, it is first and foremost important to check that packaging material and format are recyclable. Further aspects should also be checked, such as that the end consumer understands that the product is recyclable and that the product can be sorted easily in the recycling stream. In a panel discussion on opportunities for boosting recycling capacity with feedstock recycling, there was an open mic session moderated by Paul Hodges, Chairman, International eChem, that classified the challenges of current recycling solutions: “The problem is that we have just six years to work out how we are going to do it – and there are many challenges to overcome. One challenge is around technology. Mechanical recycling can handle single-layer plastics such as PET, and chemical recycling technologies such as pyrolysis can recycle multi-layer plastics. But they need a lot of development work to operate efficiently. Another challenge is that recycling will change our business models, as the recycling must be done locally to minimise CO 2 emissions and create a circular economy. We must start planning now to introduce the circular economy, or risk losing all the benefits that plastics provide for society.” On this note, the audience raised the concern of how the European market could be protected from cheaper imported packaging that does not conform to the EU Directives. In this regard, Werner Bosmans held out the prospect of an EU-CO 2 border tax. He then finished with a passionate plea: “Europe is not afraid to be at the front. Plastics pollution is a real issue. We need to do something, and the rest of the world has to follow. There is no other choice.” www.icis.com Upcoming ICIS events: The ‘Asian Recycling & Sustainability Conference - Seeking paths and working collaboratively to establish a circular economy road map in Asia’ will get to the bottom of the issues ‘How big is the problem on plastic waste today?’ ‘What strategies are the industry players exploring to create real solutions in tackling these issues?’ ‘How can brand owners, consumers and government institutions help to promote a sustainable future?’ It will be held on 19 February 2020 in Bangkok, Thailand. The ICIS conference ‘PET Value Chain: Building a positive future - Leading the change towards a sustainable industry with commitments to circularity’ will be held 17-18 March 2020 in Amsterdam, The Netherlands. AGR April 21-24, 2020 Hall 2.1 · A05 at the Krones booth German Technology","@ID":36}, "BOTTLING / FILLING PETplanet Insider Vol. 21 No. 01+02/20 petpla.net 20 Material savings in Gujarat It’s all ultralight! by Kay Barton August 2019 We met: Mr Chintan Patel, Director Western India – more precisely: Ahmedabad in the state of Gujarat – is the home of plastics processor and water bottler Optima Polyplast, and its sister company Optima Plastic Industries. In just six years, the company has developed from a straightforward closures retailer to a manufacturer and full-range supplier of closures, preforms, bottles and bottled water. Right from the start, the companies attached considerable importance to material savings and focused on the manufacturing of ultra-light products. We talked with Director Mr Chitan Patel about the development and activities of the Optima Polyplast. Tour Sponsors: “In the two years that followed our launch as a retailer of caps and closures in 2013, the market showed increasing promise,” recalls Chitan Patel, a university-qualified pharmacist. “The positive resonance convinced us that we could also become a manufacturer. Together with my partners Dhiraj Patel and Harish Patel, we founded Optima Plastic Industries in 2015. We began manufacturing closures, which led to the vision of being able to offer a complete product; that brought us to where we are today.” Optima has, since 2006, also operated a bottling plant for water in another part of the business; the complete packaging is now to be manufactured in-house. “Our idea was for the packaging to save on materials and costs, and that we could pass these savings on,” he explains. Optima’s own water brands – “La Aqa+” and “Reva” – should especially benefit from any savings coming from the reduced use of materials in the future, enabling the products to be offered on the market at a lower price. Although the bottling plant is structurally separate it is located on the same site as the plastics processing plant, after Optima decided that it wanted to channel everything into a single location. The company currently employs 120 workers on a 3-shift basis and has an annual turnover of US$12.6 million. It has invested US$4.3 million in its business which, for strategic reasons, is located on a 2,300m2 site near the centre of Ahmedabad. The city, which has almost eight million inhabitants, offers considerable potential in the beverages and supply industry. The state government supports business start-ups and expansions through attractive tax models and cutting-edge infrastructure for utilities and transportation, for example. Optima researched and developed its products for around a year, before creating lightweight preforms for water bottles that are, at the same time, designed to have sufficient resilience to handle extended transport routes. “We can now manufacture 6g preforms for 0.2l bottles, 9g for 0.5l, and 13.8g for 1l,” Mr Patel says, indicating his portfolio. “Our research findings are that the 1l bottles are among the lightest in the world. We also make what we consider to be the lightest closure in India; just 0.8g at 23mm. In using such a reduced amount of material, we can now offer the water bottle at a price which is approximately 35% lower.” Three compression machines from Sacmi manufacture the closures, with an annual output of approximately 220 million units. Around five per cent of production is exported. Optima also supplies 28mm closures for third-party fillers and 28mm and 25mm closures for pharmaceutical customers, including Torrent Pharma, Intas Pharma, Cadila Pharma and Yash Pharma. Preforms are manufactured on Ferromatik Milacron equipment, while Shyam Plastic Machinery handles the blow moulding, with two automatic systems and one semi-automatic. Total output of preforms and bottles is over 180 million units. In the filling plant, Optima uses rotary equipment from Hilden, running at 300bottles/minute for filling and capping. The material, amounting to approximately 250 tonnes per month, comes from Saudi Arabia or local Indian manufacturers. As a supplier of preforms and closures, this segment accounts for around 35% of the total turnover. “We already have a unique selling point, in our consistent lightweight claim,” explains Mr Patel. “On average, we save approximately 45% on material compared with our competition, a saving we pass on to our customers. Last but not least, the low cost of the materials is also a signal for a greener India. In the coming year, we want to install more new machines and to make further investments in a franchise model over the medium term,” said Mr Patel. “We want to gain a foothold in other Indian states both independently and through joint ventures, and manufacture there locally with the same strategy.” www.optimapolyplast.com Director Chintan Patel with a bottle of La Aqa+ 25mm compression moulding closures for pharmaceuticals","@ID":22}, "MAINTENANCE PETplanet Insider Vol. 21 No. 01+02/20 petpla.net 31 The pellets are propelled at high speeds to blast contaminants from mould surfaces. The combination of kinetic energy and thermal effects breaks the connection between dirt and surface, lifting contaminants away. Other manufacturers found that Cold Jet’s system cut cleaning time 50 to 75%. As dry ice evaporates on contact there is no run-off, rinsing or drying required. Dry ice blasting is also safe and non-toxic, does not create downstream contamination and reduces or eliminates employee exposure to dangerous chemical cleaning agents. After a Cold Jet demonstration, Silgan acquired two dry ice blasting cleaning systems. One is located on the plant floor; the other is in the maintenance room. Since integrating Cold Jet’s systems into its cleaning cycles, cleaning time for a single mould was cut from two to three hours to less than 45 minutes. The company has trained all its machine operators in their use and been able to reduce maintenance room staff to a single person. Multiple applications Silgan is now finding ways to use dry ice blasting in other areas of the plant, including a conveyor system for salad dressing bottles. It uses an anti-static spray on the bottles as they move along the conveyor system to prevent them from sticking together. The alcohol-based spray accumulates on the conveyor rollers, which slows down production. Cleaning the anti-static spray machine previously involved disassembling the system, cleaning the components by hand with food-grade cleaners and then reassembly; the process took at least a day. Operators can now use the Cold Jet system to clean the entire machine in an hour, without taking it apart and risking damage to the components. On occasions when a PET dryer overheats and resin melts inside it, workers would normally have to wait for the dryer to cool down and then remove the resin by chipping it out; a 12-24 hour process. Dry ice blasting clears the resin and enables the dryer to be restored and running in less than two hours. Saving days of downtime “We have also eliminated nearly three days of downtime by using Cold Jet’s system to clean the injection screws on our presses, a process that usually required us to send the screws offsite,” said Pond. “The time savings have been phenomenal as we have been able to clean our equipment better and faster while they are still online. We no longer have to worry about working dangerously close with hot equipment, our on-site environment and safety managers are happy, and we have dramatically reduced the amount of cleansers, degreasers and alcohol that we buy and use for cleaning.” Every 15,000 cycles, machine operators use the Cold Jet system to clean and prepare the moulds for the next round. At the deeper 60,000 cycle cleaning, the maintenance operative removes the majority of the residues by dry ice blasting the moulds, before they are removed from the presses. Line workers clean the rest of the equipment, often using only dry ice blasting. “It is because of Cold Jet’s systems that we are able to meet our high cleaning standards and customers’ mould maintenance cycles,” Pond concluded. Use of Cold Jet’s cleaning systems has enabled Silgan Plastics to reduce scheduled downtime, increase production time and reduce maintenance costs. www.coldjet.com IMDvista INOX Line Closure Inspection – 100% Inline – Complete solution out of one hand. – Robust, compact and very flexible. – One control center (HMI) for the whole line. IMDvista PECO LUX Preform Monitoring – Shot by Shot – Requires no additional floor space. – No preform orientation necessary and no moving parts. – Up to 80% part inspection. Inspection Systems for the Plastic Packaging Industry IMDvista BOCO SCAN We scan and measure your Bottle Inline – Transparent, opaque, shiny and matte bottles in one system. – Calibrated measurement +/- 5 μm. – Fast automatic product change. Swiss Made | www.imdvista.ch Cleaning injection blow mould","@ID":33}, "PACKAGING / PALLETISING PETplanet Insider Vol. 21 No. 01+02/20 petpla.net 27 mann. Finally, the system passed its factory acceptance test and was shipped to Saint-Galmier. Here, the KHS team replaced the old KHS Kisters shrink packer from 1986 with the optimised packaging machine. “At first we weren’t able to fully achieve the required packaging quality with the combination of shrink film and machine used,” admits Stuhlmann. The specialists therefore spent the following months working on the various machine components, further developing, constructing, installing and testing them time and again. Significant development for the entire Danone Waters Group One major further development on the new generation of machines was to distribute the hot air supply more accurately on both lanes. The optimum alignment of the hot air flow on both sides of the multipacks loosely wrapped in film also had top priority for KHS. “Both are crucial for crease-free pack quality as the optimum processing window for the partly inverse effects was extremely limited,” Stuhlmann explains. The Dortmund company solved this problem with the help of a number of further developments, one being the specially designed central tunnel nozzle which will also be available to other projects in the future. The special air nozzles with their optimised perforated nozzle plates also help to create crease-free packs. Furthermore, the KHS Kisters shrink packer can now process films of a much lower thickness. The machine uses an optimum width of film per pack thanks to film web control. Badoit and its operators benefit from fully automatic film web control which is easy to handle. “With this new technical feature we were able to achieve the goal set by the customer, namely of providing optimum packaging quality while using the lowest possible amount of material,” smiles Stuhlmann. The team of experts also managed to boost the packer’s performance. On the further developed shrink packer up to 37,000 bph can be formed into packs of six on two lanes at the existing line speed. The final acceptance test at the beginning of 2019 was performed to the full satisfaction of all involved. “KHS has met our requirements in every respect. The packaging quality has considerably improved compared to what it was,” explained Marie. “Thanks to the improved quality we’ve been able to double the size of the lettering on the packaging,” Marie relates. “This is a great advantage as regards product presentation. Our brand is now more visible to our customers.” The management of Danone Waters is also convinced by the final result. The French parent company considers the project to be an excellence reference for the entire company group. www.khs.com 25-26 March 2020RAI, Amsterdam www.prseventeurope.com Incorporating The Plastics Recycling Show Europe will take place at the Rai, Amsterdam on 25th-26th March 2020 The Exhibition and Conference for the European Plastics Recycling Industry Register Now for free entry at prseventeurope.com","@ID":29}, "CAPS & CLOSURES 13 PETplanet Insider Vol. 21 machine. The product characteristics of the 38mm closures that were being produced live at the booth were constantly analysed by the Intravis CapWatcher III and then transmitted via Euromap 82/OPC-UA to the machine controller of the Netstal Elion 2200. The data of the visual quality inspection of the external diameter were used to control automatic corrective measures. Malfunctions and unexpected production disruptions are unwelcome and have to be fixed quickly to ensure that the overall efficiency of the plant remains high. With Smart Operation inexperienced and less well-trained personnel will be able to start up the production quickly. The operating concept consists of four buttons, the so-called Smart Buttons, as well as a configurable dashboard on the main screen for the display of relevant process information, situational interaction messages as well as applicationspecific instructions. During production, the status transitions are activated with the Smart Buttons. All conventional operating elements can be blocked in order to make sure that the operation of the production can be made as simple and secure as possible. The machine is then operated exclusively by the Smart Buttons. Standardised handling specifications based on in-house expertise can be reliably integrated into the machine controls. “The volume of written process descriptions, checklists and instructions at the machine is reduced drastically or even eliminated altogether, since these are part of the machine and the user always knows that to do thank to the information on the main screen,” explained Schmid. www.kraussmaffei.com Higher output: Thanks to the optimisation of the clamping unit controller, the output of type 29/25 closures can be increased by 6.5%.","@ID":15}, "MARKET SURVEY 25 PETplanet Insider Vol. 21 No. 01+02/20 petpla.net Resins Company name Indorama Ventures Polymers Germany GmbH NEO Group Reliance Industries Limited NOVAPET, S.A. Postal address Telephone number Web site address Contact name Function Direct telephone number E-Mail Philipp Reis Strasse 2 65795 Hattersheim, Germany +49 69 305 6025 www.indoramaventures.com Mr Achim Heyer Business Dir. Polymer & PET Resin +49 172 614 6425 [email protected] Industrijos str. 2, Rimkai LT-95346 Klaipeda district, Lithuania +370 46466710 www.neogroup.eu Ms Justina Volček Product Development Manager +370 602 14 169 [email protected] PET BU, Build. No. 8, B Wing, 1st floor, Thane Belapur Road, RCP, Ghansoli, Navi Mumbai, 400701, Maharastra, India +91 22 7967 0000 www.ril.com Mr Rajesh K Gera Asst. Vice President - Business Development +91 2279681426 (D), +99 67033107 [email protected] P° Independencia, 21, 3°, PC 50001 +34 976 216129 www.novapet.es Mr Ricardo Monfil Head of Polymers Division +34 976 216129 [email protected] Resins 1. Brand name of the resins Polyclear PET, PolyShield Resin, XPure Polyester NEOPET Relpet and Relpet Green NovaPET 2. IV range a. of homo-polymers 0.60 - 1.05 0.56 - 0.82 0.76 0.58 - 0.96 b. of co-polymers 0.81 - 0.87 0.76 - 0.84 0.59 - 1.00 0.60 - 1.30 3. Speciality resins CSD Polyclear PET 1101 NEOPET 80, NEOPET 82 Relpet G5841 LBS Soft, CR Water Polyclear PET 1101, T94N Aqua NEOPET 76, NEOPET 78 Relpet G5761 MW Soft, CR, SPRIT Beer PolyShield Resin 2300 and Masterbatch 2520 NEOPET 80, NEOPET 82, NEOPET 84 Relpet B9845 Glasstar Edible oil Polyclear PET T94N Relpet G5801 Wine / Liquors PolyShield Resin 2300,2520; OxyClear Barrier Resin NEOPET 80, NEOPET 82 Relpet B9845 / Relpet G5801 Glasstar Personal care / Pharmaceuticals Polyclear PET T94N, XPure Polyester NEOPET 80 Relpet G5801 Glasstar, SPRIT Slow crystallisation Polyclear PET T94N, XPure Polyester Relpet S5841 (5 gallon returnable, thick sheet and thick moulded articles) Glasstar, SPRIT Hotfill NEOPET 82 HF Relpet H7761 HF Pre-coloured DCU, Luz Fast reheat Polyclear PET 1101 NEOPET 82 FR, NEOPET 84 FR Relpet QH5821 LBS Soft Other Next generation catalyst series Xpure Ultra NEOPET Relpet C1000 (CPET trays, high tenacity straps), Relpet IM5590 (thin wall products and injection moulded articles), Relept OP5821 (UHTmilk on aseptic filling line) CPET, HT, REX (for EBM), SOL (aerosol bodies) 4. Increased barrier properties PolyShield Resin 2300, OxyClear Barrier Resin Relpet B9845 barrier grade has both active oxygen barrier and passive carbon dioxide barrier Dairy, LUZ , DCU, Polygloss (Light barrier), Glasstar (Gas barrier) 5. PEN mixes available Yes 6. Recycled blends available Relpet Green (100% PCR) Yes, under customer requirements 7. Special comments EBM grades available ; NPG modified resins in development Gradeshavebeendevelopedbasedonfinerrequirementsof end-use;customisedgrades(likeEBM)areavailableonrequest. Specialised in light barrier protection for long shelf life milk products (UHT, ESL, Milk shakes, yogurt) Company name Indorama Ventures Ltd Postal address Telephone number Web site address Contact name Function Direct telephone number E-Mail 75/102 Ocean Tower 2, 37th Floor, Bangkok 10110, Thailand +662 661 6661 www.indoramaventures.com Mr W.G. Hoenderdaal Technical Marketing Manager +316 51809942 [email protected] Resins Europe USA/Canada Latin America Asia 1. Brand name of the resins RamaPET, PlantPET Polyclear PET, Oxyclear Barrier PET, Oxyclear Shield PET, Performance PET, FuTuRe-PET Resin, PlantPET Resin Polyclear PET, Oxyclear Barrier PET, Oxyclear Shield PET, Performance PET, FuTuRe-PET Resin, PlantPET Resin RamaPET, Afron 2. IV range a. of homo-polymers IV 0.58 - 0.95 IV 0.58 - 0.95 IV 0.74 - 1.25 IV 0.50 - 1.08 b. of co-polymers IV 0.58 - 0.84 IV 0.58 - 1.25 0.58 - 1.25 IV 0.58 - 1.08 3. Speciality resins CSD R1, R182C, R180 ES11, ES11 (A)-R10, 1101 1101, 1111 S1, S2, R1, N1S Water N180, W176, W170, N1, N1(S) N2R, N2R (A)-R10, N2R-Ti, 3301 3301 N2, N1 Beer N1, N1(S), N180 Oxyclear Shield PET 2310 Oxyclear Shield PET 2310 N1 Edible oil Wine / Liquors N1, N1(S), N180 Oxyclear Barrier PET 3500, PolyClear EBM PET 5505, 5507; 1708CC, 3302 Oxyclear Barrier PET 3500, Polyclear EBM PET 5505 and 5507 N1 Personal care / Pharmaceuticals N1, N1(S), N180 Polyclear EBM PET 5505/5507 Polyclear EBM PET 5505/5507 N1, G1 Clear Slow crystallisation P184 T-94 T-94 G1, G1AS (scratch resistant version) Hotfill R1, HF 2201, 1708HS 2201 H1 Pre-coloured None Fast reheat R1, R182C, R180 ES11, 1101 R1, R2, ES11 Other PlantPET R182C PlantPET Resin (Bio-MEG), High IPAmodified resins, BOPET Grades PlantPET resin (Bio-MEG) L1 (high flow blood tubes), film grades, low melting resins & silica masterbatches 4. Increased barrier properties Oxyclear Barrier PET 3500, OxyClear Shield PET 2310 Oxyclear Barrier PET 3500, OxyClear Shield PET 2310 5. PEN mixes available Co-polymers; Homo Polymer PolyClear Heat 2222, 2224, 2226, PEN PolyClear Heat 2222, 2224, 2226, PEN 6. Recycled blends available rPET flake and granulate FuTuRe-PET Resin, PolyClear Conserve PET FuTuRe-PETresin, PolyClear Conserve PET 7. Special comments RamaPET L1 for injection thin walled articles Polyclear EBM PET for extrusion blow moulding; low IV and functionalised copolyester N2G(GermaniumbasedPET);HPCGrades forcrystalclearbottles/articles,BioPETbasedonBioMEG","@ID":27}, "PETcontents 4 PETplanet Insider Vol. 21 No. 01+02/20 petpla.net 01+02/20 INSIDE TRACK 3 Editorial 4 Contents 6 News 35 Products 40 PET bottles for Home + Personal Care CAPS & CLOSURES 8 Bonded to the bottle - United Caps and LyondellBasell present three varieties of tethered caps 10 Checking all the boxes on tethered caps - Range compatible with exisiting bottling lines 12 High performance for production of closures - New control algorithm for higher outputs 14 Carefully designed - A delicate balance of precise geometry 15 Stay with me! - Bericap tethered caps solutions 16 Till recycling do them part - Solutions for attaching caps to single-use bottles for the duration of their use 18 Sustainable trends in caps - Sacmi proposal with the option of the tethered feature BOTTLING / FILLING 20 It’s all ultralight! - Material savings in Gujarat 21 Edible oil in PET: East India holds out 22 From mineral water to 60 different preform designs MARKET SURVEY 24 Suppliers of resins and additives PACKAGING 26 French design packaging - Secondary film packaging for multipacks LABELLING 28 Sustainable labelling - using PET MAINTENANCE 30 Cutting cleaning costs - New cleaning system boosts production time and productivity TRADE SHOW REVIEW 32 Circularity for polymers - ICIS recycling conference 36 K show review - part 2 38 Focus on efficiency and circular economy 39 Made to measure - Hand-held CO 2 measuring device for sealed containers and carbonated beverages BUYER’S GUIDE 41 Get listed! Page 36243628 Page 8 Page 30 CAPS & CLOSURES","@ID":6}, "35 PRODUCTS PETplanet Insider Vol. 21 No. 01+02/20 petpla.net PETproducts Newamstar launches Starbloc integrated solution Newamstar has announced the launch of Starbloc, which has been developed in line with the trend towards equipment integration, convenience and intelligence. Starbloc integrates blowing, labelling, filling and capping into a single system in a solution designed to meet the needs for water, beverage, condiment and dairy products. It has a maximum capacity of 53,000 bph for 200-2,500ml PET bottles. Newamstar says that Starbloc’s highly-integrated design enables it to occupy a small footprint and that it offers a rapid return on investment. It incorporates a sixth generation blowing machine, with output capacity of up to 2,650 bottles/ mould/hour. Full servo synchronisation control enables quick changeovers and with flexible production. Multi-label stations are compatible with different bottle types and labels and pre-adhesive labelling technology eliminates the need for glue stations, making operation and maintenance easier. Sterilisation modules and technical process control with non-contact electronic filling valves are designed to maximise hygiene and an online inspection and rejection system control preform, empty bottle and label quality. The installed MES system undertakes life-cycle management of data identification, acquisition tracking and quality traceability. Newamstar says that Starbloc is very much part of the industry’s technological progress towards “perfect” (error-free) factories. www.newamstar.com 38D-KL for dairy and non-carbonated beverages The new 38mm D-KL linerless HDPE closure (38D-KL) from Closure Systems International (CSI) is designed with consumer and dairy producer satisfaction in mind. Through its improved application performance and drop-down tamper evidence for additional security, the 38D-KL is precision engineered to deliver reliable performance on HDPE and PET dairy bottles. CSI’s 38D-KL is commercially available for applications in non-carbonated cold- and ambient-filled beverages and liquid dairy markets. CSI’s 38D-KL closure is intended to deliver a sustainable solution and can be sourced with up to 40% PolyCycle, CSI’s post-consumer recycled (PCR) HDPE resin. PolyCycle PCR is sourced from recycled milk and other beverage containers, providing an opportunity for closed loop packaging and ensuring high quality sourcing. Both the HDPE and the PolyCycle PCR version of CSI’s 38D-KL closure are 100% recyclable. www.csiclosures.com 35 PRODUCTS [email protected] Tel: +90 212 695 50 00 Fax: +90 212 694 97 24 100815dmyR .com","@ID":37}, "CAPS & CLOSURES 8 PETplanet Insider Vol. 21 No. 01+02/20 petpla.net United Caps and LyondellBasell present three varieties of tethered caps Bonded to the bottle Caps that stay attached to the bottle after it has been opened, known as tethered caps, have been presented jointly by United Caps and LyondellBasell at the K trade fair. This design requirement will be obligatory for single use beverage bottles in Europe by July 2024. PETplanet: United Caps and LyondellBasell are presenting the results of their joint project: three varieties of tethered caps. Please could you describe your cooperation on this project? Hoffmann-Leist: When the discussion about tethered caps began, we initially noticed great confusion in the market. So, we approached our long-term partner LyondellBasell to see if we could sit together and reflect on what would be required and discuss what was to be done. We initiated the Alliance for Closure Tethering (ACT) with LyondellBasell on our side as a resin producer. The brand owner Spadel is also part of the ACT and many more. This was in the middle of 2018. A big plus of the ACT is that it works very effectively with short discussion pathways. That’s why we are able to present three different solutions already today which we began to design early this year. Trocherie: Each ACT partner brought their particular expertise to the project. As a resin producer, we proposed different resins which are tailored to the requirements of still and carbonated beverages. PETplanet: What different resins have been proposed for the specific properties? Trocherie: For the non-carbonated beverages where we don’t need resistance to stress cracking, the grade chosen is Purell GC7260G, an organoleptic resin offering flexibility in terms of processing and allowing broad processing conditions. For the screw-with-hinge design for Carbonated Soft Drinks (CSD) and aseptically filled beverages, the selected resins are the grades Hostalen 5231H and Hostalen 5231H UV. They can be implemented for a very high level of carbonisation as they show good stress cracking resistance (ESCR) performance. Due to high throughput in processing, they also increase productivity and save energy by allowing the use of a lower injection temperature. PETplanet: Caps and closures manufacturers offer a variety of tethered closure designs these days. Some of them require a longer neck to attach the closure. Which designs did you choose? Reimann: We are presenting three different designs, and to anticipate, all of them can be used with standard necks. The first design is a double-slitted TE-band design, known as a “lasso” design. This design has the advantage that it allows the use of existing moulds, thus reducing implementation complexity. There is also no increase in weight compared to classic nontethered closures and it is available for all major neck finishes. The second design has been developed for still water. This presson design offers a lightweight solution. The third design – a screw-withhinge variant – can be used for all kind of beverages. This one is the most sophisticated because it has CAPS & CLOSURES Screw-withhinge design for all kind of beverages Double-slittedTE-band design (widely known as “lasso” design) for all kind of beverages Press-on design for non-pressurised beverages by Gabriele Kosmehl & Heike Fischer From left: Ms Astrid Hoffmann-Leist, Chief Marketing and Innovation Officer at United Caps, Mr Benedict Reimann, Innovation Manager at United Caps, Ms Isabelle Trocherie, Business Development Manager Healthcare & Closures LyondellBasell, Gabriele Kosmehl & Heike Fischer","@ID":10}, "BOTTLING / FILLING PETplanet Insider Vol. 21 No. 01+02/20 petpla.net 22 From mineral water to 60 different preform designs by Michael Maruschke Tour Sponsors: Aditya Dugar (left) with Michael Maruschke at the Editourmobil May, 2019 We met: Mr Aditya Dugar, Managing Director When Ruptex was founded by Aditya Dugar’s father in 1998, as a bottler for mineral water, its preform production capacity amounted to 20 tonnes per month, with blowing and filling output of 60 bottles per minute. His father encouraged Aditya, from his early schooldays, to come to the company in his free time to learn all the aspects of business – and he did so. He formally joined company in 2007. Today, Ruptex is in good shape, making healthy profits with a focus on preform production; mineral water is not part of the operation any more. Aditya considers it a difficult business with small margins and difficult to operate in, without a well-established brand. He looks after Sales and Purchasing and another relative manages production. Today, the company has an annual capacity of 8,000 tonnes. Preforms are produced in Bhiwadi, Rajasthan, approximately two and a half hours’ drive from New Delhi. It produces about 60 different designs, ranging from 7 g to 300 g, on seven Toshiba and five Ferromatik injection moulding machines. At the heart of preform manufacture is a Husky H-PET machine with a 40 cavitymould; it was the first machine of its kind in India, when purchased back in 2016. Focus on regional brands and 10% rule of thumb Today, the company’s product range includes preforms for CSD (50%); water (20%); jars (20%); and edible oil (10%). Its customer base is comprised mainly of smaller, regional brands. For Aditya it is important that he can communicate directly with the owner of a company and build up good relationships. He feels more comfortable looking after several smaller customers than a few big players. As a rule of thumb, he does not want to sell more than 10% of capacity to one single customer, as a precaution. Raw material is mainly supplied by Reliance, the market leader, and some is imported from China. He mentioned that Reliance recently introduced a kind of flat rate for its PET raw materials: all customers pay the same price per tonne, regardless of quantity. Other PET raw material suppliers in India have followed this pricing model. Aditya has a positive outlook for the years ahead for the PET and preform market in India. Because of its flexibility as an unbureaucratic, smaller company, Ruptex is in a very good position to follow new trends, explore new niches and implement new developments, rapidly. He is thinking of expanding into caps and investing in a dedicated injection moulding machine, specifically for this purpose. He openly admits that the company began cap production several years ago, but it was challenging. However, time marches on and the market has changed; he sees a good opportunity to enter this segment. www.ruptex.com Aditya Dugar at his desk","@ID":24}, "TRADE SHOW REVIEW PETplanet Insider Vol. 21 No. 01+02/20 petpla.net 32 Circularity for polymers - ICIS recycling conference by Gabriele Kosmehl The polymer industry is facing an unprecedented moment brought on by a global shift towards circularity and sustainability. The European Commission’s Strategy for Plastics and increasing brand-owner commitment to recycled content in packaging is putting pressure on an industry already challenged by supply constraints and market uncertainty. With the full value chain impacted by these challenges, the importance of industry collaboration is emphasised more than ever before. In response to this changing industry, Berlin hosted the first ‘Circularity for Polymers: The ICIS Recycling Conference’ on November 5th 2019. PETplanet selected the most important topics for those involved in the PET chain. The first speaker was Werner Bosmans, Policy Officer - Circular Economy, for the European Commission. He explained to the 100 conference participants what the initiatives of the European Plastics Strategy and the Single Use Plastics Directive would require from participants in the plastics supply chain. He talked about the EC’s targets and strategies for plastic recycling and the proposed plastic tax, including timelines and strategies to define recycling terminology. Werner Bosmans Of particular interest for the bottle industry is the directive on reducing the impact of certain plastic products on the environment, which comes into effect on 5 June 2021. Based on the identification of the ten most-found marine plastics litter items on European beaches, the directive advocates, where possible, less harmful alternatives, prevention measures and/or better waste management. In terms of the bottle caps listed in the top ten items, the product design requirements for tethered caps come into effect as prevention measures; these stipulate that caps and lids must remain attached to beverage containers & bottles (≤ 3 l) from July 2024. From 2025, single use beverage bottles must contain 25% recycled content for PET bottles (as an average per member state) and by 2030 30% recycled content for all plastic bottles (average per member state). In addition, extended producer responsibility is planned so that manufacturers of certain packaging – such as food and beverage containers – must help to meet the costs that arise from waste prevention, waste management, litter clean-up and data gathering. The separate collection target for plastic beverage bottles is 77% by 2025 and 90% by 2029. “The best way to achieve high collection and low littering is through a deposit refund system,” recommended Bosmans. “When something has value, it is not thrown away; or it will be picked up by someone else,” and he illustrated his proposal using the example of Lithuania, where a deposit refund system quickly led to a return rate of 90%. During the subsequent round-table discussions, conference participants had the opportunity to meet with key stakeholders throughout the plastics value chain and discuss the challenges and opportunities present in the market today. Topics included the challenges in reaching virgin-like quality with recycled polymers, recycling improvements in Asia, the question of how the rest of the value chain can support recyclers in improving the recycling stream and insights into achieving sustainability initiatives within a larger company. In his lecture “Evaluating the Market for Recycled Polyolefins”, Mark Victory, Senior Editor, Recycling, ICIS, discussed the challenges facing recycled polyolefin market growth, such as the lack of standardisation because of differing production and input methods, the restrictive legislative environment and how country specific legislation such as the UK’s packaging recovery note cap and trade scheme are distorting market fundamentals. Victory also","@ID":34}, "LABELLING PETplanet Insider Vol. 21 No. 01+02/20 petpla.net 29 LABELLING 29 Beyond the facestock, the adhesive matters too. It makes an impact both during manufacture and when entering the recycling stream, with which an adhesive should, ideally, be fully compatible. It should facilitate removal of itself from the stream (see CleanFlake technology, below). Release liners can make up 35% of the laminate, so improvements in this area can have a strong impact on sustainability. In the past, liners have posed a difficult recycling challenge; especially silicone-coated ‘glassine’ materials. Significant improvements have already been made with glassine recycling but one of the most important developments, for both sustainability and productivity, is that many label liners are also now made from PET. The benefits of PET release liners Sustainability gains from PET liners begin with the fact that they are thinner. Using 30 μm PET liner, or the 23 μm version, reduces the amount of material needed, compared with a conventional glassine liner. Pressuresensitive laminates can therefore be made thinner, which means more labels on an equal size roll and so fewer trucks on the road. More meters of labels on a longer roll also means longer production runs, with less startup and changeover waste. So far, so good, but PET comes into its own still further when taking recycling into account. If care is taken to remove silicone, and to keep the PET separate from other plastics, the liners can be recycled into useful products such as thermoformable sheets, for making trays, fibre or strapping. Avery Dennison has an expanding program in place to collect and recycle PET liners and has also launched the first commercially-available recycled content PET (rPET) label liner, which is made from carefully selected post-consumer waste (PCW). Dealing with post-consumer waste PET can play an important role in finding applications for PCW. CleanFlake, a recent Avery Dennison innovation, has closed the loop for PET packaging; the new technology won the 2019 FINAT Recycling and Sustainability award. CleanFlake facilitates clean separation of labels from PET containers in the conventional recycling process, leaving high quality PET flakes behind. The reduced levels of contamination from label facestock, ink and adhesive allow the production of food-grade recycled PET (rPET), suitable for making PET bottles or other food packaging – new bottles made from old bottles. A key benefit of CleanFlake technology is that it does not compromise on productivity or shelf appeal. It also meets widely varying recycling standards in many European countries, including PETcore and EPBP EU. Additional sustainability benefits can be achieved with the right choice of label release liner. For example, a million square metres of labels on an rPET23 liner (which contains 30% post-consumer waste) can reduce resource use (compared with a virgin PET23 liner) as follows: fossil fuel -30% (59 barrels of oil), energy use -11% (equivalent to 4.8 households for a year) and emission of Greenhouse gases -14% (equivalent to taking 4.2 cars off the road per year). The future Further cost-effective improvements to sustainability are urgently needed. Waste is an inevitable by-product of the labelling process but we must prevent large volumes going to landfill or incineration. Realistic ways to source and recycle responsibly do exist; the options offered by Avery Dennison are expanding rapidly, in collaboration with brand owners, packaging suppliers and recyclers. Once all parties in the supply chain are properly engaged – and the right materials made available – labelling can become part of the solution to the sustainability challenge. www.averydennison.com For more information about BERICAP TetheredCaps: BERICAP TetheredCap Easy handling Safe application No change to • Neck finish • Capper • Filling line","@ID":31}, "PACKAGING / PALLETISING PETplanet Insider Vol. 21 No. 01+02/20 petpla.net 26 Secondary film packaging for multipacks French design packaging First-class natural mineral water and an exclusive bottle design are the trademarks of the French Badoit spring. From the bottled water to the packaging the premium brand makes the highest demands of the quality of its products. KHS has supported the company, part of Danone, since 1986. With its new Innopack Kisters SP A-H shrink packer Badoit is again benefiting from KHS. France is heralded as a paradise for gourmets. The land of haute cuisine is renowned the world over for its award-winning wines, outstanding cheeses and high-class natural mineral waters. One brand which has established itself as a leader among carbonated natural spring waters is Badoit. The bottler from Saint-Galmier in the Département de la Loire, southwest of Lyon, has been working closely with the country’s top restaurants for many years. “Our customers make the highest demands of our products – and not just regarding our water. The perfect quality of the packaging also plays a decisive role,” says Etienne Marie, plant manager at Badoit. “As a premium brand our products not only have to differ from those of the competition in quality but also in appearance. The exclusive standard of our water must also be reflected in the packaging,” states Marie. The mineral water plant has therefore opted for bottles with a long, elegant neck, a unique feature on the French market. Badoit requires better packaging quality While the unusual bottle shape is a blessing when it comes to brand recognition, it has proved quite a challenge for the shrink packers used by the water bottler. “The long-necked bottle makes it extremely difficult to produce a packaging quality which is outstanding in all respects,” Marie says. “The multipacks often had creases in the film, the print was distorted or the packs weren’t stable enough to withstand the logistics.” In addition, the outmoded packaging machines were no longer state of the industrial art when it came to efficiency and sustainability and were increasingly limited in their technological capacity. Badoit received support from its parent company. Danone Waters launched a competition between its individual brands and their production plants who then turned to their respective suppliers. “Danone Waters wanted a packaging machine which, thanks to significant further developments in the shrink tunnel segment in particular, considerably improves the standard of the shrink film processing available to date,” emphasises Stuhlmann. Here, it was especially important that the lettering and brand logo on the packs was neither distorted nor creased. Intensive optimisation process The expert team’s first task was to develop new components for Badoit’s packaging machines. The packaging specialists in Kleve subjected all system parts to thorough testing. After several optimisation loops the improved components were integrated into the latest generation of the KHS shrink packer. “We then performed a series of further tests to make sure that our new developments satisfy Badoit’s high demands,” says StuhlFrom left: Christopher Stuhlmann, head of the Line Product Division at KHS, and Etienne Marie, plant manager at Badoit With its shrink packer Badoit can process films of a significantly reduced thickness. The machine also uses an optimum width of film per pack.","@ID":28}, "CAPS & CLOSURES 15 PETplanet Insider Vol. 21 No. 01+02/20 petpla.net Bericap tethered caps solutions Stay with me! According to EU Directive 2019/904 plastic closures must remain attached to the bottle even after opening. Bericap was one of the first manufacturers to develop solutions for this. The screw caps have been given a new design so that they are compatible with any technical specification. As a result, various solutions have been developed that can be adapted to all important bottle neck sizes without negatively affecting the filling or application processes. CAPS & CLOSURES Bericap has succeeded in fulfilling comprehensive requirements, even if this necessitated a re-design of the existing closures. “Within the product development process, it quickly became clear that the screw caps had to be redesigned no matter which technical solution is proposed,” states Volker Spiesmacher, Director Sales and Marketing at Bericap. “The tether requires more space in the area of the tamper evidence band. Hence, the screw caps had to be redesigned.” Bericap tethered cap for all major neck finishes The four technical proposals for screw caps now presented by Bericap can be applied to the same closure shell which is a redesign of the current closure. All proposals can be applied to all major neck finishes available on the market. However, some proposals perform better, if small details of the neck are adapted – this modification process can be closely examined and discussed with Bericap experts. The Bericap proposals allow for a market introduction of the new closure design suitable for tethered caps at an earlier stage than the actual tethered screw cap solution has to be implemented. Thus, the redesigned caps can be readily manufactured with all technical prerequisites for a tethered version set in place when they become mandatory in 2024. The redesigned cap can then be introduced at a time that is in line with marketing activities. In addition to the screw-cap solutions, Bericap also offers presson caps for standard necks as well as a premium solution with customised neck finish which offers the highest weight savings on neck and closure. “Quite typical for Bericap, the presented tethered cap solutions do not only offer products that fulfill the EU requirements for various applications and markets but more so allow a stepby-step transition of our customers’ filling lines towards the use of tethered caps with minimal to no cost implied”, Spiesmacher concludes. “We are in conversation with our customers now and fully support them during the transition process”. Less weight - more sustainability At the BrauBeviale Bericap presented its sustainable closure solutions. Bericap has achieved a weight reduction of approximately 30% in the new, lightweight CSD closures. This is realised without impairing drinking comfort or the filling procedure, as only the outer diameter has been minimised. These closures are based on the DoubleSeal technology developed by Bericap. The technology offers sealing safety and ensures that the carbon dioxide remains in the bottles even at higher temperatures; it protects the condition of the beverage. The new, lightweight CSD closures have already been introduced at various major brands. www.bericap.com ClipIn tethered cap Sustainable and recyclable – Bericap’s colourless screw caps solution presented at the Brau Beviale Nuremberg 2019","@ID":17}, "36 TRADE SHOW REVIEW PETplanet Insider Vol. 21 No. 01+02/20 petpla.net TRADE SHOW review A test of strength for the plastics industry I t has been a t es t o f strength for the plastics industry which was shown everyone’s commitment to developing projects related to recycling, sustainability and to circular economy. The same positivity overwhelmed Moretto S.p.A. which was enthusiastic about the results of K 2019, an exhibition that always presents great opportunities and motivations for the sector. As in a large stage, Moretto exhibited its systems and products for injection moulding, blow moulding and extrusion. There have been two exhibition areas: one specifically dedicated to the extrusion sector, with Contrex brand products, the other one completely dedicated to Moretto. Energy efficiency on small productions For Moretto, a great success was achieved by XComb dryer series, extended in the range to cover higher production needs. These mini dryers are a combination of patented Moretto technologies: fully electric (they do not use compressed air), equipped with powerful turbo-compressors, zeolite technology, the Dew Point equaliser and the exclusive OTX hopper. As for all Moretto dryers, the Moisture Meter device, an exclusive Moretto solution for the precise in-line measurement of residual granule moisture, can also be installed on the XComb series. Moisture Meter analyses and detects the exact content of residual moisture up to 15 parts per million, states the company. Feeding and conveying solutions for micro-moulding Big interest was gained by the solutions dedicated to “micro” conveying for the feeding and conveying of small quantities of technical materials. Compact feeders, can be used for installation on stand-alone machines, on drying and dosing systems or directly on the throat of the processing machine. These conveying systems, like all of the Moretto range, include models specifically indicated for the use in clean rooms. Energy efficiency systems for packaging and PET Particular attention was paid to the dehumidification of PET granules, a delicate phase especially for large productions, typical of the rigid packaging and beverage sectors. In a dedicated area of the stand, Moretto presented a drying system consisting of a XD 800X series dryer combined with the OTX hopper and Moisture Meter Manager, a solution with certifiable results, with high efficiency in terms of energy for any type of material and a completely automatic system of the drying process. www.moretto.com Single head bottle inspection The Total Bottle Inspection Solution (TBIS) fromAir Logic Power Systems (ALPS) is an integrated quality control system. It combines proven in-line leak testing, visual inspection, opacity check and other inspection technologies into one compact quality control solution. Highlighted at K show was the TBIS-S single head linear solution. This compact machine combines vision and leak system in one machine. Bottles from 3 cc to 750 cc are inspected by four side cameras and one top-down camera for surface defects, contamination, geometry or material defects. “The system has been introduced at NPE and is already commercialised in the USA”, explained Andrew Steiner, Application & Sales Support Manager, ALPS, and adds that the compact layout as well as the possibilities to tailor the system according to customers’ needs are especially appreciated by their customers. For example, the system can easily be supplemented with a bottom camera and additional inspection options. Despite the space-saving design, up to 200 bottles/minute can be inspected. www.alpsleak.com Andrew Steiner, Application & Sales Support Manager, ALPS in front of the TBIS-S single head linear bottle inspection system PART 2","@ID":38}, "CAPS & CLOSURES 14 PETplanet Insider Vol. 21 No. 01+02/20 petpla.net A delicate balance of precise geometry Carefully designed Closures are literally the backstop of preforms. With the perfect preform only as good as its closure, one knows that a closure has many responsibilities, from ease of opening to effective protection of the product within. Closures need to perform in partnership with the preform, both from an application and an environmental perspective. Even if a closure is consumer- and product-friendly, recent legislation on tethered closures highlight how crucial it is that designs are also in accordance with the circular economy. CAPS & CLOSURES The EU directive on Single Use Plastics in May 2019 highlighted design requirements to connect caps to bottles from 2024, with regulations extending from the Circular Plastics Alliance launched in December 2018 by the European Commission. This high-level, multi-stakeholder platform gathers the complete plastics value chain to ensure the responsible progression of plastic packaging throughout its entire lifecycle. With plastic packaging producers keen to stay ahead of the legislation, understanding how the legalities of closures is changing is integral to continued profitability, as well as crucial to the positive influence of the industry at a time when public perception of plastic is low. In addition to the tethered requirements, closures must adhere to the increasingly strict rules of additives and colourants, in order to support their ability to be recycled in standard collections and to protect the value stream of the recycled content it creates. Circular closures Appreciating that forward-thinking plastic producers can be part of the solution by evaluating and boosting their sphere of influence means that the design and production of responsible closures and preforms is more important than ever before. Global plastic packaging producer Retal operates in over 60 countries worldwide and is vocal about its commitment to the circular economy. Continued investment and expertise in design of tethered closures sits alongside its myriad actions including installing the EU’s largest solar panel roof in Lithuania, buying renewable energy wherever possible and signing up to organisations such as Waste Free Oceans and RecyClass. The technical development of responsible tethered closure solutions that enhance its preform portfolio is supported by the R&D team’s deep expertise in utilising the latest 3D CAD software. Development director Anton Sugoniaev explains how responsible use of colourants and additives rightly influences the company’s ongoing development of effective, efficient and responsible HDPE closures, saying, “Closures are very sensitive, far more than preforms, so we must concentrate our expertise on getting to that delicate balance of precise geometry. A closure that is easy to turn for consumers, including those of reduced mobility, yet also provides strength and shows excellent stress cracking resistance, has to be carefully designed by technical experts.” Retal has produced over 10 bn closures, with its closures’ portfolio initiated with the foundation of its first single-piece closure machine nearly two decades ago, with steady growth seeing today’s activities currently standing at 60 closure production lines at ten sites across Eurasia and in the US. High standards Working in partnership with many of the world’s leading food and beverage brands, Retal’s commitment to creating and producing responsible plastic packaging solutions means that these high volumes of closures are assured, certified ISO 9001:2001 and regularly inspected by local and international standards, such as the PET. RUS’ Quality Management System which meets the ISO 9001:2008 requirements. Key account director Alexander Kalinin states that Retal’s continual development in the closures category means that its current positive position in the market makes Retal a reliable closures partner. He says, “With nearly 20 years’ expertise in the closures business, we have seen continued investment alongside extensive technical understanding of how the EU regulations on plastics additives and colourants affects closures and their recyclability and performance. By adjusting our equipment, enhancing our laboratories’ capabilities and staying ahead of technical legislation, we will continue to expand our PCO1881 and tethered closures range.” Another advantage of the light weight of the new closures solution means that customers have the choice not to invest in the new standard 26/22 as it is fully compatible with the current 1881 equipment due to being practically the same weight, plus it is also suited to both carbonated and noncarbonated beverages. This predicted expansion will be supported by Retal’s centralised procurement, with closures warehousing available in every plant of the Group. Investment in super-lighweighted PCO1881 closures, including vision quality control, printing and laser engraving is projected, further boosting the performance of the closures as well as the environmental footprint, supporting Retal’s promise of being active in its sphere of influence for the good of the circular economy. www.retalgroup.com","@ID":16}, "BOTTLING / FILLING PETplanet Insider Vol. 21 No. 01+02/20 petpla.net 23 empowered by Drinktec New Zealand Australia Philippines Taiwan South Korea Japan Let Your Inspiration Flow. From Down Under to Japan It’s time for the Editour Road Show to hit the road again! The start of the new decade will see us undertaking a trip from Australia and New Zealand to Japan, via the Philippines, Taiwan and South Korea! With support from Drinktec, the world’s biggest beverages show, we will be shooting off to Australasia in April. Our journey from south to north will see our team visit a variety of locations, countries, cultures and climate zones, with different vehicles. From the legendary, biodiverse sceneries of Australia and New Zealand and with numerous interview visits in between, PETplanet and the Editourmobil will finish the Tour with a visit to Japan, the Land of the Rising Sun! Make sure you’re on board when we set off on our next adventure and get ready for in-depth analyses of the special features and trends in these bottle and beverage sectors! Interested in being visited? [email protected]","@ID":25}, "CAPS & CLOSURES 17 PETplanet Insider Vol. 21 No. 01+02/20 petpla.net stay open to an angle of at least 140°, remain tethered to the bottle, and ultimately allow reclosing of the bottle for multiple uses by the consumer.” The third tethered variant featured by Aptar at BrauBeviale, Flip Lid for still beverages, came about from consumer experience studies. Beyond meeting tethered standards, other unique features of this solution include the ability to integrate the design within a very low profile neck finish, and the hinge design making the closure capable of folding back at a 210° angle. Here too, an audible click tells the user that the lid is latched back and out of the way before pouring or drinking from the bottle. “With Flip Lid you can achieve a significant reduction in plastic from both the preform and closure,” says Kenny happily, as the snap on design of the closure makes it possible to eliminate much of the surface area required for typical thread finishes, thus shortening the overall neck finish height. www.food-beverage.aptar.com “Best Closure” award for flip lid at the World Beverage Innovation Awards 2019 The World Beverage Innovation Awards, in association with BrauBeviale, were designed to celebrate excellence and innovation across numerous categories within the beverage industry. At the 2019 Award Ceremony, Aptar Food + Beverage was rewarded with the Best Closure Award for its Flip Lid solution. A panel of nine judges considered entries from over 33 countries in 24 different categories. Aptar’s Flip Lid was identified by this jury as a “very innovative concept that is in line with today’s prevailing concerns about packaging disposal and recycling” and is “a consumerfriendly closure”. Aptar Food + Beverage has reinvented packaging for tethered closures to enhance the consumer drinking experience. A critical technical parameter for ease of opening is the closure’s protruding element, which aids in gripping and lifting the lid, allowing for a one-handed experience. This closure also offers consumers a wide opening for drinking comfort, and an audible click when the hinge is fully open and fully closed. 40 Bar Oil-Free Piston Compressors For PET Applications. www.hertz-kompressoren.com Building the future in every moment of your business","@ID":19}, "PETplanet Insider Vol. 21 No. 01+02/20 petpla.net 40 PETbottles Home + Personal Care Jar for scent pearls At irregular intervals, scent pearls are available in sales campaigns from German discount retailer Aldi Süd. At the end of October, three different scents – Red Berries, New Spa and Bergamot – were available to purchase in jar-like containers. The containers held 110g of the scented pearls, which release their pleasant aroma over a period of six weeks. Twisting the lid activates the plain scent dispenser; this has no label or printing. At POS, they are displayed in a packet with an adhesive seal and several windows to show the product. Pearls, container lid and packet colouring match one another. www.aldi-sued.de Make-it-yourself slime Under the “Elmer’s” brand, American company Newell Brands is selling a creative toy that children can make themselves. In a curving bottle with a two-part seal, which is opened by twisting the orangecoloured cap, there is a component product that becomes a stiff slime when mixed with water, baking soda and contact lens cleaner; it can be used as a type of play dough. Colour and glitter pigments are clearly visible in the transparent bottle. Two similarly curving labels provide retail information. www.elmers.com Cleaning oil from Nivea Beiersdorf has brought onto the market a new product in the facial care range, which thoroughly removes make-up residue without the use of cotton pads. The product is moisturising and creates a milky emulsion on contact with water. It is available in a light blue, 150ml bottle with a lockable pump dispenser. A transparent label on the front and a label printed on the inside at the back provide information about the product and ensure an attractive appearance on retailer shelves. www.nivea.de Mouthwash with charcoal Young American company Hello, which has the tagline “naturally friendly”, is selling products for oral and toothcare. The products work with natural ingredients, such as activated charcoal. The packaging for 16 fl oz/473ml of alcohol-free mouthwash with coconut oil and mint is a slim, black bottle. This is furnished with a screw cap with dosing function and two matt printed labels. The cap has a shrink-foil wrap as a tamper-evident seal. www.hello-products.com Spray cleaner for brushes In the USA, Walgreens is selling 5.9 fl oz/174ml of detergent for cosmetic brushes or cosmetic sponges in a transparent bottle with a screwed-on pump sprayer. A transparent cap prevents unintentional operation and protects the sprayer from damage. A semitransparent self-adhesive label describes product and usage. At POS, the bottle is displayed in an unmarked, transparent plastic packet with hanger. www.walgreens.com","@ID":42}, "MARKET SURVEY 24 PETplanet Insider Vol. 21 No. 01+02/20 petpla.net 01+02/2020 MARKETsurvey Additives Suppliers of resins & additives There is rapidly increasing demand for packaging materials that give even greater protection to their contents. Functional additives and resins are an important technology in meeting this demand for greater product protection in the plastic packaging market. A functional additive modifies the properties of packaging to impart desirable or beneficial functions. That is why we won’t stop a well-established tradition in opening our market surveys overview in 2020 with suppliers of resins and additives. These companies participated: Addform Limited, Clariant Plastics & Coatings GmbH - BU Masterbatches, Repi S.p.A, Sukano AG, Indorama Ventures Polymers Germany & Indorama Ventures Ltd, Neo Group, Reliance Industries and Novapet, S.A. Although the publishers have made every effort to ensure that the information in this survey is up to date, no claims are made regarding completeness or accuracy. Company name Addform Limited Clariant Plastics & Coatings GmbH, BU Masterbatches Repi S.p.A. Sukano AG Indorama Ventures Polymers Germany GmbH Postal address Telephone number Web site address Contact name Function Direct telephone number E-Mail Unit 21, Skypark Industrial Estate Liverpool, L24 1YL, Great Britain +44 151 659 1102 www.addform.co.uk Mr Richard Glen Sales Manager +44 151 659 1102 [email protected] Am Unisys-Park 1 65843 Sulzbach am Taunus, Germany +49 6196 757 60 / +49 6196 757 6276 www.clariant.com/masterbatches Ms Severine Wild Marketing Europe +49 6196 757 6276 [email protected] Via B. Franklin 2, 21050 Lonate Ceppino VA - Italy +39 0331 819511 www.repi.com Ms Lucia Buffoni Marketing Manager [email protected] Chaltenbodenstrasse 23 8834 Schindellegi, Switzerland + 41 44 787 57 77 www.sukano.com +41 44 787 57 77 [email protected] Philipp Reis Strasse 2 65795 Hattersheim, Germany +49 69 305 6025 www.indoramaventures.com Mr Achim Heyer Business Dir. Polymer & PET Resin +49 172 614 6425 [email protected] Additives and Colours for PET Liquid colours Yes Yes Yes No Microgranule colours No Yes Yes Masterbatch colours Yes Yes Yes UV protection additive (solid) Yes Yes Yes UV protection additive (liquid) Yes Yes Yes No AA reduction (solid) Yes Yes - SenzAA No AA reduction (liquid) Yes Yes - SenzAA No Oxygen scavenger (solid) Yes No OxyClear Additive, PolyShield Masterbatch Oxygen scavenger (liquid) No No IV enhancer Yes Yes Yes Yes Reheating Yes Yes No Blowing additive Yes No Yes (liquid) Yes Slipping agent Yes Yes Yes (liquid) Yes Other PET additives: Anti Yellow, Antiblock Matting Agent, Surface Modifier and Special Effect Anti Yellow (liquid), Process Aid (liquid) Optical Brightener (liquid) Colours for Barrier Solutions (liquid), Whites for monolayer UHT Milk (liquid), blacks with no carbon black Antioxidants, Antistatics, Melt Enhancer, Voiding Agent, Optical Brightener, Nucleating Agent, Mould Release, Matting Agent, Slip/Antiblock, Light Diffusor, Light Barrier, Impact Modifier, Flame Retardant, Antimicrobial, Plasticiser, Pinning Agent, Foaming Agent Resins & additives Preform machinery Preform production & inspection Preform & SBM mould manufacturer SBM 2 stage Compressors Caps & closures & inspection Filling equipment & inspection Recycling Palletising & shrink film machinery","@ID":26}, "CAPS & CLOSURES 12 PETplanet Insider Vol. 21 No. 01+02/20 petpla.net New control algorithm for higher outputs High performance for production of closures The Netstal Elion series has been developed further specifically for the beverage cap segment and is now equipped with new, user-specific features. The basic hybrid drive concept of the Elion was maintained: The centrally positioned 5-point dual toggle lever with horizontal servo motor is still being used because it moves dynamically, harmonically and quickly. Bucking the trend that moves toward all-electric machines, Netstal continues to prefer the hybrid approach with a combination of electric and hydraulic axles for beverage closures. CAPS & CLOSURES High performance, low energy consumption “We are relying on our hybrid injection units for the quick and precise production of closures because that way we don’t have to sacrifice performance,” emphasised Peter Schmid, the applications team leader of KraussMaffei HighPerformance AG in Näfels, Switzerland. For this reason, Netstal machines never use spindle drives. By consistently using hydraulic cylinders, Netstal ensures that the machine will deliver an optimal performance – while being operated efficiently at the same time. Netstal Elion machines with a hybrid drive concept also feature competitive energy consumption. The company states that at their upper performance limit energy values are as low as those of a comparable all-electric machine. The key factors are the efficiency of the clamping unit and the recuperation of energy, which is temporarily stored as hydraulic energy and then fed back into the system. This is something that could not be accomplished with spindle drives because, for geometric reasons, they are subject to a self-locking effect and therefore do not feature the optimal concept with regard to dynamics, efficiency and wear. New control algorithm allows higher outputs By adapting the clamping unit controller, a significant optimisation of the dry cycle times of the Elion has been achieved. Depending on the model, the dry cycle was shortened by up to 0.2 s. The optimisation applies to all Netstal Elion models with Axos version 8.2.0. and up. This release incorporates the latest control technology insights. The additional speed is made possible through the adaptive optimisation of the acceleration and deceleration ramps for the clamping unit drive. The maximum moving speed is reached faster and can be maintained longer before the moving mould plate is harmoniously decelerated and the toggle lever mechanism seamlessly transitions to building up the clamping force. This does not compromise the mould protection. A shorter dry-running time does not automatically mean a faster cycle under real production conditions. That is why the new control algorithm takes into account the potential mould weight and incorporates it in the control of the acceleration and deceleration process. “This allows our customers to further speed up their production cycles and achieve further productivity increases,” explained Schmid. For example: A Netstal Elion 4200 with a 96-cavity mould produces type 29/25 HDPE closures. One closure weighs 1.23 g. Thanks to the optimised control, the cycle can be shortened from 2.77 s to 2.6 s. The hourly output goes up from 124,750 to 132,920 closures, which equals an increase in productivity of 6.5 per cent. New plastics in the production of closures Bimodal and multimodal plastics, which are increasingly being used for the production of closures, are another market demand. These materials have various benefits that improve the quality of the closures. They particularly resulted in massive improvements in the area of ESCR. “There are – sometimes large – differences with regard to the flow characteristics and the injection process pressures during processing and production. In addition, there are also significant differences compared to conventional materials with regard to the plasticising performance. These also have to be taken into account when developing applications,” Schmid said. The injection unit was not just adapted mechanically to the new requirements but also with regard to the software. Flexible controls, intuitive operation The freely programmable Axos control technology offers operators high flexibility. An illustrative example was the control circuit which was presented at Drinktec 2017 together with partners. It featured the first integration of external peripheral data in the controller of the injection moulding The electric toggle lever clamping unit of the Netstal Elion with the horizontally arranged servo motor","@ID":14}]}}
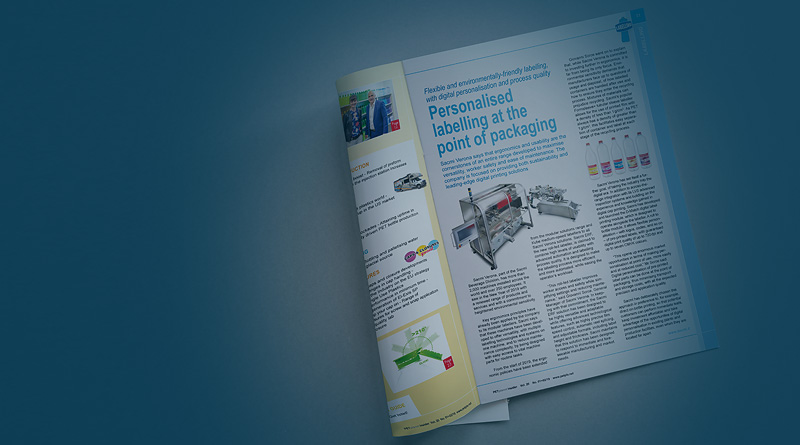