"PETplanet Insider Vol. 21 No. 03/20 petpla.net 39 TRADE SHOW REVIEW empowered by Drinktec New Zealand Australia Philippines Taiwan South Korea Japan Let Your Inspiration Flow. From Down Under to Japan It’s time for the Editour Road Show to hit the road again! The start of the new decade will see us undertaking a trip from Australia and New Zealand to Japan, via the Philippines, Taiwan and South Korea! With support from Drinktec, the world’s biggest beverages show, we will be shooting off to Australasia in April. Our journey from south to north will see our team visit a variety of locations, countries, cultures and climate zones, with different vehicles. From the legendary, biodiverse sceneries of Australia and New Zealand and with numerous interview visits in between, PETplanet and the Editourmobil will finish the Tour with a visit to Japan, the Land of the Rising Sun! Make sure you’re on board when we set off on our next adventure and get ready for in-depth analyses of the special features and trends in these bottle and beverage sectors! Interested in being visited? [email protected]","@ID":41}, "36 TRADE SHOW REVIEW PETplanet Insider Vol. 21 No. 03/20 petpla.net TRADE SHOW review PART 3 Efficiency and quality in plastic recycling The machine and plant manufacturer Herbold Meckesheim, Germany presented tried and tested process solutions for the treatment of plastic waste in Düsseldorf in addition to its wide range of machines. The solutions from Herbold are based on 40 years of experience and continuous developments in post-industrial and post-consumer applications. “Size reducing, washing, separating and drying and agglomeration are our main processes. Our customers value our wide range of machine options and the ability to obtain custom plant designs from a single source. With our focus on the circular economy, we are fully in line with the current spirit of the times and with one of the main topics of the K 2019 trade fair”, said Werner Herbold, one of the two general managers. At the booth Herbold presented machine innovations from the preshredding sector, granulators, and washing lines. Herbold machine solutions are for the following applications: post-industrial and post-consumer films, post-consumer hard plastics, PET bottles, PET trays, big bags and other monofilaments, Tetra packs and pulp waste. The new VWE 700 prewashing unit was presented. An important component in the Herbold film washing line is the multistage prewashing unit, which captures coarse foreign bodies and reduces the mineral fraction, both to protect the subsequent machines. The remainder is also gently prewashed. Herbold said that they have optimised this process step even further by increasing the throughput performance for films, optimising the flow of water, and integrating a baffle plate thickener into the unit to clean the process water, and therefore remove contaminants directly on the unit. With the new WS 60/210 shredder another highlight was presented. The demand for high-performance shredders that can process entire bales is increasing, especially when used in washing lines. Therefore Herbold presented the EWS 60/210 for the first time at the trade fair. This shredder was developed for dry operation as well as for wet operation. It has a maintenance-friendly design with a high capacity. In many plants, the crusher is the first stage in the process. In this stage, foreign bodies are often impossible to avoid. For this reason Herbold has taken some of the special features of this stage into account. “We focus on making a perfect wear-protected rotor that, in addition to custom knife configurations, is equipped in particular with bolted armor plating and a special grinding chamber seal”, stated Daniel Zeiler, Head of Sales. The time-consuming hardfacing of rotors is therefore unnecessary. The two-sided belt drive is low-maintenance, and to safeguard against foreign bodies, there is a clutch that prevents damage to the machine when uncrushable feed material is encountered. The maintenance concept is tailored to ensure optimal accessibility based on ergonomic considerations. The first machines are already successfully in use at customers in Europe. www.herbold.com Clariant, PET Engineering and Husky presented the Erit bottle, a 100% rPET bottle The problem of using post consumer recycled material is that it creates an unsightly side effect like yellowing that is not acceptable by the industry and the consumer. Clariant worked on this by definding colour solutions that could be used in recycled PET. The Clariant team decided for dark black and dark green colouring. The new Cesa Nir black colour which was used for the Erit bottle is detectable in standard sorting systems and is therefore again recyclable. Two other colours were presented: one green-effect colour and a translucent blue, the bottles are capped by a metallic looking plastic cap. Husky Injection Molding Systems Ltd. a leading supplier of injection moulding equipment and services to the PET bottle market, has developed the tooling for the preform from which the Erit bottle is blown. Husky has optimised the weight and properties of the finished bottle. Husky supported this innovation also with its tethered closure. www.clariant.com www.husky.co www.petengineering.com Mr Abdelhadi Jaga, Sales spare parts, led us over the booth. Luca Baldessin, R&D Manager, PET Engineering, after the Clariant press conference","@ID":38}, "37 TRADE SHOW REVIEW PETplanet Insider Vol. 21 No. 03/20 petpla.net 1st Aseptic blower FDA certified in USA ABF 1.2 is the Aseptic Blow-Fill system featuring the very first sterile aseptic blower approved FDA. The GEA ABF 1.2, installed and successfully validated in the USA, obtained the FDA certificate for shelf-stable, low acid beverages produced and distributed in the USA. Thanks to ABF 1.2 each single step of the sterilization process is monitored, whilst the aseptic blower, housed inside a microbiological isolator, avoids any potential risk of recontamination. Another milestone for GEA 10 years after the first FDA certificate received for its PAA based sterilization system. New generation dryer for rPET Piovan presented its GenesysNext line for the first time. The new patented PET formance and PureTech systems ensure that the GenesysNext is able to process any type or percentage of PET material, guaranteeing a high level of quality at a low cost per preform produced. This drying system is distinguished by self-adaptive technology that is optimised for the treatment of recycled PET. The new dryer can automatically manage the drying process by setting all the critical parameters: from the process air flow rate to its dew point value, from the residence time to the temperature, maintaining optimum operating conditions even as hourly production and initial temperature and humidity conditions of the plastic granulate vary. This new machine generation include more intuitive control and improved self-regulation. www.piovan.com Peter Dal Bo, CCO Piovan Group in front of the new GenesysNext line Sustainability is standard At the K show Sacmi focused on sustainability. With Sacmi’s IPS, customers are able to use standard machines to make products consisting of up to 100% rPET and use recycled PET in flake form in quantities of up to 50%: using standard hot runners, demonstrating Sacmi’s determination to make this the new market standard. Performing rPET is the most important topic, next to light-weighting. Both versions (IPS220 and IPS400, with 96 and 128 cavities respectively) offer maximum flexibility thanks to fast size changeovers and, on the larger version, compatibility with most commercially available resins. Consolidated technology - already tested and appreciated on markets - gives customers the option of heading down the sustainability route to maximise the potential return on their investment without risks or surprises. The solution showcased at the fair, designed for applications in rPET and the utilisation of PET flakes is, in fact, an intrinsically sustainable ‘native’ solution that requires no work on/modifications to the machine. From moulds to vision systems (Sacmi PVS, preform vision system), Sacmi provides comprehensive assistance on all markets. www.sacmi.com","@ID":39}, "BOTTLING / FILLING PETplanet Insider Vol. 21 No. 03/20 petpla.net 27 based products and willing to launch the new 2 litre bottle format, Yotvata decided to purchase a second aseptic complete PET line from Sidel. Sidel’s technology matches their needs and allows producing UHT and Extended Shelf Life (ESL) milk in PET bottles. “We already had a very positive experience with the Sidel Aseptic Combi Predis technology for PET production on the first line we purchased from them in 2014. This new packaging line will allow us to increase the production capacity on existing products while reducing our environmental footprint, mainly due to the switch from HDPE to PET and the bottle lightweighting potential offered by Sidel’s integrated dry preform decontamination system,” explains Achiraz Horesh, COO at Yotvata. Currently, the new flexible line is producing 1 l bottles and the newly designed two litre bottle for milk in PET, meeting the needs around flavoured, ESL and UHT milk. The recently installed aseptic PET complete line features Sidel’s Aseptic Combi Predis, complemented by Capdis, combining preform and cap sterilisation, blowing and sealing functions in a single enclosure for a 100% sterile filled and capped PET bottle. The Sidel Aseptic Combi Predis offers environmental footprint as it does not consume any water and very few chemicals. It allows unlimited bottle lightweighting. This solution has already been contributed to save seven billion litres of water and 57,000 tons of PET, while producing 46 billion bottles. In this technology, the blower oven activates the sterilising effect of the hydrogen peroxide vapour without the need for additional heating of the preforms. The same technology is used for the cap sterilisation, ensuring a 100% dry aseptic PET packaging solution. PET line from one single partner The line includes Sidel’s RollQuattro, a versatile high-speed roll-fed labeller, able to handle lightweight containers with thin labels, plus conveying and end-of-line equipment. To make its aseptic PET complete line, able to run at 13,500 bph, Yotvata relied on Sidel expertise in conveying, packing and palletising. The new installation at the Israeli site includes EvoFilm, a shrink-wrapping system able to deliver best quality/price/performance ratio. In addition, the dairy producer selected a PalKombi, an automatic palletiser suitable for crates, cartons, trays and shrinkwrapped packs, designed for medium to high speed lines that allows for easy control and access. Andrea Tondelli, Sales Manager Southern Europe, Sidel, summarises how Sidel supported the dairy producer, “Yotvata leveraged the entire set of our competences, from packaging design and industrialisation through leadership in aseptic technologies up to our longstanding expertise in complete lines. The Sidel Aseptic Combi Predis delivers utmost hygiene, high ease of operations and flexibility needed to match this customer’s needs, considering the various products they’ll process through the line.” www.sidel.com","@ID":29}, "TRADE SHOW REVIEW PETplanet Insider Vol. 21 No. 03/20 petpla.net 34 Preform mould manufacturing Canadian mould manufacturer Stackteck Systems chose to take the opportunity presented by the K Show 2019 to highlight their new technologies for PET preforms and premier their PET preform mould initiative. We met: Mr Rick Unterlander, General Manager PET Mr Vincent Travaglini, President & CEO We spoke with General Manager PET Mr Rick Unterlander about the past, the future and, of course, about PET. He began with an outline of the history of Stackteck, which was established in 1998 as a merger of Tradesco (founded in 1976) and Unique, whose history dates back to 1969. In 1991, while it was still operating under the Tradesco name, it designed, developed and manufactured the world’s first four-level stack mould. A year later, it launched another first: the Quick Product Change (QPC) stack mould. The following 22 years saw a series of worlds’ first developments from StackTeck, including innovative mould technologies such as: five-piece collapsing core; 4x32 stack mould configurations; 2x64 unscrewing cap moulds; and 2x32 co-injection stack moulds. In 2013, Stackteck released its first production mould featuring Trim (Thin Recess Injection Moulding) technology. This year, 2019, sees it launch its first Fasttrack mould capability, with automated design and an eight-week delivery. Other developments announced in 2019 saw Stackteck Asia established in South Korea, and the launch of its PET initiative. The company has, to date, built over 130 PET preform moulds, ranging from two-cavity development platforms to 144-cavity high volume production systems. Its main markets and the the majority of sales are found in North America and Asia, including Japan. At K, the company exhibited a range of its technologies, such as ISO hot runner systems; Kooltrack conformal cooling stack components; and Picool post mould cooling systems. With over 35 years’ experience in the industry, Stackteck’s new General Manager PET, Rick Unterlander, is a recognised expert. He has held a number of positions at several PET converter and equipment supply companies, ranging from PET Lab Technician through to PET Process Engineering Manager, R&D Engineering Manager, and Owner/VP PET Operations. He holds numerous patents in the industry and continues to participate in initiatives for advancing PET technology to improve performance and efficiency, and support sustainability. His focus in his new appointment at Stackteck is on PET preform projects in the Americas. He is also the liaison to Stackteck Asia in South Korea, where the company has already built a successful track record in PET preform moulds, hot runners, and post-mould cooling systems. “Our moulds, hot runners, end-ofarm-tooling and Picool, a new, patented post mould cooling technology, are compatible with all major machine brands, at very competitive costs and industry leading performance”, Rick stated. “Our hot runner technologies are designed to reduce pressure drop, improve cavity-to-cavity balance, reduce colour changeover time, and generate lower AA levels than conventional designs, while virtually eliminating PET dust”, he added. The new moulds feature conformal cooling to improve productivity, while Picool speeds up cycle times. “We need around four to 14 weeks to fulfil an order for a mould, depending on design, cavitation and backlog”, Rick added. “We are pretty well positioned in terms of sales and after sales service, with our two manufacturing locations in Canada and South Korea plus a global support network, strategically located in regions around the world.” While different markets require different solutions, meeting and overcoming the global challenges and demands from the industry for PET moulds is based on the same foundations and qualities. Reducing scrap, improving productivity “Economic value, cost of ownership, performance and efficiency are key requirements that shape success,” Rick Unterlander said. Without identifying them by name, he said that he sees the top tier suppliers for twoKay Barton met with Rick Unterlander, GM PET Preform Moulds (left), and Vince Travaglini, President & CEO (right) at the Stackteck Systems’ booth during K 2019","@ID":36}, "BOTTLING / FILLING PETplanet Insider Vol. 21 No. 03/20 petpla.net 31 Effective sterilisation When further developing its linear aseptic filler KHS focused on increased efficiency. The filling machine for sensitive products is available in both a standard aseptic and ESL version. In the KHS process sterilisation takes place in several stages. First, the machine disinfects the neck and bottle interior. Here, the inside of the container is sprayed twice with a hydrogen peroxide aerosol (H 2 O 2 ) at a speed of up to 80km/h. “This ensures that every part of the bottle is sprayed and sterilised; we even achieve this with individual designs and critical shapes,” Redeker states. Secondly, two aerosol reaction cycles are initiated. The process ends with a four-stage drying process which uses sterile hot air. Gentle filling for product protection In order to ensure the quality of the products, it is essential that the aseptic zone is absolutely clean. KHS said they are doing so by gentle noncontact filling, among other things, performed in two stages. This prevents any excessive beverage foaming. After filling the bottle is conveyed to the capping unit. Here, the closure is sterilised in the same manner as the bottle in the filling section. This entails two-step disinfection with H 2 O 2 and two drying stages with hot sterile air. “In the capper unit we’ve also made sure that all parts in the aseptic zone have a flat surface. By doing so we can prevent any air turbulence, making cleaning and disinfection easier,” Redeker comments. The bottle is then dated for full documentation of all information. “Our customers can always see which product was filled when on which valve,” explains Redeker. One-block system With its new dry aseptic block KHS reacts to the current dairy demand for flexible, resource-saving filling of sensitive products. The system boosts line availability and considerably reduces energy consumption. Operators have greater flexibility thanks to the short changeover times: format changes are facilitated by the wellcoordinated interfaces. The modular design enables customers to expand their linear aseptic filler block in order to meet current market demands at all times, KHS stated. www.khs.com High output: The new linear InnoPET BloFill ABF aseptic block is designed to fill milk, mixed milk beverages, juice, smoothies and iced tea into PET bottles holding between 250ml and 2 l. 40 Bar Oil-Free Piston Compressors For PET Applications. www.hertz-kompressoren.com Building the future in every moment of your business","@ID":33}, "TRADE SHOW REVIEW PETplanet Insider Vol. 21 No. 03/20 petpla.net 42 TRADE SHOW REVIEW 42 Standard recycling often results in down-cycling; it will turn your old plastic keg into a park bench or other low-grade plastic product. The manufacturers of Keykeg/Unikeg continue to put in place processes to recover and reuse materials for the next new kegs. This is dependent on the development of technology, techniques and other influences. Innovation projects in materials selection and sourcing, processing and up-cycling from collected used kegs are ongoing every day. Rather than opt for waste to energy, technology is sufficiently advanced to collect and sort plastics which can then be processed to be ready for re-use in the same or comparable products. This prevents the need for more virgin material to be used in the next new packaging product. It is important that the recovered materials can continuously be used for new products. Contaminating rPET with additives should not be accepted by purchasers, whether they are producers or consumers. Keykeg/Unikeg proposes that buyers ensure that post-consumer recyclate (PCR) can be used to create new transparent kegs. Chemical recycling is the least attractive method; any benefit for the environment is only slightly better than waste-to-energy incineration. Products making use of blended materials for barrier properties, most likely only to be recovered by chemical recycling, should be considered as less favourable. OneCircle Community Keykeg/Unikeg are supported by OneCircle, a community with all activities related to the use of sustainable kegs at its core. This also includes the development of global collection, sorting and re-use of materials community, with the fundamental aim to leave the world a better place. Delivering one-way kegs to the market without accountability in the supply and waste stream is no longer either socially acceptable or commercially viable. The future for sustainable plastic kegs Creating plastic kegs in today’s packaging world continues to be based on ongoing innovation and is strongly related to plastics re-use. Most providers are focused on product innovations, creating different size ranges in their portfolios and on the creation of competitive edge in the market. Simply reducing the per-litre cost of packaging does little or nothing to address re-use objectives. For companies such as One Circle and its product portfolio, Keykeg and Unikeg, the focus is as follows: 1) Handgrips and base cups are made out of 100% circular materials (PP); suppliers are requested to evidence this in their supply chain. 2) The preform is designed to reduce the amount of plastics used. The lower the weight, the less raw and PCR material is used. 3) Where possible, clear PET is used to ensure 100% re-use by mechanical recycling is possible. 4) Innovation projects, for bags and amber blended PET, are in place to support full circular principles and deliver a sustainable solution. Recyclability is no longer enough, measured against today’s standards. Keykeg and Unikeg, in addition to being made out of 100% re-used PP material, will be made of re-used clear PET material from the beginning of April 2020, which takes the total of PCR up to 45%. This number will increase further in the course of 2020. Keykeg’s recycled content will be further increased by incorporating a substantial amount of recycled material in its inner container. One Circle continues to invest to create a global keg collection network to support the re-use of plastics used in kegs. This network is currently used only by Keykeg and Unikeg but is open to other providers on the understanding that the costs are shared equally. One Circle’s aim is to leave the world a better place, to eliminate waste of resources such as materials and water, and to promote the sustainable use of plastic kegs over other packaging solutions such as steel kegs and bottles. Product design, supply chain advantages as well as a responsible approach to collection and re-use is building a platform for future sustainable kegs. www.lightweight-containers.com .com 100815dmyL","@ID":44}, "PETnews 6 NEWS PETplanet Insider Vol. 21 No. 03/20 petpla.net Bekum celebrates three anniversaries and breaks ground on a new facility The Bekum group celebrated recently three anniversaries – 60 years Bekum in Berlin, Germany, 50 years Bekum in Traismauer, Austria und 40 years Bekum in Williamston, USA. As part of the celebrations at the American location, the groundbreaking ceremony for the expansion of production capacities was made on November 26, 2019. A new building with a production area of 3,700 m² and almost 700 m² of office space will be added. This increases the site’s operational area to more than 15,000 m². Michael Mehnert, Managing Partner, who traveled from Germany for this celebration, stated: “My father founded this company sixty years ago. Today I’m standing here and lay the foundation for a new production hall in order to be able to serve the continuously increasing demand in the USA in the future!” Steve London, COO and President of Bekum America Corporation said: “The groundbreaking on our new facility was a great kick off to our 40th anniversary celebration with our dedicated employees. The Bekum team has continually been providing state of the art products for our clients, and this event is the perfect opportunity to celebrate all the individuals who complete Bekum.” Bekum America was established in 1979 with the mission to introduce top quality blow moulding machinery, designed to produce plastic bottles, containers and other large plastic parts in the North American marketplace, via blending German design and technology with American skill and ingenuity. Bekum’s customer base includes large multi-national customers, as well as owner/operator plastic bottle manufacturers. www.bekum.com Worldwide acclaim for reduce-reuse-recycle principle High accolades go to an innovation developed especially for the circular economy. The patented stand-up pouch from Werner & Mertz and Mondi has been chosen to receive the prestigious WorldStar Packaging Award in the “Household” category. “The highly innovative 100% recyclable pouch leapfrogs sorting and recycling hurdles on the way to true recyclability. […] This is Cradle-to-Cradle!”, said the competition’s jury of the World Packaging Organization (WPO) about its decision. The award will be presented during the trade show Interpack in Düsseldorf on 8 May. In a four-year project based on Cradle to Cradle principles, Werner & Mertz and the global packaging and paper firm Mondi developed a completely recyclable pouch of a monomaterial (polyethylene) with a removable sleeve or wrap-around label. The concept solves the problem of recycling printed plastic. About 80% of the packaging material is not printed and therefore can be recycled with no loss of quality as it is not contaminated by ink. The remaining 20%, the printed sleeve, is completely recyclable and, because no adhesives or bonding agents are used, the material can flow back into new applications. The independent Institut Interseroh certified that the stand-up pouch has “very good recyclability that cannot be optimised any further.” www.werner-mertz.de Managing Director Michael Mehnert (2nd from left) at the groundbreaking ceremony with the managers of the US subsidiary CFO Owen Johnston, Chairman Martin Stark, President & COO Steven London (from left) Chinaplas rescheduled to 3-6 August 2020 The organiser of Chinaplas, Adsale Exhibition Services Ltd., announced a new date for the 2020 show edition. Chinaplas 2020 will be held 3-6 August 2020 at NECC in Shanghai. The fair had been postponed in order to control the coronavirus epidemic in China. Ada Leung, General Manager of Adsale, expressed, “As an important trendsetter, Chinaplas has expeditiously responded to the market needs. Many market activities like consumption, manufacturing and investment etc. are put on hold during the epidemic. And now, some companies have already resumed work and manufacturing in an orderly manner. We believe that once the outbreak is controlled, all suppressed market demand will be released. The postponement of Chinaplas to August in Shanghai will help the upstream and downstream industries to seize business opportunities during market rebound period.” In this epidemic, plastics and rubber have been used as important raw materials for prevention supplies. Many companies in the plastics and rubber industries have donated money and materials, sped up their manufacturing process etc. to assist in the epidemic control measures. Recently, the Ministry of Industry and Information Technology of People’s Republic of China announced the scope of medical emergency protection materials. In the list, there are coated spunbond, breathable film, meltblown non-woven fabric, PE /PC anti-fogging rolls and sheets, seals, zippers, antistatic agents and other important raw materials for producing medical protective clothes and masks; as well as plastic packaging materials such as plastic bottles (barrels) and labels. The epidemic could also trigger the industries to rethink of the future manufacturing processes, consumers’ pursuit of healthy lifestyles, safe and private commute, and sterilising electric appliances. If enterprises can seize the opportunity to transform and upgrade their business, there will be a potential business growth, states Adsale. www.chinaplasonline.com","@ID":8}, "TRADE SHOW REVIEW PETplanet Insider Vol. 21 No. 03/20 petpla.net 38 India-made moulds by Kay Barton Mould manufacturer Leo Precision, based in Silvassa, in the union territory of Dadra and Nagar Haveli close to Daman in west India, was founded in 2010 and now has plans to expand more strongly in the single-stage sector. With up to 40 moulds already produced per year in this segment within the first year of expansion, the company is now roughly on a par with its other main area of business: the production of two-stage preform moulds. In the 2018/2019 financial year, it generated US$ 4 million; expectations for 2019/2020 are that revenues will increase 55%. Leo Precision currently has a market share of 35% in the highquality moulds segment, according to Managing Director Senthil Kumar. The idea behind Leo Precision is to provide equipment for single and two-stage moulds plus conversion from one single source – with a 30–50% saving compared with the corresponding original moulds. Mr Kumar has more than 20 years of experience in PET equipment and processing. “Right now, we have roughly 1,500 moulds in use worldwide,” he explained. “The demand for single-stage moulds is always high, so we want to push forwards in this area further.” Leo Precision said that its equipment is compatible with machines from Nissei ASB, Milacron or Krauss Maffei. Mould manufacturing is undertaken on CNC machines from Mazak, Haas, Makino and GF, with the use of Zeiss and Mitutoyo measuring equipment. “We currently have around 180 employees. Our company premises extend to roughly 6,000m2. The Leo Plastic divisions account for about 1,000m2, with 1,800m2 occupied by Leo Mould Tech,” Kumar explained. The majority of customers are located in India, with around 40% of production destined for export, primarily to Africa. Leo Precision’s principal competitor is Delhi-based equipment manufacturer Acme moulds. The company expects demand for single-stage equipment to grow and can generate 60% of its own revenue. “The market for beverages here in India is still growing and has a lot of potential. Nevertheless, we are noticing an increase in the proportion of small, local bottlers, for whom the innovative packaging is not the key factor,” Senthil Kumar further explained. “Overall, we can see shifts in the market away from larger brands and towards smaller brands.” Not surprisingly, Leo Precision is feeling the effects of the poor image that plastics generally have in the world. “As long as no real alternatives are found and made usable on a wide scale, the present situation will stay the same worldwide, and things will get a little more difficult for plastics manufacturers every day. The demand for alternatives is there, but we’ll have to wait and see. Our industry thrives on continual technological developments and investments. We are now focusing on the acquisition of some test machinery also.” www.leopp.in Leo Precision’s booth at K show with Senthil Kumar (left) and Kay Barton","@ID":40}, "TOP TALK PETplanet Insider Vol. 21 No. 03/20 petpla.net 10 Interview with plastic packaging converter Manjushree Technopack’s new CEO – Mr Sanjay Kapote Next level growth strategy by Kay Barton India’s largest plastics company, the Bangalore-based giant Manjushree Technopack Ltd. (MTL), has a new leader on board. After its acquisition in October 2018 by Advent, the US-based private equity fund, MTL announced that it was ready for the next level of strategic growth, dubbed MTL 2.0. The target is a trebling of revenue from current levels, a target to be achieved in the next four years. Mr Sanjay Kapote was recruited to the Board to guide the company down this transformational path. He has 22 years’ experience in diverse management roles of several businesses, both national and international, and has been working at MTL since the beginning of November 2019. We had the opportunity to discuss with him the changes he has in plan for MTL and the objectives that will drive this transformation. PETplanet Insider: After two decades and several interviews with the Kedia family, who ran what was their family business passionately, we are now meeting a new face for the first time. Please tell us something about your background. Sanjay Kapote: Prior to joining MTL, I worked with Jindal Poly films, Birla Tyres and Essel Propack, amongst others. In all these companies I spearheaded various business operations, including profit improvement, new acquisitions, business restructuring and strategic turnaround, product development and lean manufacturing. With almost three decades of experience working in the automotive and packaging industry and with the best of companies, packaging is more than a passion for me. PETplanet Insider: Sounds like you indeed like new challenges and opportunities! So how about your very new role at MTL? Sanjay Kapote: Being a part of MTL is truly empowering. We have a clear vision and a powerful and dedicated team. As part of our strategic roadmap, we have articulated our vision and values for what we call Manjushree 2.0. We are embarking on a mission to triple our sales and are driven towards this one goal. The absolutely unconstrained environment makes MTL very exciting for me. We want to be a professional organisation, with integrity, customer centricity, innovation and environment sustainability at the core of our value proposition. PETplanet Insider: MTL is going to set the bar really high in a comparably short timeframe. How are you or how is the company going to achieve that? And what will be your current and future role in terms of reshaping the company and its plastic conversion business? Sanjay Kapote: Since the acquisition of MTL by Advent, we have developed a strategic roadmap to further unlock MTL’s potential and leverage our market leader position for accelerated growth in India. And, yes, our goal of tripling our revenue in the next four years is ambitious. We plan to achieve this growth through both organic and inorganic routes. PETplanet Insider: We saw both these routes in the history of Manjushree before its acquisition as well. Could you specify the company’s endeavors towards the growth strategy further? Sanjay Kapote: Our inorganic growth plans will be focused on consolidating in the rigid packaging market and entering new segments while also acquiring allied businesses, such as closures and dispenser manufacturing firms. The rigid plastic packaging industry in India is estimated to be two million tonnes per annum; MTL addresses only 60% of the market today and has about 10% market share. We have significant headroom available for both organic expansion and mergers and acquisitions. We are looking at three to four acquisitions over the next four years. PETplanet Insider: We will be following these acquisitions and expansions closely, of course. If we look at other branches and especially when it comes to material and cost savings, you sometimes find significant reductions in terms of quality. MTL’s characteristic feature throughout the years have been quality-driven products. Sanjay Kapote: True, and MTL is committed to developing innovation that is of high quality. We have always been at the forefront of adopting new technology to deliver best manufacturing practices to our customers. Our plant in Bidadi, for example, is highly automated. The Husky machines installed there are connected to a network that can be controlled remotely. The predictive algorithm of the software monitors the machines’ wear and tear and raises a red flag for maintenance issues well in advance, to avoid any breakdowns. PETplanet Insider: You deal with all the well-known local and inter- and multinational brands. Big investments have been made in corresponding machinery and equipment to achieve that. What is your strategy to maintain both quality and a competitive price at high level outputs? Manjushree’s new CEO Sanjay Kapote","@ID":12}, "imprint EDITORIAL PUBLISHER Alexander Büchler, Managing Director HEAD OFFICE heidelberg business media GmbH Vangerowstraße 33 69115 Heidelberg, Germany phone: +49 6221-65108-0 fax: +49 6221-65108-28 [email protected] EDITORIAL Kay Barton Heike Fischer Gabriele Kosmehl Michael Maruschke Ruari McCallion Waldemar Schmitke Anthony Withers WikiPETia.info [email protected] MEDIA CONSULTANTS Martina Hirschmann [email protected] Johann Lange-Brock [email protected] phone: +49 6221-65108-0 fax: +49 6221-65108-28 LAYOUT AND PREPRESS EXPRIM Werbeagentur | exprim.de Matthias Gaumann READER SERVICES Till Kretner [email protected] PRINT Chroma Druck & Verlag GmbH Werkstr. 25 67354 Römerberg Germany WWW www.hbmedia.net | petpla.net PETplanet Insider ISSN 1438-9459 is published 10 times a year. This publication is sent to qualified subscribers (1-year subscription 149 EUR, 2-year subscription 289 EUR, Young professionals’ subscription 99 EUR. Magazines will be dispatched to you by airmail). Not to be reproduced in any form without permission from the publisher. Note: The fact that product names may not be identified as trademarks is not an indication that such names are not registered trademarks. 3 PETplanet Insider Vol. 21 No. 03/20 petpla.net In China, the coronavirus has led to an extension of the Chinese New Year break. To stem the tide of the flu-like illness, the government has put in place travel restrictions affecting all of China. In Hubai, the province worst affected by the virus, public life has come almost to a standstill. Coca-Cola has powered down many of its 45 factories in China, reports Coca-Cola Company Chief Executive James Quincey. However, the Chinese government wants to make sure the flow of food and beverages doesn’t stop for its population so some factories are active again. In another move, Chinaplas has cancelled its trade fair in April in the new National Exhibition and Convention Centre (NECC) in Shanghai. Today, we heard the announcement by Ada Leung, General Manager of Adsale, that the trade fair will take place at the NECC in Shanghai on 3-6 August 2020. She said: “Many market activities like consumption, manufacturing and investment etc. are put on hold during the epidemic. And now, some companies have already resumed work and are manufacturing in an orderly manner. We believe that once the outbreak is controlled, all suppressed market demand will be released. The postponement of Chinaplas to August in Shanghai will help the upstream and downstream industries to seize business opportunities during the market rebound period.” Since Chinaplas will be in August, we will bring forward our August issue of PETplanet so that the preliminary trade fair report can reach all our readers (new publication date: July 20, 2020, new insertion deadline: July 03, 2020). We hope that the coronavirus and all its effects are overcome as quickly as possible and the restrictions can be lifted. Yours Alexander Büchler A personal update. Dear readers, last year, an accident forced me into inactivity. Since then, I have made good progress and I can now undertake small tasks again. A visible sign of this is the Editorial written by me. Thank you for your patience and many good wishes and thanks to the whole PETplanet team for taking the weight off my shoulders. Dear readers,","@ID":5}, "MARKET SURVEY 29 PETplanet Insider Vol. 21 No. 03/20 petpla.net Suppliers of preform machinery In this issue we focus on new developments in perform machinery. We are very proud to present the most exciting brand-new data from the following perform machine manufacturers: Kronce Enterprise Development Co., Ltd., Netstal Product Brand-KraussMaffei HighPerformance AG, Sacmi Imola, Husky, Otto Systems and Sipa. Although the publishers have made every effort to ensure that the information in this survey is up to date, no claims are made regarding completeness or accuracy. Resins & additives Preform machinery Preform production & inspection Preform & SBM mould manufacturer SBM 2 stage Compressors Caps & closures & inspection Filling equipment & inspection Recycling Palletising & shrink film machinery Husky Injection Molding Systems Otto Systems AG Sipa 500 Queen Street South, Bolton, ON L7E 5S5, Canada +1 905 951 5000 www.husky.co Reinhart Drawetz Business Development Manager - PET Systems +1 905 951 5106 [email protected] Zürcherstrasse 73 8730 Uznach, Switzerland +41 55 285 22 11 www.otto-systems.com Mr Stefan Zatti CEO +41 55 285 22 09 +41 55 285 22 44 [email protected] Via Caduti del Lavoro 3 31029 Vittorio Veneto, Italy +39 0 4389 11 511 www.sipa.it Mr Pablo Fiorentini Sales Director, Preform Systems & Tooling +39 0 4389 11 511 +39 0 4389 12 273 [email protected] HyPET5e , HyPET5e+ , HyPET HPP5e NexPET Multi-Layer Co-injection PET-Series 120, PET-Series 160, PET-Series 240, PETSeries 320 XForm 250 XForm 350 XForm 500 XTreme 72 XTreme 96 Up to 144 cavities Up to 48 cavities 4/48/72/144 2-96 cavities 8 / 96 8 / 128 8 / 180 Max. 72 Max. 96 Dependent on number of cavities and preform design (max. standard shot size 8,030g) Dependent on number of cavities and preform design (max. shot size 2,323g) Dependent on number of cavities and preform design (typical preform range 10-40g, with barrier content from 2.5% up to 40%) Max. shot weight 7,980g 525 750 750 60 60 1,700 476 1,010 Up to 1,150 1,000 1,350 1,350 1,000 1,350 Adaptive System Pressure supporting improved energy consumption, integrated high speed robot with up to four stages of preform cooling supporting the fastest cycle time in the industry, capability to mould the most aggressive preform applications at the industry's highest preform quality, reflex Platens, distribute clamping forces evenly, reduce tonnage requirements and extend mould life Designed for the mid-volume market segment, system capability, tooling conversion and refurbishing are engineered to meet the needs of this market, includes many features and capabilities from the HyPET5e platform, quicker mould change-overs, adaptive system pressure & reflex platens, integrated & operator friendly controls Based on HyPET HPP5e platform, integrated and operator friendly system controls, including auxiliaries, Multi-Layer hot runner and secondary injection unit, optimised front mounted hot runner nozzles and melt delivery for best-in-class mid-layer distribution capability Consulting & engineering of preform systems, complete preform production system including auxiliaries, full electric clamping unit, hybrid injection solution with shooting pot or electric injection with Time Safe Unit (TSU) XForm: available in GEN4 XP version (low energy consumption, fast cycle time, complete new HMI) XTreme: injectioncompression technology, ultra-thin wall capability, 2 preforms can be produced simultaneously Integrated Mould Alignment increases mould life and optimises preform quality, quick colour change reduces colour change-over time, complete range of integrated auxiliaries (resin dryer, chillers, product handling) Complete range of integrated auxiliaries, partial cycle completion when power fails, options to perfectly adapt the system to the geographical conditions and many specific customer needs Includes most HyPET HPP5e options, including mould alignment and self-cleaning, optional secondary injection unit changeover feature, complete range of integrated auxiliaries Extra large preform capability (up to 380mm), co-injection technology up to 72 cavities, integrated dust-evacuation (OH-XTRACT), enhanced neck-cooling (OH-XCOOL), wear-protection coating (OHXTreme) XForm GEN4 XP: XP technology, LongLife tooling coating, XMold for ultra-thin preform injection capability, wide-mouth preforms capability XTreme: built-in inspection system for 100% quality check, 100% recyled flakes processing capability, direct connection with XTRA SBM","@ID":31}, "PETplanet Insider Vol. 21 No. 03/20 petpla.net 46 PETbottles Beverage + Liquid Food Probiotic fruit gums Under its own name and with the description “Extra Strength Probiotic Gummies”, Walgreens is selling probiotic fruit gums with active cultures of Bacillus Subtilis and Bacillus Coagulans in a clear PET container that contains 90 fruit gums. The probiotic additives are to support bacterial balance in the digestive system. The circulating self-adhesive label describes product and application and a push down and turn cap protects the product from being dispensed by small children. www.walgreens.com New mineral water at Aldi Süd Since September 2019, the Aldi Süd group has had a new still mineral water in its range. The manufacturer/bottler of the water is Urwasser GmbH, a company belonging to Molkerei Gropper. Gropper, previously known as a producer of retail brands involving milk, yoghurt products, juices, smoothies and mixed coffee drinks, is entering a new market segment with mineral water. The “riese Urwasser” [ancient crater water] comes from the Marienquelle in Bissingen, a town in Nördlinger Ries with a landscape created by the impact of an asteroid. Chosen as packaging is a 100% rPET, slightly blue shimmering, slim and tapered bottle. The sleeve label explains the history of the water and is suitably decorated. The bottle is sealed with a light blue screw seal with guarantee band. www.rieser-urwasser.de Limited Edition from hella At regular intervals, German company Hansa Mineralbrunnen GmbH is launching especially tasty flavours of its drinks brand “hella” as “Limited Editions”. This year, it was “mango picchu” with mango and peach flavour. The uncarbonated, low-calorie drink is in a clear 750ml single-use bottle with circulating reinforcement ridges and is sealed with a violet screw cap with guarantee band. A colourful circulating sleeve label contains product information. www.hella-mineralbrunnen.de","@ID":48}, "BOTTLE MAKING 16 PETplanet Insider Vol. 21 No. 03/20 petpla.net Indian PET packaging industry – Reliance’s role in its growth journey & beyond From PET manufacturer to expert adviser The move to PET packaging in India began in the mid 80’s, with the introduction of PET packs for household containers (bottles and jars) and edible oil (EO). In a departure from conventional use, PET packaging in India started with PET jars/kitchen wares, filled with spices, pickles, edible oil etc, which kept the market ticking over. Fast forward to today and all the milk variants (fresh, flavoured, UHT, Chaas, Lassi) are packaged in PET by Amul and other milk majors. Reliance Industries Ltd., September 2019 We met: Vishal Mall, Vice President PET Business - Export Market, Atanu Biswas, Vice President PET Business - Domestic Market Rajesh K Gera, Asst. Vice President PET Business - Business Development & Sustainability It is heartening to note that, last year (2018/19), India’s PET market consumption crossed one million tonnes for the first time. This total, which is 13% up on the previous year, includes PET bottles, thermoformed APET containers, PET strapping, injection moulded items, and PET masterbatches and monofilaments. In the recent past, the Indian market saw single-digit growth; it is projected to grow 8-10% annually in the coming years. With a market share of 45%, Reliance is the major player in India’s PET sector. The balance is accounted for by other Indian manufacturers and imports. Reliance believes in total cooperation and support to PET processors and brand-owners to grow the domestic market. It endeavours to provide technical services, including inputs for processing, and also supports product and market development to accelerate the in-organic growth of potential Indian markets. Reliance has always been committed in making continuous efforts to launch new products in addition to supplying a consistent quality product. “Value-positioning is today shifting more capacity in PET and giving opportunity for non-cola beverages, promoted on health and wellness platforms. This has resulted in the introduction of variants of fruit drinks, flavoured water, nimboo pani and other beverages packaged in PET”, said Rajesh Gera in describing Reliance’s role in the in-roads made by PET packaging and its continued success with Indian end-users. “The CSD majors are also working on the eco-system. We work pro-actively with brand-owners and converters to bring in niche ideas for PET packaging and undertake match-making, to speed-up launch of new products in PET. The development of special PET resins to enhance the shelf life of food and beverage products is one such example.“ The Indian consumer market is moving from ‘class to mass’, he explained, which has led to a boom in PET demand. “The big cola majors have launched CSD in 250ml PET bottles in India. There is a growing interest from regional majors across India in small size PET packs, for launching CSD in smaller packs sizes up to 250ml.” Water, CSD and juice products account for more than 55% of all PET bottles used in India. From a raw material manufacturer’s point of view, the main trends here are in developing new applications and broad-basing current packages to new locations in the country, along with supporting material savings. Country Liquor in PET is another uniquely Indian application supported by the RIL team. The majority of states currently use PET bottles ranging in size from 90ml to 750ml, which helps to achieve overall savings to end users. Shatter-proof, economical packaging options are the buzz words today for PET in the liquor segment. There is a further opportunity to save SCM cost by shrink-sleeving filled PET bottles. In the IMFL sector, PET bottles are used extensively; the trend is a further shift to PET, for more liquor variants. The use of PET in liquor has led to the emergence of niche shapes and visual effects; 1 l frosted PET bottles for vodka and 2 l bottles with externally fitted handle for whisky were both developed by UB group. The adoption of PET packaging has led to an enhanced product appeal and increased sales for these liquor variants. The edible oil (EO) market has good growth potential for PET, as it is now increasingly being used for large 5 l containers and replacing traditional HDPE and tin packs. One EO Tour Sponsors: “Value-positioning is today shifting more capacity in PET” states Rajesh Gera, Asst. Vice President PET Business","@ID":18}, "PETplanet Insider Vol. 21 No. 03/20 petpla.net 35 TRADE SHOW REVIEW stage preform moulds as Stackteck’s leading competitors. “Being innovative in finding ways to meet those requirements is essential. Recently, sustainability has become a global priority. Finding solutions for reducing scrap through improved part quality, speedy colour change-overs and building processing know-how with recycled materials have been a priority for us, as well as improving productivity through advanced technologies in the hot runner, cold half, and post mould cooling systems.” Stackteck sees clear trends for today’s PET preform industry as a wide range of market segments including rPET applications, beyond the beverage and food industry, which is creating many new opportunities for mould projects. Stackteck’s President and CEO, Mr Vincent Travaglini, confidently stated “We can cope with that. We have a large capacity for machining, to handle big programmes. In a highly competitive market, we have built a good reputation through the years for being a premium supplier in food and beverage packaging with a broad scope of offerings, from part development and mould design to piloting, prototyping, repairs and systems integrations. All that is led by industry experience. We have many long tenured people in sales, manufacturing, engineering and other company areas, too,” he concluded. www.stackteck.com Stackteck is a global provider of integrated plastic tooling solutions for the injection moulding industry. From product and mould design to complete systems integration, the company develops injection moulds and systems. Through technical innovation in mould bases, quick product change and multi-level stack moulds, Stackteck states to differentiate itself by delivering high productivity to the caps, closures, thin wall packaging, technical and medical markets. Dedicated testing, service, repair and refurbishment resources ensure the capacity to deliver global multi-mould programs which are proven and deliver ongoing performance year after year. ASEPTIC PET PACKAGING PROVEN PERFORMANCE Over 60 billion bottles have been sterilised using Sidel Aseptic Combi with dry preform sterilisation saving our customers 10 billion liters of water and over 60,000 tons of PET. Sidel, when aseptic matters. sidel.com Sidel Aseptic Combi PredisTM FDA approved Visit Sidel at Interpack, Hall 13, Booth 47 May 7th-13th Dusseldorf","@ID":37}, "7 NEWS PETplanet Insider Vol. 21 No. 03/20 petpla.net ICIS Asian Recycling & Sustainability Conference postponed because of coronavirus The Asian Recycling & Sustainability conference organised by ICIS has been postponed. The new date of the conference will be Friday 19 June (originally scheduled for February 19). The venue will remain as the Hyatt Regency Bangkok Sukhumvit. “The health and safety of our participants is of top priority which is why we have taken this decision.” says the statement of ICIS. The organiser announced that registered delegate places as well as booked rooms at the Hyatt Regency Bangkok will be automatically transferred to the new date of Friday 19 June. The one day event will focus on the theme “Seeking paths and working collaboratively to establish a circular economy road map in Asia” and aims get to the bottom of the issues related to the immensity of the plastic waste crisis, the strategies of producers and long-standing brand owners to explore and promote solutions and many more. www.icisevents.com Petcore Europe Conference 2020 focused on sustainability Each year the European PET value chain meets in Brussels for the annual Petcore Europe Conference. This year the two day conference was held at the Crowne Plaza Brussels Hotel to welcome more than 300 industry delegates. Under the theme “Circularity and Innovation - Shaping the future of PET”, the complete PET industry sector shared perspectives and strategies for a succesful and even more circular future on 5 and 6 February. From PET resin producers, masterbatch producers, packaging designers and manufacturers, equipment manufacturers, label producers to major brand owners, EPR schemes, waste management organisations, recyclers, waste sorting and recycling machinery manufacturers - the entire value chain was represented. Additionally, speakers and participants from the European Commission, the European Parliament, the Ellen MacArthur Foundation and Eunomia shared their thoughts on the PET market as well as the plastics industry in the Circular Economy. “Petcore Europe represents the entire PET value chain since 1993. The strength of the organisation is the engagement of over 90 participating member organisations working together on the circularity of PET through working groups and projects”, stated Stephen Short, President of Petcore Europe, when opening the conference. Trends and solutions in PET collection and recycling Gian de Belder from Procter & Gamble and Larry Logan from Digimarc presented the Holy Grail project on digital watermarks. Gian announced that several P&G brands will integrate digital watermarks with first shipments end of the year in Germany. We will report on this in detail in our forthcoming issue. www.petcore-europe.org NO. ONE-WAY PRODUCTION. YES. TOP QUALITY RECYCLING. How can your recycled product meet permanently increasing demands? With the CHT range of high performance process solutions with environmental relief for the wet chemical cleaning. We support you directly on site and ensure your quality controls in our laboratories with state-of-the-art equipment. Thus, your strong position in the growing market is confirmed day by day. More about us at www.cht.com PLASTIC RECYCLING SHOW | 25 – 26 March 2020 PRS Amsterdam | hall 7 | booth B23","@ID":9}, "BOTTLING / FILLING PETplanet Insider Vol. 21 No. 03/20 petpla.net 26 Aseptic PET line for the Israeli market Extended shelf life white milk in PET bottles Yotvata Dairy by Strauss Group, locally well-renowned for their chocolate milk drink, was the first producer in Israel to manufacture Extended Shelf Life (ESL) white milk in PET bottles, an extraordinary development in the Israeli market. Recently, the liquid dairy manufacturer upgraded its 2 litre ESL milk bottle from HDPE to PET, thus introducing a completely new product for the country. With a new installed complete aseptic complete PET line from Sidel Yotvata redesigned its packaging. Despite having only 8.5 million inhabitants, Israel ranked number 15 globally for per capita spend on dairy in 2016. At the moment, the majority of dairy players in Israel are bottling their products in HDPE and carton, so Yotvata’s choice to increasingly adopt PET as their preferred packaging material contributes to a distinctive brand positioning and establishes them as pioneers on the market. A leading dairy producer Founded in 1962 and located in a kibbutz in the heart of the desert, approximately 40 km north of the Red Sea, Yotvata Dairy has demonstrated – against all odds – the feasibility of milk production under desert conditions. By combining long-standing expertise and focus on uncompromising quality, the company has been able to create a variety of rich tastes, expanding their dairy portfolio into new categories and becoming a leading dairy producer in Israel. Namely, the reputation of the taste of their chocolate milk sold at the small inn at the entrance to the kibbutz since the 1960’s has made this a “must stop” for anyone traveling to Eilat. Sidel’s PET packaging expertise critical for new product launch Yotvata had clear objectives around the launch of their new 2-litre PET milk bottle, targeted towards family households: “We need to break the visual codes in comparison with the past and with our competition, as all local dairy producers – including us – were used to pack milk in 2 litre squared bottles in HDPE with a handle. Additionally, we want to ensure a great brand experience for our consumers and maximise opportunities for the bottles to be easily taken from supermarket shelves,” says Ram Srugo, CEO of Yotvata. This last point was especially challenging because the majority of Israeli retailers are storing cold-chain products in refrigerators where people need to extract goods from the top with a very limited permitted height. All these issues had to be addressed in a market that is particularly innovative in terms of product launches, while packaging formats are changing at a slower pace. However, there is also a growing awareness for new, convenient and sustainable packaging solutions – at Yotvata and across the entire industry. PET is the obvious choice, not only with regard to its sheer limitless design possibilities but also with its lightweighting potential and recyclability qualities. The material offers considerable environmental benefits in the form of lower transport costs and overall reduction of raw material use. As a long-term business partner, Sidel supported Yotvata in designing and qualifying the new 2-litre PET bottle, helping the producer overcome any obstacle placed by the big size format, while enhancing users’ convenience. The new design, which includes a reflection of the customer’s branding on the top part of the container, concentrates the material’s tightness in the gripping area to avoid any splashing effect when pouring the product in a glass. Additionally, it is also counterbalancing the vacuum effect, which may impact products distributed via coldchain. Variety of milk-based drinks While welcoming the increased demand for their wide range of milkFILLING","@ID":28}, "MATERIALS / RECYCLING PETplanet Insider Vol. 21 No. 03/20 petpla.net 12 Producing PET resin within a ‘greenbelt’ by Michael Maruschke The Dhunseri Group has been a major player in the Indian tea market for over 50 years. Until 2002, it was engaged solely in the growing and production of tea. It then branched out into other markets, including the petrochemical industry. In 2003, the company began production of PET resin. In order to have a better international sales coverage and access to PET raw materials, it decided to enter a 50:50 joint venture with Indorama Ventures in 2015. The company, which is now known as IVL Dhunseri, operates two factories in India: one in the port town of Haldia, West Bengal; and the other in the district of Karnal, Haryana. Installed capacity of 700,000 tonnes/year makes IVL Dhunseri the second largest PET resin producer in India. IVL Dhunseri Petrochem Industries Pvt. Ltd. May 2019 We met: Mr B. Chattopadhyay, CEO, Mr Pankaj Kr. Sinha, Marketing Head India We visited the facility in Haldia, which actually consists of two plants. The first plant, which commissioned in 2003, employs Zimmer polymer technology to produce the PET resin and the second, which started operations in 2012, uses Oerlikon Barmag technology. Both plants can be considered among the most advanced PET resin manufacturing facilities in the world. Ethylene glycol is supplied by Sabic/Meglobal and transported to the plant via an 8 km pipeline directly from the city’s port, while the terephthalic acid (TPA) is supplied by MCC PTA India Corp Pvt Ltd (MCPI) from its production site located just 6 km away. Certifications in place - worldwide export The company’s product range consists mainly of bottle and jar grade PET resins, with about eight per cent sheet grades. New and specialised PET grades are under continuous development; a dedicated resin composition for the popular 20 l (five gallon) PET containers being an example. It features one of the highest IV (intrinsic viscosity) currently available and can be used for the production of preforms with wall thicknesses greater than 5mm. IVL Dhunseri’s Haldia facility is one of the plants within the Indorama group that has received quality certifications from several national and international agencies, such as US FDA, European FC, Japanese and Canadian Food and Health Bodies, and from multinational brands such as Pepsi. Consequently, 50% of its PET resin production is exported, under the Ramapet brand, to over 42 countries worldwide. Within its domestic market, the material is distributed under the Aspet brand to about 280 customers across India. Factory with fruit garden The Haldia plant has its own fire station (which also provides emergency service for the local community); its own health facility for employees; and a ‘greenbelt’, with a fruit garden and a temple shrine. The plants and surrounding facilities are powered by two coal-fired power plants, which have 10MW and 8MW capacities. Diesel generators are installed as a back-up. Egyptian project IVL Dhunseri also operates a 540,000 t/a PET facility in the Ain Sokhna Free Trade Zone, North West of the Gulf of Suez in Egypt. This facility is one of the largest in the Middle East and Africa and is well placed to meet the increasing demand for PET resin in MEA region. www.ivldhunseri.com Tour Sponsors: F.l.t.r.: Pankaj Kr. Sinha, B. Chattopadhyay and Michael Maruschke View of the Haldia plant from above","@ID":14}, "TOP TALK PETplanet Insider Vol. 21 No. 03/20 petpla.net 8 PETplanet: Mr Davatz, these days it is increasingly rare for a man like you to work his way up from apprentice to CEO in the same company. Today, companies seem to be relying more on trained managers and less on technical expertise. Davatz: There are three factors at play here; the theoretical toolkit, practical experience and the personality of the person involved. People can be skilled in these three areas in different ways. The valuable building blocks of theory are definitely helpful provided they are combined with practical experience, but personality might be most important. When managers move company every six months, I don’t think that continuity can be sustained. PETplanet: Netstal is now no longer Netstal; since last summer Netstal has become KraussMaffei HighPerformance AG. What has changed for customers? Davatz: Our parent company KraussMaffei is repositioning itself by bringing together under the umbrella of a single brand, KraussMaffei, the various business areas and previous brands of KraussMaffei, KraussMaffei Berstorff and Netstal. The strong name of Netstal lives on as a product brand for our machines. The change of name is happening without any restructuring, which demonstrates the stability of the company and shows our commitment to the Näfels site. We invest a lot in our product pipeline. In addition we will build a new competence center. PETplanet: Yet didn’t KraussMaffei HighPerformance AG immediately start working reduced hours in the summer? Davatz: This applied last year to all of plastics engineering and especially to sales involving systems for automotive engineering which suffered a spectacular collapse. We weren’t able to dodge that trend, but the issue of reduced hours is last year’s issue. We’ve moved on. PETplanet: Are you thinking of the product range for preform injection moulding machines with lateral removal? That would be a minor revolution for Näfels people. Davatz: Not only that; we are in the process of developing such a machine equipped with a 4,000 kN clamping force. In terms of investment, it is one of the largest development projects in the entire KraussMaffei Group and the biggest in the history of Netstal. Rather than thinking about physical solutions or machines, we are instead focusing principally on the product which will be produced on our systems. So we are thinking about the bottle itself and offering our customers complete solutions for this application. This means that we are often able to offer a turnkey package with mould, removal device, dryer and cooler, including a service package. Interview with Renzo Davatz, CEO of KraussMaffei HighPerformance AG From the side – the new Netstal PET product range Since the summer of 2019, Netstal has been renamed KraussMaffei HighPerformance AG. We asked Renzo Davatz – almost 30 years in the company and CEO since 2016 – about the background to this. We were particularly interested in the prospects for the future. Here, Davatz tells us of the development of a new product range with lateral removal – a new approach for the Swiss company, which has previously preferred removal from above. This is how we know Netstal’s PET-Line, with a removal from above. The new 4000 model will feature a lateral removal – a new approach for the engineers from Näfels.","@ID":10}, "PETcontents 4 PETplanet Insider Vol. 21 No. 03/20 petpla.net 03/20 INSIDE TRACK 3 Editorial 4 Contents 6 News 45 Products 46 PET bottles for Beverage + Liquid Food 48 Patents TOP TALK 8 From the side - the new Netstal PET production range - Interview with Renzo Davatz, CEO of KraussMaffei HighPerformance AG 10 Next level growth strategy - Interview with plastic packaging converter Manjushree Technopack’s new CEO Mr Sanjay Kapote MATERIAL / RECYCLING 12 Producing PET resins within a ‘greenbelt’ PREFORM PRODUCTION 14 Goodbye to cans: preforms for CSD 15 Preforms for regional brands BOTTLE MAKING 16 From PET manufacturer to expert adviser - Indian PET packaging industry BOTTLING / FILLING 19 Oil bottle production in-house - Major investment in SFL linear stretch blow moulder 20 Flexible, sustainable and digital: filling technology’s future is now 24 From the source to the table - 8 l container dispenser in 100% rPET 26 Extended shelf life white milk in PET bottles - Aseptic PET line for the Israeli market 30 Taking care of sensitive products - The first linear InnoPET BlowFill ABF aseptic block from KHS 32 Towards multi-packaging 33 From stretch blow moulding to hot filling - TES STM Group’s Blueline machinery range MARKET SURVEY 28 Suppliers of preform machinery TRADE SHOW REVIEW 34 Preform mould manufacturing 36 K show review - part 3 38 India-made moulds 40 Eliminating waste and building a circular economy 44 Brau Beviale review - part 2 BUYER’S GUIDE 49 Get listed! Page 3624368 Page 16 Page 19 FILLING","@ID":6}, "BOTTLING / FILLING PETplanet Insider Vol. 21 No. 03/20 petpla.net 24 8 l container dispenser in 100% rPET From the source to the table The term “Volvic” derives from the Latin expression “Volcani Vicus” (land of volcanoes) and refers to the Regional National Park of the Volcanoes of the Auvergne natural park in France. This is the source of the natural mineral water Volvic. The water began to be sold in 1938 and in 1955 took the name of Societé des Eaux de Volvic. In 1969, the classic glass bottle was replaced by a container in PVC, one of the first examples of plastic bottles to be used in Europe to bottle spring water. In 1997, Volvic became the first food and beverage company to launch recyclable PET bottles on the market. From a recently realised new development results an 8l container of 100 per cent rPET. The whole bottling process of the Societé des Eaux de Volvic, part of the Danone group, undergoes careful controls. This starts from protecting the source to monitoring the natural environment until the moment when the bottled product is consumed. All of this is taken care of in minute detail, involving partners and suppliers, as with the recent investment in the purchase of a new bottling line for 8 l containers in 100% rPET. Italian company SMI supplied the integrated Ecobloc Ergon system. The synergy between Volvic-Danone and SMI started from the design phase, every choice rotated around the necessity to obtain higher than average bottle performance and quality, safeguarding the final product, whilst ensuring eco-sustainability and operational efficiency of the whole production process. The bottling process starts with conducting the water through stainless steel pipes from the source to the bottling plant. To protect the liquid from any external contamination the Volvic bottling plant was designed according to advanced automation and security criteria. The bottles blown, filled and capped by the integrated Ecobloc Ergon system need to go through a long series of controls within the bottling line and every day the Volvic Quality laboratory collects samples and carries out careful tests. 8 l home use, container-dispenser So that the natural mineral water arrives at the consumers’ table as pure as when it flows from the source, the container plays a vital role. Volvic’s high regard for environmental issues led the French company to develop modern solutions for the recycling of PET. Volvic states that it was one of the first companies to use rPET to produce containers, slowly increasing the percentage until it hit 100% with the new 8 l bottle. This container features a square base, in the same style as the smaller Volvic bottles, to create a practical home use containerdispenser. Its shape, part of which is slightly tilted, ensures that the bottle can be easily positioned on a flat surface. Thanks to the special cap which is used as a tap the supply of the product is claimed to be convenient and easy. The new design of the maxi container was accurately reproduced by SMI which created the moulds that are installed on the integrated system, the Ecobloc Ergon HC EV. This system has been chosen to produce, fill and cap large size containers. The new investment was studied in detail, creating strong teamwork between the experts at Volvic and Danone and the designers at SMI. The complete production process was designed so that every step of the bottling is kept under constant control, because it is here that the water comes into contact with the external environment and is at a greater risk of contamination which would compromise the sensory, chemical, physical and microbiological properties. SMI provided the French technicians with one of their own stretch-blowers, so that they could carry out a series of blowing tests while accurately testing the preforms and bottles. These tests allowed them to regulate the “top load” resistance and the material distribution, a step at a time, developing a specially made preform with a specific shape. The biggest challenge, when using preforms made from recycled material is to guarantee the constant resistance of the bottle when it is being blown. FILLING Recognisable by the green cap, Volvic 0.5 l and 1.5 l bottles were the first in France to be produced with a type of plant-based plastic that is 20% vegetable origin, favouring the use of renewable materials.","@ID":26}, "BOTTLE MAKING 17 PETplanet Insider Vol. 21 No. 03/20 petpla.net major even uses a 15 l PET container. Smaller EO pack sizes, especially 2 l, are also now packaged in PET; previously, they were available only in HDPE. Speciality PET grades have been developed by RIL for niche applications, such as “high barrier” for oxygen & carbon dioxide; opaque for light sensitive packaging; slow crystallising resin for bulk packages; and injection moulding grade resins, among others. In non-bottle segments, Reliance sees a future for PET primarily in replacing styrenics (including polystyrene) and PC (polycarbonate) in injection moulded items like stationary products. RIL has developed a special PET grade, RELPET IM5590, for this end-use. The resin has the required properties for manufacture of injection moulded products. Reliance is equally active in the field of recycling and sustainability eco-system. It has set up over 70 of a total of around 500 “reverse vending machines” (RVMs) for recycling PET bottles around the country. This initiative is helping the PET community to generate awareness of the utility of post-consumer PET bottles, both among the people and Government bodies. It is worth noting that empty used PET bottles are removed from the streets by lower social groups and then recycled. RVMs, along with the organised recycling system, has helped India to reach a PET recycling rate of 92%. RPET products are currently used for non-bottle applications; current legislation prohibits PET to be used in food product packaging. As the polyester fibre industry already has capacity, all the recycled PET bottles collected stay in India only for fibre applications. Recycled PET bottles are used as raw material in textiles such as blankets, T-shirts, pillows strappings. RELPET resin made by Reliance (in addition to that supplied in domestic market) is exported to different countries. “RIL exports globally to Asia Pacific, Africa, Europe, Middle East and Latin America, with a primary focus on adjoining geography,” said Vishal Mall. RIL’s team supports converters globally both for market development and technical services. The PET packaging market in India has grown exponentially and continues to expand into new areas. “Reliance is proud to be a part of this success story and continues to strive along with other stake holders to co-develop new packaging solutions. India is set to go far beyond the milestone of 1mn TPA of PET consumption in 2019-20!” Atanu Biswas concludes. www.ril.com","@ID":19}, "TOP TALK PETplanet Insider Vol. 21 No. 03/20 petpla.net 11 Sanjay Kapote: Our focus is to deliver “affordable customised innovations”. Over the years, we have developed some thoughtful packaging solutions for various industries. At the same time, we have invested extensively in research and development, in talent and cutting-edge technology, to make plastic packaging more cost-effective, weight effective and sustainable, with minimum carbon footprint and without forfeiting quality. We are exploring technology tie-ups with global players to bring best-inclass technologies to India. Currently, we are focused on adding more power efficient machines, as well as bolstering EBM capabilities. We recently installed zero-cooling technology; we are perhaps the first to bring this technology to India. This is a disruptive technology from Japan’s Nissei ASB, which improves productivity. PETplanet Insider: Yes, we reported on Nissei ASB’s Zero-Cooling technology several times already and had a few face-to-face meetings with them about it at the leading trade shows. Savings in material and operational costs means that you can work economically through intelligent technology, which nowadays also gives you many environmental advantages. Sanjay Kapote: Yes, and when we talk about environmental advantages, we should keep sustainability and recycling in mind. Recycling will become an important part of our business. We are committed to creating a circular economy. We have embarked on setting up our own recycling plant. We believe brands are eagerly looking for reliable solution providers who can help them with their extended producer responsibility, and with recycling of postconsumer recyclable waste material for their own products. We see the potential to become one of few players in the industry to offer brands an end-to-end solution for recycling and to deliver extended producer responsibility (EPR). We will take responsibility for collection, segregation and processing of plastic waste to create a high-quality post-consumer recyclable resin, which can be used along with virgin resin to produce new packaging. PETplanet Insider: In terms of sustainability we have already seen many efforts from MTL, such as your plant in Bommassandra, which we reported on in 2016 (PETplanet Insider issue 11, 2016), and for which you received an award from the Indian Green Building Management for its environmentally-friendly concept. Or the Reuseum information centre, the construction area of which we visited last year, during the course of the India Road Show (PETplanet Insider issue 12, 2019). Sanjay Kapote: Correct. Besides focusing on sustainable product innovation, MTL is also big on using renewable energy. We are investing heavily on adopting renewable energy at our plants; our Bidadi plant is one of the very few LEED Gold certified factories in India. And as you rightly said, with the Reuseum project we generated a pioneering information centre, which is able to teach people the importance of sustainable living and behaviour. PETplanet Insider: As mentioned, we report on MTL’s activities regularly in PETplanet Insider and on our website: petpla.net. Nevertheless, could you once again summarise your manufacturing capacities and capabilities for our readers? Sanjay Kapote: Until 2016, all our production was concentrated in Bangalore, predominantly in our factories in Bidadi and Bomassandra. In 2016, we acquired four facilities of Delhi-based Varahi Ltd. In March 2017, we started our greenfield plant in Guwahati, with a capacity of 4,000 MTPA (t/a). Today, these seven facilities, together, have an installed capacity of about 150,000 MTPA. We recently commissioned a new greenfield facility in Silvassa, which will help us expand our footprint to new clients in western India, especially in Gujarat and Maharashtra. PETplanet Insider: Thanks a lot for the interview, Mr Kapote! www.manjushreeindia.com May 7-13, 2020 Hall 13 · A73 at the Krones booth German Technology","@ID":13}, "BOTTLING / FILLING PETplanet Insider Vol. 21 No. 03/20 petpla.net 20 Flexible, sustainable and digital: filling technology’s future is now Sterilisation of containers for aseptic beverages is an important part of the filling process and there are several techniques available to manufacturers, each with their own benefits and drawbacks. Whether they use chemical or energy-based container decontamination, bottling manufacturers will be embracing greater digitisation and (best of all) can look forward to more sustainable methods of filling. Barbara Bricoli, Ph.D., Innovation Manager for GEA, and Paolo Abelli, Head of Product Development of Blow Moulding and Filling at GEA, look at the options available and speculate on what the future may hold for the technology. We live in a world in which ‘natural’ is perceived as good. Consumers want fresh tasting products, full of natural ingredients, with high nutritional value and a long shelf life. In developed countries, refrigeration and cold chain distribution networks provide the fresh products consumers crave. But where this is not available it seems that freshness and long shelf life are in conflict. With aseptic technology now available for aesthetically and ergonomically appealing plastic containers, it’s possible to achieve both, bringing fresh-tasting products to a wider audience and avoiding environmental disadvantages of maintaining the cold chain. Wanted: aseptic filling that minimises water and chemical waste Aseptic bottling technology ensures that sterile bottles are filled with sterile products and sealed with sterile caps, all within a sterile environment. Eliminating bacteria from the process in this way makes it possible to produce beverages and liquid foods with a fresh taste, which will remain safe to use for over six months, even at ambient temperatures. Although the principle of aseptic bottling is widely practiced, the way that bottles (and caps) should be sterilised in the first place is intriguing. Achieving the required level of sterility is usually not a problem; doing so while minimising water and chemical usage is more difficult. Chemicals used for sterilisation are expensive; bottles need to be purged of any residue prior to filling; and the chemical itself must be recovered safely and efficiently. Furthermore, sterile water is expensive to produce. PAA sterilisation: required for some applications PAA sterilisation, which is wellknown and effective, sterilises bottles and closures using a warm solution of peracetic acid. This provides both a chemical and a very important mechanical element to the sterilisation process; the chemical neutralises any biological contamination, while the action of filling and removing the solution purges bottles of physical debris, such as dust or plastic fragments, which may be found inside the container. The bottles then need to be rinsed with sterile water to remove any chemical residue. While this process is still the most effective, it requires a lot of water. Many applications still require PAA sterilisation and research into more sustainable methods is ongoing. H 2 O 2 sterilisation – an option, just not for everyone Other applications, such as hydrogen peroxide (H 2 O 2 ) require no water at all. Containers sterilised by FILLING Natural, fresh, safe, longlife food: sterilisation processes and aseptic filling and packaging play a major role. (Images: GEA)","@ID":22}, "BOTTLING / FILLING PETplanet Insider Vol. 21 No. 03/20 petpla.net 25 Stretch blow moulding, filling & capping The Ecobloc Ergon HC EV is a system for stretch-blowing, filling and capping the square based 8l containers in PET with a production capacity of up to 3,200bph. SMI points out that the system does not need a rinser, nor conveyors between the blower and the filler or accumulation. Other advantages include: Isolating system between the “dry” area of the blower and the “wet” one of the filler, through a jet of high pressured, sterile air in excess of 5Pa. The air flow, through 4 units of Galvani filters (HEPA filters) is situated on the top part of the filler area to avoid contamination, acting as a “clean room”. In addition, the filling valve is controlled by an electronic flowmeter. The preform suction system is situated on the oven infeed star, to remove any impurities that could be on the inside of the preform itself. The air that is inserted into the suction system is filtered and is part of the air recovery system that comes as standard on all the range of SMI stretch-blow moulders. The system combines blowing air into the preforms with the following vacuum suction process. The machine features integrated inspection systems with cameras to guarantee the quality of the bottled water, to monitor the production process and to avoid particles and/ or impurities being deposited on the inside of the unblown preforms. Maintained sterility for all the processes of blowing, filling and capping. The stretch-blow module is equipped with a double stage air recovery system, which allows the reduction of energy costs tied to the production of high pressure compressed air. The filler area is compatible with COP (Cleaning Out of Place) and equipped with optional system of stainless steel bulkheads to separate the “wet” area of the filler with the “dry” area of the blower during maintenance or cleaning operations. Electronic components are positioned on the inside of the panels to ensure a greater protection from damp. The base of the filler area is made in stainless steel and slightly sloped to ensure that any spilt liquids go down the drains. The electronic capper is equipped with cap orienting during application, a system which controls correct positioning of the cap and a rejection system for over turned caps; cap sterilisation through jets of ionised air on the cap channel Washable cap accumulation table, in stainless steel, equipped with an optional system to suction the caps to remove any impurities that might have deposited on them while moving along the hopper The increase in production speed of bottling lines, the use of lighter containers, and the change in laws that are stricter in terms of food product quality and integrity force companies in this sector to use cutting edge technology equipped with advanced inspection systems for preforms, bottles and caps. To satisfy the quality standards of the Danone group, the Ecobloc HC Ergon is equipped with Pressco inspection systems. www.smigroup.it","@ID":27}, "BOTTLING / FILLING PETplanet Insider Vol. 21 No. 03/20 petpla.net 21 this method can be purged with sterile air. While this process is effective, it has limitations. In many countries it is impossible to control the initial bioburden of supplied preforms and caps and storage conditions can often be less than ideal. Dry sterilisation provides no mechanical purging/ sterilisation effect; if there is a risk of particles in the preforms, PAA sterilisation is better. “Some customers want to use H 2 O 2 because it reduces costs and is the latest technology,” said Paolo. “But it’s not right for everyone and inappropriate use can lead to unexpected contamination during production.” Sterilising preforms requires an aseptic blower The concept of sterilising the preform prior to blowing the bottle with an aseptic blower was pioneered by GEA in 2010 and GEA is still the only company, as of today, that has obtained the FDA approval for aseptic blowing. In this process, hot preforms are sterilised inside and out simultaneously, using a flow of H 2 O 2 . The bottles are then blown within the sterile area and filled. Sterilising the preform reduces the amount of chemical necessary as the preform is smaller and more regularly shaped than a blown bottle. It reduces the weight of PET required for each bottle as there is no risk of shrinkage during treatment. This also allows manufacturers to experiment with innovative bottle designs but achieving peak levels of safety is still challenging. Electron beam technology negates the use of chemicals The future may see the development of sterilisation methods that eliminate the use of water and chemicals completely. Barbara said that GEA’s research and development of new products is always customer driven. There is a range of potential technologies that have merit, including pulse light and electron beam technology, but they have been found to be impractical, so far. “Ultraviolet and pulse light treatment are very promising for PET bottle sterilisation and electron beams can be used for sterilising preforms but there are maintenance issues,” she said. “The costs are currently too high for commercial use.” Paolo agreed that electron beam technology is very good but also complex and expensive, and operators have to be carefully screened. “I don’t believe it’s possible to recover the cost of the machine through the reduced use of water and chemicals. Moreover, energy has a May 7 -13 Hall 13 | Booth A31","@ID":23}, "PREFORM PRODUCTION PETplanet Insider Vol. 21 No. 03/20 petpla.net 14 Goodbye to cans: preforms for CSD by Michael Maruschke April 2019 We met: Mr Rupnath Roy Chowdhury, Managing Director Mr Ekbal Hossain, Manager PET Division Mr Ratan Kumar Paul, Chief Commercial Executive Tour Sponsors: Cans & Closures now has an installed capacity of about 30 t/d, which is set to increase to around 40 t/d (15,000 t/a) from early 2020. It produces preforms on Krauss Maffei machines, including a few 60 cavity CV175-1900s and a 48 cavity CV 3500. A 96 cavity Husky preform machine is in the pipeline and should start producing preforms in the near future. Its major customers include some of the largest beverage businesses in and around Eastern India, such as franchisees of Coca-Cola India; R.C. Cola; Bisleri; and other beverage and water manufacturers, as well as leading India FMCG, pharma and liquor companies. The preform product range consists of clear and green preforms for hotfill, CSD and water, while the FMCG, pharma and liquor bottle range features various shapes and designs, from 30ml to 500ml. One of its main lines is a 24.21 g preform with PCO1810 neck for hotfill applications, which is used for Maaza, one of Coca-Cola’s regional favourites. The preforms come with PCO1881 (CSD), PCO1810 (hotfill) & 29/25 (water) necks. Nitro Hotfill and seasonality According to Rupnath, the company owns the only 16 g/1 l water mould in India that is suitable for the nitrofill process of filling 1 l Kinley Water. It was supplied by MHT Tooling. Rupnath explained the effect of seasonal changes on the beverage market in India. Demand for water is pretty constant, all year round, but the production peak for juice and CSD extends to four months from March to late May/early June – the annual hot season, preceding the monsoon. Cans & Closures has the capacity to manufacture preforms, blown bottles and the capability to produce bottles from single stage ASB machines. It is the only company in Eastern India that covers all four PET market segments: beverage and water; pharma; liquor; and FMCG. It appears to be well-placed to further consolidate its leadership position in the Eastern India PET Market. Several years ago, “Cans and Closures” accurately reflected the product range of Cans & Closures Pvt. Ltd., which included aluminium ROPP closures and crown caps. But this is not the case anymore. When the price for PET came down to affordable levels, a little over 10 years ago, it fuelled a steady growth in demand for PET bottle and preforms. Rupnath Roy Chowdhury decided to diversify and, in 2008, started PET preform production, initially on a Krauss Maffei KM 175-3500CV injection moulding machine. The investment was a success; the company has grown strongly ever since, at a rate of around 10% annually over the last few years and 2019’s growth figure is forecast to be more than 20%. Rupnath considers his company to be the fastest growing preform manufacturer in Eastern India. F.l.t.r.: Ratan Kumar Paul, Ekbal Hossain and Rupnath Roy Chowdhury","@ID":16}, "MARKET SURVEY 28 PETplanet Insider Vol. 21 No. 03/20 petpla.net 03/2020 MARKETsurvey Company name Shanghai Kronce Enterprise Development Co. Ltd. KraussMaffei HighPerformance AG Sacmi Imola Postal address Telephone number Web site address Contact name Function Direct telephone number Fax E-Mail Room 06/07, Fl. 35, 6088 Humin Road, Minhang District, Shanghai 201199, China +86 21 2420 200 1 www.chinakronce.com Mr Andy Yang General Manager +86 15 000 770 587 +86 21 2420 227 8 [email protected] Tschachenstrasse 8752 Näfels, Switzerland +41 55 618 6111 www.kraussmaffei.com Mr Stefan Kleinfeld Application & Product Manager +41 55 618 6241 +41 55 618 6605 [email protected] Via Provinciale Selice 17/A 40026 Imola BO, Italy +39 0542 607111 www.sacmi.it Mr Moraldo Masi Director of Business Unit PET +39 0542 607888 +39 0542 642354 [email protected] Preform injection moulding systems Machine model number / name P-SR PET preform injection moulding system Netstal PET-Line 2400, Netstal PETLine 4000, Netstal PET-Line 5000; Netstal PET-Line 2C; PETForm 175 IPS220 IPS400 Number of cavities (min/max units) 12/72 32 - 144 16 - 72 48 - 128 Maximum individual preform weight 800g Max. shot weight 6,600g 140g 140g Max resin through-put (kg/h of PET) 400 Up to 1,350 625 125 Standard features (short description / keywords) Turnkey solution provider for production with the reasonable ROI based on reliable production cost of PET preform, PET bottle & caps, servo-motor driven system, power saving for heavy preform production, higher PET plasticization result, 24:1 L/D ratio useful for high quality PET plasticisation Intrusion Injection cylinder (shooting pot), electrical drive for plasticising screw Options / Special features (short description/keywords) Better perform, bottle and cap design, weight saving, easy for fast blow, better view for final products, various solution for selection, focus on products quality, efficiency, flexibility, clients’ requirements has been taken into account, heavy duty equipments, energy saving, fast production, trouble free in product process, engineer onsite service, fast start-up and better training for operator CPP = \"Controlled Production shutdown during a Power outage\"; NRS = Netstal remote support, energy measurement Calitec T-belt for preforms extraction, belt free robot linear motor with KERS, take out plate with three postcooling stations, HMI with control of all auxiliaries, double cylinder for preform ejection, digital valves for each actuator, water unloading system prior to mould changing, injection shot completition device (power failure) Direct preforms unloading from gripper plate, belt free robot linear motor with KERS, take out plate with four postcooling stations , HMI with control of all auxiliaries, boosters on moving platen for first phase ejection, digital valves for each actuator, water unloading system prior to mould changing, injection shot completition device (power failure)","@ID":30}, "TOP TALK PETplanet Insider Vol. 21 No. 03/20 petpla.net 9 PETplanet: So what was the trigger point for developing lateral removal? Davatz: Despite all the advantages of overhead removal, we had to recognise that the factory layout for many of our customers is geared towards systems with lateral removal. So the systems and moulds are built and installed to meet this requirement. We have listened to what our customers are telling us and we are co-operating with our mould partners on these systems. This means that moulds for lateral removal can also be used on our systems and the new product range fits in with existing factory layouts. This is delighting our existing customers and will also be interesting for customers who have previously ordered from other providers. PETplanet: Systems from Näfels have a wellknown reputation for sturdiness and long-lasting construction. Davatz: And that’s how it will stay. The new Netstal PET-Line will still be a true Netstal: precise, fast, sturdy and reliable. We intend to bring further improvements to the existing product range in terms of energy consumption and cycle times reduction. PETplanet: Why have you singled out the 4000 as the first model in the new product range? Davatz: The 4000 will certainly be the flagship model within the new Netstal PET-Line family. PETplanet: Many thanks, Mr Davatz. www.kraussmaffei.com Renzo Davatz, CEO of KraussMaffei HighPerformance AG (formerly Netstal-Maschinen AG) since the summer of 2016, completed his apprenticeship with the Glarner Machinery Company. Subsequently, he has occupied various positions in Netstal over the past 30 years – for example, he established the service organisation in the USA and was responsible for the service business worldwide for KraussMaffei and Netstal products.","@ID":11}, "PETplanet Insider Vol. 21 No. 03/20 petpla.net 47 BOTTLES Lipton Ice Tea less sweet Following consumer pressure, many drinks manufacturers are changing their recipes and are reducing the sugar content of their products. The new “less sweet” Peach-Nectarine variety contains 3.9g of sugar per 100ml. The bottle is slightly contoured and clear with irregular circular but intermittent ridges and contains 1.25 l of content. The honey contained in the product is represented in the design on the sleeve label by a honeycomb pattern. An orange coloured screw cap with guarantee band seals the bottle opening. www.liptonicetea.com Rio d’oro NFC juice from Lake Constance Under its own brand “rio d’oro”, German discount retailer Aldi Süd is for a short time selling an apple juice as a naturally cloudy NFC juice; it is 100% freshly pressed from Lake Constance apples. The producer of this juice is Molkerei Gropper GmbH and it should be kept chilled. The transparent bottle with a large drink opening contains one litre and is made from 50% recycled plastic. The bottle is decorated with a circulating paper label and the opening is sealed with a green screw cap with guarantee band. www.aldi-sued.de","@ID":49}, "43 TRADE SHOW REVIEW PETplanet Insider Vol. 21 No. 03/20 petpla.net TRADE SHOW review Natural ingredients Döhler presented pioneering ingredients, ingredient systems and integrated solutions for the beverage industry. The focus was on developments combining plant-based nutrition, naturalness and sugar reduction with unique multi-sensory experiences, to satisfy the wishes of environmentally and health-conscious consumers. From reduced-sugar adult soft drinks in innovative flavours, to fruity and fresh NFC juices, to refreshing fruit-infused water and full-bodied, alcohol-free beers, visitors to the Döhler stand were able to discover inspirational ideas for their next beverage product. All these concepts are based on a comprehensive portfolio of natural ingredients ranging from natural flavours, natural colours, health ingredients, pulses & cereal ingredients, dairy & plant-based ingredients, fermented ingredients, fruit & vegetable ingredients to ingredient systems, as well as a diverse range of certified organic ingredients. In addition, Döhler also presented its diverse ingredient portfolio which provides potential for further product concepts. From functional sport drinks containing magnesium and which are available in different flavours, to authentic tea drinks in organic quality, to alcohol-free beers and malt drinks with a typical beer character – the concepts are intended not only to impress thanks to their natural and fresh tastes, but also to provide diverse inspiration for different product positionings. www.doehler.com Piston compressors with a Plus At the show, Atelier Francois (AF) was focusing on its range of highly efficient oil-free low-pressure 6-15 bar piston compressors. These are suitable for all compressed air applications, including food and beverage and brewery applications. The capacities range from 7.2 to 58m³/min in accordance with ISO1217. The Belgian company also offers oil-free piston compressors from 20-40 bar with capacities from 150 to 3,300m³ / h in accordance with ISO 1217. The Smart Inverter Starter (SIS) is one of the options available. It ensures that the starting current never exceeds the nominal current and the full load power never exceeds 100 per cent. Additional shielded cables, line filters or other protection devices are redundant. This development comes along with the Adjustable Air Flow System (AFS). It is used when less than full air capacity is needed. When 100 per cent air capacity is needed, the first stage double-acting cylinder compresses the air on the up and down stroke of the piston. This raises the atmospheric air to 4 to 5 bar achieving the most important pressure ratio. For 55 per cent air capacity, the first stage cylinder compresses atmospheric air only on the upward stroke of the piston. AFS automatically unloads the lower part of the cylinder to match air flow required in the system. www.afcompressors.com The AF team at Brau Beviale PART 2","@ID":45}, "BOTTLING / FILLING PETplanet Insider Vol. 21 No. 03/20 petpla.net 22 level of carbon footprint that must be taken into consideration,” he said. GEA is working around these limitations to provide a chemical-free sterilising process with lower TCO compared with electron beam. Reducing downtime A key area for development in aseptic filling is in the reduction of downtime, much of which is related to cleaning and sterilisation operations with mandatory, weekly cleaning the norm for all process and filling equipment. By optimising sterilisation procedures, it is possible for both downtime and utilities to be reduced. Another factor urgently driving downtime reduction in food and beverage production is staff turnover, which bears heavily on safety and hygiene. It is essential for user interfaces to be as intuitive as possible, allowing problems to be resolved easily and limiting training needs. GEA’s aseptic blowing & filling system is now designed with software and HMI interfaces supporting TPM (total productive maintenance) methodology, providing enhanced alarms management systems and easily accessible information for problem solving and root cause identification. The search for plastics to be proud of The use, or perhaps misuse, of single-use plastic has received much publicity recently but, despite the headlines, PET bottles remain the most environmentally friendly and commercially practical way of retailing beverages. It is incumbent upon everyone in the supply chain to ensure that the environmental consequences of using plastic bottles are minimised. The battle is being fought on two fronts: recycling and biodegradability. Plastic has a major advantage in that, once collected, it can be recycled relatively easily into new bottles. Research continues to expand the amount of recycled materials in PET bottles with the ultimate aim being 100% of recovered material (rPET). Efforts are also being made to develop other materials such as biodegradable plastics that will create less of a long-term threat to the environment. Innovative materials such as polyethylenefuranoate (PEF), a plastic derived from organic material, can be used in a wide range of applications such as bottles for soft drinks. PEF’s barrier and thermal properties are superior to conventional PET, helping to provide a longer shelf life. It also offers higher mechanical strength, so less material is required. This could become the material of choice for beverage manufacturers. GEA is currently working to ensure that bottling machinery and processes are compatible with these new materials. Using data to drive process and cost efficiencies Digitisation, and the opportunities it provides for increased machine learning, is also important. GEA is part of a consortium that is researching machine learning on fillers and blowers, with the intention of increasing flexibility and efficiency in line with Industry 4.0 principles. Digitisation enables better control of the production line. It can provide accurate KPI information that can be accessed easily, on a laptop or phone. Data collected from the production line helps with troubleshooting and can provide valuable information to support preventative/predictive maintenance programs. “Digitisation also allows better communication to ERP systems and helps to make bottle or product changeover faster, reduce maintenance costs, monitor production, enable more efficient communication, and track products once they have left the factory,” said Barbara. Talk amongst yourselves: using AI to free up operators Machine learning will also have a major role to play in the future. “If we install sensors to check parameters that are important for a process, we can set up an algorithm to create a self-adjusting, self-tuning machine without any operator involvement.” Barbara explained that, if an operator needs to adjust a recipe, data could be automatically collected and the machine can learn to adjust the parameters itself. It should be possible in future to get machines in different factories talking to each other and learning from each other’s experiences. “This is the higher frontier of the digitisation project,” she said. “This is not easy, but it is our target.” Research & development GEA states to take an inclusive approach to developing new ideas. Not only does it work closely with third-party companies and universities to progress new innovations quickly and effectively, it also encourages its own members of staff to share their ideas in a constructive way. Every year, highly qualified staff members take part in a workshop to explore new ideas and make sure they were in line with customer requirements. GEA has recently received funding from the EU Horizon 2020 work program that promotes the development of a sustainable economy. Filling technology has developed rapidly throughout its history. Today the key focus is on flexibility, sustainability and digitisation, driven by customer needs and market demands. The pace of development is not slowing. It is, however, becoming more agile, more technology-oriented and more inclusive, with a spirit of cooperation between key players. www.gea.com Wet sterilisation by PAA: still the most effective method today","@ID":24}, "PETplanet Insider Vol. 21 No. 03/20 petpla.net 41 TRADE SHOW REVIEW base weight, all with the objective of using less material. Producers of larger solutions, sustainable plastic kegs in particular, are also focused on challenging their own preforms’ weight, balancing performance and weight throughout their innovation projects, while keeping safety at the forefront of their packaging design. They must do everything possible to reduce weight in other keg parts, also. Waste Waste is, clearly and of itself, wasteful. The trend that is high on the agenda and is growing in strength along the whole value chain, from producer to consumer, is the reduction of waste. Landfill or Sea Waste to landfill in the plastics packaging industry is increasingly unacceptable. Keykeg/Unikeg is fully focussed on abolishing it and is currently operating programmes to make sure waste to landfill is a thing of the past. Initiatives such as the Plastics Alliance, launched by the EU Commission, are creating a future plastics roadmap. Users should ask providers if they have signed the Plastics Alliance Declaration and, more importantly, are they actively participating in EU Commission-sponsored meetings to find long term solutions, embedded into the supply chain? Waste to sea is totally unacceptable and should be outlawed. Everyone involved, as producers and as consumers, must be pro-active. It is the responsibility of all of us to make sure we dispose of products in a responsible way; it’s not as if there is a shortage of responsible options. It is also important to hold global, national and local lawmakers to account. They have a duty to stimulate collection and proper recycling means by law making. Plastics should be recycled locally and the practice of effectively brushing the problem under the carpet by shipping end of use plastics out of sight to developing countries, which contribute to the ocean plastic problem, must be stopped. Waste to energy Incinerating plastic products to generate energy for heat, for example, are still very low down the sustainable pecking order. It may be the least sustainable option, but it is a first step on the solution ladder. Recycling Recycling keeps waste away from landfill and even waste to energy options. However, it is not acceptable to design a strategy where recycling of materials is seen as the highest sustainability goal. The aim “to leave the world a better place” must be for full circularity, to adhere to the “cradle to cradle” principle. PET BOTTLE RECYCLING LINE SUPER CLEAN PROCESS (SCP) Micro Denier Filament Grade www.bo-re-tech.com Modular Design for Flexible Layout Next Generation","@ID":43}, "BOTTLING / FILLING PETplanet Insider Vol. 21 No. 03/20 petpla.net 30 The first linear InnoPET BloFill ABF aseptic block from KHS Taking care of sensitive products The market for sensitive beverages is flourishing. Throughout the world manufacturers of dairy products have recognised the potential of wholesome beverages and expanded their product portfolio over the past few years. Most of the new products are filled into PET bottles. With the new linear InnoPET BloFill ABF aseptic block KHS reacts on the requirements of the dairy industry for flexible filling technology for sensitive products. FILLING Sensitive beverages are becoming increasingly popular all over the world. The demand for functional foods with less sugar in particular is growing. “Keeping to a healthy diet is playing a central role in the lives of more and more consumers,” explains Thomas Redeker, sales director for Dairy Europe at the KHS Group. “The demand for products that are sustainably packaged and attractively presented has also greatly increased in the last few years.” Dairy industry’s packaging of choice: PET containers PET bottles are the ideal vehicles for this new trend. An increasing number of makers of dairy products are thus relying on containers made of PET. “Not only producers but also consumers are convinced by their many different advantages,” says Redeker. In particular this includes the great capacity for individual design this type of container has. “PET bottles lend themselves to exclusive design. The cap and label can be perfectly tailored to the brand. This had a positive effect on the brand positioning at the point of sale,” Redeker states. The plastic containers score when it comes to their environmental balance as they are fully recyclable. PET bottles not only provide reliable product protection; they also have good pouring properties. KHS new linear InnoPET BloFill ABF aseptic block KHS recognised the potential of PET containers for aseptic filling 25 years ago. Its latest development is the linear InnoPET BloFill ABF aseptic block. This combines the rotary InnoPET Blomax Series V stretch blow moulder with the linear Innosept Asbofill ABF 712 aseptic filler. The block takes up less space than the individual machines; the air conveyor is also no longer required. This cuts down on energy consumption. Personnel costs are reduced as only one operator is needed in place of the former two. “By blocking the machinery and including a continuous clock module we also minimise the risk of soiling. This has a positive impact on hygiene and line availability,” smiles Redeker. Fast format changeovers within up to ten minutes help to boost system availability. They are performed under aseptic conditions, doing away with the need for any additional cleaning and sterilisation. The short change-over times let producers of sensitive beverages fill a large number of different stock-keeping units (SKUs). The linear aseptic block is designed to fill milk, mixed milk beverages, juice, smoothies and iced tea into PET bottles holding between 250ml and 2 l. The equipment outputs up to 12,000 1.0 liter bottles and a maximum of 15,000 0.5 liter bottles per hour. The modular design of the dry aseptic block allows the filler to expand at any time. Operators can retrofit their block with a chunk filler or additional filling and capping unit, for instance. “The modular design gives our customers greater flexibility. They don’t have to think about precisely which products they want to bottle when purchasing the block,” Redeker says. “KHS enables them to retrofit the required modules on site as soon as they expand their product portfolio.” This in turn permits beverage producers to react more flexibly to changing market demands. Integrating the stretch blow moulder With the integration of the stretch blow moulder the aseptic block gains a number of plus points. The heating system in the new Blomax generation consumes up to 40% less energy compared to most standard heating systems thanks to its optimised near infrared heating concept and new double gate technology. This is made possible by the near infrared heater centrally installed in the closed reflector tunnel. In the heater the preforms pass the centrally arranged heating units to both the left and right. The preforms are spaced just around 18mm apart instead of the previous approximately 37mm. The Dortmund systems supplier has been able to considerably reduce the number of heater boxes used. The air management system for heater box ventilation has also been optimised. “The fan can be set separately for the neck, reflector and lamps. This means that the machine only cools the areas which actually need cooling,” explains Redeker. InnoPET Blomax Series V: The heating system in the new Blomax generation consumes up to 40% less energy compared to most standard heating systems thanks to its optimised near infrared heating concept and new Double Gate technology.","@ID":32}, "45 PRODUCTS PETplanet Insider Vol. 21 No. 03/20 petpla.net PETproducts A PET bottle for craft beer “Beer … a high and mighty liquor,” said Gaius Julius Caesar, a famous beer lover. The drink’s origins go all the way back to ancient civilisations but the manufacturing process has evolved. Beer was first brewed only for family or neighbourhood consumption; commercialisation came later. Today’s packaging is the latest step in that evolution. Today, beer in a plastic bottle is common in some countries but novel in others. The fact that PET bottles quickly grow their market share shows that this type of packaging has several advantages. Do PET bottles “look right”? They can have glass-like appearance; they are transparent but also unbreakable. PET is resistant to damage and easy to transport. It is recyclable into other uses and has a much lower carbon footprint than glass, as PET Technologies’ joint project with Bierwelle Brewery demonstrates. Technology is what the two companies have in common: for brewing a malty beverage, on one side, and to blow-mould containers on the other. An elegant and resilient amber PET bottle is where two meet. PET Technologies developed the physical design; the decorative elements reflect Bierwelle’s corporate identity. The font used for the brand name confirms brand recognition. How is the bottle produced? Bierwelle’s craft brewery makes 31.4 g PET bottles on UPF-5 stretch blow moulding machines. Tests conducted at PET Technologies’ laboratory confirmed that the bottle can cope with 7-8bar internal pressure, without deformation. This is PET Technologies’ second project with Bierwelle. The first was an “authentic” container decorated with the views of the city of Chernihiv, the brewery’s birthplace. www.pet-eu.com Production monitoring with software solution Grafit 4.0 Digitisation, product tracking, iOT, artificial intelligence: in production, this involves using machine data to optimise and automate processes. The software solution Grafit 4.0 present the data of all connected machines in a clear, accessible form, and make it available to the operator for use and analysis. The data is displayed in real time, e.g. via the smartView app. It allows early detection, analysis and correction of errors. The central monitoring of the entire machine park offers a higher productivity, less production scrap and lower costs. The system is available for the complete Starlinger product range (machinery for the production of plastic fabric and for plastics recycling machinery). Machines of other manufacturers can be integrated as well by means of standardised interfaces. Grafit 4.0 possesses a clear data structure; in the future, it will be geared towards machine learning, which means that the system can be trained to detect errors at an early stage. The resulting predictive maintenance of the machines leads to higher machine uptime. The smartView app highlights a user-friendly interface, which includes the option to individually adjust the menu bar. Popular features are push notifications, the storage of recipes, the export of data into a computer program or ERP system as well as limiting the access to machinery with an RFID lock. Online tutorials are available for operator training. www.starlinger.com","@ID":47}, "PETpatents www.verpackungspatente.de PETplanet Insider Vol. 21 No. 03/20 petpla.net 48 Irregular preform Intern. Patent No. WO 2019 / 104394 A1 Applicant: Integrated Plastics PTY Ltd., Sydney (AU) Application date: 30.11.2018 The international application describes the structure, shaping and procedure for manufacturing a container from an irregular, asymmetrically shaped preform, e.g. because of an integrated handle. Bottle with indentation Intern. Patent No. WO 2019 / 110967 A1 Applicant: DEQ Ltd., Milton Keynes (GB) Application date: 3.12.2018 A bottle for a hot or cold drink is furnished with a specially shaped exterior into which a second container can be inserted and released. This can contain a snack or similar. Both can be held/carried easily in one hand – an additional bag is unnecessary. Plastic container Europ. Patent No. EP 3476756 A1 Applicant: Toyo Seikan Co. Ltd., Tokyo (JP) Application date: 27.6.2017 The procedure for manufacturing a thin-walled container for hot filling is shown. The interplay of temperature and pressure of the air blown in has been improved. Controlled collapsing Intern. Patent No. WO 2019 / 106347 A1 Applicant: Creanovate Ltd., Isleworth Middlesex (GB) Application date: 26.11.2018 The shoulder area of a PET bottle for soft drinks is designed in such a way that after product removal, the container can be compressed in a prescribed way to reduce its volume. Plastic bottle Intern. Patent No. WO 2019 / 106905 A1 Applicant: Yoshino Kogyosho Co. Ltd., Tokyo (JP) Application date: 5.9.2018 Multi-layer preform for manufacturing a plastic bottle with improved barrier properties for carbonated drinks. The collecting of carbonation between the layers is prevented. Plastic bottle Europ. Patent No. EP 3511257 A1 Applicant: Toyo Seikan Co. Ltd., Tokyo (JP) Application date: 15.8.2017 PET bottle with compensation areas that are arranged and dimensioned in such a way that the bottle always looks “round”.","@ID":50}, "36 TRADE SHOW REVIEW PETplanet Insider Vol. 21 No. 03/20 petpla.net Labelling trends and autosplicer There are several trends that the Italian shrink sleeve specialists Finpac identifies for the labelling market. “For PET bottles, there is a growing demand for perforated films - vertically and/or horizontally. Removing them makes it easier to recycle the bottles after they have been used,” reports Enrico Danovaro, Commercial Director Finpac. Paolo Gobrili, the company’s sales manager, is also seeing increased demand for reducing label thickness. Finpac has already completed a successful series of tests with label thicknesses of 20microns. At the Brau Beviale; Finpac featured their latest technological innovation with an autosplicer for sleeve reels. It consists of reel-holders with an automatic joining system for high-speed sleeving lines, up to 72,000 bph which can guarantee continuous production up to 40 minutes without any intervention by machine operators (based on a 500ml PET bottle configuration with a full body sleeve label having a cut length of 172mm fed by n. 2 autosplicers). The drawer reel holder combined with a jointing system between the different reels, – up to 4 reels of 1,000m – is specifically designed to guarantee flexibility, speed, reliability and high productivity combined with an intuitive and easy-to-use logic. The automatic splicer offers a system with four drawers for preparing the joint that allows the operator to work quickly and safely during the application phase of the adhesive. The prepared joint is automatically moved to the correct position eliminating any human error and eliminating the need for an operator on the line. Consisting of a sturdy, all-steel structure, and moveable drawers holding up to four reels which ensure a continuous label flow the system is stated to guarantee a simple, fast and safe preparation of the sleeve reels by the operator. Each of the reel-holding drawers is composed of a contrast roller, a support bar for preparing the joint and a reel locking bar that serves to keep the reels in position while the operator applies the adhesive without loss of line-speed. Once the adhesive has been placed, the operator needs only to confirm the preparation by pressing a button. The system automatically moves the prepared junction to the correct position thus eliminating any “human error”. The fixed joint position ensures accurate and effective control of the system and the moveable splicing heads are on board a motorised trolley where the two cutting blades are present, as well as the moveable contrast rollers and the buffer brakes. The carriage automatically aligns the relative jointing head at one of the preparation areas to then proceed to join the two ends of the coils. Once the cycle is activated, the simultaneous action produces an accurate join between the coils in a few seconds and the end result is a real overlap between the ends. www.finpac.it Mould technology for economical concepts in the field of blow moulding The independent mould maker Kiefer Werkzeugbau GmbH, based in Schwaigern, Germany, produces blow moulds for all common rotary blow moulding machines and for linear blow moulding machines. The company’ expertise includes Research and Development, innovative design in the field of light-weight & low-pressure base design, big-container design - up to 30 l, as well as for prototyping and test runs. At the trade show, Kiefer gave information about individual development of customised packaging, fast and flexible economic production of prototyping in 3-D-printing inhouse, as well as their anodised blow moulds range. The portfolio includes blow moulds for 100% recycled material. www.kiefer-mold.de F.l.t.r.: Paolo Gobrili, Sales Manager Finpac and Markus Seiler, Managing Director Aventa GmbH","@ID":46}, "TRADE SHOW REVIEW PETplanet Insider Vol. 21 No. 03/20 petpla.net 40 Pathfinding in plastics recycling and the circular economy: separating truth from hype Eliminating waste and building a circular economy by Annemieke Hartman, Global Commercial Director, OneCircle Brand owners’ packaging mix is changing, being made inevitable under pressure to act responsibly towards future generations, to inflict the lowest possible CO 2 footprint and eliminate the waste of raw materials, water and other resources. Keykeg/Unikeg has adopted a strategy of sustainable lightweight plastic kegs, rather than solutions such as steel kegs and bottles. Product design and supply chain advantages, along with a responsible approach to collection and circular use of materials, are building a platform for future sustainable kegs. ‘greenwashing’. Evidence-based knowledge must drive decision-making. Straightforward recycling has become a familiar aim over recent years. It is time to take the next step and drive business models towards fully circular lifecycle solutions. It sounds like a simple aim, but the detail reveals that the reality is rather more complicated. Reduce The most sustainable material is that which is not used in the first place! Providers of packaging solutions for Fast Moving Consumer Goods (FMCG) companies, are working on projects aimed at the reduction of weight. The small container environment has seen reduction of bottles’ neck height, reduced wall thickness and reduced Empty Keykegs crushed and ready for recycling and reuse As a provider of advanced packaging solutions in 10 l, 20 l and 30 l Keykeg and Unikeg formats, the company is continuously striving to develop solutions to reduce its environmental impact, with the objective of delivering a fully ‘closed loop’, circular solution in the near future. In this article, the company seeks to provide insight into the sustainable plastic keg market and suggest questions that users should ask of keg providers to ensure that the product’s offerings are truly sustainable options, to identify and highlight recycling opportunities and to be able to discern lip service and","@ID":42}, "BOTTLING / FILLING PETplanet Insider Vol. 21 No. 03/20 petpla.net 19 Major investment in SFL linear stretch blow moulder Oil bottle production in-house Willowton Group, a leading FMCG business and major African oilseed processor, has turned to Sipa to help it bring production of bottles for its edible oils in-house. Sipa has installed five new SFL linear stretch-blow moulding systems at Willowton’s plant in Pietermaritzburg, South Africa. FILLING “Willowton has been procuring bottles externally for some 20 years, but last year it took the decision to produce them itself, and it chose Sipa as its technology partner,” says Giovanni de Rosa, Sipa South Africa General Manager. Willowton has taken delivery of two SFL6/4 units, two SFL6/6’s, and one SFL6/8 EVO. They are now making bottles in various sizes, ranging from 375, 500, and 750 ml on the SFL 6/8 EVO, through 2 l on the SFL 6/6, to 4 and 5 l on the SFL 6/4. The outputs range from 4,400 bph on the SFL 6/4 up to 14,000 bph on the SFL 6/8 EVO. Ali Akbar Moosa, Chairman & Director at Willowton says: “The SFL is the right platform for us to meet the quick change-over requirements on our filling lines. The machines are all easy to run, and the costs of maintenance are low. They give us the flexibility to produce a wide range of containers in terms of size, complexity and shape.” This year, Willowton Group will celebrate its 50th anniversary. The family-owned business was founded in Pietermaritzburg by DH Moosa together with his brothers and sons in 1970. Since then, it has grown to become one of Africa’s leading edible oil processors, as well as one of the leading competitors in the South African FMCG market. The group operates across South Africa with manufacturing facilities not only in its home town of Willowton, Pietermaritzburg also in Johannesburg and Cape Town. It has manufacturing operations in Zambia and Zimbabwe as well, and has aspirations to further extend its reach to customers throughout Africa. Willowton’s product range stretches beyond edible oils, into margarines and spreads, beauty, toilet and laundry soaps, candles, baking and industrial fats, as well as maize meal, rice, and sugar. It has its own distribution company, Willowton Logistics. Key to the group’s success are the sound foundations of service excellence, continued investment in technology and human resources and the hands-on involvement of the directors in the day-to-day running of the business. Willowton puts a very strong emphasis on safety and hygiene. The oil and margarine manufacturing facility in Pietermaritzburg operates the Hazard Analysis and Critical Control Point (HACCP) Food Safety Management System, an internationally accepted food quality and safety management system that ensures that products are hygienic and safe for public consumption; it has attained British Retail Consortium (BRC) accreditation, which is essential for securing contracts with companies supplying food products to major UK supermarkets such as Marks & Spencer, Tesco and Sainsbury’s. www.sipasolutions.com The newly installed Sipa SFL lines at the Willowton plant in Pietermaritzburg, South Africa. 5 l PET oil bottle produced on SFL 6/4 and 2 l on SFL 6/6 Sipa equipment.","@ID":21}, "BOTTLING / FILLING PETplanet Insider Vol. 21 No. 03/20 petpla.net 33 TES STM Group’s Blueline machinery range From stretch blow moulding to hot filling TES STM’s Blueline range of PET preform to bottle linear stretch blow moulding machines includes machines with capacities of 3,000-18,000 bph, depending on the number of cavities. Output is up to 2,250 500ml bottles/hour/cavity. The machines can be equipped to produce oval PET bottles, using a preferential heating solution that allows optimisation of wall thickness; there are also options geared to production of very low volume (e.g., 10ml) bottles, and bottles that can be hot-filled. Blueline series machines are fully electric: all major movements are carried out by electric drives, most of which are servomotors. The control systems enable operators to conduct full, online diagnostics. Energy-efficient heating ovens are equipped with specially-designed ceramic panels that reflect infrared radiation and help to reduce consumption of electricity needed during preform heating, to less than two Watt-hours per 500ml bottle. Blueline HF series machines, which are designed to manufacture Hot Fill (HF) bottles, are equipped with four, six or eight cavities and have output capacity of up to 12,000 bph, depending on preform weight, material and filing temperature. The HF production process is based on the application of a hot blow mould, which allows a higher degree of crystallisation and, consequently, have increased thermal resistance. After the blow moulding process, the bottle is cooled down by compressed air, delivered through holes located in the stretch rods. After leaving the blowing mould, bottles are further air-cooled, in order to stabilise contraction. The machines’ electric heaters are located in the blowing block and in the bottom part of the moulds, which are equipped with sensors that constantly monitor temperatures and thus provide full control over the process. These features help to ensure consistent high quality and dimensional repeatability of bottle production. Preform necks are protected against deformation by water cooling. The blowing moulds are water-cooled at the point of contact between the neck and mould. The cooled part of the blow mould is isolated from the heated part in order to minimise loss of energy. Reducing production costs The Blueline series stretch blow moulding machines incorporate a number of features aimed at reducing production costs, including a system that recovers compressed air from the blowing process, in two ways. The first diverts a part of compressed air from the blowing process to the stretch blow moulding machine control system. This means there is no need for a separate supply of compressed air for the pneumatic control system. A second solution allows recovery of compressed air used in the blowing process, in order to supply other devices down the line, such as the filling machine, labeller, etc. The company says that this solution is currently unique to Blueline blow moulding machines. These two features help to reduce compressed air consumption by as much as 50%. TES STM has patented a method of using hot air from the heating ovens to pre-heat preforms. The heating oven, which is equipped with NIR lamps, is cooled with air drawn from outside the machine, which is circulated by a fan. The air that has been heated during the cooling process is then circulated to provide initial heating of preforms. This solution helps to reduce electricity consumption for preform heating by 4-5%, depending on weight and shape. The Multiflex option, available on the HF series, is designed to speed up changeovers. Retooling for production of bottles with different preform necks is cut to around 30 minutes, which means that bottles with various threads can be made on the same blow moulding machine. Blueline series stretch blow moulding machines are designed as a solution for small and medium producers. www.tes.com.pl The machines’ electric heaters are located in the blowing block and in the bottom part of the moulds. FILLING Stretch blow moulding machine from the Blueline series of TES STM","@ID":35}, "PREFORM PRODUCTION PETplanet Insider Vol. 21 No. 03/20 petpla.net 15 Preforms for regional brands by Michael Maruschke When software engineer Nishit Singhal was looking for a new business challenge, about ten years ago, he considered various different options, from services for telecommunication to industrial production. He saw big potential in the growing PET bottle business and decided to start preform production himself. From a humble start in the suburbs of Delhi with a second hand Krauss Maffei in 2010, Frystal Pet Pvt. Ltd. grew steadily and soon faced a lack of space and capacity. Two years later the company moved the manufacturing unit to Neemrana, in Rajasthan, which is still close to Delhi but offers cheaper land and also government subsidies. It continued to grow and installed two more ASB machines to cope. May 2019, We met: Mr Nishit Singhal, Director (photo) Mr Mayur Singhal, Director When we visited, we were advised that Frystal now has 60 permanent employees. A total of seven injection moulding machines (four ASB and two Demag units, with 24 cavities each, and a 72 cavity Husky HyPET 4.0) were in operation. Total processing capacity is now 7500 tons per year. Preforms for Bisleri, Jayanti and Patanjali drinks Frystal supplies preforms ranging from 160ml to 2 l for CSD, RTD, juices and water, to regional brands and corporate customers across India. Customers include corporate players like Bisleri, a leader in the water segment, Jayanti, a leader in Jaljeera flavoured CSD ethnic drink, and Patanjali for water. Frystal also export preforms to many African countries. There is a seasonal peak for CSD and water in North India from mid Feb to June. Frystal is a market leader in PET preform manufacturing in Northern India and has an innovative reputation; it introduced a 250ml preform for CSD with PCO1881 neck, weighing Tour Sponsors: only 12.6 g; previously, the standard was 13.5 g. Its focus remains on beverages; a market in which it sees further growth potential. CSD and Water show have enjoyed doubledigit growth per year, according to Nishit Singhal. Frystal may consider the production and supply of preforms for edible oil and other products in the future. It does not produce caps because the market currently has sufficient capacity for closure systems. The PET raw material situation Frystal’s PET material is supplied totally by Reliance. Asked for the reasons behind the recently introduced “flat rate” tariff, Nishit Singhal believes that this is an effort to curb imports from China and also to lower the entry level/price for manufacturers who want to switch from other materials to PET. www.frystalpet.com Manage quality issues in the blowmolder—contact us to learn how. AGR INTL . COM / / +1.724.482.2163 // [email protected] DEFECT DETECTION WHERE IT IS NEEDED Preform + Sidewall + Seal Surface + Base","@ID":17}, "BOTTLING / FILLING PETplanet Insider Vol. 21 No. 03/20 petpla.net 32 Towards multi-packaging The new Sacmi monobloc unit EquaFill ECF multi-packaging can handle several commercially available packaging types (glass, cans, PET) in parallel, with real-time size changeovers. FILLING EquaFill ECF multi-packaging is a Sacmi solution that aims to meet bottlers’ flexibility requirements from a multi-material perspective, allow frequent size changeovers and maximise filling process efficiency. Designed to fill bottles and containers (in glass, PET or aluminium), cans - all on a single platform - this Sacmideveloped solution is for all those sectors (craft beer, fruit juices and CSDs) where product uniqueness benefits from manufacturing management that’s completely free from restrictions posed by the material or the container format. Various configurations and output rates are possible. Sacmi EquaFill can handle up to 36,000 containers per hour. Process hygiene and user-friendliness are seamlessly combined with the solution’s key feature, that is, the fact that it permits multi-packaging filling via quick and easy format changeovers. With this solution Sacmi intends to take the industry forward, away from traditional dedicated production lines (glass, cans, PET) towards true multiline configurations. Initial market feedback has shown that Sacmi can, with such set-ups, increase average process efficiency, with a parallel, similarly sized reduction in fixed costs (CAPEX). Other advantages include - especially as regards revamping of existing facilities - a considerable reduction in the plant footprint, Sacmi said. In addition to net savings in terms of process-related space and costs, the Sacmi monobloc yields dividends in terms of synergy and efficiency as it’s possible to avoid - thanks to the single platform - the duplication of shared parts such as pressurised piping, palletisers and rinsers, etc. The outcome: a solution that matches the steady trend towards smaller production lots and caters to the need to get products on shelves in different sizes and materials to intercept every nuance of market demand while optimising the fixed costs of the entire process. www.sacmi.it +44 (0) 1254 584210 [email protected] petmachinery.com Active for over 25 years, our global network and specialist knowledge makes us the go-to company for the sale or purchase of a PET machine. Commercially savvy, we work closely with our customers and our global network, to make sure everyone gets the best deal. Providing comprehensive advice throughout your sale or purchase; we can arrange dismantling, loading, packing, shipping, specialist insurance and commissioning. If you have amachine to sell or you’re looking to purchase, please get in touch. THE INDUSTRY EXPERTS","@ID":34}]}}
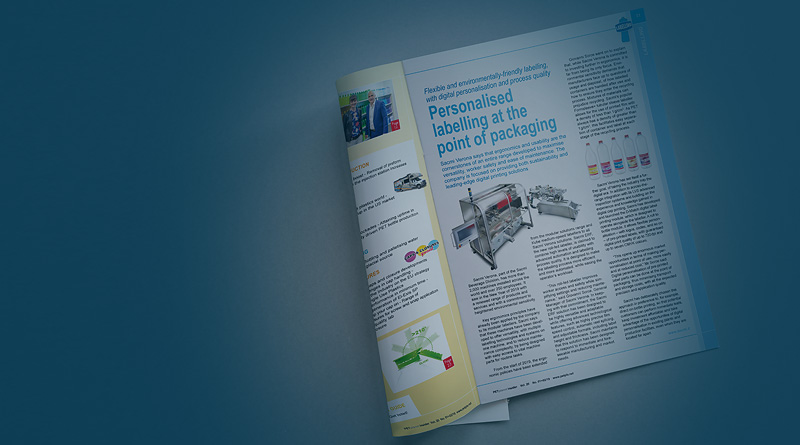