{"pages":{"page":[{"@ID":15, "MATERIALS / RECYCLING PETplanet Insider Vol. 24 No. 07+08/23 www.petpla.net 13"},{"@ID":30, "MARKET SURVEY 28 PETplanet Insider Vol. 24 No. 07+08/23 www.petpla.net 07+08/2023 MARKETsurvey Company name AF Compressors, Ateliers François S.A. Siad Macchine Impianti ABC Compressors Kaeser Postal address Telephone number Web site address Contact name Function Direct telephone number E-Mail Ateliers François, Rue Côte d'Or 274, Liège B-4000, Belgium +32 4 229 70 10 www.afcompressors.com Mr Pascal Heyden Marketing Manager + 352 26 95 66 28 sales@afcompressors.com Via Canovine, 2/4 24126 Bergamo, Italy +39 035 327611 www.siadmi.com Mr Giovanni Brignoli Compr. Div. Food & Beverage Product Leader +39 035 327609 giovanni_brignoli@siad.eu Azitaingo Industrialdea, 6, 20600 Eibar, Gipuzkoa, Spain +34 943 820 400 www.abc-compressors.com Mr Gonzalo Gabarain Global Sales & Marketing Director +34 647 413 760 ggabarain@abc-compressors.com Carl-Kaeser-Str. 26, 96450 Coburg, Germany +49 9561 640-0 www.kaeser.com Mr Henry Beyer Product Manager +49 9561 640-5017 henry.beyer@kaeser.de 1. Machine designation / model number CE & L (high pressure) OPC (low pressure) BS Line Vito Next Horizon Synchro | Horizon Synchro LP | X-PET Sigma PETAir 2. Number of models in range 30 (high pressure), 22 (low pressure) 19 models 32 30+ models 25 3. Output in m³/hour 150 - 3,300 m³/h (high pressure); 432 - 3,480 m³/h (low pressure) 1,000–6,000 100-6,000 200-6,600 336-2,772 4. Compressor type High pressure blowing air (up to 40 bar) Oil-free reciprocating piston compressor \"all-in-one\" skid Low pressure air 7-10 bar Low pressure screw Low pressure oil-free piston compressor Screw type High pressure blowing air (up to 40 bar) 20-40 bar High pressure piston (booster) Piston High pressure oil-free piston compressor (atmospheric up to 40 bar) Piston type Integrated system All in one system, high & low pressure simultaneously Atmospheric compressor including VSD with largest regulation range from 18% to 100% of the capacity 5. Lubricated or oil-free Oil-free 100% Oil-free compressor Class 0 Low pressure compressor Oil-free 6-15 bar Oil-free 100% Oil-free compressor Class 0 Lubricated Booster compressor Oil-free 0-40 bar Oil-free Not needed, it's atmospheric HP compressor Lubricated Integrated system Yes Yes Atmospheric 100% oil-free compressor class 0 6. Machine layout L shape V V and H (horizontal) Horizontal opposed cylinders, forces balanced and virtually no vibrations V (2 cylinder), W (3 cylinder) 7. Number of compressor stages 3 stages, 3 cylinders for HP, 2 stages, 2 cylinders for LP 2 screw + 2 booster= 4 total 3 2 for LP and 3-4 for HP 1+1 8. Are special foundations required ? No No No No, virtually no vibrations No 9. Cooling system Evaporative or radiator system Water Water Water cooled (Closed cooling tower or aerocooler) Air (water option) 10. Belt or direct drive V-belt transmission Belt drive Direct Drive Low pressure compressor V-belt transmission Direct drive Direct Drive Direct Booster compressor 0-40 bar, V-belt transmission Belt drive Not needed, atmoshperic HP direct drive Belt Integrated system Direct Drive"},{"@ID":32, "TRADE SHOW REVIEW PETplanet Insider Vol. 24 No. 07+08/23 www.petpla.net 30 PERMANENT MAGNE T MOTOR SYNCHRONOUS DIRECT COUPLED MOTOR 0 transmissions losses and best IE5 efficiency. VAR I ABL E SPEED DR I VE REL IABI L I TY The first compressor that eliminates idling times with the largest regulation range in the market. Lifetime mechanical warranty.* *ask your ABC Compressors contact fot futher details. IE5 magnetic motor with the best efficiency in the market. T.: +34 943 820 400 M.: +34 673 056 281 abc@abc-compressors.com www.abc-compressors.com PRESSURE PRESSURE HIGH LOW THE FIRST SYNCHRONOUS COMPRESSOR OIL-FREE AIR"},{"@ID":27, "BOTTLE MAKING 25 PETplanet Insider Vol. 24 No. 07+08/23 www.petpla.net Launching a one-stop shop to seamlessly switch to recycled PET The RePETable offer Sidel‘s ‘RePETable offer’ portfolio of services is designed to help the packaging industry make an efficient transition to rPET bottle production while offering support to improve the circularity of primary packaging. Sidel aims to facilitate a smooth and efficient market switch to recycled PET by establishing a ‘no fear’ one-stop shop for rPET - the RePETable offer. These service solutions are intended to enable customers to adopt up to 100% rPET without impacting bottle production. Sidel also offers support to the industry to develop innovative and more sustainable primary packaging materials that are designed for recycling. The offer consists of a range of services designed to extend virgin PET benefits to rPET and achieve consistent production performance and bottle quality. Sidel packaging experts are continuing to develop advanced knowledge about recycled PET resin and solutions for efficient bottle production by leveraging its unique small-scale recycling pilot line in France. The offer has been designed for customers to pick and choose services that best suit their specific needs. Sidel’s RePETable offer is additional to its packaging optimisation services for lighter bottle weight, helping customers make a cost-efficient transition to recycled PET. Consistent production performance and bottle quality With more than 40 years of blowing and PET packaging expertise, Sidel says it has developed a deep understanding of recycled PET resin characteristics, its variability and its impact on bottle production. “To reach the same level of performance as virgin PET, rPET bottle production process needs to be adapted to suit the resin used,” says Jérôme Neveu, Packaging & Moulds Product Manager at Sidel. “Therefore, our RePETable offer is made of solutions to address the challenges associated with rPET bottle production securing bottle mechanical resistance with optimum material stretchability and bottle shaping.” Sidel offers rPET-ready features with packaging services and mould solutions, equipment upgrades and process support which achieve consistent, high production performance and bottle quality, even with up to 100% rPET. The blowing process is optimised to manage challenges associated with rPET grades and outof-spec rPET is identified and rejected before processing. Primary packaging designed for recycling Sidel’s investment in its smallscale recycling pilot line is supporting primary packaging suppliers in innovating with new materials for closure, sleeve, glue, label, additives, colouring and any other primary packaging material. The services delivered through this pilot line ensure primary packaging recycling process efficiency, resin quality, and rPET bottle performance. Sidel is using this line to recreate every step of the recycling process from washing, drying and pellet extrusion to crystallisation and Solid State Polymerisation, including dedicated process and laboratory controls at every step. Sidel packaging and equipment experts study all aspects of the process from post-consumer PET bales to flakes, including pellets ready to be injected into preform up to rPET bottle blow moulding and industrialisation. A cost-efficient transition to rPET As the demand for rPET continues to rise, driven by regulations across the world and brands’ commitment to packaging circularity, the cost of rPET is fluctuating and remaining higher than that of virgin PET. Sidel’s packaging optimisation services for bottle weight reduction help to offset rPET resin costs and achieve savings with a quick payback. www.sidel.com"},{"@ID":46, "PETplanet Insider Vol. 24 No. 07+08/23 www.petpla.net 44 PETbottles Home + Personal Care Micellar water from Alverde Under its own brand Alverde, dm has launched a 2-phase micellar water with organic aloe vera and organic cucumber. The product, which is suitable for all skin types and also removes waterproof make-up, is filled in a transparent bottle made of 100% recycled material. A screw-on disc-top cap allows the product to be applied to a cotton pad - after shaking well before use - and then applied. A surrounding self-adhesive label explains the product and application and allows a view of the two phases. www.dm.de Shampoo with activated charcoal Garnier has expanded its “True Treasures” range to include a shampoo variant with attractive activated charcoal and black cumin oil. The product stands out on the shelf because the bottle appears black. Only on closer inspection does i t become apparent that the bottle is only slightly coloured, the visible black being the product i tsel f. The 100% recycled bottle con t a i ns 300 ml o f t he balancing shampoo that instantly removes residue and moisturises for 72 hours. A gold-coloured hinged lid with a dosage opening and two labels complete the eye-catching packaging. www.garnier.de Flashy colour for Duschdas For its 50th anniversary, Unilever gave the Duschdas brand a product and packaging makeover. The products are free of microplastics and 99% biodegradable. New fragrances or fragrance combinations were also created, such as watermelon, acai berry, lavender tonka or, as in the picture, lime mint. The headstand bottles made of 100% rPET contain 225 or 450ml and are easy to refill via refill bags. The almost transparent hinged lid with silicone valve allows for easy and measured dispensing of the shower gel. www.duschdas.de Mouthwash without alcohol and dye Johnson & Johnson sells a mild-tasting mouthwash in Germany under the brand name “Listerine” that contains no alcohol and no dye. The product with the suffix Naturals contains 96% ingredients of natural origin that are biodegradable. The bottle, made of 50% recycled material, is 100% recyclable and decorated with several self-adhesive labels. The childproof screw cap, which serves as a dosing cup, is secured with a shrink sleeve before the first withdrawal. www.listerine.de"},{"@ID":17, "LABELLING PETplanet Insider Vol. 24 No. 07+08/23 www.petpla.net 15"},{"@ID":49, "PATENTS www.verpackungspatente.de PETplanet Insider Vol. 24 No. 07+08/23 www.petpla.net 47 Bottle with handle Intern. Patent No. WO 2022 / 183756 A1 Applicant: Guangzhou Tech-Long Packaging Machinery Co. Ltd., Guangdong (CN) Application date: 19.4.2021 Plastic bottle with a handle with one end attached to the bottle neck and the other “free” rather than fixed. This should improve handling. Bottle with reinforcements Intern. Patent No. WO 2022 / 182833 A1 Applicant: Coca-Cola Comp., Atlanta (US) Application date: 24.2.2022 Plastic bottle with a variety of wave-shaped reinforcement ridges. Despite these ridges that are sometimes under the label area, the feel and visual appearance of the bottle are retained. Plastic bottle Intern. Patent No. WO 2022 / 209488 A1 Applicant: Suntory Holdings Ltd., Osaka (JP) Application date: 25.2.2022 A lightweight, thin-walled plastic bottle has variously shaped and placed creases that give the bottle improved resistance to distortion. Bottle with cap Intern. Patent No. WO 2021 / 118767 A1 Applicant: Niagara Bottling LLC., Diamond Bar (US) Application date: 17.11.2020 Describes a preform, a bottle made from it and a cap that remains attached to the bottle by a guarantee band. Plastic bottle European Patent No. EP 4095052 A1 Applicant: Sidel Participations, Octeville-Sur-Mer (FR) Application date: 14.1.2019 A patent application has been made for the design of a plastic bottle with an appropriately shaped bottom. Preform Publication No. DE 102021114558 A1 Applicant: KHS GmbH, Dortmund (DE) Application date: 7.6.2021 An optimised preform for the production of a container that has been reduced in weight without any significant reduction in rigidity. PETpatents"},{"@ID":6, "PETcontents 4 PETplanet Insider Vol. 24 No. 07+08/23 www.petpla.net 07+08/2023 Page 42 MATERIALS / RECYCLING 10 From wood and paper to PET - Glycol production from renewable raw materials LABELLING 14 PET bottles say goodbye to labels - Sipa and Água Monchique flip the skript 16 Breaking barriers in PET recycling - Discussing the increase in recoverability by using magnetic coatings on shrink sleeves 18 Advances in adhesive technology - Enabling PET bottles to achieve circularity 20 High speed labelling goes green - Latest generation of Opera and Kube labellers 22 Inspection system for all types of labels BOTTLE MAKING 25 The RePETable offer - Launching a one-step shop to seamlessly switch to recycled PET MAINTENANCE 26 Industry 4.0 meets PET facility equipment cleaning MARKET SURVEY 28 Suppliers of compressors TRADE SHOW REVIEW 31 Erema 40th birthday - Erema invites customers to discovery day and opens new R&D centre 32 rPET: made in West Africa and distributed from Dubai, UAE 33 Laboratory inspection & analysis - For all kinds of plastics, especially for rPET 34 Inline viscosity management - PET and polyolefin recycling 35 Plastic packaging solutions and recycling services - Interview with Dr Karl Hagspiel, Senior Circular Economy Expert at Alpla 38 Adhesive enables PET/PE component separation - Re-usage of PET/PE monomaterials from multi-layer packaging 39 Interpack 2023 review, part 2 42 Monomer purification with melt crystallisation in PET recycling 43 High-speed all-in-one solution for medium-sized bottlers BUYER’S GUIDE 48 Get listed! INSIDE TRACK 3 Editorial 4 Contents 6 News 43 Product 44 PET bottles for home + personal care 46 PET bottles for beverage + liquid food 47 Patents 54 Outer Planet LABELLING Page 16 Page 35"},{"@ID":50, "LABELLING PETplanet Insider Vol. 24 No. 07+08/23 www.petpla.net 24 LABELLING 1ST .& \"\" can inspect for short shots as well as blow byes. This ensures not only the quality of the decoration itself, but also of the decorated object. And the system also addresses the peculiarities of the IML process during daily handling. “We are aware that rapid product changes are the daily routine, especially in productions using IML labels. That’s why we equipped our IMLWatcher with a quick reference mode,” Janina Orlowski tells. This functionality helps the operator to create a new, ready-to-use reference within seconds and fully automatically. The subsequent reference evaluation also helps to find out the effects of an adjusted reference compared to the previous one. This ensures that only perfect references are activated. In addition to the already established solutions in the household chemicals and food industries, new industries are also increasingly experimenting with how they can incorporate IML decorations for their purposes. In this regard, Intravis recently announced with several partners that a new solution for IML-decorated medical products will be presented at this year’s Fakuma trade show. Sleeve labels with special requirements Compared to the other types of labels, sleeves pose special challenges for the vision systems currently available on the market. For this reason, Intravis decided to develop a system specifically designed for sleeved products, the SleeveWatcher. Undoubtedly, a major challenge is the glossy surface of sleeves. Compared to pressure-sensitive or in-mould labels, sleeve labels often lead to high reflections if illuminated incorrectly. These reflections, in turn, can result in the ejection of faultless products that actually meet all quality requirements. Intravis meets this challenge with a lighting technology. It illuminates the entire inspection area and, consequently, produces a very homogeneous light. This significantly minimises the risk of reflections but still detects typical defects like folds and holes. Another challenge presents the huge number of possibilities that can arise with sleeved objects. A large selection of object shapes with diverse combinations of colours, patterns and transparent label parts provides a particularly high degree of variation for sleeve labels. These elements, which make the sleeved product attractive to the end consumer, are often highly challenging for vision inspection. Due to the specially arranged hardware as well as a completely new developed inspection module for the IntraVision software, the SleeveWatcher is optimally adjusted to the challenging characteristics of sleeve labels. Thus, the system enables a comprehensive 360° inspection of the entire label. Once the SleeveWatcher is installed, it inspects 100% of the product flow at a speed of up to 15 parts per second. Thus, the system can easily keep up with even the fastest sleeve labelling machines, says Intravis. Its six side cameras inspect sleeves for common label inspection criteria such as presence, identity as well as horizontal and vertical offset. In addition, the system inspects for sleeve-specific defects such as smiling and frowning effects, folds, distortions, and holes. On request, code reading is also possible – with the same code range as known from the LabelWatcher. www.intravis.com About Intravis Intravis GmbH is well kown for vision inspection systems for quality testing in the plastics packaging industry. With its headquarters and production facility in Aachen, Germany, the ownermanaged company has more than 30 years of experience in quality inspection, with more than 200 employees. Intravis has subsidiaries, sales and service offices all over the world."},{"@ID":22, "LABELLING PETplanet Insider Vol. 24 No. 07+08/23 www.petpla.net 20 Latest generation of Opera and Kube labellers High-speed labelling goes green Sacmi Beverage says that the large, world-spanning industry is also multi-faceted and demands solutions that can be optimised for both high volumes and medium output rates, on which format changeover speed/adaptability are essential. LABELLING Sacmi Beverage has sold over 2,500 labelling machines worldwide, including both stand-alone systems and equipment integrated with complete stretch-blowing and filling lines. It recently presented the latest versions of its established Opera and Kube labelling machines that, the company says, provide comprehensive solutions that combine high productivity and versatility on various labelling technologies and systems. Sacmi’s Flexi Opera labeller range is designed for a full range of container types, including cylindrical or shaped, in glass, plastic or metal. The company says that it offers a combination of versatility and very high output rates. The Opera range has been available for many years, during which time it has been upgraded and evolved. Its multi-material approach is integrated with the ability to use different labelling systems, including the application of pre-cut, wraparound or self-adhesive labels, on a single platform. Manufacturers can also apply one or more labels on the same container using the same technology or a combination of different technologies, such as cold glue, roll-fed, adhesive, or hot melt. Flexi Opera is available in a range of configurations and can be installed on existing lines. The machine is designed within optimised overall dimensions and has extensive scope for customisation to customers’ particular requirements. Sacmi says that its Kube range takes a significant step upwards in a single machine’s ability to handle diversified product mixes and frequent changeovers, with all format changeover tasks able to be managed directly via the operator interface. Users can save various recipes and recall them as necessary, which means they can maintain efficiency in sectors like wine, beer and spirits, where format changeovers are standard, using multiple labelling technologies and systems. Kube offers a plug/play approach. Its modular framework allows manufacturers add a wide range of options, such as cold glue, hot melt, self-adhesive. The machine incorporates an automatic bottle positioning system and is available with Sacmi’s proprietary LVS labelling vision system, to deliver comprehensive process quality control. Sacmi labellers are also designed to incorporate new labelling systems and materials that aid the creation of a returnable PET supply chain. Sacmi Beverage has already developed and installed many exclusive solutions, across the world. These include, in partnership with key raw material producers, development and supply of new washable glues, alongside new systems that apply labels with fewer glue spots, making it easier to recycle PET containers for food use. Glue can be applied exclusively on the overlap area of the two flaps in the case of wrap-around labels. During recycling, these are separated by a Sacmi-supplied cutting tool. Sacmi says that the latest versions of its solutions aim to accompany customers through the green transition: helping them face regulatory changes being enacted across the world and ensuring they can respond to consumer demand for innovative, sustainable packaging. www.sacmi.com Flexi Kube labeller The Flexi Opera labeller is designed for a wide range of container types."},{"@ID":39, "TRADE SHOW REVIEW PETplanet Insider Vol. 24 No. 07+08/23 www.petpla.net 37 improvements will also solve the problem of too short turnaround time at professional composting facilities. Bio-based polymers do not have to be biodegradable, as they can be so-called drop-in chemicals (e.g. HDPE from sugar cane waste; it is absolutely identical to HDPE from fossil sources and not biodegradable). This development will continue and provide us with new biodegradable and bio-based materials, I am pretty sure. And our involvement in this area will also give us the opportunity to be a pioneer here. Currently, these products play a minor role in the early stages of production and use PETplanet: One last question for the recycling expert: recycling machine manufacturers do not see mechanical PET and / or plastic recycling at the end of its development. Improvements are still possible. So-called chemical recycling for plastics is also developing and should be complementary to other forms of recycling. There are some projects being carried out on this. A wealth of different studies are being conducted. However, it is clear that this costly process needs investment - but the problem also seems to be the security of investment: the research on these processes is mainly carried out with material streams like polyolefin that have already been well prepared and sorted. This means that investments are made on the basis of this material, including PET. How do you assess the situation and is Alpla interested in this type of recycling? Hagspiel: This question is probably beyond the scope of this interview to answer. Yes, there is progress in recycling polymers, but not only in chemical recycling. Mechanical recycling is also opening up new applications and reaching new levels of quality. But to come back to your question about chemical recycling and investments: in chemical recycling, we have to distinguish between the technologies for polyolefins, mainly pyrolysis, and the technologies for polyesters like PET, namely methanolysis, glycolysis and hydrolysis. These are completely different technologies with very precisely defined input parameters. Today, most major oil companies and polymer producers are focused on pyrolysis. As you mentioned, investments for such plants are in the range of 600 to 900 million euros or even more and have capacities of 100,000 t/a and more. In order to get the green light from the board members for such an enormous investment, the legal/political environment must be clear and favourable, as well as the market and the input stream must be clear and safe. At Alpla, we focus on increasing our mechanical recycling capacity as we are convinced that this is the environmentally friendly way to keep the material in the cycle. At the same time, however, we are keeping a very close eye on the market for the latest developments in chemical recycling in order to ensure, or at least strive for, a parallel existence with equal rights. Chemical recycling should be a complementary and necessary recycling technology, but it should not interfere with the input stream that is suitable for mechanical recycling. PETplanet: Thank you so much Dr Hagspiel for your time and the willingness to share your knowledge with us! www.alpla.com ® Accurate. Fast. Intuitive. Simplified dimensional and thickness measurement of plastic containers and preforms featuring AutoJob®— automated attribute recognition and job setup in seconds. Visit us on social www.agrintl.com +1.724.482.2163"},{"@ID":5, "imprint EDITORIAL PUBLISHER Alexander Büchler, Managing Director HEAD OFFICE heidelberg business media GmbH Hubweg 15 74939 Zuzenhausen, Germany phone: +49 6221-65108-0 fax: +49 6221-65108-28 info@petpla.net EDITORIAL Kay Barton Heike Fischer Gabriele Kosmehl Michael Maruschke Ruari McCallion Anthony Withers WikiPETia. info petplanet@petpla.net MEDIA CONSULTANTS Martina Hirschmann hirschmann@petpla.net Johann Lange-Brock lange-brock@petpla.net phone: +49 6221-65108-0 fax: +49 6221-65108-28 LAYOUT AND PREPRESS EXPRIM Werbeagentur | exprim.de Matthias Gaumann READER SERVICES reader@petpla.net PRINT Chroma Druck Eine Unternehmung der Limberg-Druck GmbH Danziger Platz 6 67059 Ludwigshafen, Germany WWW www.hbmedia.net | www.petpla.net PETplanet Insider ISSN 1438-9459 is published 10 times a year. This publication is sent to qualified subscribers (1-year subscription 149 EUR, 2-year subscription 289 EUR, Young professionals’ subscription 99 EUR. Magazines will be dispatched to you by airmail). Not to be reproduced in any form without permission from the publisher. Note: The fact that product names may not be identified as trademarks is not an indication that such names are not registered trademarks. 3 PETplanet Insider Vol. 24 No. 07+08/23 www.petpla.net Dear readers sweltering in the summer heat, Here I am, sitting in front of my computer penning this editorial and the mercury is almost hitting 40 °C. Who wants to sit next to an unhealthy air conditioner? But there are other ways of keeping cool indoors. Some have suggested placing a freezing PET bottle filled with water on the refrigerator. Naturally this piqued my interest. Could this be the answer – one bottle for one room? Let us look at the problem theoretically. I will spare you a lecture on thermodynamics but it is well known that 1m3 of air releases 1.2 kj (kilojoules) to cool by 1 kelvin, provided, of course, that pressure remains constant. On the other hand, 1 litre of ice requires 40 kj to go from -20° to 0°. In addition, the melting energy during the transition phase from solid to liquid is 334 kj. So, in a room of 60m3 (2.5m x 4m x 6m) we could, with a bottle of water on the fridge, reduce the air temperature by five kelvins. This should make us sit up and take notice – in theory at any rate. In practice, however, the reduction in temperature does not occur straight away but is a longer process during which cool air is transferred to walls and furnishings and its cooling effect is therefore dissipated. So, apart from a nice pool of water condensation under the bottle, nothing happens. However, as a brewer (regular readers will be well aware of my beer activities), I put the beer in PET water bottles in the freezer. Water in beer freezes at 0 °C, and alcohol at -100 °C. In the evening, I take out the freezing PET bottle, open it and turn it upside down. Only the alcohol comes out, carrying with it a concentrated taste of beer. The ice stays in the bottle. And now I have a room cooler that doesn’t work but a delicious Eisbock in my hand. I’ll give you two guesses as to which one I prefer! Cheers. Yours Alexander Büchler"},{"@ID":14, "MATERIALS / RECYCLING PETplanet Insider Vol. 24 No. 07+08/23 www.petpla.net 12 220,000 t bio-MEG and lignin-based renewable functional fillers to be produced here from the end of 2023 carbon contained in the wood and thus also make a greater contribution to mitigating climate change. Dr Duetsch continued, “We need to reduce the amount of wood used for energy generation and increase its material use to promote a circular economy and work towards eliminating the need for new fossil raw materials. Compared to the fossil MEG market, which amounts to 33Mt/a, our volumes are certainly micro-quantities, but it is a sensible step nonetheless as it clearly shows the way towards a renewable carbonbased chemistry and can enable further investments in renewable chemicals and recycling facilities. These are critically needed as almost all the carbon used in the chemical system today comes from fossil feedstocks. In general, however, we see a multitude of opportunities for bio-MEG - and PET is certainly a key application here. But we also see great potential in, for example, engine and battery coolants (MEG usually consists of 95% of this composition) and are experiencing interest from the polyester, as well as the polyurethane industry.” Applications in the PET industry The potential applications are particularly exciting for the plastic packaging industry and thus also for the PET industry. According to UPM, the wood-based chemical intermediates would offer the same chemical properties as fossil-based chemicals, but with 70% less CO2 emissions. In addition, little or no operational changes or retrofitting of existing production facilities is said to be required. “It can be easily integrated into existing PET production,” says Dr Duetsch. “Ideally, this bio-based PET will be mechanically recycled at the end of its life, just as its fossil counterparts should be. If this is not possible, there is the option of chemical recycling through glycolysis. By integrating bio-PET, we see an important step towards a holistic circular economy in the PET value chain.” Once the plant is up and running, they plan to supply CSD and water bottle manufacturers, among others. Bio-MEG from UPM’s own pilot plant has already been successfully processed into PET and verified by beverage producers. Bio-MEG also as a complement to and in rPET According to UPM, rPET will have to cover the lion’s share of carbon raw materials in the future in order to increasingly initiate and maintain sustainability and the circular economy. Dr Duetsch commented: “It is extremely important to reuse and recycle materials. But even in a functioning circular economy, there will always be losses in the process. These losses can be offset, for example, by sustainable raw materials, such as our Bio-MEG, which are already available now and help create a circular carbon economy. The admixture of bio-based MEG can also be useful in the production of rPET and the recycling-related losses. Freshly heralded partnership to produce PETG On June 1, the company made another step official, namely the cooperation with the Portugal-based international copolyester producer Selenis, a subsidiary of the IMG Group. The aim here is to produce sustainable PETG using UPM’s Bio-MEG. Selenis focuses on developing products that are fully recyclable in the PET stream and has technologies that can convert plastic waste into new polymers. This should enable converters and Selenis brand owners to adapt their products so that they too can reduce their CO2 footprint by adding bio and recycled content while maintaining performance. www.upmbiochemicals.com"},{"@ID":4, "LABELLING PETplanet Insider Vol. 24 No. 07+08/23 www.petpla.net 18 Enabling PET bottles to achieve circularity Advances in adhesive technology Changes in the food and beverage packaging sector never stop, with new materials, design updates, and sustainability demands creating challenges for manufacturers and suppliers alike. However, many believe the race to produce even thinner and low weight PET bottles might be reaching its limits with PET per litre of bottled water reaching an all-time low. Adhesives play several crucial roles, from helping to ensure the recyclability of the package and bottle, to product security, extending shelf life, and reducing waste. That is also why adhesive formulations add value to this industry while providing the necessary versatility to perform across different applications and in various production environments. For the PET bottle recycling stream, it is paramount to have the best possible collection, sorting and cleaning process to reach the highest possible quality. The entire chain, starting with the consumer participating in the collection within a separate and dedicated stream for PET bottles, reduces the need for sorting. Cleaning the PET bottles to free them from leftover liquids, labels, and adhesives is a key step in the process. A hot alkali bath washes off specifically formulated adhesives for this purpose and removes any contamination from previous filling goods. The wrap-around and full surface label adhesives are customised for efficient wash-off and are certified by third party bodies. Qualification requirements for certification bodies in Europe, the U.S., and other countries such as South Korea, South Africa, or Australia can differ somewhat. Plastic waste reduction and leakage into the oceans is on the top of the agenda of the international community with on-going United Nations negotiations to end plastic pollution and finalise a legally binding document by the end of 2024 to this effect. Considering the trends and these international forces, certification bodies are seeking greater cooperation and are working towards mutual recognition of testing institutes and possibly testing protocols and certifications. International brands seek to use packaging components that are certified for as many geographies as possible to satisfy the export strategies of international products, highlighting the need for greater international coordination. How can adhesive suppliers support beverage manufacturers using PET bottles? As a well-known adhesive manufacturer worldwide, H.B. Fuller provides global support while working to qualify and certify products for local markets across the world. The alkali wash-off labelling product line, H.B. Fuller Earthic 4001 and 4010, are wrap-around labelling grades for plastic labels on PET bottles LABELLING"},{"@ID":54, "TRADE SHOW REVIEW PETplanet Insider Vol. 24 No. 07+08/23 www.petpla.net 35 Interview with Dr Karl Hagspiel, Senior Circular Economy Expert at Alpla Plastic packaging solutions and recycling services by Heike Fischer Alpla, a plastic packaging specialist, with 23,300 employees and 190 production facilities in 46 countries worldwide, has reached a PET recycling capacity of 266,000 t in its several recycling plants worldwide. Further growth expected! PETplanet spoke to Dr Karl Hagspiel, Senior Circular Economy Expert at the PRSE trade fair in Amsterdam about Alpla’s recycling and sustainability strategy and the current challenges in the rPET market. PETplanet: Alpla has been active in plastic recycling since the 1990s. At that time, a 1,000ml plastic bottle for Lenor was made from PCR material. Thirty-three years have passed since then. Recycling is now the heart of a circular economy. What does circular economy mean to Alpla? Hagspiel: The circular economy is a central theme at Alpla. Because, as the name suggests, it’s about keeping the material in the cycle or loop for as long as possible. Together with the also very important topic of Design for Recycling (D4R), we at Alpla try to keep polymers at the highest possible level of recycling. But our contribution with focus on plastics is only one part on the way to a closed loop instead of the currently prevailing linearity in the global economy. For our part, we are trying to fulfil our responsibility by producing only 100% recyclable packaging from 2025, offering a wide variety of reusable bottles, and steadily increasing recycling capacity - for both PET and HDPE - worldwide to obtain high-quality recycled material we produce ourselves and thereby guarantee availability to our customers. PETplanet: Last year, Alpla developed Austria’s first modern PET returnable bottle for the mineral water company Vöslauer. Could you briefly outline the key data of the project and explain why Vöslauer decided on this type of returnable packaging? Hagspiel: The returnable PET bottle for the Vöslauer mineral water brand was the first modern returnable PET bottle for the Austrian market. In principle, we develop reusable packaging because our customers want and demand it and because we believe that this will be a big market in the future. For the project with Vöslauer, we were able to draw on our long experience in this field, because we have already been producing a returnable PET pool bottle for the Genossenschaft Deutscher Brunnen (GDB Association of German Mineral Springs) in Germany for many years. And we also have various sizes of returnable PET bottles in use for Coca-Cola in Central America. The reusable PET bottle for Vöslauer is a 1-litre bottle that, at just 55 g, is around 90 per cent lighter than the glass alternative. This alone reduces the CO2 footprint by around 30 per cent. The bottle is made entirely of recyclable PET monomaterial with a recycled content of around 30 per cent. This is to be continuously increased over the years. With twelve cycles, the bottle is expected to remain in use for around three to four years. From an climatic point of view, the investment is already worthwhile when it is first used. At Vöslauer, the introduction of refillable PET will save around 420 t/a of CO2 . This actually answers the question of why Vöslauer decided to use this type of reusable packaging. F.l.t.r.: Dr Karl Hagspiel, Senior Circular Economy Expert at Alpla and Casper van den Dungen, Vice President Plastics Recyclers Europe at the PRSE in Amsterdam 2023"},{"@ID":56, "OUTER PLANET 54 PETplanet Insider Vol. 24 No. 07+08/23 www.petpla.net OUTER PLANET Transformation of PET bottles into polymers for lithium-ion batteries A team of A*STAR (Agency for Science, Technology and Research, Singapore) scientists has successfully upcycled waste PET plastic into polymer electrolytes, which are key components for safer lithium-ion batteries (LiBs). The study is the first known report of a working lithium-ion battery assembled using polymers upcycled from PET plastics, which are used to make plastic bottles. The study was published in Journal of Materials Chemistry A in November 2022. “Upcycling waste plastics is a new strategy to give these ubiquitous yet commonly discarded materials a new lease of life to transform them into value-added new products for novel applications,” said Dr Derrick Fam, Deputy Head of the Polymer Composites department at A*STAR’s Institute of Materials Research and Engineering (IMRE), who led this study together with Dr Jason Lim, Deputy Head of the Soft Materials department at IMRE (Institute of Materials Research and Engineering). The researcher describes as particularly advantageous the fact that there is a well-developed waste collection infrastructure for PET plastics and that the waste streams are relatively uncomplicated, thus offering great potential for upcycling. “There is a rise in demand for sustainably-sourced materials for lithiumion batteries due to greater electrification. However, the use of waste PET plastics as a resource for polymer electrolytes has never been achieved till now. This represents our first attempt to upcycle waste PET plastics for this application”, said Dr Lim. Capitalising on existing properties Amongst the different types of plastic, PET is one of the most abundant plastics produced today, amounting to 31 million tonnes in 2019, according to data from Statista. PET plastics possess existing features that make them suitable to be upcycled into polymer electrolytes (PEs). They are made up of rigid terephthalate components, which contribute to their excellent mechanical properties and can be tapped on to enhance PEs’ mechanical robustness, which in turn facilitates device integration and fabrication. In addition, they possess easily breakable chemical bonds which allow these polymers to be repurposed into new chemical building blocks with ease. These can then be reconstituted into new polymers for fresh applications. Battery design Waste PET bottles were used by the team to design polyurethanebased PEs. Compared to conventional liquid electrolytes currently used in LiBs, PEs are promising alternative components in batteries that have the potential to eliminate safety hazards such as the risks of electrolyte leakage, uncontrolled heating, volume expansion, dendrite growth and fire hazards. After assessing the viability of the PET-derived polymers as solid polymer electrolytes, the team further evaluated their ionic conductivity and cycling performance when used as gel polymer electrolytes for LiBs. Findings from the study showed the potential of the polyurethanes derived from waste PET as polymer electrolytes for LiBs. They achieved a room temperature conductivity of 10-4S/cm as a gel-polymer electrolyte (GPE), which is comparable to existing commercial systems containing liquid electrolytes. The team also successfully assembled a working LiB using these polymers, and showed that cells can be repeatedly charged and discharged up to 150 cycles. Their promising performance paves the way for a future powered by more sustainable energy, where PET plastic waste can be transformed into PE materials for batteries, creating a circular economy. The team will also look to advance the technology for upcycling of waste plastics on a larger scale to create components for ecofriendly batteries. About the A*STAR The Agency for Science, Technology and Research (A*STAR) is Singapore’s lead public sector R&D agency. Through open innovation, they collaborate with partners in both public and private sectors to benefit the economy and society. As a Science and Technology Organisation, A*STAR intends to bridge the gap between academia and industry. www.a-star.edu.sg (Top, from left): Dr Jason Lim, Dr Derrick Fam, Dr Warintorn Thitsartarn, Dr Ding Ning, Ms Chien Sheau Wei; (Bottom, from left): Ms Loh Wei Wei, Dr Shermin Goh, Ms Tan Ming Yan and Dr Dorsa Safanama (source: A*STAR)"},{"@ID":51, "LABELLING PETplanet Insider Vol. 24 No. 07+08/23 www.petpla.net 19 that are available on a global scale. The company’s international technical teams are working with local certification bodies to obtain further wash-off assessments. To date, H.B. Fuller has the following certifications for Europe: PET Cycle, Returpack, and Veolia. In addition, the U.S. team is working on the Association of Plastic Recyclers (APR) approval process. Also, in other regions, Fuller’s experts are teaming up with customers to follow recognised standards and finalise certifications that assure the right the way in the markets served. H.B. Fuller works directly with supply chain associations such as RecyClass, APR, or Australian Packaging Covenant Organisation (APCO) to cooperate with industry partners on design for recycling guidelines and testing protocols. The input from an adhesive supplier is particularly important as adhesives, and especially wrap-around labelling adhesives on PET bottles, have a huge impact, even though they are a small component of the overall packaging. When considering the circular nature and key success factors of PET bottleto-bottle recycling, adhesives play a crucial role in ensuring high quality, direct food contact approved for PET production. As with any other business, recyclers are seeking to run the most efficient process as possible, paying close attention to water and energy usage of their own operations. The cleaning of PET bottles is an essential step of the PET recycling process when any remaining liquids, labels, adhesives, and any other contamination need to be removed. Thus, an easy and effective label removal and wash-off is paramount to a state-ofthe-art recycling process. H.B. Fuller said that they are now focusing on creating smart materials and systems that reduce costs, improve efficiency, and make products more sustainable. Advanced technologies like H.B. Fuller Earthic 4001 and 4010 need to be specifically formulated to enable easy wash-off. Elizabeth Staab, Global Packaging Sustainability Manager, H.B. Fuller, says: “We believe the next step in development is how to reduce the overall carbon footprint. Thus, with careful selection of appropriate raw materials and efficient manufacturing practices, more sustainable solutions can be achieved in future. One thing is for sure, innovation does not occur in a vacuum, but at the interface of customers, equipment, substrate suppliers, and technical services.” www.hbfuller.com 2023 will see the launch of the Plastics Recycling Show Middle East & Africa. Dubai World Trade Centre, Dubai Interested in booking a stand? Contact mabarber@crain.com www.prseventmea.com Organised by Supported by MIDDLE EAST & AFRICA 5-7 September 2023 Dubai Register for your FREE entry badge"},{"@ID":47, "PETplanet Insider Vol. 24 No. 07+08/23 www.petpla.net 45 BOTTLES Summer happiness for spraying 150ml Sommerglück - a body spray with a peach scent and a del icate shimmer due to gl itter particles - has recently been sold by the dm natural cosmetics brand Alverde. The bottle is made of 100% rPET and is sealed with a screw-on, shiny gold-coloured pump dispenser with a protective cap. The vegan product itself is free of synthetic fragrances, colours and preservatives. The peach fragrance is made from rescued organic baby peaches. www.dm.de Scented washing-up liquid from Lidl The German discounter Lidl is selling 500ml of dishwashing liquid each under the W5 brand in a limited edition with special fragrance combinations. There is “Grapefruit Bergamot” and “Raspberry Rose”, both variants are free of microplastics and lightly coloured. The handy waisted, transparent bottles are made of 100% recycled material. The screw-on hinged cap can be operated with one hand and is shaped and produced in a way that conserves resources. www.lidl.de"},{"@ID":33, "PETplanet Insider Vol. 24 No. 07+08/23 www.petpla.net 31 TRADE SHOW REVIEW Erema invites customers to Discovery Day and opens new R&D centre 40th anniversary of Erema There was plenty for the guests to admire at the Erema Discovery Day, which was held by plastics recycling machine manufacturer Erema in Ansfelden on the 1st of June. The invitation was accepted by around 400 customers and partners, mainly from Europe, to find out about the wide range of recycling technologies for PO and PET plastic waste. The technology that was presented and explained by Erema experts and guest speakers during lectures in the morning, could then be seen live in-action in the afternoon when the recycling machines were demonstrated in operation. A total of six innovative recycling technologies were on display: Intarema TVEplus DuaFil Compact, Intarema TVEplus RegrindPro + ReFresher, the Corema cascade extrusion system, a Vacurema Inline Sheet line equipped with new EcoGentle technology, the new Intrarema FibrePro:IV machine, and the PCU-TwinScrew. These allowed visitors to witness their performance and the high quality of recycled pellets that they produce. “This wide range of technologies is necessary because the recycling process each of our customers choose depends on the type of plastic, the level of contamination of the input material, and which product will be made using the recycled pellets. Following the expansion of our Ansfelden site and with the new site nearby in St. Marien, we can now demonstrate all these processes, carry out test runs with customers’ material and focus on development work independently of our Customer Centre,” says Erema’s Managing Director Markus Huber-Lindinger. Erema is driving forward research and development work in the company’s new R&D Centre. Two halls with a total area of 1,550m2 and a new office building offering space for 50 workplaces has been built. Here, the company bundles cross-departmental test machines and laboratory facilities for post consumer and inhouse recycling applications. “This is how we make it possible to implement a circular economy for plastics”, says Huber-Lindinger. “With the new R&D centre, we have laid the foundation for further important plastics recycling milestones from Erema. This innovative strength is what has made us stand out over the past 40 years, and we will continue to play this pioneering role.” Christoph Wöss, Business Development Manager, Bottle Recycling at Erema Group reinforces this statement in his presentation ‘Tailor-made PET recycling solutions’ while opening the PET Recycling session, by summarising: “Erema has an European market share of around 41% with its products for PET food end-applications.” Sophie Pachner, R&D Manager Process Engineering at Erema presented the EcoGentel plasticising technology: The core elements of the EcoGentle technology are the adjustment of compression ratios for better solids handling behaviour, the targeted utilisation of shear flows in combination with elongation flows, and a number of other process and rheological optimisations. The the coordinated clash between the shear and elongation flows increases both the melting performance and the dispersive and distributive mixing capacity in the plasticising unit. The result is particularly gentle plasticising combined with high melt homogeneity and a wide process window for more stable operation. Variations in parameters such as the bulk density of the input material, viscosity or temperature of the PET flakes can be compensated as part of the stable process. EcoGentle is claimed to be a particularly gentle method of plasticising at lower temperature that saves energy. The much lower melt temperature has a positive effect on the quality of the melt and the quality of the final rPET pellets. Christian Sommer, Technical Sales Manager, Business Unit Powerfil introduced the laserfilter for PET applications. He started by explaining how the laserfilter works. “Coming from the extruder the contaminated plastic melt flows via a circular distributor ring into the housing between two parallel configured laserdrilled screen discs. The melt is pressed through the screen discs, flows through and leaves the filter in a clean state via the collection channel. The contaminant particles collect on the screen as the melt flows through. A scraper disc with three scrapers on each side rotates between the screen discs. The scraper and discharge screw speeds depend on the pressure and are controlled fully automatically. The pressed on scrapers lift the contaminants immediately from the smooth, hardened screen discs and forward them directly to the discharge system.” The laserfilter is also playing an increasing role in the PET sector. The reason for this is that the increased use of rPET in end products requires high process stability. This stability is also required if the degrees of contamination increase – which is currently the case. The laserfilter processes input material with a degree of contamination of over one per cent. The functional principle avoids dead spaces and makes for short dwell times, which in turn prevents „black spots“ with PET. The high melt and recyclate quality is important in the case of food contact grade applications. The melt losses are reduced below 1% thanks to the newly developed discharge unit. The new LF 2/354 Quattro is able to produce up to 6,000kg/h of filtrated melt. Exciting presentations followed and the pre-evening birthday party was a great success for Erema. www.erema.com F.l.t.r.: Christoph Wöss, Business Development Manager, Bottle Recycling at Erema Group, Sophie Pachner, R&D Manager Process Engineering at Erema and Gerold Breuer, Head of Marketing & Corporate Development at Erema Group GmbH"},{"@ID":41, "39 TRADE SHOW REVIEW PETplanet Insider Vol. 24 No. 07+08/23 www.petpla.net TRADE SHOWreview Interpack 2023 review - part 2 Bericap, Thomas Schmidt, Group Marketing Director 1) Overall, what were your impressions of Interpack? As also the stats prove, the overall feedback on the show has been extremely positive. Visitors and exhibitors really enjoyed the personal get together of the packaging industry after the long absence. New packaging concepts and innovative solutions were presented ready to be touched and discussed in detail. In comparison to previous editions we also experienced that all categories: Industrial, Beverage, Food and Wine & Spirits were equally represented by visitors attending our booth. 2) What aspects of your company offer were you highlighting? Our Interpack 2023 motto “Welcome to Captown” offered a perfect platform to present our latest closure innovations from Industrial District, Beverage Hills, Foodville and Wine Valley. On the one hand we were able to show Bericap’s wide range but on the other hand also demonstrate very specific solutions covering customer needs. For sure the ClipAside tethered caps success story with executions for all relevant neck finishes from 26 to 38mm has been a highlight on display. Also of high interest was Bericap’s completely reworked sports cap range: the new models Biarritz, Mayence and Monet impressed with different functional and design features. Last but not least: Bericap’s edible oil closure range with new tamper evidence features and mono material design set new benchmarks by combining user convenience with sustainability. 3) What will be the coming trends in PET bottles? Sustainability will certainly continue to drive new developments such as further light-weighting of bottles and closures as well as the optimisation of the recycling processes (e.g. mono material designs to avoid complexity in the sorting process). At the same time, closure customisation and flexible individualisation are still important in the food and beverage segment as well as in many other industrial sectors. Digital printing services for example can maximise design flexibility in that respect. It allows to create a unique-looking, recognisable product, on the one hand, and to protect the product against copying and counterfeiting, on the other. www.bericap.com ASB, Yasukazu Mino, Section Manager International Section, Sales & Marketing 1) Overall, what were your impressions of Interpack? The trade fair was a success for us in that we were able to maintain relationships with existing customers, as well as establishing new ones. The event drew a global and diverse audience that included many visitors from North Africa and the Middle East. 2) What aspects of your company offer were you highlighting? We are here with the same machine that we showcased at the K trade fair, the ASB-12M-2INJ injection stretch blow moulding machine. It is a 1-step double layer ISBM machine based in the ASB -12M model but re-engineered with twin injection units and a six-station rotary table that comprise two separate injection and cooling stations. The patented double layer moulding process enables containers to be moulded with an inner and outer layer in the body and/or neck section in a variety of thicknesses, configurations or resins. Intended applications include airless pump containers for oxygen sensitive products, recycled flake resin as the outside layer, moisture sensitive products, or premium glass-like designs. 3) What will be the coming trends in PET bottles? We are seeing a transition from glass to PET, with many bottlers switching to PET as a result of high energy costs and the low availability of glass bottles. Being mindful of the importance of sustainability, the bottlers will have many opportunities to improve their PET balance sheet through lightweighting or by using recyclates. I am seeing another trend in large container sizes. The pandemic has made customers aware of the importance of stockpiling, which is being reflected, among other things, in the current trend for large water containers. www.nisseiasb.co.jp"},{"@ID":53, "41 TRADE SHOW REVIEW PETplanet Insider Vol. 24 No. 07+08/23 www.petpla.net PMMI addresses insights on packaging automation PMMI, The Association for Packaging and Processing Technologies, addressed significant trends in automation. In a press conference on May 5, executives from PMMI highlighted key trends and insights from a recent report, “The Future of Automation in Packaging and Processing,” which revealed continued interest and adoption of automated technologies as a result of growing labour shortages and e-commerce. According to the report, 60% of consumer packaged goods (CPG) respondents to PMMI’s study cited a lack of labour availability as a significant driver of interest in automated solutions. As a result, 31% of all CPG respondents said they were deploying automated machinery on production lines as a substitute for manpower and will continue to do so. While this pain point has been felt across the globe, it is a significant concern in Germany where the Institute for Employment Research (IAB) expects the nation’s potential workforce to fall by seven million by 2035. The continued growth across e-commerce is another driver of automated solutions in packaging. About half of CPG respondents reported that growth in e-commerce is impacting their business, increasing the need for greater flexibility in packaging operations to accommodate fast-changing consumer preferences. “Continuing labour shortages and e-commerce growth represent shared challenges among CPGs operating in the United States, Canada and much of Europe,” said Jorge Izquierdo, vice president, market development, PMMI. “However, the resulting interest in automated solutions as a remedy have accelerated adoption and carved new paths in collaboration and creative problem-solving between these companies and OEMs to fuel greater efficiency, productivity and cost-efficiency.” To ease workforce challenges, many companies are turning to robot and cobot solutions. Over 90% of respondents believe that robots and cobots have helped address labour shortages with 27% reporting to deploy cobots in their plants. That figure is expected to grow to 57% over the next five years. Maintenance represented another opportunity for automated solutions in packaging and processing. 43% of respondents reported use of predictive maintenance technology on their lines while 83% were considering it. Related, 56% reported use of remote access solutions since 2020. Even 3D printing is playing a larger role in machine maintenance while helping CPGs lower downtime and costs. About 25% of respondents claimed to use 3D printing to make and replace non-moving parts prone to quick wear and tear. www.pmmi.org Coding developments Markem-Imaje, global provider of end-to-end supply chain solutions and industrial marking and coding systems for multiple market verticals, unveiled market-first new coding technology designed to propel production of serialised 2D barcodes, three recently-developed laser designs and a host of other innovations. The new Super Piezo Inkjet (SPI) marking technology is claimed to combine the advantages of continuous inkjet CIJ and Drop on Demand. Markem-Imaje CIJ Product Division Director Sabri Mourad explained: “It’s coming to answer the demand of brands to have high quality print on the product and to serialise 2D codes. This is the right answer to the revolution coming to the market in 2D barcodes from GS1. It will give brands the capability to mark unique brands with unique codes on 3D complex surfaces”. Besides SPI, Markem-Imaje demonstrated three recentlydeveloped laser models, one to respond to the industry demands of the segment’s three technologies, each helping brands to meet their sustainability goals whilst boosting productivity at a time when manufacturers face an increasingly challenging environment. MI’s new ultraviolet technology, the UV500, excels on difficult materials where other laser technologies cannot perform so well, including on the finest, easily-damaged substrates like new more environmentally friendly thinner mono films, as well as polymer labels and thermoplastics like high-density polyethylene. A key attraction at MI’s stand was an in-line packaging line demonstration featuring laser, continuous inkjet, thermal transfer overprinting, large character inkjet, and intelligent print and apply labeling systems in action. The demo was fully integrated and managed by MI’s Packaging Intelligence software suite Colos, prepared for supply chain traceability and engaging consumer experiences. www.markem-imaje.com"},{"@ID":16, "LABELLING PETplanet Insider Vol. 24 No. 07+08/23 www.petpla.net 14 Sipa and Água Monchique fl ip the script: PET bottles say goodbye to labels Portuguese mineral water supplier Água Monchique has taken a lead in producing PET bottles that are easy to recycle: with the help of PET processing equipment specialist Sipa, it has developed label-free bottles. This means that the only part of the complete package not in PET is the PP cap, which remains attached to the bottle after opening in accordance with EU legislation, but which is easy to remove in recycling operations. Not only that: the bottles are produced in 100% post-consumer recycled material. The new bottles need no label because all the information the customer needs is integrated directly into the bottle wall by embossing during the moulding process. Sipa provided various aspects of support to Água Monchique, which produces the 555ml bottles on the Xtra 8 advanced rotary stretchblow moulding system. Sipa’s input goes even further: the Xtra 8 is in what the company calls a Sincrobloc configuration, meaning that it is directly integrated with the filler, the Flextronic S 8/50/10. From the idea to the 555ml bottle The Natura project took life last September during the Drinktec fair in Munich, when top executives from Água Monchique went onto the Sipa booth to meet the design team. While they were looking at one particular innovation, a prototype PET bottle for sparkling wine created by Sipa, the idea came up for another innovation, a label-free bottle for water. “The idea came up spontaneously, with the Sipa design team proposing the concept, as well as the idea for upsizing (from the 500ml format), in contrast to the downsizing that is generally practised today,” says Sipa’s Sales Area Manager. “A 555ml bottle gets to be positioned higher on supermarket shelves than 600- or 750ml sizes, so it will have more visibility.” The customer liked the idea and appreciated Sipa’s increasing offer of packaging solutions and its full range of technologies for preform and containers production. The goal: carbon-neutral by 2030 Água Monchique has for a long time paid considerable attention to the sustainability of its operations and its products. Its strong innovative spirit had already led it to develop a 720ml bottle in 100% rPET. The new project, called Monchique Natura, takes the company another important step down the road to sustainability: its goal is to be carbonneutral by 2030. The new bottle is not only label-free and totally made in rPET, but also very light, weighing just 19 g. The bottles will be sold individually and in six-pack cardboard containers that sport the FCS mark (FCS is the Forest Stewardship Council), indicating that they are made from 100% recycled materials. “This is a bottle completely produced from other bottles, in which we replace the use of labels with fingerprints on the plastic itself, minimising the impact of this activity on the environment and proceeding with a strategy focused on promoting a true circular economy,” says Vítor Hugo Gonçalves, CEO of Água Monchique. Monchique Natura is the first Portuguese bottle and one of the first in the world to appear on shop shelves without labels. It will go on sale in the third quarter of the year. Monchique Natura will join a group of other solutions that Água Monchique has introduced in what Gonçalves calls “the relentless search for best practices to make our business model more sustainable and more in line with circular economy models. Sustainability will remain at the forefront of our actions and Monchique Water will deliver on its promise to contribute to the betterment of the current generation, as well as generations to come.” Sipa has collaborated on other Água Monchique projects in the past. The Portuguese company already uses Sipa’s two production systems to make bottles in seven different formats. The “regular” Monchique range is available in five sizes, from 340ml through to 5 l, all with simple and attractive designs. An Xtra 8 produces the smaller sizes, while an SFL 6/4 XL, operating in a Sincro set-up with a Bigfill volumetric gravity filler, is used for the 5 l bottles. The 5 l bottles in particular stand out for their low weight: they have been validated at 66 and 64 g, which is close to 10 g lighter than the norm in Portugal. www.sipasolutions.com LABELLING"},{"@ID":40, "TRADE SHOW REVIEW PETplanet Insider Vol. 24 No. 07+08/23 www.petpla.net 38 Re-usage of PET/PE monomaterials from multi-layer packaging Adhesive enables PET/PE component separation During the first industrial trial conducted at a Krones pilot plant in Flensburg, the partners were able to completely separate as much as 69% of the PET/PE components and partially separate another 12%. This approach is special as it uses the existing infrastructure only to recycle the multi-layer packaging. Decisive for the success of the project team were the collaborative efforts of the partners BASF, Krones, Südpack, and Tomra. The companies combined their know-how in order to close the loop. The first phase of the project was initiated in early 2021 when Tomra conducted the first sorting trials with PET/PE trays. These trays had been manufactured by Südpack using a “debonding adhesive” developed by BASF. Südpack, a leading manufacturer of high-performance films for the packaging of food, non-food and medical products, has committed to becoming a zero-waste company. “Our contribution to the collaboration project was our long-standing expertise in lamination. Using our expert knowhow in water-based lamination, we were able to develop multi-layer films that can be separated by caustic hot washing,” says Carolin Grimbacher, Managing Partner at Südpack who is also responsible for R&D. To close the materials cycle, the recyclable multi-layer films first have to be sorted out of the waste stream. The main determinant of success for this step was the ability of the Autosort technology of Tomra to separate the recyclable PET/PE trays from nonrecyclable trays. “Our NIR technology made this possible because it is able to detect the multi-layer PET trays containing the adhesive of BASF. With this it’s possible to sort the trays out of the waste stream and add them to the recyclables,” David Rüßmann, Manager Special Projects, explains. The separated PET and PE can be re-used as monomaterials Krones, a company that, among other things, develops plastics recycling systems, joined the project team in July 2022. At one of the company’s pilot plants, trials were carried out to test whether it’s possible to separate laminated PET/PE films to their single layers in an industrial scale. A standard hot washing process commonly used for PET recycling was applied successfully and as a result, the separated PET and PE can be re-used as monomaterials. “At our facility, we proved that the delamination of multilayer films works. However, the separation of the films can still be improved by optimising individual process parameters as well as, for example, the particle size of the flakes,” Thore Lucks, Head of Technology Recycling Solutions at Krones, explains. Specifically developed adhesives The process of separating the PET and PE components of the film is based on adhesives that were specifically developed for this purpose. These adhesives are used during the lamination of multi-layer films to join different functional materials. The lamination adhesive has to have the best possible adhesive strength when required, but still makes it possible to easily separate the two films when it comes time to recycle. “Our waterbased Epotal adhesives already yielded very good results when separating multi-layer packaging in the laboratory. We consider it a huge success that we were able to completely separate 69% of the packaging during our very first industrial trial. We are confident that we will be able to further increase this figure by optimising our debonding adhesive,” Kresimir Cule, Commercial Marketing Industrial Adhesives, BASF SE, states. Further development of the lamination adhesive The project is still ongoing. By adjusting various parameters of the recycling process and by further developing the lamination adhesive used, the project partners see additional opportunities for improving the recycling rate for plastics. The quality of the recycled materials is a major focus. The aim is to be able to re-use the PET for the manufacture of food packaging, while the PE fraction will be used as a raw material to make new packaging for the non-food industry. www.basf.com www.krones.com www.suedpack.com www.tomra.com Multi-layer films are used for a wide range of packaging materials, particularly in the food industry. The European Green Deal stipulates that packaging must be recyclable to a large extent by 2030. However, up until this point, the recycling of multi-layer film has proven difficult because the film is made of different materials. A collaboration project involving the companies BASF, Krones, Südpack, and Tomra has now demonstrated that it is possible to separate PET/PE multi-layer packaging into its individual components and return them to the materials cycle as raw materials."},{"@ID":57, "1 The worldwide round trip with The Middle East Roadshow Editours PET world in the Middle East In a spectacular project taking us well into 2024, we will be travelling in a wide variety of ways to various countries and regions of the Middle East with different mobile editors. There we will interview machine manufacturers, the supply industry, bottle and beverage producers, as well as PET recyclers and everyone involved in the process chain. What market-specific trends are there now or will arise in the future? What developments and technologies are in vogue on the consumer and plant construction site in some of the hottest regions of the world? What special requirements are there? What role do topics such as food safety, shelf life and sustainability play in PET packaging and how are companies preparing themselves for the coming years? This, and much more we will be discussing face-to-face with all the key players and then our results will be presented to you in a series of must-read reports in PETplanet Insider. Please join on this enchanting voyage to the world of PET in the Middle East. We look forward to welcoming you on board! Our previous Road Shows at a glance 2010-2011-2012-2013-2014-2015- 2016-2017-2018-2019-2020-2022 Interested in being visited? barton@petpla.net Autumn 2023 - 2024 EDITOUR - ThE MIDDlE EAsT ROADshOw 6 countries numerous interviews with PET companies Sponsors to date"},{"@ID":3, "No.7+8 2023 www.petpla.net D 51178; ISSN: 1438-9452 31 . 07 . 23 MAGAZ I NE FOR BOT T L E R S AND BOT T L E - MAK E R S IN THE AMER ICAS, AS IA, EUROPE AND AL L AROUND THE PLANET PETplanet is read in more than 140 countries MARKETsurvey Suppliers of compressors Page 28 Page 38 Page 42 Page 35 Page 32 LABELLINGPage 14"},{"@ID":38, "TRADE SHOW REVIEW PETplanet Insider Vol. 24 No. 07+08/23 www.petpla.net 36 PETplanet: The rPET share of the Vöslauer returnable bottle is currently 30%. The company would like to use a higher proportion of recyclate. But since the logistics chains were reorganised after Covid in the second half of 2022, virgin PET is very cheap in Europe and is displacing PET recyclates. The still high inflation is also depressing consumption. Recyclers are left with a lot of material on their hands. How do you assess the current situation? Hagspiel: You are right - the current price for new PET is a real challenge for recyclers and the critical market situation is exacerbated by reduced consumption in the private sector. The first recycling plants in Germany have already had to stop production due to the current sales and price situation. But we are facing another big challenge or rather a new danger. It is the import of rPET from countries outside the EU. The material is cheaper than the material produced within the EU. Yet we have no certainty about the origin of the material, while the EU is demanding ever stricter documentation and proof of the origin and quality of rPET or other types of recyclates. At Alpla, we are countering this trend by expanding our own recycling plants. In this way, we want to ensure that we can continue to provide our customers with sufficient high-quality recyclates in the future to meet the ambitious targets set by the EU and other requirements. PETplanet: For Donat Mg mineral water in Slovenia, Alpla has developed a closed-loop system with its own recycling facilities. This closed loop makes them independent. The Slovenian government is still discussing whether and when to introduce a DRS system. In your opinion, what should a longterm strategy for the PET recycling system look like? Hagspiel: The deposit system (DRS) as an extended producer responsibility (EPR) model will be an integrated long-term strategy for recycling at a high quality level. In general, what has no monetary value has no value to the individual citizen. Sorry to put it this way, but money seems to be the most effective (maybe even the only) incentive to return the bottle. In Germany, we have a 97 per cent return rate for PET bottles through the deposit system. This clearly shows that this route can work and, of course, also enables us as recyclers to get hold of more material. However, it is important that returned bottles also become bottles again and that the material is not downcycled, which unfortunately often happens at present. We will also have a DRS system for other materials - as we currently have for waste electrical and electronic equipment (WEEE) and batteries in several EU countries. France will or has already integrated EPR systems for DIY and toys. This is a very important step towards a stronger circular economy. Why various EU member states are hesitant may be due to the projected costs of the system. But the environmental cost of “doing nothing” will be much higher! PETplanet: Laws and directives can provide investment security for the economy. What is your opinion on the EU directives such as the SUP & PPWD for the plastic packaging industry? What are the challenges for the relevant stakeholders like producers, retailers and consumers? Hagspiel: As you mentioned, EU regulations are a challenge for the plastics industry. Currently, EU regulations focus mainly on plastic and largely neglect other packaging materials. We call for fair competition for all packaging materials. The only basis for accepting or banning a packaging should be the carbon footprint or, more generally, the environmental footprint of a product or packaging material. So here we are definitely advocating for eco-modelling and we are also advocating for it at the EU level. Because, for example, producing a combination of paper with a non-recyclable plastic layer just to avoid or minimise a plastic tax is definitely the wrong way to go and does not lead to a successful circular economy. Retailers are the direct link to the consumer, and they are also affected by the SUPD and PPWR. For example, they need to offer reusable packaging. When we look at the end consumer, we need to offer them a convenient way to be part of the circular economy and raise awareness that all empty packaging is valuable raw material, even if we have to do this through a deposit scheme. PETplanet: Alpla has not limited itself to the classic PET bottle for the use of rPET. rPET is also used in thin wall injection moulding and thin wall extrusion blow moulding. The entire packaging market is covered. In addition to PET or rPET packaging, Alpla is also developing alternative packaging material that is bio-based or paper-based. For what applications is the material intended? What is the proportion of bio- and paper-based material in current production? Hagspiel: At Alpla, we are always looking for the best solution for our customers. And we notice that the demand for alternative material is increasing. Therefore, we are also looking for the best solution in this area. For PET, the only recycled material (rPET) that can be used for direct contact with food and nutrients, we have to meet the recycling target of the EU regulations. And with the development of thin-wall injection moulding, we are on the right track of this strategy. The question of paper-based or bio-based material is part of the same strategy. Why are we working on this? Because we are providing the solution for our customers and developing the packaging that is an integrated part of the circular economy. The paper bottle we develop must be recyclable in the paper recycling stream. When it comes to biopolymers, we have to distinguish between biobased and/or biodegradable. The biodegradable materials will play a role in very specific niches, for example, coffee capsules or tea bags. Currently, however, these packages cannot be industrially composted together with the (used) contents, tea or coffee. This is because they take longer to degrade than the turnaround time in professional composting plants. In this area, we at Alpla have launched a coffee capsule that is home compostable - with the used contents and the fleece. However, material"},{"@ID":24, "LABELLING PETplanet Insider Vol. 24 No. 07+08/23 www.petpla.net 22 Inspection system for all types of labels For the decoration of bottles, jars and cans, there are more different types of labels available today than ever before. Producers have the choice: established pressure-sensitive labels, indestructible IML decoration, or an outstanding sleeve solution? For the inspection of these decorations, companies are then also spoiled for choice. LABELLING Why not a “one for all” solution? Some suppliers of vision inspection rely on universal solutions that cover different label types. A customer should then be able to perfectly inspect several label types with the same kind of vision system, for example sleeves as well as pressure-sensitive labels. On first impression, this may seem tempting to many customers, as it is assumed that these solutions can be flexibly used for different label types. “At first glance, such solutions certainly look attractive to some customers due to their low initial price,” knows Janina Orlowski, Team Leader of Product Management and Marketing at Intravis. “But at second glance, these solutions come with enormous disadvantages. For instance, you need at least one absolute expert in the company to adjust the system to the ever-changing types of labels. As a company, you are therefore dependent on a well-trained employee. If this employee is absent, this can immediately have a noticeable impact on the quality of the inspection process - and thus on the quality delivered.” And this is not the only disadvantage of an ”one for all” solution. Janina Orlowski continues: “The decisive disadvantage of these solutions, however, lies in their inspection accuracy and the data determined. The systems may sort out defective parts, but they cannot tell you exactly which defect caused a part to be sorted out. So, as a customer, they know they had a bad part, but how to prevent that from happening again is something they have to painstakingly check in the quality lab and then draw their conclusions with a time lag. In that time, you may have already produced half a production slot with inferior quality. If this happens more often, the initial advantage of the low price is used up very quickly.” Special solutions for quality products Therefore, Intravis has chosen a different path for many years now. The Aachen-based company offers specialised systems for the various types of labels. “With our systems, producers ensure, on the one hand, that high quality is delivered to their customers. On the other hand, in the event of a defect, they learn directly which defect types have caused rejects and to what extent,” reports Markus Juppe, Chief Marketing Officer at Intravis. The company accomplishes this thanks to two factors. Firstly, each system is equipped with hardware explicitly designed to detect the typical defects of the particular labelling process. This includes specific illuminations that are necessary due to different surface conditions of the various label types. For example, this avoids annoying reflections that would otherwise result in false ejection or at least a restricted inspection area. Moreover, the integration of high-resolution cameras is claimed to support an optimal and detailed evaluation of the labels. The second decisive factor is the IntraVision inspection software. The software has specific modules which, on the one hand, have been developed directly for the different label types and, on the other hand, are additionally adapted explicitly for each customer product. This has the advantage that special label geometries or product shapes can be precisely addressed. In conjunction with high-resolution industrial cameras, the integrated inspection modules are then able to find defects and identify which type of defect it is. Thanks to an interface between the vision system and the customer’s ERP or MES system, this information can also be directly transmitted. Thus, line operators and plant managers can see immediately and at a glance which processes they need to check in order to keep their production quality high in the long term. The IntraVision software also solves the problem of the image processing specialist that the company has to keep on hand when using “one for all” solutions. This is because, on the one hand, the systems are completely commissioned by an Intravis service technician. They are ready-"},{"@ID":58, "MATERIALS / RECYCLING PETplanet Insider Vol. 24 No. 07+08/23 www.petpla.net 10 Glycol production from renewable raw materials From wood and paper to PET by Kay Barton Forestry and paper company UPM, a leading global producer of sustainable paper, wood, biochemicals and composite products and energy, with operations in 11 countries on six continents and headquarters in Helsinki, Finland, is about to start up its new biorefinery in Leuna, Germany. The €750 million investment to produce biochemical products is part of the company’s strategic plan to use renewable versus fossil raw materials for use in various industries, including automotive, textiles but also plastics and packaging. A key product from the new plant in Leuna will be a woodbased bio-MEG, which should soon gain a foothold in PET production. We spoke to Dr Michael Duetsch, Vice President of the UPM Biochemicals division, about a technological vision with potential and reach. May 30, 2023 We met: Dr Michael Duetsch, Vice President UPM Biochemicals “Our business is based on forests,” Dr Duetsch began the conversation. “We plant and harvest forests to make renewable and recyclable materials and products. Many applications and a variety of materials are based on organic chemistry and require carbon in their production. While decarbonisation is happening in energy production and in many aspects of transport, organic chemical compounds, which are made of carbon molecules, cannot be decarbonised,” said Dr Duetsch. His enthusiasm from the dynamism and energy with which UPM is building a new business is palpable. He sees what he is about to do with UPM in Leuna as pioneering a gamechanger. Dr Duetsch has now been part of UPM for 12 years. Before his current job, he had already worked for 16 years in the chemical industry for various companies. Now he is in the process of creating a new business area in the company - a biorefinery that converts wood, residues and sawdust into chemicals. He further explained: “The inclusion of a renewable carbon cycle and its role in durable applications is, in our view, an essential component for sustainability in chemistry.” Sustainability, the biochemical way The history of the UPM Kymmene goes back to the beginnings of Finnish forestry. The Group’s first mechanical pulp mills, paper mills and sawmills were commissioned in the early 1870s. Some 150 years later, the company, which employs more than 17,000 people worldwide and had a turnover of €11.7 billion in 2022, is putting alternatives to fossil fuels at the heart of its operations with its “Biofore Strategy”, already ten years in the making, ambitiously driving its own transformation to become a leader in the bioeconomy. “One of the first success stories based on this strategy was our biofuels business unit,” Dr Duetsch recalled. “Here we had developed a process to convert tall oil, a by-product in pulp mills, into biodiesel and bio-naphtha.” Since 2015, UPM has been operating a corresponding plant in Lappeenranta, Finland, with an annual capacity of 120,000 t, and is currently examinThe biorefinery in Leuna under construction Vice President of UPM Biochemicals Dr Michael Duetsch"},{"@ID":11, "9 NEWS PETplanet Insider Vol. 24 No. 07+08/23 www.petpla.net"},{"@ID":19, "LABELLING 17 PETplanet Insider Vol. 24 Ravish Majithia: Based on a survey conducted by the Association of Plastic Recyclers, PET reclaimers already have magnetic separators as a part of their flake decontamination process. Removal of metal contamination from PET is important and magnetic separators are commonly used to remove small metal pieces from PET flake. Magnomer’s coatings utilise this existing infrastructure to separate undesirable shrink sleeve flake as well. PETplanet: What is the percentage of separation that can be achieved compared to conventional sleeves‘ separation? Ravish Majithia: In the case of PETG, the most common sleeve resin used in North America and EU, more than 98% of sleeve flake was magnetically separated using Magmark SS coatings. This is compared to almost zero separation if our coating were not present for PETG removal. PETplanet: You mentioned that the Association of Plastic Recyclers (APR) recently awarded you the responsible innovation award for the Magmark SS magnetisable coatings. How did the process work, what kind of tests were carried out? Ravish Majithia: The Innovation recognition by APR is based on high volume commercial recycling tests. This includes: Printing over 250,000 “innovation“ bottles using standard PETG sleeves with Magmark SS coating Testing a subset of these bottles at three commercial MRFs to show that the use of Magmark SS coatings do not impact MRF operations; Introducing over 2 metric tons of “innovation“ bottles at two different PET reclaimers namely Indorama Ventures (facility in Alabama, US) and Evergreen Recycling (facility in Ohio, US) to showcase magnetic removal of sleeves. As a part of the recognition process, the MRFs and reclaimers provided public testimonials to APR’s review committee which subsequently awarded the recognition to Magnomer. PETplanet: Is Magmark limited to use on PET bottles‘ shrink sleeves or can it also be used for other types of packaging/labelling? Ravish Majithia: Magmark technology can be applied to various categories of labels or flexible packaging – indeed anywhere where sorting of said flexible film is required. Our various current products and demo videos can be found on our website. PETplanet: Thank you very much Ravish! www.magnomer.com"},{"@ID":9, "7 NEWS PETplanet Insider Vol. 24 No. 07+08/23 www.petpla.net New study presents roadmap for circular PET packaging and polyester textiles in Europe A new study published by system change company Systemiq, presents a comprehensive roadmap for achieving a high-circularity, low-emissions system for PET packaging and polyester textiles in Europe. PET packaging and polyester textiles are made from the same plastic molecule, which makes up one-quarter of consumer packaging (bottles and trays) and the vast majority of synthetic textiles (clothing, homeware and industrial) used in Europe. Today, this material is mostly made from virgin feedstocks and three-quarters of PET/polyester waste is disposed to landfill or energy recovery after just one use. The study highlights the transformative potential of ambitious and complementary circular economy approaches, including demand reduction, reuse, mechanical recycling and chemical recycling. By 2040 – compared to a continuation of historical trends – these measures could reduce overall PET/polyester consumption by one-third, waste volumes sent to landfill or incineration by ~70%, and greenhouse gas (GHG) emissions by half, while the supply of recycled content would be sufficient to meet the requirements of the draft Packaging and Packaging Waste Regulation (PPWR). Moreover, they could generate 28,000 net new jobs and an additional €5.5 billion/a in revenues for recycling industries. Titled ‘Circular PET and Polyester: A circular economy blueprint for packaging and textiles in Europe’, the study outlines six priority actions needed to transform the PET/ polyester system. These actions could slow consumption growth and establish complementary mechanical and chemical PET/polyester recycling systems that increase recycling rates and the availability of high-quality rPET. The findings come at a critical time, coinciding with the EU’s Single-Use Plastics Directive Implementing Act and the development of the draft PPWR. The study was developed under the guidance of an independent Steering Group comprising experts from the public sector, academia, civil society, and industry. It was commissioned and funded by Eastman and Interzero. www.systemiq.earth Ceresana study on the European label market Ceresana, a market research firm, has analysed the market for labels in 21 European countries: Consumption of paper and plastic labels in Europe is expected to increase by around 1.5% per year until 2032. The total area of small labels and stickers adds up to millions of square meters. As environmentally friendly packaging is increasingly in demand, labels made from biodegradable or recyclable materials can score well in conjunction with biobased adhesives. Wine and beer drinkers usually do not have to worry in this regard: labels for reusable bottles are traditionally made of paper and attached with washable starch or casein adhesives. However, market shares of glued labels are currently decreasing. The high inflation rate is troubling many consumers. Currently, the most dynamic development is occurring in the “cosmetics and pharmaceuticals” sector, which consumes more and more plastic labels. In the production of shrink film labels (shrink and stretch sleeves), the controversial plastic grade PVC is increasingly being replaced by PET. Demand is increasing in particular for PET-G modified with glycol. Labels are becoming smart and talkative QR codes, RFID tags and near field communication (NFC labels): labels are increasingly becoming as “smart” as digitalisation and the Internet of Things demand. Smart labels can communicate with smartphones or other devices: Labels report the expiration products or other important information about the contents of the packaging; they make supply chains transparent and ensure anti-counterfeiting and traceability. However, the biggest growth occurs in in-mould labels (IML) with Europe-wide growth of around 2.4% per year, which usually can be recycled well because they are made of the same plastic. The study The study presents label consumption as well as revenues generated with labels and forecasts up to the year 2032. The data on label consumption is broken down by areas of application, by different label types, and by materials. The study also provides company profiles of the most important producers of labels. https://ceresana.com/en/produkt/labels-market-report-europe Doehler Group: acquisition of SVZ Doehler, a global producer, marketer and provider of technology-driven natural ingredients, ingredient systems and integrated solutions announces the acquisition of SVZ, subject to regulatory approval. This is intended to strengthen Doehler’s portfolio of natural red fruit and vegetable ingredients and its global market presence, expanding the operations in the USA and Japan. SVZ is known for its high-quality purees, concentrates and ingredients of sustainably sourced vegetables and red berries. With production sites in the USA, Spain, Poland and Belgium, SVZ has established a strong global presence and successfully built a base of premium customers in the food, beverage and lifescience & nutrition industry. With this acquisition, customers are expected to benefit from an even broader ingredient portfolio and larger raw material base. Consumers’ interest in healthier nutrition creates a rising demand for ingredients that offer better nutritional value and superior sensory experiences from sustainable raw materials. SVZ’s portfolio contributes to this trend by offering a variety of low-calorie, high-fibre and nutrient-rich fruit and vegetable ingredients that enhances the overall nutritional content of food and beverages. SVZ’s products seamlessly integrate with Doehler’s portfolio of natural ingredients and ingredient systems. www.doehler.com"},{"@ID":10, "8 NEWS PETplanet Insider Vol. 24 No. 07+08/23 www.petpla.net The Wine Society trials PET bottles following packaging research Following the publication of its Alternative Packaging for Wine report in May, The Wine Society has embarked on the second phase of its packaging trial. Four of the British Society’s most popular wines, including its top-selling wine, The Society’s White Burgundy, will be released in rPET bottles in collaboration with Packamama. The flat-pack, recycled plastic bottles are considerably lighter than glass bottles weighing 63 g compared to an average of 460 g for glass bottles, resulting in a lower-carbon footprint, as well as offering consumers greater convenience and portability through their space-saving design. The bottles are also fully recyclable. As part of its bold Sustainability Plan and goal of halving its total carbon footprint by 50% by 2023, The Wine Society earlier this year commissioned an independent study to identify and review all available alternative packaging formats to glass, and the flat-pack, recycled plastic bottle by Packamama came out as one of the better options. Light to transport, space saving across the supply chain, and made from 100% recycled PET plastic, the bottle and cap are fully recyclable by 99% of local authorities in the UK unlike other packaging options like cartons and pouches. While a shelf life of up to 18 months is technically possible, Society members are being recommended a drinking window of six months for this bottle format. Dom de Ville, Director of Sustainability and Social Impact comments: “In our recent carbon report, we shared the news that glass bottles account for 31% of The Society’s total emissions. To achieve our ambitious reduction targets, we need to significantly reduce our emissions attributable to packaging. One way to do this is putting more of our wines into lower-carbon packaging formats. Although rPET might sound controversial, with today’s technology and in the absence of a proper system in the UK to collect and reuse glass bottles, the recycled plastic bottle is a really good option. It has a lower-carbon footprint than glass and can be recycled at home. “While we recognise there is a plastic pollution problem, it is not necessarily plastic itself that is the problem, rather it is what we do with it. This is why we are taking a practical approach to plastic, seeing its benefit in our efforts on climate change, rather than taking a black-or-white stance that all plastics are bad. This bottle is made from 100% recycled plastic and is recycled everywhere in the UK – which helps to support a more circular economy.” The trial of the Packamama rPET bottles follows the release of six of The Society’s wines in bag-in-box (BiB). The BiB trial was a great success with the wines selling out in three weeks. This second packaging trial will support The Wine Society to reduce its carbon emissions and should members back the new format, the business will commit to the bottles becoming a permanent fixture in the range. Pierre Mansour, The Wine Society’s Director of Wine adds: “We are trialling these bottles with wines designed to be drunk young and our tastings confirmed that the quality compares favourably with the same wines in glass and BiB. While rPET has less of a track record with wine, we will want to satisfy ourselves, and members, that there is no impact at all on quality. Only then, and assuming members continue to buy them and their feedback is positive, will we include them as a more permanent fixture in our range.” Santiago Navarro, CEO & Founder of Packamama concludes: “The Wine Society is taking major steps to reduce their emissions. Having been founded in 1874, when atmospheric CO2 measured 288 parts per million (ppm), they are one of the very few wine businesses still around today that knows a world below 300 ppm; which is how our Earth has been for at least the last 800,000 years, probably 3 million years. Nowadays, we have passed 420 ppm and at 430ppm we will be at 1.5 °C of warming, which the IPCC recommends that we stay below. We are very grateful to The Wine Society for their pioneering climate action and are deeply honoured to collaborate with them to help them reduce their emissions through trialling our eco-flat bottles.” www.packamama.com www.thewinesociety.com Veolia PET Germany to close Rostock recycling site Veol ia PET Germany GmbH wi l l close the PET recycling site in Rostock, Germany, on December 31, 2023 after more than 20 years due to the lack of long-term security for the production site. The closure will affect a total of around 50 employees. This decision is based on an estimation of the market with regard to the will to close the loop for PET beverage bottles. It has not been possible to secure sales of recycled PET in cooperation with the beverage industry and/or retailers, says Veolia. The willingness of all market participants to participate in a long-term perspective for the purchase of recycled PET on economic terms is the prerequisite for the PET loop. In this volatile climate, the permanent, economic operation of a PET recycling plant is not possible for Veolia. Veolia PET Germany GmbH, based in Hamburg, is part of Veolia Umweltservice GmbH and, thanks to its many years of experience, is one of the leading companies in all areas of the PET recycling market in Europe. The production sites in Frauenfeld (Switzerland), Fetsund (Norway), Norrköping (Sweden) and the central marketing company of all plants in Hamburg are not affected by the closure. www.veolia.com"},{"@ID":2, "LABELLING PETplanet Insider Vol. 24 No. 07+08/23 www.petpla.net 23 to-use, which means they are already optimally set up to meet the customer’s requirements. On the other hand, the easy-to-use software requires no time-consuming programming by the operator. Usually, the setup of a new product is already fully automated with the touch of a button. Automatic readjustment possible With the right integration of the Intravis system, the whole inspection process can even be automated. Intravis has already implemented such a solution at a German global player for many years. Markus Juppe presents it in more detail: “Essentially, the solution is that we use one of our inspection systems to detect any misalignment of the label relative to a predefined optimum position. If such an offset is detected, then our system sends a signal to the labelling machine, which automatically readjusts its dispensing head based on the detected offset.” The ingenious aspect is that even in the event that a label is dispensed from two different dispensing heads, the Intravis system can trace the offset back to the respective dispensing head, and only this head is then adjusted. According to Markus Juppe, such a solution can be implemented with both linear and rotary labelling machines in case of producing with pressure-sensitive label. However, this technical approach can also be transferred to IML labels in the injection moulding process or to a shrink or stretch sleeve application. Experience paired with new ideas The system used for the automatic readjustment of label dispensing heads is a LabelWatcher. It has already been in the Intravis product portfolio for 20 years. It is the solution for the inspection of pressure-sensitive labels on bottles, jars and cans. Regardless of whether only one side is decorated with a label or two, the LabelWatcher can be specifically adapted to all requirements. The inspection scope includes standard inspections such as presence and positioning of the label, contaminations, wrinkles and bubbles, as well as artwork inspections, and even reading codes - no matter whether barcode, QR code, data matrix code, or plain text codes. Intravis has also introduced two enhancements to its proven system this year. First, the LabelWatcher is now also available in the so-called washdown design. Janina Orlowski says: “With the washdown design of the LabelWatcher, we are once again significantly expanding the application possibilities. Each component is individually enclosed. Thanks to the specific design, the inspection unit and the control cabinet are splash-proof from all sides and meet the hygiene requirements of the producers. In addition, this makes cleaning much easier, even with aggressive cleaning methods.” The second innovation is that the LabelWatcher can now also inspect unoriented products with any object shape. The LabelWatcher 360°, the official name for this solution, is an inspection system particularly designed for the quality control of products with 360° labels in any rotational position. Thanks to a newly developed imaging as well as a referencing procedure specially developed for the LabelWatcher 360°, it can now be used to inspect unoriented products just as reliably as customers have been used to with the established LabelWatcher for oriented products. Due to the characteristic of the wrap-around label, the inspection scope of the LabelWatcher 360° is additionally extended by an inspection of the label joint line. IML on the rise IML decorations are increasingly being used on cups and jars. The IMLWatcher is a system for the quality inspection of products with in-mould labels that has already been established in the market for years. “We realised more than 10 years ago that IML labels require special handling and inspection and could only be insufficiently checked with a solution like our LabelWatcher,” reports Janina Orlowski. Due to the special manufacturing process, IML-labelled products also come with special types of defects. For example, the IMLWatcher is one of only a few inspection systems available on the market that YOU CAN HAVE FROM THE SAME RESOURCE Proven 500+ ISBM Molds Globally Enhanced Cavitation Balanced HR System Priority Development Superior Tool Steel IN-House Testing Prompt Tech Support ACME DRINKTEC SOLUTIONS LLP CREATING MOLDS WITH A DIFFERENCE +91-9810418975 +91-9819020785 +91-9810631426 Sales@acmedrinktec.com www.acmedrinktec.com"},{"@ID":35, "PETplanet Insider Vol. 24 No. 07+08/23 www.petpla.net 33 TRADE SHOW REVIEW For all kinds of plastics, especially for rPET Laboratory inspection & analysis by Heike Fischer Sikora AG, known for measuring and control technology, inspection, analysis and sorting systems, presented at the World Recycling Expo in Essen, Germany, the Purity Concept V. This system is based on optical cameras and detects contamination or defects such as black specks or yellow discolourations on transparent and coloured pellets and flakes. PETplanet talked to Mr Felix Wendt, Area Sales Manager. PETplanet: The Purity Concept Systems are used for the offline inspection, analysis and evaluation of plastic materials in the field of nondestructive testing (NDT). Which technologies are applied? Wendt: We offer two laboratory systems, which are equipped with different technologies depending on the application. The customer can choose between an optical system, which detects black specks, colour contamination and colour deviations, or an X-ray based system, for metallic impurities in the pellets. PETplanet: Which measuring principle do you use? Wendt: The material, which shall be inspected, is placed on a sample tray. The latter is moved automatically into the inspection area, where the material is inspected by the optical respectively X-ray camera. The camera image is then further analysed by our analysis software in order to detect contamination. The whole process takes less than a minute. PETplanet: What are the output options for the measurement data? How can these be visualised and qualified? Wendt: Due to the analysis software, included contamination from a size of 50μm are automatically detected, visualised, and evaluated. A projector is used to colour-mark contaminated material on the sample tray. At the same time, the contamination is highlighted on the camera image. This permits a clear assignment of the contamination at any time. Therefore, one can easily remove the contaminated material for a further analysis in the lab. The software also includes an image gallery of detected contamination as well as many statistics and report functions. PETplanet: What is special about the Purity Concept V and where is it used for? Wendt: The Purity Concet V is typically used as a laboratory testing device for quality assurance, e.g. in incoming goods inspection or for material release before delivery to the customer. The system has a colour camera and can be used for many applications. It detects black specks, white spots, colour contamination and discolourations on the surface of flakes, crystalline and amorphous pellets as well as on test plates. What is special about the Purity Concept V, is that it works semi-automatically. Whereas the analysis is fully automatic, the operator can always interact and adjust the settings. E.g., he can zoom in the camera picture and select individual pellets and contamination or adjust the sensitivity of the algorithm according to his needs. The Purity Concept V also provides a test certificate with all information on the quality of the tested material which can be used for material release and delivery. PETplanet: Sikora reports that this technology is particularly suitable for the analysis of rPET. Have you already received feedback from the recycling industry? Wendt: The exchange with existing customers is very important to us, as we want to develop further with them. What our recycling customers mainly appreciate about the Purity Concept V is that it is not a black box. The approach of the semi-automated process simply offers many possibilities and allows the operator to get a good feeling about the quality of the product. A good algorithm is of course the basis, but it can never replace the human eye. In addition, the Purity Concept V can analyse not only crystalline but also amorphous rPET pellets. This allows our customers to use the device at different points in the production chain. Besides, test plates, which are nowadays more often used in recycling industry, can be analysed as well. We received feedback from our customers that they are satisfied with the broad wide of applications that our system offers. PETplanet: Are there requests for further developments of the system? Wendt: Definitely. We get a lot of inquiries or new ideas for new applications, especially at trade shows. We always have an open ear to the market here, and especially in recycling, we would also like to broaden our base. PETplanet: Thank you so much for your time and information you shared with us! www.sikora.net"},{"@ID":28, "MAINTENANCE PETplanet Insider Vol. 24 No. 07+08/23 www.petpla.net 26 Industry 4.0 meets PET facility equipment cleaning based on an article by Steven P. Wilson, Director Dry Ice Cleaning Applications & ESG at Cold Jet LLC Many manufacturers utilising PET have adopted Industry 4.0 in their facilities, digitally connecting systems throughout the entire manufacturing process to streamline production processes, improve quality control, increase operational efficiency, and achieve cost savings. Smart dry ice blasting equipments have now made this IoT technology available to cleaning processes as well. This no longer makes cleaning practices isolated processes that cannot be measured and monitored. The human-machine collaboration that brought new insight to our manufacturing processes, is now available for the cleaning processes. Cold Jet Connect introduces Industry 4.0 capabilities to dry ice cleaning, claimed to providing a clear view of the data which helps to make decisions that will accelerate the return on investment and profitability through increased machine efficiency and uptime. Cold Jet Connect Analytics has been developed to enable continuous tracking and support for dry ice blasting equipment. Possibilities include remote monitoring, programmable cleaning recipes, and service that are now possible on the maintenance side of the operations. From moulding (injection to blow) to bottling and filling (airveyors, glue pots, labellers, conveyor belts, palletisers) manufacturers are able to gain actionable insight to make data-driven decisions to accelerate their return on investment through increased machine efficiency and uptime. Jeff Waters from Microsoft noted that monitoring equipment and processes was key to having proper Product Lifecycle Management (PLM). He reported that ability to monitor equipment reduced equipment failure by 13%, improved quality by 27%, and reduced service costs by 10%. This is very consistent with the objectives of lean six sigma initiatives where manufacturers define, measure, analyse, improve, and control their production processes. Deloitte reported in their 2023 Manufacturing Outlook Survey that Data Analy-tics was the second initiative (behind Robotics and Automation) for U.S. executives. Generally, there are six objectives manufacturers are desiring to achieve when adopting Industry 4.0. Smart dry ice blasting machines equipped with Cold Jet Connect Analytics is claimed to provide insight to all of them: 1) Asset performance management – for the ability to diagnose, predict and plan convenient maintenance schedules, Cold Jet Connect is showing whether the dry ice cleaning machine is used properly and operating properly. 2) Cycle management – the system helps understanding the process. Management can see materials being used (dry ice), time, and true cost of maintenance / cleaning practices. 3) IoT driven scheduling – it is called a time when the equipment needs to be maintained or when and how much dry ice to order. 4) Man/machine collaboration – A guidance on proper cleaning methodology is provided. Take the guess work out of cleaning a variety of substrates with stored cleaning recipes. Ensure good process and performance while minimising consumables. 5) Digital transformation – the system enables a connected process between the factory floor and management. 6) Cybersecurity – Cold Jet ensures a risk-free cyber-physical platform with continuously upgraded, strong security standards. Numerous questions about the cleaning processes can now be remotely monitored without the need to be physical present. Information are provided on questions such as how long does it take to clean that station, how much does it really cost to clean that station, how much dry ice was used during cleaning, are the cleaning crews optimising the blasting parameters, is there a pattern to the cleaning cycles, is it time to replace the blaster etc."},{"@ID":42, "40 TRADE SHOW REVIEW PETplanet Insider Vol. 24 No. 07+08/23 www.petpla.net Sidel, Pascal Lefèvre, Vice President of Food, Home & Personal Care 1) Overall, what were your impressions of Interpack? We are here with our team and exhibits from Food & Beverages and our HPC (Home and Personal Care) business and have had many visitors to our stand for very detailed discussions. We found the fair lively and international. We are particularly pleased to have received the Special Jury Prize at the PackTheFuture Awards for our 1Skin bottle here at the fair. This 1l bottle, which we exhibited for the first time at Drinktec, does without a label for easier recyclability, but provides consumer information by means of engraving and QR code. 2) What aspects of your company offer were you highlighting? We have placed the focus on the end-of-line area. The RoboAccess_Pal S palletising unit is a very compact cell with a footprint of only 12m2, in which we have applied three new patents at once: the light-weighted carbon fibre clamping head is flexible and contributes to a high load capacity; to protect the worker, we have installed a mobile curtain for safe access during pallet feeding and removal; and the patented folding guarding system that allows the whole cell to be compactly folded and moved to where it is needed. We are also introducing the new Cermex ProSelex carton infeed module for asymmetrically shaped containers. It has a capacity of up to 300 ppm (products per minute) and comes with a reduction in changeover time due to a simplified process. An average changeover now takes between 1 minute for a new collation and 2 minutes 30 seconds for a complete bottle change. Friction is reduced by the module’s collating concept, which limits the number of contact points between the collating combs and the products. 3) What will be the coming trends in PET bottles? The answer is simple: sustainability! Our customers want lightweight solutions and a new style for their packaging. Using less material – the amount of plastic required being constantly reduced – but with more recyclates. We offer our customers the option of carrying out trial runs of their materials with us. Many of them come to us with the idea of switching to 100% rPET but as soon as they realise the cost and availability issues involved, they start by testing 30% or 50% rPET. Our company is, of course, able to produce 100% rPET on our machines. www.sidel.com Unscramblers for empty bottles Spanish Posimat featured their recent developments of unscramblers and auxiliary equipment for bottle handling and transport. The robotic unscrambler Compactbot is suitable for the handling of various types of bottles at the same time, including asymmetrical ones, and is designed to automate the filling line quickly and easily even in limited floor space. Changeovers can be easily set up on the display and require no intervention in the mechanics, according to Posimat. The speed is 120 bpm. Posimat also introduced the unscrambler Micro, specially designed for small bottles, capable of performance rates of up to 200 bpm. The bottles are loaded into the unscrambler by a Hopper Elevator where they are distributed on an upper rotating disk and fed into the selectors, located around the periphery of the disk. The containers are simply moved by air and gravity. The bottles then drop from the selectors into the funnels where they are discharged upright on the vacuum conveyor. Format changeover - performable in less than 5 minutes according to Posimat - is performed by simply unplugging and reinstalling selectors and funnels, tailor made for each container format. As the operation does not require any tools or adjustments, it can also be performed by unskilled operators. Micro was developed primarily for pharmaceutical, cosmetics and food applications. www.posimat.com"},{"@ID":34, "TRADE SHOW REVIEW PETplanet Insider Vol. 24 No. 07+08/23 www.petpla.net 32 rPET: made in West Africa and distributed from Dubai, UAE Food-grade rPET with a capacity of up to 500 tonnes/month is produced by the Polysmart Group in Nigeria. The distribution partner is Shad Polymers in Dubai, UAE. PETplanet met live and remotely the dynamic business people running the companies: Wasiu Balogun of Polysmart has dedicated his career to implementing sustainable and environmentally friendly projects in Nigeria in the packaging and recycling industry. Girish Wadhwani is a co-founder of Shad Polymers DMCC. Both bring a wealth of experience in trading and distribution. PETplanet: Mr Wadhwani, could you tell us about the initial idea for rPET and the current status of the company? Wadhwani: Food grade rPET is manufactured by Polysmart Group in Nigeria and distributed by Shad Polymers in Dubai, UAE. Polysmart Packaging Ltd. started operation in January 2013 at Ota, Ogun State Nigeria. Polysmart Packaging belongs to the Polysmart Group. Polysmart Group is a fusion of three companies: Polysmart Packaging Limited, Switch and Recycling Innovations Ltd and Crystal Packaging Ltd. Faced with the increase in plastic waste and to contribute to a greener environment, the founders of the Polysmart Group decided to set up a recycling plant to support this cause and export foodgrade rPET to consumers who believe in their vision of a green planet and a reduction in global warming. PETplanet: In 2022, Polysmart Group began producing food-grade rPET. What technology do you use? What is your current capacity and to which countries and markets do you sell the most rPET? Wadhwani: Polysmart uses European technology approved by FDA and Efsa. Our capacity is 500 tonnes per month and we propose to sell to Europe and USA. PETplanet: What is the importance of the African & European market for Polysmart? Wadhwani: Africa is our home and we are committed to serving the continent that it should not become a dumping ground for the wealthy nations waste as we have enough plastic scrap from our own consumption. To meet this objective, Polysmart has taken the initiative to contribute to this cause and recycle PET waste and convert it to high quality food grade rPET. PETplanet: How do you assess the current PET packaging market? And how do you think this market will develop? Where do you see growth potential for the sale of rPET worldwide? Wadhwani: The PET packaging market is currently experiencing unprecedented growth. This is due to a number of factors, including increasing demand for packaged food and beverages, growing awareness of environmental issues, government regulations and the emergence of new technologies. By the year 2050 we expect that 50% of the material required would be recycled, reusable and environment friendly. Due to this many projects are on stream to meet this demand. PETplanet: There are more and more companies around the world that attach importance to a sustainable economy. How do you assess the efforts towards a sustainable economy in West Africa? Wadhwani: Africa has the largest bottle recycling plants in Nigeria, South Africa and Ghana. We expect many more plants to start operation in the next five years. The movement for a sustainable circular economy is catching speed and with the resources available in Africa, we expect Africa to be the leading continent to service global sustainable cycles. PETplanet: We at PETplanet will be doing an interview tour, our so-called Editour, of the Middle East this autumn. Which regions can you recommend to us? Where do you see promising developments in the packaging industry? Wadhwani: I would suggest visiting UAE, Saudi Arabia and Oman. PETplanet: Even though it is almost impossible to predict the future: Where do you see Polysmart Group and Shad Polymers in ten years? Wadhwani: We expect to be in the top five players in West Africa. We plan to increase our capacity fivefold in the near future. PETplanet: Thank you very much for your time and your willingness to share your knowledge with us! Wadhwani: Thank you for giving Polysmart Group and Shad Polymers an opportunity to share our products through your platform. www.shadpolymers.com www.polysmartgroup.com F.l.t.r.: Shad Polymers Managing Director Girish Wadhwani and Ms Heike Fischer, PETplanet, at the Plastics Recycling World Expo 2023 Mr Wasiu Balogun, CEO of Polysmart Packaging Ltd."},{"@ID":1, "No.7+8 2023 www.petpla.net D 51178; ISSN: 1438-9452 31 . 07 . 23 MAGAZ I NE FOR BOT T L E R S AND BOT T L E - MAK E R S IN THE AMER ICAS, AS IA, EUROPE AND AL L AROUND THE PLANET PETplanet is read in more than 140 countries MARKETsurvey Suppliers of compressors Page 28 Page 38 Page 42 Page 35 Page 32 LABELLINGPage 14"},{"@ID":52, "PETplanet Insider Vol. 24 No. 07+08/23 www.petpla.net 46 PETbottles Beverage + Liquid Food New variants of Vio With consumers becoming increasingly sceptical about sugar, sugar substitutes or sweeteners in drinks, manufacturers are developing new products to offer the desired products. The latest example is a beverage series from Vio that does not need a name additive such as organic or light. The new product is just called Vio - a carbonated soft drink without sugar or calories. Only the addition - depending on the variety, inspired by Spain (peach watermelon), the Caribbean (lime mint) and Italy (lemon lime) - gives clues. One litre of the transparent drink is filled in each bottle, which is made of 100% rPET. The labels are designed to match the individual varieties and an opaque screw cap with brand lettering completes the pack. www.coca-cola-deutschland.de A distinctive bottle for Valensina Wh i l e Va l ens i na uses the familiar bottle for the non-chilled juices, a distinctive bottle is used for the chilled direct juices in the “... Morgen” range, Valensina uses a distinctive bottle. The stable, transparent bottle has a rectangular basic shape and then merges into a round neck with a sufficiently large opening. It contains one litre of juice and - depending on the variety - is labelled with different descriptions such as ‘Munterer ’, ‘Klassicher ’, ‘Schwungvol ler ’ or ‘Exotischer ’ Morgen. A plastic label conveys the dates and juices contained. A raised Valensina lettering is incorporated in the area of the transition from square to round. www.valensina.de Hydration drink in PET The Dutch company Body & Fit Sportsnutrition B.V. is now selling a product without sugar and caffeine, but with vitamins and minerals, under the brand “LevlUp”, which has its origins in the gaming sector and suppl ies gamers wi th dr ink supplements or RTD drinks. The drink is designed to help gamers stay hydrated. Under the name “LevlUp Hydration Drink”, there are three flavours to choose from; Galaxy, Nuke and Bubble Gum. Each is filled in 500 ml in a transparent bottle, which is decorated with an almost full sleeve label and sealed with an opaque screw cap. www.levlup.com 2023 Training Schedule Technology&Application of PET Plastic Packaging for Hot-Fill &Aseptic Beverages Join our expert team for small group training on a variety of subjects - frommaterials to recycling. Scan to learn more & register for classes! ©2023 Plastic Technologies | 1440 Timberwolf Drive, Holland, Ohio USA 43528 www.pti-usa.com info@pti-usa.com info@pti-europe.com"},{"@ID":7, "MARKET SURVEY 29 PETplanet Insider Vol. 24 No. 07+08/23 www.petpla.net Compressors Compressors – not often in the spotlight perhaps, yet a vitally important component of PET production, and with significant potential of energy saving. Our annual market survey takes a closer look at these unsung heroes of the PET industry, featuring compressor manufacturers and their product range: AF Compressors, Siad Macchine Impianti, ABC Compressors, Kaeser Kompressoren, Atlas Copco Airpower, Nanjing Shangair Machinery Manufacturing and Dalgakiran Compressed Air Technologies. Although the publishers have made every eff ort to ensure that the information in this survey are up to date, no claims are made regarding completeness or accuracy. Resins & additives Preform machinery Preform production & inspection systems Preform & SBM mould manufacturer SBM 2-stage Compressors All about caps Filling equipment & inspection systems Palletising & shrink film machinery Recycling machinery Atlas Copco Nanjing Shangair Machinery Manufacturing Co., Ltd. Dalgakıran Compressed Air Technologies www.atlascopco.com Mr Kris Vermeulen Global Product Manager PET kris.vermeulen@atlascopco.com No.1, Xiyan Road, Binjiang Economic Dev. Zone, Jiangning District, Nanjing +86 25 8640 8239 www.shangair.com Mr Edward Zhou Overseas Sales Manager +86 1519 595 1347 rusia@shangair.com Eyup Sultan Mah. Muminler Cad. No:70 Sancaktepe / Istanbul, Turkey +90 216 311 71 81 www.dalgakiran.com Mr Alp Halil Yörük Strategic Marketing Director +90 216 311 71 81 alp.yoruk@dalgakiran.com ZP, ZP VSD ZD FF, ZD VSD FF ZD Xtend ZD Flex WM Rotary screw, reciprocating and turbo compressors 3 18 56 2,500 2 25 170-835 902-4,195 500-7,500 400-10,000 60-72 0,16 - 20,000 55-132 820-4,100 90-900 / 85-315 55-2,500 / 55-315 No No Yes, fi xed pressure setting Yes, pressure to choose Tidy, D Series 3-stage piston 2-stage screw + adsorption dryer + 2-stage piston 2-stage screw + adsorption dryer + 2-stage piston 2-stage screw or 3-stage turbo + adsorption dryer + 1- or 2-stage piston Reciprocating Pet Master, turbo compressors No yes, adsorption dryer yes, adsorption dryer yes, adsorption dryer 60m3/min, 72m3/min, air tank 150 l DPR-D Oil-free Oil-free, Class 0 Oil-free, Class 0 Oil-free, Class 0 Oil splash lubricate Piston 2-stage screw + adsorption dryer 2-stage screw + adsorption dryer 2-stage screw or 3-stage turbo + adsorption dryer 30bar Scroll Piston 2-stage piston 2-stage piston 1- or 2-stage piston Booster series Air cooled Adiabatic water cooling available Adiabatic water cooling available Adiabatic water cooling available Eagle Balance opposite piston Oil-free screw balance opposite piston Oil-free screw Balance opposite piston Oil-free screw Balance opposite piston 3 4 4 3 or 4 or 5 2 Single and double No No No No No Air cooled included Water cooled Water cooled Water cooled Air cooled No Belt Gearbox Gearbox Gearbox, direct drive Belt Tidy, Inversys Plus Belt Belt Belt Belt Pet Plus, Inversys DPR, Impetus No Heat of compression dryers for energyless drying Heat of compression dryers for energyless drying Heat of compression dryers for energyless drying DVK-D, Inversys Plus"},{"@ID":23, "TRADE SHOW REVIEW PETplanet Insider Vol. 24 No. 07+08/23 www.petpla.net 42 Monomer purification with melt crystallisation in PET recycling The chemical research and development company Shanghai Dodgen Chemical Technology Co., Ltd., based in Pudong, which has been active since 2005 in the fields of process technology for biosynthetic materials, degradable plastics and recycling or additive production, also presented itself and its fields of activity in relation to chemical PET recycling. Marketing Manager Kathy Lee explained the challenges and opportunities involved and Dodgen’s corporate approach. Mechanical PET recycling degrades the mechanical properties of the plastic and affects the mechanical performance of the recycled PET products, which limits their application to some extent. In China, mechanical recycling of PET is well established and the market for bottleto-fibre recycling is mature; bottle-tobottle recycling though has to meet the requirements of bottle processing and food packaging. This has led to the development of chemical recycling technologies such as chain degradation and re-polymerisation. Chemical recycling involves the conversion of PET polymer chains, depolymerising the polymer into oligomers or monomers. After the purification process and other treatments, these materials can be used as raw materials for the production of chemical products. Research and development is ongoing in the field of chemical recycling of PET, and significant progress has been made in areas such as alcoholysis, enzymatic hydrolysis and advanced recycling, some of which have been successfully commercialised. Chemical recycling can be achieved by processes such as hydrolysis, sugar fermentation, methanolysis or saponification, producing different degradation products. This article focuses on the development and commercialisation of the PET alcoholysis method. The commercialisation pathway for PET alcoholysis recycling DuPont has introduced methanolysis with Lewis acid as a catalyst for PET recycling. This process is suitable for recycling PET containing dyes, coatings and other polymers. It is said to have a production capacity of 50,000 to 80,000 t/a. Companies such as Goodyear, DuPont and Hoechst in the United States have already implemented EG (ethylene glycol) hydrolysis on an industrial scale. Fujita has also publicly reported on related technologies and suggested wetting shredded tissues with EG before entering the hydrolysis system to speed up the reaction. China’s Zhejiang Jiaren Company has worked with Teijin of Japan on Eco Circle technology, which can produce finer fibres at the same level as virgin PET. It is suitable for recycling waste polyester garments that contain dyes and pigments. Sabic in Saudi Arabia is the first in the industry to use chemical upcycling to produce renewable PBT polyester, turning plastic waste into valuable resources. Eastman’s polyester recycling technology uses sugar fermentation or methanolysis to depolymerise waste into base monomers to create new materials. Guangdong Shuye Environmental Protection applies ethylene glycol hydrolysis, which uses ethylene glycol as a depolymerisation agent to convert PET into BHET under high temperature and pressure. The BHET is then repolymerised into rPET, rPETG, flakes and films. Problem of the alcoholysis method The current process of PET alcoholysis is relatively complex, be it methanolysis or ethylene glycol (EG) hydrolysis. The raw products have to be refined, filtered and purified before they can be reused for the production of recycled PET or other products. As the main target products of depolymerisation are BHET or DMT, deep depolymerisation is required, resulting in long reaction times. High purity of monomers is required, making separation and purification a challenge. The process has a lengthy workflow and high energy requirements. Dodgen has achieved numerous successes in melt crystallisation for the purification of DMT and EG. www.dgchemtech.com Dodgen employees show their developments to interested guests."},{"@ID":36, "TRADE SHOW REVIEW PETplanet Insider Vol. 24 No. 07+08/23 www.petpla.net 34 PET and polyolefi n recycling Inline viscosity measurement by Heike Fischer PETplanet: In your opinion, what are the advantages for testing the rheology of thermoplastic polymers compared to other methods? Lorenz: Rheometers or viscosimeters are a relatively inexpensive and quick way to determine flow properties which are essential to design or set-up manufacturing processes for plastics. The simplest viscosity measuring device is a melt flow indexer which can be found in almost every company converting or manufacturing plastics or plastic goods. PETplanet: Would you please briefly explain the traditional offline Capillary Rheometer measurement process? Lorenz: In a typical setup, polymer is molten inside a heated cell or container, normally cylindrical, and forced by means of a piston through an orifice with specific dimensions. This can be done by simply putting a weight on that piston that would push the molten polymer through the orifice. In other methods the piston is operated by a drive that can apply either a constant load or a constant or controlled speed to the polymer melt. Characteristic properties like MFR (MVR) or viscosity can be calculated directly from the test parameters and resulting measurements (speed, force). PETplanet: You have now translated this process into an online system. How is it basically structured? Lorenz: The main goal here is to have a continuous measurement that provides real-time viscosity data. We are still using an orifice (or capillary) through which the polymer is pushed through. Instead of a piston, we are using a gear pump to convey a side stream from the main extrusion stream of polymer through a heated flow block and the capillary. This allows us to apply similar techniques as described above. Either the system operates at a constant pressure which in turn gives data like MFR or MVR or the system is operated at a controlled speed which allows to calculate shear viscosity from the data. Usually thermal or geometric corrections are applied to compare these data with numbers derived from lab tests. Typically, the comparison is very good so you not only have a real-time process overview but potentially could save a lot of lab time by implementing such systems in your production. PETplanet: You presented two types of rheometers, the Continuous Melt Rheometers (CMR IV) and the Zero Discharge Rheometers – ViscoSensor. How do they work? Lorenz: There are mainly two types of instruments: a CMR IV is an open system where the measured melt stream goes through the system (pump – flow block – capillary) and then exits the system. This small stream of polymer is then discarded but could also be used for subsequent verification. The ViscoSensor in turn is a closed-loop, return stream system. The measuring stream is being pushed through the capillary but subsequently is fed back to the main process (pump 1– flow block – capillary – flow block – pump 2). Both systems have advantages and disadvantages depending on the application. PETplanet: What about rPET applications? Lorenz: These systems are commonly used along the whole value chain from resin production over conversion into e.g. film, sheet, compounds and in mechanical or chemical recycling. The very typical scenario for us is rPET. Making pellets from flakes or other recycled sources is a very common application for our systems. A real-time continuous viscosity measurement can help to accurately determine the quality of PET pellets which is critical for all subsequent steps in the production process. Deviations in the production process and the product quality can quickly be identified and measures can be taken to keep the consequences minimal. Furthermore, our systems provide a correlation between melt viscosity and IV (intrinsic viscosity). IV has the same importance in the PET world as MFR or MVR would have with plastics like PE, PP, PS,… Knowing the IV right away can be important in time critical value chains. Lot-tolot variation can be kept to a minimum or eliminated entirely. Furthermore, lab utilisation can be reduced. PETplanet: Do you already have systems in the rPET market? What is the feedback? Lorenz: We have numerous systems in use at recyclers, film and sheet manufacturers and integrated flake-toproduct operations (bottles, film, foam, fiber). Everywhere, where IV is a critical parameter (hence everywhere) and the more detailed this information can be provided there is always benefit in using this kind of system. Specifications can be narrowed down, stock can be easily sorted and classified, incoming stock (e.g. flakes) can be utilised better and lab work can be reduced only to name a few benefits. PETplanet: Thank you very much. www.dynisco.com Polymer manufacturers need to create new materials and deliver high quality to meet ever changing end-use requirements. Precise testing and analysis are mandatory to ensure quality and to stay competitive. Dynisco analysers, including melt flow indexers, and rheometers, are well-known for testing the properties of polymers. Material analysis solutions range from the analysis of a polymer in the laboratory, to online quality control in production, to processing small quantities of special polymers or composites. At the Plastics Recycling World Expo, PETplanet spoke to Johannes Lorenz, Sales Manager at Dynisco, about inline viscosity measurement in PET and polyolefin recycling."},{"@ID":13, "MATERIALS / RECYCLING PETplanet Insider Vol. 24 No. 07+08/23 www.petpla.net 11 MATERIALS / RECYCLING 11 ing the possibility of expanding production in Rotterdam. For bio-glycol production, the business unit uses beechwood from sustainable forest management and side streams from sawmilling operations. All of the wood will be FSC- or PEFC-certified. However, the company is also involved in the planting, growing, harvesting and collecting of beech wood itself and claims not to compete with land for food production or to use any fertilisers - two of the biggest criticisms of some other organic raw materials such as sugar cane. UPM also uses wood from routine thinnings which are required for sustainable forest management. It is important to note that currently more than 60% of the beech wood harvested in Germany are burnt for energy generation. In the processing stage, the cellulose is then turned into bio-glycols, lignin into functional fillers (used mainly in the automotive and rubber industry) and hemicellulose into industrial sugar. “Unlike oil or natural gas, the use of renewable carbon from wood to make biobased products - along with carbon from direct CO2 use and carbon from recycling existing materials - will play an important role in achieving a net-zero future,” Dr Duetsch is convinced. “In a world where 96% of products, including plastic packaging, rely on chemical intermediates, the chemical industry is a key enabler and urgently needs to find alternatives to fossil feedstocks to help address the climate crisis.” Biorefinery (almost) ready for take-off The project, which does not yet exist in this form anywhere else, is scheduled to start at the end of 2023. More than 100 jobs have been created in the 16-hectare biorefinery and a total of 220,000 t of bioMEG and lignin-based Renewable Functional Fillers (RFF) sold under the brand UPM BioMotion. Use segments include textiles, packaging including PET, coolants, refrigerants, composites, pharmaceuticals, cosmetics and detergents. “We will only use locally sourced and certified beech wood as raw material,” explained Dr Duetsch. “This sustainable source will be used to produce a new generation of renewable bio-based ‘drop-in’ glycols.” Instead of burning the harvested beech wood for energy production, using it in more durable and recyclable products would make much more efficient use of the (MKMXEP VEXMSREP TVSƤXEFPI ;LEX IPWI# SACMI.COM 300 4VIJSVQ MRWTIGXMSR ERH TVSGIWW IRLERGIQIRX MRGPYHIH DIGITAL (MKMXEP TVSGIWW GSRXVSP VIEGLIW TVIZMSYWP] YRXLMROEFPI PIZIPW STIRMRK YT XLI MRHYWXV] XS -S8 WGIREVMSW RATIONAL 7%'1- 4VIJSVQ :MWMSR 7]WXIQ MRGPYHIH JSV EHZERGIH GSQTVILIRWMZI TVSGIWW GSRXVSP PROFITABLE '330 TSWX GSSPMRK MRWMHI GSSPMRK W]WXIQ\r WLSVXIRW G]GPI XMQIW ERH PIEHW XS QSVI TVSƤXEFPI TVSHYGXMSR momic"},{"@ID":8, "PETnews 6 NEWS PETplanet Insider Vol. 24 No. 07+08/23 www.petpla.net GlobalData: Asia to lead global PET capacity additions by 2027 Asia is set to lead the global PET industry capacity additions with a share of 61.8% by 2027, by gaining capacities from new-build and expansion projects between 2023 and 2027, according to GlobalData, a leading data and analytics company. GlobalData’s latest report, ‘Polyethylene Terephthalate (PET) Industry Installed Capacity and Capital Expenditure (CapEx) Forecasts by Region and Countries Including Details Of All Active Plants, Planned and Announced projects, 20232027’ reveals that the total PET capacity of new-build and expansion projects in Asia is expected to be 5.21 million t/a (mtpa) by 2027. Increased usage of plastic in end use industry segments such as food and beverages, FMCG and pharmaceuticals are the key factors for PET industry growth in Asia. Nivedita Roy, oil and gas analyst at GlobalData, comments: “For the upcoming new build projects, the region is expected to add a capacity of 5.13mtpa from six planned and announced projects, whereas, for the expansion of the existing PET projects, the region is expected to add a capacity of 0.08mtpa from two announced and planned projects.” PET capacity: China and India key countries China and India are the key countries in Asia in terms of PET capacity additions. The main capacity addition in China will be from an announced project, Zhejiang Petrochemical Daishan Polyethylene Terephthalate Plant 2, with a capacity of 2mtpa. It is expected to commence production of PET in 2026. Nivedita concludes: “In India, the main capacity will be from Reliance Industries Dahej Polyethylene Terephthalate Plant 2, with a capacity of 1mtpa. It is expected to come online in 2026.” www.globaldata.com CCL Labels acquires IML business Creaprint SL in Spain CCL Industries, a leader in speciality label, security and packaging solutions for global corporations, government institutions, small businesses and consumers, announced it has acquired privately held Creaprint S.L., based in Alicante, Spain. Creaprint is a specialist in mould label (“IML”) producer with a manufacturing facility in Alicante, Spain, and a sales office in Miami, Florida, with 2022 sales of $17 million. Creaprint has recently invested in a new production facility where operations will relocate later this year. The business will now trade as CCL Label Spain and become an integral part of the Food & Beverage unit in Europe. Coincidentally, the recently announced acquisition of Pouch Partners s.r.l. Italy (“Pouch Partners”) from Pouch Partners AG Switzerland, closed on June 6. www.ccllabel.com Recycling record for PET to PET: 17,700 tons in the first half of 2023 Following last year’s recycling record, PET to PET Recycling Österreich GmbH in Müllendorf, Austria, has once again recorded a record figure for the first half of 2023: 17,755 t of PET beverage bottles were kept in the resource cycle – an increase of more than 17% compared to the previous year (2022: 15,131 t). “We are of course delighted with the increase in the volume processed and thus an even better closing of the PET beverage bottle loop in Austria – however, we are looking forward to a very challenging future. In the second half of the year, a significant decline in recyclates used is expected on the market, due to a persistently difficult economic situation, still very high inflation and, above all, a large price difference between primary raw material (virgin) and secondary raw material (recyclate),” explains Christian Strasser, managing director of PET to PET. Innovations at PET to PET: Construction of a PV plant The site area for the storage of food-grade finished products, which was expanded in 2022, was successfully roofed over in a further step. A photovoltaic system with an area of 6,400m² and an output of 1,200 kWp is currently being installed on the completed roof structure. This will involve the use of 2,373 PV panels, which in future will cover around 8% of the electrical energy required from the company’s own generation. In further expansion stages, this value is to be further increased. In the past, the recycling company has already relied 100% on renewable energy to operate its plants. www.pet2pet.at"},{"@ID":45, "PETplanet Insider Vol. 24 No. 07+08/23 www.petpla.net 43 TRADE SHOW REVIEW High-speed all-in-one solution for medium-sized bottlers Guozhu Group from Guangdong, active in the production of blow moulding machines, turnkey blocks for beverage filling, as well as preform and blow moulds, presented its fully automatic linear blowing-filling-capping series PMLBGX-6-28-10 in Shenzhen. The lines, which are specially designed for medium-sized beverage producers, can be operated in the PMLBGX-6-2810 version shown on the stand with a choice of six cavities for 12,000bph for 600ml or three cavities for 4,500bph for 1.5 l bottles. The Guozhu Group also has a 9-cavity version in its portfolio, which is to offer 16,000bph at 600ml capacity. In addition to the compact design (total installation just about L 11.2 x W 2.1 x H 2.2m), the company points in particular to the machine’s energy-efficient processes, such as energy-saving preformer heating and short internal transport paths within the blowing and filling/capping unit. Overseas Marketing Manager Laura Cai explains, “Around 40-50KW of operating power is consumed by the PMLBGX-6-28-10 shown here. The larger 9G model is around 60-70KW.” Mould changes and basic maintenance work should also be able to be carried out quickly thanks to easily accessible areas with just a few hand movements. “A phenomenon that can be observed particularly well here in China is that nowadays medium-sized beverage producers demand a high degree of format and product flexibility while still maintaining a comparably reasonable production capacity. At the same time, investments in technical equipment are an essential issue for such companies and often the available space in production is limited. We want to react to these requirements and applications accordingly and not only offer our all-in-one solution at an attractive purchase price, but also make the processes in ongoing production more economical. www.guozhu-pet.com F.r.t.l.: Johann Lange-Brock, Media Consultant PETplanet, Laura Cai, Overseas Marketing Manager Guozhu Group and Kay Barton, Editor PETplanet PRODUCTS PETproduct Metallised coatings for PET bottles Singulus Technologies is a global provider of production technologies for the manufacture of high-tech products. The company has recently launched a range of metallised coatings that it claims are recyclable. Traditional metallised coatings often utilise non-recyclable materials and harmful substances, raising environmental concerns. Addressing this issue, Singulus Technologies says to have successfully produced metallised finishes on PET plastic that have passed key recyclability tests, including metal detection and NIR (Near Infrared) technology for resin identification. These tests were conducted by certified test facilities of the Association of Plastic Recyclers (APR). Compared to conventional metallising processes, Singulus Technologies claims that the new coatings offer a number of advantages. Using the new coatings, resin-based spray primers and topcoats can be avoided on various substrates, including PET, SAN, and glass. The coating require less energy to apply, thus offering substantial cost savings. From an environmental standpoint, the processes emit zero VOCs (Volatile Organic Compounds), eliminating the need for EPA (Environmental Protection Agency) reporting. Thin-film technology and surface treatment Singulus Technologies develops and builds machines and equipment for efficient production processes in thinfilm technology and surface treatment, which are utilised world-wide in the markets of photovoltaics, semiconductors, medical technology, packaging, glass & automotive as well as batteries & hydrogen. The company’s core competencies include processes of coating technology, surface treatment as well as wet-chemical and thermal production processes. www.singulus.com"},{"@ID":29, "MAINTENANCE PETplanet Insider Vol. 24 No. 07+08/23 www.petpla.net 27 MAINTENANCE 27 All of these new cleaning capabilities support the five pillars of predicable cleaning in manufacturing: process, people, practice, punctual, and purlieus. Cleaning with smart dry ice blasting machines, from manual to fully automated and integrated cleaning solutions, provides a powerful and reliable process, says Cold Jet. So that the benefits can be fully exploited, people in the organisation must be well trained and informed though. Smart dry ice blasters provided with the Cold Jet Connect platform put both machine and application training at operator’s fingertips via a QR code. A library of training videos ensures operators are using their machine most effectively. To better standardise and monitor practices, smart machines have on-board recipe storage to take the guess work out of operator’s hands. Machines are password protected with lockout screen capabilities. Last but not least, operators have an insight to accurate cleaning times for improved cleaning results and environmental sustainability. Reporting of proper and timely cleaning is also critical. Cold Jet Connect provides a variety customisable cleaning reports: per job reports, daily reports, monthly reports to annual reports can be generated to document the cleaning process. Smart machines provide not only unrivaled cleaning intelligence but a remote support platform including diagnostics and service. The mobile app with augmented reality to connect with a Cold Jet technician gives the ability for a virtual guided repair via the phone or tablet along with the selection between a chat function or just scheduling an in-person service visit. Cold Jet says that cleaning with dry ice offers a green, sustainable solution for those focused on ESG initiatives. Being a product of carbon capture and utilisation (CCU) process, it does not add to the greenhouse gas (GhG) emissions score or CO2 carbon footprint calculation. The cleaning process is dry, non-abrasive and does not leave a secondary waste stream behind. Industry 4.0 technology helps to understand, controll and delegate daily cleaning practices. www.coldjet.com"},{"@ID":18, "LABELLING PETplanet Insider Vol. 24 No. 07+08/23 www.petpla.net 16 Discussing the increase in recoverability by using magnetic coatings on shrink sleeves Breaking barriers in PET recycling by Gabriele Kosmehl Shrink sleeve labels have long been identified as an obstacle to PET bottle recycling. With their patented magnetisable coatings, the start-up Magnomer aims to overcome these challenges. Their Magmark coatings, when applied to shrink sleeves, are claimed to allow efficient and economical separation – utilising existing infrastructure. The technology has garnered industry recognition and is poised to boost PET recycling rates. PETplanet: Ravish, first of all, can you briefly introduce your company, please? Ravish Majithia: Magnomer is a materials startup located in Framingham, MA, USA & Mumbai, India, introducing a patented magnetisable coatings technology called Magmark to transfer sortability features for recyclable packaging. Magmark coatings are printed using industry standard techniques as a transparent varnish to impart magnetisation on flexible films such as bottle labels. This complements widely used magnetic separators in plastics recycling to economically separate problematic labels. Magnomer’s coatings technology is a packaging design tool used to resolve long standing sorting issues in package recycling such as label contamination. Magnomer has received industry recognition from the Association of Plastic Recyclers (APR) on the basis of a first ever commercial scale recyclability test of shrink labelled bottles. PETplanet: Which labels exactly belong to the “problematic” category when it comes to economic separation and how can companies implement your technology in practice? Ravish Majithia: Shrink sleeve labels are simultaneously an excellent marketing resource - they are the fastest growing label category; and a significant deterrent to circular recycling of PET bottles. Major recycling associations like Recoup in UK, the Association of Plastic Recyclers (APR) in North America and European PET Bottle Platform (EPBP), Petcore and Recyclass in Europe have identified shrink sleeve labels and specifically PETG shrink sleeve labels as one of the biggest issues in PET recycling. The problem is sortation - sorting PETG shrink sleeve labels away from the PET bottles stream is the need of the hour. Magnomer has developed a magnetisable coating which allows for easy sortation of shrink sleeve labels away from the PET stream. Magmark SS coating is a transparent, foodsafe coating which can be printed on the labels using common high speed printing techniques like gravure and flexographic printing in high speed processes. The coating can be printed along with existing graphics requiring little to no modification to the printing operations, allowing for easy adoption with no capital expenditure required. We have proven our technology on a commercial scale. Over two metric tons of bottles with Magmark SS coated shrink sleeves were introduced into regular operations at two commercial PET reclaimers, Evergreen recycling and Indorama Ventures. More than 99% of the contaminating label flake was removed using magnetic separation. Based on the positive feedback from the reclaimers and their glowing testimonials the Association of Plastic Recyclers (APR) in North America awarded Magnomer the Innovation Recognition in June 2023. The coating itself does not impact any bottling process. PETplanet: Do recyclers need additional equipment to achieve a good separation performance of magnetisable ink sleeves? LABELLING Ravish Majithia, Co-Founder & CEO at Magnomer"}]}}
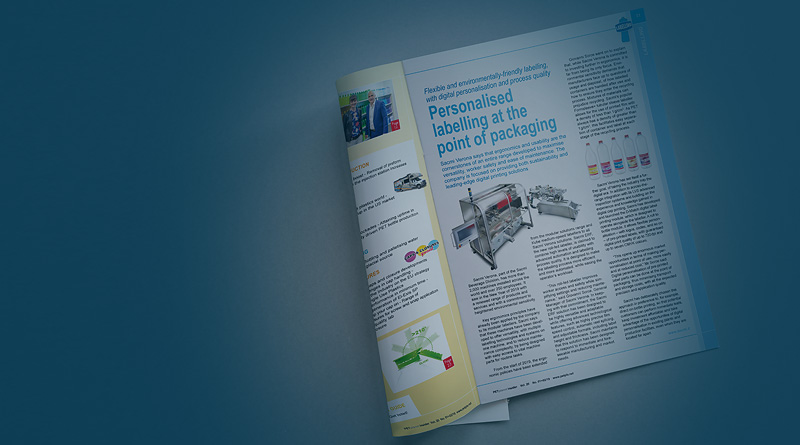