"TOP TALK PETplanet Insider Vol. 21 No. 12/20 petpla.net 11 PETplanet: If we take a look at the North American market: apart from Covid-19, what other trends in bottle sizes and design can you observe here? Eric Roegner: We have continued to focus on sustainable innovation and technology as our primary growth levers. It is an area where we have launched on average over 200 products per year. We have been able to develop proprietary technologies that have allowed us to have 170 patent families. If you look at the key products we are launching, they are around design for recyclability, lightweighting, barrier capability, as well as increased use of PCR. Design and size trends will always be built on the brand and the desired customer experience. Our role is to deliver that. This is where Amcor’s innovation engine shines. We have consistently driven innovation that enables sophisticated designs, along with lighter weight packages with more PCR. We design bottles that cater to everything from sample size to elaborate detail that delivers distinction on the shelf - what the most brand - loyal customer craves. PETplanet: To what extent has the Covid-19 pandemic changed your internal processes? And which of these can you foresee implementing in the long term? Eric Roegner: Everything we do at Amcor starts with safety. Given the context around Covid-19, we’ve also focused on keeping our teams healthy as well. As we continue to navigate the additional risk and complexity of operating during the ongoing pandemic, we remain confident that the health and safety protocols we implemented – and continue to evaluate - will enable our co-workers to remain healthy and keep our plants running as they have been thus far. We have successfully navigated and implemented technology platforms to lessen the frequency of visits and reduce the potential spread of Covid-19. From the customer visit to our manufacturing plants, our goal is to keep everyone safe. PETplanet: And which of these can you foresee implementing in the long term? Eric Roegner: It’s unclear what a post-pandemic business environment will look like. We’re prepared to meet any challenges with the ultimate goal of protecting the health and safety of all our stakeholders. PETplanet: What is Amcor’s experience with digital exchange? Do you think you will continue this approach in the post-Covid era and are you aiming for a “back to normal” as soon as possible in terms of business travel and customer visits? Eric Roegner: With travel restrictions reducing face-to-face engagement, we’ve changed how we interact with our work teams and customers by incorporating more video conferencing. This technology has become the backbone of our work-from-home practices, like so many other employers around the world. Almost instantaneously, our home and work lives have collided, but we’re managing through it with great success. At the same time, I’m very proud of our 50-plus plants that continue to run, uninterrupted, throughout the last nine months of this pandemic. Their tireless effort and unwavering commitment to our customers has resulted in the continuous supply of essential packaging during this most critical time in our history. Now, I spend most of my time in virtual meetings – sometimes those meetings include family member cameos. Today, we update profiles, share content, and incorporate the right key words and hashtags so people can find us quickly. Working through the pandemic stay-at-home orders, social media channels have enabled the supply chain to remain “open for business.” Our sales team found opportunities through social media friends and community organisation timelines. LinkedIn was where customers offered us virtual “pats on the back” for on-time deliveries and maintaining production schedules and commitments, often to their own local communities. PETplanet: How is Amcor responding to environmental challenges? Eric Roegner: Requirements for packaging are increasing with endof-life solutions and waste reduction being critical. Consumers want packaging to be cost-effective, convenient, easy-to-use, great-looking, and more sustainable and leading to less waste. Responsible packaging is the answer. Amcor packaging is already recyclable or reusable, including more than 95% of the Amcor rigids portfolio. The company continues to design packaging that uses less material in the first place. Amcor became the first global packaging company pledging to develop all its packaging to be recyclable or reusable by 2025, directly addressing a major environmental issue with its capability, scale and reach. PET bottles and jars often have the lowest carbon footprint and their production results in up to 70% less greenhouse gas emissions than other packaging materials, according to Amcor’s Asset Lifecycle Analysis. PETplanet: A big talking point currently is 100% rPET beverage bottles. Is it simply a marketing tool or is it a sensible route to sustainability? Eric Roegner: We don’t consider the use of post-consumer recycled materials to be a trend. We have been working with customers to incorporate 100% PCR materials into their packaging for over 15 years. Customers are being very strategic and have recognised the importance of a circular economy for all packaging, including PET bottles and jars. We have seen a radical growth rate in the use of PCR. As the industry leader in the use of PCR, we have many commercialised packages in 100% PCR and utilised more than 100 million lb annually over the last 3-4 years. PET, which has rapidly become the world’s preferred packaging material, is lightweight, shatterproof, resealable, reusable, and infinitely recyclable. Amcor is one the industry’s best equipped manufacturers of PCR bottles, capable of maintaining high quality and a highly stable and consistent manufacturing process. The company is a leader in advancing the use of PCR in a range of PET and HDPE packaging. Amcor incorporates varying percentages of PCR for its customers and has invested significant time and resources in developing and securing reliable sources of the highest quality PCR plastics. PETplanet: Thank you very much Eric! www.amcor.com","@ID":13}, "PREFORM PRODUCTION PETplanet Insider Vol. 21 No. 12/20 petpla.net 18 XActive-Cleaning cuts dust in hot runner systems Sipa has taken an innovative approach to tackling the problem of recycling used PET bottles in the development with Erema of the Xtreme Renew system. But this is not the only route that Sipa is pursuing: XForm systems too can produce high-quality preforms in rPET. Special measures need to be adopted to make this possible, however, since rPET does have special characteristics. One of these relates to fine PET particulates – powder, dust– and how it can accumulate in hot runner systems. These are a concern in any preform processing system, but when it comes to rPET, the concern is greater. Over time, PET dust builds up on the inside the cylinders of the actuators. Initially, this powder does not cause any problems, but as it accumulates, it inhibits the movement of the pistons, eventually severely compromising the quality of the preforms. If not treated, this accumulation can cause the system to seize up completely. Cost-effective solution Important producers of hot runners have known about this problem for a long time, and a lot of work has gone into developing ways to counter it. Sipa has developed solutions that keep production of dust to very low levels. With the growing use of rPET, Sipa decided to take a new look at dust, and to devise an easier and more cost-effective solution to the problem. Simplicity is key to ensuring that the risk of malfunction is minimised. Sipa aimed for a system that could run continuously for five million cycles before those moving parts subject to wear – piston seals, valves, and so on – needed to be replaced. In a system running with a cycle time of 7 s, that means it would be able to work continuously for 10,000 h. Guided by this vision, Sipa’s engineers came up with a system, which the company has since patented, which adapts the compressed air flows, normally used to move the hot runner valves, to also blow out the very few plastic particles that deposit inside the actuators each cycle. Sipa calls the system XActiveCleaning. XActive-Cleaning principles The hot runner system is equipped with a supplementary circuit incorporating a series of valves which, controlled with appropriate logic, govern the entry and discharge of air from the cylinders, making sure that any PET dust particles created in the system are evacuated every cycle. This solution should on its own be sufficient to keep the system clean. To be absolutely sure, there is also a “boost” function that can be activated to perform a forced cleaning cycle, at intervals that can be set by the user (every 40,000 cycles for example). This process lasts for a few tens of seconds, so it has no impact on productivity. High cavitation moulds Sipa has engineering expertise in moulds and hot runners, as well as machines for PET preform injection moulding systems. As an illustration of this prowess, Sipa conceived, designed, built, and delivered preform mould hot runner system with 192 cavities for one of the world’s leading PET container makers, based in North America. This presented an important challenge in ensuring even and consistent filling of all cavities, at high speed, without excessive force. Sipa met the challenge with the help of its XFlow melt distribution system. XFlow incorporates an innovative hot runner manifold design that Sipa believes provides the best balance of melt distribution in the industry. In fact, it exhibits the lowest pressure drop ever measured. That is one reason why the maintenance interval – five million cycles – is so long, since wear and tear are considerably reduced. XFlow makes high-cavitation systems possible, without having to compromise on balance, pressure losses, and the formation of acetaldehyde due to polymer degradation. XFlow can be applied to moulds with more modest levels of cavitation with equally impressive results. XFlow applies as an advanced concepts of polymer fluid dynamics to hot runner engineering. By taking melt rheology aspects into account, it is possible to obtain balancing results quite beyond those of traditional systems. Sipa has been implementing XFlow in its hot runner systems for several years now. www.sipa.it","@ID":20}, "MATERIALS / RECYCLING PETplanet Insider Vol. 21 No. 12/20 petpla.net 12 Producing food contact compliant rPET using Erema Vacunite bottle-to-bottle system Closed plastic cycle can be implemented One of the first Vacunite bottle-to-bottle systems recently started operation in Werne, Germany. Using this system, the RCS Group, who already produces PET flakes for the nonfood sector, is expanding their plastics recycling division to include the production of food-grade PET recyclate for food and beverage packaging, films and blisters. For the further processing of PET flakes, the waste disposal and recycling group has built a new location on a 10,000m2 site, creating 20 additional jobs. Here, the Erema Vacunite recycling system will process up to 15,000 t/a of PET flakes from the German deposit bottle collection system and other European sources to make high-quality recyclate, vacuum-assisted and in a nitrogen atmosphere. Due to the strict travel restrictions during the Corona pandemic lockdown in spring, commissioning the plant became an unexpected challenge for everybody involved. The plant components had already been delivered, but since the installation team was not permitted to travel to Germany, RCS started to assemble the recycling plant themselves. An Erema team was then able to be on site for commissioning. New standard for recycled material quality RCS now operates seven days around-the-clock to produce rPET that meets all existing FDA and efsa specifications for direct food contact and the often even stricter regulations of well-known beverage brands. It also exceeds the customer’s expectations. “Our analyses indicate that for all potential contaminants we achieve values that are significantly below our target values or are not detectable at all,” explains Alexander Rimmer, Managing Director of the RCS Group. Vacunite is based on the combination of Vacurema technology - which has been proven over the past 20 years and Erema has further developed for this application - together with newly patented vacuum-assisted Solid State Polycondensation (SSP) technology, which was specially developed by Polymetrix for this demanding application. All thermal process steps now take place in nitrogen and/or vacuum atmosphere. Discolouration of flakes and pellets is largely eliminated and additives that could lead to undesired reactions in the melt are reliably removed. In addition to these quality factors, this new technology minimises energy consumption. The process requires 40% fewer components and consumes up to 36% less energy than comparable systems on the market. The energy consumption for the entire production process from flakes to the final pellets is only 0.35 kWh/kg. Following the commissioning of the Vacunite system with a throughput capacity of up to 1.8 t/h, RCS can now offer its customers high-quality rPET flakes and rPET pellets that are food contact compliant. The cooperation between RCS and a leading PET bottle and preform manufacturer illustrates how a closed plastic cycle can be implemented, taking the PET material obtained from the German deposit system as an example. Alexander Rimmer says: “The recycling process of PET bottles returned by consumers using deposit machines begins in our group of companies as early as the collection stage. We turn the bottles into washed flakes, which are then processed using the new Vacunite system to produce food contact compliant recycled pellets. Our customer uses this in proportions of up to 100% to produce new preforms and bottles, which in turn end up in the retail trade and in households. This means that the cycle is completely closed and completely transparent to consumers, who can trace the route from the deposit machine back to the retailer.” Christoph Wöss, Business Development Manager at Erema Group GmbH, is also convinced that this route will be a successful one in the future. “Even though demand in the beverage industry has gone down due to the Corona pandemic and the situation in the recycling industry is tense due to the fall in the price of new raw materials - our customers and we are convinced that plastics recycling will not lose importance as a major contributor to the circular economy and that the demand for high-quality recycled pellets will continue to increase over the medium term.” The reasons for this are the voluntary commitment of all well-known brand manufacturers, as well as EU directives on the recycling of PET bottles and the minimum proportion of recycled material to be used in new PET bottles. www.erema-group.com","@ID":14}, "MARKET SURVEY 28 PETplanet Insider Vol. 21 No. 12/20 petpla.net Company SMI S.p.A. Postal address Telephone number Web site address Contact name Function Direct telephone number Email Via C.Ceresa, 10, 24015 San Giovanni Bianco (BG) - Italy +39 0345 40 111 www.smigroup.it Ms Daniela Dadda Marketing Department +39 0345 40.318 [email protected] Shrink film machinery: Automatic machines for packing plastic, metal, cardboard or glass containers; packs in film only, cardboard pad + film, tray only, cardboard tray + film Packaging options & output rate (packs per minute) Shrinkwrapper machines; trayformers; overlapping cardboard sleeve multipackers; wrap-around casepackers and combined machines, provide performances from 30-450 packs/min (in triple lane), depending on the model or product to pack. - print registered film (yes/no; packs/min) Yes - nested pack (yes/no; packs/min) Yes - label orientation (yes/no; packs/min) Yes - carry handles (yes/no; packs/min) Yes - pad supported (yes/no; packs/min) Yes - tray supported (yes/no; packs/min) Yes - film only (yes/no; packs/min) Yes - tray and film (yes/no; packs/min) Yes - pad and film (yes/no; packs/min) Yes Shrink process: - shrink tunnel with hot air Smiflexi tunnel distributes hot air flows in an efficient and homogeneous way on the pack, thus ensuring its good quality at the end of the process. - oven Available tunnel methan heated Footprint Single lane: smallest AFW serie (10,060 x 1,774 x 2,450mm) till the bigger size SK 1200 HS (18,752.5 x 1,774 x 2,450mm) Double lane: smallest LSK 32 (9,820 x 1,974 x 2,450mm) till SK 1202 HS (18,752.5 x 1,974 x 2,450mm) Number of possible lanes 1-3 Packaging material & possible thickness film: 30-100μm depending on the production speed and pack collation; cardboard: low wave corrugated cardboard blanks: 3mm thickness Voltage/power/energy consumption Depending on the machine model Film cutting and feeding system Manual sealing bar joins the films, film reels the machine is equipped with a dedicated reel truck, pneumatic blocking system and when the film ends, the machine stops, adjustment of the film length is electronic, equipped with a device for centering the printed film provided with reference mark. Certification CE Palletising machinery: Format changeover time The machine automation and control are entrusted to the Sercos Fieldbus technology; intuitive user interface for quick and easy management of end-of-line palletising operations; real-time machine diagnosis and technical support further enhance the machine control features. Output rate (packs/min) 35-100 packs/min (according to the size of the product handled and palletisation selected) Automatically intergrated:(yes/no) Yes Empty pack feeding Yes Insertion of interlayers Yes Connectable to shrinkwrapper Yes Special characteristics: i.e. low-level feed, cross conveyer barrier Swiftandprecisemovements:Thecentralcolumn isactuatedbybrushlessmotorswhichguaranteehighlydynamic,reliableandprecisemovementsofallaxesofoperation.Machine automationandcontrolareentrusted to theSercosFieldbus technology, featuringan intuitiveuser interface forquickandeasymanagementofend-of-linepalletisingoperations. Company Sipa Postal address Telephone number Web site address Contact name Function Direct telephone number Email Via Caduti del Lavoro n. 3; 31029 Vittorio Veneto (TV) - Italy +39 0438 911511 www.sipa.it Mr Matteo Tagliaferri Marketing and Communication +39 0521 548111 [email protected] Palletising machinery: Genius PTF Genius PTF/V Genius PTF/A Genius PTF - Active Layer Conventional automatic palletisers steady pallet type Conventional automatic palletisers steady pallet type, with double platform Conventional automatic palletisers moving pallet type Conventional automatic palletisers steady pallet type with innovative layer preparation Format changeover time 15min 15min 18min 10min Output rate (packs/min) Up to 330 layers/hour Up to 420 layers/hour Up to 700 layers/hour Up to 330 layers/hour Automatically intergrated:(yes/no) Empty pack feeding Yes, empty pallet feeding Yes Yes Yes Insertion of interlayers Yes Yes Yes Yes Connectable to shrinkwrapper Yes Yes Yes Yes Special characteristics: i.e. low-level feed, cross conveyer barrier - Operational flexibility and further reduction in change-over times - Optimisation of cycle to increase performance, with improved control of the different movements using stateof-the-art electronic solutions - Customisation of the gripping system and layer transfer according to the product to handle - Designed to accept a variable number of product infeeds - Fully automatic system requiring limited operator intervention, operating in complete safety - Possibility to handle all main pallets on the market trouble-free, with highly customisable solutions - Operational flexibility and further reduction in change-over times - Optimisation of cycle to increase performance, with improved control of the different movements using state-of-the-art electronic solutions - Customisation of the gripping system and layer transfer according to the product to handle - Designed to accept a variable number of product infeeds - Fully automatic system requiring limited operator intervention, operating in complete safety - Possibility to handle all main pallets on the market trouble-free, with highly customisable solutions - Operational flexibility and further reduction in change-over times - Optimisation of cycle to increase performance, with improved control of the different movements using state-ofthe-art electronic solutions - Customisation of the gripping system and layer transfer according to the product to handle - Designed to accept a variable number of product infeeds - Fully automatic system requiring limited operator intervention, operating in complete safety - Possibility to handle all main pallets on the market trouble-free, with highly customisable solutions - Operational flexibility and further reduction in change-over times - Optimisation of cycle to increase performance, with improved control of the different movements using state-of-the-art electronic solutions - Customisation of the gripping system and layer transfer according to the product to handle - Designed to accept a variable number of product infeeds - Fully automatic system requiring limited operator intervention, operating in complete safety - Possibility to handle all main pallets on the market trouble-free, with highly customisable solutions - Linear axes layer preparation with active pack orientation and arrangement","@ID":30}, "EDITOUR 23 PETplanet Insider Vol. 21 The Ellen MacArthur Foundation and the United Nations Environment Programme proposed the New Plastics Economy Global Commitment in 2018. Taiwan Circular Economy Network became the first signatory in Taiwan in September 2019. Taiwan has a mature recycling system and many innovative business models and solutions. More than 400 governments, financial institutions, academic research institutes, NGOs, and international companies including Unilever, Coca-Cola, Nestle, and Carrefour, have signed the commitment and promised to take specific actions. High PET bottle recycling rate Taiwan implemented the four-in-one recycling system which created a high recycling rate of PET bottles and enabled the recycling of 67 product items of 13 categories. More than 5.1 billion PET bottles are collected per year. Taiwan strives to turn wastes into resources and promote circular economy, so as to achieve the goal of total resource recycling and sustainable materials. Taiwan focuses on recycling organic wastes for renewable energy, creates reuse value with recycling technology. You will learn more about the Taiwanese beverage market in our upcoming issues of PETplanet Insider: We met Limner Technology, a family owned company specialised in cosmetics and beauty care products, manufacturing delicate heavy-wall PET bottles and jars. The second report is about the company Target Plastic producing PET bottles, particularly for hot fill applications and, more recently, ready-made ones for OEM drinks. Finally you will learn about the giant company Taiwan Hon Chuan Enterprise Ltd. expanding their business portfolio with food and dairy products. Sources: www.epa.gov.tw www.eng.circular-taiwan.org www.asiafundmanagers.com PETcast In our new Road Show podcast, PETplanet meets industry experts from Down Under to Japan and talks with them about their successes, decisions and current developments. Listen to the full conversation atwww.bit.ly/2HVwbAd","@ID":25}, "BOTTLING / FILLING PETplanet Insider Vol. 21 No. 12/20 petpla.net 31 followed in 2018 by a plant in Moers as part of a joint venture with Dr Oetker. Two PET lines from Krones are now in operation at each location. In addition, the Bissingen plant also got two new lines, in 2018 and 2019. Both lines once again feature a PET-Asept D system from Krones, each with a rated capacity of 18,000/h 1.0 l containers. This aseptic filler-capper block processes milk, dairy drinks, and whipping cream and also coffee beverages, NFC juices, smoothies, and water. The latest filler generation gives Gropper the utmost flexibility in container choice. On earlier models, changing bottle shape meant replacing handling parts. Today, all container types can be processed with a single set of handling parts. Because the clean room no longer has to be opened, cleaning times are shorter – and the line’s performance has increased by around 25% compared with earlier models. With the PET-Asept D, Gropper has chosen to keep the filler and the blow-moulder separate. One reason is to clearly segregate packaging material storage from the hygienic space around the filler. Preforms and packaging materials are fed into the lines from a central location at the front end of the bottling hall – and for that reason, the Contifeed preform feed system, the Contiform 3 Pro stretch blow-moulders, and the packer are all sited in this part of the hall. The filler stands at the opposite end of the hall. An AirCo air conveyor transfers the moulded PET containers along the 60m (nearly 200-foot) stretch between the two areas. “The air conveyor also serves as a buffer. Especially when working with higherviscosity products, we can run slow filling without impacting the thermalprocess in the blow moulder,” explains Burgmeier. Klein chuckles, adding, “At Gropper, we’re obsessed with buffers because our experience has been that Each of the two Solomodul modular labellers has two docking stations for wraparound, pre-cut, and lid labelling stations. The set-up can also accommodate integration of two Autocol labelling stations for selfadhesive labels if needed.","@ID":33}, "PREFORM PRODUCTION PETplanet Insider Vol. 21 No. 12/20 petpla.net 20 Voices from the Industry Preform production in 2020 For a preform special, PETplanet asked preform producers from all over the world about preform trends in 2020 (I), how recycling is already being considered during preform production and which components could be important (II) and last but not least we asked about their current business situation (III). We thank PDG Plastiques, Retal, Chemco Group and Eskapet for their answers. PDG Plastiques I) We are currently getting more demand for the use of rPET in preforms, but optimisation and weight lighting continue to be major trend. II) In France, we have seen growing demand for an rPET content of 15%-25%, but we are also increasingly being asked for an rPET content of 50% and 100%. The price of rPET is higher than virgin PET because there is not enough capacity available on the market. The increase in bottle collection and recycling plants capacities will benefit the market and help to develop the use of rPET in preforms. III) There were increases and decreases for preforms during the pandemic but globally the demand has increased, mainly for dairy and milk preforms, but also for hydroalcoholic gel preforms. Production globally has increased by 15%. PDG Plastiques has developed and produced the first 100% rPET Opaque UHT milk bottles for Pâturage brand (Intermarché). The material was produced from opaque post-consumer bottles (mainly milk and dairy bottles). It was the final stage in a project by a Consortium of 7 companies involved in milk bottling, PET preforms, recycling and distribution (LSDH, LSP, PDG Plastiques, SGT, Paprec, Intermarché, Carrefour). It has taken two years to finalise the complete chain of competences. PDG Plastiques, a leading producer of PET preforms for the dairy and milk sector, has also developed preforms with complete light barrier and with only 1% or even 0% of TiO2 in collaboration with Penn Color company. PDG Plastiques has specialised in PET preforms and bottles since 1990. It has 2 plants in France and Algeria. www.pdg-plastiques.com Retal Group I) Two clear trends of 2020 are lightweighting and an increased focus on rPET. In terms of lightweighting, Retal addresses this ongoing trend by saving material in the neck of our preforms. With the logical progression from the PCO1810 to the PCO1881, the next step is the 26/22 neck, a variation of which we already produce at some of our factories. Wider adoption of 26/22 neck was slower due to the SUP directive. Across the industry, we are waiting for a standard of 26/22 neck, suitable for tethered caps to be fully defined. Regarding rPET, as a B2B manufacturer we are driven by the demands of our customers, so in order to promote responsible and sustainable plastic packaging solutions, we work together with our customers to be well prepared for any upcoming regulations. II) As our main area of influence, we are committed to working with our customers to integrate design for recycling principles wherever possible, whether that is through advising different colourants or additives in order to support a higher quality collection of used plastic packaging and supporting them to make informed design decisions that positively impact on their final product’s recyclability. Our global food and beverage brand customers are certainly keen to meet and often exceed the regulations for rPET content, and we support greater use of recycled materials, gaining advantages through design engineering, and investing further in equipment that allows for the use of a variety of quality grades and colours to create rPET packaging. III) The pandemic allowed for the positive characteristics of plastics to be visible, such as the ability to protect food and to create medical-grade barriers. While we have found that a lack of tourist activity and events has reduced demand for smaller volumes, we have seen an increase in demand for larger volumes, with that shift in sales in constant flux as the situation evolves, and our production teams and extensive warehousing able to respond quickly to the needs of our customers. www.retalgroup.com Chemco Group I) For Chemco the focus remained the same; most of our machines were dedicated to the beverage, water, oil and dairy industries. Industries affected adversely by the Covid-19 pandemic also were able to access other non-traditional channels (like internet sales) to make up for some of their lost business. Recycled and PREFORMS","@ID":22}, "PREFORM PRODUCTION PETplanet Insider Vol. 21 No. 12/20 petpla.net 21 Dimensional and thickness measurements for plastic containers and preforms. • Repeatable • Accurate • Precise • Fast GAWiSD +1.724.482.2163 AGRINTL.COM SEE GAWIS4D IN ACTION post-consumer recycling content is increasing in popularity, and consumers, especially in exports, are open to trying it for their products. II) Recycled content varies from industry, customer and location. For example, in India, there are still restrictions in place for the usage of PCR (post-consumer recycling) for food and beverage packaging, with improvements in quality, this is expected to change soon. At Chemco we have our in-house dedicated recycling facilities which allow us to control the quality of the input material. The high-quality machines and a world-class laboratory attached to it ensure the material is safe and can be used for packaging. III) To a large extent, preform production at our end is primarily determined by our clients and their strategy. Based on the industry we are addressing consumer behaviour did see a radical change. Still, because of the expectations of normalty and reports of a vaccine on the way, brands were not keen on making significant changes in terms of preform developments. At Chemco we are proactive and have developed various effective online sale bottle and jar designs that maximise the content, minimise breakages/ damages in transit and allows the retailer to reduce environmental impacts by using lesser protective packaging. www.chemcogroup.com Eskapet I) Eskapet is one of Turkey’s leading preform manufacturer, exporting to more than 80 countries in 5 continents. This gives us an understanding of both Turkish and international market requirements. The Covid-19 pandemic affected the domestic and international in largely the same way. With a general lockdown and the closing down of the hospitality sector, sales fell dramatically compared with the previous year. The loss of the soft drink market was compensated by increased sales of bottled spring water in 1.5 and 5 litre bottles as consumers tightened their belts, and we have focused on this sector of the market. II) Prior to the Covid outbreak, we were increasingly asked for 100%, 50% and 25% recycled preforms, but with the pandemic, demand has fallen dramatically. The higher cost of rPET compared to virgin material is the reason. We find this puzzling; recycled material is environmentally friendly and should be much cheaper. But as demand for rPET increased, so did the price to more than double the price of virgin material. Then problems started to appear with rPET preforms, notably with mould and shade. There is also the problem of collecting sufficient waste to produce rPET. This needs to be significantly improved if the situation is to change. III) Over the three months of March, April and May many producers began to order more than they needed, thereby increasing our sales figures but this over-stocking caused a decline in sales subsequently. Nonetheless, overall we have increased our preform sales in 2020. www.eskapet.com","@ID":23}, "CAPS & CLOSURES 35 PETplanet Insider Vol. 21 No. 12/20 petpla.net Alongside the folding and slitting machines for plastic caps, PackSys Global manufactures complete lines for plastic and laminate tubes for the oral care, cosmetics and pharmaceuticals segments. Madag Printing Systems AG is a specialist in hot stamping machines for the packaging, machinery and automotive industries. Texa AG adds value to the portfolio by developing and building packing machines for tubes, cans and cartridges. Both companies are subsidiaries of PackSys Global AG. One year ago the construction of a new, company-owned, 15,000m2 facility started in Rüti, Switzerland. It is only 500m from the current headquarters away. CEO Beat Rupp is clearly proud that, despite coronavirus, they are keeping to plans and will move in a year’s time. “Whether it is finished or not, we have to be out of the old premises on October 1, 2021. The way things are going at the moment, I’d like to think we will not be moving to a building site.” PackSys: We certainly look forward to increased sales but many customers who already use our technology will be able to implement tethered solutions without buying new machines. Our systems have a machine bed with two stations; slitting is made at the first station and folding at the second. The customer must therefore only exchange the parts that touch the product at the slitter. For oriented tethered caps new machinery will required. We look forward to around 30 additional systems per year. Covid-19 impact on developments In normal times our commercial and R&D teams travel the world to listen to customers explaining their needs and visions of the future. The Covid imposed limitations on travel have meant that we had to stay close to home. While this has been a boost to our development partnerships with Swiss companies, the new communication and information sharing technologies which have boomed during 2020 have also enabled new methods of cooperation and joint developments with partners outside of Switzerland. We have developed some new solutions for the closure market which will be presented in 2021, either in traditional forums, using new digital presentation methods or some combination of both. PETplanet: Many thanks. Mr Beat Rupp CEO PackSys Global","@ID":37}, "43 TRADE SHOW REVIEW PETplanet Insider Vol. 21 No. 12/20 petpla.net SMI Machinery Beijing – Branch of SMI S.p.A. I) The global spread of Covid-19 brought trade shows and exhibitions to a halt in 2020, with large cancellations all over the world. We’ve been forced to change our habits, our behaviozrs, our consumption patterns and we have been obliged to minimise social contacts. This has also led to the cancellation or postponement of exhibitions and events that have always been a good occasion to create or consolidate social relations and to show innovations. While major economies still struggle with the impact of coronavirus, SMI Machinery Beijing Co. Ltd. China, a branch of SMI S.p.A., took part in this important event that generally attracts international participants. At this year’s edition there weren’t as many visitors as in the past; yet, many exhibitors weren’t there because of the travel and health restrictions connected with coronavirus spread. We had anyway the opportunity to discuss with some important customers, who eventually decided to visit CBB. II) During 2020, despite the physical distance we have had to keep, SMI has never stopped being by customers’ side. In addition to online services like AR smart glasses and all online help desk services, our company has decided to create a Virtual Expo, a digital space dedicated to the interaction between us and our current and future customers. Anyway, in addition to this virtual tour experience organised by SMI headquarters, it was a good idea to be physically present at CBB in order to get some important information from the market and talk about future plans of our customers. III) The number of clients visiting the trade fair was definitely lower than that of previous years. There were a few high level contacts, paying us a visit to discuss some possible projects. Further to the global corona pandemic and the associated travel restrictions, investments in machinery and equipment are temporarily in stand-by, waiting for a better economical scenario. However, the exhibition showed us that there is a high level of interest in new technologies for efficient, hygienic and flexible beverage bottling and packaging plants like those supplied by SMI: hi-tech solutions inspired to Industry 4.0 and Internet of Things (IoT) concepts, which deliver increasingly more efficient, flexible, environment-friendly, ergonomic, easy to use and control systems. www.smigroup.it","@ID":45}, "BOTTLING / FILLING PETplanet Insider Vol. 21 No. 12/20 petpla.net 30 Proactively approaching new ideas Multi-talented The town of Bissingen in Germany’s Northern Swabia region is surrounded by gently rolling hills and small tracts of woodland. The roads that lead to it pass through villages and by small farms. Livestock farming is particularly typical for the region – the source of Gropper’s raw milk. In Bissingen, raw milk is processed into a wide range of dairy products that are then stocked in the refrigerator cases of supermarkets across Europe. Last year, Gropper celebrated its 90th anniversary. The company has grown considerably since its founding: the erstwhile cheese maker is now a mid-sized enterprise producing private-label dairy products, not-fromconcentrate (NFC) juices, smoothies, and bottled water for customers across Europe. Gropper now processes around 350 million litres of milk a year. Despite these enormous quantities, regionalism still plays an important role, as Berthold Burgmeier, Head of Engineering, explains: “We source our milk from around 870 farmers within a 70 km radius of the dairy. The only exception is organic milk, which we also source from the foothills of the Alps since there are not enough organic dairy farms in our region to meet our needs.” Originally an all-dairy operation, Gropper now also produces juice, smoothies, and bottled water. The company’s spirit of innovation is strong: “When it comes to product development, we are more like a brand manufacturer than a privatelabel supplier,” says Karl Klein, Managing Director Production and Technology at Gropper. “We don’t wait for our customers to come to us. We approach them proactively with new ideas.” As a result, Gropper has been successfully making organic products for supermarket chains since 2006. That same year, the company surprised its customers by suggesting they bring smoothies to the German market – long before many of the major brands. In 2009, Gropper began producing NFC juices in PET containers for grocery discounters. “Our latest coup is our own organic mineral water brand, Rieser Urwasser. It has given our dairy a foot in the door to one of Germany’s biggest grocery discounters,” Klein says with an unmistakable touch of pride. Clear expectations Krones became familiar with Gropper’s untiring pursuit of innovation and willingness to take risks back in 2004, when the dairy decided to move into PET packaging. “PET containers make the product visible,” explains Karl Klein. “Bottles made of PET plastic are also very lightweight, fully resealable, and hygienically perfect.” The company had very specific ideas about how its first PET line should be equipped. They wanted to use a two-colour filler with dry-aseptic technology. “It’s the standard in the dairy industry. All of our cup fillers work on that principle. So it was clear that our PET containers and caps would also have to be sanitised in this way,” says Karl Klein. Since Krones didn’t have that type of filler in its portfolio at the time, the Neutraubling-based company delivered just a Contiform stretch blowmoulder and a two-colour sleeve labeller that was designed especially for Gropper. The Krones’ filling technology experts had taken the customer’s idea as inspiration and developed a four-colour filler that uses gaseous hydrogen peroxide to sterilise the containers and caps. And their efforts paid off. In 2005, when Gropper was considering its next investment in a PET line, the company chose this newly developed filler from Krones. “It was still just a prototype – so of course, there were some ups and downs,” recalls Burgmeier. “When we were looking to add yet another line in 2012, we weighed very carefully whether we should go with Krones again. In the end, though, we realised that Krones had continually improved its dry-aseptic process in the meantime – and so we did. Right now, nobody else on the market can build a dry-aseptic PET line at the same level of quality and reliability.” Championing dry aseptics Today, PET containers account for about 40 per cent of Gropper’s total production volume. The success of PET packaging is also reflected in the dairy’s capital expenditure. In 2015, the company decided to significantly increase its capacity for producing in PET containers and launched a wave of investment. That same year, Gropper opened a second plant in Stockach, near Lake Constance, which was The stretch blow-moulder and filler are installed as separate units. An AirCo air conveyor transfers the moulded PET containers along the 60m (nearly 200foot) stretch between the two areas. On the PET-Asept D, the filler and capper are housed within a cleanroom.","@ID":32}, "BOTTLE MAKING 24 PETplanet Insider Vol. 21 No. 12/20 petpla.net Interview with Limner Technology Co., Ltd. June 19, 2020 We met: Mr Aaron Lai, Managing Director Taiwan cosmetic containers for the West by Kay Barton We met Aaron Lai, head of the family-owned PET converter, Limner Technology, in Taichung, Taiwan. His company specialises in cosmetics and beauty care products and manufactures delicate heavy-wall PET bottles and jars. Next year, the team will celebrate its 20th anniversary, although its experience in plastics goes back 50 years when Mr Lai’s father, Lai Wen-Sheng, used to produce moulds for the cosmetics industry. With more and more experience and increasing popularity within the sector, the next logical step was for Limner to establish its own production line for containers. The company has set up ten production lines for containers and three for caps. 80% of all products are made from PET. Its main customers are clearly in the top-quality end of the packaging sector. With 40 staff, a turnover of US$3 million and 18% growth, the Lai family is now seeking to expand its already flourishing business in the USA, Japan and Taiwan, as well as local overseas locations to enable them to be more selective when supplying local markets. “When we founded Limner Technology in 2001 our vision was to devise an all-in-one solution by which we could provide custom bottle designs using our own moulds and matching decoration”, said Mr Lai when speaking of the concept and its early stages. “We started out by producing extruded shampoo and later drinks’ bottles, but in the medium term we wanted to use our moulds in more challenging areas. The realisation that these could possibly become thick-walled and heavy PET containers came to me during the Cosmoprof cosmetics trade fair in Bologna. I had a very hard time finding good quality containers like these there, even though the trend for using PET in cosmetics packaging had been gaining ground for some time. Obviously, it was still a real struggle to produce such containers at that time. Nevertheless, we were excited by the idea and decided, hey let’s do it! The project involved three years intensive work until we had all the difficult areas such as thick-wall preform design, material crystallisation and vials under control. We were then finally able to produce containers which looked just like glass and so take cosmetics in PET to the next level. In 2015, we launched our “Aquapet” bottle. Since then, we have been targeting two main customer groups. Firstly, those who can choose from a wide range of ready-made standard containers and designs from our portfolio, and those for whom we can develop and manufacture a complete product design”. Limner’s single stage machinery by Nissei ASB Tour Sponsors: Managing Director Aaron Lai","@ID":26}, "9 NEWS PETplanet Insider Vol. 21 No. 12/20 petpla.net Tethered capped bottles: Introduction in stores planned for the spring of 2021 Starting on July 3, 2024, closures of beverage packaging with a capacity of up to 3 l must remain attached directly to the bottle. The mineral water bottler Vöslauer Mineralwasser GmbH is the first company in the German-speaking market to implement this provision of the Directive and is presenting the tethered cap for the 4x1 l packs, which is to reach retail shelves in the spring of 2021. The Austrian market leader is taking another important step towards the responsible use of the valuable resource plastic with this innovation – four years before the legal deadline. After the introduction of the first bottle made entirely of rPET in 2018, the launch of the tethered cap is yet again proof of how committed the innovative family-run company is to sustainability and protecting the environment. “We are extremely pleased to have reached another packaging technology milestone. This innovation is the result of our good collaboration with and the outstanding expertise of our Austrian partner Alpla. We are strong partners and together are creating new opportunities to act in ways that benefit the environment,” said Herbert Schlossnikl, managing director at Vöslauer. The tethered cap is stated to lead to no compromises whatsoever in terms of quality or drinking pleasure. “The new cap can be unscrewed as easily as the previous caps, and the refreshing taste of our mineral water has not changed,” explained Schlossnikl. The cap can be turned off to the side with a slight twist so that it does not interfere with pouring or drinking directly from the bottle. Vöslauer managing director Birgit Aichinger added: “A band connects the cap directly with the bottle so that it cannot be lost. The cap can be disposed of together with the 100% rPET bottle in the yellow plastic recycling bags or collection bins in Austria, or together with the bottle in a reverse vending machine in Germany.” The new packaging solution will reach shelves in Austria in the middle or end of March 2021, and in Germany at the end of May 2021. The tethered cap will initially be launched on all mineral water varieties sold in the 4x1 l bottle packs in Austria and Germany, and will later be expanded to all packages. www.voeslauer.com/bleibt-dran KHS support-service for tethered caps The EU directive pertaining to tethered caps will come into effect in July 2024: KHS will support customers in finding a solution in good time that suits all requirements. This directive concerns all manufacturers of PET bottles with volumes of up to 3 l. From discussions with customers KHS concludes that customers are orienting themselves towards a future-proof standard with regard to the upcoming EU specification and want to implement it as efficiently as possible be it through simple conversion or lasting resource savings by using fewer materials in the production line. Depending on the type of closure, one can test versions of the tethered cap on existing systems in advance with just a few adjustments. The customer can thus put this time to good use to choose the type of closure that suits best. During this phase, KHS will be happy to advise on how customers can permanently save resources and thus cut costs by reducing the weight of closures and threads. For this, KHS consider the entire production process, because as experts in turnkey filling and packaging systems KHS focus on the complete line. From the container design to secondary packaging (or tertiary packaging), KHS looks at the options for resource savings whilst at the same time increasing the efficiency of the system. www.khs.com Erratum An article on issue 11, p 49 of PETplanet Insider, showed a wrong picture. The article “The new MRSjump recycling extruder – PET tray-to-tray recycling in a single extrusion step” from Gneuss erroneously shows Herbold’s new hot washing system at the company’s test centre (news p 6). The photo of the Gneuss MRSjump recycling extruder that should have been assigned to the article is shown below.","@ID":11}, "TOP TALK PETplanet Insider Vol. 21 No. 12/20 petpla.net 10 “The role of packaging has never been more vital” by Gabriele Kosmehl In times of rapidly changing habits, packaging manufacturers must react particularly quickly and flexibly. In our Top Talk, Eric Roegner, President of Amcor Rigid Packaging, explains what impact the pandemic is having on consumer behaviour and what role PET plays in it, and how they helped a distillery to switch from filling spirits in glass to disinfectants in PET - in just 24 hours. PETplanet: Earlier this year, you published the insights you have gained during the Covid-19 pandemic. One of the findings deals with changing consumer behaviour, including the shift in packaging formats. Can you briefly explain the changes which have had a particular impact on PET packaging? Eric Roegner: During the Covid19 pandemic, there have been clear shifts in shopping practices, product demand, and channel distribution. Despite these changing consumer patterns, the role of packaging has never been more vital, enabling the safe delivery of food, beverages, healthcare products, and home and personal care items including cleaning supplies, hand sanitiser and other essentials. PET containers are lightweight, safe and often more sustainable than aluminium cans, cartons, and glass containers. Hygiene has also emerged as an important safety concern during the pandemic. Capped and sealed PET bottles keep beverages protected from pathogens like viruses and bacteria. They are also sealed to combat contamination and re-sealable for ongoing protection. “Covid-19 is re-shaping consumer priorities” We know from industry research that Covid-19 is re-shaping consumer priorities. Consumers have an increased focus on preventative health, cooking at home, ecommerce, buying in bulk, and sustainability. All these shifts have implications to product demand as well as how those products are packaged. We’ve seen ecommerce growth accelerate during the pandemic. A McKinsey & Co. report notes that sales in this channel will see a sustained post-crisis increase. As a result, the bottles and jars produced for the ecommerce supply chain must function accordingly – no leaks, breaks, or dents. Since consumers will not tolerate a poor unboxing experience, an opportunity for PET packaging has emerged. PET bottles and jars stand up to the rigors of the ecommerce channel, providing benefits such as lighter weight, reduced carbon footprint, reduced freight costs, breakage and safety advantages, and easy handling and opening. The Covid-19 outbreak has also caused a stark shift in the products that consumer demand. For example, earlier this year, Multi-Channel Merchant reported that demand for hand sanitiser skyrocketed more than 800 per cent. This demand created an opportunity for hundreds of U.S. distilleries and wineries to rapidly transform their operations. Amcor jumped in to assist current customers from the spirits, home, and personal care segments with their bottling needs. Our teams also supported smaller distilleries as they activated locally. Shifting from wine or spirits to hand sanitiser requires adjustments to the entire operation including a necessary shift in the packaging format, typically from glass to PET bottles. PETplanet: How exactly has Amcor been able to support its clients with these changes? Eric Roegner: Throughout North America, we played a key role in enabling the availability of hand sanitiser. At the local level, producing and packaging hand sanitiser is manual and requires all hands on deck. Distilleries were accustomed to using glass packaging for its spirits products. It’s not a secret that glass bottles can break, are heavy and often more expensive to transport, and not easy to recycle. PET, however, won’t shatter – so no breaking bottle will shut the line down to remove glass contamination or to prevent an injury. In addition, according to Amcor’s Asset Lifecycle Analysis, PET bottles often have a lower carbon footprint than alterative glass bottles. We worked closely with one of our customers, Michigan-based Ugly Dog Distillery, one of the oldest craft distilleries in the U.S., which shifted its production facilities from spirits to hand sanitiser. In less than 24 hours, our teams were getting Ugly Dog the bottles it needed – and helping to enable some virus prevention for healthcare workers and the community at large. Eric Roegner, President of Amcor Rigid Packaging","@ID":12}, "TRADE SHOW REVIEW PETplanet Insider Vol. 21 No. 11/20 petpla.net 44 Special Edition & myBeviale.com Successful launch for beverage industry dialogue platform BrauBeviale 2020 For three full days, about 3,000 professionals and other interested parties from the international beverage industry gathered online for the Launch Days of myBeviale.com, where they had the opportunity to learn from more than 330 companies offering around 770 products and solutions, interact with each other, and expand their knowledge. The supporting programme and exhibitor presentations at the BrauBeviale 2020 Special Edition, which unfortunately could not be held at the Exhibition Centre Nuremberg because of the coronavirus pandemic, were held online instead, using the new dialogue platform. The result was a new digital dimension to expand the range of products and services offered by the Beviale Family from the Nürnberg Messe Group. Starting now, beverage professionals and industry insiders can meet at a virtual level at myBeviale.com throughout the year to network, interact and learn from each other – at no cost. More than 90 “actions” with about 140 individual presentations and more than 150 different speakers were the focus of the Launch Days for myBeviale.com, the new dialogue platform. Andrea Kalrait, Executive Director BrauBeviale at Nürnberg Messe says “Both experts and other interested parties were actively involved in the Launch Days, and we’ve received lots of positive feedback. It’s a very promising start for myBeviale.com.” The goal of the platform is to encourage and facilitate dialogue in the beverage industry throughout the year. The future viability of the beverage sector The theme of the current BrauBeviale Triple – the exhibition events in 2018, 2019 and 2020 – was the future viability of the beverage sector. The fact this theme was more relevant than ever during the Launch Days was evident from the strong participation in the lectures, seminars and discussion rounds relating to this subject: from the marketing slot “Beverages after the crisis” to contributions on digitalisation, automation, online marketing and trading, and trends in brewing technology, filling and packaging. The “non-alcoholic” field also proved very popular. For the first time, the German Beverages Export Forum was part of the regular programme and was openly accessible to all registered users. During times of crisis, in particular, exporting is a game-changing subject. Home and hobby brewers and small brewery operators attended the Craft Beverage & brau@home Stage at their own expense for the full three days, and made very intensive use of the contributions on offer. “The successful start to myBeviale.com showed that, as an exhibition company, we can network individuals, share knowledge and create experiences not only on-site but also online,” comments Dr Michael Melcher, Executive Director Digital Products & Platforms at NürnbergMesse. “The world and society in general are changing. Our goal is to provide players in the sector with a platform where they can get answers to their specific questions, regardless of time or location, to help them remain viable for the future.” Kalrait adds: “The response from the sector confirms that we are meeting a need. I invite everyone to work with us to develop myBeviale.com together and ensure it best meets the needs of the industry.” The next BrauBeviale will be held in Nuremberg, November 8-10, 2022. www.braubeviale.de","@ID":46}, "PETcontents 4 PETplanet Insider Vol. 21 No. 12/20 petpla.net 12/2020 TOP TALK 10 “The role of packaging has never been more vital” - Interview with Eric Roegner, President of Amcor Rigid Packaging MATERIAL / RECYCLING 12 Closed plastic cycle can be implemented - Producing food contact compliant rPET using Erema’s Vacunite bottle-to-bottle system PREFORM PRODUCTION 13 Performance, flexibility, sustainability - Response to new challenges in preform manufacturing 14 Handling dust - Ultra Hot Runners and automated Self-Cleaning Technology cuts downtime and boosts rPET preform quality 16 Systemic approach to advanced preform production 19 Versatile preform design and tooling package - Collaboration between R&D/Leverage and PET Pak for tailor-made preforms and tooling 20 Preform production in 2020 - Voices from the Industry EDITOUR 22 Taiwan - A strong tiger BOTTLE MAKING 24 Taiwan cosmetic containers for the West 26 Flexibility is the key to stability MARKET SURVEY 27 Suppliers of palletising and shrink film machinery BOTTLING / FILLING 30 Multi-talented - Proactively approaching new ideas 33 Compact flash pasteuriser for all standard container segments - KHS Innopro BoxFlash CAPS & CLOSURES 34 Slitting for tethered caps TRADESHOW PREVIEW 38 Drink Technology India 2020 goes virtual TRADE SHOW REVIEW 41 China Brew China Beverage, part 2 44 Brau Beviale 2020 - Special Edition & myBeviale.com BUYER’S GUIDE 49 Get listed! Page 41 Page 14 Page 24 INSIDE TRACK 3 Editorial 4 Contents 6 News 46 PET bottles for Home + Personal Care 48 Preform products PREFORMS","@ID":6}, "TRADE SHOW PREVIEW PETplanet Insider Vol. 21 No. 12/20 petpla.net 38 PETplanet: Mrs Desai, thank you for your time today. Could you please describe the current Covid-19 situation in India and what it means for the country’s economy? Avisha Desai: Active cases in India have fallen from a high of 90,000 a day in mid-September to 50,000 this week, and the number of deaths has also significantly declined. But the situation still seems to be spiralling out of control as cases continue to accumulate. The total number of cases in India has reached 8,958,483 and deaths currently amount to 131,578. Along with the humanitarian crisis, the Covid-19 pandemic has severely hit the Indian economy, which is expected to contract by 5.9% in 2020 because of the strict lockdown measures taken to contain the virus. While this measure was taken to nip the virus in the bud, it had many repercussions as it brought many productive activities to a standstill overnight. It is expected that the situation might improve in the next year, but the recession may translate into a permanent income loss. PETplanet: What is being planned by the Indian government or is already underway to support the industry? Avisha Desai: An integrated and comprehensive National Food Processing Policy has been proposed by the Ministry of Food Processing Industries of India; a draft has already been circulated among the stakeholders and suggestions and recommendations requested. It intends to build India’s National Food Grid and National Cold Chain Grid along with the retail markets in every corner of the country. The Ministry provides a lot of financial assistance to food processing companies, under the Pradhan Mantri Kisan Sampada Yojna (PMKSY) scheme. The Food Safety and Standards Authority of India has recently launched an initiative for reduction of plastic footprint in the F&B industry, to eliminate single-use plastic, develop environment-friendly alternatives, and develop an effective plastic collection and recycling/disposal system. PETplanet: How has the beverage industry specifically been affected by the situation and what changes can be observed or expected? Avisha Desai: The beverage industry has not been as adversely affected as other industries, which are holding on by the skin of their teeth. Fortunately, beverages and drinkables are still in great demand in the market. We have observed that the demand for immunity-boosting drinks has surged among the consumers as compared to other carbonated and soda beverages. Increased awareness among the Indian population, stimulated by the coronavirus outbreak, has driven is a growing inclination towards healthy choices in the beverage industry. PETplanet: What does the pandemic situation specifically mean for the trade show which should have been happening in December in Mumbai? Avisha Desai: The prohibition of mass gatherings and the travel restrictions imposed by the government of India as Covid-19 tightened its grip on the Indian population meant that conducting event on-site would have been preposterous. We are also concerned about the health of our exhibitors, stakeholders and visitors, whose safety would have been compromised at an on-site exhibition. Therefore, we are holding an online exhibition and conference on the originally scheduled dates of Drink Technology India, i.e. December 9-11, 2020. The next physical Drink Technology India is planned to take place from October 20-22, 2021 in Mumbai. In the upcoming edition, we will be stringently following the directives of the government and ensuring standAn interview with Avisha Desai, Group Project Director at Messe Muenchen India Drink Technology India 2020 goes virtual by Kay Barton As Group Project Director Messe Muenchen India (MMI) since 2011, Avisha Desai and her team have been in charge of the annual Drink Technology India amongst other trade shows. The event has become one of the highlights of the beverage industry. Covid-19 and governmental restrictions mean that this December’s edition will be held virtually.","@ID":40}, "BOTTLING / FILLING PETplanet Insider Vol. 21 No. 12/20 petpla.net 33 KHS Innopro BoxFlash Compact flash pasteuriser for all standard container segments KHS first presented its flash pasteuriser machine specifically developed to meet the demands of small and medium-sized breweries four years ago. The technology, proven in practice many times since, is now available for several new areas of application: where it was initially only used in keg racking, it is now compatible with the glass, can and PET container segments. Its compact design on a frame means that users benefit from lower logistics costs and faster installation. “Our space-saving Innopro BoxFlash flash pasteuriser combines precision and efficiency with a very good price/ performance ratio,” states Gerold Tandler, process technology product manager at KHS. As with all process engineering systems from KHS the Dortmund turnkey supplier uses as many identical parts as possible on the Innopro BoxFlash. Components taken from other series machines include, for instance, the buffer tank and frame from the Innopro Paramix program, KHS’ threecomponent blending system. Unlike in the standard design the buffer tank here has been placed horizontally inside the frame. “To this end, we cut the size of the tank down by 25% to a still generous 1,500 l,” explains Gerold Tandler, process technology product manager at KHS. This has the advantage that the system no longer has to be dismantled for shipping, supplied in parts and repiped and rewired on site, meaning that after acceptance at the production site it is simply shipped as a complete unit. This reduces logistics costs by at least two thirds and considerably shortens the time needed for installation and commissioning on site. Simple installation, optimum pasteurisation Besides attaching the machine feet and mounting the overpressure valve to secure the buffer tank, all that remains to be done on site is to connect up the relevant lines and the Innopro BoxFlash can go into action. The sled systems for product pumps also included greatly ease maintenance. The pasteurisation temperature can lie between 60 and 75 °C and the heat retention period is 30 s. To Tandler, the advantages are obvious. “The Innopro BoxFlash combines optimum, safe product treatment with an extremely small footprint – plus it’s effective and saves on resources.” Perfect for small and medium-sized breweries As with its big brother, the Innopro KZE C with a capacity of up to 600 hl/h, the procedure on the Innopro BoxFlash has been perfectly tailored to the requirements of the brewing industry. With a maximum output of 45 hl/h, it is specially designed to cater for small and medium-sized breweries. In combination with a KHS Innokeg CombiKeg the compact flash pasteuriser can also be equipped with the optional OnBoard CIP module. KHS fits two keg parking stations and dosing pumps for the CIP media in the system for this purpose. This means that after production both the flash pasteuriser and filler can be cleaned internally. “The system’s overall volume is so small that CIP times can be significantly shortened, readying the system for production again very quickly,” says Tandler. Prepared for Industry 4.0 Finally, the integrated IO-Link communication system improves the monitoring of the extensive sensor setup. It permits constant communication between the sensors and the controller and a permanent feed of diagnostic information right down to sensor/actuator level. This means that the Innopro BoxFlash is prepared for predictive maintenance and – with an eye to Industry 4.0 – all geared up for the future. www.khs.com The KHS Innopro BoxFlash flash pasteuriser tailored to the requirements of small and medium-sized breweries is now compatible with most container segments, including PET.","@ID":35}, "8 NEWS PETplanet Insider Vol. 21 No. 12/20 petpla.net Another Herbold washing line in the UK Herbold Meckesheim has supplied a plant with an input capacity of approximately 10.000 tpa for film recycling in England. It is designed for 100 per cent post-industrial stretch film. A demanding application for wash lines, as it represents an extremely high surface area and low bulk density. The plant is another step in covering the growing demands for high quality plastic recycling in the UK. According to its Government, an additional tax on plastic packaging is very likely to be introduced in 2022. The initial amount accounts to £ 200 per ton on packaging which does not include at least 30 per cent recycled material. This will encourage the demand for high quality recyclate. One of the highlights of the latest project is the Herbold EWS 45/200 shredder which is used as a pre-shredder prior to the wet granulator. The new concept particularly enhances the accessibility to the knives and sieves to ensure a userfriendly handling. A gearless belt-driven propulsion system in combination with a mechanical clutch offers additional protection against demolition caused by foreign bodies. The rotor can be equipped with variable knife configurations, with easy to change armour-plating as an option. In order to obtain the highest quality of the final product, a hydrocyclone is used instead of a conventional separation tank which achieves higher separation levels, exerts more friction upon the material, and hence generates purer flakes. These superior outcomes were confirmed prior to the customer’s purchase decision via tests carried out in the Herbold test centre. Herbold Meckesheim is in a good position to comply with increasing demands for high quality plastic recyclates. The latest washing plant generation is stated to make a major contribution to more circularity in the UK. www.herbold.com German Technology Innovative hotrunner optiRun Reading UFI codes – the new OCR module Intravis GmbH now offers a convenient solution for all producers and bottling companies that have to indicate UFI codes on their packaging from 2021 onwards. The new OCR module ensures fast and precise reading of various codes, whether UFI, batch or data matrix codes. Combined solutions are readable without problems. In addition to inspecting the label or product for the presence and legibility of the code, OCR can also be used to compare it with a reference code from a database. This enables producers to check changing codes for correctness at any time – without having to stop and reset the inspection system. This saves work steps and time. At the same time, production managers receive immediate information on the quality of production and can intervene promptly in the event of errors. All inspection results, including the codes, can then be exported to a database, thus supporting seamless reporting for customers. The new OCR module is now available for the Intravis systems of the SpotWatcher family and for LabelWatcher and IMLWatcher. The existing hardware will only be extended by an additional camera and an additional illumination. UFI codes will be obligatory from January 1, 2021 by EU decree for all products whose content may be dangerous for the end consumer. The UFI code – a unique recipe indicator – makes the exact composition of the content recognisable. With the new OCR module, Intravis supports all filling companies in meeting this requirement. The advantages of the new OCR module at a glance: Time savings due to higher process efficiency, extensive insight into processes due to fast and broad data acquisition, seamless recording of all codes for meaningful reporting and security in case of legal disputes due to perfect readability of the codes. www.intravis.com","@ID":10}, "TRADE SHOW PREVIEW PETplanet Insider Vol. 21 No. 12/20 petpla.net 39 TRADE SHOW PREVIEW 39 ard operating procedures to ensure a safe environment for the participants. PETplanet: How have exhibitors and visitors reacted to the suspension of the on-site event this year and what was the actual reason to opt for a virtual event rather than a physical one with appropriate hygiene concepts? Avisha Desai: In the current Covid-19 situation, exhibitors appreciated the fact that they might not be able to interact with visitors as their chances of making it to the on-site event were significantly low. So, we decided to go virtual this year, with the aim that the exhibitors can connect with buyers regardless of the restrictions levied on mass gathering and travel. Most of the companies have tried to adapt to the new measures of networking and agreed with the decision to go virtual. However, there are some exhibitors who are sceptical of virtual platforms as they are unaccustomed to technology and digitalisation. Nonetheless, there is a need to acquaint oneself with technology in these pressing times, as it offers us innovative measures to continue our endeavours. PETplanet: Could you please explain what exhibitors and visitors of Drink Technology India may expect from the virtual edition? What will be shown digitally? Avisha Desai: The online platform will allow exhibitors to conduct their business networking virtually, which is very necessary in these challenging times. Along with protecting data, the platform will provide real-time dashboard engagements with the buyers, a conference programme, and buyer-seller meetings. The simple user interface will allow easy access to data and information, and facilitate significant encounters with the buyers. Participants will also be able to make use of synergies with other shows in the Messe Muenchen India portfolio, such as Analytica Anacon India & India Lab Expo, IFAT India, Mat Dispens, Pharma Pro & Pack Expo, Pack Mach Asia Expo, World Tea & Coffee Expo and The Smarter-E. PETplanet: Will the virtual format replace ‘real’ events in future or complement them? Can you discuss the industry’s thoughts, here? www.sacmi.com Product design Product development Product validation Industrial production plant Process & quality control On-site and start-up assistance After-sales and Customer service SACMI 4.0 THE COMPLETE CLOSURE, PREFORM AND CONTAINER SOLUTION FOR YOUR SMART FACTORY ENDLESS INNOVATION SINCE 1919","@ID":41}, "41 TRADE SHOW REVIEW PETplanet Insider Vol. 21 No. 12/20 petpla.net China Brew China Beverage (CBB) took place from October 13 to 16, 2020 in Shanghai. In this second part of our review, PETplanet asked exhibitors about their experiences at this year’s fair in terms of special circumstances due to the pandemic (I), about the important issues discussed (II) and finally about the successes of the CBB and the mood in the industry (III). Enjoy reading statements of Pressco, GDXL, SMI, ABC Compressors, Heuft and Newamstar. ABC Compressors I) Despite the circumstances, it went quite well. It is true thst we found less people, but even so the quality of the visits was high. There were real projects on the table, and we felt the reaction in the market. II) The exhibition was straightforward. The uncertainty and freezing of investment were among the main topics. At the same time there was optimism among the visitors. III) Being a local exhibition and considering the current situation in China comparing to other countries, we found the CBB 2020 successful for us. Real projects are coming and some of them have been already awarded, so we should say economy and consumption are growing again in China. Still, uncertainty is on people’s mind but at the same time there is eagerness to move forward. www.abc-compressors.com Newamstar Packaging Machinery I) In this year’s exhibition, Newamstar launched the 6th + generation blow moulding machine with a capacity of 2,750 bph per cavity, which is in line with the world’s top level, and launched a newly developed StarPack, which can do both film packing and carton packing. At the 2020 China Liquid Food Equipment Intelligent Manufacturing Technology Forum held at the same time, Newamstar also presented a smart factory solution for integrated production and storage. The solution integrates intelligent production, networked collaboration, customisation and digital management, and has access to warehouse storage, inspection, production, warehousing, logistics and transportation, bringing high-efficiency, high-quality, low-consumption, clean, and flexible customised services, realising the full life cycle management of liquid products, which will help customers to achieve business success. II) Innovation has become an inevitable choice for the sustainable development of global enterprises. In 2020, due to the impact of the Covid-19, the world economic structure evolution has been accelerated, and the profound and complex adjustment about the market environment have taken place. Only by focusing on innovation and promoting innovation we can meet customer production needs better and bring consumers healthy, safe, fresh and nutritious products. III) The successful holding of the exhibition has brought strong development momentum to the technological progress of the beverage and beer industries at this stage. At present, China has achieved major results in the fight against Covid-19, and various social institutions such as enterprises, schools, and businesses have fully resumed normal operations. Newamstar is accelerating the promotion of digital transformation and intelligent upgrading. The application of digital technology will open up the intelligent manufacturing production chain, help flexible and efficient low-carbon production, and accurately serve intelligent logistics, which can bring a beautiful experience of integrated production and storage of intelligent factories and strive to win more extensive cooperation. www.en.newamstar.com F.l.t.r.: Erica Gu, Sales and Service Assistant; Tony Chen, Sales Area Manager; Xian Zhu, General Manager; and Charles Yan, Sales Area Manager at ABC Compressors China Heuft Systems Technology (Shanghai) I) We experienced quite normal exhibition business at this year’s CBB. The organiser carried out the preparations carefully and professionally according to the regulations and there was no feeling of disturbance or obstruction. Of course, there were far fewer foreign visitors but it was still a successful exhibition for Heuft. II) Project discussions as always but an important topic was also the diversification of the industry with established producers of certain fields crossing over to new market segments. The PET industry no longer seems to be growing much faster but the canning industry is on the increase. We also experienced that interest in line efficiency is becoming more and more important in China as costs are increasing, also for land and labour. III)The mood in the beverage market seems positive – it is a growing market. There are investments planned for new production lines because current lines are overloaded. Also premium products are moving forward in China. Heuft continued to pay visits to the customers who came to our booth, followed up the discussions and demands and provided solutions as always after an exhibition. Business looks good for Heuft even in a very difficult year like 2020. www.heuft.com","@ID":43}, "PREFORM PRODUCTION PETplanet Insider Vol. 21 No. 12/20 petpla.net 16 Systemic approach to advanced preform production Sipa counts itself among the very few PET technology suppliers around the world capable of providing cutting-edge equipment to make high-performance, low-weight preforms and containers. As far as preforms are concerned, it is alone in offering not only traditional injection moulding systems branded XForm, but also an injection-compression technology, Xtreme, capable of making lightweight high-performance preforms. PREFORMS Xtreme, already in commercial use at several customers, is claimed to take preform production into a new era, whether it involves virgin material or post-consumer recyclate, rPET. The advantages are especially significant when it is paired with Erema’s Vacurema post-consumer bottle recycling system in Xtreme Renew, a system, capable of producing highquality food-contact preforms from up to 100% rPET flakes. Fourth generation XForm Sipa has high hopes for Xtreme and Xtreme Renew. The company also offers quality and quantity in the form of XForm. The system was introduced in 2012, and already last year it entered its fourth generation, XForm Gen4 XP. This incorporates advanced technology to deliver lowest conversion cost alongside unmatched speed, flexibility, and ease of use. As is well-known, XForm is available in several sizes, with clamp forces of 250, 350 and 500 t. These can run with moulds holding respectively up to 96, 128, and 180 cavities. New technology incorporated into all these systems has been designed to handle the most demanding applications. It delivers short cycle times; it offers high energy efficiency; and it has low maintenance cost. As with all previous XForms, the XForm Gen4 XP accepts virtually all legacy tooling produced by any major mould maker. Powered by the latest generation of servo-driven hydraulic pumps, the XForm Gen4 XP has low lock-tolock time, paired with an increased injection rate. Total energy efficiency has also been increased: in a typical configuration with the machine set-up to full screw utilisation and PET with an IV of 0.80 dl/g, the XForm Gen4 XP consumes just 0.195 kWh of energy for every kg of material processed. One of the reasons for the improvements in dry cycle time and energy efficiency is the introduction of a kinetic energy recovery system acting on the toggle drive. New accu layout Sipa’s XForm platform has already gained a reputation for its ease of maintenance, the Gen4 XP, it is even easier. One of the reasons for this is a modified accumulator area layout: the accumulators are now mounted on a pull-out rack inside the machine frame. In addition, the oil tank has been redesigned so that it does not need to be emptied in case of maintenance. Those processors operating in the hills and mountains will be interested to know that it can also be used at altitudes of up to 3,000m without any modifications. The net result of all these improvements is that XForm Gen4 XP users can operate even more consistently, at higher speeds, spending less on energy and maintenance, using a machine that will reduce conversion cost to very low levels. The operator experience on the XForm has also been further enhanced in the Gen4 XP. This is achieved through an HMI with a large 21.5-inch touch screen with highdefinition graphics, swipe functions just like a smartphone or tablet, a multi-function control knob for onehanded operation, and fast response times unaffected by processor load. The HMI incorporates an automatic","@ID":18}, "PREFORM PRODUCTION PETplanet Insider Vol. 21 No. 12/20 petpla.net 14 Ultra Hot Runners and automated Self-Cleaning Technology cuts downtime and boosts rPET preform quality Handling dust based on an article by Bilal El Sayed, PET Tooling Product Manager, Husky Every mould requires maintenance and cleaning, at some point; PET dust particles can naturally accumulate, over time, so this is inevitable. The hot runner must deliver molten PET to each cavity equally while maintaining melt consistency. If any plastic escapes into the hot runner the temperature degrades the melt and dust accumulates. This build-up of dust can lead to cavities going down. The cold half must allow the mould cavities to properly fill and form the desired parts. Moulds need vents large enough to allow air to escape but small enough to ensure that melt is retained. Over time, this makes vents prone to clogging with dust. Clogged vents result in trapped air, and trapped air can cause defects like shorts or voids. This is why it is so important for manufacturers to find successful ways to handle dust. Keeping moulds clean is even more important when running recycled PET (rPET). Using high amounts of rPET material can increase gas, powder and dust generation caused by residual contaminants, like AA blockers or O2 scavengers, that persist in the recycling process. And as demand exceeds supply, it is possible for residual contaminants to increase and the quality of rPET to decline. With more and more brands looking to offer sustainable packaging solutions made using higher percentages of rPET, mould cleanliness becomes even more important. Increasing system speed compounds the impact of maintenance and cleaning on productivity: as cycle times reduce, moulds naturally create dust faster and require maintenance more often. How do producers solve this challenge? It starts by working with a reliable and knowledgeable partner, who has the experience and expertise to develop and deliver leading-edge solutions. Why invest in Hot Runner technologies to clean dust when there exists a solution that can avoid it completely? Husky states to have gone further and offers proven solutions that minimise dust creation in the first place, thus helping to reduce down time, for scheduled and emergency maintenance. Solutions include Husky’s Ultra Hot Runner and patented Cold Half Self-Cleaning Technology, which are designed to eliminate dust and enable producers to move to rPET with more confidence and less risk. To reduce PET dust accumulating where it should not, some PET mould manufacturers use vacuums to remove it in their hot runners. While vacuum technology may remove dust inside hot runners, it doesn’t change the amount that builds up in the cold half. This side will eventually need a thorough cleaning, causing downtime and lost productivity. Implementing an additional vacuuming step adds complexity and cost to an already complicated process. Husky’s Ultra Hot Runners have operated successfully by controlling and consistently delivering melt to each cavity. They prevent plastic from leaking, thus helping to prevent the generation of PET dust and eliminating the need for extra vacuum technology. Husky’s patented Ultra Spring technology uses a method called cold start protection, which keeps the nozzle and manifold sealed in a cold state before the hot runner reaches its operating temperature, thus reducing dust build-up in the stack. Addressing the root cause of dust creation eliminates the need for additional mechanisms like vacuums and so reduces maintenance downtime. It also minimises component failure risk and, consequently, offers a significant advantage over those technologies that are susceptible to dust build up. What if a mould could clean itself? Until recently there have existed two common methods of neck ring vent cleaning: hand cleaning and dry ice blasting. While extremely effecPREFORMS","@ID":16}, "MARKET SURVEY 29 PETplanet Insider Vol. 21 No. 12/20 petpla.net Company Productive Systems (Pty) Ltd GEA Group Postal address Telephone number Web site address Contact name Function Direct telephone number Email PO Box 7643, Centurion, 0046 South Africa +27 12 661 1250 www.productivesystem.com Mr Stefan Schonfeldt Marketing Director +27 12 661 1250 [email protected] Via Fedolfi 29, 43038 Sala Baganza, Parma, Italy +39 0521 839 0 www.gea.com Andrea Pellegrini Head of Global Sales & Marketing GEA Procomac presso +39 0521 839 411 [email protected] Palletising machinery: Semi automatic & automatic Yes Format changeover time 10-20min depending on differences in formats 5' (completely automatic) Output rate (packs per minute) 25,000bph (empty plastic bottles) 90pack/min 6x4 500ml (dia 56mm) Automatically intergrated:(yes/no) Empty pack feeding Yes Yes Insertion of interlayers Yes Yes Connectable to shrinkwrapper Yes Yes Special characteristics: i.e. lowlevel feed, cross conveyer barrier Yes Low level, high level, fully brushless palletiser permits smooth, precise movements and low energy consumption, predictive maintenance And & Or PI El Limon, Av. de Europa, 6, 41928 Palomares Del Rio (Sevilla) - Spain +34 954 779 200 www.andyor.com Mr Caridad Ortega Suárez Sales Director +34 954 779 200 [email protected] No Yes, 15-900bpm No Yes, 15-400bpm Yes, 15-400bpm Yes, 15 -400bpm Yes, 15-900bpm Yes, 15-900bpm Yes, 15-900bpm Shrinking pistols (hot air) Several models depending on speed Max. length of the pack is 1,400mm LDPE + LLDPE 40-60μm Several models depending on speed Yes CE and UL 15-20min Up to 400bpm Yes Yes Yes Yes Low-level feed; tray former possible to be integrated (display palletiser) Genius PTF - Fastlayer Genius PTF/A - Fastlayer Genius PP/PV Robby Pal Robby Pal with Fastlayer Conventional automatic palletisers steady pallet type with innovative layer preparation Conventional automatic palletisers moving pallet type with innovative layer preparation Conventional automatic palletisers steady pallet type for empty PET containers Robotic automatic palletiser Robotic automatic palletiser with innovative layer preparation. 10min 12min 15min 15min 10min Up to 330 layers/hour Up to 700 layers/hour Up to 330 layers/hour Up to 320 layers/hour Up to 320 layers/hour Yes Yes Yes Yes Yes Yes Yes Yes Yes Yes Yes Yes Yes Yes Yes -Operationalflexibilityand furtherreduction in change-over times -Optimisationofcycle to increaseperformance, with improvedcontrolof thedifferentmovements usingstate-of-the-artelectronicsolutions -Customisationof thegrippingsystemand layer transferaccording to theproduct tohandle -Designed toacceptavariablenumberof product infeeds -Fullyautomaticsystemrequiring limitedoperator intervention,operating incompletesafety -Possibility tohandleallmainpalletson the market trouble-free,withhighlycustomisable solutions -Layerpreparationwithactivepackorientation andarrangementwithrobots -Operationalflexibilityand furtherreduction in change-over times -Optimisationofcycle to increaseperformance, with improvedcontrolof thedifferentmovements usingstate-of-the-artelectronicsolutions -Customisationof thegrippingsystemand layer transferaccording to theproduct tohandle -Designed toacceptavariablenumberof product infeeds -Fullyautomaticsystemrequiring limitedoperator intervention,operating incompletesafety -Possibility tohandleallmainpalletson the market trouble-free,withhighlycustomisable solutions -Layerpreparationwithactivepackorientation andarrangementwithrobots -Operationalflexibilityand furtherreduction in change-over times -Optimisationofcycle to increaseperformance, with improvedcontrolof thedifferentmovements usingstate-of-the-artelectronicsolutions -Customisationof thegrippingsystemand layer transferaccording to theproduct tohandle vacuumheadavailable forwide mouthcontainers(i.e. jars). -Designed toacceptavariablenumberof product infeeds -Fullyautomaticsystemrequiring limitedoperator intervention,operating incompletesafety -Possibility tohandleallmainpalletson the market trouble-free,withhighlycustomisable solutions -Completerange tohandledifferent typesofcontainersandproducts: layer, rowandmultiheadand looseproduct palletisingsystems -Extremelyflexibleandmodularsolutionwithreduced footprint -Customisationof thegrippingsystem and layer transferaccording to the product tohandle -Designed toacceptavariablenumber ofproduct infeeds -Fullyautomaticsystemrequiring limitedoperator intervention,operating incompletesafety -Possibility tohandleallmainpallets on themarket trouble-free,withhighly customisablesolutions - Complete range to handle different types of containers and products: layer, row and multihead and loose product palletising systems - Extremely flexible and modular solution with reduced footprint - Customisation of the gripping system and layer transfer according to the product to handle - Designed to accept a variable number of product infeeds - Fully automatic system requiring limited operator intervention, operating in complete safety - Possibility to handle all main pallets on the market trouble-free, with highly customisable solutions - Layer preparation with active pack orientation and arrangement with robots","@ID":31}, "empowered by Drinktec New Zealand Australia Philippines Taiwan South Korea Japan Let Your Inspiration Flow. )URP 'RZQ 8QGHU WR -DSDQ G’day and Konnichiwa! Editour Road Show goes virtual This year’s Editour Road Show was planned to be our next big international editorial project. That is now impossible. For the safety of others and our own, we are all working from home during the lockdown period. But it’s still time for the Editour Road Show to hit the road – it’s just that we won’t be doing so physically, not at the moment. The start of the new decade will see us undertaking a trip starting in Australia, moving on to New Zealand and then Japan, via the Philippines, Taiwan and South Korea. With support from Drinktec, the world’s biggest beverages show, we will be ‘virtually’ shooting off to Australasia in April. The first weeks will see us interviewing PET companies along the route via Internet and phone. These encounters will appear not only in PETplanet Insider but also in a completely new way – new to us, anyway: as podcasts on our website, for the first time ever! We will keep monitoring the situation closely to decide if, how, when and where we can still go personally with our Editourmobil, later in the year, while complying with governmental rules. We will present a comprehensive review of our Tour experiences both at China Brew China Beverage in Shanghai, China, in October and at Drink Technology India in Mumbai, India, in December 2020. Make sure you’re on board when we set off on our next adventure and get ready for in-depth analyses, special features and reports of trends in these bottle and beverage sectors! Enjoy our first-ever Virtual Editour! Stay safe and healthy! Interested in being interviewed? [email protected] April - December 2020 Powered by","@ID":47}, "PETplanet Insider Vol. 21 No. 12/20 petpla.net 46 PETbottles Home + Personal Care A bottle containing oak extract The demand for detergents that contain a high proportion of natural ingredients in suitably designed bottles is a challenge for manufacturers. The German company, Fit GmbH, is selling a vegan fabric conditioner consisting of 98.8% natural ingredients with no colourants or microplastic content. The easily biodegradable one-litre bottle containing oak extract and made from 100% used plastic has been brought out as part of Fit’s “Kuschel weich/Aus Liebe zur Natur” (“Cuddly Soft/Out of Love for Nature”) range. The bottle has a matt printed plastic label with a green screw cap with dispensing function. www.shop.fit.de A vegan fabric conditioner from Vernel A vegan fabric conditioner under the name “Naturals” has been brought out by Henkel as part of its Vernel range. It comes in a slim, slightly tapered 800ml bottle which is made from 100% recycled plastic. The product consists of 99% natural ingredients and is free of silicones, microplastics or colourants. A transparent window to monitor usage is integrated within the sleeve label, which can be easily removed via a perforated strip prior to being discarded or recycled. The opaque screw cap also has a dispensing function. A sticker on the front of the bottle invites customers to take part in a “money back” free promotion by uploading their purchasing receipt. www.vernel.de A hair fragrance from Nihan The German company, Lifestyle Distribution GmbH, has brought out a new hair fragrance as part of its Nihan range following the launch of its “#queensunited Nihan Black” product. The compact 100ml bottle has a screwon pump sprayer and self-adhesive label, some of which is printed in a shiny gold colour. A protective cap shields the pump sprayer from damage. www.lifestyleperfumes.eu 10-in-1 Oil Repair 3 from Garnier Garnier Fructis is promising its customers a 10-fold effect with its new “Oil Repair 3, 10-in-1 Leave-In” hair care product. In addition to avocado, coconut and olive oil, the product also contains triglycerides to help nourish, care for and protect the hair, making it easier to style. The yellowish-coloured 400ml bottle has two clear film labels that include information on the product and instructions on how it should be used. It is applied to the palm of the hand via a lockable pump dispenser, then massaged into the hair and hair ends without the need for rinsing. www.garnier.de","@ID":48}, "MARKET SURVEY 27 PETplanet Insider Vol. 21 No. 12/20 petpla.net 12/2020 MARKETsurvey Resins & additives Preform machinery Preform production & inspection Preform & SBM mould manufacturer SBM 2 stage Compressors Caps & closures & inspection Filling equipment & inspection Recycling Palletising & shrink film machinery Palletising and shrink film machinery For the third time PETplanet Insider focuses on palletising and shrink film machinery to conclude this years market survey overview in PETplanet. Here you find the machine details of state of the art technology from participating companies: SMI S.p.A., Sidel, Krones AG, Productive Systems (Pty) Ltd, KHS Group, Jiangsu Newamstar Packaging Machinery Co., Ltd., GEA Group, And&Or and Sipa S.p.A. Although the publisher have made every effort to ensure that the information in this survey is up to date, no claims are made regarding completeness or accuracy. Company Sidel KHS Krones AG Jiangsu Newamstar Packaging Machinery Co., Ltd Postal address Telephone number Web site address Contact name Function Direct telephone number Email Rue du Commerce, 67116 Reichstett, France +33 388 183 880 www.sidel.com Mr Piero Zamboni PR Manager +39 521 999452 [email protected] Juchostraße 20, 44143 Dortmund, Germany +49 231 5690 www.khs.com Böhmerwaldstraße 5 93073 Neutraubling, Germany +49 9401 70 0 www.krones.com Mr Andreas Fritsch Product Management Packaging Technology +49 8031 4040 [email protected] No. 8 Xinjing East Road, Zhangjiagang Eco- andTechnological Dev.-Zone, Jiangsu Province, China, 215618 +86 512 5869 1111 www.newamstar.com Mr Wesley Yin Marketing Manager +86 512 56993303 [email protected] Shrink film machinery: Packaging options & output rate (packs/min) - print registered film (yes/no; packs/min) Yes, up to 120 cycles per minute (PET bottles), 150 cycles per minute (cans) in 3 lanes Yes, 540 packs/min Yes, 150 x 4 = 600ppm Yes, 60 - nested pack (yes/no; packs/min) Yes Yes, 80 packs/min Yes, 100ppm No - label orientation (yes/no; packs/min) Yes No No No - carry handles (yes/no; packs/min) No Yes, 240 packs/min Yes, 80 x 2 = 160ppm No - pad supported (yes/no; packs/min) Yes Yes, 110 packs/min Yes, 120 x 2 = 240ppm Yes, 60 packs/min - tray supported (yes/no; packs/min) Yes Yes, 110 packs/min Yes, 120ppm Yes, 60 packs/min - film only (yes/no; packs/min) Yes Yes, 540 packs/min Yes, 150 x 4 = 600ppm Yes, 80 packs/min - tray and film (yes/no; packs/min) Yes Yes,110 packs/min Yes, 120ppm Yes, 80 packs/min - pad and film (yes/no; packs/min) Yes Yes, 110 packs/min Yes, 120 x 2 = 240ppm Yes, 80 packs/min Shrink process: - shrink tunnel with hot air or gas fired opt. Yes With electricity or gas fired (option) Yes Yes - oven Yes No Yes - steam tunnel No No Yes Footprint Depend on configuration Depends on speed Number of possible lanes Up to 3 4 4 With 1 or 2 lanes Packaging material and possible thickness Low-density polyethylene (LDPE) from 27-100μm Shrink film 25-80μm thickness; corrugated board: B,C, E and F-Flute Film, min 25 - 120 60μm~80μm Voltage/power/energy consumption NC Voltage: standard 3x400V; power: min. 22KW - max. 48KW; energy consumption: depending on requirements Depends on speed, package and material AC380V, 50hz, about 110kw Film cutting and feeding system Yes Continuous feeding system from a roll Yes, fully automatic feeding, splicing, welding Yes Certification CE certification Compliant with 3c certification Palletising machinery: Format changeover time Depend on configuration Depending on machine type, automatic changeover and manual changeover (5 to 10min) 20min Output rate (packs/min) Up to 12 layers/min 100 - 650lph (layers/hour) 120 Automatically intergrated: (yes/no) If necessary Yes Empty pack feeding Yes, empty pallet feeding Yes Auto Insertion of interlayers Yes Yes Auto Connectable to shrinkwrapper Yes Yes Yes Special characteristics: i.e. low-level feed, cross conveyer barrier Available on high and low level infeed High speed with low level infeed Low-level feed, cross conveyer barrier","@ID":29}, "by Heike Fischer EDITOUR PETplanet Insider Vol. 21 No. 12/20 petpla.net 22 Taiwan – A strong tiger Due to the weak global economy caused by the Covid-19 pandemic, Taiwan’s economic output is also expected to decline. The International Monetary Fund (IMF) forecasts a 4% decline in the tiger economy this year. Some critical voices comment that the IMF’s forecast is too negative, as Taiwan managed to contain the outbreak of the virus and was able to control the situation well. Taiwan is officially part of the Republic of China. It is a small but important country for East Asia. The area of Taiwan is 35,808 square kilometres. With a population of only 23.7 million, Taiwan nevertheless enjoys enormous economic success. Due to its compact geographical location, the tiger state is one of the most densely populated states in the world. With a population density of about 651 inhabitants per square kilometre, Taiwan is the 17th most densely populated nation. In the 21st century, the country’s population has increased by 700%. In the meantime, however, the birth rate in Taiwan has fallen considerably. The country is having difficulty maintaining the current population density. According to forecasts, Taiwan’s population will have reached the climax in 2024 with about 23.7 million people and will then decline. In terms of purchasing power parity, the Taiwanese economy ranks seventh in Asia and 22nd in the world. The IMF rates the economy as progressive. The country is particularly distinguished by production facilities in the technology industry.Real GDP growth was 2.7% in 2019. Looking back, this is rather low growth. In 2011, for example, the country had a growth rate of 13% in one quarter, which was the peak of the financial expansion. From 2016 onwards the economy contracted, so the 2.7% growth rate can be considered a rocksolid figure. Sustainability - In Taiwan to recycle is a habit Sustainability is the global megatrend. It will be of great importance for Asia. In fact, the region bears a disproportionate burden of climate change. Causes for concern are water scarcity, rising sea levels, pollution and plastic in the ocean. Around 8 million tonnes of plastic end up in the sea every year. Over 90% of plastic waste comes from just ten rivers, eight of which are in Asia. Energy production is the most serious problem. As a developing country, Taiwan is highly dependent on energy to sustain its growth. Fossil fuels such as coal and oil are the cheapest and most available sources of energy. Some countries recognise the need for ambitious energy programmes to curb emissions, but reality is catching up. However, the global megatrend of sustainability also promotes the design of sustainable products and processes. Besides electric vehicles, waste treatment and alternative energies, this trend is also reflected in the production of sustainable packaging. Tour Sponsors:","@ID":24}, "BOTTLING / FILLING PETplanet Insider Vol. 21 No. 12/20 petpla.net 32 block set-ups often result in efficiency losses. We really notice that when one of our buffer towers goes down and has to be bypassed. Efficiency immediately drops by four or five per cent.” Clear favourite for labelling As a private-label producer, Gropper makes countless different products and brands. In order to meet its customers’ demands, the company has to be able to offer all labelling options. Therefore, both of the new lines include a Solomodul, each of which has two docking stations for wraparound, pre-cut, and lid labelling stations. The set-up can also accommodate integration of two Autocol labelling stations for self-adhesive labels if needed. If Gropper needs to handle special-shaped bottles on the new lines, a Sleevematic can do the labeling. “We change labels at least five or six times a day. We chose a modular labeller to keep time losses to a minimum,” says Burgmeier. Gropper has trusted Krones labelling technology ever since they installed their first PET line as Karl Klein explains: “When it comes to labelling, we’ve never gone with anyone but Krones. Their roots are in labelling and I have the greatest trust in them.” To date, Gropper has also exclusively chosen Krones Contiform stretch blow-moulders for bottle production. Direct access is a major advantage The collaboration on PET plastic packaging is just one more milestone in the two companies’ long partnership. “Krones has been a dependable partner to Gropper for more than 30 years. Even though the group has grown to be quite large, we know that we will always have a contact person there who can answer our questions and help solve any problems that arise,” says Burgmeier. Klein adds: “Since the majority of our products are chilled foods, we have to operate 24/7 filling specific orders. Line uptime is essential. Of course, you’ll have an occasional downtime or need a spare part at short notice. At those times, it’s important to have a supplier who will deliver service or spare parts quickly and dependably. Our close proximity to Krones’ headquarters is also a major advantage.” But Klein also sees the partnership as a win-win for both companies. “We get reliable machines and service from Krones, and Krones gets to observe its machinery in a longterm field test and apply its findings to future developments and improvements. Each time we come up with a new project, we have very specific ideas and expectations about how we want production to look and how we can make it even more efficient. Krones listens carefully, takes on our challenges, and does everything in their power to make our expectations reality.” www.krones.com Berthold Burgmeier, Head of Engineering (left), and Karl Klein, Managing Director Production and Technology","@ID":34}, "7 NEWS PETplanet Insider Vol. 21 No. 12/20 petpla.net FLIPPING THE WORLD OF PET UPSIDE DOWN AND EVEN SIDEWAYS. The All-New NETSTAL PET-LINE with Side Entry. kraussmaffei.com/new-petline The All-New NETSTAL PET-LINE comes with a variety of advantages to maximize output and minimize costs: - Side entry for maximum mold compatibility - Shortest cycle times for increased output - Lowest level of energy consumption to minimize the ecological footprint - Improved 100% rPET processing to enable the circular economy - New control unit including NETSTAL Smart Operation to ensure easy, fast and safe start-up and production","@ID":9}, "BOTTLE MAKING 25 PETplanet Insider Vol. 21 No. 12/20 petpla.net BOTTLE MAKING 25 The standard small bottles have a capacity of 30, 50, 100, 120, 150, 250, 350, 500 and 700 ml, with 30 ml bottles with the “dropper” cap by far the most popular. These bottles end up in the hands of foundation, serum, essence and hair care brand owners. 30, 50 and 80 ml jars are also available, with 50 ml being a best seller. Of the 80% PET content mentioned earlier, 70% is in small bottles and 30% in jars. The remaining 20% are, for example, PMMA and ABS. “70% of our products can be found in the skin care sector, 23% in cosmetics and 7% in pharmaceutical products”. “For PET processing, we use one Nissei ASB-12M, one 12N/10 and one CMS two-stage blow moulding machine supplied by the Taiwanese machinery builder. Another 12M is to be added shortly. For caps, we use six injection moulding machines from Nissei and OMC”, explains Mr Lai as he takes us around his factory where 2.4 million thick-walled bottles, 6.6 million standard-walled bottles and 2.2 million jars, together with 20 million caps, roll off the production line via this system. “On the CMS model, we only make preforms with 24/410 threads, However, I have to admit that the potential for design and productivity is not as good compared to ASB for example which is why we have scaled back developments with two-stage blowmoulding. We are outsourcing other neck finishes anyway”. Moulds made by the company are used exclusively for processing in their own machines. As well as the local market, which accounts for 40% of sales, Limner sells 40% to the USA and 20% to Japan. “Of course, we want to continue to grow and expand our client base, particularly in the USA and Europe, and are currently looking for local distributors who could help with this. We are also planning to open a sales and marketing office in California in 2022. Here in Taiwan, we want to put our new ISBM line into production next year. We have no real competition at local level since our products, like those of other converters, are unique”, said Mr Lai. Entering the company’s premises “On the other hand, we believe that those in our industry complement one another rather than inevitably excluding parts of the sector. We have also been exploring the potential for using alternative material such as rPET or PCR PET but have yet to be fully convinced. We have been carrying out some research and development in this area for nine months now given the ever-increasing demand from customers for recycled material to be used in packaging. However, our initial successful field trials showed that our products looked less attractive with added recycled material than they do with brand-new PET. So, it is hard to say at this stage if customers from the premium end of the market will really approve of this and therefore whether any further work in this area is worth the effort”, said Mr Lai. www.limner.com.tw Closure manufacturing area PETcast In our new Road Show podcast, PETplanet meets industry experts from Down Under to Japan and talks with them about their successes, decisions and current developments. Listen to the full conversation atwww.bit.ly/2HVwbAd BERICAP Tethered Cap Solutions • Easy& intuitive handling • 180° opening • No change to - Neck finish - Capper - Filling line Approved and ready for line trials now!","@ID":27}, "BOTTLE MAKING 26 PETplanet Insider Vol. 21 No. 12/20 petpla.net Flexibility is the key to stability PET Technologies has recently brought to the market a new generation of flexible PET stretch blow moulding machines called the APF-Max series. Its output varies between 3,000 and 14,000 bph, while the bottle volume is between 0.1 and 6 l. The product range includes 6 basic models and 5 special versions. The machines have already attracted favourable customer reaction. User-friendly concept and new design The company states that the machine is modular, has a streamlined design and is easy to operate. All the connection equipment is accessed at the top of the machine, whilst the electric control cabinet is located at the rear. The central lubrication system makes machine maintenance easier. For ease of transportation by land or sea, the machine can be split into two parts. The APF-Max blow moulder is equipped with a B&R PLC (since 2017, B&R has been part of the ABB group). The software program and the manuals are available in multiple languages. Flexibility APF-Max series is available in 2-, 3-, 4-, 5-,6-, 8-cavities configurations, offering a wide range of preform neck standards, enabling bottles from 100ml, for sanitisers, for example to 1 l for coffee, to be produced on the same machine. Output can be readily increased from the 7,000 bph with a four-cavity model to 14,000 by installing additional cavities and making minor changes to the heater. The machine can produce a wide range of bottle formats from 100ml to 6 l. The APF-Max 5 model, with 5 cavities can produce 2 l bottles, and by changing to 3 cavities, it is possible to produce 1 gal bottles. A hot-fill option is available on all models. Quick-change moulds The APF-Max blow moulder offers rapid mould change for different bottle formats with minimum down time, typically 15 minutes. The 108 mandrels in the heater of 8-cavity blow moulder can be changed in 4 minutes. All-electric configuration The servo drives provide more precise positioning together with high speed and a stable heater conveyor speed and blowing process. The stretching rod position is automatically controlled depending on the bottle height when switching from one bottle format to another. Preblow is also controlled via PLC. NIR heating and low total installed power The APF-Max blow moulder is equipped with the special short-wave near infrared heating system (NIR) which, although not commonly used in blow moulders, is said to be more efficient in terms of lower energy consumption. The NIR heating is said to offer various benefits including uniform temperature distribution between the inner and outer parts of preform wall reduced heating time, and a more compact heater. Ceramic reflectors are used for better preform heating and offer the advantage of automatic temperature regulation. Universal and operatorfriendly, economic and flexible These are just some of the benefits claimed for the new generation of APF-Max PET stretch blow moulders: high output combined with compact dimensions and a double air recovery system to cover the demand for low pressure and pressure for preblow. In Russia for example, Avida and the Kazan milk plant have already installed 3 blow moulders from PET Technologie’s APF-Max range. www.pet-eu.com","@ID":28}, "TRADE SHOW PREVIEW PETplanet Insider Vol. 21 No. 12/20 petpla.net 40 Avisha Desai: I am sure the entire industry is yearning to have an onsite, face-to-face interaction with their clients again. The virtual format may become pertinent in future as it will bring additional benefits to the regular on-site events. Ease of participation in case of travel issues and big data analytics, based on users’ interests, are some of the benefits that could be incorporated alongside the on-site events. PETplanet: Could you please give us a preview of what MMI is planning for Drink Technology India 2021 and other events that you host? Avisha Desai: For the first time, Drink Technology India will be colocated with Pack Mach Asia and World Tea & Coffee, giving the buyers the opportunity to connect with sellers from a larger industry. Pack Mach Asia is an international trade event for processing and packaging, which is jointly organised by The Institute of Packaging Machinery Manufacturers of India (IPMMI) and Messe Muenchen India. The World Tea & Coffee expo caters to the hot beverage industry; it brings together various exhibitors of this industry and displays technological advancements in this sector. PETplanet: Great, we’re looking forward to it! Can you tell us about the other events, like our Road Show, that were held in India last year? Why did Drink Technology India invest in that activity? Avisha Desai: The India Road Show was first time we have partnered with PETplanet, who travelled to various important cities in the country in the “Editourmobil” special vehicle. Three teams were assigned to cover the entire country. We visited over 40 PET-relevant companies to discuss everything important and forthcoming about the Indian beverage industry. Drink Technology India invested in this activity for promotional purposes and to network with various manufacturers across the country. The aim was to connect with the smallest and the largest players in the Indian beverage industry. It also allowed the Indian packaging industry to showcase their technology, potential and growth prospects on a global platform. PETplanet: Thanks a lot for the interview and stay healthy! The interview includes figures from the following sources: U.N. Trade and Development Report 2020 https://eatrightindia.gov.in/safeand-sustainable-packaging.jsp https://www.makeinindia.com/ sector/food-processing https://indiancompanies.in/indianfb-industry-beverage-and-food-sector/ Building the future in every moment of your business 40 Bar Oil-Free Piston Compressors for PET Applications. hertz-kompressoren.com","@ID":42}, "CAPS & CLOSURES 34 PETplanet Insider Vol. 21 No. 12/20 petpla.net PackSys Global, Rüti, Switzerland We met: Mr Beat Rupp, CEO Mr Ueli Kobel, Group Leader Global Sales Closures Mr Thomas LeFevre, Vice President for Sales and Marketing Ms Murielle Erard, Head of Marketing Slitting for tethered caps For a long time PackSys Global AG in Rüti, Switzerland, has specialised in manufacturing machines for the slitting and folding of the tamper evident band seen on most beverage caps. For many years, slitting was a rather unspectacular technology. Caps made by compression moulding required slitting. Producers of caps using injection moulding could choose between slitting the tamper evident band or making it as part of the injection moulding process. Discussions about recycling rates and the circular economy show that PET bottles are among the most widely recycled types of packaging however their caps are seldom recycled and are an easily recognised source of ocean plastic. As a result of this situation the EU passed legislation requiring that by July 2024 that all caps on beverage packaging remain attached or tethered after the bottle or carton is opened. Similar legislation was under discussion in California but has not yet been approved. The discussions about tethered caps have brought the technology to centre stage in cap production. We spoke to CEO Beat Rupp and Ueli Kobel about the background. PETplanet: Mr Rupp, Mr Kobel, you provide customers with systems for slitting caps. To what extent have requirements changed with the tethered cap? PackSys: Up to now, we have basically been dealing with straight cuts around the cap perimeter. This means we have rolled the cap along a knife with a specified pressure. This created the predetermined breaking points that enables the consumer to release the cap from the quality band using a specific twisting motion. PETplanet: The plastic cap must remain attached to the bottle during consumption. PackSys: Exactly. This happens only with an integrated hinge between the tamper evident band and cap and it makes the cutting geometry signifi - cantly more complex. The knife along which we rolled the cap must now not only cut horizontally; there are also vertical cutting edges on the knife. We call this technology smarTether. PETplanet: The design of the hinge, i.e. where the cut should be, is decided by the customer? PackSys: Yes. We deliberately stay out of this area. Each customer has their own trends there and that’s how it should stay. Certainly, we discuss ideas with the customer, as despite cleverly crafted hinge solutions, these can sometimes be difficult to implement in production. One very interesting area is the use of tethered caps on cartons, especially those known as gable top. Gable top cartons, which are very often used for dairy products, have an angled top instead of a flat top. For such cases the beverage is always dispensed in a certain way. Tethered caps on water, juice or carbonated soft drink bottles can be tethered in any direction. For gable top packages the tethered cap has to be oriented so that it stays out of the path of the beverage being poured. Developing orientation technology for tethered caps has been an interesting challenge but one where we have succeeded. The first oriented systems using our newly developed CapCompass technology are now in production and should deliver oriented tethered caps to the market in 2021. PETplanet: If you put the different designs from customers side by side, can you identify a trend? PackSys: A very clear trend is that the projects work with existing caps. They are trying to continue to produce the cap in the same way as usual and make the necessary adjustments just with the slitting. There is a strong pressure from all segments to make tethered caps be as cost effective as possible and certainly to avoid using more plastic for a tethered cap than for a non-tethered cap. PETplanet: Are there projects that have come through the prototype stage? PackSys: One customer has produced and tested 80 million screw caps and is now expanding its testing to several more locations. A lot of expertise has been developed by the cap makers, the bottlers and us as well. PETplanet: So there will be a significant sales increase for your business when the new regulations are implemented. Ueli Kobel, Group Leader Global Sales Closures PackSys Global","@ID":36}, "PETnews 6 NEWS PETplanet Insider Vol. 21 No. 12/20 petpla.net CCL invests in sustainable film project to boost recycling Speciality label, security and packaging solutions company CCL Industries Inc. announces plans for a strategic new capacity investment at their Innovia Films extrusion site in Plock, Poland. A new sixmetre multi-layer co-extrusion line will be installed to produce EcoFloat shrink sleeve material. This hybrid polyolefin film facilitates easy separation of labels from PET bottles and other types of plastic containers in the recycling process to enable bottleto-bottle circularity, an important goal for global food and beverage brand owners. The capacity comes on line in early 2022 with most of the capital deployed in 2021. www.ccllabel.com Alpla Group: Philipp Lehner new CEO from January 1, 2021 The Management Board of the Alpla Group, the global plastic packaging and recycling specialist based in Hard, Austria, is being restructured – Philipp Lehner will succeed Günther Lehner as CEO on January 1, 2021, making him the third generation of the family to run the company. Günther Lehner will assume the position of Chairman. The company has been preparing for this generational change for years, and it will now be effected with Günther Lehner handing over the agendas of the Chief Executive Officer (CEO) to his son Philipp Lehner on January 1, 2021. They will visit customers together in the course of 2021 in order to introduce Philipp Lehner as the new CEO of the Alpla Group. As Chairman, Günther Lehner will play a part in the company’s strategic direction in the years to come. One of the focuses of his future activities will be further developing the recycling and circular economy lines of business. He will also contribute his many years of experience in technology development and innovation and will play a significant part in shaping the company’s strategic networking with customers, suppliers and other business partners. “I am delighted to be placing the management of our company in family hands and I am confident that Philipp will do excellently in occupying this position. This will secure the continuity that our customers and business partners need,” says Günther Lehner. “Alpla has strong foundations and is excellently positioned to rise to the challenges of these times,’ says Philipp Lehner. ‘I am grateful to my family for the enormous trust they are placing in me and I look forward to shaping the company’s future together with our staff.” Philipp Lehner (36) joined Alpla in June 2014 following his business management training, study periods abroad, jobs in the finance and consultancy sectors, and an MBA qualification at the Harvard Business School. On joining the family-owned business, he spent his first six months on a plant trainee programme in Lübeck, Germany. He then served as plant manager at Alpla Iowa in the USA for 18 months. He subsequently assumed overall responsibility as regional manager of the USA for two and a half years, before returning to Hard at the end of 2018. Since January 2019, Philipp has been CFO of Alpla, making him responsible for the areas of finance, IT, digitalisation and human resources. www.alpla.com Günther Lehner (left) will place the agendas of the CEO of the Alpla Group in the hands of son Philipp Lehner. HERBOLD Plastcompactor Agglomeration with the Plastcompactor HV, ideal for: Powder Fibres Film Foam material More about our HV on www.herbold.com 'R \\RX IDFH SUREOHPV ZLWK EXON GHQVLW\\ RU PDWHULDO ÀRZ\"","@ID":8}, "CAPS & CLOSURES 36 PETplanet Insider Vol. 21 No. 12/20 petpla.net Technologies Tethered closure designs vary according to the individual applications and beverage container specifications. PackSys Global has developed two new slitting technologies to create solutions matching the EU directive requirements and considering consumers’ convenience. All technologies deliver solutions with all the traditional benefits of slit TE Band closures plus tethering. smarTether This technology can be implemented without machine modifications into all machines in PackSys portfolio. A choice and combination of multiple horizontal, together with several vertical knives, allows slitting with either a randomly positioned hinge or a lasso styled tether. Conversion of existing production machines allows quick and cost-effective product conversion. smarTether is applicable on all major PET bottle closure applications. smarTether purposely leaves a thin and controllable skin in the separation area (to not completely cut through the plastic closure side wall). This provides a high-performance tethered closure suitable for high speed capping processes. smarTether technology experTether experTether, like smarTether, is designed for multiple slitting lines on both the horizontal and vertical axes. The spindles are fully and accurately synchronised to the slitting knives, located at the outside of the rotating slitting turret. The synchronised tooling ensures unique accuracy on slit lines and is the only method able to create customised slitting pattern on plastic closures as known from standard TE band slitting. Regardless of the required speed, experTether can handle it. experTether CapCompass technology When it is important the closure stays in a consumer-friendly position after opening (e.g. carton bricks, gable top, etc.), CapCompass is the right solution. After opening, the closure will flip away to a nondisturbing position. Simultaneous spindle movements allow accurate positioning of the plastic closure before slitting process starts. Optimised machine kinematics, paired with sequential knife penetration, provide gentle closure handling and make it therefore also suitable for thin wall and light weight closures. CapCompass orientation technology can be used with both smarTether and experTether to achieve the customer’s desired tethering style. PackSys Global has applied for patents on a number of the newly developed technologies related to tethered solutions. CapCompass","@ID":38}, "PREFORM PRODUCTION PETplanet Insider Vol. 21 No. 12/20 petpla.net 17 process set-up and an in-depth part quality troubleshooting tutorial, which together will help users improve machine up-time, lower scrap rates, and depend less on highly skilled machine operators. More open One of the great advantages of the XForm concept is its openness. It has led the way in its ability to accept preform tooling from other major producers. In recent months, Sipa has added new features to further facilitate use by its customers of existing tooling. The new XForm 250 Gen4 XP preform injection moulding system, for example, accepts non-Sipa moulds and end-of-arm tooling (EOAT), it also accepts pin plates for preform cooling and removal coming from alternative suppliers. Allowing customers to use their existing pin plates on new Sipa machines is one of the latest examples of how Sipa is trying to make their lives a little easier. No shaking A short while ago, a Sipa employee was watching an XForm 500 system equipped with a 180-cavity mould running at full tilt, with a cycle time of 5.4 seconds. Normally, when a machine of that size and type is operating flat-out, it makes its presence known. The air vibrates, one may even feel throbbing through the floor. Just out of curiosity, the technician put a glass of water on the frame of the machine. There was hardly a ripple on the surface. This was not a one-off. It is a characteristic of all XForm machines. And the larger the machine, and the higher the cavitation, the more characteristic it is. Vibration obviously puts stress in a system, and when that system is running fast for a very long period – which is often the case in PET preform production – that stress is significant. It can cause premature wear on moving parts, leading to high maintenance costs on the machine and the tooling, especially on large systems. In fact, the clamping systems, linear bearings, tooling tapers – essentially the entire system structure – undergo massive stress. Component lifetimes drop. But the XForm can operate with ultra-high cavitation tooling, with very short cycle times, and still run extremely smoothly, states Sipa. What helps to make this possible is a robust clamp design and a smooth clamping profile that comes from the servo-driven toggle. This yields a smooth performance that hardly wavers over time, helping keep maintenance costs low. In fact, maintenance costs on machine and tooling on the XForm are significantly lower than almost any other PET preform system in the market, Sipa emphasises.","@ID":19}, "PETplanet Insider Vol. 21 No. 12/20 petpla.net 47 BOTTLES A certified Nature Box Nature Box, a Schwarzkopf and Henkel brand, was approved as a natural cosmetic in autumn this year during which improvements were made to its packaging. The product contains 98% natural ingredients and comes in a bottle now made from 98% social plastic which has been collected from beaches and the countryside. The picture shows the product containing cold-pressed pomegranate oil which comes in a matching-coloured 250ml bottle. A self-adhesive label with a screw-on hinged press-down cap and dispensing spout round off the packaging. www.natureboxbeauty.com An aromatic shower from Tetesept Tetesept has brought out a revitalising orange and jasmine aromatic shower product under the name “tetesept: Formula”. It comes in a 250ml bottle made from 100% recycled material and is brownish in colour, rather reminiscent of old pharmacy containers. The vegan shower gel does not contain any paraffins, silicones or microplastics and is 98% biodegradable. Self-adhesive labels include information on the product and explain the company’s ethos. A dispensing spout integrated within the hinged lid closure makes this an easy to use product. www.tetesept.de A hair oil from Wella Wella has brought out a Deluxe hair oil product which comes in a slightly copper-coloured, clear 100ml bottle. It has a transparent adhesive label on the front through which the customer can clearly see the product and its slightly milky texture. The goldcoloured label on the back of the bottle provides information on the product and instructions on how it should be used. The oil is applied via a manually operated pump dispenser which has a glossy finish. An additional cap protects against damage and inappropriate use during handling and storage. www.wella.com Love Nature: Refill bottles Henkel’s new washing and cleaning range, Love Nature, not only includes references to vegan, animal-friendly and the phrase “100% recyclable” or more appropriately “made from 100% recycled plastic” which is used by nearly all manufacturers in this sector but also that the bottles can be re-filled at selected pharmacy locations by using appropriate vending machines. In comparison to other well-established products, the brightly coloured liquids in horizontal shoulder bottles with a green cap and self-adhesive label are really eye-catching. Different bottle sizes are used depending on the product, e.g. 470ml and 960ml sized bottles for handwashing and liquid colour detergents respectively. www.love-nature.info","@ID":49}, "48 PREFORM PRODUCTS PETplanet Insider Vol. 21 No. 11/20 petpla.net New mould part coating MHT AG, based in Hochheim am Main, Germany, in cooperation with the Lüdenscheid Plastics Institute, is conducting basic research into a new type of coating for moulded parts. The first results were recently examined and evaluated. What can injection moulders expect in the near future? A thin-walled, thermal barrier layer of ceramic has been shown to be a solution with great potential: It reduces heat penetration capacity into the shaping tool components, resulting in temperature balance optimisation. Due to the thinness of the ceramic layer, there is a short-term temperature-induced viscosity change of the PET. Over a longer period, the plastic remains in a flowable state, so that even thin-walled, long preforms can be filled quickly. The overall good cooling rate of the MHT-typical conformal cooling remains unaffected by the thinness of the layer. This is how MHT AG ensures a high cooling rate over the entire injection moulding cycle. After initial series of tests, the engineers are convinced that the concept can be realised: An optimisation of the attainable flow path length as well as the filling of the moulded part could be demonstrated. In future, injection moulders will enjoy lower material consumption for the production of thin-walled, long preform geometries, and this will be accompanied by reduced energy input. Further research on coating is aimed at determining optimum layer thickness and achievable surface quality. www.mht-ag.de Industry 4.0 implementation benefits preform production To adapt more easily to the necessities and production processes in order to meet the needs of its customers more effectively, Petka has transformed its production system by introducing new technologies, and in particular by implementing Industry 4.0 in its factory. This technology has allowed the company to prevent possible anomalies, thanks to the use of sensors in its machines. In this way, the company was able to find solutions more quickly for customers, and reduce production times by 25%. During the pandemic period, the company had to meet the client’s needs in short deadlines, as all of them were making quick decisions about their investments at the same time. Thanks to the new technologies, Petka increased capacity by 25% in the last year. Since its implementation, Petka is able today to make prototypes by only producing the stack parts, thanks to its new mould designs. The prototypes range from 6 g to 70 g for preform projects, and from 100 cc to 10 l for bottle projects. Using these new technologies, the company designed a new mould for preforms which made the production of prototypes simpler. This meant that customers received the preform samples more rapidly with typical cost savings of between 15% to 20%. The Industry 4.0 system also supports more efficient use of resources, reducing waste in the manufacturing process by 8%. www.petkamold.com Optimised configuration Following the continuous improvement strategy focus on PET preform injection moulding systems, the Kronce Enterprise Development team is focusing on collecting feedback from their customers with the intention of improving cycle times and optimising configurations of the complete PET preform production line. Kronce states that PET preform demand is both rising and broadening; the number of different applications is increasing strongly. As a result, PET preform producers are looking for ways to increase output while controlling costs, both of equipment and of production. Kronce says that getting a reliable, higher output at a reasonable capital outlay, while minimising production costs and thus helping competitiveness is its focus. Continuous market research and feedback helps Kronce to turn clients’ vision and goals into reality and to help them to develop their ranges and increase productivity, using their existing equipment. For example, in 2020 the company adapted a 64-cavity PET preform injection mould to work in equipment that was capable of operating only a maximum 48-cavity machine in the past. The client’s PET IMM, with a 730x730 tiebar distance, wasfitted with a 64-cavity preform mould, using a 13g preform with 3025 neck. Output was increased by 28.4%, while power consumption was reduced by 16.91%. Kronce is eager to demonstrate the potential benefits of 64-cavity production over 48-cavity. The company is developing similar solutions for clients requiring lower output levels: 32-cavity PET preform injection mould in a Kronce PET IMM model with 520x520 tiebar 48-cavity PET preform injection mould in a Kronce PET IMM model with 580x580 tiebar 48-cavity PET preform injection moulding with single injection unit and triple PET preform ejection robot and post cooling system. www.chinakronce.com PREFORMS PREFORM products","@ID":50}, "PREFORM PRODUCTION PETplanet Insider Vol. 21 No. 12/20 petpla.net 15 tive, hand cleaning is a complex process that requires mould components be individually removed, cleaned, rinsed, dried and replaced with the use of spray cleaners, solvents and brushes. Dry ice blasting is a nonabrasive method where the mould is cleaned directly in the press while still hot. Grain-sized carbon dioxide pellets are introduced into an air stream and are shot through nozzles at high speed to quickly remove residue. Both of these methods are time consuming, require skilled maintenance personnel and must be thorough to eliminate processing defects. Repeated motions could result in operator injuries, and mould parts and inserts can be damaged during the cleaning process. Running rPET amplifies manual cleaning challenges, including the need for more frequent cleaning. Furthermore, running different qualities of rPET can cause greater risk of outgassing and dust deposits in vents, which can lead to a higher risk of defective parts. Having a reliable, fast and easy method of cleaning maximises successful rPET material running. Husky’s Self-Cleaning Technology skips traditional maintenance interruptions of 2-6h; its automatic process is simplified to the touch of a button and lasts just a single extended machine cycle. It eliminates the need for operators to enter the machine and can be performed as often as needed and helps to resolve the conflict between cycle time and mould maintenance. The secret to Self-Cleaning Technology is controlled flash, using precisely controlled gaps to ensure flash does not travel beyond the target area. During a self-cleaning cycle, the vents are filled by PET flash; the overflow of PET from the preform. The flash then sticks to dust in the vents and the flashed preforms, complete with dust, are then ejected, leaving cleaned vents behind. Effective combination While Ultra Hot Runners and Self-Cleaning Technology do not completely eliminate the need for traditional mould cleaning methods, they represent a significant evolution in mould maintenance and offer manufacturers added flexibility and reduced risk when running rPET – especially when used together. This addresses many of the common issues associated with mould maintenance, including minimising labour and downtime, streamlining the moulding process and making cleaning safer. It enables producers to be more sustainable, by supporting higher percentages of rPET to be run more efficiently. Case study An established preform manufacturer located in the United States installed Self-Cleaning Technology on a HyPET HPP5 system. Traditionally, this customer manually cleaned vents every 50,000 cycles or on detecting defects such as top sealing surface shorts, flow lines on the thread finish, or shorts in the leading thread. As their operation runs continuously, they were sensitive to downtime. Their existing mould cleaning methods had difficulty keeping up with required maintenance activities. At a glance: Self-Cleaning Technology increases uptime and production capacity: Automated mould vent cleaning significantly reduces the risk of short shots Convenience makes cleaning more likely to be performed Cleaning can be performed more frequently and consistently Ultra-spring package and enhanced seal design streamlines operations by: Eliminating dust issues and consequent downtime required for cleaning Providing cold start protection and reducing risks of air leaks and stem blockage Offering a superior balancing and processing window advantage The ergonomic and downtime concerns with dry ice cleaning caused them to explore the development of costly equipment to automate the dry ice cleaning process. After discovering and implementing Husky’s Self-Cleaning Technology, this investigation was halted. The customer was able to reach 570,000 cycles with no requirement for dry ice cleaning. Estimated savings in maintenance time are more than 320 h/a. www.husky.co","@ID":17}, "PREFORM PRODUCTION PETplanet Insider Vol. 21 No. 12/20 petpla.net 13 Response to new challenges in preform manufacturing Performance, flexibility, sustainability based on an article by Moraldo Masi, PET BU Director, Sacmi Closures, Preforms & Containers Division When the first complete Sacmi PET preform production platform with injection technology (IPS -injection preform moulding) was introduced in 2012, it had two goals: to complete the Group’s vocation as a plant engineering provider for every stage of the cap and beverage line and to respond to the burgeoning demand that reflected - especially among bottlers - the need for a solution offering reliability, low consumption and user-friendliness. This range subsequently evolved and expanded to meet the need for versatility and performance, especially among converters. As with packaging in general, the preform production sector continues to seek an appropriate response to the dual needs of productivity and flexibility. Additionally, the global market is pushing hard to make the industry sustainable, setting out the packaging industry recycling milestones that will need to be reached over the next decade. A particularly topical challenge, especially in Europe (in light of new standards on reducing virgin plastic use in packaging), is sustainability which has long been a focus of Sacmi’s efforts. Those efforts have, firstly, seen the development of a range of standard machines that can operate with recycled resins. They have also seen a focus on lightweighting (overall weight reduction of the cap-preform system, performance remaining equal). On this latter front, covering the entire production chain, Sacmi sees itself to be perfectly placed to guide innovation at global level. In light of the above, the company is investing heavily in developing machines and moulds that meet customer needs. The Sacmi IPS for the manufacture of PET preforms has been designed and produced in keeping with the following concepts: Performance, not just as regards cycle time/productivity but also in terms of line availability, reliability and energy consumption: the pillars of a modern TCO (total cost of ownership) approach. Flexibility, in terms of quick and easy mould changeovers, plus the ability to operate with legacy and existing moulds. The main players on this market require such features from systems suppliers because moulds are expensive and often last longer than the machine on which they’re assembled. Sustainability, in terms of both weight reduction (packaging performance remaining equal) and the ability to use rPET. This last aspect is gaining in importance almost daily, as everstricter national and international standards are implemented to safeguard the environment. Equipped to respond to new, pressing market needs, the Sacmi injection press range can, in the standard configuration, process up to 100% of rPET in granules and up to 50% in flakes. Moreover, expectations are high on the lightweighting front as the Italian company is also a developer of new technical and cap-preform design standards and experienced at getting them to market. For example, 2020 saw the company invest in the development of the new 26mm neck standard – lighter than the earlier 28mm but equally high-performance – and carry forward the standardisation process with the main international certifying bodies. www.sacmi.com PREFORMS","@ID":15}, "PREFORM PRODUCTION PETplanet Insider Vol. 21 No. 12/20 petpla.net 19 Collaboration between R&D/Leverage and PET Pak for tailor-made preforms and tooling Versatile preform design and tooling package When R&D/Leverage Europe was contacted by PET Pak d.o.o. Slovenia for a solution to provide bespoke preforms and tooling for a large range of bottles with a 28mm neck finish for cylindrical, dome, bullet and pharma bottles it was a technical challenge: Not only was the inquiry technically demanding for such a varied bottle range, the request was also for various weights and product sizes which included three different neck finishes. R&D/Leverage Europe focused on a versatile preform design and tooling package to provide the best possible solution. The main challenge was to design a preform with flexibility for weight change whilst maintaining optimum stretch ratios for high quality bottles. “The stretch ratios are extremely important to achieve the best possible material thickness variation. PET Pak made it very clear that the quality should not be compromised and also cycle time was very important in order to make the package cost effective.” recalls R&D/Leverage the challenge they faced. The neck finish and related preform tooling components were also designed in such a way that the three neck finishes could be used from one preform design with minimal tool change parts. Extensive testing R&D/Leverage has a testing facility in the UK (Product Solutions Laboratory) including nine single stage machines with fully equipped state of the art bottle QA capability. This laboratory is dedicated to the development of all PET, PP and other resins for single stage bottle solutions in terms of colour validation, weight reduction, high specifications, preform design flexibility, optimised cycle times and full tooling validation. Tool manufacturing is located within the same campus to provide flexible tooling developments and modifications to support the best quality and efficient service for convertor and Brand owner requirements. It was here that testing was carried out for PET Pak, as R&D/Leverage recalls: “The results were immediately very positive and achieved the high technical demand and stringent specification set out by PET Pak.” PET Pak is a manufacturer of topquality plastic packaging. Mitja Nadoh, Project Manager at PET Pak states: “When we were deciding about the tooling partner for this demanding and important project it was clear that we needed to select a company which is fast acting, understanding and cooperative; the only logical choice was therefore to work with R&D/Leverage, who closely cooperated with us and delivered the exact solution we were hoping to get. “ He continues, “Because of our ambition to work only with the best partners in order to provide top-quality products to our customers we are now able to expand with a newly build modern 10,000m2 production plant, which will allow us to improve our already high production standards and services.” www.rdleverage.com PREFORMS +44 (0) 1254 584210 [email protected] petmachinery.com Active for over 25 years, our global network and specialist knowledge makes us the go-to company for the sale or purchase of a PET machine. Commercially savvy, we work closely with our customers and our global network, to make sure everyone gets the best deal. Providing comprehensive advice throughout your sale or purchase; we can arrange dismantling, loading, packing, shipping, specialist insurance and commissioning. If you have amachine to sell or you’re looking to purchase, please get in touch. THE INDUSTRY EXPERTS","@ID":21}, "imprint EDITORIAL PUBLISHER Alexander Büchler, Managing Director HEAD OFFICE heidelberg business media GmbH Vangerowstraße 33 69115 Heidelberg, Germany phone: +49 6221-65108-0 fax: +49 6221-65108-28 [email protected] EDITORIAL Kay Barton Heike Fischer Gabriele Kosmehl Michael Maruschke Ruari McCallion Waldemar Schmitke Anthony Withers WikiPETia.info [email protected] MEDIA CONSULTANTS Martina Hirschmann [email protected] Johann Lange-Brock [email protected] phone: +49 6221-65108-0 fax: +49 6221-65108-28 LAYOUT AND PREPRESS EXPRIM Werbeagentur | exprim.de Matthias Gaumann READER SERVICES Till Kretner [email protected] PRINT Chroma Druck Eine Unternehmung der Limberg-Druck GmbH Danziger Platz 6 67059 Ludwigshafen, Germany WWW www.hbmedia.net | petpla.net PETplanet Insider ISSN 1438-9459 is published 10 times a year. This publication is sent to qualified subscribers (1-year subscription 149 EUR, 2-year subscription 289 EUR, Young professionals’ subscription 99 EUR. Magazines will be dispatched to you by airmail). Not to be reproduced in any form without permission from the publisher. Note: The fact that product names may not be identified as trademarks is not an indication that such names are not registered trademarks. 3 PETplanet Insider Vol. 21 No. 12/20 petpla.net There is no year in PETplanet’s history which has seen quite so many changes as 2020. What began slowly with an excellent interview with Rajesh Nath of VDMA India about coronavirus in issue 5 subsequently led to a series of similar conversations. Sacmi, R&D Leverage, Husky, GDXL, Sukano and, in this issue, Amcor, describe the impact, Covid-19 has had on their work. Our hugely popular Editour event was not able to take place as planned. Instead, we conducted interviews remotely which can be heard on a PETcast on our homepage or read in the magazine. This issue focuses specifically on Taiwan. Many trade fairs were cancelled, in particular Interpack, Chinaplas and the Brau event last month. We made other arrangements by holding PETinars in May, June and November, a list of which can be found on our homepage under “Postponed events” and “Services/PETinars” respectively. We also had difficulties in sending our magazine to the rest of the world as not all postal agencies were able to process foreign mail. Those countries that did not receive printed copies were sent a PDF version which also enabled the latest news on PET to reach many office staff working from home. We will maintain this level of commitment for as long as is necessary. PETplanet’s main focus will continue to be our outstanding printed publication and on-site research with Editourmobil. However, it is safe to say that many of the new formats are going to be retained. On that note, I wish you all a relaxing time over the holiday period. Yours sincerely Alexander Büchler A look back over the year 2020 Dear readers,","@ID":5}, "42 TRADE SHOW REVIEW PETplanet Insider Vol. 21 No. 12/20 petpla.net Pressco Technology I) We were very pleased that the fair organisers had implemented very rigorous safety protocols, and so the attendance at the fair was very strong - indeed better than we had anticipated. We also sanitised our stand space several times each day, and provided plenty of masks, gloves and hand sanitiser to our guests. II) The primary topics for Pressco and our customers were focused on our ability to provide a wide range of distributed inspections on a single production line, which allows the user to deploy one inspection platform which can inspect preforms, empty bottles and filled bottles all from the same system, with a single processor and interface. This also makes training and support much easier for the customer, because there is only one software to learn and there is a single relationship for any customer service needs. In addition, Pressco systems provide a tremendous amount of data to improve process visibility and enhance line productivity and efficiency. This is critical for most of our customers who operate high-speed lines. Many customers who visited our booth were very willing to share their specific inspection requirements so that we could work together with them to identify the proper solutions. III) We believe there is much optimism among the food and beverage companies. We see potential for growth in the Chinese market in particular, both for PET bottles and aluminium beverage cans. The packaging manufacturers and the filling companies are eager to do business with suppliers who are willing to work hard to help them meet very aggressive goals for quality, efficiency and profitability. Our customers see Pressco as a business partner who truly understands food and beverage packaging, and who offers them state-of-the-art technology supported by a worldwide service team. www.pressco.com GDXL Precise Machinery I) Due to the pandemic, stricter measures such as personal certification for entry pass, green health pass code, mask wearing, temperature monitoring, etc. were applied. The premise was the same one (SNIEC) with upgrades in security and health control equipment such as embedded temperature sensors at security checkpoint, entry gates with ID reader and face detection, etc. These raised participants’ confidence towards the event. There were fewer exhibition halls when compared with previous editions of CBB, as some overseas exhibitors and visitors could not attend for safety reasons. Fortunately, compared with similar expos in upper half of the year which were mostly postponed or completely turned online, the event was held successfully as scheduled, which showed a positive sign that the industry is eager to adapt to post-pandemic era and grow. II) The topics of the event were related to intelligent production and latest brew and beverage development trends. Issues including individualised and flexible production, new requirements to beverage and equipment in post-pandemic era, product life cycle management and sustainability, online service platform and unmanned sales, as well as new technologies and package designs, were discussed. III) China has been our major market for years and we have built up strong relationships with our customers. We were glad that many of them were able to attend so that we could meet them in person, discuss on-going projects and strengthen business partnerships. The pandemic is in general under control in China, and suppressed demand for consumption has been gradually released with the help of sophisticated logistics network and on-line shopping platforms. Moreover, being daily life consumables, beverage products are less susceptible to adverse effect of pandemic than other fast consumer goods, which may not be necessary during difficult times. While demand for beverage and liquid food are growing in pace with the economy, the pandemic may serve as an opportunity to optimise and discover new applications of intelligent production and marketing options. www.gdxl.com","@ID":44}]}}
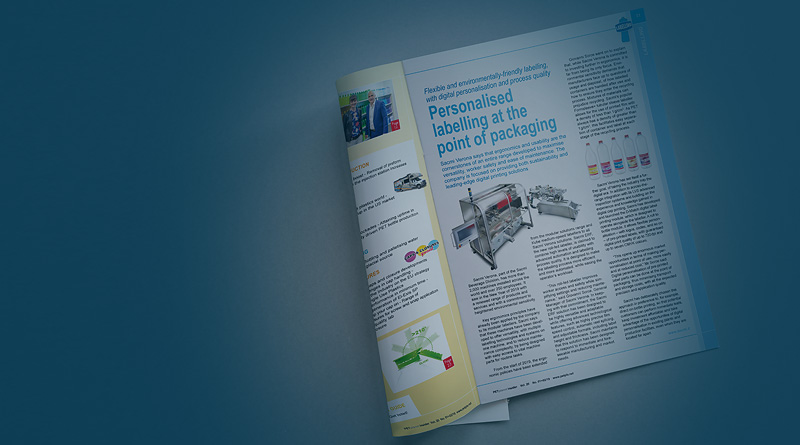