{"pages":{"page":[{"#text":"EDITOUR PETplanet Insider Vol. 22 No. 03/21 petpla.net 12 caused not only a postponement of the Olympic games but triggered a major recession with real GDP projected to shrink by more than five per cent. But Japan has surprised us all. Currently, as of early March, the benchmark index in Tokyo is higher than it has been for decades. For starters, the announcement of a Covid-19 vaccination campaign has given a boost to share values. Primarily, however, the government has published economic figures for the fourth quarter of 2020 and these have recently been gaining decent upward momentum. Furthermore, Japan is benefitting from the Regional Comprehensive Economic Partnership (RCEP), ratified in November 2020, which is a free-trade agreement between the ten ASEAN members states and five more nations in the Asia-Pacific region. A significant proportion of Japan’s manufacturing landscape comes under the plastics industry. The most commonly produced goods were films, sheets and plates, followed by containers and parts for machine tools. According to the Japan Plastics Industry Federation (JPIF), PET material production was at 307,904 t in 2020 (2019: 365,286 t). Japan’s PET bottle, beverage and recycling market Land of the rising recycling rates by Gabriele Kosmehl The last stop on our current Editour took us to Japan. The world’s fourth largest island nation stretches over 378,000km2 across the four main islands of Honshu, Hokkaido, Kyushu and Shikoku as well as over 6,800 smaller islands. Japan is one of the most densely populated countries in the world - and has the highest proportion worldwide of vending machines, more than four million, dispensing drinks that are mostly bottled in PET - and recycled after use. Tour Sponsors: Macro-economic data 2020 2021 2025 Population (millions) 126.5 123.0* Population density (population/km²) 347 GDP (annual percent change) -4.8 % 3.1 %* GDP nom. (billion) US $ 4,944 $ 5,103 $* GDP/capita nom. US $ 39,048 $ 40,733 $* Inflation (%) -0.1 % 0.3 %* Unemployment rate (%) 2.9 % 2.8 %* *preliminary figure/estimate (sources: German Trade and Invest 2020/GTAI/IMF/MOFA) Japan’s economy At the end of 2019, the longadvertised VAT increase from 8% to 10% was implemented in Japan. Many purchases were therefore brought forward, especially as there were hopes for a good year for Japan’s economy in 2020, with the planned Olympic Games expected to draw large crowds. Then, early in 2020 came the Covid-19 shock and","@ID":14} "Thewholeworldof PETplanet is read in more than 140countries petpla.net WHY PETPLANET? For more than 22 years, PETplanet Insider has been the world’s leading magazine for the PET bottling and bottle-making industry, bringing together machine manufacturers and their customers – directly, with up to date on-site reports at customer plants, providing first hand information on the latest developments and trends. Our market reports and surveys, along with interviews with the major players in the industry give our readers an excellent overview of what is happening in the world of PET. PETplanet Insider continues to be the highly specialised source of information for more than 10,000 readers in over 140 countries and the ideal publication for advertisers who wish to target decision makers in this sector. Social Media Connecting worldwide News Daily PET business news Worldwide PET magazine No.1+2 2020 Page 31 Page 10 MOULDMAKING Page 18 Editours Worldwide editorial reporting Congresses PET symposiums and lectures WikiPETia .info PET knowledge management system Pulse The monthly PET price index Events Fairs, open houses, on-site sessions ... PETinars Learn from the best PETcasts Let´s talk about PET","@ID":45} "MARKET SURVEY 36 PETplanet Insider Vol. 22 No. 03/21 petpla.net 03/2021 MARKETsurvey Suppliers of preform machinery In this issue we focus on new developments in perform machinery. We are very proud to present the most exciting brand-new data from the following perform machine manufacturers: Nissei ASB Machine Co. Ltd., Netstal Product Brand KraussMaffei HighPerformance AG, Sacmi Imola, Sipa, Husky Injection Molding Systems and Otto Systems. Although the publishers have made every effort to ensure that the information in this survey is up to date, no claims are made regarding completeness or accuracy. Company name Nissei ASB Machine Co., Ltd. KraussMaffei HighPerformance AG Sacmi Imola Postal address Telephone number Web site address Contact name Function Direct telephone number E-Mail 4586-3 koo, Komoro-shi, Nagano-ken, 384-8585 Japan +81 267 23 1565 www.nisseiasb.co.jp Mr Masato Fujii Section Manager, Sales Coordination Team +81 267 23 1565 [email protected] Tschachenstrasse CH-8752 Näfels, Switzerland +41 55 618 6111 www.kraussmaffei.com Mr Stefan Kleinfeld Application & Product Manager +41 55 618 6241 [email protected] Via Provinciale Selice 17/A 40026 Imola BO, Italy +39 0542 607111 www.sacmi.it Mr Moraldo Masi Director of Business Unit PET +39 0542 607888 [email protected] Preform injection moulding systems Machine model number / name PM-70/65NII, PM-70/111N, PM-170/111M Side Entry Systems: Netstal PET-Line 3000, 4000 / Top Entry Systems: Netstal PET-Line 2400, 4000, 5000, 2C; IPS220 IPS300 IPS400 Number of cavities (min/max units) 6 - 48 24 - 144 16 - 72 24 - 96 48 - 128 Maximum individual preform weight 240g Max shot weight 6,600g 140g 140g 140g Max resin through-put (kg/h of PET) 250 (approx.) Up to 1,350 625 900 1,250 Standard features (short description / keywords) Vertical clamping, built-in preform aftercooling stations, extremely compact All systems: Intrusion; Side Entry Systems: Smart Operation (= safe and guided operation); PETX-Screw (= optimised 100% rPET processing); Energy Recuperation (Lowest Energy consumption) Injection cylinder (shooting pot); electrical drive for plasticising screw, T-belt for preforms extraction, Cool+ system (inside cooling), belt free robot linear motor with KERS, take out plate with 3 postcooling stations, HMI with control of all auxiliaries, double cylinder for preform ejection, digital valves for each actuator, water unloading system prior to mould changing, injection shot completition device (power failure) Injection cylinder (shooting pot), electrical drive for plasticising screw, T-belt for preforms extraction, Cool+ system (inside cooling), belt free robot linear motor with KERS, take out plate with 4 postcooling stations, HMI with control of all auxiliaries, boosters on moving platen for first phase ejection, double cylinders for preform ejection, digital valves for each actuator, water unloading system prior to mould changing. Options / special features (short description / keywords) Outputs are tailored to ASB's own range of 2-step blowing machines for hot fill application. PM-170/111M is designed for bottle and jar preforms with capability of neck size up to 120mm Cycle guard (= Controlled production shutdown during a power outage); NRS (= Netstal remote support); Energy measurement; Cool plus (= Preform inside cooling); Staggered EOAT (= additional cooling station); Q-Vision control Fast change over system with plug-andplay mould fixing system, plug-and-play take out plate fixing system, water pumps for mould cooling assembled on main machine platform, secondary belts system for an easier collection of preforms sampling, quality control vision system with multiple camera, soft handling package, walkway; high temperature environment package, cooling water sensoring kit Injection shot completition device (power failure), water pumps for mould cooling assembled on main machine platform, quality control vision system with multiple camera, soft handling package, walkway, high temperature environment package, cooling water sensoring kit","@ID":38} "55 TRADE SHOW REVIEW PETplanet Insider Vol. 22 No. 03/21 petpla.net Sipa supports sustainable growth PET containers production and filling equipment specialist Sipa will demonstrate its strength in sustainable manufacturing solutions. With more than 30 years of experience in PET container manufacturing and filling technologies, Italy-headquartered Sipa has a strong presence in China. It cooperates with many famous Chinese brands – Wahaha, TingHsin International, Yihai Kerry, C’estbon, Nonfu spring, Uni-president, Dinghu, Coconuts, Jilinsengong, Zijiang, Zhuhai Zhongfu, COFCO Group, Ganten, and Beidahuang among them – as well as international brands with locations in the country, such as Coca-Cola, Pepsi, and Danone. Tailor-made solutions Sipa proposes manufacturing solutions tailormade to customer requirements – whether it be in designing new attractive bottle designs, in lightweighting to reduce materials, reducing cycle times, cutting investment costs, or increasing flexibility to re-tool. Solutions include in-house design and production of moulds that can be used on its own production systems as well on those of machines from other major brands. Its design service extends to bottle prototyping using various technologies. Sipa is also able to deliver global tooling programs for new preform moulds or mould conversions, with cavitation levels all the way up to 192. Sipa says that numerous breakthroughs over the years have provided customers with advantages in terms of sustainability in their operations. One of the latest is Xtreme Renew technology. This is claimed to be unique in the world in its ability to produce high-quality preforms directly from flakes of post-consumer scrap, in a single heat cycle. It combines Sipa’s Xtreme injection-compression moulding technology with recycling technology. Manufacturing solutions for the production of PET preforms and containers include high-speed rotary stretch-blow moulding systems (Xtra range, capable of producing a class-leading 2550 bottles per hour per cavity – and which is an ideal fit for Xtreme), linear systems (the highly flexible SFL range), and high-speed and medium/low-speed single-step ISBM systems (ECS FX and ECS SP respectively). On preform production side, the Sipa range includes the XForm GEN 4, preform injection moulding technology featuring 250, 350 and 500 t systems, capable of running with moulds holding up to 96,128 and 180 cavities respectively. Producing large containers For the production and filling of large containers, mainly used for mineral water and edible oils, Sipa highlights its SFL linear blowing machines and supporting complete line equipment. Sipa technology is already being used in China for containers as large as 12 l collapsible cooler bottles. In the edible oil industry, SFL units are hard at work making bottles from 1.8 l up to 10 l at numerous Sipa customers. Advantages include high output, low energy consumption, efficient automation, and steady operation. Local bottle design, mouldmaking and tooling refurbishment Sipa has its own manufacturing operation in China as well as a local skilled team of packaging designers and engineers. Sipa Machinery Hangzhou Co., Ltd builds and refurbishes preform and bottle moulds for local manufacturers. Last year, SMH has hugely invested in automation for preform moulds production, incorporating the latest technologies available enabling it to greatly increase production capacity and shorten delivery times. Production is supplemented by a well-stocked spare parts warehouse. The after-sales team includes service engineers with several years of experience with the company. www.sipa.it SIPA Hall 6 Booth F61","@ID":57} "imprint EDITORIAL PUBLISHER Alexander Büchler, Managing Director HEAD OFFICE heidelberg business media GmbH Vangerowstraße 33 69115 Heidelberg, Germany phone: +49 6221-65108-0 fax: +49 6221-65108-28 [email protected] EDITORIAL Kay Barton Heike Fischer Gabriele Kosmehl Michael Maruschke Ruari McCallion Waldemar Schmitke Anthony Withers WikiPETia.info [email protected] MEDIA CONSULTANTS Martina Hirschmann [email protected] Johann Lange-Brock [email protected] phone: +49 6221-65108-0 fax: +49 6221-65108-28 LAYOUT AND PREPRESS EXPRIM Werbeagentur | exprim.de Matthias Gaumann READER SERVICES Till Kretner [email protected] PRINT Chroma Druck Eine Unternehmung der Limberg-Druck GmbH Danziger Platz 6 67059 Ludwigshafen, Germany WWW www.hbmedia.net | petpla.net PETplanet Insider ISSN 1438-9459 is published 10 times a year. This publication is sent to qualified subscribers (1-year subscription 149 EUR, 2-year subscription 289 EUR, Young professionals’ subscription 99 EUR. Magazines will be dispatched to you by airmail). Not to be reproduced in any form without permission from the publisher. Note: The fact that product names may not be identified as trademarks is not an indication that such names are not registered trademarks. 3 PETplanet Insider Vol. 22 No. 03/21 petpla.net Postponement of drinktec to 2022 Guest commentary by Petra Westphal, Messe München After almost a year and a half of the pandemic, we are all eagerly looking forward to actively renewing our private and professional contacts, to exchange ideas and finally to be able to look people in the eye again. Hopefully in our own social circles this will become a reality for many of us in many countries this summer. Much more difficult for the immediate future and beyond will be for businesses to meet each other face to face again. Will we be able to cross national borders unhindered in autumn? What restrictions might be necessary in autumn in order to be able to guarantee everyone’s safety? We, drinktec together with PETpoint, are the global summit for the beverage and liquid food industry. In Munich we are not only the hotspot for technical innovations and world premieres, but in particular we are the gathering place for business meetings and the exchange of views for the sector both here and worldwide. We can only hope to make this a reality again if travel across national borders and between continents is unrestricted. Two thirds of all drinktec visitors come from abroad, half of them from other continents. In view of these facts, we cannot live up to the claim and promise of being a leading international trade fair this year. We have therefore decided, together with the drinktec advisory board, to postpone the world’s leading trade fair to autumn 2022. The new date is September 12-16, 2022. Until then, we, and our strategic partner PETplanet, will be keeping you up to date about the events, technical evolutions and revolutions of the industry. We, the drinktec and PETpoint team, will do everything we can to ensure that in 2022 you will be able to experience once again the surprises and excitement of the world’s leading trade fair. We look forward to seeing you there. Yours, Petra Westphal Cluster Director drinktec worldwide, Messe München Dear readers, participants of drinktec and PETpoint,","@ID":5} "MATERIALS / RECYCLING PETplanet Insider Vol. 18 No. 0/17 petpla.net 21 Improving PET bottle-to-bottle recycling Next Generation Recyclingmaschinen GmbH (NGR) has been a technology leader in technology Liquid State Polycondensation (LSP) for years. In the NGR process, all impurities are removed from the PET melt already in the liquid phase to such an extent that the necessary requirements for food packaging (EFSA & FDA approved), including water bottle grade, are achieved. Since the proportion of recycled material in food packaging is to be significantly increased, especially in the beverage bottle and tray production sector, numerous projects of NGR have been completed and are currently being implemented confirm the effectiveness and efficiency of the process. By mid-2021, plants for processing post-consumer PET will be operating on every continent. Compared to conventional systems, the NGR process offers an energyefficient and, in terms of melt quality, better physical cleaning process, said NGR. The intrinsic viscosity (iV value) is constantly measured and adjusted to the customer’s target value via automated control of the vacuum unit. This makes it possible tofine-tune the material quality to the customer’s product specifications, including ultra-tight IV control, which is essential for downstream production. For the operator, time-consuming batch production is eliminated and no cost-intensive additional processes are required. Thus, no additions of nitrogen or similar process aids are required for iV increase. The efficiency of LSP technology is demonstrated by direct coupling with production processes such asfilm manufacture, spun yarn production or the manufacture of preforms for subsequent bottle production. This eliminates a complete re-melting step and the associated iV degradation resulting from a downstream process. The elimination of the pelletising process again significantly increases energy efficiency. To better demonstrate the LSP process and carry out customer trials, NGR is expanding the PET pilot plant with an additional line. Customers will thus have two LSP lines available for testing purposes at NGR from March 2021, so that both bottle-to-bottle trials and other applications can be successfully tested. This will enable all customers the chance to personally convince themselves of the efficient LSP process on their own materials. www.ngr-world.com NO. ONE-WAY PRODUCTION. YES. TOP QUALITY RECYCLING. How can your recycled product meet permanently increasing demands? With the CHT range of high performance process solutions with environmental relief for the wet chemical cleaning. We support you directly on site and ensure your quality controls in our laboratories with state-of-the-art equipment. Thus, your strong position in the growing market is confirmed day by day. More about us at www.cht.com","@ID":23} "BOTTLING / FILLING PETplanet Insider Vol. 22 No. 03/21 petpla.net 39 Manufacturing and filling rPET or PET bottles Recent studies clearly show the advantages related to the use of PET plastic bottles, containers that are unbreakable, safe, with great barrier properties, light and above all recyclable. Thanks to its recyclability and to its great weight/capacity ratio, many oil producers choose this packaging material as ideal solution in terms of environmental sustainability. Bottling and packaging solutions offered by SMI include a wide range of stretch-blow moulders from the EBS Ergon range, that allow to produce rPET or PET containers, of integrated fillingcapping systems from the Ecobloc Ergon range and of different types of secondary and tertiary packaging machines capable of meeting any requirement in terms of pack format and production output. Compact rotary stretch-blow moulders for producing oil Stretch-blow moulders from the EBS K Ergon range are a solution for productions up to 9,200 bph and offer all the advantages of the rotary blowing technology, says SMI. Thanks to the compact and ergonomic design, they can be installed on small bottling plants and ensure advantages in terms of ease of use and control by the line operator. The stretch-blow moulding carousel is equipped with motorised stretch rods, controlled by electronic drives that do not require mechanical cams. This solution ensures a precise management of the movement of the stretch rod, significant energy saving and reduced mechanical interventions. The stretch-blow moulding system makes use of high-performance, low dead volume valves, that allow reducing preblowing and blowing times, ensuring greater machine performance and higher quality of the bottles produced. Precise and reliable electronic fillers SMI said that their oil filling technology is precise and reliable, thanks to the use of the mass flow meter, an electronic device installed next to each valve that detects the product flow placed in each bottle. In this solution there isn’t any contact between the valve and the bottle, thanks to a gripper that grabs the bottle by the neck, keeping it in line under the filling valve, with advantages in terms of process hygiene and safety. The wide range of solutions offered by SMI also includes that with the weight filling system. www.smigroup.it FILLING Filling edible oil in PET A challenging future for competitive market segments The companies of the edible oil sector, influenced by the trend of strong product diversification, need very flexible and efficient bottling and packaging plants in order to reach high levels of optimisation and competitiveness of production lines. In an economic environment that is increasingly oriented towards eco-friendly solutions in the use of plastic packaging, a growing number of companies have chosen to use 100% rPET preforms, that allow to produce bottles with a high mechanical and aesthetic quality in a context with low environmental impact.","@ID":41} "BOTTLE MAKING 24 PETplanet Insider Vol. 22 No. 03/21 petpla.net Next generation PET blow-moulding machine New series, new features 2020 saw Side, which has been supplying PET bottle lines and solutions for more than 25 years, introduce its new generation 3000 Series PET blow-moulding machines, which is aimed particularly at beverage and water bottling companies. The new series has been developed with the intention of contributing to efficiency and cost reduction; it has a very wide range of options. And it also includes some novel and innovative features. A new air recovery system is claimed to deliver up to 30% savings in compressed air. The new blowing blocks and circuits developed by Side’s technical team enable recovery and reuse of all air used in bottle pre-blowing and in part of the blowing process, without compromising cycle time. This is possible because the 3000 Series is a fully electrical machine, with all movements activated by Siemens servomotors. Non-pneumatic cylinders are used for component movements. The 3000 Series is comprised of four different models, covering a range of production needs: The 3008e Series can blow up to 18,000bph (500ml, 1881 neck finish). Side says that it is the only linear machine on the market that can blow bottles of up to 2l in eight cavities, with an average speed of 16,000bph. This 3008e can be equipped with a preferential oven, to produce oval and asymmetric bottles. The 3007e Series is the only machine currently on the market that can blow bottles of up to 3l, using a 150mm diameter shell mould. It is able to use a range of different moulds from other systems and has a market-leading capacity to blow many different types of bottles, at speeds up to 14,000bph. The 3005e Series, which can blow 5 l/38mm neck finish bottles at up to 6,500 bph, achieves perfect synchronisation with the fastest bottling-filling lines at water plants. This new model can process bottles up to 8 l and neck finishes up to 48mm. The final model in the range, the 3004e Series, can blow bottle of 10 l/48mm neck finish at rates up to 4,500 bph. It provides the latest technology for big bottles and delivers the largest savings currently on the market, in terms of air and power consumption. Maintenance, testing & prototyping Side’s new Maintenance Saving Programme (MSP), managed by the company’s technical support department, enables maintenance schedules to be designed in line with customers; own requirements. All Side blow-moulding machines work with the Ewon Flexy 4.0 remote connection system, an industrial modular gateway that allows universal communication with a range of field equipment, regardless of the protocol used. The company’s technical support department manages all troubleshooting, maintenance, settings and software reprogramming remotely, from off-site, saving time and cost. New bottle shape testing and prototyping is becoming increasingly popular, along with testing of new PET resins, rPET especially. The company’s bottle designers work closely with customers to obtain the best bottle and the required results. The Side plant tests and prototypes more than 40 projects each year, enabling customers to see the final bottle before market testing. The Side technical and development team provides design, mockups, prototyping moulds, sampling and lab tests and offers “closed loop” services for projects with special needs. Side’s focus is continuously on the industrial optimisation of weight and the performance of blow-moulding machines. www.sidemachines.com RANGE bph l to l 3008e 16,000 1.5 2 3007e 14,000 1.5 3 3005eG 6,500 5 8 3004eG 4,500 5 10 The 3000 Series range includes models and productions as above mentioned","@ID":26} "TOP TALK PETplanet Insider Vol. 22 No. 03/21 petpla.net 10 Interview with ir. ing. Dirk Wouters, CEO and Co-Owner of CHP A drop that matters by Heike Fischer CHP is an engineering company designing, manufacturing, installing and servicing stateof-the-art lubrication solutions, ranging from small-scale installations up to large turnkey projects. 1,500 production lines are currently operating in 720 factories in 78 countries, running worldwide without jams, while saving energy and lowering costs. Customers such as Nestlé, Coca-Cola and Danone benefit from CHP systems. PETplanet Insider talked to Mr Dirk Wouters who joined CHP as CEO and co-owner in 2020. PETplanet: Dirk, you joined CHP last year with a lot of experience in both the technical and management fields. What first impressions do you have of CHP and what first ideas did you bring with you? Dirk: My first impression of CHP is that it is driven by an experienced, young, excited & dynamic team that has only one goal for all of its clients: excellence. The products that the company manufactures are unique and designed for the future, in order to constantly meet all expectations and rapidly changing requirements in the sector. Not only from a technical point of view, but also in terms of sustainability, which is a very rare combination. It is my goal to uplift the general level of performance even more by using my expertise in an international business context, combined with my entrepreneurial DNA. This way I hope to further expand our relations and to generate an international business growth. PETplanet: How many of your initial ideas were you able to implement, and how were you able to give positive support to CHP? Dirk: Since the company is built on good foundations, it already offers a wide range of high performing products. All key elements for success are already here, which makes it easier for me to continue the great results CHP already established during the last few years. My added value today is mainly to strengthen the structure of the company and to prepare the organisation for further growth and development. The most important KPI’s will still be innovation and customer satisfaction. PETplanet: Around 80% of your business is in the PET sector. What key business strategies are you following to maintain this strong position? Dirk: We think it is very important to stay in close contact with our customers in the beverage industry, in particular those who use PET bottles. This gives us the opportunity to keep up with the evolutions and trends in the PET bottling industry, specifically those related to recycling and sustainability. CHP is committed to keep on being an ally for the PET industry by coming up with answers to their (rapidly changing) expectations and demands. It is our priority to help them overcome any challenge they may encounter. PETplanet: What are the specialties in the CHP product range? What are their particular strengths? Dirk: That would be the unique features and benefits of the MicroDry dry lubrication systems that help optimise the efficiency of filling lines. The most important challenges for plant managers in the bottling industry are mainly related to line efficiency and controlling costs. When our clients decide to make the initial investment to install the MicroDry system, we see that the line efficiency increases substantially, while the operational costs drop drastically. At the same time, the amount of lubricant (recurring consumables) needed, is limited to the bare minimum. As we all know, sustainability – in this case saving water when lubricating the lines – has gained importance over the years. Many companies already strive to reduce water consumption in their production processes to an absolute minimum, which is of course a very positive evolution. Our MicroDry dry lubrication is the perfect solution because it allows our customers to save 100% of water during the lubrication process. This makes an oversised water treatment plant redundant, because there is no more spilled water that needs to be purified or recuperated. A second unique and successful product line is the MicroDry Air coating system. Especially in the PET lines, a lot of air conveyors are still transporting empty bottles to the filler. Due to complex layouts, long supply lines and special bottle shapes quite often bottle jams occur. The MicroDry Air system eliminates these jams and guarantees uninterrupted supplies to the filler. Unfortunately, many users still don’t know that there is a perfectly simple solution to this very common problem. We are only a small component in a very complex process, but nonetheless we still feel privileged to be able to offer this ingenious and efficient solution to our clients. MicroDry Air helps them to increase efficiency and to save money, while improving safety. PETplanet: How has the pandemic affected your operations and more generally, what has been the impact on after-sales service? Has Mr Dirk Wouters, CEO and Co-Owner of CHP","@ID":12} "62 PETplanet Insider Vol. 22 No. 03/21 petpla.net ABC Horizon set compressor: Up to 6,000m3 /h The cylinders are horizontally opposed, with crankpins displaced by 180°, cancelling out the inertia loads. Horizon operates virtually without vibrations; this results in a longer life of mechanical parts as they do not transmit excessive force or produce fatigue on structural parts of the compressor’s 20 years machine life time. ABC states that there are no anti-vibration pads or special foundations required, at +2 kg/cm2 . The compressor and all peripheral components are skid mounted. There is no premature wearing of valves, rings and gaskets. When unloaded, venting the intercoolers is not required, meaning efficiency increase and lower energy consumption. www.abc-compressors.com Improved recycling technology BoReTech focuses on the technology and equipment manufacturing of PET bottle recycling. In the year 2020, the company has made a series of improvements and enhancements in the recycling process and mechanical structure of the PET bottle recycling functional equipment. The important feature of the Heat-Shrinkage Label Scrapping Machine is that it has greatly improved by 10% on the label scrapping rate compared with previous models, the service life of spare parts is twice as long as before. Spare parts can be quickly disassembled and assembled. Bale Breaker (SA Series) has a de-baling capacity of 12 t/h and is good at de-baling high-density PET bottle balers which from 450 kg /m³ to 500 kg/m³. It is to detect pressure and adjust shaft speed automatically. The Hydro Washer is a multi-functional flake washing machine, which can be used for hot washing and cold washing. Its occupation of the area is small, around 3m2 . The shaft and screen of the Horizontal Step Dryer are specially designed to be stepped. A rotating screen can be self-cleaning to prevent clogging. The gradual increasing diameter prevents sudden high centrifugal force create PET fines from flakes. The material loss will be reduced to save the benefit of the user. Paddles are changeable. Weighing Packing Station (Double-positions) for PET flakes and pellets can set the packing weight, automatically detect the filling weight then stop conveying materials, and automatically change directions for conveying to the other position. www.bo-re-tech.com PRODUCTS","@ID":64} "COMPRESSORS PETplanet Insider Vol. 22 No. 03/21 petpla.net 42 PETplanet: So the next improvement plans for the Vito Next are already on your agenda? Sandeep Gadkary: Yes – again, continuous improvement is a key focus, not only for the Vito Next compressor range, but in general for the lean culture that our company is adopting. Almost every company nowadays understands the need to deal with ever-increasing threats and disruptive changes by continually innovating. This challenge requires entirely flexible organisational structures and skills. The packaging industry is no exception and it is affected by megatrends driving innovation: sustainability and circular economy, biopolymers, rPET, light weighting, and eco-design packaging lowering outlet pressure, different packaging formats, and allpervading efficiency. Improvements that could be shown not only in the compressor design but even by its diversification for different applications, like nitrogen, or heavy-duty oilfree industrial compressed air. PETplanet: Finally, a general question: Siad has customers all over the world. Which special geographical features particularly affect the compressors and require special adjustments or maintenance? Sandeep Gadkary: Severe or extreme ambient conditions affect compressor design and performance, and clearly these can be linked to specific geographic installations. Our Vito compressors’ population, as well as our process gas compressor population, are operating in many different world locations in totally different conditions, from the frozen areas of the Russian Siberia down to the very hot and dry conditions of the Middle East, or in the hot and humid tropical countries. For air compression systems, monitoring the dew point - the temperature at which your compressed air becomes saturated - is critical to keeping the equipment running efficiently and effectively. Dryers are essential in maintaining compressed air dry and free of moisture and contaminants. This said, even the compressor installation plays an important role: for instance, we have successfully installed and operated a Vito Next reciprocating compressor on the 4th floor of a high-rise building, and this was some challenge, not only for compressor transportation, but keeping operational and maintenance parameters under a certain performance threshold. For such demanding Siad Macchine Impianti is part of the Siad Group. The Siad Group was established in Bergamo, Italy, in 1927 and it is extensively involved in industrial gases; engineering; healthcare and LPG and natural gas. Siad Macchine Impianti specialises in the design, manufacture and installation, throughout the world, of Air Separation Units to produce industrial gases, reciprocating compressors for process gases and air (including API 618 and ISO 13631) plus LNG Liquefaction plant. The company supplies the refinery, petrochemical, chemical, energy, food and beverage and industrial gases sectors. www.siadmi.com installations, the compressor package must be equipped with further special features: The noise level must be optimised to comply with very restricted limits, and the mechanical vibrations as well as the specific static weight on the supporting surface must be reduced. PETplanet: Thank you very much!","@ID":44} "PETcontents 4 PETplanet Insider Vol. 22 No. 03/21 petpla.net 03/2021 TOP TALK 10 A drop that matters - Interview with ir. ing. Dirk Wouters, CEO and Co-Owner of CHP EDITOUR 12 Land of the rising recycling rates - Japan’s PET bottle, beverage and recycling market MATERIAL / RECYCLING 17 PET toner cartridges 18 Washing lines for Japan - Interview with Boretech Environmental Engineering Co., Ltd. 20 Challenging conditions - BariQ and Coca-Cola Atlantic launch strategic partnership to increase Egypt’s domestic PET bottle collection rate 21 Improving PET bottle-to-bottle recycling 22 What does it mean to move to a circular economy in 2021? BOTTLE MAKING 24 New series, new features - Next generation PET blow-moulding machine 25 PET bottles and containers for food and cosmetics BEVERAGE INGREDIENTS 26 Functional, healthy and low alcohol - Beverage trends in Japan BOTTLING / FILLING 28 Lightweight bottles from Japan’s landmark - Extremely low material use for bottled water 30 A picture of health - Krones PET aseptic filling lines at Eckes-Granini 32 A block system for the future - Tempo Beverages invests in new PET line from KHS 34 New formats, increased speed - Oman Refreshment Company and Sidel join forces to launch three new formats 39 A challenging future for competitive market segments - Filling edible oil in PET MARKET SURVEY 36 Suppliers of preform machinery COMPRESSORS 40 Built to last - Interview with Sandeep Gadkary, Strategic Advisor of the Board of Directors and COO Compressors Division Siad INSPECTION 44 A journey into the unknown - Agr helps beverage brand owners manufacturing PET containers MOULD MAKING 46 Label-less design improves recyclability - NoLabel 100% PCR PET bottle for Danone water brands in Latin America LABELLING 48 A breath of novelty for roll-fed labellers - Simpl-Cut: P.E. Labellers’ new technology TRADE SHOW PREVIEW 50 Chinaplas 2021 preview TRADE SHOW REVIEW 57 Meet the needs - United Caps presents new products and tethered caps during interactive virtual event 58 Milk processing in India - drink technology India 2020 webinar BUYER’S GUIDE 64 Get listed! FILLING Page 32 Page 28 Page 46 INSIDE TRACK 3 Editorial 4 Contents 6 News 60 Products 63 PET bottles for Home + Personal Care 70 Outer Planet","@ID":6} "INSPECTION 44 PETplanet Insider Vol. 22 No. 03/21 petpla.net Agr helps beverage brand owners manufacturing PET containers A journey into the unkown In many beverage plants, the decision to self-manufacture PET bottles is a journey not just into the unknown, but the unknown unknown. Agr’s Process Performance Optimization Group (PPOG) consultants help processors navigate this unfamiliar terrain. The new millennium has seen tremendous advances in PET bottle blowing technology, from block or integrated blow-fill machines to the breakthrough Process Pilot automated blowmoulder control system introduced by Agr International. At the same time, there’s been an absence of demand growth for carbonated beverages, a consequence of the increasing consumer appetite for a healthier diet as evidenced by tremendous demand growth for bottled water. Several big-name converters have consolidated, changed focus, or exited the business. Not surprisingly, the industry saw a wave of retirements among plastics engineers. All this was unfolding against the backdrop of mounting environmental concerns that prompted fillers to rethink the need to ship empty bottles hundreds of miles to their plants. The beverage industry responded with a logical solution: bring blowmoulding in-house. The numbers pencil out, and it makes sense from the sustainability perspective. Making bottles on demand at the point of filling also offers the advantages of increased flexibility and closer control. According to Paul DiZinno, Manager of Agr’s Process Performance Optimization Group, brand owners have invested in hundreds of blowmoulding lines over the past decade. The seismic shift to self-manufacturing has spread far beyond the U.S. to beverage operations around the globe. But as one major CSD processor in Germany found out, there’s a lot to learn about the blowmoulding process. Labeller trouble Opening in 2018, the German plant was designed and equipped for efficiency and productivity, with the Agr Process Pilot installed inside the 20-mould KHS blow-fill machine. Prior to installation of Agr’s Process Pilot system, container handling issues were observed on the high-speed line producing 42,000 bph. Sometimes, the bottles seemed to wobble in the labeller, as though they weren’t sitting well in the cup. Further downstream, labels would pop off as the containers were going into pallets. New to blowmoulding, plant personnel didn’t know how to track down the cause of the skewed labels. Nor did they suspect that it was the symptom of a much more significant problem. As a long-term supplier of critical measuring instruments and productivity tools to the plastic packaging industry, Agr was keenly aware of the industry shift to self-manufacturing - and its pitfalls. PET bottle making is extremely sensitive to a host of variables. Dynamics like temperature, humidity, preform composition, machine condition, or even operator skill can impact material distribution, the key factor in bottle performance. Process Pilot takes and analyses realtime measurements of the thickness of the sidewall of every single bottle, then adjusts the blowmoulder control parameters if material distribution starts trending out of spec. The result is an optimised blowing process that ensures consistent container quality and performance. PPOG supplements Agr’s Process Pilot by providing plants with fundamental process knowledge. Brand owners have discovered a shortage of knowledgeable plastics personnel in the job market. The PPOG engineers, veterans with a long history in bottle manufacturing operations, have deep expertise in the blowmoulding process. They also take a holistic view of the vast chain of interrelationships throughout the production cycle. All these elements must be coordinated to achieve sustainable improvements in stability, uniformity, and productivity. Turn down the heat The issue of the wobbling bottles came up when PPOG Process Engineer Consultant Damon Choate was in the German plant for phased commissioning of the Process Pilot. Without on-site equipment to do qualitative bottle testing, Choate sent samples to the Agr service depot in Italy for analysis. There, bottle volume expansion and maximum burst pressure data, provided by Agr’s PPT3000 Packaging Pressure Tester, revealed that the bottles were subject to frequent base stress crack failures. “Half the sample bottles burst in the base just a few seconds into the test,” Choate relates. “The ones that didn’t fail had over 40 per cent volume expansion. The resin wasn’t being distributed properly, which is why the bottles wobbled and didn’t fit in the label cup.” “Agr is well known for our ability to test volume expansion,” DiZinno observes. “We were the first to do the 13-second expansion test. This is the number-one parameter PPOG engineers look at. Even if the weights are exactly centered, we can tell whether the problem resides with the material, the process, or the design.” With the PPT results indicating room for improvement in the process, the engineers reviewed the bottle recipe, or blowmoulder settings. It was clear to them that too many oven lamps were The Process Pilot interface is a window into blowmoulder operation, translating realtime data into an easy-to-understand visual format.","@ID":46} "COMPRESSORS PETplanet Insider Vol. 22 No. 03/21 petpla.net 40 Built to last by Gabriele Kosmehl Price, performance, timely delivery and a fully satisfactory user experience during the whole product life are requirements that customers place on their compressors. In our interview Mr Sandeep Gadkary, Strategic Advisor of the Board of Directors and COO Compressors Division at Siad Macchine Impianti S.p.A. explains how these demands were considered when developing the Vito Next PET compressor generation. PETplanet: Mr Gadkary, you joined Siad Macchine Impianti (Siad MI) in January 2019. Can you briefly explain the tasks that you have particularly focused on since then? Sandeep Gadkary: From my early days at Siad MI, I have been involved in a flurry of activities regarding our compressor business, mainly in the three key areas of: growth focus; operational excellence; and high performance culture. Growth can be co-related to: new products, or enhanced products, and expansion into geographic areas where Siad MI was in the past only partly present; also application diversification to various industrial and process segments. As far as product is concerned, we focused most of our efforts from the outset to improve the energy efficiency and performance of our compressors in order to provide our clients with the best available system solutions. Hence, we have recently launched the next generation of PET compressors called Vito Next. On the operational side, we are pressing ahead with the adoption of lean methodology and the use of lean tools in every functional area of the compression business stream; I am convinced process optimisation will help to deliver a continuous operational excellence to our business. Digitisation is another pillar of our activity; we understand that deploying integrated, digital tools to every step of our processes definitely represents a quantum leap in the efficiency of our daily activities and to our business performances. Last, but not least, an important aspect of my work is dedicated to high performance culture, through the improvement of employee engagement; and with our customers, by paying particular attention to the aspects affecting their relationship, interactions and satisfaction with our service to them (the “Customer Experience”). PETplanet: You mention geographical expansions that are on your agenda. How have you been able to manage this in times of travel restrictions? Sandeep Gadkary: It is not only a matter of being geographically present and actively close to our clients. We are also progressively developing different channels to market, on and beyond our traditional direct sales offices and local service centres, through the appointment of long term partners/distributors. In addition to the “physical” proximity Sandeep Gadkary, Strategic Advisor of the Board of Directors and COO Compressors Division Siad April 13-16, 2021, Shenzhen at the Krones booth 10F23 German Technology Innovative hotrunner optiRun","@ID":42} "BOTTLING / FILLING PETplanet Insider Vol. 22 No. 03/21 petpla.net 33 Productive even in lockdown As in many other countries, the corona crisis threatened to sabotage the planned schedule in Israel, too. The country was one of the first to go into full lockdown – just as the engineers were about to ramp up the finished line. It quickly became clear that the installation team was now stuck on site and that no new service engineers could be flown in – a situation that naturally caused some uncertainty as nobody knew how long it would last. After much consultation the two parties mutually decided to carry on working. Tempo went to great effort to ensure that the KHS employees on site felt safe at all times despite them having to unintentionally extend their stay. In light of Tempo’s good care and support, the twelve people on the KHS team fully backed the aforementioned decision and made the best of the situation. For its part, Tempo used the time to have its employees trained by its guest engineers and with the help of online courses so that they would be able to As the biggest producer of alcoholic beverages and the third-largest supplier of soft drinks Tempo Beverages is known to almost the entire population of 9.1 million in Israel. quickly and independently solve any problems that might arise. Once the new line had been finally accepted in June 2020, the last KHS engineers left in Netanya were able to travel back home. Satisfied customer Despite the adverse circumstances production resumed on Line 12 just seven weeks after the old filling setup was shut down. The planned increase in capacity to 32,000 bottles maximum every sixty minutes was also realised in the previously ‘underutilised’ packaging and palletising area, enabling the agreed overall equipment efficiency of 92% to be already surpassed during the acceptance test. Tempo is already looking to the next joint project: a KHS canning line with a maximum output of 40,000 cans per hour. When asked what else his company is planning for the future, Daniel Beer, deputy CEO for Tempo replies, “We have to react to the significant changes we’re noticing in consumer behaviour. We’re doing this by strengthening our core brands on the one hand and investing in innovation on the other – either by expanding our product range, introducing new brands or coming up with new forms of presentation.” www.khs.com www.en.tempo.co.il l l","@ID":35} "TOP TALK PETplanet Insider Vol. 22 No. 03/21 petpla.net 11 TOP TALK 11 Covid highlighted any areas of concern and if so, what steps will CHP be taking to resolve any problems? Dirk: As for all entrepreneurs, Covid has been a real challenge for us. CHP supports and supplies for a crucial industry fulfilling the needs of all households and families worldwide. It goes without saying that we took all necessary safety measures to protect our colleagues and our customers. The presence at the office was limited to people operating hotlines. All other employees worked – and are still working – from home. Our technicians have been given the instructions to respect rigorously all safety rules to protect our customers and their own safety. We managed to do this without letting our customers down. It’s a blessing that we have very reliable products and that we operate in an industry where hygiene and safety are top priorities. PETplanet: What challenges is the PET sector facing now and in the foreseeable future? Dirk: I predict a lot of new challenges within the PET sector. There are so many different countries, each one with different rules and legislations, different guidelines, rPET… But we are used to this changing environment and it has always been in our nature to adapt and reinvent ourselves accordingly. That’s why I’m very confident that – as a team – we will have no difficulties to keep up. PETplanet: What are your future plans in terms of business development? Where is CHP planning to invest? Dirk: The focus has been on innovation for a while now and we are not planning on changing that any time soon. We started installing our new CHP Alert system on retrofit projects and on all of our new installations. It is important for plant & line managers and operators to have a live overview of line data at all times - 24/7. Industry 4.0 and IOT are becoming a very big part of our daily lives. Besides that, we are also looking at fast growing markets within our own field of activity. We are about to invest in the USA, where we are looking for an acquisition in order to expand our presence. CHP is also realising its first success stories in China and we are currently developing our network in South-East Asia and Russia. PETplanet: Thank you very much. www.chplub.com www.sacmi.com Product design Product development Product validation Industrial production plant Process & quality control On-site and start-up assistance After-sales and Customer service SACMI 4.0 THE COMPLETE CLOSURE, PREFORM AND CONTAINER SOLUTION FOR YOUR SMART FACTORY ENDLESS INNOVATION SINCE 1919","@ID":13} "BOTTLING / FILLING PETplanet Insider Vol. 22 No. 03/21 petpla.net 34 Oman Refreshment Company and Sidel join forces to launch three new formats New formats, increased speed Oman Refreshment Company (ORC) has launched three new formats for PET bottles in order to meet changes in consumer demand. Sidel completed the line conversion within a reduced lead time. These formats are now operating with improved rated speed to satisfy consumer demand in Oman. Established in 1974 and currently employing more than 900 people, ORC is one of the pioneers and market leaders in the Omani manufacturing sector. As a franchisee of PepsiCo International, the company’s headquarters is located in Al Ghubra and it operates in different food (Lays, Cheetos and Quaker Oats, etc.) and beverage (Pepsi, Topfruit and Aquafina Water, etc) sectors. It has an overall annual beverage production capacity of around 500 million litres. The company is expanding its manufacturing and distribution capabilities to meet growing demand for its products and also to respond to diverse consumer preferences. The carbonated soft drinks (CSD) market in Oman is dominated by international companies and it is dominated by PepsiCo whose sales volume and value in 2018 reached 84.7% and 84% respectively. Although Oman is known for its high CSD consumption, changing life styles and the introduction of an “excise tax” (50% tax on CSD) have slowed demand. To maintain market share and adapt to healthier consumer habits, ORC approached Sidel to launch three new PET bottle formats (0.25 l, 1 l and 1.5 l). Tight time constraints ORC has operated a Sidel Matrix Combi12 line since 2015 and Sidel’s project was to adapt this very same line. When the order was received in June 2019, a 14-week lead time was established to meet the market launch date. However, it was initially assumed that the parts could be delayed because of the August summer break. The key to success was therefore seamless planning and execution. As a complete solution provider, Sidel achieved its goal by leveraging its expertise in production and closely cooperating with suppliers. From shipping to execution, approximately 15 experts from Sidel participated in the project. To ensure smooth operation, the original line efficiency was inspected by Sidel’s team before site execution. With consultancy from Sidel, some adjustments were made and Sidel was supported by optimal logistics and 3rd party equipment suppliers to accelerate progress. ORC also played a crucial role by providing full in-house support from the maintenance and warehousing teams to ensure that all activities went to plan. In spite of tight time constraints, Sidel displayed close teamwork, liaising with both the partners and the customer. “Sidel’s challenge was to finish the project within a very tight schedule. Sidel took swift action in manufacturing the required adaptation kits then shipping them in the fastest lead time possible. Installation, testing, and commissioning are the most challenging activities of the project wherein Sidel was able to excel by sending the best team,” says Youssef Ezzikhe, CEO at ORC. A flexible approach to project execution, together with on-going support from the product division to reduce the equipment lead time were the key factors that the company describes as contributing to an overall well planned and executed service project. Sidel finished the line conversion project at the end of August 2019, allowing ORC to fulfil their market commitment. www.sidel.com FILLING In addition to launching new package sizes, the rated speed of the filler on each format was increased: 0.25 l – 24,000bph, 1 l – 22,500bph and 1.5 l – 22,000bph. Easy machine handling through intuitive HMI","@ID":36} "54 TRADE SHOW REVIEW PETplanet Insider Vol. 22 No. 03/21 petpla.net Equipment for PET bottling Koch-Technik will be exhibiting equipment for PET bottling with the volumetric dosing unit KEM and the patented gravimetric dosing and weighing system with mixer Graviko (GK 250) KEM: Chamber volume dosing (Kochpatent) with ± 0.15% accuracy for pellets, powder & ground materials: Each chamber of the dosing roll is filled evenly before it is discharged. The constant speed guarantees a high dosing accuracy. Benefits & features are the 5 dosing rollers for shot weights from 2 g to 10,000g, an easier role replacement and a high dosing accuracy. Koch dosing unit types Kö (granules), Pu (powder) and Ma (ground materials) are stated to dose with high recipe accuracy. A large selection of pre-mixers with agitators guarantees a homogeneous premix. The modular dosing and mixing units for injection moulding, blow moulding and extrusion are designed to be adaptable and exchangeable with relevant Koch system conveyors. Benefits & features are an up to 500 kg/h machine throughput, a basic body made of GAL / So-HB 100 or V2A stainless steel and dosing via chamber volume. Patented gravimetric dosing and weighing system with mixer The patented Graviko system dispenses plastic materials reliably and with the highest repeatable accuracy using precision slides. One can choose from Graviko units with throughputs of 80, 250, 600, 800, 1,000, 1,500 and 2,000 kg/h. The system allows the user to easily dose & weigh, check, modify and evaluate the material in a single operation. The controller recognises external interference during weighing and compensates for it. A horizontal agitator ensures optimum pre-mixing. Benefits & features are a dosing using precision slides; Precise dosing & weighing, checking, correcting and evaluating - in one operation; interferences are immediately recognised and compensated; easy material change through sliding and swivelling features. www.koch-technik.com KOCH TECHNIK Hall 10 Booth H29 Otto Hofstetter & Otto Systems: High quality injection moulds and PET Systems Following the successful trade fairs of previous years, the Swiss company Otto Hofstetter is present with its own booth showing its products and services this year. Otto Hofstetter is a producer of PET preform moulds from 2 up to 192 cavities, as well as for injection moulds for thin walled packaging applications and IML solutions. Side entry moulds Side entry moulds in industry standard and the corresponding EOAT’s are now also available from Otto Hofstetter. The proven cavity lock stack design is of course also built into these moulds. Otto Hofstetter will be providing customer information on its complete portfolio of high-quality injection moulds. Besides the well-known high quality injection moulds, Otto Hofstetter‘s strength is the full portfolio around the plastic article itself, which starts with an idea for a product, followed by the expertise to consult and design the product. Once the injection mould is built, the after sales service will round off the complete package. Otto Systems AG specialises in designing, planning and implementing first-class systems to produce PET preforms. Experienced experts offer uncompromising high-quality components tailored to specific customer requirements to create optimal, top-performing systems. www.otto-hofstetter.swiss OTTO HOFSTETTER Hall 14 Booth C51","@ID":56} "BOTTLING / FILLING PETplanet Insider Vol. 22 No. 03/21 petpla.net 28 Interview with Mt. Fuji Springs Inc. August 21, 2020 We met: Ms Akiko Yokoyama, Marketing Manager Extremely low material use for bottled water Lightweight bottles from Japan’s landmark The factory of bottler Mt. Fuji Springs was built ten years ago at the foot of Mount Fuji in Fujiyoshida City, Yamanashi Prefecture. The area around the volcano is situated around 150 km to the south-west of Tokyo and is so well-known, it is a must-see for any traveller to Japan. Here, at an altitude of 1,000m, the area above the plant is a marginal development zone, and there are no livestock farms and ski resorts. Winters can be snowy and summers are pleasant and not too hot. We met Marketing Manager Akiko Yokoyama to talk about her products and the company background. “Since we started in 2010, our idea was to put the excellent quality water from Fuji to good use. At that time there was nothing up here - the entire infrastructure had to be created, of course taking into account all environmental laws and requirements. Because there are no other buildings above our company, the groundwater is extremely low in nitrates and nitrites, which is an ideal prerequisite for us.” The water for their own-brand product “Frecious Fuji” is obtained from a 273m-deep well; its initial acquisition that aimed to retain the water quality was a bit of a challenge. It is meltwater, which is filtered through a layer of natural basalt over the years. In the factory, it is filtered again to remove foreign objects and microorganisms before it is bottled. Ms Yokoyama explains: “We own a total of six wells. We also tap into other water sources to meet the different needs of different customers. These provide different water properties and tastes.” Alongside Frecious Fuji, the company also bottles “Frecious Asagiri Kogen” in another factory on the Asagiri Plateau at the western foot of the volcano. This has a high vanadium content and can only be tapped here. A third product is “Frecious Kiso”, which is bottled at Mount Ontake, over 250 km away. “In that area, there is wide biodiversity and lots of wild wasabi growing, which needs clean drinking water,” says Miss Yokoyama. Mt. Fuji Spring’s water is soft and so is suitable for making baby food. The manufacturer has had product safety confirmed with an FSSC 22000 certificate. The core business is the water delivery business, and the company has its own brand, Frecious. There are two main water dispensers and both of which are highly regarded for their design. ‘Dewo’ features a 7.2 l light weight film pack, and ‘Slat’ is a floor-mounted model that features a 9.3 l easy-to-crush bottle. The dispensers are manufactured by a third-party company. Ms Yokoyama explains: “We see a significantly expanding market for water coolers for home use rather than commercial use. Here, the functionality and design of the devices play a significant role, as well as easy handling of the water containers within one’s own home.” The coronavirus situation has also fuelled the demand for products for consumption at home. The company makes its best seller, the 118g PET container holding 9.3 l, as well as its 32g PE film packs holding 7.2 l entirely inhouse. The bottling process itself takes place in a cleanroom before the finished product is delivered directly and exclusively to customers at home. The precise equipment remains a secret, but there are eight production lines available on site. “Conventional bottles simply have a weight problem, while our packaging is very light in the hand, can be compressed or folded for disposal once it is empty and overall produces less waste,” says Ms Yokoyama. “As regards regular bottles, we are Tour Sponsors: PE film packaging Marketing Manager Akiko Yokoyama Water server “Frecious Slat” in action by Kay Barton Our reporting usually finds us in functional industrial estates on the outskirts of cities or in central urban office complexes. Occasionally however, there are special exceptions. Googling Japan quickly brings up photos of a snow-capped mountain, the 3,376m-high volcano Fuji, which is a landmark of the country. And it is precisely here, at an altitude of 1,000m and surrounded by nature, that the company Mt. Fuji Springs bottles mineral water for water coolers. With its packaging, the company consciously strives for extremely low material use. FILLING","@ID":30} "50 TRADE SHOW REVIEW PETplanet Insider Vol. 22 No. 03/21 petpla.net Chinaplas open its doors! Dear readers, dear visitors, AUS$1-trillion loss from the pandemic, estimated by the United Nations Conference on Trade and Development (UNCTAD), is an expensive lesson to learn for global economies while recovery anticipated remaining lethargic in 2021. The ASEAN region, seeing an economy fell for the first time in 22 years, has had to contend with the impacts of the pandemic since its prologue in March 2020. Despite the uncertain aftermath, the recovery is at the arm’s length. In particular, for the ASEAN-5, is expecting a GDP growth of 5.2% in 2021, according to the International Monetary Fund (IMF) audit of January 2021. China, known as the world’s factory, is estimated to garner a 2.3% growth year-over-year in 2020; and projected to reach 8.1% in 2021, according to the International Monetary Fund’s (IMF) updated January 2021 economic outlook. The country rebounded more rapidly and re-opened gradually as early as April 2020. Chinaplas 2021 will be the only international plastics & rubber exhibition this year in the world, totalling 350,000m2 of exhibition area, with more than 3,600 local and overseas exhibitors and 19 theme zones which showcase 1,100+ plastics and rubber raw material suppliers and over 3,800 advanced machines. In this issue we have also compiled a comprehensive preview of the fair with PET-related information. You will find PETplanet Insider in hall 2, booth Y87. Even if our team cannot be there in person, we would be pleased if you visit our booth, leave your contact details and take the new issue of PETplanet with you to read! Recycling solutions for PET, post-consumer and production waste recycling Erema will be presenting its full range of products and services. Although, due to Corona, the machine manufacturer will not have a recycling machine on display this time, they will still highlight the entire portfolio for PET recycling, post-consumer recycling and recycling of production waste. Visitors to the trade fair stand will be looked after by the team from Erema’s Shanghai subsidiary. From there, customers and interested parties will be able to talk to people at the company’s headquarters in Austria in hybrid meetings using video conferencing for customer-specific consultation. Now that China has had the Corona situation well under control for several months, teams of technicians who travelled from Austria were able to visit customers across the country for several weeks before the end of 2020 to start up several recycling machines. In March, a team will set out again and, following a mandatory quarantine period, will begin commissioning several more machines. With its proven Vacurema technology, the machine manufacturer offers a wide range of processing options for applications involving direct food contact, such as the inline processes PET to sheet, PET to fibre, PET to strapping and PET to preform. Growing interest is also noticeable in the post-consumer segment. In Europe, the use of post-consumer recyclate has become a major topic in the plastics industry due to legal recycling regulations imposed by the European Union. By providing the technology, Erema is playing a major role in making recyclate suitable for high-quality applications in the cosmetics and food industries, which in turn opens up new sales markets. The FDA confirmed in August 2019 that the recycling process based on an Intarema TVEplus RegrindPro machine plus ReFresher module is suitable for the production of milk and juice bottles, as well as meat trays, disposable tableware and cutlery, provided the input material comes from milk and juice bottles. In November 2020, the FDA confirmed an additional input stream and more application uses for the recyclate treated using this process. In addition to all HDPE beverage containers, HDPE closures of HDPE, PP and PET beverage bottles can also be processed. Material containing up to 100 per cent recyclate can be used in the production of containers for direct contact with food of all kinds. Erema will also be part of the Recycling Conference: Chinaplas and CPRJ Plastics Recycling and Circular Economy Conference and Showcase 2021 – subforum: Advanced recycling technologies closing the loop of industry chain Monday, 12 April, 8.30 am - 12.30 pm. Presentation by James Qiu, General Manager of Erema’s Shanghai subsidiary, on the topic: “Plastic recycling technology made by Erema: up to 100% recycled material - from postconsumer waste to high-quality product” www.erema.com EREMA Hall 10 Booth C45 PETPLANET Hall 2 Booth Y87","@ID":52} "MATERIALS / RECYCLING PETplanet Insider Vol. 22 No. 03/21 petpla.net 17 Interview with Ricoh Company Ltd. July 21, 2020 We met: Mr Tsuyoshi Imamura, General Manager, Chemical Technology and Products Division PET toner cartridges by Kay Barton When people think of Shibuya in Tokyo it is its intersection, rumoured to be the busiest of its kind in the world with its five zebra crossings and surrounded by high-rise futuristic buildings, which immediately springs to mind. Ricoh’s headquarters are located around 10 km south of the intersection in the Ota district. The association with the company is rather similar to the one with the crossroads as the name will certainly be synonymous with printers and copiers. In fact, the company has a presence in around 200 countries and manufactures far more than office products and printers such as audio-visual projection systems and camera equipment under its Pentax brand. However, we decided to restrict ourselves to printing issues and travelled to Tokyo to meet Mr Tsuyoshi Imamura, General Manager in Ricoh’s Chemical Technology and Products Division, to talk about the use of PET for it is here that their toner cartridges are produced. “Ricoh was probably the first company to use PET in its toner cartridges back in 2000”, began Mr Imamura. “We were looking for ways to keep the use of material to a minimum and used standard stretch blow moulding for our toner cartridges, a practice which was already well-known to us from the drinks’ packaging sector”. This type of production is now used in rapid supply chains in the four regions USA, Europe, China and Japan from where the manufactured cartridges are ultimately filled with toner, then delivered via the quickest route to the customer. There are two major types of toner cartridge, namely bottle-type and one-piece, depending on the local equipment available and customer preference. The cartridges are used in Ricoh’s entire printer range, from monochrome and colour machines to A3 copiers and printers for both domestic and industrial use. According to Mr Imamura, cartridges are sourced locally or from abroad, depending on demand. “Although we use PE and PS, it is PET which is mostly used in our products. The main point to stress here is that we use 100% recycled PET. We made sure our cartridge production system was cost-effective and environmentally-friendly right from the outset and have continued to enhance our manufacturing processes as we have gone along. In 2000, we switched from PE to PET. With the introduction of PET, we were able to reduce the unit price per cartridge by 25% and the amount of required material by 40%”. Ricoh developed the first post consumer resin (PCR) cartridge in 2004, obtained UL (Underwriter Laboratories) certification for the material and then began processing. “As a result, we were able to save a further 32% per unit cost and we have achieved the use of recycled materials, which was not considered mainstream in the toner cartridge field at the time. In 2017, we also achieved 100% use of recycled materials. Precise figures of actual PET conversion are not currently available but is likely to be substantial given the size of the company (90,000 employees worldwide) and net sales of US$ 19.5 billion. In conclusion, Mr Imamura said “We are currently working towards the establishment of a global recycling system for toner cartridges to implement the UN’s Sustainable Development Goals (SDGs), with special emphasis on two areas: a general expansion in the use of recycled material and an increase in the number of cartridge applications, including an equivalent recycling process”. www.ricoh.com Tour Sponsors: Tsuyoshi Imamura, GM Chemical Technology and Products Division Typical PET toner cartridge Ricoh’s plant in Numazu city PETcast In our new Road Show podcast, PETplanet meets industry experts from Down Under to Japan and talks with them about their successes, decisions and current developments. Listen to the full conversation atwww.bit.ly/2HVwbAd","@ID":19} "MATERIALS / RECYCLING PETplanet Insider Vol. 18 No. 0/17 petpla.net 19 Ibaraki. It was combined there with with food grade qualified European pelletising and SSP systems. “These two deals led to us being prioritised by Japanese recyclers,” explains Alan Ou. “Later we supplied further washing lines to Utsumi. With the import ban on plastic waste in China in 2018, numerous recycling projects emerged in Japan from 2017 to 2019, subsidised by the government by up to 50% for relevant machinery. Previously, Japan exported around 260,000 t of post-consumer PET to China each year. Without wanting to go into specific details, Mr Ou explained that current and future Boretech projects in Japan mainly involve systems with an hourly flow rate of 6 t of material for further food-grade processing. “Annually, Japan generates around 650,000 t of PET bottle waste and we estimate that by the end of 2022, around 80% of this will be recycled locally. The multinational brands are successively increasing the PCR proportions in their packaging, which in our view should bring various potentials, not least for us, in terms of highquality recyclate manufacturing.” Alongside activities in Japan, India is the second most important trading partner. Here, mechanical engineers have installed 55 lines and systems. Now, during the pandemic, everything is running a little differently. Although at Boretech itself there was just one short two-week production stop in 2020, customers have sometimes postponed their projects or delayed payments, both within China and worldwide. As a result, the situation has affected annual turnover, warehouse space and planning, with impacts also felt on the service side. Although it has been possible to provide replacement parts quickly and easily, freight handling has been an increasing logistical barrier. Onsite at Boretech, safety measures have been implemented for staff. Maintaining a public image and presence as physical events like trade fairs have fallen away is a familiar issue for large parts of the sector but the company remains relaxed. “Our products are so niche that these days we would rather invest our advertising budget in places where we want to be found, in online searches and specialist media like PETplanet,” explains Alan Ou. He continues: “In future, we want to expand our activities in Latin America so last year, we appointed a Spanish-speaking employee. The situation is similar to in Japan and offers great potential with a growing need for high-quality, foodgrade recyclate. www.bo-re-tech.com One of Boretech’s PET bottle recycling projects in Japan product development caps & closures design high cavitation moulds multi-component moulds closure production systems after sales service competent – professional – inspiring +43 5572 7272-0 | [email protected] | www.z-moulds.com","@ID":21} "7 NEWS PETplanet Insider Vol. 22 No. 03/21 petpla.net Alpla Group: 50 million euros a year for recycling The Alpla Group, a leader in the development, production and recycling of plastic packaging, is to invest up to 50 million EUR/a on average between now and 2025 in further expanding its recycling activities. In particular, it plans to globalise its activities in the area of high-quality recyclates in order to close the materials cycle in as many regions as possible. In 2018, the packaging and recycling specialist theAlpla Group signed the Global Commitment of the New Plastics Economy (an initiative of the Ellen MacArthur Foundation) and committed to spending a total of 50 million euros to expand its recycling activities up to 2025. Alpla is now significantly increasing this investment target. From 2021, an average of 50 million EUR/a will be ring-fenced specifically for recycling. “We have been very active in the past the past two years. We succeeded in initiating bottle-to-bottle projects around the world, including in Asia, Europe and Central America. We nevertheless continue to see increasing demand on the part of our customers all over the world,” explains Georg Lässer, Head of Corporate Recycling at Alpla. This sustained demand gives Alpla the opportunity to kick-start further investment projects, says Lässer. Günther Lehner, Chairman of the Company Advisory Board, stresses that the company will focus on high-quality application areas in new regions: “Our aim is to establish a bottle-to-bottle cycle – including in regions in which the recycling of waste does not currently play a large part.” Georg Lässer sees long-term development opportunities in countries outside of Europe: “Customers around the world enquire about packaging made with a proportion of recycled materials, including in Africa, the Middle East, South East Asia, China and India.” On Europe, the expert comments as follows: “This market is now highly competitive. We secured a strong market position early on in Western Europe with our own plants and partnerships, and this is something we want to further consolidate.” Key milestones Its move into HDPE recycling in 2019 represents another milestone for Alpla. This is being continued with the construction of a plant in Toluca, Mexico, which is scheduled to go into production in autumn 2021. The company is also currently creating a PET and HDPE recycling plant in Thailand together with a cooperation partner. Capacities at the existing plants in Austria, Poland and Germany have been expanded over the past two years and just recently, Alpla announced the installation of an rPET extrusion system at one of its own preform plants in Italy. In all, the annual capacity of the Alpla recycling companies, joint ventures and partnerships amounts to approximately 130,000 t of PET and 60,000t of PE. www.alpla.com Sacmi Group appoints new General Manager The Sacmi Group announces the appointment of a new General Manager. In March 2021 Mauro Fenzi is to take over from Giulio Mengoli, who has, for personal reasons, considered it appropriate to terminate his employment. Despite all the difficulties caused by Covid-19, the year 2020 still saw Sacmi achieve good results in terms of operating margins and cash flow generation. The past year has allowed the Group to further enhance its far-reaching presence around the world. Market shares have grown in all business areas. This highly positive trend was confirmed by the projected full-year results, released at the Members’ Assembly.The President of the Board of Directors, Paolo Mongardi, informed the Assembly that the change in General Management would take place “in such a way as to ensure continuity of strategic and operational corporate management”. He also thanked Giulio Mengoli for his valuable contribution to the company over the years. Genoa-born Mauro Fenzi, 59 years old, who holds a degree in engineering from Milan Polytechnic and has wide-ranging experience in the field of industrial automation systems development, has now been appointed to the role. Mauro Fenzi has gained broad professional experience in Italy, the United States and France. Since 2014 he has been at the helm of leading multinational groups. More specifically, from 2014 to 2019 he was CEO of Comau (a leader in industrial automation), where he had covered various key positions since 2001. Since January 2020 he has been CEO of Sogefi (a leading provider of automotive components). www.sacmi.com Sipa and PTI enter into strategic partnership Sipa and PTI reached an agreement to join forces on the market, with PTI now becoming part of the Sipa group. This strategic partnership will help both companies to increase their visibility and create new business opportunities. “Joining forces with Sipa makes perfect sense for PTI. We bring extensive knowledge in package development and material expertise to their capabilities’ portfolio,” said Thierry Fabozzi, PTI CEO. “This strong collaboration will also give PTI access to Sipa’s latest equipment and enable us to provide even better turnkey solutions for our brand-owner customers.” “We are very pleased to see PTI become a part of the Sipa group. In addition to the technical synergies, we also see geographic advantages. PTI’s wellestablished footprint in the United States will allow Sipa to further reinforce its visibility and success for its equipment technology in North America. Sipa’s relationships elsewhere in the world will help introduce PTI as a leader in package development, giving the possibility to Sipa to provide a very comprehensive offering to the market” said Sipa Chairman Dr. Gianfranco Zoppas. www.sipa.it","@ID":9} "MATERIALS / RECYCLING PETplanet Insider Vol. 22 No. 03/21 petpla.net 23 +44 (0) 1254 584210 [email protected] petmachinery.com Active for over 25 years, our global network and specialist knowledge makes us the go-to company for the sale or purchase of a PET machine. Commercially savvy, we work closely with our customers and our global network, to make sure everyone gets the best deal. Providing comprehensive advice throughout your sale or purchase; we can arrange dismantling, loading, packing, shipping, specialist insurance and commissioning. If you have amachine to sell or you’re looking to purchase, please get in touch. THE INDUSTRY EXPERTS PET used, the result can be anything from grey or pale yellow, to blue or greenish. The more recycled content the bottle has, the darker the end colour will appear. The Anti Yellow range comprises different liquid additives able to balance the appearance of variations in material and to regain brightness, correct a greenish or greyish tone. Mechanical challenges instead include a drop of the Intrinsic Viscosity (IV) when using rPET. This happens because PET, after several production cycles, due to degradation, shows a reduction in the molecular weight: Its chains are shorter, and the final product is mechanically weaker. Repi’s IV enhancer combine shorter molecular chain to longer ones, thus increasing the IV of the material. Besides additives, colours can also come to the rescue. When a very dark rPET is used and an Anti-Yellow additive is not enough, corrections through colour may be crucial. Repi’s Fumè colour range is made of shades like ambers, light blues, greens or greys, that are used at very low dosages (as low as 0.05%) so not to impact the recycling stream. The entire value chain of plastic packaging has been working hard and constantly for many years on making plastic recyclable and recycled. Now more than ever, cooperation and constructive approaches are crucial. Instead of blaming one packaging solution against the other, let us prepare for the “roaring 20s” with renewed energy and focus on what “delivering the circular economy” means, without forgetting the carbon footprint impact of our choices. This is the only way to get to structured solutions that will be effective and positive in the long run. www.repi.com Reducing, reusing, recycling, and refitting One way can be choosing additives and colours that add performance and aesthetics while having negligible impact on its recyclability. This is at the basis of the Refit concept. Repi as a global colour and additive solutions supplier to the packaging industry is strongly promoting its vision on circular economy, by adding a 4th “R” to the three well known: reducing, reusing, recycling and refitting. Refit means having an all-round approach to carbon footprint contribution. Protagonist is the liquid colour and additive technology that can be defined as a low carbon footprint technology. Why? A few main reasons can be found: Process: The manufacturing process of a liquid colour/additive is energy efficient since no high temperatures are needed to blend carriers (that are already liquid) with pigments or dyes. Regardless from the specific production cycle, all processes happen at room temperature. Logistics: The high concentration of liquids leads to less space needed for transport and therefore significant CO2 saving. Stockage of liquids at the customer’s site is highly space efficient, reducing space needed in warehouse. Refit comprises additives and colours that are dedicated to plastic recycling and offer a broad-spectrum support in the form of aesthetics enhancers and mechanical boosters: Anti Yellow (AY) additives and IV enhancers. The colour of rPET varies a lot from supplier to supplier (and even from one batch to the other) and depending on the ratio of recycled","@ID":25} "MATERIALS / RECYCLING PETplanet Insider Vol. 18 No. 0/17 petpla.net 18 Interview with Boretech Environmental Engineering Co., Ltd. Washing lines for Japan by Kay Barton The Chinese recycling system supplier Boretech has massively expanded its influence in the Japanese market and plans to have installed a total of nine complete systems and various individual components by the end of 2022. The focus here lies on PET bottle washing systems for bottle-to-bottle recycling with a processing capacity of 6 t/h. Along with India, this makes Japan a key sales market and could, according to the company, increase the proportion of sales from 30% in 2020 to 50% this year. PETplanet enthusiast Alan Ou, Senior Vice President of Boretech, explains the background. The company is in no way a newcomer: it has a 30-year history in recycling work and development. In 1991, Boretech in Taiwan became the second PET recycler. In 1994, its own factory in China was built for polyester fibre manufacturing using washed PET flakes. In the mid2000s, the engineering department emerged and started developing the planning and manufacturing of its own PET bottle washing lines. “With our many years of experience, we wanted to bring together economic aspects and quality,” says Alan Ou. “The crucial thing here is that almost every washing line is developed and constructed individually for the customer’s particular need and process.” Currently, over 170 recycling systems are running worldwide, including with customers such as Far Eastern, Reliance, Veolia and Polymetrix. “Companies like this have naturally fuelled our reputation within the industry. Our systems have meanwhile been considered for many high-end projects and are moreover a cost-effective alternative to the higher-priced European competition.” Now the focus is on Japan. What are the secrets of this success story? A joint venture with a Japanese recycling company, in existence since 2000, has provided years of knowledge and experience of the Japanese PET recycling market. On the basis of this information, the first Boretech washing systems for foodgrade rPET manufacturing and sheet extrusion were implemented in 2011 at PET recycler Utsumi Recycling. In 2013, there followed a washing system for Taiwanese Far Eastern Group with their first overseas bottle-to-bottle factory in Sakai-machi, Senior Vice President Alan Ou GAWiSD featuringAutoJob ™ – job set up in seconds +1.724.482.2163 AGRINTL.COM ACCURATE • FAST • REPEATABLE SEE GAWIS4D IN ACTION Dimensional and thickness measurements for plastic containers and preforms. ®","@ID":20} "BEVERAGE INGREDIENTS PETplanet Insider Vol. 22 No. 03/21 petpla.net 26 Beverage trends in Japan Functional, healthy and low alcohol Consumers worldwide are looking for food & beverages that support a and sustainable lifestyle, with mental and spiritual health benefits as well as physical, and should be natural and come with a high degree of functionality. A balanced diet should help combat tiredness, improve digestion and boost the immune system. Doehler reports that the Japanese market for ‘functional foods’, in particular, has been growing fast. It tripled in value in 2016 alone and has maintained a strong upward trend in subsequent years. As is the case in many countries around the world, there is significant demand on the Japanese market for energy drinks, sports drinks and RTD (ready to drink) coffee drinks. This segment includes what are known as “beauty drinks” – beverages claimed to support the skin and physical appearance – as a specific trend among Japanese consumers. The focus in these markets is more on functional beverages than simply quenching thirst. Canned and bottled coffee New ways of serving coffee have made it the most popular drink in Japan, with 76% of the population stating they consume it. Coffee is the most popular non-alcoholic beverage in the country, a fact that led to the invention of canned coffee in 1968. RTD coffee is now also available in PET bottles. Consumers have a pick of options; as well as coffee shops, coffee beverages are available from vending machines in supermarkets, airports, convenience stores and street corners, facilitating consumption on-the-go to and from the office. It is available both as a hot or cold drink, depending on the season, with heated cans on offer during winter months and chilled coffee available throughout the year. While flavoured coffee is not very popular, classic variations such as black and milk coffee are in great demand. In line with the consumer demand for healthy lifestyle products, reduced sugar variations of canned and bottled coffee are becoming ever more popular. Functional and healthy Reducing sugar content is also a strong driving force in other beverage categories in Japan. While the beverage market as a whole is in decline, demand for sugar-free and reduced sugar carbonated water and energy drinks variants is growing, driven by health-conscious consumers who demand new products that are more natural and less sweet. Energy drinks represent one of the most exciting and dynamic beverage categories, with innovative concepts, exciting flavours and an array of market positioning options. Consumers appreciate the invigorating effect of the stimulants and demand has grown for drinks made from naturally occurring sources of energy, such as guayusa and guarana. This new generation, with functional ingredients such as proteins, BCAAs, vitamins or minerals, offers further marketing potential. Doehler has a wide selection of natural ingredients that are tailored for functional beverages, such as supportive vitamin and mineral blends, trendy plant-based proteins and exotic botanical extracts. All of these ingredients provide improved nutritional value and taste profile.","@ID":28} "BOTTLING / FILLING PETplanet Insider Vol. 22 No. 03/21 petpla.net 31 On-site implementation time In late August 2019, the first machines were ingressed. In early November 2019, the first filled bottles came off the conveyor. In December 2019, the line was successfully validated. In early January 2020, the line was fully operational. Installed on a small footprint, the new aseptic low-output line is rated at 13,000 containers per hour. It enables Eckes-Granini to flexibly fill even relatively small batches of still juices with the requisite degree of microbiological safety. The line fills about 50 different products, all of them still beverages, in two bottle formats, both with a 38mm wide-neck cap. “One goal pursued with this new line was to reduce the complexity in the existing bigger line, thus rendering it more efficient,” to quote Hermann Naumann. Changing over between the two bottle formats, he continues, takes only about an hour, product change-overs are completed in 20 minutes – non-productive times are altogether short. BEYOND THE HORIZON PROCESS SOLUTIONS FOR POLYMER RECYCLING AND SOLID STATE POLYMER UPGRADING Polymetrix, a Sanlian Buhler Company, provides process technology including EPCM services for the polymer recycling and manufacturing industry. Leading supplier of rPET systems and intergated rPET plants for single line capacities up to 70’000 tons per year. www.polymetrix.com www.slhpcn.com “What’s more, we were able to bring the filling volumes we’d previously outsourced back into our own production hall. Since there is a general trend towards a more and more diversified range of articles coupled with decreasing batch sizes, this smaller-output line definitely makes sense,” says Naumann. “And last but not least, we just didn’t have more space available here in our plant,” adds Henning Hanisch. “That was why we needed an ultra-compact line layout, something that was neatly solved by Krones. The new line minimises legwork, and it’s very easy to access and operate.” Both lines are meanwhile utilised to full capacity in three-shift operation. As far as coronavirus restrictions are concerned, the Bad Fallingbostel facility has so far got away “more or less unscathed,” as plant manager Hermann Naumann explains, “because we hardly serve the out-ofhome segment from this plant, apart from bag-in-box packs. Sales of PET containers, on the other hand, have rather increased because consumers in the first six months of 2020 compensated for the lockdown of the hospitality industry by buying their drinks at food and beverage retailers.” Non-returnable PET containers are the most important type of package for the family-owned company. They account for 83% of sales in Germany alone. With an eye toward improved sustainability, EckesGranini therefore aims to reduce the containers’ weight still further while simultaneously substantially increasing the containers’ content of rPET, which already averages 25 per cent today. www.krones.com www.eckes-granini.com Plant manager Hermann Naumann (left) and Henning Hanisch, project and process manager. The Granini brand accounts for roughly a quarter of total group sales.","@ID":33} "PETplanet Insider Vol. 22 No. 03/21 petpla.net 63 BOTTLES PETbottles Home + Personal Care A shower gel concentrate in PET Aldi South has brought out a shower gel concentrate with different types of fragrancies under the “Abbott and Broome” brand which comes in a clear 100 ml bottle. The product, which according to the label is equivalent to a 300ml bottle of non-concentrate shower gel, is applied via a screwed-on pump dispenser with locking function. One or two pushes on the pump are said to be sufficient for the every-day shower experience. In addition, the product does not contain any microplastics. www.aldi-sued.de A bio-range from Poliboy The traditional German brand, Poliboy, is constantly expanding its range of cleaning products by using naturally active ingredients wrapped in suitable packaging. The picture shows two examples from the brand’s current organic range, namely bathroom and glass/surface cleaners. The climateneutral, vegan products conform with NCP standards and the fragrance created by essential oils. The bottle is made from 100% recycled material. A lockable trigger helps in applying the product evenly to the surfaces to be cleaned. The bottle has a label in the neck area with a QR code which provides information about a climate protection project. www.poliboy.de A laundry fragrance from 100% recycled material The German discount pharmacy company, dm, has brought out a laundry fragrance under its own “Denk mit” brand which comes in a 400 ml bottle made from 100% recycled material. The product can be used in washing machines and dryers. A bitter ingredient has been added to the liquid for child safety reasons. The cap, which is not made from recyclate, serves as a dispensing aid. The sleeve label is perforated which enables the bottle and label to be separated for easier sorting purposes. www.dm.de A nourishing shower gel from Nivea Pressure being exerted by small, new market players operating in the environmentally-friendly personal care products sector is not allowing large manufacturers to relax which is resulting in the introduction of new innovations and improvements in products. Nivea has launched a nourishing shower gel that meets both of these demands under the brand name “Natural Balance”. The opaque, shimmering vegan shower gel has a fragrance of cotton blossoms and is free from microplastics. The product consists of 99% of biodegradable raw materials and is infused with organic argan oil. The not-quite transparent bottle is made from 97% recycled material and secured via an easy-to-open hinged press-down lid with sloped brand lettering. www.nivea.de","@ID":65} "INSPECTION 45 PETplanet Insider Vol. 22 No. 03/21 petpla.net directed to turn on during blowing. The process was running too hot, and the preform temperature was higher than necessary to produce the ideal stretch and orientation of the PET molecules. “In general, when making PET bottles, the colder you can make the process, the better,” explains Choate. “The goal in blowing is to get the very best orientation of the PET, both vertically and horizontally. This gives the best container strength.” It’s true that high heat makes the PET more pliable and easier to stretch, but all stretching is not equal, he points out. Cold forces the molecules to align better vertically and horizontally. Reducing the preform temperature specified in the recipe by a few degrees will produce better overall resin distribution and better strength and rigidity, a critical attribute for shelf life. Gas permeation through the walls and resistance to volume expansion also improve with the proper orientation of molecules in a colder blow. In all, the PPOG engineers reduced the number of lamps that turned on in the oven by 15, from 69 from the original recipe to 54 in the revised one. They also lowered the preform temperature setpoint by four degrees. With these two changes, the bottle volume expansion went down to the most desirable rate of 12 to 13 per cent, from 40 per cent prior to the engagement, “a vast improvement,” DiZinno notes. Additionally, while it wasn’t a goal at the outset, the significant reduction in the blowmoulder operating temperature generated approximately $20,000 in annual energy savings. Adressing the variables While the preform temperature inside the blowmoulder was the chief cause of non-conforming bottles for the German drinks maker, in other cases the PPOG engineers often connect the dots back to a processor’s preform supply. In fact, one of the most common challenges to optimum blowmoulder performance is the lack of consistency in preforms. Given that blowmoulding is a process where uniformity is key to stability, preform variations can produce out-of-spec bottles that seriously disrupt downstream production. Especially with today’s ultra-high line speeds, just a few minutes of downtime can cause a processor to lose thousands of dollars in sellable goods. Preform variations have multiple root causes. Without strict inventory control, they can age in storage and absorb moisture, or batches can become mixed. Preform age is a major source of variation. Further up the supply chain, preform manufacturers might switch to a different resin composition or use different injection moulding machines to fill a single customer order. “Self-manufacturers aren’t always tuned in to the subtle differences in product from their suppliers, and those differences can impact the entire filling line,” DiZinno comments. As an example, he cites one plant that was having trouble with nonconforming bottles. There were multiple issues with poor bottle handling due to the preform variability causing unplanned stops, and jams in the filler, labeller, and bundler. After investigating, DiZinno found that the plant was receiving preforms made from two different resins on 10 different injection machines at five different facilities within the organisation. “The operators were making a single bottle design on a dedicated blowmoulder, but they needed 33 different recipes to accommodate the different preforms. There was so much variability in their process, they tried to compensate by fine-tuning a recipe for each different combination,” he relates. “The plethora of recipes just multiplies the opportunities for errors, and in the end, the bottles were never ideal.” To help plant personnel understand what was happening, DiZinno called up a production history chart on the Process Pilot screen to illustrate in granular detail how the thickness of the bottle sidewall jumped for 25 minutes when correlated with a specific preform batch. He explained how to interpret the data, showing operators how to use that detailed insight into thickness distribution to learn how to make better performing bottles. After assisting the customer with optimising its process and engaging Process Pilot, the plant was able to handle all its preform sources with a single recipe. Lightweight and rPET That knowledge will be of increasing value as sustainability continues to grow in importance and brand owners embark on lightweighting and rPET initiatives. While global water brand owners have already made dramatic strides in reducing bottle weights, CSD applications are just beginning to see weight reduction initiatives, Choate reports. Similarly, the commitment from major beverage producers to increase the use of rPET poses additional manufacturing challenges. “When you use recycled resin, the material in the preform is inconsistent, and the bottle becomes increasingly difficult to make,” DiZinno remarks. “Operators typically don’t have the experience to deal with the issues that can occur.” Because Agr is not affiliated with any specific blowmoulder manufacturer, the engineers can provide whole-plant assistance even in facilities where multiple blowmoulder brands are running. The PPOG engineers utilising Process Pilot have achieved a gamut of improvements that range from faster blowmoulder startups, shorter changeovers, less operator involvement, rapid jam recovery, and reduced scrap to improved bottle quality, lower material consumption, better performance in transit, enhanced shelf appeal, and fewer consumer complaints. “There will always be a bit of an art to manufacturing preforms and containers,” DiZinno observes. “Our engineers help operators develop a balanced, centered process that allows continuous operation without slowdowns or jamming despite changes like an increase in temperature or the amount of rPET in the preforms. It’s a matter of finding the right recipe for the plant, based on the unique environment. It’s very custom work,” he concludes. www.agrintl.com One of the most common challenges to optimum blowmoulder performance is the lack of consistency in preforms.","@ID":47} "MOULD MAKING PETplanet Insider Vol. 22 No. 03/21 petpla.net 46 NoLabel 100% PCR PET bottle for Danone water brands in Latin America Label-less design improves recyclability Bonafont and Villavicencio, Groupe Danone’s spring water brands in the Brazil and Argentina markets, are developing their environmental efforts by recycling all single-use PET bottles. The company designed a label-less bottle for its new 100% PCR (post-consumer recyclate) PET packaging, using Moldintec’s Advanced Freeform Laser Mold Decoration Process. PET recyclers’ views on the ideal bottle for recycling are well-known. They prefer a heavy one, made of clear PET, without colourants or additives, with a one-piece PP closure and, most importantly, without a label. Paper labels generate ink-bleeding and contain sticky paper fibres and silicone-based glues that significantly impact PCR quality, with negative consequences for its market price. Plastic labels are particularly detrimental as some are difficult to separate from the flake and affect both colour quality and yields. Good PET flake from today’s lighter PET bottle is lost during elutriation (label separation by air current) or when optical sorters reject bottles with full-body shrink sleeve labels. Even a small price sticker causes problems in the recycling process. Different inks, materials and glues require different types of solvents and more advanced process for material separation and wastewater treatment. Design & technology from South America The development of new, ecofriendly 100% PCR PET packaging was entrusted to Moldintec, a widelyknown blow-mould manufacturer. It incorporated laser manufacturing capabilities into its modern factory in 2016; initially to improve the mould etching process from craft chemical treatment to fully-digital laser engraving. The engineering team found more uses of light machining technology to keep its customers at the forefront of innovation. Light machining is not a new solution in the tool making industry; it is widely used to apply patterned etching on 2D or 3D surfaces. Moldintec’s software team created the plugins needed to shape any bottle surface with complex mesh, starting from any HD image, logo, text, or even a face from a selfie, with a multi-axis laser machine. “A simulation tool was also needed to make our company capable of showing a bottle preview to the clients, especially customers who have never before seen such a complicated bottle skin,” Mr Diego Taboada, COO of Moldintec explains. The result is a new frontier for industrial bottle design; the PET skin itself becomes the full-body label. This is new territory for graphic designers and enables them to break out of the boundaries of traditional, bidimensional labels. Creativity leads to sustainability The Moldintec’s industrial design team worked closely with Danone’s I+R&D (Innovation, research and Development) engineers, and the two nations’ marketing and compliance teams to meet its branding requirements, without using a label. Each country has its own laws covering food and bottled water, so the support of the legal and regulatory team was fundamental to obtaining governmental approvals of the innovative packaging, where the brand, spring location, physical and chemical composition and much other label information still has to be legible on the transparent skin of a PET bottle. The project was focused on developing and delivering a 100% PCR PET bottle but with the existing shape conserved as much as possible, while satisfying surface bottle decoration and NoLabelling requirements. The techniques applied included 3D shaping of the logos and brands; a contrast of shine and shade effect by etching patterns and changes on ways that the surfaces flow; high readability fonts on the nearly transparent PET material, ensuring the legally-required information is effectively transferred by the moulds onto the bottle. “The challenge was amazing for all of us, at both companies,” said Eng. Francisco Crosta, Head of Danone’s Argentina-Uruguay R&I packaging team. “We are engineers and indus-","@ID":48} "53 TRADE SHOW REVIEW PETplanet Insider Vol. 22 No. 03/21 petpla.net PET moulds and packaging solutions GDXL displays its latest products and developments in its booth at Hall 9, stand no. S41. The company fabricates preform mould, blow mould, closure mould and hot runner applied on various renowned injection and SBM machines for PET packaging. It also provides R&D and engineering services including container designs and retrofits on production lines. In recent years, GDXL has launched multilayer co-injection products and complete preform production systems together with its partners. Benefiting from the company’s effort in the times of pandemic, GDXL achieved a domestic turnover growth of 25 per cent year-on-year, offsetting the impact on international sales to attain an overall revenue increment of more than 10 per cent in 2020. The achievement was also driven by GDXL’s increasing dedication in the research and development of its precise mould products. During 2020, GDXL achieved 40 patent application acceptances and 61 patent authorisations granted by the China National Intellectual Property Administration. The new IPs covered inventions and utility models including container optimisations such as reinforced structures, barriers to gases and light for various applications, and light-weighting. They also included mould designs with strengthened structure, more user-friendly installations and improved moulding performance. Bottle designs with various market-appealing styles and textures were also part of the patent achievements. Multifaceted product optimisations create extra value for customers and partners. Apart from its core PET mould business, GDXL’s development in providing complete engineering solutions is also making progress. In 2020, together with various equipment partners, GDXL launched preform production line projects for several domestic customers. Multilayer containers with resistance to light and gas permeation, and market-appealing elements including colour gradation and imitated texture, were also developed in a number of versions. They had been tested and verified by several domestic and international customers in the course of 2020. GDXL will continue to intensify cooperation with various equipment suppliers and business partners to expand its global business, as well as develop new product portfolio in areas such as non-beverage PET packaging. www.gdxl.com Plastic cap manufacturing solutions With a market share of over 75% in China, Sacmi is the country’s leading provider of plastic cap manufacturing solutions that use compression technology. Hence the company’s pivotal role at Chinaplas where Sacmi will be showcasing a complete range that integrates the cap slitting and folding solution with in-line slit quality control. Advanced in-line controls at every stage and technological leadership in the manufacturing process allow Sacmi’s solutions to respond to the latest packaging-closure trends from a lightweight and integrated neck-capsule design perspective. More specifically, Sacmi has chosen the Chinese market - where over 650 CCM machines have been installed by key players in the local industry - as the perfect showcase for promoting major on-press technological innovations that go hand-in-hand with 4.0 controls throughout the production line. In addition to in-line total quality control systems, Sacmi has enhanced the CCM range with dedicated solutions such as the new CM-Flow system; the latter can even be installed on existing machines to provide a combination of energy savings (up to 9%) and improved extrusion process quality. Furthermore, new in-press controls let manufacturers spot any drift away from production parameters in advance, allowing for the set-up of preventive and predictive maintenance programs. Sacmi will also display the SFM slitting solution for an AB 1881 Cool+ cap for CSD applications. To meet their burgeoning demand for product personalisation, Chinese customers can take advantage of a complete range of Sacmi services that span from design to assistance, especially as regards cap design and customisation; the over 1,000 caps in the catalogue can be customised together with the customer using embossing or offset external decoration. Moreover, like the other machines in the line, the displayed slitting solution can be integrated with the Sacmi vision system; the latter comes in various versions (from 1 to 7 cameras) and features advanced CVS 360 control software. The hub for the country’s technical and sales assistance services is Sacmi Shanghai. Its 55-strong team includes highly specialised, fully trained technicians who support the customer at every stage. During 2020 this hub overcame every challenge to provide vital long-distance support and assistance, including complete machine/plant remote start-up services. Sacmi states to combine cutting-edge cap-making technology with an all-round range that covers everything from preforms to bottling, thus meeting bottlers’ and converters’ every single need. www.sacmi.com SACMI Hall 10 Booth G41 GDXL Hall 9 Booth S41","@ID":55} "COMPRESSORS PETplanet Insider Vol. 22 No. 03/21 petpla.net 41 to our clients during these challenging times, we are filling the gap of trade-shows by organising numerous webinars dedicated to our products and services, as well as on-line customer conferences. PETplanet: Last year you launched the Vito Next on the market. Can you say a little bit about the development phase and the reasons for developing an improved generation of Vito compressors? Sandeep Gadkary: The development phase was crucial for Vito Next, not only because it took many months of design and prototype testing, but because it was also driven by careful and continuous listening to market requests, represented by the so-called “Voice of Customers”. Rather than engaging in months of linear product development, we focused on the rationale of how we can create value for our customers. We “stepped out of the box” to test our hypotheses and immediately collected evidence from customer feedback. This process was reiterated using customers’ input to make further small adjustments until we had developed a product they actually want. That task involved most of our company’s functions and departments: marketing, sales, R&D, the technical department, project management, operation & logistics, quality and purchasing. Keeping our product offering aligned with clients’ requirements was the real focus behind this development. One targeted challenge was to supply a fully connected compressor option not only for new units, but even for the existing population, through an hardware and software package tool (called “SiadMI4U”). SiadMI4U is a simple, connected device, which allows our clients to have an always-connected compressor package and also allows Siad MI to offer different levels of service, from remote monitoring to the full intelligent asset management of our customers. Another opportunity is key markets localisation, starting with China for markets in the Far East. PETplanet: Can you outline the specific improvements which have been made as a result of customer feedback? Sandeep Gadkary: As I mentioned before, the starting point was the Voice of Customers, whose main needs and drivers are price, performance, timely delivery and a fully satisfactory usage experience during the whole product life. Improving compression efficiency, performance and product usage experience, anyway, is a continuous pursuit. In parallel to product upgrade, we continued improving our productivity through increasing the efficiency of our internal processes for PET compressors production, run simultaneously and with same procedures and quality standards both in Italy and in China. PETplanet: What other improvements does the Vito Next have to offer compared to the previous model? Sandeep Gadkary: Together with the optimised performances of Vito Next, we developed different options for variable speed drives (VSDs), high efficiency motors, heat recovery systems, reduced package vibrations, “zero noise” solution, and, as I mentioned, the SiadMI4U tool, valid for the whole Siad MI product range, which results in an always-digitally connected compressor package. Ultimately, the efficiency and extended lifetime achievement are the distinguishing features of Vito Next: a very low energy-intensive compressor built to last and for increased uptime and availability. PETplanet: Specifically, through which features could energy savings be achieved? Sandeep Gadkary: The first energy saving is provided by the improved efficiency of the compressor itself, thanks to an optimised fluido-dynamic design of our Vito Next compressors. Then, there are other features in the package, which contribute to the whole system efficiency: the first of these is from the energy recovery with usable heat of the compressor’s cooling water at around 80°C; another source is from the installation of high efficiency motors, which can result in a 2-3% reduction of the whole energy required compared with the use of standard motors; last, but not least, is the installation of a VSD into the compression package, to follow variable compressed air capacity requirements, which could then provide additional savings of up to 20% compared with the traditional “intermittent full load/no load” running system. PETplanet: How does the compressor react to the varying demand of an SBM machine with regard to the energy supply? Sandeep Gadkary: VSD is indeed the real feature for this task on Vito Next. As mentioned before, its installation represents the most efficient way to factually “copy” the variable compressed air capacity requirements with a proportionally variable compressor running speed, and consequently a proportionally variable power usage, in a much less power-consuming way than the traditional “intermittent full load/ no load” system when a compressor always runs at nominal speed. PETplanet: In addition to the large item “energy”, it is parts prone to wear such as those in contact with the cylinders that are charged as operating costs. Have these also been taken into account in the improvements? Sandeep Gadkary: Of course compressor energy costs represents a major portion of the operating costs, or the so-called “Operating Expenses” (OPEX), and OPEX represents the largest portion of a compressor’s Total Cost of Ownership (TCO) during its whole expected life. So, we focused on energy efficiency and component life time during the development of the improved generation of Vito compressors. Listening to customer feedback we made a major shift in value creation and generated a cylinder proprietary solution resulting in an unparalleled extension of the duration of the wear parts and compressor service life. We have successfully delivered topnotch performance and customer-proven solutions in the field of maintenance and operating costs reduction. I would like also to underline that, considering all the components to be taken into account to evaluate TCO during a typical timeframe of 15 or 20 years, reciprocating compression technology is more energy efficient and remains the best option vs. other technologies, for high-pressure, oil-free air compression. Compressor room at a water bottling plant in North of Italy (courtesy of Acqua Sant’Anna S.p.A., Italy)","@ID":43} "PETplanet Insider Vol. 22 No. 03/21 petpla.net 57 TRADE SHOW REVIEW United Caps presents new products and tethered caps during interactive virtual event Meet the needs United Caps, an international manufacturer of caps and closures based in Luxembourg, reported a strong product pipeline with a number of new lines in development and either launching or soon to be launched, during its United Virtually interactive online event. Despite the effects of the global Covid-19 pandemic, the company has continued to invest in research and development, according to CEO Benoit Henckes. higher grip characteristics and its venting feature is stated to improve end-user safety by venting pressure in the case of spoiled contents. The company says that this offers increased efficiency and improved productivity in filling of sensitive beverages, such as juices and milks. United Caps also presented its line of caps and closures for edible oils and vinegars, under the slogan of “Everything You Need, Nothing You Don’t”. The line includes its awardwinning Doubleflow closures and a family of lightweight, high performance solutions for 26mm necks. The company says that its R&D efforts continue to enhance this and its entire product portfolio. www.unitedcaps.com Tethered caps and closures The imminent arrival of European Union (EU) legislation requiring tethered caps was the subject of distinct presentations and discussion. The company places particular emphasis on collaboration, with customers, consumers and across the bottling industry. United Caps has been heavily involved in the formation of the Alliance for Closure Tethering (ACT), which is intended to bring together segment leaders in the packaging industry to conduct an impact assessment of various tethering solutions on existing finishes, and to determine what changes that might be required. The goal was to come to agreement on the best industry-wide approaches to tethered caps and closures and to support better integration into the supply chain with a united, rather than standalone, solution. The company says that the solutions presented as United Caps Tethered Closures (UCTC) resulted from its collaborative approach. As well as meeting the new EU regulatory requirements, they are reported to have been widely accepted by customers. The company has published a ‘white paper’ that describes its approach; it can be downloaded at the company’s website. Product updates and new product development United Caps says that its new 29 Flip On edible oils closure enables fast and clean pouring of liquids, with drip control. Its easy to open top features a non-detachable tamper evident band, which is claimed to make the product more sustainable. A variety of branding options and colours are available. Keeping the TE band and closure intact boosts opportunities for recycling. The Proline 2 closure for still beverages weighs just 3 g but is claimed to perform like a much heavier solution. It is suitable for use on aseptic lines and is available in a recycled material, as well as in more traditional materials, upon request. Its design is intended to offer 29 Flip On closure enables fast, clean pouring with drip control. Doubleflow closures for edible oils","@ID":59} "EDITOUR PETplanet Insider Vol. 22 No. 03/21 petpla.net 16 PETcast In our new Road Show podcast, PETplanet meets industry experts from Down Under to Japan and talks with them about their successes, decisions and current developments. Listen to the full conversation atwww.bit.ly/2HVwbAd OECD. Life expectancy for women is 87 years and 81 years for men. The industry is responding to this trend with smaller quantities and packaging for seniors as well as user-friendly handling. Recycling Since plastic packaging is common in Japan, it is also one of the leading countries to generate plastic waste. While China remains the largest generator of plastic packaging waste worldwide, the USA is the largest generator of plastic packaging waste per capita. As published in the UN report, this is followed by Japan and the EU. To simplify the recycling of postconsumer packaging materials, the Japanese population is accustomed to carrying out pre-sorting. PET bottles, glass, paper and aluminium are collected separately. The incineration rate for the remaining waste is over 70 per cent, while waste disposal at landfills is shrinking due to low remaining capacities. Japan is a successful example of PET bottle recycling. 1995 saw the introduction of the Containers and Packaging Recycling Law (CPRL) by the Ministry of the Environment to promote the collection and recycling of containers and packaging waste; according to the Japan Soft Drinks Association JSDA, these account for around 60 per cent of household waste by volume. Containers that are subject to this sorted collection are glass and PET bottles, other plastic containers, paper containers and packaging, and aluminium and steel cans as well as paper packaging and cardboard. Responsibilities are clearly regulated in the CPRL: besides the sorting guidelines for consumers, it is stipulated that the sorted waste is then collected by the municipalities and stored for collecting by the recycling companies. Manufacturers and business organisations using containers and packages have to pay a recycling fee to the JCPRA in accordance with the volume they manufacture or sell. Each year recycling business organisations are selected by a public bid in every local municipality where a waste storage site is located. They are assigned to collect and transport the waste from the storage sites to recycling facilities. To make sure the waste is recycled, these recycling business organisations receive payment only after showing a delivery report that has been signed by the recipient of the recycled products. If an item has been disposed of improperly, a large red warning sticker is put on the offending rubbish bag to shame the person responsible. Rising bottle-to-bottle rates In the early 2000s, the recycling material from post-consumer PET bottles still flowed mainly into the production of sheets and fibres but since 2010, bottle-to-bottle has risen sharply. According to the CPBR, 27,100 t of recycled PET flakes from PET bottles went into bottle-to-bottle recycling in 2012; by 2013 it was 40,300 t and in 2017, 61,300 t. A small dip in the recycling balance is to be expected in 2020 due to the pandemic, but overall Japan is showing an upward trend in bottleto-bottle recycling. One by one, large companies like distributors and trading companies are entering the PET bottle recycling business. In the PET bottle market, mechanical recycling for rPET for B2B is expected to reach 320,000 t per annum by 2022; chemical recycling is also being undertaken for B2B by brand owners. Manufacturers are already on course to make this a success. Put together in 2016, the Voluntary Design Guidelines for Designated PET Bottles cover a collection of points that, when implemented, should enable a smooth recycling process. These include aspects of the bottles (non-coloured PET, no direct printing, no base cups), the labels (separation by gravity when recycling, inks not transferring to PET, shrink sleeves with perforation etc.) or closures which are made mainly of PE/ PP with a specific gravity less than 1.0. And Japan has raised the bar even further: in November 2018, The Plastic Resource Reclamation Declaration was published by the Japan Soft Drink Association together with soft-drink manufacturers and other industry groups. Its declared goal is to achieve 100% effective utilisation of PET bottles by 2030. Sources: AHK, Euromonitor, Japan Containers & Packaging Recycling Association, CPBR, Japan Soft Drinks Association,JPIF, Statista, UN Report, World Bank, Yano Research Institute et al. photo courtesy: Suntory","@ID":18} "OUTER PLANET 70 PETplanet Insider Vol. 22 No. 03/21 petpla.net OUTER PLANET Bottles made from carbon emissions or orange peel – in this new “Outer Planet” category, we are presenting projects that you would not normally expect to see in PETplanet Insider. But bear with us, these projects are not quite as off the wall as you might think. Quirky they may be, and some may never get beyond the development stage, but some might just be the next big thing. Join us in some blue sky thinking that could energise our entire sector. Citrus peel as raw material Cosmetic bottle made from industrial carbon emissions New technology developed at the research institution VTT, Espoo, Finland, enables the use of pectincontaining agricultural waste, such as citrus peel and sugar beet pulp, as raw material for bio-based PEFplastics to replace fossil-based PET. The carbon footprint of plastic bottles can be lowered by 50% when replacing their raw material of PET with PEF polymers, which are claimed to provide a better shelf life for food. “In the near future, you could be buying orange juice in bottles that are made out of orange peel. VTT’s novel technology provides a circular approach to using food waste streams for high-performance food packaging material, and at the same time reducing greenhouse gas emissions,” shares Professor of Practice Holger Pöhler from VTT. In addition to a lower carbon footprint when comparing PET with PEF (polyethylene furanoate), the VTT also states that the barrier properties of PEF plastics are better than PETs, meaning that the food products have a longer shelf life. PEF is a fully recyclable and renewable high-performance plastic. It therefore opens up possibilities for the industries to reduce waste and to have a positive impact on the environment. VTT’s technology uses a stable intermediate for the production of FDCA (2,5-furandicarboxylic acid), one of the monomers of PEF, which enables an efficient process. In addition, utilising pectin-containing waste streams opens up new possibilities for the circular economy of plastics. VTT has patented the technology, and the research has been published in the scientific journal Green Chemistry on December 7, 2020 under the title “A unique pathway to platform chemicals: aldaric acids as stable intermediates for the synthesis of furandicarboxylic acid esters”. www.vttresearch.com As part of their innovative partnership, LanzaTech, Total and L’Oréal have unveiled the world’s first sustainable packaging made from recaptured and recycled carbon emissions. The successful conversion process takes place in three steps: 1) LanzaTech captures industrial carbon emissions and converts them into ethanol using a unique biological process. 2) Thanks to a dehydration process developed with IFP Axens, Total converts the ethanol into ethylene before polymerising it into polyethylene, which has the same technical properties as the fossil version. 3) L’Oréal uses this polyethylene to produce packaging. It is claimed to have the same quality and properties as conventional polyethylene. The partners now intend to continue working together to increase the production volume of these sustainable plastics and look forward to working with all those who wish to join them in the use of these new sustainable plastics. www.loreal.com","@ID":72} "BOTTLING / FILLING PETplanet Insider Vol. 22 No. 03/21 petpla.net 29 working with the OEM bottler Asagiri Beverage, which also belongs to our group. Asagiri fills 500ml and 2 l PET bottles, which are available in over 1000 supermarkets and food shops.” Moreover, Asagiri Beverage has been able to implement a material reduction in bottle manufacturing of 60% to date and is the first manufacturer in Japan to launch a 100% bottle-to-bottle rPET bottle with a 38% reduction of CO2 in the manufacturing process. Sustainability resonates throughout the company. Alongside the economic promotion of the local region, Mt. Fuji Spring also contributes to environmental protection and conservation, for example through donations to the Hiderou Awai Environmental Foundation. The company showed economic growth of an average of 20% on the previous year. Overall, the company employs 261 staff. www.fuji-meisui.co.jp hardness soft water vanadium Energy, protein, lipids & carbohydrates Sodium (salt equivalent) calcium magnesium potassium pH weakly alkaline Frecious Fuji characteristics 24mg/l 79μg/l 0 0.57mg (0 g) 0.59mg 0.22mg 0.08mg 8.3 Frecious Asagiri Kogen characteristics 85mg/l 180μg/l 0 8.0mg (0.02 g) 1.5mg 1.1mg 0.29mg 8.5 Frecious Kiso characteristics 20mg/l 0 0.19mg (0 g) 0.56mg 0.12mg 0.06mg 7.7 Lightweight PET bottle Each content is per 100ml Customer Factory INTRAVIS Service 1-\"45*$ 1\"$,\"(*/( 7*4*0/ */41&$5*0/ 888 */53\"7*4 $0. \"-8\":4 #: :063 4*%& */ 1&340/ 030/-*/&","@ID":31} "56 TRADE SHOW REVIEW PETplanet Insider Vol. 22 No. 03/21 petpla.net Maag Group’s technologies Maag Group, a broadly diversified global solutions provider of Pump & Filtration Systems, Pelletising & Pulverising Systems, Recycling Systems and Digitalisation for use in the polymer industry is showing its latest innovations. The highlight of the booth will be the ERF350, a high-performance melt filter for the filtration of heavily contaminated polymer feedstock. The filter is self-cleaning with a rotating, perforated drum, through which there is a continuous flow of melt from the outside to the inside. A scraper removes contaminants that are held back on the surface and feeds them to the discharge system. This enables the filter to operate automatically, without disruptions over long periods and without having to replace the screen. The advantages: ultra-low melt losses and good mixing and homogenising of the melt. Another highlight in the Maag Group booth is the Pearlo underwater pelletising system for the highly efficient and flexible production of spherical pellets with throughputs of up to 36,000 kg/h. Compact and modularly structured, it requires only a very small footprint. Electronically controlled EAC technology guarantees precise pressure of the pelletising knives during operation, thereby enabling long runtimes free of interruptions with consistently high pellet quality. In the same equipment segment, Maag Group shows a Baoli-3 third-generation dry-cut pelletiser for processing hard and soft materials. The key components of these pelletisers are manufactured in Germany, and all versions meet the requirements of applicable safety standards in Germany. Maag Group has more than 60 years’ experience in pelletisers and has already installed around 800 Baoli pelletisers in China. As with previous Baoli generations, the automated cutting chamber locking system enables fast handling while supporting operator safety. From its range of gear pumps, Maag Group will be presenting the extrex gear pump in x6 class design. As with all x6 versions, Maag Group has completely re-engineered and redesigned the components, from the shafts through to the bearings and seals, and optimised the interaction of the components. Specially developed gear teeth with low compression allow very high pressures to be achieved with low shear rates. The result is a further increase in achievable product quality, volumetric efficiency, as well as production consistency and safety. www.maag.com MAAG Hall 10 Booth Q01","@ID":58} "8 NEWS PETplanet Insider Vol. 22 No. 03/21 petpla.net After more than 20 years, Austrian brewery is withdrawing PET bottles In 2000, Austrian brewery “Mohrenbrauerei” introduced beer in PET bottles. Now the single-use container is being taken out of the product range. The main reason for this is the change in consumer behaviour due to the critical discussion about plastic packaging. The Mohren Brewery sells 97 per cent of its beverages in returnable containers, 3 per cent in aluminium cans, disposable glass and plastic bottles. Four varieties – Pfiff, Radler Sauer, Zitrone Naturtrüb and Grapefruit – were previously available in 0.33 l PET non-returnable bottles. After more than 20 years, bottling in plastic bottles is now being discontinued. In 2000, the Mohren Brewery introduced beer in PET bottles and was thus a pioneer on the Austrian market. Later, the bottle size was reduced from 0.5 to 0.33 l and the closure was further developed several times. The brewery even built its own machine to seal the bottles. “The critical public discussion about plastic is leading to declining consumer acceptance. This also affects our technically innovative PET bottle,” says Managing Director Heinz Huber. The prospect of a pandemic-related slow carnival season also contributed to the decision of the Dornbirn-based company. PET bottle sales were traditionally above average during this season. “We originally introduced the PET bottle as a niche product for on-the-go or for events,” explains co-managing director Thomas Pachole. In future, the aluminium can will remain in the range as a lightweight, disposable container. www.mohrenbrauerei.at Award for Kirin’s thin film deposition technology Kirin Holdings Company, the Packaging Innovation Laboratory, has developed a new thin film deposition technology for PET bottles using a hot wire CVD technology for an environmentallyfriendly package. In recognition of the results of this development, on January 7, 2021 Kirin Holdings was one of the Worldstar Winners in the Beverages category of the Wolrdstar Packaging Awards 2021 organised by the World Packaging Organization (WPO). The technology was also selected as a Diamond Finalist presented at the Dow Packaging Innovation Awards 2020, organised by Dow Chemical Company in the United States on November 11, 2020, as well as winner of the 44thKinoshita Award in September 2020. The technology is expected to contribute to resource conservation by forming a colourless, transparent and recyclable gas barrier film on PET bottles, which prevents oxidation and degradation of the content liquid while reducing weight. This technology uses special ceramic rods to form a thin film on the inner surface of the bottle that prevents the permeation of oxygen and other substances. By devising the type of film material and the conditions under which the film is formed, it has become possible to fill the bottles with a variety of clear and colourless beverages. In addition, the bottles are recyclable in accordance with Japan’s Voluntary Design Guidelines for designated PET bottles. www.kirinholdings.co.jp","@ID":10} "BOTTLING / FILLING PETplanet Insider Vol. 22 No. 03/21 petpla.net 30 Krones PET aseptic filling lines at Eckes-Granini A picture of health After installing a PET-Asept D system five years ago, Eckes-Granini Deutschland GmbH has now commissioned a PET-AseptBloc D with a block-synchronised blow-moulder at its facility in Bad Fallingbostel. FILLING The company’s ambitions are high: market leadership in all of Europe with premium products in the fruit-juice category. This is what the German familyowned company Eckes-Granini has successfully translated into hands-on reality. Throughout Europe, the group focuses on upmarket quality, with the aim of its brands being Number One or Two in the fruit-juice rankings. In Germany, Eckes-Granini Deutschland GmbH’s portfolio includes both of the market-leading brands: Hohes C and Granini. The Granini brand accounts for roughly a quarter and Hohes C for about a fifth of total group sales. Positive experience In its Bad Fallingbostel facility, Eckes-Granini started operation on a first aseptic line from Krones back in 2016, a PET-Asept D system rated at 36,000 containers per hour. It features dry-aseptic technology from Krones that lays claim to providing maximised sterilisation performance in conjunction with minimised media consumption. “Our first dry-aseptic line is a perfect combination of efficiency and flexibility, with marked beneficial effects on our sustainability record. Compared to our previous wet-aseptic line, we achieved savings of 20% for electricity, 30% for water and wastewater and 50% for gas needed in steam generation,” explains Henning Hanisch, project and process manager at Eckes-Granini. And plant manager Hermann Naumann adds: “Krones turned out to be the perfect vendor, with spot-on microbiological know-how and field-tested technology. Ultimately, though, it was the TCO, i.e. the total cost of ownership that helped tip the scales in favour of Krones.” Compact-size line for low outputs It was precisely this positive experience gained in the past that made sure Eckes-Granini opted for another aseptic line from Krones. This second line installed at the Bad Fallingbostel facility has been dimensioned for a rating of 13,000 bph (1.0 l and 0.75 l bottles) and comprises: PET-AseptBloc D with Contiform 3 Pro blow-moulder, H2O2 sterilisation module and modulfill VFJ volumetric filling system: Whereas in the first line it was a third-party blowmoulder that was linked up to the sterilisation and filling modules of the PET-Asept D system by means of AirCo conveyors, Eckes-Granini has now chosen to buy the complete kit from Krones, including the blow-moulder/filler block. Modularised starmodul labelling machine, block-synchronised with a sleevematic machine and a shrinkmat steam tunnel: Even though in the first line it was also possible to dress the bottles in wraparound and pressure-sensitive labels respectively, or alternatively in sleeves, two separate labellers were needed for that: a sleevematic and a modularised machine. Variopac Pro FS packer with Varioshrink tunnel and an integrated handle applicator: Which affixes the carry strap directly to the film reel in the Variopac Pro FS. After that, the sixpack is produced by wrapping the film (with the handle already attached to it) around the containers. “This method obviates the need to install an additional machine, which cuts the kit’s footprint,” says Henning Hanisch. Modulpal Pro 2A palletiser with high-level infeed Henning Hanisch had also been actively involved in the installation work for the first dry-aseptic line. “We’d already planned and commissioned the first aseptic line from Krones with more or less the same project team. Here in our company that was seen as a big advantage. And things were similar at Krones: they knew who was responsible for what here on site, they knew their way around, and some of the people they sent to handle erection and commissioning were the same who’d already worked on the first line. It was not least thanks to this good cooperation that we were able to implement the new line in next to no time. We were always ahead of the schedule,” he explains, and Hermann Naumann adds: “Our operators were also able to directly put their experience gained with the first aseptic line to good use – they quite simply knew already how to handle the various machines. Same technology, same spares – you just cannot beat that.” The line includes a modularised Starmodul labeller, block-synchronised with a Sleevematic machine, so it is possible to dress the containers in wrap-around and pressure-sensitive labels respectively, or alternatively in sleeves.","@ID":32} "PETproducts 60 PETplanet Insider Vol. 22 No. 03/21 petpla.net Bericap tethered solution available for the GME 30.40 neckfinish The International Technical Centre for Bottling and Related Packaging Cetie is in the process of defining a new neck standard for carbonated beverages. The new GME 30.40 neck standard has a thread diameter of only 26mm, reducing the weight of the neck and closure by between 1.4 g and 1.7 g, depending on the diameter of the neck support ring. The neck standard takes the latest trend of neck support ring diameter reduction – from the former standard of 33mm down to 29mm – into account. In contrast to other 26mm neck standards GME 30.40 will perform safely under all climatic conditions on bottle sizes of up to 3 l. Bericap has developed the 7049 closure for the GME 30.40 neckfinish. The closure can be equipped with a tamper evident band which remains on the neck or the ClipAside tethered cut after opening by the consumer. ClipAside improves the consumer convenience of the PET bottle because the closure can be opened and locked at an angle of 170-180 degrees, enabling unobstructed drinking from the bottle. Since the closure remains attached to the bottle it avoids littering. www.bericap.com Closures removal solution for returnable bottles While reuse and recycling schemes for beverage packaging are seen as efficient tools for reducing the environmental impact of packaging systems and for increasing resource efficiency, effective preparation of bottles PET and glass bottles is important. Arol Group’s Arol Reverse is offered as a solution for unscrewing of pre-threaded plastic caps and threaded aluminium caps from glass and refPET bottles. The company says that Arol Reverse equipment, with between three and 30 heads, delivers safe unscrewing of caps with diameters of 28-38mm, at up to 60,000 caps/h (1,000 caps/ min). The machine’s decapping heads are made entirely of stainless steel; special handling parts, including discharge piping and containers, can also be supplied in stainless steel, to prevent scratching of rPET bottles and extend component life. It can identify bottles that do not have caps; its ‘no decapping’ feature prevents bottle neck damage. The machines are equipped with advanced inspection systems to identify height variance at input and detect caps at discharge. Arol Group says that Arol Reverse is designed for quick format change and is flexible enough to be adapted to conditions in any plant. Arol is part of Arol Group, which includes Unimac-Gherri, specialist in filling and capping of glass, metal and plastic containers with twist-off and pre-threaded caps for dense, semi dense and pasty food products; Tirelli, which is focused on packaging equipment for the cosmetics industry; and Maca Engineering S.r.l, a specialist in the design and manufacture of machines for production, assembly and cut of aluminium and plastic caps and closures. www.arol.com PRODUCTS","@ID":62} "61 PRODUCTS PETplanet Insider Vol. 22 No. 03/21 petpla.net Successful research on GDS granule drying system Eisbär is proud to announce that when looking closer at their GDS granule drying systems Eisbär found a way to drastically reduce the cooling water consumption of the machine. Investing in a new drying unit draws high acquisition costs in itself already however, electricity and water consumption are also crucial factors as additional costs. Additionally, the systems’ water usage is of enormous importance from an environmental point of view. An examination of the GDS granule drying systems has revealed that the amount of cooling water used by the machines has decreased by almost 94%. GDS GDS 400 GDS1100 GDS 2000 New water consumption litre per minute 5 12 20 Water saving litre per hour 3,300 9,180 16,800 Water saving litre per year 28,050,000 78,030,000 142,800,000 (Calculation based on an assumption of 8,500 operational hours per year and a cooling water temperature of 12 °C.) Eisbär said that the GDS Granule Drying System is a new generation material dryer with a resin drying capacity of up to 5,000 kg/h. Its high product quality ensures a long service life and with fewer moving parts it enables easy maintenance and lower service costs. Moreover, the machine’s significant energy saving is made possible by means of throughput control, recusorb, dewpoint control and by an efficient plate heat exchanger. Using GDS can save litres of water each year which means significant cost savings as well as a great action towards becoming more sustainable and being more environmentally friendly. www.eisbaer.at Ultrazone O4 technology Fogg Filler is continually focused on improving technology that better serves its customers and the environment. Fogg’s newest sanitising solution for filling needs is closedlooped Ultrazone O4 solution. The sanitisation process can perform at a 3 - 6+ log reduction, resulting in a near-aseptic rinse for bottles. Ultrazone O4 is stated to create a hydrogen peroxide “like” solution from a combination of electricity, air and water, which keeps chemical cost ultra low and increases profitability on a filling machine. With the ability to filter and reuse the water-based solution, one filler can theoretically save 18,000 gallons of water a day, increasing the facility’s savings on wastewater disposal. The Ultrazone O4 solution comes complete with the Ultrazone O4 skid and fully enclosed, custom rotary bottle sanitising/rinsing turrets to match exact requirements. The Ultrazone O4 skid creates and recycles the solution continuously, while the sanitiser/rinser turrets accurately apply the solution to the bottles to achieve the desired level of sanitisation. The fully sealed door enclosure around the turrets safely contains all fumes during operation using carefully designed, Hepa pressurised airlocks at the bottle entry and discharge points and special electronic door locks only open after fumes are safely evacuated from the chamber. During the sanitisation process, bottles may need to be treated on one or more turrets, depending on the line run speed and necessary contact time. Once inside the enclosure, bottles are first sprayed aggressively inside and out with the sanitising solution in an upright position to start the contact time and loosen mechanical debris. They are then passed on to the sanitiser/rinser turrets where the bottles are rinsed upside down so that solution may flow out of the bottles. In a typical two turret installation, the first turret will sanitise the bottles with the Ultrazone O4 solution and the second turret can be used to simply drain or rinse with another solution of your choice. Lastly, the bottles pass through a Hepa pressurised degas tunnel and out through the exit airlock. Once the bottle is out of the chamber and inside thefiller, thefilling and capping process proceeds as it would on any Fogg filler. This technology can be purchased on new machines, replace existing sanitiser/rinser system, or be paired with any existing “stand alone” filler. www.foggfiller.com FILLING","@ID":63} "PETnews 6 NEWS PETplanet Insider Vol. 22 No. 03/21 petpla.net Australia’s largest PET recycling plant under construction Construction is underway on a world-class recycling facility in Albury-Wodonga that will see the equivalent of around 1 billion PET plastic bottles recycled each year. Environment Minister and Federal Member for Farrer, the Hon. Sussan Ley MP, marked the official start of construction by turning the first turf on-site at the project, which is being delivered in a joint venture between Asahi Beverages, Pact Group Holdings Ltd and Cleanaway Waste Management Ltd. The $45 million plant in the Nexus Precinct, 10 km outside the Albury CBD in NSW, is set to be fully operational by October, two months earlier than expected owing to Albury Council approving the project ahead of schedule. The facility will trade as Circular Plastics Australia PET. Excavation of the site has already started, sheds to house more than a dozen diggers have been erected and dozens of jobs will be created as construction ramps up in coming weeks. The raw plastic material that the new plant will recycle each year is equivalent to 1 billion 600ml PET plastic bottles and will be used to produce more than 20,000 t of new recycled PET bottles and food packaging, making it the largest end-to-end rPET plant in Australia. It will increase the amount of locally sourced and recycled PET produced in Australia by two thirds – from around 30,000 t currently to over 50,000 t/a according to Pact Group. The plant will also reduce Australia’s reliance on virgin plastic and the amount of recycled plastic Australia imports. The project was made possible with the assistance of almost $5 million from the Environmental Trust as part of the NSW Government’s Waste Less, Recycle More initiative funded from the waste levy, with the support of the Department of Regional NSW and the Australian Government’s Recycling Modernisation Fund. www.asahi.com.au Drinktec postponed until September 2022 The Drinktec advisory board and Messe München have taken a joint decision to postpone the world’s leading trade fair for the beverage and liquid food industry until the autumn of 2022. The new dates are September 12-16, 2022. This action was prompted by the international nature of the Drinktec event. The decision could not be delayed given that industrial goods trade fairs involve extensive planning and complex high-tech construction work. Despite the coronavirus crisis, Drinktec is registering high demand for floorspace from customers both in Germany and abroad. Three quarters of the available exhibition floorspace has already been booked. Dr Reinhard Pfeiffer, Deputy Chairman of the Board of Messe München says: “Until recently, we assumed that the pandemic situation would improve, making international travel possible. The latest developments have quashed these expectations. Two thirds of all Drinktec visitors come from abroad. Of these, half come from other continents. This means we cannot deliver the benefits of a leading global trade fair this year.” The global beverage industry meets in Munich only once every four years. “Companies synchronise their innovative developments in line with this cycle, which is why we had to find timely dates in the trade fair calendar. Cancelling altogether and leaving an eight-year gap in between trade fairs would have been unacceptable for the industry,” explains Dr Pfeiffer. Volker Kronseder, Chairman of the Drinktec advisory board, as well as Drinktec’s conceptual sponsor, the VDMA (German Mechanical Engineering Industry Association) support the decision. Preparations and plans currently underway for Drinktec 2021 and the integrated oils+fats event will now be seamlessly transferred to the new 2022 dates. www.drinktec.com CarbonLite Holdings files for relief under Chapter 11 of the Bankruptcy Code CarbonLite Holdings LLC, recycler of plastic beverage bottles, announced that it has filed a voluntary petition for relief under Chapter 11 of the Bankruptcy Code in the United States Bankruptcy Court for the District of Delaware (the “Bankruptcy Court”). The filing pertains to all three of CarbonLite’s facilities, in California, Texas and Pennsylvania, as well as to its California subsidiary, PinnPack Packaging. Production at all these facilities will continue as usual without interruption, as will payment of all employees. Layoffs are not under consideration. There will be no stoppage of supply to CarbonLite’s customers during the reorganisation period. Pressures directly related to the coronavirus pandemic contributed to CarbonLite’s decision to reorganise. This included temporary production slow-downs caused by employee illness, the low price of virgin plastic relative to rPET, and a nine-month delay in the grand opening of the company’s new Pennsylvania facility caused by travel restrictions that held up equipment commissioning by European manufacturers. CarbonLite has also incurred heavy capital expenditures for the recent expansion of its Dallas facility and construction of its state-of-the-art, 270,000 square-foot plant in Reading, Pennsylvania, which launched limited production in October 2020. This plant is outfitted with advanced robotic systems and is the largest standalone bottle-to-bottle recycling facility in the world. Its grand opening is planned for this spring. The company’s plans includes customer contract renegotiations to ensure CarbonLite’s solid financial footing. www.carbonliterecycling.com","@ID":8} "EDITOUR PETplanet Insider Vol. 22 No. 03/21 petpla.net 13 Drinks industry and trends There are a few major Japanese beverage firms and two foreign companies, Coca-Cola and Nestlé, which make up the dominant share of all beverages available in supermarkets and vending machines. Amongst the biggest Japanese firms for beer, spirits, and non-alcoholic beverages like tea, coffee or CSD are Asahi, Kirin, Suntory, and Sapporo. In its report “The Consumer Impact of Coronavirus in Japan”, Euromonitor illustrates how the habits of the Japanese population have changed in recent months. With regard to the drinks landscape, the country, whose liquor market is one of the largest in the world, is currently showing a fall in the consumption of alcoholic drinks. According to forecasts, a market volume of € 107.125 million will be reached in 2025, which corresponds to annual sales growth of 2.73% (CAGR 2021-2025). Capital growth will be driven primarily by premiumisation and the growth of out-of-home consumption. Ideas driven by the pandemic, like online drinking sessions, are currently enjoying increasing popularity and are counteracting the collapse of sales. In the beer sector, many are looking increasingly to nonalcoholic options. The market for nonalcoholic drinks has been able to grow in recent months, particularly for drinks that offer immuneboosting or stress and body-fat reducing benefits. In 2019, sales of sugar-free tea and coffee drinks and mineral water increased too and are considered to be future growth categories. Here, Suntory, BritVic and Kirin are of particular regional significance, along with the regional bottlers of Coca-Cola and PepsiCo, such as Coca-Cola European Partners (CCEP) or Femsa. As listed by Statista, market sales of non-alcoholic drinks should amount to around € 56.403 million in 2021. According to forecasts, a market volume of € 65.390 million will be reached in 2025; this corresponds to annual sales growth of 3.77% (CAGR 2021-2025). In this market, this converts to around € 447.46 per capita across the population in 2021. Share of container package in 2019, based on output (Source: JSDA)","@ID":15} "MARKET SURVEY 37 PETplanet Insider Vol. 22 No. 03/21 petpla.net Resins & additives Preform machinery Preform production & inspection systems Preform & SBM mould manufacturer SBM 2-stage Compressors Caps & closures & inspection systems Filling equipment & inspection systems Recycling machinery Palletising & shrink film machinery Sipa Husky Injection Molding Systems Otto Systems AG Via Caduti del Lavoro 3 31029 Vittorio Veneto, Italy +39 04389 11 511 www.sipa.it Mr Pablo Fiorentini Sales Director, Preform Systems & Tooling +39 04389 11511 [email protected] 500 Queen Street South Bolton, ON, L7E 5S5 Canada +1 905 951 5000 www.husky.co Mr Reinhart Drawetz Business Development Manager - PET Systems +1 905 951 5106 [email protected] Zürcherstrasse 73 8730 Uznach, Switzerland +41 55 285 22 11 www.otto-systems.com Mr Stefan Zatti CEO +41 55 285 22 09 [email protected] XForm 250 XForm 350 XForm 500 Xtreme 72 Xtreme 96 HyPET5e , HyPET5e+ , HyPET HPP5e, NexPET Multi-Layer Co-injection PET-Series 120, PET-Series 160, PET-Series 240, PETSeries 320 96 128 180 72 96 Up to 144 cavities Up to 48 cavities 4/48/72/144 2-96 cavities 69,000 preforms per hour (pph) 87,000pph 122,000pph 52,000pph 69,000pph Dependent on number of cavities and preform design (max. standard shot size 8,030g) Dependent on number of cavities and preform design (max. shot size 2.425kg) Dependent on number of cavities and preform design (typical preform range 10-40g, with barrier content from 2.5% up to 40%) Max. shot weight 7,980g 1,700 476 1,010 Up to 1,150 XForm: available in GEN4 XP version (low energy consumption, fast cycle time, complete new HMI); Xtreme: injectioncompression technology, ultra-thin wall capability, 2 preforms can be produced simultaneously Adaptive System Pressure supporting improved energy consumption; integrated high speed robot with up to 4 stages of preform cooling supporting; capability to mould the most aggressive preform applications at highest preform quality; reflex platens, distribute clamping forces evenly, reduce tonnage requirements and extend mould life; energy absorbing conveyor improving preform quality and efficiencies Designed for the mid-volume market segment; system capability, tooling conversion and refurbishing are engineered to meet the needs of this market; includes many features and capabilities from the HyPET5e platform; quicker mould changeovers; adaptive system pressure and reflex platens; integrated and operator friendly controls Based on HyPET HPP5e platform and features; integrated and operator friendly co-injection system controls, including auxiliaries; multi-layer servo valve-gate hot runner and secondary injection unit; optimised front mounted hot runner nozzles and melt delivery for best-inclass mid-layer distribution capability and reliability Consulting & engineering of preform systems, complete preform production system including auxiliaries, full electric clamping unit, hybrid injection solution with shooting pot or electric injection with Time Safe Unit (TSU) XForm GEN4 XP: XP technology, LongLife tooling coating, XMold for ultra-thin preform injection capability, wide-mouth preforms capability; Xtreme: built-in inspection system for 100% quality check, 100% recyled flakes processing capability, direct connection with XTRA SBM Self-Cleaning mould technology improves system efficiency; Quick mould change; Integrated mould alignment increases mould life and optimises preform quality; Quick colour change; Complete range of integrated auxiliaries (resin dryer, chillers, product handling); Recycle melt to preform module on HPP5e - universal connection to melt decontamination unit. Complete range of integrated auxiliaries; partial cycle completion when power fails; options to adapt the system to the geographical conditions and many specific customer needs; additional new multilayer co-injection capability Includes most HyPET HPP5e options, including mould alignment and selfcleaning; optional secondary injection unit changeover feature; complete range of integrated auxiliaries, including B-layer materials and additives Extra large preform capability (up to 380mm), co-injection technology up to 72 cavities, integrated dust-evacuation (OH-XTract), enhanced neck-cooling (OH-XCool), wear-protection coating (OHXTreme)","@ID":39} "51 TRADE SHOW REVIEW PETplanet Insider Vol. 22 No. 03/21 petpla.net Environmentally responsible dry ice cleaning solution For injection or blow moulders, moulds are a mission-critical asset and require timely, proper, fast, and efficient cleaning to ensure uptime and part quality. When the moulds are not cleaned properly and on a regular basis it may cause blemish and unwanted flash on the final product, filling problems which lead to quality problems and longer production cycle times. In addition, solvents and other waste-generating cleaning processes are bad for the environment and are not acceptable for the health of PET moulders. During Chinaplas, Cold Jet will present dry ice cleaning solutions. The company’s dry ice cleaning technology allows moulds, lock rings, cores, and gate inserts to be cleaned without the disassembly of the stripper plate and while the mould is still in the press. The system also cleans blow moulding machines, palletising equipment, conveyor belts, and glue machines. Cold Jet’s dry ice cleaning technology is claimed to provide an easy solution that saves time and improves processes. Resulting in a 3-5% increase in productivity and investment returned in just a couple of months, states the company. Additionally, with dry ice blasting equipment, PET moulders avoid the usage of chemicals. During the trade show, Cold Jet will present dry ice blasting machines life and explain the importance of daily using dry ice technology in the PET moulders production facilities. www.coldjet.com Newamstar will exhibit the 6th + generation rotary blower Up to 2,750bph single cavity capacity: The 6th + bottle blowing technology can blow bottles ranging from 0.25 to 2.0 l. It applies the rigidity design at the support structure, light weight design for rotating parts and local optimisation design for the components movement law which enables the wholes machine to run at high speed steadily with lower vibration and noise. With the precise process control and stable operation, the single cavity capacity of the blower is up to 2,750 bph. Modular design: The equipment applies a modular design, and each system is designed as a separate modular unit, which can be combined in various ways to meet the fast delivery requirements of the project. The advanced heating transmission structure guarantees even preform heating and ensures the stable and efficient preform transmission. The quick-change design of the changeover parts meets the requirements for quick switching between different bottle necks. Mould frame combined linkage mechanism: The bottle blowing system applies the tandem type of combined linkage mechanism coordinating the movement of mould frame and bottom mould. It can precisely control the opening and closing movement of the mould frame and the lifting movement of the bottom mould which can reduce the vibration and impact of the mechanism, slowing the wear of parts, enhancing the smoothness and reliability of the blowing system, and it improves the high-speed performance of the whole machine. Stretching servo flexible control: Servo stretching system can precisely control the stretching speed and distance, easily adjust the blowing process, and adjust online while blowing the bottles. The stretching and sealing linkage device realises the linkage between preform sealing and stretching. The contact between them is soft and controllable, while ensuring movement accuracy and stability. Integrated high-pressure valve group brings low energy consumption: The modular air source processing unit is placed at the back of the equipment for easy maintenance. The integrated high-pressure valve group has little dead space and achieves low HP air consumption. The six-step blowing process, with the intermediate pressure section, greatly saves air consumption, and the recovery rate is up to 35-40%. Active bottle gripper transfer: The active gripper is used to transfer the preform and the blown-shaped container to precisely control the opening and closing of the gripper. Powerful digital production control: Multiple inspection points are set up on the production line to monitor equipment abnormalities and malfunctions in real time in the Newamstar Smart Factory solution. All production lines apply ethernet technology to collect, store, and transmit data to the intelligent factory management and control platform. Analyse and process the data by Newamstar’s latest LMS system, presenting users with clear and accurate production dynamics and creating big data management. At the same time, there are online reminders for equipment cleaning, maintenance, and lubrication to keep the equipment running in the best condition. www.en.newamstar.com NEWAMSTAR Hall 4 Booth A41 COLD JET Hall 11 Booth K21","@ID":53} "MATERIALS / RECYCLING PETplanet Insider Vol. 22 No. 03/21 petpla.net 22 What does it mean to move to a circular economy in 2021? by Lucia Buffoni, Marketing Manager at Repi 2020 is over, 2021 has been invoked so much and by so many countries around the world - and now? Unfortunately, it seems that the pandemic has made it through the year without too many problems and continues to bother us and affect our lives. But the resources called in, at all levels, by the struggle against Covid will be lethal, this time for the virus itself. This is what we hope the most, and according to The Economist, we have chance that “the decade could yet roar.” If we talk of safety, plastics and packaging pop up. In such an emergency contingency, plastics have proved once more to be the most reliable and affordable solution for personal protection. The pandemic has challenged everyone’s lifestyle, habits, and daily life, even of those who are fighting for a reduction when not a ban of plastics. Many sustainability-conscious people found themselves choosing single-use plastic items, such as disposable wipes and sanitary protective devices, but also plastic bottles containing hand sanitisers up to takeaway food containers and single serve drinks packaging. If we look at the world consumption rates of 2020, single use packaging is at a record high from north to south and this will last for a while, together with the demand of plastic disposable wipes, gloves, masks, etc. This increase is challenging a lot the collection and recycling systems, which however are demonstrating to be resilient, keeping up. In such a context the best thing we can hope for, is to take the opportunity to keep pushing the development of a circular economy of which of course plastics recycling is the best example. Now more than ever the solution seems not to be the elimination of plastics, but a systems-level approach on a global scale to improve collection and recycling. Let us remain on the concept of circular economy. Reaching a circular economy means structuring economies on the virtuous closed loop of make – use – recycle in which every product is designed to be used and then disposed leaving no traces, it means being re-used to generate other products and so on. All good so far - but is this really the full picture? I mean if we recall the primary goal of a circular economy, that is to cut CO2 emissions as main cause of global warming, then the carbon footprint contribution of our activities should be the main driver. Instead, some solutions emerging and defined as 100% recyclable produce actually higher CO2 emissions than what they are replacing and can’t therefore be sustainable for the future. Looking at the single use packaging sector, plastic packaging is the most attacked material and, as a consequence, we see a shift to other materials that are not automatically more carbon footprint friendly than plastics. This is often an emotional answer to social media attacks that could be even more harmful from a system point of view. As an example, replacing a PET bottle with a glass one is not the solution. What if we try to let consumers learn what’s behind a packaging and why plastics in packaging have become so successful worldwide! The current health emergency is showing one of their unparallel advantages offered to consumers: safety. But plastic packaging does offer much more: light weight, a PET bottle is lighter than any other packaging and therefore consumers can practically carry their on-the-go snacks and drinks while commuting to job; moreover it hardly breaks and its logistic is agile and safe all over the world; lastly plastics are highly recyclable (and recycled already) to enter the packaging value chain again or to be used for a number of other applications, not of lower value (textiles as an example). Coming to the carbon footprint contribution, plastic packaging helps reduce CO2 emissions, especially when it involves recycling. A PET bottle made of 50% rPET has a lower environmental impact than a tin can or a glass bottle (be it single use and reusable), which is the least environmental unit. Having said that, there are ways to make a plastic packaging even more sustainable.","@ID":24} "9 NEWS PETplanet Insider Vol. 22 No. 03/21 petpla.net EU beverage packaging aims to be fully circular by 2030 Unesda Soft Drinks Europe pledges that EU (incl. Norway, Switzerland and the UK) primary beverage packaging will be fully circular by 2030. Launching its Circular Packaging Vision 2030, the industry commits that by 2025 its packaging will be 100% recyclable and its PET bottles using 50% recycled content. Its ambition is that by 2030, its PET bottles will be made from 100% recycled and/or renewable PET, where technically and economically feasible. It also pledges that more than 90% of its packaging will be collected and that it will use more refillable packaging. These actions are directly contributing to the EU circular economy transition and surpassing EU targets set out in legislation. A circular packaging is designed to contain recycled content, is recyclable and possibly also reusable; it is therefore part of a circular economy where the waste management and recycling infrastructure allows it to be widely collected, recycled and reused. Unesda members will deliver their vision through these three equal pillars of circularity: Collect : Striving to achieve closed-loop collection of beverage packaging supporting: Creation of closed-loop beverage packaging collection and recycling systems to accelerate achievement of the target of at least 90% collection of all its packaging by 2030. Wider introduction of well-designed Deposit Return Schemes (DRS) for PET, aluminium cans and other materials when 90% collection by existing extended producer responsibility systems is not achievable. Recycle: Using only packaging that is circular by design and boosting uptake of rPET in beverage packaging to deliver: By 2025: Beverage packaging (plastic, metal, glass) will be 100% recyclable; all soft drinks PET bottles will contain a minimum average of 50% rPET. By 2030: The ambition is for PET bottles to be made from 100% recycled and/or renewable material if technically and economically feasible – thereby moving away from fossil fuel sources. Reduce and reuse: Reducing the sector’s packaging footprint and increasing the use of refillable packaging: Aiming to use more refillable packaging by 2030 compared with 2020. Studying the best environmental and economic pathway to increase use of refillable models. The sector intends to continue investing in recycling technologies to improve their efficiency and financial performance. By combining mechanically recycled PET, enhanced recycled PET and renewable PET it is possible to reduce the carbon footprint of packaging and deliver products in a safe and sustainable packaging. Europe’s soft drinks industry fully supports the EU ambition of making Europe the world’s first climate-neutral continent by 2050 and building a European circular economy, including packaging circularity. To deliver its vision, Unesda points out that the sector will need coherent support from EU authorities and national governments including: A long-term perspective and legal certainty as well as protecting the single market. A well-functioning secondary raw materials market that gives the soft drinks sector access to sufficient high quality rPET in order to meet its obligations under EU law, without compromising on safety standards and avoiding downcycling. Increased investment in waste management and recycling infrastructure. An EU framework enabling innovative recycling technologies. EU minimum requirements for new DRS across Europe. Clear definitions of recyclability that foster innovation and investment. www.unesda.eu PETinar: EU Plastics Strategy and its impact for the PET value chain ASK THE EXPERT: Dr Rana Pant from the European Commission will give a detailed overview of the Implementation of Directive EU 2019/904 on the reduction of the impact of certain plastic products on the environment (SUPD) and Essential Requirements in Packaging & Packaging Waste Directive (PPWD). - April 22nd, 2021 at 2pm Central European Time - PETINAR","@ID":11} "EDITOUR PETplanet Insider Vol. 22 No. 03/21 petpla.net 14 Beverage packaging The Japanese drinks market is distinctive in that drinks can be sold at all times and everywhere via an enormous network of vending machines. According to the Japan Vending System Manufacturers Association, the number of vending machines in the country decreased by 4,149,100 units as of the end of 2019, amounting to 98.0% of the previous year. Looking at beverage vending machines, which account for almost 60% of the total, numbers dropped in all categories, including soft drinks (cans/PET bottles), milk (paper cartons), coffee/cocoa (cups), and alcohol/beer. Of these, the vending machines for soft drinks (cans and PET bottles), which account for the majority of the market, have an oversaturation in terms of location. The Yano Research Institute emphasises that this trend is likely to continue for some time, and, since new installations have been delayed due to the effects of Covid-19, the number of vending machines installed as of the end of 2020 was expected to drop to 97.6% of the previous year, i.e. 4,050,000 units. However, one vending machine for roughly 30 people is still very high coverage. As regards packaging material, PET dominates the Japanese drinks packaging market, followed by aluminium cans. According to The Council for PET Bottle Recycling, 25.2 billion plastic bottles were sold in Japan in 2018. This represented a 6.9% increase on the year before and amounts to about 200 bottles per person. The Covid-19 outbreak has shifted market attention from reusable containers to disposable containers, re-evaluating the convenience of single-use plastic containers. Despite this trend, which seems to have halted the plastic-free movement, the Yano Research Institute has noted that in 2020, convenience stores that endorse the use of environmentally friendly materials are promoting products in paper containers. Driven by the desire to offer more sustainable solutions, many bottle manufacturers in Japan are also aiming for 100% rPET. Examples include drinks manufacturer Suntory, which plans to convert all PET bottles to 100% rPET and bio-derived PET by 2030, and Evian Japan, which has announced that production will be with 100% rPET by 2025. Two trends are emerging with regard to container size. In recent months, large pack sizes and units have been in greater demand because of coronavirus, primarily packaged mineral water. According to the Yano Research Institute, examples of large volume containers on the rise include mineral water and RTD tea in 2 l PET bottles. However, the traditionally rather small living spaces in Japan counterbalance this as they do not support extensive stockpiling. So this trend may be rather pandemic-driven and will flatten. At the same time, reduced mobility caused by coronavirus has reduced the market shares of on-the-go sizes but this may also change again as infection rates fall. Demographic change in Japan has long been an important topic and this also influences demand behaviour. In 2020, the median age of the Japanese population was around 48 years; according to the World Bank, 36% will be over 65 years of age by 2050. In terms of health, life expectancy at birth in Japan is 84 years, four years higher than the OECD average of 80 years and one of the highest in the Collection and recycling rates of designated PET bottles (source: The Council of PET Bottle Recycling - CPBR) photo courtesy: Suntory Suntory’s bottled green tea Iyemon comes in a square-shaped bottle with a label that can be easily removed after consumption. (Photo courtesy: Suntory)","@ID":16} "BEVERAGE INGREDIENTS PETplanet Insider Vol. 22 No. 03/21 petpla.net 27 Beauty & recovery drinks “Beauty shots” have been a strongselling category in Japan since the 1970s and are especially popular with people who had to work late at night, seeking products to combat stress and tiredness. Today, these products are far more diverse and come with different and additional functionalities, such as support in recovering from hangovers, stomach aches and other ailments, as well as products targeted at beauty-conscious consumers, with claimed benefits for skin health. By using state-of-the-art technologies, Doehler offers high-quality products from nature in different ways, from minimally processed full spectrum powders that retain the entire content from the raw material, to high-end standardised botanical extracts with guaranteed amounts of certain naturally-occurring healthy compounds, like antioxidants. These valuable botanicals are paving the way for inspirational natural food and beverage applications with market positioning strongly based on health. Alongside plant extracts, strong infusions, distillates and essences, natural colours and flavours allow consumers the choice of distinctive flavour and vibrant colour. Collagen beverages are available as a diet supplement around the world; they have become very popular as novel drink shots in Japan. Enriched with vitamins, these shots are positioned as a healthy way to help boost nutrient content that consumers might be lacking. There is also great demand for rejuvenating products that work as skin moisturisers and help reduce wrinkles. Low and non-alcoholic In line with the worldwide trend amongst consumers towards nonalcoholic beverages, this movement can also be seen on the Japanese market. To create delicious non-alcoholic spirits, Doehler offers natural flavours, distillates, extracts and alcohol boosters. The company’s comprehensive selection of bonificateurs and typages provides beverages with well-rounded flavour profiles and enables top notes to stand out, while the natural ingredients complement each other perfectly and create enhanced taste experiences, with alcohol content below 0.5%. The most popular low-alcohol beverage in Japan is Lemon Sour; a lemon-flavoured mix drink made with a spirit and a soft drink and usually sold as an RTD can. The authentic and fresh taste requires high-quality citrus ingredients, with citrus oils and flavours just some of the ingredients needed for a successful beverage. Citrus oils from Doehler are available in organic quality and thus provide 100% natural citrus flavours for organic beverages, as well as being used as a base ingredient when creating citrus flavours. Doehler’s extensive production capabilities and strategic geographical positioning allows the company to work with raw materials from the main sources of citrus fruits around the world. Seventy-five per cent of all processed citrus fruits come from Latin America. Whether lemon or orange, or citrus as a whole, Doehler supplies customers globally with both high-quality natural ingredients and a range of exciting concepts for refining spirits with natural extracts. Exotic and herbal taste profiles While consumers demand healthier and more natural beverages, they also wish to experience new tastes and textures, with exotic taste profiles particularly popular on the Japanese beverage market. Flavours such as hibiscus and rose are well-known today; orange and cherry blossom are promising new taste variations. Earthy flavours, such as herbs, spices, roots and botanicals are on the rise, with botanical extracts particularly well-suited for use in a variety of both non-alcoholic and alcoholic beverage applications. Herbal and fruit flavours therefore represent new taste experiences and meet the consumer desire for more ‘naturalness’ and authentic products. Headquartered in Darmstadt, Germany, and active in over 130 countries, Döhler is a specialist producer, marketer and provider of technologydriven natural ingredients, ingredient systems and integrated solutions for the food and beverage industry. Doehler says that it develops innovative and sustainable concepts with its customers – from idea, to implementation, to shelf. www.doehler.com","@ID":29} "BOTTLE MAKING 25 PETplanet Insider Vol. 22 No. 03/21 petpla.net Interview with Daiichikako Company Ltd. May 18, 2020 We met: Mr Toshifumi Konishi, Chairman and Mr Tadafumi Konishi, Executive Director PET bottles and containers for food and cosmetics by Kay Barton During the eighth century, the city of Nara, around 45 minutes by car east of Osaka, was the capital of Japan. Nara and its surrounding area are a popular tourist destination. Among the beautifully preserved shrines, places of worship and palace ruins, some of which are Unesco World Heritage Sites, lies the famous Nara park with its free-roaming Sika deer and Yoshino cherry trees which are a magnet for visitors when the cherry blossom is in full bloom. This is where the two manufacturing plants owned by Mr Toshifumi Konishi, Chairman of Daiichikako, produce plastic bottles and caps for food and cosmetic items. The company exports some of its products to the USA, China and Thailand. Daiichikako began processing PET around 15 years ago at a time when a new trend was emerging in the cosmetics industry to switch from glass to plastic containers. Toshifumi Konishi as a veteran innovator was instrumental in shaping this change. He has been a company member since 1965 when it was still a Sekisui Chemical supplier for the manufacture of every-day products, such as household items and parts for them. In 1971, Mr Konishi decided to focus on the processing of pure plastics and set up a new business which he still runs today. The company moved to its current location near the River Saho 33 years ago when the area was developed into a business park. This is where Daiichikako now manufactures bottles, containers and closures for cosmetics, spices and sauces, as well as cleaning agents and hygiene products. Its product range includes 2,000 different types of direct blow-moulded containers, 900 stretch blow-moulded containers for cosmetics, four for spices and approximately 30 for sanitary items like sanitisers, mouthwash etc.. For the cosmetics sector the company can manufacture about 50 closure types and has four standard models for spice containers. Daiichikako also produces PE and PP bottles. The PET sector and associated PE caps account for around 40% of total production capacity. “PET bottles and containers are transported and channelled via larger processors and companies to various Japanese brand-name firms through major moulding manufacturers and container trading companies.”, explains Executive Director, Mr Tadafumi Konishi. “We produce 25 million PET containers, from 10ml to 500ml, and 6 million caps each year. The 160ml Tonkatsu sauce bottle is our best seller. We produce 53 million plastic bottles a year and process around 1,000 and 40 t of PE and PP respectively. Our material comes from local suppliers, namely Asahi Kasei, Kuraray, Japan Polyethylene, Japan Polypro and Prime Polymer, as well as Thai Indorama and Taiwanese Shinko Synthetic Fibre. Twenty-four million PET bottles remain on the local market, with around one million destined for the international market.”. Mr Konishi further explains “In our PET department we use blow moulding and stretch blow moulding machines from Tahara, the MSE series, and Nissei ASB models such as ASB-70DPH, ASB-12N or PF6-2B. We manufacture caps on equipment from the NEX series of Nissei Plastic Industry, the Si series of Toyo Kikai Metal and SE series of Sumitomo Heavy Industries. Our production plant comprises an area of 11,000m2 . Our whole facility takes up an area of 18,773m2 and employs 230 people. Daiichikako sees the mediumsized OEM bottle manufacturers as its main competitors. The company’s turnover is currently just under US$ 28 million. “Investing in the visual inspection sector is our next project”, says Mr Konishi. “We are also considering entering the market with our own brand of cosmetics and disinfectants in due course”, he added. www.daiichikako.com Tour Sponsors: Executive Director Tadafumi Konishi explaining his business activities PET bottle for cosmetics PETcast In our new Road Show podcast, PETplanet meets industry experts from Down Under to Japan and talks with them about their successes, decisions and current developments. Listen to the full conversation atwww.bit.ly/2HVwbAd","@ID":27} "MATERIALS / RECYCLING PETplanet Insider Vol. 22 No. 03/21 petpla.net 20 BariQ and Coca-Cola Atlantic launch strategic partnership to increase Egypt’s domestic PET bottle collection rate. Challenging conditions BariQ, Egypt’s first bottle-to-bottle recycled PET facility, has been operating in Egypt since 2010 and has annual production capacity of 15,000 t of food grade PET pellets that are FDA, Efsa and Reach approved. The company has announced the launch of a strategic partnership with Coca-Cola Atlantic to increase collection rates of used consumer PET bottles and to raise the quality and supply of bales. The partnership is in line with Coca-Cola’s “World Without Waste” initiative, launched in 2018. A new pre-sorting facility, installed at BariQ’s plant, with the support of Ministry of Environment and Ministry of International Cooperation, was formally opened by Coca-Cola Atlantic and Bariq in December 2020. Its advanced Tomra bottle sorter uses infra-red detection technology to sort different types of plastics, such as PVC, single/multilayer plastics and coloured PET and produces statistical analyses of the percentage of each type. It can separate clear PET bottles at up to 10t/h, equivalent to 500,000b/h. The project was fully designed and managed by the BariQ technical team alongside the technology providers, from concept through infrastructure design and all the way to the launch of the facility. Egypt’s lack of waste collection and segregation infrastructure means that it faces many challenges in solid waste management, leading to negative environmental impacts such as depositing plastic waste on the Nile River banks, in sanitary drains and uncontrolled landfills. An regulated “Informal Sector” leads to the proportion of clear PET bottles in the overall plastic bottle collection being as low as 5-10%; this badly impacts the quality of recycled products. The installation of the new presorting facility means that BariQ will be able to accept low- and medium-quality plastic waste collected from the Nile’s riverbanks and from sanitary drains, separate clear PET bottles with up to 85% efficiency, segregate other types of plastic, and produce statistical data for each type of waste. This will reduce the negative impact of plastic waste disposal on the environment and will help Coca-Cola Atlantic to implement the “World Without Waste” initiative to increase collection rates in Egypt. According to Usama Zaki, BariQ CEO, the BariQ and Coca-Cola Atlantic collaboration is the first step towards a solid alliance between government, private sector and NGOs to comply with the implementation of Egypt’s 2030 SDGs vision in solid waste management generally, and plastic recycling in particular. “With the new pre-sorting facility we expect to increase the collection rate up to 80% within the next 3 years. This will dramatically increase the recycling rate in Egypt and, consequently, help CocaCola Atlantic to achieve at least 25% recycled content in 2025 domestically,” he said. This will be in line with CocaCola Atlantic’s sustainability targets. It will create a structured closed loop that will create job opportunities, attract environmentally conscious investments and ultimately lead to a successful circular economy model. www.bariq-eg.com Tomra bottle sorter A new pre-sorting facility was opened by Coca-Cola Atlantic and Bariq in December 2020 with the aim to increase the PET bottle collection and recycling rate in Egypt.","@ID":22} "TRADE SHOW REVIEW PETplanet Insider Vol. 22 No. 03/21 petpla.net 58 Drink Technology India 2020 - Innovation in Milk Beverages webinar Milk processing in India - trends and technologies by Kay Barton The international trade fair for beverage and liquid food technology Drink Technology India (DTI) was held virtually last December because of the pandemic. Experts from the machine building industry, science and the dairy business came together in a lively round of discussions about the dairy industry in India. Besides showcasing new products, these discussions highlighted future trends in dairy and dairy-based foods and drinks, as well as packaging technologies. The webinar was jointly organised by the Indian Dairy Association. Summarised here is a selection of points from lecturers and keynote speakers. Dr GS Rajorhia, President Indian Dairy Association The Innovation in Milk Beverages webinar was opened by Dr GS Rajorhia, President of the Indian Dairy Association. He reported that the dairy industry experiences average growth of around 6.5% each year. Accordingly, 190 t of milk was produced in India in 2019, almost 22% of the global milk production of 880 million tonnes. At 394 g per day, the per-head consumption is high in comparison to the worldwide average of 302 g. He further explained that demand is also likely to increase, fuelled not least by the pandemic. “There are clear trends, for example, towards very nutrientrich and varied dairy products,” explains Dr Rajorhia. “Demand is moving towards new combinations, flavours and healthy ingredients.” Also connected with this is the omnipresent topic of food safety, leading to a rise in aseptic packing and the achievement of longer shelflife spans. “The shelf-life currently achieved is six to twelve months. It is predicted that sales of UHT milk are likely to reach US$ 24.6 billion in 2024,” continues Dr Rajorhia. Current favourites are lassi and buttermilk in various forms. Pranav Shah, Director Dairy & Food SPX Flow Joining the discussion from Denmark was SPX Director for Dairy & Food, Pranav Shah. The machinery and plant manufacturer headquartered in North Carolina, USA, is principally seeing consumer trends in healthy foods that feature great flavours but refrain from using artificial ingredients and sugar. “Also topics like functional food, on-the-go consumption, quick access and quick preparation of snacks are gaining importance in society,” says Pranav Shah. Usually, products like these are comparatively higher in price but increasing prosperity is leading to sales growth in these areas. However, at the same time, affordability is an important topic in many markets. “Origin also plays an increasing role,” says Mr Shah and he has applied a feature for addressing customers visually: local Danish products that show the national flag on the packaging sell around 33% better than the same products without a flag. In summary, Mr Shah says: “We see the principal trends for dairy products and ingredients in high-protein, natural flavours, long-life dietary fibres, milk-based snacks and sustainable, handmade products that show the value creation and process chain.” Dr Satish Parmar, Assistant Professor at SMC College of Dairy Science The Indian SMC College of Dairy Science, represented by Professor Dr Satish Parmar, talked about trends in whey-based drinks. Using a graph from the National Dairy Development Board, Dr Parmar first gave a stateby-state insight into India’s milk production. According to this, the state of Uttar Pradesh produces the highest proportion of milk in India (30.5 million tonnes) before Rajasthan (23.7 million tonnes). Dr Parmar explained: “Around one third of all milk in India goes into cheesemaking. A significant proportion of whey arises as a by-product of this process, which was traditionally considered a waste product but has since been more intensively re-processed. Whey is natural, rich in lactose, minerals, vitamins and proteins and can be used in a wide variety of applications, including drinks, particularly here in economic and technological regard.” Dr Parmar categorises milk-based drinks as milk-like, thirst-quenching and fruit-juice-type drinks. In addition to these are alcoholic and non-alcoholic drinks. Numerous whey-based drinks are already on the market, for example energy, sports and functional drinks.","@ID":60} "FLIPPING THE WORLD OF PET UPSIDE DOWN AND EVEN SIDEWAYS. The All-New NETSTAL PET-LINE with Side Entry. kraussmaffei.com/new-petline The All-New NETSTAL PET-LINE comes with a variety of advantages to maximize output and minimize costs: - Side entry for maximum mold compatibility - Shortest cycle times for increased output - Lowest level of energy consumption to minimize the ecological footprint - Improved 100% rPET processing to enable the circular economy - New control unit including NETSTAL Smart Operation to ensure easy, fast and safe start-up and production","@ID":73} "MOULD MAKING PETplanet Insider Vol. 22 No. 03/21 petpla.net 47 trial or graphic designers, who never dealt with the fonts as a tridimensional surface that will communicate through shines and shadows before; and never before in two languages.” Moldintec’s previous experience was an advantage; it was able to present the technology to the team, early in the process. That opened the Danone team’s eyes to the updated labelless concept becoming perfectly aligned with its environmental efforts. The first move was in Argentina, the home of Moldintec’s headquarters. A few weeks later, Brazil took the pilot team’s ideas and redefined their bottles, legal information and logos. The feedback loop helped to speed up development; when one country ran a test, the other improved too. “The journey gave us a lot of positive experiences. We are very grateful to be partners of a world-class blow mould manufacturer,” Francisco Crosta said. The Bonafont bottle was a ‘first’ in Brazil and a milestone for the bottled water industry. The code-bar was moved to the cap, keeping the high contrast printing capability and the full bottle shape clear of ink. The pandemic also imposed more challenges during the project. The team adapted undertaking more work from home and observing strict social distancing and bio-security measures during plant trials and initial production support. “We learned a lot with Danone’s NoLabel projects, which will be beneficial for Moldintec Brazil future,” said Eng. Thiago Tullio, Head of Moldintec Brazil. “As our workforce moves to digital, dispersed and remote working, we will gain advantage in thinking more globally about our company.” Moldintec now has a number of labelless projects ongoing, with some of its moulds ready for commercial use. Laser technology is gaining in maturity and customer acceptance, which means a more sustainable packaging future. “While the NoLabel bottle is not a solution for all our packages, it serves and meets true packaging innovators’ expectations. Our intention is that this Manifesto bottle becomes a symbol of the challenges that are moving us and awakens to conscious consumption, which can be a great link in the entire chain to promote the systemic change that we need to go through,” said Thays Rosini Sustainability Manager, Danone Waters Brazil. Groupe Danone (Danone) serves several countries worldwide with premium spring water. Evian is its flagship brand. Danone’s Latin South America operation serves Brazil under the Bonafont brand, Uruguay with Salus, and the Argentinean market with Villavicencio as their premium brands. www.moldintec.com Find a video at https://youtu.be/PdNnfj3O3fg","@ID":49} "BOTTLING / FILLING PETplanet Insider Vol. 22 No. 03/21 petpla.net 32 Tempo Beverages invests in new PET line from KHS A block system for the future A trust lasting more than 35 years: KHS recently commissioned a new non-returnable PET line for Israeli beverage producer Tempo Beverages under very special circumstances – and in doing so combined its latest-generation stretch blow moulding technology with a filler for the very first time. In Israel Tempo is literally on everyone’s lips: as the biggest producer of alcoholic beverages and the third-largest supplier of soft drinks the brand is known to almost the entire population of 9.1 million. There’s hardly a household in the country without a bottle of beer, water, juice or cola from Netanya in the refrigerator. In 1952 the story of growth and success began in the city on the Mediterranean between Tel Aviv and Haifa. At the start of the 1990s Tempo Beverages became PepsiCo’s sole bottler in Israel and Heineken’s exclusive sales partner. In 2005 40% of the company, which is also the biggest brewery in Israel, came under the ownership of the Heineken Group. And nine years ago the beverage producer was made a licensee of the French spirits group Pernod Ricard. Tempo now clocks up sales of about €375 million, 45% of this with non-alcoholic beverages. The recent joint venture centered on Line 12 in Netanya. This is where Tempo fills its own mineral water and primarily Pepsi products – sugar-free Pepsi Max in particular – into nonreturnable PET bottles. The line has now been replaced in two phases of construction. The first in 2017 focused on the packaging and palletising section, during which an Innopack Kisters TSP with an integrated handle applicator and an Innopal PB palletiser with a capacity of up to 32,000bph were installed. In 2020 it was then the turn of the filling section when the previous 25-year-old mechanical KHS filler with a maximum output of 18,000bph and the old stretch blow moulder from a competitor made room for the latest technology KHS has to offer: a stretch blow moulder/ filler block equipped with an InnoPET Blomax Series V and a modular Innofill PET DRV filler. An Innoket Neo roll-fed labeller and Innopro Paramix C blending system are also part of the line. Challenging climate plus limited space Besides the usual demands made of the quality, efficiency and performance of a new filling line, there were further challenges to be met. “The new line wasn’t just supposed to enable us to fill up to 32,000 1.5 l bottles an hour with our carbonated products. A further requirement was that we could bottle at 20 °C using 9 g of CO2 per liter,” states Haim Neori, electrical and process manager for Tempo. In view of the company’s proximity to the sea, high humidity levels and ambient summer temperatures of 30 to 35 °C, the products needed to be cooled for filling and then reheated to prevent condensation being formed in the packs. Another obstacle to be overcome was the restricted space: with a ceiling just four meters high, individual adjustments had to be made in order to accommodate the line and clean room air filters and to position the cap and preform infeed. What’s more, construction work in the limited area had to be reduced to an absolute minimum so as to keep interruptions to operation as short as possible. “KHS had the perfect remedy for each of these problems,” Neori states. With its new PET line from KHS Tempo again lives up to its role as a pioneer. The stretch blow moulder/ filler block is the very first to combine a new-generation KHS stretch blow moulder with a KHS filler. Another new path was also trod – after some initial hesitation – in a totally different area. “For the customer the KHS labeller was a first,” says Michael Roche, head of Regional Center Middle East at KHS. “Despite a willingness to experiment, our contact at first found it hard to abandon the old and embrace the new with this machine. By employing all our powers of persuasion and quoting a number of successful reference projects, however, we were ultimately able to convince our client,” Roche claims happily. “In the end Haim was full of praise for the Innoket Neo – he was really enthusiastic about how easy it is to operate and how smoothly it runs.” The KHS labeller was afirst for Tempo; after initial hesitation to try something new, the company is now very pleased with its acquisition. FILLING","@ID":34} "52 TRADE SHOW REVIEW PETplanet Insider Vol. 22 No. 03/21 petpla.net Solutions for a profitable circular economy As one of the leading manufacturers of metal detectors, material analysis and sorting systems for the plastics industry, Sesotec GmbH is placing its trade show appearance in Hall 10, Booth E03 entirely under the main theme of “Circular Economy”. The exhibits will include metal detectors from the GF, Protector and Rapid Pro Sense 6 series, as well as the Flake Purifier+ multi-sensor sorting system and the Flake Scan material analysis system. Sesotec will show metal detectors that can be used in different areas of material feeding and ensure high plant availability of processing machines by preventing unplanned machine downtimes caused by metal particles. Costs for repairs, for production losses caused by the downtimes and, if necessary, for recalls, are avoided. Especially when recyclate is processed, metal detectors are indispensable devices for ensuring high plant availability and preventing damage. Particularly worthy of mention is the Rapid Pro Sense 6 metal detector, which is equipped with a newly developed reject mechanism that offers many advantages, especially to compound manufacturers who frequently change colours or produce or process abrasive materials. Multi-sensor sorting system Flake Purifier+ for high-quality PET recyclates All Sesotec sorting systems can be equipped with a combination of up to three sensors - according to the application - sort mixed plastics, bottles, flakes or regrind according to different criteria such as colour, shape, material type or metal. The Flake Purifier+ multi-sensor sorting system exhibited at the Sesotec booth is characterised by accurate separation of foreign objects with lowest loss of good material. The Flake Purifier+ ‘s special material feed, valve bar with particularly fine nozzle grid, and integratable recovery line increase efficiency in the recycling process, especially with highly contaminated input material. The use of recycled products saves CO2 and thus - in addition to conserving resources - also contributes to climate protection. The Flake Scan Also on display at Chinaplas 2021 will be the analyses systems Flake Scan for plastic flakes. Companies producing new granules from recyclate use the Flake Scan material analysis system in incoming goods inspection. In recycling, the device is used by quality laboratories in outgoing goods inspection and for production control. In all areas, manual analyses have hitherto been carried out, which take a lot of time and whose results are not reproducible. With Flake Scan, on the other hand, reports on the composition of plastic grades and on offcolour components can be generated within a few minutes in consistently high quality and with reproducible results. Service rounds off the circular economy Starting with competent advice, through commissioning, to maintenance packages and digital service, such as predictive maintenance, Sesotec offers the whole range, ensuring customers maximum machine availability and optimum performance. www.sesotec.com SESOTEC Hall 10 Booth E03 LG Chem’s expansion & introduction of LG Chem’s caps & closures LG Chem is to announce the completion of new production lines. One highdensity polyethylene (HDPE / 200kta) line and two linear low density polyethylene (LLDPE / 600 kta) lines will be on stream during 2Q 2021. HDPE plant produces using the cutting-edge manufacturing system based on the low-pressure polymerisation method and its superior process-ability and quality is fully recognised. The new HDPE line will produce main raw material for caps & closures. With the expansion, LG Chem intends to double the global caps and closures for beverage market presence from around 100 kta to 200 kta. LG Lutene-H which is historical and verified caps & closures grade has been in the market for almost 20 years and offer customers a range of products to meet the specifications of their various application requirements. Consumers are becoming more sensitive and cautious on odour and taste of beverage. With unique organoleptic control system, LG Chem maintains excellent organoleptic property of each and every batch. Lutene-H’s Environmental Stress Cracking Resistance (ESCR) properties offer possibility of down-gauging which helps end-users to reduce cost of production. The super process-ability makes Lutene-H to fit nicely to both injection and compression moulding process. The processing zone is wide so the customers can produce caps and closures with stability. LG Chem has been preparing for the future trends and regulations like tethered caps of EU commissions of single use plastics, PCR products and etc. www.lgchem.com LG CHEM Hall 17 Booth D101","@ID":54} "PETplanet Insider Vol. 22 No. 03/21 petpla.net 59 TRADE SHOW REVIEW Massimo Pelizza, Head of Sales at Gea Procomac Besides presenting their current, inhouse solutions for aseptic bottling, the team from plant manufacturer Gea – Mr Massimo Pelizza, joining from Italy, and Mr Shrikant Agarkar from India – described their activities in India in the field of aseptics. They began educational programmes on the topic of aseptic bottling in 2010/2011. In 2013, the first aseptic PET line in India was put into operation at milk giant Amul in Gujarat. In 2016/2017, a second line was added. A system was sold to RJ Corp in Haryana for commissioning in Kenya and another to Karnataka Co-operative Milk Producer’s Federation (KMF) Nandini in Karnataka. “All four installations are in the range of 30,000 to 36,000 bph,” says Shrikant Agarkar. Shrikant Agarkar, Manager Sales at Gea Process Engineering Naresh Lalwani, Regional Deputy Director and Head at the Indian Institute of Packaging (IIP) discussed the packing of milk and dairy products initially from an historical perspective, crossing over to topics including packaging and customer engagement at POS. As important points alongside product storage, shelf-life and safety, he also mentioned marketing, design and consumption-related topics, such as product image and handling. “Liquid milk in India is up to 92% in milk bags, 7% in glass and 1% aseptically packaged,” explains Mr Lalwani. In his presentation, he illustrated the advantages and disadvantages of the different packaging. In the case of PET, Mr Lalwani discussed barrier technologies, which have a positive influence on the shelf-life of the content. Naresh Lalwani, Regional Deputy Director and Head at Indian Institute of Packaging (IIP) According to him, general packaging trends include anti-microbial, self-cooling or heating or edible packaging. Smart Packaging is also interesting: “The packaging could indicate whether the content is still good or will soon go off, for example by a change of colour.” www.drinktechnology-india.com Shenzhen World Exhibition & Convention Center, PR China 350,000 sqm Exhibition Area 3,600+ International Exhibitors 3,800+ Machine Exhibits 90,000 sqm Plastics & Rubber Raw Materials Zone","@ID":61} "LABELLING PETplanet Insider Vol. 22 No. 03/21 petpla.net 49 Increasingly appreciated and requested the pre-glued-linerless machines are currently used in various applications: from soft drinks to mineral waters, up to fruit juices and yogurt drinks. For this reason, the suppliers of pre-adhesive labels are constantly growing globally, thus guaranteeing a good supply of material to the owners of machines with adhesive technology. “When customers see Simpl-Cut at work they are impressed by its effectiveness and user-friendliness,” - concludes Bruno Negri. “Many people want to equip themselves with this innovative technology, so much so that today we already have dozens of machines installed worldwide. Famous natural mineral water brands have been among the first to benefit from it. For example, Spumador, part of the Refresco group, already has four Simpl-Cut Flex installed in different factories and intend to purchase new ones. Volvic, a brand of the Danone group, is another important reference.” The production activities of the companies that have already equipped themselves with Simpl-Cut are now widely optimised and maintenance costs have greatly reduced, said P.E. Labellers. The P.E. novelty has just been conceived and is already in the spotlight: the beverage sector needs smart solutions that can meet the need for flexibility, speed and performance. www.pelabellers.com EISBÄR TROCKENTECHNIK GMBH / Wuhrmühle 22 / 6840 Götzis / T +43 5523 55558-0 / F –50 / [email protected] / www.eisbaer.at GDS GRANULE DRYING SYSTEM 94 % WATER SAVING We took a closer look at our GDS granule drying systems. The result is astounding. We were able to reduce the cooling water consumption drastically. You are having a GDS granule drying system from Eisbär and would like to take advantage of the savings? Please contact us: [email protected] As example for GDS1100: New water consumption litre per minute 12 Water saving litre per hour 9,180 Water saving litre per year 78,030,000 Calculation based on an assumption of 8,500 operational hours per year and a cooling water temperature of 12 °C.","@ID":51} "LABELLING PETplanet Insider Vol. 22 No. 03/21 petpla.net 48 Simpl-Cut: P.E. Labellers’ new technology A breath of novelty for roll-fed labellers Customers all over the world use hot glue roll-fed labellers. While popular around the world, traditional roll-fed labellers have three disadvantages: high costs of dedicated cutter and hot-melt glue system maintenance, and for the several technical interventions required. Machine stoppages required to clean glue from vacuum drums and other surfaces. Difficult cutting blade replacement with long and expensive stop machine. “We wanted something more for our customers,” - explains Bruno Negri, Senior Vice President of P.E. Labellers. “We know roll-fed machines very well, and thanks to the experience gained in fifty years of activity we also know their limits. That’s why we created Simpl-Cut, which solves these problems in a brilliant and truly revolutionary way.” The technology patented by P.E. offers higher quality in the labelling system, optimising processes, reducing costs. There are five new steps introduced with the Simpl-Cut solution: The first is the cutting system, which is extremely simplified. In fact, the fixed contrast blade for cutting the label, usually used in roll-fed machines, is eliminated. In Simpl-Cut the blade change is immediate: it can be replaced in less than a minute, without needing any adjustments. The operation is elementary that it can be performed by any operator. The second is the hot melt applied before cutting. In this way, the drum is always clean, and this greatly affects the optimisation of the production processes of the customers, because the horrid machine downtimes, often caused by the contamination of the glue on the drum, are eliminated. The application of hot glue before cutting, in addition to preventing blockages or jams, also avoids the downtimes for the cleaning of the drums. The third evolutionary step: there is only one drum for cutting and transferring the label, which means a drastic reduction (almost cancellation) of maintenance. This also allows for much faster format changes. The fourth innovation of SimplCut: this technology allows for up to 5 stations on the drum, allowing to ensure higher flexibility and speed. Usually a roll-fed machine has 3 to 4 fixed divisions. The new Simpl-Cut can instead use a variable number of divisions (3, 4 or 5) depending on the needs. Container diameter and speed in labelling are no longer limits and each container can be labelled at its ideal speed. The fifth and new element is the “stress-free” low tension system. This innovative solution keeps labels in registration and enhances ability to run lower cost label materials such as lower gauge and non-laminated films. So, one can work with thinner and more economical films. It guarantees the optimal management of the labelling materials used, said P.E. Labellers. “But we didn’t stop here,” continues Bruno Negri. “We went further and also created the Simpl-Cut Flex version, a doubly revolutionary labelling machine. This solution proposes a further step by combining two different technologies on a single station: the roll-fed with hot glue and the linerless pre-glued. In this way, we fully meet the needs of our customers, and offer unparalleled flexibility, because they can switch from one technology to another with the maximum freedom of choice, in less than a minute and using the same drum. The Flex version also offers another great plus factor: the possibility of wraparound sleeve applications. This is a feature that the beverage and mineral waters markets increasingly require today.”","@ID":50}
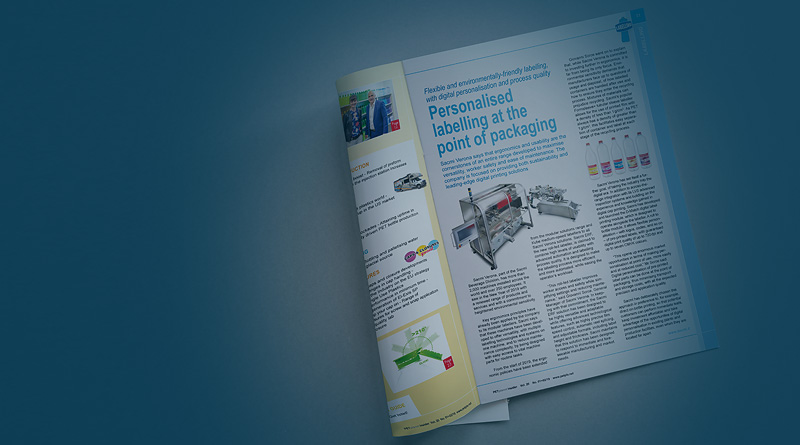