"MARKET SURVEY 27 PETplanet Insider Vol. 22 No. 06/21 petpla.net 06/2021 MARKETsurvey 2-stage SBM machinery What all types of 2-stage stretch blow moulding machines do have in common is that prior to the stretch blow moulding process, preforms have to be injection moulded in a separate machine. However, there is a diverse range of models to choose from in 2-stage stretch blow moulding. Our market survey allows you to compare specific parameters of these state-of-the-art machines from some of the market leading manufacturers. Although the publishers have made every effort to ensure that the information in this survey are up to date, no claims are made regarding completeness or accuracy. Resins & additives Preform machinery Preform production & inspection systems Preform & SBM mould manufacturer SBM 2-stage Compressors Caps & closures & inspection systems Filling equipment & inspection systems Recycling machinery Palletising & shrink film machinery Company name PET Technologies Luxber, S.L.U. KHS GmbH Urola Scoop Postal address Telephone number Web site address Contact name Function Direct telephone number E-Mail Grünlandgasse 5/1/12 2620 Neunkirchen, Austria +43 720 775 196 www.pet-eu.com Mr Maxim Poliansky CEO +43 720 902 169 [email protected] Av. de Azorin, 34-36, 03440 Ibi, Spain +34 96 555 3853 www.luxber.com Mr Ricardo Sanchez Export Manager +34 606 964 907 [email protected] Juchostr. 20, 44143 Dortmund, Germany +49 231 569 0 www.khs.com Mr Björn von Lengerke Global Product Account Manager +49 40 67907 382 [email protected] Urola Kalea S/N 20230 Legazpia (Spain) +34 943 737144 www.urolasolutions.com Mr Iñaki Unanue Commercial Director [email protected] 1. Machine designation / model number APF-Max series 8 models avaliable APF-6004, APF3002 APF-10, APF-5 APF-30 Tecnopet 1000, 2000, 4000, 6000 InnoPET Blomax Series V Linear: Urbi-2, Urbi-4, Urbi-6, Urbi-8, Urbi-2l, Urbi-4l 2. Bottle volume (from/to in litres) a) Standard machines 0.2 - 6 0.2 - 2 0.1 - 10 0.1 - 3.0 0.1 - 2 b) Machines for large containers 3 - 10 15 - 40 Upon request Up to 10 3. Maximum number of stretchblow moulds (units) a) Standard machines 8 4 1, 2, 4 and 6 36 8 b) Machines for large containers 2 1 Upon request 4 4. Output per stretch-blow mould for: 0.5 litres CSD bottle (units per hour) 1,750 1,500 2,250 Up to 2,800 1,700 1 litre CSD bottle (units per hour) 1,750 1,500 1,900 Up to 2,600 1,700 1.5 litres still mineral water bottle (units per hour) 1,750 1,500 1,800 Up to 2,700 1,800 Large capacity container 2,000 Upon request 1,250 Other 500 for 20-40l Preferential heating up to 2,000 5. Footprint / space requirement (L x W x H in metres) 9.5 x 3.3 x 3.2 APF-6004: 8.6 x 3.2 x 2.5 APF-3002: 6.4 x 2.8 x 2.3 APF-10: 8.2 x 3.4 x 2.6 APF-5: 7.4 x 3.2 x 2.7 6.7 x 2.4 x 3.1 8.02 x 5.69 x 3.75; up to 13.03 x 7.62 x 3.75 Smallest Urbi-2: 2.32 x 2.20 x 2.0; largest Urbi-8: 5.90 x 4.35 x 2.30 (without hopper-loader) 6. Special features (short description/keywords) Modular system 2-3-4-6-8 cavities, flexibility to produce 0.1-6.0l bottles at one machine, NIR heating system, hot fill option, quick changeover to other preform type, blow mould quick change Quick mould change, air recovery system, oval and complex shapes, space saving dimensions, hot fill option, patented mould closing system Lightweight containers for 3-6l with 38mm preform, APF-5: two independent blowing units to produce two bottle formats/volumes by turns Possible to blow PET kegs and 4-5 US gallon returnable and one-way watercooler bottles on one blower Preferential heating, air recovery system, wide neck, PP preforms Clever-Loc mould hanger for larger process angle and less complexity, Double Gate NIR oven for up to 40% reduced energy consumption, Focus Heater for better material usage and bottle light weighting, DuoCooling and Eco Dry for cooling energy reduction and higher hygiene due to less mould condensation; reliable and repetitive processing of rPET Fully electric, compact, low energy consumption,same residence time of all preforms in the oven, transfer of preforms to press wit fixed pitch. Options: preferential heating, air recovery, hot filling.","@ID":29} "imprint EDITORIAL PUBLISHER Alexander Büchler, Managing Director HEAD OFFICE heidelberg business media GmbH Vangerowstraße 33 69115 Heidelberg, Germany phone: +49 6221-65108-0 fax: +49 6221-65108-28 [email protected] EDITORIAL Kay Barton Heike Fischer Gabriele Kosmehl Michael Maruschke Ruari McCallion Waldemar Schmitke Anthony Withers WikiPETia.info [email protected] MEDIA CONSULTANTS Martina Hirschmann [email protected] Johann Lange-Brock [email protected] phone: +49 6221-65108-0 fax: +49 6221-65108-28 LAYOUT AND PREPRESS EXPRIM Werbeagentur | exprim.de Matthias Gaumann READER SERVICES Till Kretner [email protected] PRINT Chroma Druck Eine Unternehmung der Limberg-Druck GmbH Danziger Platz 6 67059 Ludwigshafen, Germany WWW www.hbmedia.net | petpla.net PETplanet Insider ISSN 1438-9459 is published 10 times a year. This publication is sent to qualified subscribers (1-year subscription 149 EUR, 2-year subscription 289 EUR, Young professionals’ subscription 99 EUR. Magazines will be dispatched to you by airmail). Not to be reproduced in any form without permission from the publisher. Note: The fact that product names may not be identified as trademarks is not an indication that such names are not registered trademarks. 3 PETplanet Insider Vol. 22 No. 06/21 petpla.net Dear readers, It feels like two out of three messages that land in our editorial office revolve around rPET. While the multibrands have had bottles with a significant proportion of rPET on the market for a number of years, we are also getting more and more reports from regional suppliers. For example, EckesGranini, the German high-end brand for juices, has announced that it will increase the proportion of rPET used since 2018 from 25% to 100%. “We want to be a pioneer as regards the circular economy and set a good example for the beverage industry,” states Hermann Naumann, plant manager for Eckes-Granini. Together with his machinery supplier, he has adapted production to handle the increased proportion of rPET (see page 31). In Slovenia, too, the mineral water bottler Donat, together with its preform supplier, has switched to 100% rPET. Since water bottles in Slovenia are traditionally green, the supplier has set up an extra green-to-green recycling process (see page 43). The question remains where all of the rPET is to come from. Should the trend towards very high rPET proportions prevail, well above the EU requirements of 25 or 30%, the ability to deliver will become even more difficult. Helen McGeough, Icis Senior Analyst & Global Analyst summarised this at the Icis recycling conference at the end of April (see page 39): “If we were to achieve a 50% recycled content rate in PET globally, growth rates need to be 82% per annum in comparison to 2020. This is equivalent to an additional 1,800 recycling plants with an average of 25,000 t capacity.“ Where these recycling plants might come from is a matter of debate. Yours sincerely, Alexander Büchler","@ID":5} "INSPECTION 15 PETplanet Insider Vol. 22 No. 06/21 petpla.net A new computer vision system for inspection From the individual component to the full, capped container, Sacmi provides a complete range of quality control solutions for cap, preform, bottle and labelled container lines. Patented systems and the incorporation of AI algorithms in the software combine high output rates and precise defect detection with a new approach to quality control. INSPECTION Cap inspection In short, the ‘ideal’ bottle: an already-full, capped and labelled container that undergoes dedicated checks, from the individual parts (cap and preform) to the completed container. As a leader in cap compression press production technology, focused on cap lightweighting and new tethered standards, Sacmi offers a complete line of vision systems and spark testers that allow high-speed, in-line control of 100% of output. By installing CHS solutions in-line on an injection press (made by any manufacturer) or downstream from an assembly line, the customer can inspect up to 270,000 caps per hour. Thanks to its array of seven cameras, users can perform complete image capture and quality control of both the ‘working’ and visible parts of the cap, internal sections included; each cavity number is read, allowing generation of real-time reports on any defects. The CHS machine can also mount a Spark Tester to identify typical injection defects, such as micro-holes in the gate area. Particularly noteworthy alongside the development of new standardcompliant ready-to-market solutions for tethered caps is Sacmi’s solution for inspecting caps downstream from the anti-tamper band folding and slitting station. The CVS102 is designed to be fully integrated on new or existing lines (whoever the supplier) and can be configured with 2 or 6 cameras to inspect both the interior and exterior part of the band. Preform inspection Moving on from cap to preform, Sacmi integrates on its in-line and off-line PVS inspection range a patented module that applies advanced AI algorithms and a polarised-light illuminator to detect defects in the preform body. Thanks to a broad range designed to meet producers’ specific needs (inline as an aid in quality control labs or off-line for the high-speed sorting of potentially faulty preform lots), the PVS ‘family’ leads the industry by letting users create a comprehensive set of checks that include, once again, size/ weight checks and cavity number readings. The solution can be equipped with colour acquisition and control devices or the automatic centrifugal positioner which enhances efficiency and is quite compact, thus reducing the footprint on existing lines. Sacmi has sought to bring about a new size changeover system by developing and installing the selfguided Sacmi D.R.I.V.A. (Drive and Recognise through Intelligent Vision Algorithms) system on the ‘off-line’ PVS10L range. The system consists of AI algorithms capable of identifying each type of preform via its basic characteristics (diameter, length and colour) and autonomously performing the relative size changeover and loading the correct inspection recipe. D.R.I.V.A. thus works like a true automatic brain, providing workers with close, precise, reliable support while eliminating any risk of error (e.g. in code copying) during the set-up stage. What’s more, autonomous size switches slash format changeover times from over an hour to just one minute, ensuring maximum sorting line availability. Label and container inspection Completing the range of Sacmi control solutions are the LVS (label) and BVS (container) inspection systems. Fully configurable, with up to 12 cameras, the BVS inspects every part of the container - mouth, thread, body, bottom - and has applications throughout the beverage, dairy, pharmaceutical and homecare sectors. Designed to inspect transparent PET bottles or HDPE, LDPE or PS containers, the system is designed to cover the full range of technologies on the market. All Sacmi computer vision systems feature CVs 2021 64-bit software to maximise usability and interoperability between machines. This also lets users share statistical information on the net via the use of OPC/UA, MODBUS and http protocols, making it easy to transfer production data from the vision system to ERP or MES systems. Sacmi operates worldwide with 80 production, distribution and service companies, ensuring customers can count on reliable assistance and consultancy services before, during and after the sale. www.sacmi.com Defects in the preform body are detected via a patented module that applies advanced AI algorithms and a polarised-light illuminator.","@ID":17} "MOULD MAKING PETplanet Insider Vol. 22 No. 06/21 petpla.net 18 R&D/Leverage Europe Product Solutions Lab A firm for all seasonsby Ruari McCallion R&D/Leverage’s Product Solutions Lab has overcome Covid-19 restrictions, lockdowns and travel constraints to maintain crucial services to converters and brand owners alike throughout the pandemic. R&D/Leverage’s Product Solutions Lab (PSL) in Ashfield, Nottinghamshire, England, has grown hugely since it was first established, 15 years ago. It has proved to be very popular with converters and brand owners alike and seen demand for its services rise so much that its floor space has pretty much trebled. It now occupies three adjacent units on the industrial estate to the north of Nottingham, in England’s East Midlands region. PETplanet Insider visited the PSL when it was officially extended into its second unit, in 2016; Covid-19 travel restrictions ruled that out this time, so we spoke online. “We have massively expanded, and we now have nine moulding machines in there,” said Alan Tolley, Managing Director of R&D/Leverage Europe. The machines – eight Nissei ASB models, complemented by an Aoki 250LL-75S – are the same standard and often the same range as converters and brand owners themselves use for production. The company’s speciality is single step preform and stretch blow moulding, which does away with preform transportation, eliminating even the slight risk of scuffing in transit and ensuring a high quality, glasslike finish to bottles. The company’s focus is particularly on brands whose packaging needs are for very high quality, high standard of finish packaging. Building capability “We identified a major hole in the market,” says Steve Gough, Technical manager, R&D/Leverage Europe. “We started to build a relationship with Brand Owners. We could show them what our capabilities are and position ourselves as the go-to people for them, for testing and development.” It has been a successful strategy. Over the past six years, close relationships with leading brands have been built, to the point where they come to R&D to develop a project under consideration, in the first place. The PSL offers single cavity pilot tooling for product development, material R&D/Leverage’s Product Solutions Lab comprises eight Nissei ASB models and an Aoki 250LL-75S.","@ID":20} "PREFORM PRODUCTION PETplanet Insider Vol. 22 No. 06/21 petpla.net 25 Kleinfeld: Changing material is just one way of responding to the depleted PET market and the rising prices. For example, the improved screw on our new machine shows that colour changes can be made quicker, with less PET material required for rinsing. This has a positive effect on material consumption each time there is a change of colour and material. Optimising the OEE also means that at least some of the additional costs required for purchasing material can be saved elsewhere. Our new PET line therefore offers preform manufacturers high availability and reliability. During the development process, special emphasis was given to short changeover periods, troubleshooting support and minimal downtimes. The fact that customers can carry out their production operations with confidence will help in minimising stress and costs. Härter: The new Netstal PET line also helps us to make savings in costs associated with the energy consumption of our electric toggle lever machine. Its smart main drive constantly checks the required oil levels and adapts and optimises itself automatically. The recovery of braking energy from the electrical axles also helps in saving energy costs. 60% of the energy used by the dynamic axles is recovered. Some countries provide incentives to replace old with newer, more energy-efficient machines. However, these naturally involve large, one-off, investments at a time when savings are required. With the electric, form-fitting drive, we are able to save 10% of energy compared with its hydraulic counterpart with a cycle time of 7.5 seconds. This also has a savings potential for every single cavity. Kleinfeld: Fast cycle times are, of course, ideally suited to Netstal machines. There is the potential for huge savings if cycle times can be reduced with the necessary synchronisations and a smart process system. Both are possible with the latest generation aXos controller. We are currently showing our customers an application that has an 18.58 g lightweight preform with an 1881 thread and a steady cycle time of 7.5 seconds – which is still very fast. PETplanet: Coming back to plasticising – you have already mentioned the improved screw in achieving more robust processing of recyclate as well as faster colour changes. Are there any other improvements in terms of process technology? Härter: The new PETX screw has so far proved to have very low AA values which, in our experience, reduces the proportion of an AA blocker that has to be added to the production process by at least 10%. In fact, we have already been able to achieve 20% reductions for our customers. It was also interesting to note that the amount of added colour could also be reduced by up to 45% due to the improved mixing action. With the PETX screw, the drying temperature can be reduced to 165 °C without compromising the process. This saves both energy and cooling time, thereby shortening the cycle period. Kleinfeld: Alternatively, let us also think in a broader context. As a system provider, Netstal has taken advantage of the opportunities offered by OPC-UA as well as by integrating individual system components. In this way, the machine can communicate with the dryer or camera system and exchange data. This helps to minimise waste and reduce operational complexities. The use of poorer material quality can also be detected very quickly. PETplanet: Could you again briefly summarise what all this means regarding our initial question on the shortage of PET material? Härter: Perhaps it can best be summed up as follows: A changeover in material is easily achievable today. The money needed for material can be saved, among other things, through control of the machine process and system configuration. PETplanet: Thank you both very much! Christina Härter, Head of Application Engineering Stefan Kleinfeld, PET Product Manager","@ID":27} "TOP TALK PETplanet Insider Vol. 22 No. 06/21 petpla.net 11 bottles. What solutions are you proposing to your customers? What does this mean for the production of the PET juice bottle? Will parameters such as weight etc. change? Acker: We already have numerous systems in our portfolio that promote the circular economy. First of all, the demands made of our customers are becoming ever more complex because these aren’t merely fueled by consumers but also by the changes in legal provisions you just mentioned and by the financial markets, for example. Stakeholders increasingly expect companies to engage in sustainable business practices. For us as KHS, the order of the day is thus to reduce, reuse and recycle throughout our value chain. We have to stay ecologically and economically fit for the future. We therefore offer our customers holistic expert advice for their PET and glass bottles and cans in the form of our Bottles & Shapes consultancy program that examines the entire manufacturing process. We’ve also developed a portfolio of systems and solutions for secondary packaging in order to counter the plastics debate: these include our Nature MultiPack that turns beverage containers into stable packs using easy-to-remove dots of adhesive instead of shrink film and the option of wrapping beverage cans in paper or bundling them into packs with a cardboard clip. In FreshSafe PET we have the only recyclable barrier for plastic containers on the market that protects the product and extends its shelf life. At the same time, KHS machines themselves considerably help to reduce the carbon footprint. Our InnoPET Blomax Series V stretch blow moulder, for instance, cuts electricity consumption by up to 40% and - by making effective use of materials - also saves up to 10% in PET, thus conserving valuable resources. In addition, our systems and solutions can easily process PET bottles made of 100% recyclate. The sum of all these parts is an important step towards cutting emissions in the long term, conforming with legal requirements and meeting the demands made by society. The advantages of PET are undisputed; it’s light, unbreakable and can be reclosed, for instance. This type of container will therefore continue to be very much in demand. If we manage to establish collection systems and build up closed recycling loops worldwide, acceptance among a proportion of consumers will again increase. PETplanet: KHS is a specialist in beverage filling and packaging. How do you see the future of the various materials such as glass, PET, and aluminium used in beverage filling? From the point of view of sustainability, what material for beverage filling do you see as particularly viable for the future? Acker: Regardless of the container, our contribution to sustainability and environmental protection is to strive for constant optimisation as regards reductions in weight and recyclability and for an increasing use of recycled materials. There are various movements and trends in evidence throughout the world that we can cater for with our holistic approach. There’s no one answer as to which container is the best as this depends on a number of variables. Our job is to give our customers the best possible advice based on their wishes and requirements and find the best solution for their needs and the market. Ultimately, developments also depend on the circular economy being in place in the respective countries. The entire industry should help to establish suitable recycling systems worldwide. PETplanet: A little glimpse into the near future: two of the most important trade shows in the industry have been announced for 2022 and will hopefully take place: the ‘K’ trade show in Düsseldorf and the Drinktec trade show in Munich. What are KHS’ plans for next year? Acker: We’re making preparations for various in-person shows, such as the two exhibitions mentioned, naturally while accounting for the protective hygiene concepts and in view of the continuing restrictions, such as those on travel. We’re looking forward to networking face to face. Trade shows with presentations of new machinery, with direct and personal contact are something we all miss. Parallel to this we’re continuing to work on our digital presence, one example of which is our Brand Gallery. We want to further expand this sales support tool in the future so that it forms a strong module for corporate communication independent of our physical attendance at trade shows. PETplanet: Thank you very much, Mr Acker! GAWiSD featuringAutoJob ™ – job set up in seconds +1.724.482.2163 AGRINTL.COM ACCURATE • FAST • REPEATABLE SEE GAWIS4D IN ACTION Dimensional and thickness measurements for plastic containers and preforms. ®","@ID":13} "MARKET SURVEY 28 PETplanet Insider Vol. 22 No. 06/21 petpla.net Company name SMI S.p.A. Side S.A Sipa Postal address Telephone number Web site address Contact name Function Direct telephone number E-Mail Via C.Ceresa, 10, 24015 San Giovanni Bianco (BG), Italy +39 0345 40.111 www.smigroup.it Mr Pietro Volpi Marketing Dept. Manager +39 0345 40.316 [email protected] Pol.Ind. Montguit, C/Llinars s/n, 08480 L'Ametlla del Valles, Barcelona, Spain +34 938 463051 www.sidemachines.com Mr Josep Jiménez Sales Manager +34677551928 jose.jimé[email protected] Via Caduti del Lavoro, 3 31029 Vittorio Veneto, Italy +39 0438911 511 www.sipa.it Mr Paolo De Nardi Project leader/Stretch-Blow Molders Devt. +39 0438911 624 [email protected] 1. Machine designation / model number The EBS (Electronic Blowing System) Ergon series of SBM machines includes 13 models: N° 7 models, from 4 to 16 cavities, bottles up to 3l. N° 3 HC (high capacity) models, 3 to 6 cavities, high-capacity bottles (up to 10l). N° 3 EBS K (electronic blowing system Kompact) Ergon series with 3 models from 2 to 4 cavities, bottles up to 3l. New models: 1002e-160e/c 2002eG - XL 3004e 3005e 3007e 3008e Rotary blow moulders: Xtra: 6 - 24 (8 models) Linear blow moulders: SFL 6: 6/8, 6/6, 6/6 XXL, 6/4 XL, 6/4 XXL, 6/3 XL (5 models); SFL 4: 4/4, 4/3 XL, 4/2 XL (3 models); SFL 4 wide mouth: 4/4 WM, 4/3 WM XL; SFL 2/2 & SFL 1XL 2. Bottle volume (from/to in litres) a) Standard machines 0.10 - 3 Up to 3.5 Up to 2 Up to 2 l 0.25 - 3.5 0.25 - 3.0 b) Machines for large containers 3.5 - 10 Up to 20 Up to 10 Up to 8 - - 5 - 30 3. Maximum number of stretch-blow moulds (units) a) Standard machines 16 2 7 8 24 8 b) Machines for large containers 6 2 4 5 2 4. Output per stretch-blow mould for: 0.5 litres CSD bottle (units per hour) 2,300bph per cavity (depending on the preform/bottle features) 3,000 5,000 7,000 14,000 18,000 2,550 per cavity 1,800bhc 1 litre CSD bottle (units per hour) 2,250bph per cavity (depending on the preform/bottle features) 3,000 5,000 7,000 14,000 16,000 2,550 per cavity 1,600bhc 1.5 litres still mineral water bottle (units per hour) 2,250bph per cavity (depending on the preform/bottle features) 3,000 5,000 7,000 14,000 16,000 2,550 per cavity 1,800bhc Large capacity container 1,200bph per cavity (depending on the preform/bottle features) 1,600 4,500 6,000 14,000 16,000 650bhc Other 1,200 5. Footprint / space requirement (L x W x H in metres) Standard models: min 4.2 x 3.5 x 2.75 (EBS 4 - 6 Ergon) / max 6.8 x 3.9 x 2.75 (EBS 16 Eergon). NB: without preforms hopper & unscramble; K models: 2.32 x 3.28 x 2.3; HC - high capacity models: min 4.45 x 3.46 x 2.57 (EBS 3 HC Ergon) / max 5.55 x 3.46 x 2.57 (EBS 6 HC Ergon). NB: without preforms hopper & unscrambler. 7 x 4.75 x 3.33 7.54 x 10 x 3.33 3.00 x 12 x 3.65 3.00 x 12 x 3.65 3.00 x 12 x 3.65 3.00 x 12 x 3.65 6. Special features (short description/keywords) Compact frame, ergonomic & functional design, high technological content of the solutions inspired by Industry 4.0 and Internet of Things (IoT), new preform-heating module, featuring compact dimensions, horizontal frame of the preform-holding mandrels chain and a ventilation system that optimise the preform heating process; heat-reflecting and energy-efficient panels made of composite materials; stretch-blow moulding module equipped with motorised stretching rods, mould-holder opening/closing/locking system operated by a brushless motor; the ReduxAir optional kit enables to blow bottles with lower pressure compressed air. Eco-friendly machines, enabled to stretch-blow lightweight preforms. Preferential oven, neck orientation, T-handle system, PP preform blowmoulding, on-line remote device, 5 gallons returnable / one way, beer keg, asymmetric / oval bottles, air recovery system Best output 2,700bph/cav. with best process & Active angle: easy to blow. Reduced TCO: lower air and energy consumption (-25%). 30 sec to change blow mould (toolless), simple use & maintenance. rPET easy process. Bottles for water, oil, CSD, heat resistant, oval symmetric and asymmetric, with preferential heating, neck orientation, with handle, wide mouth (up to 130mm NF), large size (up to 30l), rPET, Tritan, PE, OPP, …","@ID":30} "PETplanet Insider Vol. 22 No. 06/21 petpla.net 44 PETbottles Beverage + Liquid Food Vio in 100% recycled packaging Coca-Cola’s Vio brand has replaced all its PET bottles with those made from rPET. Unlike other manufacturers, Vio is highlighting this changeover prominently on their new bottles. The picture shows an example of a 1.5 l Vio bottle for still mineral water and a 1 l bottle for Vio Bio Limo. Customers can immediately see the change. Vio is also working on issues relating to the cap and label in terms of recycling. www.coca-cola-deutschland.de Sangria in PET Just in time for summer, retailers’ special offers areas are filling up with seasonal products for celebrating outdoors. German discount retailer Aldi Süd has a promotion of 1.5 l bottles of sangria. German company Hauser Weinimport GmbH from Fischach is responsible for bottling and distribution. The bottle is easy to grip in the neck area and is sufficiently stable to ensure easy handling of the bottle. A sleeve label presents multilingual information about the drink, which has an alcohol volume of 7%. The bottle is sealed with a screw cap with guarantee band. www.aldi-sued.de Infused Bio from Vittel Drinks with few calories and healthy, natural ingredients are in high demand. Manufacturers respond by developing suitable drinks. The “Infused Bio V” drinks from Vittel are an example of this. Here, an organic fruit infusion meets natural mineral water. The image shows the Raspberry and Blackcurrant variety. The product is sold in a transparent, 750ml, single-use PET bottle. This is decorated with a slightly milky sleeve label and is sealed with a tamper-evident screw cap. www.vittel.de/vittel-infused-bio Caribbean Style from Lidl German discount retailer Lidl has added to its range a limited availability promotion of several healthy juices with the label “Caribbean Style”. The drinks are produced by Spanish company AMC Natural Drinks and include juices like kiwi, grape, apple and lime, as well as ingredients like aloe vera and coconut water. They are available in 330ml bottles. The sleeve labels are printed in bright colours to suit the name and have suitably coloured screw caps. www.lidl.de","@ID":46} "43 PRODUCTS PETplanet Insider Vol. 22 No. 06/21 petpla.net PETproducts Colour change feature for Altanium hot runner temperature controllers Husky Injection Molding Systems, Ltd., a leading industrial technology provider to the plastics processing community, announced its collaboration with Chem-Trend on a system solution that creates repeatability during the critical colour change process to offer a fast, accurate, and optimised approach for operators. The team devised a new guided procedure made easily accessible to operators within the Husky Altanium Mold Controller operator interface. The instructions outline a simple, yet effective approach to setting up and performing the colour change process explicitly for moulds with hot runner systems. The joint approach is based on the process for using Chem-Trend’s Ultra Purge brand of purge compounds, which is designed specifically to reduce colour-change time and carbon formation in hot runner systems. Together, Chem-Trend and Husky aim to enhance their customers’ operational margins by increasing equipment and labour uptime. Trial results showed up to an 85% reduction in scrap and an 80% increase in mould cleaning efficiency when following the recommended process. Features of the new package include step by step instructions to set colour change parameters; a booster to ensure a faster colour change time; digital cycle count input, black speck removal mode and in-built memory for easy recall of settings. www.husky.co www.chemtrend.com Mineral water company Donat replaced its PET and glass packaging with 100% rPET bottles In cooperation with Alpla, the Slovenian mineral water company Donat has replaced its PET and glass packaging entirely with 100% rPET bottles. With this step, the company intends to cut its carbon emissions by up to 90%. Under the motto of ‘green to green’, Alpla initiated the use of 100% green rPET bottles to replace the 100% virgin-material PET and glass bottles conventionally used by the mineral water company Donat. The company’s decision to discontinue the use of virgin PET bottles and reusable glass packaging is resulting in an annual saving of around one million litres of drinking water and some 98,000KWh of electricity; 12,000kg of cleaning product can be eliminated in this way too. This cuts its carbon emissions by up to 90%, the company calculated. As the Slovenian market is dominated by green PET bottles, it made sense for Alpla to choose a ‘green to green’ approach. Green bottles are collected in Slovenia and recycled at the Alpla recycling plant in Wöllersdorf, Austria, and then go back onto supermarket shelves as new rPET mineral water bottles. “We have been involved in closed-loop recycling in Slovenia since 2014 and we turn 4,000-5,000 t of Slovenian PET bottles into rPET at PET Recycling Team in Wöllersdorf. When the opportunity arose for us to use green rPET for the Donat bottles, we seized it and began to collect and separate these bottles, which would normally end up in non-food recycling. The result is a sustainable recycling project with a long-term partnership and a win-win situation for both companies,” says Primoz Agrez, Multi-Country Manager, Balkan/Adria, at Alpla. Donat’s total volume amounts to 35 million bottles a year, 30% of which are 0.5l bottles and 70% 1l bottles. Around 1,300t of green bottles have to be collected a year in order to meet all of Donat’s rPET bottle needs. www.alpla.com The right tools and expertise to help with your rPETgoals! Agr is uniquely positioned to support your venture into rPET bottle manufacturing with a powerful combination of Process Control tools, Process Consultants, and decades of industry experience. AGRINTL.COM • +1.724.482.2163","@ID":45} "INSPECTION 17 PETplanet Insider Vol. 18 No. 0/17 petpla.net How to train customers in a pandemic? Sophisticated vision inspection systems require thorough user training to deliver the benefits and ROI that bottle manufacturers and fillers expect. This training typically requires a select group of staff members to attend an instructional class either at the vendor’s facility or on-site with a trainer being sent in to conduct the sessions. When the global pandemic put a halt to such in-person activities, Pressco Technology Inc., based in Cleveland, Ohio USA, immediately sprang into action. Within just a few months, Pressco developed a complete on-line training solution. The company created a digital platform where individual students at multiple plant locations could each access their own real-time, fullyinteractive system simulator. With this digital infrastructure in place, remote “virtual classroom” sessions may now be conducted by Pressco’s training experts with customers around the world. This platform proved to be a tremendous success, Pressco states, meeting a crucial need during a time when travel restrictions seemed to eliminate any possibility of obtaining high-value, hands-on training for their staff. Pressco VP of Sales & Customer Service, Tom Murphy notes, “we’ve got systems installed in over 80 countries all around the world, and our customers expect us to support them so they get the maximum return on their investment. I’m really excited at how well our team did in creating this virtual classroom, and our customers have been thrilled. With things slowly returning to normal, the ‘new normal’ at Pressco now means that our customers will have the option to acquire all the training they need either in person or remotely.” www.pressco.com INSPECTION BLOWscan www.bmt-ni.com Code: BLOWscan A unique, data-driven stretch blow moulding platform for: 9 Preform assessment 9 Material insight 9 Lab-scale prototyping 9 Quality control A scientific approach to stretch blow moulding.","@ID":19} "MATERIALS / RECYCLING PETplanet Insider Vol. 22 No. 06/21 petpla.net 38 Michelin successfully validated the use of Carbios’ enzymatic recycling technology for PET plastic waste in its tyres Getting the bottle rolling Carbios, a company pioneering new bio-industrial solutions to reinvent the lifecycle of plastic and textile polymers, and tyre manufacturer Michelin have taken a further step towards developing 100% sustainable tyres. Michelin has successfully tested and applied Carbios’ enzymatic recycling process for PET plastic waste, in order to create a high tenacity tyre fibre that meets the tyre-giant’s technical requirements. Enzymatic recycling Carbios’ enzymatic recycling process uses an enzyme capable of depolymerising the PET contained in various plastics or textiles (bottles, trays, polyester clothing, etc.). This technology is claimed to allow the production of 100% recycled and 100% recyclable PET products of the same quality as if they were produced with virgin PET. PET enzymatic recycling in car tyres: a world first The monomers resulting from Carbios’ process, which used coloured and opaque plastic waste such as bottles, once repolymerised in PET, made it possible to obtain a high tenacity fibre meeting Michelin’s tyre requirements. The technical fibre obtained is of the same quality as the one from virgin PET, processed with the same prototype installations. This high tenacity polyester is particularly suitable for tyres, due to its breakage resistance, toughness, and thermal stability. Carbios’ enzymatic recycling process therefore enables Michelin to get one step closer to its sustainable ambitions, and contributes to the entry of tyres into a true circular economy. Michelin is committed to achieving 40% sustainable materials (of renewable or recycled origin) by 2030 and 100% by 2050. The potential of the process This step constitutes a world-first in the tyre sector and is claimed to confirm the potential of Carbios’ process to engage the industry in a responsible transition towards a sustainable circular economy model. www.carbios.com www.michelin.com IPR +44 (0) 1254 584210 [email protected] petmachinery.com Active for over 25 years, our global network and specialist knowledge makes us the go-to company for the sale or purchase of a PET machine. Commercially savvy, we work closely with our customers and our global network, to make sure everyone gets the best deal. Providing comprehensive advice throughout your sale or purchase; we can arrange dismantling, loading, packing, shipping, specialist insurance and commissioning. If you have amachine to sell or you’re looking to purchase, please get in touch. THE INDUSTRY EXPERTS Every year, 1.6 billion car tyres are sold worldwide by all tyre manufacturers combined. For their production, manufacturers process 800,000 t of PET plastic fibres. Michelin has now successfully validated the use of Carbios’ enzymatic recycling technology for post-consumer PET in its tyres. In Michelin’s case, that is around three billion plastic bottles per year that the company could recycle into technical fibres for the production of its tyres.","@ID":40} "PETplanet Insider Vol. 22 No. 06/21 petpla.net 41 TRADE SHOW REVIEW “Post Covid-19 - Strategy and Trends for the Circular PET Economy” Petcore Europe annual conference 2021 part 1 “At Petcore Europe we truly value the essentiality of mutual collaborations and believe that only a comprehensive approach could efficiently straighten the PET industry in this challenging circular economy era. Following the concept of practice what you preach, we successfully hold our Virtual Annual Conference 2021 over two days, on the 2nd and 3rd of June. Moreover, we were pleased to see that we actually succeeded in drawing high interest and attention to our event among 185 attendees, 21 speakers and policymakers during the whole two days of the conference. In order to guarantee that our virtual Annual Conference could bring a definite significance to all the participants and would enhance a comprehension of the current complexities that our industry is facing at the moment, we made an attempt to look at the issues related to the circularity from various angles. By doing so, we tried to create a strategically driven conference, where all the attendees could talk openly and freely about their PET related concerns, and together with the highly experienced speakers could look for some potential solutions within existing bottlenecks. Coming back to the holistic approach, at Petcore Europe, we decided to dedicate the first day of the conference to the perspectives and strategies for the PET value chain with presentations given by Emmanuelle Maincent and Laure Baillargeon from the European Commission, executives from the sector and trade focused experts. While the second day was more technical as regards the trends in PET Collection, Sorting, Recycling and Circularity. Looking back at all the work that has been done, we can acknowledge that the game was worth the candle, and we are definitely looking forward to new challenges that the PET industry might encounter on its arduous path of becoming more recognised as the most circular material.” PETplanet thanked the management team of Petcore for this statement about the conference and Petcore’s invitation to join the two days virtual event. With the topic of “Post Covid-19 - Strategy and Trends for the Circular PET Economy”, the conference gave an overview of the challenges and opportunities for the PET industry. Experts took an analytical look at various areas of the PET value chain. The first Session “2019 PET Market, Collection & Recycling Rates” started with a presentation byHelen McGeough, Senior Analyst, Plastic Recycling, & Global Analyst Team Lead at Icis , about rPET in Western Europe 2019. She highlighted the lack of harmonisation in collection systems - which produce varied rates across Europe - and she described the impact of Covid-19 on the rPET market. Helen summarised that “traditional” rPET prices have historically linked virgin, flake, and food-grade granule prices. With the announced sustainability goals, a new demand for rPET has been created which cannot be met at the moment. To meet the SUP target by 2025, PET collection growth would need to be 60 per cent. The average growth rate to reach the target in 2029 would be 6 per cent per year. Helen mentioned wider recycled polymer issues created by the pandemic: she saw an impact on collection and sorting during the early phases of the pandemic, and added that test cycles of recycled polymers, especially polyolefins, had been postponed in 2020 and that concerns about hygiene had led to a return in the use of virgin material. Finally, she added that the consumer focus on sustainability had waned and that the closures of business and industry sectors had hit both supply and demand for recycled polymers. In Session 2 “EU Legislation - where are we headed?” Emmanuelle Maincent from the European Commission focused on the new Plastic Contribution Proposal, which is part of the EU resource system. The Plastic Contribution Proposal is statistically based. It is a contribution proportional to the quantity of plastic packaging waste that is not recycled. There will be a call rate of 0.80 €/kg. It is intended to be used to support the waste strategy, i.e. a 50% recycling target by 2025 and a 55% target by 2030, and it will provide incentives to reduce waste and foster recycling. In Session 3 “Changing supply & demand: viewpoints from the value chain” PET producers, recyclers and converters explained their positions. Antonello Ciotti, Chairman of CPME, expressed concern at the lack of rPET content definition and raised the question of imports of so-called foodgrade flakes from non-EU countries. As a result, he saw a major problem in the area of greenwashing and sustainability. He called for regulations to prevent greenwashing. He continued to note critical issues such as the unfair competition from non-EU producers. He explained that the EU is the only macro-region where there are no trade defence instruments (TDI) on PET imports. China has excess PET capacity (domestic demand is greater than total EU demand), and EU PET producers are penalised by import duties on MEG. In conclusion, he stated that PET manufacturers in Europe are ready to support their customers in reaching the goals set by the Circular Economy Directive. by Heike Fischer","@ID":43} "PACKAGING PETplanet Insider Vol. 22 No. 06/21 petpla.net 36 The sustainable package With the purpose of contributing to a circular economy, Sacmi’s intention is to meet the challenge of generating sustainable innovations every day. In doing so it draws on a broad yet in-depth understanding of materials and processes to develop solutions that reduce raw material and energy consumption and create new technologies and prototypes. The driving force behind Sacmi’s Rigid Packaging Technology Business Unit is research and development to provide lighter packaging solutions made of new, increasingly high performance materials. R&D lab: research and innovation For over 15 years, the Business Unit’s R&D facility has been developing cap and neck combinations that maximise performance and minimise weight across the full range of beverage industry applications. By the early 2000s Sacmi was already thinking – even though it did not yet have a preform production plant solution in its portfolio – in terms of ‘package development’: that is, the highest-performing combinations in terms of both seal and correct, easy breakage of the anti-tamper band during opening (e.g. development of the ML27 neck). Moreover Sacmi has been working for years actively alongside Cetie (International Technical Centre for Bottling), the body that regulates and defines PET and glass packaging standards and guidelines. Many of the solutions that are currently found in the most popular necks that are available on the market were conceived and designed in the Sacmi laboratory, as the company says. Solution for PET preforms This segment has grown considerably over the last 10 years, gradually evolving to form Sacmi’s PET preform injection proposal, the IPS (Injection Preform System) range. Progress in this area has boosted Sacmi’s ability to design solutions that take a ‘capsule-preform package’ approach right from the design stage. In addition to cap and preform solutions with everlighter caps, suitable for all standard necks and a wide range of applications, Sacmi has also developed a series of lightweight necks which, together with dedicated cap solutions (again characterised by lightweighting), aim to reduce the overall package weight, making the industrial-scale solution more sustainable. This strategy has been successful, especially on emerging markets, and has allowed Sacmi to establish itself as a key preform player, the company states. Injection press range The range of platforms includes three models (220 t, 300 t and 400 t). These feature moulds with up to 144 cavities and offer multiple combinations of hot runners in order to create combinations that match required product volumes and geometries perfectly. All these platforms have been designed with focus on performance, reliability, flexibility and user-friendliness. Combining these four characteristics was a complex, demanding exercise, Sacmi says. Yet, the IPS is achieving Sacmi’s goal of providing the market a reliable solution. Compression moulding On the closures front, the CCM platform has been the leading flattop cap technology for many years. Although proponents of injection try to link compression to heavier capsules (typical in the CSD world), the reality is that CCM machines have also achieved good results in the mineral water sector, providing cycle times of 1.44 s on the lightest capsules thanks to Sacmi’s Cool+ technology and","@ID":38} "INSPECTION 12 PETplanet Insider Vol. 22 No. 06/21 petpla.net How to maximise sleeve label quality They are mainly found in Japan. In Europe and the United States, an increasing number of bottles are decorated with them as well: We are talking about sleeve labels. To meet the special requirements of this particular decoration method, Intravis GmbH has designed a new system specifically for sleeve inspection, the SleeveWatcher. INSPECTION More and more frequently, bottles decorated with sleeve labels can be found on European shelves. Nowadays, they are very popular in the beverage sector, but they are increasingly used in other areas as well: whether it is a toilet cleaner from a German global player or a shampoo from a British consumer goods manufacturer. This is not surprising, since sleeve labels offer several advantages compared to other decoration methods. One of the most important benefits is that sleeves can be applied to any object shape while providing a very large area for advertising and eye-catching decorations. Moreover, sleeves cover large parts of the objects, which makes it easy to hide colour deviations or spots created during the recycling process. The recyclability of sleeve labels has to be mentioned as well, since no adhesive is needed in the application process. And finally, the labels can be easily recycled with the help of a perforated seam or by using special sleeve material. Special challenges in inspection Compared to other types of labels, sleeves pose special challenges for the vision systems currently available on the market. For this reason, Intravis decided to develop a system specifically designed for sleeved objects. Undoubtedly, a major challenge is the glossy surface of sleeves. Compared to self-adhesive or in-mould labels, sleeve labels lead to high reflections of light if illuminated incorrectly. These reflections, in turn, can result in the ejection of faultless objects that actually meet all quality requirements. Intravis meets this challenge with an adjusted lighting technology. It illuminates the entire inspection area and, consequently, produces a homogeneous light. This significantly minimises the risk of reflections. Another challenge is presented by the huge number of possibilities that can arise with sleeved objects. A large selection of object shapes with diverse combinations of colours, patterns and transparent label parts provides a particularly high degree of variation for sleeve labels. These elements, which make the sleeved product attractive to the end consumer, are often highly challenging for vision inspection. Due to the specially arranged hardware and a newly developed inspection module for the IntraVision software, the SleeveWatcher is adjusted to the challenging characteristics of sleeve labels. Thus, the system enables a comprehensive 360° inspection of the entire label. Inspection of sleeve-specific defects What else distinguishes the SleeveWatcher from other vision systems? Christian Schreck, Head of Marketing and Product Management at Intravis, explains: “First of all, the SleeveWatcher is a turnkey system. This means that our customer receives a system from us that only needs to be put into operation in his production line by our service technicians. We have already installed and set up the inspection modules for him upon delivery.” The system can easily keep up with even the fastest sleeve labeling machines. Its six side cameras inspect sleeves for common label inspection criteria such as presence, identity as well as horizontal and vertical offset. In addition, the system inspects for sleeve-specific defects such as smiling and frowning effects, folds, distortions, and holes. On request, OCR code reading is also possible – no matter whether plain text, data matrix codes or barcodes are inspected. Not only ejection, but also data supply The SleeveWatcher focuses specifically on sleeves and their typical defects. Janina Orlowski, product manager for Intravis inspection systems in the field of decoration, explains why customers benefit from it: “Today, sorting out defective objects is no longer a unique selling point for an inspection system. However, we have specialised in offering our customers specific information about their production processes. General data, such as the number of defective objects ejected, only helps them in a rather limited way. With our SleeveWatcher, we provide them very detailed statistics, diagrams, and reports about what specific defect type caused the ejection: no matter whether smiling or frowning effects, wrinkles or distortions occur.”","@ID":14} "A look inside the PSL MOULD MAKING PETplanet Insider Vol. 22 No. 06/21 petpla.net 20 “With an almost approved product, there might be some longer-term checks that they have to do, where they need to put it in a temperature chamber for three months or something like that, but 99 per cent of the validation procedures are completed and ticked off, here at our PSL,” says Alan Tolley. “We can test mould platforms that we manufacture through our PSL. “The attraction to the customers is potentially massive reductions in development time. “Customers want their moulds tested; they want to have some idea at the tool maker’s stage. Having this capacity in-house saves time on shipping samples back and fore and on external validation. We can, very often, receive immediate approval to finish a production tool, shaving weeks or even months from the overall project time. It’s a full turnkey offer,” he continues. “We save them from jeopardising their production plans. We ship the moulds out to them, with all validations already completed and recorded, with all the supporting documentation. By the time the mould gets to them the product is already approved and they’re up and running, immediately.” R&D/Leverage had got used to hosting four or five visits a week to the PSL, by both brand owners and converters, from Russia, South Africa, South-East Asia and all over the world. For customers new to the company, it has served as an outstanding introduction to R&D’s testing capability, encouraging them to come back again and again to use its extensive and highly rated service. Overcoming Covid-19 Then came Sars-CoV-2 ID-19, better known as Covid, which stopped all travel – especially international travel – dead in its tracks. Customer visits to the PSL went down from several each week to just one every few months. For many companies, that would have meant severely curtailing or even shutting down operations altogether. While it was unexpected and could not have been planned for, it turned out that the investment in comprehensive design, prototype, testing and validation equipment made it perfectly suited to the ‘new normal’. R&D/Leverage’s ability to fully complete all design and development, prototyping, testing and to undertake full QA during lockdown, and to send comprehensive reports to convertors and brand owners, with complete confidence that the QA control methods are of an approved standard, served both R&D and its customers very well. “Having all of the inspection equipment, all of the technical knowhow and the machines, has really been a big boost for us. Last year was a record breaking year,” says Alan. “Without having the complete cycle to offer, we would have been struggling, sending samples out, waiting a week or two for them to come back, redrafting, trying again – we have, instead, been able to do everything here and deliver complete solutions. We have actually become the customers’ trusted partner. They know they can give us the order, we will design it and we will manufacture, whether that is a one cavity pilot tool or a production tool. We will lead through all the qualifications, and then send the samples to them. With one customer in particular, over the last 15 months, it has worked very well for both sides.” Rising to the occasion Ultimately, there is no substitute for the depth of understanding that comes from getting to know each other face to face: it is how long-term partnerships are built. What the Covid situation has demonstrated is that R&D/Leverage is the firm for all seasons, equipped to deal with the unexpected – in whatever form it takes – and to deliver. The start of the pandemic saw the company get a lot of orders for sanitiser and handwash bottles but regular business reasserted itself fairly quickly, and it received a huge number of orders for cosmetics. R&D carried a lot of projects single handedly, using zoom calls and such like to set the scene, bring the brand owners and the converters together and essentially to drive whole projects. The company won respect with the agility of its response and its willingness to go the extra mile to allow the customers to keep everything on track and launch several new product ranges. “Without our capability, it would have just been absolutely impossible. As the uses and demand increase for R&D/Leverage’s PSL, we see more ways that our customers view us as a complete solution provider, rather as a commodity tooling supplier,” Steve Gough concludes. www.rdleverage.com R&D/Leverage’s Product Solutions Lab is equipped with: Aoki 250LL-75S two Nissei ASB 70 DPH V3 three Nissei ASB 70 DPH V4 two Nissei ASB 70DPW Nissei 12M The PSL offers single cavity pilot tooling for product development, material trials, colour trial and in-house training. This allows a sampling program for a customer’s product that includes inspection of samples from R&D’s stretch blow and injection stretch blow moulding lab.","@ID":22} "9 NEWS PETplanet Insider Vol. 22 No. 06/21 petpla.net Synergy between PET Engineering and Comep Born from the synergy between PET Engineering and Comep, Competek - Sustainable Packaging Solutions is a new player in the international packaging industry. The new company aims to provide food, beverage and homecare packaging manufacturers with sustainable and efficient product lines. PET Engineering has always specialised in the engineering and industrialisation of new packaging solutions, with a special view to their implementation on customer lines. The core business of the French based company Comep consists in the development and production of moulds for PET containers instead. The two companies are joining forces to focus on helping packaging manufacturers in the fast-evolving consumer goods sector to face the challenges and changes the market requires. Competek, based in France is providing a full range of packaging services; from packaging engineering and optimisation, to high quality moulds and changeover spare parts. www.competek.com Alpek acquires CarbonLite’s rPET facility Alpek, S.A.B. de C.V. announced that it has acquired CarbonLite Recycling LLC’s state-of-the-art PET recycling and pelletisation facility in Reading, Pennsylvania in the United States. The site was acquired for US$ 96 million on a debtfree basis and is subject to customary conditions precedent. Alpek was strongly interested in CarbonLite’s Reading site as it is outfitted entirely with brand-new equipment, including a state-of-the-art optical sorting system, wash line, and solid state polymeriser (SSP), which enables production of foodgrade pellet, needed in bottle-to-bottle recycling. The site has a bottle-to-flake and flake-to-pellet input capacity of 115,000 t and 49,000 t, respectively, making it the largest integrated rPET facility in the Americas. The site is expected to start operations during the third quarter 2021. This acquisition is fully aligned with the Fostering a Circular Economy pillar of the Company’s long-term strategic growth plan. It increases Alpek’s installed rPET capacity to 394,000 t, reaffirms its position as the largest PET recycler in the Americas, and achieves the company’s target of supplying selected customers with 25% rPET content before 2025. www.alpek.com","@ID":11} "PATENTS www.verpackungspatente.de PETplanet Insider Vol. 22 No. 06/21 petpla.net 47 PET bottle Internal Patent No: WO 2018/ 228921 A1 Applicant: Nestec S.A., Vevey (CH) Registration date: 7.6.2018 A light-weight PET bottle with a specially shaped neck and underside area. Container mouth European Patent No: EP 3643632 A1 Applicant: Suntory Holdings Ltd., Osaka (JP) Registration date: 6.6.2018 The mouth of a plastic container that is specially shaped to ensure functionality or tightness when the cap and its sealing features are applied. Plastic container Internal Patent No: WO 2020/ 101672 A1 Applicant: Amcor Rigid Packaging USA, LLC., Wilmington (US) Registration date: 14.10.2019 A plastic container with embossings/areas in the shoulder region which should allow a force being exerted from above to enter the side wall of the bottle. Sharp-edged bottle geometry Internal Patent No: WO 2020/ 104187 A1 Applicant: Alpla Werke Alwin Lehner Co. Ltd., KG, Hard (AT) Registration date: 5.11.2019 A system for producing a plastic container with a shape that is sharp-edged in at least a few areas. Stable bottle Intern. Patent No. WO 2020 / 109697 A1 Applicant: Sidel Participations, Octeville-Sur-Mer (FR) Application date: 19.11.2019 Plastic bottle with handle and walls with deeper inset areas and a surrounding edge that additionally stabilises the container. Plastic container Intern. Patent No. WO 2020 / 110468 A1 Applicant: Yoshino Kogyosho Co. Ltd., Tokyo (JP) Application date: 7.10.2019 Multilayer PET bottle with improved barrier properties, reinforced areas and a special base shape. PETpatents","@ID":49} "PACKAGING PETplanet Insider Vol. 22 No. 06/21 petpla.net 37 precise, consistent product size and weight. Sacmi accounts for the vast majority of sales of these light cap manufacturing applications. Compression technology has been a dominant technology in the beverage cap sector for almost 30 years, with more than 1,800 machines sold globally. This technology doesn’t just ensure consistent, precise size and weight, it also promises better performance than injection in terms of energy consumption, size/colour changeover times and the structural quality of the caps. These advantages largely stem from the broad, versatile range of resins that can be employed and the fact that extrusion and moulding systems do not use hot runners. All CCM lines feature a video camera quality control system and band slitting-folding system. Sacmi says that this solution is preferable to a band with injection-moulded bridges, also in the case of tethered cap manufacturing. As soon as the European Commission first decided on the adoption of tethered closures for bottles smaller than 3 l, Sacmi immediately developed a series of solutions for all the main standard and lightweight necks. The ready-tomarket range in this field is already a broad one. www.sacmi.com 29-30 September, 2021 MESSE ESSEN, GERMANY REGISTER FOR FREE TODAY www.ami.ltd/recycling-expo Co-located with: Organised by: Join us at Europe’s focused free-to-attend exhibition and conference for the plastics recycling industry. • Source new equipment, materials and technologies • Keep up-to-date with the latest industry trends and discussions • Put your questions to the experts in a face-to-face environment • Make up for lost time in 2020 by accessing the full supply chain in one place","@ID":39} "PETcontents 4 PETplanet Insider Vol. 22 No. 06/21 petpla.net 06/2021 Page 15 Page 31 TOP TALK 10 “We’ve undoubtedly grown even closer to our customers in the process” - Interview with Kai Acker, CEO of KHS Group INSPECTION 12 How to maximise sleeve label quality 14 Maximised laboratory output - Agr introduces a robotic handling system for its Gawis 4D measurement system 15 A new computer vision system for inspection 16 Preform colour inspection - Quality assurance developments in the rPET packaging industry 17 How to train customers in a pandemic? MOULD MAKING 18 A firm for all seasons - R&D/Leverage Product Solutions Lab BOTTLE MAKING 22 Joining forces - Olivier Serre, Managing Director of newly formed Competek in an interview on the company merger of PET Engineering and Comep 31 From 25 to 100% rPET - KHS and Eckes-Granini launch bottles made of 100% rPET PREFORM PRODUCTION 24 Tackling a shortage of PET raw materials - Netstal responds to the depleted PET market and rising prices MARKET SURVEY 27 Suppliers of 2-stage SBM CAPS & CLOSURES 32 Improved hotrunner insulation with ceramic components 34 Survey on tethered caps 35 Tethered caps & TE bands - design solutions PACKAGING 36 The sustainable package MATERIALS/RECYCLING 38 Getting the bottle rolling - Michelin successfully validated the use of Carbios’ enzymatic recycling technology for PET plastic waste in its tyres TRADE SHOW REVIEW 39 Icis 3rd Recycling & Sustainability Conference 41 Petcore Europe annual conference 2021, part 1 BUYER’S GUIDE 48 Get listed! INSIDE TRACK 3 Editorial 4 Contents 6 News 43 Products 44 PET bottles for Beverage + Liquid Food 45 PET bottles for Home + Personal Care 47 Patents 54 Outer Planet Page 22 INSPECTION","@ID":6} "CAPS & CLOSURES 34 PETplanet Insider Vol. 22 No. 06/21 petpla.net Survey on tethered caps Tethered caps – closures that stay connected to the bottle when opened and used – will become an everyday part of life for consumers in the EU starting in July 2024. Sidel carried out a survey to get a better understanding of consumers’ environmental perceptions, their requirements for closures in general and their opinions about these new tethered caps. Results show that although participants agree that tethered caps contribute to a greener perception of plastic bottles, a cap should mainly guarantee product safety and userfriendliness. From June to September 2020, more than 3,200 adult Europeans participated in a survey on tethered caps performed by Ales Research on behalf of Sidel. Through online interviews and in focus groups, consumers assessed the appeal, functionality and environmental impact of tethered caps, by expressing their environmental concerns and attitudes, overall beverage packaging requirements, visual expectations as well as their perspectives on tethered caps’ usability when pouring and drinking from the bottle and reclosing the cap. Sidel’s objective was to understand consumer acceptance of the new tethered caps and thus proactively support its customers in converting to tethered caps to comply with the new regulation and to ensure the success of their new packaging in the marketplace. User-friendliness over environmental concerns The survey results show that 87% of participants agree that plastic pollution harms the environment and that caps are a part of it. Meanwhile, 67% of consumers are convinced that changing their own behaviour in terms of waste sorting and reduction can make a difference towards a greener environment. 45% of panellists realise tethered caps reduce the risk of cap loss because they remain attached to the bottle, therefore keeping them from getting dirty or lost. Only a minority of respondents (26%) believe that tethered caps will really help reduce plastic littering. According to the results, the usability of the cap itself, i.e. how easily the cap can be opened, how easy it is to pour from or drink from the bottle, comes immediately after in terms of importance. And the last preference criteria are cap attractiveness, child safety and how easily the bottle and cap can be recycled. Preferences towards different cap types During the survey, consumers were also asked to compare existing screw caps with some tethered cap prototypes – snap-on and tethered screw caps, which are going to be introduced on the EU market – and also with existing sport caps. The survey results demonstrate that there is no solution that satisfies all needs: consumers’ first impression of snap-on caps is that the design is quite disruptive and they were surprised about the initial experience. Once they get used to it, they appreciate that it is very easy to open with one hand. Tethered screw caps were found to interfere with the lips and nose while drinking. Sport caps can be difficult to open, and their design makes it naturally difficult to pour the product into a cup or glass. www.sidel.com BEYOND THE HORIZON PROCESS SOLUTIONS FOR POLYMER RECYCLING AND SOLID STATE POLYMER UPGRADING Polymetrix, a Sanlian Buhler Company, provides process technology including EPCM services for the polymer recycling and manufacturing industry. Leading supplier of rPET systems and intergated rPET plants for single line capacities up to 70’000 tons per year. www.polymetrix.com www.slhpcn.com","@ID":36} "BOTTLE MAKING 31 PETplanet Insider Vol. 22 No. 06/21 petpla.net KHS and Eckes-Granini launch bottles made of 100% rPET From 25 to 100% rPET Since the middle of May Eckes-Granini’s 1 l Hohes C juice bottle has consisted entirely of rPET. KHS’ Bottles & Shapes experts in Hamburg were responsible for optimising the bottle. The new containers will continue to be produced on the InnoPET FreshSafe block. ity of the design with the help of laboratory tests and simulation. In the case of Eckes-Granini the specifications were clear: switch to 100% rPET while maintaining the homogeneous quality of the container. According to Eckes-Granini, the changeover of the 1l Hohes C bottle to rPET will save over 4,000 metric t/a of virgin PET. This in turn means that the bottler will cut its carbon emissions by about 8,000t/a. Challenges and solutions Finding ways of saving on resources was not the only focus of the project. The ability to do so on the KHS InnoPET FreshSafe block in operation at Eckes-Granini since 2017 also had to be investigated. “One of the concerns was whether either the preforms or machine needed adapting,” explains Dr Matthias Kruse, head of PET Technology at KHS. “We thus assessed the quality of the recycled PET material. This is crucial, for large variances in colour, molecular length and inhomogeneity quickly reduce the efficiency of production.” The fact that Eckes-Granini procures its preforms from two different suppliers presented an added challenge, Kruse says. The geometry of the preform is essential for efficient processing, especially when a high percentage of rPET is used. Through extensive testing it was established that both makes of preform function soundly on the block system. All that was needed for optimum bottle production were minor adjustments to the heater on the stretch blow moulder. KHS’ NIR or near infrared technology especially provides a wide processing window for rPET, allowing preforms to be heated prior to the stretch blow moulding process with pinpoint accuracy, for example. No major changes to the machinery or geometrical properties of the preforms were required. PET bottle with barrier properties Eckes-Granini will continue to benefit from FreshSafe PET barrier protection also after converting to 100% rPET. The company has relied on this system from KHS since 2006. The oxygen barrier of chemically pure glass, a waferthin coating on the inside of the PET bottle, is not only claimed to protect the juice from oxygen pickup but also to be fully recyclable. The coating can be washed off bottles during the recycling process. By the end of 2022 Eckes-Granini Deutschland intends to only use PET bottles made entirely of rPET for all brands, saving approximately 9,000 metric t/a of new plastic by doing so. www.khs.com Dr Matthias Kruse, head of PET Technology at KHS Eckes-Granini has been using 25% rPET in its Hohes C PET juice bottles since 2018. “Bearing the EU’s plastic strategy in mind and the increase in recyclate quotas this prescribes, we’ve now decided to switch to using recycled PET only. We want to be a pioneer as regards the circular economy and set a good example for the beverage industry,” states Hermann Naumann, plant manager for Eckes-Granini in Bad Fallingbostel, Germany. Europe’s leading producer of fruit juice beverages has pursued an ambitious sustainability strategy for years, Naumann continues. “We aim to continue steadily reducing our carbon footprint in production and in our packaging. This means not only cutting down on the amount of material used but also closing the recycling loop.” In the KHS Bottles & Shapes consultancy program, beverage producers state their preferences regarding the weight, shape or stability of the container, for instance, upon which the systems supplier assesses the feasibilSince the middle of May the 1l Hohes C juice bottle from Eckes-Granini comes in 100% rPET. (Source: Eckes-Granini) An InnoPET FreshSafe block from KHS has been in operation at Eckes-Granini since 2017.","@ID":33} "BOTTLE MAKING 23 PETplanet Insider Vol. 22 No. 06/21 petpla.net Serre: We’re receiving positive feedback from the market, the comprehensive offer and our sustainable solutions are appealing to a lot of companies in the field as they see us as the strategic partner providing all the solutions they need. Competek is perceived as a good alternative to OEMs in packaging development and line transformation. PETplanet: In your first announcement concerning the joint company, you said that your intention is to help packaging manufacturers in the fast-evolving consumer good sector to face the challenges and changes the market requires. On which main challenges and changes exactly do you focus? Serre: Nowadays Environmental Health and Sustainability are two hot topics, and countries are introducing new regulations that serve to meet today’s needs while preserving the world for future generations. Companies are therefore facing a major transformation, as they must adapt their business according to the new legal requirements. Competek’s main aim is to provide them with all solutions they need to reduce carbon impact and material wastes, achieve energy savings and packaging optimisation. For instance, in Europe the Single Use Plastic directive forces all bottle producers to use tethered caps by 2024 and to have a ratio of 25% of rPET in PET containers by 2025, which means customers will have to redesign their packaging to take those new regulation into account, preferably with a fast return on investment. We support them in the development of their projects, from preform development to injection, thanks to our capability to manage rPET protocols and thanks to our 20 years of experience with packaging. Once validated, we have all industrial capabilities and knowledge to manage the transformation of our customers’ lines in light of the new shape of the tethered cap, thereby transforming the new packaging into reality. But there’s more, thanks to some specific technologies. For example, with the Starlite supervented base we can optimise the blowing process and increase energy savings while reducing bottle weight, consequently reducing costs and emissions. PETplanet: What are the main concerns your clients come to you with regard to meeting new regulations and how can you support them? Serre: Clients are worried because adopting tethered caps means that existing lines must be evolved, which implies huge investments of time and money. But they are also worried about rPET. The main fear is that making a packaging greener thanks to the use of recycled PET will impact on the performance of the bottle and the perception of their customer. We are by our customers’ side, that’s why we have developed the right skills to help them face all of these activities, built on our expertise over the past ten years. The rPET Protocol, for instance, allows the customer to compare the actual bottle performance with the same bottle done in recycled PET, and following the test results our engineers will advise on possible modifications, if needed. In general, every customer request is a new possibility to innovate. PETplanet: Concerning sustainability - a keyword that you have integrated into the company name – which technologies are you offering? Serre: For sure, the rPET Protocol is an innovative service that will become useful and required in future months. What we would like to make clear is that our sustainable packaging solutions are designed to help manufacturers transform their business and their production to safeguard the environment but also to help them make sustainable and reasonable investments. Another example, Supervent, is a proprietary technology that allows the machine to blow at a lower cost thanks to the reduced pressure required. This has an impact on the environment thanks to the lower energy consumption, but also lowers the investment the company has to undertake. The combination of Supervent technology with other technologies we have at our disposal thanks to specific licensing agreements, will help us improve not only the costs but also the quantity of material used, therefore being sustainable under an economical point of view as well. Our engineers invest a lot of time in research and development, testing new innovative solutions to introduce in the market. “We always tailor the solution to the specific request we receive and consider the existing line” PETplanet: For which customer issues/sectors does the new brand bring the most benefits? Serre: Competek’s added value is that we have a complete and modular offer, which means that we can provide everything the customer needs: A full service, going from packaging design and packaging engineering to the implementation of a new container on existing lines, or just one of the single services. In general, we always tailor the solution to the specific request we receive and consider the existing line. Thanks to our experience and the innovation-driven mindset of the team, we can address many different issues PET bottle producers may face. That’s why we define ourselves as “The one-stop-shop for all your needs”. PETplanet: You mentioned that you do not focus exclusively on bottles for beverages, but also on other sectors such as bottles for personal care? Serre: The majority of our customers belong to the Food & Beverage industry, however, we have also been working with companies producing detergents and personal care products. To be clear, all our services are perfect for all PET bottle producers whatever required. Indeed, our moulds are available in a wide array of sizes, from 100 ml to 30 l with handles. PETplanet: Thank you very much!","@ID":25} "CAPS & CLOSURES 32 PETplanet Insider Vol. 22 No. 06/21 petpla.net Heatlock Co Ltd, which was originally founded in Sweden and remains in the hands of the second generation of the Helldin family, has been manufacturing hotrunners for over 30 years. It sold its first hotrunner system in 1977 and, in 1982 it introduced ceramics as insulation for hotrunners – the first company in the world to do so. It made a very strong statement about its future when, in 2003, it entered the Chinese market by establishing a joint venture, LKM Heatlock, with Chinese company LKM. Six years later it established its own operation, as Heatlock Co Ltd, with facilities in Hong Kong and at three locations in the People’s Republic of China (PRC): in Foshan City, Quandong; 40km West of Shanghai in Suzhou City, Jiangsu Province; and in the NE of the country in Qingdao, Shandoing Province. In 2014, Heatlock opened Tech Centres in the USA (Detroit, Michigan) and in Germany (Erbach). In 2007, four years after it entered the Chinese market, the company patented a new generation of ceramic technology, which offered improved performance compared to previous generations. Its all-in-one A3 series was launched in 2011 and remains a strong seller today. Heatlock says that its ‘workhorse’ series is “built to last, durable, with hot to cold or direct gate solutions, including valve gates”. A floating manifold system is also available; it features modular design that can be adapted to suit a wide range of mouldings. Its hot runners are designed to be easy to use, the company says. Among the standard features of Heatlock’s caps and closures hot half range are built-in flash memory with complete mould details, and a Digital Project Book that includes all documentation for individual projects, including service information. Superior insulation for energy savings The key feature and attraction of hotrunner ceramic components is their superior heat-retaining and insulation performance, compared with titanium and steel. Its ceramic parts have demonstrated performance between five and seven times better than titanium and eight to 12 times better than steel, at compression strengths of 2,100M/ mm2 , and the ability to withstand temperatures of up to 1,400 °C. The improved performance is demonstrated in Fig.1. It shows the different levels of manifold heat losses in comparable moulds that are each supported by four spacers: steel in one case (the red line) and ceramic in the other (the blue line). Over the period measured – three hours/180 minutes – the ceramic spacers saved 0.33Wh for each Improved hotrunner insulation with ceramic components Swedish company Heatlock, pioneers of ceramics in hotrunners, demonstrates clear advantages in heat loss and consequent energy usage by using ceramics in key components. Ceramic supports that are individually adapted to the respective height in the mould. Fig. 1: Comparison between steel (red) and ceramic (blue) heat losses 8-fold naturally balanced hot runner system with screw-in nozzles","@ID":34} "MOULD MAKING PETplanet Insider Vol. 22 No. 06/21 petpla.net 19 trials, colour trial and in-house training. This allows a sampling program for a customer’s product that includes inspection of samples from its injection stretch blow moulding lab. “We are now approached for guidance on how to design the product, what machine to put it on, what platform, what cavitation, and so on,” says Steve. The PSL is a key part of that development; it demonstrates that R&D/Leverage has world-class, market leading capability. “These brand owners have all visited our facility and seen our equipment, capacity and expertise,” he continues. “They see our moulding machines, which give us a lot of flexibility: we have different machines for different cavitations, outputs, sizes and finishes. We can demonstrate single cavity development tools and small and large production tool qualification.” Testing, analysis and quality assurance It’s not just physical output. The PSL is a laboratory, which implies testing and analysis – indeed, it is an important element of the offer. “For the Brand Owners, they want to do a lot of colour trials, developments to get tight corner radii, weight specifications, top load specifications and so on – we can do all of that, right here, on site,” he says. But R&D/ Leverage is not a company to rest on its laurels. It has been expanding the PSL capacity, as well its physical size. “As brand owners have come and visited, we identified areas that we needed to improve and build on, in order to support them even better. So, we expanded and upgraded our QA (quality assurance) facility to the point where it is really, now, the state of the art; it is the best you will see in our industry, anywhere.” In order to position itself as the world leader in its field, R&D/Leverage purchased some quite bespoke QA equipment for measuring plastic bottles, which provides highly accurate dimensional reports and is – crucially – non-contact, which en-ables it to deliver results very quickly. The latest iteration of the equipment was designed with input from R&D, after it worked with the manufacturing company to ensure that it met its particular needs. It raises the industry bar higher. Investing in equivalent machinery R&D/Leverage also identified the equipment that the brand owners themselves were using to undertake testing back at their own premises, once the samples had been supplied. The clients would be carrying out drop tests, putting them in temperature chambers, performing torque tests on the caps, and so on. The company bought the same sort of equipment as its customers use, enabling it to present itself as a one-stop shop and to contract the testing to R&D, as well. “The equipment within our QA facility allows R&D’s customers to validate bottles during the development process, to identify any changes that may be required at an early stage, and thus to speed up approval. Some of our equipment provides capability previously unknown to some of our customers and has set the standards for future QA procedures and requirements,” Steve says. What R&D/Leverage has put in place is a one stop shop. It can develop the tool and the product, to a position where the client is happy with both the aesthetics of it – and it goes further. Cutting development time The company can complete all the dimensional checks, top load, burst tests, volume checks, torques testing, wall thicknesses - in short, the whole range of tests. Alan Tolley, Managing Director of R&D/Leverage Europe R&D/Leverage’s Product Solutions Lab (PSL) in Ashfield, Nottinghamshire, England, has grown hugely since it was first established, 15 years ago.","@ID":21} "INSPECTION 16 PETplanet Insider Vol. 22 No. 06/21 petpla.net Quality assurance developments in the rPET packaging industry Preform colour inspection The Lithuanian company Sprana Ltd is a well-known player in the fertiliser industry. After the focus of their analysing technologies was expanded to the plastics industry, their customer Retal encouraged them to develop a PET preform inspection system to assure production quality control on-line. The PET preforms colour inspection system PSIS is designed to enable an automated colour stability check on preforms on the production line as the preforms are being transferred from the moulding machine to holding containers. According to the 2019 EU Singleuse Plastics Directive, plastic packaging manufacturers will need to integrate 25% of recycled plastic in their production process by 2025 in PET bottles and 30% by 2030 in all types of beverage bottles. This not only confirms the stringent requirement to increase rPET concentration in PET preforms but also a need for methods and tools which could improve and guarantee high-quality control and accurate analysis in the production process. Sprana states that there are still many issues that producers are facing in using post-consumer recycled material. The key challenges in increasing the amount of recyclates in PET preforms are to maintain high product quality and assure the overall performance of PET bottles. Therefore, the quality control of the production process is becoming an ever more crucial issue in the plastic industry. PSIS is designed to enable an automated colour stability check on preforms directly on the conveyor belt as the preforms are being transferred from the moulding machine to the containers. Common defects when using rPET Some of the most common defects in PET preforms with increased rPET concentration are different types of inclusions, haziness, and yellowing. Hence, for an upcoming R&D project funded by EEA and the Norwegian Financial Mechanism 2014–2021 Sprana intends to develop a new inspection system that enables the detection of black specks and other contaminations at an early stage of production. In this project, the company will carry out research and experimental activities in order to improve the quality control of PET preforms in on-line monitoring and analysis and to increase recycled materials concentration in production processes. This is realised by using machine vision and AI technology. Sprana will also develop the system’s prototype, which will be tested and installed on-site. The company states that by optimising and improving quality control of PET preform production, manufacturers will be able to reduce the routine human labour part of the quality assurance process, which is seen as inefficient, time-consuming, and increases the possibility of defective products. Released from routine tasks, staff will instead be able to carry out higher value-added processes and focus on higher quality of the products. During this project, Sprana will be collaborating with local and international partners to carry out the R&D stages and achieve the main goals of the program. In cooperation with Lithuanian PET preform producer Putoksnis Ltd. and Norwegian consulting and projects management company IDN (International Development Norway) Sprana’s objective is to adapt the resulting product/solution in a real industrial environment and to commercialise it in the EU and across world markets. Overall, the project not only aims to promote the usage of secondary PET resin in the industry and to stimulate the market for rPET trading, but the partnership will also take a further step towards the EU goal of creating the circular economy for the PET plastic packaging industry. www.sprana.eu INSPECTION Machine vision and AI technology improve the quality control of preforms.","@ID":18} "MARKET SURVEY 30 PETplanet Insider Vol. 22 No. 06/21 petpla.net Company name 1 Blow Global Pet Industries Private Ltd. Chumpower Machinery Corporation Postal address Telephone number Web site address Contact name Function Direct telephone number E-Mail 25 Chemin de Gerocourt 95650 Boissy L'Aillerie France +33 (0) 9800 820 70 www.1blow.com Olivier Perche Sales Director +33 (0) 9800 820 75 [email protected] Unit Nos. 8 to 15, 108 & 109, Karishma Ind. Estate, Survey No.36, Hissa No.5, Village Waliv, Dhumal Nagar, Near Rashmi Bung., Vasai (East), Tal-Vasai, Dist. Palghar-401208. +91 7066041070 www.globalpetind.com Mr. Bipin Panchal Managing Director +91 9819007643 [email protected] No.688-1, Sec. 3, Zhongshan Rd., Wuri Dist, Taichung City 414, Taiwan +88 6423388 289 www.chumpower.com Mr Michael Lee Sales Manager +88 6905363 828 [email protected] 1. Machine designation / model number 1XXL / 1XXLN / 1XL / 1XL Lab / 2L / 2LN / 2LO /2LHF / 2XL / 4L / 4LN / 4LO / 4LHF / 4XLS / 5M-C / 6MO All-electric servo controlled fully automatic PET SBM Machine - Electra series; cavity automatic Pet SBM Machine - Eco Series; semi automatic PET SBM Machine GPSB-20L/120 bubble top & sispenser CPSB linear series 2. Bottle volume (from/to in litres) a) Standard machines 0.10 - 12 0.2 - 2 0.5 - 2 b) Machines for large containers 5 - 30 2 - 5 gallon 14 - 20 3. Maximum number of stretch-blow moulds (units) a) Standard machines 6 2, 4, & 6 cavity - Electra series & 3 cavity - Eco series 14 b) Machines for large containers 1 1 cavity for 5 gallon bubble top 2 4. Output per stretch-blow mould for: 0.5 litres CSD bottle (units per hour) 2,000 2,400 (Eco series); 3,600 (2 cavity Electra series), 6,000 (4 cavity Electra series), 9,000 (6 cavity Electra series) 2,500 1 litre CSD bottle (units per hour) 1,800 2,200 (Eco series); 3,200 (2 cavity Electra series), 5,400 (4 cavity Electra series), 8,400 (6 cavity Electra series) 1,500 1.5 litres still mineral water bottle (units per hour) 1,700 2000 (Eco series); 3,000 (2 cavity Electra series,) 5,200 (4 cavity Electra series), 8,000 (6 cavity Electra series) 2,000 Large capacity container 1,000 for 5l ; 600 for 20l 2 Gallon - 200 Jars Per Hour; 5 Gallon - 120 Jars Per Hour 250 Other 5. Footprint / space requirement (L x W x H in metres) 2.1 x 1.6 x 2.4 Eco series - 3.6 x 2.3 x 2.4; Electra series - 3.6 x 3.6 x 2.4; GPSB20L/120 - 3.4 x 1.9 x 2.2 10 x 6 x 5 6. Special features (short description/keywords) Preferential heating (oval bottles), neck orientation (with standard preforms), hot fill, compatible with Sidel, Krones, KHS, Sipa, Side moulds, recovery of blowing air; power recovery, 5M-C available as a Combi in cooperation with Ermi and Synerlink, integrated ink jet coding unit; Sure Grip device for blow-moulded hand grip, selective access to HMI through bagde reader Introducing new range of lowest energy consuming PET SBM machines: A) Eco series - 40bpm: 3 cavity automatic PET SBM and B) Electra series - 60, 100 & 150bpm. All electric servo controlled fully automatic PET SBM 2 cavity - 60bpm; 4 cavity - 100bpm; 6 cavity - 150bpm and C) GPSB-20l/120 bubble top & dispenser. Semiautomatic PET SBM for 2, 4 & 5 gallon jars. High speed linear machine for water, CSD, cosmetic and pharmaceutical industry. Special features such as bottle viewer which allows user to monitor the machine production status in real time, and receiving error message for prompt action to avoid downtime. Company name Sidel Group Postal address Telephone number Web site address Contact name Function Direct telephone number E-Mail Avenue de la Patrouille de France, CS 60627 Octeville sur Mer 76059 Le Havre cedex, France www.sidel.com Stéphane Ménard, Mathieu Druon, Mathieu Stauder Blowing Product Managers +33 232858687 [email protected]; [email protected] 1. Machine designation / model number Sidel EvoBlow blower 109 models available Sidel EvoBlow eHR (Heat Resistant) blower, 38 models available Sidel EvoBlow PH (preferential heating) blower, 18 models available Sidel EvoBlow Predis 54 models available 2. Bottle volume (from/to in litres) a) Standard machines 0.25 - 3.5 0.25 - 2 0.25 - 2 (upon bottle dimensions) 0.25 - 2 b) Machines for large containers up to 5 Up to 3.5 Up to 3 (upon bottle dimensions) not applicable 3. Maximum number of stretch-blow moulds (units) a) Standard machines From SBO 6 to SBO 34 (three frames, three oven pitches) From SBO 6 to SBO 28 (three frames, three oven pitches) From SBO 6 to SBO 22 From SBO 6 to SBO 26 (two frames, two oven pitches) b) Machines for large containers From SBO 6 to SBO 14 (one frame, three oven pitches) From SBO 6 to SBO 14 (one frame, two oven pitches) 4. Output per stretch-blow mould for: 0.5 litres CSD bottle (units per hour) Mechanical output: 2,700 for XS mould size, 2,600 for M mould size, 2,400 for L mould size Mechanical output: 2,000 for L mould size Mechanical output: 2,000 for L mould size Mechanical output: 2,500 for XS mould size, 2,500 for M mould size, 2,400 for L mould size 1 litre CSD bottle (units per hour) Mechanical output: 2,600 for M mould size, 2,400 for L mould size Mechanical output: 2,000 for L mould size Mechanical output: 2,000 for L mould size Mechanical output: 2,400 for M mould size, 2,250 for L mould size 1.5 litres still mineral water bottle (units per hour) Mechanical output: 2,600 for M mould size, 2,400 for L mould size Mechanical output: 2,000 for L mould size Mechanical output: 2,000 for L mould size Mechanical output: 2,400 for M mould size, 2,250 for L mould size Large capacity container Mechanical output: up to 1,800 for L Jumbo mould size Mechanical output: 1800 for L Jumbo mould size Mechanical output: 1,800 for L Jumbo mould size not applicable Other Mechanical output: 2,000 for L eHR mould size for hot filled beverages Mechanical output: 2,000 for L mould size For juices, tea, sport drinks, milk-base products 5. Footprint / space requirement (L x W x H in metres) MM model: 7.9 x 4.6 x 3.7 - GM model: 9 x 5 x 3.7 - LM model: 13.7 x 7 x 3.7 MM model: 7.9 x 4.6 x 3.7 - GM model: 9 x 5 x 3.7 - LM model: 13.7 x 7 x 3.7 MM model: 7.9 x 4.6 x 3.7 - GM model: 9 x 5 x 3.7 MM model: 7.9 x 4.6 x 3.7 6. Special features (short description/keywords) Maxi output smaller model / larger model : For XS mould (up to 0.75l): 48,600 - 90,000bph; For M mould (up to 2l): 15,600 - 67,200bph; For L mould (up to 3.5l): 14,400 - 63,000bph; For L Jumbo mould (up to 5l): 10,800 - 25,200bph Maxi output smaller model / larger model: For L eHR mould: 10,800 - 56,000bph; electrical mould heating instead of oil mould heating Maxi output smaller model / larger model : 8,400 - 40,000bph for flat and complex containers Maxi output smaller model / larger model : For XS mould (up to 0.75l): 45,000 - 60,000bph; For M mould (up to 2l): 15,000 - 60,000bph for L mould (up to 3.5l): 14,400 - 57,600bph; dry preform sterilisation - Predis -, for aseptic bottling with no blower sterilisation","@ID":32} "TOP TALK PETplanet Insider Vol. 22 No. 06/21 petpla.net 10 Interview with Kai Acker, CEO of KHS Group “We’ve undoubtedly grown even closer to our customers in the process” PETplanet: After just under two years as CEO of KHS, the Covid pandemic struck. How has the pandemic affected your strategic business plans? How did KHS get through the last year? Acker: Despite the challenges, at the end of the day we’re satisfied with the last business year. One of the things that has helped us during the corona pandemic is our strategy of increased regionalisation that we’ve been consistently pursuing for several years now. The aim of this – apart from sales organisation – is to transfer our local service knowledge to the KHS Group’s entire product portfolio. This allows us to provide proximity to the customer and establish a level of expertise in the region which enables local teams to also install and commission our machinery besides just servicing it. Particularly in times of travel restrictions, our regional teams have thus proved to be a great boon. We, too, have of course felt the impact of the uncertainty in our industry. Some new investments have been postponed for the time being, for example, and the focus has instead switched to maintaining existing lines for longer. In this respect, virtual services in particular have increased in significance, especially in times of social distancing. Here, too, we’ve been able to support our customers as their reliable partner and safeguard their extremely important production processes. Digital communication and processes can of course never fully replace personal contact or the human factor. However, in the future we’ll also continue to consistently expand our range of digital remote diagnostic services. PETplanet: What were the most important changes you had to make in the company during the Covid pandemic? What areas were particularly affected? Acker: The overall situation has changed. Alongside the various economic aspects, in particular people’s health is now a prime concern. In order to protect our personnel, we’ve thus significantly increased our hygiene measures at the respective production sites. Internal company processes have also been adjusted in order to reduce the risk of infection. We’ve worked more shifts and, where possible, enabled people to work remotely or from home. At the start of the pandemic, we were also very busy bringing numerous employees back from installation sites located all over the world. What’s more, we had to introduce quarantine concepts so that work out in the field could be performed within the given time frame. Likewise, we’re in intensive and close dialog with the authorities both nationally and internationally, taking on board information that’s constantly changing. At first, this was a totally new scenario for us and a challenge for all those involved, one we’ve since mastered by working together. This has enhanced the sense of community within the KHS Group and we’ve undoubtedly grown even closer to our customers in the process, so that we’ll come out of the crisis all the stronger as a company. PETplanet: As a result of the pandemic, technologies around the field of digitalisation became an anchor for survival. Even though KHS has previously focused on digitising its machines, what specifically do you see as a clear advantage of digitalisation? Not just in terms of the machines, but perhaps also in terms of customer communication and the working environment? Acker: Primarily, digitalisation boosts efficiency in production and is thus sustainable and protects the environment as fewer resources are used and energy consumption is lowered, for instance. There are a number of clear benefits for customers in other areas, too. KHS’ ReDiS remote diagnostic system prevents long production downtimes through predictive maintenance, for example. Our web-based Innoline MES Basic Line Monitoring module assesses line efficiency, detects possible faults and thus identifies weak points in the operation of a system. Our audiovisual Augmented Reality Service helps with troubleshooting without an engineer having to be on site. Here, data goggles transfer images from the machine in real time. This can then also be much more easily operated as processes are digitalised and automated. Format or product changeovers are now much faster and less complicated. Moreover, because of the pandemic new forms of customer contact and exchange between industry stakeholders have become established, among them online expert panel meetings staged as technical talks and webinars. We’ve also introduced a number of digital tools as new internal and external platforms for communication. If I may say so, the pandemic has helped to accelerate the launch of our digital processes; this is something we all profit from. As a result, in 2020 we also saw a drop in travel expenses of 40% compared to 2019. If we manage to save half of this in the long term once the pandemic has ended without neglecting our contact with the customer, we’ll also noticeably help to reduce the impact on the environment and promote a sustainable style of corporate management. PETplanet: When it comes to the bottling of beverages in PET bottles, legislators such as the EU or the German government have recently been making new decisions that effect the entire PET value chain. One month ago, the German government introduced the extended bottle deposit for PET juice by Heike Fischer","@ID":12} "INSPECTION 14 PETplanet Insider Vol. 22 No. 06/21 petpla.net Agr International introduces a robotic handling system for its Gawis 4D measurement system. Maximised laboratory throughput As speeds increase, weights are reduced and recycled material is becoming a significant factor in bottle production, regular testing and measurement of production samples is essential to properly manage quality. However, with limited personnel and equipment, laboratory throughput can be a challenge for many production facilities, potentially compromising quality efforts. Agr International’s Gawis AF robotic handling system, in conjunction with the Gawis 4D measurement system, provides both, a solution for meeting the need for comprehensive testing/measurement of bottles and a means to address throughput demands. The Agr Gawis 4D is designed to automate quality checks by consolidating numerous dimensional and thickness measurement operations, typically performed by hand, on individual bottles or preforms into a single hands-free operation, completed in a matter of seconds. tor intervention, maximising testing throughput while freeing laboratory personnel for other, more critical, tasks. The Gawis AF robotic handling system interfaces seamlessly with the measurement system. It can be purchased with a new system or retrofitted to existing systems operating in the field. Central to the system is a precision pick and place industrial robot that manages sample selection and placement of samples into the Gawis 4D for measurement. Operation is fully integrated. All controls and operations including overall job setup, robot, sample coordination, as well as activation and control of individual test sequences are handled through the Gawis4D user interface. For sample management, samples are hosted in a multi-level carousel that is outfitted with rotating tiers designed to accurately position samples for robot access. The tiers can be configured to accommodate bottles from single or multiple mould rounds, or a complete mould set of preforms. Each tier is fitted with spring activated sample grips that provide exact bottle control and positioning for the robot yet allow fast loading by an operator. When tests on the individual samples are complete, the robot can either discard samples or return them to the sample carousel for further analysis. The Gawis 4D outfitted with the Gawis AF robotic handling system is the latest in Agr’s line of high-precision measurement systems for bottles and preforms. The Gawis 4D system offers a means to perform a range of complex dimensional measurements that are fast and precise with un-matched repeatability. AutoJob, a patent pending feature on the Gawis 4D, simplifies job setup on the system by providing automated recognition of key finish measurements, reducing job setup time to a matter of minutes. This system also offers a wide range of thickness measurement options, including thickness at single or multiple discrete points anywhere on the sidewall or heel of the bottle, and the ability to perform complete vertical or horizontal (circumferential) scans for analysing preform ovality and material distribution. www.agrintl.com INSPECTION The addition of the robotic handling system takes this to the next step. With the handling system, the Gawis 4D can not only measure individual bottles, but also perform measurements on complete sets of bottles or preforms. It can be operated on a continuous basis, without opera-","@ID":16} "INSPECTION 13 PETplanet Insider Vol. 22 No. 06/21 petpla.net NO. ONE-WAY PRODUCTION. YES. TOP QUALITY RECYCLING. How can your recycled product meet permanently increasing demands? With the CHT range of high performance process solutions with environmental relief for the wet chemical cleaning. We support you directly on site and ensure your quality controls in our laboratories with state-of-the-art equipment. Thus, your strong position in the growing market is confirmed day by day. More about us at www.cht.com Short response time for troubleshooting This product-related quality data, which can be transferred to any of the customer’s information systems via an interface, helps to detect serial defects at an early stage and to react accordingly. Whereas the quality manager previously needed to reach a conclusion by himself about the frequency and severity of a defect based on the ejected objects, he now receives a detailed overview with the help of the inspection system. This significantly shortens the response time for troubleshooting and increases the efficiency and output of production. Additionally, the customer can export all information as a report or send it automatically via email. This enables him, for example, to provide his customers with detailed information regarding the quality of his delivery. In the future, sleeved objects will be definitely found more often in our supermarkets. To ensure that quality remains at a first-class level in the long term, inspection systems are essential which deal perfectly with the special requirements of sleeve labels. Furthermore, these systems can help producers to keep their production at the most efficient level possible by providing comprehensive, specific information. www.intravis.de","@ID":15} "OUTER PLANET 54 PETplanet Insider Vol. 22 No. 06/21 petpla.net OUTER PLANET When the packaging becomes the product – and vice versa A bottle that doesn’t come to stay The clue is in the name. Soapbottle is packaging made from and for soap. Once the liquid hygiene product content is finished, the empty container can be used as hand soap or washing agent and simply “washes away”. Jonna Breitenhuber is a product and process designer based in Berlin. In her Master’s thesis, she wanted to tackle the topic of sustainable packaging for liquid personal care products. Inspired by the food industry, which already has a few examples where the product itself becomes packaging, she was wondering if she could transfer this concept to hygiene products. So, just as you can eat the cone along with your ice cream, she wanted to find a solution for hygiene products that turned the product into packaging – and vice versa. Jonna was gripped by the idea and started experimenting with soap and “project Soapbottle” was born. The concept of Soapbottle spread quickly and took off at a rapid pace: Salone Satellite, Fach Pack, Ambiente, Kunstgewerbemuseum Berlin – fairs and exhibitions showcased Soapbottle. Awards for design and sustainability followed, such as the Federal Eco-Design Award, as well as publications on various platforms. The designer received messages from people and companies all over the world showing interest in the development. This motivated her to pursue the project further. Meanwhile, project Soapbottle is now based in Amsterdam and has grown into a young, international team that works intensively on product and brand development. Zero waste goal The primary intention of the project was the zero-waste approach. Once its 100ml liquid contents are finished, the container becomes like any other bar of soap. In other words, it simply degrades over time, upon use or can be processed into a cleaning agent. Solid soap is an alkaline salt, which is produced from oil (or fat) and caustic soda and decomposes in the sewage plant after a few days. The bottle comes with a label made from recycled and recyclable paper and a stainless steel cap which can be re-used on the next Soapbottle. For the soap itself, natural and biodegradable raw materials are used. Commercialisation When designing the product, Jonna Breitenhuber chose a rectangular shape for space-saving stockage in stores. So far, the product realisation phase is still underway. Via a kickstarter campaign, the company has recently been able to generate the funding it requires. Together with partner Marie-Stella-Maris, the team is now working on the next phase of brand and product development. The goal is to launch Soapbottle in 2022. www.projectsoapbottle.com","@ID":56} "PETplanet Insider Vol. 22 No. 06/21 petpla.net 39 TRADE SHOW REVIEW 39 TRADE SHOW REVIEW Icis 3rd Recycling & Sustainability Conference by Gabriele Kosmehl The end of April saw the 3rd edition of the Icis Recycling & Sustainability Conference. The three-day event which took place in a fully virtual environment focused on new data and developments for the whole polymers world. PETplanet picked some of the PET-related cherries for you. Global supply outlook for recycled polymers In her presentation, Helen McGeough, Icis Senior Analyst & Global Analyst Team Lead, Plastic Recycling highlighted the current state of availability of recycled polymers in relation to supply demand. With regulations spreading globally and across all regions, sufficient supply becomes an issue. Supplies of recycled PET, despite being highly positioned compared to other types of plastics, are no exception here. Some big brands in the beverage sector are beginning to sense this already as they go way beyond the minimum requirements with bottles featuring rPET contents of 50% or even 100%. Helen pointed out that these brands frequently cite the challenges in sourcing a sufficient supply of recycled materials, particularly of high-quality recycled polymers. To obtain enough highquality material, the brands recognised that they have a role to play in collection, establishing facilities and commitments to collect more material. To support this, Helen shared data from Icis showing the global availability of virgin PET compared to rPET. These global capacities from 2020 showed a 10% share of rPET capacity in comparison to virgin PET. So in the context of mid- and long-term industry goals such as for instance the EU goal of 25% rPET share on average by 2025 for single-use bottles and 30% by 2030 for all bottles, a substantial growth in the supply of rPET is required as Helen vividly underpinned with figures: “If we were to achieve a 50% recycled content rate in PET globally, growth rates need to be 82% per annum in comparison to 2020. This is equivalent to an additional 1,800 recycling plants with an average of 25,000t capacity.” E N D L E S S I N N O V A T I O N S I N C E 1 9 1 9","@ID":41} "TRADE SHOW REVIEW PETplanet Insider Vol. 22 No. 06/21 petpla.net 42 Casper van den Dungen, Vice President of Plastics Recyclers Europe , pointed out that 5.3MT PET is placed on the market. 66% is used for PET beverage bottles, 5% for non-beverage bottles, 19% for trays, 6% for flexible packaging and 4% for others. In conclusion, 96% of PET is used in packaging (bottles, trays and flexible). He saw a trend in bottle production that will continue to increase at a slower pace, with tray consumption likely to grow. In PET sorting and collection, Casper saw an impact of minus 10-15% during the pandemic. For PET recycling, Casper highlighted the importance of DRS systems, where the growth of collection is the major driving force. He presented four key market developments for rPET in 2025: the first limitation remains collection, and he suggested a deposit increase is needed in the major countries. The second limitation is the quality of collection, the third is the harmonisation of direct food contact for recyclates (regulation 282/2008), and finally the fourth limitation is a lack of transparency towards developments on modulation of costs for collection & recycling. That is why Casper urged major changes to raise awareness of design for recycling, to increase bottle collection and to use the maximum value of collected PET to program new business models to finance the higher targets. Frédéric Durand from Tomra talked about Trends in Sorting – Roadmap for Digital Watermarks and Artificial Intelligence. As a member of the Holy Grail project, he called for today’s limits in sorting to be overcome. He said that this could be achieved by improving the detection and sorting of materials, especially of difficult to sort / recycle, by enabling food and non-food recycling applications among others and finally by a proof-of concept successful within the Holy Grail project. Frédéric’s ambitions for the Holy Grail 2.0 are to enable and develop a true circular economy, to identify and evaluate potential test markets and sites with project partners at the large installed base of Tomra equipment in different applications and markets (clean/dirty MRF, PRF etc.). He added that Tomra aims to establish a dedicated, ring-fenced DW project team (two additional staff planned) to build, install and support test machines for industrial trials, once funding is secured. Tomra will continue add-on module development (connected to standard NIR) based on the new defined specification. Finally with the good, established working relationship with the Digimarc R&D team, Tomra supports business development activities and shares market knowledge in HG 2.0. There will be a second part of the review on “Trends in Design for Recycling”, “Monomer Recycling - where is circular PET headed?” and “Circularity of PET - opportunities beyond recycling”. Information about the speakers and their presentations can be found on the event homepage at Petcore. November 7-9, 2021, Dubai At the KRONES booth A1-34 German Technology Innovative hotrunner optiRun www.petcoreeuropeannual-conference.eu www.petcore-europe.org","@ID":44} "PETplanet Insider Vol. 22 No. 06/21 petpla.net 46 8 Seconds Wonder Water Elvital from L’Oréal Paris promises the “fresh from the hairdresser” feeling in 8 seconds – smooth, shiny and protected hair – by applying “Dream Length 8 Seconds Wonder Water”. The coloured bottle holds 200 ml and two labels describe content and application. It is simply applied to freshly washed, wet hair, massaged in and after 8 seconds, rinsed out again. Wonder Water is applied via a two-part screw cap; the top part turns to open an outlet channel. www.loreal-paris.de Curved bottle without sprayer Under its own brand “W5”, German discount retailer Lidl is selling 1 l of classic glass cleaner in a curved, asymmetrical PET bottle. To suit the times, the bottle is made from 100% recyclate and is offered as a refill pack without a trigger. Two self-adhesive labels and a screw cap with guarantee band complete the packaging. Two “W5” imprints are embossed into the bottle. www.lidl.de Plant-based fabric conditioner from Softlan Under the brand name “Softlan”, Colgate-Palmolive has brought onto the market a plantbased fabric conditioner with the tagline Vegan. The fabric conditioner makes use of recycling in two ways. On the one hand, the bottle is made from 100% recyclate; on the other hand, the scent is obtained from recycled jasmine blossoms. The blossoms come from flowers that have not been sold at the flower markets. The bottle contains 650ml of a lightly coloured product and is intended for 27 wash cycles. To improve stability, it has longitudinal ridges that run in parallel. To indicate additional new features, an adhesive sticker is applied to the neck area. The screw cap is combined with a dosing aid. www.colgatepalmolive.com Bicycle care in PET German company Prophete GmbH is selling 500 ml of an organic bicycle care product for degreasing the drivetrains of bicycles and e-bikes in a transparent plastic bottle. According to the manufacturer, it removes stubborn dirt like grease and wax. The cleaner is free from solvents and phosphates, is manufactured using sustainable raw materials and is biodegradable. A lockable, screwed-on pump sprayer makes it easy to apply to the surfaces to be cleaned. www.prophete.de PETbottles Home + Personal Care","@ID":48} "CAPS & CLOSURES 35 PETplanet Insider Vol. 22 No. 06/21 petpla.net Slitting and folding of tamper evident bands for tethered caps Tethered caps & TE bands - design solutions New legislation in the European Union requires that by July 2024, all plastic closures must remain “tethered” (attached) to single-use beverage containers after the container is opened. This will bring a big change for the beverage packaging industry. One of Packsys Global’s core competences focuses on the slitting and folding of tamper evident bands. The company has developed multiple solutions to solve the tethered requirements. The upcoming European directive requires that plastic caps must remain attached to containers during consumption. This means a change to the creation of the tamper evident band. In addition to the protection that customers expect against tampering, closures will need to have even more complex cutting geometry to give both protection against tampering and keep the closure on the package. For a long time Packsys Global AG has produced machines which roll the cap along a knife with a specific pressure to create a straight cut around the cap perimeter. Before the EU legislation was enacted, the company was already working on developing slitting solutions which would not only fulfill the regulations but are regarded to have a positive impact on our planet. Today a significant amount of plastic closures can be found in our planet’s oceans. The EU legislation is based on the idea recognises that since there is a high rate of bottle recycling if the closure stays on the bottle the recycling rate for closures should rise and reduce future pollution. Tethered closure designs need to vary in order to match individual applications and beverage container specifications. The machine manufacturer has designed solutions that can be implemented into existing and new machines of the company’s range. For most applications closure producers do not need to invest in new machines. Consumers can benefit from the protection of traditional tamper evident (TE) closures and help the environment by having the closure tethered as well. SmarTether This technology offers a combination of various cutting segments to create perforation lines for the TE band and the tether function. This can be simple horizontal cutting, or it can be combined with multiple vertical or diagonal slit lines. It purposely leaves a thin and controllable skin in defined sections of the separation lines. It supports in the capping process and will easily break at the first opening. The technology can be applied on all existing major PET bottle closure applications. It delivers a highperformance tethered closure suitable for high-speed capping processes. ExperTether Lightweight plastic closures require a perfect support of the knives during the slitting process. A continuous support on both sides of the knives is important. ExperTether and SmarTether can both be used for the same cutting line pattern. With ExperTether the entire slit contour is 100% cut through – including the vertical and diagonal section. This is done by perfect synchronisation of the rotating spindles to the fixed slitting knives. Independent of the machine speed, the synchronised inner and outer tooling provide unique slit accuracy for customised slitting patterns for the tethered feature. Both the TE band and the tethered feature are processed on same mechanical cutting technology. CapCompass This feature is a method to bring a closure, when first opened, to a position which is locked and does not disturb the consumer while they are drinking. Gable top or other carton packaging applications are major markets for this processing method. Whether it’s a pre-moulded hinge, the thread start, an embossing, or some other feature, the slit lines can be positioned for functionality and/or marketing purposes. CapCompass is made for cutting closures at the right place and could be combined with the other two technologies additionally to TE band slitting. www.packsysglobal.com Ueli Kobel, Product Manager Closures, Packsys Global","@ID":37} "MARKET SURVEY 29 PETplanet Insider Vol. 22 No. 06/21 petpla.net Kosme Gesellschaft mbH SMF Maschinenfabrik GmbH Serac Group SAS Newamstar Packaging Machinery Co., Ltd. Technopet Machineries Gewerbestrasse 3, 2601 Sollenau, Austria +43 2628 411 0 www.kosme.at Mr Johann Gugler Managing Director +43 2628 411 125 [email protected] Stuifenstraße 59, 74385 Pleidelsheim, Germany +49 7144 888 27 www.smfgmbh.com Ms Agnes Plaska Key Account Manager +48 503 783.686 [email protected] 12, route de Mamers, BP 46, 72402 La Ferté Bernard Cedex, France +33 2 43 60 28 28 www.serac-group.com Mr Guillaume Fayrad Blowing Division Director +60 12 418 1955 [email protected] East Xinjing Road, Zhangjiagang Econ.&Techn. Dev. Zone, Jiangsu 215618, P.R. China www.newamstar.com +86 512 5869 1111 [email protected] 14/15, shree Naman Plaza, GF, SV Road, Kandivali (west), Mumbai-400067, India +91 022 28610828 www.techno-pet.com Technopet Machineries Manufacturer& Exporter Manufacturer of PET Bottle Blowing Machine +91 98210 40637 [email protected] Rotary machines (7 models) Linear machines (5 models) Over 20 models of blow moulding machines, series: Combi, Jumbo, HS, Stratos and Optima Serac Blow Linear RBM2-40 Auto 3000 PDW-OL2400 PDW-AE1800 Bottle & Jar/P-Auto 2X2X5 Jar 20Lit/ TPS 20L 0.10 - 20 0.05 - 3.0 (up to 4.0 depending on design) 0.05 - 3.0 0.10 -3 0.05 - 3 0.16 - 2.5 0.2 - 1 0.2 - 1 0.2 - 2 1.5 - 11.0 0.5 - 30.0 1 - 20 3 - 5 3 - 20 0.5 - 5 10 - 20 From 3 - 8 2 16 cavities in Optima 16 turbo 12 8 - 40 2 units 2 units 2 units 2 units From 4 - 8 From 1 - 3 4 cavities in Optima4 Max 4 2\\4\\6 1 unit 1 unit 2,500 1,700 28,000 1,400 12,000 - 81,000 3,000, 3,600, 4,500 2,400 1,800 1,000 2,500 1,650 24,000 1,400 4,000 - 60,000 3,000, 3,600, 4,500 2,400 1,800 800 2,500 1,600 24,000 1,500 4,000 - 60,000 / 4,000 - 40,000 (2.5l) 1,000 600 1,200 Up to 1,250 for 5.0l; 750 for 15.0l; 700 for 20.0l; 350 for 30.0l 6,000 (for 5l) 1,000 1,200 - 6,600 400jph/c 200jpc/c 28-120mm 46-120 6.45 x 3.18 x 3.46 (without preform feeding system) min.: 4.50 x 1.83 x 3.10; max.: 5.10 x 1.85 x 3.10 (without preform feeding system) from 4.4 x 3.4 x 2.9 up to 10.5 x 5.2 x 2.9 12.8 x 2.2 x 4.3 (with preform feeder) 2.2 x 2.0 x 2.5 1.5 x 1.1 x 2.5 2.1 x 1.5 x 2.2 2.1 x 2.0 x 2.5 3.1 x 2.5 x 3.0 Blow moulder on one platform (for all sizes); active neck cooling; patented modular oven (low energy consumption); block version with fillers for all sizes available Air recycling system, available also with PI; mould shells of linear machines are compatible with rotary machines; fast semi-automatic mould change within 10 min.; preferential heating Fully electric with servo drives & NIR lamps or classic machines with pneumatic cylinders & conventional IR ovens. Finished bottles can be discharged in upright position. Easy use & maintenance: fast neck format change, quick mould change system, central lubrication system, pyrometers, detection of cracked bottles, router for on-line support and preform dumper to load the preforms automatically from octabins. Available in ultra clean version for sensitive products. Stand alone or in bloc with Serac filler for bottle or cups (Combox, Cupbox); full electrical motions, no mechanical adjustement during changeovers; economical savings with air recovery system & low electricity consumption, preferential heating for flat, oval and complex shapes; mould boxing on large capacities for handle insertion; clean options to run ESL configuration in Bloc Efficient single mould capacity, perfect security system, quickreplaceable moulds, long-term continuously-running, energysaving and lower consumption, capable for multi-type bottles, information processing system, remote monitoring and service module Max volume: 1,000ml, neck size: 19-30mm, max dia: 100mm, max height: 330mm, mould opening: 100mm, no. of cavity: 2 Nos, type of mould: auto ejection, cavity distance: 110mm, preform PCD in oven, 38mm, mould thk: 170mm, preform neck cooling system: (360°, individual preform), IR heating station: 6 Nos","@ID":31} "TRADE SHOW REVIEW PETplanet Insider Vol. 22 No. 06/21 petpla.net 40 Although supply varies according to region (Asia Pacific dominates the rPET supply, followed by Europe and North America), collection and sorting remains the biggest bottleneck. Within Europe for instance, a lack of harmonisation results in collection rates varying between 23% and 96% according to 2019 figures. Besides the need to increase collection volumes, another focus should be on increasing the quality of the material, as was pointed out in the presentation. Deposit return schemes could help achieve higher levels both of collection and quality. Since the question of the potential of chemical recycling comes up often in this context, Helen was also able to shed light on this topic. Although she sees great potential in the process, she cautioned that it could take another 5-10 years to reach industrial levels. In their research, Icis analysts identified 200 chemical recycling processes using a variety of technologies, with the majority of them still at the pre-commercial stage. Besides this, there are uncertainties about the process relating to the possible environmental impact or lack of clarity from the legal point of view (in Europe for example). For these reasons, a decision is unlikely to be reached for the next couple of years about the contribution that chemical recycling may make to reach recycling targets. Asian and European recycled PET: Managing supply challenges amid increasing demand In another presentation, Matt Tudball – Senior Editor Recycling Icis covered the European rPET market. In 2020, major beverage brands reported falling sales. Due to the pandemic, on-the-go consumption or consumption during big events fell and with that post-consumer bottle availability. This could not be bolstered by the increased consumption of larger PET bottles as they were consumed over a longer period of time, with consumers making less frequent use of bottle return schemes. At the same time, a massive drop in crude oil prices caused a sharp drop in price for virgin PET. As a result, some companies - particularly in the thermoforming sector - were replacing rPET with virgin material, while others, especially bottling brands, due to brand commitments, sustainability targets or regulations, maintained their use of rPET. At the beginning of September 2020, rPET flakes held a 30% premium over virgin PET, while Efsaapproved food-grade pellets were double the price of PET. The situation completely changed in early 2021 with virgin PET prices rocketing. Matt pointed out that many sources he has spoken to in the European rPET market said a forecast of the further price development is very difficult to make as there is a huge uncertainty about post-lockdown Europe; will there be a rapid return to normality or will producers adopt a more cautious approach with corresponding effects on the market? Factors which are likely to play a key role are regulatory legislation which are not expected to have an impact before the end of the year, and consumer behaviour. Other important developments which are likely to have an impact on the market are the rise of tray-to-tray recycling, and the growing level of extrusion technology being employed by the bottle sector across Europe. The growth of this is expected to increase rapidly, making extrusion technology a new competitor in the scarce rPET market, with the possibility of additional competition from the tray-to-tray sector on the horizon. Hazel Goh – Senior Editor Icis looked at the Asian rPET market. Virgin PET prices have increased significantly, especially in Q1 this year. This led price sensitive downstream converters, mostly from the fibre textile industry, to use more rPET and less virgin PET in their production where possible. There were improvement in the domestic demand, resulting in less export volume availability. In addition to that, freight costs increased in October/ November last year, made rPET exports had higher total cost, and hence seemed less attractive for importing buyers. Regarding Asian recycling capacity, China houses a large percentage of mechanical recycling capacity (66% or 5,342,083 t/a). Other Asian regions with substantial PET recycling facilities are in India, Indonesia, Japan, Malaysia, Taiwan, Thailand and Vietnam. With a shift in regulations and brand owner commitments in sustainability, Hazel expected more new recycling plants to come on-stream in the near future. www.icisevents.com","@ID":42} "PETnews 6 NEWS PETplanet Insider Vol. 22 No. 06/21 petpla.net Bericap has acquired aluminium closure expert Mala Bericap, one of the leading global manufacturers of plastic closures, has taken over Mala Verschluss-Systeme GmbH, thereby extending its product portfolio to include aluminium closures. Mala is a family-owned company based in Bad Liebenstein, Germany. In 2020 it generated annual revenue of 40 million Euros from the production and sale of aluminium screw cap closures for spirits, wine, non-alcoholic beverages and edible oil. Bericap and Mala’s business models and product program are stated to complement each other perfectly. Whereas Bericap focuses on the production and sale of plastic closures for the food, beverage and chemical industries, Mala specialises in aluminium roll on pilfer proof (ROPP) and long cap closures for the wine and spirits market. Mala intends to gain access to new markets and Bericap’s product portfolio will be extended to include aluminium closures. The acquisition will allow Bericap to continue on its growth trajectory and, with Mala on board, it has the opportunity to open up new market segments and to develop innovative closure technologies combining plastic and aluminium. Completion of the product range Mala has over 200 employees at its sites in Bad Liebenstein and Schmalkalden-Wernshausen and markets its closures globally. “The extension of our product range to include Mala’s aluminium roll-on caps enables us to tailor our solutions even more precisely to the needs and requirements of our customers. The acquisition has allowed us to complete our already comprehensive range of closures for PET and glass bottles.” said Christian Krautkrämer, Managing Director at Bericap. Now Bericap is able to offer alternatives in aluminium, in addition to the established range of plastic closures, for edible oil, vinegar and mineral water. Spirits manufacturers will also appreciate Bericap’s new singlesource supplier setup covering all their needs, from simple ROPP aluminium closures to multi-stage highly safety closures. Production of aluminium closures for wine can also be ramped up thanks to the global Bericap production network. “Mala’s design capabilities and specialised production equipment for aluminium closure finishing and decoration are impressive. The company offers exceptional flexibility in customer projects with its own in-house pad printing, side offset printing and hot foil embossing technology. Together we can leverage our full potential and grow our business footprint in expanding markets,” added Christian Krautkrämer. www.bericap.com Indorama Ventures completes acquisition of CarbonLite’s Texas PET recycling facility Indorama Ventures (IVL), a global chemicals producer, has completed its acquisition of CarbonLite Holdings’ facility in Texas as part of the company’s commitment to increasing PET recycling capacity. Now known as Indorama Ventures Sustainable Recycling (IVSR), the Dallas site is one of the largest producers of food-grade recycled pellets (rPET) in the U.S., with a combined capacity of 92,000 t/a. The facility will recycle more than 3 billion PET plastic beverage bottles per year and support more than 130 jobs directly. IVL is the world’s largest producer of recycled PET for beverage bottles. With this acquisition, IVL expands its U.S. recycling capacity to 10 billion beverage bottles a year, towards its global target of recycling 50 billion bottles (750,000 metric tons) annually by 2025. Thailand-based Indorama Ventures entered the U.S. PET market in 2003. In 2019, the company acquired recycling facilities in Alabama and California, bringing a circular business model to its U.S. operations. The new acquisition in Texas allows IVL to better serve customers’ increasing need for recycled PET for beverages. America’s leading beverage companies have launched the ‘Every Bottle Back’ project to support the circular plastics economy by reinforcing the value of their fully recyclable PET bottles among consumers. www.indoramaventures.com","@ID":8} "PETplanet Insider Vol. 22 No. 06/21 petpla.net 45 BOTTLES Limited edition Müllermilch brownie flavour milkshake Transferring well-loved flavours to other products stimulates additional purchases by customers. Müllermilch is expanding its Müllermilch range with a limited edition variety, “American Style Brownie Flavour”. The product is available in the well-known 400ml / 423g bottle. This featured a sleeve label designed to suit the American style and was sealed with a tamper-evident plastic lid. www.muellermilch.de Healthy drink from Rio d’oro Two vegan multi-fruit juices with added Vitamin C, zinc, selenium, dragon fruit pulp and spirulina extract have been added to Aldi Süd’s own-brand Rio d’oro range. These are available with bylines like “In Love” or “The Blues” and promise support for physical functions. The product is available in a transparent, no-deposit, 750ml bottle with a suitably coloured paper label and an opaque screw cap with a tamper-evident seal. www.aldi.de PETbottles Home + Personal Care Wow! Glow from Guhl Guhl Ikebana from Germany is selling 250ml of a limited edition shampoo for all hair types in an upward pointing transparent bottle with two areas on the sides that make holding and handling the bottle easier. The shampoo is lightly coloured and has packaging that stands out on the shelf; it has a bold label on the front and the label on the back has a reflective surface on the inside. www.guhl.com 2 in 1 for kids German discount pharmacy Dm is selling 250ml of a two-in -one product for kids, shine shampoo and hair conditioner, under its own brand name “Saubär” in a sturdy, transparent bottle made from 100% recyclate. The transparent front label features characters from the children’s comic series “Yakari”. The back label is printed on the inside with a landscape and, together with the front label, makes a type of 3D effect for children. According to the manufacturer, the product is free from microplastics. It is dispensed via a two-colour push-pull cap, which, according to the bottle printing, should be unscrewed from the bottle before throwing away. www.dm.de","@ID":47} "BOTTLE MAKING 22 PETplanet Insider Vol. 22 No. 06/21 petpla.net Olivier Serre, Managing Director of newly formed Competek, in an interview on the company merger of PET Engineering and Comep Joining forces by Gabriele Kosmehl At the beginning of June, PET Engineering, specialised in the engineering and industrialisation of new packaging solutions, and Comep, specialised in the development and production of moulds for PET containers, announced that they would combine their expertise as the new company Competek. A focus on sustainable solutions will help companies implement new regulations, for example with regard to tethered caps or rPET content. while Comep was known worldwide for the quality of its moulds. Starting from 2020, all Branding & Packaging Design services have been provided by Gentlebrand Srl, an independent Design Agency based in Italy, while PET Engineering’s and Comep’s technical teams have joined their forces to create a new company named Competek. We address the food, beverage and homecare packaging market with a 360° offer, from the engineering of new packaging until its implementation on existing lines. Thanks to the 20-years expertise of the team, we’re able to provide solutions for all lines and for any OEM platform. PETplanet: France has been selected as the new company’s registered office. What does this mean for PET Engineering’s Italian headquarters? Serre: The Competek headquarter is based in Cognac in France where our activities are coordinated. Our teams, however, are located worldwide, and we have different core expertises in Italy and in France, making both location key for the company. PETplanet: Have you already received initial reactions to the announcement from the industry? And if so, what were they like? PETplanet: You recently announced that PET Engineering, and Cognac Moules Emballages Plastiques (Comep) – a French producer and designer of PET moulds – have combined to form Competek. Can you briefly explain what considerations led to this merger? Serre: PET Engineering and Comep were providing similar services but with some peculiarities: PET Engineering was highly specialised in Packaging Design, Packaging Engineering and Line conversion services, F.l.t.r.: Alessandro Bortoluzzi, Operations director, Olivier Serre, Managing Director, Vittorio Carrer, Packaging Director, Competek Olivier Serre, Managing Director of newly formed Competek","@ID":24} "PREFORM PRODUCTION PETplanet Insider Vol. 22 No. 06/21 petpla.net 24 Netstal responds to the depleted PET market and rising prices. Tackling a shortage of PET raw materials In recent weeks, there have been shortages in electronic supply and mechanical parts as well as raw materials, with the latter also affecting the availability of PET. The reduced volumes have been caused by a variety of factors. While the European economy remains sluggish as a result of the pandemic, China’s is booming once again. Excessive demands for raw materials in China are placing huge pressures on stocks of European plastic. These shortages not only cause disruption to supplies but also result in higher prices. In addition, several force majeure measures have been introduced in Europe and worldwide in recent months. The lack of raw material for producing PET means that PET for preforms and bottles cannot be manufactured either. Nevertheless, production at PET processing facilities is continuing and noticeably increasing with the approaching summer months. In an interview with PETplanet, Stefan Kleinfeld, PET Product Manager, and Christina Härter, Head of Application Engineering at KraussMaffei HighPerformance, highlight the technological opportunities that using the new PET line will offer processors. PETplanet: Mrs Härter, Mr Kleinfeld – you say that some of your customers are short of raw material. This is particularly devastating with the approaching top-selling summer months in mind. Kleinfeld: Some of our customers are in a very difficult situation. There are delivery obligations that cannot be honoured as a result of the shortage of raw material. Härter: Larger customers are also being affected by the lack of supplies. The smaller ones are impacted either by reduced availability or higher prices and quite often by both. Recyclate could be an alternative, especially for PET, but even here the market is very limited. PETplanet: That doesn’t sound very encouraging. What solutions can you offer your customers? Kleinfeld: There is some excellent news to report on recyclate. The new Netstal PET line’s improved screw has enabled us to achieve even more robust processing of recyclate. It can be in the form of flakes and rPET, i.e. as processed recyclate, which provides a high level of flexibility for our customers. which meant that production could be started quickly. In the case of flakes, we have so far carried out tests up to a proportion of 50%, and in line with the decrease in bulk density, we have had a reduction in throughput of about half. (See Fig. 1) PETplanet: But the amount of post-consumer recyclable bottles has still not returned to its previous high levels either. Are there other solutions? Härter: A change from virgin PET to flakes will most likely not take place, with a switch to rPET planned instead in view of its quality. The additional processing phase mainly involves removing volatile substances such as benzene levels, which are adjusted as necessary. Incidentally, we also discovered during trials that minor changes needed to be made to our processing settings in switching from 100% virgin to 100% rPET. No extra modifications were necessary, Figure 1: Throughput in relation to flake content","@ID":26} "CAPS & CLOSURES 33 PETplanet Insider Vol. 22 No. 06/21 petpla.net square millimetre of contact surface, compared with steel. In the case of Heatlock’s KE0200305 spacers, four of which have a combined surface area of 490mm2 , heat loss savings would total 160Wh. The benefit to operating companies that use ceramic rather than steel spacers is to save energy on heating, give better hotrunner temperature control, improve recovery and give less work for the chiller to undertake, all leading to better part control and quality consistency. The greater insulation properties mean that more supports can be employed, with greater support area, improving mould rigidity and without high levels of heat loss. Due to the ceramics, there is an extremely small heat input from the manifold into the mould plates. The heating elements on both sides ensure a good and even temperature in the manifold. Nozzle tip detail for a particularly fine sensitive gating point. Heatlock says that its latest generation CE-FIX ceramic clamp technology, delivered within 5micron height tolerace, offers increased sustainability, ease of installation and adjustment. Tailored hot half systems Heatlock’s hot half systems are tailored for specific customer requirements. At Plastimagen Mexico 2019, the company announced its first partnership for caps and closures moulds, with TK Mold Shenzen, of China. Heatlock says that the partnership is dedicated to “providing high quality moulds of 32 cavities and under”, which it has identified as an opportunity gap in the market. The company claims that its hot half systems, which are all manufactured from P20 or stainless steel, are more affordable than equivalent systems from established global suppliers. As well as built-in flash memory with complete mould details and a Digital Project Book that includes all documentation for individual projects, including service information, Heatlock’s hot half systems come with a full range of standard fittings and features. Insulation plates, high tolerance location elements, built-in service tools and service interval counters are all included as standard. Total quality commitment and global network Heatlock’s production processes are constantly monitored and improved using TQM (total quality management) Lean Sigma and TPM (total productive maintenance) BPM/ BPR (business process management/ business process re-engineering) techniques and tools. Its distribution network includes presences in most countries across the world with mould making or injection moulding manufacturers. www.heatlock.com High cavity hot runner with sliding nozzles Complete hot side from behind with a partially blanked insulation panel","@ID":35} "8 NEWS PETplanet Insider Vol. 22 No. 06/21 petpla.net European plastics manufacturers plan 7.2 billion Euros of investment in chemical recycling PlasticsEurope announces a significant increase in planned chemical recycling investment: from 2.6 billion Euros (US$ 3.2 billion) in 2025 to 7.2 billion Euros (US$ 8.7 billion) in 2030. To further accelerate investments in this technology and the transition towards a circular economy, PlasticsEurope calls for a harmonised and strong policy and regulatory framework. Chemical recycling is claimed to allow the recycling of plastic waste which is otherwise incinerated or sent to landfill and to deliver significant quantities of recycled material with virgin plastic properties. Scaling-up this technology, and delivering broader systemic change requires a tool kit that includes many solutions – diversification of feedstock, new infrastructure, business models, new materials, waste prevention and eco-design, amongst others. From an industry perspective, it is also vital that policy-makers create a policy and regulatory framework that provides certainty and incentivises further investment. Working with public and private partners via alliances at local, national and global level to encourage appropriate recycling, reuse and recovery of plastic waste pollution is key. With a projected contribution of 1,2 Mt of recycled plastics produced through chemical recycling by 2025, PlasticsEurope plays a leading role in delivering on the European Commission’s Circular Plastics Alliance target of 10 Mt recycled plastics used in European products by 2025. www.plasticseurope.org Registrations for K 2022 in high demand Now the deadline for registrations for K 2022 has been reached, the organisers report high demand for the trade fair which will be held in Düsseldorf from 19 to 26 October 2022. “K 2022 will again occupy the entire fairgrounds,” rejoices Erhard Wienkamp, Managing Director at Messe Düsseldorf. K 2022 will again welcome the “Who’s Who” of the international plastics and rubber industry to Düsseldorf. Some 3,000 companies from all continents have registered to exhibit their developments in the segments raw materials & auxiliaries, semi-finished products, technical components & reinforced plastic products, machinery and equipment for the plastics and rubber industry. The three major guiding themes of K 2022 will be: Circular Economy Digitalisation Climate Protection These leading themes will be echoed by both the exhibitors’ presentations and in the focus of the official special show “Plastics Shape the Future”, the Science Campus and VDMA’s Circular Economy Forum. The physical event on site will be extended to include additional digital content. www.k-online.com Food & Drink technology (fdt) Africa 2021 cancelled Food & Drink technology (fdt) Africa, the premier trade fair for the processing, filling, packaging and logistics for Africa’s food and beverage industry, has been cancelled. Suzette Scheepers, CEO of event organisers Messe Muenchen South Africa, says the event, which had been scheduled to take place at the Gallagher Convention Centre in Johannesburg from November 2-4, 2021, will not go ahead this year due to uncertainty in the market and ongoing travel bans and restrictions as a result of the Covid-19 pandemic. Further supporting the decision to cancel the event is President Cyril Ramaphosa’s recent announcement of the strengthening of restrictions as the country moves into its 3rd wave of Covid-19 infections. Under these restrictions, all gatherings are limited to 100 people indoors, and 250 people outdoors. “As a key pan-African industry event, fdt Africa was scheduled to be co-located with Ifat Africa and Analytica Lab Africa; a combined and broad-reaching event that traditionally brings together thousands of pan-African and international stakeholders for knowledge sharing and product discovery. However, due to the current circumstances, we concluded that we could not assure our valued sponsors, exhibitors and visitors of the traditional levels of international engagement.” Scheepers says. www.fdt-africa.com Suntory Beverage and Food GB&I invests £6M in sustainable packaging goals Suntory Beverage and Food Great Britain & Ireland (SBF GB&I) is investing £6M (US$8.5 million) in its Lucozade brand to help minimise its impact on the environment. From the end of this year, all of Lucozade Sport’s bottles will be made from 100% recycled plastic and will feature a label that is half the size of the original. Although they have always been recyclable, the new labels which feature on-pack recycling prompts, intended to ensure that the bottles can be sorted into the clear waste stream to be recycled back into bottles at UK recycling centres. In total the changes represent a saving of 3,500 t of virgin plastic and 9,000 t of CO2 , contributing towards SBF GB&I’s net zero and 100% sustainable plastic packaging ambition. Lucozade Sport’s new rPET bottles and reduced sleeve design have been endorsed by a raft of recycling organisations, including the Recycling Association, who praised the investment from SBF GB&I. “We have been critical in the past of brands using a full plastic sleeve around their bottles. Suntory Beverage and Food GB&I have gone above and beyond remedying this in their re-design, by not only minimising the plastic sleeve, and ensuring the whole bottle is recyclable, but they’ve moved to using 100% recycled material in its manufacture too,” Simon Ellin, CEO at The Recycling Association, commented on the initiative. www.lrsuntory.com","@ID":10}]}}
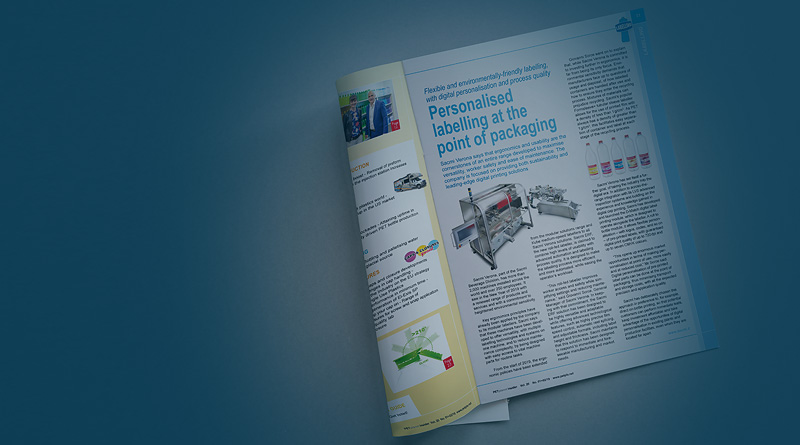