{"pages":{"page":[{"#text":"MARKET SURVEY 25 PETplanet Insider Vol. 22 No. 12/21 petpla.net SMI S.p.A. Via C.Ceresa, 10, 24015 San Giovanni Bianco (BG) - Italy +39 0345 40 111 www.smigroup.it Ms Daniela Dadda Marketing Department +39 0345 40.318 [email protected] Automatic machines for packing plastic, metal, cardboard or glass containers; packs in film only, cardboard pad + film, tray only, cardboard tray + film SMI designs and manufactures a wide range of fully automated machines for secondary packaging: shrinkwrappers machines ; trayformers; overlapping cardboard sleeve multipackers; wrap-around casepackers and combined machines. The models available provide performances from 30 to 450 packs/minute (in triple lane), depending on the model chosen and on the type of product to pack. SMI shrink wrappers and case packers can be integrated with a SMI palletizer to form a “Packbloc” compact end-of-line system. Yes Yes Yes Yes Yes Yes Yes Yes Yes Thanks to the precise analysis of thermodynamic phenomena generated by the shrink process, SMI tunnel distributes hot air flows in an efficient and homogeneous way on the pack, thus ensuring its excellent quality at the end of the process. Available tunnel methan heated Single lane: smallest AFW serie (10,060 x 1,774 x 2,450mm) till the bigger size SK 1200 HS (18,752.5 x 1,774 x 2,450mm) Double lane: smallest LSK 32 (9,820 x 1,974 x 2,450mm) till SK 1202 HS (18,752.5 x 1,974 x 2,450mm) 1-3 Film: 30-100μm depending on the production speed and pack collation; cardboard: low wave corrugated cardboard blanks: 3mm thickness Depending on the machine model Manual sealing bar joins the films, film reels the machine is equipped with a dedicated reel truck, pneumatic blocking system and when the film ends, the machine stops, adjustment of the film length is electronic, equipped with a device for centering the printed film provided with reference mark CE The machine automation and control are entrusted to the Sercos Fieldbus technology; intuitive user interface for quick and easy management of end-of-line palletising operations; real-time machine diagnosis and technical support further enhance the machine control features. 35-100 packs/min (according to the size of the product handled and palletisation selected) Yes Yes Yes Yes Swiftandprecisemovements:Thecentralcolumn isactuatedbybrushlessmotorswhichguaranteedynamic,reliableandprecisemovementsofallaxesofoperation;machineautomationand controlareentrusted to theSercosFieldbus technology, featuringan intuitiveuser interface forquickandeasymanagementofend-of-linepalletisingoperations. Genius PTF - Fastlayer Genius PTF/A - Fastlayer Genius PP/PV Robby Pal Robby Pal with Fastlayer Conventional automatic palletisers steady pallet type with innovative layer preparation Conventional automatic palletisers moving pallet type with innovative layer preparation Conventional automatic palletisers steady pallet type for empty PET containers Robotic automatic palletiser Robotic automatic palletiser with innovative layer preparation. 10min 12min 15min 15min 10min Up to 330 layers/hour Up to 700 layers/hour Up to 330 layers/hour Up to 320 layers/hour Up to 320 layers/hour Yes Yes Yes Yes Yes Yes Yes Yes Yes Yes Yes Yes Yes Yes Yes -Operationalflexibilityand furtherreduction in change-over times -Optimisationofcycle to increaseperformance, with improvedcontrolof thedifferentmovements usingstate-of-the-artelectronicsolutions -Customisationof thegrippingsystemand layer transferaccording to theproduct tohandle -Designed toacceptavariablenumberof product infeeds -Fullyautomaticsystemrequiring limitedoperator intervention,operating incompletesafety -Possibility tohandleallmainpalletson the market trouble-free,withcustomisablesolutions -Layerpreparationwithactivepackorientation andarrangementwithrobots -Operationalflexibilityand furtherreduction in change-over times -Optimisationofcycle to increaseperformance, with improvedcontrolof thedifferentmovements usingstate-of-the-artelectronicsolutions -Customisationof thegrippingsystemand layer transferaccording to theproduct tohandle -Designed toacceptavariablenumberof product infeeds -Fullyautomaticsystemrequiring limitedoperator intervention,operating incompletesafety -Possibility tohandleallmainpalletson the market trouble-free,withcustomisablesolutions -Layerpreparationwithactivepackorientation andarrangementwithrobots -Operationalflexibilityand furtherreduction in change-over times -Optimisationofcycle to increaseperformance, with improvedcontrolof thedifferentmovements usingstate-of-the-artelectronicsolutions -Customisationof thegrippingsystemand layer transferaccording to theproduct tohandle vacuumheadavailable forwide mouthcontainers(i.e. jars). -Designed toacceptavariablenumberof product infeeds -Fullyautomaticsystemrequiring limitedoperator intervention,operating incompletesafety -Possibility tohandleallmainpalletson the market trouble-free,withcustomisablesolutions -Completerange tohandledifferent typesof containersandproducts: layer,rowandmultiheadand looseproductpalletisingsystems -Flexibleandmodularsolutionwithreduced footprint -Customisationof thegrippingsystemand layer transferaccording to theproduct to handle -Designed toacceptavariablenumberof product infeeds -Fullyautomaticsystemrequiring limited operator intervention,operating incomplete safety -Possibility tohandleallmainpalletson themarket trouble-free,withcustomisable solutions -Completerange tohandledifferent typesof containersandproducts: layer,rowandmultiheadand looseproductpalletisingsystems -Flexibleandmodularsolutionwithreduced footprint -Customisationof thegrippingsystemand layer transferaccording to theproduct tohandle -Designed toacceptavariablenumberof product infeeds -Fullyautomaticsystemrequiring limited operator intervention,operating incomplete safety -Possibility tohandleallmainpalletson the market trouble-free,withcustomisablesolutions -Layerpreparationwithactivepackorientation andarrangementwithrobots","@ID":27} "BOTTLING / FILLING PETplanet Insider Vol. 22 No. 12/21 petpla.net 16 New bottle design for Iraqi National for Food High-speed PET packaging line Sidel has successfully installed its first high-speed PET packaging line for water in Baghdad as part of the greenfield project of Iraqi National Company for industrial food (Iraqi National for Food). With a speed of 48,000 bph, the line corresponds closely with the sustainability standards provided by Sidel. The new Dinar bottle produced for Iraqi National for Food comes in three sizes and is manufactured with a light preform, based on Sidel’s StarLite design. Iraqi National for Food belongs to the Iraqi National Group of Companies, which is one of the country’s leading companies in manufacturing, trade and transportation. Founded in 2019, Iraqi National for Food is recognised for its nutritional products. The company has many self-owned brands – including “Hindrin” carbonated soft drinks, “Dinar” healthy water and “Ra’eege” pasteurised juice. Iraqi National for Food initiated the new greenfield project to meet a growing demand for bottled water. After witnessing and experiencing Sidel’s solutions at two customer sites in Turkey, Iraqi National for Food chose Sidel as their partner to install the complete PET water packaging line. Two firsts in Baghdad: high-speed PET water line and light preform Following an analysis of the market and the customer’s requirements, Sidel proposed a complete PET packaging line for water featuring a Sidel Combi as a turnkey solution, covering the entire process from packaging design to equipment supply. It thus became Sidel’s first and fastest high-speed line in Baghdad. The 48,000 bph line has a line efficiency of 96%, Sidel said. The complete line solution are claimed to provide high sustainability standards which are of importance to Iraqi National for Food. For example, at the beginning of the line, Sidel’s EvoBlow blower fitted with the AirEco2 double air-recovery option reduces the required volume of compressed air by 35%. Furthermore, the Sidel Matrix Filler SF100 reduced filler enclosure provides a smaller filling environment with fewer chemicals and less water used during external cleaning. The air filtration system used in the filling process keeps the environment safe while ensuring high product quality. In terms of packaging design, the bottle is designed and manufactured in three sizes (330ml, 500ml, 1,500ml) with a light preform based on Sidels StarLite. Close cooperation overcomes lockdown obstacles To complete the installation on time, Sidel and Iraqi National for Food cooperated closely during this period, overcoming numerous logistic challenges posed by the lockdown further to the Covid-19 pandemic. “The situation made the process of dispatching our installation team as well as arranging spare parts more difficult. Although the line arrived at the site","@ID":18} "PETplanet Insider Vol. 22 No. 12/21 petpla.net 38 Healthy from Switzerland Trivarga AG from Zurich sells four different low-calorie, non-carbonated soft drinks under the brand name “moonspring”, based on natural ingredients with individual additions of Q10, folic acid, taurine and caffeine. They are vegan, gluten-free, preservative-free and gently aseptically bottled. For the naming and description concept, the sleeve labels are colourful and eye-catching with a small transparent window for a direct view of the product. Each of the transparent bottles contains 500ml and is closed with a screw cap with brand logo printing. www.planetmoonspring.com Salad sauce from Thomy In Switzerland, the Thomy brand, which belongs to Nestlé, has a wider range of ready-to-eat salad sauces on offer than in Germany. Among them is a sauce with Aceto Balsamico di Modena. The product also contains sunflower oil and herbs. It is free from gluten, lactose, flavourings and preservatives. 450ml are filled in a handy waisted bottle with sleeve label and screw cap. A transparent strip allows a view of the product and a quick check of the filling quantity. www.thomy.ch","@ID":40} "MARKET SURVEY 23 PETplanet Insider Vol. 22 No. 12/21 petpla.net 12/2021 MARKETsurvey Palletising and shrink film machinery To conclude this years market survey overview the issue focuses on palletising and shrink film machinery. Here you find the machine details of state of the art technology from participating companies: SMI S.p.A., Sidel, Krones AG, KHS Group, Jiangsu Newamstar Packaging Machinery Co., Ltd., And & Or and Sipa S.p.A. Although the publisher have made every effort to ensure that the information in this survey is up to date, no claims are made regarding completeness or accuracy. Company Sidel KHS Krones AG Jiangsu Newamstar Packaging Machinery Co., Ltd Postal address Telephone number Web site address Contact name Function Direct telephone number Email Rue du Commerce, 67116 Reichstett, France +33 388 183 880 www.sidel.com Mr Piero Zamboni PR Manager +39 521 999452 [email protected] Juchostraße 20, 44143 Dortmund, Germany +49 231 5690 www.khs.com Mr Ernst van Wickeren Product Manager Packaging +49 2821 503 200 [email protected] Böhmerwaldstraße 5 93073 Neutraubling, Germany +49 9401 70 0 www.krones.com Mr Andreas Fritsch Product Management Packaging Technology +49 8031 4040 [email protected] No. 8 Xinjing East Road, Zhangjiagang Eco- andTechnological Dev.-Zone, Jiangsu Province, China, 215618 +86 512 5869 1111 www.newamstar.com Mr Wesley Yin Marketing Manager +86 512 56993303 [email protected] Shrink film machinery: Packaging options & output rate (packs/min) - print registered film (yes/no; packs/min) Yes, up to 120 cycles per minute (PET bottles), 150 cycles per minute (cans) in 3 lanes Yes, 540 packs/min Yes, 150 x 4 = 600ppm Yes, 60 - nested pack (yes/no; packs/min) Yes Yes, 80 packs/min Yes, 100ppm No - label orientation (yes/no; packs/min) Yes No No No - carry handles (yes/no; packs/min) No Yes, 240 packs/min Yes, 80 x 2 = 160ppm No - pad supported (yes/no; packs/min) Yes Yes, 110 packs/min Yes, 120 x 2 = 240ppm Yes, 60 packs/min - tray supported (yes/no; packs/min) Yes Yes, 120 packs/min Yes, 120ppm Yes, 60 packs/min - film only (yes/no; packs/min) Yes Yes, 540 packs/min Yes, 150 x 4 = 600ppm Yes, 80 packs/min - tray and film (yes/no; packs/min) Yes Yes,120 packs/min Yes, 120ppm Yes, 80 packs/min - pad and film (yes/no; packs/min) Yes Yes, 110 packs/min Yes, 120 x 2 = 240ppm Yes, 80 packs/min Shrink process: - shrink tunnel with hot air or gas fired opt. Yes With electricity or gas fired (option) Yes Yes - oven Yes Yes No Yes - steam tunnel No No No Yes Footprint Depend on configuration 4m, 6m or 8m long Depends on speed Number of possible lanes Up to 3 4 4 With 1 or 2 lanes Packaging material and possible thickness Low-density polyethylene (LDPE) from 27-100μm Shrink film 25-80μm thickness; corrugated board: B,C, E and F-Flute Film, min 25-120 60μm~80μm Voltage/power/energy consumption NC Voltage: standard 3x400V; power: min. 22kW - max. 48kW; energy consumption: depending on requirements Depends on speed, package and material AC380V, 50Hz, about 110kW Film cutting and feeding system Yes Continuous feeding system from a roll Yes, fully automatic feeding, splicing, welding Yes Certification CE certification Compliant with 3c certification Palletising machinery: Format changeover time Depend on configuration Fully automatic changeover available - 0min operator time Depending on machine type, automatic changeover and manual changeover (5 to 10min) 20min Output rate (packs/min) Up to 12 layers/min Same as packaging machine 100-650lph (layers/hour) 120 Automatically intergrated: (yes/no) If necessary Yes Empty pack feeding Yes, empty pallet feeding Yes Yes Auto Insertion of interlayers Yes Yes Yes Auto Connectable to shrinkwrapper Yes Yes Yes Yes Special characteristics: i.e. low-level feed, cross conveyer barrier Available on high and low level infeed High speed with low level infeed Low-level feed, cross conveyer barrier Resins & additives Preform machinery Preform production & inspection systems Preform & SBM mould manufacturer SBM 2-stage Compressors Caps & closures & inspection systems Filling equipment & inspection systems Recycling machinery Palletising & shrink film machinery","@ID":25} "34 TRADE SHOW REVIEW PETplanet Insider Vol. 22 No. 12/21 petpla.net The right tools and expertise to help with your rPETgoals! Agr is uniquely positioned to support your venture into rPET bottle manufacturing with a powerful combination of Process Control tools, Process Consultants, and decades of industry experience. AGRINTL.COM • +1.724.482.2163 More homogenous injection brings benefits Stand 2105 in Hall A2 at the Fakuma trade fair was the showcase for Promix, an equipment manufacturer for plastics processors from Winterthur in Switzerland. Dr Markus Murr, Sales & Market Manager, showed us the PET mixing nozzle launched in the spring that offers constant material homogeneity and better temperature distribution during the injection process in preform manufacturing. The mixing nozzle should simultaneously optimise several areas in preform creation. At the trade fair stand, the manufacturer showed this type of mixing nozzle in cross-section to enable viewers to better visualise the technology; this offered a view of the internal, mesh-like strutting that ensures the advertised homogeneity. “The mixing nozzle was designed for quick injection times and high pressures. Its use in high-cavity moulds should prevent aberrations from local AA concentrations so as to ensure a more homogenous AA content in the preform through better dispersion in the melt flow,” explained Dr Murr. “So savings can be made for example on AA blockers, which lowers production costs. Consequently, any migration of the blocker into the food would also of course be prevented.” According to Promix, the use of the PET mixing nozzle could frequently mean that AA blockers might not be needed at all. “On average, local AA peaks can be reduced by 20-30% whereby all cavities are within the permitted limit values,” continued Dr Murr. Incidentally, the mixing should also achieve a better temperature distribution overall within the preform thus fostering more homogenous wall strengths. This nozzle should also help to optimise colour distribution for coloured preforms. To illustrate this point, the manufacturer presented two plastic examples at the stand, one made with a conventional nozzle and one with the Promix nozzle. This latter showed a significantly more uniform colour. “To avoid colour streaks or inconsistencies in preforms, the processor often adds more colour,” said Dr Murr. “When using the nozzle, colour use and therefore the related costs can also be reduced.” And these optimised results are also achieved when using recyclate. If rPET is included in the mix, the improved homogenisation of the rPET flakes in the melt flow should likewise improve the colour distribution in the resulting coloured preforms. According to Promix, the PET mixing nozzle should be easy to retrofit into existing injection moulding equipment. www.promix-solutions.ch Promix’ stand at Fakuma Promix PET mixing nozzle","@ID":36} "31 TRADE SHOW REVIEW PETplanet Insider Vol. 22 No. 12/21 petpla.net CHT Group at PRSE in Amsterdam PETplanet Insider talked with Dipl. Ing. Sebastian Laux, Global Business Development Engineer Recycling Solutions at CHT Group PETplanet: After a long time, the PRSE show was one of the first presence events. What did you expect from the show? And were your expectations fulfilled? Sebastian Laux: Our expectations were more than fulfilled. We initially expected less participants this year, due to the ongoing uncertain situation in the world. However, participation of visitors and exhibitors was above expected and we had a lot of first engaging contacts, as well as new interesting R&D projects which made in our eyes the PRSE show a success. We primarily wanted to take the chance to exchange in detail with our existing and new customers. Secondarily, we also wanted to use the time for discussions with other stakeholders of the value chain to see how we all can contribute in the future to higher quality recycling. Due to the limited time, we will have further exchanges about the new projects after the exhibition, which is already a great start. PETplanet: Recycling is one of the most important factors in the large field of sustainability. Where can you find the CHT Group in this field? Sebastian Laux: CHT initiated sustainability projects many years ago. This resulted, for example, in the award of the “Responsible Care Mittelstandpreis” of the German Chemical Industry Association (VCI) in 2018 and 2019. In general, this topic guides both the corporate vision: “The CHT Group, the preferred partner and leading reference for sustainable chemical solutions in our markets” and the supporting mission: “With smart chemistry, we make our contribution to sustainability”. Furthermore, the newly created position of “Chief Sustainable Officer” and the nomination as an important pillar of the Strategy 2025, show that sustainability is energetically considered as a strategy. In addition to a fundamental CO2 reduction, the use of recycled raw materials and biodegradable products as well as the expansion of the recycling business are strongly to be promoted in the “Sustainability Roadmap”. In PET recycling, we have been supporting our customers for more than 13 years with individual formulations and strong technical support to make their processes more efficient and at the same time save important resources such as energy and water and to protect the environment. Decisive for the utilisation of the recycled PET are a processing as pure as possible as well as an optimal cleaning. Additionally, our efficient auxiliaries used in the recycling process, Tubiwash, Tubifoam and Tubiwet are biologically removable from the wastewater and therefore do not pollute the environment. Besides this, we offer products for an efficient wastewater treatment and support the further process steps of the recycled material, e.g. antisticking for film and bottle production, antistatics for fiber production. We as CHT Group contribute in different ways to a circular economy and a more sustainable future. PETplanet: What are the news or planned projects in the field of PET processing at CHT? Sebastian Laux: There are many interesting and challenging projects waiting for us and our partners. As the news inform us with high frequency about the last-minute recycling regulations from politics and new recycling goals of brands and associations such as Petcore, Plastic Recyclers Europe, EuPC and Ceflex, we need to adapt quick to the fast changing market requirements to be able to support the value chain with innovative solutions that allow their fulfilment. The requirements on a deinking process of PET packages or a delamination process of composite products including PET are two examples of the new projects which create new requirements compared to the well-known PET bottle recycling process. PETplanet: What do you think are the current and future challenges of PET recycling and how will CHT support recyclers? Sebastian Laux: I think we need to work on different situations such as education, infrastructure (collection & sorting) and technology. The earlier we start, the better. Additional to the whole plastic and recycling value chain, politics take a key role in preparing the infrastructure and guiding us, as consumers, to a smart circular economy. Consumers need to know the benefits of recycling PET packages, how to do it and why PET is in many cases more sustainable for packaging products than paper or glass. So far, the political decisions are often taken from emotions influenced by social trends, resulting in regulations that would have come to more sustainable solutions with the proper support of experts. Fruitful collaborations between politics, brands and experts from the plastic recycling industry will lead to though-out innovations, especially for new products like e.g. composite products, which do not yet have standard recycling solutions. We, as CHT Recycling Solutions, will keep supporting these developments with our expertise and advanced innovative process solutions based on a strong exchange with the PET recyclers and machine suppliers. Our cleaning solutions will be more important than before, regarding the new requirements and challenges in the PET recycling. Needless to mention that we already actively contribute to a sustainable average usage rate of 50% rPET in new products. www.cht.com","@ID":33} "CAPS & CLOSURES 19 PETplanet Insider Vol. 22 No. 12/21 petpla.net Krautkrämer: This is due to the neck support ring (NSR) diameter. Most current 1881 necks in the market are using a very wide neck ring diameter of 33mm. The cap then touches the ring when opened and can only be fixed at an angle of 160°. We recommend using neck support ring diameters of 31mm or even as low as 29mm as these neck support rings do not interfere with a 180° opening angle. You can see how well this works on an OGEU bottle which has this smaller neck ring. (Pictures above) And by the way, the smaller neck support ring also allows further weight reduction in the bottle neck. PETplanet: Which brings us to the neck geometry. Does the bottler have to switch to new geometries? Krautkrämer: This always has to be checked on a case-by-case basis. Bottlers can continue to use their neck finishes currently in use even though we highly recommend to reduce the neck support ring diameter. Nevertheless the new CSD neck GME 30.40 has been developed and is in the stage of market introduction. GME 30.40 provides a weight saving for neck and closure of 1.4g for NSR 33mm and even 1.61g for NSR 30mm. But, of course, I have to consider a bottler’s whole production system, can he/she make step-by-step changes, do they have to switch several lines at the same time etc.? As I said, there is no general answer. PETplanet: You said that the ClipAside is a ThisCap idea and that you have a licence to use it. Does that mean that other cap producers can also obtain a licence? Krautkrämer: Yes, and I think that is a good thing. Ideally one but no more than three technologies have to become established at large scale in our market so that we are able to produce the necessary unit quantities. In my view, it does not make sense to have a hundred different alternatives. Just providing the ClipAside for all neck sizes from 26-38mm involves a huge amount of effort and investment. We have already qualified and introduced the ClipAside for the PET 26 (GME 30.40), PCO 1881, PET 29/25 and PET 38 2- and 3-start. We can also supply samples for the PET 26/1-and 3 start, PCO 1810, PET 33-2 start and the Snap-on PET 26/10. We are well prepared to support our customers with large volume line trials and accompany them through the qualification and introduction process. PETplanet: Thank you very much, Mr Krautkrämer! Opening angle of 180° with narrow neck ring (left) versus an opening angle of 160° with wide neck ring (on the right) Individual test: Opening of various tethered cap solutions The Editourmobil at Bericap’s premises in Budenheim, Germany","@ID":21} "imprint EDITORIAL PUBLISHER Alexander Büchler, Managing Director HEAD OFFICE heidelberg business media GmbH Vangerowstraße 33 69115 Heidelberg, Germany phone: +49 6221-65108-0 fax: +49 6221-65108-28 [email protected] EDITORIAL Kay Barton Heike Fischer Gabriele Kosmehl Michael Maruschke Ruari McCallion Anthony Withers WikiPETia.info [email protected] MEDIA CONSULTANTS Martina Hirschmann [email protected] Johann Lange-Brock [email protected] phone: +49 6221-65108-0 fax: +49 6221-65108-28 LAYOUT AND PREPRESS EXPRIM Werbeagentur | exprim.de Matthias Gaumann READER SERVICES Till Kretner [email protected] PRINT Chroma Druck Eine Unternehmung der Limberg-Druck GmbH Danziger Platz 6 67059 Ludwigshafen, Germany WWW www.hbmedia.net | petpla.net PETplanet Insider ISSN 1438-9459 is published 10 times a year. This publication is sent to qualified subscribers (1-year subscription 149 EUR, 2-year subscription 289 EUR, Young professionals’ subscription 99 EUR. Magazines will be dispatched to you by airmail). Not to be reproduced in any form without permission from the publisher. Note: The fact that product names may not be identified as trademarks is not an indication that such names are not registered trademarks. 3 PETplanet Insider Vol. 22 No. 12/21 petpla.net Dear readers, The Editourmobil is back on the road again! We were only able to carry out the West Pacific Tour 2020 via podcast and telephone interviews, but we have now started our tour which will ultimately take us to Drinktec in Munich. Due to the current situation, we are limiting ourselves to Europe, travelling only to those countries permitted under Covid-19 restrictions. We began with three appointments, more or less on our doorstep. In this issue you can read the interview with Alexander Krautkrämer, CEO of Bericap, on the subject of tethered caps. Much has happened on this over the past few months. The subject has dominated discussions at recent trade fairs. What will the cap look like in principle? The multinationals seem to be focusing on the Clip Aside cap. Current thinking is that this cap is consumer-friendly. We also report on our visit to the Plastic Recycler RCS Plastics. There, PET disposable bottles are recycled into PET reusable bottles. New plant has been ordered and will be added in 2022 to increase the granulate capacity to 50,000 t/a. At this point I would like to draw your attention to our third visit to Christian Wagner, CEO of the preform mould manufacturer MHT. Here, too, the theme of tethered caps was very much to the fore. MHT – an independent subsidiary of Krones – has invested heavily in the automated production of neck rings in order to be prepared for the expected conversion of moulds to new neck geometries. You will be able to read this interview in issue 1+2 / 2022 as part of our Caps & Closures Special! I wish you a very Happy New Year. Stay safe! Yours sincerely, Alexander Büchler Cover: 66 feet (20m) soda pop bottle sculpture at Route 66 (photo: Melissa Kopka via iStock)","@ID":5} "MATERIAL / RECYCLING PETplanet Insider Vol. 22 No. 12/21 petpla.net 12 Tour Sponsors: Growth potential included Bottle-to-bottle recycling at its best Back on the road on our Editour through Europe we stopped at the waste management company and plastics recycler RCS Plastic in rural Werne, Germany. Here we met the managing director Mr Alexander Rimmer with whom we talked about his state-of-the-art recycling plant. He gave us his opinion on the current situation of PET recycling and told about his expansion plans with another Erema Vacunite granulation system. Perfectly connected to motorways and major European ports as well as railways, he is investing in a sustainable future. PETplanet: Mr Rimmer, at what point and why do you recycle plastic at RCS? Rimmer: The company was founded in 1985 by the brothers Gerhard and Franz-Josef Francke in Werne. They started with the collection and marketing of paper and cardboard and have developed significantly since then. We now employ 170 people at two locations in Werne. In 2011, we started recycling PET bottles into unmixed PET flakes and in 2020 we started producing granulate at our new location. PETplanet: What types of plastic do you recycle and where do you source your material? Rimmer: So far, we have recycled disposable PET bottles. The material comes from the German deposit system of retailers. Various machines are used for recycling: The sorting is done by the sorting system of Stadler, the washing part is an own construction of our company and the granulation is done by a Vacunite system of Erema. PETplanet: What process steps does the material go through? Rimmer: The material is delivered to us from the deposit system and sorted in the first step by the Stadler sorting plant, where contaminants are sorted out and the PET bottles are divided according to colour. In the next step, the PET bottles pass through the RCS washing facility for cleaning, where CHT detergents are used. For granulation, the PET flakes are sorted by a flake sorter from Unisensor to ensure quality and then go to the Erema Vacunite granulation system and the SSP system from Polymetrix. (See issue 10/2021 PETplanet) PETplanet: What capacities are currently available to you and are you planning any expansions? Rimmer: We currently have a granulate capacity of 16,000 t/a. Next February, we will receive a second granulation plant of Erema and will thus be able to increase the capacity to 50,000 t/a. PETplanet: For which industry do you produce rPET? Who are your customers? Rimmer: We mainly produce rPET for the food and beverage industry. Our customers are well-known brands in the food and beverage industry. PETplanet: What do you think is the biggest challenge of PET recycling? Rimmer: The biggest challenge in PET recycling is societal developments. Here in Germany, we can recycle PET very well because there is a welldeveloped deposit system. Through the deposit system, the PET bottles do not come into contact with any other substances, the quality of the material is thus ensured. This also ensures that the bottles are recirculated and thus recycled again and again. As a possibility for improvement, I suggest the spread of the deposit system in other countries, so that the collection and recycling of PET bottles can also be promoted throughout Europe. It is worth mentioning that the recycling rate for PET in Germany is over 97%, which is not possible in countries without a deposit system. Another suggestion is, and this is very important to me, a better cooperation and communication between the producers of food packaging and PET bottles with the recyclers, so that new packaging is produced according to the principles of “design for recycling.” PETplanet: What is your opinion on the EU directives? Rimmer: We are neutral towards the EU plastic directives. Through the legal requirements for beverage bottle manufacturers, we and other plastic recyclers receive support and more acceptance from the very top. In addition, the distinction between single-use plastics such as cotton buds, plastic cutlery or drinking straws, which will be completely banned, and singleuse plastics such as beverage bottles will raise awareness in society, as not F.l.t.r. Mr Alexander Rimmer, CEO at RCS and Ms Jessica Böckmann, Administration at RCS","@ID":14} "MOULD MAKING PETplanet Insider Vol. 22 No. 12/21 petpla.net 20 PET preform moulds for side-entry systems Rotated by 90° PET preform moulds from Otto Hofstetter AG are now also available for side-entry systems. The family-owned Swiss company relies on its proprietary Cavity-Lock stack design, with its proven track record in the top-entry world, supplying all corresponding EOATs ranging from 2 to 192 cavities. Otto Hofstetter. For example, in Austria, a 48-cavity preform mould for 1.5litre bottles has been running without a rebuild for 22 years; in Indonesia, a 96-cavity mould for 0.6 litre bottles has been in continuous service since 2007. The hot runners are also marathon performers. In Belgium, one of Otto Hofstetter’s hot runners has been in daily use since 2014, clocking up almost 16 million cycles and counting. Side-entry moulds A few months ago, the management of Otto Hofstetter AG decided to construct side-entry moulds for PET preform systems with horizontal robot removal. This means that PET preform producers can now enjoy the durability and high availability of Swiss moulds for both side- and top-entry platforms. The move from the proven topentry to side-entry moulds basically just required a rotation of 90 degrees. For this purpose, some small technical adjustments had to be made in the design. The result is side-entry MOULD MAKING In 1977, Otto Hofstetter AG engineered and constructed the first injection mould for the production of PET preforms. The client was the Continental Can Company, which had the mandate to produce new drinks packaging for Coca-Cola and Pepsi. The order consisted of 12 injection moulds with 16 cavities, many of which were designed to produce preforms for 2-litre bottles. Since then, many leading PET producers in Asia, North and South America, Australia, Africa and Europe are customers of these Swiss-made tools, which are manufactured using high quality components assembled with great care by skilled toolmakers. In addition to this craftsmanship, achieving the performance levels of the moulds from Uznach requires even more expertise. For example, refinements like OH Xtreme coating, which enabled a 72-cavity mould to complete more than 15 million cycles before its first maintenance. Or OH Xtra surface treatment, which reduces conventional average roughness (RA) from 0.2 to 0.3 microns to 0.05 to 0.1 microns. Otto Hofstetter is proud of the reliability of their cavity-lock mould design which the company claims has a longer service life than conventional feed-in designs, often needing revisions after 10 million cycles. According to the latest data from producers, this target is often exceeded, says 96-cavity side-entry mould 144-cavity side-entry mould","@ID":22} "BOTTLING / FILLING PETplanet Insider Vol. 22 No. 12/21 petpla.net 17 before the lockdown, the project execution was still hindered by the restrictions, especially because no one was allowed to travel to Iraq at the time. By tackling the dilemma together with the customer, Iraqi National for Food managed to arrange an exceptional flight for our team a few months after the lockdown,” explained Vedat Guler, Sales Director, Middle East at Sidel. The installation and start-up only took six weeks and the first sellable bottle was produced and launched on the market by the middle of June 2020. “We are very happy that we chose Sidel for our complete water line project, in particular during the pandemic. The Sidel team provided great consultancy and conducted efficient execution so that our product could be launched in a short period of time,” said Mohammed Jasim, Executive Manager at Iraqi National for Food. www.iraqinational-group.com www.sidel.com Iraqi National Group of Companies was established in the year 2000, with a capital of 13.5 billion Iraqi dinars as set of the companies with experience in industry, trade, transport and marketing. The companies are specialised in manufacturing and in putting products in the Iraqi market. The Groups vision is to provide foods of high nutritional value and high quality that enrich the lives of consumers every day.","@ID":19} "OUTER PLANET 46 PETplanet Insider Vol. 22 No. 12/21 petpla.net OUTER PLANET What is wild plastic? Wildbag – cleaning the planet Wilplastic sources plastic from beaches, landfills, illegal dumpsites and prevents more plastics from ending up there, polluting the planet. The company works with communities of collec- tors around the world to bring these materials back into the production cycle. The goal is to empower people while driving social and environmental change. How is wild plastic processed and when does it end up in ones hands ? First step: A collector collects the wild plastic in countries without a functioning waste system. Step 2: Where possible, the wild plastic is recycled by local recycling partners or shipped to Europe, where it is washed, melted down and granulated. Step 3: The granulate is then transferred to a producer in Germany where it is processed into Wildbags. Step 4: The Wildbag arrives in Hamburg from where it can be shipped. The 35l Wildbag 35l bag with virgin plastic (average from samples) 35l recycling bag Material Made from Wildplastic High percentage of virgin plastic High percentage of recycling plastic Weight per bag 19.17g 14.74g 19.75g CO2 emissions when the bag is recycled after use 21.39g CO2e 52.03g CO2e 17.83g CO2e CO2 emissions when the bag is incinerated after use 81.62g CO2e 98.36g CO2e 79.88g CO2e Impact cleans up the planet supports collectors no further impact no further impact Wildplastic states that the Wildbag cleans up the environment and saves CO2 . Whenever the Wildbag is recycled, it emits up to 60% less CO2 than a comparable trash bag made of virgin plastic. This is the case even though the Wildplastic is transferred from many parts of the world. The analysis refers to trash bags with a capacity of 35 l. All steps from the extraction of raw materials, transport and production to the end of the life cycle were included. A distinction is made between incineration and recycling. If the trash bags are used for residual waste, they will most likely be incinerated. If they are used for the recycling bin, they will most likely be recycled. The results were calculated using data provided by partners and LCA databases. A scientific model was used to calculate the emissions. The different reference products: 35 l bags with new plastic and recycling bags are composed of samples from different drugstores and supermarkets. The company sums up that the most environmentally friendly garbage bag is the one you don’t use in the first place, for trash you don’t create in the first place. www.wildplastic.com F.l.t.r. Mr Dieter Gottschalk, Co-Founder Wildplastic and Mr Rui Carvalho, General Business Manager at RCDPLAS Plastics Recycling","@ID":48} "MATERIALS / RECYCLING PETplanet Insider Vol. 18 No. 0/17 petpla.net 15 Achieving purity for food contact applications Pure PET flakes Reiling operates plastic recycling plants in Marienfeld, Hamm, and at Burgbernheim, their newest location. New guidelines have led to an increase in the volume of PET bottles collected and this influx of bottles means that full service is becoming increasingly important. Reiling offers an complete range of services, from collection (full service or DIY), through processing (converting bottles to flakes), to creating carefully controlled end products. Post-consumer PET bottles are delivered to Reiling’s facilities in compressed briquettes or bales. Before they can be processed, each bottle needs to be separated from the compressed mass, to enable it to be washed and sorted, according to colour. After shredding and washing, flakes undergo another cleaning and sorting process. Colour and material purity are of central importance for those who will eventually buy the flakes, as high-quality starting materials are needed to manufacture new products. Reiling Kunststoff Recycling says that it uses state-of-the-art equipment to efficiently process PET flakes, ensuring that buyers receive only recyclate with the highest material and colour purity. Flake Purifier+ systems from Sesotec play an important role in Reiling‘s PET sorting process. The sorting system is equipped with an array of sensors that make it possible to separate PET flakes according to colour, metal contaminants and type of plastic, in a single run. The latest models of Sesotec equipment are currently in use at Reiling facilities in Marienfeld and in Burgbernheim. Flake Purifier+ can be efficiently integrated into the overall system, offering precise fits for connections at material feeding and outlet points. Feed hoppers transfer PET flakes to the main conveyor for sorting. Material that is rejected from the main conveyor is automatically fed back into the system via a recovery lane, which provides the benefit that the majority of good material will be recovered; losses of usable material will minimised. Andreas Schragen, Managing Director of Reiling Kunststoff Recycling stated: “Our facilities have benefited from Sesotec’s reliability and competence for many years. The new Flake Purifier+ series makes it possible to achieve a closed material cycle. We can even guarantee flakes that are pure enough for use in food contact applications.” www.sesotec.com Sorting of PET flakes with Sesotec’s Flake Purifier (photo: Sesotec GmbH) Behind the Reiling name is more than a century of experience in collection and reclamation of recyclable materials. The German, family-run, recycling company provides a variety of services, including collection, transport and processing, to delivering high-quality recyclate. Their expertise makes them a valuable partner to industry, local government, trade, and dual recycling systems. GAWiSD featuringAutoJob ™ – job set up in seconds +1.724.482.2163 AGRINTL.COM ACCURATE • FAST • REPEATABLE SEE GAWIS4D IN ACTION Dimensional and thickness measurements for plastic containers and preforms. ®","@ID":17} "CAPS & CLOSURES 18 PETplanet Insider Vol. 22 No. 12/21 petpla.net Tour Sponsors: Consumer convenience with ClipAside Tethered caps will have to be used for disposable beverage containers up to 3 litres in the EU from 2024. Two years ago, we discussed a number of potential options. Today, the industry’s solutions seem to be caps that can be moved to the side on straps or with a hinge. We spoke to Alexander Krautkrämer, CEO of Bericap, about the current situation. PETplanet: Mr Krautkrämer, two years ago, we were sitting at this very table discussing the EU Single Use Plastics (SUP) Directive and what it would mean for the PET bottle cap. What has happened in the meantime? Krautkrämer: Our main focus two years ago was on developing and evaluating a number of ideas for a tethered cap. We also discussed whether new neck geometries would be needed, or if such a cap could be produced using existing neck geometries. PETplanet: Today, we are seeing the first designs appearing on the market: among the examples on the table we also see your ClipAside design on a 1.5 l OGEU water bottle for the French market. How did you get there? Krautkrämer: We spent a lot of time searching for a closure design that was both intuitive and convenient for the consumer as well as safe for the bottler to process on existing machinery. We finally decided on a licensed solution from ThisCap. The ClipAside closure can be handled easily without the consumer ever having opened a tethered cap before. We can manufacture the cap by slitting along the tamper band. We produced a sample run of 70 million, which was very satisfying. Furthermore, the ClipAside design convinced us with its consistent performance (e.g. opening angle) on all relevant neck finishes ranging from 26-38mm. We are currently supplying ClipAside for 29/25 and 38mm 3-start neck finish, and will start serial productions also for PCO 1881, GME 30.40 and 38mm 2-start within the next two months. PETplanet: In what way is this different from other tethered solutions on the market? Krautkrämer: We will see different designs and the market will decide which of these will prevail. There will be moulded and slit tethers, interferent and folded bands as well as solutions with and without protrusion. One advantage of ClipAside lies in the design of the straps that hold the cap in place. Our ClipAside model has parallel tethering straps. The parallel tethering straps give the cap more play, which means that the consumer cannot “overstretch” the cap when pushing it to the side. Even when pushed over at an angle of 180° to the bottle shoulder, the cap will spring back into an 180° position. Overstretching with trapezoidal tethers tends to break the tethers; hence one of the significant differences is not moulded versus slit, but it is parallel versus tethers under stress. The other big advantage for our customers is the flexibility of the slitting process. The new closure shell can of course be slit with standard or tethered slit. Which means: our customers can already today qualify and test their filling lines with the new closure design including a standard slit. Once they are ready for the market introduction with tethered caps, it is only a change in the slitting geometry which then does not require any further modification on the filling equipment. PETplanet: For 1881 neck finishes you are claiming an opening angle for ClipAside within a range of 160-180° whereas the slitted cap on the OGEU bottle fixes nicely at an 180° angle. Shouldn’t the 180° opening angle be the objective? Alexander Krautkrämer, CEO of Bericap OGEU water bottle with a slitted, tethered cap On the left: Parallel tethering straps; on the right: trapezoidal tethering straps","@ID":20} "27 PRODUCTS PETplanet Insider Vol. 22 No. 12/21 petpla.net PETproducts Investment in advanced technology for rPET and large-capacity packages Petka Mold, which is based in Adana, Turkey, specialises in the production of PET preform and blowing moulds, along with aftersales support and spare parts. The company has, from its earliest days, had a focus on advanced technological expertise to drive product improvement, including weight reduction and performance in operation. İt launched its first 32-cavity mould in 2006 and a 48-cavity mould the following year. Petka has made a habit of working closely with customers and leading brands in the PET industry, producing a range of mould types that are suitable for various injection and blowmoulding machines. İn 2018, for example, it launched its first 96-cavity hot runner and, the following year, it debuted its 56 GR 33 NF full cold half mould for the largest iced tea bottle in the world, with a capacity of 2.5 l. The company has embraced Industry 4.0 to make its own processes more interactive, automated and efficient. Implementation of lean production and Industry 4.0 systems in its factory has enabled Petka to drive down waste in its manufacturing processes, which has helped to improve quality and cycle time, while controlling costs. Technologies becoming widespread in the Fourth Industrial Revolution are, increasingly, being incorporated in machinery for the food and beverage packaging industries. It has the capacity to support customers with preform and bottle sampling in its technically advanced laboratory in Adana, Turkey. It provides sample preforms and bottles with detailed quality reports that enable clients to make informed, data-supported decisions about future investments. Petka has responded to issues of sustainability with, in particular, research and development of lighter and fully reusable packaging. It is also developing moulds that are suitable for the increased use of rPET. It works with and assists customers in all phases of product development, from initial design to series production. www.petkamold.com MOULD MAKING Minimised core shift Mold-Master’s Symfill technology is intended to minimise core shift to improve part quality (straightness) of cylindrical, centre injected components having an aggressive L/D ratio. It achieves this by allowing the melt to enter the nozzle runner channel from multiple sides as opposed to the single-entry point of traditional designs. Examples of such components that would benefit from this technology include blood tubes, needle shields, over caps and other similar parts from the medical, cosmetic and stationary industries. On recent blood vial applications that leveraged Symfill technology, barrel bow was reduced by up to 90% (as little as 0.15mm) by eliminating core shift. Symfill technology is exclusively available with Mold-Masters hot runner systems. Minimising barrel bow offers downstream processing advantages which includes enabling tubes to roll concentrically in the labelling machine; increasing final stage throughput and minimising machine downtime. Mold-Masters is a leading global supplier of hot runners, controllers, auxiliary injection and co-injection systems. The company design, manufacture, distribute, sell and service highly engineered and customised plastic processing equipment that caters to every market. www.moldmasters.com Symfill technology minimises core shift to improve part quality of cylindrical, centre injected components by allowing the melt to enter the nozzle runner channel from multiple sides (right) as opposed to the single-entry point of traditional designs (left).","@ID":29} "9 NEWS PETplanet Insider Vol. 22 No. 12/21 petpla.net Alpla establishes new Asia-Pacific region The Alpla Group, global packaging solutions and recycling specialist, has announced that it is strengthening its footprint in Asia. On January 1, 2022, the AsiaPacific (APAC) head office in Singapore will go live, with a new region being created from a merger of the former regions North East Asia and South East Asia. It includes current operations in China, Thailand, Vietnam and the Philippines. The APAC region will be managed by Roland Wallner, currently Alpla Managing Director North East Asia. With 2,750 employees, Alpla APAC sees itself well situated for the Asian packaging market. Alongside extending the reach of Alpla’s industry-leading moulding technology, a focus lies on the further development of circular economy activities in the region. www.alpla.com rPET100 Designed for recycling. Made from recycling. • Heat resistant • Fully recyclable • Thermoformable like PET BENEFITS HOT CUPS · DAIRY PRODUCTS · INSTANT SOUPS · TO-GO MEALS · COFFEE LIDS foodgrade without compromise Berry announces availability of EUCertPlast accreditation With the approaching UK Plastics Tax and increasing consumer interest across the whole of Europe in the provenance of their packaging, Berry Global announces the availability of certified recycled plastic from six of its UK sites. The investment in certification underlines the company’s commitment to its customers during this transitional period and extensive, long-term capabilities to provide packaging materials with a minimum of 30% recycled content that can be supported by independent accreditation. This capability will be of particular importance after April 2022, when the UK Plastics Tax comes into force for all plastic packaging, both UK manufactured and imported, that does not contain at least 30% recycled plastic. It will also help to support brands internationally, who are seeking to demonstrate their commitment to more sustainable packaging in the light of ongoing consumer pressures and potential future legislation in other countries. The EUCertPlast certification, which works to the European Standard EN 15343:2007, helps assure customers that best practices are being followed throughout the recycling process for pre- and post-consumer waste in terms of stock management of incoming waste, recycling process, quality management, staff training and qualifications, traceability in supply chain and environmental protection. The chain of custody provides full details of the origins of the waste material and the waste management company from which it was sourced. www.berryglobal.com","@ID":11} "PATENTS PETpatents PETplanet Insider Vol. 22 No. 12/21 petpla.net 39 Plastic bottle Intern. Patent No. WO 2019 / 220327 A1 Applicant: S.I.P.A. S.p.A., Vittorio Veneto (IT) Application date: 14.5.2019 Reduced-weight container made from PET for carbonated drinks. The base is specially shaped to make it sufficiently stable, despite its lightweight construction, and easy to manufacture. Multi-component preform Intern. Patent No. WO 2021 / 065705 A1 Applicant: Toyo Seikan Co. Ltd., Tokyo (JP) Application date: 25.9.2020 The application describes the design and the procedure for manufacturing a preform with an inner layer and an outer layer that is positioned underneath the neck ring. Bottle with separate handle Intern. Patent No. WO 2021 / 081227 A1 Applicant: Niagara Bottling Inc., Diamond Bar (US) Application date: 22.10.2020 Large-volume bottle (holds 1 gallon) with a separate handle and various reinforcement ridges that give the bottle sufficient stability during handling. Optimised, lightweight container Europ. Patent No. EP 3795484 A1 Applicant: Altium Packaging LP, Atlanta (US) Application date: 22.8.2017 Thin-walled, lightweight container still stable and shatterproof enough in all areas – especially the base. Connectable bottle Intern. Patent No. WO 2019 / 241246 A1 Applicant: Jeffrey Meyer, Pomona (US) Application date: 11.5.2019 The outside of a bottle is shaped in such a way that several bottles can be joined together. Shorter thread length Disclosure No. DE 102019007519 A1 Applicant: Gomez Cao Innovations & Inventions S.L., Barcelona (ES) Application date: 29.10.2019 Preform for a bottle with a matching cap. Bottle and cap are given features that offer retained functionality but require a lesser opening angle, thus a shorter thread and therefore lower material usage.","@ID":41} "35 TRADE SHOW REVIEW PETplanet Insider Vol. 22 No. 12/21 petpla.net Sponsors to date The worldwide round trip with EDITOURS Back to Europe The second part of PETplanet’s bipartite Drinktec Editour is right ahead! After the successful first part “From Down Under to Japan” in 2020, our second stage of the project takes us back to the flourishing European hub where we will be exploring the latest technologies, news, innovations and developments that move our PET industry. It is time for a new start, for renewal and for developing new ways of thinking. During and especially after the pandemic, it will be vital to make every effort to get the global economy back on track in the medium term. Sustainability will be the key. Once again, PETplanet will be at the forefront. It will again be a partner in Drinktec, the world’s leading beverage trade fair, which is to be held in Munich from 12-16 September 2022. After the success of our previous Drinktec Road Shows, in 2017 in South East Asia and 2020 in Australasia, we will be back on the road in Europe for a whole year. Starting in Autumn 2021 with our Editourmobil, we will be ready for a new get-together with the industry. We will be revealing the results of our meetings and discussions at Drinktec with the leading thinkers in PET processing, packaging and recycling. Apart from new technologies we will be also taking stock of how things stand. We will be asking how global thinking might change as a result of Covid-19. How will bilateral business relationships cope with the aftermath of the pandemic? What opportunities will there be for the drinks industry and its suppliers? Our planning, in terms of precise timeframes and details of the countries to be visited will be flexible, in order to take account of the rapidly changing pandemic situation. However, this much we can confidently say: in these challenging times we, as the voice of the PET industry, will be at the very heart of the roadshow as usual and are already looking forward to welcoming you back on board the Editourmobil! Share this exciting experience with us! Interested in being interviewed? [email protected] Let Your Inspiration Flow. 7KH (XURSHDQ 5RDG 6KRZ PART2 Empowered by drinktec Interested in becoming a Sponsor? [email protected] Autumn 2021 - 2022","@ID":37} "MATERIAL / RECYCLING PETplanet Insider Vol. 22 No. 12/21 petpla.net 13 EDITOUR 13 all single-use plastics are the same. PET bottles are ideal for recycling and the associated circular flow, which is not the case with disposable plastics such as cotton buds. Our work is influenced by the fact that the demand for rPET for the food and beverage industry has increased significantly and development potential can be deduced from this. PETplanet: How do you feel about the statement of the big brands from the beverage and packaging industry to produce their products from 100% rPET by 2025/30? Rimmer: In general, we find the goals of the big brands exemplary, but there is currently not enough rPET capacity. The Europe-wide structures for collecting PET bottles are lacking. We would currently recommend the production of beverage bottles from recycled material in the range of 50-75% so that there is no shortage of rPET resources and all brands can meet or even exceed the legal requirements. Should the situation in Europe change with regard to the deposit system, we see the use of 100% recycled material in PET bottles as quite realistic in the future. PETplanet: What is your position on chemical or monomer recycling? Rimmer: In general, we see chemical recycling as another possibility for recycling, as pyrolysis technology is used to recover a secondary material from the plastics. However, this process tends to focus on plastic waste that can no longer be mechanically recycled for technological, economic and ecological reasons. For example, contaminated plastics, waste fractions from different types of plastics that can no longer be sorted. In the future, it will be important that manufacturers of packaging and PET bottles work together with plastic recyclers so that the packaging is produced in such a way that recycling is economically and ecologically feasible. A combination of mechanical and chemical recycling would be optimal, so that plastics made of different types of plastic can also be recycled. This could significantly increase the recycling rates of plastics and thus contribute to a stronger circular economy. In the case of beverage bottles, on the other hand, mechanical recycling works very well and is also significantly cheaper than chemical recycling. PETplanet: My final question: Where do you see RCS in ten years? What are your strategies for the company in the field of plastics? Rimmer: We see a clear development potential in the future, especially in plastics recycling. In the future, we will not only recycle PET bottles, but also by-products such as closures or other types of plastic in general. With regard to the topic of sustainability, we would also like to develop further with photovoltaic systems on roofs and systems that correspond to the latest state of the art. We are also thinking, for example, of alternative drives such as hydrogen-powered trucks. PETplanet: Thank you so much! www.rcs-entsorgung.de/en www.erema.com www.sacmi.com Product design Product development Product validation Industrial production plant Process & quality control On-site and start-up assistance After-sales and Customer service SACMI 4.0 THE COMPLETE CLOSURE, PREFORM AND CONTAINER SOLUTION FOR YOUR SMART FACTORY ENDLESS INNOVATION SINCE 1919","@ID":15} "PETplanet Insider Vol. 22 No. 12/21 petpla.net 36 PETbottles Home + Personal Care Pril as limited edition Henkel uses recycled material for the bottle and cap of the limited edition of Pril with the addition “Meeresfrische”. The bottle is made of 100% recycled material from the Social Plastic Organisation, which supports people in poor countries without recycling systems for collecting plastic waste in nature with money or social benefits. In this bottle, the hinged cap is also made of 84% recycled material. The bottle contains 450 ml of the lightly coloured dishwashing detergent and is decorated with two self-adhesive labels. www.pril.de Care with hemp Beiersdorf has added a face and beard balm with a calming effect to its Nivea Men range with the name addition “Sensitive Pro”. The product uses 100% vegetable hemp seed oil and vitamin E and is said to soothe the signs of skin stress, calm the skin, make it look healthy, absorb instantly, be non-greasy and also ideal for beard care. The dark green coloured bottle contains 150ml and is made from 97% recycled material. The balm is dispensed via a screw-on, lockable pump dispenser. A plastic label with a stylised hemp leaf conveys all trade and application data. www.nivea.de Eyeglass rinsing agent with pomegranate In October 2021, Aldi Süd had a sales promotion on glasses rinsing agent. The product with pomegranate fragrance is supposed to clean glasses and lenses easily and prevent them from fogging up. The manufacturer of the product is Hyga GmbH & Co. KG. The browncoloured bottle contains 200ml of liquid, which is applied to the glasses already moistened with water via a lockable pump dispenser. The glasses are then cleaned by rubbing with the fingers, rinsed and dried. An adhesive paper label explains the ingredients and how to use the product. www.aldi-sued.de Express body lotion by Weleda The traditional German manufacturer of body care products with natural ingredients, the Weleda company, which celebrates its one hundredth birthday in 2021, sells 200ml of a body lotion with express moisture and citrus fragrance in a curved plastic bottle. What is striking about the bottle is that it has a non-slip, frosted surface except at the bottom. The closure is a hinged cap with a dosage opening. The two selfadhesive labels explain the product, ingredients and trade data. www.weleda.de","@ID":38} "MARKET SURVEY 24 PETplanet Insider Vol. 22 No. 12/21 petpla.net Company And & Or Postal address Telephone number Web site address Contact name Function Direct telephone number Email PI El Limon, Av. de Europa, 6, 41928 Palomares Del Rio (Sevilla) - Spain +34 954 779 200 www.andyor.com Mr Caridad Ortega Suárez Sales Director +34 954 779 200 [email protected] Shrink film machinery: Packaging options & output rate (packs per minute) - print registered film (yes/no; packs/min) No - nested pack (yes/no; packs/min) Yes, 15-900bpm - label orientation (yes/no; packs/min) No - carry handles (yes/no; packs/min) Yes, 15-400bpm - pad supported (yes/no; packs/min) Yes, 15-400bpm - tray supported (yes/no; packs/min) Yes, 15 -400bpm - film only (yes/no; packs/min) Yes, 15-900bpm - tray and film (yes/no; packs/min) Yes, 15-900bpm - pad and film (yes/no; packs/min) Yes, 15-900bpm Shrink process: - shrink tunnel with hot air Shrinking pistols (hot air) - oven Footprint Several models depending on speed Number of possible lanes Max. length of the pack is 1,400mm Packaging material & possible thickness LDPE + LLDPE 40-60μm Voltage/power/energy consumption Several models depending on speed Film cutting and feeding system Yes Certification CE and UL Palletising machinery: Format changeover time 15-20min Output rate (packs/min) Up to 400bpm Automatically intergrated:(yes/no) Yes Empty pack feeding Yes Insertion of interlayers Yes Connectable to shrinkwrapper Yes Special characteristics: i.e. low-level feed, cross conveyer barrier Low-level feed; tray former possible to be integrated (display palletiser) Company Sipa Postal address Telephone number Web site address Contact name Function Direct telephone number Email Via Caduti del Lavoro n. 3; 31029 Vittorio Veneto (TV) - Italy +39 0438 911511 www.sipa.it Mr Matteo Tagliaferri Marketing and Communication +39 0521 548111 [email protected] Palletising machinery: Genius PTF Genius PTF/V Genius PTF/A Genius PTF - Active Layer Conventional automatic palletisers steady pallet type Conventional automatic palletisers steady pallet type, with double platform Conventional automatic palletisers moving pallet type Conventional automatic palletisers steady pallet type with innovative layer preparation Format changeover time 15min 15min 18min 10min Output rate (packs/min) Up to 330 layers/hour Up to 420 layers/hour Up to 700 layers/hour Up to 330 layers/hour Automatically intergrated:(yes/no) Empty pack feeding Yes, empty pallet feeding Yes Yes Yes Insertion of interlayers Yes Yes Yes Yes Connectable to shrinkwrapper Yes Yes Yes Yes Special characteristics: i.e. low-level feed, cross conveyer barrier - Operational flexibility and further reduction in change-over times - Optimisation of cycle to increase performance, with improved control of the different movements using state-of-the-art electronic solutions - Customisation of the gripping system and layer transfer according to the product to handle - Designed to accept a variable number of product infeeds - Fully automatic system requiring limited operator intervention, operating in complete safety - Possibility to handle all main pallets on the market trouble-free, with highly customisable solutions - Operational flexibility and further reduction in change-over times - Optimisation of cycle to increase performance, with improved control of the different movements using state-of-the-art electronic solutions - Customisation of the gripping system and layer transfer according to the product to handle - Designed to accept a variable number of product infeeds - Fully automatic system requiring limited operator intervention, operating in complete safety - Possibility to handle all main pallets on the market trouble-free, with highly customisable solutions - Operational flexibility and further reduction in change-over times - Optimisation of cycle to increase performance, with improved control of the different movements using state-of-the-art electronic solutions - Customisation of the gripping system and layer transfer according to the product to handle - Designed to accept a variable number of product infeeds - Fully automatic system requiring limited operator intervention, operating in complete safety - Possibility to handle all main pallets on the market trouble-free, with highly customisable solutions - Operational flexibility and further reduction in change-over times - Optimisation of cycle to increase performance, with improved control of the different movements using state-of-the-art electronic solutions - Customisation of the gripping system and layer transfer according to the product to handle - Designed to accept a variable number of product infeeds - Fully automatic system requiring limited operator intervention, operating in complete safety - Possibility to handle all main pallets on the market trouble-free, with highly customisable solutions - Linear axes layer preparation with active pack orientation and arrangement","@ID":26} "8 NEWS PETplanet Insider Vol. 22 No. 12/21 petpla.net Drinktec 2022 edition 90% booked Drinktec, the trade fair for the beverage and liquid food industry, will take place in Munich from September 12 to 16, 2022. The organisers announced a current booking status of 90% of the floor space and expressed confidence that the demand for exhibition space will be comparable to the level of previous Drinktec trade fairs. Digital tools already available offer a lot of scope for making participation in the trade fair more efficient for exhibitors and visitors. Exhibitors at the trade show can highlight their expertise in the individual topic areas through entries in the Solutions Directory. This will already be of benefit in the run-up to the trade fair, since the Solutions Directory will be available online to search through from the end of 2021. Visitors will also be shown offerings for their own application areas directly on their mobile device with the help of the Innovation Guide, a service available to trade fair visitors. By defining the main topics, Drinktec intends to demonstrate the potential for investment decisions in the coming years. Messe München is implementing these main topics throughout the event through special areas, the allocation of the exhibitors’ own offerings to these main topics, and expert sessions in the forums. These main topics include: Sustainable production & packaging, Consumer landscape & product design, Water & water management, and Digital solutions & digital transformation Drinktec will already be starting from December 2021 with the online program, Drinktec Talk. In four online events on the main topics, expert presentations on current solutions will provide compact information and enable an exchange with the speakers. The webinar series will be offered live and in English, and comprises presentations as well as an open Q&A session in which the participants can also enter into dialogue. www.drinktec.com Bekum America opens its expanded manufacturing facility Bekum America Corporation has completed construction of an expanded machine production facility to meet the high demand for Bekum extrusion blow moulding machines. The new facility adds 3,700m2 (40,000 square feet) of manufacturing and 690m2 (7,400 square feet) of office space to Bekum’s existing 10,700m2 (115,000 square foot) facility. This expansion will allow Bekum America to increase machine output, shorten lead times and will result in continued expansion of the workforce. Bekum America’s manufacturing team proudly shipped the first machine from the new machine assembly hall in May and will be busy in the months ahead fulfilling current machine demand. In addition, Bekum America will host a Customer and Community Open House on September 29 – October 2, not only to formally dedicate the new building, but to also showcase Bekum’s new state-of-theart manufacturing facility. www.bekum.com Quva signs agreement to acquire a 57.51% stake in Resilux Quva NV has reached an agreement to acquire, via a subsidiary to be established (“Bidco”), all of the shares of Resilux NV held by the Reference Shareholders, representing a total of 57.51% of the issued shares in Resilux. The purchase price payable by Quva for the Resilux shares acquired from the Reference Shareholders is equal to EUR 235 per share. The completion of the acquisition is still subject to merger control approval. The acquisition will be followed by a mandatory tender offer for the remaining shares of Resilux. Following completion of the acquisition, Quva (via Bidco) will launch a mandatory public tender offer for the remaining shares of Resilux at a price equal to EUR 235 per share. Quva anticipates that the acquisition will be completed and the Mandatory Tender Offer will be launched in Q1 2022, subject to the relevant approvals being obtained. www.resilux.com www.quva.com German Technology Innovative hotrunner optiRun","@ID":10} "33 TRADE SHOW REVIEW PETplanet Insider Vol. 22 No. 12/21 petpla.net Koch-Technik draws positive conclusion of Fakuma 2021 Koch-Technik presented its complete portfolio of mixers, dryers, dosing units and central conveying systems at a larger stand than in 2018. The highlight of the stand were the new Eko-N dry-air driers as well as the control units of the generation MC7, which now also serve for the gravimetric mixers Graviko and the mobile dry-air driers KKT. „In the run-up to this year´s Fakuma we did not know how well the on-site trade fair would be frequented. Despite the lower number of visitors in comparison to the years before, it was a successful trade fair. Especially the personal dialogue with the professional visitors as well as the quality of the talks were positive. Furthermore, there are some signs, that especially in the automotive sector, there is only cautious optimism due to the difficulties in procurement. Particularly pleasing is that our totally new trade fair stand was perceived very positively after the involuntary break“, as CEO Carsten Koch sums up. www.koch-technik.com F.l.t.r. Werner Koch, CEO at Koch Technik, and Heike Fischer, PETplanet Insider Engel: Fakuma 2021 inspires injection moulding industry Fakuma 2021 was a great success for Engel. “The positive trade fair experience underlines the economic upward trend and is driving investment in new technologies,” as Dr Christoph Steger, CSO of the Engel Group, emphasises at the conclusion of the industry event in Friedrichshafen. “Our customers grasped the opportunity to finally exchange ideas in person again and experience innovations in real and live terms.” The industry’s first major live event after the automotive crisis and Corona pandemic took place at exactly the right time. “The automotive industry has come back with a bang, and the investment backlog has cleared,” says Steger. “Even if the Corona pandemic is still preventing some travel, Engel’s stand was well attended. We had some excellent talks, concluded numerous projects and got new ones underway.” Visitors came from all industries. Besides the automotive industry, the medical technologies, packaging and technical moulding sectors were strongly represented. Leveraging the full potential of the machines In particular, innovative solutions for more sustainability in injection moulding and further digitalisation of production processes were met with great interest. The two topics are closely linked. “Digitalisation is an important precursor to the circular economy”, said Steger. “Smart assistance systems and interconnected systems help us to leverage the full potential of injection moulding machines, for more efficient production while reducing the CO2 footprint.” Engel’s trade fair stand made this vividly clear. Compared to the last Fakuma, Engel’s stand has become larger. The additional space was used to present digital products and solutions. The machine exhibits also demonstrated the new opportunities for the circular economy. Engel presented a closed process chain for polypropylene involving the production of mono-material food packaging using IML thin-wall technology and the production of protective covers from label offcuts. At the same time, the Engel e-speed 420 injection moulding machine celebrated its world premiere. “Hybrid and all-electric injection moulding machines are seeing deployment in an increasing number of applications,” says Steger, emphasising another trend that was reflected at Engel’s stand. Demanding precision applications gave insights into the performance of the various hybrid and all-electric machine series by Engel during the five days of the trade fair. Machine exhibits are still in the virtual showroom at Engel’s virtual world. www.engelglobal.com/virtual-world New dosing and mixing units With the Minicolor SG V, Motan introduced a new variant of the volumetric dosing and mixing unit series. The unit covers important requirements for the dosing of additives and ensures mixing quality with a high dosing and repeat accuracy, said Motan. The dosing and mixing unit is mounted directly on the feed opening of the processing machine and is therefore space-saving. The user-friendly microprocessor control of the Minicolor SG V can either be used for injection moulding applications or extrusion operation. The modern 7” graphic display visualises the dosing rates and supports calibration. Dosing speed is calculated automatically according to the calibrated weight and recipe. Dosing granulate with patented slider technology The new gravimetric batch dosing and mixing unit for granules Gravicolor 110 is specially designed for injection moulding, blow moulding and extrusion processes. With the system, up to four different components can be mixed precisely and with the high recipe accuracy. All components are dosed with a specially designed vertical slider. In the event of a recipe or material change, the existing material hopper can continue to be used through the variable slider opening. The slide opening is flexibly adjusted by input on the control panel by a stepper motor. The integrated IntelliBlend analysis function makes it possible to precisely record and document the recipe, material and operating environment. www.motan-colortronic.com The Gravicolor 110 dosing and mixing unit with patented slider technology for injection and blow moulding as well as extrusion processes Minicolor SG V, a dosing and mixing unit for granulates","@ID":35} "28 TRADE SHOW REVIEW PETplanet Insider Vol. 22 No. 12/21 petpla.net PRSE Amsterdam review Record numbers attend Plastics Recycling Show Europe 2021 The 5th Plastics Recycling Show Europe (PRSE) exhibition and conference hold November 4-5, 2021 in Amsterdam, Netherlands, attracted a record number of visitors and exhibitors from across Europe. The annual event had a total attendance of more than 4,400 over two days and attracted over 180 exhibiting companies. Over 3,500 attended the in-person event and nearly 900 others attended virtually. Opened in a virtual presentation by Virginijus Sinkevičius, Commissioner for the Environment, Oceans and Fisheries at the European Commission, the two-day PRSE conference showcased the latest developments in plastics recycling technology and applications, as well as exploring future industry challenges and the legislative landscape within the EU. Unique in Europe, PRSE brings together exhibitors, visitors and Plastics Recycling Awards Europe finalists representing the whole value chain of the plastics industry including recyclers, machine producers, raw material producers, converters, waste management companies and, increasingly, brand owners, retailers and investors. The hybrid event this year also allowed people unable to visit the event in person to view elements of the conference programme via livestream including the welcome address, keynote speeches and sponsored presentations as well as the announcement of winners of the Plastics Recycling Awards Europe. Online-only visitors were also able to interact directly with exhibitors. The Plastics Recycling Show Europe returns to Hall 12 at RAI Amsterdam on June 22-23, 2022. PETplanet has compiled some highlights from the PET sector and beyond in this second part of our review. www.prseventeurope.com Taking a holistic approach to PET packaging with AWArPET PET bottles containing post-consumer recycled material – rPET – have in a relatively short time become a common sight, rather than the exception that they were just a few years ago; use of rPET is destined to increase further, with a growing number of bottles made in 100% rPET. Sipa has built up experience through its expertise in bottle design and in process technologies to enable the use of rPET. This means not only creating designs that take into account differences and variations in processing characteristics of rPET, but also other less obvious factors such as the increased level of powder that rPET processing creates (more on this later). Containers incorporating rPET will only be accepted by brand owners and consumers if they perform as well as containers made from virgin material. That means rPET arriving at the converter has to be clean and consistent, and with processability during preform production and bottle blowing that is almost, if not exactly, the same as virgin PET. A new brand - AWArPET These days, Sipa’s product design experts are involved in the development of 3,000 or more new packaging designs every year. The three R – Reduce, Reuse, Recycle – are constant principles in all of these projects, as the company states. Sipa has now established a new brand – AWArPET – which stands for an environmentally conscious approach to the design and production of PET packaging. The Green Plastic Factor AWArPET bottles are very light. Sipa has for example been involved in one design project, code-named Mario, for a 1 l water bottle weighing just 16 g, far lighter than most 1 l bottles currently on the market. The company believes that over the next three to five years, the weight could come down even more. However, low weight is not a be-all and end-all. Consideration also needs to be given to the notion that a well-designed but heavier PET bottle, with a PET label, may actually in the end prove more sustainable than a lighter one that has a multilayer structure or a PVC label, both of which hinder recycling efforts. From flake to preform in a single step The joint development between Sipa and Erema on the Xtreme Renew process incorporates ground-breaking technologies that enable rPET to be converted in a fully integrated system directly into injection-compression molded preforms. Xtreme Renew eliminates an entire section of the heat history of rPET, making it considerably more cost-effective than alternative systems, while also offering extra benefits in terms of carbon footprint. Sipa believes that for converters considering the use of high volumes of rPET, it is a highly attractive proposition Recyclass rules Sipa strictly follows the Recyclass Design for Recycling guidelines established by EPBP, the European PET Bottle Platform. This voluntary industry initiative provides PET bottle design guidelines for recycling, evaluates PET bottle packaging solutions and technologies, and facilitates understanding of the effects of new PET bottle innovations on recycling processes. www.sipasolutions.com www.erema.com F.l.t.r. Roberta Gualtieri, Marketing Manager Sipa, Christoph Wöss, Business Development Manager at Erema Group and Mr Pablo Fiorentini, Global Sales Director Preform Systems & Tooling at Sipa.","@ID":30} "32 TRADE SHOW REVIEW PETplanet Insider Vol. 22 No. 12/21 petpla.net “We’re back! Finally an on-site trade fair again with innovations you can actually handle!” This is what everyone was saying at this year’s Fakuma 2021 in the exhibition halls in Friedrichshafen. After the compulsory one-year hiatus, the event was held live again from 12 to 16 October. 1,470 exhibitors from 39 countries showcased their innovations covering all aspects of injection moulding, extrusion technology, thermoforming and 3D printing on 85,000m2 of overall exhibition floor space. The fact that 40% of the exhibitors came from outside of Germany substantiates Fakuma’s great significance all over the world, especially in these exceptional times: “For the companies in our industry sector, Fakuma is one of the most important industrial trade fairs of all,” notes Annemarie Schur, Fakuma project manager at trade fair promoters P. E. Schall. “Fakuma was even more important this year. On the one hand because on-site trade fairs only became possible again in the fall of 2021, and on the other hand because the issues of environmental protection, circular economy and sustainability are an enormous task that we all have to tackle.” “Many tradition-rich global market leaders have made use of the crisis to advance their innovations. The trend towards digitalisation is accelerating. Cross-company concepts have been developed for the establishment of a circular economy for plastic products. Every crisis presents opportunities too, and many a clever mind is taking advantage of them,” confirms Sandra Füllsack as well, managing director of Motan Holding GmbH and spokesperson for the Fakuma exhibitor advisory committee. “As a business platform for innovations throughout the value-added chain, Fakuma 2021 was once again the ideal venue for presenting new products and technological solutions, as well as for discussing trendsetting issues.” Extremely practical and with high levels of professional competence, and at the same time in a friendly atmosphere – this is how exhibitors and expert visitors regard the unique and highly esteemed industry event. The next international trade fair for plastics processing, namely the 28th Fakuma, will take place from October 17-21, 2023. www.fakuma-messe.de/en/ Conical co-rotating PET extruder The conical co-rotating Mas extruder stands for a large feed opening, a high feed volume and thus for a high screw filling ratio. The Mas extruder processes A PET, G PET and GAG PET, both for repelletising and for direct extrusion to products. The large aperture in the conical extruder supports feeding of both PET grinding stock (e.g. from PET bottles and preform) and of ground cast or BOPET foils. There is no need to precrystallise or predry the PET. As the extruder’s intake volume is significantly greater than the discharge volume, a high screw filling level is achieved. This helps to achieve high output values at slow screw speeds and at a correspondingly low melt temperature. This results in good colour values and lowest possible IV loss, states the company. The low thermal load, accompanied by low specific energy consumption (≤ 0.22 kWh/kg) thus allows for highest quality extremely economically. The PET recycling process developed by Mas has been in possession of the FDA “No Objection Letter” since mid-2015 and also meets the Efsa criteria for processing washed PET bottle flakes into products with direct food contact. www.mas-austria.com/en Injection moulding technology and medical manufacturing solutions Husky Injection Molding Systems, Ltd., showcased its latest hot runner and controller technology innovations, as well as its medical manufacturing solutions. The live debut of the new UltraShot Injection System, designed to increase overall part design freedom based on function demonstrating production advantages and how to: Increase yield by reducing scrap rates; eliminate subsequent manufacturing steps; enable new part designs; introduce new resin usage. On display was also the latest addition to Husky’s hot runner portfolio, the Pronto Direct, which offers flexibility, value and performance for automotive, packaging and consumer electronics part moulding. Medical Manufacturing Solutions was presented by the company’s specialised moulding solution for pipette tip manufacturing, powered by Schottli mould solutions. This mould technology incorporates a compact cluster design and lateral symmetrical gating enabling high volumes and material savings while achieving the highest standards of quality, said Husky. An introduction to the company’s new integrated system approach for medical device manufacturing for a wide variety of medical applications, such as pipette tips, syringes, blood collection tubes was given. www.husky.co/en www.schoettli.com/en/ Fakuma 2021review part 2 Mr Stefan Lehner, General Sales Manager at Mas Plastic Processing Technology","@ID":34} "MOULD MAKING PETplanet Insider Vol. 22 No. 12/21 petpla.net 26 In-house mould making at 12 machining centres PET and rPET containers design for liquid soap In the household detergents sector, plastic packaging, whether rigid or flexible, continues to dominate. In 2020, the use of detergents and disinfectants has favoured the growth in market share attributable to rigid plastic packaging over, for example, metal packaging. The world consumption of plastic materials for producing containers for household and personal care cleaners has grown an average of 4.8% per year over the last ten years. The SMI Group is a worldwide known manufacturer of bottling and packaging systems for the industrial sectors of food and beverages, pet food, household cleaning and personal hygiene, chemical and pharmaceutical products. The company is able to meet production requirements of up to 36,800bph. With the launch of the Ergon technology, SMI has offered solutions in the domain of complete bottling and packaging lines featuring efficiency, flexibility, sustainability, ergonomics and Internet of Things (IoT) technology. The primacy of plastic for household and personal care products Plastic packaging in its totality covers 94% of the packaging of cleaning and maintenance products. Detergents, cleaners, cleaning and chemical products are often packed in PET containers with a square or a rectangular base, that make the handling easier and represent a marketing tool that gives value to the product they contain. Safety, functionality and ergonomics are the main features that the containers used by manufacturers of detergents and sanitisers must have. These characteristics can be easily achieved by using plastic packaging material. The advantages of plastics - especially of PET - in the production of containers for personal care and pharmaceuticals are: The material is cheaper than other packaging solutions; it is light, flexible and has a high resistance especially during the transport and storage of products; furthermore, the processing of plastics requires less energy compared to other materials, such as glass. From the design to the production of containers The PET bottle represent as well a perfect opportunity to highlight products such as hand soap. Thanks to a team of specialised engineers and latest generation designing tools, SMI is able to design, develop and virtually prototype a wide range of packaging solutions made from rPET and PET, which can meet customers’ specific requirements in terms of safety, functionality and ergonomics. The containers recently designed by SMI for liquid soap packaging highlight the product contained thanks to their shape and special decoration. The idea was to add a “look” that satisfies the specific requirements of customers, such as illustrating plants and flowers used as soap aromas. The best way to appeal to buyers in the points of sales is to draw their attention to the products on the shelves through a nice container as the first step to getting it into their basket. SMI relies on an advanced 3D CAD department for bottle design and graphic processing, that, after an accurate analysis of the customer’s requests, turns the container idea into a detailed project and, finally, into a physical prototype. SMI stated that until now their engineers have designed around 1,700 containers, featuring simple and highly complex shapes suitable for different products. Container moulds SMI manufactures moulds and machines for stretch-blow moulding, filling and packing containers in PET and rPET. The bottle moulds installed on SMI stretch-blow moulders are manufactured using a special aluminium alloy. The 12 machining centres installed in SMIMEC can achieve an output rate of 15,000 moulds per year and are equipped with linear motors running at 80 meters per minute and mandrels running at 30,000 rounds per minute. For large-scale production of these containers, SMI offers a wide range of rotary stretch-blow moulders from EBS Ergon series, available in stand-alone or Ecobloc version, integrated with the filling and capping modules. SMI machines from EBS Ergon range adapt to the needs of smart and green factory for productions up to 36,800bph. www.smigroup.it MOULD MAKING","@ID":28} "PETnews 6 NEWS PETplanet Insider Vol. 22 No. 12/21 petpla.net Erema awarded for Recycling Machinery Innovation At the award ceremony as part of the Plastics Recycling Show Europe (PRSE) on November 5 in Amsterdam, Erema received an award for its recycling system Intarema TVEplus RegrindPro + ReFresher in the category Recycling Machinery Innovation of the Year. Thanks to the combination of its recycling machine with the ReFresher technology that reduces odour downstream of the extrusion process, Erema has enabled the PCR-HDPE produced with it to be used in proportions of up to 100 percent for the production of packaging for direct contact with food and beverages, as confirmed by the U.S. Food and Drug Administration (FDA). The judges recognised this innovation as a step change in eliminating unwanted odour from waste plastics, allowing recyclate to replace virgin plastics in high end applications. This type of innovation is essential for meeting EU targets for recycled content of food contact plastics. www.erema-group.com Intro Sustainable Resources acquire Bariq Egyptian investment firm Raya Holding has completed the disposal of Bariq, its PET recycling specialist subsidiary, to Intro Group, a privately-owned Egyptian conglomerate comprised of a diverse group of companies in various fields including trading and commercial representation; oil and gas; and engineering. Bariq’s recent annual growth rate has been up to 20% Intro Group recently started to focus on the green economy and sustainable energy. It established Intro Sustainable Resources as a developer and operator of projects in environment and sustainability, mainly in renewable energy generation, power distribution and waste management, through Intro Resource Recovery. It is this subsidiary that has acquired Bariq, which will now be part of its waste management portfolio. Intro Resource Recovery’s projects include refuse derived fuel (RDF), waste management systems and digitalisation. Its new ownership will allow Bariq to diversify in the waste management business and strengthen its corporate image in sustainable resource recovery. It will also support its expansion strategy, including new capacity planned to be online by 2023. Bariq processes post-consumer bottles into FDA, Efsa, Reach, Health Canada & GRS compliant food-grade PET pellets. The facility complies with BRC and Sedex directions. It exports to global bottle and food container producer brands and major fibre producers throughout Europe and North America. With a combined annual capacity of 31 kt, made up of 16kt of rPET flakes and 15kt of rPET food grade pellets, Bariq currently recycles 1.6 billion PET bottles/year. Bariq says that its processes use advanced, sustainable technology from major European suppliers. Its portfolio of recycled products extends from food and non-food-grade PET (in both clear and green colours) to injection grade rPP and rHDPE. www.bariq-eg.com The Erema team with Michael Heitzinger, Managing Director Erema GmbH (left), is the proud recipient of the Award for the Recycling Machinery Innovation of the Year.","@ID":8} "PETcontents 4 PETplanet Insider Vol. 22 No. 12/21 petpla.net 12/2021 Page 46 MATERIAL / RECYCLING 12 Bottle-to-bottle recycling at its best - Growth potential included 14 Difficult climate for recyclers - South African plastics industry releases latest recycling figures 15 Pure PET flakes - Achieving purity for food contact applications BOTTLING / FILLING 16 High-speed PET packaging line - New bottle design for Iraqi National for Food CAPS / CLOSURES 18 Consumer convenience with ClipAside MOULD MAKING 20 Rotated by 90° - PET preform moulds for side-entry systems 26 PET and rPET containers design for liquid soap - In-house mould making at 12 machining centres 27 Mould special products MARKET SURVEY 23 Suppliers of palletising and shrink film machinery EVENT REVIEW 28 PRS Europe 2021, part 2 32 Fakuma 2021 review, part 2 BUYER’S GUIDE 40 Get listed! INSIDE TRACK 3 Editorial 4 Contents 6 News 27 Products 36 PET bottles for home and personal care 38 PET bottles for beverage and liquid food 39 Patents 46 Outer Planet Page 18 Page 20 MOULD MAKING","@ID":6} "MOULD MAKING PETplanet Insider Vol. 22 No. 12/21 petpla.net 21 moulds that include all the quality and features of the company’s top-entry injection moulds. The stack structure is also executed with Cavity-Lock, and the latest performance-enhancing innovations such as OH XCool and OH Xblow can also be integrated into the mould. In addition, all corresponding EOATs are available to match the selected preform. The hot runners comply with all relevant standards. In operation For initial tests, a side-entry mould from OHAG was installed in a new PET-Line 4000 at Netstal. The 96-cavity mould (for technical data see box on the right) was designed for a preform with a 38mm 2-start thread, a weight of 50 grams and a wall thickness of 4mm. The EOAT cooling ran over four positions, the air cooling over three. With a cycle time of 13.9 seconds and an injection rate of 22.5 grams per second and cavity, the new side removal mould exceeded expectations during the first tests, according to the company. Well-known PET preform manufacturers in the USA, who are already using the new side removal moulds on a daily basis, were able to confirm the high performance in the tests and attest that the side removal moulds are of the same quality as the systems with top removal. Along with the engineering and construction of preform moulds, Otto Hofstetter AG offers a comprehensive range of services for all aspects of PET preform production. Projects generally start with the clarification of the customer’s needs and end with the testing of the first preforms produced on the production system. The Swiss company believes a successful project is best achieved by early and close collaboration with all involved parties, up- and downstream. www.otto-hofstetter.swiss Tests - technical data Mould cavities: 96 pitch: 60 x 140mm Preform neck: 38mm 2-start thread weight: 50 g wall thickness: 4.0mm Material : PET-IV 0.80 dl/g Post mould cooling EOAT-cool: 4 positions Air cooling: 3 positions Performance cycle time: 13.9 s injection: 22.5 g/s/cavity","@ID":23} "10 NEWS PETplanet Insider Vol. 22 No. 12/21 petpla.net Investment in Australia’s Plastic Recycling and Sustainable Packaging Industry Pact Group has received AUD 20 million in funding from the Federal Government’s Modern Manufacturing Initiative for Recycling and Clean Energy Manufacturing projects to support its investments in technology to increase the amount of recycled materials in locally made plastic packaging. The funding will support investment of approximately AUD 76 million in new equipment and facility upgrades at 15 of Pact’s operations in New South Wales, Victoria, Queensland and Western Australia, which are to be completed by mid-2024. The upgrades will provide Pact with the capability and capacity to meet growing demand for sustainable packaging, enabling the company to provide customers with solutions that will support them in complying with the Government’s 2025 National Packaging Targets. These require 100% of packaging being reusable, recyclable or compostable with 20% average recycled content included in plastic packaging. The investments will also support delivery of Pact’s own sustainability target to provide 30% recycled content across its portfolio by 2025. The investments will be made across four areas of Pact’s manufacturing operations. Upgrades to national dairy packaging equipment at facilities in New South Wales, Victoria, Queensland, and Western Australia to enable up to 50% recycled content for HDPE milk bottles. Installation of world-leading technology at facilities in New South Wales and Victoria to boost production capability for PET drink bottles with 100% recycled content. Upgrades to Sulo mobile garbage bin manufacturing facilities in New South Wales and Victoria to increase production capacity to support the rollout of “four bin” waste management initiatives and increase the use of recycled content to 80% from the current average of 30%. New equipment at Pact’s industrial packaging manufacturing plants in New South Wales, Victoria and Queensland to upgrade production facilities to enable increased recycled content in the manufacture of plastic paint pails and plastic cubes used in agricultural chemical and industrial applications. The investments will create more than 250 permanent fulltime jobs in Pact’s facilities and a further 120 jobs during the construction and installation phase of the projects. The upgrades complement Pact’s investments in recycling infrastructure in Australia, including a new PET recycling facility in Albury, which will be operational next month, a HDPE recycling facility in Melbourne, a further PET recycling facility at a location yet to be identified, and several other projects that are under evaluation. Materials recycled through these facilities will include plastic waste collected from household recycling bins (such as milk bottles, food containers, and bottle tops), bottles from container deposit schemes, as well as old mobile garbage bins and other industrial waste. www.pactgroup.com Small bottle recycling initiative Amcor Rigid Packaging (ARP) is announcing a technological advancement that makes it possible for billions of small bottles to be recycled. ARP states to first apply the technology to 50ml rPET spirits bottles which are often lost in the recycling process due to their small size. The size of these bottles presents challenges at most U.S. material recycling facilities (MRFs). The bottles tend to slip out of the sorting process where broken glass is filtered out for disposal. With its pledge to develop all its packaging to be recyclable, compostable or reusable by 2025, Amcor is innovating to increase the recyclability of its products. Seeing an opportunity for improvement, ARP’s team of engineers examined the issue and began designing a container that collapses in a controlled way to maximise its width. With a collapsed width greater than 5 cm, this design would no longer slip through the cracks at most U.S. recycling facilities. “This discovery was made by the Amcor team when testing revealed that the bottles collapse in different ways,” said Terry Patcheak, VP of Research & Development and Advanced Engineering at ARP. “Our simulations demonstrated that when these tiny spirits bottles are designed to collapse in a specific way, fewer bottles actually fall through the cracks. The potential here is higher recyclability rates and more recycled content for multiple segments and materials.” Amcor’s bottle design includes intentional failure points and is based on the Association of Plastic Recyclers specific guidelines. Finite Element Analysis testing is being undertaken to better understand the dynamics of these small bottles during the recycling process. Additionally, ARP will partner with recycling facilities to capture real-world data about the recyclability of its new bottle. www.amcor.com","@ID":12} "PETplanet Insider Vol. 22 No. 12/21 petpla.net 37 BOTTLES PETbottles Beverage + Liquid Food Dm expands its own brand “Ivorell” The German drugstore discounter continues to expand the range of its own brand “Ivorell” used in the beverage sector. The latest example is a finely bubbly, vegan soft drink with organic fruits without sugar. It is available in the flavours organic apple extract and organic lemon with organic ginger extract. The packaging is a transparent bottle made of 100% recycled material with a capacity of 500ml, decorated with a sleeve label and closed with a screw cap with a guarantee band, coloured to match the variety. www.dm.at Health drink from San Benedetto Under the name “Aqua Vitamin”, the beverage producer San Benedetto sells drinks in some European countries that are supposed to be beneficial to health. There are four variants for different functional areas of the body such as concentration, endurance, fitness and well-being. They also differ in taste. Each is filled with 400 ml in a slim, transparent bottle with a large drinking opening with opaque screw cap and first-opening safety device. A foil sleeve label conveys all the information. www.aquavitamin.it Sport Isotonic from Silberquelle The Austrian company Privatquelle Gruber GmbH & Co KG fills 620ml of isotonic sports drink with magnesium and calcium into a strikingly decorated transparent bottle. There are two flavours - currant and grapefruit. The water comes from a spring in Tyrol and is bottled locally. On the drinks shelf, the bottles stand out because of the special design of the label; the circular rings are slightly reflective and match the colour of the drink variant. The beverage is dispensed via a sports cap that is secured against first withdrawal. www.silberquelle.at Kola from Tyrol In Austria, Privatquelle Gruber GmbH & Co KG sells a special cola under the name “Tirola Kola”. The drink, which is only sold locally, contains fresh spring water from Tyrol and kola nut as well as portions of Swiss stone pine, spruce needles and cinnamon bark. There are two variants - one with, one without sugar. The transparent bottles, which are waisted in the handle area, are made of 100% rPET and are labelled in opposite / contrasting colours for particularly easy differentiation. The bottle is closed with a matching colour screw cap with a TE band. www.tirolakola.at","@ID":39} "29 TRADE SHOW REVIEW PETplanet Insider Vol. 22 No. 12/21 petpla.net Milliken’s additive solutions boost recycling & the circular economy Milliken & Company supports the plastics recycling industry with polymer additives that allow for the increased use of recycled content by improving the properties of recycled polypropylene (rPP) itself. As a global producer of additives and colourants, Milliken offers many ways to improve resin formulations, compounds and end products. At the show Milliken showed the following products and initiatives: DeltaMax Performance Modifiers for PP used by converters processing recycled polypropylene (rPP) or impact copolymer (ICP) resins , Partnership with PureCycle Technologies to purify recycled PP, Engagement with HolyGrail 2.0, Europe’s Digital Watermark Project. Enhancing PP’s properties Milliken’s DeltaMax Performance Modifiers for PP help contribute to a circular economy by enhancing the impact strength and melt-flow properties of rPP resins, blends and PP impact copolymers. DeltaMax can raise melt flow by five times while maintaining impact and stiffness properties. This allows converters to increase operating efficiencies and create innovative part designs with easier flow through moulds. DeltaMax technology is claimed to be effective in modifying postconsumer and post-industrial recycled resins as it elevates impact strength and melt flow to the same levels as – or better than - those of virgin resin. This enables compounders and converters to incorporate up to 100% recycled PP without sacrificing performance or processing. Partners in the cause Milliken is passionate about helping to drive recycling and the circular economy but knows it cannot do it alone. Success in this area requires partnerships and collaboration. One such example is Milliken’s ongoing work with PureCycle Technologies, which began early in 2019. PureCycle’s patented recycling process, developed and licensed by Procter & Gamble Co., separates colour, odour and other contaminants from plastic waste feedstock to transform it into virgin-like PP. Milliken, whose additives will play a critical role in reinvigorating recycled PP, has formed an exclusive supply relationship with PureCycle to help solve the plastics end-of-life challenge. Additionally, Milliken’s Chemical Division has joined the Digital Watermarks Project, a large-scale initiative testing the viability of digital watermarking technologies for the accurate sorting of plastics. The project was part of HolyGrail 1.0, a pioneering initiative facilitated by the Ellen MacArthur Foundation that brought together brand owners, retailers, recyclers, packaging producers and sorting technology providers from across the plastics value chain to investigate ways to improve the sorting of post-consumer plastics. HolyGrail 2.0, the 2nd iteration facilitated by AIM, the European Brands Association, will take this initiative to the next stage by validating the concept and the technology on a semi-industrial scale. The project is due to report on its findings in mid-2022. www.milliken.com","@ID":31} "MATERIALS / RECYCLING PETplanet Insider Vol. 22 No. 12/21 petpla.net 14 South African plastics industry releases latest recycling figures Difficult climate for recyclers Plastics SA, the umbrella body representing the South African plastics industry, has released the official plastic recycling stats for the year ending December 31, 2020. Each year, data is collected from plastics recyclers around the country by Plastix 911 on behalf of Plastics SA. Petco provides figures from their listed PET recyclers, whilst raw material suppliers Sasol and Safripol provide input on the production and domestic demand of plastics raw materials. South Africa’s plastics industry is dominated by the packaging sector (which accounts for roughly 52% of the local market), followed by building & construction (13%), agriculture (9%), automotive and transport applications (7%). Due to increased awareness of hygiene caused by the outbreak of the Covid-19 pandemic, the demand for flexible packaging increased 2% in 2020. Demand for rigid packaging (linked to on-the-go meals, PET beverage bottles and take-away containers) shrank, although packaging used for domestic- and personal care increased due to the greater emphasis on cleaning and the increased demand for hand sanitisers. Packaging sheeting was also used to manufacture face shields locally. Consumption of virgin and recycled plastics in SA South Africa, like most countries around the world, has witnessed a decline in collection and recycling rates during 2020, compared to pre-Covid-19 rates. In addition, many recyclers were unable to operate at full capacity for several months during the past year due to social distancing norms. Other factors that adversely affected the plastic recycling activities include ongoing loadshedding, water shortages and high labour costs which forced many operations to scale down, or even close their doors permanently. South Africa converted 1,739,480t of polymer into plastics products during 2020, a decrease of 5.6% from 2019. This is the total amount of locally produced polymers, imported polymers and recycled polymers sold to local convertors in South Africa, and excludes polymers exported, virgin and recycled. Locally recycled polymer represented 17% of the total domestic consumption, a drop from 18.3% in the previous year. Per capita consumption for locally converted plastics (virgin and recycled) decreased to 29kg/person (down from 31kg/person recorded in 2019). Per capita consumption for virgin material only, dropped from 26kg to 24kg. Virgin consumption increased by 11% since 2011, whilst recycled tonnages, locally converted, increased by 35% in the same 10-year period. Plastic recycling in SA South Africa recorded an input recycling rate of 43.2% during 2020. 461,500t of plastic waste were collected for recycling, of which 312,600t were recycled back into raw materials. 296,500t of recyclate were used to produce new products while 97,260t of recyclate was used to produce new packaging. In an attempt to improve the quality of the incoming recyclables, as well as to reduce their high recycling cost due to contamination, an increasing number of recyclers have started going directly to the waste generators. This allowed them access to cleaner materials and maintain their margins, albeit at lower quantities. 64% of the incoming waste came from landfill and other postconsumer sources. Of this, the majority of the volume (54%) was sourced from the formal sector, collectors and waste management companies. Most plastics were baled, but some were also loose materials. Very critical to the value chain, only 3.6% of recyclables were obtained directly from waste pickers and walk-ins. A further 6% was collected from drop-off facilities and buyback centres. 2018: 74,328 2019: 69,166 2020: 54,556 Tonnages of PET recycled in SA 2018-2020 End-markets for plastic recyclate Markets for recyclate exist in most local market sectors. Only 5.2% of the recyclate was exported as raw material to plastics convertors in the SADC region and Asia. Brand owners and retailers have committed to recycled content in packaging. Although currently, only recycled PET (rPET) is suitable for food contact applications, recycled PP, PE-LD and PE-HD are used in non-food applications, e.g. personal- and domestic care packaging. Recycled flexible packaging was the largest market for recyclate in 2020. 22% of all recycled materials were used to manufacture products such as bags or general flexible packaging. www.plasticsinfo.co.za","@ID":16} "30 TRADE SHOW REVIEW PETplanet Insider Vol. 22 No. 12/21 petpla.net Fimic’s newest solution for the recycling process: SPA screw pump This year, Fimic, specialised in filtration with a range of five different models of automatic melt filters designed to covering filtration requirements specially for post-industrial and post-consumer plastics recycling, presented its technology developed by the specialists in automatic self-cleaning melt filters: a screw pump that allows to easily transport plastic melt from the extruder to the filter without using gears with a single screw. Regular gear pumps used in plastics recycling are very sensitive to contaminations and are getting damaged easily by contaminants especially in post-consumer applications. Because of this, constant maintenance is required and often, it is needed to install a safety filter to protect the gear pump itself, with an increase in investment, manpower, and maintenance costs. Additionally, gears must be periodically replaced by the operator, a further downtime leading to operation losses. Fimic’s SPA screw pump is said to allow considerable savings, because operational costs are reduced to a minimum. In fact, the company states that there is no need for maintenance, nor to install a safety filter for pump protection, nor expensive spare gears that the operator will no longer be forced to replace. While the SPA is claimed to be easy to use and not to require periodic replacements by the operators, it can be installed either before or after the filter, being perfect for applications requiring a double filtration step. Installed before the filter allows building up enough pressure to the filter without the risk of damaging gears or replacing them too often, protecting the twin-screw extruder used especially in compounding applications. And after the filter, stabilise the pressure of the material and to maximise the productivity of the filter and the extruder itself. SPA combines both Fimic’s engineering standards and high quality of manufacturing materials, to offer a reliable and high-performance product. SPA’s operation, designed in three sizes, targeting different output requirements, from SPA120, output up to 1,000 kg/h; SPA140, output from 1 t/h to 1.5 t/h; and SPA160, output from 1,500 kg/h to 2 t/h. A larger one is also being designed, to reach even higher throughput requirements, guaranteeing to all players in the recycling industry significant savings in operational costs. www.fimic.it STEPS TO THE PERFECT BOTTLE. www.roeders.de www.roeders.de Idea & Design Technology Manufacturing Blow Mould 100% Service Y O U R PA R T N E R F O R B L OW MO U L D S .","@ID":32}]}}
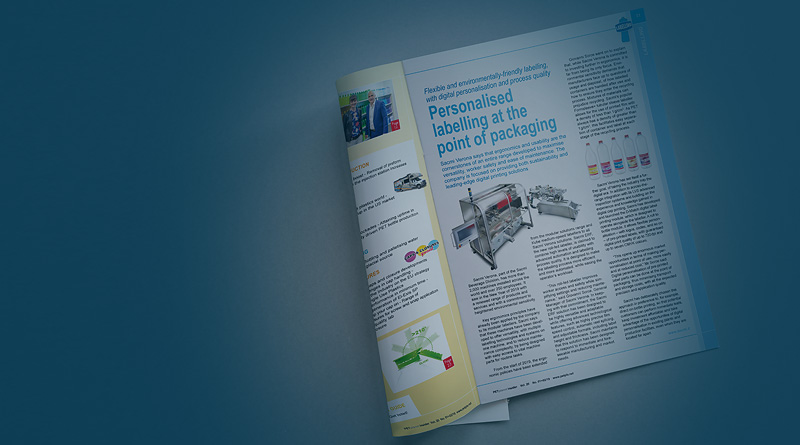