{"pages":{"page":[{"@ID":28 "26 TRADE SHOW REVIEW PETplanet Insider Vol. 25 No. 06/24 www.petpla.net TRADE SHOWreview Chinaplas returned to Shanghai After a six-year hiatus, Chinaplas 2024 made a glorious return to Shanghai and concluded successfully on April 26 at the National Exhibition and Convention Center (NECC), Hongqiao, Shanghai, PR China. The grand comeback to Shanghai immediately captured the attention of the global plastics and rubber industries. The exhibition achieved a record-breaking number of exhibitors, with 4,495 companies participating from 38 countries and regions, occupying total exhibition area of 380,000 m2, and set a new record for visitor attendance. A total of 321,879 visitors from over 170 countries and regions attended the mega event, representing a 29.67% increase compared to the 2023 Shenzhen exhibition. Among them, the number of overseas visitors reached 73,204, accounting for 22.74% of the total, marking a significant growth of 157.50% compared to the 2023 Shenzhen exhibition. PETplanet met a lot of good friends in Shanghai! www.chinaplasonline.com Bernhard Stipsits, Managing Director at Blue Air Systems GmbH F.l.t.r.: Chris Chen, Marketing at Boretech & Johann Lange-Brock, PETplanet F.l.t.r.: Johann Lange-Brock, PETplanet and Bush Hsieh, Chumpower Jason Xue, General Manager at Demark Eisbär Trockentechnik & Z-Moulds (f.l.t.r.:) John Zhang, Sales Agent China Z-Moulds. Martin Spiegel, CEO Eisbär; Michael Fink, CEO Z-Moulds; Johannes Loacker, Sales Manager Eisbär Gneuss team: Ms Luisa, Assistant of Shanghai Laoge Trade Co., Ltd & Dr Axel Hannemann, Head of Fibers & Pellets, Gneuss Guangdong Guozhu Enterprise Group: Laura Cai (left) und Heidi Cao (right), Johann Lange-Brock (middle), PETplanet Marshall Guo from Maguire Products Rolf Blaser, Area Sales Manager PET at Otto Hofstetter AG Gabriele Covin, Head of Marketing, Pegaso Industries S.p.A. Mr Zhao, Taizhou Huiyuan Mould Co., Ltd. F.l.t.r.: Johann Lange-Brock & Sakato Haruo, Nissei ASB"},{"@ID":42 "BOTTLING / FILLING PETplanet Insider Vol. 25 No. 0/24 www.petpla.net 13 Increased speed KHS has introduced three improvements to its modular Innofill PET DRV filler, enhancing its capability for faster and more effective filling of still and carbonated beverages into PET bottles - even under extreme conditions. The new Innofill PET DRV HC (high capacity) filler option provides the flexibility needed for filling large containers of 1.5 litres or more, says KHS. Two technical optimisations allow the machine output to increase by up to 15% for these sizes. The product bowl has been raised, increasing the static height between the tubular ring vessel and filling valve, resulting in a higher filling speed. Additionally, a pneumatic switching valve now features three switching steps instead of two, offering three different filling speeds. This enables optimal filling quality and time for both, small and large containers. CO2 consumption is minimised: whereas 150 g of carbon dioxide per hectolitre are needed for a 300ml bottle, as the volume rises this amount gradually decreases, reaching about zero for a 1 l container. For larger containers, no CO2 is needed at all. Manfred Härtel, Product Manager Filling at KHS, explains that the reason for this exceptionally low consumption is that KHS has dispensed with the nozzle technology in the filling valve, which was previously used to control the filling speed in the bottle. “On our new modular platform, this is regulated on the product path between the tubular ring bowl and filling valve so that gas is no longer lost.” KHS has increased the speed of its DRV fillers to meet the growing demands of markets such as Asia. With an output of up to 90,000 bph for CSDs, the system is claimed to ensure gentle and safe conveyance of beverage containers to prevent damage and spillage. Using advanced simulation technology, KHS computes the impact of centrifugal force on beverage sloshing. In CFD (Computational Fluid Dynamics) calculations the bottle contour, fill level and diameter plus the star geometries and capacities are used to determine precisely how the liquid in the bottle behaves and moves during the filling and capping process. To facilitate a reliable production process, machine geometries are adjusted on the container conveyor and stars, for example. Bottle base cooling The newly developed bottle base cooling function is part of the energyefficient and compact block system. This feature is essential for PET bottles filled with carbonated beverages, as they need to withstand the required filling pressure. The bottles, which leave the stretch blow moulder at about 80 °C, must be quickly cooled to become solid and stable. This is particularly important for bottles with complex base designs. The previous method of convection cooling with air and water often reached its limits in tropical regions with high temperatures, risking damage to the bottle base material. To address this, KHS has implemented a bottle base full jet cooling procedure that ensures containers achieve adequate stability before pressurised filling. This method reduces the risk of damage and improves the bottle’s stability and leak tightness. Water consumption is efficiently regulated by a filtered cooling water circuit. www.khs.com FILLING New SCAN Technology for your Bottle Inspection IMDvista BOCO SCAN One system for opaque and transparent bottles No size parts needed - quick product change Reflection-free bottle inspection Endless geometries and shapes Bottle base full jet cooling is claimed to be effective and gentle, ensuring stability and improving hygiene. (Source: Frank Reinhold)"},{"@ID":32 "Trade Show review PETplanet Insider Vol. 25 No. 06/24 www.petpla.net 30 The future of sustainable packaging solutions European Food & Beverage Plastic Packaging Summit The European Food & Beverage Plastic Packaging Conference presented by ACI Europe took place in Porto, Portugal, from May 15 to 16. Around 50 participants from the packaging and beverage industry discussed the future of sustainable packaging solutions. Paul Davidson, Challenge Director Smart Sustainable Plastic Packaging, UK Research & Innovation, hosted the event and presented the topics of legislation (PPWD), chemical recycling, refilling and reuse, collection and sorting technology and material development. These are the highlights of the first conference day: Graham Houlder, Founder and Managing Director of Sloop Consulting/ Ceflex, presented the Ceflex project, which aims to collect all flexible packaging so that over 80 per cent of the materials that are recycled are returned to the economic cycle and can be used by sustainable end markets to replace new materials. Adela Putinelu, Head of Policy and Sustainability at Plastic Energy spoke about chemical recycling. She discussed the advantages of the complementarity between chemical and mechanical recycling. She listed the following advantages for chemical recycling: It increases the recyclability of mixed, flexible post-consumer plastic waste and thus displaces the production of virgin material. She emphasised that the quality and properties are similar to virgin plastics and that no separation by polymer type is required beforehand. The chemical recycling process also allows contaminated food packaging to be recycled and new recyclates to be produced for food-contact, and contactsensitive plastic packaging. She said that Plastic Energy already has two recycling plants operating in Spain since 2016 and 2017, where a recycled hydrocarbon oil called Tacoil is sold to petrochemical companies for further processing into monomers and recycled plastic. She summarised that ambitious PPWR regulations provide incentives to transform the market, but that enforcement and implementation are crucial. She sees a global agreement on plastics as a unique opportunity to harmonise rules and reverse the trend of plastic pollution on a global scale. Maria Vera-Duran, Project Manager of the Industry’s Confederation (EuRIC), reported on the new PPWD in 2024, emphasising the minimum content of recycled material in plastic packaging. Recycled content must be derived from post-consumer plastic waste that has been collected in the Union in accordance with the PPWD, the national SUPD implementing legislation and the WFD; or has been collected in a third country to standards equivalent to those provided for this in the EU; She highlighted the importance of this mirror clause to level the playing field between European recyclers and importers of recycled plastic. By December 31, 2026, the sustainability criteria for plastic recycling technologies and EU equivalence of rules for plastic waste collected or recycled outside the Union should be achieved. She also spoke about the eco-modulation of EPR fees. The EPR fees can be (voluntarily) modulated on the basis of the percentage of recycled content in packaging. The modulation should take into account sustainability criteria and environmental costs of recycling technologies. With regard to bio-based content, she explained that the European Commission will review the status of the development of bio-based plastic packaging three years after the EiF. If necessary, it will present a legislative proposal that includes sustainability requirements, targets for the increased use of bio-based plastics and the possibility of achieving the RC targets if recycling technologies are not available. Ana Gascon, WWW Director in Europe at the Coca Cola Company, reported on Coca Cola’s “World Without Waste” strategy. Ana said that the world has a packaging problem. As one of the largest beverage producers in the world, Coca Cola has a responsibility to help solve this problem and is willing to be part of the solution. That’s why Coca Cola will make 100% of its packaging recyclable by 2025 and use 50% recycled material in its packaging by 2030. Ana told that by 2030, at least 25% of the volume of Coca Cola’s beverages will be sold in refillable or reusable packaging. And on the way to a world without waste, the company wants to collect and recycle one bottle or can for every bottle or can sold by 2030 - regardless of where it comes from. In addition to the 3 Rs, reduce, reuse and recycle, Coca Cola’s focus in Europe is to work with the rest of the industry to promote 16 operational DRSs in Europe by the end of 2024, and the rest foreseen in the pipeline for DRS is the collection system that guarantees the best collection rates and the best quality of feedstock. Ana summarised 3 main take-aways. Firstly, the opportunities: A lot of progress has been made, but there is still a lot of room for improvement in each pillar. Ecoinnovation and R&D are a must for continuous improvement to create a more sustainable packaging. The second fact Ana sees are the challenges: There is a great need for co-operation between all actors involved: we are all in the same boat! She emphasied that Coca Cola wants to support a systemic chance based on the principles of the circular economy. For this to happen, all stakeholders are needed: companies, governments, customers, consumers, media, non-governmental organisations. www.ceflex.eu www.euric.org www.plasticenergy.com www.coca-colacompany.com www.acieu.net"},{"@ID":43 "OUTER PLANET 46 PETplanet Insider Vol. 25 No. 06/24 www.petpla.net OUTER PLANET From simple partitions to complex ceiling structures Acoustic products made out of 100% PET bottles The company Impact Acoustic AG has the mission to make a real difference in the architecture and design industry. In 2020, the product Archisonic Felt was launched, a Cradle-to-Cradle certified acoustic absorber that forms the basis of all products of Impact Acoustic made of PET. PETplanet talked to Andrea Romano, Sustainability Manager at Impact Acoustic. PETplanet: Was there a special situation that triggered the founding of the company and what is the idea behind it? Andrea: The increasing global plastic pollution problem and the lack of effective PET recycling led Sven Erni and Jeffrey Ibañez to found Impact Acoustic in 2019. The idea behind our company is rooted in a mission to make a real difference in the architecture and design industry by driving sustainable development and innovative design. We saw an opportunity to address environmental concerns while also delivering superior acoustic control and stunning design. By embracing sustainability into every aspect of our business, from product development to manufacturing processes, we aim to lead by example and inspire positive change across the industry. Our goal is to create products that are not only beautiful and functional but also environmentally responsible, ultimately contributing to a more sustainable future for all. PETplanet: Where do you get the PET bottles from and how do you produce the material? Andrea: We purchase 60% recycled post-consumer PET from certified recycling facilities in China, which ensure strict recycling standards such as SCS Global. We then set up a Swiss start-up specialising in recycling facilities to produce high quality rPET with an efficiency of 97% using our products. This rate of 60% rPET and 40% PET represents a necessary trade-off to achieve a significant reduction in the use of virgin plastic, thereby increasing the circularity of the system and reducing the demand for new plastic. PETplanet: What is made from the material and where is it used? Andrea: Our product line, including Archisonic Felt and Archisonic Textile, offers a wide range of stylish solutions designed for environments requiring high acoustic control, such as offices, restaurants, hotels, and public spaces. Our product range features aesthetically pleasing ceiling and wall claddings, room and desk dividers, acoustic lighting, and various acoustic accessories. PETplanet: How do you create new products? Andrea: With our in-house design teams we develop and research the acoustic materials of the future. Every design process at its core includes sustainable and practical aspects to not only satisfy but also transform how acoustic products are used to improve spaces and aesthetic design. In addition, collaboration is at the heart of our ethos. We work closely with the world’s leading architects, designers and developers to bring their creative visions to life. Through open communication and a deep understanding of their needs, we create bespoke acoustic solutions that are perfectly tailored to each unique project. PETplanet: You believe that upcycling bottles is only a small part of the solution in the fight against plastic pollution. You support a worldwide ban of the production of PET bottles. What do you think is an alternative for the numerous applications in which a PET bottle is used? Andrea: It is important to note that there is no single, straightforward solution. The objective is to develop a framework that can support and facilitate collaboration between manufacturing and designers, enabling them to evaluate a prospective sustainability analysis in the context of the principles of the circular economy. One additional example is to close the loop with each material, applying the 10 R principles to ensure that the same product is used for the same functionality. PETplanet: What is your opinion on the current EU legislation? Andrea: These steps represent a significant move towards reducing plastic pollution and promoting sustainability. However, we must ensure that we have more experts in this field to guarantee thorough and effective implementation and innovation.For example, bio-PET could be produced using bio-sources on average for 30% of. In this way ethylene glycol is extracted from bio-sources. While this seems eco-friendly, it can lead to competition for resources between energy production and the food industry. Furthermore, a thorough examination is necessary of other impact categories, such as the use of pesticides in biosource cultivation, which can result in the loss of biodiversity and water consumption and so on. Therefore, a comprehensive approach involving professional expertise is essential to achieve a balance between sustainability goals and economic and resource considerations. PETplanet: How do you imagine the design and construction industry of the future? What are the three most important factors that you would change? Andrea: The design and construction industry must work together to evaluate different approaches and frameworks and form multidisciplinary teams that are able to evaluate design for X practices (design for reuse, design for remanufacturing, etc.). This will enable them to address the best optimal strategy for each specific case. The three main important factors that will change for the future are: 1. Increase collaboration and integrated design process 2. Investment in R/D and training 3. Regulation support and incentives. PETplanet: Thank you very much Andrea. www.impactacoustic.com"},{"@ID":31 "EVENT REVIEW PETplanet Insider Vol. 25 No. 06/24 www.petpla.net 29 conducted in nitrogen and/or vacuum, is claimed to set new standards in technical performance and recyclate quality. The nitrogen used in SSP is purified and recycled, reducing consumption and improving colour values. Recycled PET for the textile industry As well as in the food sector, food-compliant rPET is also playing an increasingly important role in the textile industry. Well-known brands are relying more and more on rPET as a material that meets the requirements for food grade specifications in order to be able to offer their customers textiles that are both sustainable and safe from a health perspective. This trend is reflected by the increase in sales of bottle-to-fibre applications at Erema. Asia is an important market in this segment. Ultimately, the textile industry is increasing the demand for PET recycling. Around two thirds of the total volume of PET flows into the production of synthetic fibres. Erema has responded by setting up its own business application for fibres and textiles. In addition, Erema presented their Intarema FibrePro:IV machine which was developed specifically for fibre-to-fibre recycling. For this system, Intarema technology has been combined with the new IV uptimiser. It is claimed to succeed in processing shredded PET fibre materials heavily contaminated by spinning oils in such a way that the finest fibres can be produced again from the recycled pellets. www.erema-group.com EVENT REVIEW 29 At Chinaplas 2024, the Erema expert teams were on hand to share their expertise with visitors. Erema’s booth at this year’s Chinaplas edition E N D L E S S I N N O V A T I O N S I N C E 1 9 1 9"},{"@ID":14 "BOTTLING / FILLING PETplanet Insider Vol. 25 No. 06/24 www.petpla.net 12 Advanced filling in a water world based on an article by Tommaso Tegoni, Product Manager Filling, Sidel The beverage industry has expanded rapidly over recent years, and bottled water represents the fastest-growing category driving PET growth – driven particularly by countries such as China, India and Turkey. FILLING To meet the rising demand, packaging solutions provider Sidel introduced Evofill PET at the start of this year, a compact new filling machine technology for water and still beverages. The new design is claimed to offer enhanced hygiene and quality while also reducing water and chemical consumption. Sidel designed the first PET filler in 1987. The evolution in filling design has been influenced by a range of factors. Starting with the end consumer, packaging choices are mainly influenced by lifestyle preferences, sustainability claims and budget constraints. Health and price remain key considerations for bottled water. “However, customers often have also other considerations unique to the individual markets that they operate in, such as local legislation, for example,” stated Tommaso Tegoni. “Packaging expertise and extensive knowledge of customers’ industries have led Sidel to develop the Evofill PET system, which provides enhanced water quality in a reduced footprint and is changing the way that manufacturers utilise filling machines”, he added. Enhanced optimisation & design As optimum hygiene is extremely important for all customers, the Evofill PET has been designed to be easier to operate, maintain and clean. To achieve this, Sidel has created a simplified configuration with fewer transfer star wheels and a more compact front table and process unit. In addition, the company has simplified the format changeover in both manual and automatic mode, which can be completed in less than five minutes. The filler can be integrated within Sidel’s Combi and Super Combi complete systems and can also be fully embedded into Sidel’s Evo-On digital intelligence platform to monitor and improve all aspects of the filling parameters and performance. Ease of use Tommaso explained that the ergonomic design of the new development ensures a consistent and repeatable performance that can be used by operators of all skill levels. The reduced filler enclosure is a controlled environment that keeps the water safe during production. The flowmeter contactless filling is claimed to ensure product safety and quality, while preserving bottle integrity with gentle neck handling. Starting at 24 and ranging up to 144 filling valves, with various pitch and filler diameter sizes, Evofill PET can handle bottle sizes from 0.1 to 10 l. The spacesaving filler can handle high production speeds of up to 90,000bph with a footprint that is 15 per cent smaller compared to previous generations. Reduction in water and chemical consumption “There is no doubt that improved sustainability and reducing resource consumption is a huge priority now, both for consumers and governments, with new legislation and directives coming into force around the world. Evofill PET’s integrated CIP system reduces energy by around 25 per cent, while also cutting both water and chemical consumption by 12 per cent for external cleaning. Additionally, its compact size means fewer components and less maintenance operation,” Tommaso proudly announced. Striving for a lower total cost of ownership Tommaso summarised: “While bottle designs and filling technologies have evolved over time, goals for packaging solutions has remained constant: to benefit from the lowest possible total cost of ownership (TCO). Evofill PET has been designed to enhance productivity on PET water bottling lines. The improved accessibility enables faster format changeovers and cleaning operations, reducing downtime. Combined with lower operational costs, it all adds up to a lower TCO. Evofill PET is robustly built for an extended lifespan, enabling customers to count on its reliable operation – with efficiency rates of up to 99 per cent – for years to come.” www.sidel.com"},{"@ID":7 "No.6 2024 www.petpla.net D 51178; ISSN: 1438-9452 24 . 06 . 24 M A G A Z I N E F O R B O T T L E R S A N D B O T T L E - M A K E R S I N T H E A M E R I C A S , A S I A , E U R O P E A N D A L L A R O U N D T H E P L A N E T PETplanet is read in 159 countries MARKETsurvey Suppliers of preform-, cap- & SBM moulds Page 23 EDITOUR FILLING Page 12 Page 10"},{"@ID":37 "35 EVENT REVIEW PETplanet Insider Vol. 25 No. 06/24 www.petpla.net Discover the latest solutions and materials for your next project LEARN. Unlock ways to increase efficiency and boost profits BE INSPIRED. Explore a top-of-the-range showcase of suppliers for your industry NETWORK. Engage with plastics recyclers, waste managers and end users ATTEND FOR FREE Scan the QR code to register for a free ticket www.ami.ltd/Plastics-Recycling-World-Expo-EU-register Exhibitors include: 11-12 September 2024 Brussels, Belgium Co-located with: and many more... IMH and PETform’s shared booth highlights handle bottles and moulds Integrated Plastics (IMH) from Sydney, Australia, and PETform Technologies from Daman, India, shared a booth highlighting IMH’s integrally moulded handle bottles and PETform’s advanced preform injection moulds. Nick Mellen, Managing Director of Integrated Plastics, marked the company’s first participation at NPE with a focus on entering the US market, noting significant interest from Central American visitors. The centrepiece of IMH’s display was the 2-stage stretchblow moulded PET handle bottles, ranging from 700ml to 7.5l. These bottles feature a PET handle that is injection moulded during the preform production process, eliminating the need for a separate handle attachment. The patented technology is claimed to boast significant sustainability advantages over traditional HDPE and PP solutions, including reduced warehouse and shipping costs, higher output compared to the extrusion process, and up to 40% energy savings. Made from PET or rPET, these bottles are fully recyclable without the need for handle separation. The IMH bottles are particularly advantageous for the dairy, edible oil, beverage, juice, and personal care markets. Among the preferred suppliers of IMH is PETform Technologies, which delivers preform moulds for the handle bottles and turnkey systems to inject the preforms. Shurid Mody, CEO of PETform, highlighted the company’s capabilities as a global provider of high-performance two-stage PET preform injection moulds and hot runner systems. Established in 2000, PETform is known for its innovative mould designs and partnerships with customers to develop preform designs that meet stringent industry requirements. Mody noted that this year’s NPE was particularly successful, describing it as “one of my best shows ever” with numerous contracts signed. www.integratedplastics.com.au www.petform.co Nick Mellen, Managing Director of Integrated Plastics The PET handle that is injection moulded during the preform production process"},{"@ID":9 "7 NEWS PETplanet Insider Vol. 25 No. 06/24 www.petpla.net Alpla and Re-Purpose form strategic partnership to strengthen the plastics cycle in South Africa The Alpla Group and Re-Purpose have announced a strategic partnership that will advance sustainable packaging solutions and strengthen the feedstock value chain of Alpla’s very first PET recycling facility in Africa. Alpla is investing 60 million euros in the construction of a state-of-the-art recycling plant in Ballito in the South African province of KwaZulu-Natal. Construction of the plant on the 90,000m2 site is well advanced. From the beginning of 2025, the plant is expected to produce over 35,000t/a of rPET. Durban-based Re-Purpose is one of the market leaders in the reverse logistics of post-consumer plastic waste through sourceoriented collection programmes. With four material recovery facilities around KwaZulu-Natal, Re-Purpose is developing and empowering local communities and buy-back centres to collect and divert a significant volume of plastic waste. The model is also creating hundreds of jobs and income for previously disadvantaged people.The partnership combines the recycling expertise of Alpla and the reverse logistics of Re-Purpose. By joining forces, the two companies aim to develop solutions and promote the circular economy. At the same time, a large number of jobs will be created in KwaZulu-Natal, neighbouring provinces and potentially throughout the country. As part of the collaboration, Re-Purpose will maximise the utilisation of its current baling centres and set up new centres to make it easier for people to collect PET bottles. Re-Purpose will also assist Alpla in building a strategic supplier base for PET bottle bales and work with key stakeholders to expand community reach and separation at source programmes. The aim is to contribute to the collection of 5,000t of PET per month. This volume is expected to be required for the full capacity operation of Alpla’s recycling plant from 2026. www.alpla.com CCL Industries completes acquisition of 100% of Middle East Venture C C L I n d u s t r i e s I n c . announced it has completed the acquisition of the remaining 50% equity interest in its Middle East joint venture, PacmanCCL (“PCCL”), from its partner, Albwardy Investment LLC, headquartered in Dubai. PCCL, headquartered at its Dubai manufacturing facility in the UAE, operates label production facilities in Oman, Egypt, Saudi Arabia and Pakistan. Sales for the first four months of 2024 were approximately $34 million with $14 million of adjusted EBITDA. The debtfree, all cash purchase consideration is approximately $143 million, net of cash acquired, subject to customary closing conditions. The business will immediately commence trading as CCL Label with results fully consolidated. www.cclind.com"},{"@ID":30 "EVENT REVIEW PETplanet Insider Vol. 25 No. 06/24 www.petpla.net 28 Food-safe rPET on the increase, now also in the textile industry The production of food contact compliant rPET is becoming increasingly important in Asia - and it is now extending its importance to the textile industry. Erema is at the forefront, meeting the strict food safety standards of European and North American authorities, and adhering to the specifications of global brands. The growing PET industry in Asia and Africa is driving demand for PET recycling solutions. At Chinaplas, Erema featured systems tailored for direct food contact, with the central element being the proven Vacurema technology. These PET systems are operational worldwide, utilising technologies like Vacurema Basic, Advanced, Prime, MPR, and Vacunite. The key feature of Vacurema machines is the SafeFlake technology in the vacuum reactor, which integrates decontamination, drying, and intrinsic viscosity (IV) treatment. By pre-treating PET flakes under vacuum at the correct temperature, moisture and contaminants are removed before extrusion, preventing any hydrolytic and oxidative degradation of the melt. This is claimed to ensure high-quality rPET pellets, even if input material parameters like moisture, mixture, or bulk density vary. Vacurema Prime is a version of the process where two crystallisation dryers immediately upstream from the vacuum reactor operate in batch mode alternately – also in vacuum – to decontaminate the material. IV is increased via Solid State Polycondensation (SSP) on the flake, with the system boasting a low specific overall energy consumption of 0.295 kWh/kg, making it energy efficient compared to conventional PET processing lines. Legal requirements and commitments from major brands are driving a significant increase in the use of recyclate in PET bottles. Erema’s Vacunite system addresses the challenge of producing high-quality output from lower-quality input material. In collaboration with Polymetrix, the Vacurema process includes vacuum-assisted SSP in a nitrogen atmosphere. This dual safety decontamination process, 41-\"4) 1300'&% BOE XBTIBCMF MBCFM BOE DMPTVSF JOTQFDUJPO TPMVUJPO 888 */53\"7*4 $0."},{"@ID":29 "EVENT REVIEW PETplanet Insider Vol. 25 No. 06/24 www.petpla.net 27 Sustainability and new technologies Italian auxiliary equipment manufacturer Moretto showcased solutions for feeding, dosing, dehumidification, thermoregulation and refrigeration of plastics at Chinaplas 2024. It demonstrated new developments and established solutions applicable to a range of sectors, including automotive, medical devices, optics, beverages, packaging and electronics. Moretto also exhibited products aimed white goods, technical moulding, PET and recycling. Its focus was on developments that contribute to the performance and the sustainability of the whole plastics processing sector. The market’s ongoing investment in research and development are leading to new plastics that are lighter, stronger and more sustainable. These materials offer solutions to environmental challenges and are intended to align with the sustainability expectations of consumers as well as increasingly stringent government regulations. Moretto’s MPK crystallisation system is claimed to offer PET processors easier operations when reclaiming PET scrap for re-processing. Its sensors and monitoring system are designed to enable MPK to automatically adapt its process parameters, learning the best way to set-up the operations from the material and its behaviour. The hopper is equipped with a shockproof stainless-steel finish called Spyro, which insulates the inner mixer body and minimises heat loss, thus increasing energy efficiency. MPK has an advanced digital connectivity, in line with all Moretto’s equipment. Digitalisation, the Internet of Things (IoT), AI and data analytics are radically transforming manufacturing and everyday management, enabling manufacturers to make better decisions, improve efficiency and automate processes. Mowis, Moretto’s control and management software platform, was developed in-house and based on years of experience of processes within the production plant. It is a multi-user platform, accessible on-site or remotely, for the management of complex systems that achieves total connectivity between machines, processes, departments and plants, via OPC UA protocol. Moretto invests six per cent of its turnover in R&D, which is above the industry average, and maintains that the combination of a sustainable approach towards production process and the deployment of advanced technology in its solutions can be the key for a continuous improvement in the plastic processing sector. www.moretto.com"},{"@ID":39 "37 EVENT REVIEW PETplanet Insider Vol. 25 No. 06/24 www.petpla.net Real-time analysis for material feeding, blending and dehumidification A t t h e NPE stand of US equipment manufacturer Maguire, we met IT manager Ralph Hassel, who introduced us to the company’s new IT monitoring system ‘ Tracker ’ . Wi t h this software, the company is taking a further step in terms of production data analysis, evaluation and remote parameter adjustment. In combination with the Maguire Tracker Hub Controller, information from Maguire material blenders, feeders, dryers and conveyors can be accessed online using any end device. The corresponding functions can be activated in a subscription system depending on requirements and end device usage. It should also be possible to integrate the system into existing third-party databases. “The features of the software include remote control and adjustment of recipes and material flows, for example, as well as complete queries, checks and changes to parameters and important production data,” explained Mr Hassel on the presentation screen. Tracker also has comprehensive real-time analysis and reporting functions for consumption and dosing, as well as the general functional status of equipment and error detection. The data generated in this way can be visualised and displayed in different ways. “Continuous data collection and evaluation within the production process is essential and is in high demand in almost all areas,” said Mr Hassel. “With the tool, our customers can now optimise their processes accordingly and monitor them better.” www.maguire.com And & Or’s NPE insights How would you assess your overall experience at NPE this year? The show was spectacular, even more so than in 2018. Many visitors from the Americas, north, central and south. Lots of leads and great quality of the visitors. Could you please share the key exhibits or technologies showcased at your booth during NPE? What factors influenced your decision to focus on these particular offerings, and what was the response from visitors? The key exhibit was the container bagging technology and autonomous mobile forklift robot. 1. Bagging technology: flexibility & packing material cost savings as the key benefits. Blow moulders manufacturing PET bottles, jars, jerrycans and other PET containers can pack layers of bottles on a pallet at less cost per layer than using corrugated boxes or trays, or even slip sheet. Bagging technology also offers more product capacity per layer and allows bottle manufacturers to safely pack product in cleaner and more hygienic conditions. 2 . Au t onomous mobile forklift robot: handl ing and transporting loads or pallets of finished PET products without the need of labour/operators, from manufacturing lines/areas to warehouse, direct ly benefitting companies with increased productivity and a reduction of risk. Automating the logistics of palletised finished product connects production lines with warehouses / shipping areas, without the need for auxiliary elements. The time invested by the operators on a PET bottle manufacturing facility is time largely spent moving pallets around from the production to other areas. The use of arms to move pallets between production lines, station pallet wrappers, and warehouse, offers an improvement in plant safety (avoiding the dangerous combination of forklifts and people), in the traceability of product and in the organisation and classification of the finished product in the warehouse. Overall it helps reduce production costs. www.andyor.com Ralph Hassel presents the Tracker IT system"},{"@ID":20 "INSPECTION 18 PETplanet Insider Vol. 25 No. 06/24 www.petpla.net Sacmi’s 24/7 virtual assistance for rigid packaging In step with AI: intelligent computer vision The evolution of ‘vision’, from quality control to process control, systems designed to ‘think’ like a human being, providing immediate and useful information to even the most experienced operator. Sacmi provides a wide range of vision systems for rigid packaging in the beverage industry. INSPECTION Caps, preforms, right up to the full, labelled container: today, Sacmi systems are evolving under the banner of artificial intelligence and deep learning. This is achieved thanks to the new release of the Computer Vision software (CV) suite, a set of tools that - in the name of interoperability, cybersecurity, and data availability- project quality control within a collaborative vision between man, machines and systems. Sacmi says that the GildaAI, a real ‘virtual colleague’ provides answers, further simplifies system management and troubleshooting. Quality first Sacmi seized the opportunity from the early days of software engineering to complement its range of machines with the development of data-based systems to support quality control. More recently, the radical paradigm shift in the digitalisation of systems has made these solutions a tool for quality control and a strategic tool for making the production process more efficient. The new CVs software suite The range of vision systems for the rigid packaging sector is based on the Sacmi software suite. This is the starting point of the development to train operators in their use, making process data management simpler, more useful and more immediate. In this logic, CVs includes software (CVs23) integrated into the machines and common to all systems, the remote data logging and analysis platform (CVsWeb) and the Classy AI system that improves and simplifies system operation by automatically categorising the types of defects detected, says Sacmi. In addition to the technical interface, which is always available, the Classy AI presents an advanced dashboard, trained to ‘think’ like a human being, classifying and associating each defect with its possible cause, intercepting and anticipating any process drift. Gilda-AI, the 24/7 digital assistant Sacmi’s approach to the factory of the future is based on the idea that technologies should increase productivity and ensure the safety and well-being of operators. This concept is reflected in CVS machines and devices that detect defects and offer unparalleled virtual support through Sacmi’s new 24/7 digital assistant, Gilda-AI. Gilda-AI is a ‘virtual colleague’ that speaks the language of the operators and provides immediate and intuitive solutions to any problem. Thanks to Gilda-AI and the CVs software suite, there is no need to consult manuals or search for complex solutions. The range for bottlers As part of its vision in the production of rigid packaging for the beverage industry, Sacmi offers the proven CHS solution for the in-line quality control of caps. In addition, there are the new cut and tamper-evident band inspection systems integrated into the cap line in view of the changeover to the new tethered standard. Sacmi range extends to preform production, with PVS systems for both in-line and laboratory quality control, and with the first press on the market, the IPS 300 and IPS 400, to integrate this system directly into the machine as an option for process control. For bottling lines, Sacmi develops dedicated label quality control (LVS) and filled and labelled container (BVS) quality control systems, which are designed to work with advanced software packages. Digital & on-site services Intelligent on-board machine systems complement the ability to support customers throughout the service life of the machine and plant with a timely after-sales, remote and on-site service. From this point of view, too, solutions such as Gilda-AI and the remote control of data, together with the possibility of sharing it in the cloud with the Sacmi team, are the beginning of a new approach to customer service. www.sacmi.com"},{"@ID":18 "INSPECTION 16 PETplanet Insider Vol. 25 No. 06/24 www.petpla.net Tethered Caps: From regulation to implementation In July of this year, EU Directive 2019/904 on Single Use Plastics will finally come into force. One of the consequences of this directive is the widespread introduction of tethered caps in the European Union. We spoke to Marius Pötting, Product Manager Caps and Closures at Intravis GmbH, and asked him: What impact will the directive have on the industry in general and on inspection systems for closures in particular? PETplanet: Mr Pötting, EU Directive 2019/904 comes into force on July 3. In your opinion, what are the main objectives of this directive? Marius Pötting: In general, the directive aims to reduce the impact of certain plastic products on the environment. The focus here is on reducing plastic waste, improving the recycling loop, reducing material consumption as well as using resources more sustainable. The introduction of tethered caps (plastic closures that must remain permanently attached to the packaging) is also intended to prevent the careless disposal of closures in the environment. All these measures obviously have a huge impact on the plastics and packaging industry. PETplanet: So what exactly does the directive mean for the packaging industry? Marius Pötting: The effects on the packaging industry are diverse and require adjustments to the entire process chain. In order to meet the requirements of EU Directive 2019/904, considerable investment in research and development was and still is required. However, the directive also offers opportunities for companies that can position themselves as pioneers for sustainable packaging solutions. In concrete terms, the introduction of the directive means that adjustments have to be made at various points in the manufacturing process: For example, to the injection moulding machine tool, the injection speed and injection pressure, as well as the inspection system all the way to the filling line. PETplanet: You mention that these changes will also have an impact on the inspection of objects. Can you tell us what exactly is changing for inspection systems? Marius Pötting: The introduction of tethered caps has ensured that new, asymmetrical geometries and designs have been established on the market. As a result, both the feeding and the handling of the inspection system had to be adapted. In addition, material savings mean that closures are becoming thinner and thinner and are therefore more vulnerable to process-related defects. Accordingly, the feeding system must be carefully adapted to the thinner material thickness. One example of this is the Intravis form-fit star wheel separation, which ensures perfect positioning of the closures thanks to its lateral movement. The star wheel separation does not exert any pressure on the closures and there is no friction compared to conventional separation methods. In addition, the introduction of the new tethered caps has changed the inspection approach, which means that the software must also be adapted. Intravis has implemented a holistic software solution based on Deep Learning: It does not require time-consuming “screening” and “teaching” of different defect patterns. With the new approach, you can train the system on the basis of a few good parts in a quick and intuitive process. Deviations from the defined “good” closures are automatically ejected based on the sensitivity settings you choose. The inspection system thus ensures that even minimal defects are detected and only flawless products find their way to the end consumer. PETplanet: Talking about the inspection approach: More and more suppliers in the mechanical engineering sector are now offering their systems with the addition of Artificial Intelligence. Can you tell us what customers can expect from Intravis? Many customers are certainly afraid that their data will disappear into a black box and that they cannot understand what exactly is being verified. Marius Pötting: At Intravis, the customer always retains full control over the inspection system. As already mentioned, the AI is the foundation for empowering our customers INSPECTION"},{"@ID":4 "INSPECTION 17 PETplanet Insider Vol. 25 No. 06/24 www.petpla.net to teach the system which product should be accepted as a good part and which should not. Intuitive reference creation allows the customer to define inspection areas in which all defect criteria are inspected. The customer uses tolerance values to independently define which closure he wants to evaluate as a good or bad part. Based on a large number of successfully completed projects, Intravis has already gained extensive experience of typical defects (such as flashes or short shots at the warranty band) that can occur during tethered cap production. This allows the best possible, customised solution to be found for each project. The cavityrelated data analysis enables precise monitoring and analysis in order to be able to react to potential problems at an early stage. This means that our customers always retain full control over their production quality. PETplanet: Intravis was one of the first providers to offer an inspection system that is “Tethered Caps Ready”. How much experience have With Netstal’s leading preform injection molding technology. Our PET-Line impresses with broadest compatibility, maximum throughput, exceptional ĆďĆēĈĚ ĆħĄĊĆďĄĚ ĐđĕĊĎĂč đēĐĄĆĔĔĊďĈ Đć ē÷ìû Ăďą other challenging recyclates, and with its intuitive Axos control unit. Wemaximize your added value Preforms you gained in this area in the meantime? Marius Pötting: For many years now, Intravis has been actively involved in Cetie (International Technical Center for Bottling and related Packaging), making a significant contribution to the further development of tethered caps and, thus, supporting the optimisation of safety and sustainability standards in the packaging industry. Since then, we have dedicated ourselves intensively to the inspection of tethered caps and have successfully adapted to meet the new requirements. By using the latest image processing technologies and machine learning algorithms, we are able to inspect tethered caps quickly and precisely - regardless of whether they are produced using the injection moulding or compression moulding process. As a leading provider of image processing solutions in the packaging industry, we are proud to have already successfully implemented a large number of inspection systems for closures on the market, and to be able to offer our customers high-quality and reliable solutions for tethered caps. PETplanet: Finally, let’s imagine a customer who wants to convert his existing line to tethered caps. He has already updated everything and is now confronted with the final task of adapting his inspection. How complicated will this be for the customer? Marius Pötting: Of course, I cannot speak for other providers on this issue, but Intravis took all the necessary measures early on when developing and refining the CapWatcher. So, an uncomplicated and rapid changeover is definitely possible. It is advisable to involve the inspection system provider in the changeover as early as possible. If you are interested, you can contact us at any time. We will be happy to support you with the transition of your production. PETplanet: Thank you very much Mr Pötting. www.intravis.com"},{"@ID":6 "PETcontents 4 PETplanet Insider Vol. 25 No. 06/24 www.petpla.net 06/2024 EDITOUR 10 30 million preforms daily - Visiting one of the largest plastics processors for PET in the region BOTTLING / FILLING 12 Advanced filling in a water world 13 Increased speed 14 Handling high-value liquids INSPECTION 16 Tethered Caps: From regulation to implementation 18 In step with AI: intelligent computer vision - Sacmi’s 24/7 virtual assistance for rigid packaging AUXILIARY EQUIPMENT 19 Controlled loss-in-weight gravimetric dosing unit MATERIALS / RECYCLING 20 The recycling rate for beverage cartons is only half as high as is being claimed - Deutsche Umwelthilfe has been investigating recycling streams MARKET SURVEY 23 Suppliers of preform, cap & SBM moulds EVENT REVIEW 26 Chinaplas review - Chinaplas returned to Shanghai 27 Sustainability and new technologies 28 Food-safe rPET on the increase, now also in the textile industry 30 The future of sustainable packaging solutions European Food & Beverage - Plastic Packaging Summit 31 From “maybe” to “definitely” - PET cap and closure manufacturing system 32 NPE review - part 1 BUYER’S GUIDE 40 Get listed! INSIDE TRACK 3 Editorial 4 Contents 6 News 38 Products 39 PET bottles for home + personal care 46 Outer Planet FILLING Page 31 Page 13 Page 10 EDITOUR INSPECTION"},{"@ID":21 "AUXILIARY EQUIPMENT PETplanet Insider Vol. 25 No. 0/24 www.petpla.net 19 Controlled loss-in-weight gravimetric dosing unit The DUG series of loss-in-weight gravimetric dosing unit by PET Solutions, part of the Pegaso Industries S.p.A. group, based in Borgoricco, Italy, has been developed as a cutting-edge advancement in the automatic dosing of masterbatches, additives, and regrinds in granules. Designed to optimise production process efficiency, the DUG feeders are claimed to combine innovative design with advanced technology, offering flexibility for various applications on injection moulding machines, blow moulders, and extruders. The DUG dosing unit is notable for its inclined axis configuration, ensuring precision and stability. Paired with a brushless motor, it offers precise and reliable dosing control, minimising errors. The intuitive control system features an LCD display that can be installed on the feeder or remotely. A key solution is the patented dual load cell system: The first load cell handles dosing from the hopper to the mixer, while the second provides additional precision control, ensuring maximum accuracy. Six screw sizes are available, from 8 to 30mm in diameter, and three hopper versions, ranging from 10 to 60 l. The feeder’s self-learning calibration and adjustment system, which uses data exchange between the two load cells, allows for automatic and continuous adjustment. This, combined with a bottom shutter for residual material discharge, is claimed to enhance efficiency and ease of management. The central flanged base of the DUG allows for the installation of one or two units, offering versatile configurations. An integrated static mixer ensures homogeneous material mixing, and a Modbus RS485 interface facilitates integration with other systems. Additional features and options include a remote control panel, touch LCD display, a centrally polished stainless steel hopper, capacitive sensors with a buzzer for material shortage alerts, and a remote controller kit. Other available accessories are a paddle mixer body, a Venturi loader for air-compressed material loading, and a screw cooling system for low melting point materials. PET Solutions says that the DUG dosing unit allows for efficient replicability of dosing processes, quick colour changes, and fast cleanings due to the unit’s complete accessibility, reducing downtime. The interchangeable stainless steel screws offer operational flexibility for different materials. The advanced technology of the DUG series minimises material waste during the weighing process, contributing to a more sustainable and economical production. www.petsolutions.it www.agrintl.com +1.724.482.2163 ȏ $FFXUDWH )DVW ΖQWXLWLYH ȏ 3RZHUIXO 6LPSOH -RE &UHDWLRQ DQG (GLWLQJ ȏ 3UH 'HȴQHG &RQWDLQHU 0HDVXUHPHQW 5RXWLQHV ȏ $XWR-RE® ȃ $XWRPDWHG )HDWXUH 5HFRJQLWLRQ DQG -RE 6HWXS LQ 6HFRQGV High Precision Dimensional Measurement for Plastic Containers — 6LPSOLȴHG ® The easily transferable weighing and dosing station makes the system suitable for dynamic production environments."},{"@ID":50 ""},{"@ID":11 "9 NEWS PETplanet Insider Vol. 25 No. 06/24 www.petpla.net CHANGE YOUR PERSPECTIVE CUSTOMIZED COMPLETE LINES PREFORMS AND CONTAINERS PRODUCTION SYSTEMS SINCRO BLOC SOLUTIONS FILLING & SECONDARY PACKAGING SOLUTIONS TOOLING SOLUTIONS vbr-voѲࢼomvĸ1ol \" bv |_; omѲ vrrѲb;u om |_; l-uh;| -1ࢼm] -v - om;ňv|or v_orĶ 1-r-0Ѳ; o= o@;ubm] you a full range of vhbѲѲv vr;1bC1 |o |_; ;mࢼu; ruo1;vv ث =uol |_; 7;vb]m -m7 ruo71ࢼom o= ru;=oulvĶ loѲ7v -m7 1om|-bm;uvĶ r |o |_; u;-Ѳb-ࢼom o= 1olrѲ;|; Ѳbm;vĸ ); -u; -Ѳvo ;|u;l;Ѳ Y;b0Ѳ; bm ruob7bm] mbt; -m7 _b]_Ѳ 1v|olb;7 voѲࢼomv =ou |_; lov| 7b;uv; l-m=-1|ubm] u;tbu;l;m|vĸ $_; b7;-Ѳ r-u|m;u |o _-um;vv ou bl-]bm-ࢼom -m7 0ubm] ou ruof;1|v =uol r;ѲѲ;| |o r-ѲѲ;|ĸ PACKAGING DESIGN AND ENGINEERING"},{"@ID":1 "No.6 2024 www.petpla.net D 51178; ISSN: 1438-9452 24 . 06 . 24 M A G A Z I N E F O R B O T T L E R S A N D B O T T L E - M A K E R S I N T H E A M E R I C A S , A S I A , E U R O P E A N D A L L A R O U N D T H E P L A N E T PETplanet is read in 159 countries MARKETsurvey Suppliers of preform-, cap- & SBM moulds Page 23 EDITOUR FILLING Page 12 Page 10"},{"@ID":17 "BOTTLING / FILLING PETplanet Insider Vol. 25 No. 06/24 www.petpla.net 15 when configured in synchrobloc with a blow-moulding machine. Sipa’s stated commitment to reducing running costs in the latest Flextronic W helps manufacturers to better control and manage costs. At the same time, the company says that its quality standards ensure production consistency and compliance with product specification. Safety has not been overlooked. Modular element guards prioritise safety and convenience, providing operators with added peace of mind during operation. www.sipasolutions.com Filling flammable liquids Sipa’s Flextronic W Atex version has been specifically designed for the safe filling of flammable liquids, such as 70% alcohol hand sanitisers. This specialised configuration adheres rigorously to Atex compliance standards, for mitigation of risks and safe operation in environments with hazardous atmospheres, such as explosive gases and vapours. The version incorporates features to eliminate of potential ignition sources and the integration of micro isolators around the filling valves to contain hazardous areas. Specially-designed ventilation and aspiration systems further minimise risks. The Atex version of Flextronic W caters to industries requiring the safe and efficient handling of highly flammable liquids and features safety and precision engineering. It is claimed to ensure compliance with the most stringent safety standards and provides reassurance to manufacturers operating in hazardous environments."},{"@ID":12 "EDITOUR PETplanet Insider Vol. 25 No. 06/24 www.petpla.net 10 Visiting one of the largest plastics processors for PET in the region 30 million preforms dailyby Kay Barton In the Al-Kharj industrial zone, around 100 km south of Riyadh, the Zahrat Al Waha For Trading Company produces preforms and closures under its Oasis brand as one of the largest converters in Saudi Arabia. With an enterprise value of US$270 million and a process volume of 300 tonnes of PET and 40 tonnes of HDPE per day, the giant, which has been listed on the stock exchange since 2016, is of immense importance in the plastic packaging sector not only nationally, but also in the entire Gulf region. Now the company is completing a new production facility for the manufacture of flexible film and labels, which is due to go live in three months. Plenty of reasons to take a look and ask some questions. EDITOUR Meeting with Zahrat Al Waha For Trading Co. (Oasis) We met: Mr Ahmed Hassan Ahmed Ali, Quality Director The Al-Kharj industrial area near the administrative district of the same name in Riyadh province is characterised by expansion. The large red buildings, four in number, stand out visually from the others. They are the Oasis factories. When the processor began its activities in 2012, preform and cap production were still under one and the same roof, exactly where we met Quality Director Ahmed Hassan Ahmed Ali for an interview. “We started with a Husky HyPET HPP 4.0 line back then,” he recalled. Mr Hassan, a qualified chemistry graduate has been part of the company for nine years now and has been working in the plastics sector since the millennium,” explained Mr Hassan with a smile. Since then, he has been responsible for ensuring quality at Oasis, which is achieved primarily through significant investments in well-known suppliers. What once took place in the same factory is now separate. The preform and closure production sections are meanwhile in separate buildings in the industrial estate, as is a warehouse and, more recently, a factory for the production of film and labels, which is about to be commissioned. As a result, the packaging producer soon wants to position itself as a turnkey supplier for the beverage market. A total of 18 Husky HyPET 400 and 500 systems with 96 and 144 cavities process 300 tonnes of PET daily to produce 30 million preforms, i.e. almost 110,000 tonnes of material per year. On the HDPE side, around 14,400 tonnes are processed into closures on eleven Husky HyCap 3.0 systems with 96-cavity moulds from both Husky itself and Corvaglia. During the plant tour, we see a Packsys Global slitting-folding machine for 29/25 closures. The inspections are carried out by IMD Vista Equipment. “For the preform area, further IMD Vista inspection systems are to follow in the future. At present, we only have one here,” says Mr Hassan. The current capacity utilisation is 85%, we were told. The portfolio includes 42 different preform and six cap versions. PET and PE raw materials are sourced entirely from Sabic, while masterbatch suppliers are Polyone and Colormatrix. “Everything we produce goes exclusively into the water bottling sector,” says Mr Hassan. The annual turnover is US$160 million with an average annual company growth of 10%. The company employs 250 people and has a total area of 80,000m2, of which around 20,000m2 is used for production. View into the cap factory Next to the Editourmobil with Mr Ahmed Hassan (right) and Kay Barton"},{"@ID":34 "32 EVENT REVIEW PETplanet Insider Vol. 25 No. 06/24 www.petpla.net EVENTreview NPE 2024 draws record attendance With over 50,000 registrants, NPE 2024 garnered considerable interest from industry stakeholders. According to the organisers, this year’s edition saw a notable influx of newcomers, with 63% of attendees experiencing NPE for the first time. The trade show also recorded one of the youngest audiences in its history, with 30% of participants under the age of 40, signalling a rising enthusiasm for innovation, sustainability, and the future prospects of the plastics industry. More than 15,000 international registrants marked a milestone as the most internationally diverse show in NPE’s history. Representatives from 133 countries, encompassing 68.2% of nations worldwide, registered for the global plastics trade show. This represented a 9.9% increase compared to NPE 2018, highlighting the exchange of industry innovations and ideas on a global scale and fostering international collaboration in addressing plastic-related challenges. The next NPE show is scheduled for May 3-7, 2027, in Orlando, FL. www.npe.org PET cap inspection & bottle scanning solution IMD Vista’s booth highlighted their strategic collaboration with Origin Materials in the development of the world’s premier PET cap and closure manufacturing system. The Swiss company provides subsystems tailored for conveying, orienting, and inspecting the caps. Martin Gerber, Chief Sales Officer (CSO) at IMD, emphasised the developmental ingenuity invested in these solutions: “There were several feeding and handling challenges with this new design and lightweight solution. Furthermore, we had to tailor the camera inspection to accommodate the highly transparent material.” Given the absence of reference specifications, Origin and IMD collaborated for over 12 months to ensure the same level of process reliability for the new PET caps as for HDPE or PP solutions. “Our experience in preform inspection proved beneficial here and we were able to make some adaptions with regards to camera inspection of highly transparent PET materials,” explained Gerber. Modular inspection of bottles & containers Another novelty introduced by IMD Vista is the Boco Scan, marking the company’s foray into bottle inspection territory. “It was always clear to us that when taking this leap, we wanted to offer something exceptional, setting ourselves apart from the competition,” remarked Gerber. The new system is designed for the 360° inspection of transparent, opaque, shiny, and matte bottles and containers, conducting inspections not through photographs but via a scanning method. “This has the advantage of mitigating reflections, common in bottles with intricate contours, which could otherwise distort the results,” elucidated Gerber. Crucial to the company was the system’s facile changeover and seamless integration into production lines. It has been designed as one standard system for all bottle types without format parts and ensures a plug-and-play experience, no matter which type of bottle the customer needs to inspect. “Boco Scan boasts versatile applicability, rendering it suitable for many industries. In addition to beverage and cosmetic bottles, we are also looking towards the agricultural sector. Containers for this market were hitherto unsuitable for standardised and highly automated inspection. The response from this sector at NPE was exceedingly positive,” Gerber concluded. www.imdvista.ch Martin Gerber, CSO at IMD with the Origin PET caps for which IMD provides several subsystems Using high-resolution cameras and advanced illumination, Boco Scan is able to inspect the most complex bottle geometries, shapes and colours of opaque, clear, shiny or matte bottles."},{"@ID":27 "MARKET SURVEY 25 PETplanet Insider Vol. 25 No. 06/24 www.petpla.net Röders Tec Sacmi Imola s.c. Sipa S.p.A. GDXL Precise Machinery Co., Ltd. Scheibenstraße 6, 29614 Soltau, Germany +49 5191 60353 www.roeders.de Mr Steffen Lühnung & Mr Jani Rickert Sales Manager +49 5191 603822 & +49 5191 603340 [email protected] Via Selice Prov.le, 17/a, 40026 Imola (BO) Italy +39 0542 607 111 www.sacmi.it [email protected] Via Caduti del Lavoro 3 - 31029 Vittorio Veneto, Italy +39 04389 11 511 www.sipa.it Mr Marco Brusadin Global Packaging Dev. Director +39 0438 911694 [email protected] No. 18 Changjiang Road, Guicheng, Nanhai, Foshan city, Guangdong Province, China. Postcode: 528251 +86 757 8677 7168 www.gdxl.com Mr Billy Ay Marketing Specialist +86 757 8677 7168 ext 8681 [email protected] Up to 30 3.3 (standard machines) to 12 (big format machines) 30 Up to 5 Yes No No Yes Yes Yes Yes Yes, we supply moulds applicable to various brands of SBM machines such as Sidel, Krones, KHS, Sipa, Newamstar, Tech-Long, etc. Sidel, KHS Corpoplast, Krones, Sipa, Kosme, ADS, Nissei, Chumpower, Terekas, 1 blow and other major machine types Beverage market major brand owners and licencees worldwide, together with local bottlers as well Sipa, Sidel, Krones, Kosme, KHS, SMI, Sacmi, Siapi Bottlers/converters which supply bottle to beverage brands such as CocaCola, Pepsi-Cola, Danone, Nongfu Spring, etc.; as well as applications in food, cosmetic, pharmaceutical, home and personal care industries. Bottle design development Yes Brandbuilding, product repositioning, marketing design, packaging engineering, lightweightening of existing bottles, technical feasibility; new AWArPET analysis (Design for Recycling), etc… We provide bottle design services according to customers' requirements on technical performance and appearance. Quick and fl exible bottle sampling and qualifi cation in Röders laboratory with certifi ed equipment as well as energy-saving solutions. New: Diamond milling technology and Röders Racecut system will lead to shorter lead times for customers. Double cavity concept, low pressure base moulds, stainless steel moulds Wide mouth, large sizes (up to 30 l), asymmetrical, nitrogen hot fi ll, containers with handles, HDPE to PET conversions, pharma & cosmetics Bottle and mould designs for light-weighting, optimised CSD base, re-inforced structure, market-appealing styles, imitated texture, etc. Solutions for compatibility of moulds between different machine types, new Röders RMC-system for quick mould change to reduce changeover times and cut mould costs. Corvaglia Mould AG GDXL Precise Machinery Co., Ltd. Hörnlistr. 14, 8360 Eschlikon, Switzerland +41 71 973 77 77 www.corvaglia.com Mr Albert Brunner Director Sales & Service +41 71 973 77 52 [email protected] No. 18 Changjiang Road, Guicheng, Nanhai, Foshan city, Guangdong Province, China. Postcode: 528251 +86 757 8677 7168 www.gdxl.com Mr Billy Ay Marketing Specialist +86 757 8677 7168 ext 8681 [email protected] CSD & carbonated bottled water, still bottled water (pressurised & non-pressurised), sensitive drinks (juices, teas, fl avoured waters, ...), sports & energy drinks, others (dairy, edible oil, …) Closure moulds for various beverage applications including water, CSD, aseptic and hot-fi ll, etc. Coffee, beer, detergents, other contents/applications are possible upon request Closure moulds for applications to food, edible oil, cosmetics, personal care, pharmaceuticals and other industries. Individual cap solutions are possible upon request R&D service and mould fabrications for individualised single-pc or multi-pc closures. Flat top & sports closures for neck fi nishes from 25 to 48mm, e.g. all Cetie standard necks GME 30.21 to GME 30.43 Closure moulds for one-piece cap and two-piece cap for various neck fi nish standards including 1810, 1881, 30/25, 29/25, 26/22, 38mm, etc. HDPE (PP for transparent parts) HDPE starting from 0.8g Closure moulds for: 1881 Aseptic / hot-fi ll: 2.15g 1881 CSD: 2.35 g 48mm neck water: 4.2g 38mm neck water: 2.8g 30/25 neck: 1.65 - 1.85g 29/25 neck: 1.2g 24 - 96 cavities From 12 to 72 cavities Various GDXL (we also supply hot runner) Closure design approvals from all major beverage brand owners. Most economical closure designs for private labels. Tethered cap solutions for carbonated and non-carbonated drinks according to requirements of EU Directive 2019/904"},{"@ID":35 "33 EVENT REVIEW PETplanet Insider Vol. 25 No. 06/24 www.petpla.net Modular system for flexible optical online inspection and sorting of plastic pellets Sikora has exhibited the Purity Scanner Advanced that is used for inspection and sorting of plastic pellets. Even t he sma l l es t , critical contamination is rel iably detected and sorted out by the system, says the company. Thanks to the modular concept, different camera types can be used depending on the inspected material. In addition to optical 25 μm high-resolution cameras, which detect black specks and discolourations, an X-ray camera can be installed to detect metallic contamination down to 50μm in the pellet. Purity Scanner Advanced automatically sorts out detected contamination via a blow-out unit. For optimising the by-catch, Sikora has developed a “hybrid blow-out” feature. The customer defines in advance which contaminants in the material are uncritical and selects a smaller blow-out unit for these, so that their by-catch is reduced. Both the reliable detection and hybrid blow-out are claimed to ensure high material quality. At the same time, production processes are optimised, and the reduced by-catch contributes to cost-efficient and sustainable production. www.sikora.net John Dognazzi, Managing Director of the Sikora daughter company Sikora International, in front of the Purity Scanner Advanced Improving properties with OpenairPlasma and PlasmaPlus Technologies Opena i r -Pl asma t reatment enhances the surface energy of predominantly non-polar plastics, thereby modi fying their surface properties. This activation process prepares materials for subsequent industrial treatments by increasing surface wettability, which in turn improves adhesive and coat ing strength as well as material printability. For cases where act ivat ion alone is insufficient, Plasma Plus technology offers an alternative. This process applies nano-coatings to surfaces, creating functionally enhanced surfaces with superhydrophilic properties, leading to improved adhesion. In the soft drink industry, PlasmaPlus nano-coating can improve the barrier properties of PET bottles. The nanocoating is transparent like glass yet flexible, shock-resistant, and friction-resistant, says the company. This coating reduces diffusion and extends the shelf life of soft drinks. The process applies the coating to both the inside and outside of the packaging. Securing ink bonding on caps Plastic bottle caps must be airtight while remaining easy to open. Silicone-modified compounds have low surface tension, making printing with solvent-free, food-safe inks challenging. Plasma treatments are claimed to increase surface tension on bottle caps. Plasma jets are integrated directly into high-speed pad printing machines. According to Plasmatreat, their processes are solvent-free, offer locationselective applications, and can be seamlessly integrated into existing production lines. www.plasmatreat.com Plasma treatment on bottle cap (photo: Plasmatreat GmbH)"},{"@ID":16 "BOTTLING / FILLING PETplanet Insider Vol. 25 No. 06/24 www.petpla.net 14 Handling high-value liquids Sipa’s Flextronic W filling system has been upgraded to handle personal care and homecare liquids as well as edible oils. In today’s fast-paced production landscape, precision and adaptability are essential for success. Sipa, an industry leader in PET bottle production, handling and filling, has announced the launch of an upgraded version of its Flextronic W weight filler, which it describes as a ‘groundbreaking addition’ to its existing range of monobloc filling machines. The Flextronic range was originally designed for high-value products such as edible oils; the latest version of the FlextronicW has undergone an evolutionary design upgrade to make it capable of handling a diverse range of products including salad dressings, ketchup, several types of sauces, detergents and other applications in home and personal care, such as cosmetics. Sipa says that the latest version of the Flextronic W offers higher standards of product performance and emphasises the need, in today’s production landscape, for precision and adaptability, while delivering at pace. In order to achieve these goals, Sipa has invested the Flextronic W with advanced technology and customisable features intended to deliver excellent operational performance, efficient production processes and superior product quality. These features are claimed to meet the needs and demands of businesses in the food and toiletries industries. The company says that its range of monobloc filling solutions featuring Flextronic W offer premier quality and exceptional sanitisation capabilities, while minimising operational expenses. Main features The Flextronic W’s features include a pressurised central tank for efficient product handling. Its draining frame is made entirely of grade 304 stainless steel, to achieve high standards of hygiene. For operations that require the strictest standards, an ultra-clean configuration featuring nitrogen pressurisation of the filling tank is available, along with automatic insertion of dummy bottles during CIP. Changeover times have been cut, which helps to boost productivity, and operations are made as simple as possible by a user-friendly touchscreen HMI, with intuitive control and monitoring of filling processes. In order to minimise waste, the Flextronic W is equipped with a recovery tray for rinse or cleaning oil, which enables complete product recovery at the end of production. Sipa says that the Flextronic W’s comprehensive set of features are designed to raise its performance in a number of areas. The capacity for the flexible handling of a variety of products eliminates any need for additional equipment and simplifies the production process. Likewise, its adjustable filling speed is designed to ensure the efficient handling of a wider range of FILLING products, with different consistencies, than previous models. Automatic filling engagement is designed to deliver precision and consistency, for uniform product quality through multiple fills. Its design, including the use of high-grade stainless steel, mean that the machine is ideal for industries and operations with strict hygiene standards, Sipa maintains. The improved design helps to minimise downtime and boost productivity by enabling faster changeovers and transitions between products, and easier access for simplified maintenance. The filler, available with 20 to 96 valves, can achieve output rates ranging from 6,000 to 36,000 bph in case of 1.5 l formats. Advanced weight-filling technology Flextronic W seamlessly accommodates various types of products, says Sipa. This versatility allows producers to expand their offerings without the need for multiple filling machines, thus helping to boost operational flexibility and cost-effectiveness. Its advanced weight-filling technology enables higher levels of accuracy, which minimises product waste while maintaining quality and consistency. As its design incorporates features for quick adjustments and thus cuts downtime, higher production rates and improved efficiency can be achieved, especially"},{"@ID":23 "PETplanet Insider Vol. 25 No. 06/24 www.petpla.net 21 MATERIALS / RECYCLING disposable packaging. What’s more, drinks cartons are made almost entirely from new rather than recycled materials. Thousands of trees have to be felled for the packaging. This is because slow-growing wood with long fibres is required for production purposes, most of which is imported to Germany over long transport routes.” www.duh.de right- /Quellenangaben 1 UBA, Federal Environmental Agency (2023) 2 Calculation according to sources 1, 3 and 4 3 ifeu gGmbH, Institute for Energy and Environmental Research (2020) – 11.2 % of beverage cartons not sorted for recycling 4 FKN e.V., Association for Beverage Cartons (2008) – approx. 12.5 % other external materials, approx. 17 % moisture and contaminants 5 Market information – approx. 70 % paper, 25 % plastic and 5 % aluminum content of beverage cartons 6 FKN e.V. (2019) – annual processing capacity of the Palurec plant in Cologne Knapsack of around 18,000 tons 7 bifa Umweltinstitut GmbH, Environmental Institute (2020) – approx. 22 % loss during paper recycling Actual recycling rate 2021 according to DUH e.V. Alleged recycling rate 2021 according to FKN e.V. 37.9 % 75 % Total use of beverage cartons in 2021 (empty weight)1 179,700 t Paper content (not recycled)5,7 14,603 t Plastic content (not recycled/incinerated)5,6 10,206 t Aluminium content (not recycled/incinerated)5,6 1,831 t Other external materials (e.g. plastic foils, corrugated cardboard) 16,813 t Moisture and contaminants4 22,865 t No collection via the Green Dot system (e.g. due to disposal in residual waste/paper waste, littering; empty weight)2 69,699 t (Empty weight without other external materials, moisture and contaminants) 94,823 t Recycled beverage cartons (empty weight)5,6,7 68,183 t Sorting residue (beverage cartons not sorted for recycling, incl. moisture and contaminants)3 14,843 t Status: February 2024 Collection via the Green Dot system in bins for recycables (without other external materials, but incl. moisture and contaminants)2 132,531 t (empty weight without moisture and contaminants)2 110,001 t Paper content (recycled)5,7 51,773 t Beverage cartons for recycling (after sorting, incl. other external materials, moisture and contaminants)1 134,500 t Aluminium content (recycled)5,6 2,910 t Plastic content (recycled)5,6 13,500 t Recycling of beverage cartons in Germany in 2021 (source: DUH)"},{"@ID":10 "8 NEWS PETplanet Insider Vol. 25 No. 06/24 www.petpla.net Erema Group achieves EUR 380 million revenue in 2023/24 The Erema Group, headquartered in Ansfelden, Austria, achieved a revenue of EUR 380 million for the financial year 2023/24. The group, which now includes eight subsidiaries such as Erema, Pure Loop, Plasmac, and Lindner Washtech, expanded its portfolio through a joint venture with the Lindner Group, adding washing technology to its offerings. CEO Manfred Hackl highlighted the company’s role in advancing the circular economy for plastics, recycling over 25 million tonnes annually. In the past year, Erema produced 290 plastic recycling extruders and over 100 add-on components. The group operates approximately 8,500 machines worldwide and employs 950 people. Despite economic challenges, such as competition from low-cost virgin materials and high energy prices, Hackl remains optimistic. Erema is focusing on process optimisation and increasing investment in R&D to enhance customer value and prepare for future growth. Significant investments include a new R&D Centre in Ansfelden and new machinery at the Customer Technology Center in North America. Over the past five years, Erema has invested more than EUR 110 million in expanding and modernising its facilities. Erema has also seen success with new technologies such as Duafil Compact for high-contamination applications and Refresher technology for odouroptimised recycled pellets. The DischargePro control system, which reduces melt loss by up to 50%, has been nominated for the Plastics Recycling Awards Europe. For bottle applications, Erema’s Vacurema systems boast a capacity of over 4.5 million t/a. PET recycling is also becoming important in the textile industry, supported by Erema’s FibrePro technology and a new fibre technical centre at its headquarters. Given the global plastic production of around 400 million tonnes annually with only 9% recycled, Erema sees substantial potential for growth in plastics recycling. www.erema-group.com The Erema Group with its eight subsidiaries is managed by CEO Manfred Hackl (right) and CFO Horst Wolfsgruber. Sidel expands Central Asian presence with new office in Kazakhstan Sidel, a leading provider of equipment, services and complete line solutions for packaging liquids, foods, home, and personal care products, established a new office in Almaty, Kazakhstan on June 12, 2024. The strategic decision aims to bring Sidel’s expertise closer to its customers and support their growth in the region. Sidel has been serving the Central Asia and Caucasus (CCA) region for more than ten years. The region is a significant market with Kazakhstan, Uzbekistan, Azerbaijan, Tajikistan, Turkmenistan, Kyrgyzstan, Georgia, and Armenia exhibiting growing GDP and disposable income levels. Building upon the strong relationships Sidel has already developed with fast moving consumer goods producers in CCA, the company will continue to significantly invest in this region, providing its solutions and services while supporting the local market needs. The new office will give producers direct access to Sidel’s regional expertise, including local project management, advanced engineering solutions and on-the-ground support services that understand and respond to local market nuances. Sidel is also committed to investing in the local labour market, leveraging local talent, and developing skills in all core operational functions, including sales, project management and services. www.sidel.com"},{"@ID":47 "36 EVENT REVIEW PETplanet Insider Vol. 25 No. 06/24 www.petpla.net BEYOND THE HORIZON PROCESS SOLUTIONS FOR POLYMER RECYCLING AND SOLID STATE POLYMER UPGRADING Polymetrix, a Sanlian Buhler Company, provides process technology including EPCM services for the polymer recycling and manufacturing industry. Leading supplier of rPET systems and integrated rPET plants for single line capacities up to 70’000 tons per year. www.polymetrix.com www.slhpcn.com ABC Compressors’ NPE insights How would you assess your overall experience at NPE this year? Hugely satisfied. it was very busy from the beginning to the end, and we had the chance of meeting many new potential customers. Majority of the visitors were US-based but a significant number of customers from LATAM and Caribbean countries attended the exhibition. We celebrated a dinner on Wednesday and it was a great success as we had +100 guests attending. Could you please share the key exhibits or technologies showcased at your booth during NPE? What factors influenced your decision to focus on these particular offerings, and what was the response from visitors? Service network: We have established our own service structure since 2021 and we already have ten technicians in Dallas, Philadelphia, Portland, Mexico and Miami. Service is very demanding among customers, so building up a strong team was key for success. Horizon Synchro and XPET new ranges: We were highlighting all the new developments of both new ranges.(See PETplanet 03/24) Rental services: We have developed a portable solution where we place the whole compressor package in a container, load it on to a trailer and it is delivered within 24 hours. Based on your experience at NPE and your broader industry knowledge, what developments or challenges do you observe in the American PET bottle market? I would like to have the chance to walk through the exhibition to gain a better understanding of the new developments. I know the big players are investing a significant portion of their budgets in hot fill lines. Consumers are looking forward to healthier drinks, and many new juices and energy drinks are being developed. These products are bottled using hot fill lines. We also have many customers who are transitioning from HDPE to PET. Those using PET are obtaining lower density bottles, which is something we have been seeing in other continents in recent years. Lighter PET bottles are better as they use less plastic material, and on the compression side, lower pressure is needed, which requires less energy consumption. In the end, the carbon footprint is reduced, and it is great that the US is becoming more conscious of this. We believe PET is still the most eco-friendly solution, and these kind of actions helps eliminate negative criticism. Regarding challenges, the US market is a relatively new market for ABC Compressors as we have been present for the last eight years. Entry barriers have been huge for us but we are at our very best moment now as customers are starting to know our brand and they are also recognising ABC as cutting edge technology. With 100+ installations over more than 20 states, we are currently dominating the market with 30% market share in 2023. Having this good positioning is challenging us to build up a strong service team so although we already have ten technicians, we are looking forward hiring more technicians in 2025. www.abc-compressors.com Answers provided by Nacho Urbistondo de Leiva, Sales Area Manager North America, ABC Compressors Full range of blow moulding equipment Canada-headquartered PET All Manufacturing covers North and South America for a number of technologies. It reported having a great show with visitors generally of a high calibre, ready to get down to business. The booth featured an allelectric, 2-cavity stretch blow machine from Chumpower for bottles up to 5 l. This machine is one of Chumpower’s lineup of blow moulders from 1 to 14 cavities that uses continuous movement of preforms guaranteeing that each preform is exposed to the same heat and bottles have the same wall thickness. Outputs of up to 2,800 bottles/cavity/hour are possible for light-weight water bottles. The show machine was sold on the last show day to a customer in Texas. Visitor interest in PET All’s other technologies like extrusion blow moulding and injection blow moulding was also strong, the company says, and one machine was sold on the second day of the show. Pet All’s offering includes a number of technologies for bottle applications with outputs of up to 21,000 bph. www.petallmfg.com The PET All Manufacturing team in front of their NPE booth The ABC Compressors team at NPE"},{"@ID":13 "EDITOUR PETplanet Insider Vol. 25 No. 06/24 www.petpla.net 11 Packsys Global equipment for slitting and folding Quality Director Ahmed Hassan with preforms produced on HyPET systems for the water industry One of two areas specifically for preform production PETplanet interview: Quality Director Mr Ahmed Hassan (left) and Kay Barton"},{"@ID":41 "PETplanet Insider Vol. 25 No. 0/24 www.petpla.net 39 BOTTLES PETplanet Insider Vol. 25 No. 0/24 www.petpla.net PETbottles Home + Personal Care Slim dispenser for hand soap Edeka sells a wide range of personal care products under its own Elkos brand. These include a beautifully designed, slim bottle for hand soap. The bottle contains 300 l and is printed with a sleeve label featuring a raccoon motif. The product can be dispensed via a screw-on pump dispenser. The bottle has a label with all the commercial information on the bottom, which can be easily removed at home to make the bottle look more neutral. www.edeka.de Hand soap with glitter The drugstore discounter dm’s own brand Balea advertises its hand soap with the addition “Glow” with an additional shimmer effect. 300 ml of the vegan hand soap with shimmer pigments is filled in a transparent bottle with a strikingly coloured pump dispenser. The soap is free from microplastics and smells of apricot. A label with a silvery or colourful sheen, depending on the light, completes the eye-catching appearance. www.dm.de"},{"@ID":40 "PETproducts 38 PETplanet Insider Vol. 25 No. 06/24 www.petpla.net 100% rPET wine bottle for the UK market SGT, a French manufacturer of PET packaging solutions announced its partnership with Event Wine Solutions to introduce a new mono-material PET wine bottle made from 100% recycled PET. This ambitious European project aims to meet the high standards and sensitivities of the UK event market with a unique French touch. This collaboration brings together wine producers from Bulgaria and Greece, two countries renowned for their exceptional wines, to create a premium product for the UK market. The goal is to offer high-quality wines packaged in innovative bottles that respect the environment while ensuring food safety and excellent taste. The new wine bottles developed by SGT and Event Wine Solutions are made entirely from 100% rPET and are fully recyclable, marking a significant step forward in reducing the carbon footprint of the packaging industry. These lightweight and durable bottles meet the strictest food grade standards, ensuring that the wine maintains all its organoleptic properties. SGT has been offering two neck finishes for several years: BVS 30 H and BVP 22H30. The rPET used for these wine bottles, known as CirPET (Circular and PET), is produced by SGR, the recycling unit of SGT. Additionally, the wine preforms are also available in a multilayer version for longer preservation. www.sgt-pet.com Beermaster with new packaging solutions In the heart of Moldova, nestled among scenic vineyards and rolling hills, lies the prominent brewing company Beermaster. Beermaster, in its quest for innovative solutions, particularly in the packaging of beer and various other beverages, has partnered with PET Technologies, which installed an advanced APF-Max series blow moulding machine. Previously reliant on two semi-automatic machines equipped with seven blow moulds, Beermaster faced frequent production halts. PET Technologies helped Beermaster to achieve its goals introducing APF-Max 4L blow moulder. This machine produces PET bottles ranging from 0.2 to 3.0 l, with an output of 7,000 bph. In case of 500ml bottle, the output is 8,000 bph. The APF-Max 4L is claimed to ensure a seamless production flow and brought with it the flexibility of a quick bottle format changeover, with mould changeovers taking 20 minutes. Beermaster now produces five different bottle sizes on the APF-Max 4L, including the popular 3 l format, thanks to the machine’s ability to handle larger volumes up to 3 l. The APF-Max 4L reduces energy consumption and features an NIR heating system, in line with Beermaster’s commitment to sustainable production practices. In addition, the machine’s robust design can accommodate heavy preforms, which are critical to maintaining the integrity of the bottle design, which resembles a traditional beer keg, after filling, according to PET Technologies. An essential aspect of this partnership was PET Technologies ability to tailor the bottle designs to incorporate Beermaster’s branding, embedding their logo distinctly on each bottle. This customisation has not only strengthened brand recognition but has also enhanced the visual appeal of the products. www.pet-eu.com"},{"@ID":22 "PETplanet Insider Vol. 25 No. 06/24 www.petpla.net 20 MATERIALS / RECYCLING Deutsche Umwelthilfe has been investigating recycling streams The recycling rate for beverage cartons is only half as high as is being claimed The German environmental organisation Deutsche Umwelthilfe (DUH) has calculated a recycling rate of 38% rather than 75% for beverage cartons, once again casting an unfavourable light on the use of controversial cardboard packaging. However, the new EU Packaging Regulation plans to do something about this. The current draft text calls for a mandatory deposit scheme for containers which, for technical reasons, are made almost exclusively from virgin material. CONVEYING PALLETIZING PACKAGING BLOWING FILLING LABELLING The DUH organisation is always challenging and questioning the environmental-friendliness of drinks packaging in Germany. Their research and findings can also be applied to other countries, even though Germany is different with its small-scale bottling industry and special waste system (Yellow Bag). For the German small-scale market, the DUH has concluded that returnable glass bottles are the most environmentally-friendly option for short distances between the consumer and bottler. The fact that municipal water in Germany is of drinking water quality was not taken into account, which is why no packaging is actually required for water. It is equally evident that the non-returnable PET bottle is the most eco-friendly form of beverage packaging when distances between the consumer and bottler are greater, as is the case in nearly every country. The current DUH study on drinks cartons is extremely interesting. The official recycling rate of 75% for drinks cartons claimed by FKN e.V., the association that represents the interests of beverage carton manufacturers, is far too high – in fact it is only around 38%. The 75% quoted by the FKN is based on the cartons collected in the yellow bag, the 38% recycling quota of the DUH is based on cartons produced or sold. Barbara Metz, Federal Managing Director at DUH, said “Contrary to the promises made by Tetra Pak and Co., beverage cartons have an incredibly poor recycling record. This is mainly due to the fact that more than a third of their drinks cartons do not end up in yellow recycling bags but in residual waste, a paper bin or in the environment. The Federal Environment Minister Steffi Lemke must therefore introduce a one-way deposit of 25 cents on drinks cartons as soon as possible. This would allow around 2.3 billion more units to be recycled each year. The best thing to do is to dispense with environmentally harmful drinks cartons altogether and use regional reusable bottles instead.” In addition, the EU Packaging Regulation explicitly recommends introducing a deposit scheme for beverage cartons. Drinks cartons have tended to be less eco-friendly in recent years. The paper fibre content has decreased while the plastic ratio has increased, with composite packaging having become 35% heavier during the last 20 years. They are only filled at a few locations and distributed over long distances throughout Germany. Thomas Fischer, Head of the Circular Economy at DUH, continues: “Beverage cartons are a burden on our environment due to their plastic-moulded packaging. Tops made from plastic, long-handled pouring aids or oversized screw caps are evidence of the increasing plasticisation of this short-lived"},{"@ID":46 "EVENT REVIEW PETplanet Insider Vol. 25 No. 06/24 www.petpla.net 31 PET cap and closure manufacturing system From “maybe” to “definitely” In 2022, when Jay Hanan, Senior Technical Director of R&D at Origin Materials, approached Ueli Kobel, Director of Packsys Global’s Slitting Division in Rüti, Switzerland, several companies had already rejected his idea of developing a cap made entirely from PET as impractical. From Ueli Kobel, he at least got a “maybe” in response. Now, the PET cap for CSD PET bottles is a reality, having successfully launched at NPE. Jay Hanan is well-versed in the caps and closures business, having worked for several years in the industry. However, after joining Origin Materials in 2021, his distance from the closures sector, combined with access to a wide range of materials at the California-based sustainable materials company, allowed him to fully appreciate the design freedom offered by different polymers. This prompted him to question why bottles and caps were only available as twomaterial solutions instead of making the bottle’s cap from PET as well as the bottle itself. “We aren’t doing anything that hasn’t been done before – but we’re doing it differently,” says Hanan about the launch, acknowledging, “But first, we had to find visionary people to make an idea like this work.” He found these visionaries in Rüti, and thus, Origin and Packsys Global formed a strategic cooperation to produce the world’s first commercially scalable PET cap and closure manufacturing system. At the Swiss specialist for slitting and folding of beverage closures Packsys Global, significant energy has been invested into the project, developing tamper-evident solutions for the cap made of PET. The standard equipment used for slitting and folding HDPE caps required only slight modifications to adapt it to PET. Test series at the in-house Krea Lab technology centre were successful, paving the way for the launch of the PET cap at NPE. The PET cap offers several advantages over other material solutions, not only for markets driven by recycling. “In addition to the simplified recycling that a mono-material solution provides, PET also offers performance advantages over traditional HDPE and PP caps,” explains Bamidele Ali, VP of Corporate Development at Origin. “Besides the lightweight aspect, the higher oxygen barrier of PET makes the material particularly interesting as it can extend the shelf life of the bottled products.” Beyond the beverage segment for still drinks and CSD, the PET cap could also appeal to industries such as cosmetics. Ueli Kobel, Business Director of the Packsys Global Slitting Division, highlights another advantage: “HDPE suffers from degradation when reused multiple times. Changing a closure to the same grade of PET as the container avoids the need to separate the two materials and also solves the degradation issue.” For the new development, both virgin PET and rPET can be used. Origin’s high-throughput production system – having surpassed the 100,000 caps mark during trials – aims to produce the world’s first PET caps and closures at a commercial scale and will be adaptable to all common bottle neck finishes. www.originmaterials.com www.packsysglobal.com Origin Materials introduced the world’s first PET cap for CSD at NPE. F.l.t.r.: Bamidele Ali, VP, Corporate Development Origin Materials and Jay Hanan, Senior Technical Director, R&D Origin Materials presenting the PET cap at the Packsys Global booth."},{"@ID":44 "MARKET SURVEY 23 PETplanet Insider Vol. 25 No. 06/24 www.petpla.net Preform moulds 06/2024 MARKETsurvey Suppliers of preform, cap & SBM moulds For this issue, we have decided to present a complete overview of the knowhow in mould making. Please find here new mould technology for closure, preform and stretch blow moulds. We are pleased to present highlights from Z-Moulds, Sacmi, Sipa, Corvaglia, PET Technologies, GDXL, Röders Tec, Otto Hofstetter, and SMI! Although the publishers have made every eff ort to ensure that the information in this survey is up to date, no claims are made regarding completeness or accuracy. Resins & additives Cap producers, systems & inspection systems Preform machinery Preform production & inspection systems Preform, cap & SBM mould manufacturer SBM 2-stage Compressors Filling equipment & inspection systems Palletising & shrink film machinery Recycling machinery Company name Otto Hofstetter AG Sacmi Imola s.c. Sipa S.p.A. GDXL Precise Machinery Co., Ltd. Postal address Telephone number Web site address Contact name Function Direct telephone number E-Mail Zürcherstrasse 73, 8730 Uznach, Switzerland +41 55 285 22 11 www.otto-hofstetter.swiss Mr Stefan Zatti CSO +41 55 285 22 09 [email protected] Via Selice Prov. Le 17/A, 40026 Imola (BO), Italy +39 0542 60 7111 www.sacmi.com Mr Moraldo Masi PET preforms B.U. Director +39 0542 607111 [email protected] Via Caduti del Lavoro 3 - 31029 Vittorio Veneto +39 0438911511 www.sipa.it Mr Gianfranco Perricci Global Sales Director, Preform Systems & Tooling +39 04389 11 511 [email protected] No. 18 Changjiang Road, Guicheng, Nanhai, Foshan city, Guangdong Province, China. Postcode: 528251 +86 757 8677 7168 www.gdxl.com Mr Billy Ay Marketing Specialist +86 757 8677 7168 ext 8681 [email protected] Preform moulds Horizontal opening Yes Number of cavities 2 up to 144 (side & top entry) Up to 144 2 to 200 From 32 to 160 cavities Preform sizes Up to 500g Finish ø from 25 to 43mm, lenght up to 195mm Thread up to 120mm in diameter and length over 400mm in length Various neck fi nish standards including 1810, 1881, 30/25, 29/25, 26/22, 38mm, etc. Preform weight from approx. 3.5g to 750g (for applications from pharmaceutical/cosmetic bottle to 5-gallon keg) moulds already built for (makes) Netstal, BMB, Husky, Sacmi, Sipa Beverage market major brand owners and licencees worldwide, as well as local bottlers and converters Sipa, Husky, Netstal, Sacmi, BMB, Nigon, Arburg Husky, Netstal, Krauss-Maffei, Sipa, etc. Vertical opening Yes Number of cavities 2 up to 112 2 to 96 From 16 to 96 cavities Preform sizes Up to 500g Thread up to 110mm in diameter and length up to 205mm in length Various neck fi nish standards including 1810, 1881, 30/25, 29/25, 26/22, 38 mm, etc. Preform weight up to 69g Moulds already built for (makes) Arburg, Krauss-Maffei Sipa, Krauss-Maffei Sipa, Krauss-Maffei, etc. Do you produce single stage tooling sets? (Preform moulds AND blow moulds) No No Yes, for Sipa, ASB Nissei No Other - Multilayer moulds up to 72 cavities - Moulds for PP - Moulds for thinwall packaging - Moulds for cartridges and tubes - Moulds for medical products Design and manufacturing of moulds, hot runners and post cooling systems. Complete solutions design, also compatible with third parties presses. Together with its moulds, Sipa also supplies post-moulding cooling systems for any injection system. Sipa, with more tha 30 years of experience in this sector, designs and supplies highly optimised systems capable of obtaining high quality parts, low energy consumption and low maintenance costs. We also provide: - preform R&D service for specialised container purposes; - engineering solutions together with our partners and patent holders for: multilayer co-injection containers with barrier properties and market-appealing elements, preforms with integrated moulded handle; and turn-key production systems"},{"@ID":24 "PETplanet Insider Vol. 25 No. 06/24 www.petpla.net 22 MATERIALS / RECYCLING - Advertorial -"},{"@ID":26 "MARKET SURVEY 24 PETplanet Insider Vol. 25 No. 06/24 www.petpla.net Stretch blow moulds Cap moulds Company name SMI S.p.A. PET Technologies Postal address Telephone number Web site address Contact name Function Direct telephone number E-Mail Via C.Ceresa, 10 24015 San Giovanni Bianco (BG) ITALY +39 0345 40.111 www.smigroup.it Marketing department +39 0345 40111 [email protected] Grünlandgasse 5/1/12 2620 Neunkirchen, Austria +43 720 775 196 www.pet-eu.com Maxim Poliansky CEO +43 720 902 169 offi [email protected] Stretch blow moulds Bottle size (max.) (in litres) 12 40 Moulds supplied directly to blowing machine manufacturers Yes Yes Do you supply retrofi t moulds for existing SBM machines? Yes Yes For which bottle maker have you already produced moulds Up to now, SMI engineers have produced a high number of moulds, featuring from simple to sophisticated shapes for a a wide range of companies for the industry of food & beverage, household cleaning and personal hygiene products and chemical and pharmaceutical products. Rotary and linear blow moulders: Sidel, KHS, Krupp, Sipa, SMI, Krones, Kosme, Siapi, Sipa, Mag Plastic, ADS, Lonza, Side, Chumpower etc. Bottle design service SMI designs, develops and virtually prototypes a wide range of packaging solutions in rPET and PET, according to the customers' specifi c requirements. Many major beverage and food manufacturers are committed to using rPET to reduce their carbon footprint. Thanks to an advanced CAD center for 3D design, SMI has invested in solutions for producing rPET bottles and for supporting companies in the study and graphic realisation of a wide range of containers that are 100% recyclable, of high quality and lightweight for saving energy and material. Furthermore, SMI provides solutions for manufacturing of bottles with the utmost quality, also thanks to accurate checks made on preforms and bottles. Creation of unique bottle design, branding, product naming, logos and labels, 3D models, prototyping, bottle sampling, PET containers laboratory tests, conversion of bottles from other materials to PET Specialities The moulds are manufactured using a special aluminium alloy. SMI relies on a special laboratory for the production of moulds and mechanical components, equipped with an FMS line consisting of 12 CNC machining centres: highly automated machines, running 7 days/week round the clock, even operator-less, according to pre-set production programmes (CAM). The 12 machining centres can achieve an output of more than 15,000 moulds/year; they are equipped with linear motors with a speed rate up to 80 meters/minute and mandrels achieving a speed rate of 30,000 rounds/minute. As a result, top-level quality standards are constantly provided. Moulds for 100ml - 40 l containers, fi lling line conversions, bottles for chemicals and detergents, sanitisers, hot fi ll, refPET, 5US gallon bottles with/without handle, wide neck jars, lightweight designs, laboratory tests Other The “ReduxAir” system allows to carry out stretch-blow moulding operations at lower pressures than usual. By an innovative design and specifi c technical solutions this system allows for the air in between the bottle's outer walls and the mould's surface to be more quickly released; thus, the PET bottle manufacturing process can be carried out with compressed air pressure at 15-20 bars (such a value depends on the preform and bottle features and on the stretch-blow moulding process conditions). The great advantage the ReduxAir's user can benefi t from in terms of lower power consumption of the compressor requires a few design limitations in the bottle's shape and features. Short lead time Company name Z-Moulds Sacmi Imola s.c. Postal address Telephone number Web site address Contact name Function Direct telephone number E-mail Z-moulds GmbH, Dr.-Walter-ZumtobelStrasse 9, 6850 Dornbirn, Austria +43 5572 7272-0 www.z-moulds.com Mr Michael Fink CEO +43 5572 7272-610 michael.fi [email protected] Via Selice Prov. Le 17/A, 40026 Imola (BO), Italy +39 0542 60 7111 www.sacmi.com Mr Stefano Chiozzini Closures B.U. Manager +39 0542 607111 [email protected] Filling good: - beverages Carbonated and non-carbonated drinks, water, juices, beer, coffee & teas, dairy, etc. Still water CSD and sparkling water Juice, RTD, tea, isotonic, cold fi lled / hot fi lled - other Edible oil, soy sauces and other fi lling goods possible on request Dairy, pharma & food - individial cap solutions Possible on request Closure: -type All single-piece standard closure dimensions for all neck fi nishes, sports closures, fl ip-tops, push-pulls, multi-component closures… Flat top, 25 - 48mm Flat top, 26 - 38mm Flat top, 28 - 43mm Flat top,child proof & stoppers, 18 - 63mm -material HDPE, LDPE, PP, TPE, … HDPE HDPE and PP HDPE and PP HDPE, PP and TPE -weight Lowest from approx. 0.7g From 0.8g and above From 1.45g and above From 1.65g and above From 1.35g and above Moulds: Clamping dimensions/Cavities 16 to 128 cavities From 12 to 64 cavities Preferred hot runner suppliers MHT, Mold Masters and others No need of hot runner Special features Several patented technologies for most effi - cient closure production, with low downtimes and spare parts usage Closure designs, including tethered solutions, validated by major brand owners, worldwide"},{"@ID":8 "PETnews 6 NEWS PETplanet Insider Vol. 25 No. 06/24 www.petpla.net Nadeem Amin is the new President for Netstal Americas Netstal has appointed NadeemAmin as its new President for the Americas Region, effective since June 1, 2024. He reports directly to Netstal CEO Renzo Davatz. NadeemAmin joins Netstal with over 30 years of experience in collaborating with customers in the plastics industry. After 25 years in various roles at Husky, he joined Sacmi USA in 2020 as Vice President PET Sales and Business Development. In his new leadership role, Nadeem Amin will continue to drive market share expansion throughout the Americas Region from the Netstal Technical Center located in Hebron, KY. This technical centre currently supports customers with sales, service, and training. His focus will be on maximising production efficiency for customers in the strategic application areas of PET preform, beverage closures, thin-wall packaging, and medical moulding. www.netstal.com Origin Materials and Bachmann Group to mass produce PET caps and closures Origin Materials and Bachmann Group announced a strategic partnership to mass produce PET caps and closures. In Bachmann’s existing world-class European manufacturing facilities, Bachmann and Origin will operate the lines to convert virgin and recycled PET into caps, including tethered caps, using high-speed equipment and automation. Origin’s caps are developed to be the first commercially viable PET closures to reach the mass market. Origin Co-CEO and Co-Founder John Bissell said: “Bachmann Group will help us produce billions of caps, taking pellet or flake all the way to finished closures. We share a commitment to sustainability and look forward to a productive partnership.” Origin’s PCO 1881-compatible caps, which can be made with virgin or recycled PET, will be available beginning in Q4 2024, with PCO 1881-compatible tethered caps and other cap types to follow afterwards. www.originmaterials.com"},{"@ID":2 ""},{"@ID":45 "imprint EDITORIAL PUBLISHER Alexander Büchler, Managing Director HEAD OFFICE heidelberg business media GmbH Hubweg 15 74939 Zuzenhausen, Germany phone: +49 6221-65108-0 [email protected] EDITORIAL Kay Barton Heike Fischer Gabriele Kosmehl Michael Maruschke Ruari McCallion Anthony Withers Editorial & WikiPETia. info [email protected] MEDIA CONSULTANTS Martina Hirschmann [email protected] Johann Lange-Brock [email protected] phone: +49 6221-65108-0 LAYOUT AND PREPRESS EXPRIM Werbeagentur Matthias Gaumann www.exprim.de READER SERVICES [email protected] PRINT Chroma Druck Eine Unternehmung der Limberg-Druck GmbH Danziger Platz 6 67059 Ludwigshafen, Germany WWW www.hbmedia.net | www.petpla.net PETplanet Insider ISSN 1438-9459 is published 10 times a year. This publication is sent to qualified subscribers (1-year subscription 149 EUR, 2-year subscription 289 EUR, Young professionals’ subscription 99 EUR. Magazines will be dispatched to you by airmail). Not to be reproduced in any form without permission from the publisher. Note: The fact that product names may not be identified as trademarks is not an indication that such names are not registered trademarks. 3 PETplanet Insider Vol. 25 No. 06/24 www.petpla.net The time has now come; as from “...3 July 2024, singleuse plastic beverage containers may only be placed on the EU market if their plastic closures and lids are firmly attached to the containers for the entire period of use.” This is what EU Regulation 2019/904 says somewhat cumbersomely. It cost the beverage industry a lot of effort and money to implement this. Money and effort that bottlers would have loved to invest in more meaningful projects. The preamble “...but its increasing use in short-lived items that are not intended to be reused or recycled cost-effectively means that the associated production and consumption habits are becoming increasingly inefficient and linear...” is – at least when it comes to PET bottles and their closures – way off the mark. No plastic has a higher recycling share than PET. And since the closure almost always comes with it, the polyolefin component is also in the recycling loop. But what’s the good of crying? The industry has tried to change the committees’ minds with factual arguments, but to no avail. Now we have a mess, or rather the tethered cap. Simply because the locking ring on the previous closure is cut differently or manufactured with new moulds, which is very complex, the sensitive closure now gets stuck in the feeders, and is a challenge for quality assurance as well as being extremely unpopular with consumers. The many good sides of the EU are overshadowed by these and other regulations that are difficult to understand. This plays into the hands of the EU sceptics and right-wing populists, who gained 10% more seats in the recent EU election with 370 million eligible voters, increasing their number of seats to 131 (out of a total of 720). May the future regulations make more sense and perhaps involving experts when they are drawn up. Yours, Alexander Büchler Dear readers,"},{"@ID":36 "34 EVENT REVIEW PETplanet Insider Vol. 25 No. 06/24 www.petpla.net Modular testing system for all key aspects of plastic bottles UK-based quality control equipment manufacturer Torus Measurement Systems, which specialises in measuring all aspects of plastic bottles, presented its ‘TQ Lab’. The fully automated device combines the three modular units B302, B309 and B304 to provide reliable measurements for neck and body dimensions, thickness distribution, load, volume and weight. According to Torus, the system can either be used as a standalone solution with up to 50 bottles to be tested en bloc or integrated inline into the existing production line. The B302 thread, body and thickness module is said to offer all the features of external dimensions for all areas of plastic bottles. All neck, body and height features are to be measured in seconds and industry-leading accuracies can be achieved using telecentric camera equipment. Thread and body alignment routines are designed to automatically position the bottle for measurement and significantly reduce operator intervention. The combination of white light technology and bottom-up bottle orientation enables thickness measurements at the shoulder, top and bottom to maximise material savings. The B309 inner diameter module also utilises confocal white light technology, which enables non-contact inspection of the inner neck diameter and is designed to eliminate the operator and measurement influences of conventional contact methods. According to the manufacturer, the module covers small neck openings through to wide neck finishes by combining a right-angled sensor with a precision gantry system. This setup enables measurements at user-defined heights from the seal surface. Finally, the B304 top load, volume and weight module offers the ability to check the structural integrity of the bottle and perform wet top load, brim full volume and programmable fill height measurements within a single measurement cycle. The system is therefore able to automatically fill and empty bottles for all wet test routines. The load tests range from aerated, sealed, capped or side-loaded bottles. www.torus-group.com F.l.t.r.: Chloe Coles, Group Marketing and Graphics Coordinator, and Greg Schultz, Regional Managing Director US, next to the TQ Lab"},{"@ID":49 "The worldwide round trip with PET world in the Middle East In a spectacular project taking us well into 2024, we will be travelling in a wide variety of ways to various countries and regions of the Middle East with different mobile editors. There we will interview machine manufacturers, the supply industry, bottle and beverage producers, as well as PET recyclers and everyone involved in the process chain. What market-specific trends are there now or will arise in the future? What developments and technologies are in vogue on the consumer and plant construction site in some of the hottest regions of the world? What special requirements are there? What role do topics such as food safety, shelf life and sustainability play in PET packaging and how are companies preparing themselves for the coming years? This, and much more we will be discussing face-to-face with all the key players and then our results will be presented to you in a series of must-read reports in PETplanet Insider. Please join on this enchanting voyage to the world of PET in the Middle East. We look forward to welcoming you on board! Our previous Road Shows at a glance 2010-2011-2012-2013-2014-2015- 2016-2017-2018-2019-2020-2022 Interested in being visited? [email protected] Autumn 2023 - 2024 6 countries numerous interviews with PET companies Sponsors to date Editour The Middle East Roadshow"}]}}
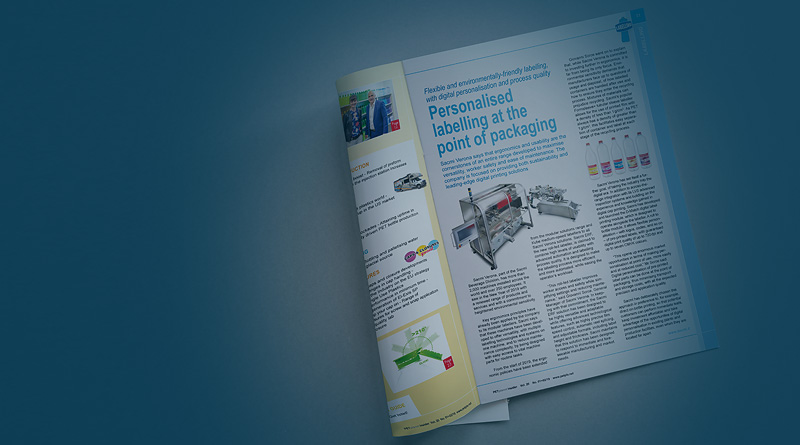