Preform mould manufacturing
We met:
Mr Rick Unterlander, General Manager PET
Mr Vincent Travaglini, President & CEO
We spoke with General Manager PET Mr Rick Unterlander about the past, the future and, of course, about PET. He began with an outline of the history of Stackteck, which was established in 1998 as a merger of Tradesco (founded in 1976) and Unique, whose history dates back to 1969. In 1991, while it was still operating under the Tradesco name, it designed, developed and manufactured the world’s first four-level stack mould. A year later, it launched another first: the Quick Product Change (QPC) stack mould. The following 22 years saw a series of worlds’ first developments from StackTeck, including innovative mould technologies such as: five-piece collapsing core; 4×32 stack mould configurations; 2×64 unscrewing cap moulds; and 2×32 co-injection stack moulds.
In 2013, Stackteck released its first production mould featuring Trim (Thin Recess Injection Moulding) technology. This year, 2019, sees it launch its first Fasttrack mould capability, with automated design and an eight-week delivery. Other developments announced in 2019 saw Stackteck Asia established in South Korea, and the launch of its PET initiative.
The company has, to date, built over 130 PET preform moulds, ranging from two-cavity development platforms to 144-cavity high volume production systems. Its main markets and the the majority of sales are found in North America and Asia, including Japan. At K, the company exhibited a range of its technologies, such as ISO hot runner systems; Kooltrack conformal cooling stack components; and Picool post mould cooling systems.
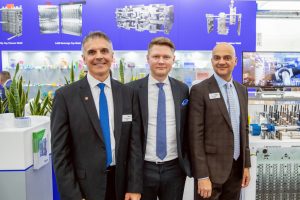
With over 35 years’ experience in the industry, Stackteck’s new General Manager PET, Rick Unterlander, is a recognised expert. He has held a number of positions at several PET converter and equipment supply companies, ranging from PET Lab Technician through to PET Process Engineering Manager, R&D Engineering Manager, and Owner/VP PET Operations. He holds numerous patents in the industry and continues to participate in initiatives for advancing PET technology to improve performance and efficiency, and support sustainability. His focus in his new appointment at Stackteck is on PET preform projects in the Americas. He is also the liaison to Stackteck Asia in South Korea, where the company has already built a successful track record in PET preform moulds, hot runners, and post-mould cooling systems.
“Our moulds, hot runners, end-of-arm-tooling and Picool, a new, patented post mould cooling technology, are compatible with all major machine brands, at very competitive costs and industry leading performance”, Rick stated. “Our hot runner technologies are designed to reduce pressure drop, improve cavity-to-cavity balance, reduce colour changeover time, and generate lower AA levels than conventional designs, while virtually eliminating PET dust”, he added. The new moulds feature conformal cooling to improve productivity, while Picool speeds up cycle times.
“We need around four to 14 weeks to fulfil an order for a mould, depending on design, cavitation and backlog”, Rick added. “We are pretty well positioned in terms of sales and after sales service, with our two manufacturing locations in Canada and South Korea plus a global support network, strategically located in regions around the world.” While different markets require different solutions, meeting and overcoming the global challenges and demands from the industry for PET moulds is based on the same foundations and qualities.
Reducing scrap, improving productivity
“Economic value, cost of ownership, performance and efficiency are key requirements that shape success,” Rick Unterlander said. Without identifying them by name, he said that he sees the top tier suppliers for two-stage preform moulds as Stackteck’s leading competitors. “Being innovative in finding ways to meet those requirements is essential. Recently, sustainability has become a global priority. Finding solutions for reducing scrap through improved part quality, speedy colour change-overs and building processing know-how with recycled materials have been a priority for us, as well as improving productivity through advanced technologies in the hot runner, cold half, and post mould cooling systems.”
Stackteck sees clear trends for today’s PET preform industry as a wide range of market segments including rPET applications, beyond the beverage and food industry, which is creating many new opportunities for mould projects.
Stackteck’s President and CEO, Mr Vincent Travaglini, confidently stated “We can cope with that. We have a large capacity for machining, to handle big programmes. In a highly competitive market, we have built a good reputation through the years for being a premium supplier in food and beverage packaging with a broad scope of offerings, from part development and mould design to piloting, prototyping, repairs and systems integrations. All that is led by industry experience. We have many long tenured people in sales, manufacturing, engineering and other company areas, too,” he concluded.