Review: rPET in stretch blow moulded bottles
Online conference on May 28, 2020, 1:00 p.m. – 2:00 p.m. CEST
Target group: Managers for recyclers, converters and bottlers with stretch blow moulding machines
The first PETinar organised by PETplanet Insider took place on the 28th of May 2020. PETplanet invited three specialists to discuss the topic of manufacturing and processing rPET right through to a blown PET bottle.
Moderator
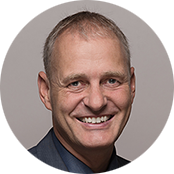
Mr Stefan Bock, CEO of RedupPET, expert in the field of preform production, moderated the discussion. The first presentation was delivered by Mr Christoph Wöss, Business Development Manager, Bottle Application at Erema Group. Christoph introduced the new bottle-to-bottle recycling technology Vacunite from Erema. He was followed by Mr Arne Wiese, Product Manager Bottles & Shapes at KHS. Arne described and analysed the processing from an rPET preform to a blown rPET bottle.
Vacunite
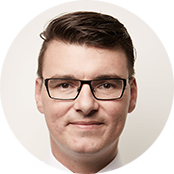
Christoph emphasised the advantages of the Vacunite technology. Vacunite is a combination of the proven Vacurema technology and an assisted SSP (Solid State Polycondensation) at reduced pressure under nitrogen, patented and designed by Polymetrix. In the Vacunite system, the extruder is short with backward degassing at the melting zone. For a higher degree of crystallisation, a new, compact inline crystallisation system was added. It shows no sticking behaviour because the shift of low melting peak is above drying temperature.
The technology reduces yellowing due to vacuum and N2 and generates a reliable decontamination, which is FDA & Efsa approved. The low IV decrease in the vacuum reactor enables a high increase of the IV in the SSP. The IV increase is determined by the process temperature (190-210°C) and pressure (100-200 mbara). Christoph concluded that the Vacunite technology is a well-controlled thermal process, has very high energy efficiency and is officially food contact approved. It has an output from flake to pellet up to 0.35 kWh/kg.
For more details, see Christoph’s presentation.
From rPET preform to bottle
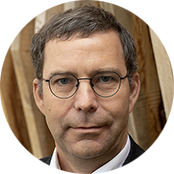
Arne explained the material difference between PET and rPET. The factor that most strongly represents a variance to virgin PET is the colour and the cost of the recycled material. The impact on the blowing process is based on experiences with an InnoPET Blow Moulder Series V from KHS. Arne stated that the colour variation results in more heat absorption, and this means more material in the shoulder area of the preform. The pyrometer at the end of the oven can only adjust an average of the preform temperature. If the quality of the bottle is not sufficient during this phase, additional hardware can help, added Arne.
With the process pilot and mould control the machine can react much faster on colour variations in the preform. The Process Pilot can improve CPK (process stability) by 28%, the Unit Mould Control can improve CPK by 16%, and the overall CPK is thus improved by 28%+16% = 44%. Another important question is the impact on the IV. During the heating process and the material distribution there was no difference compared to the virgin material measured. Differences could be measured on bottle performance due to the different IV´s of the material. Arne’s suggestion here is to ensure that the IV never drops below the critical level. Arne’s conclusion on the quality of an rPET bottle: There can be variations of material distribution and the IV, but problems only occur if minimal requirements are no longer met. The rPET bottle helps to close the loop for recycling.
For more details, see Arne’s presentation.
We thank the speakers and the numerous participants for their interest and the exciting discussions!