What to expect when you’re inspecting
by Christoph Wynands (Product Manager) and Malte Nitz (Marketing), Intravis
In recent years, the demands and challenges in the production of preforms have grown steadily due to needs for increasing material savings and the expanding use of recycled materials. The demands on inspection solutions for preforms have also risen to the same extent during this period. More and more inspection systems and concepts have entered the market.
When do you use an offline system and when is a monitoring system the better choice? Or perhaps it is best to have both together? What are the differences between 100% inline inspection and a laboratory system for random sample inspections? And how can you get even more out of your existing inspection solutions with the appropriate software?
Despite the current prevailing mood in the media that plastic packaging is responsible for all of the ills in this world, the number of drinks that have been filled in PET bottles continues to increase in recent years. Ever lower manufacturing costs, safer transportability, increased recyclability and low weight are just some of the positive characteristics that explain the increasing share of PET packaging.
Due to these advantages, the spreading use of PET bottles has increased significantly. Let’s take the developments in Germany as an example. The market share of PET bottles was still around 30% in 2003. This is when the deposit on non-refillable bottles was introduced and the share then increased to almost 72% by the end of 2017. In line with this development, which can also be observed in many other countries around the world, more and more companies are starting to produce PET preforms or expanding their capacities in this area. Due to these changes, indispensable elements in modern production lines now include inspection systems. They guarantee consistently high product quality and offer their users clear competitive advantages.
Increasing requirements
With the increase in the number of preforms produced, new requirements and expectations for inspection systems have arisen on the production side. Because the market requirements are very different and sometimes incompatible, various system types were developed over time. Whereas years ago, suppliers often only offered one “system for preform inspection”; today they often offer four or five different solutions – some of which are still adapted to meet specific customer requirements. As a result, this means an ever increasing range of systems for different situations. The customer rarely knows exactly what the best solution is for their production from the beginning without consultation.
Critical applications = 100% inline testing
Choosing which inspection system is the right solution depends first and foremost on the customer’s requirements. So he must ask himself the following questions: How demanding is my product? Which risk factors can influence product quality? How important is the job that I produce on this machine? Do I produce for a demanding customer or critical market to which I only want to deliver perfect quality? If so, even one bad preform can lead to the rejection of a delivery or, in the worst case, the end of a partnership. Accordingly, a 100% inline inspection solution is the best choice for such cases. Systems such as the PreWatcher Inline from Intravis inspect all preforms directly after an injection moulding machine and sort out the defective ones. The PreWatcher Inline inspects up to 72,000 pph with a precision that is pixel accurate for a total of 25 criteria – including the reading and correlation of data to the cavity number.
In-house production = monitoring may be sufficient
Machine downtimes due to bursting preforms in the blow moulder, responsibility for the entire supply chain and short distances in-house are more forgiving than an external customer who suffers a production stoppage and complains about an entire delivery. Due to this lower risk, 100% inline inspection may not be required. In this case, many customers rely on the results of a lower cost production monitoring system. When embedded in a production line, these systems do not achieve 100% inspection; but offer a good compromise in terms of up-front costs, space requirements and inspection performance. Also, monitoring systems can achieve the same accuracy as the more expensive and required larger footprints of inline and offline 100% inspection systems.
One of the latest monitoring systems on the market is the PreMon. Due to its new transport technology it inspects up to 70% of preform production, and costs only one fifth the price of a 100% inspection system. Therefore, it offers the optimal compromise by having a fast ROI, small space requirements and still delivers the security of high product quality.
PreMon special features include an optional ejector that sorts out defective preforms. It offers grading statistics in which the system collects and visualises real-time data, as well as, the most important information of the last 24 hours and assigns the information to the corresponding packaging units (octabins). By indicating the error rate, the corresponding error images and the corresponding evaluation statistics; the PreMon provides a stable foundation for making the right decision on whether or not an octabin meets quality requirements with certainty. With this information, the producer can reliably decide how to proceed with an octabin: recycle the entire packaging unit, send the octabin into storage and re-sort it with offline inspection, or release it for sale or for further processing.
Offline re-sorting systems
When an octabin lands in the blocking warehouse, the hour strikes for an offline inspection system. On one hand, these systems are characterised by higher inspection speeds and on another hand they are so flexible that they can be converted from one preform design to another very quickly. Compared to 100% inline inspection systems, offline inspection systems often offer a similar scope of inspection capabilities.
Laboratory systems support analysis and reporting
For comprehensive quality audits, preform producers require extensive reporting on the quality of the preforms that are made. If a company wants to offer its customers the highest possible level of detail in this area, it will use a laboratory system such as the Sample-PreWatcher. It is common practice to sort out the first and the last complete shot of a shift and to subject it to a precise inspection in the laboratory. The Sample-PreWatcher with its circa 30 inspection criteria replaces the laboratory. It offers an additional weight check, and a higher precision during inspection compared to an inline or offline vision system. Other capabilities include a polarisation test with which stress points in the preform can be detected.
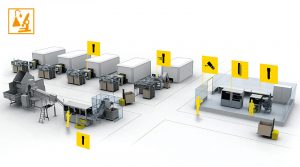
As far as speed is concerned, it must be considered in a differentiated way. Compared to an inline, offline or monitoring system, a laboratory system with up to 1,200 tested preforms per hour is considerably slower. However, a comparison with conventional test methods within a laboratory is more appropriate. Here, the laboratory system offers a higher test performance with up to 30,000 individual quality data points collected per hour; it gives a decisive advantage of an objective and reproducible test situation. The “human” influence factor is thus reduced from quality control and has no influence whatsoever on the accuracy of the measurement results. In addition, the measurements of the laboratory system can be output directly as a report with one click, thus providing comprehensive support for laboratory personnel.
Data summary and optimisation with software
All inspection systems whether they inspect inline or offline, 100%, or only partially, have one thing in common. They produce a very large amount of product-related quality data. With the right tool, a comprehensive analysis software, important insights can be drawn from this collected data. With the help of these findings, producers can then optimise their processes and compare at a glance which lines and settings may require changes for improvement. As an example of a benefit of data collection, the mould diagram function of the IntraVisualizer analysis software is described here. This feature uses the cavity numbers of preforms to create a three-dimensional graphic of the distribution of a defect within the mould for each individual defect type. Based on this graphic representation it is possible to see that the clamping force of the mould needs to be adjusted because defects such as long shots (flash) occur more frequently in one area of the mould. The benefits of timely information and findings such as these can demonstrably increase the performance of a production line and result in a large savings of material and time.
Conclusion
In summary, given the large number of different inspection solutions available, each has its own advantages and could be the best choice for certain situations and requirements. For future production, which is increasingly controlled and optimised by data and information, a combination of different system types together with additional analysis software is the best choice. If a company is aware of the accuracy and speed required for its needs and to fill its orders, the optimal quality inspection concept can be found for every producer. The right quality information can help to identify production advantages and provide a decisive competitive edge in the global preform market.