Slitting for tethered caps
PackSys Global, Rüti, Switzerland
We met:
Mr Beat Rupp, CEO
Mr Ueli Kobel, Group Leader Global Sales Closures
Mr Thomas LeFevre, Vice President for Sales and Marketing Ms Murielle Erard, Head of Marketing
For a long time PackSys Global AG in Rüti, Switzerland, has specialised in manufacturing machines for the slitting and folding of the tamper evident band seen on most beverage caps. For many years, slitting was a rather unspectacular technology. Caps made by compression moulding required slitting. Producers of caps using injection moulding could choose between slitting the tamper evident band or making it as part of the injection moulding process.
Discussions about recycling rates and the circular economy show that PET bottles are among the most widely recycled types of packaging however their caps are seldom recycled and are an easily recognised source of ocean plastic. As a result of this situation the EU passed legislation requiring that by July 2024 that all caps on beverage packaging remain attached or tethered after the bottle or carton is opened. Similar legislation was under discussion in California but has not yet been approved.
The discussions about tethered caps have brought the technology to centre stage in cap production. We spoke to CEO Beat Rupp and Ueli Kobel about the background.
PETplanet: Mr Rupp, Mr Kobel, you provide customers with systems for slitting caps. To what extent have requirements changed with the tethered cap?
PackSys: Up to now, we have basically been dealing with straight cuts around the cap perimeter. This means we have rolled the cap along a knife with a specified pressure. This created the predetermined breaking points that enables the consumer to release the cap from the quality band using a specific twisting motion.
PETplanet: The plastic cap must remain attached to the bottle during consumption.
PackSys: Exactly. This happens only with an integrated hinge between the tamper evident band and cap and it makes the cutting geometry significantly more complex. The knife along which we rolled the cap must now not only cut horizontally; there are also vertical cutting edges on the knife. We call this technology smarTether.
PETplanet: The design of the hinge, i.e. where the cut should be, is decided by the customer?
PackSys: Yes. We deliberately stay out of this area. Each customer has their own trends there and that’s how it should stay. Certainly, we discuss ideas with the customer, as despite cleverly crafted hinge solutions, these can sometimes be difficult to implement in production.
One very interesting area is the use of tethered caps on cartons, especially those known as gable top. Gable top cartons, which are very often used for dairy products, have an angled top instead of a flat top. For such cases the beverage is always dispensed in a certain way. Tethered caps on water, juice or carbonated soft drink bottles can be tethered in any direction. For gable top packages the tethered cap has to be oriented so that it stays out of the path of the beverage being poured. Developing orientation technology for tethered caps has been an interesting challenge but one where we have succeeded. The first oriented systems using our newly developed CapCompass technology are now in production and should deliver oriented tethered caps to the market in 2021.
PETplanet: If you put the different designs from customers side by side, can you identify a trend?
PackSys: A very clear trend is that the projects work with existing caps. They are trying to continue to produce the cap in the same way as usual and make the necessary adjustments just with the slitting. There is a strong pressure from all segments to make tethered caps be as cost effective as possible and certainly to avoid using more plastic for a tethered cap than for a non-tethered cap.
PETplanet: Are there projects that have come through the prototype stage?
PackSys: One customer has produced and tested 80 million screw caps and is now expanding its testing to several more locations. A lot of expertise has been developed by the cap makers, the bottlers and us as well.
PETplanet: So there will be a significant sales increase for your business when the new regulations are implemented.
PackSys: We certainly look forward to increased sales but many customers who already use our technology will be able to implement tethered solutions without buying new machines. Our systems have a machine bed with two stations; slitting is made at the first station and folding at the second. The customer must therefore only exchange the parts that touch the product at the slitter. For oriented tethered caps new machinery will required. We look forward to around 30 additional systems per year.
Covid-19 impact on developments
PackSys: In normal times our commercial and R&D teams travel the world to listen to customers explaining their needs and visions of the future. The Covid imposed limitations on travel have meant that we had to stay close to home. While this has been a boost to our development partnerships with Swiss companies, the new communication and information sharing technologies which have boomed during 2020 have also enabled new methods of cooperation and joint developments with partners outside of Switzerland. We have developed some new solutions for the closure market which will be presented in 2021, either in traditional forums, using new digital presentation methods or some combination of both.
PETplanet: Many thanks.
Technologies
Alongside the folding and slitting machines for plastic caps, PackSys Global manufactures complete lines for plastic and laminate tubes for the oral care, cosmetics and pharmaceuticals segments. Madag Printing Systems AG is a specialist in hot stamping machines for the packaging, machinery and automotive industries. Texa AG adds value to the portfolio by developing and building packing machines for tubes, cans and cartridges. Both companies are subsidiaries of PackSys Global AG. One year ago the construction of a new, company-owned, 15,000m2 facility started in Rüti, Switzerland. It is only 500 m from the current headquarters away.
CEO Beat Rupp is clearly proud that, despite coronavirus, they are keeping to plans and will move in a year’s time. “Whether it is finished or not, we have to be out of the old premises on October 1, 2021. The way things are going at the moment, I’d like to think we will not be moving to a building site.”
Tethered closure designs vary according to the individual applications and beverage container specifications. PackSys Global has developed two new slitting technologies to create solutions matching the EU directive requirements and considering consumers’ convenience. All technologies deliver solutions with all the traditional benefits of slit TE Band closures plus tethering.
smarTether
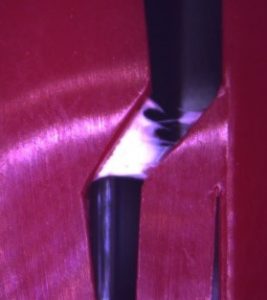
This technology can be implemented without machine modifications into all machines in PackSys portfolio. A choice and combination of multiple horizontal, together with several vertical knives, allows slitting with either a randomly positioned hinge or a lasso styled tether. Conversion of existing production machines allows quick and cost-effective product conversion. smarTether is applicable on all major PET bottle closure applications. smarTether purposely leaves a thin and controllable skin in the separation area (to not completely cut through the plastic closure side wall). This provides a high-performance tethered closure suitable for high speed capping processes.
experTether
experTether, like smarTether, is designed for multiple slitting lines on both the horizontal and vertical axes. The spindles are fully and accurately synchronised to the slitting knives, located at the outside of the rotating slitting turret. The synchronised tooling ensures unique accuracy on slit lines and is the only method able to create customised slitting pattern on plastic closures as known from standard TE band slitting. Regardless of the required speed, experTether can handle it.
CapCompass technology
When it is important the closure stays in a consumer-friendly position after opening (e.g. carton bricks, gable top, etc.), CapCompass is the right solution. After opening, the closure will flip away to a non-disturbing position. Simultaneous spindle movements allow accurate positioning of the plastic closure before slitting process starts. Optimised machine kinematics, paired with sequential knife penetration, provide gentle closure handling and make it therefore also suitable for thin wall and light weight closures. CapCompass orientation technology can be used with both smarTether and experTether to achieve the customer’s desired tethering style.
PackSys Global has applied for patents on a number of the newly developed technologies related to tethered solutions.
Visit PackSys Global