Almost 50 years of PET stretch blow mould production
If there were a synonym for PET stretch blow moulds it could be Röders. Röders, together with Corpoplast, from its very beginning made PET stretch blow moulding suitable for large-scale production almost 50 years ago. Later Röders supported well-established machine producers like Krones and Sipa with their development of modern mould concepts for their blowing machines. The PET stretch blow moulding technology is still one of the most important packaging technologies for liquids today. Jürgen Röders, managing director of Röders, has a long-held passion for PET stretch blow moulding – so we visited him at Soltau.
Röders is a sixth-generation family-run business with a history of more than 200 years. Apart from technology, there is only one matter of concern for Jürgen Röders and that is reliability. This means meeting short delivery times as well as ensuring that he provides solutions that are tailor-made to his customers’ requirements.
Röders, together with Corpoplast, was the first to venture into the PET stretch blow moulding technology for packaging soft drinks in 1975 in a move away from PVC to PET. For years, Röders had designed and produced PET blow moulds exclusively for machines from Corpoplast. Later, in the 1990s, Röders started offering PET blow moulds also for machines made by Sidel and others.
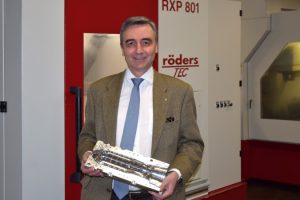
Röders has not only left its mark on the history of PET stretch blow moulding. Today, too, significant industry innovations are coming out of Soltau, including its rapid mould change system and the development of coatings for stainless steel moulds to reduce cleaning efforts at the customers as well as protection against scratches and damages.
For all innovations, it often comes down to fine details which will be decisive for whether or not a mould will fit and function. “Even within machine generations, the mounting arrangement for the PET stretch blow moulds can be different. Here, we have to take particular account of the machine’s varying and therewith special features”, says Jani Rickert, Head of PET Blow Mould Sales.
Innovations in production are very important for reducing delivery times and improving cost efficiency. More than 30 years ago, Jürgen Röders already felt challenged by the fact that aluminium is relatively easy and fast to machine, but only slow machines were available to produce moulds made of aluminium. Finally, he started the development of High Speed Cutting machines (HSC machines) and Röders became a pioneer in this evolving technology. Today, the production of its high precision, high speed milling and grinding machines account for more than 80% of Röders’ turnover.
The use of High Speed Cutting machines can dramatically reduce the processing times for mould parts and almost completely cut down the manual polishing work of the inner surfaces of those mould parts. Smallest details and complex geometries may directly be produced with this specialised machinery and time-consuming die-sinking (EDM) work is avoided.
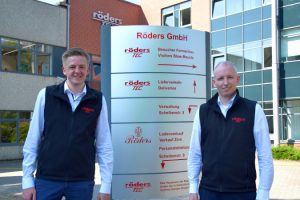
The flat company hierarchy helps shortening delivery times also. If necessary, it takes only a few days from the design stage to an initial sample mould to be completed. Processes within the plant are carefully time and quality monitored and supervised. In case a customer requires a sudden change, for example in priority, production may immediately react.
In most projects, customers usually come up with a suggestion for a bottle design and already send a detailed construction (CAD file). Then Röders with its comprehensive experience consults with respect to feasibility in PET stretch blow moulding. Sometimes, the customer only has a vague idea about a bottle design, may be a sketch. Then Röders will develop also the construction of the new PET bottle suitable for stretch blow moulding. Technical requirements like top load, minimum weight, choice of preform etc. are considered. For testing Röders has a fully certified blowing laboratory, in which also larger numbers of sample bottles may be produced and tested. Renowned companies like PepsiCo and Coca-Cola have certified Röders’ capabilities and laboratory.
A very important trend in the industry with respect to saving resources has been the development of bottle designs for low-pressure stretch blow moulding. This mainly concerns the base design. Again, Röders has made own developments and brought down the blowing pressure to approx. 20 bar helping the customers to achieve significant energy savings.
Today, Röders produces an average of 6,000 moulds/year. Business has been stagnant during the year of Covid. When answering the classic parting question “Where will Röders be in five years’ time?” Mr Röders did not mention any specific targets but said “We are flexible, follow the market and remain open for new opportunities. This has been our solid business foundation for more than 200 years company history”.