Rotated by 90°
PET preform moulds for side-entry systems
PET preform moulds from Otto Hofstetter AG are now also available for side-entry systems. The family-owned Swiss company relies on its proprietary Cavity-Lock stack design, with its proven track record in the top-entry world, supplying all corresponding EOATs ranging from 2 to 192 cavities.
In 1977, Otto Hofstetter AG engineered and constructed the first injection mould for the production of PET preforms. The client was the Continental Can Company, which had the mandate to produce new drinks packaging for Coca-Cola and Pepsi. The order consisted of 12 injection moulds with 16 cavities, many of which were designed to produce preforms for 2-litre bottles.
Since then, many leading PET producers in Asia, North and South America, Australia, Africa and Europe are customers of these Swiss-made tools, which are manufactured using high quality components assembled with great care by skilled toolmakers. In addition to this craftsmanship, achieving the performance levels of the moulds from Uznach requires even more expertise. For example, refinements like OH Xtreme coating, which enabled a 72-cavity mould to complete more than 15 million cycles before its first maintenance. Or OH Xtra surface treatment, which reduces conventional average roughness (RA) from 0.2 to 0.3 microns to 0.05 to 0.1 microns.
Otto Hofstetter is proud of the reliability of their cavity-lock mould design which the company claims has a longer service life than conventional feed-in designs, often needing revisions after 10 million cycles. According to the latest data from producers, this target is often exceeded, says Otto Hofstetter. For example, in Austria, a 48-cavity preform mould for 1.5-litre bottles has been running without a rebuild for 22 years; in Indonesia, a 96-cavity mould for 0.6 litre bottles has been in continuous service since 2007. The hot runners are also marathon performers. In Belgium, one of Otto Hofstetter’s hot runners has been in daily use since 2014, clocking up almost 16 million cycles and counting.
Side-entry moulds
A few months ago, the management of Otto Hofstetter AG decided to construct side-entry moulds for PET preform systems with horizontal robot removal. This means that PET preform producers can now enjoy the durability and high availability of Swiss moulds for both side- and top-entry platforms.
The move from the proven top-entry to side-entry moulds basically just required a rotation of 90 degrees. For this purpose, some small technical adjustments had to be made in the design. The result is side-entry moulds that include all the quality and features of the company’s top-entry injection moulds. The stack structure is also executed with Cavity-Lock, and the latest performance-enhancing innovations such as OH XCool and OH Xblow can also be integrated into the mould. In addition, all corresponding EOATs are available to match the selected preform. The hot runners comply with all relevant standards.
In operation
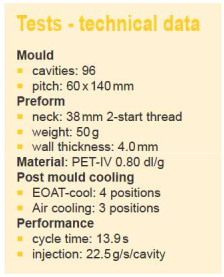
For initial tests, a side-entry mould from OHAG was installed in a new PET-Line 4000 at Netstal. The 96-cavity mould (for technical data see box on the right) was designed for a preform with a 38 mm 2-start thread, a weight of 50 grams and a wall thickness of 4 mm. The EOAT cooling ran over four positions, the air cooling over three. With a cycle time of 13.9 seconds and an injection rate of 22.5 grams per second and cavity, the new side removal mould exceeded expectations during the first tests, according to the company. Well-known PET preform manufacturers in the USA, who are already using the new side removal moulds on a daily basis, were able to confirm the high performance in the tests and attest that the side removal moulds are of the same quality as the systems with top removal.
Along with the engineering and construction of preform moulds, Otto Hofstetter AG offers a comprehensive range of services for all aspects of PET preform production. Projects generally start with the clarification of the customer’s needs and end with the testing of the first preforms produced on the production system. The Swiss company believes a successful project is best achieved by early and close collaboration with all involved parties, up- and downstream.