What’s new in preform production?
Three question-survey on the current preform product situation and future challenges
PETplanet Insider gave preform producers the opportunity to describe their current situation and plans. We are pleased to present the answers from Plastipak, SGT, PDG, Novapet and Flexblow. The companies answered the following three questions:
1) The last development steps in the production of preforms were the thin-wall-, the multilayer- and the use of rPET in a preform. What are the new challenges in the production of preforms?
2) Is there any specialisation in your company – what types of preforms does your company produce most often? Do you think this is the way you will continue?
3) Which markets are interesting for you, where will your company invest in the future in terms of preform production?
Plastipak, Pedro Martins, Executive Managing Director Europe
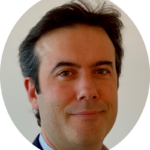
1) The inclusion of rPET, with increasingly higher percentages of recycled material, often up to 100%, is still the dominant trend we see in our business. For Plastipak, a reprocessor and producer of food-grade rPET since 1998 in Europe, the inclusion of rPET in preforms is not the challenge as this has been a core capability for many years. With three recycling plants in Europe, one in the US and another one currently under construction in Spain, Plastipak is the largest producer of food-grade rPET in Europe. Reprocessing capacity is being developed at a high rate, however collection of post-consumer PET to feed the recycling plants remains a challenge, as does the leakage of material from closed loop bottle-to-bottle recycling in to applications such as textiles. Complete closed-loop recycling is the ultimate goal, and so design-for-recycling is another critical component of the solution. For many years, the constant focus of our development team has been the design and creation of sustainable, fully circular packaging, and this philosophy is at the heart of every Plastipak innovation. Finally, our most important challenge is the production of the lowest carbon products that we can. The design and production of low carbon preforms requires the amalgamation of our key skills; design expertise, the latest light-weighting technologies, resin developments, inclusion of recycled content and best in class production. Underpinning this, 100% of the electricity Plastipak uses at its European plants originates from renewable sources. Our life cycle analysis service enables Plastipak to quantify environmental impacts, enabling our customers to make fully informed decisions on this basis.
2) With 15 plants across 12 countries in Europe, and many more in North and South America, Plastipak produces preforms and containers for the major applications of PET bottles and containers; beverage, food, home and personal care, industrial and more. Therefore, we cannot say that we specialise in any particular sector or in any particular product, apart from sustainable, innovative, high quality products. Our development centre looks at the whole life of the package and the requirements of the product that it destined to protect, so producing the lightest-weight, highest-performing package that is optimally designed to suit the filling platforms and logistical chains, right through to the end of life. This is the approach that has grown our business to the size it is today, and we anticipate that we will continue to follow this model.
3) Plastipak is customer-driven, and we develop long-term partnerships with our clients, many of which are multinational or leaders in their respective markets. This, combined with the contract-driven nature of our business, means that our investment is customer-centred, rather than speculative. Going forward, we anticipate this will not change, and we will grow with our customers. Plastipak will continue to make investment decisions on this basis, as well as with the long-term strategic intent of producing the lowest carbon, fully circular products possible, to support our, and our customer’s ESG aspirations and targets.
SGT & SGR Group, Frédéric Mignot, CEO
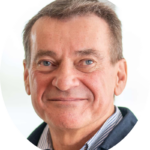
1) At SGT, we are focused on developing light weighting, sustainable and design-for-recycling preforms, three major trends for bottlers industry. Regarding light-weighting our preforms, we are currently working on a new range of ultra-lightweight PET preforms for food and non-foods applications. We are also developing a new range of preforms with the 26/22 neck finish specially designed for tethered caps. About increasing the incorporation of recycled PET, we are able to supply and incorporate 12,000 t of rPET per year in our preforms production thanks to our recycled unit – SGR – in Chalon sur Saone, in Eastern of France. To answer cosmetic customers’ requests, SGT will soon be able to propose new preforms with colouration effects based on a multilayer technology.
2) 80% of our production is dedicated to package food liquids with a catalog of more than 260 references in mono and multilayer preforms. In addition, we are also more and more developing preforms for household products, hygiene, cosmetics and laundry industries where demand for PET and rPET packaging is growing.
3) SGT is investing into new cosmetic range of preforms like the 24/410 neck finish, in mono or multi-layer. Another area of interest is the chilled dairy and spreadable markets for which we develop the preform “cup”.
PDG, François Desfretier, General Manager
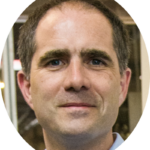
1) I think reduction of weight is still a challenge. It will be done by preform design and dimensions, by new PET material properties, by bottle design and by blouwing process. We are working on all these subjects in order to improve LCA of liquid packaging.
2) We are specialised in preforms for UHT milk and dairy products. And it will continue. However, we also produce a lot of preforms in PET and rPET for all beverages and liquids in general.
3) All the beverage and liquid markets are intresting for us and we will continue to invest in preform production because demand will continue to grow up for lighter packaging.
www.pdg-plastiques.com
Novapet, Alázaro Ires, Preform Business Manager
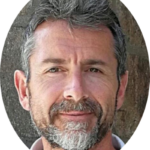
1) To improve new references/moulds for new markets; as it can be edible oils and housed hold, pharmacy and cosmetic products either. An rPET unit production is shortly added to Novapet to produce our rPET preforms.
2) We are highly producing mineral water and carbonated soft drinks preforms. In the latest 2-3 years we have already highly entered into new markets as related. In a few months we will face as well preforms for returnable and non-returnable 3, 4 and 5 galons (from 12 to 20 l.). Common uses are edible oil, mineral water and also fertilisers. A new challenge.
3) Any of them can be interesting for Novapet. We are continuously improving the investment into preform production (current year 2500 MU) with the aim to relocate the production capacity into other location in Spain with new preform machinery units.
Flexblow, Gintautas Maksvytis, CEO
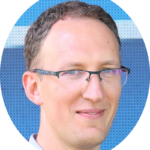
1) Biodegradable packaging has been a big thing for a while. FlexBlow’s R&D packaging team is collaborating with partners and researching the usage of recycled biomass in packaging. rPET preform solutions are still one of the major needs. It’s related to the mandatory requirement to increase recycled material content by 2025, as well as to the global shift towards sustainable packaging. Our recent preform development projects concentrate on shelf-life extension for 100% rPET containers.
2) FlexBlow has launched special preforms as a response to the market needs. We specialise in designing and engineering custom preforms for niche projects, i.e. hot-fill product launch, conversion from glass, multilayer PP or HDPE to PET, light-weighting, optimising preforms for very complicated design, etc. Our focus on customisation allows designing preforms that require no further adjustment of clients’ current filling, capping, palletising, or packing lines. Our know-how in preform, container, and mould engineering and dedicated in-house prototyping infrastructure enable us to provide custom preforms that are perfectly compatible for customers’ projects. Also, we have developed a tool dedicated to customising preforms – customers who consider custom preforms can receive instant offers through the self-service website.
3) We focus on developing customised preforms for various products: sauces, syrups, personal and home care, nutraceuticals and cosmetics, industrial chemicals, various beverages, oils, etc. FlexBlow’s in-house mould manufacturing and injection mould sharing strategy allows custom preforms with as little as 50,000 EUR on clients’ end.