Inspecting bottles with increased levels of rPET
When producing PET bottles with significant recycled PET (rPET) content, there are several factors to consider – including the visible quality issues related to rPET as well as the challenges related to processing bottles with this material.
Agr international offers a combined solution for these challenges with two products in its Process Pilot portfolio; the Pilot Vision+ inspection system and the Process Pilot blowmoulder management system. While either product can work on a stand-alone basis, the combination of Pilot Vision+ and Process Pilot provide bottle producers with a powerful duo that can manage rPET in a manner that ensures quality, maximises production efficiency and minimises waste.
Vision inspection for contaminants and defects
The Pilot Vision+ system, Agr’s latest generation of vision-based inspection systems, is designed to work in conjunction with today’s high-speed reheat stretch blow moulding equipment and identify contaminants and defects present in preforms and bottles. The Pilot Vision+ can be configured with up to six cameras, positioned at optimal locations within the blowmoulder in order to facilitate effective inspections. Typically, units are configured in four separate inspection stations; preform inspection in the oven area, and then immediately after mould takeout for bottle seal surface, base and sidewall inspection.
The preform inspection module of the Pilot Vision+ system acts as a preform filter. Multiple colour cameras provide the imaging for 360º preform sidewall inspection as well as end cap and gate. Optics, LED illumination and image analysis routines are optimised to identify preform defects that impact bottle integrity, particularly the black specs and particle contamination associated with rPET. Preforms with visible defects can be accurately identified and removed before the bottle is blown, saving energy and resources.
With the increased use of rPET, challenges related to colour consistency are also an issue. In the Pilot Vision+ system, the colour preform cameras can monitor the colour of preforms entering the blowmoulder and ensure that colours are consistent and within acceptable ranges. A valuable tool incorporated into this system provides the capability to learn multiple reference image sets for colour inspection. With this, it is possible to process a preform supply with slight colour variations and manage the range of colour by accepting those that match the reference images, while rejecting those that do not match.
The base inspection on the Pilot Vision+ system incorporates a set of inspection algorithms that identify the smallest defects and anomalies regardless of bottle base size, shape or design. In addition, the base inspection features a unique liquid lens that adjusts focus for bottle heights from five to sixteen inches, without mechanical components. This feature eliminates the need for mechanical lens adjustment when changing between bottles of different heights. Focus settings are saved with each job and focus is automatically adjusted to accommodate new bottle heights, saving changeover time and ensuring a clear, high-resolution image of the base at the start of production. The high-resolution imaging is suited for managing bottles with rPET where the presence of small particle contaminants can increase the incidences of holes in the highly stretched regions of the foot and base.
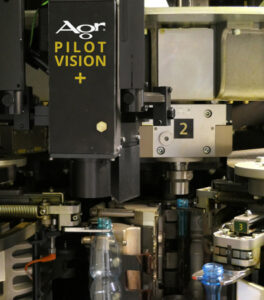
The Pilot Vision+ system offers a number of tools to assist operators with setup and job management. These include adjustable ROI tools, digital image filtering, zone scaling and the ability to display live and historical inspections images that can be used for evaluation or setup purposes. Defects are correlated to the mould/spindle to easily identify the source of a defect. Defects are also categorised using colour codes for quick and easy identification of offending characteristics.
Process control for managing rPET variability
One of the challenges to efficient bottle production is variability in the resin and as a result, lack of consistency in preforms. Recycled resin significantly compromises preform consistency, and as a result, the bottle becomes increasingly more difficult to make.
Preforms made of recycled PET, because they are inconsistent in makeup and colour, behave differently in the blowmoulder and require continuous adjustments to the blowmoulder controls in order to maintain proper material distribution.
The Process Pilot system takes and analyses real-time measurements of sidewall thickness of every bottle leaving the mould, then adjusts the blowmoulder control parameters if material distribution starts trending out of spec. The result is an optimised blowing process that ensures consistent container quality and performance over the entire production run.
Process variability related to rPET material, such as variations in colour that affect heat absorption, can be effectively managed by the Process Pilot system, eliminating the need to constantly adjust the blowmoulder. This avoids the production of defective and non-conforming containers, minimising product waste and related downstream issues.
The Pilot Vision+ and Process Pilot automated blowmoulder control system are part of a complete line of products offered by Agr International Inc. to help bottle manufacturers and brand owners manage container quality and production efficiency, particularly with the ever-increasing use of rPET.