Moulding of returnable & refillable PET bottles
Nissei ASB, Hall C5 – Booth 225
Compared to their glass counterparts, returnable and refillable PET bottles are typically 90% lighter, with a 30% lower carbon footprint. Compared to single use PET bottles, returnable and refillable PET bottles weigh around twice as much, yet as a result of their reusability, they only consume around 8-10% of the PET material of equivalent single use bottles throughout their lifetime, which may extend up to 6 years considering a typical 3-month re-use cycle.
In a typical production scenario, a single HSB-4N machine will produce up to 20 million returnable & refillable PET bottles per year, and with each bottle having a lifetime of more than 25 cycles, this represents the equivalent of at least 500 million single use bottles. At end of life, refillable PET bottles are bottle-to-bottle recyclable or can be converted into other new products. Even when moulded with 100% virgin PET, the refillable bottle already has a lower carbon footprint compared to a single use bottle, but the ability to absorb 30% of recycled materials without any impact to performance, the carbon footprint of the container is reduced by around an additional 25%.
Working with a famous brand filling company, Nissei ASB developed and launched the first returnable and refillable PET bottles for juices and soft drinks in the German market during the country’s first “green wave” way back in 1989. Shortly thereafter, ASB went on to supply similar systems to multiple companies in around 20 countries throughout the 1990s.
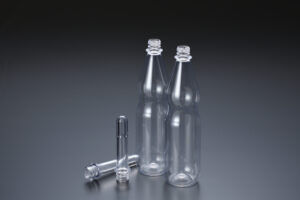
Now, with the resurgence in interest and public demand for refillable packaging, not only in Germany but also globally, ASB is well placed to take advantage by utilising its broad packaging expertise as well as its capable moulding equipment. The double blow heat-set process that is the main feature of the HSB series machines, gives the ASB bottle significant advantages over other moulding methods, says ASB. The result is higher crystallinity (density) of the material, together with less stress in the moulded bottle. Both these factors combined result in improved thermal stability and greater resistance to environmental stress cracking, ensuring higher reusability rates at a lighter weight.
At Drinktec 2022, using its well-established double blow heat-set process via its HSB series reheat stretch blow moulding machines, Nissei ASB will demonstrate live moulding of a returnable and refillable PET bottle on an HSB-4N machine that are claimed to surpass current industry standards in all respects: A 1 l sparkling water with 1.5 gas vol. (design compatible with popular German industry standard for sparkling water), weighting 53 g (current industry standard 62 g), with reuse cycles greater than 25 times (current industry practice “up to 25 times”), with a rPET content of up to 30%, without reduction in performance (in laboratory testing ASB’s R&R bottles with 30% rPET actually achieved in excess of 30 times washing and pressurisation cycles).