Always in tune with the times
Sustainable development of required preforms
The last stop on our Editour takes us to PDG Plastiques. The PET converter is for more than 30 years active in the PET industry, being one of the pioneers in Europe. As a family-owned company, integrity, reliability and partnership are key to PDG Plastiques. The company is located south of Paris and has a subsidiary plant in Algeria. It is producing approx. 2 billion preforms consolidated. Blowing activities represent approx. 70 million bottles per year.
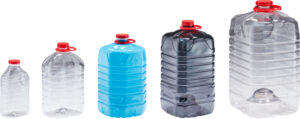
In a packaging world dominated by large companies, PDG-Plastiques seeks its place by dedicating itself to special challenges. PDG produces special solutions for the dairy industry, e.g. for barrier containers. Also especially small and very large complex preforms. Two years ago, for example, PDG launched a range of large containers with 5, 10 and 20 l capacities and mouths of 48 and 63 mm.
Light base technology
In the constant struggle to save material, PDG has developed a light base technology, Mint-Tec, together with a partner. By applying this technology, PDG removes more than 10% material from the bottom of the preform. Especially for heavy preforms it is a very interesting technology and being implemented for a new 20 l preform. Recently PDG introduced this technology for a 5 l container for a well-known French mineral water company.
Alternatives to HDPE or carton packaging
PDG Plastiques and its partners also developed Prelactia, a special injection process, leading to a 2-layer preform, where the inner layer blocks the light entrance. The outer layer covers and gives the bottle a nice white appearance. Since the introduction of the Oxy Block barrier, PDG provides also a barrier against oxygen ingress. Prelactia is offering a solution to the dairy industry in finding alternatives to aseptic HDPE and carton solutions, for any kind of dairy products. It can be combined with recycled PET material as well.
The technology used enables PDG Plastiques to comply with European directives requiring a 25% recycling rate for PET bottles by 2025 and 30% by 2030. A different mindset in the green economy, as one of the first in Europe, PDG introduced one and a half years ago the 26/22 light neck finish for carbonated and still beverages, saving almost 2 g as a total package solution towards the standard 1881 finish. The current material price increase led to the fact that brand owners now introducing this new neck finish on large scale.
Enhancing material functionality
As a researching and forward-looking company PDG is involved in a project with Keiryo Packaging. Keiryo Packaging technology for plastic processing integrates molecular ordering into the polymer melt, triggering “flow-enhanced morphological changes” in the polymer mass with the aim of enhancing material functionality. The KP technology combines a software and a hardware component. It triggers a phenomenon called Flow-Enhanced Nucleation and Induced Crystallisation (Fenic). The hardware is a 3D printed insert – the physical component of the technology, that is retrofitted on standard injection machinery. The inside of the insert is made of microchannels generating a well-defined friction when the polymer passes through the hot runner into the preform mould.
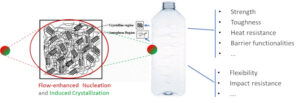
Higher level of order of the molecules improve the overall material functionality and can be advantageous for barrier applications – the ordered morphologies can act as an obstacle that delays the gasses permeation. As a result, also less material is required. Keiryo are running trials in PDG’s industrial facility as technology partner. PDG is still in the process of fully scoping these differences, but the demonstration that morphological changes are carried over in the bottle is an important milestone.
PDG Plastiques is ISO 22000 FSSC certificated. The company carries out the necessary controls on the injection process using state-of-the-art technologies to ensure that quality targets are met and that customers can market their products with a clear conscience. The laboratory, which is equipped with the modern measuring instruments, monitors the quality of the final product. PDG Plastiques contributes in its own way to the planet by caring for the integrity of its products and the well-being of the planet.
Photo top: Philippe Blonda, Business Development PDG-Plastiques (left) and François Desfretier, CEO (right)