“The hot runner is the heart and artery system of the mould”
Saving money and reducing CO2 emissions through hot runner refurbishment
The company HRC is located near the historic town of Győr in Hungary on the banks of the Danube. HRC’s core business consists of the servicing of PET hot runners and providing high-quality spare parts to the PET packaging industry. Keeping their company’s environmental impact as low as possible is something that brothers Árpád and Tamás Horváth, who founded the company in 2006, have seen as an important part of their mission from the very beginning, and they work continuously to reduce the CO2 impact of their processes.
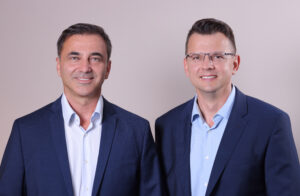
“Being owners of an industrial type of business in such a beautiful country as ours, it’s only natural to be aware of the impact on the environment”, Árpád states. “We service the plastic packaging industry, which has had its fair share of challenges in recent years, mostly coming from a growing consumer concern over pollution and emissions, and more recently the pressure to increase the re-use and the recyclability of raw materials. Since we work very closely with the industry leaders in the PET-packaging business, we are subsequently challenged too. Many multinationals that we serve have a specific corporate goal to reduce their environmental impact, looking at every link in their value chain. That also means that we as a supplier and service company have to comply, and we do that by staying ahead of the game. As a company, we have never taken the reactive approach to market trends, technological developments and challenges, so for us, it’s a no-brainer to try and reduce our carbon footprint proactively.”
Taking pride in their attention to detail, and keeping their “zero-concessions” policy at the heart of their everyday decision-making, HRC strives to lead the way in low-environmental impact performance as well. The facility has been running on 100% renewable energy since 2019, but that’s not where it ends.
Refurbishment minimises carbon footprint
“It’s often overlooked, but when comparing newly built machinery versus overhauling such machinery, in many cases there’s a huge offset in CO2 emissions. Especially when there is steel involved, a closer look is often worthwhile. Since the manufacturing and forging of steel is a pretty carbon-heavy process”, Árpád continues. “We take a standard 96 cavity PET hot runner as an example. When we make a full refurbishment on such a system, which brings the complete hot runner back to 100% new condition, the carbon footprint is up to 5.6 t less than that of a new manufacturing of such a hot runner. So, not only does a refurbishment save a significant amount of capital expenditure to the customer (without any concession versus a new hot runner), but it also helps achieve the customer’s environmental goals.”
“Without a proper working hot runner system, all other efforts tend to fall short”
But the biggest impact of the hot runner on emissions is surely its reliability and performance. “When a complete PET system is continuously running at its fastest cycle time, within quality specifications, without stops or breakdowns, that’s when emissions are lowest. When the dryer delivers the material as hot and as consistent as possible, the extruder has to “work” less hard to get to a homogenous melt within the cycle time available. If then the hot runner delivers that melt to all cavities with every shot, that’s the sweet spot of a system. Rigorous preventative maintenance on the complete line is of course a huge must to achieve this, but we take pride in being able to provide the best service to a key part of the process. Without a proper working hot runner system, all other efforts tend to fall short. The hot runner is the heart and artery system of the mould; at least that’s how we like to think of it.”
Árpád explains that on one end, there is one main channel that receives the liquid from a pump, and the hot runner has to deliver this material to all the different areas and consumers, while carefully maintaining the conditions and properties of the material. When one small corner of the melt distribution falters, the impact can eventually be dramatic. It can lead to quality issues, and cycle time losses and can even force complete system shutdowns. All of these effects are detrimental in terms of CO2 emissions. “A slower cycle time mostly means more energy consumed per tons processed. A blocked cavity means more hot runner power is consumed per cavity since the manifold system is still fully heated. And a defective preform eventually is basically more waste-material, which increases CO2 loss per definition since energy that was consumed to make the raw material and the preform is lost.”
Understanding these mechanics and the impact on the customer’s P&L and emission targets, HRC maintains that only their true “zero concessions policy” will pay dividends in the end. “We have actively collected a tremendous amount of useful feedback from the market and our customers, about the various levels of hot runner component quality which is available in the market. If we understand the problems of our customers, we can provide the right solutions more efficiently. As with many parts and components, the key is in the details. Take valve stems for example the chamfer on the edge must be precisely made. If not, the valve pin can start wearing out the nozzle tips and the injection mould gates prematurely, leading to preform faults. This is only one of the aspects of a part that we inspect 100%, to ensure there are no such effects impacting our customer’s product down the road.”
Over 700,000 units shipped
On what the future may bring, HRC is very clear: “The combination of such scrutiny on our side, and the fact that we are ready to directly contribute to our customer’s strategic goals has been our modus operandi since the beginning. We believe it’s this mentality, and the fact that we can guarantee such performance that’s helped us stay in the lead, and continuously helps to increase our market share and customer base across the globe. Our parts and services have received very positive reviews, and very importantly also from our distinguished Japanese customers, and we take big pride in that. But to be frank, we don’t expect anything different, as we for 100% know the precise condition of every part and hot runner that we ship to our customers. That means we can be sure of its performance in its designated PET production line. The future is bright, and we want to contribute to that!”
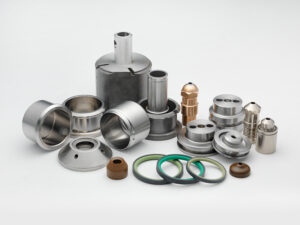
To date, HRC has overhauled more than 140 hot runner systems of various sizes, makes and types, including multilayer systems. They specialise in large 96-144 cavity systems and can handle even larger formats in their state-of-the-art cleaning lines. Over 700,000 units of HRC components have been shipped to their customers, with only positive feedback and returning orders as a result.